THE SAFETY NET
The stockings are hung by the chimney with care…and the Christmas tree is safely placed three feet away from the fireplace. OK, that might not be how the old Christmas poem goes. But it’s a good tip to keep in mind! Read on for more Christmas safety tips to keep your loved ones safe this holiday season.
1. REPLACE OLD LIGHTS AND USE THEM CORRECTLY
The lights bring holiday cheer for sure, but they can be a safety hazard. Use indoor lights indoors and outdoor lights outdoors, and always turn them off when leaving the house or going to bed. Be sure to replace the light sets that have broken sockets or frayed wires.
Psst! Check out these charming (and safe) Christmas lights cookies.
2. BE MINDFUL OF POISONOUS PLANTS
Eating mistletoe is actually toxic. Keep it away from pets, along with other potentially poisonous plants like holly berries, Jerusalem cherry and amaryllis. Don’t miss our checklist to help “pet proof” your house for the holidays
3. PRACTICE CAR SAFETY WHEN TRAVELING
It’s always important to drive safely, but the Christmas travel season can be especially dangerous. Have your car serviced before leaving on a road trip, carry an emergency kit and give yourself extra time to avoid rushing. Remember to decrease your speed if you’re driving in snow or ice and wait for snowplows and sanding trucks to clear the roadways before starting your journey.
4. WATCH OUT FOR ONLINE SHOPPING FRAUD
Unfortunately, the holiday shopping season is fraught with fraud. While you shop, carefully check that the website address is spelled correctly fraudulent websites with similar spelling can trick you into giving away your credit card information. When checking out, be sure the payment page address begins with “https” (the “s” stands for “secure”). And as always, never click a link from an unsolicited email.
5. DON’T MAKE THE TREE A FIRE HAZARD
To avoid the same fate as Clark Griswold’s tree in National Lampoon’s Christmas Vacation, be aware of fire safety. Have the tree vendor cut off about 2″ of the trunk to expose fresh wood for better water absorption, and make sure there’s always water in the tree stand. Keep your tree at least three feet away from radiators or fireplaces. And if you buy an artificial tree, check that it’s labeled “fire resistant.”
Find more helpful hints for taking care of a real Christmas tree.
6. PROPERLY SECURE THE TREE
No one wants Santa to get squished by a fallen Christmas tree. Make sure your tree is properly secured with a strong stand that doesn’t lean. If you have a fresh tree, don’t whittle or taper the trunk to fit your stand; this makes the tree less stable.
7. DON’T BURN WRAPPING PAPER IN THE FIREPLACE
Sure, a crackling fire in the fireplace is a must-have for cozy holiday events. Just avoid any fire accidents by practicing proper fireplace safety. Don’t burn trees, wreaths or wrapping paper; and always use a fireplace screen.
8. KEEP THE RAW TURKEY AWAY FROM THE SALAD
One thing is for sure, nothing will ruin your Christmas dinner faster than guests coming down with food poisoning. Handle food safely with these simple reminders: keep raw meat away from fresh produce, wash your hands frequently, use a meat thermometer and use separate cutting boards for cooked and uncooked meats. See the food safety mistakes we’re all making.
9. BE CAREFUL WITH CANDLES
The top three days for home fires started by candles are Christmas Day, New Year’s Eve and New Year’s Day. To avoid a disaster, keep candles at least a foot away from anything flammable. Make sure candles are in stable holders that can’t be easily knocked down, and never leave burning candles unattended.
10. HANG BREAKABLE ORNAMENTS UP HIGH
Those colorful and shiny vintage ornaments are just too tempting for little ones! Instead, hang breakable ornaments at top of the tree. That way, kids can get in on the decorating fun without the worry of broken glass.
Christmas Lights
11.14.2024 |
Some holiday lights and lighted decorations are only safe for indoor or outdoor use, not both, so make sure the lights you have are being used correctly.
• Replace any string of lights with worn or broken cords or loose bulb connections.
