Behind the backing gates


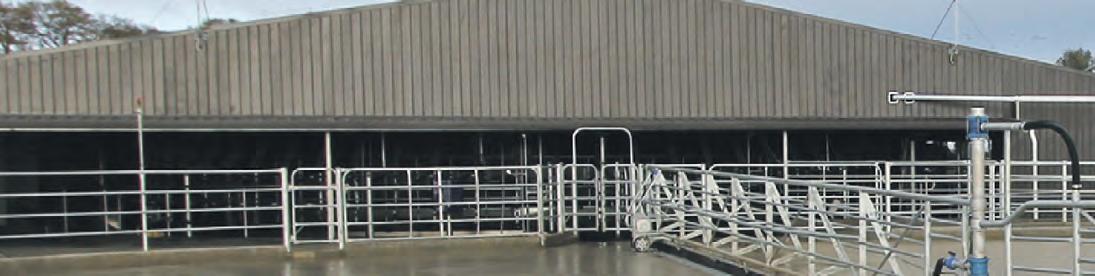
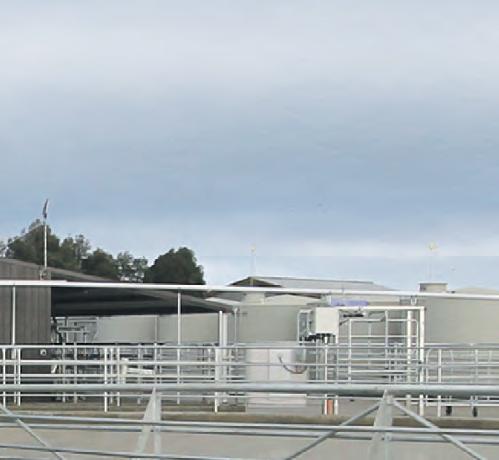
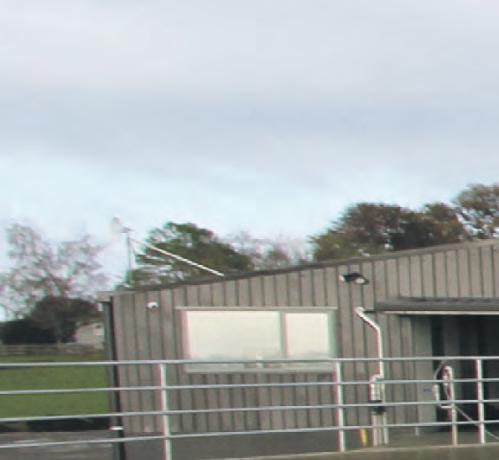
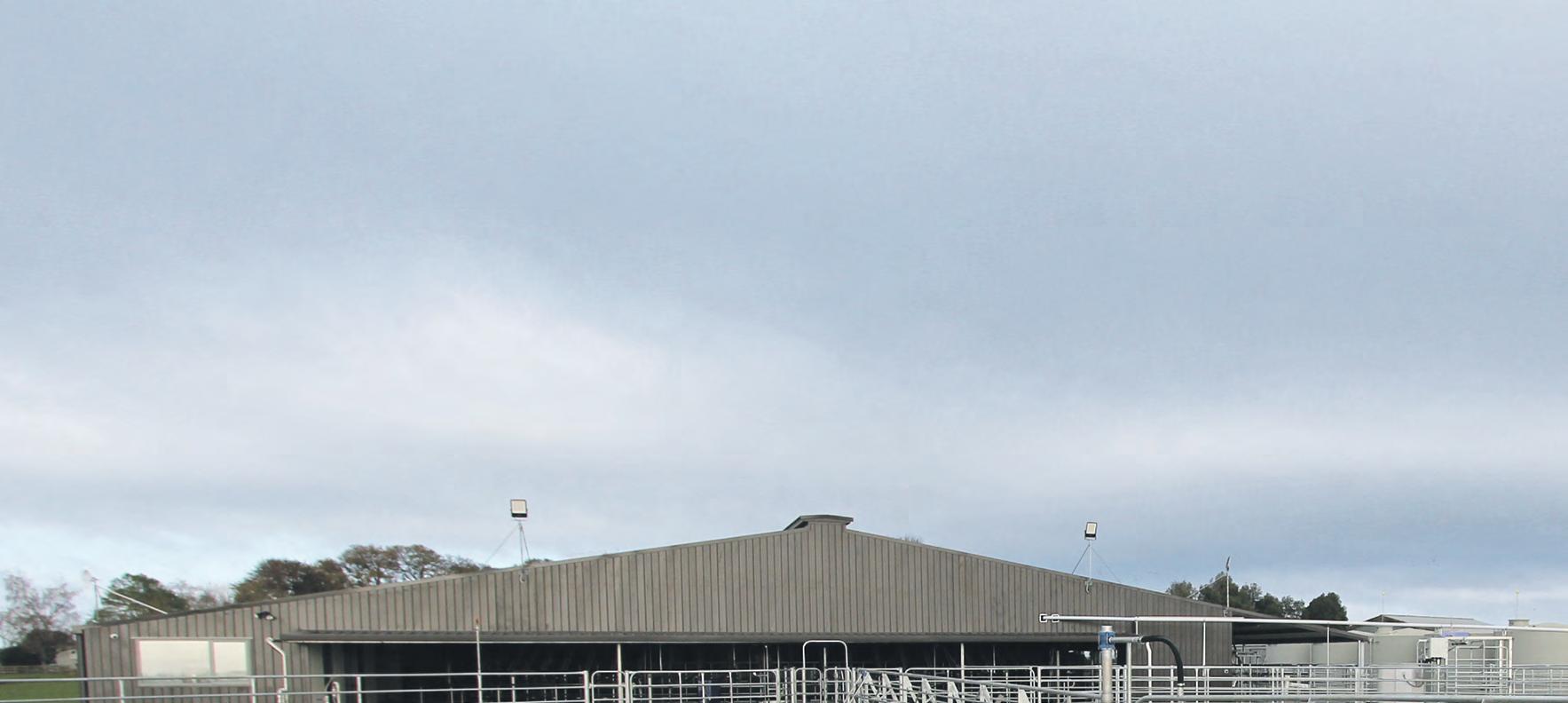
Meet Fraser Storey
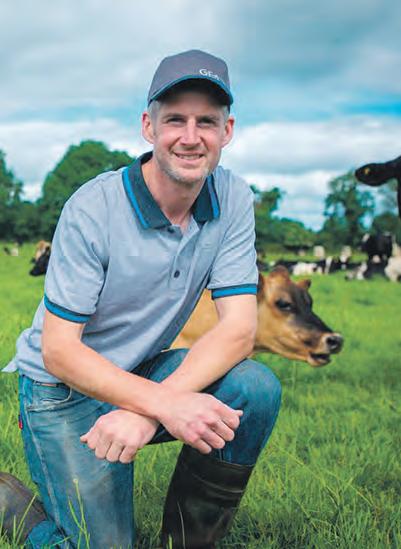
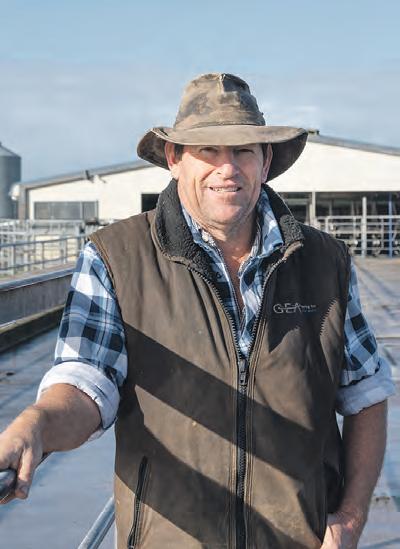
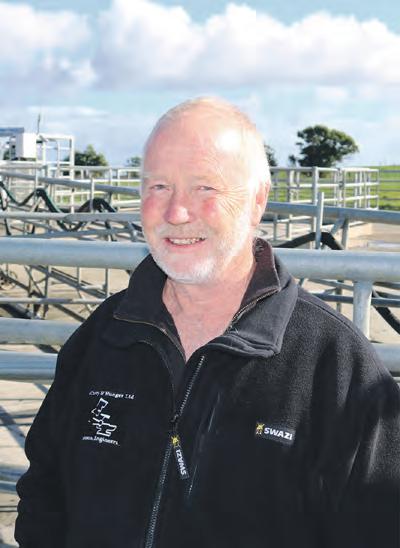
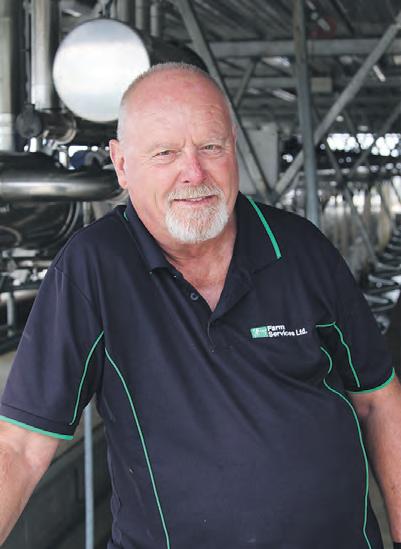

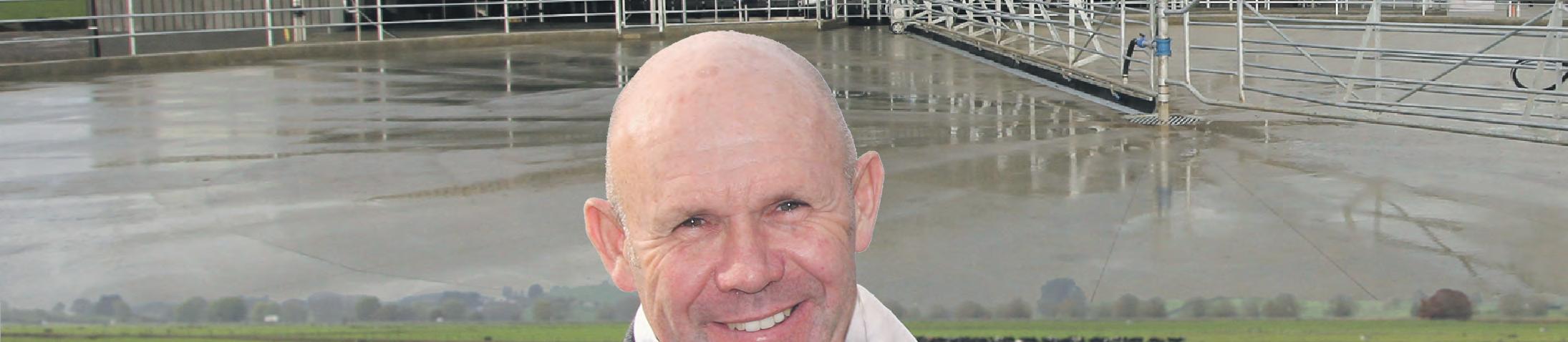
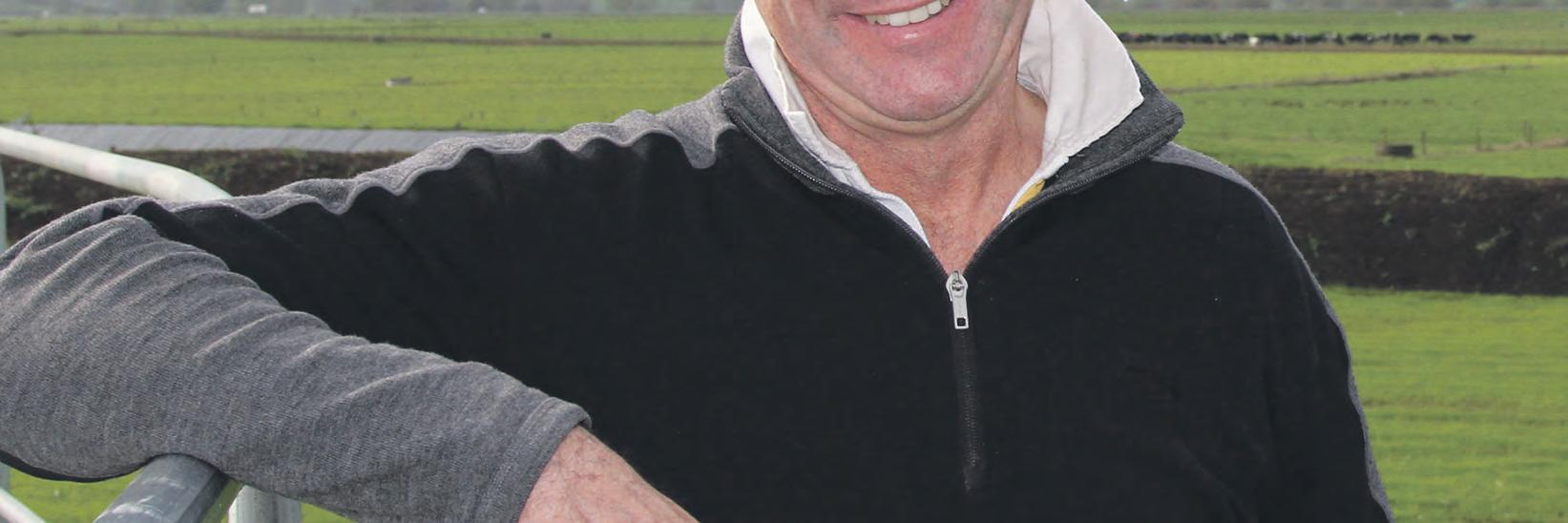
industry during the last four decades
rate of progress which will only increase in the
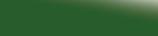
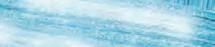


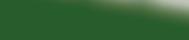

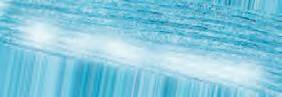


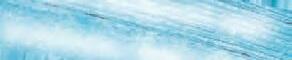
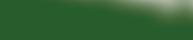
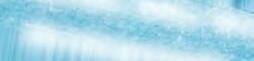


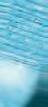




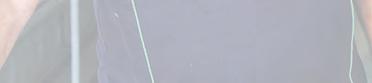
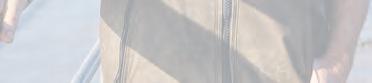
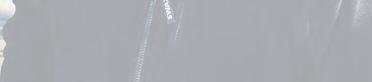
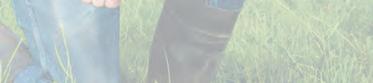
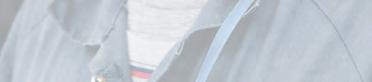
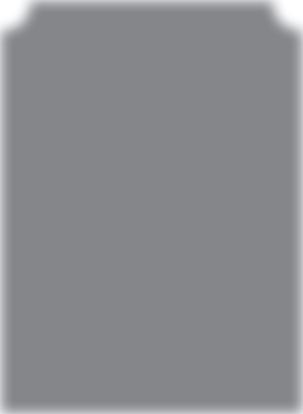
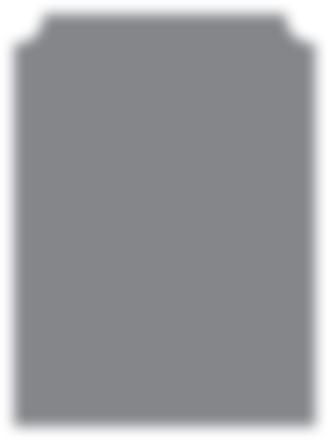
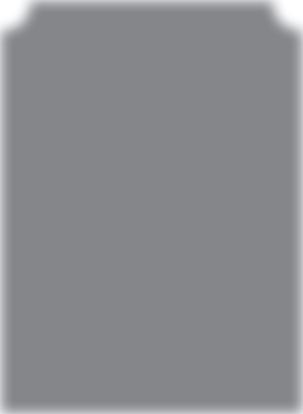
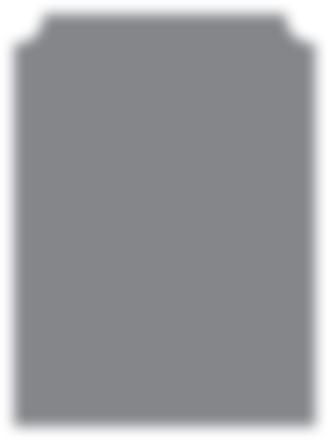
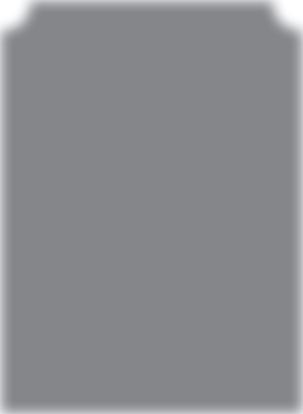
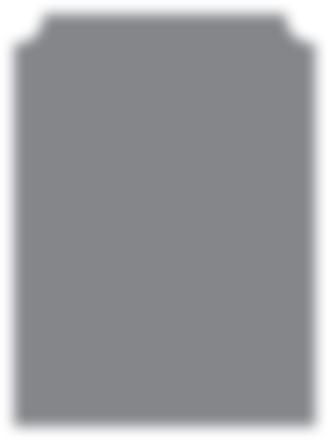
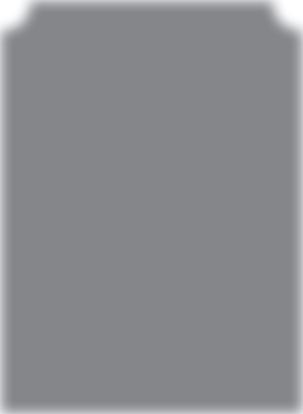
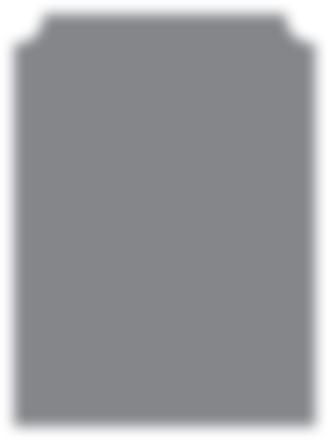
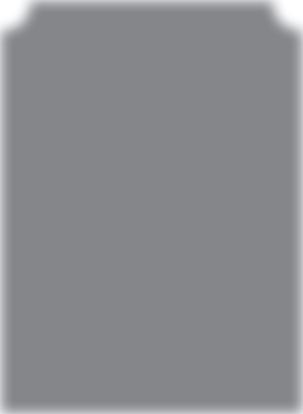
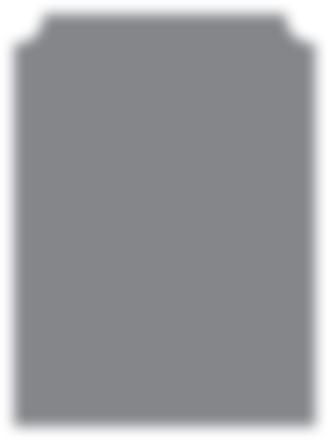

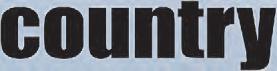




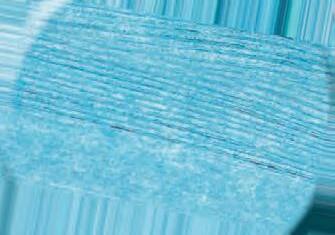


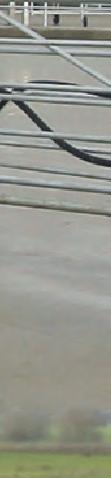
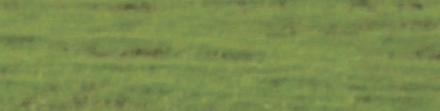



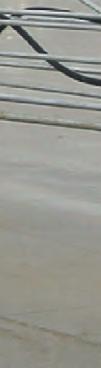

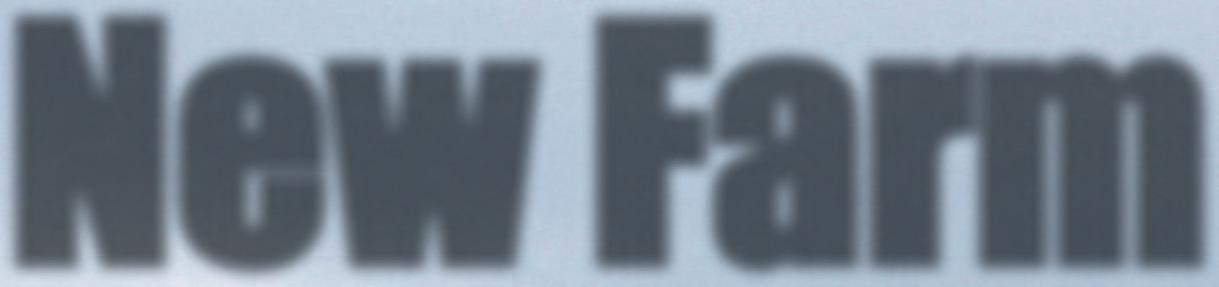
his family
new build is
and
build

Meet Fraser Storey
industry during the last four decades
rate of progress which will only increase in the
his family
new build is
and
build
New Farm Dairies was conceived more than 18 years ago after an idea about farmers who, considering the renovation or building of new farm dairies, wanted to benefit from the experience of fellow farmers.
The rural support businesses behind those developments also got on board and the rest, as they say, is history.
The concept was, and is, to present ‘the farmer’s voice’ so readers have the benefit of understanding the motivations and challenges faced by each farmer in achieving his or her goals. The mechanics of achieving those aims is then reinforced by the organisations and individuals involved in the development – so readers have a rounded presentation of all the considerations and potentials involved in achieving the desired end result.
It was, and remains, a novel approach. Each profile is accompanied by advertisements from the farmers’ rural support organisations, which provide much-needed technological perspectives and expertise to round out the logic behind the respective development.
We acknowledge that the stories we are privileged to tell are just a fraction of the many developments taking place every day on farms around New Zealand. In 18 years we have profiled more than 630 farms with an average 35 profiles taking place each year, each nominated by one or more of the organisations and/or individuals involved in the development.
New Farm Dairies’ popularity comes down to the fact that it talks to farmers about farmers. Once nominated, our journalists arrange to visit the farm and talk with the farmer and support organisations who wish to be involved in the feature. These gatherings are informal and often a rare opportunity to stop and reflect on what has been achieved.
If you have, or will shortly undertake an upgrade, renovation or new build on your cow, sheep or goat dairy farm – we want to tell that story, because the challenges you faced and overcame could benefit fellow farmers.
We hope you enjoy this year’s profiles – and if you know of someone who should be profiled in next year’s edition, please contact the doyen of New Farm Dairies, Lois Natta.
www.pppindustries.co.nz sales@pppindustries.co.nz
0800
new builds. But the reality is that each and every development was motivated by the relevant farmers’ commitment to animal welfare, the environmental sustainability of their farms, their families and the future of the dairy industry.
The profile of farming has changed in the 18 years since New Farm Dairies was first published. Back in 2004 most New Zealanders could recount an on-farm experience – they had a family member or friend who was a farmer or had visited a farm. The upshot was that they had an appreciation for what motivates and drives farmers and understood – at some level –the industry’s relevance and importance to the economy of New Zealand.
Not so today. On-farm experience among urban dwellers is becoming a rarity as distance and negative media reinforce an image that runs counter to the reality of modern farming. But if the popularity of the only farming show to screen on primetime television is anything to go by, Kiwis have an intrinsic nostalgic connection with the land, and the people who farm it. Most Kiwis want to believe in the motivations of the people behind the production of one of the purest food sources in the world.
The emergence of social media and acceleration and narrowing of news stories over the last few decades, however, has shrunk the audience for farming stories – often meaning only the sensational headlines register.
Sun Media’s New Farm Dairies was conceived to tell the stories of new farming developments but it is, in reality, one of a small number of publications which tell the story of farming, taking readers onto the farm, to understand the motivations that drive multi-million dollar investments – often without any immediate economic return.
On the face of it, the stories in this – as in previous editions – tell the story of farm upgrades, renovations or
What started out as a magazine which ‘simply profiled new builds’, has matured into ‘a virtual field day’, taking readers behind the scenes of a range of farms to learn about innovations that are demonstrably changing lives – of animals and people – for the better.
In every case, the welfare and health of the animals and the stewardship and health of the land has been improved. By nature, farmers farm because they love their animals and the outdoors; they ‘get’ that their responsibility as stewards of the land is to leave it in better condition for future generations. They live this ethos every day, in every weather, and under increasing scrutiny.
Farmers work the hours needed to get the job done, often in isolation without the social support many urban dwellers take for granted. They generally shun the spotlight, preferring to get the job done. But if they aren’t telling their stories, who is?
In many ways, the stories embody the spirit of NZ – each of the farmers profiled say they could not have accomplished what they’ve done without the support, friendship, expertise and trust of an amazing network of dairy support partners –builders, electricians, plumbers, dairy system manufacturers and suppliers, along with a varied range of rural contractors. All those organisations and individuals share a drive and determination to do whatever is needed to deliver the best outcome for their farmer clients.
Every dollar spent on-farm, of course, has a positive financial impact that spirals from the farm, across the local community and infrastructure, to the world.
Now that’s a story worth telling, and retelling.
Massey Dairy 4 Manawatu 4-11
Birdgrove McLean Trust Northland 12-13
Mt Moriah Jerseys Northland 14-17
HP Dairies Canterbury 18-19
Pahau Dairy Farms Canterbury 20-21
Twin Rivers Canterbury 22-23
Simson Farm Taranaki 24-25
Kapuni Farm Taranaki 26-27
Chislehurst Farms Taranaki 28-33
Platform Farm Wairarapa 34-35
Agriconcepts Central Plateau 36-39
White Pine Farms Eastern BOP 40-41
Red Fern Farms Eastern BOP 42-45
Willow Creek Dairies Southland 46-47
J&K Miller Southland 48-49
Drumderg Southland 50-51
Laing Waikato 54-55
Milk Makn Waikato 56-57
Jada Rocks Waikato 58-59
Wilson Sheep Waikato 60-63
Bo Sheep Waikato 64-65
Edward Farms Waikato 66-67
Matangi DairiesWaikato 68-71
Rotohipi Waikato 72-73
Aranui Farming Waikato 74-75
Van Vliet Waikato 76-77
Empson FarmingWaikato 78-81
McPherson SheepWaikato 82-83
Paramount FarmingWaikato 84-85
Lakeside KainuiWaikato 86-89
Longreach DairiesWaikato 90-93
Ormsby Waikato 94-95
Magan Ireland 96-97 Moorend UK 98-99
Located just on the outskirts of Palmerston North, Massey Dairy 4 is located not far from the Massey campus and is the larger of two dairy farms owned and run by the university.
Massey University began to purchase property back in April 1973, with the acquisition of two properties totalling 162 hectares, for use as a large seasonal supply dairy farm.
In May 1988, the adjoining property of 58.24 hectares was also purchased and amalgamated into the existing property.
In early 2012, half of the Dairy Cattle Research Unit grazing platform joined Dairy 4, and the remainder of the DCRU land, which
was then organic, was dissolved into the Dairy 4 grazing area.
Dairy 4 now has a property totalling 220ha, milking 600 cows. Hamish Doohan is operations and sustainability manager for both Dairy 1 and Dairy 4.
Allan Still, who is general manager for Massey Ag and Hort Enterprises, says about five years previous he was approached by AgResearch, which wanted to invest in a facility with Massey University as it was relocating its dairy science team to Palmerston North.
“AgResearch needed access to cows; a joint venture project which would provide access to Massey cows for their research purposes,” says Allan, “We said: ‘Yes’.”
Rather than tack on another shed to their existing rotary, Massey decided a better
option was to develop a ‘fi for purpose’ dairy research facility, which would not only cater for a host of other research projects but could also provide a suitable animal-handling component to complement Massey’s teaching functions.
“So we are setting ourselves up as a research provider of choice for external animal research while providing a base for teaching, and research for Massey University.” says Allan.
The original shed on Dairy 4 was commissioned in a hurry when the 2004 floods struck. The old shed will remain and be
converted to an animalhandling facility.
“The problem we faced with the existing facility was that with the increasing demand for more complex research, it became more difficult to manage in a commercial environment,” says Allan.
“The new dairy design allows greater flexibility in providing multiple access points, and as such is more adept at handling the constant flow of small research herds.
This was a huge undertaking and a massive project, with two fully functional dairy platforms under the one roof. A 60-bail rotary, which will be the commercial and small-scale side of things, and a 28-bail rotary that will largely be used for research purposes.
Not only is there two dairy systems, but there has also been a large covered animal-handling facility installed as well as a stand-alone classroom. A huge feed pad was under construction at the time of my visit, as well as an impressive effluent-handling feature
Hamish says the new animal handling facility is larger than what AgResearch had at Tokanui. “Massey opted for the slightly larger option so that when there is a vet student training and they have practical work to do, they have plenty of room to spread out,” says Hamish.
“The covered facilities include power, data capabilities, and good lighting.”
Due to heavy soils on the farm, a freestall barn, which was constructed back in 2013 and is used for wintering the herd, is also being integrated with the effluent side of the new project. It has a scraper system in place that
scrapes the solids into the floodwash channel, which is then flooded with greenwash from a newly-installed tank. All effluent then goes through a separator system.
The design on the Massey project had been done well in advance, then put up for tender.
Rural Building & Engineering won the tender and built the project to plan.
Lance Wilkin, who is a co-owner of RBE alongside Paul Roberts, says the tender process was a two-stage open tender – and open Registration of Interest followed by a closed Request for Tender to short-listed Tenderers for the procurement of Contract Works. The entire project was done under the NZS3910:2011 construction contract.
“The job has been so structured, with a
contract administrator and quantity surveyors overlooking the entire project,” says Lance. “You’d expect that given the value of the contract, so we needed to get up to speed with processes very quickly.”
Lance says this was the first time RBE had buil two platforms under the one roof. “The amount of auxiliary rooms, such as an entire toilet and shower block including an accessible toilet and shower to accommodate people with physical disabilities, offices, sample rooms, data room, plu the different floor levels throughout made this technically challenging job,” says Lance.
There are two underpasses installed in the 60-bail shed; one for staff and one solely for herd testing so technicians can access the shed from outside without interfering with work in progress.
The scale of this project meant a lot of RBE’s regular suppliers weren’t keen to come on board, as it was such a large project and would have taken them away from their regular clientele.
This meant RBE had to source other contractors willing to participate in a project of this magnitude.
Thousands of cubic metres of crushed aggregate had to be trucked in and compacted to build up the site, unfortunately against the lay of the land.
“The reasonably tight timeframe, and given the scale of the project and the scale of the site, and with Covid-19 in the mix as well, made things quite difficult to manage at times,” says Lance
“Even at Level 3 Covid restrictions we had to keep numbers of contractors on-site to a bare minimum to maintain social distancing. This made progress challenging.”
The test cups are in place in the centre of the platform. The Moa Platform and Waikato plant in the main shed. The receiving cans are still shiny and new. The smaller shed has its own clean up area so the shed runs as a stand-alone shed. The Waikato controls and Sema milk controller all work in together.RBE was contracted as the main contractor for the project and responsible for overseeing delivery of the entire project excluding the rotary platform, milking plant and effluen componentry. This meant RBE undertook the major earthworks, site excavation, construction of two cowsheds and vet training barn, cow yard concrete and pipework, a new silage bunker to complement the existing three-bunker silage set-up, effluent system and precast concrete infrastructure and, at the time of my visit, was part-way through constructing the new feed pad.
RBE also constructed cow races around the complex to tie everything back into the existing infrastructure.
The feedpad, covering 3500m2 will be split into two feedpads; a commercial feedpad and a trial feedpad, which is able to be divided into eight separate sections. There will be a further six greenwater tanks installed on the feedpad for flood-washing. The effluent will flow down to the flood-wash channel and in
the pump sump. All liquids run back to the pond after going through the stone trap and solids separation system. From the pond it is then pumped onto paddocks and back into greenwash tanks.
