
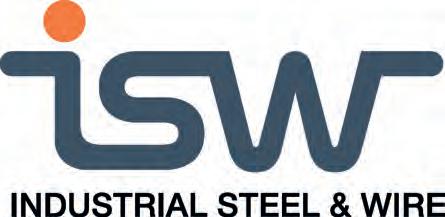

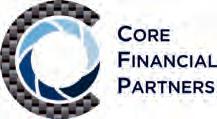

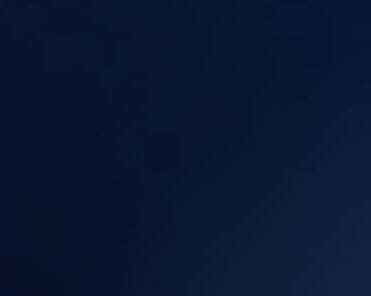

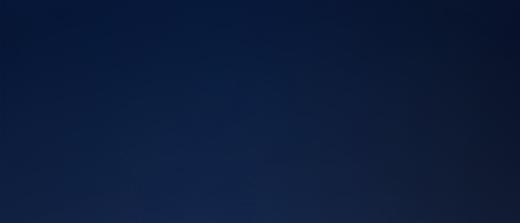
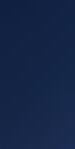



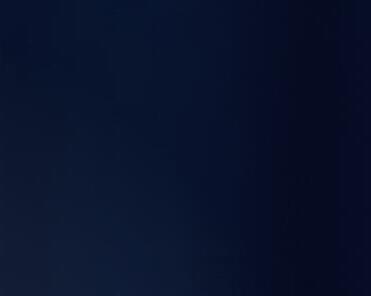
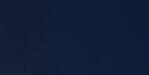
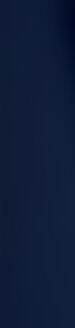


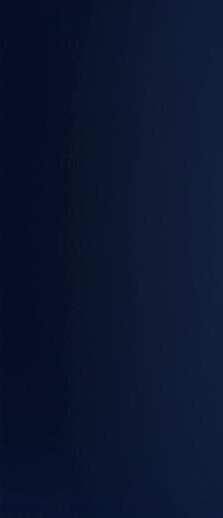




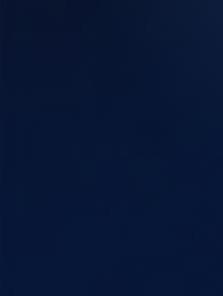

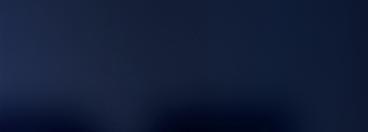
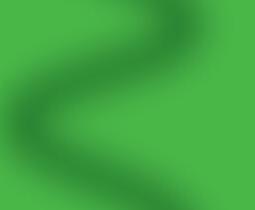

Don Jacobson III
“We need a spring to fit here, with this rate and it should be easy, right?”
If you’re a spring manufacturer, you’ve heard this before. A customer approaches you with a fully designed assembly and the spring is the last component to be considered, often squeezed into a tight space with rigid performance demands. The assumption? “It’s just a spring; how hard can it be?”
The reality? Very hard.
In today’s world of miniaturization, tight tolerances and costsensitive production, springs are frequently an afterthought. Until they become the bottleneck. As a manufacturer, it’s our job to guide engineers and designers before molds are cast and tooling is finalized. Because once those are locked in, the “cheapest part” of the assembly can quickly become the most expensive.
Let’s take a quick look at some familiar cases where spring tolerances were an afterthought and review how they turned out.
Scenario 1: A medical device company designed a tiny mechanism with zero room for spring variation. The result? A 50% scrap rate and a 300% cost increase. (Solution: They redesigned the housing to allow for a more manufacturable spring.)
Scenario 2: An automotive supplier demanded ±1% rate tolerance, not realizing that ±5% would work fine. The tighter spec added $0.50 per spring, which added up to costing them $50,000 each year of production.
When designing springs, please remember that tighter tolerances often mean higher manufacturing costs. Working with your SMI springmaker is the best way to avoid any design pitfalls or extra costs that could be eliminated with the right design partner.
“Everything should be made as simple as possible, but not simpler.”
— Albert Einstein
Don Jacobson III
Newcomb Spring Corp.
D3@newcombspring.com
Contact Us
Spring Manufacturers Institute
PO Box 5668
Elgin IL 60121
Main phone z 847-450-6848
Gary McCoy z 847-450-6240
Gaby Carrasco z 847-857-6432
SMI Executive Committee
President: Don Jacobson III, Newcomb Spring
Vice President: David DeVoe, John Evans’ Sons
Secretary/Treasurer: Dave Deerwester, The Yost Superior Co.
Past President: Gene Huber Jr., Winamac Coil Spring
At-Large: Joe Devany, Betts Company
Executive Director: Gary McCoy, SMI
SMI Board of Directors
Julie Arenz, R&L Spring/Medicoil I Markus Arnold, WAFIOS I Tim Bianco, Iowa Spring I Jodi Boldenow, IDC Spring I Adam Jacobson, FENN/Torin I Chris Kozka, MW Components I Don Lyons, JonSpring I Alex Melnikow, Midstate Spring I Keith Porter Jr., Newcomb Spring I Sanjeev Rivera, Lee Spring I Timo Roeger, Kern-Liebers USA I Monica Shafer, Novi Spring I Jason Sicotte, Associated Spring I Bernie Taylor, Hoosier Spring I Tim Zwit, Motion Dynamics Corporation
Springs Magazine Staff
Gary McCoy, Executive Director/Publisher, gary@smihq.org
Phil Sasso, Managing Editor, phil@smihq.org
Gaby Carrasco, Associate Editor, gaby@smihq.org
Lisa Plefka Haskin, Art Director, lisahaskin95@gmail.com
Communications Committee
Chair, Keith Porter Jr., Newcomb Spring I Reb Banas, Stanley Spring & Stamping I Hale Foote, Scandic Springs, Inc. I Patrick Gillum, Gilco Spring of Florida, Inc. I Adam Jacobson, FENN/Torin I Lucas Karabin, Acme Monaco I Gary McCoy, SMI I Phil Sasso, SMI I Michael Shapiro, Gibraltar Corporation I Bill Wynn, Gardner Spring, Inc.
Advertising Sales I Japan
Ken Myohdai, Sakura International Inc.
Head Office: 3F,4F, ENDO Sakaisuji Bldg., 1-7-3, Bingomachi, Chuo-Ku, Osaka 541-0051, Japan
Phone: 81-6-6624-3601 I Fax: 81-6-6624-3602
Tokyo Global Office: 5F Kamei No. 2 Bldg., 2-17-13, Kiba, Koto-Ku, Tokyo, 135-0042, Japan
Phone: 81-3-5646-1160 I Fax: 81-3-5646-1161
E-mail: info@sakurain.co.jp
Advertising Sales I Taiwan
Charlie Yu, Worldwide Services Co. Ltd. 11F-B, No 540, Sec. 1, Wen Hsin Rd. Taichung, 408 Taiwan Phone: +886-4-2325-1784 I Fax: +886-4-2325-2967
E-mail: marketing@acw.com.tw
Springs (ISSN 0584-9667) is published quarterly by SMI Business Corp., a subsidiary of the Spring Manufacturers Institute: PO Box 5668, Elgin IL 60121 Phone: 847-450-6848; Website: smihq.org
Address all correspondence and editorial materials to this address.
The editors and publishers of Springs disclaim all warranties, express or implied, with respect to advertising and editorial content, and with respect to all manufacturing errors, defects or omissions made in connection with advertising or editorial material submitted for publication.
The editors and publishers of Springs disclaim all liability for special or consequential damages resulting from errors, defects or omissions in the manufacturing of this publication, any submission of advertising, editorial or other material for publication in Springs shall constitute an agreement with and acceptance of such limited liability.
The editors and publishers of Springs assume no responsibility for the opinions or facts in signed articles, except to the extent of expressing the view, by the fact of publication, that the subject treated is one which merits attention.
Do not reproduce without written permission.
Cover designed by Lisa Plefka Haskin utilizing Shutterstock imagery.
Please archive or
Springs archives: smihq.org/springs-magazine
Ideal for torsion springs, tension springs, extended loop springs, and bent parts
FMU+ Series accomodates wire diameter ranging from .007”-.314”
Linear Transport Unit Option Available - Scan QR Code to View
• “Bend after cut” feature that eliminates need for secondary operations
• Second station increases production/output
• Allows for complex springs and bent parts with longer legs and loops to be produced
3-year license for spring+ now included in every FMU+ for easier set-up
• spring+ can be used for simulation of the production sequence, collision control, theorectical calculation of the output, and reduction of axis travel
Kern-Liebers USA, a subsidiary of Germanbased Kern-Liebers, will celebrate its 50th anniversary in July with an invitationonly event at its Holland, Ohio, facility featuring food, music, games and other activities.
With three plants in the U.S. and Mexico, Kern-Liebers USA engineers and produces springs, stampings, assemblies, heat and surface treatments. Worldwide, the company has 40 facilities.
“Our goal is to be a key strategic supplier for the automotive and industrial sectors — known for our technical expertise, reliability and uncompromising quality,” said Timo Roeger, Kern-Liebers USA managing director. “Our vision is to go beyond being just a manufacturer. We want to be a trusted development partner to our customers, supporting them from concept through production.”
The Holland, Ohio, plant specializes in stamped-bent parts and flat and round wire
Rotor Clip has launched a new educational video to help engineers better understand the function and advantages of wave springs. Unlike traditional coil springs, wave springs generate force through bending, allowing for up to 50% reduction in axial space while maintaining performance.
The video explains how wave springs can reduce assembly height, save weight and streamline components in various applications.
“Our goal is to make it easy for engineers to see the value of wave springs in solving space and weight challenges,” said Craig Slass, Co-President of Rotor Clip.
Available now on Rotor Clip’s website, the video explores the company’s full range of wave spring configurations, including multiturn, nested, round-wire and linear designs for industries including aerospace, medical devices and fluid systems.
Watch the video at www.rotorclip.com/wave-springs.
springs for several industries, all crafted using internally developed and manufactured equipment.
Since opening its U.S. subsidiary in 1975 under Dr. Kurt Steim, former CEO and current shareholder of Kern-Liebers, the company has significantly expanded its North American presence.
“We’ve made a deliberate shift to place customer needs at the center of every decision, whether it’s lead time optimization, product development or service responsiveness,” Roeger said. “True progress doesn’t come from machine investments, PowerPoint slides or even the most well-crafted strategic plans … we foster an environment where people feel ownership, take pride in their work and are empowered to improve.”
Kerns Liebers USA is part of a global network that employs more than 6,500 people worldwide. Learn more at www.kern-liebers-usa.com.
Orlando Precision has acquired Aero Spring and Manufacturing Company, Inc., a Phoenix-based supplier of custom springs and precision components for the aerospace sector. Founded in 1980, Aero Spring has served Tier 1 and Tier 2 OEMs with specialized components, including compression, torsion and extension springs, as well as wireforms.
“This acquisition further strengthens our capabilities in precision aerospace components and significantly expands our expertise in Belleville washers,” said Frank Mauro, president of Orlando Precision.
The acquisition adds in-house tensile and hardness testing capabilities to Orlando Precision’s offerings, enhancing its ability to provide vertically integrated, high-precision services across the aerospace, medical, electronics and defense markets.
The Aero Spring operation will be relocated to Orlando’s Huntington Beach, California, facility, where it will be fully integrated into the company’s existing infrastructure and production capabilities.
The Wire Association International Inc. (WAI) reported a successful turnout for its biennial Interwire Conference & Trade Exposition and 4th Global Continuous Casting Forum (GCCF), held May 13–15 and May 12–15, 2025, respectively, at the Georgia World Congress Center in Atlanta, Georgia. The events attracted 3,386 attendees from 46 countries and 42 U.S. states, with 350 companies exhibiting and 85 speakers featured across both programs.
“Interwire 2025 lived up to this year’s theme, ‘Shaping the Future of Wire Making, Uniting People & Technology,’ with courses and planning sessions focused on the wire and cable industry’s future,” said WAI’s 2025 President Eric Bieberich. “Keynote
and conference sessions showcased technological advancements and leadership insights, while the show floor buzzed with business opportunities, fostering collaboration and leaving me optimistic about our industry’s future.”
Highlights included keynotes by Andrea Pirondini, CEO of Prysmian North America, and author Chris Tuff, as well as a welcome reception at Mercedes-Benz Stadium. New additions included the Advanced Extrusion Workshop, a Fireside Chat, Taste of the South Happy Hour and WAI’s Education Center launch.
WAI’s top honors were awarded to Emmanuel De Moor, Thomas M. Heberling, Willem Sundblad and Pirondini. GCCF Chair Chris Tucker praised the forum’s global collaboration and focus on emerging technologies, calling it a “strong signal” of industry momentum.
IP Automation Inc., specialists in CNC wire bending and automation equipment, relocated its headquarters to a new facility in Carol Stream, Illinois. The 50,000+ square-foot space is nearly double the size of the previous location and reflects the company’s ongoing efforts to expand manufacturing capabilities and support long-term growth.
“We are thrilled to move into our new headquarters and take this next step in our company’s development,” said Tom Christofilis, CEO of IP Automation. “This new space will allow us to better serve our clients, collaborate with our talented team and continue to drive innovation in our industry.”
The Carol Stream location was selected for its strategic access to transportation routes and proximity to key partners, vendors and customers, the company says. It sees relocation as a step toward strengthening local relationships and supporting its workforce with a more modern, spacious environment.
While the address will change, all phone numbers will remain the same. Details about the grand opening event will be announced on the website, www.ipautomationinc.com.
Custom Wire Products (CWP) has acquired Little Falls Alloys (LFA), a Paterson, New Jersey-based wire manufacturer known for its expertise in nonferrous copper-based alloys. The 30,000-square-foot LFA facility will continue operations under its established name, expanding CWP’s production capabilities and product offerings.
LFA, which serves industries from automotive to medical devices, is known for custom redraw and electroplating services, including processing precious metals, copper and nickel. The company pioneered the production of beryllium wire in the 1940s and remains a key supplier for spring manufacturers.
“Over the past 80 years, Little Falls Alloys built a strong reputation for excellence and reliability,” said Jeff Lawrence, president of CWP. “We are excited to bring that legacy into the CWP family and leverage our strengths to provide even greater value to our customers.”
Lawrence noted that the multi-milliondollar acquisition will be accompanied by a significant investment in the Paterson site
wire 2026 takes place April 13–17, 2026 in Düsseldorf, Germany, and will include its inaugural special World of Cables section in Hall 13, featuring end product cable.
“For almost 40 years, wire has been the place to be for everyone who thinks big about wire and cable,” said Daniel Ryfisch, Director of Messe Düsseldorf. “With World of Cables, we are now putting the real stars of the industry on the big stage — the end products! Because without cables, nothing works — neither high-tech nor sustainability.”
World of Cables will highlight end products and demonstrate their key role in challenging applications — from high-voltage cables and fiber optics to automation and telecommunications. Its integration into wire 2026 means that the entire value chain of cable production will be represented — from raw materials and manufacturing to final application in key industries worldwide.
For more details about the World of Cable visit: www.wiretradefair.com/en/Visit/ Specials_Topics/World_of_Cables z
CASMI’s 2025 webinar series kicked off with a presentation on tariffs attended by 102 participants.
Guest speaker Paul Nathanson, a strategic communications expert with more than 30 years of experience in international trade policy, including Section 201, 232 and 301 tariffs, gave a clear overview of the current tariff landscape and what to expect going forward.
