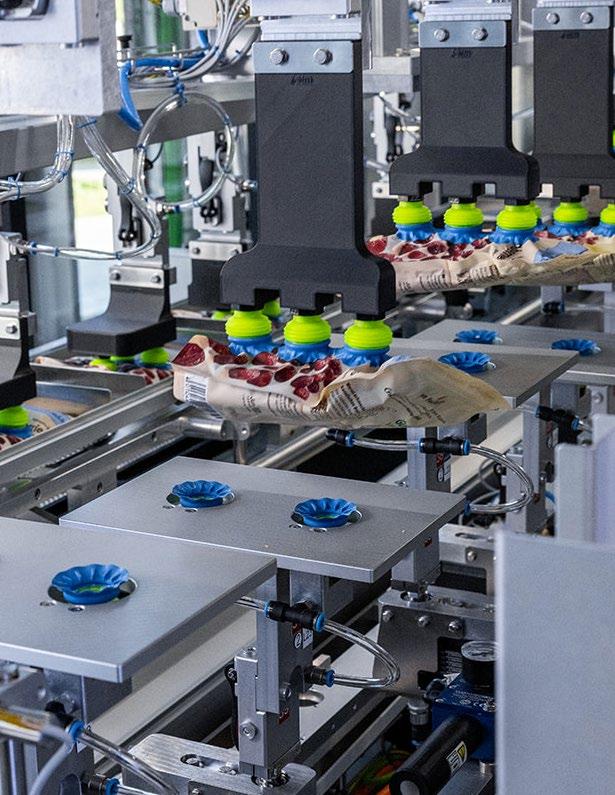
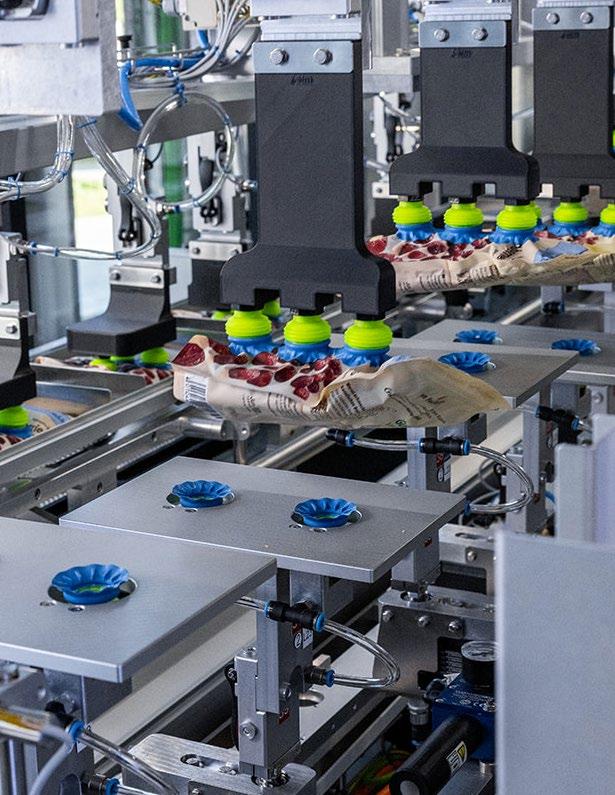
Impact Developments and Breakthrough Technologies
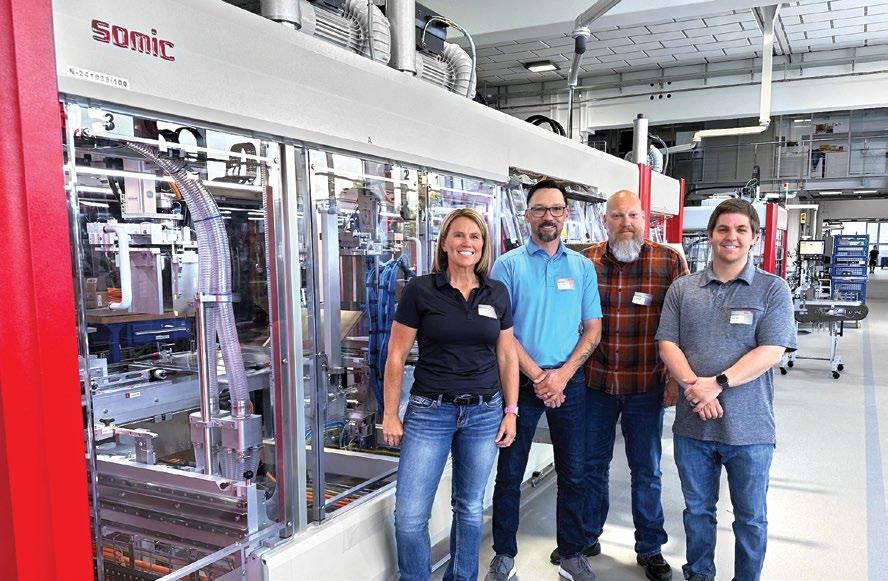
In the 11 years I have been associated with this company, never can I recall a busier environment than the one we are operating in today. And I, along with the rest of my colleagues, am enjoying every minute of it.
As I write this, the manufacturing floor here in Inver Grove Heights – our first summer since we moved into spacious new headquarters last October – is filling up fast. We are currently in the process of building or assembling 12 machines, and a few of
them are the new 434 SuperFlex. It’s a machine that is truly unlike any other.
SuperFlex will officially be unveiled to the North American marketplace in September when it will be in our booth (SU26023) at PACK EXPO Las Vegas. But we’ve decided to share details about this simply fantastic machine now instead of waiting.
As you can see on the cover of this issue, it is a strikingly impressive machine. I urge you to read all the
details in this issue because I’m certain you haven’t seen anything like it before. SuperFlex is our next generation case packing platform that checks all the boxes you look for with an end-of-line packaging solution.
One of the traits I’ve thought has always separated SOMIC from the competition is the flexibility of our equipment. This machine takes it to a whole new level and that’s a great thing to hang your hat on. Brand owners are always being challenged to come up with the next new thing for their products. SuperFlex answers that call and more.
We are now offering other 434 machines with our pioneering Carried-based Orientation Rotation Arrangement System (CORAS®) collating and grouping technology. With the help of contact-free Planar technology, CORAS flips the script for variety packs. Trackbased floating carriers – which rotate 360-degrees and ride along a magnetic field without being in contact with anything else – are really fascinating to watch in action.
We’re giving you two opportunities to do so. You can join us in booth SU-26023 on any of the three days at PACK EXPO Las Vegas, September 29-October 1. Or you can see these machines prior to the show with a side trip to Minnesota when we host our Open House on Thursday, September 25.
A team from Masters Gallery Foods was present for FAT testing of their 424 machine in Germany.
From left to right:
Jessica Ten Haken, TJ Lenz, Nick Kullman and Alex Miller.
If you haven’t already received an invitation to join us, please visit: www.us.somic-packaging.com/openhouse.
June was a very productive month in other ways. I visited our corporate headquarters in Germany with a group from Masters Gallery Foods, and I’m pleased to report they were very happy with the results. I was also interviewed by Packaging Strategies magazine for a Secondary Packaging story that you can find in their June issue.
I also did another podcast. This one was for Refrigerated & Frozen Foods magazine, and you can go to their website and listen to the conversation I had with editor Kelley Rodriguez about “Retail Ready and Other Trends in Cold Foods Packaging”.
I invite you to read the stories in this issue about other developments in progress. Weber, Inc. in Kansas City is doing some phenomenal work with new technology. A European customer is enjoying great success with our machines, and we honor more of our amazing employees.
I hope to see you in September, whether it’s here in Minnesota or in Las Vegas. Or both!
Respectfully,
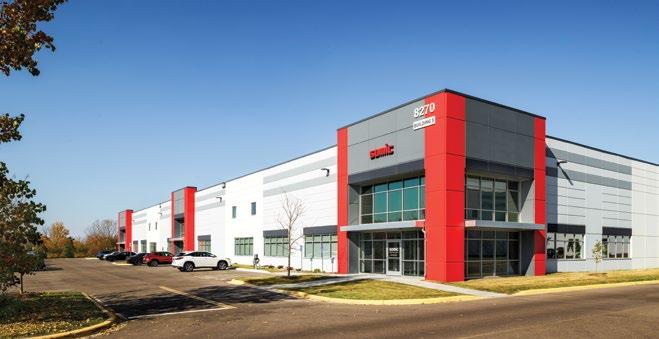
Join Us for our Open House Celebration
A few days before PACK EXPO Las Vegas begins, we invite you to join us here in Minneapolis for our Open House event on Thursday, September 25. We planned this memorable event to give you two separate experiences to enjoy.
Our morning session begins at 10 a.m. and will include a formal ribboncutting ceremony, as well as remarks from company officials and tours of our sparkling facility. Here you can watch live demonstrations of the 434 SuperFlex and CORAS technology while enjoying a freshly tapped brew from the beer tent.