“The farm is quite complex, as it is running as a commercial dairy farm and a research and training institute for students. It was important they have a decent facility,” says Lance.
The dairy sheds’ roofing has a polycarbonate ventilate bridging for heat displacement and to let more natural light into the shed. The walls are all made from precast concrete panels as well as poly panel for ease of cleaning. There are a massive four big water heater tanks in the large dairy.
Two DTS milk vats are installed, with the ability to install two more in the future.
“That’s a lot for a shed this size but when the research side of thing comes into effect, it’s totally understandable,” says Lance.
All the precast concrete panels were constructed offsite by RBE,
and the beauty of doing it that way is they were not working in around the weather on-site. “It probably saved about four-six weeks by doing precast,” says Lance.
Everything has been constructed to a very high calibre, right down to a huge array of health and safety signs.
The effluent system has a large effluent bunker to cope wit the dairy sheds, feedpad and the large wintering barn run-off. The treatment system is leading-edge technology at the minute and is not often installed on a commercial farm. “It’s great to have a solids separation system installed such as this one to cope with the large amount of effluent,” says Lance Hamish was after a large amount of solids storage because of the heavy soils on the farm; this enables them to spread solids on pasture or plough in when ground conditions are suitable. Lance says RBE would like to acknowledge the efforts of everyone involved in the project and in particular the input from Hamish Doohan and Allan Still.
Lance is proud of the fact that the first piece of soil was turned in December 2020 and milking commenced on November 29, 2021.
Bromley Dairy & Pumps from Feilding completed the full Waikato Milking Systems install. Both Bromley and Waikato Milking Systems tendered for this project, which was a big undertaking given the scope of the project and the timeline permitted for its completion. They had two weeks to pull their side of things together.
Bromley Dairy & Pumps owner Steve Bromley says the plant is an American/European spec’d plant. “It is very rare that there is one of this capability in New Zealand.”
There is both a 60-bail commercial milking plant and a 28-bail research milking plant installed under the one roof. “These are what we call fully-loaded plants, both systems have all the bells and whistles and then some,” says Waikato Milking Systems lower North Island region manager Ben Frederickson. Both plants are equipped with a Waikato Milking Systems
Centrus composite platform with MultiRoller Undercarriage installed by Nathan Hitchcock, Matt Churchill and their team at Moa Rotary Platforms. The Centrus composite rotary milking systems are unique. Unlike concrete alternatives, which are built on-site, each composite deck is manufactured in the factory to consistent stringent quality standards.
“These particular platforms are what are known in the industry as the Gen 4 version, which means they are the latest technology,” says Ben. “The Gen 4 means there have been improvements over time; for example Gen 1 came in four bail sections, whereas Gen 4 come in a per-bail section which are all clipped together.”
Each bail weighs 28kg as opposed to a concrete platform that weighs considerably heavier. The idea of the Centrus composite system is they’re completely impervious so they’ll last a lifetime. Being so light, they’re easier on running gear, meaning less maintenance and wear and tear.
Rubber mats are standard and pre-fitted in each bail
providing ideal cow comfort.
The team from Moa Rotary Platforms comes out annually for a platform service and thorough check-over, says Ben. “They check that it is running to optimal performance and recharge the grease cartridges.”
Both platforms are fitted out with the stainless perimeter drip rings to prevent the milkers from wearing the water drips from the platform; instead water escapes via the drip ring straight into the drain.
Automation for both systems is well-appointed with the standard Waikato 320 milking clusters, which are ergonomically designed for both cow and milker during milking, and to optimise the milk harvesting process. ECR Plus Automatic Cup Removers with Vortex Milk Sensors were installed.
The ECR Plus integrates with the NaviGate Dairy Management software, enabling staff alerts for withholding cows as they enter the machine, and identifies abnormal milkings as they occur.
The SmartD-TECT conductivity measuring pulsators are a labour-saving technique that give early indication of udder health in discrepancies between each quarter. A red alert will flash on the User Display so the milker can take the appropriate action. The SmartDTECT will pick up a mastitis case typically five days before it becomes clinical, which gives the milker the opportunity to get onto it nice and early to stop the spread and potentially save on higher treatment costs.
Electronic Milk Meters, Milk Samplers and User Displays complete the automation for this project.
The Waikato Milking Systems plant is equipped with a Milk Recovery System and a SmartWASH Auto Plant Wash System
A Navigate Premium Herd Management with five-way drafting has been put in place for the 60-bail, with a three-way drafting for the 28-bail system. This has a walkover weigh system incorporated into it.
The feed herd management system individually feeds cows customised amounts according to specific requirements
CowTRAQ™ Collars have been incorporated for heat, health and rumination monitoring for the entire herd.
The CowTRAQ™ collars integrate with the TracHQ™ software to provide Massey with real-time information and mobile alerts.
Massey wanted the refrigeration units to be totally water-free, which is why the plate coolers are run by glycol units. Installation of these units was completed by Bromley Dairy & Pumps.
All the glycol is stored in high density water tanks adjacent to each milking parlour, so each plant can run independently. The glycol stores in the tanks at two degrees Celsius, and as the glycol contains anti-freeze it is well suited where rapid cooling is required.
There are currently two DTS milk vats
installed, with plans to install another one in the near future.
The Sema Milk Pump Controller is, as its name suggests, a milk pump controller, which works in with Waikato Milking Systems’ milking system. The MPC features a waterproof unit that has been extensively tested for water tightness. It has been designed with rural power conditions in mind, and both the single and three-phase units operate within very wide voltage limits as well as having built-in surge suppression.
The MPC has all the bells and whistles with an incredibly simple and fast set-up and is fully optimised for the Massey sheds. All settings can be adjusted while the pump is running. The Super-Cool mode provides the slowest possible flow of milk through the plate cooler to optimise heat extraction and give the lowest possible milk delivery temperature to the vat.
Allflex now owns Protrack Milk Meter after purchasing the rights to them back in November 2021. The meters measure the likes
The larger of the two dairies has an exterior underpass for ease of access for herd testing.
The team from RBE in the process of constructing a feedpad.
of volume of milk per cow on a per-milking basis, fat content, protein contact, lactose and a conductivity reading. Essentially, they can signal whether the cow has an infection, which can be caught sooner and therefore have a faster, better outcome for the cow. These are all wired back to the computer hub for analysation after milking. Protrack Milk meters obtain accurate and realtime production information whenever the cows are milked. “Our part in this project was small in comparison to the size of the project, but an integral part all the same,” says Allflex’s lowe North Island monitoring specialist Trevor Ward.
The team from Bromley Dairy & Pump installed the effluentsystem. Steve Bromley says the automatic flood-wash system was designed by his company, and once the feedpad has been completed and the six new tanks added, they will be automated and tied in together for a fully functional operation.
“Whilst we were doing the effluent side o things we noticed that workers were coming over with the tractor and sucking out the effluen pond, so we made the suggestion to Massey about installing a pump at the cow barn and upgrading the effluent separator to accommodat the extra waste,” says Steve. “The separator actually works better with more solids.”
All effluent from the dairy sheds, vet training barn, feedpad and cow barn runs through the cross-drain, goes through the stone trap, then liquids carry on down to the effluent pond while solids pass through the Hi-Tech transfer pump and up through the valve separator to be stored in the bunkers until required.
The greenwater tanks are then filled with wate pumped up from the effluent ponds and used t clean the yards down. “The only clean water used is around the milking plant,” says Steve.
The effluent ponds are created so they can be
extended in future if required.
Because the effluent has come through the separator there are no solids to stir, so no stirrer is required in the pond. The ponds will just get cleaner and cleaner over time.
“It has been very important to think about the environment and carbon footprint,” says Steve, “and Massey want to be ahead of the game in that area as well.”
Davieth Verheij from AgFirst Engineering in Te Awamutu was first engaged by Masse University in 2017 following its market evaluation and procurement for a new low rate travelling effluent irrigator. Masse needed an irrigator that would apply to land lighter, was reliable, reduced labour requirement and applied effluent/nutrient
to land evenly. The Weta irrigator developed by Davieth and the AgFirst team ticked all the boxes.
The Weta low-rate irrigator is a travelling rain gun, which is propelled by the effluent flow via a turbine-driven hydrauli winch system. This removes the need for rotating booms and high-wearing mechanical drive systems. The Weta is also the only drag hose irrigator that will maintain its travel speed no matter where it is on the farm. This is achieved with a speed sensor and automated turbine flow bypass valve. This means the application depth is uniform over the entire farm, making nutrient management and proof of placement a breeze.
As part of the new farm dairy and effluent system upgrade in 2021, Massey University decided to purchase an additional
Weta irrigator to double capacity. AgFirst Engineering is Farm Dairy Effluent Design Accredited and worked with Bromley Dairy & Pumps to complete the Massey University effluent system design
There are plans in the future to install a big weather station up on the hill at the back of the farm, which will in turn hook back to the pond pump and will also be able to GPS where the irrigators have been.
Irrigators will be able to be switched on or off via cellphones.
Daniel Gorton, director of Reporoa Herdflow says his company supplied two Reporoa Herdflow High Lift Gates to the Massey Dairy project. Both gates included the following extra options: 4WD, breech sensors, and the on-gate camera with monitor at cups-on area.
“This new gate design was developed in 2017 and we are the originators of the High Lift Backing Gate,” says Daniel, “so over 30 years of knowledge has gone into producing this new gate which will give Massey many years of trouble free running.” The Herdflo High Lift Gate is a robust yet simple gate. Daniel says the gate droppers are constructed from heavy duty pressed steel, galvanised and U-bolted to the 25NB galvanised pipe rails. Because the pipes are U-bolted rather than welded, there are minimal welds to crack and break over time.
The backing gates run on galvanised ‘I’ beam (anti de-rail design) with side guide wheels. This stops the gate having any crabbing or jamming issues and means the gate can never come off its rails.
Massey’s backing gates have the breech sensor that prevents bulldozing of cows in the yards. It has integrated functions to look after your cow’s health and wellbeing and has a Programmable Logic Control system, which allows for many standard functions plus more can be added when, and if, Massey requires them.
The quality Acraflex Dairy Wall Coating in the Massey dairies was applied by Surfatex 2019 Ltd from Palmerston North. Owner Glen Sinclair says the interesting thing with this particular job was the architect specified waterproofing with a produc called Bituthene for the outside of the underpasses. “This was a first for our company and another string to our
bow, given it then needed to be signed off by council,” says Glen.
Site foreman Nana Ngatokorua oversaw the application of the Acrafle Dairy Wall Coating system, starting with prep work that involves a wash and light grind to get rid of any rough bits. After applying a primer coat, a three-stage Acraflex coating is the applied, followed by the flex coatin and lastly the glaze coating, which keeps the coatings easy to keep clean in years to come.
The exterior concrete walls were also painted on the entire complex. Some areas of the flooring were painted and had an added aggregate to formulate an anti-slip finish
The job was well and truly finished off prior to using the shed, which was a coup given the tight deadlines.
Brett MacDougall is the owner of MacDougalls in Pahiatua and local DeLaval dairy hygiene supplier to Massey.
Brett says as well as supplying dairy detergents and consumables, they offer full grade-busting facilities and come in and do regular DeLaval Cleaning Analysis tests at Massey. DeLaval DCA is a service that determines the effectiveness and efficiency of mechanical slugs and thermal processes during cleaning in milking machines by sending a camera down the milk lines. Its innovation lies in an algorithm that automates the way slugs in the milk line are analysed.
By evaluating the mechanical and thermal processes of the cleaning of a milking machine, DeLaval DCA improves the cleaning procedures before problems appear, securing optimal cleaning results at all times, which is essential for milk quality. “We do regular hygiene checks, chat with the farmer and make sure everything is tracking the way it should be,” says Brett.
Brett MacDougall checks the DeLaval dairy hygiene products.
There
set up to hold the glycol for the refrigeration systems.Waikato Milking Systems Bailgate.
monitoring collars - choose a system that gives you confidence, and is delivered by an unbeatable support team from a brand you trust.
Participation in a farmer-led mentoring and extension programme has paved a smooth transition from active dairy farming to retirement for a Northland dairy farmer.
Lachie McLean admits that until he joined the Northland Extension 350 programme, he had little time to lift his head from the eight hours he was spending in the shed each day, combined with running the farm.
“The programme enabled me to see the bigger picture, to get new ideas and have the advice and support I needed to implement them,” says Lachie.
“I began working on, rather than in, my business and that made all the difference. I now have a productive, sustainable farm managed
by sharemilkers enabling me to devote my energies to my other passion – theatre.”
Dating back to 1976, Lachie has produced and directed a string of successful musicals, theatre and variety shows, mostly in the Northland region, resulting in a Civic Award and, more recently, his appointment as chair of the Forum North Trust.
The Birdgrove McLean family has been part of the fabric of Northland dairy farming for more than 151 years, says Lachie, recalling that his great-grandfather emigrated from Nova Scotia, purchasing and breaking-in the original 420 acre farm in 1871.
The property was eventually subdivided into five farms for each of his sons. Lachie grew up on one of those smaller farms and, to this day, lives in the Birdgrove McLean homestead
built by his grandfather.
“I am the fourth generation to farm the property,” says Lachie. “I took over from my father and, until 2012, milked 120 cows on 72 hectares through a 17-bail rotary shed.”
“In 2012 I amalgamated the farm with my cousin’s similar-sized property and then purchased an adjoining 113 hectares, making up the current 257 hectares which comprises a 176 hectare milking platform.
“The increase in acreage demanded an increase in herd size to 350 Jerseys, which really put a strain on the old rotary, requiring me to spend around eight hours a day milking!
“I wanted to step away from the day-to-day running of the farm but needed direction –
that’s where the Extension 350 programme came in and with the help of two farm advisors and a mentor farmer I was able to redefine the future – mine and the farm’s.
The practical outputs of the succession plan included the construction of a new dairy, sale of the herd and appointment of a 50/50 sharemilker – in that order.
“The goal – and overall output of the Extension 350 programme was to improve and extend the farm infrastructure so I could get someone else to run the farm for me so I could continue to live on the farm and work on it, when I wanted to,” says Lachie.
The decision to move from the existing rotary to a herringbone is a reversal of the traditional trend but Lachie says he opted for a herringbone because there is less to go wrong.
Vaughan Webber has been a Southland based dairy farmer for the past 20 years just outside of Edendale. Initially share milking a herd size of 600 cows before taking the step into the same farm’s ownership with a 300-cow herd in 2021.
Vaughan comments, “with the changes in environmental red tape the previous owner and I were keen to make the move to a wintering barn to allow milking 11 months of the year. Previously running a grass-based production system, we wanted to add grain to the herd’s diet as part of the production system migration. At the time we engaged a farm nutritionist to help us build the right solution with respect to wintering barn configuration, herd nutrition requirements and all supplementary equipment and machinery. Through this process our nutritionist put us on to the Keenan family of gear where we bought a MechFiber 400 mixer wagon and orbital muck spreader.”
“Since making the move we have seen a marked improvement in cow health, nutrition and production. Via the Keenan mixer wagon we can ensure an even balanced diet in every mouthful and a consistent distribution of feed and trace minerals across the herd. Where necessary we can also use the MechFiber software programme to tailor the blend ratios at different times of the year to the needs of the herd.”
With regards to the muck spreader, Vaughan says, “our unit has proven very robust and performs well. These units have since become very popular in our region and we find it ideal for spreading separated effluent and composted straw from our wintering barn.”
“The move to a wintering barn was a no brainer for us and the Keenan gear has played a key part in the overall success of this change and the ongoing farm development.”
first machine of
sized range to
designed
system.
duty sealed
and
working life.
The KEENAN Orbital Spreader is a versatile heavy duty spreader. It is capable of high work rates, trouble-free operation and can be used for farm or commercial waste.
the
of the New Zealand farming and
industry,
“WITH CHANGES IN ENVIRONMENTAL RED TAPE WE WERE KEEN TO MAKE THE MOVE TO A WINTERING BARN TO ALLOW MILKING 11 MONTHS OF THE YEAR”
“We sized the dairy to 30-aside, which equates to 10 or 12 rows. A new blank site was chosen in the centre of the farm which meant we needed to achieve complete development – fencing, race, tanker loop, shed, services etc.”
The build was originally set to start at the end of March 2020 with a first milking 12 weeks later on July 8. However, due to the Covid lockdown, the project started four weeks later on April 19, 2020, resulting in Lachie and contractors scrambling to make up for lost time.
The old rotary was still operational but there came a point when we had to decide whether we were going to have the new shed ready on July 8, given the four-week delay due to Covid,” says Lachie.
“We’d committed the vat to come over and once we moved that, the old rotary became unusable. We made the final call on
month before with the commitment by all contractors that they would work whatever hours were required to ensure I was milking on July 8. Achieving that meant we had to be very well orchestrated, right up to the last day.”
Builder Trevor Barfoot, of Barfoot Construction, was charged with not only building the shed, yards and pipe work and, with Atlas Quarries the race and tanker loop, Lachie saying he had to apply for essential worker status but also worked “all hours” at the site, to ensure they finished on time
“And two years on, Trevor comes back – at no charge – to attend to the little things that sometimes need attention after months of operation. I can’t speak highly enough of his dedication and commitment to his clients, and getting things done on time, and to
budget,” says Lachie.
Advance Dairy & Pump Whangarei, in close collaboration with DeLaval, supplied and installed the DeLaval ML2100 MidiLine swing arm system that ensures perfect alignment of the MC32 clusters and EP100 pulsators. The milk pump is a DeLaval FMP220 with a SEMA variable speed drive controller. Automatic cup removers and automatic drafting were not part of the initial set-up but can easily be retrofitted in future “Initially Alan Vaile from Advance Dairy & Pump Whangarei, looked after the installation,” says Lachie. “But Gary Blackwell picked up the reins and worked all hours to ensure the dairy was completed by July 8.”
All walls in the dairy – milking area, pit and auxillary rooms – were painted by Specialised Coatings, providing an attractive, easy-care, robust paint finish.
“The installation and set-up of the dairy
The interior of the dairy.
was critical, but knowing you will get reliable, prompt service going forward is equally as important. Advance Dairy & Pump is there when I need them – and that’s all I ask.”
After what Lachie admits was a “stressful time” the build was completed 12 weeks and three days after the site was surveyed, on July 8.
Two weeks before the planned first milking, Lachie – with around three people in attendance – walked the early-calvers through the unfinished dairy once a day to familiarise them with having to walk down the row versus what they were used to – stepping onto a rotary platform.
One year on, on June 1, 2021 – and in line with Lachie’s retirement plan – Will Burnell and Anna Reinhart started as 50/50 sharemilkers milking 400 cows.
The team: DeLaval’s Hamish Browne, Advance Dairy & Pump’s Trevor Hutchinson, DeLaval’s Alex van der Klip, farm owner Lachie McLean, Advance Dairy & Pump’s Gary Blackwell, and Monica Hutchinson. The DeLaval ML2100 MidiLine swing arm system features MC32 clusters and EP100 pulsators. The dairy’s uncluttered and open environment ensures good cow flow. Extensive plantings have been done at the entrance and around the new 30-aside herringbone dairy.A ‘state of the art’ dairy – the only one of its kind operating in Australasia – is the outcome but not the beginning.
Farmer Lorna Tantrum recalls that when she and her parents, Trevor and Avril Tantrum, began talking about building a new dairy on their 80 hectare farm in Kaiwaka, Northland, it would be a ‘basic herringbone’.
“But then we started talking with DeLaval and looking at some of the innovations they have developed which transform the whole milking experience – for humans and cows,” says Lorna.
“And it grew from there. Each innovation raised the potential – and in a cost-effective way – for an enhancement which, combined, future-proofed the dairy.”
So the ‘basic’ dairy soon morphed into a
herringbone that DeLaval district sales manager capital Alex van der Klip says is “the only one of its kind in Australasia”.
The new 30-aside dairy features a DeLaval ML3100 parlour with MSA30 Swing Arm units that combines Milking Point Controllers, automatic cup removers, Delpro Herd and Milking Management and iCar approved milk metering with blood and conductivity sensors.
The Evanza Clusters weigh “a mere 1.5kg” and feature clover ‘twist and turn’ cartridges in place of more traditional liners.
The C200 automatic cleaning system is spearheaded by candle jetters which, in contrast to ‘above head’ positioning, are located on a framing that sits under the recessed pit wall when the jetters are not in use – protecting them from knocks or soiling.
When required for cleaning, the framing
simply pulls into position so the clusters can easily and quickly be pushed down onto the candle jetters – saving shoulder strain, which Lorna says is a common side effect of pushing clusters onto overhead jetters.
The ID readers at each entry point identify the cows as they enter the dairy, and a threeway sort gate, preceded by automatic weigh scales, provides automated drafting as cows exit the dairy.
All information – from milking point, to weight and drafting – is recorded on the Delpro Herd and Milking Management system to provide the family with real-time, and historic, information on each cow’s health and production.
Lorna says the family chose not to include an automatic teat spray system because they believe that manually applying teat spray provides an opportunity to inspect each udder – affording early intervention in the case of
such things as mastitis.
The new dairy is a vast cry from the 46-year-old, ‘worn-out’ 24-aside herringbone it replaced.
“I remember milking in the old shed when I was around 12 years old,” says Lorna. “We milk 280 to 290 cows split-calving so the shed was in use every day of the year and never got a break – it was worn out.
“Being in use every day also limited our ability to radically upgrade the shed, so the best option was to build new,” says Lorna.
The decision was spurred on by Lorna’s parents, Trevor and Avril, who decided to step back from milking and hand the reins of the farm to Lorna. Trevor continues to manage the family’s 60ha runoff while Avril, a veterinarian by profession, looks after animal health.
Left: Trevor, Avril and Lorna Tantrum say the promise of their new dairy has more than delivered. The Tantrum’s beloved purebred Jerseys are very settled and producing well in the new dairy. The interior of the dairy is light and bright thanks to numerous polycarbonate panels in the roof. The old 24-aside herringbone served the family well.“The original shed was in a good position so we sited the new build in close proximity, near the calf house and existing services, and developed a new tanker loop,” says Lorna.
Planning for the new dairy started in 2021 in consultation with DeLaval and its local agent Advance Dairy & Pump, which has bases across Northland.
“Service is really important,” says Lorna. “So we worked closely with Advance Dairy & Pump’s Wellsford branch manager Anton Schedewy, who guided us through all the options.
“Initially, the goal was simply to replace the old dairy with something modern but the more we learned about the innovations DeLaval has developed, and how these promote production
and animal management, the more we realised that we could change the whole dynamic of milking – for me and anyone else who ever worked in the dairy.”
“We don’t envisage milking more than 290 cows so opted for a 30-aside, which equates to 10 rows per milking,” says Lorna.
Gibson Construction built the new dairy, including concrete and yards, with construction commencing shortly after Easter 2021. The roof includes numerous polycarbonate sections, creating a light and bright interior, and extends over the AB race, protecting it from the elements.
The layout of the dairy was tailored to
incorporate and enable the new technology. The pit, for example, is slightly wider than standard to accommodate the MSA30 Swing Arms, which are longer than traditional swing arms due to the technology they contain.
Rubber matting from Numat Industries is installed on the floor of the pit, providing cushioning and – according to Lorna: “saving everyone’s knees and hips”.
The ID readers at the start of each row identify the cows as they enter the milking platform. The entry gate closing behind the last cow is triggered by a microswitch which sends a signal to the Delpro Herd and Milking Management system to confirm the order of cows in the dairy.
As cows exit the milking area, they move through a longer-than-standard race that
combines weigh scales and three-way sort gate.
The milkroom design is also tailored to accommodate the DeLaval C200 automatic cleaning system.
The future-proofing goal for the new dairy is evident in the new larger food grade stainless steel vat with laser-welded base and side-wall refrigeration that was manufactured and installed by Dairy Technology Services.
The first milking in the new dairy took place in September 2021 at the end of calving. Lorna recalls they kept the old shed functional so they were able to calve and milk in that as the new shed was being built. “Once the new dairy was completed, we only had to transfer the refrigeration unit across.”
Lorna and her parents say the cows settled fairly well to the new environment. “We have a feedpad where we feed maize and PKE but the absence of in-shed feeding didn’t impinge on the cows quickly settling to the new environment, which is so open and inviting,” says Lorna.
Until that firstmilking, Lorna and her parents admit their confidence in the new technology was based on its specifications and promise –but as the first season nears an end they say that promise has been realised.
“Becoming familiar with the computer system was a learning curve but there are so many benefits – like when the farm advisor comes an I can go into the computer and see how many litres each cow is producing, see any variation in production and also monitor liveweight.
“We can also monitor the performance of our
heifers and compare the performance of each herd. What used to be time-consuming is now so easy,” says Lorna.
“The MSA30 Swing Arms are great, moving smoothly from one side of the dairy to the other, and ensure perfect alignment.
“The Evanza Clusters are fantastic, very light and easy to handle and the cartridges, in place of traditional shell liners, fit every teat no matter what size and last 5000 milkings; twice as long as shell liners.”
Lorna says you hold them differently to conventional clusters.
“For example, by the tube not the bowl, and vacuum starts as soon as you pick them up. If vacuum doesn’t start it’s because that cow should not be milked – for treatment, colostrum etcetera. This gives you great peace of mind, especially if you have distractions – like
children helping in the shed!
“The screen on the Milking Point Controller shows the cow number, milk flow, blood and conductivity and can also show trends for that cow over time.”
“The DeLaval C200 auto wash system is fantastic,” says Lorna. “I love that I no longer have to stretch up to apply clusters to overhead jetters. I can sleep as I no longer have shoulder pain! All I have to do is push the clusters down onto the candle jetters, push the start button on the wash system and leave it to the system that follows the wash programme preset by Advance Dairy & Pump.”
Lorna says there’s no bunching of cows when they leave the row due to the long lead-in to the weigh scales and sort gate.
“Sensors in the roof detect the cow is present; closing the gates behind her so the reader can scan her ear tag, register her weight and draft her according to directions preset either from the pit or mobile phone. Being able to accurately weigh and compare heifer and cow weight has a significant impact on animal health.
Cow flow is also much better in the new dairy. “All up, it takes no more than two hours to milk,” says Lorna.
The genesis of the Tantrum’s herd of purebred Jersey cows dates back to 1980, when they had to restock after losing their entire herd to brucellosis.
Trevor recalls the herd then averaged around 300kg/ms per cow with total farm production of around 36,000kg/ms. A focus on type, production, udders, temperament and longevity has enabled the current herd to achieve a per-cow average of 450kg/ms and total farm production of around 137,000kg/ms.
The first alert that a fire had broke out in Hamish Pearse’s Temuka dairy came from exploding marker spray cans. It was around 8pm on a still February night and the sound of the cans exploding – akin to gunshots – alerted Hamish’s milker who, on seeing the flames, rang him
“It was an electrical fire which started in the office. We alerted the local fire brigade and se about trying to contain the fire but the fire ha tripped the fuses to the yard-wash hoses – so by the time we worked out which fuses we could turn out, the fire had gone through the wall and into the dairy,” says Hamish.
“By the time the fire was extinguished the
office, milk and store rooms and the poly panel wall, which separated the service rooms from the dairy, were destroyed with the damage in the dairy extending to the wooden roof beams and all rubberware.
“It was devastating. At that time it was hard to see how we’d manage given we were still milking twice-a-day – but manage we did.”
Hamish’s father Jeffrey Pearse, and Jeffrey’s business partner Evan Agnew, built the 25-aside herringbone shed in 1990, two years later adding another 18-aside herringbone alongside it rather than extending the original pit, because they didn’t want to upset cow flow,
and milked through both sheds.
Hamish took over the farm in 2011 as a 50/50 sharemilker for his father and Evan, eventually buying out the latter. Today
Hamish and wife Zoe Pearse own the 200 hectare, 650 cow, farming 48 per cent and 52 per cent respectively with Hamish’s father.
With the shed destroyed by fire and unable t be used, Hamish turned to his neighbours and milked in their rotary dairy for four or five days
“While we were milking next door our local engineers worked frantically to patch the fire ravaged shed to a stage where we could resume milking in the 18-aside.
“It looked terrible, but we were able to bring the cows home and continue milking once-aday until they were dried off on May 28.”
Hamish says once he’d gotten over the shock of the fire, he began planning a rebuild
“It was a chance to rethink the layout and efficiency of the shed. There were some aspects we wanted to retain – like the 18-aside –because repurposed, it would provide a large, covered animal handling facility.
“The old set-up had a square collection yard with no backing gate and we had virtually no technology – so rebuilding gave us an opportunity to modernise and automate the dairy for the future.
“And we wanted to extend the pit of the 25-aside to 41-aside herringbone.”
The rebuild started May 10 with the cows milked through the 18-aside until they had dried off.
A photo-board is a reminder of the devastation to the Pearse dairy.
One year on, Hamish Pearse says ‘his worst nightmare’ has turned out to be a blessing.View from the dairy – the Southern Alps. The AB facility, previously an 18-aside herringbone, to the left; and the extended 41-aside herringbone to the right.
The footprint of the new dairy would be larger than the original with a new office, milk and pump rooms, so Blake Downie Contracting was called in to develop the site.
“We were able to do most of the demolition and yard work ourselves. I’m lucky to have multi-skilled family, mates and staff,” says Hamish.
“My 2IC, Rolly Degamo, is a highly skilled engineer so we were able to do 85 per cent of the engineering – yards, gates etcetera and my father and a mate were down here every day doing the concrete.
“The steel framing for the roof of both dairies was still sound so we stripped the roofing iron and, where possible, repurposed it for things like hay feeders,” says Hamish.
“Converting the 18-aside herringbone to an AB area required the pit to be filled and raised to provide the optimum height/position for AI or pregnancy scanning.
“We changed the configuration of the collection yard, extending its size and adding a backing gate, and then topped all the original yards – which were still in relatively good condition – with 100mm of concrete.”
In terms of technology, Hamish elected to go with a GEA iEXPRESS herringbone dairy designed specifically for herds from 100 to 700 cows. The system can be customised to suit, it is cost effective and enables high throughput. Hamish says the iNTELARM guides the clusters from side-to-side, ensuring perfect alignment while creating space in the pit.
The dairy features iCR+ automatic cup removers that feature EasyStart lift or pull vacuum activation, which speeds cupping by one to two seconds per cow, and the GEA Autopuls pulsation system. The dairy is also
equipped with a GEA iNTELWASH automatic wash system.
A Protrack automated drafting gate from Allflex/MSD Animal Health Intelligence was installed. The gate is powered by easy-to-use software that enables drafts to be set ahead of time via smartphone or farm PC or during milking. The drafting gate integrates with Allflex collars, Protrack SCC, Milk and ID.
The floor of the pit is lined with NumatAGRI DuoMat herringbone pit matting providing milkers with a non-slip cushioned surface which adds milker comfort and safety.
The first milking in the new dairy took plac on 28 July – just seven weeks after the rebuild started.
Looking back, Hamish admits that what appeared to be a disaster has turned into a positive.
“The rebuilt dairy is 100 times better than it was before. At the time, the fire was ‘your worst nightmare’ but in hindsight it was a blessing because we were forced to rebuild – and we used that opportunity to build a dairy which is modern and efficient with a high level of technology, which makes milking and animal handling a breeze.
Hamish says insurance only partly contributed to the cost of redevelopment – the rest was an investment in the future.
“Until the cowshed burnt down I was milking every morning but now I only milk when I’m needed. I retained all my staff and they really enjoy milking in the new environment. It’s a one man-shed but we have two people milking – the second person getting the next herd in.”
Now – the rebuilt dairy. Yard redesign allowed the installation of a Protrack automated drafting gate. The farm’s 2IC Rolly Degamo is an engineer whose skills enabled Hamish Pearse and team to complete around 85 per cent of all engineering. The spacious new milk room. The floor of the pit is lined with NumatAGRI DuoMat herringbone pit matting. A zigzag rail in the dairy limits the cows in each row to 41.The design of rotary dairies has evolved over the years since they were first invented by a Taranaki dairy farmer in the 1960s.
