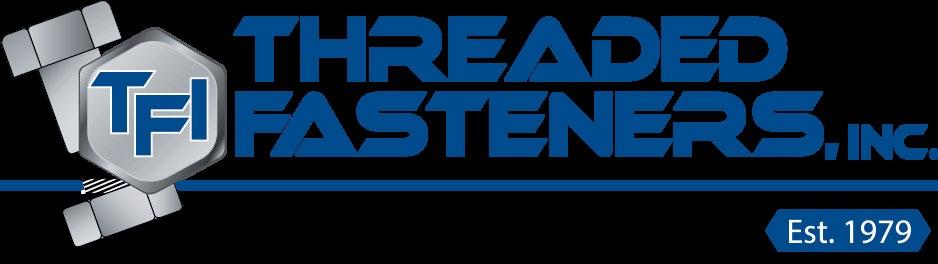
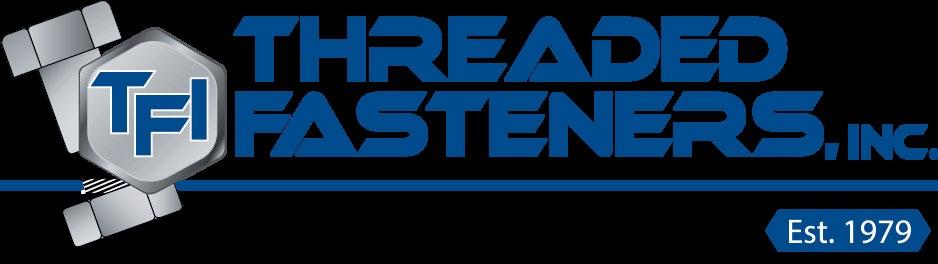
QUALITY MANUAL
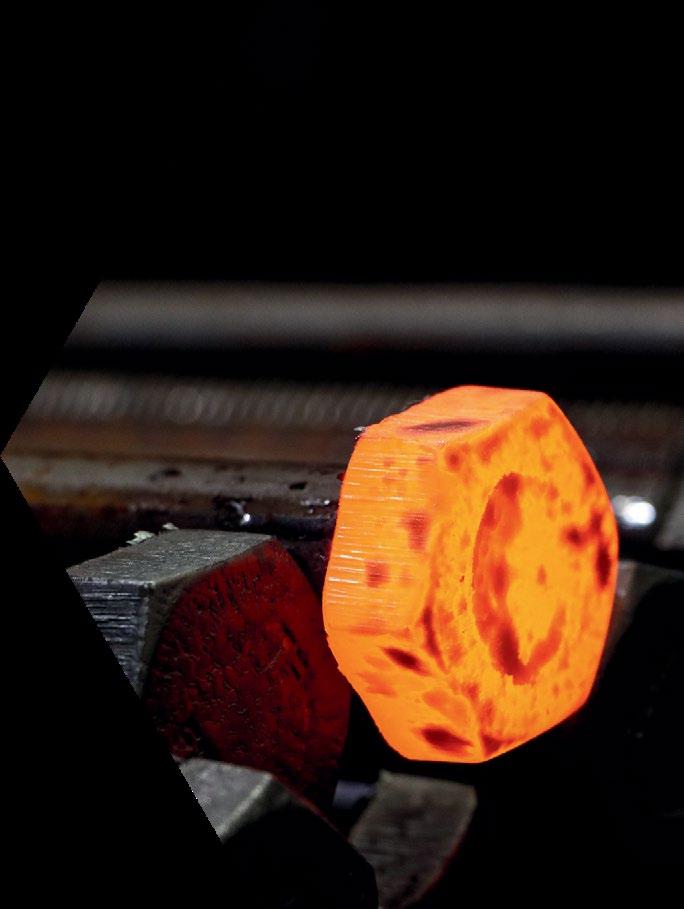
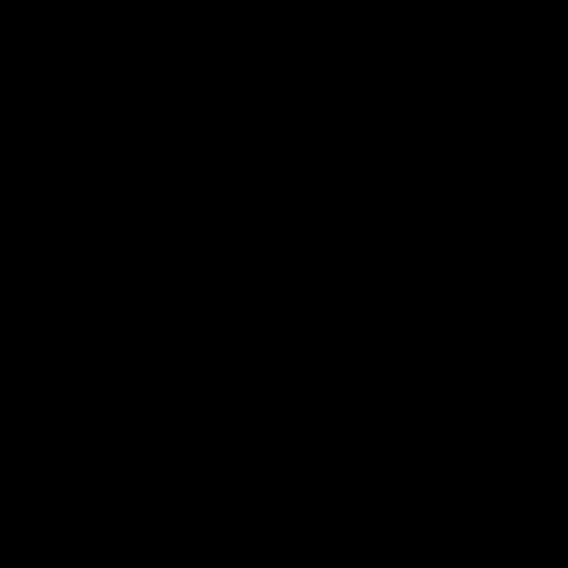
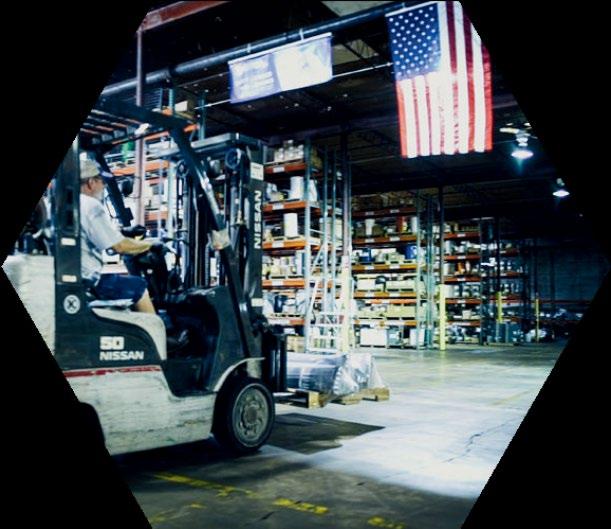
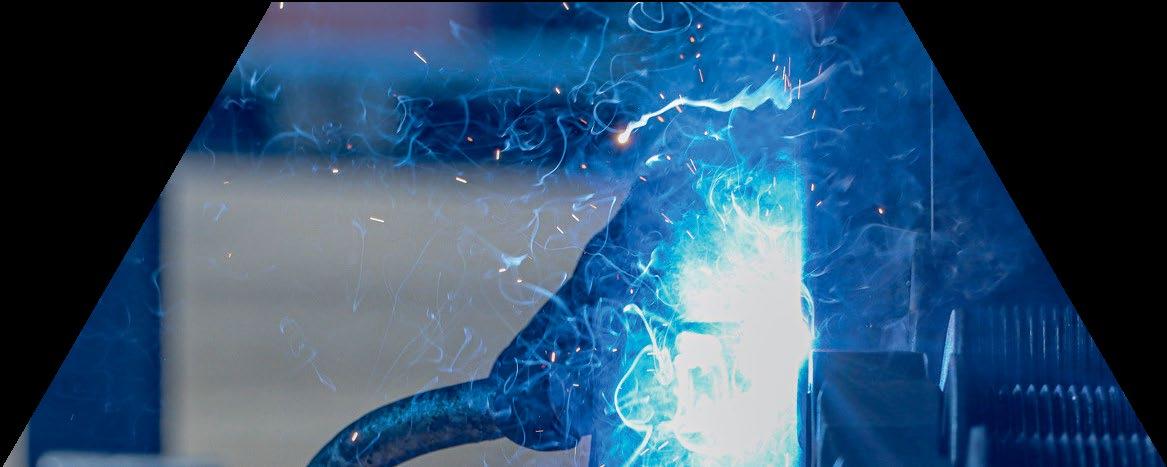
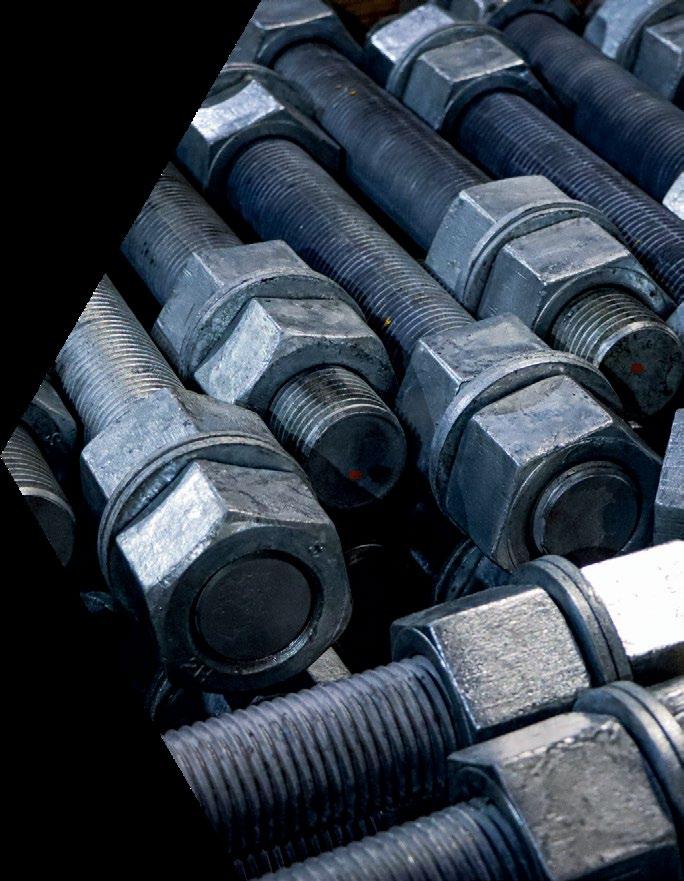
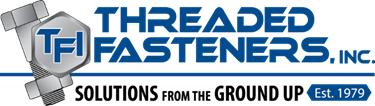
Manual Revision A 2025 Section 1 Table of Contents
TABLE OF CONTENTS
Section 1 Table of Contents
Section 2 Quality Management Procedures
Section 3 Foreword
Section 4 Quality Management System
Section 5 Leadership
Section 6 Planning
Section 7 Support
Section 8 Operation
Section 9 Performance Evaluation
Section 10 Improvement
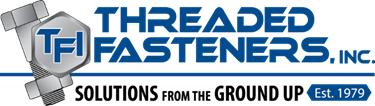
Risks and Opportunities
Objectives
Management Review
Correction Action Request
Calibration
Training
Purchasing
Document Control
Identification and Traceability
Internal Audits
Nonconforming Product
Production Control
Revision A 2025 Section 2
Quality Management Procedures
SQP-TFI-QMS-01A
SQP-TFI-QMS-02A
SQP-TFI-QMS-03A
SQP-TFI-QMS-04A
SQP-TFI-QMS-05A
SQP-TFI-QMS-06A
SQP-TFI-QMS-07A
SQP-TFI-QMS-08A
SQP-TFI-QMS-09A
SQP-TFI-QMS-10A
SQP-TFI-QMS-11A
SQP-TFI-QMS-12A Quality Manual
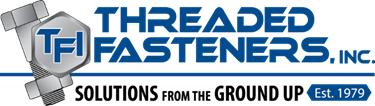
3.0 Introduction
Founded in 1979 by brothers-in-law Frank Martin and Steve Sholtis, Threaded Fasteners Inc. (TFI) has grown from modest beginnings (one chop saw and one rigid pipe threader in a borrowed warehouse) to be one of the largest fastener and steel bolt distributors in the Southeast.
Some 13 years after opening the first location on Eslava Street, a second location was launched in Pensacola to better serve Florida-based customers. Our growth has remained strategic, opening new branches in cities where longtime clients operate. Our vision for the future includes opening more than 20 additional locations to better serve the global needs of our customers.
Made in Mobile, Ala., Threaded Fasteners Inc. operates manufacturing facilities in Semmes, Ala., and Tampa, Fla., where anchor bolts and specialty headed products are built by local crews on two-shifts to meet the growing demand for quality materials. A new business venture that displays our innovative spirit – Quality Galvanizing – was launched in March 2017 when ground was broken for the plant where TFI products will be galvanized against corrosion prior to packaging, sale, and distribution.
