Rollers in Offset Printing – Ensuring Consistency and Durability
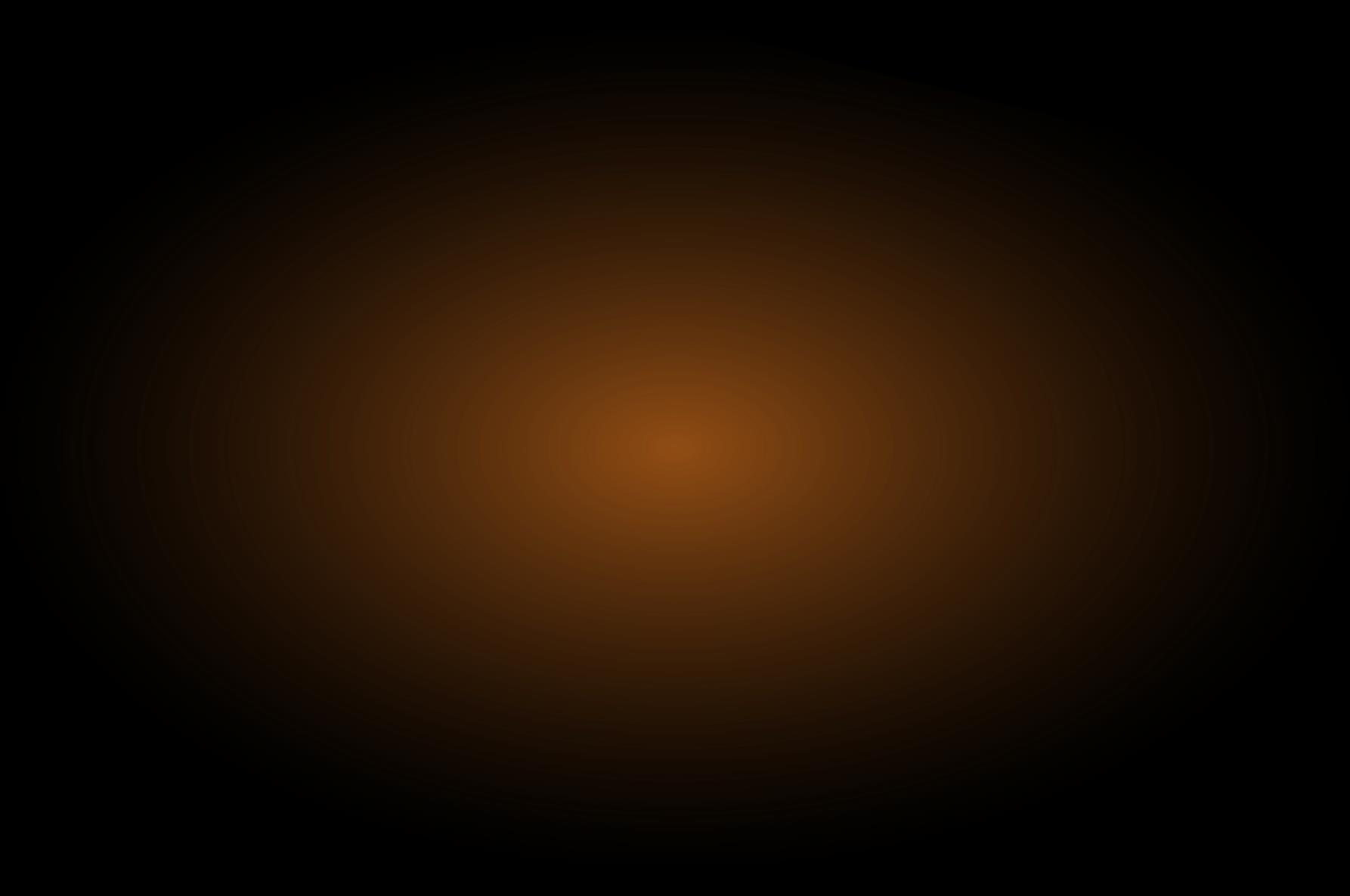
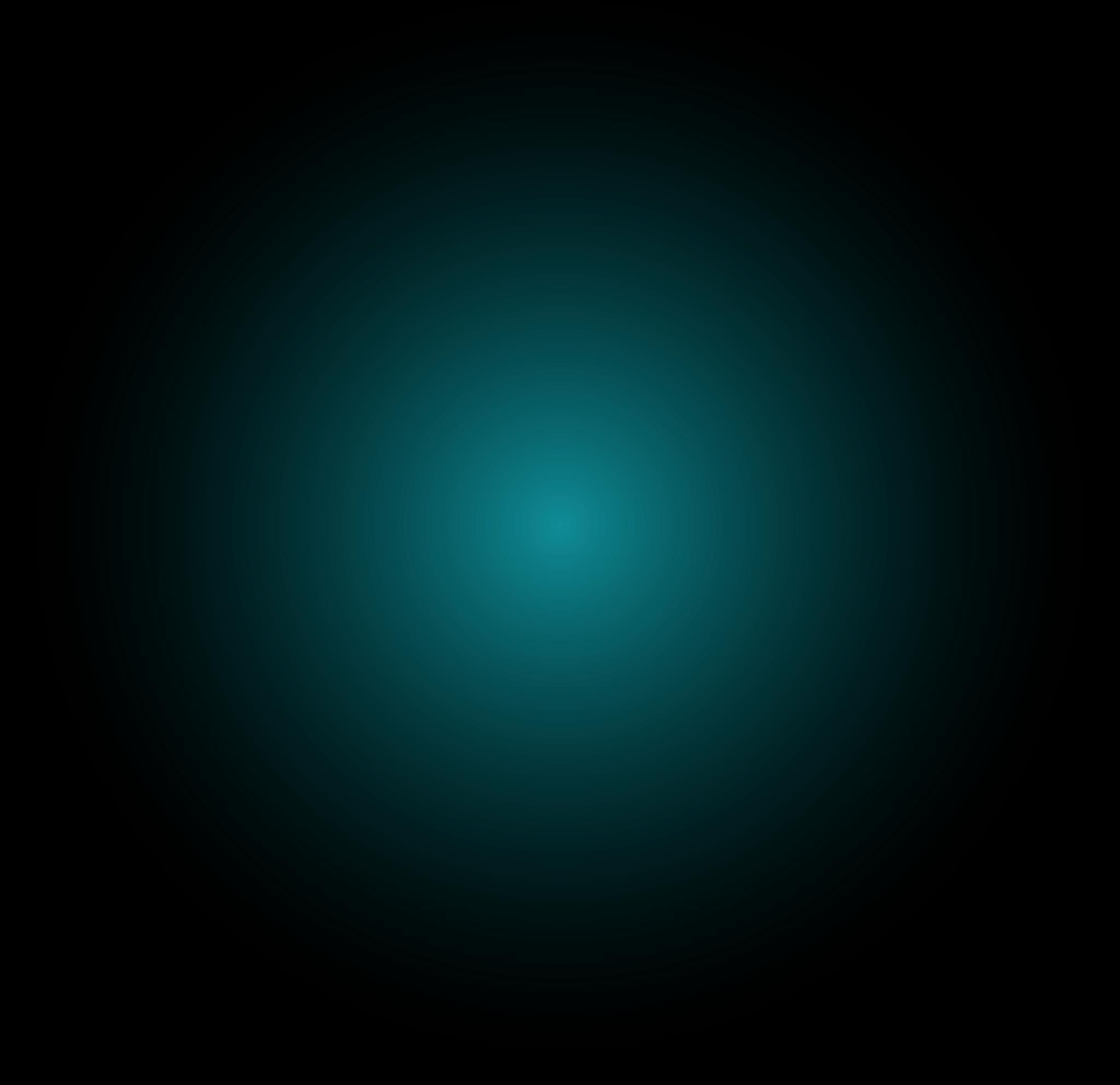
Offset printing relies heavily on rollers to transfer ink from the plate to the rubber blanket and finally onto the substrate. These rollers must maintain uniform pressure and ink distribution to achieve sharp, consistent prints, especially during large runs. Materials like rubber or polyurethane are commonly used for their efficient ink transfer capabilities and resistance to wear. Regular maintenance, including cleaning and inspection, is essential to prevent ink buildup and ensure the longevity of the rollers, thereby reducing downtime and maintaining high-quality outputs.
