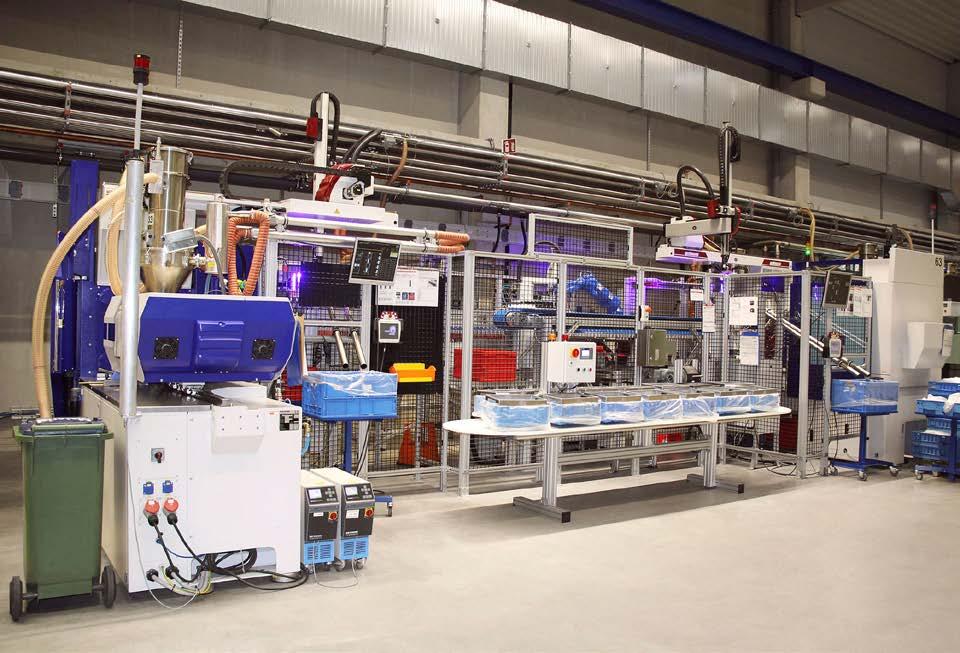
15 minute read
MASCHINEN/ PERIPHERIE
Flexible Verkettung von Spritzgiessmaschinen
Intelligenter Spritzguss
Advertisement
Happ, Hersteller von Teilen und Baugruppen für die Automobilindustrie, setzt für die Fertigung seiner Produkte Spritzgiessmaschinen der EcoPower-Reihe von Wittmann Battenfeld ein. Die flexible Verkettung zweier dieser Maschinen ermöglicht eine effiziente Produktion komplexer Baugruppen.
Die Firma Happ wurde 1964 gegründet. Die ersten Produkte des Unternehmens waren Butterbrotdosen und Möbelbe schläge. Mittlerweile beschäftigt das familiengeführte Unternehmen 70 Mitarbeiter, die im 3-Schichtbetrieb auf einer Produktionsfläche von 6000 m² qualitativ hochwertige, komplexe Teile und Baugruppen primär für die Automobilindustrie herstellen. Ein Teil des Umsatzes wird auch mit Produkten für die Weisse Ware erwirtschaftet. Das Unternehmen bietet seinen Kunden das gesamte Leistungsspektrum von der Entwicklung und Konstruktion über den hauseigenen Werkzeugbau bis hin zur Prototypen- und Serienfertigung.
Komplette Baugruppen vollautomatisch montieren
Happ verarbeitet über 1300 t verschiedener thermoplastischer Kunststoffe mit Spritzgewichten von 0,5 bis 3000 g im 1- und 2-Komponenten-Spritzguss. Zur Herstellung der Kunststoffkomponenten stehen an die 40 Spritzgiessmaschinen in den Schliesskraftgrössen von 350 bis 8000 kN zur Verfügung, darunter 7 Maschinen der vollelektrischen EcoPowerReihe von Wittmann im Schliesskraftbe reich von 1000 bis 3000 kN. Die Maschinen dieser Reihe sind zum Grossteil mit Robotern der Typen W818 und W822 ausgestattet. Zur Trocknung seines Materials setzt Happ eine zentrale Materi altrocknungsanlage ein.
Gesamtansicht der mittels staufähiger Fördersysteme verketteten Spritzgiessmaschinen der Type EcoPower 110/350.
Durch die konstante Investition in innova tive Automatisierungstechnik ist es Happ möglich, komplette Baugruppen vollautomatisch und damit mit höchster Präzision und Effizienz zu montieren. Zur Entwicklung und Herstellung dieser Automatisierungslösungen hat Happ am Standort in Ruppichteroth 2015 die Firma ErgoTek gegründet. Der Ursprung von ErgoTek geht auf ein von Happ 2014 entwickeltes Produkt für den Fitness- und Physiotherapiebereich, die sogenannte Ergo-Wall zurück. Dabei handelt es sich um eine in unterschiedliche Neigungen verstellbare Kletterwand unter Einsatz von Automatisierungsund Fördertechnik. An der Uni Potsdam werden aktuell Therapeuten an der ErgoWall ausgebildet.
