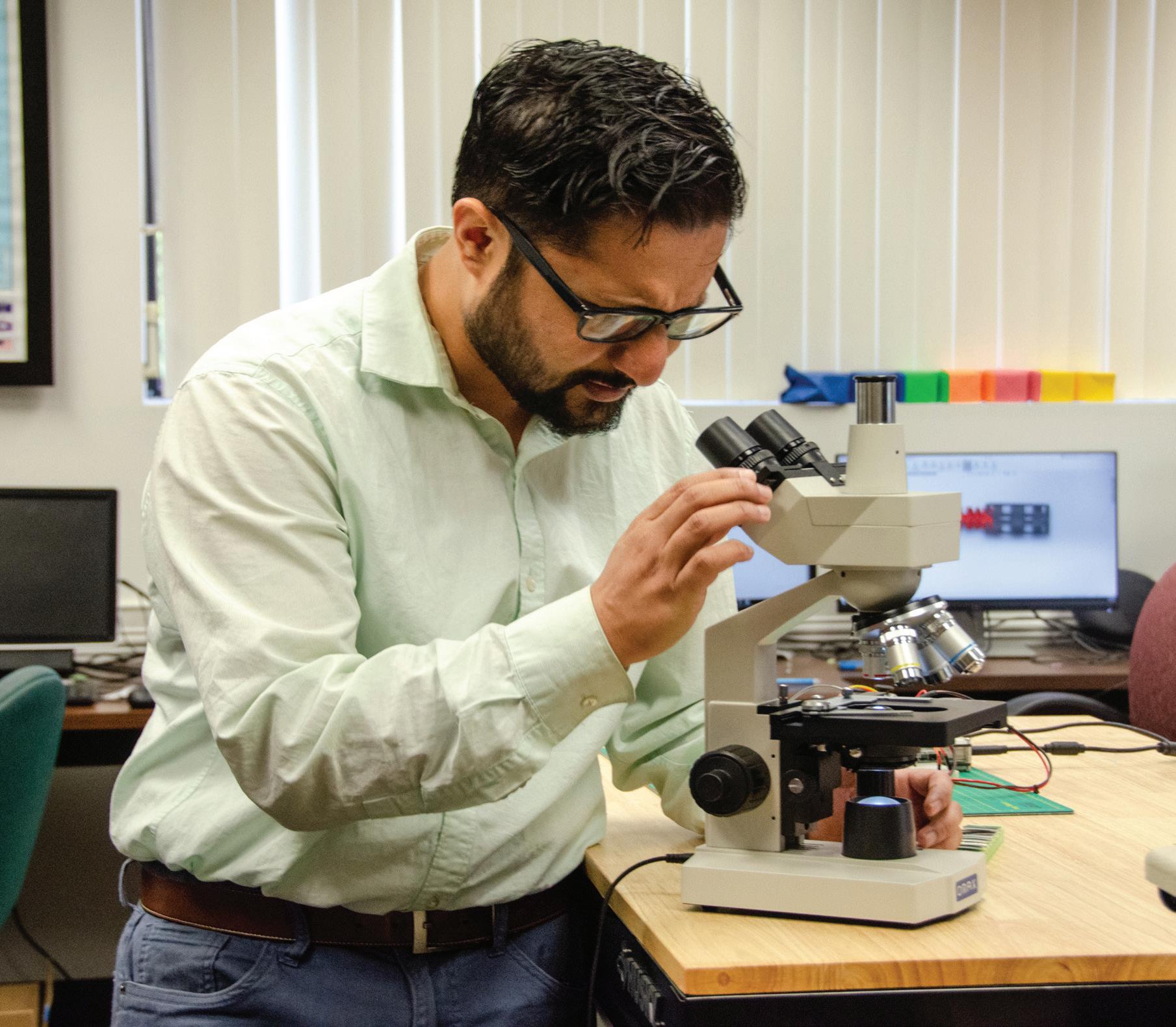
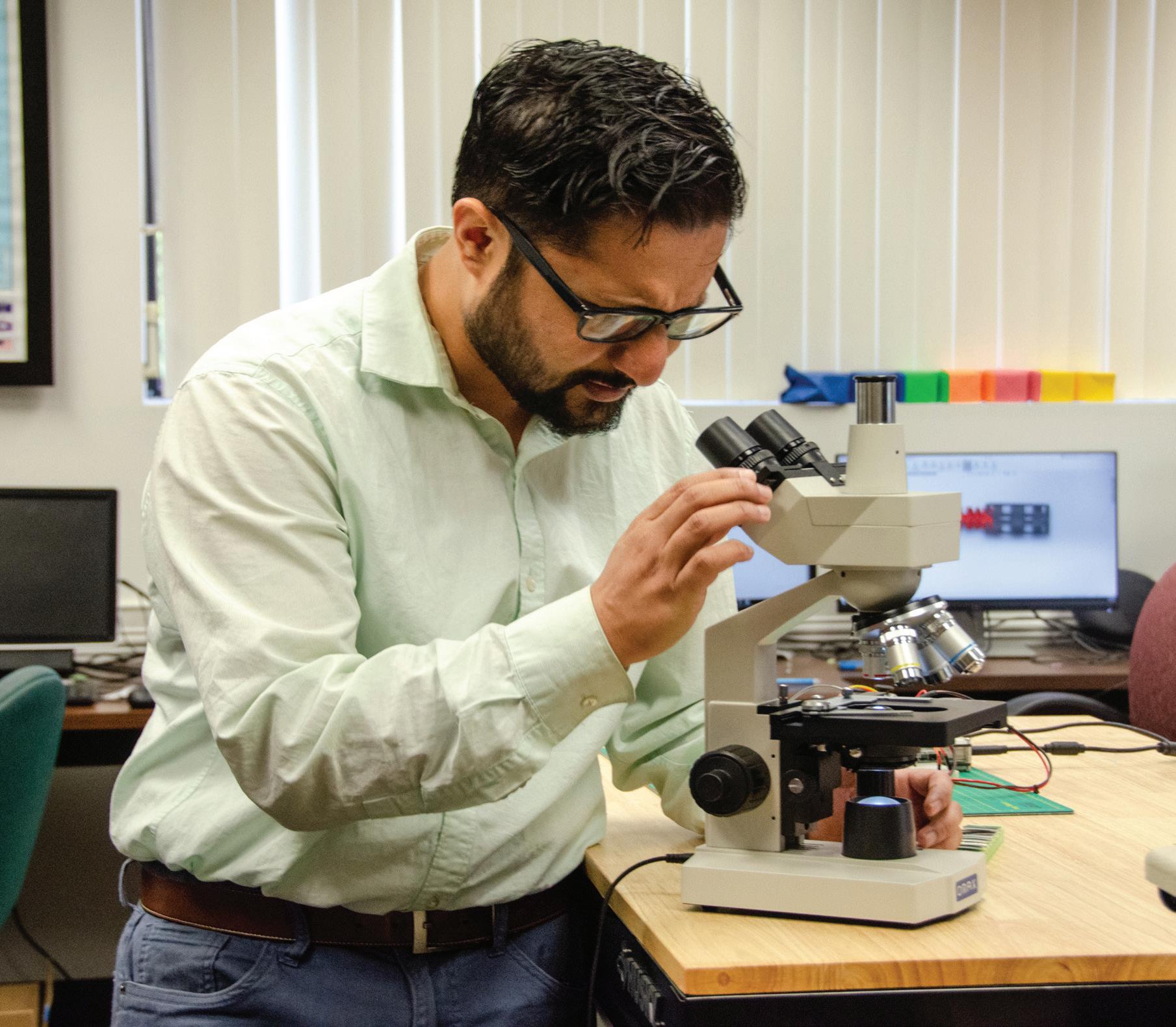
Aerospace Engineering
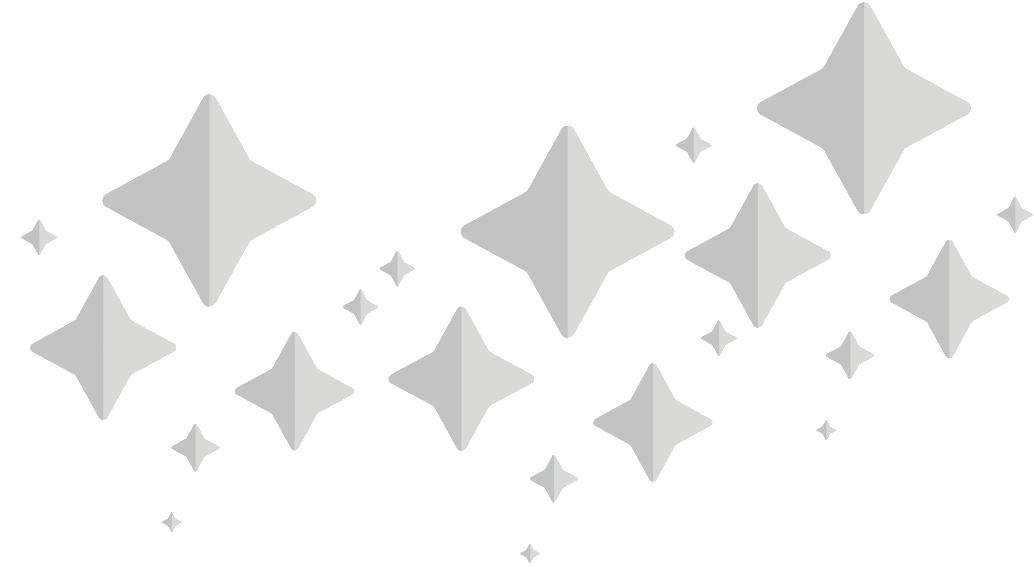
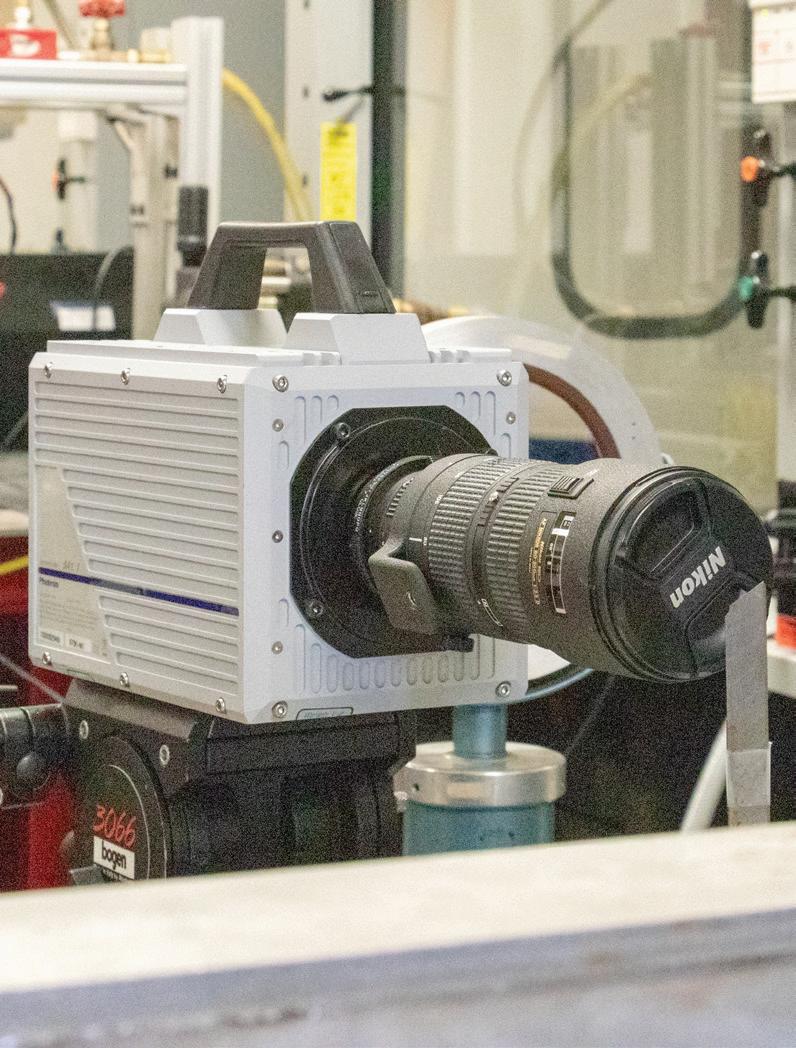
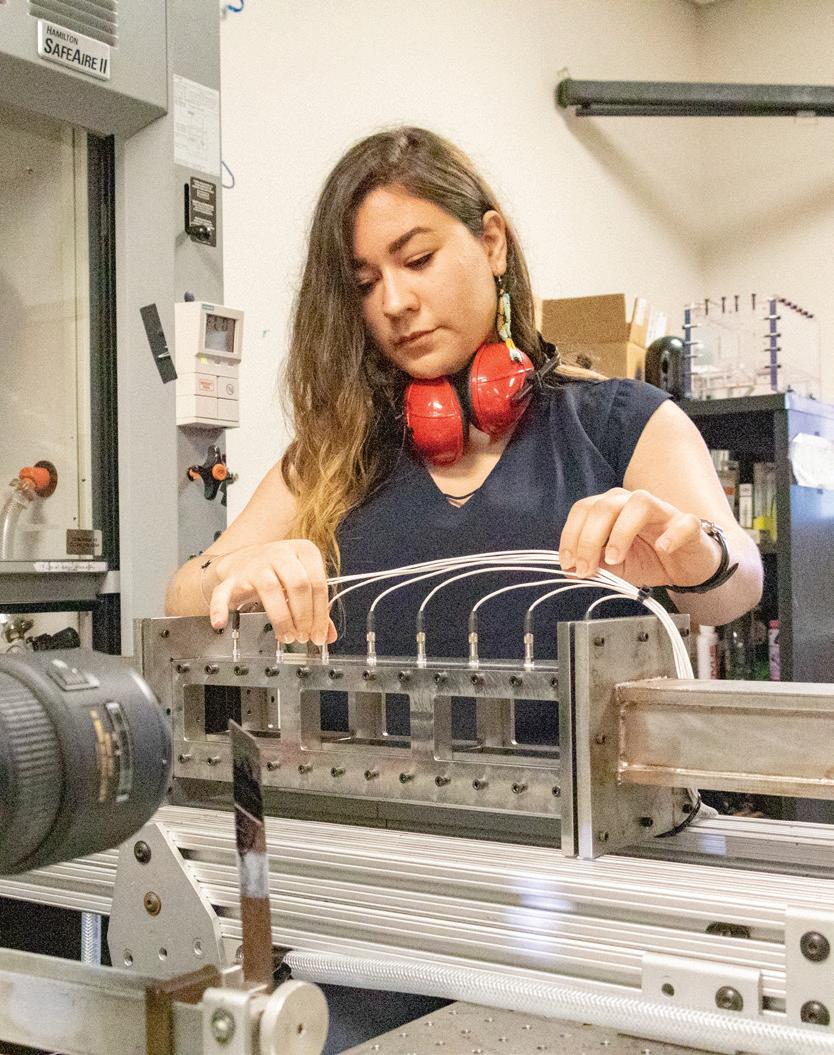
LAB DIRECTORY
Astrodynamics and Space Robotics Lab
Tarek Elgohary
Assistant Professor elgohary@ucf.edu
mae.ucf.edu/TAE
Center for Advanced Turbomachinery and Energy Research
Jayanta Kapat Professor and Director
jayanta.kapat@ucf.edu
cater.cecs.ucf.edu
Computational Fluids and Aerodynamics Lab
Michael Kinzel
Assistant Professor michael.kinzel@ucf.edu
mae.ucf.edu/CFAL
Composite Materials and Structures Lab
Jihua Gou Professor
jihua.gou@ucf.edu
mae.ucf.edu/CMSL
COSMOS Lab
Ranajay Ghosh
Associate Professor
ranajay.ghosh@ucf.edu
mae.ucf.edu/cosmos
Experimental Fluid Mechanics Lab
Samik Bhattacharya
Assistant Professor
samik.bhattacharya@ucf.edu
mae.ucf.edu/EFML
Propulsion and Energy Research Lab
Kareem Ahmed Associate Professor kareem.ahmed@ucf.edu
mae.ucf.edu/PERL
Structures and Materials Design Lab
Kawai Kwok Assistant Professor kawai.kwok@ucf.edu
mae.ucf.edu/kawaikwok
Vasu Lab:
Combustion, Propulsion, Laser Diagnostics, Absorption Sensors and Fuels
Subith Vasu Professor subith@ucf.edu
mae.ucf.edu/VasuLab

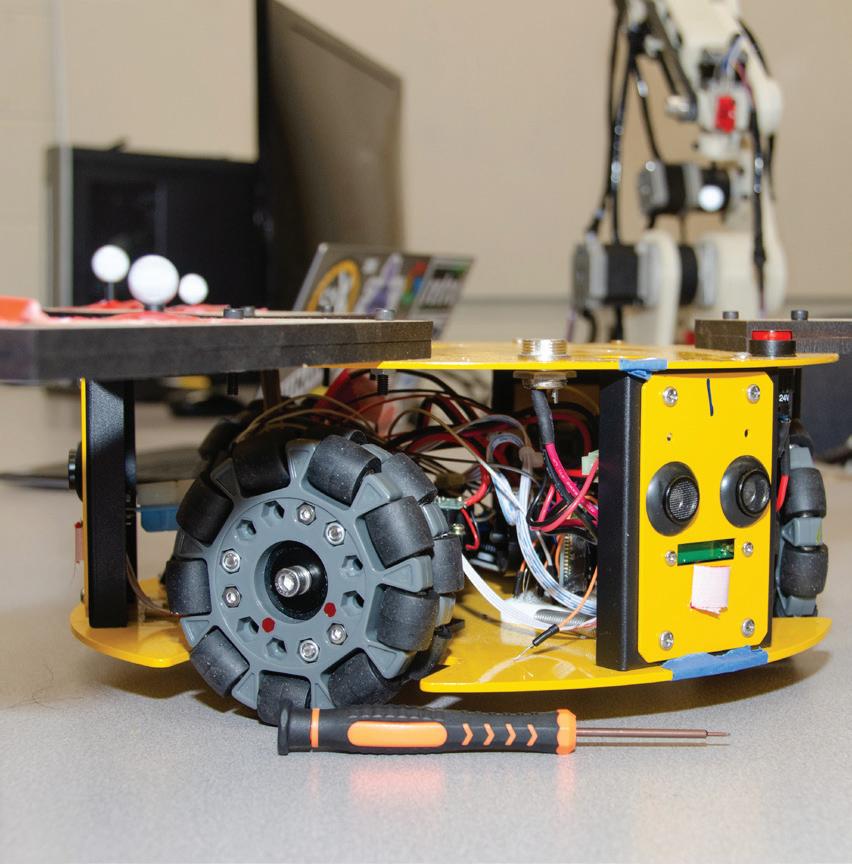
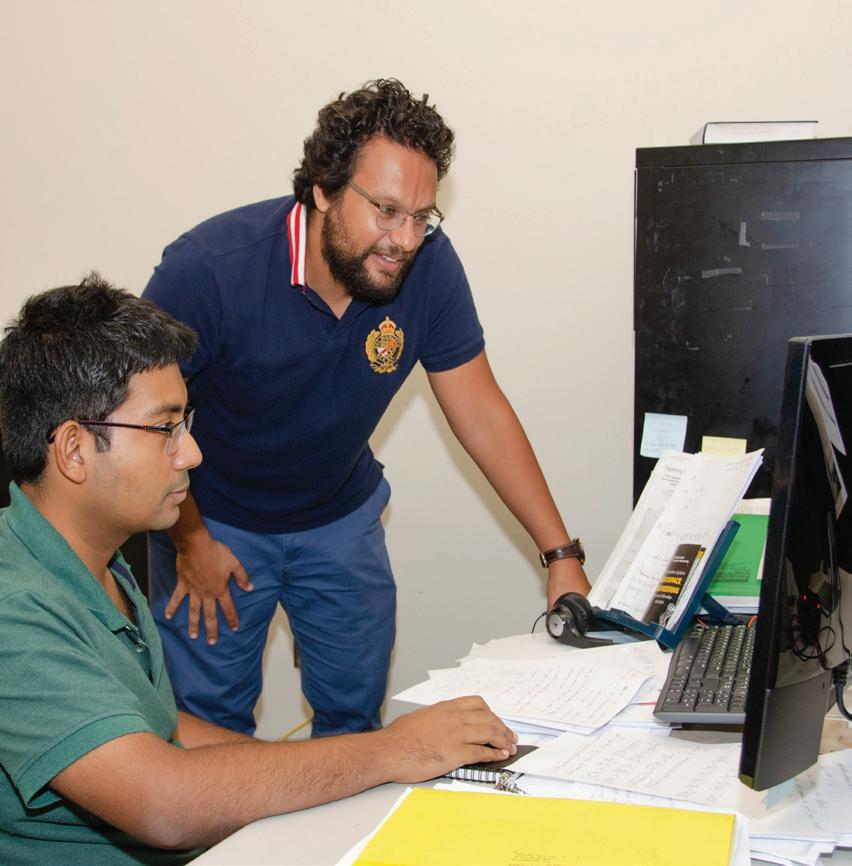
ASRL Lab
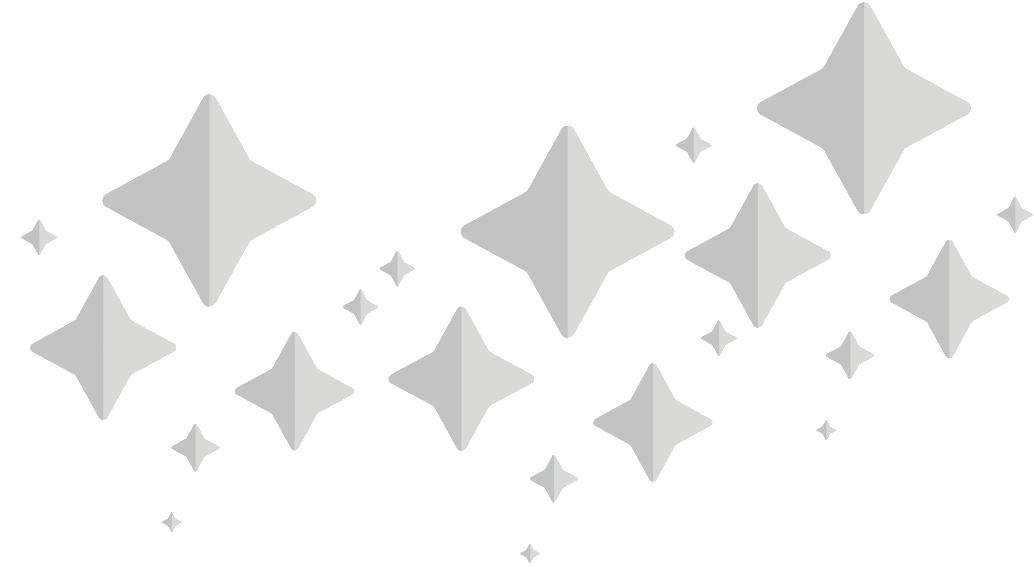
Astrodynamics and Space Robotics Lab
Led by: Tarek Elgohary, Ph.D.
At the intersection of dynamics, control and computational methods, you’ll find the research conducted in the Astrodynamics and Space Robotics Lab. With a focus on space flight applications, Assistant Professor Tarek Elgohary and his research team tackle various guidance, navigation and control problems applied to orbital mechanics, autonomous space proximity operations, space situational awareness and robotics.
One of the current projects in the lab is ROME, a Raid Orbit Motion Emulator. This compact ground vehicle is coupled with a robotic arms to emulate the motion of spacecraft in orbit and to simulate docking maneuvers.
Other work includes simulations and robotics experiments to push the boundaries of the field of space flight.


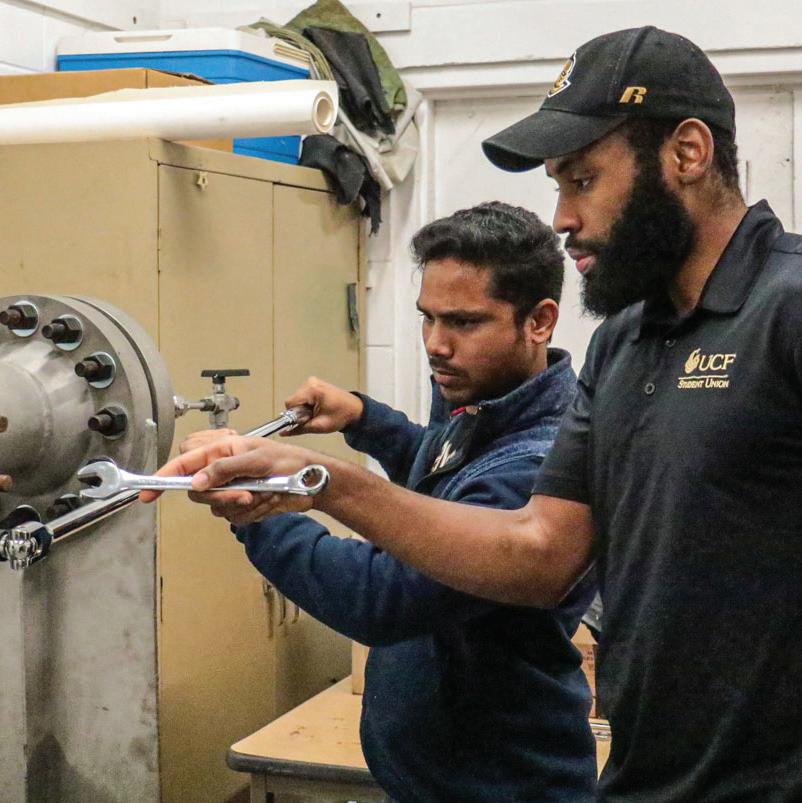
CATER
Center for Advanced Turbomachinery and Energy Research
Led by: Jayanta Kapat, Ph.D.The University of Central Florida lies in the heart of the state, at the center of the Turbine Turnpike. There’s no better setting for the Center for Advanced Turbomachinery and Energy Research, led by Pegasus Professor and Director Jayanta Kapat.
CATER Is comprised of a group of core faculty researchers that include the Department of Mechanical and Aerospace Engineering’s aerospace engineering faculty, as well as postdoctoral researchers, graduate students and undergraduate students.
The researchers have developed close ties with many major engineering companies located near the university including GE Global Research, Aerojet Rocketdyne and Embraer. Siemens has also provided several multi-million dollar grants to fund the construction of the Siemens Energy Center, which exclusively houses CATER-related research projects. The 10,000-square-foot space houses laboratories as well as well as state-of-the-art equipment inclding high performance computers and software, scientific cameras, and more.
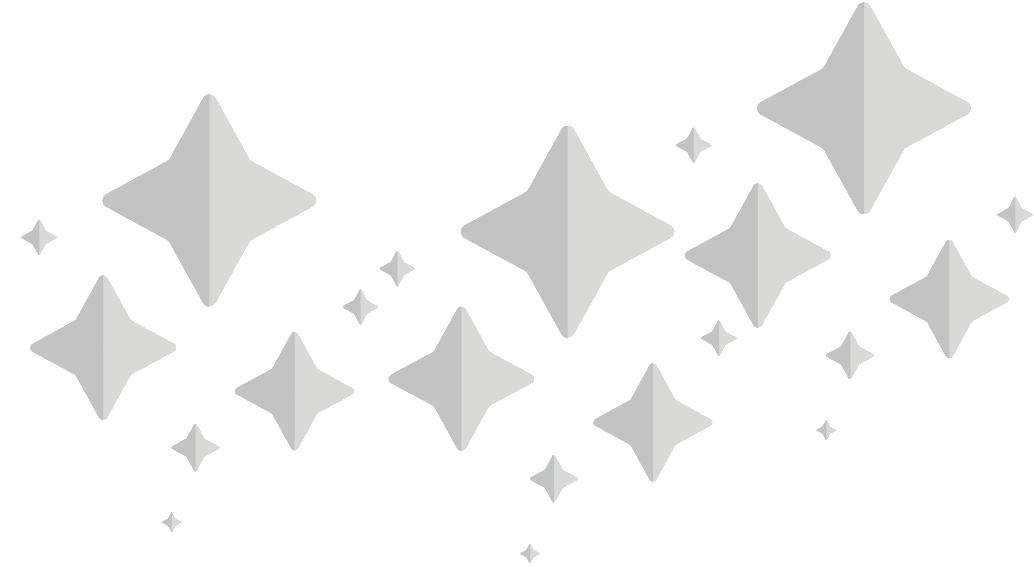
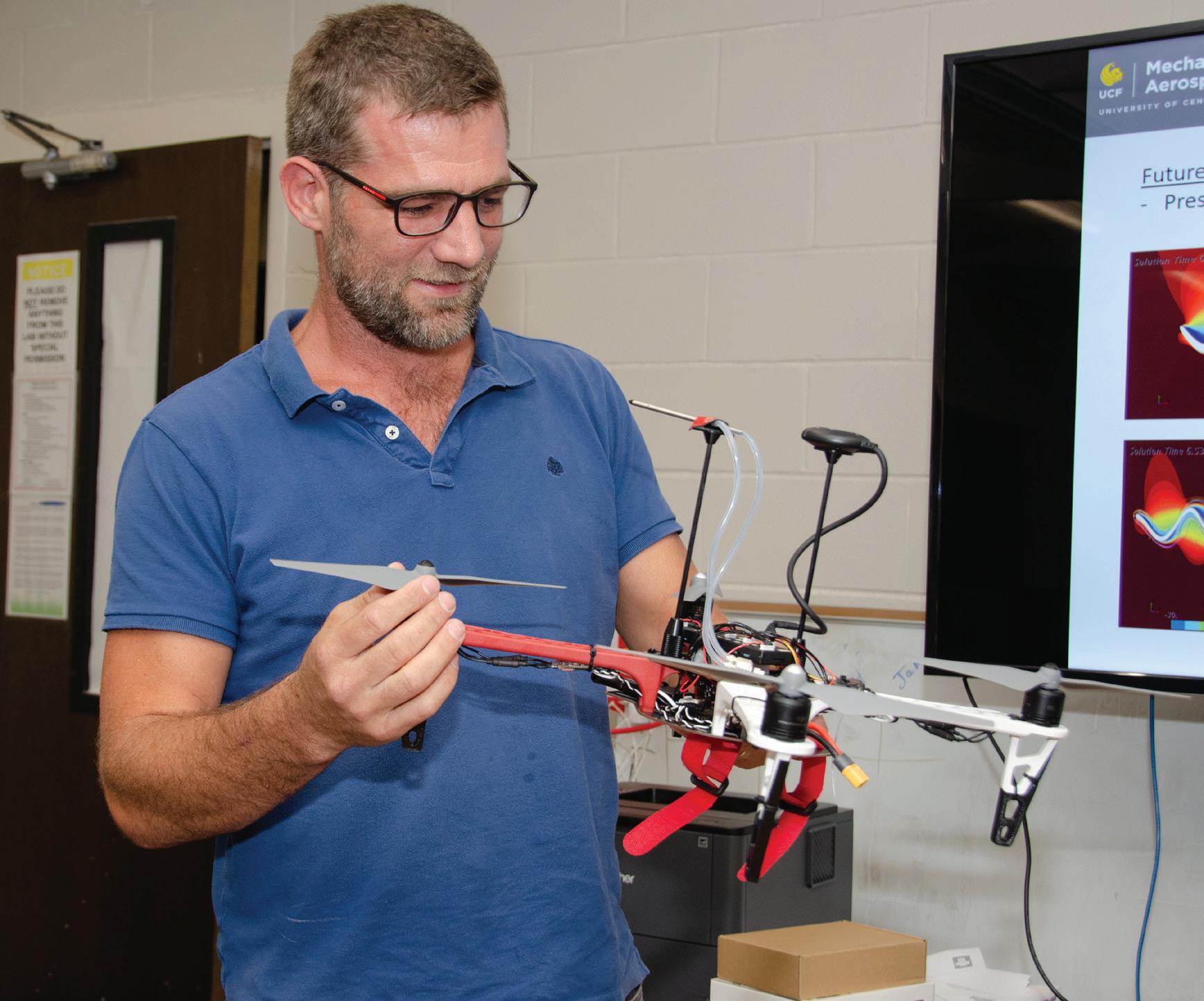
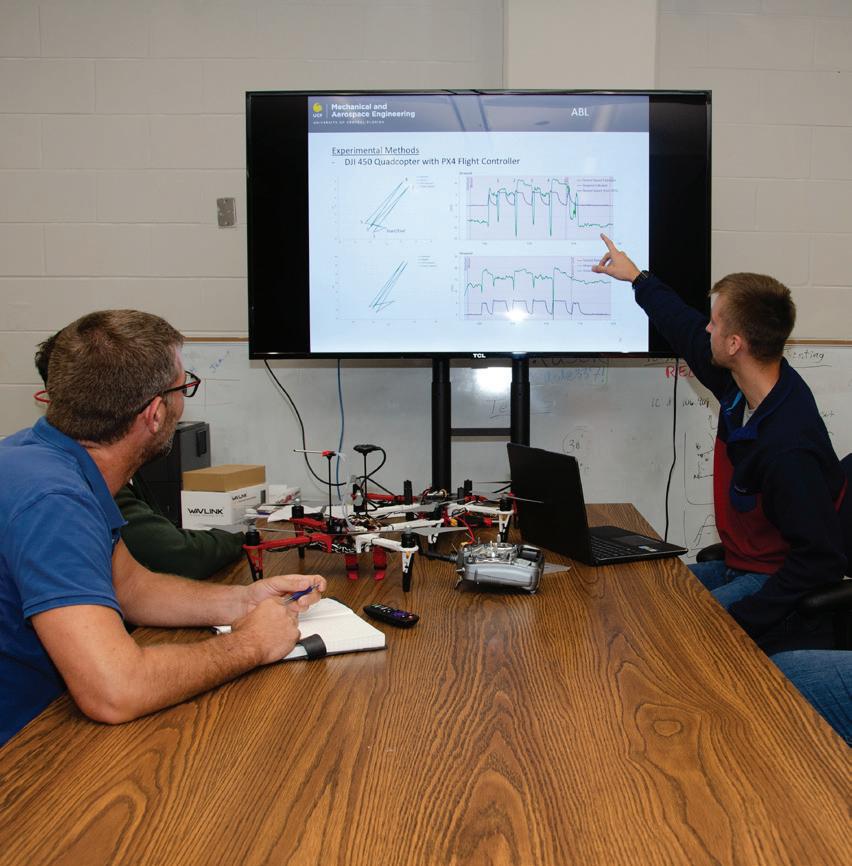
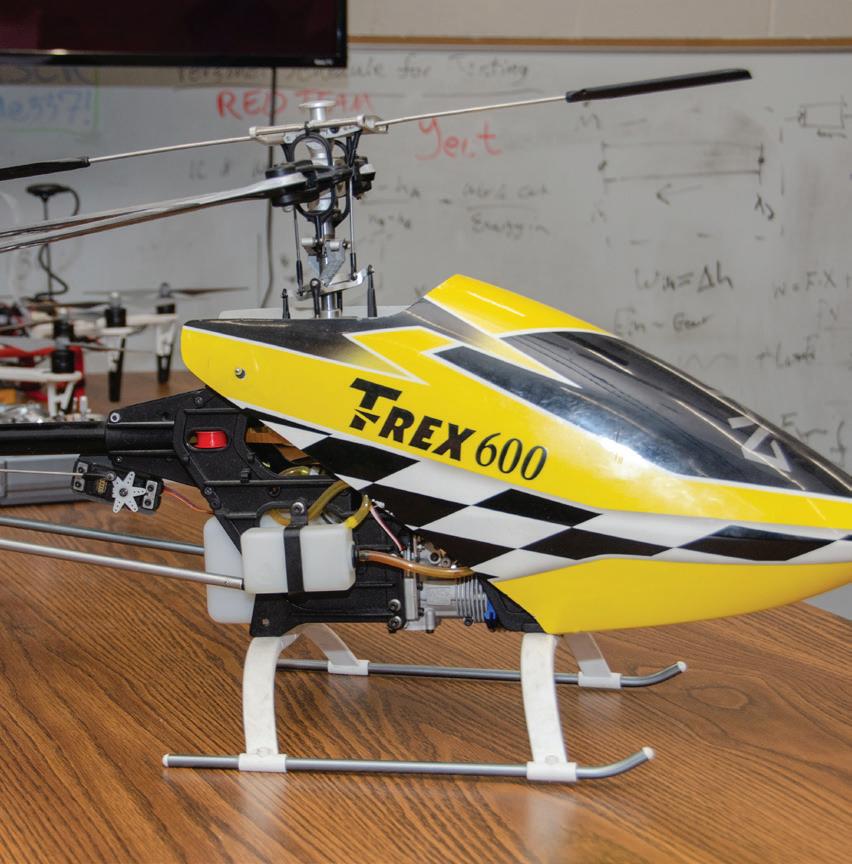
CFAL Lab
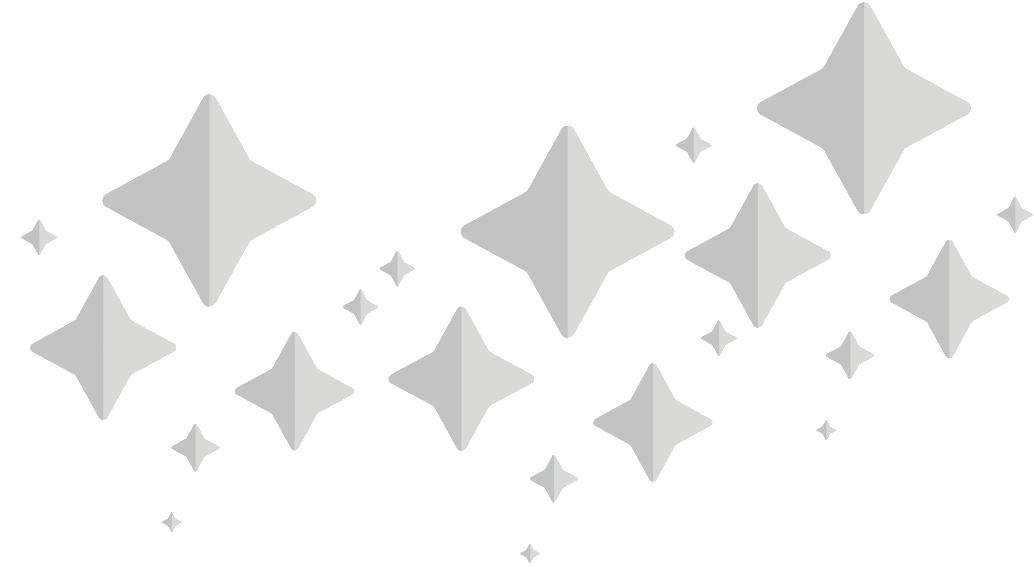
Computational Fluids and Aerodynamics Lab
Led by: Michael Kinzel, Ph.D.
