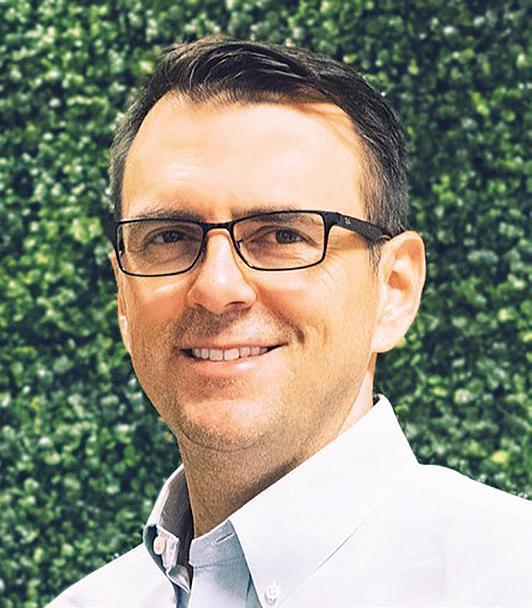

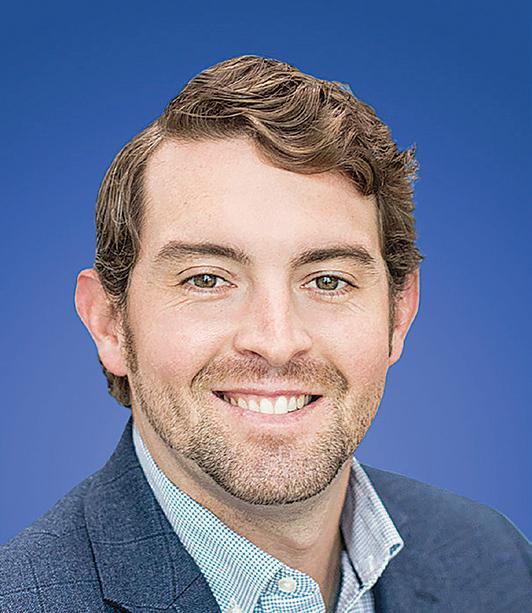

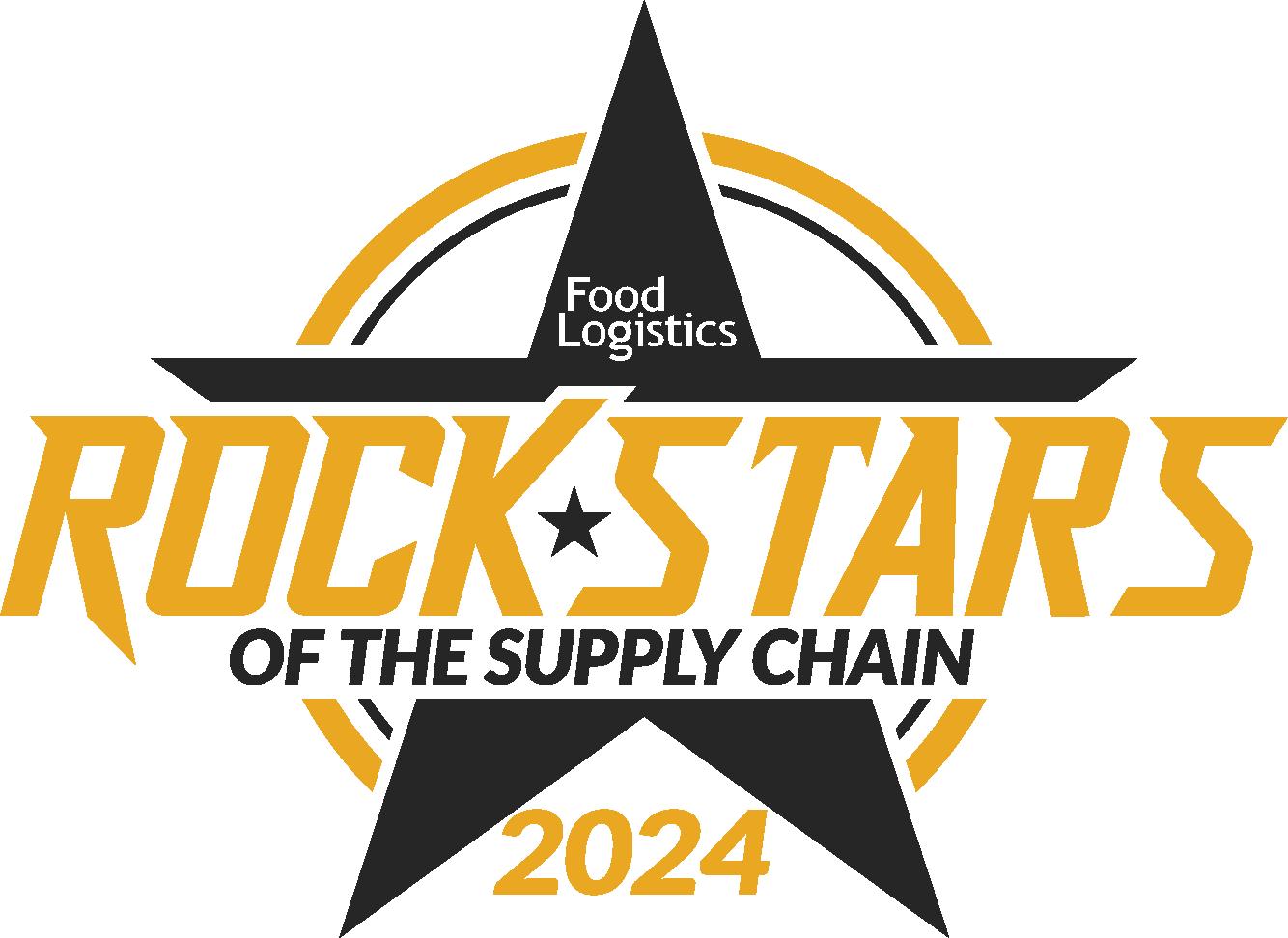

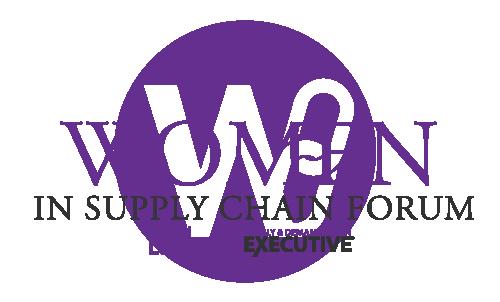
MARK YOUR CALENDARS
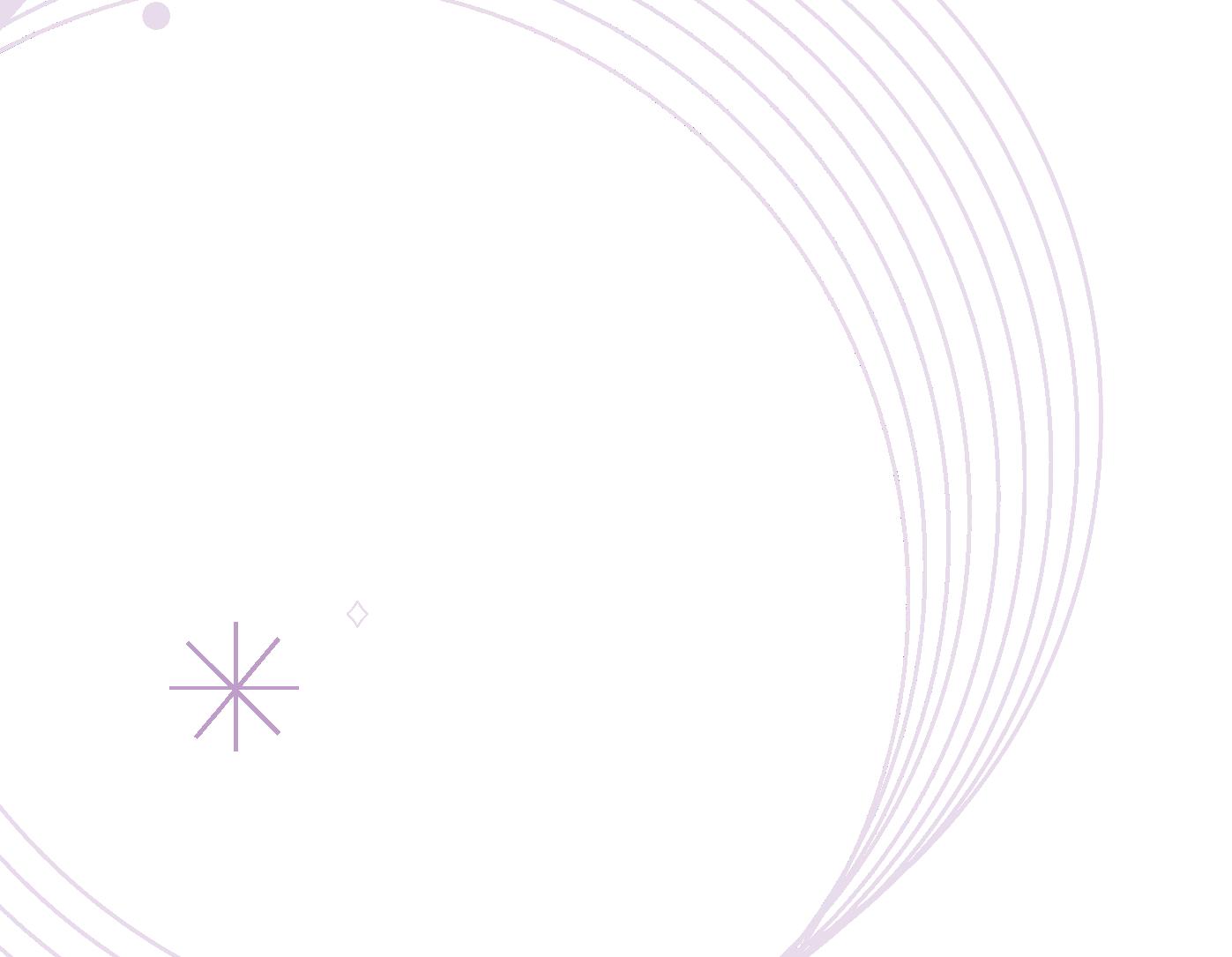
SCAN ME
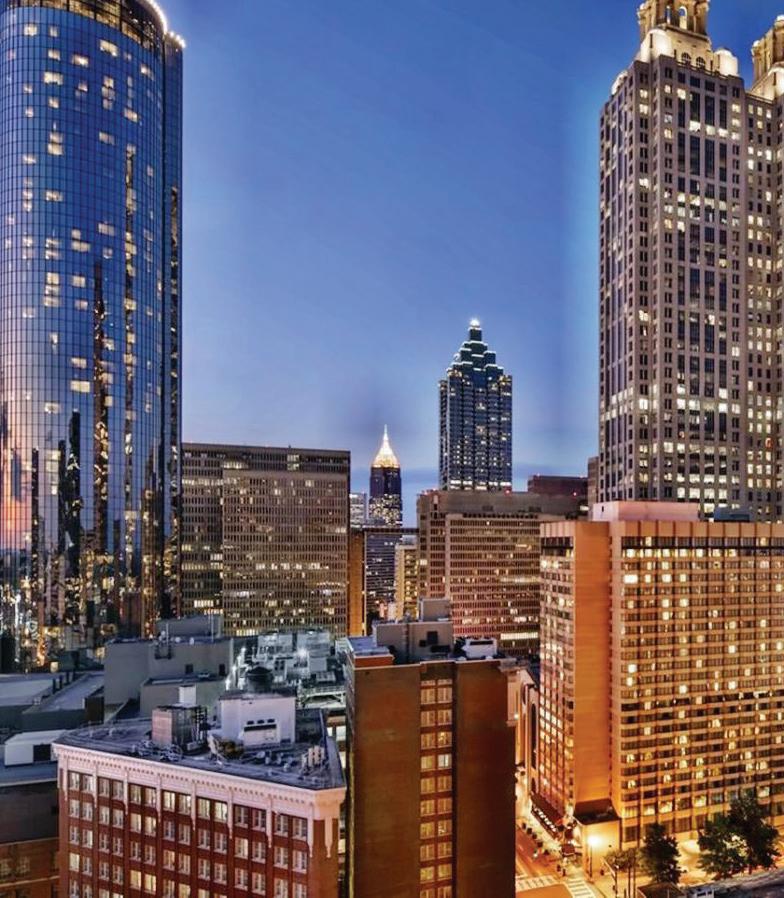
SCAN HERE TO UNLOCK EXCLUSIVE ACCESS TO UPCOMING EVENT DETAILS AND BE THE TRAILBLAZER WHO KNOWS WHEN REGISTRATION OPENS FIRST!
