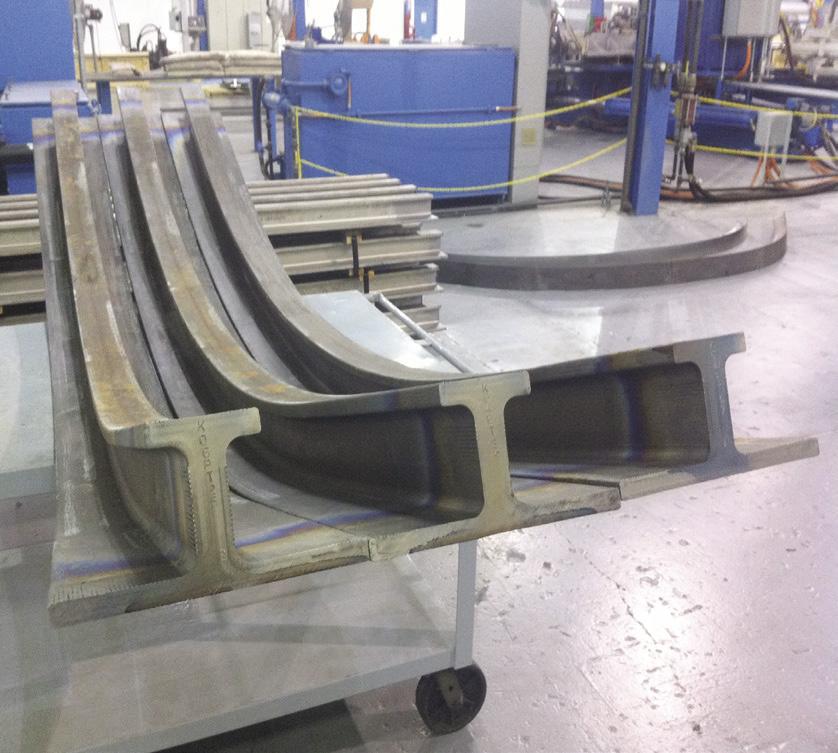
2 minute read
The solutions we create provide value to your business
ARIES Manufacturing is dedicated to the supply of complex airframe structure components, in both titanium and aluminum alloys, to leading manufacturers in the aerospace industry.
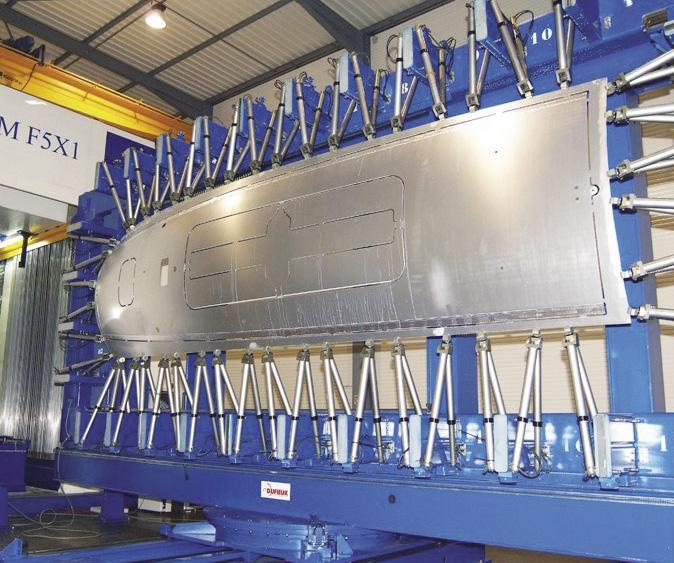
ARIES Manufacturing is part of the ARIES Alliance, a group of companies focused on developing innovative technology that creates value for the aerospace industry.