• Read manufacturer’s instructions for the maximum number of light strands to connect safely. Do not overload electrical outlets with holiday lighting.
• Inspect power cords (every year!) to ensure there is no damage to the cord or insulation.
• Check the rating on your extension cords to make sure they meet the power needs for the way they are being used.
• Use clips, not nails, to hang lights so the cords do not get damaged.
• Outdoor extension cords, lights, and decorations should be plugged into outlets protected by ground fault circuit interrupters (GFCIs) or into portable outdoor GFCIs.
• Turn off all Christmas tree lights, light strings, and any other lighted decorations before leaving home or going to bed.
• Bring outdoor electrical lights inside after the holidays to prevent hazards and to make them last longer.
• Do not stand on furniture or any other object that is not meant for climbing on when hanging your Christmas lights. Use the correct ladder for the task.
• To keep your balance, always maintain three points of contact—two hands and a foot or two feet and a hand—while climbing up or down a ladder.
• Ensure extension ladders are placed at a proper angle before climbing up.
• While hanging decorations, if a ladder must be set up in front of a door, make sure the door is locked, blocked open, or properly guarded
DISCUSSION
• What are some tips to make hanging Christmas lights on the house a safer activity?
• Why is it important that outdoor decorations be plugged into GFCIprotected outlets?
Winter is Near. Have You Addressed Your Outdoor Slip, Trip and Fall Hazards?
Q42024 | Liberty Mutual Insurance - Focus on Safety
144 workers were killed in falls on the same level in 2022, according to the National Safety Council (NSC).
Environmental conditions or particulate soil can cause outdoor surfaces to become more slippery. While we cannot control the weather, we can implement control strategies to reduce the impact of these environmental factors. In addition, you can help to reduce the likelihood of slips, trips, and falls on your outdoor surfaces through improved design of sidewalks, curbs, parking lots or structures, stairs, and exterior lighting. Maintenance, including cleaning of exterior surfaces, is also an important element of your slip, trip, fall prevention program. This includes snow and ice removal considerations for states exposed to those conditions.
HOW CAN YOU PREPARE?
You can assist your site with identifying and reducing outdoor slip, trip, and fall hazards by inspecting surfaces
and recognizing areas in need of repair. Most design standards for ground and floor surfaces define a trip hazard as a change in level exceeding one-half inch in height or one-quarter inch for abrupt changes in height as a potential trip hazard . Slip hazards can be introduced by water, such as roof drainage, soil particulates, or even fallen debris/foliage from nearby landscaping. After potential hazards are identified, you can develop a plan to address these hazards that may include:
• Filling and patching cracks and holes.
• Repairing and eliminating raised or sunken areas that can arise due to tree roots, settling, cold weather (frost heaves), and ordinary wear and tear.
• Redirecting roof drainage away from sidewalks and parking areas.
• Ensuring drain covers are flush with surrounding pavement.
• Centering and securing parking stoppers and, near entrances, painting them Safety Yellow to improve visibility.
• Defining pedestrian pathways to crosswalks to avoid car stops, landscaping, and curbs.
• Ensuring exterior stairs are in good condition and free from cracks, and that degraded stair treads and handrails are secure and stable.
• Replacing burnt out lights and ensuring exterior lighting is on and provides enough illumination when it is dark.
• If lights are on a timer, ensure they are adjusted seasonally to turn on during evening hours.
• Scheduling cleaning and maintenance to remove particulate soil or fallen leaves from exterior walking surfaces.
• Developing a plan for snow and ice removal.
• Liberty Mutual Risk Control reference note, Parking lot inspection checklist, RC 5533, can assist you with identifying potential hazards that can increase the likelihood of slips, trips, and falls on your exterior premises. Download on Liberty Mutual SafetyNetTM.
