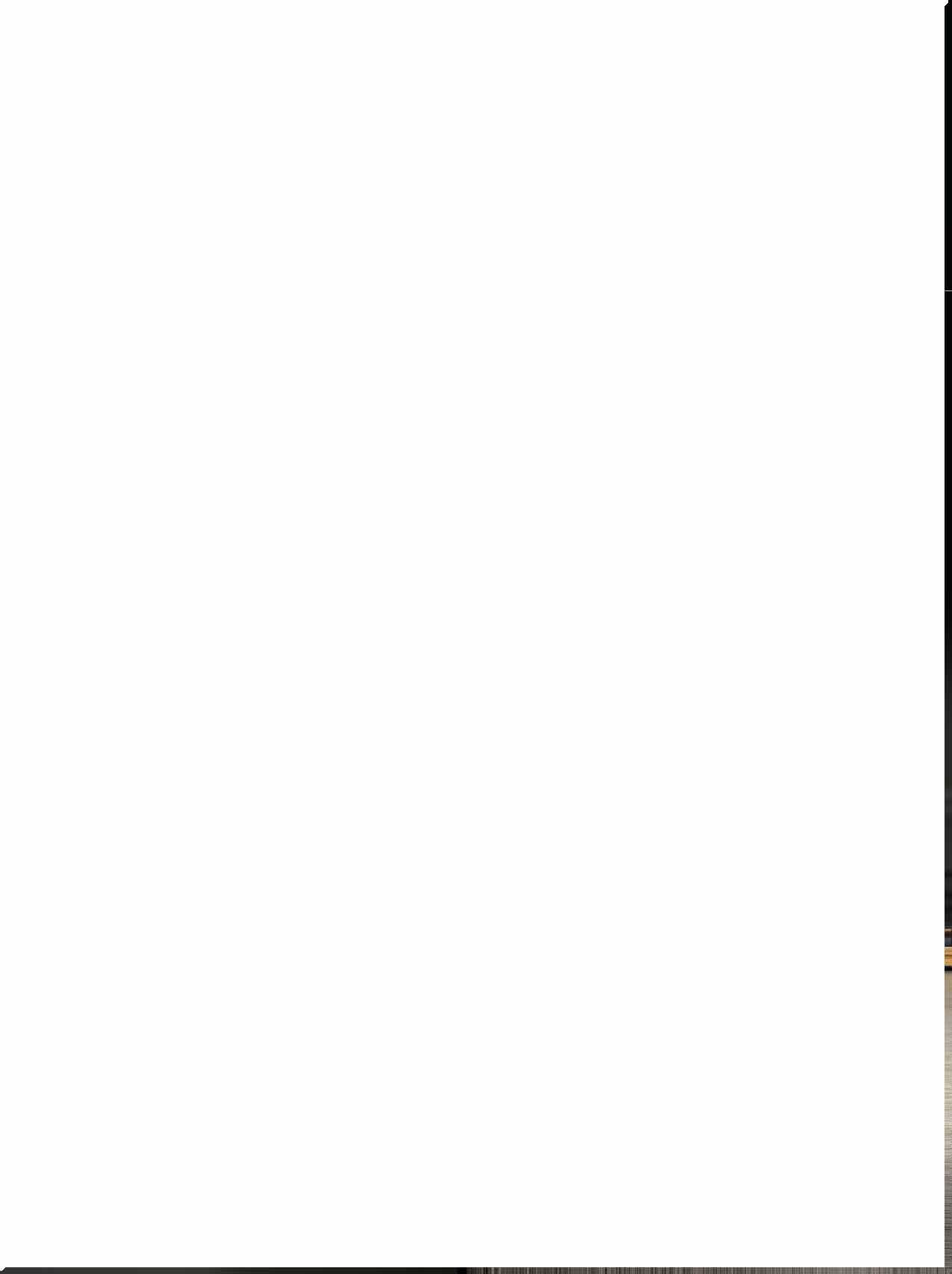
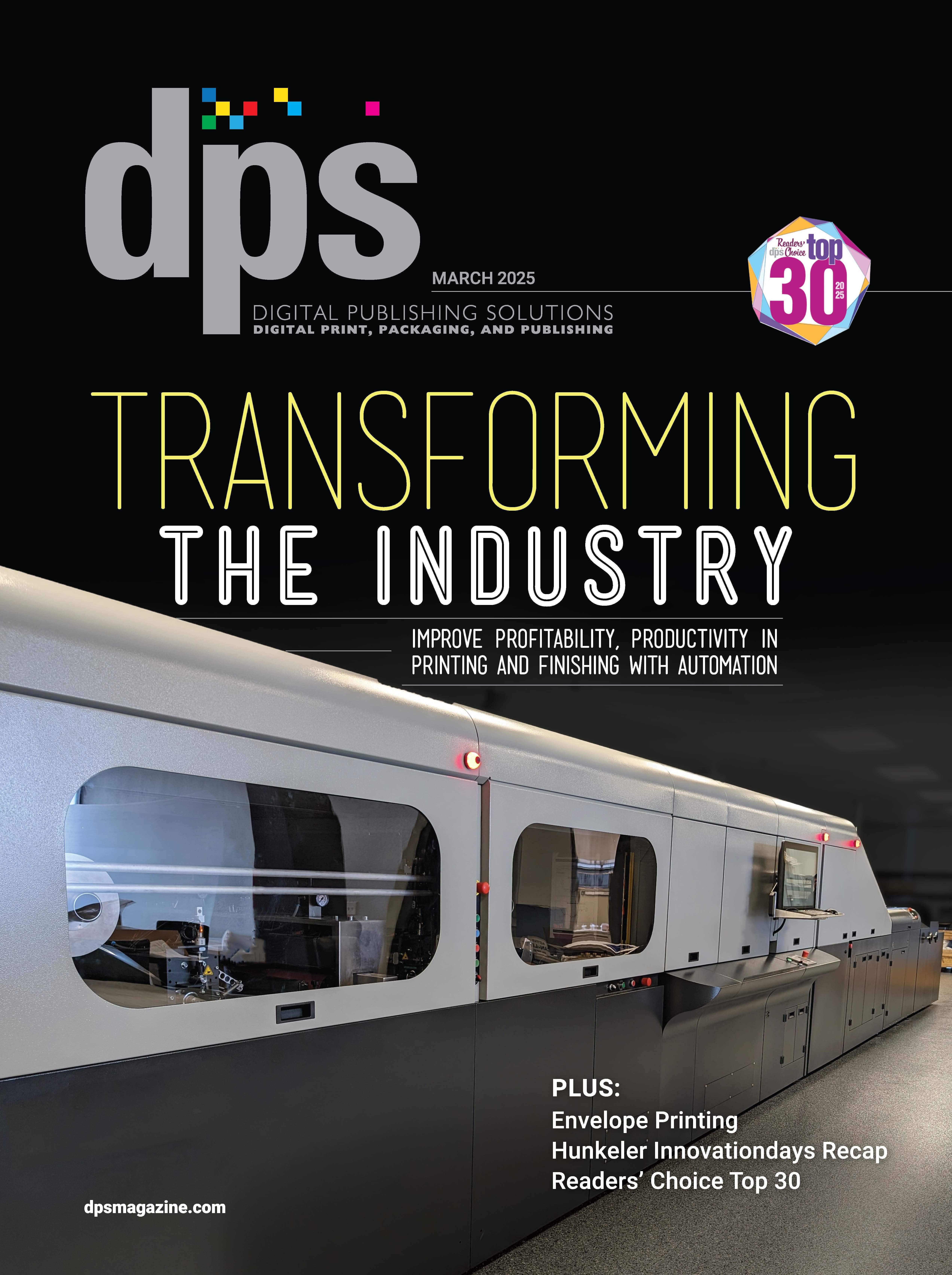
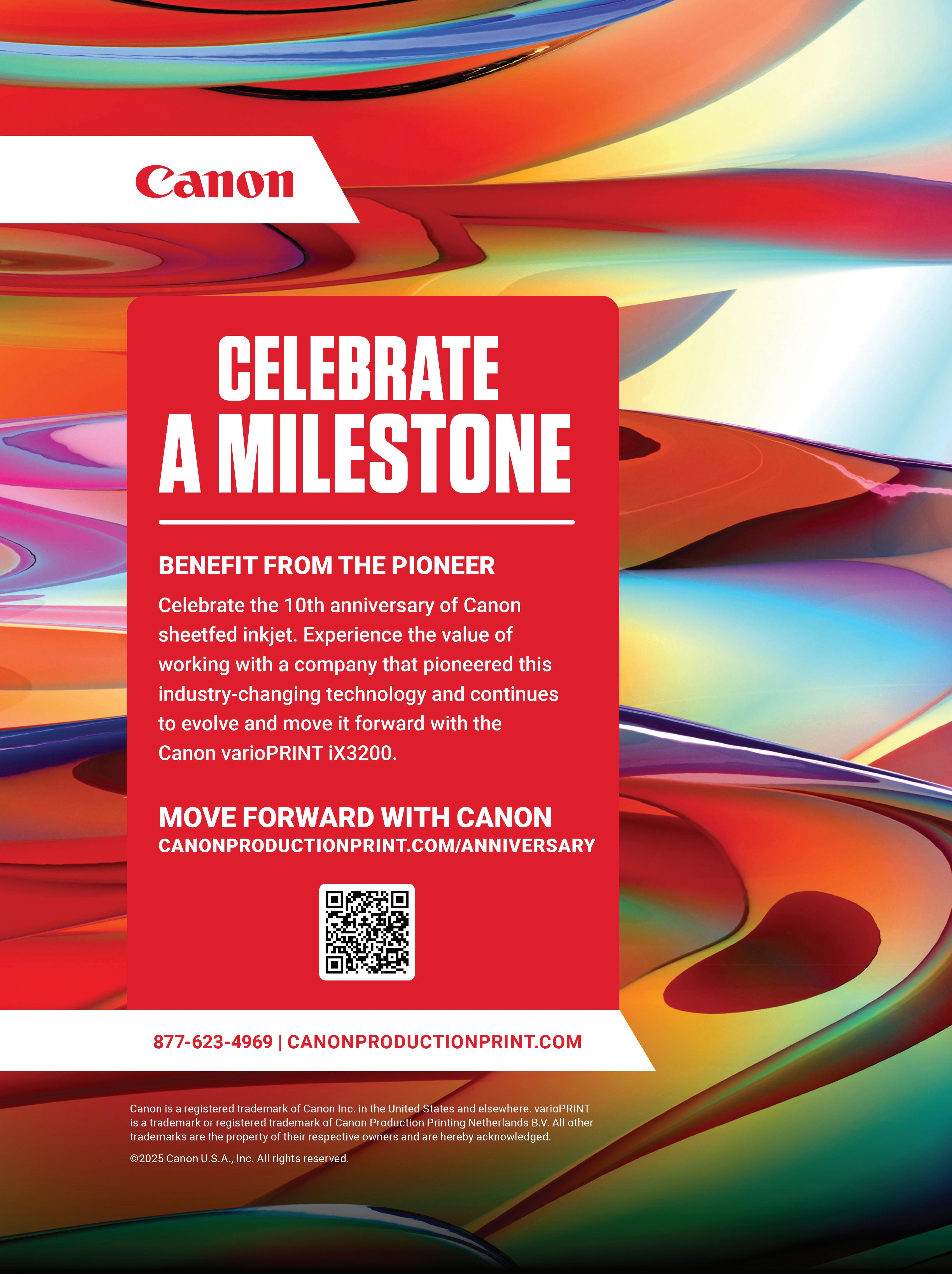

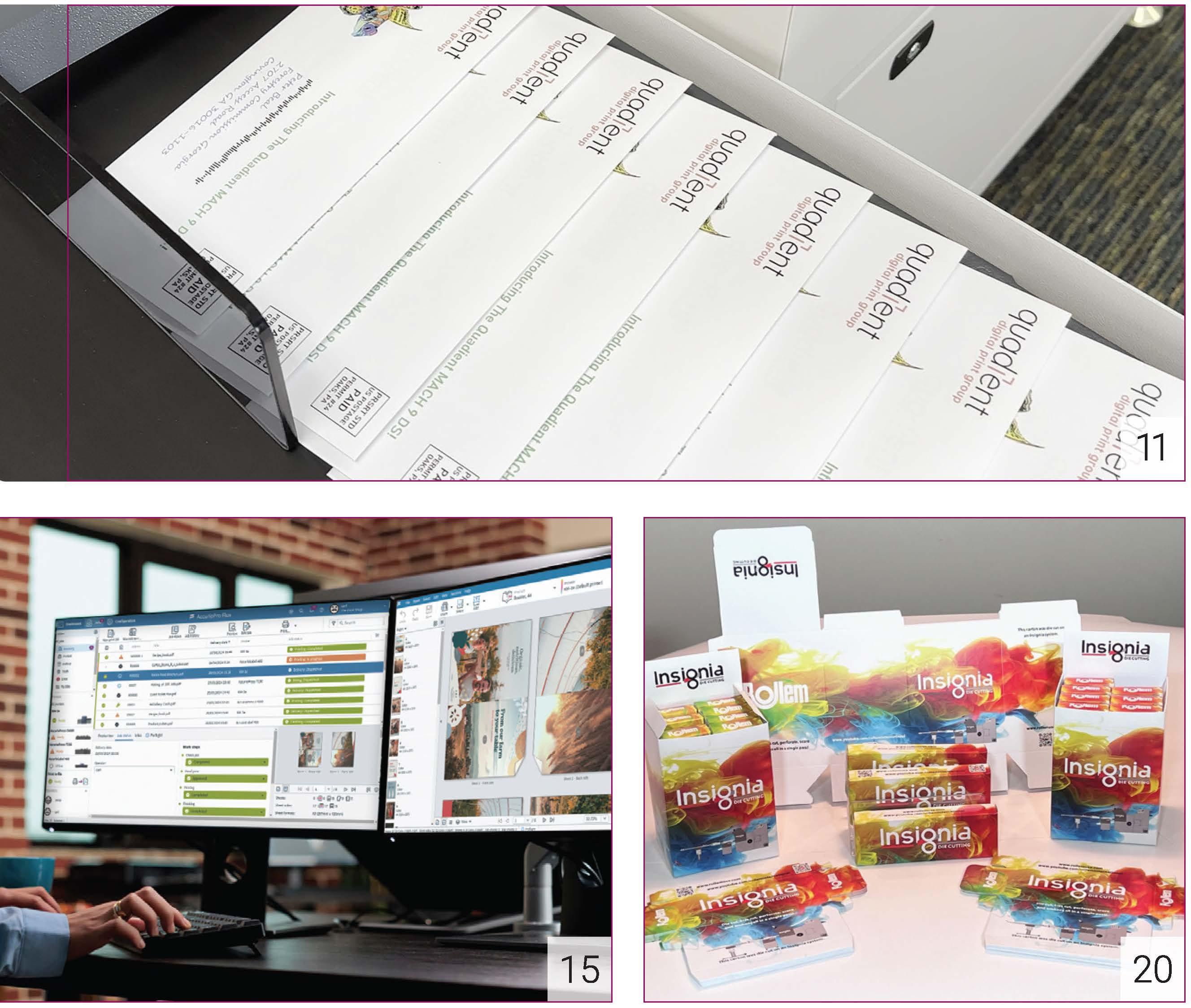


The print industry has evolved over time, utilizing new technologies to better support shifts in customer behavior. Today, automation tools are driven by the adoption of and advancements in artificial intelligence (AI) from prepress to finishing.
This issue our feature article, Paving a Path to Automation, discusses the role of automation in production workflow, including print production and finishing. For more on the impact of modern technologies like automation and AI, visit us online at dpsmagazine.com for web-exclusive content as well as a webinar on the topic.
For more on the impact of modern technologies like automation and AI, visit us online at dpsmagazine.com for web-exclusive content as well as a webinar on the topic.
This issue also marks the annual Top 30 Readers’ Choice awards. Flip to page 20 to read more about the vendors our readers were most interested this past year. Online we highlight new and flagship products and services offered. Congratulations to this year’s winners and honorable mentions!
Continuing the conversation on digital print for the mail segment, we highlight advancements in envelope printing. The utilization of inkjet in this space encourages new applications.
Finally, we provide a recap of the recent Hunkeler Innovationdays, where industry leaders focused on showcasing connectivity between printing and finishing equipment as well as a preview of the upcoming National Postal Forum show.
dpsmagazine.com
Volume 27, Number 2 • ISSN: 1529-2320
EDITOR IN CHIEF
Thomas Tetreault
978-921-7850
EDITOR