After lunch, you have the option to board a shuttle for our evening event in Stillwater. Recognized as the birthplace of Minnesota, this quaint town offers amazing architecture and a vibrant downtown district. A lively night of great food and music is planned from 4-9 p.m. at The Freight House. This charming and colorful restaurant overlooks the scenic St. Croix River and was the first building in Stillwater to be placed on The National Registry of Historic Places.
Make your plans now for a day that you will always remember!
September 25, 2025
Inver Grove Heights, MN
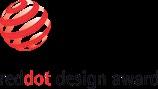
Our state-of-the-art SOMIC 434 recently was honored with a Red Dot Award as the best Product Design for 2025. Citing the machine's technical performance, the judges were impressed with its design, generous glass surfaces, slim frame construction, impressive LED corner lighting, soundproof supply cabinet, and intuitive touch controls.
Peter Fox, Chief Executive Officer
Retail-Ready Magazine is published by SOMIC Packaging, focusing on the Retail-Ready industry. We manufacture advanced mechatronic case-packing systems that collate, unitize and load cartons, trays, retail-ready packages, and wraparound cases.
See how SOMIC can bring new efficiencies to your packaging line.
8270 Courthouse Blvd. Inver Grove Heights, MN 55077
+1.651.419.6050 us.somic-packaging.com
info@somic.us
Follow us on our Linkedin page:
linkedin.com/company/ somic-packaging-usa
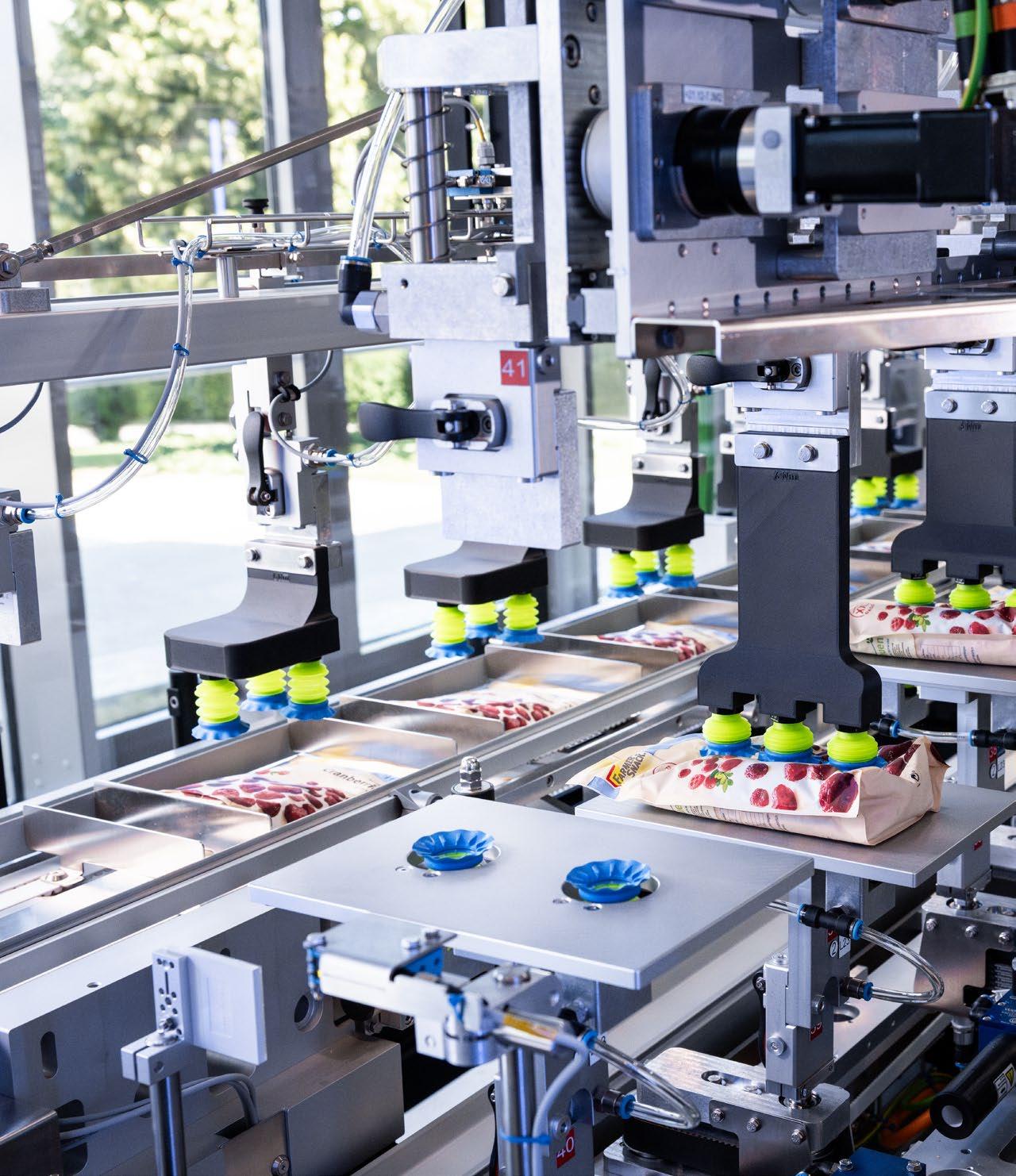
READY FOR ANYTHING AND BUILT FOR EVERYTHING
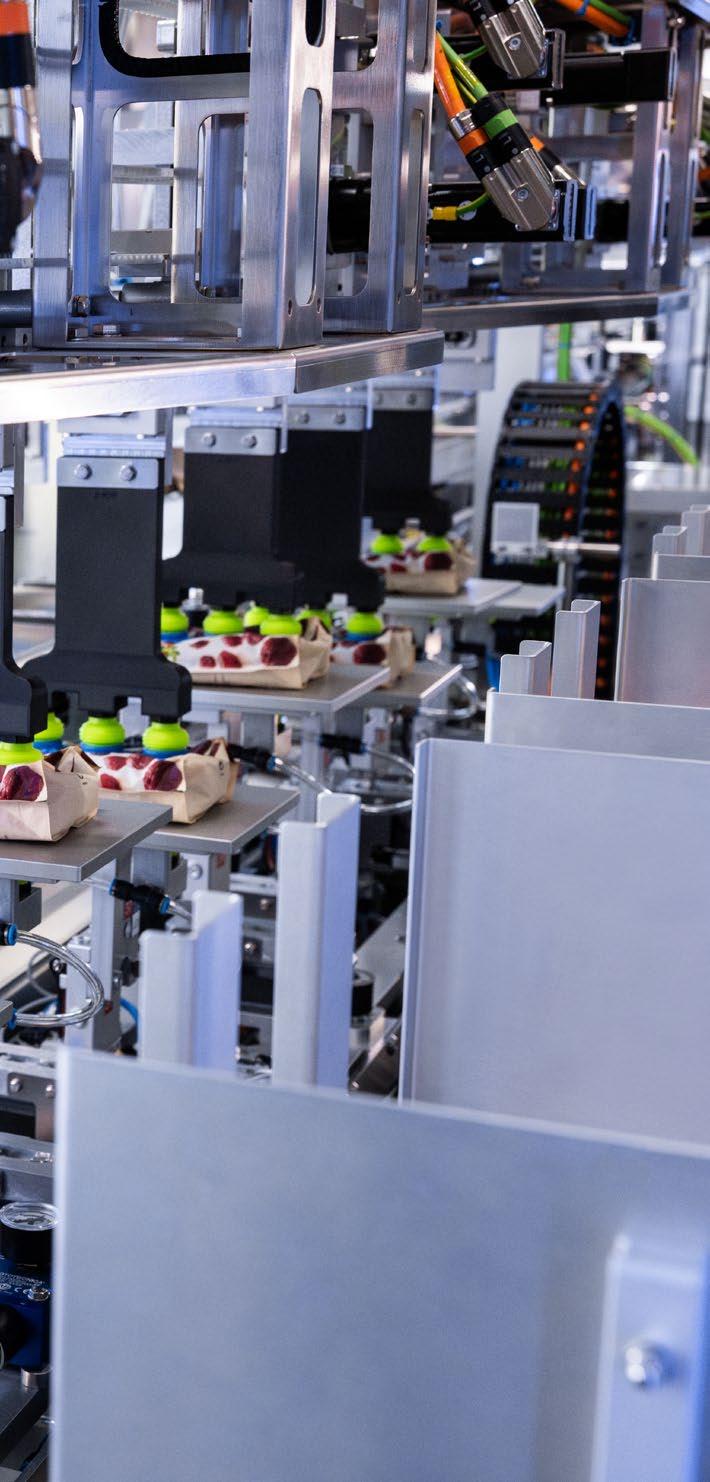
Introducing the SOMIC 434 SuperFlex, the most flexible case packer on the market today.
Every packaging engineer knows the drill. One retailer wants a wraparound tray, another wants a two-piece cover, and they both want it shipped next week.
