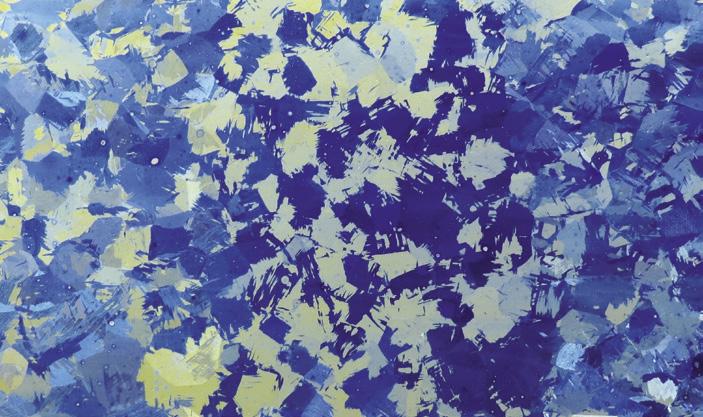
5 minute read
Rapid Response. Dependable Delivery.
Exceptional Turnaround From a Proven Partner in Titanium Materials Testing
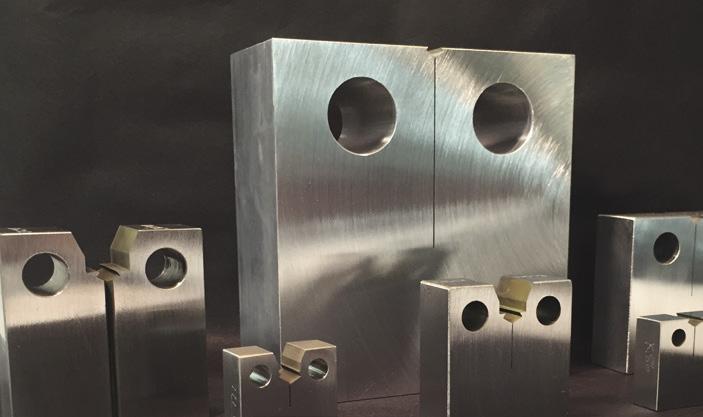
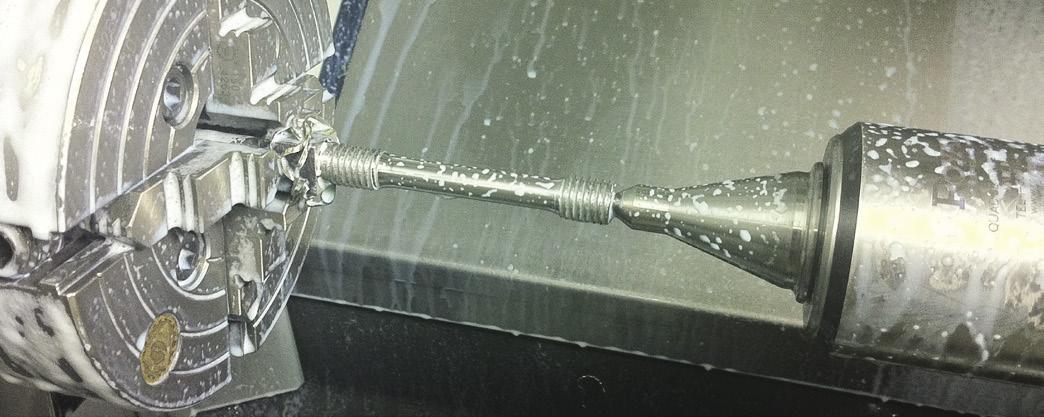

Product Evaluation Systems, Inc. (PES) is a fully accredited, independent leader in titanium materials testing for aerospace and other applications. With a dedicated, experienced staff and state-of-the-art testing facilities, we offer full-service capabilities for all of your titanium testing needs, including:
• Mechanical Testing
• Metallurgical Analysis
• Chemical Analysis for lightweight construction by enhancing mechanical properties and reduction of manufacturing costs for sheet-based titanium components by eliminating the need for additional heat treatment process.”
PES responds to your needs promptly with personal service, customized solutions and expedient turnaround. We work with clients throughout the United States and Europe on projects of all types and sizes.
To request a free quote for your titanium testing needs and to see a full list of capabilities, please visit our website at www.PES-Testing.com or call 724-834-8848.
Kaiser said that the development involves a new and unique test stand for Heat Transfer Coefficient (HTC) evaluation, and that the initial requirements were successfully realized. The results included: homogeneous temperature distribution after resistive heating; well controlled and user defined temperature profiles were implemented; and extremely high cooling rates were achieved (cool (900 °C – 500 °C) ≈ 940 K/s). There was no significant dependence of the HTC on pressure without lubricant, and that lubrication has great influence on HTC and cooling rate.