Cassandra Balentine cbalentine@rockportpubs.com
ASSOCIATE EDITOR
Melissa Donovan mdonovan@rockportpubs.com
ART DIRECTOR
Sarah M. White swhite@rockportpubs.com
WEB EDITOR
Melissa Mueller
CONTRIBUTORS
Kemal Carr, Olivia Cahoon, Gina Ferrara, Mark Hanley
ADVERTISING SALES
PUBLISHER
Thomas Tetreault
300 Newburyport Turnpike, Ste. 11 Rowley, MA 01969
Ph 978-921-7850 x110 • Fx 978-921-7870 edit@rockportpubs.com
SALES
Amanda Doyon Ph 978-921-7850 x170 • Fx 978-921-7870 adoyon@rockportpubs.com
Subscribe online at dpsmagazine.com
CORPORATE & PUBLISHING OFFICE 300 Newburyport Turnpike, Ste. 11 Rowley, MA 01969
ROCKPORT CUSTOM PUBLISHING, LLC
Cheers, Cassandra Balentine, editor cbalentine@rockportpubs.com
CHAIRMAN
Jeffrey Jensen
PRESIDENT & CEO
Thomas Tetreault
CONTROLLER
Missy Tyler
By DPS Magazine Staff
The 15th Hunkeler Innovationdays (HID) emphasized the central role of networking with the motto “CONNECT.” The event, which was hosted in Lucerne, Switzerland from February 24 to 27, 2025, attracted 6,800 participants and 120 exhibitors presenting 40 live solutions. The international print industry event is focused on high-performance digital printing and finishing.
“We are proud that, together with our partners, we were able to present pioneering solutions during the four days of the trade fair that will shape the future of the digital printing industry,” emphasized Bruno Müller, CEO, Müller Martini, in a statement about the event.
Exhibitor Highlights
Here are a selection of innovations and systems showcased at HID.
Visitors saw the BlueCrest Evolution Inserter with Hunkeler Unwinder UW8.
BÖWE SYSTEC showcased the Fusion Speed Inserter with BOXIT and Hunkeler Unwinder UW8.