Reflected in Threaded Fasteners history of creating value in and for the people we serve, TFI has invested in the development, implementation, and operation of an effective Quality Management System across all areas of the organization. The Quality Management System is intended and sustain the overall performance of the business, products, and services.
The expected outcomes of the Quality Management System are:
• The ability to consistently provide products and services that meet the customer and applicable statutory and regulatory requirements.
• To provide opportunities to enhance customer satisfaction.
• To identify and address opportunities for improvement.
• To foster an environment using the Plan-Do-Check-Adjustt cycle that creates effective process planning and interactions.
• The ability to demonstrate conformity to relevant quality management system requirements.
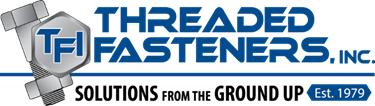
Threaded Fasteners believes in continuous improvement and utilizes the following Quality Management System principles in its daily operations:
• Customer focus.
• Leadership.
• Engagement of people.
• Process approach.
• Improvement.
• Evidence based decision making.
• Relationship management.
The purpose of the Quality Manual is to:
• Promote and Communicate TFI’s Quality Policy, procedures, and requirements.
• Describe and implement an effective quality management system.
• Provide basis for control of practices and facilitate assurance in business activities.
• Provide a documented structure for auditing the quality system.
• Provide a stable environment for an effective quality system during changing circumstances.
• Give personnel guidance and training in the quality system methods and requirements.
• Demonstrate compliance with ISO-9001-2015.
• Be able to present TFI’s Quality Management System for external purposes.
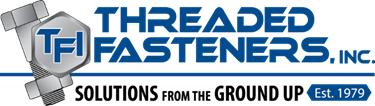
3.1 Process Approach:
Threaded Fasteners champions the process approach in the development, implementation, and continuous improvement of the Quality Management System.
TFI believes this approach will foster:
• Key processes and measurements the meet objectives.
• Definitive process that delivers intended outputs and create value.
• Achievable processes.
• Data and evaluation of processes.
3.2 What is the Plan-Do-Check-Adjust Cycle:
• Plan: establish objectives and build processes necessary to deliver results.
• Do: implement what was planned.
• Check: monitor and measure processes and results against the objectives.
• Adjust: take actions to improve results.
Threaded Fasteners has identified this approach to effectively focus on risk-based thinking at every level to promote continuous improvement.