Attendees learned about the evolving trade environment, potential impacts on the spring manufacturing sector and how new policies could shape the industry’s future. A recording of this session is available through the CASMI member portal.
Two additional webinars are planned for this year. Topics and dates will be announced.
CASMI will host its 2025 An Evening at the Ballpark on Thursday, Aug. 15, 2025, at Impact Field in Rosemont, Illinois, the home of the Chicago Dogs, an American Association of Independent Professional Baseball (AAIPB) team.
Registration includes a game ticket, seating, food and beverages. Sponsorship opportunities are not available. This annual event is a token of appreciation from CASMI to its associate members and SpringWorld exhibitors for their ongoing support.
The application deadline for CASMI 2025 Scholarship Program closed May 2. We had many qualified applicants this year, reflecting the strong interest and commitment to the program. This year’s scholarship recipients will be announced in June.
The second biennial combined CASMI Expo and SMI Educational Symposium at SpringWorld will be held Oct. 7–9, 2026, at the Donald E. Stephens Convention Center in Rosemont, Illinois. The event is held every two years in even-numbered years.
The floor plan for the CASMI Expo is now available for exhibitors online at www.springworld.org. Exhibitors can now view and select their booth spaces using the interactive floor plan, which allows for easy navigation and booth selection by size, type or location. This tool is designed to help exhibitors choose the optimal location for their booths to maximize visibility and engagement during the event.
For more information or assistance, please contact CASMI at info@casmispringworld.org.
Aug. 15 Evening at the Ballpark Chicago Dogs Game, Impact Field Rosemont, Illinois
Oct. 16 SpringWorld Kick-Off Dinner
Alter Brewing Co. Downers Grove, Illinois
Nov. 13 Member Meeting
Top Golf
Schaumburg, Illinois
Dec. 11 Holiday Party Coopers Hawk Arlington Heights, Illinois
Events are subject to change. Visit www.casmi-springworld.org for the latest information.
By David DeVoe, John Evans’ Sons, NESMA President
NESMA continues to support the advancement of the region’s precision spring manufacturing sector with a renewed focus on workforce development, networking and industry visibility.
Marketing Committee Chair Andrea Tarantino (Napcon Communications), and I have deepened NESMA’s commitment to member support and industry advancement. Planned initiatives for 2025 include:
Workforce Development Partnerships — NESMA actively collaborates with technical high schools, trade programs and colleges to build a stronger talent pipeline for manufacturers across New England. These efforts include scholarship programs, facility tours and internships.
Industry Advocacy— The association continues to represent members’ interests at the state and regional level, ensuring manufacturers have a voice in policy decisions related to labor, energy and environmental regulations.
Enhanced Member Resources — NESMA’s updated digital platform includes tools for funding opportunities, compliance support, industry benchmarking and networking — strengthening the business foundation for our growing membership base.
August 25 NESMA Annual Golf Outing Farmington Country Club, Farmington, Connecticut
December NESMA Annual Holiday Party Farmington Country Club, Farmington, Connecticut
For an updated calendar of NESMA events, visit www.nesma-usa.com
In April, NESMA hosted its Tabletop Show & Comedy Night, attracting more than 100 attendees and vendor participation from not only Connecticut but also Massachusetts and Illinois. The event underscored NESMA’s regional influence and broad industry appeal. The evening combined business networking with entertainment. Special thanks to our generous sponsors, Industrial Steel and Wire, FENN/Torin, Gibbs Interwire, NIMSCO, HW Green Company, Thomaston Savings Bank, United Wire Company, Acme Monaco, Amstek Metal, CONNSTEP, Radcliff Wire and WAFIOS, whose support made the event possible and impactful.
NESMA’s Hartford Yard Goats baseball game in May was a success, offering an evening of networking and camaraderie on the Yuengling Party Deck. We extend our sincere thanks to all the attendees and sponsors, Amstek Metal, Connecticut Spring & Stamping, FENN/Torin, Gibbs Interwire, Napcon Communications and WAFIOS, whose support made the event possible.
A highlight of the event was the opportunity for all attendees to participate in a moving and patriotic ceremony by holding a giant American flag on the field. It was a memorable experience that added a meaningful touch to an already outstanding manufacturing community event.
On August 25, NESMA will host its annual Golf Outing at the beautiful Farmington Country Club — one of the top-rated golf courses in the state. Don’t miss out on a fantastic day of golf, camaraderie and connection with fellow manufacturing professionals.
Reserve your spot today at www.smihq.org/go/nesma-golf
NESMA is more than an association — it’s a community. Through collaboration, education and shared experiences, we’re strengthening the future of manufacturing in New England.
With a vibrant schedule and a clear mission, NESMA remains a driving force for innovation and unity in the spring and metalstamping industries.
For event registration, sponsorship opportunities, or to learn more about membership, visit www.nesma-usa.com. z
Dayton Lamina delivers high-performance compression springs for OEMs—engineered for durability, precision, and peak performance to meet the toughest industry standards.
Custom sizes & materials
High load capacities
Corrosion-resistant coatings
Expert solutions for unique manufacturing needs
Extensive inventory base w/common used diameter, length and pressures
Laura Helmrich-Rhodes, CSP, Ed.D., SHRM-SCP
Since OSHA and most other federal agencies are in limbo at the time of this writing, I’ll let the dust settle before I make any predictions or concise recommendations. In the meantime, I will focus on getting back to the basics of safety and human performance as an important profit-making ingredient. I’ll share a bit about myself, my favorite sport and how it plays into the workplace.
Confessions of a Lacrosse Mom
We’re a “lacrosse family.” Our son, Sean, played goalie, starting in elementary school. His dad was instrumental in creating the first club in our town. We now have a robust youth lacrosse league for elementary, middle, and junior high students, as well as interscholastic boys’ and girls’ high school teams. Sean went on to play in college, contributing to two national title teams, and has coached extensively since, including a stint in graduate school as interim head coach for an NCAA Division I women’s team during a national coaching search.
As a longtime “lacrosse mom” with experience as a high school and collegiate athletic trainer, I can easily see the crossover of sports coaching and safety management in the workplace. Coaching is coaching, regardless of who is on your team. This came to mind as I read the April 2025 USA Lacrosse Magazine cover story “How to Curb Bad Behavior in Youth Lacrosse.” The content and its application to workplace safety are worth discussing. Have you ever witnessed “unsportsmanlike conduct” at work? If you are a parent, grandparent, dedicated fan, former or current athlete, coach or especially a referee, you will see the value in this analogy, too.
The article discusses how some communities address “bad behavior” at all levels of lacrosse — players, parents and coaches. We probably don’t need to define unsportsmanlike behavior. The term “incivility” is often heard today. It’s certainly not new to sports or the workplace. It’s the increase in occurrence that warrants our awareness and action.
Let’s face it, today’s kids are your future employees. It is even possible that those shouting, swearing and fighting adults are your current coworkers or, heaven forbid, your next applicant. The USA Lacrosse Magazine article cites the National Association of Sports Officials’ 2023 survey, indicating in a study of 35,000 officials, 69% said that sportsmanship is “getting worse,” compared to 57% in 2017.
Both surveys attributed the cause of sportsmanship problems to parents. There were incidents in which officials were chased to their cars and even events resulting in arrests. I couldn’t help but see it all through the lens of a safety and human resource professional. Writer Justin Feill offers several suggestions for preventing and improving behavior, as well as creating a better culture for all, each with a clear connection to workplace improvements.
Although throwing a red or yellow penalty flag on the manufacturing floor or in a heated work meeting might take some creativity, stopping bad behavior at work is still essential. U.S. workplaces are experiencing a rise in incivility that has escalated to workplace violence. The health care and night retail sectors have the highest risk factors. However, manufacturing is not immune. OSHA reports on its “Workplace Violence Prevention” webpage that in 2023, 740 employees across all sectors died due to violent acts at work. According to the “Census of Fatal Occupational Injuries,” in 2023, 391 fatal injuries in manufacturing were due to violence. This number includes both homicides and intentional injury by another person.
The table on the next page lists “5 Ways to Nip Bad Behavior in the Bud” on the playing field from USA Lacrosse Magazine. The list is directed to everyone at the game — players, coaches, parents and spectators. Similar strategies should be implemented at your
facility. Set expectations to create a caring culture, reduce incivility and especially prevent any workplace violence.
A written code of conduct, along with a zero-tolerance policy for unacceptable behavior, is recommended for all employees in the workplace. Discussing this document with workplace applicants is the equivalent of a coach sharing the written code with players and parents at preseason meetings. Coaches require a signature of understanding to eliminate future incidents, and so should you. Eventually, written documents can become outdated or obsolete and require updating. Be sure to include the code of conduct in the continuous improvement process to be current and work well for your organization.
Dealing swiftly with disrespectful, rude, impolite or offensive comments at work is important. Throwing a flag, or carding the offender in the game, stops the bad behavior. Something similar must happen at work. Quick intervention prevents the behavior and others’ reactions to the behavior from escalating to violence. According to the Society of Human Resource Managers (SHRM), the most common forms of incivility seen at work include addressing others disrespectfully, interrupting or silencing others who are speaking.
1. Create a Code of Conduct.
2. Card Offenders to preemptively address bad behavior of anyone, including spectators.
3. Recruit Sideline Managers to monitor behavior on and off the field and ensure consistency with the Code of Conduct.
4. Incentivize Positive Behavior and good sportsmanship with awards and social media coverage.
5. Nail the Preamble at all events with a pregame address setting expectations.
Verbal abuse, intimidation, shoving, pushing, fistfights and the threat of harm are all considered violence at work. Federal OSHA has regulations on this topic and some states mandate written prevention programs. One example of federal requirements is that injuries sustained must be recorded on the OSHA 300 log — even minor incidents, such as broken eyeglasses.
Have you ever seen an obnoxious adult ejected from a sporting event? It’s a troubling trend and creates a lot of anxiety for everyone in the moment. The rest of us feel relieved when it is over and dealt with quickly. Swift attention also sends an important message to your workforce. A 2024 SHRM HR Quarterly article reported that, in a survey of more than 1,000 U.S. employees, 66% had experienced or witnessed workplace incivility in the past month and 57% in the past week.
All workers want a safe and protected environment, both psychologically and physically. An organization that tolerates incivility can foster a fear-filled environment. This can lead to reduced morale, increased job turnover and potential long-term effects such as PTSD. Even the most valued laborer who creates consistent trouble with coworkers will negatively impact profits. Every company should have a written, clear, fair and consistent process for dealing with conflicts.
1. Create a Written Code of Conduct and include it in the continuous improvement process.
2. Deal with Offenders Quickly.
3. Recruit Quality People using employee referrals to get positive people.
4. Incentivize Positive Behavior by rewarding great employees, promoting and growing great leaders that practice open communication and conflict resolution.
5. Nail the Preamble by setting safety, quality and civility expectations daily. Remind everyone they are important and create a caring work community. Offer EAPs to help employees cope with personal problems.
Recruiting great employees — especially through referrals — can help attract candidates with similar positive attitudes and behaviors. Top workers often know others who could become your next valuable team member. Offering referral incentives is a smart way to bring in reliable, team-oriented people. Just as important as hiring skilled operators is recognizing positive attitudes, encouraging teamwork and promoting only those who demonstrate supportive, can-do leadership.
If supervisors need training in dealing with difficult employees, handling hard conversations or simply being better leaders, there are many resources for nurturing these skills. Like coaching athletes to improve their passing and catching skills, leadership skills can be sharpened through seminars, webinars, good books and mentoring. None of these needs to be a large expense to the company. Supervisory and leadership roles and authority are clearly defined to prevent confusion, and both are paramount in conflict management.
USA Lacrosse Magazine suggests league administrators “Nail the Preamble,” in other words, start each game with a review of the written expectations. Post the code of conduct for all to see. If you have been to any sports event lately, you have seen and heard a similar announcement that only good sportsmanship will be tolerated. This sets up the game for success and makes ejecting the perpetrators from the game much easier.
Reviewing your company’s “preamble” (code of conduct) at meetings, pre-shifts, toolbox talks and production or QC reviews can focus everyone on civility. It clarifies your mission, sets the priorities and encourages cranky people to leave their bad attitude at home. Fortify your culture by starting each meeting by setting positive expectations for adhering to safety rules, promptly reporting near misses or accidents and “playing nice.”
Attend an upcoming safety webinar: Supervisor Safety Leadership Thursday, July 10, 2025 1–2 p.m. ET
As an additional member benefit, SMI’s safety and compliance webinars are complimentary to members. Nonmembers may participate at a cost of $149. For a full list of upcoming safety and regulatory compliance webinars and services, visit: www.smihq.org/go/safety.
Leave it in the Locker Room?
Recognizing that not all our troubles can be “left at the door,” provide support to employees to cope with and solve personal problems such as financial, marital or illness, so that festering irritations don’t manifest themselves in coworker conflict. Open, caring communication and opportunity to seek help should be part of a company’s formal or informal employee assistance program. Employee Assistance Programs (EAPs) are confidential services that help employees address personal and work-related problems.
According to SHRM, one-third of workers surveyed expect incivility to increase over the next year. What’s considered “respectful” can also vary by generation, making it essential to set clear expectations, train employees and leaders in de-escalation and address issues promptly.
Finding a way to discuss my favorite sport while highlighting safety and human performance proves you can’t leave your “good sportsmanship” on the playing field. You carry your respectful manners and positive attitude with you everywhere you go. Companies that put effort into effective conflict management will improve relationships, increase productivity, retain talent and reduce stress in the workplace. z
USA Lacrosse Magazine
Laura Helmrich-Rhodes, CSP, Ed.D., SHRM-SCP, is SMI’s regulatory compliance consultant. She is an associate professor in the Safety Sciences Department at Indiana University of Pennsylvania, teaching graduate and undergraduate classes. Contact Rhodes at SMI: 847-450-6848 laurahrhodes@gmail.com
5 Ways to Curb Unsportsmanlike Behavior in Lacrosse | USA Lacrosse www.usalacrosse.com/magazine/misc/youth/5-ways-curb-unsportsmanlike-behavior-lacrosse
OSHA Safety & Health Topics
Workplace Violence — Overview | Occupational Safety and Health Administration www.osha.gov/workplace-violence
Society of Human Resources Management (SHRM) Magazine
Incivility Is Running Rampant in the Workplace. How Can Organizations Fix It? www.shrm.org/topics-tools/news/all-things-work/shrm-launches-civility-index
Sample Written Policy
Workplace Violence Prevention Policy www.shrm.org/topics-tools/tools/policies/workplace-violence-prevention-policy
Violence Prevention Program online course, Oregon OSHA
Oregon Occupational Safety and Health: Violence Prevention Program online course:
Online courses: State of Oregon
www.osha.oregon.gov/edu/courses/Pages/violence-prevention-program-online-course.aspx
Office of Personnel Management
What is an Employee Assistance Program (EAP)? — U.S. Office of Personnel Management www.opm.gov/frequently-asked-questions/work-life-faq/employee-assistance-program-eap/what-is-an-employee-assistance-program-eap/
Dan Sebastian
Editor’s Note:
SMI Past President, Dan Sebastian, retired from writing the “Dean of Springs” with his final column in the Spring 2025 issue of Springs (http://bit.ly/ SPR-SPR25p21). This is the first in a series of Sebastian classics. Turn to Ride of a Lifetime (p.44) for a complete Springmaker Spotlight profile of Sebastian and his storied career by SMI Executive Director Gary McCoy.
One major issue in springmaking is the use of commercial tolerances for springs. It is worth looking at the origin of the published data. Some of the first tables were presented in 1944, when A.M. Wahl copyrighted his book “Mechanical Springs.” Wahl presented tables developed by Westinghouse Electric’s research and development center in his book, which continues to be one of the most used references in the spring industry. In subsequent years, empirical data from a research team at Associated Spring augmented the original data.
