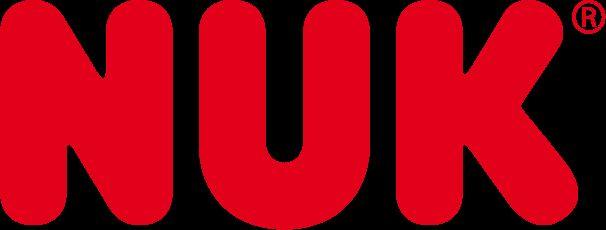
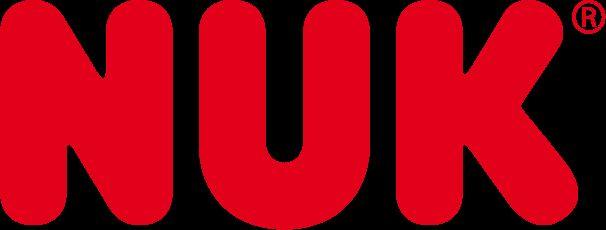
Understanding Life
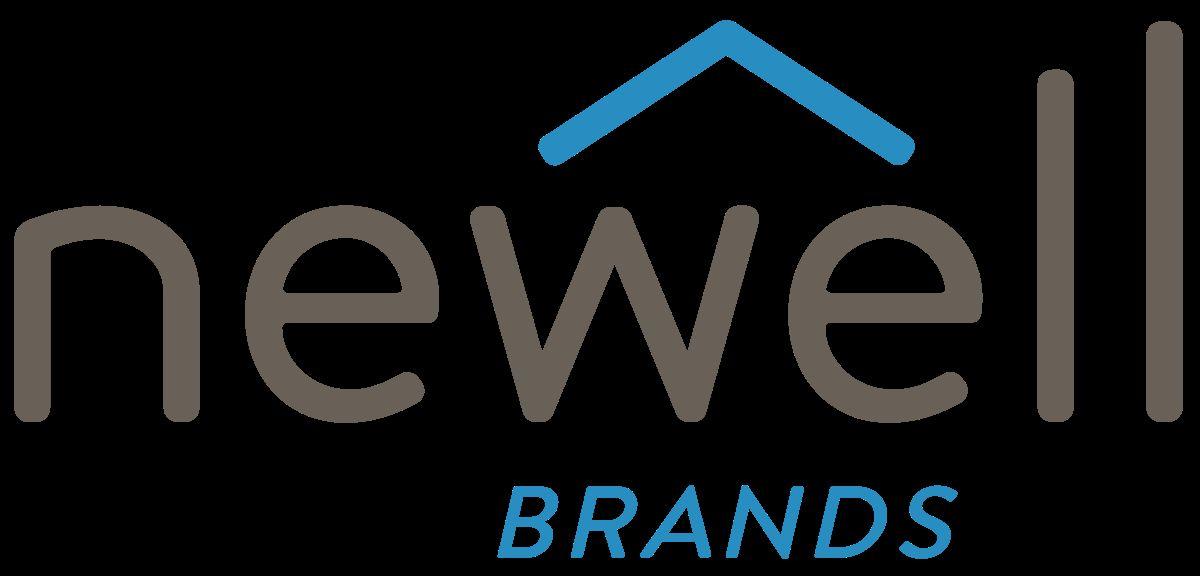
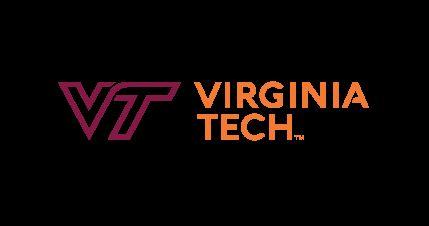
Anna Troutt, Junsik Kong, Olivia Molloy, Rohan Sarathy
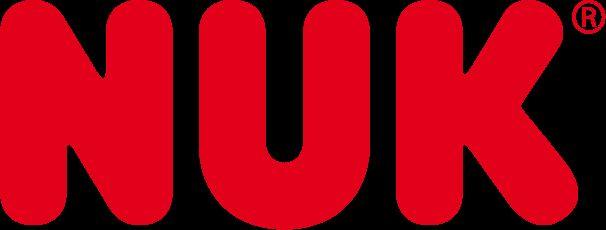
OUR CHALLENGE
MUST HAVES
Plastic free packaging
Exposed and visible product
Able to be merchandised (peg or shelf)
ISTA 3A compliant
Pack out instructions included
LIKE TO HAVES
Designed for automation
DISTRIBUTION
MANUFACTURING
Shipped on 48”x40” US GMA pallet (2 high in trailer)
Designed to be sold to Walmart, Target, Buy Buy Baby
Packed out in WI Facility - initially hand packed → automated
Ergonomic with simplification of pack out
Intuitive design for easy product placement
TARGET MARKET
Walmart, Target, Buy Buy Baby
Parents of newborns and toddlers
Note:Eachproducttestedinamastercasecontaining12products

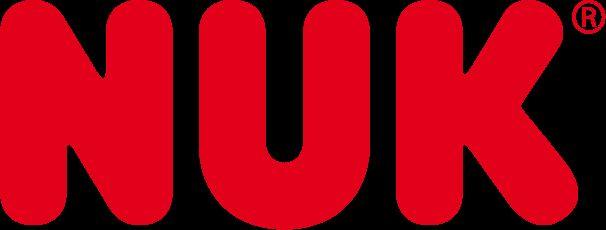
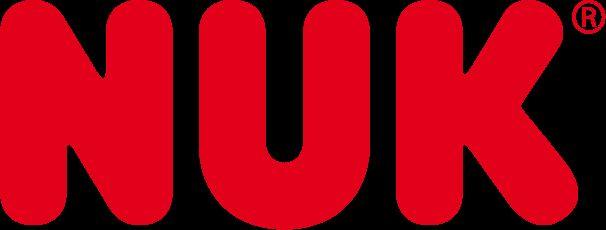
CURRENT DESIGNS
all of the current designs rely on the use of some, if not entirely, plastic
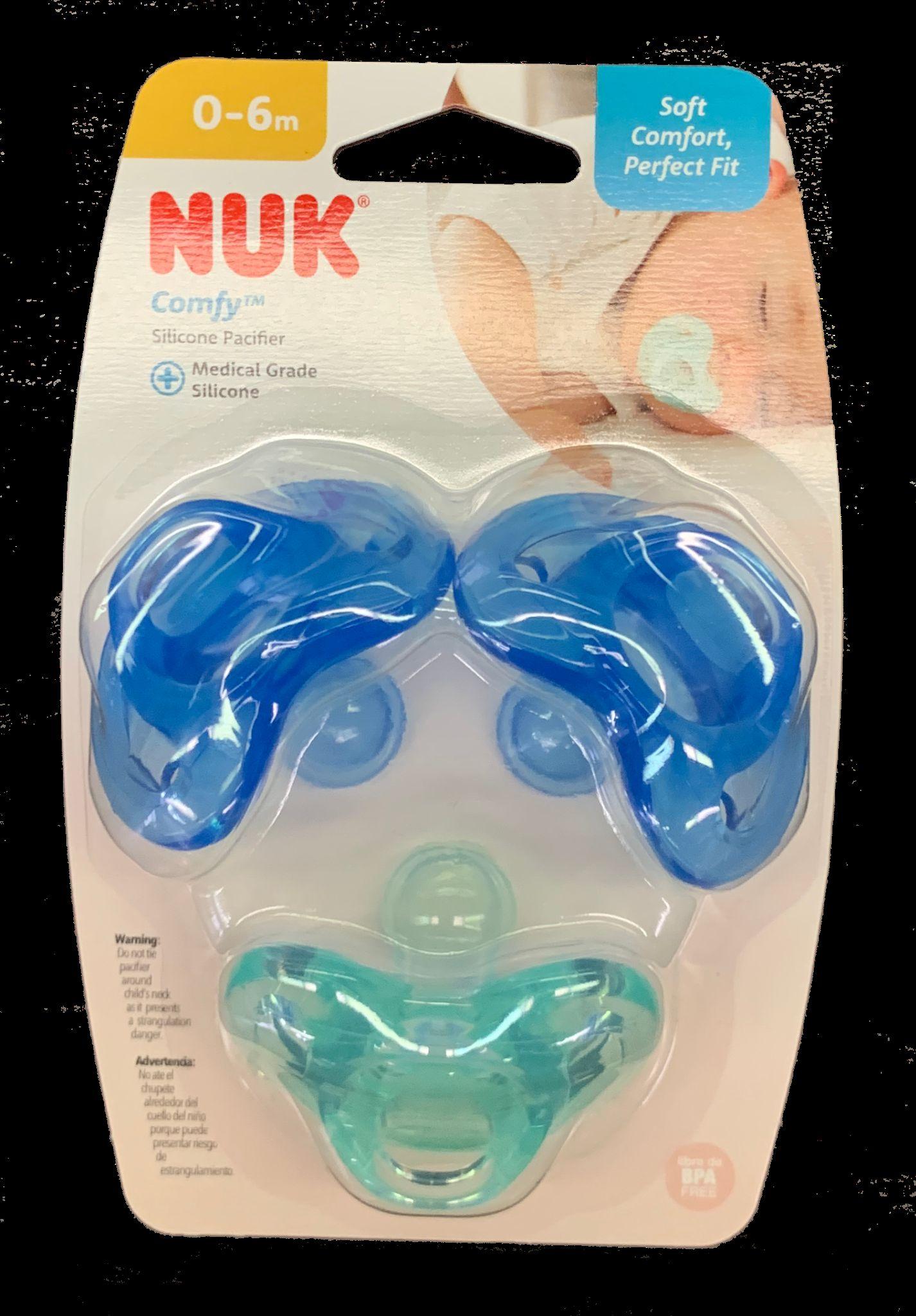
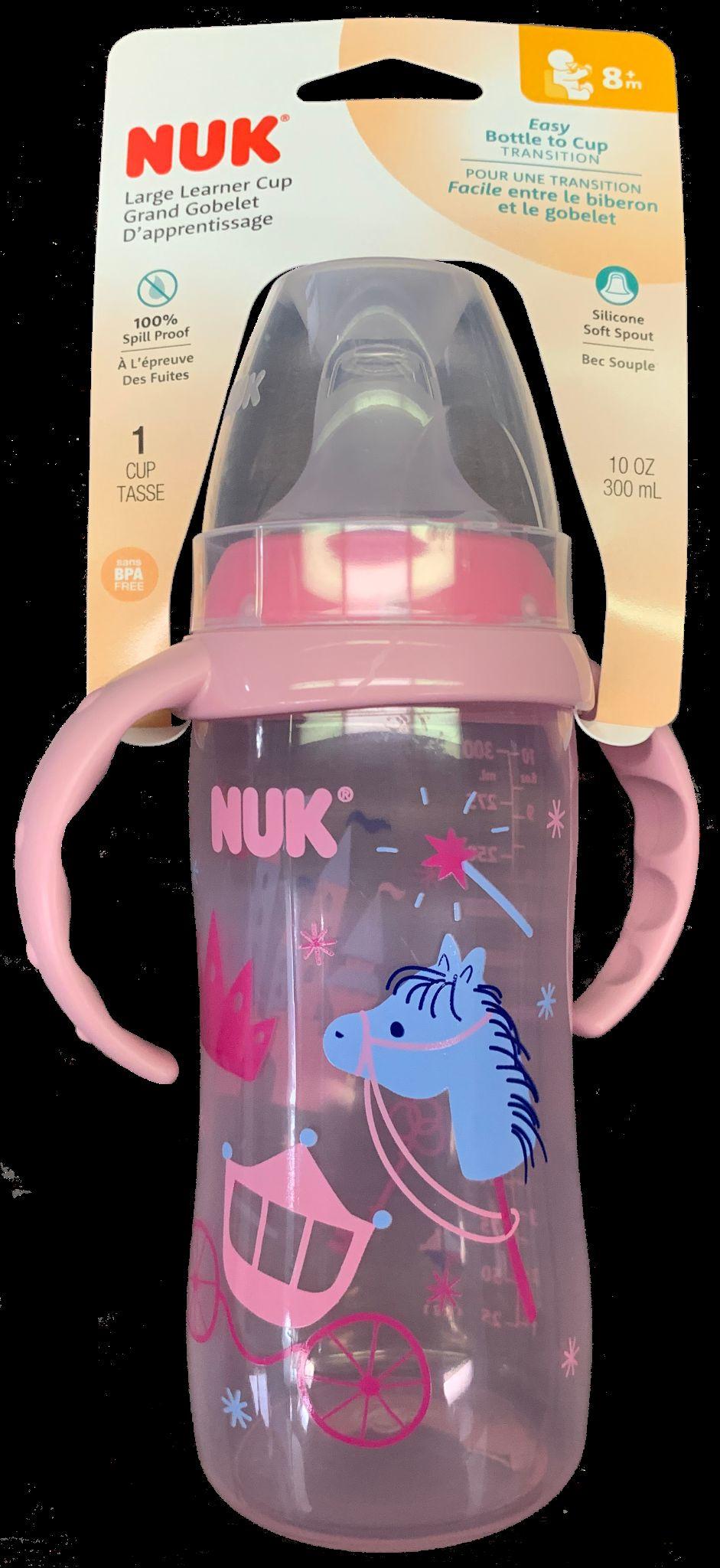


Paperboard
HDPE
Paperboard
Recreate the primary packaging of the proposed product line to:
Appeal to mothers and fathers alike by providing them sustainable, recyclable packaging while creating a cohesive line that promotes the purchase of NUK products throughout a child's development.
Meet . . .
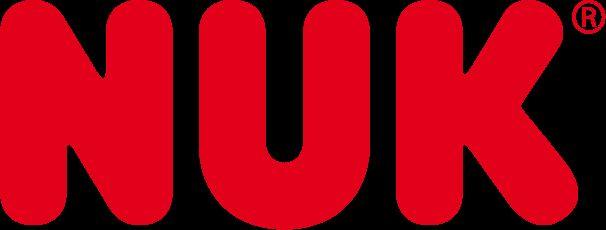

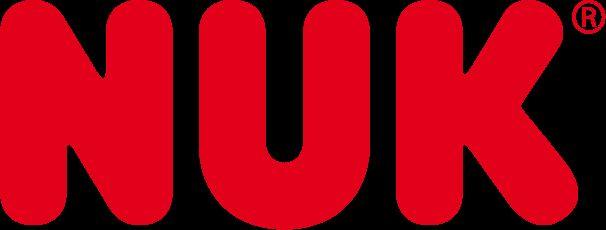
100% paperboard designs highlighting product visibility and maintaining security
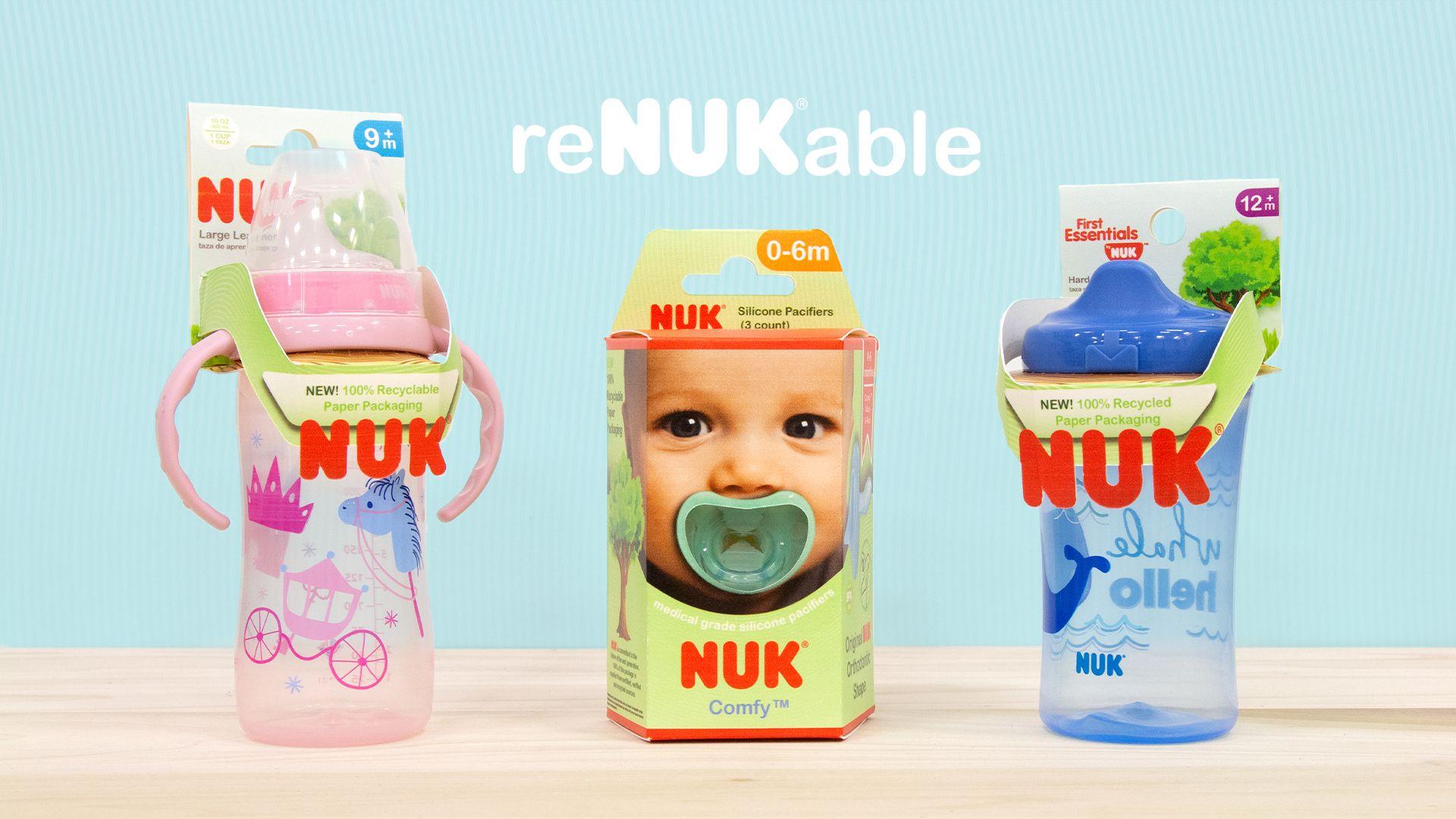