Spritzguss und Fördertechnik
Das mit diesem Produkt gewonnene Know-how sollte mit ErgoTek sowohl für die Montage bei Happ als auch für den Einsatz in der Industrie genutzt werden. Seit 2018 werden die Module, die die Basis für die Modulförderer bilden, im Industrieumfeld eingesetzt. 2019 wurden die
Der Reverse Engineering Prozess ermöglicht die Rekonstruktion fehlender Daten. Werkzeuge, Bauteile und Design Modelle werden in ein gängiges CAD System zurückgeführt.
Flexi-Förderer (Testgerät) von ErgoTek aus Kunststoffteilen von Happ.

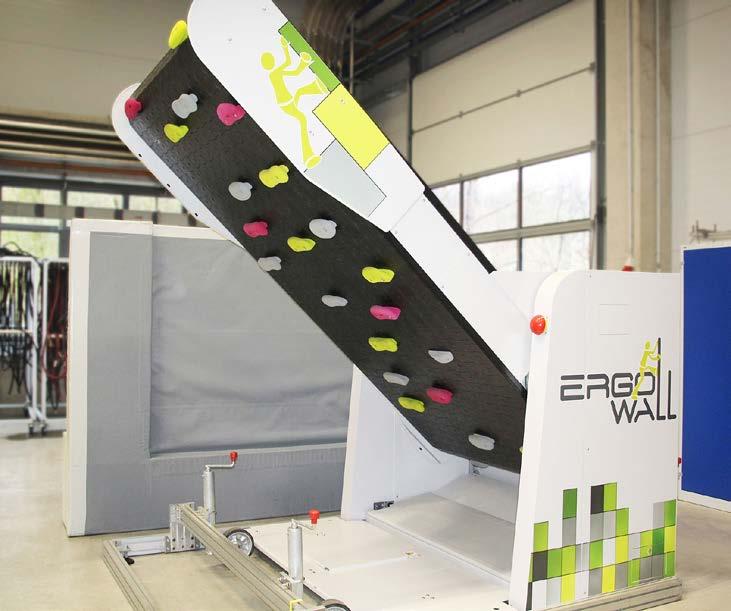
Ergo-Wall – erstes Produkt von ErgoTek für Freizeit und Physiotherapie.
Modulförderer, die im Wesentlichen für getaktete Systeme genutzt werden, um das FlexiTek-System erweitert. Die staufähigen FlexiTek-Systeme bieten hier ein sehr breites Anwendungsspektrum und sind optimal an die Anforderungen in der Spritzguss-Fertigung angepasst. Für 2020 ist eine Erweiterung des Portfolios um ein Schwerlastfördersystem für Gitterboxen geplant. Mit der Kompetenz der Firma Happ im Bereich der Kunststoffspritzguss-Fertigung und der langjährigen Erfahrung in der Förder- und Automatisierungstechnik werden Module entwickelt, die ErgoTek in den Fördertechnik-Systemen flexibel und modular einsetzen kann. Dabei wird ein besonderes Augenmerk auf die Wirtschaftlichkeit der Produkte gelegt.
Kontrolliert montieren
Ein kürzlich von ErgoTek in der eigenen Produktion umgesetztes Projekt ist die flexible Verkettung zweier EcoPower-Maschinen mittels staufähiger Fördersysteme. Mit diesem System werden vollautomatisch Aussen- und Innenrohr der Ablassschraube von Ölfiltern für die Automobilindustrie zusammengefügt, geprüft, laserbeschriftet und abgelegt. Zum Einsatz kommen bei dieser Anlage zwei EcoPower 110/350 mit einer Schliesskraft von je 1100 kN, die mit je einem Roboter des Typs W818 ausgestattet sind. Auf den Maschinen werden jeweils mit einem 2-fach-Werkzeug das Innenrohr bzw. das Aussenrohr der Ablassschraube für den Ölfilter gespritzt, mit den Robotern entnommen und einer Kameraprüfung zur Kontrolle der Masshaltigkeit der Teile zugeführt. Eine weitere Kamera prüft die Teile auf Gratbildung. In weiterer Folge werden die Rohre via FlexiTek-Förderer von ErgoTek weitertransportiert und zum Abkühlen gepuffert. Danach montiert ein Scara-Roboter das Aussenrohr auf das Innenrohr. Mit Hilfe eines Knickarm-Roboters und einer weiteren Kameraprüfung werden Tiefenmass und Winkelstellung kontrolliert und die Bauteile zur Laserbeschriftung an ein Beschriftungsband übergeben. Anschliessend erfolgt die Übergabe der fertigen Baugruppen an den Flexi-Buffer von ErgoTek.
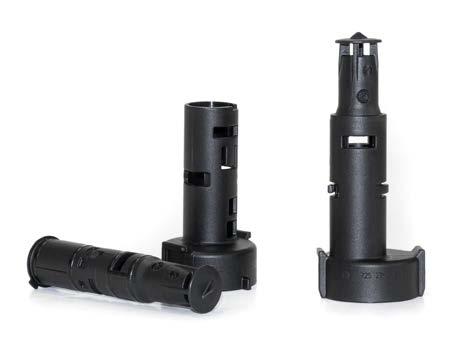
Foto: Wittmann Battenfeld
V.l.n.r.: Innen- und Aussenrohr einer Ablassschraube für einen Ölfilter sowie fertiges Produkt.
