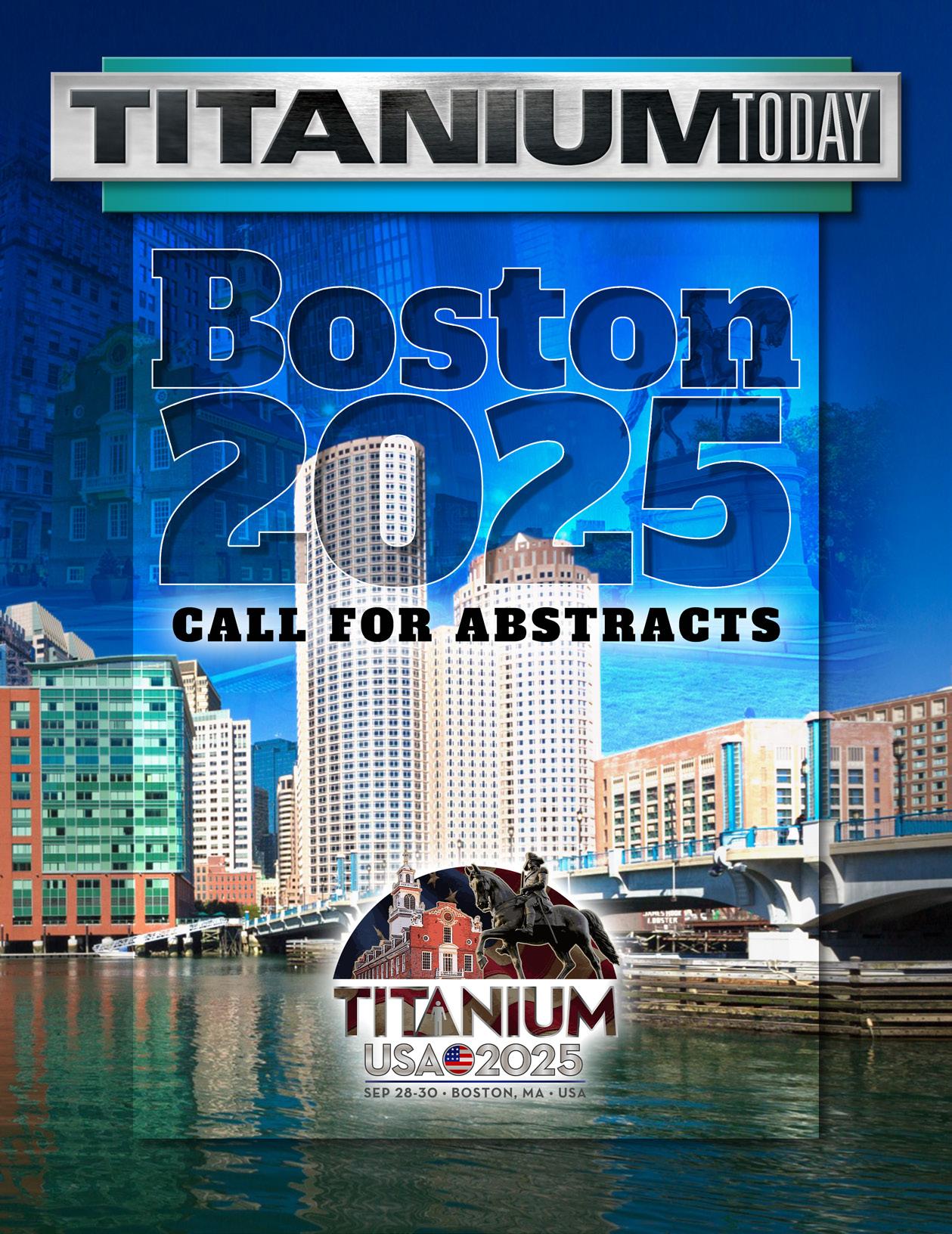
Issue 13; 2025 All Markets
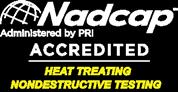
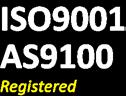
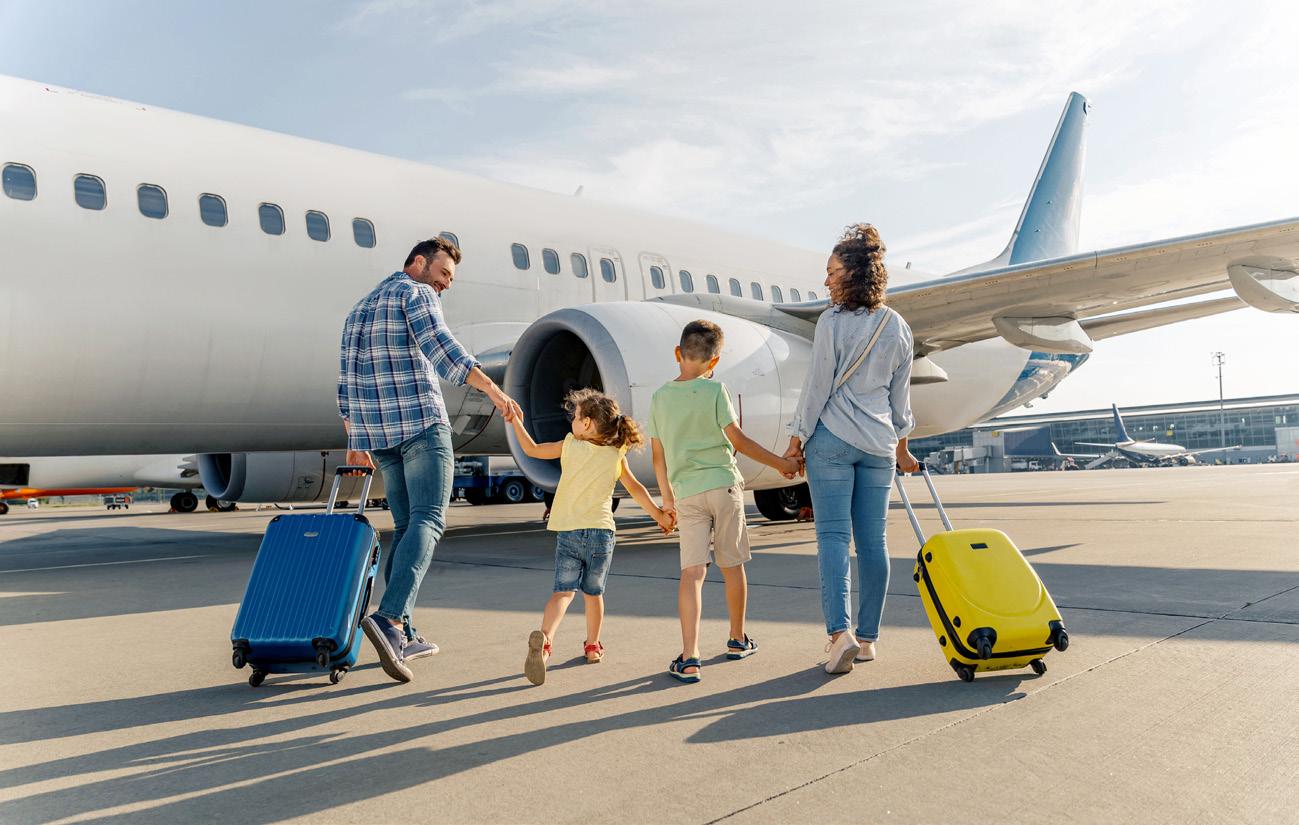

Issue 13; 2025 All Markets
Advantages
•
•
•
•
Marty Pike President ATI Specialty Materials
Sam Stiller Vice President
Howmet Aerospace
Brett Paddock Secretary / Treasurer
Titanium Industries Inc
Dr. Markus Holz
Academic Member, Professor
Jeff Easto is a supply chain and procurement executive with deep expertise in the metals industry and strategic sourcing. Since joining Precision Castparts Corp in 2021, he has led global supply chain strategies and currently serves as Vice President of Purchasing for the Metals and Forgings segment. Prior to PCC, Jeff spent 10 years at GE Aviation in various leadership roles, specializing in global sourcing, materials planning, and supply chain management. He also served as a board member of the Michigan Aerospace Industrial Association, contributing industry insight and supply chain expertise.
Steve Chavez CEO
All-Met Recycling
Jeffrey Easto Vice President Purchasing
TIMET, Titanium Metals Corporation
Olivier Maillard
Vice President Metallic Raw Material, Forgings & Castings and Fasteners
Procurement - PMM
Airbus SAS (France)
Michael Marucci
Division President
Advanced Solutions and Surface Technologies business units
Kymera International
John Scherzer
Vice President – Medical Markets
Carpenter Technology Corporation
Edward Sobota
Vice President, New Product Development
STS Metals
That’s why when it comes to the design and manufacture or the repair and reconditioning of crucibles, molds, and hearths for your ESR, VAR, EBM, or PAM installations, we draw on our more than 135 years of design, engineering and manufacturing excellence to ensure that your copper-based melting equipment is operating at peak efficiency.
Quality vessel repair services to keep you running at high production levels.
A reputation for quality work and on-time delivery. Our staff of expert millwrights, welders and machinists can tear down, assess, repair and test your valuable melting equipment.
Additionally, our manufacturing capabilities are fully supported by our staff of over 50+ engineers.
Our services include:
• Machining, welding, straightening, and sizing of stainless steel, copper, nickel, aluminum, bronze, and carbon steel
• Preventative maintenance, including cleaning, re-sizing, straightening and seal replacement
• Crucible diameter and size modifications
• New crucibles, molds, base assemblies, water jackets, etc.
To learn more about our rebuilding and manufacturing services,call (330) 337-0000, visit www.ButechBliss.com or email cu@butech.com.
Medical Technology
Dr. Colin McCracken
Product Manager, Biomedical, Titanium Oerlikon Metco (Canada) Inc
Colin McCracken gained his B .Sc , M . Phil . and Ph D in Metallurgy from Brunel University of West London, UK in 1992 Colin then joined AVX Ltd - Tantalum Division working on capacitor grade tantalum powders and left in 2005 as Head of R&D Colin then moved to the USA to join Reading Alloys Inc as Development Manager - Powder Products and in 2011 Colin was appointed to Director of Product and Market Development at Ametek SMP - Reading Alloys In 2013 Colin relocated to Ontario Canada to work with H C Starck Canada Inc and then later joined Tekna Advanced Materials before finally joining Oerlikon Metco Canada Inc . in 2017 as a Product Manager for Biomedical and Titanium products In 2016 Colin was awarded a Fellow from the UK Institute of Materials, Minerals and Mining
Global Industrial Markets
Christopher Wilson Director of Research and Development NobelClad
Chris Wilson is the Director of Research and Development for NobelClad Chris has a degree in Metallurgical Engineering and a Masters in Business Administration from the University of Pittsburgh . Trained and certified as a Six Sigma Black Belt in Lean Manufacturing Chris has worked within the metals industry for more than 25 years in various functions such as operations, quality assurance, and technical service Chris has focused and specialized on the titanium metals industry Chris is the current Chairman of the ASTM B10 01 Titanium Committee; Recording Secretary of the ASTM B10 Reactive and Refractory Metals Committee; Vice Chairman of the NACE TEG120X Reactive Metals Committee; Member of the International Titanium Association’s Industrial Application Committee as well as a participating member of the Materials Technology Institute (MTI)
Safety Education
Robert Lee (Co-Chair)
President Accushape™ Inc
Robert G Lee is the President and Owner of Accushape™ Inc Mr Lee is Chair of the ITA Safety and Compliance Committee During the past 50 years, Robert Lee has been directly involved in the processing of titanium and other special metals in many forms including, machining, welding, forging casting, screening, pressing and sintering of titanium powder Accushape™ was started in 1987 by Robert Lee for the purpose of scaling up the production of knife handles for Buck Knives made by pressing and sintering (P/S) of titanium sponge granules (titanium powder) (TSG) to produce a net shape finished knife handle . Accushape has produced over 500,000 titanium P/S parts including knife handles, golf club inserts, hex nuts and washers Accushape™ has processed and screened 100’s of thousands of pounds of titanium sponge fines to customer’s special requirements More recently, Mr Lee has been issued 7 patents for a new titanium based material system TiCarbonite® and the ODAK™ tile system TiCarbonite® is a light weight, extremely hard and tough material finding applications for ballistics armor ODAK™ tiles create many types of systems with no increase in thickness and no through gap, making possible flexible material systems that can fit contours
Michael Marucci (Co-Chair)
Division President
Advanced Solutions and Surface Technologies business units
Kymera International
Michael Marucci serves as Division President at Kymera International, a global leader in specialty materials Kymera produces silicon carbide, titanium powders, aluminum powders, copper powders, specialty alloys for titanium production, and surface technology solutions
Mike joined Kymera in March 2020, following the company’s acquisition of Reading Alloys, Inc from AMETEK In his current role, he oversees Kymera’s Surface Technologies and Advanced Solutions business units
The Surface Technologies unit specializes in high-quality thermal spray services, anticorrosion coatings for global navies, thermal spray materials, and advanced spray equipment and automation solutions The Advanced Solutions unit produces high-purity master alloys for titanium production, processes high-purity titanium scrap, and manufactures titanium powders, tantalum, ferro-titanium, copper, and bronze powders
Are you aiming to increase the recycling rates in your titanium production shop?
