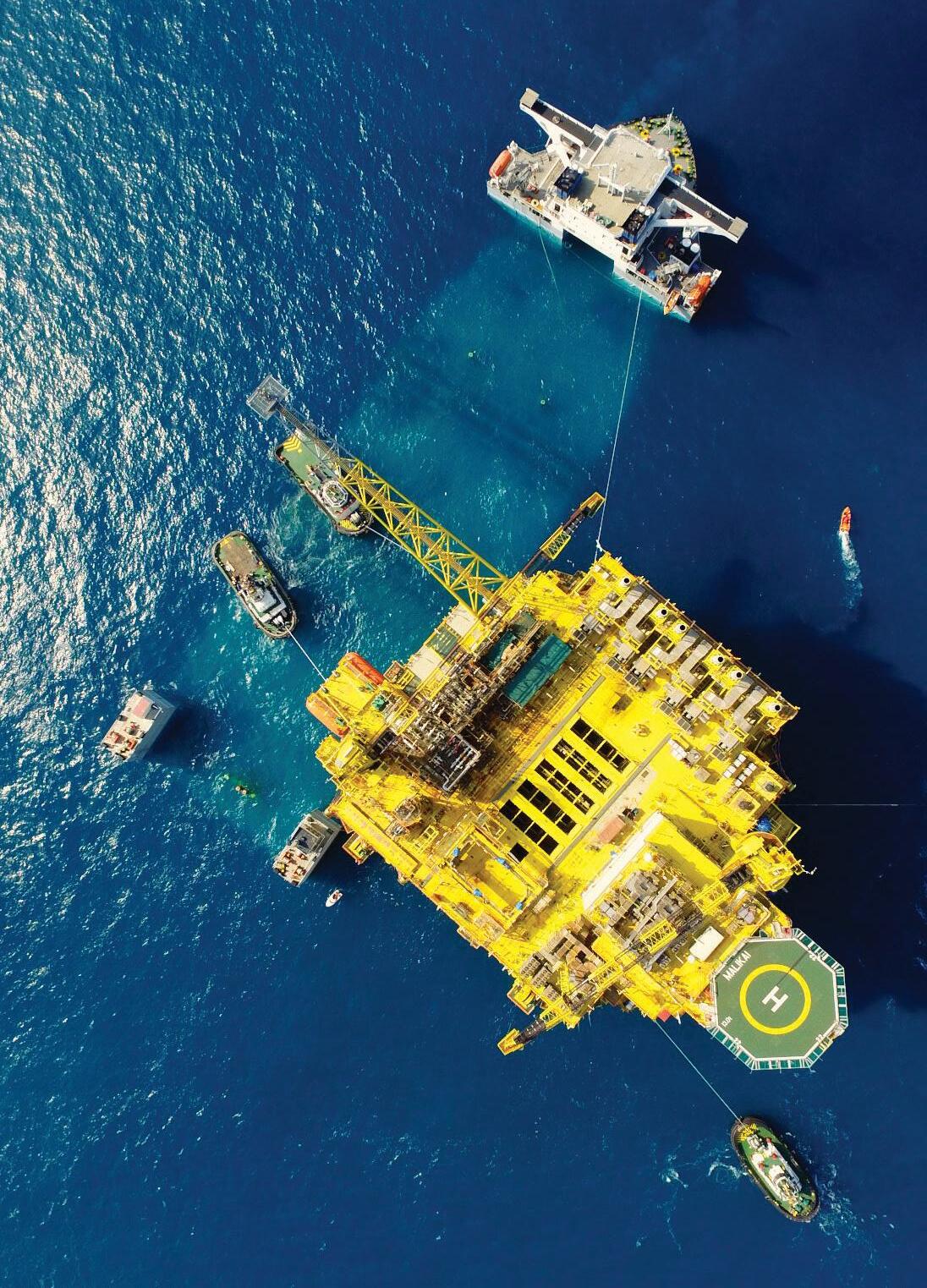
THE MONTHLY BULLETIN OF THE INSTITUTION OF ENGINEERS, MALAYSIA
KDN PP 1050/12/2012 (030192) ISSN 0126-9909 NOVEMBER 2016
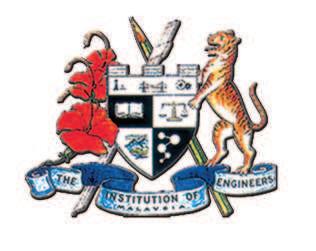
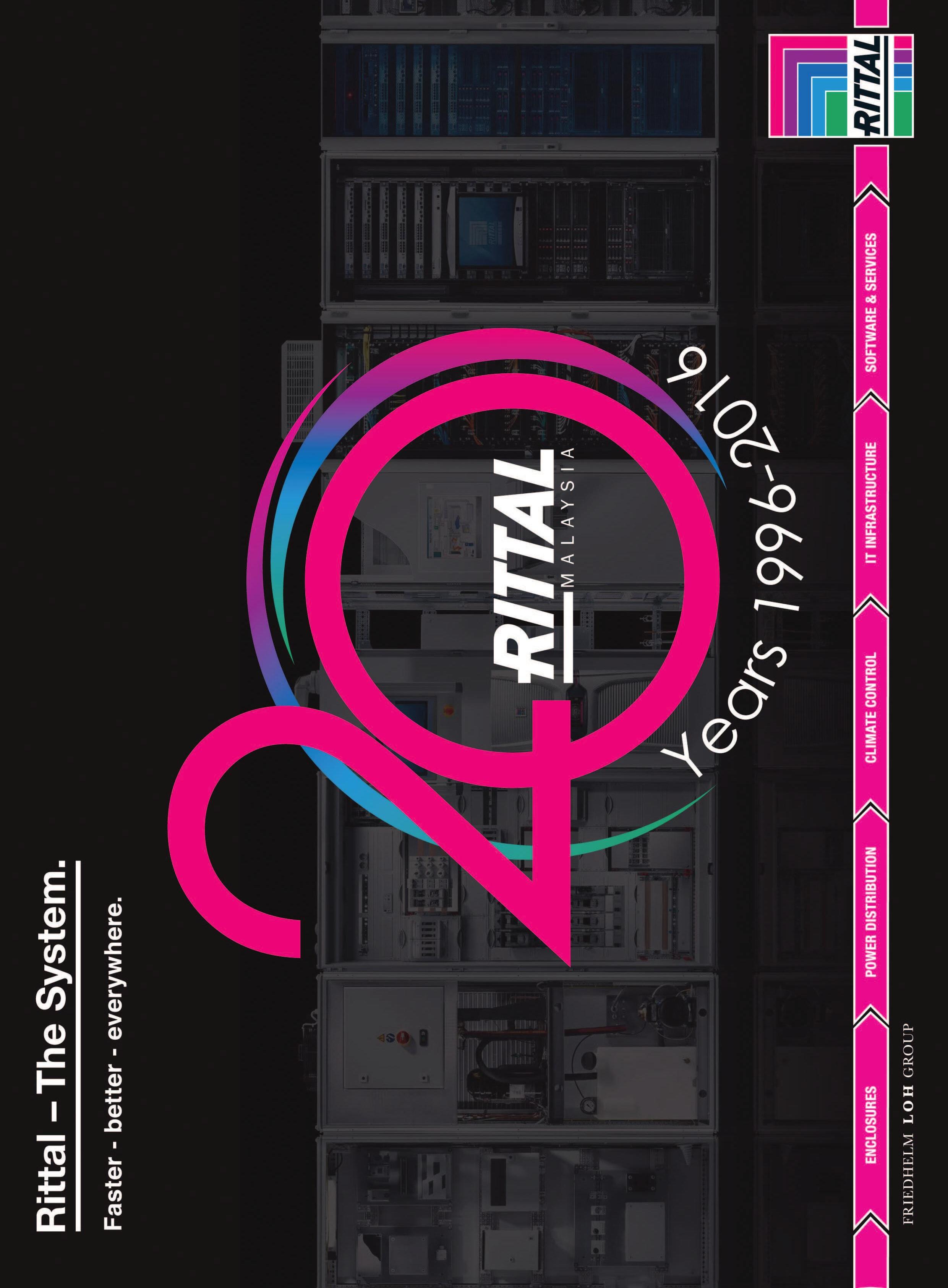
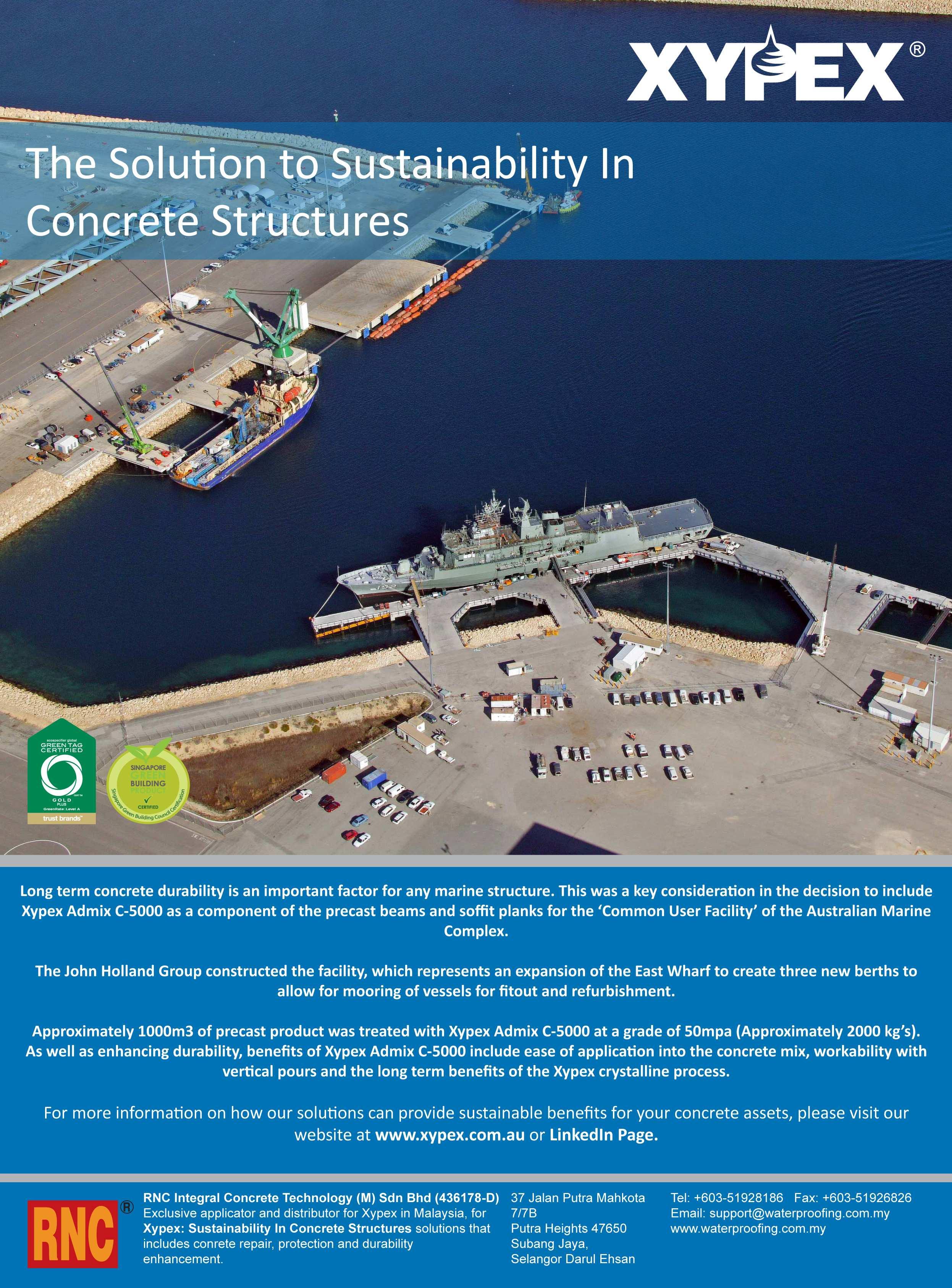
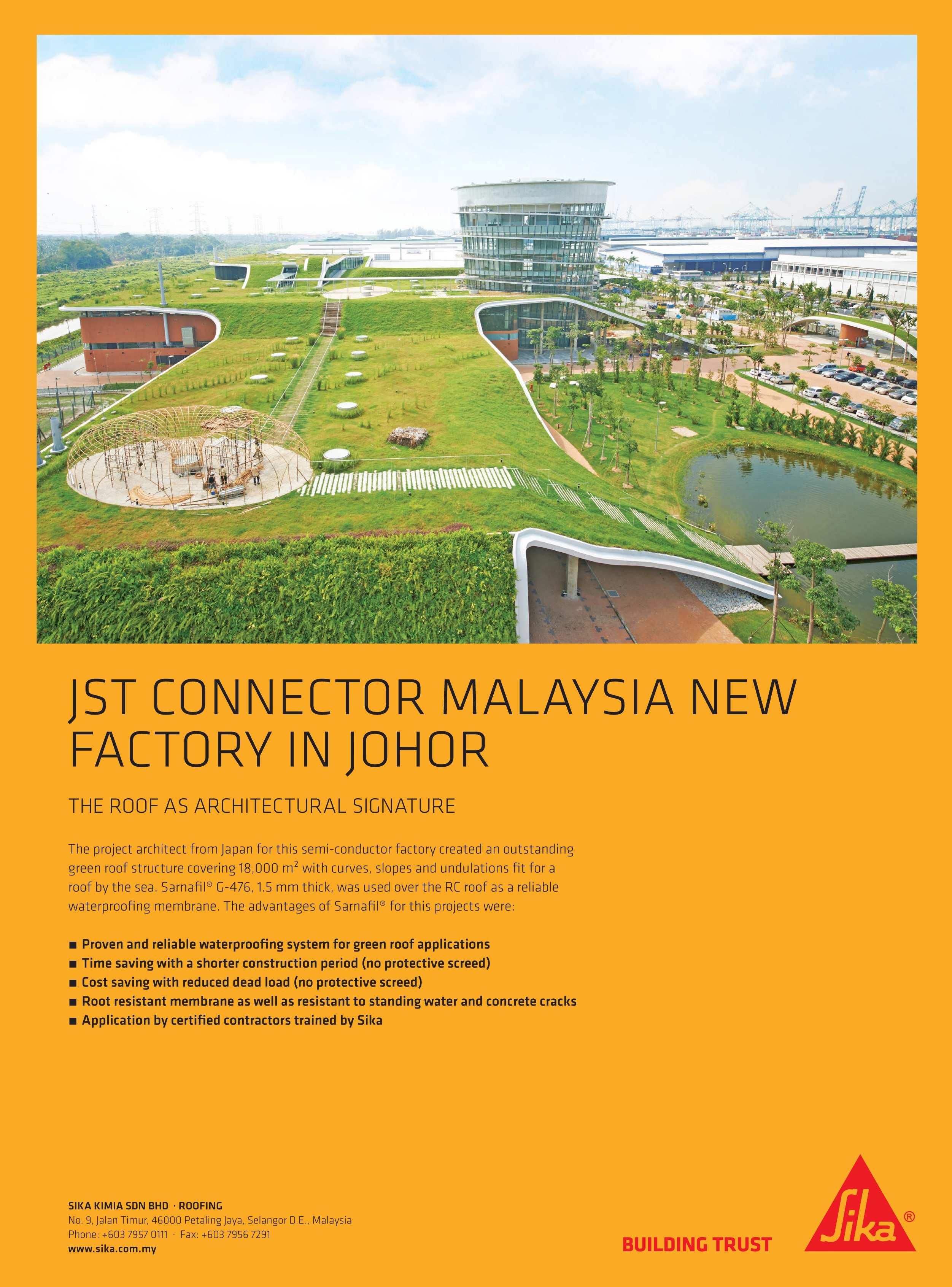
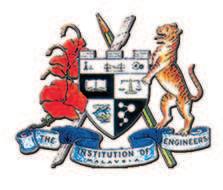
THE MONTHLY BULLETIN OF THE INSTITUTION OF ENGINEERS, MALAYSIA
KDN PP 1050/12/2012 (030192) ISSN 0126-9909 NOVEMBER 2016
Number 11, November 2016
IEM Registered on 1 May 1959
MAJLIS BAGI SESI 2016/2017 (IEM COUNCIL SESSION 2016/2017)
YANG DIPERTUA / PRESIDENT
Ir. Tan Yean Chin
TIMBALAN YANG DIPERTUA / DEPUTY PRESIDENT
Ir. David Lai Kong Phooi
NAIB YANG DIPERTUA / VICE PRESIDENTS
Ir. Prof. Dr Ruslan bin Hassan, Ir. Lai Sze Ching, Ir. Lee Boon Chong,
Ir. Prof. Dr Jeffrey Chiang Choong Luin, Ir. Assoc. Prof. Dr Norlida bt Buniyamin, Ir. Ellias Bin Saidin, Ir. Ong Ching Loon
SETIAUSAHA KEHORMAT / HONORARY SECRETARY
Ir. Yam Teong Sian
BENDAHARI KEHORMAT / HONORARY TREASURER
Dr Wang Hong Kok F.I.E.M.
BEKAS YANG DIPERTUA TERAKHIR / IMMEDIATE PAST PRESIDENT
Y.Bhg. Dato’ Ir. Lim Chow Hock
BEKAS YANG DIPERTUA / PAST PRESIDENTS
Y.Bhg. Academician Tan Sri Dato’ Ir. (Dr) Hj. Ahmad Zaidee bin Laidin, Y.Bhg. Dato’ Ir. Dr Gue See Sew, Y.Bhg. Dato’ Paduka Ir. Keizrul bin Abdullah, Y.Bhg. Academician Dato’ Ir. Prof. Dr Chuah Hean Teik, Choo Kok Beng
WAKIL AWAM / CIVIL REPRESENTATIVE
Ir. Prof. Dr Mohd. Zamin bin Jumaat
WAKIL MEKANIKAL / MECHANICAL REPRESENTATIVE
Ir. Dr Kannan M. Munisamy
WAKIL ELEKTRIK / ELECTRICAL REPRESENTATIVE
Y.Bhg. Dato’ Ir. Dr Ali Askar bin Sher Mohamad
WAKIL STRUKTUR / STRUCTURAL REPRESENTATIVE
Ir. Hooi Wing Chuen
WAKIL KIMIA / CHEMICAL REPRESENTATIVE
Ir. Prof. Dr Thomas Choong Shean Yaw
WAKIL LAIN-LAIN DISPLIN / REPRESENTATIVE TO OTHER DISCIPLINES
Ir. Roznan bin Abdul Rashid
WAKIL MULTIMEDIA DAN ICT / ICT AND MULTIMEDIA REPRESENTATIVE
Abdul Fattah bin Mohd. Yatim, M.I.E.M.