3.3 Risk-Based Thinking
Risk-Based Thinking is an integral part of TFI’s approach to operating an effective Quality Management System. Risks and Opportunities are both addressed when planning and implementing processes applicable to the QMS. The purpose of which is to achieve improved results and to prevent and/or lower the risk of negative effects.
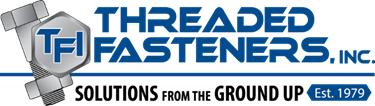
3.4 Normative References
ISO 9001:2015 contains the requirements that are applicable to the Threaded Fasteners Inc. Quality Management System. All references to ISO 9001:2015 in this document are to version:
• International Standard ISO9001:2015(E) Quality Management System Requirements, Quality Management Fundamentals and Vocabulary.
3.5 Commitment and Support
Threaded Fasteners Quality Management System is supported by Senior Leadership. Senior Leadership monitors the effectiveness of the QMS. Senior Leadership will also monitor compliance with the QMS as defined in the Quality Manual, procedures, and instructions that are developed and mandatory for all functions and personnel of Threaded Fasteners Inc.
4.1 Context of the Organization
Threaded Fasteners Inc. identifies external and internal issues through strategic and operational planning. Issues are evaluated for relevance to the Quality Management System and how they may or may not affect the ability for TFI to achieve attended results. TFI continually evaluates whether climate change is a relevant issue in relation to its QMS.
Threaded Fasteners Inc. organizational context includes:
• Knowledge of TFI’s core products and services.
• Identifying interested parties (Table 1).
• Understanding the needs and expectations of interested parties (Table 1).
• Determining the scope of the Quality Management System.
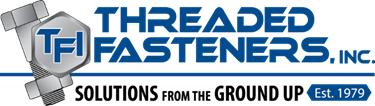
4.2 Understanding the Needs and Expectations of Interested Parties
Threaded Fasteners Inc. reviews and monitors needs and expectations of interested parties and their relevancy to the Quality Management System. Table 1 outlines the interested parties identified by TFI. Needs and expectations are reviewed using RiskBased Thinking as discussed in section 3.3. Objectives are set and reviewed at Management Review.
Table 1
Interested Party Needs and Expectations Objectives
Customers
Employees
Suppliers
Legal and Regulatory Bodies
Management
Quality, Safety, Climate Change and competitive pricing and delivery of products and services.
Safe work environment, job security, adequate training, and equipment.
Clear description of products or services requirements and/or scope of work, good working relationship, prompt payment.
Compliance with all regulations and statutes applicable to the product or service/organization.
Leadership; direction; resources; involvement; motivation.
Customer Satisfaction, achieve revenue targets and customer retention.
Produce quality products and perform quality services and follow QHSE policies and procedures.
Continuity through a relationship that benefits both parties and allows Threaded Fasteners to promptly serve its customers.
Identification of applicable statutory and regulatory requirements for the products and services provided, understanding of the requirements, application within the QMS, and update/ maintenance of the requirements.
Increased growth, sales & profitability/efficiency & effectiveness of operations.
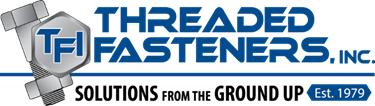
4.3 Scope of the Quality Management System
Senior Leadership determines the boundaries and application of the Quality Management System to establish its scope.
Senior Leadership takes the following into consideration:
• The external and internal issues as referenced in 4.1.