Whether it’s the fluid mechanics of a human bone or a next generation aerial vehicle, Assistant Professor Michael Kinzel uses his knowledge and expertise to come up with innovative solutions to problems related to fluids and aerodynamics. His team in the Computational Fluids and Aerodynamics Lab is a major contributor to NASA’s Dragonfly mission, which aims to land an octocopter on Titan, Saturn’s largest moon. The team also explores the area of entry, landing and descent and is working on designs for a nextgenerations capsule that can better manage heat and aerodynamics, or deliver payloads around the world in less than an hour.
But Kinzel’s work doesn’t just focus on faster, more efficient spaceflight. His team is also exploring the intricate details of inner bone fluids mechanics to discover how it drives bone health, with applications for astronauts in space as well as for patients with bone implants. Here, the team uses high-end computations as well as flight testing in microgravity.
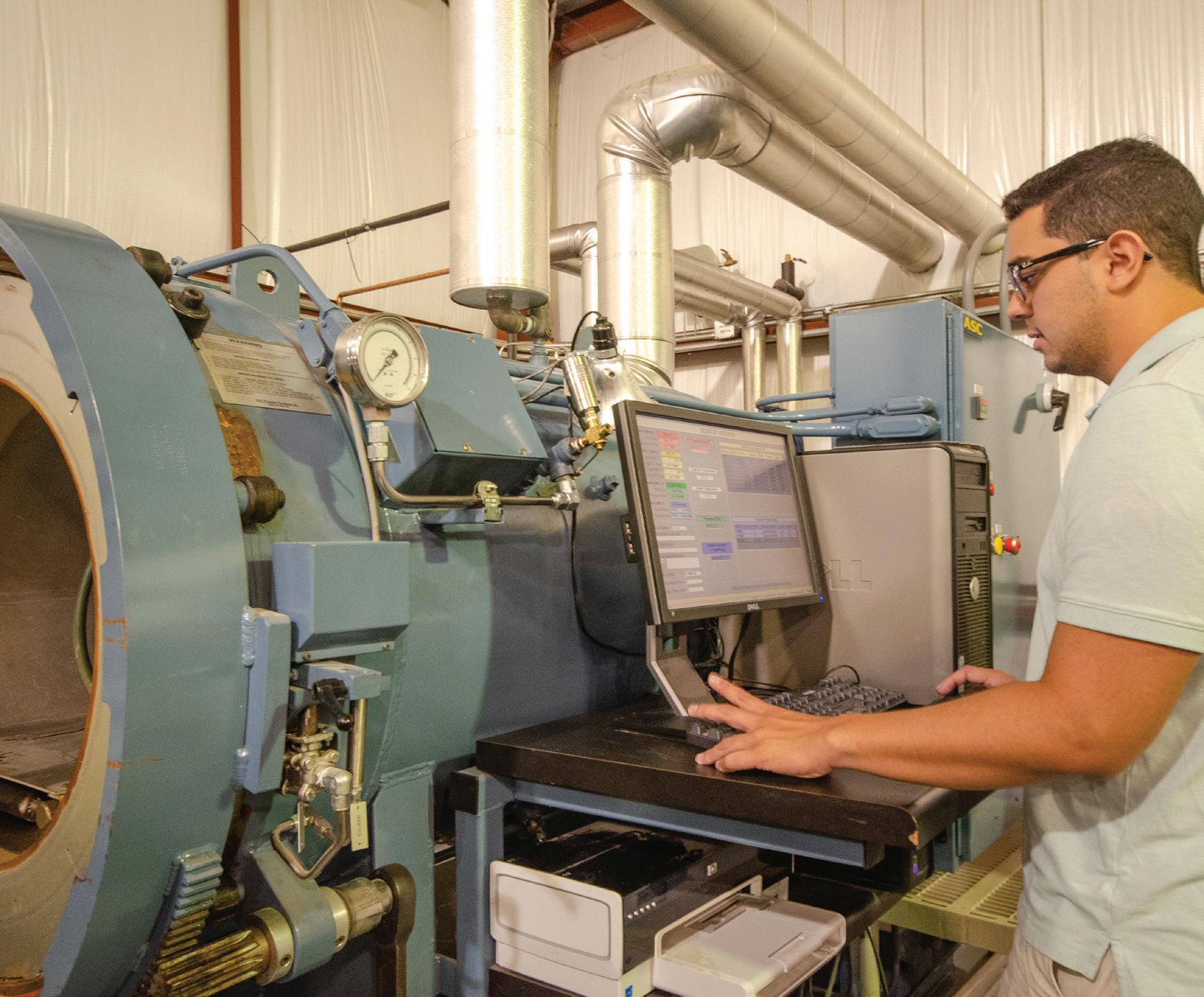
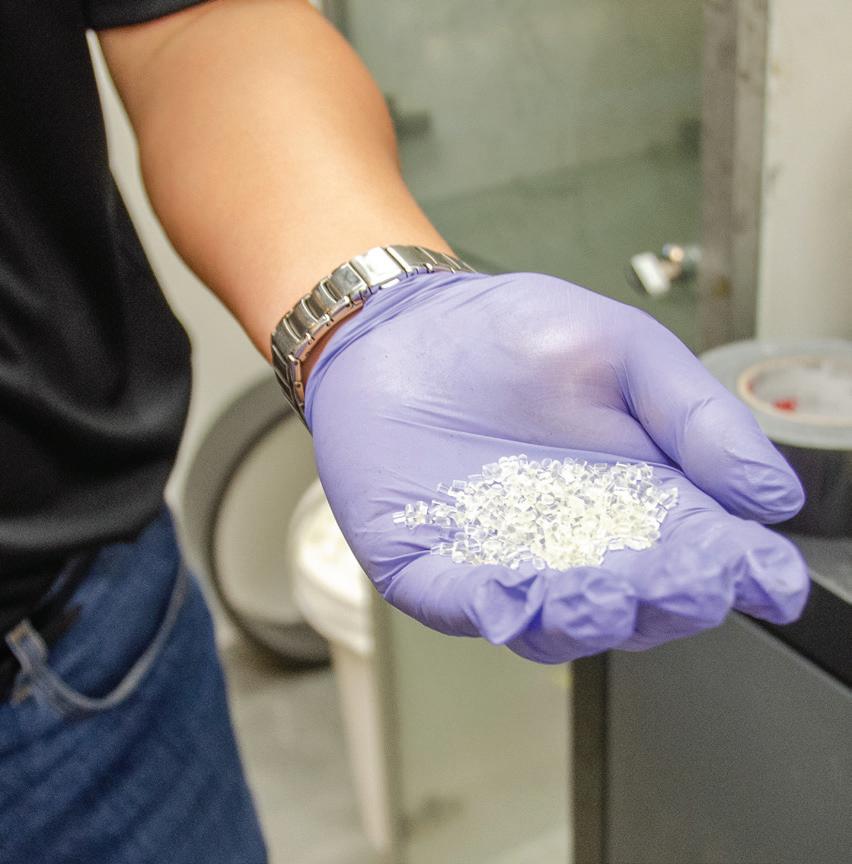
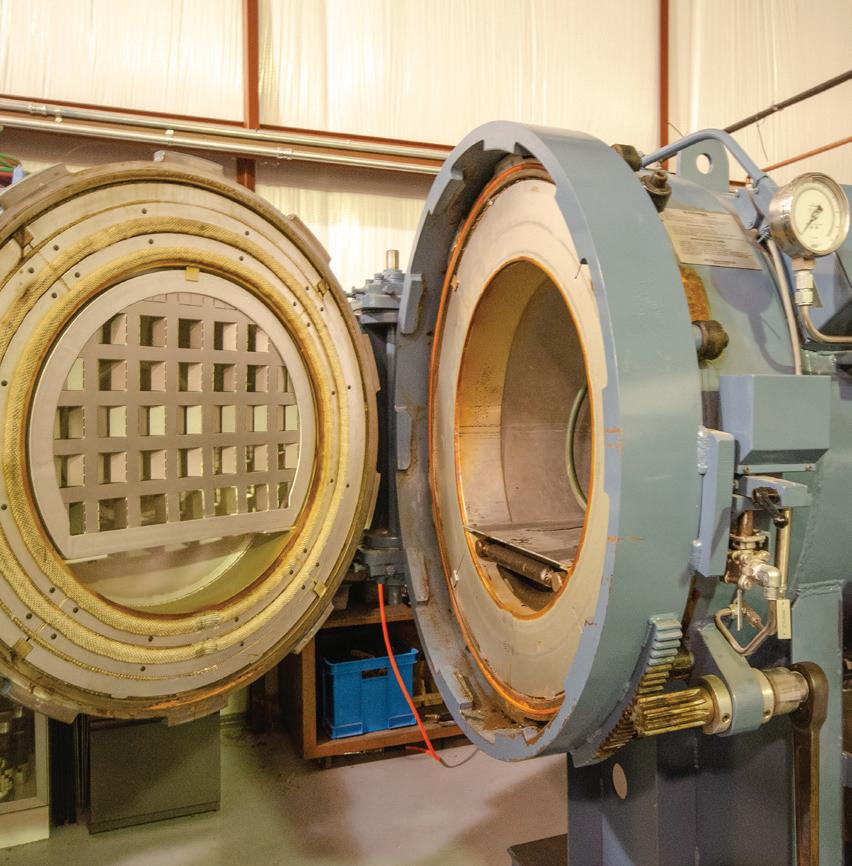
CMSL Lab
Composite Materials and Structures Lab
Led by: Jihua Gou, Ph.D.
The most advanced composite materials are used in the design and construction of aircraft and spacecraft. In the Composite Materials and Structures Lab, led by Professor Jihua Gou, those materials and structures are designed, processed, tested and analyzed.
The overarching goal of the lab is to create the most state-of-the-art capabilities for the creation and study of composite materials, as well as to provide a knowledge and technology base for the application of composites in aircraft and spacecraft, energy, ships, prosthetics, and automotive and sports goods.
Gou’s current projects are funded by NASA, the Department of Energy, the Federal Aviation Administration and the National Science Foundation. He and his team collaborate with industries and government laboratories including Boeing Co., the Air Force Research Laboratory, NASA’s Marshall Space Flight Center and the Kennedy Space Center.
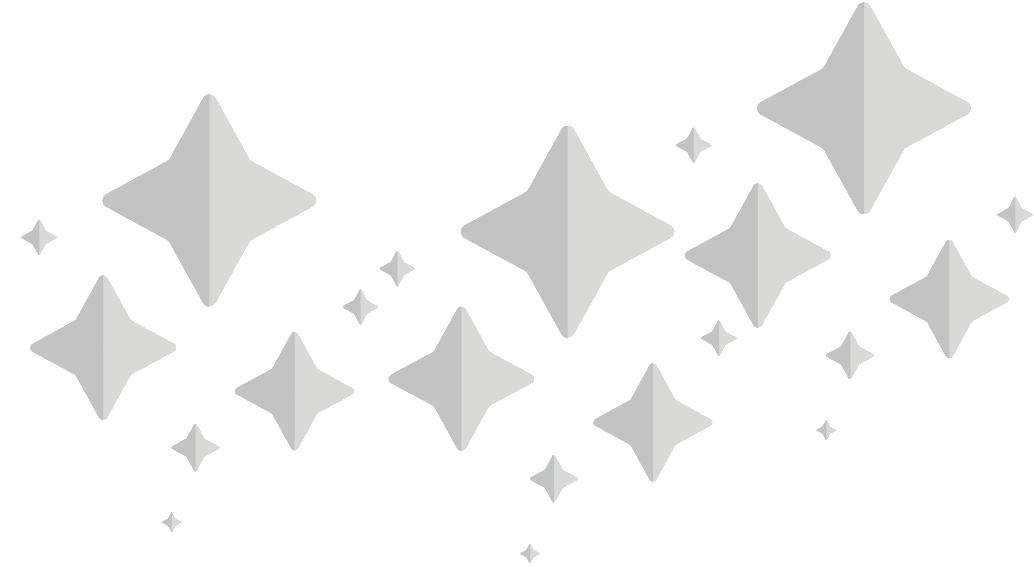
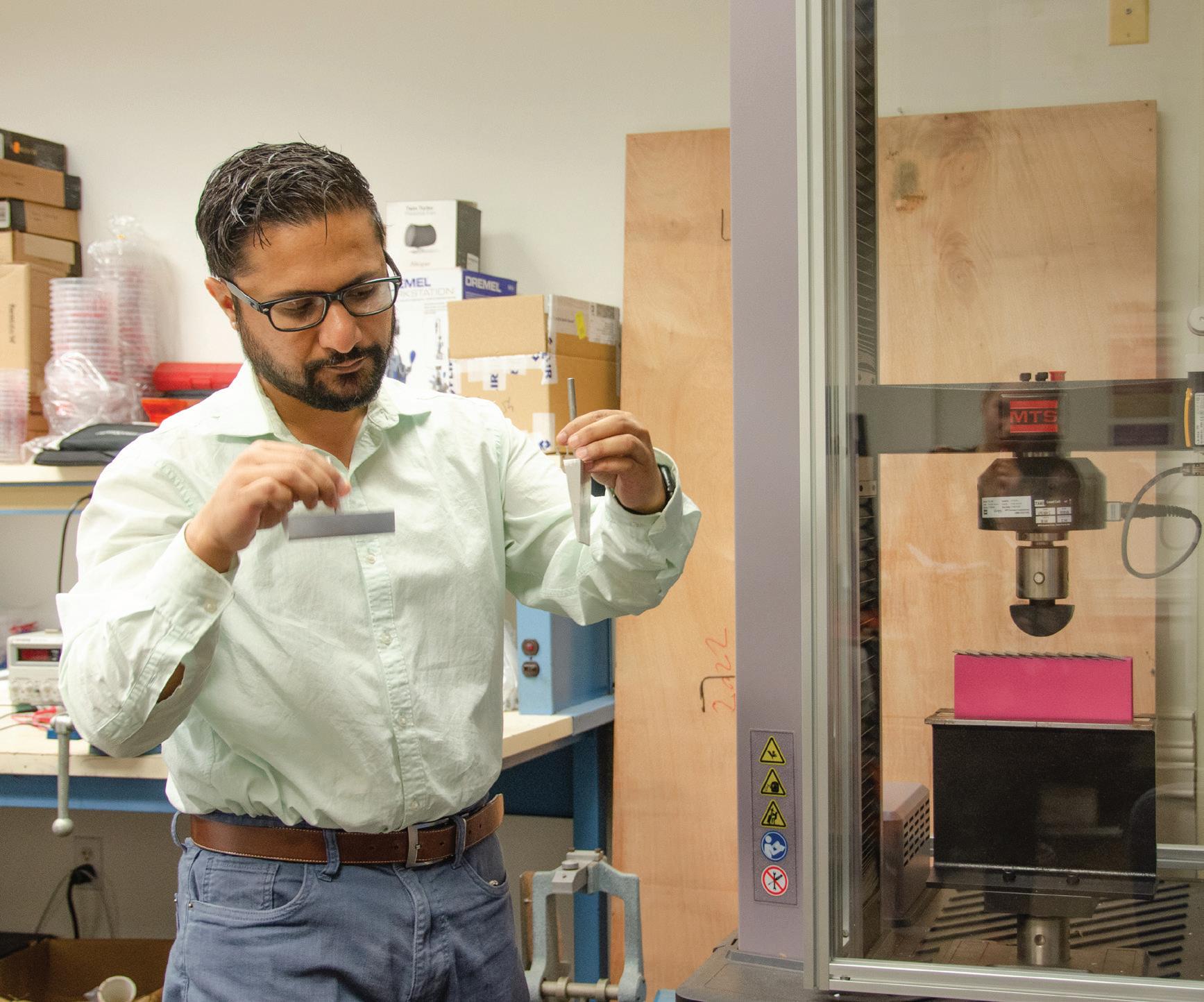

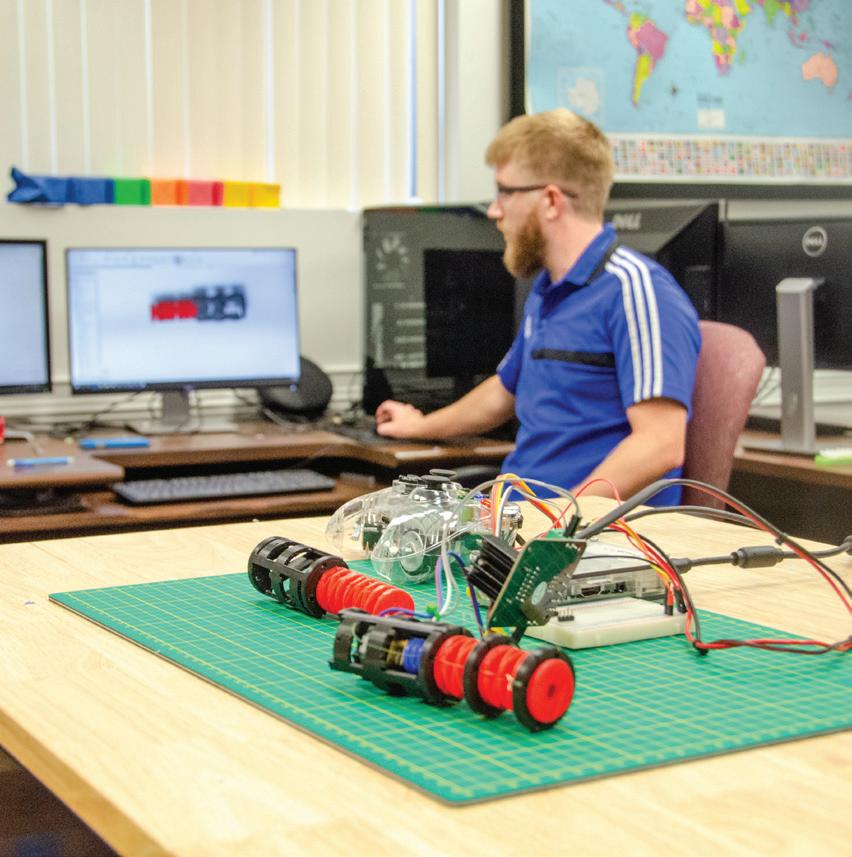
COSMOS Lab
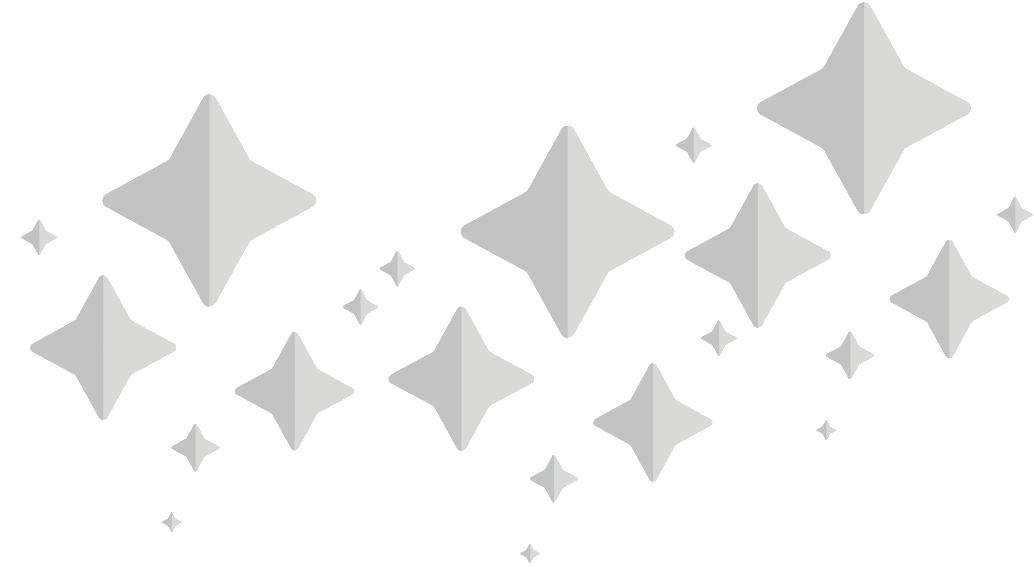
Complex Structures and Mechanics of Solids Lab
Led by: Ranajay Ghosh, Ph.D.Why don’t animals get dirty? Why don’t fish ever lose their scales?
In the COSMOS Lab, Associate Professor Ranajay Ghosh and his research team explore the answers to these questions, which could help engineers design stronger, more durable materials.
The secrets lie in the geometry of hair, fur, feathers and even fish scales. Ghosh studies their properties and behaviors to determine how to best replicate them in new, synthetic materials. With the knowledge of how fish scales can grip and move across surfaces, or how much stress and pressure they endure during a shark bite, better materials for robotics and exoskeletons can be created. This could also lead to the development of foldable, stackable structures that expand when shot into space.
Ghosh currently collaborates with Siemens to create snakelike robots that can be used for turbine inspection. These robots, equipped with borescopes, can fit and maneuver safely within all of the nooks and crannies of the turbine, leading to a more effective and efficient inspection. They can be combined and stacked together to create varying lengths, and can also be useful during search and rescue missions.
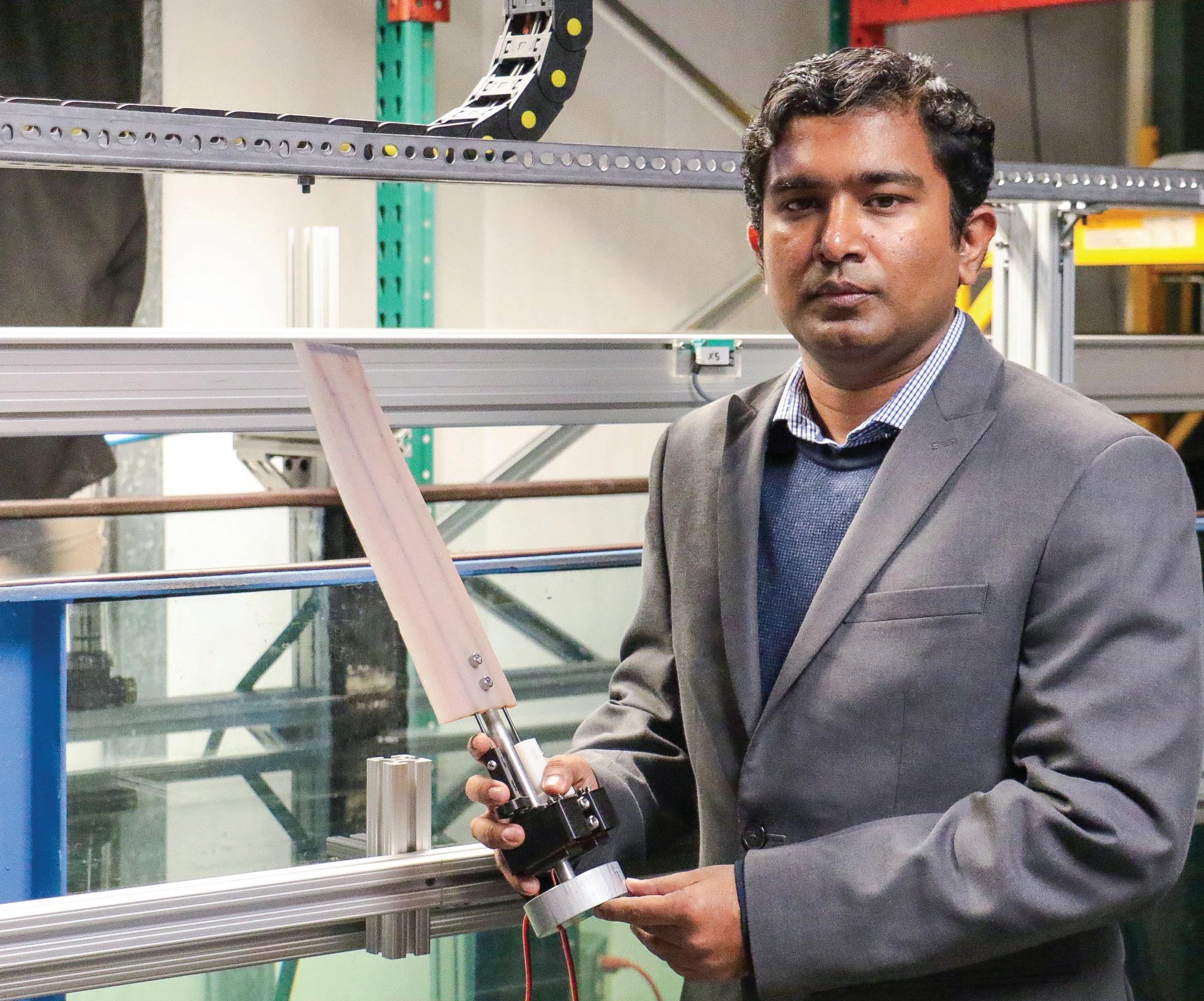
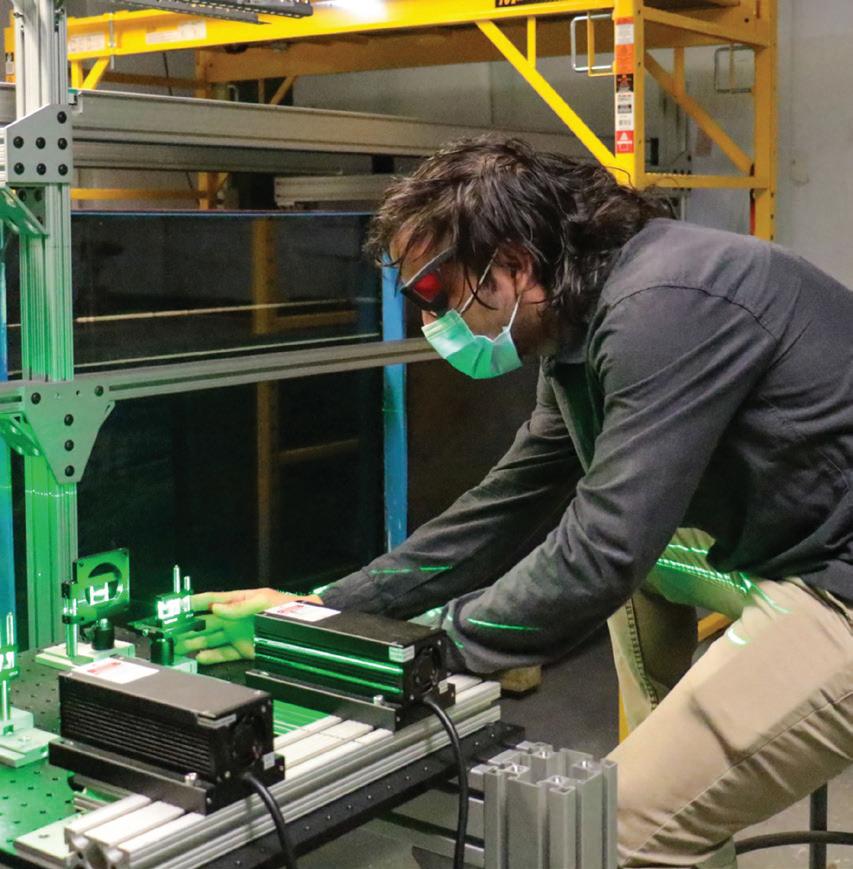
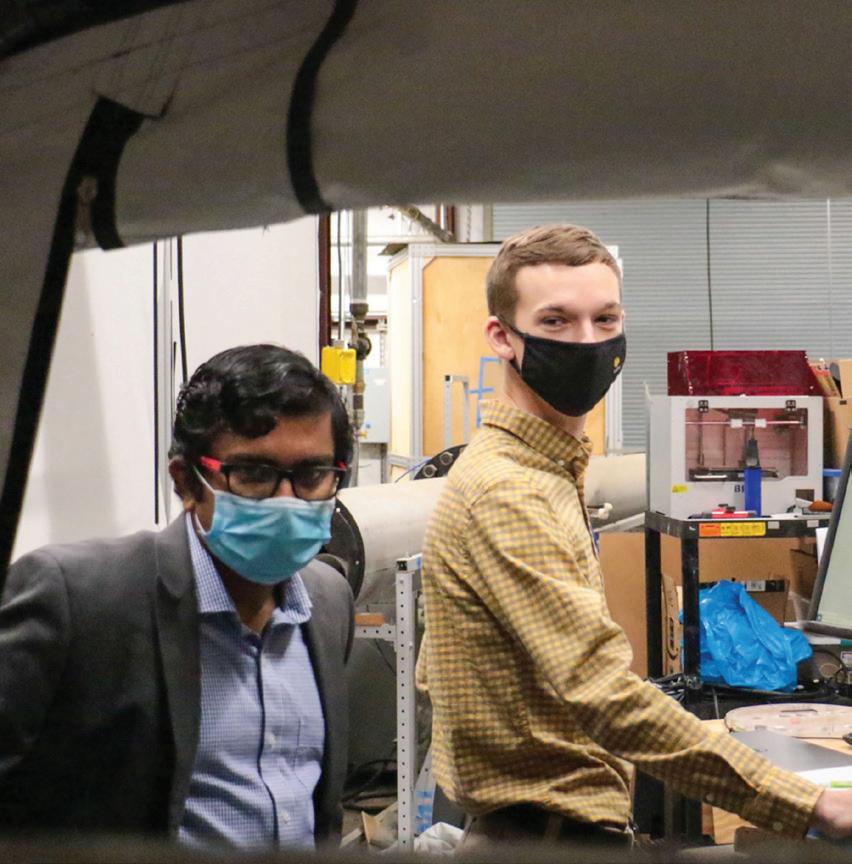
EFML Lab
Experimental Fluid Mechanics Lab
Led by: Samik Bhattacharya, Ph.D.Many airplane passengers grit their teeth, white-knuckle their armrests and say a silent prayer for their flight to go smoothly. They know that any sudden disturbance in airflow can cause turbulence — and in turn, a severe case of anxiety.