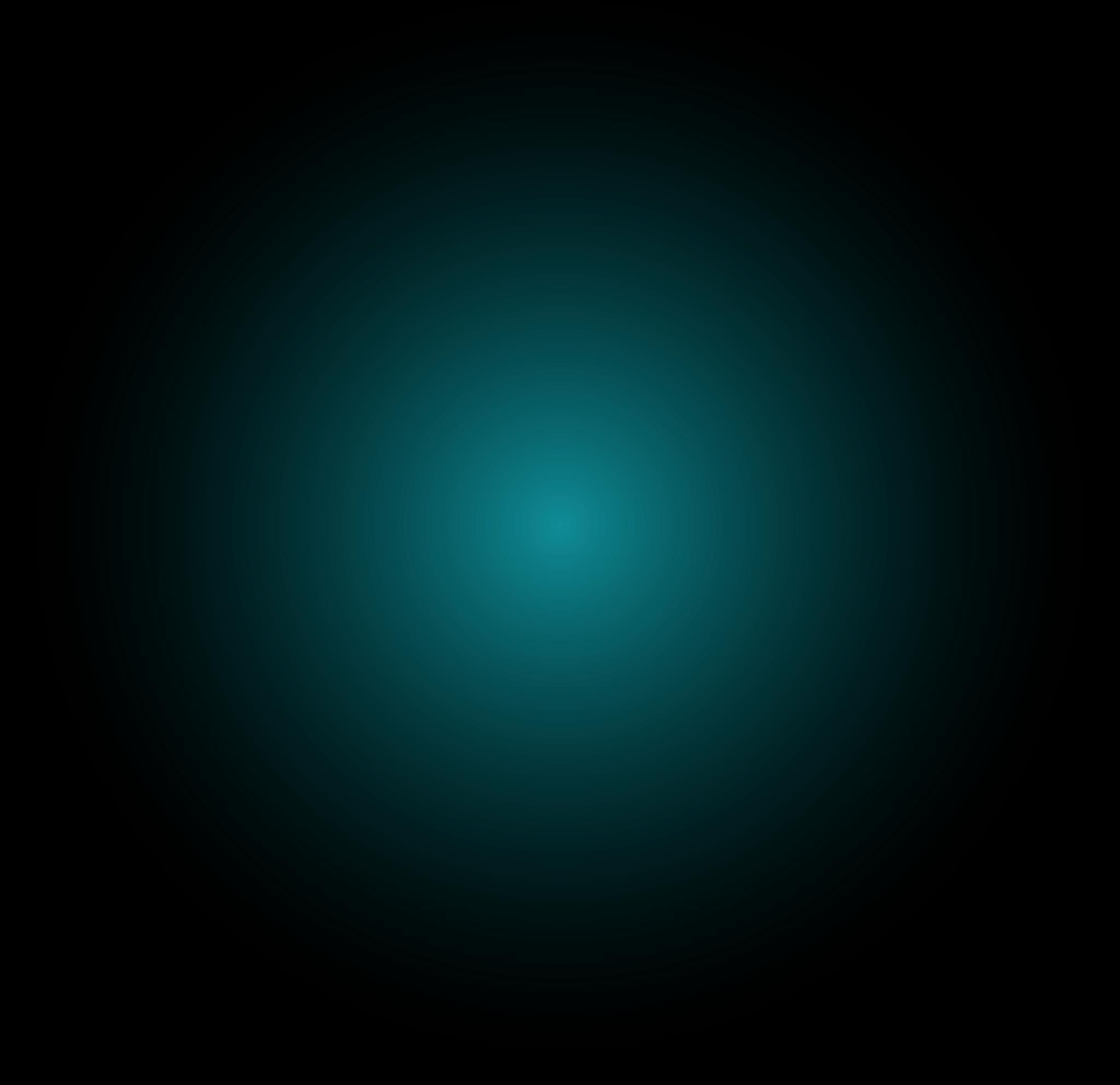
Material Composition – Enhancing Performance and Longevity
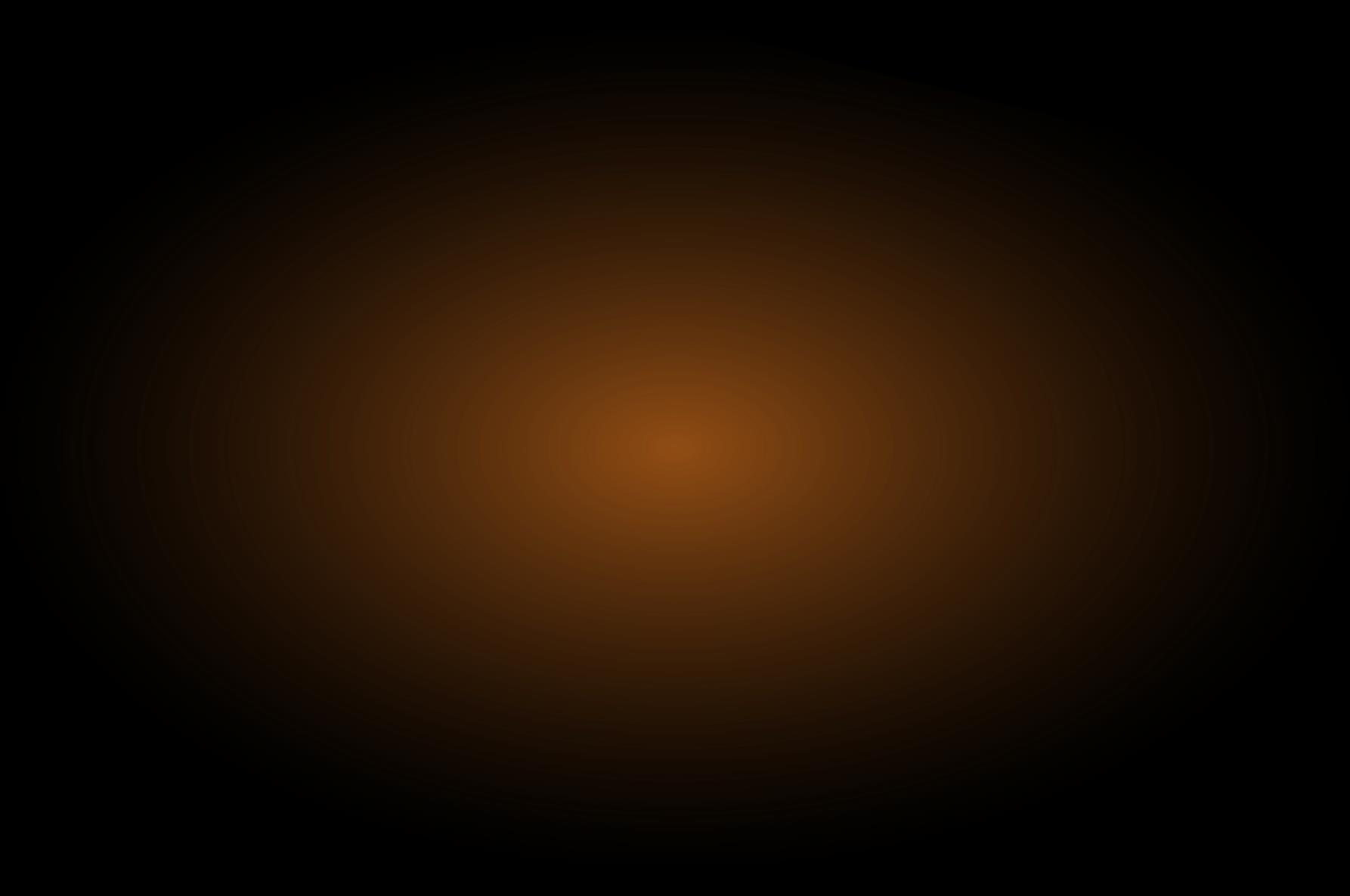
The choice of materials in roller manufacturing significantly impacts their performance and lifespan. Rubber pressure rollers and polyurethane variants are preferred for their elasticity and durability, facilitating efficient ink transfer and resistance to wear. Advancements in material science have led to the development of specialized coatings that enhance roller performance, reduce maintenance needs, and extend service life. These innovations contribute to consistent print quality and operational efficiency, making material selection a critical aspect of roller design in modern printing technology.