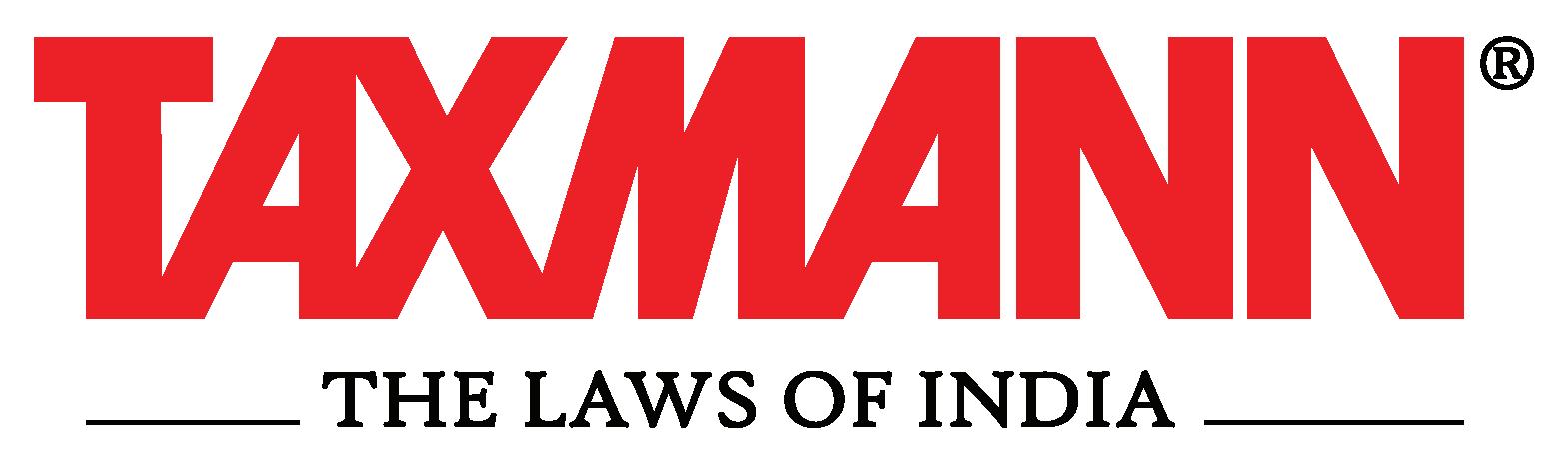
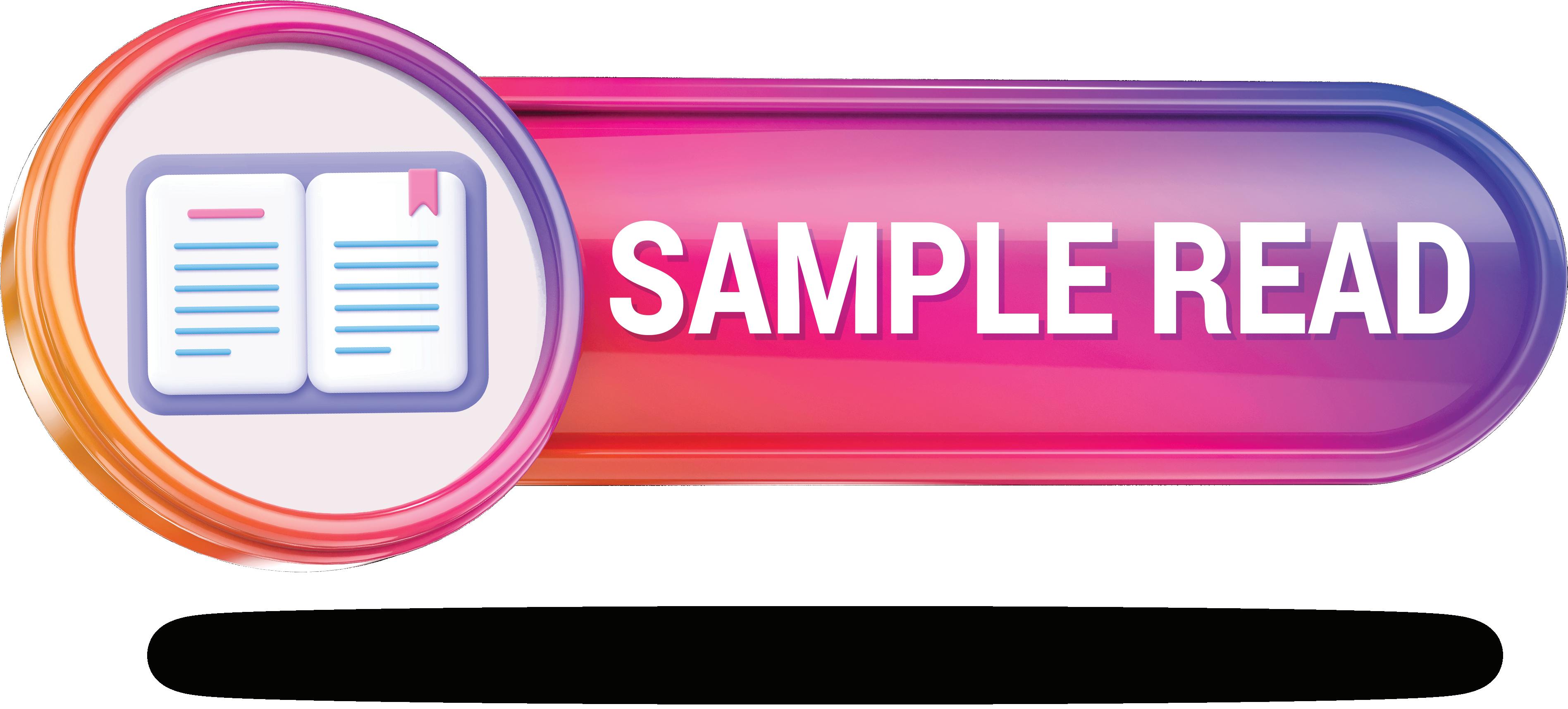
