A
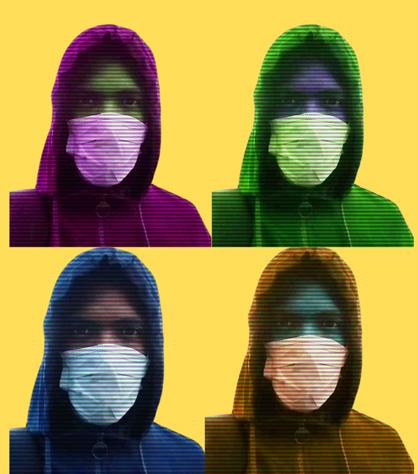
ABOUT ME
SABELO P. NDALA
Mechanical Draughtsman Z.A
I’m Sabelo, a Multi-disciplined draughtsman, CNC programmer, and Industrial design & UX/UI Design student based in South Africa.
Driven by a commitment to sustainable, innovative design, I am dedicated to exploring and mastering the full spectrum of design disciplines—spanning mechanical, architectural, petrochemical, electrical, structural, and product design.
With over five years of experience in mining equipment manufacturing, I bring a strong background in both practical and strategic aspects of the field. I spent three years working in the Research and Development division at Thriftline Products Pty Ltd., and for the past year, I have had the privilege of serving as the program lead. In this role, I manage R&D initiatives, oversee drafting and design projects, lead prototyping efforts, and ensure rigorous quality control standards. I approach each project with meticulous attention and a passion for pushing boundaries in design and manufacturing.
Sabelo P. Ndala
�� Alberton, Johannesburg, Gauteng, South Africa
�� spndala83@gmail.com
�� 081 506 2288
�� www.linkedin.com/in/sabelo-ndala
Professional Summary
Multi-disciplinary mechanical draughtsman, CNC programmer, 3D Modeller, 5+ years of experience in mining equipment manufacturing, R&D, and high-precision component design. Adept in mechanical CAD modeling, CAM toolpath generation, DFM, and casting design. Proven leadership in design and production environments with a systems-thinking approach. Currently furthering studies in UX/UI Design and Industrial Product Design.
Core Competencies
2D & 3D CAD Modelling (Fusion 360, Inventor, AutoCAD, Siemens NX, SolidEdge, Solidworks)
CAM & Toolpath Generation (Fusion 360 CAM, Inventor CAM, Mastercam)
CNC Programming & Optimization
Product Development & Rapid Prototyping
DFM & DFA Principles
Technical Documentation & Drawing Control
R&D Support & Interdepartmental Collaboration Systems Thinking & UX/UI Awareness
Education & Certifications
Professional Master’s degree in UX/UI Design (In Progress) — Tech-Global University 2025 - 2026
Advanced Master’s Degree in Industrial & Product Development (Ongoing) — Tech-Global University, 2024 – 2026
Multi-Disciplinary Draughting Certificate — Academic Institute of Excellence (AIE), 2024
CNC Programming Certificate — Ikusasa Training Center - 2024
Electrical Engineering Heavy Current N4 - Ekurhuleni East College for FET, 2003
Certified Member — South African Institute of Draughting (SAID)- Student
Certified Member — South African Institute of Steel Construction (SAISC)- Student
Software & Tools
CAD: Autodesk Fusion 360, Inventor, AutoCAD, Solidworks, Solid Edge, Siemans NX
CAM: Fusion 360 CAM, MasterCAM, Inventor CAM
Office & Design Tools: Microsoft Office, Adobe Suite
Other: Product Sketching, Drawing Sheet Setup, Basic UX/UI Tools
Professional Experience
Draughtsman & Design Lead NDA — [2025]
Led product redesigns with full 2D, 3D, and CAM deliverables
Addressed design inefficiencies in the absence of defined parameters or procedural flow
Independently utilized personal licenses and hardware to compensate for software/resource limitations
Created detailed technical documentation and drawings for casting & CNC integration
Program Lead – R&D, Design & Production
Thriftline Products Pty Ltd. — [2023–2025]
Directed technical drawing standards, prototyping, and DFM practices
Designed the reusable AXT_R/set Reaming Shell Mould improving carbon component turnaround
Oversaw in-house design-to-production transition of the MC631500 AQ casing pipe Bridged production, CNC, and QC teams with unified design workflows
Junior Draughtsman / Intern Roles
Various Student & Freelance Projects — [2019–2021]
Conceptualized mechanical assemblies, jigs, and fixtures
Participated in bearing puller project at AIE using Autodesk Inventor
Drafted components for learning-based and mock-manufacturing setups
Additional Skills
Emotional Intelligence
Managing Customer expectations
Project management fundamentals
Technical Writing
Business Mkindset for Creatives
DESIGN PROCESS & DESIGN THINKING
SKETCHING, DRAUGHTING, MODELLING & RENDERING
My design approach

AQ_REAMING SHELL SPLIT_MOULD
DESIGN
AQ_R/set Reaming shell Carbon components assembly
HIGH DENSITY CARBON
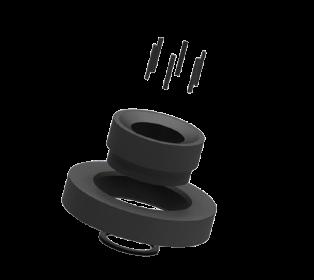
In addressing the limitations of traditional reaming shell moulds, which are often single-use and thus costly, our team innovated a solution to enhance both efficiency and sustainability in manufacturing. We redesigned the reaming shell mould, focusing on reducing its size and weight while engineering it for reusability. As a result, each mould now achieves over ten cycles or “burns” before replacement is necessary, significantly reducing manufacturing costs.
Given South Africa’s rich mining history and the dominance of large corporations in the sector, achieving this milestone was no small feat. Our efforts have redefined the manufacturing process for reaming shells, establishing a new benchmark in the industry. This breakthrough not only optimizes resource use but also contributes to a more sustainable and cost-effective approach, paving the way for future innovations in mining-related manufacturing.

Project Name: AQ_Reaming Shell Split Mould Design_2024
Company: Thriftline Products Pty Ltd.
