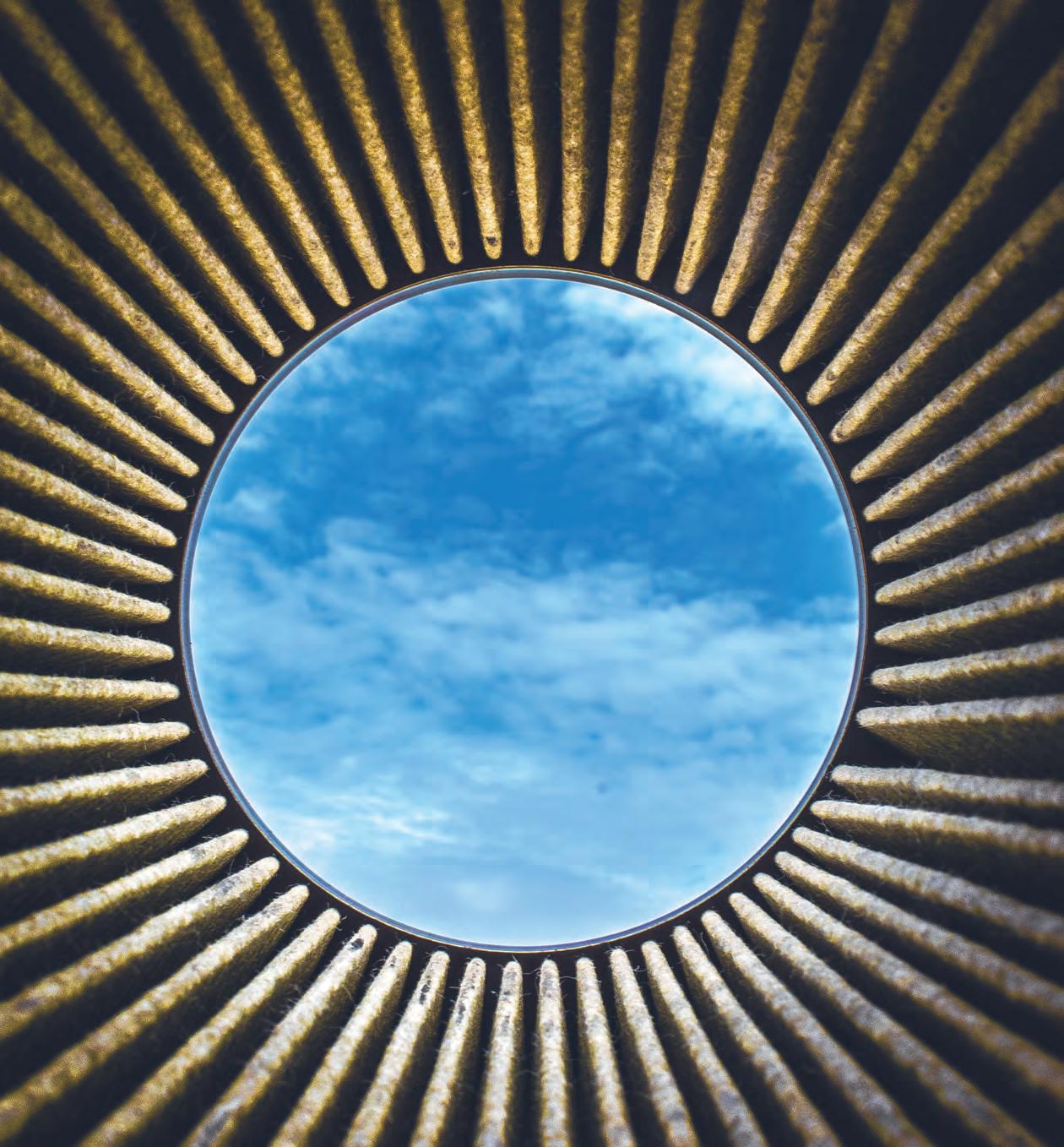
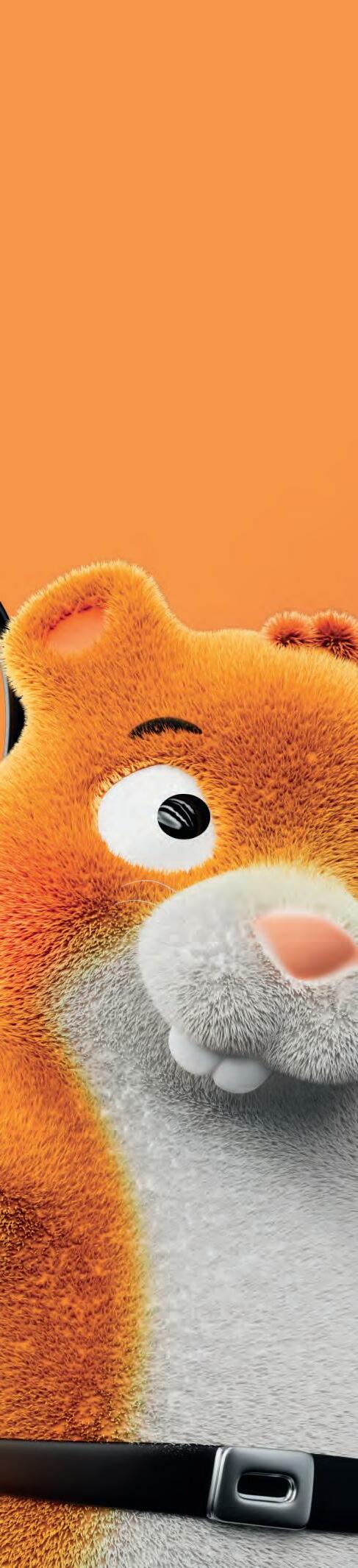






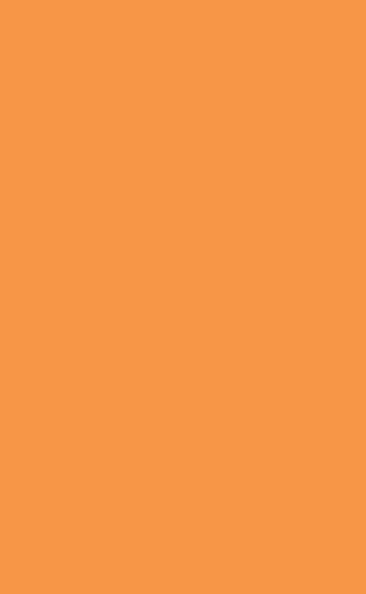


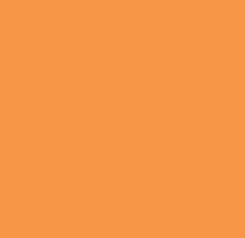

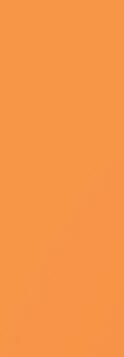

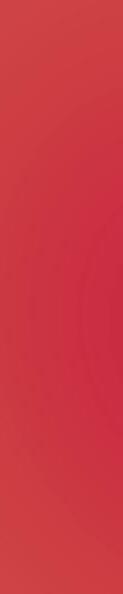
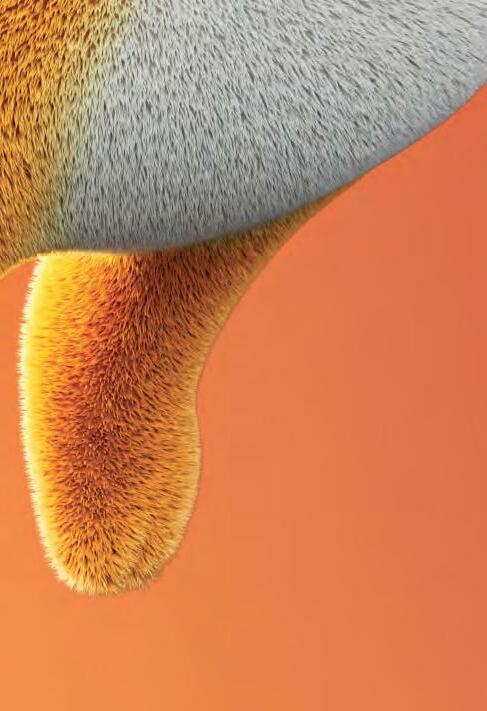
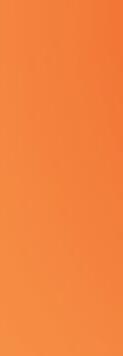
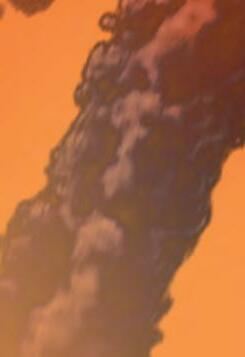
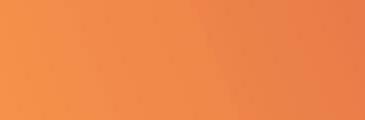
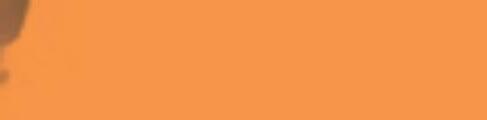
j.bush@hennikgroup.com
IF YOU’RE READING THIS then I hope you’ve just picked up your copy of The Manufacturer magazine from our stand at Digital Manufacturing Week (DMW). If you are passionate about manufacturing and you’re NOT in Liverpool this week, then I urge you, dear reader, to take a long hard look at yourself!
DMW, or the Woodstock of manufacturing as I like to think of it, is really the only place to be in November. It’s the week where the great and the good of UK manufacturing come together to celebrate this fantastic sector in which we are all proud to work. There will be events taking place throughout the week (14-18 November), including the Smart Factory Expo, now in its seventh year, which will showcase all the technologies enabling the digital manufacturing revolution under one roof - creating a carefully curated shop window for manufacturers at all stages of their digital journey.
Part of Smart Factory Expo and located at the very heart of the show floor, will be Made Smarter Innovation Alley, which will feature all the emerging and disruptive technologies from some of the country’s most innovative start-ups and scaleups looking to change the manufacturing landscape.
There will also be Manufacturing Leaders’ Summit where, as the name suggests, there will be two days of presentations and discussion from the top minds in the sector, covering key, strategic business and technical challenges across the manufacturing ecosystem. SME Growth Summit will offer much the same, but from the perspective of the UK’s 130,000+ manufacturing SMEs; available to anyone from a manufacturing organisation with a turnover up to £100m.
In addition, of course, we have our two awards evenings. The Manufacturer Top 100 (16 November), publicly recognises the heroes of UK manufacturing who stand out for their contribution to changing the face of industry. The Top 100 2022 is nominated by The Manufacturer’s 265k-strong audience, the wider industrial community, and judged by an esteemed panel of industry leaders, academic institutions and manufacturing associations.
The Manufacturer MX (TMMX) Awards, in partnership with the Institution of Mechanical Engineers (IMechE), have been described by a previous winner as “the Oscars of manufacturing”, and are widely considered as the gold standard for the manufacturing industry. They are the only peer-reviewed and judged programme of their kind.
TMMX Awards exist to encourage, benchmark and celebrate manufacturing excellence, with every stage of the programme providing value for participants, whatever their excellence maturity. The 2022 awards will take place at a gala dinner on 17 November and feature ten categories including Supply Chain Excellence, Sustainable Manufacturing and, of course, overall Manufacturer of the Year. A huge thank you to all our sponsors this year.
The Manufacturer editorial team will be conducting interviews at the TM Studio, located on the Smart Factory Expo Show floor (stand L30). Please come along and say hello. There will also be a number of fringe events taking place throughout the week including IfM Masterclasses, the Best of British Showcase and site visits. I hope everyone has a fantastic DMW and I look forward to seeing you in Liverpool.
@TheManufacturer www.themanufacturer.com
journal do not necessarily represent those of the publishers. Whilst every effort is made to ensure the accuracy of the information contained in the journal, no legal responsibility will be accepted by the publishers for loss arising from use of information published. All rights reserved. No part of this publication may be reproduced or stored in a retrieval system or transmitted in any form or by any means without prior written consent of the publishers.
To receive your copy: email memberships@hennikgroup. com, telephone +44 (0)20 7401 6033 or write to the address here.
Hennik Research Limited (part of Nineteen Group), 1 Alwyne Road, Wimbledon, SW19 7AB
Tel: +44(0)20 7401 6033 Email: info@hennikgroup.com www.hennikgroup.com ww.themanufacturer.com
www.digital-manufacturing-week.com
The Manufacturer’s editorial advisory board provides insight and guidance to the editorial team on a regular basis, helping maintain the relevance and quality of the magazine’s content, both in print and online. The board also provides diverse and expert comment on strategic developments in manufacturing.
Board members also advise on other The Manufacturer products and online publications, such as the Annual Manufacturing Report. Membership is by invitation only, but if you would like to be considered, please email j.bush@hennikgroup.com
EXECUTIVE CHAIRMAN
JJ Churchill and The Manufacturer Top 100, Exemplar 2014
DIRECTOR OF INDUSTRIAL POLICY
Manufacturing Technology Centre
DIRECTOR OF STRATEGIC BUSINESS DEVELOPMENT
Tata Steel
MANAGING DIRECTOR
Drallim Industries, and The Manufacturer Top 100, shortlisted 2014
CEO
Corrotherm, and The Manufacturer Top 100, Exemplar 2014, current Judge
MANUFACTURING OPERATIONS DIRECTOR MAI
BAE Systems and The Manufacturer Top 100, Exemplar 2017
INNOVATION LEAD
Rolls-Royce plc. Young Manufacturer of the Year, TMMX Awards 2017
HEAD
Siemens Digital Factory, Congleton
CHIEF COMMERCIAL OFFICER
SDE Technology, and The Manufacturer Top 100, Exemplar 2016
DEPUTY DIRECTOR, LAND & MARITIME TRANSPORT, MANUFACTURING & MATERIALS Innovate UK
ENGINEERING INTEGRATION MANAGER
Airbus Defence and Space, and The Manufacturer Top 100, Member 2016
MANAGING DIRECTOR
G&B Electronics and The Manufacturer Top 100, Member 2016
e speak to Professor Rab Scott, Director of Industrial Digitalisation at the University of Sheffield Advanced Manufacturing Research Centre (AMRC), to find out more.
What has changed since the launch of Industry 4.0?
RS: When Industry 4.0 was first proposed there was a dystopian view that humans would be replaced by robotics, with the factory of the future having far fewer employees than we do today. That hasn’t come to pass. In fact, there was a 2015 report by Deloitte which identified that while 800,000 jobs had been lost to automation, more than three million had been created. And those roles were worth around £10,000 more than the ones they displaced. So, we’re seeing a drive for upskilling into higher value jobs.
An emerging trend is that data is now the new oil, but like oil, it needs refining to become valuable. If you don’t do anything with data, then it has no value and becomes a cost. This is a trap which manufacturers continue to fall into; they know data needs to be collected, but not what to do with it. And they don’t necessarily know what value they’ve got in the data they’ve collected and where to go for help.
The sheer volume of data is muddying the waters. People talk about AI and machine learning, which is all very well, but taking
It’s been just over a decade since the launch of Industry 4.0 at Hannover Messe. So, what has changed? Has the vision of the 4th Industrial Revolution been delivered, and do we need to consider how the last decade will shape the future of manufacturing?
ABOVE: The COVID-19 pandemic helped accelerate technology deployment as manufacturers needed to pivot quickly into the digital age
advantage of such technology must start with the correct data being collected in the right way. That’s data engineering rather than data science. Unfortunately, those sorts of skills aren’t necessarily being trained within a manufacturing context.
We need to start teaching young people about the use and value of data at primary school level. We can’t put the technology on a pedestal as something only accessible to the few due to the skills required to work in
BELOW: The last ten years has seen a plethora of technologies arrive to assist manufacturers
that space. We’re seeing a lot of tools being commoditised, but we’ve got to get people thinking with a data-centric mindset; that’s absolutely key.
A plethora of technologies have arrived on the factory floor, but many are still siloed because of the challenges around connectivity and cyber security. Some are still stuck in proof-of-concept, or pilot purgatory, and struggle to progress beyond that phase because the broader adoption of such technologies across the enterprise has not been considered.
It’s true that some manufacturers are accelerating technology deployments and identifying the benefits; and the pandemic helped with that because it enabled companies to pivot quickly into the digital age. However, others have struggled to start that transformation journey, have become bogged down with proof-of-concepts, and continue to wrestle with three fundamental questions that still need to be answered around skills, ROI and security.
As far as skills are concerned, we’re at a tipping point, as we are going to be the only generation that transitions from analogue into digital. So, the sector is looking around for the skills to make that happen. In the future, digital will be implicit, not explicit for manufacturing and the skills to enable that will be vital.
There is still a huge question around return on investment (ROI). Manufacturers considering investment in digital technologies want to know what they are going to get back and when. Unfortunately,
the companies that have already adopted and embraced transformation view it as a competitive advantage, so they tend not to broadcast how they are saving money, time, and what is enabling them to be more productive.
In addition, due to what’s happening in Ukraine, the cyber threat has never been bigger. The protection of national infrastructure is absolutely key. And while that’s traditionally been transport, utilities and power, manufacturing is beginning to be mentioned in the same breath due to the contribution it makes to gross domestic product (GDP).
If you don’t do anything with data, then it has no value and becomes a cost. This is a trap which manufacturers continue to fall into
Professor Rab Scott, Director of Industrial Digitalisation at the University of Sheffield Advanced Manufacturing Research Centre (AMRC)
What gaps need filling to make the Industry 4.0 vision a reality?
The Made Smarter National Adoption programme is helping companies to understand the value of Industry 4.0 and to start their journey; but the impact of the programme has been slow to be realised. There’s still a lot of hype clouding the landscape, but if you distil the concept down to its fundamentals, the core of Industry 4.0 is about reduction of non-value added activity.