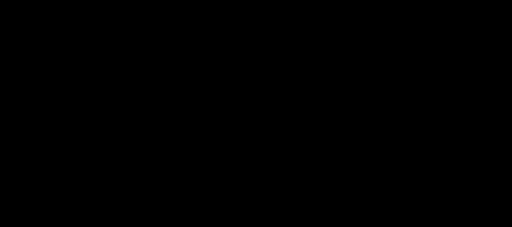
Box is angled so front and the sides can be viewed at once
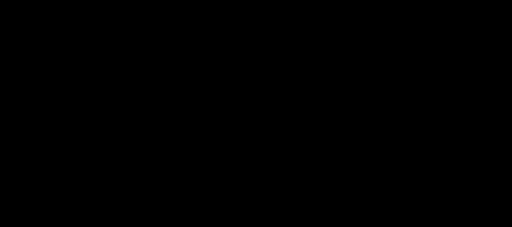
Insert allows for easy access during unboxing experience
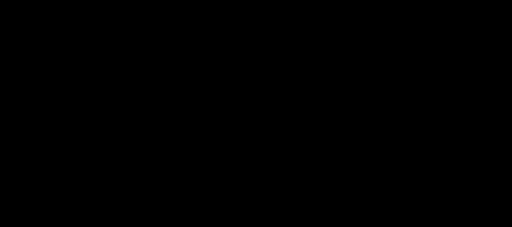
Packaging highlights unique features of the NUK product
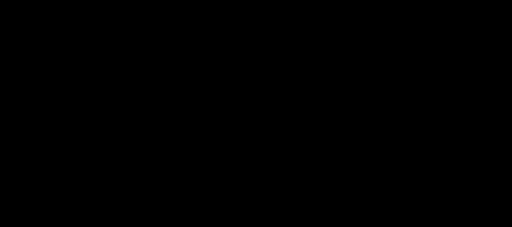
Smaller window allows for the products security in the box
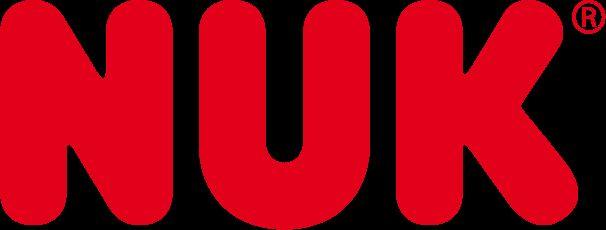
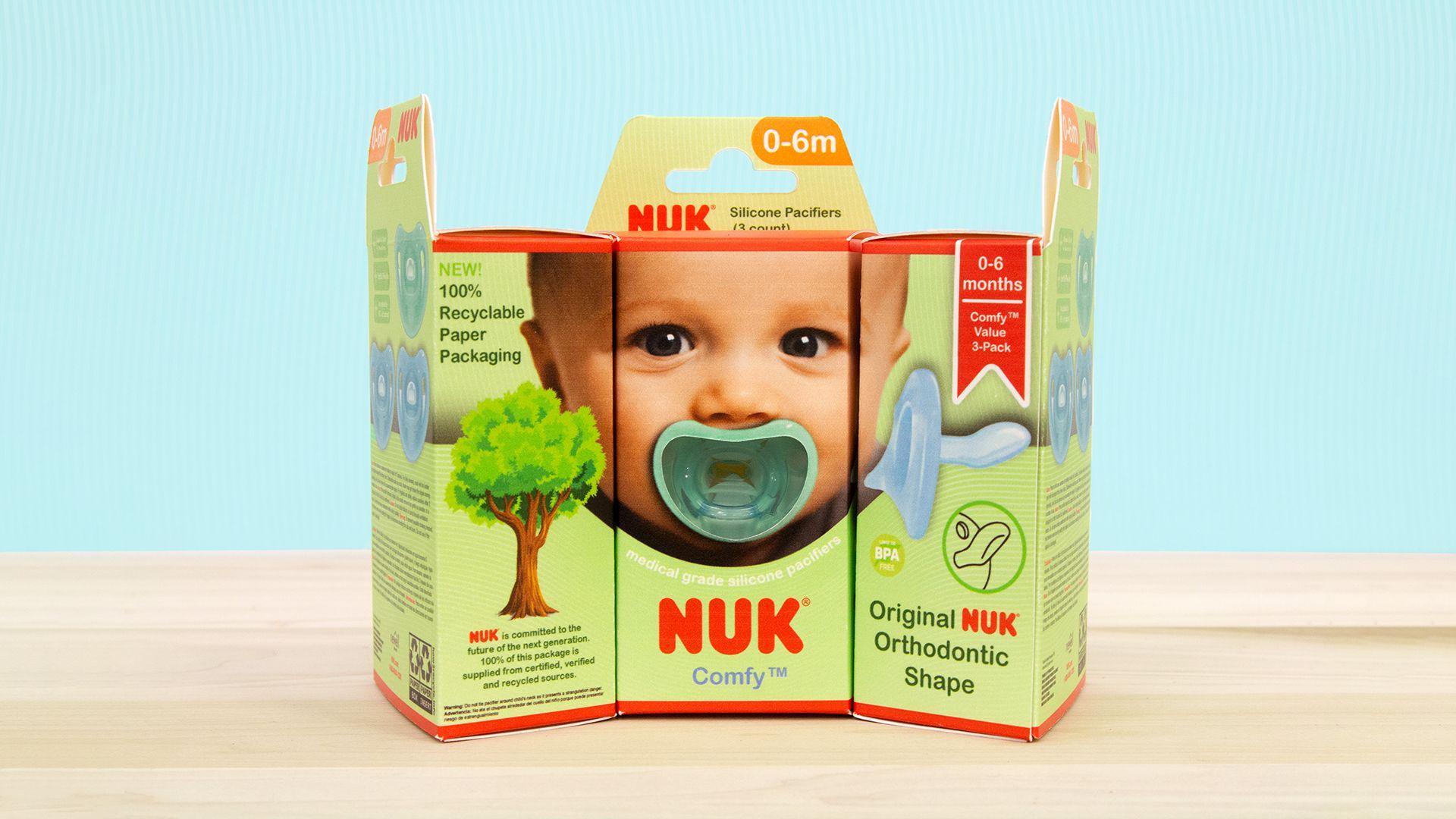

Can be hung on a peg
Exposed product
Can sit on a shelf
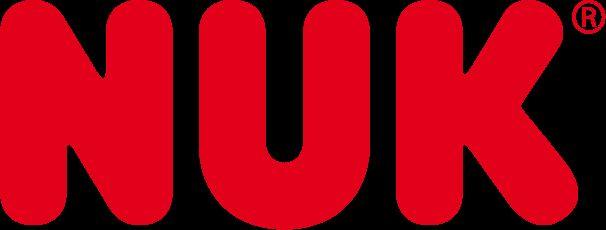



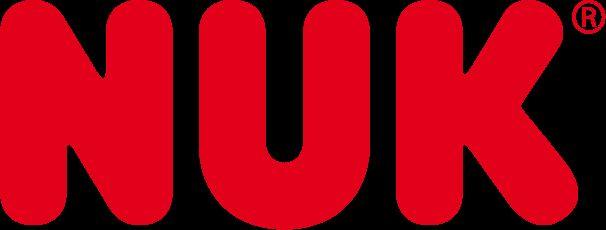
3 PK PACIFIER PACK OUT
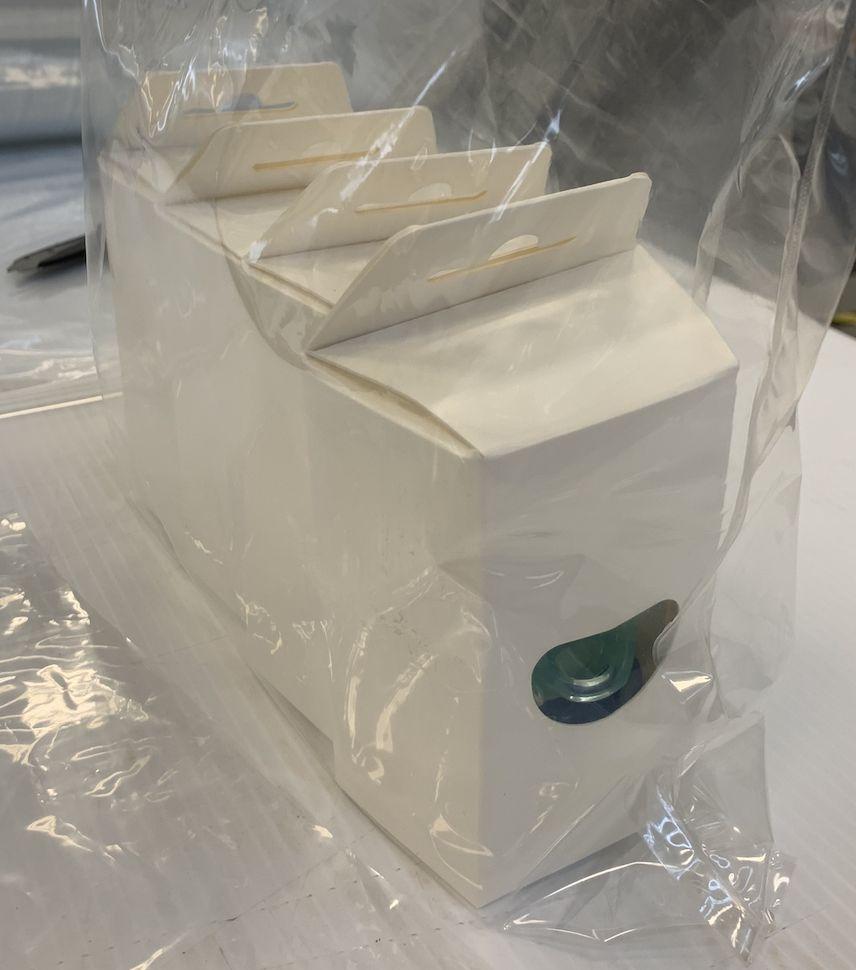

PRIMARY SHIPPER
1. Remove cutouts
2. Crease all folds
3. Adhere the glue-tab
4. Fold over hang placard
5. Close bottom flap
6. Add pacifiers to insert
7. Fit insert into the box
8. Close top flap
1. Crease all folds
2. Apply glue to glue tab
3. Square shipper sides
4. Close bottom flap and tape
5. Add 4 primary packages to inner bags - add 3 bags per shipper
6. Close and tape top flap
7. Tape top flaps in I pattern


PACIFIER TESTING SET-UP
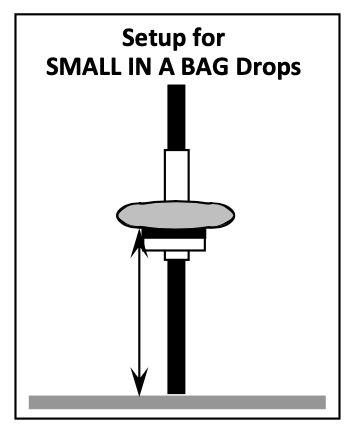
Required ISTA 3A: Small
● Top load (80lbs)
● Vibration test performed via small standard for small packaged products due to external dimensions
● Shipper tested in a bag full of dunnage
○ Top load placed on top (in another bag)
In bag vibration testing for small packages
● Face 1 for 30 minutes
● Face 2 for 30 minutes
In bag drop test for small package
● 6 drop sequences alternating between faces 2, 3, 6 at 24in.

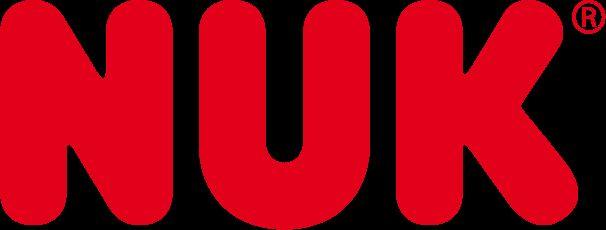

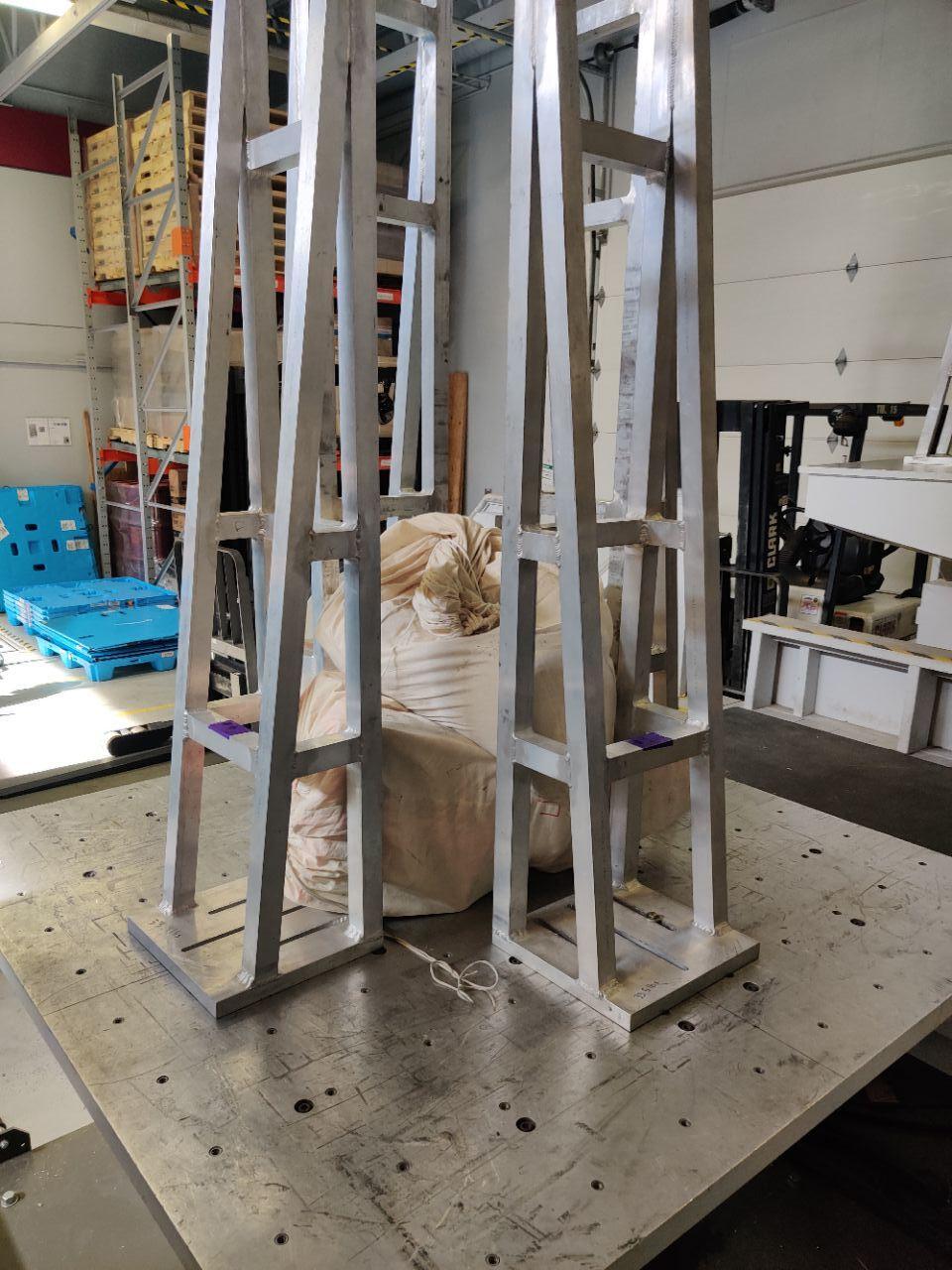
PACIFIER TESTING RESULTS

Results
Compression stress to box faces
Corners crushed due to compression and drops
No damage done to product, slight superficial damage done to shipper
○ Slight bending of primary packaging hang tabs (remedied when product is hung on peg)
○ All product remained in the packaging throughout the entirety of ISTA-3A
Challenges
Pacifier shipper was 3A standard but is designated as a “small package” due to its external dimensions
Requires testing in a bag full of dunnage with top load on top in another bag
Shipper survived a more rigorous test with topload plates rather than a dunnage bag