DON’T MISS OUT – SIGN UP AND STAY IN THE KNOW!


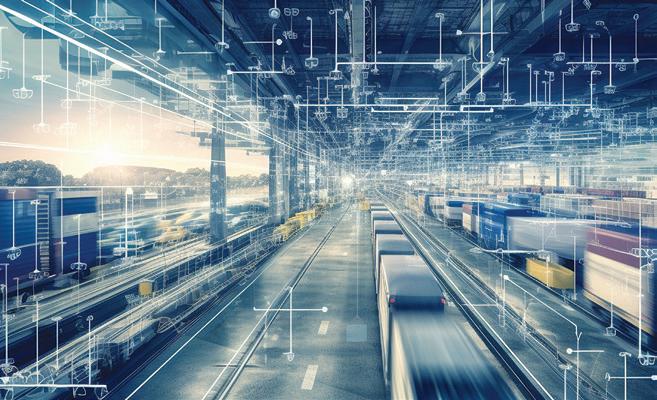
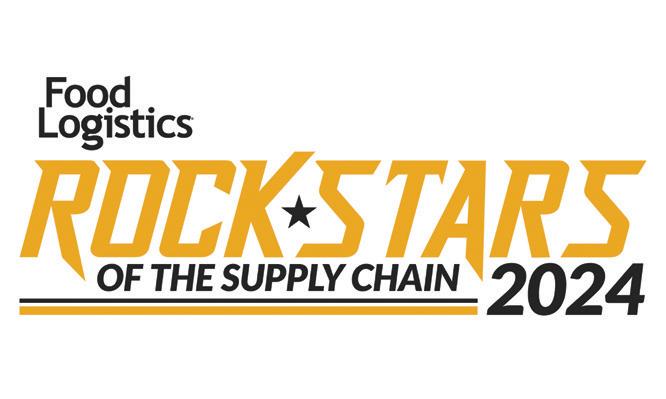

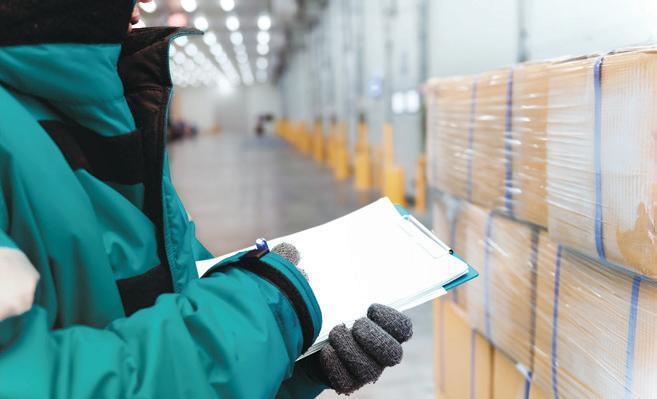

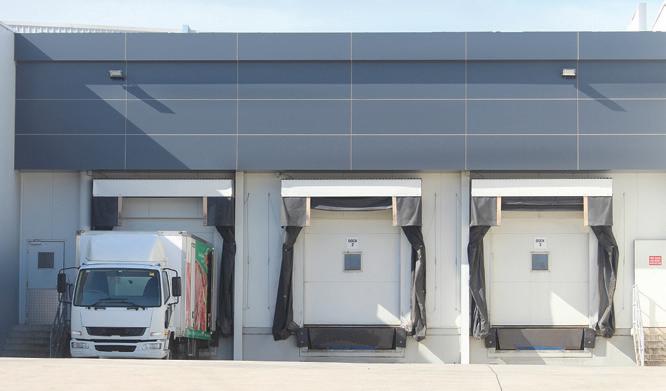
SCAN ME
SCAN HERE TO UNLOCK EXCLUSIVE ACCESS TO UPCOMING EVENT DETAILS AND BE THE TRAILBLAZER WHO KNOWS WHEN REGISTRATION OPENS FIRST!
DON’T MISS OUT – SIGN UP AND STAY IN THE KNOW!
Every year, our editorial staff sifts through the 100-plus submissions for our Rock Stars of the Supply Chain award, and every year, I am more and more impressed by the rock stars of the supply chain, who continue to go above and beyond to improve food safety, enhance efficiency and disrupt supply chain disruptions.
And this year’s roundup of winners is no different.
This year’s winners are collaborative, passionate, innovative and forward-thinking; they’re an inspiration to their teams and viewed as mentors to those entering the supply chain space; they’re dubbed as loyal, dependable, driven, visionary, ambitious and lead by example.
These supply chain rock stars are the true backbone of the cold food chain.
That’s why we upped the game and revamped the Rock Stars of the Supply Chain award, now breaking the submissions into four distinct categories:
• Top Warehousing Stars
• Top Shippers
• Rising Stars
• Lifetime Achievement
Also in this issue are cutting-edge interviews with supply
chain leaders on mitigating supply chain risk (page 12), revolutionizing the last mile (page 18) and new solutions pertaining to supply chain visibility (page 34). Check out expert columns on how to overcome cargo theft (page 33), understanding cold storage real estate regulations (page 31) and how to enhance worker safety (page 32). And be sure to sign up for our twice-weekly e-newsletter, Cold Chain Insights, at https://foodl.me/ctxgccva and become more connected to the Food Logistics community.
• Headed to MODEX in March? Come find us at booth # A9404.
• Submissions for Top 3PL & Cold Storage Providers award open Feb. 12.
• Submissions for Top Supply Chain Project award (now available to the Food Logistics audience) open Feb. 19.
• Registration is open for SCN Summit: State of the Supply Chain, covering topics such as warehouse automation, cultivating company culture, going electric, generative AI in logistics and more. Go to www. SCNSummit.com to register or learn more about becoming a speaker.
• Save the date for this year’s Women in Supply Chain Forum, set for Nov. 12-13 at the Ritz-Carlton in Atlanta. Head to to www.WomenInSupplyChainForum.com to learn more.
Hope to see you in person while out and about and looking forward to working together in the New Year!
EDITORIAL
Editor-in-Chief Marina Mayer mmayer@Iron.Markets
Managing Editor Alexis Mizell-Pleasant amizell@Iron.Markets
AUDIENCE
Audience Development Manager ....................... Angela Franks
PRODUCTION
Senior Production Manger Cindy Rusch crusch@Iron.Markets
Art Director Flatworld Solutions
ADVERTISING/SALES
Brand Director Jason DeSarle jdesarle@Iron.Markets
Account Executive Brian Hines bhines@Iron.Markets
Account Executive Jay Gagen jgagen@Iron.Markets
Account Executive Mark Pantalone mpantalone@iron.markets
IRONMARKETS
Chief Executive Officer ................................................ Ron Spink
Chief Financial Officer JoAnn Breuchel
Chief Revenue Officer Amy Schwandt
Brand Director, Supply Chain & Green IndustryJason DeSarle
Brand Director, Construction, OEM, IRONPROS Sean Dunphy
VP, Audience Development Ronda Hughes
VP, Operations & IT Nick Raether
Content Director Marina Mayer
Director, Online & Marketing Services Bethany Chambers
Director, Demand Generation & Education Jim Bagan
Content Director, Marketing Services Jessica Lombardo
CIRCULATION & SUBSCRIPTIONS
P.O. Box 3605, Northbrook, IL 60065-3605
(877) 201-3915 | Fax: (847)-291-4816
circ.FoodLogistics@omeda.com
LIST RENTAL
Sr. Account Manager Bart Piccirillo | Data Axle (518) 339 4511 | bart.piccirillo@infogroup.com
REPRINT SERVICES
Brian Hines (647) 296-5014 | bhines@Iron.Markets
Published and copyrighted 2023 by IRONMARKETS. All rights reserved. No part of this publication may be reproduced or transmitted in any form or by any means, electronic or mechanical, including photocopy, recording or any information storage or retrieval system, without written permission from the publisher.
Food Logistics (USPS 015-667; ISSN 1094-7450 print; ISSN 1930-7527 online) is published 6 times per year in January/February, March/April, May/June, July/August, September/October, and November/December by IRONMARKETS, 201 N. Main Street, Fort Atkinson, WI 53538. Periodicals postage paid at Fort Atkinson, WI 53538 and additional mailing offices.
POSTMASTER: Send address changes to Food Logistics, P.O. Box 3605, Northbrook, IL 60065-3605. Subscriptions: U.S., one year, $45; two years, $85; Canada & Mexico, one year, $65; two years, $120; international, one year, $95;
Frozen food temperatures could be changed by just three degrees to save the carbon dioxide emissions of 3.8 million cars per year, according to research from DP World . Most frozen food is transported and stored at -18°C, a standard that was set 93 years ago. A move to -15°C could make a significant environmental impact with no compromise on food safety or quality, the study found.
“Frozen food standards have not been updated in almost a century. They are long overdue for revision,” says Maha AlQattan, group chief sustainability officer at DP World. “A small temperature increase could have huge benefits but, however committed each individual organization is, the industry can only change what’s possible by working together. With this research and with our newly formed coalition, we aim to support collaboration across the industry to find viable ways to achieve the sector’s shared net zero ambition by 2050. The move to -15°C will bring the industry together to explore new, greener standards to help decarbonize the sector on a global scale. Through this research, we can see how we can deploy accessible storage technologies in all markets to freeze food at sustainable temperatures, while reducing food scarcity for vulnerable and developed communities.”
Scan the QR code to learn more https://foodl.me/oq5jgcyp
The 2023 December SCN Summit highlighted commentary from industry experts on trends, technologies, challenges and opportunities revolving around warehousing, transportation, sustainability, procurement, emerging technologies, workforce development and risk management.
These sessions featured experts from Enable, PLM Fleet, Interact Analysis, SAP and National Retail Federation, with audience engagement and polling through the live platform. Recap and catch up with all 6 sessions on demand, available now.
Scan the QR code to learn more https://foodl.me/ti9r24t8
Choco released Choco AI, a revolutionary solution designed to automate and streamline order management between restaurants and suppliers, mitigating the challenges of manual processes.
“Choco AI is a game-changer, not just for individual suppliers, but for the entire industry, opening a new chapter of streamlined operations and increased revenue. In just two weeks, suppliers can transition to a digital setup, effortlessly managing emails, voicemails, and more, pushing their business into a future of enhanced efficiency and profitability. For the first time, suppliers can centralize all their orders, enabling smarter decisions to tackle staff shortages and significantly reduce waste. This is just the beginni ng of a series of AI innovations we’re actively developing to further improve both suppliers’ and restaurants’ operations. We’ve ensured our AI technology is easy to implement, with our solid support guiding suppliers every step of the way,” says Choco CEO Daniel Khachab.
