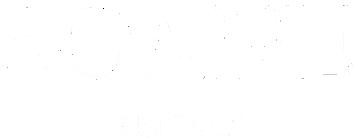
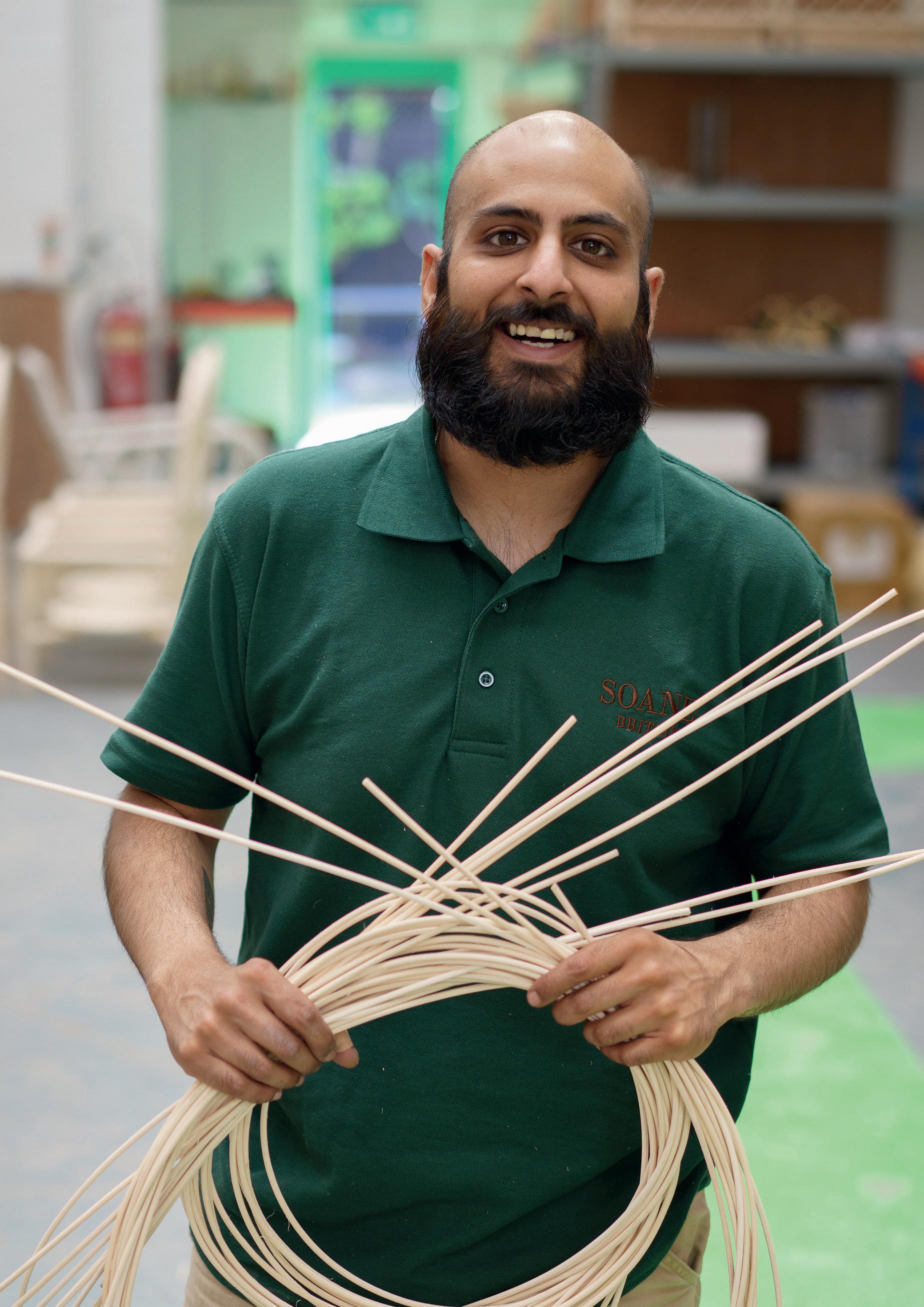
THE
MAKERS WHO MAKE US

Soane Britain is proud to celebrate over
Since 1997, the integrity of the manufacturing all Soane’s work. Every single piece is workshops that excel in traditional some of Britain’s finest makers, and of the UK’s established and
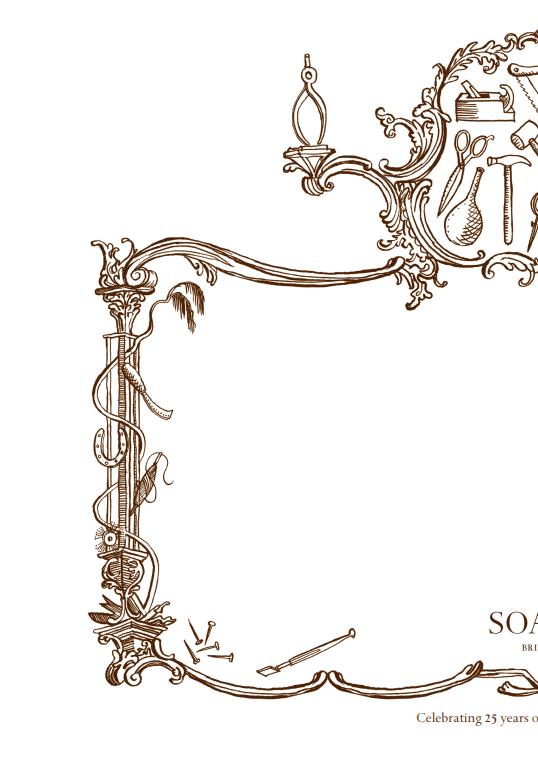

over 27 years of British craftsmanship. manufacturing process has underpinned is made in Britain, using a network of crafts. Soane now collaborates with and has become a showcase for the best and new craft industries.
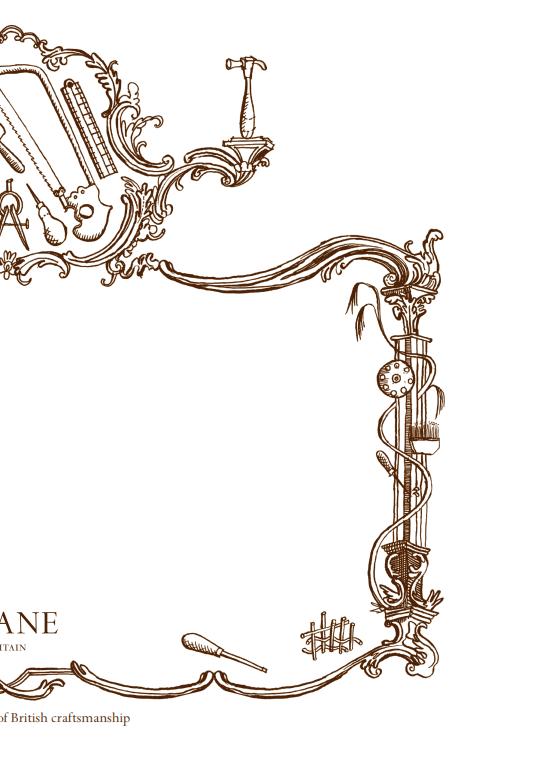
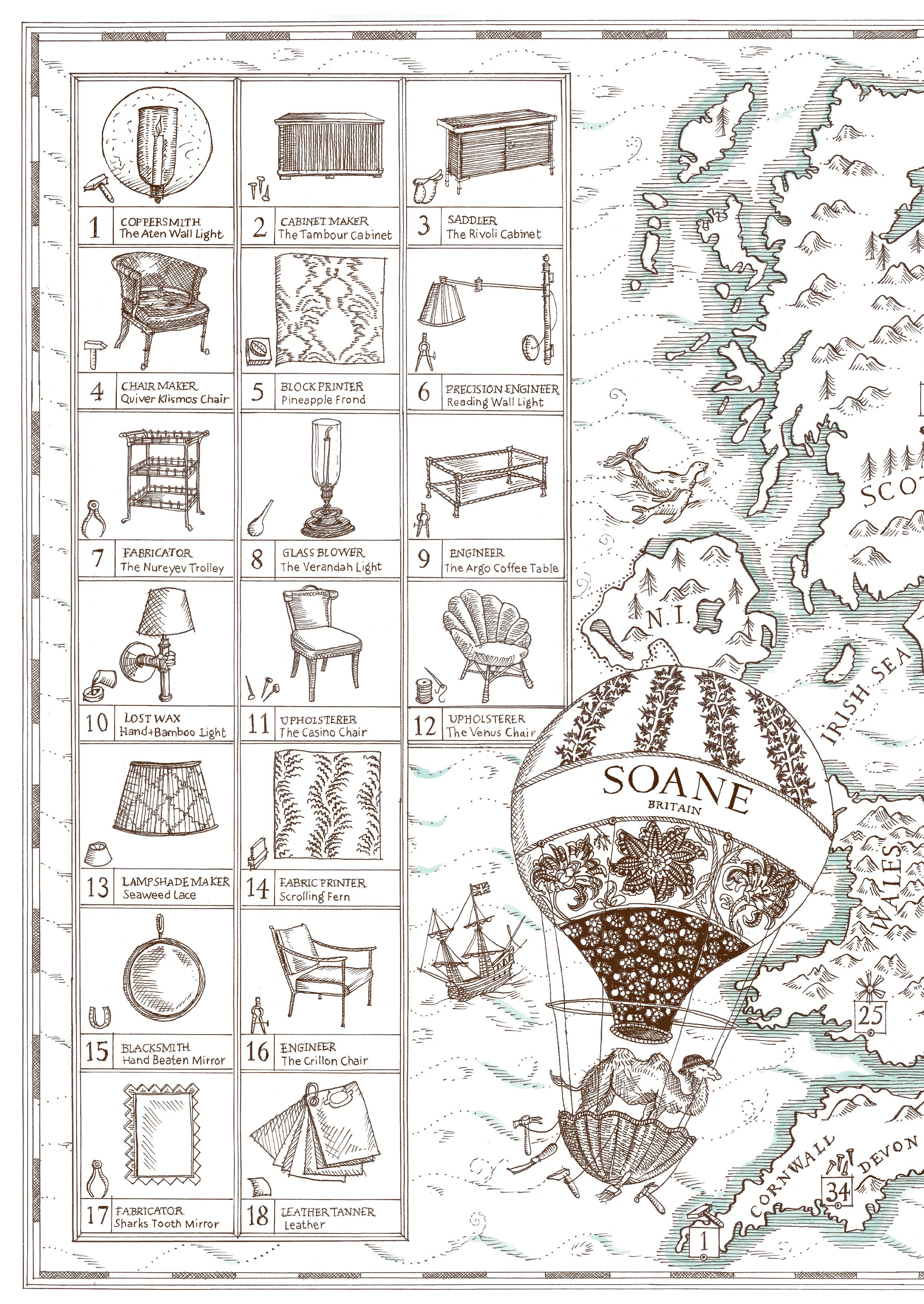
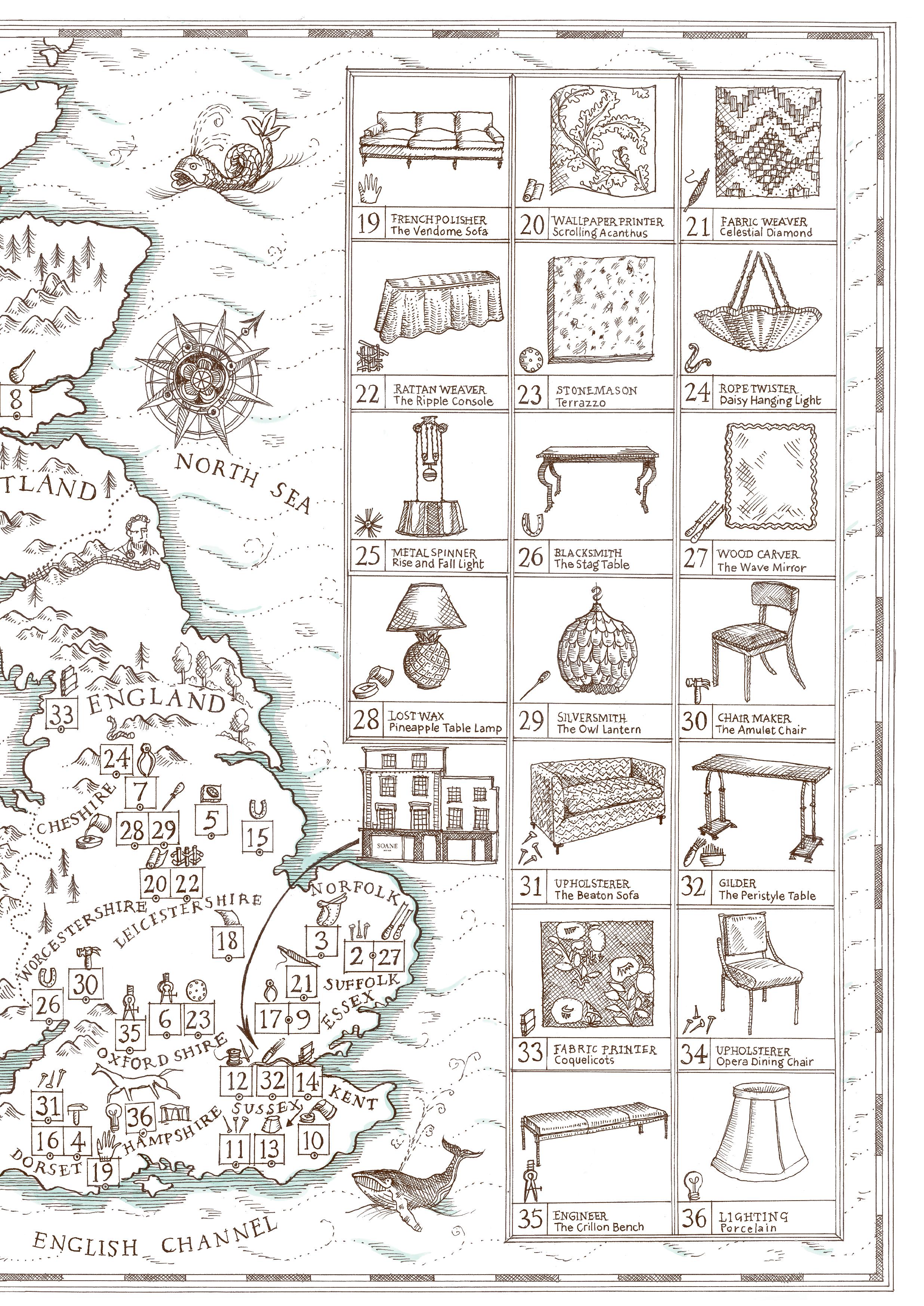
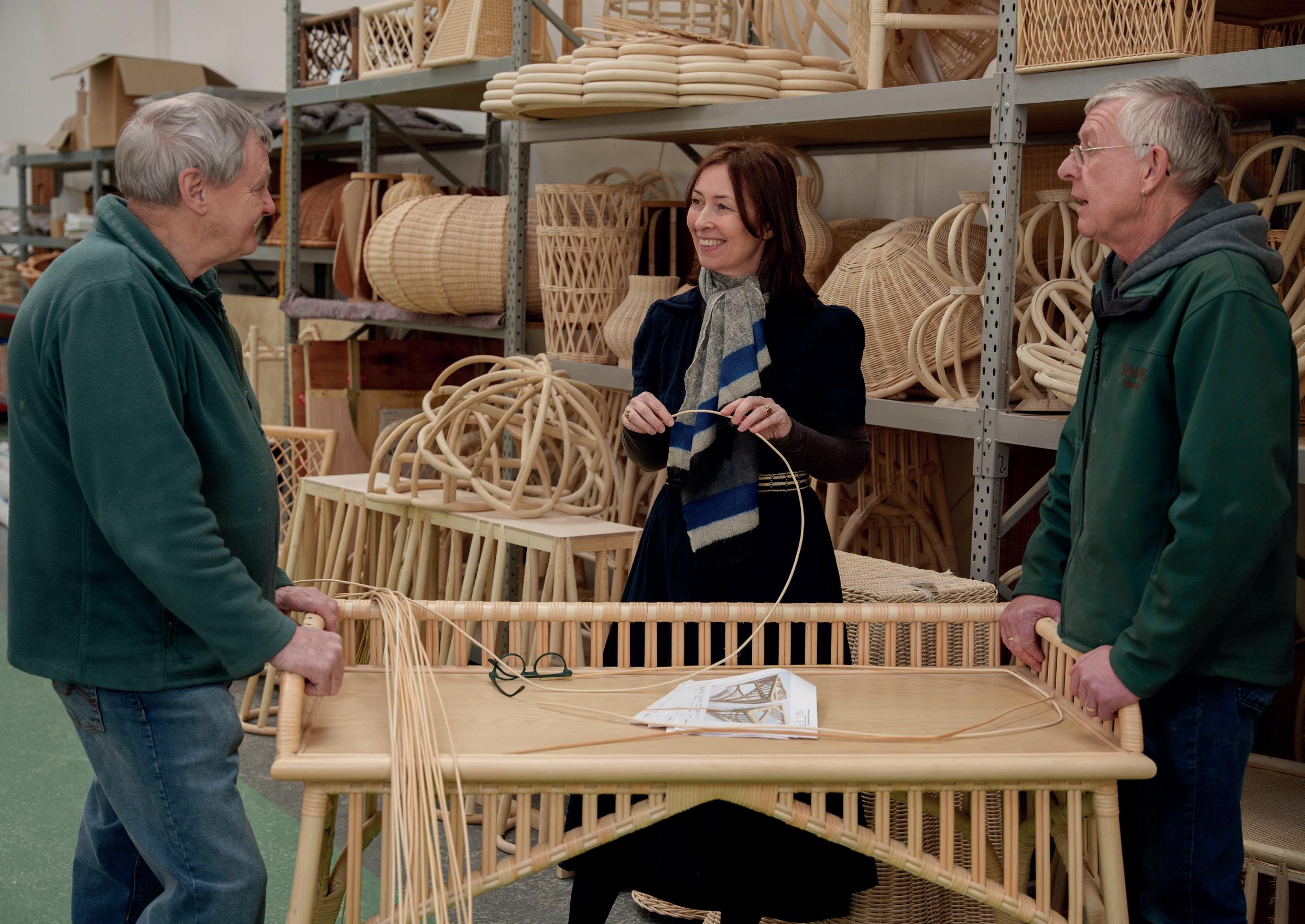
After more than 25 years, Soane’s founding commitment to champion British craft and manufacturing remains at the centre of its vision. Since launching the company in 1997, co-founder Lulu Lytle has put this heritage at the heart of the company, making it a showcase for established and new craft industries. With each and every design made in Britain, Soane’s relationship with its makers, who include blacksmiths, silversmiths, chair makers, saddlers and rattan weavers, has been crucial to its success.