VIBRATION AND DROP TEST RESULTS
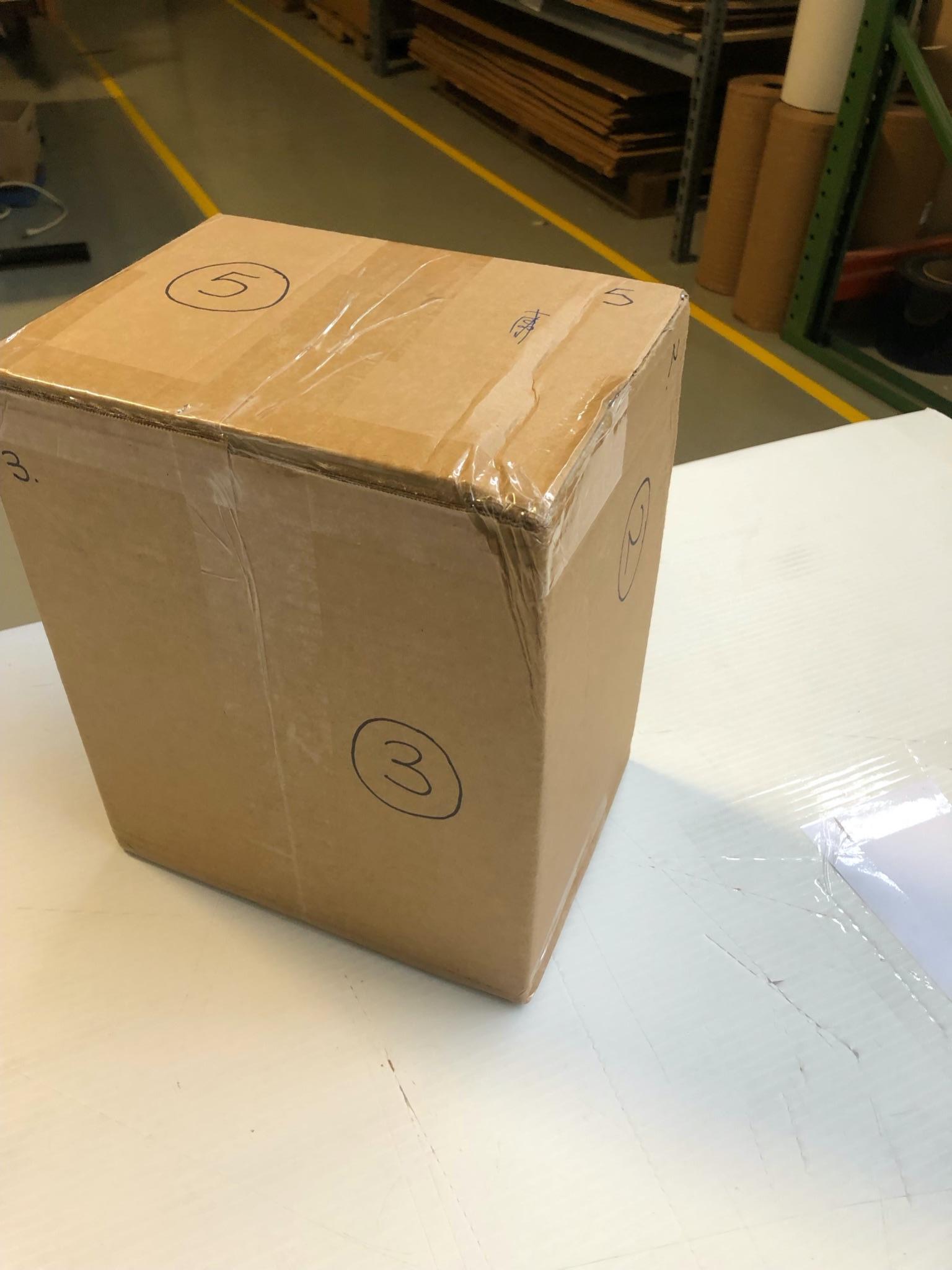
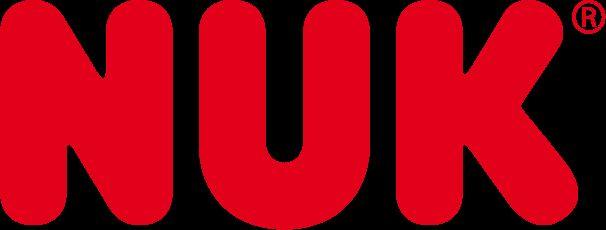

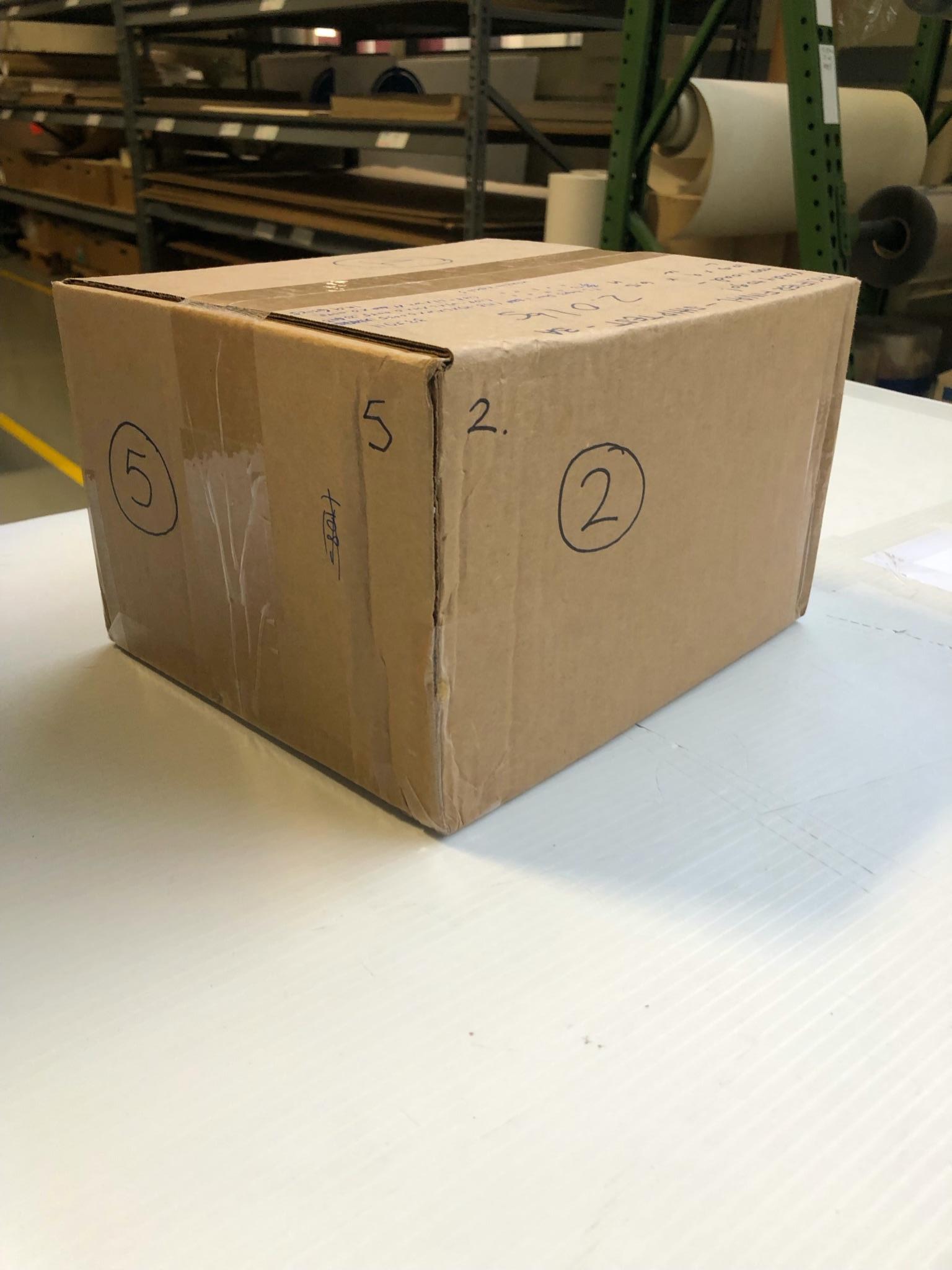
Despite slight damages on the shipper due to drops and vibration testing, there were no damage to the primary packaging inside.
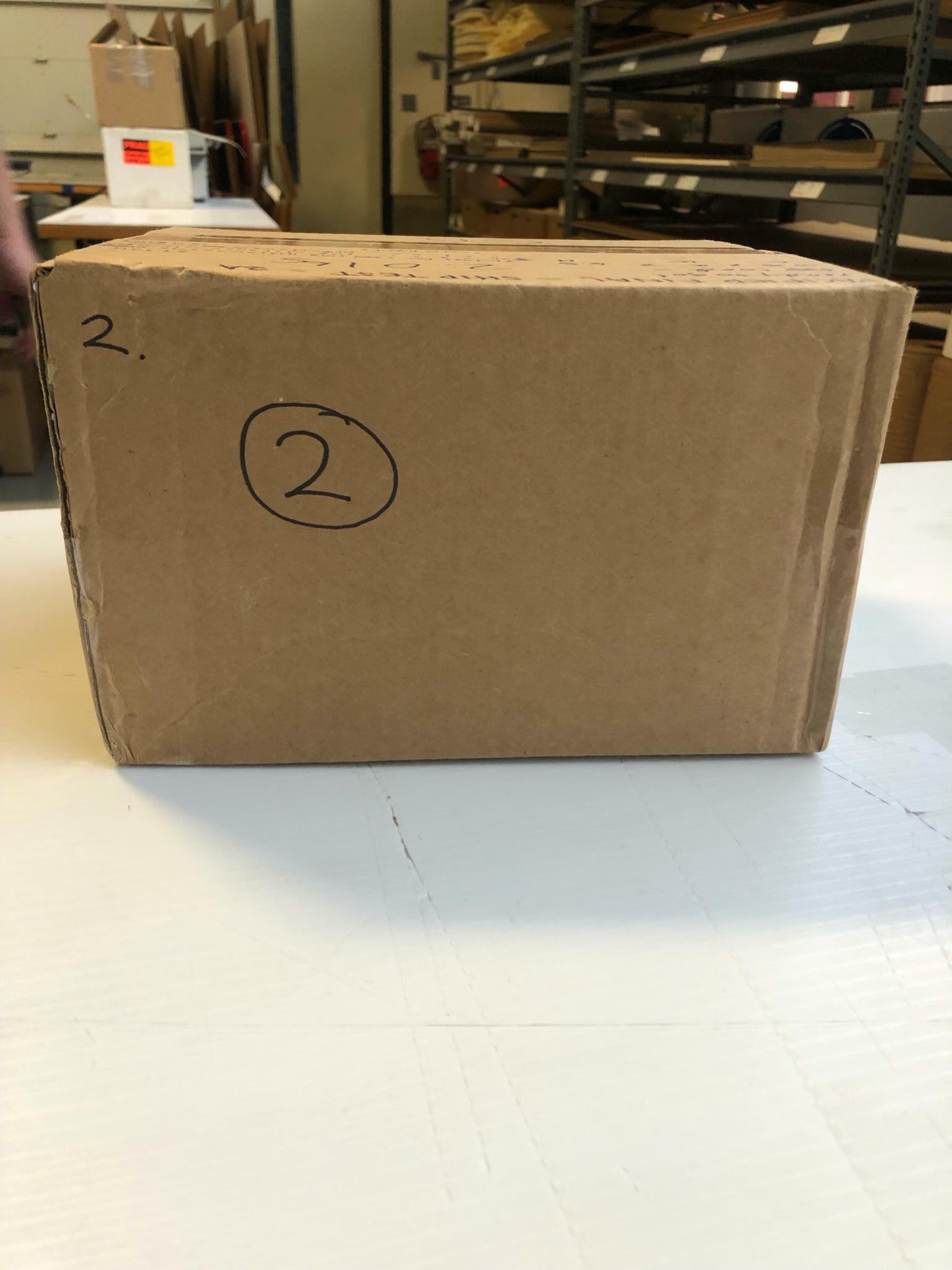

Can be hung on a peg
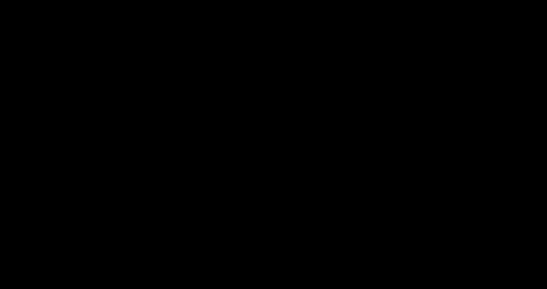
Handles fit into packaging so that it cannot be removed without full disassembly
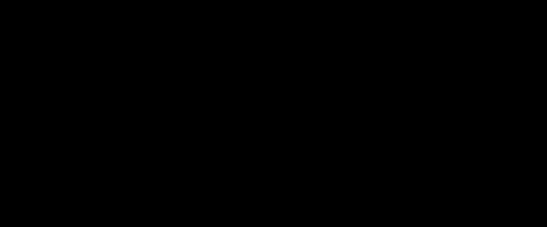
Packaging optimized so that the least amount of board is used
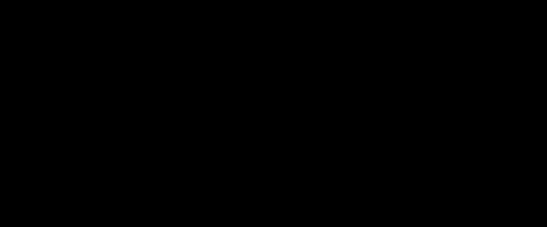
Packaging does not need to be glued, design features tabs
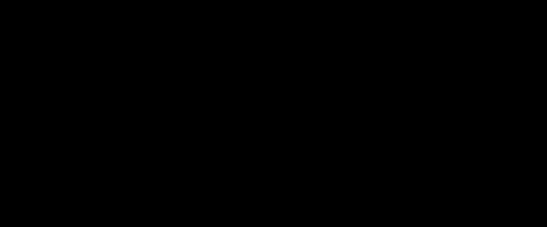
Similar iconography for better continuity and brand recognition
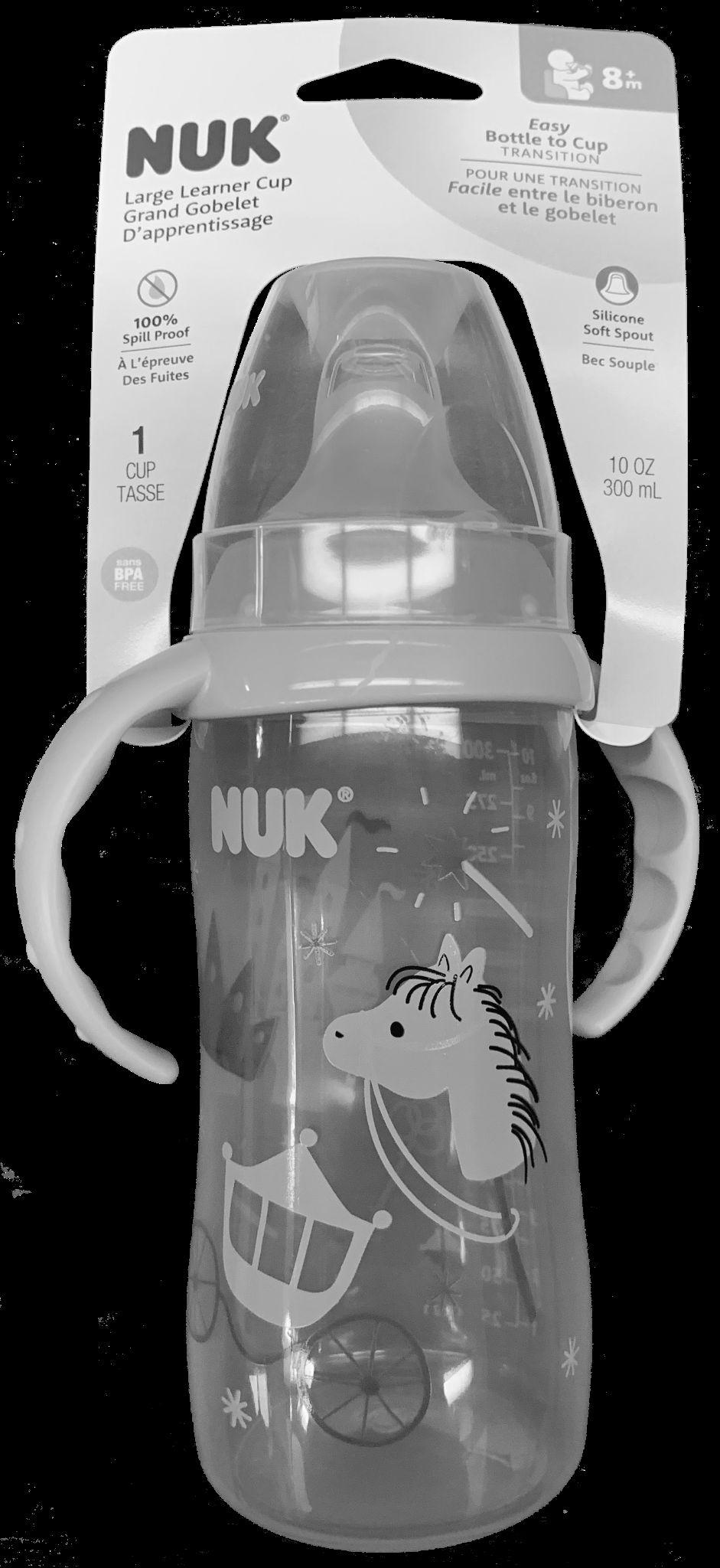
Can sit on a shelf
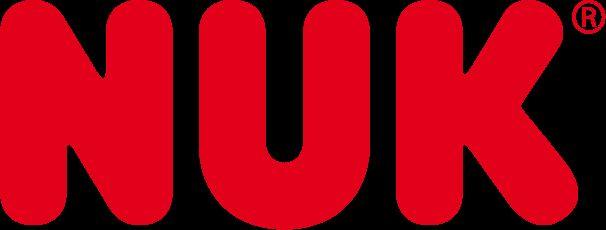
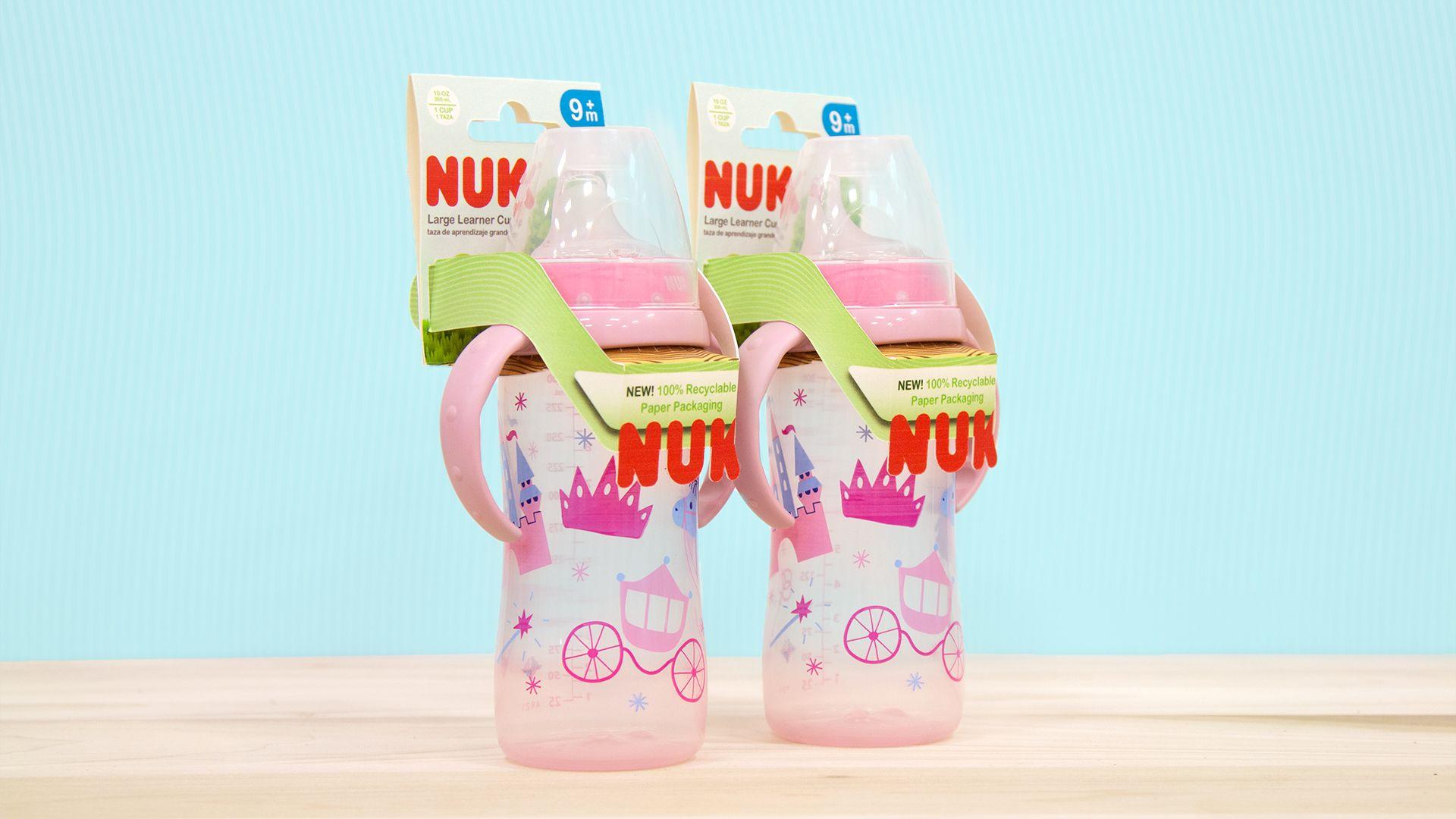