Ultimately, people and organisations need places where they can go and see this happening to have that light bulb turned on. This is where the High Value Manufacturing (HVM) Catapult and other research and technology organisations (RTOs) really have a role to play in becoming demonstration sites, where people go to see what’s relevant to them without being ‘sold to’. If it’s a question of selling the technology, quite often the best salesman, and not necessarily the best technology, wins out.
had on Industry 4.0?
When Industry 4.0 was rolled out, it was solely about productivity. Now it includes the whole net zero and environmental, social and governance (ESG) agenda; this is a positive move. It’s not just about the bottom line anymore, it’s also the generation of wealth, and by that I mean mental as well as financial wealth.
This means giving people jobs in which they’re valued and allowing them to adopt technology to improve the quality of life in
• A 2015 report identified that while 800,000 jobs had been lost to automation, more than three million had been created
• Manufacturers know they need to collect data, but not always what to do with it
• Many technologies that have been introduced onto the factory floor are still siloed
• Manufacturers are still wrestling with questions over skills, ROI and security
• Much of the education around manufacturing is based around paper on glass processes
their workplace. All of these impact on net zero; if you improve quality and reduce your waste streams, you improve productivity while having a positive impact on net zero –the two go hand-in-hand.
The question then, of course, is whether we are merely going to manufacture more parts using the same amount of energy? That could potentially happen so this is where manufacturers have to become socially, as well as environmentally and economically, responsible. But we’ve certainly seen a pivot away from being purely productivity focused towards climate change and ESG.
BELOW: There is a fail fast mentality coming into manufacturing; people are willing to experiment with technologies, and simply move on if something is unsuccessful
Comparing the landscape at the dawn of Industry 4.0 with now, in the present climate there are very few technologies that are being allowed to mature slowly. There is a definite fail fast mentality coming into manufacturing, because people are willing to experiment, and simply move on if something is unsuccessful.
Technology is absolutely integral to this ethos and to where we have to bring the digital and manufacturing ecosystems together. Currently they’re still not completely aware of the opportunities that lie within each other.
Industry 4.0?
I don't think that we are providing fit-forpurpose people out of the education system. We are still teaching in Victorian ways. Yes, we might be using tablets and screens, but what’s fundamentally changed? Essentially the process is paper on glass. We need to be looking at more problem-driven educational systems.
There is a huge challenge facing all manufacturing – the recruitment of people with the appropriate skills. This is primarily because of the salaries that can be demanded in other fields, such as fintech, using similar digital capabilities. For the people with the skills manufacturers need, there are, unfortunately, opportunities elsewhere.
ABOVE: There are huge opportunities for companies that are willing to digitalise
The answer, I believe, is to start upskilling our manufacturing workforce. And that’s got to start within the apprenticeship realm, because they’re digital natives and people who are committed to manufacturing, and we should be giving them the tools they need. Ideally, that journey would have started in secondary or primary school, but let’s start with the people who are already in the sector.
What’s the importance of transparent supply chains?
More and more, companies are being driven by the net zero and ESG agendas and going forward, that means the way supply chains transact will have to change. That will mean a change of mindset will be required among manufacturers. For example, we now need to be far more open to sharing data; data has traditionally been held back because it represents an organisation’s USP. In reality, if data is shared, then huge opportunities and benefits can emerge, because areas of collaboration that didn’t exist previously are all of a sudden opened up.
To do that, however, we’ve got to have the capability and tools to be able to share that data securely and to trust the data that’s being shared. There are two levels of
trust - the trust that the data hasn’t been intercepted and corrupted during transfer, but also the trust that the original capture of that data is being done in a proper and correct way.
So, we’ve got to trust the transmission of data and its use in making decisions. As we move towards the net zero agenda, everyone is getting worried about Scope 3 emissions. However, your Scope 3 emissions are someone else’s Scope 1 and 2. So, we need to start capturing Scope 1 and 2 in a robust, repeatable way, but then also be open to sharing it.
In the short-term, there are huge opportunities for companies that are willing to digitalise. There will have to be mindset change, however, and I don’t know when this is going to happen. A key part of the future vision from the perspective of a large volume manufacturer is to be able to reconfigure quickly to perform small batch production and increase agility and flexibility. But where does that leave the small companies that are currently filling that space? They’re going to have to reinvent themselves.
More manufacturers will need to shift from a sole focus around the products they create, and look carefully at the upstream supply chain and the downstream product in service; that’s what will drive new business models and new ways of working. I think that we’ve got the manufacturing base in the UK that can embrace those sorts of changes and really benefit from them.
Reading this at Digital Manufacturing Week 2022? On the afternoon of Day 2 of Manufacturing Leaders’ Summit (MLS), 17 November, Professor Rab Scott will look at the current global challenges, emerging technologies, the skills required, the challenges the supply chain will face, and how manufacturers can overcome these hurdles.
In the future, digital will be implicit, not explicit for manufacturing and the skills to enable that will be vital
5G is the first mobile technology designed to support the digital transformation needed to deliver Industry 4.0. However, back in 2019, manufacturers were telling us that it was hard to visualise the benefits 5G would deliver, even though many recognised how advanced digital technologies could support industry productivity. What they needed was real-world examples, results and measures, and a clear picture of what would be needed for 5G innovation.
New use cases are delivering clearer understanding
In 2020, the UK government’s Department for Digital, Culture, Media and Sport (DCMS) launched the Industrial 5G Testbeds and Trials (IG5TT) programme, coordinated by Digital Catapult. It’s one of the UK’s key programmes for experimentation and learning from early deployments of 5G within manufacturing and logistics, engaging with industry, telecoms experts, business groups and the academic sector. Eight I5GTT projects (5G ENCODE; 5GEM-UK; 5G Factory of the Future; 5G CAL; AMC2; Smart Junctions 5G; 5G Ports; and 5G Logistics) have been identifying the real-world benefits, challenges and considerations
relating to 5G adoption through a wide range of use cases in manufacturing, transport and logistics, including:
• Using augmented reality (AR) and/or virtual reality (VR) devices (such as headsets) to support design, manufacturing and training, and provide access to on-the-spot support from remote experts
• Monitoring and tracking time-sensitive assets
• Providing real-time process monitoring and analytics, plus closed-loop control to reduce waste
• Switching autonomous vehicles to remote manual operation in emergency situations
• Tracking and tracing assets to improve scheduling and performance
• Using artificial intelligence (AI) to reduce traffic congestion and pollution while improving flow
Why not stick with 4G or WiFi?
While there are situations where 4G can be used (such as for tracking containers and pallets), it simply doesn’t deliver the rapid response and speed of data transfer that industry needs. And because WiFi is constrained by regulatory conditions, covering a
Jessica Rushworth, Chief Strategy & Policy Officer, Digital Catapult Phil Young, Director for Policy, Research and Strategic Engagement at Digital Catapult, looks at how multiple new use cases are evidencing the real-world benefits and value of industrial 5GYoung, Directorfor
Policy,Research and Strategic Engagement at Digital Catapult
We have gained practical technical knowledge on how to make Industry 4.0 use cases work within 5G powered wireless digital infrastructure
comparable area at the same quality of service as 5G would be difficult and more expensive, even considering additional 5G costs.
For example, as well as securely tracking goods and equipment as cranes and containers move through ports, 5G can also enable traffic management at smart junctions around the port and support automated drone flights for port police operations. It also enables the adoption of technologies that require significantly higher throughput, such as predictive maintenance systems, without the need for a physical network.
In some trials, WiFi could potentially have met some of the requirements, but it lacks the security and reliability advantages of 5G, especially when it comes to supporting the use of mobile devices such as VR headsets.
A private 5G network also provides essential additional security for manufacturers who are cautious with their data and want to process it locally. Most projects reported that they implemented all 5G security measures, and some provided enhanced levels of security for industrial devices, such as certification for non-5G elements that could be validated when the device registered on the network.
There’s still a way to go, but we’re making great progress I5GTT project partners, industry vendors and DCMS have been able to make rapid progress in addressing some of the challenges identified, and in taking advantage of relevant opportunities through shared learnings.
“We have gained practical technical knowledge on how to make Industry 4.0 use cases work
• Real-world benefits of 5G are starting to be realised
• 5G offers speed, reliability and security advantages over 4G and WiFi
• Much of 5G is still very much consumer-focused
• Collaboration between telecoms and industry will be key
Find out more about the Industrial 5G Testbeds & Trials programme and the projects involved here: K www. digicatapult.org. uk/how-we-canhelp/what-weoffer/programme/ industrial-5gtestbeds-and-trials/
within 5G powered wireless digital infrastructure,” said Jessica Rushworth, Digital Catapult’s Chief Strategy & Policy Officer. “This has translated into a deeper understanding of the potential business value of different technologies. Most importantly, it has given us valuable insight into the challenges of adoption within industry.”
Even as understanding of the benefits of 5G increases, there are still challenges to be faced. Until recently, 5G specifications, standards and system integration guides and expertise have mainly been focused on the consumer domain. Availability of 5G compatible industrial products is limited. And there is still a lack of 5G expertise in industry.
To fully realise the value of 5G, collaboration between the telecoms industry and other industry sectors will be vital. A closer working relationship will deepen and broaden the exploration of what is possible, as organisations learn together how existing 5G and new systems can be integrated and deployed in real-world environments, and how new business models will evolve over the coming months and years.
“The next stage, as the technology matures and some of the technology barriers are overcome, is to understand better what the blueprint for a 5G-enabled advanced digital infrastructure for industrial enterprises will be, and to create the supply chain that can meet its requirements” added Dritan Kaleshi, Digital Catapult’s Director of 5G Technology.
Maintaining momentum and keeping testbeds under active development will help to create demand for Industrial 5G, so that we can consolidate the UK’s status as a growing leader in the 5G innovation space, and accelerate the transformation to Industry 4.0.
Although it took four trains to get down to Dorset to visit the Bournemouth-based factory of Parvalux, it was incredible to see how essential DC motors are to such a variety of applications as diverse as golf buggies, medical air pumps, ventilators and even honey extractors. Electric motors are the beating heart of a whole plethora of products; chances are if it moves there’s a motor involved somewhere.
Electric motors are everywhere; from the moment we brush our teeth in the morning to when we go to bed with the gentle murmur of a fan. Throughout our day at work and at home, many items we use have a motor; you could be using a Parvalux motor without even realising it. Everyday household items, including white goods such as dishwashers, washing machines, microwaves and fridges, are powered by DC motors, which convert electrical energy into mechanical energy.
Starting the day with a hearty English breakfast in our Poole hotel, my colleague Tom St John and I suddenly realised we’d spent way too long stuffing ourselves with hash browns and needed to get a move on. On our way to Parvalux, driving through the rainy streets (even though it was August), we found ourselves in a back-and-forth disagreement as to whether he drove through a red light or not - to this day I am convinced that he did; perhaps this is a mystery the editorial team can solve in a
LEFT: Parvalux’s electric motors have end application use in industrial automation, agriculture, materials handling, building automation, mobility solutions, leisure, medical devices, transport and logistics
ABOVE: Parvalux will soon amalgamate its operations from its three existing factories and the administrative functions to create a single, purpose-built manufacturing centre
future episode of The Manufacturer Podcast. When we finally arrived at Parvalux, our first task was to put on a pair of PPE over shoes with steel cap toes. These made me look like a female version of Krusty the Clown, and it’s safe to say the shoes did not match my outfit - but sometimes safety comes first.
Our hosts for the day, Managing Director, Doug Sheppard, and Marketing Manager, James Cope, explained that Parvalux was first established in 1947 by Mr L. Clark in London, where he provided motor rewinds and repairs. The business relocated to Bournemouth on England’s sunny south coast in 1957, where it began designing and manufacturing complete gear motor units for industrial applications. In 2008, Parvalux acquired Essex-based EMD Drive Systems, nearly doubling the company's turnover in the process. The Clark Group’s ownership of Parvalux came to an end in December 2018 when maxon motor, a specialist for mechatronic drive systems, acquired the company.
Parvalux’s electric motors have end application use in industrial automation, agriculture, materials handling, building automation, mobility solutions, leisure, medical devices, transport and logistics and have worked extensively with F1 teams in the automotive sector. However, its most significant sector is medical –Parvalux motors appear in stairlifts, patient hoists and crucially worked closely with the government during the COVID-19 pandemic producing ventilator motors.
Currently Parvalux has three different production sites, which we were given the opportunity to visit, starting with the headquarters that house administration, design engineering and test functions. This factory is set up to manufacture one-off and low to medium volume production motors across the company’s entire spectrum of range and options. As volumes increase, the production process adapts accordingly and hands over the production lines to the High-Volume Production team. The HQ factory is run as an independent business unit, on lean manufacturing principles that incorporate manufacturing engineering measured against daily production targets.
It’s no secret that UK engineering and manufacturing are suffering a massive skills shortage, and many manufacturers have described it as their biggest challenge. However, walking around the factory floor we saw a diverse mix of people of all ages, genders and ethnicities. Doug explained that Parvalux is very proud to have achieved a near 50/50 split in terms of the gender demographic, which is quite unusual in the manufacturing and engineering industry. The company has set a goal to become more diverse and make itself more dynamic.
He went on to explain that the company is heavily invested in improving the skills gap, acknowledging research that shows that having a more diverse workforce allows better decision making. Manufacturers in all industries are currently feeling the pinch of the skills shortage and so Parvalux has the ambition to open up its own academy over the next five years, working with schools and colleges to bring students through the
We don’t want to invest in automation to lose people; it’s a case of investment in automation to upskill our teams and allow them to go on to bigger and better things in their job roles
Doug Sheppard, Managing Director, Parvalux
Digitalisation and sustainability come with a cost. However, Parvalux has invested heavily in both. Can you explain how?
DS: Parvalux is not a short-sighted company; our owners are incredibly passionate about investing in the longterm. We have set a company mission for 2030, 2040 and 2050 and when they invested in the new site, the owners asked us to look at a 50 year plan. The goal behind that was all around Parvalux’s investment in innovation, sustainability and digitalisation. And while digitalisation isn’t accessible to everyone, I’ve noticed over the past 12 months, particularly working with The Manufacturer, that there’s a lot of digital manufacturing events taking place. While some technologies have traditionally been inaccessible for many companies, particularly SMEs, it’s now becoming more readily available and more cost effective to adopt. We’ve been able to partner with a number of companies to invest in a machine shop, which is able to measure current form and the efficiencies in our CNC machines. It’s a cloud-based system so it’s very accessible and can be up and running within two weeks. It now gives us meaningful data on our factory which we can use to improve the business going forward.
Parvalux has been in existence for 75 years. How are you planning to embrace digitalisation?
Naturally, a 75-year-old business is going to have a legacy of some old equipment, as well as new. We’ve recently approved a £3m investment in capital equipment to
go alongside our new facility, because we want to invest in our people, skillset and technology. We don’t want to move into a brand-new manufacturing building with our 50 year old machinery equipment, so we’re currently looking into how our systems are automated, but then also what that means for our people.
We don’t want to invest in automation to lose people; it’s a case of investment in automation to upskill our teams and allow them to go on to bigger and better things in their job roles.
How are you seeing the general adoption of digital in the manufacturing industry?
Electric motors are quite a functional product and they're quite mechanicalbased, but we're starting to see more innovation in that area in terms of digitalisation. We’re looking at technologies and solutions that our parent company are working with, such as how they embed cloud-based systems and maintenance into their mechanical products.
So we’re combining the service-based sector with the physical, and that's something we don't see too much of at the moment. To give you an example, it could be that in a couple of years we’ll be supplying electric motors that can tell our customers when it’s time to perform maintenance, rather than risk the product breaking down and then having a bigger issue further down the line. It’s a really exciting time to do that but it’s in an industry that’s not necessarily attuned to digitalisation; it’s motivating to be at the forefront of that while also helping the industry get on board.
BELOW: Electric motors are a mechanicalbased product, but Parvalux is starting to see more innovation via digitalisation
T-level system into apprenticeships across the business. Parvalux’s aim is to tap into local talent, but to also give back to the community by providing access to jobs.
We then travelled in convoy to visit the next facility which wasn’t far away, the High-Volume Production facility, which takes care of the higher quantity orders. It operates three independent flowlines, each supplied by Parvalux’s own in-house winding section and sub-assembly lines. It is entirely self-sufficient and delivers to customers directly. Similar to the HQ production facility, the Parvalux HighVolume Production facility operates semiautomatic winding machines to produce armatures from spindles and laminations, wound with copper. Parvalux’s lean methodology journey has begun, with its goal being to create a true Centre of Excellence for winding and assembly of custom designed, application specific, geared motor solutions.
BELOW: Parvalux is very proud to have achieved a near 50/50 split in terms of the gender demographic
The company is heavily invested in improving the skills gap, acknowledging research that shows that having a more diverse workforce allows better decision making
Doug Sheppard, Managing Director, Parvalux
Unfortunately, we didn’t have time to visit the Parvalux Machining Centre of Excellence (I’m going to blame us for overindulging on one too many hash browns for breakfast), but we were given the low-down from Doug about how the site operates. It is responsible for manufacturing a wide range of different components used in the production of motors and gearboxes. This includes shafts, machined castings, stators, rotors, and gears that are later used in the assembly of geared motor solutions. This facility is able to produce high-volume, quality components in a very short space of time. Finished, fully tested components are then sent to the assembly facilities ready for use in the production of geared motor solutions.
However, soon these sites will be no more as Parvalux is expanding. The company will amalgamate its operations from the three existing factories and the administrative functions to create a single purpose-built manufacturing centre. We got to visit the 8.75-acre development and it was amazing to see all the work that has taken place since construction begun in 2020. Speaking on the job opportunities created by the new facility, Doug explained that over 200 new faces are expected to join the company by 2030, and as Parvalux is on target for its third consecutive record year, he expects
even more to be added in the coming years. The new production development is incredibly exciting for the local community and further shows the company’s commitment to the local economy, as well as growing the Parvalux brand.