Minimaler Steuerungsaufwand
Mit dem Einsatz dieser verketteten Anlage ist eine wirtschaftliche Fertigung dieses Produktes erst möglich. Darüber hinaus bietet die Anlage eine Reihe weiterer Vorteile: –Durch die Verbindung der beiden Anlagenteile über die FlexiTek-Bänder kann auf eine Einlagerung der einzel nen Bauteile verzichtet werden, und die
Zuordnung der Nester und damit die
Nachverfolgbarkeit bleiben gesichert. –SPC-Teile können angefordert und über die Rutschen ausgeschleust werden. –Bei einer Unterbrechung an einer der
Anlagenteile können die weiteren Systemkomponenten bis zu maximal einer
Stunde weiter produzieren. –Der Boxenpuffer mit den Fertigteilen muss nur ca. alle 2,5 Stunden geleert werden. –Die Verkettung der FlexiTek-Förderer benötigt nur einen minimalen Steue rungsaufwand und lässt eine Trennung der einzelnen Sicherheitsbereiche zu.
Kontakt Battenfeld (Schweiz) AG Vogelsangstrasse 15 CH-8307 Effretikon +41 44 908 65 65 info@battenfeld.ch www.wittmann-group.com
High-Speed-Aufrüstung von Pultrusionsanlagen
Compounds aus LFT
Mit seinen Pultrusionsanlagen zur Herstellung von Compounds aus langfaserverstärkten Thermoplasten (LFT) hat der hessische Systemlieferant ProTec Polymer Processing GmbH in Asien immer mehr Erfolg. Zu den Kunden, die Kunststoffpellets auf mittlerweile zwei LFT-Anlagen produzieren, gehört Suzhou Sunway Polymer Co. Ltd. In China.
2017 kaufte der Compoundeur bei ProTec die erste LFT-Pultrusionsanlage mit 32 Strängen und einer Produktionskapazität von 500 kg/h Pellets. 2019 erwarb er eine zweite Einheit mit 64 Strängen und einem doppelt so hohen Output. Ausserdem bestellte das Unternehmen im vergangenen Jahr zwei gravimetrische Dosier- und Mischsysteme vom Typ Somos Gramix S9, die auf den Anlagen ab diesem Jahr eingesetzt werden.
Mit Hilfe des Strangziehverfahrens – die englische Bezeichnung «pultrusion» leitet sich aus den Begriffen «pull» und «extrusion» ab – lässt sich eine breite Palette an faserverstärkten Kunststoffen fertigen. Auf Pultrusionsanlagen von ProTec können Kunststoffhersteller LFT-Pellets hocheffizient und automatisiert fertigen. Für die Faser-Polymer-Kombinationen lassen sich nahezu alle gängigen Thermoplaste nutzen und je nach Anforderung mit Glas-, Stahl-, Aramid- oder Kohlefasern verstärken. Die LFT-Pellets werden im Spritzguss zu hoch belastbaren Leichtbauteilen mit sehr guter Oberflächenqualität verarbeitet und im Automobilbau, in der Elektro-, Verpackungs- und Sportartikelindustrie sowie in der Luft- und Raumfahrt eingesetzt. Abnehmer der 1998 gegründeten Suzhou Sunway Polymer sind chinesische Tier
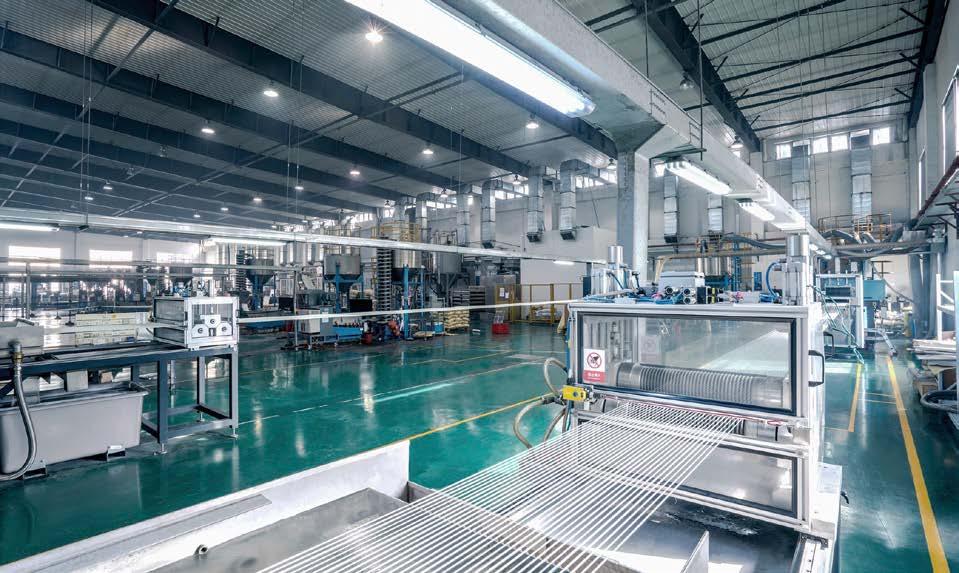
2017 kaufte Sunway bei ProTec die erste LFT-Pultrusionsanlage mit 32 Strängen und einer Produktionskapazität von 500 kg/h Pellets (im Vordergrund), 2019 eine zweite Einheit mit 64 Strängen und einem doppelt so hohen Output.