Holes for the handles
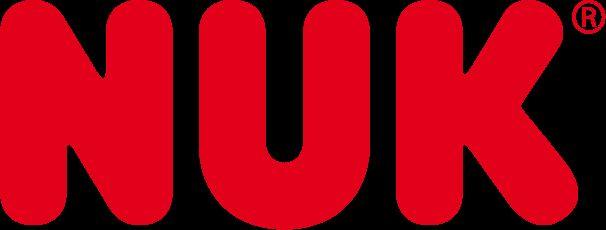
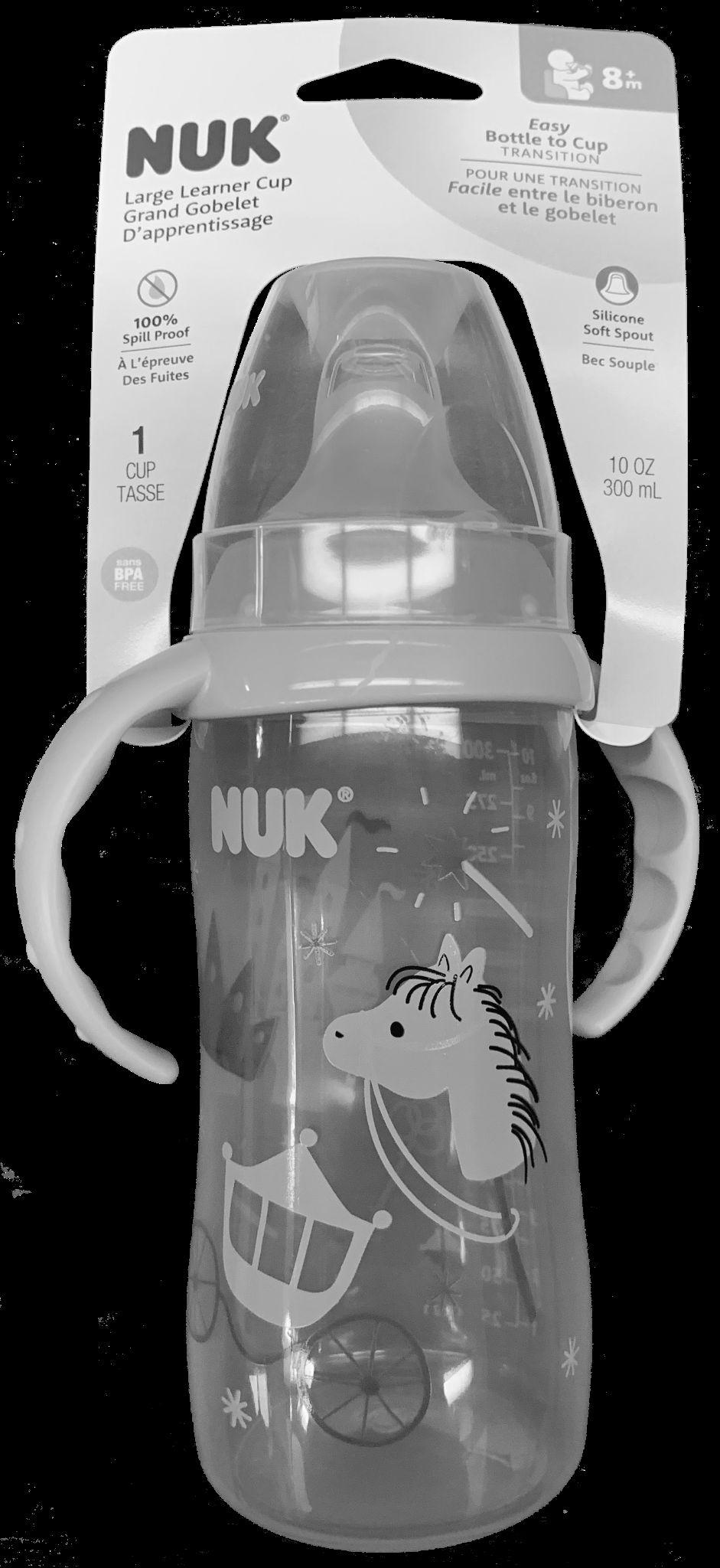
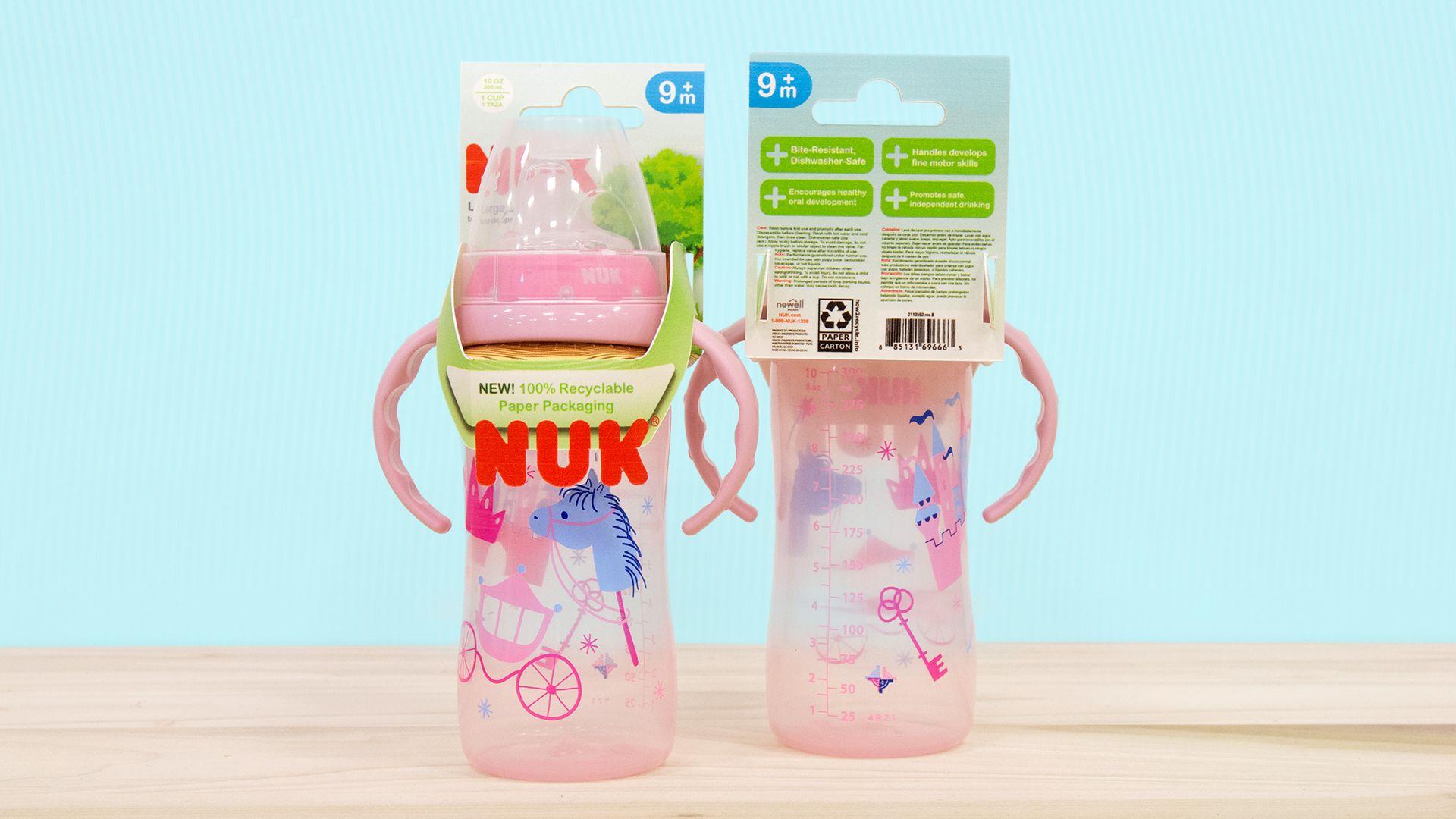

LARGE LEARNER PACK OUT
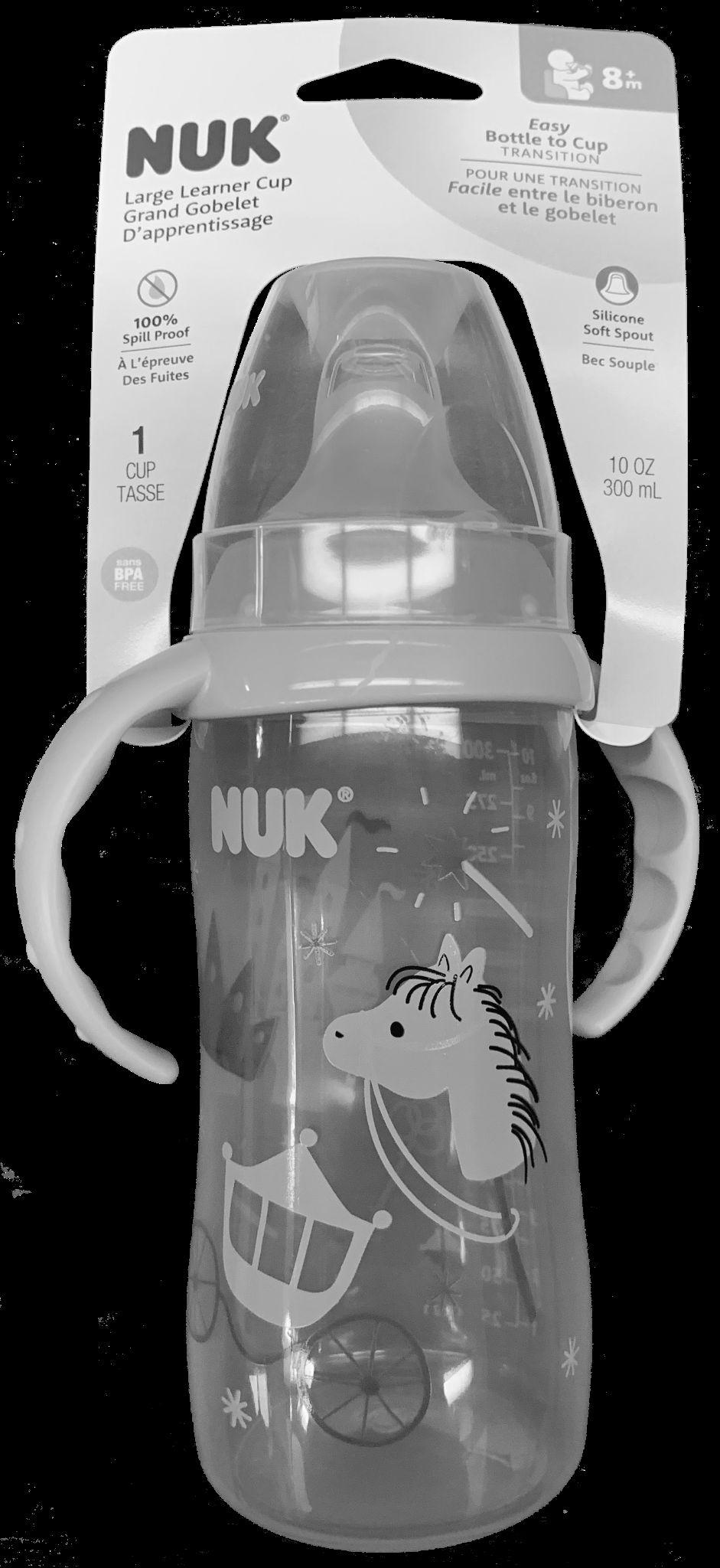
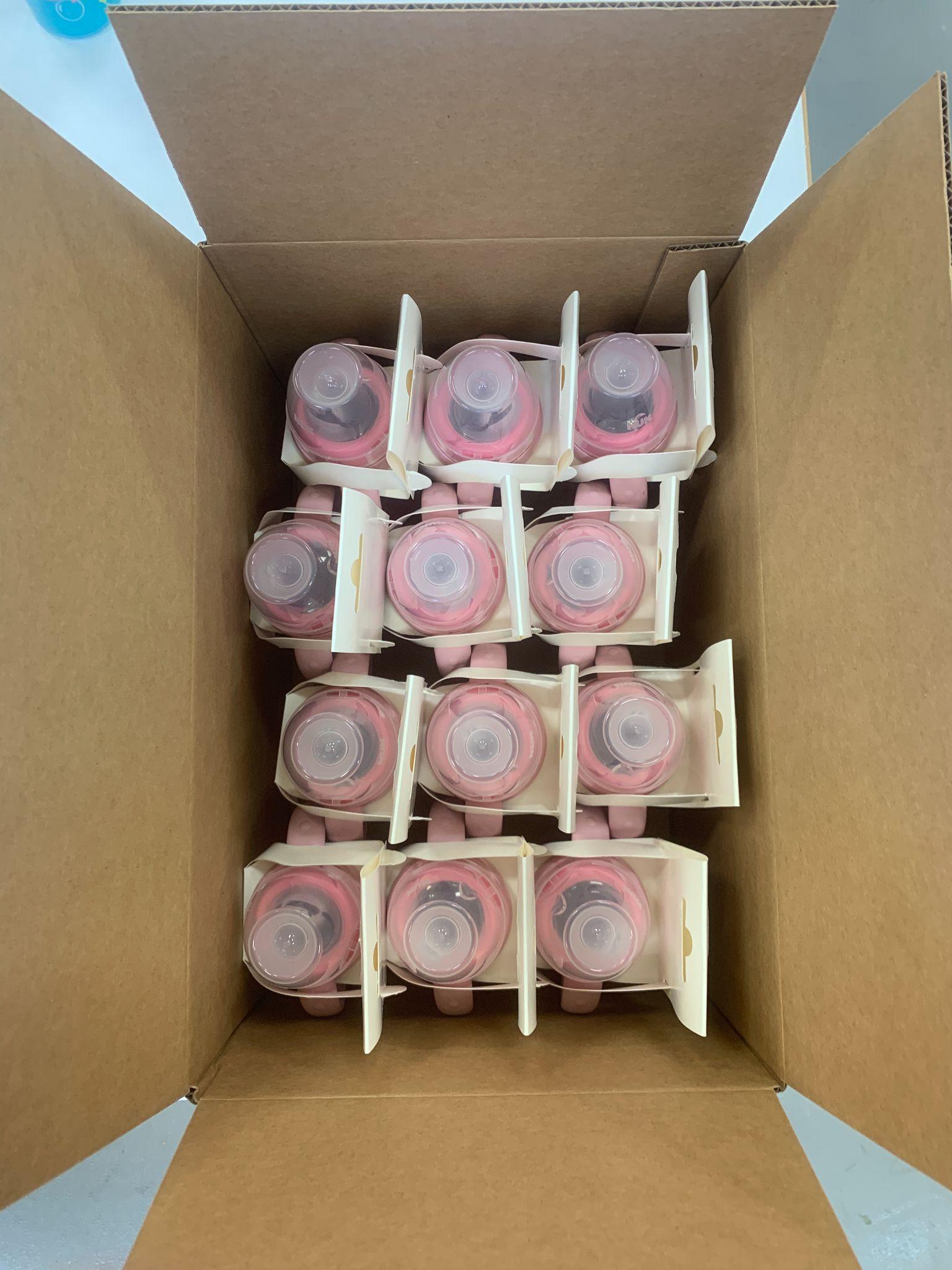
PRIMARY SHIPPER
1. Remove cutouts
2. Crease all folds
3. Attach placard to bottle mouth
4. Attach handle and screw on bottle top
5. Fold hang placard
6. Insert arm tabs into hang placard holes
7. Adjust for straightness
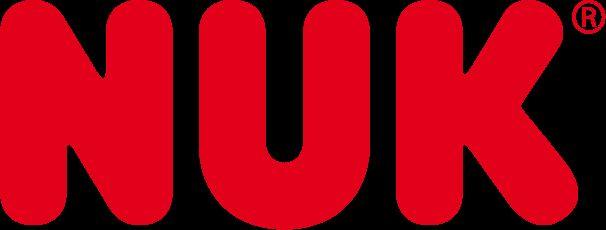
1. Crease all folds
2. Apply glue to glue tab
3. Square shipper sides
4. Close bottom flap and tape in I-pattern
5. Add primary packages with arms nestled
6. Close and tape top flap in H-pattern

