

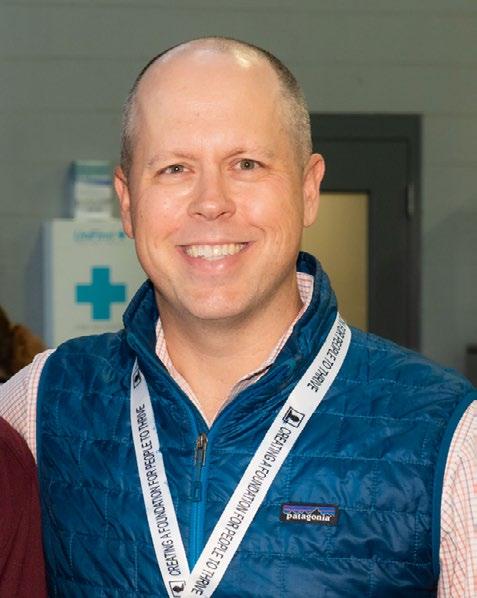
Summer is upon us, and with it comes an important moment of reflection and action in our industry. Each year, the construction world unites in recognizing Construction Safety Week, held May 5–9. It’s a time to honor the progress we’ve made in protecting the lives of the men and women who build our communities - and to recommit ourselves to the work still ahead.
At T.W. Frierson, we proudly participated in this year’s Safety Week across all of our project sites. We spent time with our incredible field teams and trade partners, men and women who make our work possible every day, focusing on what it means to adopt a true safety mindset. From live demonstrations and hands-on training in fall protection and safe work practices, we came together to learn, share, and reaffirm our shared commitment to one another’s well-being.
This industry has made great strides in ensuring construction workers go home safely every day, and we are proud to be part of that journey.
While physical safety rightly remains a top priority, May also marked Mental Health Awareness Month, and it’s a crucial reminder that safety must extend beyond hard hats and harnesses. In fact, the construction industry faces some of the highest rates of suicide, depression, and substance use of any profession. The long hours, intense deadlines, and physically demanding nature of the work can take a serious toll on mental health, sometimes in ways that remain unseen until it’s too late.
Many of us have witnessed firsthand how these challenges affect not just individuals, but entire teams, project outcomes and families. This is not a series of isolated incidents, it’s a widespread issue that demands attention, empathy, and action.
FACTS ARE CLEAR, REPORTED STATISTICS FOR OUR INDUSTRY INDICATE:
• 83% of construction workers have experienced a mental health issue
• 65% attribute those issues to job-related stress
• The industry sees 53.3 suicides per 100,000 workers - one of the highest rates across all sectors and four times higher than the national average.
• 70% report feeling anxious, stressed, or depressed on the job
These numbers reflect a reality we can no longer ignore. True jobsite safety includes mental and emotional health, and ensuring that reality starts with all of us.
The 2025 theme for Mental Health Awareness Month is “Turning Awareness Into Action.” At T.W. Frierson, we’re doing just that. We are living our core value of “Treat Others Like Family” by continuing to invest in meaningful programs like our:
• Chaplaincy Services
• Mental Health Resource Availability
• Team Training and Development
• Open Conversations Across the Organization
These are just a few of the ways we’re working to foster a culture where asking for help is a sign of strength, and where people are valued not just for what they build, but for who they are.
As industry partners and clients, you play a vital role in this mission. By supporting contractors who prioritize mental wellness, you help cultivate safer, healthier environments where our people, and your projects, can thrive.
At T.W. Frierson, our purpose is clear: To Create a Foundation for People to Thrive.
That foundation isn’t built with steel or concrete alone— it’s built with compassion, courage, and community. Thank you for walking alongside us as we continue to champion both safety and mental well-being on every project, every day.
April 28, 2025 marked a significant milestone for public safety in Tennessee as Governor Bill Lee, alongside the Tennessee Emergency Management Agency (TEMA), Goodwyn Mills Cawood (GMC) Architects, and our team at T.W. Frierson, officially broke ground on the new TEMA Warehouse and Middle Region Coordination Center.
This cutting-edge, 121,980 square foot facility will soon rise on a 110 acre property, consolidating TEMA’s critical functions into a single hub designed for rapid emergency response, operational efficiency, and long-term resilience. The new center includes a 67,302 square foot tilt-up concrete structure, a 6,784 square foot mezzanine, and will serve as a backup state watch point for the region.
Governor Lee described the project as “a key investment in the safety and security of Tennesseans,” and we couldn’t agree more. We’re proud to bring our experience and commitment to quality construction to a facility that will directly support our communities in times of crisis.
Facility Highlights Include:
• Durable tilt-up concrete construction and more than 131,000 cubic yards of flatwork
• A regional helipad for emergency deployments
• Advanced audiovisual wall for real-time monitoring
• Onsite mechanical yard with chiller system and dual emergency generators for power continuity
Approved by the State Building Commission in 2023, this project represents a forward-thinking partnership between public agencies and private industry. As Construction Manager/General Contractor, T.W. Frierson is honored to help deliver this essential infrastructure that will serve Tennessee for generations to come.