But in smaller aircraft, such as unmanned aerial vehicles or micro air vehicles, turbulence is more than a bumpy ride. It can severely affect the stability of these vehicles and cause them to lose control. On the other hand, nature’s natural fliers — birds — know how to retain control during airflow disturbances.
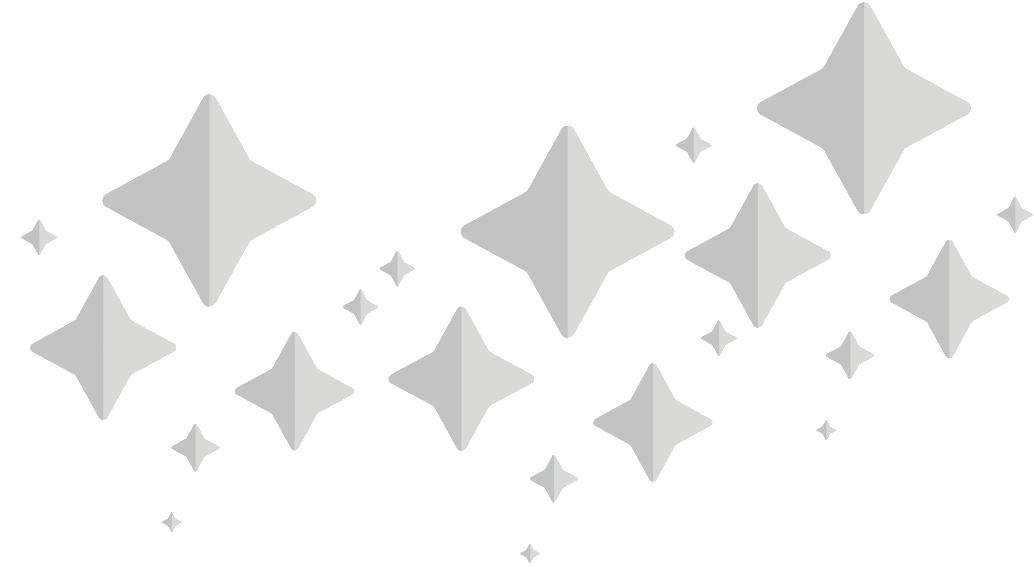
Assistant Professor of Aerospace Engineering Samik Bhattacharya is studying the morphing power of bird wings in turbulence through a three-year, $441,000 grant from the U.S. Air Force Office of Scientific Research. The goal is to uncover the secrets of bird stability and engineer a comparable solution for UAVs and MAVs.
Bhattacharya and his team are also studying the perching manuevers of birds and their implications for aircraft design. With the aid of 3D printed wings and a towing tank, the team at the EMFL lab are ready to uncover the secrets of avian flight and how they can transform modern aviation.
With the support of a National Science Foundation CAREER Award, team is also uncovering the mechanics of manta rays and how they can be applied unmanned underwater vehicles.
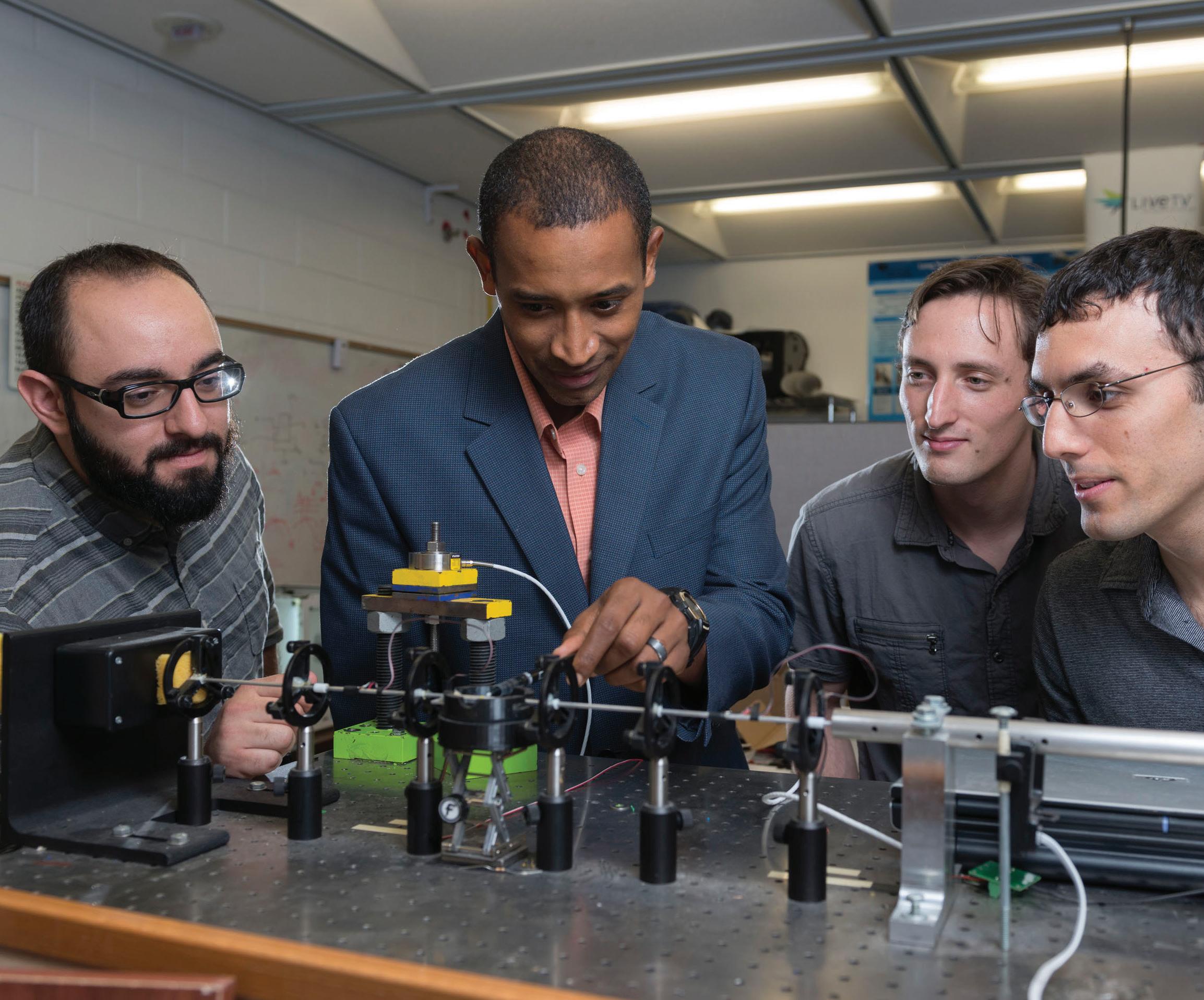
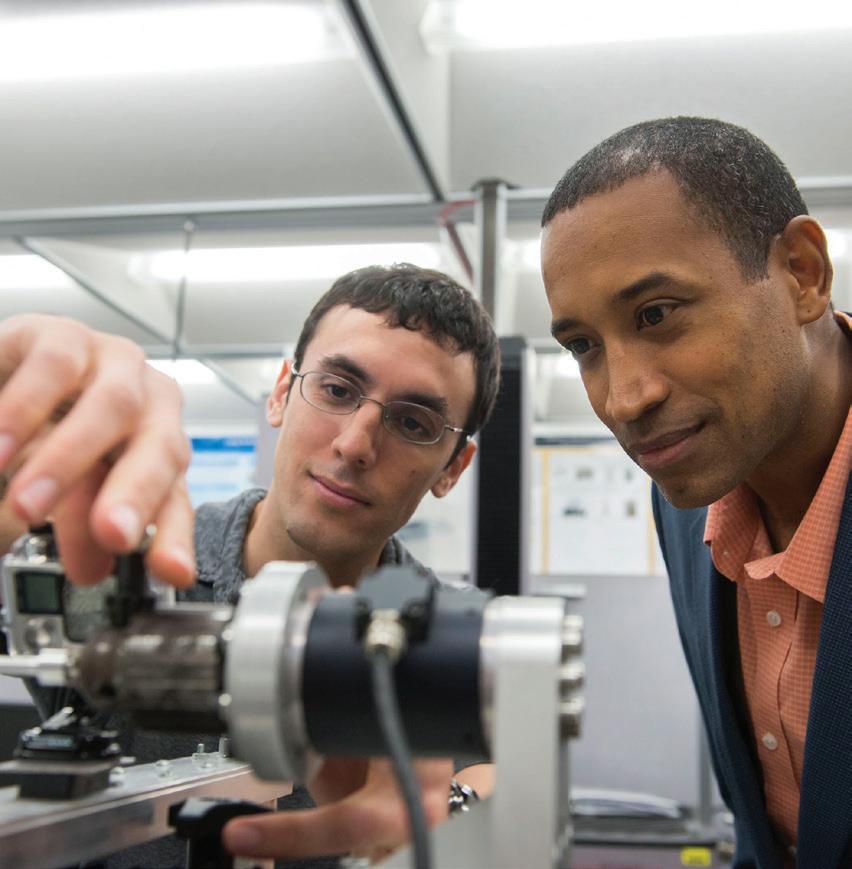
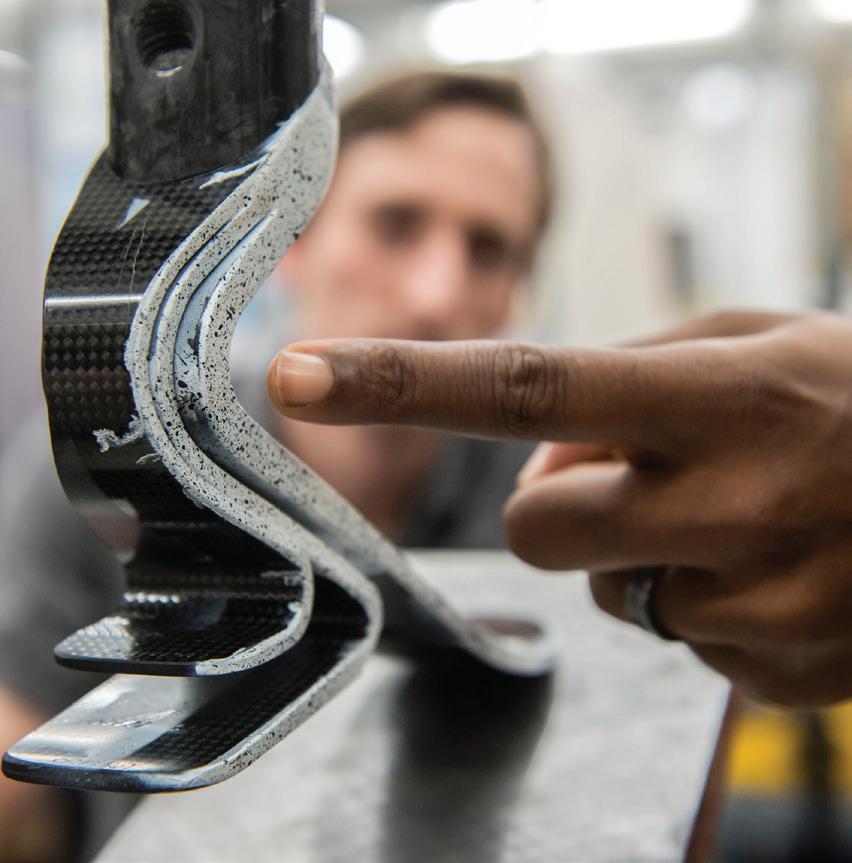
MOMRG Lab
Mechanics of Materials Research Group
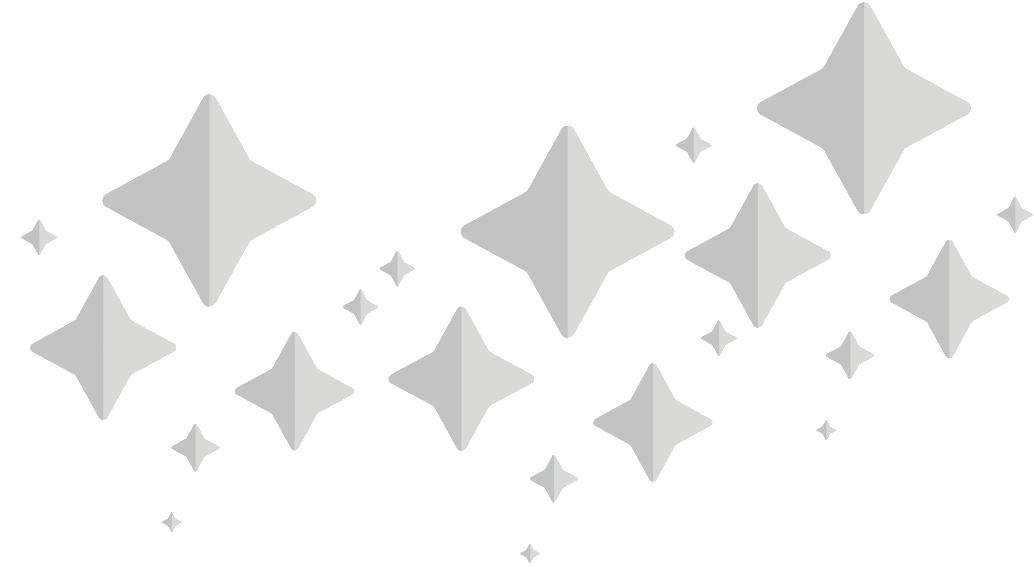
The hottest components of a machine dictate the life of a structure. If designers know how long materials will last in extreme environments, they can manufacture more durable machines. With the aid of continuum-level models, Professor Ali Gordon and his team in the Mechanics of Materials Research Group estimate the behaviors of essential materials to extend the life and reliability of aircraft and spacecraft. They continually master novel techniques in experimental, computational and theoretical mechanics while individually applying that knowledge to break ground on specific problems.
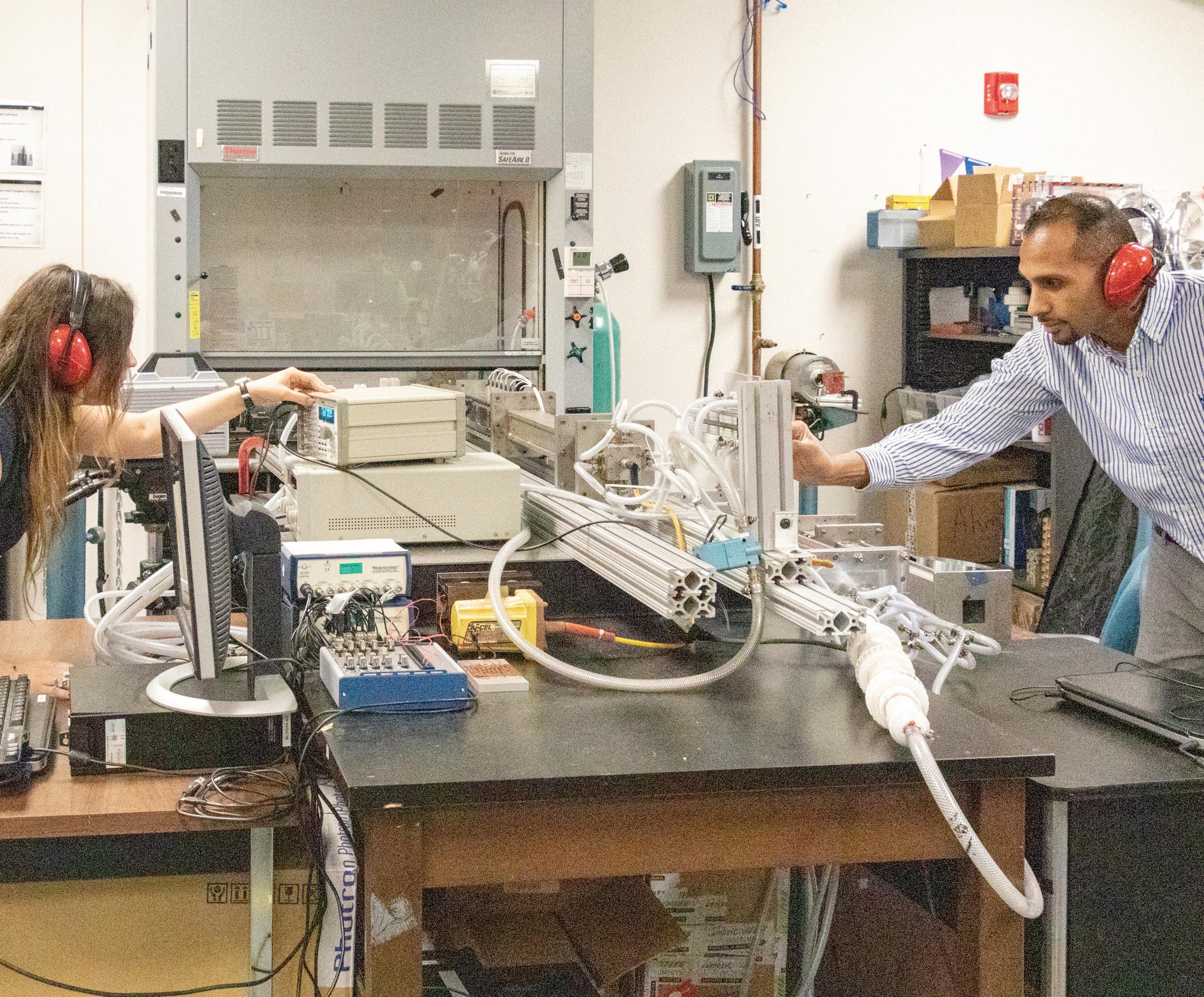
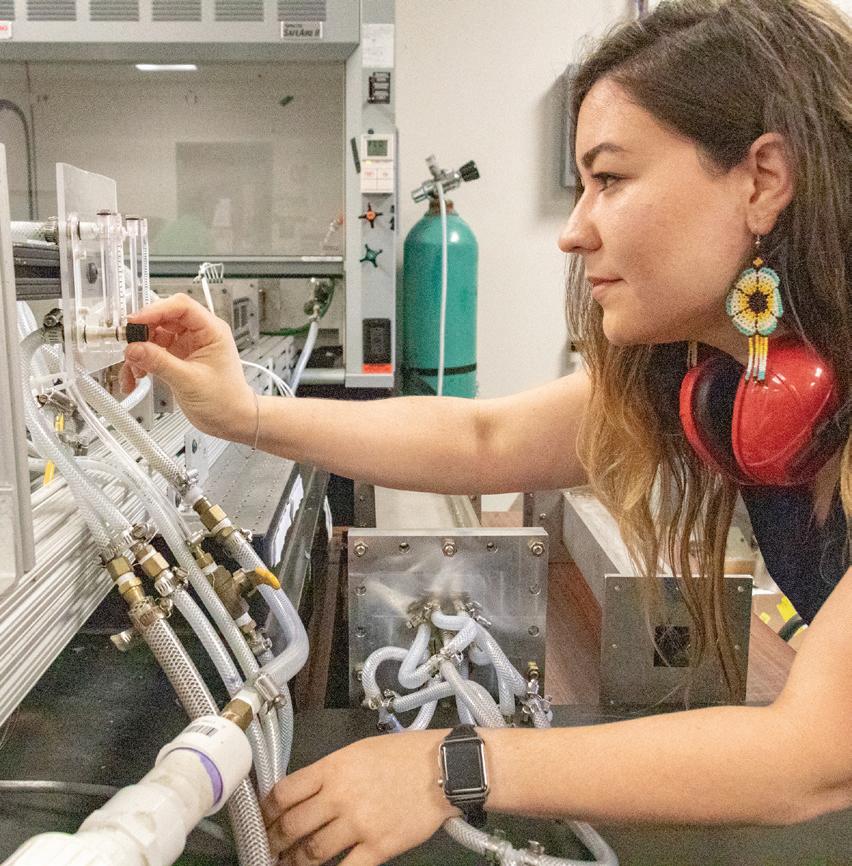
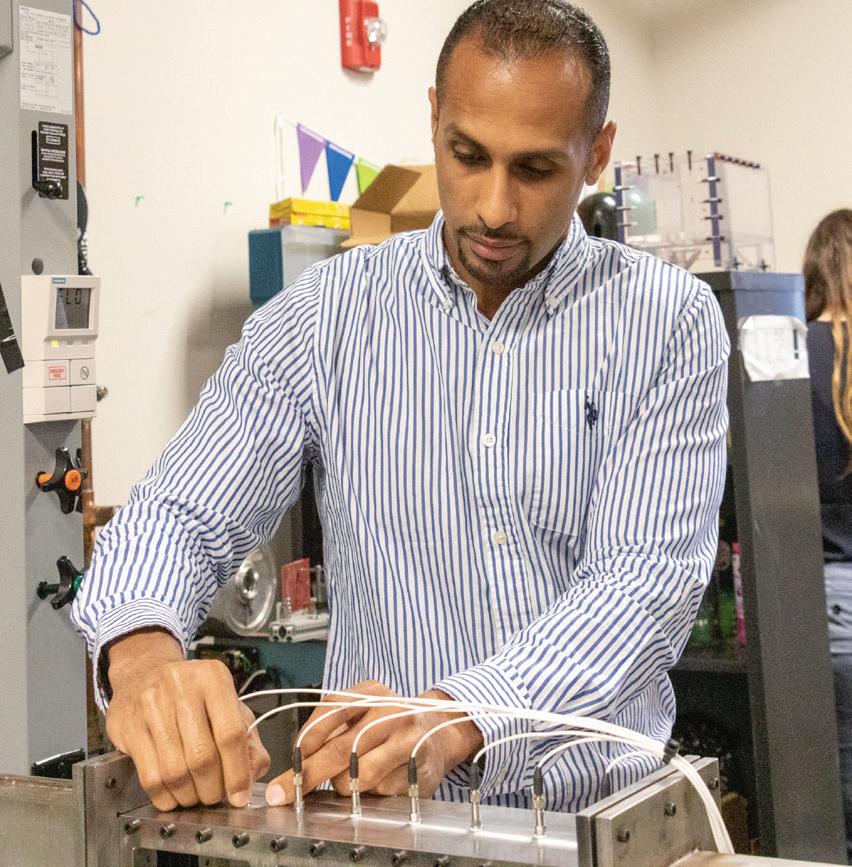
PERL Lab
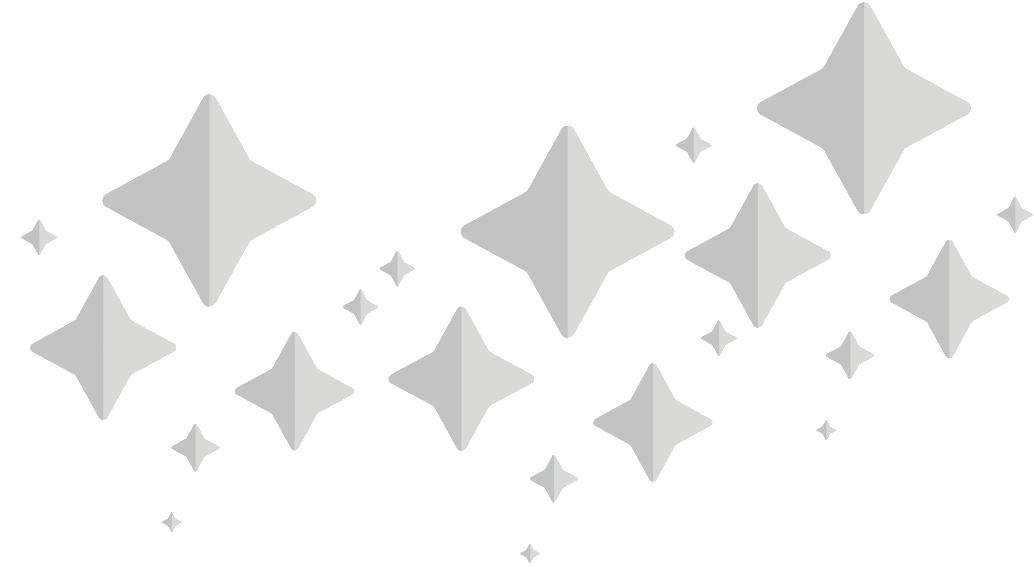
Propulsion and Energy Research Lab
Led by: Kareem Ahmed, Ph.D.What if you could travel from New York to California in 30 minutes or less? That fantasy could become a reality through the research conducted in the Propulsion and Energy Research Lab.
Assistant Professor Kareem Ahmed leads a large research team that investigates multiphase turbulent reacting flows, clean combustion strategies, hypersonic and supersonic compressible reacting flows, and alternative fuels for the next generation advanced propulsion and combustion energy technologies. The PERL Lab is the only lab in the nation that is equipped with a turbulent shock tube for testing hypersonic reactions.
The team’s recent discovery — that subsonic flames can be turned into hypersonic flames with a little turbulent mixing — could open the door for air travel five times faster than the speed of sound. The science behind is this is key to a second discovery — the mechanism behind supernovae explosions, used by scientists for models to understand the origin of the universe.
Ahmed’s research has been recognized by Science magazine, the Combustion Institute and the Department of Defense. He has also garnered more than $6.47 million in research funding from organizations such as NASA, Siemens, the Department of Energy and Aerojet Rocketdyne, that will allow him to further develop his research on hypersonic travel.

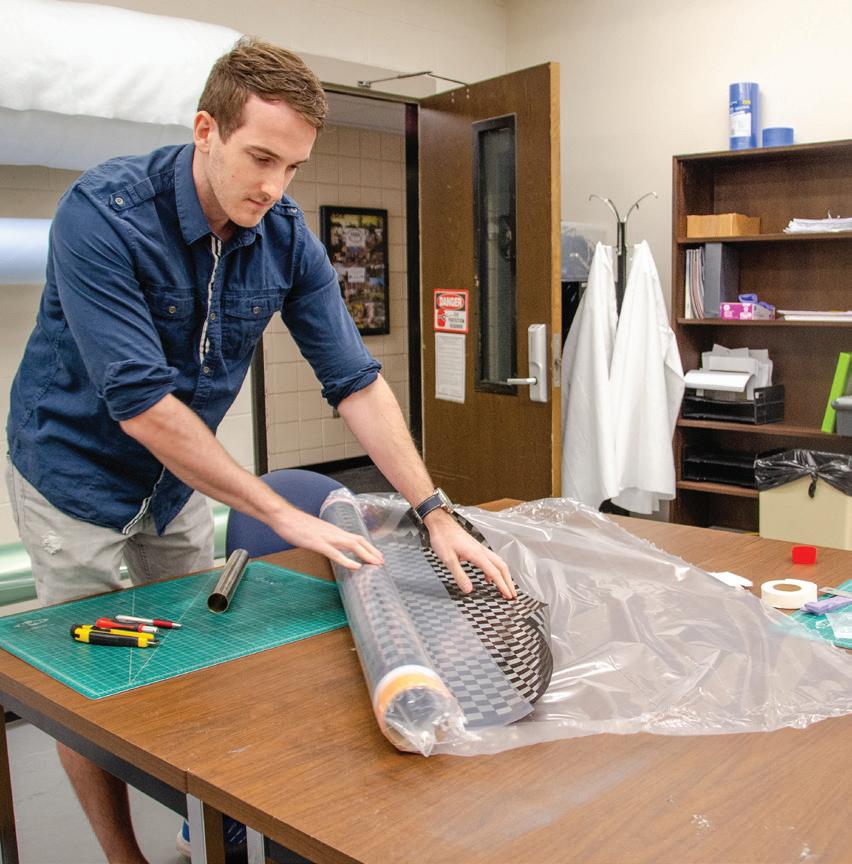
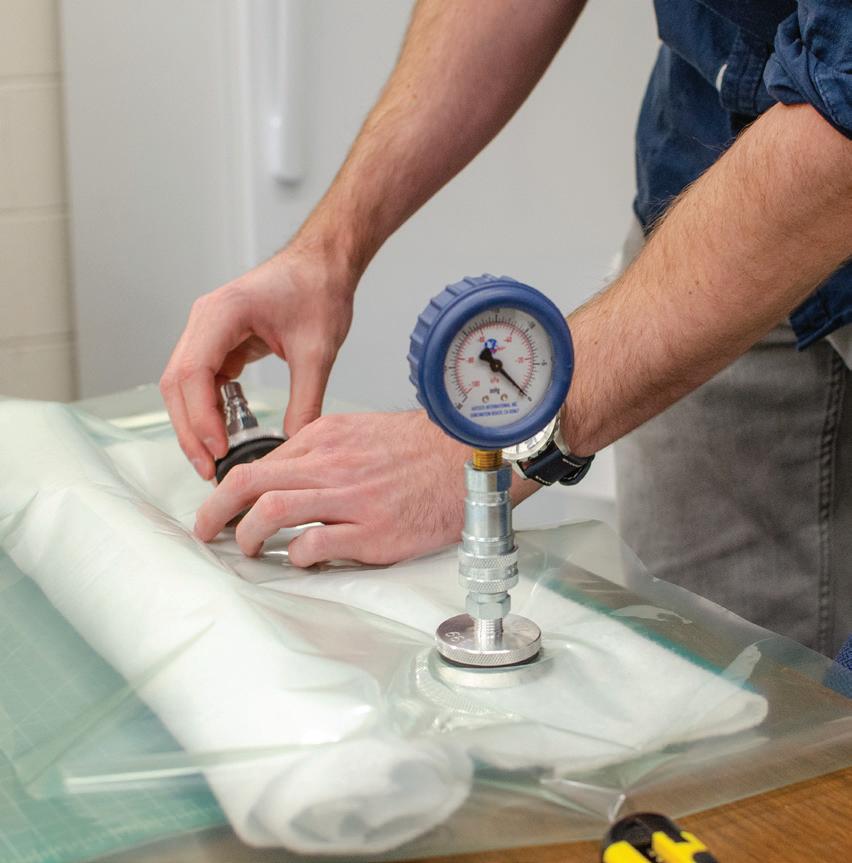
SMD Lab
Structures and Materials Design Lab
Led by: Kawai Kwok, Ph.D.
Sending devices into space is tricky — they are large in size but rocket cargo space is small. Imagine fitting a structure the length of a Boeing 737 into a truck compartment. This is the challenge undertaken by the research group of Assistant Professor Kawai Kwok.
In the Structures and Materials Design Lab, Kwok and his team use innovative concepts to design deployable spacecraft structures that can be efficiently packaged inside the payload volume of launch vehicles and reliably deployed to their functional size in orbit.
Through a combination of computational modeling, experimental characterization and prototype fabrication, Kwok and his team seek to explain the underlying mechanics of thin-shell structures and advanced composite materials, and come up with novel structure designs.
The SMD Lab closely collaborates with NASA and a few aerospace companies specializing in deployable space systems and composite material solutions.
