2024 SPOTLIGHT!

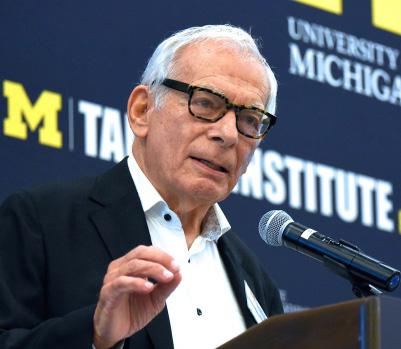
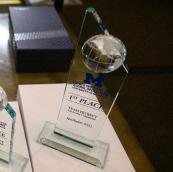
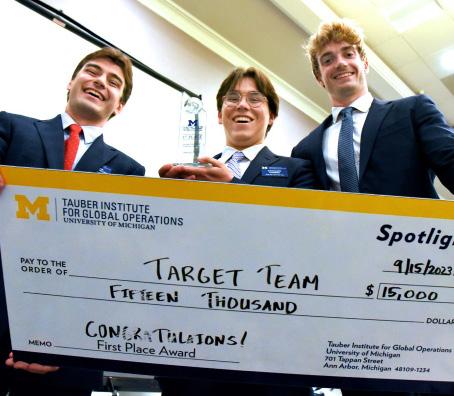

Greetings, and welcome to the 2024 Spotlight! Project Showcase and Scholarship Competition.
This year marks an incredible 31 years for the Tauber Institute for Global Operations continuing impactful work in developing new leaders for operations and supply chain careers. In addition to students completing challenging and rewarding Tauber Industry projects, students took part in our Leadership Advantage modules, participated in onsite industry experiences and factory tours, and participated in teamwork training to jump start preparation for their leadership journeys.
This year we also embrace new beginnings as we bid farewell to the leadership of Larry Seiford (CoE) and Hyun-Soo Ahn (RSB), who have been integral in forwarding the vision and impact of the Tauber Institute. As new co-Directors we (Saif and Joline) are honored and humbled to be following in the footsteps of Larry and Hyun-Soo and excited to be part of the next stage of development of the Tauber Institute.
Industry partners also strive for new beginnings, as they continue to work through disruptions to supply chains, including increasing logistical challenges, difficult demand forecasting, changing consumer attitudes, and cost pressures, all while undergoing digital transformation and restructuring. Tauber team projects support specific challenges our industry partners faced. The outcomes of the projects resulted in solutions that will drive measurable value well beyond the summer project. As you will see during the Spotlight! showcase, the results are both transformative to our student’s future careers and highly impactful for our industry partners. We are incredibly grateful to our industry partners who have invested in our students, supported these projects, and continue to raise the bar on what an academic and industry collaboration can produce.
This guide documents student teams’ regional and global impact with executive summaries describing the challenges, methodology, and results from each sponsored project. The depth and breadth of our students’ project outcomes reflect the demands faced by operations’ functions in a dynamic world. We hope these executive summaries will provide insight into the University of Michigan’s solid global reputation and partnerships with leading companies who know our students can be called upon to solve some of their most challenging problems.
HERE'S TO CELEBRATING NEW BEGINNINGS,
Goff Smith Co-Director of the Joel D. Tauber Institute
Seth Bonder Collegiate Professor of Industrial and Operations Engineering College of Engineering
JOLINE UICHANCO
Ford Motor Company Business Co-Director of the Joel D. Tauber Institute
Associate Professor of Technology and Operations
Ross School of Business
Managing Director
Head of Industry Partnerships
Tauber Institute for Global Operations
Santa J. Ono President
3190 Ruthven Building
1109 Geddes Avenue
Ann Arbor, Michigan 48109-1079 TEL: 734 764-6270
August 26, 2024
Welcome to the 31st Anniversary of the Spotlight! Team Projects Showcase and Scholarship Competition with the Tauber Institute for Global Operations at the University of Michigan. It’s a privilege to greet you all once again as we come together to celebrate the incredible achievements of our students and the lasting impact of this remarkable program.
The University of Michigan has always been committed to harnessing our strengths in research and education to serve society. The Tauber Institute exemplifies this mission by fostering collaboration between our College of Engineering and the Stephen M. Ross School of Business, driving innovation that extends far beyond our campus. By bringing together brilliant minds from different disciplines, the Tauber Institute continues to deliver solutions to complex challenges, demonstrating that the most effective answers emerge from collective effort.
This year’s projects, developed in partnership with industry leaders, exemplify Tauber’s enduring legacy of excellence. Our students continue to identify potential savings in the millions across a diverse range of initiatives. Their work not only drives substantial operational improvements but also further solidifies our standing as a world leader in innovation and impact.
Over the past three decades, the Tauber Institute has proven its value time and again, both to our students and to the broader community. The skills and experiences our students gain through these projects equip them for success as they transition into their professional careers, while the insights and solutions they generate have a lasting effect on the organizations they serve.
As we celebrate this milestone, I encourage you to reflect on the Tauber Institute’s continued growth and the extraordinary contributions of our alumni, who carry forward the knowledge and drive they developed here at Michigan. Their achievements serve as a testament to the power of cross-disciplinary collaboration and the enduring impact of this unique program.
I want to extend my heartfelt gratitude to Joel D. Tauber for his visionary leadership in establishing this partnership, as well as to our dedicated company partners whose support is vital to the ongoing success of the Tauber Institute. Your engagement and collaboration with our students are instrumental in shaping the next generation of engineers, entrepreneurs, and leaders.
The stories and projects presented in this showcase are a powerful reminder of what we can achieve when we unite our strengths. I hope you find them as inspiring as I do.
Sincerely,
Santa J. Ono President
“When I was honored with the naming of the Tauber Institute back in 1995, I never dreamed it would become the vibrant global network of operations professionals and thoughtleaders that it is today. Thank you all for your contributions to this community that inspires me with its energy and its eagerness to embrace new ideas.”
- Joel Tauber
It all began when a gathering of business advisors identified a key category of employees missing from their organizations: trained professionals who understand both the business and engineering aspects of manufacturing.
As a result of that discussion, the University of Michigan’s Ross School of Business and College of Engineering formed a new cross-unit collaboration. Named for benefactor and U-M alumnus Joel Tauber, the Tauber Institute was born — and immediately began to innovate.