INTECO´s new innovative vacuum arc cold hearth skull melting and casting furnace
› can achieve recycling rates of up to 100% by feeding virgin and scrap material (e.g. compacted chips) between melting & casting cycles
› can achieve an improved energy ef ciency compared to other cold hearth technologies
› allows static casting of ingots and slabs as well as dynamic casting of complex investment cast parts
› can achieve pouring weights from 250kg up to 3.000kg in one cast
› More than 20 years of experience as a premium supplier in the titanium industry
› Supply of melting and casting equipment for titanium including auxiliaries
› Engineering studies, project- and technology consulting for entire titanium production lines
› Know-how transfer, from selections of raw material up to aerospace certi cation
› Customized process and production management systems (IMAS) for titanium production lines
Michael C. Gabriele
ITA Contributor
Michael Gabriele is an independent freelance writer on behalf of the International Titanium Association (ITA)
Art Kracke President at AAK Consulting
An industry consultant
located in Charlotte, NC, Kracke entered the titanium industry in 1980 with Teledyne Allvac, working in many areas including the development and sale of titanium alloys, superalloys and vacuum melted specialty steels The company evolved into ATI Specialty Materials
Peter C. Zimm Principal Charles Edwards Management Consulting
Peter Zimm leads strategy, market positioning, and operations improvement consulting projects for aerospace companies A Principal for aerospace-focused management consulting firm Charles Edwards, he has delivered scores of projects for OEMs, Tier 1s, subtier suppliers, and raw materials companies across the world Peter is an internationallyrecognized market expert in aerospace raw materials, aircraft components, manufacturing process technologies, and aircraft emissions
Prior to joining Charles Edwards, Peter was a Principal at ICF Aviation’s Aerospace & MRO practice . He began his career at Timken Aerospace where he held various business development, marketing, and sales management positions and co-architected the company’s aftermarket entry strategy Peter has a Masters in Business Administration from Boston University and a Bachelor’s degree from Dartmouth College
Titanium Mill Products:
Sheet, Plate, Bar,Pipe,Tube,Fittings, Fasteners, Expanded Sheet & Ti Clad Copper or Steel.
Titanium Forgings and Billet:
Staged intermediate ingot & billet to deliver swift supply of high quality forgings in all forms and sizes including: rounds, shafts, bars, sleeves, rings, discs, custom shapes, and rectangular blocks.
Titanium, Zirconium, Tantalum & High-Alloy Fabrication & Field Repair Services: Vessels, Columns, Heat Exchangers, Piping, Anodes, Custom Fabrications, Field & In-House Reactive-Metal Welding & Equipment Repair Services Available 24/7.
Plate Heat Exchangers:
Plate Heat Exchangers to ASME VIII Div 1 Design, Ports from 1” through 20” with Stainless Steel, Titanium and Special Metals, Plate Heat Exchanger Refurbishing Services & Spare Parts.
Two Service Centers & Fabrication Facilities in Ohio & Texas with Capabilities in: Waterjet, Welding, Machining, Sawing, Plasma Cutting & Forming.
Serving a Wide Variety of Industries: Chemical Processing, Mining, Pulp & Paper, Plating, Aerospace, Power and others.
Tricor Metals, Ohio Division 3225 W. Old Lincoln Way Wooster, Ohio 44691
Phone: 330-264-3299
Fax: 330-264-1181
Tricor Metals, Texas Division 3517 North Loop 336 West Conroe, Texas 77304
Phone: 936-273-2661
Fax: 936-273-2669
Tricor Metals, Michigan Division 44696 Helm St. Plymouth, MI 48170
Phone: 734-454-3485
Fax: 734-454-7110
Astrolite Alloys California Division 201 Bernoulli Circle, Units B & C Oxnard, CA 93030
Phone: 805-487-7131 Fax: 805-487-9694
[Editor’s note: This article is based on a speech given by Peter Zimm last October at the Titanium USA Conference and Exhibition held in Austin, TX. Zimm is a principal at Charles Edwards Management Consulting and is co-author of “Aerospace Titanium—Global Market Outlook and Supply Risk Assessment,” a comprehensive report on the market for aerospace titanium mill products that is available at AeroOutlook.com. AeroOutlook offers premium aerospace industry market reports meticulously curated and authored by distinguished aerospace market experts. Zimm’s presentation at TI USA along with this article summarizes some of the key findings from that report.]
By Peter Zimm
Total aircraft production value was $150 billion in 2023 and is expected to grow to $158 billion in 2024, a 5-percent increase from 2023 but still 13 percent below 2018’s peak of $181 billion. Commercial air transports are approximately 50 percent of global aircraft production value; military is about one third and business and general aviation are about one fifth. Aerospace entered 2024 hopeful for another year of double-digit growth, but those hopes were soon dashed when a mid-cabin door plug fell out of an Alaska Airlines’ Boeing 737MAX while in flight. Most importantly, however, Boeing’s Puget Sound machinists went on strike in September. The strike lasted 53 days and workers were called back in the middle of November. Production halted not only for the MAX but also for the Boeing 767 and 777.
The production troubles were not limited to Boeing. Supply chain disruptions which have been plaguing the aerospace industry seemed to worsen in 2024. By the end of the first quarter, it was clear that air transport deliveries for Airbus were also running well behind the rates needed to achieve double digit increases again. In April, the European airplane maker lowered its 2024 delivery target from 800 total aircraft to 770. Furthermore, they moved out their
Charles Edwards estimates 2023 aerospace titanium demand was about 160 million pounds. Engines (about 40 percent), equipment systems (about 25 percent), and aerostructures (about 30 percent) consumed most of aerospace titanium. Two-thirds of total aerospace titanium consumption ends up as finished parts on either an Airbus or a Boeing aircraft. The other one-third is ultimately consumed by the rest of the aircraft OEMs.
75 per month production goal for the A320 family from 2025 to 2027. Farnborough Air Show orders were among the lowest on record but given that production backlogs remain at 8 to 10 years (depending on assumed build rates), the paucity of orders is probably not a concern.
Of greater concern are the persistent sub tier supply chain and OEM operational challenges in the industry. Supply chain challenges are worse than OEM’s expected them to be a year ago and suppliers, confronted with changing customer schedules and the specter of poor performance
Established in France (Lyon), the stockist Acnis Group is one of the world leaders in the distribution of metal alloys especially in TITANIUM, in all forms : sheets, bars, tubes and powder for 3D printing.
ISO 13485 certified since 15 years , the family business has specialized in the medical field since its creation in 1991, to meet the demand of orthopedic manufacturers and dental implants, as well as surgical instruments.
ACNIS Group acts as a buffer between producers and users, thanks to its 600 to 700 tons rotating stock and 1,300 references of different origins. Our unique cut-to-size service center (15 machines: waterjet, high-definition waterjet, plate sawing, bar sawing, shearing, machining, chamfering) allows us to reduce your costs by optimizing scrap rates.
As a result, the company is able to deliver very quickly its customers, in barely a week , no matter the ordered quantity. Major implant manufacturers among the main American and European OEMs themselves call on ACNIS Group to source their metal alloys.
The last creation of ACNIS USA stock in 2023 in Chicago has changed the game. Acnis Group is now the only distributor that can stock and deliver any quantity in North America (ACNIS TITANIUM & ALLOYS USA-Chicago), South America (ACNIS DO BRAZIL-Sao Paulo), Europe (ACNIS FRANCE-Lyon), South Asia (ACNIS CHINAShanghai) for global worldwide contracts.
Acnis is your one-stop shop for all TITANIUM grades, stainless steel (316L, 420B, cobalt chrome, 17/4 PH, high nitrogen alloy, Custom 455, Custom 465…) and polymers
Our dental subsidiary BCS , a European leading distributor of CAD CAM products for additive manufacturing, is registered with the FDA for titanium powder & discs, and cobalt chromium powder.
ACNIS TITANIUM & ALLOYS
1940 E Devon Elk Grove Village 60007 - IL - USA
dfreitag@acnis-titanium.com
kragan@acnis-titanium.com
224-550-2422
by other suppliers, have to balance OEM build rate aspirations with the risk of over-investing (in inventory or tooling and machinery) if OEM production goals are not met. Ironically, the slow ramp in aircraft OEM build rates is providing much needed stability for sub tier suppliers, enabling at least some to recovery financially.
We forecast total aircraft production value will grow at 6.1 percent compound annual growth rate (CAGR) from $150 billion in 2023 to $202 billion in 2028. This represents a shallower recovery ramp than we forecast last year.
On the aftermarket side (titanium demand is partly driven by titanium
replacement parts), the maintenance, repair and overhaul (MRO) market value was $226 billion in 2023 and is expected to grow over 8 percent to $245 billion in 2024. MRO continues to benefit from strong air traffic demand as well as under-delivery of new aircraft (old aircraft continue to fly for longer). However, MRO is also experiencing labor and parts shortages. In addition, MRO capacity is constrained and the return of air travel to pre-Covid levels is driving up wait times to get into overhaul shops.
Looking further out, we forecast MRO will grow at 3 percent compound annual growth rate (CAGR) from $245 billion in 2024 to $262 billion in 2028.
Aerospace raw material demand is based on material for aircraft production as well as material consumed in spare parts for MRO. Charles Edwards’ raw material model breaks down aircraft fly weight into material composition by material family (i.e., aluminum, steel, titanium, nickel, and composites), aircraft system (i.e., aerostructures, engines, equipment systems, interiors, etc.), and other distinctions.
Our forecast considers material substitution over time, changes in aircraft and engine OEM production mix, and other market dynamics. We then build up buy-to-fly ratios based on typical material removal during processes such as machining, forging, and melting. The result is a buy weight composition by aircraft which we apply to the production forecast to arrive at aggregate raw material demand based on production. MRO material demand is based on expected spares requirements for repair and overhaul events.
The aerospace industry demanded 1.36 billion pounds of raw materials in 2023 across all the raw material families (a relatively flat increase from 2022). We forecast aerospace raw material demand will grow at 5.9 percent CAGR from 1.36 billion pounds in 2023 to 1.82 billion pounds in 2028. The reason the CAGR is lower than overall production value is that raw material production precedes finished aircraft production by some period of time; therefore, raw material production is starting from a higher base in 2023 relative to final production.
Titanium is used throughout the aircraft: in the engine (e.g., compressor discs, blades and vanes, and cases), components/equipment systems (landing gear, ducting), and aerostructures (chords, spars, wing
boxes, and pylons). Titanium is also used in the nacelle, fasteners and brackets, and interior parts. Charles Edwards estimates 2023 aerospace titanium demand was about 160 million pounds. Engines (about 40 percent), equipment systems (about 25 percent), and aerostructures (about 30 percent) consumed most of aerospace titanium. Two-thirds of total aerospace titanium consumption ends up as finished parts on either an Airbus or a Boeing aircraft. The other one-third is ultimately consumed by the rest of the aircraft OEMs. A number of demand trends impacted the aerospace titanium market in 2024:
Aircraft production rates. Despite the production difficulties that plagued narrow-bodies in 2024, builds of titanium-rich “composite” wide-body aircraft (787 and A350) ticked upward during the year.
Aircraft production mix. Early in the post-COVID recovery, production was skewed to narrow-body aircraft more than usual due to a faster return of short-haul air traffic. However, as long-haul traffic has rebounded, the ratio of narrow-bodies to wide-bodies built was returning to pre-COVID ratios. With the interruption in MAX production due to the strike and the quality issues at Boeing, this proportion returned promptly to pre-
COVID levels but are skewed by the artificially low deliveries of MAX, 767, and 777 aircraft.
Charles Edwards forecasts that titanium demand will grow at a robust 7.2 percent CAGR from 160 million pounds in 2023 to 227 million pounds in 2028.
With Russia’s invasion of Ukraine in 2022, geopolitical risk suddenly reappeared as a factor that must be taken into account in our global industry. Civil unrest in the French island territory of New Caledonia and interruptions in shipping through the Suez Canal continue to remind us that the threats to steady supply remain real and are constantly changing.
Across all the aerospace metal families (titanium, aluminum, nickel, and steel), the various aerospace alloys that account for most of metal raw material demand are comprised of 15 different elements (e.g., chromium, cobalt, and magnesium, etc.). These elements are mined or refined in 55 different countries, one quarter to one fifth of which we consider to be high risk (risk is defined as the prospect of a force majeure event in the next three years). Because of the global nature of our industry’s sources of supply
and because of increasing global tensions, we include geopolitical risk assessments in each of our raw material market reports.