Soane’s determination to secure the future of traditional crafts, has guided the company’s growth over the last 27 years, investing in its workshops, most notably reviving the last remaining rattan weaving workshop in the country where it has established an apprenticeship programme. During this time Lulu has mentored many craftspeople and supported their growing business.
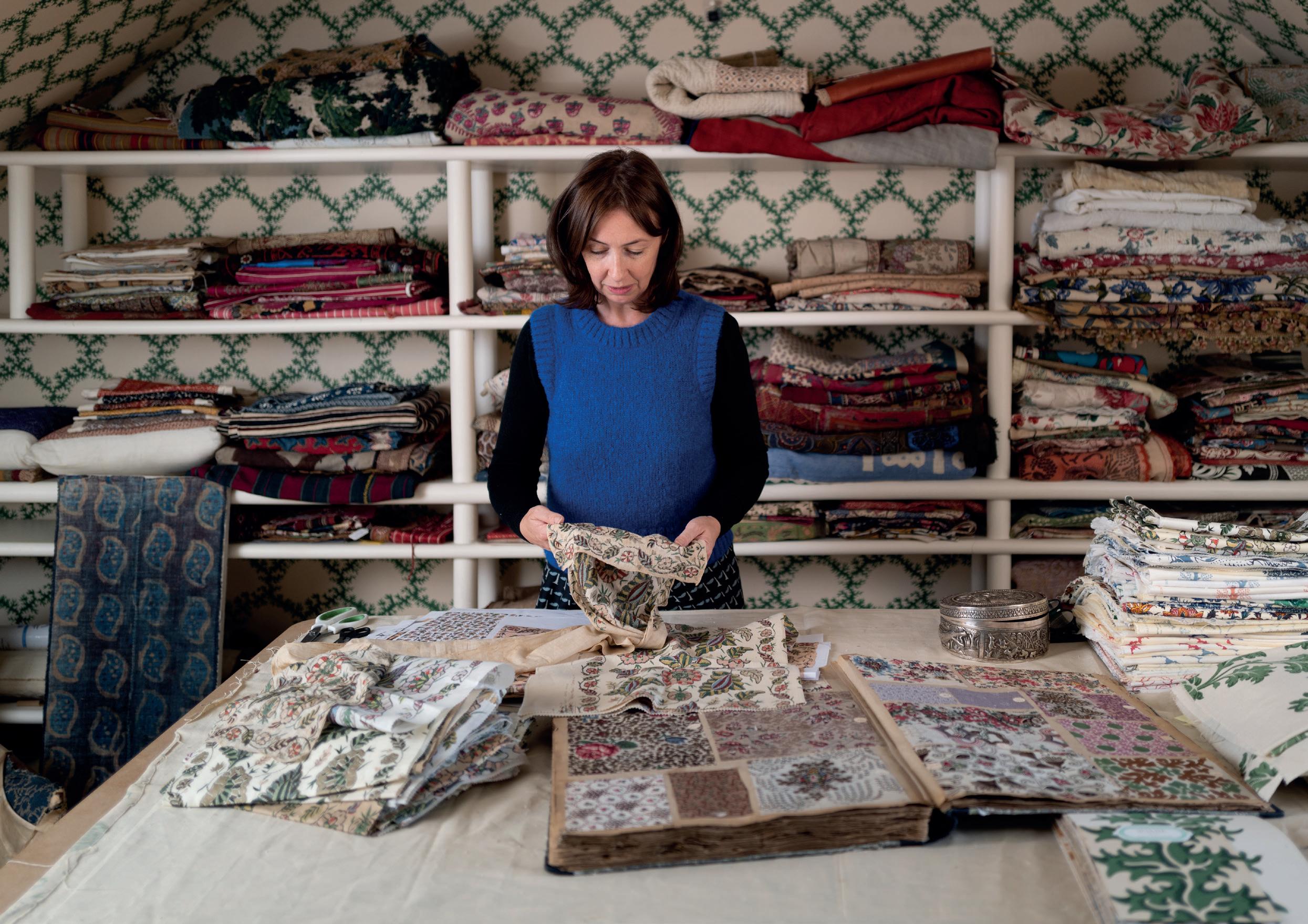

The Soane rattan story is one of making furniture and lighting, founded on integrity and longevity, whilst reviving an almost extinct British industry.

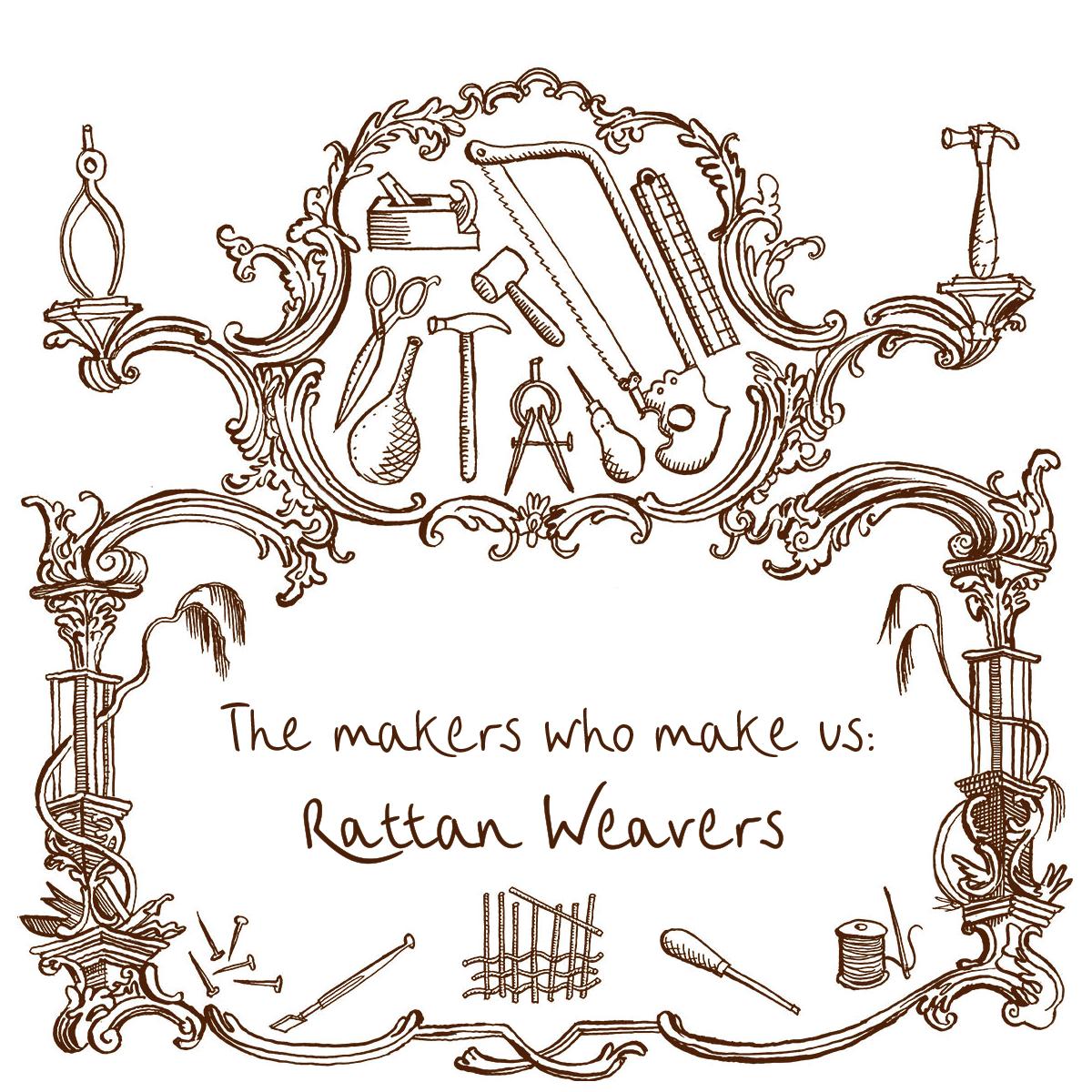
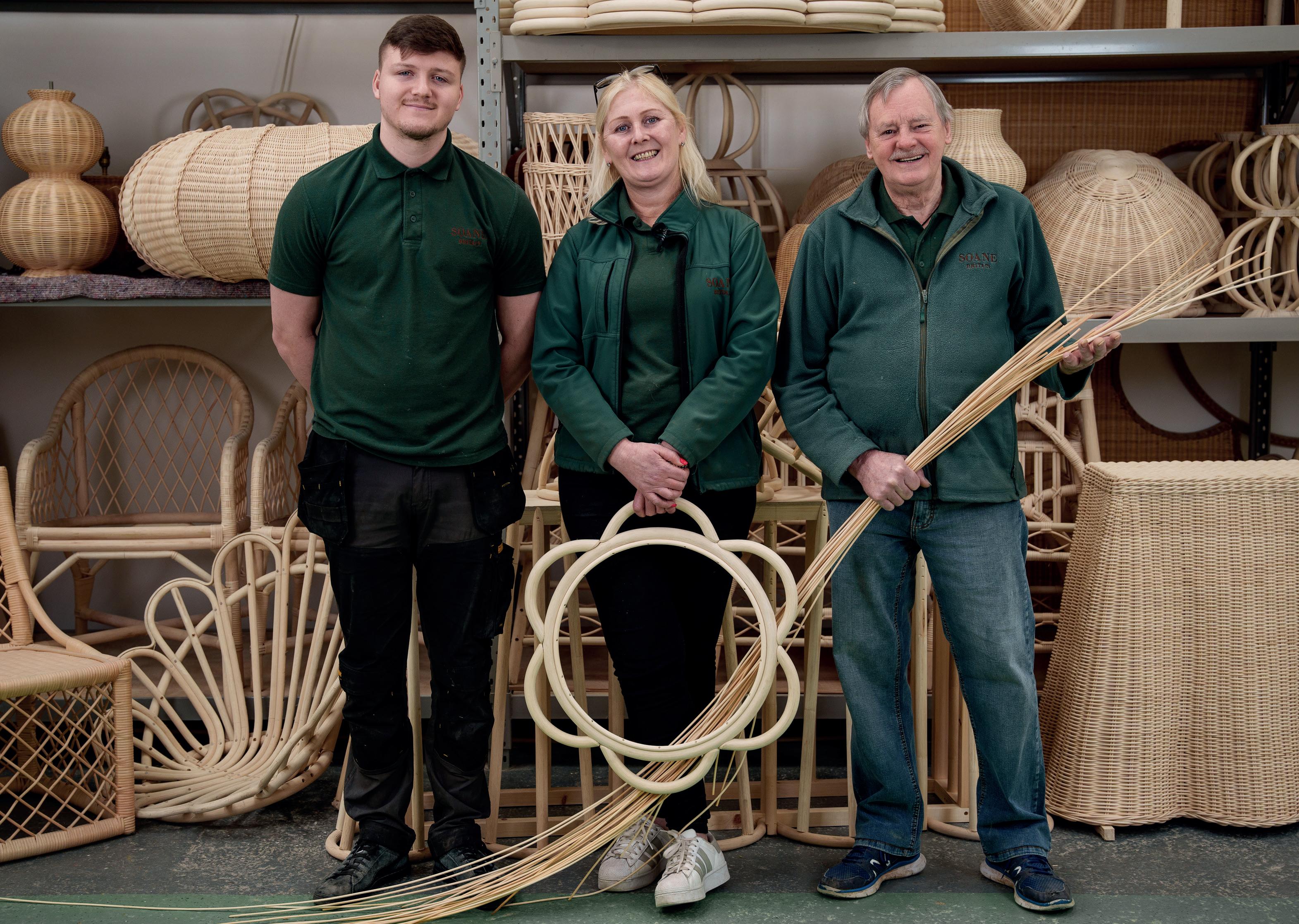

In 2010, after 8 years working with Angraves, the last rattan workshop in England, Lulu received news that it was going into administration. “Following a myriad of changes in furniture fashion and competition from cheap imports, demand for traditional handweaving dwindled. The combination of fear of losing these specialist skills from England forever and a need to fulfil client orders gave me the courage to buy the raw materials and machinery from Angraves’ administrators and rebuild the workshop.”
The team of weavers working at Soane’s Leicestershire workshop have a combined 130 years’ experience between them. Rattan weaving is often a family tradition with three generations of one family working together in the Soane workshop.
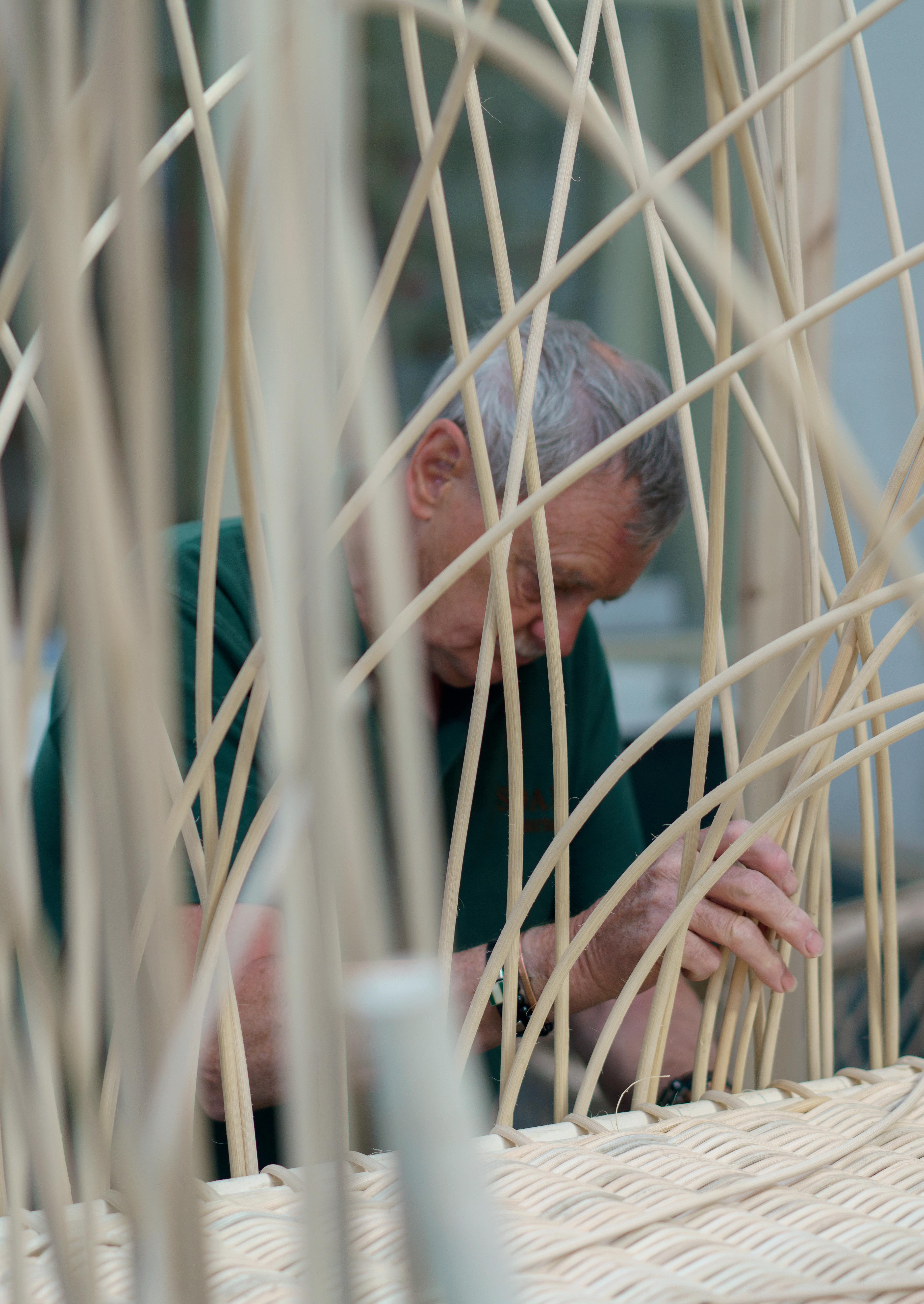
The craftsmen work skilfully with the flexible plant material to create three dimensional pieces with the distinct atmosphere and inherent strength of traditionally handwoven rattan designs.