While the principal of a circular platform –where cows are milked as they make generally one rotation – remains, time and experience has generated a raft of enhancements to improve their performance.
Johnny and Deidre Ussher are 50/50 sharemilkers on the family farm at Culverden, milking 1100 cows through a 60-bail rotary. The shed was built in 1984; Johnny says at the time it was the biggest in New Zealand.
The dairy has worked hard over the years, the
outer structure is still sound but the milking system had long since outlived its efficiency
“The original milking plant was modified over the years to keep it working but, as technology evolved, it became more and more difficult to get parts which didn’t need a huge amount of customisation,” says Johnny.
“We could have carried on with the old plant but if we had a breakdown during the season and there wasn’t a part, we would be in trouble.”
Johnny says the structure of the shed and the original concrete platform were still strong. “We knew it was big enough because there wasn’t an issue with milking times. It was more about updating the milking plant with something which was more modern, efficient and easy to use – and which would
futureproof the shed for the future.”
But the design of those early platforms compromised the Ussher’s ability to do that. “Where today the floorin the centre of the dairy is lower than the outside – where the milkers stand – when this dairy was built the entire floo of the dairy was on one level,” says Johnny.
“The centre-gland was positioned in a rectangular section at the centre of the dairy, lower than the rest of the floor. There was minimal space beneath the platform to install new technology – and this was the challenge we took to Morrison Agri who have serviced, and know, the dairy well.”
Morrison Agri is an authorised dealer for Waikato Milking Systems in Canterbury and North Otago, says Rob Morris, who recalls the issues Johnny had presented them with over the years to keep the dairy running efficiently
“Dairy upgrades are a big part of our business, from platform repairs through to I-beams, wear-strips and rollers replacement.
“We are used to pulling the stops out and improvising to solve the challenges our farmers present to us,” says Rob. “Johnny’s milking system was worn out – numerous modifications had been done over the years but the time had come for upgrading – and because of the design of the shed, this called for ingenuity and customisation.
Before – the old system had four lines falling into the pit and one through the centre-gland and receiving can.
Stable vacuum, from the larger milk lines, means better udder health because the cows are now milking out evenly.
After – the new centregland with larger 4 inch milk lines.
Morrison Agri adopts this approach to all the work they do. “Improvisation and customisation is our speciality,” says Rob.
“Everything above the platform was relatively modern and efficient– new Waikato Milking Systems Cow Restraints, Smart ECR Cup Removers and 320 claws had been retrofitted six years ago.
“Our focus was on upgrading the milking machine under the platform and centre gland…a SmartDRIVE Variable Speed Drive and blower pump had also been installed in recent times,” says Rob.
This called for a complete new milking plant – milk pumps, centre gland, receiving cans, milk lines, wash system. “The platform running gear also needed to be upgraded with new rollers and wear-strip.”
Rob says the original dairy system had four lines falling into the pit through the
centre-gland and into receiving can and then pumped away from the centre of the shed. “We wanted to change that so the milk fell into the milk cans, which would be repositioned under the platform – from there it would be pumped through the centre-gland and then out to the vat.”
Rob says the lack of clearance between the floor of the dairy and the platform presented a real challenge when it came to upgrading the deck’s running gear and installing new receiving cans under the platform where they would be out of the way and protected.
“Installing the new wear-strip and rollers required the Morrison Agri team lying in tight spaces due to the lack of clearance between the deck and the plinth,” says Rob.
“Upgrading the milklines and receiving cans also called for ingenuity because the optimum fall for a milkline is 1.2 per cent to 1.5 per
cent and the set-up of the shed meant there wasn’t enough capacity to achieve that – so we installed two receiving cans under the deck to achieve this.
“The capacity of the milk loop-line was increased to promote better flow from 2.5 inches to 4 inches, which in turn provided better vacuum stability at the cluster.”
Rob says a new centre-gland was also installed, which allowed his team to reposition the Smart ECR controller from the centre of the platform to the milkroom, making it easier for Johnny to adjust as needed.
Despite the challenges of working in confined spaces retrofitting technologie which had been tailor-made for the Ussher dairy, the work was completed in June 2021.
Johnny says the synergy between the Morrison Agri and Waikato Milking Systems teams was fundamental to getting
all the customised equipment on-site when needed so it could be installed.
“Considering the alternatives, it was a cost-effective exercise which has transformed the efficiency of the dairy,” says Johnny
“Our farm team of four are enjoying the reassurance of milking in a dairy which is automated – which works without the threat of breakdown we had before.
“We used to get a bit of slipping of the clusters but now, with the bigger milk line, that’s a thing of the past. The vacuum at the cluster is stable and the cows are milking out evenly and this contributes to improved udder health.”
Johnny’s team used to manually clean the plant before so the new automatic wash system has transformed that part of milking, enabling the team to get on with other things.
“We’re really pleased.”
Proud to support Pahau Dairy Farms Ltd The preferred milking systems partner for Dairy Farmers 577 Morrison Agri increased the size of the milk line and installed two receiving cans under the deck where they are protected. Morrison Agri’s Rob Morris, Johnny Ussher and Waikato Milking Systems’ Garry Ballantyne.The decision whether to renovate or build new came down to the figures for Canterbury farmers Graham and Adele Wells.
“The rotary dairy on our farm at Dunsandel was originally built about 30 years ago. The building was still sound but the internals had done their time and we were having to spend a lot of money to keep the shed going,” says Graham.
A detailed review of the existing plant confirmed that the bails needed to be replaced.
“While the existing bails were in good order, their design could not easily be adapted to take automatic cup removers without impeding cow entry and exit from the bails,” says Graham.
The entire milking system also needed to be replaced and preferably upgraded with automatic cup removers, so they looked at the options.
“From a cost perspective, upgrading everything above and below the existing
platform would cost around one-fifth of what it would cost to build new.
“Those figures really sharpened our focus and led to us deciding to upgrade everything other than the platform and building,” says Graham.
“In essence, we decided to retain the existing number of bails – 40 – adding new bails and automatic cup removers; and, on the underside of the platform, installing new wash and milk lines and new pulsators along with new platform rollers, bearings and wear-strip.”
Graham and Adele have owned the 206 effective hectare farm, milking 800 cows, for 18 years. Graham says the farm was 180 hectares when they bought it, so the demands on the existing 40 bail rotary have increased over the years as the acreage and herd numbers have increased.
“We had GEA in the old shed and wanted
to continue with them, especially given their bails complemented their automatic cup removers and clusters.”
Conversations with local GEA service partner, Stocker Solutions, began mid-2020 with Graham saying the overall driver for the upgrade was to modernise the dairy to make it more efficient and to create a goo working environment.
“We looked at the bail structure and even considered putting a new platform in but finall settled on new bails on the existing platform.
“The design of the new bails was quite different to the old and we needed to ensure the new bails would fit and woul not impinge on the room each cow had. Stocker Solutions resolved this concern by mocking-up one bail so we could actually
experience the difference they would make – that gave us confidence to proceed.
Graham project-managed the upgrade, planning to start demolition of the old plant on June 1, 2021, and have the revamped shed ready six weeks later on July 17, 2021.
“We were able to achieve that thanks to Stocker Solutions, which organised for all the GEA equipment to be shipped down and on-site by the time we started the dismantle.”
The first task was to dismantle the existing gear, clearing the way for the upgrade. Graham, supported by his farm team, got in and stripped the inside of the dairy, removing the bails and milking plant.
“We then sand-blasted and painted the steel deck and got NumatAGRI in to install rubber matting around the entire platform to provide an anti-slip surface which is comfortable for the cows, aiding relaxation, and also protects the deck.”
Clare BaylyThe dairy’s interior, showing the new bails, iCR+ Intelligent cluster removers, CRS cow restraints and iPUD in-bail teat spray.
Herd manager Rakesh Kumar says the new bails and milking system have transformed the dairy.
The underside of the dairy was upgraded with a new centre gland, and, on the underside of the platform, new rollers, bearings and wear-strip.
NumatAGRI’s marketing manager Jon Coursey says the vulcanized rubber Kura matting is imported from Germany and precision cut in New Zealand.
“It is made from recycled car and aircraft tyres, is 24 millimetres thick and warranted for 10 years and should last for more than 20 years. The mats used to have a straight cut between bails but, to provide an almost seamless covering of the deck, we now precision cut them with a waterjet.”
Once the upgrade and resurfacing of the platform was completed, Graham oversaw the welding and installation of the new customised GEA Iflow Gen2 bails designed to incorporate the automatic cup removers and jetters. The design of the new bails means the Friesian/ Friesian-cross cows have more room than they
had in the original bails and, according to Graham, really modernised the whole shed.
“The GEA bail hoops are angled to the ground so the cow doesn’t have to lift her head up high as she backs off and clears her hocks. They are robust and the design really protects the jetters.
“At the same time we were installing the bails, the platform’s bearings, rollers and wear-strip were being replaced,” says Graham.
The team from Stocker Solutions installed a new centre gland in the middle of the dairy along with the new milking plant which included automatic cup removers, cow restraints and in-bail teat spray.
Shane Stocker says the iCR+ Intelligent Cluster Removers, iCRS Cow Restraint System
and iPUD in-bail automatic teat sprayers combine optimum efficiency with animal health and welfare, ensuring every cow is milked out evenly and consistently with every udder receiving even application of teat spray.
“The original clusters were in good condition so these were retained and we installed new pulsators whose precise electronics deliver a perfectly controlled pulse to the cluster.
“New milk and wash lines were installed under the platform along with new vacuum and wash pumps.”
A Protrack monitor, with herd records, has been installed at cups-on, the plan being to retrofit a drafting gate from Allflex/MS Animal Health Intelligence at a future date.
Herd manager Rakesh Kumar has just finished his first season milking in th revamped dairy and says the new bails have transformed the look and function of the dairy.
“Before we needed two people in the shed but now one person can run the shed with automatic cup removers. Having the Protrack monitor with herd records at cups-on, even without the drafting gate, means an audible alert sounds when a cow needs to be drafted, enabling a higher degree of accuracy with cow ID.
“The new wash lines and wash system, preset by Stocker Solutions, have had a marked improvement on animal health, the cows are clearly more comfortable in the new bails and the quiet operation of the plant has generated a really good milking environment,” says Rakesh.
Looking back, Graham and Adele say renovation was the right choice. “We’ve got a modern, efficient dairy for a fraction of the cost of a new build.”
Milking a smaller herd in a bigger shed makes for happy campers on a South Taranaki dairy farm.
“It saves three hours a day in milking time,” says Allister Simson, who runs 540 cows on 200 hectares at Patea.
The Kaharoa Rd property once milked 630 cows in a 40-bail rotary, now replaced by a 60-bail Waikato Milking Systems’ Centrus composite rotary milking system.
Allister says there was also 100ha of drystock land involved in the operation, connected to the dairy unit but self-contained.
The old milking shed was built in 1982 and he says the platform was getting to the end of its life.
This meant that not a lot was brought over to the new greenfield site. Existing water and effluent systems have however, been incorporated in the latest incarnation.
Allister says the two-pond effluent disposal facility feeds int a travelling irrigation system. A new transformer was needed to tap into the power supply reaching a house on the property.
The updated system includes a SmartWASH auto plant
wash system and ECR-Plus automatic cup removers which control the cow retention straps, and the SmartSpray automatic individual in-bail teat spray system, courtesy of Waikato Milking Systems.
Mark Ward, monitoring and automation sales specialist with Allflex/MSD Animal Health Intelligence, says the Simson dairy shed is equipped with Protack Vantage.
This system includes Protrack Draft, an automated three-way drafting gate which Mark says takes the hassle out of drafting. At the heart of this technology in the rotary shed is Protrack ID.
Mark says this is an accurate milking shed ID system, utilising HDX eartags, and is a fully integrated Protrack module. “This system uses both audible and/or visual alerts to indicate ante any problems.”
Mark says it also features full MINDA integration including dynamic groups in the shed.
Waikato Milking Systems provided a wide array of technology and equipment for the Simson shed. This included a platform
positioning system, which attaches to the central gland.
Waikato Milking Systems’ lower North Island regional manager Ben Frederickson says this provides accurate platform positioning via QR codes for each bail, which tells the ECRPlus cup removers things like where the bridge is located. “If a set of cups comes off while the cow is in front of the bridge, she will be held to ensure she is teat-sprayed and also to not cause disruption to cows entering the platform.”
Ben says the ECR-Plus cup removers feature ‘plug and play’ capabilities through the Bail Marshal. “This allows the automation to be future-proofed, where Allister can simply plug in milk measuring technology such as electronic milk meters, yield indicators and SmartD-TECT pulsators, at any stage.”
In the plant room, Waikato Milking Systems supplied the vacuum pump, plate cooler, wash tub and SmartWASH auto plant-wash system. All the milking plant and associated technology was installed by Hawera-based Hunt Farm Services. The platform was manufactured by Waikato Milking Systems in Hamilton and installed on-site by Moa Rotary Platforms.
Allister Simson with sharemilkers Dean and Jessica Sorensen, and farm assistant Dylan McCutcheon. Hunts Farm Services’ foreman Daniel Lorde checking out the clusters. Above: The Protrack gate was installed by McCarty & Hunger.Allister Simson says that, if he grazed young stock off, the yard has a capacity for 640-650 cows. Steve Edwards FARM SERVICES 2014 LTDMoa’s Inglewood branch manager Matt Churchill says the deck sections of the Centrus are formed in a multi-layer laminated process.
“The result is a deck which is 75 per cent lighter and far more durable than traditional concrete or steel alternatives,” says Matt. “It also has a multi-roller system, which increases durability by distributing platform weight more evenly.”
DeLaval supplied the shed hygiene chemicals and wash routine. “We also transferred the DeLaval milk filter across frm the old dairy, and filter socks,” says Allister Simson
Chris Perrett, from Hawera-based Chris Perrett Electrical Solutions, says they provided “the glue to hold it all together”. This started with a new power supply, from the road, including a transformer and back-up generator.
Working in with the builders, Chris says ducting was put in under the concrete base of the shed for cabling relating to the platform and milking plant. This included the electrical work associated with the Protrack automatic identification
drafting system supplied by Waikato Milking Systems, which is interlinked with the shed radio.
Chris Perrett Electrical Solutions also installed LED lighting over the platform. “This has low consumption and is cost-effective to run,” says Chris. This includes a bird-proof cover, which he “made up”. He also carried out all electrical requirements in the vacuum and plant rooms, including a new switchboard.
Chris Perrett Electrical Solutions wired in the wash-down system provided by Waikato Milking Systems, and the water heaters and cooler pumps, and vat chillers.
The Protrack gate was installed by McCarty & Hunger from Patea. Owner John Hunger says the fourth-generation company, which started business in 1878, used two other backing gates from the old shed which they extended for the new yard.
Their work included all the railing and gates around the yard, for internal pens, at the entranceway and loading race.
Allister Simson says that, if he grazed young stock off, the yard has a capacity for 640-650 cows.
Looking after the herd is obviously top priority, and Allister says he’s used a Race Wrangler cattle crush for hoof-care for the last 15 years.
“It is mainly used for feet care and the occasional calving. Feetcare was done on the old rotary platform and once the Wrangler was installed the trimming of feet became a much safer job and the cows are also easier to manage.” Allister says cows walk in the gate and are secured with belly straps, with the offending hoof winched up in readiness for treatment.
Painting, inside and out, was completed by Surfatex. Director Glen Sinclair says interior concrete block-work around the platform, floor to ceiling, were coated with the company’s specialist product Acraflex dairy wall coating system. “This no only looks great, but is easy to clean and maintain.” His team also painted the plant-room, milk-room, staffroom and toilets with Acraflex
Exterior painting was completed by Allister Simson. “The client wanted to use light colours throughout,” says Glen.
An ex-builder, Allister Simson says he liked the idea of exposed, stained, rafters in the shed design, plus good lighting and ventilation.Allflex supplied Protrack Draft, an automated three-way drafting gate. Waikato Milking Systems provided the central control panel, bail marshalls, receiving vats, clusters and cup removers, along with teat wash and teat spray systems. Painting, inside and out, was completed by Surfatex. Acraflex Dairy Wall Coating Systems
Another chapter has been written in the 70-year history of a South Taranaki farming family.
Steve and Maria Poole’s new 54-bail rotary at Manaia is the latest addition to an operation started in the area by Steve’s father, John, now aged 91.
It all started with a sheep farm on nearby Skeet Rd, with Steve Poole sharemilking on a second property owned by his father.
Steve and Maria Poole bought the 250ha Manaia Rd property seven years ago in an equity partnership with his brother, Rob, who later sold his share.
The original block was 170ha, but Steve says another 80ha was added from a farm “over the back”.
An existing 34-herringbone shed milked 500 cows. The 54-bail one-man rotary milks 750 Friesian-cross cows. The herd is split into two and milked one after the other.
Steve Poole says the old shed was 50-100m from the road and the new one about 900m away, so it’s in a central position taking into account the extra block. A former paddock required some building up at the base to allow for fall to associated effluent ponds
Bunn Earthmoving extended the existing tanker track and created a new loop, with 600700m of new races developed.
The Stratford-based company also created the new 40m x 40m x 40m effluent pond, linked to a travelling irrigation system.
A new transformer was added, with the shed power supply coming from existing lines on the road verge.
A new water piping system was also required.
“The octagonal shape of the shed means there is no wasted space,” says Steve Poole.
Ventilation and lighting are key aspects, with a double underpass beneath the platform a
further feature of the design.
The Manaia Rd operation has a rectangular yard and neighbouring feed-pad. Steve Poole says the associated floodwash system uses recirculated greenwater.
Michael Bloeman Engineering, from nearby Kaponga, came on board with one of its specialist backing gates. The High Runner is self-aligning, making for smooth cow flow,with automatic wash programmes.
A self-confessed ‘ideas man’, Michael came up with the concept about 18 years ago. The backing gate, which Michael says minimises human error and automatically responds to the herd, is operated by a control panel in the milking shed.
Michael says the patented design ‘which just came out of my head’ was built in the company workshop and assembled on-site.
It was installed on the Poole property
by Preston Engineering when the fellow Kaponga-based company was tackling rails and gates surrounding the yard and feed-pad. Preston Engineering director Gary Preston says 98 lengths (1.5m) of 25mm pipe were used in the project.
Builders Fabish & Jackson, from Inglewood, put in the required poles. Director Steve Fabish says the octagonal design was nothing new to the company. “We designed the firs one 42 years ago,” says Steve Fabish. “In those days they had timber poles. It was a 17-bail rotary.”
Steve Fabish says the concept remains the same today however. With an octagon, there is no wasted space in the shed. Laminated timber beams were pre-cut and concrete wall panels manufactured off-site at the company factory, says Steve Fabish. “It’s basically a big kitset which we assembled on the farm.”
The roof is Colorsteel, with the design including aluminum windows. Steve Fabish says the colour scheme – in this case Greyfriars – is ‘whatever the client wants’.
After considerable earthworks were completed, Fabish & Jackson set about laying the concrete required for the platform, yard and feedpad. “It was one of our standard sheds,” says Steve Fabish. “They do look nice on the land.”
The heart of the operation - the platform - was supplied by Waikato Milking Systems and installed by Moa Rotary Platforms.
Matt Churchill, branch manager for Moa Rotary Platforms in Inglewood, says the milking platform features a multi-roller undercarriage, with twin-track running gear. The platform came as a kitset from Waikato Milking Systems in Hamilton and was put together on site by Moa Rotary Platforms. The 54-bail platform has a regular concrete deck, says Matt.
Waikato Milking Systems’ regional sales manager for lower North Island, Ben Frederickson, says Elite Farm Solutions then
came in and installed milking equipment supplied by WMS – including the central gland, milk lines, receiving cans, clusters, cup removers and jetters.
Based in Opunake, Elite Farm Solutions also installed effluent pumps on the Poole property
Waikato Milking Systems also supplied the in-bail and bailexit teat-spray system, along with the cup-wash and two platform controls. In the plantroom WMS provided the plate cooler, milk filter and wash-tub, along with a vacuum pump i a separate room.
All electrical work was undertaken by Hawera-based Mark Frost Electrical. “Current requirements for effluent and milk cooling meant we needed the owners to be very forwardthinking in the way they wanted to run the new shed,” says Mark Frost. “We worked closely with Steve Poole to look at all options and controls for interconnection and load reduction.
“He made the decision to increase the supply above the traditional standard and use a variable-speed chiller and snap chill
system, as well as interconnecting effluent systems,” says Mark Finishing touches were added by specialist dairy shed painting company Surfatex. Director Glen Sinclair says the interior of concrete wall panels around the platform were prepared, primed and coated with the company’s cornerstone Acraflex dairy wall coating system. “It’s easy to wash and keep clean.”
Glen says the Foxton-based company worked closely with Fabish & Jackson on this project and has been involved in a number of octagonal sheds over the years.
Surfatex also painted the interior of the shed office, plant-rom and milk-room staffroom and toilets – with both the latter also receiving a coat of Acraflex. An industrial coating was used on the chemical room floor. Regular exterior paint was used on the outside of the building, says Glen. “The client wanted to use light colours throughout.”
Steve Poole says the cows adapted quickly to the new shed, which is well and truly living up to his expectations. “It’s exactly what I pictured.”
The Manaia Rd operation has a rectangular yard and neighbouring feedpad. Waikato Milking Systems’ Ben Frederickson beside the central gland inside the rotary platform. Preston Engineering’s Gary Preston with some of the 98 lengths (1.5m) of 25mm pipe used in the project. Michael Bloeman’s engineering business came on board with its specialist High Runner backing gate. Contract milker Mark Ahern with farm owner Steve Poole.Chislehurst Farms in Bell Block, Taranaki, has been owned by three generations of the Slater Family. The original 50 acres was purchased by Andrew Slater’s grandparents –Leonard and Myra Slater – in 1944. Back then the herd was milked in a wooden walkthrough shed, where they used milk cans and a horse and dray.
Leonard and Myra’s son Don, and his wife Ailsa went off-farm for a couple of years to go sharemilking after they married and then returned in 1966 to carry on working the family farm.
Some neighbouring properties were purchased over the years to allow the increase in cow numbers. When Don’s father died suddenly in 1970, Don and Ailsa took over ownership of the farm.
Don and Ailsa also own a thriving cymbidium orchid orchard across the road from the dairy farm. Don, who is now in his 76th season on the farm, says their new shed is the cream of the crop.
“When we built the new herringbone shed, we thought that was the greatest – but this new shed is unreal.
“Technology has been forced upon the industry and we just have to accept it if we
want to make progress.”
Don explained that back in the day when he was farming it was a simple life but very physically demanding. “We are now in a different era with very different systems; compliances are causing a lot of issues now in the industry. Whilst they were the good old days, I wouldn’t go back,” says Don.
“The inputs may be higher now, but the bottom line is better too.”
The farm has gone from 50 acres back in 1944 to a little more than 200 hectares now.
There is a long tradition of rugby in the Slater family. Andrew was an icon of Taranaki rugby throughout the 1990s, first making his debu
as a 19-year-old in 1989. By the time of his retirement at the end of 2001, Andrew had become the third most-capped Taranaki player ever. Brother Gordon also made his debut for the All Blacks in 1997. After having played in 182 matches for Taranaki and with nearly 220 firs class games, Andrew bowed out of top rugby at the end of the 2002 season. However, his son Bradley is carrying on the tradition by playing for the Chiefs.
The farm has two herds of cows: a crossbred herd and a Jersey herd.
Andrew says he has a soft spot for the Jersey cows, which have been on farm for as long as he can remember.
This new shed is their first rotary, and Andrew is impressed with the fact that having come from the herringbone to the rotary means only one milker is required in the shed plus one hour has been deducted from milking times, freeing up time for himself and his staff.
Andrew is also finding the technology of the new shed really exciting. He loves the new NaviGATE drafting gate from Waikato Milking Systems.
Denis Wheeler from Denis Wheeler
Earthmoving is an ex-dairy farmer, so is fully in tune with the time restraints of dairy farming and he understands the urgency of getting the job done when it needs to be done and getting it done on time.
Working under the builder’s instructions to
get the system in place involved Denis working around milking times in the old shed while excavating the site for the new shed, which is right next to the old dairy.
Denis has a large range of machinery and used different machinery for different jobs at Chislehurst Farms.
Denis did all the site preparation for the new shed, he excavated the hole for the platform which was under-roof at the time, constructed the tanker track and entranceway, and also brought in his telehandler to lift all the precast tilt panels and put in place for the walls of the new dairy shed.
Brian Hill Builders from Okato constructed the new dairy shed for Chislehurst Farms. The new shed constructed for the 54-bail
The Ekochute is set up in the old herringbone area, which is now used as an entry lane to the new yards for the cows.
rotary shed is a light and airy dairy parlour and has oodles of room to move about in.
The shed is light and airy with plenty of room around the perimeter.
Surfatex’s sevencoat Acraflex painted walls make cleaning a breeze.
The new shed consists of the usual array of rooms such as a chemical room, vet area with vet drop-down platform, machinery room and the office/staff room.
Brian Hill met with Andrew to work out exactly what he wanted in his new build and then proceeded to get the designs done and submitted to council for approval.
“This build is slightly different to other builds of mine, in that Andrew has utilised the old herringbone shed as one of his entries to the yard,” says Brian.
“He has also retained his existing vat stand. It took a bit of juggling but worked out really well.”
The bottom half of the build has been
constructed from tilt panels with the upper half constructed from poly panel. Plus, clear panelling in the roof allows plenty of light in.
One of the more notable designs in the shed is the underpass to the centre of the rotary platform, which has an outside entry and gives ease of access for herd testing and saves the technicians entering through the shed at busy times.
Brian says that in all new shed builds his team now install an extra line for future technology.
“With new builds now lasting for an average of 50 years, and technology constantly evolving, it is important to have the means to allow for that new technology in the future.”
Brian is a long-standing trade customer of Mitre 10 New Plymouth, and the Chislehurst Farm build was a stand-out due to the sheer size of the building and the amount of steel and concrete involved. Timber machined for bird-proofing around the edges of the building was supplied to Brian as well as the LVL beams, including aluminium fencing for the outdoor underpass to keep it safe from children being able to enter.
All shed pipework, gates, backing gates with scrapers and portals were constructed and installed by Coastal Welders. Owner Andrew Wood says they built everything around Waikato Milking System’s NaviGATE system. Circular pens for good cow-flow were a must. Andrew supervised all the concrete work to ensure posts were placed in correct positions,
and to ensure all heights, falls and drainage were in the right place.
The Acraflex paintwork in the new shed was applied by Surfatex 2019 Ltd.
Foreman Shane Angland, who was working ‘back in the day’ with Surfatex’s original owner Frits van Echten, has continued in his role with new owner Glen Sinclair. Shane says the application is the same with all sheds –they coat using the seven-coat system. “The blockwork is prepared by polishing it with a grinder to eliminate any sharp edges on the blocks, which is followed by the acid wash water blasting. After the drying and masking process the blockwork is applied with a two-pot
epoxy to seal the concrete, followed by the first coat of Acraflex.
“The first coat of Acraflex is thinned dow and used as a priming coat to fill any holes. A second coat of Acraflex is then applied – and once this has dried, a third thicker coat of the Acraflex is applied. This is allowed to dry and then two coats of fleck are applied.”
Shane says the fleck breaks up the glarin white colour of the Acraflex. “Last bu not least is the glaze, which melds it all together and provides a high quality, durable, attractive, easy-to-clean surface that is ideally suited to the harsh-working conditions found in a dairy environment.”
As well as being used extensively throughout the dairy industry, Acraflex is also used in apiaries, viticulture, meat processing plants
and washrooms – in fact, anywhere in which a clean, hygienic, and hard-wearing environment is essential. Acraflex is acid and alkali resistant, and dirt and grime are easily washed away without the use of high-pressure cleaners and time-consuming physical methods, with its non-slip and easy-to-clean surface.
A new Waikato Milking Systems 54-bail Orbit concrete rotary platform with multiroller undercarriage was installed by Moa Milking & Pumping from Inglewood. The twin-track system uses two I-Beams and a set of industrial-grade nylon polymer rollers contained within a unique fixed carriage to ensure correct alignment.
Liz Voorend
P 027 755 6501
Page 30 Coast & CountryCHISLEHURST FARMS Liz Voorend
farmsafety@wfss.co.nz workablefarmsafety.co.nz
Liz Voorend
P 027 755 6501
Liz Voorend
027 755 6501
Liz Voorend
farmsafety@wfss.co.nz workablefarmsafety.co.nz
027 755 6501
farmsafety@wfss.co.nz workablefarmsafety.co.nz
farmsafety@wfss.co.nz workablefarmsafety.co.nz
The ONLY Health & Safety company that:
The ONLY Health & Safety company that:
The ONLY Health & Safety company that:
Brings the farm up to compliance standard
The ONLY Health & Safety company that:
The ONLY Health & Safety company that:
Brings the farm up to compliance standard
Brings the farm up to compliance standard
Organises hazardous substances, safety data sheets, inventory and plan
Brings the farm up to compliance standard Organises hazardous substances, safety data sheets, inventory and plan
Brings the farm up to compliance standard
Organises hazardous substances, safety data sheets, inventory and plan
hazardous substances,
Provide easy to use templates
Organises hazardous substances, safety data sheets, inventory and plan
Provide easy to use templates
Provide easy to use templates
Provide on the farm follow-up services
Provide easy to use templates
Provide on the farm follow-up services
Provide on the farm follow-up services
Provide on the farm follow-up services
NO MEMBERSHIP FEES!
NO MEMBERSHIP FEES!
NO MEMBERSHIP FEES!
NO MEMBERSHIP FEES!
Brian Hill of Brian Hill Builders, Waikato Milking Systems regional manager of sales & service Ben Frederickson and Moa Milking & Pumping’s director Nathan Hitchcock check out the new milk cans. Moa Milking & Pumping’s director Nathan Hitchcock explains the use of the Bail Marshall. The new shed with the PPP feed silos to the right. Electric L 2005 Ltd’s director Kerry Larsen Director checking out one of the electric meters.The fact that the nylon rollers move with the platform mean they do not require fixed housed bearings, which eliminates the need for continuous greasing and oiling, and this keeps the centre-pit clean and tidy. The outer edge of the milking platform is fitted with a stainless-steel drip ring where there is a gap between the platform edge and the drip ring, allowing water run-off from the platform to fall between the gap rather than running directly onto the milker.
Moa Milking & Pumping director Nathan Hitchcock says the Slater family’s new shed includes Waikato Milking System’s complete range of Smart technology, which starts with ECR Plus cup removers with Bail Marshals, which allows ‘plug and play’ capabilities so any automation can be easily added at any time in the future. Andrew is currently running
SmartD-TECT mastitis detection, Yield Indicators and the NaviGATE Premium 3-way drafting and herd management system.
The inclusion of CowTRAQ collars for keeping track of the herd assists with heat detection, health event monitoring and rumination. The Smart technology and the CowTRAQ collars communicate with the DairyHQ software to unify the system to give ‘real time’ monitoring of each cow that walks on the platform, as well as milking machine monitoring for each bail to maximise herd performance and farm efficiency.
The plant has a SmartWASH Automatic Wash System, and the rotary gland is fitted with a Wash Gland accessory. This allows lines
that carry wash water, teat spray solution or compressed air to move with the platform. The inclusion of a Wash Gland meant that Moa could supply the Slaters with an automatic teat spray mixer, which Andrew really liked the idea of. This automation eliminates the need to manually mix teat spray and fill a reservoir in the centre.
“By purchasing a Waikato system you won’t be required to maintain as much as another plant,” says Nathan.
“Maintenance is so easy, and we have a 10-year maintenance plan and only need to do an annual service on the system; the farmer maintains the rubberware.”
In year 10 the pulsators and centre gland get checked over.