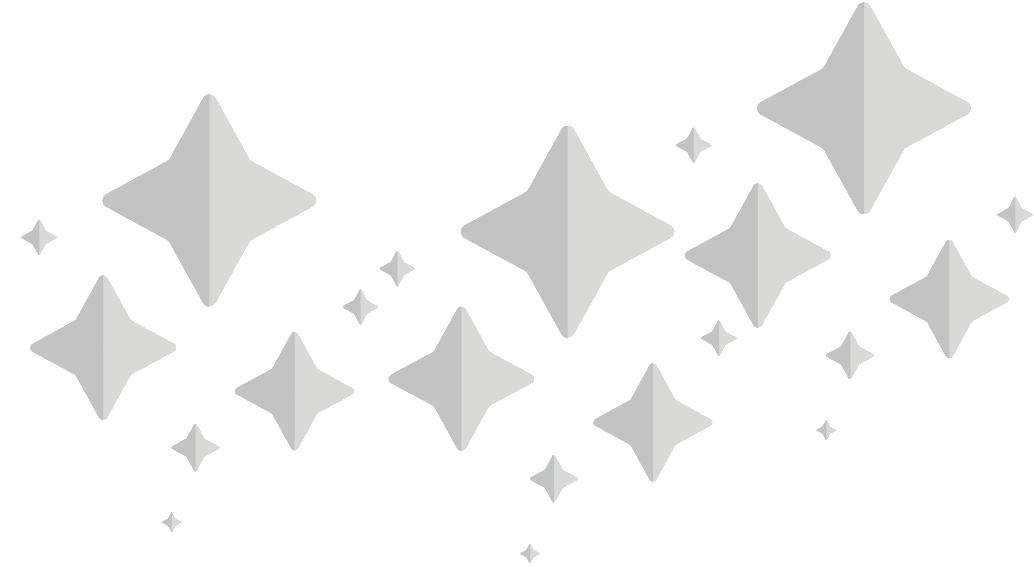

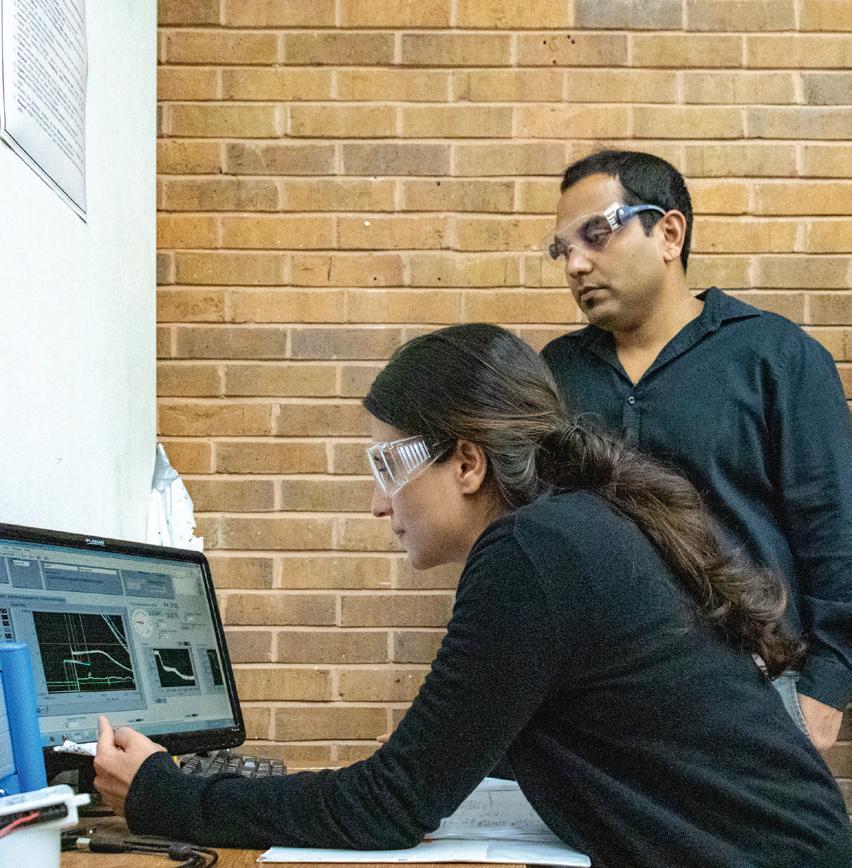
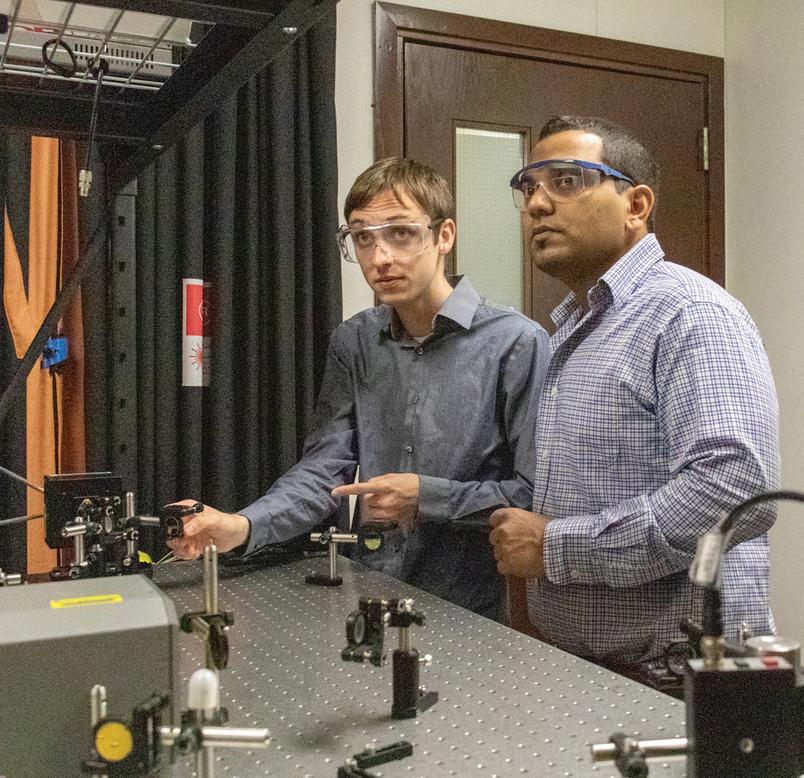
Vasu Lab:
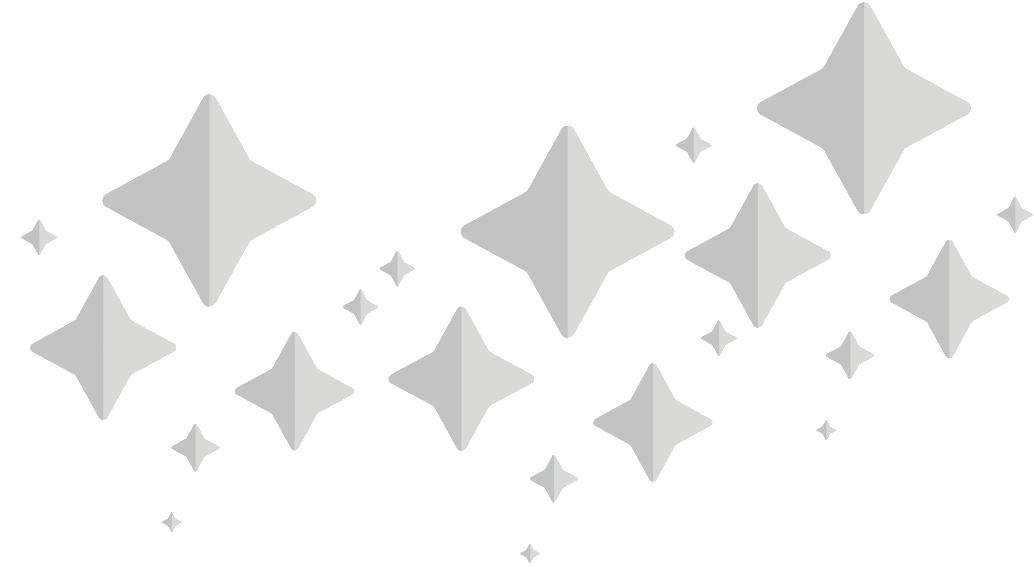
Combustion, Propulsion, Laser Diagnostics, Absorption Sensors and Fuels
Led by: Subith Vasu, Ph.D.
Not too many researchers would venture inside of a fire, but that’s exactly what Associate Professor Subith Vasu has done. With his research team in the Vasu Lab, he has developed a method that uses lasers to measure the temperature, as well as the concentrations of different molecules, in such a high-heat environment. This method could aid researchers in fighting fires and explosions, advanced energy conversion strategies using supercritical CO2, and creating cleaner, more efficient engines for space travel.
This method was also instrumental in Vasu’s recent work on the proper destruction of chemical weapons, sponsored by the Defense Threat Reduction Agency. Vasu has also received a $1 million Young Faculty Award from DARPA to develop a handheld device that can detect trace amounts of fentanyl, along with deadly toxins that result from chemical warfare. Vasu Lab has garnered more than $10 million in research funding and recognized by multiple professional agencies and international agencies including U.N. Currently, the lab has ongoing research projects from FAA, NASA, DOE, Air Force, Navy, Army, DARPA, DTRA, and several industries.
Biomedical Engineering
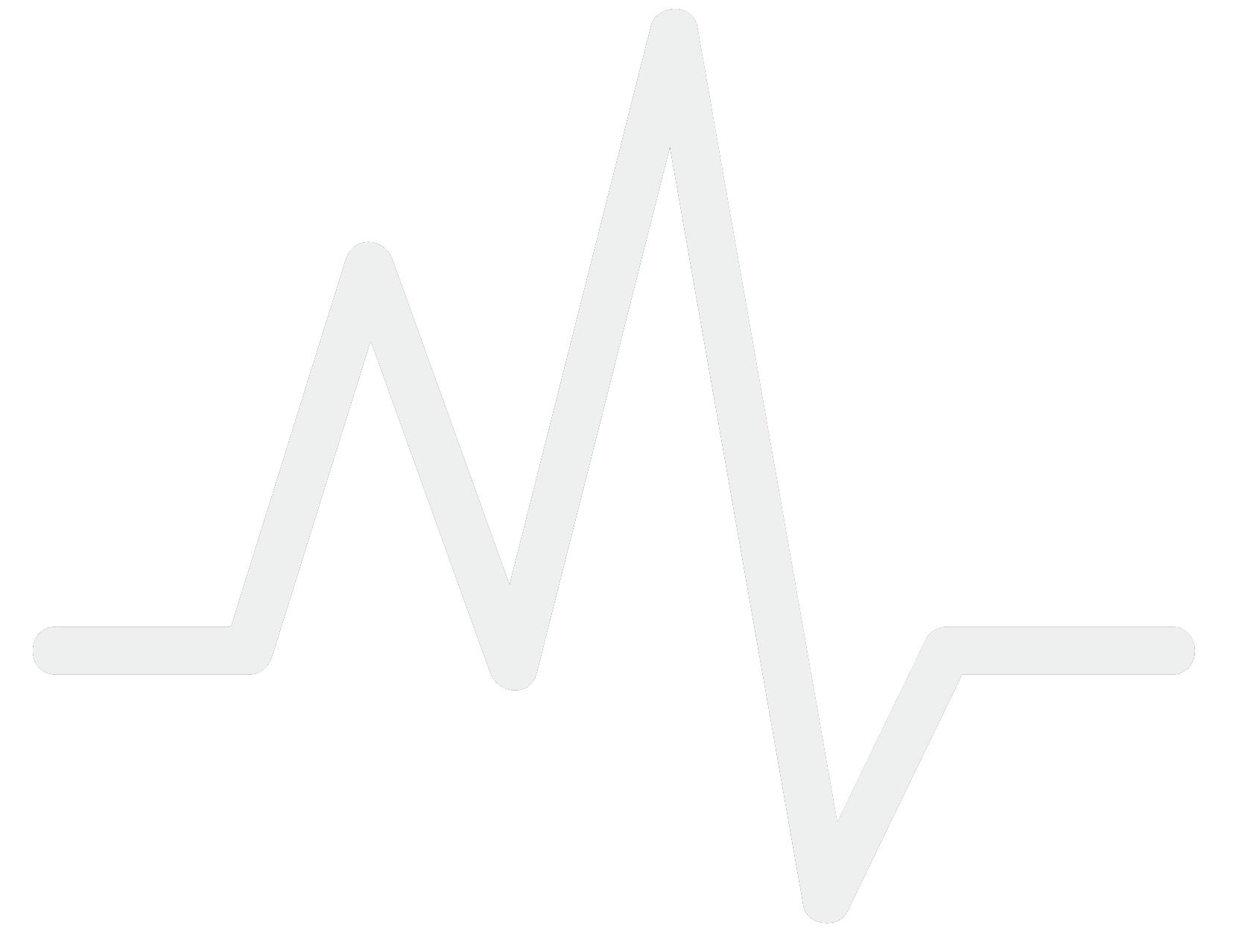
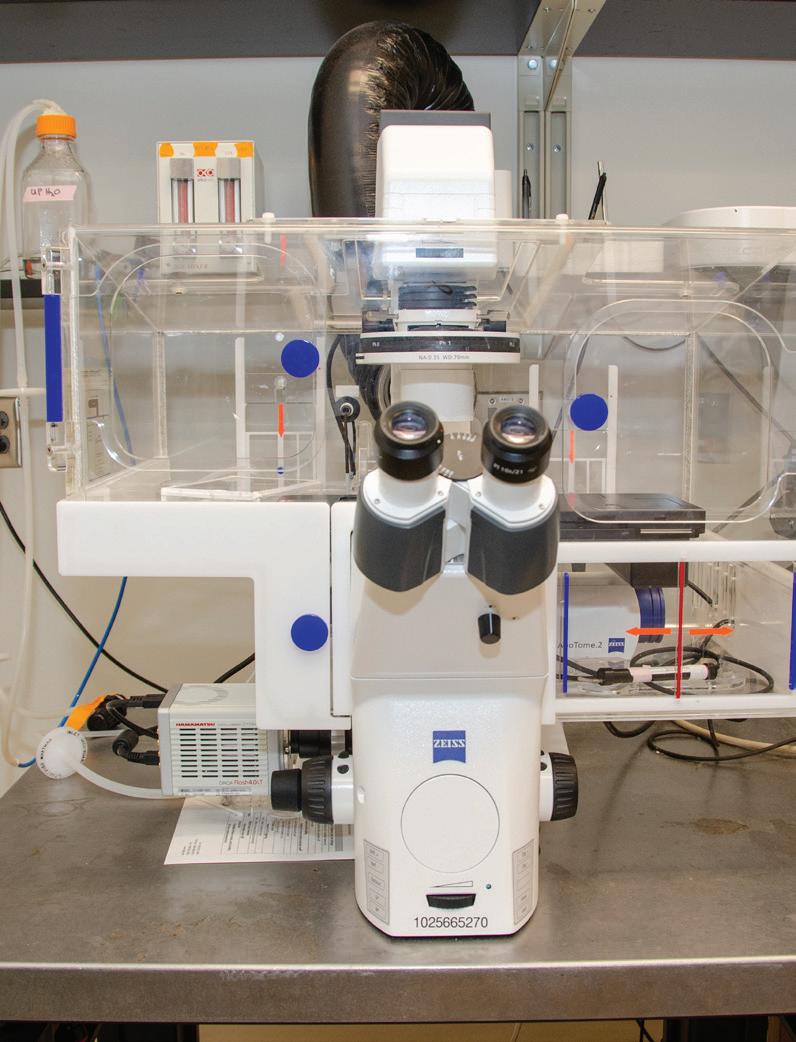

LAB DIRECTORY
Biodesign Program in Rehabilitation Engineering
Sudesha Pal
Associate Lecturer spal@ucf.edu
mae.ucf.edu/BPRE
Biomedical Acoustics Research Lab
Hansen Mansy
Associate Professor
hansen.mansy@ucf.edu
mae.ucf.edu/BARL
Biomedical and Process Modeling Lab
Olusegun Ilegbusi Professor
olusegun.ilegbusi@ucf.edu
mae.ucf.edu/Ilegbusi
BRaIN Lab
Helen Huang
Associate Professor hjhuang@ucf.edu
mae.ucf.edu/BRAIN
Cellular Biomechanics Lab
Robert Steward
Assistant Professor rstewardjr@ucf.edu
Computational Biomechanics Lab
Luigi Perotti
Assistant Professor luigi.perotti@ucf.edu
mae.ucf.edu/luigiperotti
Computational Mechanics Lab
Alain Kassab
Professor, Biomedical Engineering Program Director
alain.kassab@ucf.edu
mae.ucf.edu/
ComputationalMechanicsLab
NeuroMechanical Systems Lab
Qiushi Fu
Assistant Professor qiushi.fu@ucf.edu
REAL Lab
Hwan Choi
Assistant Professor hwan.choi@ucf.edu
mae.ucf.edu/REAL
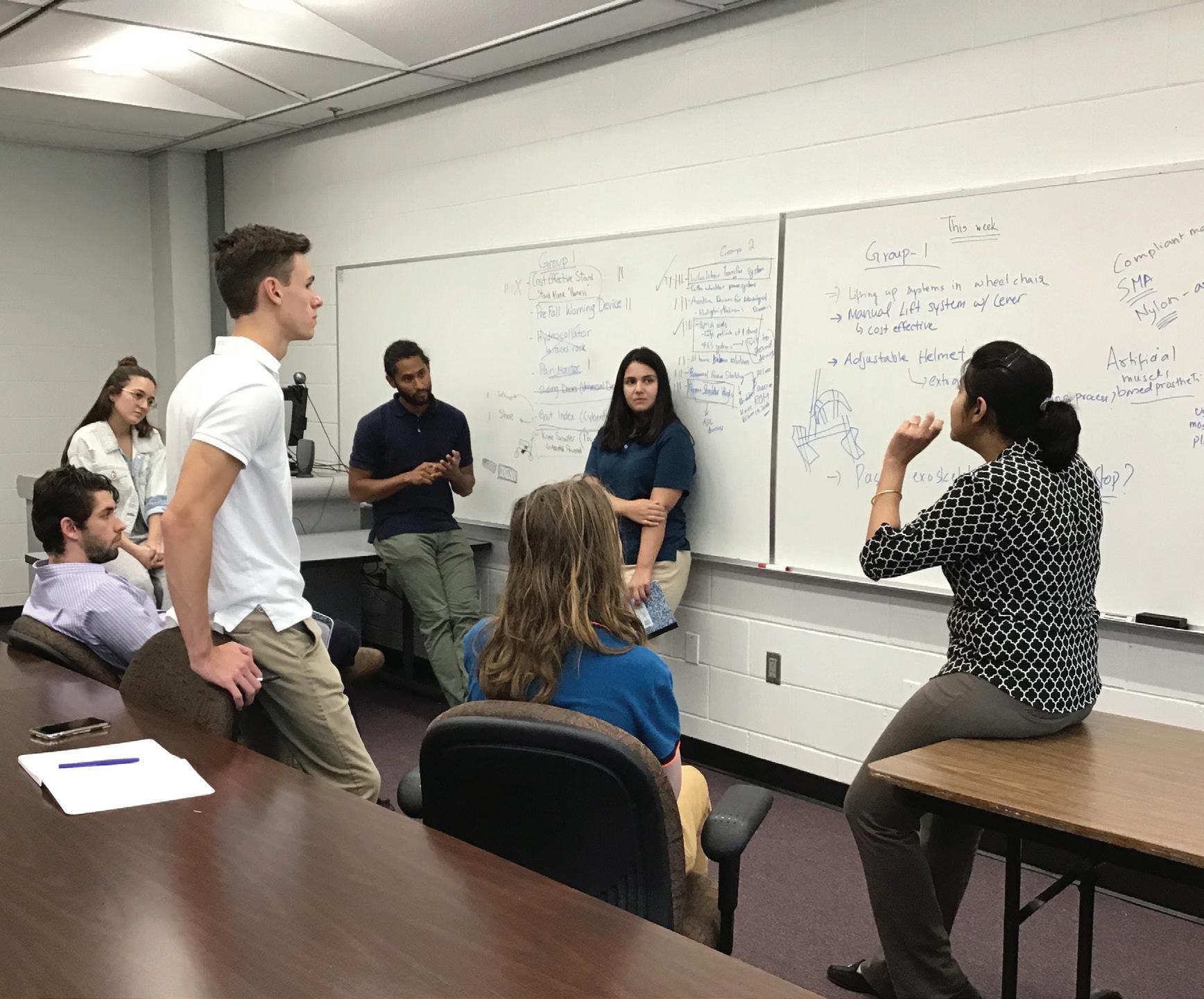
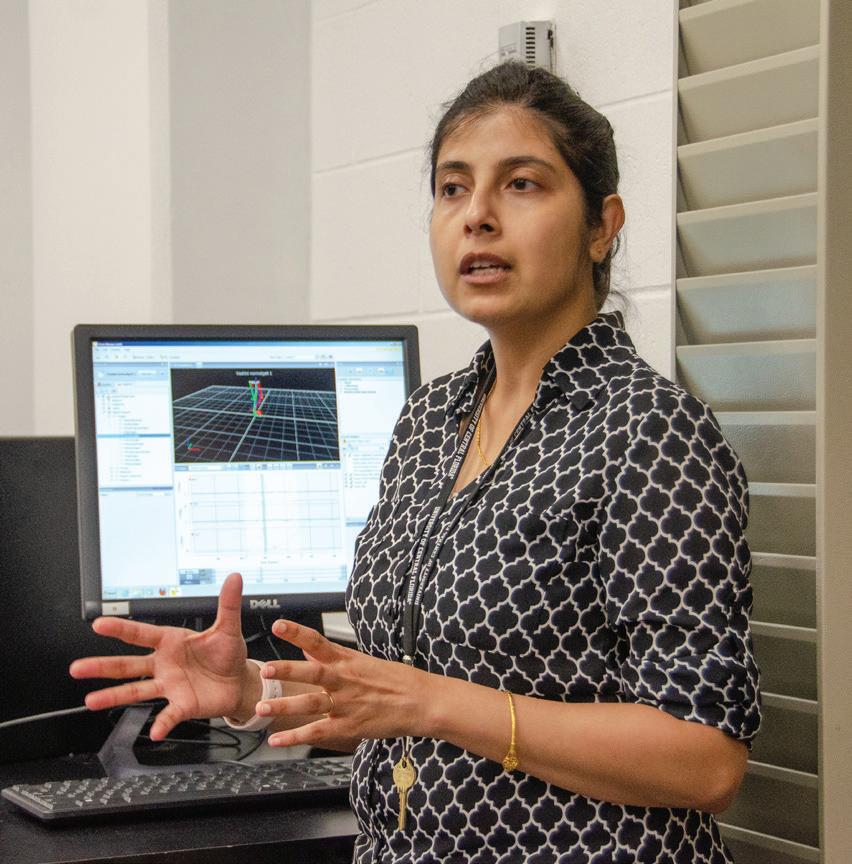
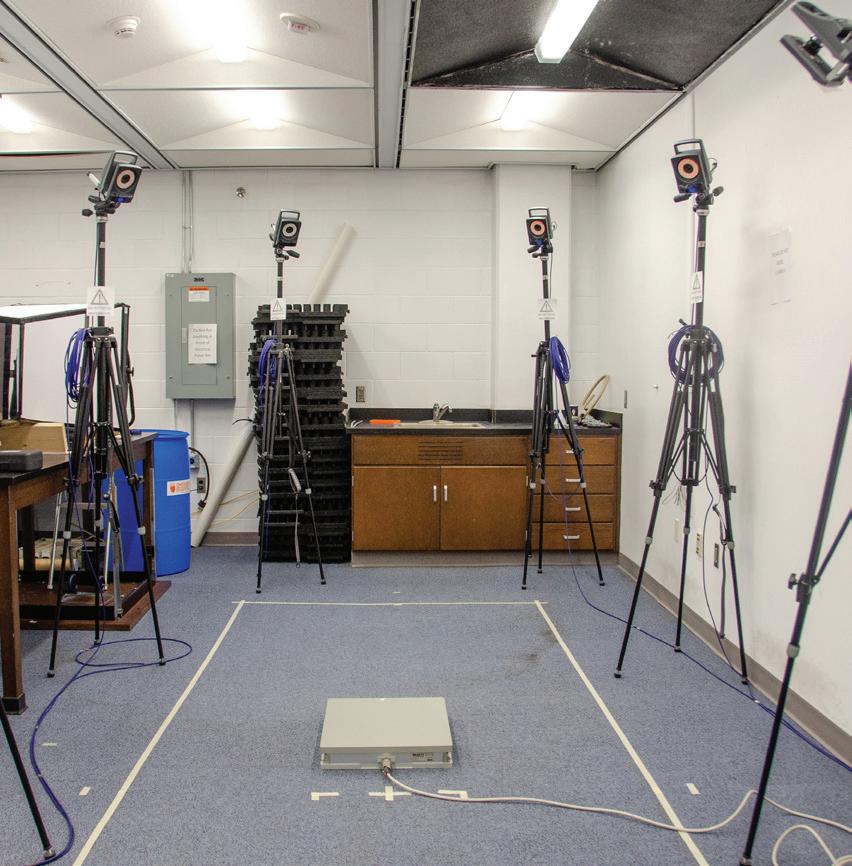
BPRE Program
Biodesign Program in Rehabilitation Engineering
Led by: Sudeshna Pal, Ph.D.For Lecturer Sudeshna Pal, engineering education is just as important as engineering research. Through her Biodesign Program in Rehabilitation Engineering, undergraduate students receive a real-world education via a six-week paid internship at various rehabilitation centers, physical therapy clinics and prosthetic clinics across Central Florida.
By the end of the program, students have a better understanding of user needs in rehabilitative devices, can more effectively comunicate with clinicians and clinical staff, and have the ability to identify unmet patient needs that could potentially be addressed in future engineering courses.
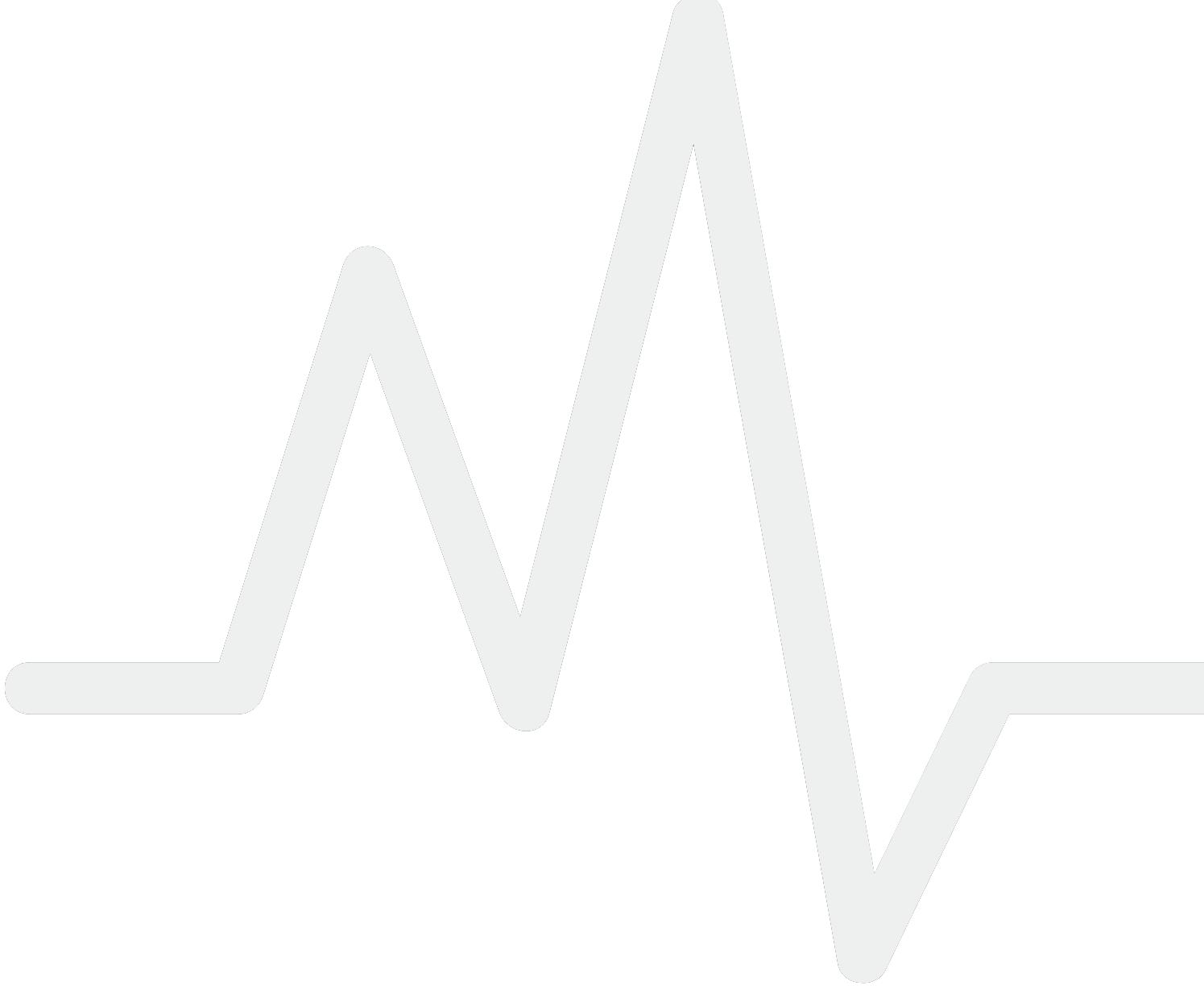
The program is a collaboration between Pal and other UCF researchers, and is sponsored by the Eunice Kennedy Shriver National Institute of Child Health and Human Development of the National Institutes of Health.
Through a second NIH grant, Pal provides an educational training program for students interested in human motion design projects. Using a Vicon motion capture analysis system, which includes multiple cameras, sensors and arm markers, Pal and her students can perform a variety of studies related to biomechanics, including a comparison of the gait in individuals with prosthetics versus those without them.

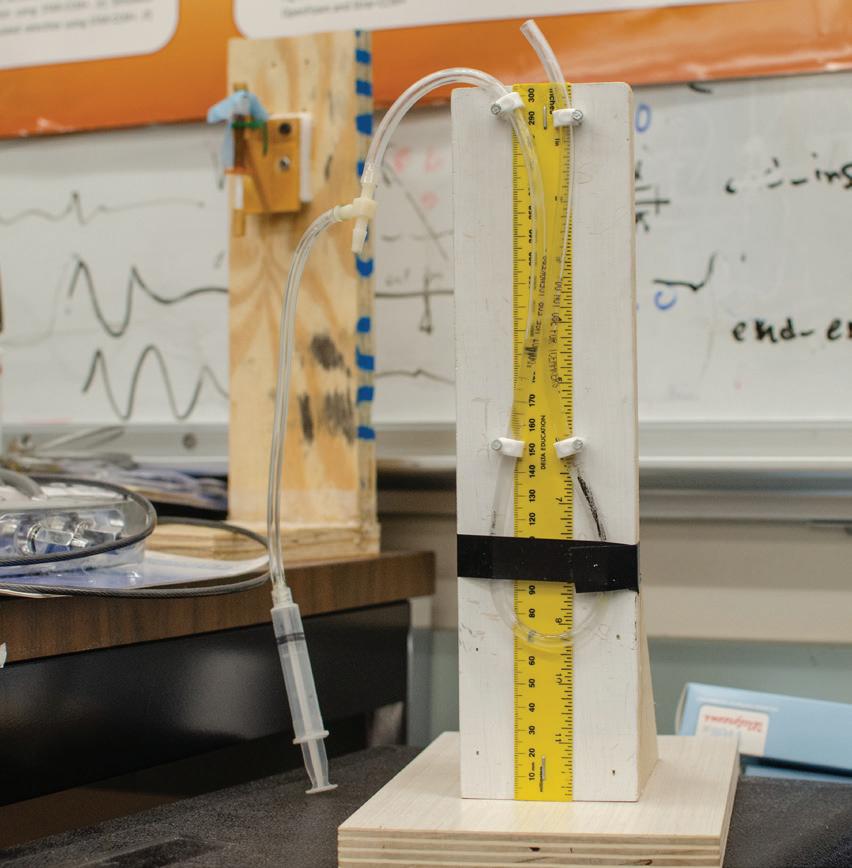
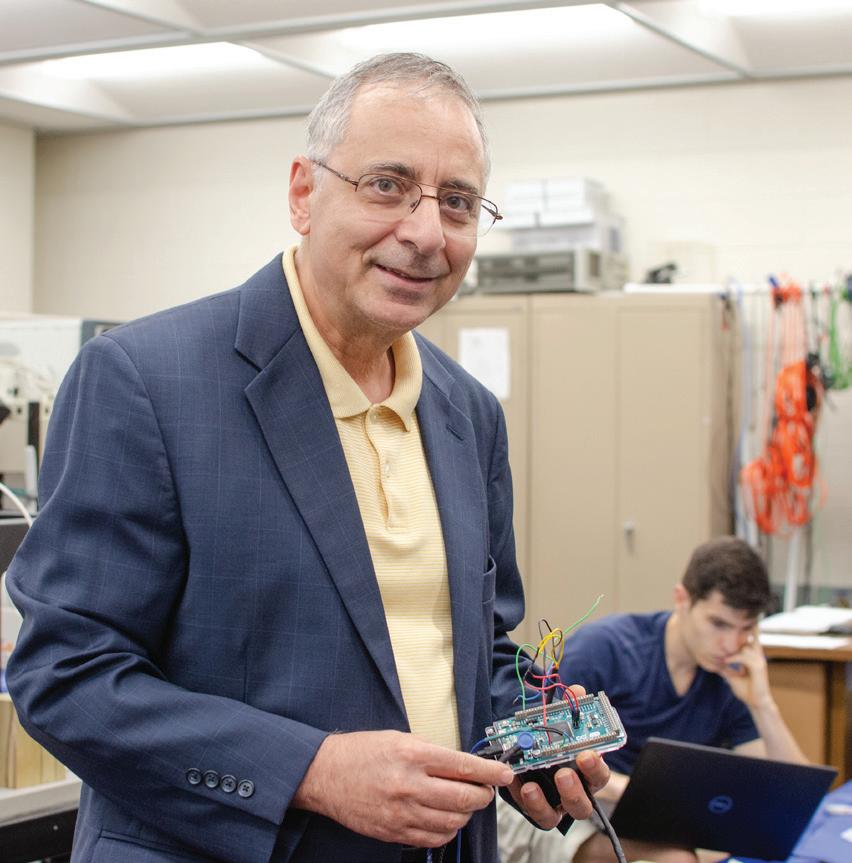
BARL Lab
Biomedical Acoustics Research Lab
Led by: Hansen Mansy, Ph.D.What if we could detect and monitor serious medical problems such as heart failure, vascular stenosis, elevated intracranial pressure, and small bowel obstructions just by listening to their vibro-acoustic emissions?
