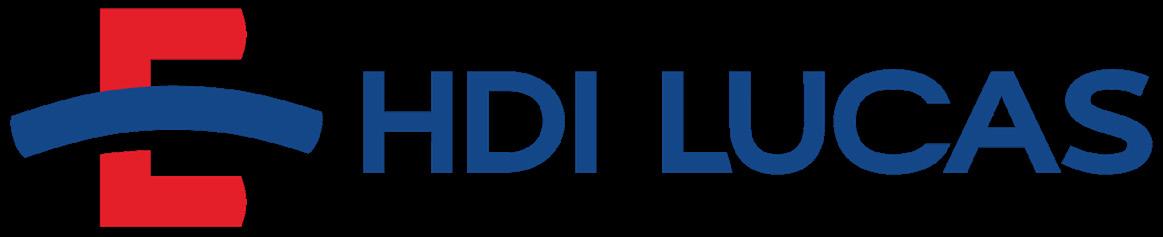
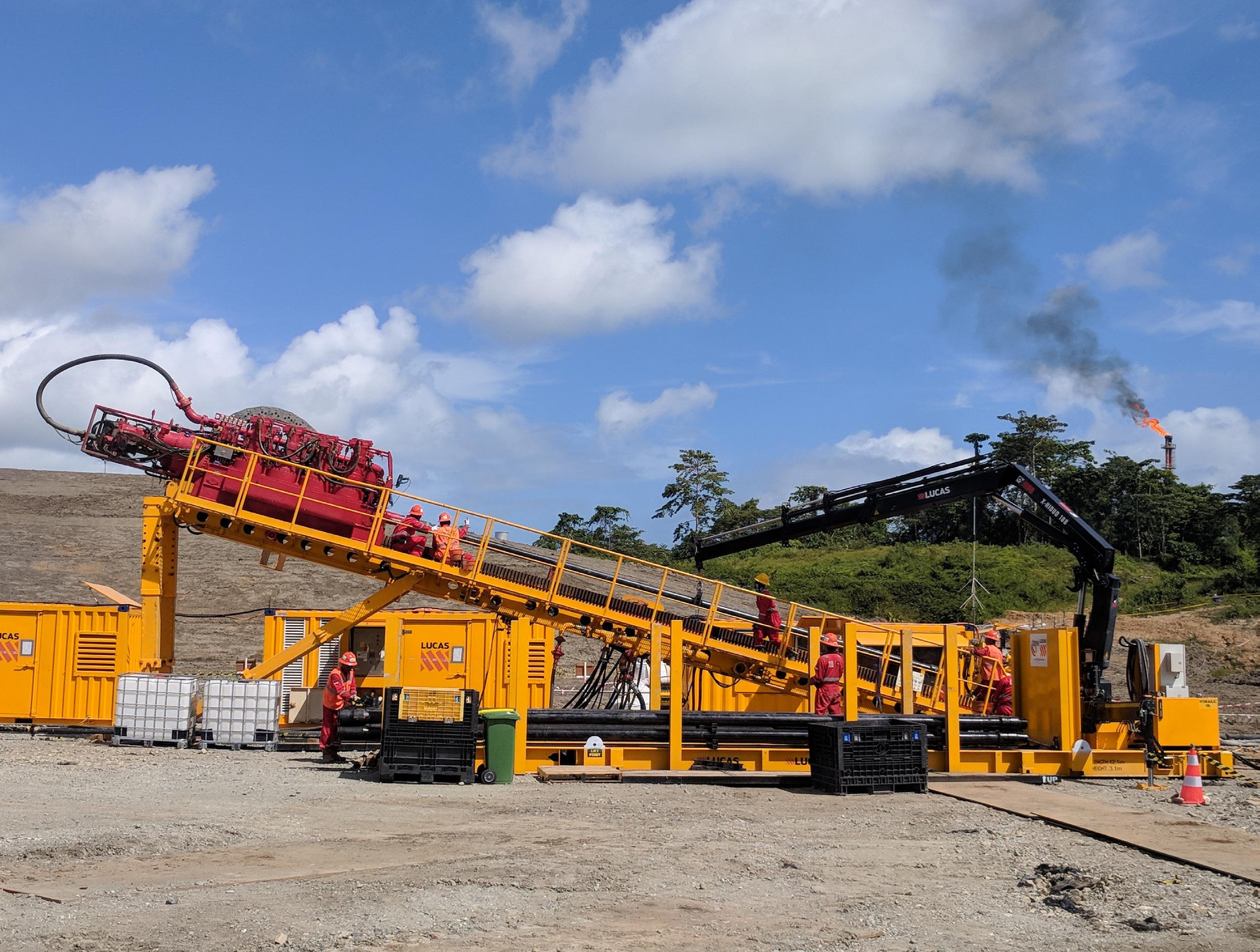
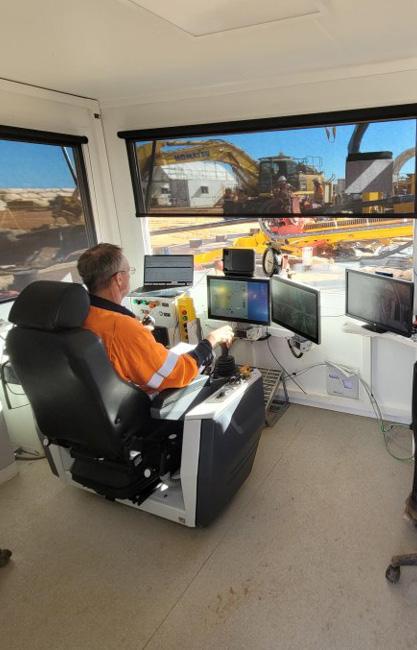
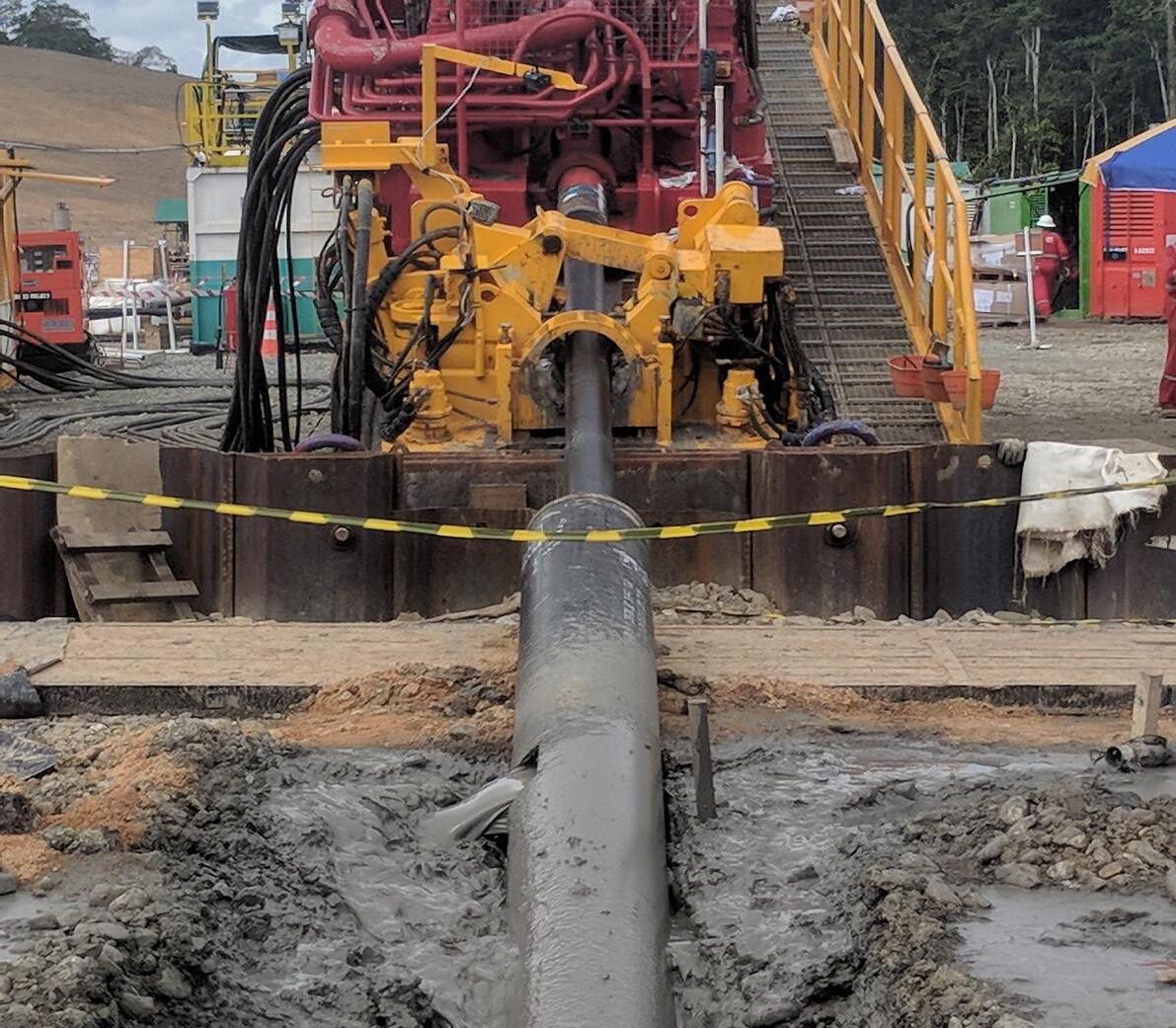
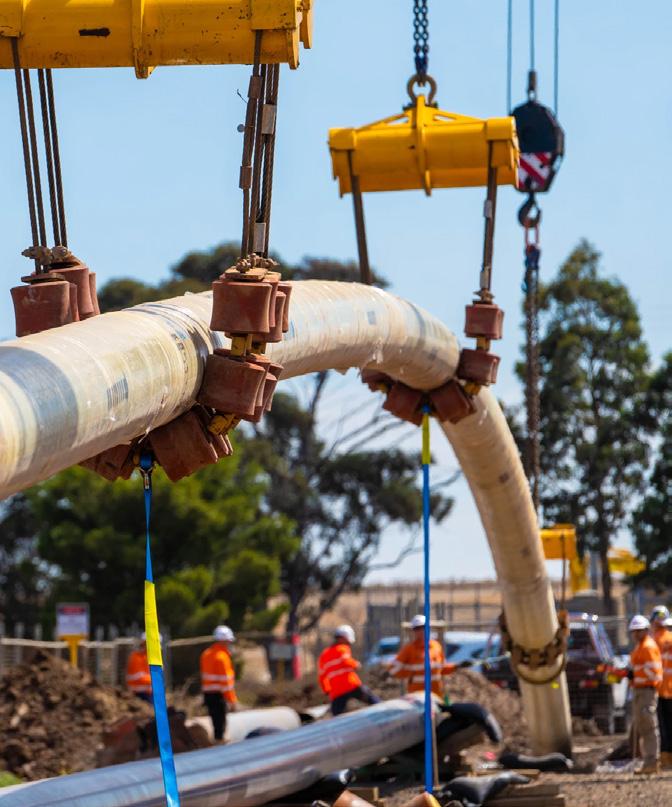
THE CUTTING EDGE OF HORIZONTAL DIRECTIONAL DRILLING
INSTALLATION OF PIPELINES, CABLES AND CONDUITS UNDER NATURAL OR ARTIFICIAL OBSTACLES

HDI Lucas seeks to build customer relationships based on trust. Working closely with our clients to get the best solutions, we keep our promises. We have built a reputation in the market as innovators and problem solvers thanks to a high-level of expertise and experience; advanced technology and equipment that we have helped to develop; and, being part of the VINCI Group, which means we can access a full range of international construction experience.
HDI Lucas has been “at the cutting edge” of HDD, leading the sector by establishing many of the major industry milestones in extending the capabilities of HDD. These include:
• First HDD over two kilometres in length under the Tamar River, Tasmania, in 2002.
• • World’s largest HDD project with nine landfalls for the Gorgon Project, Barrow Island (WA), in 2012.
• • Largest volume of pipe installed by HDD in a single shot River Axios, Greece in 2018.
We also have close relationships of trust with our staff. We have the strongest commitment to making sure our workers always go home safely at the end of every day. HDI Lucas has the best safety record in the industry.