As retailers like Costco, Aldi, and Walmart push more complexity downstream, CPG manufacturers are increasingly tasked with meeting a wide range of case configurations, retail display standards, and SKU-specific demands. All of these expectations are on timelines that leave little room for inflexible automation.
According to a report by McKinsey & Company, this rising SKU proliferation and shifting product mixes are driving shorter manufacturing runs and faster product changeovers across the consumer goods industry. In this climate, packaging agility isn’t a luxury, it’s a prerequisite for growth.
At SOMIC Packaging, we’ve been listening closely to these pressures from across the packaging value chain. That’s why we developed the all-new 434 SuperFlex -- a next-generation case packing platform designed to meet the challenges of modern end-of-line automation with unmatched versatility, precision, and compactness.
We believe it’s the most flexible case packer on the market today. Here’s why.
Retailers Move Fast. You Need to Move Faster.
We’ve all seen the scenario: A sales team lands placement at Costco with a beautiful, retail-ready case. Weeks later, a new opportunity arises with a different retailer, but the case spec changes completely. Maybe it’s a tray with a cover or an open-front display, or a flat-pack orientation that requires alternating layers. In many plants, this kind of change demands new tooling and machinery. Or worse, a new line entirely.
The new SuperFlex changes that equation. It’s built on a single integrated platform that can produce virtually every major packaging configuration demanded by today’s retailers, from upright stand-up pouch displays and wraparound cases to two-piece tray-and-cover formats, flat nested orientations, and more. As we like to say: One machine. Infinite possibilities.
The SuperFlex requires up to 50% less space while delivering the same or greater functionality.
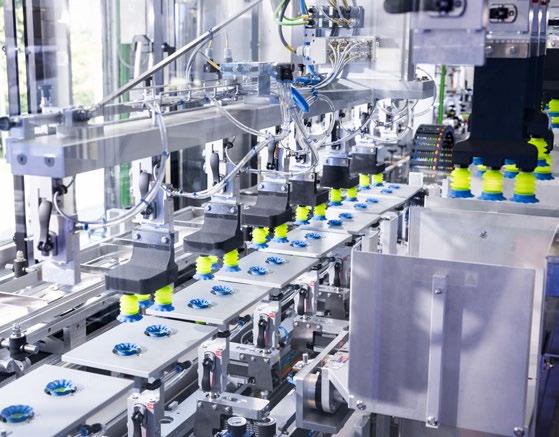
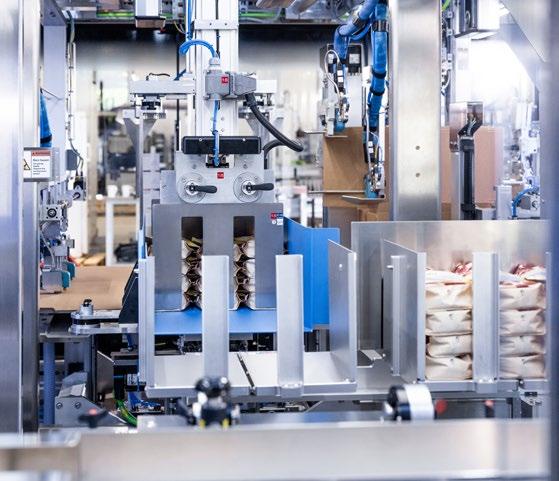
Smaller, Smarter, Faster
In North America, space is often considered abundant. But on the production floor, every square foot still counts. One of the most remarkable aspects of the SuperFlex is its compact footprint. Compared to traditional multi-component systems in the market today, the SuperFlex requires up to 50% less space while delivering the same or greater functionality.
This compactness comes from smart engineering. Rather than bolting together separate tray formers, case erectors, loaders, and closers, we’ve stacked and streamlined all of the key functions into one modular platform. This design reduces not only floor space, but also risk, maintenance complexity, and energy consumption.
We often ask plant managers, “How much is a square foot of space worth to you?” While that answer varies, the ability to free up line space without compromising performance is universally valuable.
Engineered for Variation, Built for Speed
We live in a world of packaging variability today. From fluctuating corrugated board quality due to recycled content and humidity, to inconsistencies in flexible pouches, these variations can be the enemy of automation. That’s why SuperFlex is engineered with precision servo controls, integrated product conditioning, and proprietary mechanisms for handling pouches and imperfect blanks.
With its intelligent case forming and product manipulation tools, SuperFlex accommodates warped corrugated, delicate products and irregular patterns without jamming or downtime. In fact, one customer recently asked, “How much space do you need to fold a precision front flap on a Costco tray?” When we showed them how compact the mechanism was —and how crisp the output looked — they were stunned.
Stunning is also a good way to describe the Carrier-based Orientation Rotation Arrangement System, known simply as CORAS. The 434 can operate at speeds up to 34 cartons per minute in a single cycle, or 60 per minute in a double
cycle. With CORAS collating and grouping technology, SuperFlex can increase productivity with floating carriers, thus removing the need for conventional pick-and-place sorting.
The Strategic Advantage of Flexibility
For manufacturers, SuperFlex doesn’t just offer engineering elegance, it provides strategic value. It allows CPG brands and co-packers to future-proof their packaging lines, respond to new opportunities faster, and reduce the capital expenditures traditionally required to support multiple formats.
A repeat customer recently purchased multiple SuperFlex units as part of a plant-wide modernization effort. They saw the potential immediately: fewer line changeovers, faster reconfiguration, and broader SKU support with much less equipment. This kind of responsiveness is what modern packaging success requires.
Not Just a Machine – A True Platform Ready for Anything At SOMIC, we’ve always believed that the best packaging machines are the ones that solve problems, not just pack products. That’s why SuperFlex is more than just a case packer. It’s a configurable platform that supports growth, change, and innovation.
It’s also built to scale. As more manufacturers adopt flexible pouches, new snack formats, or multi-pack bundles, SuperFlex can adapt to support those products with minimal engineering lift. In time, we see SuperFlex becoming a foundational system across a wide range of market segments, from dairy foods, candy and confectionery items, to baking mixes, beverages, and pet treats.
Ultimately, the SuperFlex is about saying “yes” to change. It’s about giving plant managers, packaging engineers, and CPG brand teams the confidence to pursue new markets, win new customers, and navigate packaging shifts without fearing production bottlenecks.
If you’ve ever lost sleep over a lastminute spec change or stared down a plant layout wondering how to fit just one more line, SuperFlex was built for you.
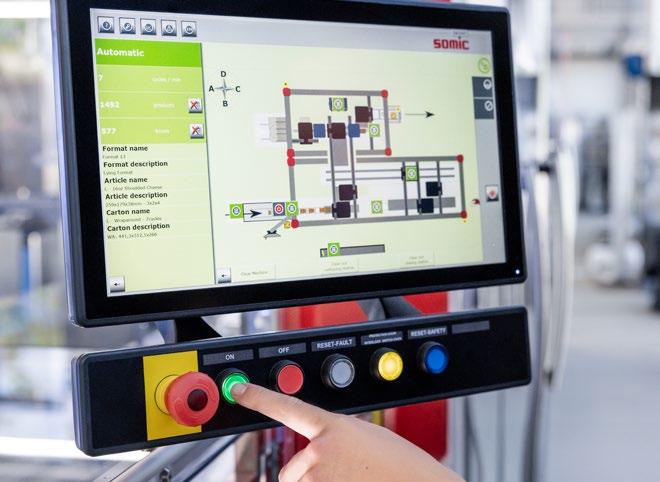
This “configured-to-order” approach drastically cuts engineering time and accelerates delivery.
80% of the machine is already pre-built using a modular, configurable design. The remaining 20%, is customized to match a customer’s specific packaging application.
A Paradigm Shift in Case Packer Design
Configured to Order - Faster to Your Floor
TheSuperFlex isn’t just a new case packer, it’s a new way of thinking about how case packing systems are designed, built, and delivered.
Traditionally, automated packaging equipment has followed a designto-order process. For each new machine, engineers start from a blank slate and tailor the system to the specific use case.
This is a labor-intensive sequence that involves custom design, systems engineering, project management, procurement, manufacturing, assembly, commissioning, and Factory Acceptance Testing (FAT). In many cases, this process can take 12 to 18 months or longer, especially when the application requires complex or novel configurations.
In most engineered projects, approximately 80% of the total timeline is consumed by projectspecific design activities, with only 20% dedicated to configuration and final assembly.
The 434 SuperFlex flips that model on its head.
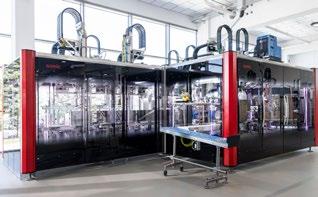
With SuperFlex, SOMIC has standardized the majority of the platform’s architecture. Using a modular, configurable design and a library of pre-engineered assemblies, 80% of the machine is already pre-built using proven components. The remaining 20%, the portion that requires customization, is configured to match a customer’s specific packaging application. This “configured-to-order” approach drastically cuts engineering time and accelerates delivery.
