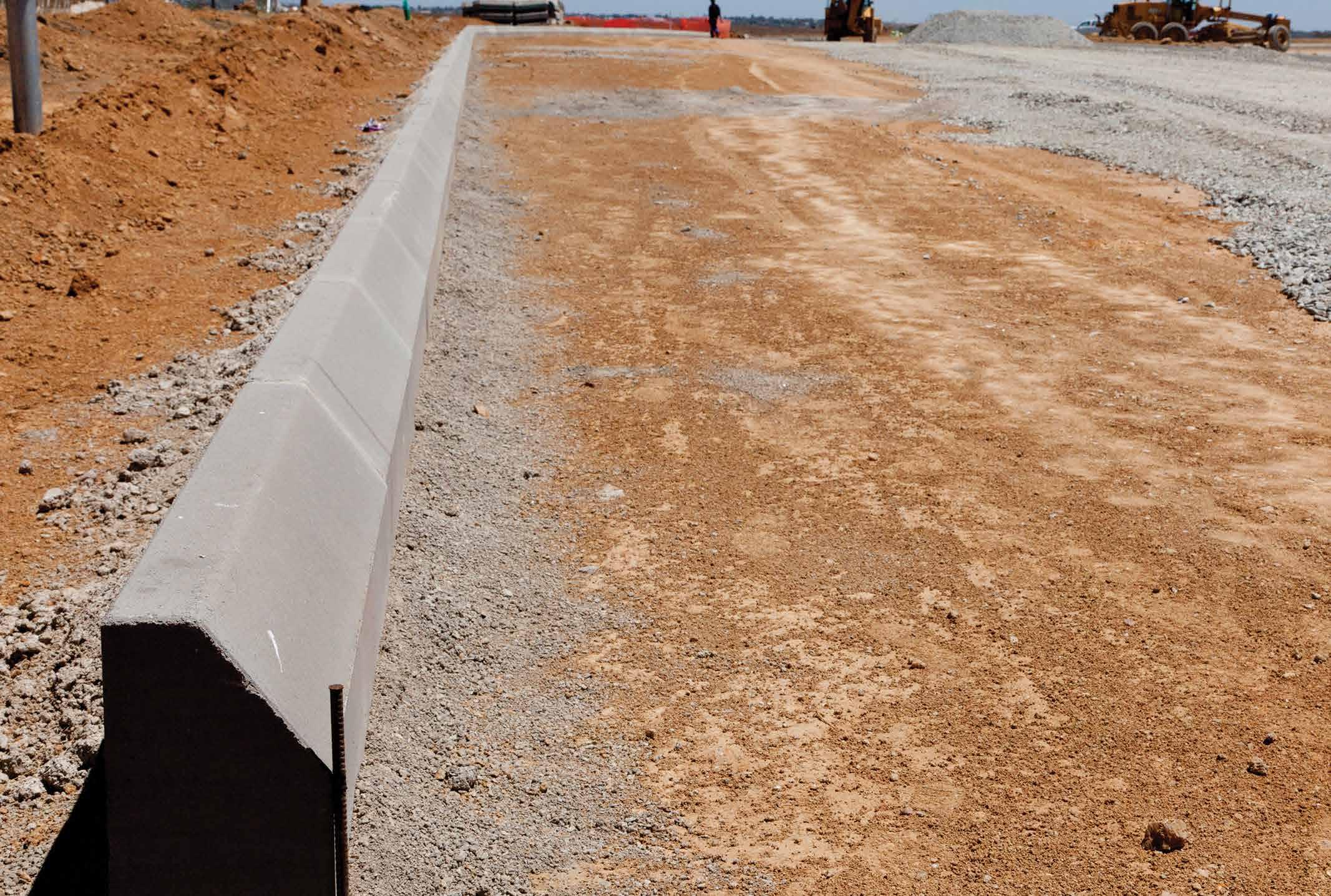
1 minute read
Installation and specification
The installation of kerbs is specified by SANS 1200MK.
In principle, the following is prescribed:
Advertisement
• Trenches on which kerbs are to be installed should be excavated and well compacted. If the engineer finds that the in-situ subsoil is not good, an imported sub-base material should be used.
• A bedding material of at least 50mm thickness should be used that consists of crushed stone, cement and sand, with a maximum particle size of 13,2mm.
• There should be close joints no larger than 10mm between kerbs and they should be filled with 3:1 sand/cement. The joints must be pointed. Ends of kerbs should be well moistened before jointing and filled joints must be covered and kept moist for 48 hours. When joints have cured, an appropriate sealant must be used, where necessary.
• Allow for expansion joints of at least 12mm at intervals of at least 20m.
• After jointing, the kerbs must be backed with concrete “haunching” of at least 15Mpa and the space behind kerbs must be back-filled and well compacted in layers.