HDI Lucas is Australia’s most accomplished horizontal directional drilling company. It is a subsidiary of Spiecapag and a sister company to Horizontal Drilling International (HDI) France.
We have decades of local experience in HDD conditions and also have access to the knowledge gained from our parent organisation’s extensive international project experience. HDI Lucas was formed in 2018 following the acquisition of Lucas Engineering and Construction, which was both a leading pipeline contractor and an accomplished horizontal direct drilling contractor.
We are renowned for our innovative approaches and practical solutions. Our reputation has been earned thanks to a combination of experience, the use of the latest technology and state-of-the-art equipment. Over the years, we have extended the capabilities of HDD beneath natural and artificial obstacles, continuously redefining the limits of HDD and setting the benchmarks for HDD in Australia.
We have a concentrated focus on safety management, risk management, environmental performance and quality systems. This culture is essential in keeping our promises to clients and to our staff. Our projects are managed with few delays or cost overruns. We have a high level of customer satisfaction and we are strongly committed to ensuring our workers always go home safely at the end of every day.
OUR STRENGTHS
• Leading expertise in horizontal directional drilling
• Operations at a global level
• Innovation through R&D
• Adaptability as a core value
• Latest technology and state-of-the-art equipment
TGE first landfall using HDD (ESSOBass Strait, Australia
First company to install HV electrical lines using HDD (Garonne River, France) 1991
First HDD in rock (SNAM-Sicily, Italy & TPCN iagara, USA)
First 48’’ pipeline installed by HDD (GASUNIE-Canal Noord Holland, Netherlands)
First HDD over 2km in length (DUKE Energy-Tamar River, Tasmania, Australia)
Longest landfall project at the time (1850m) (Pohokura Gas Field Landfall, New Plymouth, New Zealand) 1991 2002 1989
2007
World’s largest HDD project, including 9 landfalls at DN800 (ChevronGorgon Gas Project, WA, Australia
Largest volume of piping by HDD in a single shot 1820m of 48’’ pipe (TAP-River Axios,Greece)
HDI Lucas is part of VINCI Construction, one of the branches of the VINCI Group. It is an international contractor that designs, builds and operates production, transport and storage infrastructures for the oil & gas and other energy markets. VINCI Construction employs over 100,000 people in over 100 countries. The business provides a wide range of services for its infrastructure projects, including financing, design, construction, and maintenance.