SNOW AND ICE REMOVAL PLANNING
For locations that are exposed to snow and ice, it is important to pre-plan and develop a plan for snow and ice removal that addresses the following:
• Frequency and timing of removal activities before building occupants and guests arrive and periodically as Periodic inspections to ensure snow removal activities are adequate.
• Placement of snow piles to ensure snow does not melt and refreeze in pedestrian walkways including the parking lot surface.
• Use of deicing and ice melt chemicals to remove ice.
• Heated surfaces can potentially promote melting and evaporation. Maintenance associated with these surfaces should also be addressed.
• Use of friction additives to increase traction.
Leading Practices for New Hire Orientations
Q42024 | Liberty Mutual Insurance - Focus on Construction
According to a poll by Gallup analytics , “one in five employees either report that their most recent onboarding was poor, or they received no onboarding at all.”
While there has been a reduction in fatal worker accidents, the construction industry remains one of the most dangerous workplaces. The most recent published data from the Bureau of Labor Statistics shows that there were 1,069 fatalities in construction in 2022, with 233 being from the construction of buildings. Across the U.S., the construction industry loses nearly $10.7 billion a year to serious, nonfatal workplace injuries. One way to help reduce the frequency of injuries and their costs is to ensure new hires and experienced hires receive project orientation and onboarding. While the process can run the gamut depending on the type of contractor, there are best practices when implementing an effective new hire and experienced hire orientation process.
SOME OF THESE BEST PRACTICES INCLUDE THE FOLLOWING:
INTRODUCE IMPORTANT PROJECT PERSONNEL
• During the new contractor orientation, it is important to introduce the project managers, safety manager, safety coordinators, and other site staff that help facilitate the project’s daily activities. This helps any workers know who they can talk to and where to find them should they have questions or concerns.
COVER SITE SPECIFIC SAFETY REQUIREMENTS (OR EXPECTATION SETTING)
• Outline and review the specific rules and policies that need to be adhered to as a requirement for working on the job site. This part of the orientation should cover expected safe work behaviors at the project and highlight site specific rules, like PPE policies or 100 percent fall protection policies.
• Other topics could include the following:
• Permit requirements such as welding, ladder use, confined space, work-at-height, etc.
• Safety pre-planning requirements including site specific forms that must be used.
• Review project specific safety plans and emergency egress
• Ensure that the new contractors know the emergency procedures and the muster points in an emergency evacuation. Cover the emergency evacuation plans, emergency exits, muster points, and other relevant information that pertains to the project’s emergency safety plan.
• Talk about the plans for weather emergencies like tornadoes and where workers should gather.
PROVIDE A PHYSICAL OR VIRTUAL PROJECT TOUR
• Give contractors and their workers a tour of the site, either virtually or in person so that they can become acquainted with the different exit points and huddle locations or explain the project environment. This will help them visualize the project and see what obstacles they may be facing. These tours can help contractors become familiar with their surroundings and understand the scope of the project and high-risk areas and provides an opportunity for them to ask additional project-specific questions.
TAILOR THE ORIENTATION TO YOUR ORGANIZATION’S SPECIFIC REQUIREMENTS
• Discuss insurance specific requirements for the project. Cover any owner specific requirements; for instance, if the project is for a hospital or education institution, there may be specific rules set forth by the owner. The project owner may also require workers to take specific training prior to starting work.
CONSIDER UTILIZING ORIENTATION SOFTWARE OR ONLINE PLATFORMS
• Software or online platforms can help streamline repetitive tasks and help eliminate the same process day–in and day-out. This creates consistency in material presentation as well as efficiencies for both the contractor and the trade partners.
• Provides for a streamlined accounting of attendance at orientation and/or who has participated in orientation. This can then be linked to electronic badging for access to the project.
• Gives workers an opportunity to complete educational training at a pace they need to learn the material and may also include quizzes to help ensure the content was received.
REQUEST FEEDBACK
• Obtain feedback about the orientation process from new contractors to ensure they received the most effective and efficient orientation training. This feedback allows for improvements to be made for the next sessions.
