
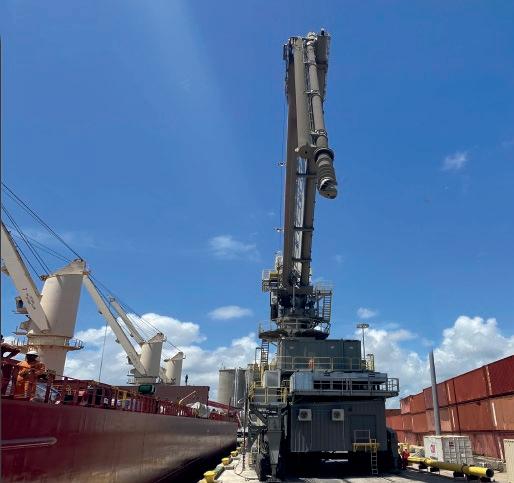
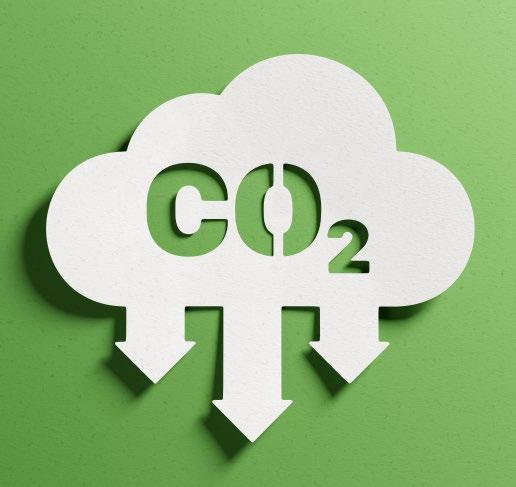

After eight successful years at the helm, Peter Jonsson has stepped down as CEO, Bruks Siwertell Group.
“On behalf of JCE, I want to extend my sincere gratitude to Peter Jonsson for his leadership and dedication over the past eight years. Under his guidance, Bruks Siwertell Group has grown into a strong and innovative company, well-positioned for the future,” says Sofia Sahlberg, Board
member, Bruks Siwertell Group, and COO, JCE Group, majority owner of Bruks Siwertell Group.
Effective immediately, Clas Gunneberg has been appointed interim CEO as the process begins to establish a permanent successor. “My immediate priorities will be to maintain our strong performance, support our business units, and ensure a continuous focus on our strategic goals,” says Clas Gunneberg.
Gunneberg brings extensive leadership experience from a range of industries, including automotive, industrial engineering, automation and electronics, making him wellequipped to steer the company through this transition.
Following a competitive public request for proposals (RFP) process, a new Bruks ship loader has been ordered by the US Port of Long Beach, California.
“The Port of Long Beach is one of the busiest and most influential ports in the US, and also has some of the country’s strictest environmental protection regulations,” notes Daniel Pace, Sales Manager Americas, Port Technology, Bruks Siwertell. “We offered a ship loader with a low weight, efficient design that fits seamlessly within the existing dock space. Additionally, our ability to meet the Port’s strict delivery timeline, and our financing capabilities, were key factors in securing this contract.”
The Port of Long Beach, one of the most influential ports in the US, will be served by a new Bruks ship loader
The fully enclosed traveling and shuttling Bruks ship loader will handle a wide range of dry bulk materials, including coal and petcoke at a rated capacity of 5,000t/h, and soda ash, pyrobor, and sulfate at 2,000t/h, loading vessels up to 120,000 dwt. It is planned to commence service towards the end of 2026.
A new next-generation Siwertell 15 000 S road-mobile unloader order has been received from an undisclosed owner. The largest model Siwertell road-mobile ship unloading solution will offer environment-friendly, efficient grain handling and comply with European Union (EU) directives for ATEX-classification, ensuring the safe handling of organic commodities.
“In mobile ship unloading terms, this is a significant contract, with a specialized configuration,” highlights Jörgen Ojeda, Sales Director, Mobile Unloaders, Bruks Siwertell. “The good reputation of our road-mobile ship unloading technology was fundamental in securing the order, along with the fact that we are the only manufacturer capable of delivering such a large, efficient mobile ship unloading system.”
The Siwertell 15 000 S road-mobile unit will offer a continuous rated wheat unloading capacity of 400t/h, discharging vessels up to 15,000 dwt. It will be delivered fully assembled towards the end of 2025.
The Siwertell type-1B ship loader will offer a rated capacity of 1,000t/h
Sky Ports, Egypt, part of the Sky Logistics Group, has placed an order for a screw-type Siwertell type-1B ship loader. It is destined for a new multipurpose terminal in
East Port Said, which has been developed to grow the region’s economy and align with its ‘green’ port ambitions.
“We are increasingly called upon to be part of large-scale, regional infrastructure projects, and have a reputation for delivering quality, dynamic, tailored solutions that offer a competitive advantage against established suppliers,” says Per Hansson, Operations Director, Bruks Siwertell.
The ship loader will offer a rated capacity of 1,000t/h, and is scheduled for delivery at the end of 2025. It will come equipped with a tripper arrangement that will be integrated into the operator’s jetty conveyor gallery, and will also feature advanced digital technology, such as the Siwertell SmartView IIoT tool for enhanced operational monitoring and support.
Bruks Siwertell company, Bruks Klöckner, has launched a next generation industrial drum chipper, which delivers enhanced performance and increased efficiency, setting a new benchmark in drum chipping technology for handling sawmill byproducts and waste wood.