HDI Lucas is sistered with Horizontal Drilling International (HDI), an international construction company established in 1984, specialising in the installation of pipelines under natural or artificial obstacles using trenchless methods, particularly HDD. HDI is headquartered in France with divisions in the UK, Poland, Ivory Coast and, since 2018, Australia.
Within the VINCI Group, there are companies with expertise in all construction fields, bringing many opportunities for collaboration and joint-ventures. Closely related to HDI Lucas activities are:
Spiecapag has completed some of the most complex pipeline construction projects in the world. Success has been achieved by continually pushing the boundaries of construction techniques using innovative design and systematic construction techniques. The company maintains fleets of specialised equipment, specifically designed to safely build pipelines in some of the most challenging environments in the world. Its capabilities encompasses:
• Onshore pipelines and associated facilities for energy, resources and utilities sectors.
• Onshore and near-shore pipelines for the oil and gas sector. Procurement and logistics to regional and remote sites.
Geocean has successfully delivered marine work projects for more than 30 years. It has worked on all continents, in diverse climatic conditions and with multiple logistical challenges. Geocean performs turnkey projects under EPCI-type contracts, or for public works contracts in the oil and gas, mining and chemical industries.
Geocean specialises in landfalls in shallow-water zones using unique equipment that it has developed. Geocean has expertise in design and turnkey construction of offshore and coastal works including:
• Submarine pipelines, import and export terminals moorings, wharves and jetties.
• Trenching for submarine pipelines, pipeline landfalls and other bespoke works.
Largest cable landing project installed by HDD (Chevron, Jansz-Io Project, WA, Australia)
HDD uses a directional drilling machine and associated equipment to accurately drill along a specified bore path (the shot) and then ream the hole until it reaches the required diameter to fit the pipe or conduit. Each project has unique requirements. We develop the project methodology to suit the conditions, technology requirements and the equipment to be used. However, the basics of HDD are summarised here.
The first stage of HDD consists of drilling a small diameter pilot hole using a long guided flexible stem equipped with a wire-line guidance system and ending with a beacon housing and drill bit.
HDD drilling fluid
HDD drilling fluid is a mixture of water and bentonite or polymer. It is continuously pumped to the drill bit, also known as the cutting head, to produce a high-pressure jet that assists the bit to grind the soil or rock ahead. It also helps remove the cuttings, stabilises the bore hole, cools the cutting head and lubricates the passage of the product pipe. Importantly, this fluid is not toxic to the environment.
Monitoring drill location and direction
Monitoring the position of the pilot hole uses a wire-line guidance system. A transmitter located near the cutting head sends a signal to the location engineer. It provides the exact location of the drill stem from the readings of inclination and azimuth. The guidance system is accurate to over two kilometres with an accuracy of 2% at depth.
Steering the drill head
Corrections are made by the operator and location engineer to steer the pilot hole along the specified bore path. The speed of the drilling varies between soil or rock conditions and the amount of steering required. When exit point is reached the wire-line guidance system, transmitter, beacon housing and drill bit are detached and replaced with a reamer.
The pilot hole now needs to be enlarged to install the liner (pipeline or conduit), this is known as (forward or back) reaming. A reamer is either push or pulled as it is rotated and lubricated with drilling fluid to expand the diameter of the pilot hole. The drilling fluid is pumped back to remove cuttings as the hole is enlarged. An evenly mixed drilling fluid prevents blockages of the bore hole. Reaming speeds will vary depending on conditions. The added bentonite creates a “cake-layer” around the hole. This helps make the bore stable and reduces fluid loss and infiltration.
Once the bore is at the desired size the pipe or duct is either pushed in (pipe thrusting) or pulled back (pipe pullback) within the pre-reamed hole. The drill rod and reamer are attached to a swivel to prevent torsion stress from the rotating drill being transferred to the product pipe. Drilling fluid is pumped down the bore hole to provide lubrication.
Horizontal directional drilling allows pipelines, cables and other services to be laid without impacting the surface along the installation. Because the process replaces the need for trenches, the impacts on the surface are focused on the entry and exit points.