• Electric motors are the beating heart of a wide variety of products
• Automation doesn’t have to mean losing people; it can upskill teams and allow them to go on to bigger and better job roles
• Tap into local talent to ensure you are giving back to the community by providing skilled jobs
• Despite the cost, investing in digitalisation is worth it when it gives back meaningful data that can be used to improve the business
Scan the QR code to view the video of The Manufacturer’s site visit to Parvalux
sustainable goals
Manufacturing is the largest emitting industrial sector, generating 16% of total UK greenhouse gas emissions in 2019. This means that if the UK is to meet its target of becoming net zero by 2050, manufacturers have a considerable part to play. With such a big push towards sustainability and renewable energies, it felt a little silly to be asking what Parvalux is doing in this regard when we were stood on top of its solar panel lined roof.
Doug explained that the company is incredibly passionate about sustainability, further strengthened by the maxon motor acquisition, a company which also has sustainability and environmental impact at the forefront of its business.
A key feature of the new multi-million pound facility, and one of Parvalux’s primary aims, was to create a carbon neutral factory. The site is on target to achieve this thanks to approximately 1,500 installed solar panels, with capacity to add more as the company grows. The installation will give Parvalux the foundation to achieve carbon neutrality by 2030.
Only around 19% of the approximate 90 billion tonnes of raw materials extracted worldwide each year is currently recycled or composted, with about 81% dumped, incinerated or sent to landfill, according to Deloitte's estimates, and that volume is expected to double by 2060.
Meanwhile, the Ellen Macarthur Foundation, the global group focused on promoting the circular economy
By harnessing technology-driven insights, manufacturers have the capacity to redesign themselves and their products to maximise reuse and recycling as a share of overall resource use
concept, has estimated that developing circular business models, in clothing manufacturing alone, could be worth $700bn overall by 2030. However, that won't happen if 'circularity' is treated simply as an add-on to a traditional, more ‘wasteful’ way of doing business.
Instead of campaigns that simply incentivise customers to return products for resale, remanufacturer or recycling (by offering vouchers for new product purchases), the foundation urges businesses to rethink performance indicators as well as customer incentives and the customer experience in ways that encourage increased and more sustainable use of the same raw materials.
“Products need to be designed and made to be physically and emotionally durable, and able to be remade and recycled at the end of their use,“ the organisation states. “Co-create supply networks able to circulate products locally as well as globally.“
Operations and logistics expert Emile Naus, Partner at supply chain consultancy BearingPoint, suggests that this really puts the onus on redesigning products so they can be rented, resold, remanufactured or otherwise reused.
“With product design, that's something where, as manufacturers, you can do a lot; probably 75-80% of the issues are created at the beginning. So if you design well, you can build in circularity,“ he said.
Sectors such as automotive parts, and increasingly in some electronics such as smartphones, already have some solutions involving supply chain collaboration.
A blast from the past?
Other past collaborative efforts include the Netherlands' previous glass bottle standardisation programme for exchange and recycling. Schemes of that sort might look ripe for revival, especially when supply chains can use digital analytics and computers to share data and work together for economies of scale.
“Manufacturers agreed to use the same shape, colour and spec of bottle. Any bottle could go back to any manufacturer for cleaning, relabelling and reuse via a deposit system where retailers charged customers, incentivising them to bring them back,“ Emile explained.
This may entail jettisoning ideas around differentiating via packaging to some extent, and may not even require any fancy tech.
Ultimately, organisations can collaborate on the materials to use, the most efficient storage strategies, how to put it all together and create a 'return' revenue stream - as well as redesigning the supply chain itself to meet these needs.
Some changes will need to depend on top-down regulatory shifts to ensure that value can be created, but there's little stopping manufacturers from sharing data and developing more circular industry-wide approaches, meanwhile.
“The question becomes how committed are you to this sustainability?“ Emile added. “Is the product merely technically recyclable, or is it economical to recycle - that's much harder. Too many things are branded as recyclable because you can put them in recycling, but that often doesn't happen if it's cheaper to buy new raw materials.“
The benefits could be huge Roger O'Brien, Project and Technical Lead at the University of Sunderland's Sustainable Advanced Manufacturing project, said working together towards reducing waste and achieving a more circular economy within manufacturing could deliver “huge“ economic and environmental benefits, with manufacturers reducing purchases of raw materials and therefore the associated costs.
“One of the most efficient ways is through the introduction of alternative recyclable materials into the production process, allowing end-of-life products to be fully recycled,“ he said.
For those reasons, manufacturers should collaborate on removing obstacles to achieving this, especially in terms of education. Many companies
RIGHT: BearingPoint's Emile Naus: Collaborations can redesign the supply chain itself to meet circular economy needs
Investing in recyclable materials could increase demand for products due to their green credentials
Roger O'Brien, Sustainable Advanced Manufacturing project at the University of SunderlandFleur Doidge is a contributing writer to The Manufacturer and themanufacturer.com
are reluctant to switch to new, greener materials and processes due to the perceived costs, when closing the loop could offset “significant“ capital outlay over time.
Data-based insights from ERP and other business software platforms are already able to help prove the business case, incorporating new technologies such as 'near-net' manufacturing, including additive manufacturing, which reduces additional operations and finishing, he added.
“Investing in recyclable materials could increase demand for products due to their green credentials and there could be cost savings from reusing recycled material or even remanufacturing products,“ Roger said. As an example, the SAM project stands ready to help with the education task of breaking down barriers to process and product improvement.
ABOVE: Schneider's Mark Yeeles: A partner programme has helped Schneider reduce resource consumption by 157,000 metric tonnes through retrofit, recycling and take-back
• 81% of extracted raw materials is dumped, incinerated or sent to landfill
• In clothing alone, 'circular economy' business models could return $700bn by 2030
• Measuring and metrics is keywhich means leveraging data using digital technology
• For maximum benefit, data and insights should be shared up and down the supply chain
• With this information, the industry becomes empowered to increase circularity
Jinender Jain, Head of Sales for the UK and Ireland at digital transformation and business re-engineering services provider Tech Mahindra, suggested that data-driven insights can as easily help businesses trying to achieve circularity while managing inflation, cost of living and resilience pressures in the same breath.
“From a strategic vision perspective, there is a huge drive to avoid waste,“ he agreed. “And demand from consumers is driving discussion.“
Jinender echoed the overall perspective of Emile Naus, Roger O'Brien and others. Business intelligence and analytics, garnered via monitoring and management software in the enterprise, is key to driving collaborative efforts on circularity and the elimination of resource waste, because
BELOW: Improved policy and practice can be devised and applied to single organisations and across the supply chain as a collaborative effort
it increases the availability of quality information that can be used to make valid business decisions.
Data on how products might be repaired and reused can be analysed and conclusions founded on sufficient bedrock for the enterprise to move forward, without waiting for regulation to mandate change.
It can also free up in-house resource to focus on collaborative or individual efforts, not only on developing but implementing improved designs that help reduce waste and reach circular economy goals. Repairs and maintenance can be made easier and shelf lives lengthened, all of which helps move an industry nearer an ideal of zero waste.
“That's the first thing which is going to help in the circularity of the economy. Right now, we are in the region of being at somewhere less than ten percent of the economy - with billions of tonnes of waste going to landfill,“ Jinender said.
Extracting core materials for recycling and reuse must be coupled with a linked-up approach that takes in the whole supply chain through traceability of materials for retrieval, for example.
Suppliers of goods and services, including IT, to manufacturing and retail, are also key partners here, he noted, especially because, while solutions vary, accurate data sharing for transparency which can be acted upon is crucial.
“There are different ways of going about these things. You may need to change your manufacturing or shop floor design. You may need to keep the cost down as well. It is not easy,“ Jinender added. “Cost per unit may go up.“
Collaborative efforts should devise more approaches that can be implemented without top-down mandates from government. Without grassroots and industry action from the first instance, progress on circularity may remain glacial, he noted.
Jinender gave a practical customer example in packaged medicines, typically retail, with mandatory, multilingual leaflets detailing side effects and other information. The company realised that almost no one reads the leaflets, and the resources for creating them are largely wasted.
A team-and-customer hackathon came up with a solution: adding a scannable code or link to full details
online on the box, instead of providing the traditional leaflet.
“It was a large saving,“ said Jinender. “It has completely done away with the need for putting a paper inside a three-package medicine box. It is now rolling out in Asia-Pacific. For some other countries permissions are sought.“
Regulations in force sometimes leave considerable scope to make changes that aren't always explored. In this case, the actual stipulation was only that the information needs to be provided to the end user; it is left to the manufacturer to decide the best way of fulfilling this, the appropriate packaging materials to choose, and so on, Jinender noted.
“Then newer business models will appear,“ he said. “And technology is also going to catch up with this, providing the right level of information on the solution or problem. Can I have accurate information on tracking or products I am using? If I need to wash jeans 25 times, can I do it with a less water, or can I extract something more, or use less hazardous materials in my processes?“
Mark Yeeles, Vice-President of Industrial Automation at industrial IT manufacturer Schneider Electric, said the drive for circularity should become “more than a mindset“ - nearer a way of life for manufacturer communities.
“Many large industrial companies have said reducing carbon footprint is a top-three strategy - OK, great. But then you look at reports that show one in six hasn't done any mapping (of carbon use) at all,“ said Mark.
So a 'smart factory' programme will of course help as a start. Once you've got measurements, you've got data that can be analysed, with resulting strategies then thought through, defined and applied to improved policy and practice around organisations across the supply chain, as a collaborative effort.
Working with clear expectations scoped out, and applying an optimum circularity methodology, helps ensure the right principles are applied for the right purposes, which can be bigger than simply working with your own data and experiences.
“If you're a consumer packaged goods manufacturer, for example, your focus might be on packaging challenges, because that's the bit the customer 'feels', as it were,“ Mark explained. He added that devising and applying simple and partial changes that reduce waste can be a better way to go than trying to “boil the ocean“.
understanding of what peers are doing. Look for industry benchmarks on, for instance, energy use. He suggested that more of that sort of activity needs to happen.
SoftwareCollaborative efforts existbut could grow Certainly getting government funding can be “a bit complex“, but there are also catafalque-type groups around the country - or like the Manufacturing Technology Centre (MTC). In such groups, manufacturers can share insights and work towards developing circularity endto-end, with the right partners.
Mark Hughes, UK and Ireland Regional Vice-President at business software vendor Epicor, gave The Manufacturer some pointers on how to start closing loops further and faster by using data, noting that aspects of circularity have been applied by segments of manufacturing for decades (automotive being an honourable example). Epicor has worldwide automotive spares supplier Carwood as a customer as well as industrial equipment focused Radwell.
“It used to be the grey market. Now it's the green market,“ Mark quipped. “There's long been good examples, but it hasn't been mainstream.“
Quality traceability, trackability and reuse or repair rely on quality information about resources and supply chains, which means collaboration and communication must be rock-solid, especially if there is to be a return on investment.
ABOVE: Tech Mahindra's Jinender Jain: Regulations in force can leave considerable scope to make changes that aren't always explored
With supply chain disruptions and price pressures altering the sustainability versus cost and availability balance, using software to record, analyse and manage the required data will become a key method to meet challenges for resource, materials or product reuse, especially when intelligence can be shared to help make circularity efforts cost-effective.
“You can
look at machine builders and ask how they optimise their circular loops.“
Schneider's 'green premium' partner programme has helped it reduce its own primary resource consumption by “about 157,000 metric tonnes“ through retrofit, recycling and take-back programmes.
Understand objectives, establish baselines and set goals with an
“For some, sustainability is becoming integral in their manufacturing cycle because they can't source product from anywhere else,“ Mark reported. “Companies like Radwell are coming to the forefront because they've got product.“
Collaborative marketing efforts could include a focus on making end users more aware of the opportunities to source or purchase remanufactured or refurbished, as well as any add-on services such as extended warranties.
“So we've got to get better at using technology such as B2B or B2C collaborative selling tools,“ Mark said.
also
We've got to get better at using technology such as B2B or B2C collaborative selling tools
Mark Hughes, Epicor
Manufacturing is the largest emitting industrial sector in the UK, generating 16% of total greenhouse gas emissions in 2019. If the UK is to meet its target of becoming net zero by 2050, manufacturers have a considerable part to play
As more manufacturing businesses place sustainability at the top of their agenda, the benefits are becoming increasingly clear.
Commercially, moving toward greater sustainability can reduce costs and increase profits. However, it can also have a positive impact on talent attraction, development and retention – these days people want to work for a business with a social and environmental conscience. This is a topic Joe Walton, Director at Michael Page Manufacturing, discussed in a recent panel discussion on employee engagement with sustainability issues at the 2022 Sustainability Symposium hosted by The Manufacturer.
In September, Michael Page’s Senior Operating Director, Ruth Hancock, participated in the judging process for the ‘Sustainable Manufacturing’ category at The Manufacturer’s MX (TMMX) Awards. Here, she discusses the exciting innovations she saw during the judging week.
RH: Following the initial sift of participating companies, I visited the final five manufacturing facilities with the other judges and a moderator. The remit was the same for each business: a 20 minute presentation, followed by a site tour, Q&A and feedback.
The passion and commitment to sustainability was incredible. Every business had a clear and relatable strategy, and sustainability was the backbone to every business decision. The determination to make a positive difference shone through.
Each facility had their own unique challenges, from enabling low carbon energy generation to waste management and recycling, and they were all working in environments where
Ruth Hancock, Senior Operating Director of Michael Page Manufacturing
Ruth Hancock, Senior Operating Director of Michael Page
LEFT: The UK’s manufacturers are showing a passion and commitment to sustainability
Joe Walton, Director of Michael Page Manufacturing
The gala dinner and ceremony takes place on 17 November in Liverpool themanufacturermxawards.com
cost and quality were factored in at every stage. Some had been focused on sustainable manufacturing for over a decade, while others were just a few years into the journey.
By using the clarity and guidance that science-based targets provide, the manufacturers had all approached change differently. Some concentrated their efforts on their facilities for instance, by upgrading lighting and installing onsite wind turbines. Others looked at the broader ESG agenda, factoring in how sustainable and engaged their teams were. Many aimed big and adopted the
‘shoot for the moon, and even if you miss, you'll land among the stars’ mentality. If the idea is to reduce plastic in packaging, aim to eradicate it entirely.
Those businesses who have made steps towards engaging their entire workforce have an ace up their sleeve when it comes to attraction and retention. Increasingly, candidates are drawn to businesses which live and breathe their green credentials, and they want to be part of the shift. For that reason, businesses need to consider how they will approach ESG and sustainability, then build a communication strategy so that their employees, suppliers and customers can be part of the shift, without greenwashing.
Websites and internal communication platforms are an obvious starting point for this. I saw some great examples in a number of facilities where the business’s sustainability journey and plan were proudly displayed on the walls of the factory. This led to an increase in engagement and ideas.
I think there are a few key approaches which will stand manufacturers in good stead:
Be unique: One size doesn’t fit all, and the way in which a manufacturer becomes more sustainable depends on their product, process, facility, people and culture. For progress to be made at the pace required, sustainability needs to be at the core of everything. Some of the most innovative initiatives I saw came not from the senior leadership team or head of sustainability, but from the shop floor.
Be clear: Avoid getting lost in the details; there is so much that can potentially be changed, improved and achieved, that sustainability risks being a very noisy place where little gets done. Defined, quantifiable goals, and a succinct plan with regular reviews, are the route to success.
Be brave: Don’t wait for the solution to reach a standard of absolute perfection before embarking on change. Time is not on our side.
Be loud and proud: Tell your employees what you’re doing, what’s going well and what’s not. Tell your suppliers and hold them accountable for their green credentials. Tell your customers and ask them to come on the journey with you.
Finally, be generous: Share your success, failures, challenges and ideas with other manufacturers. Join forums and industry discussions and help the industry come together and succeed together.
At Michael Page Manufacturing, we are proud to be driving sustainability and transformation through our partnership with The Manufacturer.
To discuss any talent needs you may have, please get in touch today on the details below:
Ruth Hancock, Senior Operating Director of Michael Page Manufacturing
k Ruthhancock@michaelpage.com
Joe Walton, Director of Michael Page Manufacturing
k Joewalton@michaelpage.com
Increasingly, potential employees are drawn to businesses which live and breathe their green credentialsPEOPLE & SKILLS PARTNER CONTENT
Four years ago, Digital Manufacturing on a Shoestring was started by a team at the Institute for Manufacturing (IfM), University of Cambridge. Kate Price Thomas, the programme’s Marketing and Engagement Lead, tells us how Shoestring solutions have been deployed in 14 companies, helping them to start to digitalise
In 2018, we established Digital Manufacturing on a Shoestring in partnership with the University of Nottingham, a number of industrial supporters, and with initial funding from the UK Engineering and Physical Sciences Research Council (EPSRC).
Our aim was to try and help small and medium-sized companies (SMEs) to start digitalising; particularly those who didn’t know where or how to start or didn’t think they had enough budget or the right inhouse skills.
We began to survey and classify all the very low-cost technologies and organise them into a set of solution areas to meet the digital solution needs of small manufacturers. Our idea was to assemble solutions from ‘building blocks’ that could be reused, adapted and combined repeatedly.
By running workshops with over 300 companies and talking to them about their business priorities and barriers to growth, we combined priority business needs with potential digital solutions. And from those workshops, we extracted a list of 59 digital solution areas that address the needs of small businesses.
Solution areas included systems like job tracking, so you know where a job is at any one time on a production line, or inventory tracking so you can order products in time.
These are all simple, easy-to-implement solutions using low-cost tech, but which can have a massive impact on efficiency and customer satisfaction, as well as a company’s sustainability credentials.
In the past year alone, 14 industry partners
have used a Shoestring solution on their shop floors, and we’ve found that once one solution has been successfully applied, partners are keen to expand it, try another solution or go beyond Shoestring and purchase a more complex commercial digital system.
This was the case with Kemdent, a small dental manufacturer based in Swindon. The company was a classic example of a company ready to digitalise, but every time it looked at the market, it was left feeling bewildered. So, Kemdent approached us at Digital Manufacturing Week to see if we could help.
We organised an in-company workshop with its production supervisor and operations director to really understand and identify its top business needs. We then suggested solutions which could help.