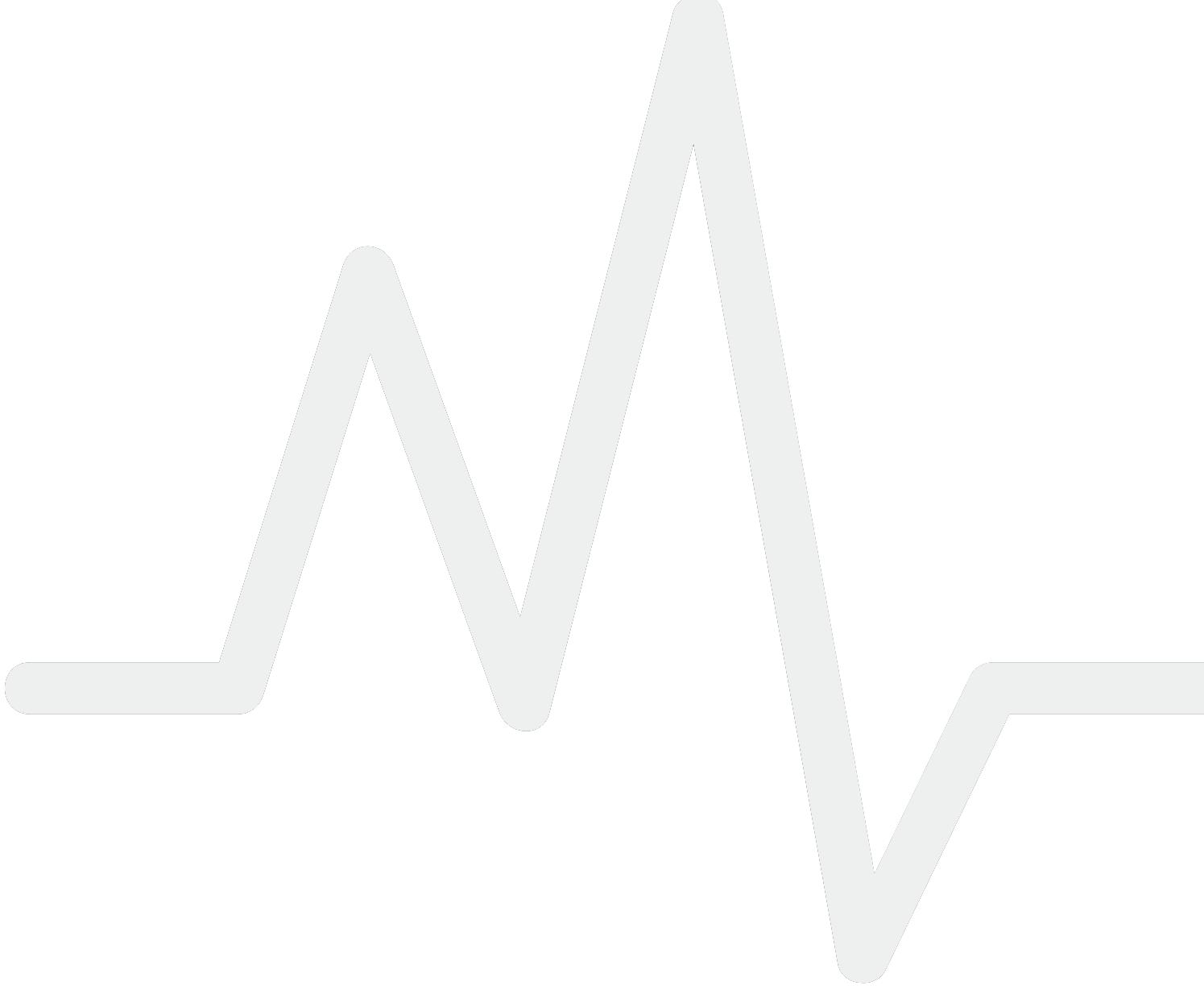
In the BARL Lab, Professor Hansen Mansy has spent the past 25 years investigating vibroacoustic phenomena in the human body and defining their time and frequency signatures. He combines knowledge in novel sensor design, computerized measurements, digital signal processing and machine learning, medical imaging and medical sciences to find the acoustic correlates of certain pathologies. This research has catalyzed the development of low-cost, noninvasive, portable technologies that are suitable for clinical use, home monitoring and telemedicine.
Mansy is developing several revolutionary devices, including one that can detect elevated intracranial pressure using high-sensitivity sensors that can measure the tiny pulsation of the tympanic membrane. Another device under development will be able to detect hip dysplasia in infants using vibro-acoustic stimulation and a cell phone. Through a $1.3 million grant from the National Institutes of Health, he is also creating a device that captures low-frequency chest wall vibrations, which contain signs of cardiac deterioration in heart failure patients. While this heart monitor would initially be used by healthcare providers, the long-term goal is to create a second-generation monitor that could be used for home monitoring. This aims to improve patients’ quality of life and reduce mortality and healthcare costs.
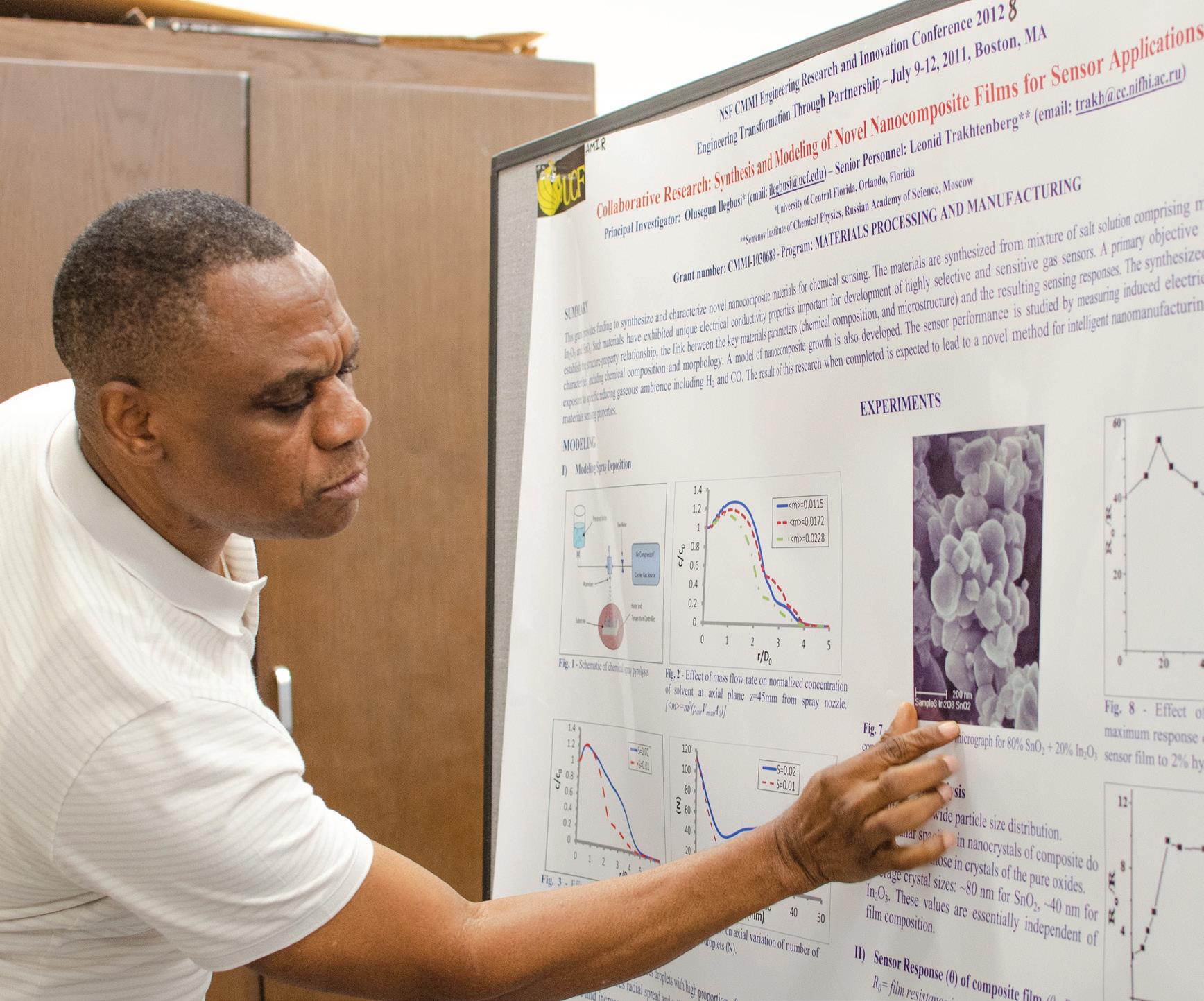
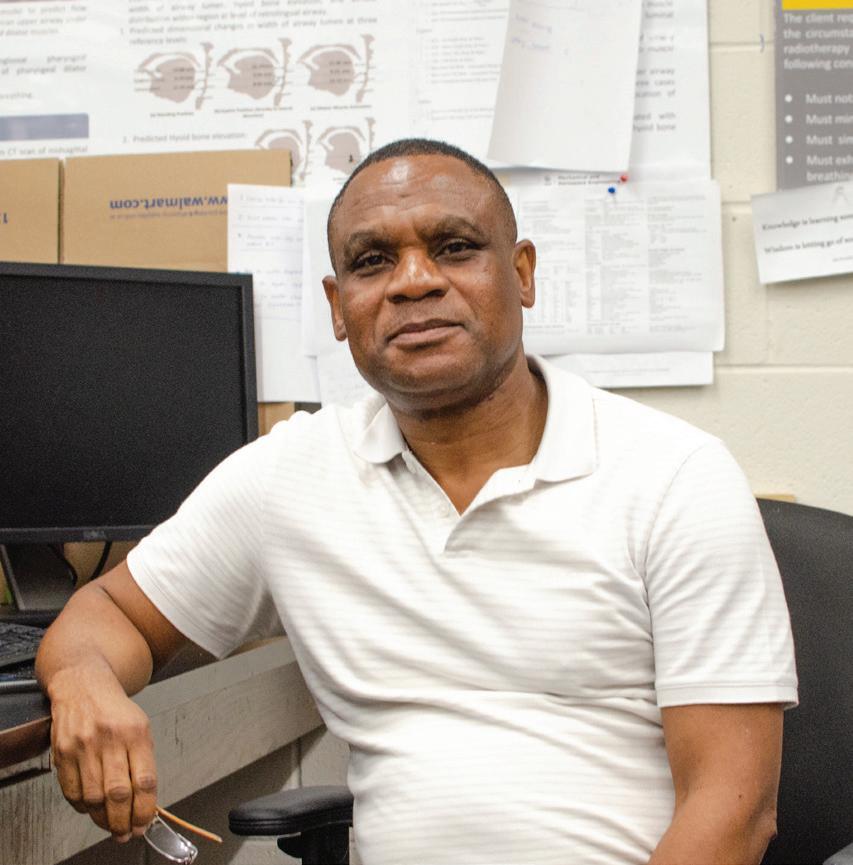
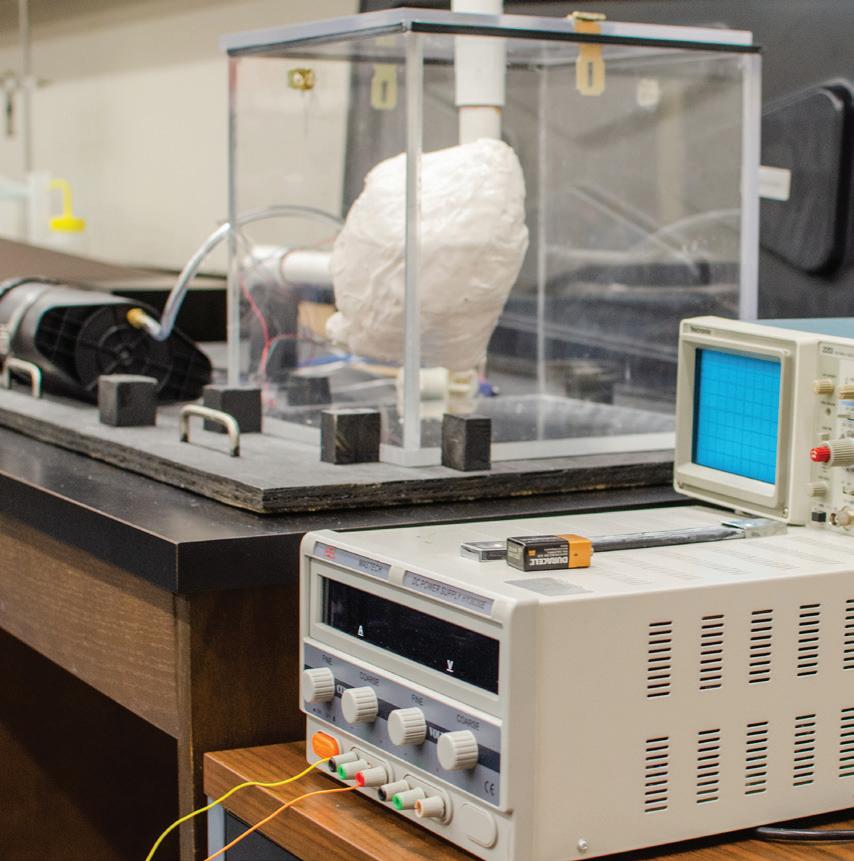
BPML Lab
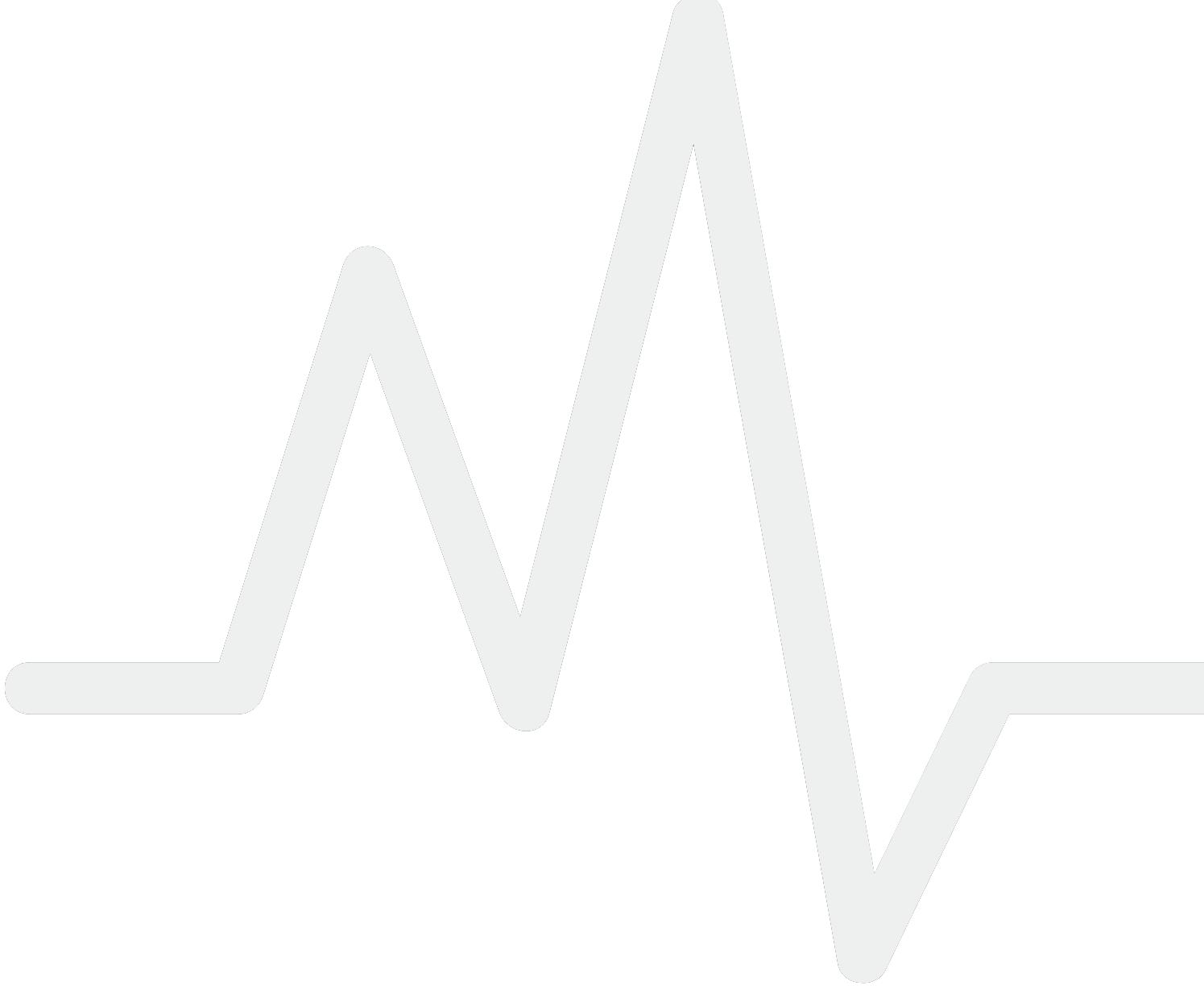
Biomedical and Process Modeling Lab
Led by: Olusegun Ilegbusi, Ph.D.Lung cancer treatment is difficult — not only for the patient, but for the doctor as well. The lungs are constantly in motion, so targeting tumors without killing healthy tissue is next to impossible.
But in the BPM Lab, Professor Olusegun Ilegbusi has found the solution to this problem. In collaboration with aerospace engineering Professor Jihua Gou and a UCF alumnus, Ilegbusi created a 3D lung simulator that can mimic patients’ breathing patterns. With this information, doctors can more precisely treat lung cancer patients, leading to fewer side effects and fewer rounds of treatment.
The trio of researchers also founded SegAna, a startup that develops the patented software for the simulator. SegAna has already been awarded a $250,000 grant from the National Science Foundation and has raised $4 million dollars from investors. The simulator has been tested at six different hospitals across the U.S. and recently received approval from the FDA.
Ilegbusi collaborates with UCF researchers to determine how tongue cancer affects patients’ ability to swallow and how the coughing mechanism is affected in individuals with throat cancer or Parkinson’s disease. He has also unlocked the key to stem cell generation by calculating the precise conditions needed for them to grow.
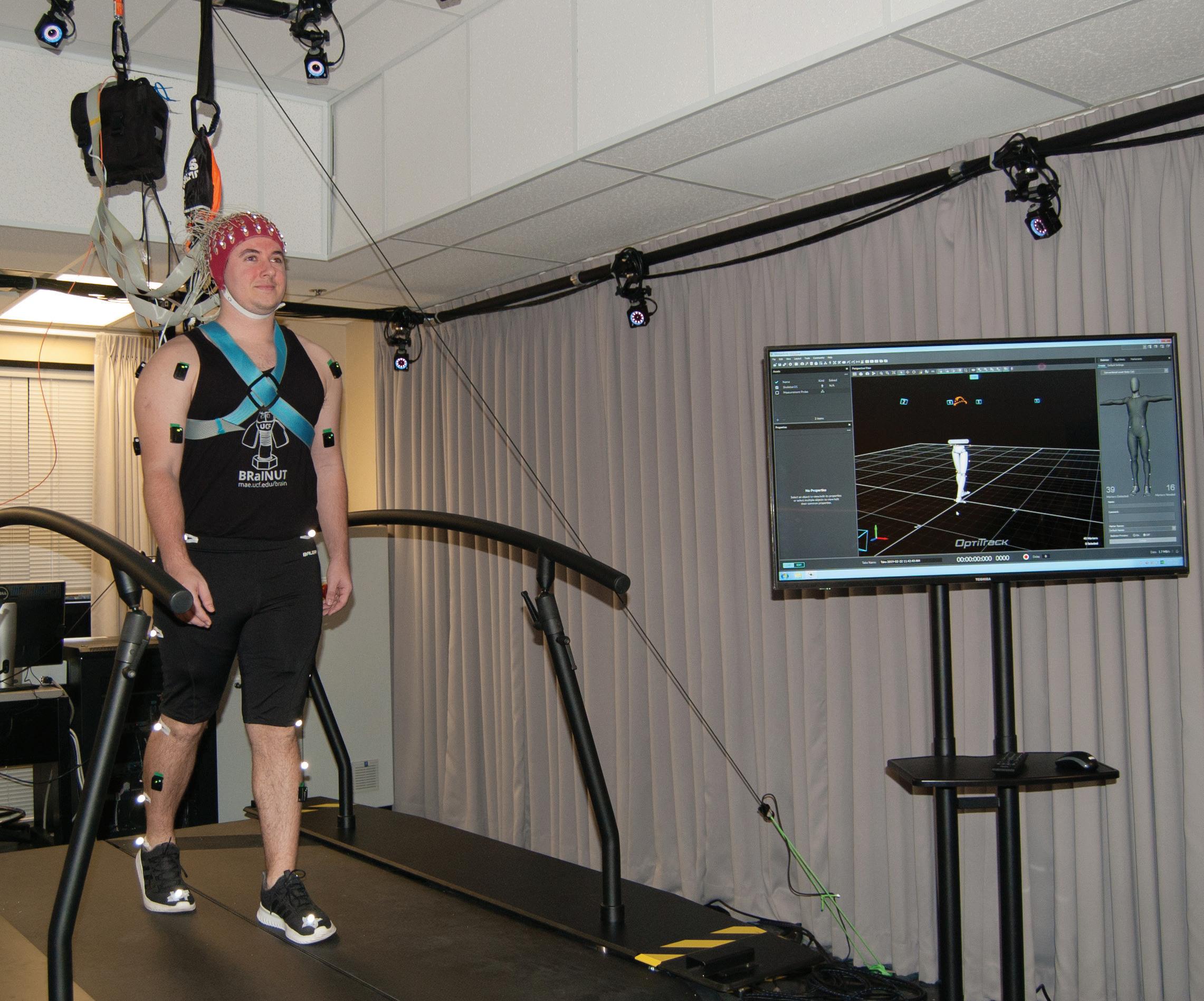

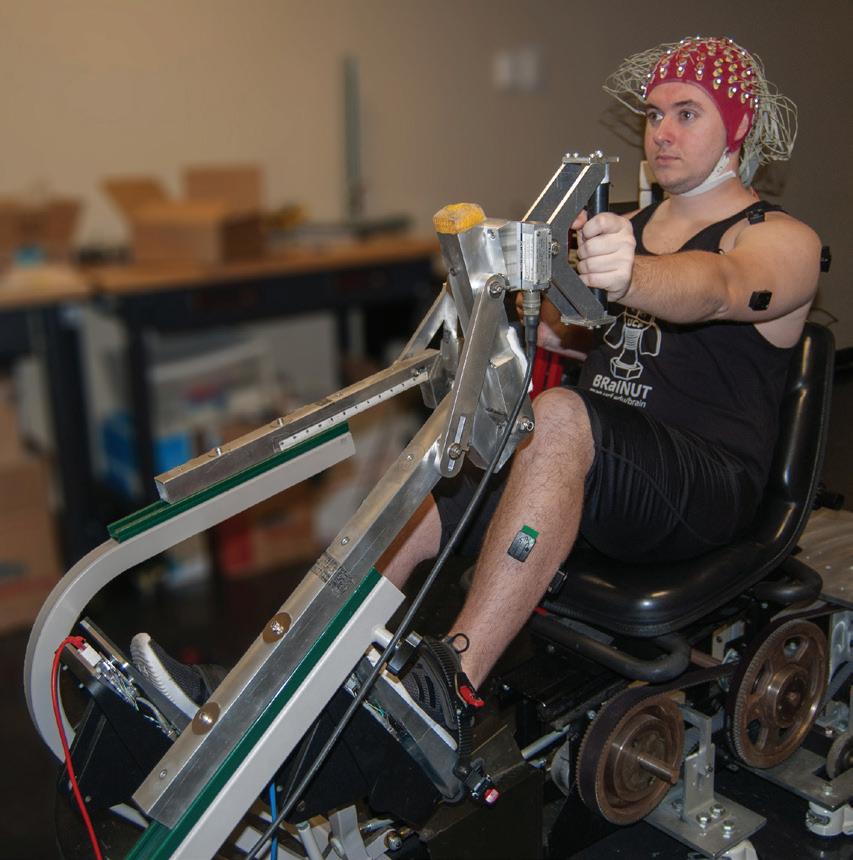
BRaIN Lab
Biomechanics, Rehabilitation and Interdisciplinary Neuroscience Lab
Led by: Helen Huang, Ph.D.When we walk, we don’t think about what it takes to make us move – we just do it. But as we age, walking and maintaining a steady gait can become difficult.
At the BRaIN Lab, Associate Professor Helen Huang combines her engineering skills with human subject experiments to gain a better understanding of how the brain, muscles, and body work together to make humans move. The motivation behind her research is the belief that studying brain processes as we move is crucial for understanding how and why we move the way we do and for developing smarter devices to help people balance and walk.
Using electroencephalography (EEG) to record brain waves, a suite of sensors to record muscle signals and body motion, a treadmill, and computer programs to analyze large sets of data, Huang and her team can map the areas of the brain that become active during walking and losses of balance, and also measure when and how much they activate.
Huang’s research has been supported by the National Institutes of Health and the National Science Foundation. Most recently, she was part of a research team that received a $1.8 million grant from the NIH to create an educational program to give underrepresented students opportunities to learn about and conduct aging research with a holistic approach.