HDD has the least environmental impact on fauna, flora and people in built-up areas. It allows traffic and other stakeholder activities to continue without disruption during the drilling process.
Site conditions change little during the project duration so that site safety is easier to manage and enforce. Lost time injuries are reduced and rare.
Avoiding onshore obstacles
The use of HDD Is particularly useful in avoiding onshore obstacles where an open-cut excavation is unsuitable. Obstacles that can be avoided include:
Waterways (rivers, streams, canals, etc.),
Roads, motorways and airport runways
• Utility services such as telecommunications, gas and electricity
Railways
Airport runways
• Rock outcrops
Environmentally sensitive or protected areas
Residential areas
• Dump sites
Operating quarries
• Golf courses
Construction of shore approaches (landfalls or outfalls)
We have delivered many complex directional drilling works from sea to shore (Landfalls) and shore to sea (Outfalls) for clients due to the advantages the HDD processes offer:
Overcome the difficult conditions experienced by marine or standard land-based equipment.
Significantly reduce the environmental impact on coastlines (protected beaches and sensitive areas); the flora and fauna (often protected species considerations); and on residents and visitors (tourists and holidaymakers).
Safe crossing of surf zones.
• Protection of the service (usually pipeline) against erosion (drilling needs to be at sufficient depth)
In 2007, we drilled the Pohokura offshore Gas Field Landfall (New Plymouth, New Zealand), which was the longest landfall project at the time (1850m).
HDI Lucas uses innovative and flexible contracting practices to deliver high levels of client satisfaction. We provide a flexible approach to our customers’ project requirements to make sure we get a best for project result.
We prefer to work in collaboration with our clients at the early planning stage of projects to optimise project value for all parties. We promote and encourage ECI— early contractor involvement—with clients. With ECI, the cost-timeline equation can be optimised at the initial design phase based on close dialogue with the customer. This results in more cooperation, greater cost control, lower risk and a design phase that benefits both parties and ultimately boost their performance.
We approach projects from the perspective of a partner helping our clients to succeed. In our experience collaboration provides the best result for the client and for us.
HDI’s drilling rigs offer a pulling capacity ranging between 35 and 400 tonnes. They allow for the installation of small size pipelines over short distances as well as large diameter pipelines (up to DN 1400) over very long distances.
Rigs are trailer or crawler mounted and consist of a central beam rack with a carriage moved by pinions powered by hydraulic motors. Hydraulic rotary motors located on the carriage provide the necessary rotary force.
Each drilling rig has its own control cabin, steering kit, high pressure pump and other ancillary equipment, forming a complete and autonomous drilling spread. The HD 650 and HD 350 models are designed and manufactured in-house.
We have a concentrated focus on safety management, risk management, environmental performance and quality systems. This culture is essential in keeping our promises to clients and to our staff. Our projects are managed with few delays or cost overruns. We have a high level of customer satisfaction and our workers always go home safely at the end of every day.
The HDI Lucas vision is “injury free every day”. To achieve this HDI Lucas recognises it must maintain a proactive approach to health and safety; provide visible leadership at all levels, have in place effective management systems that reflect the operating environment and community standards relevant to HDI Lucas service delivery as well as ensure the right culture is embedded in the organisation.
Our quality systems have been proven time and time again as we tackle some of the most challenging horizontal drilling projects in the region, and those systems are regularly reviewed to ensure we learn and stay ahead of the curve.
• Construction permits are granted quickly
• Unrivalled protection for pipelines
• Surface traffic is not disrupted
• No harm to the environment
• Cost and schedule optimisation
• Safety
• Ease of maintenance
One of the key benefits of directional drilling over alternatives such as trenching or overland pipelines is its ability to avoid or substantially mitigate environmental impact.
HDI Lucas is committed to meeting all environmental regulations. Our policy requires all operations to be conducted in a way that will preserve and protect the environment.
We are rigorous in identifying environmental risks and developing management or engineering solutions to avoid, minimise or mitigate them. We work closely with all stakeholders to ensure our activities have the least effect on land use, the environment and cultural heritage.
HDI Lucas has a risk management framework aligned with ISO31000. Comprehensive risk management processes underpin our operational and governance activities.
Our people are formally trained in hazard identification and risk management at levels appropriate to their roles and responsibilities. Their skills are maintained through daily application of those processes.
Well established consultative and communication processes ensure risk is well understood and communicated across the business. We constantly monitor integration of our risk management framework across all of our operations
HDI Lucas’s membership of the Vinci Group provides our clients with assurances of solid parent company backing. At $113 Billion AUD (€68 Billion) in 2023 revenues, VINCI Group’s financial strength ensures the continued viability of HDI Lucas.
FINANCIAL STABILITY
• Part of a profitable group that has an annual turnover of
• $113 billion AUD.
