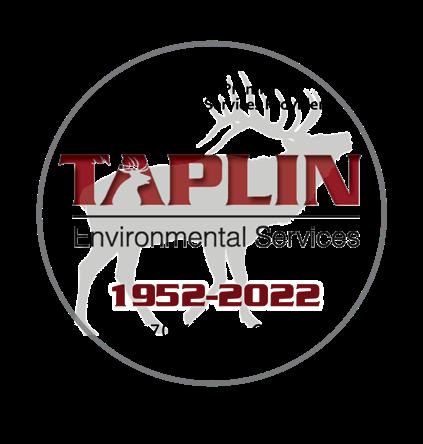
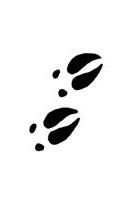
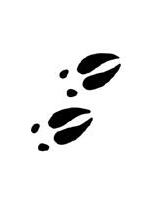

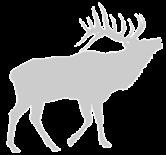
ROW CLEARING SERVICES
KEEP THE LIGHTS ON
Taplin provides critical service to major energy and pipeline providers and ensures energy for all
MACOMB COUNTY
Efficient and effective underground inspections
BCPS K-8 ARTS ACADEMY
Asbestos abatement on a major renovation in Battle Creek helps create a legacy of fine arts learning for community
EYES UNDERWATER
Underwater asset inspection - new tech changes the game
Taplin Group has fostered a longstanding relationship with a major North American natural gas supplier, providing essential Right of Way (ROW) Clearing services. This critical service ensures that the pathways for pipelines remain free from trees, brush, and other obstacles, adhering to federal regulations that mandate clear routes for both aerial and ground inspections.
Over the years, Taplin Group has executed numerous ROW clearing operations across various locations in Michigan, spanning state forests, wetlands, and residential areas. The geograph-
ical diversity of these projects necessitates a flexible approach, although the core objectives and methodologies of the work remain consistent.
The process of ROW clearing involves the deployment of specialized equipment tailored for efficiency and safety. This includes skid steer mounted fecon units, tractors equipped with brush hogs, chainsaws, chippers, and occasionally boom lifts for addressing larger trees. Each piece of equipment is strategically employed to ensure thorough clearance while minimizing environmental impact.
Central to the success of each project is a meticulously planned procedure that begins with marking the pipeline and delineating the boundaries of the ROW.
Advanced pipeline locating equipment is used to precisely mark the pipeline’s path, measure the proper distances for ROW boundaries, and outline the edges to guide the fecon operators. This upfront marking process not only ensures compliance with regulatory requirements but also enhances safety and operational efficiency.
Prior to the commencement of clearing operations, Taplin
Group’s marking crews conduct thorough surveys of the ROW terrain. This proactive approach helps identify and mitigate potential hazards such as buried steel materials, abandoned vehicles, discarded appliances, and large stones. Addressing these hazards before clearing begins is crucial for maintaining crew safety and preventing equipment damage.
Throughout each project, Taplin Group emphasizes comprehensive documentation and reporting. Detailed reports are compiled, documenting cleared segments, providing daily before-and-after photos, and offering narratives that outline the work completed and any encountered challenges. This documentation serves not only as a record of project milestones but also as a tool for evaluating performance and addressing any issues that may arise.
Safety remains a top priority throughout every phase of ROW clearing projects. The nature of the work involves navigating rough terrain, managing equipment in adverse weather conditions (often during winter months), safely felling trees, and navigating potential water hazards. Taplin Group’s commitment to safety is reinforced by a rigorous safety program and extensive experience in ROW clearing, which collectively enable them to successfully undertake projects of considerable scale and complexity.
In conclusion, Taplin Group’s expertise in ROW clearing is characterized by a blend of advanced technology, rigorous planning, and a steadfast commitment to safety and environmental stewardship. Their ability to navigate diverse terrains and regulatory landscapes underscores their capability to deliver effective solutions for maintaining crucial pipeline infrastructure across varied geographical settings.
In early 2023, the Macomb County Public Works Office, acting on behalf of the Macomb Interceptor Drainage District and the Eight & One-Half Mile Relief Drain Drainage District, issued a bid for inspecting their respective systems. This project presented unique challenges, but Taplin approached it with confidence in operational ingenuity and determination to overcome any obstacles.