When responsibly harvested, where it grows naturally in primary rainforest, rattan is an admirably sustainable material. It is cheaper and much faster growing than timber and is completely biodegradable. It is reliant on the existence of healthy vegetation to flourish which encourages the preservation of forest habitats.
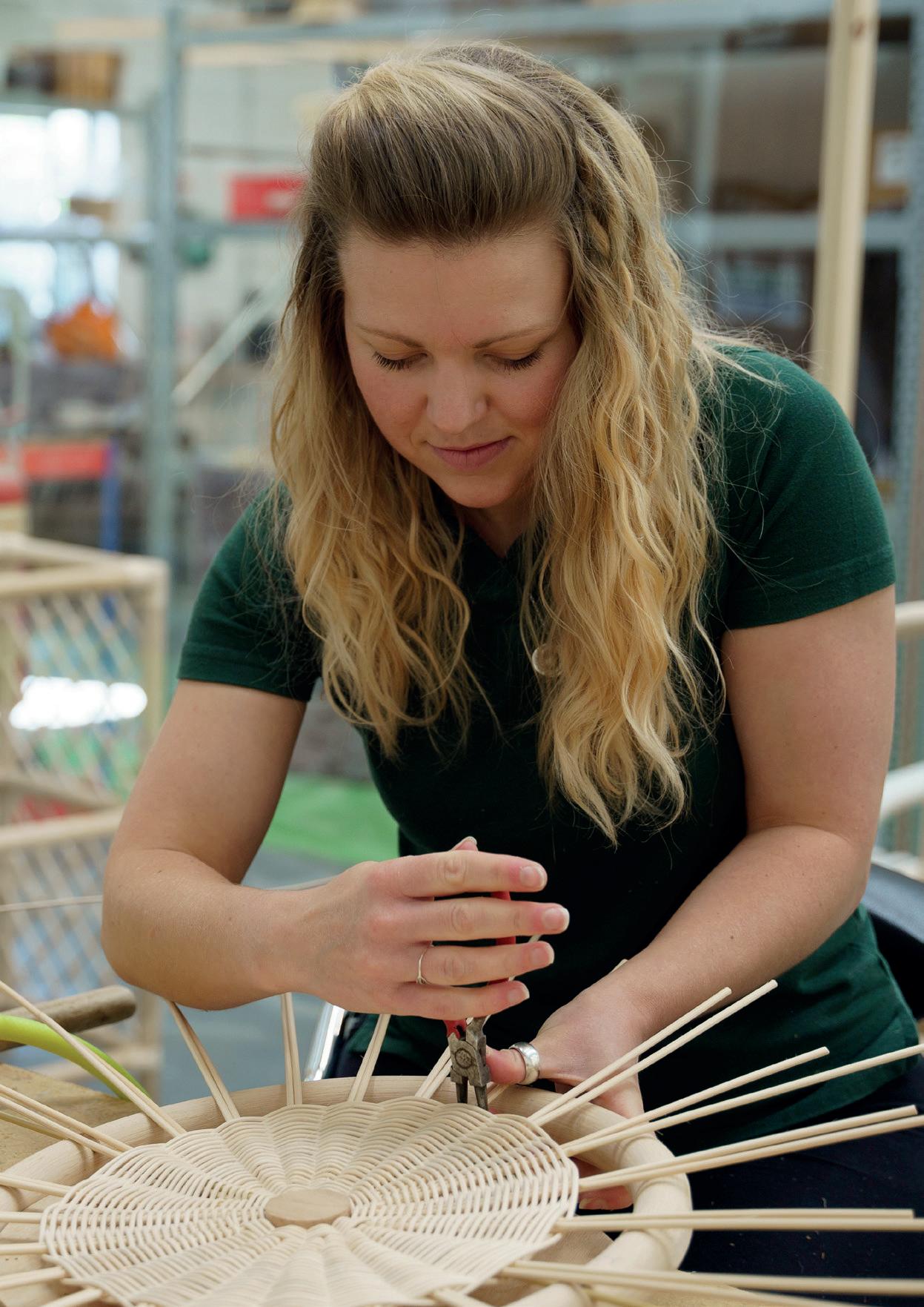
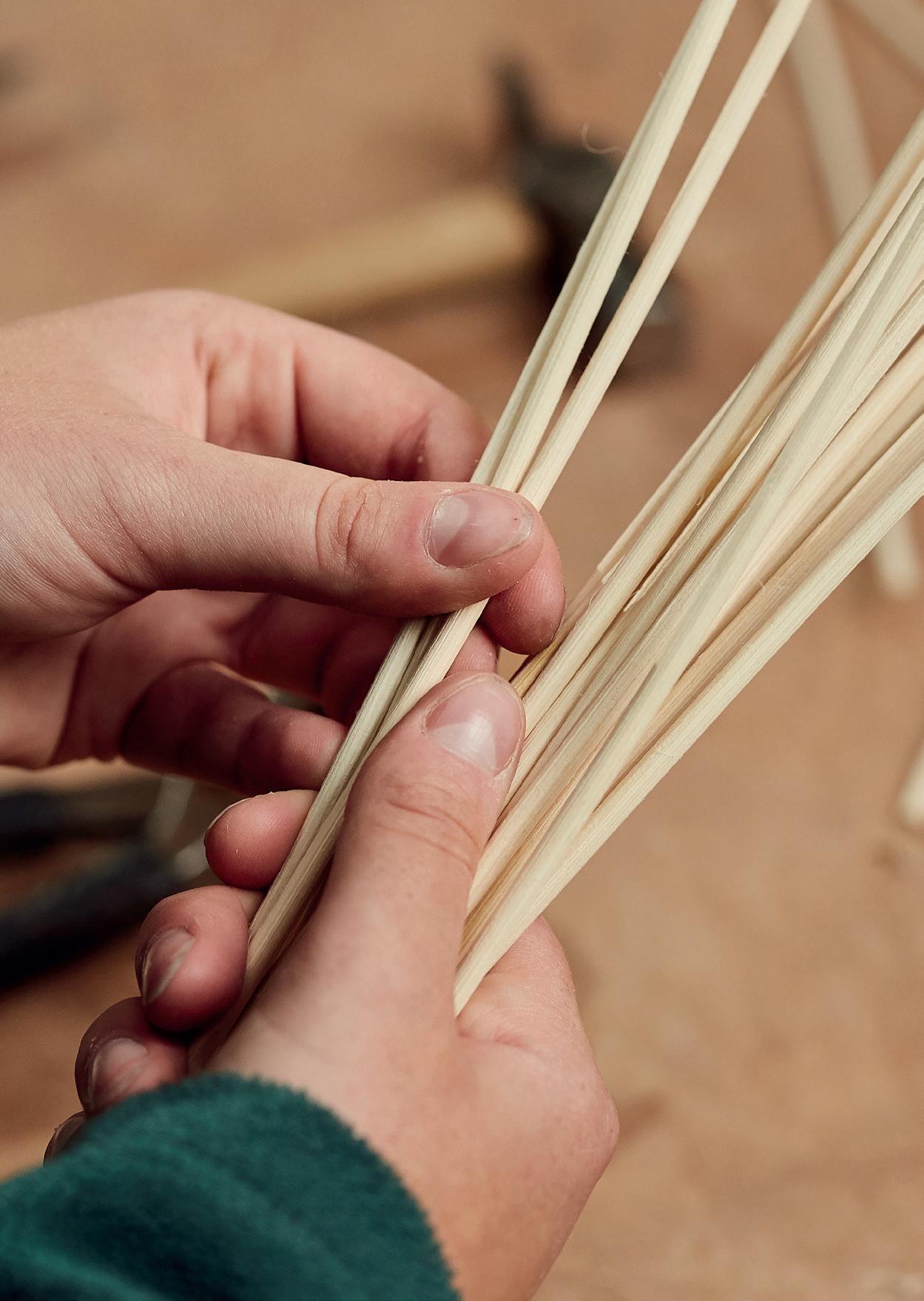
At a time when we are scrutinising the origins of materials more than ever, rattan’s ecological credentials are particularly sound.
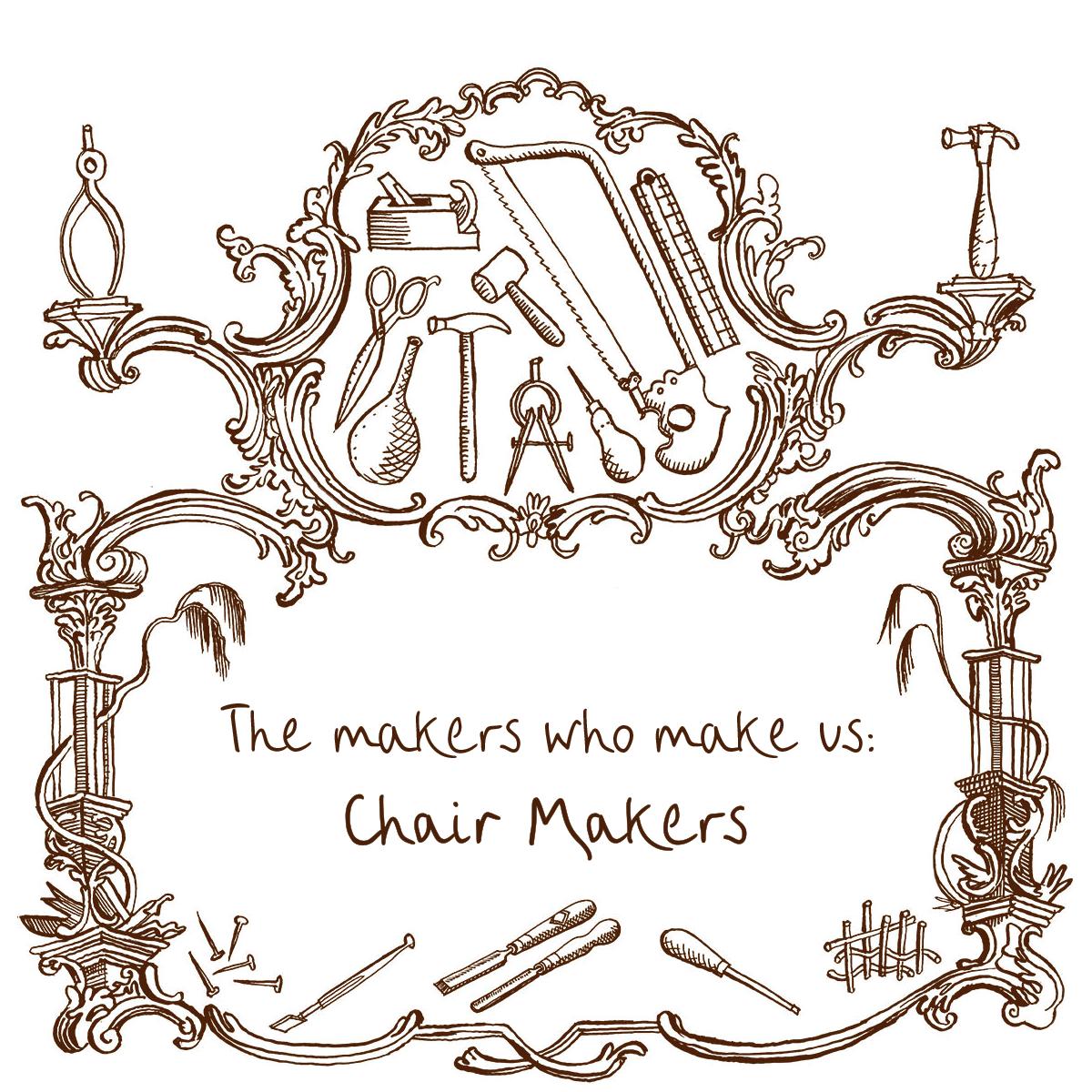
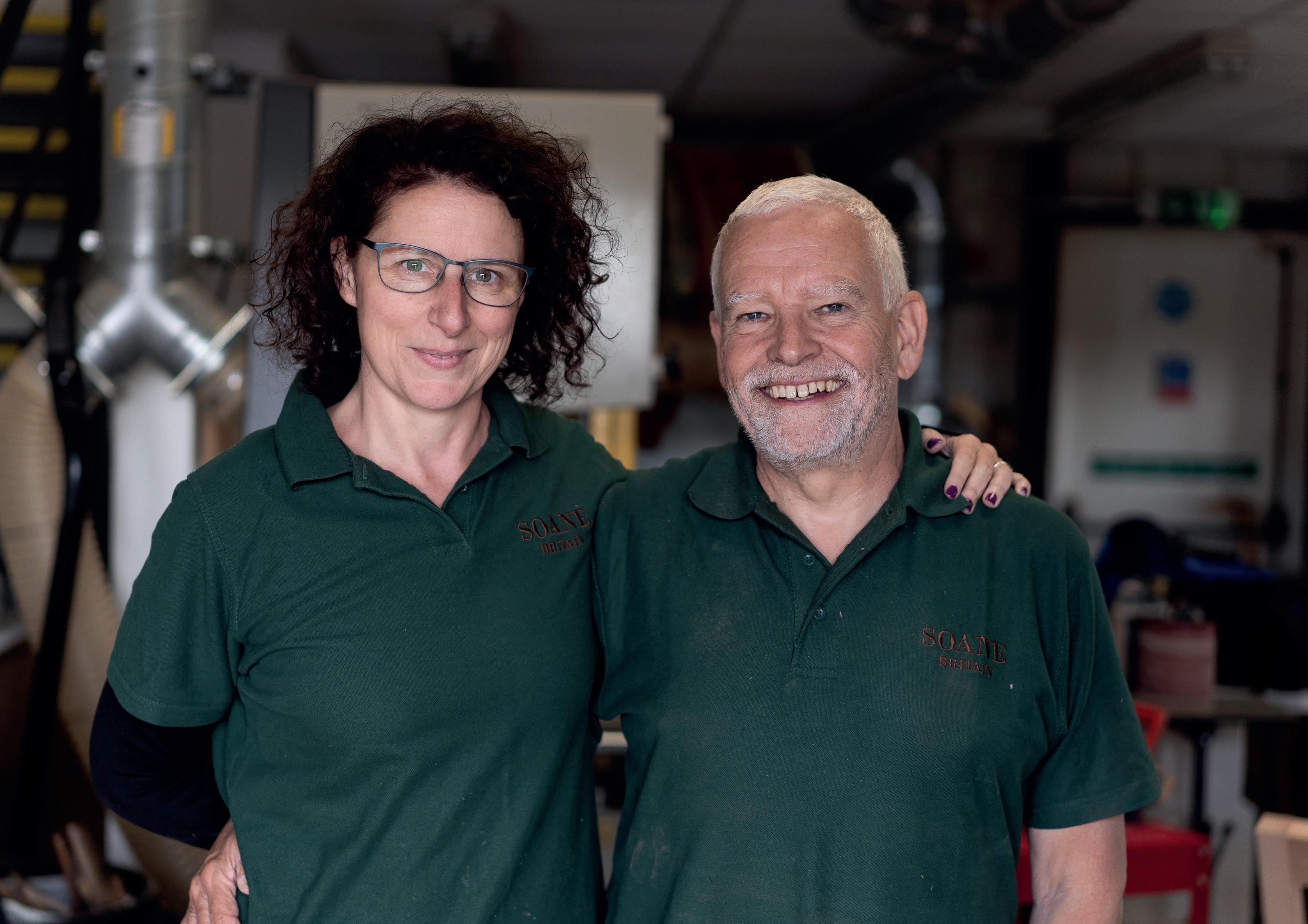

Chair making is a highly specialised craft requiring exceptional joinery skills to make chairs of great quality and comfort.
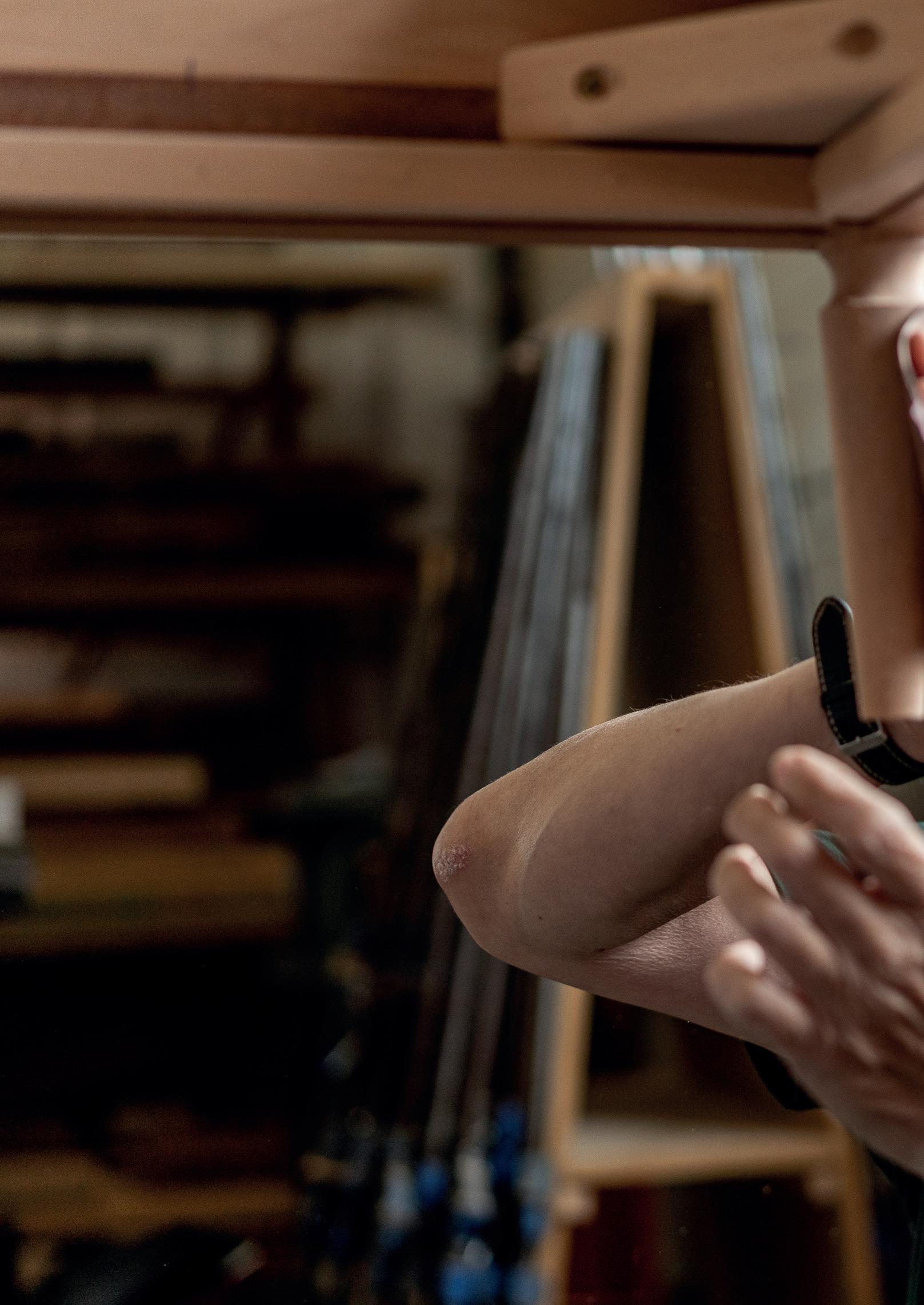
Soane has taken ownership of one of a very few workshops in Britain still making chairs exclusively by hand in Dorset and continuing the traditions of eighteenth century master chair makers.
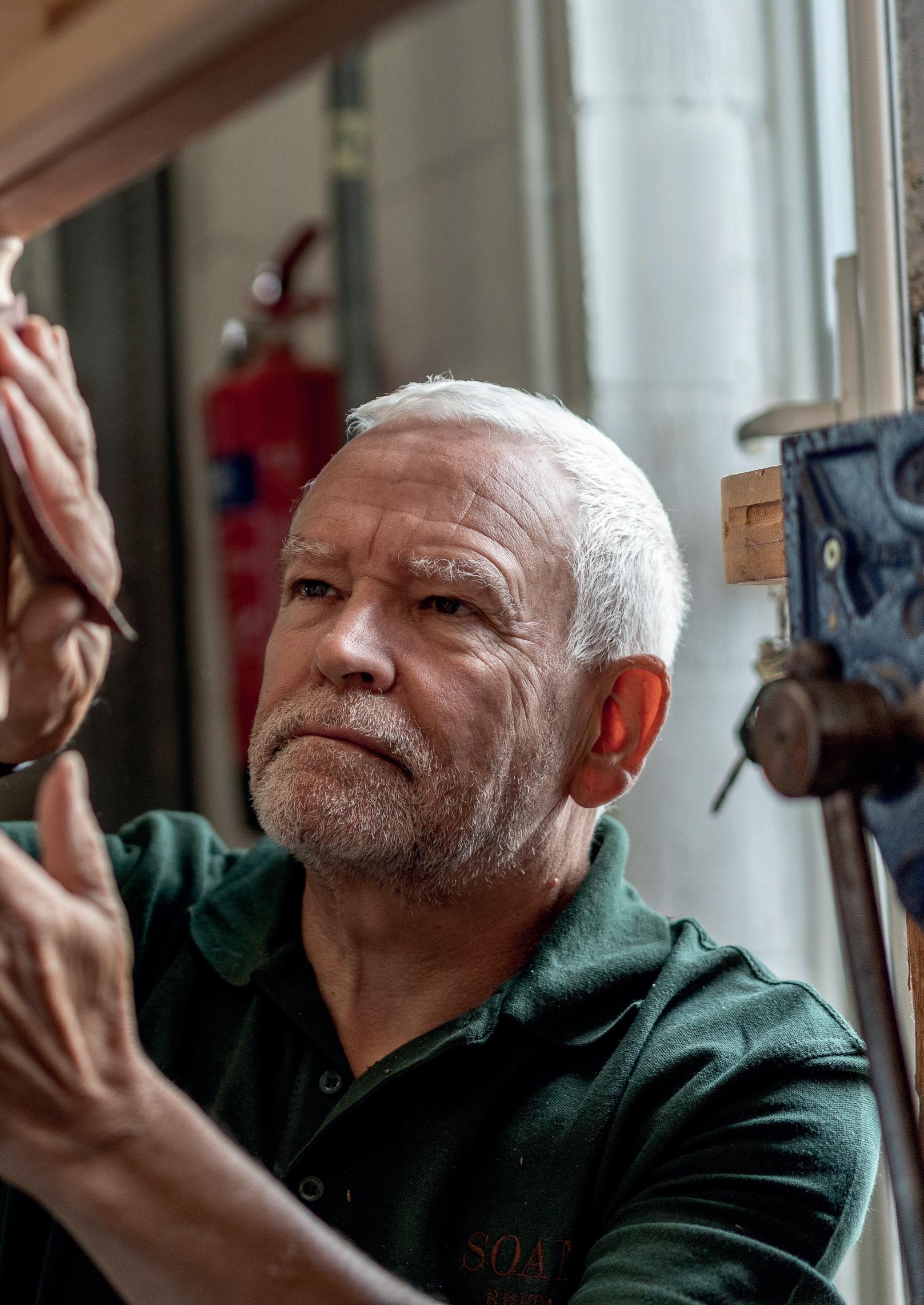
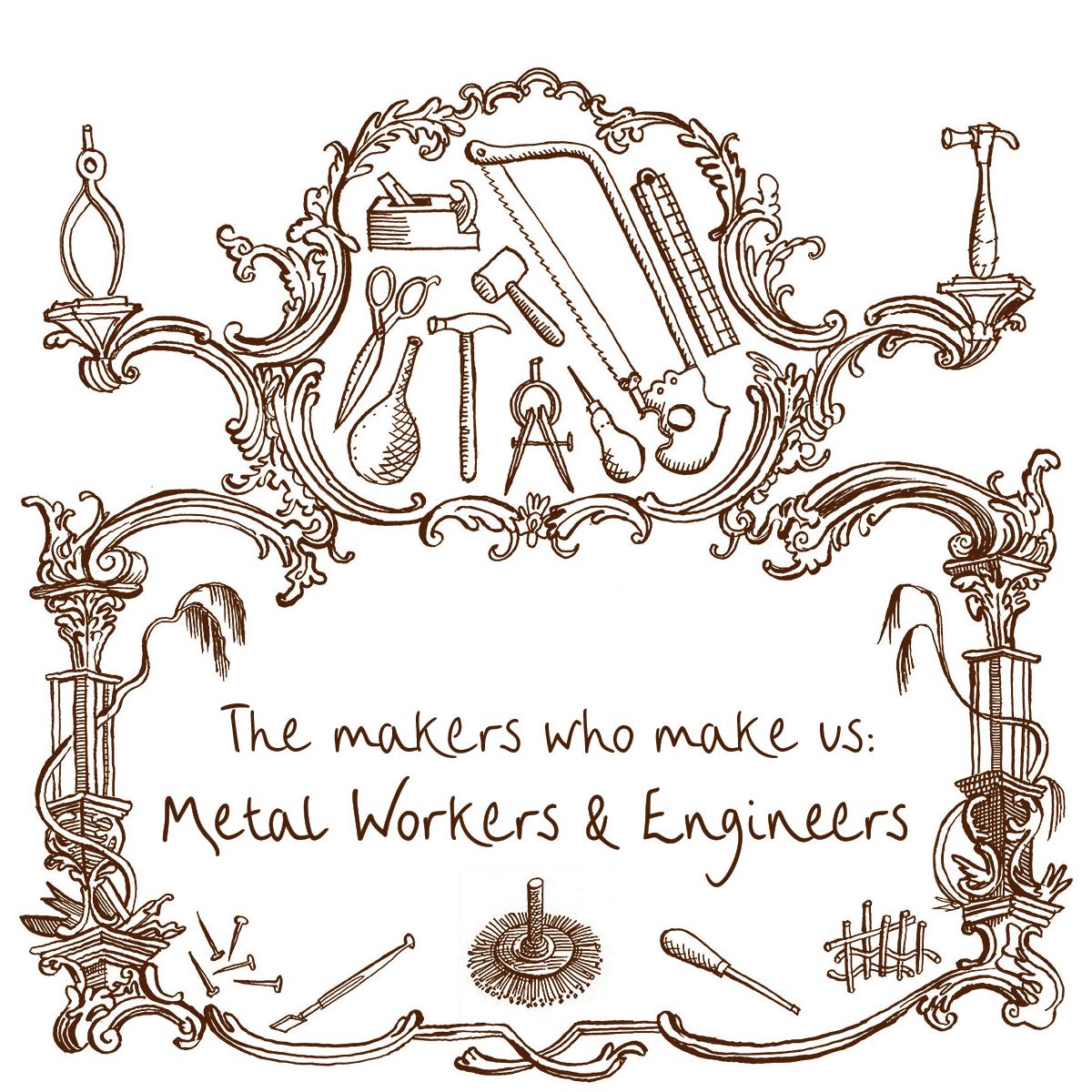
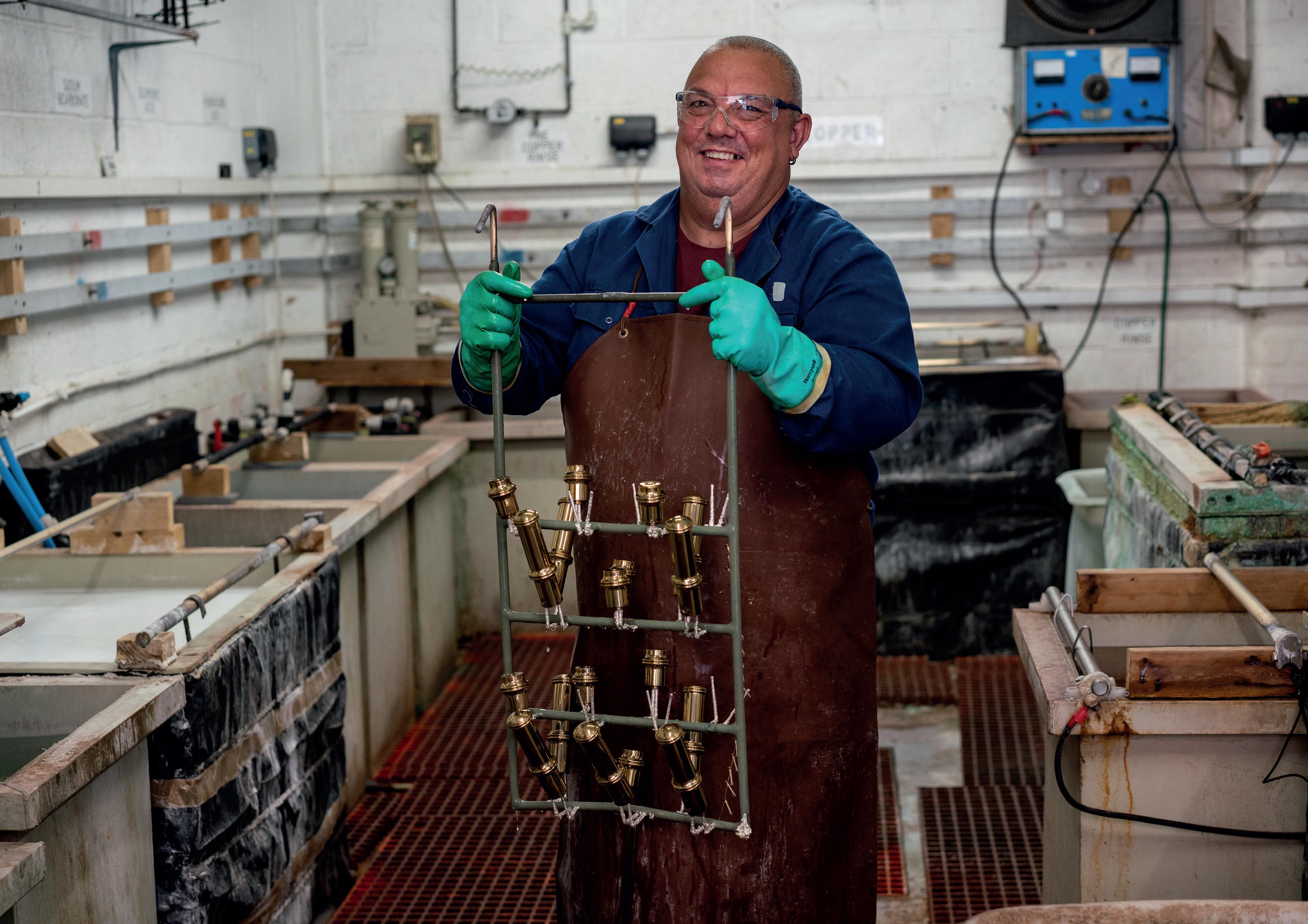

