BREAKING DOWN THE DIGITAL SUPPLY CHAIN
While digitization means different things to different companies, a digital supply chain presents the same benefits across the board.
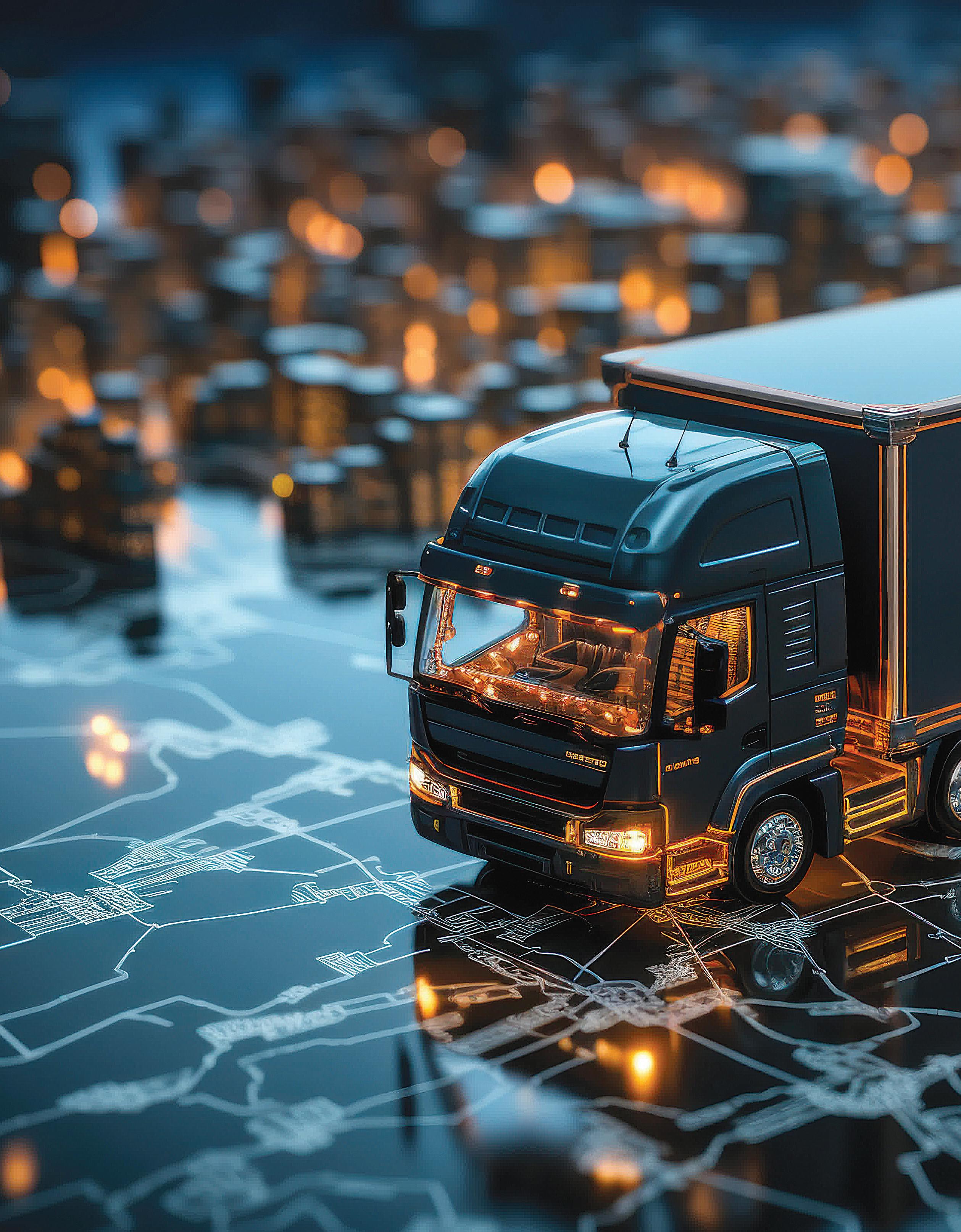
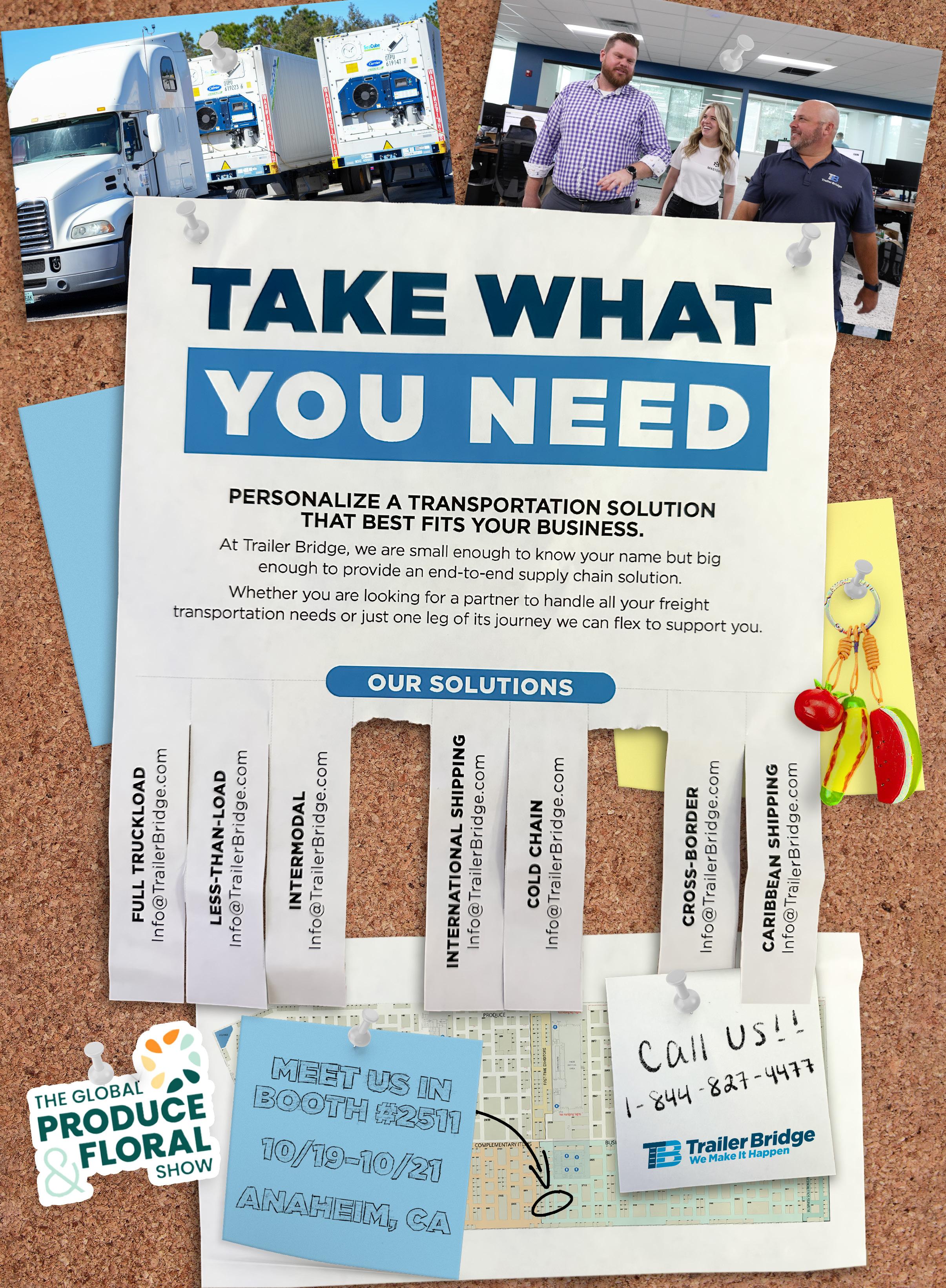
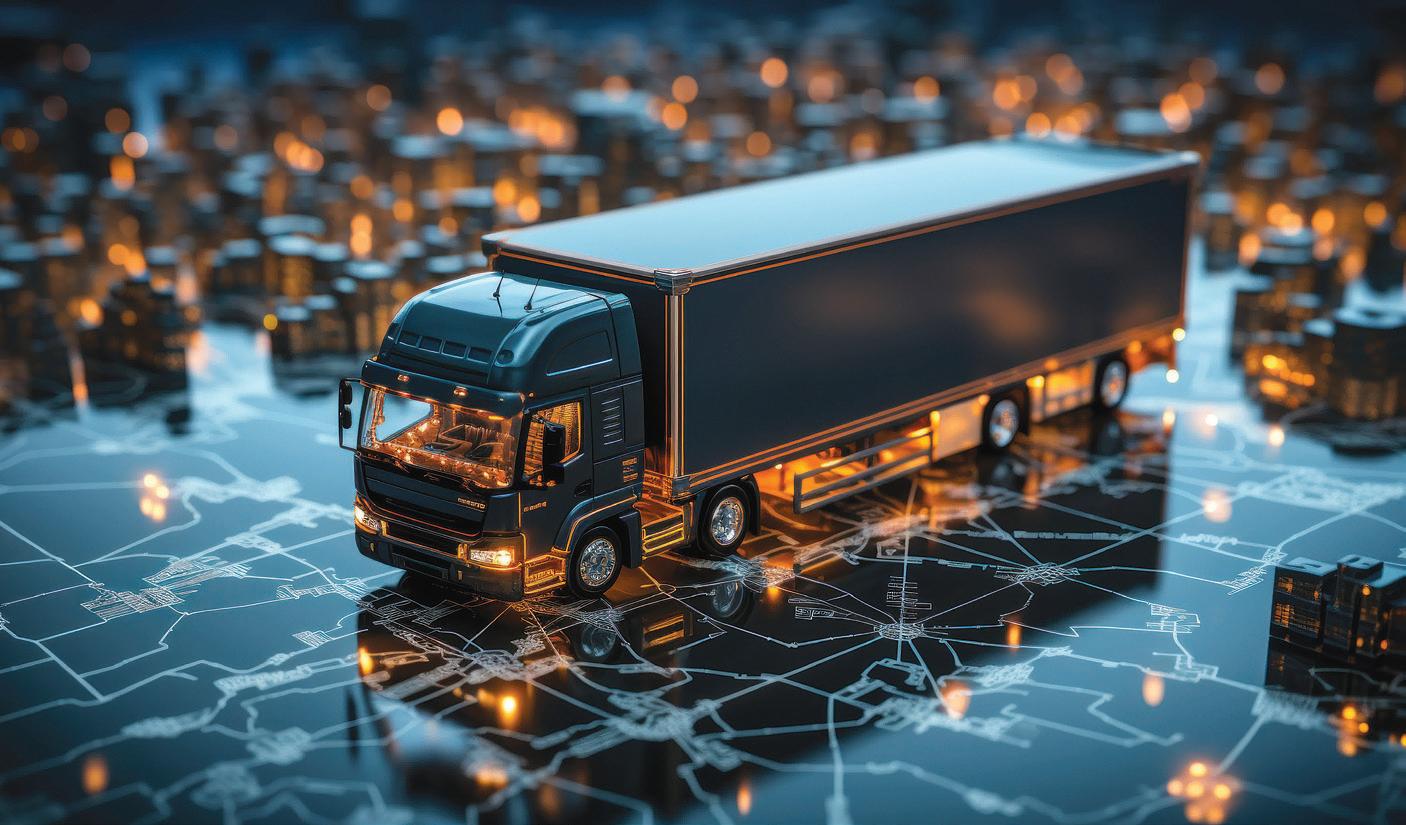
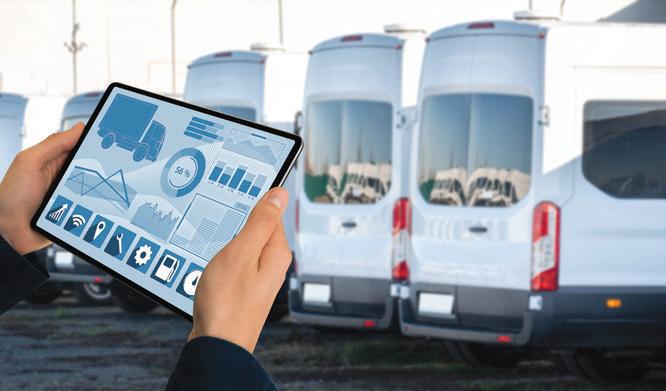
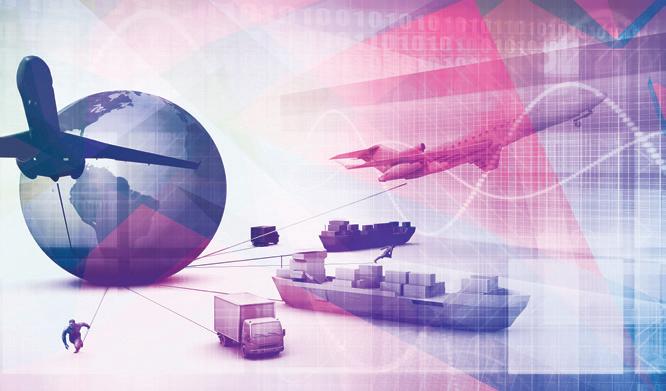
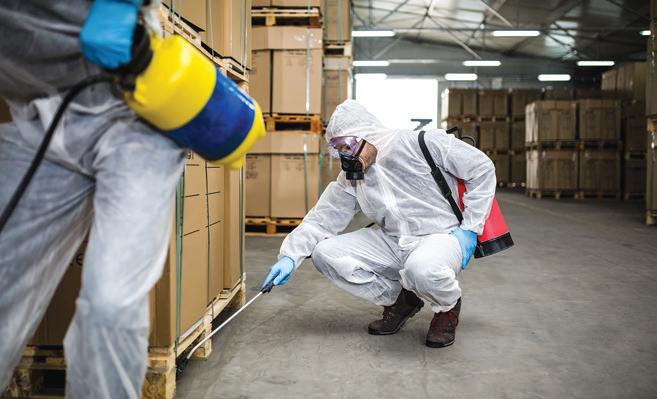
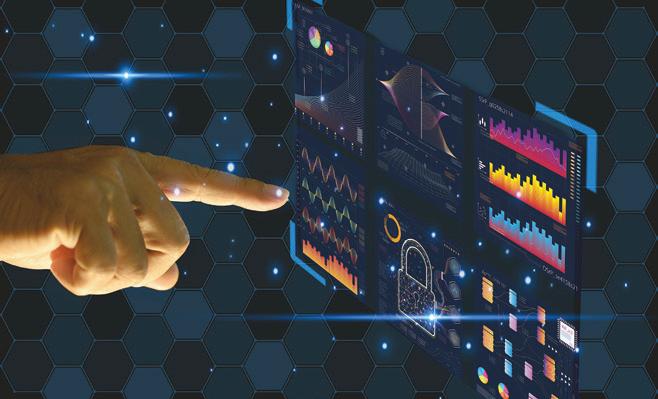
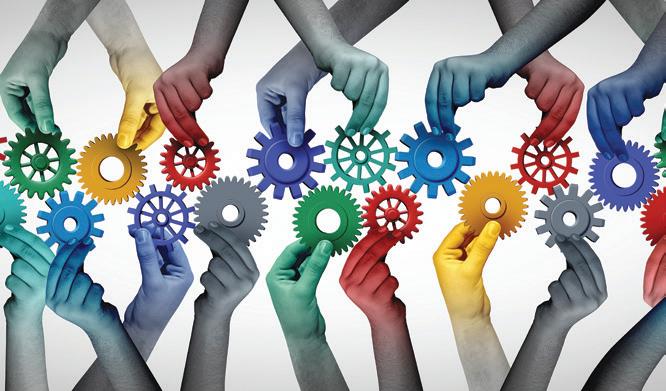
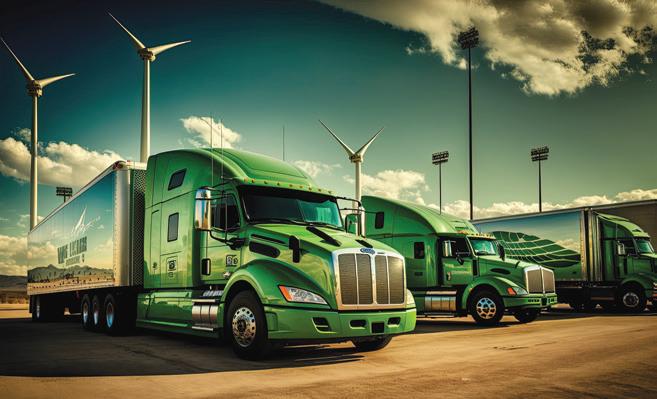
While digitization means different things to different companies, a digital supply chain presents the same benefits across the board.
These days, a digital supply chain in some way, shape or form is all everyone can talk about. From blockchain and artificial intelligence (AI) to telematics, visibility and electrification, the future of logistics depends on the adoption and implementation of digitization.
In fact, a digital supply chain closes the gap to build resiliency and mitigate risk. It automates what has traditionally been manual tasks and enhances sustainability along the way.
That’s why our upcoming SCN Summit: Future of Supply Chains virtual webinar series focuses on everything impacting today’s supply chains.
The webcast kicks off Dec. 5 with a State of the Industry report, providing insight on everything from FSMA 204 and worker strikes to inflation, friendshoring, electrification and more.
Rowan Scott, research analystfrom Interact Analysis, will lead the session on warehouse automation, discussing importance of warehouse management systems and how automation, robotics and/or wearables can provide forecasting, inventory refill, traceability and visibility to help mitigate future bottlenecks and congestion.
Meanwhile, Jonathan Gold, VP of supply chain and customs policy for the National Retail Federation, will talk State of E-Commerce, detailing the online retail landscape for department stores, online marketplaces, grocery retailers and foodservice establishments.
Other topics entail cold chain fleet management, electrification, supply chain visibility and AI. Go to www.SCNSummit.com to register for one, two or all sessions. Join live and participate in polls, surveys and receive the latest in all things supply chain and logistics in real time.
Hope to “see” you in December!