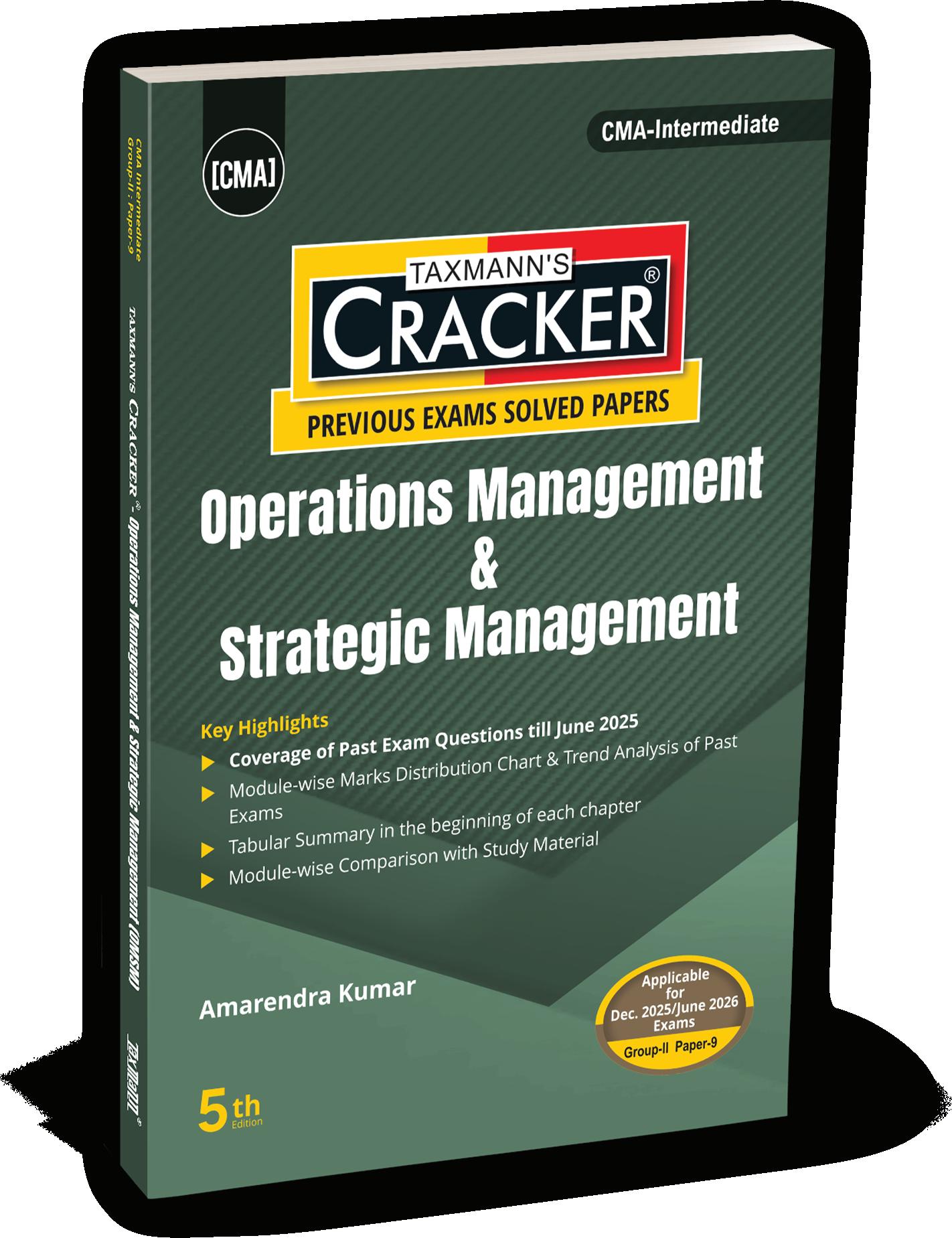
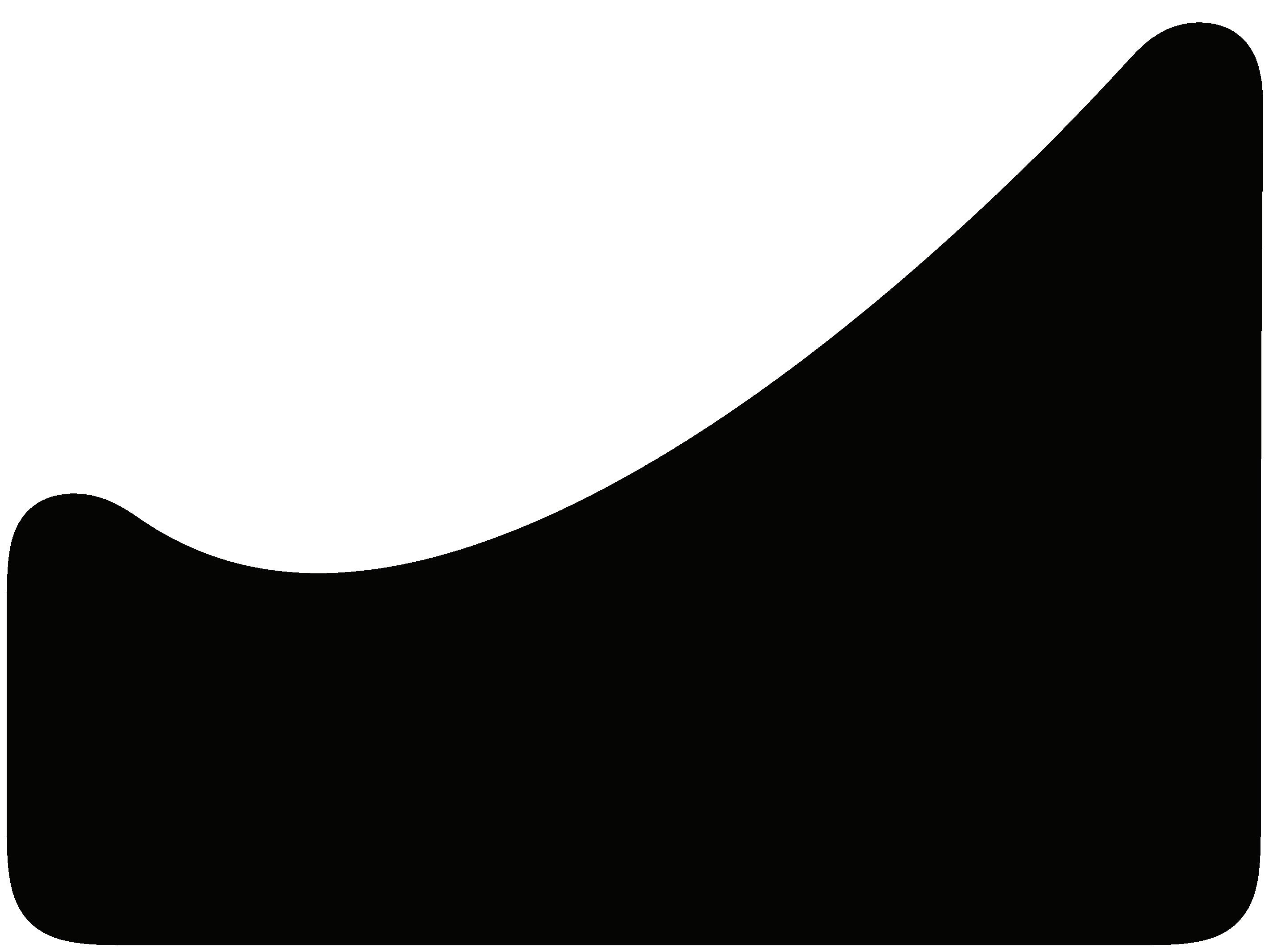