Product Description: AQ_Reaming Shell Split Mould Components
Software: AutoCAD, Autodesk Inventor and Keyshot
Manager: R. Hogan
Collaboration: Carbographite /F. Benadie (Turner)
PROJECT DOCUMENTATION
Product Requirements Document (PRD)
Project Title: The Claw – Heavy-Duty Wrench Spanner
Prepared by: S.P Ndala
Date: 08 April 2025
Version: 1.1
1. Purpose
To design, test, and manufacture a high-performance wrench spanner specifically optimized for PQ, HQ, NQ, BQ, and AQ drilling systems. This tool addresses failures and inefficiencies found in conventional off-the-shelf wrenches under extreme mining and drilling conditions.
2. Scope
The product is intended for field technicians, drilling operators, and maintenance personnel working in core drilling, exploration mining, and retrieval equipment setups.
3. Background
Conventional wrench solutions failed due to inadequate material strength, poor ergonomics, and inability to withstand high operational torque. A custom-engineered solution, named The Claw, was initiated to meet both functional and durability requirements.
4. Product Description
Core Features:
- Dual-Jaw Design: Semi-circular, pivoting jaws with high-grip inserts or optional serrated metal teeth.
- Replaceable Inserts: Rubber or polymer inserts for pipe protection and grip versatility.
- Curved Ergonomic Handle: Enhances user comfort and torque leverage.
- Pin and Clip Mechanism: For adjustable or removable components during service.
Physical Characteristics:
- Material (Prototype V1): High-strength, low alloy steel
- Mass: ~24.6 kg
- Volume: 3,131,280 mm³
- Finish: Industrial-grade powder coating or oxide treatment
- Optional Upgrade: Switch to quenched & tempered alloy steel or lightweight 6061 Aluminum for lighter-duty variants.
5. Functional Requirements
Requirement ID
FR-001
High
FR-002
FR-003
FR-004
FR-005
FR-006
6. Non-Functional Requirements
- Durability: Minimum design life of 3 years in field use
Description Priority
Must fit and operate on PQ, HQ, NQ, BQ, AQ tube sizes
Must withstand torque forces generated from a minimum of 137,900 N axial load High
Must include a handle designed for two-handed operation
Medium
Grip surface should not damage pipe/tube surface High
Replaceable grip elements must be field-serviceable Medium
Spanner should maintain alignment under operational strain High
- Maintainability: Easy access to parts for inspection/replacement
- Safety Factor: Minimum of 3.0 under max loading
- Compliance: ISO and SABS tooling safety standards (if applicable)
- Ergonomics: Must allow for comfortable repeated use in harsh environments
7. Performance Criteria
Metric Target Value Notes
Von Mises Stress ≤ 90 MPa Based on yield strength / safety factor Safety Factor ≥ 3.0 All high-load regions
Displacement ≤ 1 mm Under full load Jaw Grip Retention No slip at 137,900 N Simulated and physical testing
8. Constraints
- Manufacturing Tolerance: ±0.25 mm on functional areas
- Material Availability: Should consider cost and availability of alternate steels
- Weight Limit (Optional Variant): < 15 kg for lightweight field-use model
9. Dependencies
- Accurate modeling and simulation in Autodesk Inventor
- FEA-based validation using realistic load cases
- Prototyping and physical validation required before production release
10. Acceptance Criteria
- Passes FEA simulation with ≥3 safety factor
- Physical prototype survives full-load torque without yielding
- Grip inserts function across all five tube grades
- Operator usability verified through field simulation or controlled testing
11. Appendix
- FEA Summary (from April 2025 report):
- Max Stress (V1): 2.6 MPa
- Max Displacement: 2.18 µm
- Safety Factor: 14+
- Rendered Design Concept (attached image): Lightweight optimized claw with improved ergonomics and replaceable inserts.
THE CLAW - HEAVY DUTY WRENCH SPANNER
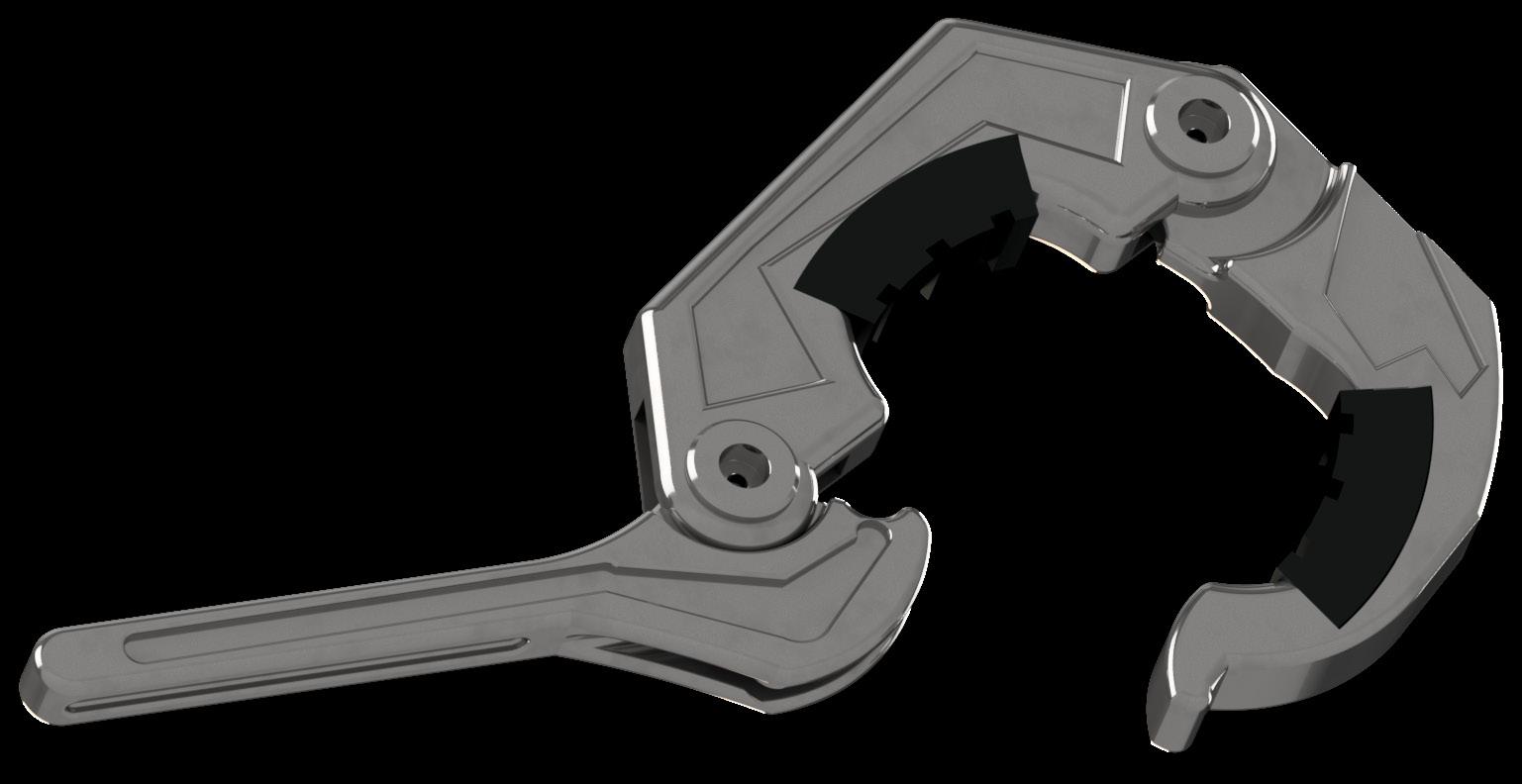

The development of The Claw wrench spanner was driven by a need to solve key operational challenges in core drilling. Recognizing the gaps in the original design and the absence of a defined manufacturing process, I took it upon myself to independently develop a complete solution. This included designing the 3D model, creating detailed 2D technical drawings, and generating CAM programs for CNC machining.