By installing a low-cost temperature sensor (for less than £10) above one of its production lines, Kemdent was able to check that the dental wax cooled at the right rate to avoid hardening too fast and causing defects in the final product. The sensor, attached to a Raspberry Pi microcomputer, sends data to a dashboard so the company can see and collect data in real-time. It quickly discovered the optimal working temperature at which to control its process to minimise damage to the wax sheets during production.
Since installing that first sensor, the Kemdent team has now implemented sensors onto several production lines, improving the efficiency and quality of operations. It has also installed a large monitor on the shop floor to show employees the real-time temperature of all the production lines, helping them to identify problems quickly and have less wastage. And with a better understanding of how digitalisation can help the company and
the low-cost way
armed with better confidence, Kemdent has gone on to develop a second Shoestring solution, Overall Equipment Effectiveness.
Another SME, Snug Homes, a Bristolbased company who supply modular homes, came to Shoestring to explore if we could provide a solution which would help trainees identify potential issues so that they could rectify quality issues quickly and avoid repetition of error.
The company implemented a unified change management solution which meant users could upload new quality issues on a database while performing their tasks at the construction site or office, and then could assign these issues to a person to be solved and tracked. The solution, built using open-source database software, allows all quality issues relating to a project or set of tasks to be exported for review at the project review stage.
Lean manufacturing the Shoestring way One of the biggest roadblocks to creating fast sustainable improvements is the belief that sustainability is expensive. However, in practice, businesses can target quick no-cost, low-cost improvements like Shoestring solutions to improve efficiency, reduce waste and improve profits.
At least half of our solutions have clear sustainability impact. For example, one of the most popular Shoestring solution areas is process monitoring which gives you hotspot visibility of how to improve and use your equipment better. This helps companies to do things more efficiently and quickly, meaning less energy usage and therefore less wastage. Another one which has high impact is product use monitoring – these solutions let you know how much equipment is being used so you can plan maintenance more effectively.
Recently we completed an evaluation of 15 Shoestring industry pilots that have been developed for 14 companies.
We found that already, over 60% of the deployed pilots are starting to see benefits such as labour time and cost saving; improved process and production efficiency; increased information availability and accessibility; and increased knowledge and enthusiasm about digitalisation.
What we’ve learned is that Shoestring is about organising and involving a small business in the digitalisation process, rather than just providing it with solutions and hoping those solutions meet its needs.
The selection and specification workshops are crucial - making sure that the solution fits the company’s top business need. Everyone’s language is
different, so you need to take time to break down what people really need. Working very closely with, and listening to companies and making sure they are engaged from the outset is key to helping develop and facilitate the solution. It’s about engaging senior and junior level employees too, and building a team that is working together to develop their skills.
Reduction in product defects or human error
Saved employee time
Increased production efficiencies and improved processes
Increased information availability/ accessibility
Increased knowledge/enthusiasm about digitalisation
Reduction in waste and the use of energy/raw material
Increased worker satisfaction
Working very closely with, and listening to companies and making sure they are engaged from the outset is key to helping develop and facilitate the solution
24
The Shoestring solution has been easy to deploy, lowcost, low-risk and has given the staff something new to engage in. It has given us a great introduction into digital manufacturing and to anyone out there who is thinking about getting involved, I would say give Shoestring a call, you’ve got nothing to lose
Implementing this system while working on our single module tiny home has enabled us to start small and test with our core crew and on-site team prior to our next multi-module home. We anticipate the tool being of great value as we scale up operations and are currently writing new starter inductions that cover the use of this tool
Ford, Consultant, Snug Homes1. Process monitoring: To visualise and understand key variables or outputs within production processes.
2. Supply chain monitoring: To understand and keep track of the status and health of activities conducted in supply chains.
3. Energy wastage monitoring: To record and report energy usage with the company so that it can be understood and reduced.
4. Wastage monitoring: To measure, record and report waste within the company so that it can be understood and reduced.
5. Equipment monitoring: To streamline the process of diagnosing and correcting issues with equipment.
The Digital Manufacturing on a Shoestring approach shows how it is possible for smaller companies with small budgets to capitalise on advances in technology and implement low-risk digital solutions. Looking ahead, we are now transitioning Shoestring into a community programme. Having proven that this approach works, we are now looking at testing the best ways for companies to build the solutions themselves, including how to facilitate low-cost external support. We will also work with the community to help create a library of Shoestring solutions for other companies to use or adapt.
• The Digital Manufacturing on a Shoestring approach offers lowrisk digital solutions to smaller companies without big budgets
• Solutions are all being developed so that they are simple, easy-toimplement and use low-cost tech
• At least half of the Shoestring solution areas have clear sustainability impact - improving efficiency, reducing waste and improving profits
• Shoestring is about organising and involving a small business in the digitalisation process
• Once one solution has been successfully applied, partners can see the impact and are keen to try the next one, or specify a more complicated commercial digital solution
Our vision is that Shoestring will be a hub with all the tools, resources and expert advice, but is driven by regional experts who understand how to use Shoestring and can really drive uptake. These experts may be working in further education colleges, be representatives in the local manufacturing networks, or regional business development managers who support the work of the local enterprise partnership, district council, innovation centre or growth hub.
Shoestring is still in the development phase, and keen to work with any company or organisation who think it might like to get involved in one or more of a range of Shoestring Digital Manufacturing activities. Visit www. digitalshoestring.net to find out more.
If you are interested in finding out how your company or organisation can get involved with Shoestring, or would like to know more, come and visit us at Digital Manufacturing Week 2022. There will be live demonstrations of Shoestring solutions and a keynote talk by our Founder, Prof Duncan McFarlane.
Meet Neil.
Whilst driving, Neil spotted a distressed woman frantically waving. The woman had been stranded for hours with a young child.
Despite many passers-by, no one had helped. Neil turned around and stopped. He called for a recovery unit and made sure both she and her child were safe.
Digital
Jonny Williamson reports
Three things dominate current discourse: economic growth, wealth equality and the race to net zero. Reasons for why this is the case are starkly evident. How these goals can be successfully delivered, however, is a source of intense debate, one which cost Liz Truss her premiership and in record time, no less. The task is made harder by the trio being intrinsically linked; they cannot and should not be tackled in isolation.
As countries strive to create fairer, greener and yet more productive societies and economies, relatively few acknowledge the vital role manufacturing plays. The UK government is especially guilty, with no industrial strategy and seemingly no desire to implement one. Indeed, the Minster for Industry, Jackie Doyle-Price (at time of printing), has said she doesn’t even like the term ‘industrial strategy’.
Yet, manufacturing – specifically, digitally-enabled manufacturing – will be a core enabler of the future we want. One in which everyone has the things they need at a price they can afford without causing harm to the environment or society. That was the message to delegates who attended the inaugural InterAct Network conference in October.
A diverse roster of speakers drawn from across industry, policy, think-tanks and academia shared their unique insights and perspectives on what it will take to create a future digital manufacturing ecosystem that delivers for everyone.
technologies are reshaping our economy, manufacturing ecosystem and workplace. Though painful, these changes will enable us to meet our net-zero ambitions, while being resilient and productive.
In his opening keynote, Tamim Bayoumi, Deputy Director at the International Monetary Fund, described how technology has historically widened many forms of inequality, particularly during the IT revolution which took hold around 1980.
Tamim explained that new technologies require new skills. This raises demand for such skills at a time when supply is limited. The resulting wage premium skilled workers can command increases inequality, albeit only initially. Over time, demand for new skills slows and the supply increases which leads to less of a wage premium and lower inequality.
This notion, introduced by American economist Simon Kuznets in the 1950s, broadly holds true for all three Industrial Revolutions to date. Steam, electricity and computers have each provided a myriad of uses that have transformed our lives and the economy. Their impact on inequality has also been similar – an initial rise followed by a plateau.
Does this mean the current Fourth Industrial Revolution will follow the same path? Not necessarily, but we have to accept that IT has created greater inequality than any other technology. This is due to the profound effect IT has had on the economic geography of prosperity.
“Historically, manufacturing required low-skilled labour and land. Factories were therefore located in relatively small towns or on the fringes of larger cities. In 1985, for example, Toyota built its largest US plant in Georgetown, Kentucky; population 30,000.
“By contrast, the main input to IT is skilled workers. Hence, why most IT companies base themselves in cities and large towns,” Tamin noted.
The relocation of cutting-edge industry from small, less prosperous towns to large, wealthy cities over the past 50 years has deepened inequality along three dimensions:
1. Higher demand for skilled labour has benefitted the educated versus the unskilled
2. Rapid urban growth has raised land prices which has benefitted (generally) old and well-off land-owners versus the young and poor
3. Urban prosperity has come at the expense of towns, even as the high cost of housing has made it more difficult for people to move to these prosperous cities
Manufacturing is being disproportionately affected by the recruitment woes facing numerous sectors, with around four vacancies for 100 manufacturing jobs in the country. This is more than double the usual level of vacancies which typically stands at 1.9 per 100 jobs, and even surpasses the hard-hit hospitality sector, which is running at 3.6 per 100.
Industry’s long-standing recruitment challenges are being compounded by the very nature of manufacturing undergoing a transformation. This can be seen on four fronts, said Bhavina: “Automation, digitalisation, greenification [sustainability] and flexible work.”
Bhavina Bharkhada, Head of Policy and Campaigns, Make UK
IT’s transformation of multiple sectors, not least manufacturing, has seen the zone of prosperity widening out from major cities to other places. However, this can’t be allowed to result in a corresponding expansion, or indeed continuation, of inequality.
Avoiding such a scenario means providing places that have been left behind with the tools to win in the IT age. Most obviously, education that is focused on the skills needed in the future digital age.
“We also need to do more to help those with talent but limited means to move to where opportunities are through housing support,” Tamin suggested. “We need to pay for both these initiatives. Those who benefited most from the IT revolution, the skilled and landowners, should contribute most via an increase in the marginal tax rate.”
The theme of skills was picked up by Bhavina Bharkhada, Head of Policy and Campaigns at Make UK, who noted that labour is the primary challenge facing manufacturing businesses. The sector is battling to fill 95,000 vacancies which Make UK estimates equates to around £7bn in lost output for the wider UK economy or £21m a day in lost GDP per worker.
Skills are at the heart of each of these areas, with the digital skills gap considered the biggest barrier to wider technology adoption. On-site working practices are changing rapidly thanks to digital developments such as virtual reality, artificial intelligence, 5G, robotics and additive manufacturing. This has led to a rise in demand for skills such as cyber security, programming and software development, among others.
Additionally, almost two-thirds of manufacturers are changing their skills strategy in order to manufacture products more sustainably, with 40% believing greenification is a key factor driving changes to how they operate and the skills and jobs which their businesses need. As a result, Make UK has seen rising demand for skillsets relating to:
• Resource efficiency (carbon accounting, lean manufacturing)
• Low carbon economy (nuclear and renewable energy generation, carbon emission minimisation)
• The development of new or amended products (circular design)
Something often overlooked is the importance of strong management and leadership during times of change, Bhavina noted. Most manufacturers agree that these skills are key to increasing the adoption of new technologies, yet less than ten percent of training budgets is spent on leadership. This is something being acutely felt by SMEs, many of which identify a lack of access to management skills as a barrier to their future growth.
Bhavina concluded by outlining how government policy could help smooth the transition toward the future of work:
The fight
means manufacturers need to FIGHT for talent
• Create an Employer Training Fund by reforming the Apprenticeship Levy: a portion of unspent levy funds should be ringfenced to support the upskilling and retraining of existing employers
• Introduce a Training Investment Allowance: expand the current tax exemption for work-related training, providing a tax rebate on investment in training for existing employees
• Expand the government’s Help to Grow Management scheme; the current eligibility of ten to 250 employees is restrictive
The UK is the ninth largest manufacturing nation in the world; France is eighth and Italy is seventh. All three countries have a similar manufacturing output but France and Italy have twice the UK’s level of automation. Moving up the rankings requires the UK to invest in automation and upskilling. Yet, automation frequently carries a negative connotation.
Troy Barratt, Managing Director of Kent-based Contracts Engineering Limited (CEL), passionately advocated a quick and effective change leaders can make when discussing the arrival of new technology, especially automation.
“Deskilling is a horrible word used to describe the process where skilled people are replaced by machines, but in most instances, this is not what actually happens,” Troy noted. “Usually, when companies invest in software or plant to drive productivity, it leads to workforce upskilling.
“Not only is deskilling the wrong word but it also drives a wedge of distrust creating an ‘us and them’ attitude between teams that should be working together.”
Automation will be crucial to successfully reindustrialising the UK, it will provide much-needed capacity and enable the country to manufacture cost-competitively on the world stage. Troy encouraged reframing the discussion to change people’s views of automation from a job-killing negative to a careercreating positive.
“What sounds better?” he asked. “Let’s deskill manufacturing jobs and add automation to reindustrialise the UK, or let’s upskill our manufacturing workforce using automation to reindustrialise the UK; which will add more well-paid jobs?
“It’s a trick question because we’re talking about the same thing. An automated factory will need skilled operators, engineers, computer scientists, programmers and technicians.”
Troy is speaking from experience having invested in both factory and back-office automation. CEL currently has one cobot and one robotic welding cell, with plans to be at five-plus by the end of 2023.
“We spend a lot of time and effort on training and upskilling the team in the factory and the offices. This helps to create buy-in for investments,” Troy concluded. “Additionally, because we’re coming from a small base, investments are a win-win for the company and the team. And yes, since investing in automation, our workforce has grown.”
Aimee Doole’s keynote expanded on the points made by Tamim earlier in the day. Aimee, Strategy Head for integrated engineering company Booth Welsh, noted how previous industrial revolutions have largely prioritised maximising profit, whereas the Fourth Industrial Revolution prioritises:
• Profit: using digital technologies to improve and grow manufacturing
• Planet: using digital technologies to reduce the sector’s environmental impact
• People: using digital technologies to better enable and empower teams
Booth Welsh has coined the term ‘Environment 4.0’ to reflect how smart technologies are helping businesses to deliver tangible results in efficiency, performance, resilience and waste
Automation is scarier for SMEs because the solution will touch a higher percentage of staff
Troy Barratt, Managing Director, Contracts Engineering
reduction, while also delivering a positive impact on profitability.
“The workforce of the future will be much more purpose-driven. Purpose drives a human-centric approach with greater resilience and societal value,” Aimee explained. “Environment 4.0 taps into the power of purpose using technology and will help businesses cross the bridge to the next phase of industry, from Industry 4.0 to Industry 5.0.”
Environment 4.0 has four defined technology pillars, according to Booth Welsh, all of which have become increasingly commonplace in industry:
1. Collaborative robots (cobots)
2. Digital twin technology
3. Industrial Internet of Things (IIoT) sensors
4. Remote support and testing with virtual tools
“We believe that Environment 4.0 comes with an in-built sense of paying it forward. When you follow these principles as you adopt new business solutions, doing the right thing balances people, planet and profit — with no need to worry about a trade-off.
“As we’re all aware, adopting a change in your way of working isn’t easy. It requires a collective effort. Joining meaningful networks has been key for us.” concluded Aimee.
It was a fitting conclusion as the theme of collaboration ran through the entire agenda. Indeed, it is InterAct’s raison d'etre.
The questions facing business leaders, policymakers and wider society are multifaceted with no easy answer. Equally, the scale of change needed and the timeframe in which to achieve it is intimidating, to say the least. The key will be adapting a systems approach and working together in order to combine expertise from the broadest range of perspectives around common goals.
As Made Smarter Challenge Director, Chris Courtney, commented: “Yes, the future looks daunting but consider what we have already achieved in our lifetimes. Twenty years ago, Tesla hadn’t built anything, Apple hadn’t introduced the iPhone, no one was on Facebook and the term ‘cloud computing’ hadn’t been coined.”
The day closed with an in-depth panel discussion featuring some of the day’s speakers and several new voices. The takeaways from this discussion will be summarised in an upcoming article, look out for it on TheManufacturer.com.
ABOVE: The inaugural InterAct Network conference was held at the historic Institution of Engineering and Technology (IET), London IMAGE: COURTESY OF INTERACT
• Realising the future we want will require knowledge, skills and technology
• Businesses require much greater support to embrace innovation and increase technology adoption
• We need a radical redesign of our education and skills system to ensure future skills needs will be met
• Collaboration and adopting a systems approach are crucial
• The lack of an industrial strategy needs to be addressed
InterAct is a £4.4m Made Smarter Innovation funded network that aims to bring together economic and social scientists, UK manufacturers and digital technology providers to address the human issues resulting from the adoption of new technologies in industry. Its long-term vision is to build an engaged interdisciplinary community to support UK industry in the adoption and development of digital technologies that will result in a stronger, more resilient, manufacturing base. www.interact-hub.org
Emerging digital technologies provide a world of possibilities to fully align both your business and your environmental goals
Aimee Doole, Strategy Head, Booth Welsh
The end of September saw the pound fall to a record low against the dollar. Despite the wellreported negative consequences in the mainstream media, John Mills , economist and Founder of The John Mills Institute for Prosperity, claims that such an event could result in a silver lining, and growth opportunities for UK manufacturing
Speaking in the days following the pound’s devaluation, John highlighted the UK’s historic national obsession with policies that lead to an overvalued pound which have contributed to driving down manufacturing productivity, creating an unproductive and lowgrowth economy.
He also identified that a lower value pound represents an opportunity to boost manufacturing and for the government to make UK exports more competitive and increase the profitability of our domestic manufacturing sector. This would encourage investors to site new manufacturing plants and operations in the UK rather than elsewhere. The Manufacturer Editor, Joe Bush, caught up with John to find out more.
Why has the UK traditionally had an obsession with a strong pound?
JM: We’ve had this ethos for a few hundred years, going back to before the days of the gold standard. There’s always been a general perception that the stronger the pound, the better off the economy. In fact, when you analyse it, the reverse is true. A higher pound actually makes us less competitive, which means there is lower growth in exports and less investment. That results in lower living standards and lower productivity gains.