The next generation DH 365 is an advanced development of Bruks Klöckner’s proven drum chipper model.
“For years, the DH 365 has been a trusted solution for sawmills, delivering high-capacity, precision chipping of waste wood,” says Patrick Wicharz, Area Sales Manager, Bruks Siwertell.
“The next generation DH 365 offers a number of enhancements and features,” Wicharz explains. “With no steel frame or pit required underneath the machine, the discharge conveyor arrangement can be at ground level, which delivers significant cost savings and installation benefits for customers, and improves accessibility for maintenance.”
The DH 365 can be substantially tailored to meet a customer’s specific needs
The DH 365 is specifically designed for processing sawmill waste wood, handling material with a maximum infeed diameter of 250mm. It is available in two configurations and offers a broad range of wood chip lengths from 19mm to 36mm, enabling customers to tap into different markets.
Orders for Bruks Siwertell’s innovative Siwertell Careaugmented reality (STC-AR) service agreements continue. STC-ARs are nextlevel digital service agreements, which integrate augmented reality (AR), revolutionizing maintenance and service tasks, and maximizing operational efficiency for road-mobile unloader users.
A second Bruks truck tipper platform has been ordered by long-standing customer Domtar for its Windsor paper mill in Quebec, Canada. The new contract follows the completion of a similar installation at the facility in August 2024. Both units have been ordered as part of an ongoing modernization program at the mill and are designed to perfectly integrate with the existing infrastructure.
The second Bruks truck tipper platform is planned for delivery in August 2025. All systems handle wood chips, which are destined for the mill’s 450,000 metric ton annual capacity fiber line. The
They are designed to complement regular mechanical, hydraulic and electrical inspections and maintenance work, and combine cutting-edge hardware, including AR glasses and headsets, with pre-paid, fixed-cost support and discounts on spare parts.
Bruks tipper platforms offer a lifespan of around two million lift and lower cycles
Windsor mill generates 90 percent of its energy from renewable resources, reuses more than 97 percent of its manufacturing byproducts, and plants half a million trees a year in Domtar-owned forests.
AS CLAS GUNNEBERG STEPS INTO HIS NEW ROLE, he brings a wealth of knowledge, an energetic leadership style, and a clear vision for the company’s future. His first priority? Ensure Bruks Siwertell Group continues delivering world-class dry bulk handling and wood-processing solutions, while meeting as many customers as possible.
Gunneberg graduated as an engineer over three decades ago. “Since then, I have worked in a diverse range of international manufacturing industries, with 25 of those years as a managing director or CEO,” he shares. “This experience has given me valuable insight into driving profitable growth in complex business environments.
“The companies that make up Bruks Siwertell Group are all high-quality businesses with impressive histories and fantastic offerings. I see great potential in combining their strengths to create an even stronger customer
With over 25 years’ experience in senior leadership roles, a strong customer focus and a valuable understanding of how to create profitable growth in complex business environments, Bruks Siwertell Group welcomes its new CEO, Clas Gunneberg
offering, and the healthy underlying growth in dry bulk handling and wood processing provides a strong driver for building a much bigger company,” Gunneberg adds.
With business continuity and delivery on current projects a key priority, Gunneberg will visit all Group companies and connect with personnel to gain a deeper understanding of operations. He is also finalizing the company’s future growth strategy and will drive digitalization, sustainability, and innovation.
“Customers are at the core of our strategy,” says Gunneberg. “Everything we do should benefit them. I want to meet as many as possible, and sooner rather than later.
“We will focus on digitalizing internal and external processes, as well as our products and services, to increase customer value. Innovation is key to ensuring our offerings integrate the latest advancements,” he notes.
Gunneberg’s values reflect those central to Bruks Siwertell Group. “My leadership is inclusive, open, and direct,” he emphasizes. “I am 100 percent committed and never give up before achieving my goals. Teamwork is essential, and I work closely with the management team and other stakeholders.”
Looking ahead, Gunneberg identifies several industry challenges, including the shift from global to regional supply chains, minimizing carbon impact, and global trade uncertainties. “We will continue to address these through established action plans and by staying flexible to reduce any negative effects from sudden trade shifts. I am excited about the future and eager to work with our talented teams and valued customers to take Bruks Siwertell Group to new heights,” Gunneberg concludes.
The huge variety in wood-processing installations and operations means that ongoing service support needs to be flexible and tailored to suit needs; Bruks Siwertell has introduced a new model of service agreements that does just this
LIKE ALL INDUSTRIES RELIANT ON HEAVY MACHINERY, in the dynamic and demanding world of wood processing, operational efficiency and equipment reliability are paramount. Recognizing this, and the fact that few customers want exactly the same packages of ongoing service support, Bruks Siwertell’s wood technology division has introduced a new, flexible planned service agreement model.
It is designed to allow customers to select the support that they need and meet the unique requirements of their wood-processing installation, ensuring optimal lifetime performance and longevity of their machinery.
“Bruks Siwertell’s commitment to customer-centric solutions is evidenced in its technology and lifetime service support,” emphasizes Jennie Lindh Olsson, Service Account Manager, Bruks Siwertell. “These new model service agreements are structured to provide transparency and adaptability, allowing high degrees of customization to meet the specific requirements of each operation. The form is clear about what the contracts contain and allows us to tailor the contract to the customer’s wishes and needs.
