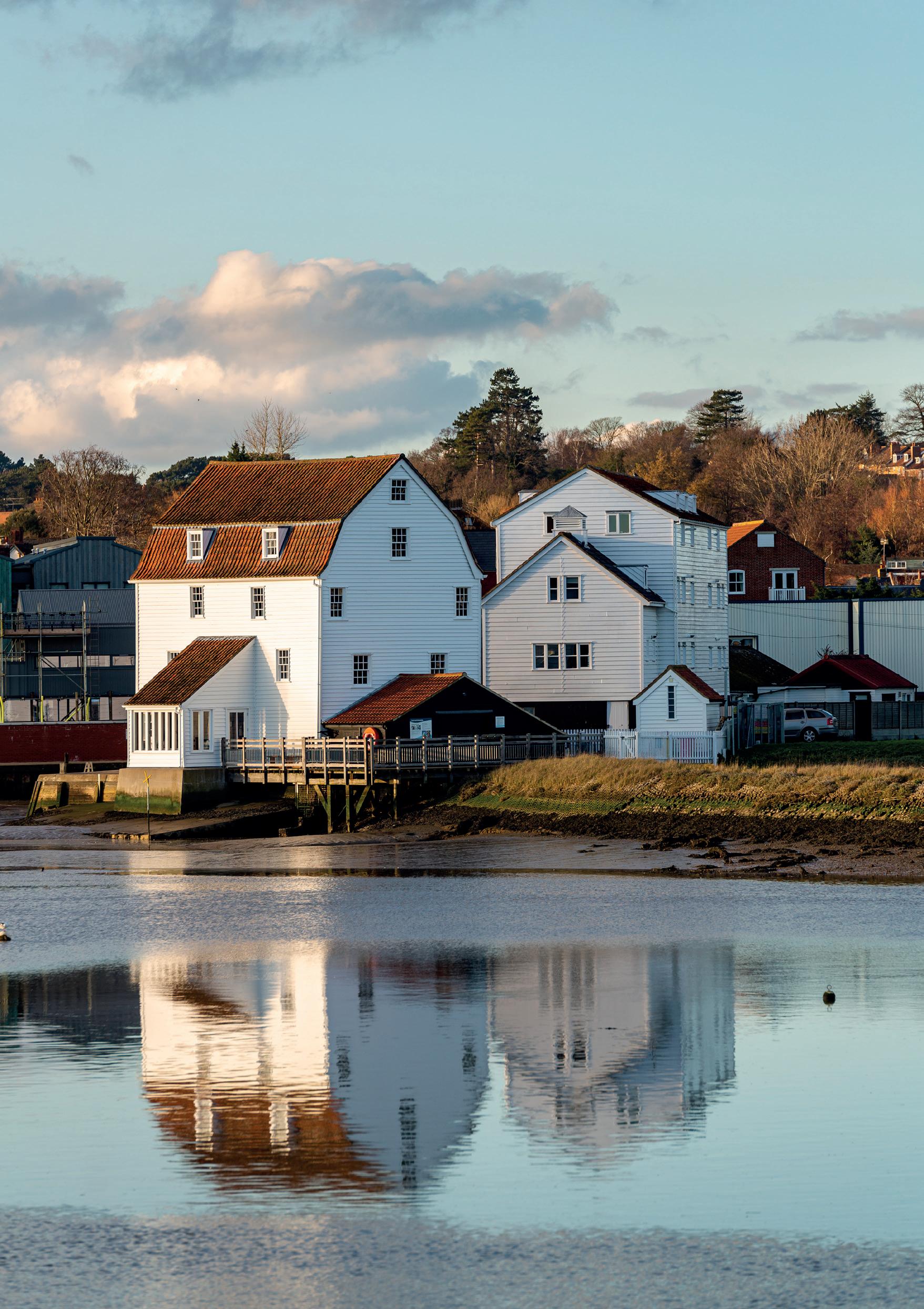
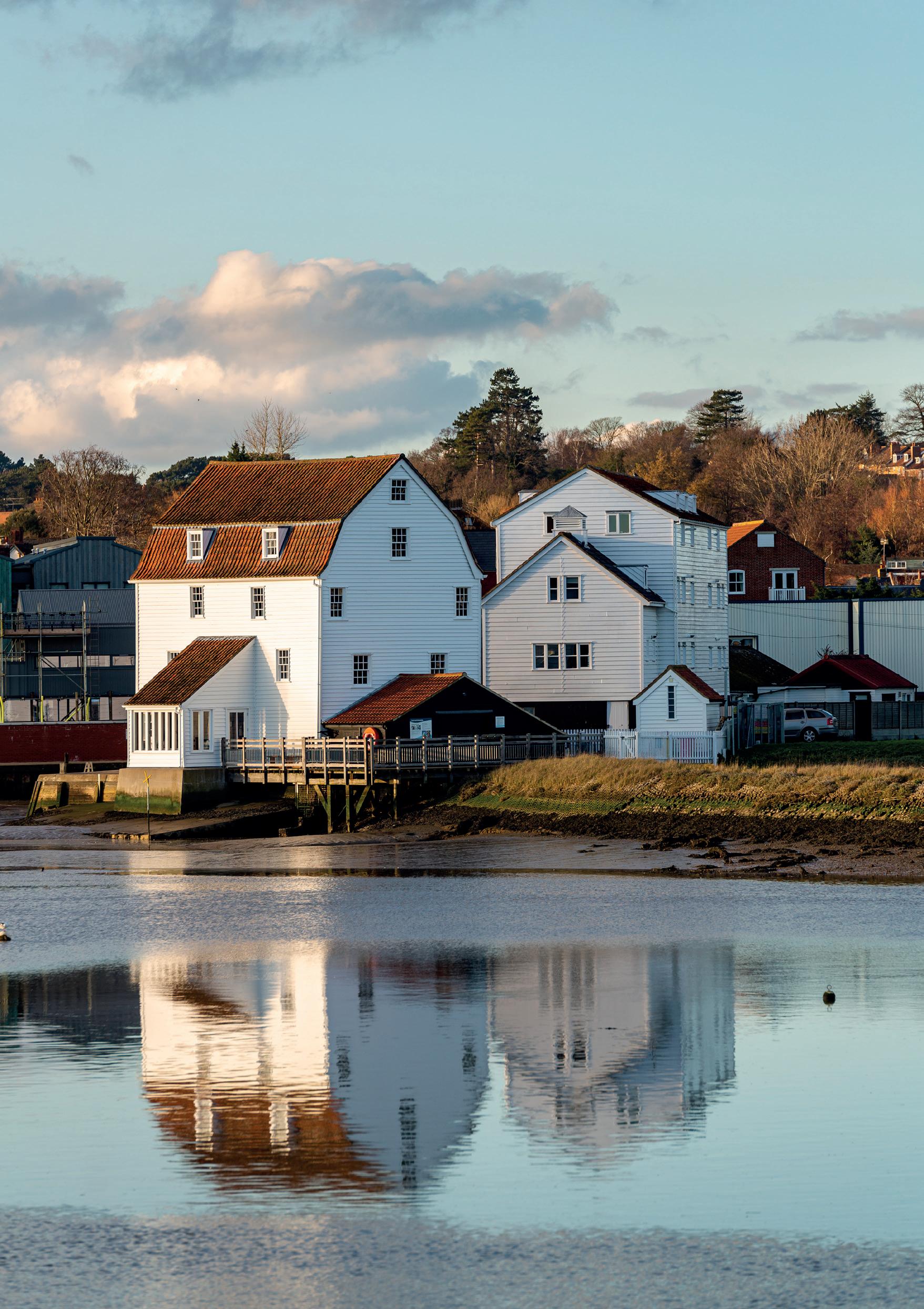
Advertising
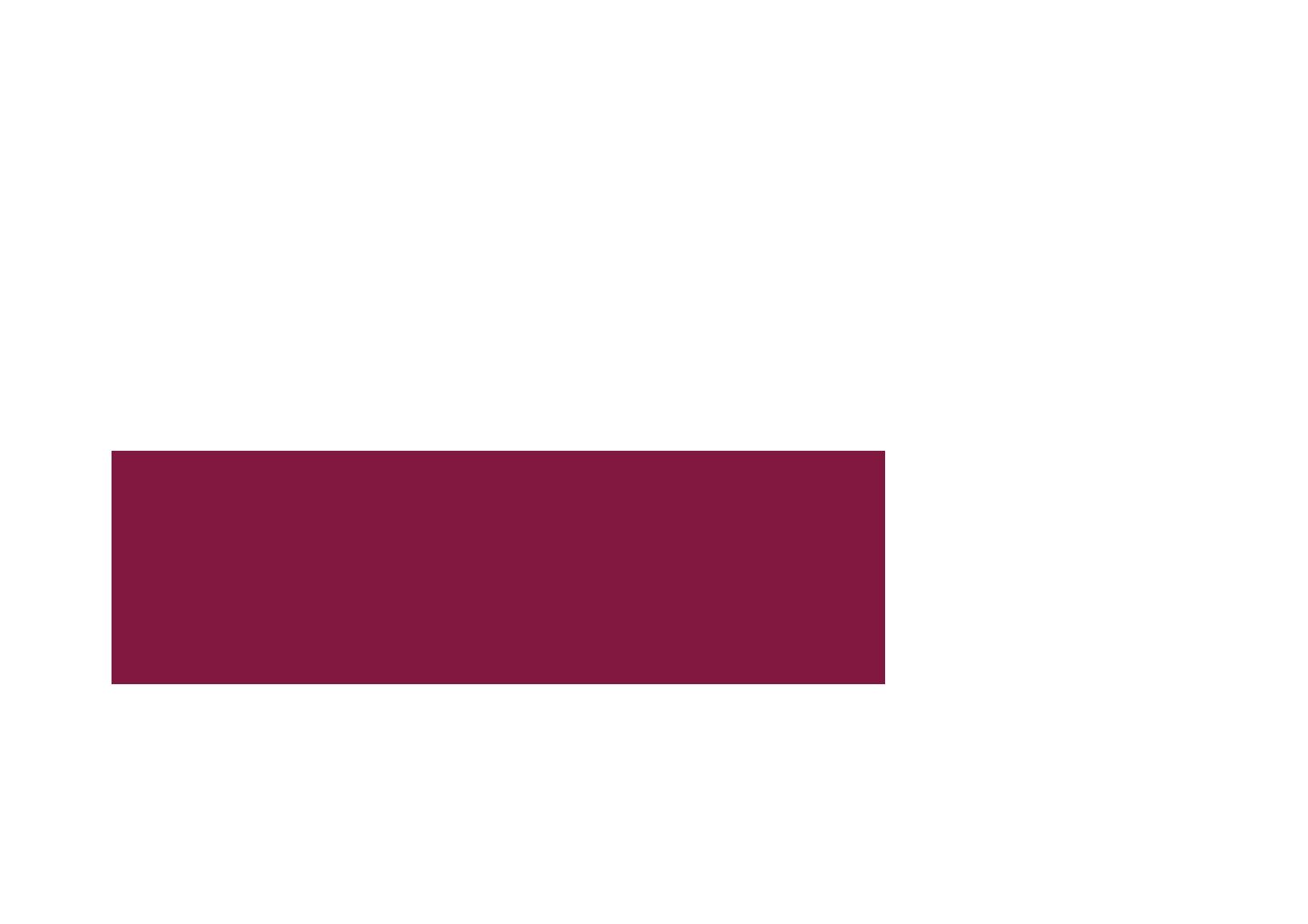
A GUIDE & SHORT HISTORY
WELCOME TO THE TIDE MILL
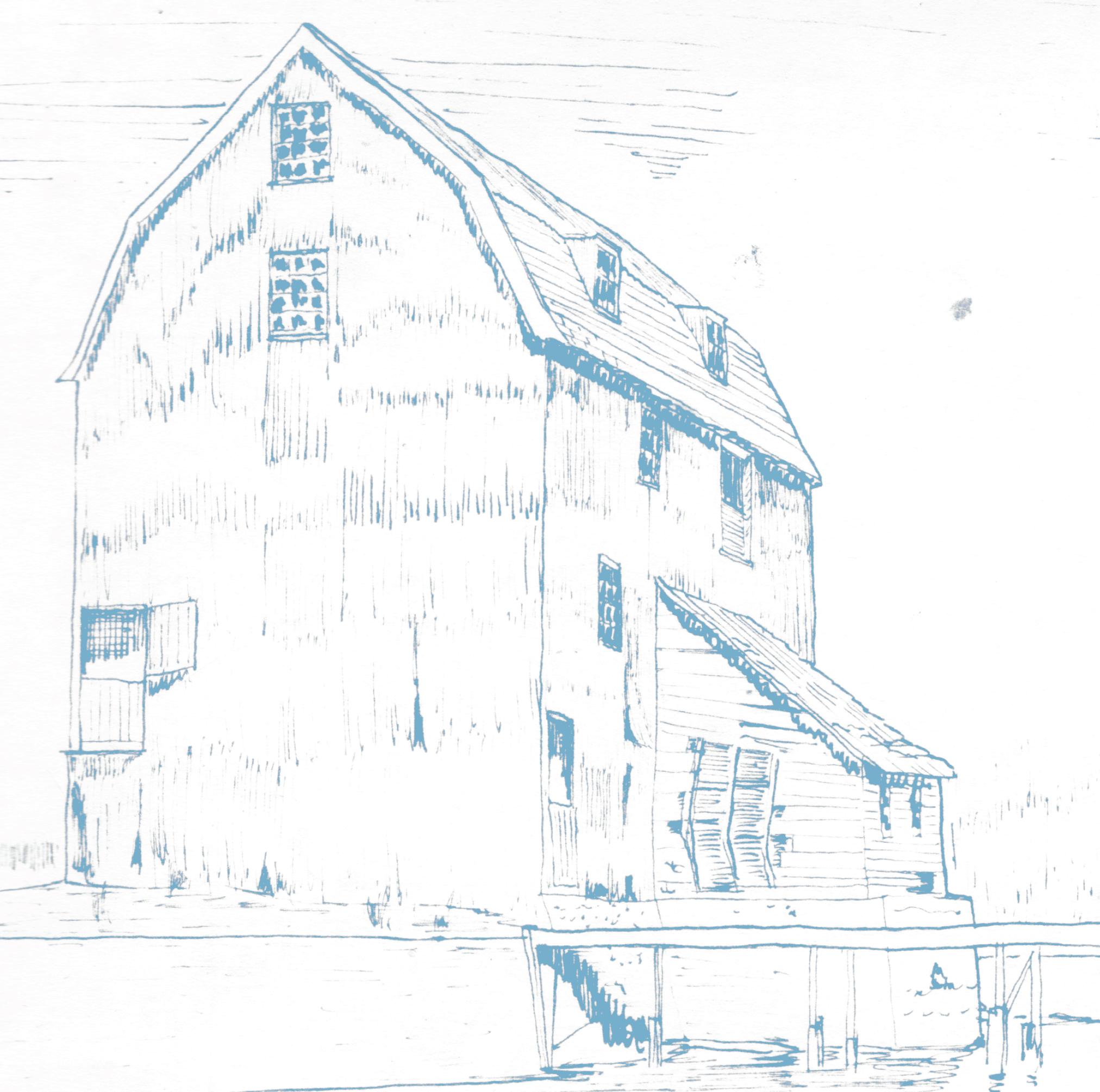
Woodbridge Tide Mill is a rare survivor. A mill has stood on this site by the river Deben since before 1170. The current mill, built in 1793, is the fourth on the site.
The Tide Mill team hope you enjoy your visit and find this guide helpful in pointing to the many different aspects of life over the centuries that the Mill displays. These range from the technology employed since the mill was built by the Normans to deal with part of the river Deben where the tides rob the riverbanks of water for hours every day, to the problems of higher tides today because of global warming. The mill is and has always been powered by renewable energy. We have installed a small electric generator powered by the Crown Wheel to emphasise the point. This is an important part of school visits.
The team is proud of the restored Mill, and we hope you enjoy your visit. Thank you for supporting the charity which maintains and runs the mill. Without your support, the Mill could end up a shell as it was before its rescue in 1968.
The Trustees are very grateful to XXXXX…. for their generous sponsorship of this Guide.
John Carrington. Chair of TrusteesWoodbridge Tide Mill Charitable Trust.
TIDE MILL TOUR
THIS IS A GOOD WAY TO SEE THE MAIN PARTS OF THE MILL
Entrance area –introductory video of how a tide mill works and Mill history
Gift Shop –and voluntary donation point - please?
