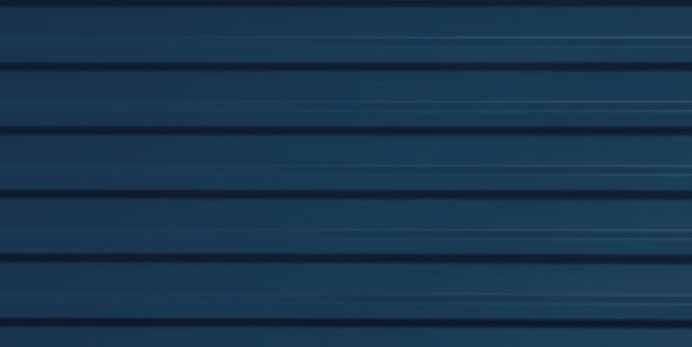
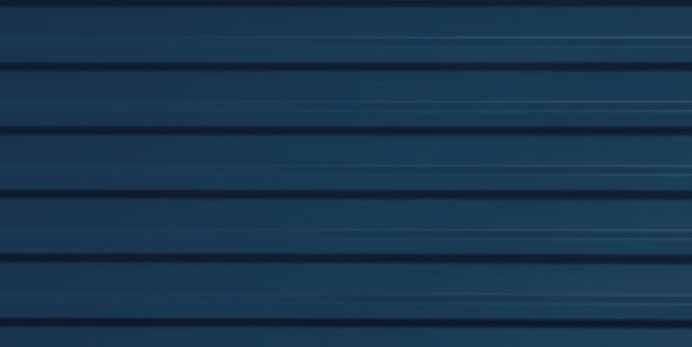
Be Seen in the Foundation Auction
www.floridaroof.com/item
Your company will be seen online and onsite at FRSA's 101st Annual Convention and Expo at the Gaylord Palms Resort in Kissimmee and recognized in Florida Roofing magazine. Expo exhibitors also receive a ribbon to display in your booth.
Your company will be seen online and onsite at FRSA's 100th Annual Convention and Expo in Daytona Beach and recognized in Florida Roofing magazine.
Your company will be seen online and onsite at FRSA's 100th Annual Convention and Expo in Daytona Beach and recognized in Florida Roofing magazine.
Auction Dates
Auction Dates
July 15-22 Online
July 19-22 Onsite
July 7-14 at www.floridaroof.com/items
July 12-14 at Gaylord Palms Resort
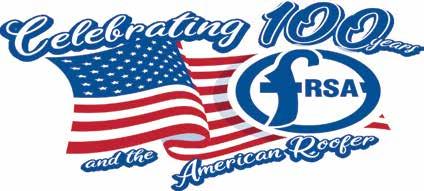
Your Donation Supports the Industry Through Scholarships + Research + Education
Your Donation Supports the Industry through Scholarships + Research + Education
ROOFING
Roofers Work to Save a Bat from Extinction


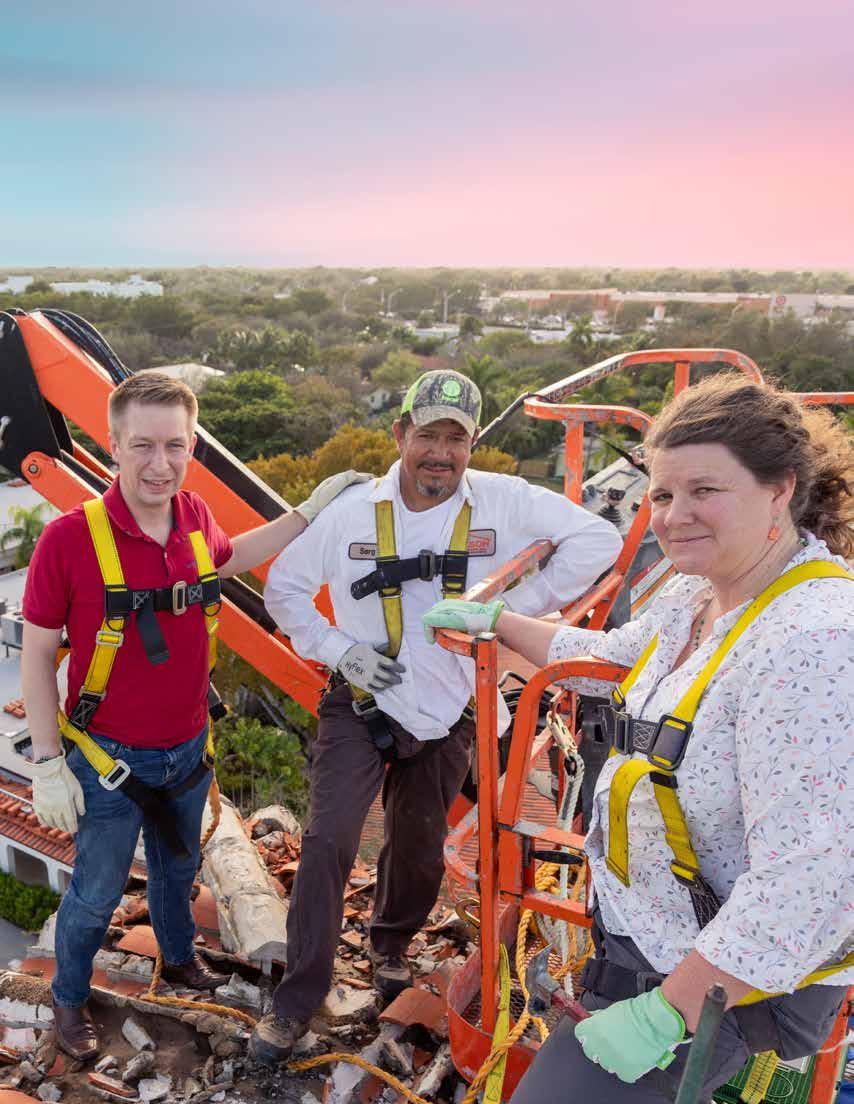
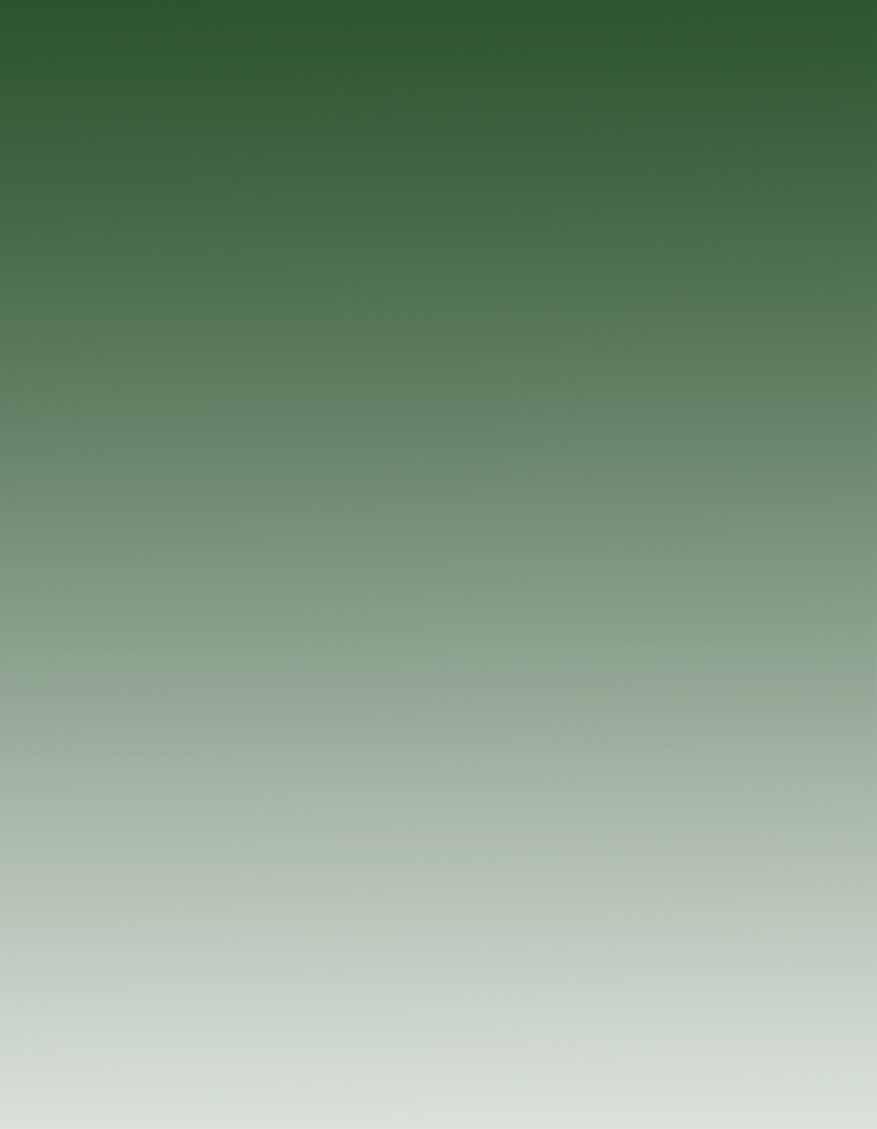

FRSA-Florida Roofing Magazine Contacts:
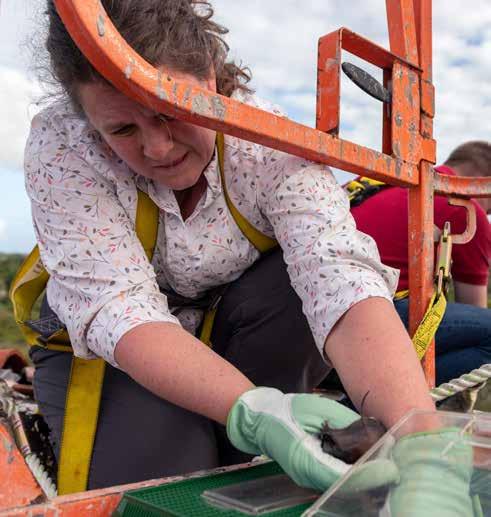
For advertising inquiries, contact: Lisa Pate at: lisapate@floridaroof.com
(800) 767-3772 ext. 157
All feedback and reprint permission requests (please include your full name, city and state) contact: Lisa Pate, Editor, at: lisapate@floridaroof.com
(800) 767-3772 ext. 157 Florida Roofing Magazine, PO Box 4850 Winter Park, FL 32793-4850
View media kit at: www.floridaroof.com/ florida-roofing-magazine/ #FRSA #roofingprotects
2023
S unshine S tate S olution

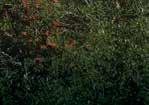
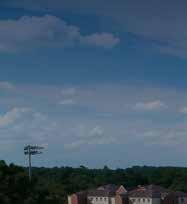
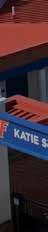
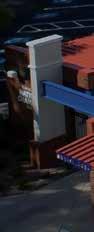
Equally strong and attractive , these metal roofing panels are available in Florida in our full line of PAC-CLAD painted steel, aluminum and Galvalume Plus coatings, ensuring that your roof will endure whatever comes its way. All panels are Miami-Dade County and Florida Building Code approved.








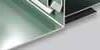
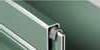
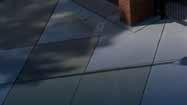



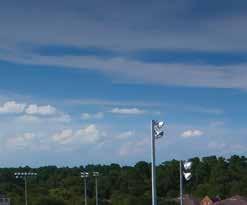

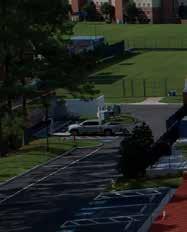
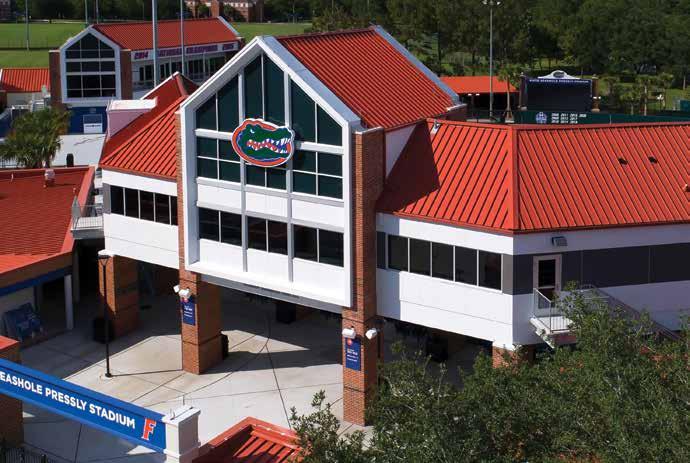
Supporting The Faine House
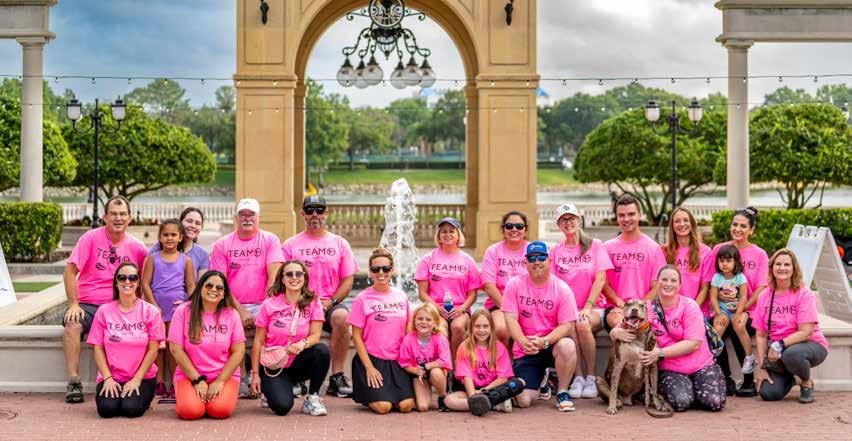
The Faine House is an Orlando-based group home for young adults on the verge of homelessness where dozens of Central Florida young adults have lived, opened their first bank account, found employment, attended technical school or earned a college degree. Through The Faine House, young adults have the chance to discover themselves and to see what a future outside the system can hold.
Regardless of their background, every young adult deserves access to dedicated mentorship, quality education and strong emotional support.
The Faine House, co-founded by retired NFL player, businessman and philanthropist Jeff Faine and financial executive and philanthropist Jeff Sharon – two local leaders with a strong spirit and heart for creating change – incorporates their spirit in all that it does. For the past 11 years, The Faine House community, comprised of dedicated volunteers and business leaders,
has empowered young adults in overcoming past challenges and realizing their true potential.
The Faine House operates a 7,000-square-foot facility in the Pine Hills community of Orlando. They host 10 private bedroom suites, accepting 18 to 23-year-olds into the residential program who are in desperate need of access to safety, stability, opportunity and mentorship. Each young adult sets their own financial, occupational and educational goals and participates in a curriculum designed to heal and empower them.
FRSA President Matt Criswell and wife Jackie, chose The Faine House as the 2023 Charity of Choice. In addition to raising funds through the FRSA Convention registration site, Affiliate chapters throughout the state have made donations. Recently, Team FRSA, which included members and staff, participated in a 5k walk and raised over $4,200 for the charity. Thanks to the following companies that generously supported Team FRSA!
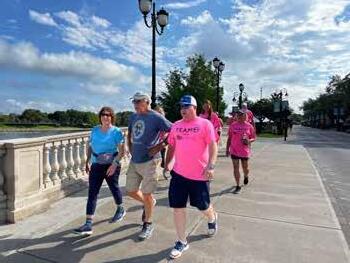
■ A.C.T. Metal Deck Supply
■ All Weather Roofing
■ Davis Roofing & Sheetmetal, LLC
■ DuPont Tile Bond & TCParker & Associates
■ Insurance Office of America
■ O’Hara’s Son Roofing
■ Rodman Roofing
■ WeatherShield Roofing Group
Interested in supporting this wonderful charity, please visit, www.floridaroof.com/charityofchoice.
Updates on OSHA’s Heat Injury and Illness Prevention Efforts
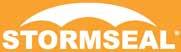
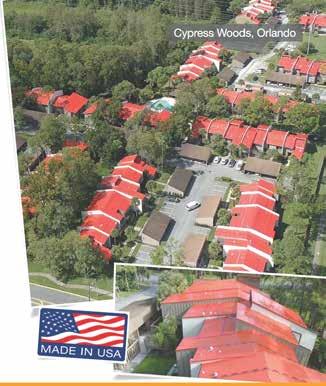
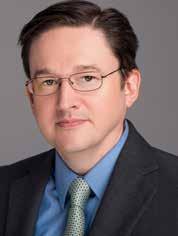
Employers know that working in the heat can be a health hazard, especially with summer temperatures already here. Workers in several industries can be affected, so OSHA continues to review and adapt its standards.
On May 19, the Small Business Association’s Office of Advocacy held a Small Business Labor Safety OSHA/MSHA Roundtable. Among the topics discussed was an update on the National Advisory Committee on Occupational Safety and Health (NACOSH) Heat Injury and the Heat Illness Prevention Campaign. The meeting was led by Lisa Long, Deputy Director of OSHA’s Directorate of Standards and Guidance and Pamela Barclay, OSHA health scientist.
Goals of the Work Group
OSHA created the Heat Injury and Illness Prevention Work Group of NACOSH to assist that committee in providing recommendations for heat injury and illness prevention. The first goal (Task One) was to evaluate
OSHA’s heat illness prevention resources and provide input. The second goal (Task Two) was to assess stakeholder input for the Heat Injury and Illness Prevention in Outdoor and Indoor Work Settings advanced notice of proposed rulemaking (ANPRM), then make rule recommendations for OSHA to consider.
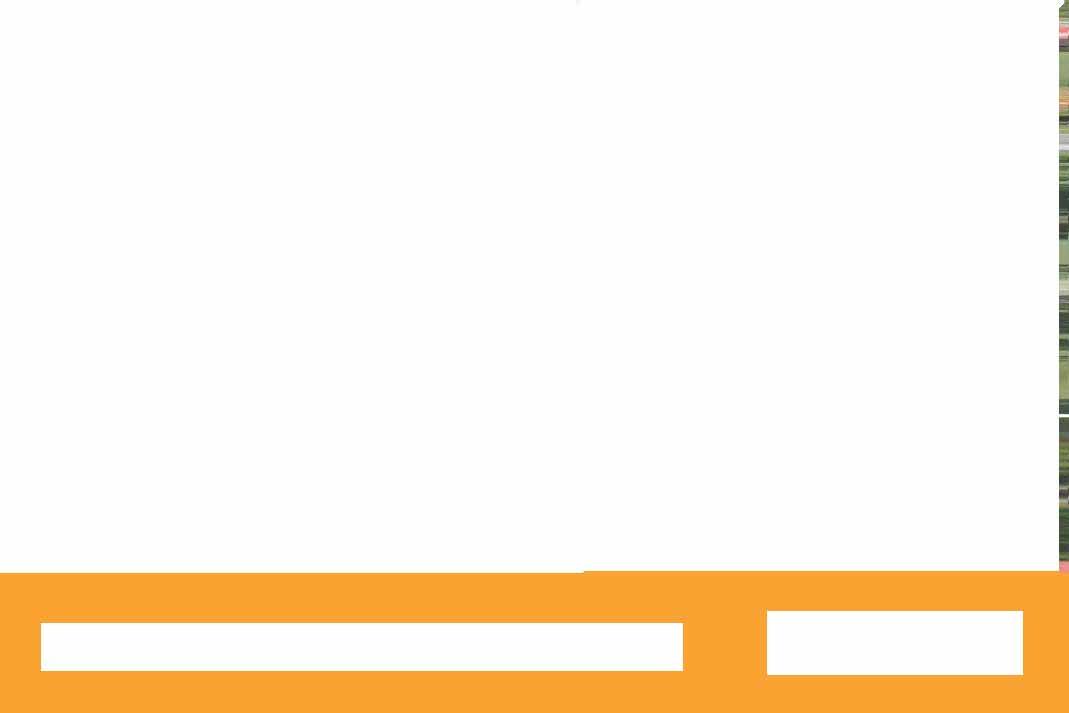
Work Group Recommendations for Task One
The group met five times from February 2022 to April 2023 and submitted recommendations for Task One. These included the following:
■ Ensuring that all heat injury and illness documents clearly identify worker rights and employer responsibilities
■ Ensuring that all materials and solutions have been technically reviewed and are based on evidence
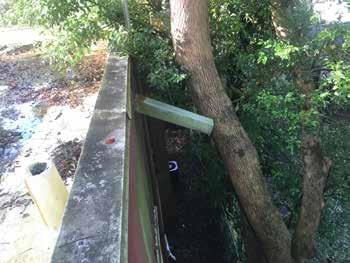
■ Revising any materials with errors or broken links
■ Targeting a wide range of workers
■ Increasing outreach to temporary and youth workers
■ Creating more multi-lingual materials
■ Continuing community outreach efforts related to heat issues
■ Expanding information for healthcare providers, especially first responders
■ Increasing the use of social media and apps for messaging
■ Identifying best practices and technology for employers and workers.
Work Group Recommendations for Task Two
The group continues to deliberate on the issues related to Task Two and will provide a written report. This report will include ways to measure and define heat exposure, strategies for reducing work-related heat injury and illness and how existing industry and state standards apply. Task Two recommendations were presented at the NACOSH meeting on May 31.
Heat Illness Prevention Campaign
OSHA launched the Heat Illness Prevention Campaign in 2011 and modeled it after Cal/OSHA’s campaign. Its purpose is to educate both employers and workers about the hazards of working in the heat.
To raise awareness about heat-related dangers, OSHA is sponsoring a Beat the Heat National Contest. It has also launched The Heat Source newsletter which can be found on OSHA’s website, www.osha.gov/heat.
Final Thoughts
It will be interesting to see what results from the Heat Injury and Illness Prevention in Outdoor and Indoor Work Settings ANPRM.
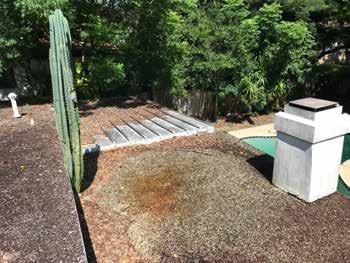
In the meantime, if you have concerns about following OSHA guidelines and protecting your workers from the heat, meet with your HR staff to ensure that all policies are current. You can also consult legal counsel. A seasoned OSHA attorney can assist you in being compliant and advise you on new rule proposals.
The information contained in this article is for general educational information only. This information does not constitute legal advice, is not intended to constitute legal advice, nor should it be relied upon as legal advice for your specific factual pattern or situation.
Trent Cotney is a Partner and Construction Practice Group Leader at the law firm of Adams and Reese LLP and serves as FRSA General Counsel.
Free Legal Helpline for FRSA Members
Adams and Reese LLP is a full-service law firm dedicated to serving the roofing industry. FRSA members can contact Trent Cotney to discuss and identify legal issues and to ask general questions through access to specialized counsel. They offer free advice (up to 15 minutes) for members. If additional legal work is required, members will receive discounted rates. This is a pro bono benefit provided to FRSA members only. Contact Trent at 813-227-5501.
What’s Wrong with These Pictures?
Industry Updates
EagleView Technologies Appoints New Leadership
EagleView Technologies, a leading provider of aerial imagery and data analytics, announced the appointment of Piers Dormeyer as its new Chief Executive Officer. Piers, who has been an integral part of the EagleView team for the past ten years and most recently served as President of the Commercial Group, brings a wealth of expertise in business strategy, organizational development and operational excellence. With this transition, EagleView looks forward to a seamless leadership succession.
“It is an honor to assume the position of CEO at EagleView,” stated Piers Dormeyer. “The company has seen unparalleled growth in the recent past and I believe that we will continue to lead the industry by focusing on our cutting-edge technology. We have a talented team and I look forward to continuing our work together to scale our innovative solutions and deliver unparalleled value to our customers.”
Piers has consistently demonstrated his strategic vision, leadership skills and passion for driving growth. As President of the Commercial Group, he successfully spearheaded key initiatives, building strong relationships with customers and partners while expanding the company’s market presence. Piers’s extensive industry knowledge, combined with his deep understanding of EagleView’s operations, uniquely positions him to lead the company into an exciting new chapter of innovation and continued success.
As Piers takes the helm as CEO, Chris Jurasek will move into the role of Executive Chairman. During Chris’s tenure as CEO, his strategic vision and dedication played a crucial role in shaping EagleView’s growth and establishing the company as a market leader in aerial imagery and geospatial data analytics. “I am exceptionally proud of the innovative products we’ve brought to market, the process improvements implemented and the remarkable growth we have achieved. It has truly been my honor and pleasure to lead EagleView these last three years,” said Chris. “I’m confident that Piers is the right leader to drive the accelerated EagleView growth plan into the future. His experience, passion and deep understanding of EagleView’s operations make him the perfect choice.”
Insurance Office of America Appoints Phillip Lane to Managing Partner Insurance Office of America (IOA) announced the appointment of Phillip Lane, CLCS, to the role of Managing Partner. Phillip joined IOA in 2018 as a commercial lines producer and, since, has served as a Vice President. In his new role, he will oversee IOA offices in Kissimmee, Melbourne and Ormond Beach.
“There is a reason Phillip has been recognized for prestigious industry awards year after year. He is a consummate professional and embodies IOA’s focus on protecting our clients’ dreams,” said IOA Group Chairman and CEO Heath Ritenour. “As an integral member of the IOA team, he is deserving of this promotion to Managing Partner and I look forward to his continued success for many years to come.”
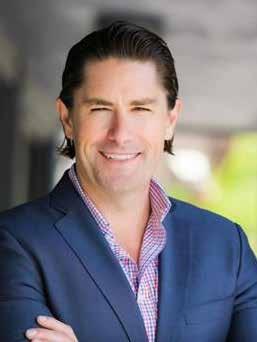
153,000 Monthly
Phillip is a demonstrated leader in the commercial insurance industry where he specializes in contracting, manufacturing, banking, technology and professional services. He has been active in key associations, including the Florida Roofing & Sheet Metal Contractors Association (FRSA), FRSA Credit Union, Space Coast Licensed Roofers Association, Treasure Coast Roofing & Sheet Metal Association and the National Roofing Contractors Association (NRCA).
“Phillip has been an important addition to the IOA team and I’m thrilled for him to progress in leadership within the organization,” said IOA Division President Danny Anderson. “His focus on the risk management
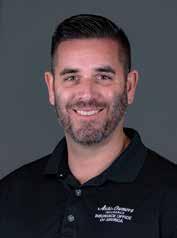
and insurance needs of clients is impressive and he inspires those around him.”
“Phillip is one of IOA’s top producers and through his actions, he has shown he embraces and exemplifies the heart and soul of IOA and what we stand for,” said IOA Regional President Nathan Brainard. “We look forward to welcoming Phillip into this new role as his opinions and leadership will have a further positive impact in the Central Florida region and IOA as a whole.”
Among his many accomplishments, Phillip has been named a Risk & Insurance Power Broker and for three consecutive years and has been named an Insurance Business Top Retail Broker.
Atlas Web Technologies to Add Capacity at Paper Mills

