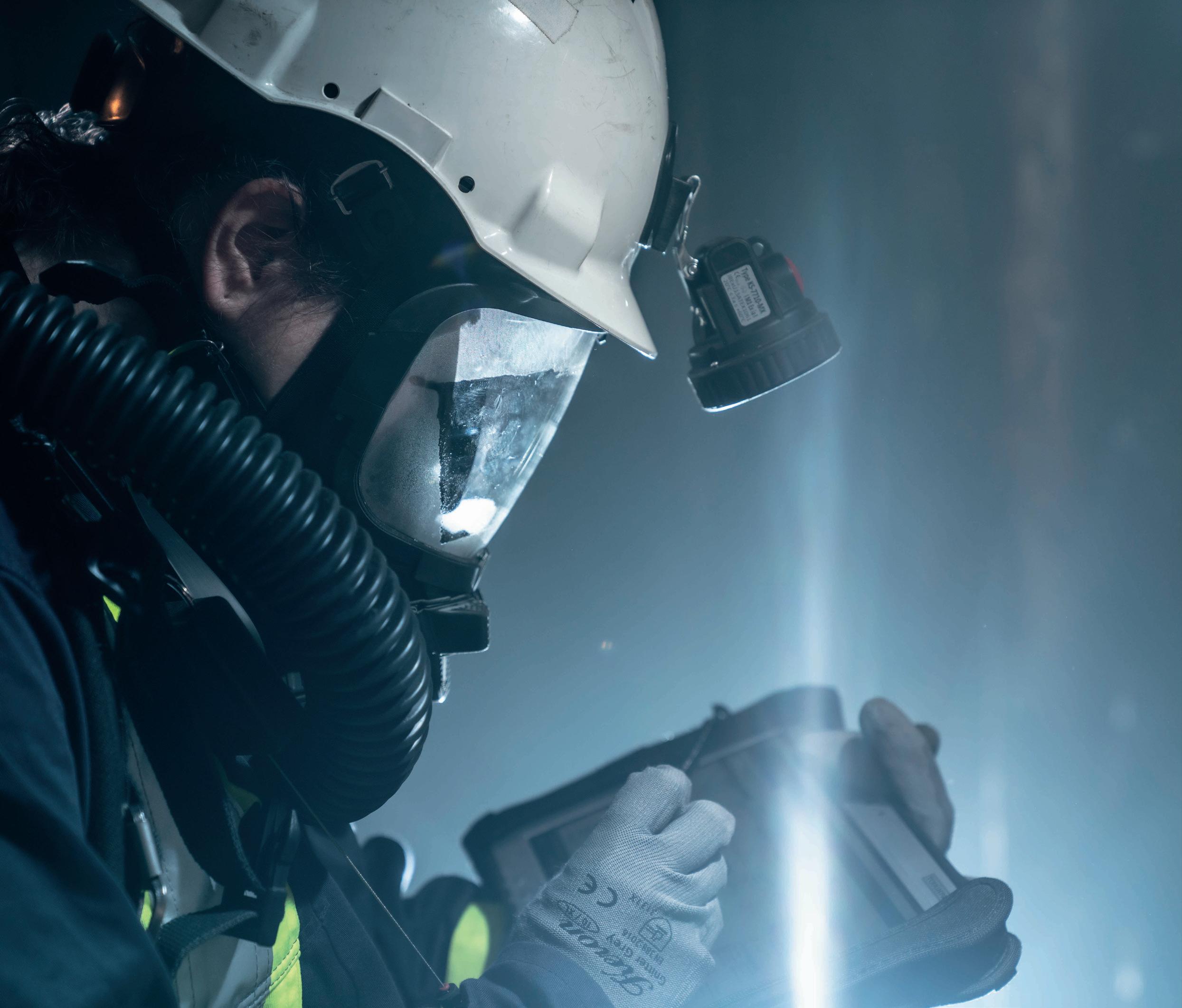
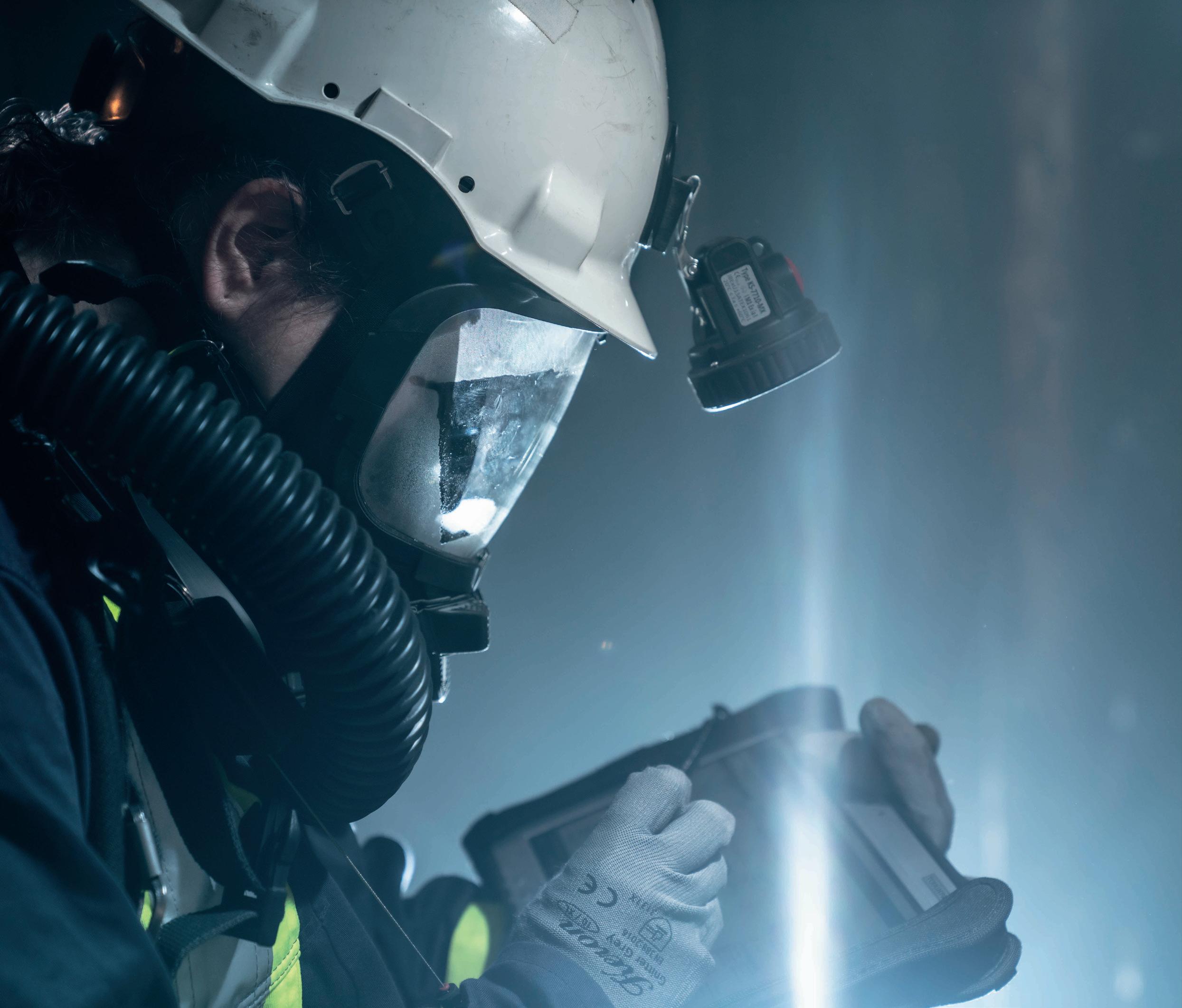
Discover potential. Drive performance.
With over 30 years’ experience working in the rail industry, specialising in the safety sector, the OPC provides practical, reliable ways of improving performance and assessing ability.
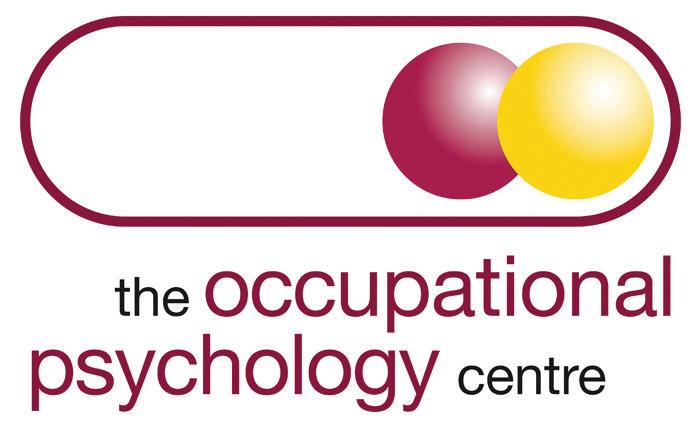
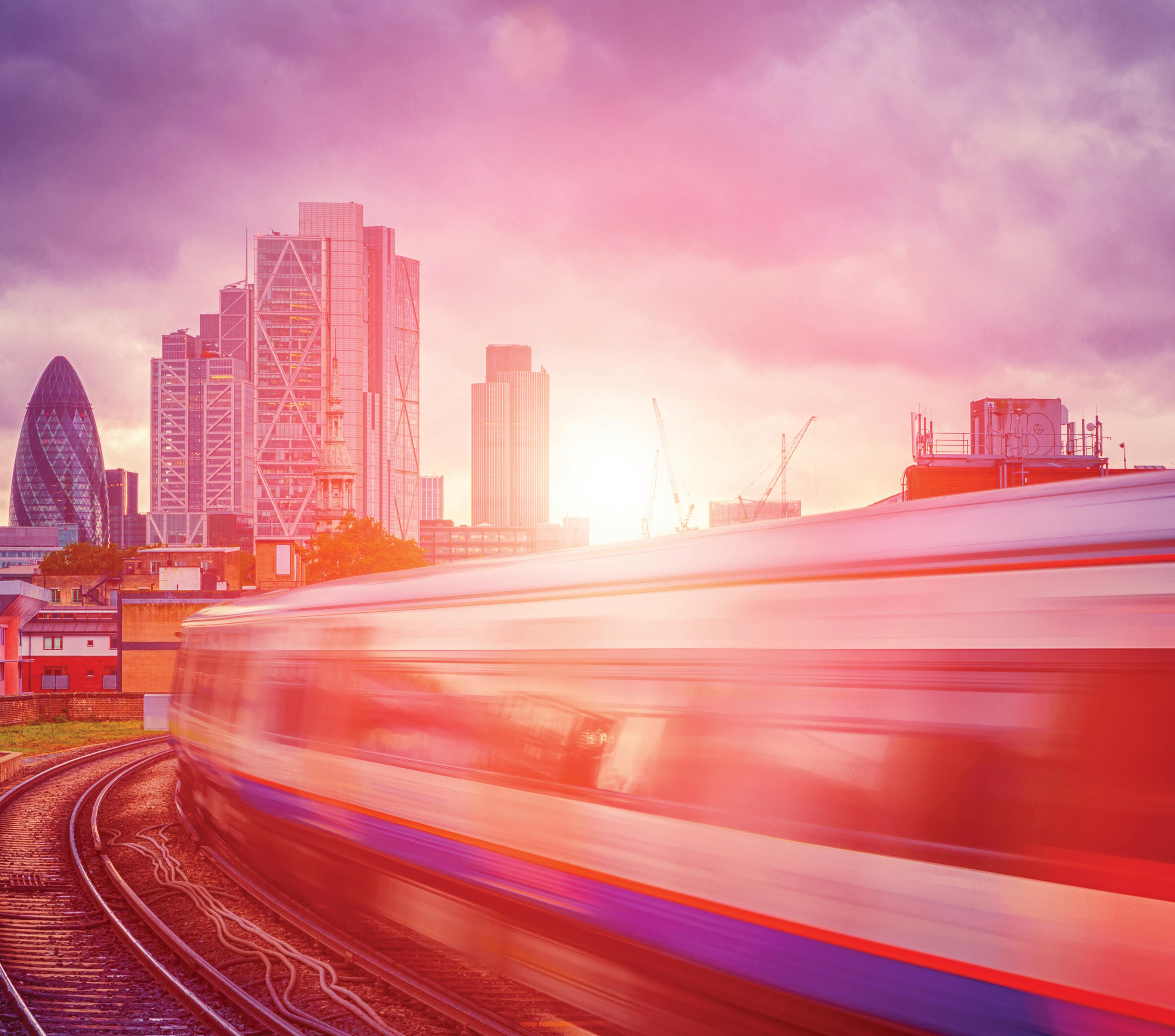
railprofessional @railpromag
PUBLISHER
EDITOR’S NOTE
EDITORIAL EDITOR
Sam Sherwood-Hale editor@railpro.co.uk
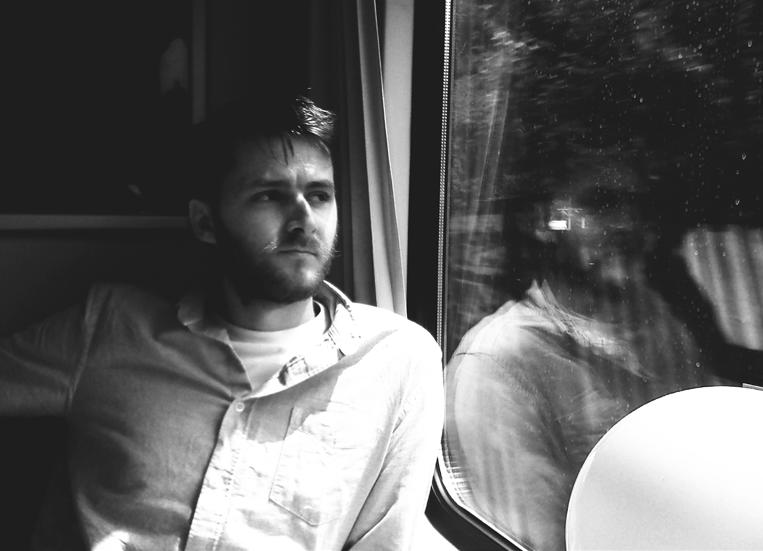
DISPLAY ADVERTISING
Adam Overall adam@railpro.co.uk
Jamie Tregarthen jamie@railpro.co.uk
RECRUITMENT ADVERTISING recruitment@railpro.co.uk
SUBSCRIPTIONS subscriptions@railpro.co.uk
ADMINISTRATION
Cherie Nugent info@railpro.co.uk
Lisa
admin@railpro.co.uk
Summer is finally here! We’ll be stepping outside in a few weeks for Rail Live and the convivial spirit will continue with the Chartered Institution of Railway Operators annual conference taking place this month as well. The High Speed Rail Group’s (HSRG) annual conference which is also being held in June.
Centred on the theme ‘Delivering HS2 in Full: Spreading Prosperity and Driving Growth’, the event follows the recent announcement of delays to the project and will consider the ways in which delivering HS2 in full will benefit the UK, including job creation, economic growth, connectivity and the ability to reach net zero.
The event will feature speeches from members of both the Cabinet and Shadow Cabinet on the value high-speed rail brings to the UK. Attendees will also be able to hear a number of industry professionals speak, including Mark Thurston, CEO of HS2 Ltd.
We’re focussing on high-speed rail in this month’s issue with a story about a procurement solution providing a constantly replenishing supply chain for HS2. We also look at electrification, signalling, and trackside with features from Asa Whitfield, Fellow of the Institution of Civil Engineers and Leo Scott Smith of safety technology startup Tended.
As always, we have our usual collection of opinion pieces with comments this month from Andy Bagnall at Rail Partners, Mark Phillips CEO of RSSB, Alison Bell People & Corporate Affairs Director at MTR UK and our regular columnists.
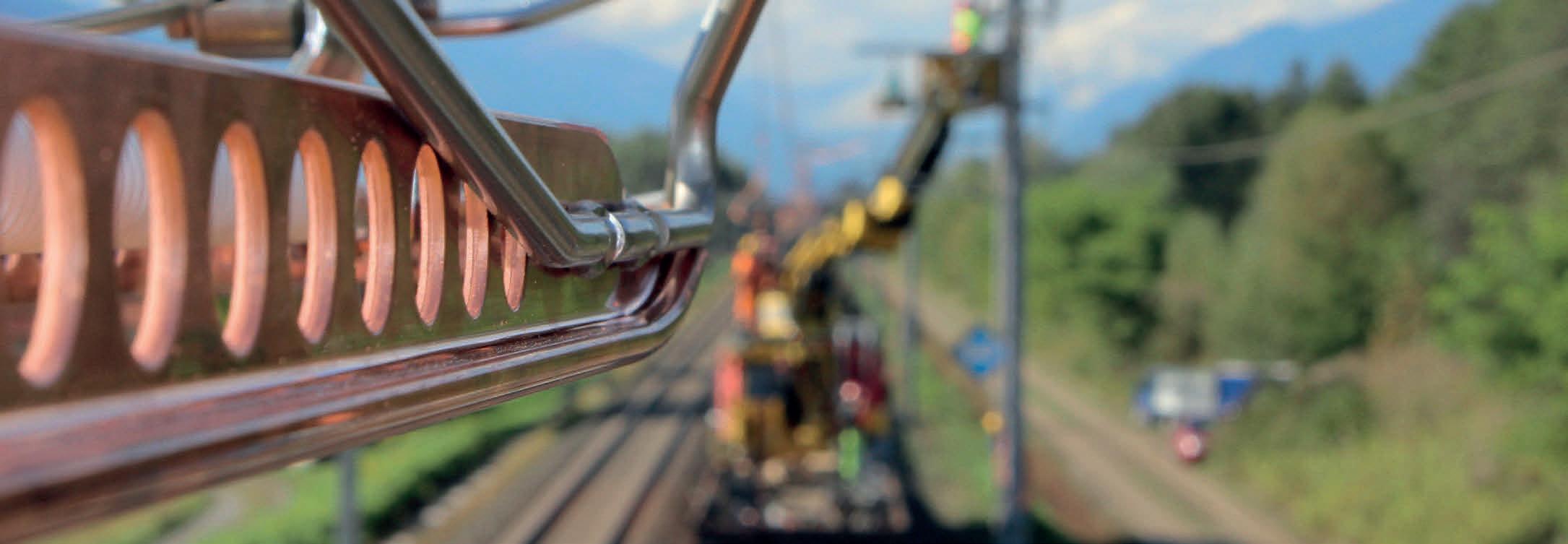
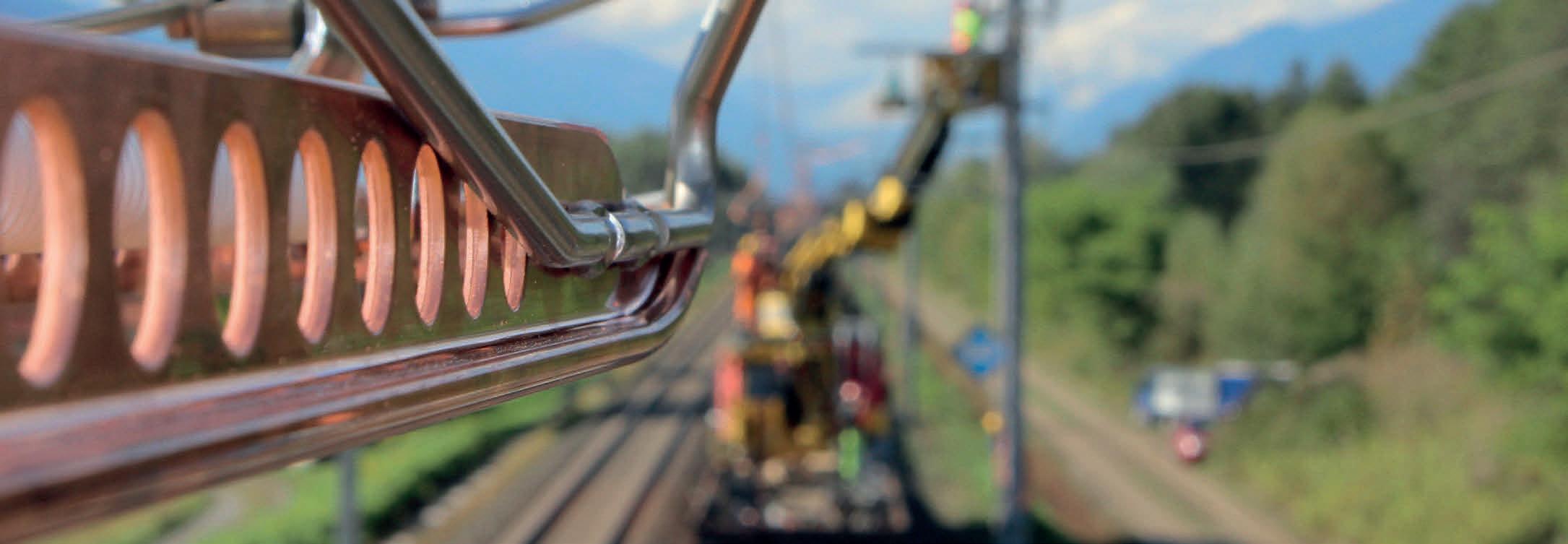
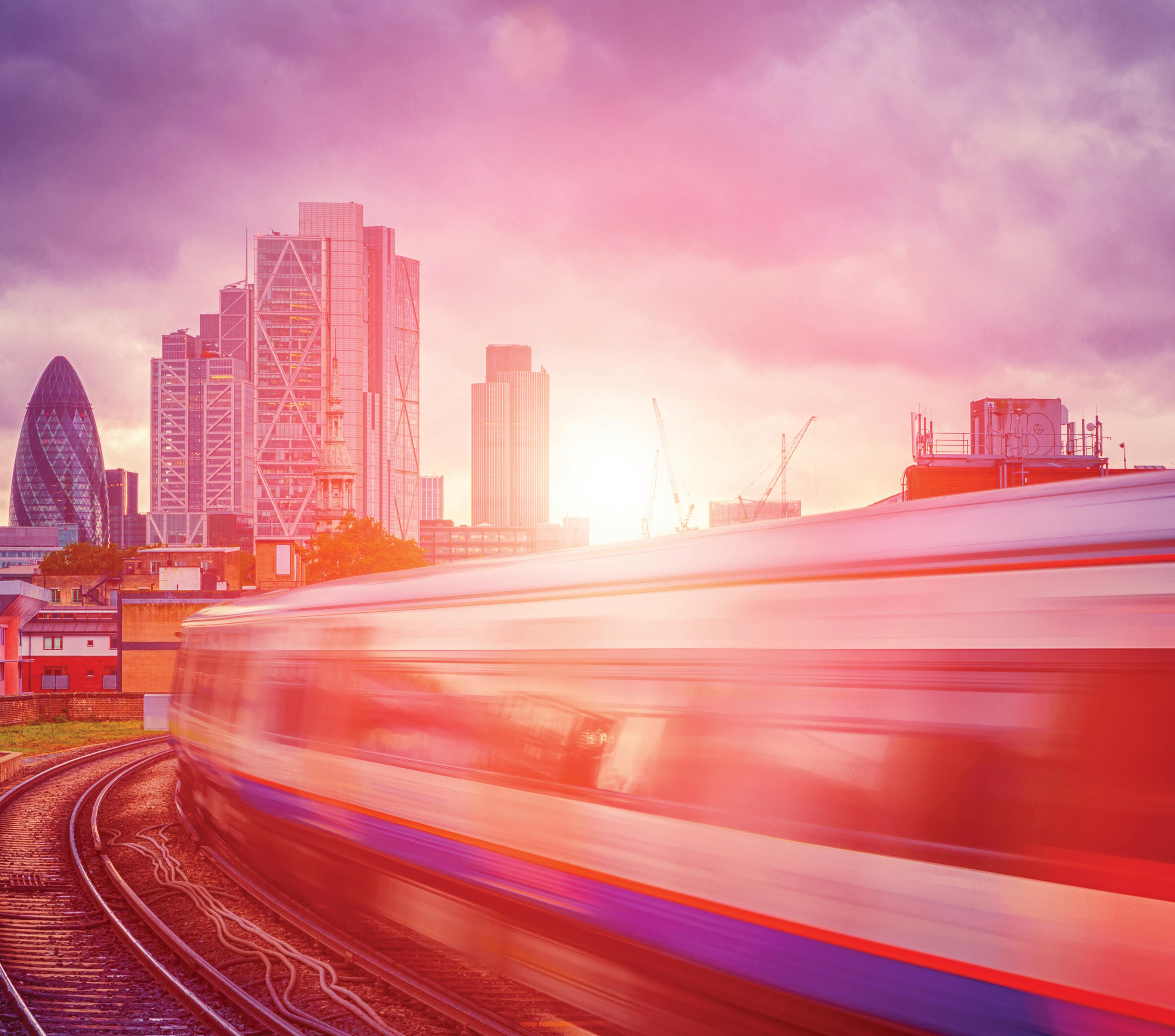
We also have a whole suite of interviews this month. We talk to Sarah Sanderson at Dräger Safety UK Ltd, Clem O’rourke at Frazer-Nash Consultancy, Steve Whitmore of Engauged, Ric Kirman of Korec Group, Martin Osman at Chevron Green Services, Kevin Babstock at Advanced New Technology Ltd, Chris Renshaw of Bratts Ladders and Chris Manning from Sumo Services Ltd.
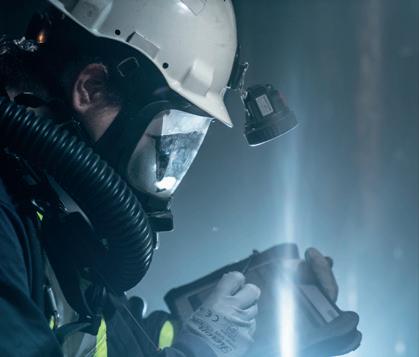
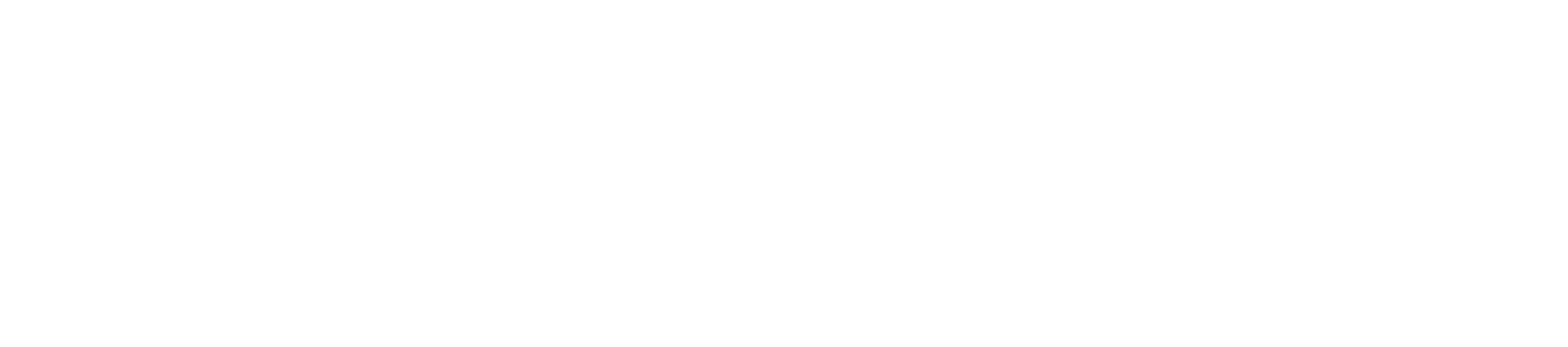
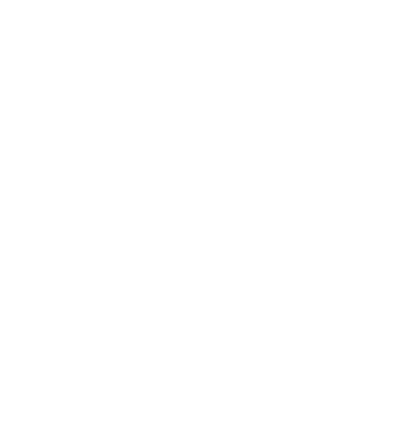
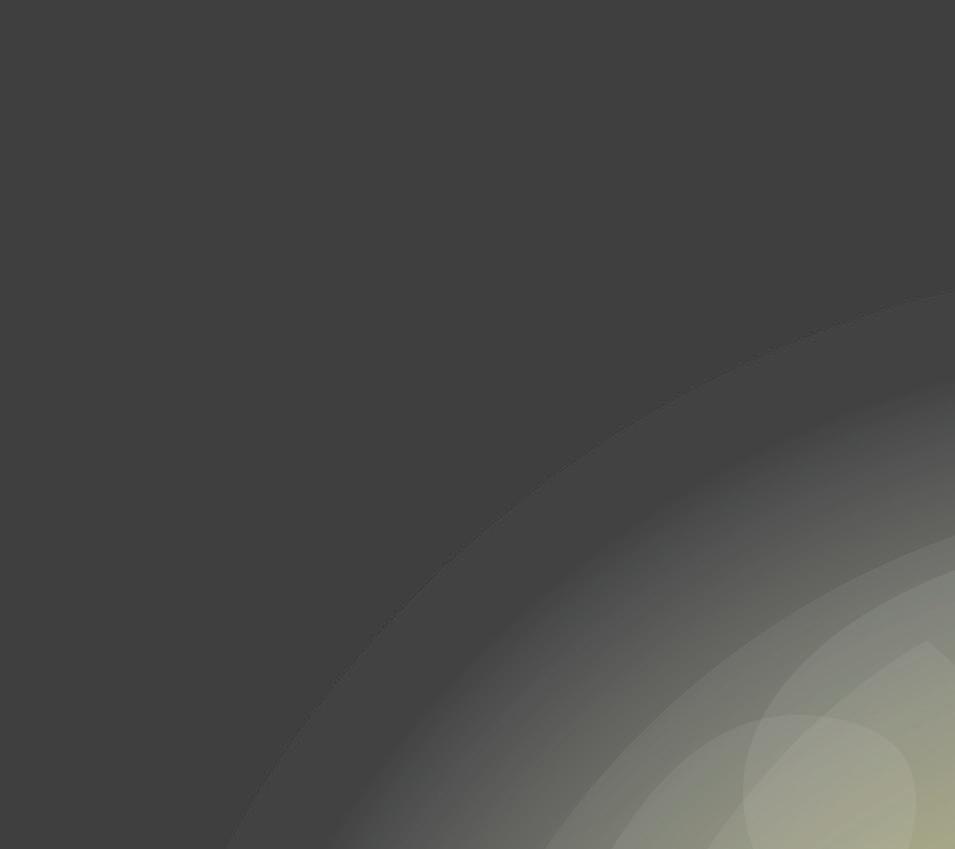
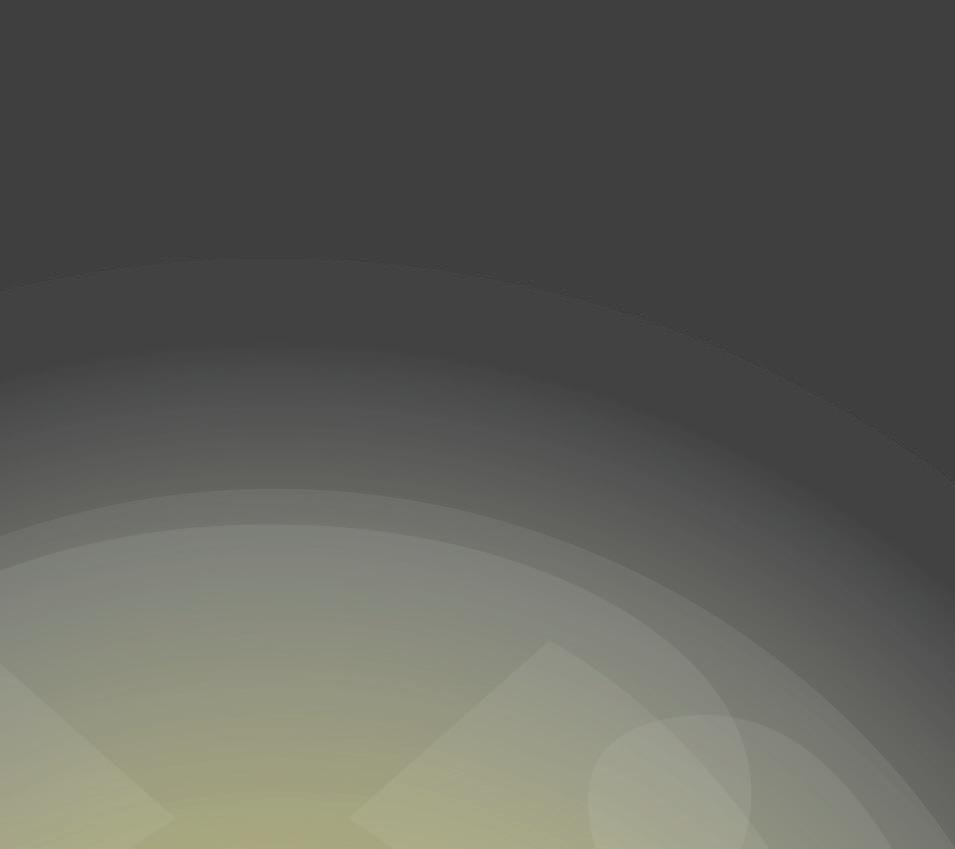
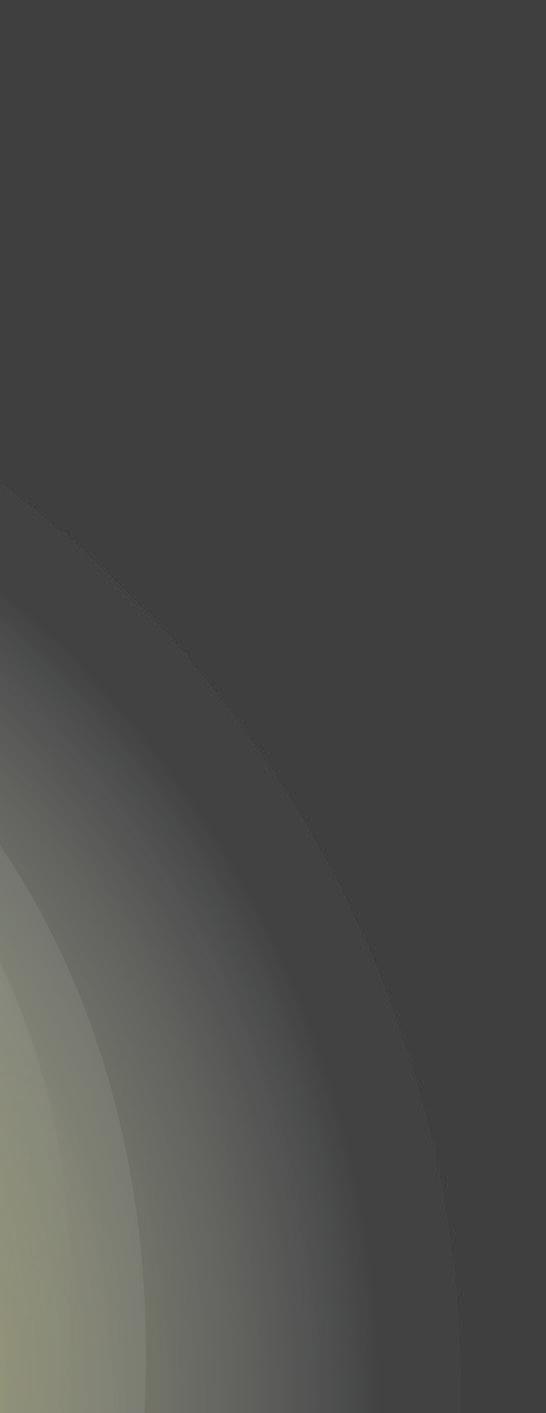
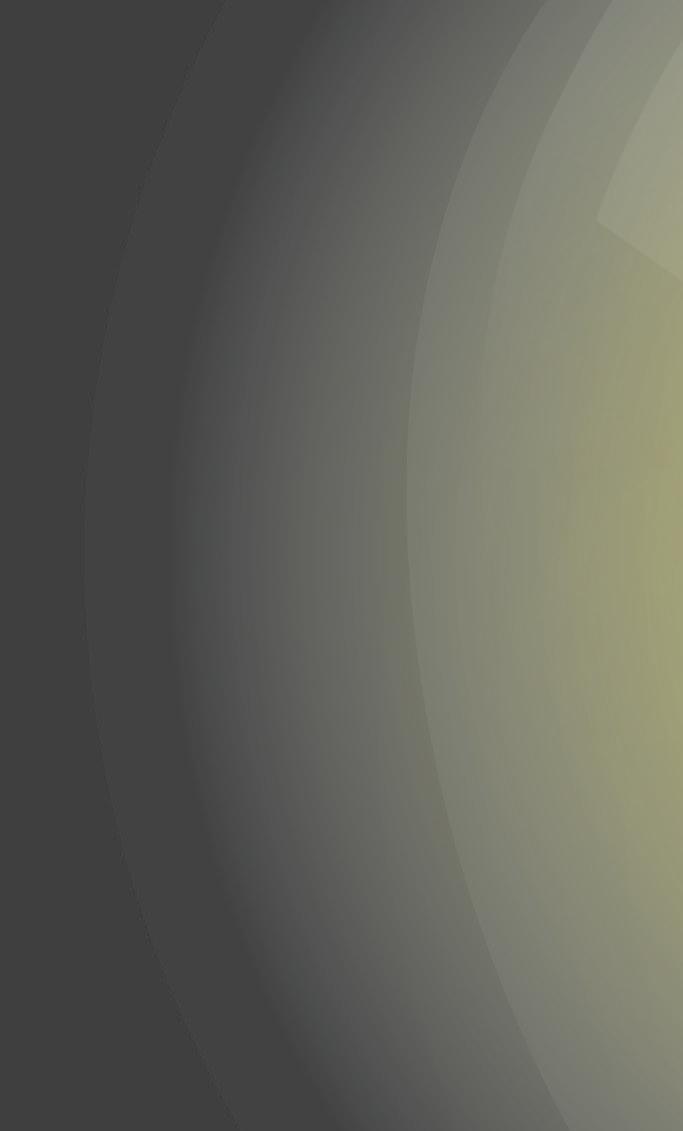
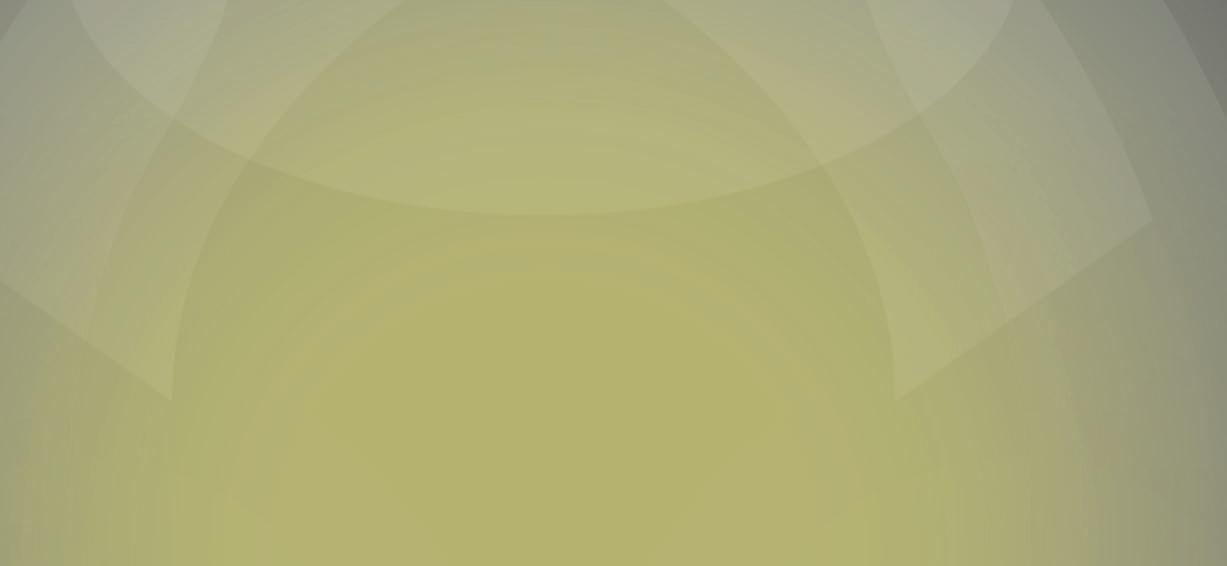
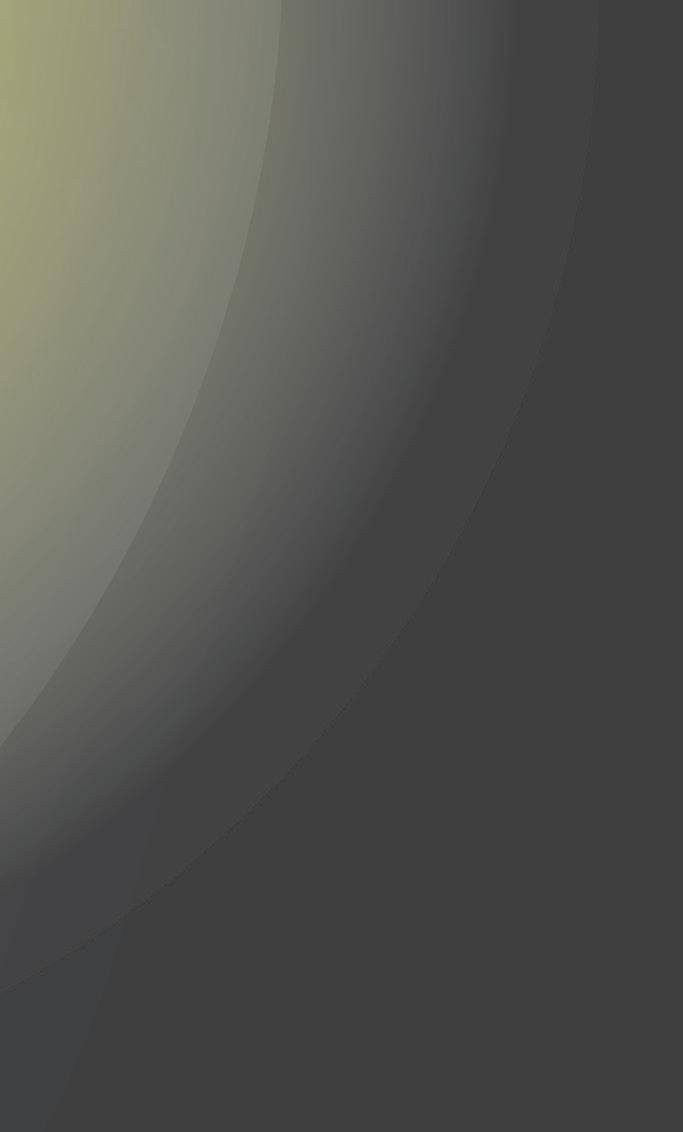
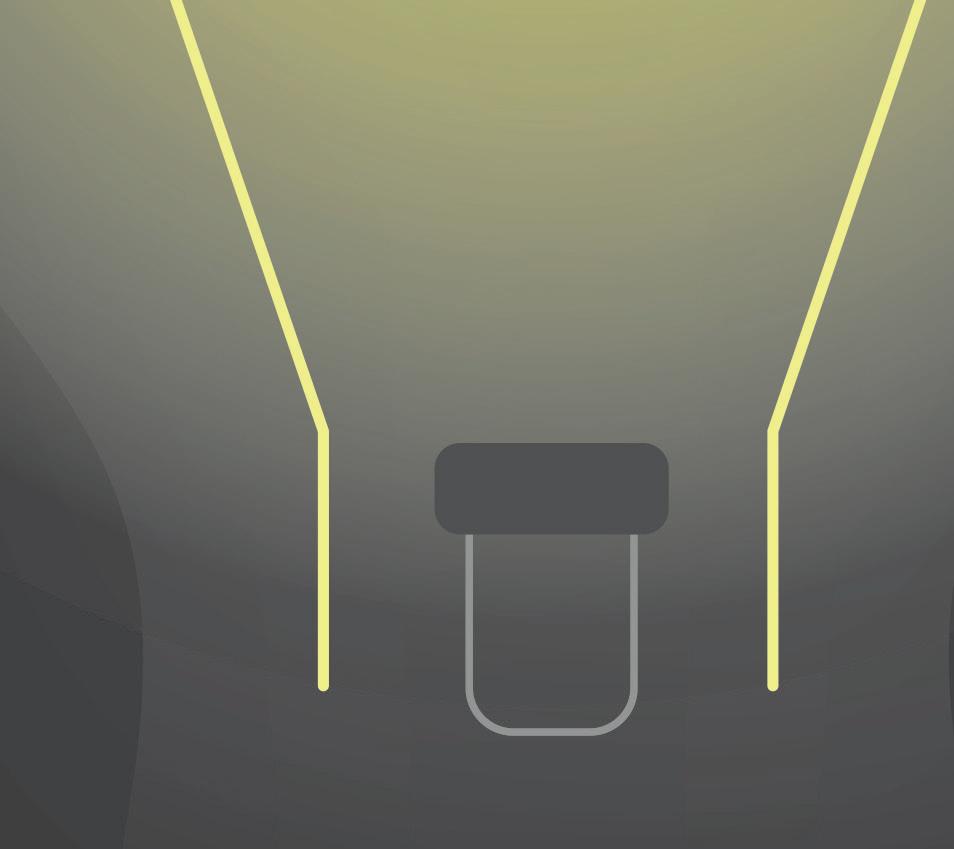
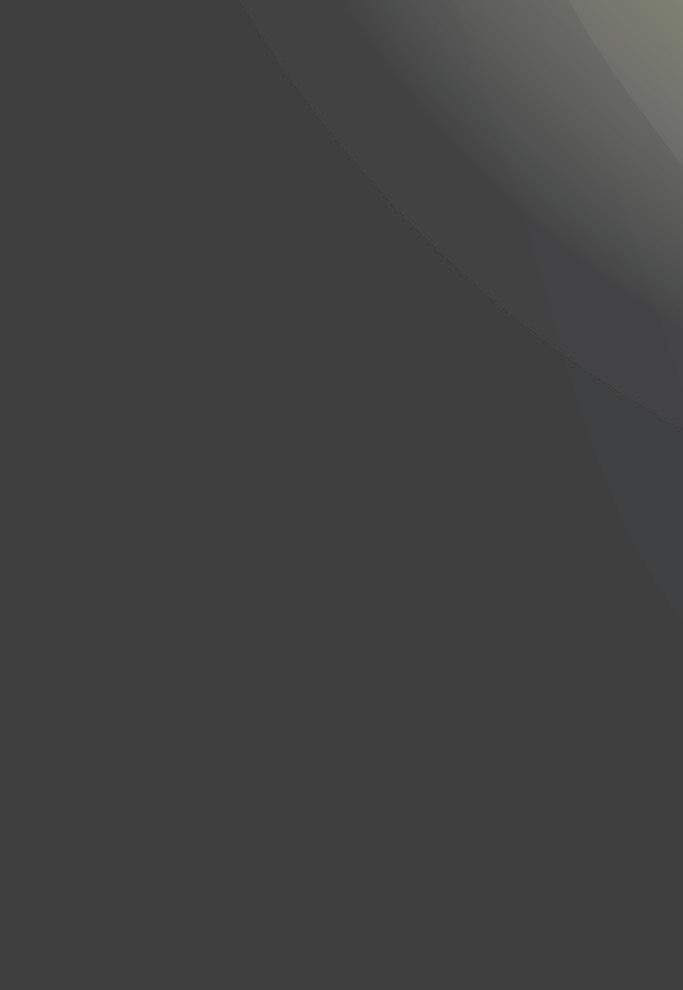
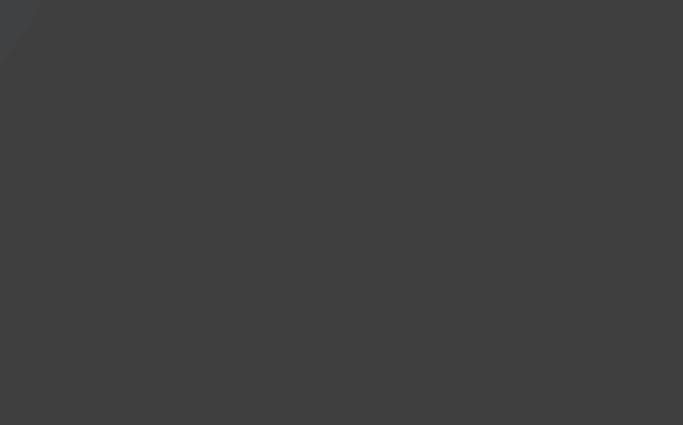
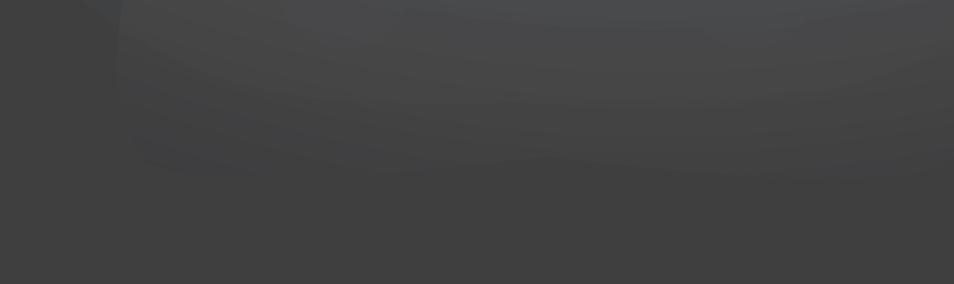
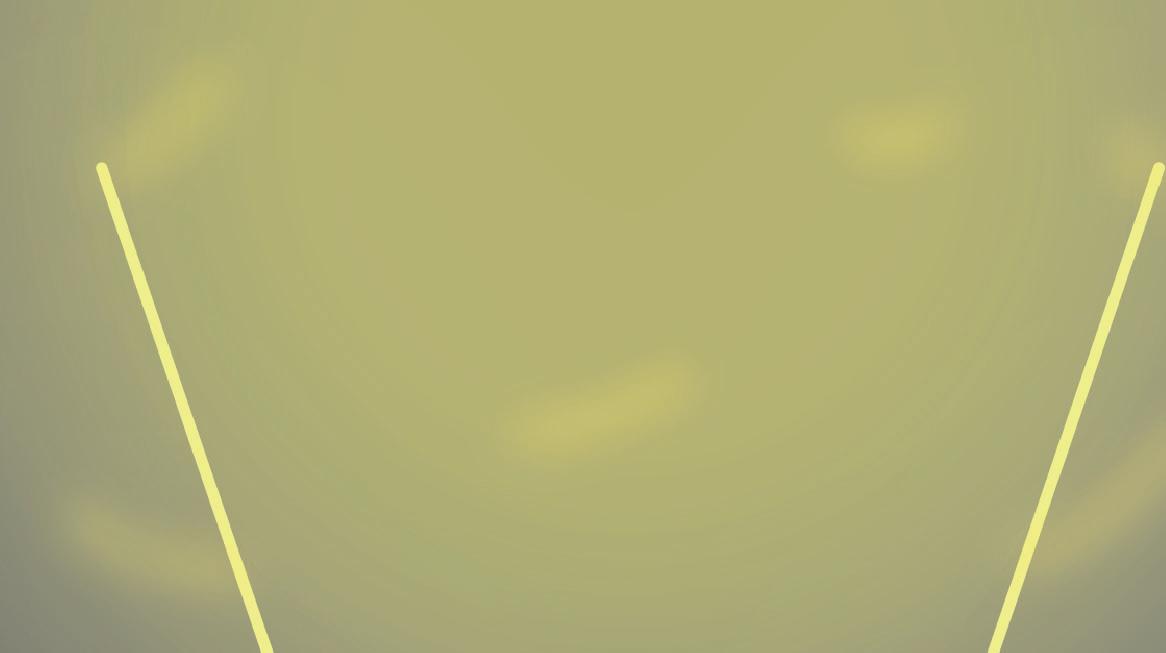
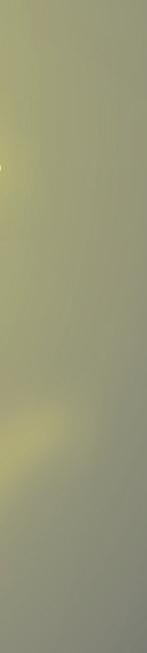
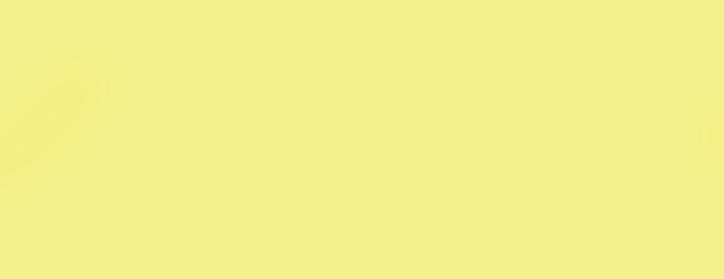

