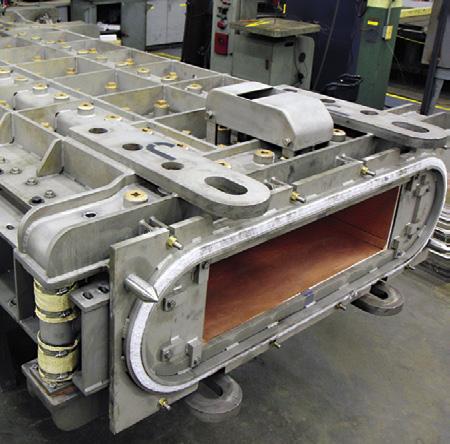
6 minute read
Butech Bliss delivers excellence in melting equipment repairs
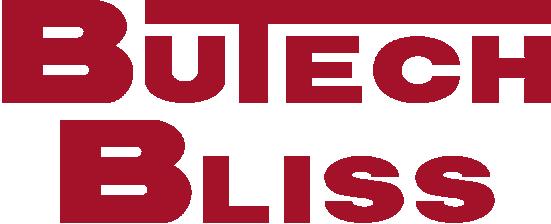
That’s why when it comes to the design and manufacture or the repair and reconditioning of crucibles, molds, and hearths for your ESR, VAR, EBM, or PAM installations, we draw on our more than 130 years of design, engineering and manufacturing excellence to ensure that your copper-based melting equipment is operating at peak efficiency.
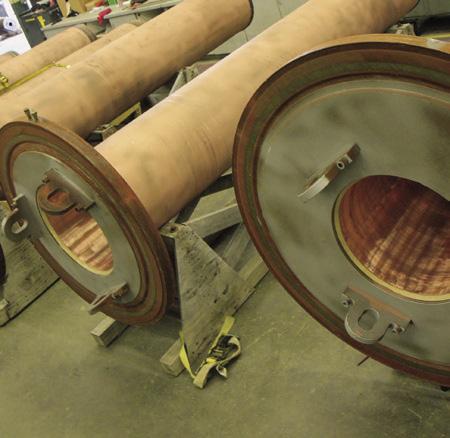
A reputation for quality work and on-time delivery.
Our staff of expert millwrights, welders and machinists can tear down, assess, repair and test your valuable melting equipment. Additionally, our manufacturing capabilities are fully supported by our staff of over 50+ engineers. Our services include:
• Machining, welding, straightening, and sizing of stainless steel, copper, nickel, aluminum, bronze, and carbon steel


• Preventative maintenance, including cleaning, re-sizing, straightening and seal replacement
• Crucible diameter and size modifications
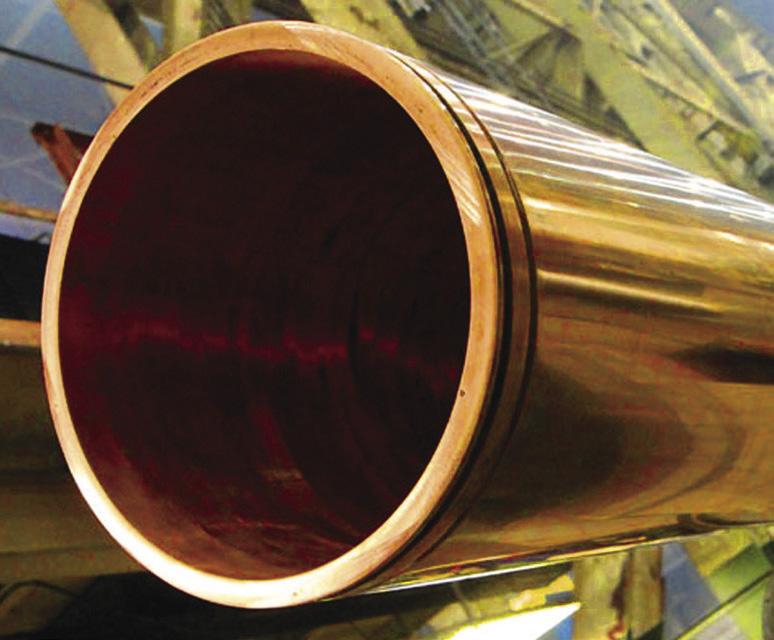
• New crucibles, molds, base assemblies, water jackets, etc.
