MY ADVICE FOR SAFETY PROFESSIONALS?
CONSIDER THESE THREE TIPS:
1. Weave psychological safety into your safety education. From toolbox talks to microlearning modules, look for ways to educate workers about psychological safety and its importance.
2. Clearly connect the psychological to the physical. Make sure workers understand how psychological safety directly influences physical safety at work. This will make it easier to achieve the team-wide understanding and buy-in you need to support a psychologically safe environment.
3. Measure success. Engagement surveys can help you assess improvements in psychological safety. Keep an eye on physical safety indicators, too. An increase in, say, incident or near-miss reports could actually be a sign that workers feel more comfortable flagging safety concerns.
When your safety efforts focus on the psychological, you’ll find it easier to cultivate a workplace where employees don’t hesitate to take action on critical safety matters. Your Safety Culture Depends on Psychological Safety Trust and comfort are powerful motivators in the workplace. Without it, even the most well-intentioned safety initiatives will fall flat.
That’s why it’s so important to invest in fostering psychological safety. What you’ll unlock: a culture where employees feel more secure, engaged, and committed to the long-term safety of your team.
Your Way To Safety
Whether it’s walking the factory floor, taking a stroll outside during a break or getting from one meeting to another, we’re on our feet at least part of the day. With all of that foot traffic, the potential for a fall is always present.
Walking has been a leading cause of workplace injury for many years, the National Safety Council says, adding that “we need to watch out for all of the hazards tied to walking just as we would any other part of our jobs that poses a safety risk.”
So, what are some of the dangers tied to walking? Distractions, improper footwear, damaged surfaces and poor housekeeping.
STAY SAFE – FOLLOW THESE TIPS FROM NSC:
• Don’t read a text message, email or any kind of written material while walking. If you need to do so, step to the side and put your back to a wall while you read.
• Save in-depth conversations for the conference room or a private office.
• Leave your headphones behind. They block out noises and may prevent you from noticing people or obstacles in your path.
• Watch where you’re going. You need to be able to see changes in elevation, cracks or holes in flooring, as well as other hazards.
• Slow down.
• Don’t let packages or boxes block your view.
Walking has been a leading cause of workplace injury for many years...
When workers don’t feel safe, they’re usually hesitant to report dangerous conditions at all.
Can A Strong ‘Working Memory’ Help Prevent On-The-Job Distraction?
05.01.2024 | Safety and Health
Ann Arbor, MI — “Working memory” may play a key role in helping workers avoid getting distracted, results of a recent University of Michigan and Google study suggest.
“Working memory” is defined as the “ability to hold and manipulate information simultaneously in one’s mind,” a U-M press release states. “In other words, when intrusive thoughts enter the mind, working memory is needed to keep track of the thoughts one should remain focused on.”
Researchers analyzed data from nearly 2,600 people who reported their physical and psychological happenings at work and home. Participants assessed job demands and resources, as well as disclosed family problems from the past 12 months.
To assess working memory, the researchers gave the participants a series of numbers one at a time. The participants attempted to repeat those strings of numbers backward, beginning with sets of two numbers all the way up to an eight-digit set.
The researchers found that “as people reported experiencing more family problems during the last year, the more they felt their job was demanding. This showed family problems seeping into their assessment of work,” the release states.
It continues: “This relationship does not hold for individuals with high working memory because they had an increased ability to prevent the stresses of the family domain from acting as a distraction to their work. This does not suggest that individuals with higher working memory experience fewer family problems – they’re just better able to fend off those distractions.”
Can You Get Traction on Distracted Driving?
07.03.2024 | SafeStart
A new fact sheet on traffic fatalities brings some mixed news on distraction-related safety outcomes. It reveals optimistic top-line numbers while highlighting several underlying concerns about drivers and distraction. Importantly, it underscores how much work still needs to be done to combat the dangers of
STATISTICS OF MASS DISTRACTION
First, the good news. The fact sheet, authored by the Traffic Injury Research Foundation (TIRF), says that distraction-related deaths on the road decreased from 458 fatalities in 2000 to 359 in 2021. But these positive results come with a caveat. The report notes that “the number of distraction-related fatalities has declined more slowly than the number of nondistraction-related fatalities.”
More concerningly, while the number of fatalities has declined, the rate of distraction-related fatalities rose from 19.1% in 2000 to 28.8% in 2021. That’s almost a 10% rate increase in fatal roadway incidents involving distraction. Furthermore, this increase can’t be pinned to a single demographic.