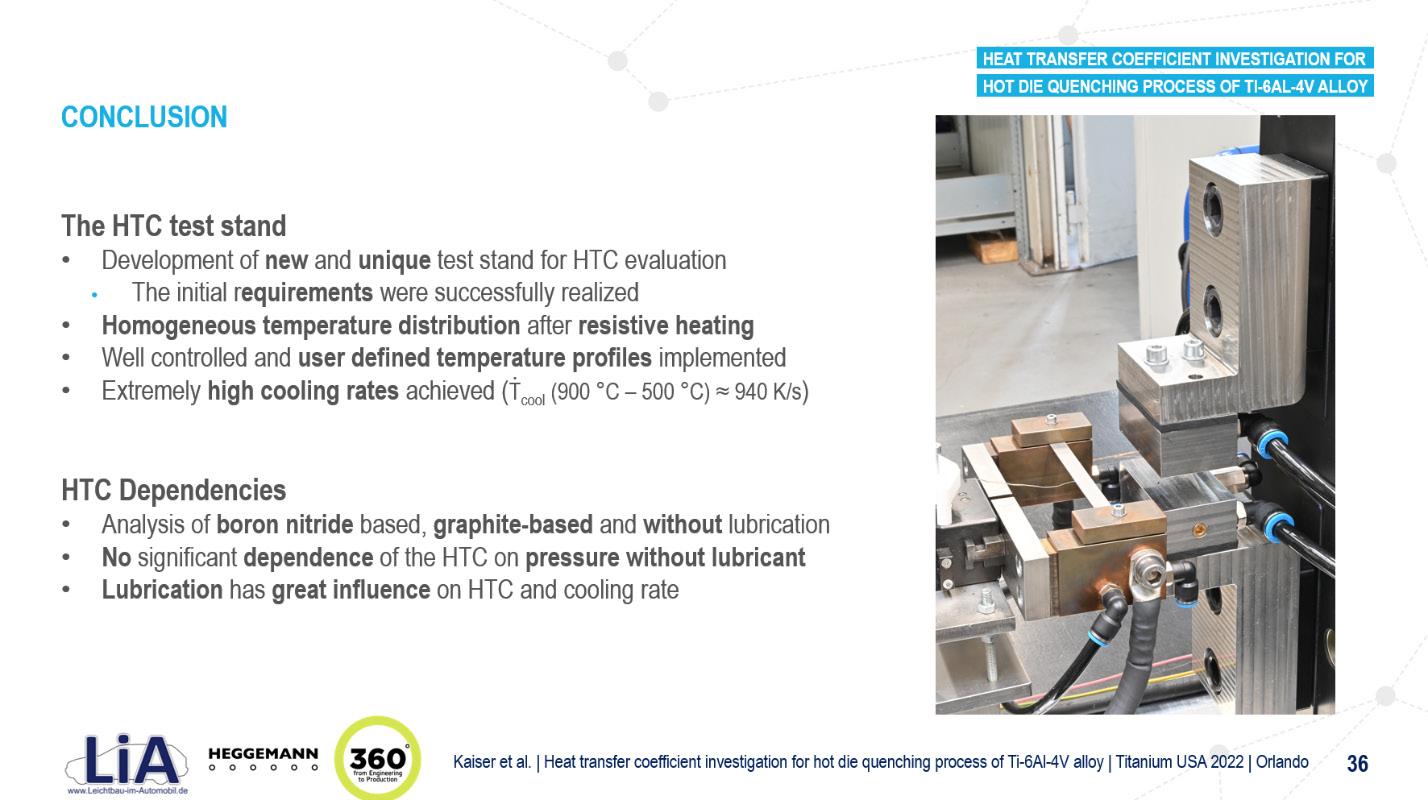
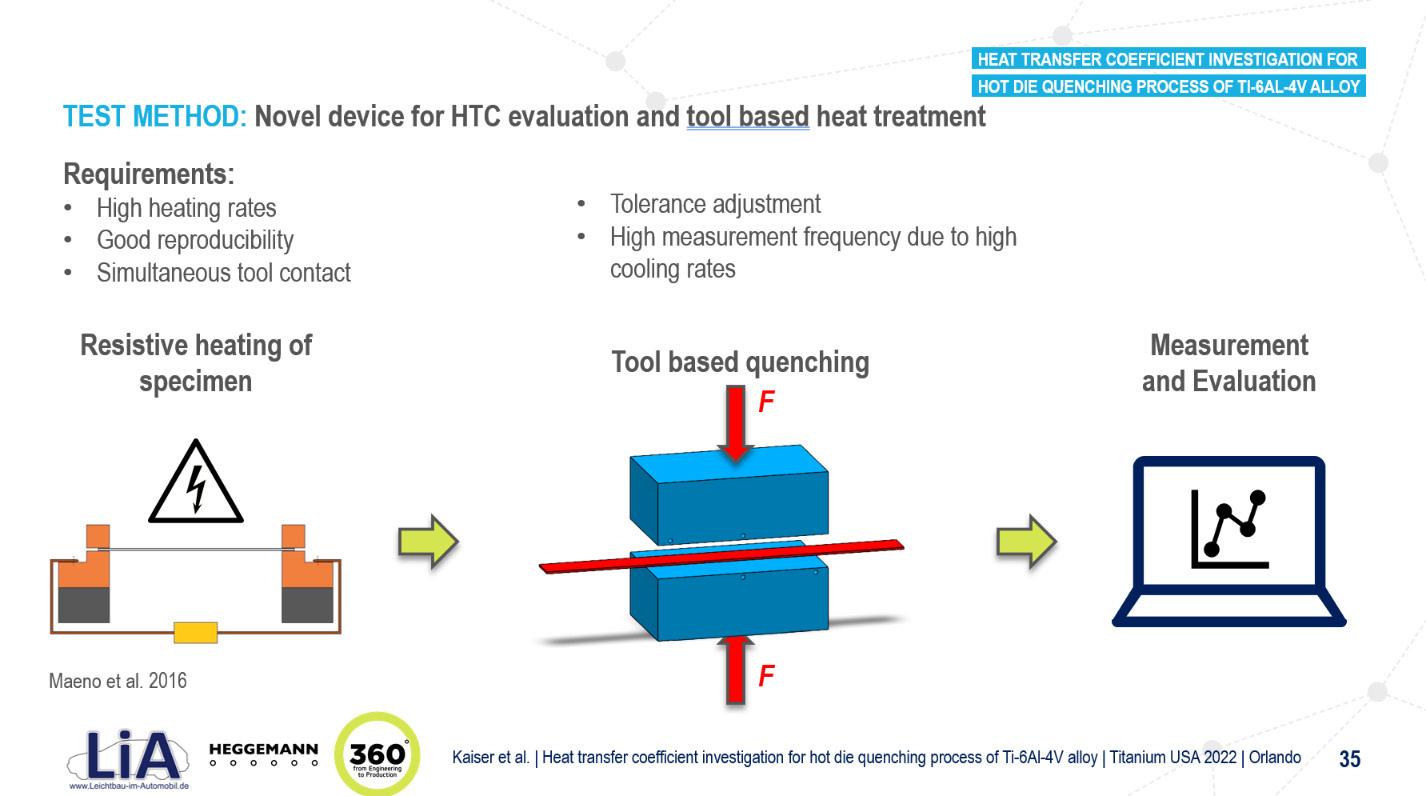

Harald Korbel, Inteco melting and casting technologies GmbH, shared information on the “Development of a New Type of Vacuum Arc, Cold Hearth Skull Melting Furnace and Process.” Korbel describe a cold hearth skull, explaining that it’s a special process phenomena related to water cooled copper crucibles. “Liquid titanium solidifies rapidly in the contact area towards the copper crucible wall while inside the skull/crucible the titanium remains liquid. The physical appearance and properties of the skull are created by the energy balance between provided melting power, latent energies and adjusted heat transfer. The cold hearth skull becomes the prerequisite for effective metallurgical work in vacuum metallurgy, such as removal of metallic inclusions, removal of non-metallic inclusions, and a reduction of interstitial dissolved nonmetallic elements.”