We’re proud to be part of building a stronger, safer Tennessee.
With great enthusiasm, T.W. Frierson is delighted to congratulate Jack Barrett on his promotion to Vice President of Self-Performance, a new role to the organization established to support Design Systems Builders, Professional Concrete Solutions, and Armory Door Openings. Since 1958, T.W. Frierson has partnered with clients across the southeast to design, develop and construct world-class facilities for the world’s leading businesses including FedEx, Polaris, Prologis, and Nissan. Rooted in service, team development, and organizational support, the Vice President of Self-Performance signals a significant milestone as T.W. Frierson pursues excellence in integrated industrial project delivery, and Jack Barrett is the ideal candidate.
Having served in multiple roles, including field leadership in other notable Nashville construction firms, Jack joined T.W. Frierson in 2017. During Jack’s tenure, most recently as Project Executive, he led an operations team in executing several challenging projects, including Project Volt and the Prologis City View project, a landmark in the history of industrial development in Nashville’s core market. Additionally, he championed a refreshed corporate program to pre-qualify T.W. Frierson’s trade partners for multiple metrics, with a heightened emphasis on safety performance.
Jack’s leadership is highly regarded by those who have worked alongside him. One of Jack’s team members notes, “Jack has consistently been available to provide direction when needed and has often ensured I have the tools and resources needed to succeed. He steps in during challenging moments to offer guidance and assist with difficult situations while maintaining the ability to step back and allow me to handle challenges on my own.”
From his first interview at T.W. Frierson, Jack made a lasting impression on his colleagues. One employee owner shared, “From the very first interview at TWF, Jack made me feel like part of the family. That warmth continued when I officially joined and received my J Team plaque. Through every challenge, he has led with integrity, support, and a true team-first mentality. Not just overseeing but truly investing in the people around him. His leadership has made a lasting impact, and while he will be greatly missed in OPS, his next team is incredibly lucky to have him.”
Jack’s leadership style is defined by his commitment to his team and collaborative approach. Another team member
describes him as “the best superior I have had in my career” and highlights the qualities that set him apart:
• Caring: Genuinely invested in the well-being of his team
• Collaborative: Works alongside you, not above you
• Engaging: Willing to jump in and solve problems
• Empowering: Gives you autonomy without micromanaging
With his strong character and depth of experience, Jack seeks to streamline the external performance and internal integration of a longtime hallmark of T.W. Frierson’s core business—selfperforming concrete, steel, and overhead doors and docks.
On behalf of all employee-owners at T.W. Frierson, President Kit Ozburn expresses gratitude and admiration for Jack’s continued leadership: “On behalf of all employee-owners at T.W. Frierson, we extend a heartfelt congratulations to Jack, Cindi, and his family for accepting the challenge to serve clients through excellence in self-performance and to enhance the experience of craft labor not only at T.W. Frierson but also throughout our industry.”
Jack himself shares his excitement for this new chapter: “It has been an honor and privilege to serve our clients, trade partners, and fellow Employee Owners in my various roles during my years at TWF. I am so thankful and excited to step into this new opportunity to serve and support our incredible self-performance teams as these men and women work so hard to put quality work in place for our clients each and every day.”
Congratulations to Jack on this well-deserved promotion! We are excited to see the impact he will make in his new role and look forward to continued excellence in self-performance under his leadership.
NES is preparing to begin Phase 2 of the Central Substation project at Gay Street & 2nd Avenue North. This major infrastructure upgrade replaces a substation that has served Nashville since 1914 and plays a key role in enhancing power reliability and supporting the city’s long-term growth. Phase 2 continues the momentum of modernizing the downtown grid with new power transformers, advanced arc-resistant switchgear, and increased capacity to meet future demand - all while keeping the existing substation fully operational.
ARCHITECT TMPartners
PROJECT TEAM
David Turner, Sr. Superintendent
Myles Ayers, Project Manager
Lee Ann Watson, Project Mgmt. Assistant
Andy Zimmerman, Project Executive
Nate Logsdon, DSB Sr. Project Manager
Donnie Hiers, DSB Superintendent
The Village at Church of the City is a thoughtful campus expansion aimed at enhancing community engagement and functionality. The project includes three new buildings for administration and gatherings, improved and expanded parking, a new entrance to ease access, and a central courtyard for outdoor connection. Sustainability is prioritized through stormwater upgrades, including new bio-retention ponds and an expanded retention pond. A new maintenance building will also support long-term campus upkeep and operations.