Second Floor –where the Crown Wheel operates the hoist and wheat is stored
First Floor –the Stone Floor where wheat is ground
Outside –the Millwheel, millpond, River Deben
Ground Floor –Pit Wheel, stone nuts
ENTRANCE AREA – introductory video of how a tide mill works and Mill history
• Facing the welcome desk on your right you can view an 18-minute video (also available on YouTube) - worth watching before or after your tour
• The first 6 minutes cover how the Mill works followed by 12 minutes on the Mill’s long and fascinating history
• The video and interactive model shows how the Mill uses free tidal power
• Throughout the Mill there are boards with Mill history and details of its workings
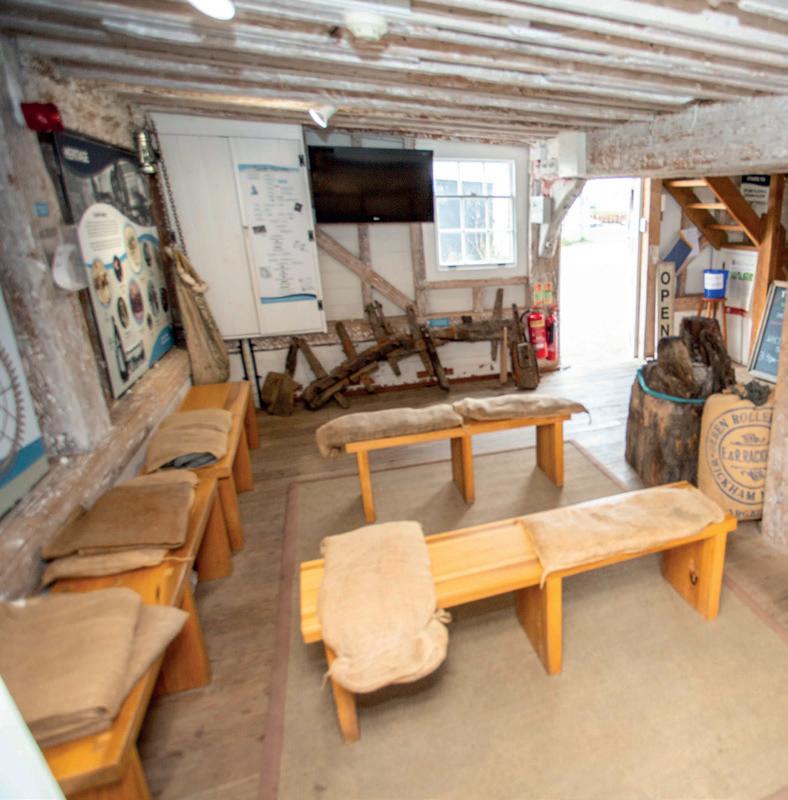
Seating Area
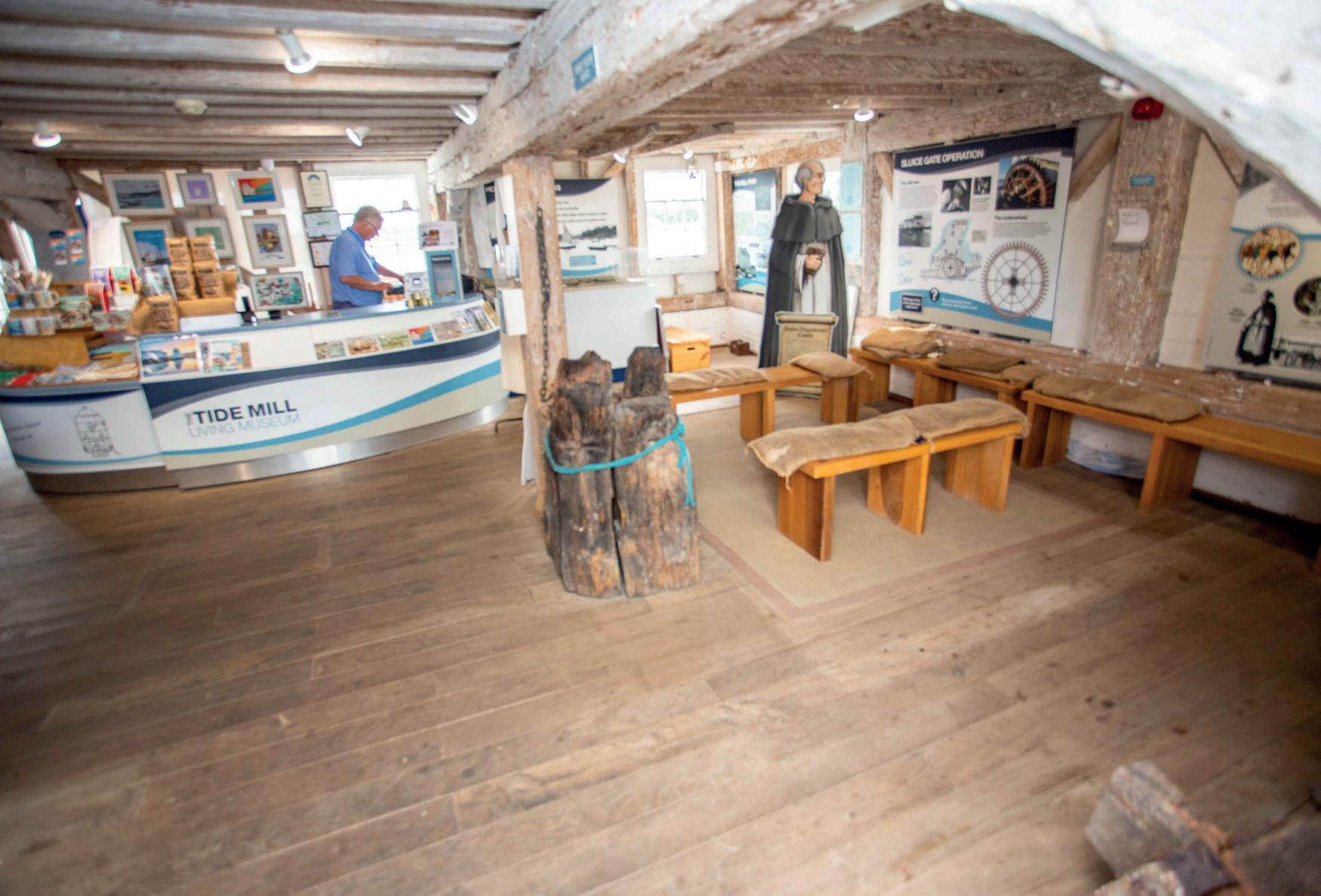
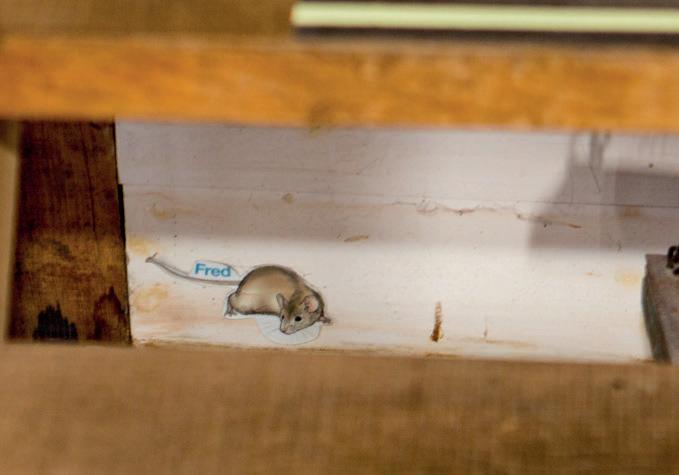
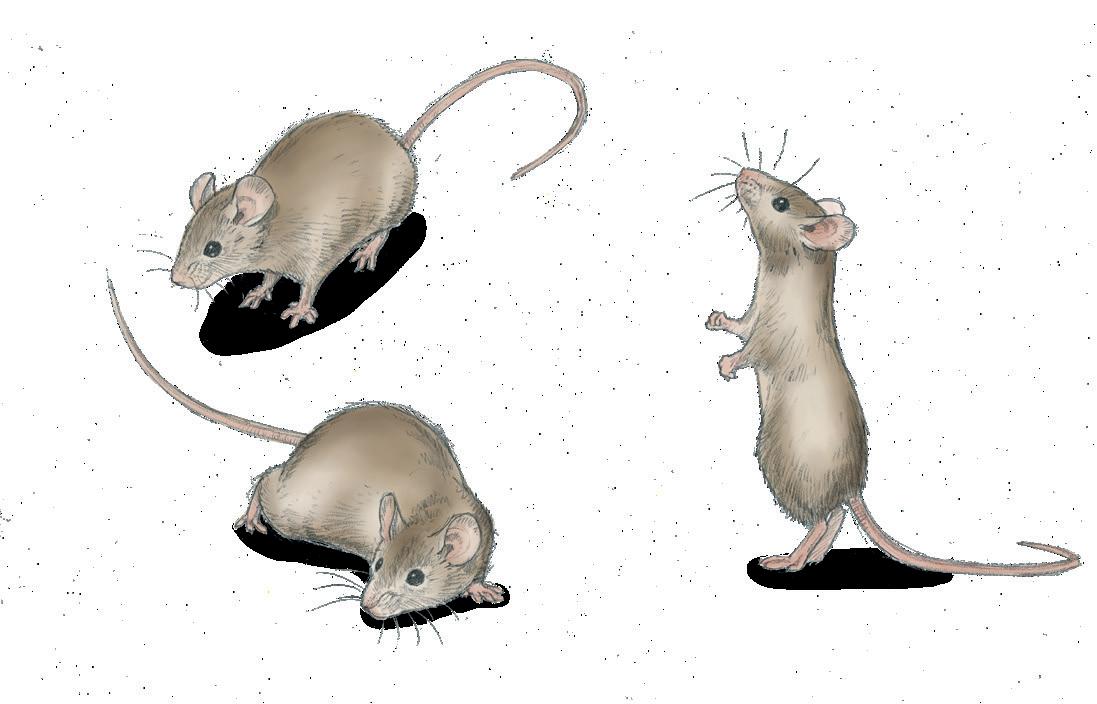
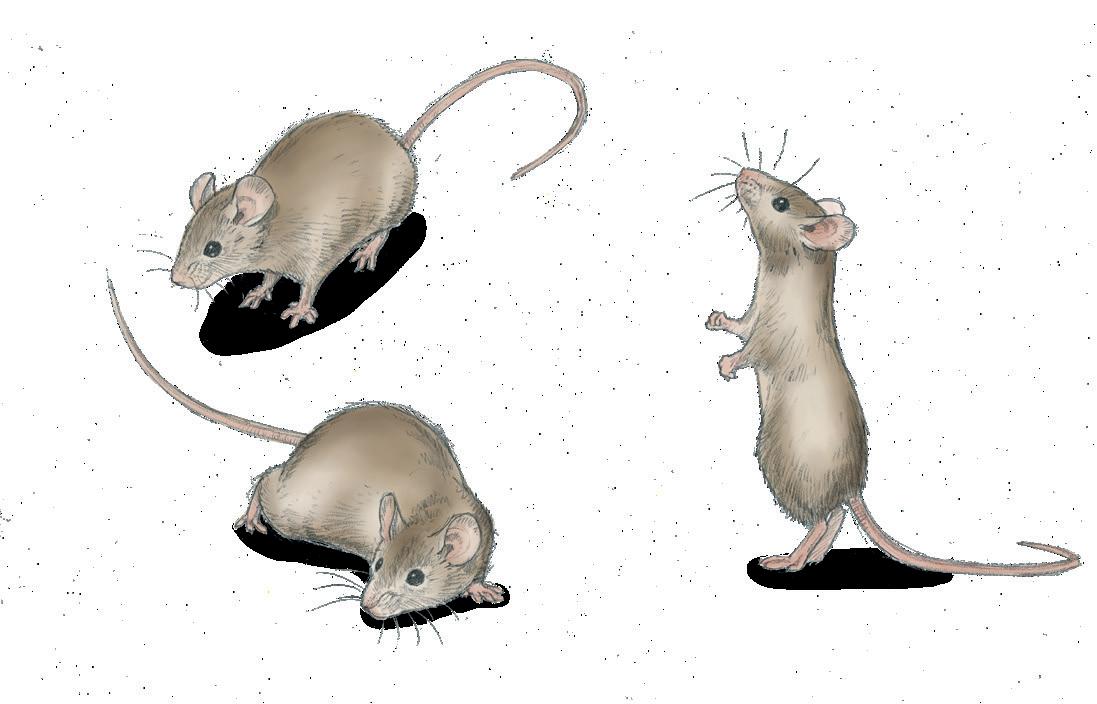
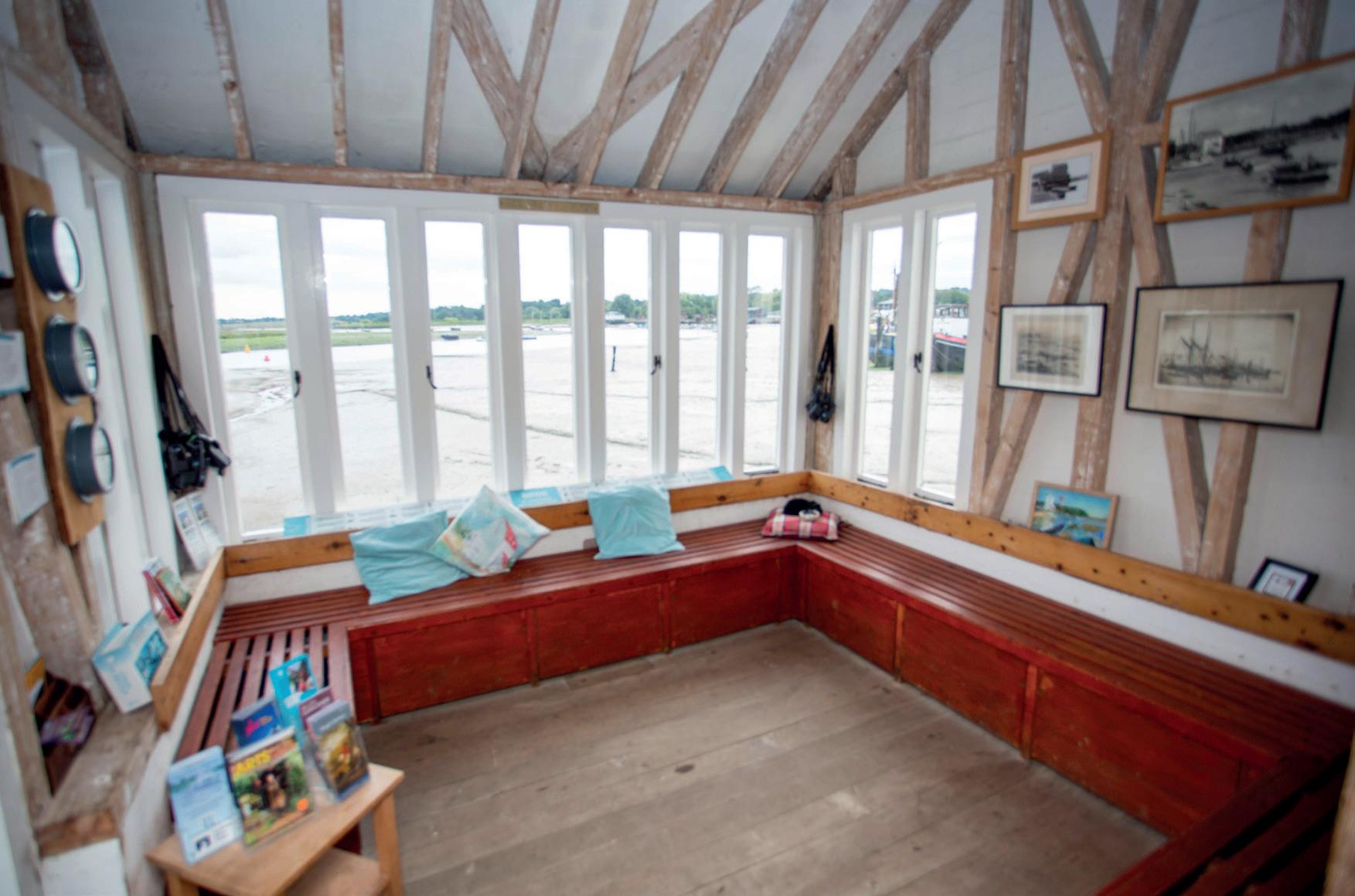
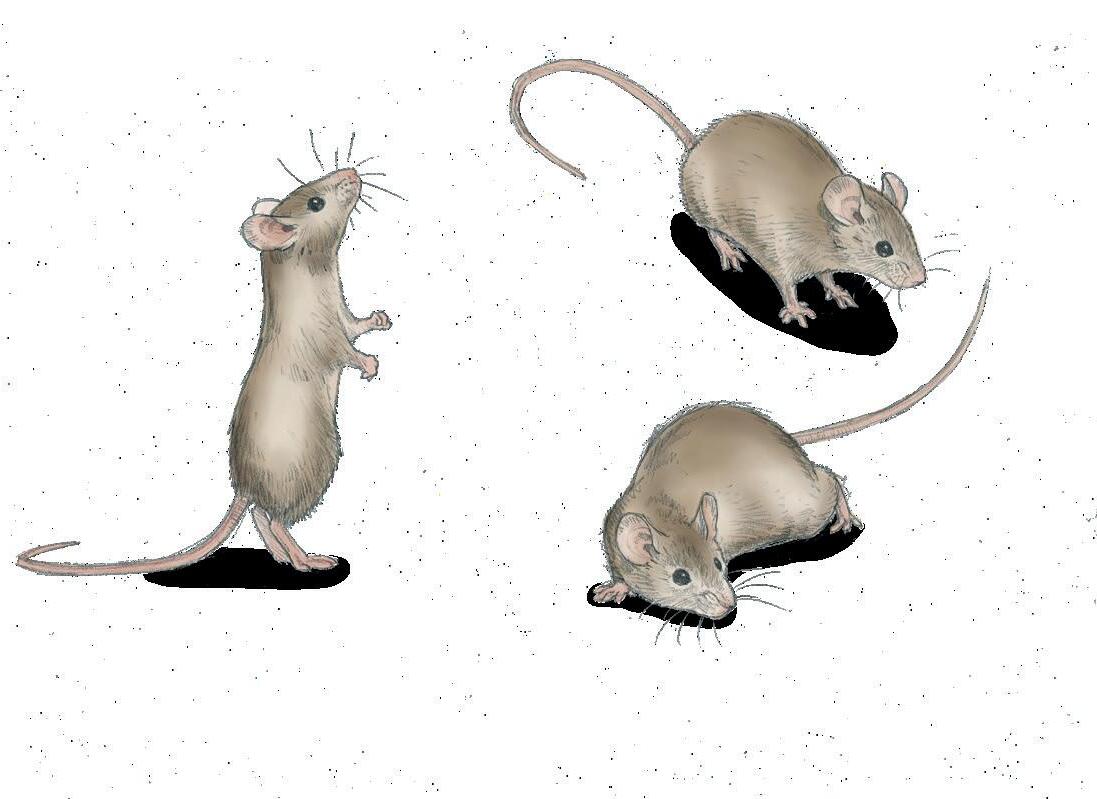
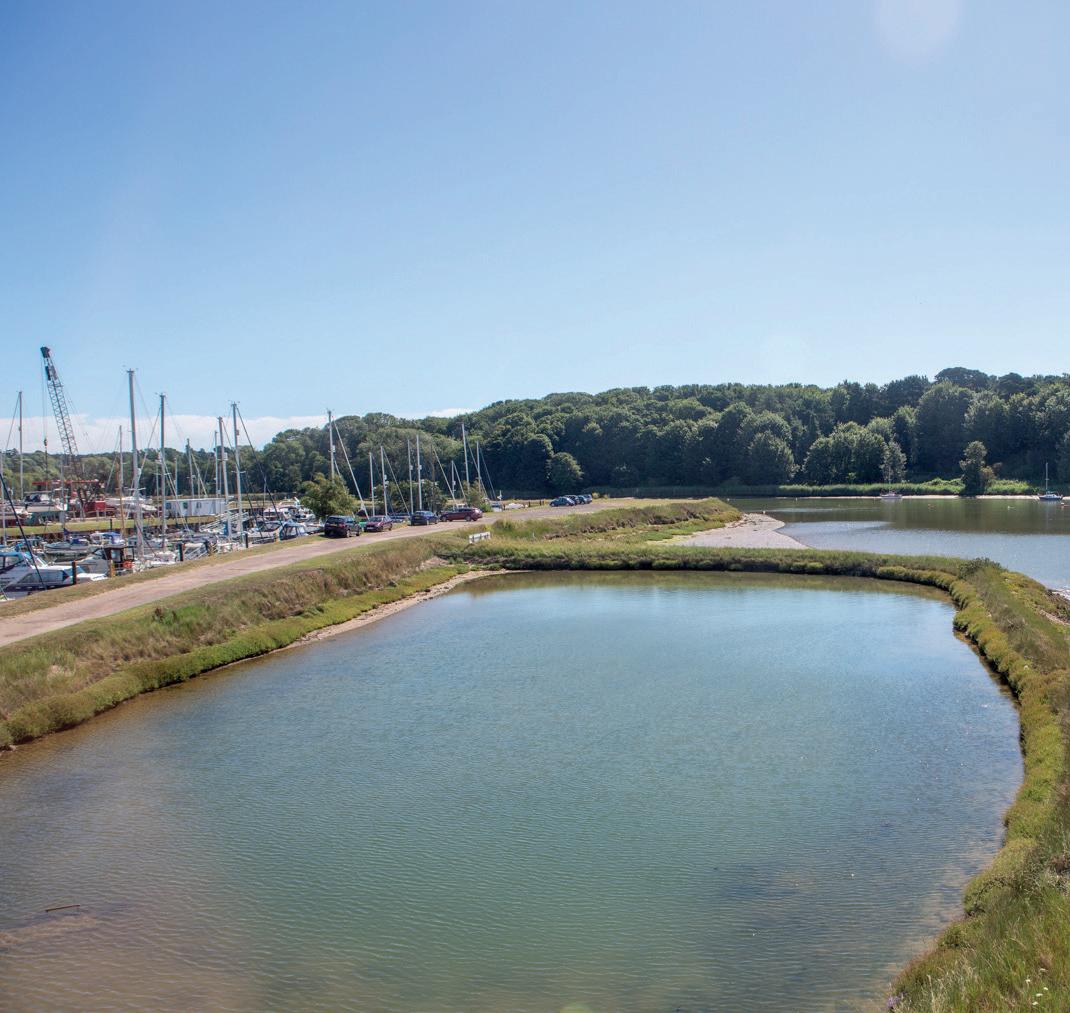
the Millwheel, millpond and River Deben
TheMillpond
This is a good place to begin because this is where the process starts
• On the way outside you walk through the riverside outhouse ‘(Weaver Room’) great for bird watchers, but originally an extra workshop for the miller.