Faculty in the two schools created new courses to deliver an integrated education addressing the challenges of modern manufacturing, with an emphasis on leadership skills.
The Tauber Institute sought every opportunity to immerse students in real-world experiences — leading to the development of Tauber team projects and the annual Spotlight! event, where students compete for academic scholarships through their presentations about their work at top companies across the U.S. and around the world.
The Tauber Institute has enjoyed many accolades — including receiving the UPS George D. Smith Prize for effective education in the fields of operations research, management science, and analytics. But a truer measure of Tauber’s success is that its graduates quickly secure rewarding employment, making an immediate impact in their respective companies, and rising to positions of authority.
Tauber Institute students are admitted through either the College of Engineering or the Stephen M. Ross School of Business. They bring with them significant experience in fields such as product engineering, manufacturing, supply chain, and consulting. Most Tauber students also have undergraduate training in engineering or other technical fields. They have made a substantial commitment to careers in operations or supply chain management and pursue an education specifically designed to meet the needs of today’s firms.
ALL TAUBER STUDENTS ARE ENROLLED IN ONE OF THE FOLLOWING DEGREE PROGRAMS:
BTS (BBA + TAUBER + MASTER OF SUPPLY CHAIN MANAGEMENT)
This 5th year master’s degree program utilizes the Tauber Institute to bridge the BBA with a Master of Supply Chain Management (MSCM) degree. The STEMcertified, 10-month MSCM program offers a comprehensive curriculum focused on end-to-end, global supply chain management.
MASTER OF BUSINESS ADMINISTRATION (MBA)
This two-year program prepares students to accept general management leadership positions. The Tauber program includes a sequence of operations management, supply chain, and manufacturing-related engineering courses.
ENGINEERING GLOBAL LEADERSHIP HONORS (EGL)
This five-year honors program prepares students to enter a variety of firms as engineers, while giving them the necessary management skills to quickly assume business leadership roles. A highly valued element of this program is a cultural concentration in a global region of choice. The EGL program leads to both a BSE and MSE.
ENGINEERING GRADUATE PROGRAMS (EGP)
A graduate-level engineering degree program that, coupled with Tauber Insitute requirements, provides intensive course work in operations and manufacturing technologies paired with business elective courses. EGP students are pursuing MEng, MSE, PhD, or Doctor of Engineering degrees.
The Spotlight! Project Showcase and Scholarship Competition is one way to introduce your company, culture, and fulltime opportunites to the Tauber Institute’s supremely qualified candidates. Some additional recruitment opportunities are listed below:
• Opportunities to work with the Tauber Institute to share your company's culture and values and to showcase career opportunities in operations and supply chain management.
• Opportunities to host an industry experience, participate in a Speaker Series, participate at our Global Operations Conference, etc.
• Coffee conversations and opportunities to connect with current students.
• Access to post job opportunities on the institute’s website, accessed by current students as well as our expanding network of 1500+ alumni.
• A connection to career centers and employment events at the College of Engineering and the Ross School of Business.
• Connect with the Tauber Institute Team to explore more opportunities to engage.
Team projects are just one way that Tauber students distinguish themselves from other business and engineering graduates. Tauber programs and courses also enhance their employability:
› The LeadershipAdvantageSM program of learning modules and workshops emphasizes leading and influencing an organization through collaboration, creativity, communication, and analytics.
› The Tauber Leadership Speaker Series invites highlevel executives to share insights with students about their careers, the qualities needed in today’s global economy for strong leadership, and tangible steps students can take to achieve excellence in their own career paths.
› Facility assessments/industry partner experiences provide students valuable insights and learning into real world application of operations and applied technology. Students are provided exposure to plant audits, agile software, and various manufacturing/ operations/agile environments across industries.
› The Global Operations Conference brings leaders in industry and academia together to strategize new ways to advance the practice of operations worldwide.
› The Leadership Forum allows Tauber students to learn about ethical leadership directly from current leaders in operations from top global firms.
Many Tauber students assume leadership roles in organizing the Global Operations Conference, Leadership Forum, Industry Panel, and Tauber Leadership Speaker Series, gaining valuable experience in the complexities of event planning and developing rapport with the seasoned executives they bring to campus. Student groups plan Tauber’s Community Service Day and organize networking events, and Student Advisory Board members work closely with Tauber leadership to strive for continuous improvement in our own operations
AMY MCLAUGHLIN 3M Company, Senior Vice President, Enterprise Customer Operations
BRIAN TAUBER BLT Ventures LLC, CEO
SHARON PFEUFFER
DTE Energy, Vice President of Distribution Engineering and Construction
JOANNE RZEPPA Amazon.com, Inc., VP, NASC Operations
JASON CLARK
The Boeing Company, Vice President, Boeing Commercial Airplane, Fabrication and Supply Chain Engineering
JORGE RAMIREZ
General Motors Company, Global Director and Chief Manufacturing Cybersecurity Officer
DAVIS American Industrial Partners, Partner
WEISS ConAgra Brands, Senior Vice President, Supply Chain
JASKIRAT SOHI
Howmet Aerospace, Global Product Integrity and Warranty Manager
Kearney Inc., Partner and Americas Lead, Automotive and Industrial Practice
The Industry Advisory Board (IAB) offers advisory guidance and support consistent with the Institute's mission and objectives. Spanning many industries from tech to non-profit, manufacturing and consulting, the IAB actively assists the institute in achieving its goals through sponsoring Tauber projects, lending industry insights, supporting Tauber events and scholarships, and providing pathways for full time career opportunities.
THANK YOU, SHARON!
A very special thank you to Sharon Pfeuffer (DTE Energy) for her many years of service on the Tauber Institute's Industry Advisory board, her close partnership, and her dedication to our student's multidisciplinary education through Tauber projects.
The Tauber Institute wishes you the best in your retirement.
Receive access to highly-talented, exceptionally-prepared candidates to solve complex operational and supply chain challenges facing the industry today. Our students are thought leaders who embrace innovation and industry disruption. Projects address critical needs and realize substantial savings and/or operational efficiencies.
For more information:
Anne Partington (aparting@umich.edu) or Mary Crosby (marcros@umich.edu)
the date: February 20-21, 2025
Hosted by the Tauber Institute for Global Operations, this year’s conference will focus on the theme of “Tech-Driven Transformation: Revolutionizing Operations for the Future.” The conference will consist of networking opportunities, a case competition, product demos, and expert panels.