“Our service agreements encompass a range of benefits aimed at minimizing downtime and reducing maintenance
“ New model service agreements are structured to provide transparency and adaptability
JENNIE LINDH OLSSON, SERVICE ACCOUNT MANAGER, BRUKS SIWERTELL
costs,” continues Lindh Olsson. “They include regular inspections that can be scheduled at a customer’s convenience. Inspections are critical assessments in service support, as an experienced surveyor can often spot issues ahead of time, and prioritize potential problem areas, enabling proactive measures. This can significantly contribute to decreased downtime and reduces maintenance costs.”
Also included in the agreements are periodic reviews with the contract manager; the frequency is dependent on a customer’s needs. They can focus on inspections, spare parts recommendations, and identify opportunities for facility improvements and optimizations.
“Detailed reports, such as post-inspection reports, are available as well. ’These provide actionable insights, including suggestions for necessary actions, recommended wear and spare parts, and potential facility enhancements,” adds Lindh Olsson.
factories, and timber yards. Approximately half of its products are exported, with the remaining half serving the Swedish market, including 25 percent supplied to Setra’s own units, primarily in Långshyttan, for further wood processing.
The Heby sawmill uses a comprehensive suite of Bruks Siwertell equipment, including wood chip screens, vibrating conveyors, drum chippers, a Rotom hammer hog, and screw and belt conveyors. By adopting a tailored service agreement, the sawmill ensures that all machinery operates at peak efficiency, benefiting from the full spectrum of services offered.
At the core of all Bruks Siwertell service agreements is a commitment to building reliable partnerships. Each customer is assigned a dedicated service contact for consistent communication and periodic follow-ups.
“We prioritize a safe working environment, collaborative planning of services and actions, and offer prioritized support, ensuring that customers receive the attention and expertise they deserve.
JENNIE LINDH OLSSON, SERVICE ACCOUNT MANAGER, BRUKS SIWERTELL
“Bruks Siwertell’s new model flexible service agreements represent a significant advance in supporting the wood-processing industry. By offering tailored solutions that address the specific needs of each customer, maintenance burdens are cost effective and equipment can continue to operate safely, efficiently and reliably. Our customer-centric approach not only enhances an installation’s overall performance, but also strengthens long-term partnerships built on commitment and trust,” concludes Lindh Olsson.
High-quality original equipment manufacturer spare and wear parts keep wood-processing machinery performing at its best
Flexible dry bulk handling arrangements on the quayside are proving to be invaluable solutions for multipurpose ports; mobile Siwertell ship unloading systems are offering significant operational advantages to operators that need agile assets that perform on every level
can be moved very quickly to shore, dramatically reducing the time a ship stays in port and freeing up capacity for other activities on the berth,” explains Karlsson.
When finished, using a self-propelled rubber-tire gantry and an advanced steering system, the port-mobile unloader can be moved away from the quayside and even stowed when not in use. To secure the gantry in all directions when parked, the end pairs of axles, both on the sea-facing and land-facing sides, are turned by 90 degrees.
The port-mobile unloader has a low weight design and does not require rails or any other additional infrastructure or preparatory reinforcement to the quay. It is available in two sizes; a 400t/h and a 600t/h unit, both of which are capable of servicing vessels of up to 70,000 dwt.
As standard, they feature a double-truck loading system, with an optional third system. As they are not interlinked, one, two or all three loading positions can be used independently and simultaneously, delivering
the fastest truck loading operation possible; a largevolume intermediate surge hopper also smooths any truck changeovers.
“When fully road-mobile ship unloading systems are required, the agility, capability and overall performance of our road-mobile ship unloading range is impossible to beat,” says Karlsson. “They can literally transform a quay with minimal infrastructure into a terminal.”
Road-mobile units have a folding structure, which is mounted on a semi-trailer for easy transportation between ports. It only takes 30 to 45 minutes to complete the set-up procedure, with packing away being equally rapid. The road-mobile ship unloader can be deployed by a single operative, keeping staffing costs low.
Siwertell road-mobile unloaders are available in three different sizes: the Siwertell 5 000 S, 10 000 S and 15 000 S; the largest offering an unloading capacity of up to
An all-electric WSM grinder is setting construction, demolition and recycling industry standards for GreenWay Recycling; its owner, Terrell Garrett, shares how this has been both an investment in machinery and in a long-term partnership
THE GLOBAL CONSTRUCTION AND DEMOLITION INDUSTRY IS CHANGING; rising costs and stricter regulations to reduce landfill waste and reclaim wood and other recyclables, along with sustainability targets becoming an increasingly urgent and a key priority, means that establishing reliable, environmentally responsible construction and demolition recycling plants is essential.
GreenWay Recycling, a mixed construction, demolition sorting, and processing company, which operates in Northwest Portland, Oregon, USA, has relied upon an all-electric grinding solution from Bruks Siwertell company, West Salem Machinery (WSM), for well over a decade.
With a focus on reliability, longevity, and cost efficiency, the WSM machine has helped maintain seamless operations while minimizing costs, and even contributed to GreenWay Recycling being named construction and demolition (C&D) ‘Recycler of the Year’ in 2024, by the US Construction & Demolition Recycling Association (CDRA).
In 2008, GreenWay Recycling made a game-changing decision, it purchased a previously-owned and refurbished horizontal-fed 4864 model grinder from WSM. It was completely rebuilt, installed with a new motor, and made ready for long-term performance. Over 15 years later, this same grinder is still in operation, handling a relentless workload with minimal downtime.
GreenWay Recycling’s facility operates on a small footprint, leaving no room for material storage. The company relies upon its equipment to work without interruption, making the dependability on WSM machinery even more critical.