Waikato Milking Systems’ regional manager of sales & service Ben Frederickson says the Yield
Indicators measure each cow’s milk volume, which goes back to the herd management system. “If there is a sudden or consistent drop in volume, then that indicates an alert to the farmer to make the decision to either feed more or dry off.”
Kerry Larsen’s team from Electric L 2005 Ltd did all the electrical work for this project. Kerry says all the conduit and ducting is installed prior to concrete going in, and that he and builder Brian Hill, when doing joint builds, always ensure they install in-ground ducting internally right around the outside of the shed so they can access cables routes at a later date, should they require and for futureproofing. “All ducting is then cappe off and vermin-proofed.”
A beautiful view out over the farm.Don Slater has lived on the farm since he was born.
The solar panel that runs the backing gate.
The nylon rollers are very lowmaintenance.
In this build, Electric L designed, built and installed two electrical distribution and motor control centre boards; the main one is in the machine room, with the second board in the staff room up the front of the shed to control the feed system and backing gates.
“We had to come up with a wireless system to run the two water-driven backing gates,” says Kerry. “This was a first for us. The yard centre has no power out there whatsoever, therefore the two backing gates are water-driven and have their own solar panel systems located on top of each gate, with wireless control of each backing gate from the cowshed console.
“There are amazing technology advancements in these modern cowshed builds,” says Kerry.
Hoof-It owner Stuart Rogers says it was a pleasure to demonstrate the features of the Ekochute hoofcare crush to the folks of Chislehurst Farms at the regional field days
“They knew that all hoof crushes are different, in spec, in function and in price.
I was keen to show and explain the key features that have set the Ekochute as the superior manually operated farmer crush,” says Stuart.
The Ekochute hoofcare crush is designed with cow comfort and farmer safety in mind, making it simple and easy to use. “I have never
Another beautiful view out over the farm.
The capped ducting is vermin-proof.
had a crush system to do lame cows before, so I am finding it brilliant and it has some really good features,” says Andrew.
NumatAgri sales consultant Anthony Garton says their product supplied and installed in the Chislehurst rotary is the premium quality Kura 25mm interlocking mat.
Installed on the high-wear area of the entry and exit to the rotary platform, the matting prevents lameness and hoof wear, as well as providing cow comfort.
“It is essential to have rubber matting on the high wear areas where the cows are pushing and turning as they enter and exit the rotary milking platform,” says Anthony.
Not only is the Numat matting good for the cows, but it is also environmentally-friendly.
Did you know there are more than one billion tyres manufactured worldwide each year? Numat’s dairy matting products are made from rubber recycled from waste vehicle tyres and the average dairy yard installation of Kura mat recycles around 2300 tyres, sparing the environment around 20 tonnes of CO2 emissions.
Chislehurst Farms use a combination of customised silo-blended meal and liquid molasses throughout the year. Working closely with his local territory managers from GrainCorp Feeds, Andrew can adjust and address any feed imbalances that might occur during the season, allowing his cows to meet their nutritional requirements and ensure they are producing to the best of their abilities.
The side entry to the new shed, with the outdoor underpass entry to the right.To say a Greytown farm is close to town is an understatement. Wilfred van Beek, who sharemilks on Platform Farm with his wife Rachel, laughs that he has 40 “near-neighbours” in the form of town residents.
The operation, owned by James and Jane Smallwood, is in fact two farms divided by a public walkway. A natural boundary is formed by the Waiohine River.
Two herringbone sheds – a 20-aside and an 18-aside – on each have become a single 30-aside herringbone on the State Highway 2 block. A mat is used for cows to cross the walking trail from the second property when required, says Wilfred.
He says a herd of 340 cows – that is 60 per
cent Jersey and 40 per cent Friesian – is run on a combined holding of 160 hectares.
The single shed has obvious efficiencies i time and labour, says Wilfred, with two milkers putting through the herd in less than two hours.
It was built on the property closest to the highway, involving an upgrade/extension of the existing herringbone. Wilfred says the existing structure was 30 years old, ‘but still in good nick’.
The existing yard and races remain, with the pit extended and new drafting gate supplied by GEA Farm Technologies.
Brad White, lower North Island sales manager for GEA, says the AutoSelect AS 3000 minimises cow-flow interruption, with animals identifi with a drafting alert as they enter the gate. “It
only closes the entry gate behind those animals, allowing all others to pass straight through.”
An auto teat-spray system is activated when cows walk through the drafting gate. Brad says identification is via GEA’s CowScout technology, which sees each animal fitted with a special electronic collar, used in heat detection and animal health alerts.
This 24/7 monitoring uses a cellular station based in the milking shed and another remote version from the paddock. Information is fed back to the shed computer or to staff mobile phones.
Brad says GEA also added a new milk line, milk pump and variable-speed vacuum pump to the Platform Farm shed, along with a reticulated cluster wash system. A feature is the swing arm milking system, which he says provides staff with more space in the pit and greater cup alignment behind the cow. GEA
also supplied iCR+ cup removers and new milk cans.
Installation of all this plant and technology was undertaken by Cooper Farm Services from nearby Carterton. Director Wayne Cooper says he took his job brief from GEA representative Brad White.
This included the swing-arm cluster system, cup removers, cup wash and receiving cans.
Cooper Farm Services also installed the drafting gate, walkover teat spray and herd management system.
In the plant room, Wayne says the company installed the milk filtering system, variable speed vacuum pump, snap chiller and vat wash.
“Milk has to go into the vat at six degrees Celsius or less,” says Wayne.
Wilfred says Carterton-based Hodgkiss Refrigeration worked with Cooper Farm Services to ‘hook up’ the snap chiller. Existing milk vats are used, with the chilling system brought over from the old herringbone on the neighbouring block. The operation uses bore water, while the power supply was upgraded in the expansion.
Wilfred says the farm effluent disposal system was upgraded four years ago, with a bladder feeding a travelling irrigator. This method was chosen because of the public walkway.
Wilfred says the bladder doesn’t release any smell and is safer as it is enclosed, and nobody can potentially fall into it. They now have 1.1 million litres of storage.
The existing shed on the other block is now being used to weigh calves and for stock drenching.
“We run a farm system 1,” says Wilfred,
“which means that we are self-contained as far as feed is concerned. They produce 142,000kg/ MS off a 100ha milking platform.
As such, the van Beeks say their key focus is on optimal pasture utilisation and maximising pasture grown. They now calve on August 1 to match the demand for grass on the unit when they typically have plenty of cover.
Wilfred says they prefer not to make baleage, although a silage stack came in handy this season, instead concentrating on fully feeding the cows.
This focus on grass has led the couple to individually soil sample each paddock to optimise their fertiliser regime, making it specific to each paddock
Wilfred is the first to admit that he’s a ‘bit of a numbers man’ when it comes to farming.
“Three is the ideal number of leaves each grass stalk should have. Less than that, it’s not enough to feed a cow properly; more, the grass takes too much energy to digest.”
The van Beek/Smallwood relationship also extends to half-shares in a 90ha dairy beef unit at nearby Featherston.
In 2013 the Greytown dairying operation featured in the Greater Wellington Ballance Farm Environment Awards, winning the Meridian Energy Excellence Award, Waterforce Integrated Management Award and LIC Dairy Farm Award.
Wilfred and Rachel van Beek have sharemilked on the Greytown property since 2009, after a two-year stint in a similar position south of Martinborough. Originally from Holland, Wilfred came out to New Zealand in
2000 after completing a university degree. “I always wanted to be a farmer,” says Wilfred.
He studied farming in his home country, coming to New Zealand on a holiday, where he met future wife Rachel.
She grew up on various dairy farms in Nelson, the Kapiti Coast, Upper Hutt and Masterton.
The couple started their farming careers on Rachel’s parents’ 145ha effective lease farm north of Masterton, milking 420 cows.
When the farm was later sold, they took a year off to visit the Netherlands then returned to NZ as lower order sharemilkers on part of the same Masterton farm, milking 270 cows for three years.
They then spent two years on an 115ha unit near Martinborough milking 360 cows, before arriving at their present position. Outside of farming, Wilfred and Rachel have a family of six ranging in age from six-17.
The milk filter (above) and blower vacuum system (right) with VSD drive were installed by Cooper Farm Services. The plate cooler (above) was installed by Cartertonbased Cooper Farm Services. New milk cans were supplied by GEA Farm Technologies and installed by Cooper Farm Services. New technology includes a cup wash system supplied by GEA Farm Technologies. A feature is the swing arm milking system, supplied by GEA Farm Technologies and installed by Cooper Farm Services.It is a wholesome food story – a lowcost sheep dairy where 600 ewes get to rear their lambs before entering the milking flock
Farmers Sean Nixon and Ruby Mulinder began planning a sheep dairy seven years ago while living in the United Kingdom. They were there for their OE – Ruby as a farm consultant and Sean as a process engineer – the plan was always to come back to New Zealand to develop a farming business.
“We realised sheep dairy was a good story environmentally, sustainably and ethically so we became involved in the British sheep dairy industry, all the while firming our plan to develop a low-cost milk/meat farm where the
lambs stay on their mums for the first 30 to 40 days and reach 16 to 20kg,” says Ruby.
“There is a cost to doing that of course, in terms of reduced milk production, but we felt that the ethical benefits and reduced labour requirements outweighed any downside.”
The couple arrived home in 2017 and began building sheep numbers on various lifestyle blocks around Atiamuri and Central Hawke’s Bay all the time looking for a property they could convert to sheep dairy.
That property – a beef fattening block of 142 hectares at Tihoi overlooking Lake Taupo – was purchased in December 2019.
“We were working to a tight timeline and budget so Sean continued to work as a process
engineer – often away in the South Island Monday to Friday – right up to the start of lambing, and I ran the farm while also working as a farm consultant,” says Ruby.
Conor, the couple’s son aged five months at the time of writing, also arrived in time to coincide with the first milkings in the new dairy, adding to the challenge, says Ruby. Fortuitously, Ruby’s father and Hawke’s Bay sheep and beef farmer, Roger Mulinder, was on hand to help with the lambing and milking.
The farm plan was to milk around 600 ewes on the 75ha flexible-boundary milking platform The shortened dairy season, due to the ewes rearing their lambs, would run from September to March/April. The farm also finishes all lamb and fattens cattle, allowing cross-grazing, pasture management and income diversification
Ruby and Sean say that Maui Milk provided invaluable advice and support in the build-up to, and since, those first milkings. By that time they had built a flock of 600 mixed age ewes due to start lambing on August 1, 2021.
The farm conversion and construction of a sheep dairy commenced in March 2021 with a target completion date of midSeptember 2021.
Being a greenfield site, development of the tanker track and shed groundwork were the firsttasks; and they had to get power to the site.
Development of the tanker track and site was carried out by Taupo-based W.R. Mankelow Earthmovers, which specialises in farm development.
Built Wright Construction was charged with developing the dairy. Mainland Engineering and Dairy Systems installed the structural steel, steel rails, completed the fit-out of containers and installation of plant, milking, water, effluent system and meal feeding systems
Sean says the dairy was designed to enable operation by one person once the sheep were trained. “We made use of automation, so starting all shed functions is a one button process.
“We only have single-phase power supply on our road, so we also made use of Variable Speed Drives and single to three-phase converters, which enabled us to use standard dairy industry motors for pumps etc.”
Sean says they looked at a range of sheep dairies from a human perspective but also for the welfare of the ewes in terms of the heat
stress they can suffer during summer and were particularly taken with a fabric dome cover over the collection yard on a farm in Rerewhakaaitu.
“The shade provided fantastic shelter from the sun for the ewes while they waited to be milked –so we included that in our design concept.”
All auxiliary rooms – pump and milk rooms – are located in a 40ft container fitted out by Mainland Engineering while the dairy was being built and delivered to site.
“Ruby and I are tall, so we wanted the pit deeper than standard – 1100cm – to position us at a good height to monitor udder health as we apply the cups. It’s also more ergonomic for cupping because we are not hunched over,” says Sean.
“The length of the pit – and size of the GEA Rapid Exit swing over – was spec’d to the speed one person could milk; in this case, 30 ewes.”
For example, the last ewe in each row is cupped as the first ewe in the row finishes milking
“We opted for a Packo Horizontal vat because it was going to be positioned outside; the vat has exceptional insulation and a large cooling area which speeds the cooling of milk,” says Sean.
“It’s a liquid cooled vat which uses a one degree Celsius glycol solution as the cooling medium so there is no chance of freezing our milk – even with low volumes.”
Taupo Refrigeration coupled the vat to a New Zealand-designed and built Glycol Chiller.
Power consumption and current draw had been a concern at design/concept stage, when it looked like refrigeration would not be able to be used while the shed was running.
“However, thanks to Taupo Refrigeration, that has not been an issue and milking temperatures are around 2.5 degrees Celsius within one hour of completion of milking,” says Sean.
The heart of the new dairy is a 30-aside swing-over GEA European Rapid Exit stalling system, which features animal indexing stalls, stainless-steel feed bowls and group feeding hoppers and controls.
Pneumatic dual controls on either side of the pit control the entrance, feeding and lifting of stalling for animals to exit. The dairy is equipped with Ovi twin sheep milking clusters with silicone milk tubing and liners and automatic cup removers. The dairy also has Intelwash automated plant wash.
The sheep exit race from the dairy has screening.
A 30-aside swing-over GEA Rapid Exit is the heart of the new dairy.The dairy features wide exit races from the GEA swing-over rapid exit. Inside the dome cover that shelters the ewes from the sun and heavy rain.
The PPP feed system, installed by Mainland Engineering and Dairy Systems, automatically provides ewes with a measured amount of feed at each milking.
The umbrella/dome roof over the collection yard provides shade from the sun and, while limited rain does come through the fabric, the sheep are sheltered from extreme rain.
“It was a big investment,” Ruby says. “But it has paid off, as the ewes love it.”
Farmlands Taupo supply a tailored hygiene programme developed by FIL of locally-made detergents and teat sprays dispensed through the automated wash controller.
The sheep effluent system was installed by Mainland Engineering and Dairy Systems. The
yard catchments feed the plant wash, yard wash and effluent to a stone-trap which has a debris catcher to capture unwanted floating solids, including wool
The effluent then gravity feeds to a 150m3 effluent bladder that is the main storage facility. Sean says they chose a bladder over a pond because it would not cause any odours or collect rainwater. Tailored Controls designed the dairy’s effluentpump control system, which communicates with the main shed controller (PLC) via a wireless link.
An 18m3 per hour Bellin PC pump draws from the centre of the bladder and pumps to pasture through a stationary rain-gun which delivers 7mm per hour.
Sean says during the milking season they generally irrigate twice a week, depending on weather.
“We use a progressive cavity pump and a raingun which is moved around to suit. We have flow and pressure monitoring on the efflue line, and the PLC automatically shuts it down if there is a problem like a blocked or burst pipe.
“We operate it on a timer, based on the target application depth, enabling us to press ‘go’, and walk away. The PLC does the rest.”
Ruby recalls they planned for the dairy to be completed before lambing so they would have a chance to run the ewes through it. “But in reality we had to wait until they had weaned their lambs before we ran them through.”
“The majority of the ewes have twins – feeding two lambs ensures the udder is evenly milked out – but we had to milk some singles to ensure udder health and avoid mastitis,” says Ruby.
The couple say the first season was a challenge. “I was pregnant, and then had Conor in a front pack while we were all quickly learning the art of training milking sheep. It was busy!
“Once they knew the routine – aided by in-bail feed and the collection yard shelter – the ewes settled and milking became streamlined.”
Sean and Ruby are pleased with the way the sheep dairy operation has come together.
“Currently, one person is able to easily milk at a rate of 480 ewes per hour.
“The dairy is a pleasure to milk in and our first crop of lambs have grown exceptionall well, validating our decision to create a lowcost milk/meat farm which is economically, environmentally and ethically sustainable,” says Ruby.
Thanks again for bringing the feeder down. It went straight to use that afternoon and immediately had an impact.
I am now saving and they are eating about 95% of my previous loss.
- Clive, Upper Hutt
GEA’s Grant Coburn alongside the GEA Rapid Exit in raised position. FIL’s Robbie Kirk says FIL provides a tailored programme through Farmlands Taupo. A generator, beside the dairy’s glycol chiller, installed by Taupo Refrigeration, future-proofs the dairy against power outages. Built Wright Construction’s Ben Wright, and Mainland Engineering’s Daniel Gorton.Our unique range of wheeled and hanging feeders protect feed from bad weather and ensure your stock have feed when they need it.
GOING TO WASTE
MONEY WITH A WILCO HAY/MEAL FEEDER
Trailers
Strong, completely mobile and in a range of sizes to suit your farm’s needs.
of products.GRUNDFOS ® Ewes are a mix of Lacaune, East Friesian and Coopworth. The milk room is one of three auxiliary rooms in the converted container.
Alan Shaw describes the new herringbone on his Whakatane farm as “a dream come true” – and he’s not exaggerating. He’d been thinking of building a new dairy for years.
For 20 or more years Alan had been milking cows through a 16-aside herringbone shed.
With the purchase of three small blocks, and leasing of the neighbours’ farm, this meant in practical terms milking went to 24 rows, or 3.5 hours, twice-a-day. And it was during those milkings that the dream and real need of a new, larger herringbone, took shape.
However, it wasn’t until he acquired a 7ha property next door to the home farm that the dream became real – but even then it required a lot of planning, including talks with trusted
advisors Focus Accountants Whakatane which looks after the farm’s business accounts. This is because the farm was mostly consolidated peat.
“Acquiring the new piece of land gave us a milking platform of around 100 hectares and the opportunity to increase cow numbers to 400 cows,” says Alan.
“The new dairy had to be sited on the new property because our farm is all flat and there was really only one position it could be built, and that was on a sand ridge that ran along the front of the farm.
“The sand, of course, was on top of peat. So we top-loaded the building site with two metres of
rotten rock and waited for it to settle,” says Alan “That took two years from getting plans, to engineers signing off the site, that the base settled allowing us to start the build.”
Steve King of King Farm Services, the local De Laval dealership, has worked with the Shaw family for longer than he can remember. “I knew the farm and we did quite a bit of work keeping the old hybrid shed going.
“Needing to consolidate the peat gave us a window to look at a variety of sheds, and to begin to buy and stockpile the equipment in a container on-site so it was on-hand when the site finally settled,” says Steve
The new dairy was, according to Alan, always going to be a herringbone. “Having milked for more than 50 years, I know that milking
can be a solitary job. It’s more efficient and enjoyable to have company in the pit so we decided not to have automatic cup removers and, instead, build a dairy which required two people milking.”
“The simplicity and overall style of the Don Chapman dairies appealed, so we elected to build a 36-aside with some variations like all milk and water piping being constructed of stainless steel for longevity,” says Alan.
Other variations to the ‘standard Chapman herringbone’ include a deeper pit, providing Alan and son Jason Shaw – who are both tall – with a comfortable cupping position. The drenching races are also wider than standard to allow for meal feeding.
Clare Bayly Alan Shaw and son Jason Shaw say the dairy is the realisation of years of planning. The herd’s view of the dairy from the collection yard with the PPP feed silos to the right. The stainless-steel feed bins and feed dispensers –looking down the dairy.Pumps have their own defined room separate from the dairy to keep noise levels down during milking.
Construction of the new dairy started in February 2021.
All concreting – yards and floors throughout the dairy – was undertaken by Whakatane-based concrete specialists Beulah Services.
Bill Dippie of W.J. Dippie designed and built all pipe yards in the new dairy. Bill says the majority are standard height but the drafting yards are one rail higher than standard, adding a level of safety and disincentive for cows trying to jump over the rails.
The dairy is equipped with a Protrack Draft 3G drafting gate from Allflex Livestock Intelligence that automaticall sorts cows according to drafts preset either ahead or during milking. The system’s animal lists automatically sync with Minda Live generating ‘drafting’, ‘missing animals’ and ‘animals drafted’ reports.
King Farm Services supplied and installed the DeLaval MidiLine swing arm milking system, which ensures optimal alignment. The dairy also features DeLaval automatic teat spray
and chemical dispenser for efficient and hands-free plant wash
Milk cooling is provided by a DeLaval CWC30 Compact Water Chiller system with built-in heat recovery, which chills milk to around six degrees Celsius as it goes into the vat.
Alan recalls that when he purchased the block, three years ago, stock and shed water came from a bore located ‘down the farm’ which drew water which was heavy in iron. “The cows didn’t like it and this had an impact on their production and health.”
He called in Carlyle Drilling from Te Puke, which found an aquifer midway between the new dairy and the house. “A 40 metre bore accessed pristine, drinkable water, which supplies the house, dairy and all stock water.” The water quality is superb and has contributed to improved production and peace of mind knowing the cows are now getting in-trough minerals year-round.
Until the new dairy was built, the Shaws fed supplementary feed to cows on a feedpad. “They’d come out of the paddock at 1.30pm each day but now – with in-shed feeding – they stay in the paddock grazing till 3pm” says Alan.
“The PPP in-shed feed system gives us more control; we can add minerals and when grass is short we can increase feed levels to maintain condition and production.
“Compared to the feedpad, we now have zero feed waste – and better utilisation is a significant cost-saving, especially whe you consider the labour which is no longer needed to daily service and maintain a feedpad,” says Alan.
Kevin Mathis of Mathis Electrical did all the central metering at the start of the build and all wiring for the new water pump, progressively undertaking all electrical wiring required for the new dairy and its support systems.
Animal handling facilities include a Race Wrangler, which is used mainly for feet – but the Shaws say the simplicity and safety of restraining animals mean it will receive wide use for anything requiring a cow to be comfortably restrained.
The first milking in the new dairy took place in September 2021. Alan and Jason Shaw say they’re very happy with the new dairy. “We’ve gone from 24 rows per milking to 10, and that’s transformed milking.”
Built in 1974, the rotary dairy with a Spanish style façade was a ‘show dairy’ attracting busloads of farmers to watch a milking through a viewing window in the vat stand.
The one million litre Flexi Tank NZ bladder only holds effluent, compared to a pond which – by nature of it being open – also collects rainwater.
‘Back in the day’, Allen Wardlaw’s dairy in Waimana in the Bay of Plenty drew crowds – as much for its Spanish style façade as for the ‘revolutionary’ rotary platform it encased.
Allen grew up over the road and recalls the dairy being built in 1974. “I was just a kid at the time but remember that bus-loads of farmers used to call to stand in awe at the viewing window and watch the platform turning. It was a real show place.
“Herringbone dairies were the norm in those times, so the opportunity to experience a rotary milking was popular and the dairy’s fame grew when it was featured on the popular farming television show, ‘Country Calendar’.”
Allen is the third-generation Wardlaw to milk in the Waimana area and eventually took over the family farm, which was located across the road from the farm with the Spanish-style dairy. In 2017 the property came on the market and he purchased it, creating a total milking platform of 166ha.
“Up until that time I had milked my 280-cow herd through a 15-aside herringbone, so the opportunity to purchase the 102ha block over the road gave me the opportunity to increase cow numbers which would, eventually, be milked through one dairy.
“The old rotary was the obvious one of the combined farm’s two dairies to ‘do up’, because it was structurally sound and well located in
terms of the distance the cows had to walk.
“We planned to milk around 430 cows on the combined farm and wanted the dairy to be a one-person operation, so it made sense to upgrade the old rotary.”
Until that renovation happened, and for the next five years, Allen and his son Blair milked 430 cows through the original dairies.
“Milking in the old rotary confirmed that platform aside, it was sound and able to be upgraded.
“The old vat stand wasn’t needed for the purpose it was originally built of course, but we were fond of the old Spanish façade and viewing window – it gave the building character and had become a bit of a landmark in the area, so we retained it.”
Richard Palmer, rotary platform engineer with Milking and Water Systems, knew the old dairy well, having maintained the rotary platform and milking system for around 20 years. He was, according to Allen, the best person to talk to about retrofitting a new platform
“After taking all the measurements he advised that we could add another eight bails, extending the platform from 28 to 36 bails.
“He was confident he could design and build a custom platform without increasing the footprint of the old dairy or raising the roof,” says Allen.
“The new platform would be 500mm bigger in diameter than the old one, and the bails would be 100mm closer together but, because the traditional ‘twin rail’ service gap would be omitted, the cows would actually have more room.”
from
The renovation began May 5, 2021, with a planned completion date of July 2, just eight weeks away.
Demolishing and removing the old platform called for a ‘new door’ in the side of the dairy, revealing a concrete floor that was still in good condition and requiring only slight modification – at the cow entrance and exit –to match the curve of the new, larger platform.
Richard says that designing and building custom rotary platforms is his speciality.
“Normally you would have a roof height of 3000mm plus – we had 2200mm, so we had to make custom brackets for the automatic cup removers, feed bins etc. All the bail supports were pre-bent and galvanised offsite.
“The 50mm concrete platform was poured on-site in sections three bails wide so it would be easy to simply replace one section – and not
the entire platform – should that be necessary in the future.
“The platform revolves on ‘old time’ steel rollers with bearings; it has more rollers than normal to spread the weight,” says Richard.
Milking and Water Systems’ Innes Richardson has been looking after the Wardlaw farms ‘for a long time’ and was well positioned to advise on the optimum milking system to save energy and labour input for the refurbed dairy.
The dairy is equipped with Waikato Milking Systems ECR-S automatic cup removers which feature an auto start and which also trigger the Waikato Milking Systems BailGates.
Allen says the cows were not used to being fed in the dairy, and the lure of feed can see some of them want to stay on for another revolution once they have finished milking but the BailGate ‘puts paid to that’. “The only cows
Waikato Milking Systems’ regional sales manager for Waikato and the Bay of Plenty, Gary Feeney, says the refit is testament to the dealership, Milking & Water, “knowing what they are doing”.
which stay on the platform are those who have not milked out.”
Once each cow has milked out, the ECR-S automatic cup removers release the cluster, signalling the Waikato Milking Systems SmartSPRAY to automatically apply a consistent layer of teat spray to every udder before the cow leaves the platform.
Due to the height of the deck from the floor of the dairy, brackets had to be customised to take the milk lines through the top of the bails because there was insufficient room under the platform.
Allen says the Waikato Milking Systems technologies simplify and improve the effectiveness and consistency of milking and mean one person can easily milk the herd in around 2.5 hours – from start to finish – during the bulk of the season, with two required during calving.
Milking & Water Systems supplied and
installed a Sema vacuum pump controller on a Waikato BP400 blower vacuum pump to keep vacuum at +/- 2kPa from the set point during milking to save power costs. A Sema milk pump controller installed on the Innox milk pump keeps milk flow during milking to the lowes optimum flow through the Waikato double bank plate heat exchanger to allow milk to enter the bulk milk silo at a low, even temperature to save energy costs of cooling milk.
In 2020 the milk room was completely refitted with the technology the new milking system would require.
The Wardlaw farm tends to dry out in summer and, wanting to maintain production, Allen installed a PPP feed system that delivers a predetermined amount of feed to every cow at every milking. The stainless steel feed bins were designed, manufactured and installed by Richard.
The team behind the retrofitted platform – from left Waikato Milking Systems’ Gary Feeney, Milking & Water Systems’ Innes Richardson and Richard Palmer, farm owner Allen Wardlaw, The Wrangler’s Wilco Klein-Ovink, and farmer Blair Wardlaw.The Wrangler’s Wilco Klein-Ovink demonstrates the system’s underbelly girths, winch, feet support, leg winch and vet rope that extend its usefulness.
‘The brains’ behind the custom-made rotary platform: rotary platform engineer Richard Palmer of Milking & Water Systems.
Allen Wardlaw is delighted with the retrofit of his 1970s dairy.
The nearly 50-year-old yards were in excellent order, the only new section being to accommodate the curve of the larger platform at the entrance and exit point.
The 50mm concrete platform was poured on-site in sections three bails wide so, if required, it would be easy to simply replace one section.
Allen says when he purchased the farm the effluent system comprised a 2000L septic tank “So we called in the experts, Archway Group, to advise on the best option given that our water table is only three metres above sea level.”
Archway Group recommended that a bladder would provide the optimum storage as, in contrast with a pond, it is enclosed and so does not catch rainwater in the same way an open pond would. The site for the bladder along with installation of a stone trap and solids bunker, was undertaken by Archway Group.
A one million litre bladder was provided and installed by Flexi Tanks NZ. The enclosed effluent system means the Flexi Tank can b filled, emptied or stirred by the same pump making effluent management a simple operation
Flexi Tanks’ Anton Meier says the bladders
The milk room was refitted in 2020 with the technology the new milking system would require.
The new 36-bail platform is eight bails larger than the original one – 500mm bigger in diameter – but still has plenty of space around the outside.
are easily installed; simply rolled out onto a 100mm horizontal bed of sand and attached to the effluent system.
“Economic, safe, self-supporting, the height of the bladder goes up or down depending on how much liquid is inside. With a 25 per cent per annum depreciation tax advantage, Flexi Tanks are the perfect solution.”
Allen says the farm received a 21-year effluent consent from Bay of Plenty Regional Council, which were “bloody brilliant to deal with”.
A Race Wrangler was installed in place of the dairy’s old head bail on a race that is slightly elevated above the yard around it.
Allen reckons his son – and farm manager –Blair and his 2IC Buddy Akuhata say the Wrangler’s usefulness goes far beyond feet issues.
“They use it for everything you would normally use a head bail for – because the Wrangler’s under-belly girths, winches and ropes mean it safely restrains cows for such things as calvings, veterinary treatment and, of course, foot issues.
“The fact the floor level is raised also makes it even easier to attend to feet issues.”
The refurbished dairy was completed one week later than the target date and Allen says he couldn’t be happier with it.
“Getting the cows, which had been milked through the herringbone, used to the rotary was made easier by feeding them on the platform, so they settled in a relatively short time.
“We’re finding they are very relaxed on the platform.”
As for the milking experience, Blair and Buddy really enjoy milking in the renewed shed. “Cutting the door in the wall of the dairy [to remove the old platform] has introduced a lot of natural light and airflow, so it’s a much nicer working environment,” says Allen.
Now that the dairy has been refurbished and is operating well, Allen says they will turn their focus to any enhancements which improve its operation.
Installing NumatAGRI rubber matting in the off and on ramps is one such improvement. Allen says the mats will minimise slipping, especially in wet weather, and avoid hoof damage.
Gibb-Gro is a 90% (900g/kg) strength naturally occurring growth promoter obtained from the culture of the fungus Gibberellic fujikuroi, and contains natural gibberellic acid GA3.
You get a rapid increase in dry matter (DM) production during the cooler autumn and spring feed shortfalls.
Increases of up to 30% or more can often be achieved especially when nitrogen has been applied.
We have many customers that have been using Gibb-Gro for a number of years to reduce the amount of Urea or other nitrogen products they apply.
In cases where they might have been adding 70kg/ha of Urea they are able to reduce this down to 40kg/ha and still get great increases in pasture growth.
Apart from making it easier for you to meet your nitrogen input targets, the savings are significant.
Apply at 9g/ha of Gibb-Gro +25ml of GibbGro Wetter per 100-200l water.
Apply a minimum of 100-200L per hectare when soil temperatures are above 6-8 degrees C.
When applied with wetter Gibb-Gro is rain fast within 2 hours.
CALL US ON 0508-442 247 FOR MORE INFORMATION
Gibb-Gro is registered pursuant to the ACVM Act 1997, No P8012. Approved pursuant to the HSNO Act 1996, No. HSR000747
•True monogerm cultivar
•Low drymatter type (12-15%)*
•60-80% of the bulb above ground
•Larger bulb type
Suited to grazing with all stock classes
•Above ground bulb colour: orange
•True monogerm cultivar
•Medium drymatter type (16-18%)*
•50% of bulb above ground
•Proven to perform across all stock classes and environments in New Zealand
•Above ground bulb colour: orange
Wewillsolveyourproblems.Wecanhelp identifythattrickyweedyouhavebeen strugglingtokill.Thenwewilldeliver quicklytoyouevenatyourruralfarm address,savingyouthehassleofhavingto gointotown. Plus,becauseweimport,manufactureand selldirectly,wecanusuallysaveyou money.