Titanium is extracted from ore, refined into sponge and then into primary metal, then melted into alloys used in aerospace production. The locations where all three levels of titanium production take place (mining, refining, and alloying) are important, but titanium is alloyed with other elements. The most-utilized aerospace titanium alloys include elements such as vanadium, aluminum, magnesium, and molybdenum. These elements are mined or refined in 36 different nations, seven of which are considered medium-high- or high-risk places to do business. The upstream supply risk assessment in our report helps consumers of titanium evaluate vulnerabilities and identify areas for which to develop contingencies.
Four titanium suppliers – ATI, Howmet, Timet (part of PCC), and VSMPO – supply the majority of titanium alloy mill product to the aerospace industry. Of course, ever since Russia’s invasion, there have been concerns about sourcing from Russia’s VSMPO. Those concerns seem to have lessened with time as neither specter— EU sanctions or Russian government export restrictions—has manifested itself to date. That said, a number of capacity expansions have been announced by Perryman, ATI, and Timet which will come online over the next several years.
Our aerospace titanium raw material report profiles aerospace market demand in detail for titanium mill product, assesses upstream supply risks, and comprehensively analyzes aerospace titanium supply. It’s available via the website www. aerooutlook.com n
The medical and dental industries began using titanium and titanium alloys, referred to as titanium in this article, as far back as eight decades ago. The initial applications were niche dental implants. The volume was small, but it was the platform on which the interest in titanium for medical applications grew.
The application that brought titanium to prominence in the medical industry was orthopedic implants. Implants were initially made from stainless steel. Stainless steel worked, but it was found that nickel ions were migrating out of the stainless implant into the body and becoming sights for inflammation. The solution was titanium, specifically Ti 6Al-4V. Ti 6Al-4V was replaced by Ti 6Al-4V ELI. ELI means extra low interstitial, specifically lower oxygen content. The lower oxygen content results in the alloy having greater ductility.
Replacing stainless steel with titanium solved the nickel ion problem. It also brought to bear the multiple beneficial properties of titanium. The advantages of using titanium in the human body are numerous and have become well known. They include: lighter weight than stainless steels, nickel alloys, and cobalt alloys which improve implants as well as medical tools; high strength to withstand the stresses placed upon implants; corrosion resistance to human bodily fluids; temperature resistance at elevated sterilization temperatures; and unlike many other metals titanium is biocompatible with the human body.
These advantages make titanium a good solution for medical applications
and often result in improved patient outcomes after implant surgery. Improved outcomes can be defined as faster recoveries, reduced risk of complications, and a greater probability of returning to an active, pain-free life for an extended period of time. Titanium helps achieve this through its biocompatibility with the human body. Bone tissue will grow into titanium, a process known as osseointegration, helping ensure that implants remain securely in place and function effectively. Biocompatibility is considered by the vast majority of people to be titanium’s most important property for medical applications.
The consumption of titanium for medical applications has grown to become a recognized and significant part of the titanium industry. While the pounds consumed for medical applications are small when compared to pounds consumed by the aerospace industry, the average cost to produce products for medical applications exceeds that of products for aerospace, and therefore commands a higher average price. The economic value of titanium for medical applications punches over its weight class, to borrow a phrase. Improved patient outcomes are
the bottom line for the medical industry. Improved outcomes are the sum of the parts required to treat a patient. Titanium is playing an important role in the material portion of the process but is secondary to the talents of the numerous surgeons, scientists, and engineers involved in the medical industry and procedures. Titanium usage in the medical industry varies across its segments. Major applications and the primary titanium used for applications include:
• Dental implants and orthodontic wires: CP, Ti 6Al-4V (grade 5), Ti 6Al-7Nb (vanadium allergies) nitinol (orthodontic wires)
• Bone, joint, spinal, and heart valve implants, bone plates, screws, intramedullary nails: Ti 6Al-4V ELI (grade 23), Ti 6Al-7Nb, CP
• Titanium powder overlays thermally sprayed onto the metalto-bone surfaces of implants to improve bone adhesion: CP, Ti 6Al-4V
• Trauma devices: Ti 6Al-4V ELI
• External fixation devices: Ti 6Al4V ELI
• Pacemaker wire: Nitinol (titanium nickel alloys) for its super elastic properties.
• Patient moving devices such as wheelchairs: Ti 6Al-4V
• Stents: Nitinol for its shape memory properties
• Surgical tools, prosthetics, scalpels, forceps, and fixtures: Ti 6Al-4V, CP, and the beta titanium alloys
efficiency
More reliability: Built robust, with high precision as the benchmark Innovation and reliability for your success: The KASTOtec
More innovation: Intelligent control and user friendly operation
Smarter storage for maximum space efficiency: UNITOWER More space
More efficiency: Save time with direct access—no additional lifting equipment needed
More flexibility: Modular, heightadjustable supports for up to 3 loading heights
Low in price, high in performance: KASTObloc
More precision: excellent performance for smaller block dimensions or lower plate weights
More safety: perfect for cutting remnant pieces
such as Ti 15-333 where higher strength is required.
Titanium’s light weight, strength, and corrosion and temperature resistance make it an ideal material for medical tools. The titanium product forms used to make medical devices are smaller dimensionally than products used in aerospace and industrial applications. The reason for this is obvious: People are smaller than airplanes and industrial vessels. But there are a lot of people on earth and our numbers are growing. The list that follows contains many of the typical titanium products forms and the parts they are used to manufacture:
• Rolled bar forged into hip stems and cups and to a lesser degree knee femoral and tibia parts
• Round, rectangular, and shaped rolled bar to be machined into bone and joint replacement parts, bone plates, screws, as well as internal and external fixation devices
• Powder metals for additively manufacturing into spinal implants, customer specific and trauma implants, custom surgical tools, and others
• Powder metals for metal injection molding (MIM) into spinal cages, surgical equipment and tools, orthodontic brackets and others
• Wire for pacemaker lead wires and stamped sheet for cases, and
• Formed wire for stents.
Titanium consumption has grown year-over-year in the medical and dental industries since its inception except for 2020 and 2021 when it stagnated due to the impact of the pandemic. The industry rebounded rapidly after medical professionals and hospitals overcame the surge of viral hospitalizations. It is important to keep in mind that medical procedures requiring titanium are not elective surgeries. The compound annual growth rate, CAGR, is around 4-5% in recent years and is projected to continue at this growth rate.
Long-term agreements are signed that allow producers to allocate their production to meet anticipated
demand in a timely fashion. Finished mill products are purchased and strategically placed in warehouses to meet unexpected, immediate demand and volumes not large enough to warrant a mill run. New alloys are in development to meet the expanding needs from new and innovative applications.
Powder titanium provides the foundation for metal injection molding (MIM) and additive manufacturing. Medical applications are believed to be the largest consumer of Ti 6Al-4V ELI powder. Additive manufacturing builds complex geometries that are not practical or possible using subtractive manufacturing processes.
Innovative titanium powder making processes are being developed and moving towards initial production that promise to increase the availability of titanium powder and lower the cost of powder making. Additive manufacturing also facilitates patient-specific implants. These implants are built by melting very small spherical powder particles one voxel at a time creating an
Fe, Ni, Co, & Cu Alloys
600 Pound Capacity
6" Rounds or 6” x 11” Slabs
Vacuum Arc Remelting
Reactive and Non-Reactive Alloys
6”–20” Crucible Diameters
100–5000 Pound Ingots
R&D Melting
300
Bar Peeling - 0.5" - 6" Diameter
Bar Polishing - 0.5" - 8" Diameter
Lathe Turning - up to 17" Diameter
Saw Cutting - up to 30" Diameter x 5,000 Pounds
implant’s cross section. This process is performed repeatedly building an implant one thin layer at a time. The implants have unique geometries that closely match a patient’s body geometry. Powder is expected to erode the consumption of rolled bar products, however the impact of additive manufacturing will be buffered by regulations, the high liability aspect of and growth the medical industry.
Additive manufacturing can enhance bone in-growth. Implants are being designed and built with surfaces that have specifically design “pores”. Bone tissue will grow into the pores simulating what occurs in nature when a broken bone heals. The number of additive manufacturing businesses building medical parts is growing. The driving force is improved, innovative implants and better patient outcomes. The spinal implant segment of the implant industry is perhaps the medical segment benefiting the most from additive manufacturing and implementing it at the greatest rate.
Additively manufactured patient-specific implants will grow significantly as the additive industry matures. It is likely that the building of patient-specific implants will become a service performed in hospitals that focus on orthopedic implant surgeries.
Implants surgeries have been performed primarily in developed nations but as health care improves around the world the number of implants is expected to grow. Robots are becoming a surgical tool preferred by a growing number of surgeons. The reasons vary but can be summarized as robots can improve patient outcomes. Improved outcomes
make it desirable for more people to choose to have implant surgery thereby increasing the consumption of titanium.
The number of implant surgeries is expected to grow as people live longer, stay more physically active, and surgeries continue to be less invasive. Innovative surgical techniques, implant design, and tools by surgeons, hospitals, and implant manufacturers will drive growth of the implant market and titanium usage. The high liability aspect of the medical market will moderate the rate of change.
Growth by acquisition will continue to be an important business dynamic for OEMs as well as companies in the medical supply chain.
consumption will grow. n
Titanium producers must continue to work closely with OEMs and medical professionals to relentlessly innovate, to paraphrase an ATI registered trademark and to provide improved alloys and product forms. The bottom line is that the properties of titanium and titanium alloys make it a foundational technology for the medical industry. When used in conjunction with the diverse skills of medical professionals, titanium
[Editor’s note: Art Kracke, an industry consultant located in Charlotte, NC, led the effort to compile the information in this article, along with members of the International Titanium Association’s Medical Technology Committee. Kracke entered the titanium industry in 1980 with Teledyne Allvac, working in many areas including the development and sale of titanium alloys, superalloys and vacuum melted specialty steels. The company evolved into ATI Specialty Materials.]
Last year Sen. Catherine Cortez Masto (D-Nev.) led a bipartisan group of Senate colleagues including Senator Marsha Blackburn (R-Tenn.), Shelley Moore Capito (R-W.Va.), Joe Manchin (D-W.Va.), and Thom Tillis (R-N.C.) in introducing bill S. 4025 “The Securing America’s Titanium Manufacturing Act of 2024” to support America’s titanium supply chain and promote investment in the U.S. defense industrial base: [Link]
A spokesman from Sen. Masto’s office, contacted via email in late February, confirmed that Sen. Masto’s bill is still in play in Congress. “Sen. Masto introduced the legislation in the last Congress, which ended on January 3, 2025. It was referred to the Senate Finance Committee. She has yet to reintroduce the bill in the 119th Congress. However, we are working to reintroduce the bill in the coming weeks/
months once a new lead for the bill is found in the House of Representatives. The previous lead retired at the end of the last Congress.”
The Securing America’s
Titanium Manufacturing Act would remove the existing 15-percent tariff on titanium sponge imports from nations with preferential trade status until the end of 2031, according to a press release from the office of Sen. Cortez Masto. The legislation would also require the President to monitor any efforts by China or other hostile countries to move into the U.S. titanium supply chain, and would give authority to the President to reapply the tariff if it becomes necessary to support U.S. businesses, workers, or national security in the
This link provides the full text of Masto’s bill: [Link]
Masto stated that the legislation is supported by Nevada company Timet, the United Steelworkers, the Aerospace Industry Association, as well as other American titanium companies. Restructuring titanium sponge tariffs to strengthen U.S. national security was also a recommendation of the Titanium Sponge Working Group, an interagency commission established during the first term of President Donald
Echoing concerns expressed in “The Securing America’s Titanium Manufacturing Act of 2024” (bill S. 4025), attendees at the 2023 TITANIUM USA Conference and Exhibition, held in Colorado, weighed the potential for titanium metal shortages in the near term.
As reported, the situation is complex and involves many industry (and geopolitical) developments, not the least of which is that the United States no longer is a domestic producer of titanium sponge. The Covid-19 pandemic snarled supply chains and upended many business operations around the world. Russia invaded Ukraine in February 2022 causing turmoil among two major titanium producers. The United States Geological Survey recently discontinued its titanium report.
In March 2022 ATI announced the termination of Uniti, LLC, its joint venture with Russian-based VSMPO-AVISMA [Link].
A Financial Times article posted online on May 3, 2023, quoted Guillaume Faury, the chief executive officer of Airbus [Link]. The story indicated that Airbus still sees problems in the global supply chain for titanium and aluminum, a hangover from the pandemic years, as well due to disruptions from the current Ukraine/Russia conflict. Faury,
At Kymera International, we’re at the forefront of advanced titanium solutions for the aerospace industry, delivering precision-engineered materials that power the future of flight. Our titanium powders, master alloys, and fully integrated titanium metallurgical products are trusted by leading aerospace manufacturers worldwide to meet the most demanding performance standards.
• Superior Strength & Lightweight Performance – Ideal for critical aerospace applications
• Unmatched Purity & Consistency – High-quality titanium powders and alloys
• Global Manufacturing & Supply Chain Strength – Delivering reliability at scale From high-performance jet engines to structural airframe components, Kymera International is the trusted partner for aerospace engineers and manufacturers looking for cutting-edge titanium solutions.