• The requirements of relevant parties referred to in Table 1.
• Consistency in the quality of the applicable products and services of our company.
• Customer satisfaction through effective application of the Quality Management System.
• All statutory, regulatory and/or legal requirements.
• Establishment of suitable processes for improvement of the Quality Management System.
The scope of operation for Threaded Fasteners Inc. is as follows:
• Distribution and manufacturing of fasteners for commercial and industrial businesses, markets including but not limited too electrical utility, marine construction, plant maintenance, steel fabrication and OEM.
• On site inventory management specialized to meet customer needs.
• Stocking and consignment programs designed to meet customer specific requirements.
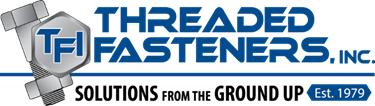
Facilities within the Scope of the Quality Management System:
Home Office
3200 Crichton St. Mobile, AL 36607 (251) 432-0161
National Distribution
3200-A Crichton St. Mobile, AL 36607 (251) 432-0161
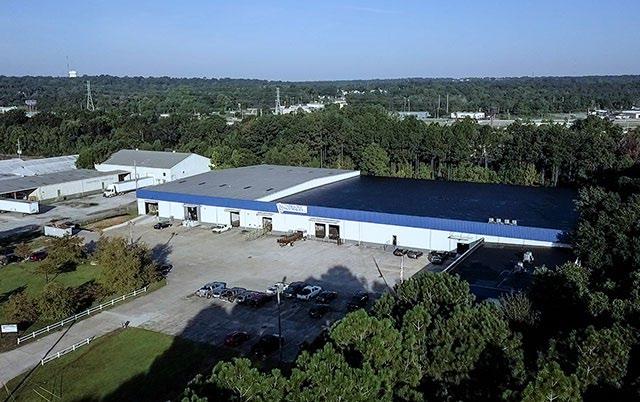
Mobile, Alabama
3200-B Crichton St. Mobile, AL 36607 (251) 432-0107
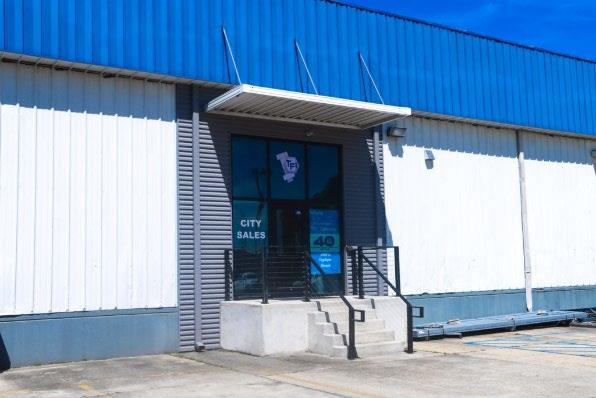
Semmes Manufacturing
2650-B N. Schillingers Rd. Semmes, AL 36575 (251) 645-3301
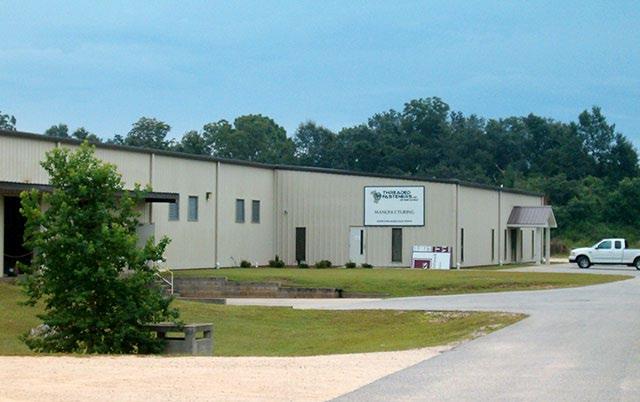
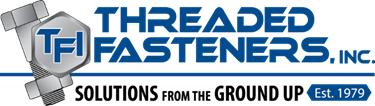
Semmes Distribution
8010 Morris Hill Road
Semmes, AL 36575
(251) 645-3301
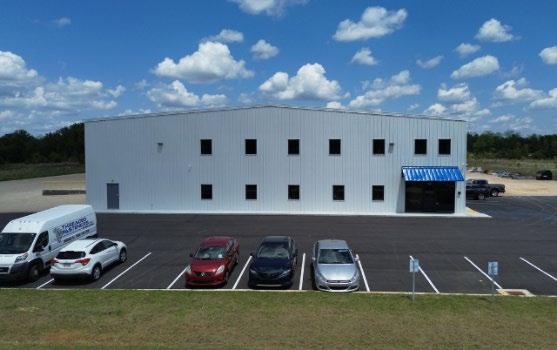
Orlando, Florida
8350 Parkline Blvd., Unit 16 Orlando, FL 32809
(321) 200-0508
Gulfport, Mississippi 1479 34th Street
Gulfport, MS 39501 (228) 575-9559
Chattanooga, Tennessee 1606 Wisdom Street
Chattanooga, TN 37406 (423) 803-5535
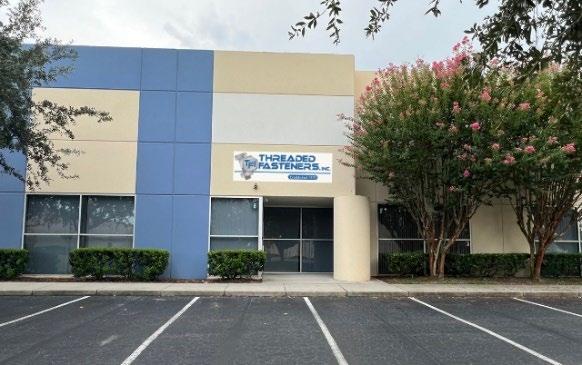
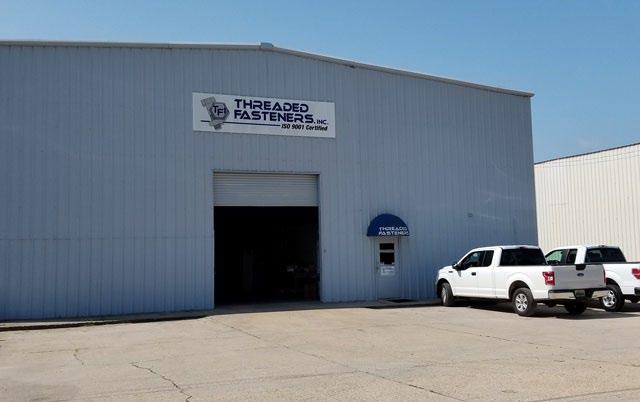
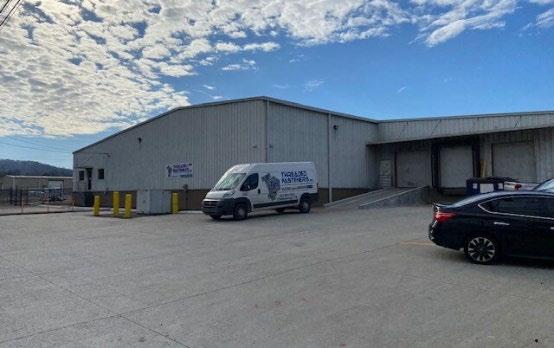
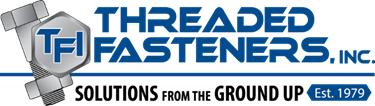
Meridian, Mississippi 5122 Arundel Road
Meridian, MS 39307
(601) 482-2658
Pensacola, Florida
3839 Hopkins Street Pensacola, FL 32505
(850) 436-2121
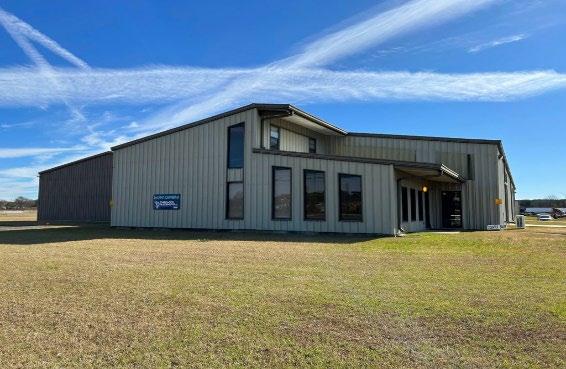
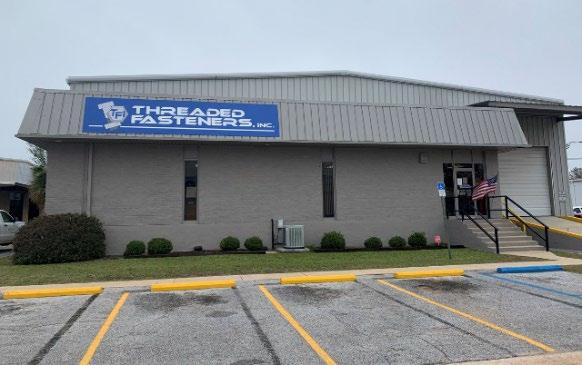
Tampa, Florida
10704 N. 46th Street Tampa, FL 33617
(813) 283-1850
Panama City, Florida
2630 Segrest Dr. Panama City, FL 32405 (850) 784-4442
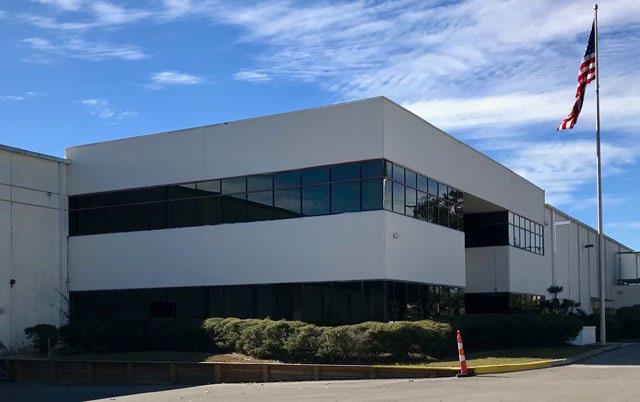
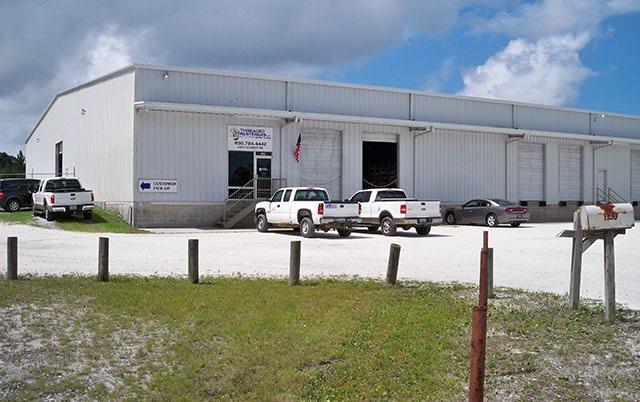
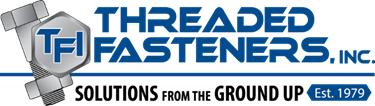
Tulsa, Oklahoma 1119 N. Iroquois Ave. Tulsa, OK 74106
(918) 587-3309
Dallas, Texas 984 E Main Street Lewisville, TX 75057
(972) 436-9781

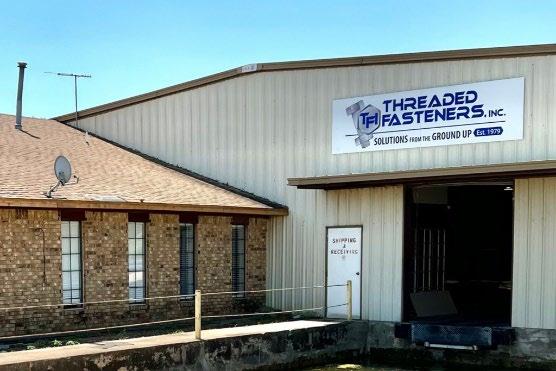
Tifton, Georgia
3394 US Hwy 41 South Tifton, GA 31794 (229) 5070
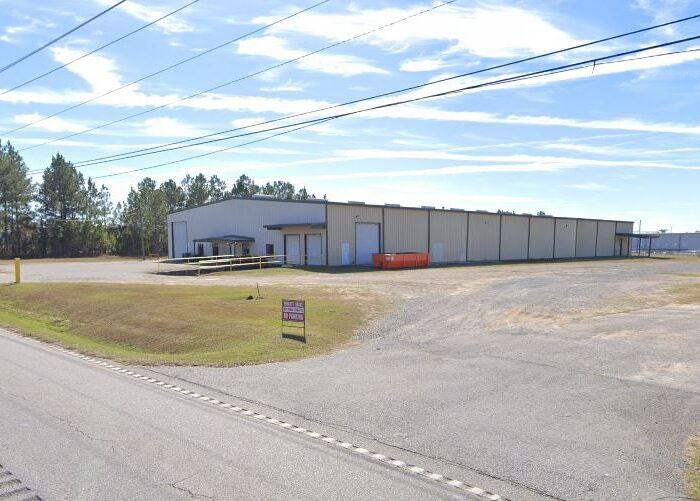
Florida – Regional Office
140 Lurton Street Suite B Pensacola, FL 32505
(850) 361-3250
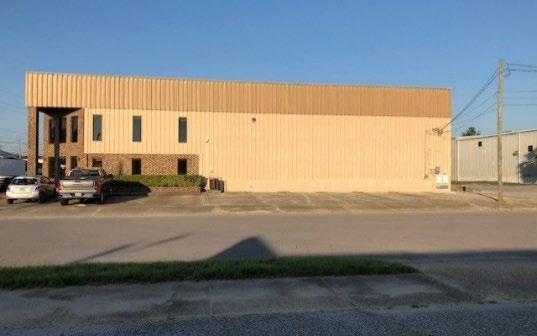
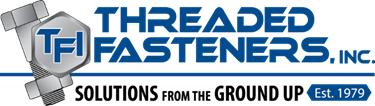
4.4 Quality Management System and it’s Processes
Table 2 outlines TFI’s flowchart of its processes. TFI continually monitors processes for operational relevancy, sequence, interaction, and assigned responsibilities. These processes shall:
• Determine the inputs required and the outputs expected.
• Determine the sequence and interaction of processes.
• Determine and apply the criteria and methods needed to ensure the effective operation and control of these processes.
• Determine the resources needed for these processes and ensure their availability.
• Assign the responsibilities and authorities for these processes.
• Address the risks and opportunities as determined in accordance with the requirements of 6.1.
• Evaluate these processes and implement any changes needed to ensure that these processes achieve their intended results.
• Improve the processes and the quality management system.
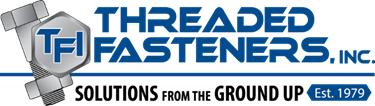