Additionally, I applied a thorough static stress analysis using Autodesk Inventor to validate the design under expected operational loads. This analysis not only confirmed the spanner’s robustness but also highlighted areas for improvement, which were incorporated to enhance the tool’s performance and durability in highstress environments. The result was a practical, well-engineered solution designed to meet the demanding needs of the drilling industry.

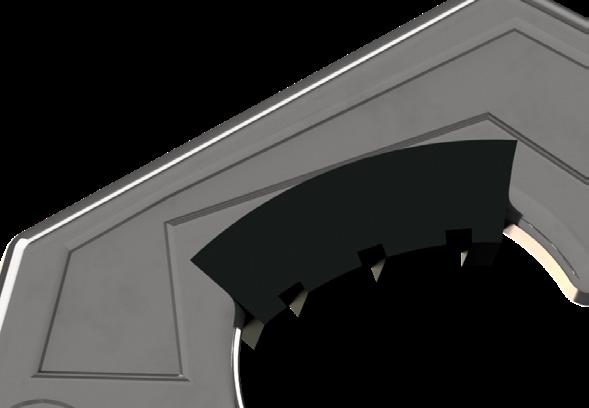
Applied to the Wrench Spanner Project
Project Title: Wrench Spanner Product UI/UX Review
Feedback Session Date: April 10, 2025
Participants: Reviewer: K. Mbele
Reviewer 2: R. Hogan
Designer: S.P Ndala
Feedback Structure
A. Functionality
�� Users can rotate and explore 3D views of the wrench.
�� Tooltip descriptions appear when hovering over grip zones or features.
�� No animation indicating adjustable length — this caused confusion.
B. Aesthetics
�� Clean, minimal look with a monochrome palette – very professional.
�� �� UI elements on mobile feel slightly cramped; consider more padding.
C. Usability
�� Drag-to-rotate is smooth and intuitive.
�� Users didn’t notice the toggle for metric/imperial sizes – needs clearer label or icon.
D. Accessibility
�� �� Text contrasts are just below WCAG standards — use deeper color contrasts.
�� No voice descriptions or screen reader tags yet.
E. Feedback Notes
Users liked the industrial design integration with UI. Struggled to locate hidden interactive features.
Wanted a quick “How to Use” button on the splash screen.
F. Suggested Improvements
Add animated toggle or icon hints for adjustable parts.
Increase padding and font sizes for mobile users.
Integrate onboarding step or tooltip tutorial.
Implement color and text contrast adjustments.
G. Designer’s Response
Will prototype onboarding and animation for next review
Project Name: Wrench Spanner AKA “The Claw”
Company: Personal Development
Product Description: PQ - HQ - NQ - BQ and AQ Wrench Spanner
Software: Inventor, Keyshot and Inventor Stress Analysis
Will test mobile responsiveness with Figma Mirror and adjust spacing.
H. Status
Implementation in progress; follow-up review scheduled in 7 days.
PDC BIT STEEL - BODY DESIGN
NOTES
Addressing Key Issues and Design Challenges in a Team / Work environment
It’s important to highlight the technical reality that 2D drawings are foundational to the design process. They contain the essential dimensions, geometric constraints, and reference placements that inform and drive the accuracy of 3D models. In turn, CAM (Computer-Aided Manufacturing) operations such as toolpath generation, surface machining, and cutting sequence planning are derived directly from the 3D geometry. Without properly structured 2D drawings and verified design data, the downstream process of generating usable CAM data becomes compromised— regardless of the designer’s skill.
I identified and attended to the problem areas concerning the 4 Wing PDC Steel body design , which had no clear design or manufacturing roadmap. I independently developed a new and complete design, including 2D technical drawings, a 3D model, and CAM programming for CNC machining purposes.