Metal workers across the country are employed in the production of Soane’s metal designs. Small workshops, each with their own specialisations – casting, engineering, fabricating, machining, finishing and plating metal – combine old and new techniques and tools for the best results.
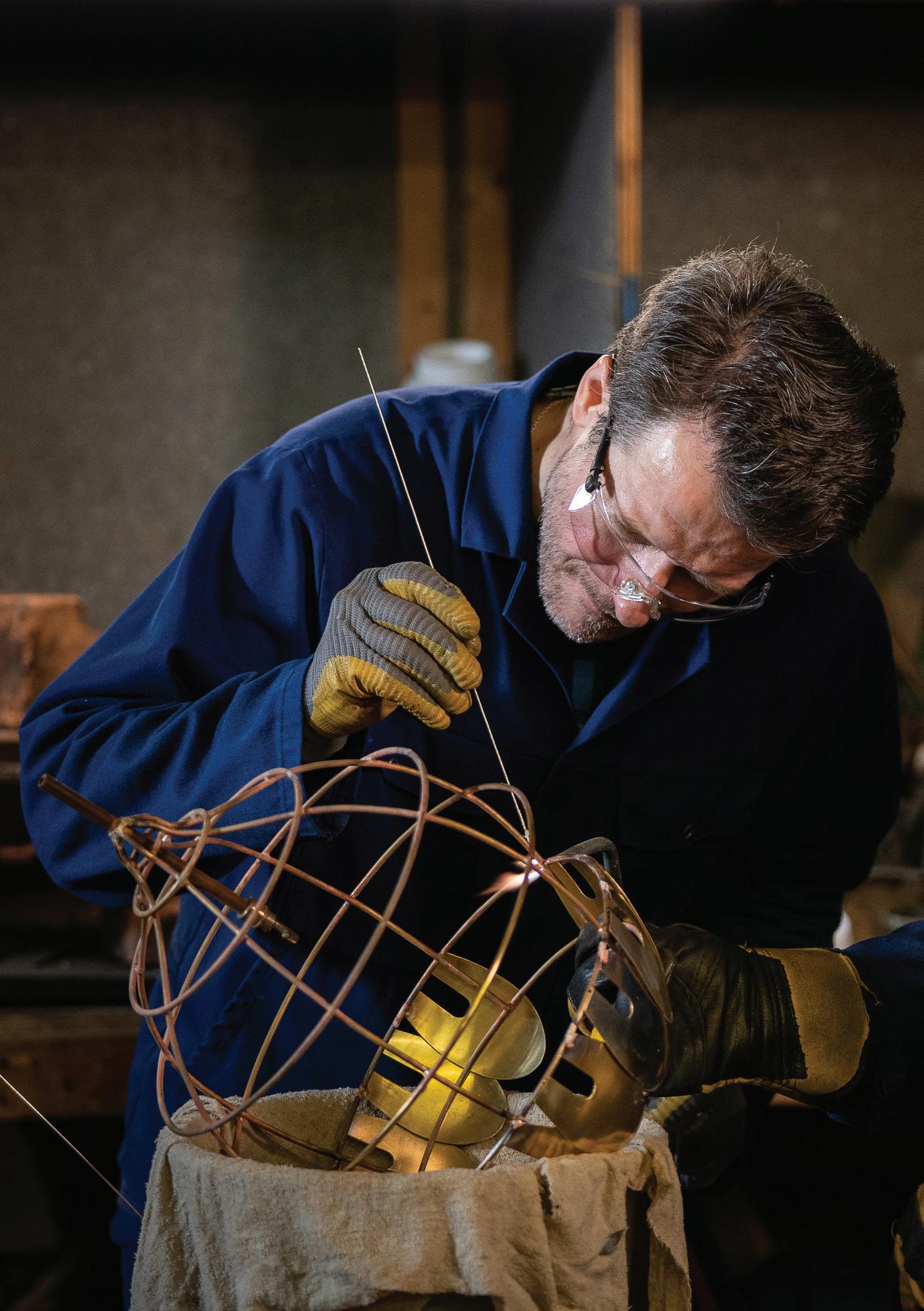

The distinctive Owl Lantern is made entirely by hand by skilled Sheffield silversmiths. Brass ‘feathers’ are cut to graduating sizes and welded in layers to the bodice-like frame.

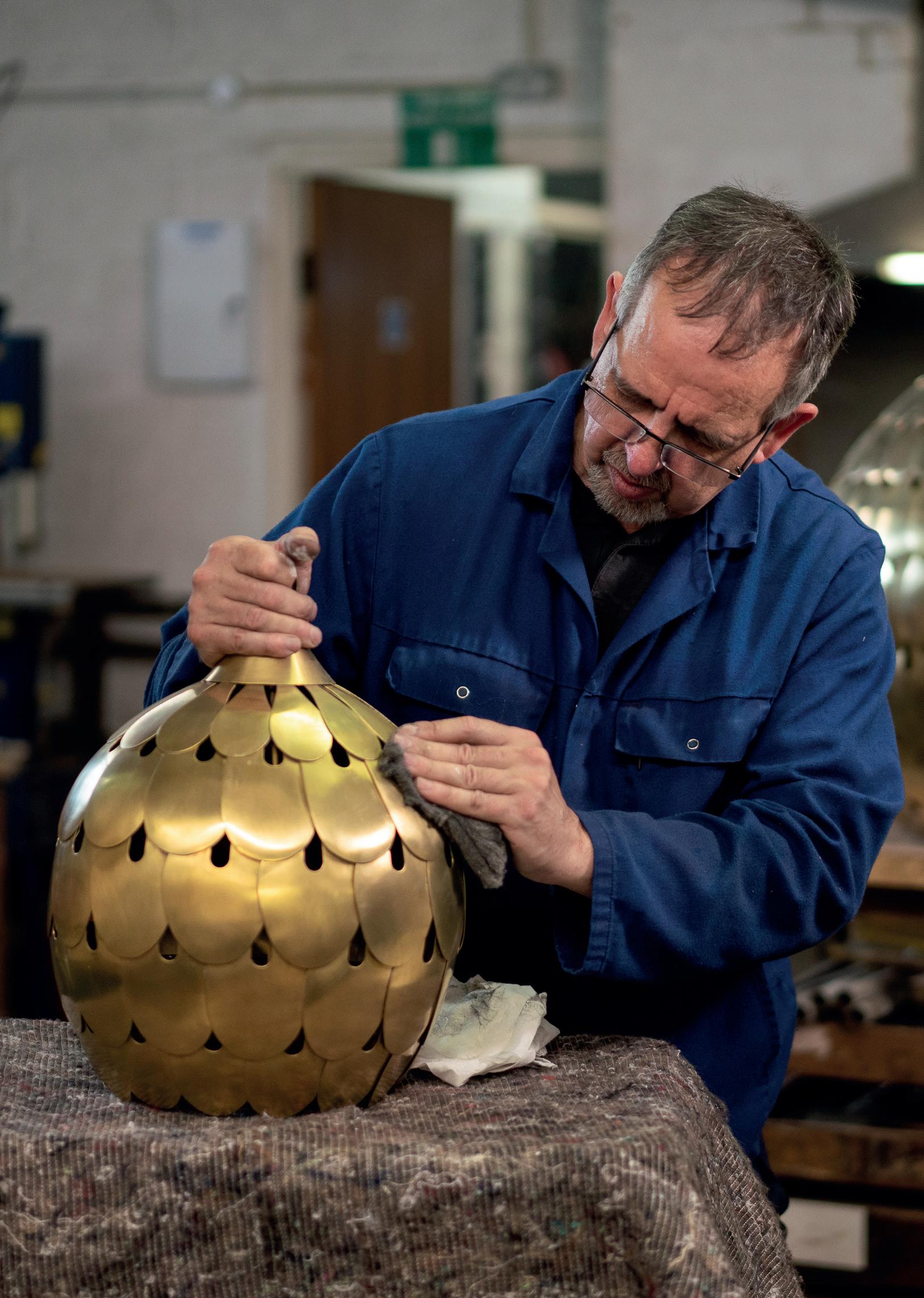
Soane’s lighting designs require the skills of several craftsmen, from precision engineers in East Sussex, expert at making designs with moving parts, to fabricators that meticulously ‘fit and finish’ components in South Yorkshire. Silversmiths, renowned for their fine craftsmanship, fostered through a British tradition of guilds and apprenticeships, are also employed to sheet metal on designs such as The Owl Lantern.
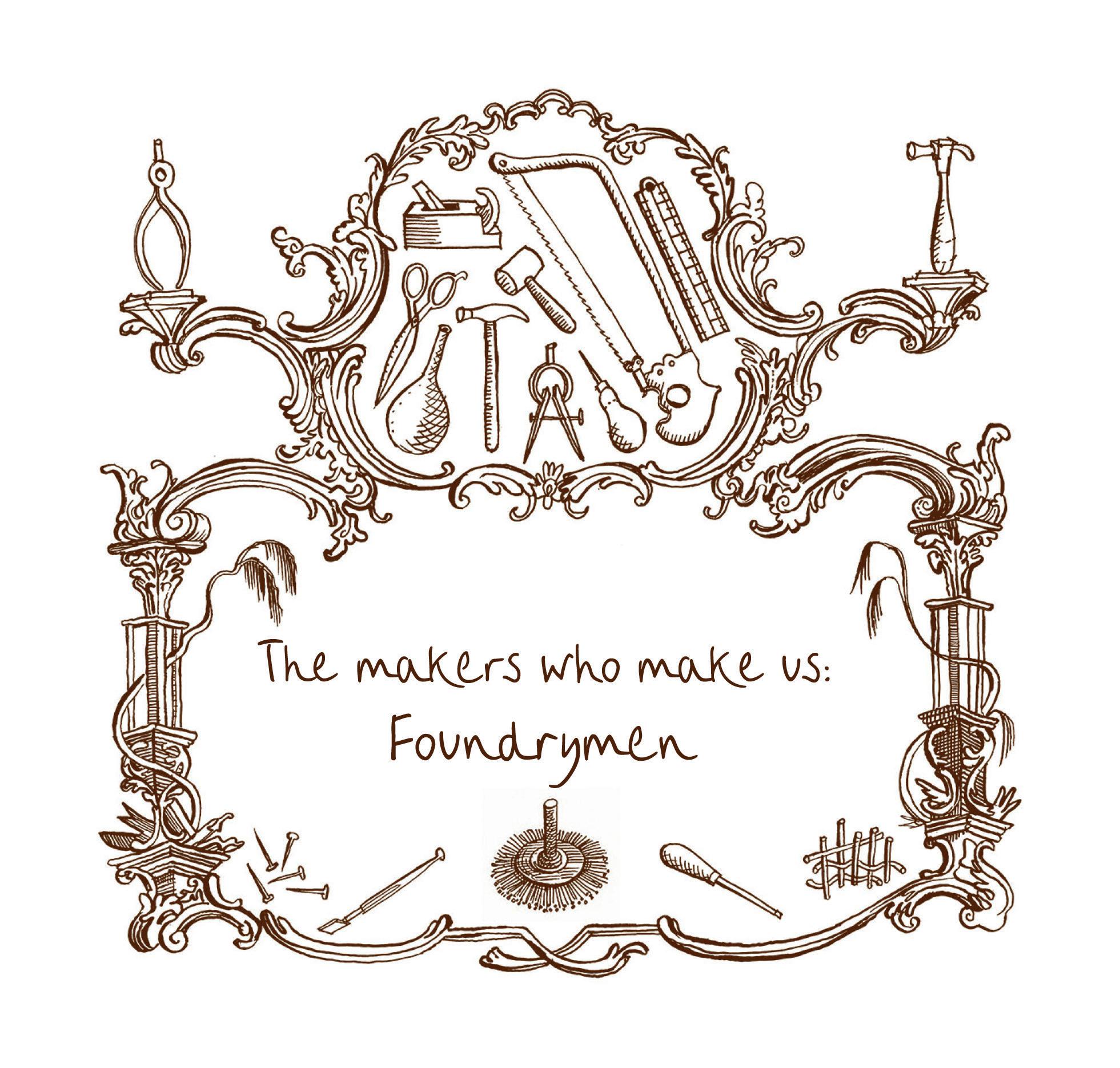
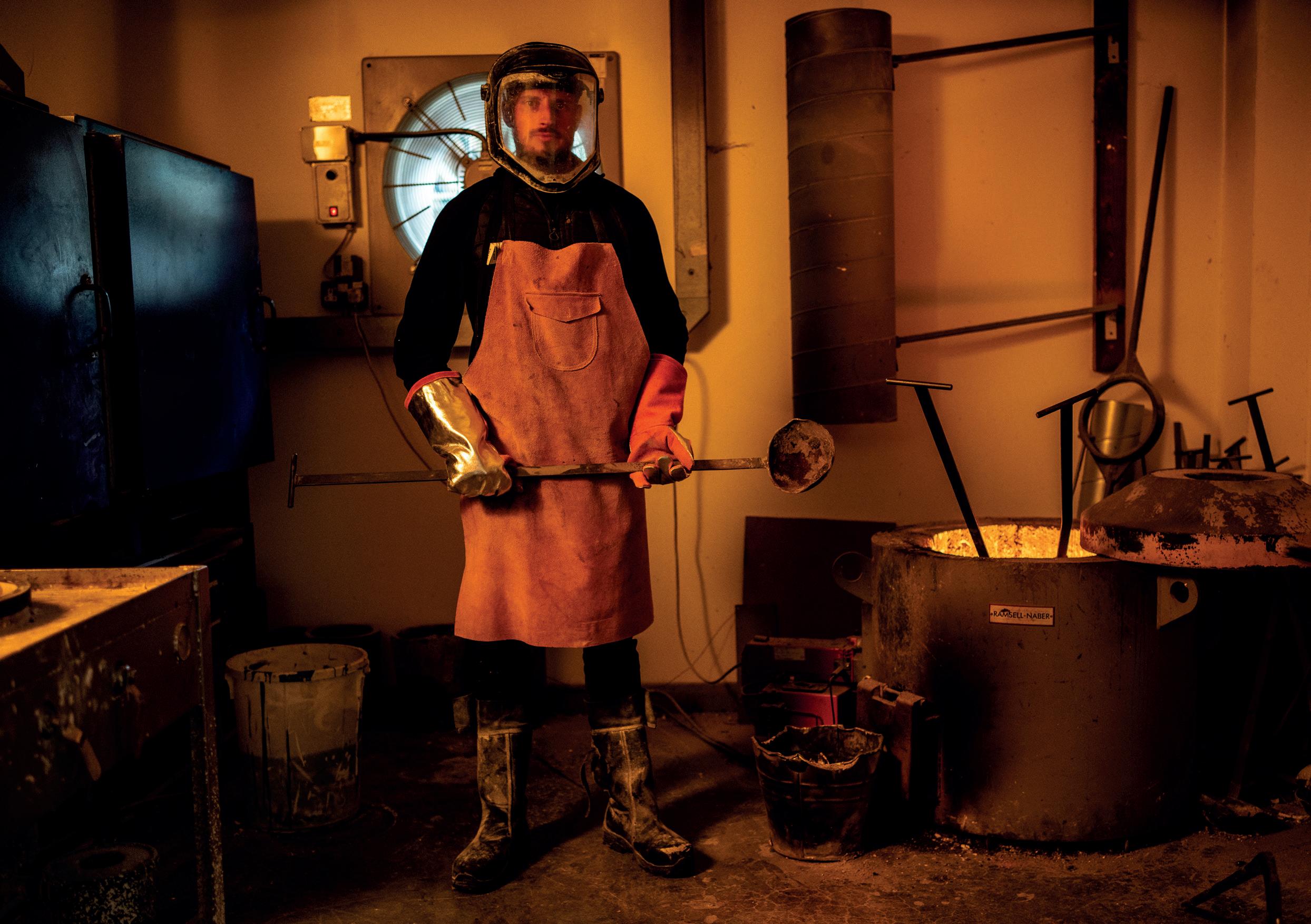