Oncewehelpyougetontopofyour weeds,wecanthenhelpyougrowmore qualitypasturewitharangeofnatural fertilisers,soilconditionersandgrowth promotersincludingSeaweedextractand GibberellicAcid
GIVEUSATRYANDCHECKOUTTHE GREATSERVICE
Herbicidesinclude;
Rainbow&BrownGlyphosate360.
Rainbow&BrownGlyphosate540.
Granny(solubleglyphosategranules).
MSF600-metsulfuronmethylforlow costgorsecontrol. 2,4-D720Amine Buckshot-picloramgranules.
Decision-flumetsulamforbuttercup control.
GA200-glufosinateammoniumfor weedcontrolinorchards. Dicamba500SL
GrassMate-abrushkillerandgrass friendlybroadleafspray.
MCPA750forthistlecontrolinpasture.
Ranger-lowcost,pasturefriendly,dock andbuttercupcontrol.
Halox100EC-haloxyfop,grasskiller. Cut'n'Pasteherbicidegelsandpastes. andmanymore
Three weeks after the McKenzie herd moved into the family’s new wintering barn, a weather bomb hit the Invercargill region with torrential rain and a wind chill factor of -1 degree Celsius. The event coincided with New Farm Dairies’ visit, showing the writer first-hand the difference from being out on paddock and in a wintering barn in an extreme weather event.
That comparison could not have been more extreme. Outside, winds were icy and gale-force but inside the Comfort Cow Barn the 600 cows were either contentedly eating silage, getting a
scratch on the barn’s numerous cow brushes, or lying in padded, dry stalls.
Eoin McKenzie is used to the challenges the weather can bring in Southland. He’s lived in the Woodlands area all his life. He’s moved five times – all within a 4km radius.
The 310 hectare effective Woodlands property is now leased to Eoin and Jayne’s son, Matt and his wife Sarah. Eoin is clearly an active, supportive member of the farm team.
Eoin says the decision to invest in a wintering barn has been a long time coming. “I hate mud – particularly the effect it has on animals which have to stand in it during bleak icy weather, and the psychological impact that reality has on everyone on the farm.
“We started planning the barn around two
years ago, our goal being to have a facility where the cows could be off the paddocks all winter, enabling us to bring eight or 10 ‘sacrifice paddocks’ back into the grazing round and meaning we could extend lactation to 305 days per cow.”
Matt and Eoin looked at a number of wintering barns. “Our preference was Southland Farm Services’ Comfort Cow Barns which are sized to allow room for cows to move, turn around, socialise and feed.”
“At peak we milk 780 cows, so we settled on a 6194m2 barn with 632 stalls and two calving areas,” says Eoin.
Southland Farm Services’ Mark McMillan says the barn features six rows of 1200mm wide DeLaval free-stalls; three either side of the central feed lane.
“The floor of the barn has two levels; the stall
areas are raised above the scraper and feed alleys to provide a warm and dry area for the cows. Comfort is ensured with 40mm DeLaval Cow Mattresses which have a soft interior encased in a waterproof envelope which is resistant to manure, urine, milk acids, UV light and microorganisms – making it easy to clean and long lasting,” says Mark.
Eoin and Matt included ‘brisket walls’ which are small walls that, together with the stalling, frame the stall for each cow.
“The scraper alleys feature two hybrid DeLaval chain scrapers which move up and down the barn collecting effluent at set times The scraper system has a pressure sensor which stops if it detects a cow lying down,” says Mark.
Clare Bayly From left: Southern Electrical’s Gerhard Lategan, Doug’s Engineering’s Andrew Johnstone, Matt McKenzie, Southland Farm Services’ Mark McMillan, Eoin McKenzie; and Milne Building Contractors’ Greg Milne. A curtain above the tilt frame walls provides protection from the prevailing south-westerly wind. Willow Creek Dairies’ road sign. A larger wagon and teleloader were needed to maximise feed efficiency“Gathered effluent is deposited into a channel from where it is transferred to precast effluent tank and through a separator before sending liquid to a 7 million litre storage pond.”
The pond liner is manufactured by Aspect Environmental Lining.
Matt McKenzie says the ideal barn site was adjacent to the farm’s rotary and side-on to the south-westerly prevailing wind.
“In May 2021 Cameron Contractors developed the barn building site and the new effluent pond.
The main structure of the barn and overall project management was undertaken by Milne Building Contractors. Greg Milne says the rise in demand for wintering barns has seen the company develop quite a few in recent years but Eoin and Matt’s would be one of the largest.
McGregor Concrete supplied all concrete
for the barn and surrounds. Construction of all concrete aspects of the build –including tilt slab walls, floor, silage bunkers, races, lanes and turnarounds – was undertaken by GT Chamberlain Builders.
Doug’s Engineering manufactured the feed rail down either side of the barn, with engineer Andrew Johnstone saying the round rail has no brackets or sharp edges that could injure cows. Doug’s Engineering also constructed all steelworks other than stalls and roof beams, yards and gates.
All electrical wiring was undertaken by Southern Electrical with refrigeration operations manager Gerhard Lategan saying this included all power to the barn, lights in the main barn and dedicated calving area, wiring of cow brushes and hoof trimmers, along with the scraper system and effluent, eparator and
transfer pumps. “A dedicated control panel is positioned at the entrance to the barn, providing easy access to the light control, and an emergency stop for the scraper system is located at each end of the barn.”
Matt says the cows went into the newlycompleted barn mid-May. “It was the first time they’d been housed, so it was a big adjustment – not just being under a roof but also learning about the various sections of the barn.
“Initially some cows lay down in the scraper lane but three weeks on, more than 80 per cent happily lie on the stall mattresses.”
The barn’s 6200m2 roof captures around six million litres of rainwater. Matt admits they collect and store a fraction of that volume.
“Cows’ need for water increases when they’re housed because they naturally ingest a lot of water when outside grazing but the roof water,
supplemented by our existing bore, means we’re able to meet the demand.”
Cows are fed a diet of silage and straw supplied and harvested by Hughes Contracting.
Eoin says the wintering barn is a huge investment but there are some immediate paybacks.
“We will milk more days, so production will increase and our feed bill will reduce – before, dry cows got 15kg of dry matter per day but now they’re not fighting to stay warm and dry, we should be able to reduce that to 9kg. With feed costs of around 40 cents/kg, this is a massive saving – with no wastage.
Eoin says in terms of time and motion, it’s now easier to monitor cows, particularly during calving. “It will transform the lifestyle and ease of farming – particularly in winter and during calving or adverse weather.”
Any parent who has milked cows understands the dilemma of needing to mind children while milking.
Resolving this was factored into the design of John and Kirsten Miller’s new dairy at Te Tipua in Southland.
“We looked at the new shed holistically,” says John. “We wanted to create an environment which would attract and retain the best staff and provide the optimum environment for our cows now and into the future.”
Achieving those aims is evident in the new 60-bail rotary, which has a high level of technology and animal handling facilities and a very large office/lounge for staff and, inevitably, the children of staff.
“We extended the standard office space to generate a warm, comfortable lounge where staff can relax,” says John. “We are parents to two young boys and understand that, while it isn’t ideal, there will be times when workers need to bring their children to the cowshed, and we wanted to provide a facility which is safe and warm.
“The room is equipped with couches and a television – with Netflix – and a large viewing window into the dairy so milkers can easily check and reassure themselves that their children are occupied and happy.”
The new dairy is a far cry from the old 40-bail rotary that John’s father built.
John and Kirsten Miller have created a facility for the future – combining technology in an environment that is comfortable for animals and humans alike.
Milking the 320 effective hectare farm’s 700 cows was taking up to five hours per milking and, combined with rising maintenance needs and costs, John and Kirsten made the decision to build new.
“The optimum herd size here is 800 cows, so we settled on a 60-bail rotary platform,” says John. “We looked at a few dairies and liked those built by Baz Janssen because they were highly functional and a pleasure to work in.”
Baz Janssen Building’s dairies have a unique style – functional, stylish, spacious and with wooden purlins. The company offers a complete service from yard design through to site development, engineering and construction yards and building.
“Baz Janssen tailored one of his standard layouts to suit our specific needs – for
example, we wanted additional clearlite panels in the roof, the large office/staff room and a rectangular collection yard,” says John.
“We like the timber purlins because they look great and are 100 per cent bird-proof. Timber purlins also absorb sound better than steel, adding to a quiet milking environment.”
Development for the site of the new dairy commenced in June 2021. “Building the new shed in a central location also meant a reorientation of paddocks and this was achieved by Batt Contract Fencing, which came in and assisted in the redesign and implementation of refencing the paddock layout to reorient to the location of the new dairy,’ says John.
“The old dairy had a circular collection yard but we wanted the new shed to have a rectangular yard because we feel they generate better cow flow and are better for the cows’ feet because they don’t have to turn as much as they do in a circular yard. The result is healthier feet and less lameness.”
John says the yard wash is simple and effective with three flood washes, which dump up to 60,000 litres of greenwash from cleaning the dairy, which is stored in two tanks to the side of the collection yard.
The 60-bail concrete Donald Engineering platform was sized to efficiently milk 800 cows. All bails are made from galvanised steel pipe fitted with purpose-built bracketing. The platform has two iBeam nylon rollers per bail, spreading the load evenly and ensuring the platform is well supported. The two heavy duty dual drive motors are connected to a
Right: The dairy is equipped with an Allflex/MSD Animal Health Intelligence Protrack 3G Automated Drafting Gate.
Left:The 60-bail concrete Donald Engineering platform is complemented by Read Industrial Electronic Cup Removers, Read Slide Pulsators, Bail Restraints and Milktech inbail teat spray.
variable speed control system which is easily managed via control consoles.
NumatAGRI rubber matting was installed in the off and on ramps to the platform, which John says is the point where cows are under the most stress. “The mats minimise slipping, especially in wet weather, and hoof damage.”
Dairytech South supplied and installed the Read Industrial milking plant, which features Read Industrial Electronic Cup Removers, Read Sliding Pulsators, Bail Restraints and Milktech inbail teat spray.
Dairytech South general manager Simon Knight says the Read Electronic Cup Removers feature auto start, which triggers cluster release as well as cup end vacuum and bail arm lowering.
“Read Sliding Pulsators are renowned for their simplicity and reliability. The system is so reliable that there is no need for pulsator filters, vacuum levels remaining stable over time regardless of ambient air quality,” says Simon.
“The Milktech teat spray applies spray to every udder within 10 seconds of the cluster being removed.”
The dairy’s Read circuit wash system is renowned as one of the simplest, most effective and robust, featuring a large bore 4” milk line with a valve at the receiver can end, hot cylinders and a water reservoir.
The Miller herd is fitted with Allflex/MS Animal Health Intelligence collars, which monitor health and heat, and an Allflex/MSD Animal Health Intelligence Protrack 3G Automated Drafting Gate was installed.
Allflex Intelligence’s lower South Island sales specialist Laura Christensen says the automated three-way drafting gate takes the hassle out of drafting. Easy-to-use software enables drafts to be preset via the shed PC or smartphone ahead or during milking.
“The system generates simple reports
including live drafting, missing animals and animals drafted,” says Laura.
The interior and exterior walls of the dairy are coated with Acraflex dairy wall coating, whic was applied by BB Cunninghame. Acraflex i acid and alkali resistant and easy to clean. The coating is backed by a 10-year guarantee.
John says the original plan was to have the new dairy completed by August 15 but there had been a few supply issues, thanks to Covid lockdowns, which added a month.
“In the end we started milking November 1. By that time the dairy was functional, if not entirely finished.
John says the biggest change for the cows, other than the new location, was the fact the turntable went clockwise – they were used to an anti-clockwise rotation in the old shed. “It probably took around 10 days for them to get used to the rotation of the new platform but they settled well.”
The dairy’s interior has a high degree of natural light thanks to a proliferation of corflute panels in the roof.AllflexIntelligence’s Laura Christensen says the Protrack 3G Automated Drafting Gate ensures effortless and accurate drafting. The dairy’s spacious pump room. NumatAGRI rubber matting at the entrance and exit minimises slipping and hoof damage.
A composting barn nearing completion in Edendale, Southland, incorporates some of the best design features of traditional wintering barns.
Logan and Mel McKenzie, in conjunction with Logan’s parents, own two adjacent farms which combined total 350 hectares milking 900 cows: 400 on the home-farm and 500 ‘next-door’.
The logic and popularity of wintering barns is evident across Southland, with new barns becoming almost commonplace and, for the last five years, Logan has been looking at the pros and cons of the various barns.
“We started off thinking that we needed a barn which would house all the cows all winter but the realities of scale and cost sharpened our
focus to what we really wanted to achieve – and that was to develop a barn which would house early-calvers through to calving.
“We start calving in early-August and our calving pad is located a fair distance from the farm dairy – in the bleakest of Southland weather this can compromise calving efficiency and animal welfare. Resolving this – with a warm barn close to facilities – was our number one priority.”
Logan looked at a range of barns and conducted extensive research over about five years before deciding that he would build a hybrid composting barn.
“Composting barns generally have a deep bed, which the cows eat and sleep on for the period of time they need to be off grass, with a tractor lane down the centre. I wanted a barn which
had the fibre bed, but which had three concrete centre lanes – a central tractor lane, and, on each side of that, a feeding lane.
“My reasoning was that the cows would have a deep, warm fibre bed but would feed on the adjacent feeding lane where at least half of their daily effluent would be excreted and captured by a floodwash system
“The floodwash would fall into a sump across the end of the barn and be piped to a weeping wall and then either direct to pasture or back into storage tanks for reuse as floodwash.
“It was quite a radical concept so I discussed it in detail with Rodger Short of Winton Engineering, which builds wintering barns, with Lindsay Lewis of Clean Green Effluent, and Nathan McDermott Building. Their expertise in their relevant fields enabled some
great refinements,” says Logan Winton Engineering’s Rodger Short says the company has experienced spectacular growth in demand for wintering barns in the Southland Region; “So much so, we developed a kitset option which farmers could spec to their requirements, and build.”
“Logan wanted a composting barn but we future-proofed it for him so, if required, it could be modified to be a traditional free-stall barn with the installation of stalls, matting and effluent scrapers.
Rodger says building a barn is a huge investment, so this gave Logan a ‘bob each way’.
“He was looking for some different sizings to our traditional barns, so we modified our standar design to give him a kitset barn, which would house 300 cows. The dimensions of the shed are 100m long by 36m wide, i.e. a total of 3600m2 or, in cow terms, around 10m2 per cow.”
Clare Bayly composting barn Logan McKenzie has built a hybrid composting barn on his Edendale farm. Under construction it is easy to see the floor divisions – 150-cow beds on each side, paired with feed lanes which face onto a central tractor lane. Natural light and ventilation – essential for effective composting – have been built into the roof of the new barn.Logan says the groundwork for the new barn was undertaken by himself with backup from Marshall’s Excavating and began in February 2022.
“The site has a fall of 2.6m from one end to the other, providing a natural gradient for the outflow of effluent from t cow beds into the effluent system.
Nathan McDermott then began construction of the foundations, portal pads and precast concrete slab panels along with the structure of the kitset barn.
A 200mm nib between the cow beds and the concrete lanes contains the bedding. The composting bed is made up of a clay base with novaflow inlaid to catch effluent, the fall of the sh providing good flow into the effluent system. The first lay over the clay base is made up of 700mm of drainage gravel with 300mm of wood chip on top, and then a final covering of 200mm to 300mm of untreated sawdust.
The pre-cast concrete panels on the side of the barn facing the prevailing wind are topped with wind cloth.
The 700mm of drainage gravel is topped with 300mm of wood chip with a final covering of 200mm to 300mm of untreated sawdust.
Lindsay Lewis from Clean Green Effluent has worked with the McKenzies providing effluent systems for their dairy farms and says they looked at a range of options, designing the ideal system for the new hybrid composting barn.
“It’s a great concept – feeding the cows off the beds means that half of their daily effluent output will be collected and treatd by the floodwash and effluent system, with the balance bein turned over each day by tractor.
“The shed’s fall will also generate natural flowof liquid effluent which, combined with the flood wash, will go into the Clean Green capture pit which, in contrast to traditional systems, is long (36m) and narrow with a weeping wall in the centre. The Parallel Timber weeping wall enables more solids to be extracted than would be possible with a standard weeping wall. The bulk of the NPK is captured in the organic humus.
“Solids are dried faster so they can be dispersed to pasture.
Liquid effluent is either irrigated onto pasture or returned tothe storage tanks for floodwash,” says Lindsay
“The system is very environmentally-friendly – the green wash going down the feed lanes, through the wall and back into the floodwash
“The distribution system allows controlled application to land at low-rate low depth application rates of 0.25mm, thereby eliminating nitrate leaching, ponding or overland run-off. Due to the low-rate low depth distribution system, effluent can be dispersed on a daily basis, all nutrients stay in the root base and minimal storage is required.”
At the time of publication, Logan’s barn was nearing completion, enabling the bulk of early-calving to take place under cover.
“In the future every cow will be calved in this barn – earlycalvers will spend all winter in the barn and as they calve, the next mob of calvers will move in. We will also be able to milk out of it in the autumn when it gets wet,” says Logan.
“The barn is a luxury but it’s also an investment in the future of the farms, in our farm team and their enjoyment of their work and lifestyle, and in animal health and the environment.”
The Clean Green Effluent patented effluent system under construction. Protection from the prevailing wind is provided by wind cloth panels above pre-cast concrete panels on the side of the barn. Six weeks on from New Farm Dairies’ visit, the cow beds are nearing completion.Ross and Tracey Laing have been farming on the same land for more than 30 years, with Ross running the farm.
He’s been adding improvements to the farm ‘since day dot’. The latest project is a new effluent system and tank to meet new environmental requirements.
The area was once all rehab farms for returning soldiers from World War II, and Ross’s farm is ex-rehab farm land. It has a 4km boundary with the Waerenga Stream with extensive riparian planting and fencing,
preventing cows from reaching the water.
“As a family, my parents, brother Brian and I bought six farms over six years that were all close to each other. At one point I was leasing my brother’s land and milking 1000 cows, but I wouldn’t want to do that now,” says Ross.
The family financially ‘jiggled around’ the different properties, until each member independently owned a farm. Ross now farms 200 hectares and has a 50ha support block close by.
He milks 520 pedigree Friesians, with autumn calving and winter milking under a Production
System 2 model. He had a 50-bail rotary dairy shed constructed in 2005 and runs the farm with two other full-time workers.
“For our land, winter milking just makes sense, as we are dry in the summer but in winter have options due to our quality, free-draining soils. In summer we grow 37 hectares of maize, which is 20 per cent of the dairy platform, and it loves the sunshine. We do any re-grassing in late-March and get a good growth response from late-flowering tetraploid rye grass during the winter.”
Mating starts on May 24 and Ross’ key to success is feed, feed and more feed. The cows are dried off on January 15 each year.
“It’s important that the cows are in good condition for mating outside the traditional season, and that they are well fed with supplements throughout the winter milking.”
The farm has a low stocking rate, but Friesians are big cows. During summer they eat pasture but during the winter they eat pasture plus 10kg of maize dry matter and 2-3kg of meal per cow, per day.
“I liken it to them getting their Weetbix (bulk feed) on the feed pad before milking, and then the Moro Bars (higher calorie and protein meal) while milking.”
Last year’s statistics were 500 to 550 kg/ MS per cow, working out as 1300kg/MS per hectare, and 260,000 kg/MS for the farm overall – and Ross is happy with that.
New environmental regulations meant that Ross had to rethink his effluent system in 2019. The 190,000 litre concrete collection pond and sand traps that had been servicing the farm since 2005 needed updating.
“It was an opportunity to future-proof and make good use of our effluent on the farm. I shopped around before settling on Tasman Tanks, feeling that what they offered was the most effective option for our land.”
The farm is low lying and has a high water table, so an inground tank was not an option. Although a rare occurrence, a leak in an inground pond is harder and more expensive to fix than one in an above-ground tank
Ross says his tank is much larger than the farm needs, but he feels that having a large storage capacity for effluent covers a really we season when irrigation is not appropriate, and
it’s always good to future-proof for expansion.
“The new tank is 2.7m high and 57m in diameter and can hold 6 million litres. With farm real estate being so valuable, a smaller footprint is important,” says Tasman Tanks NZ regional manager Greg Lilly.
The tank is made from galvanised steel panels bolted together and is lined with a FPP (flexible polypropylene) liner. The tank is highl engineered and has ground anchors ensuring reliability during high winds and seismic activity.
“The key to the tank working well is that it is on stable ground, with the weight evenly dispersed. “Earthquakes in the South Island have shown that our tanks are very durable, staying intact due to the flexibility in their structure,” says Greg.
Ross organised a Geotech report and had already confirmed the site for when
Broughton Contracting came in to complete the groundwork.
“We prepared the site by stripping topsoil, levelling the ground and digging a 2m circular trench for the walls. Ross was also very hands-on and assisted with the work,” says Broughton Contracting owner Tim Broughton.
The trench was back-filled with GAP 65 t deter rats from digging through and the fine levelled before the tank was installed. The tank has a structural and design life of 50 years, and design and durability life of 25 years.
The new system still utilises the old collection tank initially, but the effluent is then pumped to the new tank. The effluent passes through a GEA slope screen where the liquid goes into the pond and the solids slide off into a storage bunker. This eliminates the need for a stirrer in the tank.
“We spread the solids on the maize paddocks in mid-September and being rich in magnesium, nitrogen, potassium and phosphorus it causes maize to flourish, saving on fertiliser.
“The greenwater collects in the tank, and we use it to irrigate 60 hectares in the spring and we fil two 30,000 litre concrete tanks to floodwash th feedpad. It’s a real win-win situation to be able to utilise our effluent so effectively,” says Ross
The farm has two bores of its own, and a permit to use water from the Waerenga Stream. At the yard, one 30,000 litre tank holds filtered bore water for the plant wash, and one 30,000 litre tank holds creek water for washing down the yard.
The whole water and effluent system ca easily be controlled from the shed as well as near the tank itself, a system which Ross describes as “making things as easy and automated for the staff as possible”.
Cambridge farmer Matt Weatherhead has always been a country boy. Raised on a farm, he loves working outside and studied for a Bachelor of Commerce (Agriculture) at Lincoln University.
The Weatherhead family already have a 105 hectare dairy farm, milking 240 cows, in Te Miro, outside Cambridge in the Waikato. They purchased a 33ha neighbouring property to use as a run-off in 2020.
It was re-grassed in September 2021, with summer crops of chicory, clover and fodder beet. The farm grazes their stock and makes silage from any surplus.
“I saw an advert for Maui Milk in the paper and they were looking for sheep milk
suppliers,” says Matt.
After further investigation and a few meetings with Maui, Matt and Amelia decided that they’d like to convert the run-off.
“Sheep milking is environmentally more sustainable, has more health benefits, an by intensifying our run-off new jobs have been created.”
The run-off had an old, decommissioned cowshed which still had the ‘basic bones’ to work from.
“It was last used in 2002. The roof had gone, but the plant shed, concrete base and railing were still there,” says Matt.
In January 2021, work began on converting the old shed into a modern sheep dairy to be ready to send in milk to Maui from July 2021.
Builder Hamish Herdman raised the milking pit walls to a comfortable height to milk the sheep, added a new roof, and carried out concreting as required. Matt completed the painting himself.
“We were able to keep the existing round yard as it was and, with the help of an engineer, we utilised most of the existing steel work,” says Matt.
The mains switchboard needed replacing and electrical work was carried out for the new plant.
Matt specifically wanted a Waikato Milking Systems plant and had been consulting with Qubik’s Nick Heffer to design the shed and organise the installation.
“I suggested a Qubik designed and manufactured stainless steel rapid exit system that is designed to work efficiently, especially if the dairy shed has tight gaps between the
milking pit and wall,” says Nick.
“Once the sheep have finished milking, the whole rapid exit system lifts up, allowing the sheep to exit underneath the whole stalling and they can exit on an angle, rather than straight out and then having to turn,” says Nick.
“The rapid exit system was built locally from high grade 304 stainless steel to withstand the continual washing down required and meet good hygiene standards.”
The milking shed is running a 36-aside Waikato Milking Systems plant with ECR-S cup removers supplied and installed by Qubik.
“Sheep have delicate teats, and the auto cup removers prevent over-milking, as well as reducing the amount of labour required in the milking shed,” says Matt.
The sheep milking plant is using the Waikato Milking Systems SmartPULS pulsators which provide gentle, accurate pulsation with rippled timing to ensure a stable milking vacuum. The digital pulsation system opens and closes the sheep liners consistently and reliably every milking – providing optimum milking performance.
“The SmartPULS works in harmony with the sheep for maximum milk quantity and quality. It helps stop any congestion and oedema in teat tissues during milking, reducing sheep discomfort and new mastitis infection,” says Nick.
Qubik also installed a BP200 with 7.5KW motor and VSD SmartDRIVE. “The SmartDRIVE is a Variable Speed Drive
that compensates for vacuum use by increasing or decreasing the vacuum pump speed on demand,” says Waikato Milking System’s regional manager sales and service, Ben Frederickson.
“Using a transducer mounted into the main airline, the variable speed device will monitor and adjust the vacuum, sensing every minute airflow change and compensating for this b altering the speed of the vacuum pump,” says Ben.
Matt needed to meet the strict milk cooling regulations with sheep milking, so he was advised to install the stainless steel 5000L double-bank plate cooler alongside a Waikato Milking Systems top-loading milk filter for ease of use and effective cleaning.
“We bought a second-hand stainless steel milk supply vat with a Qubik-supplied and installed vat refrigeration unit to keep the milk below three degrees between our four-day pick-ups,” says Matt.
Qubik also supplied and installed the water system for the shed, including two dairy hot water cylinders, a heater stand and a Qubik custom-made and designed stainless steel wash tub. The new washdown and cooler pumps are linked to the existing dairy shed framework.
The shed water supply comes from the original concrete tank and a second-hand 25,000L plastic tank.
Matt finds the automatic plant wash, which is quickly activated by the push of a button, speeds up the whole washdown process and frees up the milker for other work.
“It also ensures the correct amount of acid
and alkali, and the correct volumes of hot and cold water are automatically used,” says Matt.
He sourced a second-hand grain silo, and during milking, auger lines supply whole maize and wheat DDG (distillers dried grains) to the sheep.
In February 2021, a total of 550 ewes arrived from Maui and the ram was put in with them.
Matt had built two 12m x 6m canvas-roofed lambing sheds himself.
“That first season only 500 ewes had lambs, but we still had 750 lambs to rear and started milking on July 28.”
Matt and one other full-time staff member run the farm, with three part-time staff for relief milking and lambing.
Overall, Matt is happy with their first seaso milking sheep, and during peak milking they
Waikato Milking Systems’ Ben Frederickson with Cambridge farmer Matt Weatherhead. Qubik’s Jeremy Collett and farmer Matt Weatherhead checking the top loading milk filter Qubik’s Nick Heffer and farmer Matt Weatherhead discuss the plate cooler. Matt Weatherhead built the lambing sheds himself. An aerial view of the newly-converted dairy shed, and the shed set-up for lambs.A South Waikato dairy shed has gone high-tech without incurring huge demolition or relocation costs.
James McConnell says his old 44-aside herringbone at Lichfield was ‘staff hungry’.
Running 700 cows on the 200 hectare Wiltsdown Rd property, James says the herringbone also made for tricky cow identification and automation.
Its successor is a DeLaval E100 54-bail rotary featuring the latest herd management technology.
James says the computerised system records accurate individual cow milk yields from milk meters, making feeding decisions and drafting for each cow ‘a breeze’.
The platform boasts on-deck teat-spraying, automatic cup removers and retention, along with auto plant-wash and DeLaval compact milk chiller system.
James says the rotary shed requires just a single milker and another to get the cows in and help with the clean-up.
Designed by Chapman Dairy and built by Don Chapman Waikato, the existing yard is retained and the rotary built on the opposite side of the site to its predecessor.
“‘It’s there, let’s use it’ was my philosophy,” says James.
He says the design also meant the stock races remain the same, with the tanker loop the only change in layout.
The rotary was built on a former holding paddock and butted up against the existing yard.
Don Chapman Waikato director Shanan White says significant earthworks were required to bring the base of the new rotary up to the level of the existing yard. Base-work included ducting for associated cables and pipes, making for a clean and uncluttered finish.
Shanan says the design was ‘pretty stock standard’ and similar to a project undertaken by Chapman Dairy and Don Chapman Waikato – also featured in this edition of New Farm Dairies – for Arco and Yvonne van Vliet at Tahuna.
The McConnell build included the milking shed, milk room and plant room, plus pipework, with polystyrene panels forming the building walls, topped with a Colorsteel roof.
“It didn’t present too many challenges,” says Shanan. “There was certainly a saving on yarding.”
James says the ‘real kicker’ for the revamp was electronic cow identification, both on the platform and in the yard.
DeLaval Rotary supplied the fully automated milking system, which includes DelPro herd management software, with installation undertaken by Tanner Industries.
Graeme Middlebrook, technical specialist for DeLaval in New Zealand and Australia, says
ear-tag identification is used to monitor each cow in the parlour, including the quantity and quality of the milk each animal produces, while data also comes from a drafting gate in the yard.
“Milk meters inside the platform capture the cow’s performance and this information is sent back into DelPro.”
Graeme says the system is fully integrated with automatic cup removers, on-deck teat spraying, weighing and drafting all controlled by the DeLaval DelPro system.
“Information from each bail is fed into a central control system, monitored in real time via a big screen at the milking platform.”
Data is collected on the shed computer and accessible on staff mobile phones. “Information on each cow is available immediately, so staff know if treatment is required and what each cow is producing,” says Graeme.
Steve Edwards The new rotary butts up with the existing yard. The fully integrated milking system includes automatic cup removers supplied by DeLaval and installed by Tanner Industries. Sharemilker Daniel McConnell, with owner James McConnell.The same technology is used in establishing individual feed ratios for the in-bail feeding system.
Graeme says a specialist drafting gate provided by DeLaval also ‘communicates’ with the DelPro herd management system. “Farmers today want information at their fingertips,” says Graeme.
The design features on-deck teat spray, automatic cup removers and plant autowash.
Tanner Industries also had a hand in installing the water lines and tanks, washdown and cooler pumps, and effluent system.
Lloyd Tanner, who owns the Putaruru-based company, and head fitter Kain Tanner say their work at the platform included installing the milk meters and cup removers, along with milk lines and receiving cans, plus the snap chiller.
They also had a hand in the clusters, cup wash and teat spray, along with the feeding system and plant-wash.
Tanner Industries hooked up two 600L water heaters, plus plate chillers, milk filters, washdown and cooler pumps, the vacuum pumps and another pump associated with the effluent disposal system.
Chemical pumps used in plant cleaning were also part of Tanner’s brief, along with installation of the teat-spray mixer.
Lloyd and Kain say they also plumbed to the milk vat, along with installing the drafting gate.
On the other side of the installation equation, was input from Laser Electrical Putaruru.
Director Mark Camp says the company completed all electrical work relating to the new rotary. This started with a new
underground main from the roadside power supply, plus associated wiring and ducting.
“Laser Electrical Putaruru wired all the DeLaval equipment in the new shed, including the central gland, platform control and drafting gate.
“This electrical work extended to the plant room, milk room, water heaters, wash pumps, vacuum pumps, vats, chillers and lights.”
Mark says Laser also set up a wireless link between the two milking sheds for backing gate and effluent transfer pump controls.
Using the existing yard meant James could continue to take advantage of Kura matting originally provided by NumatAGRI. North Island sales representative Anthony Garton says the product was installed three-four years ago to serve the old herringbone. “Our brief was to do the whole yard.”
Anthony says the anti-slip matting provides cow comfort and is also easy to clean.
“Imported from Germany by Numat, the material is laid in 25mm thick interlocking squares and secured by stainless steel anchors.”
Anthony says the product, with a lifespan of 25 years or more, is placed straight on to the existing concrete yard. With a focus on preventing lameness in the herd, he says it can also be used on a rotary platform or herringbone bails.