NOTE: Dimensions, geometric data and constraints removed to protect -interlectual property
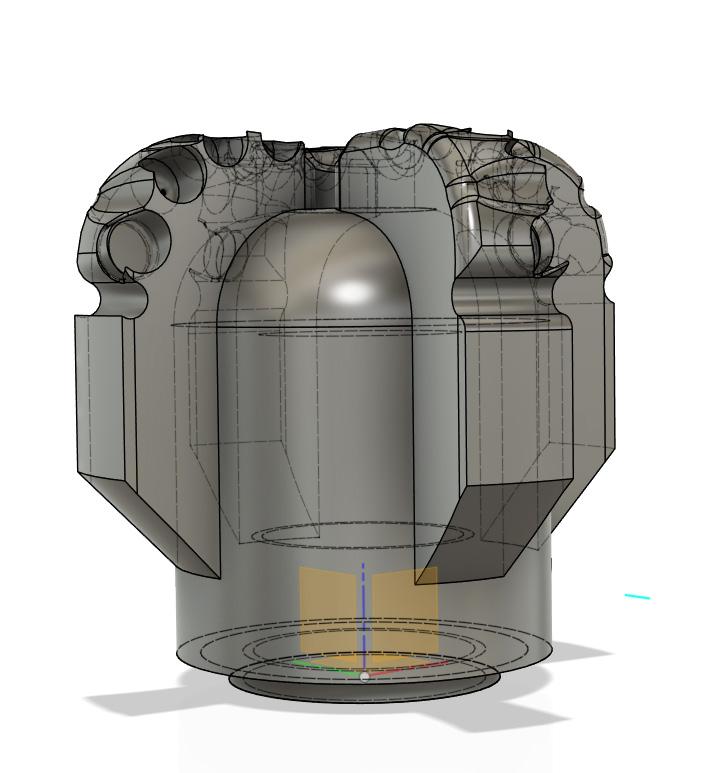
Project Name: 6 1/2 Inch 4 PDC Steel Body Design_2025 Company: NDA
Product Description: 6 1/2 Inch 4 Wing pdc steel Body Software: AutoCAD, Autodesk Inventor and Fusion 360 CAD/CAM Manager: NDA
Collaboration: NDA
PCD - PATTERN RINGPLATE
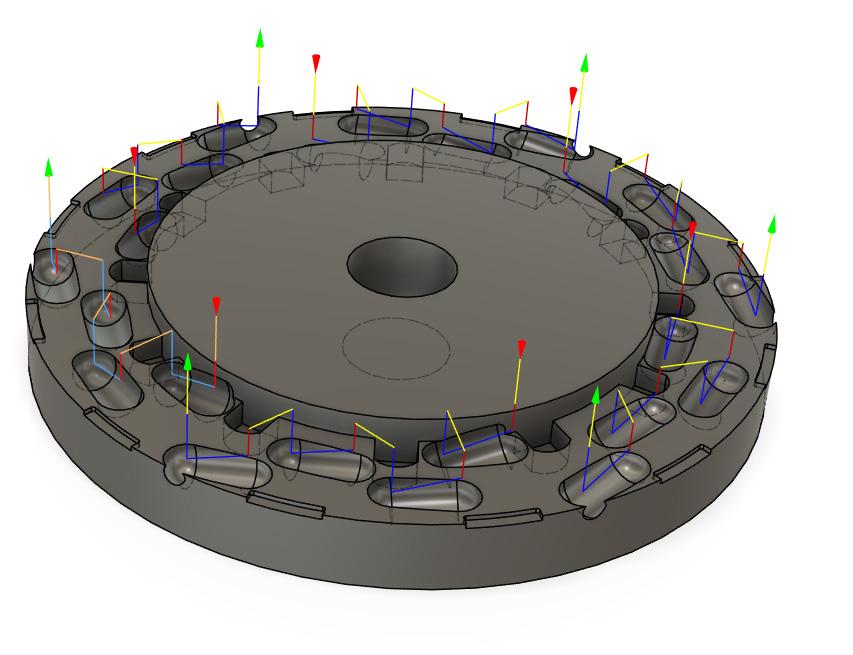
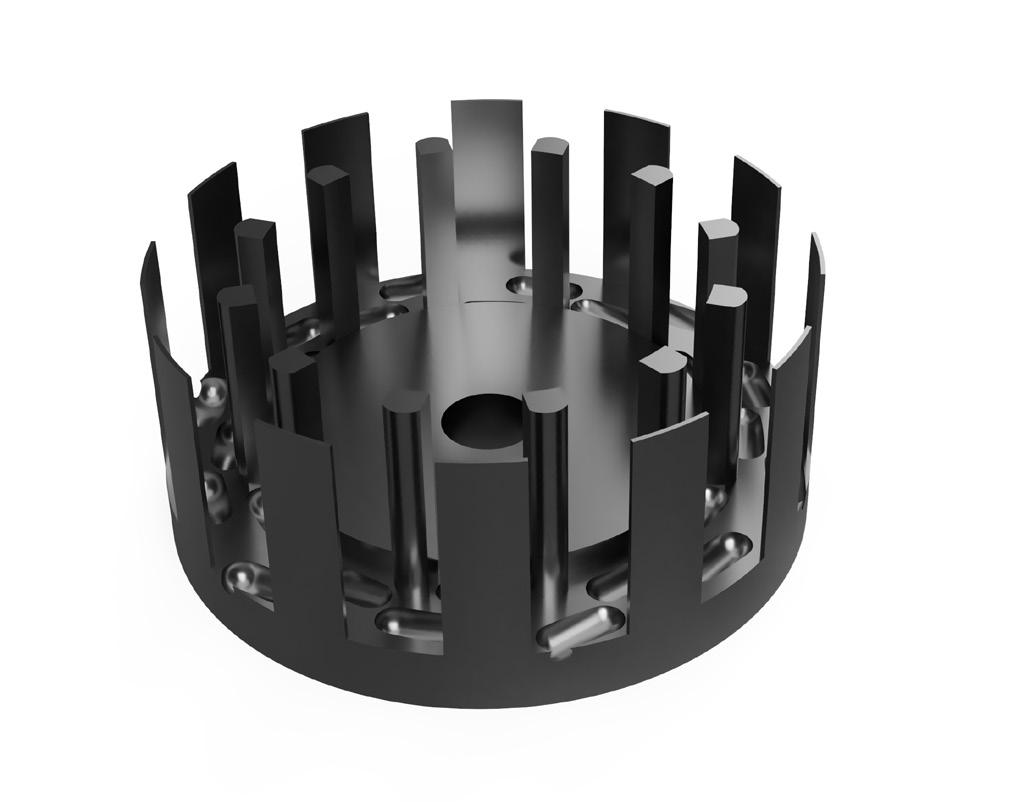
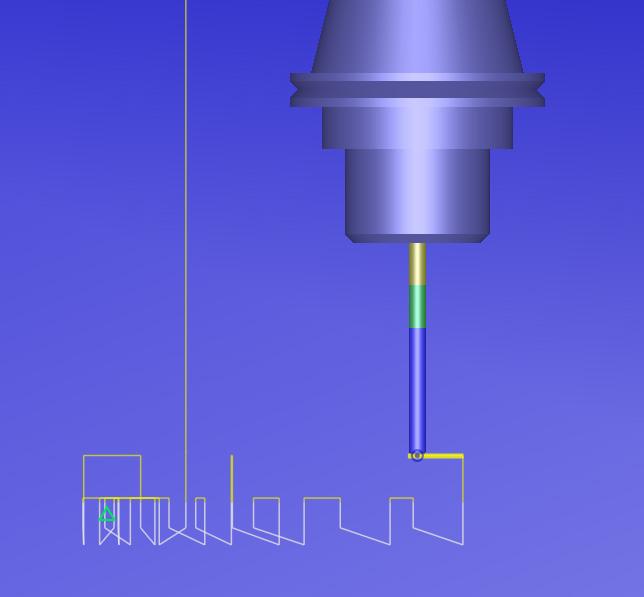
Project Name: PCD Pattern RingPlate Company: NDA.