Tauber Colloquium Kresge Hall Ross School of Business
Project Showcase and Scholarship Competition
Today's global
is nothing like it was thirty years ago.
The thinking shouldn't be either.
The world of business has changed. New ways of thinking and new leaders are needed. It's why the Tauber Institute for Global Operations at the University of Michigan was created. Today's leaders must manage the larger scope of operations, from the plant floor to the boardroom. This kind of leader doesn't just happen. The Tauber Institute develops and delivers superior talent utilizing the strengths of Michigan's top-ranked business and engineering schools overlaid with a comprehensive leadership development program. Combined with strong support and input from industry, the Tauber Institute for Global Operations has become one of the premier multidisciplinary operations programs in the world.
You're invited to put the power of Tauber Institute thinking to work for your business as a sponsoring company.
To find out more, visit www.Tauber.umich.edu
OVER 730 PROJECTS OVER 150 LEADING PARTNERS ACROSS EVERY INDUSTRY SECTOR
Tauber team projects provide students with opportunities to tackle operations-related challenges at top companies. Over the summer, 40 business and engineering students worked on 17 team projects sponsored by 13 global firms.
Harnieka Rachmala Master of Business Administration
PROJECT SPONSOR:
Gustavo Frattini – Advanced Manufacturing Engineering
Paul Seay – Head of Advanced Manufacturing Engineering
Ira Yun Master of Business Administration
FACULTY ADVISORS:
Damian Beil – Ross School of Business
Judy Jin – College of Engineering
AMAZON ROBOTICS (AR) is the division of Amazon.com Inc. responsible for developing and providing robotic automation to empower a more efficient and consistent customer experience through automating Amazon’s overall operation process in fulfillment and delivery. With the Covid-19 pandemic highlighting the importance of Amazon in customers' lives, the company recognizes the need to continually innovate its complex logistical infrastructure to fulfill customers' needs. Consequently, Amazon Operations faces the challenge of shifting from high-volume to high-mix production, which requires increased flexibility and efficiency. To address some of these challenges, Amazon has developed its first Autonomous Mobile Robot, Proteus.
While Proteus was primarily designed to move Go-Carts, a core component of Amazon’s logistics operations, Amazon recognizes the potential for Proteus to serve many other purposes. To meet this need, AR tasked the Tauber team with identifying new use cases for Proteus, both internal and external to Amazon. Overall, the team concluded that in the short term, Amazon’s internal opportunities have much greater return on investment compared to external ones. This conclusion was derived from the observation that the net cost savings of the top five internal opportunities is greater than the projected operating profit of the entire AMR market segment for manufacturing in 2027.
The Tauber team identified 28 different potential internal use cases through six site visits and 30+ interviews, then selected two use cases to prioritize. The final deliverable for each use case includes: (1) gap analysis, (2) layout, (3) technical requirements, (4) implementation roadmap, (5) financial analysis, (6) risks and issues assessments, (7) next steps.
The first use case proposed involves utilizing a Proteus fleet to automate the replenishment of parts to the stations in the AR production lines. The team estimated that the use case can result in an annual cost savings of ~$450K based on current demand forecasts. When considering AR full production capacity, the annual savings is estimated at $2.3M.
The second use case proposed involves using Proteus to replenish Totes in the Amazon fulfillment centers (FC). The team estimated that this use case can bring $2.84M of labor savings per year for a single FC, with an 8.6-month payback period compared to the current manual handling process. Considering all new fulfillment centers in the pipeline, the use case has a potential impact of $76.7M in three years.
Overall, the two use cases the team presented could save up to $79M in three years.
EGL (BSE Electrical Engineering / MSE Electrical and Computer Engineering
Project Sponsors:
Amazon Robotics Champion: Troy Cutler Amazon Robotics Supervisor: Pat Dunbeck
Master of Business Administration
MSE Industrial and Operations Engineering
Faculty Advisors: Samantha Keppler – Ross School of Business Dawn Tilbury – College of Engineering
THE AMAZON ROBOTICS’ FACTORY TRANSFORMATION project team, Nora Desmond (B.S.E. in Electrical Engineering), Jane Huang (M.B.A.), and Praveen Karunakaran (M.S.E. in Industrial and Operations Engineering), proposed a series of automation initiatives that, if implemented, could save a combined $5.4 million over three years.
We evaluated Amazon Robotics’ inbound and outbound processes for drive unit (DU) and manipulation system factories to save time with automation initiatives. Our team sought to integrate automation into AR’s workflow to streamline production by: 1) designing our own framework to assess existing processes, 2) prioritizing potential proposals, and then 3) suggesting quantifiable solutions. Our key deliverables are the current process flow map, process automation scorecard, proposed solutions, and a 3-year roadmap.
Among 19 processes mapped across inbound and outbound shipping, we suggest AR prioritize 7 processes based on higher business, organizational KPI impact, and the presence of a bottleneck. Based on their automation feasibility, we categorized them as “Quick Wins” or “Major Projects.”
For Quick Wins, our key recommendations include configuring the internal sales order (ISO) process to scan the pallet as a whole reducing ISO scan time by 50% to 60%; reconfigure the distribution of skill sets on the palletization floor to reduce hazardous queueing; implement dock-mounted scanners to automate scanning while unloading and saving $666K in labor costs over three years, and leveraging mounted scanners in workstations to reduce cycle time and increase production capacity by 2.4% and save $233K over three years. For Major Projects, our key recommendations include implementing a passive RFID (Radio Frequency Identification) scanning system to save $1.6 MM in labor over three years with NPV (net present value) of $257K and implementing autonomous guided vehicles (AGV) for automated restocking to save $2.7 MM in labor over three years with NPV of $655K. The total three-year impact of these proposals would be around $5.4 MM.
Throughout the course of this internship, we learned how to strategize from scratch, a new simulation software to simulate manufacturing processes, and how manufacturing works. In addition to the potential value our project brings to Amazon Robotics, we feel most proud of the scalability of our project, the practicality of our recommendations, and helping to make palletization safer. We are very grateful to our project champion Troy Cutler; our project manager Pat Dunbeck; our faculty advisors, Sam Keppler (Ross School of Business) and Dawn Tilbury (College of Engineering) for their guidance and support this summer.