C.P. Bourg debuted the Bourg Booklet Maker 40/60+. The new machine introduces the ability to incorporate sheet converting and stacking on the same production line as the booklet maker.
Canon displayed the ProStream 2000 series, a compact version of its web-fed inkjet presses. The ProStream 2133 printed a variety of applications live, which were then finished nearline at the Müller Martini booth using its Connex automated workflow. The solution also features inline finishing equipment including the new Hunkeler Web Extender WE8 for optimal print quality and Weko’s new remoistening unit.
Diversified Nano Solutions Corporation (DNSC) highlighted its x-nano ink product line.
Enfocus featured the latest versions of its automation solutions for printers like Switch, PitStop, Phoenix, and Griffin.
Fujifilm exhibited its Jet Press 1160CF, a high-performance inkjet printing system designed for transactional printing and book publishing.
Gelato showcased GelatoConnect, its AI-powered software solution designed to help print producers unlock their full potential and shape the future of production.
The Hönle Business Unit Curing presented its LED-UV and UV curing systems as well as infrared/hot air dryers for digital printing.
Heidelberg demonstrated the Jetfire 50, the company’s latest sheet-fed inkjet printer designed for new, future-proof production methods in commercial printing. Paired with the Müller Martini Vareo Pro and InfiniTrim, this setup transforms a blank sheet into high-quality finished books with unmatched efficiency.
1., 2., & 3. The 15th HID event followed the motto— “Connect,” emphasizing the central role of networking in the print industry. The event was hosted in Lucerne, Switzerland from February 24 to 27, 2025. Image 1 courtesy of Hunkeler AG Paper Processing.