To learn more about our rebuilding and manufacturing services,call (330) 337-0000, visit www.ButechBliss.com or email cu@butech.com.
650 employees, and 60 percent of its production sold to U.S. customers
The Velta Titanium Process features the implementation of special technology which controls particle size distribution (PSD) for titanium metal powders, resulting in the production of non-spherical, spherical titanium powders and its alloys, with low and extremely low oxygen content. The high economic efficiency of the process allows the production of different types of titanium metal powders (non-spherical and spherical shape) at low cost. The representatives said the cost of titanium powder from the Velta Process could be lower by two to three times compared to Kroll-HDH powder for commercially pure titanium grades; three to four times lower for Grade 5PM alloy; and three to four times for different types of spherical powders (both pure titanium and its alloys). They said the Velta Process can produce alloys directly through the reduction of titanium-containing raw materials (technical titanium dioxide).
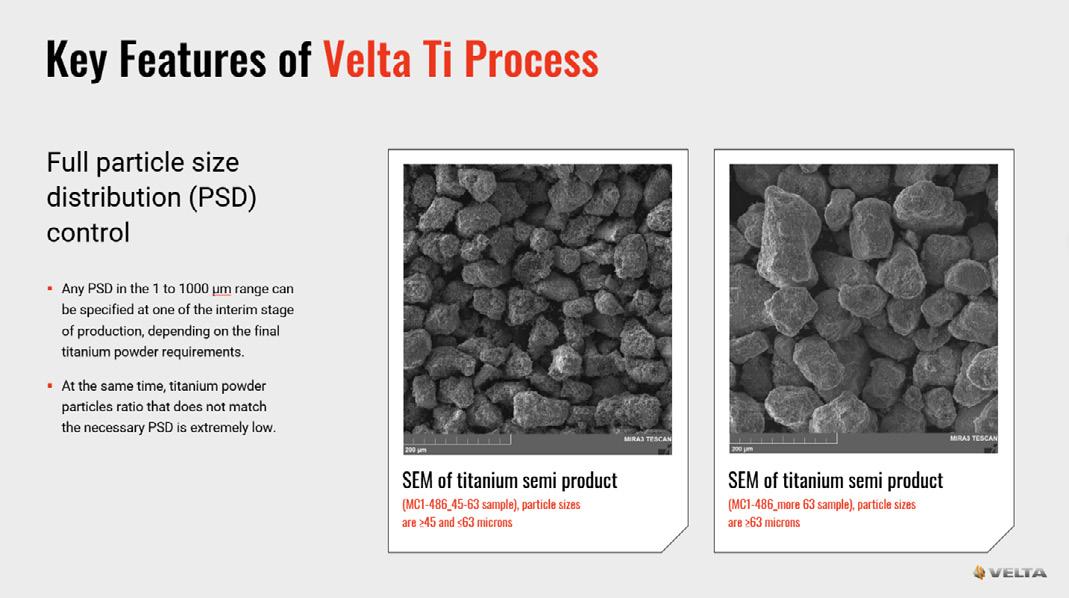
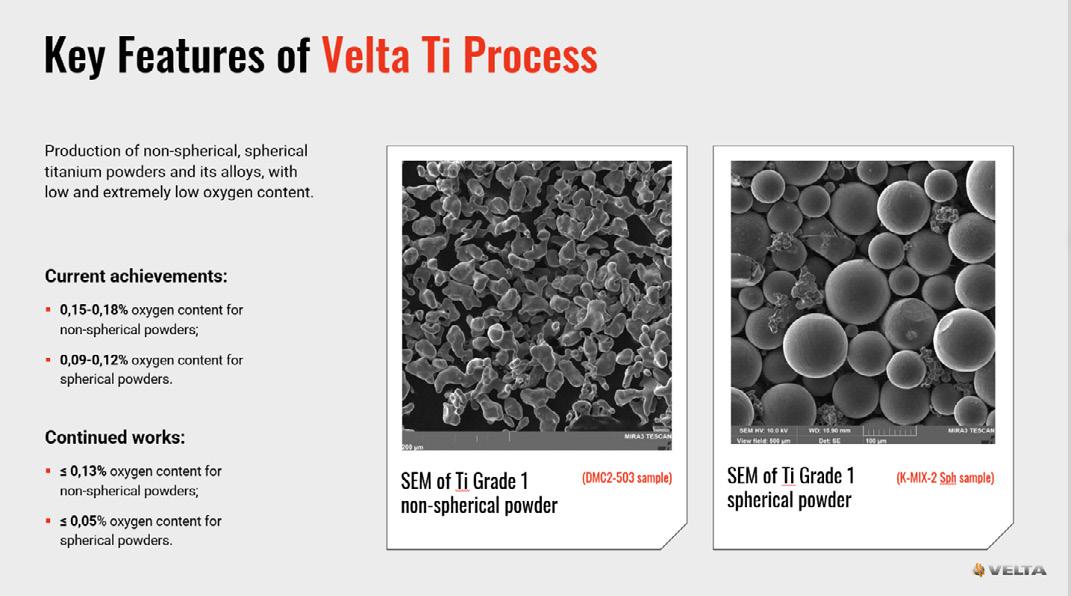

“As a result, a powder of the corresponding titanium alloy is formed without the need for additional stages, as is the case with the Kroll process. These capabilities open the way for intermetallics production and production of a large number of high-quality alloys, especially those that are currently either difficult or even impossible to manufacture in industrial quantities due to engineering constraints or economic inexpediency.” They said Velta is planning to launch a titanium manufacturing facility with a capacity of 10,000 tons of titanium powder and titanium finished parts per year.