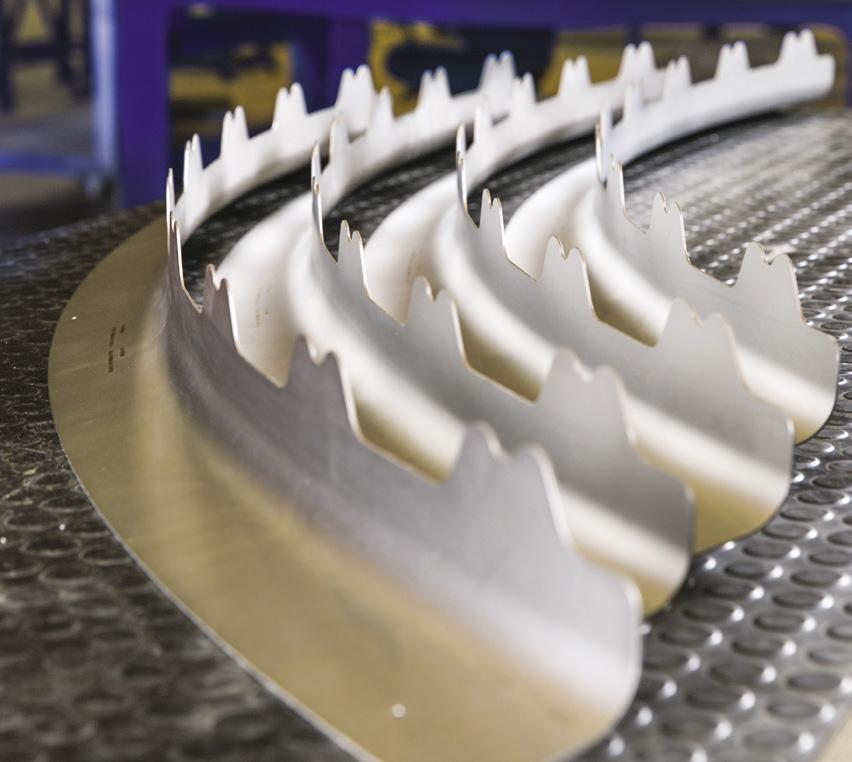
low cost parts manufacturing; and a microstructure and mechanical properties that are equivalent to wrought products.
The challenge to achieve the desired results is to use hydrogen, as it destabilizes Ti-O, making the reaction of Mg with Ti-O from being thermodynamically unfavorable to being favorable. Two steps to reduce oxygen (reduction and deoxygenation) ensures low oxygen. Molten salt (MgCl2 bearing salt) is used to facilitate the reaction.
“Our team (at the University of Utah) has developed a novel thermochemical process to extract titanium metal from ore that substantially reduces the cost, energy consumption, and emissions of titanium metal production,” Fang said. The HAMR process is a thermochemical process to obtain titanium metal from titanium oxides. A technical challenge in the production of titanium metal is the formation of oxide impurities. The Kroll process addresses this challenge by converting titanium ore (an oxide) into titanium tetrachloride (TiCl4). This intermediate material is readily purified. It is reduced to titanium metal with magnesium. This technology is capital, energy, and carbon-intensive. One advantage of the Kroll process, and several like it, is that it starts with titanium ores (e.g., illmenite), not a purified dioxide.
Fang said the HAMR technology is a two-step process, starting withTiO2 under an atmosphere of hydrogen gas. The product (TiH2) can be further processed to titanium metal through standard methods. “The reduction of titanium oxides to titanium metal using magnesium does not occur. The novelty of the HAMR process is the inclusion of hydrogen.”