Scan the QR code to learn more https://foodl.me/30l0twul
Meet the winners from this year’s Top Tech Startup Award. Now in its second year, this award presented by Food Logistics and Supply & Demand Chain Executive spotlights top software and technology startups in the supply chain and logistics space. The future of the supply chain industry is now. Congratulations to the winners of this year’s Top Tech Startup award. Thank you for disrupting the supply chain in a positive way.
Scan the QR code to learn more https://foodl.me/rq58q5v8
It is imperative for organizations to monitor evolving adverse weather events and disease outbreaks. For instance, with El Niño, companies should closely track its development and consistently evaluate the potential repercussions it may have on crucial territories and suppliers. An innovative approach some food producers have employed to combat rising ingredient costs is reducing the use of commodities in their products.
According to Nidhi Jain, associate specialist at The Smart Cube, as a consequence of supply constraints, sugar and cocoa prices are poised to remain elevated in the short to medium term. Furthermore, these price increases may continue for an extended duration, especially if the El Niño weather phenomenon persists. This scenario could result in continued high confectionery costs beyond Halloween and the rest of the holiday season.
Scan the QR code to learn more
https://foodl.me/cjeoi7nq
“In my supply network, it’s the things I can’t see that keep me up at night.”
Every supply network has blind spots where inefficiencies and waste are hidden.
CHEP is now using AI and advanced analytics to connect even more of the data from our extensive end-to-end network to deliver more valuable efficiency insights – and give you more visibility into the depths than anyone else could.
More efficiency. More innovation. That’s what you can expect when you partner with CHEP.
Expect more with CHEP.
See how
Jim Hansen, chief product officer at Advantive, explains that traceability has become a necessity in manufacturing, allowing manufacturers to provide suppliers with the data they need to ensure a product has been prepared properly, and is validated with the quality of ingredients and the accuracy of processes specified. From there, suppliers can continuously improve efficiencies and find cost savings opportunities without sacrificing safety and quality.
When fully optimized, prevention and traceability in food manufacturing can have positive operational outcomes while also ensuring compliance, offering businesses an opportunity to invest in the tools that drive higher levels of manufacturing productivity and quality. With the adoption of traceability tools, businesses are empowered to make informed decisions in real-time that analyze trends, solve problems, and move the business forward.
Scan the QR code to learn more https://foodl.me/pvso1ls4
Canada’s Assessment and Revenue Management Initiative Canadian importers and their partners are preparing for a massive, generational shift in the way the government collects, manages and reports on import revenue and trade information— not just for food and beverage imports but for all commercial goods entering Canada, explains Glenn Palanacki, VP industry strategy, forwarding and brokerage at Descartes.
Canada Border Services Agency’s Assessment and Revenue Management project, better known as CARM, is a multi-year digital initiative that will modernize how the government interacts with the trade community—importers, customs brokers, freight forwarders, carriers, customs bonded and sufferance warehouse operators, duty-free shop operators, financial security providers and software service providers—to assess and collect over $30 billion in annual revenue . While all parties have work to do to ensure readiness for May 13, all parties also have a vested interest in a more modern and streamlined system for importing commercial goods into Canada, including food and beverage imports.
Scan the QR code to learn more https://foodl.me/60kxi3u7
Drivewyze launched Drivewyze Free, a free service that uses telematics devices, tablets and smartphones to deliver in-cab safety alerts and advisories to fleets and drivers.
“This is a monumental day for our company, our safety partners, and the industry,” says Brian Heath, CEO of Drivewyze. “In collaboration with our telematics and transportation agency partners, we are excited to be giving this essential safety service to the trucking industry at no cost. There are no strings attached. We’re a safety-driven company joined by like-minded agencies and telematics partners to leverage vehicle-to-infrastructure networks to improve highway safety for everyone. We know many of our Essential Alerts and Advisories modify behavior—drivers slow down and apply less hard braking. It makes them safer behind the wheel. We’re hoping all fleets will utilize this free offering to give their drivers technology that can truly make a difference to their safety.”
Scan the QR code to learn more https://foodl.me/i0ekleam
The dry bulk and LNG segments have borne the brunt of restricted transits, according to recent research from Container xChange. In contrast, liner shipping has faced minimal consequences from transit reductions but has been significantly affected by draught reductions.
The immediate impact includes a halved number of vessels passing through the canal, resulting in shipping companies re-routing vessels, blank sailings, longer transit times, and potential higher shipping costs in the coming times. The mid- to long-term repercussions of Panama Canal situation will run easily throughout the next year because of the irreversible environmental concerns that will dwindle the performance of the canal in time.
Scan the QR code to learn more https://foodl.me/rbftxhy0
This year’s Top Software & Tech award spotlights new-to-market software and technology solutions designed to provide automation, efficiency and visibility to the supply chain space.
This award was broken down into two main categories (Small Business <$50 million and Enterprise >$49 million) and then five sub-categories within each main category: Procurement/ERP Software, Robotics; Supply Chain Visibility Solutions; Warehouse Automation; and WMS/TMS Software, with one overall winner from each category. Check out the 2023 winners and a huge congratulations from Food Logistics.
Scan the QR code to learn more
https://foodl.me/55ykjcef
AIT Worldwide Logistics launched its Middle Mile Network, a groundbreaking service that offers a faster, more secure, and cost-effective alternative to traditional expedited less-than-truckload (LTL) services on vital routes covering more than 90% of major U.S. metropolitan areas.
“In a market where industry consolidation is limiting options and potentially reducing service quality, AIT stands out by offering a robust, internally controlled network,” AIT’s chief business officer, Greg Weigel, says. “This initiative is not about rapid, unchecked expansion; it’s about providing a consistently higher standard of service that connects with AIT’s first and final-mile options to deliver a world-class, end-to-end supply chain solution for our customers.”
Scan the QR code to learn more https://foodl.me/29o04qjs
The freight industry showed signs of life, bucking a trend of weak performance that began in the second quarter of 2022, according to third quarter 2023 data from the Transportation Intermediaries Association (TIA). However, sluggish freight volumes and trucking over-capacity will likely keep future results tepid until at least the back half of 2024.
“Our forward-looking data has had us bracing for continued weakness in the freight economy,” says TIA president and CEO Anne Reinke. “However, the surprising strength we saw during the third quarter goes to show that the market can still outperform forecasts. Our members continue to be incredibly resilient and have made the most of less-than-stellar conditions in recent quarters.”
Scan the QR code to learn more https://foodl.me/onhs313l
The theme for the 2023 Women in Supply Chain Forum, “Better Together: How Collaboration Promotes Women in Supply Chain,” hit on all the right notes. Panelists spoke about diversity and inclusion, how to be a mentor and a mentee, what it’s like to have imposter syndrome (hint hint, everyone suffers from it) and how to better communicate with a remote team.
Marina Mayer, editor-in-chief of Food Logistics and Supply & Demand Chain Executive, reports that there was no podium, no PowerPoint presentation, no egos. Women met with one common goal of lifting each other up and sharing creative ideas, stories and strategies. The Forum proved that “better together” isn’t just a fancy hashtag. It’s a movement. It’s a community. It’s a journey. And it’s the future. Hope to see you later this year, Nov. 12-13 at the Ritz-Carlton in Atlanta.
Scan the QR code to learn more https://foodl.me/6b9e96nd
Overhaul launched the Intelligent Door Seal Solution, a smart door seal that incorporates Bluetooth and GPS and immediately notifies users when a trailer door opens.
“Our customers have had a consistent need to understand what’s happening with their cargo trailers, especially as pilferage continues to be an issue in the market,” says Barry Conlon, CEO and founder of Overhaul. “For the past 18 months, we’ve been developing a solution as an answer to those calls and a way to better identify potential theft activities.”
Scan the QR code to learn more https://foodl.me/vaenxczy
Veterans bring a wealth of skills and experiences to the supply chain industry that offer a unique advantage. Their ability to make critical decisions, work effectively in teams, adapt to changing circumstances, pay attention to detail and maintain a strong work ethic is highly beneficial in the supply chain space.
The economy is currently experiencing a “slowcession,” as the freight industry pushes through what feels like a recession, according to data released by ITS Logistics. In addition, wage rates and access to general warehouse labor continue to show an overall reduction, but the industry will still need to pay well above the average for good talent.
“Over the past few months, the supply chain industry has experienced an imbalance with supply and demand for the movement of freight, which has resulted in very challenging conditions,” says Ryan Martin, president of assets for ITS Logistics. “Although true, GDP grew at an annual rate of 2.1% in the second quarter of 2023, and growth in the third quarter rounded out at a robust 4.9%. From this information alone, it shows that we are not in a recession, but instead experiencing a ‘slowcession.’ We are finding ourselves in a sluggish economy that doesn’t quite tip over into a full on recession.”
Scan the QR code to learn more https://foodl.me/q69shpqg
Alexis Mizell-Pleasant, managing editor of Food Logistics and Supply & Demand Chain Executive and Navy veteran, talks with Michelle Saks, COO of Gently.io, about reinventing U.S. supply chains with teams who have spent their careers tackling the security of America’s future. With the right strategies and support, veterans have the chance to offer a fresh outlook on the growth and success of logistics, while finding a rewarding and rising career.
Scan the QR code to learn more https://foodl.me/gbfnd73s
Not being able to see ahead and predict and plan accordingly is what sometimes plagues many of today’s supply chain companies. Here’s why mitigating supply chain threats is of upmost importance heading into 2024.
Over the years, executing a risk mitigation plan has transformed from something that’s nice to have to something that every company must have, at all times, in all facets of the organization.
From the influx of cargo theft, cybersecurity threats, food safety and driver shortage to geopolitical tensions, strikes from rail/dock workers, natural disasters and more, even the smallest gap can pose serious threat to people, product and plant.
Liken it to the blind leading the blind, getting lost in a maze or driving while blindfolded.
Not being able to see ahead and predict and plan accordingly is what often plagues many of today’s supply chain companies.
What’s more, the shifting business
landscape forces freight shippers, brokers and carriers to shift tactics and accelerate the use of market data and artificial intelligence (AI)-driven analytics, according to DAT Freight & Analytics.
That’s why mitigating supply chain threats is of utmost importance heading into 2024.
In fact, resiliency is now table-stakes for the supply chain, as the next disruption is just around the corner, says Adheer Bahulkar, global supply chain lead for consumer goods and services, Accenture.
There are many other challenges facing cold food chains, ranging from weather shocks and staff shortages to inefficiencies in transportation and storage, to name a few, according to Bahulkar.
“For example, we know a large propor-
tion of food produced for human consumption is lost due to the lack of effective refrigeration,” Bahulkar adds. “Manufacturers are constantly dealing with the ripple effects of supply chain disruptions such as changes in consumption, adverse weather events and changing regulations and trade policies. It’s easy to see why this could leave them feeling they’re in constant ‘response mode’ to keep pace. We are also seeing shifts in food consumption, with many consumers shifting preferences toward convenience and ready-to-eat food. This increases the demand for cold chains.”
And, while macro factors such as cargo theft, war, and driver shortages add complexity to cold chain logistics, the persistent challenge of inventory loss
and spoilage arguably poses the greatest threat, says Himanshu Mehrotra, VP of product management at FourKites.