ARCHITECT Bauer Askew Architecture
PROJECT TEAM
Scott Peterson, Sr. Superintendent
Logan Schaible Asst. Superintendent
Chris Andrews, Asst. Superintendent
Jake Garren, Sr. Project Engineer
Mike Nolan, Sr. Project Manager
Amy Whiffen, Project Management Assistant
Luke Maddox, Project Executive
The Thompson Machinery Sales & Service Center in Cookeville, TN, is a state-of-the-art facility designed to support the company’s equipment sales and service operations. Situated on an 18-acre site, the project includes a 40,000 square foot building featuring modern office spaces and a fully equipped shop with multiple bay doors to accommodate a variety of equipment servicing needs. The site development incorporates a gravel lot, concrete paving, and heavy-duty asphalt to provide durable, functional surfaces for equipment storage, movement, and customer access.
ARCHITECT DCi
PROJECT TEAM
Jeff Landis, Superintendent
Jason Hedge, Project Manager
Amy Whiffen, Project Mgmt. Assistant
Justin Cochrane, Project Executive
Donnie Hiers, DSB Sr. Superintendent
Tory Rice, DSB Project Manager
Jesse Gomez, PCS Superintendent
Zack Bryant, PCS Project Manager
Kandy Mallory, Sr. Design Project Manager
Marc Oakley, Design Project Manager
Located off Madison Street/Highway 41A in Shelbyville, TN, this new 45,000 square-foot, single-story school will provide a dynamic and functional learning environment for students and staff. The facility will feature 12 modern classrooms, administrative offices, a library/media center, dedicated art and music rooms, a full-service kitchen, and a versatile cafeteria/multipurpose space. Additional highlights include a welcoming lobby and atrium, an iconic bell tower, and various support areas designed to enhance day-to-day operations and campus life.
ARCHITECT Davis Stokes Collaborative
PROJECT TEAM
Griffin Jones, Superintendent James Merritt, Sr. Project Engineer
Stephanie Mendoza, Project Engineer
Mike Nolan, Sr. Project Manager
Amy Whiffen, Project Management Assistant
Andy Zimmerman, Project Executive
THOMAS WEST
DSB Project Engineer
DYLAN TAYLOR
TWF Project Engineer
NEAL BELCHER
DSB Superintendent
ASHLYNE GILBERT
TWF Project Engineer
ALEX GRAEF
TWF Assistant Project Manager
STEVEN KNIGHT
TWF Carpenter
JOSE AGUILAR LEIJA
DSB Ironworker
JUAN HERRERA Carpenter Helper
KYLE LUDWIG
PCS Project Manager
RON PARRISH
Safety Engineer
SHAYNE DIETRICH
DSB Ironworker
DERSIM YASIN
DSB Field
MATT JACOBSON
Construction Technology Leader
TONY MARTINEZ
DSB Field
DAKOTA WHITAKER
DSB Field
MARLON CENTENO GONZALEZ
PCS Field
At T.W. Frierson, we believe the best way to learn is by doing. That’s the heart behind our Work-Based Learning (WBL) Program, an initiative designed to give high school students real-world experience in the construction industry long before graduation.
This isn’t just a job shadow. Our WBL students join the team and contribute in meaningful ways out on the jobsite gaining exposure to field operations and safety practices. The goal? To give them a clear and informed look at a career path available in construction.
Each WBL participant is paired with a mentor who provides guidance, feedback, and encouragement throughout the summer. We’re passionate about supporting workforce development and investing in the future of our industry. That starts with education and access, giving young people a chance to see themselves in roles they may have never considered.
To our current WBL students: we’re proud to be part of your journey. Thank you for showing up, asking questions, and getting your hands dirty. You're helping us create a foundation for people to thrive.
MARK WALSH
Senior Project Manager
KEITH FUSSELL
PCS Superintendent
DENIS ALAGIC Laborer
ARMANDO RAMIREZ
DSB Ironworker
CARLOS VAZQUEZ ALVAREZ
DSB Ironworker
EDINSON MOLERO Carpenter Helper
ZOLAN MILES
DSB Ironworker
JAYTHAN PLEASANT
DSB Ironworker
A well-designed metal building system isn’t just for warehouses and distribution centers... they are also ideal for unique, mission-driven spaces like this one.
Design Systems Builders is proud to be erecting the metal building for T.W. Frierson on the new Metro Nashville Mounted Patrol Barn at Peeler Park. The project includes an 11,016 square foot barn and a 3,870 square foot hay storage building, forming the core of a nearly 15,000 square foot operational hub. This facility will become the shared home for the horses and equipment of both the Metro Nashville Police Department (MNPD) and Metro Parks mounted patrol divisions. The greater project also includes approximately 40 acres of surrounding pasture to support the care and training of the horses in a natural environment.
This facility highlights the adaptability and efficiency of pre-engineered metal building systems, offering both durability and speed of construction, which is critical for community-serving projects like this one. From the riding arenas to the equipment bays, every inch of this structure is designed to support public safety and recreational services in a shared, purpose-built space.
DSB PROJECT TEAM
Angel Gonzalez, Superintendent Tory Rice, Project Manager
Javi Salazar, Assistant Superintendent
On February 22, 2025, our T.W. Frierson family gathered for a truly unforgettable evening of fellowship, fun, and celebration at our Annual Stock Price Reveal Dinner. Themed “A Night at the Races,” the event brought out everyone’s inner jockey and southern charm, complete with bowties, big hats, and bold Kentucky Derby style.