AHLI MAJLIS / COUNCIL MEMBERS
Ir. Gary Lim Eng Hwa, Y.Bhg Dato’ Ir. Hj. Noor Azmi bin Jaafar, Ir. Dr Aminuddin bin Mohd Baki, Ir. Mohd Radzi bin Salleh, Ir. Ong Sang Woh, Ir. Mohd Khir bin Muhammad, Y.Bhg Dato’ Ir. Hj. Hanapi Bin Mohammad Noor, Ir. Dr Ahmad Anuar bin Othman, Ir. Ishak bin Abdul Rahman, Ir. Chong Pick Eng (PE Chong), Ir. Ng Yong Kong, Ir. Tejinder Singh, Ir. Sreedaran a/l Raman, Ir. Roger Wong Chin Weng, Ir. Assoc. Prof Dr. Ahmad Kamil bin Arshad, Ir. Dr Tan Kuang Leong, Ir. Hoo Choon Sean, Y.Bhg. Lt. Jen. Dato’ Wira Ir. Ismail bin Samion (Ret. RMAF), Ir. Hj. Anuar bin Yahya, Ir. Mah Way Sheng, Ir. Gunasagaran a/l Kristnan, Ir. Chen Harn Shean, Ir. Mohd Aman bin Hj. Idris, Ir. Gopal Narian Kutty, Ir. Yap Soon Hoe, Ir. Santhakumaran a/l Erusan
AHLI MAJLIS JEMPUTAN/INVITED COUNCIL MEMBERS
Y.Bhg. Datuk Ir. Adanan bin Mohamed Hussain, Y.Bhg Dato’ Ir. Ahmad ‘Asri bin Abdul Hamid, Y.Bhg. Dato’ Ir. Low Keng Kok
PENGERUSI CAWANGAN / BRANCH CHAIRMAN
1. Pulau Pinang: Ir. Dr Mui Kai Yin
2. Selatan: Ir. Lee Meng Chiat
3. Perak: Ir. Lau Win Sang
4. Kedah-Perlis: Ir. Prof. Dr Rezuwan bin Kamaruddin
5. Negeri Sembilan: Dato’ Ir. Zainurin bin Karman
6. Kelantan: Ir. Hj. Mohd Zaim bin Abd. Hamid
7. Terengganu: Ir. Atemin bin Sulong
8. Melaka: Ir. Dr Tan Chee Fai
9. Sarawak: Ir. Vincent Tang Chok Khing
10. Sabah: Ir. Hj. Yahiya bin Awang Kahar
11. Miri: Ir. Paul Chiew Lik Ing
12. Pahang: Y. Bhg. Dato’ Ir. Tn. Hj. Abdul Jalil bin Hj. Mohamed
AHLI JAWATANKUASA INFORMASI DAN PENERBITAN / STANDING COMMITTEE ON INFORMATION AND PUBLICATIONS 2016/2017
Pengerusi/Chairman: Ir. Prof. Dr Ruslan Hassan Naib Pengerusi/Vice Chairman: Ir. Mohd. Khir Muhammad Setiausaha/Secretary: Ir. Lau Tai Onn
Ketua Pengarang/Chief Editor: Ir. Prof. Dr Ruslan Hassan Pengarang Buletin/Bulletin Editor: Ir. Mohd. Khir Muhammad Pengarang Prinsipal Jurnal/Principal Journal Editor: Ir. Prof. Dr Ruslan Hassan Pengerusi Perpustakaan/Library Chairman: Ir. C.M.M. Aboobucker Ahli-Ahli/Committee Members: Y.Bhg. Datuk Ir. Prof. Dr Ow Chee Sheng, Ir. Prof. Dr Dominic Foo Chwan Yee, Dr Wang Hong Kok F.I.E.M., Ir. Santha Kumaran a/l Erusan, Abdul Fattah bin Mohamed Yatim M.I.E.M., Ir. Chin Mee Poon, Ir. Yee Thien Seng, Ir. Ong Guan Hock, Ir. Dr Oh Seong Por, Ir. Tejinder Singh, Michelle Lau Chui Chui Grad. IEM
LEMBAGA PENGARANG/EDITORIAL BOARD 2016/2017
Ketua Pengarang/Chief Editor: Ir. Prof. Dr Ruslan Hassan Pengarang Buletin/Bulletin Editor: Ir. Mohd. Khir Muhammad Pengarang Jurnal/Journal Editor: Ir. Prof. Dr Ruslan Hassan Ahli-ahli/Committee Members: Ir. Ong Guan Hock, Ir. Lau Tai Onn, Ir. Yee Thien Seng, Dr Wang Hong Kok F.I.E.M.
Secretariats: Janet Lim, May Lee
COVER NOTE Surviving The Current Oil Price Uncertainty 5
COVER STORY CORAL 2.0 for Long-Term Survival 6 - 11
13-31
Systems for Repair and Rehabilitation of Corroded Oil & Gas Pipelines ...............................13
Sustainability of Safety Culture in Times of Turbulence ...........................................................18
Persevering Despite Oil Price Uncertainties .........23
LEANing Forward .................................................26
32 - 39
Design and Construction of Stabilised Subgrades for Roads .............................................32
Training Workshop on Maintenance of Infrastructure ........................................................33
IEM-WE on Bandwagon to Dabong School Which was Affected by Floods ............................35
Slope Stabilisation and Flood Mitigation ............37
Advancement in Tunnel Lining Monitoring Using Fibre-Optic Distributed Sensing ...............38
PINK PAGE
Professional Interview 44 BLUE PAGE
Membership List 45 - 47
by Ir. Mohd
Azmi Chairman, Oil, Gas and Mining Engineering Technical Division (OGMTD).
The Oil & Gas market has not shown much progress in the past two years since crude oil prices started to dip in 2014 from a high of over US$100 per barrel to a low of US$27 a barrel (early 2016).
The price of crude oil price in August 2016, stood at around US$45 per barrel. Given its volatile nature, no one can really predict if the price will ever go back to over US$100. Industry players have felt significantly the impact of the lower oil prices. Most have exercised their “survival strategies” such as adjusting their business models, resetting cost structures with suppliers, cutting down staff, eliminating bonus, reducing salary and consolidating office locations.
To survive, the industry has to change its current business approach. This shift will require the industry to think out of the box and with an open mind. The necessary adjustments made during this period will, in any case, offer new business opportunities to players who have the courage to innovate and to try out the new ways of doing business.
This issue of JURUTERA highlights how our national petroleum company, PETRONAS, ensures its survival with its Cost Reduction Alliance Programme (CORAL 2.0) for Upstream Malaysia.
DIMENSION PUBLISHING SDN. BHD. (449732-T)
Level 18-01-03, PJX-HM Shah Tower, No. 16A, Persiaran Barat, 46050 Petaling Jaya, Selangor Darul Ehsan, Malaysia. Tel: +(603) 7493 1049 Fax: +(603) 7493 1047 E-mail: info@dimensionpublishing.com Website: www.dimensionpublishing.com
For advertisement placements and subscriptions, please contact: DIMENSION PUBLISHING SDN. BHD. (449732-T) at +(603) 7493 1049, or E-mail: info@dimensionpublishing.com
Subscription Department E-mail: info@dimensionpublishing.com
Printed by
HOFFSET PRINTING SDN. BHD. (667106-V) No. 1, Jalan TPK 1/6, Taman Perindustrian Kinrara, 47180 Puchong, Selangor Darul Ehsan, Malaysia. Tel: +(603) 8075 7222 Fax: +(603) 8075 7333
Mailer
(648839-P)
14 Jalan TSB 2, Taman Perindustrian Sungai Buloh, Sungai Buloh, Selangor Darul Ehsan, Malaysia. Tel: +(603) 6156 5288
JURUTERA MONTHLY CIRCULATION: 40,000 COPIES
Submission or placement of articles in JURUTERA could be made to the:Chief Editor
THE INSTITUTION OF ENGINEERS, MALAYSIA (IEM) Bangunan Ingenieur, Lots 60 & 62, Jalan 52/4, P.O. Box 223 (Jalan Sultan), 46720 Petaling Jaya, Selangor. Tel: +(603) 7968 4001/4002 Fax: +(603) 7957 7678
E-mail: pub@iem.org.my or sec@iem.org.my IEM Website: http://www.myiem.org.my
(IEM) and
Chairman ROBERT MEBRUER CEO/Publisher PATRICK LEUNG
General Manager SHIRLEY THAM shirley@dimensionpublishing.com
Head of Marketing & Business Development JOSEPH HOW joseph@dimensionpublishing.com
Editor TAN BEE HONG bee@dimensionpublishing.com
Contributing Writers PUTRI ZANINA & ZOE PHOON putri@dimensionpublishing.com zoe@dimensionpublishing.com
Senior Graphic Designer SUMATHI MANOKARAN sumathi@dimensionpublishing.com
Graphic Designer NABEELA AHMAD beela@dimensionpublishing.com
Advertising Consultants AZIM SHAARI & THAM CHOON KIT azim@dimensionpublishing.com ckit@dimensionpublishing.com
Accounts cum Admin Executive YEN YIN yenyin@dimensionpublishing.com
PUBLICATION DISCLAIMER
COPYRIGHT
The PETRONAS-driven Cost Reduction Alliance 2.0 (CORAL 2.0) Programme for Upstream Malaysia and its resulting structural changes will enable its survival beyond the “lower (oil price) for longer” phenomenon
When Bacho Pilong joined our national oil company, Petroliam Nasional Bhd (PETRONAS), more than 20 years ago, some people told him that Oil & Gas (O&G) was a sunset industry.
“I’m still here today,” said Bacho, who joined PETRONAS as process engineer in 1992, armed with a degree in chemical engineering from University of Texas in Austin, the United States.
“The future will continue to be exciting for Malaysia. Deepwater drilling, complex reservoir structure and unmanned operations are among the new frontiers to look out for.
“The O&G industry outlook is exciting for the innovative and agile who are able to adapt to new situations. There is still plenty of room for technical and technological advancements which we will need.”
Currently, Bacho is Chairman of the Steering Committee of CORAL 2.0 Programme as well as head of Production & Operations, Malaysia Petroleum Management (MPM).
Oil companies around the world have been the main casualties of the relentless fall in oil prices since the jawdropping plunge from a peak of US$113 per barrel in June 2014. Consequently, they prepared for the worst, planning for lower prices for a longer period of time.
PETRONAS is no exception. As to how the PETRONASdriven CORAL 2.0 started, Bacho said the declining global oil prices from mid-2014, have significantly impacted our O&G industry. On top of that, projections of production and development costs indicate increasing costs across all operators.
He said the low oil price environment persisted in June this year and is expected to remain for some time. This phenomenon, known as “lower (oil price) for longer”, has further necessitated the need to respond and adapt swiftly.
As custodian of petroleum resources, PETRONAS’ MPM has been entrusted with the responsibility of managing and steering the overall exploration and production (E&P) activities in Malaysia, including optimising the country’s E&P assets and management
of all E&P companies operating locally.
“
CORAL 2.0 is not about squeezing margins and bleeding players. It is about how to make Malaysia cost competitive and the regional hub for Oil & Gas in Asia Pacific. It’s for business sustainability of all industry players. We can’t afford to see any party
“In ensuring we are equipped to weather the downturns and capitalise on upsurges in a measured and profitable way, MPM has revived the second wave of the Malaysia-wide cost optimisation programme in 2015,” said Bacho.
suffer because of CORAL 2.0.”
– Bacho Pilong
“Under CORAL 2.0, PETRONAS collaborates with all Petroleum Arrangement Contractors (PACs) and the industry to build long-term stability and sustainability into our operational strategies.
“In late 2014, we saw an imbalance in demand and supply. We could see a downturn coming up. With oil prices falling from US$100 to US$60, we needed to respond fast.”
As time was of the essence, CORAL 2.0 took off in November 2014 although it was only officially launched in March 2015.
“CORAL 2.0 is about the whole ecosystem in the country. It’s led by PETRONAS with the support of its PACs, O&G service providers and the Malaysia Oil & Gas Council (MOGSC). We have a spectrum of players, from the small and independent to medium and big players. We bring in everyone to bring cost down for the benefit of Malaysia,” he said.
According to Bacho, a dedicated Steering Committee and a Programme Management Office were set up to engage and streamline collaboration with PACs and the industry as well as to provide guidance for deploying initiatives. In 2015, 11 initiatives were targeted for implementation, delivering RM2.4 billion in savings.
“Thetargetfor2015wasRM1.8billioninsavings.In2015, the focus was on drilling and completion activity which accounted for RM1.1 billion of the RM2.4 billion saved. We drilled 114 wells and managed to push every well to save costs. This year, we aren’t drilling as many wells.
“The whole idea of CORAL 2.0 is to optimise cost, increase efficiency (i.e. getting more for less) and bring in industry innovations. We can’t deliver all of these alone. We have to be supported by PACs and service providers,” he said.
CORAL 2.0 is a long-term industry-wide programme with the aim to inculcate a cost-conscious mindset across Upstream Malaysia. Bacho noted that it will support sustainability of the country’s O&G industry and prepare for industry challenges by optimising cost, increasing efficiency and driving industry innovation across all operators.
“Our aspiration is not just about surviving now; it is also about preparing for the future and building an industry that’s sustainable,” he said.
CORAL 2.0’s strength stems from the collective intelligence derived through strong cross-PAC collaboration, with emphasis on transparency and visibility via analytics and benchmarking. The latter was not a focus of CORAL 1.0 then.
“Our PACs’ willingness to share data is one of CORAL 2.0’s successes. Because people are willing to collaborate, open up and share their best practices, other players can learn and apply these in their operations,” he said, adding that he makes it a point to ensure that Senior Management attends meetings on CORAL 2.0 as that helps to push the agenda across the country.
He noted that through CORAL 2.0, the analytics and benchmarking role is being institutionalised in MPM, supported by the PACs’ active involvement in providing input for benchmarking and applying the results from benchmarking to improve cost and efficiency.
CORAL 1.0 brought about total savings of RM2 billion in 10 years (1995 to 2005) of implementation, which, Bacho said, “can’t be compared with the current situation”.
HesaidonesignificantoutcomeofCORAL1.0wasthe formation of MOGSC which promoted the capabilities of local service providers and showcased Malaysia as the regional hub for the O&G industry.
With CORAL 2.0, Bacho said PETRONAS and its PACs targeted savings of between RM1.4 billion and RM1.8 billion in the first year (2015) and a further RM1.9 billion this year. The amount of annual savings is expected to grow each year to reach a steady state of cumulative RM17 billion of savings by year 2019.
“Since CORAL 2.0’s inception to July 2016, we have recorded realised savings of RM3.68 billion to date, which is at par with our cumulative target of RM3.6 billion for the whole of 2016,” he said.
On the targeted RM1.9 billion of savings for 2016, Bacho said RM1 billion was achieved as of June and his personal aspiration is to hit RM2 billion, adding, “We have four months to drive the team. We think we can do it”.
On the cumulative RM17 billion of savings aimed by 2019, he said “we can achieve it but it would be tough”.
So how do the industry players or those in the supply chain respond to CORAL 2.0? What are the challenges and ways to overcome them?
Bacho shared: “Industry players have been one of the pillars of our success. We have continued to work with them to drive industry-wide changes and deliver innovative actions. Our key partner, MOGSC, acts as speaker for the industry.
“As CORAL 2.0 involves collaboration with all parties in the industry, the challenge is to achieve the right balance between all parties. Hence, we need to agree onawin-winsituationandCORAL2.0ensuresthatweput in place a strong governance structure to steer, discuss and reach a consensus before a decision is made in support of longer term strategic objectives.
“Apart from that, CORAL 2.0 is also spearheading the implementation of a few ‘nation’s firsts’, which comprise best practices learnt from other parts of the world. As that involves a new concept of operation and that is not familiar to everyone, it takes courage to implement such new scale changes to the industry.”
According to Bacho, there will be big-scale changes out of CORAL 2.0. One example is that logistics support will be run in an integrated manner, unlike that being run by the PACs individually at present. It is time to consolidate the logistics to optimise use of assets to serve the right needs.
Other concepts are Vendor Managed Inventory (similar to Just-in-Time) to avoid costly overstocking of inventories and Analytics Value Management, which involves continuous benchmarking on how to improve or learn from each other’s best practices.
The whole essence of CORAL 2.0 is making Malaysia cost competitive and the regional hub for O&G in Asia Pacific, he said, emphasising that “CORAL 2.0 is not about squeezing margins and bleeding players but is for business sustainability for all industry players. We can’t afford to see any party suffer because of CORAL 2.0”.
CORAL 2.0 encountered challenges, of course. Bacho said these included players’ response to new ideas but added that these have been overcome, noting, “CORAL 2.0 is not about PETRONAS. It’s about us, the industry. It’s a compelling story. We are all in the same boat; we cannot allow it to sink.”
Does he expect the programme to continue after the oil price bounces back to normal?
“For now, we believe it's ‘lower (oil price) for longer’. What’s important is we have braced ourselves for the low oil price environment, regardless of whether it’s US$40 or US$50 per barrel. We can’t afford to hope that the oil price will go back to US$100 per barrel. We’ve got to execute structural changes,” he noted.
“While we do not expect CORAL 2.0 itself to be permanent, we are working on building structural changes that will change the way we do business in Upstream Malaysia. We expect these structural changes
to be the new norm in taking us forward, so we will be agile in facing future cycles of dip in the oil price,” he said.
“For instance, the analytics and benchmarking activity will be converted into Business-as-Usual, through establishing an Analytics & Value Management unit in MPM. This unit will continue to perform analytics and benchmarking activity for PETRONAS and its PACs to sustain value generation from future day-to-day operational activities.”
He continued: “Another example is that we have also consolidated cross-PAC logistics operations, infusing global best practices to derive more value out of crossPAC logistics resources.
“As this will change the landscape of upstream logistics operations in Malaysia, a cross-PAC unit has been set up to establish this new concept of operations as Business-as-Usual.
“Moving forward, the spirit of CORAL 2.0 – i.e. optimising cost, increasing efficiencies and driving innovation – will be embedded as an integral part of the way we do things.”
“Because people are willing to collaborate, open up and share their best practices, other players can learn and apply these in their operations.”
– Bacho Pilong
On what else industry players can do to weather the current difficult phase other than the CORAL 2.0 Programme, Bacho said the impact of the situation has been rapid and dramatic. While massive cost cutting may offer shortterm breathing space, it is a myopic response which may leave the business ill-equipped for the next turn of the cycle.
With the current O&G market, he noted that companies need to reinvent themselves to improve productivity. This is the time to reassess the company’s strategic direction and to find a profitable role to play in the new O&G landscape.
Transformation is needed to adapt to this new normal within the maelstrom of change. Innovation is a key driver, with the potential to transform operations and create additional profits from existing capacity that can further reduce costs, unleash unparalleled productivity and boost performance significantly.
Collaboration is crucial in order to have shared success across all players in the country’s O&G ecosystem.