Trump, and led by the secretaries of Defense and Commerce: [Link]
The U.S. titanium industry imports virtually 100 percent of its titanium sponge, a product which is made into titanium metals and alloys. Those materials are critical components of military fighter aircraft, submarines, satellites, and many other defense technologies. Almost 90 percent of titanium sponge is imported from Japan, a key national security partner. However, Masto said that an outdated tariff on titanium sponge is putting U.S. producers at a disadvantage relative to foreign titanium producers in hostile nations including China and Russia, who do not pay this tax. This bipartisan legislation would remove the 15-percent tariff on titanium sponge imports, cutting millions of dollars in unnecessary costs for U.S. companies that produce critical defense materials.
“American manufacturers rely on titanium sponge to build everything from fighter jets to satellites, and my bipartisan bill will ensure we have a safe, secure, and reliable supply chain for these critical components,” Sen. Masto said. “By eliminating this burdensome tariff, my commonsense legislation would cut costs for U.S. producers, protect our national security, and support jobs in Nevada and across the country.”
“Titanium sponge is critical for both commercial and military manufacturing. Dropping tariffs on these imports, the majority of which come from Japan, will make titanium more affordable, Sen. Blackburn said. “This legislation will reduce prices for
consumers and American companies while ensuring that titanium sponge from our allies keeps an edge over material made in Communist China.”
Sen. Capito said West Virginia is known for its manufacturing
‘American
manufacturers rely on titanium sponge to build everything from fighter jets to satellites, and my bipartisan bill will ensure we have a safe, secure, and reliable supply chain for these critical components. By eliminating this burdensome tariff, my common-sense legislation would cut costs for U.S. producers, protect our national security, and support jobs in Nevada and across the country.’
—Sen. Catherine Cortez Masto
capabilities and has a proud tradition of involvement within the titanium industry. “West Virginia hosts operations that create titanium products to strengthen national security through domestic supply chains and boost our aerospace industry. This legislation would help ease costs on this vital industry, increase access to materials, and encourage economic development
while maintaining U.S. authority to adjust tariffs as needed,” Sen. Capito said.
“I am proud to introduce the Securing America’s Titanium Manufacturing Act with senators Cortez Masto and Blackburn, Sen. Joe Manchin said. “Titanium is a critical mineral essential for engines, military fighter aircraft, satellite parts, and many other military technologies, and our bipartisan legislation would help ensure the United States has a reliable titanium sponge supply chain from countries that share our values, like Japan. I will continue working with my colleagues on both sides of the aisle to get this commonsense bill across the finish line and signed into law.”
“We must do everything we can to protect jobs in North Carolina and across the country,” Sen. Tillis said, “I’m proud to co-introduce this bill that will ensure America’s titanium supply chain and defense industrial base remains strong.”
“Timet wants to express its sincere appreciation for Senator Cortez Masto’s critical work and leadership in introducing the Securing America’s Titanium Manufacturing Act. This bill will enhance American competitiveness in the global titanium market and strengthen our American national security supply chain,” Ryan Ramsey, general manager of Timet Henderson said, quoted in the press release. “In addition to helping the U.S. industry; this effort will also have a positive effect on Timet’s hardworking employees in Henderson, NV.” n
Editor’s note: Sen. Cortez Masto introduced bill S. 4015 to the Senate on March 21, 2024. The text of a similar bill (H.R. 8912; “Securing America’s Titanium Manufacturing Act of 2024”) was introduced last year in the House of Representatives by Rep. Brad R. Wenstrup (R-OH). Wenstrup’s bill can be found here: [Link]
IperionX is a leading American titanium metal and critical materials company - using patented metal technologies to produce high performance titanium alloys, from titanium minerals or scrap titanium, at lower energy, cost and carbon emissions.
in the article, described supply chain delays as an “overall challenging situation that would last all along 2023 and potentially till (2024).”
Willy Shih, a senior contributor to Forbes and a teacher at Harvard Business School, penned an online article, posted March 2, 2022, stating that “the terrible war in Ukraine and subsequent sanctions placed on many Russian organizations have raised questions about potential supply chain vulnerabilities. While Russia is mostly an exporter of resources like oil, gas, and metals, one market where it is a dominant player is for titanium and titanium forgings. Many people are waking up to the potential consequences of a longerterm stoppage in the flow of these critical materials” [Link].
Takeshi Nakashima, the deputy general manager of the titanium division of Toho Titanium Co. Ltd., Japan, a producer of titanium sponge, during his presentation at TITANIUM 2023, warned that the global aerospace supply chain will face a sponge shortage. “The sponge demand and supply gap will keep increasing, even if OEMs ramp up production gradually. A shift of sponge allocation from the industrial market to the aerospace market might occur to catch up with increasing demand.”
The worry is that these developments, taken as a whole, are altering the U.S. titanium industry landscape, which might result in a supply pinch. Underlying all these dynamics is that titanium remains a
“strategic” metal for U.S. industrial and military manufacturing. However, concerns on this topic are not new and have been raised by industry and government agencies in recent years.
The Federal Register, in an online post dated Oct. 26, 2021, indicated that the Bureau of Industry and Security (BIS) published a report completed on November 29, 2019. The report’s executive summary stated that “titanium sponge is essential to the manufacturing and maintenance of U.S. defense systems. Titanium sponge is the intermediate product resulting from the conversion of titanium ore into a form of titanium metal that can be melted to manufacture slab or ingot, which in turn is used to produce finished titanium products. Consequently, titanium sponge production is essential to the production and sustainment of many U.S. defense systems, and preserving this critical capability is imperative to the national security” [Link].
The Titanium Sponge Working Group (TSWG), established under the Trump administration in 2020, released an online report, dated August 3, 2023 and posted on the Washington Tariff and Trade Letter, which highlighted the increased dependence of the United States on imported titanium sponge. The report came in the wake of the closure of the Timet’s Henderson, NV, plant, marking the end of domestic sponge production [Link].
The TSWG reported that “U.S.
dependency on imported titanium sponge rose dramatically from 68 percent in 2020 to 100 percent today, emphasizing a severe reliance on overseas supplies. These findings underscore the urgency for measures ensuring access to this critical input, which plays a pivotal role in the defense and industrial sectors, particularly in aerospace applications. The top four global producers of the sponge since 2010 have been China, Japan, Russia, and Kazakhstan. The TSWG report found Japan has exhibited the capability and willingness to meet varying U.S. titanium demands. Similarly, six respondents cited Kazakhstan as a reliable alternative to Japan, offering high-quality sponge.” n
[Editor’s note: the following is a collection of recent press releases and news stories offering business forecast for the 2025 commercial aerospace industry—the showcase market for the titanium industry. The thought here is to provide readers with a variety of perspectives from authoritative sources for how business conditions might play out in the near term. Readers are encouraged to review the entire article from different sources to determine how these many projections might affect business conditions in the titanium industry.]
By Michael C. Gabriele
As airlines and the commercial aerospace industry embark on 2025, most outlooks weigh positive business conditions with some nagging concerns, especially regarding the global supply chain. What’s clear is that virtually all the forecasts applaud the aerospace sector for successfully gaining altitude following the dark days of the Covid years.
For the titanium industry, the basic equation is that a positive outlook for commercial aerospace would spur demand for more titanium, as airlines work to meet the demand for expanding business and leisure travel. The demand for titanium components and assemblies would occur in orders for new jets as well as well as for titanium parts needed for maintenance, repair and overhaul (MRO).
“We’re expecting airlines to deliver a global profit of $36.6 billion in 2025,” Willie Walsh, director general of the International Air Transport Association (IATA) said, quoted in a Dec. 10, 2024 press statement [Link]. The IATA, headquartered in Montreal, with executive offices in Geneva, Switzerland, is the trade association for the world’s airlines, representing 340 airlines and over 80 percent of global air traffic.
“This (projected profit) will be hard-earned as airlines take
Forbes reported that supply chain woes, with delays at OEMS and engine manufacturers remain the top concern for the 2025 commercial aerospace market. However, Forbes pointed out that “this may be the most important trend because, in truth, delays in aircraft delivery are saving the airline industry from itself. Normally in prosperous times, airlines acquire airplanes and add routes, some of which turn out to be unprofitable. Forbes added that overall aerospace demand remains strong, despite questions regarding the supply chain.
advantage of lower oil prices while keeping load factors above 83 percent, tightly controlling costs, investing in decarbonization, and managing the return to more normal growth levels following the extraordinary pandemic recovery. All these efforts will help to mitigate several drags on profitability which are outside of airlines’ control, namely persistent supply chain challenges, infrastructure deficiencies, onerous regulation, and a rising tax burden,” Walsh said.
Highlights for the IATA outlook include: net profits are expected to be $36.6 billion in 2025 for a 3.6 percent net profit margin, a slight improvement from the expected $31.5 billion net profit in 2024 (3.3% net profit margin). Average net profit per passenger is expected to be $7 (below the $7.9 high in 2023, but an improvement from $6.4 in 2024). Operating profit in 2025 is expected to be $67.5 billion for a net operating margin of 6.7 percent (improved from 6.4 percent expected in 2024). Passenger numbers are expected to reach 5.2 billion in 2025, a 6.7-percent rise compared to 2024 and the first time that the number of passengers has exceeded the five billion mark. Cargo volumes are expected to reach 72.5 million metric tons, a 5.8 percent increase from 2024.
According to the IATA, the
Master alloys for Titanium Industry.
Nickel based Master Alloys.
Ni, Co, Mo & Fe based Super Alloys Bar Stock.
Equiaxed, Super Alloy Bar Stock suitable for making
Directionally solidified Single Crytsal Investment Casting.
significant risks to the aerospace industry in 2025 include disruptions from military conflicts in Europe and the Middle East, uncertainties over tariffs and possible trade wars, ongoing supply chain issues and concerns over fuel costs.
The New York Times, in a Jan. 11 feature article [Link], found the outlook for U.S. airlines was upbeat, according to airline executives and industry analysts. The Times reported that many major airlines upgraded forecasts for the all-important last quarter of 2024. Delta Air Lines, one of the major U.S. carriers, said it collected more than $15.5 billion in revenue in the fourth quarter of 2024, a record. “As we move into 2025, we expect strong demand for travel to continue,” Delta’s chief executive, Ed Bastian, said in a statement.
Delta’s report offers a preview of what are expected to be similarly rosy updates from other carriers that will report earnings in the next few weeks, the Times reported. “That should come as welcome news to an industry that has been stifled by various challenges even as demand for travel has rocketed back after the pandemic.” However, the Times report added a word of caution. “Geopolitics, terrorist attacks, air safety problems and, perhaps most important, an economic downturn could tank demand for travel. Rising costs, particularly for jet fuel, could erode profits. Or the industry could face problems like a supply chain disruption that limits availability of new planes or makes it harder to repair older ones.”
The positive outlook for 2025 is probably strongest for the largest U.S. airlines: Delta, United and American. All three are well positioned to take advantage of buoyant trends, including steadily rebounding business travel and customers who are eager to spend more on better seats
and international flights. But some smaller airlines may do well, too. JetBlue, Alaska Airlines and others have been adding more premium seats, which should help lift profits. Business improvements and positive industry trends, along with the stabilization of fuel, labor and other costs, have created the conditions for what could be a banner 2025. “All of this is the best setup we’ve had in decades,” Ravi Shanker, an analyst focused on airlines at Morgan Stanley, said, quoted in the Times article.
Jet engine manufacturer GE Aerospace forecasted stronger profits in 2025, saying it is better prepared to meet jet engine demand with progress in resolving supply chain issues that previously had hobbled production, according to a report on Reuters. GE stated that the production of LEAP engines, which power Airbus and Boeing narrow-body aircraft, is expected to increase 15 to 20 percent this year after a 10 percent year-onyear decline in 2024.
An online Reuters wire story [Link] quoted GE Aerospace CEO Larry Culp, who said “we have obliterated countless constraints in the supply base,” and that primary suppliers are now shipping over 90 percent of the committed volume, compared with about 50 percent a year ago.
Forbes [Link] reported that “supply chain woes, with delays at Airbus, Boeing, engine makers and other suppliers,” remain the top concern for the 2025 commercial aerospace market. However, Forbes pointed out that “this may be the most important trend because, in truth, delays in aircraft delivery are saving the airline industry from itself. Normally in prosperous times, airlines acquire airplanes and add routes, some of
which turn out to be unprofitable. Also, employee costs rise due to added capacity and improved union contracts. This time, the contracts are clearly better, but capacity growth has slowed, despite strong demand.”
Forbes pointed out that demand remains strong, despite questions regarding the supply chain. “Every carrier has noted the continued strength on its most recent earning carrier. Strong demand explains the increase in new destinations or frequencies, particularly European, which the carriers have scheduled for the coming summer.
Honeywell, in its Global Business Aviation Outlook, forecasted up to 8,500 new business jets worth $280 billion will be delivered over the next decade, an increase in value from last year’s forecast [Link].