Distracted driving and roadway fatalities are often chalked up as an issue with more youthful drivers, but TIRF’s traffic fatalities fact sheet suggests that the issue is much more complicated. According to TIRF, distracted driving kills drivers of all ages. In fact, for both young drivers (ages 16–19) and older drivers (ages 65+), over 20% of total driving fatalities are distraction-related.
And it’s worth noting that while the fact sheet is focused on Canadian roadway fatalities, distracted
driving is an issue that affects people around the world. Most notably, distracted driving is a more common issue than ever before in the United States, killing thousands of people and causing over a quarter-million incidents every year. Distracted driving is an indiscriminate hazard.
DISTRACTED DRIVING KILLS MORE THAN JUST THE DRIVERS
The fact sheet also points out that “non-distracted victims are more likely to be killed in distracted driving collisions than distracted road users.” This means that other drivers, cyclists and pedestrians who might otherwise diligently avoid distraction are nonetheless at risk of being killed by a distracted driver. All told, it’s clear that distracted driving is a widespread social concern rather than an issue of individual safety.
The President and CEO of TIRF, Robyn Roberston, recently joined the SafeTalk safety podcast to discuss the issue. In an episode called “Driving Distractions: Turning Highways into Fortresses of Focus ”, Robertson discusses the many factors fueling the increase in the proportion of distracted driving fatalities.
Robertson says that smartphones play a role in distracted driving deaths but they’re hardly the only contributing issue. Vehicle design can also lead to fatalities on the road, and so can our brain’s natural habits. The whole episode is a fascinating look at why distracted driving is such a pernicious problem and why it can be so challenging to mitigate distraction behind the wheel.
HOW TO FIGHT DISTRACTION 24/7
As a safety professional, the TIRF fact sheet is a good opportunity to re-evaluate your driving safety initiatives. Even though most driving-related fatalities occur outside the workplace, safety interventions can have a dramatic impact on off-the-job injury outcomes. And employees who stay safe at home are more likely to show up on the job healthy and ready to work. This is among the reasons why it’s so important to discuss off-the-job safety topics in the workplace and why there’s a direct connection between workplace driving safety and off-the-job driving fatalities.
It’s never a bad time to conduct an anti-distracted driving campaign to help reinforce the need for employees to stay safe behind the wheel. As you do so, don’t forget Robertson’s insight that distracted driving isn’t simply an issue with cellphones. Structural issues with cars and road design matter, and any workplace distracted driving interventions should take a holistic approach that addresses these concerns.
Human factors are another major and unavoidable contributor to all sorts of transportation issues, from flying to driving. A comprehensive anti-distraction effort should include discussions of human factors like rushing and frustration, which can contribute to distraction.
ADDRESSING HUMAN FACTORS FOR SAFER ROADS
Distraction is a notable human factor in its own right, and effectively curtailing it requires a dedicated effort. This can include everything from human factors training that educates workers on how to recognize and respond to distraction, to training supervisors to be more conscious of human factors and other safety issues.
As Ward Vanlaar, TIRF’s COO, says, “General messages may be falling on deaf ears, particularly if people don’t recognize they are distracted.” This makes a good human factors education program even more vital, as it can help workers understand the degree to which they can be affected by distraction. This will make employees much more receptive to learning anti-distraction skills and then making use of those skills when they are most likely to be influenced by distraction and other human factors.
The TIRF fact sheet is a good reminder that distraction is never static, and if left unchecked, distracted driving is likely to continue to grow as a problem. TIRF’s organizational mission is to increase education and awareness in order to reduce driving-related deaths, and safety professionals can follow their example. By proactively educating workers on the dangers of distracted driving—and sustainably introducing human factors training—you can play your part in keeping people safer on the roads.
12 Types Of Technology That Can Make Jobsites Safer
05.08.2024 | Construction Dive
Recent innovations such as wearables, drones and predictive analytics help improve hazard detection and incident prevention.
Lena Kenny is safety manager at New York City-based contractor JT Magen & Co. Opinions are the author’s own.
Construction Safety Week is an annual opportunity for people, companies and even competitors to work together and celebrate the incredibly hard work done by people in our industry who make safety the foundation of everything they do and demonstrate their continued commitment to building a stronger, safer industry.