Strategic Improvements for Crossdock Container Labeling in Amazon Operations
Ankita Bansal Master of Business Administration
Project Sponsors:
John Benson – Director of Operations
Jake Greaves – Senior Program Manager
JoAnne Rzeppa – Vice President NASC Operations
Karen De Souza Martins Master of Business Administration
Faculty Advisors:
Bhavarth Shah MSE – SEAS
Kate Astashkina – Ross School of Business
Max Li – College of Engineering
AMAZON.COM, INC., a leading multinational technology company, is continuously optimizing its supply chain operations, known as "The Mile," to enhance customer satisfaction and operational efficiency. The Mile encompasses three key components: First Mile (Fulfillment Centers), Middle Mile (Sort Centers), and Last Mile (Delivery Stations).
The North America Sort Center (NASC) facilities play a crucial role in providing the fastest path to customers while optimizing transportation lanes, reducing package dwell time, and addressing inventory placement challenges.These facilities receive packages through multiple pathways, break them down by locality, and prepare them for delivery by downstream partners. The network can ship over 35 million units per day with a remarkable 99.6% customer promise accuracy rate.
The company's focus on improving cross-dock (XD) operations, an integral part of its strategy to reduce delivery times, is crucial for ensuring a seamless transfer of pre-sorted containers directly from inbound to outbound trailers. The project aims to standardize cross-dock processes at Sort Centers (NASC), with the goal of improving performance containers per hour (CPH), reducing waste (walking distance), and ultimately enhancing customer satisfaction.
The proposed recommendations have the potential to increase CPH by 27.25%, reduce associate walking distance by 13%, and generate $115 million in profit over three years. The project suggests additional strategies for cross-dock optimization, including streamlining Transportation Operation Management (TOM) processes, ensuring efficient hostler moves, and smooth Under the Roof (UTR) operations.
Key inputs have been proposed to the existing NASC cross-dock process document to incorporate new tenets for improving overall crossdock operations. The project aligns with Amazon's commitment to continuous improvement and customer-centric approach, positioning the company for further growth and success in the rapidly evolving e-commerce landscape.
Danny ColÓn
EGL (BSE /MSE Industrial and Operations Engineering)
PROJECT SPONSORS:
Tim Brasher – Senior Director Market Development
Joseph Calmese – Chief Executive Officer
Leslie Hardin – Managing Partner
Jack Simmons – Operations Associate
Annelise Lemaire
EGL (BSE Chem / MSE Industrial and Operations Engineering)
FACULTY ADVISORS:
Jeff Alden – College of Engineering
Steve Leider – Ross School of Business
AMERICAN INDUSTRIAL PARTNERS, a results-driven middle-market private equity firm, founded ADDMAN, a leader in advanced manufacturing. ADDMAN focuses on integrating 3D printing technologies to provide comprehensive solutions in engineering, design, production, and post-processing. Serving industries such as space, defense, and medical devices, ADDMAN emphasizes sustainability and employee development. As part of a companywide Artificial Intelligence (AI) for Every Desk initiative, the 2024 Tauber Team’s project focuses on implementing an AI tool to enhance ADDMAN's business efficiency by 25% by 2025, measured through labor hours saved, increased revenue, and cost reduction. Initial stakeholder discussions identified pain points and potential areas for automation.
The team interviewed 14 business leaders at ADDMAN and identified key problems within the business operations. The areas with the most room for improvement were quoting, contract review, request for proposal (RFP) searching, dynamic pricing, customer tracking, marketing analytics, and contact management. The team conducted research to explore existing AI tools and their applications. Based on the interviews and research, the team concluded that the highest-impact initiative was contract review.
The team concluded that the manual review of long-term agreements and purchase orders resulted in human error and oversights, leading to millions of dollars in lost profit annually. The review process creates a bottleneck, slowing down operations and requiring multiple personnel. In 2023, ADDMAN employees spent 5198 hours reviewing contracts and the company lost $10.8MM in part due to contract related issues.
The team leveraged the AI tool Hebbia to create a custom contract review tool with the goals of reducing contract review labor time by 80% and protecting against the historical 7% margin erosion which equates. Through user feedback and testing, the team engineered custom prompts to compare customer purchase orders with quotes, extract and summarize key information, alert to unusual terms, and initiate the negotiation step of contract review by rewriting risky clauses. The team configured two unique matrices, one for purchase order (PO) reviews and another for long-term agreement (LTA) reviews.
ADDMAN’s continued implementation of this tool is projected to save 10,057 labor hours and $25.4- 34.1MM in margin erosion over the next 3 years. ADDMAN's strategic initiatives and AI integrations are set to enhance operational efficiency, reduce costs, and drive innovation, positioning the company for continued growth and competitive advantage in the advanced manufacturing sector.
G9 Lighthouse Project
Matt Alrutz Master of Business Administration
Project Sponsors:
Russel Bennet – Senior Manager Manufacturing
Leslie Hardin – Managing Partner
Crichton Waddell – Vice President Global Operations
Nam
Le EGL (BSE ME/ MSE Industrial and Operations Engineering)
Faculty Advisors:
Monroe Keyserling – College of Engineering
Vijay Pandiarajan – Ross School of Business
AMERICAN INDUSTRIAL PARTNERS (AIP), an operating and engineering-focused private equity firm, has made a strategic investment in Attindas Hygiene Partners. Attindas is a rapidly growing, global personal hygiene company selling baby diapers, adult incontinence products, and clinical products, with 4 sites globally in North Carolina, Ohio, Sweden, and Spain. The company has ambitious goals to achieve 100% EBITDA growth by 2027, but is challenged by below standard operational efficiency caused by high turnover in the labor market and outdated knowledge transfer processes.
The Tauber Team worked at Attindas’ Greenville, North Carolina facility to address these challenges in the G9 Lighthouse Project. Their objective was to increase and sustain overall equipment effectiveness (OEE), reduce scrap, and accelerate knowledge transfer through a standardized, scalable digital solution. In recent years, the high turnover rate on the manufacturing line has created the need to quickly fill knowledge gaps. As a generation of experienced operators retires, valuable institutional knowledge is lost. Simultaneously, the younger generation of newly hired operators turns over frequently, not staying on the job long enough to gain the institutional knowledge lost with the older generation. Consequently, operators on the Attindas manufacturing line face difficulty in performing their tasks without assistance.