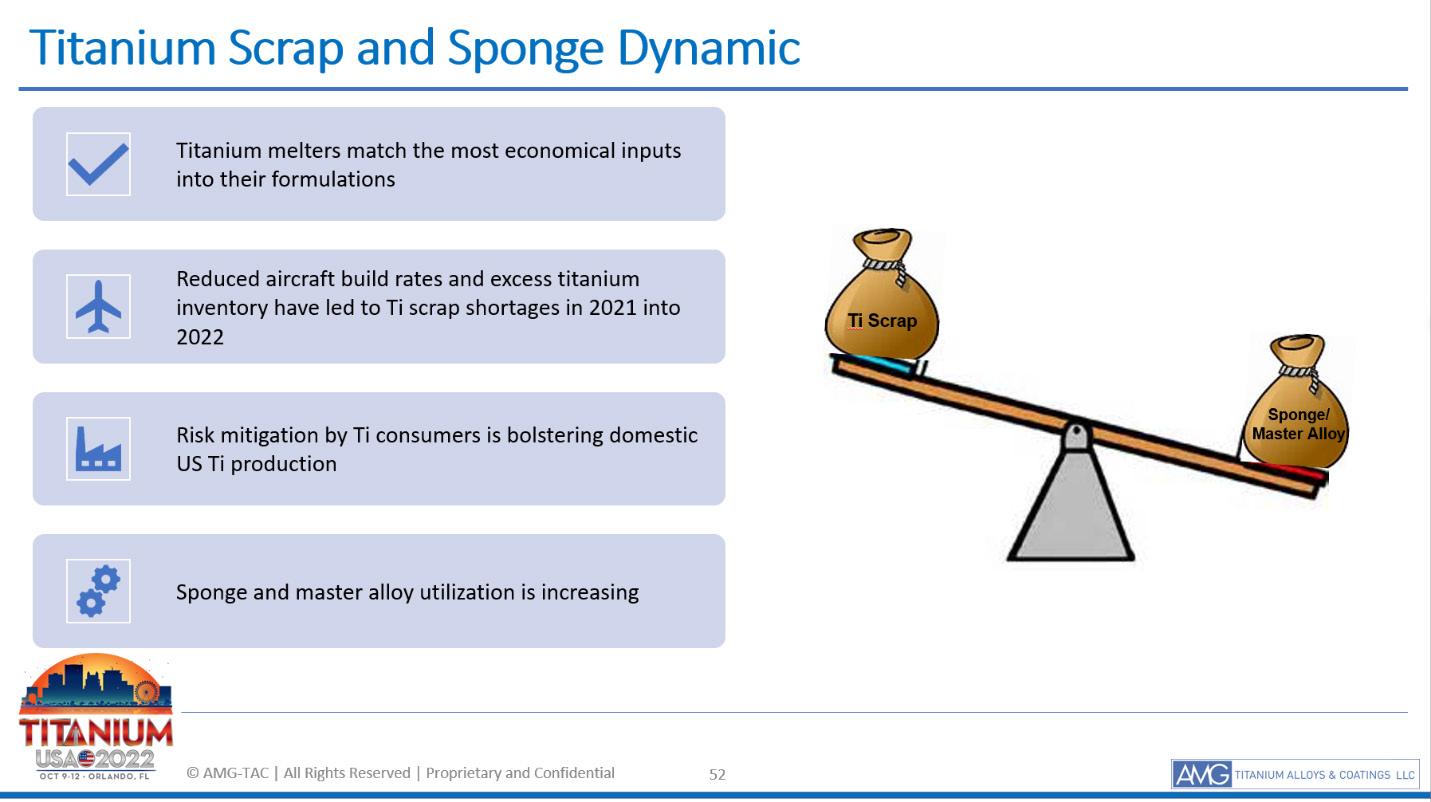
Titanium Cladding
Dr. Edgar E. Vidal, vice president of marketing and business development, NobelClad, a DMC Global Inc. company, explained why “Titanium Cladding is Critical to the Chemical Processing Industry in Times of War.” As of 2021, China dominates with over half the world production of titanium sponge, followed by Japan. “The supply of titanium has shifted to Asia, in particular China. The increase in demand of titanium in the aerospace industry and the uncertainty of the world order will only cause titanium prices to increase. The once-stable supply of titanium to other industries like chemical processing (CPI) is now very volatile. Can you fulfill the mission in CPI with less titanium? The answer is, sometimes yes, with cladding”