Innovating construction safety involves implementing new ideas, technologies, processes and practices to reduce risks, prevent accidents and promote a culture of safety.
At JT Magen & Co., we already implement many steps to innovate our construction safety, including everything from risk assessment and management to training and education.
We also embrace technologies such as wearable devices, drones and artificial intelligence-powered analytics to improve safety monitoring, hazard detection and incident prevention.
Innovations such as these have the potential to significantly improve workplace safety in the construction industry by providing better risk assessment, enhanced communication and real-time monitoring of workers and environments. By leveraging these emerging technologies, construction
companies like JT Magen can create safer working environments, reduce accidents and injuries and improve overall productivity and efficiency in the industry.
HERE ARE SOME EXAMPLES OF TECHNOLOGIES WE STRIVE TO DEVELOP AND IMPROVE, AND HOW THESE TECHNOLOGIES CAN CONTRIBUTE:
Wearables: Devices such as smart helmets, vests and wristbands equipped with sensors can monitor vital signs, detect hazardous substances and provide real-time alerts in case of accidents or dangerous conditions. These devices can also track workers’ movements to prevent collisions and ensure they stay within safe zones.
Virtual reality/augmented reality: VR and AR platforms can be used for immersive safety training simulations, allowing workers to practice handling hazardous situations in a controlled environment. AR can also provide onsite guidance and visual overlays of safety protocols, equipment instructions and hazard warnings, improving situational awareness.
Drones: Unmanned aerial vehicles equipped with cameras and sensors can conduct surveys of construction sites to identify potential hazards, monitor progress and inspect hard-to-reach areas without risking worker safety. They can also be used for inventory management and security monitoring.
Innovations such as these have the potential to significantly improve workplace safety in the construction industry.
Artificial intelligence: AI-powered algorithms can analyze vast amounts of data from sensors, cameras and other sources to predict safety incidents such as falls or equipment malfunctions before they occur. AI can also optimize resource allocation, schedule maintenance tasks and automate safety inspections to minimize risks.
BIM: This type of software enables architects, engineers and construction teams to create digital models of buildings and infrastructure projects. These models can simulate construction processes, identify safety hazards and plan logistics more efficiently, reducing the likelihood of accidents during the construction phase. While already in use, the expansion of this technology can only improve our safety profile.
Robotics: Robotic systems can perform repetitive or dangerous tasks such as heavy lifting, demolition and welding with precision and consistency, minimizing the need for human intervention in hazardous environments.
Collaborative robots, or cobots, can work alongside human workers, enhancing productivity and safety.
3D printing/additive manufacturing: 3D printing allows for the fabrication of complex structures and components with high precision. It can be used to create custom safety equipment, tools and building materials tailored to specific project requirements, enhancing worker safety and efficiency.
Predictive analytics: By applying predictive analytics to historical safety data, construction companies can identify trends, patterns and risk factors associated with workplace accidents and near misses. This information can be used to develop proactive safety measures and targeted interventions to prevent future incidents.
Autonomous vehicles and equipment: AVs and robotic construction equipment can perform tasks such as material transport, excavation and site preparation with minimal human intervention. These technologies reduce the risk of accidents caused by human error and improve overall construction site safety.
Remote monitoring and telepresence: These innovations enable supervisors and safety managers to oversee construction activities and provide real-time guidance to workers from a centralized location. This capability enhances communication, facilitates quick decisionmaking and ensures adherence to safety protocols.
Environmental monitoring and control: These advanced systems can measure air quality, noise levels, temperature, humidity and other factors that affect worker health and safety. By continuously monitoring and controlling these environmental parameters, construction companies can create safer and more comfortable work environments.
Exoskeletons: Wearable robotic devices augment human strength and endurance can help reduce the risk of musculoskeletal injuries by providing support and assistance to workers when performing physically demanding tasks such as lifting heavy objects or working in awkward positions.
Construction Safety Week reminds us that at all times, safety is priority No. 1 for our industry, and that it’s our responsibility to follow, expand and enhance safety procedures every day.
Construction Safety in 2025: Trends, Statistics & Best Practices
05.05.2025 | ISHN By Mub Pathan
With almost 8.3 million workers, the construction sector in the US achieved a major milestone in January 2025, according to Statista. This is the highest employment level since the early 2000s. The best practices for identifying and mitigating hazards in construction environments are to ensure that worker safety and training programs adhere to the ANSI/ASSP A10.2-2025 standard. These training programs provide a range of instruction tailored for new hires, considering factors such as job site conditions, regulatory requirements, pre-job assessments, effective supervisor leadership, and the need for regular retraining.