Horizon demonstrated the inline Horizon iCE STITCHLINER Mark V with Canon’s varioPRINT iX3200 B3 sheetfed inkjet press. This inline solution achieves one-pass booklet production with a high level of quality.
HP showcased an integrated book production solution alongside advancements in its HP Indigo and HP PageWide portfolios.
Hunkeler demonstrated the new GEN8 EVO roll to stack solution. At the Hunkeler booth, the Starbook Sheetfolder—which debuted at drupa 2024—ran in a nearline configuration with the newly launched Pallet Feeder. The Sheetfolder features innovations, including the multicut function and a perforation dust extraction system. With multicut, it can now process formats up to B2 and eight-up printed sheets, while the dust extraction system minimizes dirt buildup from the perforation wheel. Hunkeler also displayed the DocuTrim in its B2-plus version, featuring a singlesheet cutter. Set up in a nearline configuration with a Pile Feeder; the Gen8 Direct Mail solution, which consisted of the Hunkeler modules Unwinder UW8,
Dynamic Processor DP8, Web Folder WF8, and Cutter CS8, connected to Horizon folding equipment AFV-566DF and PSX-56; and the Hunkeler Control Platform, a flexible and modular solution for end user production monitoring.
Ironsides Technology presented its open and agnostic tracking system that enables the company to collect machine and client production data across all production platforms.
IST showcased its latest advancements in Smart Curing Technology. Kern featured the K3200 Inserter with Hunkeler Unwinder UW8.
Kodak demonstrated the speed of the KODAK PROSPER 7000 Turbo Press web-fed inkjet press, which was on show in Europe for the first time, by printing excerpts from the movie, The Last Showgirl and two music videos, Kesha’s JOYRIDE and AntsLive’s CAPTAIN ANTS that were all shot on KODAK Film to simulate the effect of a movie being projected.
KURZ presented the DM-MAXLINER 2D in live action.
MBO America exhibited its M9 Buckle Folder, a new dimension in folding technology designed to redefine efficiency and precision in the print finishing process.
Meccanotecnica featured the Universe Web for book sewing with Hunkeler Unwinder UW8 and Cutter CS8.
Müller Martini demonstrated three Smart Factory solutions. Visitors experienced how a finished softcover book was produced inline from both the white roll and the white sheet—from the digital web- or sheet-fed printing machine to the cutting robot with subsequent sorting
line, fully automated and without manual intervention. The Prinova Digital saddle stitcher produced eight different saddlestitched products in very short runs from the roll in a continuous process.
OneVision Software highlighted its modular automation solutions that seamlessly integrate production processes— from file preparation, printing, and finishing to postpress.
Quadient unveiled the DS-1200 G5iQ and highlighted its MACH 9DS full-color dynamic envelope printing solution for personalized envelopes.
Ricoh’s high-speed inkjet and sheetfed production portfolio, represented by RICOH Pro VC80000, Ricoh Pro VC40000, and RICOH Pro C9500 technologies, as well as an interactive presentation of the RICOH Pro Z75B2 inkjet press, demonstrated how everyday capabilities can be elevated to create a highly productive concept to completion environment.
RISO displayed its inkjet technology with the SDD Press Trim Module.
Scodix introduced collaborations with premium uncoated substrates vendors, Winter & Company, Gmund, as well as Fedrigoni.
Screen highlighted the Truepress JET 560 HDX and the updated Screen TruePress Jet 520NX, which featured a new five-inch printhead module.
Solimar Systems, Inc. presented in key partner stands—RISO and Screen— where it demonstrated the benefits and use cases of its industrial PDF optimization solution, ReadyPDF Prepress Server.
Under its Winkler+Dünnebier (W+D) brand, BW Converting launched the BB816+ high-performance mail inserter.
XMPie showcased its advanced, datadriven and variable data print solution.
The next HID will be held from February 22 to 25, 2027 at the Lucerne exhibition centre in Switzerland. Find a more extensive recap at dpsmagazine.com. dps
By Joan Perez Pericot, VP and Global Head of HP Industrial Print Software & Solutions Business
Automation has been the buzz word of the last decade as organizations across every sector have looked to its transformative potential to accelerate gains in sales, productivity, quality, sustainability and much more. Today however, we’ve moved well beyond “potential” and you need look no further than the HP portfolio of highly automated presses, robotic solutions like MoviGo and HP PrintOS and Site Flow solutions to see that automation is here and now, driving real and transformative change for print service providers (PSPs) and brands alike.
2024 was yet another monumental year for HP PrintOS and Site Flow, with customers producing more than 650 million items in 2024 marking continued and consistent growth of the solution since its launch in 2016. This success lies in the solution’s ability to address the unique production challenges of the web to print industry leveraging the robust infrastructure and advanced capabilities of Site Flow. Customers are equipped to fulfil the influx of high and often unpredictable volumes of micro-orders based on a wide SKU portfolio that demand quick turnarounds as well as shipping direct to end users.
In fact, during the peak holiday season our Site Flow customers processed over 150 million items and over six million orders. This growth also owes its success to the thousands of brands and PSPs that are already integrated with Site Flow and submitting orders to HP customers, and we’re constantly connecting new brands while simplifying the connection with PSP’s through end-to-end production workflow automation.
We also continue to see strong growth in HP PrintOS as PSP’s look to overcome the challenges of a fundamental lack of data and optimize their production floors. Today PrintOS serves over 28,000 organizations with more than 44,000 connected devices worldwide, a testament to the power of the platform. And, when leveraged in tandem, Site Flow and PrintOS are providing a powerful and unrivalled holistic
automation solution for PSPs to scale and grow.
The success of Site Flow and HP PrintOS comes down to our mission to invest in the solutions that support our customers to navigate the ever-evolving industry challenges, and sustainably grow their offerings.
With escalating ecommerce expectations for customization and speed, PSPs are bogged down with the challenge of growing in to print on demand in an increasingly complex print landscape.
That’s why we created the HP Industrial Print Software Solutions Division, bringing the power of solutions like HP PrintOS and Site Flow, and innovation with AI, to address industry challenges and the fragmented print production ecosystem head on. Through continued investment in our innovation, expertise and network of partners we are equipping PSPs to become more productive, reduce their costs and ultimately better collaborate for sustainable business growth.
A great example of how we’re helping brands and platforms connect with our network of PSPs and streamline production flows is our collaboration with Canva that we announced last year. Canva has expanded access
to professionally printed products from HP PSPs around the world so that anyone creating visual content on its platform can seamlessly design and print with a fully integrated system. Leveraging HP PrintOS and Site Flow, Canva is also able to automate production and shipping processes for PSPs providing an end-to-end solution that streamlines print jobs for greater productivity, and with PrintOS features, the Canva Print Operations team can better identify, connect and manage a global SKU catalog across HP-enabled PSPs at scale.