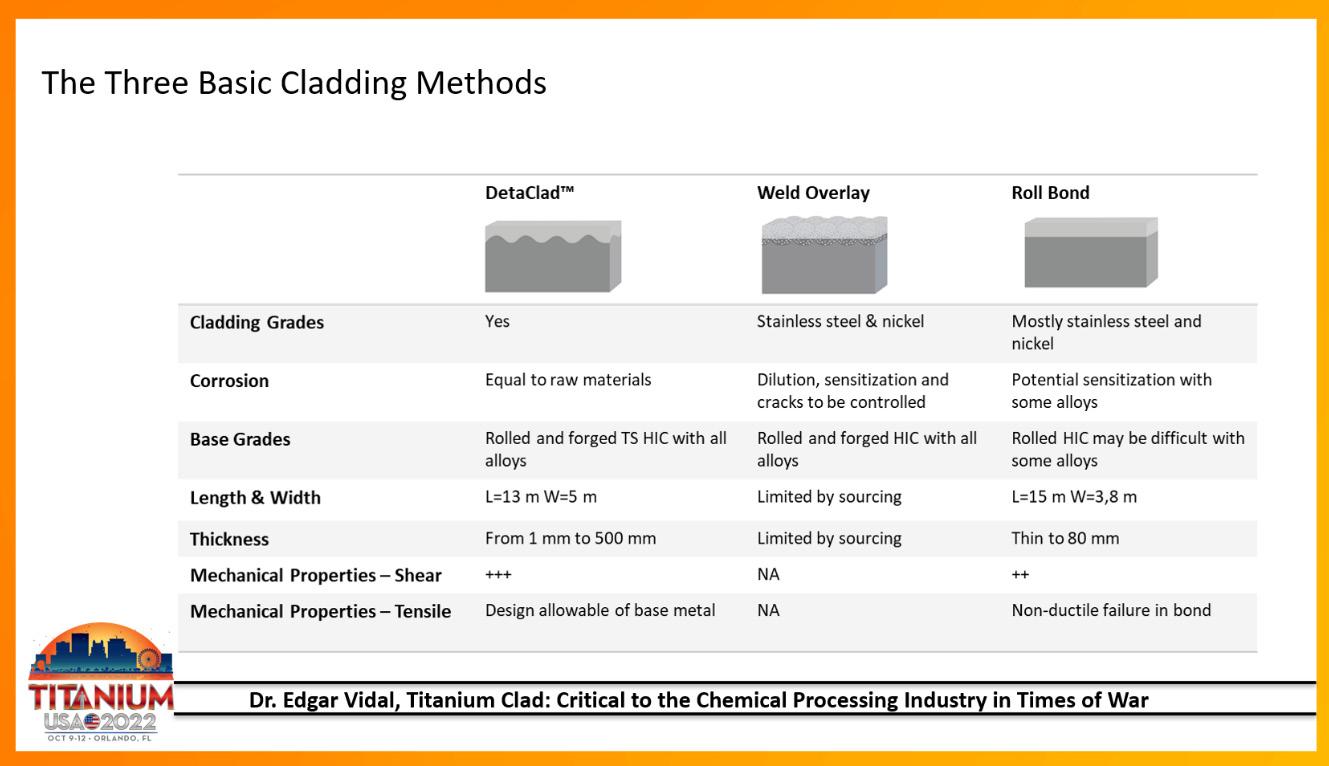
Vidal offered examples, such as Clad-Head fabrication. “Titanium clad plates can be formed into heads by either cold or hot forming, dependent upon fabricator equipment forming capabilities (up to 5m in diameter). Depending on available plate size and size/geometry of heads, segmental construction may be necessary for head forming.” He also cited DeltaPipe, titanium clad pipe, where the titanium alloy undergoes the DeltaPipe™ cladding process, resulting in a lock-tight fit to the pipe spool and is capable to withstand exposure to both ambient and elevated temperatures while at operating pressure in service.