Quality Management System
Table 2
Overview Flowchart of Company Processes
SUPPORT PROCESSES
CALIBRATION
CORRECTIVE ACTION
LINE PROCESSES
ORDERS
PURCHASING
PRODUCTION
CUSTOMER SATISFACTION
DOCUMENT AND RECORD CONTROL
DATA ANALYSIS
HUMAN RESOURCES
INTERNAL AUDITS
MANAGEMENT REVIEW
NCP CONTROL PLANNING
RISK MANAGEMENT
Quality Management System Structure Includes:
• Quality Manual
• Quality Policy
• Quality Objectives
• Standard Quality Procedures (SQP)
• Standard Operating Procedures (SOP)
• Work Instructions
• Applicable National, International, and Industry Standards
• Customer Requirements
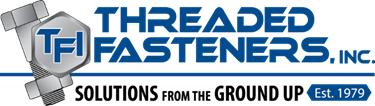
Leadership and Commitment
5.1 Leadership and Commitment
Senior Leadership provides leadership and commitment to the Quality Management Systems development, implementation, and continuous improvement by:
• Being accountable for the effectiveness of the QMS.
• Establishing the Quality Policy and Quality Objectives, and aligning them with the strategic direction of Threaded Fasteners Inc.
• Ensuring the integration of the QMS and the TFI’s business process.
• Promoting the use of the process approach and risk-based thinking.
• Ensuring the availability of resources necessary to an effective QMS.
• Communicating to TFI’s employee owners the importance of an effective QMS and the importance of compliance with the QMS.
• Ensuring that the QMS achieves its desired results.
• Engaging, directing, and supporting personnel to contribute to the effectiveness of the Quality Management System.
• Promoting and supporting improvement initiatives.
• Supporting other management roles to demonstrate their leadership as it applies to their areas of responsibility.
5.1.2 Customer Focus
Senior Leadership demonstrates leadership and commitment with respect to customer focus to ensure that:
• Customer and applicable statutory and regulatory requirements are met.
• Risks and Opportunities that can impact products and services are determined and addressed (SQP-TFI-QMS-01A)
• The continuous focus on enhancing customer satisfaction.
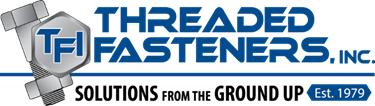
Quality Manual
Revision A 2025 Section 5
Leadership and Commitment
5.2.1 Quality Policy
Senior Leadership has established, implemented, and maintains a Quality Policy that:
• Is appropriate for the purpose, context, and supports the strategic direction of Threaded Fasteners Inc.
• Provides a framework for setting Quality Objectives (SQP-TFI-QMS-02A)
• Includes a commitment to customer satisfaction.
• Includes a commitment to continuous improvement.
The Quality Policy is:
Built on employee owners who are humble, hungry, and aware, Threaded Fasteners is committed to providing unrivaled customer service.
We achieve this by promoting a culture of engagement in the Quality Management System, operational excellence through continuous improvement, and a focus on customer satisfaction.
5.2.2 Roles, Responsibilities, and Authorities
Threaded Fasteners Inc. Senior Leadership ensures that the responsibilities and authorities for relevant roles are assigned, communicated, and understood within the company.
Senior Leadership has assigned responsibility and authority for:
• Ensuring the Quality Management System conforms to the requirements of ISO 9001:2015.
• Ensuring the processes are producing intended results.
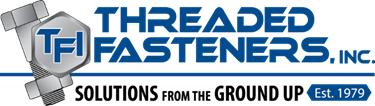
Quality Manual Revision A 2025 Section 5 Leadership and Commitment
• Reporting on the performance of the QMS and on opportunities for improvement (See 10.1).
• Ensuring the promotion of customer focus throughout the company (See 5.1.2)
• Ensuring that the integrity of the QMS is maintained when changes to the QMS are planned and implemented.