EDITORIAL
Editor-in-Chief Marina Mayer mmayer@ACBusinessMedia.com
Managing Editor Alexis Mizell-Pleasant amizell@ACBusinessMedia.com
AUDIENCE
Audience Development Manager Angela Franks
PRODUCTION
Senior Production Manger Cindy Rusch crusch@ACBusinessMedia.com
Art Director Willard Kill ADVERTISING/SALES
Brand Director Jason DeSarle jdesarle@ACBusinessMedia.com
Account Executive Brian Hines bhines@ACBusinessMedia.com
Account Executive Jay Gagan jgagan@ACBusinessMedia.com
AC BUSINESS MEDIA
Chief Executive Officer Ron Spink
Chief Financial Officer ........................................ JoAnn Breuchel
Chief Revenue Officer .......................................... Amy Schwandt
Brand Director, Supply Chain & Green IndustryJason DeSarle
Brand Director, Construction Sean Dunphy
VP, Audience Development Ronda Hughes
VP, Operations & IT Nick Raether
Content Director Marina Mayer
Director, Online & Marketing Services Bethany Chambers
Director, Demand Generation & Education Jim Bagan
Content Director, Marketing Services Jess Lombardo
CIRCULATION & SUBSCRIPTIONS
P.O. Box 3605, Northbrook, IL 60065-3605 (877) 201-3915 | Fax: (847)-291-4816 circ.FoodLogistics@omeda.com
LIST RENTAL
Sr. Account Manager Bart Piccirillo | Data Axle (518) 339 4511 | bart.piccirillo@infogroup.com
REPRINT SERVICES Brian Hines (647) 296-5014 | bhines@ACBusinessMedia.com
Published and copyrighted 2023 by AC Business Media. All rights reserved. No part of this publication may be reproduced or transmitted in any form or by any means, electronic or mechanical, including photocopy, recording or any information storage or retrieval system, without written permission from the publisher.
Food Logistics (USPS 015-667; ISSN 1094-7450 print; ISSN 1930-7527 online) is published 6 times per year in January/February, March/April, May/June, July/August, September/October, and November/December by AC Business Media, 201 N. Main Street, Fort Atkinson, WI 53538. Periodicals postage paid at Fort Atkinson, WI 53538 and additional mailing offices.
POSTMASTER: Send address changes to Food Logistics, P.O. Box 3605, Northbrook, IL 60065-3605. Subscriptions: U.S., one year, $45; two years, $85; Canada & Mexico, one year, $65; two years, $120; international, one year, $95; two years, $180. All subscriptions must be paid in U.S.
The ACF rule will have a profound impact on the agricultural and food supply chain given California’s substantial food and agricultural footprint and the trucking industry’s importance to agriculture. In short, Matt Clark, president and COO at Corcentric, says the supply chain in this region would become more microscopic and less resilient to shocks. Likewise, the shrinking radius of available processors (buyers) could have an adverse impact on the milk basis market for dairy farmers. In all, California’s ACF rule will uniquely impact the intersection of trucking logistics and the food supply chain through the costs of transitioning to ZE-MHDVs and the creation of less resilient food supply chains.
Scan the QR Code to learn more
https://foodl.me/fxkfmx
For the past 3 years, the trucking industry has faced numerous challenges stemming from the onset of COVID-19. However lately, the disruptions have become more… disruptive and less predictive. Present day, it’s not just a lack of visibility that’s creating bottlenecks along the way; today’s challenges run deep, are more personal and stem from a variety of causes such as the passage of certain laws, the lack of agreements to better protect contract workers and more.
Marina Mayer, editor-in-chief of Food Logistics and Supply & Demand Chain Executive, talks exclusively with Jai Ranganathan, chief product officer for Motive, on the importance of the Advanced Clean Fleets rule and what the industry can expect once in effect.
Scan the QR Code to Learn More https://foodl.me/9ix2l1
When it comes to sales, service should be more than a snack; it should be an entire five-course meal. By adopting
AI technology, your food and convenience distribution company can quickly earn loyal customers in a challenging market. Benj Cohen, founder and CEO of Proton.ai, lists these 4 ways AI is advancing the sector:
1. You can close wallet share gaps in a hurry.
2. New reps can acclimate quickly, and veteran reps won’t get burned out.
3. You’ll find plenty of hidden sales opportunities.
4. Your customer engagement will skyrocket.
Scan the QR code to learn more https://foodl.me/wqy4wj
The Women in Supply Chain Forum, scheduled to take place Nov. 14-15 in Atlanta, is the industry’s premier networking and educational forum tailored to men and women in executive-level positions to expand their professional network and enhance their businesses through thought-provoking discussion panels.
This year’s theme “Better Together: How Collaboration Promotes Women in Supply Chain,” brings together a host of content sessions and topics designed to deliver a powerful networking event rich in industry knowledge, education and key editorial insights that will help attendees grow their business and create meaningful professional connections.
Scan the QR code to learn more https://foodl.me/7fa79c
Many in logistics are accustomed to thinking about severe weather as a “seasonal” concern. But as climate changes, every month should be considered a potential “storm month”—this means you must monitor and track severe weather in any region at any time and have reliable, rapidly actionable plans in place for when extreme conditions do arise.
The first step for shippers is to be proactive in planning for such disruptions. Zach Gilstrap, general manager, humanitarian logistics at Coyote Logistics, explains that at the end of the day, human relationships are still the most important factor in navigating any of these challenging scenarios. Laying the groundwork to maintain an established rapport with people or organizations you can call on a moment’s notice will save time and energy when severe circumstances are rapidly approaching.
Scan the QR code to learn more https://foodl.me/qgx38l
The food industry is undergoing a seismic shift driven by the proliferation of ingredients, rapid responses to trends, and the transformative influence of social media. Businesses that navigate these trends successfully are poised to thrive in a landscape where innovation and consumer connection are the cornerstones of success. By embracing agility, leveraging data-driven insights, and maintaining a discerning eye on the evolving market, industry players can turn these trends into opportunities for growth and longevity.
According to Francesco Fazio, partner and head of innovation at Treacy & Company by Cherry Bekaert, advanced data analytics and sentiment analysis tools can aid in this endeavor, helping companies identify the trends that resonate strongly with their target audience. Genuine, authentic engagement with consumers on social media platforms can provide valuable insights and establish brand loyalty in an era when transparency and responsiveness are key.
Scan the QR code to learn more
https://foodl.me/mpbqat
Envision Cold launched its cold chain platform thanks to a $500 million investment from an undisclosed capital partner. This investment allows Envision to acquire and develop over $1.5 billion of cold storage assets and participate in the full scope of cold chain, including transportation, import and export services and real estate development. The company plans to continue acquiring and developing a network of facilities across North America, focusing on markets underserved by cold storage from both a physical infrastructure and customer service perspective.
Scan the QR code to learn more https://foodl.me/sn5081
Registration is open for SCN Summit: Future of the Supply Chain, the premier virtual event aimed at educating logistics professionals on critical issues impacting the supply chain industry. Scheduled to take place Dec. 5-7, attendees can register for one, two or all sessions. Topics include everything from State of the Supply Chain and State of E-Commerce to roundtable discussions on Electrification, Supply Chain Visibility, AI, Cold Chain Fleet Management and more.
Scan the QR code to learn more https://foodl.me/kxaizu
Spire Global, Inc. launched DeepVision, a cutting-edge weather monitoring and alerting solution designed to revolutionize global weather awareness for the energy, supply chain and logistics industries. Powered by space-driven weather forecasts, proprietary global modelling, and sophisticated machine learning, DeepVision offers proactive weather monitoring and advanced insights tailored to global supply chain management. With the visualization platform, customers can proactively monitor weather conditions, anticipate potential disruptions and take immediate action to mitigate risk and optimize operations across every layer of complex trade and supply networks.
Scan the QR code to learn more https://foodl.me/z448z5
PCS Software launched FreightNet, a new network designed to foster direct connections between bigbrand shippers and carriers. Carriers that meet PCS quality standards will be visible to PCS Software’s shipper clientele. This enables carriers to maximize exposure with shippers, connect with leading brands and build more profitable relationships. Shipper customers can leverage the ability to connect with quality carriers within their transportation management system or register their private fleet to gain visibility into backhaul opportunities and reduce empty miles.
Scan the QR code to learn more https://foodl.me/t25n3t
Every farm is different, and it is impossible to predict when and where the next climate change disaster will strike. However, the impact that drones are having on the agriculture industry is undeniable. Ensuring that U.S. farmers can continue to produce crops to fuel the food supply chain is critical to protecting the health and financial prosperity of the country. As the climate evolves, farmers will need to rely on technology more and more to adapt their growing methods and maintain their harvests. From water management to overcoming worker shortages and controlling costs, Arthur Erickson, CEO of Hylio, explains how drones can help farmers and the supply chain continue to thrive despite the many food security challenges faced today.
Scan the QR code to learn more https://foodl.me/p948s5
Arctic Xtreme™ labels resist moisture and frost build-up for 100% accurate scans every time. They also feature a durable top coating for added protection from warehouse bumps and knocks.
No wonder the readers of a leading magazine just named it a product of the year.
ID Label engineers Arctic Xtreme labels to your unique requirements, including preprinted barcode sequences and custom colors and sizes. Our professional crews can even install them for you.
Contact us today to request samples or a quote.
Our new Arctic Xtreme™ labels feature a freezer-grade, hybrid adhesive specially formulated for cold storage environments. They’re rated to perform at temperatures as low as -65F. And they can be applied at -20F to avoid any interruptions to operations.
When loads available to haul decrease and so too do trucking rates, independent owner-operators start getting out of the business and the larger fleets start scaling back their hiring. Eventually that tip the balance, capacity gets tight again and rates go up again.