Atlas Web Technologies, a division of Atlas Roofing Corporation, announced it will be making investments in two of its paper mills to significantly increase capacity. The premier manufacturer and supplier of 100 percent recycled paper and coated glass flexible facers to the polyiso and gypsum building materials markets. Atlas will make these improvements at its Meridian, Miss. and Franklin, Ohio paper mills, increasing capacity by approximately 30 percent over the next two years. This comes on the heels of a recent capacity expansion project at the Meridian coated glass facer plant and will help Atlas grow their coverage as the largest flexible facer manufacturer in North America.
“We are very excited to be making these improvements in Meridian and Franklin,” said Matthew Bennett, Vice President and General Manager of Atlas Web Technologies. “This move demonstrates a commitment to the industry, to our customers and to improving our position as the largest and most innovative flexible facer manufacturer in the country.”
The capacity improvements will help satisfy growing demand in the polyiso and gypsum facer businesses. The improvements in Meridian and Franklin are scheduled to be completed by the middle of 2024.
ROOF AND PLAZA PAVERS


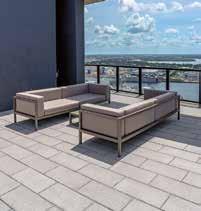
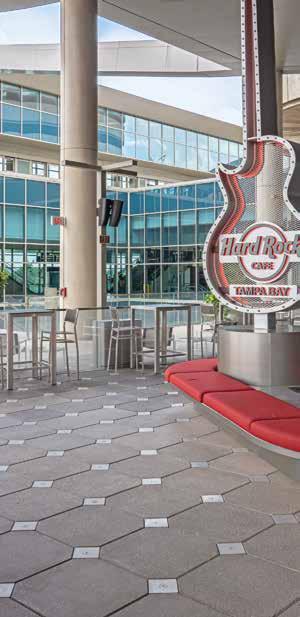
Help Save the Rarest Bat in the U.S.
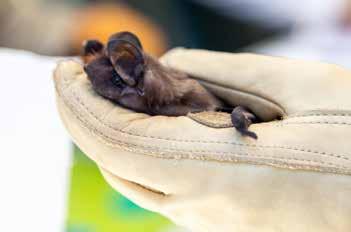
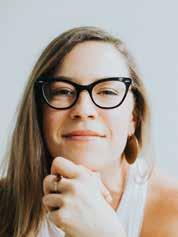
Homeowners love the distinctive look of Spanish tile roofs, but occasionally, when roofing professionals pull up a few of these barrel tiles, they find an unexpected surprise: Florida bonneted bats. These federally endangered bats sometimes seek cover and protection from predators under the nooks in these tiles. Since they are quiet and unobtrusive, Florida bonneted bats often go unnoticed until tiles are removed during construction. This is why roofing professionals have such an important role in helping save this species – which is the rarest bat in the U.S. – from extinction.
Florida bonneted bats only live in southern Florida and have one of the smallest home ranges of any bat in the U.S. They’re voracious insect eaters and one of the largest bats in North America, with a 20-inch wingspan and skinny wings that make them very fast fliers. Their large, forward-facing ears make them look like they’re wearing a bonnet.
“Florida bonneted bats live from south of Orlando to Miami and it can honestly be said that it’s a Floridian species,” says Dr. Melquisedec Gamba-Rios, Bat Conservation International’s Endangered Species Interventions Research Fellow. “They’re our neighbors and it is a responsibility for all of us to take care of our neighbors.”
Florida bonneted bats didn’t always live in roofs. Their native habitat includes the Pine Rocklands that once covered large swaths of Miami-Dade County, but only two percent of these forests remain today. Since their natural habitat is almost entirely gone, the bats make do with other spaces, like the nooks in Spanish tile roofs.
“With a lot of species, when their habitat disappears, they disappear,” says Dr. Frank Ridgley, Zoo Conservation and Veterinary Services Manager at Zoo Miami. “But these smart little adaptable bats are figuring out that there are cavities under barrel roof tiles or other kinds of cavities in buildings. But it seems like Spanish tiles are a favorite of theirs and it’s a very popular roofing style down here.”
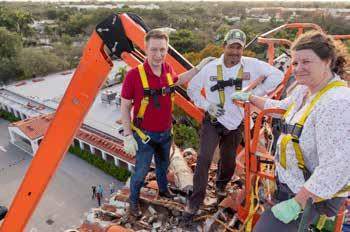
• High-performance products for roofing professionals
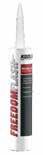
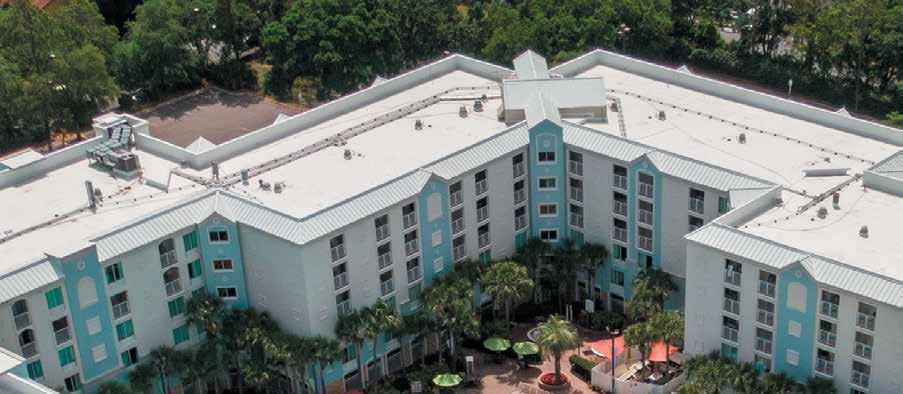
• Ideal for large commercial projects
• Warranty options for qualified jobs
• Uniflex ® is sold exclusively in Sherwin-Williams stores uniflexroof.com
• Exceptional weather resistance
• Residential roof applications for metal, concrete and tile
• Full line of roof paints, coatings and patch & repair products
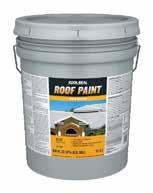
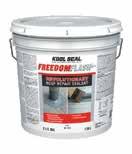
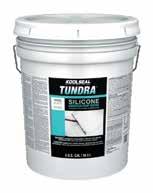

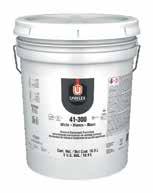
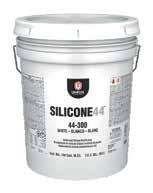
• Ideal for DIY and residential/light commercial contractors koolseal.com
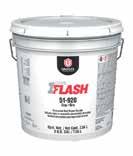
When you think of bats, you might think of massive caverns with millions of bats making noise and the distinctive scent of guano – bat poop – in the air. Since Florida bonneted bats roost in small groups, generally consisting of 12 to 15 bats, they are quiet and unobtrusive. They don’t smell and you won’t see them unless you happen to be looking at the right spot at exactly the right time, when they fly out of their roosts to forage at night. This is why people often don’t know there are bats on a home until the roof tiles are pulled up.
When a bat is seen on a project site – Florida bonneted bats are most likely to be spotted either on roofs or in attics – it is crucial to stop work immediately, notify homeowners if necessary and contact the appropriate state or federal agency or the Miami Bat Lab, which will work closely with both agencies.
“We can help the homeowner and the company navigate the best way to deal with the bats in a humane way, where we’re protecting the bats and helping the contractor to accelerate the process so they can continue working,” Dr. Gamba-Rios says. “With a few simple steps they can really help us save the Florida bonneted bats.”
Scientists with Miami Bat Lab may even be able to visit the site to look for bats, identify them, collect valuable data and help develop a plan for next steps, which could include contacting wildlife specialists to safely remove the bats.
Professional bat removal involves hiring a licensed company to close all possible roof entrances, while leaving one small spot where the bats can emerge, but not return. It may take a few days for the bats to leave and sometimes if there are only a few bats, specialists may be able to relocate them.
These voracious insect-eaters pluck a substantial number of insects out of the sky, including an array of agricultural pests, reducing the need for pesticide on crops. One study found pregnant female bats can eat their own body weight in insects each night. Dr. Ridgley said a Zoo Miami study found that if one Florida bonneted bat artificial roost was 80 percent occupied, those bats could eat 21 pounds of insects in a single night.
Florida bonneted bats are perilously close to extinction and according to Dr. Ridgley, protecting even a few bats on a jobsite can have a significant impact on the species as a whole.
“If you’re in an area where a Florida bonneted bat could be using a roof and you just go in and don’t pay attention to the bats and you happen to harm or kill the bats on a project, you may have wiped out an entire colony and population of this rare bat and it could literally take decades for the species as a whole to recover from that loss because they aren’t the fastest to reproduce and they have a very complex social structure,” Dr. Ridgley says.
Learn more about the Florida bonneted bat at https://floridabonnetedbat.org/
Since all bat species are protected by state regulations and some, like the Florida bonneted bat, are federally protected, bat exclusion should only be conducted by certified professionals to ensure bat protection and a quick resolution for homeowners.
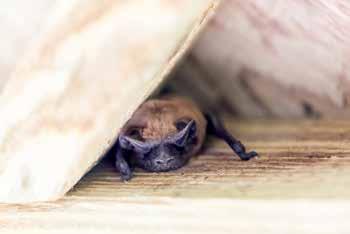
He points out how unique and incredible these bats are and how with just a little help, they can thrive. “They don’t exist anywhere else in the world except south Florida,” Dr. Ridgley says. “And the fact that they’re living in the middle of a city and survived this massive transformation and they’re just hanging in there, it’s probably that they just need a little help from us and they’ll be able to make it and recover. They’ve made it through the last 120 years of Miami transforming from a forest to a major metropolis and they’re still hanging around. It may be hard for them right now, but we can make improvements that make it easier for them and they can continue to be our neighbors – unique neighbors that no one else has.”
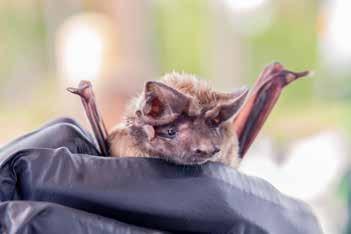
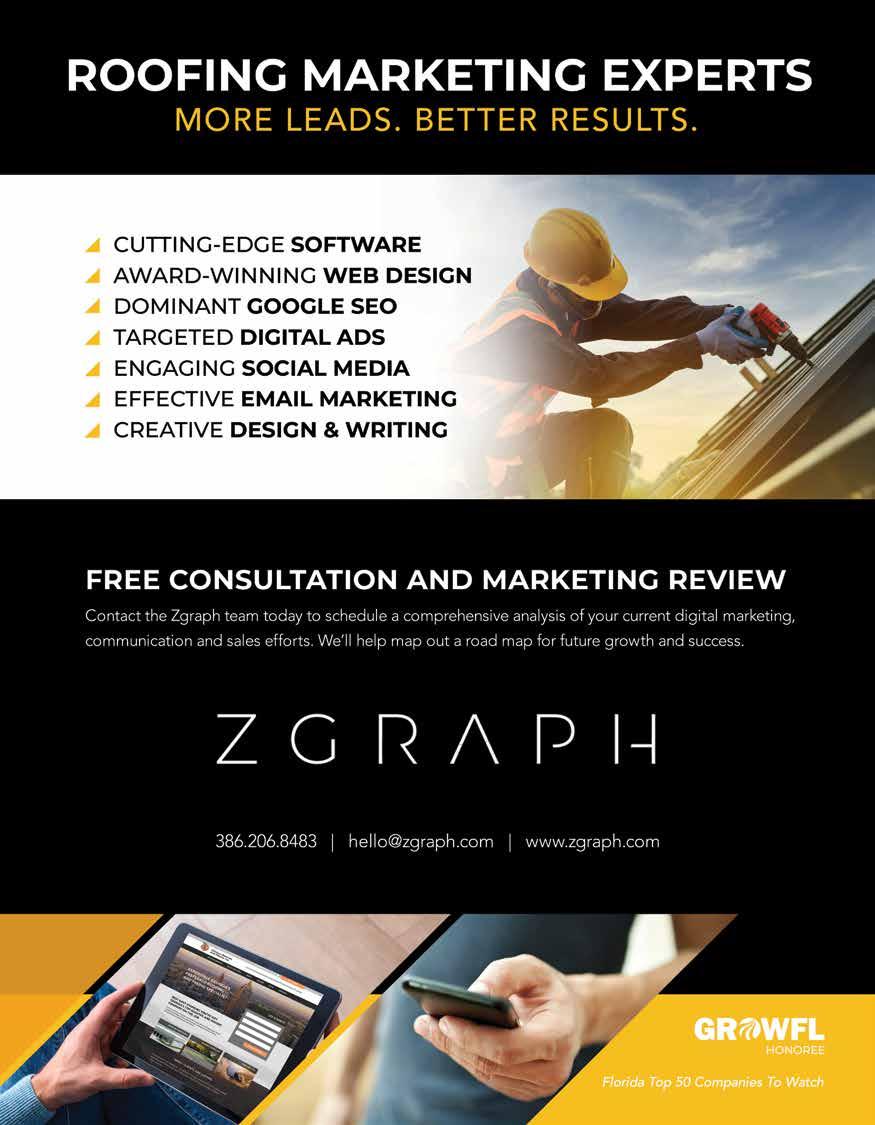
Words Matter: Roofing-Related Definition Changes
Mike Silvers, CPRC, Owner Silvers Systems Inc. and FRSA Director of Technical Services
Since we were children, we’ve been told “words matter”. Then we go to school and learn “sticks and stones may break my bones, but words will never hurt me.” So we were left to wonder which is it? Life very quickly teaches us that the former is definitely true and the latter is…not so much. Words offered with the right motives can lift us up and carry us forward, while negative sentiments from people we care for and respect can very definitely hurt. Words left unsaid may be the most unforgiving of all. You may be asking yourself what does this have to do with codes? Well, after almost 70 of these articles some of this can be chalked up to literary license, while also hoping you can indulge an old man who wants to share a few life observations along the way. I hope the connection to the code will become clearer when we are done.
When dealing with the building code, as with most things in life, words definitely matter. If the words in the building code are to be properly understood, the definitions must play a big part. Terms used in construction do not always perfectly align with those used in our everyday language. Some are not seen in any other context and are specific to a given trade or discipline. We look to the definitions within the code to help us understand the code’s intent. Those definitions are found in several areas. Most are located in Chapter 2 of any given code or subcode. Some that are trade-specific will be contained in their respective chapter as is the case with roofing-specific terms that are included in the Florida Building Code (FBC), Building Chapter 15 Roof Assemblies and Rooftop Structures. Most of the code definitions that impact roofing are shown in the following sections of the code:
■ FBCB (Building) Chapter 2 Definitions and Chapter 15 Roof Assemblies and Rooftop Structures
■ FBCR (Residential) Chapter 2 Definitions
■ FBCEB (Existing Building) Chapter 2 Definitions
■ FBCEC (Energy Conservation) Chapter 2
Definitions
The High Velocity Hurricane Zone (HVHZ – MiamiDade and Broward Counties) has its own set of definitions with some minor variations from those shown here. They can be found in:
■ FBCB (Building) Chapter 15, Section 1513 – HighVelocity Hurricane Zone Definitions
The first group of definitions shown below are some of those that have been added or revised in the FBC 8th Edition (2023). There are others too, but these are the ones that are clearly roofing-related. After the list of those that have been revised or added, I also provide some definitions that didn’t change but will serve as examples of the types of things included in the code’s definitions sections. Understanding the building code requires an understanding of the definitions. A thorough review is advised. The entire FBC can be found free of charge at floridabuilding.org/c/ default.aspx. Note: Words underscored below are new to the 8th Edition FBC.
FBC 8th Edition (2023) Added or Revised (Partial List)
EMITTANCE. The ratio of radiant heat flux emitted by a specimen to that emitted by a blackbody at the same temperature and under the same conditions
GYPSUM BOARD. The generic name for a family of sheet products consisting of a noncombustible core primarily of gypsum with paper surfacing.
GYPSUM PANEL PRODUCT. The general name for a family of sheet products consisting essentially of gypsum complying with the standards specified in Tables 2506.2 and 2507.2, and Chapter 35. Gypsum board and glass mat gypsum panels are examples of gypsum panel products.
GLASS MAT GYPSUM PANEL. A gypsum panel consisting of a noncombustible core primarily of gypsum, surfaced with glass mat partially or completely embedded in the core.
GYPSUM SHEATHING. Gypsum panel products specifically manufactured with enhanced water resistance. For use as a substrate for exterior surface materials.
GYPSUM WALLBOARD. A gypsum board used primarily as an interior surfacing for building structures.
INSULATING SHEATHING. An insulating board. A rigid panel or board insulation material having a thermal resistance of not less than R-2 of the core material with properties suitable for use on walls, floors, roofs, or foundations.
NAILABLE SUBSTRATE. A product or material such as framing, sheathing or furring, composed of wood, wood-based materials or other materials providing equivalent fastener withdrawal resistance.