• Feedback can be via a short feedback form which can be tracked electronically and then trends identified to improve the material.
The Austin Company is a Member of The University of Colorado
The Austin Company has been a member of the University of Colorado - Construction Safety Research Alliance (CSRA) organization since 2023. A special thanks to the Austin management team for allowing Craig Herndon (Eastern Safety Manager), Steve Lotz (Michigan Safety Director) and myself to attend the CSRA 2024 summit.
The CSRA is part of the University of Colorado doing scientific research into safety issues or situations where workers could get seriously injured or fatality on a construction project.
AS A MEMBER OF THE HIGH ENERGY CONTROLS TEAM LAST YEAR (2024). THE TEAM CONSIST OF:
High Energy: Controlling the Uncontrollable
Controls save lives. But what makes a control adequate? Leveraging principles of energy-based safety and human performance, a control is now considered adequate if it:
1. Effectively mitigates a high-energy hazard;
2. Is installed, verified, and used properly; and
3. Is immune to unintentional human error. When these criteria are met, a control is labeled a Direct Control. Although a clear definition now exists, initial site testing revealed that Direct Controls are often infeasible, even in common work scenarios.
This project will explore why Direct Controls are sometimes challenging; how to determine if an alternative work plan is sufficient; and how to continuously monitor the state of high-energy when workers are exposed.
In pursuit of a future where all high-energy hazards have Direct Controls, this project will also create a long-term roadmap that includes a technological, engineering, psychological, and managerial solutions.
• If our vision is the elimination of serious injuries and fatalities (SIFs), we need to eliminate SIF conditions.
• Thus, every high-energy hazard should have a corresponding direct control.
• If a direct control is not feasible, we should have an alternative control.
Left to Right – Steve Lotz, Ayleen Perez - Operations Manager, Charlie Engel, Dr. Matt Hallowell - Executive Director, Craig Herndon, Dr. Siddharth Bhandari - Associate Director of Research
What Will OSHA Look Like Under New Administration?
11.14.2024 | EHS Today
“I THINK WE WILL SEE INNOVATION FROM TRUMP 47 LIKE WE’VE NEVER SEEN BEFORE.”
It’s been a long time since OSHA has come under scrutiny. “With a leadership change, often long-standing regulatory agencies will change as well,” says Philip Russell, partner at Ogletree Deakins. ”
And this change could be dramatic, says Russell. “I think that you could see from Trump 47 innovation like we’ve never seen before.”
To understand the practical implications of that viewpoint, EHS Today spoke with Russell, who has been practicing law in the EHS space for a number of years working with companies across a range of industries.
EHS TODAY: WHAT DO YOU THINK WILL CHANGE WITH THE NEW ADMINISTRATION?
PR: OSHA has been around since 1970, and it’s operated essentially the same administration to administration. It really doesn’t matter who’s in the White House, but I think now perhaps we will begin to see a reorganization or shift in resources away from politically popular targets.
I’ll point out one in particular, the warehousing and distribution industry. I think this industry has had an inordinate amount of attention and resources focused on it. And I don’t think there is data to show that it’s the most hazardous. Yet you have other industries where hazards and fatalities are occurring. One in particular is the roofing industry. It really struggles with having too high of a rate of fatalities, hospitalizations and injuries.
More resources should be directed there.
So, with this new administration I hope to see a substantial shift in resources. I’m advocating for that because I think it’s time that we take a fresh look at the agency, how it’s organized and what its role is.
EHS TODAY: DO YOU SEE ANY PARTICULAR POLICY CHANGES?
PR: I think the current proposed heat standard goes away as it is now written. Right now, it’s a long document that has a lot of details and a lot of gotcha opportunities for citations, even if the employer has already done things to minimize the risk from heat. That part will go away but in its place you’ll see performance standards in which the employer has some discretion as to what to do while addressing the hazard.