This perception was reinforced by the inflationary problems we had in the 1970s. Between 1977 and 1982 the exchange rate for the pound rose by about 70%. No wonder manufacturing (mostly operating in highly price sensitive international markets) as a percentage of UK GDP,
went into a steep decline. At this higher exchange rate, swathes of manufacturing investments became unprofitable.
Despite all the efforts to increase UK productivity, this is the reason why we’ve slipped down the international rankings. Something like 30 countries now have higher living standards than the UK, whereas 150 years ago, we were the preeminent country.
Policies introduced to stabilise the economy in response to the inflation of the 1970s, resulted in a rising exchange rate. This was not replicated in the east; countries in that part of the world got exchange rates down. The imbalance we've seen ever since has meant that economies in the east have grown significantly faster than those in the west. Our growth rate has steadily fallen and, if we're not careful, we’ll have no growth at all for the next five to ten years.
What have been the consequences of an overvalued pound on UK manufacturing?
It’s been disastrous; manufacturing as a percentage of GDP has fallen from around 30% in 1970 to less than ten now. We’ve lost share of world trade and for a highly competitive market, like the one for manufactured goods, we've suffered as a result.
In addition, there is a cultural problem, as well as one based around competitiveness and economics.
A lower pound will make UK exports more competitive and increase the profitability of our domestic manufacturing sector
Other countries enjoy much stronger manufacturing lobbies than we do in the UK. A look at the history of Germany, for example, will show that they’ve always had a very competitive exchange rate; the Bundesbank and big export companies have always insisted on that remaining the case, which was the basis on which the Euro was set up.
In the UK there’s never been that drive from industry to make sure that we have a competitive pound. Rather, industry has been prepared to accept the services view of the world, which is very strong in the UK and represents approximately five percent of GDP export surplus.
We’re good at services, helped by all manner of natural advantages such as our language, geography, legal system, universities and training. But because services is so dominant, it tends to set the economic climate. Services can live quite happily with $1.50 to the pound, but unfortunately, that exchange rate is completely lethal for manufacturing.
A further problem is that it’s more difficult to increase productivity and sell abroad in the services sector than it is in manufacturing. Therefore, if there is an over reliance on services, a large balance of payments deficit can result, which then leads to the levels of inflation like we currently have and a weak economy.
How could a more competitive pound impact UK manufacturing and how could businesses take advantage?
All the evidence is that the lower the pound, the more competitive, relatively speaking, exports become and the better the balance of payments. I think the recent strengthening of the pound (following the recent dramatic fall) won’t be reflected in an improvement in the balance of payments; far from it.
If the pound had stayed down, it would have made a lot of competitive difference. Generally speaking, the lower the pound, the faster the growth of the economy. Therefore, what we have right now is a policy choice on the level at which we try and get the pound to settle. In terms of what our economic targets should be, currently it’s to try and keep inflation at two percent. A better target, in my view, would be for the Bank of England to maintain an exchange rate to produce enough investment to get our growth rate to two and a half or three percent per annum. Unfortunately, that’s a very long way from where the present government or opposition
are. Right across the political spectrum, it’s not something that’s being considered. However, it’s crucial that we get the rate of business investment up. Currently, the total amount of investment in the UK, including R&D, is approximately 17% of GDP. The global average is about 25%, and in places like China, it's over 40%.
It’s that investment that can really make the difference. Further to that, however, there are particular types of investment, particularly around mechanisation, power and technology, which produce very high rates of return. It’s these that really drove the first Industrial Revolution.
brought up to believe that it would, but when you look at the international figures, the evidence would suggest something different.
A striking example was when the UK came out of the Exchange Rate Mechanism (ERM) in 1992. A year previous the inflation rate was around six percent, and despite some politicians claiming it would be a disaster to come out of the ERM, inflation actually went down, dropping to around one percent in 1993/94.
Following that we had 15 years of growth through to 2008 at a reasonable rate. That shows, first of all, that inflation doesn't necessarily follow from devaluation. But also, if we’re trying to get the percentage of GDP from investment to something like 25% (from 17% currently) to keep pace with the rest of the world, then we need to shift eight percent of consumption into investment.
That means we need to find the resources to do that i.e., via savings from government, borrowing from abroad, the corporate or household sector. It's not easy, but it's possible, and there are plenty of other countries that have achieved it.
Maintaining a competitive pound will require a combination of two things; first of all, everything on the supply side needs to be in place - better education and training, infrastructure, longer-term capital, etc. Second, we also need to make sure that’s balanced by having enough competitiveness on the demand side, to make sure that we've got a reasonable amount of exports and investment flowing from that. An iron rule of economics is that if you’re losing your share of trade, then the economy will grow more slowly than the world average; that’s been the UK’s problem for a long time.
Would a more competitive pound benefit all manufacturers, both large and small?
These elements are all part of manufacturing, but the weaker manufacturing is, the less benefit there is from this sort of investment, and the slower the growth rate. So, by driving manufacturing forward it will increase regular investment.
Will the benefits of a lower pound on manufacturing mean negative trade-offs elsewhere?
Of course, no economic policy is without its downsides, and certainly any policy of a lower exchange rate means higher import prices. Whether that actually adds to inflation is a moot point. I was always
A more competitive exchange rate would benefit manufacturing businesses of all sizes. Economies of scale mean that larger manufacturing businesses are able to bring down their unit cost for manufactured goods. However, that’s much more difficult for smaller manufacturing businesses. For that reason, a more competitive exchange rate could actually be more impactful for smaller manufacturers – it will boost their margin on goods that they sell internationally.
Plus, many smaller manufacturers have also historically put off international expansion because of the costs of exporting. A lower exchange rate would
An iron rule of economics is that if you're losing your share of trade, then the economy will grow more slowly than the global average; that's been our problem for a long time
“
give many such companies the nudge they need to start selling abroad, and the fact that it will be more profitable to sell abroad will help offset the upfront costs of setting up all the administration that is needed in order to do so.
Are these goals achievable with such a negative perception of a lower valued pound?
It’s going to be a hard sell for sure. Devaluation has got a very bad name, partly because when we have devalued in the past, it has tended to be at times of crisis (sometimes of our own making when the exchange rate has been too high).
If you ask the average person in the UK whether they would like a strong or a weak pound, their reply will inevitably be for the former.
That creates a tricky starting point for politicians who have been persuaded by the arguments addressed here. The problem is that if we go with public opinion and get the pound as strong as possible, then we’re going to end up going down the path that we’ve trodden before, where we continue to lose our share of world trade. We will have lower and less profitable
investment in manufacturing, productivity will decrease and income will stagnate, in turn leading to political instability, and I’m concerned that’s where we're heading.
This situation is even more serious now because of the heavy costs that are coming down the track around climate change, health and social care, pensions, increased military expenditure and further interest charges as a result of increased debts. With all these headwinds against us, we need to drive as much economic growth as we can to offset this.
Most of the costs heading our way will hit the public sector; that means taxes will go up and living standards will go down. That’s not where the government, of any hue, wants to be.
First and foremost we need a debate where the academic and practical policy world engage about the pros and cons of this sort of policy. Currently, that isn’t happening. If you talk to anyone about the exchange rate, the response will be that it’s fixed by the market and there’s nothing we can do. It’s like the weather, you just have to put up with it.
I don’t believe that’s the case, particularly if you look around the world at policies that have been pursued by other countries. A very striking example is China which devalued its currency by about 75% between 1980 and the mid-1990s. The result was that they could produce more or less any goods at around half the price of that in the west. Unsurprisingly, their economy grew very rapidly, whereas ours languished. Manufacturing declined in the west, whereas it advanced at huge speed in the east.
So, a lower exchange rate would undoubtedly make the pound more competitive. There would also need to be settled government policy; we’re not going to attract investors if they believe that the pound will go back up, so we need consistency.
We will also need all the complementary policies on the supply side in place; education, training etc, because it’s the two together that really make the difference. We also need to raise the prestige of manufacturing and get it from where it is at the moment (about ten percent of GDP) to around 15%.
At the current level the economy will never get rid of the very serious imbalance it has
• A strong pound doesn’t necessarily mean a strong economy
• A more competitive pound will encourage investors to site new manufacturing plants and operations in the UK
• The exchange rate isn’t like the weather – you don’t just have to put up with it
• A debate needs to be generated around a more competitive currency
• We need to raise the prestige of manufacturing
The John Mills Institute of Prosperity is a cross-party research initiative that seeks to provide new, innovative and fresh ideas to increase levels of prosperity and growth. By working with policy stakeholders, legislators, business and industry leaders, trade union representatives, economists, commentators, regional leaders and the public, the Institute for Prosperity aims to bring policymakers together to affect change and find new solutions to Britain’s economic problems.
currently; we’ll never get the traditional, industrial red wall areas of the country back to a reasonable level, where they have enough to sell to the rest of the world. And we’ll never close the gap between London and the South East, and the rest of the country, so there’s a huge amount at stake, and it’s not an exaggeration to say that a more competitive pound would help to steer us out of the economic crisis.
Our political leaders must shift away from our national obsession with policies that lead to an overvalued pound
The world’s cities are forever growing, which means more vehicles clog our roads daily. Traffic management doesn’t just aim to make mobility safer and less complex, but environmentally cleaner with digital progress and connected data systems at its core. The Manufacturer’s Tom St John was given the green light to investigate Yunex Traffic
Yunex Traffic marked the third and final stop of our ‘A Fine Pool(e) of Manufacturers’ tour.
Lush (the cover story of our October issue), Pavalux (see page 12) and Yunex Traffic make Poole the jewel of the South when it comes to manufacturing excellence.
We could see the Yunex factory from the roof of the new, soon to be completed, Parvalux facility. The Siemens signage is still visible on the side of the building, owing to the fact that our host remains a Siemens business, despite a change of name and logo from Siemens Mobility, Intelligent Traffic Systems, to Yunex Traffic.
“We won’t get lost then,” I said to my colleague Lanna as we gauged which way to approach the facility before leaving Parvalux.
Yet somehow, we did get a bit lost –as we attempted to access the wrong entrance. We drove a short distance to where we were supposed to be and were met by Simon Martin, Head of Global Manufacturing.
Welcome to Yunex
We were taken into a boardroom where the Yunex team had certainly pulled out all the stops (traffic pun intended). There were between 10 and 15 members of the team, all selected to give us interviews.
I informed Simon that we can’t possibly interview everyone. “These are the whittled down selections,” he said, and followed this up by explaining, “We’ve got so many products.”
Yunex Limited has over 56 years’ experience in the field of intelligent traffic
management and control, making it the UK’s leading manufacturer and service provider of traffic control equipment and systems. Over 920 people work for Yunex Limited across the UK, with around 200 workers at the Poole facility.
Simon wasn’t lying when he said the company has a lot of products and solutions; this wide portfolio extends from electric vehicle charging infrastructure to criminal enforcement products.
“It’s basically everything that's related to traffic management infrastructure,” said Martin. “We make the standard products that you all know, traffic lights and the controllers, all the way through to some of the latest technology around integrated vehicles i.e., how vehicles communicate with infrastructure.
“We're also very closely linked to a lot of the initiatives around clean air zones, we produce enforcement cameras for low emission zones, average speed zones and bus lane management. There’s a mixture of the traditional products and services that you’d expect to see, but we’re also involved heavily in new technology.”
I should point out, in the last few months, I’ve been spotted driving in a bus lane and was caught exceeding the limit in a variable speed zone. On both occasions, it was almost certainly a Yunex enforcement camera that got me. So, they do work.
At the heart of traffic management, I’m sure you’ll be unsurprised to hear, is smart technology. The site in Poole is the sole production facility for Yunex
LEFT: Yunex Limited has over 56 years’ experience in the field of intelligent traffic management and control
globally, where manufacturing technology expertise are centralised, ensuring full lifecycle management from production of new products through to aftermarket operations.
Enter Cassy Russell, Digitalisation Manager within the manufacturing sphere at Yunex. We met him on a packed factory floor, with rows upon rows of machinery. “It's a really exciting time for us, because we’re
going through a big level of expansion in terms of the technology that we're harnessing here,” he explained.
“This is everything from your day-to-day traffic management all the way through to some cool AI technology. What that means for us as manufacturers is we've got to make these products for the team, and we can only do this through huge amounts of innovation to keep ourselves on the cutting edge.”
Solutions grounded in digital technologies produced by Yunex include intersection controllers, cloud-based urban traffic control solutions, real-time optimisation, adaptive control, motorway and tunnelling solutions and connected mobility.
“Our digital success falls into two categories,” explained Cassey. “Firstly, we have the agile elements which ensure that what we’re doing day-to-day allows us to deliver for tomorrow – we’re constantly adapting and improving. Secondly, we’ve got the innovation element, which means we’re always thinking about what technology we can deploy to ensure we're the best at manufacturing these products.
“Ultimately, we've seen huge success in simply having a plan,” he continued. “Of course, you've got to be agile and able to add or take away elements of that plan, but really understanding what your vision is as a company, and also as a manufacturing sphere, allows you to take the steps you need to achieve this.”
“Has there been some difficulties in recent years around getting that adoption right?” I asked Cassey. “I think all manufacturers have been hit hard by some of the same issues over the last couple of years,” he replied. “We’ve been trying to implement solutions while going through a transition period and have found that tricky when we haven’t had everyone in the factory or in offices at the same time. We've got component and software shortages in the factory, which means that we find it hard to implement at the pace we want to.”
The future of technology within traffic management promises to be wonderfully
exciting. Using innovative concepts, cities will soon be able to actively manage traffic. Intelligent infrastructure systems will continue to help make optimal use of the available resources through centralised control and management.
Within the factory, Cassey predicts a similarly exciting future, but is wary of the challenges that it could bring to digital manufacturing operations. He said: “In the next ten or 20 years, we're going to see huge amounts of automation coming into the factory. We're looking at real life robotics at the moment alongside our software robotics.
“But that brings a lot of technology along with it; it throws up challenges around understanding the data and what we're producing. It’s going to be even more important to ensure our quality is up to scratch and the products are meeting the demands of the customer.
“A great example of that is some lowcost Automatic Optical Inspection (AOI) that we’re looking at. Normally, AOI is hugely expensive and currently, we put every single product through that process. We're looking at really innovative solutions where we can take that board and inspect it in other ways.
One of my projects at the moment is looking at the effects on boards in real-time as a robot is building it. This takes away that really expensive piece of machinery to let it work on other things.
Supply slows
We’ve probably sounded like a broken record at times over the last year, but we’re here to report on the problems that are giving manufacturers sleepless nights
There’s a mixture of the traditional products and services that you’d expect to see, but we’re also involved heavily in new technology
Simon Martin (below), Head of Global Manufacturing
I think ultimately, we've seen huge success in simply having a plan (for digital transformation)
Cassy Russell (left), Digitalisation Manager
– supply chains are at the top of the list of nightmares.
Yunex has worked hard on this front and is still exporting successfully to over 60 countries. This includes anything to do with traffic equipment, i.e., traffic lights and controllers. But the trials of the last couple of years have still taken their toll.
“We’ve got a global supply chain problem,” said Sharon Byrne, Head of the Tactical Sourcing Operational Procurement Team. The seven buyers that work under her purchase the materials that make up every product in the Poole facility.
“The supply problem doesn’t just exist in electronics,” she continued, “Although that's the biggest issue, the challenge extends more broadly to other raw materials. Most of that is born from the COVID pandemic. The demand is a lot higher than the global supply for most industries. This means we've had to really adapt our procurement practices.
“Traditionally, we had lots of Kanban items, we had call ins, buffer stocks and safety stocks at suppliers - we can't do that anymore. An awful lot of effort had to go into planning; we had to order in advance, sometimes years, looking as far ahead as 2024. We’re not seeing any changes in that supply at the moment, but we've had different allocations before in previous years. So hopefully, we're starting to see a little bit of improvement out there – stuff is becoming more available, unfortunately no one can tell us when.”
As mentioned, global trade remains strong for Yunex; the Brexit hump has been overcome because of the preparatory work that was done to mitigate the impact.
“We had some difficulties at first,” said Sharon. “Deliveries were getting stuck in customs and suppliers weren’t quite understanding the details around the new paperwork and the incoterms. Now, we’re at a point where we’re just two days late, or rather there’s two days difference to where we were prior to that, which is a huge achievement.”
An area not yet touched on, and deliberately left until last, is the company’s commitment to sustainability. Traffic congestion and air pollution are often complained about aspects of cities around the world and staggeringly, 99% of the global population breathes air that exceeds WHO air quality limits – an uncomfortable statistic.
To address the issue of air quality, an increasing number of authorities are deploying targeted clean air and low emission zones. Take the recently expanded Ultra Low Emission Zone (ULEZ) in London, a world first. Yunex Traffic infrastructure and technology is behind this, as well as Clean Air Zones in Birmingham and Portsmouth. Yunex is also working on the delivery of schemes with transport authorities in Manchester, Newcastle and Sheffield.
“Our sustainability goals are very much aligned to the UN Sustainable Development Goals,” said Sasha Sequeira, Environment and Sustainability Advisor at Yunex Traffic.
She continued, “We're focusing on being net zero for our operations by 2030, targeting energy and the fleet to achieve that. We’re also aiming for 2050 to be net zero across the supply chain. So, we're looking at our supply chain as well as the end of life for our products, and how we impact our customers. Two areas of focus for our products centre around improving
LEFT: At the heart of traffic management is smart technology
The demand is a lot bigger than the global supply for most industries. This means we've had to really adapt our procurement practices
Sharon Byrne (below), Head of the Tactical Sourcing Operational Procurement Team
air quality, for instance, we’re incentivising active travel through low level cycle signals as well as clean air zones.”
Outside of the factory, the impact that Yunex is having on the Low Emission and Clean Air Zones in Britain's two largest of cities, London and Birmingham, has been almost immediate – remarkable achievements have been realised when it comes to air quality. Using camera-based enforcement solutions, the schemes have resulted in far fewer polluting cars.
After the first ten months of operation, research carried out by the Mayor of London’s office showed that ULEZ had contributed to a 44% reduction in roadside nitrogen dioxide within the central zone and 44,100 fewer polluting vehicles were being driven every day.