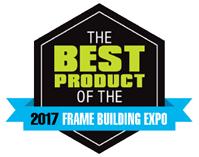
POSITIVE ROOF DRAINAGE. The drainage condition in which consideration has been made for all loading deflections of the roof deck, and sufficient slope has been provided to ensure drainage of the roof within 48 hours of precipitation.
RISK CATEGORY. A categorization of buildings and other structures for determination of flood, wind, tornado, snow, ice and earthquake loads based on the risk associated with unacceptable performance.
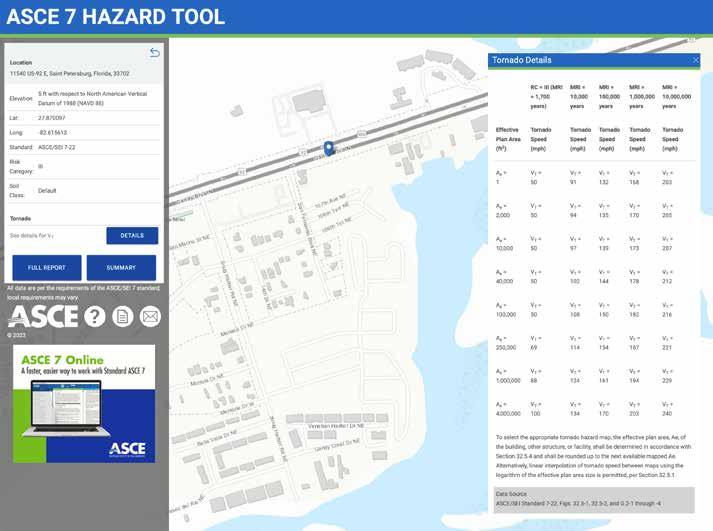
ROOF ASSEMBLY. A system designed to provide weather protection and resistance to design loads. The system consists of a roof covering and roof deck or a single component service as both the roof covering and the roof deck. A roof assembly includes the roof covering, roof deck, and may include a vapor retarder, thermal barrier, insulation or similar substrate.
ROOF COVERING. The covering applied to the roof deck for weather resistance, fire classification or appearance.
ROOF SYSTEM. A roof system consists of a roof covering and other interacting roofing components and may include vapor retarder, thermal barrier, insulation or other similar substrate. The system does not
include the roof deck unless it is part of a single component serving as the roof covering and the roof deck.
SPRAY-APPLIED FOAM PLASTIC. Single- and multi-component, spray-applied foam plastic insulation used in nonstructural applications which are installed at locations wherein the material is applied in a liquid or frothed state, permitted to free rise and cure in situ.
STEEP SLOPE. A roof slope two units vertical in 12 units horizontal (17-percent slope) or greater
VAPOR DIFFUSION PORT. An assembly constructed or installed within a roof assembly at an opening in the roof deck to convey water vapor from an unvented attic to the outside atmosphere.
As you can see, there have been extensive changes dealing with gypsum board, panels and sheathing. This should help clarify the many types of gypsum products now offered in the market and how they should be described. For roofing, a few products that would fit the definition of a glass mat gypsum panel would be DensDeck, Securock or other similar products.
The change in the definition of positive drainage will be helpful by changing additional slope to sufficient slope. The term additional slope has been
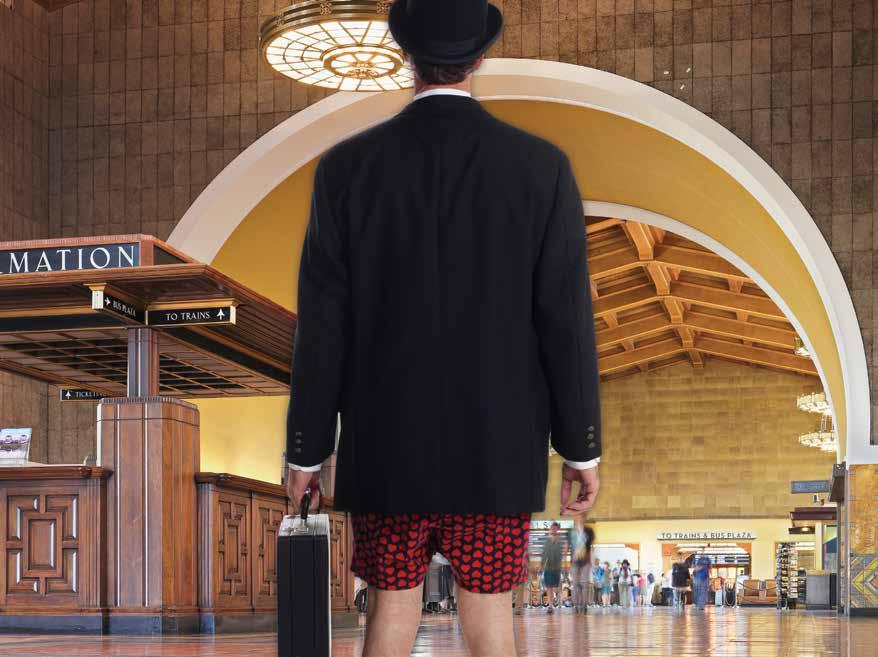
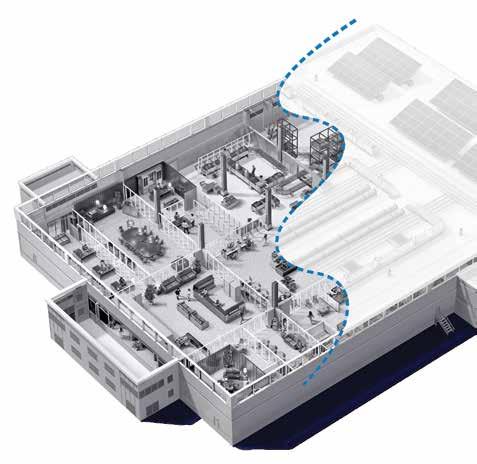
interpreted to require some type of additional slope be added during reroofing. The old language that stated additional slope has been provided was meant to confirm that the designer of a structure added slope to accommodate deflection of the roof deck to ensure drainage of the roof within 48 hours of precipitation
The addition of tornados to the Risk Category definition would seem to be concerning, but when you use the ASCE Hazard Tool (asce7hazardtool.online), it will help you understand whether or not tornado loads apply to a particular structure (see page 16). It primarily applies to buildings that have a risk category and a large footprint. The risk category inclusion is understandable, but the footprint portion requires some explanation. In principle, the larger the building the more likely it is to be hit by a tornado. Basically, a large building provides a bigger target for what is (compared to hurricanes) a fairly confined event. For most buildings in Florida, it will not apply.
A definition of roof system has been added, replacing the old definition of roof covering system which said: See roof assembly. The definition of roof assembly includes the deck, which is not typically part of a
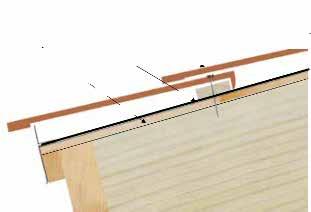
roof system and should not have been part of the previously named roof covering system. Roof assembly was tweaked to clarify that some components (vapor barriers, insulation, etc.) may or may not be present in an assembly or system. The diagrams below serve as examples to help clarify these terms.
FBC 8th Edition (2023) Definitions Which Remain Unchanged (Partial List)
ACCESSORY COMPONENTS. Components used in the installation of pedestals and pedestrian deck panels or pavers of the exterior elevated flooring system. Accessory components are made of either plastic, metal or other approved materials. Accessory components may be used to provide lateral bracing of the pedestals, to provide vertical support, for leveling the pedestal, to restrain the pedestrian deck panels or pavers to the top of the pedestal, or for other system requirements.
AGGREGATE. In roofing, crushed stone, crushed slag or water-worn gravel used for surfacing for roof coverings.
Example of a Low-Slope Roof
Roof Membrane
Upper Layer Thermal Insulation
Mechanically Fastened Base Layer Thermal Insulation
Steel Deck
Roof Tile
Underlayment
Sheathing
Roof Covering
Roof System
Roof Assembly
Vapor Retarder (may not be present)
Example of a Steep-Slope Roof
RoofCovering
RoofSystem
RoofAssembly
A definition of roof system has been added, replacing the old definition of roof covering system
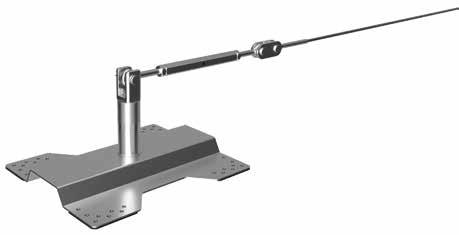

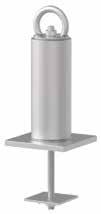

ARCHITECTURAL METAL PANEL. Water shedding (hydrokinetic) roof panel fastened to a roof deck.
BALLAST. In roofing, ballast comes in the form of large stones or paver systems or light-weight interlocking paver systems and is used to provide uplift resistance for roofing systems that are not adhered or mechanically attached to the roof deck.
BASE SHEET. The bottom or first ply of a roofing assembly over which subsequent roofing plies are applied. A base sheet may be designed for mechanical attachment, full or partial adhesion to the substrate.
BUILDING. Any structure used or intended for supporting or sheltering any use or occupancy.
BUILDING INTEGRATED PHOTOVOLTAIC ROOFING. A roofing product consisting of electricity generating
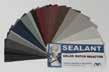
photovoltaic component integrated into a roof covering.
BUILT-UP ROOF COVERING. Two or more layers of felt cemented together and surfaced with a cap sheet, mineral aggregate, smooth coating or similar surfacing material.
“CLASS A” ROOFING ASSEMBLY. A roofing assembly that, in combination with the roof slope, has been classified by an approved testing agency, with a listing and follow-up service, as “Class A” in compliance with ASTM E108 or UL790.
“CLASS B” ROOFING ASSEMBLY. A roofing assembly that, in combination with the roof slope, has been classified by an approved testing agency, with a listing and follow-up service, as “Class B” in compliance with ASTM E108 or UL790.
“CLASS C” ROOFING ASSEMBLY. A roofing assembly that, in combination with the roof slope, has been classified by an approved testing agency, with a listing and follow-up service, as “Class C” in compliance with ASTM E108 or UL790.
CONTINUOUS ROOFING SYSTEM. A roof covering, composed from a single or multiple layers, forming a homogenous membrane over the entire roof surface, applied to either a flat or pitched roof surface(s).
COUNTERFLASHING. Formed metal or elastomeric sheeting secured on or into a wall, curb, pipe, roof-top unit or other surface to cover and protect the upper edge of a base flashing and its associated fasteners.

DISCONTINUOUS ROOFING SYSTEM. A roofing system with unsealed overlapping components, where the combined roofing system has openings at the point of overlap, applied to a sloped surface with a pitch of 2:12, or greater. Discontinuous roofing systems include asphalt shingles; concrete, clay or metal tile; wood shingles or shakes; and cement fiber roofing systems.
DRY-IN. The process of applying the first layer of felt in a roofing system.
FASTENER WITHDRAWAL RESISTANCE TEST. A static pullout test of mechanical fasteners, which are used to anchor any roofing component, to determine the force required to withdraw a fastener from the substrate. Testing shall be in compliance with the test procedure detailed in TAS 105.
FIRE-RESISTANT ROOF COVERING. Any Class A, Class B or Class C roofing system applied to the appropriate deck type within the specified slope of the listed classification.
FLASHING. The roofing component used to seal roofing systems, where the system is interrupted or terminated.
FLAT ROOF TILE PROFILE. Those tiles with less than 1/2-inch (12.7 mm) rise.
EXISTING BUILDING. A building erected prior to the date of adoption of the appropriate code, or one for which a legal building permit has been issued.
EXTERIOR ELEVATED FLOORING SYSTEM. An assembly installed over a roof assembly or other exterior supporting structure consisting of a walking surface of pedestrian deck panels or pavers mounted on pedestals using other accessory components, mechanical fasteners or adhesives as required by the manufacturer’s installation instructions for attaching pedestrian deck panels or pavers to pedestals and other accessory components. Exterior elevated flooring systems may have pedestals attached to the roof or other supporting structure or pedestals installed independently of the roof or supporting structure with the restraint of the pavers at the perimeter and discontinuous edges. Exterior elevated flooring systems are not part of the roof assembly.
Attached systems. Attached systems are those where pedestals are attached to the roof or other supporting structure by mechanical fasteners, adhesives or both.
Independent systems. Independent systems are those where pedestals are not attached to the roof but rest on the roof or other supporting structure.
HIGH ROOF TILE PROFILE. Those tiles having a rise to-width ratio greater than 0.20.
HIGH VELOCITY HURRICANE ZONE. This zone consists of Broward and Dade counties.
HURRICANE-PRONE REGIONS. Areas vulnerable to hurricanes defined as:
1. The U. S. Atlantic Ocean and Gulf of Mexico coasts where the ultimate design wind speed, Vult, for Risk Category II buildings is greater than 115 mph (51.4 m/s);
2. Hawaii, Puerto Rico, Guam, Virgin Islands and American Samoa.
LIVE LOAD, ROOF. A load on a roof produced:
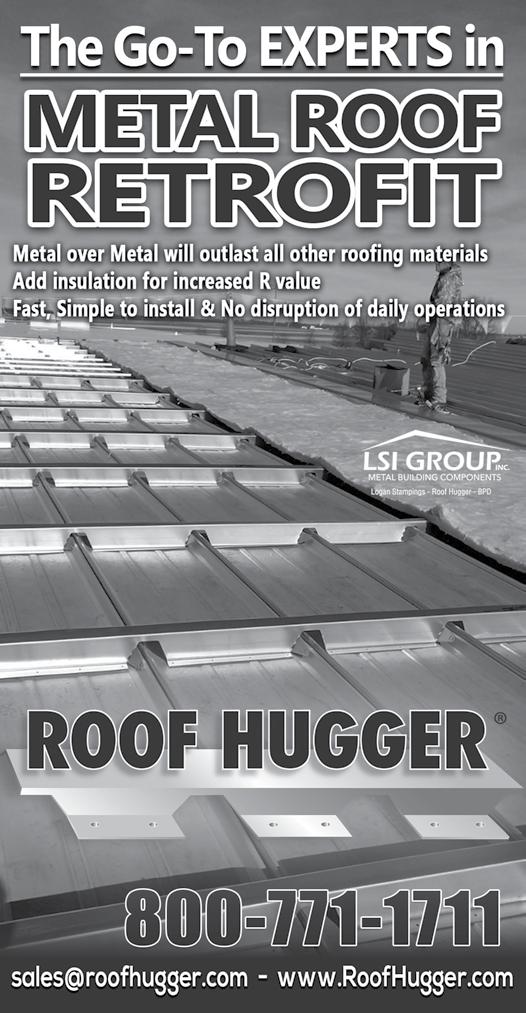
1. During maintenance by workers, equipment and materials;
2. During the life of the structure by movable objects such as planters or other similar small decorative appurtenances that are not occupancy related; or
3. By the use and occupancy of the roof such as for roof gardens or assembly areas.
LOW ROOF TILE PROFILE. Those tiles having a riseto width ratio less or equal than 0.20; except those tiles meeting the flat profile definition.
METAL PROFILE. Including but not limited to eave and gable drip, gravel stop, raised edge systems and fascia systems. All composite and nonmetallic flashing materials shall have a product approval.
METAL ROOF PANEL, METAL ROOF SHINGLE MANUFACTURER. The party responsible that forms raw material into metal roof panels and/or metal roof shingles used in building construction.
METAL ROOF SHINGLE. An interlocking metal sheet having an installed weather exposure less than 3 square feet (0.279 m2) per sheet.
MODIFIED BITUMEN ROOF COVERING. One or more layers of polymer-modified asphalt sheets. The sheet materials shall be fully adhered or mechanically
attached to the substrate or held in place with an approved ballast layer.
PHOTOVOLTAIC SHINGLES. A roof covering resembling shingles that incorporates photovoltaic modules.
PREPARED ROOF COVERING. Any manufactured or processed roof covering designed for use as the top layer of a discontinuous roofing system applied to a sloped roof.
RAS. Roofing Application Standards.
RECOVERING. The process of covering an existing roofing assembly with a new roofing system or a prepared roofing system.
REPAIR. The work of corrective procedures by replacing or altering an existing roofing component or system to eliminate water intrusion.
REROOFING. The process of recovering or replacing an existing roofing system, either in its entirety or in existing sections.
RIDGE VENT. A ventilator located within 18 inches (457 mm) of the ridge that allows the escape of warm and/or moist air from the attic area or rafter cavity.
ROOF COVERING. An assembly of multiple fieldapplied components or a single component designed to weatherproof a building’s top surface. A roof covering may be a roofing assembly or form a portion thereof.
RISK CATEGORY. A categorization of buildings and other structures for determination of flood, wind, snow, ice and earthquake loads based on the risk associated with unacceptable performance.
ROOF DECK. The flat or sloped surface constructed on top of the exterior walls of a building or other supports for the purpose of enclosing the story below, or sheltering an area, to protect it from the elements, not including its supporting members or vertical supports.
ROOF REPAIR. Reconstruction or renewal of any part of an existing roof for the purposes of its maintenance.
ROOF REPLACEMENT. The process of removing the existing roof covering, repairing any damaged substrate and installing a new roof covering.
ROOF SECTION. A separation or division of a roof area by existing expansion joints, parapet walls, flashing (excluding valleys), difference of elevation (excluding hips and ridges), roof type or legal description; not including the roof area required for a proper tie-off with an existing system.
ROOF VENTILATION. The natural or mechanical process of supplying conditioned or unconditioned air to, or removing such air from, attics, cathedral ceilings
or other enclosed spaces over which a roof assembly is installed.
ROOFING ASSEMBLY. An assembly of interacting roofing components [includes the roof deck, vapor retarder (if present), insulation, and roof covering].
ROOFING COATINGS, ADHESIVES AND MASTICS
Any and all liquid materials applied to the roofing membrane layer to enhance ultraviolet light resistance; increase resistance to fire; increase reflectivity of the roofing assembly; or, in some way, enhance the performance of the roofing assembly. Roofing coatings, adhesives or mastics shall not contain asbestos materials.
ROOFING COMPONENT. A roofing product that is incorporated into various roofing assemblies.
ROOFING MAINTENANCE. The work of extending the longevity of a roofing system through preventative care, such as refilling pitch pans, applying coatings, regraveling, resurfacing and recaulking.
ROOFING SYSTEM. A system of interacting roofing components, generally consisting of membrane or primary roof covering and insulation (not including the roof deck) designed to weatherproof, and sometimes to improve, the building’s thermal resistance.
SCUPPER. An opening in a wall or parapet that allows water to drain from a roof.
SHINGLE FASHION. A method of installing roof or wall coverings, water-resistive barriers, flashing or other building components such that upper layers of material are placed overlapping lower layers of material to provide for drainage via gravity and moisture control.
SINGLE-PLY MEMBRANE. A roofing membrane that is field applied using one layer of membrane material (either homogeneous or composite) rather than multiple layers.
STRUCTURAL METAL PANEL. Roof covering intended to be self-supporting between structural members (see Sections 2003.8.2 and 2222.4).
TAS. Testing Application Standard.
SUBSTANTIAL IMPROVEMENT. Any repair, reconstruction, rehabilitation, alteration, addition or other improvement of a building or structure, the cost of which equals or exceeds 50 percent of the market value of the structure before the improvement or repair is started. If the structure has sustained substantial damage, any repairs are considered substantial improvement regardless of the actual repair work performed. The term does not, however, include either:
1. Any project for improvement of a building required to correct existing health, sanitary or safety code violations identified by the building
official and that is the minimum necessary to assure safe living conditions.
2. Any alteration of a historic structure provided that the alteration will not preclude the structure’s continued designation as a historic structure.
UNDERLAYMENT. One or more water-shedding layers applied to a sloped roof prior to the application of a prepared roof covering. The primary purpose of an underlayment is defined as a water shedding layer to function in combination with a prepared roof covering.