“With SuperFlex, we’ve finally cracked the code,” says Peter Fox, SOMIC Packaging’s CEO. “We can now configure, build, and ship these machines in a fraction of the time it used to take. The base case packer
comes in fully assembled, and when the engineered content is ready, we just attach it and go. We're off to the races.”
This approach enables faster changeovers, tighter plant integration, and quicker installations, which are especially important for manufacturers trying to meet tight production schedules or shift to new formats in response to customer demands.
In addition to saving time, this shift also saves space. The SuperFlex design eliminates the need for long, complex machine footprints. “Look how small that footprint is,” Fox noted during a machine walk-through. “It’s a lot smaller than typical systems on the market. And that matters when you're trying to get right into your palletizing system without reconfiguring the whole floor.”
As Fox puts it: “It’s a standard platform configured to your needs, rather than one built from scratch. That’s what makes SuperFlex so powerful.”
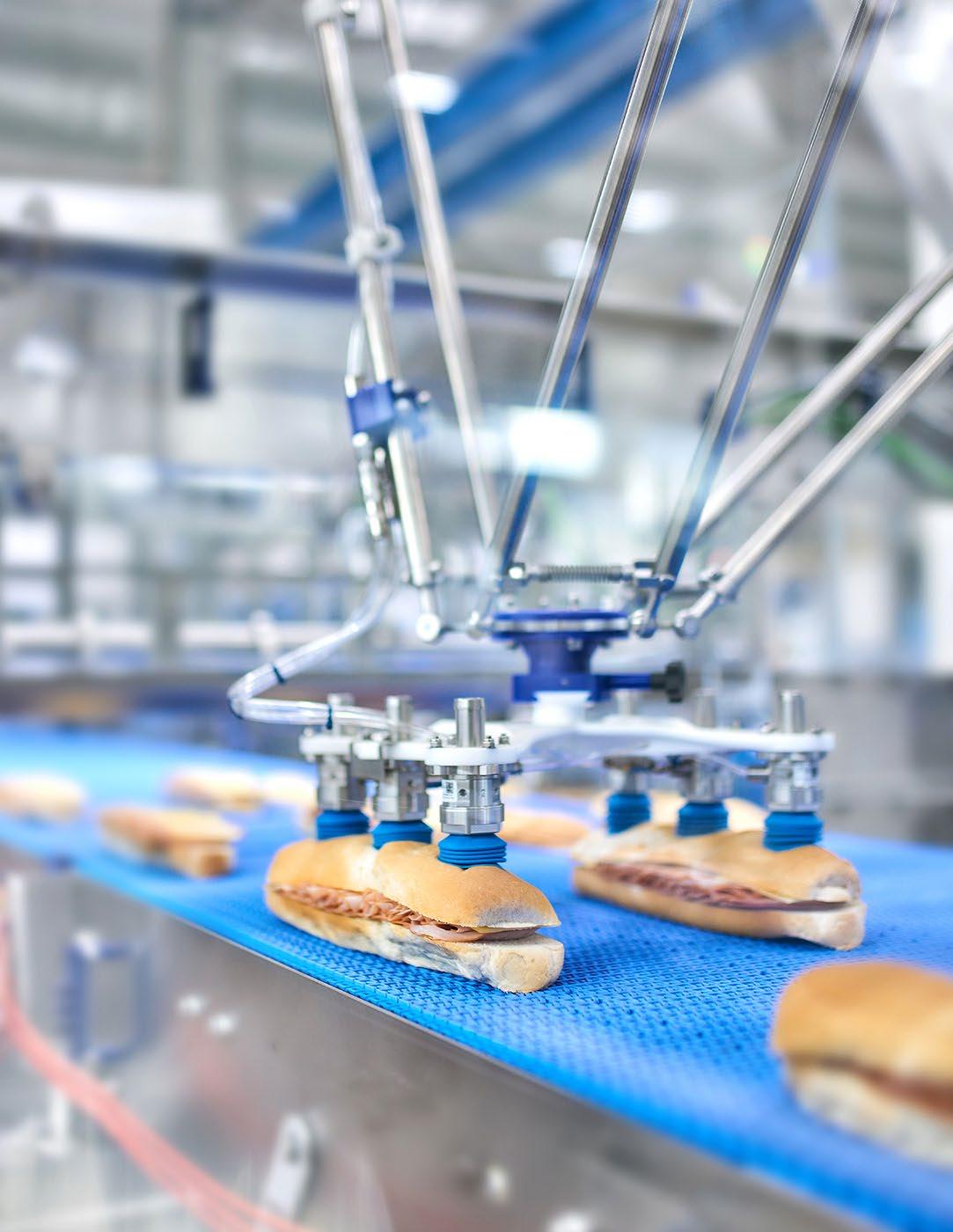
How Weber and SOMIC
Make Convenience Meal
Packaging Easier ONE LINE, ONE PARTNERSHIP:
When you start with the shelf in mind, you make the smartest decisions all the way back to the first slice.”
In today’s grocery aisles, convenience meals, from artisan sandwiches and wraps to snack trays, are a growth story that’s impossible to ignore. Evolving lifestyles, busy families, and rising demand for nutritious on-the-go options are fueling a market that’s expected to grow at more than 5.3% CAGR* through 2034.
“The days of long runs of the same product are gone,” says Jarrod McCarroll, CEO of Kansas City-based Weber Inc. “Today’s consumers want variety, portion control, and the confidence that every pack stays fresh and looks great on the shelf.”
And they want it across every daypart. Breakfast sandwiches in the morning, snack trays in the afternoon, wraps for lunch, and ready-meal kits for dinner. Organic, non-GMO, gluten-free and reducedsugar are no longer niche, they’re table stakes. Food processors and their supplier networks must keep up.
A New Turnkey Automation Partnership
Meeting that demand takes more than a good slicer or case packer; it takes a system that works endto-end. That’s why Weber and SOMIC formed a partnership built on one simple goal: make it easy for processors to produce high-quality, retailer-ready meal solutions with less labor, less real estate, and fewer headaches.
“Customers told us they wanted a single-source solution for snack trays, wraps, sandwiches, you name it,” says McCarroll. “When we asked them who they trusted on the packaging side, SOMIC’s name kept coming up. They’ve got an incredible track record for retail-ready case packing, especially with their heritage in Europe. Their compact, modular approach was exactly what we needed to close the loop.”
