SUPPLY CHAIN Market Update Bulletin

September 2023
Lead Author: David C. Hamilton, Vice President, Dir. of Purchasing

Introduction
Reporting from major sources like CoStar have shown optimistic data about the number of leases being signed recently for commercial office space, albeit many for smaller square footages. Major financial companies are targeting investment in distressed real estate, signaling that the weakness in the market can be an opportunity. Recently Fortress announced a $1bn acquisition of commercial real estate loans, leading some to believe that they too feel bullish about a rebound of real estate. These points underpin our belief that commercial office construction could remain strong this fall, along with already strong activity continuing in industrial manufacturing and data center construction. As a result, demand for equipment such as electrical and HVAC gear continues to remain high, leaving little improvement in lead times.
Economic Outlook
• As reported in multiple publications, outlook for the economy has improved and recession fears have abated somewhat, but high interest rates continue to linger, adding to uncertainty.
• Mandatory return-to-work policies implemented by multiple corporations hints at a potential increase in the commercial interiors market
• Electrical gear and related component prices continue to stay inflated, in addition to supply shortages, with little to no sign of relief well into 2024.
• Copper demand from the growth of EVs, solar, and green technologies remains a concern for material costs, availability, and lead times, coupled with continuing geopolitical unrest in many producing countries.
Mitigation Strategies
In our white paper, find strategies and solutions to help navigate issues like these
Scan or click to link to our White Paper here:
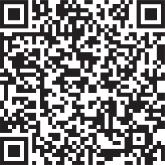
Logistics
• Importers are receiving good news as ocean freight prices decrease along with state and federal grants to modernize and reduce congestion at California ports.
Subcontractor Financials
• Risk of subcontractor default remains elevated in the US North East and West Coast markets, specifically for commercial interiors projects.
• Careful evaluation of bids and, more importantly, bidders using thorough prequalification from various angles is crucial to gaining a holistic evaluation
• Effective cashflow management is vital for the sustenance of subcontractors. Ensuring timely compensation guarantees that our partnering tradespeople have the necessary funds to efficiently acquire materials and sustain an appropriate labor force.
• Subcontractor Default Insurance (SDI) is more essential than ever, helping to ensure projects have minimal delays should a subcontractor default.
SECTORS



• Mass Timber – An emerging product which, due to its versatility, strength, fire resistance, and environmental impacts, is of great interest to us. The choice of wood species affects sourcing. Design to installation is taking 9-12 months. Foreign producers entering the market will boost capacity and efficiency on the US East Coast in the coming years.
• Industrial / Light Manufacturing – Strong increases in construction of manufacturing facilities has been balanced by decline in distribution center development. Concrete, steel, and roofing remain level risk for now, but we do expect pricing to start to increase more significantly over the next months.
• Mission Critical – Rapid and sustained development of cloud-based technologies and AI has meant a spike in the growth of data centers The heavy use of concrete, HVAC, and electrical equipment on these projects has is impacting the availability of these products and materials.
NOTABLE COST CHANGES
• General – Deviations between national cost trends and regional markets continue, as certain areas have a stable backlog, while other areas have slowed. Areas that have slowed are experiencing more competition, which is generating more favorable costs and curbing escalation. Overall, this rebalancing is prompting some market correction. Prices on most commodities are fairly stable, but openings for volatility exist due to fluid geopolitical pressures.
• HVAC & Electrical Equipment – Although at higher pricing, we are anticipating further increases due to the rise in demand in each of the sectors noted above.



• Labor – Labor cost forecasts continue to hover around a 4% rise into 2024. Subcontractors in labor-intensive trades with worker availability can charge a premium and adversely affect budgets. This is highly dependent on geographic region; areas with a union workforce are more stable.
• Healthcare – Reports specific to the NYC region suggest an anticipated decline in projects for 2023, which will gradually recover by 2027. As the market speeds up, pre-purchasing long-lead items such as switchgear and panels, HVAC equipment, modular ceilings or wall systems, and casework becomes key.
• Hospitality – This sector is one of the most active and robust recently. As many hotels rebrand, they are overhauling infrastructure and upgrading HVAC systems.
• Interior / Conversions / Repositioning – With reduced office demand, more buildings outside prime business districts are being converted to residential spaces. As the rental focus is in the mid-market, the related materials, finishes, and systems are generally available with the exception of generators, which have lead times exceeding 12 months.
CURRENT IMPACTS
• Doors/Frames/Hardware – Lead times for solid core and veneer doors remain elevated nationally.
• MDF/IDF Infrastructure – CRAC, UPS, and other server room equipment remain constrained due to continued Mission Critical sector growth
• Green and Novel Materials – Amenity spaces and new builds increasingly turn to cutting-edge materials and equipment, funneling demand to niche producers and manufacturers.
• Labor – Uneven demand for skilled labor has created challenges nationally Many Commercial Business Districts have surplus labor while rural megamanufacturing projects are constrained by lack of workers. Slowing residential and distribution starts have eased labor availability in many labor markets compared to 2020.
CONTRIBUTORS
DAVID HAMILTON (Group Lead)
Director of Purchasing, National
STO BUILDING GROUP
David.Hamilton@structuretone.com
212-251-9389
STEPHEN DENNIS
Estimating Manager
STRUCTURE TONE
Philadelphia, PA
Stephen.Dennis@structuretone.com
215-563-7875
BRIAN S. LYNCH
Purchasing Manager
STRUCTURE TONE
Boston, MA
Brian.Lynch@structuretone.com
617-348-2800
JUSTIN ACQUAVIVA, LEED® AP
Purchasing Manager
STRUCTURE TONE
Woodbridge, NJ jacquaviva@structuretone.com
609-658-6347
BRET FIELDS
Director of Preconstruction, CA
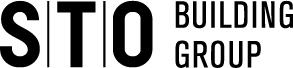
BCCI
Bret.Fields@bcciconst.com
415-817-5116
TIMOTHY PAPPS
Purchasing Manager
PAVARINI NORTHEAST
Stamford, CT tpapps@pavarini.com
203-978-2340
ROSS ALLEN, LEED AP® Senior Estimator
LAYTON CONSTRUCTION
Ross.Allen@layton.com
801-563-3847
JASON FRENCH
Director of Purchasing, TX STRUCTURE TONE SOUTHWEST
Jason.French@structuretone.com
214-525-5142
MARC PARSONS
Estimator
ABBOTT CONSTRUCTION
mparsons@abbottconstruction.com
206-467-8500
GREG COURTMAN
Estimating Manager
NATIONAL STRUCTURE TONE GLOBAL SERVICES
Gregory.Courtman@ STOBuildingGroup.com
347-491-2813
NAVLEEN GHAI
Purchasing Agent STRUCTURE TONE
New York, NY
Navleen.Ghai@structuretone.co
m
212-251-9328
SILVIU STOIAN
Vice President, Estimating GOVAN BROWN & ASSOCIATES
Toronto, Ontario, Canada
sstoian@govanbrown.com
416-703-5100