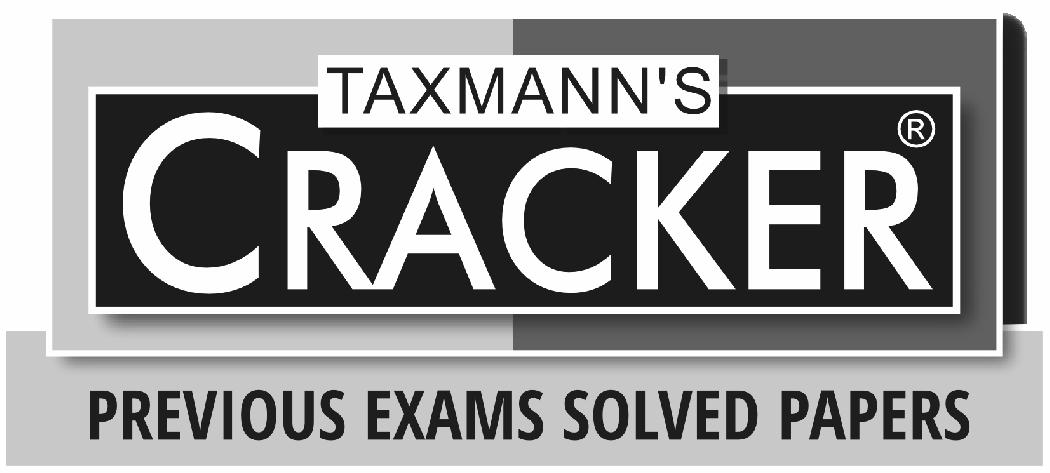
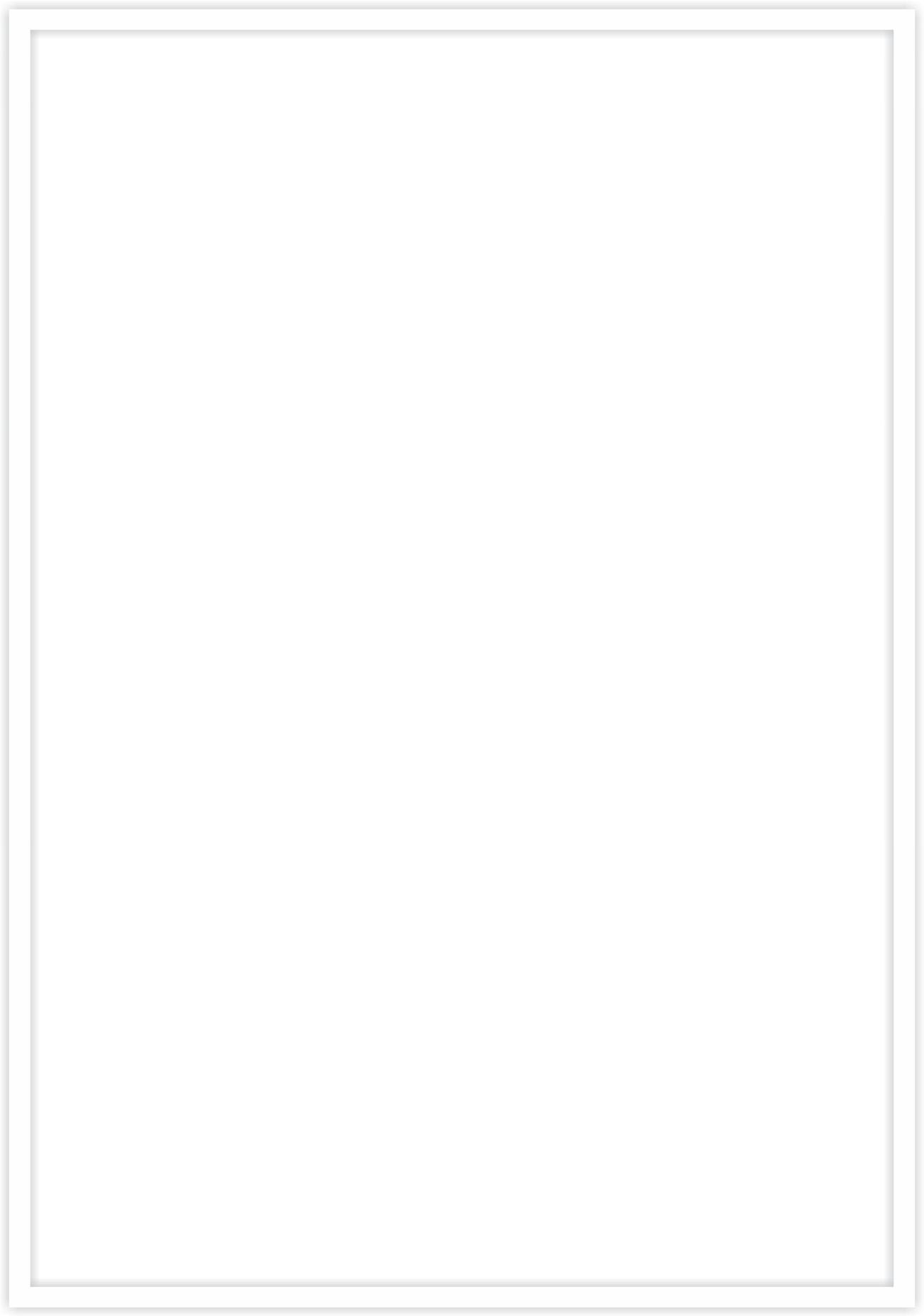
© All rights reserved
Price : ` 375
Fifth Edition : June 2025
Published by :
Taxmann Publications (P.) Ltd.