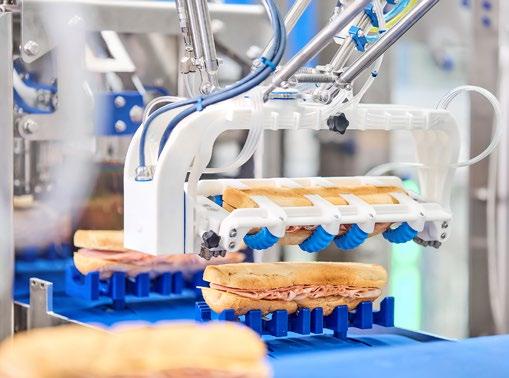
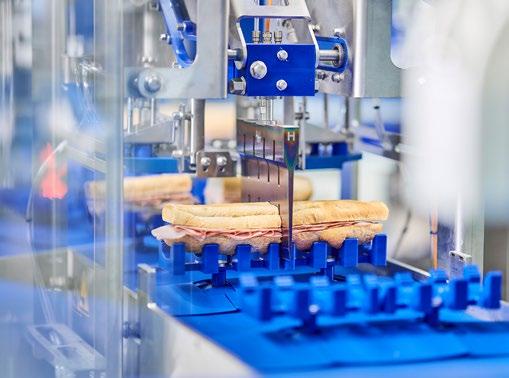
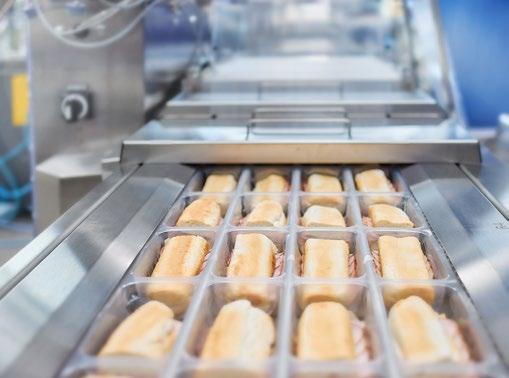
Peter Fox; CEO, SOMIC Packaging
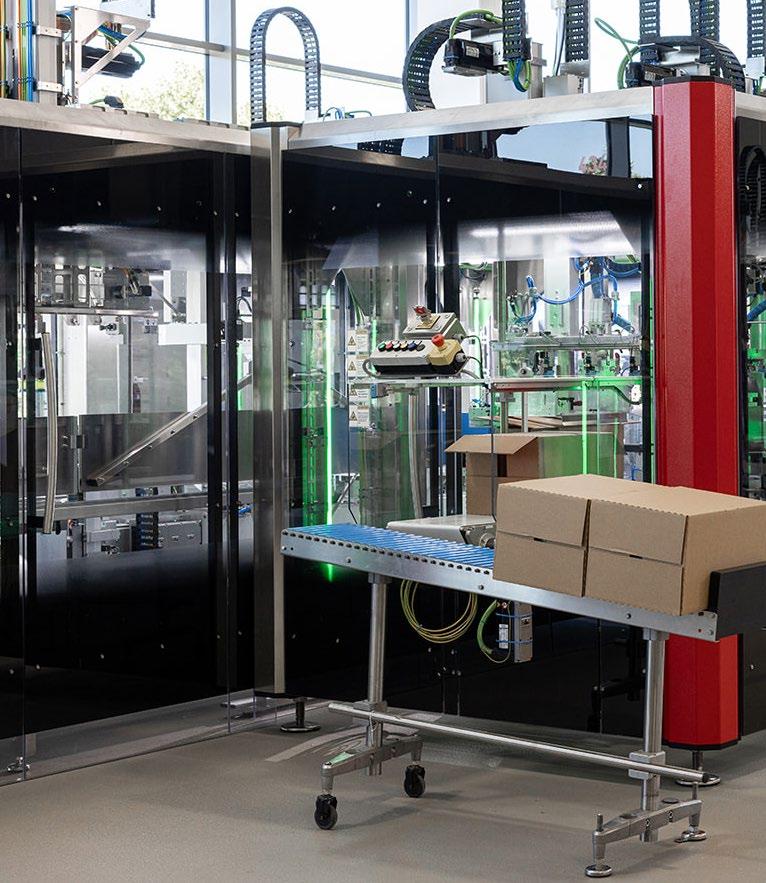
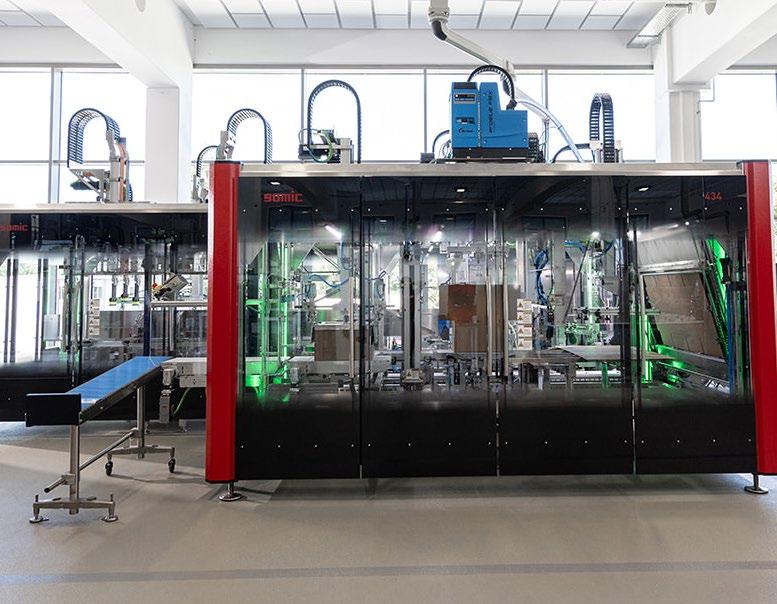
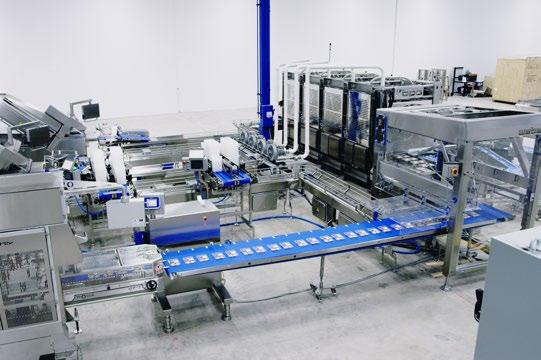
SOMIC Packaging’s CEO Peter Fox, agrees: “Retail-ready is in our DNA. We know how to handle intricate formats, from tear-off trays to club packs for big box stores. By teaming up with Weber’s upstream slicing and automated meal assembly, we’re helping producers deliver exactly what retailers expect.”
At the heart of the system is Weber’s next-generation “we” platform: weSLICE7500, weSHUTTLE, wePICK, and wePACK, all orchestrated to transport products efficiently through each processing stage. The final step is weSORT, which hands off to SOMIC’s 424 or next-gen 434 case packer. From there, SOMIC organizes finished packs into pristine shelf-ready displays. The result is a line that operates like a smart train system.
“The weSHUTTLE is built in modular sections that can turn 45, 90, or 180 degrees. It’s like having flexible, intelligent train cars that know where to go and at what speed as each one has its own IP address,” says McCarroll. “We can fit around columns, work in tight spaces, and create a flow that reduces our footprint and the labor needed.”
According to Fox, that space efficiency is a big deal for prepared meal producers.
“Some customers come in thinking they need an aircraft hangar to automate this. They’re shocked when they see our machine’s footprint. And they’re even more surprised when they realize how fast they can switch formats to handle new SKUs.”
Proof in the Plant
In real-world terms, that means more sandwiches, wraps, and snack trays per square foot, with fewer plant staff touching the product. Traditional lines rely on long, linear conveyors and big teams of manual labor. The Weber–SOMIC system consolidates that with smart automation and a single, seamless line.
“When you show a customer their product flowing from slicing to portioning to assembly, then straight through to a retail-ready carton, all fully automated, it really clicks,” adds McCarroll. “They see they can scale up, launch new SKUs, and still meet tight retailer requirements without adding square footage or people.”
One recent system includes SOMIC’s 424 T2W case packer with four case formats and a case-flipping function to ensure sandwiches are oriented exactly right.
“That detail matters,” says Fox. “Retailers want consistent shelf presentation, and Weber-SOMIC delivers that.”
Built on Shared Values
The partnership wasn’t born overnight. McCarroll credits their early conversations with SOMIC back in 2021 for laying the groundwork.
“We learned a lot from past experiences where lines fell short because too many vendors were pieced together,” he said. “Now, we can sit at the table with Peter’s team, align on what success looks like, and deliver it as one.”
SOMIC‘s case packer infeed integrates seamlessly with Weber’s line, creating efficient, shelf-ready packaging with minimal footprint and labor.
Fox agrees. “We start with the end in mind; that perfect retail-ready pack and then build backwards. It’s not about selling a slicer or a case packer, it’s about giving the customer what they sell: a premium product in a format that moves fast off the shelf.”
Ready for What’s Next
With the first full systems up and running, Weber has already invested in SOMIC’s newer 434 case packing platform with even greater format flexibility.
“This category is growing fast,” McCarroll says. “Retailers are going to keep pushing for new formats. Our system makes it possible to say Yes to those changes without starting from scratch.”
See It In Action
Weber and SOMIC are inviting customers to see their equipment solutions live at PACK EXPO Las Vegas in late September (Weber is N-7656 and SOMIC is SU-26023), as well as during SOMIC’s Open House on September 25. Expect working demos of SOMIC’s latest innovations, plus sample configurations, Q&A with leadership and engineering teams, and more.
For food producers in the convenience meal space, the message is clear: automation doesn’t have to be a patchwork of siloed machines. It can be one connected platform that turns sliced ingredients into premium, shelf-ready meals quickly, efficiently, and profitably. They can expect more.
Fox sums it up: “When you start with the shelf in mind, you make the smartest decisions all the way back to the first slice.”
Jarrod McCarroll; CEO, Weber Inc. "
They see they can scale up, launch new SKUs, and still meet tight retailer requirements without adding square footage or people.”
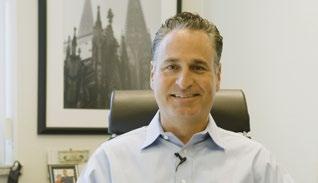
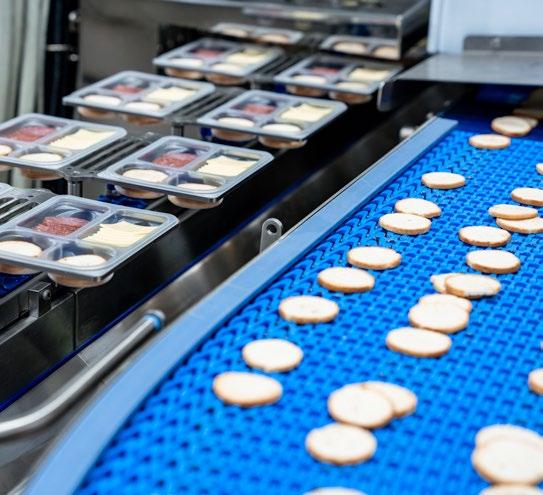
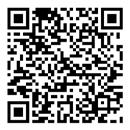
Watch the complete sub sandwich line in motion: Scan the QR code to see Weber’s end-to-end convenience meal solution.