1-Zulieferer der Automobilindustrie, die für nationale, amerikanische, japanische und deutsche Pw-Hersteller Exterieur- und Interieurbauteile fertigen. Das Unternehmen produziert jährlich rund 100000 t Kunststoffcompounds, 2018 erzielte es einen Umsatz von etwa 150 Mio. EUR. Sowohl in der Fertigung als auch bei der Messund Prüftechnik vertraut Sunway auf europäische und japanische Lieferanten.
Produktpalette erweitert
Auf ProTec aufmerksam wurden der Sunway-Produktionsleiter Chang Chun You und Produktentwickler Qi Bang Huang durch eine LFT-Pultrusionsanlage der Deutschen bei einem anderen Anwender in der Region. Sie sahen für Sunway die Möglichkeit, ebenfalls in die wirtschaftliche Fertigung von Langfaserthermoplasten einzusteigen. Damit will das Unternehmen sein Sortiment vergrössern, erklärt Produktentwickler Qi Bang Huang: «Unser Ziel ist es, Sunway-Kunden aus der Automobilbranche stets innovative Produkte und Lösungen anzubieten und dadurch Qualitäts- und Kostenvorteile zu verschaffen.» Mittelfristig will das Unternehmen auch nach Europa expandieren.
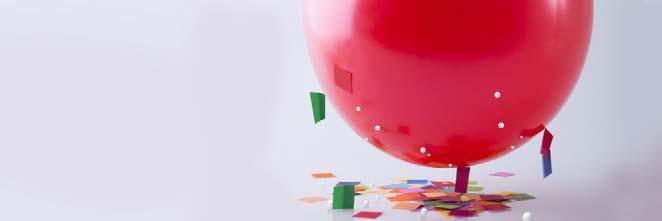
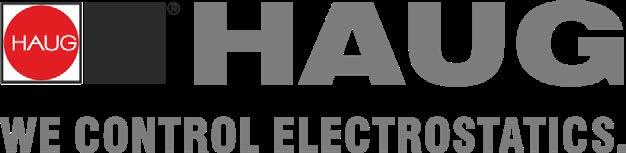
HAUG BIEL AG
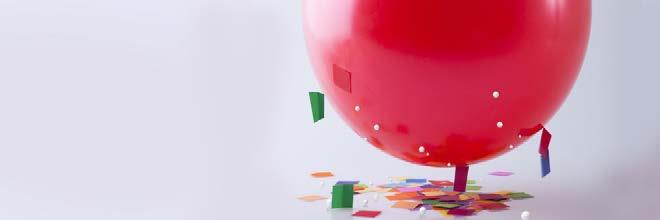
Johann-Renfer-Str. 60 Postfach CH-2500 Biel/Bienne 6 Tel.: +41 (0) 32 344 96 96 Fax: +41 (0) 32 344 96 97 info@haug.swiss www.haug.swiss
Auf den Pultrusionsanlagen von ProTec fertigt Sunway LFT-Pellets hocheffizient und automatisiert.
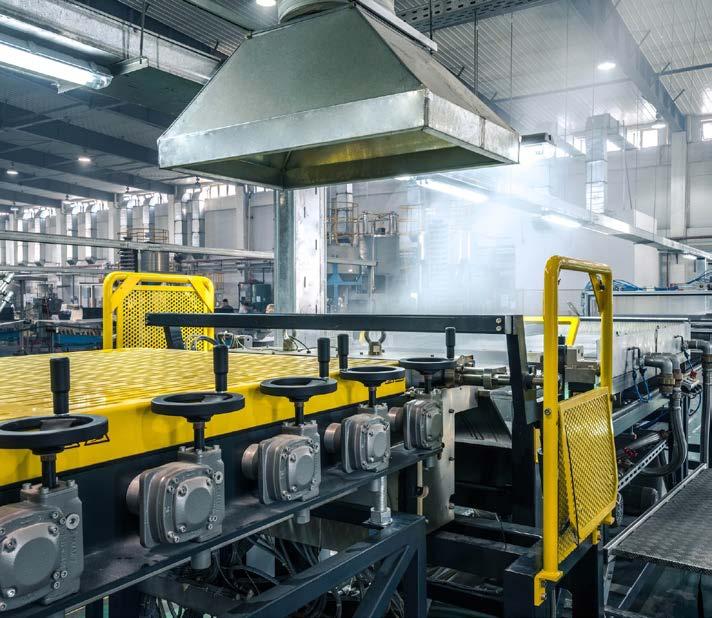

Für die Fertigung von LFT-Pellets lassen sich nahezu alle gängigen Thermoplaste nutzen und je nach Anforderung.
Alles aus einer Hand
Auch Produktionsleiter Chang Chun You war von der ProTec-Referenzanlage überzeugt: «Die Qualität, Sicherheit und Effizienz hat mich begeistert.» Fei Peng, General Manager bei ProTec Polymer Processing in Shanghai, war zentraler Ansprechpartner und half bei der anwendungsspezifischen Konfiguration der Sunway-Anlagen: «Planung, Bau und Inbetriebnahme kommen bei ProTec aus einer Hand. Denn wir bieten neben LFT-Pultrusionsanlagen Komponenten, Lösungen und schlüsselfertige Anlagen für das gesamte Materialhandling einschliesslich Dosieren, Trocknen und Fördern.»