• From the Weaver Room you can see if the tide is clear of the mill race because the miller could not start the machinery until it was. There are many images of the Mill on the wall.
• Today’s small millpond used to cover 7.5 acres - the Marina you can see today
• The river Deben is tidal and as the tide comes in it enters the millpond through a one-way valve
• The water is trapped and released at low tide back to the Deben to turn the wheel
• The wheel is made of English oak, is 5m diameter and weighs 4 tonnes
GROUND FLOOR – Pit Wheel, stone nuts
• The waterwheel turns a large wheel inside (Pit Wheel) with oak teeth
• Horizontal drive becomes vertical drive using the angled iron wallower gear
• Look up and spot the great iron spur wheel. It turns four ‘stone nuts’ directly above
• These ‘stone nuts’ turn the millstones above on the first floor
• The wooden chutes bring finished flour down to be bagged up for sale
• On the left is the ‘control room’ where the miller could control all aspects of his craft.
- turn the large metal ‘steering’ wheel to raise or lower the sluice gate
- raise or lower the running stone and to adjust the coarseness of flour
- control the flow of grain into the stones.
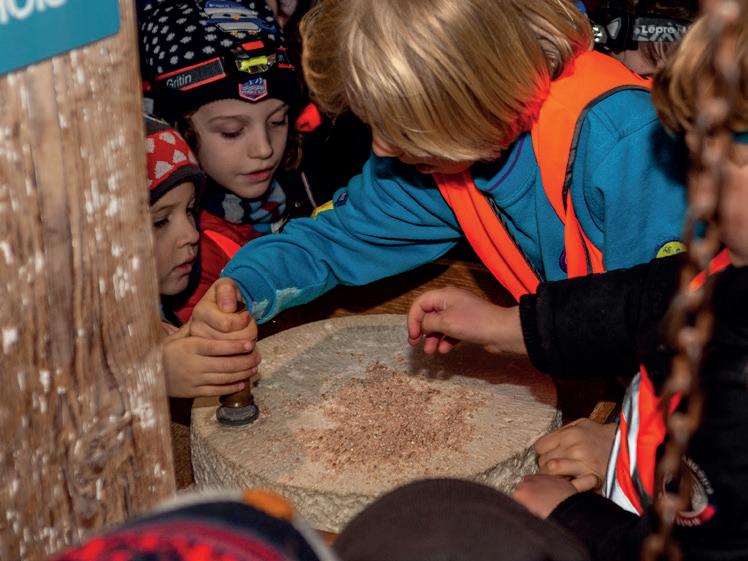
ControlRoom
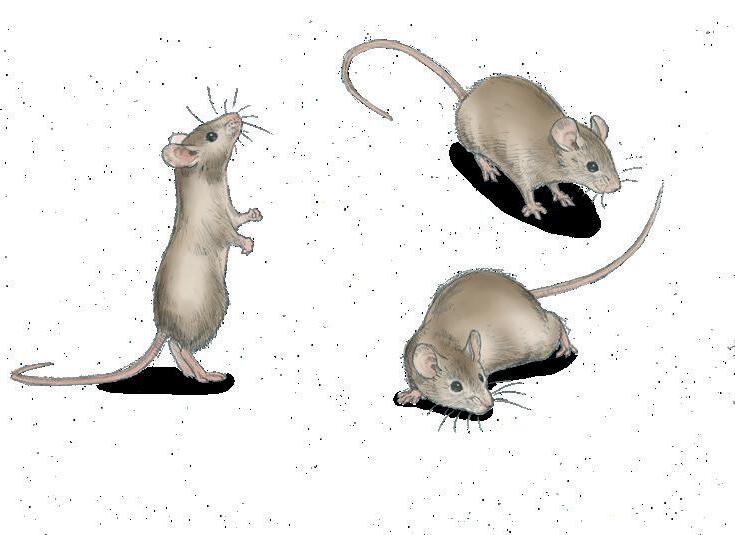
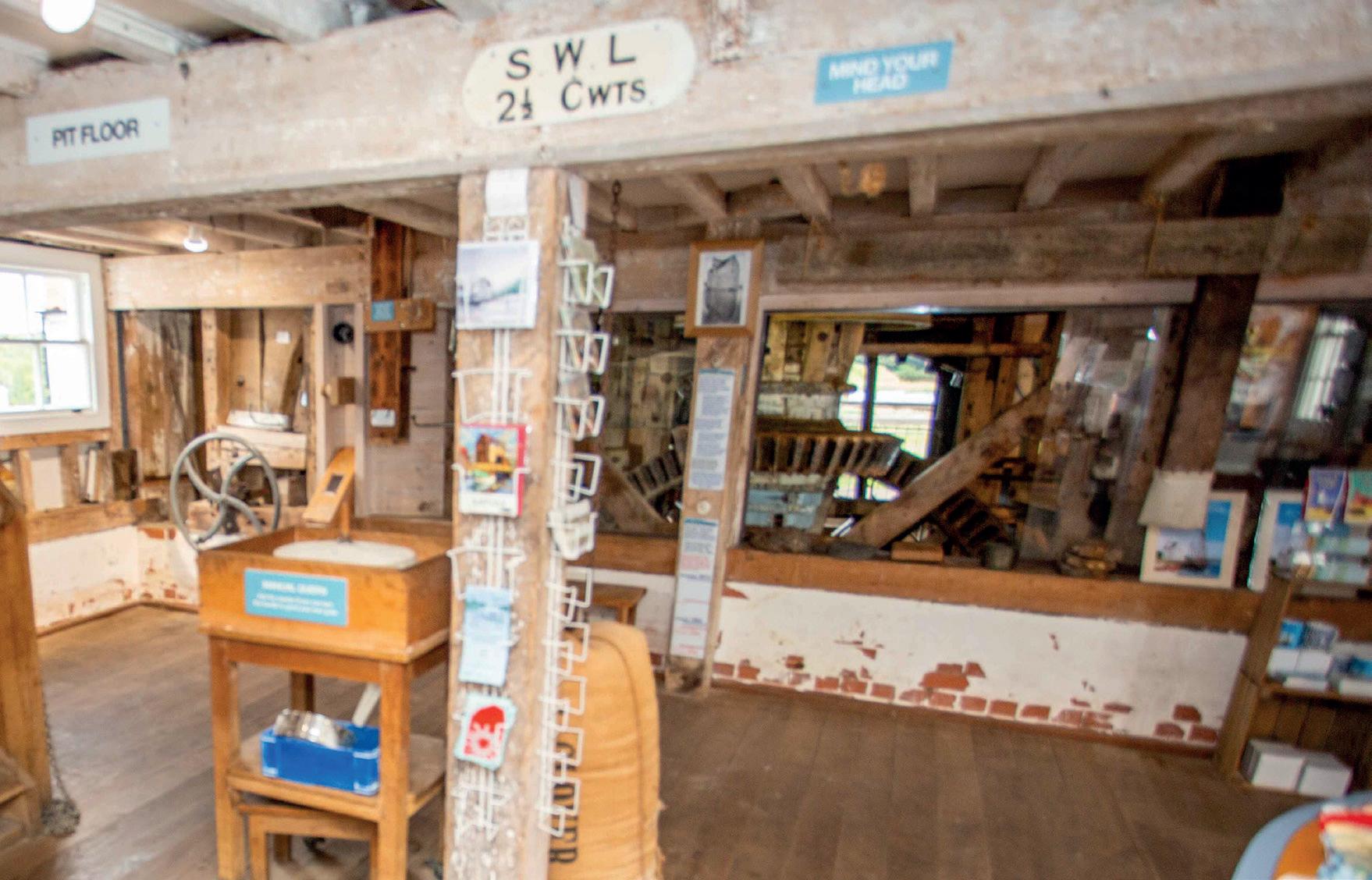
StoneNuts
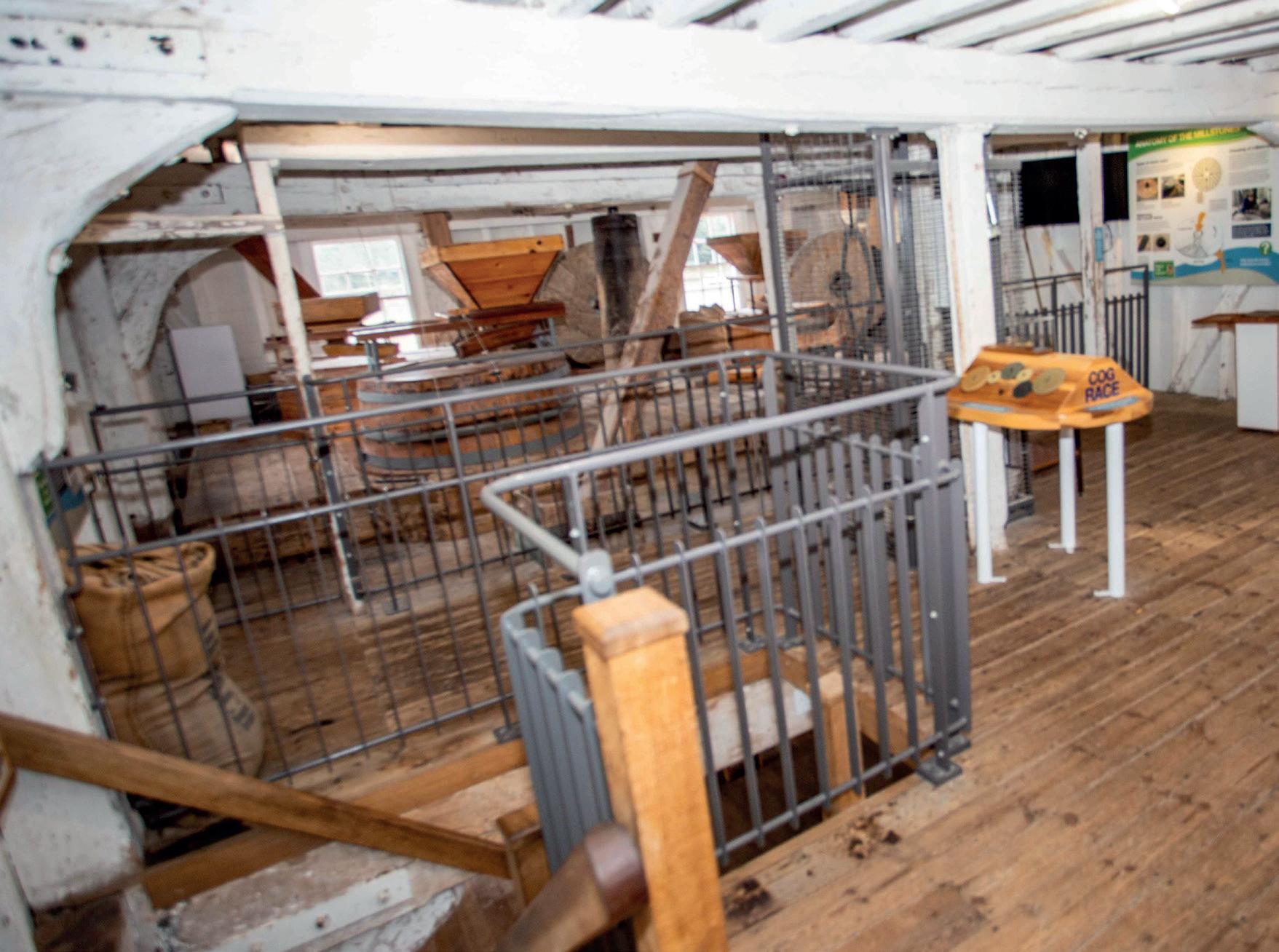
FIRST FLOOR – the Stone Floor where wheat is ground
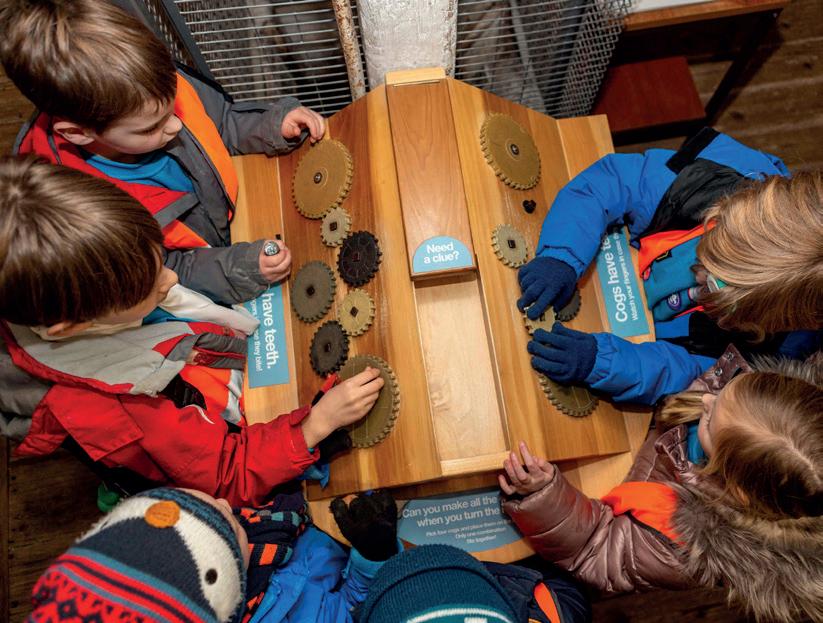
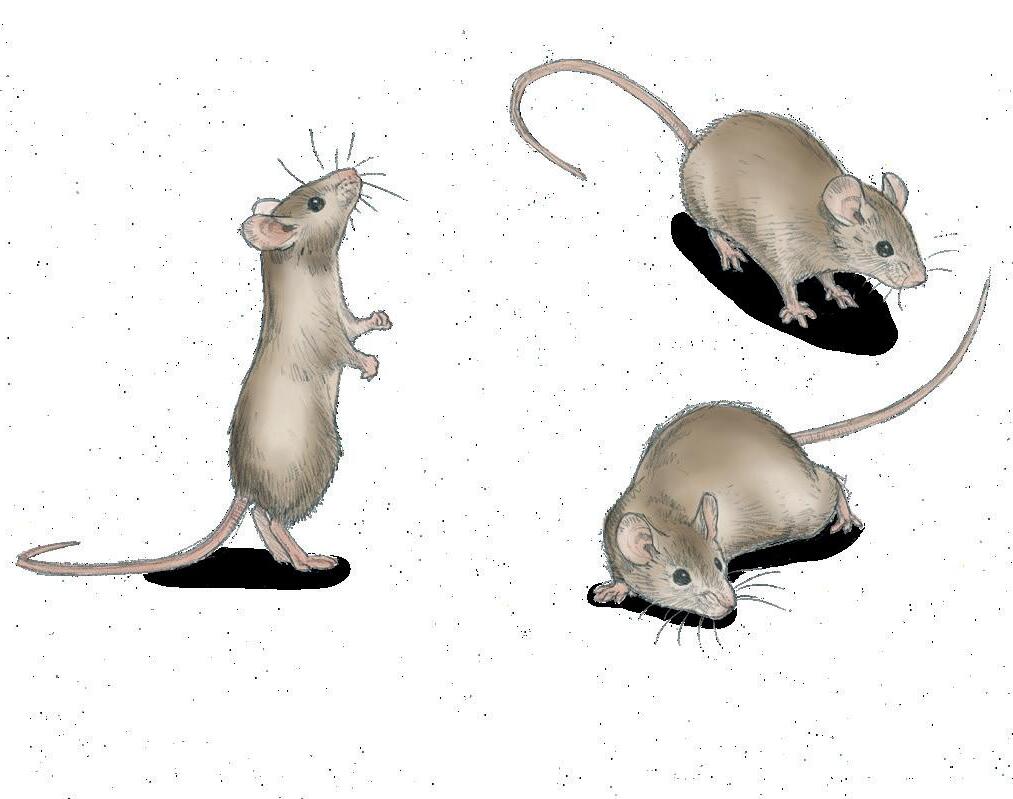
• Climb the stairs to the Stone Floor - the heart of the Mill
• There are four pairs of stones, some covered by a wooden tun with chutes bringing grain from hoppers above
• The two pairs of stones on the left are both in use today
• Stones had to be lifted every 400 hours or so of use, for dressing sturdy lifting gear is in place
• There is a cutaway tun and runner stone to show how the grinding worked
• There are a number of children’s games and puzzles on this floor
Crown Wheel Area
SECOND FLOOR –operates the hoist and wheat is stored
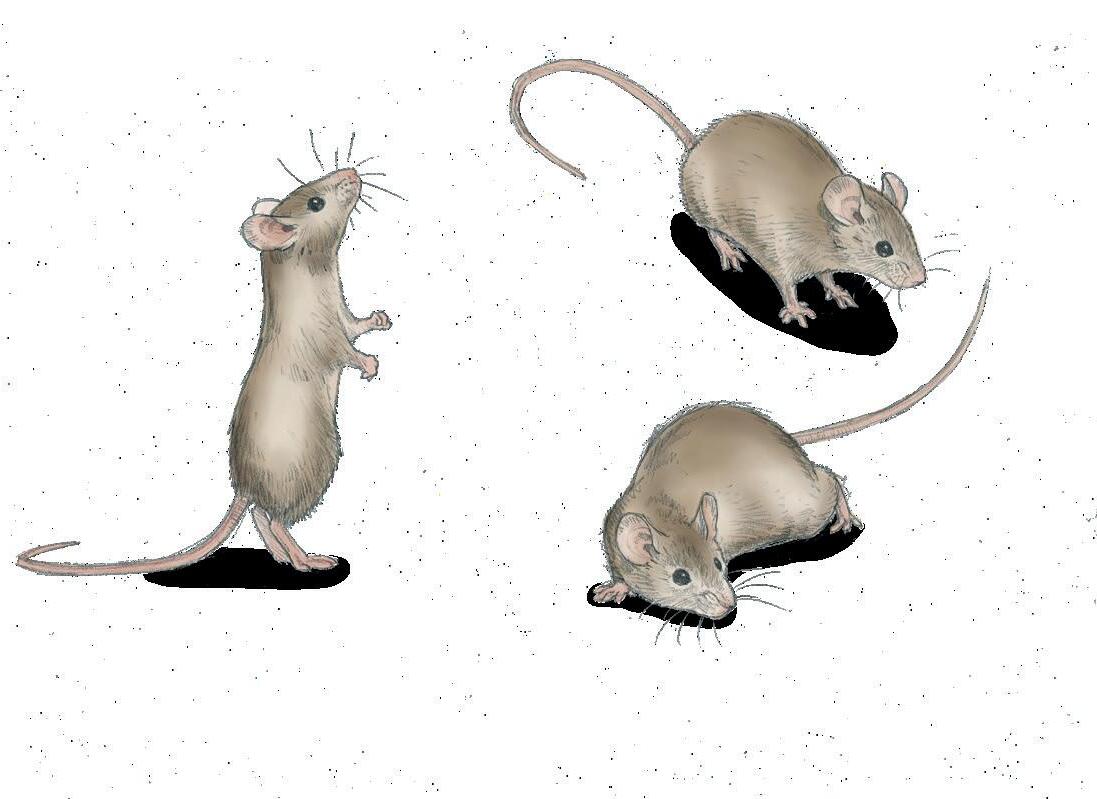
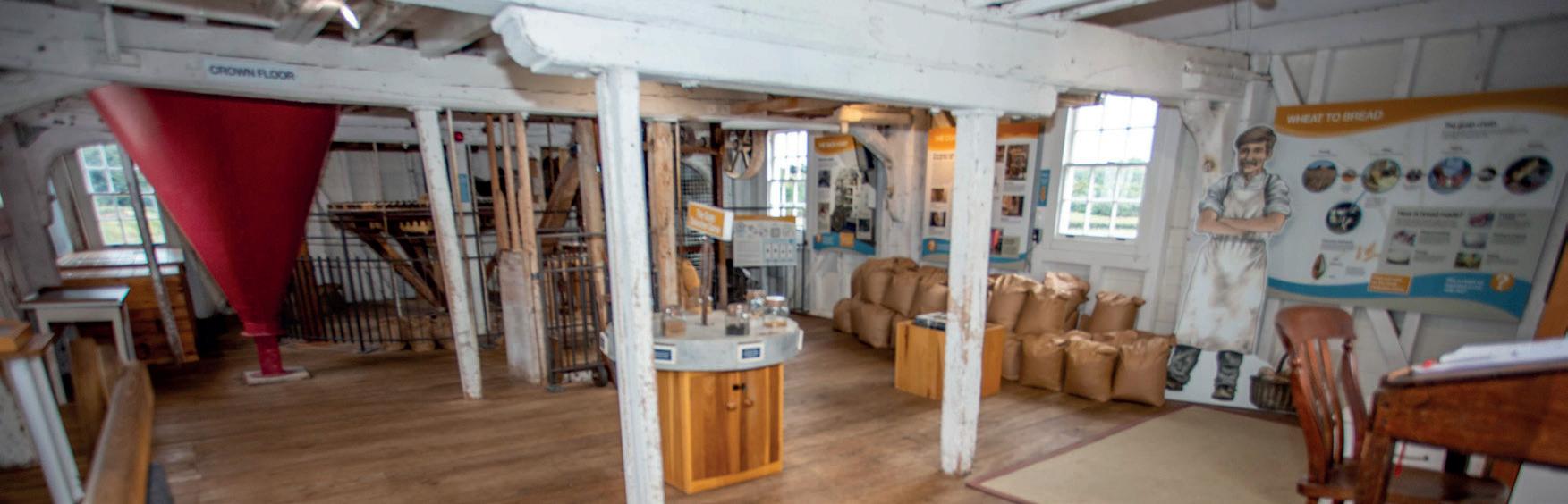
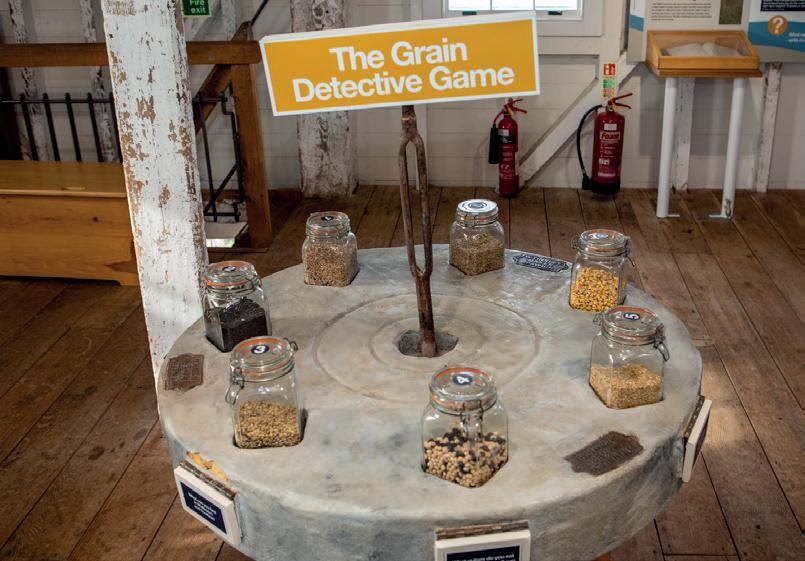
me
• The large red metal hopper dominates this floor It’s a post-WWII addition and served a temporary diesel hammer mill
• The large, horizontal Crown Wheel drives a metal pinion with several pulleys on its shaft
- The sack hoist pulley is the first, easily identified by the loose belt around it
- Next are pulleys for auxiliary machinery, like the Dressing Machine
• The Dressing Machine, in the eaves above, removed foreign bodies - like mice?
• Look out of the window to see the marina - the old millpond
• There are fine views of the river Deben from this floor.
We hope you have enjoyed your tour of the Mill and this brief tour. Our aim, set out in the original Trust Deed nearly half a century ago remains —
To promote the restoration and permanent preservation for the public beneft of the Tide Mill at Woodbridge, as a building of architectural and historical interest and as an installation of historical and technical importance which should be retained for the education of the present and future generations.
HOW THE TIDE MILL WORKS
TIDAL POWER
DID YOU KNOW...?
Tide Mills operate at low tide, not high tide as often assumed.
The pressure of the incoming tide opens a sluice gate in the riverbank and the river fills the millpond (1). As the tide falls, the first water escaping from the millpond closes the sluice gate and holds it shut (2). When the tide had fallen sufficiently the miller would open another sluice gate to release the water trapped in the millpond to turn the waterwheel on its return to the river (3).
Tidecomesin
fillsmillpond
AthightidemillpondisfullAtlowtidethe millpondemptiesturningthemillwhee andl pressure closessluice
Tide Mills were usually situated along shallow creeks some miles from the buffeting waves of the coast with a large millpond constructed to hold the water of the incoming tide. Sometimes a dam was built across a small inlet branching off a tidal estuary, creating the large millpond, such as Eling near Southampton, or Carew near Pembroke. At these mills small rivers also feed the pond.
The Mill worked for around two to two and a half hours either side of low tide. The miller’s day depended upon the movement of the tide so his working hours were highly irregular. A full working day of around 8 hours would have required split shifts of around four hours each, and at least one would be at an inconvenient time of the day. The variation in the height of the tides at different seasons added to the miller’s difficulties.
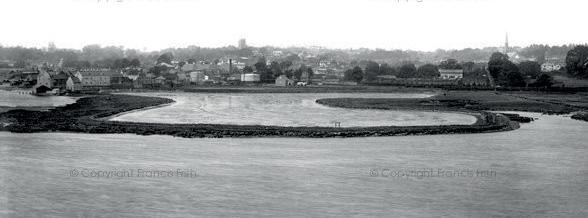
THE WATERWHEEL
There were four main types of waterwheel; backshot (or pitchback), overshot, breast shot and undershot. They operated as shown.
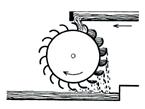