• The group has a credit rating of: A- by Standard & Poors: and A3 by Moody’s.
GLOBAL BEST PRACTICE
HDI Lucas holds the following certifications:
• ISO 9001: 2015 Quality Management accreditation
ISO 14001: 2015 Environmental accreditation
• ISO 45001: 2018 Health & Safety accreditation
FLEXIBLE & COOPERATIVE MANAGEMENT
HDI Lucas has the experience to quickly integrate with and work with other contractors on site, joint venture partners or financiers.
We bring new ideas to the table in the areas technology and equipment, delivery partnerships, safety, quality, procurement & logistics, community engagement, financing or contracting.
SAFETY TRIFR
Total Recordable Injury Frequency Rate of 0.0 for HDI Lucas activities
EFFICIENCY & PROFICIENCY
Use of HDI Lucas’s in-house specialist HDD plant, overseen by experienced, in-house project managers and site supervisors.
HDI Lucas has worked on many landmark oil & gas pipeline projects in Australia and SouthEast Asia. We have created innovative solutions to extend the capabilities of HDD on many of these projects:
• Kurri Kurri Lateral Project (NSW): Seven crossings of DN350, totaling 5.5km.
• Jansz-Io Compression Project (Barrow Is, WA): Four 550m landfalls up to DN630 HDPE casings.
• WORM (Melbourne, VIC): Seven crossings of DN500 totaling 4km.
• Channel Island (Darwin, NT): 1350m, 200mpa rock crossing.
Kewdale White Oil Line (Perth, WA): Eleven crossings of DN300, totaling 11.85km.
• The Gorgon LNG Project (Barrow Island, WA): Nine 800m landfalls up to DN800.
• Tangguh LNG Project (West Papua, Indonesia): Three 2065m landfalls up to DN600. Hangzhou Bay Pipeline Crossing (Shanghai, China): Two 1750m landfalls up to DN600.
• Tamar River Pipeline (Tasmania): 2065m of DN200 in single crossing length.
• Tasmanian Gas Pipeline (Tasmania): Thirteen crossings with total length of 3350m.
SeaGas Pipeline (SA & VIC): Eight crossings of dual DN350 & DN450 with total length of 3750m.
• Pohokura Gas Field Development (New Zealand): Two 1850m landfalls up to DN600.
• Casino Gas Field Development (VIC): Two 1650m landfalls up to DN600.
HDI Lucas has delivered many world firsts for telecommunications and power utilities. We have helped bring fibre-optic to the tops of inaccessible sandstone mountains. We have taken highvoltage electricity cables under waterways to protect them from severe weather conditions. The use of HDD in these situations has increased service levels and reduced maintenance costs.
• EDF Garonne River (France): World first HDD for high-voltage (225kV) cable.
• Telstra Mount White (NSW): Optical-fibre duct - 2:1 height ratio gained over 400m.
China Light & Power (Ma Wan Island, Hong Kong): Largest cable installation by HDD in 2001, with six separate 1400m crossings.
• Telstra Mount Sugarloaf (NSW): Optical-fibre cable drill, setting world record for height gained using HDD.
• TUAS (Singapore): Multiple 700m+ drills for fibre-optic ducts.
HDI Lucas has constructed many drinking water and wastewater pipelines projects. We have also installed intake lines for desalination plants and discharge lines for treated sewage.
• TK2050 (Lihir Is, PNG): Removal and replacement of 300m of DN1200 HDPE outfall pipeline.
• Simberi (Simberi Is, PNG): Replacement of a ruptured 800mm OD HDPE pipeline with a new 600m of DN1000 HDPE pipeline.
• Mardi to Warnervale Pipeline (NSW): Two 700m+ DN800 crossings.
• Northern Interceptor (New Zealand): More than 5000m of DN560 over six crossings. TK050 (Lihir Is, PNG): Recovery and reinstallation of 200m of DN1200 HDPE liner pipe at a vertical depth of more than 100m.
• Western Corridor Recycled Water Pipeline (QLD): Four 1200m DN600 crossings. Tauranga Southern Wastewater Pipeline (New Zealand): 1600m of DN900.
• Chatswood Graded Sewer Pipeline (NSW): 1860m of DN820.
• Illawarra Wastewater Transfer Pipeline (NSW): 1962m of DN900. Cascades Upper Blue Mountains Sewer Pipeline (NSW): Two 2440m crossings with pipe diameters up to DN450.
• Merewether Wastewater Pipeline (Newcastle, NSW): 1350m of DN900.