Sales & Marketing :
59/32, New Rohtak Road, New Delhi-110 005 India
Phone : +91-11-45562222
Website : www.taxmann.com
E-mail : sales@taxmann.com
Regd. Office : 21/35, West Punjabi Bagh, New Delhi-110 026 India
Printed at :
Tan Prints (India) Pvt. Ltd.
44 Km. Mile Stone, National Highway, Rohtak Road Village Rohad, Distt. Jhajjar (Haryana) India
E-mail : sales@tanprints.com
Disclaimer
Every effort has been made to avoid errors or omissions in this publication. In spite of this, errors may creep in. Any mistake, error or discrepancy noted may be brought to our notice which shall be taken care of in the next edition. It is notified that neither the publisher nor the author or seller will be responsible for any damage or loss of action to any one, of any kind, in any manner, therefrom. No part of this book may be reproduced or copied in any form or by any means [graphic, electronic or mechanical, including photocopying, recording, taping, or information retrieval systems] or reproduced on any disc, tape, perforated media or other information storage device, etc., without the written permission of the publishers. Breach of this condition is liable for legal action.
For binding mistake, misprints or for missing pages, etc., the publisher’s liability is limited to replacement within seven days of purchase by similar edition. All expenses in this connection are to be borne by the purchaser. All disputes are subject to Delhi jurisdiction only.
Exams Trend Analysis
Comparison with Study Material
SECTION B
STRATEGIC MANAGEMENT

PRODUCTIVITY MANAGEMENT AND QUALITY MANAGEMENT
A Quick Review
The I.L.O. publication, “Higher Productivity in Manufacturing Industries” has defined productivity as the ratio between output of wealth and the input of resources used in the process of production.
The European Productivity Agency (EPA) has defined productivity as follows: “Productivity is an attitude of mind. It is a mentality of progress of the constant improvement of that which exists. It is the certainty of being able to do better today than yesterday, and continuously. It is the constant adaptation of economic and social life to changing conditions, it is a condition, it is a continual effort to apply new techniques and methods, it is the faith in human progress.”
The term productivity can be defined in two ways. In simple terms, productivity is defined as a ratio between the output and input – between what is produced and what is required to produce it. A continual effort to apply new techniques and methods, it ids the faith in human progress.
Productivity
= Output obtained
Inputs consumed
In a broader sense, productivity is defined as a measure of how well resources are brought together in organisations and utilized for accomplishing a set of results.
Productivity
=
Performance achieved
Resources consumed
Effectiveness
Effectiveness
=
Efficiency
= Target achieved
Target achievable
Actual consumption
Input efficiency
=
Desired or Standard consumption
The importance of the concept of productivity can be viewed from the following points:
1. To beat the competition: It is an age of cut-throat competition. There may be other commodities which can serve as the substitutes of the terms ‘product’ and can attract the consumers’ purchasing power. The rm whose
SECTION A : OPERATIONS MANAGEMENT
productivity is higher can only beat the competition and can exist in the market for long.
2. Guide to Management: The productivity indices are very useful for the management and can be used for different purposes. These indices can serve as a valuable guide to the management for improving the performance of its enterprise. The productivity measures can be used for the following purposes:
(
a) Strategic: With the help of productivity indices, the ef ciency of different rms can be measured, analysed and compared. The necessary steps can be taken to improve the productiveness of the rm taking in view the productiveness of the other competitive rms.
(
b) Tactical: Different units or the sectors of the rm can also be compared as regards to their productivity and the productivity of the less productive units or sectors can be improved.
(
c) Planning: A rm uses different inputs in producing the goods. A comparison of relative bene ts accruing from the use of different inputs can be had and the most bene cial input can be used in production. It helps the management to plan for the future.
(
d) Administration: Productivity indices indicate the progress of the rm over a period of years. The productivity of different inputs, including labour, can be measured individually. The individual productivity indices help the management in bargaining with the labour leaders, trade unions and the Government in case of labour disputes regarding welfare activities. Thus administration can be improved with the help of productivity indices.