VEGETATIVE ROOF. An assembly of interacting components designed to waterproof a building’s top surface that includes, by design, vegetation and related landscape elements.
VENTILATION. The natural or mechanical process of supplying conditioned or unconditioned air to, or removing such air from, any space.
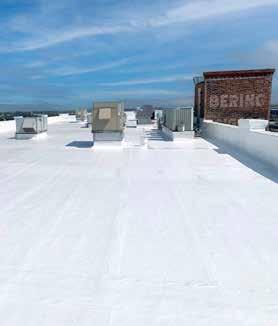
WIND-BORNE DEBRIS REGION. Areas within hurricane-prone regions located:
1. Within 1 mile (1.61 km) of the coastal mean high water line where the ultimate design wind speed, Vult is 130 mph (58 m/s) or greater; or
2. In areas where the ultimate design wind speed, Vult, is 140 mph (63.6 m/s) or greater.
For Risk Category II buildings and other structures and Risk Category III buildings and other structures, except health care facilities, the wind-borne debris region shall be based on Figure 1609.3(1). For Risk Category III health care facilities, the wind-borne debris region shall be based on Figure 1609.3(2). For Risk Category IV buildings and other structures, the wind-borne debris region shall be based on Figure 1609.3(3)
HYBRID PREMIER SYSTEM
WIND SPEED, Vult. Ultimate design wind speeds.
WIND SPEED, Vasd. Nominal design wind speeds.

WOOD SHAKES. Tapered or straight pieces of red cedar, or other wood types, of widths ranging from 3 inches to 14 inches (76 mm to 356 mm) ranging in lengths from 18 inches to 32 inches (457 mm to 813 mm) applied to a sloped roof, in conjunction with an approved underlayment, forming a discontinuous prepared roof system.
WOOD SHINGLES. Tapered pieces of red cedar, or other wood types, sawn on both faces, of widths ranging from 3 inches to 14 inches (76 mm to 356 mm) and lengths of 16 inches (406 mm), 18 inches (457 mm), and 24 inches (610 mm) applied to a sloped roof forming a discontinuous prepared roof system.
As you can see by this partial list of definitions, words – and their definitions – definitely matter when it comes to the building code. Words can definitely hurt you if you install something that’s not compliant based on a lack of knowledge regarding their presence or definitions. And words left unsaid like the word ROOF as well as others that are not defined in the building codes can be unforgiving if an important one is left unsaid. And for you of little faith…see I brought it back to codes in the end!
Mike Silvers, CPRC, is owner of Silvers Systems Inc. and is consulting with FRSA as Director of Technical Services. Mike is an FRSA Past President, Life Member and Campanella Award recipient and brings over 50 years of industry knowledge and experience to FRSA’s team.
Wind Uplift Engineering
Riku Ylipelkonen, Owner, Standard Building Advisors and FRSA Technical AdvisorOne of the fundamental concepts in engineering is that context matters. Getting soaked with a garden hose is a fun summer way to cool down. Using a pressure washer to do the same is dangerous and not recommended. Similarly, wind at 5 miles per hour (MPH) is pleasant, but wind at 105 MPH is not.
Wind behaves predictably as it is scaled. This is useful because we can observe wind behavior at lower speeds and smaller dimensions to model how hurricanes and other wind events affect whatever gets in their path. As shown in Figure 1, the scale model of a building can be built along with the surrounding topography to learn how the wind loads act upon the building.
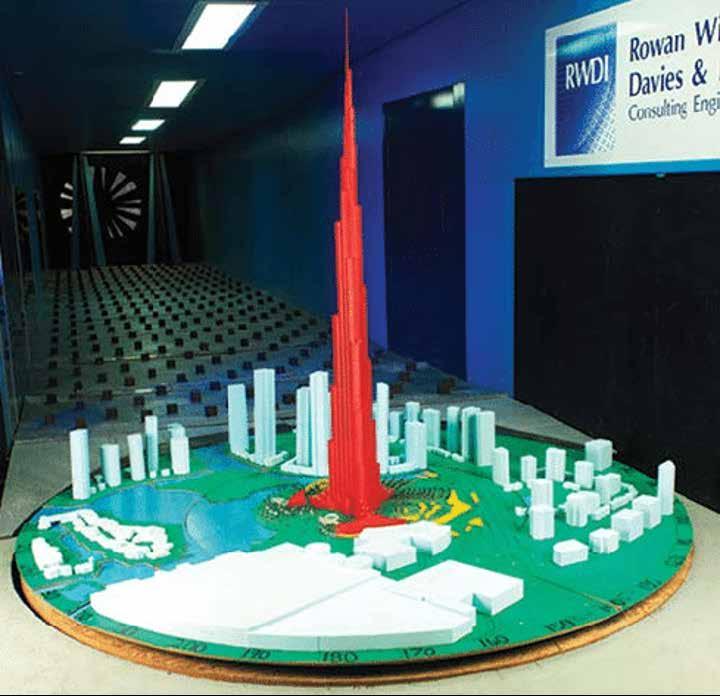
There are some important estimations shown in Figure 1. First, the fan at the end of the tunnel must have a path designed with features to mimic how wind is experienced on land. The surface roughness bumps help to shape the wind into a proper profile. Next, the turntable has the surrounding buildings assembled to scale because these features affect how the subject building observes the wind. This turntable also spins 360 degrees or completely around, because the direction of the wind event cannot be known. The features and shape of the building affect the final wind loads on the building itself. There are more variables accounted for in the testing itself, but these basic facts get the point across. The scientific community that publishes ASCE 7 Minimum Design Loads and Associated Criteria for Buildings and Other Structures has been getting better and better over time. The critical feedback of this process is the improved ability to collect data from wind events like hurricanes where concepts like surface roughness, topographical effects and more are validated with analysis. With advances in computers, data collection in wind events and communication abilities of researchers, the information and analysis to substantiate the standards have been revised with greater accuracy and precision.
This kind of wind tunnel testing has also been performed on steep-slope roofed building models, much like the projects Florida roofing contractors work on every day. Recent changes to roof zones on hip and gable roofs are a prime example of this work. When the modeling shows that the ridge end of a gable rake has a higher-pressure load than the eave end of a gable rake, the changes in roof zones take that into account. This is the same way we learned that the eave course of a steep-sloped roof covering is more susceptible to wind loads. Anyone that has seen the aftermath of a wind event in Florida can attest to that.
When a roof is modeled for pressure readings, there must be enough taps in the model to account for the changes and to predictably identify the shape of the pressure areas so we can apply that to real world roofs. The readout can show how the wind is creating negative pressures across the roof area. As shown in Figure 2 (page 26), the output of a wind tunnel test shows the pressures and how it changes on a sample low-slope roof.
The areas of perimeter, corners and the new 1 Prime Zone are defined well in the results. Please
Redefining Roofing Excellence


Discover the leader in high-quality metal roofing products – Worthouse. With our cutting-edge European technology and design, we bring excellence to the US metal roofing industry. Our mission is simple: to deliver roofing systems that are long-lasting, energy-efficient, and resilient in the face of harsh weather conditions.
WHY CHOOSE WORTHOUSE?
Unparalleled Wind Uplift Parameters – all our roofing panels are Miami Dade Approved, boasting outstanding wind uplift parameters. With Worthouse, you can trust in the strength and durability of our products, capable of withstanding winds up to 200mph.


INTRODUCING OUR LATEST INNOVATIONS.
Atlantic Sand NEW COLOR OPTION
Noble Matt
Specifically designed for sunny regions this color option perfectly complements your surroundings while providing reliable protection.
Modular Metal Roofing
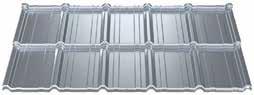
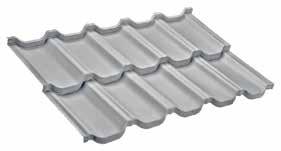
Simplify installation with our new modular metal roofing tile design. It’s modern,
Como comes with our revolutionary Magnelis® cover – cost-efficient cover option, offering long-lasting durability, shiny look and excellent corrosion resistance.
color of a peaceful soul.
bear in mind that this is just one readout of the turn table. As the source direction of the wind is rotated around this roof model, the corner and 1 Prime Zones become more defined.
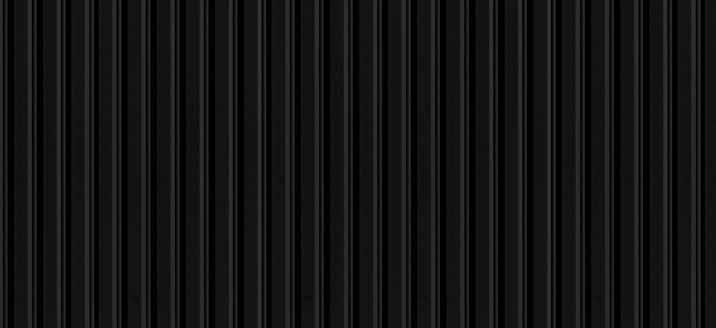
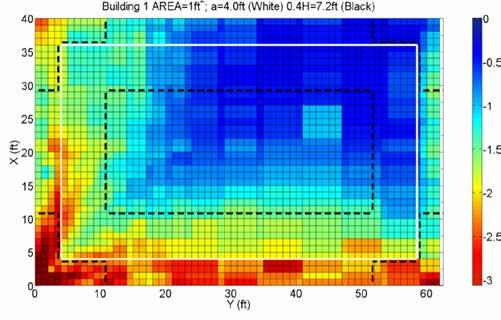
This may be a little counterintuitive, but the problem with roofing is not just that windborne debris and rain are blown onto the roof, but the moving wind causes low wind pressure areas that cause uplift force on the roof covering trying to suck it up into the sky. Think of any time you have had a light load in the back of your pick-up truck and it gets sucked out as you speed up. That napkin or receipt wasn’t blown out, it was sucked out.

With all this in mind, there is a connection to how current roof coverings are tested at third-party independent laboratories. The fundamental science is there and so is a lot of work to verify that the test methods used not only represent what happens during a wind event, but also that the wind event levels and pressures reflect what happens in real life. The vacuum chamber testing for underlayments and low-slope roof coverings, as well as the various test methods for steep-slope roof coverings, all produce results that allow us to predict how well the products will perform in real-life wind events. All this effort comes together to provide roofs that better withstand wind tests – and the test of time. FRM
Riku Ylipelkonen, Owner, Standard Building Advisors has been in the roofing industry for 15 years working for Polyfoam Products. When Polyfoam Products was acquired by 3M, the name was changed to ICP Building Solutions Group. Riku worked at ICP as Technical Services Manager until March of 2023, when he left to begin his own company. Riku is an Engineer and is working as a consultant with FRSA. He is a member on FRSA’s Codes Committee, Codes Subcommittee, Tile Committee and on the FRSA-TRI Manual Rewrite Committee. Riku is also a member of the American Society of Civil Engineers (ASCE) and the Single Ply Roofing Industry (SPRI).
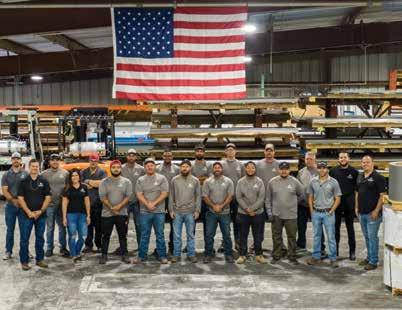
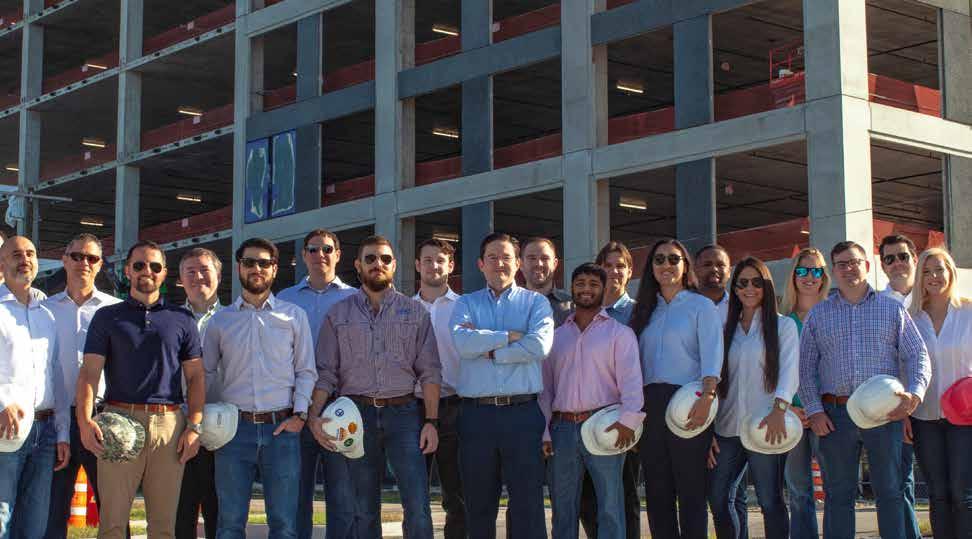

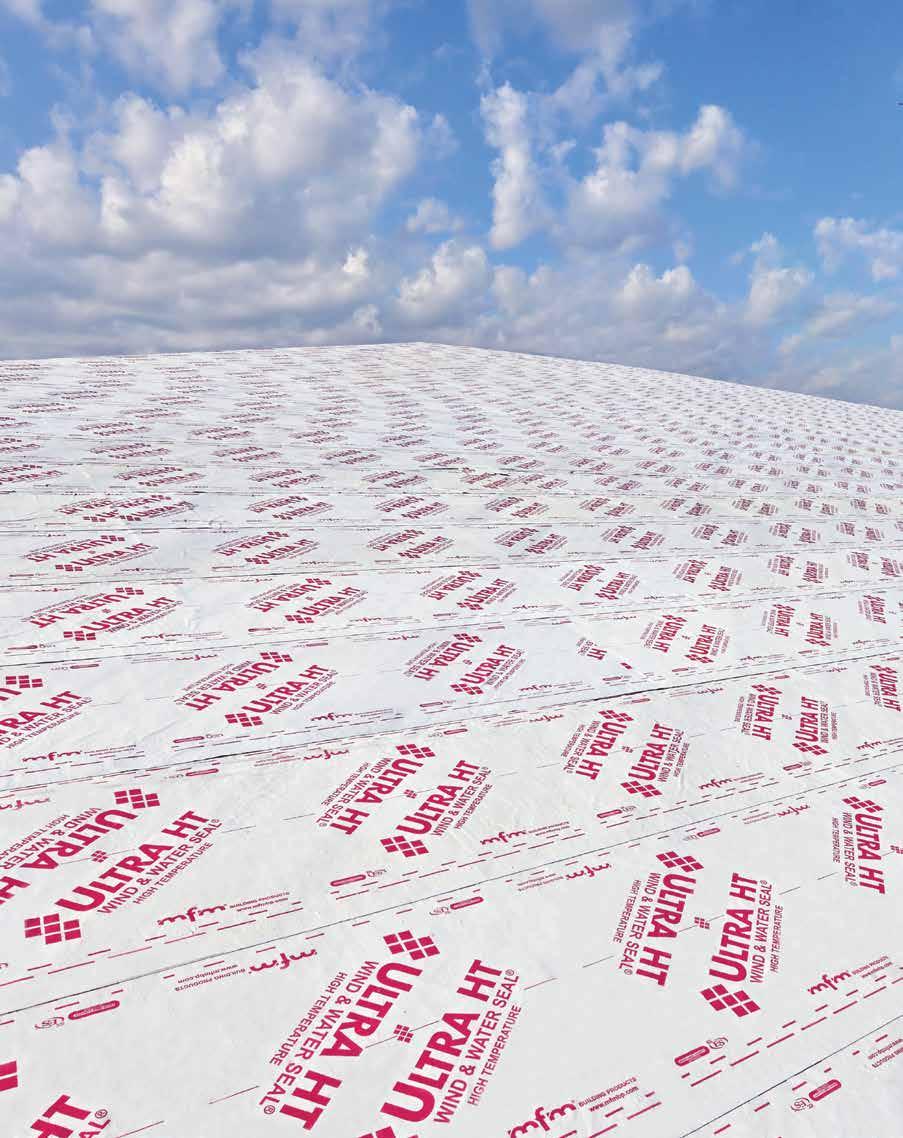

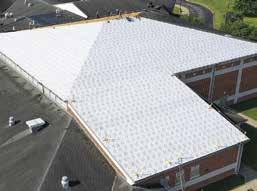
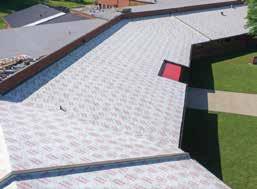
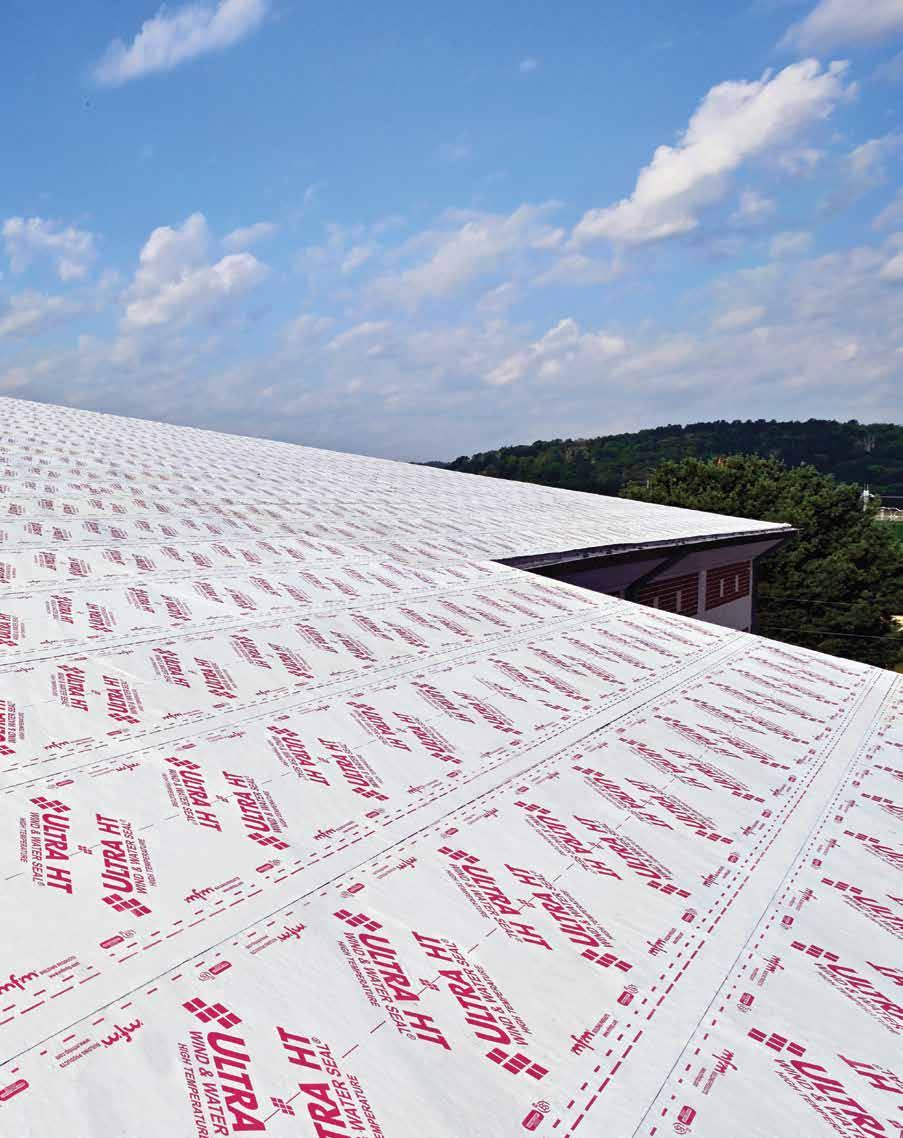
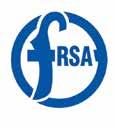