The McConnell family connection to the area goes back to 1979 when James’ father Norm bought what was then a 320ha sheep farm.
A conversion in 1984 saw the first cowshed built there, with 160ha used for dairying and the balance for drystock.
Two years later a second herringbone milking shed was added, with 400 cows milked in each on what had become a total dairying operation
Farm owner James McConnell, sharemilker Daniel McConnell, Tanner Industries’ head fitter Kain Tanner and fitter Regan Henare. Graeme Middlebrook, technical specialist for DeLaval in NZ and Australia, tests out the touchscreen at the central control system. A specialist drafting gate provided by DeLaval ‘communicates’ with the DelPro herd management system. Platform technology includes on-deck teat spraying. Page 59PH 07 578 0030 Using the existing yard meant James McConnell could continue to take advantage of Kura matting originally provided by NumatAGRI.Owning a commercial sandpit came in handy for a Waikato family building a sheep-milking facility requiring more than 4000 cubic metres of foundation material.
Four generations of the Wilson family have owned property near Matamata since 1908, including the sand quarry, dairying land and now sheep.
Operations manager Ryan Wilson says together with his parents and farm-owners, Murray and Leanne Wilson, they were ‘looking at the next step’ when he attended a sheepmilking open day.
“We are still learning,” says Ryan, with 60ha on Puketutu Rd used for the family’s ‘first crack’ at sheep-milking and 120ha for an existing dairying operation.
Murray Wilson says 10 years ago he looked at diversifying into goat-milking but ‘couldn’t get
in’ with processors.
The block now used for sheepmilking had a previous life associated with grazing, maize and dairying.
At its peak, 1500 Southern Cross sheep will be milked in a new 72-bail GEA SR internal rotary shed.
“Some had been milked before, so picked it up pretty quickly,” says Murray.
He says three staff will be able to put through the entire flock in about two hours.
Also including a rearing barn and effluent pond, the new complex was all built on a greenfield site.
Murray says the barn can accommodate 1800-2000 lambs, while also being used for shearing and rearing calves.
Construction of the milking shed was undertaken by Matamata-based Randrup Dairy Parlours International.
Managing director Chris Randrup says the company has more than 30 years’ experience in dairy shed building, particularly in the United Kingdom and Ireland, but this was their first foray into a sheepmilking operation.
He worked with the Wilson family on the design and says they ‘had a picture in their mind after viewing other sheep-milking sheds around the country’. “They picked the bones out of that.”
Chris first met with Murray and Ryan in December 2020, and the inaugural milking went ahead in August 2021. “We started with a blank canvas,” says Chris.
He says coming from a farming background himself in the area obviously helped put the
project together, as did his ‘global’ knowledge of dairy shed construction.
Once earthworks were completed at the Puketutu Rd site, one of his company’s first jobs was laying 700m of pipe underground for the shed wash-down system.
A basic electricity supply for the builders and others working on-site came from an existing water pump shed.
Once positioning of the milking shed and rearing barn were established, Chris says the next step was laying a 4000 cubic metre concrete pad.
The design includes an underpass allowing easy access for contractors and farm staff to the inside of the milking platform.
Along with the rectangular yard, there are also cells including spaces for drafting and animal health.
Six cells are foot-ponds, plus two smaller foot-baths, which Chris says helps minimise sheep loss through lameness.
Our market-leading SR Internal rotary offers a milking experience like no other. With fast, uninterrupted loading, a gentle and relaxed milking process and the ability to efficiently milk more sheep, and goats with fewer operators, it’s simply second to none.
Steve Edwards The Wilson’s Southern Cross flock will peak at about 1500 this year. Ryan and Murray Wilson say the sheep venture really just came ‘out of the blue’ for the family operation near Matamata. The family business logo added a finishing touch to the milking shed.This means the overall shed design has 85 gates compared to about 30 in a traditional dairy cow complex.
Chris says foot care is aided by matting leading on to and off the milking platform. The roof was built on the ground next to the building, which he says saved about 10 days’ building time.
“The building is about 1m higher than a traditional design, offering greater natural light and air flow,” says Chris.
Galvanised iron was used throughout, finished with freezer panels, with no timber at all in the mix. The design includes a staff office and adjoining deck.
Chris says top class joinery, windows and fittings were used throughout. “It exudes class.”
His company was also responsible for separate pump, plant and electricity supply rooms,
plus a staff toilet and central concrete strip for feeding in the sheep barn.
Washdown of the yards and cells involves both freshwater (from a high-pressure hose) and recycled greenwater, with material ultimately piped to a new effluent pond.
Chris says the exit/entrance design into the yard and onto the milking platform provides a ‘good flow’ for the flock.
Typical of a sheep milking operation, blinkers are used on yard railings so the animals are not distracted.
GEA Farm Technologies supplied a special teaching platform at the entrance to the platform in which a milker can literally steer an animal in the right direction.
GEA area sales manager Grant Coburn says this is particularly beneficial in a new shed and when introducing replacements to the set-up.
Considering the technology and sheep numbers involved, he says a rotary milking shed was always deemed the best option for the Puketutu Rd operation. “And 72-bail is the biggest you can go on an internal rotary.”
Grant says a feature of the platform design is its running on an I-beam rather than the traditional chain-driven system. The platform has a stainless-steel top and rubber deck.
GEA supplied the in-bail feeding system, automatic cup removers and central plant wash gland, along with the associated wash-down technology in the plant room.
Installation was undertaken by Matamatabased Milk & Water Services. “They fitted out the milking plant and clusters,” says Ryan. Milk & Water Services’ contribution also included installation of equipment in the pump room and washdown system. The final step by Milk & Water Services involved piping from the milk room to the vats.
Matamata-based Jimmy Neal Electrical undertook all electrical work required in the project. Director Jimmy Neal says an existing power supply in a pump-shed was initially used by contractors before a new transformer was installed.
“We were first on-site and worked with Chris Randrup on the ducting and set up mains electricity to the site, barn and effluent pond.”
Jimmy says building the roof on the ground made wiring of the lighting over the platform and yard a lot easier than usual. “Floodlights were also installed at the end of the shed.”
Jimmy Neal Electrical completed wiring involved in the milking platform including drive motors and an in-bail feeding system. This also extended to electrical work relating to the milking plant, pump room, wash down and refrigeration equipment, vacuum pump and water heaters, says Jimmy.
Chris Randrup says the building is about 1m higher than a traditional design, offering greater natural light and air-flow.The sheep milking shed was a first for global cowshed builder Chris Randrup, general manager of Randrup Dairy Parlours International. The milking shed roof was built on the ground, which saved about 10 days’ construction time. Photos: Randrup Dairy Parlours International. NATION WIDE
His team wired up the vat wash and chilling system, and the power supply, lighting and water heating in the rearing barn. “A dedicated switchboard room was included in the design, giving a clear and dry environment,” says Jimmy. Detergents and teat-spray are supplied by GEA’s FIL.
FIL’s area manager for Cambridge/Matamata/ Putaruru, Greg Duncan, says the wash programme sees chemicals mixed with water in a tub and pumped automatically through the plant after each milking. “It’s a hot wash, with acid and alkali chemicals,” says Greg.
Chlorine is also added to the alkali to help remove protein build-up. Two 6700L milk vats receive similar treatment thanks to FIL after each pick-up.
Greg says the teatspray used is prescribed by Maui Milk, which Wilson Sheep
supplies. “It kills bacteria and through emollient helps with teat care.” The spray is applied manually by staff after the cups are removed following milking.
Matamata-based BCL Feed Systems has set up a feed system to provide tasty treats to the Wilson flock during milking.
“We installed two 16-tonne meal silos with dual feedlines into the shed,” says BCL director Talya Raumati. “It was a very good project to be involved with.”
A new effluent pond was required, with lining undertaken by Hamilton-based Aspect Environmental Lining.
The company’s project co-ordinator Louise Collins says the 30m x 30m, 3m deep pond was lined with 1.5mm thick high-density polyethylene (HDPE) liner.
Louise says the HDPE liner comes in a roll 170m long and 7.5m wide which is suspended with AEL’s lifting equipment and pulled out in sectional lengths.
The edge of the liner is ‘tucked’ into the top of the trench, held down by the weight of the effluent.
Louise says a gas venting system was also installed to release methane gas generated by the effluent.
“The HDPE liner is welded and tested before commissioning to ensure the pond is fully sealed. The pond is signed off with a pond-specific quality assurance documentation and a 20-year liner warranty.”
When full, the pond holds 1931 cubic metres of material, which is ultimately used as farm fertiliser via a travelling irrigator.
Changing from dairying to sheep and catering for the new milking shed and barn also required extensive fencing work, undertaken by McLaren Fencing.
Bob McLaren, who runs the Puketutu
Rd-based company with son Lachie, estimates they erected about 10km of new fencing for Wilson Sheep. This included post and rails, netting (a sheep specialty) and traditional wire fencing.
Bob says given the stature of sheep, rails are placed closer together than on dairy farms while 7-9 wires are also used. “Every fence has a hot wire.”
“Tanalised timber was used throughout, while the netting fences do not require battens,” says Bob.
“They are a quiet breed, so don’t put quite so much stress on the fencing.”
McLaren Fencing was also responsible for work along the new driveway from Puketutu Rd to the milking shed, and in the creation of paddocks to hold sheep rather than dairy cattle.
When Brendan and Jess Bouma decided to go into partnership with Brendan’s parents, Steve and Alison, on a new sheep milking venture, they bought a new 56-hectare property near Morrinsville. It already had a cowshed, large barn and space for winter grazing and growing silage.
With a deadline for milking to start at the end of July 2021, the lambing shed had to be ready for the arrival of 750 pregnant ewes from Spring Sheep Co. The newly-built barn is 50 metres x 48 metres with two concrete feed lanes, ready for use during lambing and the heat of the summer.
It is designed to accommodate 700 sheep at a time so they can be in the pasture from 8am to 2pm and then under cover overnight and
fed wheat straw, meal, molasses and grass silage prior to lambing. Four 25,000L water tanks service the barn.
The lambing pens can take 500 lambs at either end of the barn, and Steve takes the lead with the lamb care.
GEA Farm Technologies’ Waikato area sales manager Grant Coburn was called in to assess the requirements for the dairy shed conversion to sheep in time for milking to start after lambing. He describes it as a ‘big, brave step’ for the family to go into a full commercial venture without another business in the portfolio.
“I know Brendan well, he comes from a dairy background, both sharemilking and goat milking, and Steve has experience with sheep,” says Grant.
GEA helped with the design layout of the shed and yards. The existing 24-aside herringbone set-up was ripped out and
Brendan himself did the brickwork required to extend the pit by four metres.
Gibson Construction owner Blair Atkinson raised the floor by 300 millimetres for the sheep stalls.
“We lowered the yard for the sheep and put in steel yard fencing with hard-wearing aluminium panels,” says Blair.
“Considering we were retrofitting to milk sheep, it was the easiest shed I have converted. The shed already had a high pitch, making it possible to raise the floor; and it offers good airflow during milking, making it cool in the summer.”
Gibson Construction also carried out concreting for the new PPP industries-supplied and installed 17-tonne galvanized feed silo, with a 60-degree base, ladder cage and pole operated lid opener.
PPP Industries also supplied and installed the auger refill systems. PPP Industries
national sales manager James Kellow says underneath the silo going to the shed, there is a large 90 millimetre PKE auger to get the meal into the hoppers. “Each side of the shed was supplied with a single phase 1.5kW motor and gearbox, controlled by a high-quality feed sensor and control box to stop and start the system,” says James.
Graincorp provides a custom-feed blend to Bo Sheep. “It’s important to balance the changing nutritional needs of the milking ewe throughout lactation, and we work closely with Bo Sheep to achieve this for their flock,” says Graincorp technical support manager Glen McFarlane.
GEA Farm Technologies supplied a European-style SR Rapid Exit 42-aside milking parlour with 84 stalls in total and an individual indexing system.
“It’s a simplistic set up using one milk line. The highline swing-over system means all cups can be used on one side at one time for faster milking,” says GEA’s Grant Coburn.
GEA’s accredited service partner, Milk ‘n’ Water Services, led by owner Shaun Jellie, installed the milking plant. Shaun has installed many milking plants and views each project from an animal welfare and environmental perspective.
“Once the existing cow milking plant was ripped out, this was a fairly straightforward conversion as we were able to utilise a lot of the existing plant such as the plate cooler, milk pump and filter, but everything else was new,” says Shaun.
A new compressor was installed with a dryer to stop moisture getting into the airlines.
Keeping all the internals of the compressed air equipment moisture free is important as the Waikato is known for its high air moisture content.
“The new shed is not automated but does have controls for the stalling at each end, lending itself to automation further down the line with a fully retrofittable automation pathway,” says Grant.
“As this is a brand-new shed, everything has been completed for functional milking but some of the labour and time-saving features have been left until both numbers and production rise,” says Grant.
Brendan installed the backing gates and drafting system himself. For sheep handling he bought a Hecton Sheep Handler – the fastest, most versatile sheep-handler on the market.
It is ideal for dagging, crutching (full and half belly), foot trimming, vaccinating, wool sampling, mouthing, eye wigging, and loading of AI cradles.
“It allows full access to the underside of the animal. No heavy lifting is required, and operation is easy on the back,” says Hecton Products owner Aaron Bremner.
When it came to choosing the chemical supplier for the new shed, as GEA approve both FIL plant chemical cleaning products and teat spray products for their installations, Brendan went with FIL for his sheep plant installation.
“I went to the farm and assessed the water quality and used information about the plant dynamics from trial work carried out, so I could recommend a suitable chemical product,”
says FIL area manager Mark Mohring. “I prescribed a comprehensive milking plant and silo wash programme.”
After consulting with Mark and taking into consideration the more delicate teats of sheep and their other health requirements, FIL Teatshield was selected as the teat spray.
Keith Bell of KR Bell Electrical says this was his first sheep dairy shed project but it was easy to convert because all the fixed wiring was already there. Some needed moving to accommodate the installation.
“We fitted all the new appropriate machinery for sheep, and also wired the new undercover sheds for housing and lamb rearing,” says Keith.
Brendan and his family live on-farm and Brendan does the milking. He still can’t quite believe that everything came together so well and in time for lambing and the first season to start.
Farmer Brendan Bouma with Milk ‘n’ Water Services’ Shaun Jellie, and GEA International’s Grant Coburn. GEA milk receiving cans. PPP Industries highquality feed sensor and control box to stop and start the feed system. The 42-aside herringbone milking system with in-shed feeding. PPP Industries’ James Kellow with the 17-tonne galvanized feed silo. Gibson Construction builder Blair Atkinson.Malcolm and Claire Edward bought their 160 hectare drystock farm in 2016 – by 2021 they’d made the bold move into sheep milking using a decommissioned dairy shed on the property. They have ended up with a well-converted shed with modern plant and technology, complete with future-proofing for when they expand.
“Initially we had dairy grazers, and sheep and beef, but with rolling to steep contour and about five per cent flat land, the decision was made to primarily run more sheep due to the lower impact on the farm’s environment,” says Malcolm.
The Edwards attended two Maui Milk open days, before deciding to go ahead with a sheep milking venture on their property. The milking
platform is 75ha. “Maui’s Southern Cross sheep is not a large sheep and can handle our property’s contour well,” says Malcolm.
GEA area sales manager - Northland, Bay of Plenty and North Waikato, Paul Convery, was involved in the project from day one.
“I met with Malcolm to discuss his options and which old dairy was most suitable for the installation of a new GEA Milking System,” says Paul.
Once the choice was made, Shanan White of Don Chapman Waikato Ltd laid concrete for the silo and vat stands, and the tanker pad.
“We also had to box and pour the bail area floor to get a suitable milker’s pit depth and to suit the rapid exit stalling system,” says Shanan.
“Shanan knows all the compliance rules for pads and stands and that was very helpful,” says Malcolm.
Claire and her dad, Brian, spent hours painting the dingy old shed with bright white paint both inside and out, and painted all the trim in black. The shed looks like new and provides a pleasant working atmosphere.
The Edwards wanted to start out small and grow from there if all was successful. Paul planned a customised milking system with basic spec plant that could be added to in the future.
“The sheep milking industry came about in a very short space of time, so we’ve really had to think on our feet to come up with great, customised solutions to assist farmers with their new, dairy ventures,” says Paul.
Each set-up is very specific, and the Edward’s farm installed a 24-cluster high-line parlour and an auto wash system which reduces the operator workload and eliminates chemical handling. They are also using a GEA TopFlow
S sheep cluster specifically designed for sheep milking with an even milking-out process.
Plant such as milk yield metering, auto drafting or automatic cup removers can easily be installed in the future, without too much disruption to the current setup.
McLaren’s Rural Services’ Tony McLaren installed the complete milking plant and waterworks for the shed.
“Initially we were looking at installing a double-up lowline but as it was an existing cowshed, the old pit wasn’t deep enough for the gear. After discussing with Malcolm, we opted for a highline swing over set up,” says Tony.
While this only gave 24 sets of cups, operation of plant is still fast and efficient. Tony describes this particular job as pretty straightforward, using the same equipment as used to milk cows but different cups to suit sheep.
Catherine Fry The Edward Farms dairy shed and yards converted for sheep milking. The Edward family love farm life, from left: Marty, 5, Rebecca, 9, Claire, Hannah, 4, Brooke, 2, and Malcolm. The beautifully presented new sheep dairy. Coast & CountryEDWARD FARMS Malcolm and Marty Edward in amongst the ewes.Crossroad Engineering’s Graeme McIntyre has carried out work on this farm over many years, for previous owners. He was called in to complete all the yard work, pens and drenching race, and loading ramp for the sheep.
“We used all the existing railing and exit races and Graeme added bottom bars and visual barriers to sheep-proof the yard,” says Malcolm. He has bought a Hecton sheep handler for easier handling of the sheep.
Effluent is processed through a sump and around four hectares is irrigated with it.
Damian Silvester from Silvester Electrical completed all the electrical work, including digging a new mains trench through from the road.
“We upgraded the old switchboard and wired everything in, including the auto wash system, 9100L vat, effluent system and upgrading all the light fittings,” says Damian.
“Damian had done several dairy sheds before and he connected a lot of dots for us, and gave us lots of advice,” says Malcolm
Once all the plant systems and water had been connected and commissioned with several test runs, FIL area manager Mark Mohring became involved.
“We analysed the water to ascertain the correct products and rates to ensure uncompromised hygiene cleaning for the HB plant and silo.
“Acid, alkali, and chlorine chemicals are auto dispensed into the wash programmes through the auto Intelwash system. After initial testing and several commissioning site visits, the plant and silo programme settings were regularly checked to ensure all systems were performing
as programmed,” says Mark.
PPP Industries installed a 24HB feeding system into the Edward’s shed.
The systems consists of a 17 tonne feed silo with two auger lines coming out of the silo, conveying feed into dispensers down each side of the shed. A double auger lines gives the farmer more flexibility in how much feed their animals can be fed, with as little as 60 grams up to 4kg of feed dispensed during any one milking.
“Milking of small ruminants is limited by the minimum drop of standard feed dispensers, with the minimum rate of a standard feed dispenser being about 250 grams. There are large costs savings over a season if you only wish to feed your small ruminants on average 100 grams to 250 grams,” says PPP Industries
general manager Nick Morison.
In February 2021, 700 ewes arrived from Maui and lambing took place from the end of July. In a purpose-built 100m2 shed, Claire cared for the lambs with help from the couple’s children, Rebecca 9, Marty 5, Hannah, 4, and Brooke, 2.
“We have two ad lib auto feeders, and we assist the lambs until they get the hang of it. When they reach 15kg, they go outside on meal,” says Claire.
The Edwards experienced some issues with scald on lambs that first season which will be rectified for this season with the addition of a footbath for them. The ewes pass through one at every milking.
The goal is to get to 1000 ewes for the 2023 season. The farm has Malcolm working with another two staff and is set up so they each get every other weekend off.
Graeme McIntyre from Crossroad Engineering. GEA milk receiving cans. The Hecton sheep handler. The 24 high line GEA milking system and custom-made rapid exit stalling. FIL chemicals for the plant auto wash system. Malcolm Edward with Silvester Electrical’s Damian Silvester.Producing milk and income all year round is being achieved by Matangi Dairies with two species – cows and sheep.
The 107 hectare farm is owned by Giles and Clare Hailwood, Mark and Vicki Dewdney and the Luxton-Scholtens family.
“Mark and Vicki owned and milked cows on the farm for five years, but the plan was always to take in equity partners and maximise the productivity of the land by milking all year round with sheep and cows,”
says Giles Hailwood.
“The cows calve in autumn and are milked through winter, drying off in late-January; the sheep lamb in July and milk through to April. Having both species in production through peak grass growth ensures good feed utilisation and, overall, contributes to the profitability of the farm.
“Sheep are fussy eaters, so we crossgraze with the cows and this ensures good utilisation of grass. The ewes get one-third of
their diet in the shed – maize grain and protein pellets.
“We currently milk 690 ewes on 38 hectares with the cows on the balance – the Matangi Dairies’ cap illustrating the location of each farm – sheep to the left of the drive, cows to the right,” says Giles.
The diversification of Matangi Dairies milking operation took shape in 2019 with the decision to build a new dairy to milk sheep in.
Shanan White, of Don Chapman Waikato
Ltd, says they worked with the shareholders on the design of the dairy.
“We start with a knowledge of the technology which will be housed in the dairy and then customise the structure to accommodate that. We’ve earned a reputation in cow dairy sheds but, in recent years, have added goat and sheep dairy.
“Our focus is on building a dairy which is future-proofed, providing the owners with a facility where there will be fantastic animal flow, and which will be a pleasure to work in.
The roof of the new dairy extends beyond the yards to provide shade for sheep and also captures rainwater for washing down, avoiding it going to the effluent system.
“We built the concrete floor and yards, all the pipework and gates and the ancillary rooms. A feature of the dairy is the extended roof line, around 720m2, which covers all the yards; providing protection from the weather for animals and humans alike. The cladding of the building is insulated panels – as is the ceiling in the ancillary buildings. The roof of the dairy is Zincalume long run iron.
“As with goats, the entrance/exit races are screened so sheep are not distracted by others going in a different direction.”
Pratt Milking Machines installed the rapid-exit stalling system, and DeLaval milking machine, along with the water and effluent systems.
Director Zakk Pratt says the all-stainless
steel 30-aside double-up rapid exit stalling system is designed and manufactured by Pratt Milking Services.
The heart of the dairy is a DeLaval Low Line Double-Up 30-aside – 60 sets of cups –parlour with full DelPro Flock Management System. The clusters are TF100ML S100-s, with MPC580 Cup Removers and MM25SG ICAR approved milk meters. The dairy is also equipped with a DeLaval Sort Gate and DeLaval Portal ID.
Farm manager Lisa Clark says the parallel parlour system enables faster loading and exiting with perfect animal position, which
allows for faster cluster attachment and milking routine.
“The DelPro Flock Management System means we have real time data on such things as stall position, milk yield, animal numbers, milk flow and milking duration, which is really essential with sheep – which, unlike cows, all look the same,” says Lisa.
As each ewe enters the dairy, the DeLaval Portal ID automatically identifies her from her ISO eartag and sends information to the DelPro Flock Management System. On exit, the DeLaval Sort Gate automatically drafts selected animals.
Existing vats, for milk and colostrum, were repurposed and installed – along with milk cooling – by Dairy Technology Services. DTS
area manager Dave Gray says milk goes into the vat at around six degrees Celsius, the 6hp Ryker refrigeration unit taking it down to under three degrees in less than an hour.
In relation to the effluent system, Zakk says the existing bore is supplemented by rainwater collected from the large roof area and supplies shed washdown and stock water. “Effluent goes to a sand trap and gets pumped to the existing cow shed bladder which has a diverter – for rain and effluent.”
A meal feeding system is a key component of a rapid exit dairy, and the in-shed meal feed system was manufactured and installed by Landmore Agri.
From inside the dairy looking back down the collection yard, showing the screening which prevents distraction as ewes enter the dairy or leave the rapid exit.
All sheep walk through two footbaths as they exit – the first contains water to clean hooves and the second a copper or zinc solution to treat and prevent foot rot.
Landmore Agri’s Shayne King says that the drive motor brings feed from the Big Dutchman silo and individually dispenses it to each sheep. The PML bins raise to release the sheep and are replenished so the meal is available for the next row when they enter the bale.
All electrical work for the new dairy was carried out by Electronz. The construction of the new dairy commenced on February 10, 2020, with the first milking taking place on July 20, 2021.
Lisa recalls that the first few milkings were busy. “I grew up on a dairy farm and have had
a lot of experience milking cows on contract/ share milking jobs.
“I had only milked sheep once through a rapid exit dairy before I joined Matangi Dairies on June 1, 2020. Compared to milking cows, you are working at speed in a sheep dairy. The milking machine is timed to four-minute rows and we have automatic cup removers so you’re walking 6000 to 7000 steps per milking!
“The floor of the pit is lined in rubber though, so it’s easy on your knees.
“The 690 Zealandia ewes were supplied by Spring Sheep, who were incredibly helpful with advice and support. We lambed around
20-30 per day for six weeks and, thanks to the meal, they settled fairly easily to the milking routine.”
The Hecton Sheep Handler is, according to Lisa, ‘brilliant’. “It saves your back as you’re trimming feet every day.”
In all it takes around two hours to milk the 690-ewe flock from start to finish, Lisa admitting she enjoys the change of pace and species. Mostly milking is carried out with two people in the shed and one person collecting
The view from the entrance to the dairy showing the DeLaval Portal ID which automatically identifies each ewe from her ISO eartag and sends information to the DelPro Flock Management System.
the herds. The wider-thanstandard pit means if required, three or four people can work in the pit without getting in each other’s way.
Giles and his wife Clare split their time between the cow and sheep farms to provide assistance and oversight of both operations: “So we can capture and maximise synergies,” says Giles.
“The first year has provided lots of learnings, particularly through lambing. Milking has been great – we have an excellent milking crew and lamb-rearers”.
Farm manager Lisa Clark says the Hecton Sheep Handler is a critical piece of equipment.
The rapid exit system is raised, to the left, for sheep to exit and lowered, to the right, when sheep are in their stalls and being milked.
Until 2021 the only experience the Kirkham family had with sheep was rearing and training pet lambs for school agricultural days.
Parents Gordon and Linda Kirkham purchased 96ha on the outskirts of Te Awamutu in 1986, gradually adding adjacent properties as they came on the market.
By 2020 the combined property comprised 305ha – a long, narrow farm which meant a long walk for the 900-cow herd from the furthest reaches.
“The kids [son Scott and daughters Emma and Holly] were working off the farm and, wanting to step back, we looked at the property to decide how we could maximise its production and profitability to provide a future for our family,” says Gordon.
“We had a friend who was a shareholder in Spring Sheep and he encouraged us to consider
subdividing the furthest part of the property (from the dairy shed) to a sheep dairy farm.
“Milking sheep was, at that time, an emerging industry and being early adopters had some appeal, so Linda and I discussed it with the kids, and the rest is history,” says Gordon.
Those discussions led to the decision to subdivide 35ha to be developed as a dairy sheep farm.
“We’ve always had DeLaval technology in our cow dairy and were impressed with their innovation and experience with small ruminants, so it was a no-brainer to have DeLaval equipment in the new dairy,” says Gordon. “I then drew on past skills as an architectural draftsman and designed the building which would house it.”
The resulting building is striking. The dairy and auxiliary buildings, which house the office/
staff, machine, vat and pump rooms, have complementary roof lines that take advantage of the weather and provide shelter.
The design called for a horizontal vat and Gordon says while a 6800L vat would have been sufficient in the early years the potential for a larger flock in the future meant they settled on a 9700L horizontal DeLaval vat, which gives room for growth.
The design and construction of the dairy and yards was undertaken by Te Awamutu-based Elite Services, which specialises in rural, engineering, and residential steel building services. Gordon says their expertise brought his design to life.
Gordon and Linda’s son Scott returned to manage the new sheep dairy and says that, with no experience with dairy sheep, he drew on the knowledge and experience of Spring Sheep.
“They supplied 610 Zealandia in-lamb ewes,
260 of which were hoggets and the rest mixed age. “This balance was vital when it came to milking, as the ewes familiarity helped settle the hoggets,” says Scott.
Construction of the new dairy commenced in March 2021 with a completion date to coincide with lambing.
Pratt Milking Ltd supplied and installed the 42-aside Pratt Rapid Exit, DeLaval milk plant and horizontal vat.
Director Zakk Pratt says PML developed and manufactured the rapid exit in response to growth in dairy sheep and goat farming.
“The system is very simple and encourages good flow of sheep into their individual stalls, where they are fed a measured amount of feed.”
The Kirkham dairy is the first in New Zealand to feature the unique DeLaval Euro Swing Over (MidiLine SG200) system.
The new dairy’s entrance collection yard.
The pit is uncluttered thanks to the adjustable cluster slide rail of the DeLaval Euro Swing-over.The exterior of the new dairy.
“I saw it online,” says Zakk. “There were none in New Zealand at the time – but the design was evolutionary, taking all the clutter out of the pit.
“It’s an incredibly simple and effective alternative to the traditional swing-over with an adjustable cluster slide rail system, which ensures perfect alignment.
“The milker simply ‘swings’ the cluster from side-to-side, the system itself supports all the weight of the droppers and uniquely positions the cluster with perfect alignment.”
PML supplied the 9700L litre DeLaval horizontal vat and the necessary refrigeration plant was installed by Robin McGregor of Power Chill NZ Ltd.
The dairy’s effluent system was designed and installed by Pumpn and consists of a 22m3 sump and sand trap. A bladder will be installed
in the future as growth demands.
Lambing started July 17, with Scott recalling that for the first few weeks he and his father milked eight ewes at a time via a mini-milker in the adjacent old herringbone, which had been converted for lambing.
“The Spring Sheep team were outstanding and provided a lot of much-needed support in those early days and weeks.
“They would come and give advice and we also got a lot of support from other dairy sheep farmers. The camaraderie across this fledgling industry is quite amazing. The first lambing tends to be fresh in most people’s memories, so we got a lot of support,” says Scott.
Foot maintenance is a daily necessity and the Hecton Sheep Handler, which is located
in the yards of the old herringbone, makes this simple, reducing stress for the ewes and saving our backs.
“No lifting is required and each ewe is safely and securely held so we can attend to any feet issues,” says Scott.
The new dairy was operational in the first week of August and the flock gradually adjusted to the routine of milking.
“The cluster slide system is great,” says Scott. “The clusters move effortlessly and silently from one side to the other and the automatic wash system is very simple and effective.
“It takes around one hour to milk and by the time we’ve hosed the yards, the system wash is finished.
“The vat’s automated wash system is a real
labour and time-saver as it is triggered when the tanker empties the vat – avoiding need for anyone to be at the dairy to turn on a wash system.”
One year on, Gordon is very happy with the decision to develop the sheep dairy.
“It has delivered so many benefits in terms of family succession with the kids home, but has also contributed to the overall sustainability of the entire farming operation.
“The learning curve at the start was bloody steep. Scott and I were milking and Emma was rearing the lambs with a few part-timers and there weren’t enough hours in the day.
“But we accomplished a lot in a short time and, looking back, it was worth it. It all came together in a relatively short time.
“Twelve months ago, where the new dairy is today, was an old race with trees everywhere. Now it’s the heart of an efficient, productive sheep dairy unit. It’s exceeded my expectations.”
PML’s Aaron Murphy demonstrates the simplicity of the DeLaval Euro Swing-over’s adjustable cluster slide. The controller for the DeLaval C200 automatic wash system. The 9700L horizontal DeLaval vat takes milk to less than three degrees Celsius in 20 minutes, avoiding need for a water chiller. The complementary rooflines of the auxiliary building and dairy. Page 73PH 07 578 0030 ROTOHIPI The PML Rapid Exit system in raised position, showing the stainless-steel feed bins and feed hoppers.The literal translation of the Maori word ‘Aranui’, is path (ara) and great (nui) – a ‘great path’ – which is a fitting name for a farm that set Chris and Claire Walton on the path to farm ownership.