Savvy shippers know that now is the time to build greater resiliency into their supply chains and solidify their carrier relationships. Drop trailer is highly attractive to carriers of all sizes, because it solidifies relationships for them too. Whether the market is tight or loose, they don’t have to chase spot freight when they have committed freight. Ronnie Davis, VP of North American surface transportation at C.H. Robinson, says if you’re thinking about expanding use of drop trailer, talk to a logistics provider with a nationwide carrier network that can flex with your needs.
Scan the QR code to learn more https://foodl.me/cnrzlg
End-to-end visibility and transparency in global supply chains, particularly within the food supply chains, have become hot topics of discussion. From major food and beverage companies to small-tomedium enterprises, organizations are increasingly automating their supply chain processes and striving to achieve comprehensive visibility. For food and beverage companies, this shift in perspective transforms a visibility solution into a potent competitive advantage, according to Nidhi Gupta, CEO and co-founder, Portcast.
Scan the QR code to learn more https://foodl.me/t7mfn6
Less-than-truckload (LTL) shipping has become increasingly popular in recent years, and for good reason. When shipping LTL freight, the shipper pays for the portion of a standard truck trailer their freight occupies, while other shippers and their shipments fill the unoccupied space. This provides many benefits to shippers and carriers—from cost to speed to environmental efficiency.
Dustin Kreigh, operations manager at TA Services, lists 4 things a good 3PL partner will look for when it comes to identifying and executing LTL shipping opportunities.
Scan the QR code to learn more https://foodl.me/pqr09b
Overhaul recorded a total of 1,090 cargo thefts throughout the United States in 2022, 271 in Q1, 246 in Q2, 242 in Q3, and 331 in Q4. The average value of these thefts was $361,986. These numbers represent a 29% increase in volume and a 58% increase in average value when compared to 2021. With an average of 90.8 reported cargo thefts per month, the United States sustained cargo thefts at a rate of 2.99 per day in 2022, up from 2.15 in 2021.
Cargo thieves in the United States largely tend to target loaded trailers and containers that are stationary and unattended. From 2021-2022, pilferage rates increased 5% while theft of full truckload rates decreased 27%. Meanwhile, facility theft and deceptive pickup increased to a combined 13% vs. just 5% in 2021. In 2021, 55% of all thefts with a known location occurred within unsecured parking, a rate which decreased to 44% in 2022. Truck stops/fuel stations recorded the second highest theft rate at 22%, up from 19% in 2021. While these were the two most frequently targeted locations, warehouse/ distribution centers (+23%), company yard/premises (+184%) and boarding houses/carrier facilities (+72%) all recorded increases, representing a combined 26% in 2022, up from 25% in 2021.
Scan the QR code to learn more https://foodl.me/zwzdi6
The need for better frontline worker training across the manufacturing industry is evident and organizations today are taking notice. To achieve stronger organizational success and reduce crime overall, implementing robust and continuous training will empower frontline workers to play an active role in responding and preventing warehouse and truck theft. Companies must also utilize different training methods to help workers become adept at handling any situation. A well-trained, alert and supported workforce means less risks and losses for a company, explains Christine Tutssel, co-founder and SVP of strategic initiatives at Axonify.
Scan the QR code to learn more https://foodl.me/ojfqsc
By embracing sustainable practices, connecting customers with premier quality products, and envisioning a future where every aspect of the journey is aligned with environmental values, the industry is unlocking the true potential of luxury food items—a spirit that transcends borders and embraces the spirit of sustainability.
Michael Fernandez-Ferri, co-founder of Vela, urges stakeholders to join in on this transformative journey leveraging on the power of wind, and explains why together, the industry can redefine the path of exported products, ensuring a commitment to both exceptional taste and a greener world.
Scan the QR code to learn more https://foodl.me/ejpdfe
As wholesale inventories dwindle in the United States, the ongoing restrictions at the Panama Canal could have implications for holiday stocks and supply chains, according to new research from Container xChange. The Panama Canal plays a critical role for U.S. shippers en-route to Gulf and East Coast ports. The United States accounts for 73% of Panama Canal traffic representing about $270 billion in cargo. The ongoing efforts by the Panama Canal Authority to conserve freshwater amidst the prevailing drought conditions have contributed to a substantial backlog of vessels—currently numbering around 200—awaiting their turn to transit through the canal. As this queue lengthens, waiting times have surged to a peak of 21 days, introducing significant delays across multiple segments of the shipping industry.
Scan the QR code to learn more https://foodl.me/6jjg7c
According to new data from the Women in Trucking Association (WIT), the percentage of female safety professionals in corporations with for-hire or private fleets in the commercial freight transportation industry continues to increase. The index shows that 41.6% of safety professionals in companies in transportation are women. Additionally, the 2023 WIT Index found that nearly 16% of respondents report having 90% or more of women in safety roles, with more than 25% reporting they have 50-89% women in those roles. More than 29% of respondents report having 20-49% of women in safety roles, while more than 13% report having 1-19% of women in safety roles and more than 16% report they have no women in safety.
Scan the QR code to learn more https://foodl.me/6uevwv
With nearshoring, the trucking industry has an opportunity to drive economic development, generate employment and create an interconnected marketplace. As the domestic economy could potentially see great growth through this, it’s essential to invest now in a reliable transportation management system. Getting ahead of the game and optimizing routes now will help operations when the floodgates of orders open. Vanessa Galvis, marketing director at Tai Software, explains that the road ahead is filled with promise, and as nearshoring gains momentum, the trucking industry stands ready to navigate this exciting new chapter with solid technology at its core.
Scan the QR code to learn more https://foodl.me/fxkfmx
No matter your role or position in the food supply chain, you are now commissioned to get with leadership or business channel partners to explore opportunities on how the business can take advantage of today’s digitalization technology to drive out operational cost and achieve supply chain visibility. The velocity for which food must travel through the supply chain from farm to fork can be dizzying but can be done with technology. Commodities on the Food Traceability List under FDA’s FSMA 204 Rule will be mandatory to capture KDEs and CTEs and retain the data for 2 years and produced within 24 hours of request. Don Durn, VP of customer solutions for PLM Trailer Leasing, says the time is now to get started.
Scan the QR code to learn more
https://foodl.me/6sk134
Thank you to our customers, partners and employees. You’ve helped keep shelves stocked, families fed and the supply chain moving through it all.
By choosing to use CHEP pooled pallets and containers, you already play an essential role in advancing the circular economy.
And now you can expect even more from us.
The summer 2023 peak season created spot market volatility without much disruption to contractual service levels. However, the gap between spot and contract rates is still large and driving downward pressure on contract rates, according to recent Arrive Logistics data. Rates eased in the weeks following July 4, but are beginning to tighten in certain regions as produce seasons shift and back-to-school shopping begins. Still, the National Retail Federation reports that yearover-year retail imports are trending in the right direction and should be positive by year-end after peaking in August.
Scan the QR code to learn more
https://foodl.me/nor5un
We are investing more than anyone else to make your supply secure. We’re also finding new ways of using data to drive out even more waste from your end-to-end operations.
Together, we can help every supply network to be more sustainable, more efficient and more resilient. Now and for the future.
Tell
While many believe that the COVID-19 pandemic is responsible for pioneering the digital supply chain age, what many don’t know is that digital transformation in some form dates back to the 1940s.
Claude Shannon, dubbed the founder of modern digital communications theory, paved the way for digitalization with his philosophy on how an information source, a transmitter, a channel, a receiver and a destination together form the basic elements of communication.
It’s these basic elements that still to this day make up the complete form of communication, digitally connecting people, product and plants.
And, while digitization means different things to different companies, a digital supply chain presents the same benefits across the board in moving temperature-controlled foods in a safe and efficient manner.
“In the cold food chain, a connected digital supply chain helps companies determine potential threats to the business and product, determine hazard origins through tracing, accurately forecast demand to
minimize waste and optimize inventory, and continue to ensure only the best product makes its way to the consumers,” says Jacob Olson, director, manufacturing solutions, Cleo.
“For the food/cold food chain industry, digitizing the supply chain means more accurate demand sensing and fulfillment, reduced food wastage, fewer and faster trips through optimized logistics and more,” adds Prashant Agrawal, founder and CEO, Impact Analytics.
A digital supply chain also closes the gap to enhance visibility, build resiliency and mitigate risk along the way. That’s because it provides that complete view of everything from farm (raw material) to fork (grocery story/foodservice establishment).
“Digital supply chains are very complex. They’re designed to offer a complete view of everything that needs to happen to create food, from raw material traceability and management (including land usage, animal usage, etc.) to packaged goods production facilities to B2C traceability of consumption, inventory and stocking management. Organizations must consider all these
factors to get every piece of a (sometimes) international supply chain right and enable traceability and sustainability tracking, all while ensuring that logistics, demand planning and forecasting, etc. are integrated, interconnected and driving toward common goals,” says James Newman, head of product and portfolio marketing at Augury. “For the cold food chain in particular, this becomes even more interesting when we consider things like energy costs for refrigeration, transportation costs (including refrigeration) and production costs for creating and storing refrigerated foods.”
At its core, a digital supply chain is a series of process automations that relieves humans of the responsibility to micromanage, adds Chirag Modi, corporate VP, industry strategy, supply chain execution, Blue Yonder.