CHANGING REQUIREMENTS AND INCREASING RISKS
Additionally, Construction Safety Week is scheduled to take place from May 5-9, 2025, in collaboration with OSHA. The purpose of this event is to raise awareness of construction safety by presenting a range of incident scenarios and providing advice on how to stay safe while working. This
sector has a high accident and fatality rate, making it the most dangerous workplace in the United States. According to the BLS , there has been an increase in both fatal and non-fatal injuries on construction sites compared to 2023. In particular, roofers, laborers, helpers, carpenters, and maintenance workers experienced increased injuries. Falls, slips, and trips account for the highest number of casualties.
Approximately 20% of all worker fatalities occur among construction workers, despite their making up only 6% of the US labor force. In 2023, the industry reported 1,075 workrelated deaths, the highest number since 2011. It is critical to comprehend how construction safety is evolving as we approach 2025, identify new trends, and put best practices into action in order to lower risks and safeguard employees. According to the important construction safety statistic, 1,075 construction-related deaths occurred in 2023, the most since 2011. More than one-third of construction site fatalities are caused by falls, which continue to be the most common cause of death.

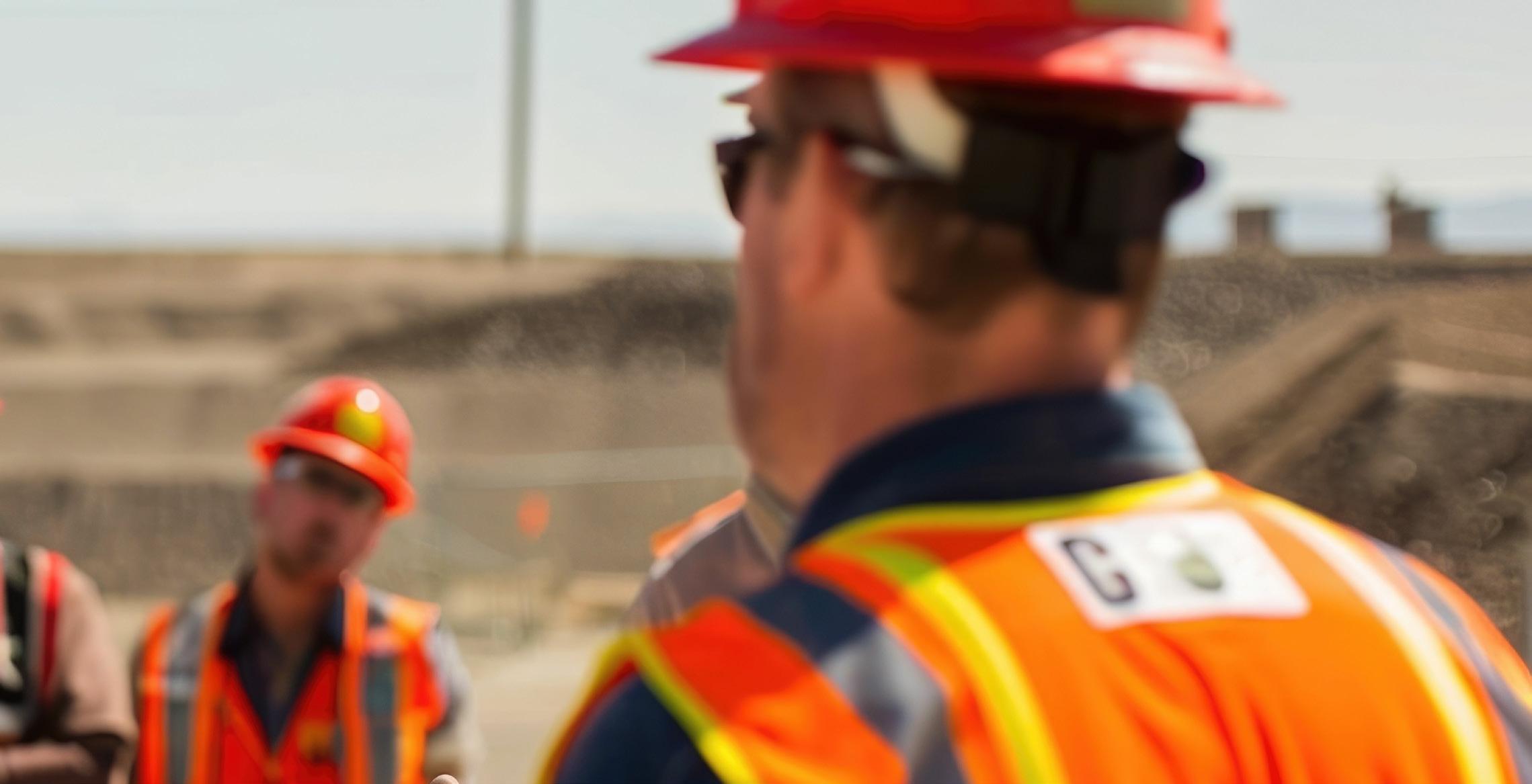
OSHA’s new rule emphasizes the importance of proper PPE (personal protective equipment) fitting on construction sites. By offering resources and best practices for workplace safety during Construction Safety Week, OSHA is actively raising awareness of safety issues, as was previously mentioned. Furthermore, specific rules about the required safety gear and apparel that must be worn on the job site have been established by ANSI and OSHA.