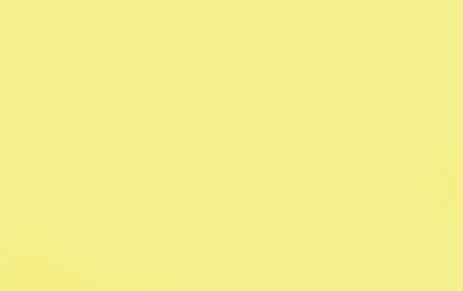
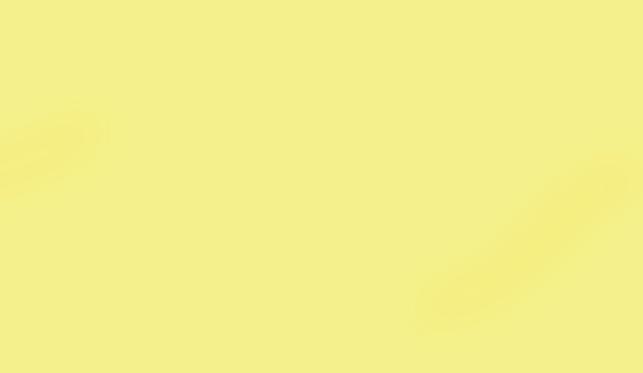
In this issue
11
NEWS
16
30 Twenty years ago, the Rail Safety and Standards Board was born, Mark Phillips, Chief Executive Officer takes us through the journey since then

33 Jonny Campbell on customer service in the transport sector
34 Nikhil Kaitwade on embracing sustainability in transportation FEATURES
38
Clem O’rourke Advance Modelling Group Leader at FrazerNash Consultancy BUSINESS
40 Central Scanning
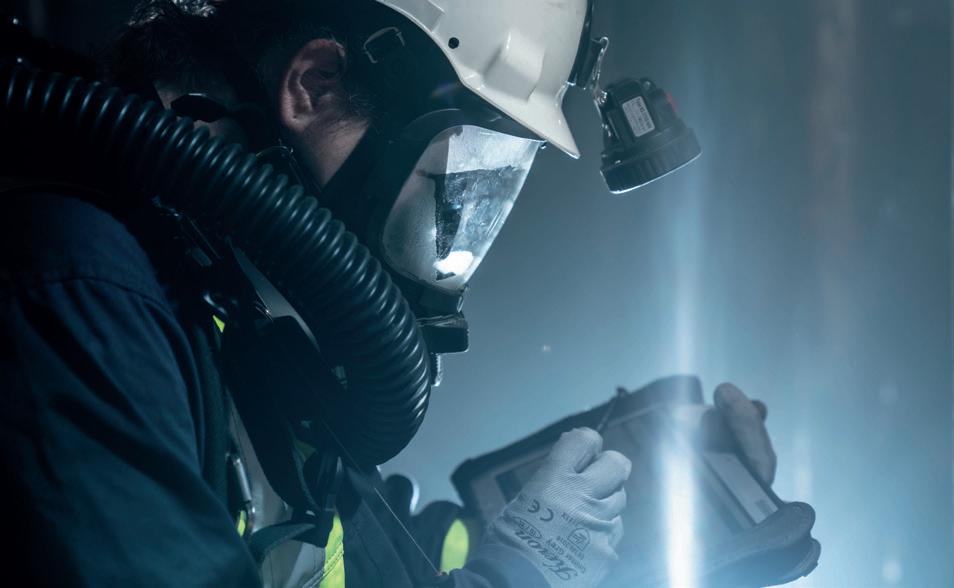
43 Axiomtek
48
Steve Whitmore Managing Director of Engauged
Ric Kirman Business Area Manager Rail & Monitoring at Korec Group
51 RAIL LIVE 2023
Innovation Emerging technologies
Health and wellbeing
Research Data insights
Sustainability Standards
Safety RSSB
Efficiency
We’re with you every step of the way
Leading and facilitating continuous improvement for rail
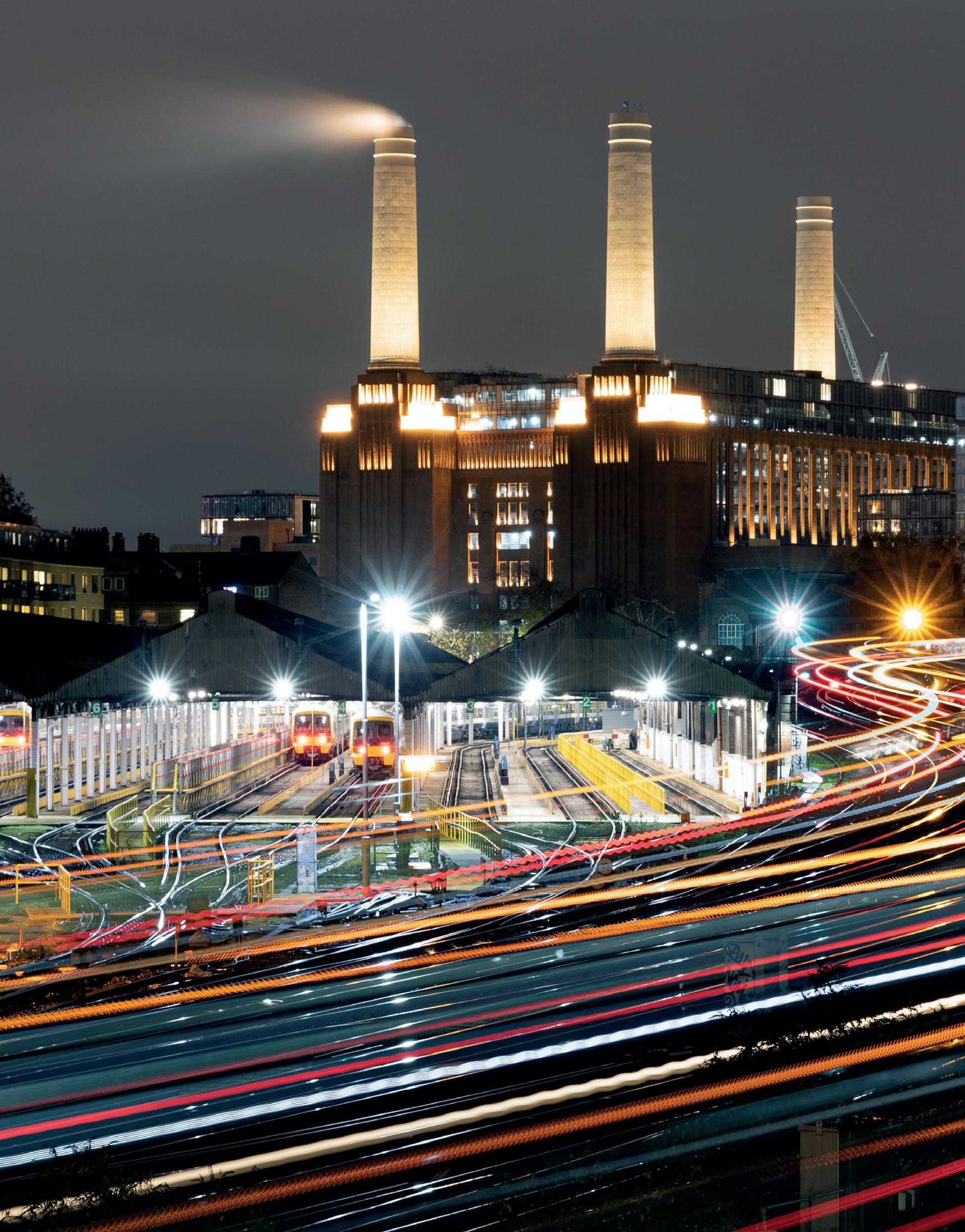
Twenty years ago this month, the Rail Safety and Standards Board was born. RSSB was created after the Ladbroke Grove crash, as a direct recommendation of the Cullen inquiry.
For two decades, we’ve worked hand-in-hand with the rail industry to make the network safer, more efficient and more sustainable. Now our materials and insights form a dynamic, impartial link between innovation, standards and safety. We close knowledge gaps, ensure new technology can be used safely and efficiently, and help codify and share best practice.
For more about our plans for the future, visit rssb.co.uk/RSSBat20
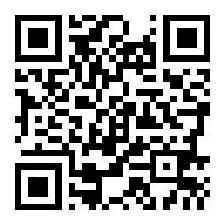
FEATURES
56 IN CONVERSATION
Martin Osman Consultancy Director at Chevron Green Services
60 IN CONVERSATION
Kevin Babstock UK Sales and Customer Service Manager at Advanced New Technology Ltd. (Ant)

64 IN CONVERSATION
Chris Renshaw Business Operations Manager at A. Bratt & Son Ltd (Bratts Ladders)
66 IN CONVERSATION
Chris Manning Head Of Rail And Infrastructure at Sumo Services Ltd.
69 HIGH-SPEED RAIL
Align JV chooses unique onsite procurement solution to support HS2 construction

VIEWPOINT
71 Nuclear Success at the Northern Power Women Awards
73
Andy Bagnall, Chief Executive of Rail Partners takes stock of the plan to revolutionise the country’s railways
FEATURES
75 TRACK & TRACKSIDE
Fit more Square Vehicles through Round Tunnels
79 TRACK & TRACKSIDE
Due to the high-risk nature of trackside environments, ensuring worker safety continues to be an industry priority, says Leo Scott Smith
83 ELECTRIFICATION
Asa Whitfield, Fellow of the Institution of Civil Engineers and rail electrification expert on what the UK is doing in this area and why, and whether goals will actually be reached
86 COSS & SIGNALLER NTS
Laura Hedley, Senior Occupational Psychologist at the OPC shares reflections on the inter-dependent safetycritical relationship between Controllers of Site Safety (COSS) and Signallers and how key Non-Technical Skills (NTS) closely fit together to keep track teams safe
90 TRACK & TRACKSIDE
A Geogrid for Demanding Geotechnical Conditions
101
92
102 PEOPLE
Jon Bradley, John Downer, Jessica Ellery, Katy Dowding, Mike Cliffe, Nick Millington MBE, Marcus Jones, Sophie Bancroft, Kevin Storey, John Dowie, Mattias Bjornfors, Llewelyn Morgan, Dr Peter Weldon
KEEP PRODUCTIVITY ON TRACK
When critical industry processes and concerns require the elimination of lost tool issues, the solution is to minimise human error. Let Snap-on ATC handle the control and tracking automatically
CUSTOMER BENEFIT
• Standardise Work
• Improve Productivity
• Control Inventory
• Reduce Losses
• Control FOD
• Improve Security
• Audit Trail
• Increase Accountability
• Oversight Prevention
• Calibration and Maintenance Reminders
AUTOMATED TOOL CONTROL
With advanced digital imaging technology and proprietary software, Level 5 Automated Tool Control System (ATC) scans the tool drawer and records which tools are removed and replaced in real time. You know where everything is at all times without your techs being slowed down for a second. The system also knows when tools are broken, allowing you to replace or repair them right away. It’s tool control that works hard to keep your techs working at their best.

