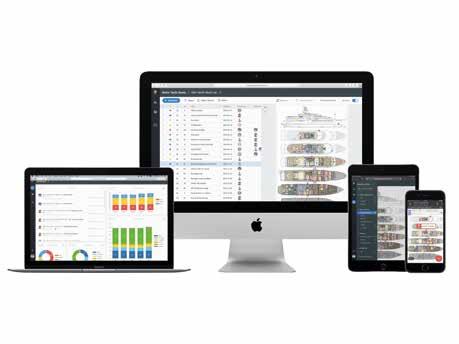
6 minute read
Why the human element matters
OPINION
with Max Stott
WHY THE HUMAN ELEMENT MATTERS
The physical toll of building, maintaining and operating yachts under current conditions is just not sustainable, says Max Stott.
This summer has seen an unusual number of fires on superyachts, causing them to sink or run aground. The overwhelming majority of stakeholders are pointing towards lithium batteries as being the source of many of these incidents, even when there’s no hard evidence to back this up.
Lithium batteries are a problem, and they do sometimes cause fires, but in the absence of official reports, they are also being used as an excuse to avoid taking a step back and looking at the bigger picture. There’s a human element to the superyacht industry that has long been disregarded, and it wouldn’t be wildly inappropriate to suggest that this is consequently having some effect on the condition of the fleet.
I’m not saying stakeholders are to blame, but I do think more consideration should be given to the people who are literally working tooth and nail to keep the industry afloat. The number one justification for the very existence of these giant hunks of floating machinery is that they provide a lot of costly work for a lot of people who will gladly make a career out of cleaning bilges, applying antifoul and fairing surfaces. The market is tightening daily and you could argue that this increase in pressure on the industry’s already struggling workforce is starting to cause some cracks in the system.
On the crew side, you have an increase in the number of charters per season and an increase in the number of superyachts joining the fleet, but there’s not enough quality crew to sustain these increases. Superyacht crews are trained to pass exams, not to maintain superyachts. They often work 18-hour days, live in tiny cabins and are under a lot of pressure to meet the owner’s demands. Many yachts are a breeding ground for mistakes and miscalculations.
Following on from the global pandemic, the world is now staring down the barrel of an economic recession – another event that will hit the poorest the hardest. Statistics have revealed that hospitality workers are struggling more with mentalhealth problems now than they were during the height of the pandemic. A new survey by Censuswide and hospitality marketing firm Flipdish reveals that 80 per cent of hospitality staff had experienced mental-health issues as a result of their work, with antisocial hours and performance pressure cited as the cause. It has already been proven that this statistic is being reflected in the superyacht industry. [See Jack Hogan’s article ‘Quay Crew and MHSS publish stark crew mental health report’ on Superyacht News.]
If a refit project is condensed while it’s in a shipyard, and the vessel is having to go straight out for a charter, then it’s the crew who will have to deal with any issue out at sea, but that doesn’t necessarily mean any issue is their fault. People cause accidents, but when incidents occur there’s often a long line of those who share the blame. The industry, unfortunately, tends to prefer short-term profit to pausing and making calculated moves that consider the long-term effects.
On the shoreside, workers in shipyards are being pushed to make compromises and find solutions for ludicrous designs that favour extravagance over seaworthiness and functionality. This problem isn’t exclusive to yachting. Renowned car companies such as Chevrolet have had to recall vehicles due to the risk of their high-voltage battery packs catching fire. The bid to become sleeker, slimmer and higher performing pushes manufacturers to come up with more compact designs that ultimately have a higher risk of causing an accident.
There’s a serious lack of appreciation and recognition for all the workers and craftsmen in the superyacht industry, especially towards junior crew and blue-collar workers at the coalface. They are the ones who are bearing the brunt, working ridiculously long hours and putting themselves at risk while trying to meet tight deadlines. These are the people who are paying for the lack of foresight from those above them.
One dreads to think how many millions of pounds worth of assets have gone up in smoke or sunk to the bottom of the ocean, or how much oil and fuel have seeped into the ecosystem over the past couple of months. But when we see accidents proliferating, there should be more consideration for the human element of the industry and the lives it is putting at risk. The boundaries have been pushed far enough. MS
Why the superyacht industry is turning to Pinpoint Works for refit and maintenance planning.
There’s no doubt the superyacht industry is booming, and during this growth period of the global fleet, demands on yacht service, maintenance and refit resources are increasing.
To adapt, it will be imperative for the industry to revisit and revise practical working processes. This shift will be particularly important for companies reluctant to swap to more modern, efficient practices – ‘adapt or die’, as the saying goes.
With most yachts undergoing a shipyard maintenance period annually or biannually, substantial time and money are dedicated to the upkeep and preventative maintenance in their lifetime. Terms such as ‘lifecycle management’ – how to optimise each stage of a yacht’s life – will be increasingly heard in conversations as the industry searches for more pragmatic yacht-management practices.
Given the extensive material and personnel resource allocation for these projects, Pinpoint Works’ founder James Stockdale sums it up: “Seamless worklist management is critical to successful communication and collaboration between specialist teams. It’s become an essential commodity of the superyacht industry.”
So how can processes be improved to facilitate effective communication and collaboration during these refits and shipyard periods to optimise both the asset and our time?
Old ways of working with notepads, Excel sheets and email chains are still regularly being used because of a reluctance to move to more advanced systems. But, in this digital age, these methods are outdated, unprofessional and costly due to their inherent inefficiencies. Pinpoint Works was created to challenge these methods by improving communication and organisation of tasks through a simple and user-friendly platform – a true upgrade in worklist management for the yachting industry.
The chief officer on board 75m M/Y Huntress says of his experience with Pinpoint Works: “Pinpoint has been an absolute game-changer on board Huntress, and I believe it has revolutionised the yachting industry in terms of monitoring shipyard works, general ships’ maintenance and helping departments communicate efficiently and effectively on board.”
By using Pinpoint Works to define a detailed scope of works before a refit or general yard period, stakeholders can document, facilitate and coordinate the required work using a vessel’s GA (general arrangement), creating a realtime, interactive worklist. One simple platform replaces the historical ways of working.
Adding photos, videos and documents helps to clarify the detail with a precise location of works on the yacht’s unique GA, making it clear to contractors where they’re needed when on board.
This scope of work can be used to source reliable cost comparisons between shipyards, allowing for better budgeting. Keeping communication open and transparent means crew, management, owners, contractors and project managers can work together more efficiently.
Pinpoint Works has been adopted and implemented by more than 350 superyachts, hundreds of smaller pleasure yachts and dozens of companies within the superyacht industry, including some of the largest, most prestigious shipyards in the world.
There are numerous benefits of having one place where everyone can see up-to-date information in real time. However, the time/cost savings based on improved communication and fast implementation make using Pinpoint Works a worthy investment for captains, operational crew and project managers.
If you’re not already leveraging an intuitive digital solution to project manage your refits and shipyard periods, it’s time to get started.
Pinpoint Works uses the latest technology in web and mobile apps and can be used during all lifecycles of a yacht: build, warranty, operation, refit, repaint and surveys.