3. An Indicator of Progress: In economically backward countries, productivity movement is basic aspect of progress. It implies the development of an attitude of mind and a constant urge to better, cheaper, quicker and safer ways of doing a job, manufacturing a product and providing a service. In an urge to improve the productivity, new inventions take place. This productivity is an aspect of basic progress.
4. Maximum utilization of Scarce Resources: In order to provide the articles or commodities to the consumers at the lowest possible cost, the productivity urges to utilise the available resources to the maximum to the satisfaction of customers. The productivity processes and techniques are designed to facilitate more ef cient work involving less fatigue to workers by improvements in the layout of the plant and work, better working environment and simpli cation of works.
5. Key to National Prosperity: The productivity, in fact, has become the synonymous to progress. Higher productivity is an index of more production with the same inputs at lower cost. It enables industry to offer goods to the general public at cheaper rates and results in expansion of markets. The working conditions and wages of workers will improve and industrialists too will get larger pro ts. Thus higher productivity is the key to national prosperity. The secrets of Japan and Western countries’ prosperity lie in increased productivity.
6. Prosperity to Labour: The higher productivity is a boon to labour also. It brings improved working conditions, better wages and salaries to workers, better labour welfare activities to labourers. Thus their standard of living is improved.
QUALITY CERTIFICATION
Many international businesses recognize the importance of quality certification. The EU, in 1987, established ISO [International Organization for Standardization] 9000 certification.
Two of the most well known of these are ISO 9000 and ISO 14,000.
ISO 9000 pertains to quality management. It concerns what an organization does to ensure that its products or services are suitable to customers expectations.
ISO 14,000 concerns minimization of harmful effects to the environment caused by its operations.
Both ISO 9000 and ISO 14000 are related to an organization processes rather than its products and services and they stress continual improvement.
ISO 9000 is composed of the national standard bodies of 91 countries. About 90 countries have adopted ISO 9000 as national standards. This certification is intended to promote the idea of quality at every level in the organisation.
ISO certification is an elaborate and expensive process. Any firm seeking this certification needs to document how its workers perform every function that affects quality and install mechanisms to ensure that, they follow on expected lines.
ISO 9000 certification entails a complex analysis of management systems and procedures. Rather than judging the quality of a particular product.
ISO 9000 evaluates the management of the entire manufacturing process, from purchasing, to design, to training. A firm that seeks this certification must fill out a report and then be certified by a team of independent auditors.
With certification comes registration in an ISO directory, that firms seeking suppliers can refer to, for a list of certified companies. They are generally given preference over unregistered companies.
There are essentially five standards associated with the ISO 9000 series. The series, if we place them on a continuum, would range from design and development through procurement, production, installation and servicing. Whereas, ISO 900X3 and 9004 only establish guidelines for operation, ISO 9001, 9002 and 9003 are well-defined standards.
QUALITY SYSTEM
9001 Model for Quality Assurance in Design, Production, Installation and Servicing. (To be used when conformance to specified requirements is to be assured by the supplier during several stages that may include design/ development, production, installation and servicing).
SECTION A : OPERATIONS MANAGEMENT
9002 Model for Quality Assurance in Production and Installation. (To be used when conformance to specified requirements is to be assured by the supplier during production and installation). 9003 Model for Quality Assurance in Final Inspection Test. (To be used when conformance to specified requirements is to be assured by the supplier solely at final inspection and test).
GUIDELINES FOR USE
9000 Quality Management and Quality Assurance Standards – Guidelines for Selection and Use.
9004 Quality Management and Quality System Elements – Guidelines.
ISO 9000 Standards, their Areas of Application in Production Flow and Guidelines for Use
PAST EXAMINATION QUESTIONS
OBJECTIVE QUESTIONS
MULTIPLE CHOICE QUESTIONS
Q. 1 Which one of the following ISO standard evaluates the management of the entire manufacturing process, from purchasing to design to training
(a) ISO 9000
(b) ISO 9001
(c) ISO 9003
(
d) ISO 14000
Ans. (b) ISO 9001
Q. 2 ISO Standards are reviewed every:
(
a) Year
(b) 2 Year
(
c) 5 Years
(d) 10 Years
Ans. (c) 5 Years
[July 2023, 1 Mark]
[Dec. 2023, 2 Marks]
Q. 3 Which one of the following ISO Standards evaluates the Management of the entire manufacturing process, from purchasing to design, to training?
(a) ISO 9004
(b) ISO 9003
(c) ISO 9000
(d) ISO 9001
Ans. (d) ISO 9001
[June 2024, 2 Marks]
Q. 4 A Zinc of ZOS Ltd. manufactures product Z of 30 units per shift of 8 hours. If the Standard time per unit is 12 minutes, what is the productivity per shift of 8 hours?