Product Description: PCD Pattern RingPlate - 4 x 6 pattern
Ringplate – Design Intent & Execution
The design of the Ringplate was approached methodically, following a step-by-step process. I identified critical design and manufacturing issues in the 4-Wing PDC steel body, which lacked a defined development pathway. In response, I independently created a complete and manufacturable solution—this included a new 3D model, detailed 2D technical drawings, and CAM programming for CNC machining.
Software: AutoCAD, Autodesk Inventor, Fusion 360 CAD/CAM, CIMCOEdit and Fusion Render engine Manager: NDA
Collaboration: NDA
Tool-Path Generation on Fusion 360 /CAM NC-Code
% O00111 (Created by Sabelo P. Ndala) (post version: 0001) (post modified: 2025-03-07 12:41:08) (Machine) (vendor: HAAS) (model: VF-4) (T1 D=8. CR=1. - ZMIN=-6. - bullnose end mill) / N10 M0 (Read note) (With BLOCK DELETE turned off each tool will cycle through) (the spindle to verify that the correct tool is in the tool magazine) (and to automatically measure it) (Once the tools are verified turn BLOCK DELETE on to skip verification) (T1 D=8. CR=1. - bullnose end mill) /G65 P9023 A0. T1 H85.34 D8. G90 G17 G21 G28 G54 G91 Z150. G90 N1 T1 M6 S6000 M3 #100=1000. #108=333.33(Cutting) (Plunge) G17 G90 G94
CONTRIBUTIONS AND RESPONSIBILITIES
DAILY OPERATIONS
Key Contributions and Responsibilities
In my role at Thriftline Products, I was entrusted with overseeing the daily operations of the drawing office, a dynamic environment that serves as the backbone of innovation and precision in our production processes.
My responsibilities include:
Document Control: Managing technical documents and ensuring compliance with quality standards.
Research & Development: Driving new product research, generating innovative concepts, and integrating the latest industry trends.
Drafting & Design: Creating detailed technical drawings and 3D models that seamlessly transition from concept to production-ready designs.
Prototyping & Manufacturing: Collaborating with cross-functional teams to prototype and manufacture products that meet exact specifications and performance requirements.
Design Maintenance: Updating and revising existing drawings to reflect design changes, material updates, and supplier adaptations, while maintaining version control.
Supplier Coordination: Ensuring optimal material selection and supplier alignment to uphold consistent quality across the production line.
As a key supplier of core-drilling bits and accessories, Thriftline Products demands excellence and innovation. I stand at the forefront of these efforts, continuously updating 3D models and contributing to the full product lifecycle—from ideation to the final product. My role is not just about maintaining standards but elevating them, ensuring each product reflects the quality and reliability our clients expect.
This opportunity has allowed me to merge technical expertise with creative innovation, shaping both my professional growth and the success of our product range.
Stress Analysis Report
Analyzed File: Assembly11.iam

Autodesk Inventor Version: 2025.2 (Build 292293000, 293)
Creation Date: 2025/04/09, 01:27
Study Author: Sabelo Summary:
Static Analysis:1
General objective and settings:
Project Name: Daily operations
Design Objective Parametric
Company: Thriftline products Pty Ltd.
Product : All product ranges and their respective components
Last Modification Date
Software: AutoCAD, Inventor Analysis
Software: Microsoft 365, Canva, Indesign, Google docs,
Manager: R. Hogan
01:19

AQ_CASING PIPE MOD &
NOTES
FITTINGS DESIGN
1. INTERPRET DRAWING PER SABS 0111 CODE OF PRACTICE
2. ASME Y14.5-2009 STANDARDS FOR TOLERANCING AND DIMENSIONING
3. MATERIAL: 1541 - EN8 - ST52 MILD STEEL
4. REMOVE ALL BURRS AND SHARP EDGES. EDGE BREAK .001
5. TOLERANCE: 0.125mm Standard Engineering Tolerences
6. FILLET RADII - 1.5mm
Cost effective and innovative design
Problem: Production of the MC631500_AQ casing pipe and fittings faced significant cost and time constraints.
Solution: To overcome these challenges, we integrated drafting and programming functions to streamline the manufacturing process, reducing costs and lead times. The optimized casing pipe design exceeded industry standards by withstanding pressure tests at 500 KPa. This innovation enabled the transition of production from outsourcing to in-house operations, resulting in substantial improvements in cost efficiency, quality control, and time management. This shift demonstrates our commitment to delivering high-quality products while maintaining operational excellence.

Project Name: MC631500 Casing & Fittings_2024
Company: Thriftline Products Pty Ltd.
Product Description: AQ Casing pipe & Fittings
Designed by: S.P Ndala
CNC Programmer/Setter/Operator S.P Ndala
CNC consultant: advanced programming :Urban Beeby Manager: R. Hogan
Software: AutoCAD, Autodesk Inventor and Keyshot
Collaboration: J.R (Welder)
8’’ - 10’’ CONVERSION T-NUT CUSTOM DESIGN

Project Name: 8’’ - 10’’ Conversion T-Nut Custom design_2024
Company: Thriftline Products Pty Ltd.
Product Description: 8’’ Chuck - 10’’ Jaws Conversion T- Nut
Designed by: S.P Ndala
Software: AutoCAD, Autodesk Inventor and Keyshot Manager: R. Hogan
Collaboration: Jerrad / Vector Precision Engineering (Machinist)
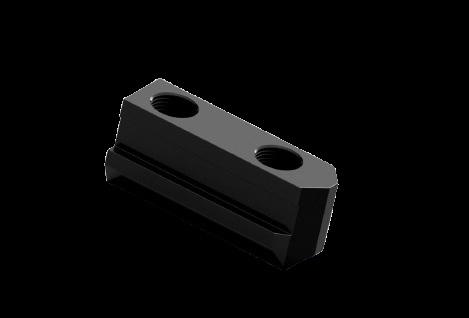
We successfully retrofitted an 8-inch Smart Machine Chuck to accommodate 10-inch soft jaws by engineering a custom T-nut adapter. Faced with the challenge of unavailable market-ready solutions and the limitations of standard 8-inch soft jaws, our team designed and implemented this cost-effective and efficient solution. This innovation has proven successful, addressing the problem without resorting to expensive alternatives.