From the thrill of horse racing-themed entertainment to the moment we’d all been waiting for the unveiling of our new TWF stock price, the evening was filled with high energy and even higher spirits.
But this event is about more than just a good time. It’s a powerful reflection of who we are. As a 100% employee-owned company, this annual tradition is a celebration of the incredible value we’re building together. Every project completed, every challenge overcome, every act of teamwork, it all contributes to our shared success.
Our stock price is determined each year through an independent valuation conducted by a third-party firm, ensuring fairness, transparency, and an accurate reflection of our performance and future outlook.
Since launching our ESOP in 2016, our stock price has grown an astonishing 424%. That number tells a story of hard work, ownership mentality, and a team that shows up every day with purpose.
Here’s to another year of creating a foundation for people to thrive!
We are proud to celebrate the completion of Brentwood Academy’s new on-campus chapel, a project rooted in purpose, community, and spiritual growth.
Designed with intention and beauty, the chapel features a striking combination of glass and timber, creating a warm, light-filled sanctuary that accommodates up to 175 individuals. More than just a building, this space was envisioned as a place where students, faculty, and families can gather, reflect, and grow together in faith and fellowship.
Since opening its doors, the chapel has quickly become a beloved destination on campus. It now hosts a wide range of events, including student Bible studies, worship nights, parent gatherings, and faculty professional development sessions. Whether it’s a quiet moment of prayer or a full house for a community celebration, the chapel stands as a beacon of Brentwood Academy’s mission to cultivate both the heart and the mind.
But the chapel is just one part of a broader vision to enhance the Brentwood Academy campus experience.
Central to this transformation are several key infrastructure improvements designed with accessibility, safety, and convenience in mind.
A new main entrance on Granny White Pike now serves as a welcoming gateway for families and visitors, offering a safer and more intuitive arrival experience. The addition of a traffic light at the intersection of Virginia Way and Granny White Pike helps streamline traffic flow during busy drop-off and pick-up times. To further support the growing needs of the school community, an additional 60 parking spaces have been added, addressing a longstanding challenge and providing greater ease for students, staff, and guests alike.
These enhancements reflect Brentwood Academy’s commitment to fostering an environment where students can thrive, spiritually, academically, and communally. We are honored to have played a role in bringing this vision to life and look forward to the lasting impact it will have for years to come.
view more photos of the Chapel by scanning or clicking on the QR code!
We are proud to announce that our work on Portobello America and the Nashville Women’s Rescue Mission has earned two National Excellence in Construction® Eagle Awards, presented during ABC National Convention in Las Vegas on February 26, 2025. The Excellence in Construction (EIC) Awards recognize the top construction projects in the nation each year, honoring outstanding achievements in areas such as healthcare upgrades, sports complexes, government buildings, and major infrastructure. This year, ABC recognized 96 of the nation’s best projects from 2024, and T.W. Frierson is honored to be among the winners.
“Through these awards, the employee-owners of T.W. Frierson are fulfilling our core purpose to Create a Foundation for People to Thrive. With a 67 year legacy of excellence in project delivery and client care, we extend our gratitude to our clients and our projects teams for the opportunity to serve.”
We extend our heartfelt gratitude to our dedicated team, trade partners, and clients who made these projects possible. Our success is a direct reflection of the collaboration, expertise, and passion that each of our team members brings to every project. These achievements are a testament to the commitment an dedication of our workforce, and we are incredibly proud of what we have built together.
Eagle Award (1st Place)
Category: Pre-engineered Up to $100M
This nearly 1 million square-foot porcelain tile manufacturing facility showcases the expertise and precision our team brings to large-scale construction. Leveraging advanced VDC modeling and a steadfast commitment to safety, the Portobello America project stands as a testament to our ability to deliver complex advanced manufacturing projects.
PROJECT TEAM:
Andy Zimmerman Joe Slate Rob Holtby Myles Ayers Lee Ann Watson Guy Harris Tory Rice Donnie Hiers Alex Martin James Merritt
NASHVILLE WOMEN’S RESCUE MISSION
Eagle Award (1st Place)
Category: Public Service Up to $100M
This project expanded the Rescue Mission’s capacity to serve women and families experiencing homelessness, creating a space where hope and support thrive. From enhanced bed capacity to additional family units and critical services, the project reflects our dedication to addressing community needs through thoughtful design & construction.
PROJECT TEAM:
Justin Cochrane Steve Mignoli Tommy Manley Sean Foote
Lee Ann Watson Luke Maddox Paul Downer Ben Carraway
ERIC DAVIS
Assistant Safety Manager
MARC OAKLEY Design Project Manager
DERIC WESSELER Preconstruction Project Manager
BRIAN CRISWELL Talent & Training Manager
JUSTIN COCHRANE Project Executive
IKAIKA TUIPULOTU Foreman
CHRIS ANDREWS Assistant Superintendent
Please join us in congratulating Brian Criswell on completing the Certified Professional in Training Management certification!