Mehr Produktivität, weniger Kosten
Sunway gehört zu den ersten Unternehmen, die sich für die neue High-SpeedAufrüstung von ProTec-Pultrusionsanlagen interessieren. Die Produktionsgeschwindigkeit bestehender Anlagen lässt sich dadurch mit geringem Aufwand von 30 m/min auf 50 m/min steigern. Der Output hochwertiger LFT-Pellets wird so um bis zu zwei Drittel erhöht, entsprechend sinken die Produktionskosten. Mit der Neuerung reagiert der international tätige Systemlieferant für die Kunststoffindustrie auf die zunehmende Nachfrage nach seinen Anlagen aus China. Sie sollte ursprünglich auch zu den Highlights des ProTec-Messeaufritts auf der abgesagten Chinaplas zählen.
Mehr LFT-Pellets schneller produzieren
Für die High-Speed-Aufrüstung sind an bestehenden Pultrusionsanlagen nur wenige Modifikationen und Ergänzungen notwendig. Unter anderem wird eine zusätzliche Vorheizung integriert und die Werkzeuggeometrie optimiert. Dadurch beschleunigt sich die Temperierung der Fasern, so dass sie auch bei einem deutlich höheren Produktionstempo perfekt imprägniert werden. Durch ein zweites Wasserbad wird ausserdem die Kühlkapazität erweitert. Den Granulator hat ProTec ebenfalls verändert. In der High-Speed-Variante schneiden speziell angeordnete Rotormes

ser die Pellets bei hohen Geschwindigkeiten auf die optimale Verarbeitungslänge von 6 bis 12 mm.
LFT zur Verstärkung von Bauteilen
Momentan entwickelt ProTec weitere innovative Anwendungen, die mit Hilfe seiner LFT-Pultrusionsanlagen hergestellt werden können. Dazu gehört eine Technologie, um auf Pultrusionsanlagen langfaserver stärkte Thermoplast-Profile produzieren zu können, beispielsweise für den Einsatz als Armierungen in der Bauindustrie. Darüber hinaus arbeitet ProTec an besonders stabilen imprägnierten Fasersträngen, mit denen sich Spritzgussteile in der Automobilund Luftfahrtindustrie verstärken lassen.
Kontakt ProTec Polymer Processing GmbH Vertretung in der Schweiz: Ingenieurbureau Dr. Brehm AG Lettenstrasse 4 CH-6343 Rotkreuz +41 41 790 41 64 info@brehm.ch www.brehm.ch
Moderne Vakuumtechnologie zur Schmelzeentgasung beim Extrudieren
Entgasung ohne Betriebsmittel
Der Compoundierer PolyComp setzt bei seiner breiten Produktpalette auf Entgasungssysteme der Firma Busch. Deren umweltverträgliche Lösung benötigt kein Betriebsmittel, das anschliessend teuer entsorgt werden müsste.
Die Firma PolyComp GmbH ist als Compoundierer sowohl Auftragsfertiger als auch Lizenzhersteller komplexer techni scher Kunststoffe. Die Rezepturen reichen von Hochtemperatur-Kunststoffen über hochfeste technische Thermoplaste bis hin zu weichen, flexiblen thermoplasti schen Elastomeren, denen auf Wunsch verschiedene Additive zugesetzt werden. Das grosse Produktportfolio erfordert eine flexible Produktion mit unterschiedlichen Extrudern und teilweise speziellen Schneckenkonfigurationen. Bei den Extrudern gibt es allerdings eine Konstante: Bei der Absaugung von Dämpfen und Gasen aus der Schmelze in den Schneckenzonen verlässt sich PolyComp ausschliesslich auf Plastex Entgasungssysteme der Firma Busch Vacuum Solutions. Die mit MinkKlauen-Vakuumpumpen ausgestatteten Systeme sind äusserst betriebssicher und einfach zu warten.
Breites Produktportfolio
PolyComp ist im Jahr 2000 als Management-Buy-Out entstanden und hat seinen Hauptsitz in Norderstedt vor den Toren Hamburgs. Seit 2013 gehört PolyComp zur Hamburger Feddersen-Gruppe, deren Unternehmen sich auf den weltweiten Handel mit chemischen und technischen Produkten konzentrieren. Zum Kerngeschäft von PolyComp gehört die Compoundierung von Polyolefinen (PP/PE), aber auch von EVA, PA, PBT, PC, ABS, EVOH, POM und PMMA. In diese Compounds werden verschiedene Additive von Carbon- oder Naturfasern, einfachen Füllstoffen bis hin zu Glaskugeln, Farbadditiven oder Wachsen eingemischt. Eine Spezialität von PolyComp sind Foliencompounds, bei denen extrem niedrige Gelanteile gefordert werden. Dabei wird mit speziellen Schneckenkonfigurationen

Die beiden Seitendosierungen am Doppelschneckenextruder. Ein Plastex-Entgasungssystem sorgt für eine Volumenreduzierung bei der Füllstoffzufuhr.
extrudiert und ein Siebwechsler mit hoher Filtriergenauigkeit verwendet. Insgesamt wird auf acht Ein- oder ZweischneckenExtrudern gearbeitet. Bei sechs Extrudern wird die Schmelze entgast.