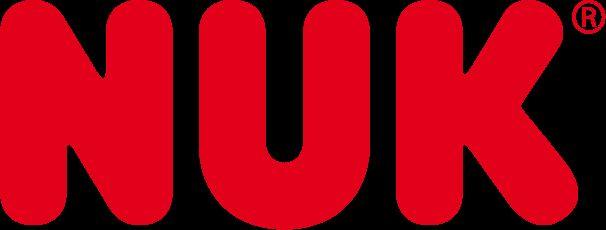
Top of the bottle is captured without sacrificing mouthpiece visibility
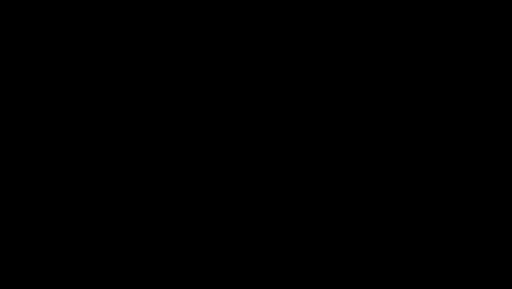
Bottle is able to sit on shelf and packaging takes minimal space
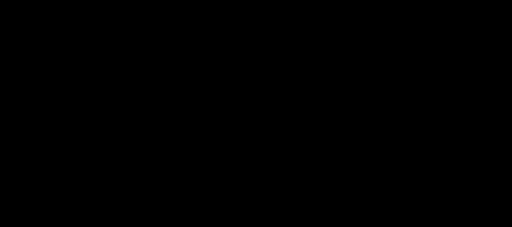
Packaging does not need to be glued, design features tabs
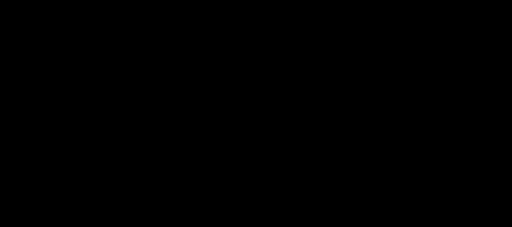
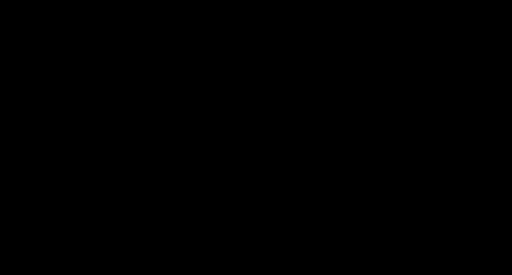
Similar iconography to pacifier and learner for better continuity and brand recognition

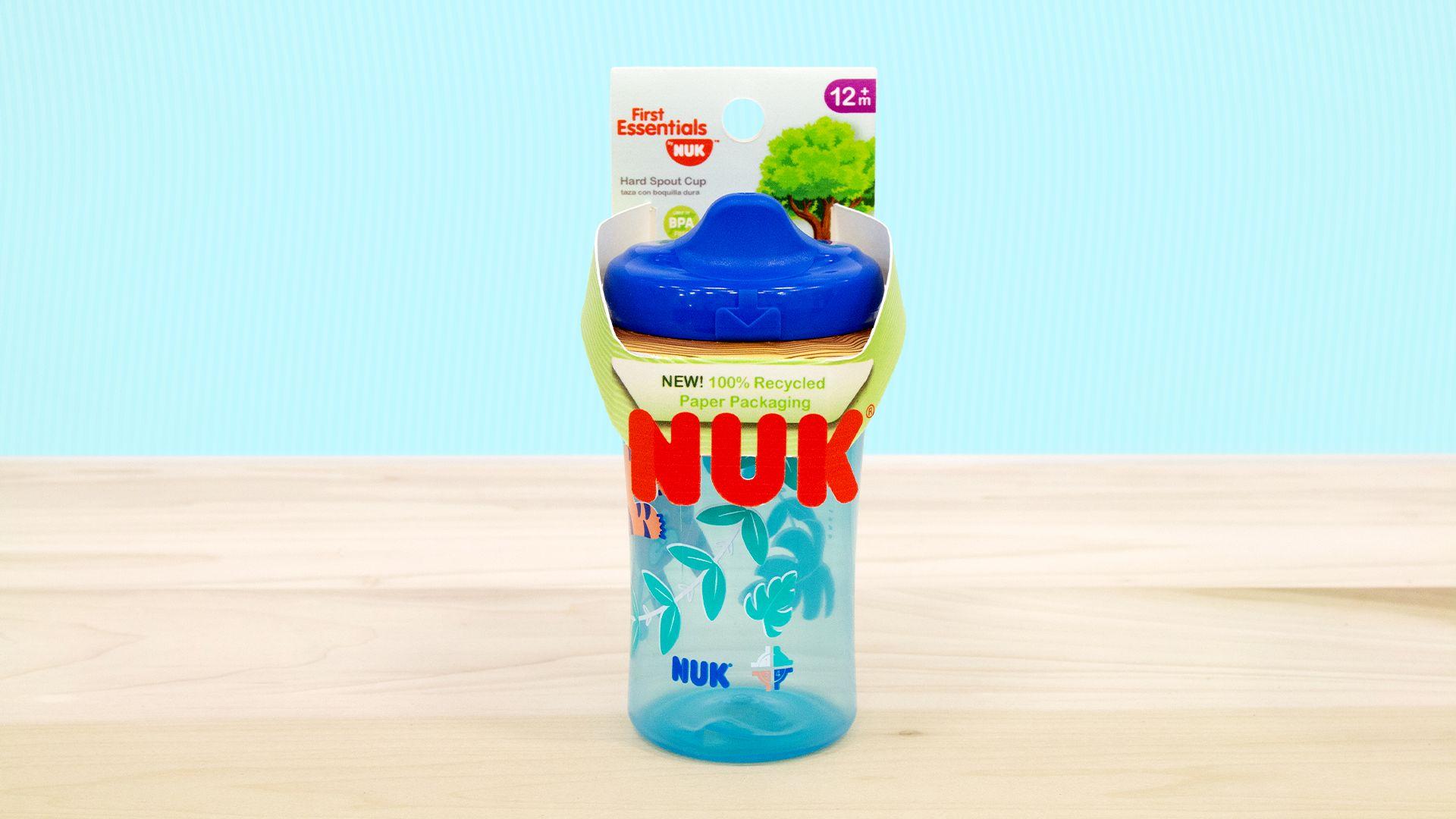

Can be hung on a peg
100% Paper
Can sit on a shelf
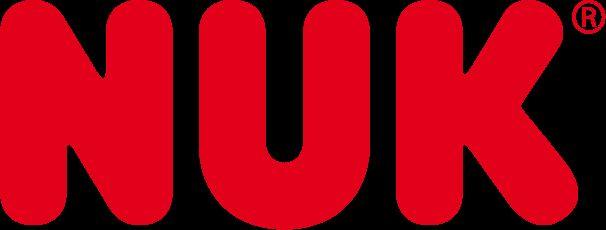



HARD SPOUT PACK OUT

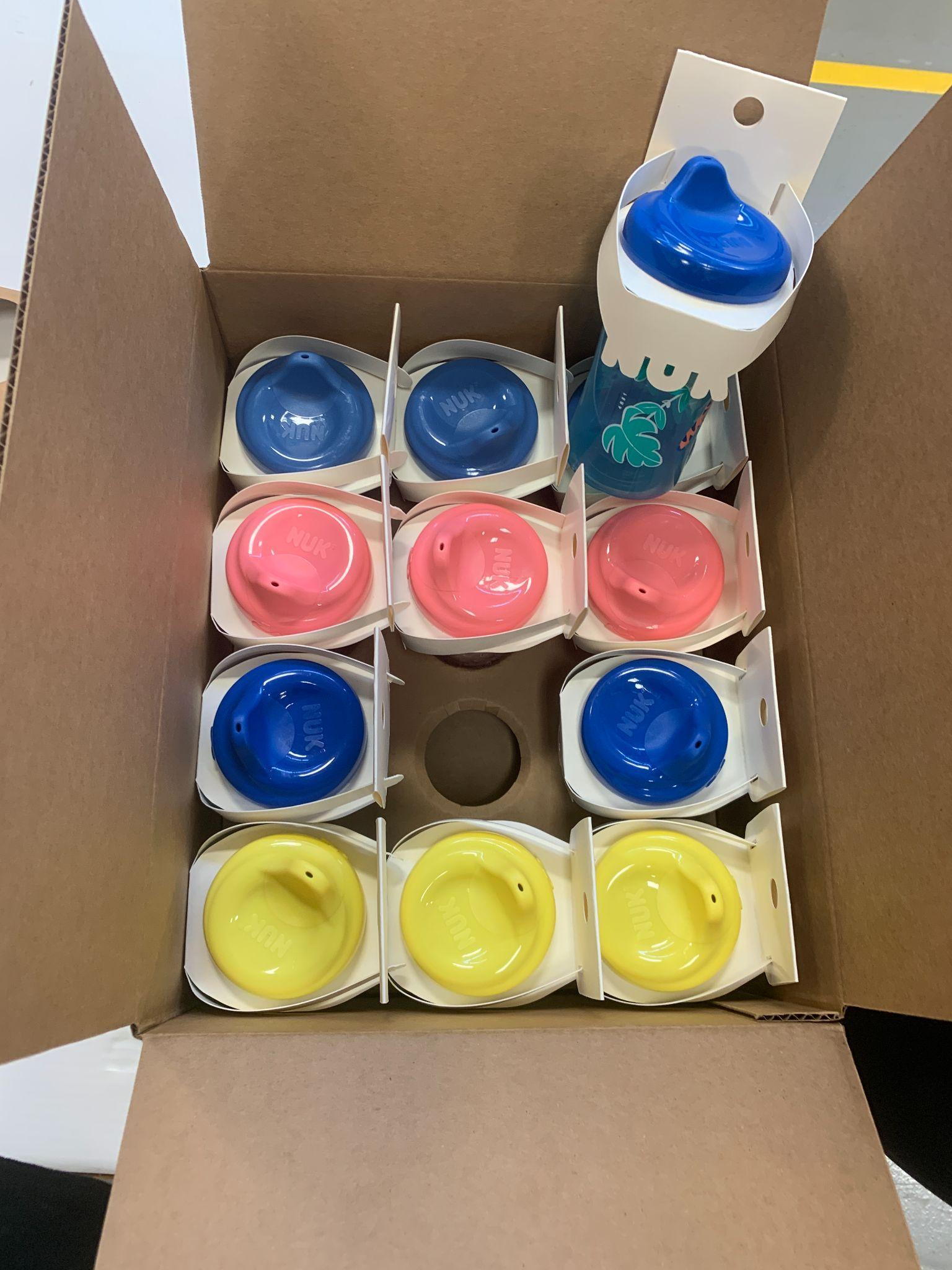
PRIMARY SHIPPER
1. Remove cutouts
2. Crease all folds
3. Attach placard to bottle mouth
4. Screw on bottle top
5. Fold hang placard
6. Insert arm tabs to hang placard holes
7. Adjust for straightness
1. Crease all folds on box and inner, set inner aside
2. Apply glue to glue tab
3. Pop shipper up
4. Close bottom flap and tape
5. Insert corrugated inner
6. Add primary packages to shipper in insert
7. Close and tape top flap
8. Tape shipper in H pattern
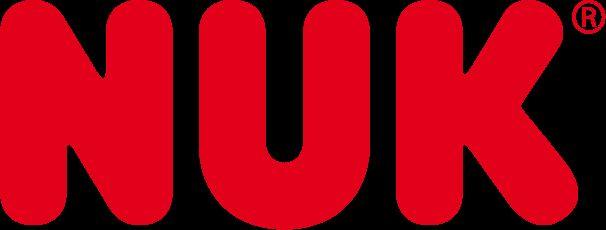