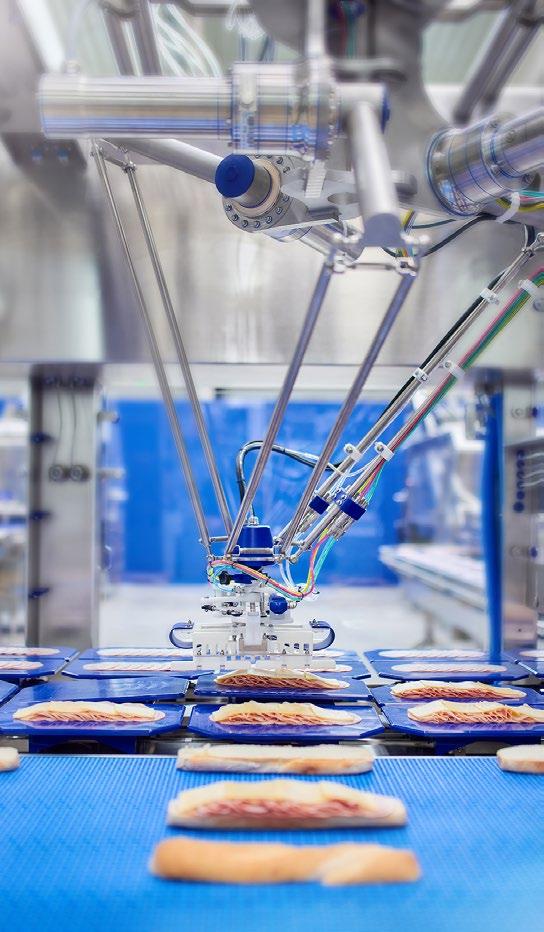
WHERE TRADITION MEETS INNOVATION
Matthijs B.V. relies on modern SOMIC Packaging solution
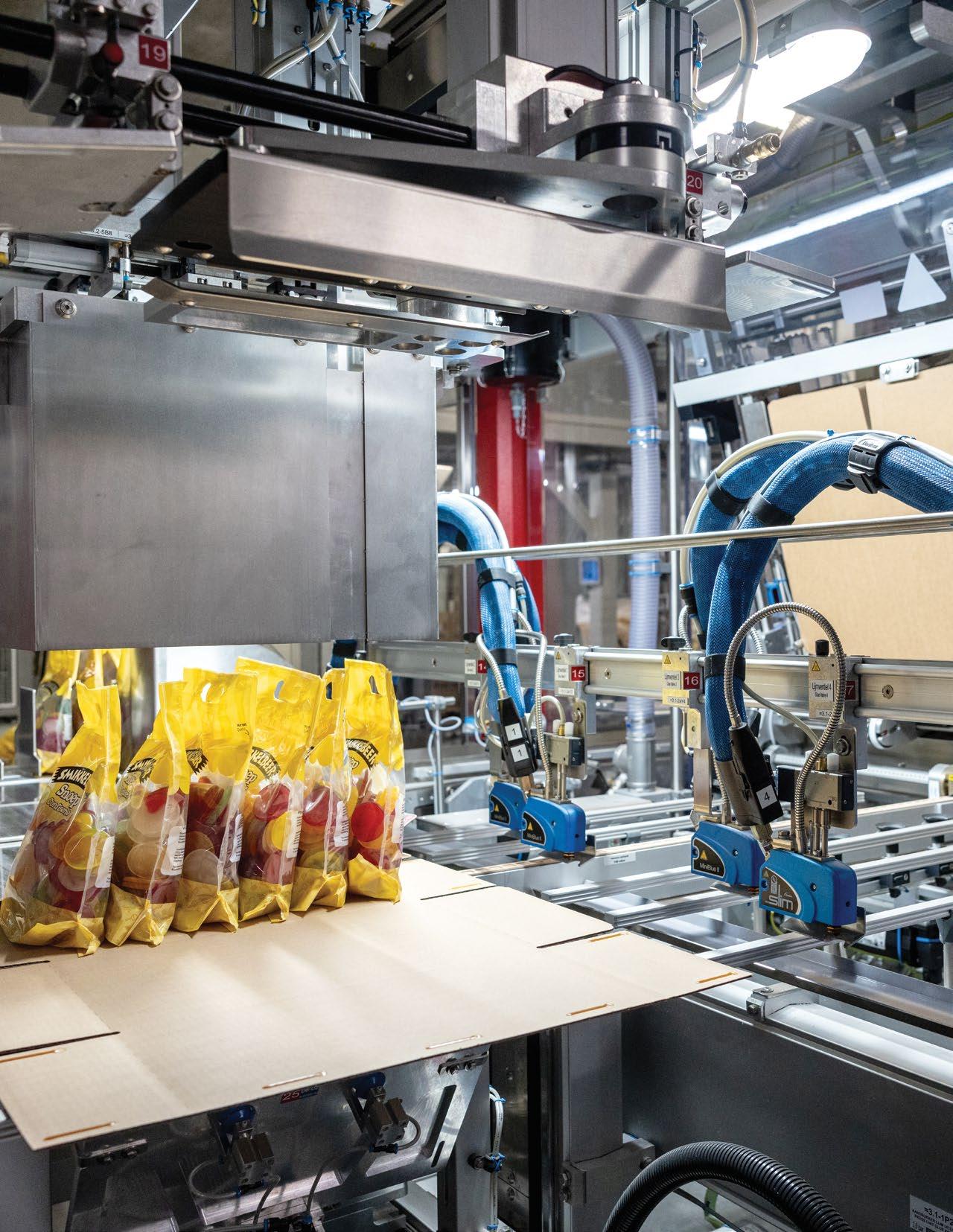
Since 1922, a confectionery manufacturer in the Netherlands has produced various brands. Matthijs B.V. in Hoogerheide are known for their unique products and produce both premium and private label brands. One such product is Manneke Pis licorice, also known as “Echte Mannekes” and available in various flavors.
Until recently, the company for over 100 years hand-packed their products until they saw the SOMIC 424 wraparound packer at a trade show. Since installing the machine for its new packaging line, they have doubled their secondary packaging capacity. They also improved both their sustainability and efficiency since they need less packaging material and labor.
Flexibility in Packaging creates perfect interaction between machines
Nick Matthijs, the company’s managing director, said the “Echte Mannekes” are packaged in 225gram (8 ounce) stand-up pouches, which plays to one of the many strengths of the SOMIC 424.
“We will also be offering other sizes in the future,” he says. “We sell our other confectionery, including the Original Manneke Pis licorice, in kilogram packs to confectionery stores.”
The 424 wraparound packer fit the company’s needs for a flexible packaging machine that could pack all of the different sizes and products in outer cartons. When Matthijs and his father, Walter, saw the 424 at a trade event in Antwerp, they were able to experience the possibilities for their packaging line first hand.
“We showed Nick and Walter how we can pack booth 225-gram and 1,000-gram (35 ounces) bags in cartons of the same size without having to change the machine,” recalled Jan-Willem Cornelisse, area sales manager for SOMIC. “A few days after this demonstration, they bought their first SOMIC machine. Together, we then planned the rest of the process, from the machine to bringing it into the production hall.”
Jan-Willem said to ensure the most efficient operation possible, Matthijs B.V. has connected the infeed belts of several products directly to the SOMIC machine which collects, groups and packs their products quickly and efficiently into cartons.
“The entire planning process was of central importance. You have to make sure that the right combination is made for all product formats,” explained Jan-Willem.
“A good example is the Pareto principle. At the request of the technical department, we determined a carton size that can be used for different contents and pack sizes. The entire packaging line at Matthijs B.V. is tailored to this. The products are filled in a VH flowwrapping machine, weighed, checked by an OCS-Wipotec system, packed in coded outer cartons, and finally loaded into the appropriate pallet.”
Nick Matthijs agrees.
“It all works perfectly together. All the machines work and communicate closely with each other. For example, the SOMIC wraparound packer can stop the upstream machines and the palletizer can stop the entire line. From the planning phase to the handover of the machine, the entire process ran extremely smoothly. Shortly after installation of the line, the SOMIC machine was ready for use and production could begin.”
Automation increases efficiency: Twice the capacity, half the staff, and less packaging material Matthijs says his company plans to push ahead with automation and standardization for good reasons.
“Perhaps another SOMIC machine will be added in the future, but at the moment we can cover our production output very well with this wraparound packer,” he revealed. “Mannekes are still a relatively new product with many flavors, so we often produce them in small batches.
“Thanks to the possibility of processing kilo packs on the same machine, we are very flexible and efficient,” he continued. “Our packaging capacity has increased from 35 to 70 bags per minute, and that is with half as many employees. Doubling capacity while increasing quality is the perfect solution for us. We want to offer more packaging sizes in the future. With the SOMIC wraparound packer, this is easy because SOMIC’s QuickChange technology allows us to easily adapt the machine to new formats, such as 100-gram (3.5 ounce) mini-packs.”