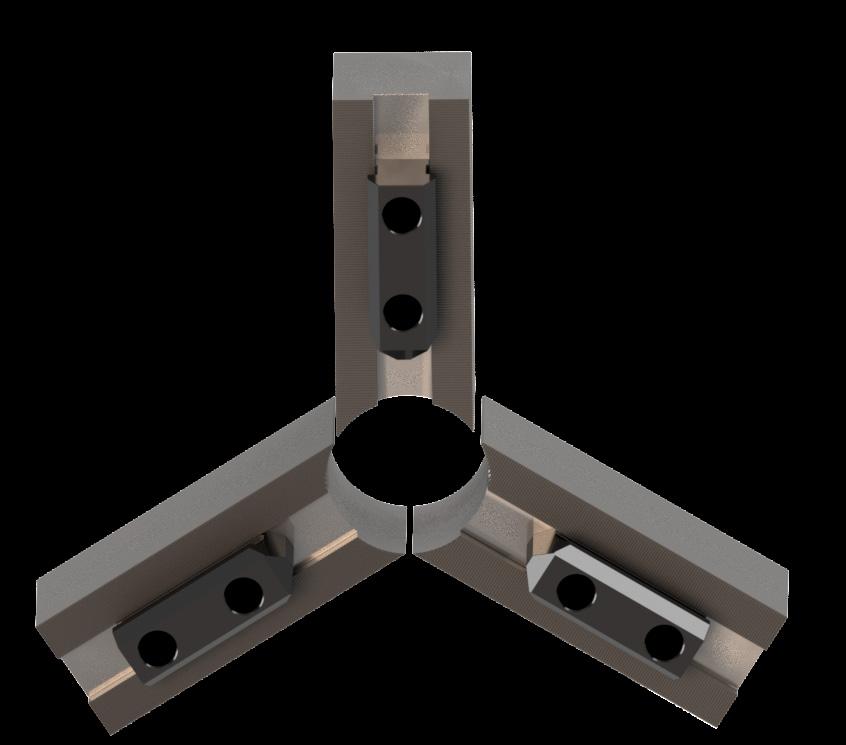
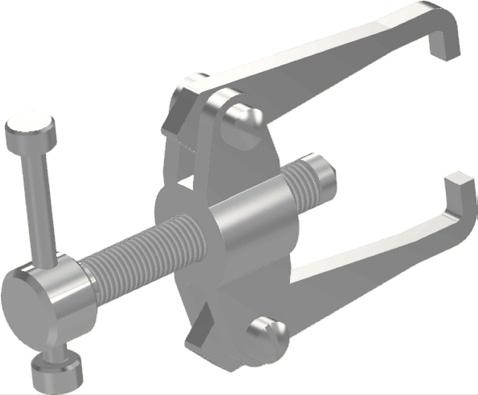
BEARING PULLER DESIGN PROJECT
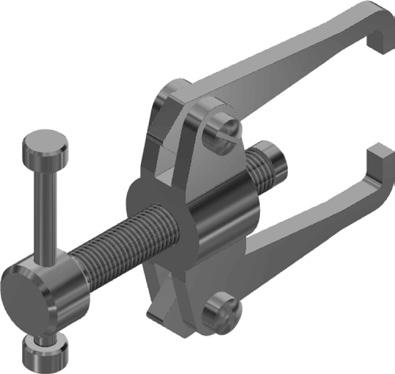

Bearing Puller Design Project Academic Institute of Excellence, Midrand Campus, South Africa
The bearing puller project marked a significant milestone in my journey as a designer. As my first encounter with CAD modeling software—Autodesk Inventor—it became much more than just an academic exercise. This experience ignited a profound curiosity for mechanical systems and engineering design.
Through meticulous modeling and problem-solving, I discovered the power of translating ideas into precise, functional designs. The project challenged me to grasp core mechanical principles while honing my technical skills. It was both a springboard and a confirmation, leading me to confidently select the Mechanical Elective as my specialization.
This project represents the moment where I turned a passion for design into a career pathway, with optimism and ambition driving me forward into the world of industrial innovation.
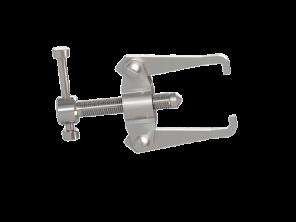
Project Name: Bearing Puller_2023
Company: Student Project
Product Description: Bearing Puller
Software: AutoDesk Inventor
Lecturer: M. Botha
EXPLORATION MINNING DRILLING EQUIPMENT ASSEMBLIES
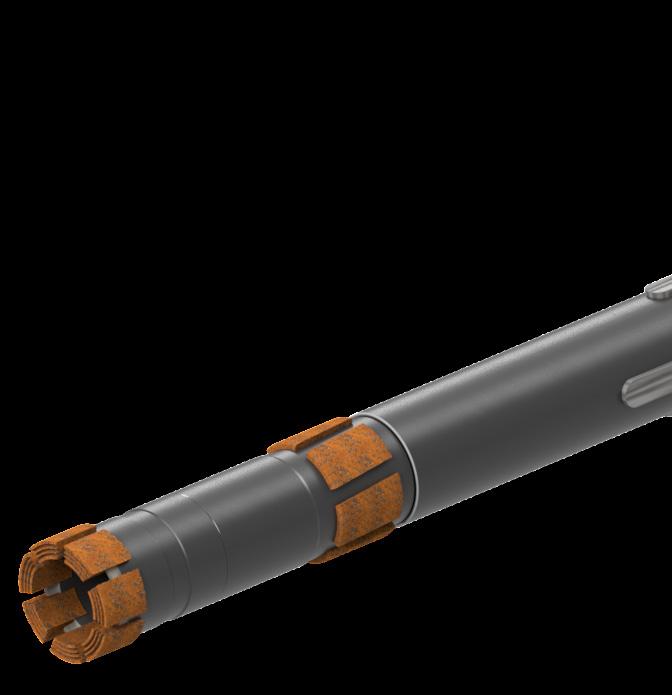
Product Design, Draughting and Modelling
Throughout my design journey at Thriftline Products Pty Ltd and a recently engaged, undisclosed manufacturing company, I have consistently applied my expertise in draughting, product design, and 3D modelling as an integral part of daily operations. These skills have been central to the development and production of equipment for exploration mining, core drilling, and sample retrieval. With over 5 years of hands-on experience in the mining equipment manufacturing industry, I’ve honed this capability into one of my core professional strengths.