For cold hearth skull melting and casting, Korbel said that any type of scrap can be used and virgin feedstock can be blended with the scrap. “Scrap is a low gas load feedstock compared to the virgin sponge raw material. Every common and commercially pure (titanium) grade and alloy grade can be produced. Improved homogenization of the melt (can be achieved) through a large, turbulent bath volume induced by the electric arc and magnetically induced bath movements. The presence of gravitational segregation effects (force) larger or insoluble particles in the liquid phase to sink and get stuck in the ‘liquid/solid transition zone’ of the cold hearth.”
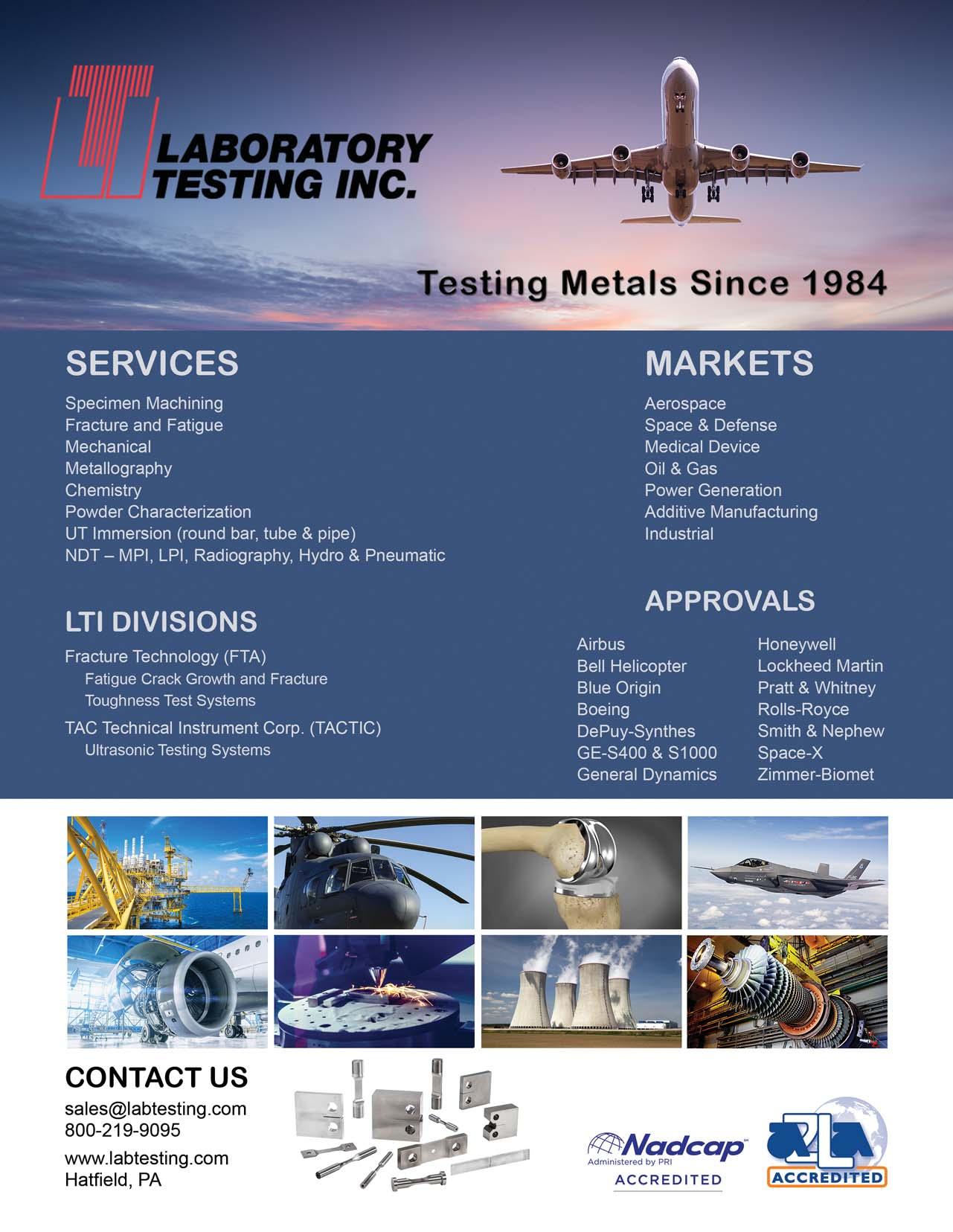
Inteco’s innovative furnace concept involves intermediate scrap, sponge and alloy additions during the melting & casting process cycles Two Titanium casting techniques are combined in one plant: static casting for ingot, slab, and Investment casting Centrifugal casting by means of a rotary casting table to achieve extended product complexity and properties. The skull melting furnace either acts as primary melter (electrode feedstock) for vacuum arc remelting (VAR) furnaces or final melting and casting plant for investment castings using VAR/EB /PAM electrodes.”
