Wafer Etch A Cutting-Edge Technology Revolutionizing Semiconductor Manufacturing
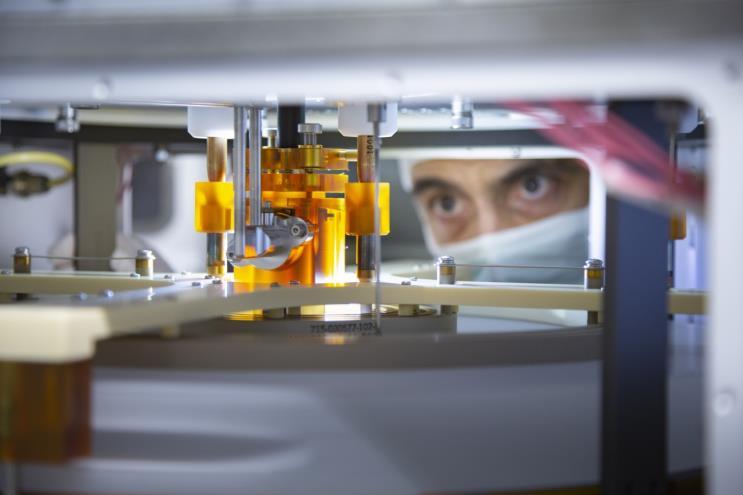
The world of semiconductor manufacturing has witnessed remarkable advancements over the years, leading to the development of smaller, faster, and more efficient electronic devices. Among the crucial processes in semiconductor fabrication, wafer, and etching holds a prominent place. Wafer etching involves selectively removing materials from the surface of a semiconductor wafer to create intricate patterns and structures necessary for integrated circuits. In recent years, a groundbreaking technique called Wafer Etch CA (Chemical Assisted) has emerged, revolutionizing the field and pushing the boundaries of what is possible. The intricacies of Wafer Etch CA, its benefits, and its impact on the semiconductor industry.
The Importance of Wafer Etching:
Before delving into the specifics of Wafer Etch CA, it's essential to understand the significance of wafer etching in semiconductor manufacturing. wafer machine etching is a critical process that enables the creation of precise patterns and structures on a semiconductor wafer. These patterns are essential for the formation of integrated circuits, which form the backbone of modern electronics. The ability to etch patterns with high precision and accuracy directly impacts the performance, power consumption, and overall functionality of electronic devices.
Traditional Etching Techniques:
Historically, two primary methods have dominated the field of wafer etching wet etching and dry etching.
• Wet Etching
Wet etching involves immersing the wafer in a liquid chemical solution that selectively removes the desired material. This technique relies on chemical reactions to etch the wafer surface. While wet etching is relatively simple and cost-effective, it suffers from limitations such as isotropic etching, where the etch rate is equal in all directions, leading to imprecise patterns and undercutting.
• Dry Etching
Dry etching, also known as plasma etching, employs plasma, a highly reactive gas, to remove material from the wafer surface. The most commonly used dry etching methods are reactive ion etching (RIE) and plasma etching. Dry etching offers better control over etch rates and enables anisotropic etching, which results in more precise patterns. However, it often requires complex equipment and can cause damage to delicate structures due to its high-energy nature.
What is Wafer Etch CA?
Wafer Etch CA, or Chemical Assisted Wafer Etch, is a cutting-edge etching technique that combines the advantages of wet and dry etching methods while mitigating their limitations. This innovative approach introduces chemical assistance during dry etching, resulting in improved control, precision, and selectivity.
How Does Wafer Etch CA Work?
In Wafer Etch CA, a carefully designed combination of gases and vapors is introduced alongside the plasma in the etching chamber. These chemicals interact with the wafer surface, enhancing the etching process by promoting selectivity and reducing damage to the underlying materials. By leveraging the synergistic effects of chemical and physical reactions, Wafer Etch CA achieves superior control over etch rates and profile shapes.
Advantages of Wafer Etch CA:
• Enhanced Selectivity
One of the significant advantages of Wafer and Etch CA is its improved selectivity. By introducing specific chemicals, the etching process can be fine-tuned to selectively remove target materials while leaving others intact. This selectivity allows for the creation of intricate structures with high precision and minimizes the risk of damage to adjacent features.
• Reduced Damage
Traditional dry etching methods often inflict damage on the wafer surface due to the high-energy nature of plasma. However, Wafer Etch CA significantly reduces the damage caused during the etching process. The chemical assistance acts as a buffer, preventing excessive sputtering and reducing the occurrence of defects. As a result, the overall quality and reliability of the fabricated devices improve.
• Improved Profile Control
Wafer Etch CA offers remarkable control over etch profiles, enabling the creation of complex three-dimensional structures. By manipulating the chemical composition and concentration,
engineers can achieve highly desirable profile shapes with steep sidewalls and minimal roughness. This level of control opens up new possibilities for advanced device architectures and novel manufacturing techniques.
• Compatibility with Advanced Materials
As semiconductor technology continues to evolve, the demand for etching techniques compatible with a wide range of materials grows. Wafer Etch CA meets this requirement by offering compatibility with various advanced materials, including compound semiconductors, IIIV materials, and low-k dielectrics. This compatibility ensures the versatility of the technique, making it suitable for next-generation device fabrication.
Impact on the Semiconductor Industry:
• Pushing the Boundaries of Miniaturization
The semiconductor industry is constantly striving for miniaturization, aiming to fit more components onto a single chip. Wafer Etch CA plays a vital role in this endeavor by enabling the creation of intricate patterns with high precision. With improved selectivity and profile control, semiconductor manufacturers can push the boundaries of miniaturization, resulting in faster, more efficient, and more powerful electronic devices.
• Enabling Advanced Device Architectures
The enhanced control and compatibility offered by Wafer Etch CA open up new possibilities for advanced device architectures. Three-dimensional structures, such as FinFETs and nanowires, can be fabricated with greater ease and precision, allowing for improved performance and reduced power consumption. This advancement paves the way for the development of novel semiconductor devices that were previously unachievable.
• Accelerating Research and Development
Wafer Etch CA's ability to provide precise control over etch rates and profiles accelerates the research and development process for new semiconductor technologies. Engineers and researchers can iterate faster, fine-tuning their designs and optimizing device performance. This increased efficiency in the development cycle fosters innovation and facilitates the rapid introduction of cutting-edge technologies to the market.
• Enhanced Cost-Efficiency
While Wafer Etch CA introduces additional complexities compared to traditional etching techniques, it offers significant cost-efficiency benefits in the long run. The improved selectivity
and reduced damage result in higher fabrication yields, reducing waste and increasing overall productivity. Additionally, the ability to etch a wider range of materials expands the utilization of existing manufacturing equipment, optimizing resource allocation and reducing capital expenditures.
Conclusion:
Wafer Etch CA represents a remarkable leap forward in semiconductor Wafer Machine Etching. By combining the strengths of wet and dry etching methods while mitigating their limitations, this cutting-edge technique unlocks new possibilities for device miniaturization, advanced architectures, and accelerated research and development. With enhanced selectivity, reduced damage, improved profile control, and compatibility with advanced materials, Wafer CA is poised to reshape the semiconductor industry, enabling the production of smaller, faster, and more powerful electronic devices that drive technological progress forward.