CONSTRUCTION SAFETY ESSENTIALS 2025
PROPER PPE FITTING
OSHA’s new rule highlights the importance of proper fit for PPE to provide maximum protection. This revision addresses concerns that standard-sized PPE may not accommodate diverse body types, which can compromise safety.
CONSTRUCTION SAFETY WEEK
The industry’s dedication to safety is emphasized at this yearly event, which takes place from May 5–9 and offers a forum for exchanging resources and best practices. The 2025 theme, “All in Together,” emphasizes how businesses and employees must work together to create a safe workplace.
MENTAL HEALTH
The importance of mental health and well-being, in addition to physical safety, is becoming increasingly recognized in
the construction industry. This entails helping staff members discuss their challenges and addressing depressive symptoms like decreased interest in activities, irritability, anger, irregular sleep patterns, and appetite changes.
FALLS
In the construction industry, falls are a leading cause of injuries and fatalities. OSHA requires fall protection measures for work over six feet in height, and implementing safety nets and guardrails is a crucial step in minimizing fall risks. Also, wearing a hard hat is essential for such fatalities.
CONSTRUCTION SAFETY WEEK RESOURCES
Organizations like Construction Safety Week, which offer resources and best practices to help businesses plan and execute their Safety Week events, further bolster the industry’s commitment to safety.
By introducing state-of-the-art technologies and preventative measures and requiring the use of safety gear and apparel, the construction industry is showcasing its commitment to safety in 2025. Businesses can make workplaces safer and ultimately prevent injuries and fatalities by adopting best practices and keeping up with the latest trends.
TACKLING AED READINESS IN DYNAMIC WORK ENVIRONMENTS
Sudden Cardiac Arrest (SCA) doesn’t wait for the perfect time or place. It can strike anywhere—on a rooftop, in a warehouse, along a highway, or miles from the nearest emergency response team. For safety professionals responsible for mobile teams, this raises a critical question: Are your AEDs truly ready to respond, no matter where the work takes them?
In many industries, including construction, utilities, energy, and logistics, the traditional, facilitybased approach to AED readiness no longer fits. Teams are constantly in motion. Worksites change daily. Gear gets loaded into trucks and hauled across cities—or across states. AEDs travel with them, often without the same level of oversight they’d receive in a fixed location. That’s where gaps form—and where risk begins.
THE CHALLENGE OF MOBILITY
AED programs were designed with static environments in mind. Safety officers typically set up inspections, track expiration dates, and conduct drills in offices or centralized facilities. But when AEDs go mobile, they leave the infrastructure behind.
WITHOUT PROPER CHECKS IN PLACE, MOBILE AEDS MAY:
• Be stored in extreme temperatures that degrade batteries or pads.
• Go unchecked for weeks—or months—between job sites.
• Be relocated or be removed from service/working order without documentation.
• Appear compliant on paper but be non-functional in the field.
These challenges aren’t hypothetical. In many organizations, mobile AEDs fall through the cracks simply because there’s no system designed to follow them. Yet the expectation remains: that these devices will work, instantly and flawlessly, when lives are on the line.