GreenWay Recycling’s founder and CEO, Terrell Garrett, shares how his partnership with WSM has been instrumental in the company’s success. “We have had a great ongoing relationship over all these years,” says Garrett.
A defining moment in GreenWay’s relationship with WSM came in 2014 when the 4864 grinder struck a large piece of iron, bending the center shaft 3.8cm (1.5in) out of alignment. The situation could have halted operations indefinitely, but WSM stepped in immediately.
“ The cost savings are significant
TERRELL GARRETT, CEO, GREENWAY RECYCLING
“WSM dropped everything to help us,” Garrett recalls. “They pushed aside some manufacturing that was scheduled and got us back up and running. They took care of us on all the replacement parts and really acted as our business partner.”
From this challenging situation came innovation. Recognizing that the grinder was hitting a lot of tramp metal, and the risk of encountering further larger pieces, which
“ WSM machines just run and run and run. You treat them as a heavy industrial machine and do the preventive maintenance and replacements, and they last forever
TERRELL GARRETT, CEO, GREENWAY RECYCLING
could pose a significant problem to its operations, WSM introduced the limited swing hammer; a design now widely used in its machines. “It does a great job of grinding, but it also helps protect the equipment when we hit big iron,” Garrett explains.
Currently, GreenWay Recycling is the only company in the Portland metro area operating a large stationary all-electric grinder, setting the construction, demolition and recycling industry standard for efficiency and environmental protection.
“Quite frankly, I don’t understand why everybody doesn’t have one,” says Garrett. “They can take the tramp metal; they can take the hits. They are also durable, having a 2.5-inch wear liner; we are still running the same wear liners we started with back in 2008, we have not worn them out yet.
“These WSM machines just run and run and run. You treat them as a heavy industrial machine and do preventive maintenance and replacements, and they last forever,” notes Garrett.
Garrett also firmly believes in the benefits of electric over diesel-powered machinery. “The cost savings are significant, not having to change the oil all the time, avoiding engine and clutch issues, and dealing with fewer moving parts overall,” he says. “There are considerable costs that we avoid, which others have to absorb. So, it is not just about consistency and reliability; it is also about lower operating costs.”
WSM stationary electric-drive wood-processing machinery has been delivered since 1947. Switching to
electric-drive wood-processing equipment can often transform operations. Compared with diesel-driven or hydraulic-driven alternatives, electric drives deliver substantial environmental and operational advantages to users. They are quiet, clean, highly efficient, and deliver stepless, precise controls, and also offer substantial energy savings, which reduces operating costs.
Furthermore, all-electric equipment is easy to maintain and is relatively simple to integrate and install, and condition-monitor, where applicable, through the use of all electric components.
Over the years, GreenWay has expanded its investment in WSM products, incorporating vibrating screens, conveyors, and disc screens into its operations. Each addition reinforces the company’s trust in WSM’s engineering and technology and in its customer service.
“The relationship with WSM has developed into a friendship,” Garrett notes. “We have a great back-and-forth dynamic. It has been an excellent ongoing relationship.”
WSM has a reputation for designing tough, long-lasting equipment, ideally suited to the demanding construction and demolition recycling sector. When combined with all electric-powered solutions, with their excellent environmental and efficiency capabilities, customerfocused service, and forward-thinking innovations, WSM ensures that companies, like GreenWay, are able to continue to thrive.
GreenWay Recycling’s success story is a testament to the power of making the right investment, not just in equipment, but in a trusted partner.
Bruks Siwertell Group’s sustainability goals and ambitions are assessed from an environmental, social, and governance (ESG) perspective, with each initiative falling into one or more of these categories.
Environmental factors consider an organization’s impact on the environment and the risks and opportunities in relation to it.
Social factors include how an organization performs in relation to its internal and external stakeholders.
Governance factors examine how an organization regulates itself, focusing on internal policies, best practice and legal compliance.
The outcome of our materiality analysis has resulted in challenging but clear focus areas and ambitions for 2030: Bruks Siwertell Group wants to set the sustainability standard for the industries that we serve and with ambitious targets, make a positive impact on surrounding ecosystems.
FOCUS AREAS
» Product development
» Reduce and limit CO₂ and greenhouse gas emissions
» Reduce energy use
» Reduce waste
FOCUS AREAS
» Health and safety
» Employee satisfaction
» Diversity and inclusion
FOCUS AREAS
» Anti-corruption
» Supply chain management
» Management systems
MEASURABLE GOALS
» 50% reduction in CO₂ emissions
» 90% circularity of products
» Zero waste in our office units
» 100% renewable energy
MEASURABLE GOALS
» Zero workplace accidents
» 30 eNPS score
» 30% female managers
MEASURABLE GOALS
» 100% of work processes updated and improved
» 100% compliance with Codes of Conduct for both suppliers and customers
Handling the Future is Bruks Siwertell Group’s sustainability commitment logo and communicates its ambitions to drive positive social, environmental, and governance change. Handling is a key word within the company; from ports to industrial settings, Bruks Siwertell technology handles material transfers. Together, the Group’s 2030 sustainability targets, along with collaborations with customers, suppliers, business partners and other stakeholders, aim to shape a sustainable future.
An ambitious 18-month rebuilding and modernization project at Bruks Siwertell Group company, Bruks AB, based in Arbrå, Sweden, is delivering both social and environmental benefits.
“This project has especially focused on increasing personnel satisfaction, diversity, and inclusion,” says Pär Eriksson, Managing Director, Bruks AB. “We already exceed the Group’s 2030 target of 30 percent female managers, achieving a gender-equal management team in 2024, but we are not complacent.