Jan-Willem says SOMIC analyzes customer requirements and uses format parts for different packaging sizes whenever possible.
“This keeps investment costs and changeover times low for our customers. For example, the format parts can be used for the 225-gram (8 ounce) pouches as for the kilo packs. There are twice as many bags in one carton,” he explained, ensuring that cartons with stand-up pouches are just as stable as those with silos.
“Manually packed RSC cartons sometimes result in unstable cartons
or pallets. The cartons can deform or collapse, which jeopardizes palletizing. With a wraparound packer, we avoid this problem as the products are first grouped and then slightly compressed. The result is stable, evenly packed cartons. We also eliminate the need for adhesive tape and labels, making the cartons truly recyclable.”
Matthijs said the company once packed its sweets in silos – buckets and trays made of hard plastic.
“Back then, we needed seven employees to manually pack the silos into boxes. Now with the SOMIC machine, the operator only has to refill the granulate for the hot melt and carton blanks. Only very rarely does the machine operator have to intervene if something goes wrong,” he said.
“The machine works very reliably and is less prone to errors than a human operator. Thanks to SOMIC’s advice, we were also able to significantly reduce the amount of packaging material, which has improved both our sustainability and efficiency. Instead of 33 pallets of silos and folding (RSC) cartons, we now only share one pallet of film and one pallet of flat cardboard blanks. The more efficient transportation alone saves us around 80% of CO2 emissions.”
Looking ahead, Matthijs B.V. is focused on future growth. Jan-Willem says automation plays a key role.
“The world’s population is growing and demand is increasing, but at the same time the number of available workers is shrinking. Automation is therefore inevitable,” he states. “It is critical to implement automated systems in order to remain competitive and future-proof.”
Matthijs says his company is already planning their next steps.
“We will certainly invest in more SOMIC machines in the future. As soon as you start automating, you quickly realize how much the investment pays off. In addition, the total cost of ownership of the SOMIC packaging machine is very low. The machine quality and the service is well organized. We receive immediate support in the event of problems, and 80% (of these situations) can even be solved remotely.”
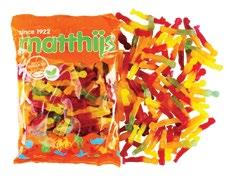
"
We want to offer more packaging sizes in the future. With the SOMIC wraparound packer, this is easy."
Nick Matthijs; Managing Director, Matthijs B.V.
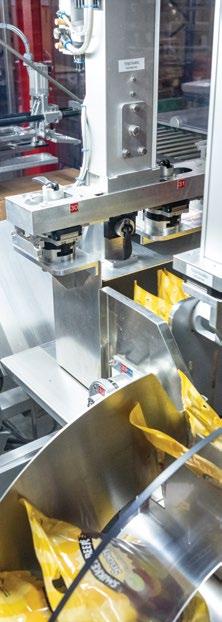
HAPPY ANNIVERSARY!
In our last issue, we recognized many of our employees who reached milestone hiring dates. We continue by acknowledging more people who recently celebrated their work anniversaries. Here is some background about who they are and what they do, both at work and during their time off:
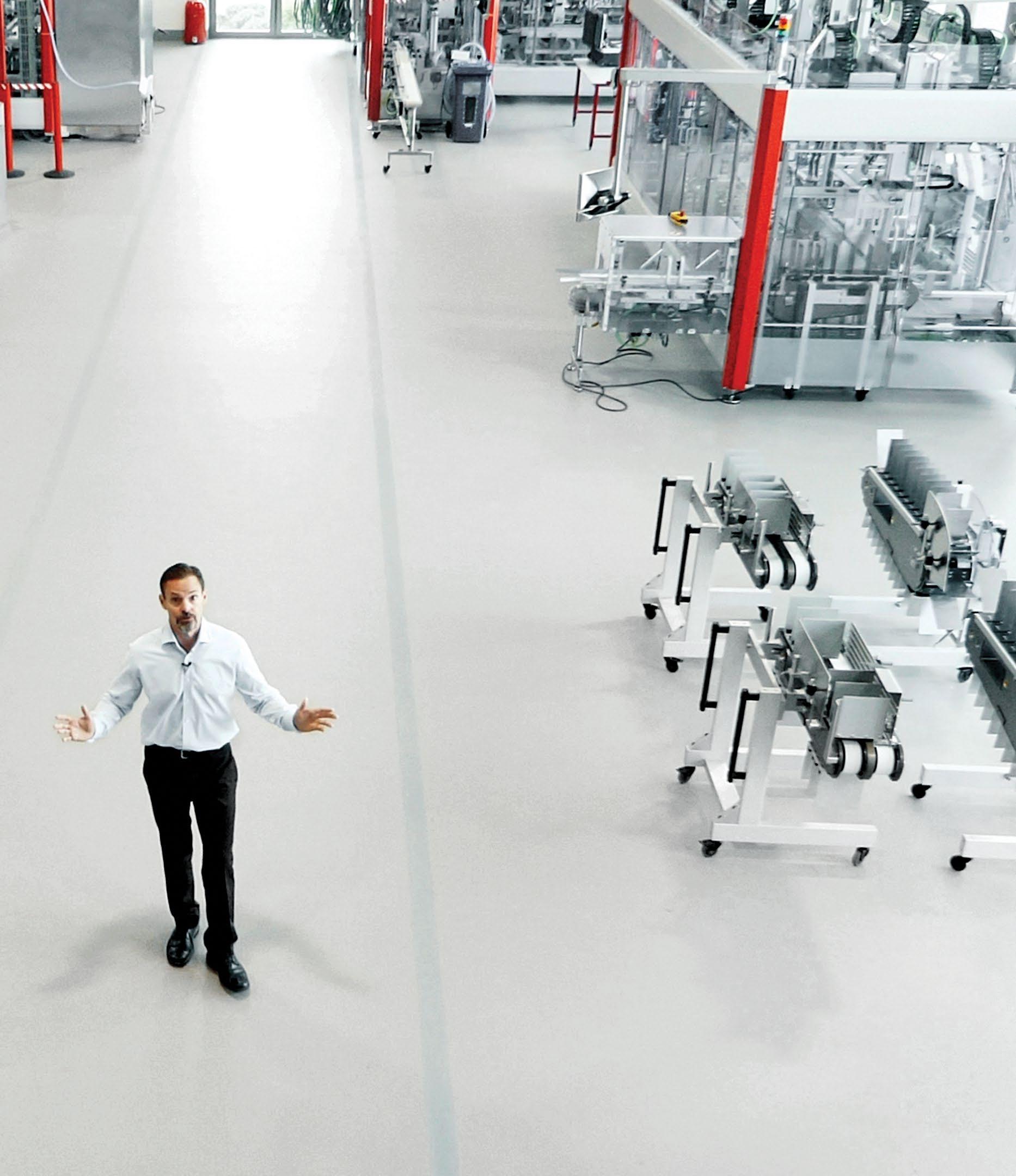
Peter Fox –Chief Executive Officer
“What I enjoy most about working here is the endless variety of products and customers. I’m especially proud of being involved in the development of our SuperFlex machine. Most people don’t know that I have seven siblings and that I live in Wisconsin; in fact, several of my co-workers do, too. I am a health nut, I love to hunt, and I enjoy cutting firewood – it warms you twice.”
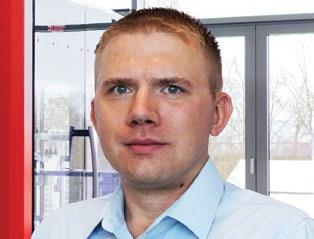
Anton Trofimov –Mechanical Assembly Lead
“I’ve been working at SOMIC for seven years. I moved to the United States two years ago with my family, and I plan to return to Germany in the next year. My family speaks four different languages, and we like to camp, fish, ice skate and travel together.”
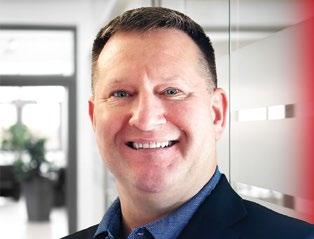
Stacy Schmeiser – Western Regional Sales Manager
”What I like most about packaging is the ever-changing landscape and the opportunities they represent. It is exciting to make a difference for both our customers and the consumer of the product they produce. I like seeing projects I’ve worked on and implemented in stores, and able to tell my son that the machines I sold put that product on the store shelves.”
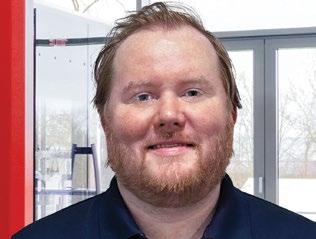
Andrew Gordon –Field Service Technician
“I live in Pennsylvania but was born overseas in England. My favorite hobby is golf and I have played at courses on four continents. In my spare time, I like to spend time outdoors and with my family.”