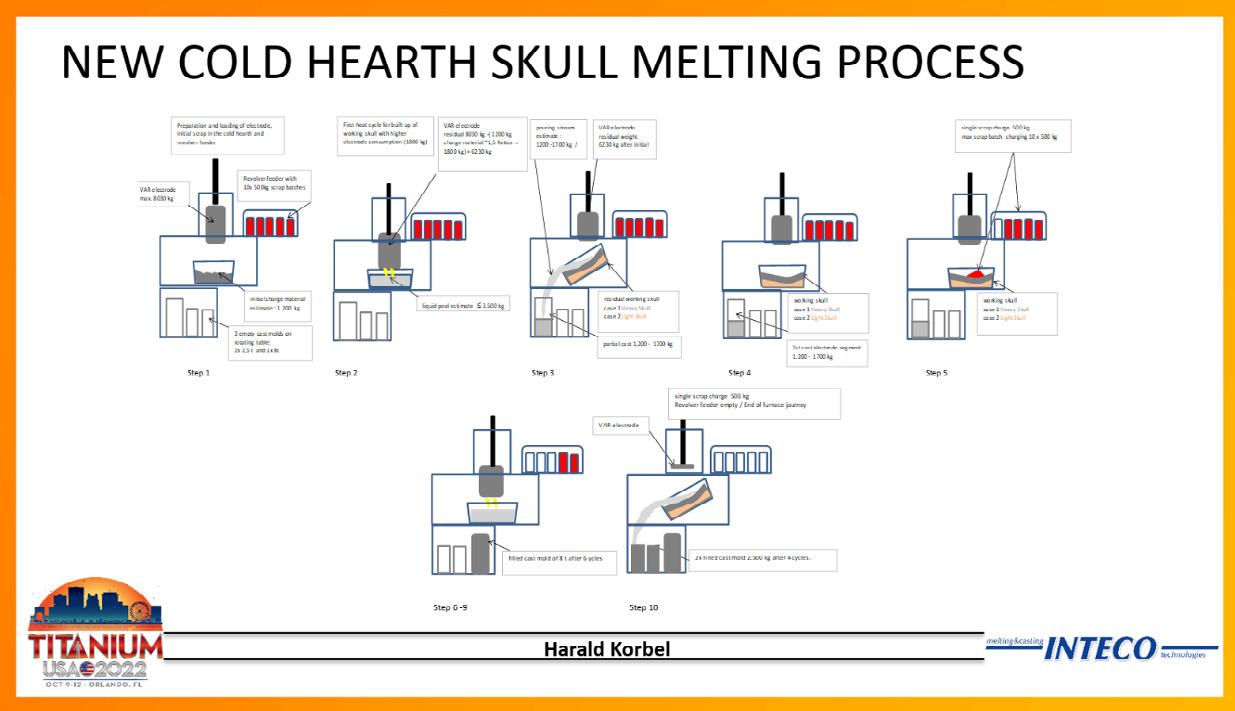
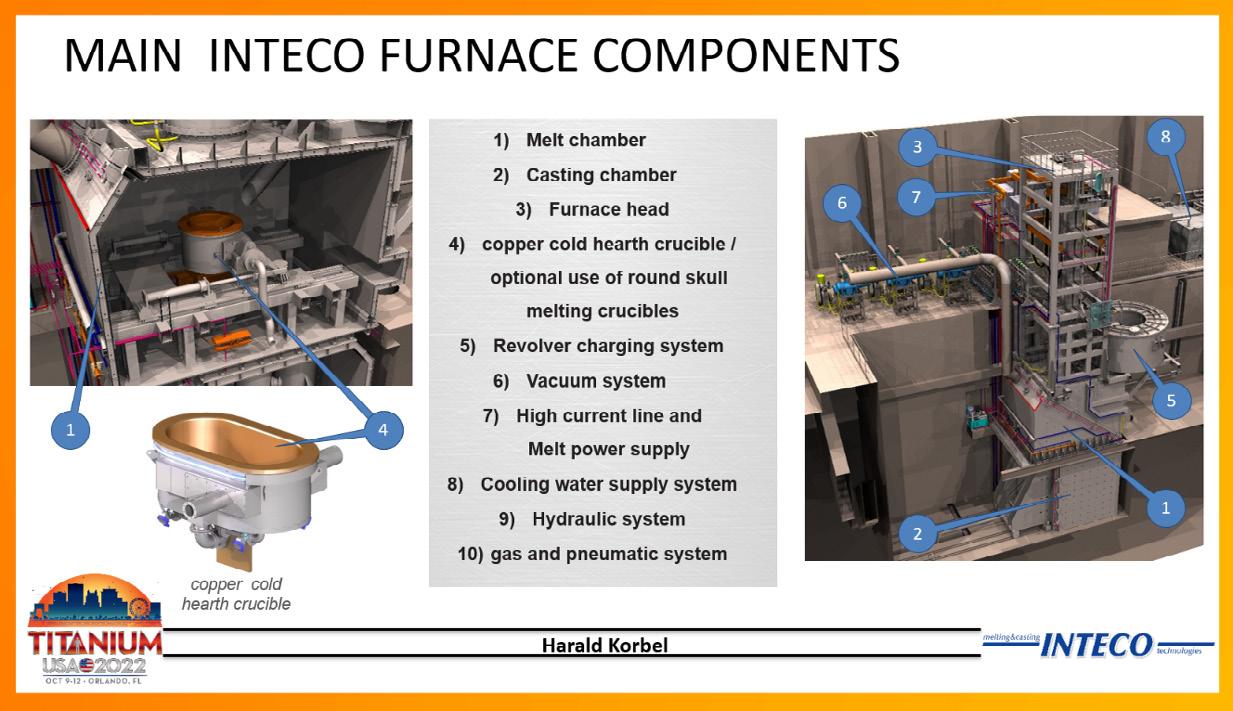
Korbel summarized by saying all other reactive metals and demanding alloys such as (zirconium, nickel, cobalt) Zr, Ni- and Co-based alloys can be melt and cast under vacuum into each any kind of shape and format. “Improved solidification conditions for the cast product can be integrated in the casting chamber concept to control.”
