
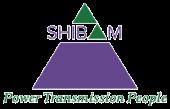

V-belts are one of the most commonly used power transmission belts, popular for their ability to transmit high torque efficiently while reducing slippage. They have been in use for over a century and are still widely used today. There are several types of V-belts available in the market, and it is essential to understand the differences between them to choose the right one for your application. In this blog post, we willdiscussthe varioustypesof V-belts andtheirapplications.
Classical V-belts are the most common type of V-belts, also known as standard V-belts. They have a trapezoidal cross-section and come in different sizes, designated by letters. The most common sizes are A, B, C, D, and E. Classical V-belts are suitable for low to medium power transmission applications and are commonly used in agricultural machinery, HVAC systems, and othergeneral-purpose applications.
Narrow V-belts, also known as Micro V-belts, have a narrower cross-section than classical V-belts. They are designed for high-speed, high-torque applications and are commonly used in automotive applications such as power steering pumps, air conditioning compressors, and alternators.Theyalsohavealongerservicelifeandaremore efficientthanclassicalV-belts.
Double V-belts, as the name suggests, have two V-shaped groovesontheirinnersurface.Theyaredesignedtotransmit higher power than classical V-belts and are commonly used in industrial applications such as machine tools, compressors, and pumps. Double V-belts offer better stabilityandreducedvibrationcomparedtoclassicalV-belts.
Cogged V-belts have a notched or toothed design on their inner surface, which increases their surface area and allows for better flexibility. This design also reduces slippage and increases power transmission efficiency.
Cogged V-belts are suitable for high-torque, high-speed applications and are commonly used in lawn mowers, snow blowers, and other smallengine applications.
Raw edge V-belts have a flat top surface, which increases their surface area and allows for better power transmission. They are suitable for high-speed, hightorque applications and are commonly used in automotive applications such as engines and transmissions. Raw edge V-belts are also more durable and have a longer service life than classical V-belts.
Variable speed V-belts are designed to operate efficiently at different speeds. They have a tapered cross-sectionthatallowsforbetterflexibilityandadapts to different pulley diameters. They are commonly used in industrial applications such as conveyors, compressors,andgenerators.
Banded V-belts consist of several classical V-belts joined together with a band. This design offers better stability and reduces vibration compared to classical V-belts.
Banded V-belts are suitable for high-torque, high-speed applications and are commonly used in industrial applications such as pumps, compressors, and generators.
Kevlar V-belts are made from Kevlar fibers, which are known for their strength and durability. They are suitable for high-torque, high-speed applications and are commonly used in industrial applications such as agricultural machinery, lawn mowers, and snow blowers. Kevlar V-belts offer better resistance to abrasionandheatcomparedtoclassicalV-belts.
In conclusion, V-belts come in various types and sizes, eachwithitsuniquefeaturesandapplications.Choosing the right V-belt for your application is essential to ensureoptimalperformanceandlongevity.