The five-year new jet purchase plans of business aviation operators surveyed remained on par with last year’s results, indicating that demand for new aircraft is stabilizing well above pre-pandemic levels, according to the Honeywell forecast. Its survey reveals ongoing plans by business jet manufacturers to ramp up production in response to strong backlogs and stable book-to-bill ratios persisting through 2024. According to information posted on its website (https://www.honeywell.com/us/en), “Honeywell Aerospace Technologies products are found on virtually every commercial, defense and space aircraft, and in many terrestrial systems.”
Separately, The Wall Street Journal, on Feb. 7, reported that Honeywell “plans to separate its aerospace division from its automation business and move ahead with plans to spin off its advanced materials arm.” The separation of Honeywell’s aerospace and automation units is slated to be finalized by the second half of 2026. The Journal article stated that
Honeywell gets “about 40 percent of its annual revenue from the aerospace business, which makes engines and cockpit systems. An independent Honeywell aerospace business would be one of the largest aerospace suppliers, having booked $16 billion in revenue in 2024.”
Representatives from the commercial aerospace giants weighed in on near-term business forecasts at the 2024 TITANIUM USA Conference and Exhibition, held Oct. 6-9, 2024 in Austin, TX. Olivier Maillard, Airbus vice president of metallic material procurement, offered a forecast that there would be a strong demand for 42,430 new commercial aircraft between 2024 and 2043. In addition, Maillard said the commercial aerospace market has recovered faster than expected (since Covid-19), “with a strong focus on Airbus’ single-aisle family, and an increasingly one over the past two years on the wide-body market. The continued steady ramp-up on all Airbus’ programs is calling on the titanium industry to prepare and anticipate demand in 2026 and beyond.”
Jeff Carpenter, senior director, supply chain contracts and operations, Boeing Commercial Airplanes, spoke to the TITANIUM USA audience virtually, reminding the “titanium world” that Boeing’s 787 is still operating normally and is still our major consumer of titanium.” News sources estimate that titanium accounts for about 14 percent of the
Carpenter stressed the importance of titanium scrap for Boeing’s manufacturing operations. “Our scrap utilization for melt operations has increased dramatically, especially due to sponge pricing and availability. Sponge is tight, but more producers are coming online. We need your help. We’re going to see you soon. If you’re a machine shop or a forger, we’re going to be buying back our titanium scrap and we’re going to be enforcing that.”
Carpenter also noted that the global fleet for commercial jets has seen constrained capacity by Boeing and Airbus, delaying retirements of aging fleets. “It’s not a demand problem; it’s a capacity problem. Average fleet age is rising. We’re flying older airplanes longer. But our planes are safe. Markets are resilient and the industry is recovering (from Covid). Long-term growth looks promising.”
Flightplan Forecast, the aerospace analysis group based in Sandy Hook, CT [Link], reported that Boeing and Airbus finished 2024 on a high note both in terms of orders and aircraft shipments, which could signal a positive momentum for 2025. “Boeing’s deliveries jumped to 30,
compared to just 13 in November and 14 in October. Meanwhile, Airbus delivered 123 units, up from 84 in the prior month.”
Flightplan reported that Boeing’s jet deliveries rebounded in December following a labor strike that disrupted production last fall. However, the company’s annual deliveries in 2024 fell to their lowest level since the COVID-19 pandemic. The company delivered 348 commercial jets last year, down from 528 in 2023. New orders also declined significantly in 2024 compared to the prior year. Boeing recorded 569 gross orders and 377 net orders after accounting for cancellations and conversions.
Airbus delivered 766 commercial aircraft to 86 customers worldwide in 2024, a slight increase from the 735 delivered in 2023. The company also secured 878 gross new orders, resulting in a year-end backlog of 8,658 aircraft. “Key highlights of 2024 included the first-ever delivery of the A321XLR and the first A330neo and A350 deliveries to several new customers. Airbus CEO of Commercial Aircraft, Christian Scherer, acknowledged the sustained demand for new aircraft and the strong momentum in wide-body orders. He also emphasized the significant team effort required to achieve these results and expressed gratitude to both the Airbus team and their customers for their continued trust and partnership.” n
This program will open for applications again beginning April 3.
Please return then to view the updated Eligibility and Awards! If you are an applicant who would like to discover more scholarship opportunities you might qualify for, please continue to the Scholarship America Hub and sign up!
�
Oak Brook, Illinois – January 8, 2025 – A. M. Castle & Co.™, a global leader in the supply of highperformance metals and valueadded services, proudly announces the launch of its new unified brand identity. This strategic rebranding effort reflects the company’s commitment to delivering specialized solutions across its core industries— Aerospace, Industrial, and Medical— while enhancing its global service capabilities and optimizing supply chain operations.
The rebranding comes a little over a year after the November 2023 merger of Castle Metals and Banner Industries under the ownership of MiddleGround Capital, a private equity firm specializing in industrial investments. This milestone marks the integration of eight specialized divisions—Banner Commercial™, Banner Medical™, Banner P&M Supply™, Castle Metals Aerospace™, Castle Metals Industrial™, Edge International™, National Kwikmetal Service® (NKS), and Supra Alloys™— under the historic A. M. Castle & Co. name, a legacy that dates back to 1890. Each division will maintain its name and specialized focus, with updated branding that reflects a cohesive corporate identity.
This rebranding aligns the company’s operations by leveraging expertise across three industry-focused verticals:
• Aerospace: Supported by Castle Metals Aerospace and Supra Alloys.
• Industrial: Represented by Banner Commercial, Banner P&M Supply, Castle Metals Industrial, and NKS.
• Medical: Led by Banner Medical and Edge International.
This new structure is further supported by operations across five global regions: APAC (Asia-Pacific), Canada, EMEA (Europe, Middle East, and Africa), Mexico, and the USA.
The rebranding will also improve cross-industry collaboration and provide customers with broader access to A. M. Castle & Co.’s complete portfolio of highperformance metals and processing capabilities. Notably, the company’s newly integrated supply chain structure will enable more efficient logistics, faster response times, and expanded access to specialized materials in key markets. Customers will benefit from:
• Localized, responsive service tailored to regional needs.
• Cross-selling opportunities enabling customers to benefit from a comprehensive range of solutions.
• Enhanced supply chain operations to reduce lead times and ensure consistent product availability.
• Updated sales materials and resources to reflect the unified brand and current offering.
“Our commitment to quality, innovation, and service remains unwavering,” said Dan Stoettner, CEO of A. M. Castle & Co. “This rebranding isn’t just about refreshing our look—it’s about aligning our operations, supply chain, and resources to serve our customers and partners more effectively. Under the leadership and support of
MiddleGround Capital, we are better positioned to meet the evolving needs of the industries we serve.”
The transition to the unified brand begins today and will occur in phases through early 2025. Customers, vendors, and partners can expect continuous communication and support during this transition to ensure a seamless experience.
Founded in 1890, A. M. Castle & Co. is a leader in the supply of highperformance metals and value-added processing services. With over 30 locations worldwide, the company serves industries across Aerospace, Industrial, and Medical market verticals, delivering expertise, innovation, and a legacy of excellence. The company operates through eight specialized divisions—Banner Commercial ™, Banner Medical™, Banner P&M Supply™, Castle Metals Aerospace™, Castle Metals Industrial™, Edge International™, National Kwikmetal Service® (NKS), and Supra Alloys™—and serves customers through five global regions: A. M. Castle & Co. APAC™ (AsiaPacific), A. M. Castle & Co. Canada™, A. M. Castle & Co. EMEA™ (Europe, Middle East, and Africa), A. M. Castle & Co. Mexico™, and A. M. Castle & Co. USA™.
MiddleGround Capital is a private equity firm specializing in middlemarket industrial investments. As experienced operators with a handson approach, MiddleGround serves as a reliable partner, working alongside portfolio companies across all organizational levels to drive growth and build sustainable, long-term value.
Kenosha, Wis., February 27, 2025 –Bahco is expanding its portfolio with a line of reciprocating and bandsaw blades designed for the pallet disassembly saws used in the pallet dismantling business. Bahco is a world leader in the bandsaw market with more than 140 years of experience manufacturing saw blades and cutting tools. The company provides tailored solutions to meet the changing needs of highperforming professionals.
These new Pallet Dismantler Blades are designed to easily cut through the nails and staples found in pallets while standing up to the shock of interrupted cuts. These tough bimetal blades can withstand the cutting heat that can quickly destroy the temper of carbon steel blades traditionally used to cut wood pallets and skids.
• The M42 Pallet Dismantler Bandsaw blades are 1-1/4” x .042” (34 x 1.1mm) with 5/8 teeth per inch.
• Welded loops are sold in bulk packs of 20 and are offered in a variety of lengths to cover numerous applications. Lengths include: 18’6”, 19’, 20’, 20’6”, 22’, 22’4”, 23’, 23’8”, 24’ and 25’4”. The 3840 Pallet Dismantler Reciprocating Bimetal Saw Blades
have a unique design that prevents the blade from getting stuck in the closed position when cutting nails in damaged parts of the pallet. The tooth design allows for excellent rate removal in wooden material with nails, and its elevated strength prevents tooth breakage.
• The 7-1/2” (190mm) Reciprocating Bimetal Saw Blades come in 10/14 teeth per inch and 10 teeth per inch and are sold in packs of 100.
• The 8” (210mm) Reciprocating Bimetal Saw Blades come in 10 teeth per inch and are sold in packs of 100 or 500.
• The 10” (269 mm) Reciprocating Bimetal Saw Blades come in 10 teeth per inch and are sold in packs of 100.
For more information on this latest line of Pallet Dismantler Reciprocating and Bandsaw Blades from Bahco, visit www.bahco.com.
About Bahco
Bahco is a leading manufacturer of tools, cutting tools, saws and other equipment tailored to the
most demanding professionals and industries. As innovators for more than 165 years, Bahco has introduced the most advanced tools in the world and sell through distributors with whom we build long-term partnerships. Bahco products are overwhelmingly manufactured in our own factories located across Europe and offered by our partner distributors to the professionals. Visit www.bahco.com/us_en.
About Snap-on Industrial
Snap-on Industrial is a division of Snap-on Incorporated, a leading global innovator, manufacturer and marketer of tools, diagnostics, equipment, software and service solutions for professional users. Products and services include hand and power tools, tool storage, diagnostics software, information and management systems, shop equipment and other solutions for vehicle dealerships and repair centers, as well as customers in industry, government, agriculture, aviation and natural resources. Products and services are sold through the company’s franchisee, company-direct, distribution and Web-based channels. Founded in 1920, Snap-on is a $4.25 billion, S&P 500 company headquartered in Kenosha, Wisconsin.
This past year IperionX achieved transformational progress, accomplishing a step change in our growth with the development of our Virginia Titanium Campus and the fast-tracked innovation activities there. We are rebuilding an industry that America once led – ushering in a new era where we manufacture high-performance titanium with ground-breaking, low cost, and energy efficient technologies – right here in the United States.
The ‘Wonder Metal’
that is inherently challenging
Titanium has long been recognized as a superior metal – stronger than steel and aluminum, with low density and nearly impervious to corrosion. Yet the current standard method of production, the Kroll process, developed in the 1940s, remains an energy-intensive, batchbased and high-cost method that is inherently challenging to scale. These inefficiencies have consigned titanium to use in only specialized, high-performance and high-cost applications. That is about to change.
The Breakthrough That Titanium Has Been Waiting For
Industrial history shows that when a new scientific breakthrough reduces the cost of a superior material, entire industries emerge around it. We saw this with steel in the 19th century and then aluminum in the 20th century.
• The Bessemer process transformed steelmaking in the 1850s by reducing production costs by 80% and dramatically increasing scale. This scientific breakthrough not only made steel affordable for railroads, bridges, and skyscrapers, but catalyzed the rapid industrial growth that drove the U.S. economy.
• The Hall-Héroult process did the
same for aluminum in the late 19th century. Previously a precious metal, used only sparingly, a single industrial process innovation made aluminum cheap enough to be used widely- in automobiles, aircraft and packaging.
In both cases, the companies that adopted and innovated with new production processes - Carnegie Steel, Bethlehem Steel and ALCOA - recognized that technological breakthroughs could not rely on fragmented supply chains or distribution channels. These companies built fully-integrated supply chains, controlling the raw material supply to their final products, to improve efficiency and lower costs.
Titanium’s equivalent transformation requires its own revolutionary process. This is where IperionX, with its proprietary technologies, believes it will revolutionize the titanium
industry.
The traditional Kroll and subsequent ingot melting processes are inherently inefficient.
Kroll relies on titanium minerals first being subjected to a carbothermic chlorination process to produce titanium tetrachloride (TiCl4), a high energy, high carbon intensive and highly corrosive material.
The TiCl4 is then reduced with molten magnesium metal and subjected to a lengthy distillation process (often more than 2 weeks) to manufacture titanium metal sponge, a porous intermediate material that must be melted multiple times in a vacuum furnace to form titanium ingots.
These large ingots must then go through numerous high-temperature
ARIES Manufacturing is dedicated to the supply of complex airframe structure components, in both titanium and aluminum alloys, to leading manufacturers in the aerospace industry.
