Speleothems Resonance in Nature
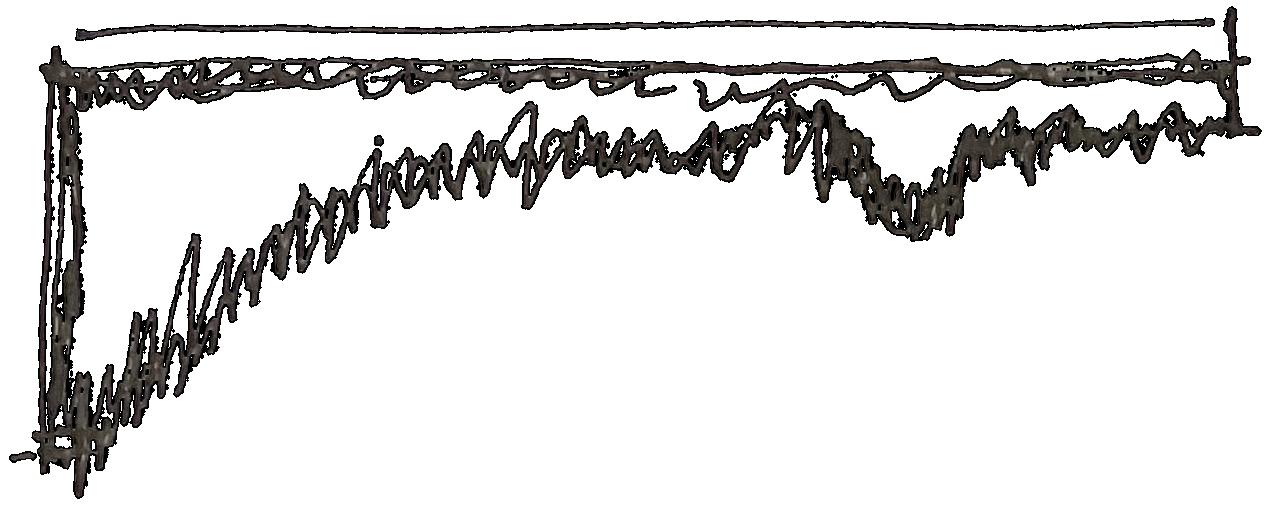
Speleothems are mineral deposits formed in caves through the movement of water. The most common forms of speleothems are stalactites and stalagmites (White 2019, Encyclopedia of Caves). Stalactites are the formations on the ceiling and stalagmites are the formations on the ground.
The design takes inspiration from the sharp, pointed rhythms of the stalactites and stalag mites. The ceiling mimics the random heights of a stalactite which is formed by the natural drip ping of water, resonating through the variable volume of the space and filling the space as it sees fit. The design aims to evoke the unique feeling of being inside a cave, resultant due to its qualities of being a enclosed space with organic geometry found in nature. This enclosure creates an intimacy that allows for a unique re lationship that resonates between the physical artefact and the person experiencing this space.
The space is interpreted as a prehistoric museum cum experiential centre which takes the visi tor on a journey through the cave, exploring the trough and crests of the speleothem surfaces. The design shall resonate with the primitive ex perience of the human brain, when homo sapiens were still hunter-gatherers living in caves.
Fig 3. Stalacites Restaurant,Melbourne. Stalactites.com.au. Fig 2. Stalacites. Speleo-mandeure.fr/IMG/jpg/crotot.jpg Fig 1. Speleothems in a cave. Livescience.com/stalagmites-and-stalactitesNational Museum of Qatar Shop Interiors,Doha, Qatar.
Fig. 4 Koichi Takada Architects.
Archdaily.com/916244/national-museum-of-qatar-shop-interiors-koichi-takada-architects, 2019.
Fig.
Cave Restaurant, Sydney, Australia.
Fig 6. Koichi Takada Architects.
Archdaily.com/56011/cave-restaurant-koichi-takada-architects, 2009.
Fig 7. Sharrin Rees.
1. Troughs and Crests formed through “Point Deform” grasshopper component.
2. Sharpness increased by modifying the range of the “Motion” parameter of “Point deform.”
3. Variable sized boxes created by inserting the deformed surface in a “Bounding Box” component.
4. Steel Mesh created by inserting the de formed surface in a “Delaunay Edge” component folled by a “Pipe” component.
The ceiling space has been divided in 5 parts to create the sharp rhythm of the stalactites and stalagmites as well as respect the room dimensions and walkability of the space. This can be clearly seen in both sche matic plan and section of the 12m x 12m x 6m space.