“We want modern facilities to provide an inviting, healthy, and happy workplace while attracting future talent. Diversity and inclusion are about more than numbers – we actively seek individuals with different backgrounds and personalities to create a dynamic leadership team.”
Beyond the social gains, the rebuild supports sustainability efforts, reducing energy consumption through better insulation, a new ventilation system, and high-specification windows. Waste handling, sorting, and recycling systems have also been significantly enhanced.
Recognizing the importance of a positive workplace culture and supporting its 2030 sustainability ambitions, Bruks Siwertell Group has rolled-out its Group-wide comprehensive diversity and inclusion training program, Gender Equality, Diversity, and Inclusion – from a business perspective.
The three-hour workshop challenges existing perspectives and provides practical tools to address biases, discrimination, and foster inclusivity in the workplace. A key element of the training was to help managers reflect on how their decisions impact inclusivity and what changes they could implement immediately to create a more inclusive and diverse environment.
“This was a course of great significance,” says Linda Hagengran, Finance Manager, Bruks AB, in Arbrå, Sweden. “I am
proud to be part of a company that prioritizes equality, diversity, and inclusion. We gained many valuable insights.”
The training was attended in person by management teams across Bruks Siwertell Group’s European sites in 2024, with online participation from its American operations.
Bruks Siwertell Group is advancing its environmental sustainability targets, aiming to reduce carbon emissions by 50 percent and transition fully to renewable energy by 2030. The installation of solar panels at Bruks Siwertell Group company, Bruks Siwertell AB, in Bjuv, Sweden, is helping to meet both of these goals.
“This project required cross-departmental collaboration and good communication,” says Peter Gustavsson, Logistics Manager, Bruks Siwertell. “It also highlights how we can integrate advanced renewable technologies into operations for tangible environmental benefits.”
Completed in late 2024, the project included the installation of 758 panels, each with a capacity of 590W, along with three Sungrow SG125CX-P2 inverters, each providing 125kW AC. The panels are estimated to generate approximately 400,000 kWh annually, which is equivalent to around a third of the site’s total energy consumption.
Bruks Siwertell Americas, Bruks Siwertell Group’s Atlanta-based business unit, has partnered with the Georgia Department of Natural Resources (GA DNR) to help restore Sprewell Bluff Park in Thomaston, a crucial conservation area.
The 26.3km² (6,495-acre) park, part of a wildlife management zone along the Flint River, is home to diverse ecosystems, including ancient longleaf pines.
“We see this as an ongoing commitment to the environment and our local community,” says Ken Upchurch, Senior Vice President, Sales and Marketing, Bruks Siwertell.
Working their way along 10km worth of Sprewell Bluff’s remote access roads, Bruks Siwertell volunteers removed around 400kg of litter and debris from the verges. The first annual clean-up event was held in September 2024.
FOLLOW THIS LINK TO SEE MORE SUSTAINABILTY INITIATIVES
LINDA HAGEN GRAN, FINANCE MANAGER, BRUKS AB “
I am proud to be part of a company that prioritizes equality, diversity, and inclusion
As the world transitions to circular carbon economies, solid biomass is emerging as a leading alternative to fossil fuels; Bruks Siwertell’s unique portfolio of biomass handling and wood-processing technologies is playing a critical role in these global shifts
“ The US could sustainably triple its annual biomass production
US DEPARTMENT OF ENERGY (DOE), 2023 BILLION-TON REPORT (BT23)
A CIRCULAR CARBON ECONOMY IS IN THE SIGHTS of many a heavy industry and global government. According to the International Energy Agency (IEA), by 2030, renewable fuels are set to account for around 5.5 percent of global energy consumption from the industrial, construction and transport sectors.
The IEA notes that demand is due to expand in all regions, but it is concentrated in China, Brazil, Europe, India and the United States, which collectively support more than two-thirds of the forecasted growth. Although policies for renewable fuels vary by fuel, sector and country, many include a combination of mandates, greenhouse gas performance criteria, and incentives to invest in direct production.
For numerous sectors, including transportation, industrial processing, and power generation, bioenergy, produced through the combustion of biomass, is driving their zero-emissions policies and decarbonization ambitions. Currently, bioenergy stands as the largest source of renewable energy globally, accounting for 55 percent of renewable energy and over six percent of the global energy supply, says the IEA.
The adoption of strong renewable energy targets and governmental policy developments often have a dual purpose, in addition to sustainability commitments, they are often seen as areas that can stimulate innovation and job creation, driving diverse, robust economies and supporting transitions to cleaner energy solutions.
Bioenergy is nothing new. In fact, it is the oldest source of energy used by humans. What is truly remarkable is today’s technological wood-processing and biomass handling capabilities, and the extraordinary potential that this market holds.
The world’s annual biomass production currently stands at an estimated 146 billion metric tons, derived predominantly from natural plant growth, says the IEA, and it forecasts a substantial role for bioenergy in achieving the Net Zero Emissions (NZE) scenario by 2050, while also contributing to negative emissions through bioenergy carbon capture and storage (BECCS), targeting 1.3 billion metric tons of CO2 per year.
Bruks Siwertell is uniquely positioned to facilitate sustainable bioenergy developments, and is already supporting these huge changes in power-generation plants, as they have switched from coal-fired to biomass-fired facilities.
For example, the UK stopped burning coal for power generation in 2024. A green transition supported by almost all aspects of Bruks Siwertell biomass handling and wood-processing portfolio.