Hohe Kosten für die Entsorgung
Bis 2009 wurden dazu FlüssigkeitsringVakuumpumpen eingesetzt. Instandhal tungsleiter Stefan Stolp kann sich noch gut daran erinnern: «Die Entsorgung des gebrauchten Wassers wurde mehr und mehr zum Problem, da Gase und Dämpfe sich damit vermischten beziehungsweise darin auskondensieren konnten. Die Kosten für die Aufbereitung oder Entsorgung des Wassers wurden immer höher.» Henning von Brühl, Assistent der Produktionsleitung, ergänzt: «Wir konnten auch nie genau vorhersagen, was sich für Stoffe im Wasser anreicherten. Es waren nicht nur Gase, Dämpfe und Polymere aus den Grundstoffen, sondern auch Bestandteile aus Additiven konnten sich im Betriebsmittel dieser Vakuumpumpen ablagern.» Grund dafür war auch ein häufiger Wechsel der Rezepturen. Selbst bei gleichen Grundstoffen konnte sich durch verschiedene Additive die Zusammensetzung der Stoffe im Wasser verändern. Da bei Poly Comp im Drei-Schicht-Betrieb in FünfTage-Wochen gearbeitet wird, kamen erhebliche Wassermengen zur Aufbereitung zusammen.
Umweltfreundlich entgasen
Auf der Suche nach einer umweltverträglichen Lösung kam 2009 der Kontakt zur Firma Busch zustande, die ein Plastex Entgasungssystem ohne Betriebsmittel anbot. Das System besteht im Wesentli
chen aus einer Mink-Klauen-Vakuumpumpe und einem vorgeschalteten Standund Feinfilter. Die Filter dienen der Abscheidung von Kondensaten und Feststoffen. Mink-Klauen-Vakuumpumpen benötigen keine Betriebsmittel wie Wasser oder Öl. Das heisst, die zu fördernden Dämpfe und Gase kommen mit keinerlei Betriebsmitteln in Berührung, mit denen sie sich vermengen oder reagieren könn ten. Trotz sorgfältiger Abscheidetechnik lässt es sich nicht immer vermeiden, dass dennoch Restmonomere in das Pumpeninnere gelangen und dort vercracken können. Deshalb ist die Mink-Klauen-Vakuumpumpe mit einer Spülvorrichtung ausgestattet. Damit kann nach einem definierten Intervall eine Spülflüssigkeit genau dosiert der Vakuumpumpe zugeführt werden, sodass die Vercrackungen aufgelöst werden. Instandhaltungsleiter Stefan Stolp hat je nach extrudiertem Material die Spülflüssigkeitsmenge und die Intervalle festgelegt, in denen gespült wird. Dies kann während Stillstandzeiten oder auch während des laufenden Betriebs erfolgen.
Geringer Wartungsaufwand
Nach Anschaffung der ersten PlastexEntgasungssysteme wurden nach und nach alle Flüssigkeitsring-Vakuumpumpen ausgetauscht. Stolp zeigt sich damit äusserst zufrieden, zum einen wurde das Problem mit dem Abwasser gelöst, zum anderen arbeiten die Entgasungsanlagen absolut zuverlässig und mit geringem Wartungsaufwand. Die Filter müssen re
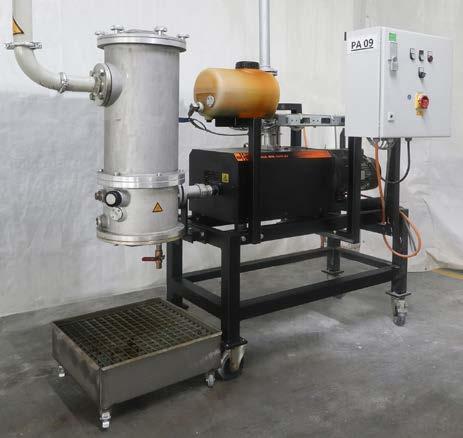
Eines von insgesamt sieben Plastex-Entgasungssystemen bei PolyComp. Sie sind jeweils ein Stockwerk über den Extrudern aufgestellt. Mink-Klauen-Vakuumpumpen sind das Herzstück von Plastex-Entgasungssystemen. Durch das berührungsfreie Funktionsprinzip wird kein Betriebsmittel wie Wasser oder Öl benötigt.