The original tables were segregated based on key design variables. The tables were later converted into an algorithm. These key variables included:
d = wire diameter
C = index
D = mean diameter
N = number of coils
The basic variables fit neatly into mathematical modeling. In basic predictability, other factors that cannot be modeled contribute to variability. Among these are the material, the equipment and the setup quality. The good news is that empirical data established a basic standard with the equipment and setup quality that was within the best industry standards.
The material was from a limited number of sources. The collected data was evaluated and reported after applying a statistical confidence factor. The material may be one of the most significant factors in any specific design and setup (that is why we do process capability studies on each setup).
Early in my career, I worked at one of the greatest statistical laboratories in the spring industry, a plant that made high-volume engine valve springs. Our studies uncovered fundamental differences between material suppliers meeting tolerances.
Some differences were so significant they impacted our procurement practices (price is not the only factor). These differences forced us to look more carefully at the material by considering factors beyond traditional specifications.
One of the things we discovered was the cast in the wire; the curvature and the pitch had a significant effect on the tolerances. You can see this phenomenon by cutting a few coils loose and letting them sit on the floor. You will see what looks like a snake coiled up. This appeared to be related to the material packaging at the mill. A secondary material factor that impacted the tolerances was the roundness.
Another factor causing tolerance variation was the distance from the coiling point to the unspooling reel. The distance must be sufficiently large to compensate for the torque created in the coiling process, allowing it to be dampened.
The original tables and subsequent algorithms used were from empirical data, which varied from the material and equipment/ setup built in. The factor designed to give +/- 3 sigma capability was the basis for the “standard tolerances.” Most springmakers can easily manufacture within the standard tolerance band, but the standard was for all. After accounting for the natural variation based on geometry, material becomes a significant source of variation. In any manufacturing process, statistical controls will ensure quality and adherence to specified tolerances are maintained. z
Dan Sebastian is a former SMI president. He holds a degree in metallurgical engineering from Lehigh University and his industry career spans more than four decades in various technical and management roles.
C. Richard (Rick) Gordon
As part of this issue on tolerances, this article compares tolerance values calculated using SMI’s Advanced Spring Design (ASD7) software for commercial and precision grades with those calculated according to international standards. Springmakers know different international standards bodies calculate tolerances in different ways. There will also be a demonstration of ASD7’s ability to accommodate tighter tolerances.
Spring manufacturing, like any other production process, is not exact1. It will produce variations in characteristics such as load, mean coil diameter, free length and relationship of ends or hooks. The very nature of spring forms, materials and standard manufacturing processes causes inherent variations. However, the overall quality level for a given spring design can be expected to be superior at manufacturers who specialize in high-quality springs using modern equipment.
Normal or average tolerances on performance and dimensional characteristics may vary for each spring design. Manufacturing variation in a particular spring largely depends on factors such as spring index, wire diameter, number of coils, free length, deflection and the ratio of deflection to free length.
Dan Sebastian’s article, “Spring Tolerances” (see p. 17), discusses both the factors included in tolerance calculations and those not included, which can significantly impact a springmaker’s ability to meet tolerances. Factors that can be modeled include:
d — wire diameter
D — mean spring diameter
C — spring index (D/d)
Na — number of active coils
Factors that cannot be modeled include spring material, equipment used and machine setup quality. Spring material parameters such as wire cast and helix2, out-of-round condition and distance from the supply spool to the machine can impact spring variation.
Spring tolerances are covered in the SMI 304 Dimensioning, Tolerancing and Testing course, which is offered annually. The class presents details from the “Encyclopedia of Spring Design” on how tolerances are calculated3. Tighter tolerances are generally associated with increased costs, which is an important consideration.
In SMI’s 201 Compression Spring Design class, several worked examples are presented. Example 1 uses the following design input parameters:
• Material: 4.8 mm oil-tempered wire
• Ends: Closed (squared) and ground
• Fits in a 40 mm diameter hole
• Outside diameter: 38 mm (95% of the hole diameter)
• Must exert 275 N at 60 mm
• Must exert 500 N at 50 mm
• Does not compress past 50 mm height
• Works in static loading conditions
In Figure 1, the ASD7 input screen shows input values in bold and commercial-grade
tolerances selected. Figure 2 shows the same screen with precision-grade tolerances. Quality factors are applied to calculate different tolerance levels: 1.6 for commercial tolerances and 1.0 for precision tolerances.
Figure 3 compares ASD7 commercial and precision tolerance values for free length, outside diameter, load 1 and load 2, along with calculated tolerances from international standards.
In general, ASD7 precision tolerances align with EN, DIN and IS Grade 2, while commercial tolerances correspond to EN, DIN and IS Grade 3. JIS values are similar for some parameters and different for others.
If a client specifies a tighter load 1 tolerance of ±28.0 N, instead of the ±43.8 N precision value, entering that value shows a new calculated load 2 tolerance of ±31.375 N. The new free length tolerance is ±1.0611 mm. Input values for any italicized field can be entered.
In ASD7, if inputs are made for both load tolerances, a value is also required for the free length tolerance. Conversely, if only the
free length tolerance is overridden, both load tolerances will be calculated.
Calculated parameters are for reference only and are not toleranced.
Sometimes springmakers are presented with customer-engineered designs that specify extremely tight tolerances. As taught in spring design classes, commercial engineering software often uses templates that include block or box tolerances (Figure 5). These are
meant for machined parts and should not be applied to formed parts like springs. This topic often prompts spirited discussions during contract reviews. In many cases, once the spring designer understands the distinction, a satisfactory solution is found.
Summary
The different tolerance options available in SMI’s ASD7 software were illustrated using a compression spring design. Tolerance values from several international standards were shown for comparison. The software’s flexibility in accommodating tighter tolerances was also demonstrated. z
References
1. Advanced Spring Design Software, SMI Inc. and Universal Technical Systems Inc., 1982–2024
2. Gordon, C.R., “Cast and Helix Measurements,” Springs, Vol. 61, No. 3, p. 19
3. “SMI Encyclopedia of Spring Design,” Tolerancing and Testing, 2000
C. Richard (Rick) Gordon is SMI’s technical director. He has more than 50 years’ experience in the steel and wire industries and is available to help SMI members and non-members with metallurgical challenges such as fatigue life, corrosion, material and process related problems.
Contact Gordon at 574-514-9367 or c.richard.gordon@gmail.com.
Enroll in Spring Design 206 — Snap Ring Design Training Program Webinar scheduled for Thursday, July 17, 2025 1–5 p.m. ET on Microsoft Teams.
To register for this class or others, go to http://bit.ly/SMItech.
At Anchor Abrasives we specialize in the design
For
Today, in our modern manufacturing facility, we are ready to continue our tradition of innovative quality products and unmatched customer service. For more information contact Anchor Abrasives Company, 7651 West 185th Street, Tinley Park, IL 60477 U.S.A. Phone: 708-444-4300; Fax: 708-444-1300.
Park, IL 60477 U.S.A. Phone: 708-444-4300; Fax: 708-444-1300.
At Anchor Abrasives we specialize in the design and manufacture of resin, epoxy and oxychloride bonded nut inserted discs and cylinders...plus centerless and rollwheels. Today, in our modern manufacturing facility, we are ready to continue our tradition of innovative quality products and unmatched customer service. For more information contact Anchor Abrasives Company, 7651 West 185th Street, Tinley Park, IL 60477 U.S.A. Phone: 708-444-4300; Fax: 708-444-1300. www.anchorabrasives.com
contact Anchor Abrasives Company, 7651 West 185th Street, Tinley Park, IL 60477 U.S.A. Phone: 708-444-4300; Fax: 708-444-1300.
Starrett offers a complete line of innovative force solutions for spring testing. High volume production testing solutions are available with both basic (L1) and advanced (L2) software.
For more information visit starrettmetrology.com/force
BY PHIL SASSO
By any measure, tight tolerances are springmaking’s inherent challenge.
Why do customers demand them? How can springmakers best achieve them? When are tolerances extreme? And how can you tactfully address expectations?
To answer these questions, I spoke with three springmakers who understand both technical demands and business realities. Together, they shed light on the fine line between precision and overengineering, offering practical insights into customer expectations, manufacturing capabilities and how education can bridge the gap.
Two associate members also contribute to this issue. Maintaining Tight Tolerances in Heat Treatment (p. 26) takes a technical look at ovens and stress relief. Meanwhile, The Racing Force of Springs (p. 28) is a case study of Roush Yates Engines’ use of advanced force testing to precisely manage valve spring performance in championshipwinning NASCAR engines.
“Tolerance is a customer specification of what they can live with and not live with in their application,” said Don Jacobson III, SMI president and vice president of business development at Newcomb Spring.
In spring manufacturing, tolerances refer to a spring’s physical dimensions or performance characteristics, such as force or deflection. But not all tolerances are created equally — or realistically.
“A spring is an elastic element,” explained Jason Sicotte, director of engineering at Associated Spring. “It’s being wound, coiled, formed … and has spring back to it.” Forming makes springmaking fundamentally different from machining, where components are cut from solid blocks of material and maintain static shapes.
“You’re typically machining a solid block of something that won’t readily deflect,” Sicotte said. “So, it’s much easier to hold tolerances that are measured in terms of a thousandth or a tenth of a thousandth. With springs, you can still measure tolerances in thousandths, but usually not tenths of thousands.”
“Forming is different than machining,” noted Gene Huber Jr., SMI immediate past president and executive vice president at Winamac Coil Spring. “Spring back and spring material is typically somewhere around five degrees. That variation is something customers need to understand.”
This fundamental difference creates expectations that don’t always align with reality. Also, many industry tolerance standards were established long before computer numerical control machines and modern inspection tools.
“Some of the spring tolerances come from pre-CNC equipment,” Huber added. Many of the industry’s legacy tolerance tables were set by SMI decades ago based on mechanical coiling. “Back then, all the axes of motion were mechanical … There wasn’t a thing called a probe.”
“Over engineering is the pretty common practice of asking for a spring — every spring — to be perfect,” Jacobson said. “And in our industry, springs are like snowflakes, each one is just a little different.”
The impact compounds quickly. Meeting unnecessarily tight tolerances often requires slower production speeds, more expensive equipment or dramatically higher scrap rates. Each adjustment increases costs that ultimately flow back to customers.
“If you do 100% inspection at the end of the process, and your yield is 90%, you’re throwing away 10% of your springs,” Sicotte said. “That effectively means your line is running 10% slower.”
Huber pointed out another culprit: heat. During stress relief, springs are exposed to high temperatures to release internal stresses. But slight variations can affect geometry. (See “Maintaining Tight Tolerances in Heat Treatment,” p. 26.)
“You have cold dimensions, and you have finished dimensions. So, if you happen to be making a spring out of music wire, when it goes through stress relief, the outside diameter will constrict,” Huber said. “If you have 10 coils of wire in the spring at a one-inch outer dimension (OD), when it goes down to 0.980 on the OD, all that extra wire actually makes the wire feed look like 10.25 coils.”
Torsion springs are especially sensitive. When stress is relieved, their leg position can change substantially.
Unnecessarily tight tolerances often come from engineering workarounds.
“It may be easier for customers to just assign a very tight tolerance to solve some other problem they may have,” Sicotte said. But that shortcut can create downstream consequences for cost, performance and manufacturability.
In our industry, springs are like snowflakes. Each one is just a little different.
Don Jacobson
“Every thousandth of an inch difference in wire diameter is magnified to the fourth power in the spring rate,” Huber said. That means even the slightest variance in input material can throw off the final performance, unless manufacturers are allowed flexibility in other areas, such as coil count or outside diameter, Huber explained.
“There’s a dance that we have to do,” Jacobson said, “where we have to find out what their actual needs are.” That might include fit constraints, specific loads or assembly requirements. But rarely is it everything at once.
Not all springs that look right are easy to make. One of the most deceptively difficult factors in spring design is the spring index — the ratio of the coil diameter to the wire diameter.
“It’s one of those tricky ones,” said Don Jacobson III. “They’ll always look like a spring, but it’ll be very difficult to manufacture once you get outside of a certain range.”
Problems arise at both ends of the spectrum. Springs with a low index, typically under 4.0, require the wire to wrap almost back on itself. That creates tool clearance issues and makes the wire difficult to bend. On the other hand, an index above 12 can lead to oversized, unstable coils that are difficult to control.
“If it gets too big, like a slinky or even bigger, it turns into this big wobbly monstrosity,” Jacobson said. “When it’s coming off the machine, making this big giant loop, and then you’re trying to make another big giant loop behind it, it’s very hard to control and be consistent.”
Spring index doesn’t often get top billing in design conversations, but it can have a big impact on production efficiency and scrap rates. And it’s one more reason for customers to consult with their springmaker early in the design process — before a simple-looking spring becomes a manufacturing headache.
“You can measure either geometric or force tolerance,” Sicotte said. “We never want a customer to put a tolerance on both a dimension and a load … then you become over-constrained.”
Diplomacy plays a critical role in helping customers understand the trade-offs of tight tolerances.
“The important part of it is load,” Huber stressed. “The real critical thing should be tolerance. Overengineering says, ‘It’s got to be just perfect.’ Well, it doesn’t have to be to really do what you want it to do.”
“Your customer is typically not a spring expert,” Jacobson noted. Most buyers work with multiple parts, not just springs, and aren’t trained in coil dynamics. “So, it’s our job as the spring manufacturers to be the experts in our field.”
“We would ask them first directly: ‘Do you really need this type of tolerance for the application?’” Sicotte said. “Very, very often they come back with, ‘Actually no … tell me what’s more appropriate.’”
Huber takes a similar approach. “I would say, ‘OK, I’m meeting your loads. You want to hold the OD plus or minus 0.005. Can you live with SMI tolerance at plus or minus 0.020?’”
From there, the discussion shifts to form, fit and function.
While overengineered tolerancing is common, there are cases where precision is nonnegotiable.
“Aerospace customers have extremely tight tolerances that are difficult to achieve,”
The tighter the tolerance, the slower the process usually has to go.
Gene Huber
Sometimes, achieving a tight tolerance can be a competitive advantage. If we can do it and others can’t, that wins us the business.
Jason Sicotte
Sicotte said. “Similarly, we’ve seen very tight tolerance in automotive transmission washers … it may affect transmission calibrations.”
Huber added that military applications and coil-over shocks often demand tight control for life-and-death or performance-critical reasons. In those cases, careful analysis is necessary to predict bowing or spatial conflicts.
“Tight tolerances aren’t always bad,” Sicotte said. “Sometimes, achieving a tight tolerance can be a competitive advantage. If we can do it and others can’t, that wins us the business.”
Material variation and upstream control are often fundamental to success. And control isn’t just about precision — it also protects against production delays.
“You may want to control material thickness to a very, very tight tolerance that is sometimes beyond what’s commercially available,” Sicotte said. “Because then your rate becomes very repeatable.”
“If your yield becomes 50%, you’re not going to have enough material to make all the parts you need,” he warned.
In some cases, tight tolerances are mistakenly transferred from other disciplines. “If the engineer specifying it came from a different industry, his experience may be more with machine tolerances,” Sicotte said. “That’s fine — just not when you’re bending wire.”
Huber noted that most engineers don’t get formal spring training in school. “They might get a spreadsheet off the internet,” he said, “but seeking the willingness to discover with them … takes a little bit of diplomacy.”
“That’s why we offer our 201, 202, 203 and 300-level classes,” Jacobson said, referring to SMI’s spring design training. “To help educate our industry as well as customers.”
So, how should springmakers approach the question of tolerances?
“That may mean offering two quotes,” Huber advised. One for standard tolerances and one for tight tolerances — so the customer can weigh performance against cost.