“It allows professionals to make decisions based on digital information and with complete confidence the information is accurate. Digital supply chains have been a game-changer for cold food chains, particularly since the start of the COVID-19 pandemic. Food manufacturers
and retailers have heavily invested in digital tools that optimize visibility and efficiency. Expiration dates are top-of-mind for cold food professionals, and with digital supply chains they can monitor their warehouses and distribution networks like never before,” he adds.
The digital supply chain also means collecting, organizing and using data in electronic format, accounting for things such as visibility, collaboration and credibility, according to Igor Rikalo, president and COO at o9 Solutions.
“At its most basic level, digitization means paper transactions or verbal communications are captured and used electronically. This would encompass cloud infrastructure, laptops, mobile devices, etc. Basically, you’re taking something managed by paper or instructed by voice and making it electronic,” adds Rikalo. “[It] means you get efficiency and performance improvement and can make better decisions.
Digitization is a distinct business advantage for food and logistics, where the lead time and shelf life can be short, and decisions must be made quickly. It means you can
make better decisions faster, your route to market is quicker, and you have less waste.”
Post-pandemic, a digital supply chain is more about transforming the many manual processes into a more automated fashion, likens Mike Bush, chief growth officer of CDL 1000.
“Let’s call this ‘Digitization Phase 1.’ For instance, we’re able to identify a malfunction in a reefer truck’s cooling system in real-time, which can mean deploying a second vehicle to rescue the goods before they’ve been stored at the wrong temperature (and saving the value of the goods by avoiding spoilage), and sending a repair service to fix the failing reefer unit so the driver doesn’t spend a day on the side of the road,” Bush adds.
In order for any type of Phase 1 to begin though, companies within the supply chain space need to invest in technologies designed to better automate processes, both in the plant and on the road.
One particular area that has seen significant benefit from the introduction of digital management platforms has been the sourcing, buying and selling of pallets, says
John Vaccaro, president, Bettaway Supply Chain Services and founder, PalletTrader.
“PalletTrader, launched last year, is a neutral, online platform, open to all, that digitizes the process of finding, sourcing, negotiating, buying, selling, settling and arranging transportation of pallets,” Vaccaro says. “PalletTrader has reimagined with technology how pallets sales are transacted, bringing a common e-commerce-like platform and process that is streamlining the process and delivering value to thousands of pallet buyers and sellers.”
Another topic impacting the adoption of digitization is the continued use of automation and how to leverage artificial intelligence (AI) and digital twins as they specifically relate to supply and demand planning, says Casey Jenkins, owner, Eight Twenty-Eight Consulting LLC.
“Essentially digital twins are modeling tools that create replicas of a supply chain (or twin) to be able to test ‘what-if’-type scenarios. In other words, it allows modeling of outcomes to test different actions, approaches, or potential risks to see the consequences; both positive and negative,”
says Jenkins. “It’s important for companies to keep in mind though that these are simply tools that can be leveraged. Even AI needs some oversight until we’re able to understand it better and how to use it effectively within our operations.”
It’s the leverage that has many in the supply chain turning to other technologies such as smart sensors, robotics, cloudbased solutions, smart labels and smart packaging, machine learning and GPS tracking, among others; basically any technology that produces data that can be measured, tracked and used to tell a story behind the journey of certain temperature-controlled foods.
However, factors such as capacity planning and demand forecasting pose challenges to some supply chain companies, but leveraging any kind of emerging technology may present the resolutions needed to keep product moving.
“This challenge can arise because, often, companies rely on week- or month-old inventory reports to determine, ‘Do we
have space for this?’ But, when you have up-to-date data, you can use it to make recommendations on how to optimize the space that you have, and how much product you can take on. For example, if, thanks to real-time reporting, you know your capacity up to the moment, it becomes much easier to decide: ‘Can we transfer products from one facility to the other?’ Or, if you are a 3PL, to decide, ‘Can we help a new client out based on their requirements?’ Effective capacity planning boosts efficiency and helps to ensure product integrity,” says Kaitlin Mercier, VP of partnerships, Routeique. “Once this baseline is established for the network, then you can start to leverage AI to solve problems that rely on having good-quality data.”
Sometimes, that digital supply chain goes beyond the traditional warehouse management system (WMS) and in some cases even the warehouse execution system (WES). That’s why some companies are venturing into a combined WMS/ WES, as well as manufacturing execution
systems (MES) “to provide visibility into item location and quantity throughout the manufacturing process, which they do not receive with just the MES,” says Christian Nixel, senior director of technology, enVista Corp. “There is also a lot of opportunity for robotics and MHE to increase the effectiveness, efficiency and timeliness of the movement of goods in the warehouse.”
Other technologies such as Internet of Things (IoT) and blockchain enable what’s dubbed the “smart cold chain,” which predicts environmental disruptions, raises real-time alerts and even self-corrects, says Agrawal.
“There is also digital collaboration via virtual situation rooms that connect suppliers, distributors and retailers to facilitate better decisions faster and advancements in AI demand forecasting to predict hourly demand and maximize the shelf-life management, including intraday markdowns of fresh and prepared foods and the reduction of waste and spoilage. Finally, there are last-mile innovations focused on the cold
The „Supply Chain – Project of the Year 2022“ Award for the best European logistics project of the year was presented by the European Logistics Association (ELA) to the French food retailer E.LECLERC Socamil and its project partner WITRON. Both companies were awarded for the design and implementation of the new fully automated omni-channel / multi-temperature distribution center in Castelnaudary. In addition to the implemented OPM solution in the dry and frozen food area, the world’s debut FPM will be used for the fi rst time for the picking of fresh and ultra-fresh items.
E.LECLERC Socamil and WITRON were able to convince the international jury of experts with a variety of criteria that were successfully implemented “end-to-end” - economically, ecologically, with the focus on customers and employees.
General contractor for the design, realization, and operation of logistics and picking systems for retail business, e-commerce, and industry.
www.witron.com
chain to ensure that shoppers receive undamaged and fresh product regardless of the buying channel,” adds Agrawal.
From food production to the retail and/ or foodservice outlet, the digital supply chain helps to transform the way food is moved from Point A to Point B. But, for many companies still relying on the good ‘ole pen-and-paper method, starting the digitalization journey can be intimidating, cumbersome and costly.
However, it all starts with one thing, and that’s determining the largest blockers the business is facing.
“Often, digital projects start as ‘proof an idea’ rather than ‘can we solve a problem for the business.’ As a result, numerous research studies and analyst groups agree that 75-85% of all digital projects get stuck in pilot mode, and they are never able to scale across an enterprise. In many cases, that is a direct result of not being able to translate the pilot results into an achievable business outcome at scale,” says Newman. “If the issue is to solve raw material
availability due to waste, look at where that is happening in the supply chain, what you are doing today and what success looks like for the entire business if you eradicate this issue. Then, focus on a technology selection process that can address and realize the actual core business need. Many times, this means foregoing the idea of generic platforms that could potentially solve numerous challenges someday and instead focusing on purpose-built solutions that can immediately tackle the problem they were designed to solve and have already cracked the scalability issue.”
“Many organizations and consultants talk about starting small with digital projects, but in reality, this has led to many bad practices. The best companies don’t start small. They start smart with a real focus on what the global outcomes to be realized are and then choose digital solutions that meet those requirements,” he adds. “This methodology doesn’t care where in the supply chain you start, whether it’s in raw material handling, finished product loss and waste improvement, or raw materials to finished product processing. But it does require the business to take a hard look at
what is really driving the need for change and be willing to tackle that problem head on, very specifically.”
For others, it’s about starting from the bottom-up.
“Companies can start with something as simple as KPI tracking. Once you define success for each step of the supply chain, you can begin improving your processes. From there, map out the entire supply chain—the production, the handling, the distribution, the storage—and try to automate every aspect through technology. This iterative approach is a good way to get started. Once companies have a baseline established, they might consider more top-down solutions like warehouse or transportation management platforms. These full-scope tools will help track and improve every step of the supply chain,” says Modi.
Another starting point is simply looking at the data.
“In analytics, the saying is ‘garbage in, garbage out.’ If the data you’re building models on is unreliable, the insights of the model will be unreliable. For the supply chain, which starts with understanding
what metrics are most critical to the firm and what data is needed to drive those metrics. Compare what data is available to what data is needed, and gaps start to appear in what data is necessary to measure performance,” says Barry Bradley, head of supply chain, Crisp.
Case in point: Digital transformation will require new ways of thinking and focused change management, according to Omer Rashid, VP, Ops Ex, automation, innovation, analytics for DHL Supply Chain.
“The first thing needed is to define your digital strategy. Once you have determined what you are trying to achieve (whether that is reduced costs, improved lead times, more accurate inventories, fresher product, etc.) that will guide your approach and solutions,” Rashid says. “Then I would suggest a practical approach. Dip your toe in to get comfortable with solutions that you know can scale, understand value propositions and develop talent that can harness the technology while continuing to execute.”
Just like any new problem-solving journey, it’s also important to understand the problems before looking at solutions.