snapon-industrial.co.uk snaponlevel5.com
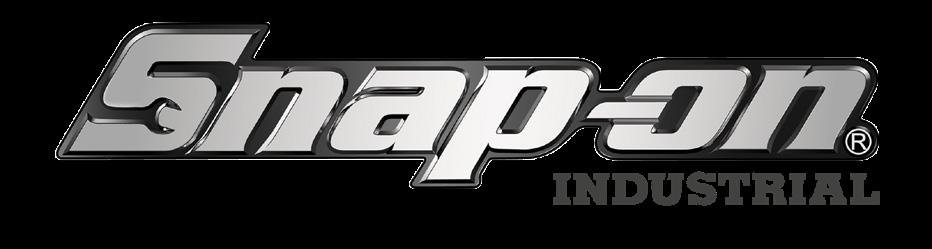
ATC BOX
PRODUCTS AND SERVICES
• Automated Tool Control Box
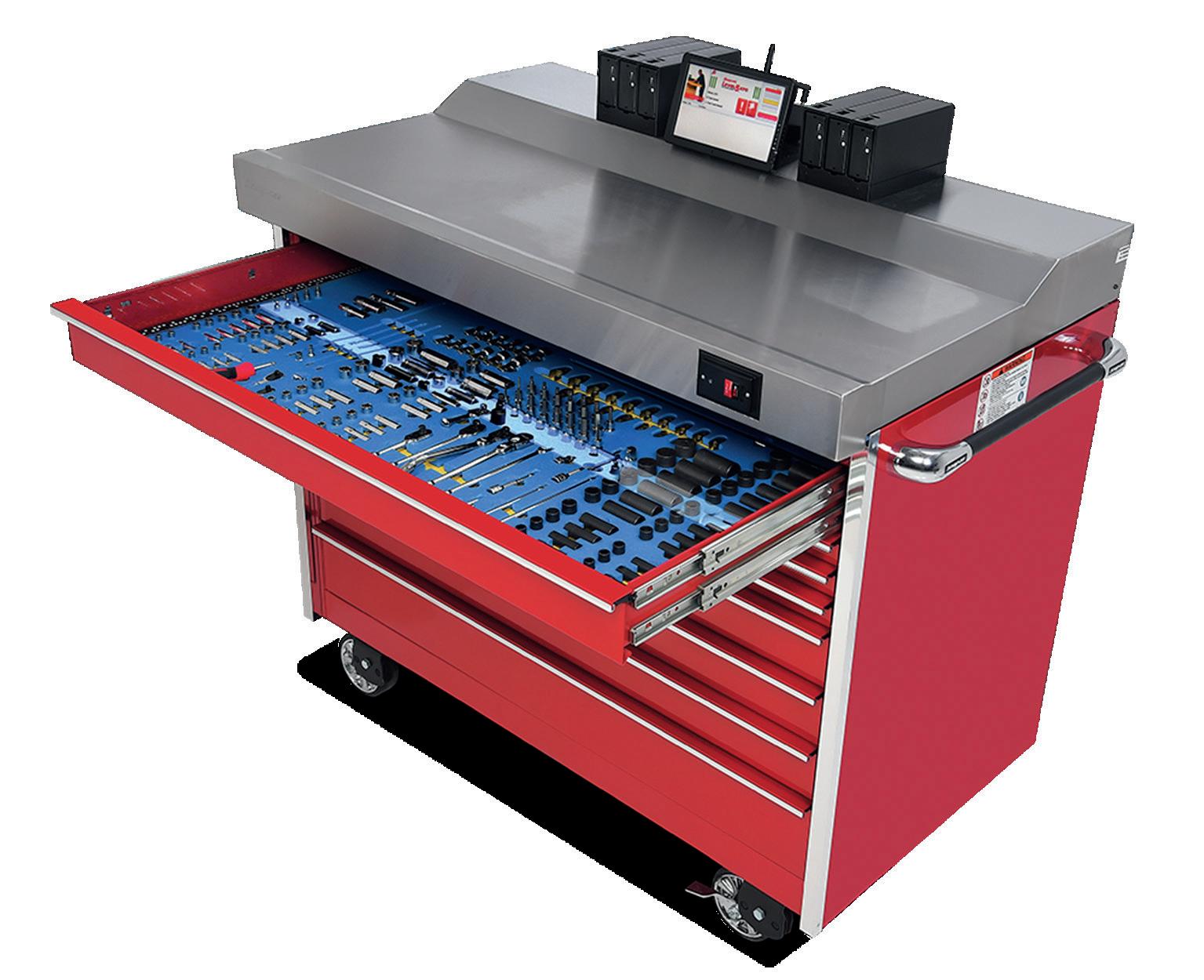
• Automated Tool Control Locker
• Value Add: Networking

• No individual scanning required
• No RFID tags to install
• No limitations on tool sizeif it fits in the drawer, it works
• Optional polyurea elastomer coated top vs. stainless steel
WORKS WITH
AUTOMATION
FEATURES & BENEFITS
CONVENIENCE
• Intuitive touchscreen interface
• Audible voice confirmation of tool removal and replacement
• Automatic locking
• Errors announced and displayed for incorrect tool position
• 10.1” widescreen, 16:9 LED, resistive touchscreen
• Dual wireless antennas for improved connectivity
• Hardware – 64-bit processor with 8GB RAM
ATC LOCKER
• Track irregularly shaped items like extension cords, tools kitted in plastic or fabric carrying cases, personal protective equipment and more
• Track serialised items like torque wrenches, multimeters or micrometers



• Fully networkable – connects to Level 5™ administrative interface
• Recharge while storing power tool
ALL THE ACCESSORIES YOU NEED
• FastFlag™ adds status display lights
• ZoomID™ gives you the ability to track serialised, certified and calibrated assets in the ATC Box

ZoomIDTM
FastFlagTM
Tel: 01536 413 904
industrialuk@snapon.com
POWERFUL ADMINISTRATIVE SOFTWARE WITH REAL TIME REPORTING
• Comprehensive analysis, reporting, and inventory tracking can be performed from administrator workstations located anywhere on the network in real time
• Reports are fully customisable and exportable to Excel or PDF
• Registers transactions in real time – both at the box and between the box and the admin client
• Real time communication includes email alerts when tools are used, when calibration is required, when tool status changes and lost or broken events
STATE-OF-THE-ART BATTERY POWER
• 16+ hours of battery run-time; 30 minutes of backup power for uninterrupted power supply
• Snap-on rechargeable batteries feature state-of-the-art circuit protection that prevents overload
SPECIFICATIONS
• 1 year electronics warranty
• Extended warranty available
• Unlimited number of assigned users
• Networking through Ethernet or wireless
• 1 copy of ATC software required for each administrator
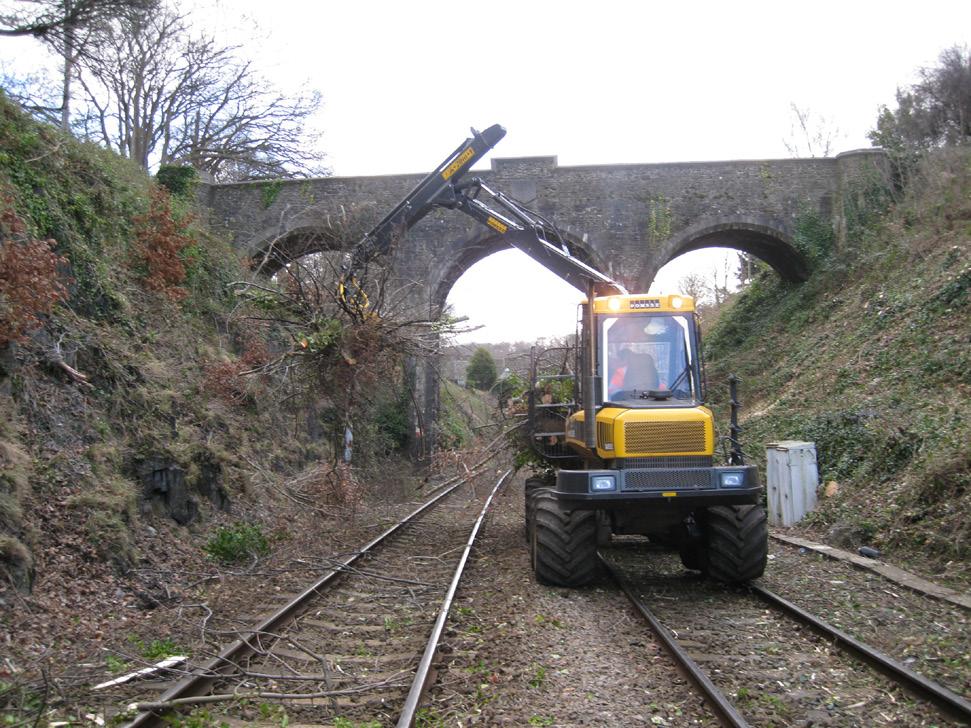
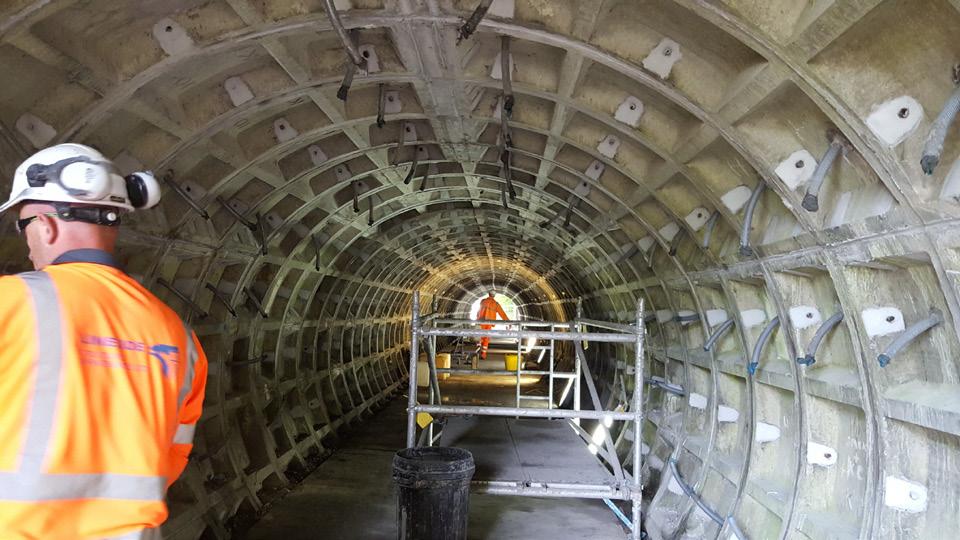

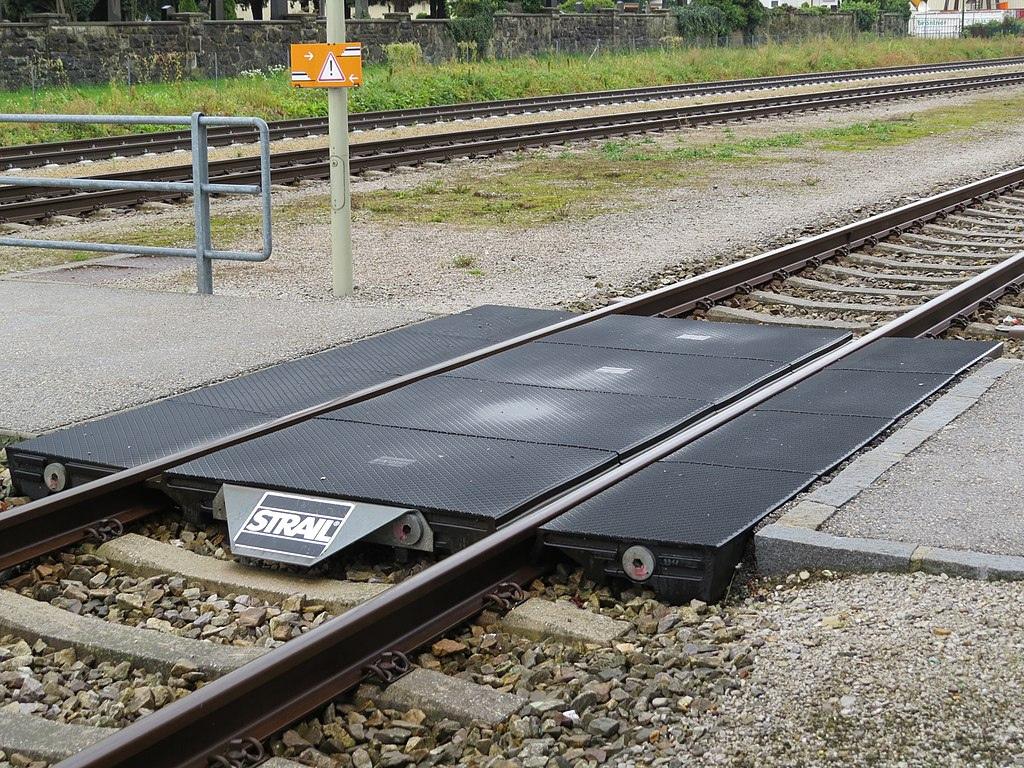
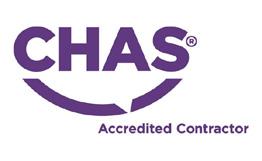
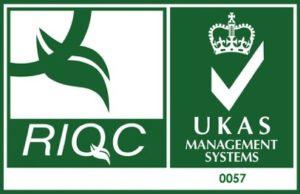
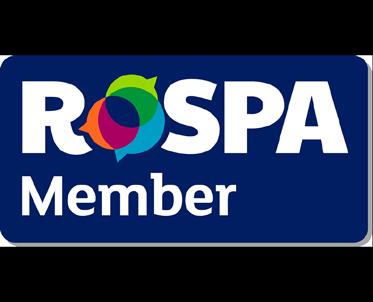
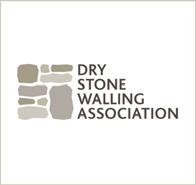

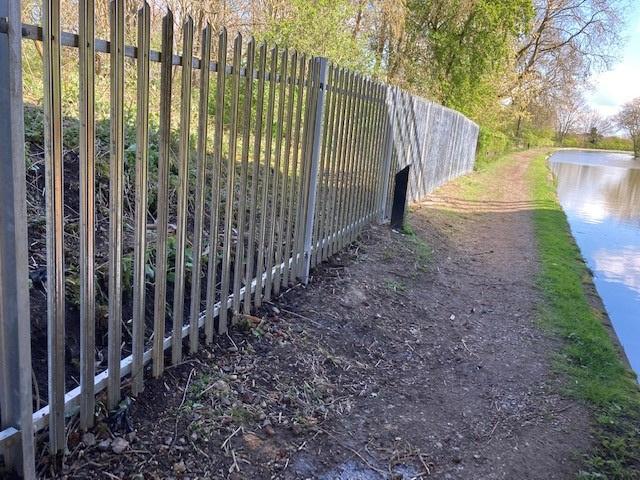
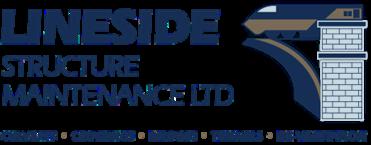
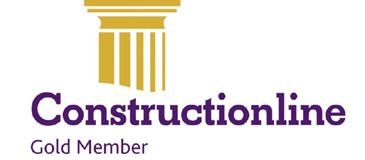
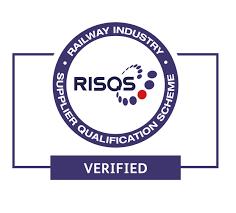
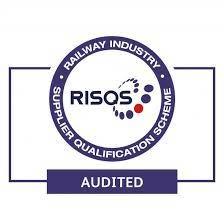
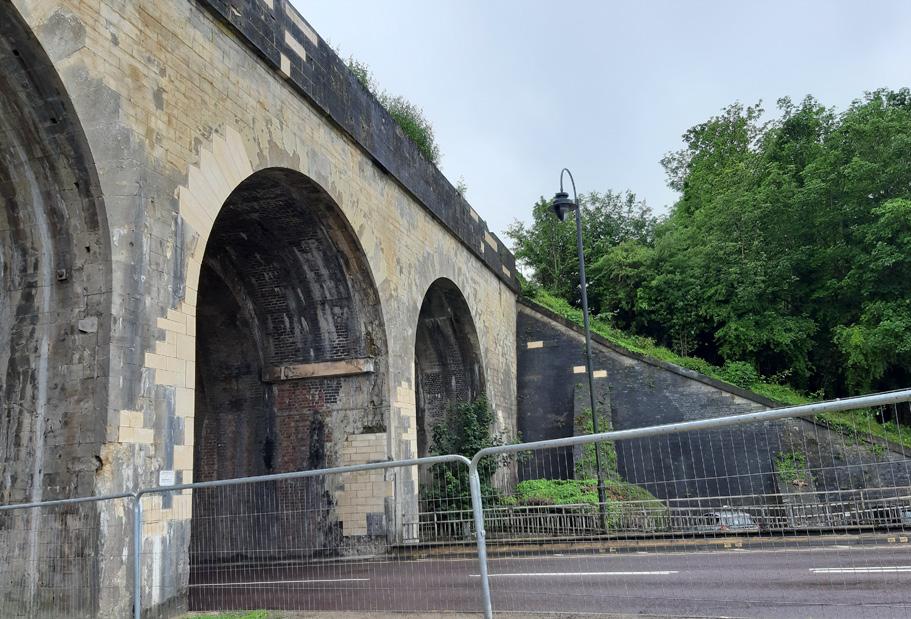
Improvement Works to Begin at Chester Station
As part of Transport for Wales’ (TfW) Station Improvement Vision, work to deliver improvements to customer facilities at Chester station will begin next month.
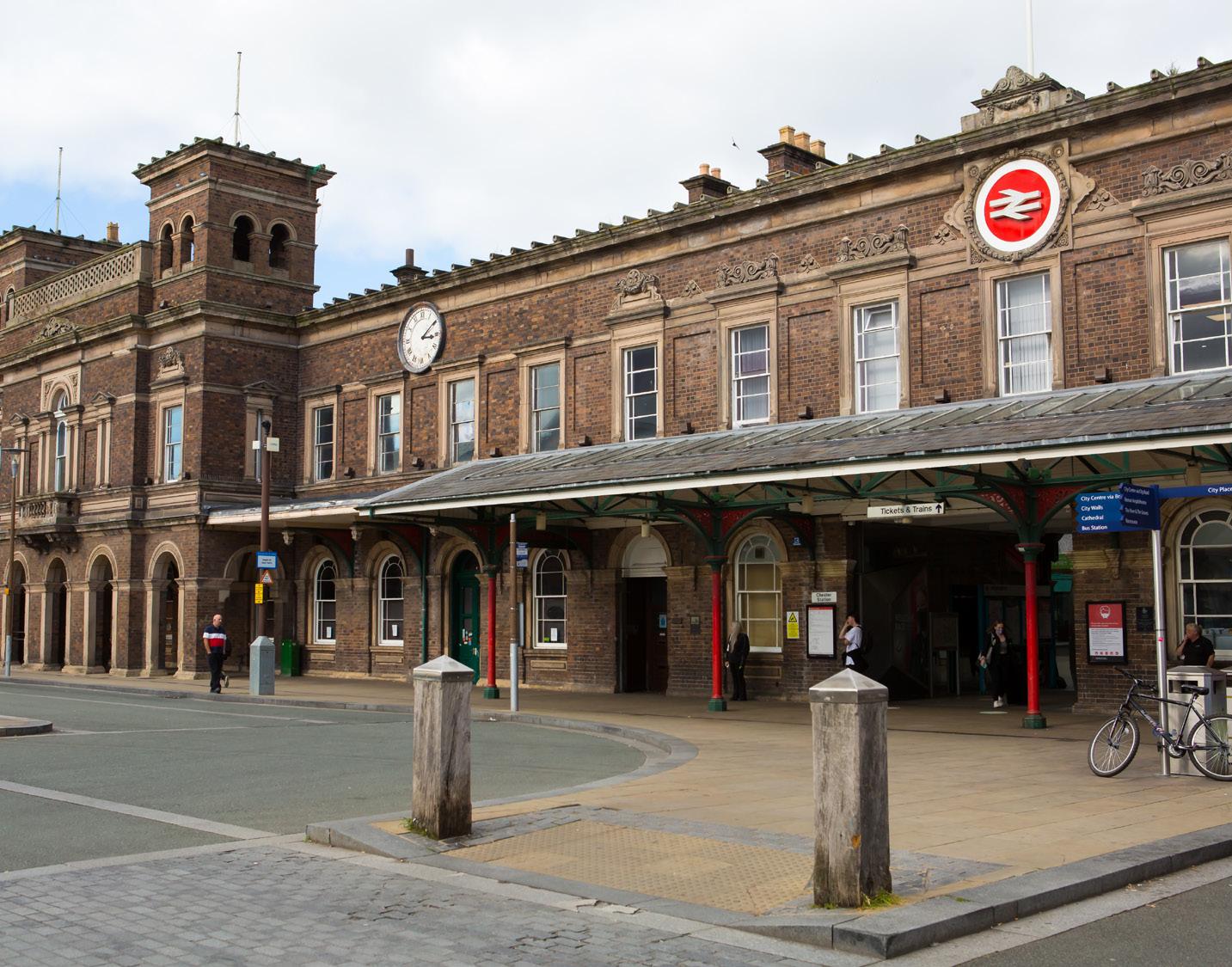
At the beginning of June MPH Construction will begin work on a number of upgrades that aim to enhance the overall customer experience of visitors to Chester station, including new branding and signage, a new passenger assist point, cycle stands, roaming mics and hearing loop systems, full station new CCTV system, toilet refurbishments on the concourse and platforms 4 and 7, a new changing place toilet, water refill unit, platform and concourse seating, waste facilities and LED lighting upgrades.
New Customer Information Screens will be installed throughout Chester station in current and additional locations. This will increase the train service information on the platforms and within the station waiting rooms. New screens will be installed for onward journeys, including bus information, and an interactive screen will be installed within the concourse.
Improvement works in the concourse also include, repurposing of the ticket office to create a new retail unit for the future, a new customer service desk with ticket selling facilities, additional ticket vending machines and a repositioned gateline with additional standard and wide aisle gates. A new quiet room will be introduced as a place for customers who require a safe, isolated space while waiting for their train.
TfW is working closely with industry and local partners to minimise disruption during these works for both customers and
the local community. An essential work site compound will be in place during these improvement works in the Chester West car park from Saturday 27 May until early 2024 and will result in a small reduction in the number of spaces available in this car park. Chester Station East car park will be unaffected.
The aim of these improvements is to provide an enhanced customer experience
and work is currently scheduled to be completed by Spring 2024. TfW is encouraging customers to plan in extra time to allow for potential disruption.
As part of TfW’s Station Improvement Vision, improvements at Flint and Runcorn East stations will begin later in the Summer, with Taziker contracted to carry out the works.
Feasibility Study for Rail Link between Oxford, Witney and Carterton is Published
The case for a railway route connecting Carterton, Witney, and Eynsham to Oxford has been set out in a new feasibility study. The preliminary strategic outline case for the Carterton-Witney-Oxford Rail Corridor (CWORC) was commissioned by Oxfordshire County Council, following proposals from the Witney Oxford Transport Group. The aim was to establish if there is a strategic need for the proposed railway line and to give an indication of the likely investment required.
The study has shown that building a rail link would be feasible and could be justified in transport strategy terms but identifies a number of planning and environmental issues. It also warns about the high financial cost and difficulty involved in undertaking such a project. However, if it went ahead, it would be predicted to be profitable.
The study suggests the journey to and from Oxford could take as little 23 minutes from Carterton, 16 minutes from Witney, and eleven minutes from Eynsham (subject to a more detailed assessment of track and platform capacity). This would represent a saving of around an hour compared to anticipated bus and car journey times in 2031. However, construction costs of building the rail line alone are estimated by the report at between £700 - £900 million, with the scheme potentially being delivered in phases – although no route has been decided at this stage. It would therefore be a long-term project and would also depend on other rail improvements being funded and completed, including the planned upgrade to the North Cotswold Line. West Oxfordshire District Council welcomed the CWORC study and said it strongly supports the work being done to explore the potential new rail link.
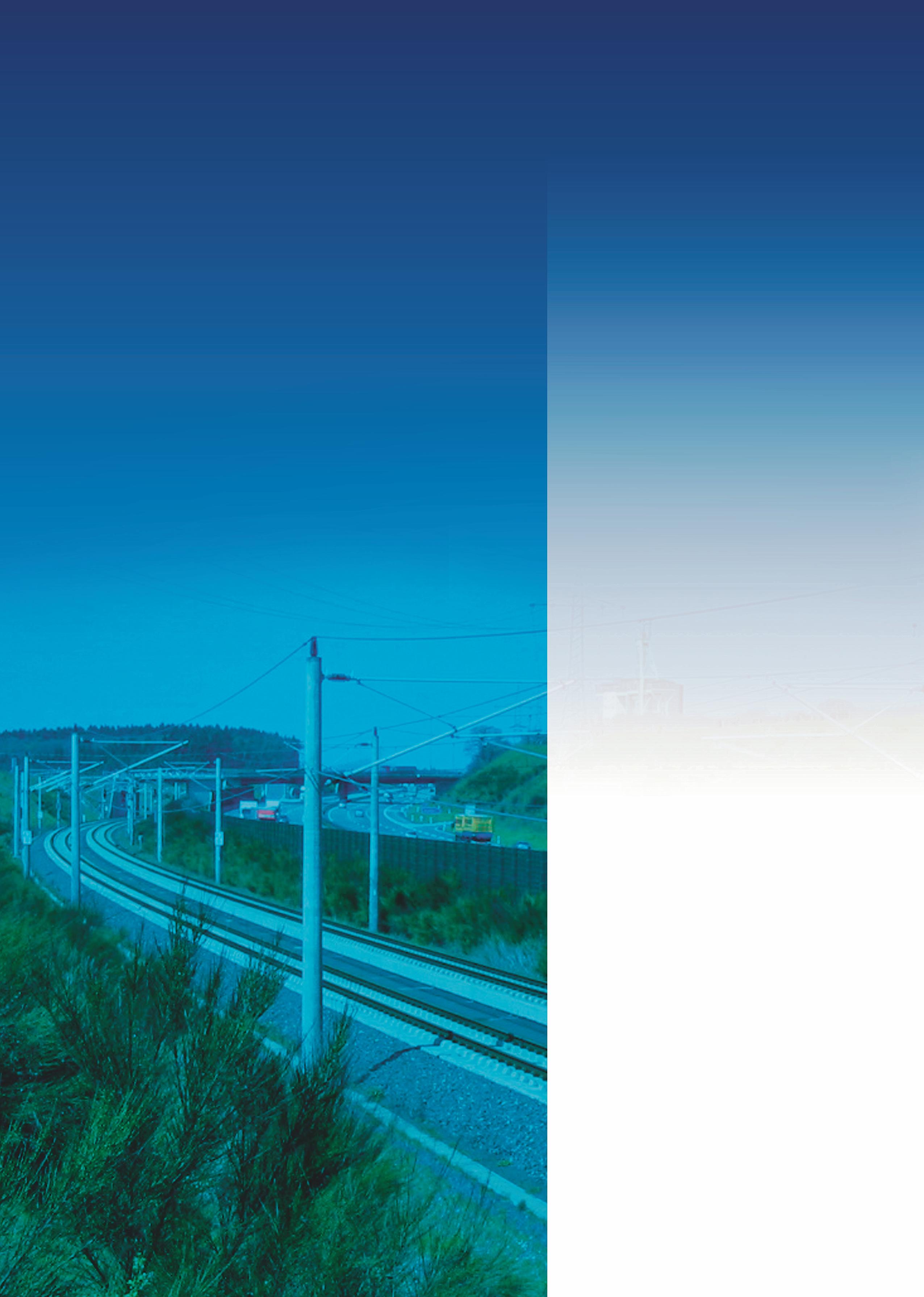