Marcus Lindholm, global purchasing manager-metals for Alfa Laval, spoke about “New Opportunities for Industrial Titanium; Accelerating Sustainable Solutions.” Lindholm said that collaboration and strong, lasting partnerships “are critical for accelerating sustainable solutions and reshaping our economy and the world we share. That is why Alfa Laval works closely with customers and other partners to find new answers to the most challenging questions of our time.”
“We already have the technology,” he continued. “Now it’s time to work together to build a more sustainable future. We want a solid titanium industry (that has) a diverse customer base to safeguard unforeseen events and new technologies; meets customer demands; transitions to green energy sources; (with) increased competitiveness, sustainable materials and a broadened scope of affordable business opportunities.”
Lindholm observed that, going forward, 25 to 30 percent of the titanium volumes sold are used for industrial applications. “The market for industrial titanium is growing, but where is the focus from the titanium community? Buyers of industrial titanium can offer stable volumes over time. Diversification generates flexibility and spreads the risks.”
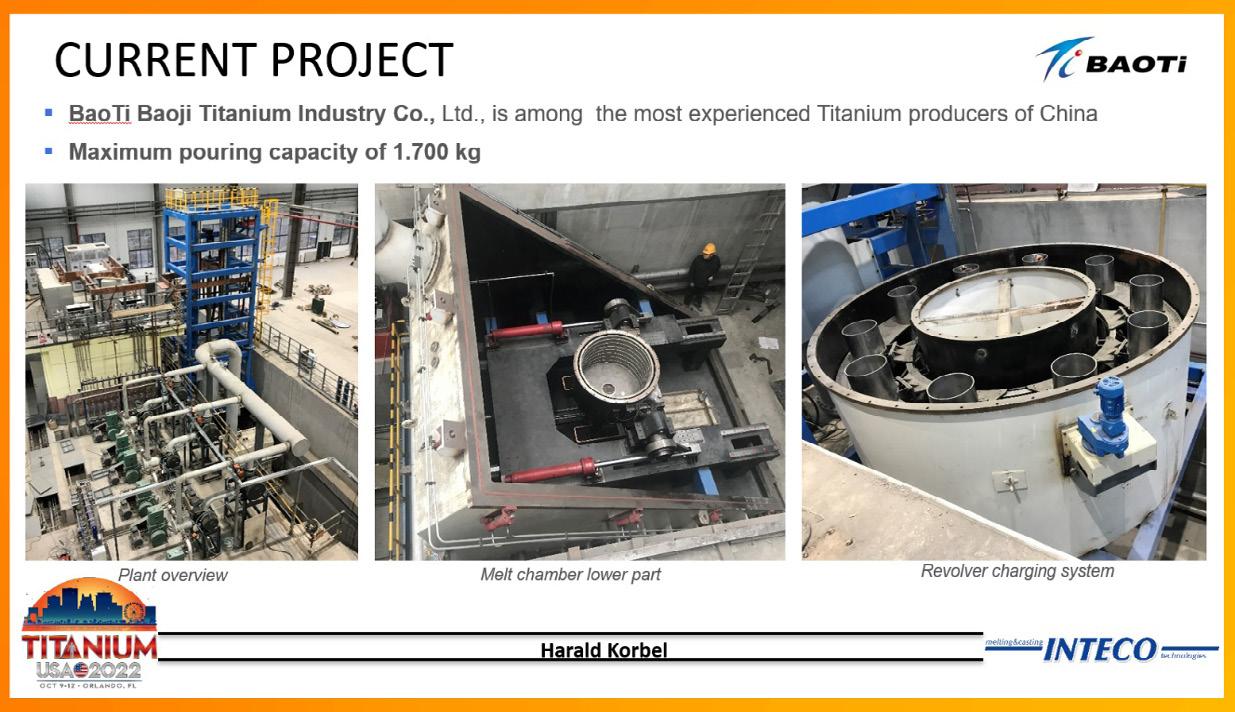
Sustainability drives innovation, he said. “(Alfa Laval) makes the existing industry more sustainable. Our technologies and solutions enable the transition to clean energy and circular economy. We continue to build on our legacy and strive towards a sustainable future. Alfa Laval’s purpose is to accelerate success for our customers, people and planet.”