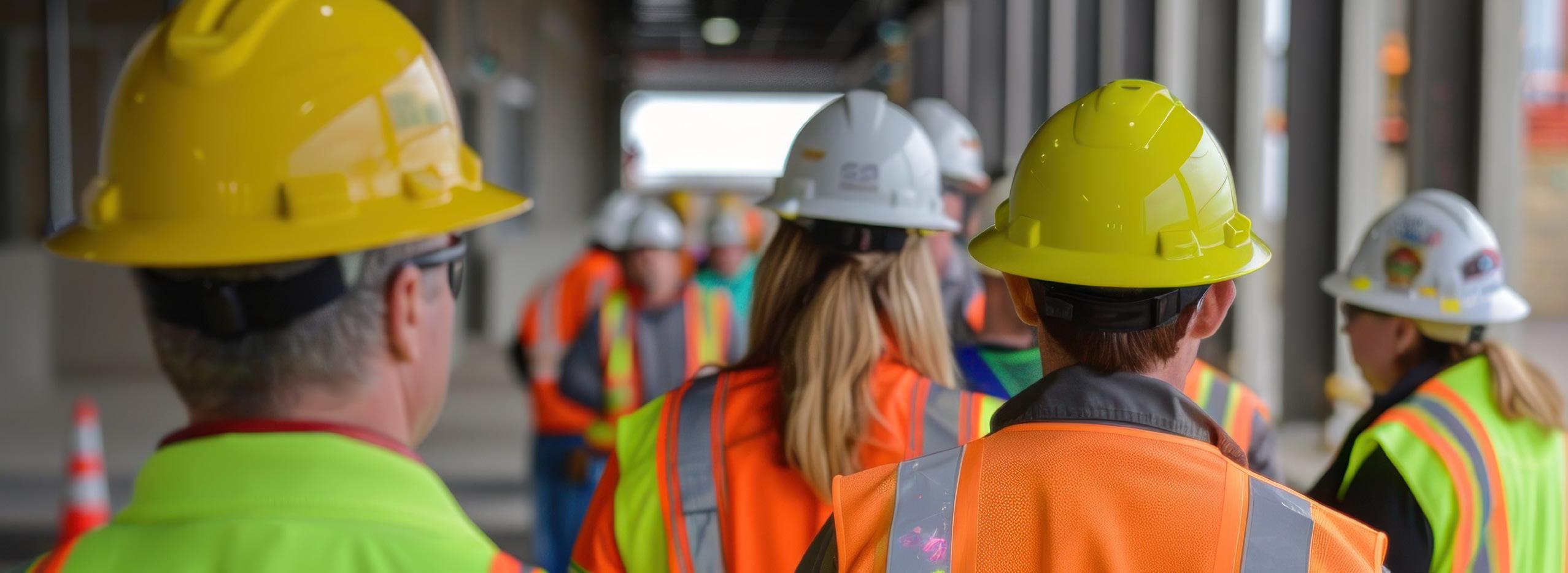
As far as the walkaround rule, I’m less confident the walkaround rule is going to go away. However, there are going to be legal challenges because I think that on its face it exceeds the authority that the OSHA Act gave to OSHA as an agency. And I think that the challenges, especially following the Loper Bright decision which ended the Chevron deference earlier this year, might mean that this goes away legally. But politically speaking, I don’t think it goes away, as lot of rank-and-file union members showed up big for Trump. Also, Vice President-elect JD Vance has been more open to labor unions than you might expect.
EHS TODAY: WHAT TYPE OF LEADERSHIP DO YOU EXPECT TRUMP TO APPOINT AND HOW WILL THIS AFFECT OSHA’S POLICYMAKING?
PR: I’m looking for balance and innovation. The balance is for someone to look at the agency, look at statistics and industries and say we need to make sure that we are going after what the data tells us. We need to make sure that we’re pairing up resources with our focus. An example of this alignment is when OSHA issues a heat or fall protection emphasis program, yet there is no increase in resources for those programs. That’s something that needs to change.