2m walkways have been left around the stalagmite zone, and a minimum of 2.1m soffit height of of the stalac tites ensures that users of the space do not accidentally bump into the sharp edges.
Schematic plan showing the clear space for movement
Schematic section showing the ceiling resonating through the space and minimum clear height of 2.1m
Step by step process of the computa tional ceiling design, primarily created by using the point deform compo nent of grasshopper.
Creating a polyline curve in Rhino as per the inner dimensions of the ceiling space, internalising it in in grasshopper and making a bound ary surface through it.
Rebuilding the surface by using lunchbox plugin and dividing it into a 30 x 30 grid, thereby creating 900 points which will deform the surface at a later stage.
Using polylines and interpolated curves to split the rebuilt surface as per the design requirements of the ceiling, in order to utilize the variable volume of the space.
Shrinking the indexed surfaces to isolate them, as well as isolating their bounding curves to gain a visual idea of the points within it.
The surface points within the surfaces are isolated using a series of cull patterns, with points within a distance of 40 to the isolated bounding curve getting culled.
Using point deform with a reversed Z-vector to create random pointed forms with a maximum distance of 1500mm. This area will also a de formed surface rising from the ground below.
Running point deform on the ceiling above the mezzanine area with a maximum range of 500mm, to allow to for a minimum clear height of 2100 mm.
Reducing the points above the staircase by 50% to allow for a less deformed surface with a maximum range of 800 mm.
Increasing the maximum range above the first part of the double-height space to 2500mm to get a much sharper fall which can fill the double height volume.
The range at the last level is set at 3500 mm to create the cascading effect of a cave as well as allow to for a minimum clear height of 2100mm.
The resultant breps are then flattened and stitched together using a solid union, before being baked in grasshopper.
Step by step process of the computational ceiling design, primarily created by using the point deform component of grasshopper.
The three iterations were created by changing the various parameters of the “point deform” and “rebuild sur face” (Lunchbox plugin) components of the grasshopper script.
This changes the troughs and crests of the deformed the surface, as well as the level of sharpness.
Iteration 1
Increasing the range of most surfaces using the number slider to create a heavy,sharp ceiling.
Iteration 2
Increasing the u and v degree of the rebuilt surface to achieve a smoother deformed surface.
Iteration 3
Decreasing the range using the number slider, except for the central area in the mezzanine.
Step by step process of the 3D fabrication achieved by dividing the ceiling into 16 parts and creating a secondary structure.
Offsetting the small grids to locate vertices for hooks
Creating a closed polysurface from the parametric ceiling brep formed in the previous assessment
Dividing the surface into a 4 x 4 grid to split the polysurface into 16 pieces for 3D printing
Drawing a line through points with the same x-coordinate, using pipe and then a bounding box to create rectangular sections for the hooks
Creating a circle using the points, shattering the circle into 4 and rejoining 3 of the curves with the vertical line
Using the pipe component to create hooks using the curves isolated in the previous step and splitting it with the closed polysurface
Creating rectangular sections below beams in order to attach the ceiling to the primary structure
Creating C-sections using the bounding box, deconstruct brep and offset components based on location of beams and rectangular sections (step 6,7,8 repeated for tertiary grid)
Step by step process of the 3D fabrication achieved by dividing the ceiling into 16 parts and creating a secondary structure. 1 2
3 4
5
6 7 8
Tertiary Grid with C-sections
C-Sections
Primary Grid (Beams)
Secondary Grid
The ceiling design is divided into 16 pieces of approximately 148 mm x 148 mm by using a 4 x 4 grid. This size was arrived at after looking at the maximum printing size of the 3D printers. The hooks were printed sepa rately, in order to give the ceiling pieces a solid base to print on. Tiny slots were created for ease of joinery.
Polywood Hooks(3D Print)
Polywood Ceiling (3D Print) Stalacites
Deformed Floor Stalagmites Base structure
The hooks of the ceiling hang on the secondary grid. The secondary grid is attached to the primary grid (beams) through opposite facing C-sections. The tertiary grid provides critical additional support to the secondary grid and thus the ceiling itself. C-sections are used to attach the grids with the primary grid sandwiched in between.
Thin pigmented concrete shell panels (1m x 1m) created using formwork.
Ref: https://parametrichouse.com/concrete-shells/
Aluminium channels, adjustable hanger brackets with clips, and galvanized suspension rod.
The parametric ceil ing design uses res onance in nature as its inspiration, and interprets the sharp and random rhythm of speleothems (sta lacites and stalg mites). Hence, the suitable program would be along the lines of a prehistoric museum cum experi ential centre.
The image of the model and section offer an accurate picture of this interpre tation.