• Performed work in over 40 countries
• Drilled over 2,000 holes
• Completed 2 million metres of HDD pipework
JANSZ-IO COMPRESSION PROJECT
Client: Chevron
Location: Barrow Is (WA), Australia
Completion: Est. 2025
Pipe Diameter: 24” (DN630)
The Jansz-Io Compression Project is a life extension activity, providing compression to the Jansz-Io field to maintain plateau gas supply to the Gorgon LNG plant and maximise recovery from the reservoir. The Jansz-Io field is located approximately 130km northwest of Barrow Island (BWI) in Western Australia in water depths of approximately 1350m and supplies gas to the Gorgon LNG plant on BWI.
The scope included:
• 3x HDD 550m DN630 HDPE casings installations.
• 1x HDD 500m DN355 refurbishment of an existing liner.
Onshore trenching and supporting cable pulling / cable lay for 300m and 400m.
• Support for live cut-over works.
Large pre-cast concrete installation.
Excavation over existing services
Interfaces included management of a bulk earthworks civil subcontractor, offshore marine HDD support, and offshore marine cable installation teams.
Barrow Island is an “A Class” nature reserve and operates under strict quarantine measures in order to protect the island’s natural fauna and flora from the introduction of nonnative species and to preserve the island’s unique biodiversity. All work on BWI is subject to strict quarantine requirements.
Client: APA
Location: Kurri Kurri (NSW), Australia
Completion: Est. 2024
Pipe Diameter: 14” (DN350)
The Kurri Kurri Lateral Pipeline (KKLP) is a buried gas transmission pipeline and storage pipeline that will connect the proposed Hunter Power Project at Kurri Kurri, in New South Wales, to the existing Sydney to Newcastle pipeline, near Newcastle.
The scope included seven HDD crossings up to 1,100m with a total length of 5.5km in sand stone formation up to 80MPa in strength.
Client: APA
Location: Melbourne (VIC), Australia
Completion: 2023
Pipe Diameter: 20” (DN500)
The Western Outer Ring Main project is a high-pressure, buried gas transmission pipeline, approximately 51km long, which will provide a new connection between existing pipelines at Plumpton in Melbourne’s west and Wollert in the north. The project also includes an upgrade to the existing compressor station at Wollert.
The project included 3km of trenchless crossing across seven HDD (six of them major waterway crossings) and twelve bores.
PROJECT
Client: APA
Location: Darwin (NT), Australia
Completion: 2021
Pipe Diameter: 12” (DN300)
Territory Generation operates the Channel Island Power Station, which is the largest power station in the Northern Territory and the main source of electricity for the Darwin-Katherine interconnected system.
The section of Amadeus Gas Pipeline that crosses the Channel Island Bridge near the power station reduced in nominal diameter from DN300 to DN200. This existing DN200 pipeline under the bridge needed to be replaced by installing a replacement DN300 pipeline under the waterway.
A new 1350m long HDD crossing was completed through varying geology up to 250MPa rock strength. The profile was very complex with a compound curve arrangement completed to minimum pipe bending radius during the last 400m of the crossing.
PIPELINE REHABILITATION PROJECTS (TK050/TK2050)
Client: Newcrest
Location: Lihir Is, Papua New Guinea
Completion: 2021/2023
Pipe Diameter: 48” (DN1200)
The first Lihir Island Tailings Pipeline Rehabilitation Project TK050 involved the recovery and reinstallation of a DN1200 HDPE liner pipe used for the placement of tailings to water depth of more than 100m. The project was located on Lihir Island at a gold mine with dense infrastructure, 643km off the coast of mainland Papua New Guinea. At over 200m in length the tailings pipe was connected to a submerged tank that gravity fed to the ocean at an angle of 37 degrees.
The second, TK2050, involved the relining of another existing DN1200 pipe (approximatively 300m in length) laid at 33 degrees.
Client: JTC Corporation
Country: Singapore
Completion: 2019
Pipe Diameter: 10" (DN250)
A significant reclamation project being completed by JTC Corporation at the Tuas Western Coast in Singapore. It was necessary for SingTel’s undersea cable systems, to be diverted to allow the dredging works to proceed.
Two 700m shore approaches (250mm OD Casing) were installed 45m deep beyond the proposed dredging zone.
Project works included all required support activities; construction and maintenance of launch pit and work area; provision and transportation of consumables, material and equipment.
Client: Fletcher (Watercare)
Country: Auckland, North Island, New Zealand
Completion: 2020
Pipe Diameter: up to 20” (DN500)
The Northern Interceptor Pipeline Project is new wastewater pipe designed to redirect flows from the North-western areas of Auckland (New Zealand) to the Rosedale Wastewater Treatment Plant in Albany.
The final pipeline design incorporates dual DN500 HDPE PN16 sewage rising mains and a DN200 HDPE conduit for future fibre optic cable installations under the Upper Waitematā Harbour and Te Wharau Creek.