(a) 60%
(b) 75%
(c) 80%
(d) 90% [June 2024, 2 Marks]
Ans. (b) 75%
Standard Qty. Produced in 8 Hrs = 60 × 8 = 40 units 12
Actual Qty. Produced = 30 units
Productivity = 30 × 100 = 75% 40
THEORY QUESTIONS
Q. 1 Kindly mention the Principles of Total Quality. [Dec. 2013, 2 Marks]
Ans.
1. Quality oriented management
2. Focus on customer
3. Involving (entire) work force
4. Continuous improvement
5. Supplier Partnership
6. Measuring performance
Q. 2 What are the advantages of KAIZEN Technique? [Dec. 2013, 4 Marks]
Ans. Kaizen is focused on making small improvements on a continuous basis. In simple terms Kaizen is Japanese for ‘a change for better’, which results in ‘continuous improvement’.
The advantages of KAIZEN are as follows:
1. Kaizen involves every employee in process of change mostly in small, incremental changes. It focuses on identifying problems at their own source, solving them at their own source, and changing standards to ensure the problem stays solved forever.
2. By involving employees they start looking about change at their environment to bring up results in their work area and improved morale as employee begins to nd work more enjoyable and easier.
3. Kaizen reduces waste in area such as employee skills, waiting time, transportation, worker motion, over production, excess in inventory, quality and process.
4. Kaizen improves product quality, use of capital, production capacity, communications, space utilization and employee retention.
5. Incorporation of visual action oriented tasks.
SECTION A : OPERATIONS MANAGEMENT
Q. 3 State the three models of Productivity Measurement. [Dec. 2013, 3 Marks]
Ans. The models of Productivity Measurement can be classified into three on the basis of the type and coverage of the output and input variables, (a) Ratio method (b) Production Function method (c) P-O-P method.
Q. 4 State the three levels of quality. [June 2014, 3 Marks]
Ans. Three levels of Quality:
1. Organization level: Satisfying requirements of external customers.
2. Process level: Meeting the needs of internal customers.
3. Performer level (job level or task design level): Meeting and maintaining the requirements of accuracy, completeness innovation, timeliness and cost.
Q. 5 Write the formula for Input Efficiency and Effectiveness. [Dec. 2014, 2 Marks]
Ans. Input efficiency = Actual consumption/Desired or standard consumptionEffectiveness = Target achieved/Target achievable.
Q. 6 State the Eight Most Common Benchmarking Errors. [Dec. 2014, 8 Marks]
Ans. The Eight Most Common Benchmarking Errors:
1. Lack of Self-Knowledge: Unless own operations are thoroughly analysed, the benchmarking efforts will not pay off. One has to know how things work in a company, how effective current processes are, and what factors are critical. That’s why internal benchmarking is an important rst step.
2. Benchmarking everything: Be selective. Benchmarking another company’s employee food service will usually not be worth the time, energy, and cost. Own TQM effort as a whole will point out the areas where benchmarking is most likely to pay off.
3. Benchmarking projects are broad instead of being focused: The more speci c the project, the easier it is and the more likely it will generate useful ideas. Benchmark a successful company’s hiring procedures, not their entire human resources operations. Focus on accounts receivable handling, not the accounting department as a whole.
4. Benchmarking produces reports, not action: Studies have indicated that 50% of benchmarking projects result in no speci c changes. The process is not an academic exercise. It should be geared toward generating and implementing actual changes.
5. Benchmarking is not continuous: Benchmarking is a process. Even before one reaches the benchmark one has set, one should take another look at partner’s performance, or at other companies. New goals should be established and new techniques adopted. The process never ends.
6. Looking at the numbers, not the issues; While the measures are important, they are not the heart of the process. At some companies, benchmarking is used to set goals, but not to generate the important changes needed to meet them.
7. Participants are not motivated: Make sure benchmarking team members have the time to do the job. Even if the project is simply added on their regular jobs, make sure each has a stake in the success of the project. Benchmarking should not be considered as “busy work” to be assigned to a group of low-level employees.
Q. 7 What are the different approaches to overcome hurdles in the management of productivity improvements? [June 2015, 2 Marks]
Ans. The different approaches to overcome hurdles in the management of productivity improvements are as follows:
(a) Management by internal motivation (i.e., KAIZEN).
(b) Management by incentives.
(
c) Management by fear.
Q. 8 What is TQC and what are its principles? [June 2015, 5 Marks]
Ans. TQC is Total Quality Control, It is quality control and improvement from shop floors to board rooms. It is an effective system for integrating quality development, quality maintenance and quality improvement efforts of various groups in an organization.
Principles of Total Quality Control (TQC)
(1) Top management policies-Zero defects, continuous improvement etc.
(2) Quality control training for everyone.