To put that into perspective, that’s a saving of around 12,300 tonnes of carbon dioxide emissions – enough to fill the Gherkin in London 22 times over. At the end of December 2020, compliance with the central London ULEZ stood at 85% for all vehicles, with over 90% of cars (excluding black cabs) compliant.
“Road traffic is one of the biggest contributors to carbon emissions in the UK and air quality is a massive health risk,” said Sequeira. “While driving remains very much a necessity, we can help with solutions like clean air zones or reduced congestion. We’re directly combatting these environmental problems through our products and solutions - that makes me feel very fulfilled. I'm helping with not only our own operations as a company, and how we're being more sustainable, but also helping our customers to improve these aspects.
“Right now, I don’t think it’s always very convenient to be sustainable,” she continued. “We need more encouragement and accessibility – we’re trying to do this by working with a lot of local authorities who engage directly with people living in those communities. Reducing emissions and improving air quality are two of our big focus areas within our products.”
We also discovered that there are significant financial and carbon savings to be had in LED signal lamp retrofit programmes. In Greater Manchester, 52,000 traditional traffic signal bulbs were replaced with Helios LED. This transition gives lifetime
LEFT: In Greater Manchester, 52,000 traditional traffic signal bulbs were replaced with Helios LEDs
• Increased use of technology and automation presents further challenges in data capture
• Yunex is another example of a sustainable approach being right for the environment and for cost
• Yunex has reported clear signs of manufacturing agility – be it through production or supply chain
• The central London ULEZ has seen immediate and dramatic reductions in carbon emissions. Other global cities must follow
savings of £5m in electricity charges, £1.5m of maintenance charges and a hefty 37,000 tonnes of CO2. Add to that an annual saving of £600,000 in maintenance costs and you’re well in the green, in more ways than one.
We bid farewell to the Yunex team, and subsequently to Poole. I couldn’t tell you much about the town itself, we didn’t get a chance to look around. Its manufacturers are nice though. With Yunex Traffic, I was struck by its commitment and passion, not just for the management of its factory operations, but for the transformational power of its innovative products, and the clear environmental and technological progress that they’re enabling.
Cities are often a pain to drive around or navigate, and you may feel, even after reading this, that they’re getting even more complex. Having witnessed firsthand the work and innovation that goes in to managing traffic, I’m assured that our roads are in safe hands. Watch out for the Yunex enforcement cameras thoughbecause they do work.
Scan the QR code to view the video of The Manufacturer’s site visit to Yunex
Right now, I don’t think it’s always convenient to be sustainable. We need more encouragement and accessibility
Sasha Sequeira (above left), Environment and Sustainability Advisor
Data-minded manufacturing leaders will be coming together for the sixth year to discuss the role of data and analytics in their business. They will be exchanging views on the best practice to collect, manage, and leverage their data to enable them to run their factories and businesses in a more efficient and cost-effective way, which is critically important in this present economy.
industrial-data.uk
A crash course in business growth tailored for the strategic leaders of SME manufacturers - linking together strategy, product, and the workforce to your wider business ecosystem.
The Summit is designed to identify the most effective avenues of growth and equip you to act on them - growing your revenue, profitability, and workforce, as well as dealing with the growing pains that come with business growth.
For businesses with a turnover <£100m.
The home for directors and C-Suite of manufacturing businesses interested in networking with their peers.
Regular virtual roundtable discussions over a glass of wine, focussed on key business issues to drive efficiency, sustainability, and innovation. Apply to join: directorsforum@hennikgroup.com
World-class, case-study driven content delivered by best-inclass manufacturing speakers from around the globe.
Over the 2 days we will be covering key strategic, business and technical challenges across the manufacturing ecosystem – with maximum opportunity to network, debate and engage with your peers. Manufacturing Leaders’ Summit is the go-to event for 2023.
For businesses with a turnover >£100m.
The reveal of the Best of British manufacturers - 700 industry professionals will enjoy a three course dinner, guest speakers, live entertainment and a lively awards ceremony.
Delivered by The Manufacturer in partnership with the Institution of Mechanical Engineers (IMechE), The Manufacturer MX Awards have a combined heritage of over 50 years and are widely regarded as the gold standard in industry awards.
Entries are open until 7 July.
Concise deep dives in to specific topics led by industry specialists. Watch a back catalogue of practical how-to webinars on demand, or watch live and ask questions to stay on top of the latest trends and technologies with our fortnightly schedule.
themanufacturer.com/webinars
Celebrating the best in manufacturing and engineering excellence and innovation.
Manufacturing & Engineering Week brings the entire community together for a festival of innovation featuring a dynamic, interactive series of digital and live events to inspire, inform and entertain.
For the exighth year, Smart Factory Expo brings together all the technologies enabling the digital manufacturing revolution –creating a carefully-curated shop window for manufacturers at all stages of their digital journey.
Source the very best innovative solutions on offer, including the latest technology offerings from start-ups, alongside established brands and companies that truly support and advance the manufacturing sector.
Digital-minded manufacturing leaders will be discussing how to successfully plan and implement a digitalisation strategy across their businesses.
The symposium will investigate key issues such as organisational and operational change, upskilling the workforce and when and where to implement enabling technologies.
manufacturing-digitalisation.com
A crash course in business growth tailored for the strategic leaders of SME manufacturers - linking together strategy, product, and the workforce to your wider business ecosystem.
The Summit is designed to identify the most effective avenues of growth and equip you to act on them - growing your revenue, profitability, and workforce, as well as dealing with the growing pains that come with business growth.
For businesses with a turnover <£100m.
For product designers and engineering professionals from all tiers of the supply chain looking for the latest solutions to reduce costs, streamline & optimise future design and engineering strategy.
Bringing together key suppliers of drives, power transmission & motion control equipment. Representing the multi-tasking culture of today’s design engineer, covering critical areas such as energy efficiency, machine safety, drives, motion control, robotics and automation plus more all under one roof.
The Manufacturer Top 100 are the very best UK manufacturing has to offer.
Now in it’s tenth year, we want to continue to showcase the people who make a truly exceptional contribution to the sector every day. Join us for the reveal of this year’s cohort at a glittering drinks reception honouring industry’s movers and shakers!
Nominations are open until 10 March. Find
The UK’s longest standing event dedicated to the maintenance, reliability & asset management industry, attracting major buyers from the industrial, buildings, transport & supply chain maintenance sectors.
3D printing is creating a whole new world for design engineers, enabling rapid creation of functional prototypes and end use parts. However, as The Manufacturer editorial team found out on a trip to 3D printing services provider Materialise, in Leuven, Belgium, it is far from a one-size-fits-all technology
Additive manufacturing, to give 3D printing its proper title, is a multi-faceted technology involving a myriad of processes, techniques and materials (including metal, plastic and ceramics), each suited to different functions and end use applications.
Not only that, but those end uses for the technology are also becoming more varied. In the past, 3D printing was the sole domain of rapid prototyping. Now, more than 50% of the parts printed by Materialise are for end use. Here, we look at some of the technologies available to manufacturers thinking of introducing 3D printing into their processes.
Metal 3D printing, or selective laser melting (SLM), combines the design flexibility of 3D printing with the mechanical properties of high-performance metal alloys to create unique, strong and lightweight parts.
In the process, laser beams heat and fuse selected parts of the upper layer of a metal powder with underlying areas that are already solid. Once a layer is complete, the metal powder bed is lowered by one layer width and a new powder layer is appliedthe laser then fuses selected areas of the metal powder again. By continuously repeating these steps, the component with its support structures is created layer by layer.
The supports are of great importance in SLM because they not only hold the component in position, but also absorb internal stresses, dissipate heat and thus prevent deformation and other construction errors.
The strengths of SLM lie in the combination of the design freedom of 3D printing with the material properties of the various metals that can be used. The technology makes it possible to implement highly complex geometries in a single component. This makes it possible to create lightweight structures that bring major benefits not only to car manufacturing and aerospace, but also to all other applications in which parts are frequently accelerated and decelerated.
SLM production can be useful for many end products, especially if they are required individually or in small batches. These include production tools, moulds and inserts, but also spare parts.
The fast build time offered by MJF provides an attractive alternative to injection moulding. With no support structures needed and surfaces that require minimal post-processing, this technology is well suited for functional prototypes and small series of even complex end use parts.
Although it is based on powder as the printing material, it does not use lasers. Instead, it uses two liquids as well as infrared light. The powder bed in the build area is heated evenly at the beginning, and the individual powder layers are applied stepby-step.
Due to this process, MJF offers good timing predictability; since the melting process is not based on laser movement, which varies depending on the area to be exposed, the printing process takes exactly the same time for each layer. This means that the printing time can be precisely predicted. Therefore, users can benefit from shorter lead times and the ability to produce more components of sufficient quality in one build job.
The strengths of components produced by MJF result from the fine-grained nature of the powder used. It enables ultra-thin layers of 80µm which produce components with higher density and low porosity when printed.
Fused Deposition Modelling (FDM)
FDM, also known as Fused Filament Fabrication (FFF), is one of the most popular 3D printing processes for the additive manufacturing of plastic components. FDM is based on thermoplastic modelling filament, which is meltable plastic provided in wire form on rolls. The filament is fed through an extruder nozzle, where the material is heated and then applied in layers to the required areas on a build platform. Once all areas of a layer have been applied, the nozzle is moved up and the next layer is printed on top of the one below.
FDM combines 3D printing’s design freedom and fast lead times with production-grade thermoplastics to create durable parts with excellent mechanical properties. FDM is a 3D printing process that can be used to create almost any geometry with Continues on p46...
Additive manufacturing has shown that parts and components can be manufactured on-demand, where and when they are needed
Bart Van der Schueren, CTO, MaterialiseLEFT: Technological evolution has made 3D printers far easier to use, and there are more materials available so manufacturers have more choice
BvS: As we know, the first use cases for 3D printing were in the field of prototyping. The most important evolution we’ve seen is customers are now looking to use the technology to make end use parts.
If you look at the production of implants as a typical example of an end use part, because additive manufacturing doesn’t require any product specific tooling, we can make huge advancements in mass personalisation. Plus, there is also a growing trend towards smaller series sizes which also lends itself well to additive manufacturing.
JL: More than 50% of the parts we print are for end use applications. Therefore, we are putting a lot of effort into the process control of 3D printing. We collect a lot of data from the printers and from post-processing, for example, and bringing all this data together has helped the industry to have a better understanding of what is happening in the machine and has enabled us to develop end use part applications.
A key difference from prototyping is that safety needs to be guaranteed for end use parts, particularly in highly regulated sectors such as aerospace and medical (where many of our products end up) – plus you need to ensure that the material and part characteristics are the same, day-to-day and year-to-year. You need repeatable production and data has been key to the evolution of the technology beyond merely prototyping.
BvS: 3D printing by nature has always been a digital technology, but for many years it has been isolated. That is something which is changing rapidly; that post-
processing phase is undergoing a digital transformation and that fits into the general trends of Industry 4.0 where conventional manufacturing technologies are becoming more digitised. What that means today is additive manufacturing is no longer a siloed technology, but rather one of the steps in a larger production chain. And that is something that is enabled by digital technologies.
What advantages can 3D printing bring to help manufacturers navigate recent challenges?
BvS: There has been all manner of challenges over the last few years which have made manufacturers ask how to make production more resilient, and additive manufacturing certainly has a role to play. That is something manufacturers have learned from the COVID crisis, for example, where supply chains were suddenly broken.
Here, additive manufacturing showed that parts and components could be manufactured on-demand, where they are needed. That kind of change in the market, which was initiated during COVID, has been picked up by manufacturers to further mitigate against supply chain uncertainty. Moving towards additive manufacturing can increase resilience, because it helps companies to have a level of production capacity near to where they need parts.
This local production allows product development to be looked at in a completely different way. Parts can be produced and optimised immediately
There has been a growing interest around 3D printing and a number of manufacturers now want to see what the technology has to offer
Jurgen Laudus, Vice President, Manufacturing Segment, Materialise
and manufacturers can even go into agile development and involve customers to really develop products that perform as required. This means that manufacturers can get to market quicker and at less cost, while also having a digital asset of the product to fall back on should there be further disturbances in the supply chain.
JL: We’ve seen a dramatic rise in manufacturers wanting to talk to us over the last few years because of the issues they are experiencing within their supply chains. Many have a huge inventory of stock lying around just in case there’s further disruption. We can greatly reduce the number of stock items thanks to a digital inventory where, if a manufacturer needs a part, they can simply print one.
Manufacturers have become aware that the supply chain should not be taken for granted; that not all parts which are produced on the other side of the world can be here in a matter of days or weeks. That has created a lot of interest for 3D printing and a growing number of manufacturers now want to see what the technology has to offer.
What benefits can 3D printing provide manufacturing?
JL: Firstly, you don’t need to make a mould, which eliminates the start-up costs typically associated with traditional manufacturing methods. Secondly, there is more freedom, enabling the design of parts to become far more complex without extra cost. And thirdly, parts can be produced more locally, minimising supply chain disruption.
More and more manufacturers are starting to become aware of these benefits. However, while some manufacturers have an idea of where they want to get to, others are struggling with knowing where to start.
As discussed, there is a wide landscape of technology and materials available, so what should manufacturers look at first? And how do they ensure that 3D printing provides them with the same outcome (or better) as they received from traditional manufacturing methods?
That’s why we believe our Mindware offering is so important. It shows manufacturers how to use technology in the best way; what are the right applications and parts to start with that involve taking the least risk. We help our customers get on the journey.
BvS: Technological evolution has made 3D printers far easier to use, and there are more materials available so manufacturers have more choice. In addition, the digital process is becoming more developed, and that is important because additive manufacturing is still a technology which is in its infancy.
There are still a lot of unknowns but by digitising the whole process, collecting data on the machine and making it available, it helps end users to better understand how the process is working and what you need to do to keep your production process stable. That is an important step towards mid-size volume production for additive manufacturing.
There are also environmental benefits. Additive manufacturing is not necessarily environmentally friendly per se, because a lot of energy is required to make the raw materials and to create the actual parts.
However, as discussed, producing parts where you need them is a feature of additive manufacturing, but this also has an environmental advantage. Most people don’t realise how many spare parts are produced. These are filling up warehouses and are often never used. 3D printing can mean on-demand production; manufacturers don't have to go into overproduction and produce spare parts, and so the inventory risk is reduced.
In addition, additive manufacturing can provide weight savings. This is important
for anything that features moving parts, because movement needs energy. So, the lighter the parts, the less energy required, and the better that product is for the environment.
What will be the role 3D printing in the future of manufacturing?
BvS: I'm convinced that additive manufacturing will become an integral part of the production chain. The freedom of production allowed by additive manufacturing enables the combination of more functions in a single component. That means you can save on assembly costs and create complex parts which couldn’t be produced with conventional technologies. Additive manufacturing is really growing into an established production technology.
Additive manufacturing enables savings on assembly costs and the creation of complex parts which couldn’t be produced with conventional technologies
Bart Van der Schueren, CTO, Materialise
Continued from p43...
particularly low distortion, as no thermal stresses are introduced into the component since heating is only carried out at specific points.
In principle, the construction dimensions are unlimited, as the components can consist of different segments that can be joined together very easily after printing. One of the major advantages of the process is that the mechanical properties of materials that can be used with FDM remain stable over time. As a result, the components are not only of high quality, but also last an exceptionally long time.
Laser sintering is a popular and versatile 3D printing technology thanks to its high precision, design freedom and wide range of production-grade materials. Suitable for all stages of the production lifecycle, from prototyping to small series or custom manufacturing, laser sintered parts need no support structures, making it possible to produce even the most complex geometries.
In laser sintering, plastic powder is distributed over the entire surface of a build platform using a roller or squeegee and then selectively bonded by melting with a high-power laser beam. Once the laser has completely processed the first layer, the platform lowers, and a new layer of powder is applied. The laser now melts the areas defined in this layer. This procedure is continually repeated, gradually creating the component.
One of the advantages of SLS is that no support structures are required, since overhanging structures are stabilised in the powder bed. As a result, any three-dimensional geometries can be created. These can have undercuts that cannot be produced in conventional mechanical or casting manufacturing. The process can also be used to create highly complex designs such as moving parts, hinges and chains in a single piece, which saves subsequent assembly steps or enables completely new design solutions and applications.
• There are a variety of processes and materials to meet different 3D printing requirements
• 3D printing is now moving beyond the realm of prototyping and into end use parts
• 3D printing allows manufacturers to produce parts on-demand, when and where they need them
• 3D printing means less tooling costs and allows designs to be more complex and flexible
• Challenges of recent years has seen a growing number of manufacturers adopting 3D printing
Another strength of laser sintering is that several independent components can be printed simultaneously in the build space. By strategically arranging the parts (nesting), the available build space in each machine can be optimally utilised, which makes the production of small series or different prototype variants, for example, relatively fast and cost-effective.
Stereolithography is one of the most widely used 3D printing technologies. Its surface quality, ability to produce fine details, and wide selection of materials make it well suited for highquality visual models and prototypes, complex aesthetic parts, and masters for techniques like vacuum casting and lost wax casting.
The basic version of the technology is based on UV sensitive liquid resins that are applied to a platform and then selectively cured by laser beam, from which different variants have evolved over time. During the manufacturing process, the platform gradually lowers and the component grows layer by layer. To prevent the printed object from moving in the resin bath, it is fixed to the build platform by means of support structures.
The strengths of SLA lie in the combination of very high dimensional accuracy, high surface quality and relatively short production times. Furthermore, apart from Polyjet, SLA is the only additive manufacturing technology that can also be used to create transparent objects. Stereolithography can also be used to produce large components in one piece.
In addition to its high detail and smooth surfaces, PolyJet offers the unique ability to print precision parts and assemblies with multiple materials, all in a single build. A single part can contain different colours, levels of transparency, and diverse physical and mechanical properties, making PolyJet well suited for complex visual models and prototypes.