LIABILITY DOESN’T TRAVEL LIGHTLY
When AEDs fail due to oversight, organizations don’t just face emotional consequences—they face legal ones. Courts have consistently held employers responsible for maintaining life-saving equipment, especially when they’ve made a commitment to having it available.
Failure to monitor, inspect, or respond to device alerts can all result in legal action. In mobile environments, where tracking is tougher and documentation is sparse, proving readiness becomes even more difficult after the fact.
That’s why safety leaders are rethinking how they manage AED programs outside the building. Documentation, visibility, and accountability are no longer “nice to have”— they’re essential.
MODERN TOOLS FOR A MOBILE WORKFORCE
As AEDs have become more portable, so has the technology that supports them. Today, innovative remote monitoring systems can travel with the device—automating status updates, expiration alerts, and overall readiness.
WITH THE RIGHT SYSTEM IN PLACE, ORGANIZATIONS CAN:
• Receive automatic alerts for battery or pad issues
• Confirm readiness at-a-glance for every unit, regardless of location
• Maintain audit logs and compliance records effortlessly
• Ensure AEDs are never “out of sight, out of service”
This kind of real-time visibility enables safety professionals to focus on strategy and training, rather than routine inspections. It also ensures that whether an AED is sitting in a warehouse or bolted inside a work truck, it’s ready to save a life.
DON’T LET READINESS STALL OUT IN THE FIELD
Readiness isn’t static—especially when your workforce isn’t. Creating a culture of preparedness means extending oversight beyond the four walls of your facility. Mobile AED programs need the same level of attention, structure, and support as those in fixed locations—if not more.
That starts with asking the right questions:
• Who is responsible for mobile AED checks?
• How often are they verified?
• Can you prove the AED(s) are functional if an incident occurs?
• Do your devices send readiness alerts—or are you relying on guesswork?
If the answers are unclear, it may be time to modernize your program.
PREPAREDNESS SHOULDN’T BE TIED TO A ZIP CODE
In the moments that matter most, your AED needs to work— no matter where it is. The good news is, tools now exist to ensure that’s possible. With smart monitoring and thoughtful program design, mobile AEDs can be just as reliable as their wall-mounted counterparts.
Because when a life is on the line, “we didn’t know” isn’t good enough.
3 Tips to Make a GREAT Inspection Checklist!
07.29.2024 | EHSVoice
Know the exact goal of the inspection before creating the form.
Lately, we have been talking a lot on the blog about the importance of checklists. Atul Gawande, the author of ‘The Checklist Manifesto’ reminds us that although simple, checklists work! Even the most specialized professionals like pilots and doctors can rely on this simple tool to improve their performance and reduce risk.
‘The Checklist Manifesto: How to get things right’ goes on to explain, that while vital, not all checklists are created equal:
“There are good checklists and bad… Bad checklists are vague and imprecise. They are too long; they are hard to use; they are impractical. They are made by desk jockeys with no awareness of the situations in which they are to be deployed”
“Good checklists, on the other hand, are precise. They are efficient, to the point, and easy to use even in the most difficult situations.”
I’m sure those of you who have attempted to utilize checklists as part of your Environmental, Health, and Safety (EHS) program have experienced this. One area within EHS that makes regular use of checklists is inspection programs. In essence, an inspection is simply a checklist, and like any checklist there are good ones and bad ones. Today we’ll explore three tips to help you make sure your EHS inspection checklists are GREAT!
TIP 1: KNOW YOUR GOAL
As mentioned, good checklists are precise. This means that we need to know the exact goal of the inspection before creating the form. It sounds so simple it should go without saying. But often, we’re so eager to get to the task at hand that we skip over the step where we stop to determine WHY we are doing this in the first place. Determining your goal can take some research on the front end.
If your goal is to make sure you’re in compliance with a particular regulation, you may need to determine what part of the regulation applies to your facility. If your goal is to support a corporate sustainability initiative, you may need to gather some corporate goals and guidelines. If your goal is proactive risk reduction, you may need to not only understand the guidelines and regulations- but also be able to back them up a few steps so you can check for indications something may be heading the wrong direction before a regulation is actually violated.
If you don’t take the time to determine your goal before writing your checklist, you may end up with a list that’s either too specific or too vague for your purposes.
Knowing your goal before creating a checklist will help you be more precise because your overall goal will dictate the level of urgency and detail that need to go into your checklist. For example if your goal is compliance with a strict regulation, you’ll need to ask more pointed and specific questions than if your goal is a more general sweep of the facility. You may find that you need to do both of these things at your facility from time to time.