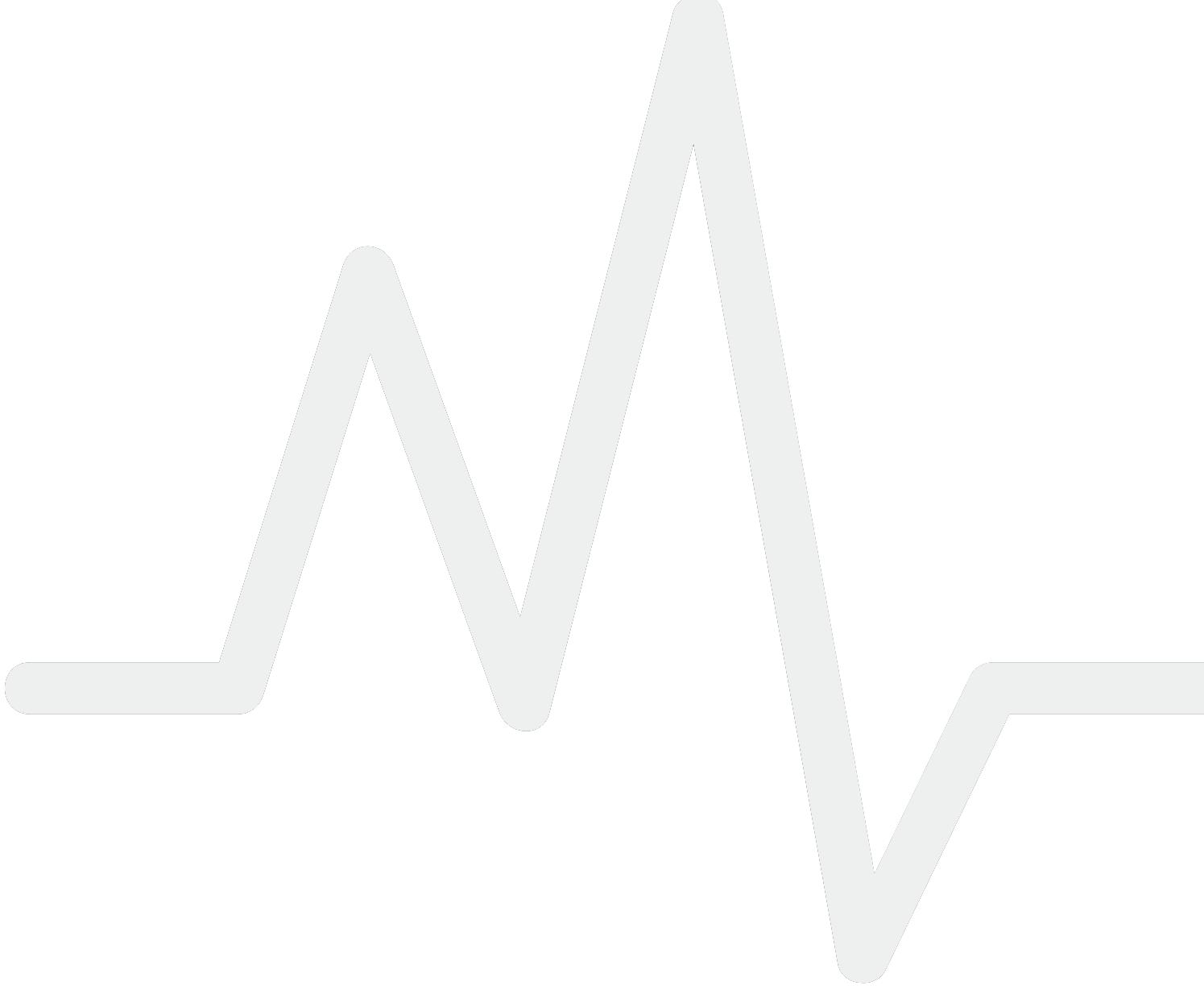
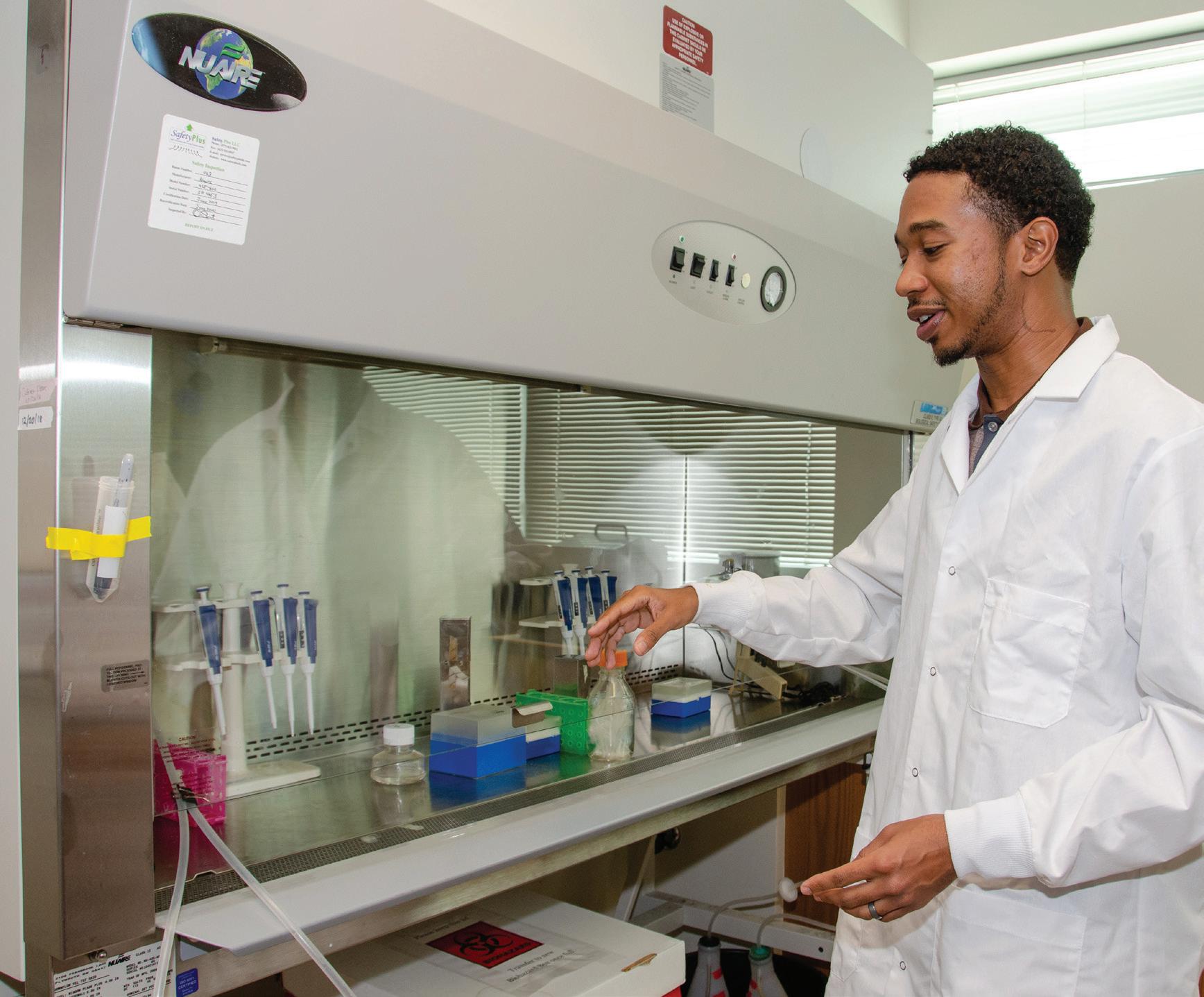
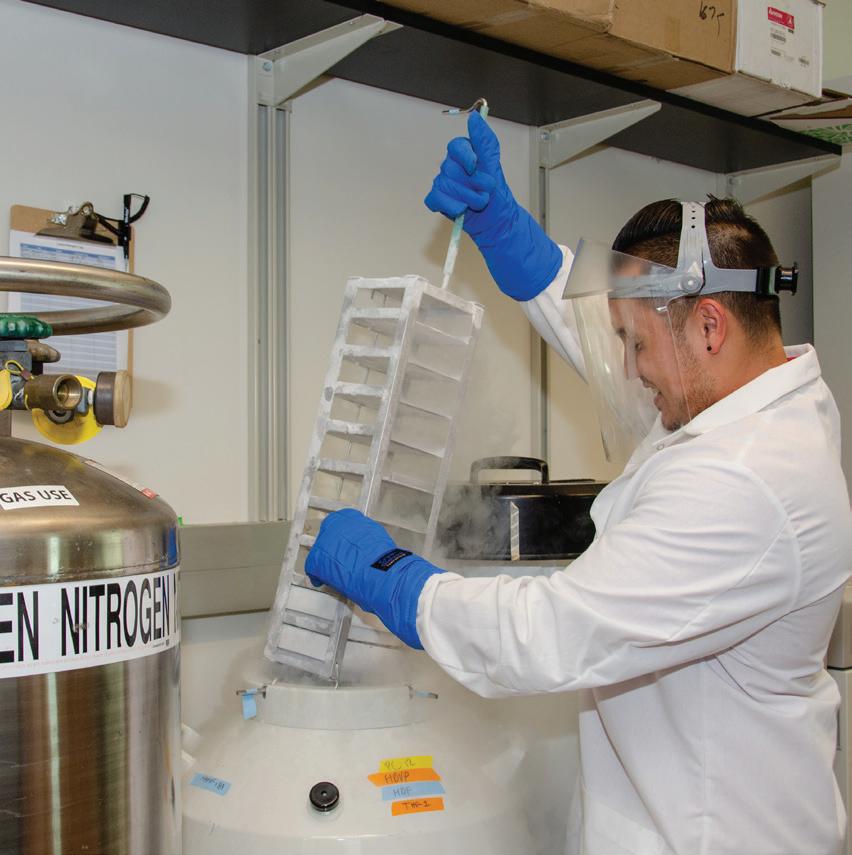
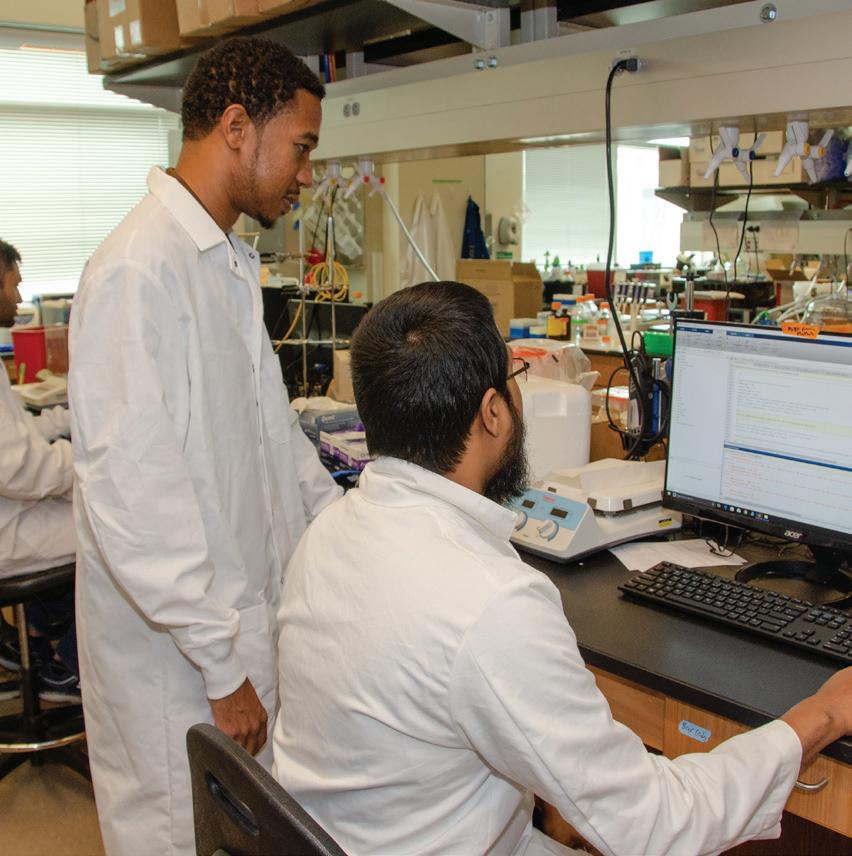
CB Lab
Cellular Biomechanics Lab
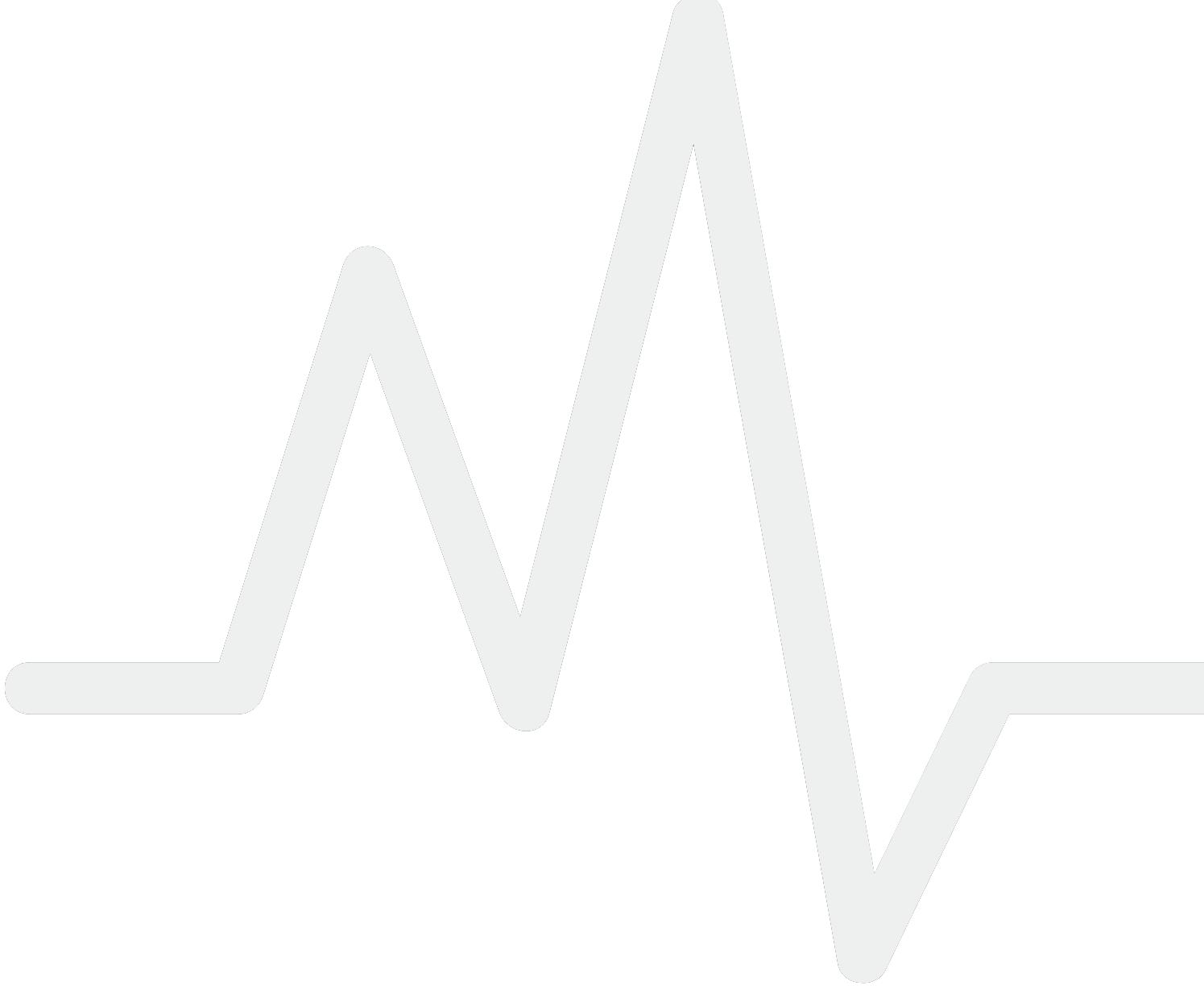
Led by: Robert Steward, Ph.D.
Research happens at the microscopic level in the Cellular Biomechanics Lab. Robert Steward and his research team cross the bridge between mechanical engineering and medicine by studying the mechanical forces that play a role in human health.
Through a grant from the National Institutes of Health, Steward studies the role that endothelial cells — and the mechanical forces they respond to — play in the early stages of cardiovascular disease. He and his team also investigate diabetes and how cells behave in a high glucose environment.

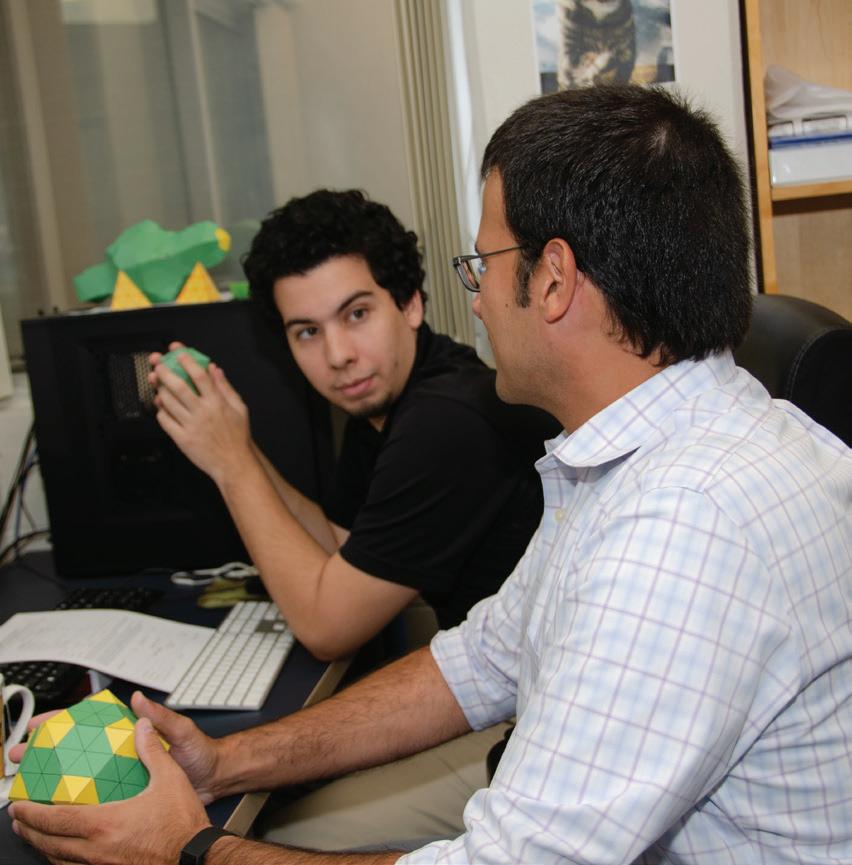
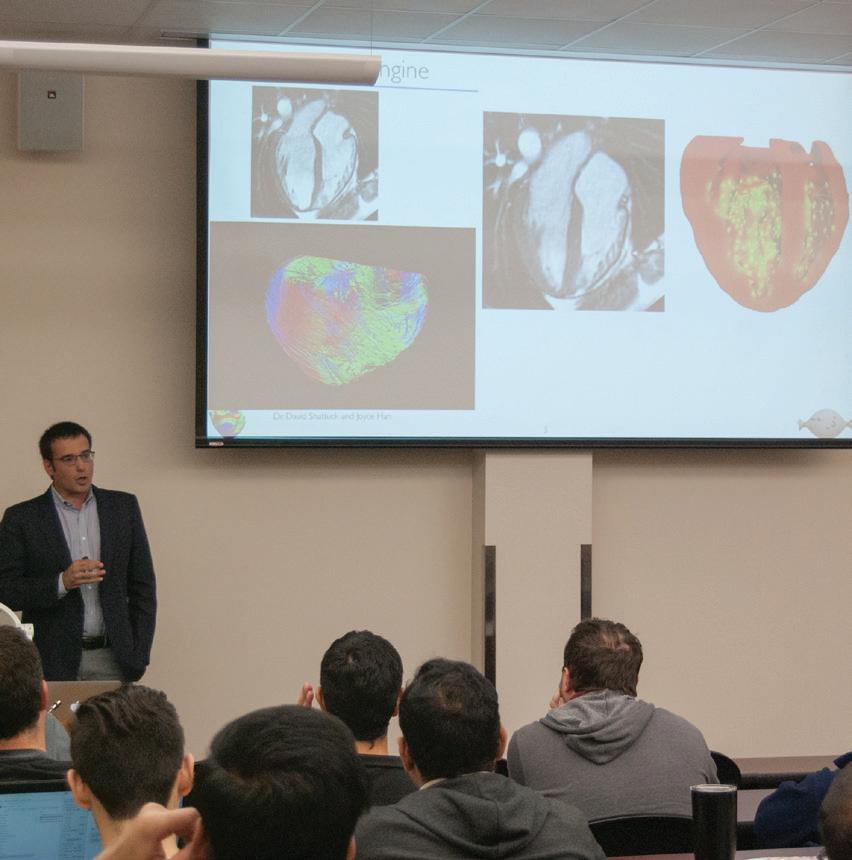
CB Lab
Computational Biomechanics Lab
Led
by: Luigi Perotti, Ph.D.Millions of patients in the U.S. are affected by cardiac diseases. However, common strategies to evaluate cardiac health often rely on inadequate measures. In addition, the motion of the heart across scales is still poorly described. These issues limit our understanding of heart function and our ability to diagnose and monitor cardiac diseases.
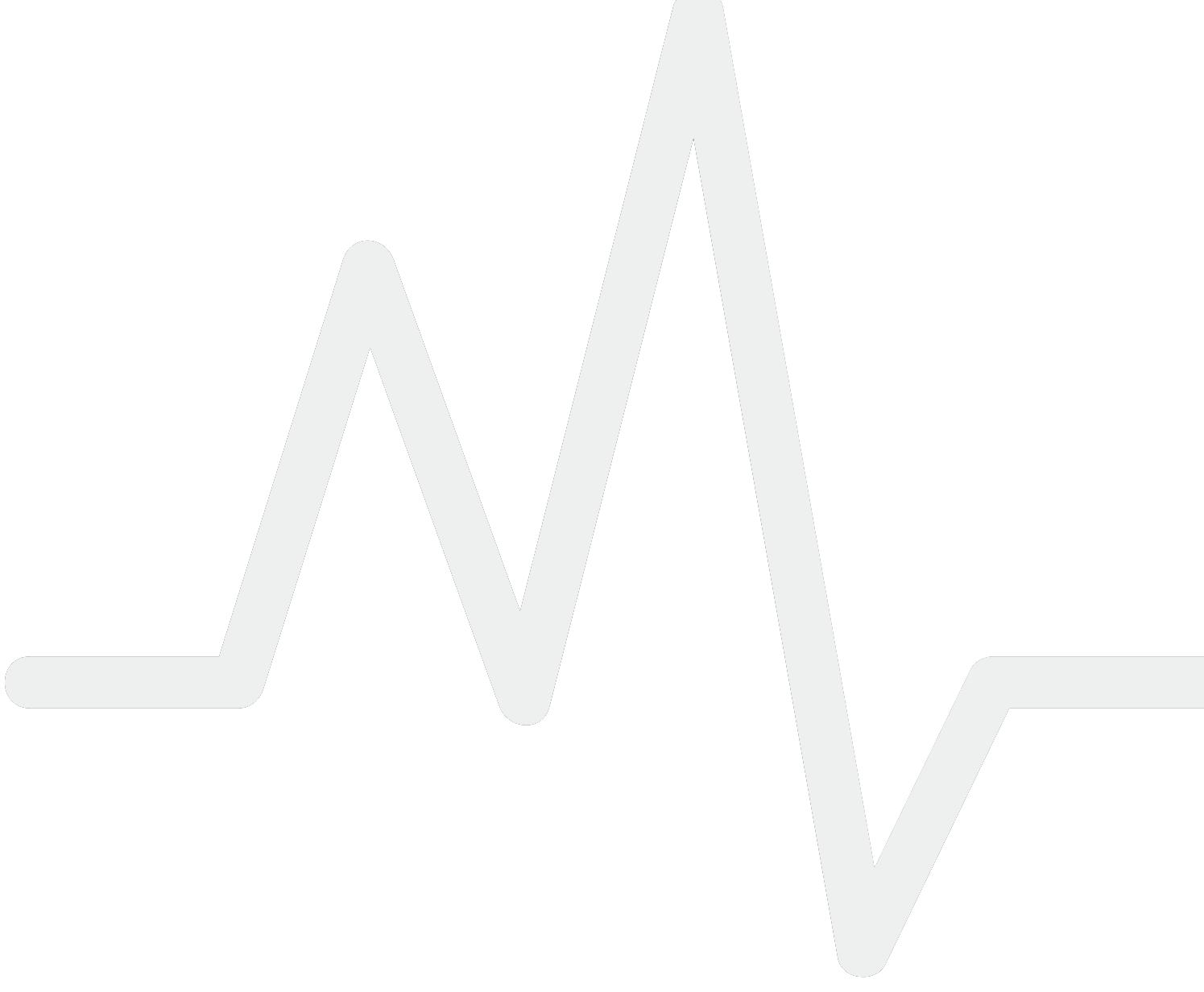
In the Computational Biomechanics Lab, Assistant Professor Luigi Perotti and his research team strive to better understand cardiac function and dysfunction. They combine MRI anatomical, microstructural and motion data with computational mechanics to build models that allow them to study cardiac kinematics, mechanics and electrophysiology.
Perotti’s goal is to identify measures of the heart’s motion and microstructure, which may serve as biomarkers to detect the onset and progression of cardiac diseases. He and his team focus on computing measures of cardiac deformation that can be estimated from imaging data routinely acquired in the clinic and using fast and robust algorithms. They also develop multiscale and multiphysics models to better understand cardiac mechanics in health and disease and better interpret motion imaging data. These research efforts are currently supported by two awards from the National Science Foundation.
Through the use of the same theoretical and modeling tools of continuum and computational mechanics, Perotti also studies the assembly and maturation of viral capsids and the packing of colloidal particles on 3D surfaces. The end goal is to eventually design bio-inspired deployable, self-morphing, thin-shell structures.
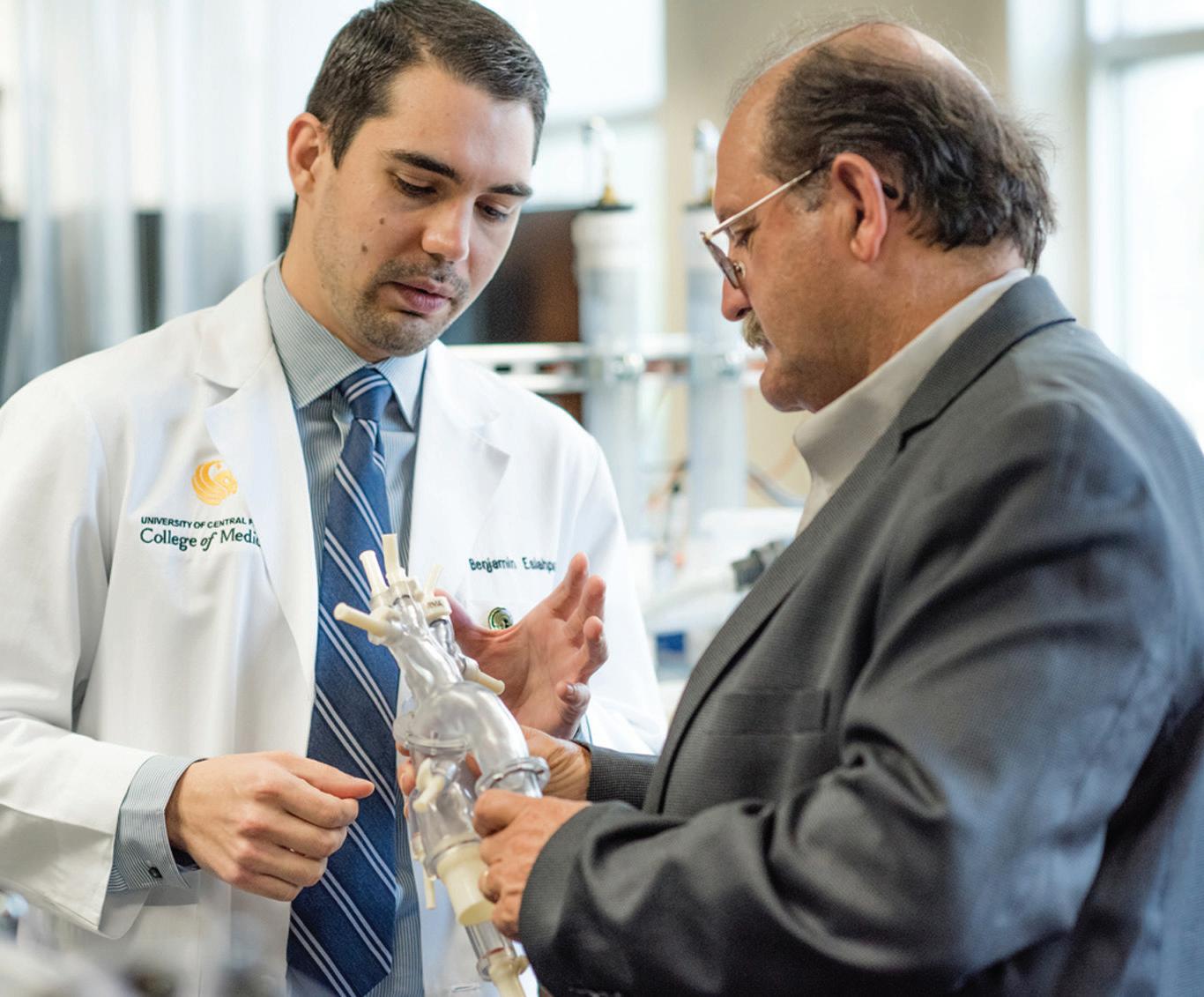

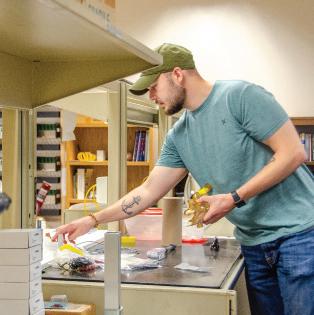
CML Lab
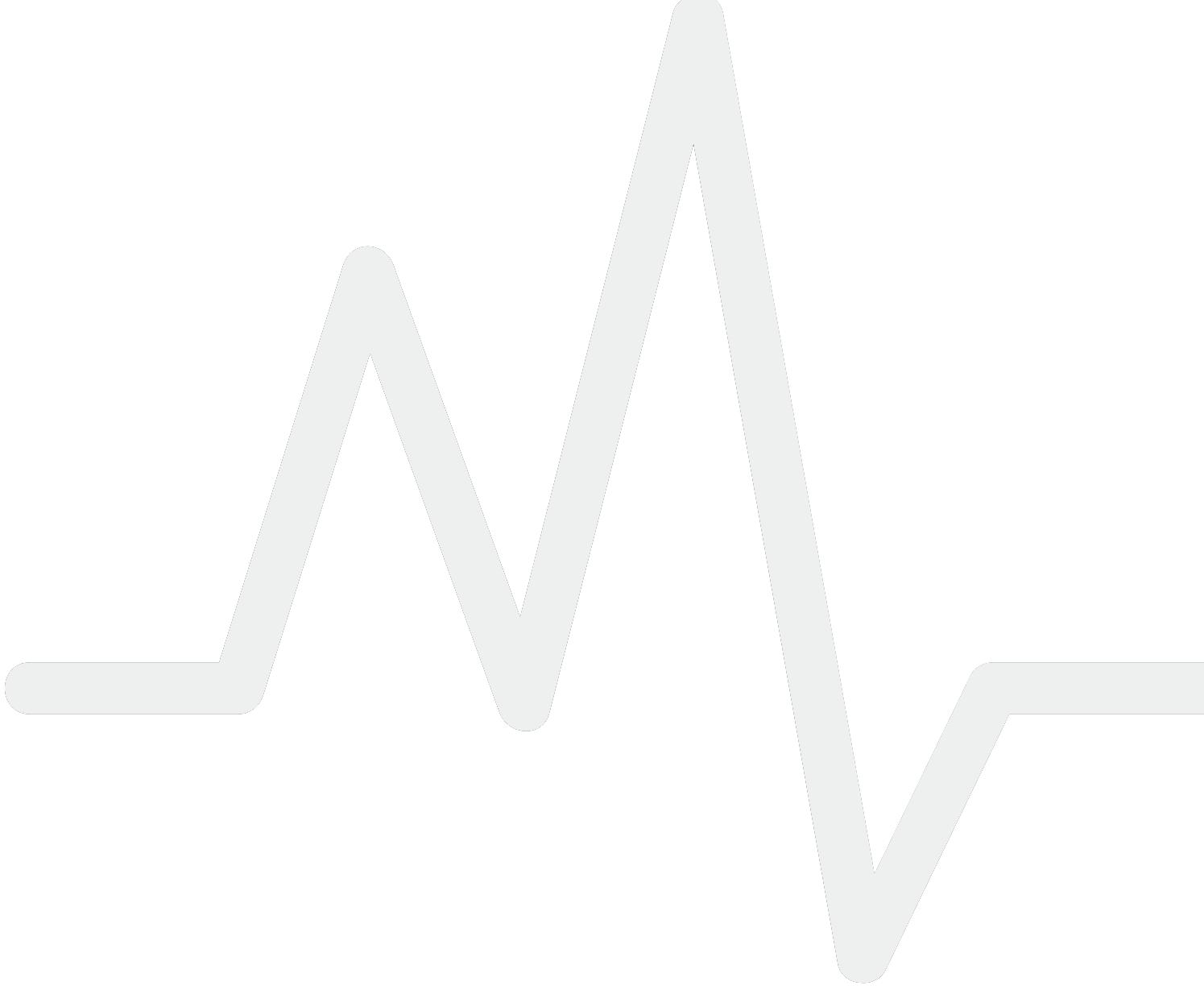
Computational Mechanics Lab
Led by: Alain Kassab, Ph.D.
Alain Kassab currently leads a three-year study under the support of American Heart Association Transformative Grant that is utilizing multi-scale computational fluid dynamics modeling to investigate a novel surgical manoeuver aimed at reducing stroke risk in left ventricular assist devices by tailoring the outflow graft implantation. Over the past 10 years, his research group has been engaged in a general program bridging engineering and medicine by utilizing computational modeling to aid in treatment planning of congenital heart disease. These studies include the investigation of the hemodynamics of a novel hybrid approach to the comprehensive stage II operation for single ventricle, the design of a self-powered Fontan circulation, and the detailed hemodynamics resulting from a range of placement of shunts and varying diameters in the hybrid Norwood palliation of single ventricle congenital heart disease.
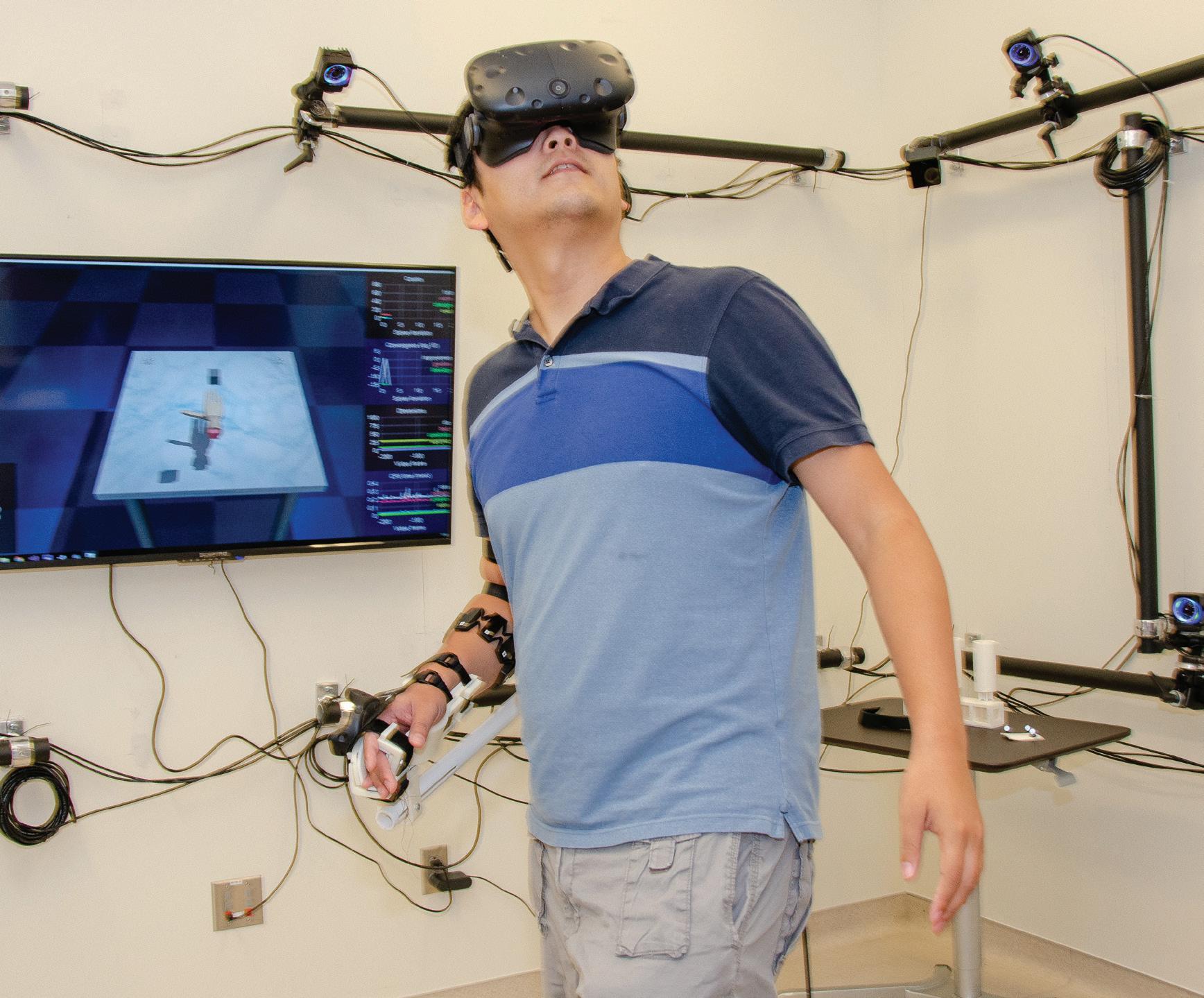
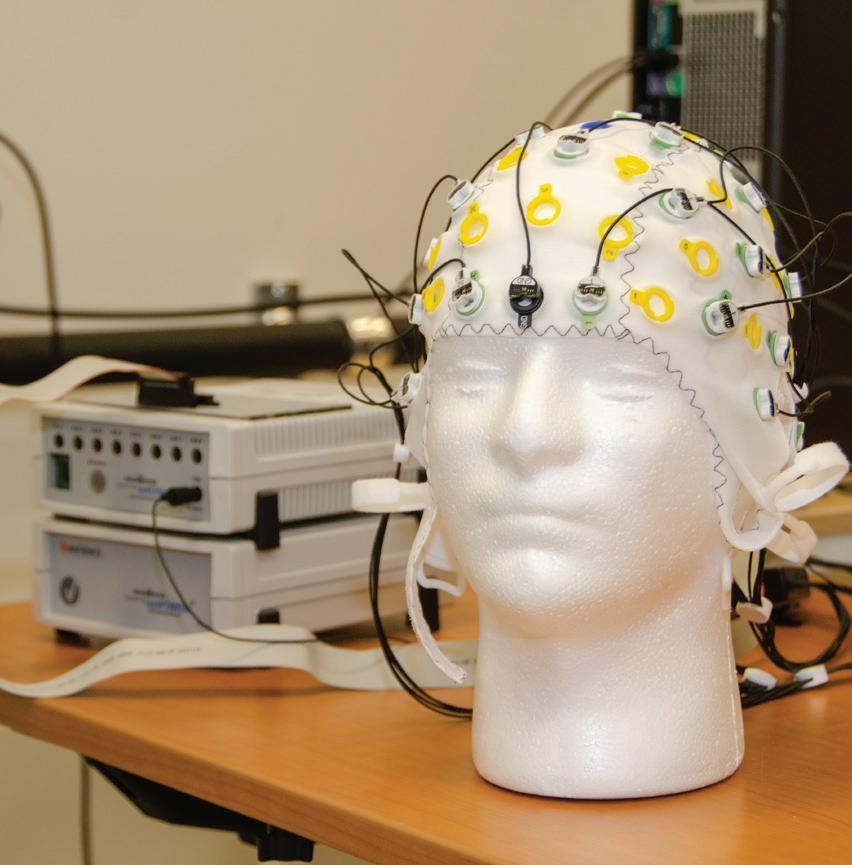
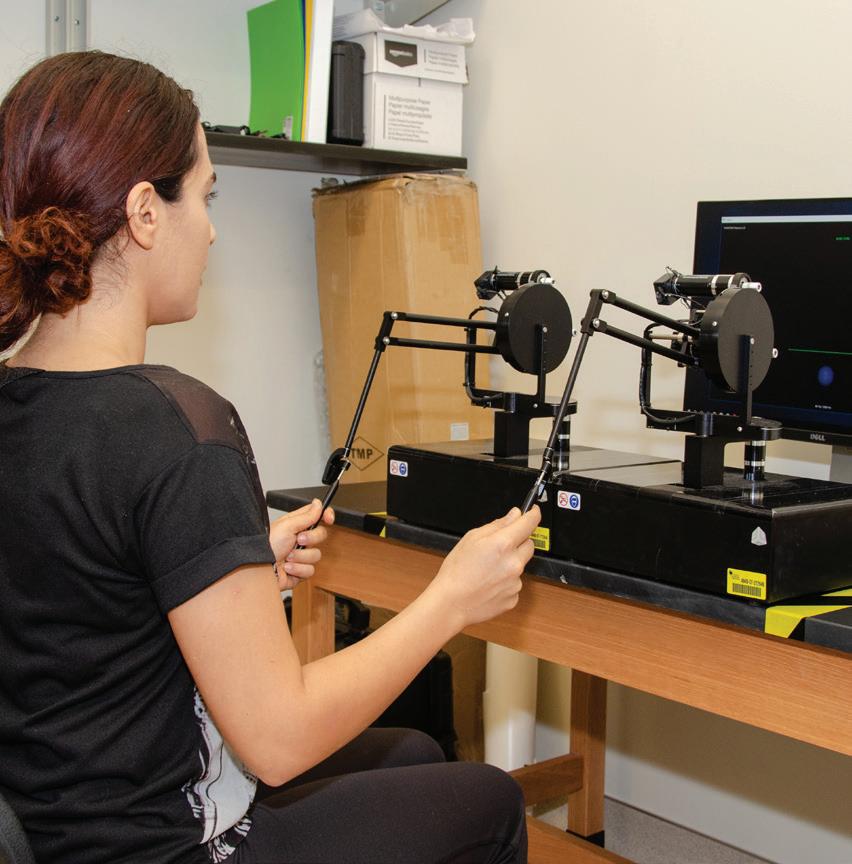
NMS Lab
NeuroMechanical Systems Lab
Led by: Qiushi Fu, Ph.D.