Current written instructions to assist operators are incomplete and difficult to use, and completed tasks often fail to meet Attindas’ standard of “what good looks like”. Operators also lack a formal venue to submit feedback or continuous improvement ideas, meaning gaps in documentation are left unaddressed and binders of work instructions collect dust on the line.
The Tauber team conducted extensive stakeholder engagement including field studies, surveys, interviews, focus groups, and leadership check-ins to gain insights into key pain points and potential solutions. These observations were used to assess the current state of the line performance with quantitative (e.g., OEE, scrap) and qualitative (e.g., team morale, leadership) evaluations.
After conducting the current state assessment, the team crafted a vision for the future state of the digital solution on the manufacturing lines and established three criteria to define success: usability; effectiveness; and accountability. The team then translated the future state vision into functional and technical requirements, crafted product wireframes, and developed a prototype of the digital solution. Throughout the development process, the team continuously sought feedback from the primary stakeholders through testing and implemented an iterative process to improve the final solution.
Finally, the team rolled the solution out to the floor with a three-step implementation plan: inform, standardize, and sustain. The implementation of the pilot focused on one capability (bagger changeover) on one line (G9) to prove the concept of the digital, tablet-based solution before scaling. The team collaborated with leadership to establish a 5-year roadmap for scaling the solution across capabilities and lines, with one capability alone capturing $7.2M of value with a 1.5 year payback period.
At scale, across lines with a suite of capabilities, the solution will transform the knowledge transfer process at Attindas by addressing the original challenges of low OEE and high turnover.
Optimizing Manual Processing in Fulfillment Centers
Cheyenne Chang
BBA / Master of Supply Chain Management
PROJECT SPONSOR:
Rasika Deshmukh Master of Business Administration
Maria Masangkay – Senior Leader - Industrial Engineering (Everett Delivery Center: Paint, Pre-flight, & Delivery)
Cameron Myers – Director Manufacturing and Safety
FACULTY ADVISORS:
Dylan Rich EGL (BSE/MSE Mechanical Engineering)
Richard Hughes – College of Engineering
Andrew Wu – Ross School of Business
THE BOEING COMPANY, a leading global aerospace company and top United States exporter, develops, manufactures, and services commercial airplanes, defense products and space systems for customers in more than 150 countries worldwide. In addition, Boeing employs more than 170,000 people across the United States and in more than 65 other countries. Their employees represent one of the most diverse, talented, and innovative workforces anywhere. Boeing’s diverse team is committed to innovating for the future, leading with sustainability, and cultivating a culture based on the company’s core values of safety, quality, and integrity.
For Boeing Commercial Airplanes, Foundational Training Centers are where new employees develop essential skills and gain their first exposure to Boeing’s rules, protocols, and codes of conduct. Boeing’s rules and regulations are in place to ensure the highest levels of safety, security, and quality in our manufacturing operations. In the company’s current production environment, there is opportunity to incorporate and enforce compliance practices in the Foundational Training Centers and change behaviors in their staff and students.
For this internship, the team was tasked with designing a robust, repeatable, and scalable audit procedure for Boeing Commercial Airplanes Foundational Training Centers. The new audit procedure would ensure compliance is being followed and drive accountability across all Boeing Training Organizations including Boeing Commercial Airplanes sites globally.
As a result, a holistic audit package was created by the team consisting of: (1) Audit process to enforce compliance throughout the Training Organization. (2) Automated tool to randomize audit scheduling cadence worldwide . (3) Audit checklists tailored to the 3 different regulatory elements in the FTCs. (4) Metric tools to enter and store all data from the audits. (5) User-friendly report out template to present findings to Leadership.
Throughout the project, the team communicated with all stakeholders that the goal of the audit was not intended to be a policing system but rather; showcase the health of the business by collecting and sharing results for operational transparency, drive continuous improvement, and start the careers of these Aerospace Professionals with safety and quality in mind. Consequently, by design, the audit procedure asks for compliance findings as well as exemplary behavior, or “best practices”. Looking for the good and fixing any compliance issues found along the way, improves training quality, and new employee readiness will be ensured across the enterprise. Additional expected benefits this project will drive are the reduction in expensive defects and rework costs to the company, but also initiate an investment in a long-term culture shift with emphasis on compliance and accountability within the company that will lead to higher safety, quality, and integrity outcomes.
Ufuoma Odje
Master
of Business Administration
Leveraging AI for Scaffolding Parts Identification
Akhil Ramesh
EGL (BSE Biomedical Engineering, MSE Industrial & Operations Engineering)
Shri Harshini Shanmugam
EGP (MSE Industrial & Operations Engineering)
Project Sponsors:
Mark Choe - EVP/CTO
Nicholas Green- Director of Digital Transformation
Project Advisors:
Wei Lu - College of Engineering
Mohamed Mostagir – Ross School of Business
BRANDSAFWAY is a leading global provider of access, specialized services, and forming & shoring solutions to the industrial, commercial and infrastructure markets. In an ever-evolving construction and industrial landscape, BrandSafway recognizes the need for modernization to address inefficiencies in its operations and identified an opportunity for significant improvement- an automated tracking of scaffolding components at job sites. Traditional paper-based systems used to monitor scaffolding assets are not only time-consuming but also prone to errors, leading to data inefficiencies, lack of visibility on assets, increased costs and inaccurate billing.
To address these inefficiencies, the Tauber team developed an AI image recognition model to automatically identify and count scaffolding system components in real-time through 2D object detection. Given extensive internal research, the Tauber team addresses the bottlenecks in the onsite inventory management system to ensure implementation of an intentional optimized solution. The AI model utilizes advanced computer vision techniques like instance segmentation to analyze images and accurately identify scaffolding parts from built scaffold structures. Additionally, the team created a comprehensive training dataset by systematically collecting images from the yard, assembling scaffold structures from scratch to enhance the model’s accuracy to 93.7%.
The Proof of Concept (PoC) AI model initiates the transition from manual to automated processes aiming to streamline operations, cut costs from manual inspections by 70% and achieve a $9M ROI within 3 years post implementation. AI-driven scaffolding part identification will provide BrandSafway with deeper insights into asset utilization, increasing returns. Additionally, it will improve capital expenditure predictions and strategic decision-making, ultimately boosting long-term profitability and sustainable growth for the organization.