Many of Soane’s metal lighting designs are made by a workshop in Hastings, on the South coast of England, that is highly specialised in the technique of lost wax casting.
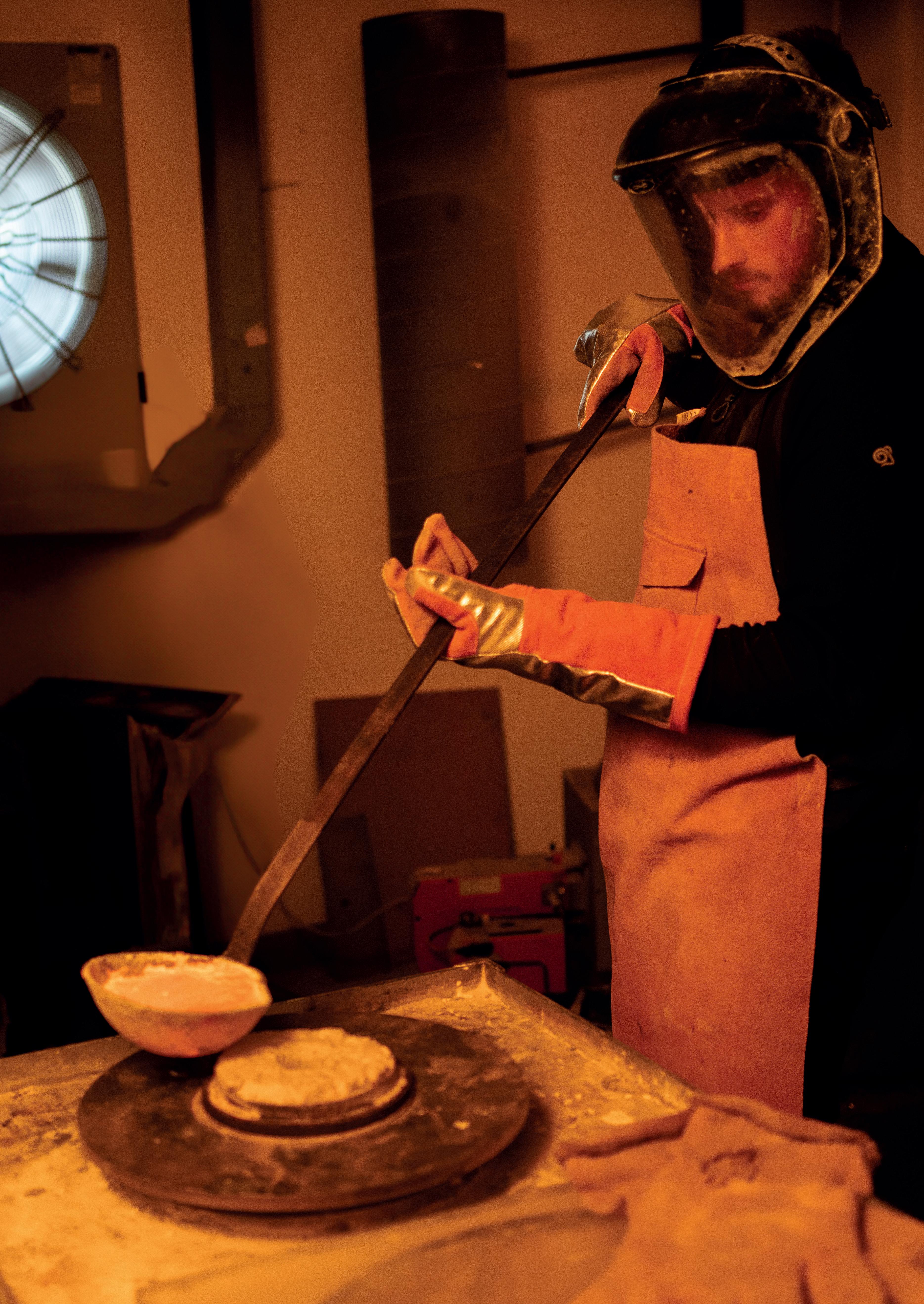

Traditionally used by artists to cast bronze sculptures, the art of lost wax casting allows for great freedom and flexibility of form while retaining exceptionally fine details and beautifully smooth surfaces.
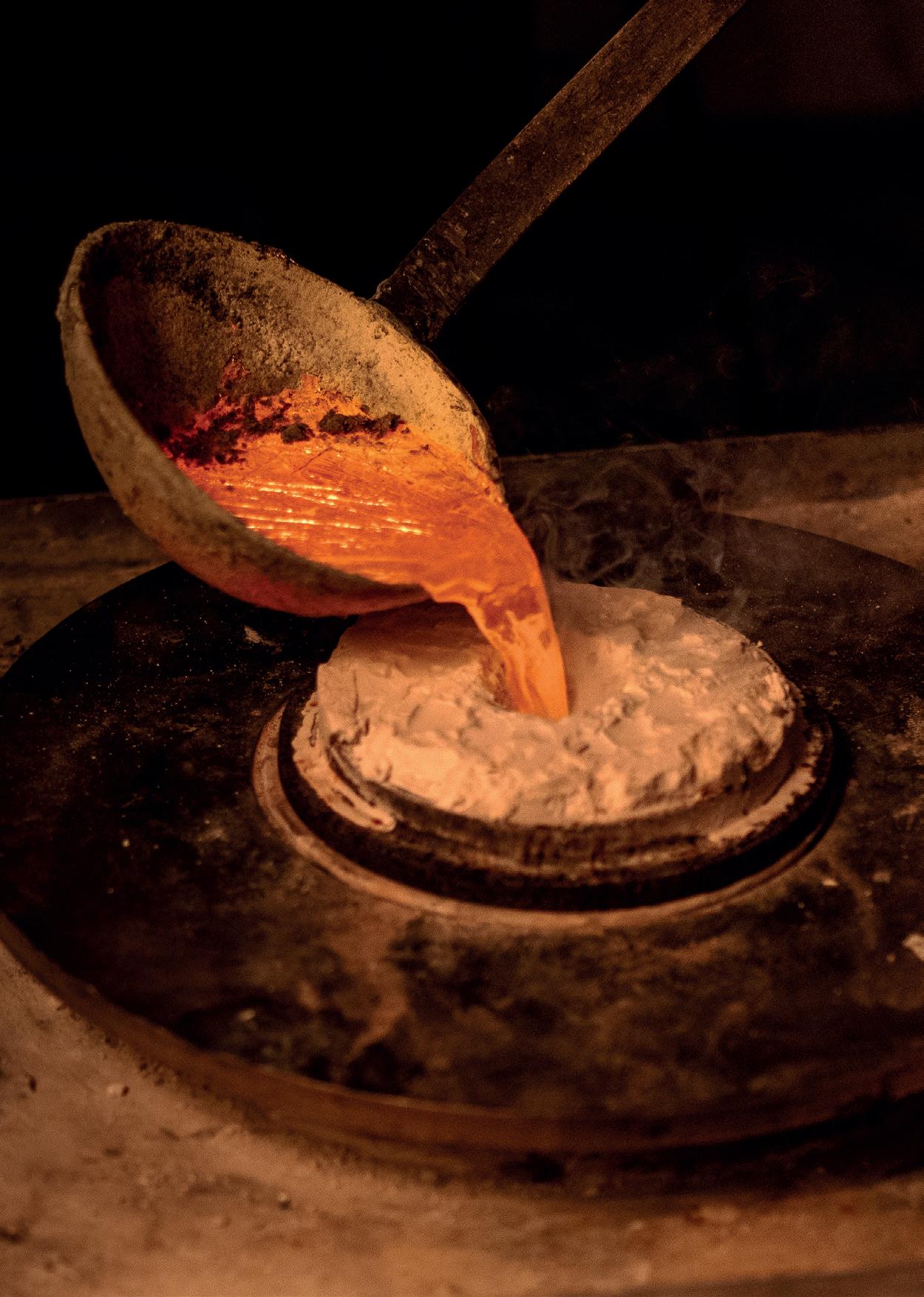

Made from solid brass, every cast metal lighting design passes through the hands of numerous craftspeople, epitomising the great expertise and extraordinary skills of the workshop.

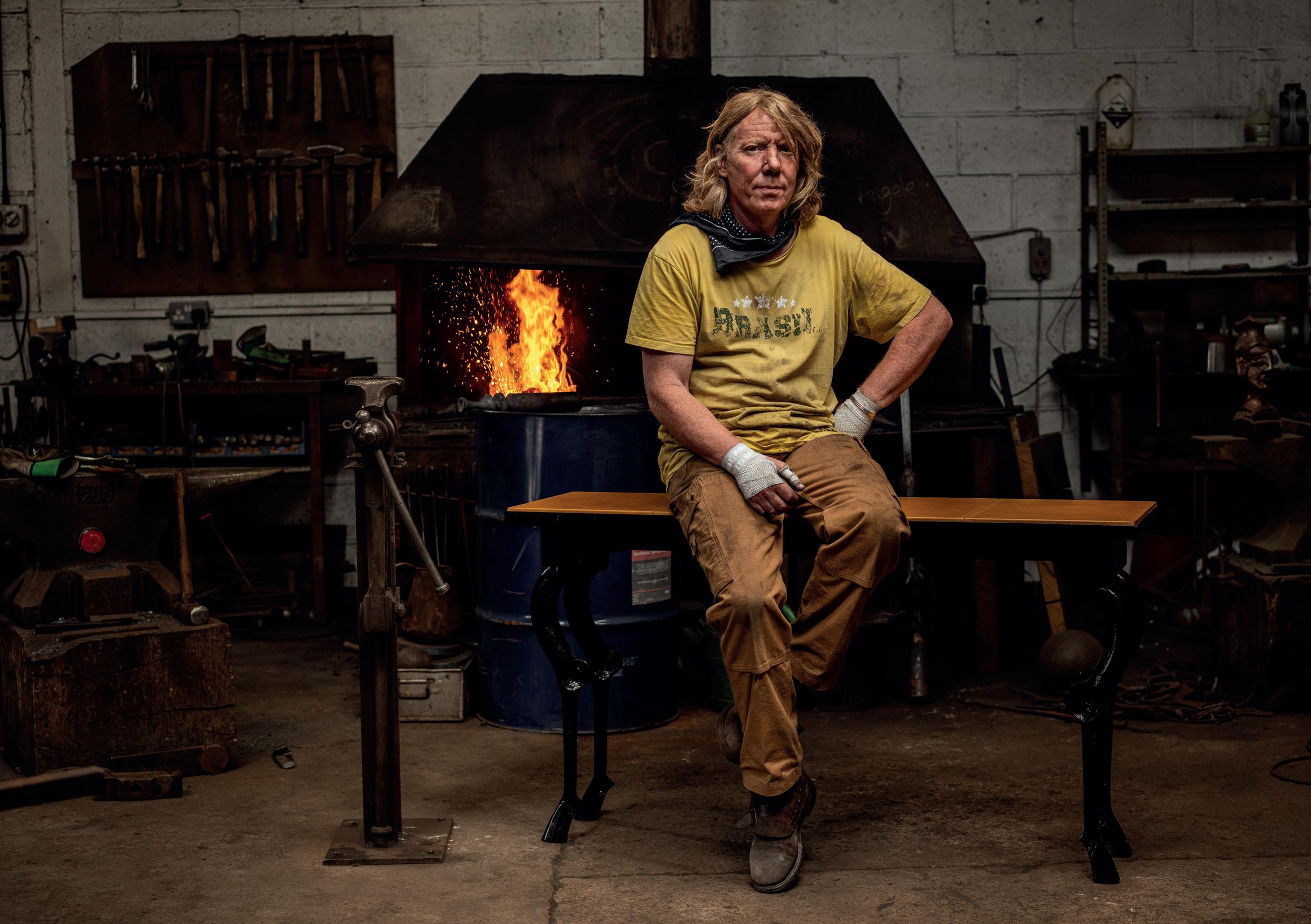
Exceptional blacksmiths create some of Soane’s most distinctive pieces, transforming inert steel bars, through hours of heating, hammering and cooling.
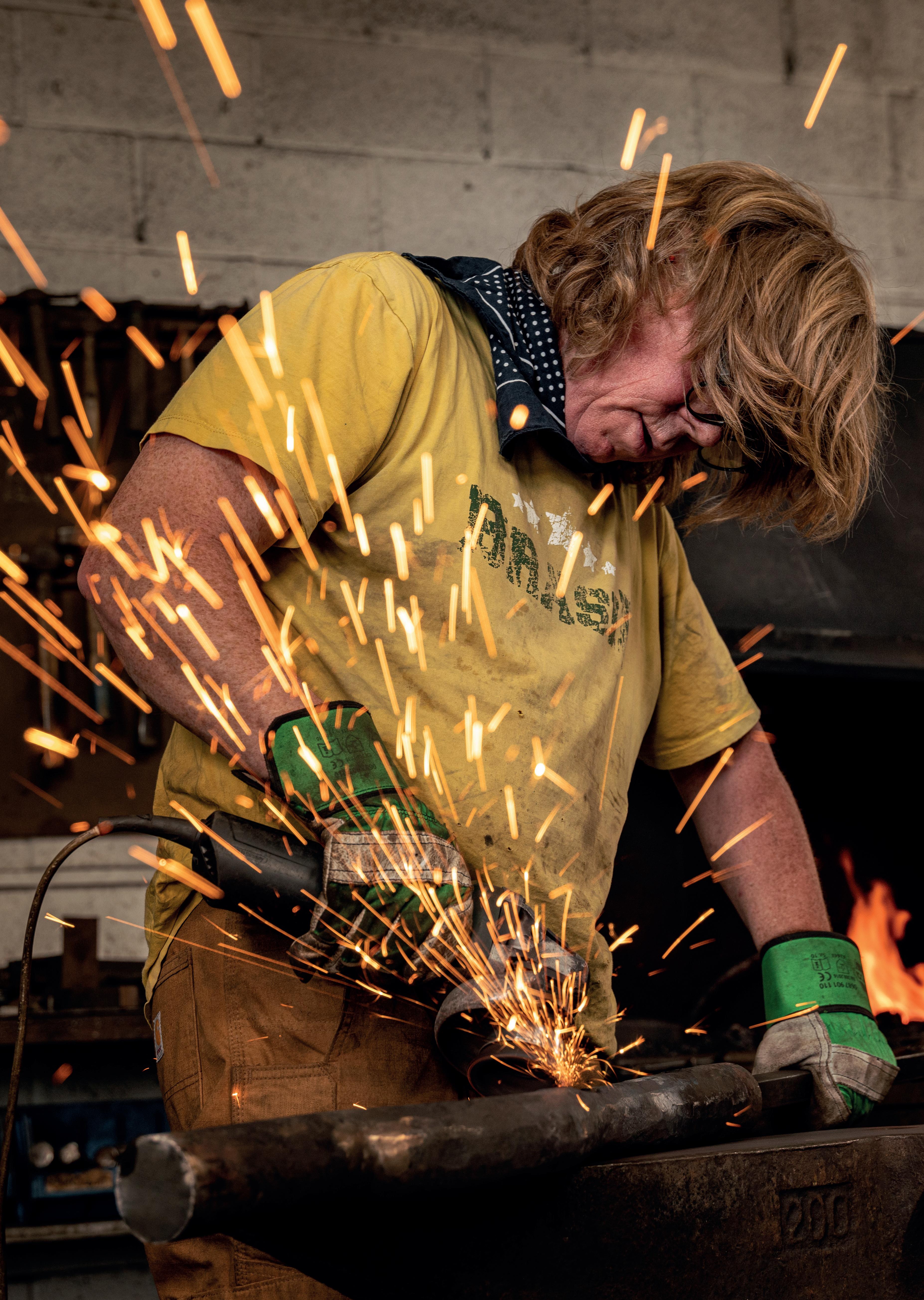
Forging iron and steel is one of the oldest known metal working processes.
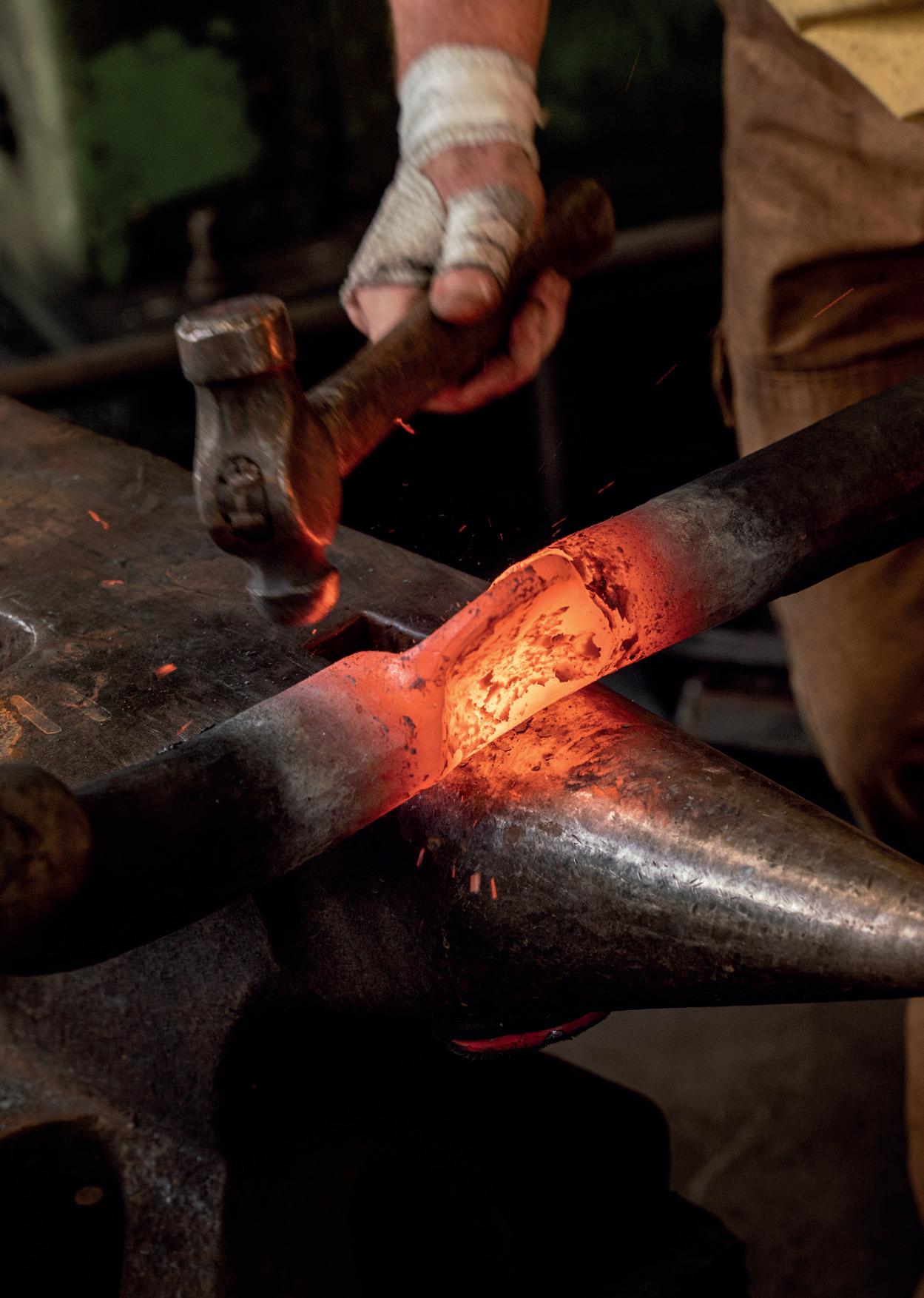