When you pick up a pen or grab a water bottle, it may seem like a simple task. But the dexterity of the human hand is more complex than you think.
In the NeuroMechanical Systems Lab, Qiushi Fu and his research team study the chain of command between the brain and the hand, with a specific focus on rehabilitation and prosthetics for those with impaired manual functions.
Through experiments that combine virtual reality, motion capture and robotics techniques, Fu measures neural signals through electromyography and electroencephalography, generated when the hands grasp and manipulate objects.
This data can be used to uncover neural mechanisms underlying sensorimotor dexterity, which provides the scientific basis for fine-tuning prosthetics and creating rehabilitative robotic devices that allow patients to bolster their manual skills.
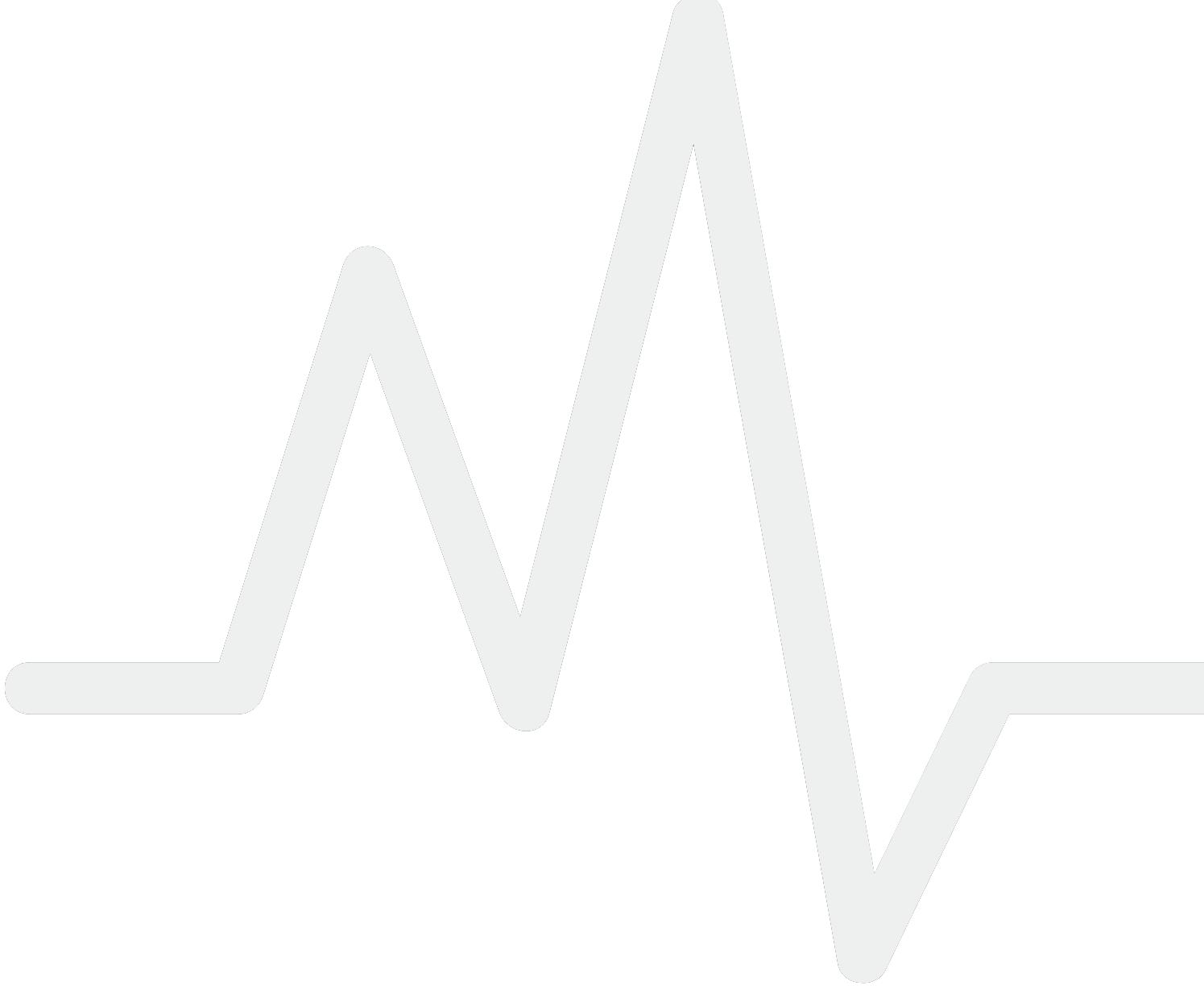
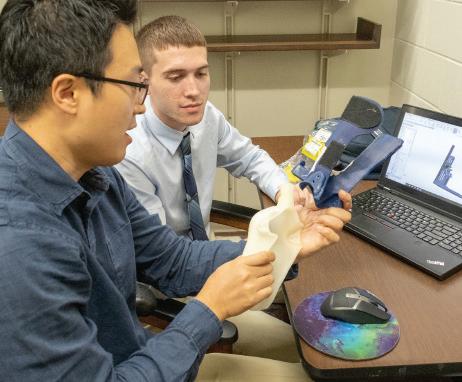
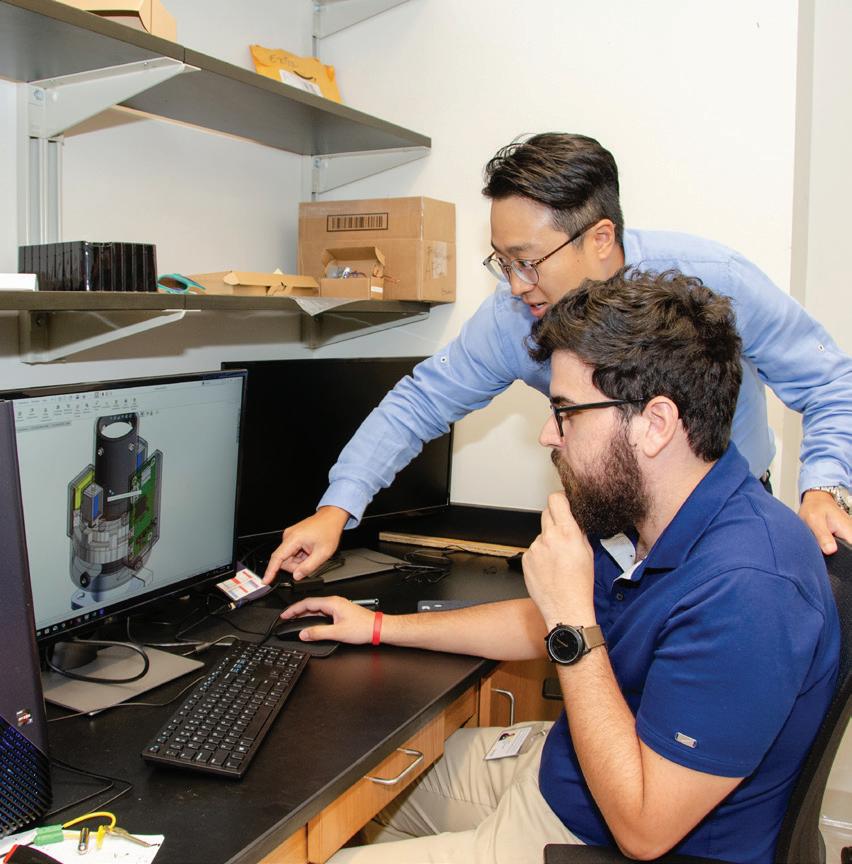
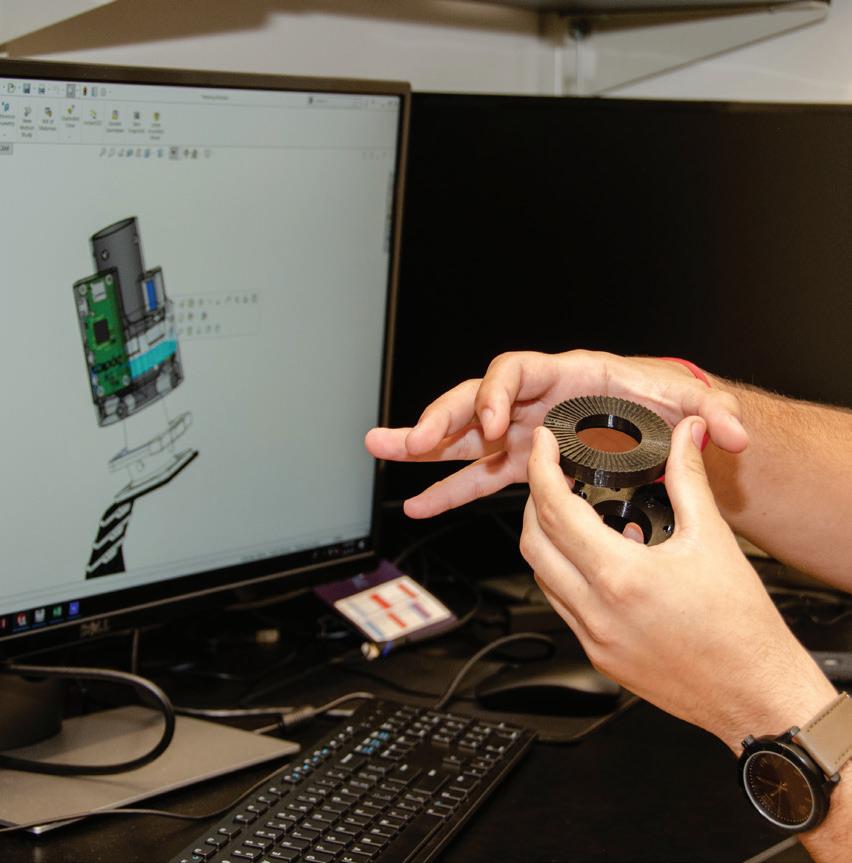
REAL Lab
Rehabilitation Engineering and Assistive Device Lab
Led by: Hwan Choi, Ph.D.When it comes to assistive devices, such as prosthetics and orthotic devices, Assistant Professor Hwan Choi has a different philosophy than most researchers. He believes that they not only improve walking function, but they can provide muscle rehabilitation through daily living as well.
This philosophy drives Choi’s work in the REAL Lab, where he develops devices that can serve both functions. His real-time variable stiffness module give prosthetics a greater range of flexibility and comfort by accounting for factors such as weight, muscle strength and walking patterns.
A second device, the real-time variable timing module, captures and releases stored energy at the appropriate time to allow amputees to propel themselves forward more easily. Both devices are designed to be affordable and to fit on any existing ankle prosthesis, eliminating the need to buy a larger, more expensive device.
Choi is a member of the Biionix Faculty Initiative Cluster, which brings together faculty with engineering, science and medical backgrounds to develop novel technologies that can be used to manufacture prosthetics. In collaboration with Melanie Coathrup, the director of the Biionix cluster, he conducts research on osseointegration, a surgical procedure that integrates the prosthetic with the bone. His long-term research goal is to figure out how to minimize the negative effects of this new type of surgery.
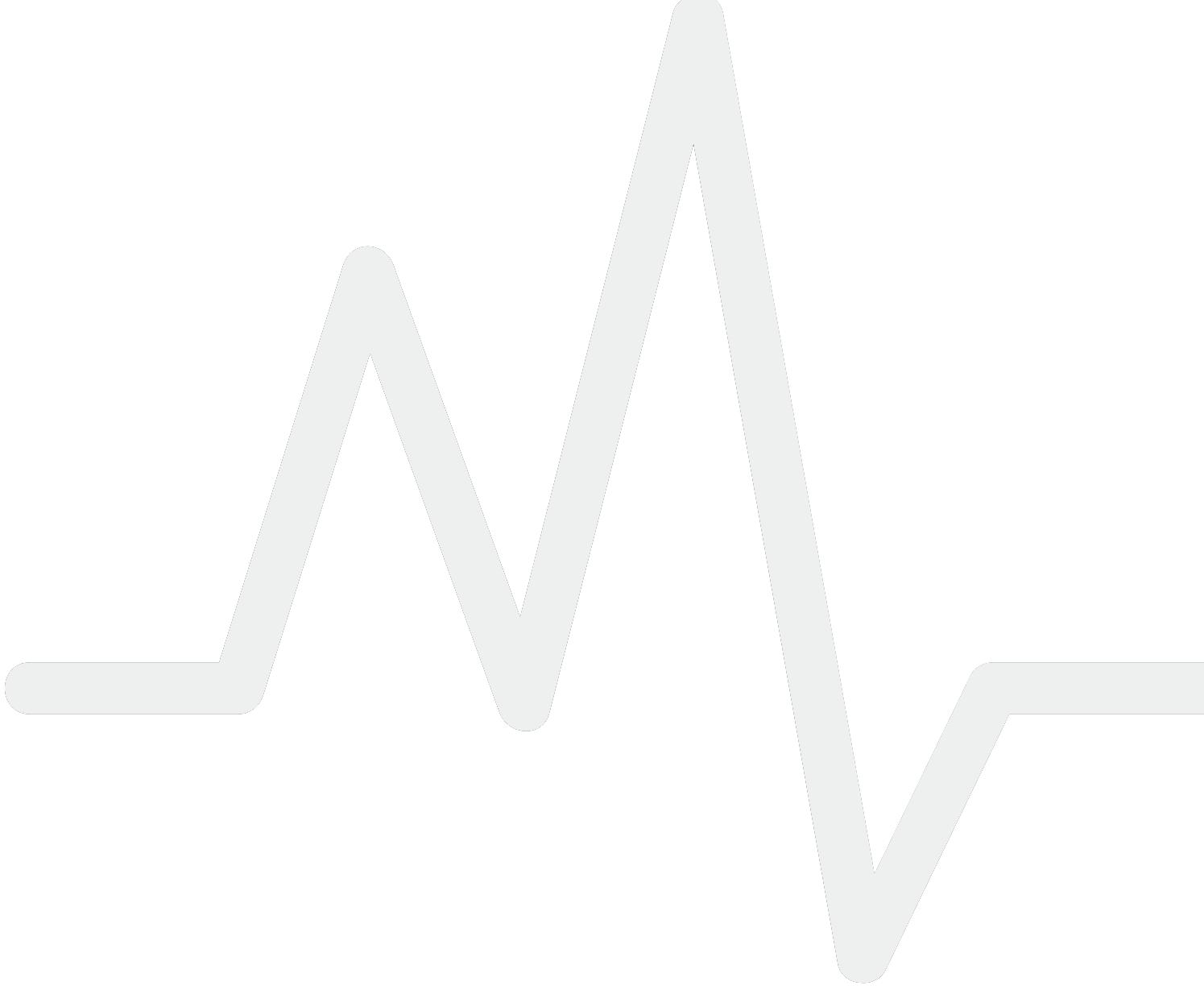
Mechanical Engineering
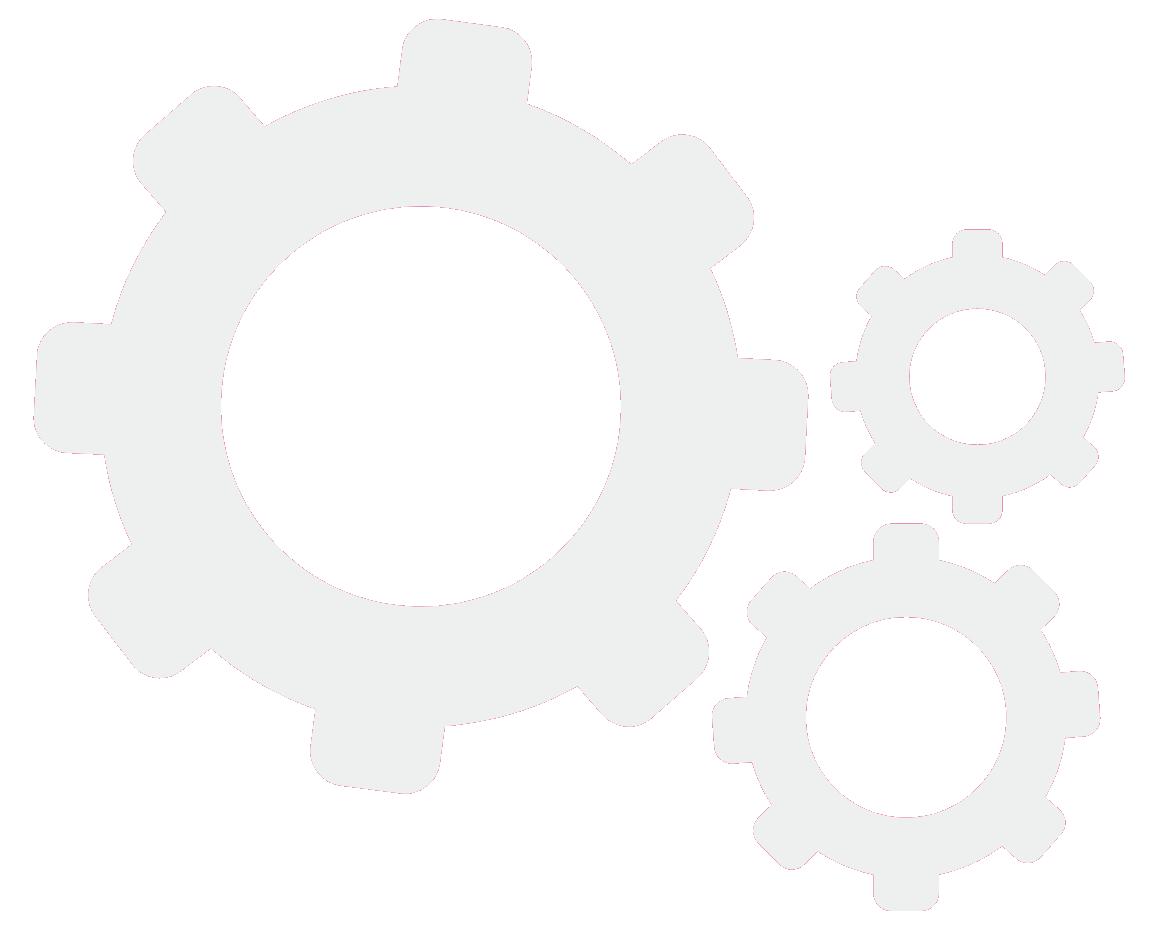
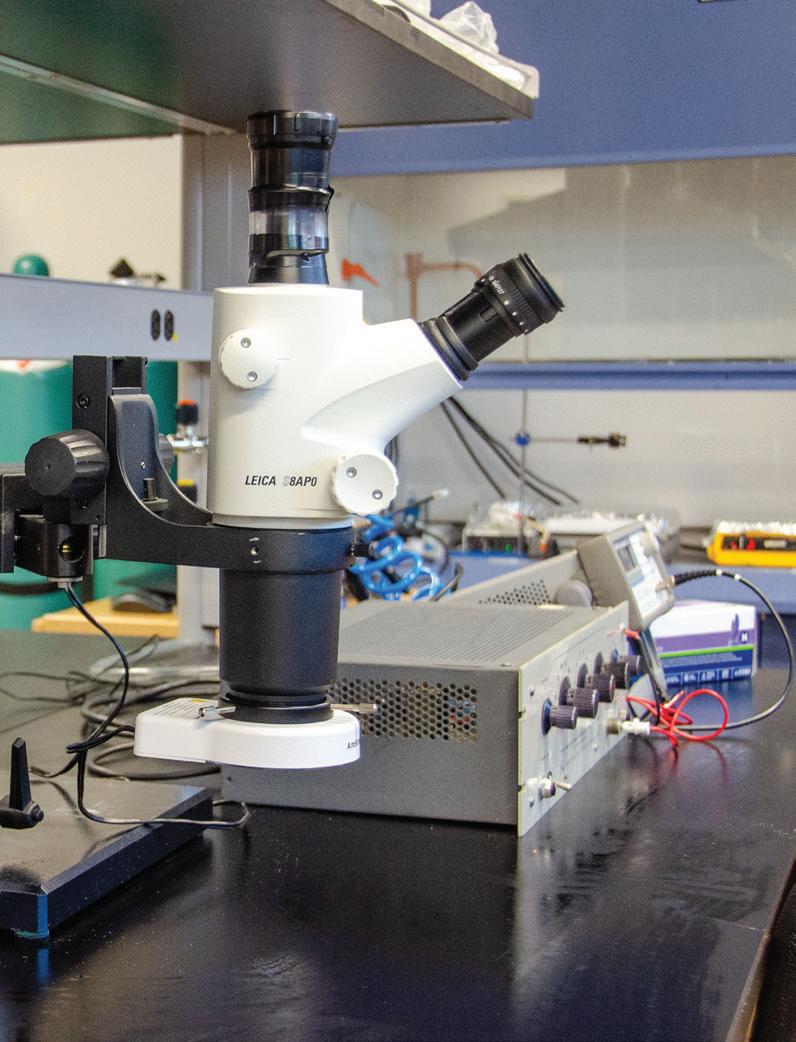
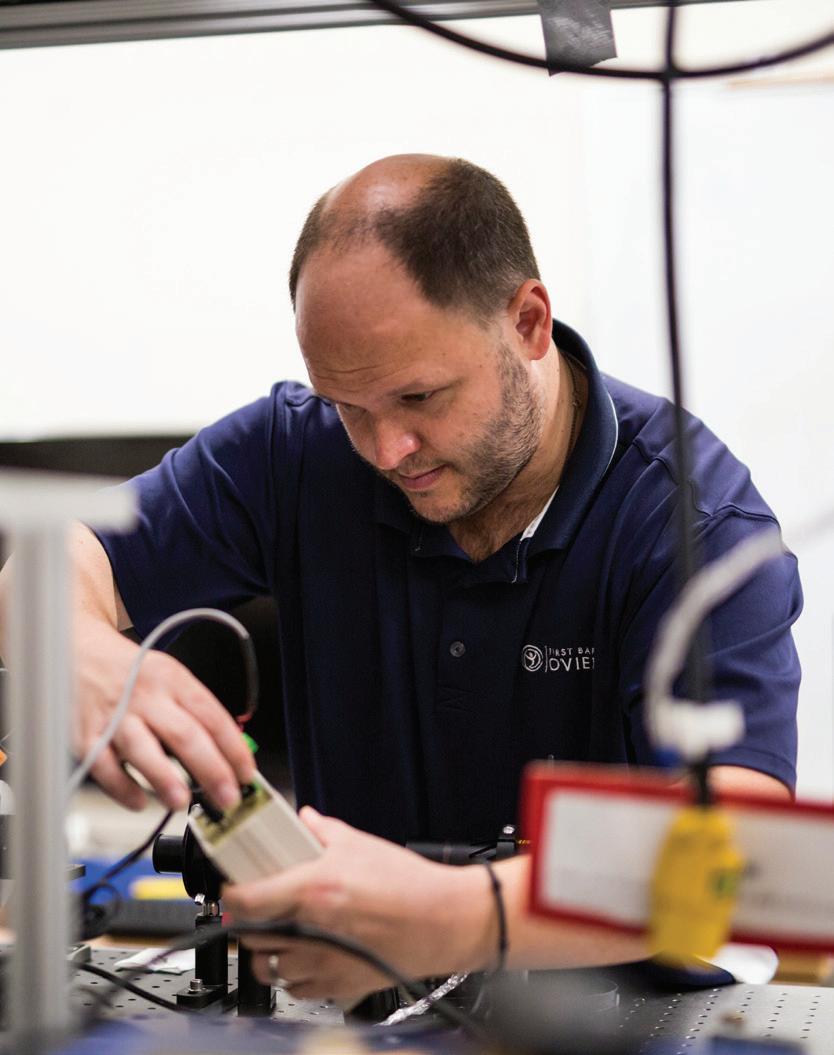
LAB DIRECTORY
Additive Manufacturing and Intelligent Systems Lab
Dazhong Wu
Assistant Professor dazhong.wu@ucf.edu
mae.ucf.edu/dazhongwu
Hybrid Sustainable Energy Systems Lab
Tuhin Das Associate Professor
tuhin.das@ucf.edu
mae.ucf.edu/TDas
Miniaturized Multifunctional Devices Lab
Hyoung Jin Cho Professor hjcho@ucf.edu mems.cecs.ucf.edu/web
Microfluidic Heat Lab
Yoav Peles Professor, Chair of the Department of Mechancial and Aerospace Engineering yoav.peles@ucf.edu
mae.ucf.edu/mfh
Putnam Lab: Interfacial Transport Lab
Shawn Putnam
Associate Professor shawn.putnam@ucf.edu
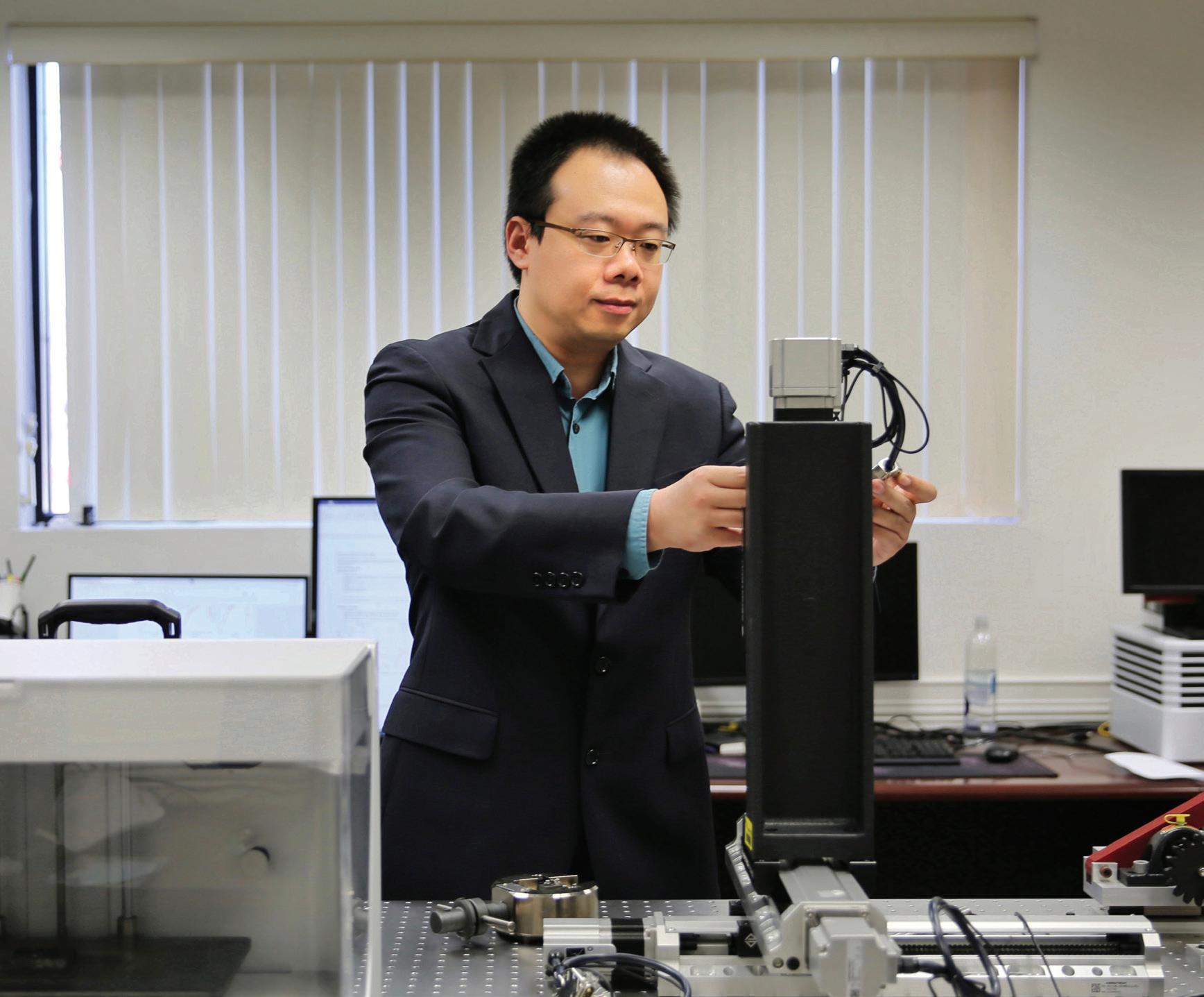
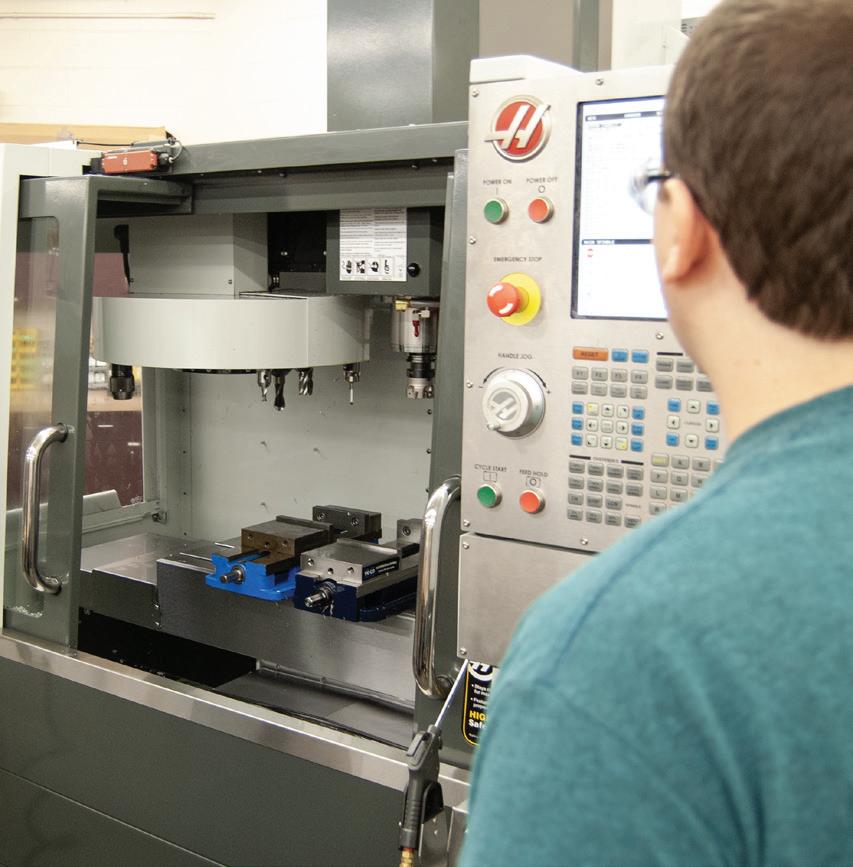
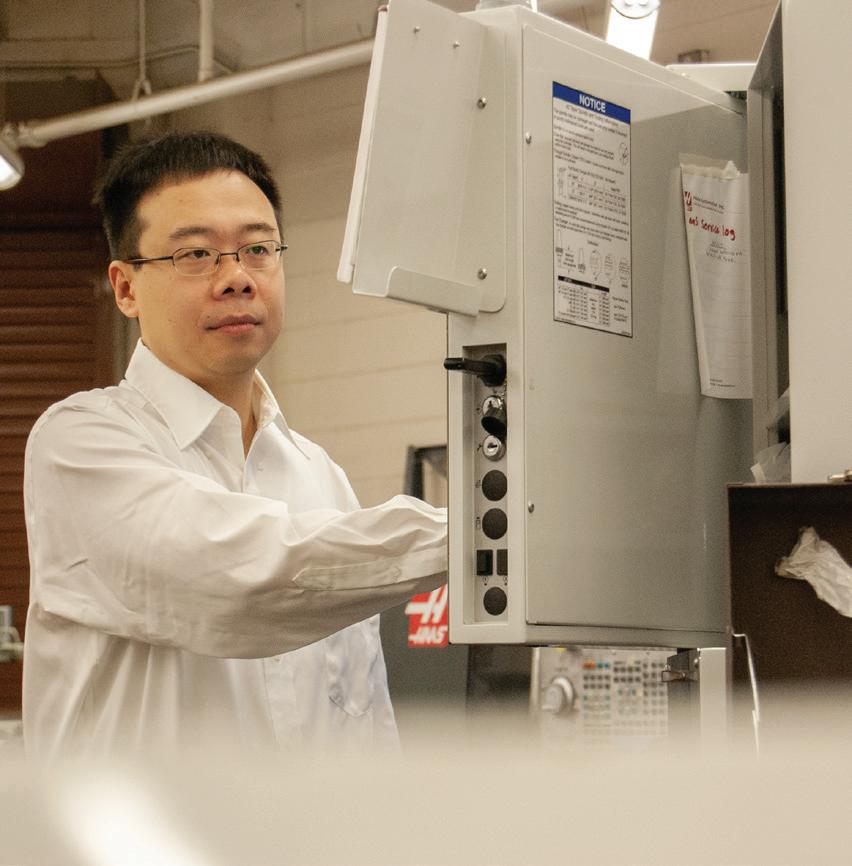
AMIS Lab
Additive Manufacturing and Intelligent Systems Lab
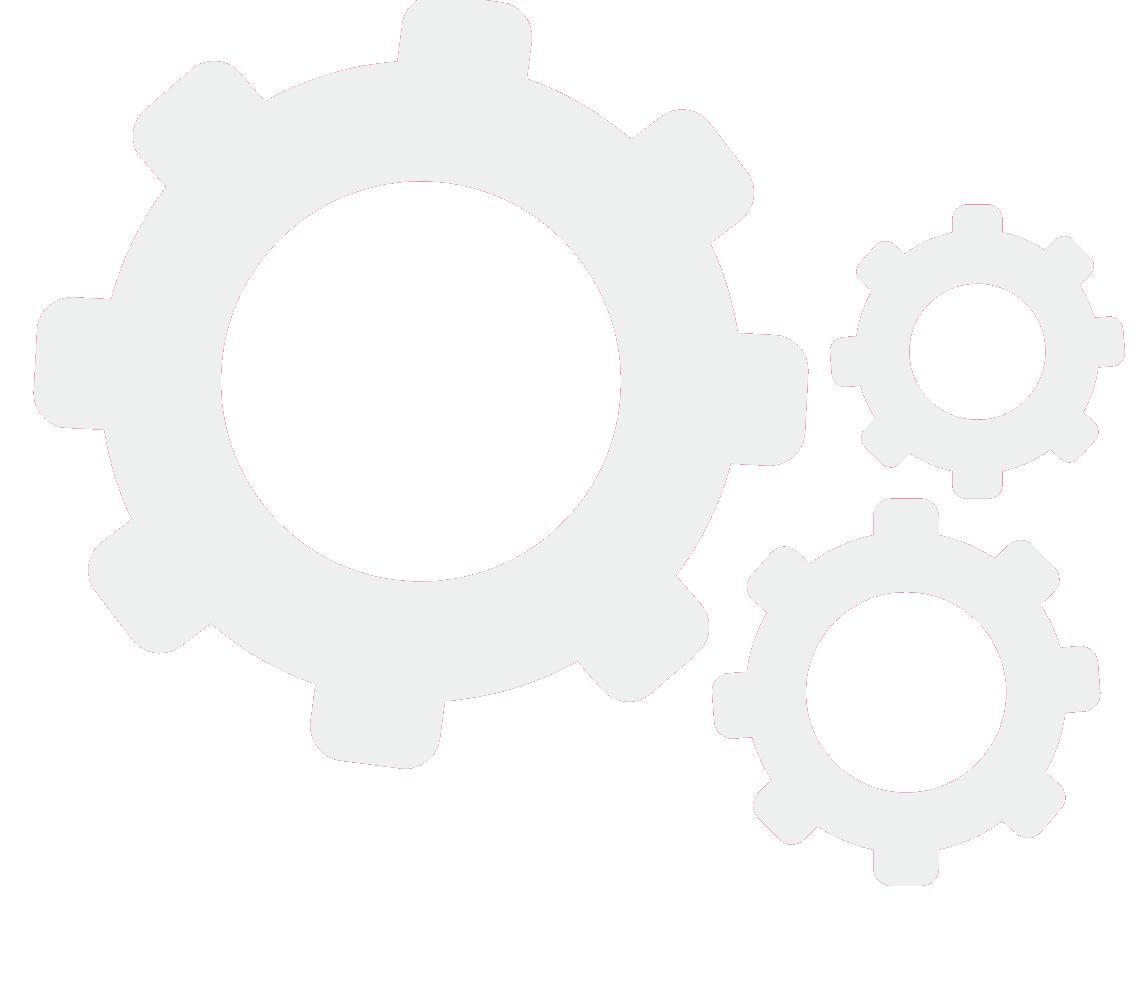
In the Additive Manufacturing and Intelligent Systems Lab, Assistant Professor Dazhong Wu and his team develop novel smart manufacturing systems and improve the reliability and safety of complex systems. They’ve created tools and processes to fabricate lightweight and high-performance carbon fiber reinforced composite materials that can significantly improve the fuel economy of automobiles and aircrafts.