“A report by the Food and Agriculture Organization (FAO) indicates that approximately 14% of the world’s food is lost from harvest to retail, largely owing to inadequate cold chain facilities and poor temperature management during transit. For businesses, especially those operating with slim margins, the financial repercussions of such losses are profound,” adds Mehrotra. “But the risk extends beyond mere inventory loss. Companies also face the possibility of shipment rejection. If a shipment fails to meet stringent temperature compliance standards, it’s often rejected unless the shipper can convincingly demonstrate that the correct temperature was maintained throughout transit. The implications of a rejected shipment go beyond the immediate financial loss. It causes a ripple effect in the supply chain, leading to delayed
delivery schedules and adversely impacting customer relations.”
Increased cost of capital also poses underlying challenge behind many of the threats impacting the cold food supply chain, says Peter Cadigan, consumer products senior analyst with RSM US LLP.
“The dearth of cold and frozen storage infrastructure in the U.S. presented challenges dating back to before the pandemic. When demand surged in 2020 and 2021, we saw developers start to build cold storage facilities on spec in a meaningful way for the first time. Now, with interest rates changing the math on those investments, there could be a slowdown of similar investments,” he adds. “The issue touches on labor challenges as well. Many of the lower wage jobs in the cold storage supply chain simply aren’t attractive. We’ve seen the industry raise wages to attract and retain workers, but we’ve seen real benefits for business that have invested in automation and robotics to offset their reliance on those jobs and get more out of their higher waged labor force. With capital costs on the rise those types of investments have become more expensive.”
In its right, food safety still remains a paramount concern, “as any break in the cold chain can lead to spoilage or contamination of both raw materials and finished products, posing health risks and strong financial consequences,” says Eric Linxwiler, SVP at TradeBeyond. “Geopolitical tensions and wars, like the conflict in Ukraine, disrupt global trade routes and create supply shortages. Looming strikes from rail and dock workers can cause severe bottlenecks, delaying shipments and leading to spoilage. Finally, natural disasters, amplified by climate change, create unpredictable crop shortages and pose unpredictable risks to transportation and storage infrastructure.”
“Multiple disruptions in the supply chain experienced over the last few years, such as the shortage of raw materials due to political, social, or weather disruptions, have compelled companies to test alternative suppliers with untested cold chain performance,” says Linxwiler. “Delays in shipment, whether of raw materials or finished goods, increase the potential of the cold chain being broken. There are multiple
examples of refrigerated containers being on standby at ports with inadequate cold chain capabilities, ruining the products.”
From a digital perspective, ransomware ranks as a big threat to the cold food chain. In fact, ransomware attackers extorted at least $449.1 million in the first half of 2023 alone, according to the Department of Homeland Security.
“Cyber risk can be mitigated by having robust backups and recovery plans and by using cloud services. Also, there’s a shortage of cybersecurity talent. Technology schools and universities aren’t producing enough to meet the ever-increasing demand, and what few there are get snapped up by bigger organizations or government entities. So, organizations should also look to more managed services for cybersecurity and need to upgrade to modern and secure software, specifically their ERP software,” says Kevin Beasley, CIO, VAI.
But, supply chain threats aside, instability in the supply chain, such as geopolitical sanctions, natural disasters, inflation and more will impact and influence the way companies can mitigate supply chain threats.
Collectively, these factors contribute to a complex set of cold chain challenges.
“With so many dynamic variables seemingly out of their control, companies need the tools to help them simplify cargo management and strengthen the performance of their supply chains. This starts by ensuring that every link in their perishable cold chain is equipped with a proper monitoring toolset and adhering to their quality assurance (QA) best practices,” says Amy Childress, VP of monitoring, cargo for Copeland.
According to multiple sources, the average value of cargo stolen during reported events in 2023 was $214,104, equivalent to an estimated $223 million in cargo across 1,778 reported theft incidents.
BSI’s Supply Chain Risk Insights Report 2023 reveals several key factors behind the increases in supply chain disruptions and in the theft of food and beverage commodities.
“These include rising food prices con-
tributing to the increased demand, natural disasters and climate change, which has had a significant impact on the availability of crops, geopolitical incidents, including the war in Ukraine, trade relationships between major economies like the U.S. and China, and the frequency of cyberattacks on the food industry and its supply chain,” says Neil Coole, director food and retail, BSI.
The report also shows that last year, food and beverage were the top commodities stolen in transit.
“One of the main reasons behind this trend is that food and beverage products are always in high demand, and inflationary factors have resulted in sharp price
increases over the past two years,” says Coole. “In a living supply chain, access to these goods in transit can be relatively easy in comparison to higher-value commodities (e.g., fuel, electronics, medical supplies and machine parts). Additionally, food and beverage commodities tend to have little to no tracking devices and anti-theft technologies.”
According to a recent report from CargoNet, Q2 of 2023 saw a 57% increase in cargo theft compared to Q2 of 2022. Documented strategic cargo theft events increased 430% year-over-year and theft of a loaded conveyance such as a full trailer increased 4% year-over-year. These kinds of thefts were most common in
California, Texas, Florida, Georgia, and Illinois. CargoNet also recorded a significant increase in the “other” category, which combines several categories of reports like identity theft complaints, hostage loads, late shipment complaints, and other kinds of criminal intelligence records.
“This unprecedented increase largely can be attributed to shipment misdirection attacks, a strategic form of cargo theft in which thieves and criminal networks steal the identities of motor carriers and logistics brokers. After assuming their victims’ identities, thieves can then obtain their freight, misdirect it from the intended receiver, and steal the cargo,” says Childress. “This emerging scheme makes
the onset of the pandemic in 2020, the FBI observed an uptick in strategic cargo theft and fictitious freight cases. To combat this increase in activity, a Truckstop report details the seven Major Theft Task Forces located throughout the United States trained to identify and mitigate cargo theft cases. The most common types of theft they track and investigate are traditional theft of a truck-tractor semi-trailer, identity theft, fictitious pickups, hijacking, pilferage and warehouse burglaries.
markets, QAD, Inc. “Leveraging advanced technologies like artificial intelligence, machine learning, and data analytics can enhance supply chain visibility. Real-time monitoring and predictive analytics can help companies identify potential disruptions early on, allowing for proactive mitigation strategies.”
cargo tracking a mandatory element in companies’ security strategies.”
But, while rising cargo theft is often attributed to inflation and rising prices, the larger root causes perhaps are quite structural, says Bahulkar.
“For example, the rise in e-commerce has meant that more cargo is spending time in warehouses and in transit. Other disruptions and bottlenecks, such as staff shortages or delays in transportation can also lead to more inventories being stuck in transit or sitting for longer in warehouses. This raises the risk of theft, not to mention lost sales,” he adds.
What’s more is, thieves have always targeted high-value, high-profile goods. Since
“Freight’s high volume and mobility over land, sea, and air make cargo theft a crime of opportunity. Other factors contributing to cargo theft desirability include the cash-based nature of the business, lenient punishments if caught, and multiple methods used to commit the crime (fictitious pickups, identity theft, straight cargo theft, pilferage, etc.). It’s also incredibly easy to disguise the scam as a legitimate trucking company and hide in plain sight,” according to Truckstop.
A study from Container xChange reveals 82% of industry professionals acknowledge the importance of technology for resilience in 2024, with predictive analysis and forecasting tools taking center stage.
And, while some factors are predictable in the sense that there is always a threat for hurricanes, earthquakes and natural phenomena, others are not predictable. Therefore, having a risk management strategy in place helps soften the blow.
“There are a number of tools and processes that exist to help with improving machine usage and throughput. But very few of the systems in the areas of manufacturing execution really focus on the empowerment of the line worker. Having systems and processes in place to have the workforce informed and communicating better throughout the plant can seriously improve efficiencies and production as well as protecting the integrity of the cold chain. Building a skilled and adaptable workforce is essential. Employees should be trained in risk management, crisis response, and the use of relevant technologies to ensure a proactive and efficient response to supply chain disruptions,” says Stephen Dombroski, director, consumer
The influx in technology is what continues to encourage companies to rethink their supply chains. This could relate to the adoption of emerging technologies and putting in place specific parameters to track, trace, measure and plan accordingly.
“The future of supply chain management largely depends on the adoption of technologies in automation, IoT, AI and more in order to bring sustainability, visibility and reliability to operations,” says Bahulkar. “Along with alternative sources of supply and right-shoring, a combination of full value chain visibility combined with predictive analytics and read-and-respond capabilities are key for supply chain to mitigate the impact of disruptions. We can expect resiliency in supply chain to become a critical advantage for companies enabling them to not only ensure business continuity but systematically gain market share as consumers increasingly rely on them through all disruptions.”
Rethinking supply chains could also mean utilizing analytics and solutions in different ways to better allow for pre-emptive action.
“New playbooks are constantly being written and with the emergence of generative AI, we will see new processes be established that five years ago, weren’t even dreamed of. Critical to these strategies are deep, data-driven insights into the supply chain supported by subject matter experts who are embracing change,” says Mehrotra. “For instance, predictive analytics can be utilized to foresee bottlenecks caused by natural disasters, allowing for preemptive action such as rerouting shipments or adjusting inventory levels before the storm even hits. Another example is using real-time data to monitor supplier performance, enabling quick responses to delays or quality issues. This approach also facilitates strategic diversification of suppliers, reducing dependence on any single source and thereby mitigating risks
associated with supplier reliability. Having insight upstream and downstream can also help companies optimize inventory levels, striking a balance between minimizing holding costs and ensuring sufficient stock to handle demand fluctuations.”
Labor disruptions are also substantially higher this year, up 136%, according to Resilinc data. This includes company and site-level strikes, national strikes, layoffs and labor protests, among others. But what does this mean for the future of cold food supply chains?
“Labor disruptions and more importantly sustained labor shortages are expected to have a significant impact on future design of supply chains,” says Bahulkar. “Demographic as well as socio-economic trends are resulting in a shrinking workforce ready for skilled labor in manufacturing and distribution and a high turnover becoming commonplace for many manufacturers. What this means for future supply chains is two things: Rising wages as companies compete to fill the gaps in their workforce in the near to mid-term; and a gradual but steady shift
to automation on the shop floors over the mid- to long-term.”
Worker strikes and labor shortages continue to have significant impacts on the future of the food supply chain. But, it’s how the cold food supply chain will respond that makes or breaks the disruptions.
“There are opportunities and solutions available to these organizations, including creating a more inclusive culture that prioritizes its people, putting health, safety and mental well-being at the core of organizational culture, investing in people, upskilling the workforce and creating a more balanced work/life arrangement to mitigate against staff burnout, improve the industry’s reputation and help to attract future talent,” Coole says.
For many organizations, the future of a safer supply chain lies in the hands of leveraging automation.
“Firstly, we see automation creating exciting careers in supply chain for talented people, and that builds in labor loyalty through better career prospects, so there’s less volatility. Secondly, we see automation by its very nature reducing the risk of labor disruptions to operations – a risk that is inherent in traditional manual
warehouses,” says Jonas Swarttouw, EVP and chairman of NewCold North America. “So, you insulate your organization from labor shocks in the warehouse by automating key bottlenecks in your operations, enabling your associates to upskill and develop and take on elevated roles, while you drive efficiency, accuracy, and resilience with smart automation to deliver always-on high-level service.”
To stay ahead of the disruptions, food and beverage shippers, cold chain distribution providers, refrigerated carriers and others in the chain must invest in understanding partners’ health, forecasts, and operating models, says Mehrotra.
“This includes details such as financial health, capacity commitments and constraints, facility dwell, customer requirements, claims, and what happens as the bullwhip effect occurs. The leaders in cold chain have invested heavily in a strong horizontal supply chain with the right strategic partners,” he adds.
And, of course, timing is everything.