Senior Leadership and Authorized Designees have the organizational freedom to:
• Create the Quality Policy, business planning, and objectives.
• Define organizational principles and practices.
• Assign authorities and responsibilities.
• Appoint the Management Representative.
• Foster continuous improvement through Corrective Actions (SQP-TFIQMS-04A)
• Establish and effective culture at all levels of the organization.
• Review annually the Quality System effectiveness.
• Provide internal communication relative to effectiveness of the QMS.
• Meet industry standards, Threaded Fasteners Inc Quality Policy, stated objectives, and customer satisfaction.
• Provide the resources and personnel necessary to maintain the system.
Management Representative
Threaded Fasteners Inc. Senior Leadership appoints as the Management Representative the Quality Manager. The Quality Manager has the authority and responsibility to:
• Ensure that the Quality System is established, implemented, and maintained in accordance with the requirements of the ISO 9001:2015 standard.
• Report on the performance of the Quality System to Senior Leadership (SQP-TFI-QMS-03A).
• Retain the organizational freedom to identify problems related to quality and consequently correct, initiate action for correction, or stop any work or activity that violates the established quality standards.
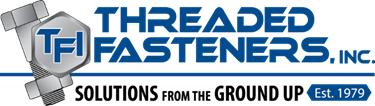
6.1 Planning
Threaded Fasteners Inc. considers issues referenced in Section 4.1 and the requirements referred to in 4.2 to determine the Risks and Opportunities that need to be addressed.
These will be addressed to:
• Assure the Quality Management System achieves its intended results.
• Enhance desirable results.
• Prevent, or reduce undesired results.
• Achieve improvement.
Standard Quality Procedure TFI-SQP-01 is established to:
• Address Risks and Opportunities.
• Establish how to implement the actions into QMS (See 4.4).
• Evaluate the effectiveness of these actions.
6.2 Quality Objectives
Threaded Fasteners Inc. commits to setting Quality Objectives that focus on customer satisfaction and support the Quality Policy.
Senior Leadership has designed Quality Objectives that are measurable, monitorable, and communicate objectives to all relevant parties. When Quality Objectives are established, the following will be taken into consideration:
• Quality Policy.
• Measurability
• Applicable requirements.
• Conformity of products and services
• Customer Satisfaction.
• How to monitor objectives
• Communication of the objectives.
• Plan for updates.
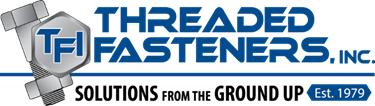
When planning how to achieve the Quality Objectives, the following actions will be determined:
• What needs to be done.
• What resources will be required.
• Who will be the owner of the objective.
• Expected completion date of the objective.
• How will results be measured and evaluated.
(SQP-TFI-QMS-02A) outlines Threaded Fasteners approach to implementing and evaluating Quality Objectives.
6.3 Planning of Changes
Threaded Fasteners Inc. understands the unique challenges presented by a growing company and changing industry. Changes made to the Quality Management System may be warranted and these changes will be developed in a planned manner (See 4.4).
The following will be taken into consideration when planning for change:
• The reason for the change and the potential effects.
• The integrity of the Quality Management System.
• The availability of resources.
• The assignment or reassignment of responsibilities and authorities.
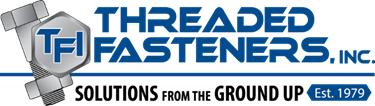
7.1 Resources
Senior Leadership monitors the effectiveness of the Quality Management System (See 3.5). Capabilities and constraints on internal resources will be considered when determining the resources needed to provide effective management, product knowledge, training, and internal audits.
In addition, Senior Leadership examines resources needed from external providers. Senior Leadership is commits to providing the necessary resources, both internally and externally, to achieve Threaded Fasteners Inc. objectives and conform to product and service requirement.
7.1.2 People
Threaded Fasteners Inc. maintains the necessary persons to effectively implement the Quality Management System. Senior Leadership will determine and provide the means necessary for the effective implementation and operation of the QMS.
Threaded Fasteners Inc. is an 100% Employee-Owned Company. Every employeeowner at TFI has a vested interest in conforming to TFI’s Quality Objectives and conforming to customer requirements.
7.1.3 Infrastructure
Senior Leadership evaluates the infrastructure necessary to effectively operate business. appropriate resources and personnel will be provided to develop and maintain infrastructure to assure Quality Objectives and Product Requirements are achieved.
Infrastructure may include, but is not limited to:
• Buildings and Utilities.
• Hardware and Software Equipment
• Transportation
• Information and Communication Technology.
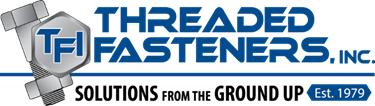
7.1.4 Environment
Senior Leadership determines, provides, and maintains the environment necessary for the operation of its processes and to achieve conformity of products and services. All employee-owners are responsible for producing a suitable environment which includes both human and physical factors such as:
• Social
• Psychological
• Physical
Threaded Fasteners Blueprint
Core Mission: To Create Value in and For the People We Serve
Core Values: Humble Hungry Aware
Strategic Anchors: Solution Based Services
People Development
Operational Excellence
7.1.5 Monitoring and Measuring Resources
Threaded Fasteners determines the and provides the resources needed to ensure valid and reliable results when monitoring or measuring is used to verify conformity of products and services required.
Resources provided will be:
• Suitable for the specific type of monitoring and measurement activities being undertaken.
• Maintained to ensure their continuing fitness for their purpose (TFI-SQP05)
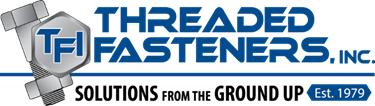
7.1.6 Organizational Knowledge
Senior Leadership determines the necessary knowledge needed to adequately perform its processes and achieve conformity. When applicable, Knowledge will be maintained and made available as necessary.
This may include knowledge and information obtained from:
Internal Resources such as:
• On the job training
• Knowledge from experience.
• Lessons learned from failures and successes.
• Capturing and sharing undocumented knowledge.
• Results of process improvements.
• Internal Audits
• Continuous Improvement Activity
• Intellectual Property
External Resources such as:
• Industry Standards.
• Customer Standards.
• Conferences and Trade Shows.
• Academia
• Statutory and Regulatory Requirements.
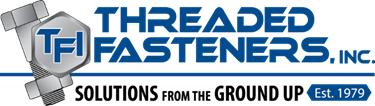
7.2 Competence
Threaded Fasteners Inc. recognizes the importance of qualified employees. TFI’s investment in its employees begins at the hiring process and continues throughout the employee’s tenure at the company.
TFI ensures that it has:
• Determined the necessary competence of persons doing work under its control that affects the performance and effectiveness of the quality management system.
• Ensured that these persons are competent based on appropriate education, training, or experience.
• Where applicable, taken action to acquire the necessary competence, and evaluate the effectiveness of the actions taken.
Threaded Fasteners deploys several activities to help enhance employee knowledge and engagement: Activities include, but are not limited to:
• Tools For Success (SQP-TFI-QMS-06A)
• New Employee Orientation (NEO)
• On the Job Training (OJT)
• Seminars
• Trade Shows
7.3 Awareness
Threaded Fasteners Inc. ensures that employees are aware of:
• The Quality Policy
• Relevant Quality Objectives
• Employee’s contribution to the effectiveness of the QMS, including benefits of improved performance.