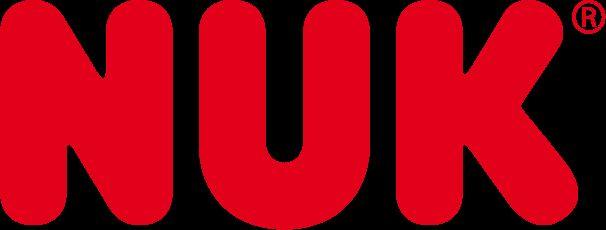
HARD SPOUT AND LARGE LEARNER TESTING
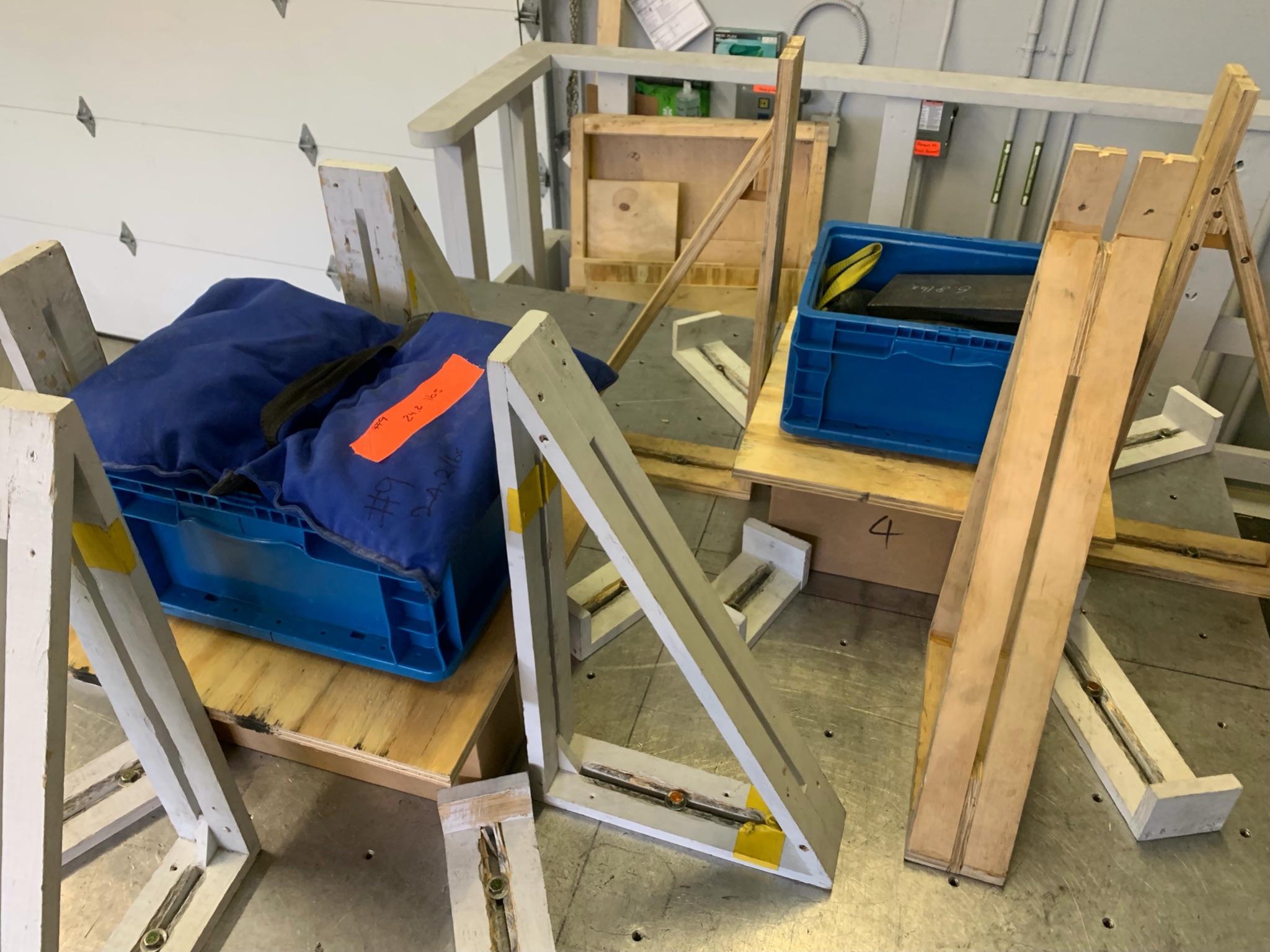
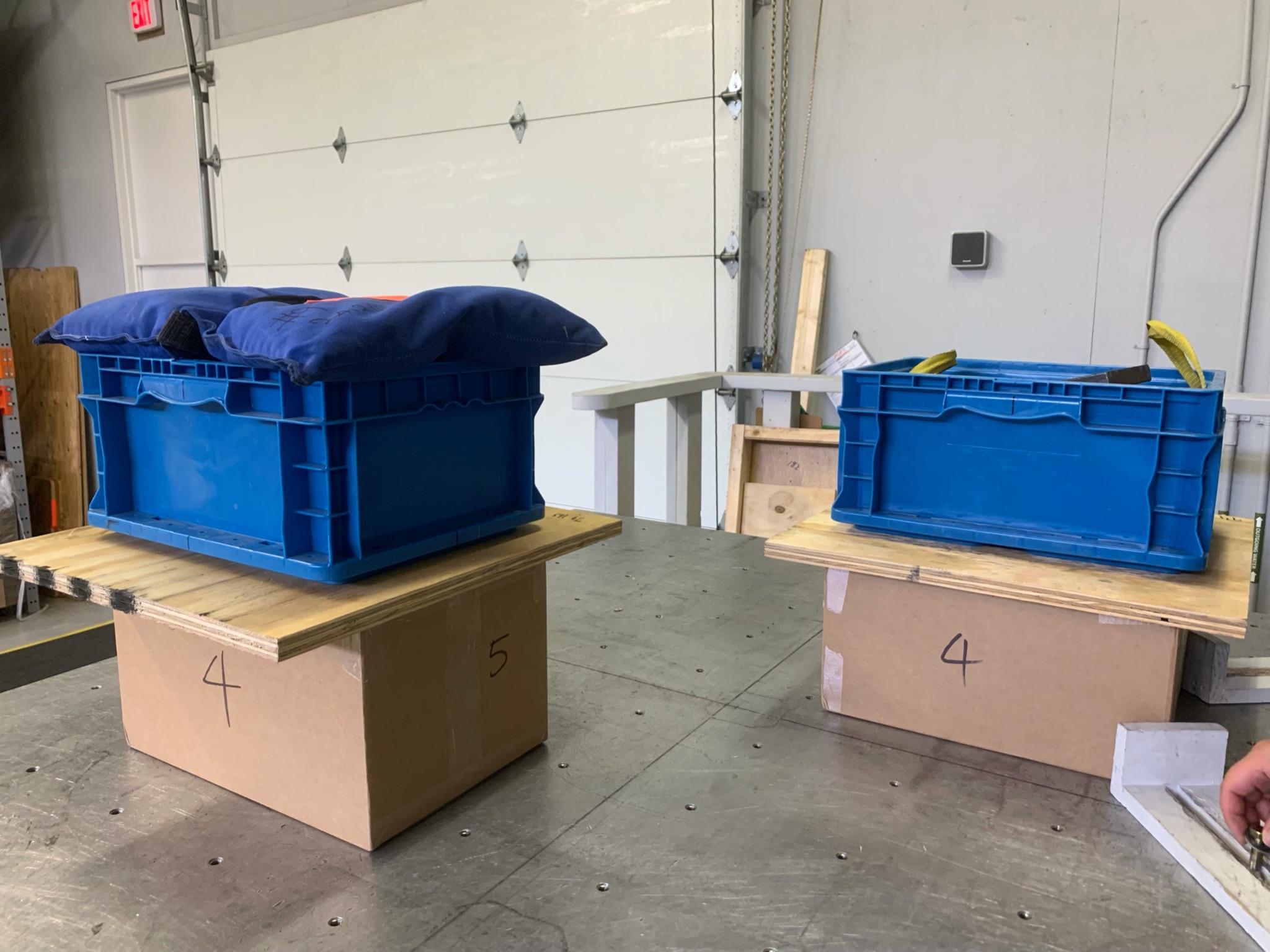
Both shippers tested to ISTA 3A Standard
Drop Sequence 1
● 8 drops at 18 inches
● 1 drops at 36 inches
Vibration testing
Top load calculated in accordance to outside dimension
● 1 hour on face 3
● 30 minutes (each) face 4 and 6
● 30 minutes face 3 - no topload
Drop Sequence 2
● 7 drops at 18 inches
● 1 drops at 36 inches
● 1 drops at 18 inches with hazard block

RESULTS OF HARD SPOUT AND LEARNER BOTTLE TESTING
Because of damage criteria, we determined that the creasing and folding that occurred to the packaging was not deemed a failure and this did not require a second round of ISTA 3a testing. Only damage that occurred was to packaging and not product
Bottle closure screwed on too tight
Teeth diameter is too small which causes pressure and friction
Minor warping/bending of the primary packaging
Packaging support on the sides of the bottle snaps
Solution:

Adjusting the dimensions of the teeth (diameter of circle)
Ensuring the cap is not screwed on too tight
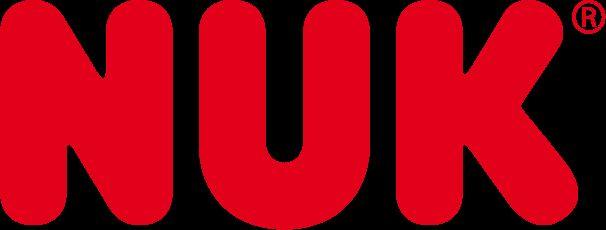

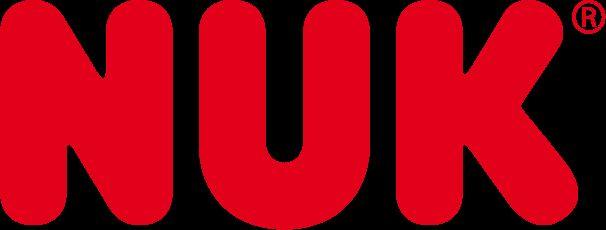
NECESSITY OF TRAYS IN HARD SPOUT SHIPPER

Hard spout 1st testing without tray E-Flute Corrugated Tray

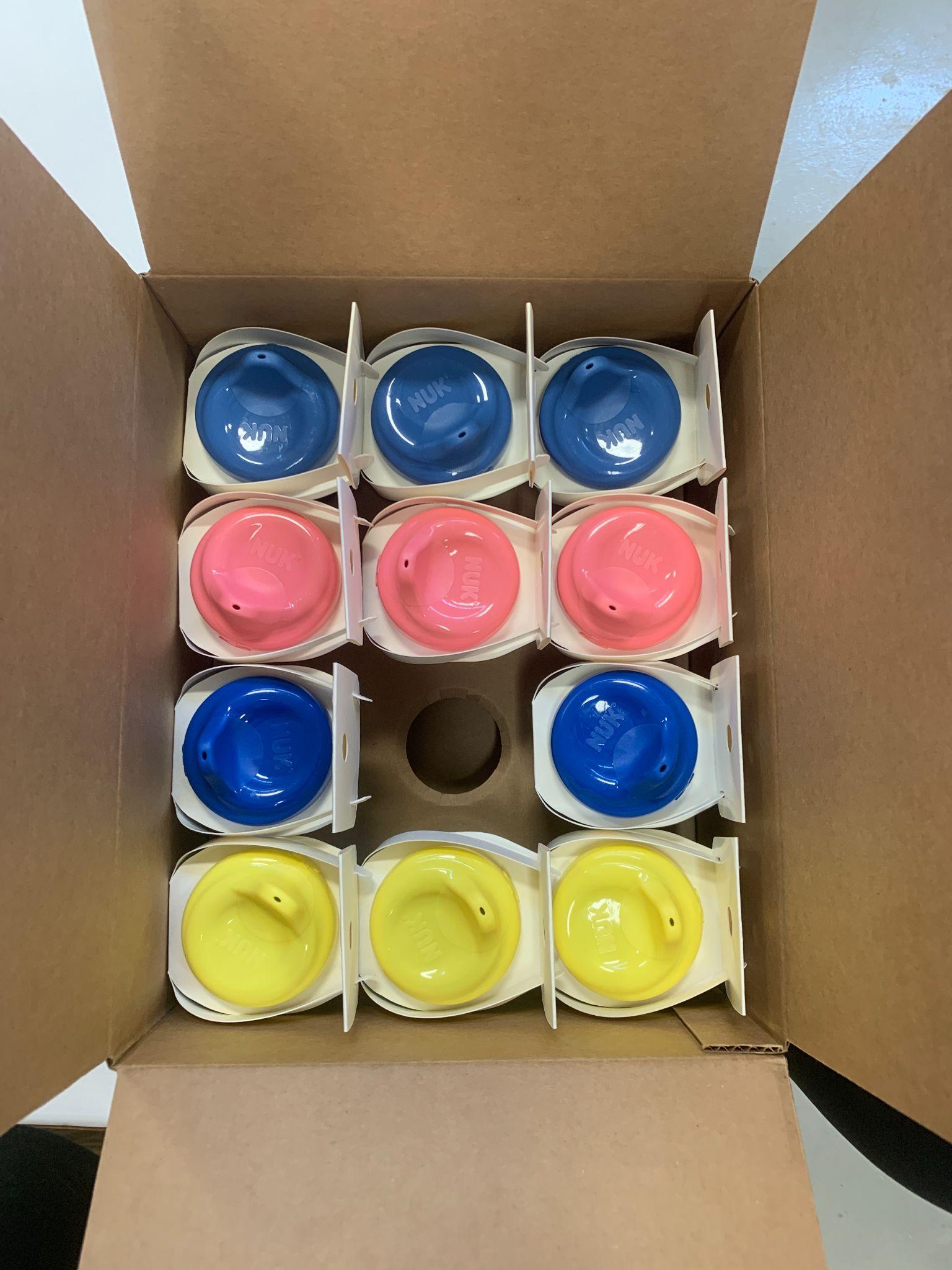

Because of hard spout bottle geometry, specifically when the bottle is captured from the top, the bottle can rotate and nestle under each other. This resulted in significant damage during testing. To pass testing, we have created an insert. This can be a point of optimization in the future.

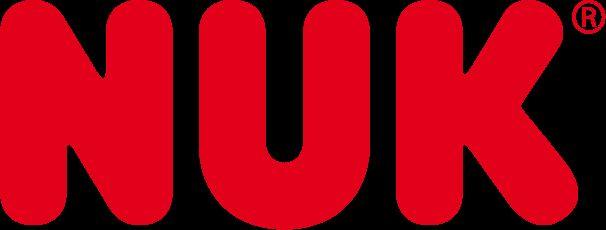
Newell Brands Sustainability Goals and Commitment:
Commitment to achieve carbon neutrality by 2040 for all Scope 1 and 2 emissions and 90 percent waste to landfill reduction by 2025
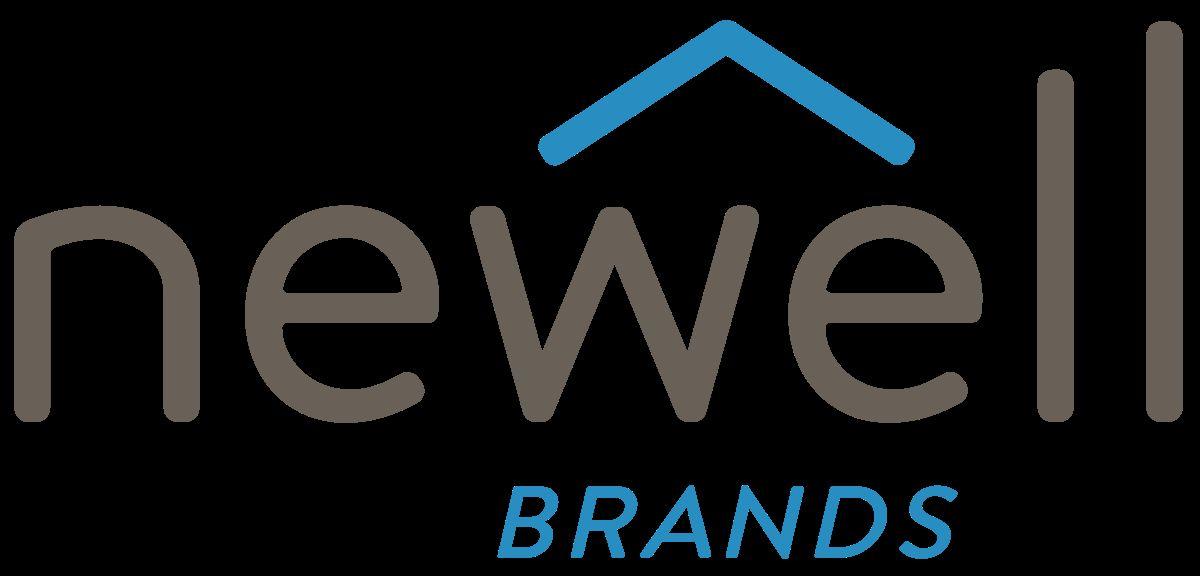

Upstream
SUSTAINABILITY
sustainability analysis from from all 3 perspectives of the life-cycle
Downstream Distribution & Use
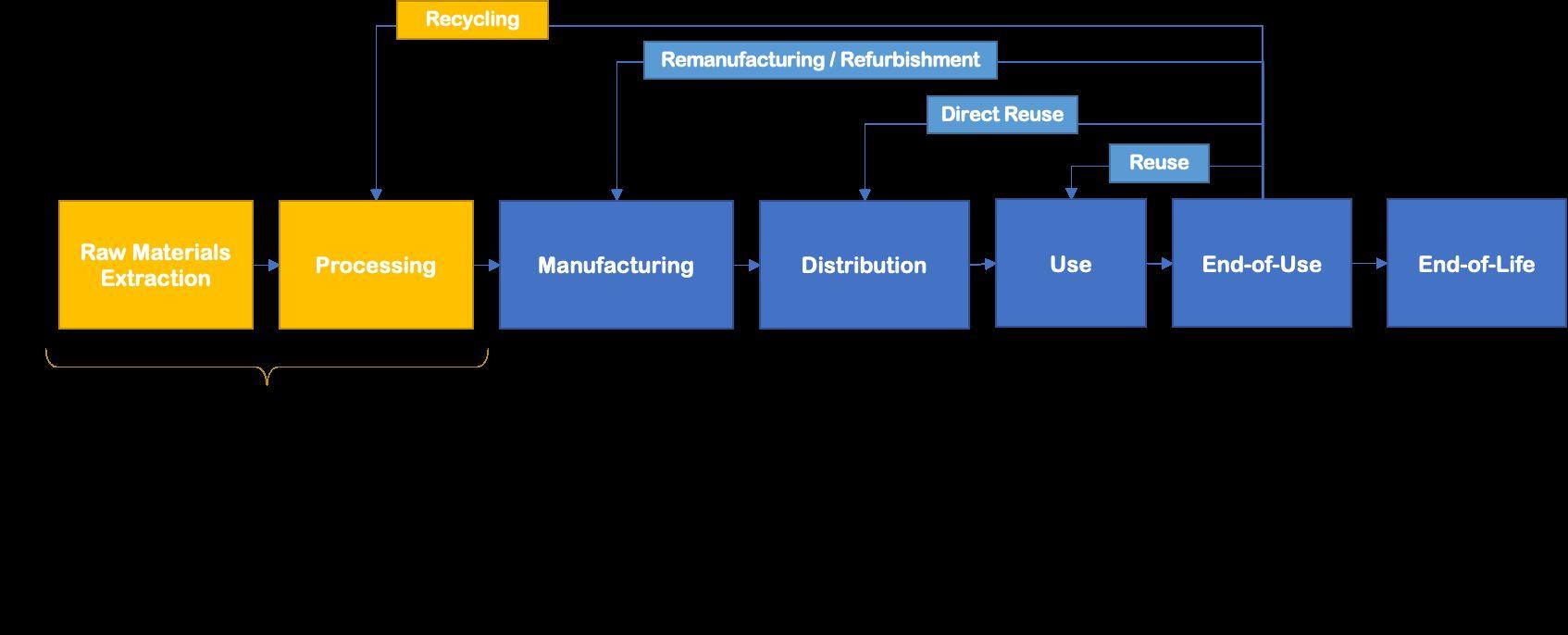
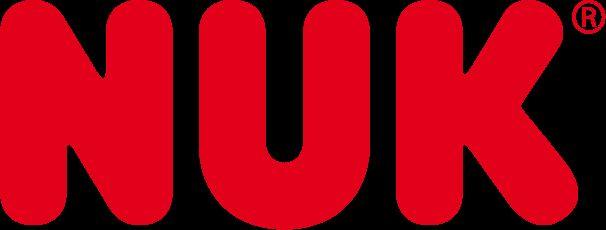