Thomas Adelman
EGL (BSE / MSEIndustrial and Operations Engineering)
Project Sponsors:
Sam Beadle – Sr Director - Productivity Programs
Patrick Persichilli – Human Resources
Craig Weiss – SVP Supply Chain
Journey to One Percent Yield Loss
Breanna Allen
BTS (BBA and Master of Supply Chain Management)
Faculty Advisors:
Benjamin Collins
EGL (BSE-DS / MSEIndustrial & Operations Engineering)
Ravi Anupindi – Ross School of Business
Brian Love – College of Engineering
CONAGRA BRANDS, headquartered in Chicago, unites a lengthy legacy of producing quality food while continuing to pioneer in the consumer goods industry. As such, Conagra seeks to further distinguish itself with excellent productivity and sustainability. The overarching goal of the Tauber Team this summer is to identify practical and technological opportunities to drive production processes to 1% yield loss or less across manufacturing production lines and capture the sustainability gains that come as a byproduct.
The first phase of the project is enhancing Conagra’s Connected Shop Floor (CSF) program. Currently, CSF is a developing program that seeks to leverage digitization and data insights to improve line efficiency in terms of a few key metrics including uptime and waste reduction. To start, the Tauber Team immersed themselves with the frontline production operations and current CSF architecture at the Council Bluffs (CB) plant. After identifying the largest savings opportunity and gaps in data visibility, we developed a dashboard for a specific line enabling frontline workers to see line performance in near real time, 20x quicker than before.
After gaining technological expertise of production processes, we observed best practices of a less tech-operated plant with impressive yield performance. Relative to Council Bluffs, Marshall engages its workforce with a more yield centric culture that culminates in a handful of best practices. The project strikes a balance between the modernization of production and strategic labor allocation. We developed scalable recommendations based on our observations to strive for 1% yield loss across all frozen-food plants.
Reliable Cost Management in the Pole and Pole Top Maintenance and Modernization Program (PTMM)
Mohsen Khabir
Master
of Business Administration
Project Sponsors:
Morgan Elliott Andahazy - Director, Service Operation
Kevin Tomaszewski - Manager, Distribution Operations
Sebastian Taboada
EGL (BSE / MSE Industrial and Operations Engineering)
Faculty Advisors:
Salar Fattahi – College of Engineering
Ran Zhuo – Ross School of Business
DTE ENERGY, a key player in the energy sector, serves 2.3 million customers in southeastern Michigan with its 11,084-megawatt system capacity. The Pole Top Maintenance and Modernization (PTMM) Program, a cornerstone of DTE Energy’s operations, is responsible for inspecting and replacing defective DTE-owned utility poles and pole top equipment. The Cost Management component of the PTMM program is not just a part of the process but a vital element that sets the stage for effective financial and budgeting management, project oversight, data science expertise, and other essential business strategies.
The Tauber project, a transformative initiative aimed at enhancing the PTMM’s cost management process, yielded significant findings. Through extensive investigation and data analytics, the Tauber team gleaned insights from 50 completed work packages. They identified anomalies, mismatches, and variations between DTE's initial expectations and contractors' work, providing a clearer understanding of the range and types of variations. This knowledge will enable DTE Energy to set more accurate expectations and enhance predictability when budgeting for future and ongoing projects. By scrutinizing all available records, the Tauber team developed a model to estimate initial costs and identify variations and mismatches, such as those due to weather, operational reasons, and technical authority on-site.
The Tauber team's pursuit of excellence was fueled by cross-functional collaboration, a key factor in identifying several opportunities for improvement and insights through data analytics. This collaborative effort will guide DTE Energy toward a future marked by improved cost identification, estimation, control, comparison, optimization, monitoring, and reporting. With a solid commitment to progress, DTE Energy anticipates an 18% increase in estimation forecasting and budgeting due to a $773 million investment in the PTMM Program over the next five years.
Stafford, TX Machine Shop Makeover
Nathan Richtarcik Bachelor of Business Administration/MSCM
Project Sponsors:
Cooper Barth - Plant Manager, Stafford
Joseph Zarzana - Global Materials Planner
Gus Sawicki Master of Business Administration
Faculty Advisors:
Len Middleton - Ross School of Business
Luis Garcia-Guzman - College of Engineering
EMERSON is a global leader in technology, software, and engineering solutions that serves customers across industrial, commercial, and residential markets. This summer’s project team collaborated with Emerson’s Stafford, Texas facility, which specializes in supplying final control valves and parts solutions, predominantly safety and relief valves, to its global customers. Despite its profitability, the Stafford plant has been grappling with suboptimal utilization rates, stagnant sales, and not reaching expected service levels within its internal machine shop. Key challenges identified include inadequate data collection and analysis of setup and run times, information silos, lack of operational support on the manufacturing floor, and an unstructured make-buy strategy. The "Machine Shop Make-Over" project aims to address these issues by performing a comprehensive current state analysis, implementing “Run the Shop” tools and enhanced operational best practices, and provided additional proposed solutions to establish a continuous improvement culture.
By implementing changes, the project anticipates a significant decrease in information siloing and an increased support mechanism for the operators to effectively and efficiently process production orders The additional solutions of optimized planning processes, effective communication tools, data collection mechanisms, and relevant KPIs will collectively transform operational workflows, ultimately setting a new benchmark for productivity and profitability. When the fundamental operational best practices are set, the management team in Stafford can then begin to work on a comprehensive make-buy strategy in partnership with the University of Michigan Industrial Operations Engineering department.
Project Sponsors:
Sanjay Shah–SVP
Charan Lawani- Sr.Director
Namitha Elsa John
EGL (BSE in Computer Science & MSE in Systems Engineering)
Faculty Advisors:
Saif Benjaafar– College of Engineering
Lennart Baardman– Ross School of Business
GOPUFF is a leading Instant Commerce platform that brings thousands of everyday products to customers in minutes. Gopuff delivers a wide variety of goods from toiletries to fresh groceries. The company sells its own inventory of about 4k products in about 400 local microfulfillment centers (MFCs). Gopuff has about 3-4k employees in the US and UK.