On how he thinks the current difficult phase in the O&G industry will shake up the local market, he said: “The industry had been enjoying high oil prices and unfortunately, this had resulted in complacency.
“Now, there is a huge paradigm shift in how business is being operated. It is hard to change long established ways of working, yet the current oil price environment has presented a unique opportunity and it’s imperative that the industry addresses structural inefficiencies. The local market will change and players need to come together to seize opportunities in the changing business landscape.”
He felt that industry players have to be more adaptable, steadfast and innovative. They must also strive to have the competitive edge to survive the turmoil. They have to rise to the bar and deliver results.
Elaborating, he said: “When oil was US$100 a barrel, of course players made huge profits. But at the same time, costs went up tremendously, such as paying for rigs. This meant that rental for rigs, which used to be US$60,000 a day, went up to US$100,000 a day.
“In today’s low oil price environment, we need to lower costs to survive. If there’s no project, which means
no work, how do we create balance? The industry must be resilient in such an environment. It’s about innovation. The industry cannot just hope for the return of high oil prices. It doesn’t work like that.”
So how can the Institution of Engineers, Malaysia (IEM) support PETRONAS and other local O&G industry service providers?
Bacho said that engineers play vital roles at all levels of modernising and improving engineering processes innovations to increase economic viability of projects and development of O&G resources.
He noted that IEM, as a strong voice for local engineers, can contribute significantly by promoting the conceptofinnovationandtechnologyasadifferentiator for future economic growth. He said IEM can enhance its members’ ability and expertise to undertake technically advancedprojectsandincreasingmoreskilledresources to take up the challenges of working within the volatility of the O&G business environment.
“We must step up and showcase Malaysia’s capability to provide such solutions in line with CORAL 2.0 aspirations and then share the message across the engineering fraternity.”
How does he see the local industry landscape in the next 5-10 years for youths who aspire to venture into the O&G arena?
The sanguine Bacho said: “Opportunities are endless in this sector. Technological breakthroughs make it possible to develop huge resources. The increase in unconventional O&G production is a good example.
“We will always need bright, talented, enthusiastic andyoungengineerswhocanfaceuptothechallenges
and deliver cost effective and innovative solutions to propel the country forward as the leading O&G hub in the region and ultimately, be the preferred global choice.”
He capped the interview with JURUTERA by highlighting that PETRONAS recently delivered PETRONAS FLNG SATU, the world’s first floating liquefied natural gas (FLNG) facility, and had launched the second unit, PETRONAS FLNG DUA. Another highlight, he added, was that Malaysian engineers were involved in assembling the two facilities in South Korea.
What’s game changing about the FLNG is that an entire onshore LNG plant is fitted on a single floating LNG vessel; it’s a world’s first. It’s described as a megastructure of unconventional proportions and a technological marvel that has changed the landscape of LNG production forever. PETRONAS pioneered the technology to facilitate the processing of natural gas, hundreds of kilometres away at sea.
In other words, PETRONAS is now able to tap into stranded gas fields or unlock gas reserves in Malaysia that are previously considered uneconomical to explore, evaluate and develop.
The current situation in the Oil & Gas industry demands players to reimagine traditional cost optimisation methods and to focus on industry-wide optimisation, said Hajejah Ali, Programme Manager for CORAL 2.0 (Cost Reduction Alliance 2.0).
She said an alliance is necessary as under CORAL 2.0, the synergy between PETRONAS, operators and service providers will bring a more sustainable response to help our O&G industry (especially the Upstream sector) remain regionally and globally competitive.
“The collaboration of a few good ideas will multiply the results, leveraging on the collective intelligence of everyone involved. When you are surrounded by people (or teams) who share a passionate commitment to a common goal, wonders can be achieved,” she added.
According to her, PETRONAS embarked on CORAL 2.0 when the slowdown in global demand and the downtrend in oil prices changed the O&G business globally.
To weather the situation, Malaysia needed a longterm, sustainable and structural response which was embedded in CORAL 2.0.
The implementation of CORAL 2.0 will reduce the cost for the entire upstream sector domestically. The cost reduction will support the economic viability of projects in the country and give our O&G industry further competitive advantages.
Hajejah Ali said CORAL 2.0 is a five-year (2015-2019) programme. Through the years, the initiatives under the programme will transition to the new normal practice in the industry domestically.
In essence, CORAL 2.0 is an industry-wide programme driven by PETRONAS to inculcate a cost-conscious mindset across Upstream Malaysia.
CORAL 2.0 will support sustainability of the industry in the country and prepare for future challenges by optimising cost, increasing efficiency and driving industry innovation.
CORAL 2.0 is a continuation of CORAL 1.0, which was implemented from 1994 to 2005.
The key objective of CORAL 2.0 is to deliver rapid and sustainable cost optimisation through the following: Optimising cost, increasing efficiencies and driving innovation.
The objectives will be achieved through 11 core initiatives driven by collaborative cross-operators, PETRONAS teams and others in the industry.
Steering Committee Chairman of CORAL 2.0 Programme since 2015, Sabahan Bacho Pilong graduated in chemical engineering from University of Texas in Austin, USA, and attended Advanced Management Program of INSEAD in Singapore and Wharton Business School at the University of Pennsylvania, USA. In 1992, he joined PETRONAS as a process engineer. His overseas postings included Vietnam, Sudan and South Sudan. Since April 2013, he has been heading Production & Operations, Malaysia Petroleum Management and serves on the boards of PETRONAS companies and associated companies.
Steel pipelines are the most effective and safest way for the transporting of oil and gas over long distances. It is normally formed by connecting spools of pipes, bends and joints by welding. According to a database published by the United State of America’s Central Intelligence Agency, there are over one million kilometres of pipelines laid around the world to transport oil and natural gas [1], and new pipelines are expected to be installed in the near future.
Damage caused by third parties, material and construction defects, natural forces and corrosion have been identified as significant factors contributing to failure of pipelines worldwide [2-5]. Damaged pipelines are a common and serious problem which involves considerable cost and inconvenience to the industry and to the public [6].
A recent explosion in an underground pipeline network in Kaohsiung, Taiwan, killed 27 people and injured 286. Initial investigations showed that the cause was probably due to a leak in an underground pipeline owned by a local chemical producer which used a 4-inch propene pipeline [7].
Therefore, inspection and repair technology are critical for the prevention of accidents, safety in operations and the extension of running time of the long-distance pipelines [8]. In order to extend the safety and durability of such pipelines, methods to repair damages have been developed.
At present, the inspection technology for both internal and external corrosion is quite reliable, using various techniques such as magnetic flux leakage (MFL) detection, pipeline current mapping (PCM) and ultrasonic detection [9]. When defects are detected, the operators will assess the pipeline condition and
decide if repair is necessary. If it is, there are a variety of repair systems available. But before the repair work, the operators have to check a list of parameters including pipeline operating characteristics, geometry and materials so that the best choice of repair systems can be made [10]. This is very important to ensure that repair system selected is safe, cost effective and reliable.
Most underground pipeline systems consist of metal pipes due to their high strength, relative simplicity of joints and low cost. Conventionally, the most reliable repair system is to remove the entiredamagedpipeandreplaceitwithanew one. Or one can remove just the damaged section and cover it with a welded steel patch. Alternatively, the repair can also be done by installing a full-encirclement steel sleeve or steel clamp. These conventional repair systems incorporate external steel sleeves that are either bolted or welded to the outside surface of the pipes (Figure 1).
If a section of the pipe is severely damaged, the operator can remove the entire spool of pipe or cut out the damaged section. A new spool/section will then be connected to
EASTERN PRETECH (MALAYSIA) SDN. BHD . 28, Jalan 7/108C,Taman Sungai Besi, 57100 Kuala Lumpur.
Tel: +603-7980 2728
Fax: +603-7980 5662 www.epmsb.com.my
the pipeline. The use of full-encirclement steel sleeve was developed in the early 1970s.
There are two basic types of full-encirclement steel sleeves. The Type A sleeve functions as reinforcement for the defective area by welding two pieces of steel sleeves longitudinally. The Type B sleeve is welded in the same manner as the Type A sleeve but, in addition, the ends of the sleeve are welded circumferentially to the carrier pipe. This type of repair is capable of repairing leaking defects or defects that may leak in future because the ends are fillet welded to the carrier pipe.
Besides welded sleeves, steel clamp repair is another alternative for repairing corroded steel pipes. Instead of welding, the sleeves are joined by mechanical fastening. The operation principle of the previously mentioned repair systems has proved to be effective by restraining the corroded section from bulging, hence the reinforcement. The long-term performance of steel repair systems is a great advantage which contributes to the relevance of this system until now.
There are several shortcomings in the repair systems mentioned. For example, these methods are generally suitable for straight pipe sections but not for joints or bends. Besides, welding or clamping of pipelines is bulky, costly and time consuming especially if the pipelines are underground [11]. In most cases, heavy machinery is required to perform this cumbersome job. Furthermore, welding involves hot work that poses a potential risk of explosion.
So, researchers started looking for alternative repair systems that were relatively lightweight, easily applicable and be an effective repair solution.
The use of fibre-reinforced composite materials to repair damaged pipelines started in the late 1980s. Since then, numerous institutions and companies have conducted their own R&D to develop commercial composite repair products. The trend is likely to accelerate.
The acceptance of composite based materials as an alternative to conventional repair materials, is indicated through the recent development of several codes and standards, including ASME PCC-2 [12] and ISO/TS 24817 [13]. Both standards recognise composites as a legitimate repair material. To date, repair systems using fibre-reinforced composites can be categorised as precured layered, flexible wet lay-up, pre-impregnated and split-sleeve systems. Although the products made by different companies and research institutes have varied performances, the composite material repair system will mainly include three parts:
1. High strength glass fibre or carbon fibre reinforcing materials;
2. Adhesive materials with high curing speed and high performance;
3. High compressed strength material for pipeline defects filling that conveys the load [14].
The pre-cured layered system involves bonding of pre-cured composite materials that are held together with an adhesive applied in the field. The repair using these systems is generally
limited to straight sections of pipe. Figure 2 (a) shows basic components of a commercially available pre-cured layered system, Clock Spring® repair system: (1) composite sleeve, (2) interlayer adhesive, and (3) infill material. The infill material is used to fill the damaged area to create a smooth surface. A composite sleeve will then be used to wrap around the repair segment. An adhesive that serves as a bonding agent, is apply in every single layer of the composite sleeves.
When the infill material and adhesive are cured, the repair is considered done. Flexible wet lay-up utilises resin matrix that is usually uncured during application but forms a stiff shell after curing. Finally, a composite cloth will be used to wrap around the repaired area to strengthen the loading capacity as shown in Figure 2 (b). Since it is flexible, it can be used to repair joints or bends.
Figure 3 is an example of a pre-impregnated split-sleeve repair system. ProAssure™ Wrap Extreme in Figure 3 (a) was developed by a team of researchers from Commonwealth Scientific and Industrial Research Organisation (CSIRO) and Petronas. The fibre is pre-impregnated with resin and stored in a specific environment (normally sub-zero degree Celsius) prior to repair. After repair, the composite will undergo in-situ curing and finally form a stiff shell.
Figure 3 (b) is the world’s first pipeline repair clamp to be made of the advanced composite material, ProAssure™ Clamp, as claimed by the manufacturer. The repair concept is similar to that of steel repair clamp. In case of material loss, either by corrosion or gouging, infill is used to ensure a smooth bed for the composite clamp. This also can be an effective leak containment solution for repairing defects that may causes pipeline leaking due to future deterioration such as corrosion and erosion.
Benefits associated with composite repair systems include short length of time needed to complete a repair, undisrupted product transmission in the piping system while the repair is made and eliminating the possibility of explosion since no welding or cutting of the pipeline is required.
Industry analysis shows that composite repair systems are, on average, 73% cheaper than completely replacing the damaged section of the steel pipe and 24% cheaper than welded steel sleeve repairs [15]. Despite these
advantages however, long-term performance is a main concern for composite repair system. In response to that, an extensive research programme sponsored by Pipeline Research Council International, Inc. and 12 composite manufacturers from around the world was conducted to better understand the long-term performance of composite repair systems [16].
This article provides an insight into widely-used systems for repairing corroded oil and gas pipelines. In general, these can be categorised as conventional steel sleeve repair system and composite repair system. Both systems have advantages and limitations, so pipeline operators need to carefully evaluate the problem to determine which repair system is most appropriate for used. These include (but are not limited to) type of defects (leaking or non-leaking), operation constraints (allow for operation shutdown or not), permission for hot work, location of defect and future concern (future deterioration). For example, if hot work is not permitted, the welded repair system is not an option. On the other hand, if further corrosion is not a concern and the section to be repaired is a straight pipe, a steel sleeve/ clamp may be sufficient to do the job due to its proven long-term performance. This is important to ensure pipelines can be operated safely within the designated operation lifespan.
[1] Central Intelligence Agency. (2015). The World Factbook Field Listing: Pipelines [online]. Available: https://www.cia.gov/library/ publications/the-world-factbook/fields/print_2117.html [Accessed: Sept. 29, 2015]
[2] EGIG, “7th EGIG report 1970–2007: gas pipeline incidents,” European Gas Pipeline Incident Data Group (EGIG), Groningen, MA, Netherlands, 2008.
[3] H.A. Kishawy and H.A. Gabbar, “Review of Pipeline Integrity Management Practices;” International Journal of Pressure Vessels and Piping, vol. 87, pp.373-380, 2010.
[4] CONCAWE, “Performance of European cross-country oil pipelines: statistical summary of reported spillages in 2009 and since 1971,” Report no. 3/11, Brussels, Belgium, 2011.
[5] K.S. Lim, N. Yahaya, S.R. Othman, S.N.F. Mior Mohd Tahir, and N. Md Noor, “The Relationship between Soil Resistivity and Corrosion Growth in Tropical Region”, The Journal of Corrosion Science and Engineering, vol. 16, Preprint 54, pp.1-17, 2013.
[6] S.N.F. Mior Mohd Tahir, N. Yahaya, N. Md Noor, K.S. Lim, and Abdul A. Rahman, “Underground Corrosion Model of Steel Pipelines Using In Situ Parameters of Soil,” ASME. J. Pressure Vessel Technol., vol. 137(5), pp.051701-051701-6, 2015. doi:10.1115/1.4028424.
[7] J. W. Hsu and F. Liu. (2014). Taiwan Gas Blasts Likely Caused By Faulty Pipe. The Wall Street Journal [online]. Available: http:// online.wsj.com/articles/taiwan-gas-blasts-likely-caused-by-faultypipe-1406964902 [Accessed: Sept. 11, 2014]
[8] M. Shamsuddoha, M.M. Islam, T. Aravinthan, A. Manalo, and K.T. Lau, “Effectiveness of Using Fibre-Reinforced Polymer Composites for Underwater Steel Pipeline Repairs,” Compos. Struct., vol. 100, pp.40-54, 2013.
[9] X.D. Zhao, G.F. Xi, and J. Yang, “Application of Corrosion Detection Technology of Long-distance Pipeline in Material Application Engineering,” Advanced Materials Research, vol. 578, pp.211-214, 2012.
[10] R. Batisse, “Review of Gas Transmission Pipeline Repair Methods,” in Safety, Reliability and Risks Associated with Water, Oil and Gas Pipelines, G. Pluvinage, and M.H. Elwady, (Eds.). Netherlands: Springer, 2008, pp.335-349.
[11] J. Kou, and W. Yang, “Application Progress of Oil and Gas Pipeline Rehabilitation Technology,” in Proceeding of the International Conference on Pipelines and Trenchless Technology (ICPTT), 26–29 October 2011, Beijing, China, pp.1285–1292, 2011.
[12] Repair of Pressure Equipment and Piping, The American Society of Mechanical Engineers, ASME PCC-2-2011, 2011.
[13] Petroleum, Petrochemical and Natural Gas Industries – Composite Repairs of Pipework – Qualification and Design, Installation, Testing and Inspection, International Organization for Standardization, ISO/TS 2481, 2006.
[14] W.F. Ma, J.H. Luo, and K. Cai, “Discussion about Application of Composite Repair Technique in Pipeline Engineering,” Advanced Materials Research, vol. 311-313, pp.185-188, 2011.
[15] G.H. Koch, M.P. Brongers, N.G. Tompson, Y.P. Virmani, and J.H. Payer, “Corrosion Cost and Preventative Strategies in the United States,” Federal Highway Administration, Office of Infrastructure Research and Development, pp.260-311, 2001.
[16] C.R. Alexander, “Advances in the Repair of Pipelines Using Composite Materials. Article 1 in a 4-part series, Pipeline & Gas Technology Magazine,” Hart Energy Publishing, LP, July 2009 edition.
Lim Kar Sing is with the Faculty of Civil Engineering and Earth Resources, Universiti Malaysia Pahang (UMP) and Faculty of Civil Engineering, Universiti Teknologi Malaysia (UTM), Johor. He is currently pursing his PhD in the field of structural repair and rehabilitation. AuthorsBiodata:
Siti Nur Afifah Azraai is pursuing her M. Phil. in Faculty of Civil Engineering, Universiti Teknologi Malaysia (UTM), Johor. Her research focus is on developing guidelines for repair and rehabilitation of corroded oil and gas pipelines.
Assoc. Prof. Dr Norhazilan Md Noor is Associate Professor Faculty of Civil Engineering, Universiti Teknologi Malaysia (UTM), Johor. His research interest includes reliability engineering, pipeline integrity assessment, risk assessment and hazard identification, soil-corrosion engineering, microbiological-induced corrosion, riskbased inspection, repair and maintenance. His is also the Editor-inChief for Malaysian Journal Of Civil Engineering.
Prof. Dr Nordin Yahaya is with Faculty of Civil Engineering, UniversitiTeknologiMalaysia(UTM),Johor.Hisprofessionalinterest is in pipelines engineering, structural reliability & assessment, corrosion and risk management. He is also senior director of UTM International Office.
IEM would like to congratulate Datuk Ir. Prof. Dr Wan Ramli Wan Daud FASc being the recipient of the Anugerah Merdeka 2016 Award from the Sultan of Perak, Sultan Nazrin Muizzuddin Shah on 24 September 2016.
Ir. Lee Chang Quan graduated with a Mechanical Engineering degree and MBA. He is currently the HSE manager in a PETRONAS subsidiary. He is also a committee member in Oil, Gas and Mining Technical Division, IEM.
Safety is always easier said than done. In the oil and gas industry, companies have established policy statements to make safety and health a priority in business operations. Such a commitment, normally in the form of a company policy statement on Health, Safety and Environment (HSE), will be put to test amidst cost cutting pressure resulting from the fall in price of crude oil. The price of crude oil tumbled to US$45 per barrel (Brent Crude, at the time of writing in Aug 2015) from the price range of US$90-100 per barrel in year 2013, causing a sharp profit drop among the oil majors. With the economic challenges clouding the oil and gas industry, how can the industry prevail in upholding the high standards of safety? Let us look at two major safety cases in the oil and gas industry for some insight.