“It’s easy to fall in love with a tool that
doesn’t end up meeting your needs. Once you define the problems, look for solutions. That doesn’t have to mean a new tech stack; you can add functionality without replacing everything. Partner with IT and sourcing using a balanced scorecard and include users in the evaluation process. Talk to experts who aren’t trying to actively sell you something,” says Hillary Drake, CEO and co-founder of Liminal Network. “The trend I’m most excited and worried about is data availability and its partner analysis paralysis. We’re all analysts now. It’s not enough to have a carrier-level, on-time service; we need to understand on time in full for a single customer or product, and we need to be able to fix it. Building the right data architecture is crucial. That can mean partnering with IT or bringing an analyst onto the team, but you as the business expert must drive it. Don’t expect IT to know what you need. At the same time decisions must be made. Don’t get hung up on best when good enough will satisfy your customer now.”
Another way to look at it is to measure the percentage of a supply chain that is not digital, Rikalo says.
“The more manual the activities, the more
impact digitization will have. This impact can either be through internal improvement possibilities or the effect of competitors becoming more digital and gaining efficiency advantages,” Rikalo adds.
It’s also best to understand (and acknowledge) that no digital supply chain solution solves all problems, says Alex Haar, chief product officer, Parsyl.
“When looking into digital supply chains, one potential pitfall is using tools that operate in a data silo, where the data is effectively trapped within that single solution. Finding a solution that interoperates easily with other products is critical,” Haar adds. “For example, companies who have a traceability solution that helps them comply with food safety laws will want to share their traceability data across other systems as well, such as their temperature monitoring solution and their ERP. Now more than ever it is critical that digital solutions play well with others.”
On the bright side, when it comes to digitization, Bush says, “the path of least resistance is the path of most likely success. Companies should start by identifying a specific issue they want to solve, then
trying a solution to the issue, tracking the results, and then adding another issue once the first solution has proven successful.”
What’s more is, the real hurdle to adopting a digital supply chain is in fact the digital execution, says Lee.
“There’s a ton of data out there, but much remains unusable because of a lack of connectivity. The most significant challenge in supply chains is creating, managing and maintaining the channels through which data flows between systems. I’ve always advocated for a dual approach: develop modular systems with that connectivity built in and prioritize strengthening the links between systems that require constant communication,” he adds. “Another misconception is that digital solutions are ‘plug-and-play’ or ‘set it and forget it.’ On the contrary, maintaining connectivity, which makes it all work, takes consistent work.”
Another challenge with digital supply chains is speed.
“Consumers have an appetite for faster and faster delivery, especially from their local grocery retailers. Businesses will have to increasingly rely on technology and automation to meet this demand,” says Modi. “In some global regions like APAC, delivery is often achieved in 30 minutes or less, and I think we might see demand for that type of efficiency in North America. Speed is also a factor in the digital platforms themselves. Customers are demanding simple tools that only require, say, three steps or fewer to place an order. We have the technology to meet this demand for speed; it’s a matter of leveraging the right tools and training food professionals to use them.”
Regardless of where you are in the journey to digitalization, or if the decision to go digital is even in existence, one thing is for certain—digital supply chains are here.
“Companies should embrace digital technologies, otherwise, they run the risk being left behind,” Rashid says.
And, digital transformation doesn’t have to be done entirely alone.
“Plenty of great software and supply chain solutions can be brought in to accelerate the transformation. Creating a digital transformation team and building all the in-house solutions has a huge oppor-
tunity cost. Each organization needs to understand what pieces they will build, and where they will partner with experts,” says Bradley.
Adopting a digital supply chain also doesn’t need to happen all at once.
“For example, you can’t go from using spreadsheets to using full automation in one initiative,” Jenkins says. “That’s setting yourself up for failure. Instead, approaching digital transformation with a realistic perspective will help to embrace the change. It’s being realistic about where your company is at, where your knowledge base around these concepts are at and having expectations that there will be some bumps in the road along the way. Small changes and steps forward are still steps forward.”
“It’s also important to note that the only way a true digital transformation can occur is if all parties of the supply chain are approaching business-to-business interactions as a partnership” Jenkins adds. “There has to be a level of trust and security with data and information flows so that there is true visibility and collaboration.”
And, you don’t need new top-tier systems to achieve real improvements, Drake adds.
“Dig into the data that already exists on
your POs and invoices, leverage your CRM and OMS, and look at tools that bolt onto existing systems vs. replacing everything at once. Finally, don’t customize. It’s easier in the short term to keep everything the way you’ve already done it, but in the long term, customization leads to expense and frustration. In supply chain, we all use similar processes and there are off-the-shelf tools that will exceed your needs.”
What’s more, because every day presents a new supply chain disruption of some kind, integrating multiple systems will become more prevalent in the digital supply chain world, according to Nixel.
“With so many available systems and an ever-expanding technology field, more integration frameworks are becoming necessary to enable multiple systems in the same supply chain to communicate with each other when moving product through every process. It is becoming more common to add an interface layer that can act as the communicator between any two systems. This is a really effective way to reduce the complexity involved in maintaining integration even in the most complex technology environments,” Nixel says. “As digital supply chains become more complex, we’re starting to see systems
function at higher levels than they were traditionally designed for. Many systems are branching out into more and more functionality to be able to provide more value to each customer.”
However, going fully digital doesn’t mean you lose the human aspect to the supply chain.
“When transforming your supply chain, the human aspect is crucial,” adds Brenig-Jones. “Focusing on training, managing changes and promoting constant improvement leads to long-term success. It’s equally important to seamlessly integrate supply chain systems with other business functions for increased efficiency and data accuracy. Staying updated with industry changes and new technologies is essential for competitiveness. In short, focusing on technology, processes and training will help improve your supply chain in the long run.”
Plus, food shippers that leverage today’s emerging technologies are better positioned to unlock better control and visibility over the entire lifecycle of shipments, says Armon Shahpar, senior lead, enterprise partnerships, Uber Freight.
“This includes everything from real-time pricing and procurement tools, facility insights to solve for warehouse inefficiencies, and tracking capabilities to ensure shipments get from Point A to Point B. We also take a holistic approach to optimize our customers’ supply chains, consulting with global food companies, beverage distributors and food shippers to spur millions in cost savings, reduce greenhouse gas emissions and ultimately provide them with actionable tools to get goods delivered with ease and on time,” Shahpar says.
At the end of the day though, going digital isn’t just about the technology; it’s about “your team’s ability to take action based on what the data says and make proactive decisions,” says Haar.
Resilient supply chains have been highlighted as a necessity in recent years. For 3PLs, efficiency is the backbone to remaining agile in transportation and distribution. In an increasingly complex and unpredictable business environment, creating resilient fleets is key to long-term success. According to Rene Vallejo, senior executive at SAP Business Network for Logistics, the journey toward logistics resiliency is a key ingredient for businesses to survive—and thrive—in the current financial and logistical environment. Maintaining solid relationships, contingency plans and implementing managing technology can improve fleet resiliency in the future.
Resiliency in fleet management refers to the ability to adapt and recover quickly from disruptions, whether they are caused by natural disasters, supply chain disruptions, technological failures or other unforeseen events. Resilient fleets can continue to meet customer demands even when faced with challenges, ensuring the seamless flow of goods. How? A good start is implementing a management strategy. According to Hadley Benton, VP of business development at Fleet Advantage, the best fleet management strategies
today are designed to enable flexibility and business agility to rapidly evolve with changing market dynamics and conditions, as well as shifting economic demand.
“Supply chain disruptions in food retail and cold chain are more common than ever and businesses need to adapt. The pandemic shut down manufacturing and distribution facilities all over the globe, and even now, businesses can’t reliably source many materials in a timely manner. Businesses are facing material shortages and production delays with both inbound and outbound logistics,” says Benton. “This is also the case for truck equipment manufacturers, who are facing ongoing
truck and part shortages. This means longer lead times for new equipment. To meet customer demand, it will be important for businesses to act with agility and transparency.”
Today, Benton explains, companies utilizing equipment finance are seeking partners who offer financial and operational flexibility and agility with programs such as:
• Sale-leaseback programs
• Leveraging advanced data analytics for optimum truck utilization modelling
• Fleet modernization reports
• Financial metrics such as lease vs. purchase analysis
• Full-service vs. unbundled decisioning All of these operational programs come with the need for communication and good relationships with partners. Andrew Lynch, president at Zipline, explains that fleets and carriers need to be treated exactly like shippers and clients to deliver the same value proposition through each transaction.
“The ability to be flexible and resilient in our business means having a flexible
and resilient network of partnerships. So, in an increasingly dislocated environment, leaning into building a combination of trust and a mutually agreed-upon definition of success in those partnerships is more critical than ever,” says Lynch.
Benton extends on this idea, reporting that when it comes to fleet management, having a partner with the flexibility to modify the financing term/structure in the face of change is critical to maintaining fleet resiliency.
“A financial structure that closely mirrors ownership is a great start. Be sure you have the ability to analyze crucial fleet data for making optimal financial decisions. Right-sizing the fleet can only be done if your financial partner has the flexibility to help early term, extend or exchange assets,” says Benton.
In a survey by Orbus Software, enterprises that suffered disruption experienced knock-on effects spanning staff shortages (56%), supply chain issues and increased business costs (48%) coupled with increased technology costs (44%).
How do you prepare for these impacts from disruption?
A back-up plan. I
In the ebb and flow of food logistics, contingencies are among one of the only ways to prepare for the unexpected disruptions that can’t be avoided.
“First, having a fleet replacement strategy and sticking to that strategy is important, but just as important is having a contingency plan when the market changes. A strong focus on operational efficiency and automation where possible can help maintain fleet resiliency. Make use of automated tools to support your operations from end to end. For example, you can use chatbots and help desk solutions to help customers answer questions easily and navigate your site, which will reduce customer support tickets and help customers get answers to their questions more quickly,” says Benton.