Adopting a methodology of using precise checklists with clear goals would mean you’d create a separate checklist for each goal, one to check compliance with the regulation you need to meet, and another for your more general observations. Keeping each checklist distinct will help you quickly identify and fix issues in a more targeted way, it will also help those reviewing inspection reports prioritize any corrective actions required.
TIP 2: USE A SIMPLE SCORING SYSTEM
Just as we want our checklist of inspection questions to be focused and precise, we also want our method of answering those questions to be quick and to-the-point. An inspection checklist is not the place for open-ended questions or long essay-like responses. There are several different ways to create a scoring system; the one that works best for you will depend on the overall goal of your inspection
SOME GOOD METHODS FOR SCORING INSPECTIONS INCLUDE:
• Yes/ No
• Pass/ Fail/ Warning
• In Compliance/Not In Compliance
• Rating
If you’re checking to make sure you’re in compliance with a strict regulation, a more binary system like yes/no or pass/ fail might be a good choice for you. If you have some room for interpretation or are looking to catch things proactively, a rating system or options with a warning in addition to pass/ fail may better suit your needs.
A rating system makes it easy for the inspector to answer the question. They can select a response and move on. They may need to add some images or extra information, but the overall answer can be added quickly and, importantly, is not open to interpretation.
The distinctness of a scoring system vs. open ended answers also makes it easier for those reviewing inspection documentation. They should be able to quickly scan the inspection and see where issues are without having to dive into additional documentation.
TIP 3: PROVIDE THOUGHTFUL CONTEXT
We want our inspection checklists to be precise and simple. However, we don’t want them to be so stripped down that our inspectors are left scratching their heads wondering why they are asking a particular question, or what the impact of a failed response is.
A simple way to do this is to provide a citation if the question is related to a particular regulation, or some points to remind the inspector of the regulatory or corporate guidelines. What we’d want to avoid here is quoting an entire regulation in all its legalese glory into the checklist.
Planning for the Human Factor in Construction Project Safety
05.01.2025 | Construction Executive by Grace Calengor
New construction technology is helping construction companies predict, plan for and embrace the human factor—both risks and rewards—on jobsites.
As Construction Safety Week 2025 approaches, companies are taking a harder look at one of the predominant factors pertaining to jobsite safety—or lack thereof—and how they can mitigate its inherent risk: the human factor. Under the theme “All in Together,” the week of May 5-9 will focus on how teams can plan, own and commit together, and that comes with planning for and owning up to mistakes. From individual behaviors to group interactions, from physical wellbeing to mental health, humans aren’t perfect and even the best of them introduce variables from day to day that leave room for error.
Jerry Shupe, chief health and safety officer at Hensel Phelps, sat down with Construction Executive to help elucidate how the human factor in construction should be considered to actually improve projects.
WHAT IS THE HUMAN FACTOR?
One thing that makes humans unique pertaining to navigating the complexities of the construction industry is their emotion. Emotion leads to creativity in design, compassion for a site’s rich history and passion for bringing a vision to life. However, emotion also leads to occasionally glossing over details and inciting disagreements.
“When we’re looking at an incident on a project,” Shupe says, “and as we start trying to figure out where the failures occurred, I think oftentimes there’s a tendency for people to blame people. But what we often forget is that no one goes to work and wants to get hurt. And oftentimes there are so many different contributing factors to why an incident occurred.” Human emotion can blind people in the moment to the true contributors to injury or accident. That doesn’t mean the human factor should be eliminated—as many are worried AI or robotics will replace them—but rather supported to properly serve the project.
Shupe says, “No matter how much we preach safety and doing things the right way, I think a lot of times what people hear is we have to get the job done. How this really ties to human performance is making sure that we’re giving people the right tools, we’re creating the right working environment and we’re really setting people up to work safely and successfully.”
FIRST AND FOREMOST
Training in construction is paramount, and the industry is typically spot-on at providing proper jobsite training. But to ensure that training is effective, it must be pertinent to person and project.
“If someone’s going to be working in a trench,” says Shupe, “we’re giving them the right training for that. If they’re going to be working at height, we’re giving them the right training for that. But sometimes where the industry can fail is by not looking at the broader training that we might give to a salaried professional in the office. Are we giving our foremen leadership development training on how to have difficult conversations? Are we giving our craft professionals actual skills to use the tools we expect them to use every single day and to use them while working amongst each other? It really comes down to understanding what training is available and providing a greater catalog of training.”