Systems For Aviation Industries
Systems For Aviation Industries

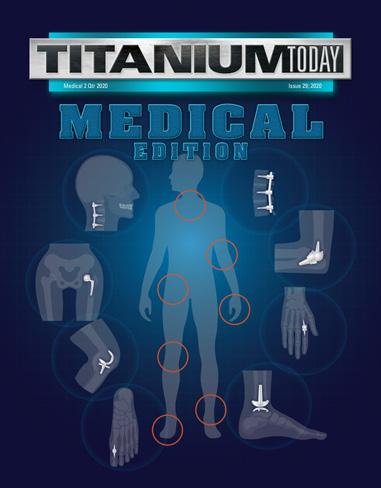
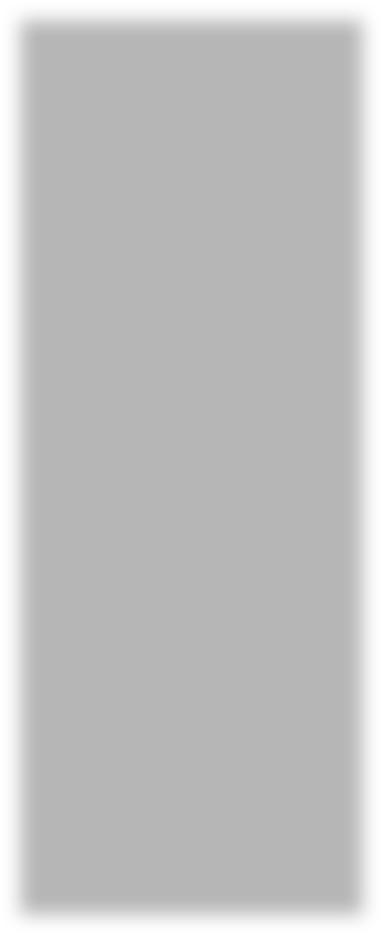
NEAR NET SHAPE TECHNOLOGY COATING SYSTEMS
CASTING SYSTEMS
� Leicomelt with Cold Crucible
� VAR Skull Melting
HOT ISOTHERMAL FORGING (HIF)
METAL ADDITIVE MANUFACTURING
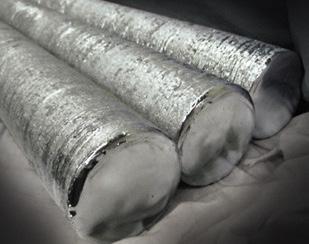
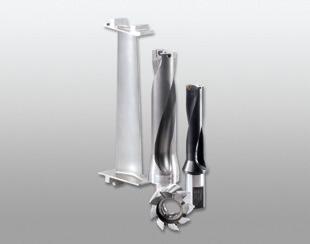
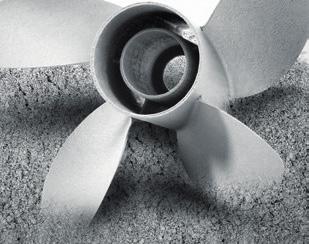

� EIGA: Ceramicfree Metal Powder Production


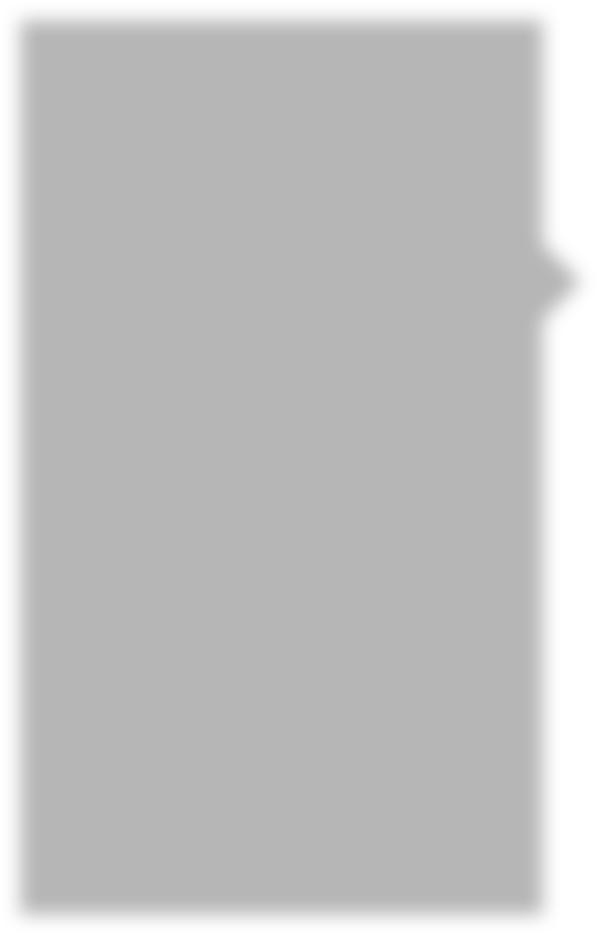
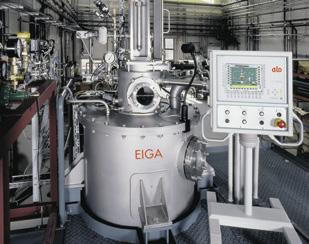
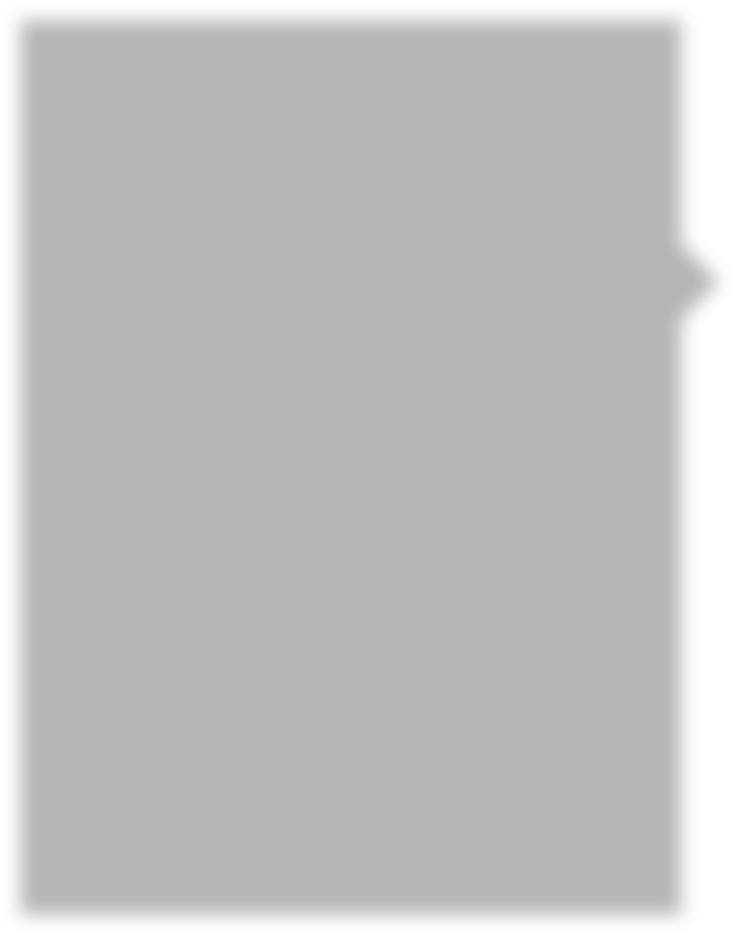
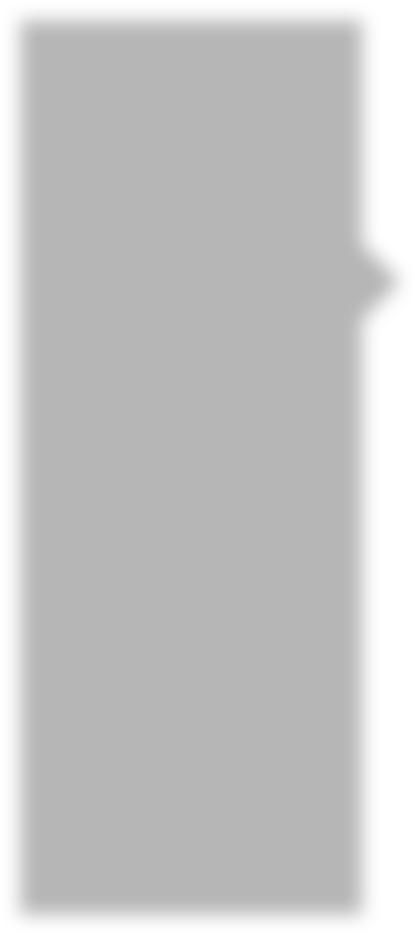
� VIGA: Inert Gas
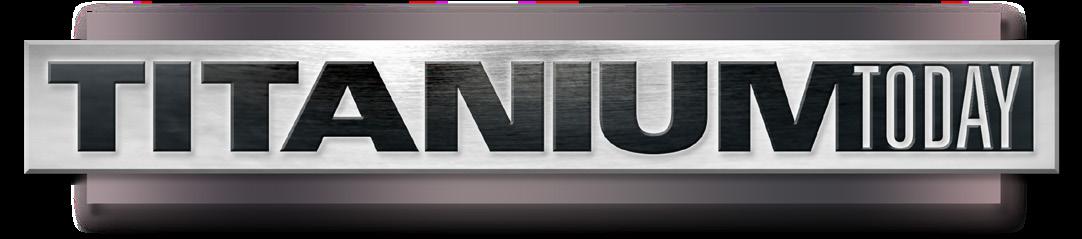
� EB-PVD SYSTEMS
Electron Beam Physical Vapour Deposition
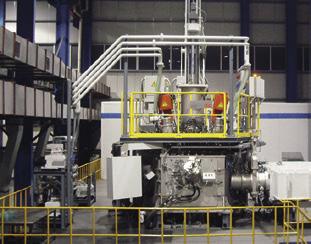
� EB-PVD SYSTEMS Electron Beam Physical Vapour Deposition (EB-PVD) of Thermal Barrier Coatings (TBC)
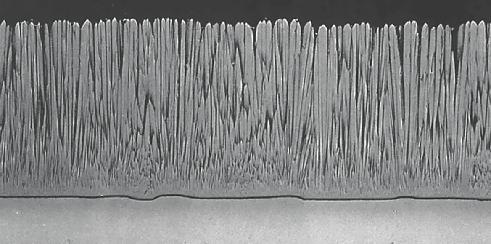
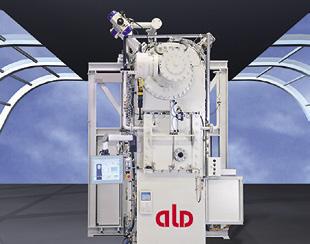
HEAT TREATMENT SYSTEMS
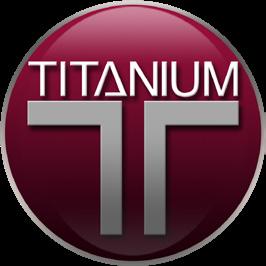
� SYNCROTHERM®
Total Integration of Heat Treatment into Component Manufacturing key technology areas of heat transfer, separation and fluid handling. “With more than 3,700 patents, we provide worldwide solutions in areas that are vital to society both today and for the future. Alfa Laval’s worldwide organization, with over 17,000 employees, helps customers in nearly 100 countries to optimize their processes.”