The Piper Alpha explosion in July 1988, which had caused the death of 167 people, remains a painful learning experience for the oil and gas industry. The incident has become one of the most common case studies in the industry. Many of the lessons learnt from the Piper Alpha explosion incident have been incorporated for improvement in operations. The industry safety standards, e.g. pressure relief valves management, emergency shutdown valves design and installation, permit-to-work (PTW) management system and emergency evacuation were also established after the incident. Hazards identified from investigations andlessonslearntaredealtwiththroughhazard elimination, engineering control, operational control or administrative control. People are up-skilled through training to ensure they can carry out their routine tasks safely.
However, all these measures will be futile if safety does not have priority over production or profitability, especially where there is an imminent threat to human lives, damage to equipment or impact on the environment. For example, in the Piper Alpha incident, the severity of the explosion could have been reduced if the neighbouring platform had adopted safety-priority behaviour. This means if they had cut off the production as soon as they were aware of the fire, they could have avoided further fuelling the fire at the Piper Alpha platform.
Will we suffer the same fate 37 years after the incident if we are posed with the same threat today? Will the front-liners be
“courageous” enough to make the decision to stop production, risking revenue loss, customer loss and management action against him or her?
In 2005, an explosion occurred at BP Texas City Refinery, United States. The incident claimed 15 lives and injured 180 people. The explosion and fire occurred during the plant start-up of an isomerization unit. A raffinate splitter tower (distillation tower) was overfilled, causing the pressure relieving devices to open. This led to flammable liquid streaming from a blowdown stack which was not equipped with a flare system.
Following the incident, the U.S. Chemical Safety Board (CSB) investigation team found several lapses in process safety. These included shift hand-over, alarm failure and start-up safety management. The investigation team also raised concerns about the safety management system effectiveness and corporate safety culture. Meanwhile, the Baker Panel, which examined the investigation of the incident, came up with a few key learning points (Hopkins, 2010):
• A lack of operating safety culture and discipline,togetherwithtoleranceforserious deviations from safe operating practices, posed serious process safety risks.
• Top management must provide effective leadership and establish appropriate goals for process safety, articulating a clear message and matching this with policies they adopt and actions they take.
• Developing and implementing a process
safety management system to ensure that all levels of management possess an appropriate level of process safety knowledge and expertise. Poor hazard identification or risk awareness throughout the organisation had contributed to the inability to see risks and therefore, toleration of a high level of risk.
• A good process safety culture requires a positive, trusting and transparent environment with effective lines of communication between the management and the workforce.
In addition, it was found that there were unclear accountabilitiesandcommunicationacrosstheorganisation which had gone through frequent structure modification without improving the safety behaviour required. Poor communication across functions, either vertically or horizontally with workers tending to work in silo, had created confusion in work and deviation from the basic requirements for safe and efficient operations.
There is a similar trait in these two major accidents that points to organisation safety culture as an underlying cause. Organisation culture is “how we do things around here” and it is also “a shared perception of daily practices” (Hofstede, 1997). Meanwhile, organisation safety culture is how safety is perceived and practised in daily work.
Currently, though oil and gas companies are facing economic headwinds and taking multiple cost-cutting measures, organisation safety culture should not be neglected. Capital projects may be postponed, training budgets reduced and manpower downsized; however, the way safety is perceived and practised in daily operations, should continue to be of the utmost importance in order for companies to uphold high safety standards.
In fact, poor organisation safety culture is the cause of many major accidents in the oil and gas industry. It was also identified as one of the causes in the Columbia space shuttle disaster in 2003 which killed the seven-member crew and shook NASA to the core.
Studiesonmajorincidentshaveestablishedlinksbetween organisation safety culture and major incidents (Hopkins, 2006). Therefore, it is necessary to always improve safety culture based on the lessons learnt from incidents. Quite often, companies take pride in providing the best protective gear, high-standard operating procedures, high-capital engineering control, intensive training and development on operation standards rather than emphasise on the sharing of learning.
Other than knowing what incident had happened, it would be more crucial that companies turned the “knowwhat” to “know-how”. The safety department should understand why the incident had happened and then reflect on the current practices before coming up with any action to avoid a similar incident. To prevent repeated failures, the safety fraternity can take the Kaizen approach tosafetyofcontinuouslearning,effectiverootcauseanalysis and sharing of lesson learnt.
Other than lessons learnt from incidents, how can companies improve their safety culture? Fortunately, we don’t need to apply rocket science to find out. There have been many research works done on the subject of safety culture. According to Reason (1997), an effective safety culture organisation would have:
• A transparent and easy-to-access safety information system that collects, analyses and disseminates information on incidents, near misses and audit findings;
• A transparent reporting culture where people are prepared to inform any near misses, errors, mistakes and non-compliance, without fear, irrespective of rank;
• A culture of trust and accountability throughout the hierarchy, where people understand the roles and responsibilities towards safety.
• A strong will to continue improving its safety system.
To apply the above points to further improve the organisational safety culture, leadership and commitment are essential. Leadership is the key to changing safety culture. Leaders can influence safety through “walk the talk” exemplary actions.Perceptionanddemonstrationofsafetybehavioursbyseniormanagers will shape the behaviour of workers and therefore, the safety performance of the organisation (Clarke, 1999).
Similar emphasis should also be given to supervisory level employees due to the longer contact time and intermediary role between senior management and workers at ground level. The synergy between the senior management and supervisors can play an influential role in moulding the safety behaviour of the workforce. Frequent and open communications among the managers, supervisors and shop floor workforce are instrumental to good safety performance (Parker, et al., 2006).
Assessing the current state of organisation safety culture is beneficial to identify opportunity for improvement to safety performance. There are various tools and studies available in the market for this. Parket, et al., (2006) have also formulated an organisational safety culture maturity framework. Using research work on oil & gas company executives, they developed and proposed a set of short cultural descriptors. Companies can use the following sample questions and descriptors to do a quick assessment of their organisation safety culture maturity:
In the eyes of management, who causes accidents?
• Are individuals blamed? Are faulty machinery and poor maintenance identified as causes as well as people? Or
• Does Management accept that it is their responsibility, that they could have done something to remove the root causes? They can take a broader view, looking at the interaction of system and people.
What happens after an accident? Is the feedback loop closed?
Balance between Health, Safety, Environment and profitability
Work-site job safety techniques
• The focus is on the employee after an accident. An accident report is not shared to the line if possible. Or,
• The top management shows a personal interest in individuals and the investigation process. All employees take accidents to others personally.
• Profitability takes priority and safety is seen as a cost. Operational factors dominate. Or,
• HSE and profitability are in balance. The business accepts delay to ensure contractors live up to the safety standards.
• Astandardworksitehazardmanagementtechnique is brought in but without much systematic use. Or,
• Job safety analysis or safety observation techniques areacceptedbytheworkforceandrevisedregularly for improvement.
How do employees feel about safety meetings?
Who checks safety on a day-to-day basis?
What is the size/ status of the HSE department?
• Meetings are seen as a waste of time and attended reluctantly. Or,
• Meetings can be called by any employee. Toolbox meetings are short and are focused on ensuring that everyone is aware of risks that may arise from work.
• There is no formal system. Cursory site checks are performed before management/external inspector visits. Or,
• Internal cross safety audits take place. Everyone checks for hazards. There is no problem demanding shutdown because of hazard.
• The department is small and has little power but is sometimes seen as police force. Or,
• HSE is seen as an important job given to high flyers. All senior people in operation must have HSE experience. Department is small but powerful with equal status to other departments.
[Source: Parker, et al., (2006)]
During economic turbulence, other than protecting the thinning bottom line,companiesmustpayattentiontothehealthandsafetyofthestakeholders, especially employees. The last thing a company needs is having to manage a crisis due to a major accident as this cost lives and money. Therefore, it is important that companies commit to their pledges in safety and health policies and review the business wholesomely, together with the safety and health management system, before making any drastic change to the organisation. Any change has to be assessed on its risks. Any change has to be followed through deeply for a smooth and clear changeover on how routine work is conducted.Agoodunderstandingoftheorganisationsafetyculturewillenable a company to grasp, assess and manage the risk of change more effectively. Open communication and well-informed workforce on safety incident, nearmisses, safety learning and sharing, violations and safety improvement action will propel the organisation to a higher safety culture maturity.
In a nutshell, cognisance in the organisation safety culture, together with improvements in procedures and safety systems, will mean improvements in safety performance. Even though organisation safety culture improvement is not rocket science, it still requires leadership and commitment to engineer the change as well as consistent follow-up to sustain the culture. So will oil and gas companies be able to keep the safety standards and their commitment to safety when faced with economic challenges? Only time will tell.
[1] Clark, S., 1999. Perception of Organizational Safety: Implications for the Development of Safety Culture. Journal of Organizational Behaviour, 20(2), 185-198.
[2] Columbia Accident Investigation Board, 2003. Report, Vol.1. Washington NASA.
[3] Hopkins, A., 2006. Studying Organization Cultures and Their Effect on Safety. Safety Sciences 44, 875-889.
[4] Hopkins,A., 2010. Failure to Learn: The BP Texas City Refinery Disaster. CCH,Australia.
[5] Hofstede, G., 1997. Cultures and Organizations. McGraw-Hill, New York.
[6] Lutchman,C.,Maharaj,R.,andGhanem,W.,2012.SafetyManagement:AComprehensive Approach to Developing A Sustainable System. CRC Press, Taylor & Francis Group.
[7] Parker, D., Lawrie, M., and Hudson, P., 2006. A Framework for Understanding The Development of Organizational Safety Culture. Safety Science-Pergamon, (44), retrieved from www.elservier.com
[8] Pennachio, F., 2008. Going Beyond Limits. Occupational Hazards, 70(9), 34-35.
[9] Reason, J. 1997. Managing the Risks of Organizational Accidents. Ashgate.
[10] U.S. Chemical Safety and Hazard Investigation Board Investigation Report: Refinery Explosion and Fire, 2007. Downloaded from http://www.csb.gov/file. aspx?DocumentId=345
Ir. Razak Yakob Razak has been in the O&G industry for over 20 years and is currently an Independent Drilling Consultant and a part-time lecturer. He was a PRODIGY Technical Review Committee Member when he was with one of the Petroleum Arrangement contractors. He was also an assessor for the PRODIGY’s Drilling Engineering programme.
Not many people are aware of the existence of PRODIGY (Program for the Development of Ingenious Young Talents) in Malaysia. It was created to address the serious issue of a shortage of competent resources in the upstream oil & gas (O&G) sector.
As mentioned in Oil & Gas Talent Outlook 2016 byMercer,“Despiteforecastedgainsinnuclear, hydro, biomass, and solar energy production, the predicted growth rate in global energy demand will outstrip the growth of all these alternative fuels”.
Hydrocarbons will still need to make up for the difference, so the O&G industry shall still thrive for a very long time despite comments that the industry is heading for a sunset.
A survey conducted by Mercer Energy Vertical, Asia Region, indicated that we would be facing manpower shortage in the Oil & Gas Sector by 2017 (Figure 1). This survey was conducted in 2013 before the oil price slump. Demand for resources has eased since then.
In the beginning of Q3 2014, the price of oil started to slide. A 10-year chart from Macrotrends shows this trend (Figure 2).
O&G companies around the world started to be cautious in the launching of new projects. Marginal projects were the first to be shelved and kept for future consideration when the demand and price of oil increased. When new projects were shelved, the demand for manpower reduced. Companies such as TH Engineering, Schlumberger, and Shell were among the first to launch their “right sizing” initiatives.
At the time of writing (June 2016), the demand for manpower in the upstream O&G sector had eased quite significantly. Even though the price of oil went back to US$50 per barrel, the market would still need to stabilise and find a new economic level before new projects could be launched. However, many world experts are positive that oil price will bounce back to a level where projects can, economically, be approved at the FIR (Final Investment Review) stage. When that happen, therewillbeahighdemandforresourcesagain though exactly when this will happen, is raising many views and opinions. Many believe that,
based on historical trending, the price goes in a cycle.
The O&G industry is usually divided into three major sectors: Upstream, Midstream and Downstream. The upstream sector includes the search for potential underground or underwater crude oil and natural gas fields, drilling of exploratory wells and subsequently, drillingandoperatingthewellsthatrecoverand bring the crude oil and/or raw natural gas to the surface. The downstream sector commonly refers to the refining of petroleum crude oil and the processing and purifying of raw natural gas as well as the marketing and distribution of products derived from crude oil and natural gas. Midstream operations are often included in the downstream category and considered to beapartofthedownstreamsector(Wikipedia).
O&G requires highly skilled professionals to design and manage the projects for successful execution. The execution has to be safely completed with time and cost effectiveness. Therefore, it is pertinent to have initiatives such asPRODIGY,toaddresstheissuesofcompetent resources shortage in the Upstream O&G sector and to provide a long-term strategy for growing the capability of our people, not only for Malaysia but also the international market.
PRODIGY was created with the strategic collaborationbetweenPetronasandPetroleum Arrangement Contractors (PAC) to address the issue of manpower. It was launched on 27 February, 2015, in conjunction with the initiative for Upstream Long Term Integrated Manpower Assurance (ULTIMA). The first intake was successfully accomplished on 20 July, 2014, focusing on Petroleum Engineering and Process & Operations. The second intake was on 26 April, 2015, with the addition of Drilling Engineering into the programme.
PRODIGY was formed with the aim to focus on young talents, fresh graduates or crossdisciplinestrainingorredeploymentofresources
from other disciplines. Apart from creating the platform for a sustainable supply of local graduates for the industry, it also aims to:
• Provide additional options for the fresh graduate.
• Increase employability of Malaysian graduates.
• Enhance the capability, competency and marketability of graduates.
• Develop, attract and retain talents via collaboration with operators and service contractors to ensure the sector has sufficient work-ready talents.
PRODIGY was also created to increase awareness among graduates to consider O&G as a career, to attract the best talents to join the industry and to address the issue of unemployed local graduates and develop them to be industry ready.
The programme is led by Petronas via its strong arm, Malaysian Petroleum Management (MPM). The members comprise all Petroleum Arrangement Contractors (PAC), which includes PSC – Petronas Sharing Contracts and Risk Service Contracts. O&G Service Contractors such as Schlumberger, Halliburton and others, are also closely involved in the programme since they provide facilities for some programme segments as part of On-The-Job exposures.
Practically every party involved with the O&G industry in Malaysia is working together hand-inhand to ensure the success of this initiative. The programme is managed by INSTEP (Institut Teknologi Petroleum Petronas), which handles all training programmes by Petronas.
It is designed as a 2-year programme for fresh graduates or re-skilling of resources from other industries. It comprises approximately 10-20% classroom work (technical modules, HSE modules, soft skills modules) and 80-90% OnThe-Job training. This is what sets it apart from other programmes offered by other institutions of higher learning. Because of the collaboration between the PACs and Service Contractors, this will seem like the candidates start work in an organisation right after graduation.
What is different is that the programme is intensive, very structured and is a complete module to ensure that the graduates are ready to accept actual workload from the organisation as soon as they start.
The programme focuses on 4 disciplines: Petroleum Engineering, Project Management, Drilling and Process & Operations.
The candidate who applies for this programme, goes through a rigorous evaluation and interview process, where eventually, less than 20% of applicants are placed. The successful ones will be sponsored by PAC or Service Contractors, so upon completion of the programme, the candidates will serve in the sponsor organisation or some other arrangement, as according to the contract requirements.
With the drop in oil price, the programme faces the challenge of staying relevant to thrive in a period when everyringgitspentmustadduptopositiveeconomicmargin for an organisation, if it is to be approved for execution. Training programmes for operators are non-profit generating expenses, so they are at the bottom of spending lists.
In an effort to stay relevant today, the programme was re-reviewed rigorously for every single line item. The result was a reduced programme period, from 24 months to about 18 months, depending on the disciplines. The challenge is to accomplish the same objectives without reducing the quality of programme. With the focus on increasing the efficiency of the programme, the mission is to ensure candidates can “run” the moment they land in the job, with specific skills that they have been assessed at various levels of the programme.
Despitethecurrentoilpriceuncertainty,thecompetency developmentofcandidatescurrentlyintheprogramme,and
new intakes in future, must continue to proceed because they will be the ones to fill in the gaps in the industry. The market condition will either get back to what it used to be or will find an equilibrium point where the work must go on and the supply of hydrocarbon will continue to be in demand as an energy source. Fossil energy will continue to be a relevant source for years to come.
The need for highly skilled professionals in the upstream O&G sector will be an issue again once the demand for fossil fuel is back. Do we wait for the price of oil to go up to start training again or do we soldier on and prepare our resources for future needs? Do we choose to be proactive or whinge about the lack of resources like we did in the past?
• PRODIGY website for pictures and information: http://www. prodigymalaysia.com
• Presentation Package by Mercer’s Energy Vertical, “Workforce Planning in Oil & Gas”, 29 October 2013, Kuala Lumpur Convention Center
• Crude Oil Chart website: http://www.macrotrends.net/1335/dollar-goldand-oil-chart-last-ten-years
• Bangkok Post, 15 March 2013, “Malaysia faces oil & gas brain drain” • The Star, 8 August 2013, “Chua: Many Factors Behind Brain Drain” • Wikipedia
Title: 1-Day Course on Safety Integrity Levels (SIL) Training for Workshop Participants 15 November 2016
Organisedby :ChemicalEngineeringTechnical Division
Time : 8.30 a.m. – 5.30 p.m. CPD/PDP :6.5
Kindly note that the scheduled events below are subject to change. Please visit the IEM website at www.myiem. org.my for more information on the upcoming events.
Ir. Davendren Vereya is with Aker Engineering Malaysia as a PDMS Coordinator and plays an active role as a Lean Navigator. He holds a Bachelor in Mechanical Engineering (UNITEN) and MBA in Construction Management.
“One thing you cannot recycle is time wasted.” – Taiichi Ohno (who invented the Toyota Production System which later became Lean Manufacturing). The lean philosophy is founded on three key principles: Respect for people, eliminate non-value-adding activities (remove wastages) and maximise the efficiency of value-adding activities.
The Malaysian oil & gas industry faced a difficult 2015. In February 2015, Petronas posted a RM2 billion loss for the final quarter of 2014. This was followed by an announcement that it would be cutting capital expenditure by 10% and operational expenditure by 30% that year. Across the world, international oil giants slashed exploration and production budgets and scaled back projects.
To add to this, productivity in the oil and gas services industry had a negative development of 55% over the last few years while manufacturing improved by 61%. The situation is clear. Customers have cut spending and are expecting engineering companies to respond to their needs for lower costs and more efficient work.
Leanisthebestwaytoproviderevolutionary improvements with changes to the process of product and service delivery. This differs from Value Engineering which provides changes to the actual product/service. While Value Engineering is described as delivering “less for less”, Lean is delivering “more for less”. During this challenging period, Lean is capable of providing the much-needed paradigm shift.