“A springmaker may say: ‘If we make these changes, it’ll be much more efficient,’” Jacobson said. “And if it’s more efficient, your price is going to be better — and if your price is better, we all win.”
The approach requires moving beyond the “customer is always right,” mentality toward cooperative problem-solving. Success comes from understanding application requirements, explaining manufacturing realities and finding solutions that balance performance with practicality.
As an old Associated Spring slogan once said: “We will meet all tolerances.” Sicotte laughed. “That was the marketing at the time.”
Today’s approach to tolerances needs to be more nuanced and more collaborative. In the end, the goal is not to chase perfection, but to deliver precision where it matters most. z
Read how Gene Huber uses the Theory of Constraints to manage consistency in tight tolerances at www.smihq.org/go/sum24-constraints
By Alex Grenier-Desbiens
In modern spring manufacturing, precision is paramount. Industries such as aerospace, automotive and medical rely on components with exceptionally tight tolerances to ensure functionality, reliability and safety. Achieving these stringent tolerances requires meticulous control over material properties, processing conditions and environmental factors. Heat treatment, particularly stress relief, has a significant impact on dimensional stability.
Pyromaître has manufactured stress-relieving ovens since the mid-80s. A turning point in our oven manufacturing journey was more than three decades ago when a customer asked us to design an inline oven capable of stress relieving high precision 0.250” CrSi torsion springs with zero rejects. In a joint effort, we produced our Pyro High Speed process and ovens. In this article, we’d like to share our knowledge of heat transfer mechanisms and their relationship to tight tolerances.
Stress relief mitigates residual stresses induced during forming. Without proper management, these stresses lead to dimensional inconsistencies. The extent of stress relief directly impacts spring geometry, with variations causing deviations in final dimensions. Meeting stringent specifications requires uniform and repeatable stress relief across all components.
The effectiveness of stress relief depends on the precise energy applied to the metallic crystal structure. The main parameters affecting the thermal process are the temperature reached, the part temperature ramp rate and soak time (see “Predicting Deflection Angles on Torsion Spring Arms During Stress Relieving,” Springs, Summer 2023 - www.smihq.org/go/sum23p37). The Larson-Miller relation offers a simple equation to calculate and compare the thermal effect (TE): TE = T × (C + log(t)), where T represents temperature, t is time and C is a material-specific constant. The desired stress relief can be achieved using lower temperatures over longer durations or higher temperatures for shorter periods, provided the overall energy input remains equivalent.
The uniformity of heat transfer has a significant impact on stress relief effectiveness and the ability to maintain tight tolerances. Several key factors influence thermal behavior during heat treatment.
Heat transfers from the surrounding hot air to the object’s surface, depending on the temperature gradient and material properties. A thin boundary layer of air absorbs and
transfers heat, creating localized temperature variation. Uniform conduction requires precise temperature regulation and consistent airflow.
Convection in the Oven: Heat moves through circulating air in the oven, with efficiency depending on airflow velocity, turbulence and oven design. Forced convection systems enhance heat transfer by ensuring continuous circulation, reducing temperature differentials across the object’s surface and preventing localized over- or underheating.
Turbulent Air Movement: Airflow can be either laminar or turbulent. Laminar flow moves smoothly across surfaces, creating steady heat transfer. Turbulent airflow creates irregular, swirling movements that enhance mixing and ensure heat transfer through all part surfaces. Controlling airflow patterns and optimizing oven geometry helps minimize heat losses and cold air infiltration.
Radiation Heat Transfer: Thermal energy transfers through electromagnetic waves, primarily between oven heating elements and the object. Radiation doesn’t require direct contact but can be highly directional, leading to uneven heating in complex shapes. Surfaces directly facing the heat source may absorb more energy, while shaded areas receive less. This presents challenges for springs with complex geometries processed in bulk with random positioning.
Impact of the Oven Belt: In conveyor systems, the contact between springs and the belt is typically minimal, resulting in insignificant thermal conduction between them. However, the belt can act as a heat sink, drawing heat from the oven atmosphere. If the belt cools significantly on its return path and heats more slowly than the objects, it may create temperature inconsistencies. Well-designed conveyor systems minimize these effects by reducing temperature loss and optimizing belt speed.
Heat Conduction Within the Object: Once heat reaches an object’s surface, it must conduct internally for uniform temperature distribution. The rate depends on material properties, including heat capacity and thermal diffusivity. Springs with high thermal conductivity distribute heat more evenly. Uniform heat transfer to all surfaces reduces thermal gradients, allowing process optimization and improved dimensional stability.
Stress relief depends on the spring’s temperature evolution during processing. Spring temperature is influenced by more than just
air temperature. Areas with higher air velocity or radiation may cause temperature gradients, leading to variations in stress relief and final dimensions. Measuring actual spring temperatures throughout the process ensures uniform heat transfer across the chamber. This approach helps detect areas where temperature deltas occur and address their causes.
Achieving precision for tight-tolerance springs requires a heat treatment process that is both repeatable and uniform. Precise temperature control, optimized airflow, low radiation and consistent processing conditions are critical. Beyond monitoring oven air temperature, direct part temperature measurement is essential for high-precision applications.
Tight tolerances in spring manufacturing ensure optimal performance in demanding applications. Manufacturers can minimize dimensional variations and enhance product stability by controlling heat transfer mechanisms and maintaining uniform stress relief. As industries push the boundaries of precision and efficiency, the demand for precise heat treatment solutions continues to grow. z
Alex Grenier-Desbiens is the product and service manager at Pyromaître Inc., Quebec, Canada. Pyromaître designs and manufactures industrial conveyor ovens and furnaces featuring the latest technologies and premium components that meet or exceed spring industry standards. He can be reached at agrenier@pyromaitre.com or 418-831-2576.
By Michael McCue
One of the most mission-critical applications for springs lies in the valvetrain of high-performance racing engines. Recoiling 75 times per second, even the slightest, typically undetectable difference in prime functionality of the springs can easily cost a race. It is one of the most highly stressed components in a racing engine. Indeed, a racing engine valve spring is analogous to a valve in the human heart, even though their life spans differ profoundly. Valve springs only last between 500 and 1,000 miles on average.
Roush Yates Engines (RYE) of Mooresville, North Carolina and its manufacturing division, Roush Yates Manufacturing Solutions (RYMS), know all too well how critical springs are to their success. So, in 2019 when The L.S. Starrett Company recommended that RYE consider evaluating the use of its force testing equipment as a very finite means of measurement for determining load characteristics of its valve springs, it took them up on the offer and began using an advanced force testing system to provide extensive load data and analysis. What RYE discovered was very revealing and led to a totally new paradigm for its spring testing.
Demanding Performance and Precision
RYE has three well-equipped, high-quality labs that feature the tools necessary to measure and inspect a wide variety of parts manufactured and supplied for its racing engines, as well as for external customers.
RYE is the exclusive engine builder of Ford Performance racing teams in the NASCAR Cup and Xfinity Series. In addition, Roush Yates Manufacturing Solutions (RYMS) is a precision CNC parts manufacturing division of Roush Yates Engines with expertise in the multi-axis machining of metal and plastic parts with complex geometries. RYMS’ in-house production includes machined solutions for Ford’s FR9 V-8 NASCAR programs, chassis motorsports components, aerospace, defense, medical and high-tech industries. RYMS’ quality management system is AS9100 Rev D and ISO 13485 certified, as well as International Traffic in Arms (ITAR) and Cybersecurity Maturity Model Certification (CMMC) compliant.
To help achieve its demanding performance and company goals, RYE uses precision measuring tools and metrology systems to ensure that critical design specifications are being met at the level expected and required by engineering. Motorsports, defense, aerospace and medical manufacturing require strict standards to achieve consistent quality. Adding complex requirements for high-performance, reliable parts makes the testing and measurement processes even more demanding.
The ultimate precision required to build racing engines cannot be fully attained without comprehensive data. Historically, valve spring load has been measured with a mechanical “spring rater,” a basic benchtop device with a pull-handle that is connected to a rod and stand with a dial indicator. While this method provides simple load values, it has limitations in terms of accuracy, repeatability and the inability to provide force analysis data.
“So much of what we do is data-driven,” explained Todd English, vice president of strategic partnerships and marketing at RYE. “The valve spring is a highly stressed component that requires data validations at various positions and stress points via a highly repeatable process and system. The Starrett force measurement system has given us a tremendous amount of data, enabling us to fully leverage spring component validation as it relates to our engine development programs. The amount of detail required in performance racing engines is staggering. We look into our processes at a microscopic level day in, day out.”
The plethora of valuable force measurement data has not only enabled RYE to consistently validate spring load data every time, but it has also spawned unique programs and measurement methods.
“We study load characteristics of various spring positions, measuring dynamic load, validating spring metrics and testing load after races. However, we have also learned to apply the data in areas we had not initially used it for, such as in research and development,” said Eric Kerley, valvetrain engineer at RYE. “The flexible software has allowed us to create customized, proprietary test programs for valve spring measurement and development projects that require comprehensive force analysis.”
“In addition, its ability to measure force in two directions has allowed us to measure not only compression springs, but also tension springs and other applications where friction may be at play,” Kerley said. “It has even given us the ability to develop and calibrate proprietary measurement tools in the development of our valvetrain systems, as well as adapting unique fixtures for many force measurement applications.”
RYE primarily uses the Starrett force testing system for load testing. The Starrett force testing system can test loads up to 5000 Newtons. In addition, it can measure distance, break points and material properties including Young’s modulus, tensile strength, stress or strain.
Determining the bottom-line value of what a force measurement system represents for a company that designs, builds and tests racing engines might be considered esoteric to some, but when RYE was asked the question, the answer was clear.
“Force measurement of our valve springs has pushed our development of high-performance engines and has been key to our success, resulting in four out of seven NASCAR Cup Championships in the past seven years,” English said. z
Michael McCue is the president of McCue & Associates LLC and former marketing manager of The L.S. Starrett Co. He has nearly 40 years of experience in manufacturing technology in a wide range of industries from machine tools and instrumentation to cutting tools and abrasives, CAD CAM, and metrology at Starrett for 13 years.
To view a Starrett video on metrology and force testing NASCAR race engines, go to: www.starrettmetrology.com/roushyates
To contact the L.S. Starrett Co., call 949-348-1213, email force@starrett.com or visit www.starrett.com.
By
Surrounded by the world’s finest jazz, gumbo and beignets, SMI held its 2025 Annual Meeting at the Kimpton Hotel Fontenot in New Orleans, March 29–April 1. While the focus remained on education and networking, downtime allowed for personal excursions to the French Quarter, Jackson Square and local attractions.
“SMI’s ongoing focus on education, technology and leadership really came to life at our Annual Meeting in the historic and lively city of New Orleans,” said Don Jacobson III, SMI president and vice president of business development at Newcomb Spring. “We came together, paraded through the streets, talked openly about the challenges and opportunities in the spring industry and heard from some truly inspiring speakers.”
The Emerging Leaders Conference found its stride this year with 15 young professionals participating in the half-day event (see p. 36).
“Our Emerging Leaders group is quickly becoming the heartbeat of SMI’s future,” Jacobson said. “Seeing such passionate, driven professionals in action — as they build leadership through collaboration — gives us every reason to be optimistic about the direction of spring manufacturing in North America.”
The Newcomers Reception welcomed 20 first-timers (affectionately known as “green-dotters”). The Opening Reception provided an opportunity to mingle with familiar colleagues and establish new contacts over hors d’oeuvres and drinks in an indoor/outdoor setting. Ideas, energy and interaction fueled Sunday’s committee and board of directors’ meetings.
“This year, SMI’s educational content was engaging, interactive and packed with fresh insights,” Jacobson said. “Our speakers brought practical strategies and a deep understanding of the challenges manufacturers face today.”
An opening panel discussion of industry leaders included Ryan Cutter of FENN/Torin, David DeVoe of John Evans’ Sons, Dan Foster of ISW, Don Jacobson of Newcomb Spring and Steve Kempf of Lee Spring, moderated by SMI executive director Gary McCoy.
Panelists shared “aha moments” that impacted their businesses, including attracting younger talent, improving employee engagement and building company culture. They distinguished the difference between being a leader versus a boss by emphasizing listening, supporting and empowering employees rather than dictating tasks. The discussion also touched on servant leadership, employee empowerment and creating an environment of trust and open communication.
During the concluding session of day one, author and workplace strategist Jeff Butler spoke on “Building an Effective Multi-Generational Workforce.”
“[Researchers] looked at Australia, Canada, rural parts of Alaska and different parts of the U.S. that barely had any electricity. How do you get young people to stay there outside of money?” Butler asked. “Well, they found out there was something that the leaders would do differently. They’d integrate them into the cultural practices. What you need to do is get them to shift their self-image from ‘I’m visiting’ to ‘I’m staying.’“
SMI Technical Director Rick Gordon opened day two of the educational sessions with an “Overview of SMI Technical Services.” He covered SMI’s Advanced Spring Design (ASD7) software, webinars and on-demand training. He also discussed SMI’s metallurgical services, including answering questions on fatigue life, corrosion problems and material-related issues.
Author and speaker Chris Dyer provided a closing session and workshop centered on his “Seven Pillars of Amazing Culture.”
“Great culture is not declared. It’s created. We have to really spend time on the right things,” Dyer said. “If we focus on the wrong things, we lose. We lose market share. We lose profitability. We lose great people. We keep losing if we’re just trying to do too many things.”
More Photos
See our 2025 Annual Meeting photo gallery: www.smihq.org/go/am25-photos
As part of the “March Forward to Success,” a Big Easy-style parade took attendees from the Hotel Fontenot down city streets to the Opening Reception and Dinner at The Chicory. Led by a brass and drum marching band, a stilt walker and two showgirls, a second line of more than 100 SMI participants followed. (A second line is a unique NOLA tradition of revelers joining a parade instead of just watching it go by.)
Optional activities included a tour of the National World War II Museum and Mardi Gras World, along with golf and pickleball tournaments.
The Closing Reception and Dinner recognized board members, committee chairpersons and SMI staff, as well as presented service awards to Linda Froehlich and Anthony Pesaresi (see SMI Thanks Outgoing Board Members p. 60).
The 2026 SMI Annual Meeting in Puerto Rico will include the induction of a new SMI president, executive board introductions, board and committee meetings, educational sessions, networking and more on the Island of Enchantment.
“We look forward to seeing everyone next year,” Jacobson said. “Puerto Rico will be the perfect backdrop to connect, collaborate and celebrate our springmaking community.”
Mark Your Calendar
2026 SMI Annual Meeting
March 5–8, 2026
Wyndham Grand Rio Mar Río Grande, Puerto Rico
Show us your SMI Annual Meeting 2025 photos and videos! Tag your photos with #smiNOLA or mention @smihq1933 on LinkedIn, Facebook or Instagram.
SMI’s Emerging Leaders has had many names throughout its history, but its goal has remained the same: provide a platform for the voices of a younger generation The Emerging Leaders Conference originated as an idea during the 2021 annual meeting in Scottsdale, Arizona, by chairs Alex Melnikow of Midstate Spring and Adam Jacobson of FENN/Torin. With its inaugural conference in 2024 in Coronado, California, it has since been refined to the successful one-day format presented this year.
“The group was developed out of a strong need for SMI to get younger and refresh itself with the voices of next generational leaders,” Jacobson says. “Through our format, bonds are quickly developed allowing new faces the confidence and understanding of making the most of the annual meeting.”
The Emerging Leaders Conference was designed to focus on industry-specific content and opportunities for peer connection. It is tailored to the needs of critical nonowner employees, and emerging, future and next-generation leaders within the spring industry, equipping them with practical knowledge and connections.