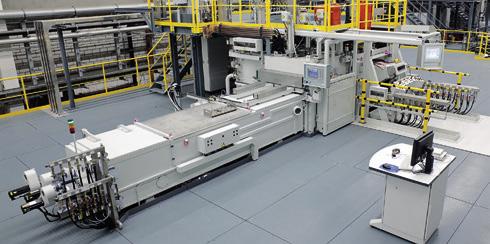
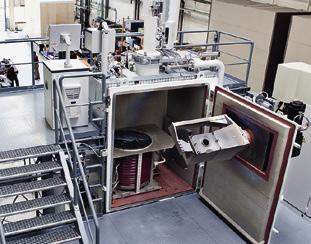

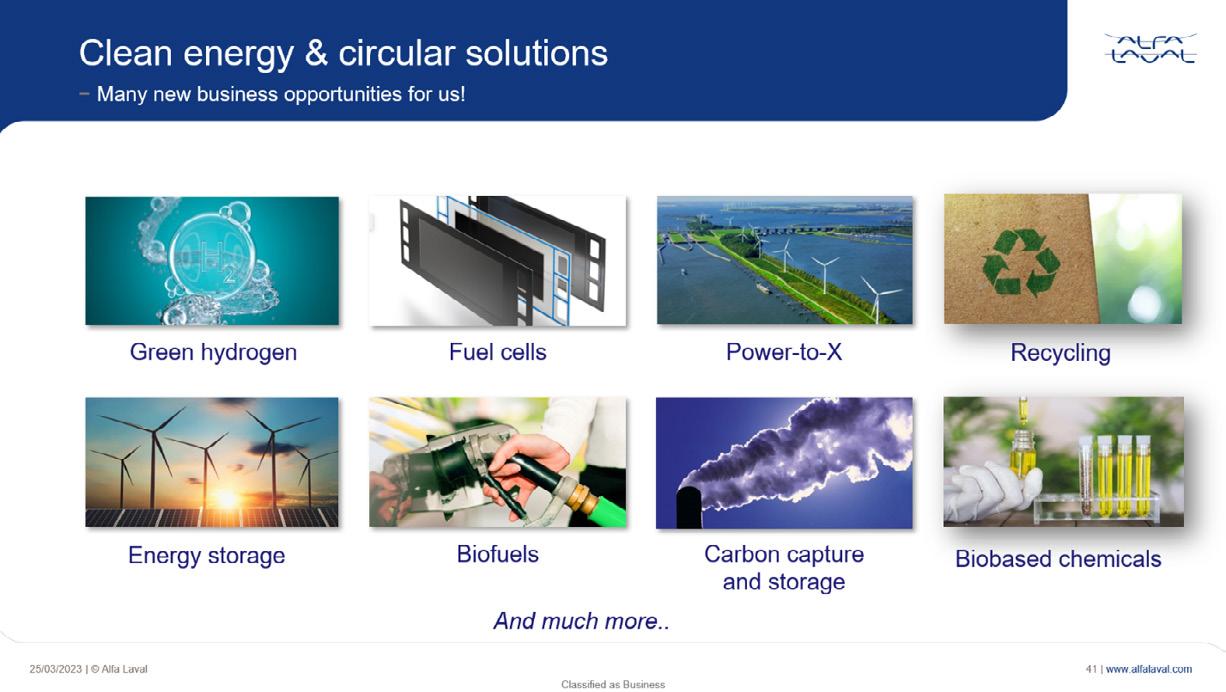
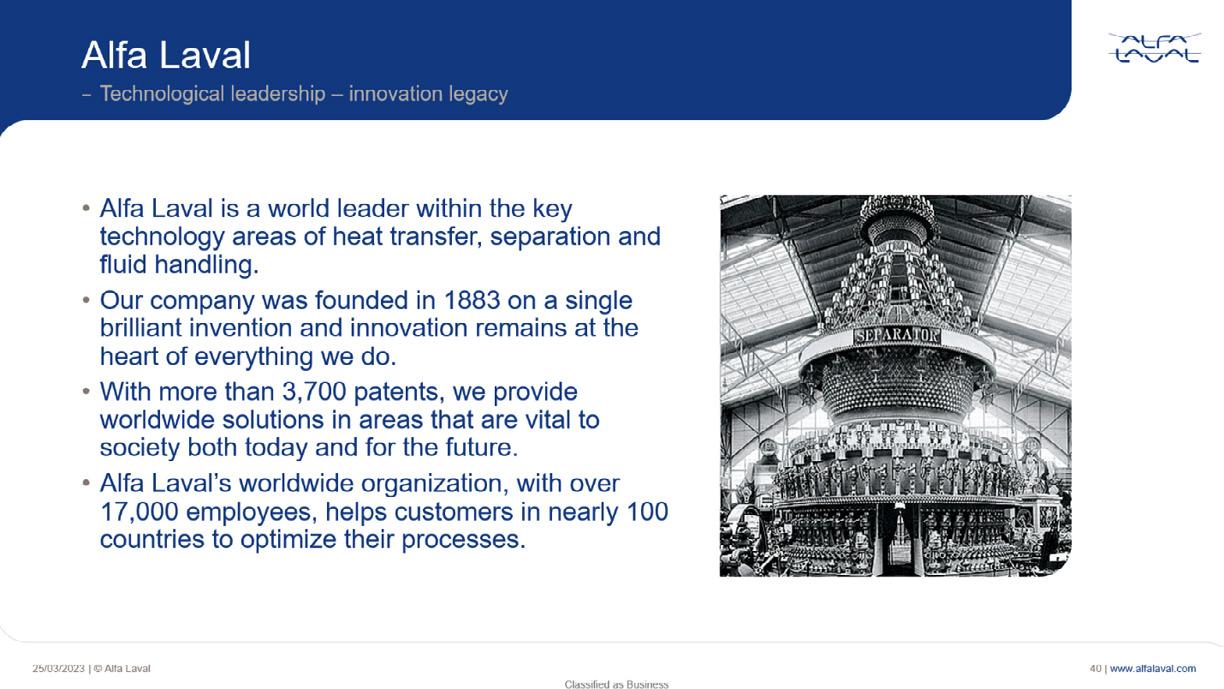
Titanium Feedstocks
David McCoy of TZMI gave a titanium feedstock market update, focusing on a rutile feedstock supply/demand outlook to 2026. “The global rutile market is experiencing extremely tight market conditions, with a deficit position of 104,000 TiO2 units in 2021, but ‘balanced’ in 2022. Near-term rutile demand has been moderated to reflect the declining supply availability. TZMI has made provisions for greater chloride slag supply during the next few years, on the basis that there is some latent capacity in the supply chain that can be re-commissioned to meet chloride feedstock demand growth. This will displace higher-cost rutile in the TiO2 pigment sector as chlorinator head grades are reduced as pigment demand drops.”
McCoy identified new rutile projects in Australia, such as West Balranald Iluka Resources, Sembehun Sierra Rutile Holdings Ltd., Avonbank WIM Resources, as well as other projects in Norway, Sierra Leone, and Malawi.
Regarding feedstock demand for a sponge outlook to 2026, McCoy said that titanium sponge end use resumed the upward trends since 2016 and peaked at 486,000 TiO2 units in 2019 before Covid-19 impacts; 2022 is expected to be 7.3-percent higher than 2019. “TZMI believes that the strong demand from aerospace and newenergy automobiles will support demand growth for titanium sponge in the foreseeable few years. Industrial market demand may be impacted in the next 24 months.” He also observed that chloride slag is replacing rutile and other high grade TiO2 feedstocks outside of Japan, while China is dominating the production of this feedstock into the metal supply chain. “Metal supply chains that require ‘back to source’ certification for rutile feedstocks might have less leverage on future prices. Sponge producers will be competing for feedstocks against a growing global chloride TiO2 sector. However, the next 12 to 24 months are forecast to be downcycles for TiO2 pigment demand.”
TZMI is a global, independent consulting and publishing company with offices in Australia, the United States, Europe, Africa and China. TZMI consulting services include practical experience in mineral sands, titanium dioxide and coatings industries.