- Embodied Carbon
- Embodied Energy
- Material Requirement
- % Recycled vs Virgin Material Inputs

- Light-Weighting
- Transportation Emissions
- Recyclable vs Recycled
- Cost of Non-Recyclable

SUSTAINABILITY
upstream perspective: embodied carbon and embodied energy for each design (scope 2)
Embodied Carbon (kgCO2-eq./kg): the CO2 emissions from the sourcing and processing of a raw material
Embodied Carbon and Embodied Energy per kg by Material:
Carbon
Comments
MJ/kg Feedstock Energy (Included). High Density
(HDPE)
1.93 54.3 MJ/kg Feedstock Energy (Included). Doesn’t include the final fabrication.
Embodied Energy (kWh/kg or MJ/kg): the sum of all the energy needed in producing the material
Actual Embodied Carbon Emissions and Embodied Energy per Unit:
Excluding calorific value
of wood, excludes carbon sequestration/biogenic carbon storage.
Source:InventoryofCarbon&Energy(ICEModel),BathUniversity
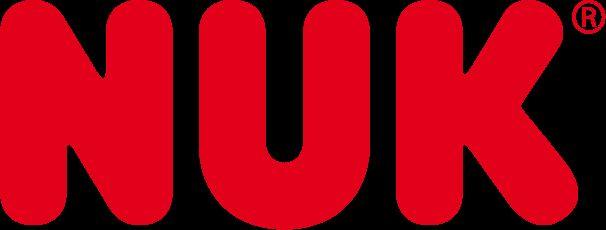
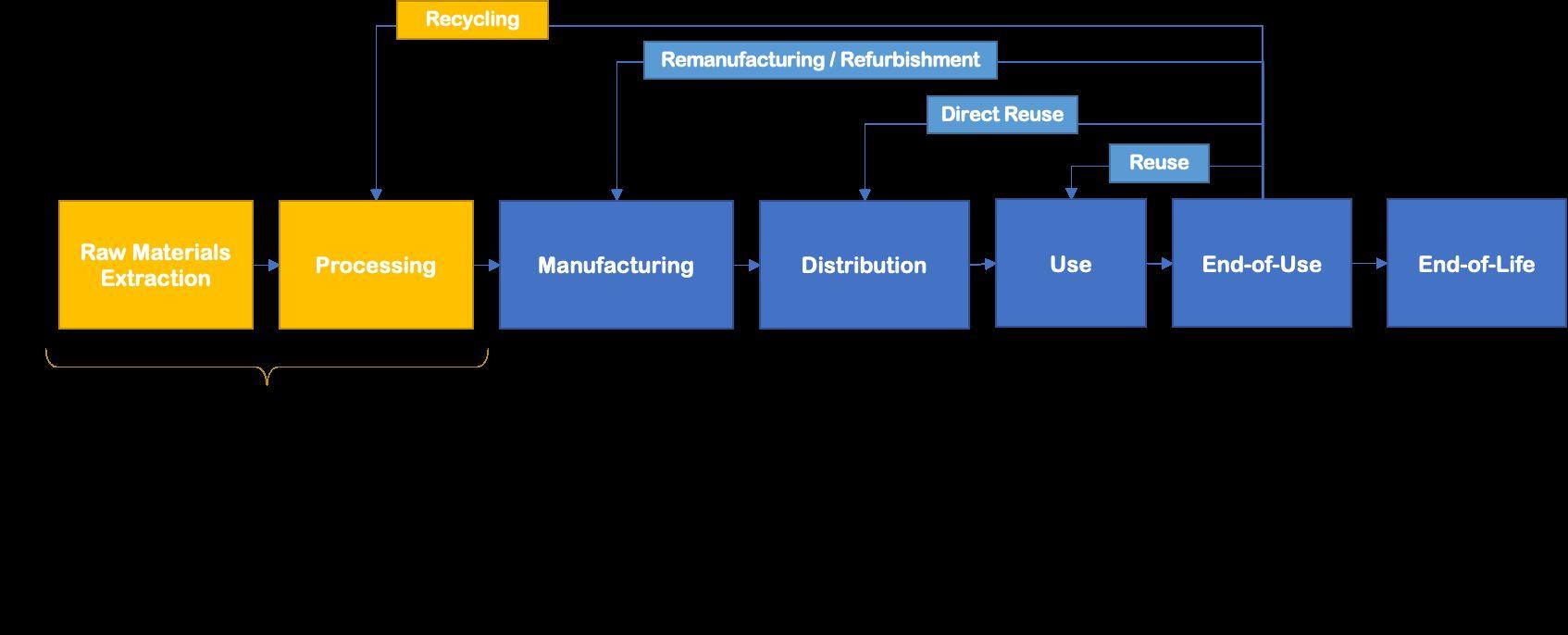

SUSTAINABILITY
distribution & use perspective: transportation carbon emissions for each design (scope 1)
Source:https://timeforchange.org/
Assumptions:
All NUK products are made in the USA
- Assume modern truck transportation and maximum emissions, 0.150 kgCO 2-eq.
According to U.S. Dept. of Transportation, 2020: 30% of truck freight trips are <100 miles
- Use max of 100 miles, or 161 km, for transportation distance
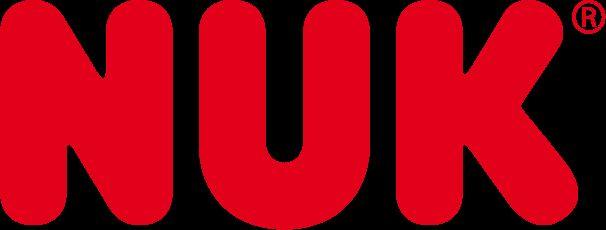


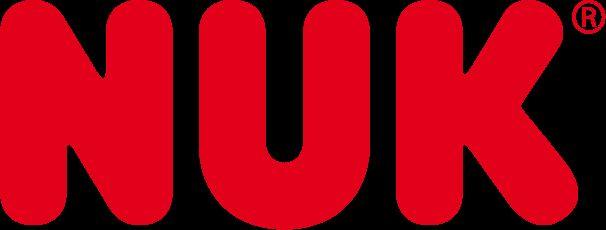
SUSTAINABILITY
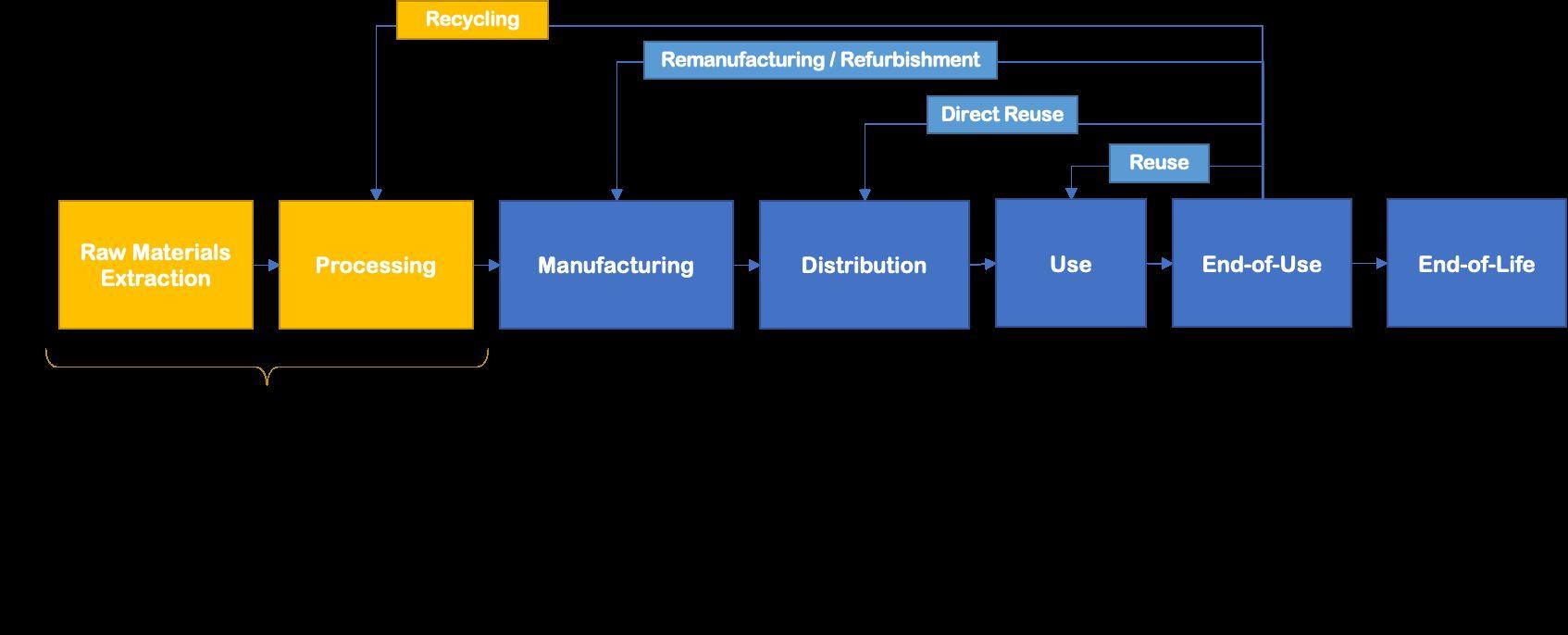



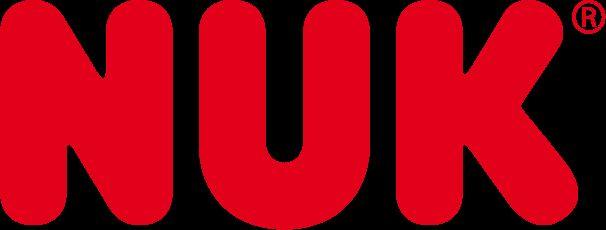
PROJECT GOALS
achieved the must haves for all three products
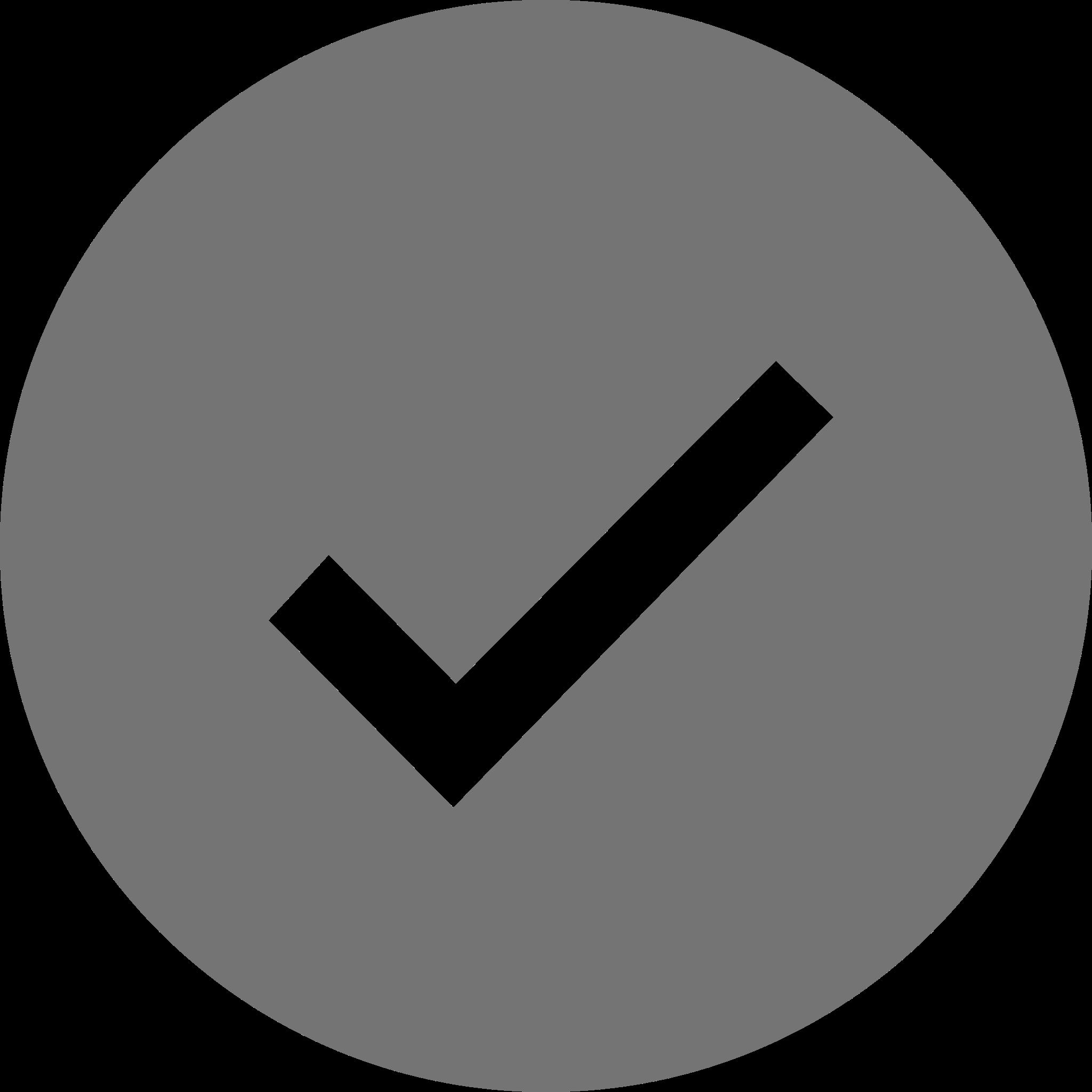

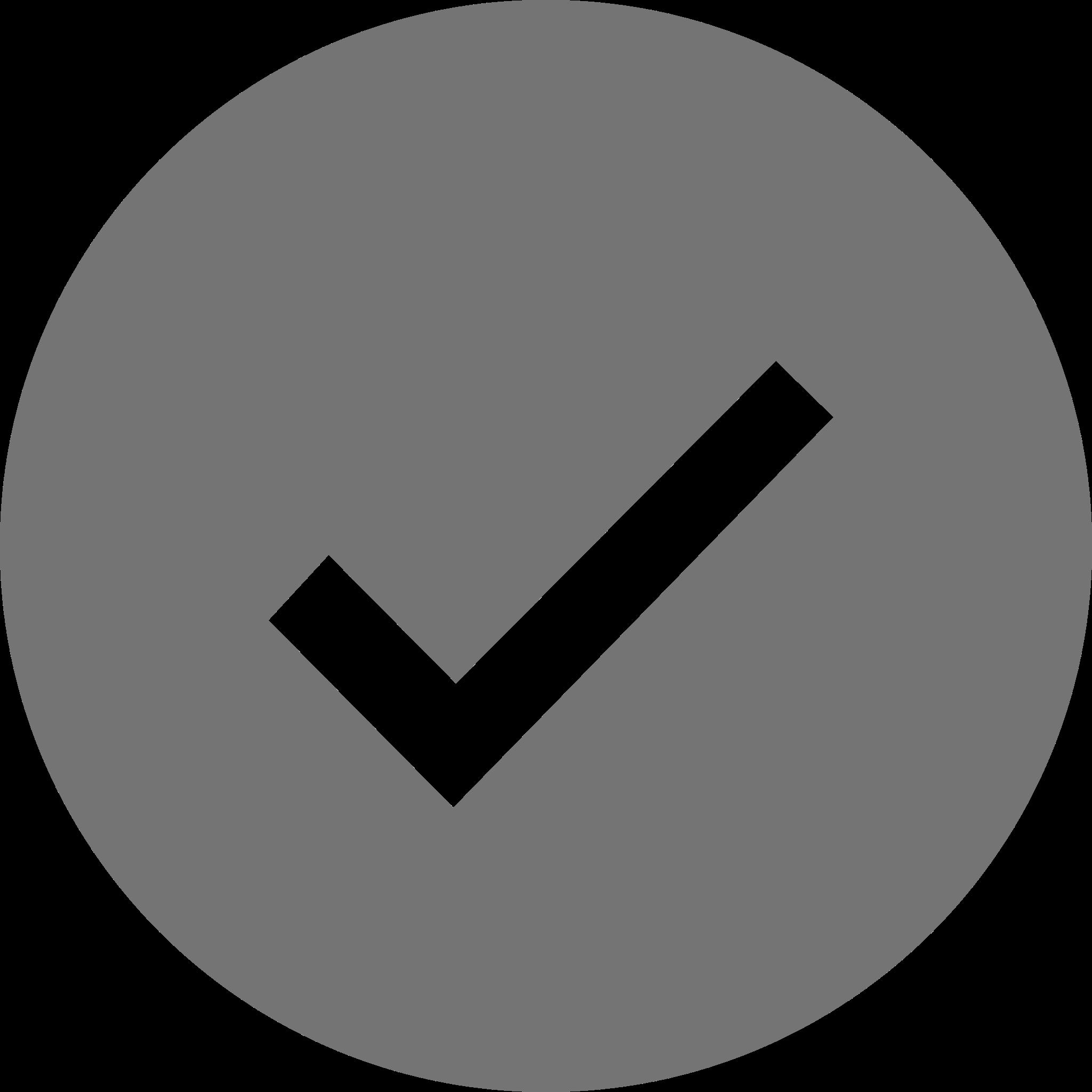
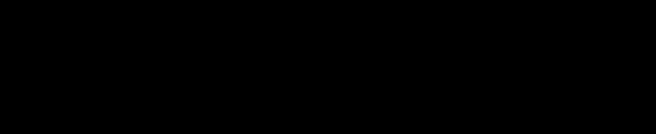