“Globalization has its benefits, but has also shown the weaknesses (in the supply chain) in times of war,” Vidal said. “Titanium has become an indispensable metal, and sourcing is dependent on a handful of countries. Aerospace applications will demand more titanium, thus limiting availability to CPI and other industries. Efficient usage of titanium is more important than ever.
Medical Trends
Eliana Fu, industry manager, aerospace and medical for the Trumpf group, explained how “3D Printing Titanium Takes a Bite Out of Dental Applications for Laser Additive Manufacturing.” They presented the processing and printing parameters of the Trumpf TruPrint 1000 or 2000 Laser metal fusion machine, which has a laser with a 1064nm infrared (IR) wavelength, typical power of 200300W for dental procedures, a laser beam spot size of 55m, and a circular build plate 200mm diameter
Fu said it’s demonstrated that the
3D printing components allows for innovative design and customization, particularly in medical applications.
“No two people are alike, and our teeth, gums and mouth shapes are all individual. Dental components, which includes braces, bridges, crowns, roots, abutments, and Removable Partial Dentures (RPDs), other fixation devices as well as instruments and tools, can all be individualized to create patientspecific parts using laser additive manufacturing (laser AM) processes.”
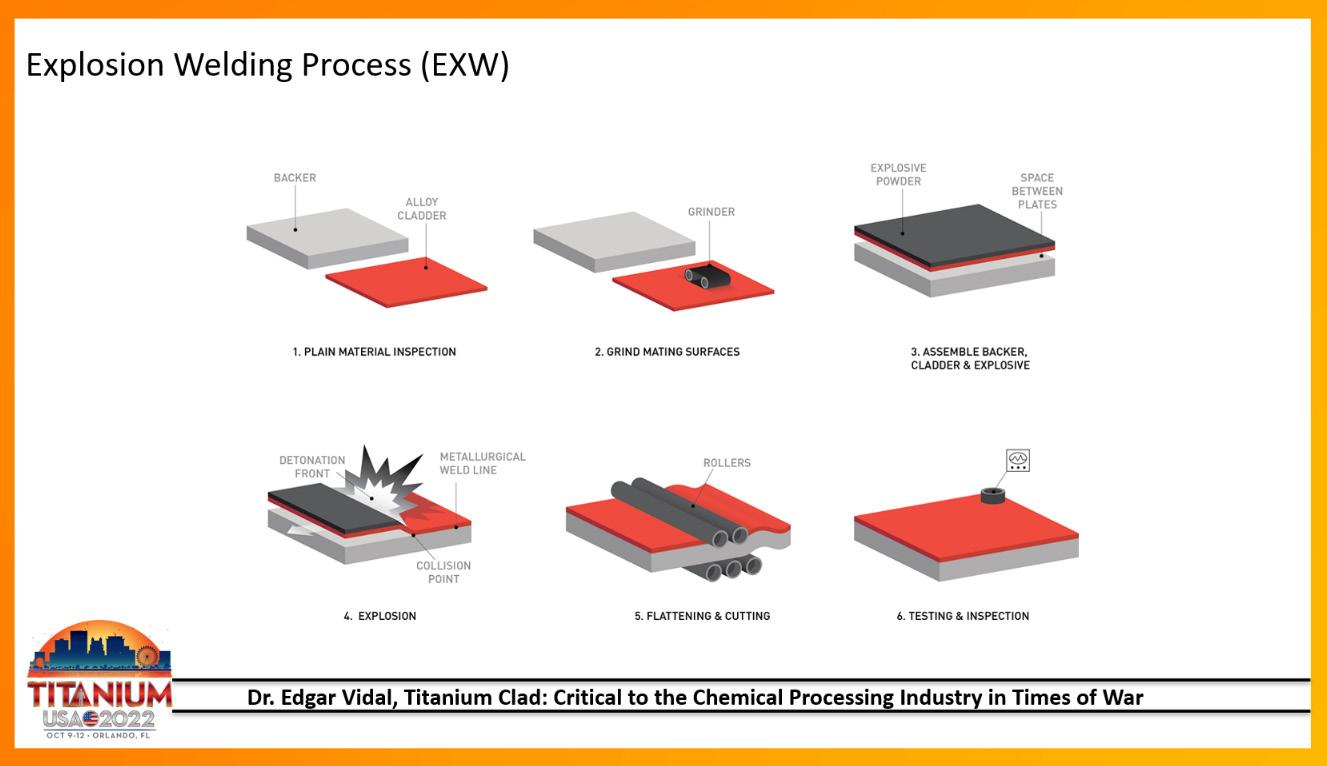
“The 3D printing dental applications is overtaking the use of traditional processes like casting as patients become more confident in these medical components and appreciate the time saving and individualization. Improvements in laser metal fusion (LMF) processes have made these parts faster, more reliable, with better quality. Smaller machines which are designed to be compact and easy to locate in a medical practitioner’s office, bring high precision solutions closer to the end user. With the latest improvements in AM powder bed processes, such as improved gas flow and laser controls, the use of 3D Printing titanium is taking a bite out of dental applications.”

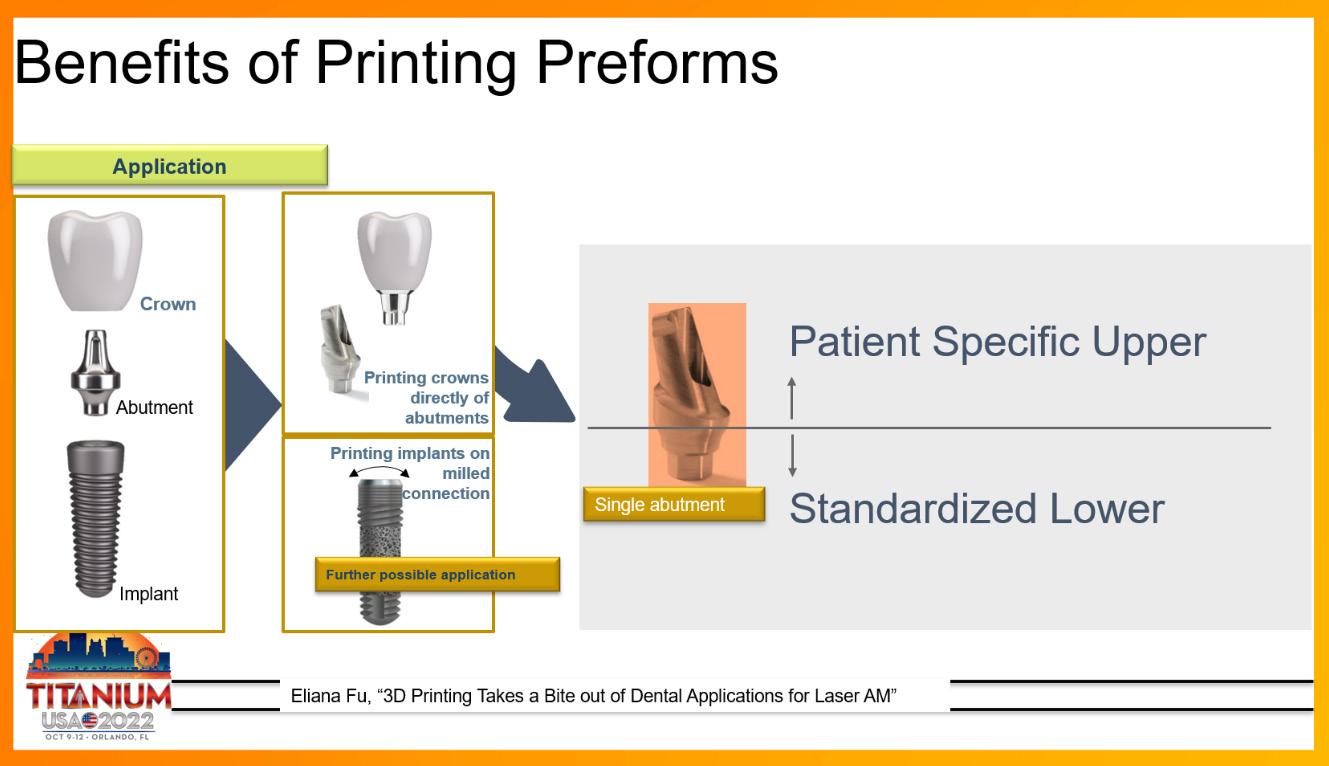

Prabhu Gubbi, Ph.D., the senior lead program manager for regulatory affairs, NuVasive, Inc., discussed “Titanium in Spinal Applications & EU MDR Implications on Ti Producers.” Spinal device categories include spinal fusion (Interbody Fusion Devices (IBF); Vertebral Replacement Devices (VBR) Spinal and Pedicle Fixation Systems such as rods, screws, plates, hooks, connectors) and spinal motion preservation (lumbar and cervical disc prosthesis; and dynamic spinal and pedicle fixation systems).