• The implications of not conforming with the quality management system requirements.
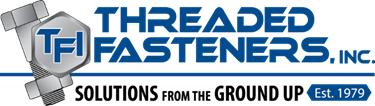
Quality Manual
Revision A 2025
7.4 Communication
Section 7 Support
Senior Leadership provides communication throughout the company on the effectiveness of the Quality Management System. Senior Leadership will determine the following:
• What will be communicated.
• When to communicate.
• With whom to communicate.
• How to communicate.
• Who communicates.
Communication will be provided through various means of media or forums including but not limited to:
• Management Reviews.
• Operational Meetings.
• Planning Meetings.
• One on One Meetings.
• Performance Reviews.
• Website and Social Media.
• Posters or Visual Displays.
7.5 Documented Information
Threaded Fasteners Inc. Quality Management System has defined the documented information required by the ISO 9001:2015 standard to assure effective operation of the company.
Documented information maintained by Threaded Fasteners Inc. will include:
• Documented information required by the International Standard.
• Documented information determined by TFI as being necessary for the effectiveness of the Quality Management System.
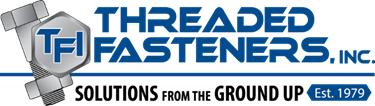
7.5.2 Creating and Updating
When creating and updating documented information, Threaded Fasteners will ensure the ensure the following key factors are included:
• Proper identification and description.
• Proper format.
• Review and approval for suitability and adequacy.
7.5.3 Control of Documented Information
Documents required for the Quality Management System are controlled. (SQP-TFIQMS-08A) has been established and implemented to ensure the control of documents relevant to the Quality Management System.
Documents and document changes may be initiated by anyone in the organization but may only be issued after being reviewed and approved by an authorized department manager. Document changes are reviewed and authorized by the same authority that issued the original and/or the authority that has assumed ownership of the document.
At a minimum, documents are subject to review during internal audits.
Threaded Fasteners Inc. has implemented this requirement ensure that controlled documents are:
• Available and suitable for use, where and when needed.
• Adequately protected.
Threaded Fasteners has addressed the following activities as they pertain to the control of documents (SQP-TFI-QMS-08A):
• Distribution, access, retrieval, and use.
• Storage and preservation, including preservation and legibility.
• Control of changes.
• Retention and disposition.
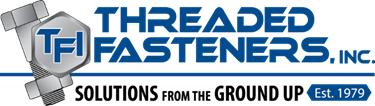
8.1 Operational Planning and Control
Senior Leadership plans, implements, and controls the processes needed to meet the requirements of the provision of products and services, and to implement the actions determined in Section 6 by:
• Determining the requirements for the products and services.
• Establishing criteria for the processes, and the acceptance of products and services.
• Determining the resources needed to achieve the conformity to the product and service requirements (See 7.1).
• Implementing control of the processes in accordance with the criteria.
• Determining, maintaining, and retaining documented information to the extent necessary (SQP-TFI-QMS-08A).
8.2 Requirements for Products and Services
8.2.1 Customer Communication
Threaded Fasteners Inc. communication with customers may include:
• Providing information relating to products and services.
• Handling inquiries, contract, or order changes.
• Obtaining customer feedback relating to products and services, including customer complaints.
• Handling or controlling customer property.
• When relevant, establishing specific requirements for contingency actions.
8.2.2 Determining the Requirements for Products and Services.
Reviews of customer information are evaluated to determine the requirements that need to be achieved. Reviews will consider any statutory or regulatory requirements and requirements considered necessary by Threaded Fasteners Inc.
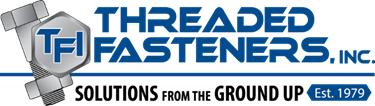
Threaded Fasteners Inc. may receive customer requirements in the following format:
• Standard Operating Procedure
• Customer Notes
• Order Notes
• Line Notes
• Via Email
• Verbally
Threaded Fasteners Inc. Production Control Procedure (SQP-TFI-QMS-12A) outlines the processes in place to ensure the effective communication with TFI’s customers and TFI’s ability to meet all requirements.
8.2.3 Review of Requirements for Products and Services.
Threaded Fasteners will include the following factors when reviewing its ability to meet the requirements:
• Requirements specified by customer, including delivery requirements.
• Requirements not stated by customer, but necessary for the specified use, when known.
• Requirements specified by Threaded Fasteners Inc.
• Statutory and regulatory requirements applicable to products and services.
• Contract or order requirements differing from those previously expressed.
8.3
Design and Development
Threaded Fasteners Inc. does not perform design activities, therefore fulfillment to the requirements of the clause for Design and Development are not applicable to our QMS.
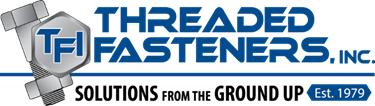
Revision A 2025 Section 8 Operation
8.4 Control of Externally Provided Processes, Products, and Services
Threaded Fasteners Inc. evaluates its external providers and purchases only from those that can satisfy the quality requirements of TFI (SQP-TFI-QMS-07A).
(TFI-SQP-07) is put in place to determine controls applied to externally provided processes, products, and services when:
• Products and services from external providers are intended for incorporation into the organizations own products and services.
• Products and services are provided directly to the customers by external providers on behalf of Threaded Fasteners Inc.
• A process, or part of a process, is provided by an external provider because of a decision by the organization.
Threaded Fasteners Inc. ensures that externally provided processes, products and services do not adversely affect the organization’s ability to consistently deliver conforming products and services.
Purchasers will prepare the necessary purchasing documents. Documents will state and describe the products to be purchased. This will include any identification requirements of the products, applicable standards, and any TFI requirements.
Purchased products are subject to inspection by receiving and/or Quality. Nonconforming product will be segregated as explained in (SQP-TFI-QMS-11A).
8.5 Production and Service Provision
Threaded Fasteners Inc. production activities are planned and documented. Critical operations are provided with work instructions and performed in accordance to written procedures.
(SQP-TFI-QMS-12A) specifies the requirements and responsibilities for controlling production processes. Quality Manual
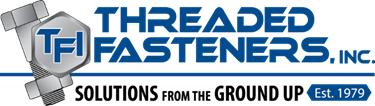
8.5.1 Control of Production and Service Provision
When applicable, the following controlled conditions at Production will include:
• The availability of documented information that defines characteristics of products being produced, services provided, the activities to be performed, and desired results.
• The availability and use of suitable monitoring and measuring resources.
• The implementation of monitoring and measurement activities at appropriate stages to verify that requirements have been met.
• The use of suitable infrastructure and environment for the operation of processes.
• The appointment of competent persons, including and required qualification.
• The validation, and periodic revalidation of the ability to achieve planned results of the processes for production and service provision, where output cannot be verified by subsequent monitoring or measurement.
• The implementation of actions to prevent human error.
• The implementation of release, delivery activities.
8.5.2 Identification and Traceability
Threaded Fasteners Inc. uniquely identifies all purchased and manufactured materials. Item IDs are used on all parts. When applicable, items may also be uniquely identified by a lot and/or heat number.
(TFI-SQP-09) ensures that suitable means are in place to identify purchased and manufactured goods.