The HP Industrial Print Software Solutions Division is taking an AI-forward approach to innovation, already encompassed in many of the advanced solutions available today across the entire print ecosystem. Read more at dpsmagazine.com. dps
By OPS Magazine Staff
Professionals of the mailing and shipping industry convene April 27 to 30, 2025 at the Gaylord Opryland Convention Center in Nashville, TN. The event is touted as a one-stop destination for attendees seeking to strengthen their services, find tools, technologies, and solutions to improve their mailing and shipping operations.
Withover100exhibitorsondisplay across 150,000 square feet, visitors are encouragedtodiscoverthelatestintechnologies, innovations, products, and services that helpmovetheindustryforward.
Exhibitor Highlights
Here are some innovations visitors can expect. For up-to-date news and an extendedpreviewvisitdpsmagazine.com.
Complete Mailing Lists, booth 761, highlights how the right data makes all
ProShip, booth 238, demonstrates how it enables enterprise shippers to optimize operations and enhance customer experiences.INFO#202
Quadient, booth 519, showcases the Quadient iX-Series mailing systems, which are powered by S.MART. mailroomsoftware;theDS-77iQfolderinserter; andthe MACH 7 colorinkjet envelope printer.. INFO#203
Scentisphere, booth 532, is a scent marketing agency that helps brands, the difference and its expertly curated agencies, and printers enhance direct mailing lists, advanced segmentation, and i-data hygiene ensure that your campaigns reach the right people at the right time. INFO#200
Mail-Gard, booth 334, provides a Disaster Recovery Solution to keep your business solvent in the event a disaster strikes. INFO#201
mail campaigns with its innovative scent marketingsolutions. INFO#204
XMPie, booth 916, features its datadriven and variable data print solution. Ideal for high-volume, high-speed direct mail jobs, users can inject real-time data to guaranteetimely,relevant, andpersonalizedcustomer journeys. INFO#205
Zebra Technologies, booth 912, exhibits its solutions tailored for the postal deliveryservice industry. These technologies include mobile dimensioning, ring scanners, printers, andhandhelddevices. These solutions work together to streamline package measurement for precise billing, boost productivitywith hands-free barcode scanning, barcode and RFID printing, and help ensure dependable performance with connectivity in mobile environments. INFO#206
NPF25
Don't miss this chance to engage with USPS leaders, gain actionable insights, and look forward in2025. dps
1. Zebra Technologies showcases its innovative solutions tailored for the postal delivery service industryinbooth912. 2. The QuadientiX-5mailing systemishighlightedinbooth519.
By Melissa Donovan 0--
Envelope printers are advantageous to any size print environment. There is a solution for every envelope printing need, whether it is at the industrial level to something designed for one-off stationary requests. Advancements in inkjet, workflow automation, and finishing components influence popularity, especially in the last decade or so.
"Digital printing to envelopes has come a long way in the last 15 years, yet we have only seen the new generation of printers take performance leaps up to near production-level speed with excellent output quality and durability in the last few years. These are exciting times to be in the industry," admits William Longua, senior director, digital print group, Quadient.
BlueCrest, lists key factors like color capability (CMYK or monochrome), print resolution, print speed, cost per thousand, and the type of substrates or materials the press supports.
"These segments help differentiate printers based on functionality, performance, and cost efficiency to meet specific pricing needs," explains Bruce. Certainly, how envelope printers
manufacturer. For example, Quadient classifies its products into two main segments-commercial and production; and then breaks them down into entry-, mid-, and high-volume presses.
Entry level, based on Quadient's product line, includes mail centers, print shops, and marketers of all sizes looking to achieve around 7,500 envelopes an hour, like its MACH 5 color printer. Mid are categorized can also depend on the volume, the MACH 7 isdesignedfor print-
Theresurgence ofdirectmail, combined withautomation, has positioned digital envelopeprintingas essential formodern marketing campaigns.
Classification of Printers �- � ing up to 10,000 envelopes per Due to the sheer scale ofoptions, envelope printersarecategorized by a number of factors, for example desktop versus industrial, inline versus online, or a function ofthe press itself-entry-, mid-, or high-volume printing.
Andy Bruce, product manager - inserterand digital solutions,
-Bill Frederick, director of sales and Tim Murphy, president, Printware LLC
hourorcommercialprinterslooking to print 50,000 envelopes per month or more. Finally, high-volume speeds are illustrated by its MACH 9DS, for those printingup to 1,000,000 pieces per month.
1. Acloseupofprinted envelopesfromthe Quadient MACH 90S. 2. The RISO ComColor FT.
The past five to ten years, we have witnessed digital printing’s increased role in envelope decoration.
“The resurgence of direct mail, combined with automation, has positioned digital envelope printing as essential for modern marketing campaigns. Affordable equipment and trade-in programs have further made these solutions accessible to businesses of all sizes, allowing them to create impactful, customized communications efficiently,” note Bill Frederick, director of sales and Tim Murphy, president, Printware LLC.
Jesse Heindl, marketing manager, RISO, Inc., says the economy is creating a boost in interest for cutsheet production inkjet in general. “Wages, labor, and paper have all gone up in cost, with the end user bearing the brunt of those increases. They have cut their jobs in half to protect budgetary requirements. The number of jobs to the print shop have doubled but all for the same volume—or less,” continues Heindl.
For example, what used to be a job of 100,000 envelopes is now two jobs of 50,000, printed months apart. “That makes for a world of short-run jobs, where the new requirement is smaller production engines, but more of them in order to print multiple jobs simultaneously. That is the new production formula, and mid-size inkjet units with the ability to print envelopes are perfect in that type of workflow,” suggests Heindl.
“Over the past decade, the cost per thousand prints, including both CAPEX and operating expenses, has dropped. This decline has made it possible to integrate printing directly into non-print
work cells, streamlining workflows, consolidating work cells, reducing costs, and boosting efficiency,” agrees Bruce.
The ability to print variable data addresses along with personalized marketing messages on the face of the envelope is big for municipalities and school district in-plants. “Print buyers are coming around to the reality that envelopes are disposable pieces and refuse to spend big dollars on them. One of the improvements we made over the last five to ten years was the clarity with which barcodes could be printed and more easily scanned, which makes a huge difference to the USPS,” explains Heindl.
Advancements in inkjet technology, workflow solutions, and automation are in demand for envelope printers.
“Improvements to inkjet allow for much faster printing with higher contrast color and more durable inks, which are also more affordable,” says Longua.
“Advancements in inkjet technology drive demand for versatile, high-resolution printing solutions. These advancements also encourage seamless workflow integration and automation, ensuring higher efficiency, scalability, and reduced manual intervention,” explains Bruce.