BRENTWOOD ACADEMY CLASSROOM
Brentwood, Tennessee
Kaden Frasier, Asst. Superintendent
Dan Hasselbring, Project Manager
Romenda Basha, Project Engineer
Amy Whiffen, Project Mgmt. Assistant
Jack Barrett, Project Executive
Zack Bryant, PCS Project Manager
Matt Self, PCS Asst. Superintendent
BRENTWOOD UMC PHASES 2 & 3
Brentwood, Tennessee
Del Perry, Superintendent
Owen Wheelock, Project Engineer
Christian Brinkley, Sr. Project Engineer
John French, Sr. Project Manager
Lee Ann Watson, Project Mgmt. Assistant
Luke Maddox, Project Executive
CHARLIE IRWIN PAINTING OFFICE RENO
Shelbyville, Tennessee
George Crenshaw, Superintendent
Steve Mignoli, Project Manager
Amy Whiffen, Project Mgmt. Assistant
Luke Maddox, Project Executive
Trent Robinson, DSB Assistant Superintendent
Neil Lambert, DSB Project Manager
Marc Oakley, Design Project Manager
COOPER CHRISTIAN ACADEMY
Shelbyville, Tennessee
Griffin Jones, Superintendent
Ikaika Tuipulotu, Foreman
Stephanie Mendoza, Project Engineer
James Merritt, Sr. Project Engineer
Mike Nolan, Sr. Project Manager
Lee Ann Watson, Project Mgmt. Assistant
Andy Zimmerman, Project Executive
DEPARTMENT OF ELECTRIC
Gallatin, Tennessee
Rob Holtby, Superintendent
Christian Brinkley, Sr. Project Engineer
John French, Sr. Project Manager
Lee Ann Watson, Project Mgmt. Assistant
Luke Maddox, Project Executive
Neil Lambert, DSB Project Manager
Nashville, Tennessee
Angel Gonzalez, DSB Superintendent
Neil Lambert, DSB Project Manager
JENKINS & WYNNE LINCOLN SALES
Clarksville, Tennessee
Joe Slate, Sr. Superintendent
Christian Brinkley, Sr. Project Engineer
Mike Nolan, Sr. Project Manager
Amy Whiffen, Project Mgmt. Assistant
Andy Zimmerman, Project Executive
Ray Woodby, DSB Superintendent
Neil Lambert, DSB Project Manager
Keith Fussell, PCS Superintendent
Zack Bryant, PCS Project Manager
Madison, Tennessee
Zach Brayton, Asst. Superintendent
Jason Hedge, Project Manager
Amy Whiffen, Project Mgmt. Assistant
Jack Barrett, Project Executive
Angel Gonzalez, DSB Superintendent
Tory Rice, DSB Project Manager
NSCC CLARKSVILLE EXPANSION
Clarksville, Tennessee
Jorge Leal, Sr. Superintendent
Jon Patrick, Asst. Superintendent
Justin Cochrane, Sr. Project Manager
Josh Coquillard, Asst. Project Manager
Lee Ann Watson, Project Mgmt. Assistant
Andy Zimmerman, Project Executive
NISSAN BAY 01 XL PRESS
Smyrna, Tennessee
Jeff Waggoner, Sr. Superintendent
Owen McCann, Asst. Superintendent
Craig Karaszewski, Sr. Project Manager
Lee Ann Watson, Project Mgmt. Assistant
Luke Maddox, Project Executive
Neil Lambert, DSB Project Manager
NES CENTRAL SUBSTATION
Nashville, Tennessee
David Turner, Sr. Superintendent
Myles Ayers, Project Manager
Lee Ann Watson, Project Mgmt. Assistant
Andy Zimmerman, Project Executive
Nate Logsdon, DSB Sr. Project Manager
NISSAN P33C
Smyrna, Tennessee
Jason Watson, Superintendent
Steve Mignoli, Project Manager
Craig Karaszewski, Sr. Project Manager
Lee Ann Watson, Project Mgmt. Assistant
Luke Maddox, Project Executive
PROJECT VOLT
Mt. Juliet, Tennessee
Alex Martin, Superintendent
Jeff Neely, Asst. Superintendent
Alex Graef, Asst. Project Manager
Jay McGinnis, Project Manager
Amy Whiffen, Project Mgmt. Assistant
Jack Barrett, Project Executive
Kyle Torrence, DSB Sr. Project Engineer
Ben Carraway, Project Architect
Marc Oakley, Design Project Manager
RUNWAY LOGISTICS 1
Nashville, Tennessee
Jason Powell, Superintendent
Phil Gaines, Asst. Project Manager
Dan Hasselbring, Project Manager
Lee Ann Watson, Project Mgmt. Assistant
Andy Zimmerman, Project Executive
Neil Lambert, DSB Project Manager
TEMA MIDDLE COORDINATION CENTER
Nashville, Tennessee
Michael Leahey, Sr. Superintendent
Christian Brinkley, Sr. Project Engineer
Mark Walsh, Sr. Project Manager
John French, Sr. Project Manager
Amy Whiffen, Project Mgmt. Assistant
Luke Maddox, Project Executive
THE VILLAGE AT CHURCH OF THE CITY
Franklin, Tennessee
Scott Peterson, Sr. Superintendent
Logan Schaible Asst. Superintendent
Chris Andrews, Asst. Superintendent
Jake Garren, Sr. Project Engineer
Mike Nolan, Sr. Project Manager
Amy Whiffen, Project Mgmt. Assistant
Luke Maddox, Project Executive
THOMPSON MACHINERY
Cookeville, Tennessee
Jeff Landis, Superintendent
Jason Hedge, Project Manager
Amy Whiffen, Project Mgmt. Assistant
Justin Cochrane, Project Executive
Donnie Hiers, DSB Sr. Superintendent