The UK’s wood pellet supplies are predominately US imports, which are processed and handled using Bruks wood-processing equipment, truck receiving and ship loading systems. Once their transatlantic journey is complete, biomass is received and unloaded at several locations using five different rail-mounted, high-capacity ST 790-D Siwertell ship unloaders, the majority of which previously handled coal; change is possible.
Bruks Siwertell’s bulk handling solutions, including ship loaders, ship unloaders, and conveying systems, ensure that biomass is transferred safely, efficiently and at the high capacities required. Also, through totally enclosed, screw-conveying systems, which minimize material degradation and dust emissions, and eliminate spillage, these systems help meet industrial-scale biomass demands while reducing environmental impact.
Bruks Siwertell’s wood-processing expertise and innovative technology, with a strong US presence, supports the global biomass industry and its ability to reach its huge potential in securing a sustainable future. This position has been strengthened even further with the acquisition of the North American engineering and manufacturing company, West Salem Machinery (WSM).
According to the 2023 Billion-Ton Report (BT23), released last year by the US Department of Energy (DOE), the US could sustainably triple its annual biomass production to over one billion metric tons. This production level could meet the projected demand for sustainable aviation fuel (SAF), effectively decarbonizing its aviation industry.
Bruks Siwertell is actively involved in supporting this growth, providing advanced waste wood and agricultural byproduct processing technology and biomass handling solutions, which enhance the efficiency, environmental
protection and sustainability of biomass pellet production and feedstock operations.
Beyond aviation, biomass is increasingly used in heavy industries like steel and cement manufacturing, where lowcarbon fuel sources are being used for heating processes.
For example, in the steel industry, where traditional manufacturing methods are responsible for around five percent of CO2 emissions in the EU and seven percent globally, ‘green steel’ production is emerging as a cleaner, more environmentally friendly alternative.
A notable reference in this arena is Bruks Siwertell’s involvement in a new biocarbon pellet plant, based in Columbus, Mississippi, USA. The plant is part of a US joint venture company between Steel Dynamics Incorporated (SDI), the fourth largest steel producer in the US, and Aymium, SDI Biocarbon Solutions.
The new pellet plant will produce biocarbon, a carbonrich biomass-based anthracite replacement, which will supply SDI’s electric arc furnace steel mills with a renewable alternative to fossil fuel-based carbon sources using Aymium’s patented technology.
Bruks Siwertell’s equipment delivery scope for this project includes: a large, high-capacity Bruks Klöckner horizontal drum chipper; WSM screening and vertical green hammermill systems; and a Bruks radial stacker, as well as the complete conveyor system from receiving to the dryer delivery. The vast majority of equipment was sourced for supply from North America.
“ There are many stakeholders vying for raw materials in growth biomass sectors
KEN UPCHURCH, SVP SALES AND MARKETING, BRUKS SIWERTELL
The ability to tailor equipment into existing sawmill arrangements can not only maximize the effectiveness of byproduct handling, new systems can also offer higher levels of operational flexibility, enabling sawmills to unlock new markets
TEXT Maic Dillbahner and Rainer Benner PHOTOS Bruks Siwertell
SAWMILLS ARE PROCESS-DRIVEN FACILITIES that demand reliable, efficient, and durable equipment. A significant portion of a log, often up to 50 percent, becomes a byproduct, which must be effectively processed to minimize waste and maximize profits. Wood chips, in particular, are a key sawmill byproduct that serve multiple industries, including pulp and paper manufacturing, renewable energy, and composite board production.
“Wood chips from slabs, edgings, and trim ends must meet strict specifications for different applications,” explains Maic Dillbahner, Area Sales Manager, Bruks Siwertell. “For example, pulp mills require chips within a precise size range, typically 4mm to 6mm thick and 15mm to 20mm in length and width to ensure optimal fiber yields.
“We address these challenges by offering extremely robust, low-maintenance and high-performance equipment that enables sawmills to: produce consistent wood chip sizes for pulp, bioenergy, and other industries; minimize energy consumption and maintenance costs; efficiently process diverse wood residues; and enhance operational efficiency, sustainability and profitability,” Benner highlights.
“Key to the wood chip, is the chipper,” adds Dillbahner. “Sawmills need high-performance chipping, coupled with screening equipment, to maintain consistency despite natural wood variability. By offering flexible solutions, they can optimize byproduct handling, reduce waste, and tap into different markets. For example,
Integrated designs can include significant height differences between pieces of equipment
“ The new Bruks line didn’t just meet our expectations, it exceeded them
FRANCOIS SCHNEPF, MANAGING DIRECTOR, STEINBOURG SAWMILL
adjustable cutting lengths on industrial drum and disc chipping machines enable the sawmill to deliver wood chips to a variety of end users.”
Bruks Siwertell offers a wide range of industry-leading solutions for handling and processing sawmill byproducts. These include wood waste grinders, disc and drum chippers, hammermills, scalping screens, oscillating screens, vibrating conveyors, and low-friction, air-cushion conveying systems such as the Tubulator™ and The Belt Conveyor™.
Germany-based Bruks Siwertell company, Bruks Klöckner, has a reputation for setting the standard when it comes to high-capacity, reliable, precision chipping, with numerous sawmills relying on these capabilities for their byproduct handling systems.
A notable example is an installation at the Steinbourg sawmill, Scierie et Caisserie de Steinbourg, in northeast France, which has specialized in beech wood for over fifty years. It needed a new chipping solution to enhance its byproduct handling and
processing efficiency and mitigate unplanned downtime.