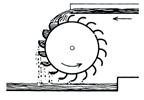
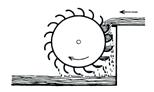
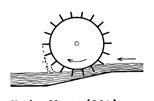
PitchBack OverShot BreastShot UnderShot
Typically, the first three of these wheels would have either buckets or curved using gravity to add power.
Woodbridge has an undershot wheel, the earliest and least powerful type with flat paddles and no help from gravity. It boasts two sluice gates, one vertical and one inclined. Although currently it uses only one gate and operates as an undershot wheel, it is certain that it was originally operated with both gates in use, allowing it to be a breast shot wheel when the millpond was full, but an undershot wheel as the head of water dropped.
It is said that famous Scottish engineer, John Rennie, developed the idea of a ‘sliding hatch’, a gate, initially lowered so high water flowed over it (breast shot), then lifted so lower water flowed beneath (undershot). Woodbridge had a modified ‘double hatch’ version of this using two gates, a rare arrangement worth preserving.
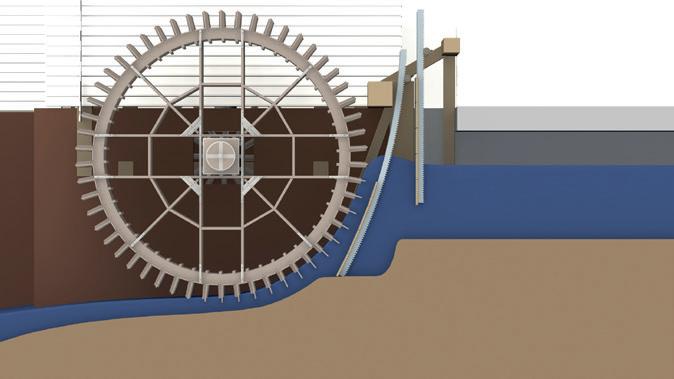
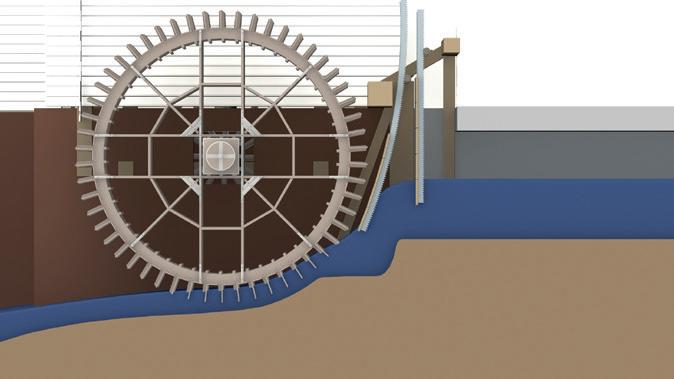
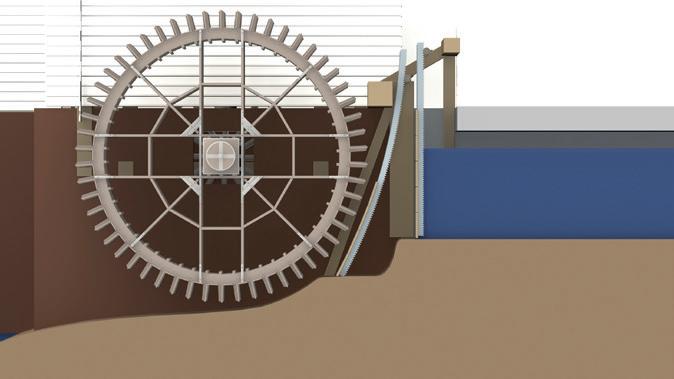
1. High tide - tidal water flls pond - gates closed
2. About two hours before low tide - Breast Shot Wheel
3. Low tideUnder Shot Wheel
The waterwheel itself is English oak, 5m (18ft) in diameter and weighs around 4 tonnes. At its centre is a huge wooden shaft on the other end of which is the pit wheel.
THE PRINCIPAL MACHINERY
The pit wheel is made of four cast iron sections with 104 shaped wood teeth set into the rim. Cast iron was an 18th century innovation with obvious advantages over wood.
Meshing of iron on iron was to be avoided as much as possible, wooden teeth engaging iron was quieter and smoother as they gradually became moulded to the iron teeth. Broken or worn-out wooden cogs were easily replaced,
whereas worn iron teeth needed re-casting - prohibitively expensive. The choice of wood for cogs was important. Oak usually for the pit wheel; holly, hornbeam or beech for the spur wheel; the crown wheel had cogs of strong close-grained apple or pear. Millers had strong favourites and some, it is said, trusted only wood from their own trees.
By engaging with the cast iron wheel (wallower) on the main vertical shaft the pit wheel’s horizontal drive becomes vertical. The vertical shaft is mounted on a footstep bearing on a large beam and extends up to the second floor.
DID YOU KNOW...?
Above the wallower is a wooden pulley that drives a governor, an automatic tentering gear. It alters the gap between the stones to compensate for variations in waterwheel speed. Although common on windmills where windspeed varies, we don’t know why ours is the only known British tide mill to have one.
The great spur wheel located, above the wallower, engages with the much smaller stone nuts in each corner that drive the upper (runner) miIIstones on the floor above The runner stone turns above the fixed bed-stone and grinds the grain. The four stone nuts are mounted on wrought iron axles and can be disengaged by means of a crank which pushes them up and into a slotted collar on the axle so that they miss the spur wheel.
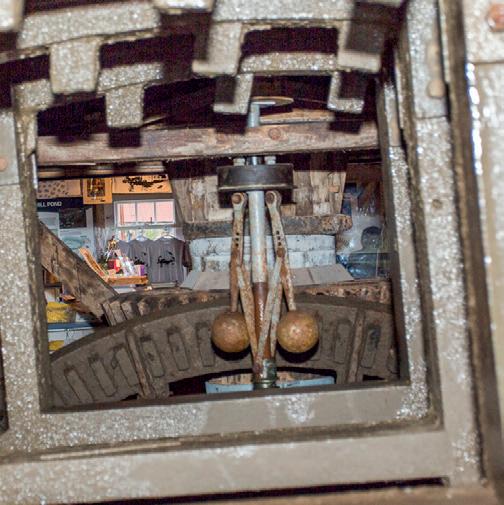
The Governor
DID YOU KNOW...?
It was unlikely that the miller would have all four pairs of stones working at the same time, but probably would have had different grains feeding to different stones.
At the top of the vertical shaft, on the second floor, the crown wheel meshes with a 45cm (18in) diameter cast iron wheel that drives a lay shaft used to turn three pulleys. Two for the dressing machine and bucket elevators, and the third which still drives the sack hoist in the middle of the Mill and which also used to work through the lucam, lifting sacks directly off lorries outside. The sack hoist shows the simple ingenuity of the 18th century engineer. The belt which drives it remains slack on the lay shaft until the miller operates it by tightening the belt on the pulley with a lever and rope. It’s still used today.
THE GRINDING PROCESS
PULLEYS FOR ANCILLARY MACHINERY
LAYSHAFT
VERTICAL SHAFT
RUNNER STONE
BED STONE
STONE NUTS
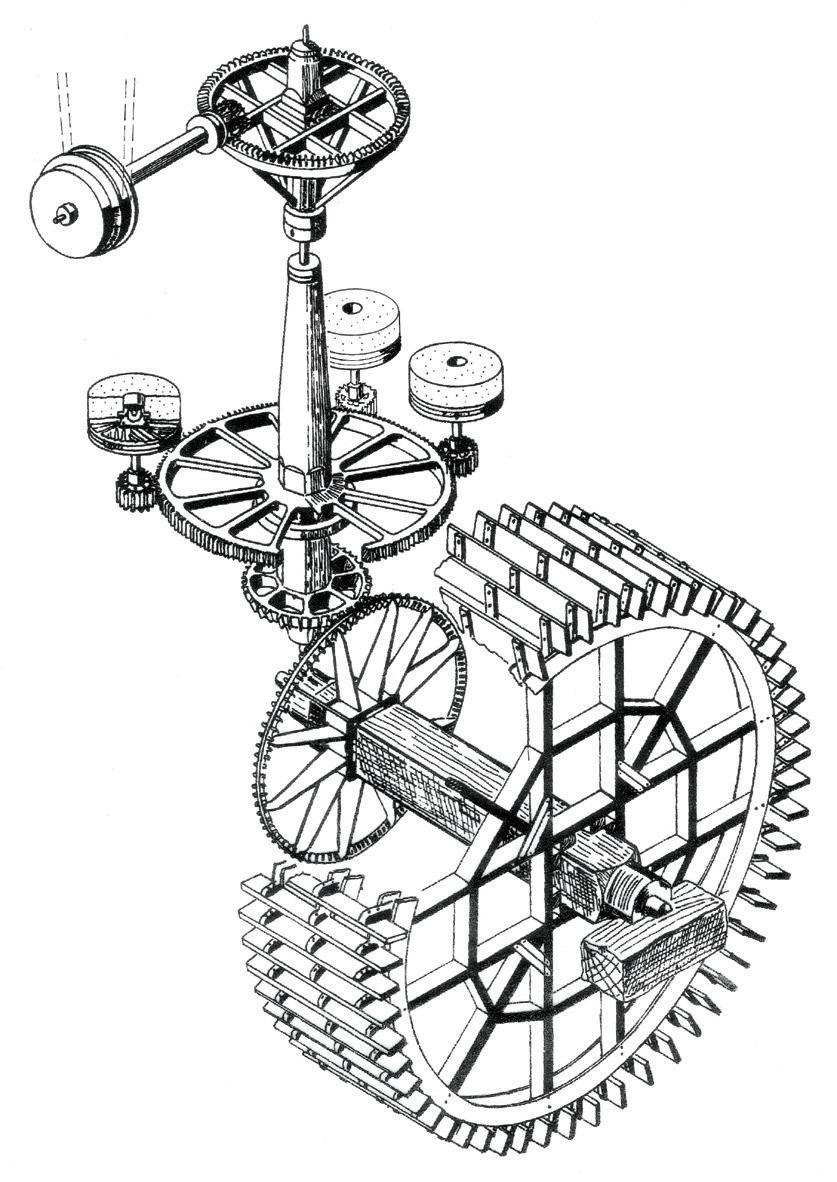
CROWN WHEEL
The principal machinery
GREAT SPUR WHEEL
MAIN OAK SHAFT
WATERWHEEL
Grain is delivered and raised to the top (bin) floor by sack hoist and stored in grain bins to be fed through chutes to the hoppers above the mill stones. From the hopper the grain runs through the shoe or slipper, a shallow trough vibrated by contact with the damsel. The damsel is an iron spindle with three or four ridges which revolves with the runner stone, constantly tapping the shoe to shake the grain into the eye of the stones. The miller controls the grain’s rate of flow using the crook string to adjust the shoe’s angle from the floor below. The rate varied considerably across different types of grain.
