How Do You Play Classic Casino Games Like Blackjack and Roulette?
Pressure vessels are critical components in industrial systems where fluids or gases must be stored or processed under varying pressure and temperature conditions. The design of these vessels is far from one-size-fits-all It requires deep engineering expertise, a solid understanding of material science, and compliance with strict industry standards. In this article, we’ll explore how pressure vessels are designed for different pressure and temperature ranges and why working with an experienced manufacturer like RR88 ensures safety, durability, and regulatory compliance.
Understanding the Basics of Pressure Vessel Design
Designing a pressure vessel begins with understanding the operational environment The pressure range whether low, medium, or high determines the required wall thickness, the type of welding, and the overall configuration of the vessel Temperature also plays a vital role, especially in applications involving extreme heat or cryogenic conditions At RR88, our engineering team starts every project with a comprehensive design phase, considering operating pressure, temperature, type of contents, and installation location These inputs help define the material of construction, corrosion allowances, joint types, and safety features. For example, vessels operating at elevated temperatures require materials that maintain strength without deforming, such as chrome-moly alloys or stainless steel
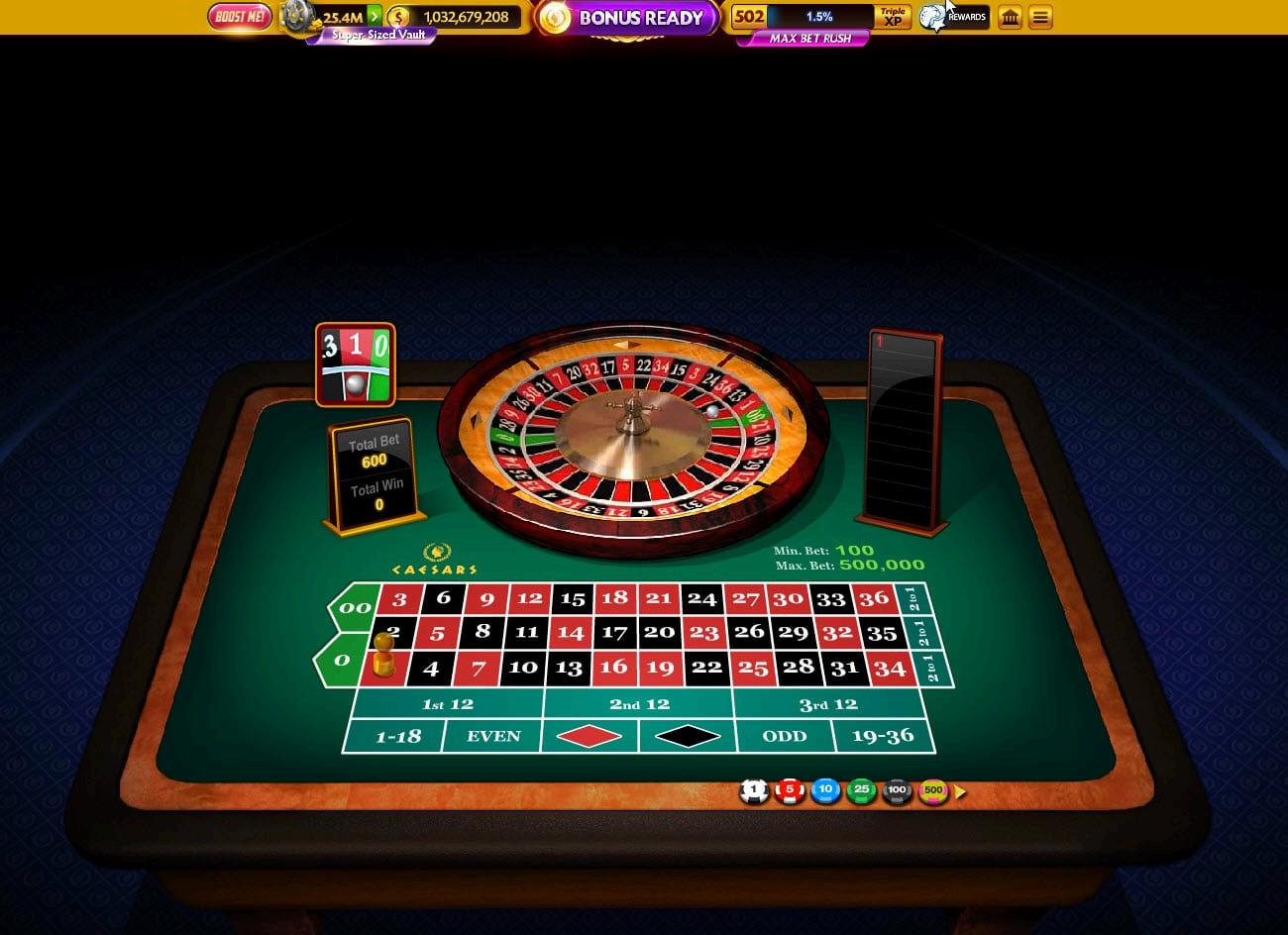
Design codes such as ASME Section VIII are followed to ensure every vessel meets structural integrity requirements under specified conditions Failure to match material properties to operating ranges can result in catastrophic failures, which is why customization is essential. RR88 excels in creating vessels tailored for diverse industrial demands, ensuring reliability under the most challenging scenarios
Materials Selection Based on Pressure and Temperature
Choosing the right material is the backbone of designing a vessel for varying pressure and temperature ranges Common materials include carbon steel, stainless steel, and high-performance alloys. Each offers different tensile strengths, corrosion resistance, and temperature tolerance
For low-pressure applications at ambient temperatures, carbon steel is often sufficient. However, it becomes unsuitable in highly corrosive or high-temperature environments. In such cases, materials like 316 stainless steel or Hastelloy are used due to their excellent resistance to corrosion and thermal expansion.