One of the key elements of Gopuff that differentiates from other instant commerce companies is their speed of delivery due to stocking their own inventory. However, having their inventory leads to a major economic loss in Damage and Expiry of their products. Therefore, Gopuff partnered with the Tauber Institute for Global Operations to develop the project Root Causing Damage and Expiry. The purpose of this project is to develop a new data analysis model, aiming to use current data tables and recognizable trends in data to identify the root causes of D&E. After root causes are identified, it is possible to consider suggestions to ultimately decrease the amount of D&E caused by preventable circumstances and reduce operational costs. The Tauber team, consisting of Namitha John (BSE CS, MSE Systems engineering and design), will assess and understand the current state of D&E, ordering, forecasting, marketing, and operations to develop a data-driven process and model to identify the true root causes behind excessive D&E.
To carry out this analysis, preliminary research was conducted by interviewing employees throughout the many departments of Gopuff, including but not limited to, ordering, marketing, supply chain, and forecasting. Each employee interviewed was asked about their personal interactions with D&E and opinions on root causes. The results of these interviews were collected, discussed, and analyzed to narrow down a list of possible root causes. Trends within data were identified for a quantitative method to correlate a product and its D&E root cause. A list of recommendations was also compiled based on the interviews conducted and the output of the model. The overall estimated impact of this project is around $2 million dollars and the opportunity to greatly decrease the amount of D&E Gopuff experiences.
Communication
Max Carter Master of Business Administration
Project Sponsors:
Bryan Geha – Director , Strategic Supplier Management Operations
Scott Bostic – Sr. Manager, Supply Chain Sustainability
Alan Liang – Manager, Strategic Supply Chain
Faculty Advisors:
Anne Partington – Ross School of Business
Mary Crosby – Ross School of Business
Lei Ying – College of Engineering
KLA CORPORATION, a global technology leader, has witnessed significant growth over the past five years. KLA is seeking an improved, streamlined and efficient supplier communication system. Currently, KLA's supplier communication processes are reliant on manual methods, which can lead to inconsistencies across the global supply chain.
To address these issues, the Tauber project manager conducted a thorough analysis of KLA’s current supplier communication practices and recommended the implementation of a Supplier Information Management (SIM) solution, including a supplier portal. By providing a unified space for supplier communication and collaboration, the portal has the potential to enhance engagement with KLA’s global suppliers.
The financial implications of implementing a SIM solution and supplier portal can be significant. Based on several assumptions, by enhancing supplier data management and optimizing communication processes, KLA could potentially realize a cost-benefit from reduced manual processes, increased supplier compliance, improved negotiation outcomes, and streamlined procurement processes.
User-Driven Application Design to Optimize Bulk Ingredient Inventory in the Dry Pet Food Network
Tori Caracciolo
EGL (BSE Mechanical Engineering, MSE Industrial & Operations Engineering)
PROJECT SPONSORS:
Roger Brecht - VP Digital Manufacturing
Chris Micena - Sr. Director Digital Manufacturing
Maxwell Master of Business Administration
FACULTY ADVISORS:
David Kaufman - Ross School of Business
Ray Muscat - College of Engineering
NESTLÉ PURINA is a multi-billion dollar company and a prominent player in the global pet dry food, wet food, and litter product space. The company’s dry pet food factories utilize multi-story bulk ingredient bins to facilitate processing millions of pounds of raw material a day. To make this operation possible, hundreds of trucks and dozens of railcars deliver to the ten dry factories on any given day. So how is it that with the sheer enormity of material involved, they are still recording key inventory levels manually on paper?
In each Purina dry pet food factory, a piece of paper called the “bin sheet” is used by operators to record the inventory levels of each ingredient bin. Understandably, this piece of paper can create a real disconnect on actual inventory levels. This lack of information can be costly. Logistics can unknowingly schedule trucks and rail cars out of sequence, driving up delivery penalty fees. If rail and trucks are out of sequence, there can be a risk that the right material is not available at the right time, resulting in lost revenue. Furthermore, a piece of paper does not allow any foresight into bin mixing issues, leading to product waste. The result is a lack of trust in the inventory levels in the factory. Each of these scenarios can result in a cost to the business of hundreds of thousands of dollars per year at any of the ten factories.
So how did the Tauber team solve this problem? They put the Flagstaff factory operators in the driver’s seat to build a digital application from scratch that would replace the paper bin sheet. While it might seem simple to take a piece of paper and turn it into an app, there are an abundance of considerations that must be taken into account. Ultimately, the goal was to develop a user-friendly digital bin sheet application that integrates with Nestlé Purina's larger inventory management toolset, enhancing visibility and unlocking trend analysis capabilities for raw material inventories. The team estimates that implementation of the application will save Nestlé Purina $5.3M over the next three years, which includes minimizing delivery penalty fees, saving multiple departments time on processing manual data, and reducing raw material product loss costs.
Optimizing WIP: Advanced Manufacturing Excellence
Katherine Qiu
EGP (MSE - Industrial and Operations Engineering)
PROJECT SPONSORS:
Nate Dietrich - Director of Advanced Manufacturing & Engineering Process
Jeff Brower - Operations Director
EGP (BSE & MSE - Industrial and Operations Engineering)
FACULTY ADVISORS:
Navaneeth Rajan
EGP (MSE - Industrial and Operations Engineering)
Izak Duenyas – Ross School of Business
Fred Terry – College of Engineering
STANLEY BLACK & DECKER (SBD) is a globally recognized Fortune 500 company with over $15.8 billion in revenue, operating in more than 60 countries. SBD is a leader in the power tools and fasteners sectors. Stanley Engineered Fasteners (SEF), a subsidiary of SBD’s Industrial division with $2.5 billion in revenue from fastener and assembly technologies.
The company engaged the Tauber team to enhance the visibility of Work-in-Progress (WIP) at the Chesterfield plastics plant, which faced significant operational inefficiencies due to the absence of an intermediate WIP tracking system. These inefficiencies led to 2,750 hours lost per year due to long search times for parts, disrupted production flow, and overproduction costs of approximately $48,000 to compensate for perceived inventory shortages. We were tasked with developing sustainable strategies to control WIP inventory, reduce waste and delays, and streamline packaging processes. By addressing these critical issues, we aimed to improve material flow, operational decision-making, and customer service outcomes. Using value stream mapping to identify bottlenecks, define non-value-added activities, and enhance flow, we set a goal to generate at least $1 million over three years, while implementing at least one physical change and identifying quick wins.