“When you are talking about the operations of a supply chain, there are many factors that go into managing them. It starts with planning; demand (forecasting),
distribution, production, procurement planning functions. You need to have a plan in place. However, executing that plan is a different story. You can have the most accurate product forecast, the best distribution plan, the best capacity plan and have all your materials and ingredients ready to go. When dealing with a cold supply chain, timing is everything because it revolves around perishability,” Dombroski says.
In general, small- and medium-sized businesses in the food industry will need to expand their digital footprints in response to increased regulation in 2024, says Beasley.
“In particular, the sector will increasingly adopt blockchain and IoT to comply with regulations that call for end-to-end traceability. This will require having advanced modern ERP software with food industry-specific capabilities necessary to deal with these cutting-edge technologies,” he adds. “These and other emerging technologies will generate an enormous amount of data that can be used to train AI models. Beyond 2024, we may see an explosion of AI deployment in small and medium-sized businesses in this sector.”
At the end of the day though, a unique threat to one company’s logistics operations may be urgent and need to be mitigat-
ed immediately, while the same threat to another company’s logistics operation may be trivial, says Ron Greene, VP of business development at Overhaul.
“All logistics operations are similar with unique attributes; the threats to cold food chains and associated risks follow this same structure. For example, a food company operating in Mexico and Los Angeles need to take a proactive approach to mitigate theft, while the same company’s operations in Nebraska will likely not have to mitigate this specific risk. Companies need to assess risks continually and make decisions on the appropriate mitigation approach as threats can change in real-time,” Greene says.
Analytics and networks connect last-mile transportation.
Last mile is a critical frontier. Often considered the most complex and costly leg of the supply chain, the rise of e-commerce and increasing customer expectations for fast and reliable deliveries has highlighted this complex part of the journey.
A recent report by Extensiv found that while a majority of third-party logistics (3PL) providers still show positive order and profitability growth, a larger group of 3PLs are now seeing flat or declining
profits as the economy fluctuates. The report includes that, although approximately one-third of 3PL respondents showed more than a 25% increase in order volume growth year-over-year and 42% indicated an increase of up to 24%, 22% of respondents either remained the same or saw a decline.
Years of innovation to revolutionize the last mile has answered the call to improve these costs and drive efficiency, culminating in the latest advances in artificial
intelligenice (AI) that synthesize analytics and tracking to transform the future of 3PL operations.
Route optimization and demand forecasting at large Planning is a critical component to the last mile, which often requires route optimization to make the most out of the trip. This is where AI excels. Through predictive analytics and machine learning algorithms, AI can analyze historical data, including
traffic patterns and weather conditions to dynamically adjust delivery routes. This not only ensures the fastest and most efficient paths but also allows for real-time adaptations to unexpected disruptions such as traffic jams or road closures. By mitigating the risks associated with unpredictable variables, AI-driven route optimization minimizes delays and enhances the reliability of deliveries.
Armon Shahpar, senior lead, enterprise partnerships, Uber Freight, says that modern supply chains tap into intelligent, data-driven tools to optimize the way goods, like food and beverages, are delivered.
“Today’s supply chains are more complex than ever, and so it’s critical that the tools to power them are data-informed and offer real-time insight into the market. Shippers in the cold food chain need to be nimble, so technologies that can offer instant access to a variety of capacity options and real-time tracking/pricing/billing have become table stakes,” explains Shahpar.
AI is also a huge component for demand forecasting. Through the analysis of datasets that include customer order history and seasonal or market trends, AI can find and accurately predict demand patterns. This is the kind of foresight that enables
3PLs to adjust inventory levels, which reduces the risk of stockouts or excess inventory.
This is becoming exponentially more important moving into 2024. E-commerce sales are predicted to increase by 7% this holiday season to $273.7 billion, according to the National Retail Federation and CBRE estimates a maximum value for this season’s returns of online purchases at $82.1 billion. By aligning supply with demand, AI-driven demand forecasting enhances overall supply chain resilience and ensures that the last mile is well-prepared to meet fluctuating customer demands.
Through advanced sensors and location services, AI enables logistics providers to monitor the exact location and status of deliveries in real time.
Many cloud-based solutions use Internt of Things (IoT) sensors to provide real-time cargo monitoring from distribution centers to final destinations. This monitoring can offer temperature alerts in food logistics that safeguard the integrity of cargo, and this level of visibility is invaluable for addressing delays and providing customers
with accurate information.
AI tools now excel in predictive analytics for the last mile. The analysis of data collection through monitoring systems and tracking aids allows AI to offer predictions of potential delays and bottlenecks. It’s proactivity before reactivity, improving costs upfront and possibly providing risk mitigation in the process.
Tire tracking, for example, can automatically begin to generate preventive maintenance inspections and tasks, improving fleet management.
Fred Kraus, VP of product at Eptura, says that to ensure that fleets are operating safely and effectively, organizations can monitor and analyze the performance of their tires to gain visibility into usage, age and repair history. In doing so, fleets can protect drivers, equipment and goods for which they are responsible.
It’s the little things AI, predictive analytics and “smart” services can do for the accuracy of the last mile. Today, same-day delivery options are almost commonplace.
One such detail helping to improve the same-day delivery process is address
validation which uses databases to verify the end point of delivery and reduce the risk of error.
Berkley Charlton, chief product officer at Smarty, says incorrect addresses drive up operational costs significantly, which is a crucial component to a 3PL’s last-mile services.
“Delivery drivers spend extra time and fuel on fruitless journeys caused by inaccurate addresses. In addition, every returned package due to a bad address adds more sunk costs to a business’s operation. These unnecessary expenses can pile up and eat into profit margins, impacting the overall financial health of a delivery business. On the flip side, address validation optimizes delivery routes, improves delivery speed, saves fuel costs and minimizes returns for delivery companies,” says Charlton.
Ultimately, the ability to anticipate and
address issues before they impact lastmile operations is one of the top advantages that AI brings to the table.
AI is also behind the insurgence of autonomous vehicles (AVs). Tyson Foods recently started utilizing driverless options to haul meat and it’s possible that the last mile will see more of these options in the near future. Why?
“Enhanced efficiency is one of the key benefits AI promises to the business world. By automating tasks previously delegated to human workers, AI empowers a new generation of always-on business processes. The work AI does—from coding to customer service to driving AVs—can happen 24/7, without a break,” says Anar Mammadov, co-founder and CEO of Senpex. “AVs also promise to increase efficiency and speed through platooning. Because AVs use AI-empowered navigation, they are capable of safely following other
AVs very closely in platoon formations. This allows for increased throughput, which enhances the speed and efficiency of the overall delivery process.”
It’s clear that AI is bringing more optimization to the last mile. The most prevalent options are the use of route optimization and demand forecasting, which has, since conception, been a vital tool for 3PLs in general and might be the easiest to integrate from a system already in place.
But growth is happening despite disruption and economic lows, and now more than ever, the opportunities afforded to the sector at the hands of AI range from detailed reporting and tracking to full scale autonomous fleets. The choice for AI in the last mile is not will I use it—the answer is you likely already are. The real question lies in which avenues you will go to build upon the efficiency that AI offers.
Annually, Food Logistics showcases individual and corporate leaders in the end-to-end supply chain. Plan now to enter your company - or a cutti ng-edge client or vendor - in one of these industry-leading recogniti on programs.
Spotlights top software and technology startups in the supply chain and logistics space.
Recognizes influential individuals in the industry whose achievements, hard work and vision have shaped the global cold food supply chain.
Recognizes leading third-party logistics and cold storage providers in the cold food and beverage industry.
2024
Profiles innovative case study-type projects designed to automate, optimize, streamline and improve the supply chain.
2024
2024
Honors female supply chain leaders and executives whose accomplishments, mentorship and examples set a foundation for women in all levels of a company’s supply chain network.
Honors software and technology providers that ensure a safe, efficient and reliable global cold food and beverage supply chain.
2024
Supply chain rock stars are the backbone of the cold food chain. The words used to describe many of this year’s winners range from collaborative, passionate, innovative and forward-thinking to inspired, driven and dependable.
NEW THIS YEAR: This year’s Rock Stars of the Supply Chain award was broken down into four distinct categories:
• Top Warehousing Stars—Recognizes professionals in the cold storage and warehousing space.
• Top Shippers—Recognizes professionals in the transportation space, including freight, trucking, rail, air cargo, ship/ports, etc.
• Rising Stars—Recognizes young or newer professionals (39 and under) whose achievements, hard work and vision have shaped the supply chain network.
• Lifetime Achievement—Honors company leaders who’ve made outstanding contributions to the supply chain space. Must have at least 10 years’ documented experience in supply chain and logistics.
Each category consists of a bevvy of winners who continue to go above and beyond to improve food safety, enhance efficiency and disrupt supply chain disruptions.
WHAT’S ALSO NEW THIS YEAR, we now have four overall winners, one for each category, whose application and their journey stood out above the rest.
Let’s first meet the four overall winners:
www.freshfreight.com
Matt Heroux, founder and CEO of Fresh Freight, embodies the essence of entrepreneurial spirit, extending his involvement across every aspect of the business, ensuring the seamless operation and continual growth of the company. On a day-to-day basis, Heroux immerses himself in numerous operational and strategic activities that are critical to the success of Fresh Freight. For example, he oversees transportation operations, ensuring that all processes run smoothly and efficiently. He ensures that required key performance indicators (KPIs) are met for the client base, as well as for Fresh Freight’s own business. He sees his primary responsibility as ensuring that the company not only meets but also exceeds customer expectations. Heroux is also diligent in making sure all aspects of the business are aligned with the company’s strategic objectives, including sales, HR, IT and its own fleet of trucks.
As president ad CEO of Lineage, Greg Lehmkuhl provides strategic leadership
But, what separates Heroux from the others is that over the past 12 months, Heroux continues to make swift, informed decisions, proving crucial in safeguarding Fresh Freight’s market position and ensuring its continued viability. For instance, Heroux developed a produce consolidation project for a major produce client in Washington, where Fresh Freight implemented a streamlined and efficient solution to create more efficiency in loads out of the Pacific Northwest. As a result, carriers now experience fewer stops, saving of 1-2 days on transportation time for loads. Under Heroux’ direction, Fresh Freight also launched a new site in Dallas, strategically positioning Fresh Freight in a major food market. In just a short period of time, this one-employee location has grown to housing now 8 employees and represents 32% of Fresh Freight’s business.
What’s ahead for Heroux? Under his leadership, Fresh Freight secured a partnership deal with an AI software startup to integrate the AI technology and enhance the team’s capability to deliver industry-best service levels. Scan the QR code to watch our video interview. https://foodl.me/20b22cmf
and oversees all facets of the company’s operations worldwide. Under his leadership, Lineage has experienced significant growth, expanded its international reach through acquisition and development activities and secured long-term investors to fuel innovation. Meanwhile, Lehmkuhl has created a strong company culture rooted in Lineage’s values and purpose-driven work. Since stepping into his role in July 2015, Lehmkuhl has led
Lineage to more than double the number of facilities operated through acquisition, built or expanded several facilities in the United States, entered new country markets, introduced a series of energy-saving innovations and coordinated the financial stability of the company. Perhaps more important from his perspective is engaging with frontline workers to help them do their jobs more efficiently.
It’s this boots-on-the-ground mentality that separates Lehmkuhl from others.
During the past year, Lehmkuhl led Lineage’s acquisitions of Burris Logistics, NOVA Coldstore and Kennedy Transportation, as well as a new joint venture with SK Logistics in Vietnam. He has also directed the building of new cold storage facilities in Windsor, Colo.; Savannah, Ga.; and Tauranga, New Zealand, and the expansion of locations in Aarhus, Denmark; Harnes, France; and Swedesboro, N.J., to accommodate customer demand.