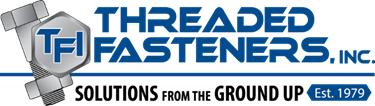
8.5.3 Property belonging to customers or external providers
Property provided from external sources that are used for processing or for incorporation into products are handled in the same manner as other purchased products. When specified in a contract, special handling instructions from customers will take precedent over Threaded Fasteners Inc. operating procedures. Any loss, damage, or unsuitability of a customer’s products is recorded and reported to the customer.
8.5.4 Preservation
Threaded Fasteners Inc. preserves outputs during production and service provision to ensure conformity to requirements. See Section 8.5.2 and Section 10.2.1 for preservation examples relating to Identification and Nonconformities.
8.5.5 Post Delivery Activities
Threaded Fasteners does not provide post-delivery activities.
8.5.6 Control of Changes
Threaded Fasteners recognizes changes to production or service provision may be required. Proper review and control to these changes will occur to ensure conformity with requirements.
8.6 Release of Products and Services
See Section 8.5.1 for Threaded Fasteners Inc. Control of produced goods and services. Manufactured and purchased goods are subject inspection during all phases from time of receipt to being released for shipment.
Nonconformities (SQP-TFI-QMS-11A) discovered during inspections are documented for internal review.
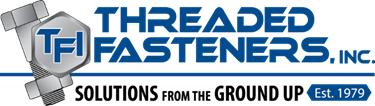
Release of products or services to the customer will not proceed until the planned arrangements have been satisfied, unless otherwise approved by a relevant authority and as applicable, by the customer.
8.7 Control of Nonconforming Outputs
Threaded Fasteners Inc. policy is to identify any nonconformities and document the findings of the nonconformity (SQP-TFI-QMS-11A). Nonconforming product is tagged and moved to a segregated area. The nonconforming product documented on the Nonconforming Product Form and is recorded in the Nonconforming Product Log. Not all nonconformities are subject to Nonconforming Product Form. Minor nonconformities discovered during Quality checks or inspections will be documented and recorded using a separate form.
Relevant parties are notified, and necessary course of action is taken.
When required, the customer is contacted for concession. Repaired or reworked product is reinspected.
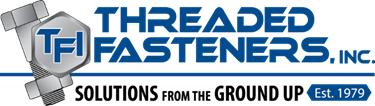
9. Performance Evaluation
9.1
Monitoring, Measurement, Analysis, and evaluation
Senior Leadership has determined:
• What needs to be monitored and measured.
• The methods for monitoring, measurement, analysis, and evaluation needed to ensure valid results.
• When the results from monitoring and measurement shall be analyzed and evaluated.
The goal of Threaded Fasteners Inc. is to obtain necessary data to measure the effectiveness of the Quality Management System and promote continuous improvement.
9.1.2 Customer Satisfaction
Threaded Fasteners Inc. mission is to “Create Value in and for the People We Serve”.
Threaded Fasteners Inc. recognizes the importance of building lasting relationships with its customers.
Customer feedback is essential for measuring TFI’s effectiveness in serving our customers. Senior Leadership is dedicated to having an open line of communication with customers. This communication includes contact by phone, email, video meetings, and in person visits.
When applicable, TFI will offer other means of gathering feedback such as surveys, and reviews.
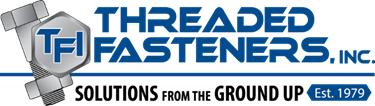
Revision A 2025 Section 9
9.1.3 Analysis and Evaluation
Threaded Fasteners Inc. analyzes and evaluates applicable data and information arising from monitoring and measurements. Results of analysis will be used to evaluate:
• Conformity of products and services.
• The degree of customer satisfaction.
• The performance and effectiveness of the Quality Management System.
• If planning has been implemented effectively.
• The effectiveness of actions taken to address risks and opportunities.
• The performance of external providers.
• The need for improvements to the Quality Management System.
9.2 Internal Audits
Threaded Fasteners Inc. commits to comprehensive, planned, and documented Quality Audits. The Management Representative established an Internal Audit Plan and Schedule. All activities and areas are audited at least once a year. More frequent audits may be performed as required.
Threaded Fasteners Inc. has identified Qualified Auditors to conduct Internal Audits. Areas of business that are the responsibility of the Quality Manager are audited by personnel independent of these responsibilities. Audit preparation includes the review of applicable standards, operating procedures, work instructions and quality records. Questionnaires and checklists are created to be used during the audit.
Noncompliance’s found during an Internal Audit result in a Corrective Action Request (SQP-TFI-QMS-04A). The Corrective Action Request will be recorded, and the respective manager notified. The results of the Internal Audits are recorded and made available to the respective manager. Activities associated with the auditing process are governed by (SQP-TFI-QMS-10A). Quality Manual
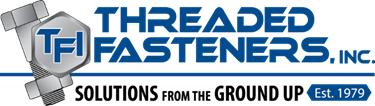
9.3 Management Review
Senior Leadership will review the Quality Management System at least once a year (TFISQP-04). The purpose of the reviews is to assess the effectiveness and continuing suitability of the Quality Policy, system, objectives, and preventative actions. The Quality Manager is responsible for scheduling and conducting the Management Review.
9.3.2 Management Review Inputs
Management review will include the following inputs:
• Follow up on open items from last meeting.
• Process and product performance.
• Customer satisfaction and feedback.
• Nonconformities.
• Corrective Actions.
• Internal Audit Results
• Changes to the Quality Management System.
• Assessment of the Quality Management System.
• Effectiveness of actions taken to address Risks and Opportunities.
• Adequacy of resources.
• Management Review Outputs.
Outputs from Management Review Outputs may lead to actions that address:
• Opportunities for improvement.
• Need for changes to the Quality Management System.
• Identify resources needed.
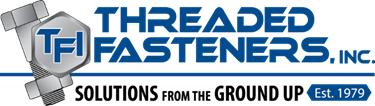
10.0 Improvement
Threaded fasteners Inc. takes a proactive approach to continuous improvement. Production and Distribution teams meet on a regular basis to discuss safety, personnel, risks and opportunities, industry trends, and opportunities for improvement.
Opportunities for quality and productivity improvements are identified and appropriate improvement projects initiated. Improvement projects may include:
• Improving products and services to meet requirements as well as to address future needs and expectations.
• Correcting, preventing, or reducing undesired effects.
• Improving the performance and effectiveness of the Quality Management System.
10.2.1 Nonconformity and Corrective Action
Processes, work operations, quality records, and customer complaints are analyzed to detect an sources of potential quality problems and determine preventive actions if required. Causes of the nonconformity’s are investigated and recorded using the CAR form. Corrective Actions (SQP-TFI-QMS-03A) and Preventive Actions that are implemented and effective result in continual improvement.
Corrective Actions will be taken to the degree appropriate to the significance of the problems in relation to the risks associated with the nonconformity.
Any Threaded Fasteners Employee has the right to issue a Corrective Action. Corrective Actions may be initiated because of:
• Identification of product nonconformity.
• Process and quality problems.
• Noncompliance’s observed during audits.
• Customer complaints, and/or return analysis.
• Nonconforming deliveries from suppliers or subcontractors.
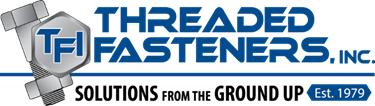
10.3 Continual Improvement
Threaded Fasteners continually seeks opportunities to improve the suitability, adequacy, and effectiveness of the Quality management System. Results from analysis, evaluation, and outputs from Management Review will be used to determine if there are needs or opportunities for improvement