Five-year Investment Plan for ‘Backbone of Britain’ Railway Revealed
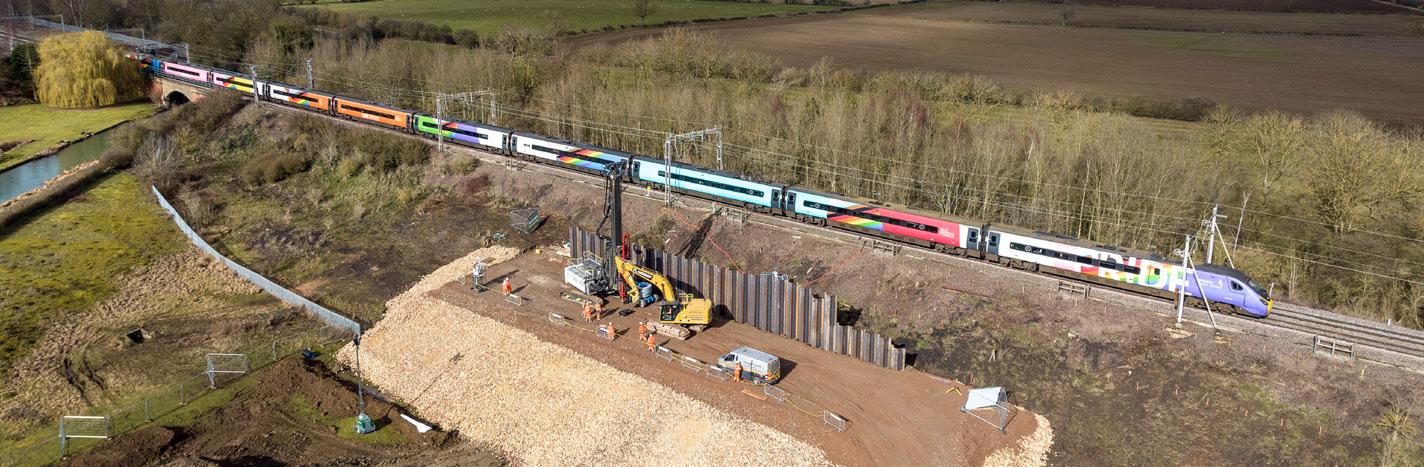
RIA welcomes continued Government support for rail reform legislation and Network Rail’s publishing of Strategic Business Plans for CP7.
Passengers and freight customers are at the heart of the multi-billion pound 202429 business plan revealed by Network Rail’s North West and Central region on 19 May. The regional Strategic Business Plan (SBP) covers the projected activities, outputs and cost of operating, maintaining and renewing its railway infrastructure between 2024 and 2029.
The publication is a major milestone in the ongoing process to determine Network Rail’s funding requirements for the five years to 2029, which are known as ‘Control Periods’, and the next five years will be Control Period 7 (CP7).
The North West and Central region is the economic spine connecting the country’s main cities – London, Birmingham, Manchester and Liverpool, with vital links to Scotland.
It is devolved into three ‘routes’ – West Coast South, Central and North West –all working closely with train operators, politicians and partners to address the local needs of passengers while working together across the regional and national railway network to get passengers and vital freight goods to where they need to be.
In the North West and Central region the main priorities over CP7 will be:
• Improved train performance: Running a cost-effective and efficient railway for the taxpayer while keeping passengers and freight trains moving safely to a reliable timetable. Major investment will take place to prevent delays caused by adverse weather and climate change in the form of drainage upgrades to reduce the risk of tracks flooding, earthwork projects to prevent landslips and upgrading overhead power lines and track to make them less likely to fail in extreme temperatures.
• Environment: A focus on sustainability so the railway not only remains the greenest form of public transport, but its operations do too with the introduction of electric fleet vehicles and employing latest carbon-saving technology across offices and maintenance depots.
• Sustainable growth: Improving current infrastructure to improve
passengers’ experience and make the railway accessible for all. Plans include investment in technology and research and development, and will facilitate the introduction of major projects such as Transpennine Route Upgrade, preparing for HS2 and other targeted investment across the country, along with supporting the continued growth of rail freight through an ambitious but realistic target of 7.5 per cent growth across the national network.
Tim Shoveller, Network Rail’s North West and Central region managing director, said: ‘Running a safe, green and efficient railway on the West Coast and Chiltern main lines along with the Midlands, North West and Cumbria is crucial to the country’s economic success which is why our plan for CP7 is ambitious, focussed on our passengers and customers and reflects the current complexities and challenges facing the industry.
‘Yet it’s not only about running the railway we already have, but making sure it works in harmony with the construction of the new zero-carbon railway HS2 which continues at pace, and also East West Rail with services due to start running on Phase 2 by December 2024. This will no doubt be challenging, but when complete will transform Britain’s railway – and this funding from Government means the North West and Central region will continue to be a foundation stone of these new rail routes for the future.’
Network Rail’s funding is made available from governments over five-year periods, known as control periods, with control period 7 (CP7) starting on 1 April 2024 and running until 2029.
The Office of Rail and Road (ORR) will now review this initial strategic business plan and review how it measures up against the Government’s HLOS (high-level output specification) and SoFA (statement of funds available), and publish its draft determination on this plan later this year including targets, measures and incentives it will hold Network Rail to deliver over CP7.
The Railway Industry Association (RIA) has welcomed Number 10’s recommitment today to rail reform, and its confirmation that no decision has yet been made on legislation for the fourth session of this Parliament. This follows a letter to Prime Minister Rishi Sunak on 9 May, signed by the Railway Industry Association and over 65 rail business leaders, calling for him to ensure legislation creating Great British Railways in this Parliament is enacted.
RIA has also welcomed the publication of Network Rail’s Strategic Business Plans for 2024-2029 in England and Wales, following their approval by the Secretary of State for Transport, Mark Harper. The Strategic Business Plans provide important details about Network Rail’s spending proposals over the next five-year period (Control Period 7, which commences April 2024), which can help businesses plan ahead and deliver work as efficiently as possible. However, the plans have been published later than usual in the five-year funding cycle, and the equivalent Network Rail plans for Scotland have not yet been published, which are needed for rail supply companies to make their own plans.
Darren Caplan, Chief Executive of the Railway Industry Association, said: ‘The Railway Industry Association and our members will welcome the confirmation today that the Government still supports rail reform, and that no decisions have been made on the timing of legislation to create Great British Railways for the fourth session of this Parliament. We continue to call on Prime Minister Rishi Sunak to ensure the legislation necessary to create GBR is enacted in this Parliament, to ensure there is no hiatus either in key decisions about the future of UK rail or in work by the rail supply sector.
‘Rail supply companies will also welcome today the publication of Network Rail’s Strategic Business Plans and the additional clarity that they provide. We will study them carefully to understand the implications for the railway, including on whether they support a smooth pipeline of investment. We note that these plans have come later than usual, and so may make it more challenging for companies to make the full preparations they would normally be able to make – rail suppliers do need earlier visibility of the plans in future. We urge the publication of the outstanding plans for Scotland as soon as possible.’
TPE Set to Unveil Latest Investment at Hull Paragon
Train operator TransPennine Express is putting the finishing touches to its latest six figure investment at Hull Paragon Interchange. A new gateline, designed to reduce ticketless travel and provide a safer space for rail customers, is set to ‘go live’ next week following an installation process that has transformed the station concourse.
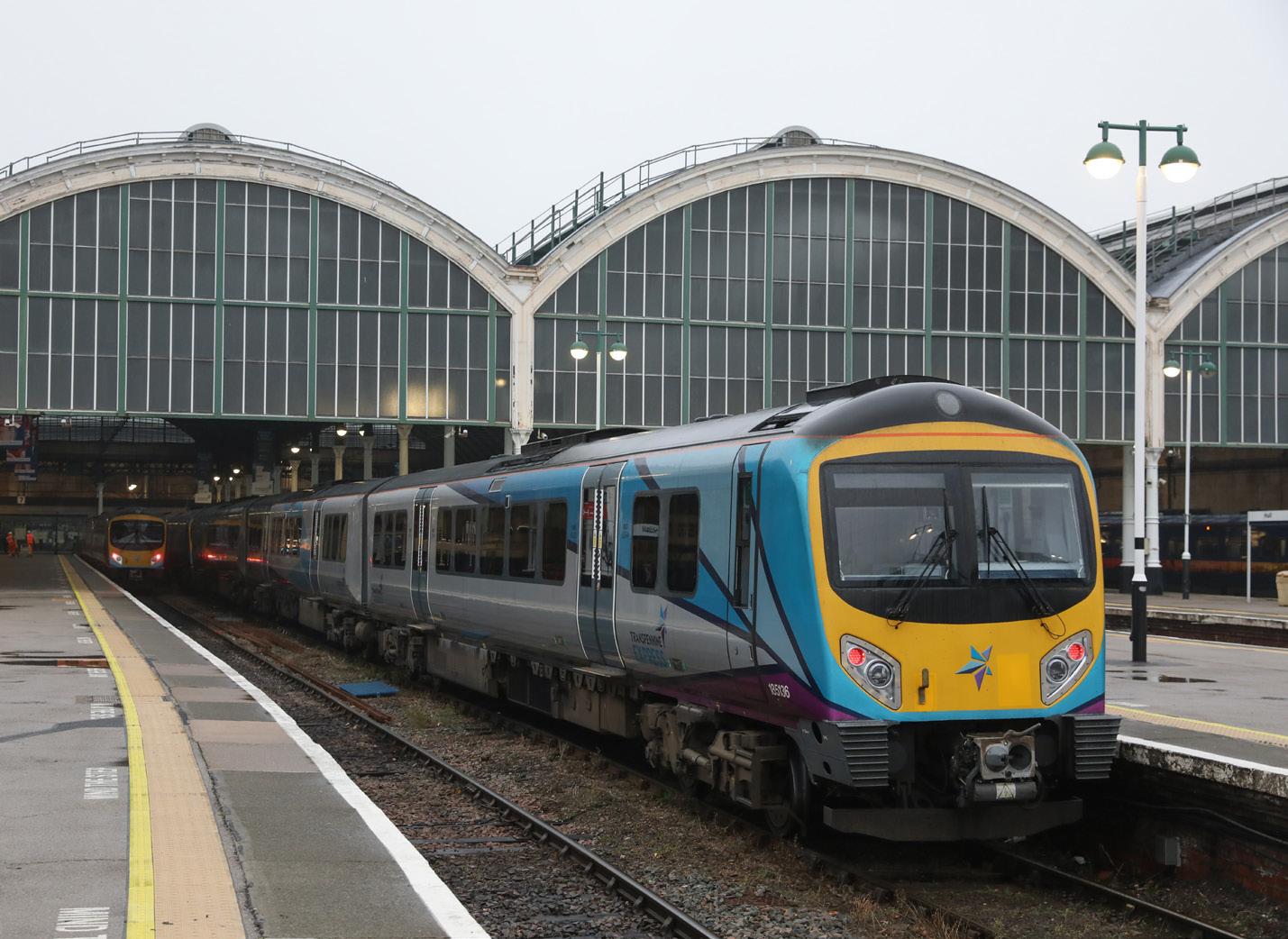
The automatic barriers, which will be staffed when operational, mean rail customers will now need a valid ticket to access the platforms at Hull station. People who want to access the platform to say goodbye to friends or family – or help them to the train – should speak to barrier staff who will use discretion to grant limited access.
Darren Higgins, Commercial Director at TPE, said: ‘The new gateline represents our latest investment in Hull and has been installed to provide an even safer travel environment for our customers.
‘The barriers mean customers will now have to buy before they board at Hull station and tickets for travel are available at ticket vending machines, via our website or mobile app, or from the ticket office at the station.’
Darren added: ‘As with any new technology, it will take people time to adjust to using the barriers and our staff at the station will be on hand to help customers and ensure the gates are used properly.’
Full peak Elizabeth line timetable introduced
Frequencies on the line have now been increased to up to 24 trains per hour between Paddington and Whitechapel at peak time, a train roughly every two and a half minutes. The Elizabeth line's full peak timetable commenced on Monday 22 May 2023 following the May timetable change. The introduction marked the final milestone of the Crossrail project, realising more of the benefits that were promised by Transport for London (TfL) and the Department for Transport (DfT) as joint sponsors including higher frequencies, greater connectivity and faster journey times.
From today, peak time frequencies will increase from 22 to up to 24 trains per hour between Paddington and Whitechapel, with 16 trains per hour running off-peak. The peak will also now last for longer, increasing capacity even further. On the east, more services at peak time will run between Liverpool Street National Rail station and Gidea Park, providing a faster route for those using the Bishopsgate entrance, and in the west, there will be an increase in peak services from Reading, with some trains that were previously operated by Great Western Railway transferring to become Elizabeth line services with reduced stops. The removal of any significant pauses for trains
outside Paddington, will also bring reduced journey times for customers travelling from the west into central London.
The week marked the first anniversary of the opening of the Elizabeth line to passengers on 24 May 2022. In its first week, more than 2.5 million journeys were made on the entire route. Now with journeys from the east and west running through central London, there are an average of around 3.5 million Elizabeth line journeys each week - with around 600,000 journeys on weekdays. This means that the transformational railway, which is on track to break even by the end of the 2023/24 financial year, has already become one of the most used railways in the country as it continues to support easier journeys and new jobs, homes and economic growth.
The railway has been crucial to helping London and the UK economy recover postpandemic, driving public transport demand. TfL figures suggest that the Elizabeth line has attracted around 140,000 additional journeys in London each weekday than otherwise would have been the case. Customer satisfaction is also high on the railway with a score of 82 per cent in TfL's Quarter 4 2022/23 Customer Satisfaction Survey (covering January - March 2023). It has transformed the accessibility of the transport network – with 41 step-free stations unlocking new journeys for disabled and older customers as well as parents with buggies and customers travelling with luggage.
An estimated 30 per cent of Elizabeth line journeys to and from Heathrow have
come from those who might previously have used Heathrow Express to the airport, and in the new timetable there are also more frequent Elizabeth line services to and from Heathrow with trains from Shenfield in the east now going all the way to Heathrow Terminal 5 all day. The airport overall now receives six Elizabeth line trains per hour all day. All Heathrow trains stop at Terminal 2&3, with four trains per hour continuing to Terminal 4, and two per hour continuing to Terminal 5.
Tottenham Court Road has seen the largest (absolute) growth in demand on the Elizabeth line since it opened, with more than 100,000 additional journeys passing through the station each day, more than doubling usage over the year. Farringdon, Whitechapel and Abbey Wood have also seen large rises in demand with 100,000, 60,000 and 30,000 extra journeys respectively, again doubling or nearly doubling the customer journeys that were seen through these stations before the Elizabeth line opened.
Journeys to Canary Wharf as a whole (Elizabeth line, London Underground and DLR) on Tuesdays, Wednesdays, Thursdays as well as at weekends are regularly outstripping pre-pandemic demand to the area. There are now twelve trains per hour running between Canary Wharf and Abbey Wood in the peak, restoring the frequency that was in place when the Elizabeth line opened last May, with a train around every five minutes. The morning and evening peak times also now last for longer, increasing capacity even further.
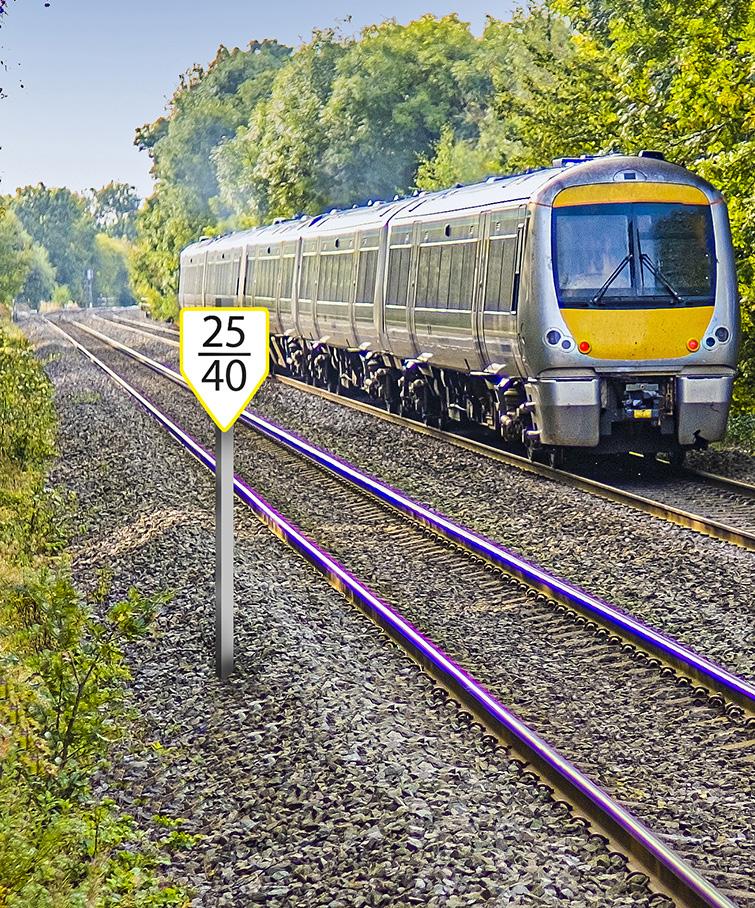


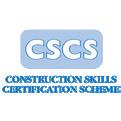
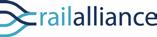
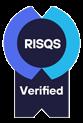
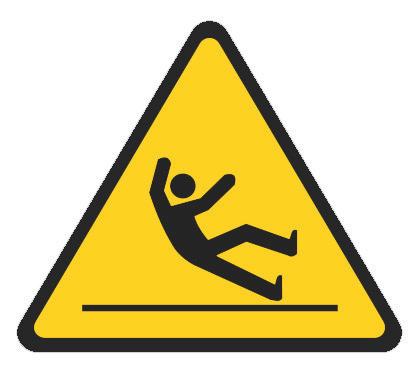
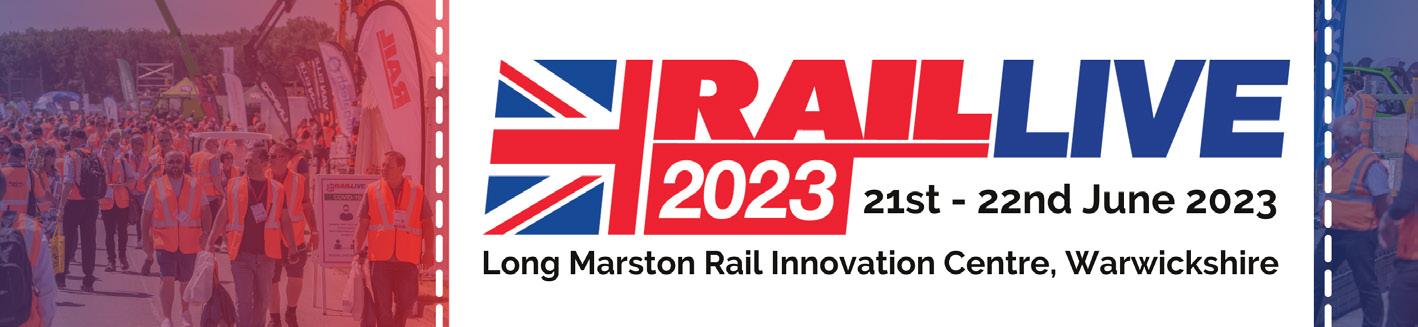
Technology for Life
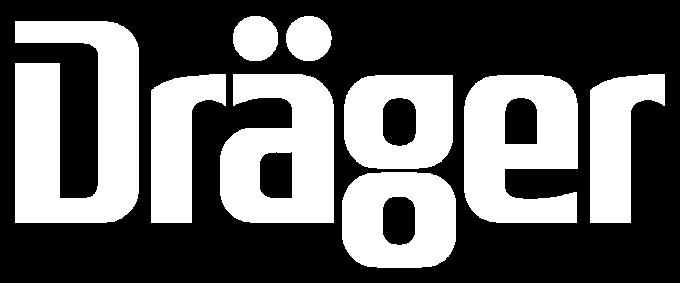
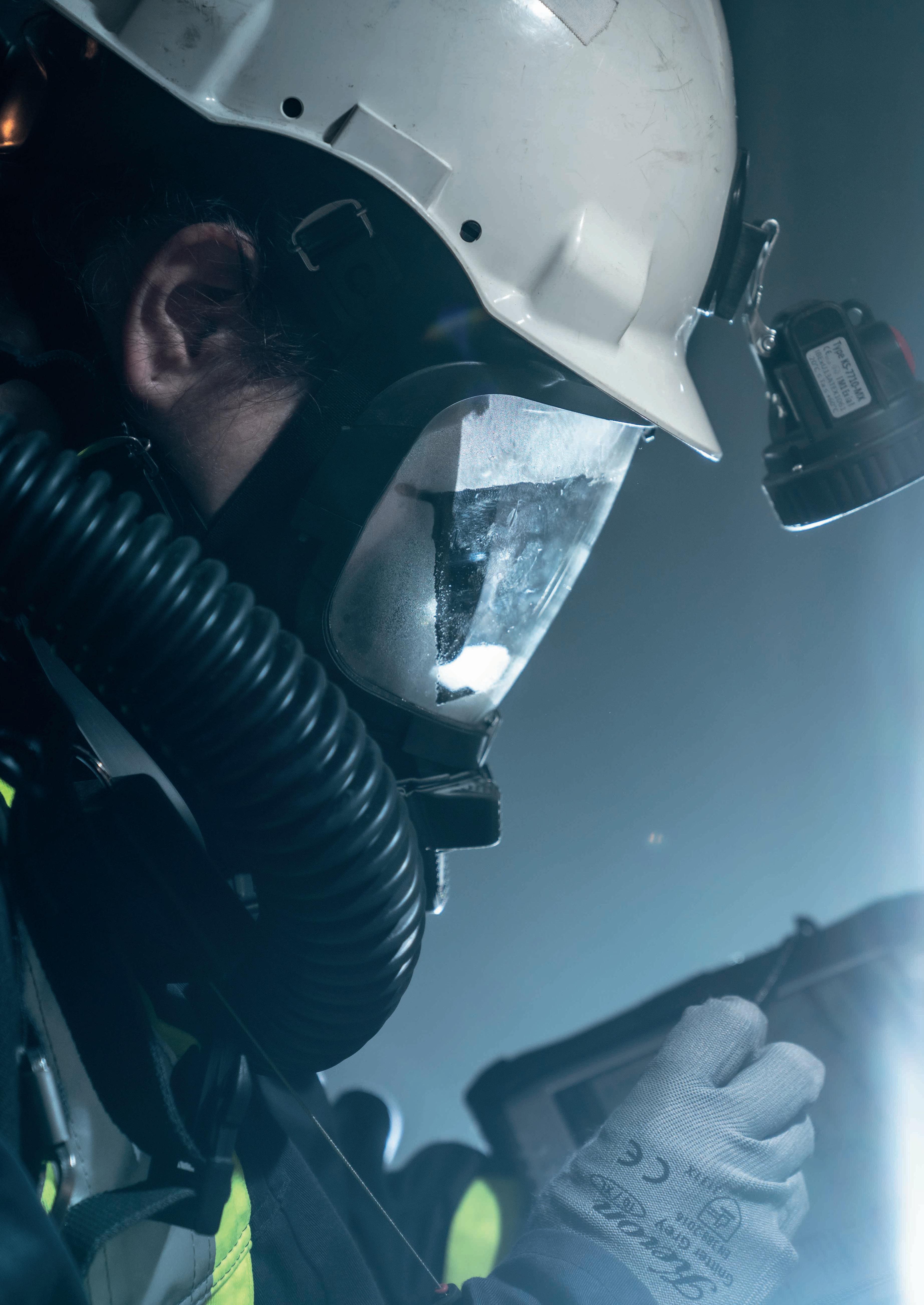
Sam Sherwood-Hale spoke to Sarah Sanderson, Tunnelling Product Specialist at Dräger Safety UK Ltd about medical and safety technology and how their products protect, support and save lives
SSH: What was the founding inspiration behind Dräger?
SS: Dräger are a leading manufacturer of both medical and safety technology products. In so doing, we protect, support, and save people's lives around the world within hospitals, through fire departments, emergency services, authorities, and within both tunnelling and its associated industries.
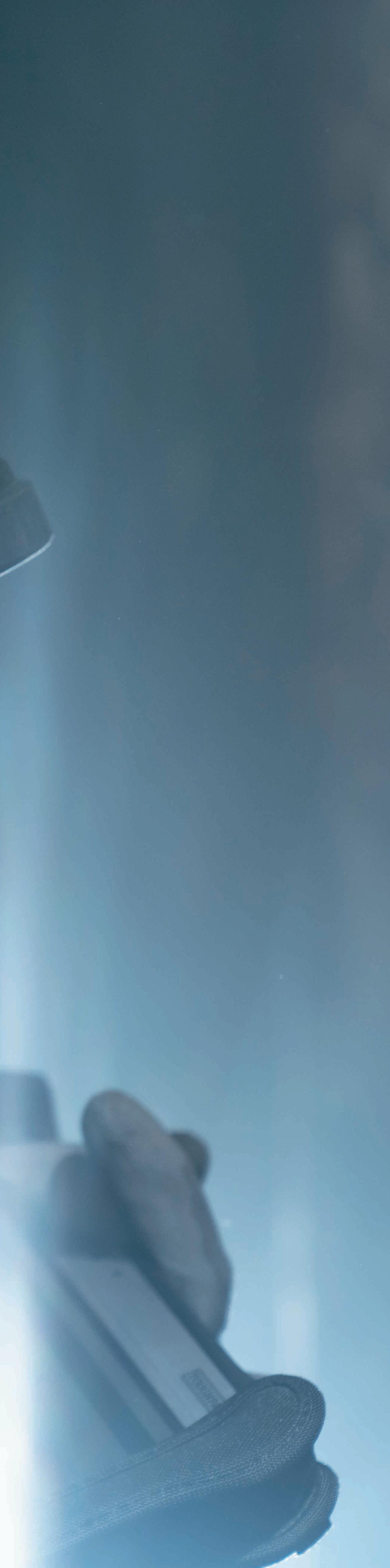
Founded in 1889, Bernhard Dräger invented the Lubeca valve, ultimately resulting in the first high pressure controlled-release valves and closed-loop technologies being created. While first designed to release carbon-dioxide gas into beer taps, this technology developed to become a crucial component of medical and safety technologies in the many years that have followed.
In 1906, following a mining disaster, Mr Dräger travelled to France taking with him a Dräger breathing apparatus he had developed two years earlier. Its continued use gave rise to the term ‘Drägerman’ –given to a group of extraordinary men and women all across the world who have volunteered to be trained in mining/ underground rescue. Whilst the technology has of course been modernised over the years, the ethos of the business remains the same: to protect and save lives in challenging environments.
SSH: How long has your company been in business?
SS: Dräger has been synonymous with technology for life for more than 130 years. Protecting, supporting, and saving lives is a key part of our DNA. The company was founded in Lübeck in 1889, and is now in its fifth generation as a family-run business. From humble beginnings, the company now has over 16,000 employees across the globe and is present in over 190 countries.
SSH: What types of products and services do you offer?
SS: The products and services we offer are vast and encompass numerous different sectors. Within the fields of emergency response and personal safety technology, our products include gas detection devices, self-rescuers, breathing apparatus, thermal imaging cameras, mine refuge chambers, impairment monitoring and detection alongside assorted PPE solutions and ancillaries.
But with great products, you need great support; the Dräger Training Academy
and Dräger Services teams are designed to enhance the efficiency of equipment, to consolidate best-practice and equip teams with industry-leading knowledge and experience to enable users to maintain and operate its technology for use in hazardous environments with minimised risk. Service agreements are also part of our offering, packages such as: TotalCare, PreventiveCare, ExtendedCare and PartnerCare are all available to our customers to ensure effective maintenance of equipment, extend manufacturer warranties and include provision of repair parts and labour, dependent on the level of care selected.
SSH: What are some major projects you’re currently working on?
SS: Several rail projects require, or have required, Dräger Safety equipment, utilising different products at different stages of the project timeline. Most recently, several stages of the HS2 project use the Dräger Oxy range of self-contained selfrescuers. These 30 minute and 60-minute devices provide additional options for the emergency planning concept and ensure the highest standard of breathing protection for personnel. Rescue trains are also in operation in Europe, across Switzerland and Germany to provide emergency aid for rail networks in the absence of road or air access through difficult and unpredictable terrain. Speaking more broadly, most major projects, including rail, require some form of PPE. Examples of the Dräger PPE range include reusable and disposable suits, head protection, respiratory protection and safety eyewear, continuing to protect personnel in the harshest and most dangerous environments with the confidence that they are safe from harm.
Whilst technology develops at fast pace, we anticipate future focus to be built around information and data processing with interconnected functionality.
Hazardous environments carry enough risk alone, so both Dräger Alcohol and Drug screening devices alongside Vehicle Immobilisers are used in a growing number of industries including many rail, transport and industrial applications, ensuring control of risk due to impairment.
SSH: What would you say is the most exciting technology in the industry?
SS: Whilst technology continues to advance at fast pace, real excitement has risen through the development of interconnected and multi-purpose emergency response systems that not only prevent dangerous incidents from taking place but also provide early identification.
Designed for long-duration deployment in hazardous environments, Dräger’s flagship Closed Circuit Beathing Apparatus (CCBA), the BG ProAir, prevents harmful substances and contaminants from entering the sealed breathing system. With the ability to allocate oxygen dosage according to your work rate and specific environment, rescue tactics can evolve according to the surrounding environment to further protect against danger. But where this technology is especially innovative, is in its ability to integrate with additional life-safety devices, and smart onboard electronics.
Hands-free thermal imaging cameras such as the UCF® FireCore added provide
hands-free vision in low-visibility, unfamiliar terrain that tunnelling personnel may encounter. This innovative product provides constant vision from a display screen within the Dräger full-face mask, meaning emergency and rescue teams have greater situationally awareness and an improved level of orientation.
SSH: What are some of the biggest challenges this sector currently faces?
SS: One of the biggest challenges within the tunnelling industry is that the numerous, on site, contractors and sub-contractors have different preferences between not only brands but also product types, a situation which can make safety planning and procurement particularly challenging. These challenges, however, are understandable, given the huge scale of certain projects.
The industry also suffers in the form of overlapping, or indeed underlapping guidelines and safety precautions that intersect with those found within the wider construction industry. Tunnelling often sits between the more stringent mining regulations and construction regulations in this regard. So, for example, a project manager working on a tunnelling project may be from a construction rather than a mining background, and that can lead to inconsistencies in how underground safety is approached.
Whilst presenting significant difficulty to industry professionals, the answer to both challenges can be found through greater transparency and cross-company collaboration. We as an industry need to work together to ensure that safety planning is as straightforward as possible, and that procurement can be viewed holistically thereby reducing project timescales and protecting industry personnel in the same breath.
SSH: How can we make tunnelling within the rail industry an environment people want to work in?
SS: Tunnelling environments can be extremely hazardous, with a variety of different machinery being used within a confined space, often at the same time. We regularly hear of global projects where stakeholders have been extremely relieved when there have been no major incidents after a year. The fact that these incidents are relatively common goes to show that serious accidents are not that rare, and safety equipment and planning should not be considered a ‘nice to have’ but deemed critical and essential.
Manufacturers hold responsibility to keep tunnelling personnel as safe as possible in the confines of such environments. Detailed safety and rescue strategies must be planned, coordinated, and agreed across all interest groups. These efforts must be made to increase the health, safety, and wellbeing of tunnelling professionals, to retain and indeed attract new staff in an industry with falling numbers.
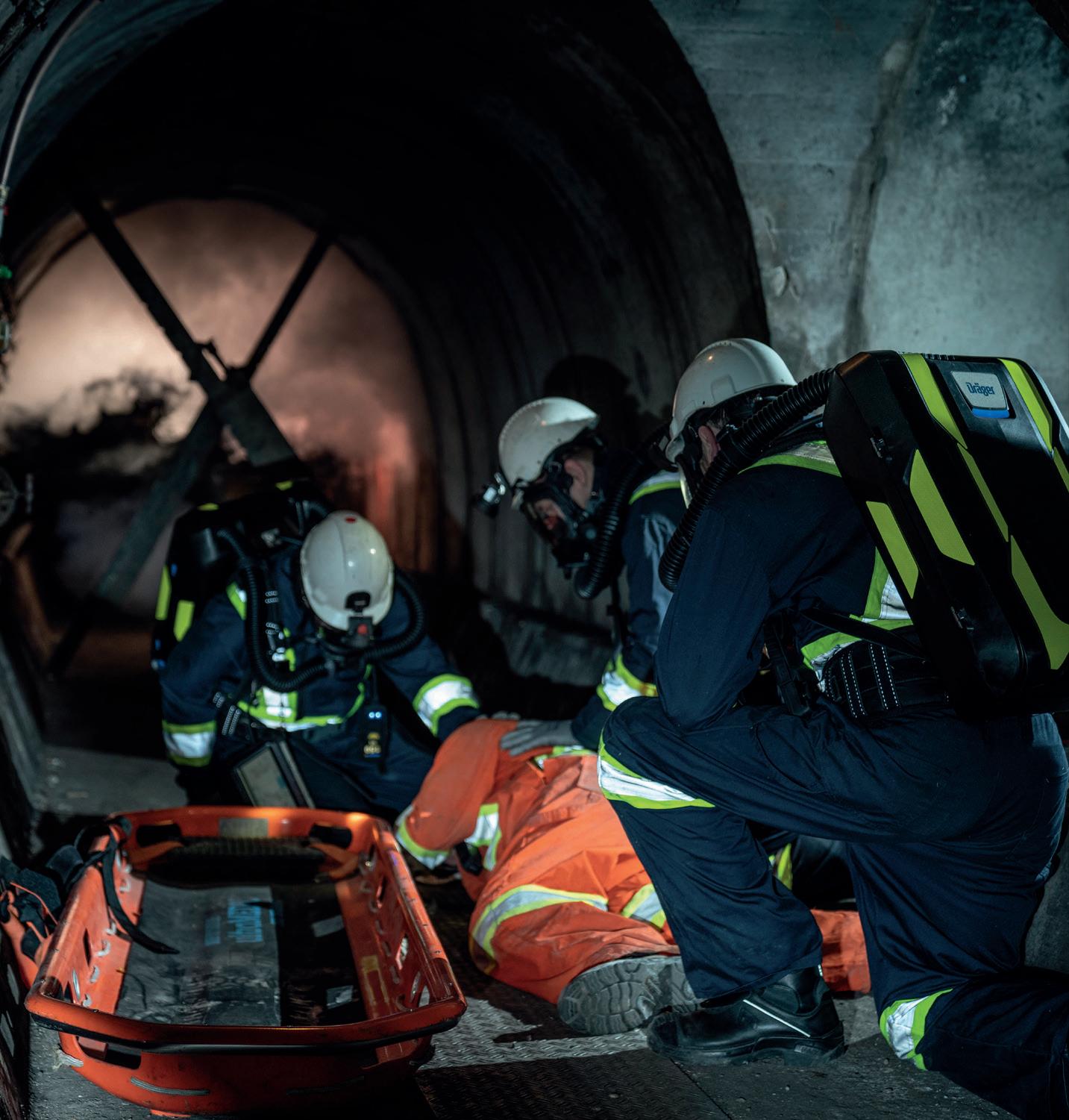
If we can’t retain staff through feeling valued, safe, and healthy, the industry is failing in its mission.
SSH: In terms of technology, how do you anticipate things might change in the next five to ten years?
SS: Whilst technology develops at fast pace, we anticipate future focus to be built around information and data processing with interconnected functionality.
Knowledge, as the saying goes, is power and in an emergency, the quality of information received about an individual and the risks that they face can be the difference between life and death. By combining technologies, such as gas detection, SCBA/CCBA equipment and thermal imaging cameras with sufficient monitoring oversight, we can detect changes to a person, or their environment and adapt rescue or operational tactics to prevent potential dangers before they present worry.
Whilst Bluetooth® provides shortrange connectivity to several products, the development of long-range transmitters would be revolutionary in the tunnelling and associated industries, providing the ability to enhance communicative channels, present clearer commands and provide sufficient oversight to keep individuals and teams safe from harm.
RIA Annual Conference 2023
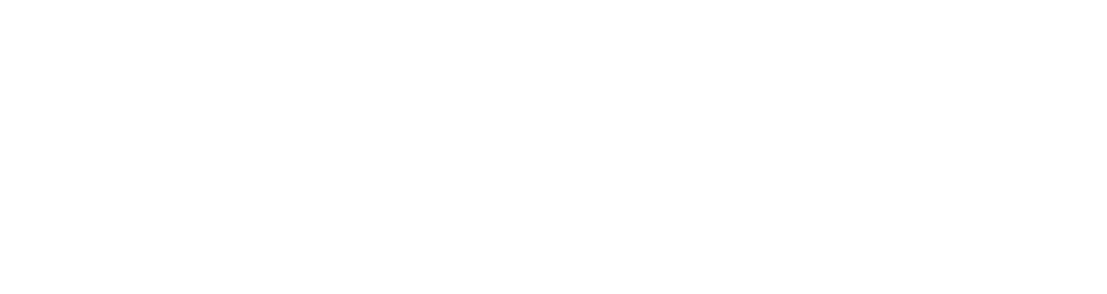
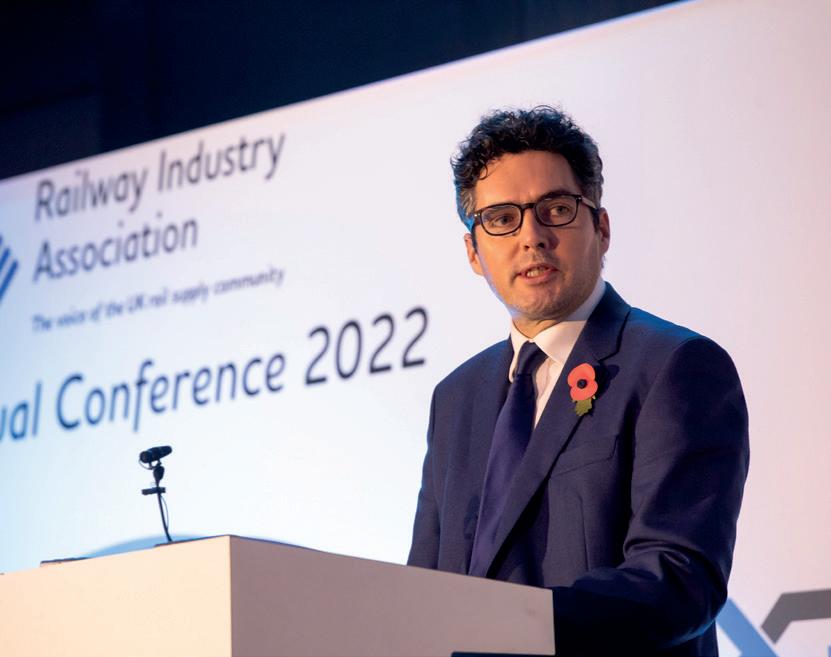
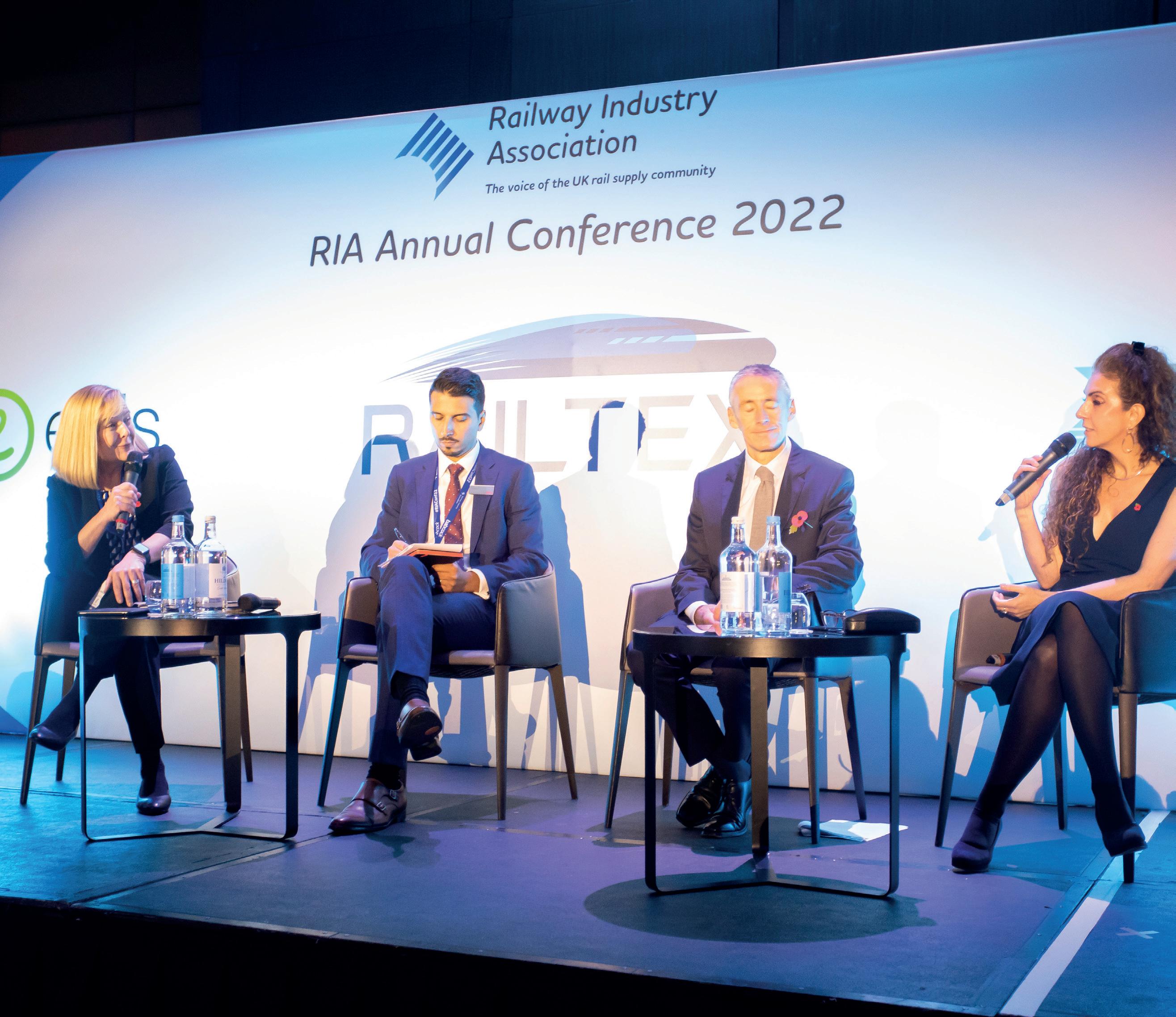
Promoting the case for rail and investment in uncertain times
1 and 2 November
Early Bird tickets now available!
2-day conference with inspiring keynotes, interview sessions and panel discussions
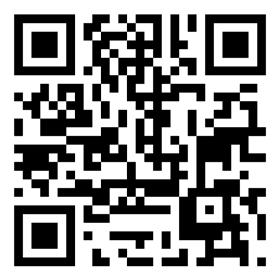
Large interactive exhibition area with spotlight pitches presenting services, products and solutions
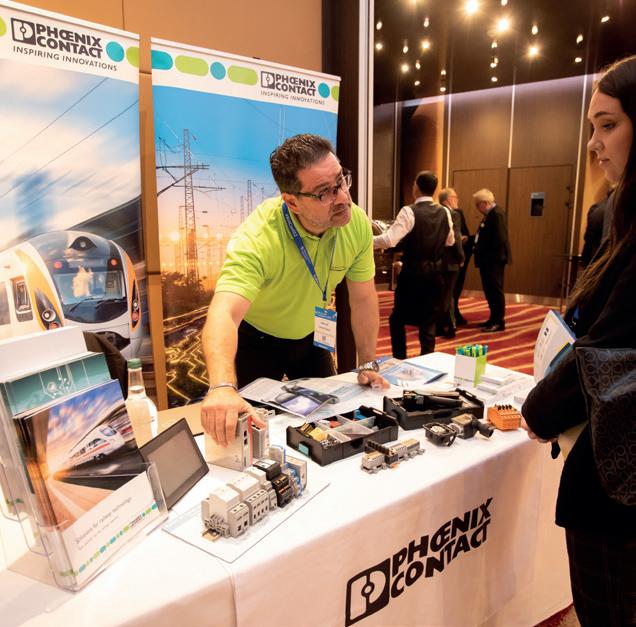
Evening programme including networking drinks, dinner and entertainment
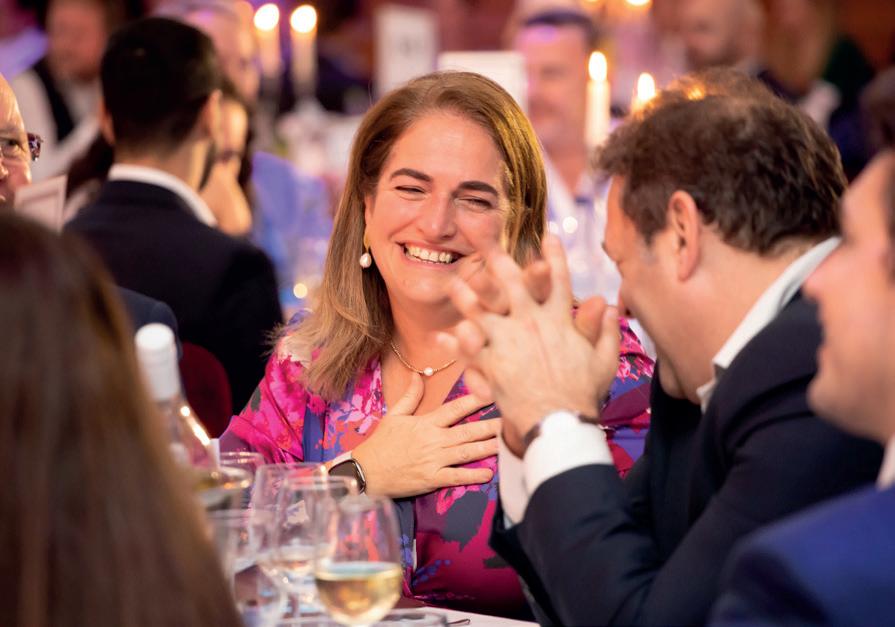
New to The Rail Industry and Want to Kickstart Your Career?
CIRO have three dates available throughout 2023 for a one-day Introduction to Rail training session, designed specifically for those who are new to the industry or more experienced members from support functions within rail.
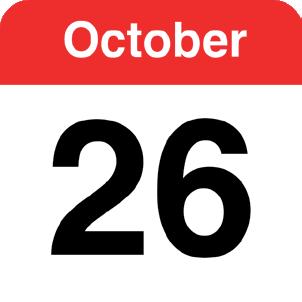
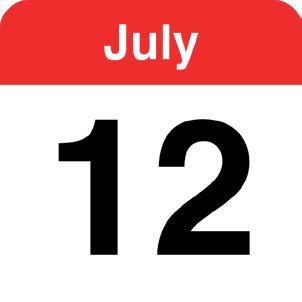
What will I learn?
Throughout the day learners will gain a comprehensive picture of the rail environment and enjoy highly participative sessions where they are guided through interactive exercises. There are also regular opportunities for the learners to ask questions to affirm their understanding of the topics.
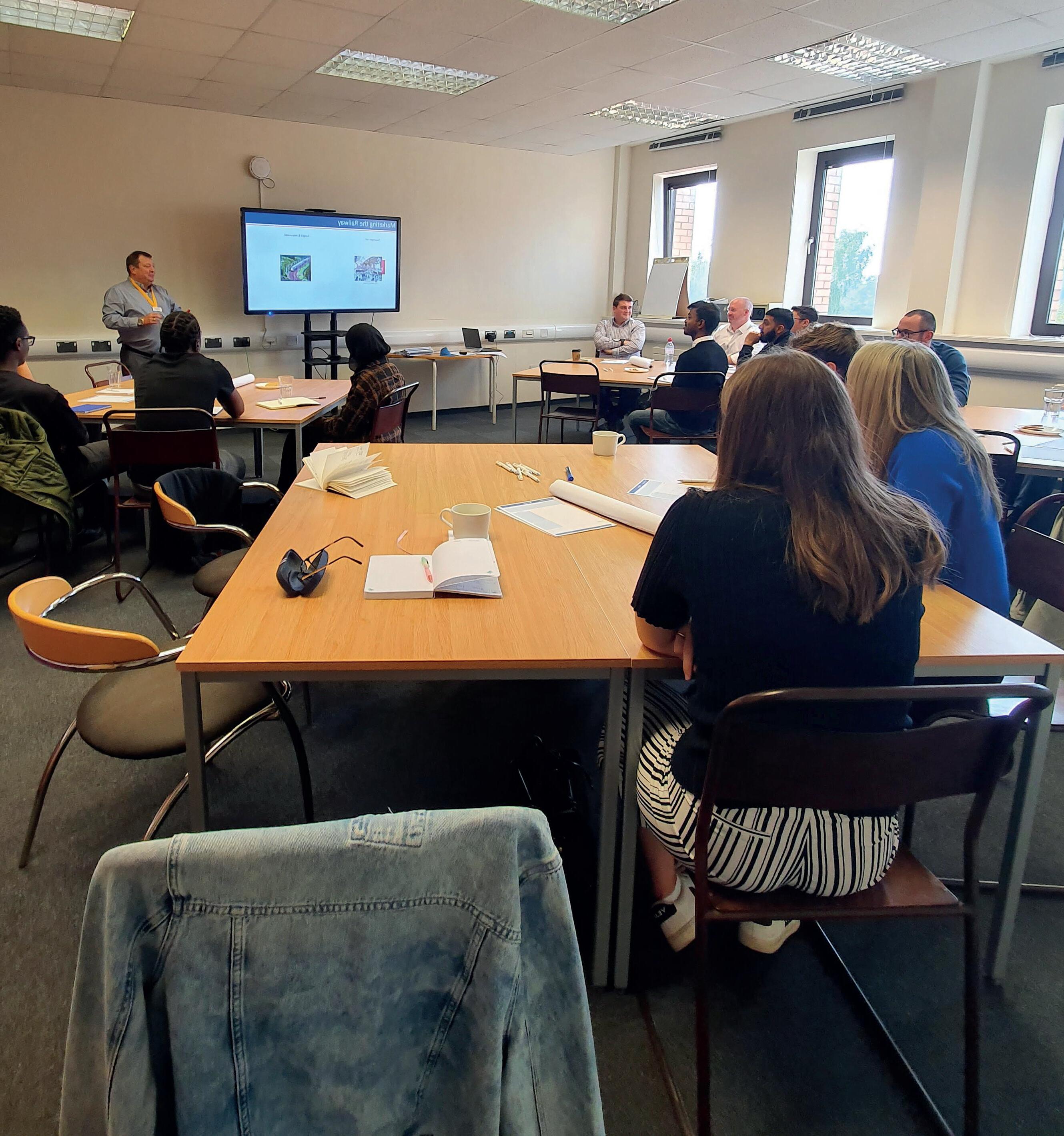
When and where is the training
Dates: Tuesday 7th Feb, Wednesday 12th July, Thursday 26th October
Times: 9.30am - 4.30am
Location: Beacon Building 2nd Floor, Stafford Enterprise Park West, Weston Road, Stafford, ST18 0BF
Refreshments and a light lunch will be provided for attendess on the day.
What is the cost?
Members: £350.00 inc vat
Non Members: £400.00 inc vat
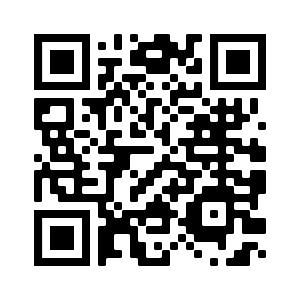