“Currently, for materials used in implants and surgical instruments, the CMR element of concern is cobalt,” Gubbi said. The materials need rationale/justification for continued use of the devices through material consideration, and have to meet certain device labeling requirements.
Gubbi provided information on the European Union’s Medical Device Régulation 2017/745, which outlines the impact of processes on material properties, referring to raw materials used to manufacture a medical device; wear, debris, degradation products, processing residues; risks linked to size and properties of particles, referring to considerations for nanomaterials or wear debris. Substances having endocrine-disrupting properties for which there is scientific evidence of probable serious effects to human health and which are identified either in accordance with the procedure set out in Article 59 of Regulation (EC) No 1907/2006 of the European Parliament and of the Council (2) or, once a delegated act has been adopted by the Commission pursuant to the first subparagraph of Article 5(3) of Regulation (EU) No 528/2012 of the European Parliament and the Council (3), in accordance with the criteria that are relevant to human health amongst the criteria established therein.
Justin Hertzler, Zimmer Biomet Research Biomechanics, reviewed “Current Considerations for Titanium in Orthopedics.” He said titanium alloys (Ti-6Al-4V, Ti-6Al-7Nb, cpTi) have a long history and proven track record in orthopedics, with biocompatibility, “bone friendliness,” and corrosion resistance. Hertzler examined the drivers for AM implants. The challenges and areas of focus include evolving regulatory environment, many AM technology options (hardware, software, materials), fatigue characterization, residual powder removal, and post processing.
Profile of the ITA
The International Titanium Association (ITA; website: https://titanium. org) is a membership-based international trade association dedicated to the titanium metal industry. Established in 1984, the ITA’s main mission is to connect the public interested in using titanium with specialists from across the globe who may offer sales and technical assistance. Working through our extensive membership resources, we seek to expand the knowledge base for the metal, providing technical literature and sponsoring seminars and conferences.
Each year our signature industry events are the TITANIUM Conference and Exhibition gatherings held regularly in the United States, Asia and Europe. Executive summaries and video proceedings are all available immediately following the events for public viewing on the ITA Website. The ITA publishes the trade publication TITANIUM TODAY.
For nearly four decades we’ve instructed thousands of professionals in all aspects of titanium usage. We look to educate engineers, designers and business executives on titanium’s superior properties and explain how those properties can be exploited to enhance products and services. We also strive to advance ideas in research, design, metallurgy and engineering, and serve as the leading forum to cultivate the exchange of ideas and support a diverse, dynamic, global industry. Current ITA membership includes 115 member organizations comprised of over 1,200 individual affiliate members worldwide.
The next Titanium USA 2023 Conference & Exhibition will be held October 1-4, 2023 at the Gaylord of the Rockies Resort in Colorado. Exhibition booths are sold out for this year but Housing & Registration is available at www.TitaniumUSA.org
SAVE THE DATES for TITANIUM Events:
2023 October 1-4
2024 May 6 – 8
October 6-9
2025 Sept. 28 – Oct. 1
Aurora, Colorado
Dublin Ireland
Austin, Texas
Boston, Massachusetts