ARIES Manufacturing is part of the ARIES Alliance, a group of companies focused on developing innovative technology that creates value for the aerospace industry.
Panel mechanical pocket milling, drilling and trimming
Superplastic Forming and Hot Forming for titanium airplane structural and engine components
HSF® process technology for titanium airframe components
process steps to fabricate titanium bar, plate and sheet to produce semifinished titanium products, often with substantial yield losses.
To manufacture a final titanium component, a surprisingly wasteful and expensive manufacturing step takes place. Manufacturers typically must machine away up to 80-90% of the titanium plate, bar or rod to create a final titanium component. This machining step alone can be responsible for ~50% of the final titanium part cost according to joint study by the U.S. Department of Energy’s Oak Ridge National Laboratory (ORNL) and Boeing.
In short, the Kroll process and its subsequent ingot melting process require a chain of complex, capitalintensive, and high-cost steps to produce titanium metal parts. This lengthy chain of process steps leads to long lead times for products that can extend well over a year.
IperionX can eliminate the complex process steps, thereby reducing inefficiencies and costs.
Our Hydrogen-Assisted Metallothermic Reduction (HAMR™) process produces lowcost titanium powder directly from either recycled titanium scrap or domestic mineral feedstock— completely eliminating the need to make titanium metal ingots. Instead, IperionX makes a high purity “ingot” in a powder form that transforms into metal products with traditional powder metallurgy techniques and our Hydrogen Sintering and Phase Transformation (HSPT™) process. Combining the efficiency of traditional powder metallurgy processes like cold isostatic and uniaxial press operations (a widely
used manufacturing method to produce high-volume and low-cost steel parts for the automotive to energy industries) with our HSPT process, allows us to achieve high quality and low-cost near-net-shape and final parts at a fraction of the cost of the traditional titanium metal supply chain.
Historically, titanium parts made via the traditional argon sintering process resulted in products with inferior properties compared to forged titanium metal parts. The incumbent industry could not find a way to take advantage of traditional powder metallurgy to produce lowcost and high-performance titanium metal parts.
IperionX’s technologies revolutionize this outdated model. Our process is
designed to produce mill products like bar, plate and sheet, and also produce near-net-shape titanium components that reduce manufacturing yield losses (in some cases from 10% yield to 90% yield, an order of magnitude improvement) and the significant costs associated with machining the parts.
Our revolutionary process fundamentally changes the economics of titanium production.
For decades, use of titanium has been constrained by its manufacturing complexity and high costs. With our patented technologies, we reduce waste,
For decades, use of titanium has been constrained by its manufacturing complexity and high costs. With our patented technologies, we reduce waste, energy use, and slash costs - making titanium viable for industries that previously did not find it economical
from these two countries, creating unacceptable vulnerability not only to critical industries like aerospace and defense, but also to U.S. national security.
energy use, and slash costs - making titanium viable for industries that previously did not find it economical.
The Boeing 787 is an illustrative example. The 787 requires around 53 tons (116,000 pounds) of semifinished titanium (‘buy’) to yield just 9 tons (19,000 pounds) of finished titanium components (‘fly’)
A 2012 study by ORNL and Boeing1 found that lowering this ‘buy-to-fly’ ratio from 6:1 (six tons purchased for every one ton used in the aircraft) to 2:1 could deliver substantial cost savings in both material and machining - especially given that machining can account for up to 50% of a part’s total cost. Boeing is but one example of how critically industry needs a way to make titanium less costly.
The Boeing 787 is an illustrative example. The 787 requires around 53 tons (116,000 pounds) of semifinished titanium (‘buy’) to yield just 9 tons (19,000 pounds) of finished titanium components (‘fly’). A 2012 study by ORNL and Boeing1 found that lowering this ‘buy-to-fly’ ratio from 6:1 (six tons purchased for every one ton used in the aircraft) to 2:1 could deliver substantial cost savings in both material and machining - especially given that machining can account for up to 50% of a part’s total cost. Boeing is but one example of how critically industry needs a way to make titanium less costly.
1 Bowden, David M and Peter, William H. “Near-Net Shape Fabrication Using Low-Cost Titanium Alloy Powders.” , Mar. 2012. https://doi.org/10.2172/1040632
IperionX believes it can unlock even greater cost benefits than in the 787 example. In addition to reducing the buy-to-fly ratio and associated machining costs, our production process eliminates the high-energy ingot melting and hot working steps required to produce semi-finished titanium. The same ORNL/Boeing study indicated that hot working from ingot to semi-finished product can represent nearly half of its cost - or about 25% of a final machined titanium part’s cost.
Using this logic, at the point where IperionX produces titanium at the same cost as conventional titanium
IperionX believes it can unlock even greater cost benefits than in the 787 example. In addition to reducing the buy-to-fly ratio and associated machining costs, our production process eliminates the high-energy ingot melting and hot working steps required to produce semi -finished titanium. The same ORNL/Boeing study indicated that hot working from ingot to semi -finished product can represent nearly half of its cost - or about 25% of a final machined titanium part’s cost.
1 Bowden, David M and Peter, William H. "Near-Net Shape Fabrication Using Low-Cost Titanium Alloy Powders." , Mar. 2012. https://doi.org/10.2172/1040632
ingots, we estimate the potential for a ~75% reduction in the cost of a titanium part. In applications with buy-to-fly ratios of 10:1 or higher - such as consumer electronics, fasteners, and other small or complex components - cost savings may exceed 90%.
4
Using this logic, at the point where IperionX produces titanium at the same cost as conventional titanium ingots, we estimate the potential for a ~75% reduction in the cost of a titanium part. In applications with buy-to-fly ratios of 10:1 or higher - such as consumer electronics, fasteners, and other small or complex components - cost savings may exceed 90%.
IperionX aims to build an uninterruptible titanium supply chain - in America, for America. Our twin-feedstock strategy eliminates dependency on foreign sources through two complementary approaches: sourcing unused American-generated titanium scrap metal, or using titanium mineral feedstocks from our 100% owned and permitted Titan Project in Tennessee, once developed.
IperionX Titanium Product Cost Reduction Potential Boeing 787 Airframe
Part Machining
Mill Product Hotworking
Kroll-Ingot Melting / HAMRHSPT
Titanium Ore
Re-Shoring an Uninterruptible American Titanium Supply Chain
For far too long the United States has depended on foreign sources for its titanium, with global supply chains dominated by China and Russia. Over 70% of the world’s titanium sponge production comes from these two countries, creating unacceptable vulnerability not only to critical industries like aerospace and defense, but also to U.S. national security
IperionX aims to build an uninterruptible titanium supply chain - in America, for America. Our twinfeedstock strategy eliminates dependency on foreign sources through two complementary approaches: sourcing unused American-generated titanium scrap metal, or using titanium mineral feedstocks from our 100% owned and permitted Titan Project in Tennessee, once developed
The Titan Project is America’s largest fully permitted, undeveloped source of titanium and rare earth minerals hosted in a simple, low-cost sand deposit. The Titan Project ensures that IperionX controls a key feedstock solution to establish an end-to -end uninterruptible titanium metal supply chain. Once developed, the Titan Project has the potential to supply IperionX’s metal production processes with titanium minerals at a significantly lower cost than even purchased titanium scrap metal
For far too long the United States has depended on foreign sources for its titanium, with global supply chains dominated by China and Russia. Over 70% of the world’s titanium sponge production comes
The Titan Project is America’s largest fully permitted, undeveloped source of titanium and rare earth minerals hosted in a simple, low-cost sand deposit. The Titan Project ensures that IperionX controls a key feedstock solution to establish an end-to-end uninterruptible titanium metal supply chain. Once developed, the Titan Project has the potential to supply IperionX’s metal production processes with titanium minerals at a significantly lower cost than even purchased titanium scrap metal.
IperionX’s first end-to-end production run
I am pleased to say that we accomplished all of the goals outlined in last year’s letter to shareholders, with some of our key advancements in 2024 including:
• Launching commercial operations with the commissioning of our large-scale HAMR furnace in Virginia;
• Completing our first end-to-end production run that delivered exceptional results and opened possibilities for further process improvement opportunities;
• Advancing simple and highly efficient manufacturing capabilities through traditional powder metallurgy pressing and our revolutionary HSPT process;
• Securing more strategic partnerships, including contracting with a major automotive company and collaborating with the U.S. Department of Defense to explore how IperionX’s titanium reshoring solution can strengthen
U.S. national security;
• Completing the acquisition of the intellectual property that comprises the Company’s breakthrough titanium technology portfolio; and
• Ensuring strong liquidity to scale our operations through two financings for ~US$100 million, which introduced new high quality institutional investors as IperionX shareholders.
As we look ahead to the future, we remain focused on building the only fully integrated end-to-end titanium metal supply chain in the United States. This year, our key goals will be to:
• Ramp-up and optimize commercial production with our scrap to final titanium product technologies;
• Build on our customer demand with an increased range of prototypes, product development and lower-volume commercial production runs;
• Continue to optimize the immense
opportunities we see for efficiency gains, including eliminating process steps and reducing production costs to make our titanium powder;
• Continue to innovate with our HSPT process technology, where we can take our titanium powder and make highquality titanium products, either as near-net-shapes or mill products, with material properties equivalent to or exceeding forged titanium products; and
• Expand and deepen our role in the defense industrial base in collaboration with the U.S. Department of Defense.
Success with these and other initiatives will allow IperionX to lead the way in making titanium the metal of choice for advanced industries.
None of this would be possible without the hard work and dedication of the IperionX team, and the unwavering support of our stakeholders. To our shareholders, customers, suppliers, and government associates: thank you for your trust and partnership throughout 2024.
As we embark on this exciting journey into 2025, I wish everyone a happy and successful new year. Together, we are shaping the future of the titanium industry and driving meaningful change for generations to come.
Our continued investment and expansion has us in the right place to meet your needs.
Our capacities and resources are aligned. We are prepared and well positioned to supply a full range of products including ingot, centerless ground bar, precision coil, additive wire, premium fine wire and shapes – all at competitive lead-times.
We are expertly equipped to address the growing demands of the aerospace, medical, recreation, infrastructure, and industrial markets worldwide. We understand the ever-changing factors of the industries we serve and are committed to supporting the growth of your business.
Rohr-Mertl has used KASTO sawing and storage solutions for roughly 55 years. The specialist for steel tubes values not only the highquality products but the exceptional maintenance and repair service as well. Even the first saw, constructed in 1970, still operates just as it did on its first day.
Tubes as far as the eye can see – with diameters ranging from 3 to 660 millimetres and wall thicknesses from 0.5 to 100 millimetres made of steel and stainless steel. Rohr-Mertl cuts, picks and stores 8,000 tonnes of steel tubes in more than 5,000 dimensions and qualities on 30,000 square metres of building space.
Karl Mertl Handelsges.m.b.H. specialises in steel tubes in various forms. Since its establishment in 1949, the company has consistently broadened its product range and services. The company currently has 90 employees. Rohr-Mertl is located in Schwechat, southeast of Vienna, and supplies various customers throughout Europe, including industrial corporations as well as workshops. The distributor acquired the 90,000 square meters at the former brewery site from the City of Vienna in 1968. “One of our warehouses is located in the historic vaulted cellar, which also houses one of our KASTO bandsaw machines,”
explained Marie Gruscher-Mertl, CEO. The family-owned company is currently managed by the fourth generation, with both daughters active in management. Additionally, son-in-law Jürgen Spannraft has served as CEO Ing. since 2019.
Rohr-Mertl currently operates ten bandsaw machines and two KASTO hacksaws, the oldest of which dates back to 1970. “We’ve been using the EBS 400 U hacksaw for well over 50 years, and it is still performing superbly,” says a satisfied Marie Gruscher. The saw is located in the in-house workshop and is used whenever employees perform any maintenance or repair work on the buildings or racks. “Over this extended period of time, occasional breakdowns occurred, but KASTO
promptly restored the machine to working order,” Marie Gruscher explains.
This is precisely the customer service that Rohr-Mertl values in its partnership with KASTO. Christian Wunderlich describes the collaboration as “High-quality products, timely deliveries, and, above all, reliable service.” As the warehouse manager, he knows he can count on KASTO. “A new machine is quickly purchased, but when spare parts become necessary, that’s when the wheat is separated from the chaff. In this regard, our experience with KASTO has been outstanding.“
Continuous growth
Since 1970, Rohr-Mertl has continuously expanded its machinery pool with new KASTO sawing machines. For instance, the company purchased two heavy-duty, fully hydraulic, high-performance bandsaw machines, model KASTOhba AU, in 1994. The parallel horizontally moving sawband is ideal for cutting profiles, tubes and solid material in any quality. Even difficult-to-cut materials such as Hastelloy can still be cut reliably and quickly to this day. “The system has been running like clockwork for 30 years,” Christan Wunderlich emphasises.
Product Evaluation Systems, Inc. (PES) is a fully accredited, independent leader in titanium materials testing for aerospace and other applications.