Book to Attend
Available Dates
To book a place on any of the three Introdcution to Rail training days, or for more information about the day or course content, contact our learning and development team at learnserve@railwayoperators.co.uk. learnserve@railwayoperators.co.uk
Learning by Doing in a Virtual World
MTR’s UK operations continue to drive a technology-first approach and adapt to external challenges, to ensure that their driver training programme remains one of the most successful in the industry. Alison Bell outlines the company’s virtual learning programme
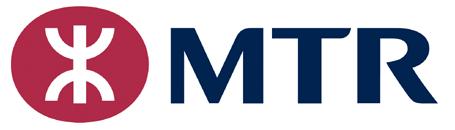

Change and innovation is critical to business success – bringing it about includes working with long-established professions to establish practical solutions to emerging challenges. One such profession is that of a train driver; a role that has changed beyond recognition in recent years.
Today’s drivers not only need to be fully conversant with the safety regulations and the routes they operate, they also need to have an unprecedented level of technical knowledge of the trains they drive. Traditionally, acquiring such knowledge comprised a mixture of classroom learning, shared experience with peers, and comprehensive practical experience in the railway operating environment.
Across the industry, there is a steady demand for new train drivers, and there is no shortage of candidates. However, the rigorous training programme acts as a pipeline, designed to deliver qualified drivers when they are needed.
The pandemic not only disrupted global supply chains; it also disrupted traditional methods of training, impacting the supply of newly qualified drivers to the rail industry. Effective training programmes usually require a high degree of social interaction; in the case of the rail industry this can include confined and enclosed spaces such as driving cabs. None of this is conducive to social distancing.
While MTR had already developed the technology to deliver experiential training, the pandemic accelerated the need for us
to draw on these techniques to develop the way we deliver mission-critical training in the future.
We chose to use our own in-house specialists to develop a toolkit for trainee and qualified drivers that includes Augmented Reality (AR) apps, targeted training video content, a bespoke learning portal, and Virtual Reality (VR) supported learning.
Previously we had delivered core operational and rule book principles either using a tabletop simulation kit (akin to a plastic ‘toy’ railway) or visuals in the classroom. Traditional forms of assessment, such as exams and tests, could be uninspiring and rigid, making it difficult for learners to receive immediate feedback on their performance.
VR technology can overcome this limitation by providing learners with realtime feedback on their progress, allowing them to adjust and make improvements immediately. This type of immersive learning recognises the benefits of an experiential learning style as outlined by David Kolb, an American psychologist and educational theorist. In layperson-speak, this means ‘learning by doing’. Whether we are learning to ride a bike or learning to walk, we achieve this by practising and refining our technique.
The course syllabus was enhanced to encourage experiential learning, resulting in the evaluation of various applications. We chose to develop our own mixed-use experience. This included our application
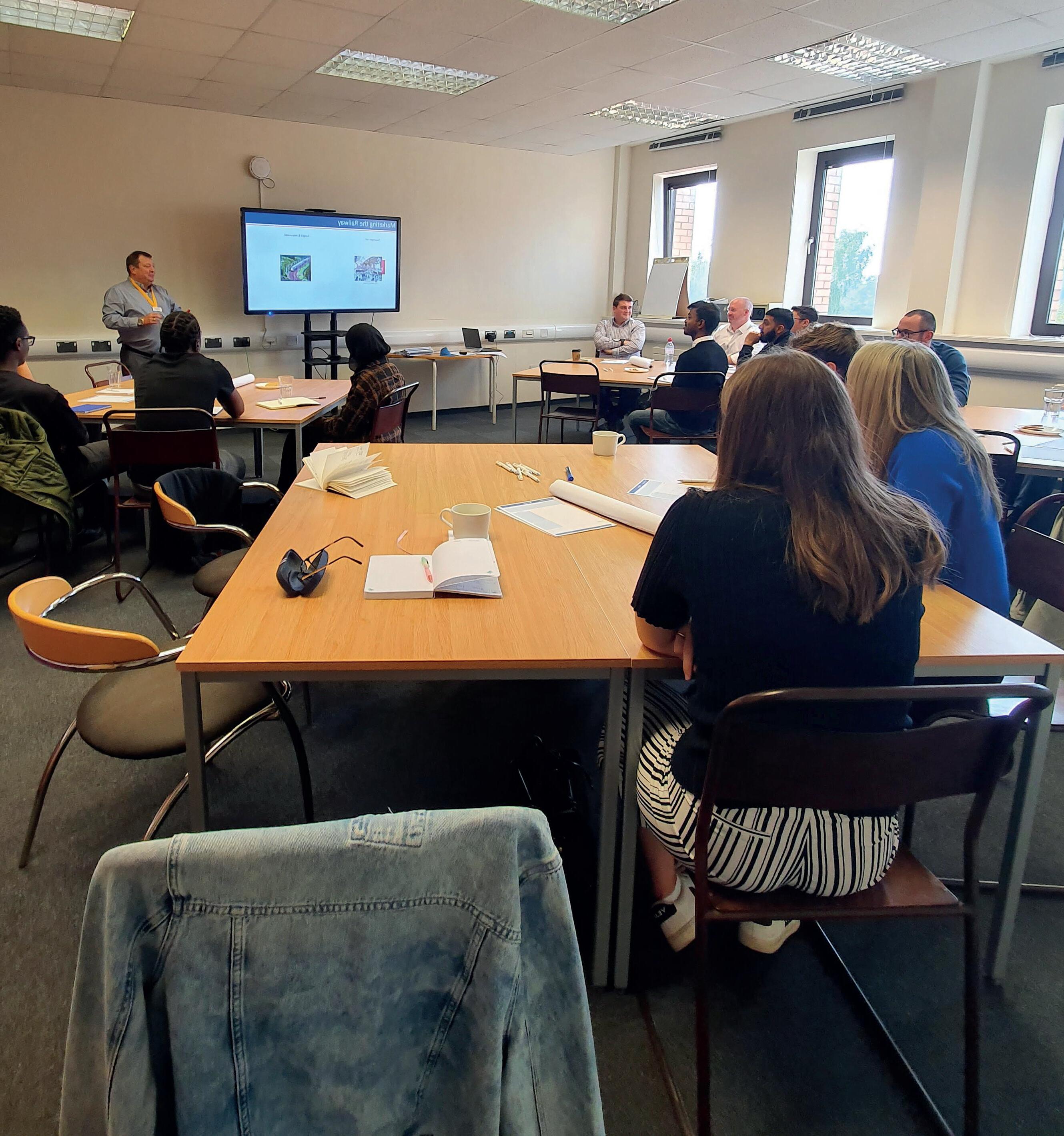
that can be used almost everywhere. It ensures that the user can access the same essential training remotely and not be tied to classroom delivery.
Our App is used to build and interact with anything railway related, including all elements of track, infrastructure, and signalling including European Rail Traffic Management System (ERTMS) principles. A key function of the App is that it is networked. By using built-in Voice over Internet Protocol (VoIP) networking, it allows a facilitator to deliver core operational rules and regulations for both training and assessments, whilst candidates are working remotely.
Adopting technology to enhance this type of training delivery helped us to introduce a much more immersive experience of driving a train. It not only allows a user to build railway infrastructure, it also acts as a train simulator and allows a trainee to simulate driving a train in the built environment.
Although there is no substitute for the real thing, mixed-reality applications have been used to allow a candidate to access traction training without the need for a depot or a real train. The application allows the candidate to place an augmented reality train anywhere they want, whether they are sat in a classroom, or if they are based at home or elsewhere. The principle is a candidate can access the App and use it for self-learning, revision, or during a facilitated session.
The technology being used introduces the ability to both build and explore. For example, a question-and-answer style format helps the trainee to identify how a train is built. Although the train in the application is built on a Class 345 EMU
‘VR technology can overcome this limitation by providing learners with realtime feedback on their progress, allowing them to adjust and make improvements immediately. This type of immersive learning recognises the benefits of an experiential learning style … ‘learning by doing’.’
NEWS IN BRIEF

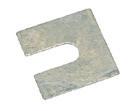

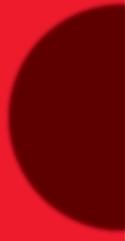

GREAT GARDEN RAIL TRAIL BRINGS

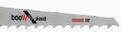

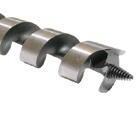

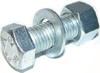


NEW TWIST TO ST ELIZABETH HOSPICE FUNDRAISER
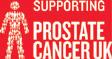
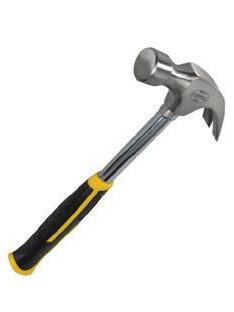



Suffolk rail station gardens will join St Elizabeth Hospice’s Great Garden Trail this summer to help raise funds for the charity. The Hospice has partnered with Greater Anglia and the East Suffolk Lines Community Rail Partnership to add an exciting new element to its annual fundraiser, creating the Great Garden Rail Trail event, which will take place on 9 July 2023. Meeting at Ipswich at 10.30, guests will take a special trip by train for a guided tour of the East Suffolk Line between Ipswich and Lowestoft, highlighting the stunning station gardens that can be found along the route.
foundation, the concept is generic enough that it can be used by anyone who would like to understand how a train is constructed. Users can ‘build’ a train from the ground up, encompassing every aspect of traction familiarisation, including the electrical system, braking system and all other associated equipment required to get a train moving.

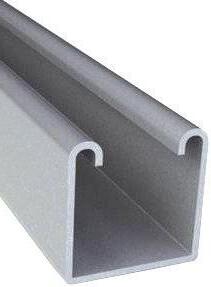
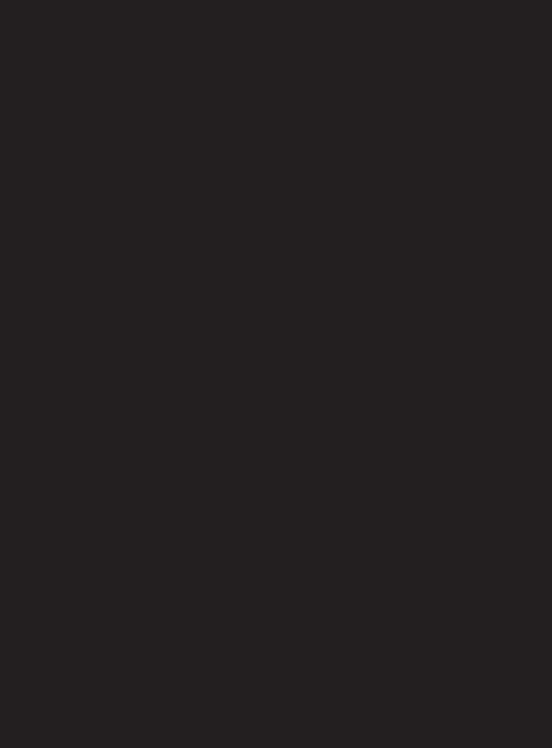
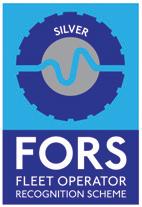
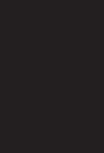

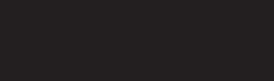


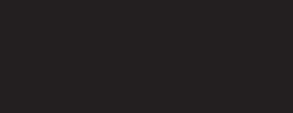
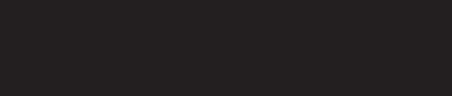

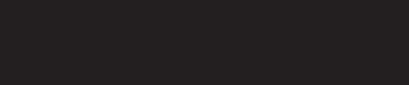
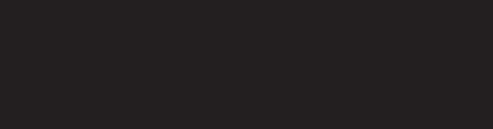
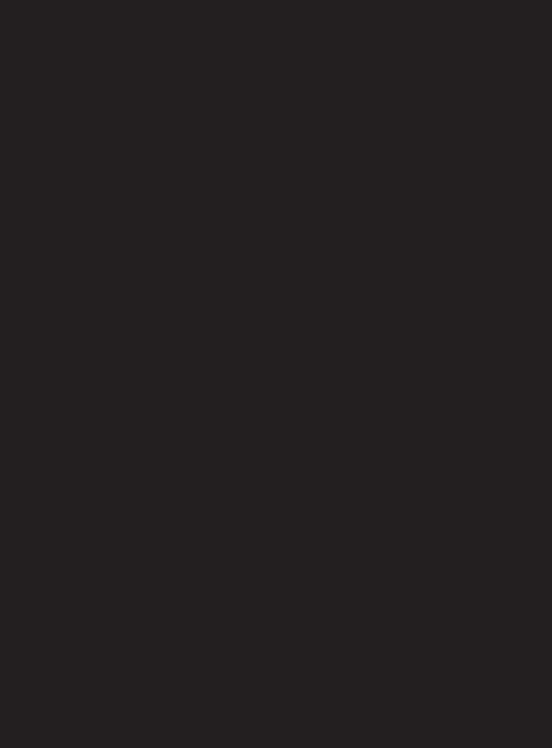
Another section focuses on the principles of identification and location of equipment. The candidate can ‘walk’ through the train and highlight all equipment while, at the same time, receive narration explaining details about that equipment.
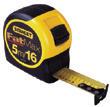
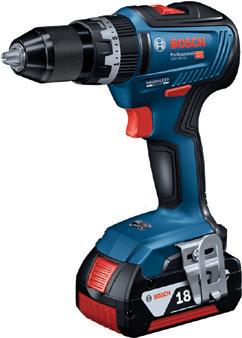
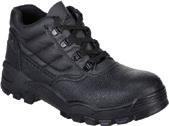
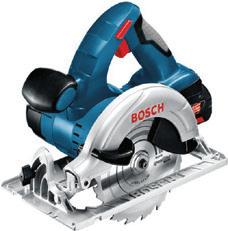
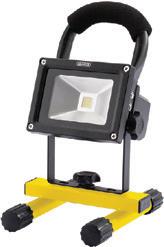

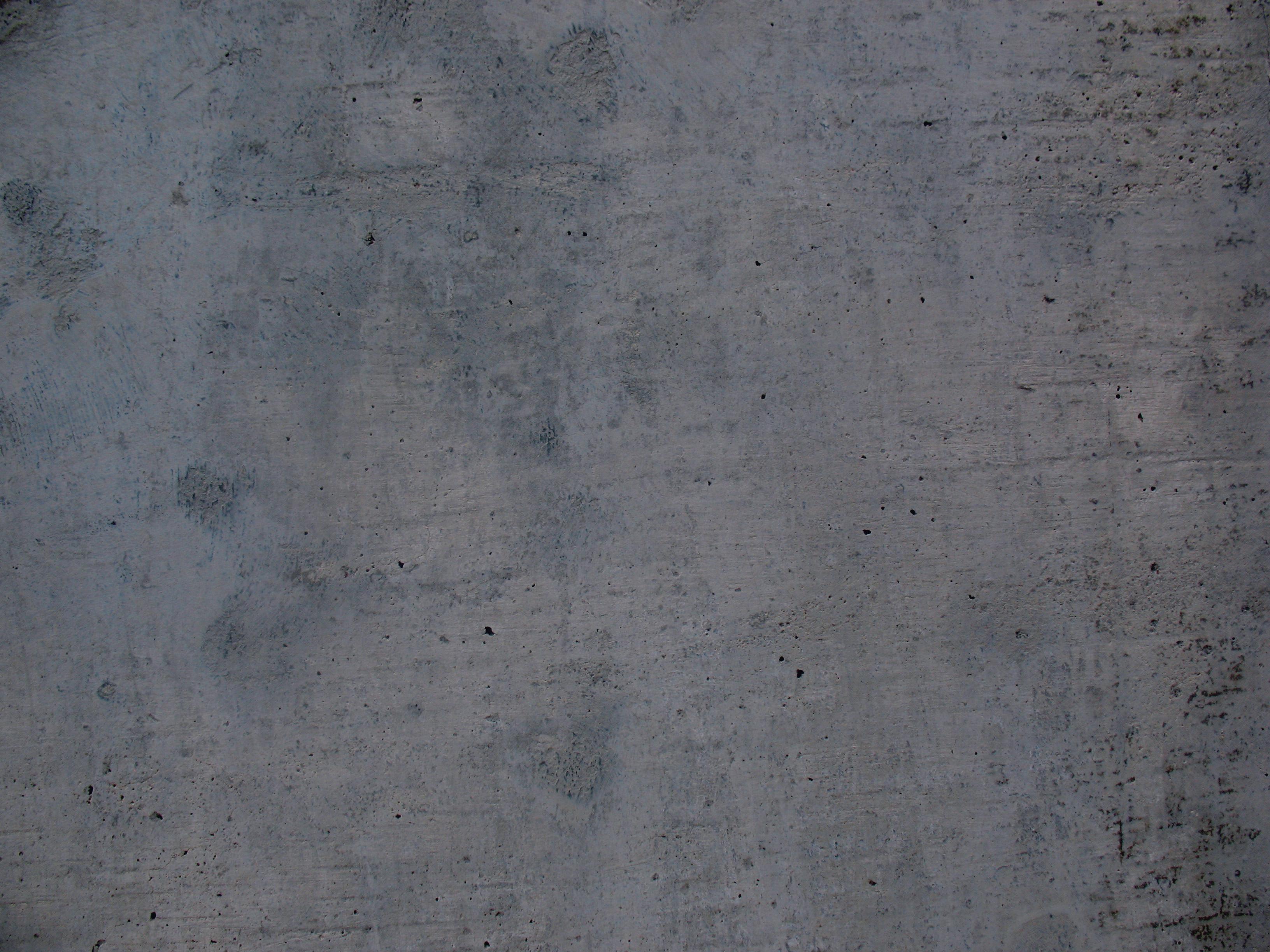
Finding a train for initial training can be difficult, but once a driver is qualified, securing a unit for continual competence development can be even more challenging.
The application also introduces the functionality for a potential assessor to ask the candidate to identify the train equipment and the candidate can highlight that equipment. This removes the need for a train and allows the candidate to form traction-related competence management at a distance virtually.