The task at the Eight & One-Half Mile Relief Drain Drainage District involved inspecting a total of 48,557.5 linear feet of pipes, ranging widely in size from 24 inches to an imposing 12 feet in diameter. Safety was paramount, particularly concerning personnel performing entries for equipment setup and transport. The team employed air movers, live air monitoring systems, and specialized air apparatus to safeguard crew working underground. These precautions ensured that the working environment remained safe and compliant with stringent safety standards throughout the inspection process.
One of the most significant challenges encountered during this project was managing haze and particulate matter that often clouded the quality of video inspections in the larger tunnels. Due to the infrequent significant flows in these tunnels, mainly occurring during rainy periods, the air within the tunnels remained stagnant, exacerbating the visual obstruction caused by haze and particulates. To effectively address this challenge, Taplin devised a strategic solution.
By positioning air movers at both upstream and downstream manholes, the crew created a controlled airflow system. This method generated positive and negative pressures, effectively clearing the haze and particulates and significantly improving the quality of the video inspections. This innovative approach not only ensured compliance with inspection requirements but also enhanced the overall efficiency and accuracy of operations.
Meanwhile, in the Macomb Interceptor Drainage District, the scope encompassed inspecting 80,371 linear feet of pipelines. These pipes varied in length from 36 feet to a half-mile, with the longest single segment measuring an impressive 2,143.5 feet. The challenge was managing the flow velocities within these pipes, which posed significant obstacles to inspection efforts. To effectively navigate these challenges, Taplin developed and implemented a specialized continuous tag lining system. This innovative approach allowed the crew to maintain an average daily inspection pace of approximately 2,100 feet. By carefully controlling the speed of inspection, the crew ensured compliance with NAASCO’s stringent standard of maintaining a consistent pace of 30 feet per minute. This system not only optimized efficiency but also enhanced the precision and reliability of inspection outcomes, thereby meeting and exceeding client expectations. Accessing these pipelines presented another layer of complexity, given the average frame clear openings of approximately 24 inches at access points. This necessitated meticulous planning and coordination to ensure safe and effective equipment deployment and operation within the confined spaces of the pipelines. In some instances, equipment assembly had to be performed inside the pipes themselves, often under challenging conditions. This required team members to utilize harnesses, man-winches, and Personal Rescue Lifts (PRLs) to ensure their safety and facilitate efficient equipment deployment.
Operational challenges extended beyond technical aspects, encompassing logistical complexities associated with working beneath busy thoroughfares like Garfield Road and 15 Mile Road. The need to perform inspections required careful traffic management, including temporary lane closures during nighttime hours on roads with multiple lanes. This strategic approach ensured both the safety of team members and the uninterrupted flow of traffic, demonstrating a commitment to minimizing disruption to the community while executing essential infrastructure maintenance activities. Moreover, the project overlapped with ongoing rehabilitation, operation, and maintenance contracts
within the same vicinity. Coordinating crew activities alongside those of other contractors posed additional logistical challenges. To accommodate the county’s operational needs and ensure the efficient completion of the contract, the team adapted their working hours. This flexibility entailed working extended night shifts, totaling up to 15 hours per shift, to align with the schedules of other contractors and mitigate potential disruptions to pump stations and flow operations.
A critical component of Taplin’s responsibilities involved inspecting and reinstalling gaskets and bolts on a 48-inch force main located off the Clinton Dale Pump Station. This task required sourcing highquality materials from local Michigan manufacturers. The Taplin team devoted significant effort to reviewing as-built plans and collaborating closely with engineering teams to ensure the procurement of gaskets and bolts that met and exceeded industry standards for durability and performance. Prior to installation, thorough cleaning of the access point structures was necessary to remove accumulated sediment from historical leaks and runoff. This proved crucial in ensuring the successful installation and reliable operation of the gaskets and bolts, minimizing the risk of future failures.
Following the completion of the work, Taplin’s comprehensive approach and innovative solutions garnered positive feedback and recognition from Macomb County officials. Their request for specifications regarding our gaskets and bolts served as validation of their satisfaction with our performance and the quality of our materials and workmanship. This acknowledgment underscored Taplin Group’s commitment to excellence and our ability to deliver superior results while overcoming complex challenges with professionalism and efficiency.