The total drilling length was more than 5,000m with each of the triple harbour crossings each exceeding more than 1,100m in length and through parallel curves. The triple Te Wharau Creek crossings each exceed 560m in length. The crossings were completed in challenging rock and clay conditions,
requiring detailed planning and preparation to ensure the crossings were constructible and risk was as low as possible. The bottom hole assemblies were manufactured utilising variable jet configurations to overcome the East Coast Bays Waitematā rock and sticky clay. The project also needed to complete detailed planning and negotiation to secure suitable stringing areas, as the urban location of the pipeline meant that options large enough to be safe and suitable were severely limited.
Working in remote locations to improve production
Client: BP/SAIPEM
Location: West Papua, Indonesia
Completion: 2018
Pipe Diameter: up to 24” (DN600)
The Tangguh Expansion Project was an expansion of the Tangguh liquefied natural gas (LNG) facility located on the southern shore of Bintuni Bay in Teluk Bintuni Regency of Papua Barat Province (West Papua).
The expansion increased the production capacity of the LNG plant by approximately 50% to 11.4 Mtpa. The full project included the construction of two offshore platforms, thirteen new production wells, an expanded loading facility and associated infrastructure. The Tangguh LNG Expansion HDD project required:
• Three HDD landfalls 2065m in length.
• Two 16-inch diameter boreholes for installation of 10inch casings.
• One 40-inch diameter borehole for installation of 24-inch product pipe.
Project works included all required support activities; construction and maintenance of launch pit and work area; provision and transportation of consumables, material and equipment.
CROSSING)
Future-proofing the city and improving the environment
Client: Tauranga City Council
Location: Tauranga, North Island, New Zealand
Completion: 2018
Pipe Diameter: up to 40" (DN1000)
The scope of the Tauranga Southern Pipeline included design and construction of a major wastewater pipeline between Memorial Park Pump Station, across the Tauranga Harbour to MaTauranga Southern (Wastewater) Pipeline on the North Island of New Zealand.
The purpose of the pipeline was to relieve the burden on the city’s sewage treatment plant, allowing it to improve its performance. The harbour pipeline was HDD drilled at a depth of 40m under the seabed.
A drill length of approximately 1570m from Memorial Park to Matapihi.
A 1500mm outer casing was driven in on both sides of the Harbour.
A 1000mm steel casing was installed by HDD, to accommodate an inner 800mm PE pipe.
Project works included all required support activities; construction and maintenance of launch pit and work area; provision and transportation of consumables, material and equipment.
Part of Australia’s largest resource project
Client: Chevron
Location: Barrow Is (WA), Australia
Completion: 2012
Pipe Diameter: up to 34” (DN860)
Gorgon is one of the world’s largest LNG projects and the largest single resource project in Australian history. Located on Barrow Island, a Class A Nature Reserve, Gorgon comprises a three-train, 15.6 million tonnes per annum LNG facility and a domestic
gas plant with the capacity to supply 300TJ of gas per day to Western Australia.
The Gorgon project required:
• Nine HDD landfalls, all 490m in length.
Three 26-inch diameter boreholes for installation of 18-inch casings.
• Four 16-inch diameter boreholes for installation of 8-inch and 10inch product lines.
• Two 48-inch diameter boreholes for installation of 34-inch product lines.
Project works includes all required support activities, construction and maintenance of launch pit and work area, provision and transportation of consumables, material and equipment.
The world’s longest landfall at the time
Client: Shell Todd New Zealand
Location: New Plymouth, North Island, New Zealand
Completion: 2007
Pipe Diameter: up to 24” (DN600)
The project’s HDD landfall traverses a 33-metre cliff and an offshore reef. At 1,850m overall, at the time this was the world’s longest landfall
One of the key challenges was traversing the many different geological layers along the HDD alignment. In order to drill through the surface layers of pyroclastic boulders and cobbles, a casing was hammered approximately 146 m using a 2,000-ton pneumatic hammer. We used an American Augers DD1100 rig. It has 500 tonnes of push/pull capacity and 136 kNm of torque. It is the largest rig in the Asia Pacific, and among the five largest in the world. We used a centrifuge to control the superfine cuttings from the siltstone and mud.
Project works included all required support activities, construction and maintenance of launch pit and work area, provision and transportation of consumables, material and equipment.
International headquarters – FRANCE
Horizontal Drilling International (HDI) 2313 Boulevard de la Défense 92000 Nanterre - France
Phone +33 1 57 98 86 02 communication@hdi.fr
Regional headquarters – AUSTRALIA
HDI Lucas
Level 12, 145 Eagle Street
Brisbane, QLD 4000 - Australia
Phone +61 7 3014 2190 australia@spiecapag.com
Regional headquarters – PAPUA NEW GUINEA
Spiecapag Niugini
Level 11, MRDC Haus
Port Moresby - Papua New Guinea
Phone +675 309 2000
png@spiecapag.com