From the eye in the centre of the stones, the grain passes slowly towards the edge, being crushed into finer and finer particles by the scissor action of the grooves cut in the face of the stones. The expelled flour falls off the edge, down a chute to the floor below to be bagged, weighed ready for collection.
DID YOU KNOW...?
The constant chattering sound is said to have given the damsel its name; like its reputed namesake it never stopped talking!
SACK HOIST PULLEY WALLOWER PIT WHEELTHE FLOUR
Stones revolving at around 160rpm produced pretty coarse flour called meal. To make it more acceptable the meal was hoisted back up to the top floor and fed into a flour dresser, essentially a large sieve that separates the flour into its different parts. The flour was fed into a rotating cylindrical mesh drum, about a metre long, and beaten against the mesh by rotating beaters. The mesh varied from fine to coarse along its length. Only the finest particles of flour would drop through the fine mesh to produce a fine, white flour. Slightly larger particles of flour, semolina, would follow through the next coarser stage of mesh with the larger flakes of bran left behind.
The Tide Mill was one of many small country mills ill equipped to meet huge demand for refined white flour in the 20th century. In the last years of the Mill’s working life peas and beans largely replaced wheat for grinding.
THE MILLSTONES
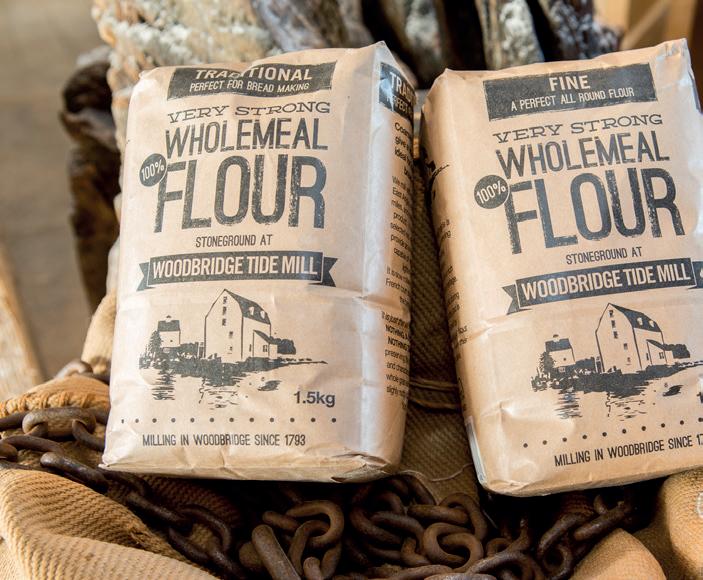
DID YOU KNOW...?
French Burr was so valuable that even at the height of the Napoleonic Wars, dealers, with government permission, bought it from the enemy at high prices.
The selection and use of the right type of stone and its maintenance required technical expertise and experience. Sources in Europe were limited making good quality stone valuable.
Two sorts of millstone were generally used.
• Peak stones, made of Derbyshire millstone grit, were used for grist work, grinding barley, oats, peas or beans.
• French burr stones were used for milling flour and were constructed from a hard freshwater quartz from the Paris basin.
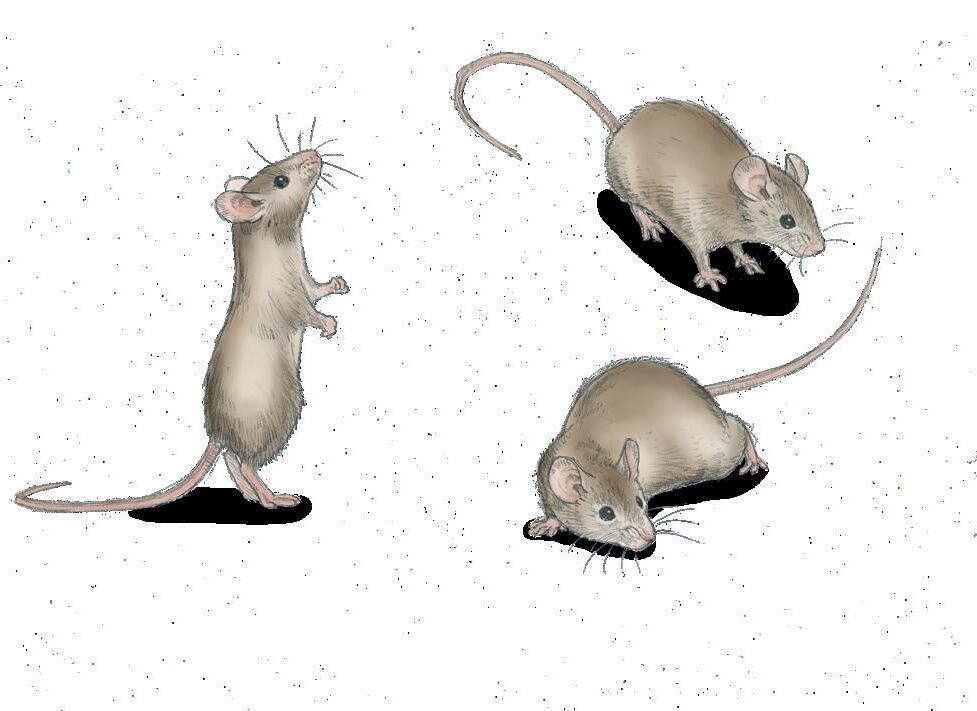
Used daily, the stones became dulled with wear so re-dressing was required every 400 hours or so. This involved the renewing of the ‘furrows’ and ‘stitching’ of the large and small grooves in the stone’s surface. The runner stone had to be raised with lifting tackle so dressing could be done with the ‘bill’, a cutting tool resembling a double-edged wedge. The runner-stone was replaced carefully so the two stones did not touch but rested fractionally apart. Dressing was carried out by the miller himself or travelling dressers. In the 1890s they would take three days to dress a pair of stones and charge 30 shillings (about £650 today).
On the second floor, the crown wheel engages with a cog driving the layshaft driving the sack hoist. The wheel and cogs are mainly apple wood.
The stones are on the first floor, enclosed within wooden tun covers. In the foreground, two brass bushel measures, and the stone crane.
The great spur wheel and disengaged stone nut. Throughout the mill, wood always meshes with iron. In the background is the wallower.
The wallower engages with the pit wheel. The horizontal drive is converted to the vertical, turning the upright shaft, driving all the machinery above.
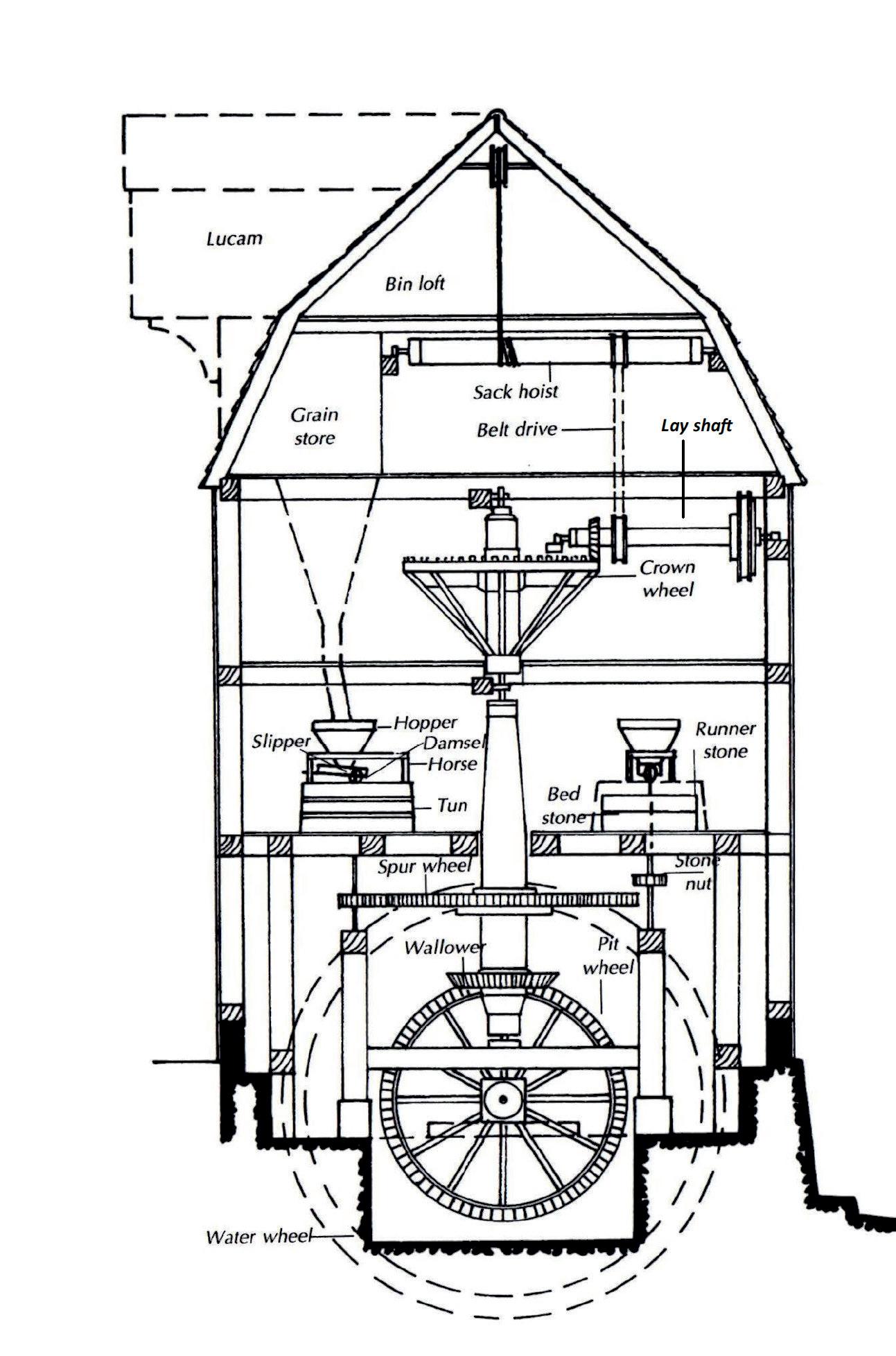
section of the Tide Mill
HISTORY
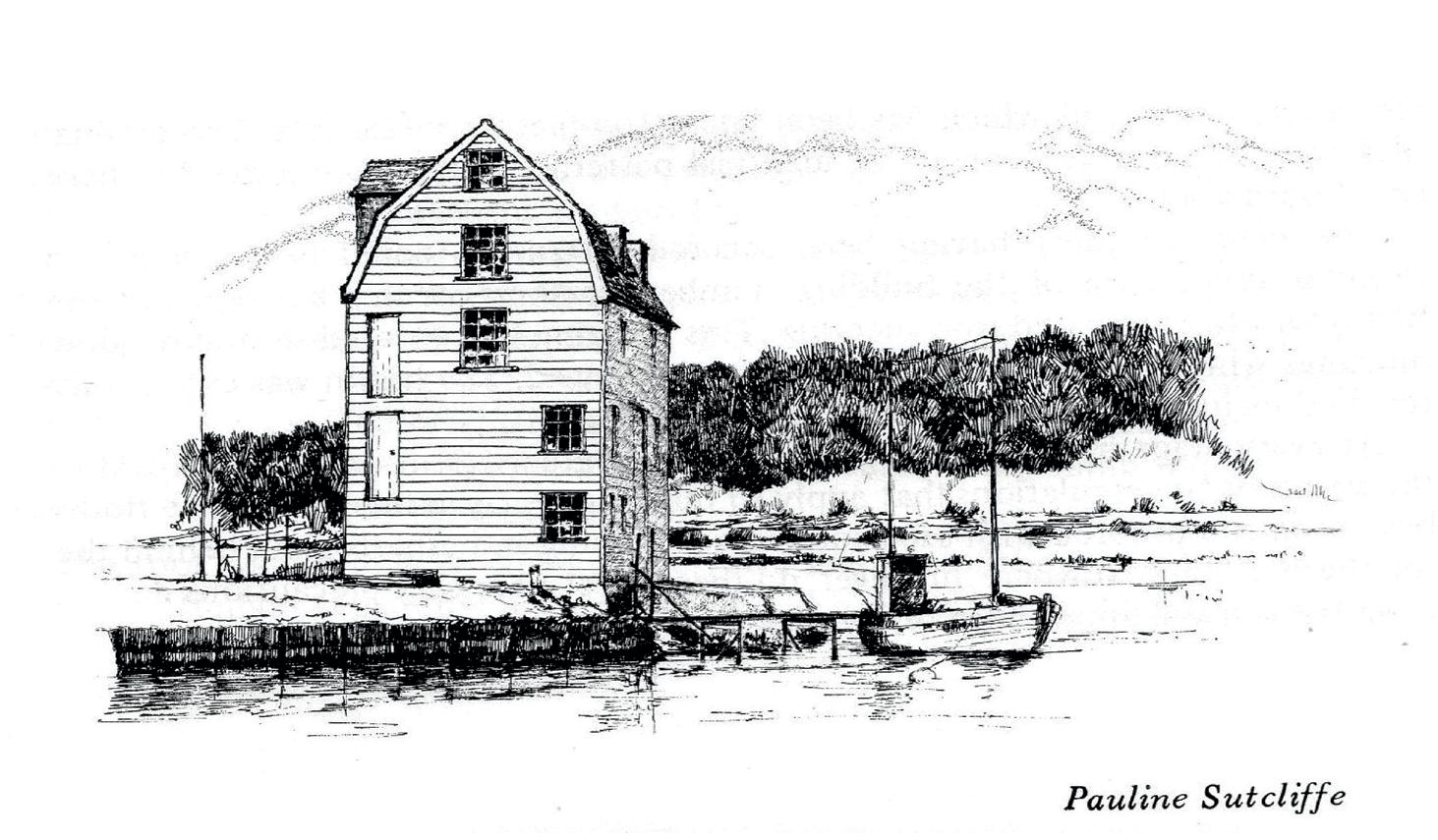
Included in the frst edition in 1973, an artist’s impression of the mill just before its frst restoration
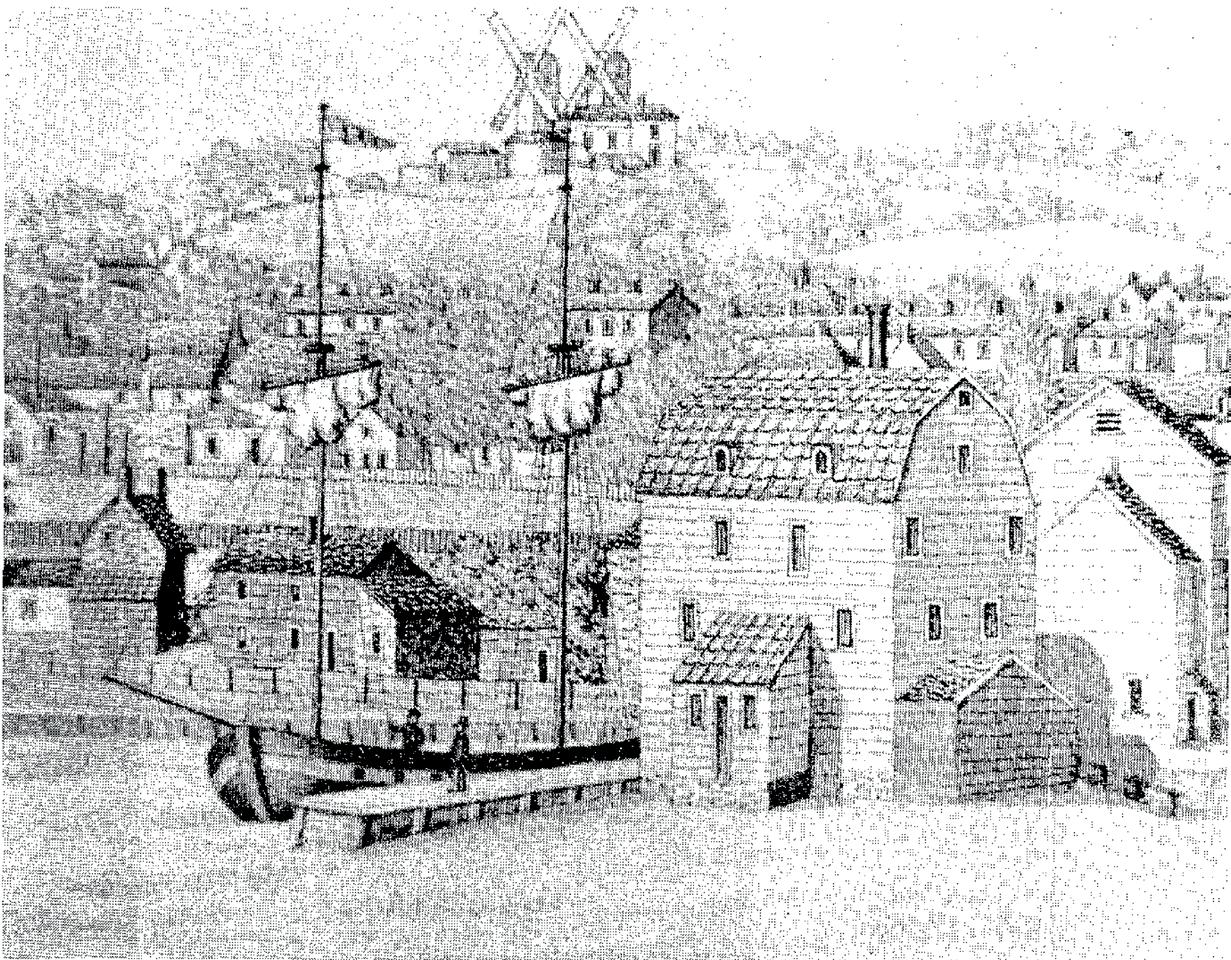
‘I may venture to assert with great confidence; that there is not one miller in 20 that knows anything about grinding well. There is 2s per quarter difference between grinding well and in but a middling way and more than 4s per quarter difference between grinding very well and ill.’
Nineteenth century milling engineer
WORKING HISTORY
Woodbridge Tide Mill is one of the few surviving examples of a specialist form of the watermill designed for grinding wheat into flour. It is a living monument to our social, historical and cultural past.
The story of Woodbridge Tide Mill begins over 800 years ago. A mill has stood where the Woodbridge Tide Mill now stands since the 12th century. The first reference to it appears in a 1170 document in which Baldwin of Ufford was given easier access to it. During the Middle Ages the Mill was owned by the Augustinian Canons of the local Priory who exercised their ‘soke rights’, compelling tenants to grind grain at the Mill and collect their share.