The Stag Table is one of the most challenging designs, requiring each leg to be beaten into shape in minutes (a second attempt would weaken the iron’s structure) and to match its three siblings whilst having individual character.
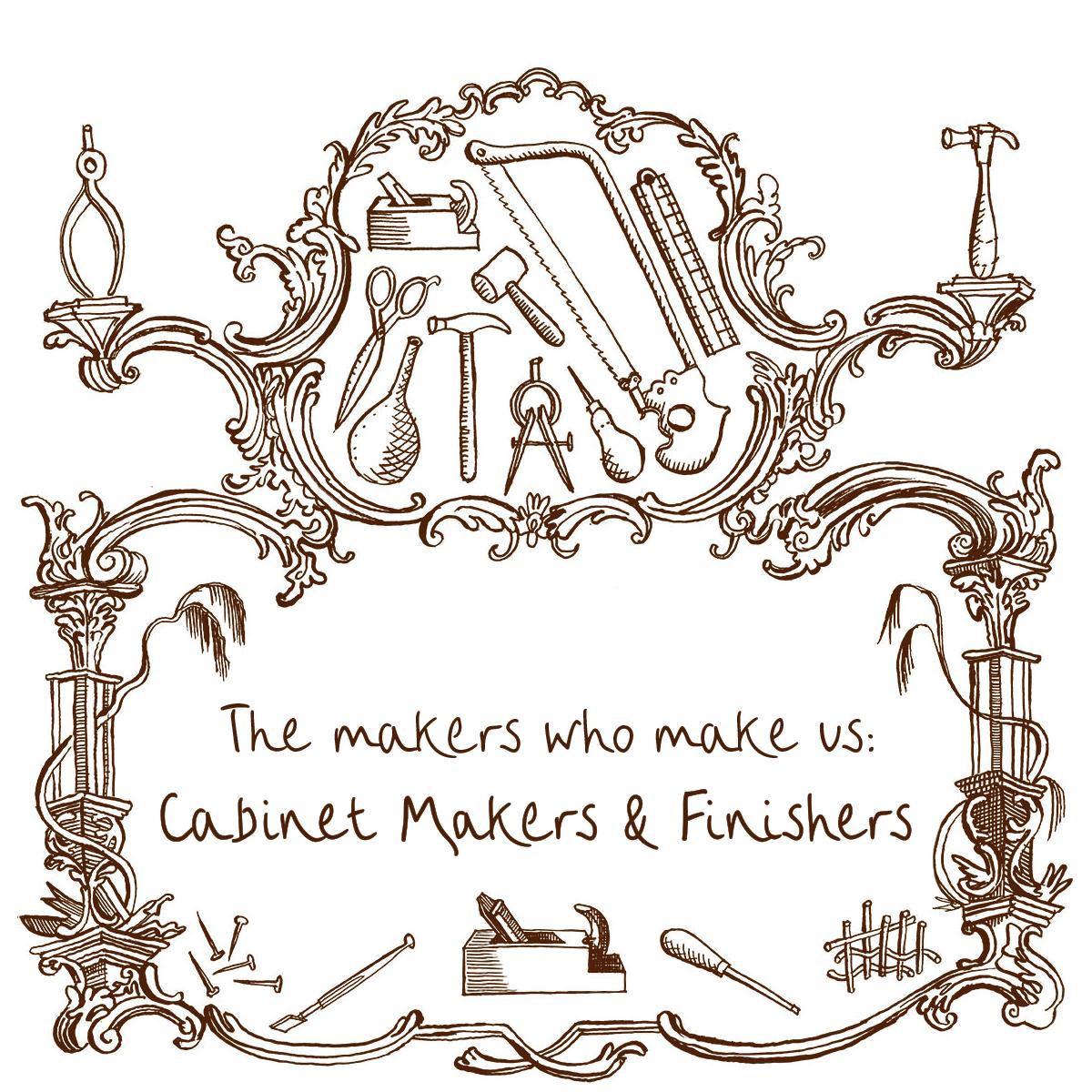
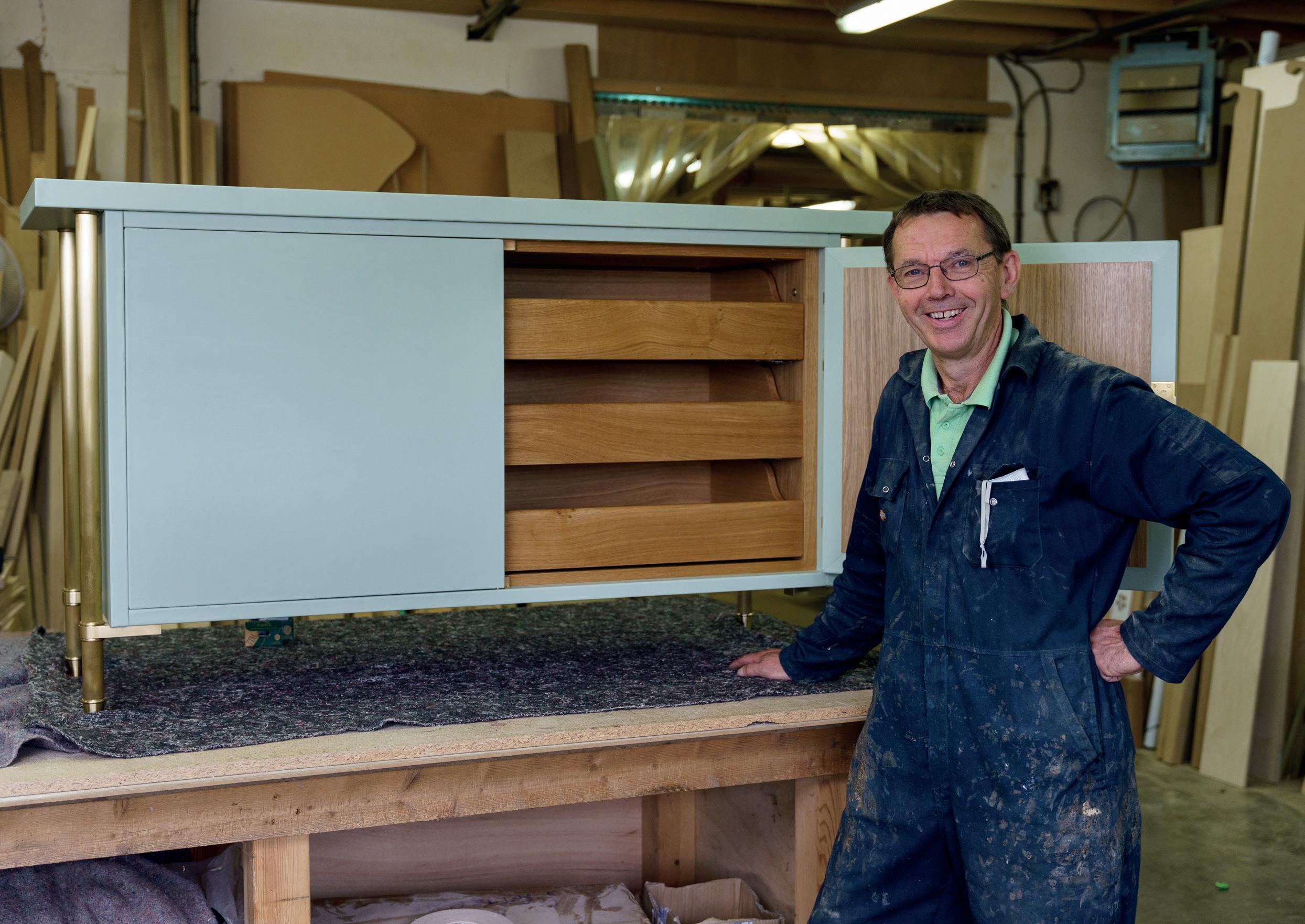
Soane Britain’s wooden furniture designs are made by a family business in Suffolk that has perfected cabinetry skills across generations.
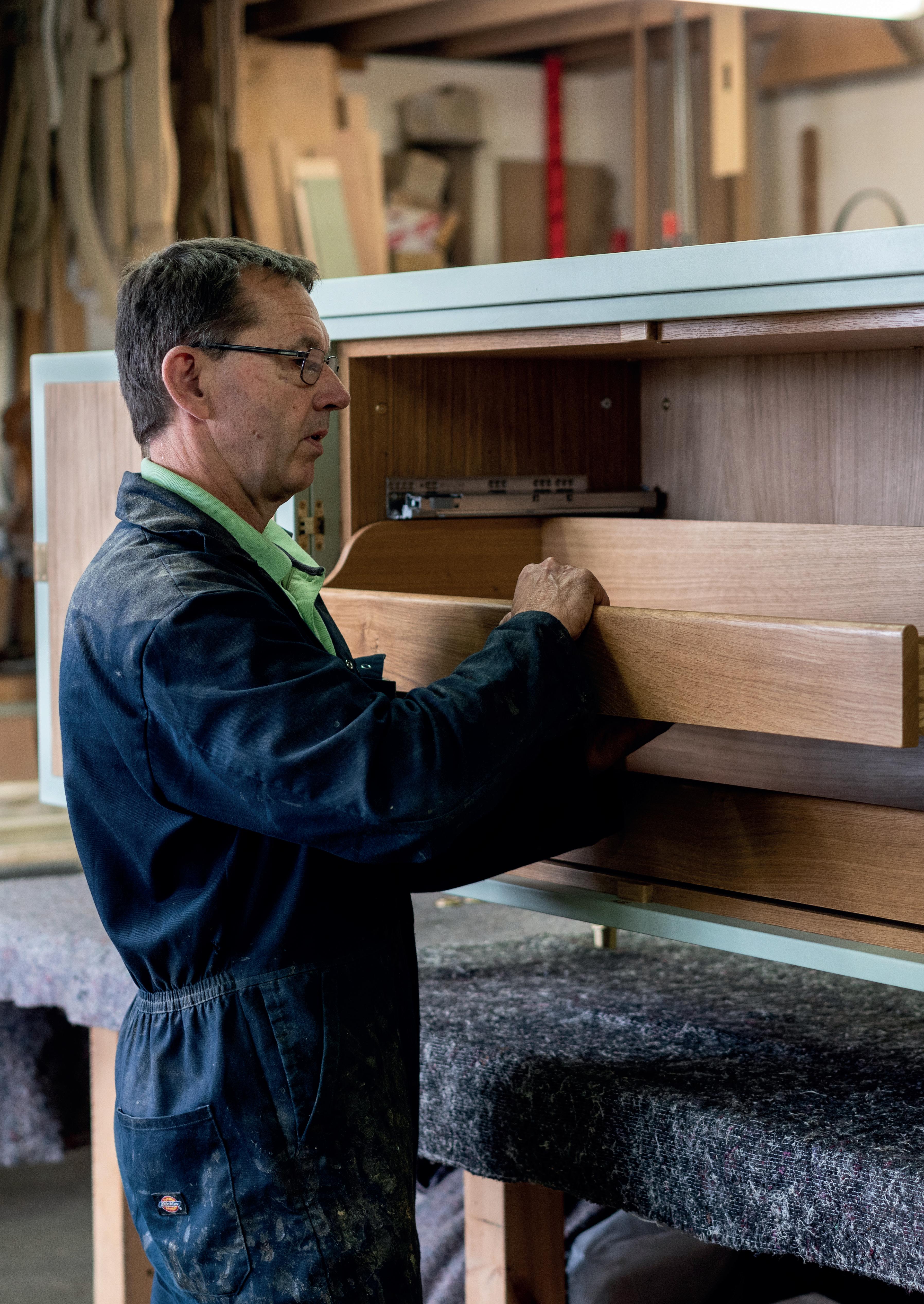
Soane’s made to order designs, including tables, cabinets and chests of drawers, are all hand made with high-grade woods and veneers selected for best effect in each piece.
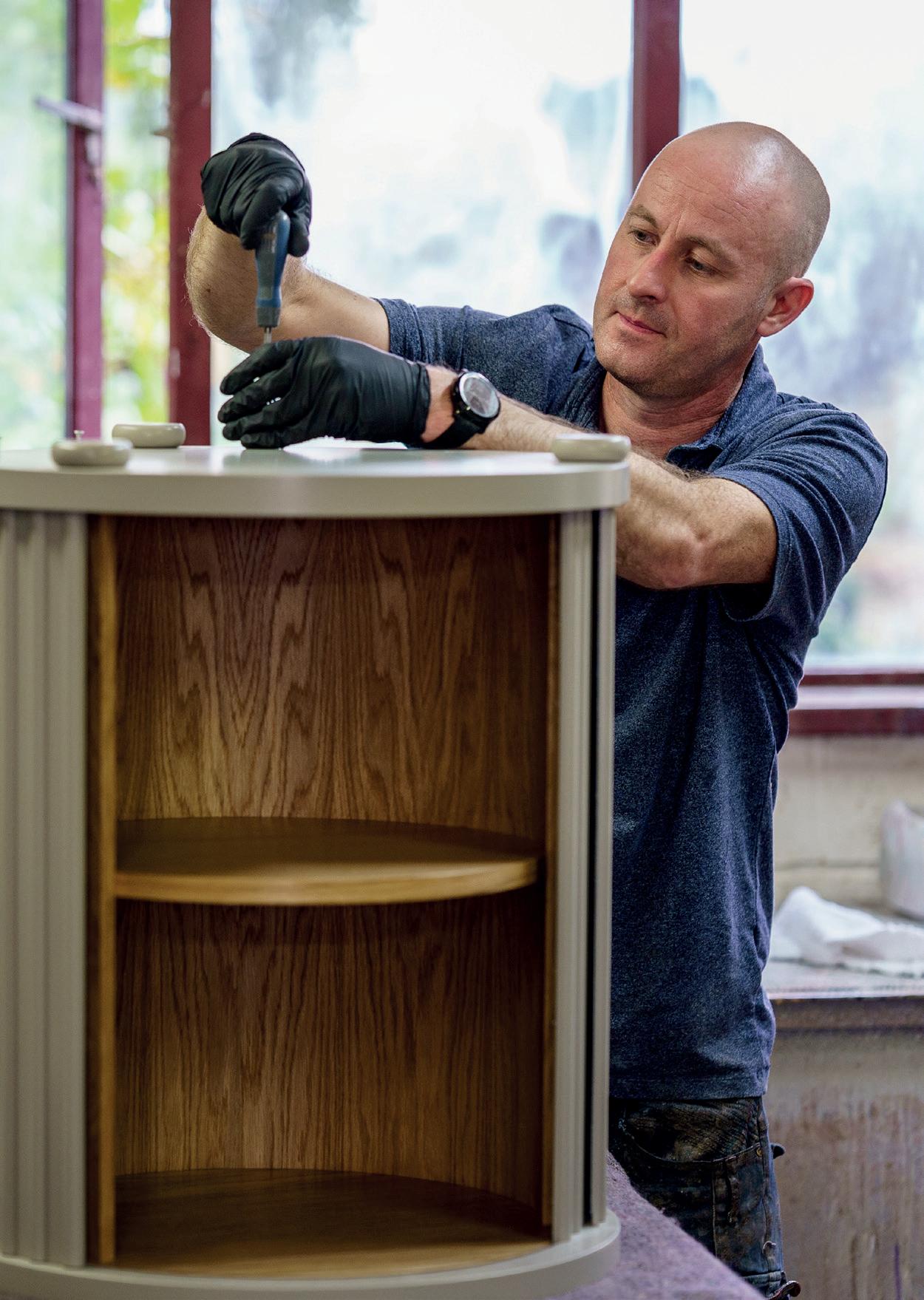

The workshop that makes Soane’s Tambour Cabinets uses traditional methods unchanged from the early 19th century. Each spleen is made individually from oak, walnut or mahogany then glued to a very strong denim backing which allows the tambour to move fluidly through bends and curves. Once the cabinet is complete, the grooves cut to take the tambour are rubbed with candle wax – the final ingredient for perfectly gliding doors.
Several specialist finishers are employed to achieve the best results possible. Of particular note are the traditional French Polishers that work methodically building up layers of polish that give great depth to pieces.
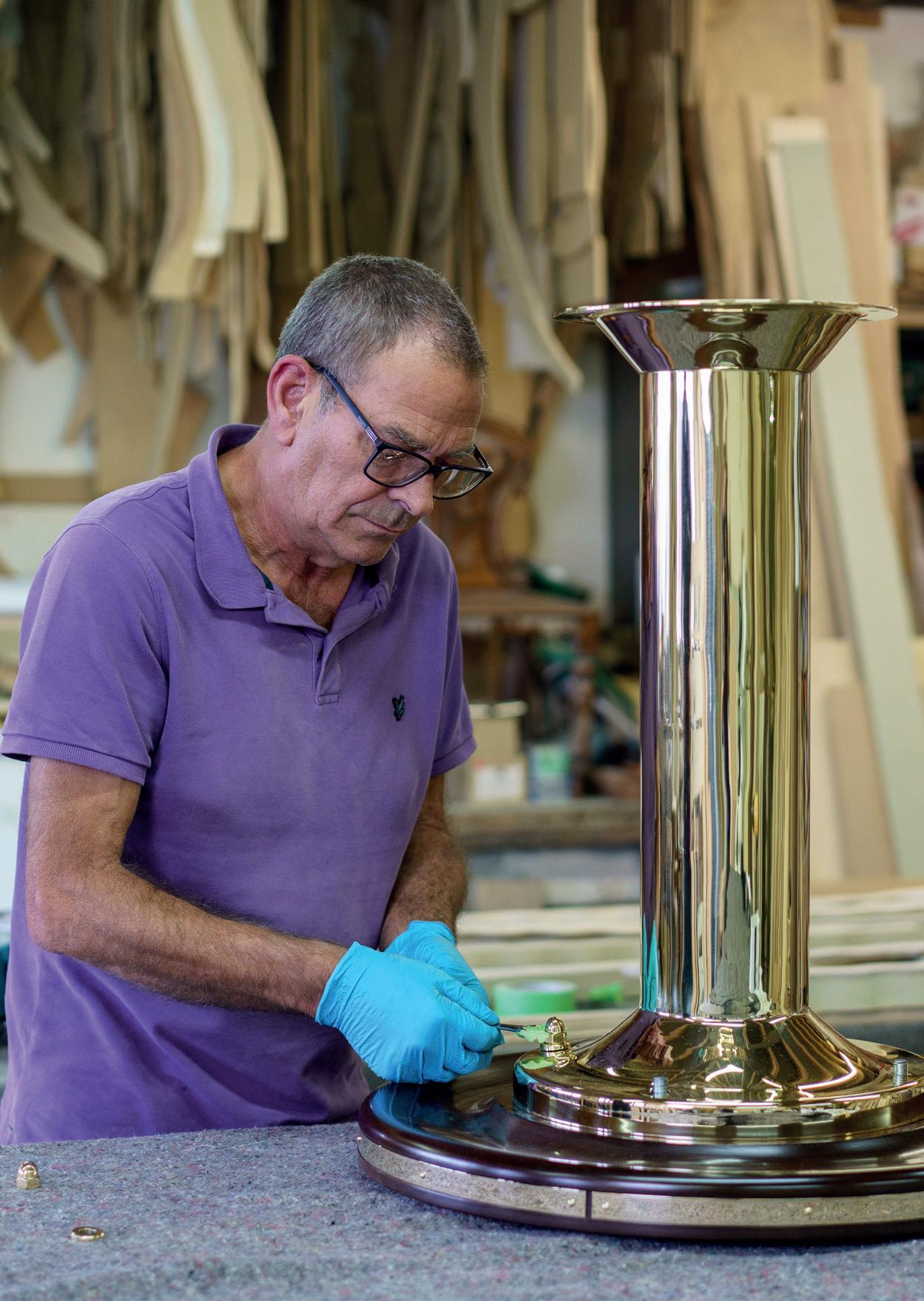
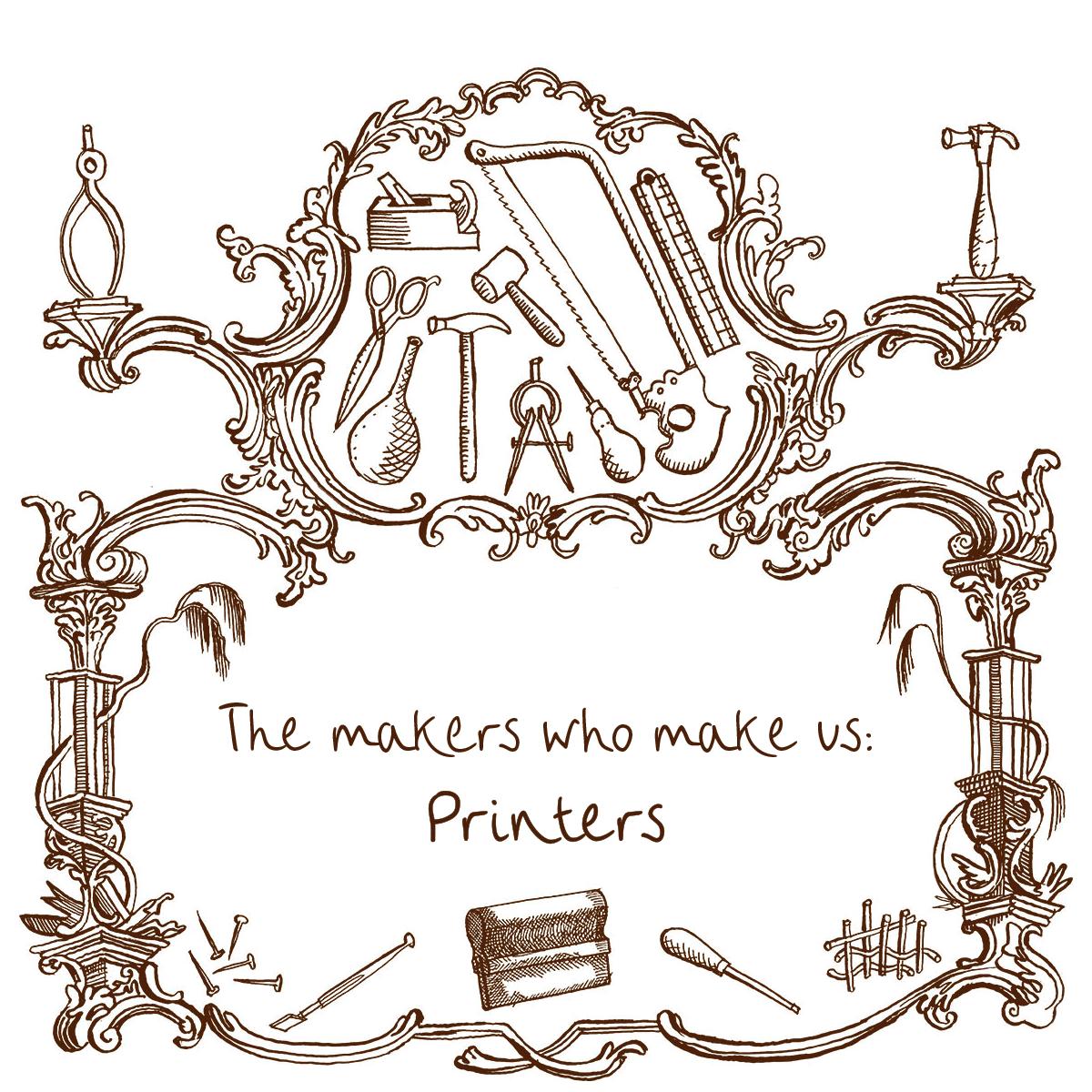
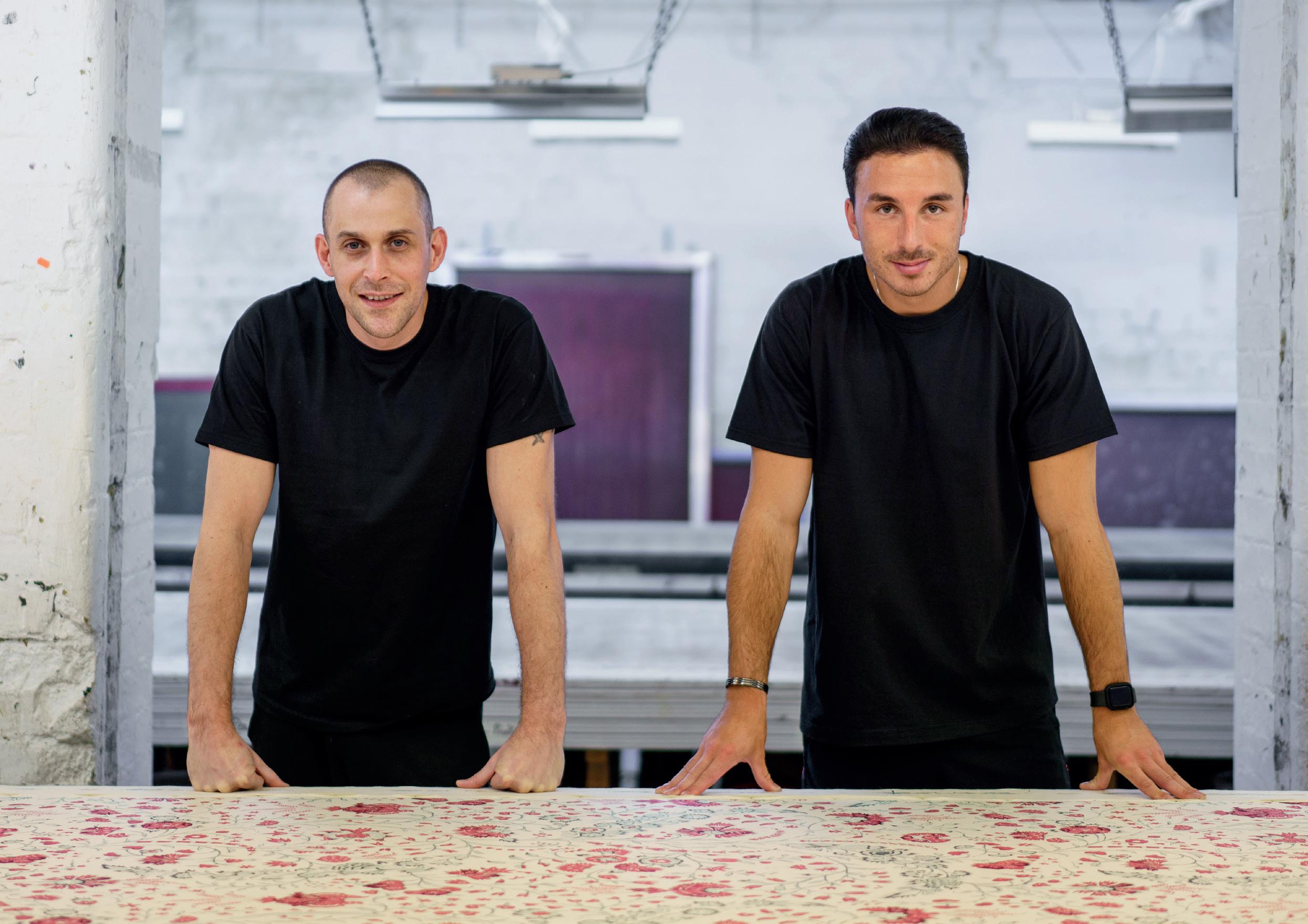
Soane collaborates with small, established printing mills in Kent and Lancashire to develop the repeating artwork and colours for patterns that are in turn hand printed onto linen or silk base cloths using flat bed silkscreen printing techniques. Flat bed silk screen printing is a labour intensive process and one that requires concentrated levels of care and attention throughout.
Screens are made using a photographic technique whereby the acetate sheets are stencil. A screen is made to a human scale, dictated by the