Tory Rice, DSB Project Manager
Jesse Gomez, PCS Superintendent
Zack Bryant, PCS Project Manager
Kandy Mallory, Sr. Design Project Manager
Marc Oakley, Design Project Manager
WIRTGEN OFFICE RENOVATIONS
Antioch, Tennessee
Cliff Manley, Superintendent
Steve Mignoli, Project Manager
Lee Ann Watson, Project Mgmt. Assistant
Luke Maddox, Project Executive
Kyle Torrence, DSB Sr. Project Engineer
Kandy Mallory, Sr. Design Project Manager
SANDERSON PIPE ADDITION
Clarksville, Tennessee
Jesse Kaufman, Asst. Superintendent
Josh Coquillard, Asst. Project Manager
Andy Zimmerman, Project Executive
Lee Ann Watson, Project Mgmt. Assistant
Nate Logsdon, DSB Sr. Project Manager
Neal Belcher, DSB Superintendent
Kyle Ludwig, PCS Project Manager
Nic Watson, PCS Asst. Superintendent
Kandy Mallory, Sr. Design Project Manager
ST. LUKE CPC GYM & CLASSROOMS
Madison, Tennessee
Tim Blakeney, Superintendent
Myles Ayers, Project Manager
Lee Ann Watson, Project Mgmt. Assistant
Andy Zimmerman, Project Executive
Kyle Torrence, DSB Sr. Project Engineer
Zack Bryant, PCS Project Manager
Amy Whiffen, PCS Project Mgmt. Assistant
Craig Polancich, Sr. Design Project Manager
Marc Oakley, Design Project Manager
Provided by Hannah Fisher, Project Engineer
“If you're thinking about doing a construction internship, my biggest piece of advice is to take some time to think about your career goals and find the internship that feels like the best fit for you. You might not know exactly what you're looking for right now, and that’s okay! I’ve found that internships offering a variety of learning experiences and opportunities for growth are the best way to figure out what you enjoy most. That’s why I chose to intern, work part-time during school, and now continue full-time with T.W. Frierson.”
I had my first internship with T.W. Frierson in the summer of 2022. At the time, I wasn’t very familiar with the world of commercial construction, but the employees at T.W. Frierson supported me every step of the way. I was eager to learn and excited to get to work. My experience as an intern was nothing short of amazing. Everyone welcomed me with open arms and made sure I had what I needed to succeed. I got to spend time in each department and really understand how all the parts of the company work together. After the first summer, I stayed on part-time during college and then completed a second internship before graduating.
T.W. Frierson’s internship program helped bring me out of my shell. From public speaking and giving presentations to equipment training and earning certifications, I was able to grow in both knowledge and confidence. The internship helped me connect what I was learning in school to real-world work. Anytime I had questions, someone at T.W. Frierson was always there to help—and it really pushed me forward, both personally and academically. You can tell that they truly care about the growth of each employee. I never felt like just a number.
One of the many reasons I chose to work for T.W. Frierson full-time is because of the family-oriented culture and strong core values. These values have meaning behind them, and the employees really live them out. I felt valued as a new employee and was excited to dive into projects on a full-time basis.
The biggest difference between being an intern or part-time employee and now working full-time is that I can really focus my time and energy on my projects. I’ve already gotten to be part of multiple jobs and have learned so much in the process. Right now, I’m in T.W. Frierson’s 18-month rotation program, which is broken into three six-month phases—operations, field, and pre-construction. With this program, I have been able to take a deeper look into the roles and responsibilities and decide what best fits my career goals.
This summer, we’re proud to welcome our largest and most diverse intern class to date! With students representing five different universities, this group brings a wide range of perspectives, energy, and ambition and we can’t wait to see how they grow with us over the next several weeks.
At T.W. Frierson, we don’t believe in coffee runs and busy work. Our internship program is built with intention, giving students a hands-on, full-circle experience of how a construction project is born and brought to life.