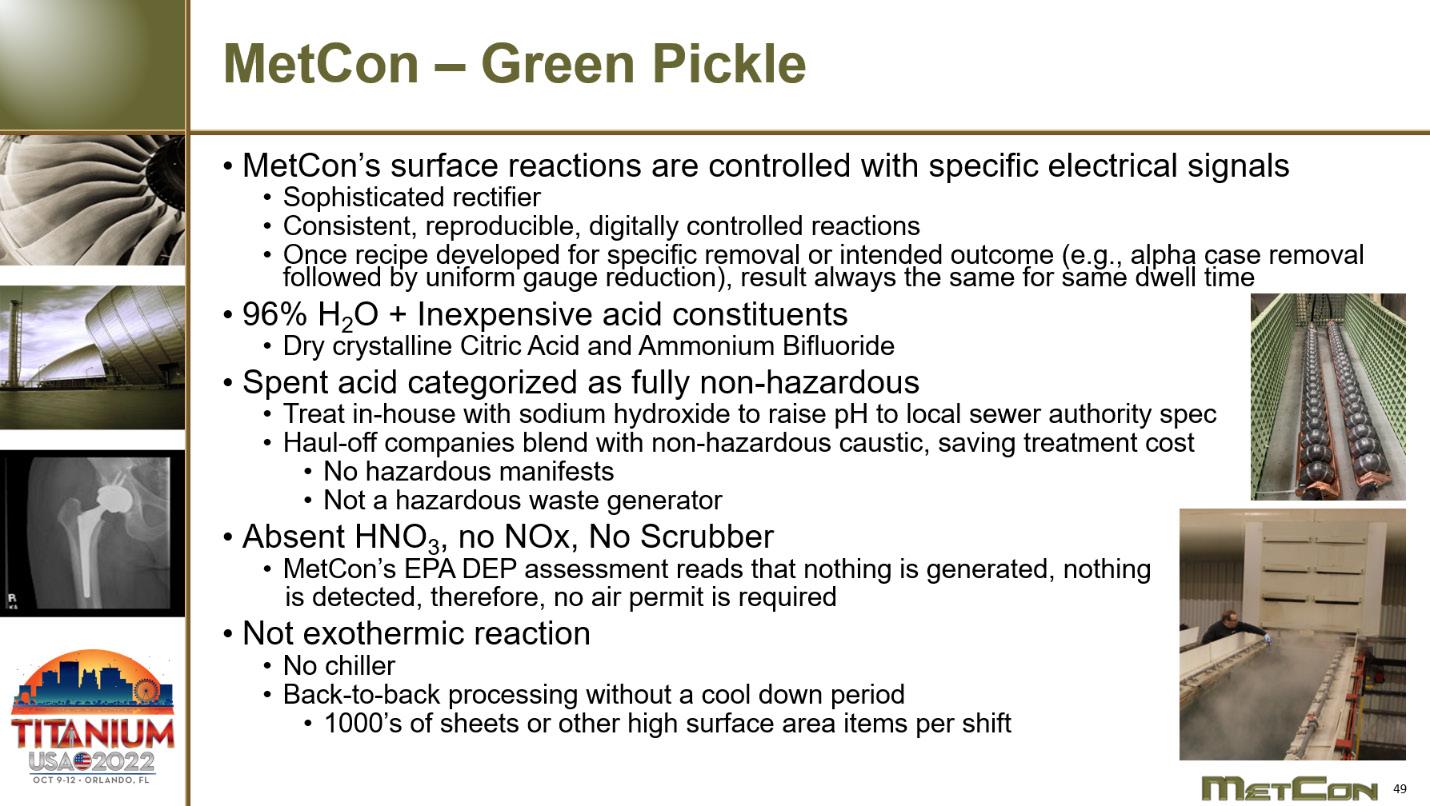
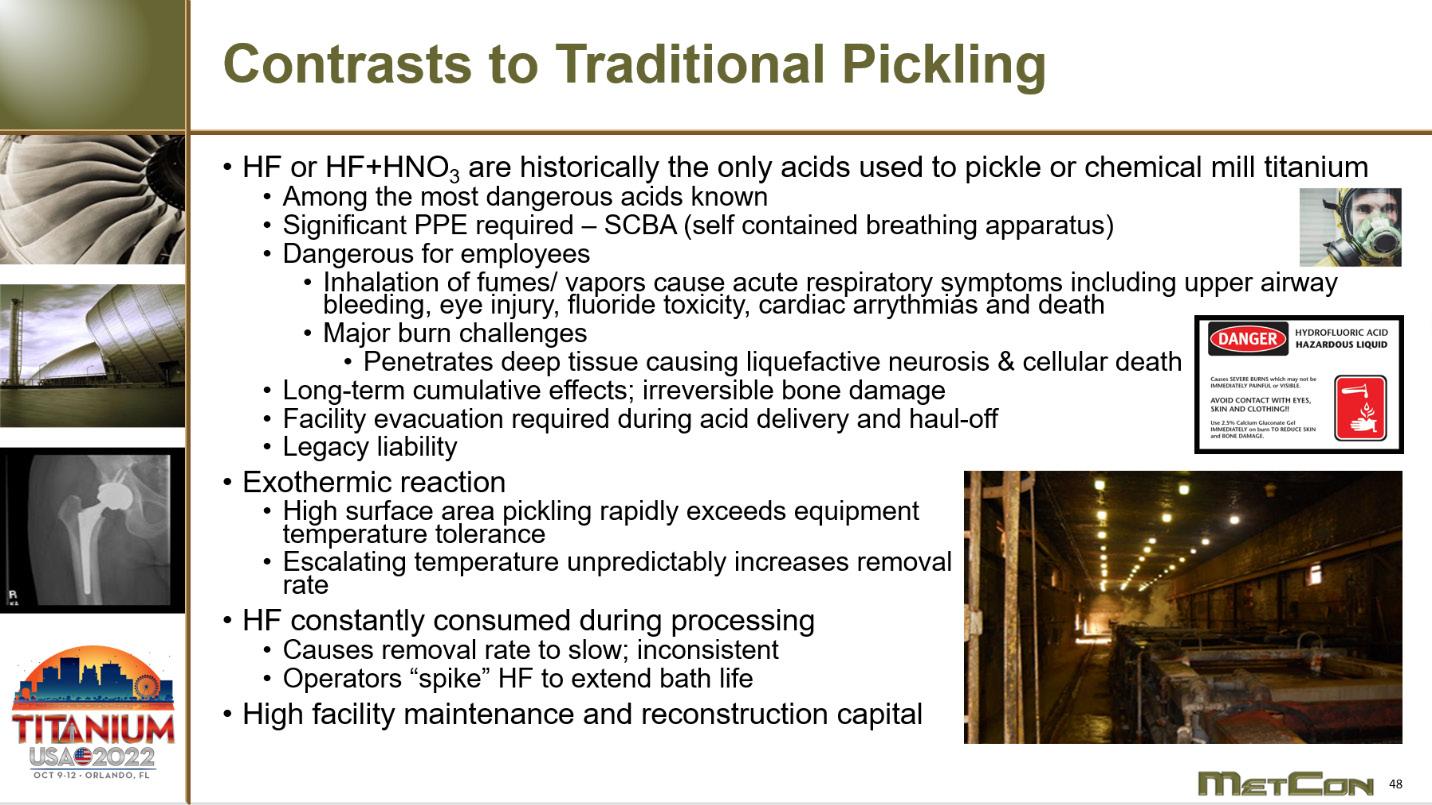
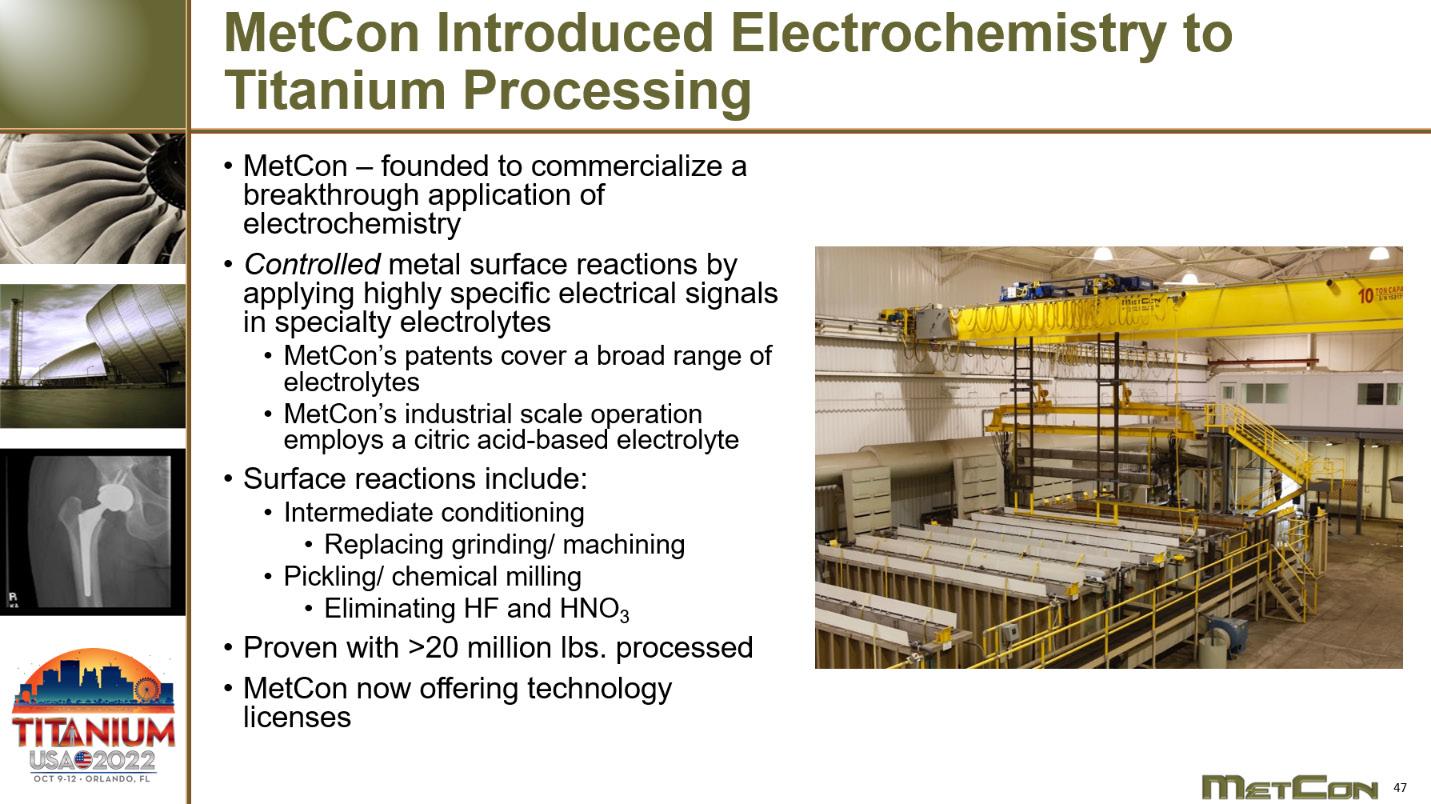
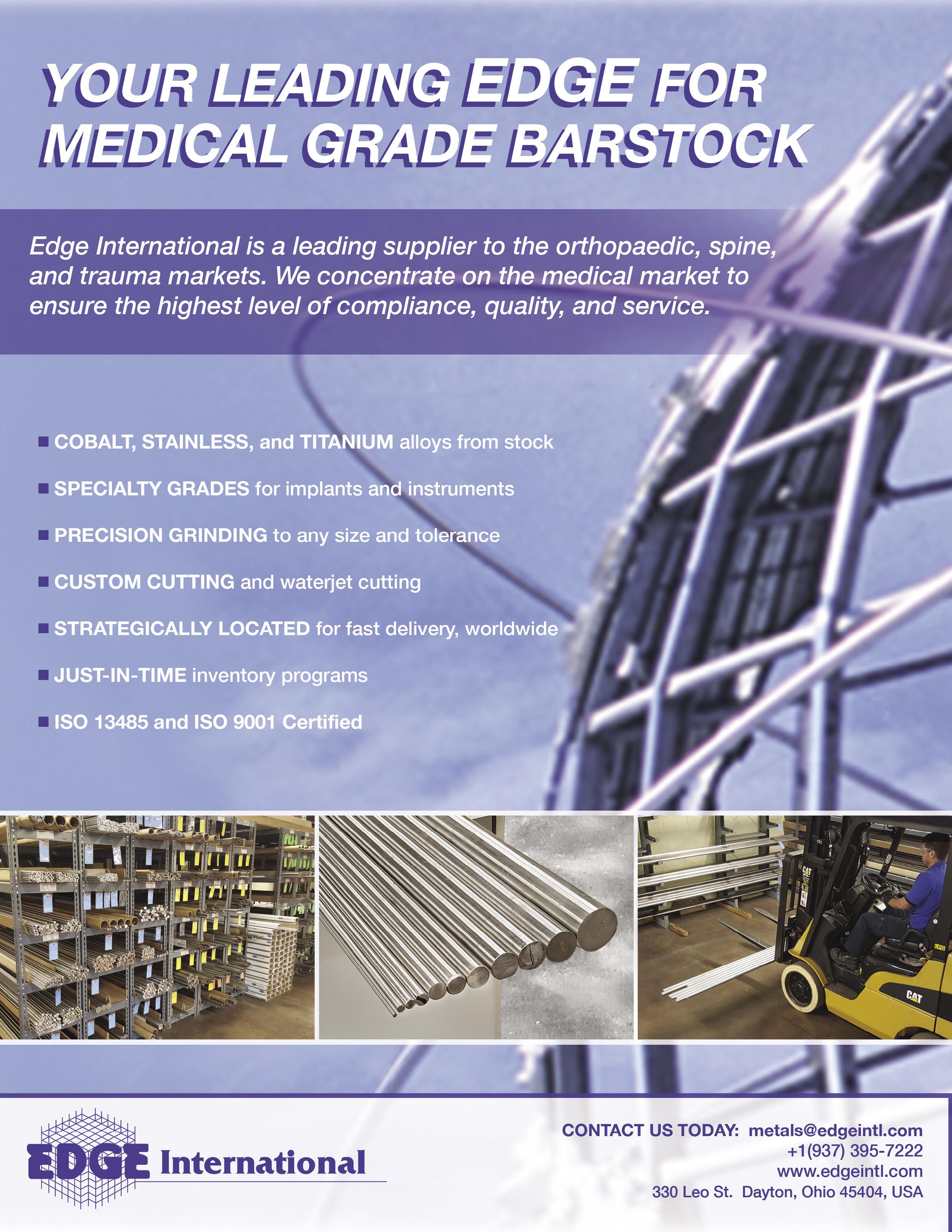
Master Alloys
Vince Rocco, vice president, sales and marketing with AMG Advanced Metallurgical Group N.V., focused his presentation on “Accelerating the Energy Transition – Titanium Master Alloys: the Hidden, Yet Critical Part of the Titanium Supply Chain.” Rocco said master alloys allow titanium producers to add alloying elements into titanium melts. “They contain two or more alloying elements that are needed for a particular titanium grade. The alloying elements enhance the properties of titanium to increase strength, weldability, and temperature resistance.”
The production of master alloys involves an aluminothermic reaction (elemental oxide plus aluminum powder), which yields a master alloy plus Al2O3 slag. “The fuel for the reaction comes from the aluminum powder and the reaction is initiated. An exothermic reaction consumes the aluminum powder and elemental oxide. A metal ingot forms with slag settling on the top, and no external energy is used for the process.”