Project Name: Explorational Mining Equipement and Core-drilling _2025
Company: Personal Design Journey
Product Description: AQ Drilling Equipment Assembly
Software: AutoCAD, Autodesk Inventor and Fusion 360, Keyshot, Adobe Indesign
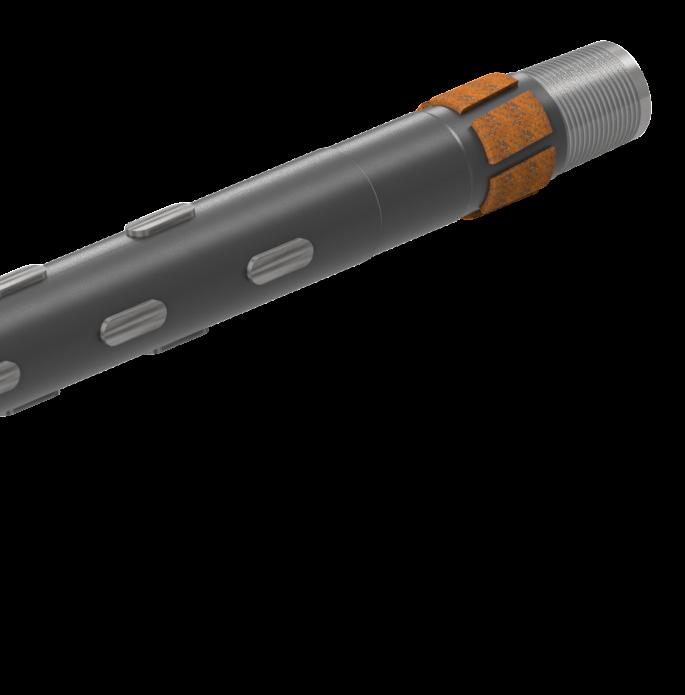
THE CONVEYOR BELT PROJECT
The Conveyor Belt Project
The Conveyor Belt Project was a pivotal component of a larger multidisciplinary initiative for my student portfolio, offering invaluable insights into the interconnected nature of design and the seamless transition between disciplines.
As part of the student brief, we were tasked with designing a comprehensive mail-sorting facility. My contribution, aligned with my mechanical elective, focused on designing the conveyor belt system—a critical element to demonstrate progress and proficiency in mechanical design.
This project served as a significant milestone in my journey, showcasing not only my technical capabilities but also my ability to integrate mechanical design principles into a broader system. The experience refined my problem-solving skills, reinforced my understanding of design workflows, and solidified my passion for innovative and functional design solutions.

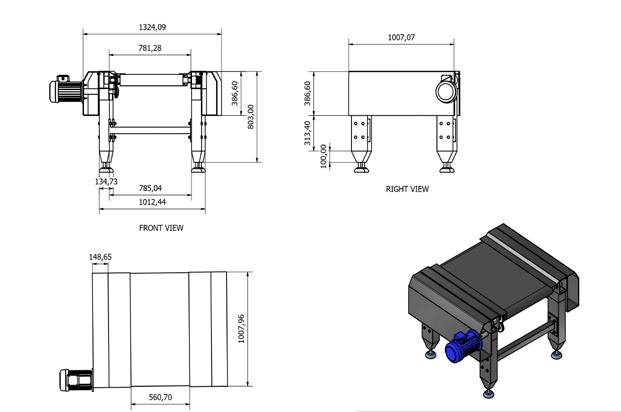
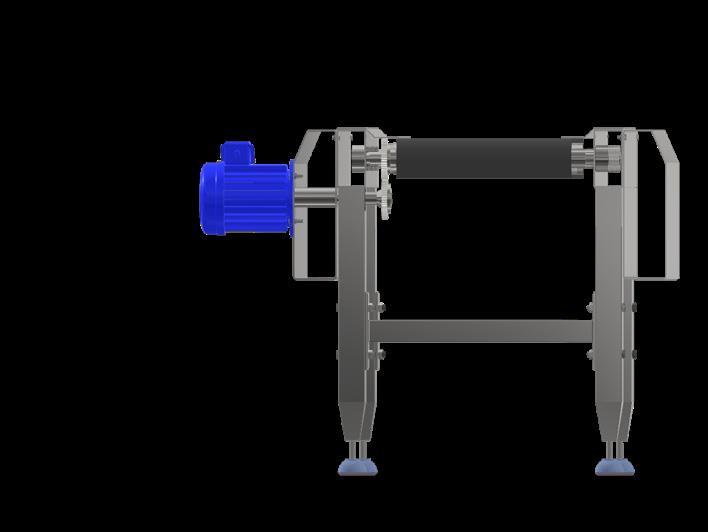
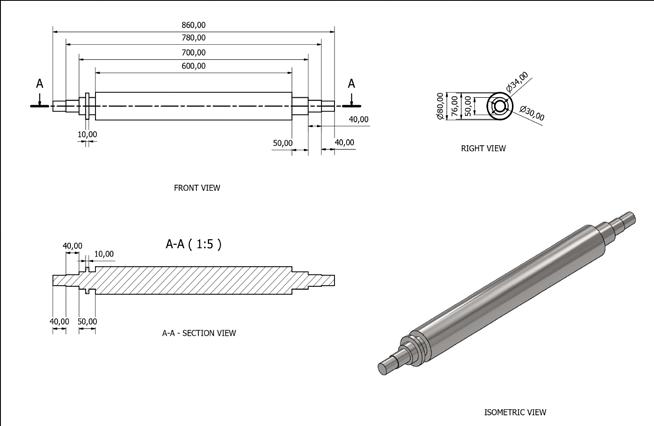
Project Name: Conveyer belt
Institution: Academic institute of excellence