The concept of Lean can be summarised into what I would address as P(3p). The alphabet P stands for Perfection Perfection can be described as the effort of continuous improvements.
The 3p in parentheses stands for Product, Process & People Product is what we want to achieve or produce at the end of each process. Process refers to the series of activities involved in order to achieve a particular end and People refers to the person involved in the process, either directly or indirectly.
Lean is the collective effort to improve the quality of the product, the efficiency of the process and the involvement of the employee. In Lean thinking, it should be noted that cost is targeted at reduction, not profit. Lean is not
about trimming to the bone and squeezing more from the remains. Applying lean also doesn’tmeantherestructuringofthecompany.
Applying the Lean Manufacturing philosophy to engineering may appear to be a little tricky and even discouraging at first. In Lean Manufacturing, the value is visible at each step and the goal can be defined. In Lean Engineering however, the value is not as easily visible while the goal is emergent as we move along the lean transformation process.
In Lean Manufacturing, value stream is formedbypartsandmaterialflowwhileinLean Engineering, it is the flow of information and knowledge. As far as the flow is concerned, in Lean Manufacturing, iterations in a process are considered as waste. However planned iterations are accepted in Lean Engineering as long as efficiency remains. Another distinguishing difference will be in the definition of perfection, P. In Lean Manufacturing, perfection happens when a process is repeatable without errors while in Lean Engineering, it is achieved when process enables enterprise movements.
Figure 1: Commitment, system-specific knowledge, and cost (source: B.S. Blanchard & W.J. Fabrycky, Systems Engineering and Analysis, 3rd Ed., Prentice Hall, 1998, Figure 2.11).
Engineering companies need to adopt a strategy to focus on differences from competitors and to be the preferred partner to
work with. The key enabler will be focus on performance improvement and improved efficiency. Lean thinking should start as early as the Front End stage, when critical decisions are made. At this stage, management control and ease of change are high while the costs incurred, costs committed and knowledge applied, are low. Engineers must make the right choices early in the process, to ensure customer satisfaction and low lifecycle costs.
To eliminate waste and to create value from the customer’s perspective, requires close collaboration with the internal and external customer in order to truly understand what creates the value.
In delivering engineering service, it is important to know what it is that we can deliver which will create customer value? Time, Cost and Quality are the 3 aspects which form customer value. Apart from knowing what to deliver, when to deliver and the cost, it is also necessary to understand the needs of the customer and to make the overall process comfortable for the customer, in order to create true value.
The objective of Lean is to increase customer value with less effort by removing the “waste” that the customer is not willing to pay for. In Lean, the goalis nottorunfaster,buttorunshorter. Eliminatingwastagealongtheprocess will make product delivery shorter.
There are 8 categories of waste: Defects, Over-production, Waiting, NonUtilised Skill, Transport, Inventory, Movement and Extra-processing.
DOWNTIME. When we talk about waste, we are not referring to people doing wasteful actions but to the product not being worked on. For example, a document sitting in a box waiting to be worked on, is non-value added. We are not talking about people being idle but the product that we are producing, being “idle”. The waste categories and examples are as below:
Defects
Something that renders the product, unfit for purpose due to poor quality.
Producing more than the customer requires, “just in case”, to make up for poor quality.
Waiting for materials, equipment, drawings or for others to complete the tasks.
Under-utilising human skills, talent, and knowledge. Employees are not fully engaged to maximise value creation.
Moving material, information around between stages in the production process.
Keeping more materials than needed for current process stage.
Physical movement of personnel or material within a process stage.
Generating more work products or quality than the customer will pay for. Exceeds “fit for purpose”.
Typically, 40% to 80% of effort is wasted in terms of a significant amount of rework, waiting for information and unnecessary bureaucracy. This results in significant delays in a process (time), wasted time and overruns (cost) and variable quality and significant reworks (quality), resulting in frustrated employees, management and customers.
Lean Transformation is not just about using new concepts and tools. It is about changing an organisation’s culture, thinking and behaviour. The process requires excellent leadership and a strong vision to be sustainable and successful. It is a difficult journey but one that is well worth the effort. Typically, the Lean Transformation process can be executed in six phases as follows:
1. Call out. This phase is a “defining moment” where overall lean strategies must be developed. The call out should be a strong driving message from the topmost level to everyone. The idea is to instill in every employee the driving force or purpose for getting Lean.
2. Lean Education. The concept of lean may be new to some. Lean may be simple but it’s not easy. Basic education is essential to all. Lean Training sessions have to be rolled out to provide clear and precise information on the lean concept. At this stage, it is very important for managers to play their role well in being the fore-runner in welcoming the initiative.
3. Value Stream Mapping. This phase is where the visual representation of workflow and information flow are developed. The current state and the future state are charted. The visualisation will help identify the area of improvements. A Priority List is developed as an action plan.
4. Initial Lean Projects. In this phase, small projects are initiated as an improvement initiative. Projects usually involve a small team (process owner) who will benefit the most from the process improvement. This phase also helps to build the comfort level in utilising the lean tools. The results from these small projects are shared and demonstrated across the organisation to gain broader support.
5. Intermediate Lean Projects. Small pockets of Lean will begin to appear. This will serve to increase the Lean Appetiteanddrivethepositivemomentum.Atthisphase, an in-depth lean education is rolled out. The driving force in the phase one is re-validated.
6. Advanced Lean Projects. After grabbing the “low hanging fruit”, it now becomes more difficult to squeeze out simple waste. At this stage, an increase in flow and capacity should be seen. Savings can be projected on a larger scale. Major opportunities still remain as the next action plan. This phase never ends.
• Engineers should play an effective role in a Lean Transformation Process. They need to transform themselves into Lean Thinkers. The optimist – Why is the glass half full? The pessimist – Why is the glass half empty? The Lean Engineer – Why is the glass double the size it should be?
• Engineers must challenge the way they work in order to eliminate waste and increase customer value.
• The only person who can determine the quality of an engineer’s work is the internal customer. Engineers should
ask: “What do I need to do so that the next person can do his job? What do I need (i.e. what are my requirements as an internal customer) in order for me to do my job?
• Engineers should emphasise the usage of visuals rather than plain reports. Visualisation or workflow, progress and performance will allow the team to take immediate corrective action and deliver right the first time as well as on time just as the disruption surfaces.
• All work needs to be performed in accordance to a defined standard. Engineers must measure their performance to identify deviations from the standard way of working. Performance measurement is used to understand how to deliver in accordance with the standard or to improve the standard.
• Identify the root cause of each problem. Instead of jumping to solutions, an engineer should find the root cause of the problem and implement a solution to actually fix the problem.
The oil and gas industry will recover from the present challenges but things will not be the same anymore. With this understanding, a culture change is a must in order to remain relevant. The contribution of an engineer is instrumental in determining the success of this change initiative. Together we should LEAN forward for a sustained positive change, and come to grips with a core concept that embraces and promotes change. "An organisation's ability to learn, and to translate that learning into action rapidly, is the ultimate competitive advantage." Jack Welch (Chemical Engineer and former CEO of GE).
[1] Gilles Valentin. (2015). The Who's Who of the Global Energy Industry Malaysia 2015. The Oil & Gas Year.
[2] Ibrahim, A. H. (2016). Resource - The Magazine for Malaysian Petroleum Club Members. Malaysian Petroleum Club. Volume 23 No 3.
[3] Prince, J and J.M Kay. (2003). "Combining Lean And Agile Characteristics: Creation Of Virtual Groups By Enhanced Production Flow Analysis". International Journal Of Production Economics 85 (3): 305-318
[4] B.S. Blanchard & W.J. Fabrycky, (1998) Systems Engineering and Analysis, 3rd Ed., Prentice Hall Lean White Belt & Orange Belt Training Material Aker Solutions.
Title: Technical Visit to IJN's Biomedical Engineering Facilities
15 November 2016
Organised by : Senior Special Interest Group
Time : 9.00 a.m. – 1.30 p.m.
CPD/PDP : 3
Kindly note that the scheduled events below are subject to change. Please visit the IEM website at www.myiem. org.my for more information on the upcoming events.
reported by Ir. Dr Ng Soon Ching Chairman, Civil and Structural Engineering Technical Division (CSETD).
The Civil & Structural Engineering Technical Division (CSETD) organised an evening talk on the design and construction of stabilised subgrades for Malaysian roads on 7 April, 2016, at Wisma IEM, chaired by Ir. Chong Chee Meng and attended by 41 participants.
The talk was delivered by Mr. Scott Young, who had vast experience in both design and construction of pavement stabilisation here and in Australia. He is also a guest lecturer at undergraduate and postgraduate level at the University of New South Wales and University of Technology Sydney.
This talk focused on the design procedures for the improvement of non-conforming subgrade layers for new pavement construction and the rehabilitation of existing pavements. IT also emphasised on the construction aspect of stabilised subgrades which included specifications, equipment, process and verification of CBR.
On pavement design, Mr. Young asserted the importance of subgrade modelling. Whether building a new road or rehabilitating an existing one, subgrade stiffness is, by far, one of the highest risk elements to ensure the finished pavement meets the design life expectations. According to the new Design Guideline published in 2013, a minimum CBR of 5% is recommended for pavements that have to support traffic volumes corresponding to Traffic Classes T1 through T5. Mr. Young argued that at least 1m depth of subgrade shouldbemodelled in the determination of design CBR to be used for the input into the pavement design process; he added that this was international practice. Such an approach can yield savings in the upper pavement layers. There are many methods to model the subgrade stratum using different CBR values within the profile. One common and well accepted approach was developed by the Japanese Road Association (as shown in Eq 1).
Where:
CBRi = CBR value in the layer thickness hi ∑hi = the total subgrade depth, is taken up to 1.0m
In the second part of the talk, Mr. Young presented the construction process of subgrade stabilisation, starting with the specification requirements as stated in Standard Specification for Road Works published by JKR. Following that, he presented the equipment used for the construction of stabilised subgrades namely stabiliser/reclaimer, mechanical spreader, roller compactor, motor grader etc. Lastly on the construction process, subgrade stabilisation work starts with:
1. Site preparation – relocation of utilities, removal of topsoil, cutting or filling of existing material
2. Spreading of stabilising agent – the required quantity of stabilising agent is distributed as per design. Normally, this is achieved by controlling the spread rate of the spreader
3. Mixing – the optimum moisture content is crucial during the mixing process and it must be checked
4. Compaction – compaction is carried out to ensure that it has achieved minimum density requirements.
5. Grading – to level the stabilised subgrade
6. Curing – this is critical especially for cement based stabilisers. It is to ensure the proper hydration of cement.
Attheendofthetalk,therewerequestionsfrom thefloorwhichMr.Youngansweredandclarified in detail. He also shared some of his personal experience and tips in stabilisation with the participants.Thetalkendedwiththepresentation of a memento to Mr. Young by CSETD Chairman Ir. Hooi Wing Chuen.
After numerous meetings, careful planning and efforts to get keynote presenters, speakers and foreign as well as local participants, the Training Workshop on Maintenance of Infrastructure kicked off. The aim of the workshop was to emphasise the importance of Infrastructure Maintenance and its role in the 16 United nations Sustainable Development Goals. It is the International Science Technology and Innovation Centre (ISTIC) program to assist developing countries to get the prerequisite frameworkforinfrastructuremaintenance.
A consortium of six organisations involved in maintenance was formed to take turns to host the annual workshop and showcase Malaysia’s expertise and commitment in Infrastructure Maintenance, especially to foreign delegates. The six are Malaysian Service Providers Confederation (MSPC), Malaysian Highway Authority (MHA), Construction Industry Development Board Malaysia (CIDB), The Institution of Engineers, Malaysia (IEM), Master Builders Association Malaysia (MBAM) and Indah Water Konsortium (IWK).
This year, MSPC hosted and conducted the workshop from 25-28 July, 2016, at the Sri Petaling Hotel, Kuala Lumpur. It was attended by 52 participants – 32 locals and 20 delegates from countries such as Brunei Darussalam, Cambodia, Kenya, Myanmar, Sri Lanka, Thailand and Vietnam. They were introduced to the national framework necessary for Sustainable Infrastructure Maintenance such as laws, regulation, policies, guidelines, advance technology and various financial models as practiced here. Afternoons were reserved for visit to projects.
The workshop opened with greetings from the ISTIC Chairman Dato Dr Samsudin Tugiman and the host, MSPC President Mr. Choo Kok Beng. The Deputy Minister of Works, Datuk Rosnah binti Abdul Rasid Shirlin, declared the workshop openandhighlightedtheneedtohaveagoodmaintenance culture. She stressed that the public too must be taught to appreciatetheneedtocultivategoodmaintenancehabits. She said maintenance was a generic term that included planned maintenance, repair, refurbishment and provision for replacement of the structures. The workshop started with a keynote address each morning. The speakers for the keynote addresses were:
• Datuk Ir. Ellias Ismail, Senior General Manager, Technology Development Sector, CIDB Malaysia, Topic: The Challenges of Infrastructure Maintenance.
• Mr. Choo Kok Beng, President of MSPC, Topic: Overview of Financing Infrastructure Maintenance.
• Academician Dato Ir. Lee Yee Cheong, Honorary Chairman of ISTIC, Topic: Developing A Preventive Maintenance Culture.
A speaker each from MHA, IWK and IEM made up the paneltotalkabouttheirrolesrelevanttothe various themes.
For Day 1, the theme was “Ascertain Malaysian Legislation on Infrastructures Maintenance. ”The speakers spoke on the institutional legislation for highway maintenance and legislation for sewerage treatment, with emphasis on privatising sewerage management. An advocate and solicitor also presented on Maintenance and Management of Strata titles, Buildings and Common Property Act 2007.
In the afternoon, MHA arranged for a technical visit to the North-South Expressway.
OnDay2,afterthekeynoteaddress,thesessioncontinued with speakers from MHA and IKRAM, IWK and IEM covering advancetechnologyonpavementmaintenance,focusingon ride comfort/riding quality, safety performance for highways, system development, monitoring and rehabilitation work for sewerage treatment plants and assets management system for buildings. IWK then hosted a visit to Pantai 2.
After the keynote address on Day 3, the panellist spoke on the different models to finance infrastructure maintenance, citing their experience on roads and highways, sewer systems and commercial buildings.
The afternoon technical visit was to Sunway Lagoon Shopping Mall in Bandar Sunway. Participants were introduced to multi-tasking skills required to keep the mall in top operating conditions. The event ended with the delegates doing a bit of shopping at the mall.
On the last day, the morning started with business matchmaking, when the participants and delegates visited the booths of the 6 consortium members. This was followed by a round table discussion with Puan Noraini of CIDB, Mr. James Warren of IWK, Tan Sri AK Nathan of MBAM, Ir. Tan Yean Chin, President of IEM and Dato Ir. Hj. Ismail Md Salleh, the DG of MHA. Each panellist spoke on their organisation’s role with respect to maintenance.
IEM President Ir. Tan Yean Chin introduced IEM’s role in the international arena and international registers. He encouraged engineers to have businesses beyond Malaysia as engineers need to be active, not only locally and within the region but also internationally. He encouraged IEM members to not only participate in local institutions in the region or in the country but also to join activities of international organisations so as to gain more exposure to how people worked in different parts of the world and to share information.
He stressed that no man can be an island. If one thinks he can work on his own, then he will be working away from success, said Ir. Tan. He urged engineers to take bold steps to go where the timid cannot or dare not, in order to discover new horizons.
Foreignparticipantswereimpressedwithourmaintenance frameworkputinplacetodevelopasustainablemaintenance culture. They would be reverting with a request to share our experiences in their respective countries. The Myanmar Shan State Minister of Industry and ElectricityhadrequestedthatISTIC conductamaintenanceworkshopwithfocusonroads,electricity facilities and mining in November 2016, in Shan State.
Theworkshopclosedwiththepresentationofappreciation certificates to sponsors and the certificate of attendance to delegates. Everyone agreed it was a fruitful and enjoyable workshop. Next year, IWK will host the workshop.
The team from Universiti Teknologi Malaysia’s Razak School of Engineering and Advanced Technology, made a commitment to contribute back to the society. The success of the first project undertaken in March 2015 was a catalyst for the team to continue with the second initiative, which was the development of a Fun Learning Toy Library for pre-school students in the rural Sekolah Kebangsaan Kuala Geris, Dabong. In particular, this project was a follow-up action to assist victims of the 2014 flood in Kelantan.
The team had the support of several NGOs and groups of people who contributed in cash and kind. IEM-WE seized the opportunity to jump on the bandwagon for the trip to Dabong on 26 February, 2016.
A Fun Learning Toy Library is useful in many ways to the target audience. It provides a conducive environment for pre-school children to develop an interest in science and technology and to
understand its basic concepts at a very young age. With this in place, these young rural children will be motivated to develop a deep interest in science, technology, engineering and mathematics (STEM) education.
The fun learning approach to understanding “difficult” subjects like science and mathematics will, hopefully, overcome or reduce the trauma of the natural disaster that the students experienced. It was reported that many of these young children had lost their homes and found it difficult to go to school. Some were fearful of being separated from their families. With a toy library in school, these children became excited and were motivated to go to school. Additionally, the intangible benefit of this project was the networking and bonding that developed among the volunteers, partners and the local community. The teachers who participated to implement relevant activities, proved to be of great help.
The team is planning a third visit to the school to monitor and follow-up with several other activities and IEM-WE will take part again. n
Women Engineers (WE) of Penang Branch, in collaboration with WE at HQ, organised a half-day technical seminar on Engineering Challenges for Slope Stabilisation and Flood Mitigation in July, 2016, at IEM Penang branch office. The case study sharing was indeed a good experiences exchanged between branch members.
The first speaker was the Immediate Past Chairman of WE Section, Ir. Raftah Mahfar, who is currently Director in a Structural, Civil, Infrastructure, Geotechnical and Railway engineering consultant firm; she has more than 29 years of experience in Geotechnical Engineering design and construction.
Slope stabilisation is a significant challenge for geotechnical engineers. Slope stability decreases when slope angle increases. Underground water plays a major roleinslopefailureasitwillincreasethedriving force by filling previously empty pore spaces and fractures, adding to the total weight of the subsoil. Increased pore water pressure in slopes can also decrease the shear strength of the slope material. Chemical weathering slowly weakens slope material, reducing its shear strength, thus reducing resisting forces. During the case study sharing session on the Slope Stability chronological event, Ir. Raftar thoroughly interpreted the sequences of slope failure and solutions to slope stability. The presentation was very comprehensive, complete with the information on the findings, design and construction phase.
The second speaker was Ir. Suhana Abdul Majid, Vice Chairman of the WE Section and managing director of an engineering consultant firm. She has 25 years of experience in various fields of Civil and Structural Engineering Services, such as feasibility study, infrastructure design, project management and asset management services in transportation sector as well as mixed development projects.