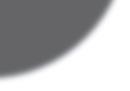
It is important to emphasise this will not replace practical traction training but can enhance it in a way that provides a driver
with more experience. This negates the need to secure a physical train as often, whilst providing drivers with an opportunity to learn wherever and whenever they need to.
We now have the capability to provide accessible and flexible content that is designed to adapt to the various ways individuals learn and can be tailored to specific roles. Moving forward, we are exploring approaches to utilise technology further as we develop a range of training programs. For example, training on communication skills, problem-solving, and conflict resolution.
By developing new techniques, MTR has created innovative and engaging processes to adapt and future-proof training delivery. We now prioritise a blended approach to training and an experience-based learning environment, including a mixture of classroom, practical and virtual learning when a training module is constructed.
While our virtual learning approach to driver training has played a crucial role in demonstrating the benefits of innovation, we must not stand still. As an industry, we must continue to seek out new ways to embrace and adopt technology to remain forward-thinking and progressive. MTR intends to do just that.
Rail Industry Celebrates the Women in Rail Awards 2023
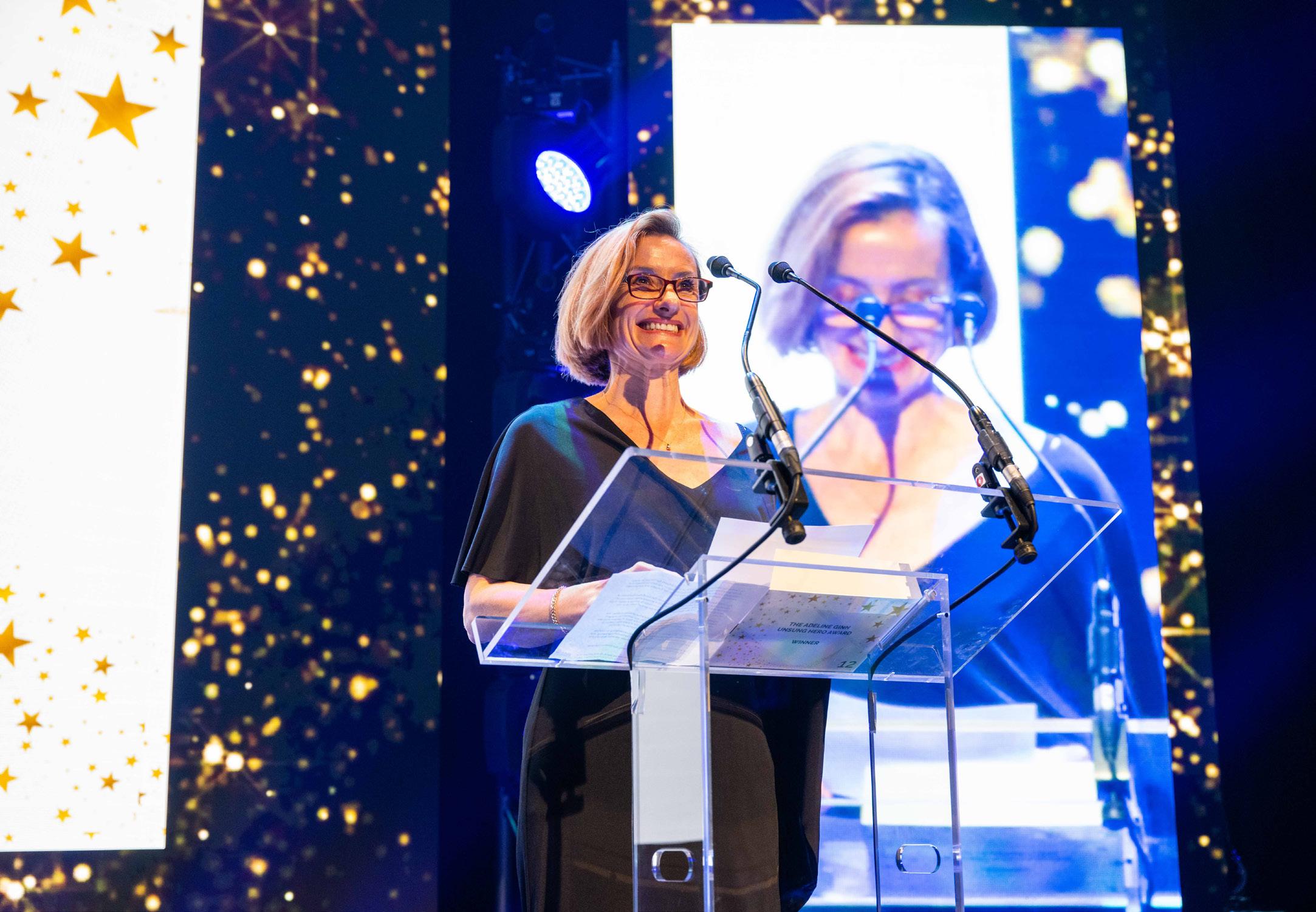
The sixth Women in Rail Awards took place on Thursday 18 May at the stunning and iconic Roundhouse, Camden London
The evening saw 14 awards being presented across 13 individual and team and corporate categories, with a further ten Highly Commended awarded to exceptional shortlisted nominees. Delivered by Nimble Media, the event was attended by over 760 individuals from across the rail industry, coming together to celebrate colleagues, teams and companies, who work hard to support others and to help create a more gender balanced, diverse and inclusive work culture in our industry.
Following the Champagne Reception, guests were serenaded to their seats by the Southeastern TRAXChoir. A welcome address from Huw Merriman, Minister for Rail and HS2, marked the opening of the ceremony, followed by Vice-Chair of Women in Rail, Shona Clive, then an inspirational address by Anit Chandarana, Lead Director, Great British Railways Transition Team. Returning host, Gemma Cairney - Broadcaster, Youth Rights Activist and Author – and selfdeclared rail enthusiast – added a witty commentary to the evening.
For more information about WR visit https://womeninrail.org/.
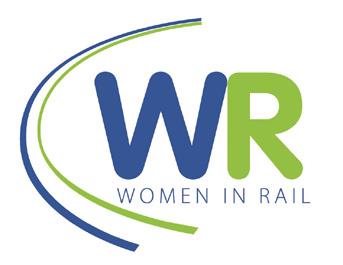
For 2023, a celebration of the allyship shown to Women in Rail over the past decade was rewarded, with the introduction of Male Rising Star and Apprentice of the Year categories. In addition, to add to the legacy left to the charity by its Founder, Adeline Ginn MBE, two categories were created to recognise an Unsung Hero and the dedication of a long serving member of the industry with the Lifetime Achievement Award.
The 2023 Adeline Ginn Unsung Hero was named as Laura Warwick of Avanti West Coast – who the judges felt went ‘BEYOND
above and beyond’ to support local charities, with a focus on mental health support, making a huge difference in the lives of her community’s most vulnerable people. Neil Pepper MBE of Transport for London was presented with the Adeline Ginn Lifetime Achievement Award, to honour his inspirational 36-year career in rail - during which he continues to be an avid STEM ambassador, inspiring thousands of children in London and the home counties, a passionate advocate for women within the industry – and a champion of equality, diversity and inclusion for all.
In a first for the event, the judges chose to celebrate the efforts of two exceptional women for The Equality Diversity and Inclusion Individual Award. Elizabeth O. Umoke of Arriva Rail London – London Overground – and Laura Phoenix of Alstom – both deserving winners and incredible EDI Champions, who, as part of their working and voluntary roles within their organisations, have spearheaded changes for EDI within their companies and the wider industry.
The judges specifically requested that all the nominees be commended for their hard work, selfless dedication, and commitment and that a huge thank you be directed to all those, and especially male allies, who nominated for this year’s Women in Rail Awards. The full list of Winners, Highly Commended and Shortlist is available to view on the Women in Rail website. Shona Clive, Vice-Chair of Women in Rail and Project Lead for the Rail cluster project and the Forth and Tay Offshore project, Scottish Engineering said: ‘The calibre of this year’s nominations was truly exceptional. We received over 430 entries from – and in respect of – a wide range of individuals, teams and companies in the railway sector, many of them from male allies nominating their female co-workers.
The judges admitted having a very difficult task selecting who should be shortlisted and ultimately win. Congratulations to everyone who was nominated – and of course to our winners –who continue to promote and improve EDI across the sector.’ Women in Rail would like to extend a big thank you to all the 2023 Sponsors:

• Headline Sponsors – SPL Powerlines UK Ltd.
• Category Sponsors – BAM Nuttall Ltd, Worldline IT Services UK LTD, Morson Group, Egis, KeolisAmey Docklands, West Midlands Trains, Beacon Rail Leasing Limited and Hitachi Rail Limited.
• Fundraising Sponsor – Telent Technology Services Ltd.
• Table Gift Sponsor – Kier Infrastructure and Overseas Limited.
• Table Decoration Sponsor – Rail People Solutions.
The awards received tremendous feedback and we look forward to celebrating our inspirational colleagues with you again next year at the Women in Rail Awards 2024!
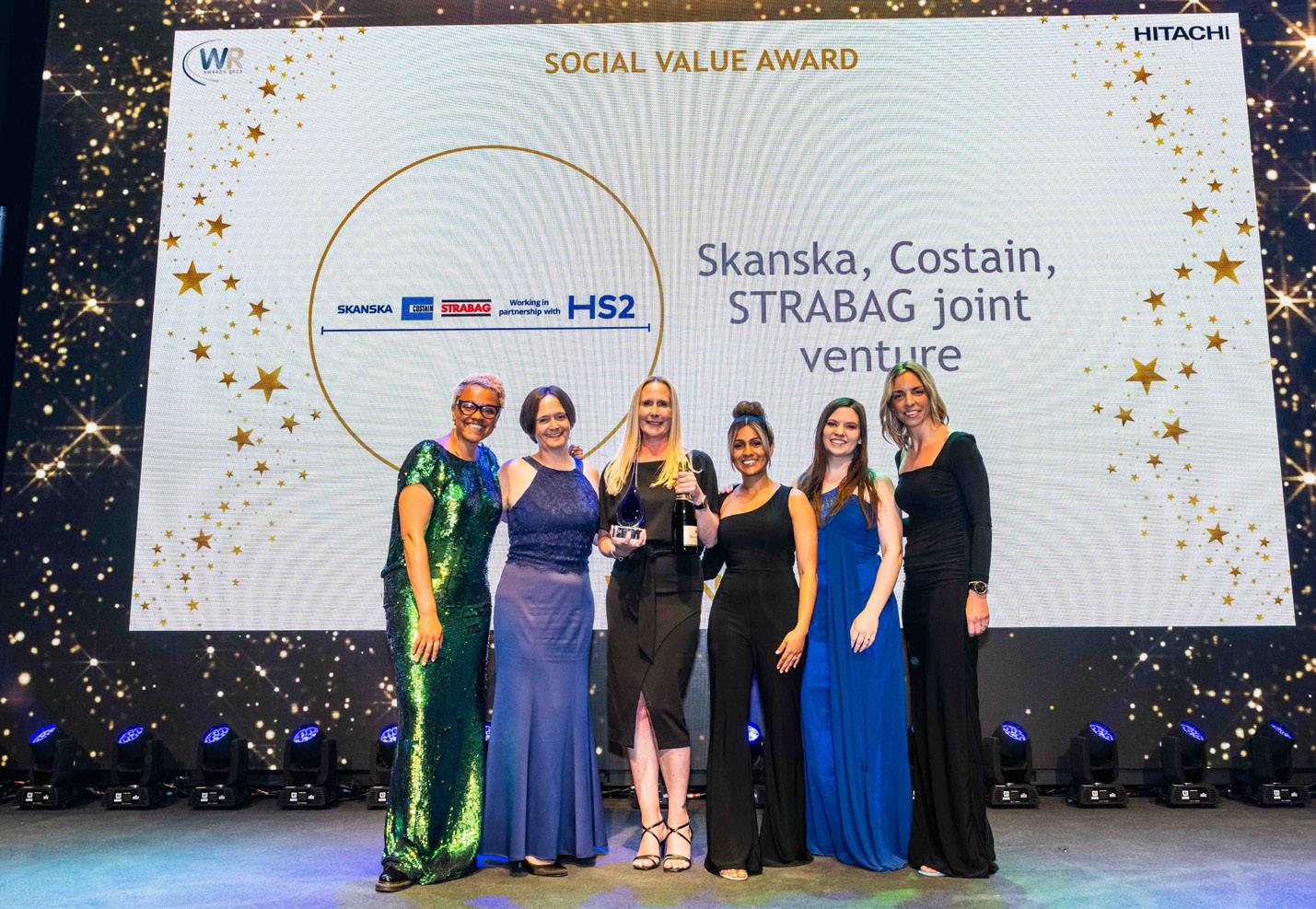
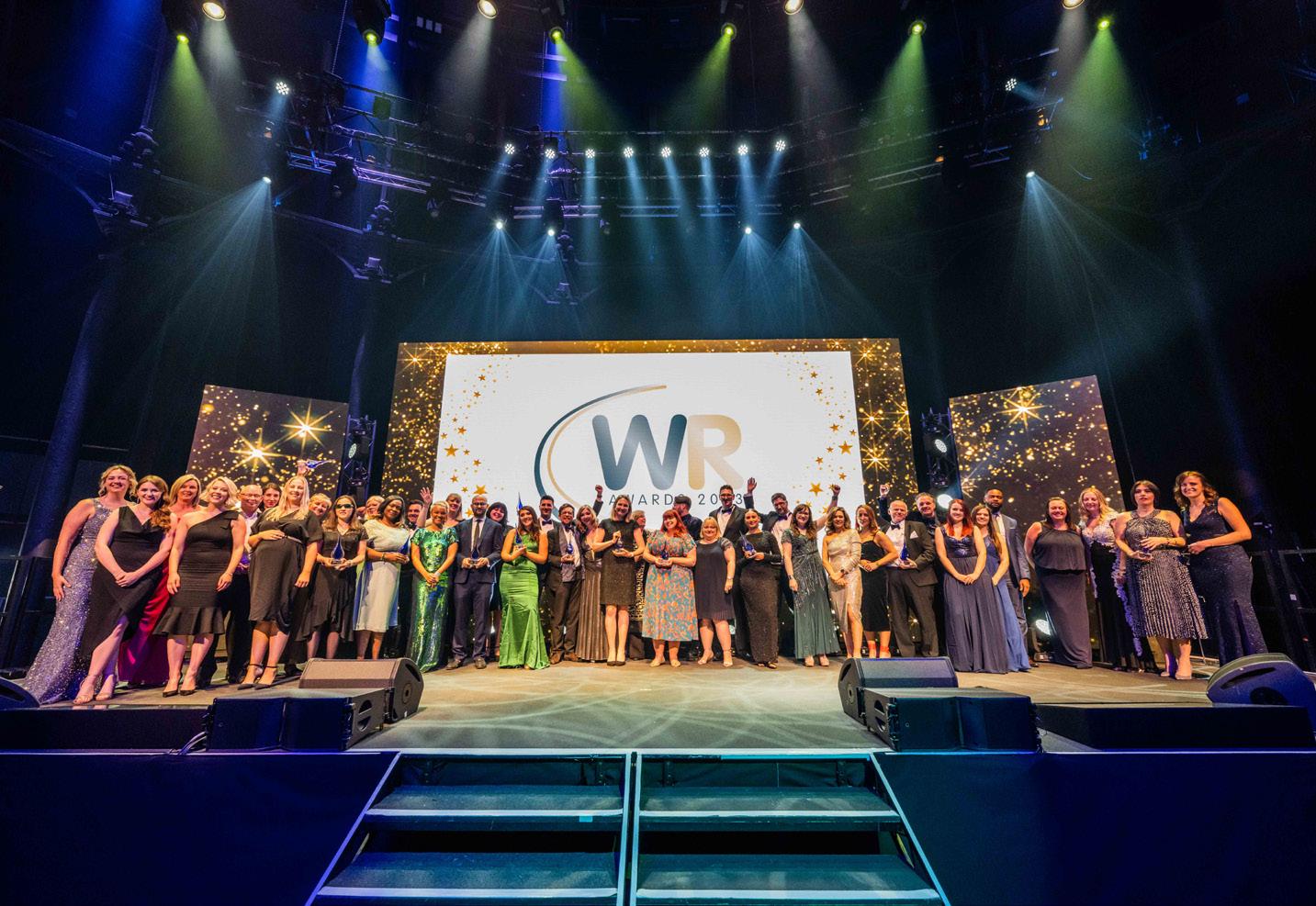
Approved Hydraulics have been supplying some of the largest rail build and maintenance firms for over 10 years, now considered some of the best in the world!
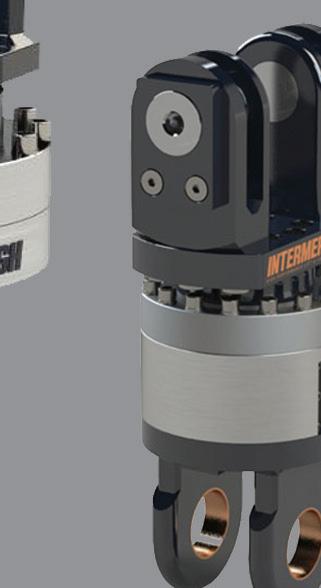
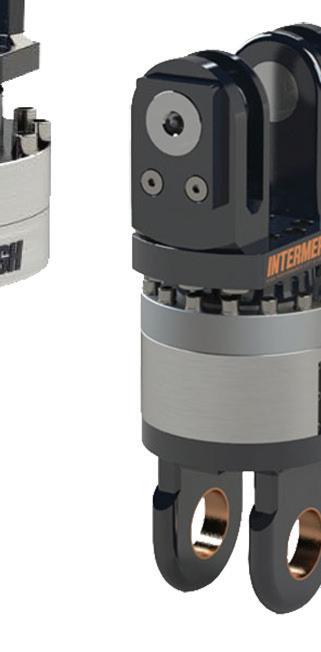
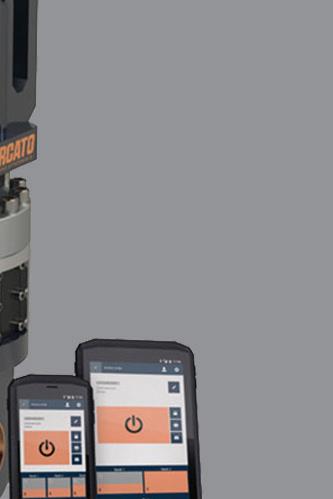
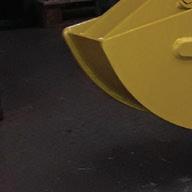

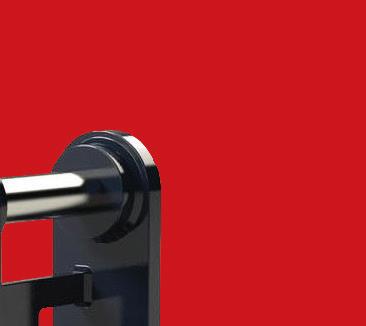
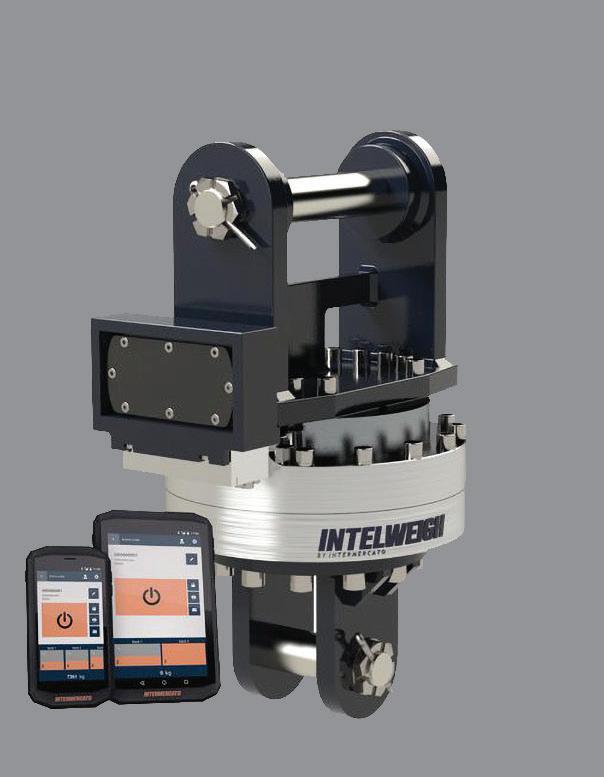




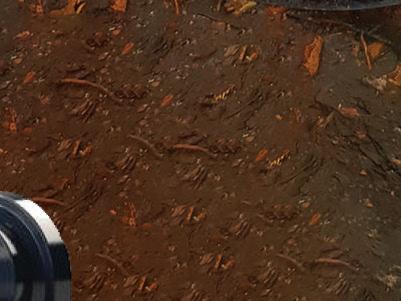
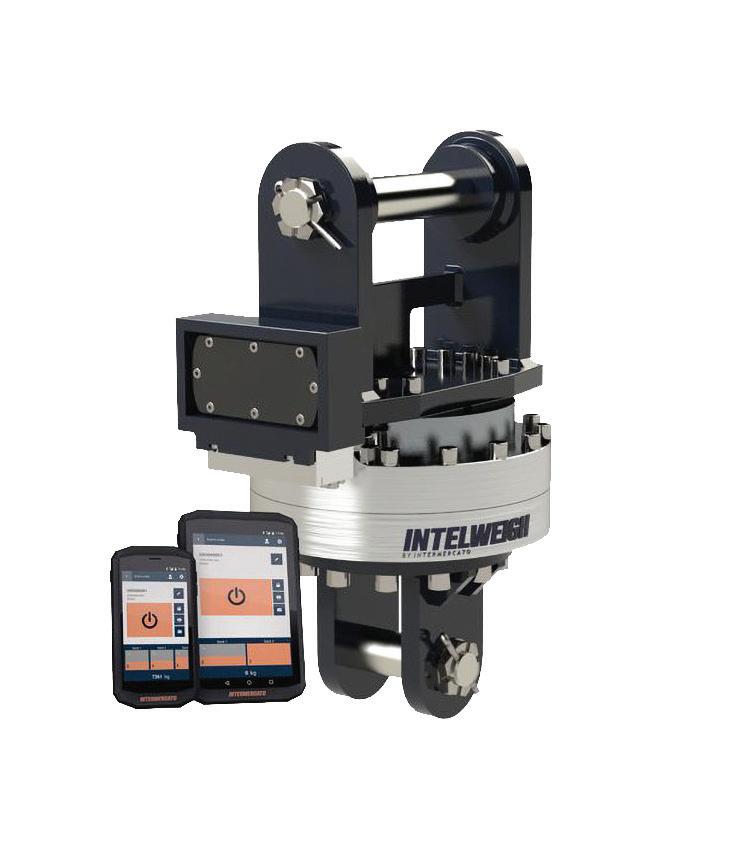
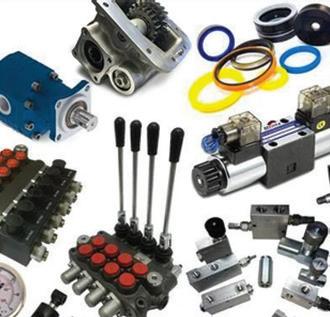
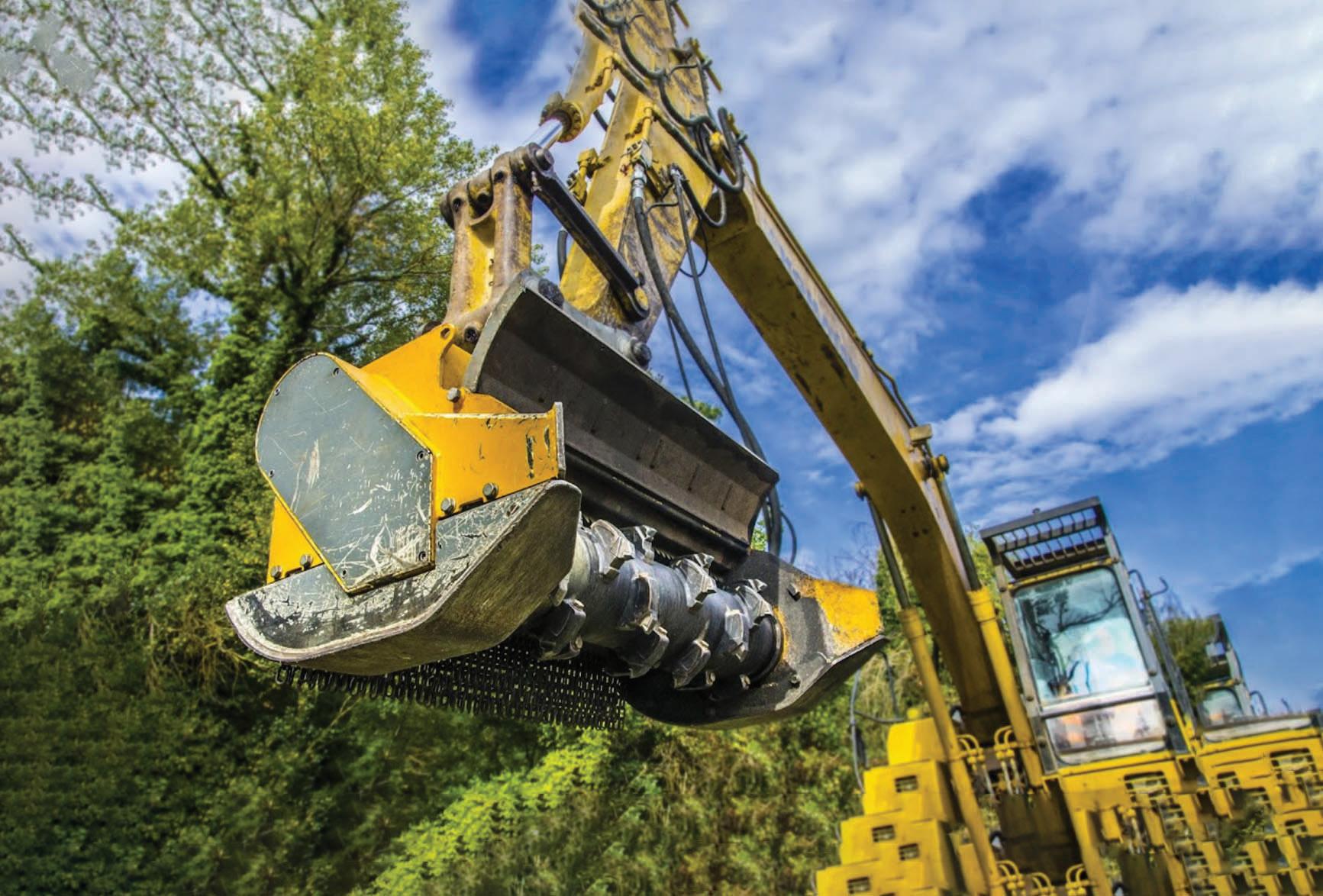
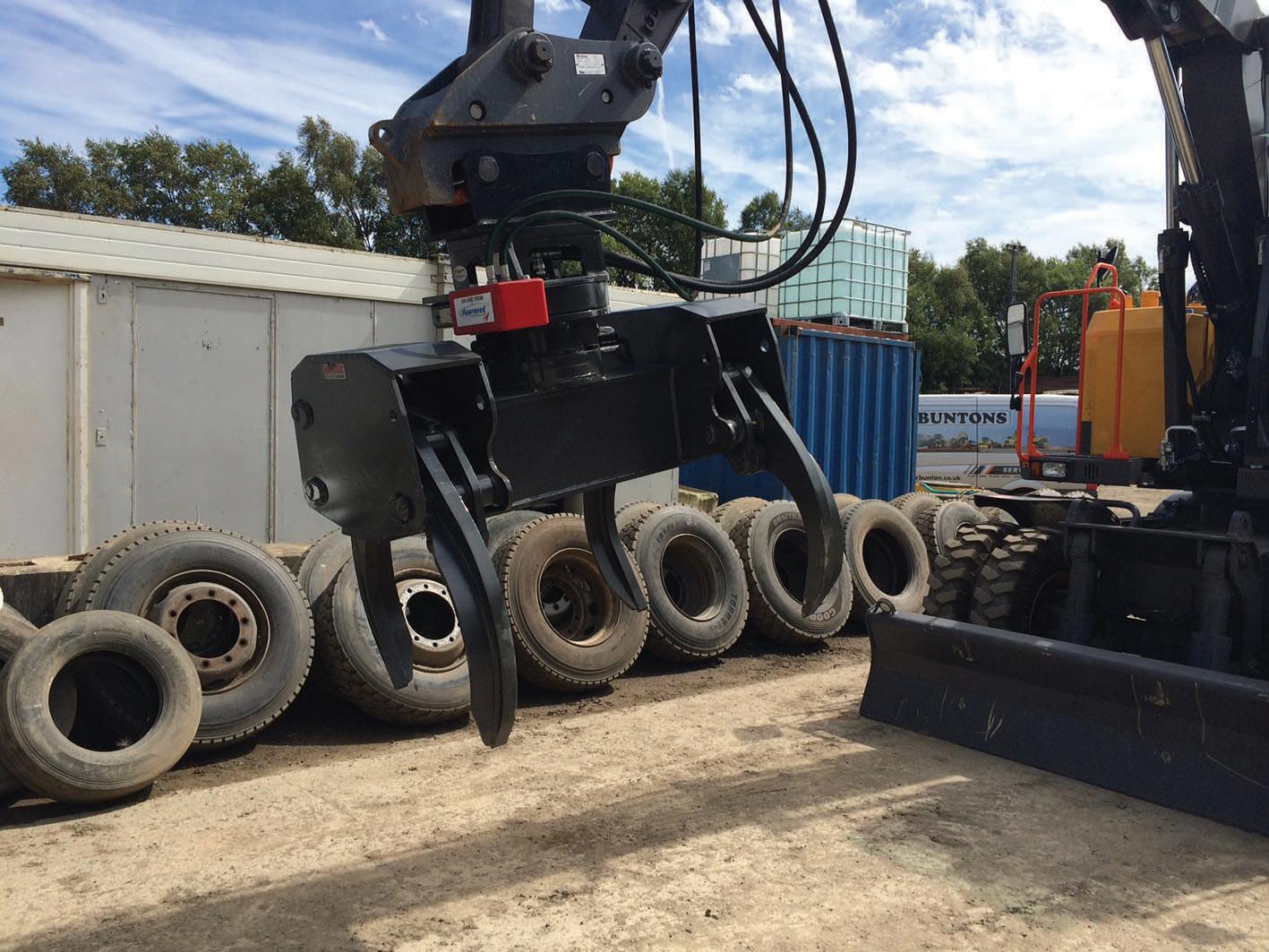
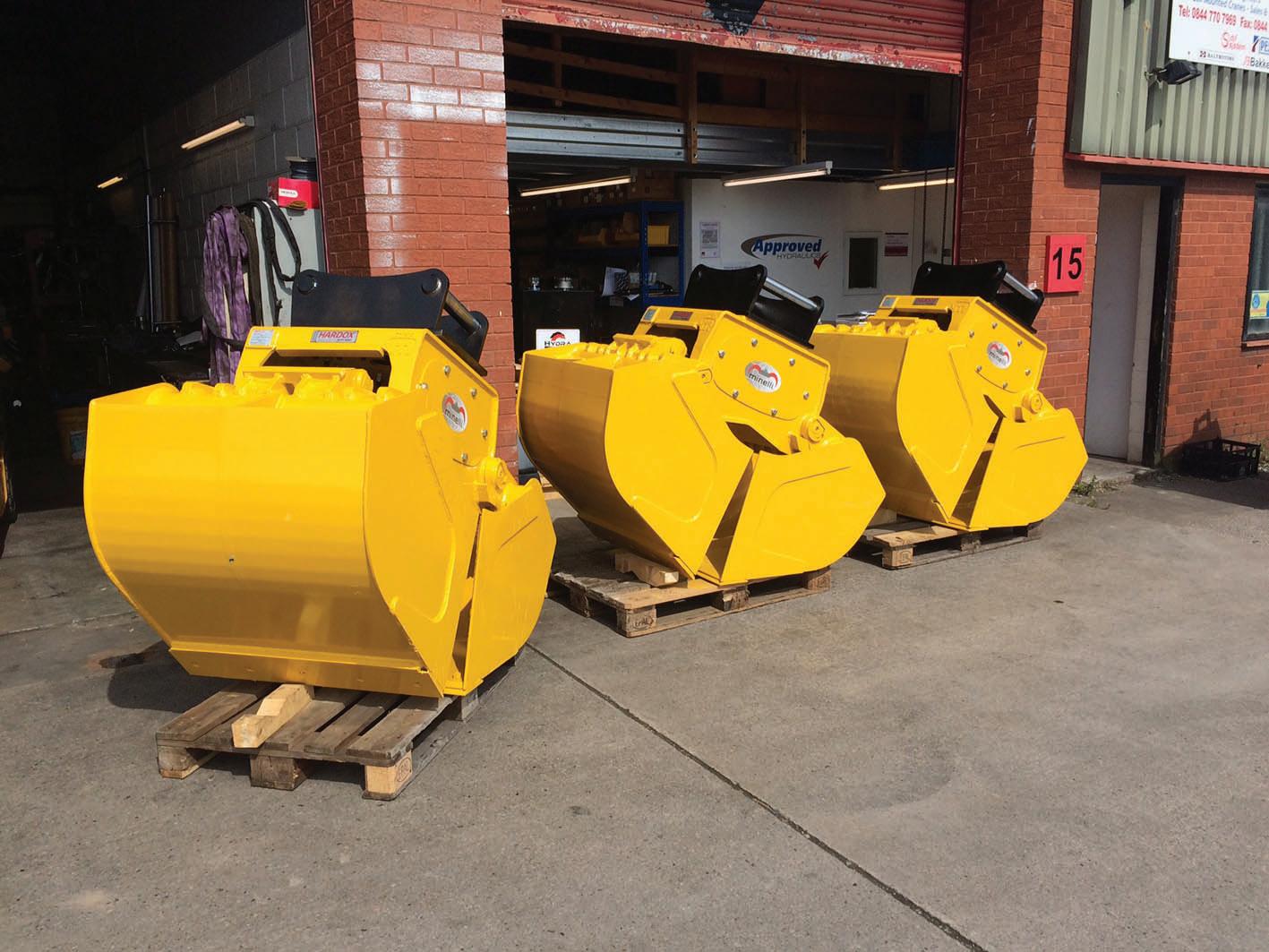