Options like automated returns management tools help reduce time spent managing refunds and returns, resulting in faster customer service and reduced manual labor needs.
Benton explains, “Rather than relying on a manual returns process, which can
be slow and frustrating for customers, 3PLs can integrate seamless returns management technology to provide a simple, fast user experience for customers to return products via a self-service portal.”
Forecasting the supply chain is difficult but not impossible. Data, analytics and visibility into nearly any metric is an option that helps fuel decision making, cultivating a reasonable level of preparedness. Geoff Coltman, VP of Catena Solutions, explains how critical data management has become.
“This requires robust data management systems (like data quality and governance software, automated reporting and dashboards with ERP data) that can handle the complexity and volume of supply chain data and make it actionable. By implementing advanced data management and supply chain visibility strategies, a company’s time and resources can be freed up, allowing leaders to strategize and execute improvements instead of spending valuable time mining and analyzing fragmented data,” says Coltman. “We have seen it work best when supply chain decisions for an organization are integrated with finance data and reporting.”
Previously, many businesses were unsure of how they could transform their supply chain data into insights and soundbites they could use for action, according to Vallejo. But now, he says, due to adaptability, businesses can “make the data actionable” across a variety of other businesses.
“By connecting and collaborating with other businesses and then automating and optimizing their networks, businesses will be able to achieve adaptability consistently, and they’ll be more proactive, rather than reactive, to challenges,” says Vellejo.
Resiliency boils down to these key elements: strategy, partnerships and preparedness. Simple enough to lay out in an article but more complex in practice as an ongoing process.
By embracing diversity, technology, data-driven decision-making and strong relationships, 3PLs can better prepare respond to disruptions as they arise. With these actionable ideas, resilient fleets can weather the storm, any storm, disaster or upheaval, and continue to deliver exceptional service to customers, ensuring longevity today and tomorrow.
Consumers are consistently making sustainable end eco-conscious decisions as part of their buying process. For food logistics companies, the warehouse space is paramount to eco-friendly practices. When it comes to building a more sustainable business practice, shifting to a greener warehouse is key and the ability to do so may come from an unlikely place—automated data collection.
Building a technologically enhanced warehouse can yield a strong return on investment for food logistics companies. The seamless coordination, adaptability in the face of fluctuating circumstances like recalls or surging customer demand and the interconnected nature of devices all leads to a more efficient operation.
Yet, smart factories only work when they have a strong foundation in automated data collection.
For instance, consider the process of inventory control. Almost half of the RFgen Digital Inventory Report participants cited over/understocking and inaccurate inventory data as significant challenges affecting their warehouses. By automating the collection of data through mobile barcoding and a linked inventory control software, warehouses can work to reduce overstock and keep pace with shifts in consumer behavior. Tracking real-time means better
planning for future orders and reduced rack space when it comes to overstock. Further, by reducing the amount of on-hand product, space and human capital are freed to be used in other areas.
The use of automated data collection allows organizations to gain full visibility into their warehouse and supply chain. Mobile devices and warehouse management systems collect real-time data on every aspect of inventory from location to shipping. This allows your team to spot waste and redundancies, including how long inventory sits on shelves, where workflows fall short, and how heavy equipment is being used.
What does this look like in action? Companies utilize barcode software and scanning technology to aid their supply chain traceability. Handheld scanners transmit data directly to their business management system, including tracking incoming shipments, picking out current shipment orders, and sending out finished products for distribution. Through this process, companies are able to trace all products and materials in their warehouses, trucks, stores, and even at their supply chain partner locations.
The future of digital warehouses is built on
data. Without data accuracy, warehouses and supply chains will be unable to make real-time decisions, let alone embrace sustainable efforts.
Automated data collection allows you to replace manual, paper-based approaches within the warehouse, which have a 60% accuracy rate at most. Not only does this benefit sustainable initiatives, but it also helps eliminate error-prone data collection.
Automated data collection should not only be a warehouse best practice, but a nonnegotiable for food logistics companies of the future. By driving accurate data collection and real-time visibility into operations, your warehouse can streamline processes and eliminate waste. The result is the ability to create a more sustainable business model that will answer customer desires while also optimizing your operation for future success.
Scan the QR code to read the rest of this column in full:
https://foodl.me/fca7rj
ABOUT THE AUTHOR BY ROB BRICE CTO and founder,In April, the California Air Resources Board (CARB) approved the Advanced Clean Fleets rule, a first-of-its-kind ruling that requires a phased-in transition toward zero-emission medium-and-heavy duty vehicles by 2045.
What this means is, fleet owners operating vehicles for private services such as last-mile delivery and federal fleets will begin their transition toward zero-emission vehicles starting in 2024. Other fleet owners will have the option to transition a percentage of their vehicles to meet expected zero-emission milestones. For example, last-mile delivery and yard trucks must transition by 2035, work trucks and day cab tractors must be zero-emission by 2039, and sleeper cab tractors and specialty vehicles must be zero-emission by 2042, according to CARB.
As a result, fleet owners are projected to save an estimated $48 billion in their total operating costs from the transition through 2050.
But what does this mean for the cold food chain? How does this ruling impact how temperature-controlled foods and beverages move across state lines?
For starters, while much of the focus is on power units, companies in the cold chain should know that CARB also updated its standards for transport refrigeration units (TRUs).
“CARB’s Airborne Toxic Control Measure now requires lower-GWP refrigerants on truck and trailer units, and the zero-emission truck TRU rule requires fleets operating in California to phase out at least 15% of their diesel-powered truck TRUs annually over seven years until none
operate in California on or after Dec. 31, 2029,” says Bill Maddox, senior manager, product management, Carrier Transicold.
“These new provisions affect fleets based in California or doing business in California. They also provide a standard for fleets that want the flexibility to operate in California in the future or have their own rigorous sustainability goals.”
Something also to consider is how to collect, measure and analyze the data from fleets converting to zero emissions.
“The future of sustainable fleets in the supply chain must start with data. When setting sustainability targets, data should pave the way. An integral step is quantifying current vehicle emissions, inclusive of miles driven, EPA vehicle rating and the CO2 output these vehicles are producing, which most businesses don’t have insight
Propane is the safe, reliable energy for material handling.
Propane-powered forklifts produce fewer emissions than those using an equivalent amount of electricity. That can improve air quality inside your facilities—for a healthier, more productive workforce. And because they only require a quick and easy cylinder change to get back to work, your propanepowered equipment does more than move inventory—it gives your bottom line a big lift, too.
To learn more, visit propane.com/for-my-business/material-handling/
into. This would include both company-owned fleet vehicles as well as grey fleet vehicles, those that are personally owned by employees but that are driven/ utilized for work-related purposes,” says Jon Bernstein, VP of product management at Motus. “Collectively, without a baseline understanding, it truly becomes difficult to accurately project their sustainability efforts, which can lead to setbacks, poor results and wasted costs. The goal of moving towards medium-and-heavy duty vehicles with zero-emissions starts with companies analyzing their current vehicle program data.”
However, the challenge with data is that it can be difficult to understand the measurable impact on emissions, particularly when it comes to miles driven and the CO2 impact those miles have on the environment, Bernstein adds.
“In addition, driving behavior can have a material impact on the amount of emissions being placed into the envi-
ronment. That’s where a data collection and management system can be critical. Accurate and visible data is vital. By consolidating into a single source of truth, better data will be produced and help accurately plan for future initiatives, as well as track against current ones. In addition, optimization of route planning can play an important role to ensure those vehicles that are sub-optimal from an emissions perspective are being utilized in the most efficient and effective way,” he adds.
Infrastructure also plays a role in how quickly and easily companies can transition their fleet accordingly.
“Two of the biggest challenges in operating a sustainable fleet include ZEV infrastructure and the cost of new EV equipment,” says Jeff Jackson, EVP, dedicated contract carriage, Penske Logistics. “We are hopeful that utilities, energy suppliers, governmental agencies and private entities will work effectively together to solve the infrastructure chal-
lenges. To solve some of the infrastructure challenges, Penske Truck Leasing has done an excellent job of creating a charging network to support EVs in California for light-, -medium and heavy-duty trucks. Penske is also actively seeking grants and other available funding to offset the costs of equipment.”
For those companies just starting to assess their fleet’s options, it’s important to understand how and where to start.
For its part, Penske Logistics has been testing various sustainable technologies for its fleet and customers.
“We are currently operating Freightliner eCascadias and Orange EV yard tractors for food and beverage customers in California. We also recently announced that we are working with ConMet eMobility as the first 3PL to pair their zero-emission refrigerated trailer with an eCascadia, to the benefit of a quick-service food retail
customer for their daily delivery routes,” says Jackson. “Penske is also an active participant in a robust tire retreading program, which offers sustainable solutions on multiple levels. A key connector to our EV fleet’s success is the Penske Truck Leasing electric truck charging network that has been well established in California.”
Beyond the fleets is a change that involves the use of low-GWP refrigerants. R-452A has a global warming potential 45% lower than that of R-404A, the traditional TRU refrigerant, is non-toxic, non-flammable and delivers similar performance to R-404A.
“Carrier has made R-452A standard across our TRU product lines for trucks and trailers,” says Maddox.
What’s more is, diesel-powered TRUs have cleaner, more efficient engines.