With a dedicated, experienced staff and state-of-the-art testing facilities, we offer full-service capabilities for all of your titanium testing needs, including:
• Mechanical Testing
• Metallurgical Analysis
• Chemical Analysis
PES responds to your needs promptly with personal service, customized solutions and expedient turnaround. We work with clients throughout the United States and Europe on projects of all types and sizes.
To request a free quote for your titanium testing needs and to see a full list of capabilities, please visit our website at www.PES-Testing.com or call 724-834-8848.
Because the old SNLS 3000 S overhead storage system with 1,012 cassettes was bursting at the seams, Rohr-Mertl built a new hall in 2012. The new UNICOMPACT 2.0 honeycomb storage system, equipped with 2,633 honeycombs and fully automatic bandsaws, has since provided increased capacity and efficient processes. “It was not a difficult decision to opt for KASTO,” recalls Marie Gruscher-Mertl “We were already familiar with the quality of the products and the great service. KASTO’s recommended solution was also the best fit for our requirements. We were also able to seamlessly connect it to our packaging machine.”
The name UNICOMPACT for these storage systems is well-suited: since the overhead gantry crane (OGC) has a small footprint. Rohr-Mertl can then utilise a large amount of space for storage purposes. “The new hall was a significant milestone for us”, Marie Gruscher-Mertl emphasises. “Not only have we significantly increased our storage space, but also our level of safety.” The goods now come to the person and no longer the other way round. “Reduced manual handling and movement in the warehouse leads to a lower risk of accidents. That is very important to us,” emphasises the CEO.
Rohr-Mertl utilises a variety of KASTO bandsaws at the UNICOMPACT stations to process mostly seven-metre standard length bar stock: KASTOtwin LE 4,
KASTOssb A 2, and KASTOtec A 4. KASTOtec demonstrates impressive performance, particularly for large series production and extremely hard materials. Innovative technologies such as the intelligent control system achieve maximum throughput. For example, this includes the automatic assignment and permanent storage of the cutting technology. This can be adjusted to the respective material qualities and the bi-metal or carbide sawband used. KASTOtwin is an all-rounder. The machine can be used flexibly with various sawband models and is suitable for a wide range of applications, thanks to its tried-and-tested technology.
The KASTOssb cuts bars precisely and quickly – particularly in series production. Thanks to the vertically moving sawband, the machine is extremely compact and delivers high performance within a small space. Special feature: The KASTOssb A 2 has a sturdy feed roller conveyor with fixed yet adjustable sides. This makes the saw the perfect choice for bundle and large-scale cutting jobs.
The UNICOMPACT has enabled Rohr-Mertl to automate the storage and picking of goods since 2012. In conjunction with the sawing
machines, the system processes orders without human intervention. The orders are prepared for shipping by a packaging machine at the end of the line. “We use a proprietary ERP system that is tailored specifically to our needs,” explains Christian Wunderlich. In collaboration with KASTO, RohrMertl’s IT department connected the highrack storage system to the ERP system. “This allows us to maximise the use of the automated system,” adds Marie Gruscher-Mertl.
Trustful collaboration
The CEOs of Rohr-Mertl have considered KASTO a reliable partner since 1970. “The sales representative responsible at the time thoroughly impressed us with his solution,” recalls Alfred Gruscher, Director and authorised officer at Rohr-Mertl.
“We have never once regretted our decision because the collaboration has been very pleasant over the years, both in person and on the phone.”
When new investments are in the pipeline, Rohr-Mertl gladly accepts KASTO’s offer to inspect systems at reference customers and speak with users directly on site about their respective experiences. “Three of our employees are experts on our high-rack storage system and our saws. Over the years, they have gathered a lot of experience,” says Marie Gruscher-Mertl. This is hugely helpful when issues arise. “They can speak to the KASTO service technicians at eye level,” explains Christian Wunderlich. Which means that each problem can be solved quickly.
Albany, OR – Kittyhawk Inc. continues to lead the Hot Isostatic Pressing (HIP) industry with the successful integration of its newest facility in Albany, Oregon. First acquired as part of the Stack HIP acquisition last year, the state-ofthe-art facility significantly expands Kittyhawk’s capacity to process complex and large-scale components for aerospace, defense, and other high-performance industries.
The Albany, Oregon, facility fi rst broke ground in March 2019 under the supervision of the General Manager, Brice Winney. By November of that same year, one of the largest HIP vessels in the United States was being installed, and by February 2020, the facility had achieved Nadcap certi fication. What typically takes well over a year was accomplished in less than 12 months, thanks to the team’s dedication and expertise.
Brice reflects on those early days with pride. “Many in the industry were surprised when we hit our early target. That was a good feeling, to accomplish something we were told we couldn’t do.”
Participating in building a new facility from scratch and commissioning machinery gave Brice and his team a deep understanding of the equipment and processes. With their hands-on experience, the team created the fi rst recipes for their HIP equipment and quickly established a culture focused on safety, quality, and continual improvement.
Being acquired by Kittyhawk was a milestone for the Albany team, and a recognition of their hard work. Joining an organization that focuses exclusively on Hot Isostatic Pressing with a long history of excellence has opened new opportunities for growth and collaboration.
The Albany facility houses some of the most advanced HIP equipment in the industry including:
286 HIP Vessel: One of the largest HIP vessels in North America, capable of high pressures up to 28,000 PSI and rapid cooling for faster production cycles.
122 HIP Vessel: Capable of achieving pressures up to 30,000 PSI and quenching rates comparable to traditional heat treatment processes. These capabilities allow Kittyhawk Albany to process larger and more complex parts than most facilities, making it an essential part of Kittyhawk’s broader service offerings. With the ability to handle high-pressure requirements and shorter cycle times, the process is not only more productive but also more cost-effective for customers.
The future is bright for Kittyhawk Albany. With room for equipment expansion in both Albany and the nearby Canby facility, the team is well-positioned to capture a larger share of the HIP market. Throughout the journey, the goal has
always remained clear: to become an industry leader in Hot Isostatic Pressing services and process-related technical support.
“We always challenge ourselves,” Brice shares. “We support each other, and stay focused on quality and safety. Growth and culture aren’t one-time initiatives—they’re ongoing efforts that we nurture every day.”
“The Albany team has been a fantastic addition to the Kittyhawk family,” said Kittyhawk President Brandon Creason. “Their deep knowledge of HIP technology and dedication to customer satisfaction aligns perfectly with our mission. We’re proud to have them on board and excited for what’s ahead.”
Through teamwork, innovation, and a relentless commitment to excellence, the Kittyhawk Albany team is helping drive the future of HIP forward—one cycle at a time.
Kittyhawk Inc. has been at the forefront of Hot Isostatic Pressing (HIP)since 1981, trusted by top aerospace and defense manufacturers to improve mission-critical components. With three West Coast facilities and some of the largest HIP vessels in North America, we deliver precision, reliability, and rapid turnaround times across industries like aerospace, defense, automotive, oil & gas, medical, and more. We are AS9100 and NADCAP certi fied, ITAR and EAR compliant, and a CLASS 07 FFL holder, ensuring the highest standards of quality and service. Visit www.kittyhawkinc.com to learn more.
January 13, 2025, Souderton, PA – Solar Atmospheres in Souderton, PA, is currently commissioning two additional 2-bar vacuum furnaces, expanding its capabilities to meet increased demand in the aerospace, industrial gas turbine sectors, and for specialized hydride/de-hydride processing of Titanium, Tantalum, and Niobium. These vacuum furnaces, produced by Solar’s sister company, Solar Manufacturing, feature large working hot zones (45” x 45” x 72”) and are rated for operations up to 2400°F with a precise temperature uniformity of ±10°F.
Mike Moyer, Solar’s Vice President of Sales, commented, “We’re thrilled to add these advanced furnaces to Solar
Souderton’s lineup. Equipped with Solar Manufacturing’s latest control systems, they ensure efficient, safe operation—meeting our customers’ needs for competitive pricing and fast delivery. This installation reinforces our commitment to consistently high-quality service.”
For additional information, contact Mike Moyer, VP of Sales, Solar Atmospheres at 215-721-1502 x1207, or mikem@ solaratm.com, and visit www. solaratm.com
Mumbai, India – Star Alucast
Private Limited, under its trademark brand Remal, has commenced production of aerospace-grade master alloys for the titanium industry in Maharashtra, India.
To address the increasing demand for high-quality master alloys in India and international markets, Star Alucast has installed advanced reaction lines and vacuum melting lines to support the processing and development of critical alloys for titanium manufacturers.
Dedicated to creating a sustainable future, Star Alucast is striving to achieve carbon neutrality. The company is already ISO-certified and adheres to both Environmental Health and Safety (EHS) and Occupational Health and Safety Assessment Series (OHSAS) standards.
The company is also establishing a
state-of-the-art quality laboratory that aims to secure Nadcap and NABL certifications.
With the launch of this production facility, Star Alucast seeks to bridge the supply-demand gap in the Indian and international titanium industry for master alloys and critical raw materials. This initiative aligns with the Government of India’s vision to indigenise the supply chain for vital materials and reduce dependence on imports.
Parthiv Rokadia, Managing Director of Star Alucast, states:
“This project and division represent our shared dream, along with our dedicated technical team that is to enhance India’s aerospace and space infrastructure. We aim to create a platform where young metallurgists and engineers can learn, innovate,
and develop in this sector. Our commitment to quality and attention to detail will set a new benchmark for India in the global aerospace and titanium industries.
We invite you to join us in our journey as we strive to make a difference.”
Established in 2022, Star Alucast Private Limited is the realization of a collaborative vision between a metallurgist and an entrepreneur. The company currently employs a team of over 100 skilled professionals from various regions of India, USA and Europe all committed to the precise and disciplined processing of high-quality alloys. Star Alucast is dedicated to providing world-class master alloys to meet the evolving demands of the aerospace and titanium industries.
Premium Quality, Stability and Reliability.
One-Stop titanium alloy production and service.
A dozen years of titanium alloy production and research experience, with more than 100 patents and achievements to its credit, mastering a number of core technologies; Accredited with Nadcap non-destructive testing certificate and AS9100D, ISO14001, ISO 45001 and other certifications;
Titanium bar/billet
Size range: Φ15-500mm
Grade: Ti6Al4V, Ti-6242, Ti-6246, Ti-38644, Ti-15333, etc.
Titanium wire rod coil
Size range: Φ1.0-20.0mm
Grade: Ti6Al4V, Ti6Al4V ELI, Ti-38644, Ti-6242, Ti-6246, Ti-15333, Ti-422, etc.
Titanium forging
Size range: customized, disc, bar, ring, etc.
L(max):14m, W(max):4m, H(max):4m.
Grade: Ti6Al4V, Ti6246, Ti6242, Ti662, Ti38644, Ti15333, Ti1023, Ti422, etc.
more information, please visit www.tcae.com/en/
My name is David (Dave) Gildemeister. I am a professor in the School of Materials Engineering at Purdue University and I also serve as Technical Editor for CINDAS, LLC.
CINDAS is a private company that distributes materials properties data as a subscription service for our customers. We maintain several large databases that contain extensive physical and mechanical properties data, applications, and processing information on numerous metals and alloys, as well as for composites, electronic materials, and organic and inorganic materials. We contract with authors to compile published data from many heavily vetted sources.
I am hoping to find an author to update our chapter on cast Ti-6-4, last updated in 1999. We would also be interested in updating and adding other titanium alloys to our database as well. Our list of current alloys in our collection can be found at the link.
Microsoft Word - AHAD-AlloySheet-May2024 (cindasdata.com)
Most of our authors write the chapters in their spare time and are compensated for their work. Some write as part of their job responsibilities to help disseminate information about their companies’ alloy products. If you might share this opportunity with your contacts, colleagues, and friends it would be much appreciated. Anyone interested may contact me at dave@cindasdata.com or dgildeme@purdue.edu.
Dave Gildemeister, Technical Editor, CINDAS,LLC
Christian Décaillet
Retiring from VSMPO-AVISMA
Phil MacVane
Retiring from PCC Metals Group
Global Sales
George L. Durfee (Sept. 19, 1929 – Nov. 21, 2024)
Grafton – George L. Durfee, 95, passed away Nov. 21 at UMass - Memorial. George was raised in Falls City, NE. He graduated from Michigan Tech, attended MIT and Harvard Program for Management Development. George was a lifelong employee of Wyman-Gordon, where he worked in various metallurgical and engineering management positions.
Rob Lindquist
Pompton Plains, New Jersey 07444, (973) 765-4337, roblindqu@gmail.com https://www.linkedin.com/in/rob-lindquist1/
SUMMARY
Results-driven Product Development Executive with extensive experience in product management, business development, marketing, and strategic planning. Proven ability to drive product road maps, competitive analysis, and lifecycle management while collaborating with executive leadership to achieve aggressive growth goals. Highly skilled in building and motivating high-performing teams, leading successful product launches, and maximizing revenue. Recognized for exemplary leadership, communication, and organizational skills that drive innovation and sustained business success.