As a long-standing customer, Steinbourg turned to Bruks Klöckner for an integrated industrial disc chipper installation. “The new Bruks line didn’t just meet our expectations, it exceeded them,” says Francois Schnepf, Managing Director, Steinbourg sawmill.
“For our wood chip production, we need consistently high quality, which can only be achieved with a machine like the one from Bruks Klöckner,” continues Schnepf. “After more than ten years of collaboration, we see Bruks as a European reference for such technologies. We were particularly impressed by the machine’s ability to easily process even challenging materials, such as pieces of dry or fresh beech wood in different sizes.”
The Steinbourg installation was completed at the beginning of 2024 and includes a horizontal-fed RH 2000 Bruks Klöckner disc chipper, designed specifically for chipping hardwood, particularly beech, with a 470mm infeed and a powerful 160kW
main drive motor. The chipping disc has a diameter of 1,990mm and is equipped with five precisionengineered knives. It has a rated capacity of up to 20t/h and processes sawmill waste, including splinters, bark, and beech cuttings, simultaneously during the sawmilling process.
The Steinbourg system uses frequency converters for the main drive motors, optimizing power consumption, and a refined knife geometry further enhancing energy savings.
“Chipping short, dry hardwood pieces presents a notable challenge for many machines, mostly because of the wood’s density, coupled with the variation in feedstock size,” explains Dillbahner. “To ensure precise control over wood chip size, our design solution included the integration of an SH 8/2 free-swinging chip screen, which separates oversized pieces, and an additional DG 200 x 400 secondary drum chipper for processing them.
“Every sawmill installation is different and the integration of new machines into existing configurations always requires careful consideration,” he says. “For Steinbourg, a key hurdle
to overcome was the height difference between the chipper and the screening system. Essentially, the chip screen and secondary drum chipper needed to be installed on top of an 8m-high concrete wood chip silo. Our solution incorporated the use of fan blades mounted on the chipping disc to propel the wood chips up to the vibrating screen, eliminating the need for an additional blower.”
Crucial for the flexibility of this operation is that the chipping lengths can be adjusted on the disc chipper, enabling the sawmill to precisely meet the demands of different markets. “This enables Steinbourg to expand its customer base as and when different wood chip lengths are required,” Dillbahner says.
To maintain redundancy and operational continuity, the new machine was installed alongside the sawmill’s existing disc chipper. The flexible infeed technology allows residual wood to be processed through either system without requiring extensive modifications, ensuring a seamless transition to the new line and enhanced reliability.
“Communication with Bruks was outstanding from day one,” notes
Schnepf. “The team was highly flexible in implementing necessary adjustments and overcoming structural challenges. Their efficiency and reliability ensured that the project was completed on time, which was a key factor for us.”
“Our Steinbourg installation enables the sawmill to meet its capacity demands, and secure the operational reliability, efficiency and future market agility that it requires. It also demonstrates that by integrating advanced chipping, screening, and conveying technologies, we help sawmills process their byproducts effectively and unlock new revenue streams.
“Whether producing precision-sized chips for the pulp and paper industry, optimizing waste wood for bioenergy, or ensuring seamless byproduct handling, Bruks Siwertell empowers sawmills to meet industry demands with confidence. Our innovative solutions support operational reliability, future market adaptability, and environmental sustainability, ensuring that no wood is wasted and every byproduct has a purpose,” Dillbahner concludes.
“ We need consistently high quality, which can only be achieved with a machine like the one from Bruks Klöckner
FRANCOIS SCHNEPF, MANAGING DIRECTOR, STEINBOURG SAWMILL
Climates are changing, and the interface between land and sea is experiencing some of its most extreme effects; port terminals need to be ready for more climatic turmoil, and have access to dry bulk handling equipment that can be adapted for the challenge
UNPREDICTABLE CHANGE IS ON THE HORIZON. The Global Maritime Trends 2050 report, published in 2023 by shipping services group Lloyd’s Register (LR), notes that: “Of the world’s 3,800 ports, a third are located in a tropical band vulnerable to the most powerful effects of climate change, and other key ports are already under pressure; some of the world’s largest, could potentially be inoperable by 2050 with a rise in sea levels of only 40cm.”
Climates that were once temperate could become less so, leaving others becoming even hotter, and some wetter and stormier. Although the impact of modeled climate changes varies depending upon global location, according to TT Club, a leading independent provider of mutual insurance and related risk management services to the international transport and logistics industry, in general, port and terminal infrastructure are likely to be increasingly vulnerable.
It notes that port terminals face a climate trilemma: flooding from rising sea-levels and increased intensity of storm surges or heavy rainfall; high winds resulting in infrastructure damage, along with operational disruptions due to limitations on the safe working windspeed of the port or terminal assets; and high temperatures that may exceed design limitations of equipment, potentially resulting in asset failure or increased fire risk, together with welfare considerations for personnel in high temperatures.
TT Club says that these impacts are being felt now around the globe and the climate model predictions indicate that they are likely to grow in significance. The insurer explains that although there is variation in climate model predictions: “development and asset management plans must have a degree of flexibility built in
“ Operators investing in equipment now, must be doing so with climate change in mind
JAN KARLSSON, SALES DIRECTOR, BRUKS SIWERTELL
can be adapted to perform in temperatures from as low as -35 degrees Celsius up to +55 degrees Celsius.