are used with light sensitive emulsion which, when exposed, effectively creates a the arm reach of two printers across the printing table.
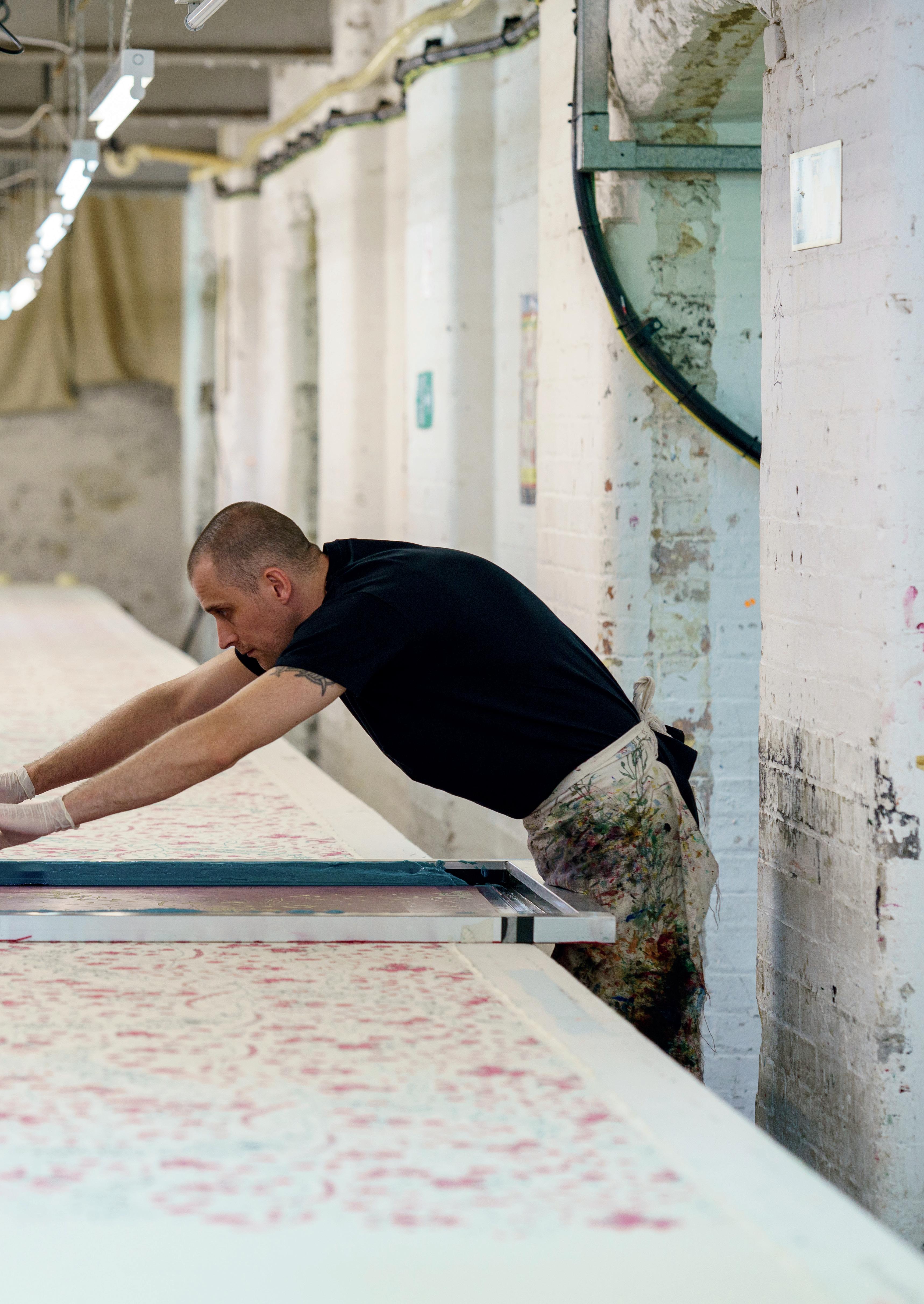

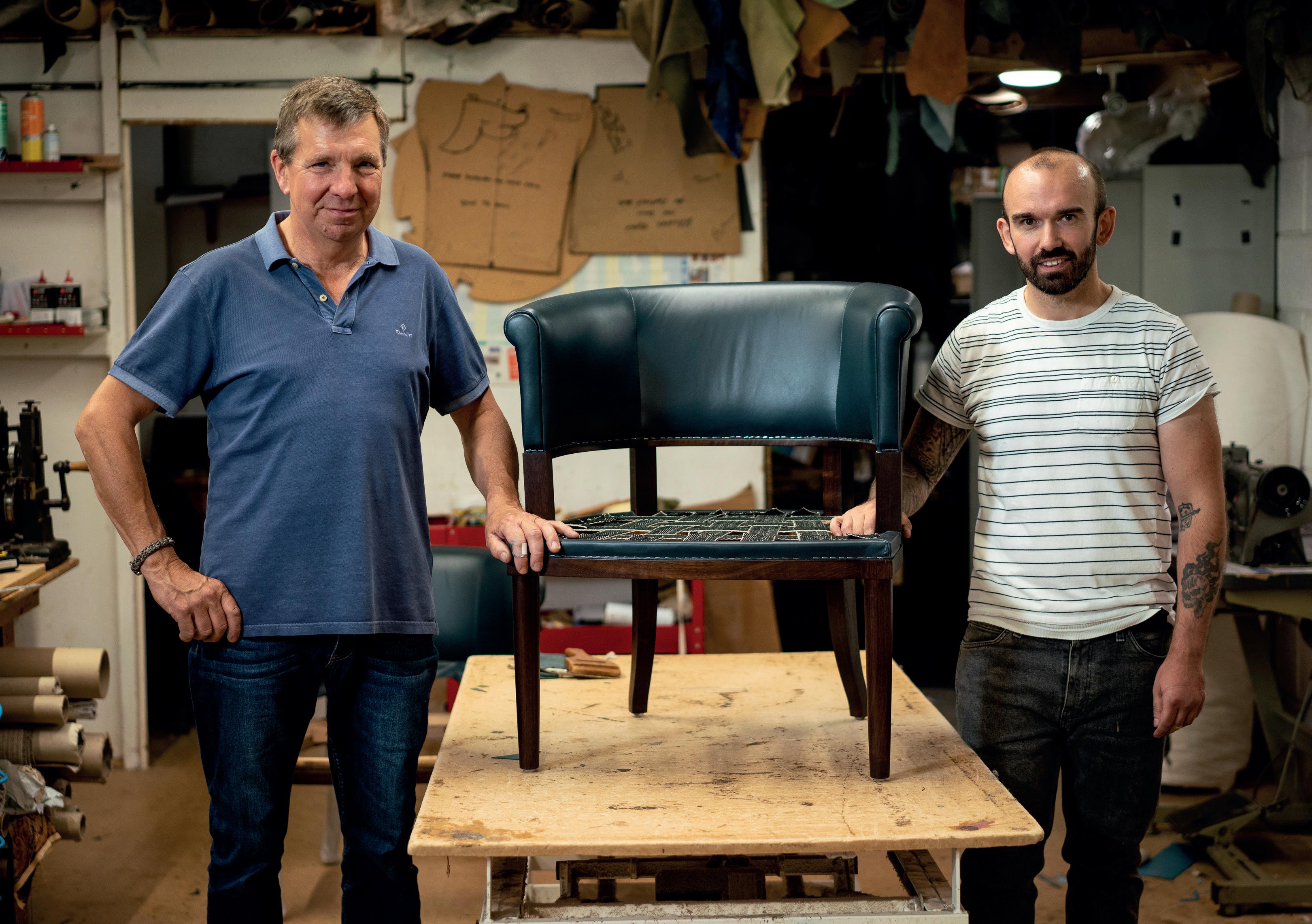
Soane’s traditionally upholstered chairs, sofas and stools are made by numerous specialists in Somerset employing diverse materials to meet the demands of each design.
Frames are delivered from the chair makers ready to be hand-sprung, hand-stitched Soane in-house fabric or leather, or using
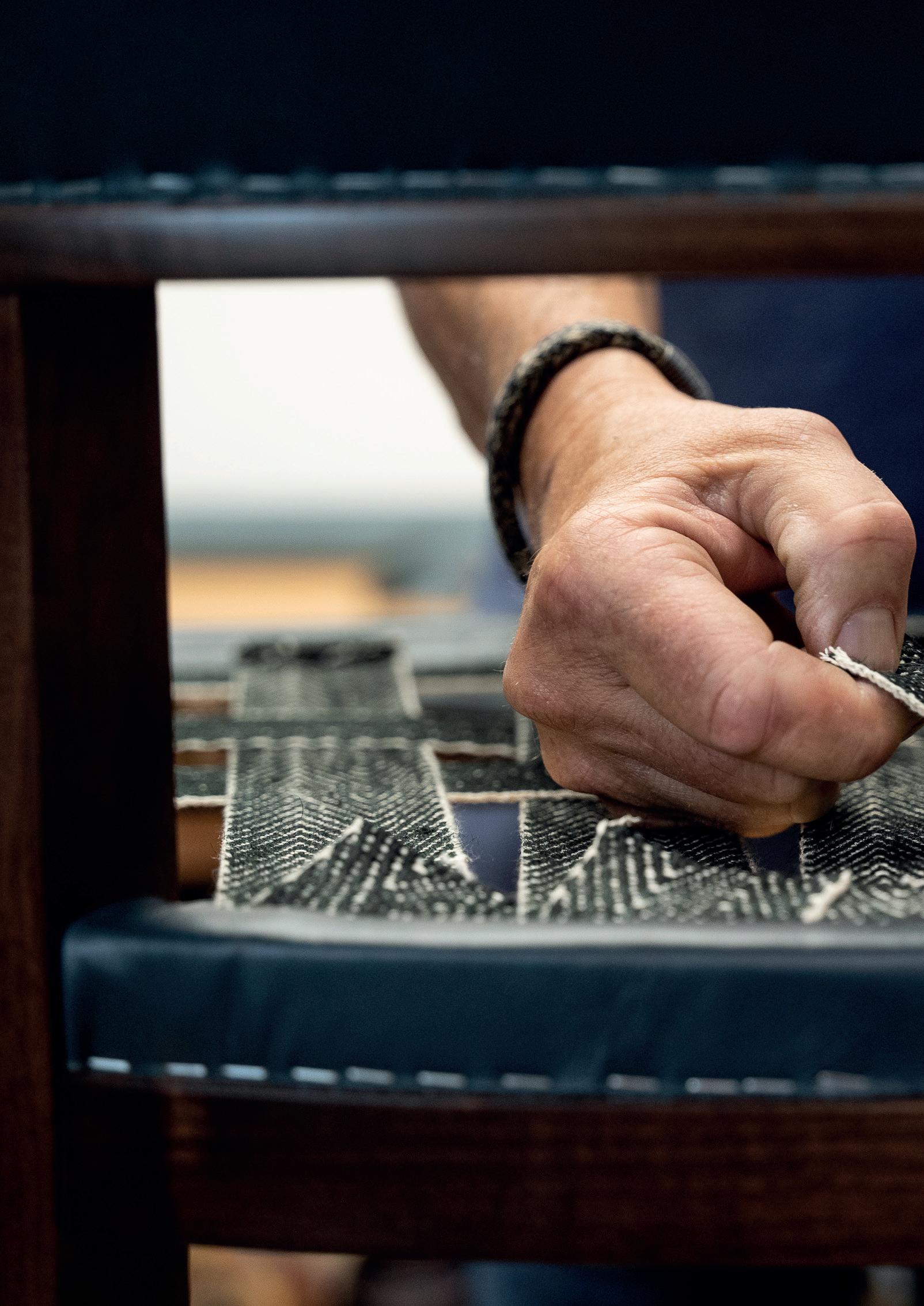
hand-stitched and webbed, using feather and down cushions. Pieces are upholstered in a using the client’s own material.
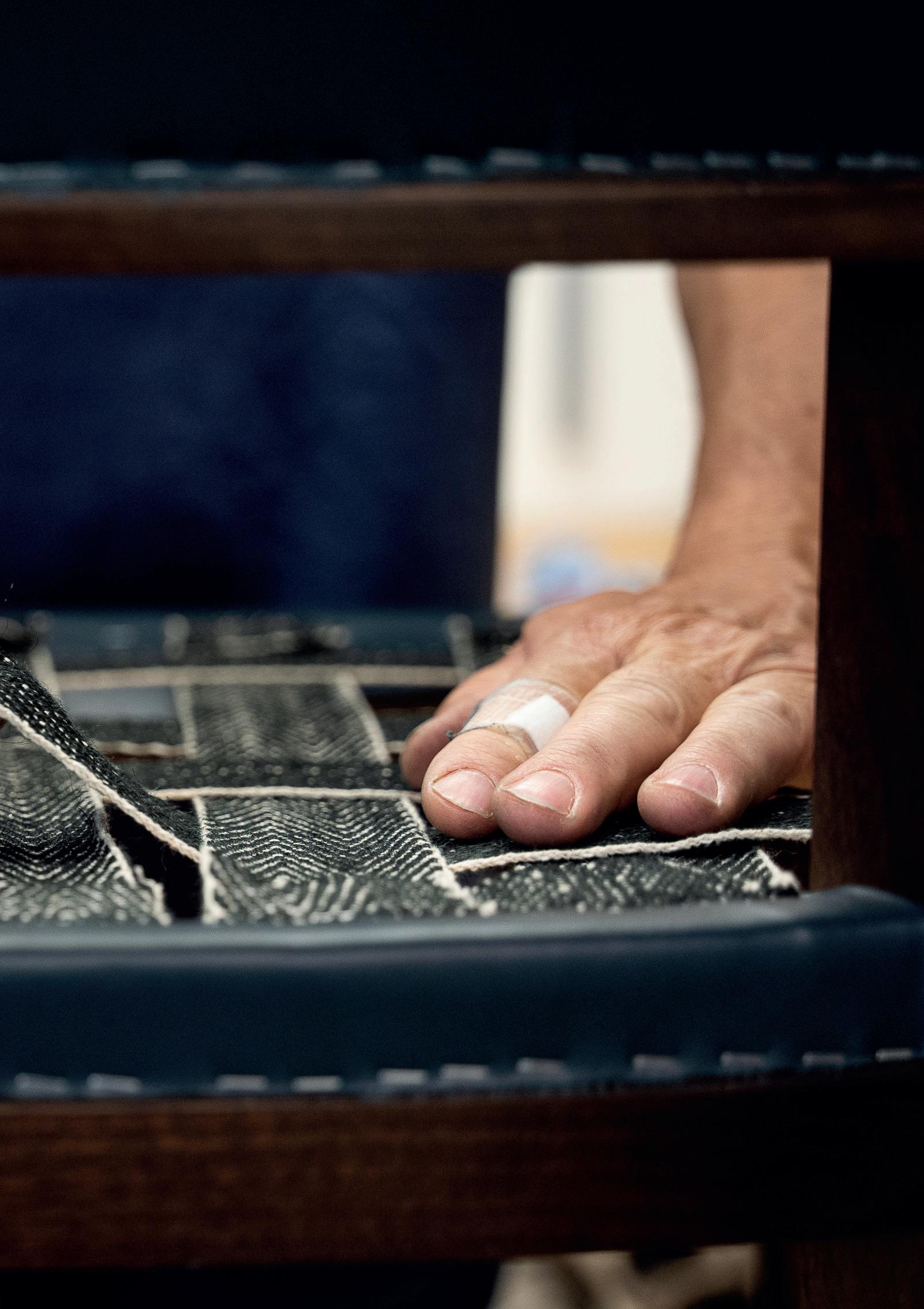
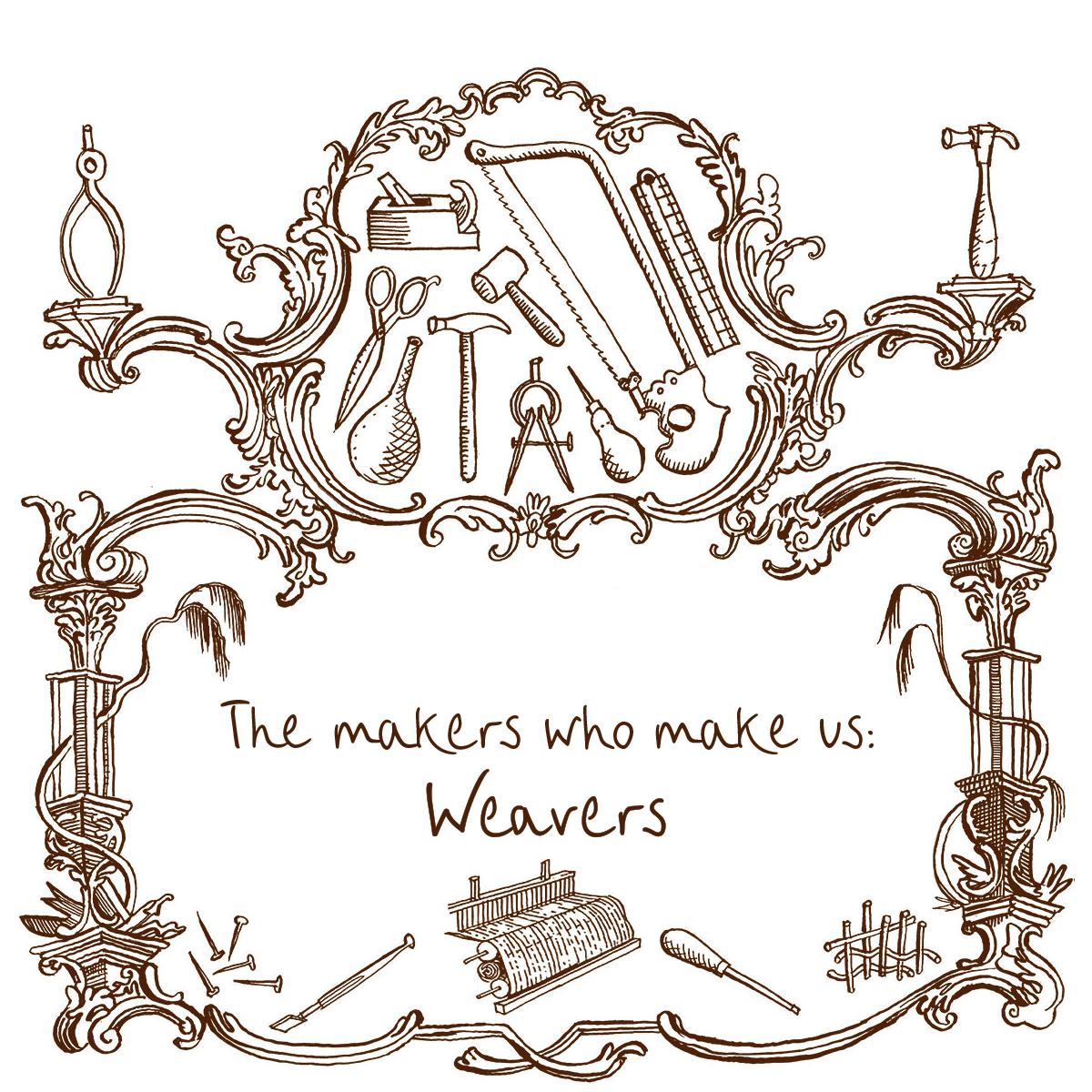
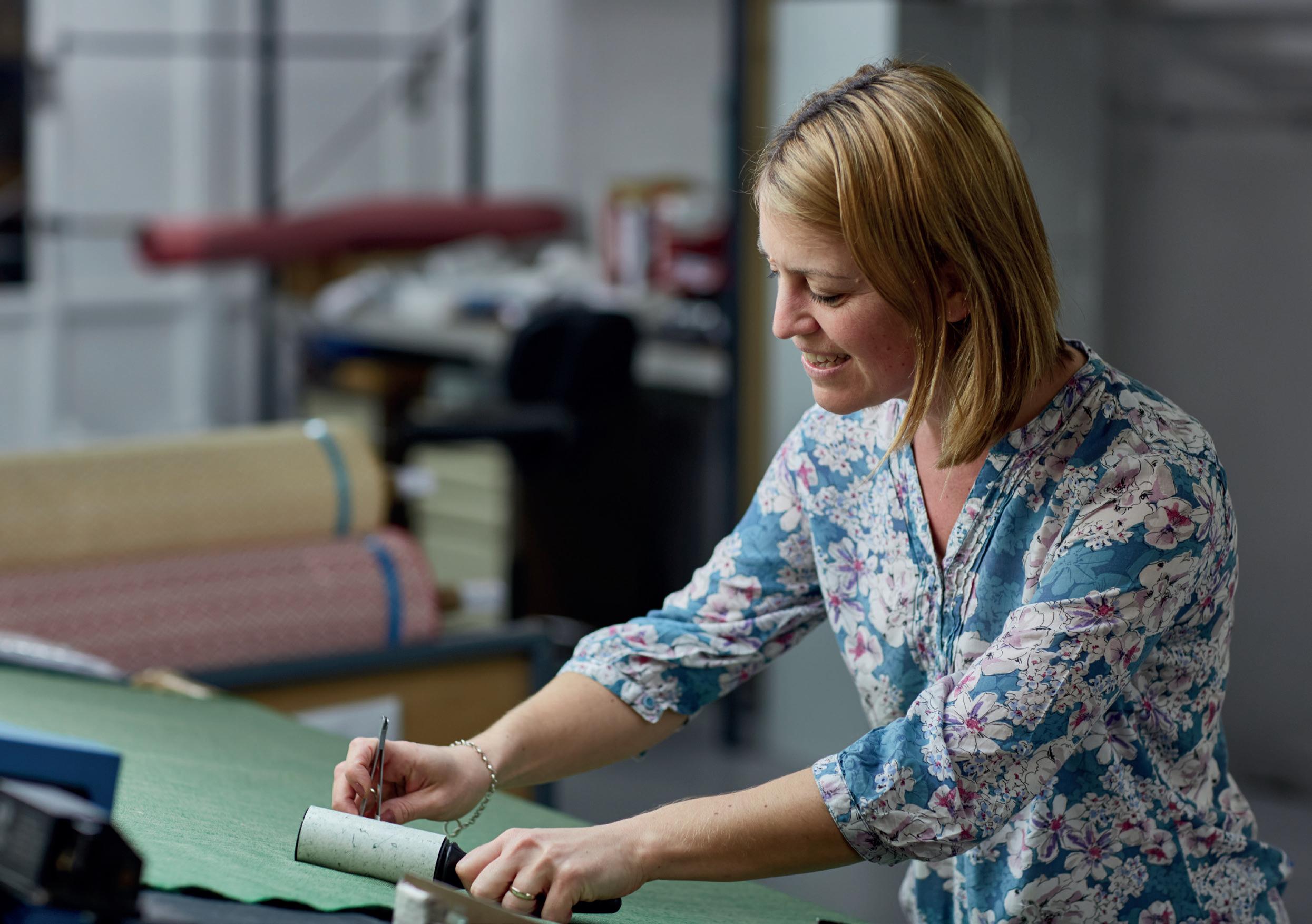