In summary, the Macomb County project exemplified Taplin Group’s dedication to innovation, safety, and meticulous planning in tackling multifaceted infrastructure challenges. By leveraging advanced technologies, strategic methodologies, and a proactive approach to problem-solving, we successfully navigated diverse operational environments and delivered exceptional outcomes that met and exceeded client expectations.
In Battle Creek, Michigan, a significant endeavor is underway to revitalize the educational landscape and foster creativity among its youth. The Battle Creek Public Schools K-8 Arts Academy renovation project is not just about renovating buildings; it embodies a visionary effort driven by community collaboration and a steadfast commitment to holistic education.
The initiative aims to transform the former Northwestern Middle School into the K-8 Northwestern Academy of Visual and Performing Arts. This ambitious undertaking is rooted in the belief that arts education plays a pivotal role in developing well-rounded
individuals. By infusing state-ofthe-art facilities and resources into the academy, Battle Creek Public Schools seek to empower students to explore, express, and excel in the arts.
The project’s inception dates back several years with the approval of a nearly $45 million bond proposal to fund extensive renovations. Physical work commenced in 2023 and is slated for completion by 2025, preparing the new facility to welcome students for the 20252026 school year.
To facilitate seamless construction, Northwestern will temporarily close for the 20242025 academic year. During this period, students will relocate to
other district buildings, allowing for comprehensive renovations without disrupting their education.
However, the project encountered a significant hurdle when asbestos was discovered within the existing structure, a common challenge in older buildings undergoing renovation. Recognizing the critical importance of creating a safe and healthy learning environment, Taplin partnered closely with Battle Creek Public Schools to address this issue.
Taplin’s abatement division undertook a meticulous asbestos abatement process, removing approximately 36,000 square feet of tile flooring, mastic,
and asbestos-containing pipe insulation from the building’s tunnel system. This intricate process required careful execution at heights of up to 20 feet in the auditorium, emphasizing stringent safety measures throughout.
Using state-of-the-art techniques and adhering to rigorous safety protocols, Taplin ensured the hazardous materials were safely removed and disposed of, allowing the renovation to proceed unhindered. This proactive approach not only mitigated health risks but also safeguarded the project’s timeline and budget.
Asbestos in school buildings is a common issue encountered during renovation projects and requires careful and thorough removal in order to keep students, staff and the community safe.
(EPA guidelines and detailed information about asbestos in schools can be found at https:// www.epa.gov/sites/default/files/ documents/abcsfinal.pdf)
Northwestern Academy of Visual and Performing Arts symbolizes hope and opportunity for future generations. Beyond its physical transformation, the academy represents a commitment to nurturing creativity, curiosity, and academic excellence. By providing a dedicated space for arts education, Battle Creek Public Schools aim to cultivate confident, innovative leaders capable of making meaningful contributions to their communities.
The project underscores the transformative power of education, particularly in providing a conducive
environment where creativity can flourish. In the revitalized halls of the Northwestern Academy, students will be inspired to explore their artistic passions and pursue their dreams. The academy’s holistic approach aims to prepare students not only for academic success but also for personal growth and community engagement.
Ultimately, the Battle Creek Public Schools K-8 Arts Academy renovation project serves as a testament to the community’s dedication to investing in its youth. Through collaborative efforts and strategic partnerships with safe and effective contractors like Taplin, Battle Creek Public Schools are poised to usher in a new era of inspiration, innovation, and educational excellence.
Since 2021 Taplin has utilized a Safety Award program in the form of a hardhat sticker denoting recognition of excellence. Employees who earn stickers are eligible for year-end prizes.
The Taplin safety award program recognizes and rewards employees who consistently use safety best practices that help reduce losses and prevent injuries.
The purpose of the program is to acknowledge safe habits and to promote quality work and adherance to Taplin’s safety protocols.
2024 SAVE THE DATE TO JOIN US!
Client Open House and Meet & Greet
FRIDAY, OCTOBER 11TH , 2024
Come see our incredible new Kalamazoo facility! Warehouse, fleet maintenance and custom fabrication and metal working, all in-house and ready to serve YOU. Event details to follow. Scan the barcode below to RSVP and join us. We look foward to seeing you in October!
Updating JSA’s, stop work instances that prevent a potential loss, and quality LPO’s written by field staff all earn recognition.
Since its inception, Taplin has awarded nearly 200 stickers to employees for various safe acts and habits preventing loss and injury.