Mill owners were made wealthy from this valuable monopoly. Geoffrey Chaucer, in ‘The Reeves Tale’ refers to the miller as having a “golden thumb”; a reference to their dubious practice of pressing the scales to show a greater weight and higher fee.
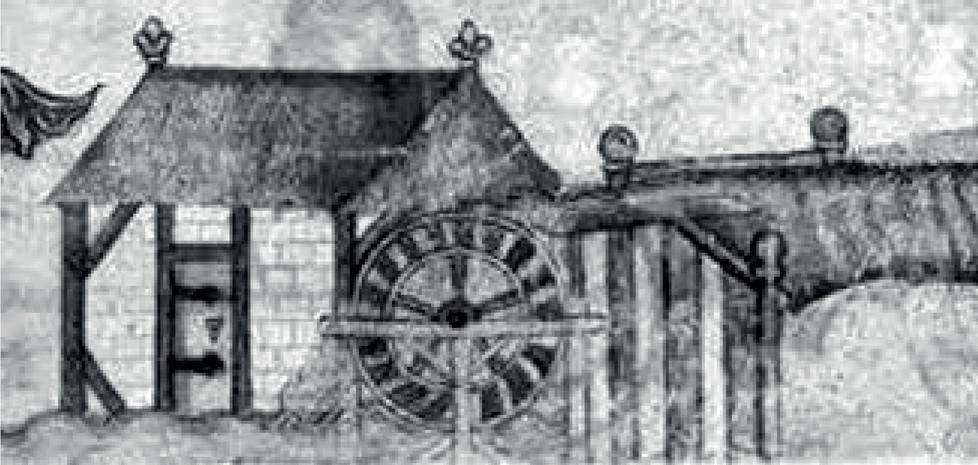
We don’t know what this mill looked like then, probably like this, one of the few images of a mediaeval mill from the mediaeval Psalter commissioned by Geoffrey Lutrell in the 14th century.
A 1340 tax survey for Edward III to finance wars against the French, the Mill’s tithe (the bit given to the church) was three shillings pa—about £2,000 today. Two hundred years later, when the Bishop of Norwich’s visited, the monks used the expense of repairing and maintaining the Mill to explain their poverty. The Mill was in a ruined state. Life spans of early mills rarely exceeded 300 years or so, and it may be that the Mill was rebuilt in this early Tudor period. But the Priors didn’t benefit as Woodbridge Priory was one of the first dissolved by Henry VIII in the early 1530s.
The rebuilt Mill would have differed from the original, probably like the picture here, neither a mediaeval mill nor the modern one we know today.
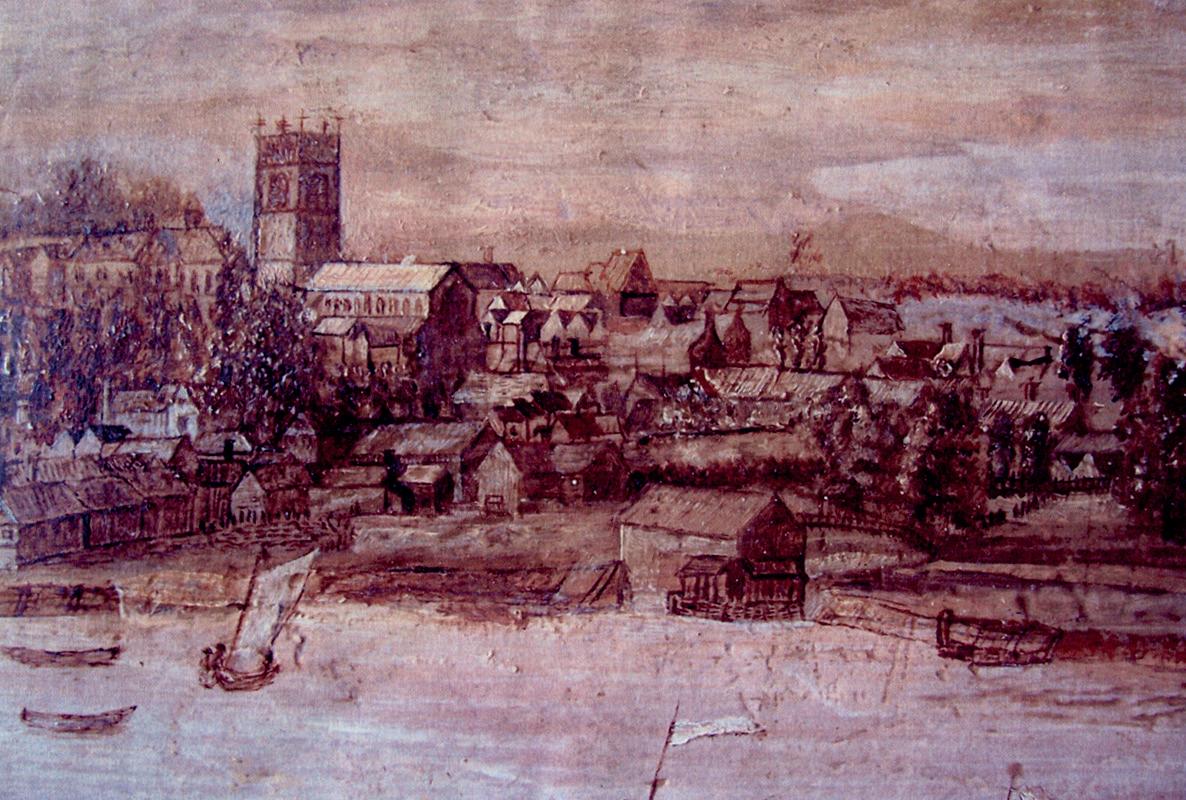
Detail from a painting dated 1770
“Turning southward over grassy hummocks; you come to clustering furze, whence; if you look over your shoulder; you see a picture that is pure delight - the old Woodbridge watermill. Many a time have I loitered here, that I might watch the barges, wheat- laden, with red-sails flowing, gliding along the fairway to the quay. Nine men working for two days were needed to unload the cargo. It was a picturesque sight - the busy men crossing and re-crossing the plank laid from barge to wharf, and sacks of wheat swung high on a crane.”
Cecile Bunn’s description of Woodbridge Tide Mill at work in its last golden age, the 1930s, reminds us that it was a source of inspiration to writers and artists even at the height of its working life. She writes of visiting the Mill and being shown around by the miller, Mr Runnacles:
‘I saw the great burr stones revolving, grinding wheat exceeding small. For forty years he and the mill had laboured together, in sympathy and understanding. That one man should master it so, was to me a marvel almost past comprehending.’
The Priory’s lands and Mill were given to Sir John Wingfield, a courtier in Henry VIII’s court, but Sir John died childless so the Mill reverted to the Crown. Few mills in Britain can claim four monarchs (Henry VIII, Edward VI, Mary I, and Elizabeth I) as owners! But in 1564 Elizabeth I granted the estate of the Priory it to Thomas Seckford, one of her court officials, for £764.8s.4d, some £3 million (at the time of writing). An example of the huge ecclesiastical wealth confiscated by Henry VIII.
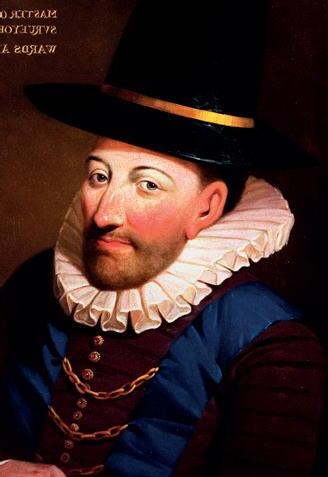
Thomas Seckford is known as a great benefactor to Woodbridge. The Seckford Foundation is still responsible for Woodbridge School and the Seckford Almshouses. The Tide Mill remained in the hands of the Seckford family until 1672 after which it passed from the Bass to the Burward family then to the Cuttings in 1792. “Bass Dock” remains only a few paces from the Mill. The Cutting family, coal merchants and farmers, undertook the next reconstruction of the Tide Mill in 1793 and including new warehouse space and improvements to the quay. Today’s Mill may be accurately dated to this year.
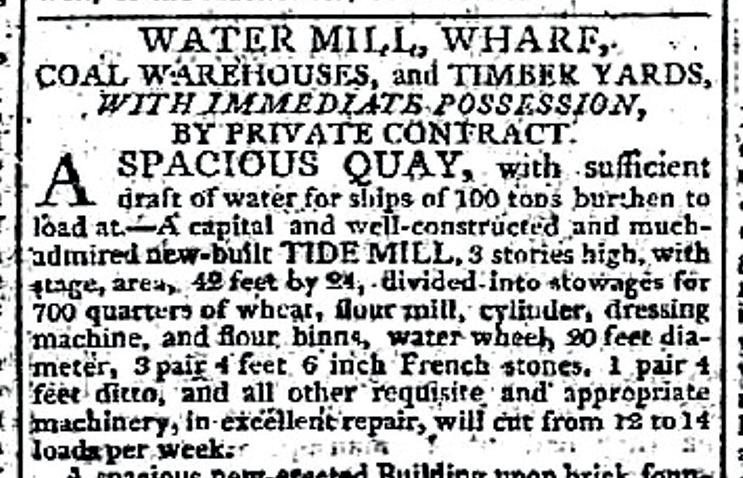
In Jan 1808, the family advertised the Mill, possibly to pay off heavy debts, in the ‘Bury Post’.
It was sold in 1811 to George Edwards and remained in the family for 150 years. It passed to his son-in-law,
John Manby in 1836 and later to his inlaws the Haywards. In the late 1870s Alfred Hayward insured it for £500, the machinery at £250 and the tenant’s fittings at £40. So, despite traditional milling being in decline, its value was around £500,000 today. Alfred Hayward also refurbished the granary nearby.
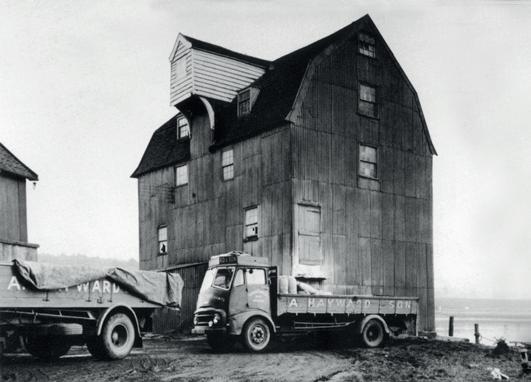
Hayward’s Trucks
Visitors were told that part of the Mill had once been an inn where there had been a bed slept in by William Rufus, the Black Prince, Queen Elizabeth I and Stanley Baldwin: ‘Not all on the same night, of course,’ the earnest story-tellers pointed out.
A. Hayward and Sons flourished, opening branches in Walton and Leiston. A steam mill was constructed near the Tide Mil and in the later years of Hayward ownership, prior to the turn of the century, the Mill’s weatherboarding was clad in corrugated iron. Some were angered, the Mill being popular with artists and photographers, but it certainly saved the old building. The tight sheeting skin protected the decaying timbers. This and the extra strength also helped when a diesel engine and a hammer mill were introduced in the 1950s.
By the late 1920s the Mill’s condition was a concern. The wheel’s oak frame and floats were deteriorating and advertisements for a second-hand wheel went unanswered. The old Mill worked at full capacity nevertheless. An observer in Dec 1926 noted that it would take nine men to unload a barge with 500 quarters of wheat from the Millwall Docks.
A spritsail barge unloading grain brought from London Docks, July 1929
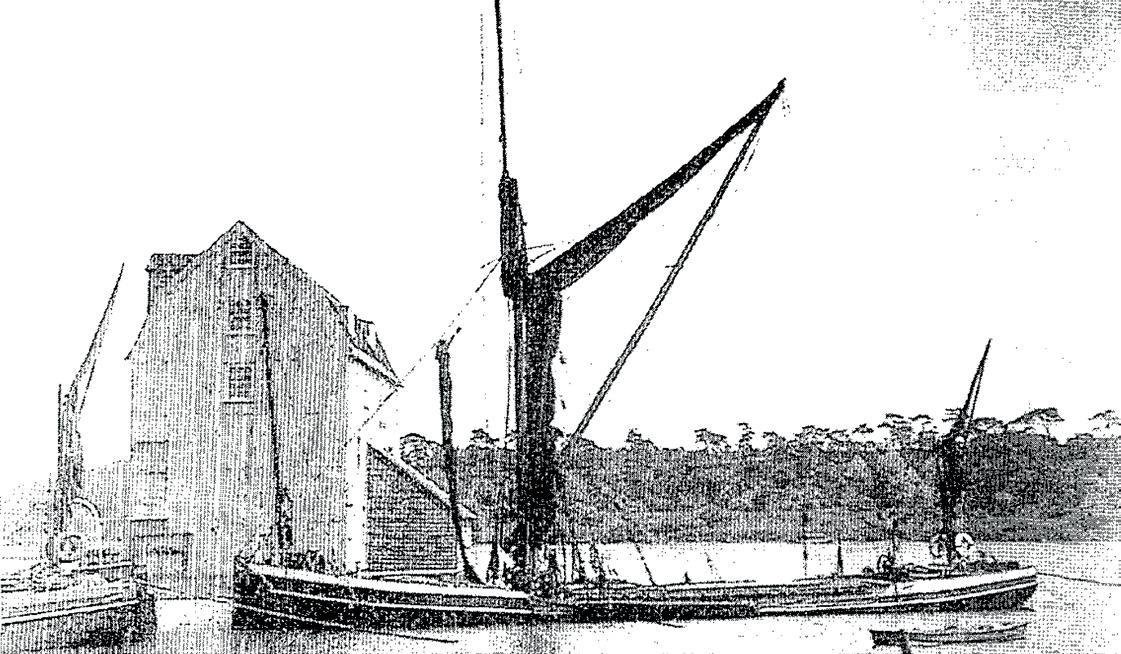
As for the future of the Mill, local worthies on the quay side were convinced of one thingthat Iike ‘the old hoss shay’ of Mark Twain, the Mill would a few centuries hence collapse all at once into a pile of dust.
In the early 20th century old locals told gullible visitor that the Mill had once been used to grind pepper, a famous pepper grown in large quantities at Kyson Point. They related a tragedy when a visiting barge’s skipper fell into one of the bins and sneezed himself to death!
In 1932 Amos Clarke an Ipswich millwright, constructed a new wheel on the old shaft and tidal milling continued innovations from the Industrial Revolution were effecting traditional mills. Steam, and later electrical power, were more efficient and reliable than wind or water, and the roller mill was significantly more productive than grinding stones. At the turn of the century an estimated 70 tide mills were left in the UK and by 1938 a leading authority on mills, Rex Wailes, estimated that there were only 9 tide mills working in Britain. At the end of the 1930s and during the Second World War Woodbridge’s rivals closed one by one. By the early 1950s it was the sole survivor. Shell filmed the Tide Mill at work in its Craftsman series - a unique working relic of a bygone age.
The roof was repaired at this time following an appeal for funds. Certainly there was a growing awareness of the importance of the Mill as part of our industrial heritage.
“On the afternoon of 9th August Woodbridge Mill was at work. I was on the top floor examining the roof framing. Suddenly the whole mill frame shuddered and then the turmoil ceased. We found the wooden packing wedges which secured the water-wheel on its shaft were all out and floating away on the tide, but the wheel had continued turning in a drunken fashion on the stationary shaft, fouling the sluice and culvert.”
Noted by Mr. D. S. Sanders in 1951
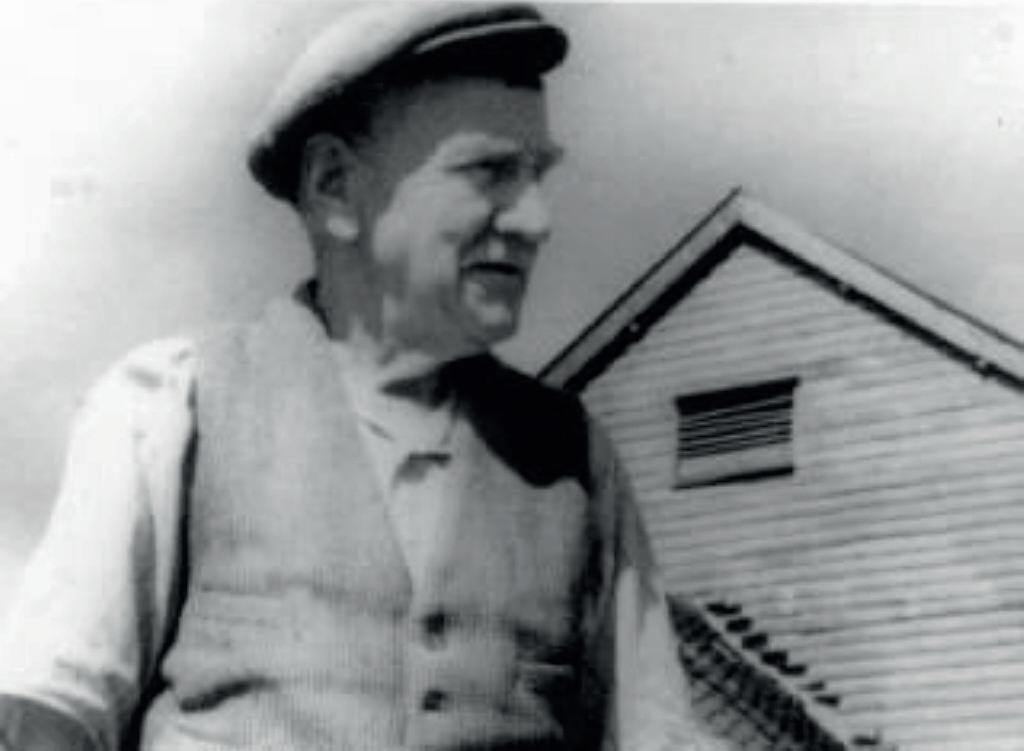
Despite these problems the Tide Mill continued. Geoffrey le Mare Atkinson, a former partner of the Haywards, had taken over in 1933. Young Jack Hawes worked at the Mill in 1939 and relates how he took the train to Framlingham, hired a bike and cycled to farms to buy grain. Despite using a ready-reckoner (a table of calculations) it couldn’t have been easy to compete with the men from Clarke’s or Warne’s to drive a bargain with the canny Suffolk farmers. Back at the Mill he would find Sid Desborough and his assistants, Ollie Wood and Ernie Cotton, covered in flour dust, working the most inconvenient hours to catch the low tide.
It is likely that the flour ground in the post-war years was poor quality. Barley meal was ground for animal feed and distributed widely in the area. When changing from barley to peas mixed meal was produced before the stones produced saleable product. Local carts would carry away the odd load of mixed meal for the family pig or poultry.