“We are bridging the gap between generations and ensuring that SMI continues to serve all of its members. It is clear that these emerging leaders are prepared to move the industry forward,” adds Melnikow. “Through vulnerable and open exchange of ideas, they have demonstrated the values of grit, integrity and ingenuity that have been so critical to the success of the generation of spring makers they follow.”
This year, 11 members attended the conference with a mix of returning and new faces. The conference began with a team-building activity and a roundtable discussion of peer tips and recommendations. After a brief break, the group reconvened to discuss managing relationships with senior
By Gaby Carrasco
leadership, company culture and managing a work/life balance.
The new format was well received. First-time attendee Katherine Pepka of Renton Coil Spring noted, “The Emerging Leaders Conference was the perfect kickoff for a ‘green dotter’ and newer members — fostering connection, collaboration and shared growth. We exchanged strategies, challenges and successes not just as leaders but as individuals, creating a space where we were able to show up as cohorts.”
One unique aspect of the conference is the pre-event “homework” assignment. Participants were asked to submit a short bio, photo and respond to a few fun personal questions. This year, one of the questions was: “Reverse bucket list — Instead of listing what you want to do, what are three amazing things you’ve already done or accomplished in your career or life?” This thoughtful assignment helped break the ice, foster connection and create a welcoming environment — especially for first-time attendees.
“As someone fairly new to the organization, the Emerging Leaders Conference was a great way to get acclimated with SMI,” says newcomer Julie Arenz of R&L Spring. “I took away valuable insights and feedback from other leaders in the industry and made connections that will carry forward for many years to come. I’m already excited to see the group again next year.”
The next Emerging Leaders Conference will be held at the 2026 SMI Annual Meeting at the Wyndham Grand Rio Mar in Puerto Rico, March 5–8, 2026. z
Education is at SMI’s core. Between our spring design and safety webinars and our annual scholarship program, your SMI membership provides educational opportunities for you and your family. Each year, all SMI member companies’ employees and their dependents are encouraged to apply for the many available scholarships. This year, $29,000 in financial aid was distributed to 12 students throughout the U.S.
“This scholarship program is a reflection of who we are as an organization — committed, compassionate and deeply invested in lifting one another up,” said SMI president, Don Jacobson III. “It’s not just about funding education; it’s about believing in people, nurturing potential and creating pathways for future leaders to thrive. We are proud to support this next generation of students as they work towards their future.”
Since the SMI scholarship fund started in 2011, a total of $411,500 in financial assistance has been granted to 190 students.
To be eligible for an SMI scholarship, award winners must be a full-time employee or a dependent child of a full-time employee who works for an SMI member company.
In 2025, SMI awarded five regional scholarships for $2,000 each. In addition, seven at-large scholarships were selected for the following amounts:
Ronald and Adrienne Banas Scholarship • $5,000
Alexander and Joanne Rankin Scholarship • $4,000
Callaghan-Hart Scholarship • $2,000
The Gibraltar Company Scholarship • $2,000
Lynne Carr Scholarship • $2,000
Goldberg Family Foundation • $4,000, two students were awarded $2,000 each
Information about the 2026 scholarship program will be distributed to SMI members in the fall by email and on SMI’s website, www.smihq.org. z
Uriel Chavez
Hometown: Garden Grove, California
SMI Member Parent: Uriel Chavez, Orlando Spring
Attending: California State University, Fullerton
Major: MBA
Mia Harrison
Hometown: Pontotoc, Mississippi
SMI Member Parent: Ramey Harrison, MW Industries Pontotoc Division
Attending: Mississippi State University
Major: Poultry Science
Marissa McManus
Hometown: Grand Haven, Michigan
SMI Member Parent: John McManus, Motion Dynamics Corporation
Attending: Ohio State University, Columbus Campus, College of Optometry Major: Optometry
Brooke Sipsy
Hometown: Mary Esther, Florida
SMI Member Parent: Becky Christensen, Newcomb Spring Corp.
Attending: Kennesaw State University
Major: Organizational and Professional Communications
Gwen Truesdale
Hometown: Whitewater, Wisconsin
SMI Member Parent: Stephen Truesdale, R&L Spring Company
Attending: University of WisconsinRiver Falls
Major: Agricultural Engineering
“This scholarship alleviates the financial burden of pursuing my education, which will allow me to focus more on my studies … Your belief in my potential inspires me to work harder and strive for excellence.”
— Rachel Chandek, Lake Geneva, Wisconsin
Alexander and Joanne Rankin Scholarship
Connor Burrows
Hometown: Zeeland, Michigan
SMI Member Parent: Brad Burrows, Automatic Spring Products Corp.
Attending: Michigan State University, College of Human Medicine
Major: Doctor of Medicine (MD)
Rachel Chandek
Hometown: Lake Geneva, Wisconsin
SMI Member Parent: Janelle Chandek, Medicoil
Attending: University of WisconsinWhitewater Major: Business
JeeAnne Peterson
Hometown: Kewanna, Indiana
SMI Member Parent: Jovy Peterson, Winamac Coil Spring Inc.
Attending: Indiana University South Bend
Major: Dental Hygiene
Callaghan-Hart Scholarship
Valerie Pollock
Hometown: Muskegon, Michigan
SMI Member Parent: David Pollock, Motion Dynamics Co.
Attending: Muskegon Community College
Major: Psychology
“Thank you for your generosity and support. I am committed to working hard in my academic pursuits and hope to contribute to the field of poultry science and veterinary medicine in meaningful ways.”
— Mia Harrison, Pontotoc, Mississippi
By Gaby Carrasco
“My ultimate goal is to become an optometrist … Thank you for this scholarship. It means a lot to receive this recognition as I continue to work towards my dreams.”
— Marissa McManus, Grand Haven, Michigan
Leah Pennington
Hometown: Randolph, Mississippi
SMI Member Parent: Christy Pennington, MW Components, Pontotoc Spring
Attending: Mississippi State University
Major: Student Affairs and Higher Education
Javier Gonzalez Grimaldo
Hometown: Clovis, California
SMI Member Parent: Javier Gonzalez Jr., Betts Company
Attending: California State University, Fresno
Major: Mechanical Engineering
Ronald and Adrienne Banas Scholarship
Liliana Koehl
Hometown: Otsego, Michigan
SMI Member Parent: Susanne Koehl, HyTech Spring & Machine
Attending: Loyola University Maryland
Major: Finance/Accounting
“I am humbled by SMI’s continued financial backing of my journey to this point. It has allowed me to focus on improving my patient care abilities and refining my clinical acumen.”
— Connor Burrows, Zeeland, Michigan
“As a graduate student in the student affairs and higher education program at Mississippi State University, this support will significantly impact my educational journey.”
— Leah Pennington, Randolph, Mississippi
“It is an honor to have been selected as a recipient and this generous support will play a pivotal role in helping me achieve my academic and professional goals.”
— Brooke Sipsy, Mary Esther, Florida
By Roy Vinderine SMI President 2001–2003
Editor’s Note:
Today, we take our time machine back to Dec. 2002 when
“The Lord of the Rings” sequel was in movie theaters and we were on the brink of the Iraq War. Yet this message by SMI President Roy Vinderine could have been written yesterday. It discusses, among other things, global competition and customers demanding lower prices, higher quality and tighter tolerances.
How important is quality to all of us, engaged as we are in the challenging pursuit of making springs and components, or supplying raw materials, machinery and services to the spring industry?
Clearly, over the past 20 years, the demand for quality products has escalated exponentially. I used to think that our company delivered superb quality products back then. However, we are simply miles ahead now, both as an organization and in the products we bring to market. I firmly believe that this is true throughout our industry in North America, brought about by the very justifiable demands from our customers for higher-quality products to enable them to better compete in the world marketplace.
We have all invested huge sums to achieve these increased levels of quality and strive endlessly for improvement in every aspect of our operations. The irony is that, despite these enormous advances, the overall net worth of SMI’s members, or their annual net incomes, has not increased commensurate with their investments.
This is partly because there is an overcapacity in the spring industry worldwide, which gives encouragement to our customers, as if they needed it, to continually press for more and more in the way of design, value engineering and closer tolerances, while at the same time demanding lower and lower prices. There are undoubtedly savings that have resulted from our improved production methods, lean manufacturing and greater emphasis on quality. However, I submit that the line of reason has been crossed, and
once again purchasing agents and those who control them have become “price” buyers, paying little or no heed to the necessity for us to maintain reasonable profitability such that we may continue to strive to further improve on the gains that have already been accomplished.
Having defined the problem, which is easy, what, you may ask, is the solution?
There isn’t an easy answer, but I firmly believe that all of us need to educate our customers and, if possible, our customers' customers, as well as those industry association watchdogs and anyone else who will listen — the message being that we are no different from any other business. Quality comes at a price — a price we all pay quite willingly when we purchase the things we desire, such as houses, automobiles, appliances and services. We make our decision to buy something, and obviously, we aim to buy the best for the money we have available. Market forces are always at play, and one may negotiate discounts based on that market. Nevertheless, we expect to, and do, pay more for a high-quality product than for one of a lesser caliber.
For those of us who are continually striving to maintain or further improve quality levels, there is no escape from the need to invest in R&D and the latest machinery and equipment, none of which comes for free. If there is value in superior quality, and I have no doubt this is so, then our prices should reflect that reality. It will take ages, perhaps, but we must all devote the time and effort to try and convince our customers that “zero defects” and superior quality do come at a price. z
Five Questions allows SMI associate members to tell the spring industry about their products and services. In this edition, we talk with Carl Atwater from
1
Tell us about your company’s history and products.
A.I. Technology, Inc. (A.I.T) was established in 1997 as a partnership between Ichiro Itaya of The Itaya Engineering Ltd., my wife, Alicia and me. At the time, our product line consisted of spring and wireforming machinery produced by Itaya Engineering, tooling produced by Spring Tooling Ltd., payoff reels produced by Coilmaster and in-line conveyor belt ovens produced by Tokyo Gasden-Ro. Over the next 20 years, we forged relationships with additional manufacturers who are leaders in their fields and we’ve brought this technology to the U.S., Canada and Mexico.
2 What trends are impacting your industry? How does it affect springmakers?
One of the bigger trends we have seen over the past few years has been a push toward more automation in our customers’ factories. For springmakers, this can mean utilizing new machinery such as robots to perform tasks on springs or feeding systems to help move springs from one process to the next.
3 What products and services do you provide springmakers?
A.I.T. offers one-stop shopping. This benefits springmakers because we collaborate with everyone involved to find the solutions needed to automate industrial processes. Our current product lines include: Itaya springmaking and wireforming machinery, tooling, and payoff reels; G+M Dorn spring end grinding machines with high-performance control and feed technology, and a wide variety of feeding systems; Spring Tooling Ltd. tooling for spring machinery; MicroStudio high precision measurement
instruments, life testing machines, feeding systems, payoff reels and software development for SPC production overview and management of production phases; and Agibi Progetti industrial furnaces for heat treatment, oiling machines, container changers and automation solutions.
Between our two technicians here at A.I.T. and me, we have more than 100 years of setup experience on all types of springmaking machinery — from Sleeper torsion winders and Baird spring generators to state-of-the-art Itaya RX-Series machines. We are springmakers, and as such, we understand the industry’s needs.
4 What role does logistics play in serving springmakers?
The majority of our products are sourced from Japan, Italy, Germany and England. Logistics plays a major role in the smooth transfer of equipment from our suppliers to our customers’ factories. We have extensive experience dealing with the brokers, ship lines, transporters and rigging crews. In most cases, AIT will be the importer of record and handle the entire import process for our customers.
5 What was a recent challenge you solved for a customer?
This is still ongoing, but a customer of ours has approached us to integrate an automation system with their existing Itaya machines. Since the Itaya machines do not support this type of system, we have been working with the customer and with Itaya on a software update that will integrate with it. After much back-and-forth in the last few months, we are confident we will have an update for our customer to help achieve their goal. z
Carl Atwater
A.I. Technology
30503 Andersen Court Wixom, Michigan 48393
Phone: 248-624-3767 catwater@aitechnology.us www.aitechnology.us
Follow SMI on social media for bonus content on Carl Atwater and A.I. Technology.
By Gary McCoy, Executive Director
With little fanfare, Dan Sebastian’s first column, “Fatigue Life for Springs,” appeared in the spring 2015 issue of Springs. That issue focused on a “Salute to the Troops,” where SMI took time to honor the spring industry’s military veterans. Just like we saluted the troops 10 years ago, we take time to honor a notable industry veteran.
This article and the accompanying “Dean of Spring Tributes” (p. 50), serve as a small way to thank a special individual who has made numerous contributions to the industry as a mentor and friend to many.
Sebastian was president of SMI from 2005–2008. In addition to writing for this publication, he also served for many years as SMI’s technical advisor.
Dan’s first column started with a modest goal.
“Over the next few issues of Springs, I hope to relate to you a few of the technical and business-related issues I have encountered on my journey through the world of springs. It started way back in 1968 when I was lucky enough to get an internship at the research and development center of Associated Spring. At the time, I was studying metallurgical engineering at Lehigh University and was convinced that after completing my studies, I would go off to NASA and work on the moon landing project. Lyndon Johnson was president, and we were still trying to find a way to land on the moon. At that time, the fax machine, cellphone and
300 channels of TV were all science fiction. Somehow that summer, springs bit me and I got on the ride of a lifetime.”
What a ride it has been! Dan’s unique ability to share deep technical knowledge and practical management advice characterized the columns he wrote during 10 years for Springs
Unless you were born into a family that manufactures springs, most everyone has a unique story of how they entered the industry. A Connecticut native, Sebastian went to an area technical school out of high school to major in metallurgy with a minor in mechanical engineering.
After earning an associate degree, Sebastian wanted more education and ended up at Lehigh University in Bethlehem, Pennsylvania. “I thought it would give me the greatest advantage in basic fundamental ferrous metallurgy,” he explained. The program provided him with the fundamentals of materials, and during his senior year, the class spent Fridays at the nearby Bethlehem Steel Mill.
Growing up, Sebastian had little knowledge of the spring industry. That changed in the summer of 1968. Desperate to find a summer job, Sebastian applied to many places in Bristol, Connecticut, including Associated Spring. He was told openings were reserved only for children whose parents worked at the company.
He ended up getting a call from the human resources department at Associated to come in for an interview. They had been trying to hire a metallurgical engineer out of college for about three years and could not find anyone.
As a typical college kid, Sebastian put on the only shirt, tie and jacket he owned and interviewed with the company’s director of research, Perry Smith. After about an hour, Perry inquired about the pin on Sebastian’s coat.
Sebastian’s pin signified he was an Eagle Scout. Smith had also been an Eagle Scout, and with that connection, he told Sebastian, “You’ve got the job.”
Including internships, Sebastian enjoyed a 23-year career at Associated Spring. In his first year as an intern, he completed research projects on the stress and relaxation characteristics of garter springs. In his second year, Sebastian got broader exposure to many projects, including an approval process for new wire source vendors as Japanese companies attempted to break into the U.S. valve spring market.
Sebastian graduated from Lehigh in 1970 with a B.S. degree in metallurgy and materials science. He had four job offers, but Smith at Associated Spring had told him to call before he graduated because they were interested in discussing a full-time
job. He called, and Smith asked Sebastian, “What’s your best offer?” After telling him the amount, Smith offered him $500 more and Sebastian accepted. At the time, Associated Spring was the largest North American spring company with a total of 14 plants in the U.S., Canada and Mexico.
Learning and Growing
Sebastian spent his first year and a half in the research center before the company asked him to join its management development program. The program exposed management trainees to different disciplines within the company over a six-month period. Sebastian was reluctant and initially said, “No, I’d rather be an engineer.”
Dan’s unique ability to share deep technical knowledge and practical management advice characterized the columns he wrote during 10 years for Springs.