Another aspect of balance is that I think all too often OSHA looks at all employers the same without regard to the fact that some employers actually have robust programs and keep workers safe. One bad thing happens to good employers, and they are treated as those they are the worst of the worst.
That’s where we’ve lost balance. There is too much focus on politically popular targets. We need to focus more on the high-risk industries and the truly bad actors. OSHA needs to go back to focusing on data which shows which
industries are the most hazardous to workers. That’s where you move the needle. And then you can innovate to make things better.
EHS TODAY: ANY PARTICULAR STEPS YOU ADVISE EMPLOYERS TO TAKE TO ENSURE A SAFER WORKPLACE?
PR: All employers need to have four things in place for every single hazard in the workplace. These will saves lives and keep OSHA away:
1. Have a rule, a process or a procedure for every hazards. Whether it’s fall protection, trenching, lockout/ tag out, whatever it is you need to have a rule.
2. Have robust training on each of those rules. Make sure that everyone who is going to be working around, near or exposed to a hazard in any way goes through training about that process or procedure to avoid the hazard.
3. Have a compliance program and be certain that employees are following the rules and their training.
4. Maintain discipline around these process. Enforcement is key. What do you do to enforce the rules if they’re not being followed? Are people being put in harm’s way?
These four things are the elements of the unavoidable employee misconduct defense. What it really asks is did an employer do all yhey could do to avoid tragedy? If you do these four things, I guarantee that you will have a safer place to work, and you will save lives.
Hidden Subcontractor Risks Lurking in the Supply Chain
Uncover the significant risks subcontractors bring to supply chains and the potential fallout for hiring companies when those risks are unchecked.
Many companies only vet and prequalify their prime contractors and suppliers, leaving subcontractors unchecked. This can lead to hidden risks due to a lack of visibility.
• Relying solely on prime contractors to manage subcontractor compliance and risks is problematic as the hiring company may be unaware of the qualifications, safety records, or compliance of all subcontractors involved.
• Subcontractors can introduce various risks, including safety incidents, workforce and human rights issues, financial instability, quality concerns, and cyber threats.
• Incidents involving subcontractors can lead to severe consequences such as reputational damage, project delays, business disruptions, and dissatisfaction among customers, employees, and investors.
SUBCONTRACTOR RISKS ARE INHERENTLY HIDDEN
Subcontracting is more prevalent than ever in today’s supply chains, with estimates showing that 60-70% of outsourced work is performed by subcontractors. This practice can be efficient for hiring companies and prime contractors to meet project needs, but it also comes with significant risks. One report found that 32.3% of supply chain disruptions originated not from prime contractors but from lower-tier subs.
The key reason for subcontractor risk is a lack of visibility for the hiring company (and sometimes even for the original contractor, as subcontracting can often go down multiple tiers). Many companies vet, prequalify, and require MSAs/ contracts only with their prime contractors and suppliers, with no direct link or visibility to subcontractors.
In our previous post we explained the key terms, responsibilities, and common challenges related to subcontractor management.
IN THIS POST WE WILL EXAMINE:
• Why hiring companies shouldn’t rely on their primes to vet and manage subcontractors.
• The risks that subcontractors introduce to a supply chain.
• The potential fallout for a hiring company.
RELYING ON PRIMES TO MANAGE SUBCONTRACTOR RISK IS RISKY
When a hiring client has a network of subcontractors without full visibility, the risks are significant. For many clients, the answer is to rely on prime contractors to properly vet potential subs, ensure adequate qualifications, and enforce compliance requirements. This expectation may even be written into contracts with the prime, holding them liable for any damage caused by their subcontractors. Unfortunately, such an approach does not fully insulate an organization from risk by today’s standards or stakeholder expectations.
HIRING CLIENTS ARE STILL ON THE HOOK
Organizations that rely on prime contractors to manage subcontractor compliance usually justify that approach with strong contractual agreements with the prime, releasing the hiring company from legal or financial liabilities arising from a subcontractor.
