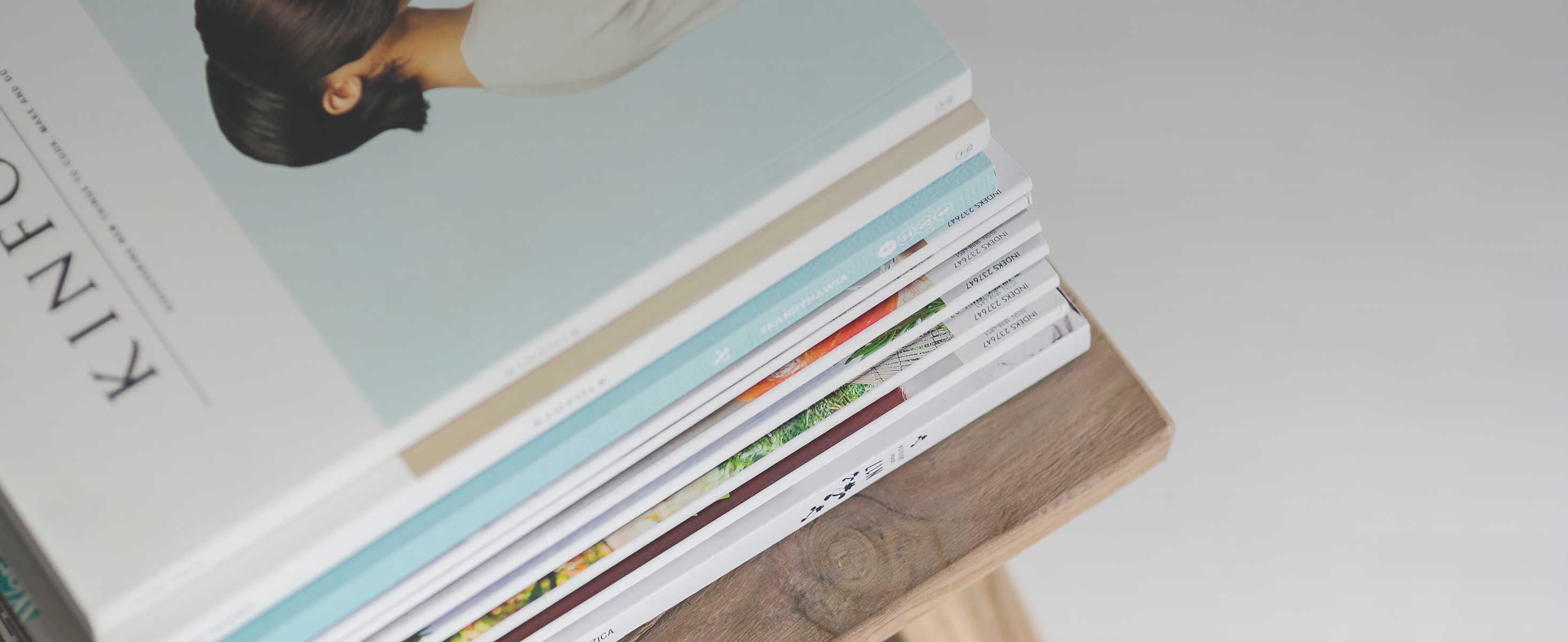
6 minute read
Environmental Law Update
Evaluation of Activity and Use Limitations in Real Estate Transactions
Noted industrial widget manufacturer, Johnson Co., is considering a move from their dilapidated facility to fancy new digs. All is going well with the property acquisition until Johnson Co. begins its obligatory environmental due diligence. Lo and behold, it turns out that the sparkly new property is hiding a deep, dark secret—residual contamination! Sitting beneath the beautiful new building and its newly-paved parking lot is a whole bunch of contaminated soil and groundwater. And that’s not all! The property is also subject to the dreaded Activity and Use Limitation (AUL)! Should Johnson Co. instruct their attorneys to go pencils down and look for a better option? Or does their intended use for the property work within the confines of the AUL?
Known by a handful of different monikers across the country, AULs are an indispensable tool for property owners to address contamination in a cost-effective manner that protects human health and the environment without hamstringing the future beneficial use of a property. Typically implemented through a covenant recorded in the chain of title, AULs restrict access to or disturbance of contaminated soil or groundwater through a combination of engineering and institutional controls.
Engineering controls are physical barriers that prevent direct contact with the contaminants in question. They can be as simple as a concrete cap or a specific depth of clean fill over contaminated soil. Engineering controls also can prevent the migration of impacted groundwater to or from a property through the use of so-called vertical engineered barriers (VEBs), such as slurry trenches or sheet piling, or the infiltration of vapors into a structure through the use of passive vapor barriers or sub-slab depressurization systems.