Soane’s woven designs are made in a 300 year old family mill in the English county of Suffolk. Combining traditional weaving techniques and knowledge of old textiles, with the latest loom technology, our weaves maintain the atmosphere and quality of the antique textiles that they replicate.
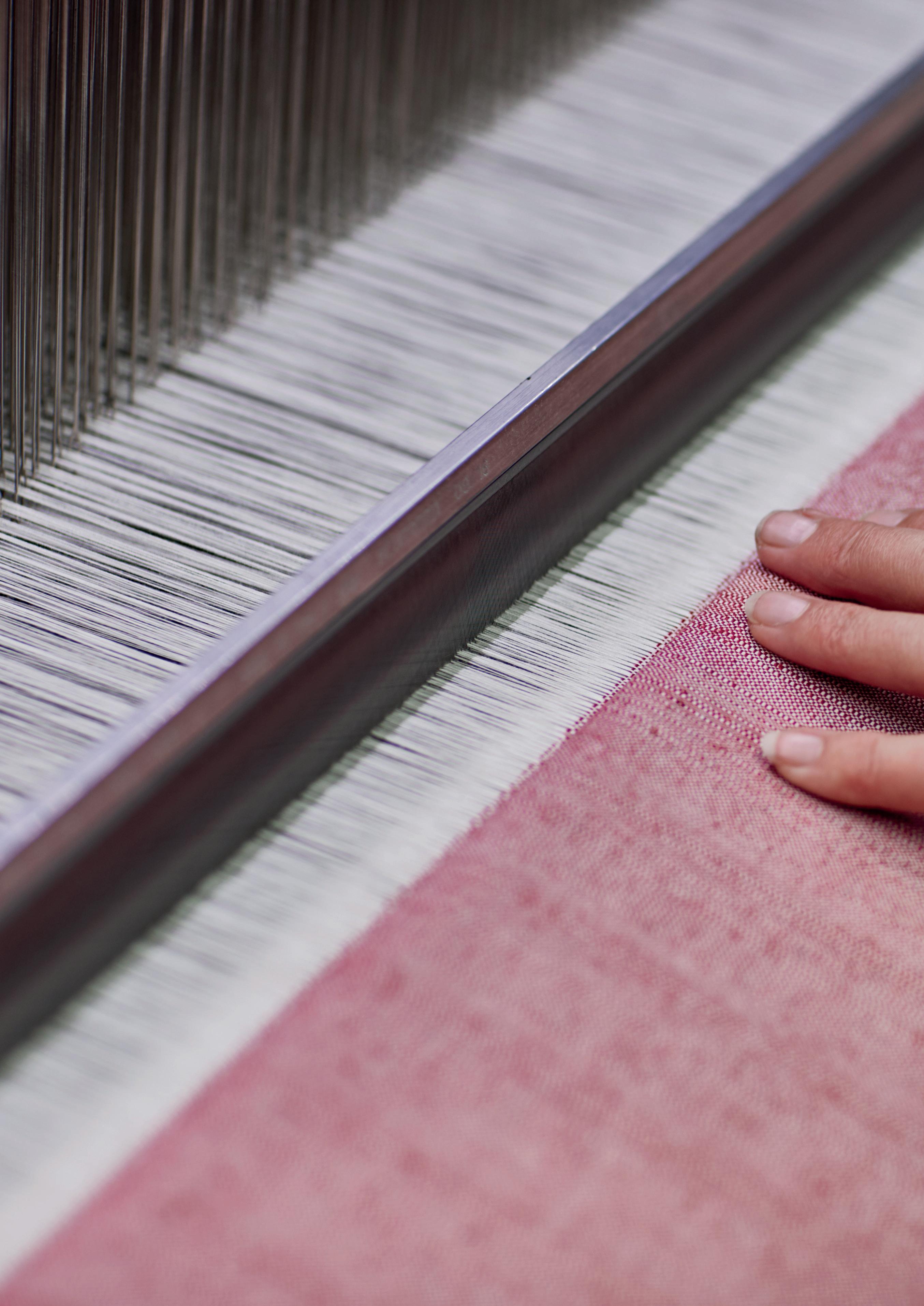

The intricate weaving process requires the skills of yarn operatives, warpers, weavers, tacklers and inspectors, beginning with the selection of the best yarns for the warp and weft and finishing with an inspection of every inch of the newly woven cloth.

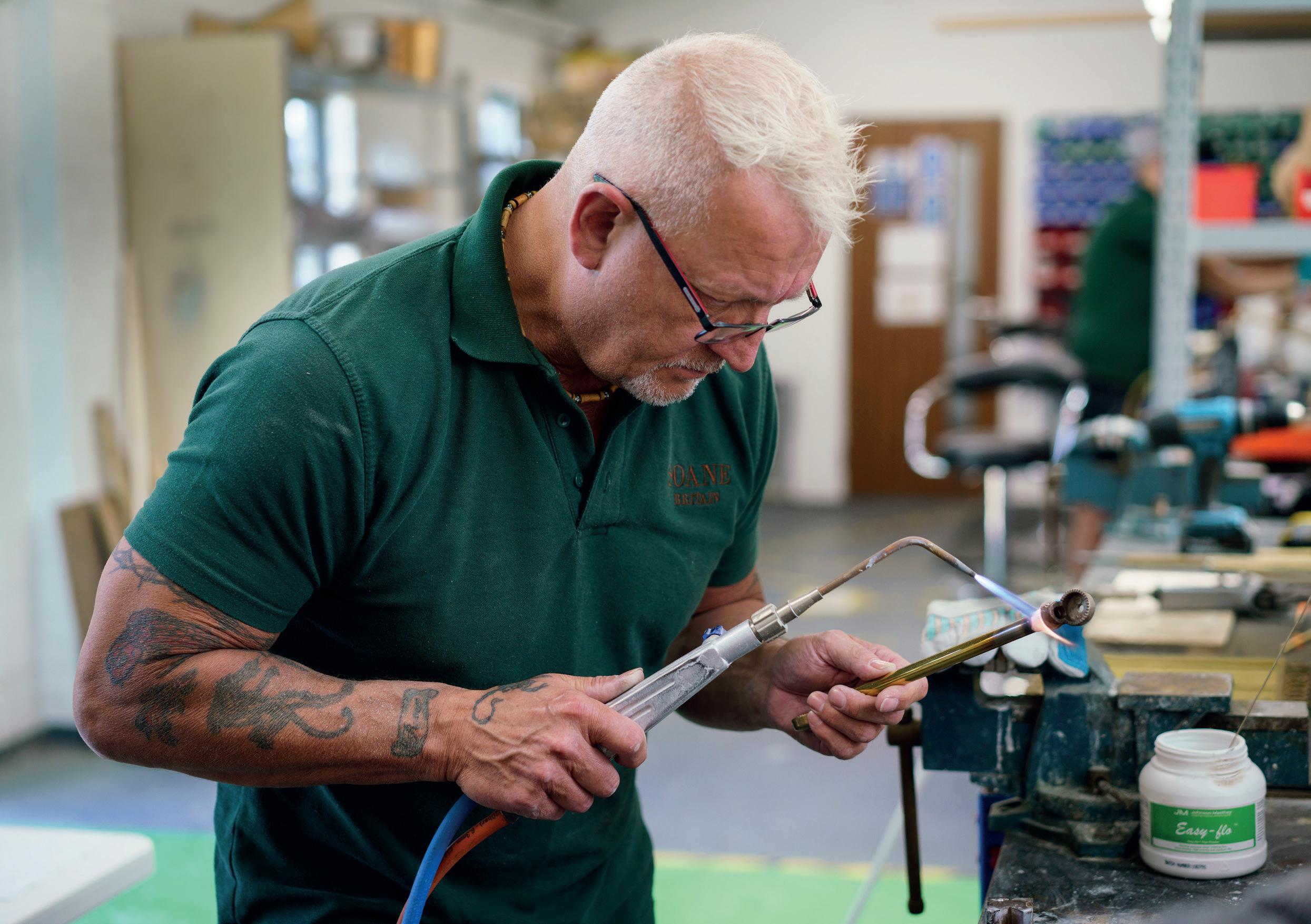

Patination is the all-important, final process in the creation of all of our metal designs and is carried out at Soane’s own Leicester workshops. The technique requires our craftsmen to carefully apply oxidising chemicals to our lights to give them a beautiful finish or ‘patina’ and requires great skill and patience. It is crucial to ensuring that every piece made by Soane has depth and atmosphere.
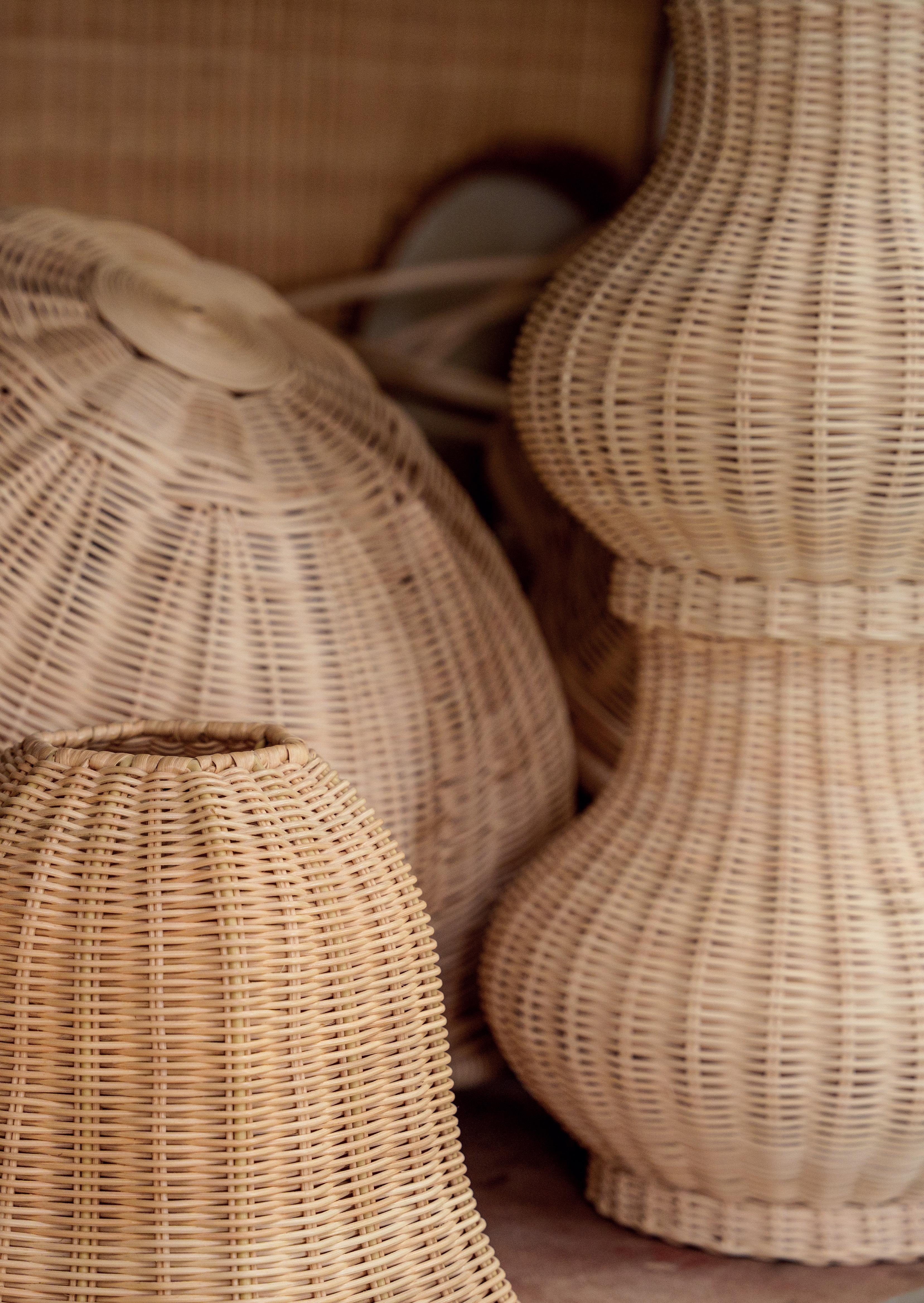