(3) Quality at product/service design stage.
(4) Quality materials from suppliers.
(5) Quality control in production (SQC).
(6) Quality control in distribution, installation and usage.
Q. 9 Write a line to define the following terms with reference to measuring productivity:
( a ) Validity, ( b ) Completeness, ( c ) Compatibility, ( d ) Inclusiveness, (e) Timeliness, (f) Cost effectiveness, (g) Partial productivity [June 2015, 1 × 7 = 7 Marks]
Ans. Measuring Productivity:
Bain suggests that a good productivity measure should possess the following properties. The more closely the measurement meets these criteria, the more useful it is for improving productivity.
(a) Validity: It re ects accurately the changes in productivity.
(b) Completeness: It takes into consideration all components of both the output and the input for a given productivity ratio.
(c) Compatibility: It enables the accurate measurement of a productivity change between periods.
(d) Inclusiveness: It takes into account and measures separately the productivity of all activities.
SECTION A : OPERATIONS MANAGEMENT
(e) Timeliness: It ensures that data is provided soon enough for managerial action to be taken when problems arise.
(f) Cost effectiveness: It ensures that data is provided soon enough for managerial action to be taken when problems arise.
(g) Partial Productivity: This measures productivity of one factor or input, keeping other factors or inputs constant or unchanged.
Q. 10 Define Quality Triology under Total Quality Management. [Dec. 2015, 2 Marks]
Ans. Quality Triology: Under Total Quality Management quality takes a holistic approach to quality and his concept of quality revolves around what is called a quality trilogy, which is composed of:
(i) Quality planning,
(ii) Quality control, and
(iii) Quality improvement.
Q. 11 “Higher productivity has manifold advantages.” State these advantages. [Dec. 2015, 6 Marks]
Ans.: Higher productivity has manifold advantages:
A. To the Individual Concern:
(
a) Higher productivity means more wages directly to the piece-workers and more production bonus to all workers. It means satis ed staff and harmonious staff relations.
(
(
b) The factory earns more pro t because of the reduction in costs.
c) Continuous higher productivity may induce the management to reduce selling prices so that sales and production may increase.
B. To the Industry: Higher productivity in some concerns will enable less efficient firms to follow them for their own survival.
C. To the Government:
(a) Higher pro ts earned by factories will bring more revenue to the government by taxation.
(
b) Export trades may develop bringing more foreign exchange to the nation.
(c) Overall higher productivity will raise an all-round standard of labour.
Q. 12 Explain ‘Eight Steps Benchmarking Process’. [Dec. 2015, 6 Marks]
Ans. Eight Steps Benchmarking Process:
1. Select Benchmarking subject and appropriate team
2. Identify performance indicators and Drivers
3. Select Benchmark partners
4. Determine data collection method and collect data
5. Analyse performance gaps.
6. Communicate Findings and identify projects to close gaps
7. Implement plans and monitor results
8. Recalibrate benchmarks.
Q. 13 Write the formula for Input Efficiency. [June 2016, 2 Marks]
Ans. Input Efficiency = Actual consumption/Desired or standard consumption Effectiveness = Target achieved/Target achievable.
Q. 14 List the benefits of Benchmarking. [June 2016, 8 Marks]
Ans. Benefits of Benchmarking:
Benchmarking is particularly helpful in validating proposals for change. Benchmarking often results in creative imitation and the adoption of new practices that overcome previous industry barriers.
This search for diversity and for innovative breakthroughs, applied elsewhere is at the core of benchmarking bene ts.
By sharing information, all parties bene ts, because it is dif cult to excel in all activities.
Sharing information and data is often rst hurdle to be overcome in the Benchmarking process.
Do not, however, attempt benchmarking in areas in which trade secrets or sensitive information determines the outcome of the process.
Benchmarking, used in conjunction with other quality techniques or used alone, can in uence how an organisation operates.
If the search for “Best”, or just “Better” practices is performed correctly, then the likelihood of successful outcomes is quite high.
Q. 15 List causes of low productivity in the Indian context. [Dec. 2016, 2 Marks]
Ans.
In the Indian context, the causes of low productivity have their origin in two distinct sources.
The rst category consists of the exogenous or external factors like shortages of essential inputs-power, raw materials, transport facilities etc. - over which the management of an enterprise has little or no control.
The second basket contains the endogenous or internal factors mainly in the form of system de ciencies preventing the optimum utilisation of resources.
Q. 16 Identify the objectives of Quality Control and also Quality requirements from customer point of view. [June 2017, 2 + 5 = 7 Marks]
Ans. Objectives of quality control are to provide products/services which are dependable, satisfactory and economical.
Quality requirements from customer point of view:
1. Conformance to speci cations (requirements).
2. Value for money