Tablet Manufacture with Pharmaceutical Granulation
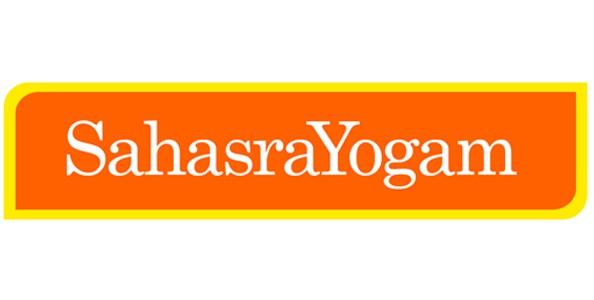
• Tablet manufacture in the pharmaceutical industry often involves granulation, a process that improves the properties of powder mixtures to ensure uniformity, flowability, and compressibility. Granulation can be broadly classified into two main types: wet granulation and dry granulation. Here's an overview of these processes:
1. Wet Granulation
• In wet granulation, a liquid binder is added to the powder mixture to form granules. The process involves several steps:
• Mixing: The active pharmaceutical ingredients (APIs) and excipients are mixed to achieve a homogeneous blend.
• Binder Addition: A liquid binder (often water, ethanol, or a polymer solution) is added to the powder mixture. The binder helps the particles adhere to each other, forming granules.
• Granulation: The wetted mass is agitated to form granules. This can be done using equipment like high-shear mixers or fluidized bed granulators.
• Drying: The granules are dried to remove the moisture content. This step is critical to ensure the stability of the final product. Drying methods include fluid bed drying, tray drying, or microwave drying.
• Sizing: The dried granules are passed through a sieve to achieve uniform size. Oversized granules are milled and reprocessed.
• Blending and Lubrication: The granules are mixed with a lubricant to prevent sticking to the equipment during tablet compression.
2. Dry Granulation
• Dry granulation is used when the API is sensitive to moisture or heat. It involves compacting the powder mixture into large pieces, which are then broken down into granules. There are two primary methods for dry granulation:
• Slugging: The powder mixture is compressed into large tablets called slugs. The slugs are then broken down into granules.
• Roller Compaction: The powder is compacted between two rollers to form a ribbon of material. The ribbon is then milled into granules.
3. Tablet Compression
• After granulation, the granules are compressed into tablets using a tablet press. This involves:
• Filling: The die cavity is filled with granules.
• Compression: Upper and lower punches compress the granules into a tablet.
• Ejection: The tablet is ejected from the die.
4. Quality Control and Packaging
• Finished tablets undergo various quality control tests, including:
• Weight variation
• Content uniformity
• Disintegration time
• Dissolution rate
• Hardness and friability
• After passing quality control, tablets are packaged and labeled for distribution.
• Advantages of Granulation
• Improved flowability: Granules flow more easily than fine powders.
• Enhanced compressibility: Granules are easier to compress into tablets.
• Uniformity: Granulation helps achieve uniform distribution of APIs and excipients.
• Reduced dust: Reduces dust generation, improving safety and cleanliness.
Choosing the Right Granulation Method
• The choice between wet and dry granulation depends on factors such as the physical and chemical properties of the API, stability concerns, and the desired characteristics of the final product.
Sahasrayogam health sciences is a trusted name for finest quality and effective formulations. Overall, granulation is a critical step in tablet manufacturing, ensuring consistent quality, efficacy, and safety of pharmaceutical products. Our units are certified with GMP and WHO. We strictly adherence to sterile manufacturing unit for Microbial contamination free manufacturing process.