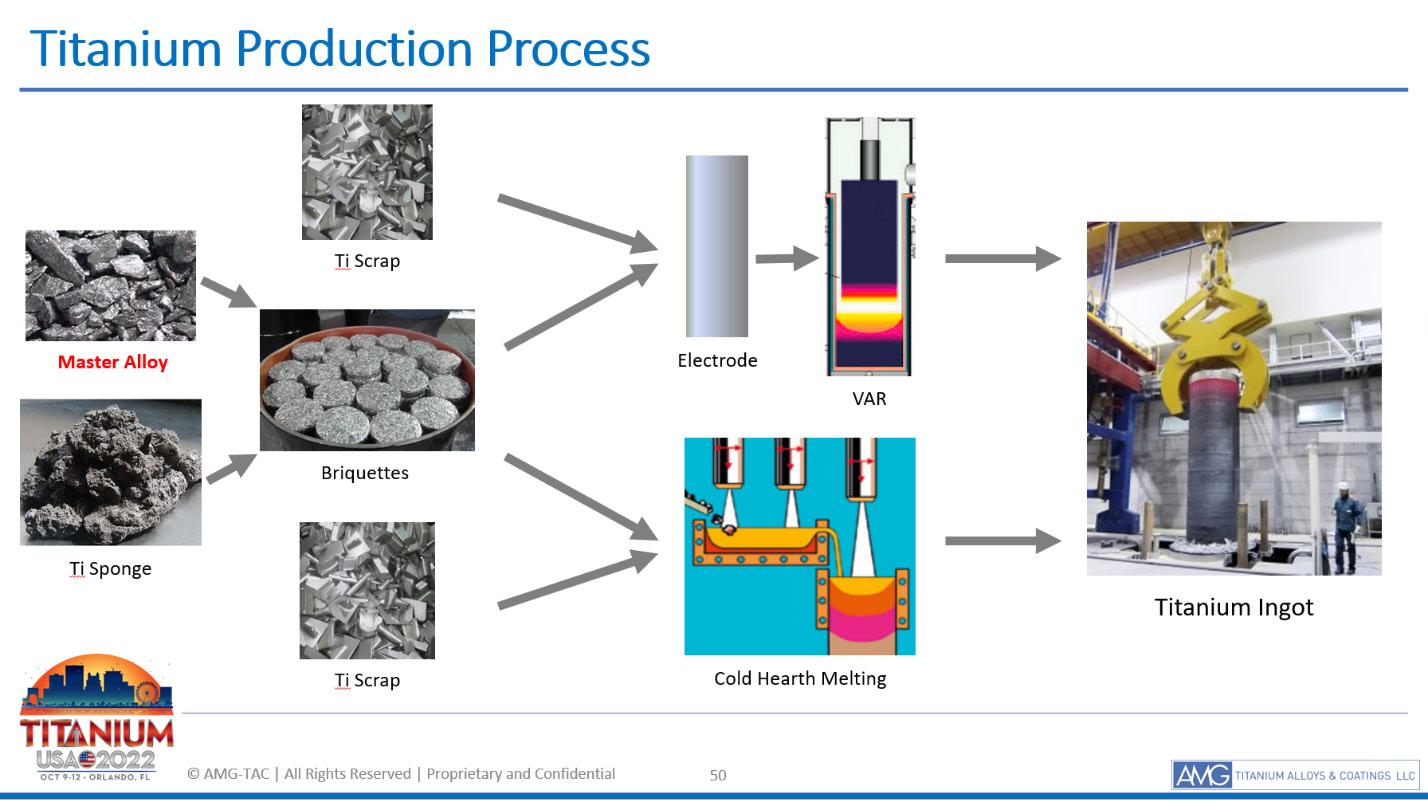
Regarding vanadium and molybdenum, Rocco said China dominates vanadium production, while Russia is a key player in vanadium production and the aerospace industry uses vanadium from primary ore and secondary production. Vanadium demand is dependent on steel production.
The molybdenum market is expected to grow at a CAGR of 4 percent between the years 2022-2027, according to Morder Intelligence. Molybdenum growth will be fueled by the automotive, aerospace and energy markets. The trend towards electric vehicles could reduce molybdenum consumption, but in the aerospace market, global demand for new jets is forecasted to increase about 80 percent.
The dynamic for titanium scrap and sponge will involve titanium melters matching the most economical inputs into their formulations, according to Rocco. Reduced aircraft build rates and excess titanium inventory led to titanium scrap shortages in 2021 into 2022. Risk mitigation by titanium consumers is bolstering titanium production in the United States. Sponge and master alloy utilization is increasing.