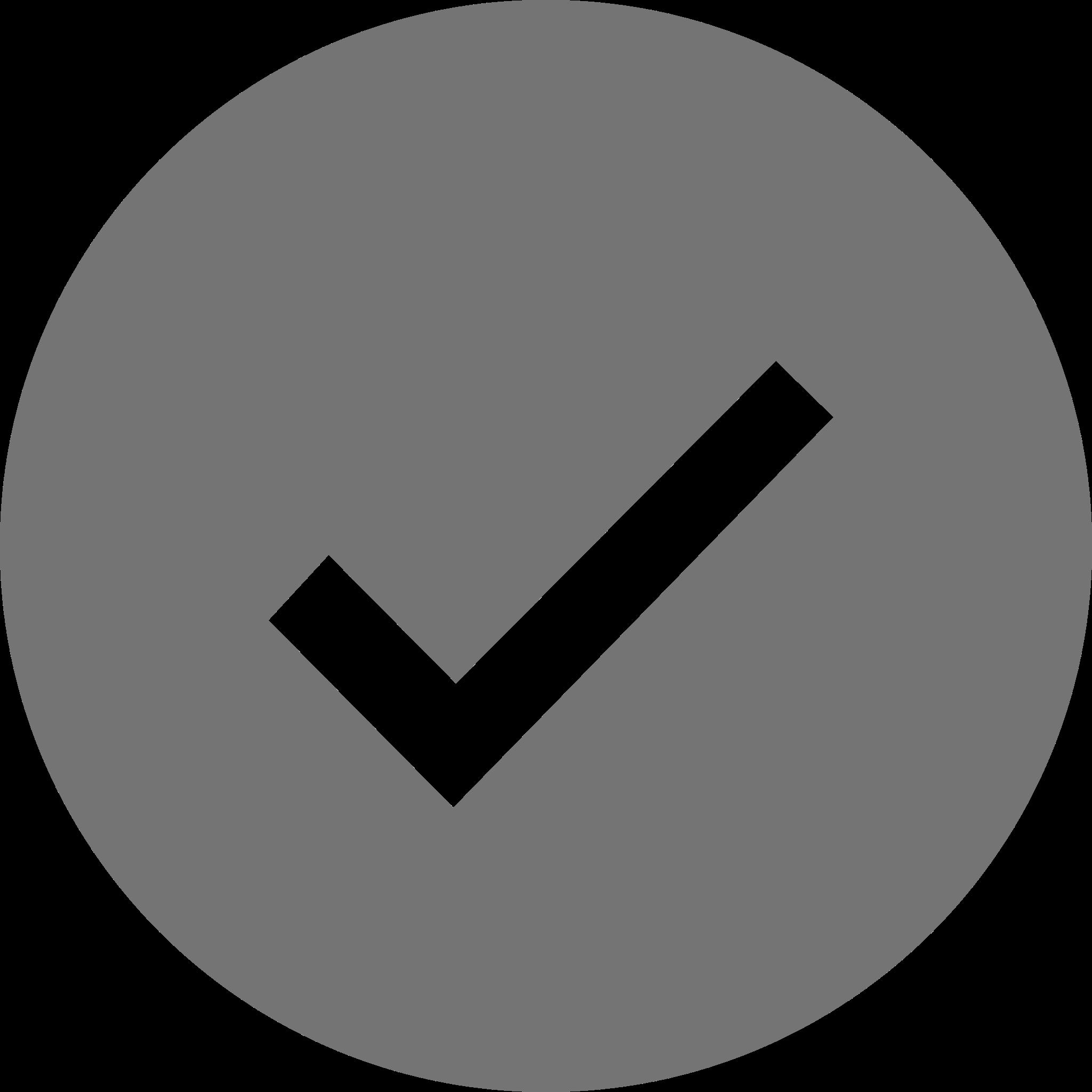
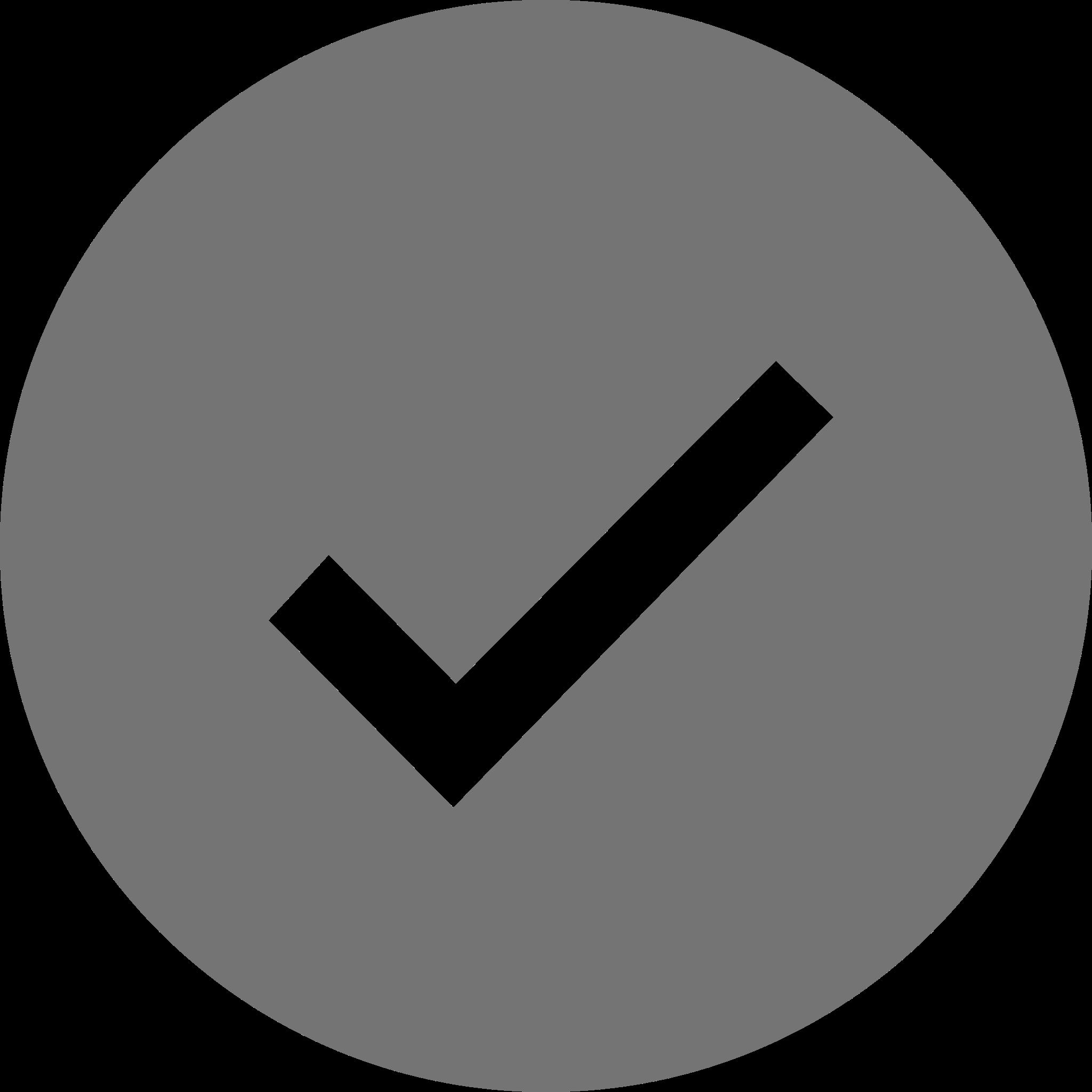
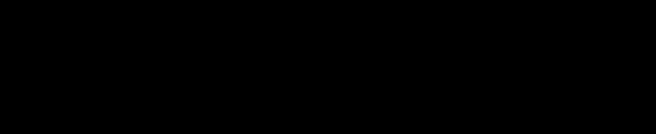

Plastic free, sustainable Exposed and visible product Able to be merchandised
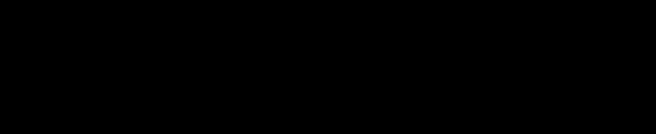

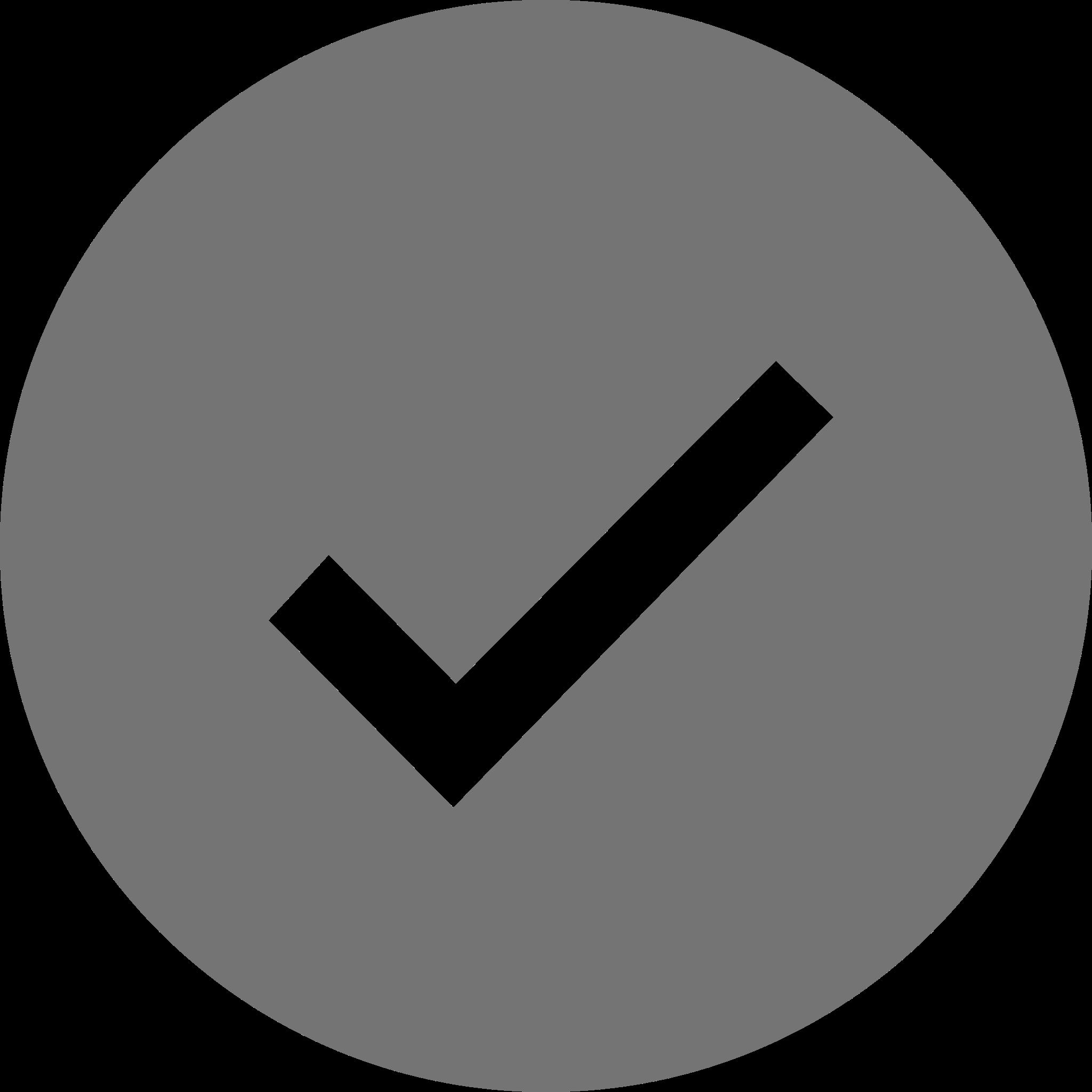
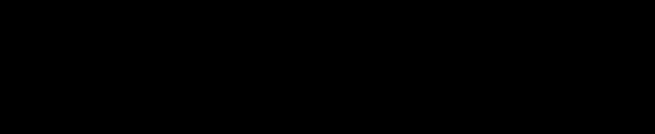

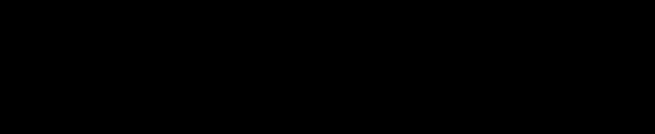
instructions given


FUTURE RECOMMENDATIONS
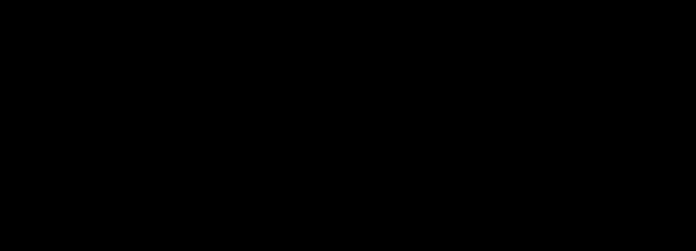
Remove inner packaging - to eliminate all plastics and unnecessary corrugated weight

Add paper stickers for tamper evidence
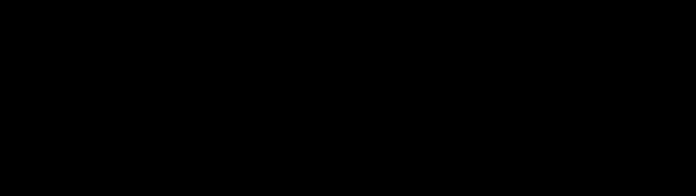
Experiment with glue tabs to aid automation in pack out.
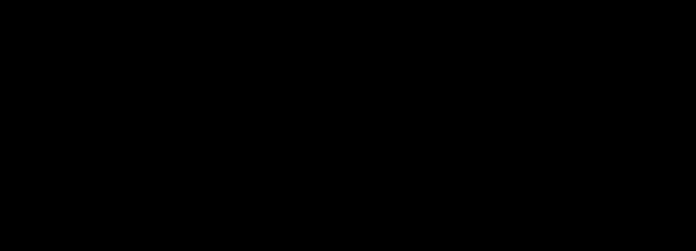
Sacrifice pacifier visibility to reduce overall carbon emissions and material cost
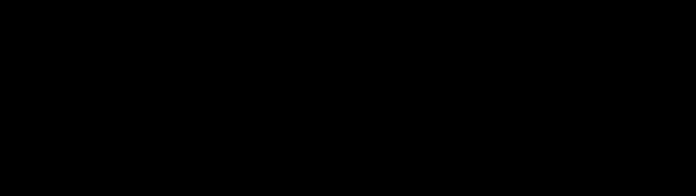
Use recycled material to further reduce environmental impact
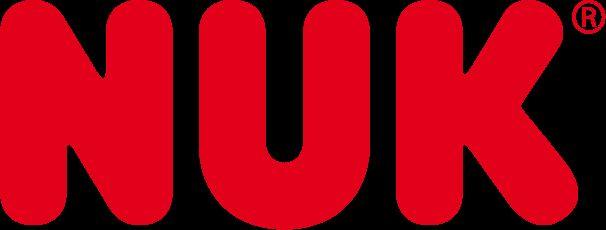


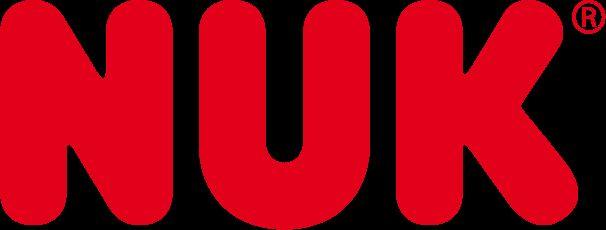
QUESTIONS?