The program kicks off where all great construction careers do: Safety. From there, interns rotate through every major department of our company:
BUSINESS DEVELOPMENT & MARKETING – learning how we pursue projects and build strong client relationships
PRECONSTRUCTION – getting into the details of estimating, planning, and early-stage decision-making
PROJECT MANAGEMENT – understanding how we coordinate teams, track budgets, and lead successful projects
FIELD OPERATIONS – where the boots hit the ground and the work comes to life
Throughout the summer, interns follow the path of a real TWF project, tracking it from early pursuit through final construction. By the time they land in the field, they’ve already seen the full story unfold in our office—offering a unique, immersive experience they can’t get from textbooks alone.
Each week during their rotations, interns deliver a presentation about what they’ve learned. These presentations are scored by TWF team members, adding a fun and competitive twist to the experience. At the end of the summer, one intern will walk away with bragging rights as our official TWF Intern Champion. ��
We’re excited to invest in this incredible group of future builders—and even more excited to learn from them along the way. With their fresh ideas, diverse academic backgrounds, and growing industry knowledge, they represent the future of our company and our industry.
Welcome to the TWF family—we’re so glad you’re here. Let’s build something amazing together.
At Armory, our sales team brings passion, industry knowledge, and just the right amount of personality to every project. Whether it’s high-speed doors, dock equipment, or custom solutions for manufacturing facilities, this crew is all in, matching our customers with the right products and the best service in the business.
Outside Sales Representative
With 3 years of experience and an OSHA 30 certification, Bryce thrives in fast-paced manufacturing environments, especially when it comes to selling high-speed products.
Fun fact: he’s walked the Great Wall of China, now that’s going the distance!
Outside Sales Representative
Cory has 2 years of experience and a sharp eye for dock equipment solutions. Outside of work, he competes in ranch versatility and reining horse shows, he knows a thing or two about precision and control.
Outside Sales Representative
With 5 years under his belt, Luke is all about overhead and high-speed doors. A former Central Michigan football player, he brings grit and drive to every sale, even if he’s never seen Star Wars (yes, really).
Our team offers a comprehensive range of services, ensuring that businesses operate smoothly and efficiently:
Overhead Door Installation & Repair
Loading Dock Equipment Maintenance
Bug Screens Installation
Planned Maintenance Programs
Fire Door Drop Testing
Modular Offices Setup
Security Partitions and Cages
Ergonomic Equipment Solutions
High-Volume Low-Speed (HVLS) Fans
PCS PROJECT TEAM
Nic Watson, Asst. Superintendent
Kyle Ludwig, Project Manager
Professional Concrete Solutions is working on a project for our repeat client, Sanderson Pipe, in Clarksville, TN. This expansion included a new storage shed and a two-story office addition, with PCS handling a wide-ranging scope of concrete work across the site.
Our team poured 12,000 square feet of turndown slabon-grade between the new shed and office, installed 22 spread footings, and completed the elevator pit and walls for the office structure. We also placed 2,300 square feet of slab-on-metal-deck (SOMD) for the second floor, along with excavating, setting rebar, installing anchor bolts, and pouring and finishing concrete across all elements.
One of the most unique aspects of the project was the need to design and install a custom bridge footing for the office foundations. This allowed our team to span over an existing electrical duct bank without disrupting operations, a true collaboration between field expertise and engineering ingenuity.
The PCS team also poured 4-foot-wide aprons around the new shed and handled demo and repair work on several sections of aging concrete paving across the site.
Despite a tight site, multiple redesigns, and weather delays, our crew delivered the project on schedule with zero safety incidents—a testament to the professionalism, planning, and precision that defines the PCS approach.
We’re proud to continue building strong relationships (and solid foundations) with Sanderson Pipe, and we look forward to what’s next.
At DCi, we’re constantly seeking innovative tools that help us bring clarity to complex ideas and create a smoother path from concept to construction. One of the most game-changing tools we’ve embraced in recent years is drone technology, revolutionizing how we capture data, visualize environments, and communicate design intent.
A recent example of this is our work with Long Hollow Church in Hendersonville, TN. As part of a planning department meeting for a proposed building alteration, the church needed to request a height variance. To help illustrate the vision and impact of the proposed changes, DCi architect Ben Carraway combined DroneDeploy aerial imagery with advanced design software to create a powerful massing study.
This approach allowed us to overlay a digital model of the proposed building directly onto site photography captured by drone, giving county officials a true-to-life visual of the design in context. The study included multiple vantage points, showing how the new height would compare to existing campus structures such as the chapel steeple, children’s building, and fly loft.
Drone technology isn’t just a cool tool, it’s fundamentally changing the landscape in which we design and build. Drones enable us to:
Capture high-resolution aerial data in real-time, improving the accuracy of site analysis and reducing the need for repeated field visits.
Create context-aware visualizations that help stakeholders understand spatial relationships and potential impacts with greater clarity.