“We see a big surge in inkjet for highvolume mailing, and the reason usually cited is the increase in uptime. High-speed printing lets print shops burn through long runs quickly, and our heatless imaging process means that they experience fewer breakdowns, fewer service calls, and more time printing and meeting their service level agreements. Improvements in workflow also streamline the printing process
and reduce a lot of the labor involved for running specific jobs,” admits Heindl.
Frederick and Murphy provide examples of workflow and automation advancements like auto-loaders, streamlined software integration, and reduced manual handling. “These further boost demand by increasing efficiency, reducing production times, and enabling seamless integration into existing print and mail workflows.”
Digital envelope printing can be performed inline, offline, or near line.
Printing and finishing inline offers a host of benefits, but also has its challenges.
With printing and finishing inline, everything is streamlined. “The advantages of inline envelope printing include streamlined workflows with fewer touch points, resulting in greater efficiency and the potential for a reduced headcount. Additionally, the system enables faster and more effective quality control, which contributes to accelerated production times, ensuring a smoother overall operation,” says Bruce.
Longua agrees, citing fewer touch points or faster setup time as key to eliminating the need for highly skilled labor to operate more complex equipment, which saves in cost and time.
Hurdles to overcome include what Bruce refers to as “reduced flexibility and increased complexity” since the entire process is inline. This means offering additional training or adjusting existing processes. He also says that inline systems require a higher initial investment, which poses a barrier to adoption.
Longua also sees challenges related to substrate availability and compatibility. “This is depending on the printing technology chosen, but new media options are appearing all the time that address this.”
“Challenges include ensuring consistent print quality on various envelope
stocks and managing feeding mechanisms to handle diverse sizes and materials without jams or misalignments,” admit Frederick and Murphy.
Alternatively, an envelope printer can stand on its own, with finishing near or offline configurations.
A standalone envelope printer offers cost savings on printing and inventory requirements. “Direct printing eliminates the need for a warehouse to store racks of printed envelopes. It also enables variable data and graphics printing at the same time. A print provider can service hundreds of customers with a lower investment in physical space and a simplified system where they minimize capital tied up in printed inventory. It also makes
setup time and sample printing easy, so customers can see exactly what they will get,” shares Longua.
“Standalone envelope printing systems offer advantages of greater flexibility to handle varied print jobs and a lower initial investment compared to inline systems,” agrees Bruce.
Variable print beyond the address is possible with standalone devices, which as Heindl points out studies have shown that personalization on the outside of the envelope itself increases the likelihood of the recipient opening the piece. And, echoing Longua, with the ability to generate the printed pieces on demand, there is no need to keep an inventory of preprinted shells.
These printers also enable printing beyond an envelope. “Standalone systems
can be adapted to newer printheads and feeding, allowing more products to be printed and personalized. Examples are coffee sleeves, coasters, bags, and boxes,” share Frederick and Murphy.
There are challenges, “such as additional steps and touch points that increase the risk of integrity errors, slower overall production speed, and a more labor-intensive process,” admits Bruce.
“A short, straight paper path is the key to printing on this challenging substrate,” notes Heindl.
Today’s envelope printers offer everything from feed mechanisms to sophisticated software management to enhance production efficiency for low-, medium-, and high-volume environments. dps
runs as low as one is not just possible and profitable for the happy few, but for any print service provider (PSP).
"To achieve this, printers need to take a holistic approach to the entire printing process from concept and order through to production and delivery, instead of focusing on single tools. This means looking for automation solutions that will be scalable as they grow and, more importantly, that will enable them to integrate their management information systems with both their input and output systems."
With shorter print runs, tighter delivery schedules, and varying printing substrates, anintelligentworkflowisamust to organize and prepare jobs. "This intelligent workflow must not only affect printing but also finishing-it must be a complete closed loop," explains Carlos Martins, head solutions management, Muller Martini North America.
"The numerous benefits of a complete closed loop workflow from printing to finishing include optimizing efficiency in finishing to eliminate makeready times and reduce errors by eliminating manual interventions," he adds.
The benefits of automation are well understood. However, many PSPs are
1. Konica Minolta offers both proprietary and partnered solutions for workfiow automation.
stuck with manual, inefficient, and siloed processes.
It can be challenging for PSPs to narrow down what is holding them back from implementing more automation. "It could be one of many possibilities, but the most important thing for the company manager or owner to recognize is that automation is coming and it's coming fast. If you don't recognize the potential, your competitors surely will," suggests Ray Hillhouse, VP sales and marketing, Plockmatic Group Offline Business Unit.
Suzi Hagay, director of workflow solutions, Landa Digital Printing, sees the order submission process as the biggest challenge towards implementing automation. "If you can streamline the order placement from an upstream system, you'll be on the right track."
The sheer volume of information available about automation and workflow optimization can be overwhelming, particularly for companies that may not have in-house expertise. ''Adding to this challenge is the fact that much of the advice or many of the resources might not apply to a specific company's needs, making it difficult to determine the best path forward," offers Bob Waddington, product line leader for curing and drying, BW Converting.
Finding the right partner is critical to success. "Trying to reinvent the wheel on your own and learning all the potential
costly lessons that others have already solved will not benefit an organization looking to effectively implement automation. It may take some trial and error to find the right partner and what level of automation you require," recommends Tim Bolton, manager, inkjet technology, Ricoh USA.
Don Dubuque, director of marketing, Standard Finishing Systems, suggests visiting vendors' demonstration centers to see these automated solutions in action as well as connecting with other print providers who have already made these investments.
Company culture often prevents PSPs from embracing automation.
''A well-trained production staffworks to get orders through as completely and accuratelyas possible based on the tools and methods that have been available to them. The roadblocks can often bethose members of the staff that have been so 'good' at their job using what they have, that they may have lost sight that there may be additional/alternate ways of doing things, and taking time to learn something new is, from their perspective, taking time away from production," explains Joe Lehn, director of product management, PressWise.
"Change is hard and our day-to-day work often means we deprioritize the future. To be able to transform the workflow, a PSP must understand where the bottlenecks are located and redesign the process. This issue involves hardware, software, people, and processes," says Kevin McPherson, senior client executive, digital, Quadient.
To overcome these challenges, Ernie Crawford, president/CEO, Crawford Technologies, says businesses must shift their mindset and view automation as a long-term investment, not a risk. The best approach is to start small with manageable changes that provide immediate value and build momentum.
Lehn admits that introducing and successfully implementing an automated
workflow is an investment in both time and money.
“When a print provider automates something, it means new ways of doing things. Like any newer technology, investing in the equipment and training resources to implement these changes can be a challenge. The technical know-how and expertise to operate and get the most out of automated systems can require investment in machines, software, and personnel, but the benefits of optimizing production workflow can help offset those initial costs in time,” notes Lisa Weese, director, product strategy and business planning marketing, Digital Press Printing Solutions, Canon U.S.A., Inc. Integration concerns also play a role. “One of the biggest roadblocks to automating production print workflows
is the integration of new automation technologies with existing systems and equipment, especially in operations with a mix of old and new equipment. Additionally, ensuring different systems can communicate and work together seamlessly requires detailed planning, investment in training, and possibly seeking external expertise to ensure a successful transition to automated workflows,” says Matt Raab, marketing director, global product offerings, Xerox Corporation.