But how does a company decide what to put in this catalog? Determining a project’s risk profile is a concrete place to start—and this is done by measuring the human factor. All contractors know that culture on a jobsite is palpable thanks to that human factor of emotion. At Hensel Phelps, Shupe and team have found a way to measure 20 separate indicators that affect the risk profile of projects. “We found that we were able to accurately predict an incident within 30 days with 78% accuracy,” says Shupe—a remarkable and optimistic statistic. Some of what Hensel Phelps measured and learned include:
• PTO—People are more likely to have an incident within the first 24 to 48 hours of returning from PTO.
• Safety Observations—If project teams are not consistently making safety observations or only focusing on unsafe behaviors (versus recognizing what people are doing well), there is increased risk.
• Weather—Weather such as rain, temperature, snow, wind, fog, etc. increases risk.
• Turnover—As you hire people, transfer people to a new project, bring on trade partners, etc., risk increases.
• Project Start/Finish—The first 6 months and last 6 months of a project have increased risk.
In recognizing the human factor, construction companies are also recognizing that risk is inherent and accidents will
happen. While all companies strive for optimal safety, the best companies also prepare for recovery after a variety of accidents. When people hear ‘accident’ in relation to ‘human error,’ their instinct is to picture someone operating a piece of heavy machinery, not someone in a C-suite office. What they also don’t picture is how those two images correlate. When considering the human factor, it makes sense that all accidents—and individuals—are related, and so must be all responses to those accidents. “How we respond as an organization,” says Shupe, and not just as individuals, is ultimately what determines what can be learned from an accident and how trust can be restored.
IMPERFECTION MAKES PERFECT
An appropriate response to an accident stems from proper preparation. As mentioned earlier, people tend to blame each other when an accident occurs, but it’s also imperative to acknowledge that accidents will happen, and to have a recovery plan in place for when they do.
“One of the core things that any organization really needs to do is build trust from the moment someone walks onto their project,” says Shupe. “Finding common ground is really important. Like I mentioned earlier, nobody wants to go to work and get hurt. We as an employer, we don’t want people to get hurt on our project. So if we can really try to find that common ground and get to know the people that we’re working with every single day, so they know we have their best interest in mind and they know we’re trying to do what’s best for them and best for the organization, I think that’s really what’s paramount in building trust and gaining respect.”
THE INHUMAN FACTOR
Acknowledging the human factor is imperative in establishing construction safety culture, but there are inhuman factors that can facilitate this establishment. As construction technology has evolved, so has the human factor. This is not to say that contech is replacing people ...continued on next page
on the jobsite or that it is eliminating risks altogether, but it is empowering people to be more aware of their own risks— the ones they pose and the ones they assume.
“We are seeing safety technology become widely adopted over the past few years,” says Shupe. “One thing we’ve been working on is a safety application that uses artificial intelligence to predict risk on the project because we know that certain things on projects do drive risk. For example, we seem to have more incidents around the holidays— Christmas, Thanksgiving, New Year’s—and we’ve felt that for a very long time. But when we started working with this company, we wanted to figure out if that is really true. What we learned is that when people come back from PTO, we are more likely to have an incident within the first 24 to 48 hours.”
This was one of the twenty indicators Shupe mentioned above that Hensel Phelps is using to provide a risk score to each of its projects and project leaders. “That score is constantly being reevaluated and will hopefully provide actionable insight that leadership can act on,” says Shupe.
Perhaps people will be more vigilant as the holidays approach and pass by, “when we know a lot of people are taking PTO,” he says. “Let’s make sure we’re doing additional safety stand downs and pre-test planning, and that everyone is bringing their best self to the job.”
The human factor has always and will always pose risk to construction projects, but there are ways to empower humans to identify, plan around and recover from those risks. This Construction Safety Week—and every week— companies have the opportunity to create a really positive safety culture, where people feel really good about going to work every day. “I tend to think you’re going to see a lot fewer incidents on those projects,” says Shupe.
Make sure your company is prepared to be All in Together during Safety Week 2025. With events happening every day from May 5-9—and the industrywide safety stand-down on Wednesday, May 7—start planning today to ensure your company doesn’t miss out. Find more information at constructionsafetyweek.com.