Tyler Hoffmeister
Assistant VP, Operations, Sheer Logistics
https://sheerlogistics.com
Tyler Hoffmeister serves as assistant VP of operations for Sheer Logistics, where he’s responsible for overseeing the operational side of Sheer Logistics, managing a diverse team of 20 professionals, while executing a comprehensive and strategic approach to supply chain management, including his core commitment to Sheer’s fully outsourced managed transportation services (MTS) clients, navigating and addressing the myriad challenges and issues that arise in the complex realm of supply chain management and putting extra focus on client engagement. Hoffmeister takes a high-level view of client challenges, evaluating options to mitigate issues ranging from cost and service to warehousing and carrier performance. This extends to his view of customers, carriers, vendors, and shippers as collaborative partners rather than mere transactions. And, he sees Sheer Logistics as an extension of these partners’ supply chains.
But it’s his attention to efficiency, ability to optimize operations,
https://www.bluediamond.com
Steve Schult is a seasoned professional with over two decades of supply chain experience and more than eight years of dedicated service in the U.S. Coast Guard. Currently, he serves as VP of global supply chain at Blue Diamond Growers, where he manages a highly integrated and complex supply chain that spans from the farm to the table, moving approximately 1 billion pounds of product annually. Depending on the day, Schult can be found wearing boots and walking the almond orchards as
Lehmkuhl also oversaw the development of Lineage’s first ever Sustainability Report; signed The Climate Pledge, committing to achieve net-zero carbon emissions across global operations by 2040; and helped form the Lineage Foundation for Good, an independent philanthropic arm of Lineage that aims to redirect food that would otherwise go to waste and address hunger to support the social and economic mobility of communities. With this pledge, Lineage has donated more than 300 million meals over the past three years.
Scan the QR code to read our exclusive interview.
https://foodl.me/sqgkyk3v
maintain a forward-thinking approach and constantly challenge the status quo that separates him from the others. He fosters a positive and empowering workplace culture. His diverse background includes tenures at FedEx, YRC Freight, and HUB Group/Unyson. And, he continues to invest time and effort in the development of his team, particularly those without prior experience in logistics.
Over the past 12 months, Hoffmeister has spearheaded several initiatives that enhance internal efficiency and directly contribute to the seamless execution of client needs. One notable accomplishment is his identification of a critical need to streamline internal communications. In response, he identified and implemented the use of a third-party operations and communications tool that streamlined internal operations and fostered enhanced teamwork and accountability within the organization. In the next 12 months, Hoffmeister is committed to supporting the company’s aggressive growth plans, continue to build a capable and trusted team and showcase commitment to continuous improvement, adaptability, and the pursuit of excellence.
Scan the QR code to watch our video interview. https://foodl.me/j6cm7vbh
he works closely with the growers. But his role also includes him frequently walking the aisles of retail partners, leveraging his expertise to ensure that Blue Diamond Growers’ products meet the needs and expectations of both retail partners and consumers. He oversees the planning, receipt, and processing of almonds, has led the company in expanding its product portfolio to encompass refrigerated, dry and foodservice channels, and actively engages in addressing national supply chain issues as part of the National Federal Maritime Committee, where he chairs a subcommittee on chassis; and the California Freight Advisory Committee, where he advocates for sustainable and efficient practices on behalf of the agricultural industry.
But, it’s his ability to be innovative and multi-faceted while maintaining a deep-rooted connection with Blue Diamond Grow-
ers as a business of innovative farmers that separates him from the others.
Over the past 12-18 months, Schult has spearheaded several transformative initiatives within Blue Diamond Growers’ supply chain, delivering on 98% fill rates and 92% on-time delivery to cooperatives customers. One notable accomplishment during this period is the shift from brokered transportation to directly managing carrier relationships. By doing so, Schult’s team sought to transform Blue Diamond Growers into a “shipper of choice.” To support this, Blue Diamond Growers rolled out the SAP Transportation Management System (TMS) solution, which improved the efficiency and accuracy of transportation and logistics operations, resulting in enhanced on-time delivery performance, stronger connectivity with transportation partners, and greater visibil-
www.bsigroup.com
Category: Rising Stars
Serving as practice director of security and resilience for BSI Group, Tony’ Pelli’s role involves working on client projects, managing his team across the United States and UK, and developing a strategy. He meets with clients regularly to discuss their supply chain risk management issues, assisting them on various projects such as gap assessments, risk management programs, and supplier assessments. He also ensures his team is actively supporting clients in these same areas and completing projects in a timely manner. A vital aspect of Tony’s role is proactively learning about new and emerging supply chain risks. This year, Pelli spearheaded a key initiative--helping clients integrate supply chain risk management into their overall organizational
Thomas Stretar
VP, Technology; Labor Management Practice Leader, enVista https://www.envistacorp.com
Category: Lifetime Achievement
Tom Stretar serves as VP of technology at enVista, as well as the practice area leader for enVista’s labor management practice, where he leads a team of over a dozen consultants in completing critical labor and warehouse-related projects for enVista’s clients.
Charles Tuck
Co-Founder and SVP of Energy & IoT Solutions, Ndustrial www.ndustrial.io
Category: Lifetime Achievement
Charles Tuck serves as co-founder and SVP of energy and IoT solutions at Ndustrial, tasked with everything
ity of inventory in motion, delivering $1 million in savings and improved on-time delivery. Another initiative under Schult’s helm is the opening three new third-party logistics (3PL) hubs, while optimizing its supply chain, leading to 2,300 metric tons of CO2 reduction.
In the upcoming 12 months, Schult is set to lead Blue Diamond Growers toward several strategic goals, including supporting a number of new product introductions, increase Blue Diamond Growers’ international footprint and a collaboration with an AI-driven demand planning company to better understand internal and external demand signals.
Scan the QR code to watch our video interview.
https://foodl.me/czppvxlj
resilience strategies. In doing so, he aligned companies’ goals for organizational and supply chain resilience, helping organizations see supply chain risk management as a key strategic priority, and communicating this to executives. He helped clients connect these systems to enable real-time risk understanding, fostering proactive identification and resolution of potential supply chain issues. For one client, Pelli and BSI developed a risk management approach across over 40 global sites that are managed by several third-party logistics companies. Pelli and his team worked to align these companies’ approaches to inventory management, cybersecurity and privacy, and physical and supply chain security. This allowed the client to achieve consistency across their distribution network, increasing efficiency and speed to market, while lowering cost and disruption. Over the next year, his primary focus is on advancing digital transformation in supply chain risk management and to integrate risk management seamlessly into procurement processes, supplier selection, and overall organizational resilience and risk management frameworks.
His responsibilities include overall project management, customer training and delivery of supply chain management projects such as supply chain assessments, warehouse and labor management implementations, incentive pay programs, process optimization, and slotting. Over the last 12 months, Stretar has been involved in many successful labor management projects; contributes significantly to company collateral, tradeshow speaking sessions, trade publication articles and more; and maintains significant influence as a mentor to the company’s annual summer internship program.
from business development and public speaking to scoping and implementing client projects worldwide. He is often traveling to facilities like cold storage warehouses across the globe, consulting with clients on their energy and IoT strategies and deploying hardware and software solutions tailored to their needs. In the past 12 months, Tuck led the deployment of energy and IoT solutions at over 100 cold chain facilities in 8 countries, bringing his total to over 400 facilities in 17 countries over the last
several years. Collectively, these installations have helped large cold storage facilities save energy costs and support carbon neutrality across the globe. For example, one recent project helped a cold storage facility save over $175,000 in energy costs over 4 months by responding intelligently to real-time electric prices. In the next year, Tuck and his team are looking to onboard over 100 additional sites to Ndustrial’s energy intensity platform,
Don Durm
VP, Customer Solutions, PLM Fleet, LLC
https://www.plmfleet.com
Category: Lifetime Achievement
Don Durm is a 28-year veteran at PLM Fleet, LLC, after serving 12 years in law enforcement. As VP, customer solutions at PLM Fleet, he spends time helping food shippers meet the demands of customers and regulators by providing guidance on supply chain efficiencies and food safety for temperature-sensitive products. He currently manages PLM TrustLink, which delivers on transparency, traceability and trust; has been active in the greening of fleets with new EV technology in refrigerated transport with
https://yale.com/en-us/north-america/
Category: Rising Stars
Brendan McCann was promoted to his current role of director of major accounts for food processing and distribution at Yale Lift Truck Technologies in August 2023, where he runs a team responsible for 165 strategic accounts and 14,651 logistics locations across the United States and Canada. This promotion marks his third in five years. McCann takes the approach of immersing himself in the needs of the customer and uses those insights to optimize their lift truck fleets. He does this by studying their most pressing challenges and building solutions that address current and future priorities, such as productivity, safety, finances,
expanding into other verticals, and bringing on energy analysts and Certified Energy Managers. Lastly, he will be resurrecting a program to help clients achieve ISO 50001 certification and earn recognition from programs like GCCA’s Energy Excellence Recognition Program, ENERGY STAR, and the DOE’s Better Climate Challenge.
all electric, solar and wheel generating energy axles; and is skilled in understanding and educating on FDA’s and DOJ’s New Era of a Smarter Food Safety. Durm has worked with both governments and industry on navigating regulatory rules and bringing safe foods to the consumer using industry best practices. He was one of the primary creators of the Certified Cold Carrier accreditation through the Global Cold Chain Alliance that recognizes carrier organizations for their commitment to sanitary and safe transportation of perishable products. He’s written for several publications on food safety guidelines; consulted the Trump Administration’s “Operation Warp Speed” on the distribution of COVID-19 vaccines in the United States; and works with cold chain industry on solutions using technology to mitigate regulatory disruptions.
ergonomics and more. This process produces a range of recommendations, from plans targeting near-term productivity gains to holistic, long-term roadmaps that guide customers through adoption of advanced lift truck technologies like operator assist systems and automation as their business evolves. McCann is also responsible for the tip of the spear sales strategy for Yale in food and agriculture verticals, leading thought leadership and guiding new products and technologies. Prior to joining Yale, McCann was a senior account manager for Briggs Equipment, a Yale dealer, where he was named Salesman of the Year in 2017. During his three-year tenure at Briggs, McCann learned from experience in a wide range of industries, from auto manufacturing to food processing. What sets McCann apart from others in his profession is that he never begins with the sole goal of making a sale. Instead, he takes the time to understand the customer’s current needs and long-term priorities, and matches them with the right lift truck technologies to help realize their vision.
Mike Ryan
Director of Logistics, REED Tms/Werner Enterprises
Category: Lifetime Achievement
Shortly after notifying winners, Food Logistics learned that Mike Ryan, director of logistics at Reed TMS, passed away from Stage 4 colon cancer. Ryan was instrumental in helping manage Reed’s day-to-day business activities and developing personnel on the operations side, building solutions both operationally and commercially for produce and foodservice shippers. Ryan was passionate about mentoring individuals new to the industry, helping them find their footing and talent. His main goal was to leave the industry a better place from when he first started.
Ryan began his career in logistics and transportation in 2002 as a sales manager with C.H. Robinson. Throughout his 20-plus years in the refrigerated logistics industry, his intelligence,
passion and natural proclivity for logistics and refrigerated goods led to a rapid ascension up the career ladder. After almost a decade with C.H. Robinson, Ryan transitioned to a COO role with Reed TMS (now a Werner company), where he was responsible for managing operational employees and account managers. During this time, Reed tripled in revenue. Despite his passion for the industry, he took a brief hiatus from trucking and tried his hand at running his own produce brokerage, Bayshore Produce, alongside his father. After four years of success with Bayshore, Ryan returned to Reed TMS, where he tackled every new challenge head-on. He was heavily involved with company philanthropy efforts, including serving as the auctioneer at Reed’s fundraisers. He also served on the Southeast Produce Council Board of Directors. His legacy extends far beyond mentorship, friendship and admiration, and of course, his love for the Kentucky Wildcats. He is survived by his wife and two daughters.