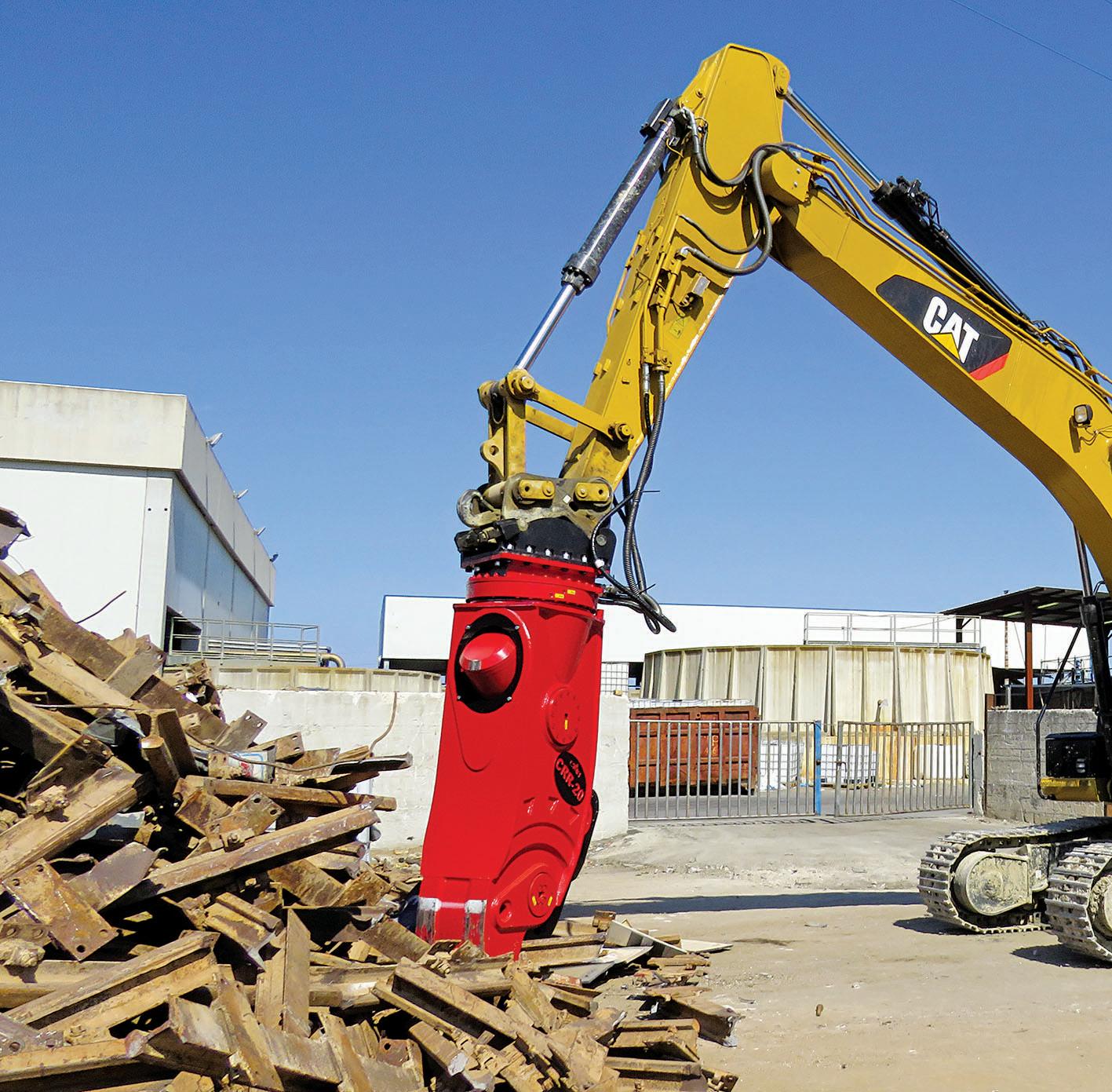
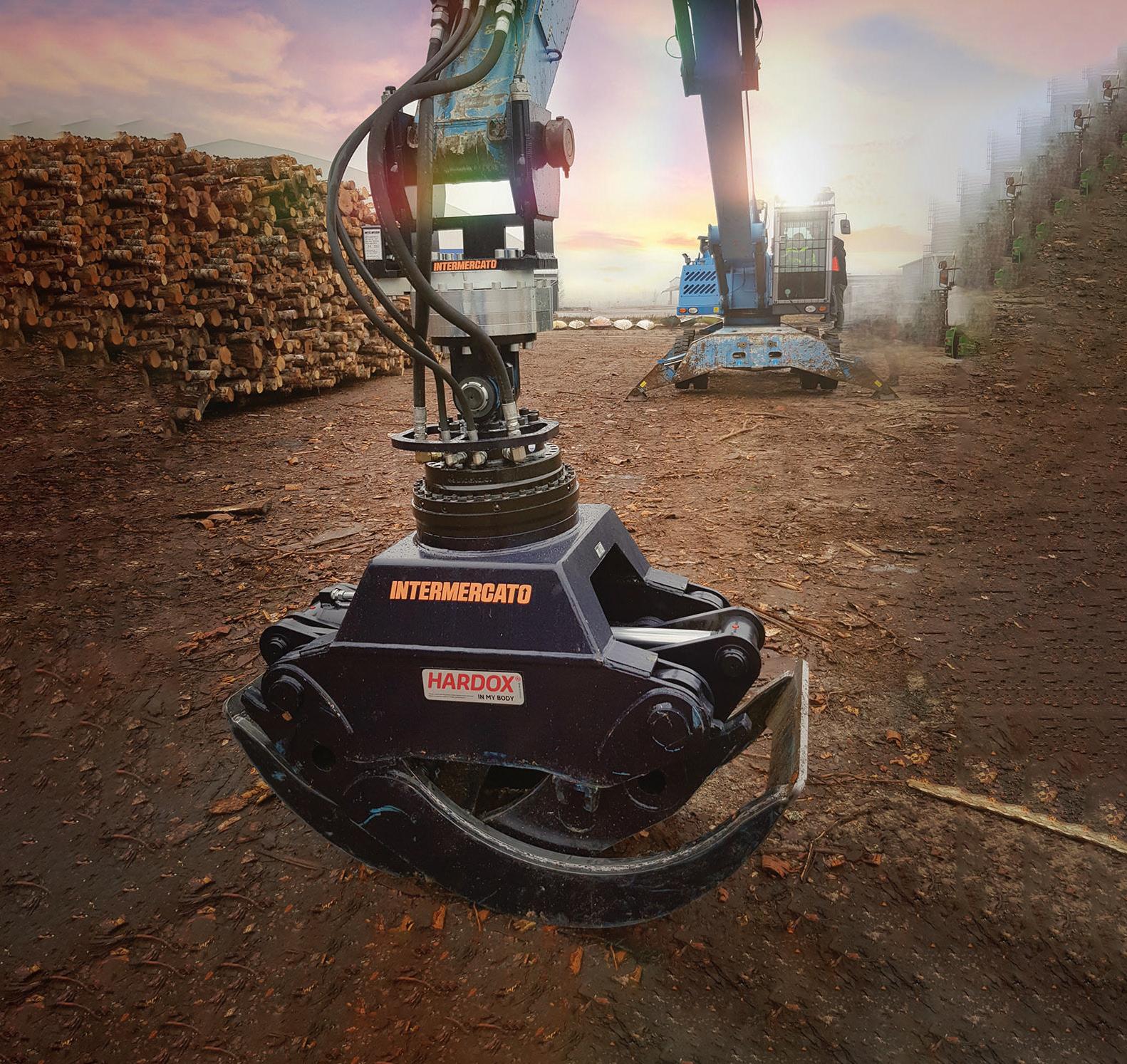

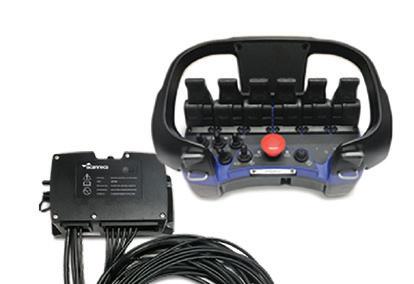
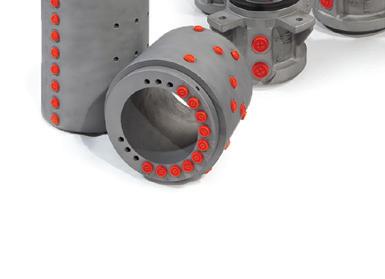
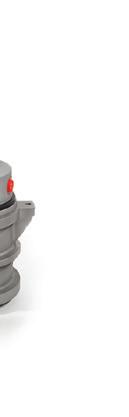
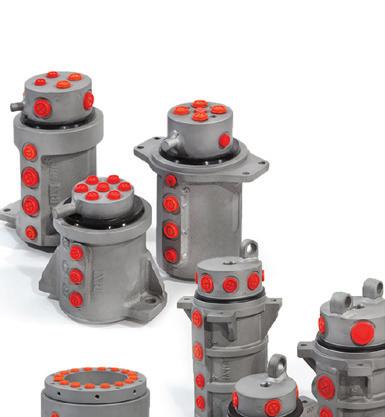
Over the past 20 years Gall Zeidler Consultants has completed 550km of tunnelling projects across the globe, establishing our position as a world-leader in tunnel design and consultancy services. Our specialists relish a challenge and always deliver – it’s why we’re a leader in innovative underground solutions, geotechnical engineering, bespoke tunnel design, tunnel rehabilitation, and project/construction management.
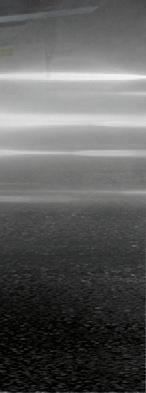

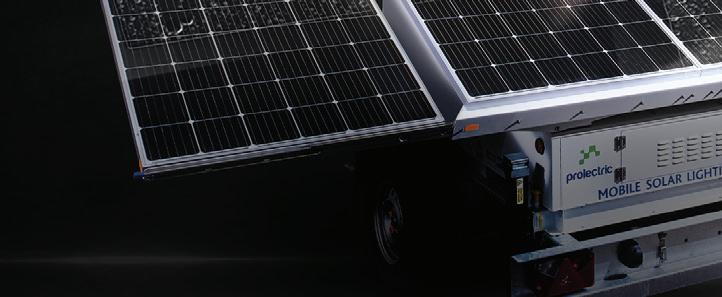
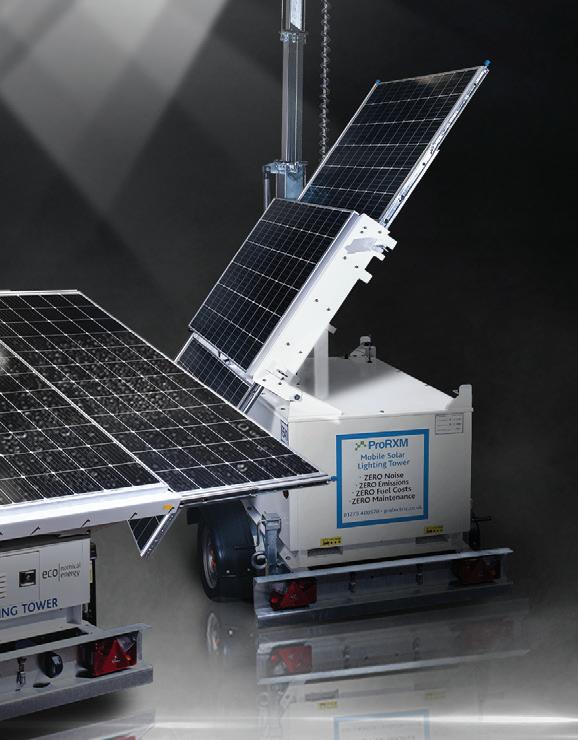
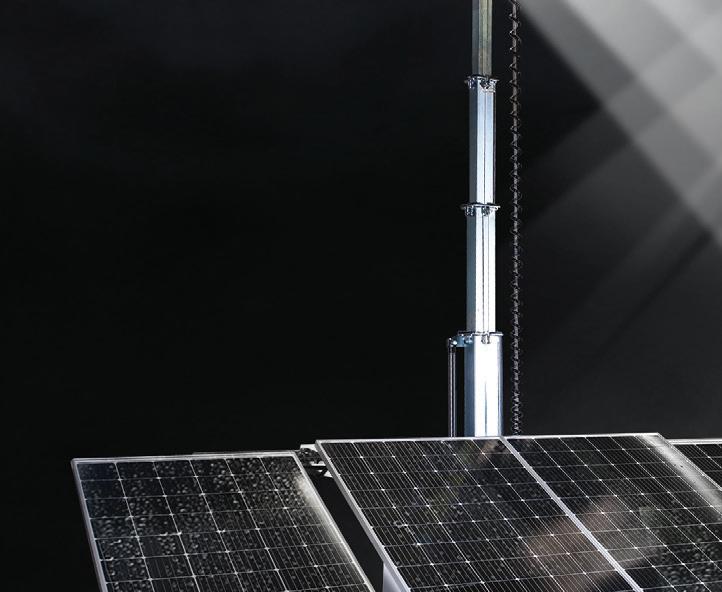
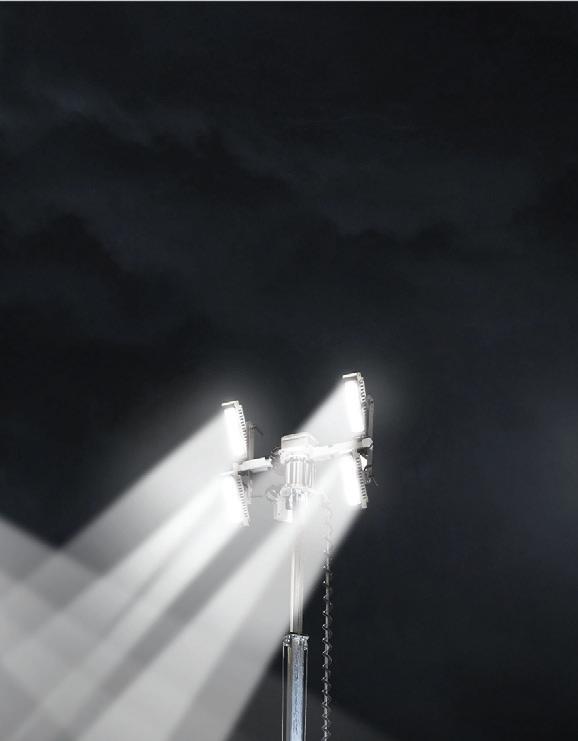

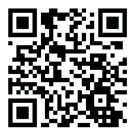
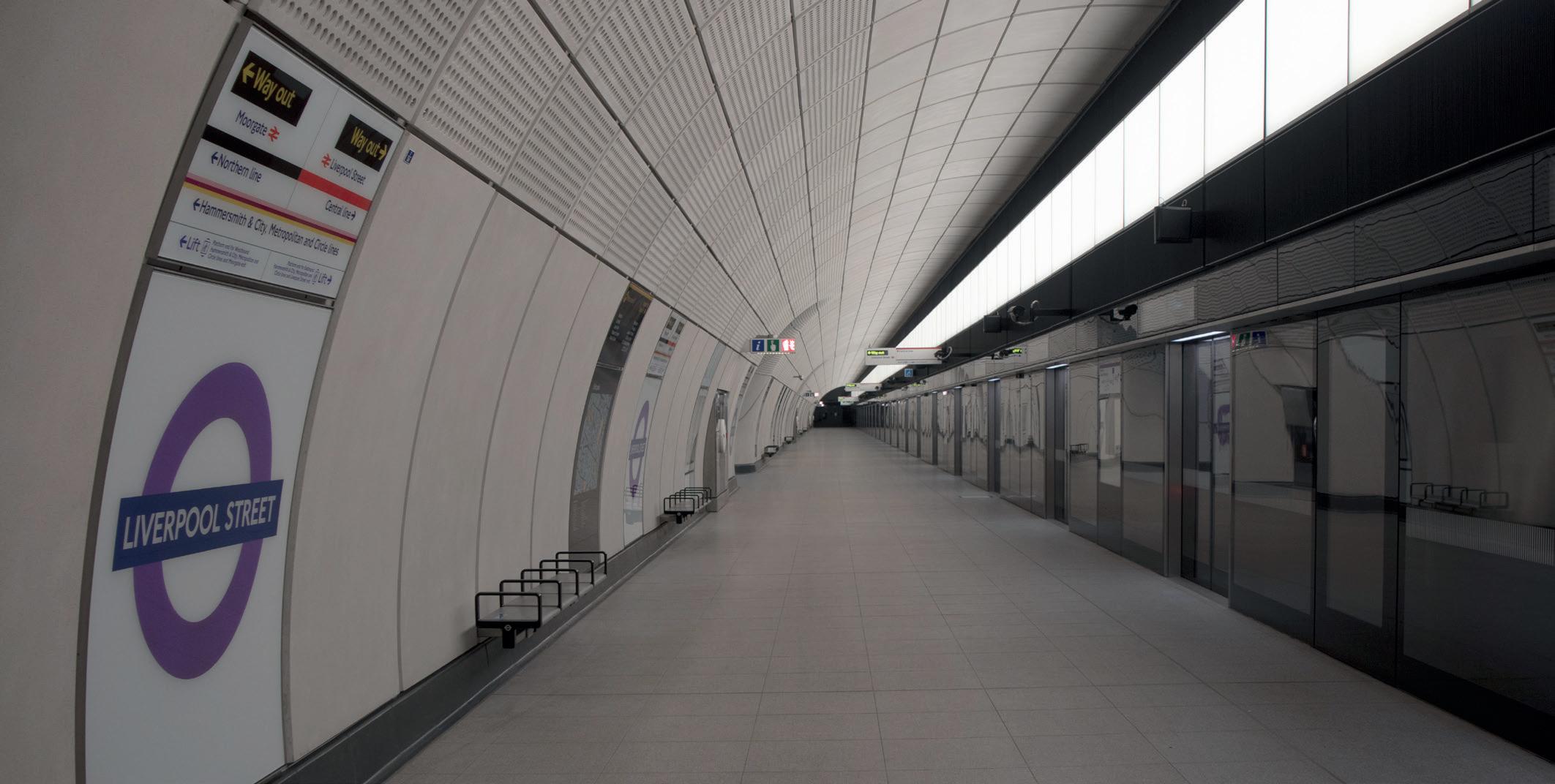
LAYING DOWN THE LAW
by Martin FleetwoodAnother Push Towards Greater Energy Efficiency in Commercial Property
The aim to reach carbon net zero by 2050 within the UK's rail sector tends to lead most people to think about power supply issues, with proposals for more trains and support vehicles to run on electricity, hydrogen or other alternative fuels
Others look at how electricity is produced to heat and light railway buildings. However, there is much more to reaching net zero, including considering the energy efficiency of the buildings being used on the railway estate and those of the contractors working in the rail industry.
Tenants are increasingly requesting ‘greener’ properties with better and more efficient facilities which will generally lower the operating costs of those properties. This is not just a cost issue but also a social responsibility one as businesses look to promote themselves as being energy
efficient alongside other green credentials. In addition to the desire for tenants to push for greener benefits, the law is also starting to bite on energy efficiency and is setting higher minimum standards for commercial landlords to comply with.
Energy efficiency regulations tightening their grip
Back in 2015 minimum energy efficiency requirements were established through the Energy Efficiency (Private Rented Property) (England and Wales) Regulations 2015 (MEES Regulations). While they only apply to property required to have an EPC rating (established under the Energy Performance of Buildings (England and Wales) Regulations 2012 (EPC Regulations)) a significant amount of commercial property will fall within this requirement.
Some types of commercial property and certain very long or very short leases are expressly excluded from the MEES Regulations, but in practice these exclusions are fairly limited. The MEES Regulations look at the substance of the relationship rather than the name given to the relevant document, thereby reducing the opportunity for parties to try to circumvent the regulations.
The MEES Regulations came into force in 2018 and made it unlawful to grant a new lease of a property with an EPC rating of F or G (as defined in the EPC Regulations) unless one of the exemptions set out in the MEES Regulations applied. However, any existing
Martin Fleetwood is a Consultant at Addleshaw Goddard’s Transport practice. The Rail Team has over 30 lawyers who advise clients in both the private and public sectors across a wide range of legal areas. As well as contractual issues, the team advises on operational matters, franchises, concessions, finance, regulatory, property, employment, environmental and procurement issues.
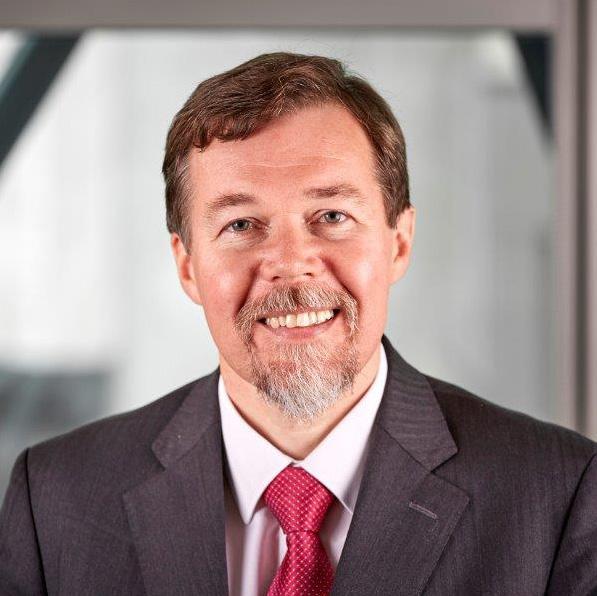
Disclaimer: This article is for informational purposes only and does not constitute legal advice. It is recommended that specific professional advice is sought before acting on any of the information given.
leases of properties with an EPC Rating of F or G were unaffected and remained lawful at that time.
An important role of the MEES Regulations is to create a slow tightening of the energy efficiency requirements of buildings which a commercial landlord can let. There is an aspiration of the minimum standard reaching an EPC Rating on B by 2030, with a number of stepped changes to increase the minimum permissible rating between 2018 and 2030. The first of these key dates has now been reached.
With effect from 1 April 2023, it has become unlawful for landlords to continue to let a commercial property with an F or G EPC rating, even if the lease was granted prior to the MEES Regulations coming into force in 2018.
Compliance is primarily the duty of the landlord
Where a commercial property continues to be let in breach of the MEES Regulations, it is the landlord, rather than the tenant who will be liable for the breach. The MEES Regulations do not require a landlord to actually carry out the necessary works to improve the EPC rating, but instead imposes a number of penalties, which include financial penalties (ranging from around £5,000 to £150,000) and reputation risk as breaches are published on a public register. It is intended that these penalties will encourage the landlord to undertake the relevant remediation work to increase the
‘With effect from 1 April 2023, it has become unlawful for landlords to continue to let a commercial property with an F or G EPC rating, even if the lease was granted prior to the MEES Regulations coming into force in 2018.’
EPC rating appropriately. Repeat penalty notices can also be served for a breach which has not been appropriately rectified, thereby increasing the cost of non-compliance to the landlord. Breaches are enforced by Local Trading Standards and to date there has been little evidence of any enforcement. 59 local authorities have recently been awarded government funding to help with enforcement, so it should be expected that more fines and listings on the public register will begin to take place.
An important part of the MEES Regulations is that while fines may be imposed and lack of compliance publicised, the lease itself continues to be valid and binding. This means that the tenant can continue to use the property and their business should not be particularly interrupted. The main source of business interruption is likely to come from the landlord wanting to carry out remedial works to improve the EPC rating. Such works should be carried out in accordance with the relevant terms for landlords works set out in the lease agreement.

In addition to the penalties imposed on landlords, there is a potential for some aspects of the MEES Regulations to affect tenants too. Tenants who grant sub-leases will take on the responsibility of the landlord
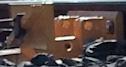
and be subject to financial penalties if the EPC rating of the property being sublet is below the relevant threshold. If a tenant refuses to allow a landlord access / permission to undertake works which would improve a below standard EPC rating to meet the relevant threshold this information may become publicly available on the national register. Such an action could have a negative effect on the tenant's own ‘green’ credentials.
Managing the squeeze on EPC ratings

In 2022, the Government estimated that around 18 per cent of commercial properties within the UK were F or G rated. While a number may have been brought up to a minimum EPC Rating of E by 1 April 2023, it is likely that there will remain a significant number of properties which fall below this. As a result, there is expected to be some tension between landlords and tenants as each party grapples with the risk of noncompliance and additional costs to raise the energy performance of buildings to higher levels.
If parties are unsure as to whether the EPC Regulations and the MEES Regulations apply to some or all of their properties, a review should be conducted on a propertyby-property basis. Simply assuming that all will be treated the same would be unwise.
As the minimum rating increases the potential fines and required remediation works could become more of an issue, particularly if the work that the landlord wishes to carry out is relatively disruptive. Ensuring that the relevant powers of the landlord are not too onerous will be important to the tenant, particularly when negotiating any lease renewal. Energy efficiency regulations tightening their grip.
Both tenants and landlords should be aware of their EPC rating, and any terms within their lease which permit the landlord to undertake remediation works to improve that EPC rating. Such works may also have an effect on the rental that can be changed. Tenants should take note of how increases may be calculated and when rents may be increased as a result. It will be interesting to see the extent to which landlords will balance the cost of remediation works compared to potential fines for having below standard EPC ratings, particularly in the first year of the process. The next part of the process will be the extent to which new terms which take account of the EPC rating changes are incorporated into lease renewals.
WHAT’S THE COST OF LIVING?
Rail Still Needs Industry Skills
A City & Guilds report – released in February 2022 – states that only 23 per cent of people looking for work would consider a career in transport and logistics, and with the ongoing shortages, Ellis Shelton, Policy Advisor at Logistics UK explains why it is vital this is addressed
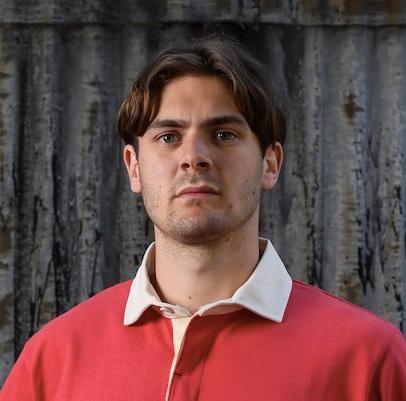
The UK’s most vital industry is still being threatened by skills shortages due to factors such as poor reputation and a lack of understanding surrounding the opportunities and progression available for employees.
The rail network is essential to keeping the country moving through a greener, more efficient mode of transport that delivers sustainability for logistics businesses. Yet rail is one of the sectors being seriously affected by the shortage, with the UK experiencing eight days of rail strikes leading up to and over the Christmas period as part of a long-running dispute over pay, jobs and conditions. A record high was recorded in January 2023 with Avanti West Coast cancelling the equivalent of 18.9 per cent of their services – one of the highest figures recorded for any operator in records dating back to April 2014.
An industry report ‘Keeping Talent on Track’ released in February 2023, outlined that up to 120,000 additional people will be required in the rail sector over the next five to ten years, with pinch points coming as an ageing workforce retires. Currently, 28 per cent of all rail workers are aged 51 and over with the potential for 15,000 to retire by 2025 and focus therefore needs to be on recruiting employees at a younger age and providing them with proper training and development prospects.
Diversity is a significant challenge in the sector. Women make up a significant portion of the UK workforce however only 16 per cent of workers in the rail industry are female, and only two per cent of those are engineers. Encouragingly, the percentage
of women in engineering roles across all sectors has increased from 12 per cent to 14 per cent over the past three years however, the same progress has not been reflected in rail and therefore the sector is missing out on a larger opportunity for recruitment. Upskilling of the workforce is also crucial as the use of digital technologies becomes more frequently used, with approximately 80 per cent of the industry requiring training over the next two decades. Government’s £96 billion investment for the integrated rail plan, published in November 2021, has the potential to create up to 12,000 jobs every year over the next five to ten years, but without the proper training and support in place to create a younger and more diverse network, the rail sector cannot thrive and grow.
Prior to Covid-19, the industry was not training enough apprentices to keep up with demand which contributed to the acute staff shortages the country is now facing. Apprentices play a key role in our economy as they provide significant support to the development of a skilled workforce and solving the sector’s long-term skills shortage. It is estimated that about 5,000 apprentices per annum, or two percent of the workforce, will be needed to meet current demand – effectively a doubling of current average levels.
The current funding model for the Apprenticeship Levy does not provide the support and accessibility needed by industry, with 94 per cent HR leaders reporting at least one barrier to accessing their levy funds. Logistics UK is therefore calling for the current format to be amended into a Training Levy which will allow greater
Logistics UK is one of the UK’s leading business groups, representing logistics businesses which are vital to keeping the UK trading, and more than seven million people directly employed in the making, selling and moving of goods. With Covid-19, Brexit, new technology and other disruptive forces driving change in the way goods move across borders and through the supply chain, logistics has never been more important to UK plc. Logistics UK supports, shapes and stands up for safe and efficient logistics, and is the only business group which represents the whole industry, with members from the road, rail, sea and air industries, as well as the buyers of freight services such as retailers and manufacturers whose businesses depend on the efficient movement of goods. For more information about the organisation and its work, including its ground-breaking research into the impacts of Covid-19 on the whole supply chain, please visit logistics.org.uk.

flexibility so that businesses can utilise the funding available. Workers currently looking to access apprenticeships are facing challenges due to the minimum skills requirement which dictates that people can only take up an apprenticeship if they have achieved a minimum standard of maths and English. Following conversations with members, Logistics UK believes this requirement is preventing a potentially valuable group of young people from joining the workforce via the apprenticeship route. The implementation of a Training Levy would support development at all ages from those without academic qualifications and new to work, to those looking for a career change.
Logistics UK believes that government must take steps to plug the skills gap through collaborating with schools and colleges, to challenge the current perceptions about industry. In addition, government must review and update its Industrial Strategy and Rail Strategy, so it is fit for purpose and benefits the logistics sector. Further investment in training and development for rail workers is crucial for reducing recruitment issues and improving job retention. There are still not enough apprenticeships being offered for logistics roles in general and with 99 per cent of logistics businesses being classed as SMEs, which are not able to access funding for apprentices aged over 18 years if they employ fewer than 50 employees, the sector’s ability to retain workers is hindered.
Mark Phillips was appointed Chief Executive Officer of the RSSB in 2016. He is a member of the Transport for London Board and a member of the Department for Transport’s Transport Research and Innovation Board. Mark is a Fellow of the Institute of Railway Operators and a Fellow of the Institute of Logistics and Transport.
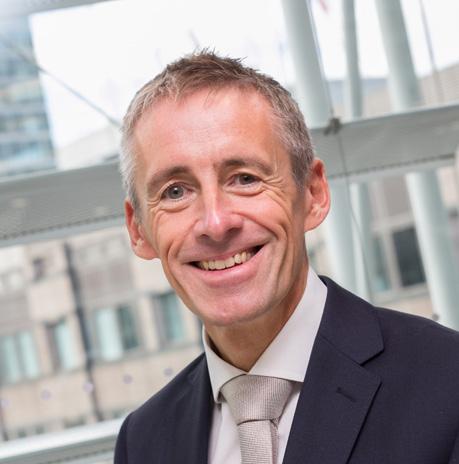
Twenty Years of the RSSB
Twenty years ago, the Rail Safety and Standards Board was born, Mark Phillips, Chief Executive Officer takes us through the journey since then
When we were founded, Britain’s rail industry was very different. The Ladbroke Grove crash in 1999 was one of the country’s worst train accidents, and RSSB’s creation was a direct recommendation from Lord Cullen’s wide-ranging inquiry, as part of separating the setting of standards, investigation of accidents, and regulatory functions for rail. It proved a turning point.
Since 1999 Britain’s railways have enjoyed a lot of success; becoming the fastest growing and safest railway in Europe, with rail journeys doubling over 20 years. By the mid 2010s the UK was experiencing the largest shift by passengers to rail from other modes. 1.8 billion trips were made by more than 8 million people in the last year before the pandemic. Together with the wider supply chain, the UK rail sector supports tens of billions of Gross Value Added to the economy, helps promote social mobility and brings opportunity to deprived communities.
But there have been challenges too. The railways have experienced varying levels of state and private sector intervention, fluctuating economic health, accidents have not been consigned to history yet and, of course, the Covid pandemic. Rail has not always been prepared or resilient enough to manage climate change and extreme weather events. Many people feel rail doesn’t offer the frequency, reliability or price that they need. We are still working to adapt to new travel patterns, with commuting at roughly 60 per cent of pre-pandemic levels but leisure travel is over 120 per cent.
RSSB has been by industry’s side through both the good and bad times, as a dynamic, impartial link between innovation, standards and safety. We ensure that knowledge gaps are addressed,
new technology can be operated safely and efficiently, that innovation benefits the industry and passenger, and that best practice is codified and shared. With no commercial interest in the underlying data, we can offer independent knowledge of all rail systems and their interfaces.
Our research has allowed existing and new vehicles to operate at different speeds on the same track, optimising journey times and maximising route capacity. Our revised standards for AC electrification have the potential to save over £700 million over the next 25 years. This is mainly by reducing costs in the design, construction and maintenance.
Our insights and analysis have helped put rail at the cutting edge of health and wellbeing practice. We’ve started a programme to gather consistent sustainability-related data from across the industry, and our Rule Book ensures industry knowledge is reliably applied in train operations and maintenance.
The railways have a critical role to play in growing, connecting, and decarbonising our economy, with immense social value and huge opportunities for young people and career-changers. Unlocking this potential is crucial, but needs to be achieved while also getting to grips with cost.
We’re enhancing our data science abilities with new datasets, like weather data, to model how the changing climate will affect fixed assets. We have access to more data than any other rail organisation, and are working with academia to lay the groundwork for blue-sky innovations.
As industry embarks on a period of change, we will ensure we can play our part in enabling the public policy agenda, whatever the party in government, maintaining our role as an independent, objective counsellor to efficiency for the future.
NEWS IN BRIEF
BRIDGE SET TO LIGHT UP THE BIRMINGHAM SKYLINE
HS2 Ltd has received Schedule 17 approval for a 150-metre section of viaduct carrying trains into Birmingham’s new Curzon Street Station, including a 25-metre-high truss which will create a new icon on the ci¬¬ty’s skyline. Birmingham City Council have approved the design of the Curzon No.2 viaduct, which is the tallest structure in the sequence of viaducts and structures that make up the Curzon Street Approaches taking HS2 trains into Birmingham.
The bridge consists of a gently curved truss in weathering steel which carries HS2 over the Victorian brick rail viaduct below, and which will reach 40 metres into the air, resting at least 17 metres above the ground. The bridge will carry three parallel high speed rail tracks over the existing east-west rail line. Closer to Curzon Street, the tracks will split further to serve the seven platforms being built at the station.
RIA NORTH RESPONDS TO TFN’S STRATEGIC RAIL REPORT
RIA North Chair, Justin Moss, said: ‘We very much welcome the publication of this report, which is strikingly consistent with RIA’s own calls for the full delivery of the TRU, HS2 and NPR and for a rolling programme of electrification. The prediction of a growth in demand is an important reminder that investment is needed now to prepare for the future.
‘The report demonstrates a clear link between investment and the delivery of desired outcomes for people in the region. With Oxford Economics data showing that for every £1 invested in the railway a further £2.50 is generated in the wider economy, RIA North stands ready to work with TfN and DfT to help make the case for this investment and provide practical support when it comes to developing and procuring major projects.
‘Separately, RIA North will be making the case for improving the procurement process to make it easier and more cost-effective to ultimately bring about transformational rail upgrades.’
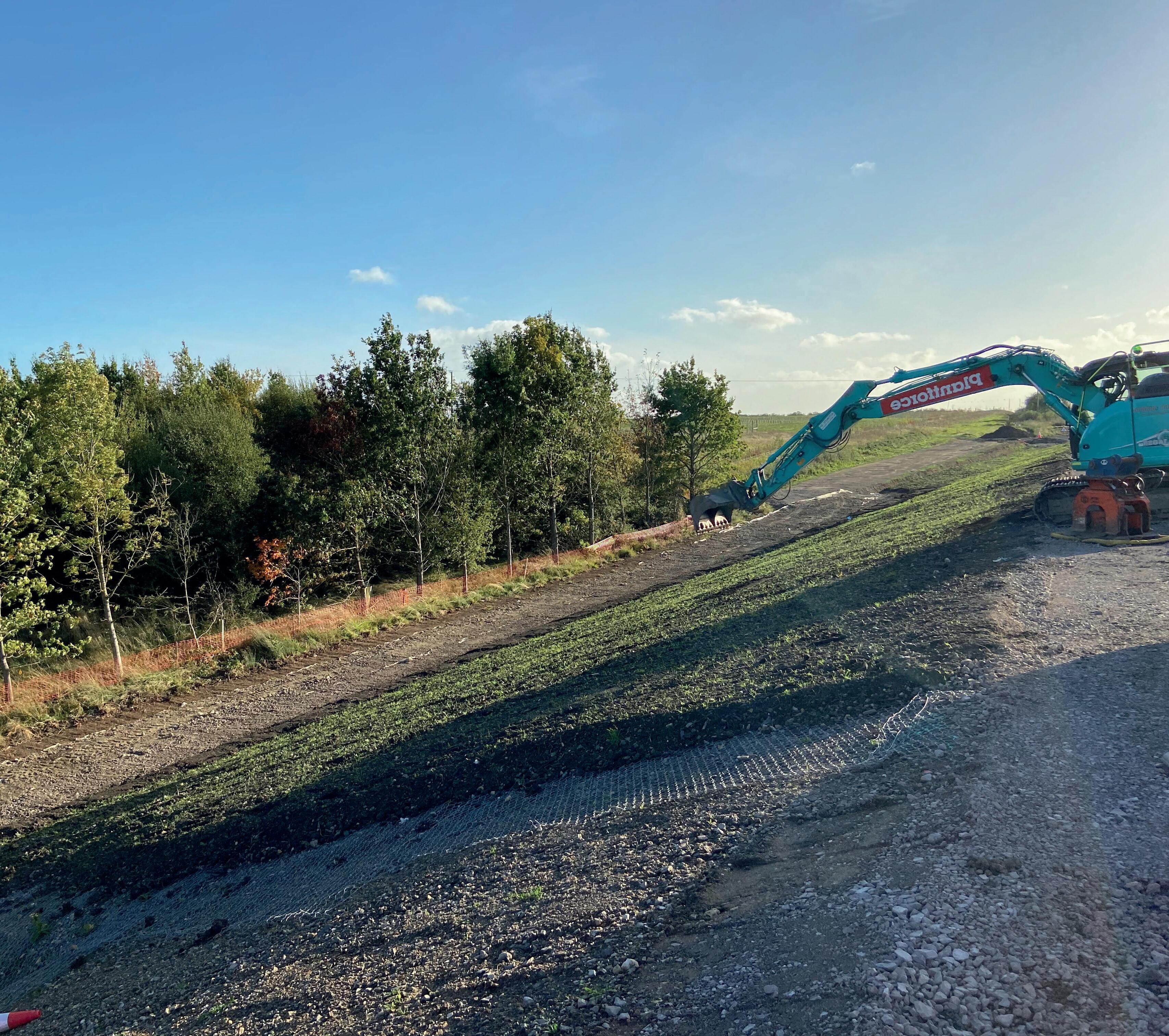