Ir. Suhana shared her experience on flood mitigation and its challenges during the construction of the On-Site Detention
Pond at Sg. Rasau Toll Plaza. Flood mitigation involves the management and control of flood water movement, such as redirecting flood run-off and methods used to reduce or prevent the detrimental effects of flood waters. Challenges from flood mitigation, such as rapid urbanisation, climate change and construction activities due to population growth, will intensify the risk of the flood. Ir. Suhana focused her case study sharing on the complexity of solutions for design and assessment, problems faced at the construction stage as well as public protests during the execution of the project.
The half-day seminar was an interactive and informative session that benefitted the participants greatly. n
The Tunnelling and Underground Space Technical Division (TUSTD) organised an evening talk on “Advancement in Tunnel Lining Monitoring using Fibre-Optic Distributed Sensing” on 25 May, 2016, at the C&S and TUS Lecture Room, Wisma IEM. The talk was delivered by Associate Professor Ir. Dr Hisham Mohamad from Universiti Teknologi Petronas. There were a total of 35 participants.
First, Dr Hisham gave a brief introduction to tunnel-induced ground movements and various in-tunnel instrumentation schemes available such as Automated Total Station, accelerometer, crackmeter, tilt beam and strain gauges. However all the systems are primarily limited to discrete or localised sensing. Then, he presented a novel approach to monitoring tunnel lining deformation and crack detection in a distributed manner, where a single optical fibre cable can potentially replace hundreds of point-wise sensors and detect tunnel movements of kilometres in length in a cost-effective manner. This technology is called Brillouin
The speaker, Assoc. Prof. Ir. Dr Hisham Mohamad
Optical Time-Domain Reflectometry (BOTDR) or Brillouin Optical Time-Domain Analysis (BOTDA).
Optical fibre sensing in general relies on the interaction between laser light and glass material in an optical fibre. Strains and deformations alter the refractive index and geometry of the optical fibre material. These changes perturb the intensity, phase and polarisation of the light-wave propagating along the fibre. A complete strain profile along the full length of the fibre can be obtained by resolving the back-scattered signal in both time and frequency, which is shifted by an amount linearly proportional to both the temperature and strain applied at the scattering location.
Dr Hisham said a particular advantage of optical fibre technology is that low propagation losses can be obtained with a single-mode optical fibre, which means the strain can be measured along the full length (up to 10 km) of a suitably installed optical fibre by attaching a BOTDR analyser at one end. He further discussed the various types of distributed fibre optic sensing and gave a comparison of the various strain sensor technologies.
From the many applications of distributed fibre optic sensing in civil engineering for smart infrastructure, the talk focused on tunnel monitoring. Case experiences of tunnel monitoring at London’s Channel Tunnel Rail Link (CTRL) and Singapore’s MRT Circle Line were presented in detail. Other examples of recent implementations of BOTDR/A fibre optic monitoring were National Grid London Cable Replacement Tunnels in the UK, Telecom tunnels and NATM tunnel of Tokyu Toyoko Line in Japan. Its application in monitoring ground movement caused by pipe-jacking was also briefly discussed. These examples of distributed optical fibre sensing illustrate the advantages of the technique, compared with conventional instrumentation devices, owing to its ability to monitor both the overall deformation of the structure and the detection of local movements such as cracking.
Dr Hisham ended his talk by highlighting issues and challenges faced in the development of optical fibre sensing technology for civil engineering application. He fielded several questions from the floor before the talk ended with a round of applause. The Chairman of TUSTD, Ir. Syed Rajah Hussain Shaib, presented Dr Hisham with a token of appreciation. n
Title: Talk on Moving from ISO 9001:2008 to ISO 9001:2015 What will be needed to upgrade your QMS to the new edition?? 19 November 2016
Organised by : Project Management Technical Division
Time : 11.00 a.m. – 1.00 p.m.
CPD/PDP : 2
Kindly note that the scheduled events below are subject to change. Please visit the IEM website at www.myiem.org.my for more information on the upcoming events.
We are a supplier of high quality geosynthetic products used for soft soil stabilization, slope reinforcement, coastal erosion protection, river bank protection, landfills, drainage, road and railway construction.
We also provide design, specification, bill of quantities, cost estimate and drawings free-of-charge.
Sending reminders to members to pay their annual subscriptions three times annually had been a run of the mill affair to the membership department of IEM. Each year, the first reminder is sent in the month of June when subscriptions become overdue while the second and final reminders would be sent in September and November respectively.
IEM, being a membership driven organization depend heavily on annual subscriptions to finance its operations. Membership subscriptions make up about 60% of IEM’s annual income. Inability to fully collect the due sums would greatly hamper the operation of the Institution and the service which it provides to members.
IEM would therefore like to appeal to members to promptly pay their subscriptions to ensure that the Institution would be able to sustain.
Membership subscription rates of IEM is one of the lowest in comparison to other professional bodies such as doctors, accountants and architects. Benefits of IEM membership is something that members do not realise or forget as the days go by.
IEM members enjoy benefits such as reduced rates for attending courses/seminars for their professional development. Non-members sometimes have to pay more than double the rate of members. The reduced rates enjoyed by members would be able to encourage their employers to send them for more training which will definitely benefit the engineers.
Comparison of some of the rates can be seen below:
Joint Seminar on Geophysical Techniques and Experiences in Ground Engineering Applications
Two-Day Course on “Boiler Design & Efficiency”
One-Day Course on “Maintenance of Lifts and Escalators”
RM450RM450RM900
RM900RM600RM1200
RM500RM300RM650
In comparison, such seminars and courses organized by private training providers would range around two to three times the rate which IEM charge.
It can be noted that the difference in training fee payable for non-members or for other training programmes is also two to three times more than IEM’s annual subscription fee.
In the past three years, IEM had organized on average 200 subsidised events annually which translate into about 4 activities per week. This is an impressive record compared to other professional bodies and can be even considered world class by any standard.
Besides tangible benefits such as the Bulletin and the Journal, IEM provides a platform/avenue for members to network during events/activities organized where members could mingle. This allows transfer of information as well as experience. The network set up can come in handy in times when a member is in need of advice, business or career opportunities within as well as outside the country.
In addition, IEM would also like to highlight that in accordance with the IEM Constitution and Bylaws, only members of the Institution are eligible to use the post nominals of F.I.E.M., M.I.E.M., Grad. IEM etc.
IEM’s existence depends on its members and we greatly hope that you will assist us to sustain the Institution set up by our forefathers for the benefit of all in the engineering profession. It will only cost RM0.40 a day which is less than the price of a glass of Chinese tea.
IEM has introduced the FULLY-PAID Membership Scheme with effect from 2013. By subscribing to this scheme, your membership will be:
• IMMUNE to increase in future subscription rates increase
• IMMUNE to inflation
• IMMUNE to increase in rates when you upgrade your membership. YOU WILL NOT NEED TO TOP UP THE DIFFERENCE WHEN YOU MOVE TO A HIGHER GRADE.
• IMMUNE to interruption in receiving IEM’s services. The IEM Bylaws state that all privileges due to a member will cease if his subscriptions is not paid by April each year.
Why not take the opportunity to sign up for fully-paid membership now and pay less!!
KepadaSemuaAhli,
Tarikh:11Oktober2016
SENARAI CALON-CALON YANG
MENDUDUKI TEMUDUGA PROFESIONAL TAHUN 2016
Berikut adalah senarai calon yang layak untuk menduduki TemudugaProfesionalbagitahun2016.
Mengikut Undang-Undang Kecil IEM, Seksyen 3.8, nama-nama seperti tersenarai berikut diterbitkan sebagai calon-calon yang layak untuk menjadi Ahli Institusi, dengan syarat bahawa mereka lulusTemudugaProfesionaltahun2016.
Sekiranya terdapat Ahli Korporat yang mempunyai bantahan terhadap mana-mana calon yang didapati tidak sesuai untuk menduduki Temuduga Profesional, surat bantahan boleh dikemukakan kepada Setiausaha Kehormat, IEM. Surat bantahan hendaklah dikemukakan sebulan dari tarikh penerbitan dikeluarkan.
Ir. Yam Teong Sian Setiausaha Kehormat, IEM,
PERMOHONAN BARU
NamaKelayakan
KEJURUTERAAN AWAM
MOHD SOFIAN BIN ISWADYBE HONS (UTHM) (CIVIL, 2007)
ROSILAWATI BTE MAZLANBE HONS (UTM) (CIVIL, 2003)
KEJURUTERAAN ELEKTRIKAL
AZREEN HAZREE BIN BAHAROMBE HONS (UNITEN) (ELECTRICAL & ELECTRONICS, 2009)
CHANDRAMOHAN A/L
BALACHANDRAN BE HONS (UNITEN) (ELECTRICAL POWER, 2009)
KAMARUS ZAMAN BIN AHMADBE HONS (UTM) (ELECTRICAL, 2007)
MOHAMAD IZHAM BIN PAZARIZALBE HONS (UTM) (ELECTRICAL, 2010)
MOHD ADAM B. MOHD ZAINALBE HONS (UTM) (ELECTRICAL, 2005)
MOHD ARIEF ZAKI BIN TOGINBE HONS (UTM) (ELECTRICAL, 2008)
MOHD FAKHRI BIN MAHAMAT SUKIS BE HONS (UiTM) (ELECTRICAL, 2012)
MOHD FARIZ BIN BACHOKBE HONS (UiTM) (ELECTRICAL, 2005)
MOHD HAFEEZ BIN MOHAMEDBE HONS (UTM) (ELECTRICAL, 2011)
MOHD MAZWAN BIN MOSTAKIMBE HONS (UiTM) (ELECTRICAL, 2010)
NOR AFNI BINTI MOHAMAD RUDZALAN BE HONS (UiTM) (ELECTRICAL, 2006)
NURHISYAM B. MOHAMED MUSTAFA BE HONS (UTM) (ELECTRICAL, 2010)
NURMADINA BINTI YUSOH BE HONS (UKM) (ELECTRICAL & ELECTRONIC, 2005)
ROSNIZAH BINTI GHAZALIBE HONS (STRATHCLYDE) (ELECTRONIC & ELECTRICAL, 1997)
SHARIDA BINTI BAHARIBE HONS (UiTM) (ELECTRICAL, 2005)
SYAZREEY IZUANSYAH BIN
ZAKARIA BE HONS (UNITEN) (LECTRICAL POWER, 2007)
TAN WENG SENGBE HONS (USM) (ELECTRICAL, 2008)
TENGKU MOHD RUSYAILAN BIN
TENGKU ABDULLAH BE HONS (UiTM) (ELECTRICAL, 2011)
KEJURUTERAAN MEKANIKAL
ZURADZMAN BIN MOHAMAD RAZLAN BE (YAMAGATA) (MECHANICAL, 1993)
KEJURUTERAAN KAWALAN & INSTRUMENTASI
NUR ALINA JELANI BE HONS (UTP) (ELECTRICAL& ELECTRONICS, 2006)
KEJURUTERAAN ELEKTRONIK
LEE MENG CHUANBE HONS (MULTIMEDIA) (ELECTRONICS-COMPUTER, 2006) ME (MULTIMEDIA) (MICROELECTRONICS, 2012) PhD (MULTIMEDIA) (2015)
PERPINDAHAN AHLI
No. Ahli NamaKelayakan
KEJURUTERAAN AWAM
47953CHEONG WEI HAOBE HONS (UTAR) (CIVIL, 2011)
23641ER CHIN NEEBE HONS (UTM) (CIVIL-CONSTRUCTION MANAGEMENT, 2002)
34320FADZIL BIN MAT YAHAYABE HONS (UTM) (CIVIL, 2000)
53728MD KAMARZAN BIN MD RAISBSc (MISSISSIPPI) (CIVIL, 1991)
24178MOHAMAD ODIL BIN SABRIBE HONS (UTM) (CIVIL, 2000)
17741 MOHD AZHARI BIN ABDULLAH BE HONS (UiTM) (CIVIL, 2000)
43181TING EE CHUENBE HONS (UNITEN) (CIVIL, 2006)
15096WAN ABDULLAH BIN WAN OMARBE HONS (UiTM) (CIVIL, 1992)
29485WAN JEE KHEENBE HONS (UPM) (CIVIL, 2008)
KEJURUTERAAN KIMIA
26337 LEE TECK LII BE HONS (UTM) (CHEMICAL, 2007)