In theory this should protect the hiring client from any associated risks with subcontractors. In practice, however, many other consequences can significantly impact a hiring company when a subcontractor is involved in an incident within its network, including project quality concerns, project delays, cyber threats, reputational fallout, and regulatory violations.
It will not matter to shareholders, workers, customers, investors, and regulators whether or not the hiring company is “contractually liable” if there are labor violations, massive project delays, or devastating media coverage about an incident associated with that company.
...continued on next page
COMMON RISKS POSED BY SUBCONTRACTORS
All the risks associated with hiring a contractor are present with lower-tier subcontractors. In the same way any prime could have a safety incident, quality issues, or a cyber threat, so could a subcontractor. The difference is that hiring companies generally have much more robust vetting, qualification, and monitoring processes to manage those risks with their direct contractors.
When the risk is at the subcontractor level, however, it can often be left unnoticed or unmanaged due to the lack of direct visibility and communication with the hiring client. The signal attenuation that takes place between the client, contractor, and subcontractors leads to a larger number of hidden and unmitigated risks that can have enormous financial and reputational consequences.
COMMON SUBCONTRACTOR RISK SCENARIOS
• Safety incidents: Without direct vetting, a hiring company can’t know the qualifications of subcontractors working on a project. Untrained workers and unsafe work conditions endanger everyone on a job site, making accidents more likely.
• Workforce and Human Rights Issues : When a hiring company lacks oversight into its extended network of subcontractors and lower-tier suppliers, workforce issues such as working conditions, fair wages, child labor, modern slavery, and more can hide beneath the surface.
• Financial instability: Subcontractors are often small businesses that tend to be more financially vulnerable. Without direct vetting, a hiring client can’t know if a sub of a sub of a sub is on the verge of bankruptcy which may lead to delays or poor-quality work.
• Quality: When a prime contractor outsources manufacturing, production, distribution, or labor to one or more subs, the hiring company loses crucial visibility into the quality of all components that result in the end product.
• Cyber Threats: Every member of a value chain is a potential vulnerability when it comes to cyber threats. A cyber-attack on even the smallest subcontractor could have severe ramifications up and down the supply chain.
IMPACT OF SUBCONTRACTOR INCIDENTS
The above examples can have serious consequences for the hiring company, regardless of direct financial or legal liability:
• Severe reputational damage due to widespread media coverage of an incident or event.
• Project delays when a subcontractor becomes unable to fulfill a job due to bankruptcy, an accident, or other adverse event.
• Business disruption in the face of cyber threats, recalls, investigations, and more.
• Customer, employee, and investor displeasure.
• Penalties, fines, and project shutdowns due to subcontractor regulatory violations.
EXAMPLES OF SUBCONTRACTOR INCIDENTS WITH MASSIVE FALLOUT
In 1999, a massive crane collapsed in Milwaukee, WI, during the construction of a new baseball stadium for the Milwaukee Brewers. A subcontractor was operating the crane when the collapse killed three workers. The subcontractor and prime faced millions in lawsuits and OSHA penalties. The Milwaukee Brewers (the hiring client) were on the hook for $100 million in repairs and significant negative media coverage, ultimately leading to a project completion delay of one year.
In 2013, Nestle was forced to suspend product deliveries and issue recalls for all products that contained beef from a particular subcontractor. Traces of horse DNA were found in quality tests of these products. Though the quality issues came from a subcontractor, not a direct contractor, Nestle still had to endure the severe reputational and financial consequences of the recall and negative media coverage.
CONCLUSION
Subcontractors are vital to most companies’ supply chains but also bring risks that should not be ignored. Relying on prime contractors to ensure subcontractor qualifications and compliance is an outdated model of managing subcontractor risk. Instead, hiring companies should be proactive in applying the same rigorous vetting and compliance requirements to subs as they do to their prime contractors.