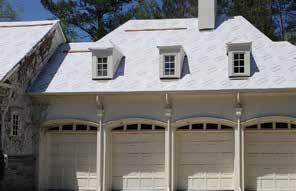
Pros and Cons of Different Roof Coatings
Amir Khan, SVP Research and Development, ICP Building Solutions GroupRoof coatings are an important way to protect and maintain roofs in residential and commercial settings. They are available in a variety of materials, popularly ranging from asphaltic blends to acrylic elastomeric, polyurethane and silicone coatings. Each type offers different advantages and disadvantages for roofing contractors and their clients. This article provides an overview of the various types of roof coatings, along with their individual strengths and weaknesses.
Know Your Roof Coatings
Roofing contractors must naturally consider the type of roof they are working with, the climate of the region and the specific needs of the home or building when choosing a roof coating. Understanding the material composition of the roof, how the environment will affect the coating and the desired performance of the product helps to narrow down the best options.
Roof coatings form a durable and often reflective surface on built-up, modified bitumen and asphalt roofs as well as concrete, metal, wood and many other types of surfaces. Many of these products can be quickly and easily applied using a professional brush, roller or spraying equipment. Contractors should do their own research and consult their peers about the different types of roof coatings and their associated benefits and limitations that are broadly discussed here. One advantage that all coatings have in common is they do not add dead load to existing roof systems because they do not count as additional layers for code purposes, thereby avoiding the cost and complication of tearing off, disposing of and replacing an existing roof. Always be sure to evaluate repair and restoration options before deciding to replace an old roof because coatings offer many benefits, including the opportunity to improve your profits by keeping your crews moving quickly from one job to the next.
Also note that because many roof coatings are rolled or sprayed on, application can require a steady hand and trained eye to avoid filling up any fissures in the roof that might include vents and drainage openings, which can lead to problems like clogs as well as lumps, bumps and other minor imperfections in the finished roof surface. Take time to consult with the coatings manufacturer or other trusted expert if you have any questions concerning proper installation of roof coatings.
Asphaltic Blends
One of the most common types of roof coating, asphalt coatings are manufactured with select asphalt and solvent blends and are popular for their good weathering qualities such as resisting the damaging
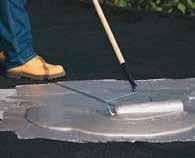
effects of heavy rainfall, large hail, snow or ice accumulation and UV radiation.
These coatings are also preferred for their low-tomoderate cost compared to other types of roof coatings, combined with their fast and easy applicability. These advantages have made asphalt roof coatings the industry-standard choice and backbone of countless successful businesses for decades. Their flexibility is further appreciated by contractors who commonly use them to seal other surfaces like foundations and retaining walls.
Asphalt roof coatings are susceptible to heat damage and can become brittle with age, so they may not be as effective or long-lasting as other types of coatings when applied to certain substrates. This means asphaltic blends may not be ideal in areas of the country that experience extreme high temperatures or greatly fluctuating hot and cold cycles.
Poorly applied, these coatings can trap moisture and create a breeding ground for mold and mildew, so it is important for crews to have some experience installing them. They also tend to be less reflective than other types of coatings, so owners may not experience the full benefit a “cool roof” can provide in terms of energy savings. Many asphalt coatings contain varying quantities of aluminum flake to make them more reflective; however, average solar reflectance (between 45 to 50 percent) is marginal relative to what is commonly considered a cool roof (80 to 90 percent reflectance).
Asphaltic coatings are generally safe to work with; however, some formulations may emit volatile organic compounds (VOCs), making it important to ensure that the product being specified will comply with all federal, state and local VOC regulations. Warranties
connections that endure
PROVIDING STRENGTH IN EVERY DIRECTION
When you join materials together, you create a precise bond, a vital connection that builds strength in every direction. This is not just how our products functionit’s how we function too. ICP delivers innovation and excellence from roof to floor. Our extensive array of professional grade coatings and adhesives builds the first layer, but our bonds extend well beyond the surface.
At ICP, we stand behind our solutions, and we’re constantly pushing the building envelope towards enduring success.
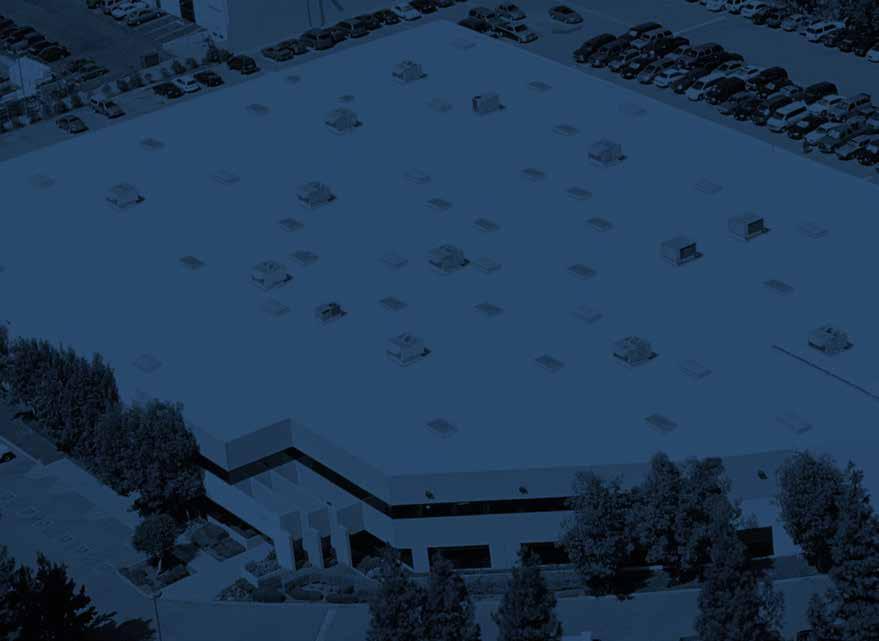
meanwhile may extend anywhere from 5 to 20 years but are generally shorter-lived than the guarantees that come with other types of roof coatings, depending on the type of substrate, system and mileage.
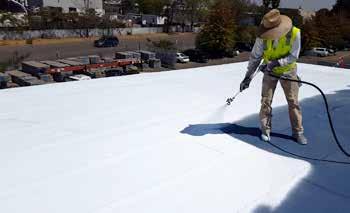
Acrylic Elastomeric Coatings
Sometimes called “rubberized” coatings, these products are generally composed of acrylic polymers that allow them to stretch and move with the structure as temperatures change. Elastomeric roof coatings create a uniform surface that remains flexible even at low temperatures, so the thermal stresses that can tax an asphalt roof are not as much of a concern. Importantly, the chemistry behind acrylic elastomers is as diverse as any roof coatings category, so there are many different options to achieve desired performance and durability. Most acrylic coatings offer outstanding UV protection and, when applied correctly, create a strong watertight seal to withstand nature’s wrath.
These coatings also tend to be bright white, having an 80 to 90 percent solar reflectance that makes them the popular choice for creating cool roofs. A California study found cool roofs stay up to 50-60ºF (28-33ºC) cooler than conventional materials during

however, some products may give off VOCs, making it imperative to read and follow all manufacturer instructions carefully.
Take note that while they are UV-resistant, acrylic coatings can oxidize over time, resulting in loss of mil thickness. Most acrylics will require at least two coats because of their tendency to lose mil thickness over time, meaning potentially more labor time and cost for installers compared to products having higher solids content such as silicone roof coatings discussed later below.
Also important is that, as a water-based product, acrylic elastomers are more susceptible to freezing temperatures at the time of application. Temperatures should be at least 50ºF when the coating is applied because dry time significantly slows down at lower temps.
Warranties for acrylic elastomeric roof coatings typically range from 10 to 20 years though, as discussed, this can vary depending on the type of coating and its desired qualities. Regular cleaning and resealing of the finished roof surface meanwhile will help to maintain its bright appearance and high solar reflectance over the long run.
Polyurethane Coatings
Polyurethane coatings form an elastic, watertight film over the roof and offer what is widely considered best-in-class tensile strength, making them among the strongest, most impact-resistant roof coatings available to minimize the damaging effects of cracking, peeling and fading. These highly durable coatings come in two types: aromatic and aliphatic.
peak summer weather and provide an average yearly net savings of almost 50 cents per square foot. Generally, cool roofs help reduce annual air conditioning use in buildings up to 15 percent according to the U.S. Department of Energy and home and building owners are taking note because the market is expected to grow by approximately $4 billion over the next four years. Roofing contractors who want to take advantage of this trend are wise to consider the latest acrylic elastomeric products for their cool roof projects.
Easy application is another key benefit of acrylic coatings that can mimic the flow and adhesion qualities of household paint, so crews can work quickly and confidently. Cleanup is also simple and fast because these coatings are water solvent.
Costs will vary given the wide range of options available though, in general, acrylic coatings are priced lower than competing silicone and polyurethane formulations. The ingredients used to make them are also safe for the user and environment in most cases;
Aromatic coatings cost less and are typically used as a base coat because they are not UV stable, meaning they can degrade under sunlight over time. Yellowing of the roof surface due to dirt pickup can also be a concern. Aliphatic coatings on the other hand provide superior elasticity as well as long-term UV protection. They have good color retention qualities and are typically used as a topcoat. Alone or in combination, these coatings can provide short- or long-term rooftop protection. They also may be used as a base coat for silicone roof coatings.
Polyurethane coatings are a popular choice for creating reflective cool roofs and offer good resistance to
Polyurethane coatings have good mechanical properties and high abrasion resistance that are ideal for where a
water pooling and UV exposure. Versatility is another key benefit: they have outstanding adhesion qualities and can be easily applied to practically any sloped or flat, textured or smooth roof system. Roofing contractors will further appreciate how polyurethane products can be applied in colder, more variable weather conditions compared to some other types of roof coatings.
Depending on the project, polyurethane coatings may not be the low-cost solution a client is seeking and some products can emit a strong odor that, while not harmful, can be unpleasant for crews and building occupants. These solvent-based coatings can also be hard on professional spraying equipment and require more steps to clean up, which can lead to inconsistent results if the equipment is not maintained properly with the use of cleaning solvents. For instance, if applied too thickly or in poor conditions, pinholes can occur within the film of the coating or air can become trapped as the product cures, which can cause the film to bubble, compromising the overall integrity of the coating. For these reasons, it is important to ensure you hire a certified installer to apply your polyurethane coating properly.
The outstanding durability of polyurethane roof coatings is evidenced by warranties extending up to 25 years for some products. Like acrylic coatings, the ambient temperature should be at least 50ºF when polyurethane coatings are applied.
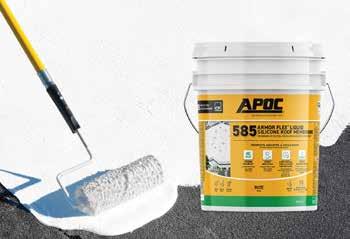
Silicone Coatings
Silicone roof coatings are most often solvent-based and have high solids content. These roof coatings are applied in a single layer (one or two coats) of silicone-based liquid material in order to form a monolithic membrane. Silicone coatings are extremely durable against weather and are also highly reflective, which can save home and building owners money when air conditioning equipment doesn’t need to work as hard year after year.
Because the product is made using moisture-cured materials, water is no longer absorbed by the coating after it has cured, making silicone coatings more resistant to ponding water situations and eventual breakdown compared to asphaltic and acrylic options. Additionally, silicone products having high solids content (typically greater than 90 percent) require less coating material during application to achieve the desired dry mil thickness. Applying more coating in a single pass is one way contractors can save time on the job while creating a watertight seal, thanks to multiple thin layers of coating.
Another benefit is that silicones are one of the most environmentally friendly roof coating options because they contain fewer solvents than most moisture-curing products, with some versions being entirely free of solvents. Silicone roof coatings are also highly versatile because they can be applied to most substrates.
The ability to apply silicone coatings at a greater thickness means crews can correct minor slope problems and ponding water situations during the application process.
Potential drawbacks of silicone include: they tend to cost more than other coatings; it can be more difficult to recoat silicone over silicone and roof surfaces coated with silicone can become slippery. Dirt pickup is another factor to be aware of because silicone easily attracts airborne dust that may cause a roof to turn shades of yellow or brown. Frequent cleanings may be necessary to maintain its reflective qualities.
Due particularly to their strong water resistance, silicone roof coatings can carry warranties from 10 to 50 years or what is effectively a lifetime guarantee of the product’s performance in some cases. For projects that are not on a tight budget, silicone roof coatings can provide the added protection and peace of mind that project owners appreciate.
Making the Best Choice
By closely examining your options, you can make an informed decision and find the ideal roof coating for your next coating project. Be sure to carefully consider the pros and cons of each type of coating and evaluate how it will meet your particular needs. Always read labels and research products to ensure that the one you select will protect from the elements and save on energy costs while prolonging the roof’s life span. If you have other questions or would like more details, please contact your chosen products technical department.
Amir Khan serves as Senior Vice President of Research and Development at ICP Group. He is recognized as an authority in the fields of asphalt, low- and steep-slope roofing, adhesives, paving and binder technologies, coatings and mastics. In his current role, he leads all research and development efforts at ICP with a special focus on helping develop new industry-leading products and identifying global business opportunities. With nearly three decades of professional chemistry and chemical engineering experience, Amir holds 19 patents.
The Power of “NO”/KNOW for Roof Coatings
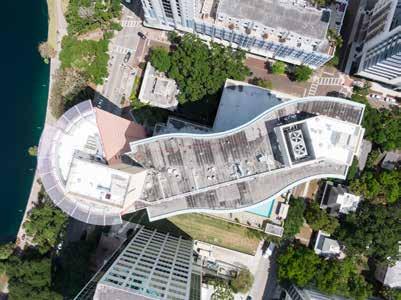
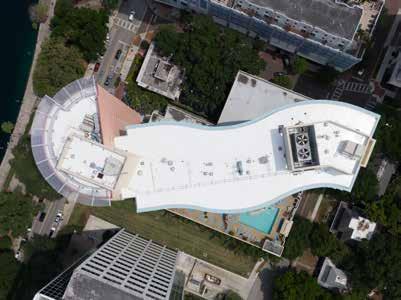

If your firm installs roof coatings beyond the scope of maintenance and repair for low-slope metal commercial roofing, you should read this article. There is a significant change in the acceptance by insurance companies for new spray polyurethane foam (SPF) roof systems and other roof recovers that use the existing roof covering for attachment. This is based on the wind uplift requirements of the Florida Building Code (FBC). After collaboration with several key individuals in the roofing industry, including key individuals in the Florida market, your building owner and manager clients are faced with a tough dilemma.
The “power of no” is being leveraged by insurance companies for structures when SPF roof systems are used. While doing the research for this article, which I started in January, there have been numerous examples of roof coating installations being denied insurance coverage. This has been confirmed by a representative for a Florida commercial insurance company, an active Florida registered roof consultant, a retired roof consultant (on his multi-family residential roof), as well as multiple roof coating manufacturers.
During a conversation in February with Mike Silvers, FRSA’s Director of Technical Services, we discussed his article, “When is it Too Late for Maintenance or Coating?” (from July 2020 – www.floridaroof.com/frm7-20p29). In that article, Mike identifies that the then applicable 2017 (and current 2020) FBC Existing Building (Chapter 7 – Section 706) clearly states the requirement for use of the existing roof as attachment for a new roof recover must comply with current up-lift requirements. Typically, the use of roof moisture surveys and detailed scope of work is developed to restore an existing roof when utilizing SPF or other new roof recovering. In some cases, the contractor and manufacturer of a roof coating will offer extended labor and material warranties when this process is followed. In one case, an engineering study was developed and submitted to the insurance company for the roof coating installation. It was still rejected by the insurance company. When submitting a proposal for this type of assembly, a wind uplift test is often not performed. If the existing low-slope commercial roof has been in place between 7 to 15 years, the possibility of the existing roof being code-compliant is slim to none. Although the state legislature has passed several laws in response to Florida’s tumultuous insurance market, including Senate Bill 2-D in May 2022, Senate Bill 2-A in December 2022 and most recently Senate Bill 7052, House Bill 881 and
THE LOOK OF CLAY. THE STRENGTH OF STEEL.
Introducing ProVia Barrel Tile Metal Roofing
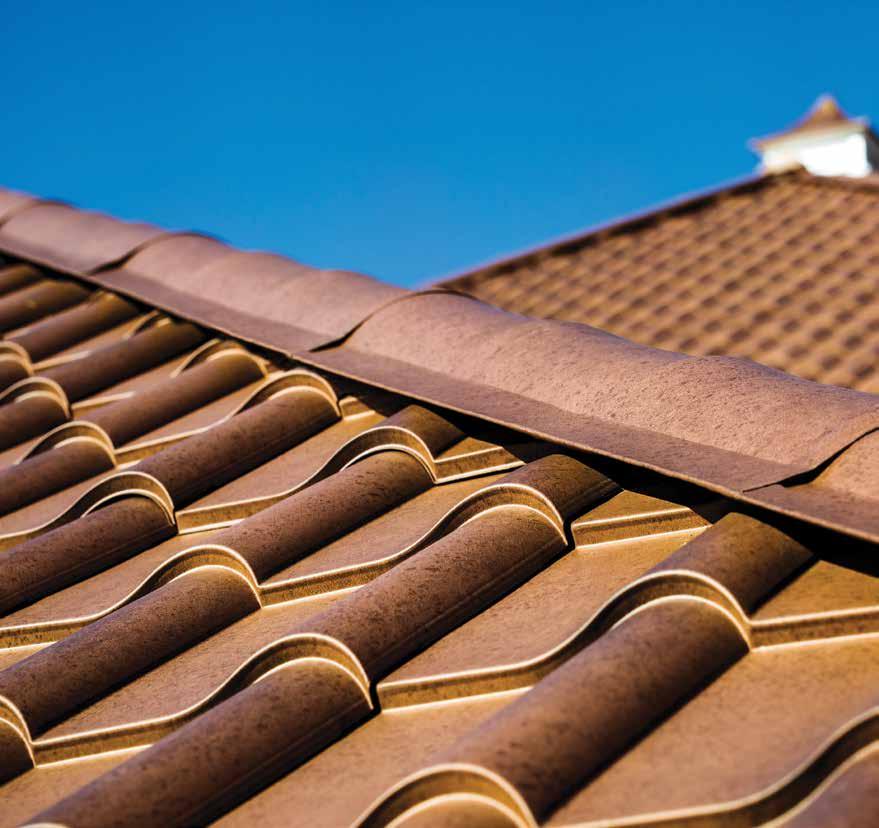
ProVia barrel tile metal roofing combines the timeless beauty of Spanish clay tile with the unrivaled strength of metal roofing. This 26-gauge galvanized metal roofing system is engineered to withstand 130-mph winds, damaging hail, torrential rain, and intense UV rays, and is backed by a limited lifetime transferable warranty. Give your customers the best of both worlds: style and substance.
It’s the right thing to do.
Learn More provia.com/metalroofing/barrel-tile/
House Bill 799 on June 1, 2023, these new laws remain primarily focused on residential roof claims, new hurricane mitigation programs for qualifying homeowners and curbing rising premiums for residential property insurance lines. According to Trent Cotney, Adams and Reese LLP and FRSA’s General Counsel, “While the new laws passed in Florida do provide additional accountability and oversight on the manner in which insurance companies generally handle claims, they provide little to no guidance on such nuanced commercial roof repairs or coating applications that commercial and multi-family property owners often assume and expect would be covered under their applicable insurance policies. It is imperative that both roofing contractors and commercial owners are apprised of potential coverage issues and scope of work considerations, concerning contemplated repairs to low-slope commercial and multi-family roofs, while we await necessary future legislation to more aptly address the commercial insurance sector,” says Cotney.
Although the state passed Bill 2-D in May 2022, this does not include commercial properties. According to Cotney, the bill is dedicated to residential construction and protection for homeowners. “I do not see any protection of re-insurance of low-slope commercial or multi-family construction in the bill.”
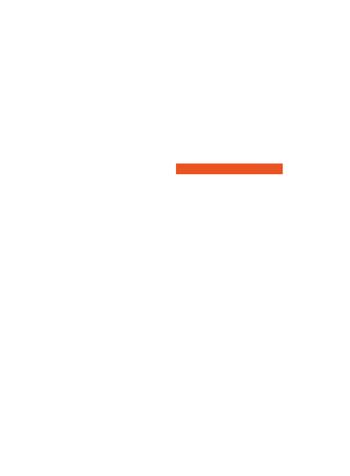
For decades, roof coating manufacturers have offered protective roof coating products, extending
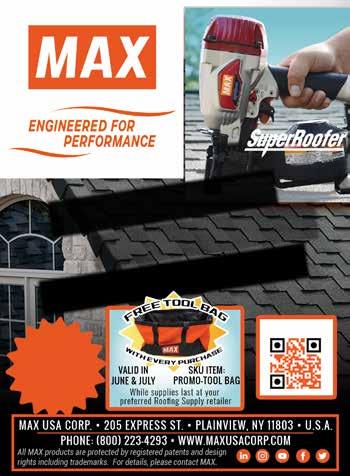
the useful service life of a roof system. Several roof coating manufacturers have offered contractors and building owners labor and material warranties that have been in existence since the mid-1980’s. These are like those offered by low-slope commercial roofing manufacturers after the roof bond era. In addition to warranties of 10, 15 or 20 years, roof coating manufacturers have offered renewable warranty terms beyond the initial warranty. These renewable warranty programs created a sustainability concept that many roofing contractors and building owners have embraced. This restoration paradigm is challenged by the decisions being made at present by the insurance carriers in the state of Florida. We have a “perfect storm” combining the current state of the insurance industry and the Florida Building Code wind uplift requirements. Since the attachment of the existing roofing assembly is what holds a new SPF covering in place, the power of “no” – as in no coverage – by insurance firms is a legitimate concern.
It is important to differentiate between maintenance and repair as opposed to a code compliant roof system when proposing roof coatings or roof recovers to a building owner. As Mike Silvers stated during FRSA’s April Codes Committee meeting, “When it comes to wind uplift resistance requirements, there is no difference between new roof systems and roof recovers.”
There is a legitimate concern for any contractor proposing this type of roofing alternative to a building owner, property manager or design firm that is unaware of the potential issues with insurance coverage. Although we know there are liquid-applied (fluid-applied) roofing assemblies that are Factory Mutual (FM) and Underwriter Laboratories (UL) approved assemblies, that does not stop an insurance carrier from denying coverage to this type of installation on your client’s structure. It is important to be transparent prior to submitting a proposal or intent to perform work. If you do not share this potential issue with your client, it can become a tragedy for them and your firm. The power of “no” is much more powerful than yes.
If it was not for a Florida roofing industry professional raising his concern, this article would not have been written. Thank you – you know who you are.
Joseph O. Sorrentino, RRO, is the Florida Regional Account Manager for Geocel and Kool Seal Roofing Solutions, a division of The Sherwin Williams Building Solutions Group. Previously, Joe was Market Development Manager for Uniflex Fluid Applied Roofing Systems and Chief Operating Officer for Sustainable Weatherproofing Solutions Inc. He has over 40 years of experience in the roofing industry and is active in IIBEC and on FRSA’s Codes and Membership Committees. You can contact him at Joe.O.Sorrentino@sherwin.com.
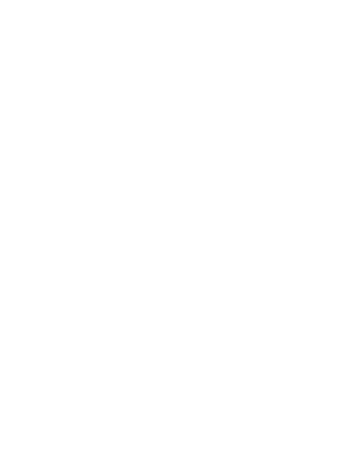
Forklift Safety
Jorge Castanon, Safety Consultant, FRSA Self Insurer’s FundHaving a forklift at your workplace to help lift, move, stack and store raw materials or finished product helps get the job done efficiently. Powered industrial trucks or forklifts are the workhorses often used to get these jobs done and, as with any piece of equipment being used on the job, safe operating procedures are a must.
A forklift operated by an inexperienced or poorly trained employee can lead to accidents, injuries or even death. The Occupational Safety and Health Administration (OSHA) requires that all forklift operators be certified in forklift safety. The OSHA forklift certification requirements are:
■ Operators must be at least 18 years old.
■ New operators must complete forklift training and become officially certified.
■ Certifications must be updated every three years.
■ Forklift operators must carry proof of their certification.
Having untrained operators can create hazards. Falling loads caused by overloading, unbalanced loads, improper loading, loads stacked too high obstructing the operator’s view, forklifts operating too fast and
improper maintenance may cause unwanted harm to workers. Operators are not only responsible for themselves, the cargo and the forklift but also responsible for everyone around them. The following guidelines will help maintain a safe workplace for yourself and your coworkers:
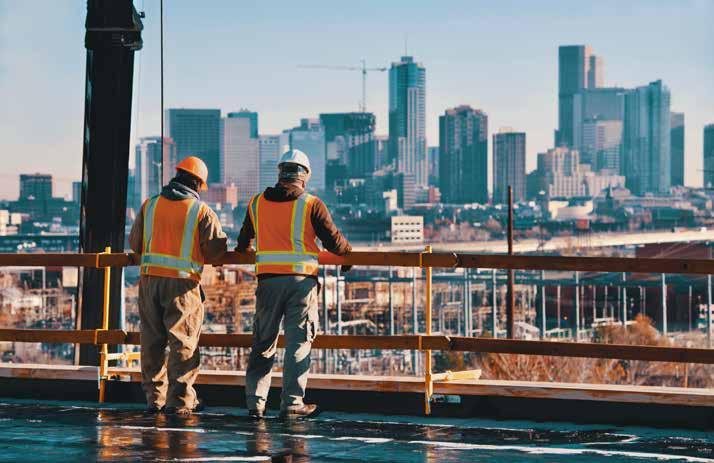
■ Before operating any forklift, you must become familiar with the location and function of the controls and other general operating functions.
■ A pre-operation inspection must be done before using a forklift.
■ It is important to recognize that operating a forklift is very different than operating a car. While the forklift is probably smaller than your car, it can be up to two-to-three times heavier. Because of the weight of a forklift, it is not as easy as stopping a car, so give yourself plenty of time to react by driving slowly.
■ You should always read the operator’s manual before operating a forklift. Do not forget to read the warning labels, nameplate data, load capacity and other important safety reminders.
EVERY ROOF IS OUR REPUTATION
For over 160 years, Johns Manville has delivered quality commercial roofing systems.
Between having one of the broadest system offerings in the industry and a dedicated team for every step of the roofing project; JM is more than a commercial roofing supplier. We are your commercial roofing partner.
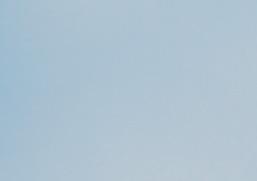
■ If the forklift has a seat belt, wear it in case of a tip over. The seat belt will keep you within the protective framework of the unit. If you try to jump off during your tip over, you could be thrown under the forklift or the load, which can lead to injury or even death.
■ Always raise the height of the forks about two to four inches above the ground while traveling and keep the load at the lowest safe height.
■ Always drive at slow speed.
■ Visibility is restricted while carrying a load and you will encounter blind spots. Always check to make sure no one is in your path before moving.
■ Pedestrians always have the right of way. Sound the horn at intersections and proceed slowly.
■ Keep three truck lengths between forklifts and never pass another forklift.