61180UMI FAZARA BINTI MD ALIBE HONS (MALAYA) (CHEMICAL, 2003) MESc (MALAYA) (2006) PhD (IMPERIAL COLLEGE LONDON) (2011)
25267CHUA CHOON HONGBE HONS (UTP) (CHEMICAL, 2003)
KEJURUTERAAN ELEKTRONIK
78902TEE KIAN SEK BE HONS (UTM) (MECHATRONICS, 1997) ME (UTHM) (ELECTRICAL, 2007) PhD (LEEDS) (2012)
62011MOHAMED SULTAN BIN MOHAMED ALI BE HONS (UTM) (ELECTRICAL-MECHATRONICS, 2006) ME (UTM) (ELECTRICAL-MECHATRONICS & AUTOMATIC CONTROL, 2008) PhD (BRITISH COLUMBIA) (2012)
KEJURUTERAAN ELEKTRIKAL
34625CHONG KIAN FOOBE HONS (UPM) (ELECTRICAL & ELECTRONICS, 2009)
60021CHRISTIANA LINUS MAJAILBE HONS (UMS) (ELECTRICAL & ELECTRONICS, 2004)
37269HONG CHIN SOONBE (RMIT) (ELECTRICAL, 2005)
34102MOHD FADLY BIN RAZAKBE HONS (UiTM) (ELECTRICAL, 2010)
61123MOHD FIRDAUS BIN SHAARIBE HONS (UiTM) (ELECTRICAL, 2008)
54598MOHD HAFIZ BIN ZAINUDINBSc (ILLINOIS) (ELECTRICAL, 2008)
51327NORAZIAH BINTI HUSSINBE HONS (UMS) (ELECTRICAL & ELECTRONICS, 2006)
51326RINA BINTI RASHIDBE HONS (UMS) (ELECTRICAL & ELECTRONIC, 2006)
43160 SOE BOON TAKH BE HONS (MALAYA) (ELECTRICAL, 2009)
51699SUDALLI BIN SABTUAHIMBE HONS (UMS) (ELECTRIC & ELECTRONIC, 2009)
57994SYAHIRAH BINTI MOHD SAHARBSc (KOREA) (ELECTRICAL, 2009)
KEJURUTERAAN MEKANIKAL
36938 JAYASILER A/L KUNASAGARAM BE HONS (UNITEN) (MECHANICAL, 2007)
72465MUSADDIQ BIN OTHMANBE HONS (UTM) (MECHANICAL, 2009)
37670LEOW CHEE HUANBE HONS (UTAR) (MECHANICAL, 2011)
KEJURUTERAAN BAHAN
40703 FAROUQ BIN AHMAT BE HONS (IIUM) (MATERIAL, 2012)
PERMOHONAN BARU/PEMINDAHAN MENJADI AHLI KORPORAT
KEJURUTERAAN MEKANIKAL
49254LEONG WEI CHIATBE HONS (USM) (MECHANICAL, 2010)
Pengumuman yang ke-97
Institusi mengucapkan terima kasih kepada semua yang telah memberikan sumbangan kepada tabung Bangunan Wisma IEM. Ahli-ahli IEM dan pembaca yang ingin memberikan sumbangan boleh berbuat demikian dengan memuat turun borang di laman web IEM http://www.iem.org.my atau menghubungi secretariat di +603-7968 4001/5518 untuk maklumat lanjut. Senarai penyumbang untuk bulan September 2016 adalah seperti jadual di sebelah:
NO. NO. AHLI NAMA
169516ABANG NIZAMUDDIN BIN ABANG MOHD KHALID
229101AMIR BIN MUSTAFA
364705LIM JUN NIAN
414154LOW CHIEW KEAT
579475MOHAMMAD IZWAN BIN ABDUL WAHID
680559POUL BIN JOANNES
729411SDR. MUHAMMAD NUR IZNEI BIN HASHIM
815123ZAINOLARIFEN BIN SAID
69005MOHD FADZLIN NOOR AIN BIN MOHD YASIN
69007MOHD FAWWAZ BIN MD ISA
74396MOHD FUZI BIN BERAHIM @ IBRAHIM
69012MOHD IZAD IZUDDIN BIN ABD AZIZ
69013MOHD KHAIDIR BIN MAT GHANI
69014MOHD KHAIRIL BIN AWANG
54426 MOHD KHAIRIL RIZAL BIN ISMAIL
42624MOHD NIZAM BIN ABDUL LATIF
28229MOHD REDZUAN BIN MOHAMAD YA'AKOB
69020MOHD SYAFIQ FIRDAUS BIN ZOLKEFLI
69024MUHAMAD BOKHARI BIN OMAR
69026MUHAMAD FIRDAUS BIN ABDUL MAJID
69028MUHAMAD HAZIQ BIN KHIRUDDIN
56677 MUHAMMAD AFIQ BIN AZMY
69036 MUHAMMAD AMIRUL FAEZ BIN ABDUL FATAH
56680MUHAMMAD FADHZRUL BIN IBRAHIM
69050MUHAMMAD FAIDHI B. ABDUL HAIYEE
53606MUHAMMAD NASRIN BIN MOHD NASERDDIN
69474MUHAMMAD NAZREEN B. SAIDIN
69073MUHAMMAD SHAHFIQ B. ABD HALIM
69077MUHAMMAD SYAFIQ B. ZURAIDI
44684MUHAMMAD SYAFIQ BIN NOTZIR
69082MUHAMMAD ZULFAQUR B. ABDUL MANAB
69090 NADIAH AMIRA BT. MOHAMAD YAZID
69093NASIBAH BT. OTHMAN
69094NASIHA SAKINA BT. MD AZMI
B.E.HONS.(UITM)(CIVIL, 2015)
B.E.HONS.(UITM)(CIVIL, 2015)
B.E.HONS.(UTM)(CIVIL, 2015)
B.E.HONS.(UITM)(CIVIL, 2015)
B.E.HONS.(UITM)(CIVIL, 2015)
B.E.HONS.(UITM)(CIVIL, 2015)
B.E.HONS.(UITM)(CIVILINSFRASTRUCTURE, 2014)
B.E.HONS.(UTM)(CIVIL, 2014)
B.E.HONS.(UTM)(CIVIL, 2007)
B.E.HONS.(UITM)(CIVIL, 2015)
B.E.HONS.(UITM)(CIVIL, 2015)
B.E.HONS.(UITM)(CIVIL, 2015)
B.E.HONS.(UITM)(CIVIL, 2015)
B.E.HONS.(UITM)(CIVIL, 2015)
B.E.HONS.(UITM)(CIVIL, 2015)
B.E.HONS.(UITM)(CIVILINSFRASTRUCTURE, 2015)
B.E.HONS.(UITM)(CIVIL, 2015)
B.E.HONS.(UKM)(CIVIL & STRUCTURAL, 2013)
B.E.HONS.(UITM)(CIVIL, 2015)
B.E.HONS.(UITM)(CIVIL, 2015)
B.E.HONS.(UITM)(CIVIL, 2015)
B.E.HONS.(UPNM)(CIVIL, 2014)
B.E.HONS.(UITM)(CIVIL, 2015)
B.E.HONS.(UITM)(CIVIL, 2015)
B.E.HONS.(UITM)(CIVIL, 2015)
B.E.HONS.(UITM)(CIVIL, 2015)
27251NICHOLAS LIMB.E.HONS.(USM)(CIVIL, 2006)
69117 NOOR ASYIQIN BT. MOHD SIDEK
B.E.HONS.(UITM)(CIVIL, 2015)
69113 NOR AINAAZWA BT. MISWAN B.E.HONS.(UITM)(CIVIL, 2015)
69127NOR SYAMIMI BT. AHMAD B.E.HONS.(UITM)(CIVIL, 2015)
69132NORAMIRA LIANA BT. MOHMED NOR B.E.HONS.(UITM)(CIVIL, 2015)
69135NORAZIAH BT. YUNUS B.E.HONS.(UITM)(CIVIL, 2015)
69160NUR EZWANNI BT. MOHAMMAD ILLAHI B.E.HONS.(UITM)(CIVIL, 2015)
69161NUR FADILA BT. GHAZALI B.E.HONS.(UITM)(CIVIL, 2015)
69176NUR HIDAYAH BT. AB RAOF B.E.HONS.(UITM)(CIVIL, 2015)
69179NUR HIDAYU BT. ABDUL KADIR B.E.HONS.(UITM)(CIVIL, 2015)
69181NUR LIANA BT. MOHAMED B.E.HONS.(UITM)(CIVIL, 2015)
69182NUR MIZAH BT. JOHARI B.E.HONS.(UITM)(CIVIL, 2015)
69184NUR NAZIHAH BT. ABDUL SATAR B.E.HONS.(UITM)(CIVIL, 2015)
69185NUR QISTINA BT. IMRAN B.E.HONS.(UITM)(CIVIL, 2015)
69191NUR SYAHIDA BT. ABD MANAF B.E.HONS.(UITM)(CIVIL, 2015)
69205NURHAFIZAH BT. HAMZAH B.E.HONS.(UITM)(CIVIL, 2015)
69209NURIAH SYAIRAH BT. MD ZAWAWI B.E.HONS.(UITM)(CIVIL, 2015)
69217NURTASHAFIZRAH BT. ABD RAHMAN B.E.HONS.(UITM)(CIVIL, 2015)
69224 NURULATIQAH BT. MOHAMAD HASSAN
69228 NURUL FATIN ALIA BT. PUASA
69230NURUL HARIYANTI BT. MOHD RAIS
69235NURUL NADIA BT. IBENIL HARJAD
B.E.HONS.(UITM)(CIVIL, 2015)
B.E.HONS.(UITM)(CIVIL, 2015)
B.E.HONS.(UITM)(CIVIL, 2015)
B.E.HONS.(UITM)(CIVIL, 2015)
57620OOI CHI HUIB.E.HONS.(UTM)(CIVIL, 2013)
57620OOI CHI HUIB.E.HONS.(UTM)(CIVIL, 2013)
16709PRATHAP KUMAR A/L GOBI
69253ROSEHEMILLIA BT. AMIL
69256ROZLINDA BT. MOHAMED
69258SAIFUL HAKIMIE B. SULAIMAN
56734SARIYRABANI BIN BASAR
69262SHAHRINA BT. BAHRUDIN
69263SHAHRUL IKHWAN NASIR B. SHOABANI
69264SHAHRUL NAZRIN B. AHA
69265SHAMSUL FAHMEE B. SHAMSUL FEKREY
56740 SITI AISHAH BT AZMI
69266SITI AISHAH BT. MAT FIAH
69276SITI KHADIJAH BT. MAKHTAR
69277SITI KHADIJAH BT. MOHAMED KAMAL
69280SITI MUNIRAH BT. ZULKIFLI
69281SITI NABILAH BT. SHARIPUDIN
69288SITI NUR BAITSHAS BT. ISMAIL
69293SITI RAHMAH BT. HAMINUDIN
69297SITI SYUHADA BT. MOHAMMED IZAM
61016 SITI TAHIRAH BT. ROSLAN
69299SITI ZAKIRAH BT. MIOR OSMAN
69305SURAYA SOHFIA BT. ISHAK
B.E.HONS.(USM)(CIVIL, 1997)
B.E.HONS.(UITM)(CIVIL, 2015)
B.E.HONS.(UITM)(CIVIL, 2015)
B.E.HONS.(UITM)(CIVIL, 2015)
B.E.HONS.(UITM)(CIVIL, 2015)
B.E.HONS.(UITM)(CIVIL, 2015)
B.E.HONS.(UITM)(CIVIL, 2015)
B.E.HONS.(UITM)(CIVIL, 2015)
B.E.HONS.(UITM)(CIVIL, 2015)
B.E.HONS.(UITM)(CIVIL, 2015)
B.E.HONS.(UITM)(CIVIL, 2015)
B.E.HONS.(UITM)(CIVIL, 2015)
B.E.HONS.(UITM)(CIVIL, 2015)
B.E.HONS.(UITM)(CIVIL, 2015)
B.E.HONS.(UITM)(CIVIL, 2015)
B.E.HONS.(UITM)(CIVIL, 2015)
B.E.HONS.(UITM)(CIVIL, 2015)
B.E.HONS.(UITM)(CIVIL, 2015)
B.E.HONS.(UTHM)(CIVIL, 2013)
B.E.HONS.(UITM)(CIVIL, 2015)
B.E.HONS.(UITM)(CIVIL, 2015)
69306SYAFEEZ B. SABRIB.E.HONS.(UITM)(CIVIL, 2015)
56748SYED IMRAN BIN SYED ALIAS
44652SYED MUHAMMAD SHAFIQ BIN SYED NORIZAN
43452 TAN KAI YANG
43452 TAN KAI YANG
B.E.HONS.(UITM)(CIVIL, 2015)
B.E.HONS.(UPNM)(CIVIL, 2013)
B.E.HONS.(CURTIN)(CIVIL & CONSTRUCTION, 2012)
B.E.HONS.(CURTIN)(CIVIL & CONSTRUCTION, 2012)
47945TAN KIEN HONGB.E.HONS.(UTAR)(CIVIL, 2011)
58859 TAN TEIK NING
B.E.HONS.(USM) (CIVIL, 2012)
M.SC.(USM)(STRUCTURE, 2013)
29357TAN WEE CHENB.E.HONS.(UPM)(CIVIL, 2010)
69316TUAN MOHAMAD FAIZAL B. TUAN ABDULLAH
B.E.HONS.(UITM)(CIVIL, 2015)
72499WAI-LUN NG, NICKYB.E.HONS.(UKM)(CIVIL & STRUCTURAL, 2014)
69322WAN MUHAMMAD RAMZI B. WAN ZAHARI
B.E.HONS.(UITM)(CIVIL, 2015)
45557YAP VOON CHUANB.E.HONS.(USM)(CIVIL, 2014)
28298YAP WEE GHIANB.E.HONS.(USM)(CIVIL, 2009) M.SC.(USM) (STRUCTURAL, 2010)
27857YEONG KANG LOONG
B.E.HONS.(USM)(CIVIL, 2007)
71159YONG ZI LIPM.E.HONS.(NOTTINGHAM) (CIVIL, 2015)
50664 ARVIND A/L RAJAN B.E.HONS.(MONASH) (ELECTRICAL & COMPUTER SYSTEMS, 2015)
44361 BELOUMIE @ ABU ANSYAARI BIN JAMALUDIN
B.E.HONS.(UTEM) (ELECTRICAL-POWER ELECTRONICS & DRIVE, 2011)
34160CHAN KOK WAIB.E.HONS.(UCSI) (ELECTRICAL & ELECTRONICS, 2015)
57713 JANARTHAN A/L KRISHNA MOORTHY B.E.HONS.(UTM) (ELECTRICAL, 2014)
44297 MEOR AHMAD HARIZ BIN MEOR AHMAD TAJUDIN B.E.HONS.(UTEM) (ELECTRICAL-CONTROL, INSTRUMENTATION & AUTOMATION, 2011)
66573MOHD KHOMAINI B. MOHD NOOR B.E.(UMP)(ELECTRICALPOWER SYSTEM, 2014)
44364MOHD SHAHRANI BIN KASSIM B.E.HONS.(UTEM) (ELECTRICAL-INDUSTRIAL POWER, 2011)
60513TEE WEE LIANGB.E.HONS.(UTP) (ELECTRICAL & ELECTRONICS, 2014)
KEJURUTERAAN ELEKTRONIK
28489LEE MEI PINGB.E.HONS.(MMU) (ELECTRONICS, 2009)
32740LIZAROZIYANTI BINTI YUSRI B.E.HONS.(UTM) (ELECTRICAL-MEDICAL ELECTRONICS, 2009)
53346TENGKU MOHD FIRDAUS BIN RAJA MAULUD B.E.HONS.(UNIMAP) (MICROELECTRONICS, 2012)
KEJURUTERAAN KIMIA
67172ABDUL FAIZ SAIFUL BIN ABD RAZAK B.E.HONS.(UITM) (CHEMICAL & BIOPROCESS, 2014)
28457AZDUWIN BINTI KHASRI B.E.HONS.(UKM) (CHEMICAL, 2009) M.E.(UTM)(CHEMICAL, 2012)
56826MOHAMMAD KHAIRULANAM BIN AZEMAN B.E.HONS.(UTP) (CHEMICAL, 2013)
74618NG JOO LINGB.E.HONS.(UTAR) (CHEMICAL, 2015)
44922 QUAH ZHI YONG B.E.HONS.(UTM) (CHEMICAL, 2014)
KEJURUTERAAN MEKANIKAL
48993ABDUL HAKIM BIN ALIAS B.E.HONS.(UITM) (MECHANICAL, 2014)
57282ABDUL SYAZWAN B. ABDUL NASSER B.E.HONS.(UNITEN) (MECHANICAL, 2015)
49024FARID WAJDI BIN MOHAMAD ISA B.E.HONS.(UITM) (MECHANICAL, 2014)
33116 MOHAMMAD AIMAN BIN MOHD YANI B.E.HONS.(UTHM) (MECHANICAL, 2009)
32390MOHAMMAD RIDZWAN BIN ABD RAHIM B.E.HONS.(UITM) (MECHANICAL, 2010)
32401MOHD ARZAIMIRUDDIN BIN ARIFFIN
B.E.HONS.(UITM) (MECHANICAL, 2010) M.E.(MALAYA)(MATERIAL & TECHNOLOGY, 2015)
38150MUHAMAD HAFIZ BIN ABD MALEK B.E.HONS.(UITM) (MECHANICAL, 2010)
36719MUHAMAD HILMEE BIN IBRAHIM B.E.HONS.(UITM) (MECHANICAL, 2010)
40385MUHAMMAD FADHLAN BIN MARZUKHI B.E.HONS.(UTM) (MECHANICAL, 2014)
44800MUHAMMAD NASRULLAH BIN ANNUAR B.E.HONS.(UTP) (MECHANICAL, 2014)
40639MUHAMMAD SYAFIQ BIN A BAKAR B.E.HONS.(UTM) (MECHANICAL, 2011)
60397 SAADEESH A/L GUNASEKARAN M.E.HONS.(NOTTINGHAM) (MECHANICAL, 2015)
45476 SUKEDEVE A/L RAJA B.E.HONS.(USM) (MECHANICAL, 2013)
45465 THOR MING TZE B.E.HONS.(USM) (MECHANICAL, 2013)
KEJURUTERAAN PETROLEUM
35965MOHAMMAD ASHRAFUNNUR BIN YEOP
B.E.HONS.(UTM) (PETROLEUM, 2012)
KEJURUTERAAN SUMBER MINERAL
KEJURUTERAAN ELEKTRIKAL
36602ADI SYAFIQ BIN MD AMIR
B.E.HONS.(UMP) (ELECTRICAL-POWER SYSTEMS, 2012)
30015MOHD SHAFREEN BIN MAD ISA B.E.HONS.(USM)(MINERAL RESOURCES, 2011)
PERMOHONAN MENJADI AHLI SISWAZAH
No. Ahli NamaKelayakan
KEJURUTERAAN ALAM SEKITAR
80196 EDWARD AJIE ANAK DENIS GASAN
80744 SUMESHINI A/P SUBRAMANIAM
KEJURUTERAAN AWAM
80707ALBERT ROBINSON WEE
80638 AZMEER AMIR BIN MAT YUSOF
B.E.HONS.(MALAYA) (ENVIRONMENTAL, 2010)
B.E.HONS.(UNIMAP) (ENVIRONMENTAL, 2014)
B.E.HONS.(CURTIN)(CIVIL & CONSTRUCTION, 2010)
B.E.HONS.(UITM)(CIVIL, 2015)
80567 CHAI CHEE YOONG B.SC.(NATIONAL CHUNGHSING)(CIVIL, 1999) M.E.SC.(HONG KONG) (INSFRASTRUCTURE PROJECT MANAGEMENT, 2011)
79569CHAI MEI HWAB.E.HONS.(BRADFORD) (CIVIL & STRUCTURAL, 2007) M.E.(UKM)(CIVIL, 2014)
80665CHAN CHUNG HONGM.E.HONS.(SHEFFIELD) (CIVIL & STRUCTURAL, 2014)
80730CHANG BOON FUUNN, VICTOR M.E.HONS.(NOTTINGHAM) (CIVIL, 2015)
79573 CHANG SHIANG YI B.E.HONS.(UTM)(CIVIL, 2014)
80188CHENG CHEE SHINGM.E.HONS.(NOTTINGHAM) (CIVIL, 2011)
80721CHIN LON CHEONGB.E.HONS.(CURTIN)(CIVIL & CONSTRUCTION, 2013)
80656CHU CHEE PENGB.E.HONS.(USM)(CIVIL, 2004)
80174CHUA PEI SHANB.E.HONS.(UMP)(CIVIL, 2014)
80662ENG WEI QIB.E.HONS.(UTM)(CIVIL, 2014)
80566 FATIN AMIRAH BINTI MOHD ANOR B.E.HONS.(MALAYA) (CIVIL, 2014)
80682GOH SIANG HUO, RAYMOND B.E.HONS.(UNITEN)(CIVIL, 2010)
80729HASLINDA BINTI HAJI MOHAMAD HAMRAN B.E.HONS.(MALAYA) (CIVIL, 2005)
80167 HERMAN BIN TAWIL B.E.HONS.(UTM) (CIVIL, 2007) M.E.(UTM)(CIVILSTRUCTURE, 2014)
80737 JAMIL BIN AHMAD B.E.HONS.(UTM)(CIVIL, 2004)
79557 LEE JIAN YANG, DENNIS B.E.HONS.(UTAR)(CIVIL, 2015)
79592 LEE TECK SHIN
B.E.HONS.(LEEDS) (CIVIL & STRUCTURAL, 2010) M.E.(UTM)(CIVILSTRUCTURE, 2014)
79579LEE WEI SZERB.E.HONS.(UPNM)(CIVIL, 2014)
80723LEONG QI WENB.E.HONS.(UNIMAP) (CIVIL, 2014)
80552LIM CHIANG LINGB.E.HONS.(UCL) (CIVIL, 1997)
M.SC.(UCL)(BUILT ENVIRONMENT, 1998)