• MWEA PFAS Seminar - August 22, 2024 @ Eagle Eye Banquet Center (Lansing, MI)
• MWEA Collections Seminar - October 24, 2024 @ Eagle Eye Banquet Center
new tech and taplin equipment ready to serve you
PEINEMANN EQUIPMENT: MODULAR TUBE CLEANING | UNPARALLELED PERFORMANCE
When addressing demanding cleaning challenges, few solutions rival the Peinemann TLX flex lance feeder in versatility and performance. Taplin, equipped with skilled technicians, offers this equipment and service to its clients. What distinguishes the TLX is its unique capability to adapt for use with multiple lances using optional kits, enabling efficient cleaning of evaporators, heat exchangers, and various industrial applications.
The 1-TLX Pipe Cleaning Setup, featuring the highly efficient Peinemann 1-TLX feeder, aims to innovate pipe cleaning operations. This feeder delivers exceptional performance and unparalleled versatility.
The 1-TLX feeder is notable for its exceptional attributes: a lightweight design, remarkable versatility, and enhanced durability. With a 30% weight reduction compared to previous models, it enhances maneuverability without sacrificing robustness. Its modular design facilitates easy customization and maintenance, ensuring optimal performance.
Experience the capabilities of the 1-TLX feeder, delivering up to 200 kg (441 lb) push/pull strength in slow gear mode. This feature enables efficient handling of even the most challenging pipe cleaning tasks.
Constructed from the TLX Drive Unit and the 1-TLX conversion kit, the 1-TLX can be easily configured into dual (2-TLX), triple (3-TLX), quadruple (4-TLX), or quintuple (5TLX) lance feeders with additional conversion kits.
Our brand new 41,000 sq ft shop and fleet maintenance facility is up and running!
The custom built facility houses our equipment maintenance garage, fabrication shop, wash bays, parts warehouse, storage bays and more. With this new resource our crews will be able to expand our bestin-class service, innovative project fabrication needs as well as keep our full fleet of heavy equipment on the job and in service.
In an effort to de-water their main effluent structure for installing a water control gate, a local wastewater treatment plant (WWTP) faced challenges despite installing a temporary outer gate and using large sandbags at the effluent pipe’s end where it discharges into a nearby river. Despite pumping efforts, the water level inside the structure remained constant because the submerged pipe continued to allow water ingress. Taplin stepped in with their newly acquired Deep Trekker submersible ROV to investigate.
Taplin’s team deployed the ROV to inspect the pipe up to the river’s edge gate and discovered that the pipe’s end had
degraded. This degradation was allowing effluent to escape, eroding the riverbank and rendering the gate ineffective in preventing river water from entering the pipe. The findings prompted the WWTP to plan for rehabilitating the pipe to halt erosion and enable the effective installation of the water control gate.
Taplin’s use of advanced ROV technology exemplified their commitment to providing innovative solutions. By pinpointing the pipe’s degradation without excavation, Taplin enabled the WWTP to make informed decisions swiftly, ensuring efficient repairs and safeguarding both infrastructure integrity and environmental concerns.
Underwater asset management refers to the monitoring, inspection, and maintenance of assets and infrastructure, such as oil pipelines, cables, bridges, and dams to ensure the efficient and safe operation of these structures while minimizing hazards. Regular management plays a critical role in ensuring the reliability, safety, and longevity of these assets located beneath the water's surface, supporting various industries such as oil and gas, renewable energy, marine transportation, aquaculture, and scientific research, to name a few.
ROVs have proven to be excellent resources for underwater asset management. Equipped with cameras, sensors, and manipulator arms, they are able to perform underwater tasks that are difficult or dangerous for a human diver to access.
They can be deployed to inspect conditions and capture details of underwater infrastructure, perform repair tasks, and collect data that can be further utilized for photogrammetry and 3D modeling, or making decisions that improve efficiency in maintenance schedules. Ultimately, regularly scheduled inspections with ROVs can help with identifying potential risks early and preventing costly damage.
Prioritizing the adoption of photogrammetry and laser scanning in the energy sector, for example, enables teams to create digital twins with these technologies. These virtual replicas empower engineering teams to proactively plan for component replacements long before any outages occur. By identifying critical paths and potential issues beforehand, the chances of unexpected complications during outages are significantly reduced, ensuring that regular plant operations can resume on schedule.