Nick Bruno, president, Harris & Bruno International, warns that the road to optimization isn’t always smooth, and for many providers, this can make the journey seem daunting. “One of the most common challenges is the upfront investment cost—automation systems require a significant initial outlay that
can deter smaller providers. There’s also the challenge of revamping workflows, as adopting automation means training staff and reevaluating production strategies to ensure a seamless transition.”
On top of that, Bruno believes there’s the lingering perception that automation is too complex or not a fit for smaller operations. “The biggest hurdle is uncertainty about return on investment (ROI). Providers often hesitate without clear data showing how quickly automation can pay for itself. However, once the benefits of faster production speeds and reduced material waste become evident, the hesitancy is replaced by enthusiasm.”
PSPs are able to address labor challenges through automation.
Industrialized automation is not new but it is gaining traction in the printing industry. “We are talking about new technologies on different levels. There is software and mechanical automation and joining those together creates automation where ‘the whole is greater than the sum of its parts,’” shares Alan McLean, regional sales director, Duplo USA.
Those looking to adopt automation have many areas of opportunity to explore, notes Raab, including quality
control systems, workflow, job management, fleet production monitoring and management systems, finishing tasks, and inventory management.
Start with an assessment of the process. “The differences between facilities and existing equipment and automation mean there is no silver bullet answer to where to start,” says Dr. Mark Bohan, director, Color Solutions, Konica Minolta.
Jamie Reber, product manager, Software, Kodak, suggests first evaluating
and understanding where your inefficiencies reside when automating print workflow. “In order to select the right software and equipment to help you automate it’s important to have a solid understanding of your current set up, where the gaps are, and what those gaps are costing your business. Being proactive upfront will ensure that you research, select, and implement the right software for today and tomorrow. Automation platforms need to be flexible and adaptable to inevitable business and marketplace changes.”
The best place to start with any automation is where it’s needed the most. “Identifying the manual steps in the worklow is extremely important because those are the areas that can benefit the most from automation—in time, efficiency, and accuracy—all that directly impact the bottom line,” adds Lehn.
You must have a crystal-clear understanding of your current print production processes in order to effectively implement end-to-end automation technology. “Once you have clearly defined your processes from the time a job comes in, you’ll be better able to identify steps that can be automated, areas of redundancy, or other processes that can be improved. This is referred to as ‘mapping the process,’” stresses Marc Raad, president, Significans Automation.
Fiery fiery.com
Four Pees fourpees.com
Harris & Bruno International harris-bruno.com
Komori America komori-america.com
Konica Minolta kmbs.konicaminolta.us
Kodak kodak.com
Landa Digital Printing landanano.com
Muller Martini mullermartini.com
PressWise presswise.com
Plockmatic Group Offline Business Unit plockmaticgroup.com
Quadient quadient.com
Ricoh USA ricoh-usa.com
Significans Automation significans.com
xerox.com
2. Müller Martini offers its complete Connex workflow solution, which is broken into Connect LineControl, ImpoWhiz, and Info Cloud. COMPANIES
Next, detailed process documentation ensures that everyone involved in the production process is on the same page. This is usually followed by creating standard operating procedures. “These are essential for establishing consistent processes and ensuring that they are followed on a daily basis. Once the processes are mapped and areas of opportunity are identified, creating new, more efficient automated procedures will become much easier, setting the stage for future success,” says Raad.
It may be wise to start by taking reasonably sized steps. “Automation of some single processes might be good for a learning experience and yield fast returns. This could set up great awareness of next steps and a foundation for larger scope projects. A large scope can be daunting, and some experience is valuable,” suggests Lance Martin, VP product marketing, Komori America.
Weese agrees, pointing out that looking for small wins is a good place to begin while simultaneously starting the conversation in regard to larger investments and longer term solutions that may need to be made in order to streamline processes and improve productivity. “Moving to automation may be as simple as going from an analog
piece of equipment to one that’s digital or, it could get much more complex with new software to aid in automation or even robotics.”
Raad says many printers choose to deploy customized automation in stages, realize the immediate productivity gains and fast ROI, then move on to other areas of their business that would benefit from automation.
Production print automation is increasingly important and prevalent in modern print environments.
Production print automation is able to eliminate cost and errors resulting from manual touch points, streamline workflow from raw materials in to finished goods out, reduce overall production
time, and minimize the impact of labor shortages, offers Jacquie Perno, business development manager, ACCO Brands.
However, the complexity of automation can be daunting for companies new to the process. “Understanding where to begin and which solutions to adopt often feels overwhelming, especially with so many options available. It’s critical for businesses to engage with companies offering automation tools and to clearly articulate the value these tools can add to their operations. Gaining this understanding helps secure internal support and capital expenditure approval for automation investments,” says John Cusack, product line leader, BW Converting..
Find a webinar and web-exclusive articles on print automation online at dpsmagazine.com. dps
Kodak
Kodak is a leading manufacturerin commercial print and advanced materials and chemicals. With 79,000 patents earned over 130 years, we believe in the power of technology and science to enhance what the world sees and creates. Ourinnovative, award-winningproducts, with our customer-first approach, make us the partner of choice for commercial printers worldwide. Kodak is committed to environmental stewardship, including industry leadership in developing sustainable solutions for print. INFO# 111
to "Give Shape to Ideas" by supporting their digital transformation through its expansive Intelligent Connected Workplace portfolio. Its business technology offerings include IT services, intelligent information management, video security solutions, and managed print services, as well as office technology and industrial and commercial print solutions. INFO# 113
MBO America offers an array of cutting edge, high-performance finishing solu-
the print and packaging industry. From essential gloss and matte films to premium finishes and special effects, our solutions enable digital printers and converterstomakeproducts brandslove. Wealsooffer innovative solutions for the digital flexible packaging market,includingprintwebfilms, thermal pre-laminations, and PE films that support recyclable applications. Our line of thermal laminators includes units for nearly any print application, including single-sided lamination, double-sided lamination, embossing, cold foiling, and more. Nobelus provides industry-leading service and support in nearly every market, including commercial print, prime labels, flexible packaging, publications, digital photo finishing, and print on demand. INFO# 116
Designed by a visionary printer burdened by the traditional manual workflow process that still plagues many printers today, PressWise is an end-toendsoftwareasaservice-basedMISand tions for inkjet and other digital print print workflowautomationsolution that Komori America
Komori America Corporation, Rolling Meadows, IL, is a premier manufacturer of offset and digital presses for printing and packaging. Komori's world-class technology is known for product reliability, outstanding print quality, and substrate
production environments. Whether cutsheet or roll-fed, inline or nearline, commercial print or packaging, MBO America can offer solutions expertise to make your production process more efficient. INFO# 114
flexibility. From unsurpassed print quality MUiier Martini and impressively fast makeready to intuitive software, Komori is committed to the advancement of print and dedicated to helping its customers navigate the print industry's digital transformation.INFO#112
Konica Minolta
Konica Minolta Business Solutions U.S.A., Inc. aims to partner with clients
1. MUiier Martini Prinova digital saddle stitcher with Hunkeler Unwinder UWS and Cutter CSS. 2. Applications cut with the Rollem lnsignia7H die cutter.