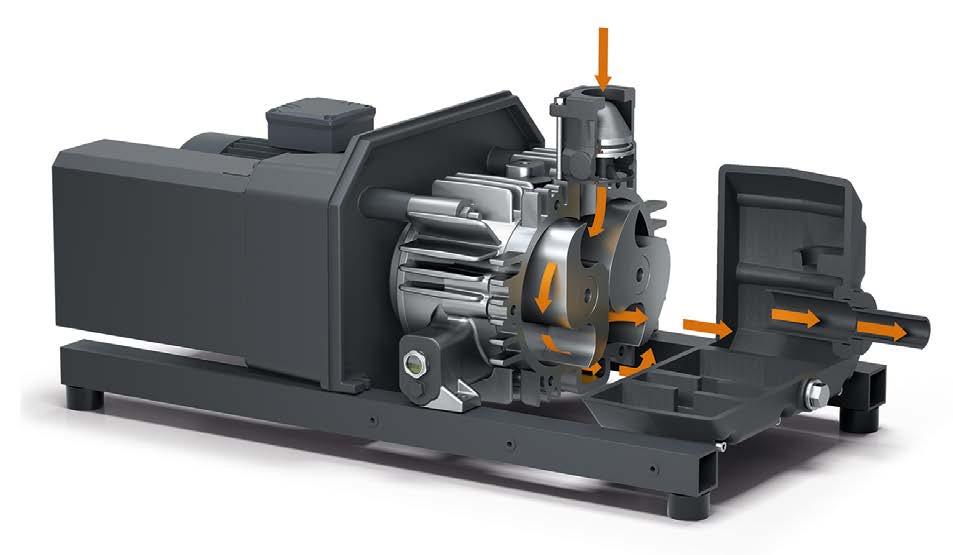
gelmässig gereinigt werden und die Spülflüssigkeit wird bei Bedarf aufgefüllt. Je nach zu verarbeitendem Material ge schieht dies unterschiedlich oft. Diese Arbeiten werden direkt vom Personal in der Produktion durchgeführt. Durchschnittlich nach 10 Monaten wird von der Instandhaltung jede Vakuumpumpe demontiert und gereinigt. «Alles in allem ein sehr überschaubarer Aufwand, verglichen mit den Arbeiten an den früher eingesetzten Flüssigkeitsring-Vakuumpumpen», so Henning von Brühl.
Hoher Wirkungsgrad
Einen weiteren Vorteil durch den Einsatz der Plastex-Entgasungssysteme sieht Simone Patermann. Sie hat als Bereichsleiterin Produktion auch stets den Energieverbrauch im Blick, zumal PolyComp nach dem Energiemanagementsystem ISO 50001 zertifiziert ist. Mink-Klauen-Vakuumpumpen haben den höchsten Wirkungsgrad aller mechanischen Vakuumtechnologien. Das heisst, die Stromaufnahme ist, verglichen mit anderen mechanischen Vakuumpumpen, bei gleicher Leistung stets geringer. Das hängt im Wesentlichen von zwei Faktoren ab. Erstens: Durch den Wegfall des Betriebsmittels entfällt die Leistung, die aufgebracht werden muss, um dieses zu fördern. Zweitens: Die Vakuumpumpen arbeiten völlig berührungsfrei. Daher gibt es keine Bauteile, die aneinander reiben und es muss keine Kraft zur Überwindung der Reibung aufgebracht werden.
Keine Ausfälle mehr
PolyComp hat 2018 eine weitere Extrusionslinie in Betrieb genommen, deren Herzstück ein Doppelschneckenextruder mit einer Durchsatzleistung von bis zu 1500 Kilogramm pro Stunde ist. Durch die beiden Seitendosierer können verschiedenartige pulverförmige Füllstoffe gleichzeitig eindosiert und mit hoher Ausstossleistung eincompoundiert werden. Ein Seitendosierer kann an eine Plastex Entgasungsanlage angeschlossen werden. Dadurch verringert sich das Volumen von Füllstoffen, und die Schüttdichte kann, im Vergleich zu einer Seitendosierung ohne Entgasung, bis zum Dreifachen gesteigert werden. Dies steigert die Gesamtdurchsatzleistung erheblich. Die Verantwortlichen bei PolyComp sind sich einig, dass sie mit den Plastex-Entgasungssystemen von Busch die richtige Wahl hinsichtlich Betriebssicherheit, Wartungsaufwand und Wirtschaftlichkeit getroffen haben. Die hohe Zuverlässigkeit wirkt sich auch positiv auf die Produktion aus. Stillstandzeiten durch Ausfälle oder durch plötzlich notwendige Reparatur- oder Reinigungsarbeiten wie früher bei den Flüssigkeitsring-Vakuumpumpen sind passé.
Kontakt Busch Vacuum Pumps and Systems Waldweg 22, CH-4312 Magden +41 61 845 90 90 info@buschag.ch www.buschvacuum.com
Moderne Recompoundieranlage neu im Technikum von KraussMaffei
Anlagenkompetenz trifft Rezeptur-Know-how
Hohe Recompoundqualitäten bei hohen Durchsatzleistungen von mehreren Tonnen pro Stunde – dafür steht die Edelweiss-Compounding-Technologie von KraussMaffei. Der Maschinenbauer hat das bereits bekannte Verfahren jetzt nochmals optimiert und erweitert.