Over the summer, we focused on three main solutions. Through stakeholder identification and daily Gemba walks, we pinpointed bottlenecks and analyzed the current packaging state at SEF’s Chesterfield facility. The first solution was implementing a physical dashboard system for WIP inventory tracking, reducing search times by 67%, and improving inventory accuracy, leading to significant labor and process time savings. In addition to the physical system, we recommended integrating the Tulip digital system with barcode scanners to enhance accuracy and efficiency. This system would provide real-time tracking and visibility of WIP across departments, improving operational decision-making and customer service. The second solution redesigned the DC layout to optimize space utilization and improve material flow, reducing overtime costs and minimizing inventory losses. The third solution addressed scheduling optimization by automating the generation of the two-week look-ahead schedule using VBA macros and JD Edwards queries. The optimization balanced demand with packaging capacity minimized non-value-added activities during changeovers, improved throughput, reduced changeover times by 1.2 hours per day, and saved 85% of the time spent on schedule creation.
We calculated the value of their implemented solutions in productivity increases, hard cost savings, and operational efficiency improvements at SEF’s Chesterfield facility to be $1.6 million over three years, and implementing physical changes. We also identified several quick wins and opportunities to scale these improvements to other plants, ensuring sustained operational excellence and cost-effectiveness across SEF’s manufacturing network.
Standardizing Inbound Planning by Enhancing OM Tools for Optimization
Jaidyn Chauhan
EGL (BSE and MSE in Industrial & Operations Engineering)
Project Sponsors:
Matthew Butryn – VP GSCL Field Operations
Kyle Murphy – Director of Supply Chain
Kate Howard
EGL (BSE and MSE in Industrial & Operations Engineering)
Chase Arnett – Lead Process Manager of Process Excellence
Jack Naidrich
EGL (BSE and MSE in Industrial & Operations Engineering)
Faculty Advisors:
Joline Uichanco – Ross School of Business
Raed Al Kontar – College of Engineering
TARGET CORPORATION is a U.S.-based retailer renowned for its diverse range of high-quality and cost-effective products, spanning from household essentials to fashion and electronics. Target has established itself as a go-to store for millions of shoppers nationwide, generating $107B in revenue in 2023. Target maintains both small-format stores and SuperTarget hypermarkets, totaling 1,956 locations in the U.S. and employing over 400,000 team members in over 20 offices globally. Additionally, Target has an extensive supply chain network, receiving goods from over 8000 vendors and operating 62 supply chain facilities that replenish stores and fulfill online orders directly to guests. In 2024, Target expects to receive 1.165 billion cartons into their Regional Distribution Centers (RDCs) through their Automated Receiving Technology (ART) and Manual Receiving dock.
This project leveraged Target’s 8-step problem-solving methodology to develop solutions for improving inbound receiving efficiency by optimizing trailer receiving decisions. The team analyzed data sources, interviewed operations managers and Target team members (OMs and TMs) in various RDCs, and observed the inbound receiving process at Regional Distribution Center (RDC) T-551 in Fridley, MN to form their solutions. The team developed several models to predict the optimal receiving location of trailers, expected unload time, and understanding how to better navigate inbound receiving given a trailer's composition.
The project’s deliverables include important metrics implemented into an updated planning tool that provides greater data visibility for OMs such that they can make more informed decisions when slotting trailers. The implementation of these solutions aims to reduce mental and physical burden on Target OMs through decreasing time to plan their shift, and leverage time given back to conduct other tasks that will increase TM productivity.
These improvements are projected to bring Target labor cost savings of $1.9M over the next three years. In addition, the team identified that the potential improvement opportunity could result in up to 10,600 planning hours for OMs saved per year.
Developing a Energy Strategy Model to Transition Residential Energy to NetZero
Alvin Li
EGL (MSE in Energy Systems Engineering)
Project Sponsors:
Amit Nagpal – Director of Strategy
Andrew Kent – Senior Manager, Strategy
Vraj Mehta
Master of Business Administration
Faculty Advisors:
Ruslan Momot – Ross School of Business Prakash Sathe – College of Engineering
WASHINGTON GAS LIGHT (WGL), a leading energy provider, has been delivering reliable natural gas services for over 170 years. Today, WGL services over 1.1 million customers across Washington DC, Maryland, and Virginia, with a strong focus on sustainability and innovation. Addressing the urgent need to reduce greenhouse gas emissions and promote energy efficiency in residential homes, the Net Zero Ready Homes project aligns with WGL's commitment to environmental stewardship and energy sustainability.
The Net Zero Ready Homes project aims to develop Net Zero Energy (NZE) certified natural gas homes by integrating energy-efficient technologies and renewable energy sources to significantly reduce on-site CO2 emissions while preserving customer energy choices. The Tauber team developed a comprehensive data collection and analysis methodology, segmenting homes based on location and building type, and created a robust net-zero model to provide personalized recommendations for each home.
The net-zero model assessed key parameters such as insulation, infiltration, windows, duct sealing, and heating and cooling efficiency to estimate energy savings and emissions reductions. These estimates informed the development of financial models and benchmark pricing. Three financial pathways were explored: (1) a 5-year subscription model with just marketing, (2) a 5-year subscription model with revenue sharing, and (3) a rate change for all customers with revenue sharing.
The analysis shows that the most promising pathway is the rate change with revenue sharing model, projects a net present value (NPV) of at least $415 million over 20 years, ensuring a predictable revenue stream and high adoption rates. By reducing gas flow from 135,684,008 MCF to 107,812,872 MCF, the model projects an increase in the distribution charge to $0.67 per therm to maintain financial viability. Despite this increase, customers would see overall cost savings due to significantly reduced gas usage.
The Net Zero Ready Homes project is projected to save $15.9 million in energy costs over three years with a reduction of over 16 million tons of CO2 in the next 20. By focusing on impactful energy efficiency upgrades, supporting renewable energy integration, and exploring innovative financial models, the project contributes to a cleaner, more efficient, and economically viable future for all stakeholders involved. The Tauber team's work has the potential to directly generate an additional revenue of $1.32 billion over the next twenty years.