Miiller Martini is the world's largest producer of print finishing solutions for commercial and book printers, trade binderies, and newspapers as well as short-run and digital book manufacturers. INFO# 115
Nobelus
Nobelus offers a range of thermal laminates, adhesive-free films, pre-laminations, and thermal laminating equipment to digital print service providers across
comes complete with robust features such as unlimited web storefronts, estimating, quoting, orderprocessing,workflow management, complete shipping integration, fulfillment, and the ability to integrate with most other third-party storefronts. INFO# 117
Ricoh USA, Inc.
Ricoh USA Graphic Communications is committed to helping you grow your business, improve customer engagement, and increase operational efficiencies. Ricoh boasts an expansive portfolio of services, hardware, and software that includes sheet-fed systems, expert professional services, software, and finishing. As part of a global leader, Ricoh creates competitive advantage and solves problems for 1.4 million-plus
businesses—both large and small. INFO# 118
RISO, Inc., headquartered in Woburn, MA, is a wholly owned subsidiary of RISO Kagaku Corporation, Japan’s leading manufacturer and distributor of high-speed inkjet printers for the production print market. Its compact design and heatless imaging system reliably produces millions of variable data prints at speeds of up to 320 images per minute/160 pages per minute duplexed. RISO machines are environmentally friendly, inexpensive to operate, and easy to use. INFO# 119
Rollem International
years, SCREEN Americas has created satisfied customers in the commercial, transactional, publishing, direct mail, 2
Rollem specializes in automated slitting, scoring, and perforating systems and sheet-fed, rotary die-cutting systems. The Insignia die-cutting system offers ease of operation and quick changeovers. It is ideal for folded cartons, packaging, gift cards, and more. Proudly made in the U.S., Jetstream is a bidirectional slitting, scoring, perforating system, well suited for postcards, business cards, and shelf tags. With a folder/gluer it is a fully automated direct mail finishing system. The Semi-Slitter kiss-cuts pressure-sensitive adhesive stock for stickers and labels. The Champion 990 is our economical scoring and perforating system. Tell us about your finishing issues or bottlenecks and we’ll provide you with options to streamline production and eliminate excess labor and waste while expanding your product offerings. Sizes compatible with all press sizes up to B2 sheets. INFO# 120
SCREEN Americas, a SCREEN Graphic and Precision Solutions group company, provides a range of solutions to meet
graphic communications needs with a strong focus on production-class inkjet printing technology. For more than 50
label, folding carton, and flexible packaging markets by delivering the latest innovations to help printers grow their businesses. INFO# 121
Sharp Imaging and Information Company of America (SIICA) helps businesses achieve simply smarter work by assisting in workflow management, creating immersive environments, and increasing productivity. SIICA offers secure production printers, office printer and copier solutions, commercial displays and projectors, Dynabook laptops, management and productivity software, and fully managed services. INFO# 122
Signs365 is a grand format, trade only wholesale printer. We offer a wide variety of full color, high-quality printed products all produced in 24 hours. $10 Overnight Anywhere shipping is available on all products. Signs365...We Are Only Trade Only! INFO# 123
saddlestitchers, die cutters, slitters/ creasers, and bookletmakers; and Hunkeler unwinders, rewinders, cutters/ stackers, dynamic perforators, and inspection systems for continuous-feed printers. Standard has applied its knowledge of the conventional offset print finishing industry to engineer effective solutions for the expanding digital and inkjet print markets. INFO# 124
Therm-O-Type digital finishing products include the new Glue-Tech Sheet-toSheet gluer, the NSF Elite, Excel, Ultra die cutting/foil stamping/embossing presses, RDC-Flex rotary die cutter, Zip cutter/slitter/creaser/finisher models, RAS-meright angle slitters, and traditional business card slitters. Therm-O-Type also produces foil fusers and handfed thermography equipment. Therm-O-Type has supported the printing industry with equipment, supplies, and technical expertise since 1977. INFO# 125
Korean venture VALLOY is a global Standard distributes a broad line of digital printing solution company. BIZfeeding and finishing products including PRESS13R is a Xerox engine based roll Horizon perfect bind- labelpressandDUOBLADEWX is afully ers, collators, folders, automatic blade-driven, roll-to-roll digital
Ilabel finisher.
WX II has eight cutting heads to catch up with the speed of laser cutters, showing clean cutting edges without dust nor scratches. DUOBLADE FX is an intelligent sheet fed sticker cutter, which produces various kiss- and full-cut outputs in unmanned environments. INFO# 126
Videojet Technologies is a world leader in the product identification market, providing inline printing, coding, and marking products, application specific fluids, and product lifecycle services. With customer application experts and technology leadership in continuous inkjet, thermal inkjet, laser marking, thermal transfer overprinting, case coding and labeling, and wide array printing, Videojet has more than 400,000 printers installed worldwide. INFO# 127
Xeikon America, Inc.
A division of the Flint Group, Xeikon is an innovator in digital printing technology. The company designs, develops, and delivers web-fed digital color presses for label and packaging applications, commercial, and graphic arts printing. These presses utilize LED-array-based dry toner electrophotography, open workflow software, and application-specific toners. Xeikon Dry Toner is FDA-compliant for food labels and packaging applications. INFO# 128
Xerox Corp.
For more than 100 years, Xerox has continually redefined the workplace experience. Harnessing our leadership position in office and production print technology, we've expanded into software and services to sustainably power the hybrid workplace of today and tomorrow. INFO# 129
3. Xerox Primelink C9200. 4. The RISO VALEZUS T2200 is a high-speed, duplexing cutsheet inkjet device.
1 Amplify Print 19 amplifyprint.org
2 Canon U.S.A., Inc.2 canonproductionprint.com
4 Duplo USA Corporation27 duplousa.com
6 Graphic Whizard Inc.21 graphicwhizard.com 13 HP, Inc. 9 hp.com
Kodak 5 graphics.kodak.com
Komori America17 komori-america.us
National Postal Forum 14 npf.org
Nobelus 26 nobelus.com
PressWise by SmartSoft25 presswise.com
ijetcolor.com
rollemusa.com
sharkmachinery.com
28 signs365.com
Systems 7 standardfinishing.com