In the process, photopolymer resins are applied in ultrathin layers to a build platform via print heads - similar to inkjet printers - and cured immediately after application using UV light. For complicated geometries and overhangs, a gel-like, water-soluble support material is also applied via the print head. Once a layer is complete, the platform moves down by one layer thickness and the next layer follows.
PolyJet printers have several print heads which allow different materials and different colours to be combined during printing. As a result, not only can specific colours and hardness be achieved, but a component with several colours and different mechanical properties can also be produced in a single printing process.
Another special feature of the polyjet process is that the light transmission of the material can be varied. Even complete transparency is possible. Furthermore, the technology enables the printing of very fine details, as the layers are only 32µm thick.
The Manufacturer’s Lanna Deamer speaks to Natalie Watson, Group Head of Sustainability at The Vita Group, a manufacturer of flexible polyurethane (PU) foams, who will be delivering a keynote at Manufacturing Leaders’ Summit 2022, around delivering valuable environmental impact data
Natalie will also be sharing a case study on The Vita Group’s emissions data journey, challenges faced around the company’s decarbonisation strategy and how to display data in a way that simply tells the whole story.
Manufacturers all around the world are facing chronic supply chain issues with resilience, agility and visibility being key challenges. This is all against the background of rampant global inflation and the complex question of who pays.
The issue of skills availability continues to worsen in UK manufacturing. While the skills requirements in this digitalised world continue to change, manufacturing still struggles to attract the right talent and be perceived, by the general populace, as a good career path. The final two wider issues, which are heavily interwoven, are digitalisation and sustainability.
The COVID-19 pandemic and other recent global issues, have demonstrated beyond all doubt that a more digitalised and automated operation is the only way of safeguarding the future. Throw in the moral
LEFT: While PU foam is traditionally made from non-renewable chemicals, The Vita Group is moving towards using more sustainable feedstock
(and soon to be legal) impetus for a net zero future and manufacturers clearly have a plethora of challenges to overcome.
There are no clear roadmaps or onesize-fits-all solutions. Only by discussing with peers and experts, sharing experiences and lessons, and a spirit of cooperation and collaboration can UK manufacturing navigate its way through these turbulent times. Manufacturing Leaders' Summit (16-17 November) is where all these issues will be aired, discussed and solutions offered.
Working with multiple stakeholders, The Vita Group is at the forefront of using lower
carbon and more sustainable alternative raw materials. While PU foam is traditionally made from non-renewable chemicals, the company is moving towards using a more sustainable feedstock and developing circular economies through partnerships with industry bodies, universities and suppliers.
In her current role, Natalie is responsible for driving through advocacy and partnerships and leading the transformational change to deliver against each of The Vita Group’s four principal areas of the ‘Enhancing everyday life’ sustainability plan; driving circularity, optimising resources, empowering people and acting ethically. Prior to this role, Natalie was Responsible Business Lead for the property services company Extentia Group - leading the responsible business and sustainable development strategy across 11 legal entities.
What has The Vita Group’s sustainability journey been like so far?
NW: Sustainability has been embedded into the business since its earliest days. The founder realised that there was an opportunity to add social value with the formation of latex products. As early as the 1990s, The Vita Group started to innovate in more energy efficient products, although in those days it was more about production efficiencies.
ABOVE: The Vita Group is focused on driving circularity, optimising resources, empowering people and acting ethically
We’ve carried this across the board for the past 30 years, but it’s only just become a structured sustainable development plan over the last decade, and only in the last five years have we consolidated our ESG measurement against our sustainability strategy. To reduce that reliance on the petrochemical side of the business, we’ve brought to market products that have used bio polyol and renewable feedstocks instead of virgin hydrocarbons. We have made a lot of progress and we will be continuing that journey to ensure that all our products will become fully circular, and The Vita Group aims to do that in a way that fulfils our net zero ambitions.
How integral is sustainability to The Vita Group’s overall business strategy?
Sustainability is at the front and centre of our business. We have a very proactive executive team; the passion shown by Ian Robb, CEO of The Vita Group, really shines through and is contagious throughout the whole company. Since joining The Vita Group, every meeting I’ve attended has included ESG or sustainability as part of
Capturing data in our value chain emissions is a challenge but it’s one we’re leaning into by working with key partners who have expert knowledge that can be leveraged to make further progress
Natalie Watson, Group Head of Sustainability, The Vita Group
the key components, and that’s not just because of the role I do but because it’s key on our agenda. The publication of our annual sustainability report highlighted that the strategy drives trust through enhancing the traceability of our products, but also the transparency of what we’re doing.
Our annual sustainability report is an open window that shows the sector what we’re doing. The release of our second report, which will be published in 2023, will hold us accountable as a business and offer a comparison of what we have done against what we said we were going to do. We are more than happy to share our experiences and challenges, which is fundamental to understand your impact as a business, to be able to manage it. After all, you can’t manage what you can’t measure!
As of September 2022, The Vita Group is now the first flexible PU manufacturer to have its climate targets approved by the Science Based Targets initiative (SBTi). As a society, if we are to limit global warming by 1.50C, we need rapid and far-reaching transitions, and business participation is critical to achieve this. Our ambitious greenhouse gas emission reduction targets align with The Paris Agreement and have been validated by independent climate scientists, which gives us the confidence that as a business, we are supporting the global economy to halve emissions by 2030.
We have set some ambitious targets, specifically to reduce Scope 1 and Scope 2 emissions by 46% by 2030. And in 2021, we achieved this target nine years ahead of schedule; but we are not stopping there, as we’ve committed to reaching net zero in our Scope 1 and Scope 2 emissions by 2050. We have also set another target to
• Tell a story that’s worth listening to when you talk about data
• You can’t manage what you can't measure
• Reducing Scope 1 and Scope 2 emissions effectively reduces Scope 3 emissions
• Becoming fully circular should be the goal to help achieve net zero emissions
• Don’t wait for the right time; start your sustainability journey now because strategies can be amended along the way
BELOW: As of September 2022, The Vita Group is now the first flexible PU manufacturer to have its climate targets approved by the Science Based Targets initiative (SBTi).
reduce our Scope 3 emissions by 13.5% by 2030. Capturing data in our value chain emissions is a challenge but it’s one we’re leaning into by working with key partners who have expert knowledge that can be leveraged to make further progress.
There have been many but one significant impact occurred with the breakout of war in Ukraine when the inflation of raw materials hugely impacted our spend data. Therefore, our Scope 3 emissions data shot up exponentially even though there wasn’t a great change in our emissions. Our behaviour across Scope 3 reduced but because of the inflation of prices and the way we calculated our emissions to begin with, this really affected us as a business.
With our Scope 3 emissions, we’re now calculating our intensity and examining our data over the next three years to ensure its accuracy as we’re now collecting it at source; we just wanted to make a start. It goes back to the age old saying: ‘Don’t let perfect be the enemy of good’. We didn’t want to wait until we had every single component aligned as we just wanted to get started on our journey; it’s okay to amend and adapt along the way because sometimes the biggest step can be the first. A key challenge for us was really making sense of the sheer amount of data coming through and this is an issue I know we were not alone in facing.
How much harder are Scope 3 emissions to measure and manage than Scope 1 and 2?
Roughly 95% of our emissions lie in Scope 3 so we knew we had to make a start and it’s become easier now thanks to our partnership with Schneider Electric. We’ve taken the necessary steps to map out our supply chain to pull out where we’ve aligned on various targets and collaborated with data collection. Having a digitised supply chain has helped us when carrying out these exercises, we’re also sending out ‘Know Your Supplier’ surveys which help pick out certain data.
We’ve got the SBTi which is naturally a vigorous data collection piece and Scope 3 is included in that. A key selling point for our products now is that we’re able to tell our customers and suppliers that we’re working hard to reduce our Scope 1 and 2 emissions and that effectively reduces their Scope 3.
With the sheer amount of data at their fingertips, how can manufacturers ensure they are extracting data that is useful and meaningful?
I would suggest two ways that we found to be enlightening. The first was the SBTi which is externally validated by climate scientists; aligning with these targets would allow manufacturers to make sense of the data with the guidance provided as it gives a clear structure to follow. The fact that they are also externally validated means that it is a rigorous process, and it allows high standards of measurement that can be inputted into an algorithm that already works.
It was important for us to be aligned with a standard ESG reporting framework, and for us that was EcoVadis. Approximately 85% of our suppliers have also embraced that framework and it’s a real consolidation of standards which allows for continuous improvement. It offers a clear structure of where we need to align ourselves in order to make life easier. And there was a lightbulb moment as we went through EcoVadis, where we had that realisation.
For example, I'm the authorised representative for the UN Global Compact for the UK network. From a business perspective that enabled us to increase our sphere of influence within the system around policy makers, legislation changes and other industry parties beyond our own sector. So it allowed us to catch the wave. In addition, as we went through the questions in the EcoVadis process, it highlighted gaps in areas where we
LEFT: The Vita Group has set targets to reduce Scope 1 and Scope 2 emissions by 46% by 2030
perhaps didn’t have a policy or didn’t know how to collect data on a certain process. It allows for continuous improvement once you've aligned with the ESG framework, and from those two perspectives, it has certainly allowed us to gain momentum in the data disclosure process.
Sustainability cannot be achieved in isolation, so how important are partnerships and collaboration?
We openly accept that we don’t have all the answers and expertise to achieve everything we want, so our partnership with Schneider Electric has enabled us to lean on them as a consultant to work together and harness its knowledge and experience.
For us, when everyone is ‘all in’, that is success. If we all work together, then we can achieve what we want a lot quicker. However, there is turbulence ahead for the industry so it’s important to stand strong on our narrative. I hope that my keynote at Manufacturing Leaders’ Summit will highlight how open and transparent The Vita Group is on its sustainability journey.
What tips would you give to manufacturers who are just starting out on their sustainability journey?
As a first step, it’s important to understand materiality to your business. Manufacturers should sit down with key stakeholders to discuss what impacts the business, what influences stakeholders and what drives business growth. Once you’ve established these core elements then the material risks to the business can be calculated, as well as finding out what impact areas the business has of both good and bad. This will give you a solid foundation to start building your sustainability strategy.
My advice would always be to find your interested parties – particularly people within your organisation; the more diverse the better. If you work within a diverse group, then you will ensure cognitive dissonance. Sustainability is such a complex topic that you need to have various viewpoints being openly discussed. Establishing a sustainable leader to facilitate these interested parties is really important – they can be that conduit for collaboration to happen.
As a society, if we are to limit global warming by 1.50C, we need rapid and far-reaching transitions. Business participation is critical to achieve this
Natalie Watson, Group Head of Sustainability at The Vita GroupReading this at Digital Manufacturing Week 2022? On the afternoon of Day 2 of Manufacturing Leaders’ Summit (MLS), 17 November, Natalie Watson, Head of Sustainability at The Vita Group will share the challenges of The Vita Group’s decarbonisation journey, including understanding, validating and tracking emissions generated in the value chain. As well as how to display data in a way that tells the whole story in a simple way.
During Digital Manufacturing Week 2022, Innovate UK will be launching its 2050 vison for materials and manufacturing, sharing its thoughts on how manufacturing might look in 30 years and on the challenges and opportunities that lie in front of the UK materials and manufacturing sectors. Paul Gadd, Deputy Director, Innovate UK explains
We want to achieve three things in releasing this vision:
• Inspire: Create a shared vision platform, proposing aspirational and realistic manufacturing futures
• Involve: Provide an open structure for collaboration, making the opportunities for the UK visible and compelling
• Invest: Design innovative interventions and supporting policies to realise the vision, attracting UK inward investments
We see manufacturing and materials as mission critical for the UK and the world.
We must act now to hit climate targets, secure sustainable supply and improve productivity and prosperity. It’s a big challenge, but one we think is achievable and a huge opportunity for the UK. We have world class manufacturing, materials excellence, creativity and design expertise, digital excellence, leadership in standards and regulation, and an enviable network of research and technology organisations (RTOs) including the catapult centres.
Linked directly to the vision, Innovate UK is delighted to announce a new £15m programme focused on manufacturing and materials. Innovate UK will be investing in Resource Efficiency for Materials and Manufacturing, REforMM. The programme will focus on the delivery of resource efficient and competitive manufacturing and materials across sectors, with an initial £1m feasibility studies funding round in November 2022.
Alongside this, Innovate UK and our partners, the Biotechnology and Biological Sciences Research Council and the Engineering and Physical Sciences Research Council, will invest in a £14m sister programme BIO-REforMM. This will focus on sustainable biomanufacturing at scale across sectors with the aim to displace petrochemical-derived materials and products. Again, an initial feasibility studies funding round will open in December 2022.
Both programmes will look to inspire a common vision, involve aligned communities and invest to support innovation. Look out for more details in the next issue or head to the Innovate UK website to get involved: K www.ukri.org/councils/innovate-uk
Some fascinating projects have received almost £14m in combined backing from UK Research and Innovation’s latest funding opportunity under the Made Smarter innovation challenge, the Sustainable Smart Factory competition.
The collaborative research and development competition sought to identify and support digital innovations to improve the sustainability of manufacturing processes, resulting in either reduced material or energy consumption.
In total, 12 projects were successful in their applications, which involved securing between £1m and £8m in funding each. The projects offer solutions for a wide range of manufactured goods and industrial processes across a number of sectors spanning food, aerospace, automotive, plastics, electronics and various engineering disciplines.
ABOVE: Project Butterfly brings together a consortium led by GKN Aerospace Services of UK manufacturing organisations, solution providers and research organisations, working across a number of UK sectors
MAIN PIC: EdgeMethods and Victrex are developing reusable machine learning models to improve energy efficiency within an existing manufacturing plant
A variety of projects have received almost £14m in combined backing from the Sustainable Smart Factory competition
• Project Butterfly brings together a consortium led by GKN Aerospace Services of UK manufacturing organisations, solution providers and research organisations, working across a number of UK sectors. They share best practice and demonstrate the power of Industry 4.0 to deliver nearterm impact on the road to net zero manufacturing.
• EdgeMethods and Victrex are developing reusable machine learning models to improve energy efficiency within an existing manufacturing plant, to both save on rising energy costs and help achieve sustainability objectives. Following a successful proof of science
project, EdgeMethods will implement its ‘Energy of Things’ software as a service solution within the Victrex polymer manufacturing site in North West England.
• Eco-Sprint led by FitFactory Technology focuses on the aligned sustainability and productivity needs of manufacturing SMEs. Starting with a focus on energy intensive aerospace special finishing processes, it will go on to demonstrate scalability through deployment in other sectors.
Projects will run for up to two years and are expected to open the door to significant carbon dioxide equivalent (CO2e) savings and a cleaner manufacturing economy.
UK registered businesses can apply for a share of up to £1.5m to research, test and develop step-change circular economy approaches.
This funding forms part of the UK Research and Innovation National Interdisciplinary Circular Economy Research programme (NICER). It enables SMEs to engage with and benefit from access to expertise at five research centres and hubs via collaborative research and development (CR&D) activities.
The closing date is Wednesday 7 December – for more information please see Competition overview - Circular Economy for SMEsinnovating with NICER, round 2 - Innovation Funding Service (applyfor-innovation-funding.service.gov.uk).
Projects are sought to share £5m in funding and improve power electronics, machines and drives (PEMD) manufacturing supply chains in the UK. Run by Innovate UK the ‘PEMD scale-up’ competition from the driving the electric revolution challenge at UK Research and Innovation supports the growing need to invest in UK PEMD manufacturing.
Being run in two strands the £5m funding competition will enable the scale-up of PEMD manufacturing in the UK. These projects are designed to develop a resilient, cross-sectoral, UK supply chain for these enabling technologies critical for net zero.
The deadline for applications is Wednesday 7 December – for more information please see: New funding announced to help the UK PEMD industry scale-up – UKRI.
The UK’s ambitious plans to significantly reduce industry carbon emissions could end up hamstrung by a myriad of ‘almost useless’ data, according to the High Value Manufacturing Catapult (HVMC). The Manufacturer’s James Devonshire delves deeper
In March 2021, the UK government laid out the country’s ambitious Industrial Decarbonisation Strategy (IDS); a roadmap for the decarbonisation of UK industry and manufacturing, and the first of its kind in a major economy.
Under the IDS, the government is targeting a carbon emissions reduction of at least two-thirds by 2035 and at least 90% by 2050.
The government says the wider Net Zero Strategy will secure 440,000 well-paid jobs and unlock £90bn in investment by 2030. Furthermore, by boosting clean energy as part of the nation’s journey to net zero, reliance on imported fossil fuels will be reduced, insulating British consumers from global price spikes and strengthening the UK’s energy security.
It all sounds very impressive, resolutely determined and, let’s face it, not a moment too soon. However, merely sounding proper isn’t going to cut it. The proof is going to be in the end results, which is why industry needs to be stepping up now, not later.
Sustainability-first agendas afford many benefits
According to the latest figures from the Office for National Statistics, consumer expenditure aside, the manufacturing sector accounted for 16.8% of total UK greenhouse gas (GHG) emissions in 2020. Transport and storage, a sector very closely linked with manufacturing, accounted for 11.3% of total GHG emissions.
Positively, though, UK industry has managed to reduce its carbon emissions significantly over the last 30 years, removing around 55.5% since 1990.
Nevertheless, there is still a long way to go if the manufacturing sector’s net zero journey is going to be successful. The good news, however, is while we’ve still got a challenging road to travel, the benefits of sustainability initiatives are numerous, making the transition all the more worthwhile.
First, there is the moral gratification associated with knowing you are manufacturing your products as sustainably as possible. It’s the right thing to do and will benefit our future generations.
Then there are the financial incentives to adopt net zero initiatives. From access to finance for green investments, to reduced energy bills as a direct result of taking advantage of renewable sources, operating more sustainably can have a direct impact on an organisation’s bottom line. And this is before we even consider any potential regulatory requirements and associated penalties for not demonstrating a sustainability-first focus.
Rounding out my top three benefits of following sustainable manufacturing practices is the reputational boost companies can afford as a result. Today, amid a severe skills and talent shortage, coming across as an attractive place to work has, arguably, never been more important.