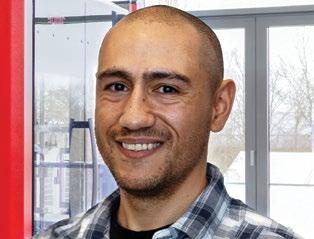
Arman Koehler – Senior Commissioning Technician
“I’ve always found joy in spending time outdoors, whether it is hiking along the North Shore of Lake Superior, casting a line for walleye, or enjoying a peaceful afternoon at Minnehaha Falls. Nature helps me slow down, recharge, and appreciate the simple beauty around us.”

Scott Welker – Eastern Regional Sales Manager
“I truly enjoy helping our customers solve their packaging challenges. Our automated solutions give them the highest degree of flexibility when offering various packaging concepts to their potential clients. When I’m not working, I spend time with my family and as a firefighter and president of our local volunteer fire company.”
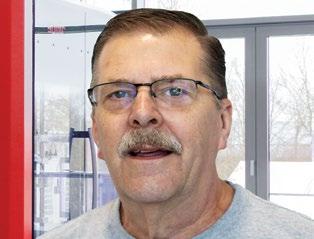
James Eidem –Mechanical Assembler
“I am a civil service retiree after serving in the Air Force for 25 years. I currently have six RC (Radio Controlled) cars and a couple of RC planes. I also own half a dozen pistols, and hope to retire and travel this great country.”
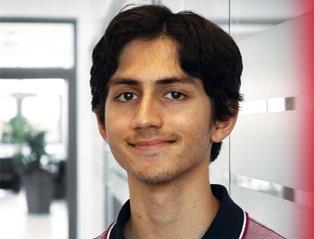
Shamroze Kahn – Mechanical Engineer Intern
“What I enjoy most about working in packaging is how each customer’s machine is like a puzzle. There are all of these intricate parts that you must figure out one by one. When you finish doing so, there is a great feeling of accomplishment.”
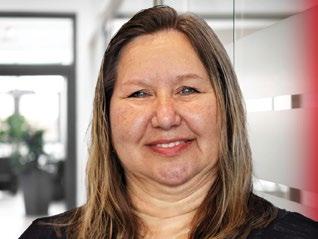
Jeannie Muller –Controller
“My husband and I have three daughters who played tennis all through middle school and at the high school level. Our youngest is a senior and is captain of the tennis team. Since my husband likes to coach from the sidelines, I suggested we take tennis lessons together. We are currently in a beginners class.”
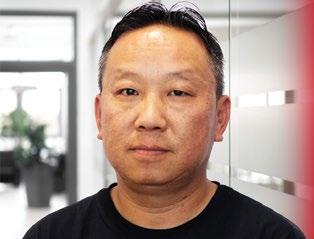
Lue Yang –Mechanical Assembler
“I like working with the people here at SOMIC and building the first 434 machine in the United States. In my free time, I like playing golf. My other hobbies are fishing, working on cars and hanging out with family. One of the items on my bucket list is to one day travel to Thailand and return to the city I was born in.”

1.651.419.6050 us.somic-packaging.com
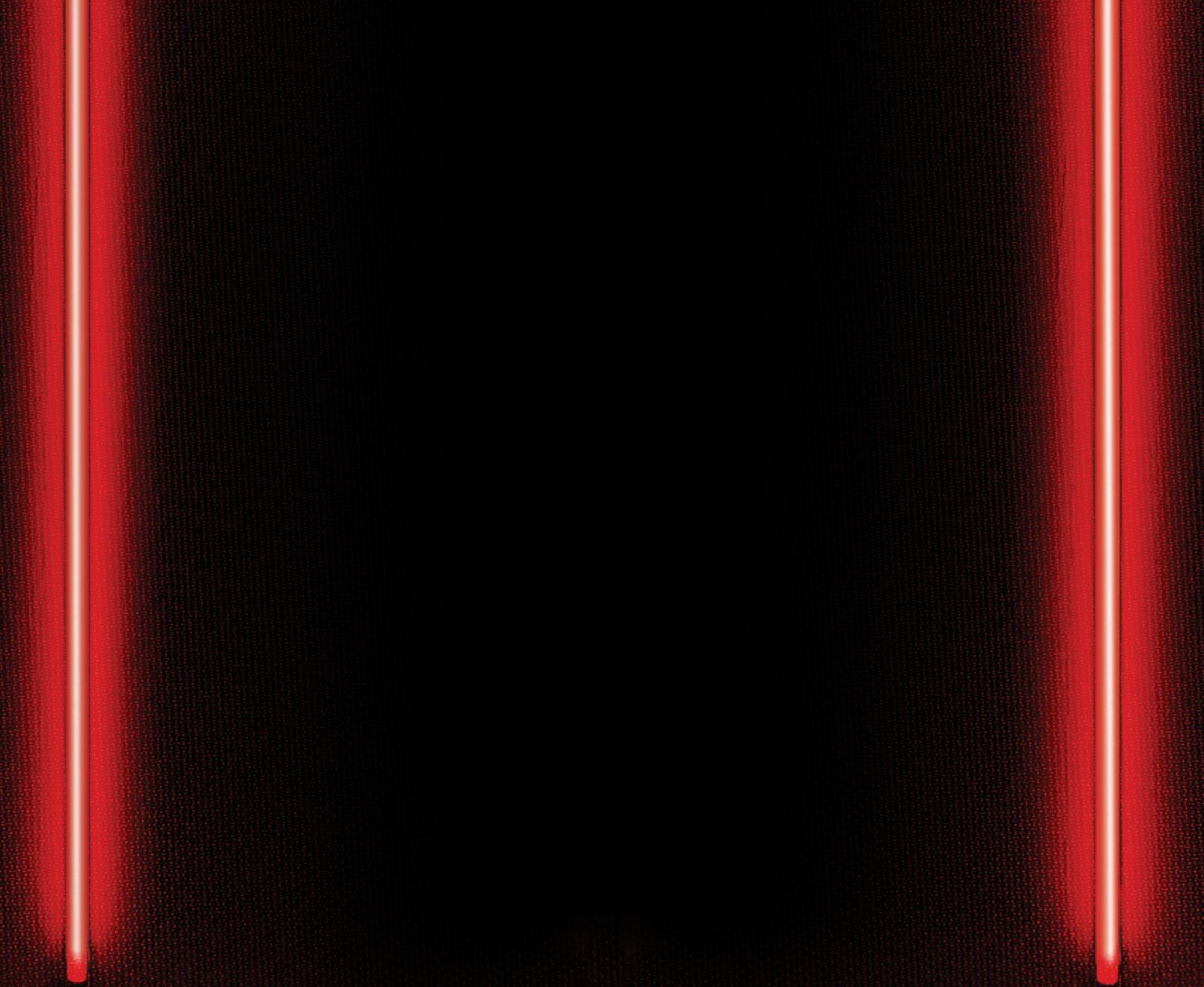

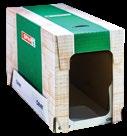
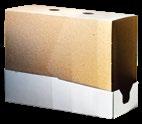
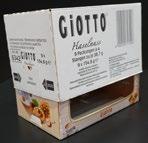
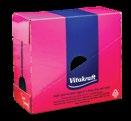
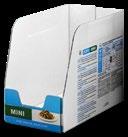
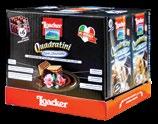
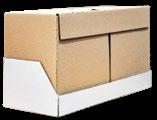
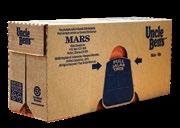
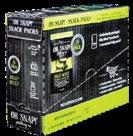
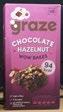
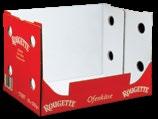
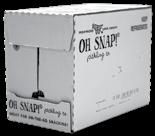
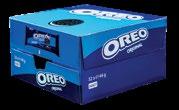
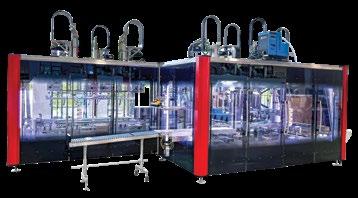
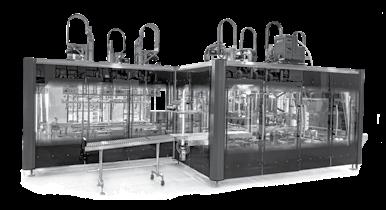
Always be ready to say yes to
When a retailer wants a new case configuration, you can respond fast with the SOMIC 434 SuperFlex pouch case-packer. Built on a simple integrated modular platform, it can produce almost every major configuration, orientation, or grouping of your product before cartoning. The modular design enables fast changeovers, even in the same shift, to help you meet demand. We can build, install, and configure the SuperFlex over twice as fast as industry standards. You’ll build your business with the confidence to always say yes to change.