■ When lifting, make sure the load does not exceed the capacity of the forklift. The capacity is listed on the identification plate and in the operator’s manual.
■ If the load has to be raised, check for overhead obstructions such as lights, pipes or sprinkler systems.
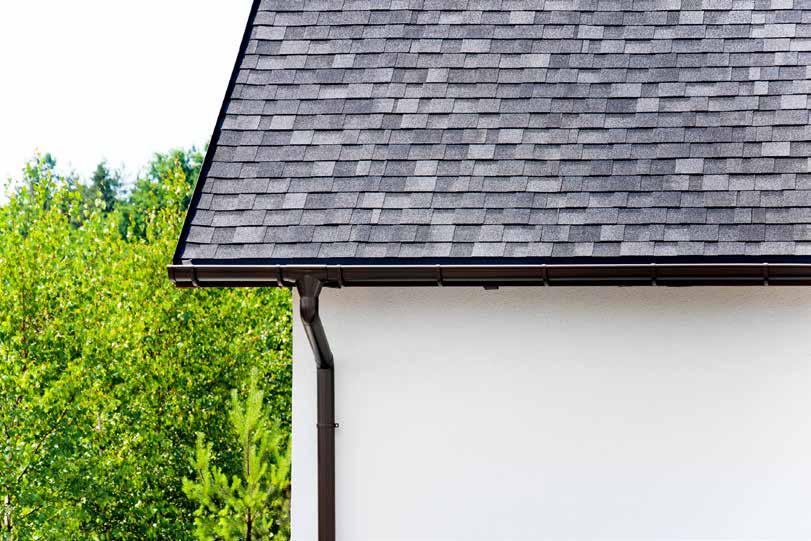
■ Never allow anyone to walk under a raised load.
If you are using a forklift outdoors or at a construction site, you are bound to encounter rough, uneven terrain. Pneumatic tires are used on these forklifts because they are more forgiving, making the unit easier to handle. This helps increase safety and stability.
Forklifts are our industries’ workhorses, moving, storing, stacking and loading everything from raw materials to finished product. As a forklift operator, you must always keep one goal in mind: the safety and efficient operation of your unit.
The FRSA Self Insurers Fund (FRSA-SIF) has professional safety consultants throughout the state who provide SIF members with safety training at no additional cost. To find out if you qualify for FRSA-SIF workers’ comp insurance, please contact Alexis at 800-767-3772, ext. 206 or email alexis@frsasif.com. To learn more about the FRSA Self Insurers Fund, visit www.frsasif.com.
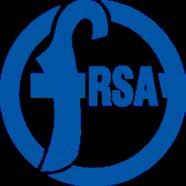


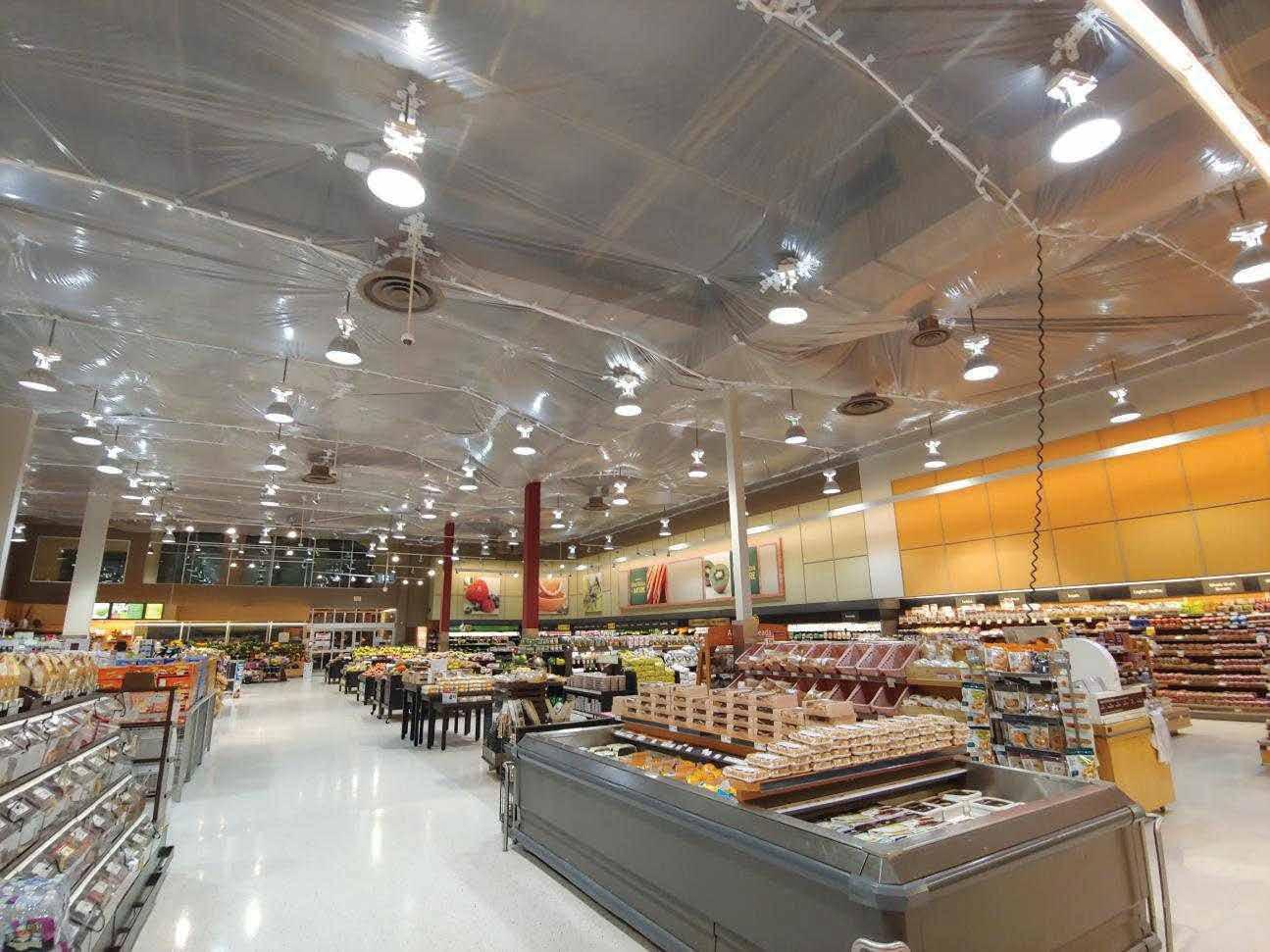
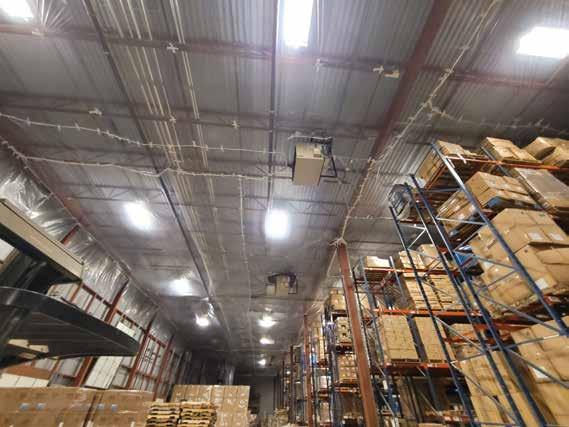
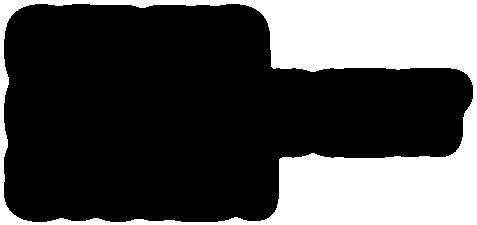
FRSA Convention Seminar Speakers
This year, FRSA is offering 31 hours of continuing education seminars that feature the best-of-the-best industry instructors. Many of the seminars focus on changes in the Florida Building Code presented by instructors who possess strong insight into the code and its application. They provide real-world examples and can respond to specific questions that you face in your day-to-day operations. We’re also offering nine hours of non-CE seminars that focus on business operations, sales, management and finance taught by experts in these fields.
Alexis Ayala
Alexis has over 10 years of insurance industry experience with the last six years exclusively in workers’ compensation. Along with her underwriting duties at FRSA-SIF, she is responsible for the direction of the Premium Audit Department and directing all issues with the state rating organization (NCCI).
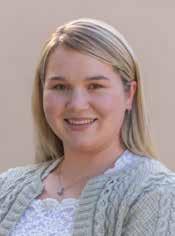
Tray Batcher
Tray represents clients in all aspects of construction law, including liens, bonds, construction defect litigation, OSHA defense and licensing. Previously, he worked in construction as an estimator for a multimillion-dollar structural contracting company.
Ben Briggs
Ben represents clients in all aspects of labor and employment law, including wage and hour, discrimination and retaliation claims, drafting employment contracts, restrictive covenants and more. Ben has been recognized by Florida Super Lawyers for his work.
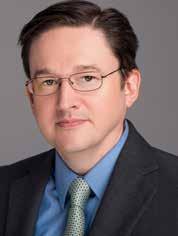
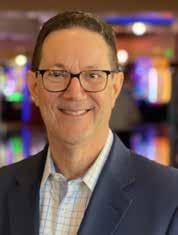
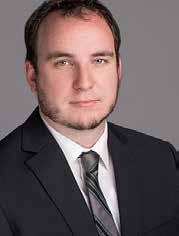
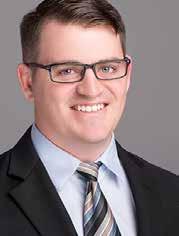
Brian Chamberlain
Brian has been with Carlisle Construction Materials since 1987. He graduated from the University of Wisconsin at Milwaukee and earned a bachelor’s degree in the Science of Architectural Design. Brian has been assisting architects, consultants and specifiers on assemblies focusing on performance, sustainability and resilience.
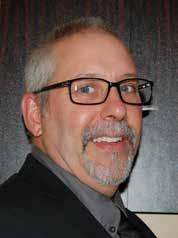
Gary Cohen
Gary is VicePresident at Certified Contractors Network, helping small and mid-sized contractors develop a plan to increase the size or profitability of their business. He is a seasoned business executive and Certified Professional Coach with a PCC credential from the International Coach Federation and a CPC credential from the International Coach Academy.
Trent Cotney
Trent is a Partner at Adams and Reese LLP and National Construction Practice Group Leader. He is well known throughout the roofing community on the local and national level. Trent is FRSA’s and NRCA’s General Counsel and is dedicated to serving the roofing industry. He routinely represents contractors on construction-related matters.
Debbie Guidry
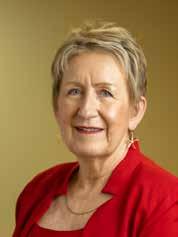
Debbie has been at the FRSA Self Insurers Fund since 1993 and serves as Administrator. SIF is a self-funded workers’ comp insurer for the roofing, sheet metal and air conditioning industry in Florida and has paid nearly $200 million in dividends back to members since the 1990s.
Greg Hayne
Greg owns Hayne Coaching Group, which helps contractors find and implement better, smarter, more innovative ways to work. His proven Creating Great Service training, support and implementation program helps commercial roofers grow their service departments.
John Kenney, CPRC
John has over 50 years of experience in the roofing industry. He started his career by working as a roofing apprentice at a family business in the Northeast and worked his way up to operating multiple Top 100 roofing companies. John is CEO of Cotney Consulting Group.


Greg Keeler
Greg is the Technical Services Leader for Owens Corning Roofing and Asphalt LLC with decades of experience in architecture and as a building official. He serves on or chairs several ASTM D08 task groups and is a member of FRSA’s Codes Committee and Codes Subcommittee.
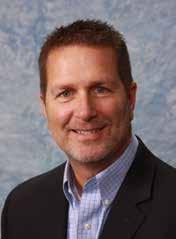
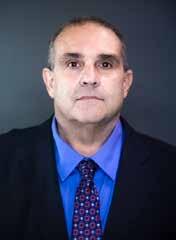
Brad Mang
Brad has been with the FRSA-SIF since 2008 and his prior 18 years of experience were as a Construction Manager, Project Manager and field Superintendent. He is a certified general contractor and OSHA certified in Construction Safety as well as in CPR and First Aid Training.
Steven McCommon
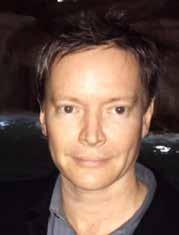
An Associate at Adams and Reese LLP, Steven focuses his practice on construction law, infrastructure and commercial litigation. Within these practice areas, Steven represents clients in contract review and drafting, contract negotiation, lien law, bond law and more.
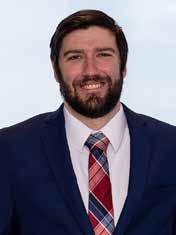
Paul Oleksak
Paul serves as the Technical Trainer at Westlake Royal Roofing Solutions and has worked in the roof tile industry since 1990. He holds a Florida roofing license and has been active on FRSA’s Codes Committee and the FRSA-TRI Roof Tile Committee for over 20 years.
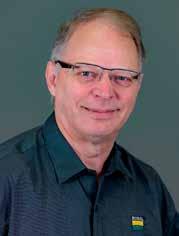
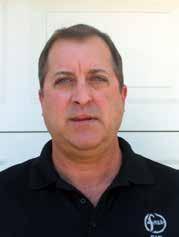
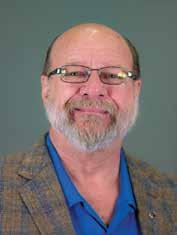
Manny Oyola, Jr.
Manny is Technical Manager Eastern Region for Eagle Roofing Products and holds a Florida roofing license. He is FRSA’s Vice President and teaches roof tile courses for FRSA and TRI. He serves on FRSA’s Codes Committee and is the Chair for FRSA’s Codes Subcommittee.
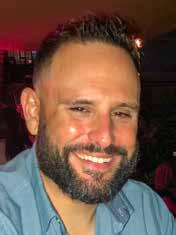
Frank Peydro
Frank serves as Vice President at Cellucrete Corp., where he has been installing lightweight insulating concrete roof decks in Florida for over 30 years. Since 1995 ,and has worked in all Cellucrete departments in the company from field operations to upper management.
Mike Silvers, CPRC
Mike is the owner of Silvers Systems, Inc. and a licensed roofing contractor with more than 50 years of industry knowledge and experience and serves as FRSA’s Director of Technical Services. He is an FRSA Past President, Life Member and Campanella Award recipient.
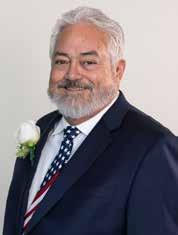
Bill Zachary
Bill is the owner of Zgraph, a web design studio and digital marketing agency based in Daytona Beach with offices in Orlando, Miami and Atlanta. Zgraph helps its clients achieve a one-of-a-kind online presence with leads, beautiful websites, social media and more. Zgraph designed and hosts FRSA’s website.
Everyone pays the same workers' comp rate, but does your workers' comp insurance carrier provide you with the potential for a yearly dividend for operating safely? If not, you need to consider the FRSA Self Insurers Fund. These members received their share of $3 million during FRSA's Convention. For more information about joining the Self Insurers Fund, contact Alexis at 800-767-3772 ext. 206 or by email: alexis@frsasif.com
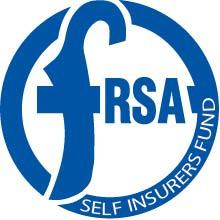
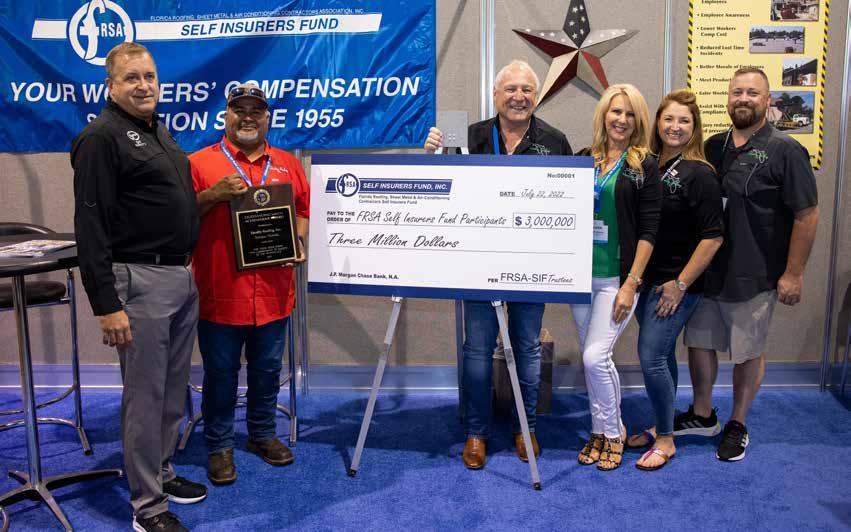
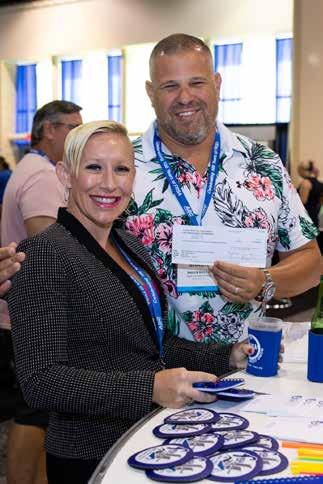
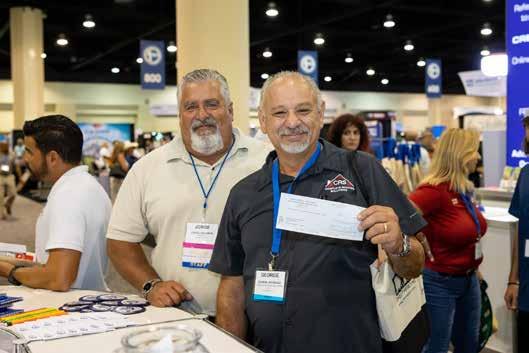
2023 FRSA Foundation Scholarships
The FRSA Educational & Research Foundation is awarding $29,000 in industry scholarships – ranging from $500 to $5,000 – to 22 students. Named scholarships originating from either endowment earnings or Foundation donations designated for scholarships, were awarded to 10 of this year’s recipients.
Cole Hepworth