“We emigrated to New Zealand from England in 2018 having visited and worked here in 2013 and 2015,” says Chris.
“In the UK and Scotland I worked on sheep and beef farms and our original intention was to do the same in New Zealand, with the ultimate aim of farm ownership. However, reality bit and we realised the margins would never allow us to purchase a property on our own.”
Chris says at the time sheep milking was
emerging as a new industry and they were fortunate to have friends who had developed a sheep milk farm at Carterton.
“We spent time there and were excited by the prospect of becoming involved in a fledgling industry which had so much potential.
“That early enthusiasm and some fortuitous networks led to the purchase of this farm with four partners, who are all involved but who leave the day-to-day management of the farm to us.”
Chris and Claire took over the 118 hectare property on the outskirts of Te Awamutu in June 2021.
“The farm was an operating dairy farm with an existing 22-aside cow herringbone. The dairy
and yards were sound but required extensive renovation to convert it from cows to sheep.
“Working with Qubik, we developed a plan to extend the dairy to, initially, a 42-aside with the potential to add another six stalls on each side to make it a 48-aside.
“We purchased 650 mainly two-tooth ewes from Maui Milk, which were mainly a mix of Southern Cross and Coopworth.
“Our long term plan is to milk around 1200 ewes but the flock of 650 was a start, giving us the potential to retain ewe lambs over the next four to five years to reach the target number. And while we’re doing that we have taken on dairy grazers to help manage grass growth,” says Chris.
Qubik sales specialist Nick Heffer says they started working with Chris and Claire in October 2020 providing design options and getting a full understanding of what they wanted to achieve in the short and long term operation.
“Lambing was due to start in August, leaving around 10 weeks to convert the dairy,” says Nick.
The last cow milking took place by the previous owner on May 30, 2021, and three days later Qubik began to remove the old milking plant ready for the conversion.
“The old shed was gutted, one of the first priorities being to change the height and fall of the pit floor,” says Chris.
The original shed was a gull wing that drained to the centre, so the floor had to be levelled so it fell to the end of the pit. Overall the floor was dropped by 300mm.
Clare BaylyAfter a lifetime as a sheep and beef farmer, Chris Walton admits he really enjoys being a sheep dairy farmer.The original 22-aside cow dairy transformed to a 42-aside sheep dairy. Chris and Claire’s three children immortalised in the concrete of the yard extension. The 650-sheep flock is predominantly Southern Cross bred and supplied by Maui Milk.
Qubik supplied and installed the stainless-steel heater stand which eliminates the need for a manifold, two hot water cylinders and stainless steel washtub.
Screening on the entrance and exit races ensure the flock’s smooth entry and exit.
The roof was extended by 7m at the collection yard end to future-proof the dairy by enabling a further six stalls to be added to the new 42-aside system that was to be installed.
Nick says the Qubik Rapid exit system, exclusive to Qubik, is the only fully stainless rapid exit system on the market in New Zealand.
“A feature of the Qubik Rapid Exit System, particularly applicable to Chris and Claire’s dairy, is that it is designed to work efficiently with tight pit-to-wall gaps, so the sheep exit underneath the stalling at an angle which is faster and smoother than if they had to go straight out of the stall and then turn a corner,” says Nick.
The dairy is equipped with Waikato Milking Systems ECR-S Cup removers, which speed and simplify milking, avoiding any potential for over-milking. SmartPULS Electronic Pulsators feature rippled pulsation which ensures excellent vacuum stability and quiet operation.
The 5000L double-bank plate-cooler enables Chris to meet the industry’s strict
milk cooling regulations. Qubik also installed the Waikato Milking Systems Top Loading milk filter and the Fristram Lobe milk pump and VSD Controller, which moves the milk gently and efficiently. The Waikato Milking Vacuum system BP200 with 7.5kw motor and SmartDRIVE compensates for vacuum use by increasing or decreasing the vacuum pump speed on demand; this also equates to power savings.
“Qubik Automatic plant wash gives Chris and Claire peace of mind when they are off-farm or using relief milkers,” says Nick Heffer. “The wash programme activates after every wash, allowing the milkers to focus on other farm jobs once milking has finished.
“We also supplied and installed the shed water system, which includes the stainlesssteel heater stand that eliminates the need for a manifold; two hot water cylinders; and Qubik custom-made and designed stainless steel washtub. In addition, we linked the new washdown and cooler pumps to the existing
dairy shed framework, supplying all new washdown, hoses and re-piped the shed.”
Qubik Refrigeration supplied and installed the 9100L stainless steel vat and the colostrum vat for the early and late parts of the season.
Chris says Liam Carter from Phase Electrical provided excellent service and helped out especially through the Covid lockdown as the project was coming to an end.
“We called them out at the start of the job to disconnect the shed and once everything was finished, they came back and wired the rapid exit system, pumps and all electrical components of the shed,” says Chris.
Lameness is an ongoing issue with milking ewes so, along with regular on-farm treatment, Chris uses Waikato-based Goat Care to give the ewes a pedicure twice a season. “This minimises foot care during the season and reduces stress for the ewes.”
Five months on from their first lambing as dairy sheep farmers, Chris and Claire reflect on achieving their dream of farm ownership.
The original collection yard transformed, with screening, for milking sheep.
“The last few months have been hectic –particularly lambing when we had six people to ensure that all the critical things got done and done well – but now we’re into the rhythm of milking sheep twice-a-day. On average it takes two people 1.5 hours to milk the flock.
“The sheep milking community – particularly Maui Milk and fellow dairy sheep farmers – is fantastic, so friendly and supportive.
Throughout we’ve been buoyed by their friendship, help and camaraderie.”
The Qubik Rapid Exit is designed for tight pit-towall gaps, enabling a faster exit as sheep leave at an angle versus straight then turning a corner. From left: Qubik’s Nick Heffer, sheep dairy farmer Chris Walton, Phase Electrical’s Liam Carter, Qubik’s Jeremy Collett, and Waikato Milking Systems’ Ben Frederickson.A new rotary dairy shed development in the Waikato is a marriage of old and new.
Arco and Yvonne van Vliet have run their 150ha Tahuna-Ohinewai Rd farm for nine years, initially milking a 480-cow herd in a 40-aside herringbone shed.
This was updated in 1983, but Arco says it would have taken ‘a fair whack’ of money to keep it up to standard.
Two years ago they decided to build a new rotary milking shed, catering for the same size herd, which could be operated by a minimal number of staff. “A one-man band,” says Arco.
A building to accommodate a 60-bail rotary was designed by Morrinsville-based Chapman Dairy and built by Don Chapman Waikato.
Having to keep milking through the construction phase, Arco says they took
advantage of an existing feed-pad and effluent system, along with farm races.
The new milking shed, built directly beside the old herringbone, also uses a good chunk of the existing yard which has been added on to by Don Chapman Waikato.
Don Chapman Waikato director Shanan White says the same scenario, blending old and new, was used for an enlarged concrete slab at the base of the feed silos.
He says the shed also involved new rails, while using part of the existing tanker loop. “The site was an old paddock and part of the tanker track,” says Shanan.
The Don Chapman design is ‘standard layout’ including an office, storeroom, chemical room and pump room.
Shanan says earthworks for the site,
undertaken by Waihou Excavation, saw a significant amount of topsoil needing to be moved. The contour of the land saw a pit required around the milking platform.
Waihou Excavation owner-operator Frank Teague says close to 2000 square metres of soil was removed from the site.
This saw the existing tanker loop re-shaped to link with the new milking shed, which Frank says had to be completed around tanker pickups from the old herringbone.
“Creating a pad for the rotary milking area, at the same level as the existing yard, saw soil removed to a depth of 3m from the former paddock.”
In addition to this, Frank says a 2m deep trench was required around the pad for a drainage pipe.
Waihou Excavation also filled in the old pit in the herringbone and carried out required
Staff and cow comfort are top priority, including natural light via skylights and NZSSapproved LED lighting installed by McMillan Electrical Solutions.
earthworks for new drafting races.
Frank says the excess soil – volcanic clay – was used to contour paddocks on the farm.
Morrinsville-based McGregors Farm Services worked closely with the van Vliets to supply DeLaval plant, equipment and technology right from the outset of the project.
Technical sales manager Shaun Killalea says McGregors installed a DeLaval Rotary E100 milking system which includes DelPro herd management software.
EID ear-tag identification is used to monitor each cow in the parlour, including the quantity and quality of the milk each animal produces.
Shaun says there are ICAR rated milk meters inside the platform, which capture the cows’ performance and this information is sent back into DelPro.
The system is fully integrated with automatic cup removers, on-deck teat spraying, weighing and drafting all controlled by the DeLaval DelPro system.
“Cluster drop and autowash are also standard on this 60B DeLaval Rotary E100,” says Shaun.
The in-bail feeding system can be set for different amounts per cow according to the season.
Shaun says the technology is centred on a touchscreen control panel (IDD), sited just outside the platform, dubbed ‘the cockpit’.
“It takes a lot of the guesswork out of herd management and makes things simple,” says Shaun.
Information goes into the shed office computer and can also be accessed by the owners and staff via their mobile phones.
Shaun says a feature of the design is a hydraulic platform at the spot outside the platform where cups are applied, which can be raised or lowered according to the height of the milker.
McGregors Farm Services general manager Daniel Peake says they worked with DeLaval in the plant room including the autowash system, wash tub and milk filters, plus the vacuum and water pumps.
Water from existing tanks was used for the cup wash and teat wash systems.
Daniel says the chilled water system was brought over from the old milking shed, as was a 350L hot water cylinder. Two new cylinders were required for the van Vliet shed.
Mike Hampshire, McGregors’ project manager on-site, says cleaning up after milking is user-friendly, with a ‘skirt wash’ installed for the stainless steel platform.
“It’s just the push of a button,” says Mike, as
is the vat wash system activated by the tanker driver after collection.
All electrical work was completed by Morrinsville-based McMillan Electrical Solutions. “It was pretty much a new fit-out,” says owner Steve McMillan.
This started with a new transformer and mains supply from the main line along TahunaOhinewai Rd.
Steve’s team wired up all the milking equipment and plant, along with associated washdown, chilling and feed systems.
Looking to keep the complex tidy and uncluttered, Steve says numerous cable ducts were formed under what would become the pit and plant-room during the earthworks before concrete was laid.
Required to meet New Zealand Safety
Standards, for staff and cow comfort, a qualified lighting engineer oversaw the LED lighting in the new shed.
Steve says McMillan Electrical Solutions also integrated the existing effluent disposal system into the new complex, while adding a new submersible stirrer.
With power supplies changed, the old switchboard was downgraded while implement sheds were re-wired and a data link established from the staff house to the milking shed.
Arco van Vliet says the old buildings will remain, however the milking pit from the former herringbone shed has been filled in.
He and Yvonne farmed at nearby Kiwitahi for nine years before moving to Tahuna. The new shed is capable of catering for a bigger herd in future, but Arco is happy with the current set-up.
“We’ll see how we go.”
The site of the new dairy was influenced by the gas pipeline that traverses the farm.
Building a new dairy is one of the biggest decisions a farmer will make – after land and herd acquisition – and whether that be a rotary or herringbone came down to one simple equation for a Te Awamutu farming partnership.
Cameron and Aotea Empson farm a 160 hectare property which was, until recently, two 200-cow farms.
“The farms are owned by my parents, Chris and Helen Empson, and had been run as separate units for around 20 years. Each had a herringbone – a 15-aside and 12-aside respectively,” says Cameron.
“I grew up on the family farm across the road but left farming in favour of banking. Aotea and I were based in New Plymouth and had two young boys; we wanted to be closer to family and so came back to the farm.
“We farmed on the property with the 12-aside shed which, like its sister shed, was nearing the end of its productive life. When I talked to dad about building a new shed he suggested we combine the properties and build one shed,” says Cameron.
“The cost of combining two farms – new races, fences etc – is considerable so, initially, I wanted to build a herringbone to keep costs down,” says Cameron.
“However, when you are milking 450 to 500
cows through a herringbone you are committing to two or three people in the shed, so it came down to a shed which was more easily operated by one person – and that was a rotary.
“Everything else flowed from that decision – technology, animal handling etc. We aimed to build a dairy which would futureproof the farm and make it easy for one person to operate other than in peak periods like calving and mating,” says Cameron.
The location of the new dairy was, Cameron says, ordained by the location of a gas pipeline that traverses the farm further down the hill.
“The two original sheds were located at the top of the hill but we were able to extend the entrance race to a site which had the scope for
the size dairy we were going to build along with the chilled water and effluent systems,” says Cameron.
“Dad had made a study of shed design and so when it came to which way the ridge-line would run, we opted in favour of the highpoint in the roof covering at one end the vat stand, and at the other the animal handling facilities. Traditionally the high point would have been over the cow entrance and exit. It just made sense to have the vat out of the sun.”
Cameron says the width of the shed also allowed them to cover an area alongside the colostrum vat so the calfeteria can be easily filled, and cleaned, out of the weather and –similarly – dosing equipment can be prepared and stored.
“We also wanted easy access to the centre of the dairy but wanted the entrance and exit positioned on the outside of the dairy, removing clutter from the interior,” say Cameron.
When it came to choice of a platform, Chris and Cameron had no hesitation in electing to work with Waikato Milking Systems.
“They are a local company. We are fortunate to have a company which supplies milking machines all over the world based in Hamilton; this meant we were able to visit their headquarters to meet the people behind the brand and experience the innovation and quality behind their products. Having that insight only added to the confidence we already had,” says Cameron.
“We’ve had Waikato Milking Systems gear in other sheds – it’s reliable – and the local dealers, Qubik, are here on the spot.
Cameron says the new dairy is sized for a maximum of 500 cows and after some discussion with Jason Hare from Qubik they opted for a 40-bail Waikato Milking Systems’ Centrus Composite Rotary Platform.
“We considered going for a 50-bail but I didn’t feel the size of the platform would hold up the speed of milking, because if you only have one person cupping there’s a limit to how quickly you can go.”
The lightness – 74 per cent lighter than concrete alternatives – and strength of the Centrus Composite Platform appealed to
the Empsons as did the ease of maintenance, long life and enhanced cow comfort thanks to rubber mats in every bail.
“The need for the dairy to be a ‘one man operation’ meant we chose a relatively high level of automation from Waikato Milking Systems – automatic cup removers, teat spray, automated drafting and wash down – all items which individually and collectively improve the efficiency of the dairy,” says Cameron.
“Going with Waikato Milking Systems also meant we were able to minimise the number of computers required in the dairy. All their systems are integrated and complement each other, a good example being the NaviGate Premium Farm Management System which, in addition to drafting, manages our automated feed system.”
A new effluent system was required and development of the pond was carried out by Waikato-based rural, industrial and commercial longreach excavation specialists Roy Cullen Excavation, and commenced in January 2020.
Owner-operator Roy Cullen says when working with farmers on effluent systems the pond is built to the required size and with an appreciation for the pond liner.
Te Awamutu-based Gibson Construction director Blair Atkinson says his team undertook all the engineering and construction of the new dairy including all concreting: i.e. the floor of the dairy along with internal and external yards.
“Concrete slabs were used in place of concrete blocks for speed of building and overall streamlined appearance of the building,” says Blair. Gibson Construction also built the effluent system weeping wall.
Once the concreting of the dairy floor was complete, Moa Milking & Pumping installed the Waikato Milking Systems 40-bail Centrus Composite Platform, which features the multiroller twin-track undercarriage.
Moa’s senior service engineer Matt Churchill says: “The Multi Roller system incorporates dual i-Beams which effectively bear the weight of the platform on a set of industrial grade nylon polymer rollers”.
“The system requires minimal maintenance and provides increased durability,” says Matt.
With the new platform in place, Qubik
installed the milking machine which features Waikato Milking Systems ECR Plus electronic cup removers, SmartD-TECT Mastitis Detection, SmartSPRAY automatic teat spray, SmartWASH automated plant wash and BailGate straps which automatically restrain or release cows from the platform. A Fristam centrifugal milk pump ensures trouble-free pumping of milk around the dairy, supported by a variable speed blower vacuum pump.
A Waikato Milking Systems NaviGate Premium Dairy Management system automates and simplifies efficient three-way drafting of
cattle. The system’s sort gate’s quiet movement ensures cow flow is not interrupted as they move through the sort gate.
The dairy’s refrigeration system comprises of Qubik’s unique 30kw Chilled Water System and 25,000L Manicon concrete tank which is buried in the centre of the tanker loop.
Qubik sales manager Nick Heffer says combined with Waikato Milking System’s double-plate cooler, the system is very efficient and environmentally-friendly, chilling milk to around six degrees Celsius when it enters the vat while generating significant electricity savings.
“The system’s heat recovery unit heats water
to around 60 degrees Celsius which means the hot water cylinders then only need to heat it a further 20 degrees Celsius to the required 80 degrees Celsius,” says Nick. “This is a huge saving in electricity over the more traditional methods of milk chilling.”
Pratt Milking Machines installed the hot water cylinders along with the washdown and auxiliary pumps for the shed and stock water. They also installed greenwater on the backing gate for the yard wash. PML also designed, constructed and installed the stainless steel fencing and gates around the entrance/exit to the underpass to the centre of the platform.
The dairy is very spacious and bright with natural light from all four sides. Above: The dairy interior, hot water cylinders and, beyond, the side door giving a glimpse of the exterior entrance to the dairy’s centre. Rubber matting on the Centrus Composite Rotary provides a quiet and comfortable footing for cows. Qubik’s Jason Hare in the dairy’s milk room. Left: Moa Milking & Pumping’s Matt Roberts near the Centrus Rotary Platform’s unique i-Beams, which bear its weight on a set of industrial grade nylon polymer rollers that need minimal maintenance.Waikato-based Corohawk installed the dairy’s feed system featuring a Chore-Time silo and 1.2m 100 per cent stainless feed trays, which features a safety edge along the front. All seams are sealed and welded for strength, hygiene and durability. The rotationally moulded dispensers are known for their strength and feature a ‘Y’ end, which halves the number of dispensers required without impeding the flow of feed.
All electrical wiring for the new dairy was carried out by electrician Paul Chestnut of Waipa Electrical. Paul says this required numerous visits to the site to accommodate the various stages of the dairy’s development, but being on-call is a vital part of any large-scale project.
Cameron says the original goal was for the dairy to be completed by June 2020 but then Covid-19 intervened, uncertainty about essential
worker status causing a pause in construction.
The first milking in the new dairy took place in mid-August and by that time threequarters of the herd had already calved, with Cameron’s team milking them through the old 15-aside herringbone.
“Their familiarity with the herringbone system presented us with some challenges when we began converting them to the rotary but we did this progressively, rather than the whole herd, and the lure of feed – they’d never been fed in the shed before – soon saw them flowing onto the platform.”
Cameron says in-shed feeding has a number of advantages – settling cows on the platform is an obvious one. We are also able to monitor and supplement minerals and ensure they are fed to every cow.”
“The NaviGate Access Farm Management System’s integration with the feed system
The dairy’s interior is light and bright thanks to large side doors and clearlite panels through the ridgeline.
enables me to have up to four different rations for the cows, which can be sorted into different mobs with different feed regimes. It’s fantastic.”
“One of the things on a rotary platform is the cows quickly learn that, if they do another round, they can get more feed but the precision feeding possible with NaviGate means that each cow gets a specified amount of meal at every milking so if she goes around again, she doesn’t get a second allocation.
“All up – from start to finish – it takes around two to two-and-a-half hours to milk our 450 cows, twice a day.”
Cameron says changing the ridgeline so the vats, dosing equipment and animal handling facilities were protected from the weather was a ‘fantastic initiative’. “The farm quad and
calfeteria can be parked out of the weather so that colostrum can be added and then the calfeteria cleaned on concrete and out of the rain, which is a real boon during calving.”
The area is also used for mixing dosing and spraying equipment can be stored, mixed and cleaned.
“The exterior entry to the centre of the platform is also a significant feature, removing clutter from the interior of the dairy and allowing easy access regardless of whether milking is taking place,” says Cameron.
“Similarly, the under-cover location of the animal handling yards and facilities means we are able to attend to all animal needs, again out of the weather and mud.”
Combining the farms and building one automated rotary has proven to benefit the overall efficiency of the dairy. “It’s a pleasure to milk in,” says Cameron.
The Waikato Milking Systems’ NaviGate Access Farm Management System sort gate and, to the right, the animal handling facilities. From start to finish it takes one person two to two-and-a-half hours to milk 450 cows. Pratt Milking Ltd’s Josh Ferguson. The collection yard view of the dairy.As if lambing close to 600 sheep for the first time wasn’t enough of a learning curve, 24-year-old Ryan McPherson accomplished it wearing a moon boot after breaking his leg.
“That bit wasn’t planned, but everything else was,” Ryan laughs, “so I just got on with it. It was sink or swim. Mum and Dad had given me a great opportunity to manage the farm and I was determined to make the most of that.”
And make the most of it he did. As his first season as a dairy sheep farmer draws to a close, Ryan reflects on a year of challenge and change.
“It was the end of 2019 and I had just finished a business management degree at Waikato University but, due to Covid-19, I hadn’t secured a job, so Mum and Dad
suggested I run their two run-offs while I looked around.
“Sheep milking was starting to become popular and the appeal of getting into a new industry which had a smaller environmental footprint and –hopefully – a big future, had a lot of appeal.
“Spring Sheep was holding a conference in September 2020, so I went and came back armed with a lot of information, and the reassurance of genetics, support and advice from Spring Sheep.
“Fortunately, my parents agreed to convert 40ha of their 70ha property to sheep milking.”
Ryan grew up on his parents’ dairy farms spending the obligatory time in the dairy but admits he never considered milking any other species.
“Spring Sheep really took me under their wing, putting me in touch with another farmer, Rhys Darby, who had done a similar conversion to the one we were planning.
“I did one milking with him and found his 42-aside GEA Rapid Exit and milking system to be easy to use and efficient, so we decided to replicate his set-up as much as we could at home.
“GEA’s Grant Coburn followed up by measuring our old shed and determining that, with appropriate extensions, we could accommodate a 42-aside GEA swing-over Rapid Exit with a slightly modified sheep entrance due to the angle of the wall of the old shed,” says Ryan.
The conversion started in February 2021 with the gutting of the shed and extension
and narrowing of the pit. The bail area was raised to achieve the optimum milking height and the roof was extended and replaced.
The 42-aside GEA European Rapid exit stalling system was then installed. The system included animal indexing stalls, stainless steel feed bowls and group feeding hoppers and controls. Pneumatic dual controls on both sides of the pit control the entrance, feeding and raising of stalling to allow the ewes to exit after milking.
The GEA milking system was installed by Tokoroa-based Fire n Ice and includes the Intelgen controller with auto pulse pulsation, Ovi twin sheep milking clusters feature silicone milk tubing and liners. The dairy was fitted with a new blower vacuum pump with Intelvac controller.
Fire n Ice electrician Grant Gall says rewiring the dairy saw the removal of all wiring from the old shed and relocation of the original switchboard. “We had to keep the water going to service the dairy run-off and then pre-wired the shed as it was being built,” says Grant. “We also added a second hot water cylinder.”
Fire n Ice managing director Lance Felton says bore water provides primary milk cooling, with the chilled water system chilling the milk to three degrees Celsius when it enters the vat. The refrigeration unit then takes it down to around one degree Celsius.
Lance says that, as happens with so many old sheds, they had to customise fittings – for example, the soak pit was customised to capture water from plant wash. “We also installed a stainless steel heat shield over the exhaust with a second muffler on the roof to dampen the noise,” says Lance.
FIL area manager for South Waikato and Taupo, Robbie Kirk, says FIL tailored a wash regime to address and manage
the unique nature of sheep milk. “The requirement for milk to be cooled to less than two degrees Celsius and four-day pick-ups means the milk, which has a high fat content, has more contact in the vat, calling for greater use of hot water and water volumes.”
A Hecton Feed System was installed comprising of custommade stainless-steel bins, feed lines, and silo. All ewes receive the same amount of feed. The bins rise with the Rapid Exit system and are filled so feed is available for the next row of sheep when the system is lowered.
The dairy also has a Hecton Sheep Handler which simplifies and speeds daily foot maintenance. No lifting is required and each ewe is safely and securely held while any feet issues are addressed.
Ryan says the conversion was completed in July 2021 ready for the start of lambing.
“Our mixed age ewes came from Spring Sheep. Having never worked with sheep, the prospect of lambing 600 ewes was a little daunting but I just got on with it, supported by a fulltime staff member and a couple of lamb-rearers.
“Breaking my leg didn’t help of course and certainly added a degree of difficulty when it came to catching lambs but the Spring Sheep team was regularly on hand – either on the phone or on the farm – for advice and support.”
“The new shed is better than we thought it would be,” says Ryan. “The first few weeks the sheep were unsettled but once they knew the routine – knew that feed would be in their bails and understood how the rapid exit would rise – they settled well.
“The end of the season is approaching, so I have dried off any with high somatic cells and am currently milking 580 ewes. Next season we’ll take numbers up to around 850. Much of that increase will be made up by the 400 ewe lambs I kept from our first lambing.”
Ryan says that with the first season behind him, he is planning a few enhancements which will increase the overall efficiency of the dairy – a main one being shade cloth over the collection yard to minimise heat stress.
‘You can’t judge a book by its cover’ is borne out by McPherson Sheep’s sheep dairy which, from the tanker loop, retains its cow dairy past. Left: Ryan McPherson checks the milk lines at the sheep exit of the new conversion while chatting to FIL’s Robert Kirk. GEA receiving cans and milking system and pump controls are all centralised for optimum efficiency. The Hecton Sheep Handler is a ‘Godsend’, saving your back with daily foot trimming, according to Ryan McPherson. The GEA Rapid Exit System is raised, to the left, as it would be to release sheep from their bails after milking. Kiwi ingenuity on display on the side of the exterior sheep exit from the dairy –Ryan and his father installed ordinary farm gates which simply drop down when required to form a race.Cambridge farmers Kieryn and Jennifer Tapper bought their 127 hectare beef and maize farm in 2016. Kieryn was raised on a Matamata dairy farm, but when his parents moved to Southland in 1994 he went to boarding school, then university. He returned to the farm in 2004, where he worked on their 500cow dairy farm for 15 years. Jennifer is a qualified lawyer but has been a mother to their three children for the past 10 years.
For the first few years in Cambridge, the Tappers transported the 80kg dairy beef calves up from the Southland farm to finish and trade
them. In November 2020, a friend invited Kieryn to attend a sheep milking field day and that really caught his attention.
“I actually love getting up early and the routine and structure that dairying offers, and I enjoy the process of pasture management,” says Kieryn.
He finds the ability to measure results daily and work to a season that ends on a specific day appealing.
“I spoke to a couple of the dairy sheep companies and realised that the financial turnover per hectare would be far superior to beef or maize.”
Maui Milk’s general manager milk supply Tom Woutersen was quick to respond to the Tapper’s enquiry and Maui general manager breeding and genetics Peter Gatley visited them on-farm.
“We decided to go with Maui. Their threeyear fixed price high payout gave us security
while we found out feet. Combined with their dairy sheep genetics and buy-back of young stock, what they offered really appealed to us.”
Of the farm 40ha was set aside for the sheep dairy platform and all fencing was upgraded to five hot wires. Three-hundred Maui Southern Cross dry ewes arrived in February 2021, and rams went in on February 21. The rest of the flock arrived in May.
The Tappers had been working on their milking shed design with Shanan White, from Don Chapman Waikato. The approximately 20-year-old, 16-aside herringbone existing dairy cow shed was solid and could be used for
The pit and roof were extended by seven metres, with Shanan carrying out all concreting and building work. The pit needed to be deeper for milking sheep – the easiest way was to raise the walkway of the herringbone by 150mm.
“The shed was high enough but needed to be extended to fit a 42-aside swing-over herringbone and allow contingency for a further six bails to expand to 48-aside as the Tappers expanded their flock,” says Shanan.
He worked on the yard extension required, adding railing around the new entrance and exit races. “Sheep move better with covered railing, so we added blackout panels. The exit needed to be longer to accommodate the foot bath.”
Qubik Te Awamutu sales specialist Nick Heffer managed the project with Kieryn after months
Nick suggested using a Qubik locally designed and manufactured stainless steel rapid exit system that is designed to work efficiently with tight milking-pit-to-wall gaps. Once sheep have finished milking, the whole rapid exit system lifts up, allowing them to exit underneath the whole stalling on an angle, rather than straight out and having to do a right-turn.
The unit is made from high grade 304 stainless steel to withstand continual washing down required to meet good hygiene standards.
The milking shed is running a 42-aside herringbone Waikato Milking Systems plant with ECR-S cup removers. Sheep have delicate teats, and this eliminates over-milking as well as reducing the amount of labour required in the milking shed.
Rippled pulsation through the SmartPULS
electronic pulsators gives excellent vacuum stability and quiet operation, and cleanly and gently milks the sheep.
Waikato Milking Systems’ regional manager sales and service Ben Frederickson says the company also supplied a vacuum system BP200 with 7.5kw motor and SmartDRIVE.
“The SmartDRIVE is a variable speed drive that compensates for vacuum use by increasing or decreasing the vacuum pump speed on demand. Using a transducer mounted into the main airline, the variable speed device will monitor and adjust the vacuum, sensing every minute airflow change and compensating for this by altering the speed of the vacuum pump,” says Ben.
For Kieryn to meet strict milk cooling regulations, a stainless steel 5000L double-bank plate-cooler is installed alongside a Waikato
Milking Systems top loading milk filter for ease of use and effective cleaning.
“We have a 9100L stainless steel vat with a Qubik supplied and installed 10hp vat refrigeration unit to keep the milk below three degrees Celsius between our four-day pick-ups,” says Kieryn.
Qubik also supplied and installed the shed’s water system, including two hot water cylinders, a heater stand and Qubik custommade and designed stainless steel wash tubs. The new washdown and cooler pumps are linked to the existing dairy shed framework.
“We’ve been really pleased with the Qubik automatic plant wash. It activates at the push of a button after every milking, allowing one of us to hose up and the other milker to concentrate
on other farm jobs,” says Kieryn.
The automatic system ensures correct amounts of acid and alkali, and correct volumes of hot and cold water, are used.
The sheep pass through a footbath containing either zinc sulphate or copper sulphate on their way out of the shed. Kieryn uses Laurie Wahanui from Goat Care to look after the flock’s hooves.
“Foot problems are common with dairy sheep, whether it be scald or foot rot. Regular hoof trimming is an essential for their health and to maximise production.”
The Tappers managed to start milking July 28. An existing seven-bay shed took the lambs, which Jennifer and farm staff teach to feed before they progress to outside.
For 2022’s season the flock numbers have increased to 1000, with the plan to peak-milk around 850 ewes.
Last season’s lambs. An aerial view of the shed showing the extension (white roof). Farmer Kieryn Tapper in the pit with Waikato Milking Systems’ Ben Frederickson. Qubik’s Jeremy Collett and Kieryn Tapper discuss the automatic wash system. Page 85PH 07 578 0030 PARAMOUNT FARMING Qubik’s Nick Heffer with the plate cooler.Gerry Gerrand does not call himself a farmer. He owns dairy farms but has never milked a cow in his life. From the age of eight all he ever wanted to be was either a boat builder or a beef farmer. He chose the former, founding and still steering nationwide boat builders, Buccaneer Boats.
But his heart is clearly on the farm. In his own words “you can’t take the farm out of the boy”. Gerry and his wife Jenny both grew up on dairy farms, with both sets of parents breeders of pedigree Jerseys – and they still live on one of their farms located at Taupiri on the outskirts of Hamilton.
The farm’s name – Lakeside Kainui – is a nod towards the couple’s twin passions – the sea and the land.
The farm is located close to Lake Kainui, and the Maori translation of Kainui is ‘abundant food’.