Scan the QR code to watch exclusive videos with some of our standout winners.
https://foodl.me/ao2z1130
Nick Gamrath
Director, Client Services
EASE Logistics
Matt Heroux
President Fresh Freight
Sam Kheir
Carrier Procurement Manager
iGPS Logistics
Diron Bell
National Accounts Director
iGPS Logistics
Alicia Bly
VP, Corporate Operations & Legal Affairs
Johanson Transportation Service
Ken Johnson
Executive Chairman
Leonard’s Express
Tracie Echols
Senior Manager of Inbound Transportation National DCP
Pratik Jagad
Chief Product Officer
nuVizz
Jon Nass
President & Executive Director
Port of Gulfport, MS
Alan Reuber
VP, Modal Operations
Redwood Logistics
Adam Gurga
Sales Manager, North America Cimcorp Automation Ltd.
Frank Hurst
EVP, LTL Echo Global Logistics
Trevor Peterson Depot Manager
iGPS Logistics
Aaron Nussbaum
Director, Logistics & Operations
Jarrett Logistics
Greg Lehmkuhl President & CEO Lineage
Jason Stoker
Operations Support Analyst
Martin-Brower Company, L.L.C., The
A.K. Schultz
CEO & Founder
SVT Robotics
Murali Venkatasamy
VP, Operations Excellence & Business Development
TA Services
Lane Ennis
GVP, Operations
Universal Chain Group Inc.
Stephen McKinley
Co-Founder & VP, Operations
Ambi Robotics
Mitchell Mazzaro
Director, Temperature Controlled Solutions
Arrive Logistics
Trent Wilson VP, Carrier Sales Arrive Logistics
Keith Moore CEO AutoScheduler.AI
Tony Pelli
Practice Director, Security & Resilience BSI Group
David Miller Senior Director Container Maintenance Corporation
Anthony Finney
Senior Account Manager EASE Logistics
Joe Amici
Director, Consolidation Echo Global Logistics
Heather Kosztowny
Director, Data Science Everstream Analytics
Tracy Derival Marketing Assistant Fleet Advantage
Brandon Anderson
Director, Fleet Operations
FST Logistics
David Blume
Director, Supply Chain Analytics Hy-Vee, Inc.
Fouad Abu-Kazam
Senior Director, Sales KlearNow.AI
Diane Ngabire
VP, Business Development Logility
Chris Reed
Director, Warehouse, Westampton Distribution Center National DCP
Ryan Polakoff
President Nexterus
Codye Satterwhite Managing Director Plantensive
Xavier Alcala
Business Solutions Manager Quality Custom Distributions
Shannon Curtis Senior Manager, Technology Solutions & Marketing
Raymond Corporation, The
Cley Saunders Senior Development Manager, Global Project Delivery RELEX
Tyler Hoffmeister
Assistant VP, Operations Sheer Logistics
Nate Schwandt Director, Marketing Sheer Logistics
Michael Lowe
CEO & Co-Founder Sunswap
Tyler Scogin Director, Brokerage Operations TA Services
Krenar Komoni CEO & Founder Tive
Emma Killough Director, Professional Services Trustwell
Armon Shahpar Senior Lead, Enterprise Partnerships Uber Freight
Brendan McCann
Director, Major Accounts, Food Processing & Distribution Yale Lift Truck Technologies”
Benoit de la Tour
CEO Advantive
Kenny Lund
EVP
Allen Lund Company LLC, ALC Logistics, AlchemyTMS
David Fredericks
Managing Director Alpine Supply Chain Solutions
Darlene Wolf
SVP, Strategic Partners Arrive Logistics
Steve Schult
VP, Global Supply Chain Blue Diamond Growers
Marc Tomkinson
CTO C3 Solutions
Nicole Glenn
Founder & CEO Candor Expedite
Derek Rickard
Director, Sales Cimcorp Automation Ltd.
Brian Carlson
Founder & Principal Cornerstone Edge
Fred Wu
Founder & CEO DeltaTrak
Doug Waggoner
CEO
Echo Global Logistics
Thomas Stretar
VP, Technology; Labor Management Practice Leader enVista
Mark Russo
Chief Science Officer
Everstream Analytics
Jon Davis
Chief Meteorologist Everstream Analytics
Brian Holland President & CEO Fleet Advantage
John Rickette
VP, Portfolio & Manager of Transaction Management Team Fleet Advantage
Chris Smith
EVP, Warehouse Operations FST Logistics
Suresh Babu
VP, Supply Chain & Procurement Great Lakes Cheese
Marcel Koks
Industry & Solution Strategy Director, Food & Beverage Infor
Mikael Bengtsson
Industry & Solution Strategy Director, Food & Beverage Infor
Kristy Knichel
CEO Knichel Logistics Inc.
Allan Dow President Logility
Will Whitehead EVP, Operations National DCP, LLC
Charles Tuck Co-Founder & SVP of Energy & IoT Solutions Ndustrial
Smital Naik Director, Client Services Open Sky Group
Don Durm
VP, Customer Solutions PLM Fleet, LLC
Jay Matthews
President Prosponsive Logistics
Mike Ryan
Director, Logistics REED Tms/Werner Enterprises
Sanjay Sharma
CEO Roambee
Bob West
VP, Food & Beverage, Industrial Ryan Companies US, Inc.
Prasad Gandhikota
Senior Business Advisory Consultant SAP
Lynn Blasio
VP, Inventory Control SpartanNash
Urs Grütter
CEO & Chairman
Stoecklin Logistics, Inc./Stoecklin Logistik AG
Raphael Bertholet
CTO, Supply Chain SymphonyAI Retail CPG
Reo Hatfield VP, Corporate Services TA Services
Doug Niemeyer President & GM TEKLYNX Americas
Tom Moore
CEO & Founder Transportation Warehouse Optimization
Tim Hinson
Head of Transportation Management Uber Freight
Hear from industry experts, as they discuss trends, technologies, challenges and opportunities revolving around warehousing, transportation, sustainability, procurement, emerging technologies, workforce development, risk management and more.
Live Sessions Taking Place: June 4-6, 2024
If you’re not already familiar with integrated data solutions and new sustainability initiatives, now is the time to optimize your current supply chain operations. From greater fleet connectivity to operator assist technologies to investing in electrification solutions, industry leaders need to think boldly—and quickly—to maximize productivity and combat new challenges.
Above all, two key trends stand out as we kick-start 2024: intralogistics solutions that prioritize connectivity through data, and sustainability measures that improve energy efficiency while minimizing environmental impact.
With a variety of applications, processes, systems and management strategies designed to capture data, it can be easy to lose sight of the bigger picture: Why are we collecting this information, and how can that information improve our operations? Is it enough to simply track time, equipment and energy usage separately to increase productivity where inefficiencies exist?
Under the principles of Industry 4.0, the answer is, it’s not. Instead of simply flagging and solving challenges that arise, interconnected data allows us to understand the ways in which various systems contribute to those challenges in the first place.
If a particular lift truck is experiencing greater wear and tear than other equipment, the tenets of Industry 4.0 can help pinpoint better long-term solutions. For example, if operators know which specific routes, loads or operator behaviors are contributing to faster tire degradation, they can then create targeted maintenance strategies that extend the life span of the equipment and reduce downtime all at once.
Connectivity also helps to reinforce best practices among operators and invest in
new assist technologies.
Many facility managers can relate to the challenges posed by overseeing a small pool of qualified, experienced operators who must constantly train new hires to get them up to speed.
Learning based in virtual reality, for example, can help new hires become more capable and confident in basic lift truck operation. When operators make the transition to full lift truck use, other tools—such as location systems or object detection systems—are designed to offer valuable peace of mind.
Location systems enhance security, efficiency and productivity by offering the ability to track, locate, monitor and control the movements of lift trucks within user-defined zones and by tracking personnel and assets in the warehouse. Object detection systems are designed to alert lift truck operators when an object is detected in the travel path.
Location systems also can be combined with fleet management tools to allow supervisors to remotely manage operator vehicle access and offer instant feedback on performance metrics.
Sustainability is now a core tenet of maximizing supply chain productivity.
Take, for instance, the rise of lithium-ion batteries as a means to achieve faster fleet charging, longer run-times, superior capacity retention and greater efficiency all while lowering total cost. Improved battery chargers and battery handling systems can help reduce turnaround time and ensure proper operator handling and servicing when storing energy equipment.
Choosing to tackle trends head-on is the best way to ensure your facilities remain productive, efficient and lean. Consider working with an end-to-end intralogistics solutions provider who can help solve for the unique challenges.
The cold storage sector continues to boom as a result of the rise in e-commerce adoption by consumers, specifically around the use of online grocery platforms. This boom has accelerated demand for cold storage, which has significantly outpaced the 3.73 billion cubic feet of existing supply, much of which is dated product built nearly 40 years ago.
Adding to the sector’s significant inventory challenges is the specialized nature of developing cold storage facilities, coupled with high construction costs, interest rates, lead times and supply chain backlogs. This, along with a significant number of outdated and obsolete facilities requiring retrofitting, it is little wonder that tenants are frustrated with current market conditions.
The challenges: high demand, limited inventory, very expensive
The shift in consumer behavior accelerating cold storage demand has caught the attention of investors, real estate investment trusts (REITS) and developers who are now active players in the market.
This pent-up demand is forcing many users to turn to third-party logistic (3PLs) companies to support their cold storage needs. But as their companies grow, so do their space requirements.
But building a cold storage facility takes time.
While retrofitting an older building can be accomplished within a 12-month timeframe, a typical greenfield development takes roughly two years to complete. However, before that can even happen, finding a suitable location for the facility is an added challenge as land in such areas is often limited.
Then there is the cost and highly specific design features. Once a suitable location is secured, building a cold storage facility is a more complex and costly process compared to a standard warehouse. These specialized facilities require significant
@kokliang1981.stock.adobe.com
financial investment and have considerably higher upfront costs to outfit the infrastructure with the necessary features and equipment to operate effectively.
Investors and developers are having to carefully assess the risk associated with this type of investment. Not only because of the initial upfront costs, but also because it is a highly customized asset up for lease to a niche user.
In Q3 of 2023, U.S. industrial saw a record 171.8 million square feet of construction completions, representing an 18.7% uptick quarter-over-quarter and a 10.4% increase compared to the previous record set in Q3 2022.
Since the start of the year, more than 451 million square feet of new deliveries have been completed across the nation, 23.5% higher compared to this time last year. The south region continues to outpace the nation, accounting for 47% of the year-to-date deliveries, representing 34.4% of the nationwide inventory.
While only representing 1.7%, or 289 million square feet, of the entire industrial market, the cold storage market will
continue to be a vital part of the industry and remain constrained as e-commerce and the convenience of online grocery shopping continues to gain traction.
To effectively navigate the challenges and opportunities in this highly specialized sector, occupiers and investors alike should start to plan at least two years ahead and leverage the expertise of commercial real estate brokers. Additionally, having access to real estate expertise and practices, including zoning regulations, land acquisition, property development, and site selection tailored specifically to cold storage requirements as well as understanding the drivers of demand, trends, and market gaps is critical for making informed investment decisions, developing strategies, and mitigating risk to address future needs.
With skyrocketing costs—from groceries to housing—it makes sense that most workers are concerned with fair pay. But despite the reality of out-of-control prices, there’s one issue that carries even more importance for frontline workers: safety.