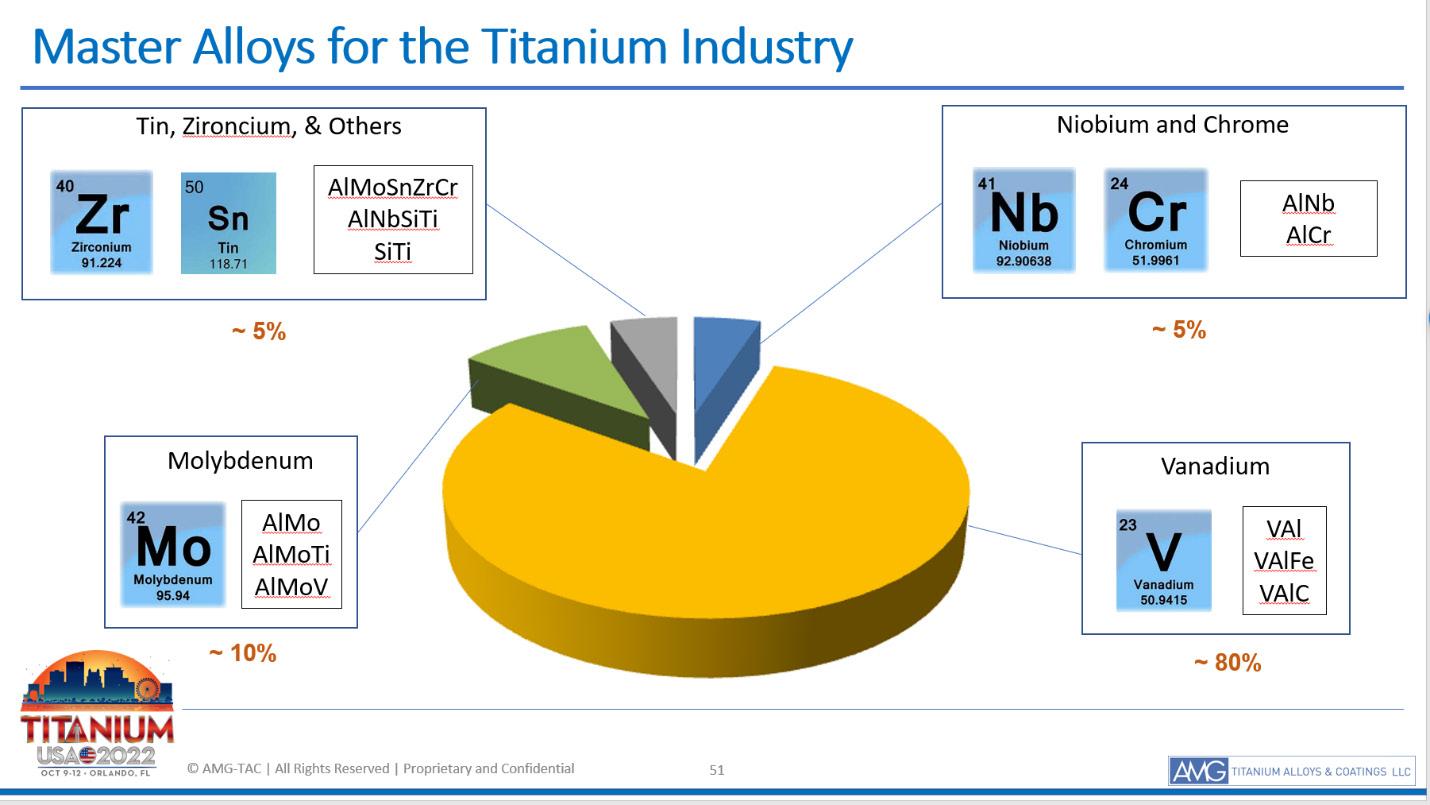
Rocco summarized his remarks by saying master alloys “are highly engineered products important to the titanium industry. Master alloy raw materials are sourced from all over the world. Ongoing supply chain issues also affect master alloy producers. (The current, tense) geopolitical environment has added an additional element of risk to the industry.”
The Velta Titanium Process
Andriy Gonchar, technical director, and Artem Yarovinsky, sales and marketing director, Velta Holding US, outlined the Velta Titanium Process. Velta LLC is a feedstock producer and the only privately owned company in Ukraine, which has built a mining and processing complex. Founded in 2006, Velta has