Mit einem hohen Investitionsvolumen baut KraussMaffei die Möglichkeiten für Kunden- und Eigenversuche rund um das Thema Recycling und Recompoundierung aus. Seit einigen Monaten ist am Standort Hannover eine Recompoundieranlage im Industriemassstab in einem Technikum aufgebaut. Die Edelweiss-CompoundingAnlage besteht aus zwei Zweischnecken extrudern ZE 65 Blue Power und erreicht eine Maximalleistung von rund 2000 kg/h. War es bisher üblich, einen Ein- und einen Zweischneckenextruder zu nutzen, so ist die Nutzung von zwei Zweischneckenextrudern ein Novum. Die Vorteile sprechen für sich: hohe Entgasungsleistungen, Geruchsentfernung, ideale dispersive und dispergierende Mischwirkung, schonende Schmelzebehandlung und das alles bei hohen Durchsatzleistungen. In Stufe 1 übernimmt der Zweischneckenextruder ZE 65 Blue Power zunächst die Aufgabe, die mit bis zu 10 % Feuchtigkeit ankommende Eingangsware zu entgasen. Gleichzeitig erfolgt hierdurch die Entfernung von anhaftenden Geruchsstoffen, was gerade bei PostConsumer-Ware sehr wichtig ist. Mit Hilfe der Schleppmittelentgasung mit Wasser, Stickstoff oder auch Kohlendioxid lässt sich eine Geruchsminimierung erzielen. Im zweiten Zweischneckenextruder, in den die Schmelze über eine Schmelzeleitung gelangt, liegt in Stufe 2 der Fokus auf der Compoundierung. «Füllen, Ver stärken, Einfärben, Additivieren – mit dem Zweischneckenextruder ist jede Verfahrensaufgabe problemlos umsetzbar. Dazu sind unsere Extruder mit allen Zusatzaggregaten zur Dosierung von Granulat, Pulver, Fasern und Flüssigkeiten ausgestattet», hebt Carl-Philip Pöpel, Direktor Produkt-Management Extrusionstechnik, hervor.
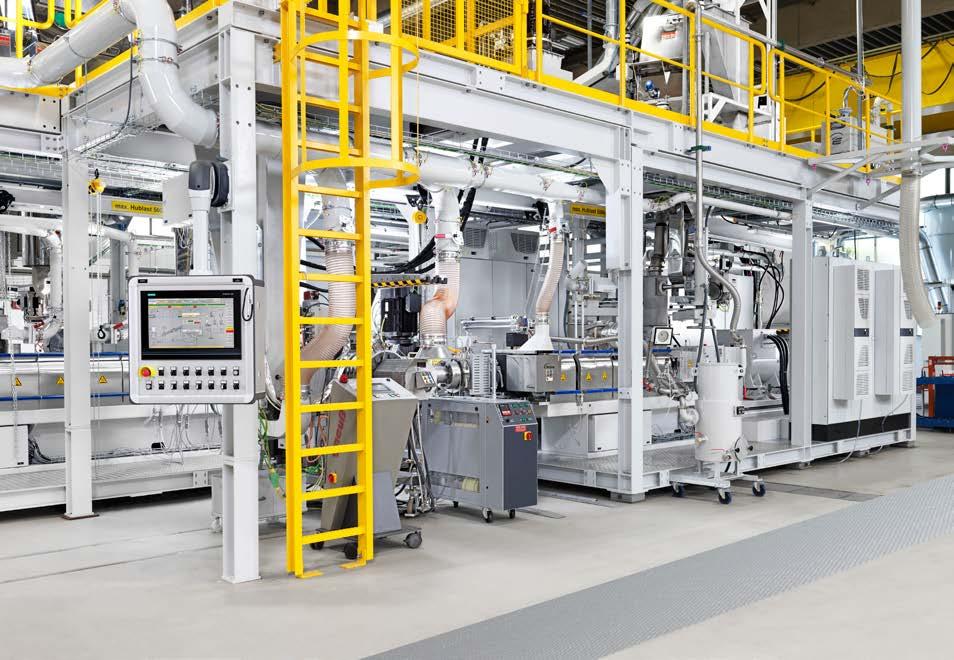
Die Compounding-Anlage mit zwei Zweischneckenextrudern ZE 65 Blue Power ist ausgelegt für eine Maximalleistung von rund 2000 kg/h.
Eigene CutterCompactor-Einheit
Eine weitere Neuerung der Anlage ist, dass die Cutter-Compactor-Einheit offline betrieben und das erzeugte Agglomerat auf eine Bandwaage ausgetragen wird. «So stellen wir eine gravimetrische Zudosie rung sicher, die eine Genauigkeit von 99,8 % erreicht», stellt Pöpel den entscheidenden Unterschied zur bisher verwendeten volumetrischen Dosierung heraus. Damit sind Dosierschwankungen, die sich beispielsweise bei sehr fluffiger Eingangs ware wie der Folien- oder Faserfraktion ergeben, ausgeschlossen. Nun lassen sich alle Post-Consumer-Fraktionen aus LDPE, HDPE, PP oder PS problemlos zu einem hochwertigen Recompound, das sowohl in Spritzguss- als auch Extrusionsanwendungen als Neuwaresubstitut Einsatz findet, aufbereiten.
Verarbeitung von PostConsumer-Recyclingware
Last but not least ist der Clou der im Technikum aufgebauten Anlage ihre Komplettintegration in ein Turnkey-Modul. Hauptvorteile für den Betreiber sind die einfache Inbetriebnahme, der flexible Einsatz und der Aufbau ohne jegliche Vorbereitung. Das Turnkey-Modul ist so ausgeführt, dass es in jeder Halle aufgestellt werden kann. Es muss bei Anlieferung lediglich an die örtliche Strom-, Wasserund Druckluftversorgung angeschlossen werden und kann die Produktion sofort aufnehmen.
Kontakt KraussMaffei Extrusion GmbH An der Breiten Wiese 3-5 D-30625 Hannover www.kraussmaffei.com