At a time when tremendous focus is on sustainability, manufacturers can appear particularly favourable in talent’s eyes by highlighting their net zero ambitions and achievements.
Furthermore, pushing sustainabilityfocused initiatives also reflects favourably in the eyes of consumers. Indeed, recent research by Deloitte, on how consumers are embracing sustainability, revealed the five sustainable practices consumers value most are:
• Producing sustainable packaging and products
• Reducing waste in the manufacturing process
• Committing to ethical working practices
• Reducing carbon footprint
• Respect for human rights
Even as B2B companies, manufacturers need to seriously consider these factors. After all, there is a knock-on effect along the value chain, whereby end consumers may make different choices based on organisations’ sustainability credentials. The bottom line is that by displaying they are following a net zero agenda, companies will give themselves another differentiating factor for customers and consumers to consider.
Industry needs set standards if it’s to really drive decarbonisation
The manufacturing sector has made some significant net zero strides, and the benefits of following a sustainable agenda are numerous and well known. Yet, the High Value Manufacturing Catapult (HVMC), UK manufacturing’s strategic research group, has recently issued a stark warning.
In its HVMC Embodied Emissions and Net Zero. A Review of Standards, Recommendations for Consistent Green House Gas Emissions Accounting in the UK report, released in early October, HVMC warns that industry’s net zero plans are at risk because of a volume of data which it describes as ‘almost useless’.
Given manufacturing’s significant contribution to GHG emissions, it stands to reason that there should be a set of common carbon emissions reporting standards across the sector. However, as the HVMC research highlights, organisations are faced with a number of different carbon accounting standards, which use varying terminology and can be broadly separated into corporate/ organisational standards or product standards. The problem manufacturers have is deciding which standard to use.
In addition, the HVMC research outlines how currently there are no definitive guidelines when it comes to reporting on Scope 3 emissions – the emissions that are not directly produced by the company itself. Accurately reporting on Scope 3 emissions is crucial as 60% and 90% of industry’s emissions occur in the early materials extraction and materials processing stages of the manufacturing value chain.
Except for the GHG Protocol Scope 3 Standard, Scope 3 emissions are typically either totally optional, or the organisation can decide which ones it includes in its calculations. As a result, Scope 3 reporting among manufacturers varies wildly and without a consistent approach across the board, it will be
near impossible to measure gains and, indeed, losses.
Finally, current reporting standards are inconsistent, using varying formats and terminology. If the manufacturing sector’s carbon emissions are to be reviewed and verified accurately, the HVMC states that a ‘robust reporting and monitoring system should be implemented – overseen by an economy-wide carbon regulator.’
As the HVMC report warns: ‘Without a proper auditing and monitoring system in
• Under the Industrial Decarbonisation Strategy, the government is targeting a carbon emissions reduction of at least two-thirds by 2035 and at least 90% by 2050
• The government states the wider Net Zero Strategy will secure 440,000 well-paid jobs and unlock £90bn in investment by 2030
• UK industry has removed the equivalent of around 100 metric tonnes of carbon dioxide in air emissions since 1990
• Adopting a sustainability-first agenda can reap numerous benefits for manufacturers
• Setting standards, common terms and consistent reporting are crucial if industry is to make measurable net zero gains
place, there is no way of knowing where the UK manufacturing industry is in terms of working towards and meeting net zero targets.’
Commenting on the report, HVMC Chief Executive Katherine Bennett said: “Tracking carbon emissions is now an integral part of a company’s annual audit. Yet, a myriad of different carbon accounting standards and methodologies are used, meaning that the data is rendered almost useless when combined across the manufacturing sector.
“Given the energy intensive nature of manufacturing, this lack of common data makes tracking overall emissions reductions almost impossible and vital information can be obscured or lost. This risks completely undermining the UK’s drive to net zero. We would be delighted to work with relevant government departments, such as BEIS, to address this shortfall and jointly develop these universal standards.”
Start with small steps Something we hear frequently from manufacturers, particularly SMEs, is that they do not know where to begin when it comes to reducing emissions. There is a definitive perception that adopting a sustainability-first agenda will inevitably involve making significant investments. The reality, however, is that organisations can often take small steps and realise quick gains, without spending large sums of money.
It could be installing solar panels to reduce reliance on grid power or switching energy providers as part of Scope 2 reduction initiatives – the important part is to do something. That could even be getting to grips with the plethora of net zero related terms that are out there.
Once organisations take their first steps towards decarbonisation and see the results that can be achieved, it often leads to a snowball effect, with more changes following in quick succession.
Industry’s net zero plans are at risk because of a volume of data which the HVMC describe as ‘almost useless’
The results of the 2022 Manufacturing Agility Assessment, researched and produced by The Manufacturer, and commissioned by HSO, will be released at Digital Manufacturing Week 2022, industry’s premier event. The report will provide powerful insights into just how agile the nation’s manufacturing organisations are
One key insight the report will reveal is how, despite surviving the COVID-19 pandemic, set against a backdrop of high energy prices, ongoing supply chain disruption and the conflict in Ukraine, many manufacturers are still questioning how agile they are.
Indeed, since 2021, when the inaugural Manufacturing Agility Assessment was conducted, manufacturers’ agility has witnessed a significant drop.
This may come as a surprise to many, which is why the follow-up interviews, conducted by The Manufacturer to add much needed context, are so valuable. In the new report, the insights from these interviews serve to highlight both where
manufacturers are in terms of agility and explain why so many organisations believe they aren’t as agile as they were in 2021.
Discover the reasons why so many manufacturers overestimated their agility last year; how supply chain disruption actually has a silver lining; and why, despite being faced with an array of challenges, many organisations are still actively investing in key business areas.
This year’s Manufacturing Agility Assessment is a deep dive into the current state of industry’s agility, building on last year’s first iteration, to provide a holistic view.
Concluding this year’s assessment, Matt Birtwistle, Manufacturing Industry Director at HSO, said the results were “eyeopening”, but that they also reflected many of the conversations HSO has been
having with its customers. In the report, Matt also provides some insights into how manufacturing organisations can quickly and effectively boost their agility, with a relatively small investment.
Matt and The Manufacturer’s James Devonshire, author of the report, will be unveiling the results of the 2022 Manufacturing Agility Assessment at 3.00pm on 16 November in the Leadership & Strategy Theatre within the Smart Infrastructure Zone at Smart Factory Expo, part of Digital Manufacturing Week.
Book a ticket for Smart Factory Expo and be among the first to learn the results of this year's Manufacturing Agility Assessment.
There has never been a more important time for our sector to pull together and to work together, to create a shared agenda and Manufacturing and Engineering Week will do exactly that. I am delighted to be part of the Advisory Board and that MAKE UK are a partner of this groundbreaking event.”
Phipson CBE, Chief Executive, MAKE UK and M&E Advisory Council Chairman
Eliyahu Goldratt must have loved trade-offs. In his work on the Theory of Constraints (TOC) in operations, he invented the evaporating cloud to address dilemmas; trade-offs where there was no acceptable compromise. He would have relished the challenge most CXOs find themselves in today; a trilemma on how to drive improved financial performance, supply resilience and sustainability impact, simultaneously (see Figure 1).
In this article, we will focus on the value chain trilemma as a concept, apply it to a subset of companies (industrial OEMs), and identify key levers to resolve this, based on our experience. Whilst we have focused on industrial OEMs for our analysis here, the trilemma is relevant for all sectors.
Industrial OEM value chains have unique characteristics that make them difficult to manage: Multiple value chains
industrial OEMs ($1.9tn in market cap and $1.1tn in 2021 revenues) over 2018-21 on financial, resilience and sustainability dimensions. Whilst there are multiple metrics for each of the dimensions, we focused on three key metrics from publicly reported data for an indicative and focused analysis: financial (% EBIT margin), resilience (coefficient of variation of WIP) and sustainability (S&P ESG index – environmental score).
Figure 2 (see over) summarises the conclusions from this analysis across the three dimensions. Across each of the three sides of the trilemma, we assessed the proportion of these 97 companies that perform in the top quartile and the top two quartiles of the two dimensions. The results were revealing. None of the 97 companies assessed had top quartile performance on both EBIT margin and on
• Maximum value sits at the interface of functions: For instance, at a mid-sized industrial client in a turnaround, driving product modularisation and platforms (managed by R&D) unlocked maximum cost benefit in external spend (managed by procurement) due to a rationalisation of part numbers and simplification of specifications.
• Driving step-change on often conflicting dimensions: A large electrical OEM client was able to drive a >40% reduction in lead time, >10% reduction in cost and >25% reduction in inventory, simultaneously through an organisation wide, cross-functional approach. The reduction of lead time spanned order bound engineering, materials supply and manufacturing. Challenging individual functional lead time buffers (e.g. after engineering, material receipt and production) was a key driver. A narrower functional focus would have missed this opportunity.
(ETO/CTO) and corresponding supply models (ATO/MTS/MTO), long lead times often running into years, unclear or delayed demand signals, lack of flexibility and limited sustainability focus. In an increasingly volatile business and geopolitical environment, the impact of these challenges gets compounded, impacting growth, margins, resilience and sustainability.
Going from good to great In resolving this trilemma, some companies have done better than others. We analysed performance of 97
environmental scores, while 23% had top two quartile performance across both dimensions. Across all three dimensions, no company was in the top quartile and 14% were in the top two quartiles across all three dimensions. This indicates that driving improved performance across all three dimensions of the trilemma is difficult, but progress is being made. We will now focus on our approach to do just that.
Based on our experience, it is critical to have an end-to-end (E2E) approach for three reasons:
• Cross-functional execution and programme management: The ability to identify, prioritise and execute few, targeted initiatives that drive end-toend value is often poor. At several clients, the improvement agenda is rooted in the annual functional budget planning exercise and excludes an end-to-end perspective of driving value across functions.
We have outlined three areas (with 14 levers) across the value chain to solve for the trilemma (see Figure 3). There is no silver bullet solution - not every lever will have a significant impact on every
Driving improved performance across all three dimensions of the trilemma is difficult, but progress is being made
• High investment hurdle rates
• Need for quantified benefits for each investment case
• Investment cases do not meet hurdle rates
• Difficulty in quantifying benefits
• Lower costs
• Greater Low Cost Country (LCC) sourcing
• Lower inventories
• Competition for Investment from same pool of CAPEX and Resources FIG. 1: THE VALUE-CHAIN
• More efficient/Lean capacity
• More Redundant/Flexible capacity
• Near shoring
• Higher inventory
dimension, however, combined, these have the potential to transform.
1. Segmented customer offer and supply models: Segmenting the customer offer into standard, non-standard and bespoke, and aligning the supply model (e.g. ATO for standard offer vs. MTO for non-standard); supporting these three customer offer types helps shape demand and drive efficiency. This enables differentiated lead times and pricing and
greater resilience as the customer can finalise their design specifications later, without impacting the value chain.
2. Next level customer interface: A seamless customer interface for quotation, order clarification, order confirmation and design freeze can drive significant cost efficiencies and improve quotation win rates. Significant automation of order bound engineering and reduction in quoteto-order lead-time is achieved.
• More Redundant/Flexible capacity
• Competition for Investment from same pool of CAPEX and Resources
Operations and Supply Chain
3. E2E project management and visibility: At several of our project-based industrial OEM clients, we have introduced backward planning and scheduling based on a target delivery date. This was followed by improved visibility of project status, cost to complete (CTC) and estimate at completion (EAC) down to the project work breakdown structure (WBS) level. Improved E2E project and engineering change management can have an outsized impact on reducing
Sumeet Ladsaongikar, Partner at Kearney Londonproject delays and associated penalties. This level of monitoring also helps with an agile response to demand changes, supply shocks and resource challenges.
4. Cross-functional strategic sourcing: Building a carbon-cube, that combines the traditional spend cube with Scope 3 emissions insight into the supply base is a key first step. Fully leveraging a combination of commercial and non-commercial levers from the two Kearney chessboards - purchasing and sustainability - would drive further emissions and cost reduction.
5. Differentiated supply-in methods: Based on the nature of demand for externally sourced materials, selecting the optimal supply-in method (e.g. VMI, ROP, BTO, etc.) can help balance the level of inventory carried and the supply resilience needed to deal with variability. At a leading industrials client Kearney introduced a tailored framework to choose from a variety of supply-in methods based on various demand and supplier characteristics. This was a key driver in a ~15% reduction in materials inventory whilst simultaneously reducing material stock-outs.
6. Resilience in the supply base: Kearney’s PRISM (Proactive Risk Intelligence in Supply Management) is a tech-enabled supply risk management toolkit that helps identify risks, plan mitigation actions and transform the operating model to embed this approach. The tool collates information on the supply base from a wide range of sources. Using a combination of commercial and non-commercial levers; these risks are then addressed.
7. Control manufacturing flows through pull: Demand for industrial OEMs are typically characterised by low volume, high mix and high demand variability. Many industrial OEM manufacturing plants are organised as production departments, with each
optimising for departmental productivity and throughput. At a large industrial client, we implemented CONWIP at multiple manufacturing plants to drive 2040% reduction in WIP turns, lead-time and improvement in customer NFS.
8. Manufacturing productivity:
Whilst year-on-year direct labour productivity improvement is the norm at most companies, the opportunity is in the ambition level on productivity improvement and the use of i4.0 technologies to enable this. At most large industrial players, we have identified and improved direct labour productivity by 15-20% and enabled annual productivity gains above inflation. Improved asset productivity (e.g. OEE) also drives improved energy and emissions productivity and lower waste.
Productivity improvement in indirect functions is often a missed opportunity because it is difficult to have a similar level of transparency on value-added and non-value added activity as is with direct labour. Using an Orgalytics focused approach, we can get an indicative understanding of the drivers of non-value added activity in indirect functions. This can then drive improvement typically through more focused roles, systems enablement and automation.
9. Resilience in manufacturing: In industrial OEMs, increasing flexibility in manufacturing capacity to absorb disruptions and maintaining constant lead time is a key resilience objective. This is often achieved through a range of levers such as flexible labour models
and make vs. buy. At a large industrial player, we implemented a series of resilience levers in the early 2010s. When the COVID crisis hit, they were able to build on this to gain market share as they could be flexible with their manufacturing capacity at short notice.
10. Service and spares optimisation: Aftermarket service is a key profitability driver for most industrial OEMs. Improvement across the full lifecycle of a service intervention from preintervention (including product reliability), intervention (e.g. repair or swap), and post-intervention (e.g. service centre optimisation) can drive customer responsiveness and cost efficiencies, simultaneously.
11. End-to-end supply chain footprint: The design of the end-to-end supply chain footprint is one of the most effective levers to address the trilemma. Deploying advanced analytical tools to assess the implications of strategic choices, portfolio decisions, local content requirements, supplier base, fiscal incentives, emissions impact etc. on the location and product-site allocation decisions is often key due to the number of options and variables involved.
12. Product platforms and LCA: At a recent mid-sized industrial client ~90% of individual material codes had less than
three months/year of usage. Moving to product platforms focusing on common components for product families drove a >10% reduction in direct material costs whilst enabling an ATO model with shorter lead time. Complementing this with a Life Cycle Assessment (LCA) of products to baseline current emissions and to simulate potential emissions reductions through changes in material origin and emissions efficient processes, is a key lever to reduce Scope 3 emissions.
13. Integrated Business Planning (IBP):
A functioning IBP process with the underlying support planning processes (demand and supply planning, master production schedules, production scheduling and MRP) is key. In an industrial OEM environment, fully mining CRM information on current quotations, expected RFPs and customer project portfolio information can drive significant impact.
14. Digitalisation: While the selection of the right IT and OT tools and systems to drive digitalisation is important, even more critical is orchestrating the execution of the overall strategy, IT, OT and operational excellence roadmap with external vendors in a co-ordinated manner. At Kearney, we call this the Quorum principle. The quorum principle is the combination lock that can unleash the full potential of digital transformation, going beyond subscale pilots.
One of Goldratt’s key insights was that every dilemma arises because of at least one underlying erroneous assumption that needs to be challenged and solved. By challenging long-held assumptions across all dimensions of the trilemma through an end-to-end approach, this too can be resolved.
author would like to thank Colin Glasgow, Nigel Pekenc
Kautovaara, all partners in Kearney for their contributions to this article
Industrial OEM value chains have unique characteristics that make them difficult to manageThe and Antti
Costs are significantly rising in paper, energy and even pallet production, which in turn is likely to have a detrimental effect on all forms of packaging.
Add to this the fact that consumer behaviour has dramatically changed to online shopping in the past few years, with the equivalent of five years growth in 2020 alone, it is no surprise that the country is using far more packaging than ever before.
So what can businesses do to reduce their costs in the current climate? Using Right Size packaging allows the creation of a more sustainable packaging process, while reducing packaging costs. Right Size packaging also helps to eliminate the use of void fillers, which are often one of the reasons costs are so high, especially following the introduction of the plastic packaging tax.
Ribble’s Right Size solution combines Fanfold material and state-of-the-art technology to create the perfect size box for all products.
In addition, making packaging flexible and cost-effective means it can be converted back into Fanfold packaging. Fanfold is a long piece of corrugated board scored at regular intervals and folded neatly and compactly. Fanfold can then be used to pack single or multiple products by feeding it into fully automated packaging machines to create an exact size box, therefore eliminating waste.
Ribble Packaging manufacture and supply corrugated Fanfold, in addition to pioneering Right Size packaging solutions in the UK.
Some of the benefits of changing to a Right Size packaging solution include
• Saving around 30% on packaging costs by using Right Size and only buying Fanfold
• Eliminating obsolete packaging purchases by making only the boxes required
• Eliminating plastic packaging by using the Right Size box
• Reducing transport costs by fitting more onto vehicles
One of Ribble’s customers, Dextra Group, stated that by using Right Size solutions, it could produce specifically designed packaging on a ‘just in time’ method to suit its factory. As a result of producing perfectly sized boxes, Right Size solutions can eliminate void fillers, reduce corrugated costs, improve vehicle utilisation and lower transportation costs.