Institutional controls, on the other hand, typically restrict the uses of the property or the activities that can take place at the property. Institutional controls can be relatively simple, e.g., restricting the use of the property to non-residential uses or prohibiting groundwater usage; or more complex, e.g., restricting soil disturbance in certain designated areas of the property. Institutional controls also will set forth obligations related to engineering controls, if any. For instance, the property owner may have to conduct inspections related to maintenance of a cap or other engineering controls or periodically monitor groundwater or air quality to ensure the efficacy of VEBs or sub-slab systems.
So what engineering or institutional controls are in place at the proposed location of the new Johnson Co. world headquarters? You name it! The site is limited to non-residential uses and there is a prohibition on the use of site groundwater. There is also a cap over the entire site, a VEB preventing migration of site groundwater, and a sub-slab depressurization system to prevent vapors from entering the building. Okay—so the contamination is capped, the groundwater is contained, and vapors are being vented to the outside air. That’s it, right? Johnson Co. can purchase the property and not have to worry about a thing, right? Yes and no. Will Johnson Co. have to address the residual contamination at the property? Probably not. Will it have to maintain the cap and sub-slab systems? Absolutely, and it won’t be cheap!
Although AULs are an important tool to address contamination, they are not without costs and other obligations going forward, potentially in perpetuity. Between ongoing groundwater monitoring, cap inspections, and other ongoing obligations, costs associated with AULs can easily breach six figures over the life of a property. Understanding these obligations and the costs associated with them during the acquisition of a property allows buyers to address them upfront and potentially to keep some of the obligations and costs with the seller.
There are several cost areas for Johnson Co., or any party, to keep in mind during the transaction. The first is costs associated with long-term maintenance obligations related to engineering controls. For a cap over contamination, periodic inspections to ensure the integrity of the cap are likely to be required on at least an annual basis, and possibly as often as quarterly or monthly. Although one could rely on onsite personnel to conduct the inspection, it is probably better to rely on an environmental consultant trained in identifying issues with engineered caps. Depending on the frequency of inspections, inspections could easily cost tens of thousands of dollars per year. Inspections of sub-slab depressurization systems or VEBs are also a likely possibility.
Directly related to inspections is the corrective action required as a result of the inspection. If the cap or sub-slab system is no longer protective of human health or otherwise operates at less than peak performance, the responsible party will need to take action to repair the cap or to ensure that the engineering control operates as intended. Cap maintenance is likely to be a bigger cost in the coming decades because recordbreaking heatwaves and unprecedented rain and snowfall events are likely to be particularly hard on engineered caps.
Another item to consider is possible financial assurance requirements associated with AULs. Although not a direct cost per se, financial assurance mechanisms are typically required to ensure that adequate funds are in place to meet the AUL obligations. Most states allow a variety of different financial mechanisms, including insurance, guarantees, letters of credit, or surety bonds. Most states will allow so-called self-insurance with proof that the ownership entity’s net worth is over potential remediation costs. With the widespread use of single-purpose entities to purchase properties, demonstrating sufficient net worth can be a challenge for some entities.
So how should Johnson Co. deal with these liabilities and costs? One option is an environmental escrow or holdback arrangement. This type of arrangement is particularly helpful to a seller that wants to ensure it can walk away from the property without having to allocate future resources to operation- and maintenance-related activities. Rather, the parties agree to hold a certain amount of the sale price in an interestbearing escrow account that the buyer can draw against to deal with costs related to cap maintenance, groundwater monitoring, etc. Importantly, the escrow arrangement should provide the seller an opportunity to approve of the incurred costs so that it can ensure that the necessary work is being done by the new buyer.
From the buyer’s perspective, this may not be ideal as it still has to meet the necessary AUL obligations (and likely financial assurance requirements) even if those costs aren’t coming out of pocket in the near term. Moreover, the buyer continually has to get approval from the former owner to get reimbursed from the escrow account. This can lead to unnecessary and costly negotiations over every single drawdown. The buyer instead may prefer a purchase price reduction that essentially “pays” for the future costs associated with the AULs. We typically rely on environmental consultants to provide a ballpark estimate of likely costs associated with the AULs requirements to inform the purchase price reduction.
There is the option to have the seller retain all obligations associated with the AULs. This may be a big ask, especially in situations in which the seller is a single-purpose entity, but certainly not an impossibility. Finally, a combination of the above approaches may be a viable option as well—e.g., an environmental escrow to cover the buyer’s yearly or periodic inspection costs, while the seller retains responsibility for cap maintenance and repairs. The preferred approach will likely be highly specific to the facts at issue, but buyers should go in knowing that an AUL, and its associated obligations, is a manageable hurdle that should not kill a potential deal.
As always, remember to get your environmental attorney involved early and often!
Environmental Law Update Editor: Kyle R. Johnson, Brown Rudnick LLP, 185 Asylum Street, Hartford, CT 06103, kjohnson@ brownrudnick.com.