A recent survey from SafetyCulture found that frontline workers place a high priority on their job safety, even putting it ahead of a higher paycheck. If forced to find a new job, the majority of workers said they would prioritize safety over a better salary.
But would higher pay lure them to a higher-risk job? Not necessarily. Only 22% of workers said they’d choose a job that offered a higher salary, but also had a higher level of risk, proving that the dollars don’t compensate for the danger. Younger workers were still cautious, but a little more likely to take the risk than Baby Boomers. Meanwhile, 28% of Gen Z workers, 29% of Millennials, and 23% of Gen X workers said they’d take the riskier job with higher pay.
But even so, most workers aren’t jumping at bigger salaries if it means a bigger threat to their personal safety. The data shows they want the same level of risk (or even lower risk) than their current jobs, even if it means sticking with the same pay.
Leaders in the supply chain space who want to keep their frontline workers and attract new talent need to emphasize safety and a culture of ongoing improvement. Here are three ways to help employees feel respected, supported, and most importantly, protected.
1. Empower workers with a voice. Frontline workers are the ones doing their jobs day in and day out, and they understand their safety better than anyone. Accord-
ing to survey data, nearly half of workers believe the best ideas for operational improvements come from their own ranks, but not all feel heard and understood by upper management.
One of the best ways to show workers that you’re prioritizing their safety is to give them regular opportunities to voice concerns and share feedback. While this may sound time-consuming and difficult to scale, gaining full visibility into the business while giving employees an easy way to voice concerns is invaluable, and can be accomplished with a mobile-first solution.
2. Offer competitive hazard pay. Safety takes the cake, but pay is still in the spotlight. Providing hazard pay is a way to recognize the inherent risks and physical demands that come with a dangerous job. It garnered a lot of attention among frontline workers during the pandemic. With the right amount and the right timing, this additional compensation can make frontline workers feel even more supported and appreciated.
However, hazard pay is a complement, not a substitute. It’s a way to recognize the risks of frontline workers on top of providing adequate safety precautions, training, equipment, and resources.
3. Continue to iterate and improve. An organization may have a solid grasp on
safety measures right now, but technology (and risks of all sorts) are ever-evolving. New team members, technology, processes, equipment, and products are shifts that could turn existing safety procedures on their heads.
Survey data found that most workers believe at least a few injuries in their workplace or industry could have been prevented with better training and work instructions.
For that reason, a commitment to safety is an ongoing process and not a one-time initiative.
Frontline jobs are demanding—physically, mentally, and emotionally. And if workers are going to put it all on the line to benefit an organization, the data shows that they need to know you quite literally have their back.
ABOUT THE AUTHOR
Cargo theft is a year-round threat to the transportation and logistics industry. More than $96 million in cargo was stolen across the United States and Canada through the third quarter of 2023, according to data from CargoNet, which also reports that:
• Incidents of theft increased year-overyear for each quarter: 64% for Q1, 57% for Q2 and 59% for Q3.
• “Strategic” cargo thefts, in which actors use fraud to obtain and misdirect freight, increased 430% year-over-year.
• Theft of a loaded conveyance, such as a full trailer, increased 4% year-over-year.
• Food and beverages were the top targeted commodity, followed by electronics and household goods.
• Truck stops, parking lots and warehouses and distribution centers were the top targeted locations for thefts.
There are plenty of precautions that carriers should consider for preventing theft, such as using high-security trailer locks, not leaving trailers unattended and adding surveillance cameras to facilities and yards.
In addition to measures like these, fleet telematics technology has emerged as a powerful tool in combatting cargo theft. Telematics, leveraging a blend of GPS, telecommunications, and connected sensors offers an array of functionalities.
A key benefit of fleet telematics technology is its ability to provide real-time tracking and monitoring of vehicles, trailers and other assets. GPS-enabled devices deliver continuous location updates, enabling carriers to easily track their fleet’s movements, and with cloud-based management platforms, fleets can be monitored anytime from anywhere via mobile devices. This level of visibility allows for immediate detection of unauthorized stops or deviations from planned routes.
In addition, trailer tracking helps carriers increase efficiency, boosts trailer uptime, and reduces driver frustration.
Geofencing technology is another feature associated with fleet telematics. Carriers can establish virtual boundaries (called geofences) around specified areas. If a vehicle or trailer equipped with telematics crosses one of these pre-defined boundaries or leaves designated zones, fleet managers will receive automated alerts, enabling rapid response to potential operational or security issues.
Geofencing technology serves as a valuable tool for trucking companies overall, offering benefits such as improved fleet visibility, route optimization, enhanced security, efficient asset management, better customer service, regulatory compliance, driver monitoring and data-driven insights.
Many telematics solutions are compatible with a host of sensors that trigger alerts upon unauthorized access or tampering with cargo containers or trailers. These sensors provide immediate notifications to carriers, enabling prompt intervention and preventing theft attempts. Door sensors, for instance, can alert to when a trailer door
is opened or closed.
Tire sensors, for example, provide near real-time data on trailer tire pressure and temperature, helping carriers avoid blowouts, costly roadside repairs and underinflation violations, not to mention wasting a driver’s time by having them hook up to a trailer with a flat. Other sensors provide data on brake health, cargo status, lights, reefer temp and more.
In general, driver behavior data provides information on where to improve safety and take measures to eliminate driver behaviors that waste fuel or subject vehicles to excessive wear and tear.
Fleet telematics technology serves as a powerful weapon for motor carriers in the fight against cargo theft. Through tools like real-time tracking, geofencing, connected sensors, driver behavior monitoring and others, telematics technology helps deter theft and aids in evidence collection, investigation and recovery of stollen goods and assets.
The cold food supply chain is undergoing a transformative phrase with companies leveraging innovative software and technologies to address challenges, increase efficiency and ensure the integrity of perishable goods.
Adoption of these technologies for supply chain visibility is critical for modernizing processes, optimizing logistics, and navigating global supply chain complexities.
Matt Heerey, president of manufacturing for ECI Software Solutions, indicates its capacity is at 70% of previous levels. He identifies key issues as limited capacity, resource shortages, disrupted material flow, transportation, and logistics problems.
As the industry moves to return to 100%, “one of the major trends we will continue to see evolve is the integration of robotics and software to streamline repetitive and mundane processes such as packing, sorting and processes,” adds Heerey.
Heerey also emphasized the importance of automation and technology in cold food systems in enhancing inventory management, temperature control, and reduc-
ing manual processes, which increases efficiency and contributes to the quality of perishable goods, he adds.
Glenn Koepke, FourKites’ general manager of network collaboration, notes one trend in the cold food chain is the use of sophisticated artificial intelligence (AI) and machine learning (ML) engines for accurate forecasting, addressing growing season challenges, capacity allocations, distribution, and order demand.
The adoption of AI- and ML-based tracking to collaborate with third-party logistics (3PL) providers, temperature-control carriers and the end customer grows each quarter, he adds.
But, companies are faced with legacy technical debt from acquisitions and/ or a lack of investment in overall infrastructure, Koepke says, with many cold food chains starting with farmers in the field whose core business is growing and harvesting, not supply chain tech.
“As part of modernization efforts, companies continue to invest in their enterprise technology stacks to digitize their process from farm to final customer,” he says.
Profitability and growth are being slashed up to 10 times or more in certain cold chain commodities, putting pressure on budget priorities, leading companies to prioritize roadmaps addressing infrastructure impact, process optimization, growth, and customer experience.
Jonathan Raemdonck, Trimble’s director of operational marketing, notes companies realize the dispersed set of systems need to work more closely together, not just within the boundaries of their companies, but also in between companies. Real-time visibility into goods’ conditions, such as temperature ranges, is crucial for both inbound and outbound traffic flows.
“When a critical production error has occurred, a food manufacturer wants to immediately identify impacted batches, which stores they have been delivered to, and which impacted products are still in transit,” says Raemdonck.
That’s why food and beverage companies integrating spot transportation into their tactical toolset for assigning transports, enabling them to manage seasonal volume spikes and reduce costs in times of a loose market, he adds.
Addressing the benefits software and technology brings to the industry, Heerey notes numerous ones, including resiliency, reliability, sustainability, and integrity of perishable goods throughout the supply chain to minimize risk and enhance product quality and safety.
Advanced analytics and data-driven insights enable proactive decision-making, optimizing logistics and reducing operational costs through supply chain traceability, fostering transparency and accountability, he adds.
David Warrick, Overhaul’s EVP of enterprise, notes the transformation of technology in the supply chain industry from potential possibilities to practical realities. Automation, enhanced visibility, and real-time processing have become key components, allowing the industry to anticipate and act proactively.
Barry Bradley, Crisp’s supply chain expert, notes improved forecasting through the provision of visibility to real-time demand from retailers and distributors. Doing so mitigates challenge through sales data by getting an accurate picture of holistic demand to use in forecasting supply, manufacturing, and logistic needs, he says.
Sales information can be automatically ingested, cleaned, and routed to analytics and a brand’s internal systems, providing an accuracy level and granularity not previously available to demand planning teams, Bradley says.
A transportation management platform helps fast-moving consumer goods
shippers keep a close eye on shipments and manage potential issues promptly through effective event management, notes Raemdonck. It enables efficient timeslot management at shipping and receiving facilities, considering specific shipping and delivery windows and the time-sensitive nature of perishable goods shipments, he adds.
“Technology accelerates decision-making, gets dispersed data across many sources and can be translated into insights that humans wouldn’t be able to infer alone,” notes Koepke.
It also protects the cold chain threshold from risking lost sales, damaged product, and customer illness.
“The real game-changer in temperature tracking is the disposable active tracker, which utilizes cellular networks,” says Koepke. “These devices continuously monitor temperature conditions. When integrated with visibility software, active trackers trigger alerts when something is out of the set temperature tolerance range, empowering timely interventions, and more cold chain control.”
Automatic notifications and customizable threshold limits help shippers detect critical events, avoid false positives and improve overall efficiency.
Combining advanced temperature tracking with end-to-end supply chain visibility, growers, shippers, distribution providers and carriers can boost on-time delivery, eliminate product loss, reduce overhead costs, and enhance customer satisfaction,
Koepke says.
Added visibility improves retailer relationships by reducing the frequency of spot buys, reducing operational costs, streamlining dock operations, and utilizing staff more efficiently, he adds.
A Food and Agriculture Organization report suggests approximately 14% of the world’s food is lost between harvest and retail, mostly due to inadequate cold chain facilities and poor temperature management during transportation. The financial implications are significant, particularly for businesses operating with narrow margins, Koepke adds.
“If a shipment does not meet temperature compliance standards, it’s often rejected, unless the shipper can provide a verifiable record of maintaining the correct temperature during transit,” says Koepke.
Despite high adoption rates, Heerey cites a McKinsey & Company study indicating many companies, especially small- and medium-sized businesses (SMB), still rely heavily on pen-and-paper operations, emails, and phone calls.
The reluctancy of SMBs to adopt cloud solutions speaks to existing challenges, says Heerey, but he warns, the longer companies wait, they will open themselves up to cybersecurity attacks, falling behind the competition and alienating the new generation of workers.
Improperly used tech stacks are another challenge.
“Local business units acquire niche applications without the broader network in mind, leading to a mixed bag of solutions that may optimize the part but not the whole,” Koepke says.
Another challenge: signal noise.
“Are teams being bombarded with alerts from every corner of their operating system?” he adds. “Can they determine which ones are actually a worry?”
To address these issues, chief supply chain officers must partner with chief technology officers and chief information officers to re-evaluate their tech stack to create a platform approach to real-time supply chain execution, says Koepke.
Scan this QR code to read the article in full.
https://foodl.me/b7dcaz66