Portfolio Management and Simplification • Price Positioning Customer Value Proposition • SaaS Product Growth Customer-Focused Innovation
By joining the International Titanium Association, you become part of an international network of titanium professionals unlike any other. You will have access to an expanding organization of committees, strategic partners, and international members. Like any investment you make on behalf of your company, you want assurance that it will provide strong returns. An investment in Corporate Membership with International Titanium Association is a wise strategic decision, whether you are a small distributor or a large producer of mill products. Whether you buy from or sell to the titanium industry, our array of benefits will provide just what you and your team are looking for. We are so certain that membership is worthwhile, we provide each Corporate Member with a ROI and engagement scorecard.
Producers & Suppliers of Titanium:
Over 700 in attendance at the 2023 & 2024 Events:
“I’ve attended numerous virtual conferences. You and your team built and executed a conference far better than others. The ability to stop the presentation to read and comprehend slides and rewind and re-listen to speaker commentary was great. The real-time meetings were also well executed.”
Unlike other industries, Titanium Producers, Distributors and Stockists are all customers of each other. If your organization is producing or distributing titanium, you know how important it is to keep connected with other suppliers. ITA is the global trade association of the world’s primary titanium metal producers who together account for over 90% of worldwide titanium production. As you lead and grow your organization, it’s on you to recruit, hire, train and retain the best staff possible. ITA will become your partner, providing you with valuable, proven resources not available anywhere else to help growth and strengthen your team.
Selling to the Titanium Industry:
You need to grow your business by raising the visibility of your firm with titanium decision-makers. By joining the ITA, you have come to the right place. We have built a niche community of over 100 organization members worldwide and growing. Make the most of your marketing investment by focusing on a relevant, targeted audience with the help of the ITA.
Consumers of Titanium:
No where else will you find a network of Titanium producers, distributors & stockists to meet all your titanium needs. ITA can introduce you to the membership who may provide you with sales and technical assistance. Attending the annual conferences will keep your team up to date on the world supply & demand trends which will help you plan lead times for the future.
“I want to give to you and your colleagues of ITA the thanks about these two days dedicated to the Titanium applications, developed with professionalism and capacity.”
“First and foremost, I just wanted to say how impressed I am with the virtual conference and how much respect I have for the ITA with the way they went about it. Secondly, I really think the presentations this year were a cut above presentations I’ve seen at other conference events in other metal sectors.”
“Congratulations on a terrific conference. I thought everything went very well and enjoyed meeting with people virtually. Thank you for your help and support!”
“I want to congratulate you and the organization for the fantastic job done. Everything was available and very easily reachable.”
Since 1984, ITA’s mission has been to promote and support the use of titanium metal in new and existing applications. ITA provides a forum for the exchange of ideas within the industry and educates the public on every aspect of using titanium metal within their design. From life cycle costing to welding, from metallography to metallurgy, ITA offers literature, webinars and in person instruction on all aspects of education.
ITA currently hosts member organizations from North America, Europe, Asia and Australia.
Here is a sampling of our valuable corporate membership benefits.
Everyone in the company is welcome to join ITA’s affiliate Membership. FREE
Exclusive access to all members through the ITA Community includes an online member directory and libraries of resources. FREE
Members may volunteer to participate in market oriented committees including Medical Technology; Industrial Applications, or Consumer Products. FREE
Women in Titanium offers networking opportunities and mentoring through in-person gatherings at the annual conferences across the globe. FREE
Access to past historical conference proceedings including the Corrosion Solutions, TMS World Conference, and TITANIUM annual Conference. FREE
Access to the annual Titanium Statistical Review report. FREE Members get noticed by highlighting Linked-In Profiles rotated on the ITA Home Page. FREE
Company Profile included in the Online Titanium Resource Center. FREE
Optional enhanced advertising available on ITA Home page, Titanium Today and in the Titanium Resource Center. *Corporate Exclusive
Your choice of booth placement at Titanium Europe. FREE
Your choice of booth placement at Titanium USA FREE
Complimentary full page, full color ad in 4 editions of Titanium Today magazine. FREE
Opportunity to submit press releases to be published in the On the Wire section of Ti Today trade publication.
*Corporate Exclusive
Online Events Calendar Listings
*Corporate Exclusive
Host an Industry Spotlight custom designed for your organization”
*Corporate Exclusive
The Titanium Educational Series is a video-on-demand web portal where your employees may view the Fundamentals of Titanium, Metallography of Titanium & Its Alloys, Safe Handling of Dust, along with technical & market oriented presentations from past Titanium conferences to keep up to date on current supply & demand trends. FREE
Safety Education: Members are invited to participate in quarterly discussions about promoting safe handling and transporting of titanium materials. Meetings are hosted with live discussions for high engagement. FREE
ITA is actively involved with programs that examine the role of titanium in human health and the environment through the administration of the REACH Titanium Consortium.
ITA pursues market development through a worldwide network of highly qualified specialists, offering free technical knowledge about titanium, its properties and long lifecycle.
ITA promotes the long-term use of titanium metal to contribute to a sustainable future
ITA invests in the future growth of industry by underwriting academic and STEM-related programs through the Education committee.
ITA shares knowledge freely and does not conduct commercial or trading operations of any kind.
ITA does not provide forecasts or comments related to titanium pricing, capacity, or forecasts from the past, present for future.
Titanium Today is a narrowly targeted trade publication serving the global titanium industry. The magazine performs two major functions: First, it carries advertisements to audiences comprised of the business-to-business segment of the economy within the titanium industry. Second, readers consult Titanium Today for editorial information they need to develop business strategies or to further their careers.
Issue 11 of Titanium Today on Issuu recorded impressive engagement metrics, totaling 5,484 impressions and 1,020 reads, with an average read time of 7 minutes and 9 seconds. The publication reached a global audience, with the highest readership in the United States, followed by Germany and the United Kingdom, showcasing its strong international presence and relevance in the titanium industry.
Regardless of size, every successful company is built on proven advertising techniques. By advertising in Titanium Today you connect with a specific target market unlike any other.
All these benefits and more are included in one flat annual membership fee of $4,985. Complete this membership interest form to start your membership today.
The premier publication delivering key industry insights, technological breakthroughs, and expert analyses to the titanium industry. With a focus on actionable intelligence, each issue provides critical information to navigate the complexities of the market. From in-depth features to exclusive interviews, TITANIUM TODAY fosters collaboration and innovation, empowering stakeholders to stay informed and ahead of the curve in this dynamic field.
7 mins 33 seconds
Average read time in 2023
16,764
Online Reads in 2023
TITANIUM TODAY delivers key industry insights, technological breakthroughs, market trends, and expert analyses to an engaged readership across our online format.
The premier publication delivering key industry insights, technological breakthroughs, and expert analyses to the titanium industry. With a focus on actionable intelligence, each issue provides critical information to navigate the complexities of the market. From in-depth features to exclusive interviews, TITANIUM TODAY fosters collaboration and innovation, empowering
We regularly publish specialized editions of TITANIUM TODAY tailored to the aerospace and medical industries, as well as emerging markets, powder applications, industrial themes, and specialized editions coinciding with titanium conferences.
Artwork requirements for
Full-page Ad Specifications:
Trim: 8.375 in. x 10.875 in.
Bleed: 8.75 in. x 11.25 in.
Type/Image Safe Area: 7.875 in. x 10.375 in.
Email artwork to: ita@titanium.org
Any files over 50 MB please do not send by email. Please send download instructions for a dropbox separately.
Due Date to Receive
Artwork: May 23, 2025
Please provide artwork in PDF/X-1a:2001 compliant file format
• The Document Size Must be Correct: If your source document is not built to the correct size, the final output may not look like you expect it to.
• Bleed: We need a minimum of .1875” bleed. If you send files with less than .1875” bleed and they are not designed to the correct trim size we may have a difficult time with your job throughout production.
• Margins: We ask that you don’t place anything important less than .25” from trim, especially type. If the type closer than .25” to the edge, it could be cut off. This includes body copy, graphics and page numbers.
• Do Not Use Spot Colors: If your job prints in process color (CMYK) Please make sure that NO Spot colors are in use in the document.
• Fonts: Some fonts are restricted from being embedded in the PDF file by the fonts license. InDesign will warn you if the font cannot be embedded due to licensing restrictions. If this happens, please either choose another font, or submit the font with the job, or create outlines of all fonts.
• Image Resolution: The correct resolution for print is 300 dpi at final size. We will flag images that are below 200 dpi.
• Image Color: Please make sure that your images are CMYK, or Grayscale.
International Titanium Association (ITA) PO Box 1300, Eastlake, Colorado 80614-1300 USA (303)404-2221 Telephone | ita@titanium.org Email | www.Titanium.org Web
Accushape Inc.
ACNIS® International
Advanced Metal Industries CO (AMIC)
Aeropro Industries
Airbus SAS France
ALD Vacuum Technologies, Inc
Alleima Tube AB
All-Met Recycling
Alta Alloys
Aries Manufacturing
ATI
ATX Co.,Ltd.
AW Bell Pty. Ltd.
Bahco
Banner Industries
Baoji Hongsen Titanium Metal Manufactory Co.,Ltd
Baoji Sino-Swiss Titanium Co.,Ltd
Baoji Titanium Industry Co., Ltd
Bodycote
Butech Bliss
Carpenter Technology Corporation
CCMA, LLC
CHAOYANG JINDA TITANIUM CO., LTD.
CKOE
Consarc Corporation
Coogee Titanium PTY LTD
CSM Tech Co., Ltd.
Dr. Markus Holz, Academic Member
Duferco SA
Element Materials Technology
ELG Utica Alloys, Inc.
ForceBeyond
Fort Wayne Metals
FRIGGI N.A. Inc.
GfE Metalle und Materialien GmbH
Goldman Titanium
Grandis Titanium
Greystone Alloys, LLC
Hangsterfer’s Laboratories, Inc.
Hempel Special Metals AG
Horie Corporation
Howmet Aerospace
Hunan Xiangtou Goldsky Titanium Metal Co., Ltd.
ICD Alloys & Metals, LLC
Independent Forgings & Alloys Ltd
Industrial Metals International Ltd.
Inteco Melting & Casting Technologies
IperionX Limited
Jezhiang Shenji
Jiangsu Hongbao High-Precise Pipe & Tube Co., Ltd.
KASTO Inc.
Keywell Metals LLC
KineTic Engineering
Kings Mountain International (KMI)
Kittyhawk Inc.
Kymera International
Laboratory Testing Inc.
Largo Inc.
Leybold USA Inc
Lockheed Martin Corporation
Luoyang Sunrui Wanji Titanium Industry Co Ltd.
Luxfer Graphic Arts
M3 Metals
Medart Processing Technologies
Mega Metals LLC
Messer North America Inc.
Metals & Alloys UK
Metalwerks, Inc.
MetCon Technologies, LLC
Metraco, FE Mottram and Eesti Titaan oü
Mistras Group, Inc.
Monico Alloys, Inc.
MPS Technology Sp. Z o.o.
NEOTISS High Performance Tube
Niagara Specialty Metals
NobelClad
NOTZ Metall AG
Novametal
Nu-Tech Precision Metals
Oerlikon Metco (Canada) Inc.
Osaka Titanium technologies CO., Ltd.
Paris Saint-Denis Aero
Perryman Company
Plaxys Inc.
Plymouth Engineered Shapes
Precision Abrasives
President Titanium Co., Inc.
Product Evaluations Systems, Inc (PES)
PTC Industries Limited (Aerolloy Technologies)
Quantum Design Inc. / Centro Metalcut
Radiac Abrasives Inc.
RENTON COIL SPRING CO. INC.
Retech Systems LLC
Rex Heat Treat
Rolled Alloys Inc
Ross Precision Manufacturing
S+D Metals / Bibus Metals
SAN-EKI, Ltd.
Service Steel Aerospace
SES, LLC
Shaanxi Lasting Titanium Industry Co. Ltd
Shaanxi Tian Cheng Aerospace Co., Ltd. (TCAE)
Shasta Services LLC
Solar Atmospheres
Specialty Metals Company
Specialty Metals Processing Company
Star Group, India
State Nuclear Baoti
STS Metals
Sumitomo Corporation of Americas (SCOA)
TiFast Srl
Timesavers International B.V.
TIMET, Titanium Metals Corporation
TITAN Metal Fabricators, Inc.
Titanium Consulting & Trading S.r.l.
Titanium Engineers, Inc.
Titanium Fabrication Corporation
Titanium Industries, Incorporated
Titanium International Group SRL
Titanium Processing Center
Toho Titanium America Co., Ltd.
Tricor Metals
Uhr Corp.
Ulbrich Stainless Steels & Special Metals
United Alloys & Metals Inc
United Performance Metals (UPM)
United Titanium
US Vanadium
Vested Metals International, LLC
VSMPO Tirus US
Weiler Abrasives Group
Wellmet International Inc.
WST Western Superconducting Technologies Co., Ltd.
Xi’an Metals & Minerals Import & Export
XI’AN XRUN NEW MATERIAL