Product : Conveyer belt
Software: AutoCAD, Inventor, Fusion 360,
Software: Microsoft 365, Canva,
Lecturer: M. Botha
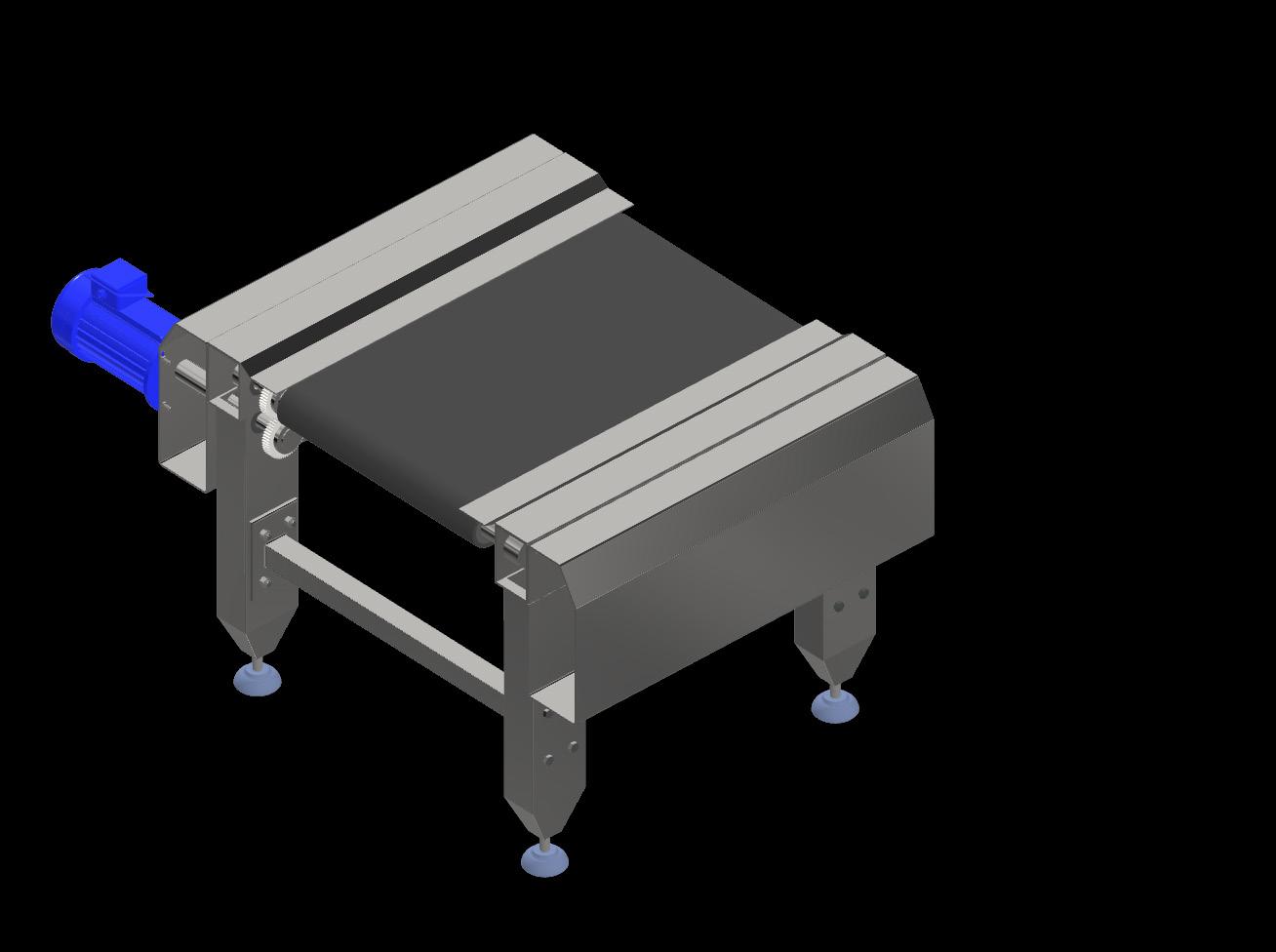
RECYCLED ADAPTOR DRILLING GUIDE
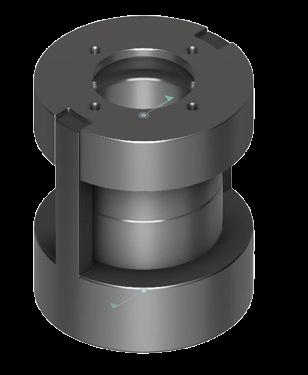
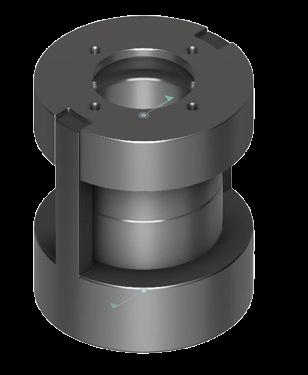
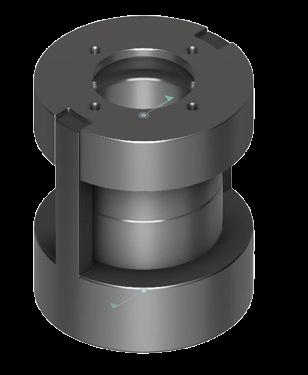
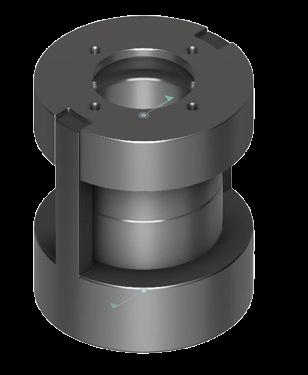
Compact and Purpose-Driven Design
The_Recycled Adaptor Drilling Guide is a prototype solution engineered for precision and efficiency in field drilling applications. Tailored for use with portable drills, this innovative tool eliminates the need for a rotary table, providing exact alignment for 45-degree, 3mm holes. These holes accommodate 3mm x 5mm tungsten pins, crucial for re-tipping the AQ_drilling crown to a refurbished steel adaptor.
Crafted with portability in mind, the design fits seamlessly into a standard toolbox, ensuring convenience for on-site maintenance and repairs. This sustainable, solution-driven tool is ideal for professionals seeking precision and adaptability in demanding field environments, setting a new standard for mobile engineering solutions.
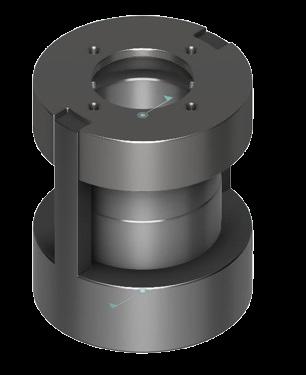
Project Name: AQ_Recycled Adaptor retipping drilling guide
Company: Thriftline Products Pty ltd.
Product Description: Compact Drlling guide
Software: AutoDesk Fusion 360
Manager: R. Hogan
Prototyping: 3D Plug