But the company thought he was management material and Sebastian relented and joined the program. “Back in those days, Associated would take a collection of people from different disciplines through a sixmonth training program and expose them to everything like accounting and sales,” Sebastian said. “It was an eclectic mix of people going through the program.”
After the training program with just a year and a half on the job, Associated Spring’s chief metallurgist took a three-month medical leave.
The management team told Sebastian, “You’re now the chief metallurgist of the spring division.”
Sebastian said he had a “ball” in that role because it was the first time he was exposed directly to day-to-day factory operations.
Later, Sebastian took a job transfer to be the chief engineer at the Associated Spring plant in Mattoon, Illinois. He quickly became responsible for quality control and estimating, leading to his appointment as head of the manufacturing plant.
Regarding his Mattoon tenure, Sebastian said, “It was probably the biggest learning experience of my career.”
Sebastian said he had learned a lot by studying Dr. Joseph M. Juran, who, along with Dr. W. Edwards Deming, were the originators of many quality management techniques still in use today.
“Juran said if you’re going to be successful, you have to learn how to speak two languages,” explained Sebastian. “He said the language in the factory is totally different from the language in the front office.”
Sebastian said he quickly realized the truth of that statement, “because the language in the factory was completely not understandable to a disciplined engineer.” He said those in the plant did not care about part numbers. They instead assigned each part a nickname. Sebastian said once he understood both languages, he was able to apply fundamental manufacturing principles. “Instead of focusing on speed, I quickly figured out that if we could have a sequential process and everything was manufactured at the same speed, we could get something through the entire plant much quicker. We built manufacturing cells, and we did things most people had not ever thought about doing,” he explained.
Sebastian said he turned around the plant not because of his genius, but with the help of the factory workers. “It was just because no one had ever taught them this.”
In 1981, Sebastian took a transfer to become head of the Associated Spring valve spring plant in Ann Arbor, Michigan. “It had fallen on hard times, and they sent me there to fix it,” Sebastian said.
Returning the plant to profitability, Sebastian realized that building a new factory could help them reach even further heights. He got the go-ahead, and a new plant was built in nearby Saline, Michigan.
“Typically, when you move a plant, the first six months are terrible,” Sebastian explained. After six months, Sebastian and the plant’s CFO had the opposite response.
As a result, Sebastian said, “We produced a record 65 consecutive months of productivity improvements.” The plant continued to produce superior results even after Sebastian left in 1991 to take the job as head of MW Industries.
His successful turnaround of the Mattoon and Ann Arbor plants demonstrated his ability to apply a holistic, process-oriented approach to manufacturing.
Sebastian tackled his next assignment with vigor. His leadership over the next 20 years in turning around and expanding MW Industries through strategic acquisitions further illustrated the value of his broad, cross-functional understanding of the industry.
Of the assignment, Sebastian said, “It was kind of like when I got to Ann Arbor, they had all the fundamentals but didn’t know how to put it together.” He admits that when he got to MW’s headquarters in Logansport, Indiana, it turned out to be even worse than he had imagined.
He quickly assembled a new team. Many of his new hires, such as Jim Callaghan, CFO, had previously worked for Associated Spring. “We put all these people in the right places and turned the thing around.”
Sebastian admits it was a challenge to collaborate with people and assimilate plants with different cultures into a single unified company.
“It was another great learning lesson,” Sebastian explained. “When you train to be an MBA, they teach you about the efficiencies of combining and making things more centralized.”
Sebastian said he quickly learned that centralization was not necessarily the most important thing.
“The entire key at MW was that we had this wide collection of plants across the company,
each with their own unique culture, but all of whom became part of an overall MW culture that we were able to blend together,” Sebastian said. “And that, truly, to me was the greatest part of the success.”
By the time Sebastian had left MW Industries as president and CEO in 2011, he and his team had added 14 operations to their portfolio.
Sebastian could author a book or hold a master class on the things he has learned during his time in the spring industry. His work, from research to manufacturing to management, allowed him to develop a deep understanding of the industry. A couple of observations he made:
“The spring is a critical and often overlooked part of manufacturing, with the ability to significantly impact the success of larger companies that rely on springs as a key component.”
“To be successful in the spring industry, it’s important to have a well-rounded understanding of the entire manufacturing process, rather than being a specialist in a single area.”
During Sebastian’s time in Mattoon, Associated Spring was a member of the Chicago Association of Spring Manufacturers,
Sebastian is known as the Dean of Springs, but very few know the origin of his nickname. As the story goes, one of the private equity (PE) firms that owned MW Industries was having trouble explaining the importance of technology in the spring industry and its relationship to customers.
A person from the PE firm started telling investors that the spring business they owned was run by the “dean of springs.” He went on to say, “He’s the guy who knows more about springs than anybody else I’ve ever met in my life.”
Sebastian considered it a gross exaggeration. Nevertheless, the PE firm started using Dean of Springs in their sales pitch, and everybody thought it was funny. “The tag stuck, whether I liked it or not!”
To be successful in the spring industry, it’s important to have a well-rounded understanding of the entire manufacturing process, rather than being a specialist in a single area.
Inc. (CASMI), which gave Sebastian exposure to the organization and the SpringWorld show. After his move to Michigan, he became the president of the Michigan Spring Association and served in that role for about six years.
At that time, Associated Spring did not allow its managers to attend SMI meetings, so Sebastian had little contact with the industry’s North American association. After becoming head of MW Industries, Sebastian traveled to Puerto Rico to attend his first SMI meeting. Not long after, SMI President Park Blatchford (1991–1993), recruited Sebastian to the technical committee, knowing he was a “technical geek.” He eventually became the committee chairperson.
Sebastian served in many roles as an SMI volunteer, eventually becoming SMI president in 2005. Due to unforeseen circumstances, Sebastian volunteered to serve an extra year as president until 2008. Before 1960, when SMI adopted a two-year term for its presidents, the term of the president was indeterminate. SMI’s first president, Fuller Barnes of Associated Spring, served twice as president (1933–1941 and 1943–1946).
The highlight of Sebastian’s term as president was leading the organization when SMI celebrated its 75th anniversary in 2008 in Palm Desert, California.
During his presidency, Sebastian was instrumental in hiring Luke Zubek as SMI’s technical director and in developing
SMI’s spring design software. Later, when Zubek left SMI, Sebastian stepped in to help fill the gap as a technical consultant for the association.
In retirement, Sebastian continues to be busy. He sits on the boards of several companies and does consulting work. He also helps his daughter and son-in-law with their business, OEM Laundry Parts, as a senior advisor.
Sebastian loves consulting work, analogizing to “being like a kid in a candy store.” It has allowed him to do what he enjoys the most. “Which is to look at things from a creative perspective as opposed to the craziness that happens in day-to-day operations.”
He boasts that it keeps him active and “keeps my brain going.”
During his career, Sebastian witnessed the industry’s shift toward automation and CNC technology.
“When I started, all of the manufacturing was done using basic mechanical machines,” Sebastian said.
Sebastian marvels at today’s CNC machines, which can make a spring or wireform, including some secondary operations, on one machine in a single operation. He says the best part of today’s technology is the ability to control more variables in the manufacturing process.
“And now with artificial intelligence (AI), we’re able to use the mathematics of AI to hook up with the electronics to be able to control all kinds of motions on machines that manufacture springs, wireforms, including fourslide machines,” Sebastian marveled.
Hear Dan Sebastian on the SMI Podcast
Listen
Apple https://apple.co/3OJODed
Spotify https://bit.ly/sae-sp
YouTube https://bit.ly/sae-yt
As Sebastian looks to the future, he is optimistic and desires that every SMI member company experience robust growth.
“I am excited about our country as we begin to seriously consider reshoring,” says Sebastian. “Our industry lost a lot of business, not necessarily from outside forces shipping in, but more from our customers taking their entire products to foreign companies and then getting their springs from local markets. As we begin to reshore, I hope that it creates great opportunities for other members in the spring world, which would bring us back to where we were in the ’60s and ’70s.”
With the respect Sebastian has earned over the years, do not be surprised if his prediction regarding the future comes true.
“I believe with what’s going on today, this could bring a whole new renaissance to the world of springs.” z
I believe with what’s going on today, this could bring a whole new renaissance to the world of springs.
P S F O N A E S G N I R
During
his long industry career,
Dan Sebastian touched many lives through his wit, wisdom and ability to connect with a variety of people. Here are a few tributes we received to honor his retirement as a regular contributor to Springs.
Thank you, Dan, for your dedication to the spring industry and SMI. Fifty-seven years in the industry and still counting!
About 10 years ago, Dan called to tell me he would be writing a couple of technical and business columns for Springs. Forty columns later, he is finally handing in his columnist license.
The Dean of Spring’s topics varied from company culture to tensile strength and fatigue life to EBITDA to hydrogen embrittlement. Thank you for the education and experiences that you provided in your columns.
On a personal note, thank you for the leadership and positive company culture that you brought to MW Industries for 21 years.
All the best, my friend!
Jim Callaghan, Lee Spring Former CFO, Matthew Warren/MW Industries SMI Honorary Member
I first met Dan in Mattoon, Illinois, in 1977 while interviewing for a job as a metallurgist for Associated Spring (a position I did not take). I remember thinking during that interview process, “Wow, this guy is smart, kind and friendly, I would really like working for him!”
I have been blessed with an amazing friendship with Dan spanning almost 50 years. Our paths crossed again in the early 1980s, as we served on SMI committees and the board of the Michigan Spring Association. Over the decades that followed, I learned that my initial impressions of Dan were spot on. He is a very smart guy. He is exceedingly kind, very warm and friendly.
There are few people who have had such a positive impact on my life as Dan. Whether he knew it or not, growing up in the industry, working side by side with him in countless roles for the SMI, I counted him not only as a great mentor but also a dear friend. Besides sharing the common bond of being metallurgists, we also shared similar personal experiences with losing our sons too early in life and those shared experiences only strengthened our friendship to deeper levels.
I could go on and on, but certainly there are few, if any, in our industry during my lifetime who have had such a profound impact on SMI and the entire North American spring industry as Dan Sebastian. His leadership, warm, friendly personality and superior technical knowledge and experience are simply unmatched!
Steve Moreland, CEO, Automatic Spring Products Corporation SMI President (2012–2014)
TDan, I have always admired your unwavering commitment to your work and SMI. You have always been a role model for me, and I am so grateful for your guidance and support with SMI.
Your positive attitude and willingness to help myself and others have made a real difference at SMI. We are so lucky to have you as a friend, mentor and shoulder to lean on. I remember when the “transition” period of the executive vice president started and the entire process (which seemed to last 18 months, especially in Las Vegas), with curveball after curveball. You managed that like a true professional, unfazed. That is just one example of the many ways you have touched my life and administered professional problem-solving 101.
I hope your retirement from writing for Springs is filled with joy, relaxation and plenty of time to wear your famous Cabellero Western Shirt. Not too bad for a University of Michigan fan (Go Irish!).
Reb Banas, President, Stanley Spring & Stamping SMI President (2008–2010)
By Gary McCoy, Executive Director
UT E S
Dan and I first met when we were both “green dot” first timers at the SMI meeting held in Puerto Rico in the early 1990s.
Since I began my work life as a CPA, I was always fascinated by my manufacturing clients; I never missed an opportunity to trade my “green eyeshade” for a “hardhat” plant tour.
I have Dan, among many others, who mentored me, to thank as I transitioned from a numbers guy to actually making things. Dan was one of three outstanding metallurgists who helped me along in our steel businesses over the years, while he also added springmaking knowledge to the mix.
Dan embodied the spirit of the SMI founders, whose goal was to improve the industry. We both were lucky to have met some of those individuals early in our careers and I am hopeful as SMI’s 100th birthday approaches that the current members will remain true to that goal.
Tom Armstrong SMI Honorary Member
Dan was the host for SMI’s 75th anniversary in Palm Springs in 2008. He was always the first person to show up at each event during our SMI conventions, which became a joke between the two of us.
As the only modern president to serve three years as SMI president (between 2005 and 2008), Dan was a driving force in the development of SMI’s Advanced Spring Design (ASD) software. He was also instrumental in hiring Luke Zubek as SMI’s technical director. Dan saw the need to provide members with access to vital technical support. Members agreed and thought it was a great idea, and it was all because of Dan’s idea to move in this direction.
There is so much I can say about Dan and what he means to me and the spring industry. He played a vital role for me as a mentor.
Lynne Carr, Retired SMI Executive Director SMI Honorary Member
During my tenure as SMI president, Dan Sebastian provided invaluable assistance on two significant topics. As a former SMI leader himself, his insights were instrumental as I settled into my new role. He was always gracious and thoughtful in helping me understand and appreciate the history on various matters and I was grateful to have his perspective on SMI.
In addition, my two-year term was primarily dedicated to the development and production of SMI’s first Metal Engineering eXpo, held in Charlotte in the fall of 2015. Dan played a crucial role in supporting the board with the conceptualization of the eXpo. He also played a key role in the nuts-and-bolts work of fleshing out how that vision would be presented. As a key member of the team, his contributions continued throughout the event itself and in the wrap-up afterward, his experience, knowledge, availability and general helpful nature played a significant role in the event’s success.
Thank you for your help, Dan and best wishes in retirement!
Hap Porter SMI President
(2014–2016)
Many terms come to mind when I think of my interactions with Dan over the years. Words like leader, entertainer, storyteller and experience come to mind, but two that really stand out are mentor and steward. Dan has exemplified these two qualities throughout the time I have known him. This is evident in the ways he has taught many of us with his wisdom and expertise he has gathered throughout his years as a springmaker, designer and flat-out expert. I have personally benefited from this wisdom many times with answered questions or assurances when I asked about something I had finally figured out.
He also has not only mentored many of us in the SMI but also stewarded the industry by his selfless work by serving on the executive committee, to eventually serve as president. His many articles in Springs have been “must read” materials for many of us! All of these efforts have led to many of us giving him the moniker of the “Dean of Springs,” but I would like to add one more title behind Dan’s name: the Ambassador of the spring industry.
In closing, I could fill several more paragraphs with specific examples of times Dan helped me personally, but would like to shorten that up by simply saying: “Thank you, Dan.” To a personal friend, mentor and steward of our industry. May you feel God’s richest blessings in all of your future endeavors!
Gene Huber Jr., Executive Vice President, Winamac Coil Spring SMI President (2022–2024)
When I entered the spring industry in 2005, I didn’t expect to stay long. Then I met Dan Sebastian. It began with a phone call — Dan encouraging me to attend SMI’s annual meeting. Though Lee Spring had been a founding member of SMI, we hadn’t actively participated for decades. That conversation and the warm welcome that followed changed everything.
When I met Dan in person, he was gracious, approachable and incredibly generous with his time and insight. His passion for the industry was infectious. As I learned about his own journey — from engineer to industry leader — I found inspiration to pursue a path of my own within the industry and SMI.
Dan’s enduring contribution to the industry has been a steady voice of wisdom and perspective. I’m deeply grateful for his guidance, encouragement and example over the years.
Steve Kemp, CEO, Lee Spring SMI President (2018–2020)
Dan Sebastian’s retirement marks the conclusion of a remarkable career defined by technical excellence and unwavering dedication. As a brilliant materials engineer during his early years at Associated Spring in Bristol, Connecticut, Dan laid the groundwork for much of the data that continues to guide our industry today.
Though my tenure at Associated Spring didn’t coincide with his, I consider myself fortunate to have had the opportunity to get to know Dan through SMI, where his expertise and passion for advancing our field were always evident. His contributions have left an indelible impact on our industry, and his legacy will undoubtedly endure.
Wishing Dan all the best as he embarks on this new chapter.