E.H. Engelmeier Family Endowment
Cole graduated from Gulf Breeze High School and will attend the University of West Florida to study Construction Management. He enjoys fishing, surfing, free-dive spearfishing and lacrosse. He plans to develop a local construction company after graduating. He is the nephew of FRSA Past President Adam Purdy, CPRC, Edwards Roofing Co. Inc., Pensacola.
Kaylee Murray
Carlos Perez Memorial Scholarship
Kaylee is pursuing a Business Marketing degree at Pensacola Christian College and has been working as a Chick-fil-A Grand Opening Trainer since graduating from high school. She plans to operate her own Chick-fil-A franchise after graduating from college. FRSA Past President Gary Register, Register Roofing and Sheet Metal, Jacksonville, is her uncle.
Leslie Sims
Austin Ebersold Memorial Scholarship
Leslie attends Stetson University pursuing her Juris Doctorate in Small Business. She plans to study small business at law school focusing on business contracts. She was Co-Director of the 2023 Putnam County Fair. Leslie’s parents are Gina and FRSA
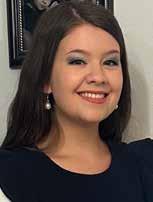
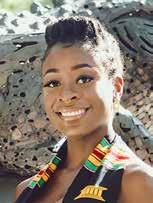
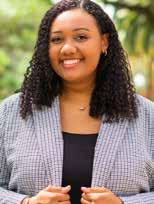
President Elect Les Sims, CPRC, Armstrong Roofing Inc., San Mateo.
For more information about opportunities to support the FRSA Foundation, contact John Hellein, Foundation Director, at 800-767-3772 ext. 123 or by email at john@floridaroof.com.
Congratulations to the 2023 scholarship recipients and thank you to the generous donors who make these significant awards possible.
Rylee Rauktis
Trent Cotney Scholarship
Rylee graduated from Edgewater High School and will attend Santa Fe Community College and the University of Florida School of Construction seeking a Construction Management degree. She wants to eventually become a general contractor. She plays volleyball and enjoys paddle boarding. Her father, Todd Rauktis, works in Sales at Commercial Roofing Specialties.
Morgan Curry
Bowen, Hilson, Turner Endowment
Morgan Curry attends University of Florida, studying Physical Therapy. She works full time at Advent Health Sports Medicine and Rehabilitation and her long-term goal is to be an orthopedic physical therapist. She volunteers at Shands Hospital Medical Intensive Care Unit and has a passion for bodybuilding where she has taken home four First Place awards.
Daniella Masso
Don Springer Family Scholarship
Daniella graduated from Florida Atlantic University High School. A National Honors Society member, she will attend the University of Florida to study Environmental Engineering. She wants to contribute to the development and implementation of sustainable energy systems. Her parents are Alfredo Masso, Boundless Builders, Pompano Beach and Jeannette Masso.
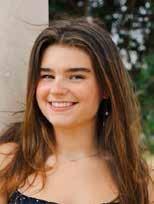
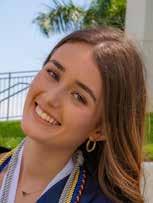
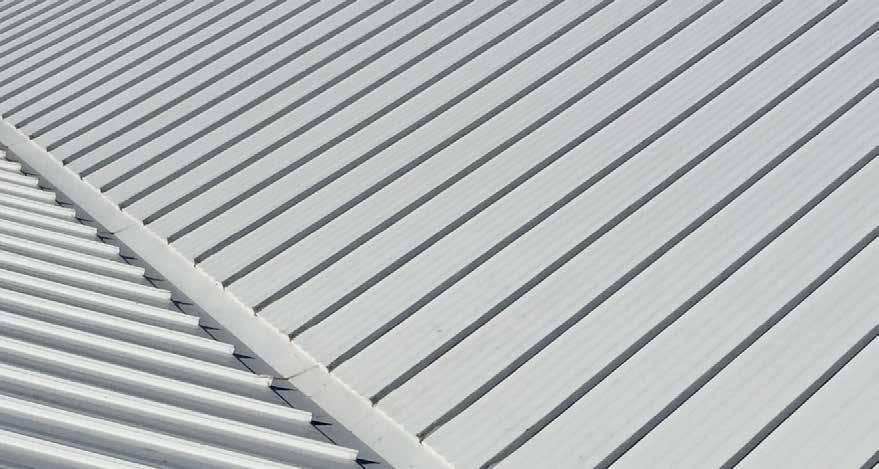
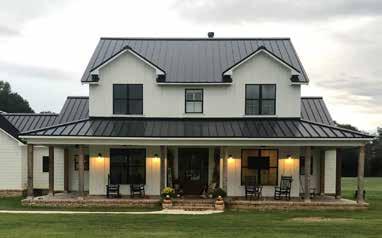
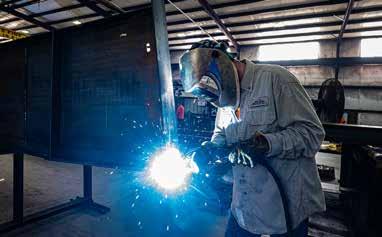
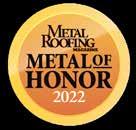
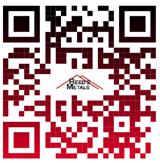
Jorge Rodriguez Edwards Roofing Co. Inc. Endowment
Jorge completed high school at Miami Art Studios and will continue his studies at Florida International University where he plans to conduct a case study on the Florida roofing industry as part of a Business degree. He played first chair violin in his high school orchestra and enjoys basketball. His brother is Rene Rodriguez, Vice President at Rouen Services.
Simon Scott
FRSA Self Insurers Fund Endowment
Simon attends at EmbryRiddle Aeronautical University, studying Aeronautical Science. He plans to become a flight instructor and then a commercial pilot. He also intends to use the construction skills he has learned in his family’s business to renovate houses. His parents are Shannon and Steven Scott, Advanced Roof Technology.
Emma Crutchfield
George Pepin Family Endowment
Emma attends the University of Central Florida where she is earning a Business degree. She served as President of her school’s Volunteer Club and helped raise over $30,000 for The Ronald McDonald House. Her father, Philip Crutchfield, is a Managing Partner at Mighty Dog Roofing, Bradenton.
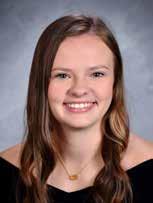

Cecilia Reboredo
Tom Walker Scholarship
Cecilia graduated from Our Lady of Lourdes Academy as a National Honor Society member. Dance is an important part of her life and the Dance Honor Society was one of several organizations in which she participated. She will attend the University of Florida to study Biology and intends eventually to practice medicine. Her parents are Michael and Ana Reboredo.
Sarah Reboredo
Sarah will graduate from Santa Fe College in August and attend the University of Florida at the College of Design, Construction and Planning to complete studies in Interior Design. She co-founded “Two Sisters Miami” with her sister Cecilia to facilitate student collaboration with local nonprofits. Her parents are Michael and Ana Reboredo.
William Ostrum
William graduated from Gulf Breeze High School and will attend Florida State University to study Environmental Sciences. He wants to better understand the effects of microplastics on marine organisms and find a solution. His uncle is FRSA Past President Adam Purdy, CPRC, Edwards Roofing Co. Inc., Pensacola.
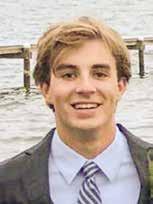

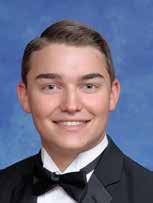
Emma Ostrum
Emma attends Florida State University pursuing an Advertising degree in the College of Communication. She works part-time as an advertising and marketing intern. Emma’s uncle is FRSA Past President Adam Purdy, CPRC, Edwards Roofing Co. Inc., Pensacola.

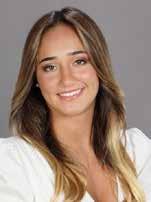
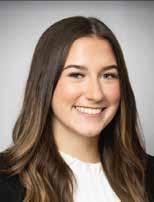
Paige Bankston
Paige graduated from Newberry High School with a 4.46 GPA and plans to pursue a Health Sciences degree at St. Petersburg College in preparation for a medical career. She played Varsity volleyball and softball and plans to play softball at the college level. She is the sister of Tyler Wilson, a Senior Operator at Gulf Coast Supply & Manufacturing.
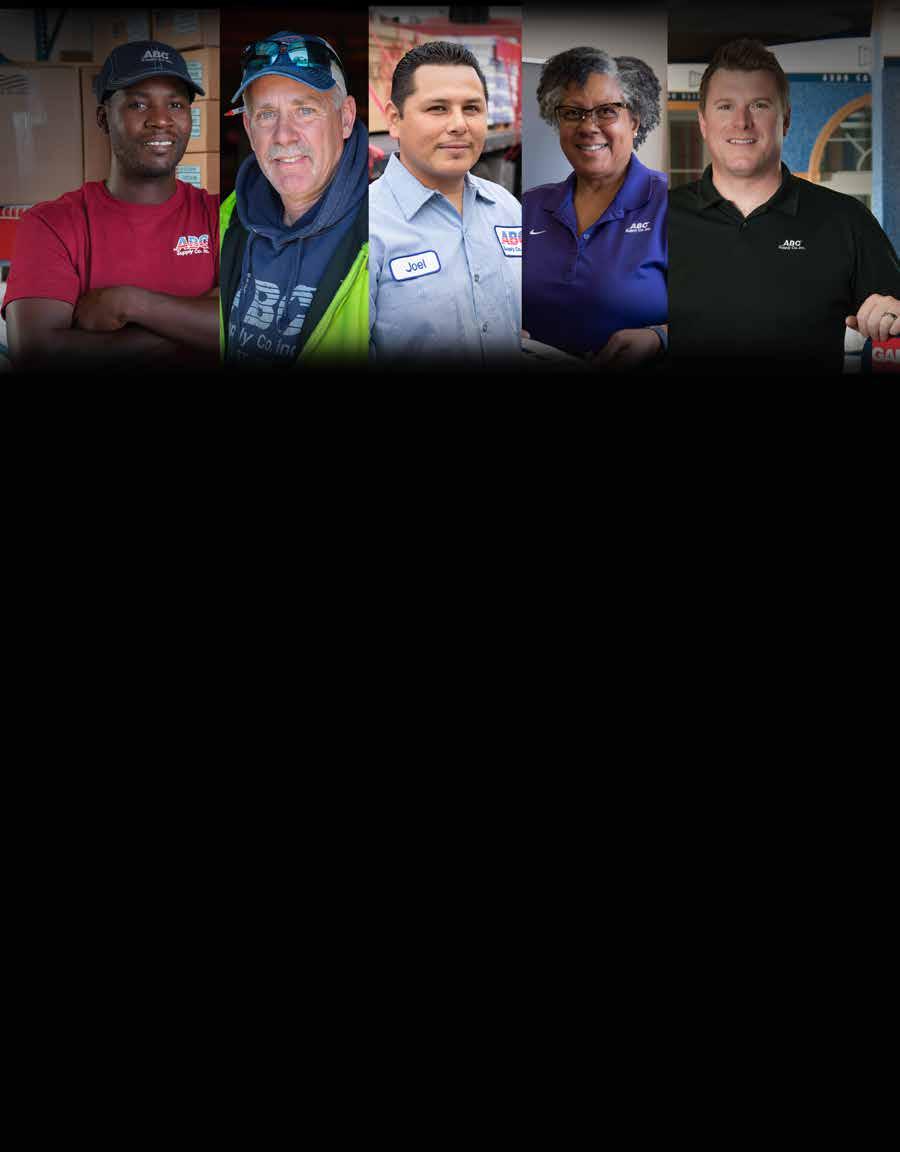
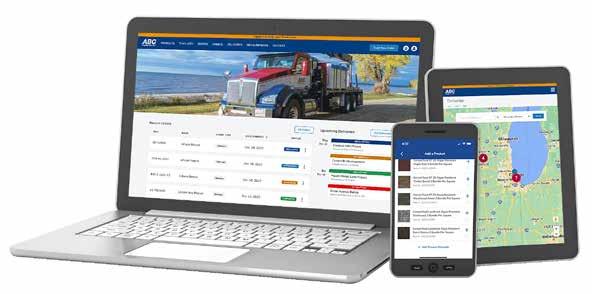

Kathleen Kennedy
Kathleen graduated from Mt. Dora High School. She plans to become an Architect and will begin her studies at Seminole State College. She works part-time at BranamJames Construction and Restoration. She bowls, swims and served as a baseball announcer for her high school team. Her father, Paul Kennedy, works in Sales at Collis Roofing.
Jessica Borowski
Jessica attends the University of Florida, studying Finance and Information Systems. She intends to pursue post-graduate work in finance, focusing on either Wealth Management or Information Systems. Her father, Robert Borowski, who founded Allied Roofing & Sheet Metal, Ft. Lauderdale, passed in 2020.

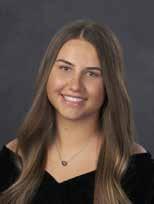
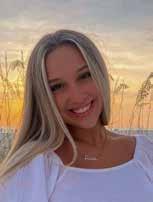
Caroline Belcher
Caroline attends Santa Fe College to study Diagnostic Medical Sonography. Her goal is to become either a pediatric or labor and delivery nurse, working at a hospital and, eventually, at a doctor’s office. She volunteers in support of cancer fundraising, teaches dance classes at The Dance Studio and works as a nanny. Her parents are Tracy and Jon Belcher, Marion Service Roofing and Sheet Metal Co., Ocala.
William Kemp
William graduated from Gulf Breeze High School and plans to attend Florida State University to study Mechanical Engineering. He wants to build and is considering whether to enter FSU’s ROTC program or follow a civilian path. His parents are Chris and Amy Kemp.
Mason Swetz
Mason attends Georgia Southern University studying Civil and Structural Engineering. He interns at engineering firm Mills, Short and Associates nad plans to become a Structural Engineer. His parents are Andrew and Melinda Swetz.
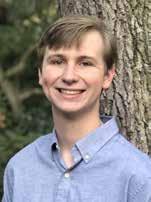
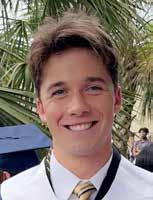
Tanner Templeton
Mason E. Liftig Scholarship
Tanner graduated from Edgewater High School and will attend Valencia Community College and the University of Central Florida seeking a degree in Construction Management. He plans to become an Estimator. His father, Brent Templeton, is a General Branch Manager at Collis Roofing.
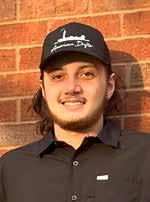
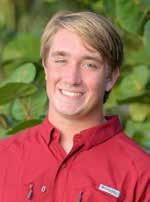
Luke Stersic
Luke attends Florida State University, studying Criminology. He hopes to serve the FBI as an organized crime investigator. Luke’s parents are Chris and Lisa Stersic.
Emma Toohey
Emma graduated from Lake Mary High School and plans to attend Seminole State College and then St. Petersburg College in pursuit of a Veterinary Tech degree. Long term, she plans to become a Veterinarian with her own practice. She works at Central Florida Veterinary Clinic.
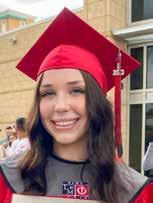
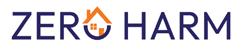

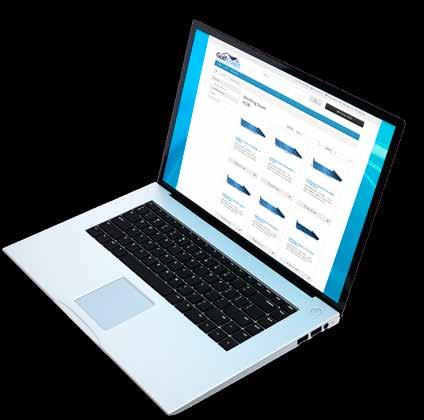

COTNEY CONSULTING GROUP
Project Management and Cash Flow
Managing roofing projects involves various tools and techniques to oversee them. Many tools have changed with the advances in methods and technologies. Cash, however, is the one constant tool that contractors will continue to rely on. While cash is not necessarily actual dollar bills and coins, a positive flow of money into the bank is essential to the financial health of contractors. The lack of cash flow is likely the most common reason for contractor failures. Contractors who report profits and have a good reputation for quality work may still have financial difficulties if they are not paid on time and do not have a positive cash flow.
Each roofing job is seen as an individual revenue base and contractors rely on roofing projects to bring in cash in the form of monthly payments from clients. Cash flow should not be just the focus of your CFO or Controller: it should be a priority and the primary focus of everyone from the owner down to the project team.
The concept of cash flow has several elements, most of them included in the broad concept of cash outflow and cash inflow. Jobsite expenditures, including labor, material, equipment, subcontractors and indirect costs, have a negative impact on cash flow and require tracking. The only significant positive cash flow is revenue received from the client. Contractors always want to operate in the black; that is, to make their cash inflow greater than their outflow. There are various methods a contractor can use to improve their cash position, some of which we will discuss in this article.
Preparing a cash flow curve for a roofing project is vital to managing costs and ensuring positive cash flow. The cash flow curve is a projection of the total value of work to be completed each month during the project’s construction. The curve is created by cost-loading the schedule and plotting total monthly expenditures.
To create the cash flow curve, the estimator or project manager must develop a cost-loaded schedule, starting with a summary schedule and estimate. The activities on both schedules should be similar and not be overly detailed for clarity and ease of use.
Construction-specific accounting software should make preparing a cash flow by job report easy, if not automatic. Some systems even incorporate this report into their executive dashboards, so the information is displayed graphically and available in real-time.
Tracking Job Costs
Tracking job costs is one of the most time-consuming but essential aspects of cost control for a roofing project. Direct labor costs are tracked by filling out
time sheets for the crew, which report hours worked against a description of work activities and cost codes assigned to those activities. Direct material costs are tracked by recording material deliveries and matching them with supplier invoices, with the appropriate cost code assigned to those materials.
Subcontractor invoices are submitted to the roofing contractor and logged as accounts payable before being forwarded to the project manager for approval. Your accounting team should verify that the total amount billed does not exceed the amount approved in each contract and assign the appropriate cost code for each subcontractor. The project manager or superintendent should verify the percentage completed for each subcontractor request.
The cost of jobsite general conditions includes indirect expenses such as equipment rental and labor costs not directly associated with job-specific costs. Indirect labor expenses include salaries for personnel such as superintendents, project managers and other supervisory personnel.
Salaried personnel, including the project manager, superintendent and other supervisory personnel, may not be required to complete time sheets like crew leaders do for their crews. If your company tracks these to projects rather than general overhead, they are individually assigned to a different cost code within the project’s general conditions estimate. The company routinely records a portion of its monthly salary against its individual cost code, which is incorporated into the labor and job cost history reports.
There is only one source of positive cash influx for a roofing contractor: receipt of payment from the client. This usually occurs once a month, after the work has been done. Residential contractors and some commercial contractors on private reroofing projects often receive a check at the time of sale or mobilization of the project.
The CFO or Controller is responsible for processing cash flow to make payments on all jobsite expenditures and receiving monthly client payments. The company relies on positive cash flow when revenues exceed expenses. The CFO or Controller may have an established line of credit with their bank and may call

on those funds in case of a short-term cash shortfall but pays them back as soon as possible. Still, your goal should be to finance your projects from a solid cash flow position that keeps additional cash for times when you may need to cover expenditures. The contractor usually pays direct and sub-labor weekly and does not withhold retention from the worker’s checks. Revenues typically lag expenditures early in the project when an increased amount of direct labor and material is expended to mobilize and start the project. Later in the project, cash flow needs are eased during the punch-out and close-out phases.
The lack of positive cash flow is one of the most common reasons for contractor bankruptcy. Contractors continually relying on the bank to fund their operations will fail. Negotiate terms with clients and subcontractors to improve cash flow, prepare timely, accurate and fair pay requests and obtain financing.
Below are some methods you can incorporate for cash flow improvement within your company:
■ As a subcontractor, you finance the general contractor in that you are not paid until the client pays the general contractor and retention is withheld from your payment; the same as what the client withholds from the general contractor. You can significantly improve your cash flow position by incorporating a lower mix of general contracting work and more privately negotiated reroof projects.
■ Include a mobilization charge in the schedule of values; this should be standard practice.
■ Require the client to make a down payment or invoice the client twice monthly. You must negotiate this into your contract, but the answer will always be no unless you ask.
■ Negotiate retention withheld from 10 to 5 percent.
■ Request retention released on portions of the work completed and accepted. This is also done during contract negotiation.
■ Have a solid estimating practice in place. By doing so, you will beat the budget or have significantly fewer overruns and performed work will cost less, considerably improving the cash flow position.