79505 LIM TECK HUAT B.E.HONS.(IUKL)(CIVIL, 2014)
80663MARIAHTI BTE BERAHIM B.E.HONS.(UTM) (CIVIL, 2012)
M.E.(UTM)(CIVILHYDRAULICS & HYDROLOGY, 2014)
80641MOHAMAD BIN ABDULLAH
79587 MOHAMED AHMED ABDULAHI
B.E.HONS.(UITM)(CIVIL, 2005)
B.E.HONS.(UNITEN)(CIVIL, 2014)
80560MOHAMED SUFIAN BIN SABARUDDIN B.E.HONS.(UTM) (CIVIL, 1999)
79565 MOHD AFIQ BIN RAMLI
79564 MOHD AIZAT BIN MOHD HANIF
80699MOHD HAIZUL BIN OMAR
80550MOHD NAZAWEE BIN MOHD ZAKI
80182MOHD NUR SYAZWAN BIN MOHD HANIF
80451MOHD SHAHNAZ BIN SANI
79589MOHD. SHAMSURIZAM BIN SHAFIE
80716MOO HONG SHINB.E.HONS.(UTP)(CIVIL, 2014)
79568MPS ELANGO VADIVELOO
80639 MUHAMMAD AZIM MUIZ BIN ABU BAKAR
80738MUHAMMAD NADZIR BIN ABDUL RAHIM
79584MURNI BINTI MAHADI
M.E.(UPM)(WATER, 2007)
B.E.HONS.(UTM)(CIVIL, 2014)
B.E.HONS.(UMP)(CIVIL, 2012)
B.E.HONS.(UTM)(CIVIL, 2013)
B.E.HONS.(UTM)(CIVIL, 2006)
B.E.HONS.(UITM)(CIVIL, 2015)
B.E.HONS.(MALAYA) (CIVIL, 2004)
M.E.(UTM)(CIVILSTRUCTURE, 2012)
B.E.HONS.(UITM)(CIVIL, 2003)
B.E.HONS.(USM)(CIVIL, 1999)
B.E.HONS.(UITM)(CIVIL, 2015)
B.E.HONS.(UITM)(CIVIL, 2008)
B.E.HONS.(UTM)(CIVIL, 2011)
80732NG WEE CHOONB.SC.(STATE UNI. OF NEW YORK)(CIVIL, 2014)
80181 NICHOLAS ARAVEN A/LARULANANDAM
80189NOOR DEWIANNA BINTI ZAKARIA
79581NORAM IRWAN BIN RAMLI
80172NORMUSLIZAM BIN ABDUL MUTALIB
80637 NORRULAZMI BIN YAHYA
80640 OLIVIA NALAANAK MEXMILLIN
80722 ONG HERN YEE
B.E.HONS.(UTM) (CIVIL, 2005)
M.SC.(NEWCASTLE UPON TYNE)(OFFSHORE, 2014)
B.E.HONS.(UKM)(CIVIL & STRUCTURAL, 2010)
B.E.HONS.(UITM)(CIVIL, 2004)
B.E.HONS.(UTM)(CIVIL, 2013)
B.E.HONS.(UITM) (CIVIL, 2006)
M.SC.(UITM)(CIVILSTRUCTURES, 2007)
B.E.HONS.(UITM)(CIVIL, 2015)
B.E.HONS.(UTM)(CIVIL, 2010)
80559POUL BIN JOANNESB.E.HONS.(UITM)(CIVIL, 2003)
80720QUSANSSORI NOOR BIN RUSLI
80183RAJA HAIQAL ARIFFARHAN BIN RAJA IBRAHIM
80653ROHAIDIN BIN MOHD GHAZALI
80652ROSIDAH BINTI NULKASIM
80661SHAZWANI HANIS BINTI HIDAYAT
80724SHEIKH LUQMAN AQEEL SHEIKH AHMAD
80180SUKHVEER SINGH BHATT
79555SULIANA BINTI JAMALUDDIN
79560 TAN CHEY YIE
B.E.HONS.(UITM)(CIVIL, 2011)
B.E.HONS.(UITM)(CIVIL, 2015)
B.E.HONS.(UITM)(CIVIL, 2015)
B.E.HONS.(UITM)(CIVIL, 2015)
B.E.HONS.(UKM)(CIVIL & ENVIRONMENTAL, 2010) M.E.(UKM)(CIVIL, 2014)
B.E.HONS.(UNITEN)(CIVIL, 2014)
B.E.HONS.(VICTORIA) (CIVIL, 2013)
B.E.HONS.(UTM)(CIVIL, 2014)
B.E.HONS.(CURTIN)(CIVIL & CONSTRUCTION, 2013)
80190TAN CHOO KHINGB.E.HONS.(UTAR)(CIVIL, 2011)
80726TAN WEI CHUANB.E.HONS.(UTM)(CIVIL, 2002)
80658TEE CHIN FANGB.E.HONS.(UNIMAP) (CIVIL, 2014)
80170 TEOH KHAI YING
79567 THUN YIT ZHEN
B.E.HONS.(UNIMAP) (CIVIL, 2014)
B.E.HONS.(UTAR)(CIVIL, 2012)
80660WONG JEE KHAIB.E.HONS.(UKM)(CIVIL & ENVIRONMENTAL, 2004) M.E.(UKM)(CIVIL, 2009)
79593WONG KIN WAHB.E.HONS.(IUKL)(CIVIL, 2012)
80596WONG SIE KIAT, NATHANIEL
80736WONG WAI HOE, DEREK
80565 WONG YIN FU, ALEX
KEJURUTERAAN BIO KIMIA
80655NIK MOHD FAHMI BIN DRAMAN
B.E.HONS.(WESTERN AUSTRALIA)(CIVIL, 2014)
M.E.HONS.(NOTTINGHAM) (CIVIL, 2014)
B.E.HONS.(CURTIN)(CIVIL & CONSTRUCTION, 2014)
B.E.HONS.(IIUM) (BIOCHEMICALBIOTECHNOLOGY, 2014)
KEJURUTERAAN BIO PERUBATAN
80664WONG CHIN WEIB.E.HONS.(MALAYA)(BIOMEDICAL, 2014)
KEJURUTERAAN ELEKTRIKAL
80725AHMAD RIDHWAN BIN MAT YAMIN
80452 AIZUDDIN BIN A RAHIM
80547 AMIR ANWAR BIN SHABUDIN
80598ARNOLD DEBULLY SALIANG
B.E.HONS.(UTP) (LECTRICAL & ELECTRONICS, 2010)
80718CHONG JIACHYI, JEANNINE B.E.HONS.(UMS) (ELECTRICAL & ELECTRONIC, 2011)
80654 DR. GOH YEH HUANN B.E.HONS.(MALAYA) (ELECTRICAL, 2004) M.E.SC.(MALAYA) (CONTROL SYSTEM, 2007) P.HD.(MALAYA)(WAVE & PROPAGATION, 2013)
79391DR. SIOW CHUN LIMB.E.HONS.(UPM) (ELECTRICALELECTRONIC, 2011) P.HD. (UPM)(2014)
80186FARLIYANA BINTI ABU KHORI
B.E.HONS.(UNITEN) (ELECTRICAL & ELECTRONICS, 2009)
80191GAN SOON SHENGB.E.HONS.(UKM) (ELECTRICAL & ELECTRONICS, 2012)
80595HARVINDER SINGH A/L HARCHAREN SINGH
80594IFFA ILANI BINTI ISMAIL
79594ISNARAISSAH MUNIRAH BT. MAJILIS @ FAKHARUDY
80646 IZZAH AMANI BINTI TARMIZI
80593 KHAIRULANUAR BIN MUDA
B.E.HONS.(UNITEN) (ELECTRICAL & ELECTRONICS, 2012)
B.E.HONS.(UNIMAP) (ELECTRICAL SYSTEMS, 2014)
B.E.HONS.(UMS) (ELECTRICAL & ELECTRONICS, 2011)
B.E.HONS.(UTP) (ELECTRICAL & ELECTRONICS, 2009)
B.E.HONS.(UTM) (ELECTRICAL, 2014)
80727 KONG SHYANG YAU B.E.HONS.(UNITEN) (ELECTRICAL POWER, 2006)
80597LEE CHUN HOEB.E.HONS.(UMS) (ELECTRICAL & ELECTRONICS, 2014)
79595 LEE YEN LING B.E.HONS.(UNIMAP) (ELECTRICAL SYSTEMS, 2013)
80553 LEE YOU WAN B.E.HONS.(UTM) (ELECTRICAL, 2007)
80733MD RIDZUAN BIN TALIB
B.E.HONS.(UTEM) (ELECTRONICSINDUSTRIAL ELECTRONICS, 2008) M.E.(MALAYA) (ELECTRICAL, 2013)
80728 MOHAMED ELAZIZI BIN MOHAMED B.E.HONS.(UITM) (ELECTRICAL, 2013)
80649 MOHD AZREE BIN MOHD NOOR
B.E.HONS.(UNIMAP) (ELECTRICAL SYSTEMS, 2009) M.E.(UTHM) (ELECTRICAL, 2012)
80683MOHD DAIM MOHD DIAH B.E.HONS.(UMP) (ELECTRICAL-POWER SYSTEMS, 2011)
80687MOHD HAFIZ BIN JUSOH B.E.HONS.(UITM) (ELECTRICAL, 2008)
80708MOHD HASNAN BIN NORDIN B.E.HONS.(UMP) (ELECTRICAL-CONTROL & INSTRUMENTATIONS, 2010)
80696MOHD HELMI BIN SAMTA B.E.HONS.(UMP) (ELECTRICAL-POWER SYSTEMS, 2009)
80549MOHD NOOR BIN ABDULLAH B.E.HONS.(UTHM) (ELECTRICAL, 2008)
80710MOHD PADELY BIN MOHD PAMAN B.E.HONS.(UITM) (ELECTRICAL, 2001)
80554MOHD RAZANI BIN MOHD RAZALI B.E.HONS.(UTM) (ELECTRICAL, 2014)
80563 MOHD YASSIR BIN ALI B.E.HONS.(UITM) (ELECTRICAL, 2009)
80591 MOHD YUSWARDI BIN AB. YAMIN B.E.HONS.(UTM) (ELECTRICAL, 2014)
80684MUHAMAD HAZIEQ BIN ABD MANAN B.E.HONS.(UTHM) (ELECTRICAL, 2012)
80564MUHAMMAD FADHIL BIN MOHD NAWAWI B.E.HONS.(MELBOURNE) (ELECTRICAL, 2012)
79556MUHAMMAD FARID BIN MOHD PAUZI B.E.HONS.(UNISEL) (ELECTRICAL, 2013)
80702MUHAMMAD NAJMI BIN HAMZAH B.E.HONS.(UITM) (ELECTRICAL, 2010)
B.E.HONS.(UNITEN) (ELECTRICAL POWER, 2013)
B.E.HONS.(UMP) (ELECTRICAL-CONTROL & INSTRUMENTATIONS, 2009)
B.E.HONS.(UNITEN) (ELECTRICAL POWER, 2012)
80648 MUSLIM BIN TARMIZI B.E.HONS.(UTHM) (ELECTRICAL, 2011)
80212NOOR HESHAM AZLEE BIN ABDUL AZIZ B.E.HONS.(UTM) (ELECTRICAL, 2014)
79561 NUR AZYYATI BINTI ISHAK B.E.HONS.(UNITEN) (ELECTRICAL POWER, 2011)
80692NUR ZUHDI BIN ZAILAN B.E.HONS.(UTP) (ELECTRICAL & ELECTRONICS, 2012)
80739PENGIRAN NORAINI @ DAYANG KU NORAINI BINTI PG MOHD HUSSEIN AL-HASHIM
79576RAJA NASUHA BIN RAJA CHIK
80592RETTY FELICIA SIMOK
80741 ROFINO ANAK RANTAI
B.E.(LEICESTER) (ELECTRICAL & ELECTRONIC, 1999)
B.E.HONS.(UNITEN) (ELECTRICALELECTRONIC, 2009)
B.E.HONS.(MALAYA) (ELECTRICAL, 2005)
B.E.HONS.(UTM) (ELECTRICAL, 2007)
80166ROYMELVIN RICKY C NYONG B.E.HONS.(UITM) (ELECTRICAL, 2010)
80194 SAFWAN BIN ABD AZIZ
80168SALINA BINTI MOHMAD
79563SHAHIDAN BIN YA @ SALLEH
80743 SUBRAMANIAM A/L MOGAN
B.E.HONS.(UTEM) (ELECTRICAL-INDUSTRIAL POWER, 2014)
B.E.HONS.(UTP) (ELECTRICAL & ELECTRONICS, 2002) M.SC.(SOUTHAMPTON) (MICROELECTRONICS SYSTEMS DESIGN, 2005)
B.E.HONS.(UTM) (ELECTRICAL, 2013)
B.E.HONS.(UTEM) (ELECTRICAL-POWER ELECTRONICS & DRIVES, 2013)
80589SYAZWAN BIN SELAMAT B.E.HONS.(UNITEN) (ELECTRICAL & ELECTRONICS, 2014)
80647 TAN SWEE THAI B.E.HONS.(UTHM) (ELECTRICAL, 2013)
80706 THAWATCHEI A/L EH DI B.E.HONS.(UTHM) (ELECTRICAL, 2009)
80571WONG LEONG MINGB.E.HONS.(BRADFORD) (ELECTRICAL & ELECTRONIC, 2010) M.SC.(NOTTINGHAM) (POWER ELECTRONICS & DRIVES, 2012)
KEJURUTERAAN ELEKTRONIK
80714DR. ANI LIZA BINTI ASNAWI B.E.HONS.(IIUM) (COMPUTER & INFORMATION, 2003) M.E.(UKM) (COMMUNICATION & COMPUTER, 2006) P.HD.(SOUTHAMPTON) (CONPUTER SC., 2012)
80713DR. NOR FADHILLAH BINTI MOHAMED AZMIN B.SC.(OKLAHOMA STATE) (ELECTRICAL, 1999) M.SC.(UPM)(MEDICAL & BIO-MECHANICS, 2007) P.HD.(NEWCASTLE UPON TYNE)(FINGERPRINTING OF COMPLEX BIOPROCESS DATA, 2013)
80173 ELIAS BIN ABBAS B.E.HONS.(SHEFFIELD) (ELECTRONICS, CONTROL & SYSTEMS, 1993) M.E.SC.(MMU)(2005)
79570GAN ENG FOOB.E.HONS.(MMU) (ELECTRONIC-ROBOTICS & AUTOMATION, 2007)
79553 MOHD ANUAR BIN ADIP
B.E.HONS.(UTM) (ELECTRICALELECTRONIC, 2006)
79578MOHD HAFIDZ BIN MOHD ALI B.E.HONS.(UTM) (ELECTRICALMECHATRONICS, 2008)
80709MUHAMAD SYAFIQ BIN JAMALUDIN B.E.HONS.(UITM) (ELECTRONICINSTRUMENTATION, 2013)
79571NORIZAN BIN MOHAMAD
79574SAMSUL BIN SETUMIN
B.E.HONS.(MISSOURI) (ELECTRICAL, 1997)
B.E.HONS.(SURREY) (ELECTRONIC, 2006)
M.E.(UTM)(ELECTRICALELECTRONICS & TELECOMMUNICATIONS, 2010)
80642TAN SEE KAIB.E.HONS.(USM) (ELECTRICAL & ELECTRONIC, 2003)
KEJURUTERAAN KIMIA
80719 AHMADATTORELLAH SHARIFUDDIN
80695ARFANUDDIN BIN YAAKOB
80509ARYANORE NAFARINE ANTUNI
80538 AVINASH A/L KISHORE KUMAR
80645 AZIMAN BIN ARIFFIN
80703CHE RAHMAT BIN CHE MAT
80551DR. JIBRAIL BIN KANSEDO
79591HAWAIAH BINTI IMAM MAAROF
B.E.HONS.(UTM) (CHEMICAL-GAS, 2013)
B.E.HONS.(UTM) (CHEMICAL, 1997)
B.SC.(SOUTHERN CALIFORNIA)(CHEMICAL, 2013)
B.E.HONS.(UTP) (PETROLEUM, 2006)
M.E.SC.(UNSW) (PETROLEUM, 2009)
B.E.HONS.(UITM) (CHEMICAL, 2016)
B.E.HONS.(UITM) (CHEMICAL, 2010)
B.E.HONS.(USM) (CHEMICAL, 2006 ) M.SC. (USM)(CHEMICAL, 2010) P.HD.(USM)(RENEWABLE ENERGY, 2015)
B.E.HONS.(USM) (CHEMICAL, 2002) M.SC(USM)(CHEMICAL, 2005)
79572IYLIA BINTI IDRISB.E.HONS.(UITM) (CHEMICAL & PROCESS, 2011)
79566 KHAIRULAZLY BIN ZAHAN
B.E.HONS.(UTM) (CHEMICAL-BIOPROCESS, 2010) M.E.(UTM) (BIOPROCESS, 2014)
80712KONG SHANG ERNB.E.HONS.(UPM) (CHEMICAL, 2009)
80499KUHANESAPATHY A/L THAVARAS PATHY
79577LAVANESWARAN KRISHNAN
B.E.HONS.(UTP) (CHEMICAL, 2011)
M.E.HONS.(NOTTINGHAM) (CHEMICAL, 2014)
79562LEONG ZI WEIM.E.HONS. (MANCHESTER) (CHEMICAL, 2014)
80175 LOH YIN CHYUAN
B.E.HONS.(UNIMAP) (BIOPROCESS, 2014)
80734MAH SIEW HOEB.E.HONS.(UTAR) (CHEMICAL, 2015)
80694MOHAMAD SHAFIQ BIN A. GHAFAR
80698 MOHD NUR ASMADY BIN ALIAS
80644MOHD RIDHUAN BIN HASAN
80474MUHAMMAD JUFRI BIN ROSLI
80462 MUHAMMAD YUSOF BIN MOHD AZISS
B.E.HONS.(UTM) (CHEMICAL, 2012)
B.E.HONS.(UTM) (CHEMICAL, 2001)
B.E.HONS.(UITM) (CHEMICAL, 2010)
B.E.HONS.(UNSW) (CHEMICAL, 2012)
B.E.HONS.(UITM)(OIL & GAS, 2012)
80187MUSA BIN MA'AMORB.E.HONS.(UITM) (CHEMICAL, 2009)
80711NG BOON PINGB.APP.SC.(BRITISH COLUMBIA)(CHEMICAL, 2012)
79590 NUR AZRINI BINTI RAMLEE B.E.HONS.(UTM) (CHEMICAL, 2005) M.E (UTM)(CHEMICAL, 2009)
80590NUR HASHIMAH BINTI ALIAS
80735NUUR MOHAMAD FIRDAUS BIN MOHAMAD RASIDI
B.E.HONS.(UTM) (CHEMICAL-GAS, 2008) M.E.(UTM)(GAS, 2012)
B.E.HONS.(USM) (CHEMICAL, 2008)
80555ONG SENG HENGB.E.HONS.(MALAYA) (CHEMICAL, 2002)
79558PRISHAM NAIR GOPAL
80466RAYMOND DAYAN PIUS JAUA
80693REEZA FARHAN BIN RAMLAND ROSS
B.E.HONS.(NOTTINGHAM) (CHEMICALENVIRONMENTAL, 2011) M.SC.(HERIOT WATT) (SUSTAINABILITY ENRG., 2012)
M.E.HONS.(BIRMINGHAM) (CHEMICAL, 2014)
B.E.HONS.(MALAYA) (CHEMICAL, 2010)
80659SIM LAI HAHB.E.HONS.(UTM) (CHEMICAL, 2004)
80543SITI NUR FADHILAH BINTI ZAINUDIN B.E.HONS.(UKM) (BIOCHEMICAL, 2009) M.SC.(UKM)(CHEMICAL & PROCESS, 2014)
80731 SURESH A/L SUKUMARAN B.E.HONS.(UTP) (CHEMICAL, 2011)
KEJURUTERAAN MEKANIKAL
79552ABDUL HADI BIN ALIAS
B.E.HONS.(UTP) (MECHANICAL, 2010) M.SC.(UTM)(PETROLEUM, 2015)
80650 AHMAD AKMAL BIN CHE MOHAMED B.E.HONS.(UTP) (MECHANICAL, 2011)
80164 AHMAD AKMAL SHAH BIN SARUN B.E.HONS.(UPM) (MECHANICAL, 2010)
80515AHMAD HILMI BIN ZULKIPLI B.E.HONS.(UTP) (MECHANICAL, 2012)
80561AHMAD NIZAM BIN JAMALUDIN B.E.HONS.(UPM) (MECHANICAL/SYSTEM, 1994) M.E.(UPM) (INNOVATION & ENRG. DESIGN, 2014)
80717 AHMAD THIBRI BIN MASHRI B.E.HONS.(UITM) (MECHANICAL, 2011)
79582AIZAT SYAFIQ BIN ZEINUDDIN B.E.HONS.(UKM) (MECHANICAL, 2011)
79588AMIR SAFWAN ANUAR B.E.HONS.(UNSW) (MECHANICAL, 2014)
80745AMMAR ZARIR BIN HARISON B.E.(TOYAMA) (MECHANICAL & INTELLECTUAL SYSTEMS, 2009)
80508ATHIQURRAHMAN BIN ABDUL HAMID B.E.HONS.(UNITEN) (MECHANICAL, 2014) 80192CHAU SHEN SHUNGB.E.HONS.(UTAR) (MECHANICAL, 2011)
80569CHEE HON CHEONG, ALEXANDER B.E.HONS.(UTHM) (MECHANICAL, 2003)
79585CHEW HAN JIEB.E.HONS.(MALAYA) (MECHANICAL, 2010)
Note: Remaining list of the “PERMOHONAN MENJADI AHLI SISWAZAH, PERMOHONAN MENJADI AHLI ‘INCORPORATED’ & PERMOHONAN MENJADI AHLI ‘AFFILIATE’ would be published in the December 2016 issue. For the list of approved “ADMISSION TO THE GRADE OF STUDENT”, please refer to IEM web portal at http://www.myiem.org.my.