Jason Sicotte, Director, Global Engineering, Associated Spring SMI Board Member
Dan Sebastian, often called the “Dean of Springs,” has been a true mentor to many of us, including me. As a past president of SMI, Dan’s deep technical knowledge and passion for springmaking are unmatched. Over the past 30 years, his dedication to the spring design program and training has helped shape countless careers and strengthened our industry. As the current president of SMI, I’m grateful for his ongoing commitment and the lasting impact he continues to make, thanks to all the knowledge he has so openly shared with our industry.
Don Jacobson III, Executive Vice President, Newcomb Spring Corporation Current SMI President
Dan is the man, the myth and the legend of all things springs. From the engineering end of design and stress nuances, to manufacturing and process mastery, to vast metallurgical knowledge, to business / financial proficiency, Dan has been an incredible mentor to many of us over the decades of dedication to our industry.
Despite being a walking encyclopedia of technical and business knowledge, his humble and warm persona makes him one of the easiest to meet and connect with at my early SMI conventions.
I was fortunate to be on the SMI Board with him, where he would consistently add pearls of knowledge to all of us, and later on I was blessed to serve as part of his executive committee, where he exhibited incredible leadership skills with both members of his executive team as well as the SMI board.
Dan was the only modern era SMI president to serve multiple terms … not out of ego, but out of supporting SMI in challenging times, again demonstrating his dedication to our industry.
Bert Goering, CEO & President, Precision Coil Spring SMI President (2020–2022)
SMI and our industry members have been blessed to have Dan lead the way as our “Dean of Springs” for decades. Dan has selflessly given of himself for the betterment of our SMI members and the industry he loves. His leadership has been appreciated by all who know him. His friendly and optimistic approach to solving some of the most difficult design questions is something I appreciate most.
Dan, please know we are thankful for your service and dedication in making SMI the best it can be. Wishing you well on your next journey!
Mike Betts, Chairman & CEO, Betts Company SMI President (2016–2018)
By Sara Scullin
“Most of my family has been in springs at some point, and it started with my dad, Marshall Jackson,” says Rhonda Miller, CEO of Action Spring in Tulsa, Oklahoma and longtime SMI member. “He was 18 and driving around downtown Tulsa on a motorcycle that had crash bars on it, and he was turning a corner and scraped the side of this man’s Cadillac. This was in the ’50s, and he didn’t have insurance.”
“The guy says, ‘OK, here’s what we’re going to do. You’re going to work for me to pay off the damages.’ It turned out that man was Larry Babb of Ebsco Spring in Tulsa,” Miller says. “My father worked for Larry for several years, and when I was eight, [my father] started his own company.”
Over the years, Miller and her siblings helped their dad at Action Spring Co. Inc. While few women were involved in the business, she made it a point to learn about the company in its various capacities. She took on increasingly larger roles over time.
“I just made it a point to know what was going on and I’m glad I did,” she says.
After her father passed away in September 2005, Miller and her husband took over leadership of Action Spring. She took on the role of CEO and her husband became president. Among other projects and initiatives, Miller had an innovative approach to automation. She saw it as a way to keep production running smoothly amid persistent (and still prevalent) workforce challenges.
When Miller started working full-time at Action Spring in 1993, the company employed 50 people and everything was done manually. “From 1993 to 2008, we still had quite a lot of people, and because of automation, we’re down to about 20 people today,” she says.
Miller first saw the benefits of automated machinery when she attended SpringWorld sponsored by CASMI in the ’90s with her father and husband in Chicago.
“I kept trying to get my dad to buy equipment, and he didn’t want to spend the money. But when you start weighing everything, yes, you can buy that machine and it’s going to save you time and money. Believe me, we have,” Miller says.
Action Spring purchased its first automated wire former in 2008. The equipment made short work of a traditionally twoperson job.
“At that point, I knew, with the workforce like it is, we just need to keep automating. And it’s worked out well,” says Miller.
“Most everything we do is custom,” she says. The spring, wireform and metal stamping manufacturer does a large share of business with cargo trailer companies, a fairly competitive market. They also build to specifications for clients in oil, HVAC, electronics and recreational industries, among others.
Miller believes one of the most important ways a family-owned business can thrive is if leadership stays involved in all aspects and processes of the company. Learning (and sometimes doing) the work — on the manufacturing floor and in the office — has given her a unique advantage.
“If you don’t stay involved, you can’t know what’s going on,” she says. “I love working with my team and seeing the outcome of their work, especially when it’s something new and the employee is trying to figure out how they are going to run it. When they finally get it to where it’s working, and you can see they’re happy — there’s a lot of excitement there.”
Miller carries her family legacy and the confidence that comes with years of experience with her into the next era of spring manufacturing — whatever that looks like.
“My dad was my role model, because he taught me about so much important
information relating to springs and the spring industry,” says Miller. “And my aunt Kathy Magrini was the owner of Gardner Industries, a spring manufacturer in Tulsa, until she died in 2020. I learned so much from her, too. Things like ‘Stand your ground,’ ‘Keep going and you’ll do fine’ and ‘Just don’t ever give up.’” z
I love working with my team and seeing the outcome of their work, especially when it’s something new, there’s a lot of excitement there.
By Dijam Panigrahi
As U.S. manufacturers anticipate a boost from new tariffs, the widening skills gap has turned eyes to workforce enablement.
Workforce enablement is the strategic process of providing employees with the tools, resources, training and support needed to do their jobs effectively and efficiently. This includes everything from technology and processes to learning and development, designed to improve productivity, engagement and satisfaction.
Immersive AR and VR simulations accelerate training and improve knowledge retention … and transfer expertise from retiring employees.
While optimistic about increased activity, many executives are concerned about their ability to hire, train and retain the skilled labor needed for modern production. A recent workforce enablement survey1 says that more than 70% of manufacturing leaders cite workforce enablement as their top priority, with the most pressing challenges being skill gaps, training and development, retention and employee engagement.
These concerns are echoed in broader industry research, such as Deloitte’s 2025 Smart Manufacturing and Operations Survey2, which highlights the struggle to fill production and operations management roles and equip workers for the digital “factory of the future.”
Why Technology Holds the Key
To address these challenges, manufacturers are turning to technology as a strategic solution. More than 40% are already leveraging augmented reality (AR), virtual reality (VR) and automation technologies, with another 40% planning to implement them soon.1
AR overlays the digital content onto the real world, while VR creates a completely simulated, immersive environment. AR uses devices like smartphones to enhance the user’s real-world view, while VR typically requires a headset to fully immerse the user in a digital world.3
These tools are transforming plant floor operations in several ways. Immersive AR and VR simulations accelerate training and improve knowledge retention, enabling companies to onboard new workers more efficiently and transfer expertise from retiring employees.
Remote assistance powered by AR connects frontline workers with remote experts, improving first-time fix rates and reducing downtime. Automation, robotics and
offer hands-on, industry-relevant experiences that mirror real-world plant operations.
AI-driven analytics are streamlining repetitive tasks, enhancing quality control and providing actionable insights to optimize production, ultimately helping manufacturers do more with less.
The adoption of workforce enablement technologies is also being measured. Key metrics include productivity, employee performance, retention rates and satisfaction surveys.
Results are promising, nearly 62% of executives find these technologies effective in addressing workforce challenges, with almost 30% rating them as “very effective.” However, barriers remain. Manufacturers cite complexity, integration with existing systems, cost and employee resistance as significant hurdles. Overcoming these obstacles requires careful change management, robust training and a culture that embraces innovation.
Real-world examples show that using digital tools to reskill workers is transforming plant floor operations. AR-guided instructions, personalized training modules through learning management systems (LMS) and virtual collaboration are enabling companies to onboard employees quickly, ensure quality and tap into a broader talent pool.
Manufacturers are also increasingly partnering with career and technical education programs to integrate workforce enablement technologies into training and upskilling efforts. By leveraging AR/VR simulations, digital LMS, and AI-driven performance tracking, CTE programs can offer hands-on, industry-relevant experiences that mirror real-world plant operations.
This strategy accelerates skill acquisition for students and incumbent workers alike, ensuring graduates are job-ready and existing employees can adapt to advanced manufacturing roles. The result is a more robust talent pipeline and improved operational efficiency, as workers are better prepared to meet the evolving demands of modern, technology-driven production environments.
As demand rises and the labor market tightens, investing in workforce enablement technologies is no longer optional but essential for closing the skills gap, boosting productivity and retaining talent. Success, however, depends on combining digital tools with effective training, communication and a culture of adaptability, positioning manufacturers to lead in the new era of American manufacturing. z
References
1. SDC Executive, “Supply Chain Organizations to Invest More in Emerging Technologies to Boost U.S. Manufacturing,” https://bit.ly/SDC-05-06-25
2. Deloitte, “Survey Reveals Smart Manufacturing Is Driving Advantage but Needs Focused Investment and Implementation,” https://bit.ly/DPR-05-01-25
3. PC Mag, Definition of AR/VR, pcmag.com/ encyclopedia/term/arvr
Dijam Panigrahi is co-founder and COO of GridRaster Inc., a company transforming industrial manufacturing, training and sustainment using AI. For more information, visit www.gridraster.com.
Gary McCoy
The journey of leadership is often paved with unassuming beginnings and quiet contributions that ripple through time, shaping the very fabric of industries and communities. Such has been the case with the dedicated leaders of SMI, whose efforts have built a foundation of excellence and innovation in the spring manufacturing world.
I started working as editor of Springs back in 2008, and what always struck me was the hours of dedication that SMI leaders had poured into the association’s work. I don’t think anyone thought about the legacy they were building at the time. They just did their work as volunteer leaders with little or no fanfare, while at the same time building successful spring companies.
The same thing can be said about Dan Sebastian. I’ve known Dan for more than 15 years, and when he talks about his service to SMI, he recently told me, “It was my honor to do so.”
I have always respected Dan’s steadiness, depth of knowledge and his ability to listen to and understand people. In this issue of Springs, we devote space to acknowledge Dan’s contributions to the spring industry through his work as a business leader, association volunteer and consultant. He may no longer write articles for the magazine, but his influence continues.
I hope you enjoy my Springmaker Spotlight article (p. 44) about Dan and the many tributes (p. 50) that poured in. In addition, I had the privilege of interviewing Dan for the Springs Are Everywhere podcast (Season 2, Episode 2), as he took me on his journey through the spring world that all started back in college during an internship at Associated Spring. What you will note about Dan is he always talks about “team.”
Dan explained one thing he did with his manufacturing team at MW Industries. “At least once a year, all of the general managers from all the plants would get together and exchange their successes and failures amongst the other general managers. We would use the entire team then to go forward and improve everything that was going on.”
As my friend David Robinson, a leadership coach, says, “With great leaders, there are no failures, only learning opportunities for those who will not quit.”
Building a legacy of leadership is an intentional and continuous process, not something that happens only at the end of a career. It includes self-reflection, consistent action and a focus on empowering others and making a difference that outlasts one’s immediate presence.
Thank you, Dan, for leaving us a leadership legacy to follow.
Gary McCoy Executive Director
At the 2025 Annual Meeting in New Orleans, SMI President Don Jacobson III presented service awards to outgoing board members, Linda Froehlich, president of Ace Wire Spring & Form Co. in McKees Rock, Pennsylvania and Anthony Pesaresi, president of Winamac Coil Spring in Kewanna, Indiana. Both Froehlich and Pesaresi served two, three-year terms on the SMI board of directors from 2019–2025. Jacobson, vice president of business development at Newcomb Spring Corp., said that Froehlich’s legacy is the strong network of women she helped empower through her work as the founding chairperson of the Women in Spring Manufacturing Committee.
“She was not just a board member — she’s been a mentor, a friend and a force for good in our industry,” Jacobson commented.
“Working with Linda has been equal parts inspiring and fun. Her passion, humor, relentlessness and heart made every board meeting memorable.”
Jacobson expressed his gratitude to Pesaresi for his efforts in uniting SMI and CASMI under a new vision for SpringWorld.
“Tony’s dedication to both CASMI and SMI was on full display when he was able to bring the two groups together,” Jacobson said.
“Tony was the spark that lit the path forward. Our combined SpringWorld Expo and Educational Symposium is a testament to his ability to create opportunity from possibility.”
Jacobson went on to say that it takes a special kind of leader to turn an idea into a partnership. “Tony helped lay the foundation for something truly transformative for our spring manufacturing community.”
In May, SMI launched a new online Member Center through GrowthZone, a membership management program. GrowthZone is a software platform that helps associations manage, engage and grow their membership.
Our new member center includes access to:
Member Directory — Update your contact information in the SMI member directory and public directories to assist outside companies looking for springmakers.
Resources — Gain access to key sites, documents and other member-only information.
Events — Register for our upcoming events and pay online using an ACH or credit card payment.
Referrals — Refer new regular or associate members to SMI to help grow our membership.
Email Lists — Subscribe to receive regular communications from us.
Committees — Increase your involvement in SMI by participating in a committee.
If you are an SMI member and have not done so already, you’ll need to create a member login to access the Member Center. Please visit: https://bit.ly/smi-gz1.
After you log in to the Member Center, you will be prompted to update your contact and directory listing information and add your payment profile.
If you would like these same benefits on your phone or tablet, please download the MemberPlus App (by Micronet Inc.).
For assistance with your membership profile in GrowthZone, please contact Gaby Carrasco at gaby@smihq.org.
To access the Member Center visit https://bit.ly/smi-gz1
SMI president Don Jacobson III recently announced the addition of five new members to the SMI Board of Directors. Each of these individuals will serve a three-year term. The board meets four times a year to review the association’s business.
The new board members are Julie Arenz, R&L Spring and Medicoil, Chris Kozka, MW Components, Timo Roeger, Kern-Liebers USA, Sanjeev Rivera, Lee Spring and Jason Sicotte, Associated Spring.
“Adding five new board members and diversifying the composition of our board is a great testament to SMI’s executive committee and staff,” said Jacobson. “It is very exciting to see where we are as an association and the direction we are headed.”
Arenz, Rivera and Roeger are actively involved in SMI’s Emerging Leaders group.
Arenz is a recent third-generation family business owner of R&L Spring and Medicoil in Lake Geneva, Wisconsin. She has been working in the company for more than eight years now and is passionate about continuing her family’s legacy of making highquality, precision springs, coils and formed wire products. She values her partnerships with other communities and looks forward to becoming more involved with SMI. Away from the office, Arenz is a mother to two young boys, so spending quality family time and being active outdoors with them is a top priority.
As a product manager at MW Components, Kozka utilizes his diverse background in customer service, engineering, estimating and quality control to help clients achieve significant process improvements. His expertise includes waste reduction strategies and optimization techniques. Certified in Six Sigma and fluent in Polish, he is actively engaged in the manufacturing community, currently serving as president of CASMI. Outside of work, Kozka cherishes spending quality time golfing and enjoying long walks with his twin daughters.
Rivera is the president of Lee Spring, a leading manufacturer of stock and custom springs, wireforms, fourslide parts and stampings. Headquartered in Brooklyn, New York, Lee Spring serves a diverse range of industries, including aerospace, medical, robotics and electronics, offering more than 25,000 stock spring products and extensive custom capabilities. In addition to spring manufacturing, Rivera also has experience in consumer products and semiconductor manufacturing, bringing a broad industry perspective to his leadership. He holds a degree in mechanical engineering from the University of Pennsylvania and an MBA from the New York University Leonard N. Stern School of Business.
Since 2023, Roeger has served as the managing director of the Smart Springs & Smart Parts division for Kern-Liebers USA. In that role, he leads the U.S. operations of the division, with overall responsibility for strategic development, financial performance and operational excellence. From 2014–2023, Roeger served as the head of product development and planning for the Smart Springs division at Kern-Liebers in Germany. He earned an MBA from IUBH Internationale Hochschule in Germany in 2020, in addition to a master of science in engineering and a bachelor of engineering degree from Hochschule in Düsseldorf, Germany.