Enhance transparency in public meetings and planning reviews, which can expedite approvals and build trust with local authorities and communities.
Monitor site conditions and progress during construction, improving coordination and documentation throughout the project lifecycle.
For Long Hollow Church, this drone-powered massing study wasn’t just a presentation, it was a strategic advantage in communicating their vision effectively.
WORK
Provided by Kit Ozburn, President
*We have all worked with a “Jerry”. While this story is not a reflection of a singular person, it is sadly a reflection of someone we all know, someone we have worked with, or someone we greatly care for. We are sadly working side by side with someone struggling with their mental health right now. We are all familiar with someone who was a hard worker and always showed up to work. And then one day they didn’t. This is Jerry’s and countless other’s story.
For decades, you could count on Jerry. He was steady. Reliable. Always fulfilled his obligations. So, when the lights of his truck didn’t sweep across the gravel parking area and he didn’t walk through the gate that morning, the concern was immediate and deeply personal.
The chest-tightening concern is as fresh today as it was on the day Jerry didn’t show up for work. Unfortunately, this is far too common in the construction industry. We have made tremendous strides in physical safety, protecting workers from the visible hazards that surround every jobsite. But what if the dangers for the industry exist beyond the eight-foot-high chain link enclosing the jobsite? What if the industry’s greatest risk exists unseen in the mental health struggles of the 6 million hardworking women and men who proudly wear high-vis and hard hats every day?
This isn’t just Jerry’s story. Ironically, statistics indicate the jobsite may be the safest place for the industry’s workforce. Beyond the fence, thousands of workers face accumulating stress and carry unseen burdens. Long hours, physical pain, job insecurity, isolation… it adds up. When support systems are lacking, the impact can be devastating.
The construction workforce is 16 times more likely to die from an overdose and 5 times more likely to die by suicide than from a jobsite incident. For too long, mental health has been an unspoken topic in an industry that prides itself on toughness. But the cost of that silence is far too high. A 2020 study from the National Academy of Engineering, Suicide and Mental Health Challenges in the Construction Industry, reports that “83% of construction workers have struggled with mental health issues.” Read those statistics one more time. Think of the people on your team… the ones who show up early, stay late, and keep your projects running strong. Now imagine they were the ones quietly fighting battles no one talks about.
At T.W. Frierson Contractor, we are distinguished by a remarkable passion for people. We realize to truly protect people, we cannot focus only on physical safety, we must care for the whole person. T.W. Frierson is pushing back against this health crisis, assuming a leadership role in this crusade, and investing in a multi-prong approach by establishing a support architecture within the organization.
We take great pride in the relentless pursuit of our Core Purpose Creating a Foundation for People to Thrive. Jerry’s experience encouraged us to look even more closely at what it means for people to thrive. We have recommitted strategies “upstream” to prevent team members from reaching a breaking point and “falling in the river.” Who on your team might be struggling silently?
Available to all employees regardless of role or hourly status, support offerings include:
• Free confidential mental health counseling
• Sabbatical program designed to reduce burnout and promote balance
• On-site chaplain services for emotional and spiritual connection
• Purposeful communication strategies removing the veil and speaking openly about mental health
We cannot stop there. Imagine a jobsite where an aching shoulder is not a dread-filled precursor signaling the early end of a career, but recognized as a signal, an opportunity to step in with care and support. Imagine a team where mental health worries are not stuffed away in a toxic toolbox to detonate another day, but rather are met with professional resources ready to shoulder the load together. These steps are worth celebrating, but at T.W. Frierson, we know there’s always more we can do.
“There comes a point where we need to stop just pulling people out of the river. We need to go upstream and find out why they are falling in.”
Desmond Tutu, Archbishop Emeritus
Can you imagine leading-indicators that exist upstream and prevent members of our industry from entering these challenges rather than reacting to the incidents? Imagine an organizational strategic plan that includes mental health critical numbers with annual initiatives accountable for action. Imagine a corporate culture that celebrates team members’ raising their hands to the bench to call out of the game for a rest.
We are responding to this crisis by bringing the issues surrounding mental health into the light. Since opening this conversation, I have had the privilege of connecting with many individuals who have bravely fought a mental health issue from a place of solitude and loneliness, and have moved into an environment of trust and support. Jerry’s unexpected absence could be more than a wakeup call- it could be a turning point and call to action for your team.
Thankfully this time, Jerry’s story did not end in tragedy. Thanks to the support of his teammates and available resources, he experienced a beautiful redemption in his personal life with his well-being graciously restored. But not every story ends this way, and that’s the hard truth our industry must confront.
I wish we had started on this journey sooner, long before Jerry didn’t show up for work. Every company has the power to transform their workplace culture from one of silence to one of support. By taking these steps, we not only protect our workforce - we strengthen our entire industry. Let's build a future where mental health conversations are as natural as discussing physical safety protocols. Your actions today could save lives tomorrow. I hope you will join us on this vital journey of transformation into a more compassionate industry.