■ Most clients and general contractors understand that roofing contractors are not banks and will allow a small
amount of front-loading of the schedule of values, just not an excessive amount.
In conclusion, cash flow management is crucial to the success of any roofing project. The lack of positive cash flow can lead to financial difficulties and even contractor failures. It is essential to track job costs and prepare a cash flow curve for each project to manage costs effectively and ensure positive cash flow. By incorporating these methods and prioritizing cash flow management, roofing contractors can maintain financial health and achieve success in their projects and business.
John Kenney, CPRC has over 50 years of experience in the roofing industry. He started his career by working as a roofing apprentice at a family business in the Northeast and worked his way up to operating multiple Top 100 Roofing Contractors. As CEO, John is intimately familiar with all aspects of roofing production, estimating and operations. During his tenure in the industry, John ran business units associated with delivering excellent workmanship and unparalleled customer service while ensuring his company’s strong net profits before joining Cotney Consulting Group. If you would like any further information on this or another subject, you can contact John at jkenney@cotneyconsulting.com.
Giving Back
FRSA Members Giving Back to the Community
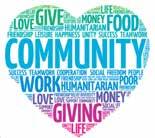
Veterans Front and Center at Indy 500: Over $3 Million Raised for Homes for Our Troops
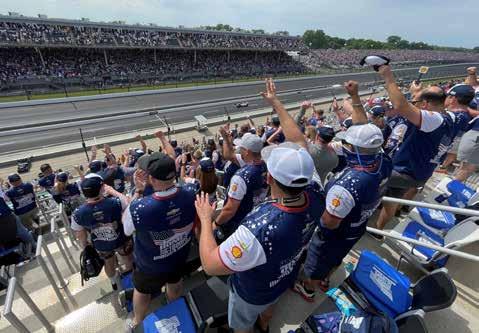
ABC Supply Co., Inc. announced that over $3 million has been donated to Homes for Our Troops (HFOT) as part of a fundraiser held by the company in conjunction with the 107th Running of the Indianapolis 500 presented by Gainbridge.
Among millions of viewers tuning in for the race, several HFOT Veterans were invited to experience the whirlwind weekend. The Veterans got a garage tour of the No. 14 AJ Foyt Racing Chevrolet driven by Santino Ferrucci, walked the fabled Yard of Bricks and got a front-row seat to the patriotic, starsand-stripes-clad HFOT Indy car racing to a thrilling third-place finish.
“The events at the Indy 500 were an incredible experience for our Veterans, including one-on-one interactions with the AJ Foyt Racing team as well as celebrating driver Santino Ferrucci’s third-place finish. We are so grateful to ABC Supply for not only hosting HFOT at the event but for raising national awareness of our mission of ‘Building Homes and Rebuilding Lives’ through both the car’s patriotic design and by matching donations throughout the month of May. Our Veterans had the experience of a lifetime and the exposure we gained ensures we can build and donate specially adapted custom homes to many more of our nation’s most severely injured post-9/11 Veterans,” says HFOT President and CEO Brigadier General, USA (Ret) Tom Landwermeyer.
ABC Supply has been a passionate supporter of HFOT since 2020 and donated the design of the Indy car to create more awareness for the organization,
which builds and donates specially adapted custom homes across the U.S. for severely injured post-9/11 Veterans, enabling them to rebuild their lives. HFOT has built 355 specially adapted homes since its inception in 2004.
“We were excited to host this monthlong donation match campaign and now, we’re simply humbled by the overwhelming support that has poured in for HFOT,” says Mike Jost, Chief Operating Officer at ABC Supply. “Our relationship with HFOT means a great deal to us and we’re so thankful to the team at AJ Foyt Racing for helping us bring light to the incredible work the organization does for our nation’s Veterans.”
“The entire AJ Foyt Racing team has been honored to represent such a wonderful organization,” said Team President Larry Foyt. “From meeting some courageous heroes who attended the race to carrying the beautiful red, white and blue livery on Memorial Day weekend, this program has been special to our team and fans alike. We’re thrilled that we could have a fantastic finish and hopefully raise a great deal of awareness about Homes for Our Troops.”
Those who missed the donation matching window can still support HFOT by visiting www.hfotusa.org.
FRSA is proud of the volunteer work completed by members in the industry and would like to share those projects as often as possible. If you have a community service project you’ve completed, please send it to Lisa Pate at lisapate@floridaroof.com.
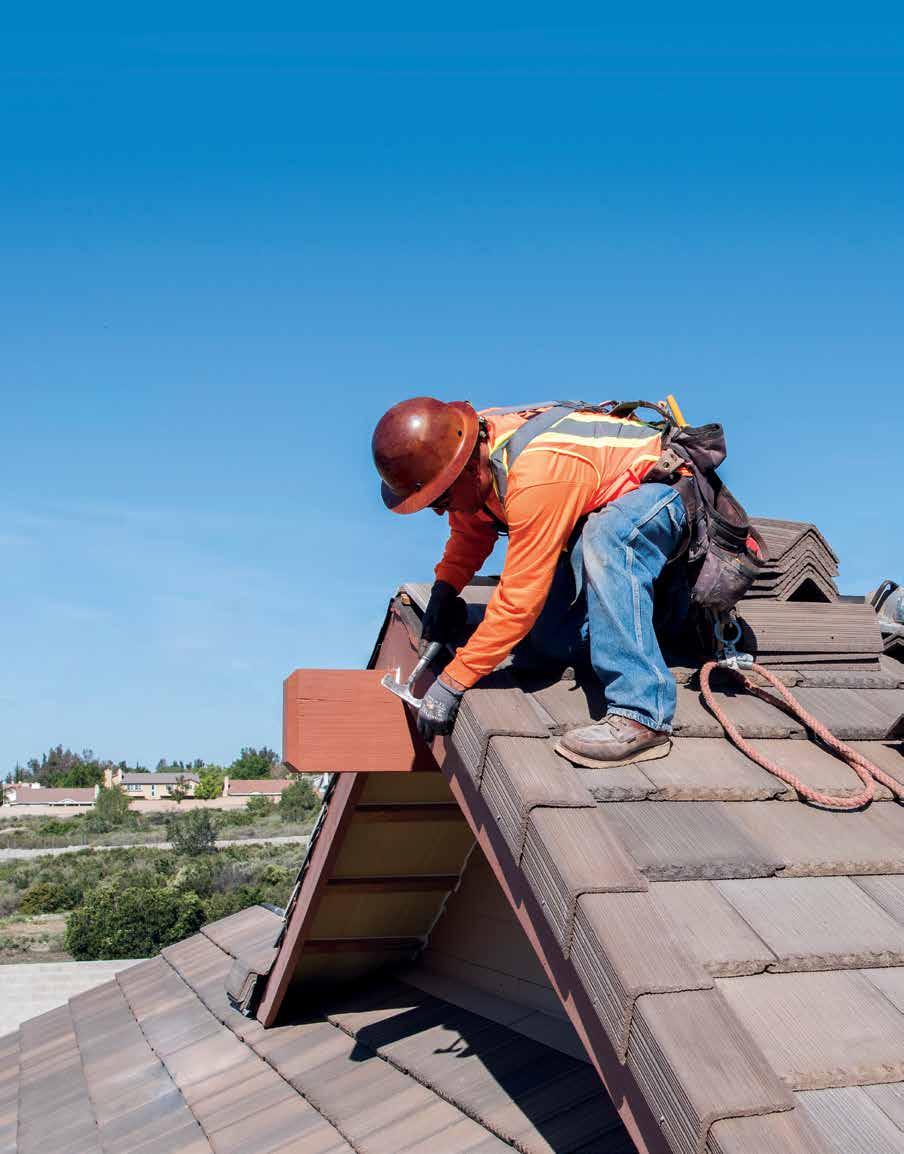
Rick Jenkins, President & CEO, Quality Roofing, Inc.
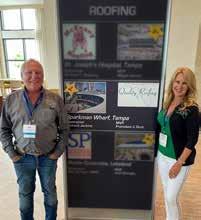
How did you get started in the roofing industry?
My father, Harrison, made me! He had a family roofing business and I was trained by my father to install the best roofing systems, to the best of our ability. I then tried a few other trades, but roofing is in my blood. I’ve been in business for 29 years.
What’s your favorite part of the job?
Designing and specifying jobs and negotiating contracts with customers. I like to give my customers the best product and value for their project.
What’s the most unusual roofing project that you’ve been a part of?
There have been two. The first was the Crystal River Nuclear Plant. This was the first fluid-applied roofing system that I installed when I was younger. Being at that facility and standing under the shadow of the nuclear reactors was incredibly intimidating. I couldn’t help but feel like I would disintegrate at any moment. The second was the Wish Farms Treehouse. This is another project I am extremely proud of. The premise of the treehouse roof design was undulated, so it looked like a kid drew it in Pre-K. The original spec for the project was to install a copper standing seam roof, which wouldn’t have worked. As a team, we decided to custom cut and fabricate individual copper shingles and it came out beautiful. It was featured on the December 2021 cover of FRM.
What would you do for a career if you weren’t doing this?
I originally thought I may want to be a pharmacist, but I realized that if I wasn’t a roofer I would starve. Joking aside, some type of sales or marketing for a company or product that I would be proud of. I prefer to sell things that I believe in.
How do you define success?
Honesty, quality of workmanship and integrity. I also play well with others. Having a friend and partner in business like John Garrison, Vice-President of Quality Roofing, Inc., has contributed to my individual success as well as the success of the company.
What inspired you to join FRSA?
I have been a member of the FRSA for a long time. The main reason I have stayed with the FRSA is because of

Morris Swope. In my opinion, he turned the FRSA into what it is today: a true benefit for the roofer! FRSA is also extremely beneficial for instigating continuing education, providing financial support and ensuring jobsite safety. What advice would you give to someone interested in joining the roofing industry?
1) Be honest, work hard and strive to install the best quality roofing systems available to you. Master what you are good at and stick to it. 2) Find mentors and rely on them for advice and guidance. My mentors have been my dad James H. Jenkins, Sr., Morris Swope, Salvatore (Big Sam) Ferlita, as well as suppliers and partners like Jim Resch, Jim Coston, Les Thompson and Eric McKenzie.
What do you consider a waste of time?
Dealing with clients that don’t want a proper roofing system for their building; the ones whose motivation is price and not a quality product. It goes against my goal of providing a quality product, every time.
What’s your favorite vacation?
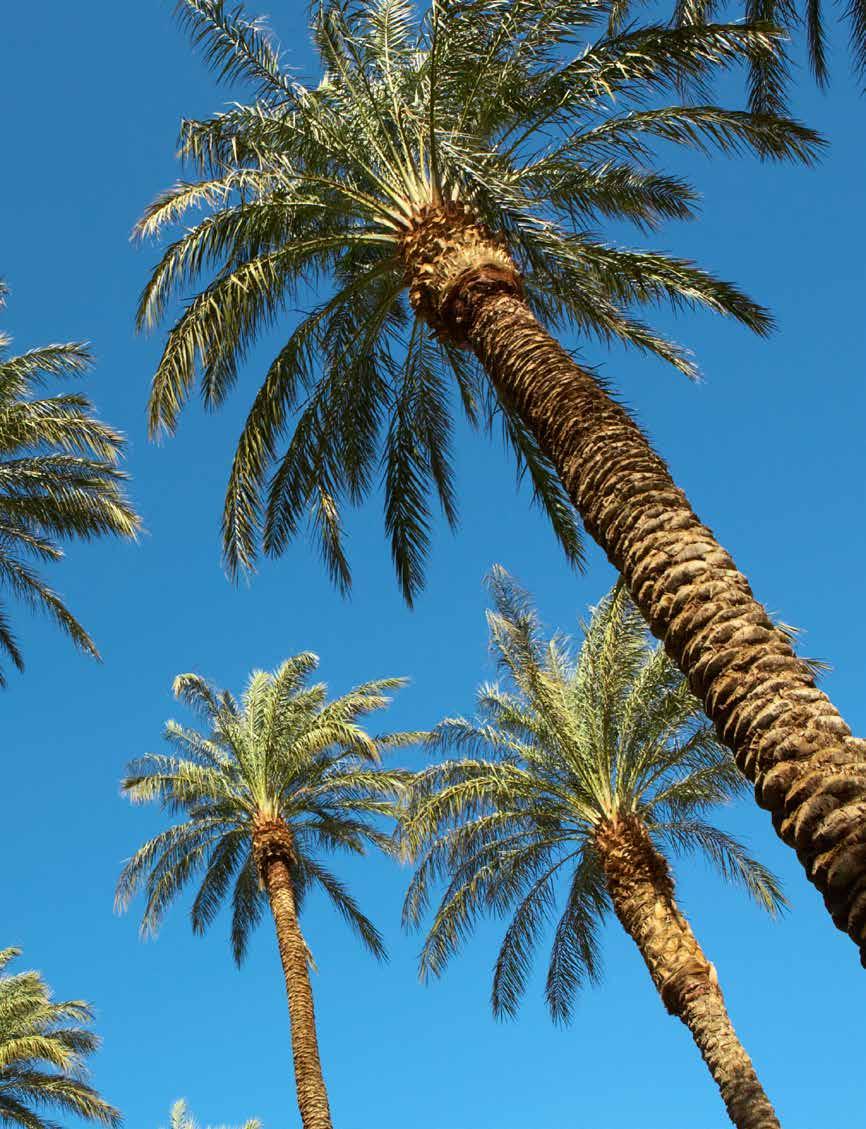
Spending time with my wife, wherever that destination is. Especially when we spent time in the New England area watching our son play college football and had our kids, grandkids and other family members join us.
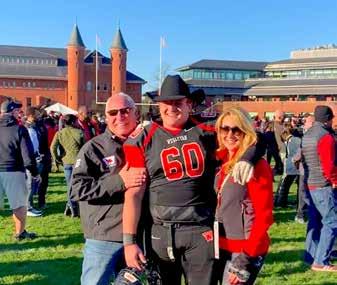
What’s your favorite pastime activity?
Going out on my boat, hunting and snow skiing. I also enjoy, like many of my fellow roofers, drinking and partying, but not golfing.
Where would be your ideal place to live and why?
Right here in Tampa, Florida. I love it here! Especially in the house that I designed, built and plan to die in – but hopefully not today!
What would surprise others to learn about you?
Basically, I am a bionic man, but not in a good way. When I was four weeks old, I had to have a left lung lobe removal. At that time, it was the second successful surgery of this type in the U.S. I was lucky and now it’s performed arthroscopically. Since then, I’ve also had a hip replacement, ankle graph and asphalt burns. As you can imagine, I have a lot of scars.
the power of INNOVATION
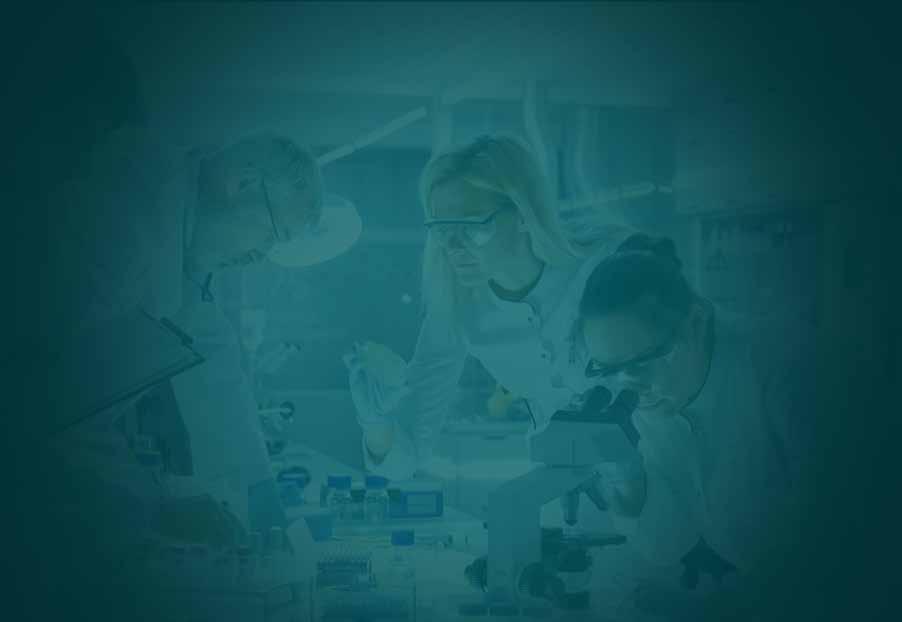
superior
technology MADE FOR YOU
PolyFlash® 1C is a state-of-the-art flashing compound designed for sealing various roofing and waterproofing details, and unusually shaped penetrations on a wide variety of roofing systems.
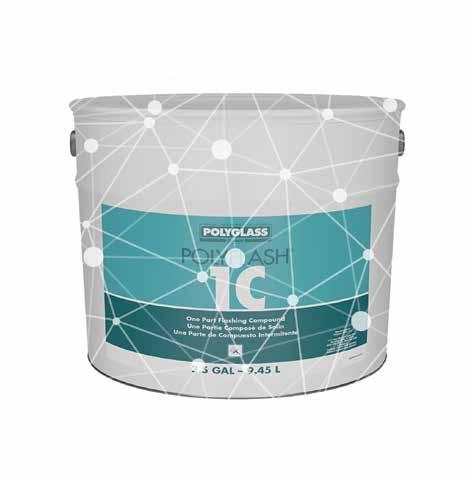


polyglass.us

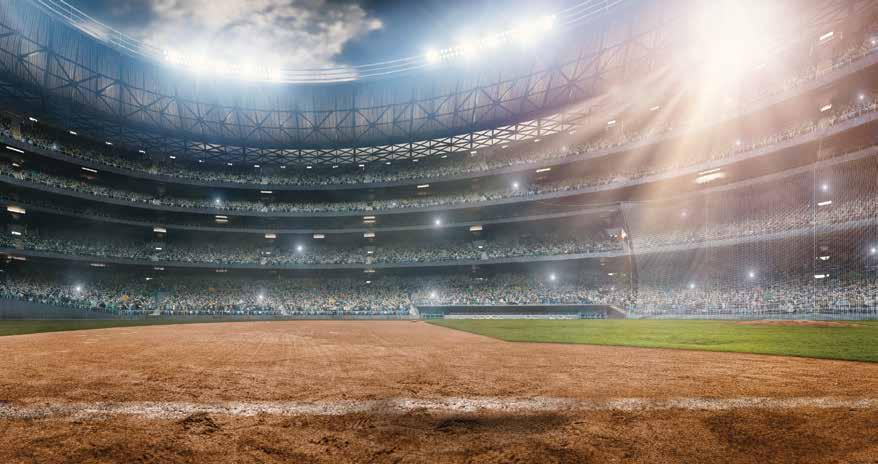

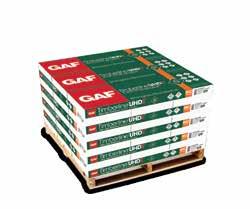


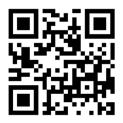


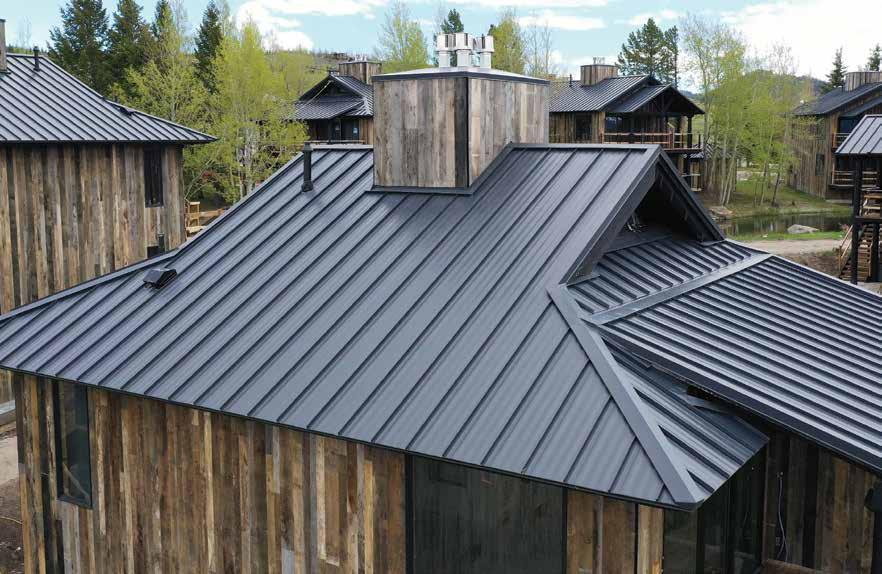
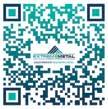