For operating in very cold climates, the highest grades of steel have to be used, along with specially-adapted cabling, and hydraulics. Applicable for extremely cold, but especially very hot operations as well, all components, such as electric motors, have to be protected within housings.
Bruks Siwertell has a number of cold weather references, and a notable example includes the Yara fertilizer plant in Glomfjord, within the Arctic Circle. It is being served by its second Siwertell unloader, retiring its first after more than 30 years of operation.
Able to discharge vessels of up to 20,000 dwt, the unloader is equipped with a dust-suppression system
and an advanced electrical control unit, including the Siwertell monitoring system, known as SiMon. It started operating in 2019, and handles demanding dry bulk materials such as various rock phosphates and potash fertilizer at a continuous rated capacity of 600t/h, with a peak capacity of 700t/h.
The unloader meets strict environmental criteria, managing high prevailing winds and operating successfully in exceedingly cold conditions. When windspeeds are excessive, Bruks Siwertell equipment always comes with applicable storm locking devices and additional tie-downs if requested. All ensure the capability of withstanding the location’s weather conditions.
At the other extreme, Bruks Siwertell has numerous references for operating in very high temperatures. For example, returning customer Kuwait Portland Cement Co has been operating a Siwertell ST 490-F rail-mounted unloader for over two decades in Shuaiba Port, Kuwait City. It was joined in 2022 by a second similarly-sized ship unloader.
Both unloaders are adapted to operate in Kuwait’s extreme climate. To accommodate predicted temperature rises in the region, the latest unit is designed to withstand ambient summertime temperatures of up to 55 degrees Celsius.
“ Siwertell technology is tailormade and designed to be adapted to prevailing conditions
JAN KARLSSON, SALES DIRECTOR, BRUKSSIWERTELL
Stormy conditions have always existed, but are likely to become more problematic. Bruks Siwertell delivers equipment with lightning rods to withstand a lightning strike, and systems can be adapted to mitigate the impact of earthquakes, ensuring that they do not tip
over during seismic activity. This includes a 2024 order for a ship unloader that is designed to withstand seasonal typhoons and earthquakes and will serve one of the Philippine’s largest companies. Also, the new Siwertell ST 640 M-type unit will be installed on a particularly exposed jetty, and will be able to discharge grain from vessels from both sides.
For many terminals, scrupulously clean material handling is now a prerequisite to being granted an operating licence. Siwertell screw-type ship unloaders and loaders are totally enclosed, minimizing dust emissions and preventing spillage. Some installations require very strict environmental regulations. For example, the Boliden Tara Mines terminal in Dublin, Ireland, which handles extremely hazardous zinc and lead, required its ship loading system meet close-tozero dust emissions and very low noise levels.
Bruks Siwertell developed a totally new system, comprising a triple-enclosed belt-type ship loader, with luffing and slewing capabilities, a reversible shuttle-belt conveyor, with doubleembedded covers, as well as a triple-enclosed jetty and overland conveyor. The tailor-made dust extraction system consists of a two-stage filtration approach, with special high-efficiency particulate air (HEPA) filters forming the final stage of the process. The clean air released to the atmosphere from this filtration process contains no measurable particles.
Other adaptations and optional features include an emergency power supply, operator cabins, including a cabin arm, CCTV monitoring, surface treatments, and semi-automatic unloading and loading capabilities when operating with additional laser- and radar-based anti-collision systems.
“We know that every operation is different, but we also understand that every installation has to work in situ, accommodating environmental, geological and climatic considerations, as well as meeting any operatorspecific requirements and performance criteria,” stresses Karlsson. “This is why our technology is tailormade and designed to be adapted, offering peak market-leading performance whatever tomorrow’s conditions.”
Our strength lies in our people; Christian Ratzke, a mechanical technician based in Hirtscheid, Germany, brings his keen focus, dedication and engineering passion to enhancing wood chipper construction, installation and maintenance
I SPECIALIZE IN WOOD CHIPPING TECHNOLOGY and the manufacture of wood chippers, ensuring that they meet the highest performance standards for our customers worldwide. As well as concentrating on the technicalities of their production at Bruks Klöckner, which is a Bruks Siwertell Group company, my engineering background is used to focus on installation methods and their integration within existing systems, and global maintenance strategies, making sure that they operate efficiently wherever they are deployed.
The challenge of continuously improving the industrial chipping machines and making them more efficient fascinates me. There is always room to optimize performance, and that is what keeps my work exciting.
In my role, I work closely with apprentices, guiding them through their training and helping them develop essential skills. Beyond mentoring, I provide crucial technical expertise to customers, ensuring that their equipment is well-maintained and running smoothly. My work also involves coordinating with various companies, helping to ensure seamless project management and making smooth operational starts a reality.
Precision and attention to detail are essential in my job. Additionally, teamwork and the ability to find solutions collaboratively is an essential part in successfully completing projects.
What excites me most about my job is the process of developing new solutions, seeing machines in action, and ensuring that customers receive top-performing equipment. It is rewarding to see a machine that I have worked on performing as expected, helping customers achieve their operational and maintenance goals.
For me, working at Bruks Siwertell means being part of a company that delivers complete systems and collaborates across international branches. We work closely with our colleagues in Sweden and the USA, which makes every project dynamic and globally connected.
The company offers opportunities for personnel to work on sites around the world with high-quality machinery and cutting-edge technology. With a dynamic and global work environment, personnel gain invaluable experience while contributing to large-scale industrial projects. This means that we are all developing our skills, ensuring that we continue to set industry benchmarks and deliver excellence in every machine that we build, which is great for us personally, our customers and the company.