Nothing was wasted. Alfred Heywood’s log book covering the early 1900s to 1931 records maize, peas, beans, barley, oats, and middlings. Middlings (sometimes called floor sweepings and often deliberately produced) were a by-product consisting of coarsely ground wheat mixed with bran, often used as animal feed.
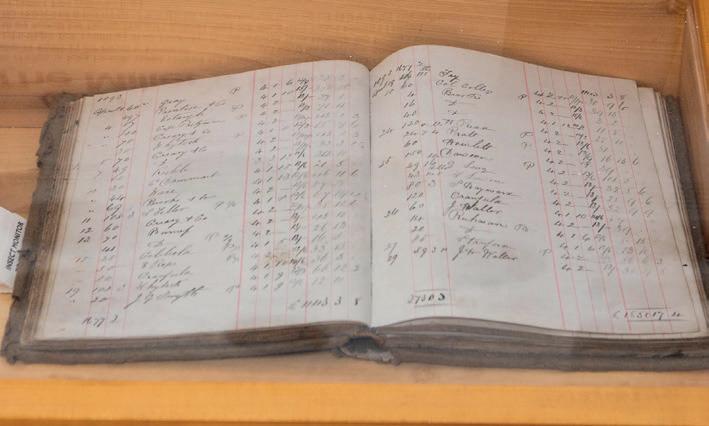
Geoffrey Atkinson died in 1954. The Mill’s new owner John Mathews installed a diesel hammer mill and an electric motor replaced the sack hoist. The hammer mill ground a ton per hour leaving the great waterwheel idle for weeks, soaking in the tide, becoming water-logged, heavy and turning erratically. The Tide Mill survived like this until 1957 when the 22 inch square oak shaft of the waterwheel broke. With little chance of repair; the long history of tide milling on the Deben appeared at an end.
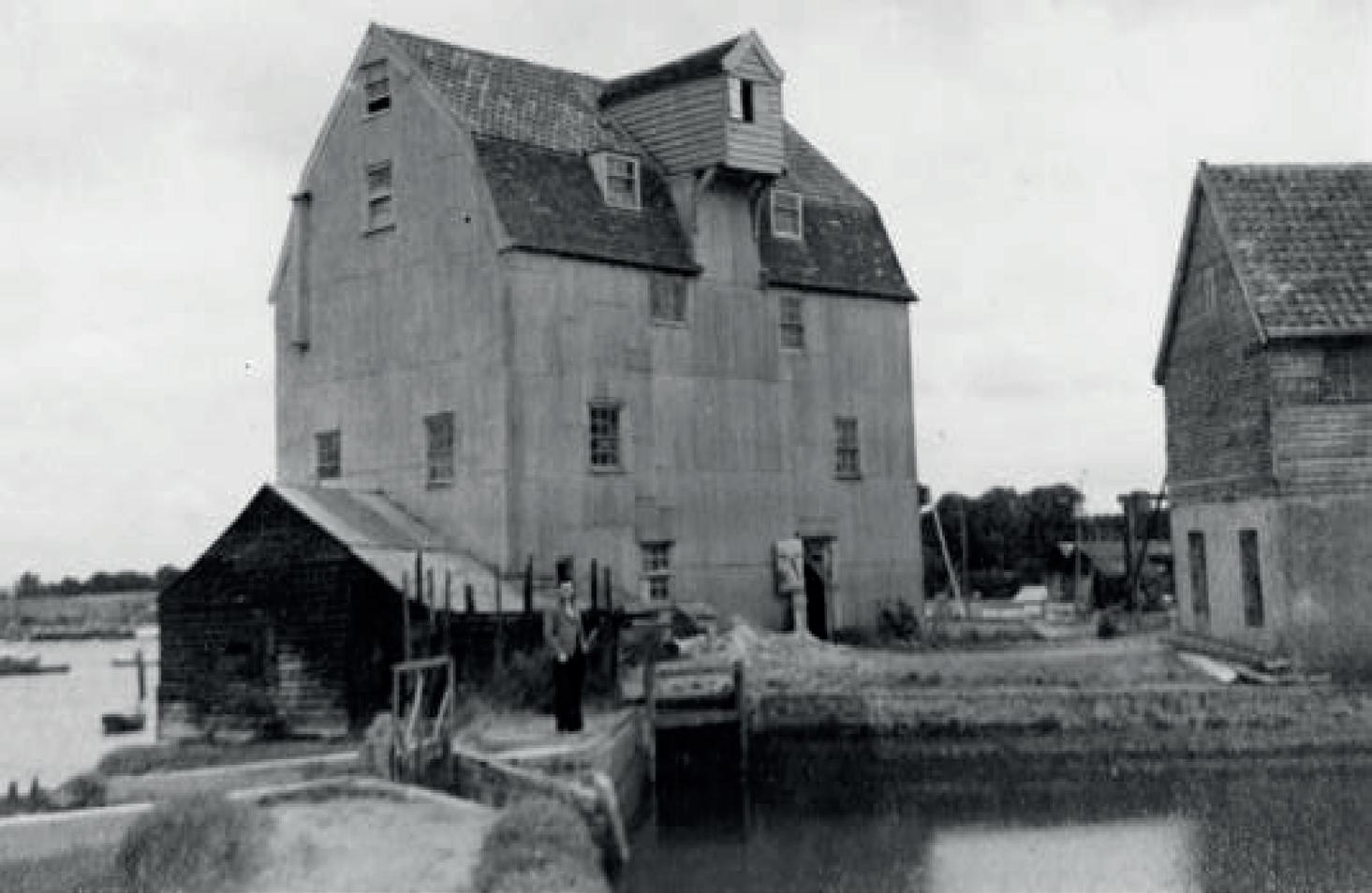
SAVING THE MILL
Interest in the Tide Mill intensified after the oak shaft broke and the conversion of the 7.5 acre mill pond into a marina. The Society for the Protection of Ancient Buildings drew attention to the Mill and its millwrights and engineers stressed the need for urgent action. In 1961 J Kenneth Major published detailed 3D Mill drawings and elevations. The following year the Ancient Monuments Board for England, highlighted the plight of the Mill. Within two years of this, ‘Illustrated London News’ wrote:
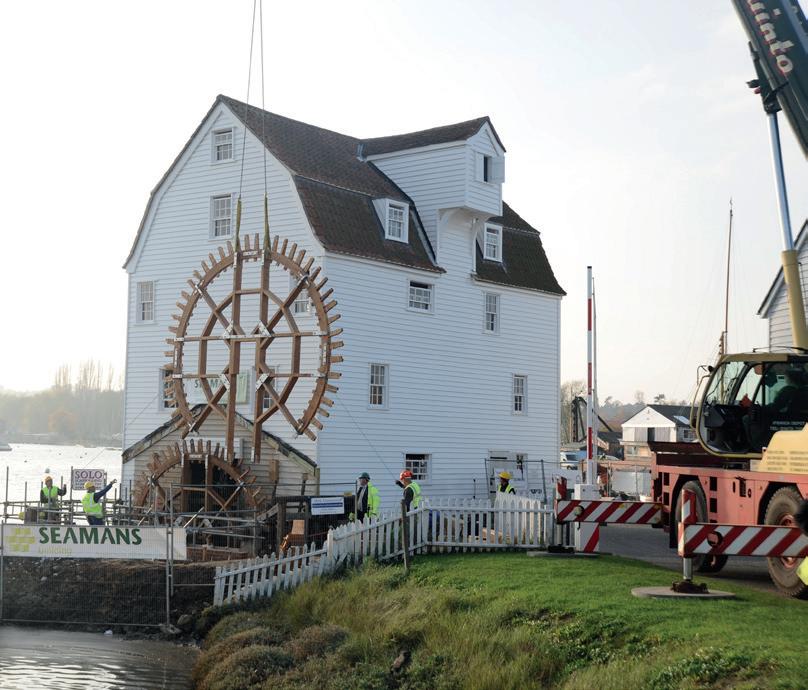
“.... now it is too late. At this stage the mill is a stretched skin structure; if the cladding were removed the whole edifice would collapse. The wheel end itself is already a ruin. Something in the region of £12,000 would be needed to make what repairs are possible.”
The working Mill in 1952 from the tidal pond showing the original mitre gates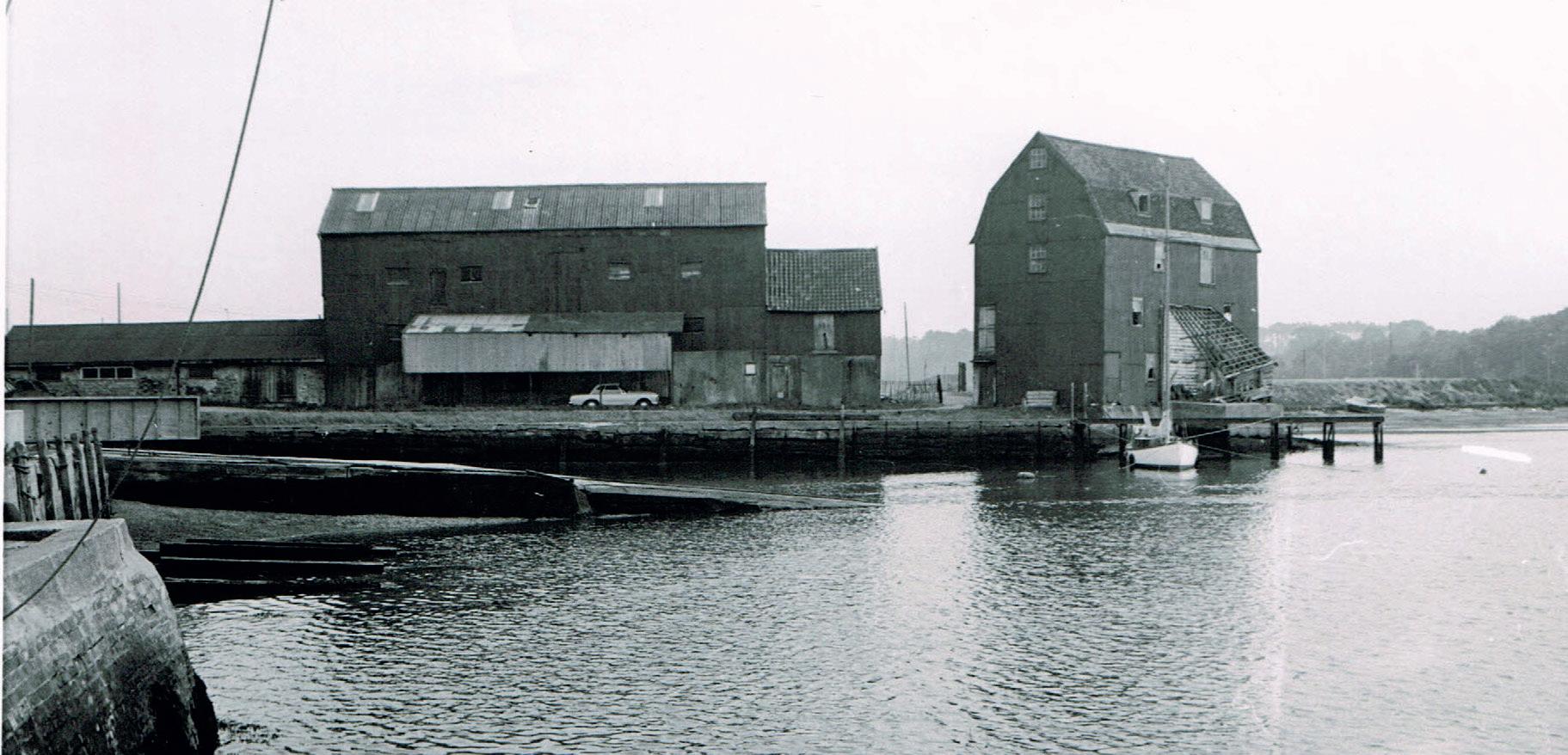
The Mill and Granary at the time of the auction; 1968
£12,000 then is some £500,000 today, a huge sum of money. Local interest in the Tide Mill remained strong despite the dire outlook. Local historian, Norman Scarfe, was a prominent supporter with the support of one of Britain’s leading molinologists, Rex Wailes. Some saw no justification for preserving it for historic and sentimental reasons.
We cannot therefore overstate the importance of Mrs Jean Gardner who purchased the Mill to save it. Mrs Gardner approached Norman Scarfe after hearing him lecture on the Mill’s plight. They discussed the possibility of her buying and restoring it. Time was short but at its auction in May 1968 Mrs Gardner became the proud owner of a ruined Mill and granary!
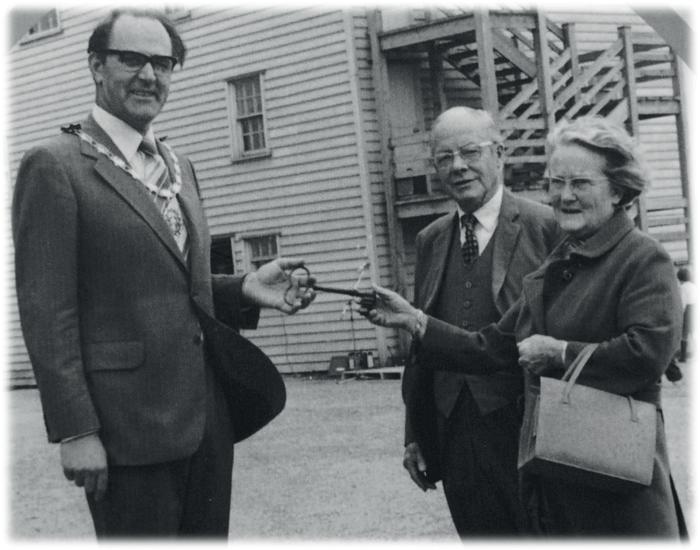
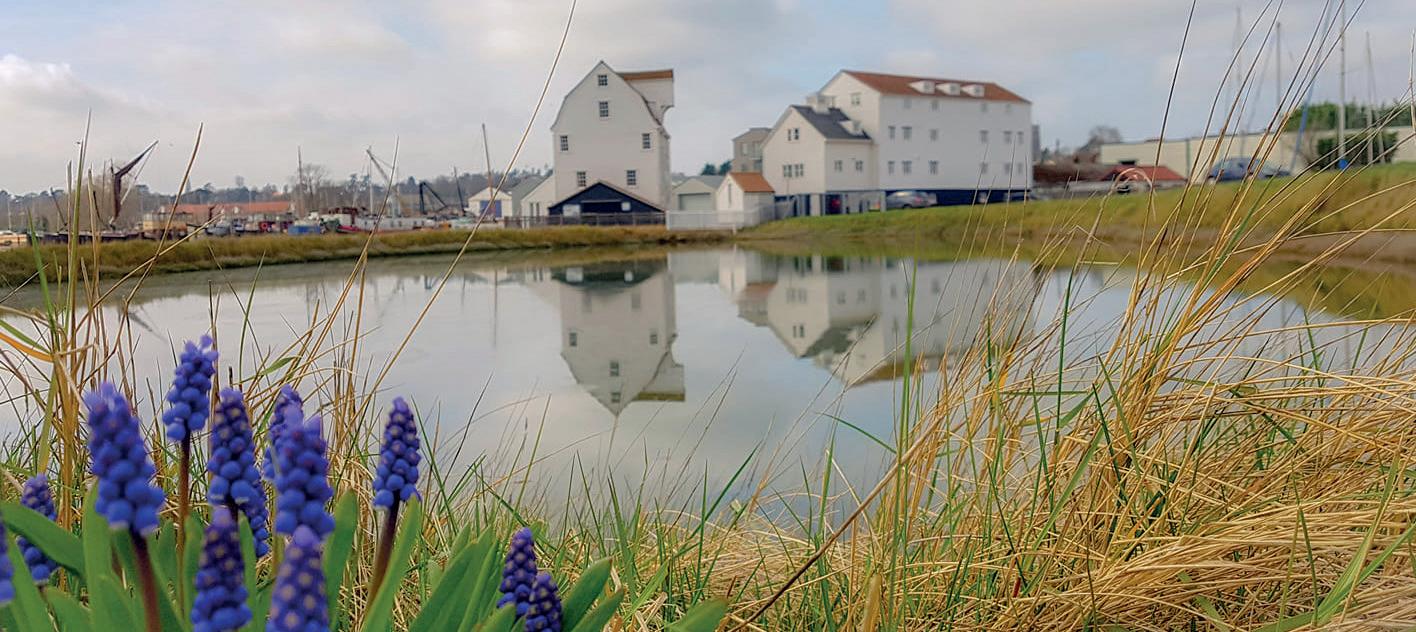
The Mill was put into the charge of The Woodbridge Tide Mill Trust, a registered charity and an appeal was launched in 1971 for £50,000 (a little over £600,000 today). The waterwheel and machinery were removed as were the roof pantiles to relieve the creaking timbers of an almost intolerable weight. A concrete slab was laid to stabilise the building behind a rough concrete apron in front of the Mill to protect the new base. This foundation wall was strengthened and raised to resist flooding and the timber frame was repaired using the original wood where possible and the roof was re-laid, with replacements of the identical pantiles coming from a derelict barn near Southwold. The corrugated iron sheeting was replaced with distinctive white timbers. An exterior fire escape was also added spoiling the appearance.
The Mill opened to the public for the first time in 1972, while further restoration works were continuing. By 1976 the main machinery was fully restored, and a new waterwheel installed.
In 1977 Mrs Gardner handed the Mill and nearby granary to Woodbridge Town Council. The Woodbridge Tide Mill Trust, an independent registered charity is responsible for the Mill.
The granary was later sold by the Town Council on a long lease for conversion into riverside dwellings, its white weatherboarded appearance complements that of the Tide Mill.
In 1981 a quantity of clay became available and the next year a bank was built forming a new small mill pond. It was named ‘Wyllie’s Pool’ after Peter Wyllie, who started the Friends of Woodbridge Tide Mill and, in earlier days, had led helpers to maintain the wheel by turning it using their feet, like a treadmill.
INTO THE NEW MILLENIUM
After 35 years the state of the Mill and displays were showing their age. Despite half a million visitors numbers were reducing. Visitor admissions insufficient to keep the Mill going.
Much of the fabric of the building needed attention too; displays needed rejuvenating; the waterwheel was deteriorating; machinery was suffering; the foundations were under threat from the tides; the pond was silting up, and milling was impossible.