“I work four days a week with Buccaneer and one day on the farm – but not in the shed,” says Gerry. “Until the early-2020s Lakeland Farm, at Taupiri in the Waikato, was two farms which shared a contiguous boundary.” Gerry and Jenny owned one farm but acquired the neighbouring property when it came on the market.
“For around 15 years we ran the farms independently; each had a herringbone shed –20-aside on the original farm and 16-aside on
the acquired property. The 50/50 sharemilker – who worked for us for 11 years and left last year to buy his own farm – milked on both properties, out of the respective sheds. It had always been our intention to combine the farms and the opportunity arose when our sharemilker moved on.”
Today, a new herringbone dairy sits on an elevated site overlooking the 126ha farm – the third shed to be positioned on this site. “It’s a good position, close to the road, its elevation generating natural fall to the effluent pond,” says Gerry.
He reckons the new dairy was always going
to be a herringbone. “It’s the most efficient system for the number of cows we will be milking and nothing goes wrong with them; they’re low maintenance and have low ongoing costs.”
That decision flowed on to the choice of Waikato Milking Systems – for the dairy and milking plant – with Qubik providing and installing the technology.
Demolition of the 16-aside dairy began midway through January 2021, the goal being to build and complete the new dairy in time for calving that was due to start in July.
“The old shed had already been demolished so we had no fall-back; the new dairy had to be completed on time. I thought we had plenty of time but in reality we finished one week before calving started,” says Gerry.
The new dairy is a 38-aside herringbone milking 380 cows or, in Gerry’s words: “10 rows”. “If required, one person could milk but most times there will be two people in the shed.”
Tim Broughton of Huntly-based Broughton Contracting was called in to develop the building site and undertake the landscaping for the tanker track, which included installation of the 25,000L concrete chilled water tank and system.
Don Chapman Waikato Ltd’s Shanan White says construction commenced end of January 2021.
“We did everything except the electrical, milking system, effluent, water and feed system.
Don Chapman Waikato built the foundations, laid all concrete, designed, manufactured and
erected all yards and gates and constructed the dairy and ancillary buildings,” says Shanan.
“We have a standard design which is tailored to suit the requirements of each farmer.”
Shanan says the walls of the dairy and ancillary buildings are insulated panel and the roofs are long-run iron.
“The pit is wider than standard to accommodate the swing arms and provide plenty of room for two people to easily work around each other in the pit.”
The dairy features a drenching race on both sides, providing easy access to the cows. “The cow entrance and exit to the dairy is also wider than standard to minimise the chance of cows bunching when entering or leaving the dairy. Manual drafting levers in the pit enable easy drafting of individual cows as they leave the dairy.
“The overall design objective was to create
a dairy which was streamlined, simple, quiet, uncluttered and a pleasure to milk in. For that reason the pump room is separate – reducing noise in the dairy.
The farm’s proximity to Hamilton means that relief milkers often want to be able to shower at the end of their shift, so the dairy features a bathroom complete with shower and toilet. A kitchen/staff room also provides facilities to make a coffee, store food and relax.
According to Qubik’s Nick Heffer, the dairy is a great example of the complete solution which Qubik can offer all farmers.
“Undertaking major work to the farm dairy shed can be one of the biggest distractions for farmers from the daily routine and discipline of farming, so we offer a ‘one stop shop’ for most aspects of the build or renovation, other than
the electrical, building and yard construction.
“This means that, instead of multiple contacts, the farmer has one company responsible for pretty-much the entire fitout of the dairy shed. Having a single overview of the entire installation means all aspects are synchronised so there is less downtime and more efficiency,” says Nick.
Qubik was able to offer Lakeside’s owners the milking machines and complete installation, new shed water, refrigeration, pre-cooling, effluent, farm reticulation and the feed system.
The 38-aside dairy features a Waikato Milking Systems Supa4 midline system with Swing Arm cup removers, which ensure perfect cluster alignment. The 38 Waikato Milking Systems 320 Clusters feature lightweight stainless steel shells and Quadrant Square liners. G2 cluster washers ensure optimum plant hygiene with adjustable flow control.
The
The desire to minimise noise and long term maintenance in the dairy is achieved with Reed 2+2 mechanical pulsators.
Highest levels of hygiene are achieved thanks to Qubik’s automatic plant washer controller, which has 12 fully programmable output relays for both wash and rinse sequences and automatically changes over from acid and alkaline chemical routines, says Nick.
The system also has full data logging, recording and digital display of peak wash temperatures for compliance when the shed inspectors visit.
“Precooling is provided by a 30kw chilled water system and 25,000L Manicon concrete tank. The superior insulation qualities of concrete are amplified by the tank being buried in the ground so it is out of the sun.
“Combined with the Waikato Milking
Systems’ stainless steel double-plate cooler, this is a highly efficient and environmentallyfriendly system which ensures milk is chilled to around eight degrees Celsius when it goes into the vat.” Qubik also supplied the 10hp vat refrigeration unit to cool and maintain the milk at required MPI regulations.
“The chilled water system generates 60 degree Celsius hot water, which means that the dual 350ml hot water cylinders only need to increase the temperature 20 degrees Celsius to the required 80 degrees Celsius. When compared to traditionally heating water from 16 to 80 degrees Celsius, this is a huge saving in electricity,” says Nick.
Qubik also supplied and installed the in-shed feed system, with the 304 grade seamless stainless-steel feed bins with stainless steel droppers for durability and additional strength.
FIL provides Gerry with a tailored range of locally-made detergents and teat sprays to suit the farming operation. FIL’s Quantum Red acid, Quantum XL alkali and C3 chlorinated cleaning chemical are programmed and dispensed through the automated wash controller.
All electrical componentry and wiring for the new dairy was provided and installed by Laser Electrical, which is based in Morrinsville. Gerry says the service he received validated the ‘totally dependable’ commitment they make to all services. They were here when we needed them, right from the start. Their availability, often at short notice, was one of the factors which enabled us to smoothly progress the build.”
The new dairy was completed one week ahead of calving at end of June 2021.
Contract milker Julie Giles says the new dairy is a delight to milk in. “It’s been designed for
the cows and the people who milk them. Cow flow is fantastic, they enjoy being fed in the shed and, from a human perspective the widerthan-normal pit makes it very easy to work with two people in the pit.
“The farm is only 20 minutes from Hamilton so all the ‘people aspects’ of the dairy –bathroom, showers, kitchen with fridge and coffee-making facilities – increase its appeal to city-based relief staff. They’re able to milk and clean up before returning home.”
Gerry, who works off-farm at Buccaneer four days a week, is quick to add that he has ‘good people’ to milk his cows – so there’s no need for him to be in the pit.
“We had some challenges when we decided to demolish the old shed and rebuild – one of them being the unknown of Covid – so I was relieved and very pleased with the way the project came together. The new dairy is everything I hoped it would be – cows are happy, staff are happy.”
The construction team: Don Chapman Waikato Ltd’s Shanan White, Qubik’s Kyle Osborne, farm owner Gerry Gerrand, contract milker Julie Giles, and Qubik’s Nick Heffer at the now-operational dairy. The 38-aside dairy features a Waikato Milking Systems Supa4 midline system with Swing Arm cup removers which ensure perfect alignment. Qubik’s Nick Heffer with the Aqua Storm plant autowasher which has 12 fully programmable output relays.When it was built 38 years ago, this 40-bail rotary was state-of-theart; now it is dwarfed – in size and innovation – by the 70-bail rotary which sits across the tanker loop.
The new dairy is, in many ways, a microcosm of the advances which have taken place in the dairy industry during four decades – a rate of progress which will, according to farmer Fraser Storey, only increase in the future.
Fraser is the fifth generation of the Storey family to farm the now 380 effective hectare property in the Waikato.
“Until two years ago the farm was 250ha milking 720 cows. It was taking six hours a day to milk the herd and the old dairy was showing its age, so my partner Robynne Ross and I started thinking about building a new dairy,” says Fraser.
“But then a neighbouring 120ha farm came on the market, raising the potential to add this to our existing acreage. The increase in farm size would, in turn, enable us to increase cow numbers to around 1000.”
Fraser says the new block had an equally old 36-bail rotary dairy which they continued to utilise – along with the home shed – for the first
season while they revised their earlier plans for a new dairy.
“We had looked at a number of sheds and liked the design and build quality of those built by Gibson Construction. Initially we considered a 60-bail but, given the objectives we’d defined for the new shed, we increased the size of the platform to 70 bails.”
In the old dairy Fraser needed five people to milk every day, so reducing the number of people in the dairy was a primary objective.
“While efficiency is important, we believe milking should be an enjoyable process for our farm team, and so we wanted two people at cups-on, for fast and efficient cupping,
with automatic cup removers and one person bringing in the next herd.
“Reducing the number of people required for milking changed the job description of our team but introduced a whole new level of job satisfaction.”
Fraser says some aspects of the dairy’s design were personalised – an obvious one being a stainless-steel drip rail, which runs around the circumference of the platform preventing water dripping onto milkers’ legs. “It’s a small innovation but one which makes applying cups to cows much more pleasant.”
When it came to the ideal site for the new dairy, Fraser says there was really only one position given the farm is consolidated peat.
“The building site is just across the tanker entrance from the old dairy. It is central to the larger property, each of our three herds having to walk no more than 1.7km to the furthest reaches of the farm.
“We have a digger and tractors with trailers on the farm, so were able to do the groundwork for the building site and the new effluent pond.”
Fraser says they dug the pond first, initially hoping the material would be suitable for the building site that needed to be raised 1.5m in places. “But it wasn’t the quality required for the building site, so we brought in clay and sand to construct a consolidated building site. “We used the fill from the pond site to develop
the carparking area which is adjacent to the new dairy.”
Otorohanga pump, irrigation and effluent management specialists Pumpn was called on to install the farm’s new effluent system. Owner Shane Phillips says effluent gravity feeds from the new dairy to a 20m x 6m x 1.2m sand trap/ solids bunker, and from there liquid gravity feeds into the 11m litre pond.
In contrast with many effluent pond stirrers which fail to stir below the surface of the pond, according to Shane, he says Pumpn’s SP stirrer maintains the liquidity of the pond, enabling liquid effluent to be easily sucked out and dispersed by a shore mounted pump. Liquid effluent is irrigated to around 50ha of the farm via a self-propelled Torpedo Travelling Effluent
Cannon which has a spread diameter of up to 102 metres.
Fraser says the construction of the new dairy, which commenced September 19, 2021, was accompanied by a protracted wet period. “It didn’t hold us up too much because we were able to do our own ground work and site development.”
Construction of the building, concrete and yards was undertaken by Gibson Construction working to one of their ‘tried and tested’ rotary cowshed designs. In addition to the 70-bail rotary platform, the building, which has an external diameter of 27m x 23m, houses an office, staffroom, toilet, viewing area plus plant and pump rooms. Construction consists of precast concrete
panels to 1m above floors, with framing and cladding above this. Bird-proofing to the vent ridge spans the length of the building with a canopy above the bridge and entry and stainless steel handrails in the viewing area.
Roof cladding is Metcom long run iron, and interior and exterior walls are clad in Metclad steel wall cladding. All internal blockwork and wash areas feature a coating system to ensure compliance with dairy hygiene.
Fraser says Gibson Construction project managed the entire project. “Their contractors designed and constructed all pipework to our specifications – for example, we wanted extensive animal-handling facilities to be positioned undercover on one side of the dairy so that response to any planned, or unplanned, animal health issues provides the ultimate safety and comfort for animals and staff alike.”
The interior of the new dairy is very light and spacious.
Page 92 Coast & CountryLONGREACH DAIRIES The stainless steel rail around the circumference of the platform stops water dripping onto milker’s legs.
The new animal-handling yards include a selfclosing head crush, AI race and foot crush.
The heart of the new dairy is a Waikato Milking Systems 70-bail Orbit Rotary Milking System installed by Moa Rotary Platforms.
Moa Rotary Platforms is the exclusive installer of Waikato Milking Systems’ platforms throughout the North Island. Their experienced team provides specialist services to farmers across the entire North Island and the reassurance of 24/7 back-up service provides Fraser with peace of mind.
Fraser says over the years various elements of the old milking system had been upgraded. We were pleased with the ruggedness and innovation of the Waikato Milking Systems gear, so it was a no-brainer to continue working
The old rotary served the farm well.
with a brand we knew and had faith in.
“The fact that the platform seamlessly integrates with Waikato Milking Systems’ current and future dairy automation technology gave us reassurance that we would be able to easily maintain the currency of the dairy as new technological advances are developed.”
Waikato Milking System’s regional manager sales and service, Ray Stowe, says the design and technology of the Orbit Rotary Platform has been proven during more than 25 years.
“They are renowned for a fast milking environment, which facilitates excellent cow flow both onto and off the platform.”
The outward-facing sloping deck of the Orbit Rotary Platform facilitates easy cow entry and exit to the dairy and improves effluent run-off and cleanliness of the deck area.
The Waikato milking system was installed by
The dairy’s new Protrack automated drafting gate.
Qubik of Te Awamutu, with Jeremy Collett saying Fraser Storey and Robynne Ross settled on a high level of technology to provide the optimum environment for their staff and animals – both now and in the future.
“The milking system includes Waikato Milking Systems ECR-S electronic cup removers, Cow Restraints, SmartSPRAY automated teat spray and the unique, recentlylaunched 320HP Milking Clusters which feature the new triangular HP1 vented liner.
Jeremy says the 320HP Milking Clusters are lighter than conventional clusters and the vented triangular liners improve milking performance and udder health.
“The effectiveness of the clusters is maximised by Waikato Milking Systems SmartPULS, which is an exceptional digital pulsation system that opens and closes the
liners consistently and dependably at every milking. The robustness of SmartPULS pulsators is incredible – the solenoids are designed to exceed 200 million cycles.”
The dairy features Qubik auto plant and vat wash systems – one for the plant and one for each of the three milk vats. Fraser says the automated systems provide a level of reassurance and simplicity which is invaluable.
“Milkers simply have to push a button to start the automated pre-programmed plant wash cycle, which is preset by Qubik, freeing them to attend to cleaning of the milking area. And the vat wash is activated by the tanker driver after each pick-up. Overall the wash systems provide a high degree of reassurance around dairy hygiene.”
The dairy’s large collection yard.Qubik supplied and installed the dairy’s refrigeration system. Qubik’s Jason Hare says the dairy’s precooling system comprises a Glacier Plus 60kW chilled water system that chills water in a 25,000L manicon tank to six degrees Celsius before it is pumped through a second-stage plate heat exchanger. Milk then goes into the vat at eight degrees Celsius and is further cooled by the vat chiller.
The chilled water unit also provides heat recovery, generating between four and five litres of 55 degrees Celsius hot water per minute, which is a significant saving in electricity over the course of just one milking.
Qubik also provided the water pumps including the Variable Speed Drive washdown pump that saves power and also ramps water pressure down, making it easy to handle one hose.
The majority of the plumbing in the new dairy
is stainless steel, including the stand on which the dairy’s three 600L hot water cylinders are mounted. The stand is also plumbed to provide water to and from the cylinders.
A Protrack automated drafting gate was retro-fitted into the old rotary, the ease and consistency of drafting leading to Fraser installing a gate in the new dairy.
The Protrack Draft Automated drafting gate from Allflex/MSD Animal Health Intelligence is powered by easy-to-use software which enables drafts to be set ahead of time via smart phone or farm PC or during milking via the Protrack pit PC at cups-on. The drafting gate integrates with Allflex Collars, Protrack SCC, Protrack Milk, Protrack ID and Protrack Heat which can control the dairy’s in-shed feeding system.
Fraser says the first milking in the new dairy took place on May 9, 2022. “All the
functional aspects were completed by that date, with a few enhancements being finished over following weeks.
“The proximity of the new dairy to the old rotary meant there wasn’t a drastic change of environment for the cows – other than the platform in the new dairy rotating clockwise in contrast to anti-clockwise in the old dairy.
“The change in direction didn’t faze the cows though and, right from day one, they went onto and off the platform calmly from the first milking.”
Fraser says the new platform is delivering a number of additional benefits. “One being that the larger platform gives cows, which previously needed to go around twice, more time to milk out in one revolution. The cows are also more relaxed in the new
The dairy’s three 600L hot water cylinders are mounted on a stainless steel stand plumbed to provide water to and from the cylinders.
environment and this has a direct correlation to animal health.
“The new dairy and milking system also provides reassurances around milk quality.”
Attracting and retaining the right staff was a significant factor to developing the new dairy. “It was hard to attract great people to work in the old shed but there is a whole new dynamic in the new environment,” say Fraser.
“The dairy itself is spacious and modern with technology which eases milking, animal handling/feeding and data recording. We have six full-time staff and they all love working in the new shed. Staff morale is great.”
Fraser and Robynne have twin daughters, who are currently ‘real farm girls,’ but they’re only five and this could change as they grow, they say.
“One of the aims to developing the new dairy was to create a facility which could be retrofitted with new technologies as they are developed and needed to maintain animal welfare, staff engagement and milk quality.”
Rubber matting provides good footing at the entrance and exit.The roof extends over and protects the animal handling facilities.Plenty of room around the outside of the platform. The entry to the centre of the dairy. The staff smoko room.
The Ormsby family take their role as guardians of the land seriously.
An effluent disposal incident on their Waikato property was the catalyst for extensive and expensive effluent and water work upgrades.
Project manager Ross Ormsby says the red flag was raised two-and-half years ago when an irrigator tipped over in a hillier spreading paddock and continued to discharge effluent by pooling into a waterway unnoticed.
The 202 hectare effective property near Te Awamutu, milking 600 cows, was broken in from bush by his parents and farm owners Keith and Margaret Ormsby. “We were horrified this happened, as we care so much
about looking after the environment and waterways,” says Margaret.
Keith and Margaret have previously received Ballance Farm Environment Awards for planting more than 34,000 plants, with the help of family, in riparian waterways’ restoration on the farm and at the local Ngutunui School.
It was identified that the effluent pond on the farm was too small for regulations and an increase in cow numbers, so a larger pond and area of land was needed to hold and spread effluent on.
Ross says the existing effluent pond spread effluent on farmland immediately adjacent to
the milking shed. “The pond’s capacity meant spreading on damp soils and sometimes in rain, which was something that concerned us.”
AgFirst Engineering Waikato recommended a system to create capacity for a potential stand-off yard/herd home. The design also factored in extending the effluent field further in the future.
“Our family recognised how a weeping wall and large capacity pond of 5 million litres with a Harvest monitoring system met all our needs for now and future,” says Ross.
“The large pond allowed us more than 90 days’ storage, so in a wet winter/spring our sharemilkers didn’t need to do any spreading or sludge maintenance on damp soils and at busy times.
“We are happy to utilise the nutrients on a wider field and target spreading of solids
on crops and land at the perfect time,” says Ross. “Our big fail-safe is a monitor on the irrigator, which also creates ease for workers as they run the irrigator at the paddock site through their phone.”
At the same time, the ageing water supply system on the property was also looked at while a trench was open for effluent piping.
“We weren’t getting great pressure through gravity-feed in some areas,” says Ross.
The old piping was between 29 and 50 years old, served by a bore near the pump shed at the milking site. “We put in a larger capacity 63mm pressure line to a new 30,000 litre tank at the top of the farm.”
Ross says the pressure pipe serves troughs directly and especially on the top plateau where lack of gravity pressure was a problem. This part of the project included two new water pumps for the down-hill and up-hill sections of farm requiring different pressures.
In order to counter farm water leak problems affecting milking shed water needs, Ross says AgFirst advised the installation of two 30,000 litre water tanks near the dairy shed, close to one of two bores. “The dairy shed and stock water systems are kept separate,” says Ross.
In future, the Ormsby family also plan to clean the milking shed yard with recycled green water.
It was a similar story for the farm effluent disposal system, with a much larger pond developed along with a more extensive irrigation system to deal with future effluent needs of a herd home and regional council/
dairy company regulations.
AgFirst Engineering Waikato engineering consultant and director Davieth Verheij says in 2020 AgFirst investigated the existing effluent pond and in paticular its storage capacity. “It was just too small,” says Davieth. “It worked for that point in time (when it was first constucted), but time has moved on.”
Davieth says there was no space to expand, so a decision was made to build a bigger pond on a separate site. “Downhill from the dairy shed, the new site on a former paddock had space and gravity.”
The 4.5m deep pond is 42.5m long by 42.5m wide and pond can hold up to 5 million litres of effluent
“It’s designed for 600 cows and can also cater for a stand-off feed-pad in the future,” says Davieth.
The pond liner was installed by Aucklandbased Viking Containment. Head of sales and
installation Brent Whitehead says the 1.5mm thick liner is made of HDPE (high density polyethylene), a strong, long-lasting material.
Manufactured in Malaysia, it comes in 1.7 tonne rolls, which are cut and welded in situ on the farm property.
“It’s basically like a big carpet,” says Brent, with 8m-wide strips welded at a rate of 3m per minute.
Brent says the liner is held in place by the weight of the effluent, with edges slotting into a trench and backfilled with soil
Part of the AgFirst design is a double weeping wall for separation of solid material. Davieth says raw effluent fom the cowshed is held in beds, separated by walls, in a concrete bunker.
In a three-way filtration system, liquid ‘weeps’ into the adjacent pond, leaving solid material behind for use as pasture fertiliser.
Davieth says the existing effluent disposal system – small capacity/ storage on sloping land – was ‘high risk’. The pumping/piping system associated with the new pond means effluent can nw be fed to the back of the farm, rather than just the immediate area around the milking shed.
Davieth says a new pump shed at the pond features flw metering and has pipelines to both the existing and extended irrigation systems. Hydrants – which travelling irrigators plug into – now dot the landscape, covering two paddocks at a time.
The water and effluent systems ere fied up by Te Awamutu-based Gibson Electrical. Director Chris Gibson says his team wired the bigger water pumps at the milking shed, linking to an existing electricity supply.
On the effluent side of the poject, Gibson Electrical completed all wiring work for the associated pumps. “It was a major overhaul,” says Chris. “Things were breaking down regularly.”
It is fair to say that Mike and Michael Magan’s new GEA iFLOW Rotary Parlour has transformed the process of milking cows on their Longford farm in the Irish Midlands.
Until 2018 it took four hours to milk the Magan’s 200-cow herd, requiring them to stand for up to eight hours on concrete per day.
That all changed in 2018 when the Magans installed a 40-bail GEA iFLOW Rotary Parlour.
“We went from 50 cows an hour, to 200,” says Mike.
Labour efficiency was the key driver behind Mike and Michael’s decision to upgrade to a rotary milking platform.
“As a small family-run dairy farm, we understood that a good infrastructure would create a better work-life balance,” says Mike.
“My son Michael and I manage the farm together, milking 200 pedigree Holstein cows twice-a-day. Labour is one of the biggest constraints in farming today and we felt that installing a rotary system would enable us to overcome those issues quite quickly.”
Mike admits the size of the herd is smaller than what is normally associated with a rotary parlour. “But for us labour efficiency outweighed capital cost and, four years on, we have absolutely no regrets about going down this route.”
The decision to install a rotary parlour was, in part, influenced by son Michael’s experience with rotary parlours
when he worked in New Zealand prior to joining the family business in Ireland.
“His experience milking in rotaries convinced him that they enabled faster throughput, generated increased labour efficiency and enabled better control over the cows than other systems,” says Mike.
“When he came home we talked about the need for a new parlour and agreed that we wanted a system which would be simple to operate, robust, reliable and which had a proven track record.
“GEA’s iFLOW Rotary Parlour ticked all those boxes; and, in addition to GEA’s international reputation for excellence, it came with the recommendation of other local farmers.”
The milking system of the GEA iFLOW Rotary Parlour is mounted below the reinforced concrete deck so it is physically protected and easily accessed for maintenance. Minimal wear and tear is an enduring feature of the platform thanks to the largest circumference drive wheels on the market placing less pressure on the double ‘I’ beams and using nylon rollers – one every 600mm – avoiding the need for a wear strip. The platform does not have bearings and has an automatic lubrication system.
In 2018 the Magans installed a 40-bail GEA iFLOW Rotary Parlour with automated iCRS cow restraints, iCR intelligent cluster removers and iPUD automatic teat spray. They also installed a GEA milk tank and the
AutoSelect 5000 three-way drafting gate.
“The cluster removers mean only one person is needed in the parlour and they are linked to the bail restraints so cows which have not milked out remain on the platform for another rotation.”
The iCR Automatic Cluster Remover has some unique features, which improve ease and efficiency of milking. LED and warning lights, for example, give a visual cue of the milking status in each bail, alerting the milker to any problems. When each cow has finished milking, the cluster is vented and the vacuum shuts off, allowing the cluster to detach from the udder. Release activates the iPUD automatic teat spray system which applies a consistent amount of teat spray to every cow.
The AutoSelect 5000 three-way drafting gate, positioned at the exit of the milking
parlour, has simplified animal segregation. Each cow is identified as she enters the platform and is drafted according to drafts either set ahead of, or during, milking via the farm office or parlour monitor.
Mike says since they have been operating the iFLOW they don’t do things differently, they simply work more efficiently. “All the things we did in a more labour-some way in the past are now more streamlined.
“We have also realised unforeseen efficiencies and opportunities for doing other things like applying tail paint and artificial insemination.”
Mike says cow comfort is a major outcome of the new platform. They are out on pasture more than they were before, due to each
milking taking only one hour compared to nearly four hours, and this obviously benefits animal health and production.
“They also need no encouragement to enter the rotary, simply walking on and reversing off.”
An unexpected bonus has been improved water efficiency, with Mike explaining that water comes from a well to cool the milk.
“Now the same water is collected and used to hose down the plant then collected again and used to floodwash the yard.”
Mike and Michael say they are very happy they chose GEA. “They are a good company to work with and the system has enabled the improvement in quality of life we were after,” says Mike.
Sixty-one years ago Moorend Farm, situated in Herefordshire in the West Midlands of England, was milking 20 cows using buckets. Today, the herd has grown tenfold to 200 cows milked through a GEA 36-point iFLOW rotary parlour.
The transition of milking system – and herd size – is, according to farmers Ken and Andrew Cox, testament to the global evolution of the dairy industry and demand for more efficient systems and practices.
Back in 1961 the first bucket milking system was introduced for the Cox’s 20-cow herd, and then in 1984 this was replaced by an eight-point abreast parlour.
By 1992 the herd had grown to 70 cows and a ‘state of the art’ Trigon parlour was installed consisting of a triangle-shaped milking platform with three milking sides – two with
That was back in 2019, and Andrew Cox says he and Ken decided that in order to move their business forward, a new milking parlour was needed. The old one was causing a bottleneck and it was taking up too much time to milk the cows, twice-a-day.”
“We decided that the aim was to put in a machine that could be operated by one person and still be able to milk the 200 cows, including washing down, in under two hours,”
“After having a good look around at a variety of systems we concluded that a rotary parlour
Each bail is equipped with a GEA iCR automatic cup remover, which operates the iCRS bail retention straps, cluster drop down and in-deck teat spray units.
The iCR cluster removers detect whether a cow has finished milking – releasing the cluster if she has finished or signals the cow retention straps to keep her on the platform for another round.
was the way forward, as it meant a lot less walking, and it would do the job properly and quickly.
“We opted for a 36-point GEA iFLOW rotary parlour because our old Trigon was GEA Westfalia and it never gave us any bother or problems. As a consequence we had a lot of confidence in GEA and in their innovation and products, and also in our dealer Wooldridge Dairy Services Limited.
Andrew says the reason they went for a 36-point is because that was the size that would fit into their existing shed.
One of the reasons the Cox family decided on a 36-point GEA iFLOW rotary parlour was it would fit into the existing parlour building.
The GEA iFLOW rotary parlour’s bail system provides superior cow comfort thanks to two opening size options, adjustable neck rail positions and height-adjustable kick and shin rail positions that accommodates cows of all sizes.
“Farm succession was also a consideration –our son Tom is keen on farming and is studying agriculture at Reading University and it made sense to set the farm up for the future with a modern, efficient rotary parlour which would easily and efficiently milk the current herd and accommodate growth in the future,” says Andrew.
The GEA iFLOW rotary parlour is a simple modular system so the farmer is able to select the technologies appropriate to the farm at the time of installation, with the ability to easily upgrade as the budget and herd size allow.
The milking machine is mounted underneath, and protected by, the concrete platform. The double I beam carriage system reduces point loading, with one nylon roller every 600mm ensuring even distribution of the platform weight. Cow comfort and flow is an outcome of adjustable rail positioning, optional rubber mats and easy entry and exit on to and off the platform.
The GEA 36-point iFLOW rotary was ordered in late 2019, with the first milking in August 2020.
In order to meet the requirement that the parlour be easily and efficiently operated by one person, the Cox family included automatic iCR automatic cluster removers, iCR cow retention straps to keep the cow on for another rotation if she had not finished, and the GEA iPUD automatic teat sprayer for pre and post spraying.
As the cows enter the dairy they are identified by means of their ear tag, and all the milking information – such as yield, conductivity, fat, and protein percentages – is collected and analysed thanks to iCORE milking point management which feeds milk data through to the Dairy Plan Management System.
“The dairy information system also controls the drafting gate, which is revolutionary as it
never misses a cow,” says Andrew.
“The range of technology in the parlour calls for a certain amount of ability on the part of the milker, as they need to be alert to cows coming onto and leaving the platform and to also be aware of any issues that may arise during milking.”
The milking system is given two hot washes per day, after each milking, resulting in bactoscan levels of around 12, and Somatic Cell Counts around 130,000.
Andrew believes that teat condition has improved with the introduction of the new rotary and attributes this to the lower and more consistent vacuum levels in the new parlour due to milk and air separation in the iFLOW milk lines.
“The square liners also seem to be milking cows out faster and cleaner. Other
improvements we’ve noticed include how quickly heifers adapt to being milked and the fact that the kick bar is never used.
“We keep the hospital cows separate and bring them in at the end when the pipe is disconnected from the tank. This prevents any accidents and makes life easier for the operator,” says Andrew.
The Cox family’s Holstein cows calve allyear-round, and on an average year go out to grass for about seven months a year. The rest of the year they are fed on a total mixed ration. They are housed on loose housing, utilising the farm’s home-grown straw.
Andrew summarises how the family feels about their new rotary parlour, saying they have no regrets. “It was the right decision and has transformed the farm.”
High energy curding CMR for optimal performance and fast growth rates
Improves future robustness of the animal
Osmolality similar to cow’s milk –improves digestion and reduces risk of scours
Balanced mineral composition to meet calf requirements
Premium quality Calf Milk Replacer
Can be fed to calves from 4 days old Whey protein for faster digestion
Hydrolysed wheat protein aids digestibility (no soya)
Dissolves easily, even in cold water
>
For improving the environment and minimising proliferation of bacteria, viruses, fungi, parasites, fly larvae
Remains active for several days, even in the presence of manure and bedding
Powerful drying agent, absorbing ammonia and moisture to improve bedding quality in animal housing
ABSORBS
TO
For maintaining gut health in calves, lambs, kids, foals and piglets
Contains plant fibres, glucose and electrolytes
Non-medicated; does not contain antibiotics
Whole colostrum powder containing 18% IgG for best immunity protection
Minimum 18% fat provides excellent energy boost
Jenna McLeod, Areare Farms, Waikato
Jenna rears 190 calves in autumn and 480 over spring – a mix of dairy heifer replacements, beef, and Friesian bulls.
Read her story here
“Launchpad18 colostrum powder is the best, Sprayfo Blue is a great fit for our system and Biopect is my absolute favourite product… I feel like we have a fine-tuned (calf rearing) system in place.”
It’s time to rest easy (knowing that your cows are too). Thanks to an innovative waffle shaped, air-cushioned underside, Siesta matting provides both stable footing and comfortable support in wintering barns, on feed and stand-off pads and indeed anywhere cows need to rest. Don’t risk inferior products. As New Zealand’s farmers have discovered, cows prefer Siesta.