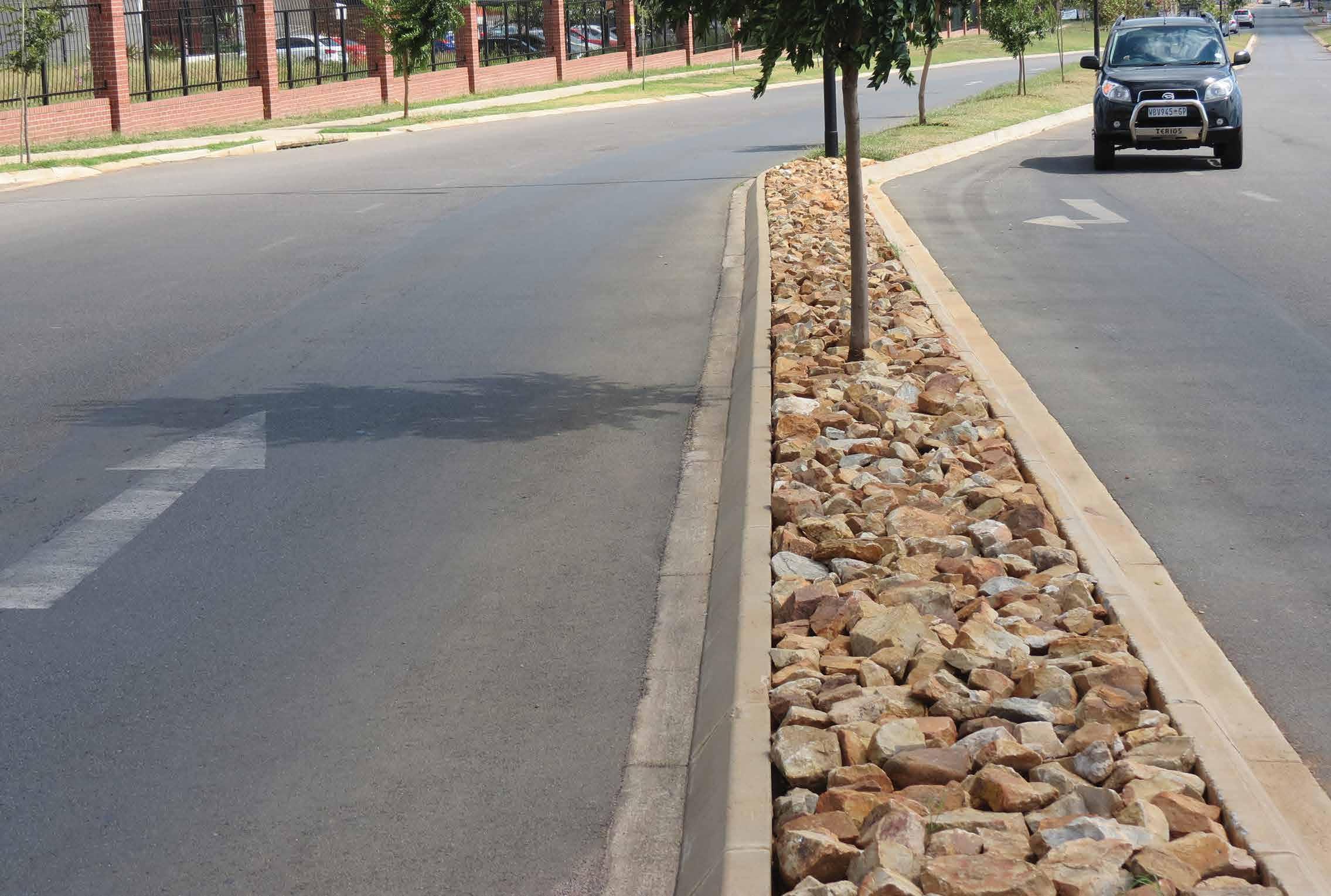
SANS specifications for concrete kerbs explained
The South African National Standard for precast concrete kerbs, edgings and channels SANS 927:2013:
• Bosun kerbs all adhere and are manufactured to SANS specifications. Product guarantees are based on the same rules.
• Kerbs are made up of high-quality materials.
• The kerbs must be free of cracks, other than hairline cracks. They must also be free of visible twists and dents.
• Kerbs dimensions must remain within ±3mm in length and straightness.
• Kerbs must comply with strength specifications.
• Kerbs must be sampled and tested in a lab.
Reality check
Don’t expect kerbs to look like the smooth, shuttered concrete seen on buildings. Dry-cast kerbs might initially appear to be darker than wet-cast ones. In the construction of roadways, kerbs will take a beating from heavy machinery used in layer works. Contractors should be aware that kerbs are not unbreakable.