“The latest trailer products in our X4 and Vector series use an advanced version of the smart engine used throughout our existing trailer platforms. Its common-rail fuel injection optimizes fuel delivery, reducing fuel consumption by 5% to 10%, and a new third speed, called ‘eco speed,’ adds to the fuel savings by automatically decreasing TRU engine RPMs during intervals where conditions permit,” adds Maddox.
An Accenture survey found 61% of companies are planning to increase their investment in sustainable supply chains over the next three years.
For some companies, like Penske, this translates to expanding its carbon-neutral, energy-efficient facilities program, Jackson says.
For others, like Carrier, it means introducing new CARB-compliant products, such as the X4 7700 single-temperature trailer refrigeration unit; the Vector 8700 single-temperature trailer reefer unit; the Vector 8800MT multi-temperature trailer reefer unit; and the Supra e11 all-electric unit for medium-duty straight trucks.
“Carrier is collaborating with other industry leaders to advance the development of all-electric refrigeration technology and help fleets comply with CARB’s requirements for the adoption of zero-direct emission truck refrigeration technologies in the state,” says Maddox. “In May, PFG, Navistar, Great Dane and Carrier launched a commercial evaluation program using all-electric refrigeration technology on a battery-electric truck for sustainable, direct-emissions-free refrigerated and frozen food distribution.”
Maddox also emphasizes the importance of implementing telematics, and how doing so can “help fleets create automatic records to demonstrate the use of plug-in electric standby power when TRUs are stationary, which can be an emissions compliance strategy in California,” he adds. “TRU telematics can support fleet operations more broadly, helping to capture data regarding fuel use, dwell time and maintenance matters that may arise while a trailer is in use.”
The cold food chain continues to adopt and implement measures, equipment and technologies to better achieve a sustainable fleet, and with the help of the Advanced Clean Fleets rule, will eventually see benefits such as lower operating and maintenance expenses, other state and federal financial incentives and providing an overall better, cleaner place to live and operate.
When thinking about the idea of fleet optimization, the prevailing mindset is that there is a binary state of being either optimized or not. This perspective fails to acknowledge that optimization can mean different things to different fleets, and that value can be achieved at intermediate steps between optimized or not.
There is no one-size-fits-all way to achieve optimal status; some fleets might benefit from simple manual planning, while others would gain the most value from decision support tools.
Understanding where you are on your optimization journey will ensure your fleet is utilized most effectively and customers are served to the best of your ability.
There was a time not long ago when a route planner or dispatcher would use a paper map to plan the day’s deliveries before hitting the road. They relied heavily on tribal knowledge about traffic, time windows and other data needed for decision making.
Enter mapping software, which calculated the distances and drive time between stops, presenting a visual route plan to interested stakeholders.
Route optimization software soon followed and further automated the process, providing feedback like an electronic copy of the plan and better ETAs. As those planners and fleets matured, they were able to take advantage of continuous planning (not batch planning), scenario creation and prescriptive suggestions for moves that could be made.
At each step in this journey, immense value was gained; time was saved, customer service was enhanced, and the organization benefited.
Although many foodservice distributors aren’t doing home delivery, it does not mean they are exempt from the complexities of final-mile distribution.
Fleets must grapple with complex road networks, evolving customer expectations, increased competition, rising inventory costs and stricter government regulations. In this dynamic environment, fleet optimization is essential for businesses to stay ahead of the competition and meet the evolving demands of the market.
Optimization should not be thought of as
a one-time event, but rather a continuous journey that varies from one business to another. It requires a comprehensive analysis of the network and the identification of key metrics to inform strategic decision-making.
Fortunately, obtaining and managing data presents the biggest opportunity for scaling businesses to significantly reduce costs and improve performance.
Dispatch optimization is a higher rung, enabling effective route planning, increased asset utilization, and maximizing available hours of service compliance.
Route optimization software can offer many benefits, even for fleets not willing or able to jump into full optimization immediately.
Scan the QR code to read this column in full.
https://foodl.me/nro0qr
All businesses want effective pest control, but it is non-negotiable for food handling verticals such as the cold chain environment. Facility managers cannot risk pest introductions when the safety of perishable goods and the standard of their reputations are on the line. Plus, food is a natural attractant for pests, and supply chains offer several opportunities for pests to infiltrate your product. This is why it is crucial to implement integrated pest management (IPM) practices along the cold chain.
IPM is a sustainable, comprehensive approach to pest control that prioritizes prevention techniques over chemical treatments. An IPM helps limits chemical treatments to last-resort situations, and when necessary, employs the leasthazardous options available for each situation. At its core, an IPM program is based on assessing the situation, implementing solutions and monitoring results.
Here’s some IPM best practices:
1. Inspect. The first step in any IPM program is a thorough inspection of the facility. The goal is to identify any potential pest entry points, such as cracks in the building’s foundation, damaged weather stripping on doors and windows or pest “hot spots,” which are areas that often offer food, water and/or shelter to pests if not frequently monitored, such as:
• Loading zones. As products come and go, so can pests. Areas where doors are frequently left open should be thoroughly inspected for signs of pest activity.
• Storage closets. This relatively undisturbed environment appeals to pests that like warm, dark places. Storage closets also frequently harbor materials that attract pests, such as cardboard and damp rags or mops.
• Dumpsters. Pests, especially rodents,
love gnawing through boxes and food debris that can be found in the garbage at your facility. A pest management professional should see if trash cans have well-fitting lids, and make sure dumpster areas are well-maintained and in appropriate locations.
• Floor drains. Although they’re easy to overlook, these hiding spaces are a perfect environment for pests like flies and cockroaches. It doesn’t matter if they are wet or dry because they like both options. Pest management professionals will look to make sure drains are clean and provide recommendations for keeping pests out.
2. Prevent. The best offense is a good defense. The foundation of any successful IPM program is the prevention of pests in the first place. This is done through regular sanitation practices and keeping up with building maintenance. Regularly clean storage facilities, processing equipment, break rooms, restrooms and transportation vehicles to limit pest attractants. Replace any broken window screens, seal holes and install loading zone air curtains to help keep flying pests from entering. Consider your landscaping—keeping shrubbery and tree limbs at least two feet away from the foundation will help avoid insects from using foliage as a freeway into the building.
3. Treat. Once a pest management professional has inspected the property and provided recommendations for pest prevention, the next step in an IPM program is treating any existing pest issues. This could include anything from bird abatement services to placing cockroach bait, and treatment should be catered to your unique situation, such as the facility’s location and the types of products it handles.
4. Monitor. Pest management programs are ongoing; they do not stop once existing pest problems are resolved. Consistent monitoring is essential to ensure the program is adapting to your needs and that any pest introductions are caught before they evolve into infestations.
By following a pest management professional’s recommendations for exclusion and sanitation practices, and by training staff what to look for, pest control becomes more manageable—and successful— as part of day-to-day operations.
The success of any organization relies heavily on its ability to cultivate a strong leadership pipeline. Nurturing a robust leadership channel is a vital necessity for sustainable growth and longterm success.
Business leaders must be proactive in identifying and mentoring talent from within the organization who can step into critical roles when needed. A well-prepared pipeline enables leaders to minimize disruptions during times of transition and empowers them to tackle unforeseen challenges with confidence. Nurturing the next generation of leaders creates a sustainable and resilient organization that can weather the storms of change and continue to thrive.
Building a strong growth path is about fostering a culture of growth and development across the organization. When team members see clear opportunities for mobility and advancement and that their efforts are recognized and rewarded, they become more engaged and committed to their roles. This environment stimulates
innovation, collaboration, and a sense of purpose, driving the entire organization forward.Leadership development programs also play a vital role, as they provide team members with the skills, knowledge, and experiences necessary to take on leadership roles. Investing in development and training also helps organizations demonstrate their commitment to professional growth, which in turn, cultivates loyalty and commitment to the company’s mission and vision.
A leadership pathway can act as a powerful retention tool. When employees see a clear succession strategy, a diverse array of development paths, and feel that the organization is invested in their professional growth, they are more likely to see the advantages of continuing to invest their own talents in your company. Additionally, a leadership development program and a culture that enables and promotes career mobility send a message to team members that the organization values and rewards its internal talent.
Providing equal opportunities for development and advancement ensures that talent is recognized and promoted
based on merit, rather than bias. A diverse leadership team brings a multitude of perspectives, ideas, and experiences to the table, which can lead to better decision making and improved business outcomes. Cultivating a succession path that encourages diversity and inclusion can lead to greater innovation, creativity, and adaptability in an ever-changing business environment.
To succeed in today’s dynamic environment, organizations must adapt and embrace a multi-generational approach to leadership development. By nurturing a diverse pool of talent and one that spans different generations, companies can effectively navigate the challenges and opportunities presented by shifting demographics.
Scan the QR code to read this column in full.
https://foodl.me/rg06cv
HURRY AND SECURE YOUR SPOT AT THE UPCOMING NETWORKING AND EDUCATIONAL FORUM EXCLUSIVELY CRAFTED FOR WOMEN AND MEN SUPPLY CHAIN EXECUTIVES
DATE: NOVEMBER 14 & 15, 2023
LOCATION: HOTEL COLEE, ATLANTA BUCKHEAD - ATLANTA, GA
WE LOOK FORWARD TO SEEING YOU AT THIS YEAR’S FORUM