Wu’s work in predictive modeling, which uses machine learning and industrial sensors to detect and prevent the manufacturing defects of high-end products such as turbine blades, won him recognition as one of the Society of Manufacturing Engineers’ 20 Most Influential Academics in Smart Manufacturing. He’s already created predictive modeling tools that are key enablers of manufacturing automation, known as Industry 4.0 or the Fourth Industrial Revolution.
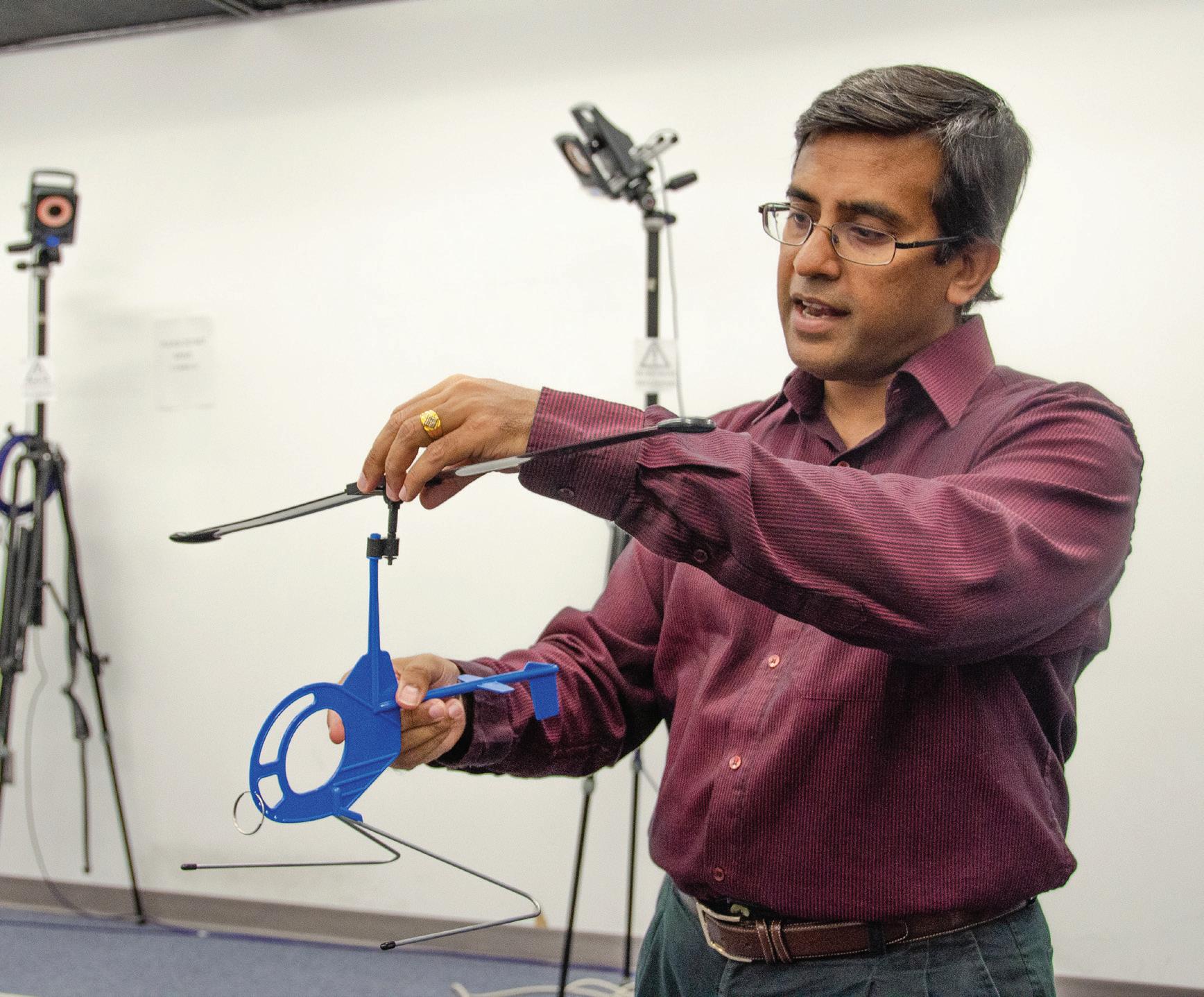
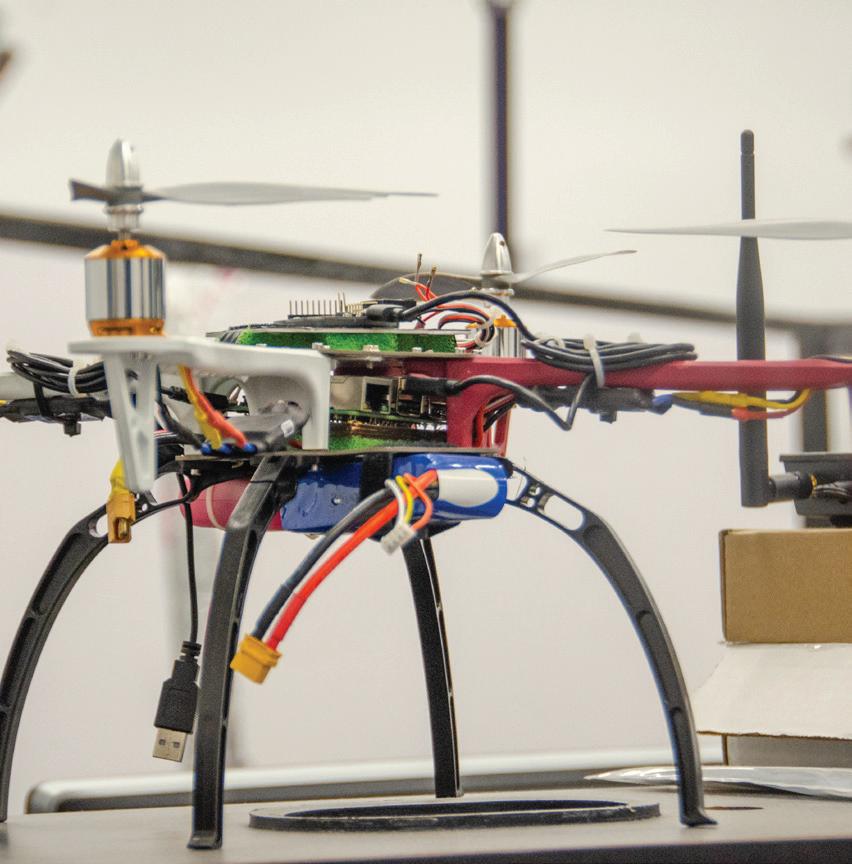
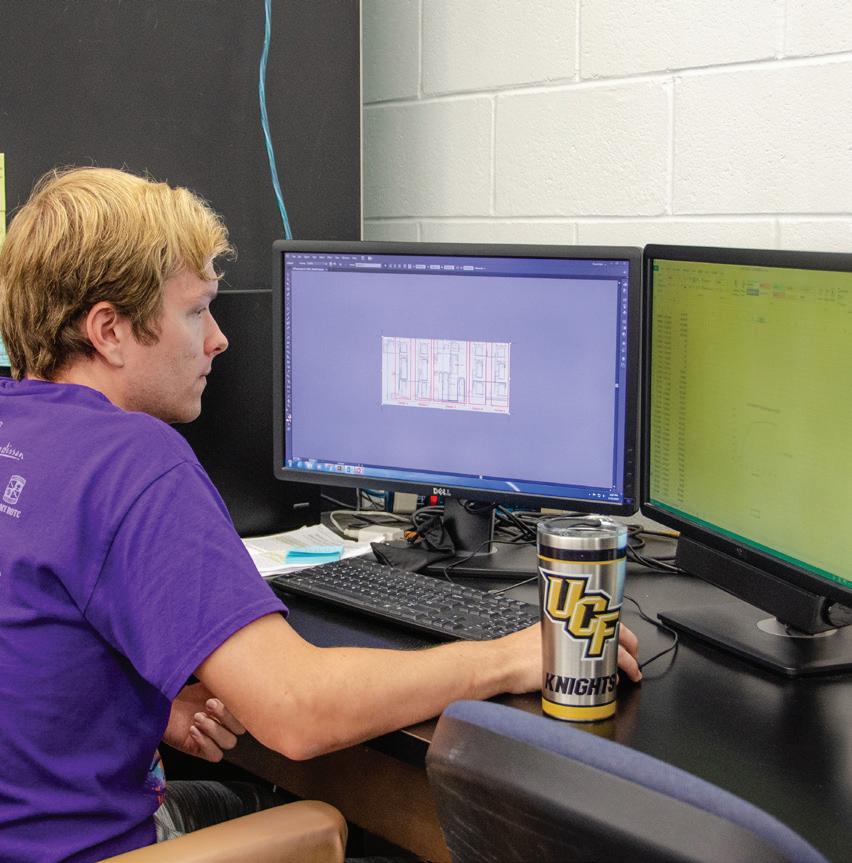
HYSES Lab
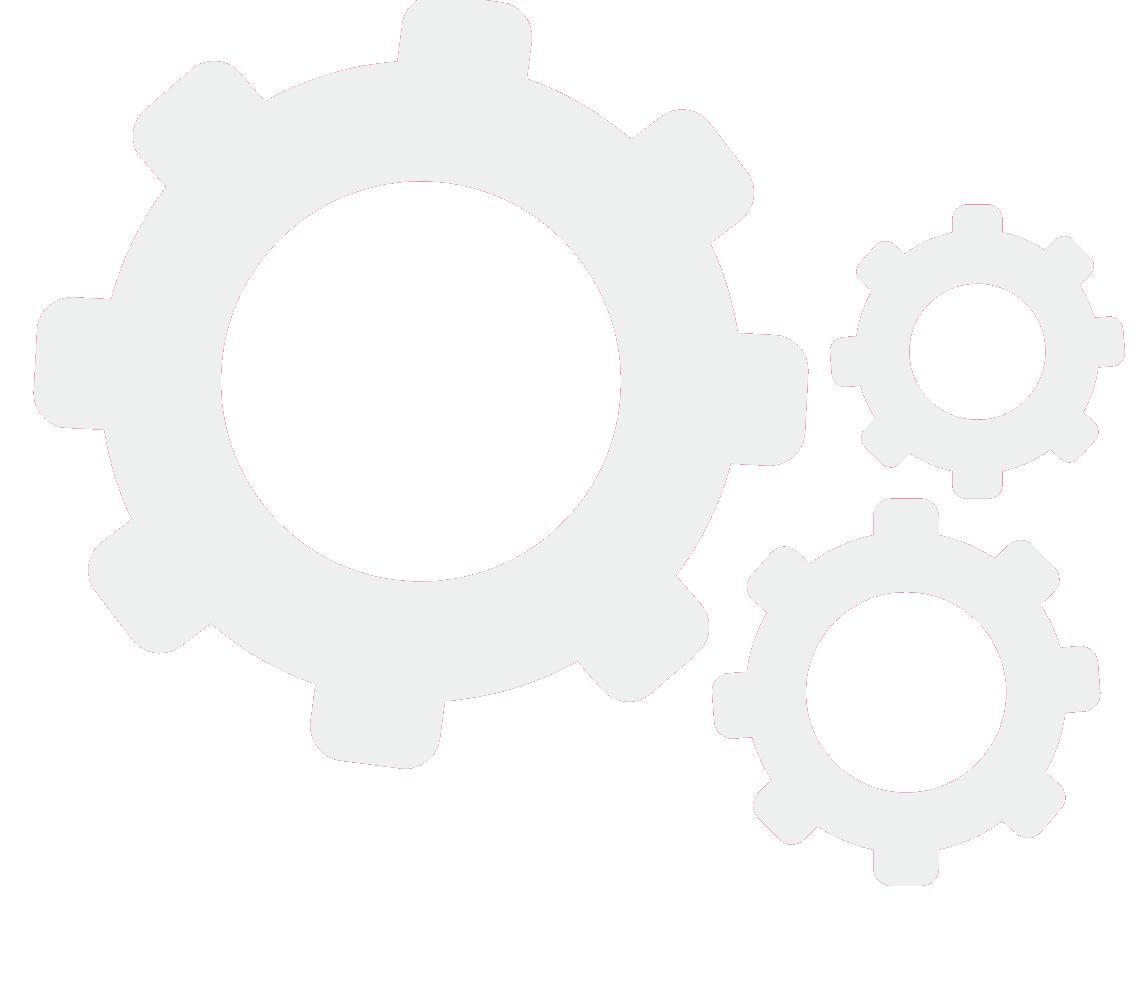
Hybrid Sustainable Energy Systems Lab
Led by: Tuhin Das, Ph.D.
Associate Professor Tuhin Das stives to create a more sustainable future through his work in the Hybrid Sustainable Energy Systems Lab. He and his team carry out independent and collaborative research in theoretical system dynamics and control as well as in application areas. Over the past several years, his team has developed a dynamic model for heat recovery steam generators, investigated aspects of energy efficient flight in unmanned aerial vehicles and created control-oriented models of floating offshore wind turbines. Das is the first UCF researcher to receive funding from the Advanced Research Projects Agency—Energy, a division of the U.S. Department of Energy that promotes and funds the research and development of advanced energy technology. ARPA-e recently awarded Das with a $1.3 million grant to develop simulations that can predict how floating offshore wind turbines and their platforms fare against the turbulent conditions of the sea. Das has received two prior awards from ARPA-e for similar research, and has also been funded by Siemens, the Office of Naval Research and the National Science Foundation.
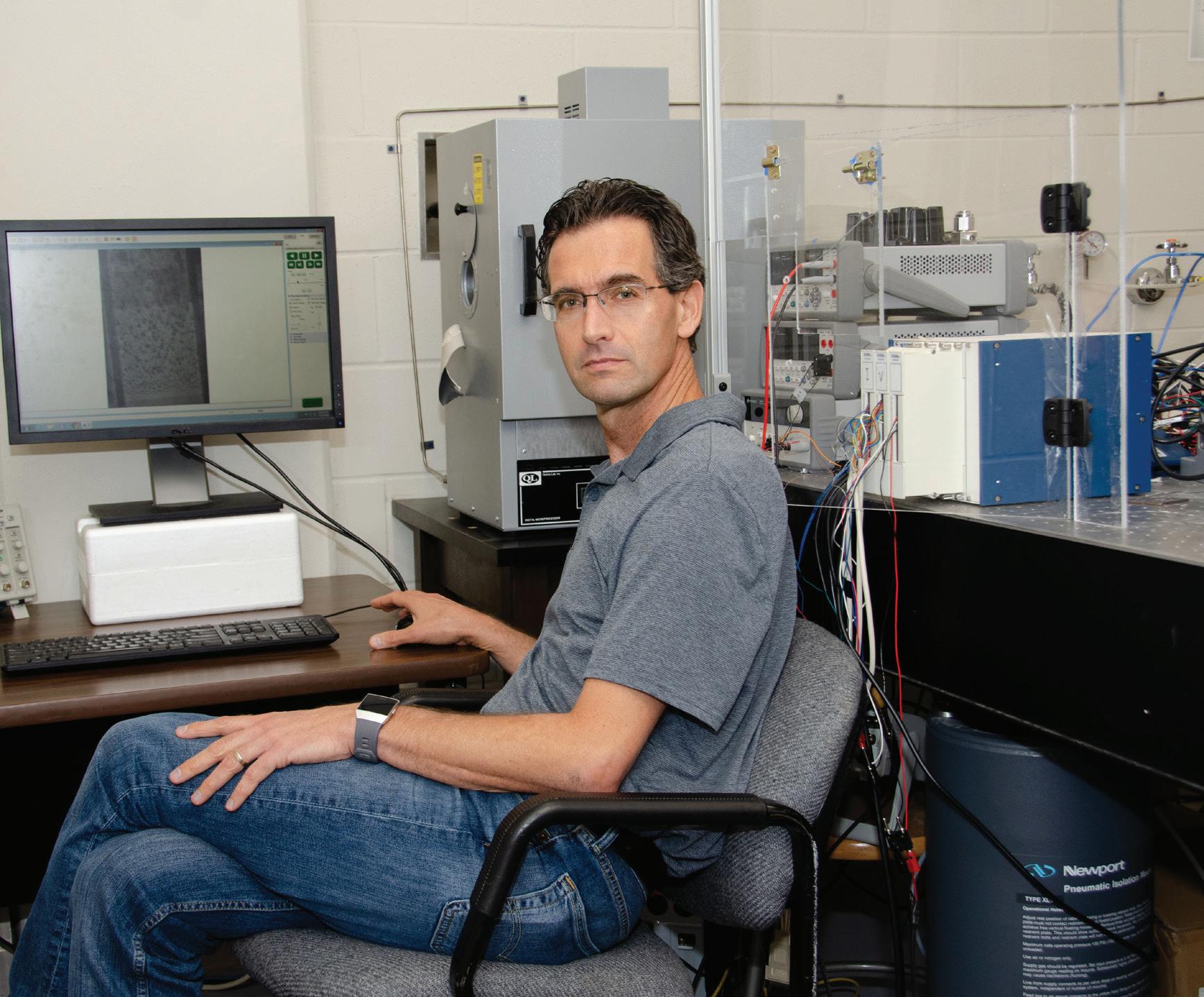
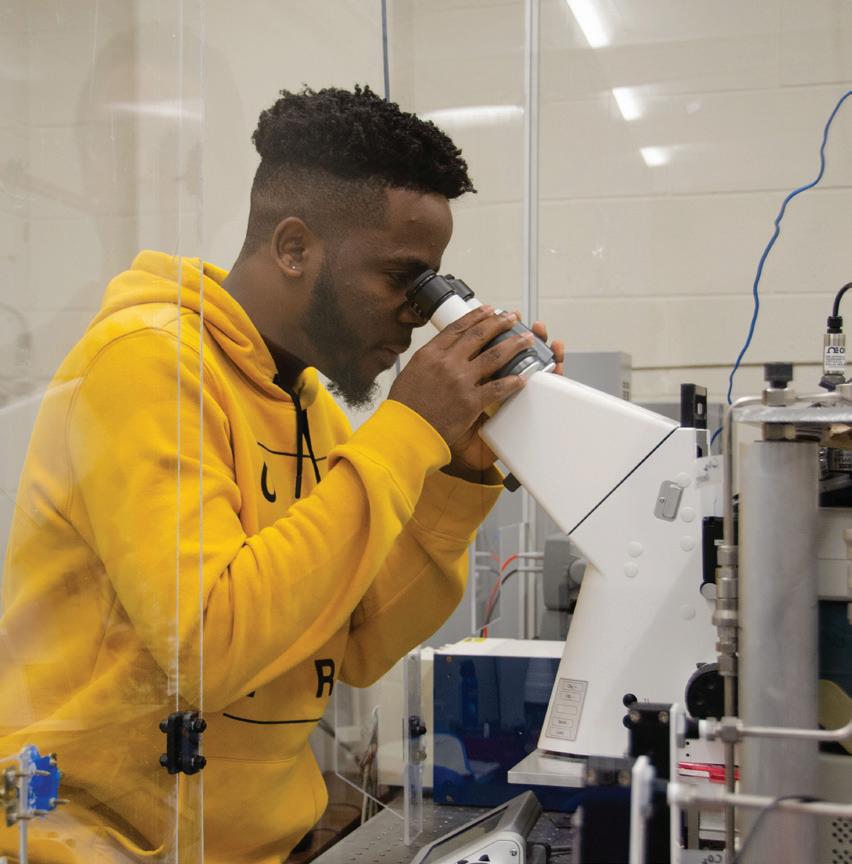
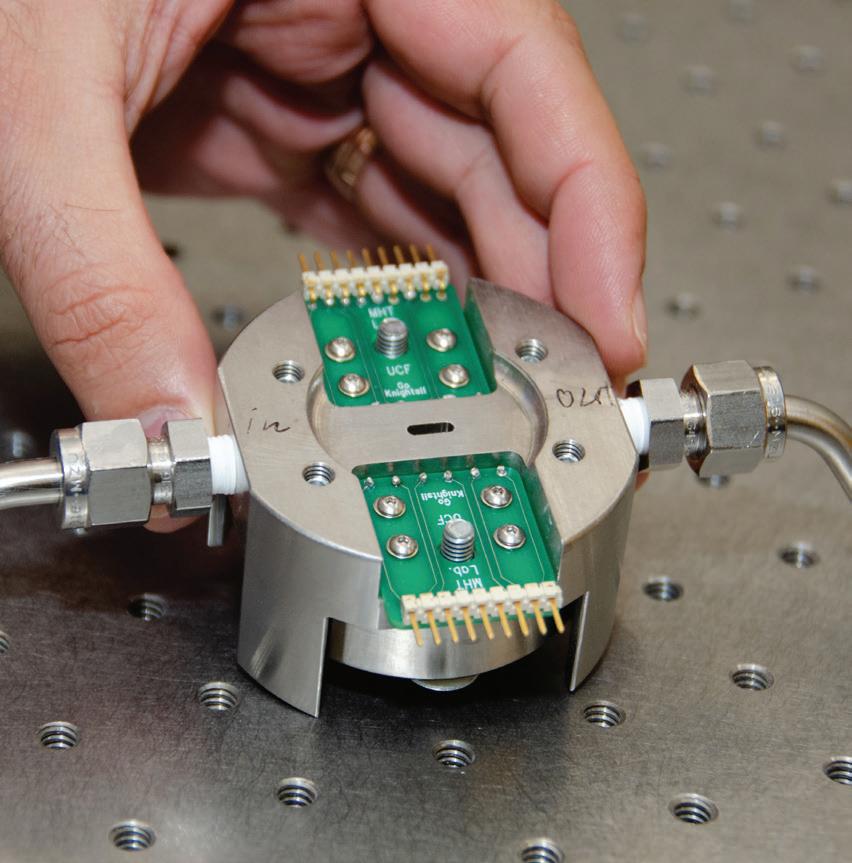
MFH Lab
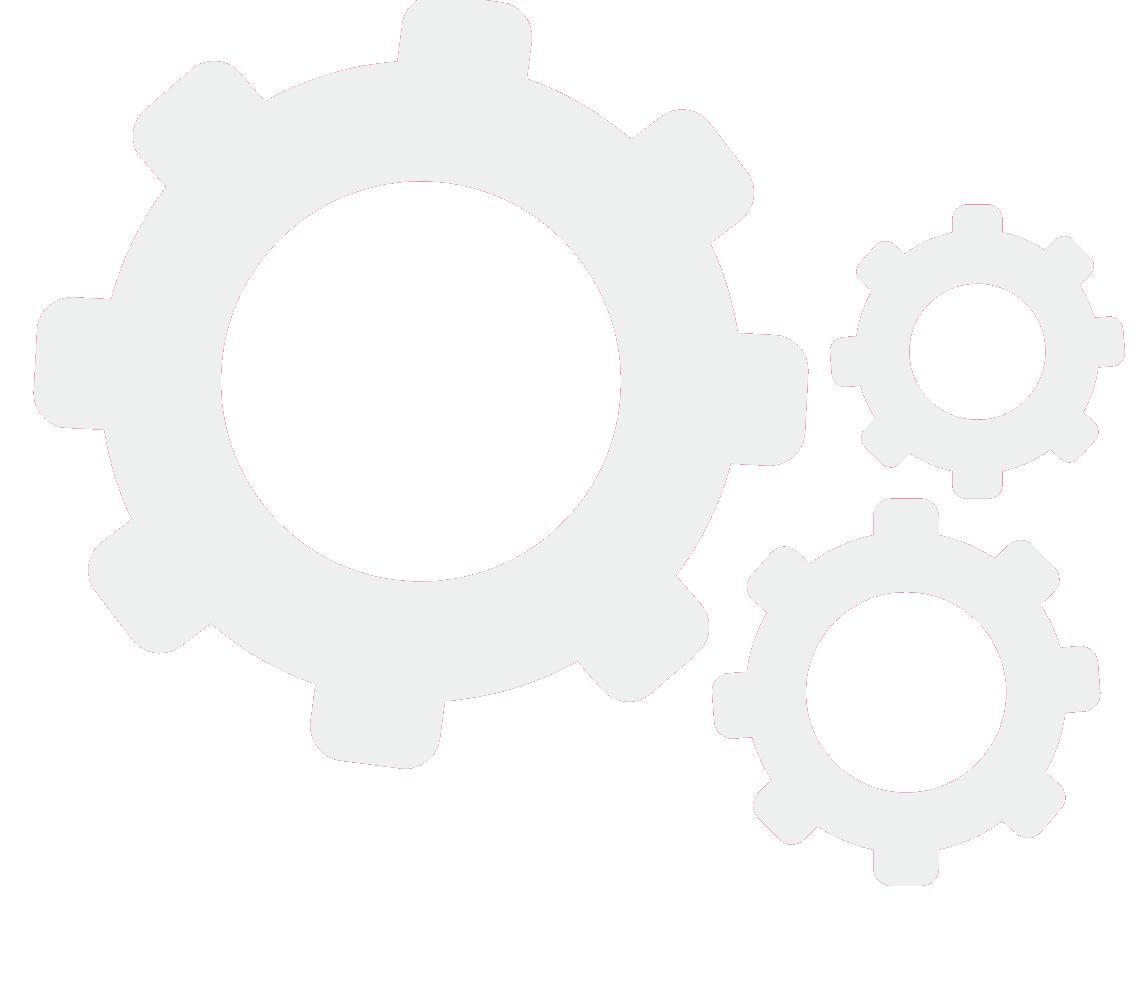
Microfluidic Heat Lab
Led by: Yoav Peles, Ph.D.
The high-powered electronics that we use every day generate vast amounts of heat, making the need for efficient cooling methods critical. Professor Yoav Peles and his team in the Microfluidic Heat Lab study a range of techniques used to improve the heat transfer process in electronic devices, including convective cooling at the microscale. The goal is to determine how fundamental heat transfer processes can affect the performance of our tech tools and toys.