When designing for high-pressure scenarios, the material must withstand not only the internal load but also maintain its shape and structural integrity over time. RR88 often recommends materials that exceed minimum requirements to extend the vessel’s lifecycle and reduce long-term maintenance. For high-temperature applications such as in refineries or chemical plants materials are chosen based on their creep resistance, oxidation tolerance, and thermal conductivity At RR88, we utilize advanced simulation software to evaluate material behavior under fluctuating conditions, ensuring long-term durability and safety.
Stress Analysis and Design Calculations
Once materials are selected, detailed design calculations and stress analyses are performed These include wall thickness determination, reinforcement calculations around openings, and analysis of external loads such as wind or seismic activityDesigning for high-pressure environments requires thicker walls, often leading to increased weight and fabrication complexity. Stress analysis ensures that each section of the vessel can handle the internal pressure without yielding or bursting For thin-walled vessels, hoop stress (circumferential stress) is typically the governing factor, while for thick-walled vessels, radial stress must also be considered.
Temperature-induced stress is another key factor As materials expand and contract, they experience thermal stress, which can weaken the vessel over time if not accounted for. At RR88, our engineers use Finite Element Analysis (FEA) to simulate these stressors and optimize vessel geometry We also consider cyclic loading in environments where pressure and temperature vary frequently. Fatigue analysis helps us design vessels that resist crack formation and material degradation over repeated cycles This proactive approach is what makes RR88 a preferred partner for mission-critical pressure systems.
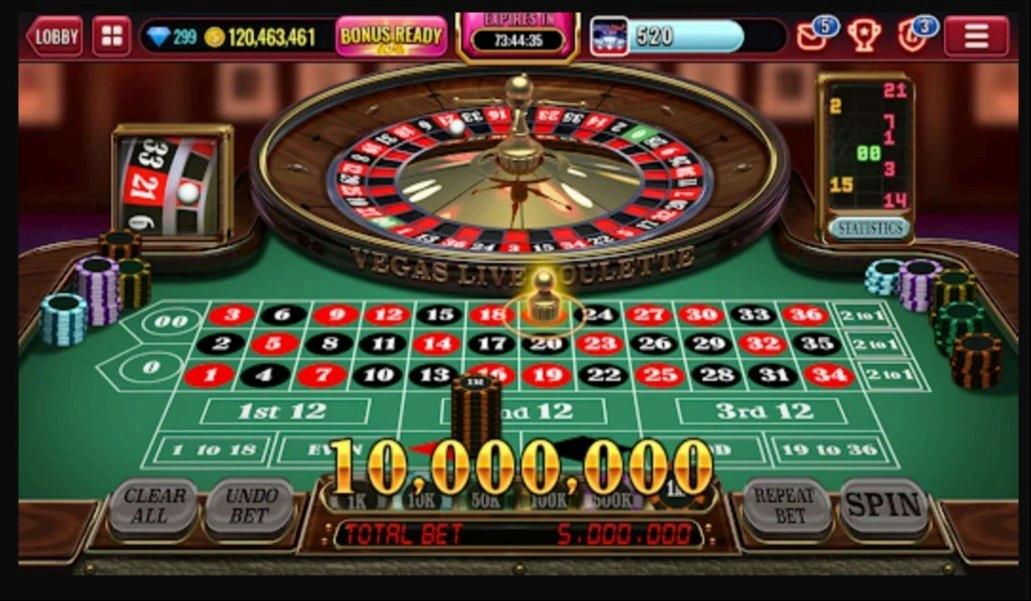
Safety Features and Design Standards
Safety is paramount in pressure vessel design, particularly when dealing with extreme conditions Every vessel must include safety devices such as pressure relief valves, rupture discs, and fail-safe controls Codes like ASME, PED (Pressure Equipment Directive), and API standards specify the minimum safety features required. For instance, ASME Section VIII mandates hydrostatic testing, where vessels are pressurized beyond operating limits to ensure they hold under stress
RR88 incorporates advanced safety protocols into every design We also provide comprehensive documentation, including material certificates, welding records, and inspection logs, ensuring full traceability and compliance.In addition to physical safety features, insulation and heat protection may be added for high-temperature vessels Insulation not only preserves energy efficiency but also protects operators from accidental contact with hot surfaces. RR88 engineers work closely with safety managers to implement these protections during the design phase