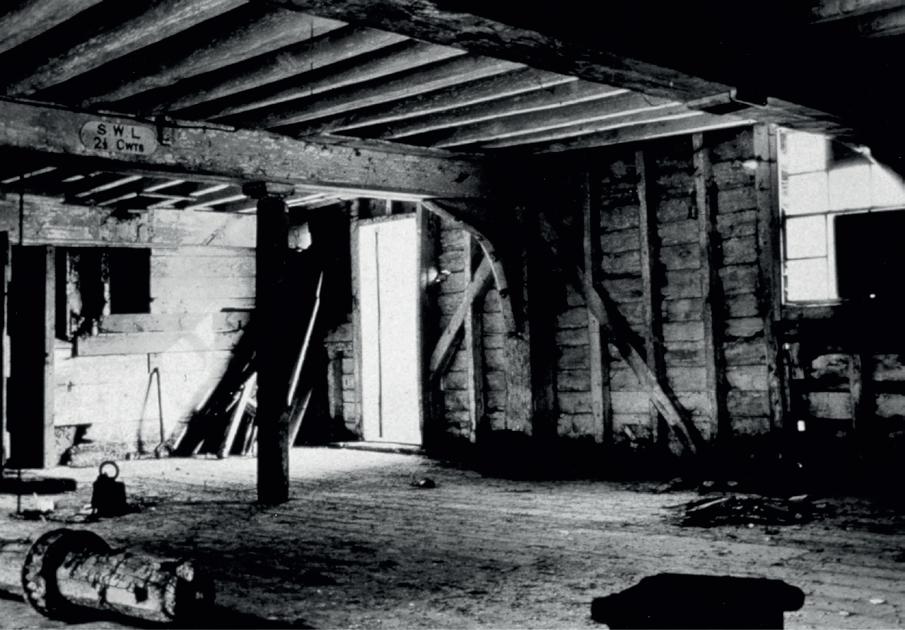
Interior of the derelict mill, 1968. Ground floor: looking towards the riverside outhouse
Local funds were pledged to completely overhaul the Milland an unsuccessful application was made to the Heritage Lottery Fund in 2009.
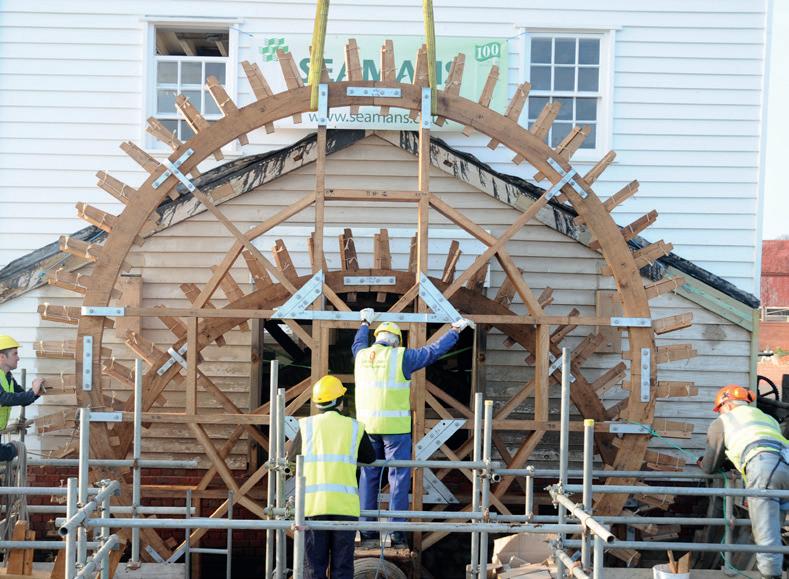
By 2010 some of the wedges holding the waterwheel in place slipped, and the wheel could no longer turn. Nigel Barratt, Chair of the charitable trust, submitted a successful bid to Heritage Lottery Fund (started by his predecessor Fred Reynolds), and raised the remaining funds required. The Mill closed in 2011 to allow the works to take place.
Weatherboarding was replaced, with a similar amount repaired, and remedial works were undertaken to the roof. The pond and the mill race were dredged out, and a new wheel was commissioned from the International Boatbuilding Training College (IBTC) in Lowestoft. The wheelhouse and the old walkway were rebuilt with the new walkway wrapping round the Mill to a new door. This provided a vastly improved visitor experience in viewing the wheel, as well as better maintenance. IBTC installed the new waterwheel, and an outside disabled toilet was provided.
The Norfolk Millwright Alliance overhauled all the machinery and dressed the stones to bring the Mill back into productive use. One set of stones was dedicated for use with the waterwheel, but a concession was made to modern technology with a second set of stones powered separately by an electric motor. This was necessary to give maximum flexibility in demonstrating grinding flour, as the size of the pond at around half an acre would only allow full operation by the waterwheel for around 8 – 10 days in the month, and then for only around half an hour at a time.
As well as being an attractive and up to date visitor attraction, it is now a fully working Tide Mill again, one of only two in the entire country, now capable of producing and supplying wholemeal flour, using the same renewable energy and machinery as it did over 200 years ago, and which its forerunners had done for over 800 years.
A completely new and up to date visitor experience was added as well as static illustrated display panels, interactive models, children’s games, audio stations, computer generated graphic displays, and a short film about the Mill – all designed to show off and explain the three themes that the Mill can demonstrate for the visitor; culture and history, technology and engineering, and agriculture - from field to flour (fork?).
This unique and attractive part of the Woodbridge Riverside is a tribute to the generosity of Mrs Jean Gardner, without whom it would surely have been lost. The Tide Mill remains a symbol of the Suffolk tourist industry. It is one of the most photographed, painted and drawn buildings in the East of England, and attracts the attention and interest of mill enthusiasts worldwide.
The Mill’s considerable maintenance costs must be met from grants and admission charges. Any additional donations are always gratefully received.
A GUIDE & SHORT HISTORY
originally written by Michael Weaver
now revised and updated by Nigel Barratt
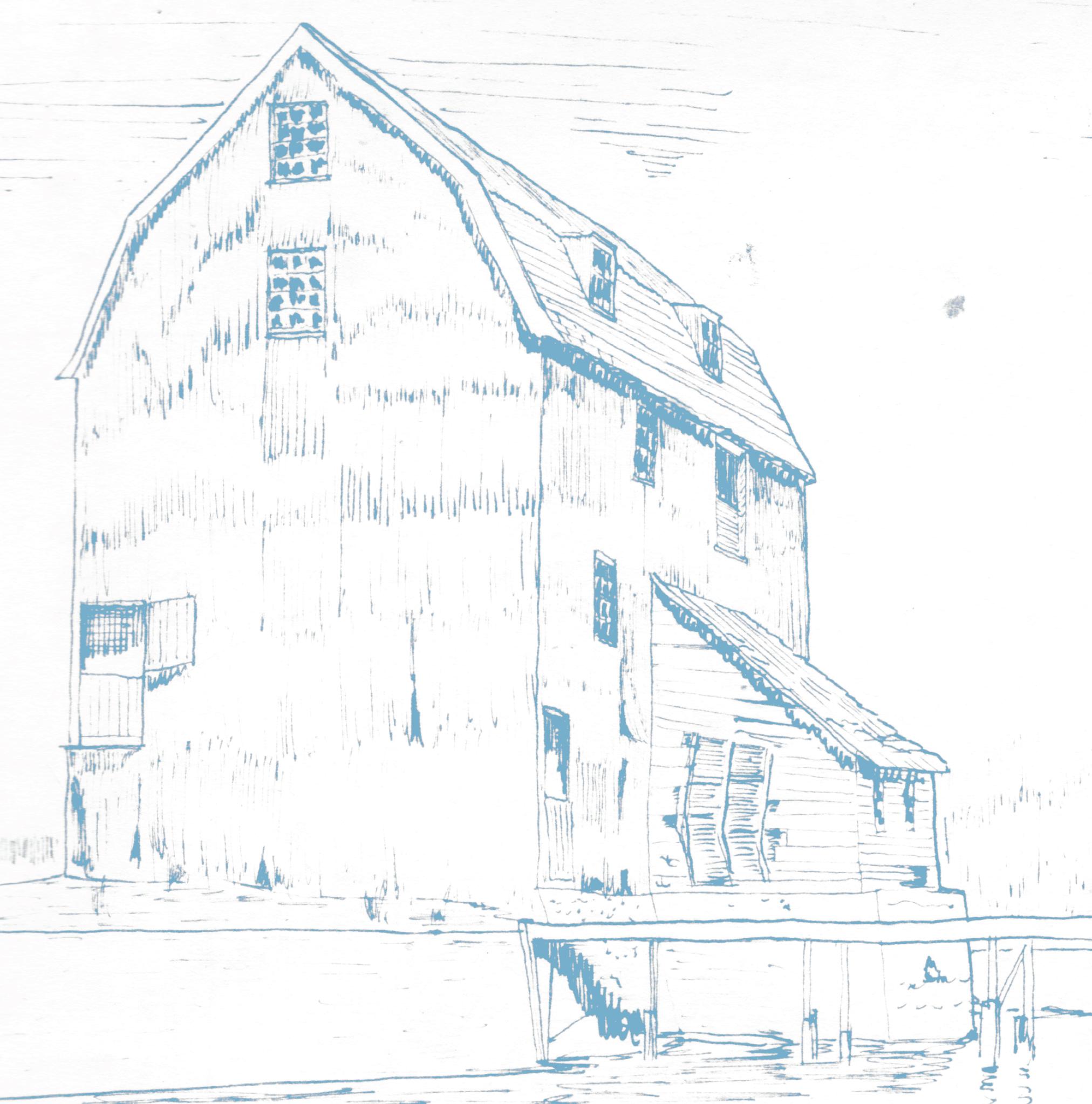
PREFACE TO THE 2024 EDITION
This edition was published after Mike Weaver’s sad death in December 2011, and following the major restoration and improvements project which took place in 2011. Mike researched and wrote the first guide book in 1973, and his 40 year knowledge of the Mill was unsurpassed. He was part of the original group who first saved the Mill in the 1970s, and until his untimely death in 2011 was a part of the recent project. He embraced the changes we introduced, and even though he didn’t live to see the end result, he would certainly have approved. As well as Mike Weaver, contributions to the early editions were made by Pat King, Geoffrey Day, and Edward Booker, some of whose contributions survive in this edition.
Published by the Woodbridge Tide Mill Trust Tide Mill Way Woodbridge, Suffolk, IP12 1BY
Registered Charity No. 274146
Sponsors, Trustees, Staff, Council, Appeal etc
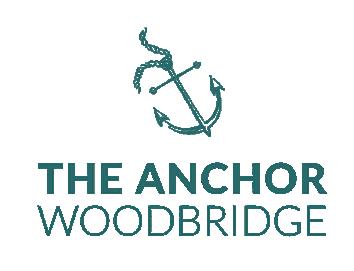
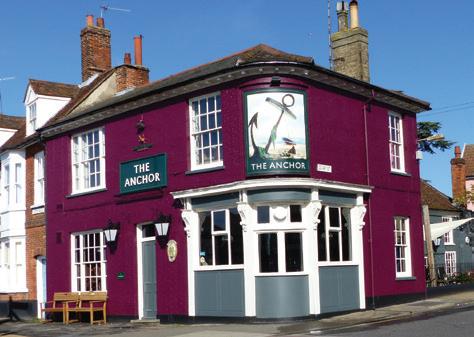
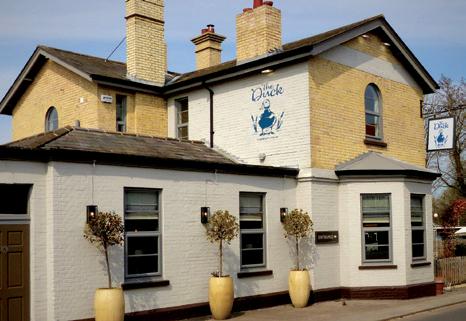
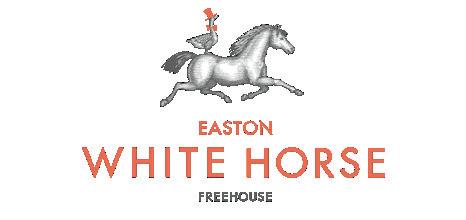
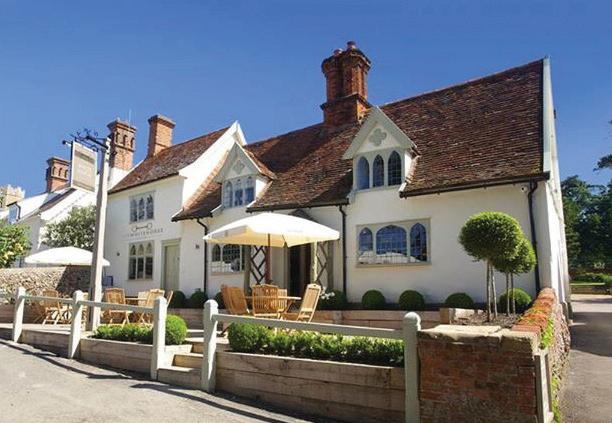
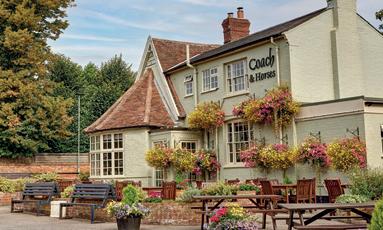
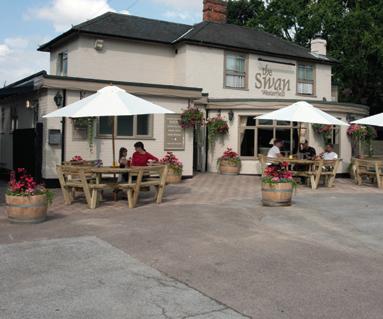
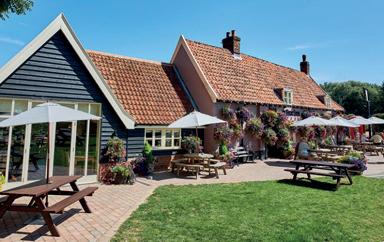
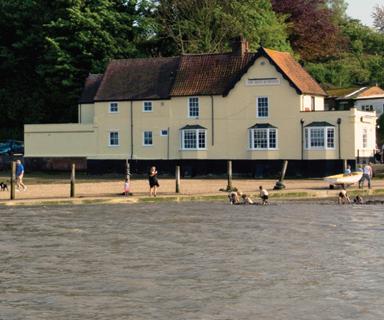
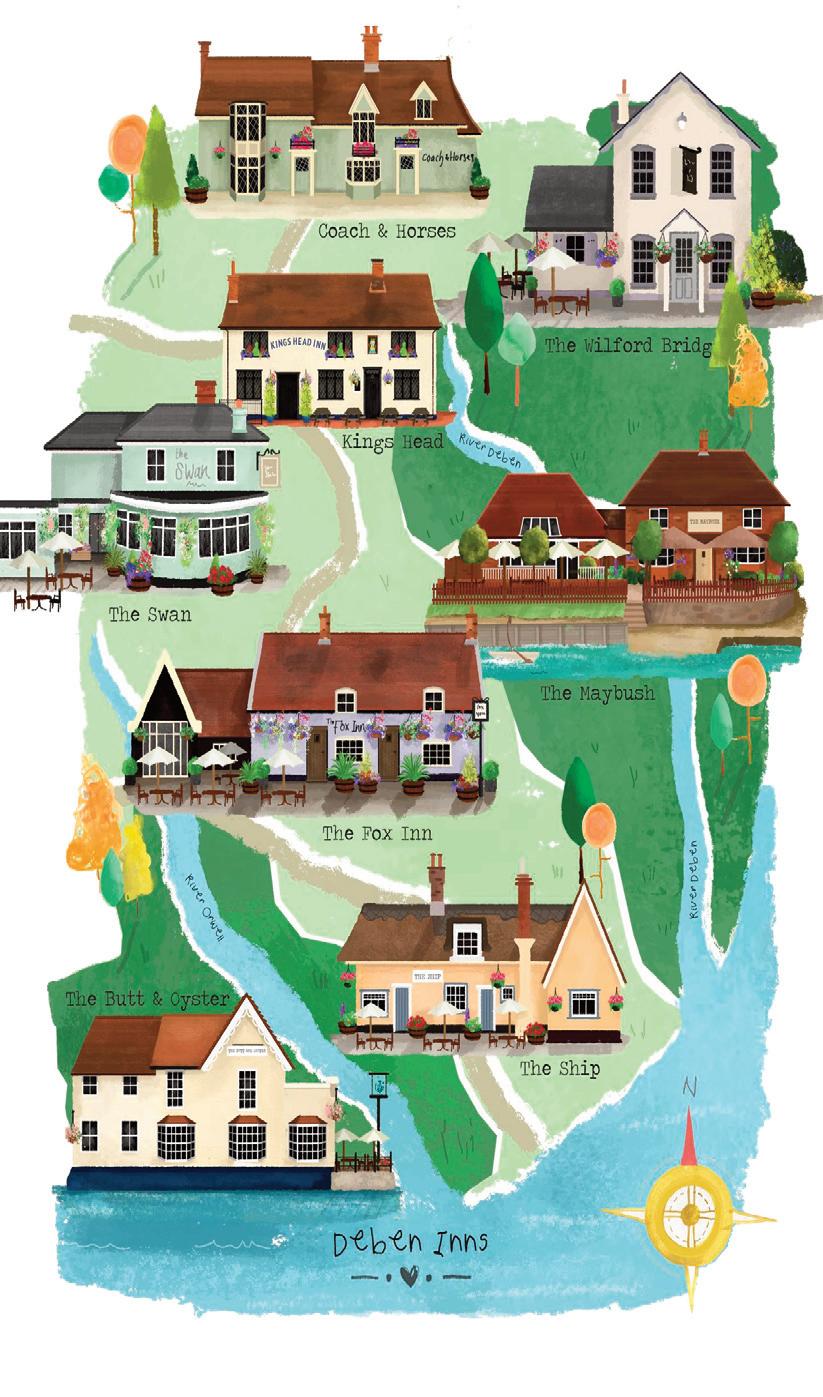
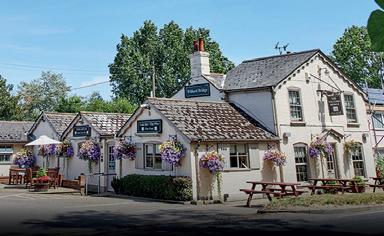
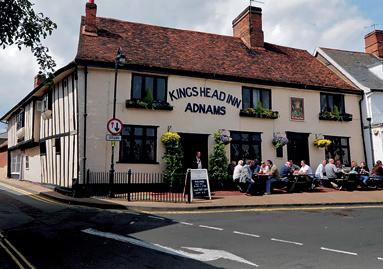
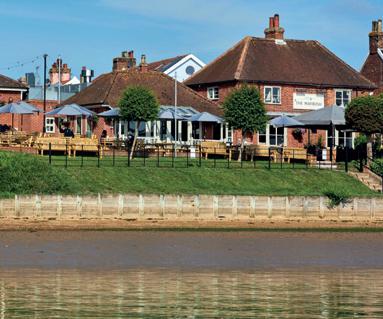
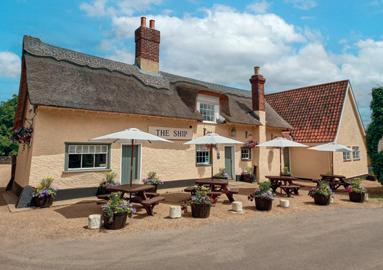