Sicotte has more than 30 years of experience in the spring industry. He currently serves as the director of global engineering for Associated Spring. During his career, Sicotte has gained valuable experience analyzing failures, designing new products and working closely with wire and steel mills on process improvements. Sicotte holds several patents and was a guest speaker at SMI’s Educational Symposium at SpringWorld 2024 on “Shot Peen Innovation.” Sicotte has also written several articles for Springs
To register for a safety webinar, visit: https://bit.ly/smi-cal.
SMI’s regulatory compliance consultant, Dr. Laura Helmrich-Rhodes, CSP, SHRM-SCP, will present four webinars this year to help members understand the latest information regarding OSHA and company safety issues.
All webinars are presented at no charge to SMI members and are scheduled for 1 p.m. EST on the dates listed below. Nonmembers may participate for $149.
Thursday, June 26
This webinar is directed toward safety committee members and others interested in the topic.
“So often, safety committees become boring and ineffective,” Rhodes explained. “Some companies avoid them because of this reputation. Who can forget the old saying: ‘When you don’t want anything done, form a committee.’”
This webinar focuses on the characteristics of effective safety committees, especially how they can contribute to a company’s overall OSHA compliance efforts. The content will be directed at not only managers but also committee members, so that they can improve their personal contributions. Resources will be provided for further information, and certificates of attendance will be issued upon request.
Thursday, July 10
This webinar is designed for department supervisors, safety committees and other company leaders. It focuses on answering the question: What are the roles and obligations of a department supervisor in leading safety in the shop?
This webinar will help supervisors identify their leadership strengths and areas
We’d love to hear from you!
Springs welcomes your notes and comments on the contents of our publication. Please email Phil Sasso, managing editor, at phil@smihq.org
for growth. Resources will be provided for further information, and certificates of attendance will be issued upon request.
Thursday, Aug. 7
An OSHA inspection remains a possibility despite a conservative federal agency administration.
“It is still likely if you sustain a reportable injury or your experience is over the national average,” Rhodes said. “Employee complaints have triggered inspections at many companies in the U.S.”
This webinar will review the step-by-step process of an inspection and review your rights as an employer in the process. (This is NOT the OSHA Top Ten Most Frequently Cited Webinar) The discussion will focus on Federal inspections. Some of the information is very similar for state-run OSHA programs. Resources will be provided for further information, and certificates of attendance will be issued upon request.
Thursday, Sept. 18
You cannot rely on auditors to evaluate your workers’ compensation (WC) cost. This webinar will combine current research data on workers’ compensation (WC) nationwide with key points to consider in self-assessing your WC costs. The session will highlight practical processes you can implement in your organization to control the loss of profits. Certificates of attendance will be provided upon request.
SMI members receive priority placement for their product, company, personnel and events announcements in the magazine. Your news releases should be roughly 50 to 100 words and may be accompanied by color photos (high-resolution .JPEG photos at 300 dpi preferred). Send to gaby@smihq.org.
2025
Sept. 8–11
FABTECH
McCormick Place
Chicago www.fabtechexpo.com
Sept. 6–8
wire Middle East Africa
EIEC — Egypt International Exhibition Center
Cairo, Egypt www.wire-mea.com
Sept. 17–18
wire Southeast Asia
Bangkok, Thailand
Bangkok International Trade & Exhibition Centre (BITEC) www.wire-southeastasia.com
Sept. 19
12th International Congress of Spring Industry Paris, France www.esf-springs.eu
Sept. 25–26
ISO/TC227 — Springs Beijing, China
2026
March 5–8
2026 SMI Annual Meeting
Wyndham Grand Rio Mar Río Grande, Puerto Rico
April 13–16
wire 2026 — International Wire and Cable Trade Fair Fairground Düsseldorf Düsseldorf, Germany www.wire-tradefair.com
Oct. 7–9
SpringWorld 2026
Donald E. Stephens Convention Center
Rosemont, Illinois www.springworld.org
As a component of SMI’s Advanced Spring Design (ASD7) computer software, SMI offers spring design training programs to help industry newcomers and veterans increase their knowledge. Training is available to both members and nonmembers.
Class
Date*
206 Snap Ring Design July 17, 2025
301 Springs — Fatigue Aug. 21, 2025
201 Compression Spring Design Oct. 16, 2025
202 Extension Spring Design Nov. 20, 2025
203 Torsion Spring Design Dec. 18, 2025
Webinars are scheduled from 1–5 p.m. EST. *Dates are subject to change.
For more information and to register for classes, visit www.smihq.org/go/tech-classes or contact Gaby Carrasco at gaby@smihq.org.
SMI regularly surveys its members to help them understand how they are performing compared to others in the industry. We respect your privacy and recognize the importance of confidentiality. No company data is ever shared with SMI members, SMI itself or any third parties. 2025–26 Schedule
Key Business Trends (regular and associate members) Survey Sent Responses Due Results Sent
Second Quarter 2025 July 7, 2025 July 17, 2025 July 18, 2025
Third Quarter 2025 Oct. 4, 2025 Oct. 14, 2025 Oct. 15, 2025
Fourth Quarter 2025 Jan. 6, 2026 Jan. 16, 2026 Jan. 17, 2026
First Quarter 2026 April 7, 2026 April 17, 2026 April 18, 2026
Wages & Benefits (every other year — regular member contacts) Survey Sent Responses Due Results Sent 2026 Sept. 3, 2026 Oct. 1, 2026 Nov. 15, 2026
(every
Annual Market Survey (regular member contacts and prospective members) Survey Sent Responses Due Results Sent
Industry Report to SMI April 2, 2025 May 31, 2025 July 15, 2025
Individualized Reports to SMI Members July 31, 2025
For more information about participating in SMI’s benchmarking programs, contact Gaby Carrasco at gaby@smihq.org.
CNC Wire Coilers, CNC Wire-Forming / Torsion Machines, High-Speed Stamping Presses & Servo Feed Lines, Link Belt Conveyor Ovens, Shot Blast Equipment, CNC Machinery, Tool Room, Insertion / Visual Inspection Cells, Test & Inspection Equipment, Laboratory Equipment, Rolling Stock, Plant Facilities, Plant Support Equipment, and more.
Gaby Carrasco
The Diary of A CEO | Steven Bartlett
May 28, 2025 | 13 min.
With so much technology at my fingertips, my attention span has definitely taken a hit. I find myself often skipping long movies in favor of quick TikTok or Instagram videos. That’s why I love podcasts that offer a range of episode lengths, longer ones for tasks like cooking or walking, and short, no-commitment episodes when I just want a quick hit of insight. The Diary of A CEO nails this balance, offering both deep one-hour-plus interviews and short under-15-minute episodes that get straight to the point.
This issue’s review is of a 13-minute interview between host, Steven Bartlett and Brian Chesky, cofounder and CEO of Airbnb, as he discusses the brutal truth about rejection, resilience and company culture. The episode begins with Chesky reading a rejection letter he received in 2008. He recounts how he was initially rejected by nearly every investor he approached. Despite this, he and his cofounders pushed forward. Chesky emphasizes the importance of resilience and staying true to one’s vision, even when faced with skepticism.
The discussion also touches on leadership philosophies, with Chesky sharing his views on what makes a great leader in today’s rapidly changing business landscape. He emphasizes the importance of vulnerability, listening and designing a company with intention, not just building a product but crafting a culture. His leadership became more people-focused, especially after tough moments like the COVID-19 pandemic layoffs.
Additionally, Chesky candidly discusses mistakes he made along his journey. One of his biggest acknowledgements is trying to grow too fast and getting distracted from his core mission. He cautions founders not to chase growth at the expense of clarity. He believes many founders mistake product innovation for company building — forgetting that people, purpose and culture are foundational.
Despite its brevity, this episode of CEO Diaries is incredibly insightful. To listen to the longer episode, check out The Diary of a CEO wherever you listen to podcasts. z
Want to share a business development podcast for me to review? Please send your suggestions to gaby@smihq.org.
RK Trading’s CSX series of Herdon formers keeps your operation running smoothly. This technology offers a high-speed 20-Axis All-Servo Wire Former that supports multiple servo spinners, the 4-axis AT system and the EA attachment. With a next-generation processor and larger touch-screen monitor, this enhanced operating system provides increased versatility and faster production speeds so you can make more parts complete in less time.
Give us a call today to get up and running with a 20-Axis All-Servo Wire Former from Herdon. SCAN HERE
Reviewed by Phil Sasso
In “The Power of Company Culture,” Chris Dyer, a featured speaker at the 2025 SMI Annual Meeting, lays out a blueprint for building a culture that improves productivity, performance and profits. He distills culture into seven pillars: transparency, positivity, measurement, acknowledgment, uniqueness, listening and mistakes.
While in New Orleans, I met Dyer the night before his presentation in the Peacock Room at the Kimpton Hotel Fontenot and told him I was reading his book.
Curious about his “Seven Pillars of Amazing Culture” — the subject of both his book and his presentation the next day — I asked about the final pillar: mistakes. How, exactly, could mistakes be a good thing?
Making mistakes a pillar of corporate culture may seem counterintuitive — if not reckless. But Dyer does not encourage a culture that accepts incompetence. He sees mistakes as growth opportunities. And he clearly distinguishes between errors and mistakes.
“Errors come from carelessness, overwork, multitasking and asking people to do work they are not inherently suited to doing,” Dyer writes. By contrast, he defines a mistake as, “An action motivated by good intentions, undertaken after careful research and in the light of positive indications of success — but one that still goes wrong.”
He shares a personal experience of buying a pet pig as a birthday gift for his daughter. He did his homework. But despite that, the family dogs saw the piglet as food, not a friend.
“After a few expensive trips to the vet for them and to the doctor to treat a large gash on my own hand, the situation was not getting better,” he writes. “But you can also bet that I learned from that mistake.”
In a business example, customer service agents need freedom to use their best judgment to quickly resolve situations. That can sometimes lead to mistakes.
“Southwest openly lets staff and customers know they will stand by their employees 100% — whatever their choices,” he notes, citing his interview with Shari Conaway, director of people at Southwest Airlines, on his TalentTalk radio show in 2016.
“This is the main reason Southwest’s customer experience is so different from other airlines,” Dyer suggests. “The employees are fun and loose. They are accommodating and empowered … because they know their employer has their backs.”
The remaining seven pillars are just as thought-provoking. For anyone interested in corporate culture, Dyer’s book delivers strategy and inspiration with the same energy New Orleans’ Café Du Monde serves up beignets and chicory coffee. z
Have a favorite business book you would like us to review? Email your suggestion to phil@smihq.org.
At Admiral Steel, we understand that your product is your reputation. That’s why we take pride in specializing in premium quality high carbon steel that meets specs such as AMS, QQS, and ASTM certified. Our commitment to providing certified material means that you can trust that you are receiving the highest quality steel available. Don’t settle for seconds and rejects. Choose Admiral Steel for the assurance of premium quality steel products. Call us at 800-323-7055 or email sales@admiralsteel.com
WAFIOS, a developer, designer and producer of specialty machinery for the wire and tube processing industry, has updated the operating system (OS) of its SNA series ring coiling and wave spring machines. The SNA series’ software has been improved to produce wave springs and single- or multi-turn rings from profiled wire, with or without crimps. The SNA series offers machines for 7-320 mm OD rings and 7-250 mm OD wave springs.
The new iQwavespring and iQtorque programming are designed to improve spring production.
iQwavespring automatically calculates motion sequences and corrects the diameter based on variations in pitch. The setup process is faster and yields fewer rejects, according to the company.
The iQtorque software detects workpiece or tool breakage and automatically stops the machine. The operator can choose to stop the machine immediately or at the end of a cycle. This minimizes possible damage to the machine or tool. The individual machine axes are monitored by an envelope curve of the motor torque. The iQtorque can reduce downtime, repair costs and improve safety during automatic operation, says WAFIOS.
For additional information on the SNA series, visit www.wafios.com.
Forming Systems Inc. has introduced HSI industrial ovens to North America that meet the latest AMS2750 aerospace standards. HSI ovens are available with an optional AMS2750 configuration, equipped with sensors and instruments certified by an International Laboratory Accreditation Cooperation-recognized, ISO/IEC 17025-accredited calibration laboratory, says the company.
These HSI industrial ovens feature a heavy-gauge stainless steel 304 interior, a three-phase heating element with broken detection, Incoloy-sheathed heating elements and a digital error diagnosis and display system. The PID controller and solid-state relay offer high efficiency in on/off heater control and precise temperature control, according to Forming Systems.
For more information, contact Forming Systems at info@formingsystemsinc.com or 269-679-3557.
Send us Your News
SMI members get priority placement of their product news. News releases should be roughly 50 to 100 words and may be accompanied by color photos (HiRes .JPEG at 300 dpi preferred). Send to gaby@smihq.org.
Your source for the best in close tolerance
strip: cold rolled high carbon/pre-tempered spring steels, coated, low carbon stainless, copper based alloys and aluminum ultra-narrow width, close-tolerance slitting edging: round, square, semi-round, deburred, custom, etc.
oscillate (traverse) and ribbon wound coils
ISO 9001: 2015 certified 43 years servicing the industry
tel. 847.537.2881 toolkinginc.com
Wheeling (Chicago), Illinois 60090 USA
SWP-A, SWP-B; EN10270-1; AMS5112N; military specifications, and others. Call for special wire needs and solutions, including restricted tensiles and size tolerances.
Name: Katherine Pepka.
Company name and city: Renton Coil Spring (RCS), Renton, Washington (just outside of Seattle).
A brief history of your company: Since 1949, RCS has been manufacturing high-precision springs and wireforms in Renton. Family-owned and engineering-led, we’ve built a legacy of quality and innovation across aerospace, defense and highperformance sectors.
Job title: Executive Vice President.
What I like most about being a springmaker: There’s something rewarding about working in a field that’s both highly technical and quietly essential. Springs may be behind the scenes, but they keep the world in motion. Plus, being part of a legacy while bringing new energy to it keeps the work meaningful.
Birthplace/Current home: Seattle.
Favorite food: Someone else’s fries.
Favorite books/authors: “A Gentleman in Moscow.”
Favorite songs/musicians: The Garden State Soundtrack.
Your hobbies: Yoga/dancing, vintage shopping, traveling and pursuing my Wine & Spirit Education Trust (WSET) certifications.
Favorite places: Spain, the San Juan Islands and anywhere I can take my dog, Bandit.
Podcast you’re listening to: How I Built This.
What’s on your bucket list: The Orient Express from Venice to Istanbul, sailing down the Nile and living a long, healthy life. Aside from necessities, what is one thing you could not go without: My passport.
Best times of my life: I’m sure having a good time right now.
A great evening for me is: Cooking for my friends, opening an excellent bottle of wine and laughing.
The one thing I can’t stand is: When people microwave fish for lunch at the office. Why? Just why?
People who knew me in school thought I was: Unlikely to become a springmaker.
I knew I was an “adult” when: April 15 became a deadline.
The most difficult business decision I ever had to make was: Pretty much everything during COVID.
I wonder what would have happened if: I never said yes to trying two years at RCS (that was 2014).
My role models: My dad (SMI Past President Chuck Pepka), the eternal problem solver who is always a few steps ahead (literally and figuratively). My grammy who is witty, stylish and lethal with a deck of cards.
I’d like to be remembered in the spring industry for: Bringing fresh perspective to a legacy business.
But people will probably remember me for: Being Chuck’s daughter and bringing my dog to New Orleans.
March 5-8, 2026
Wyndham Grand Rio Mar
Rainforest | Beach | Golf Resort
Río Grande, Puerto Rico