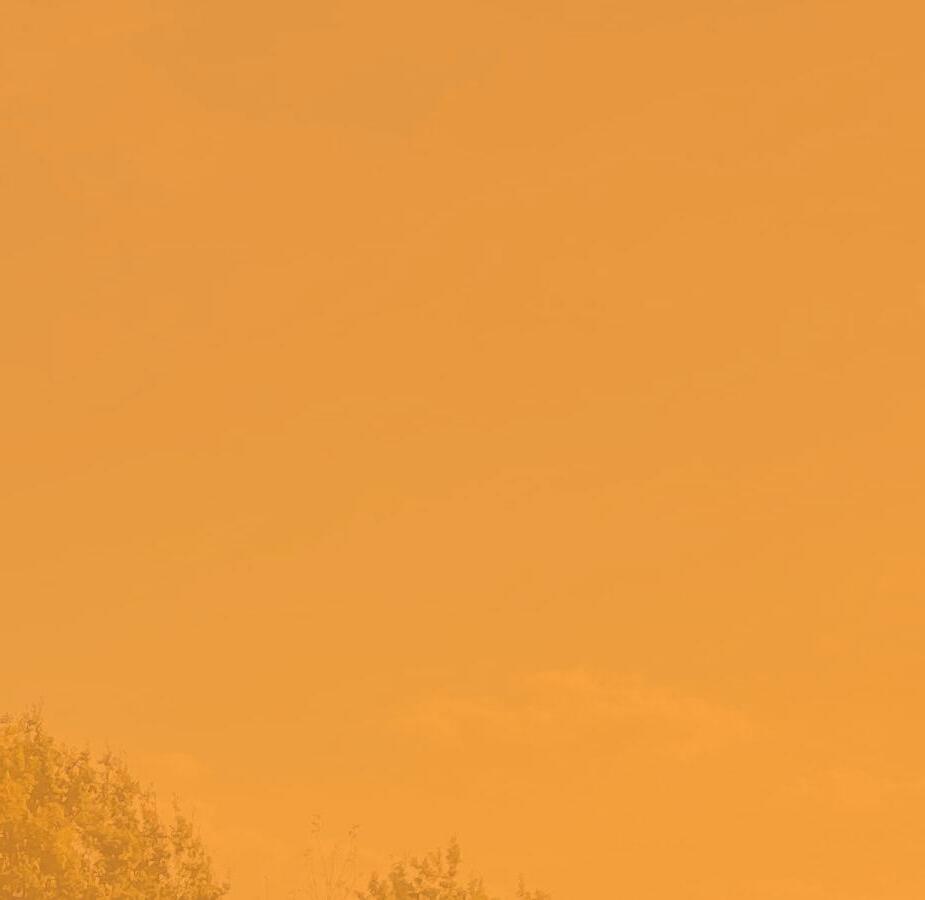
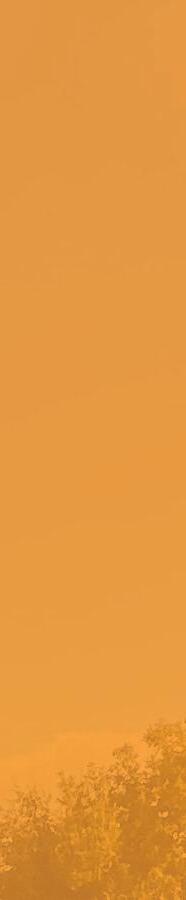
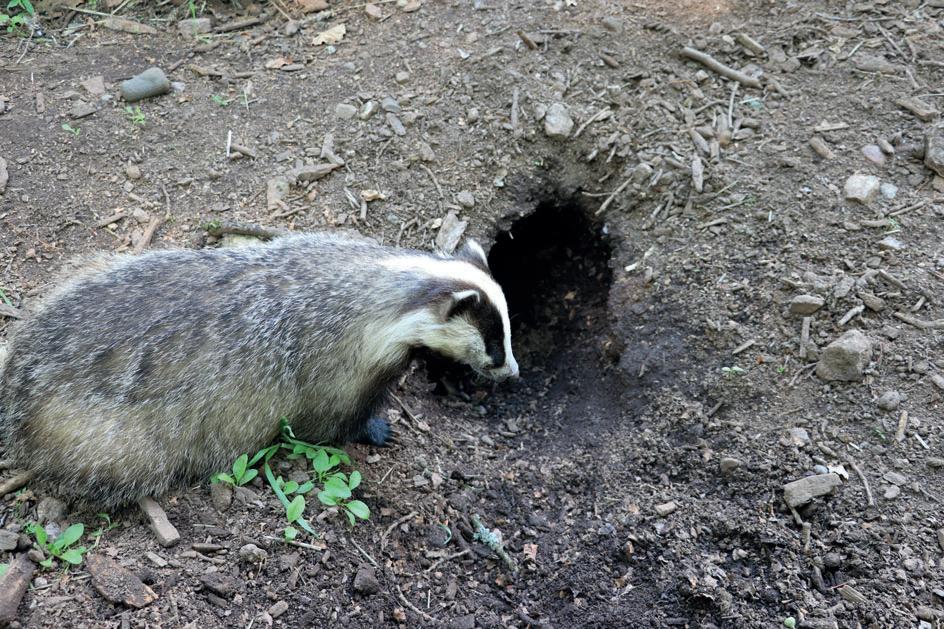
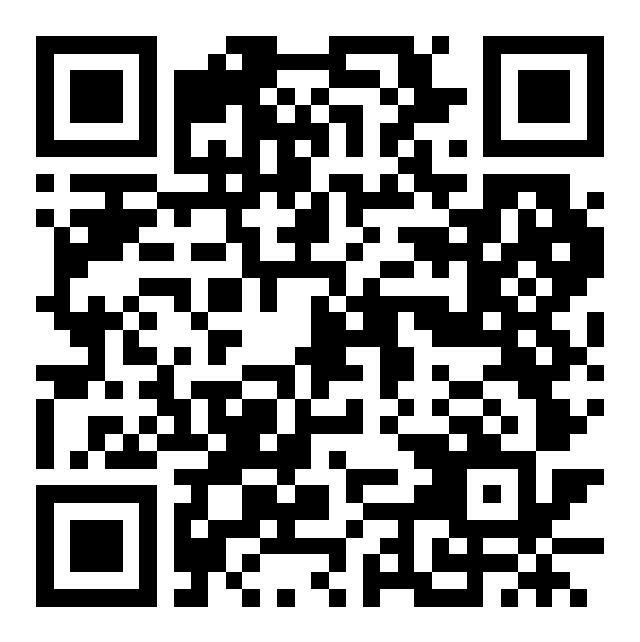

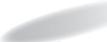


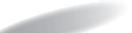




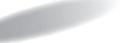


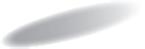

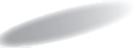
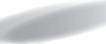



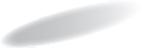


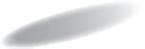
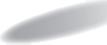

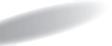
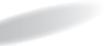
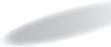




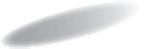
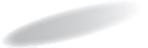

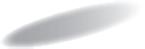
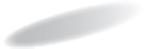
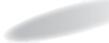
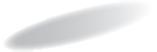
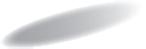

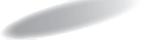
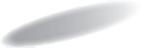

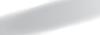
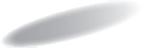
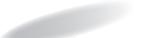
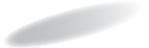
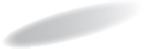
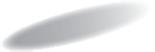
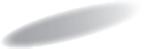
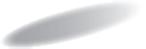
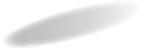
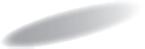
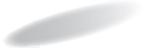
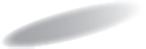
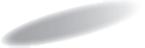
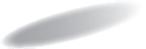
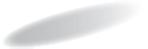
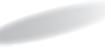
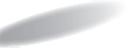

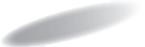
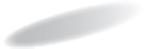
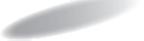
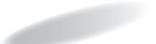




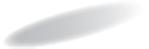

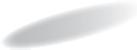




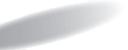
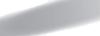
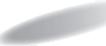


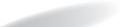

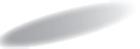


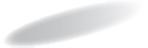
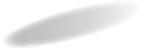
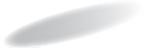
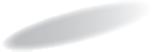

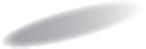
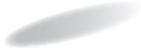
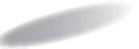

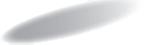
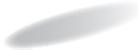
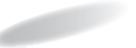

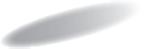
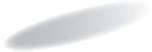

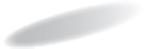
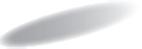



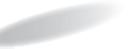

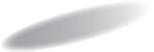
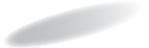
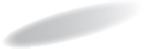
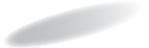
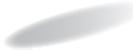
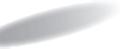
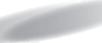
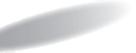

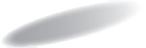
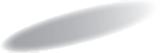
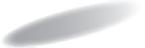
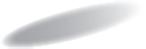
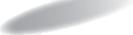
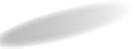

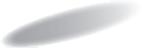


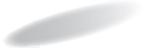
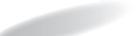
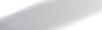
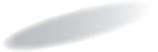

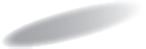
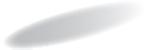

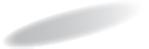

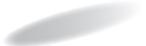
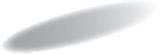
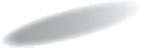
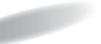
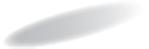
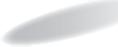



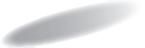
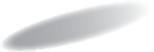
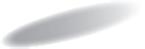
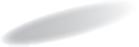
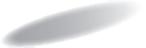

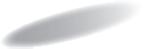
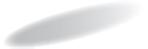

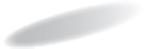
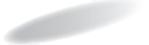
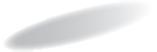
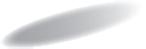

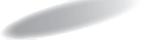

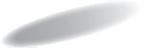
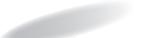
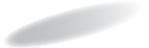

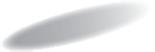
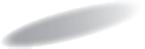
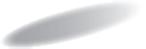
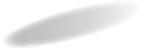
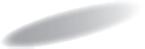
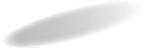
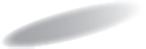
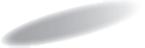
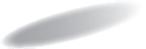
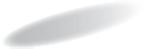
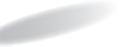
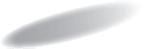
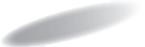

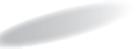
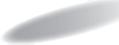



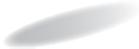


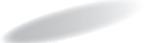

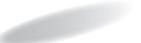
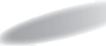


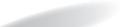

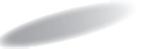


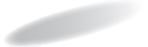
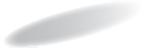
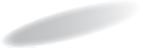

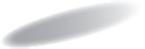
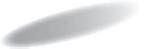
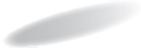
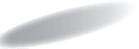

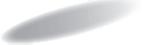
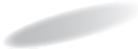
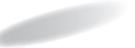

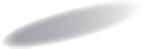
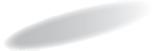
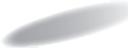
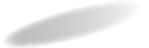
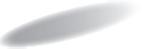


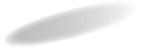
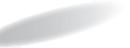

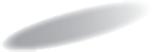
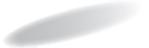
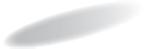
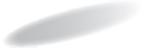

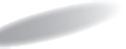
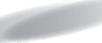
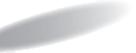

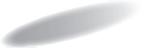
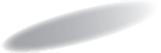
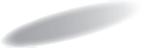

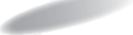

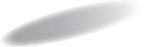
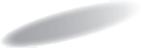
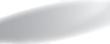

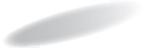
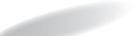
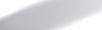


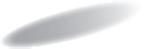
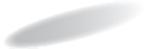
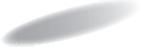
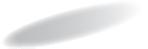


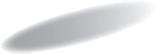
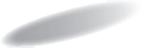
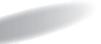
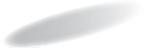
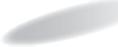



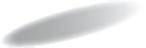

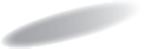
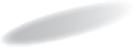
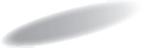

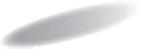
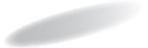
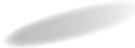

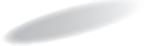

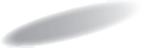
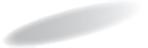
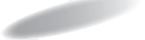
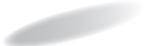
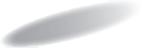
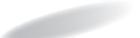

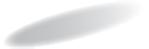
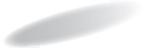
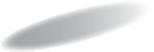
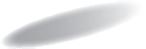
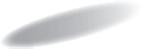
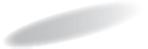
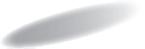
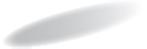
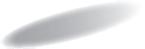
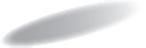
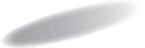
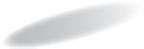
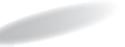
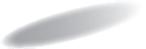
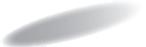

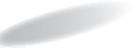
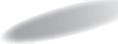



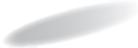
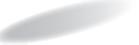

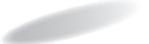

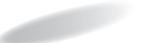
Customer Service in the Transport Sector
The latest UK Customer Satisfaction Index from the Institute of Customer Service (ICS) paints a bleak picture for businesses, revealing an average decline of 0.7 points compared to July 2022 and January 2022. The transport sector produced particularly concerning results, with a drop in customer satisfaction of 1.7 points.
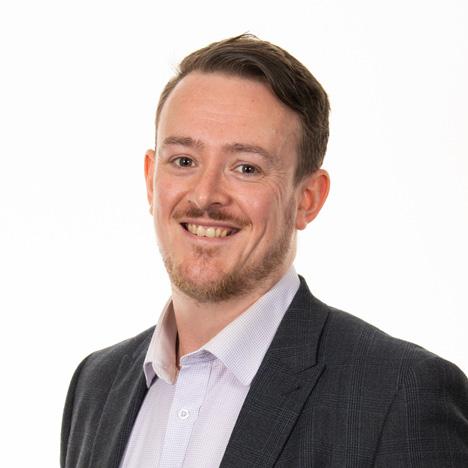
The UKCSI score is based on how customers rate organisations across 26 measures, from satisfaction with transactional experiences to broader relationship needs, out of 100 points.
This drop in customer satisfaction should be extremely concerning to the rail industry. In the midst of a cost-of-living crisis, rail companies are facing increasing competition from other modes of transport, reputational issues as a result of ongoing industrial action, and growing regulatory scrutiny. It’s therefore more important than ever that the industry is not taking its customers for granted and looking for ways to nurture customer loyalty.
There are of course several factors that will help to improve satisfaction scores, including improving on-time performance and pro-actively investing in the workforce and rolling stock maintenance. However, the value of outstanding customer service shouldn’t be overlooked, with it playing a critical role in customer retention and loyalty, and reputation management.
The ICS data highlighted issues with consumers’ satisfaction with the transport sector’s complaint handling, which dropped by 2.5 points year on year, as well as operators’ ability to express an emotional connection or ethics, which dropped by 1.0 point. Both indicate a greater requirement to address customer service provisions. So, what can be done?
Embracing new technology
Technology such as self-service platforms and AI-powered chatbots can be used to quickly and efficiently handle certain customer queries and complaints. With 1.8 billion passenger journeys made in the UK each year, finding more efficient ways to handle huge numbers of customer queries is vital. Although our research has shown that a proportion of consumers remain sceptical about the benefits of chatbots in the context of customer service, this is likely because some businesses have sought to cut costs by relying too heavily on the technology before it was sophisticated enough to do so.
Used correctly, however, chatbots can be a fantastic way to ease the burden on human operators by providing answers to simple queries and signposting customers to useful resources. In order to avoid frustrating customers, it’s crucial that when in conversation with a chatbot they always have the option to begin interacting immediately with a human agent instead. This way, customers with the most straightforward queries can be dealt with instantly by the chatbot, and those with more complex or sensitive issues can reach a highly trained operator more quickly as the overall number of customers waiting to speak to them will be reduced.
And given the recent rapid developments in conversational AI, widespread access to large language models such as Chat-GPT and Google’s Bard is likely to make chatbots far more effective for customer service purposes in the very near future. This will free up human operators even further to ensure that the most complex complaints are dealt with as sensitively as possible, driving up the quality of complaint handling and allowing them to build the emotional connection that the UKCSI showed is lacking.
Providing 24/7 customer service
Research has shown that 72 per cent of customers expect businesses to offer 24/7 customer service, and that businesses that offer 24/7 service have higher customer satisfaction ratings than those that do not.
Despite this, many businesses are still only contactable via phone or live chat within typical working hours. This means that customers with a query or complaint that occurs outside of these hours need to wait until the next working day to deal directly with an agent, and those who are unable to contact customer services during this time due to conflicts with their own work schedule might find it almost impossible to speak with an operator at all.
By making their customer service team available 24/7, rail companies can not only improve their competitive advantage, increase their customer loyalty and enhance their reputation amongst travellers, but they will also reduce the workload for their customer service agents during peak hours. Spreading the workload over a longer period can help to manage their resources more effectively, which can have a positive impact on quality.
Working with an outsourcer
Although there are clear benefits, offering 24/7, omnichannel customer service can be challenging for in-house customer service teams. With businesses facing tighter budgets in line with rising costs and inflation, many organisations are reluctant to employ more advisors. Using an outsourced team is the best way to scale up operations quickly and cost-effectively, with potential savings of £18,000 per annum, based on an average of 5,000 contacts a week.
A team of highly trained representatives can be fully onboarded into an existing team within just a few days to quickly increase access to resource. Support can also be scaled up and down at very short notice, ready to meet demand at peak times or in the event of a sudden influx of queries due to unexpected incidents such as extreme weather events or industrial action.
Final thoughts
The transport sector is facing a challenge: it needs to improve its customer satisfaction as both costs and customer expectations are rising. This may appear daunting, however there are some simple changes rail companies can make to improve customer satisfaction. By moving to more effective 24/7 customer care, with the use of AI-powered technology and a supportive outsourced team, companies can adapt their current offering to cope better with customer communications. Without doing so, they risk losing valuable customers during an already financially difficult period.
Nikhil Kaitwade is Chief analyst Automotive and Associate Vice President at Future Market Insights. He has more than a decade of experience in market research and business consulting having delivered over 1,500 client assignments predominantly in the automotive, chemicals, industrial equipment, oil & gas, and service industries. Learn more about Nikhil at: https://www.linkedin.com/in/nikhil-kaitwade-a45b7313/
Future Market Insights Inc. is an ESOMAR-certified business consulting and market research firm, a member of the Greater New York Chamber of Commerce, and is headquartered in Delaware, US. Find out more at: https://www.futuremarketinsights.com/
Battery Train – A Step to Embrace Sustainability in Transportation
Nikhil Kaitwade, Chief analyst Automotive and Associate Vice President at Future Market Insights explains how battery electric multiple units (BEMUs) can lessen the impact on the environment
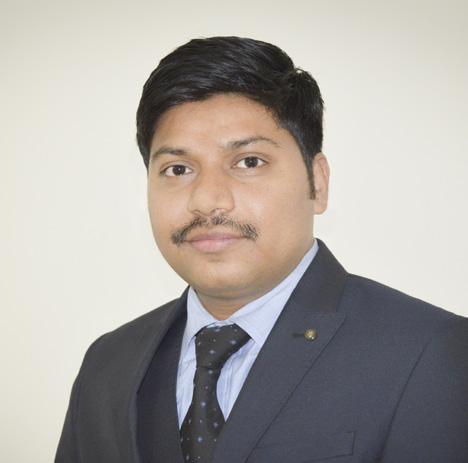
An increase in demand for eco-friendly solutions and sustainable alternatives for diesel trains has been witnessed globally. Although batterypowered trains can be seen on rails, the refuelling and recharging infrastructure is still a work in progress.
50 per cent of energy consumption and CO2 emission.
To meet the challenge and provide an innovative alternative, the United Kingdom started a battery-powered train project. Several manufacturers have shown interest in the technology to bridge the gap between electrified parts of the network.
Therefore, the need for alternative fuel options such as hydrogen and battery trains for non-electrified railway lines is widely coming to the fore. The solution for non-electrified lines will not only reduce
of the railway networks in the urban areas use electric traction. The purpose of electrification is to reduce rail’s carbon footprint by replacing diesel-powered trains. Although around 80 per cent of the traffic is running on electrified lines, upgrading and electrifying the rail infrastructure is still an issue. Several battery train projects have been undertaken by governments with pioneer firms to replace conventionally fuelled generators.
A study was conducted in 2015 by the University of Cambridge, the University of Minnesota, and Minnesota State University Mankato on diesel engines. It claims that enclosed train stops for diesel trains not only put people at risk but also worsen air quality because of exhaust emissions. The trains powered by diesel emit nitrogen dioxide and sulfur dioxide does not comply with air quality standards imposed by the regulatory authorities.
With 22 per cent of global emissions, railways account for 0.8 per cent, according to stats provided by the European Environmental Agency in 2013. Though, new reduction standards were outlined by the International Union of Railways, to cut
emissions but also improve travel comfort.
Despite the pandemic, the increase in railway electrification over the past decade continued its investment toward e-mobility. This has led to around one-third of the tracks globally being electrified. A gradual shift in electrification especially in Western Europe with 57 per cent and Asia Pacific with 55 per cent has been seen in 2022.
How battery trains are finding their route in Europe
Currently, 60 per cent of the rail network in Europe is electrified and the majority
For instance, České dráhy is planning to acquire battery trains for several regions in Czechia. According to the CEO, Michal Krapinec, the first battery train is likely to be deployed in and around 2025 to advance the region of Moravian-Silesian. ČD plans to purchase 15 battery units along with the spare parts and required services with an investment of €140 million.
Škoda Group, similarly, found a way to use the roof’s free space to house three battery packs. The battery train RegioPanter can cover non-electrified lines and can fully replace diesel trains. It can be recharged by driving under traction and can save considerable costs for the carriers. The units are equipped with a recuperation system, allowing the electricity to be produced during braking and returned to batteries, mitigating the energy demand.
In 2022, the two entities, Stadler and the German Aerospace Center joined hands to work together on the project MOSENAS. The project is based on a scalable battery concept to save weight and optimise space. Although it is adapted to cover short distances, the entities believe that the concept can enable operators to deploy BEMUs on the network without overhead lines. Moreover, the companies are looking for charging and loadbalancing options for the routes that are not feasible for battery electric trains.
60 PER CENT OF THE RAIL NETWORK IN EUROPE IS ELECTRIFIED
WITH 22 PER CENT OF GLOBAL EMISSIONS, RAILWAYS ACCOUNT FOR 0.8 PER CENT
IN 2022, THE TWO ENTITIES, STADLER AND THE GERMAN AEROSPACE CENTER JOINED HANDS TO WORK TOGETHER ON THE PROJECT MOSENAS
The hybrid mode can be a game changer for rail mobility
The tri-mode train that can easily switch between electric, battery, and diesel is currently supporting the transition to sustainable electromobility. The train can be operated on electrified and non-electrified lines with the ability to cut emissions by 50 per cent. The train is designed in trimode so that it can function in areas that don’t yet have the right infrastructure or electrical lines.
For instance, the Blue Train that has made its way to some parts of Europe uses this combination and runs by drawing power from overhead lines. The bonus point of this train is that it can recharge its battery when in operation – both in electric and diesel mode.
Electric train technology is drawing attention in Asia Pacific
Currently, Asia Pacific has the largest rail network in the world. With a track length of around 200,000 kilometres, China is the leading country in the region. Japan covers a track length of 28,000 kilometres. When thinking of autonomous vehicles, self-driving cars are the first thing that pop-up into my mind, but with changing innovations, we are moving toward driverless railways.
For instance, Japan has tested a selfdriving train that connects Tokyo, Shibuya, and other major cities around the country. This unmanned automated driving train is likely to run on rails by 2027. The Chuo Shinkansen can run at a speed of 500 kph and is considered to be the fastest railway in the world with an automated driving system. The driverless train will be run on a Magnetic Levitation linear motor railway, as it consists of an electromagnet lift that will push the train forward.
JAPAN COVERS A TRACK LENGTH OF 28,000 KM
In 2022, Beijing unveiled a driverless bullet train, Fuxing, for the Beijing Games. The custom-made train can carry around 500 passengers in its eight carriages. Moreover, the bullet train is fully equipped with a broadcast studio for journalists. Progressing toward a green network, India has completed 22,000 kilometres of electrified railway in Meghalaya. The electric locomotive is focused on increasing the speed whilst reducing emissions. The
Things not moving quickly enough for your products and services?
Want to speed up access into the rail market?
Need to quicken approvals or change standards and processes?
Struggling to find sponsors and engage clients?
electric power for the locomotive train of 25KV is drawn from a substation located in New Bongaigaon. Additionally, the recently launched Vande Bharat Express may see an entire change in its network from diesel to electric. The system has already been implemented in China, Japan, and South Korea.
We will find the quickest path into rail for your business, unlock issues, find clients, drive the change and deliver growth.
www.jpldiversified.co.uk
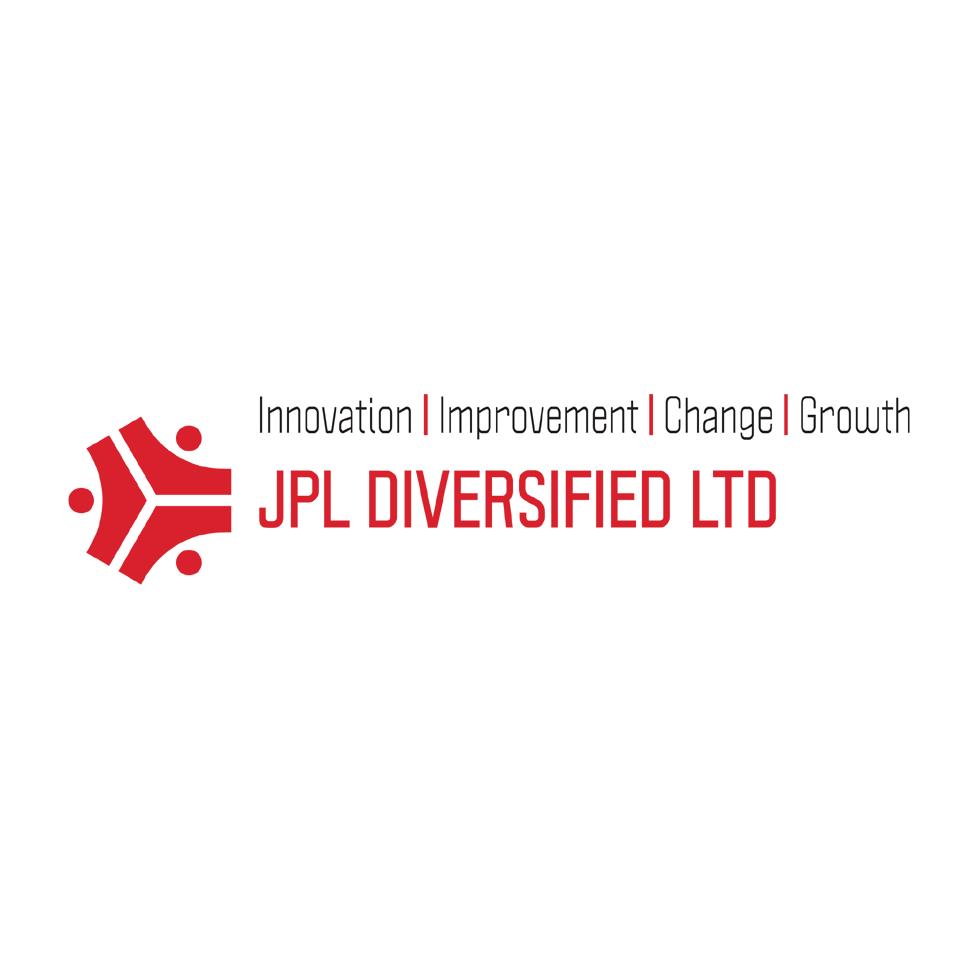
PROGRESSING TOWARD A GREEN NETWORK, INDIAN RAILWAYS HAS COMPLETED ITS FIRST ELECTRIC TRAIN OF 22,000 KILOMETRES IN MEGHALAYA
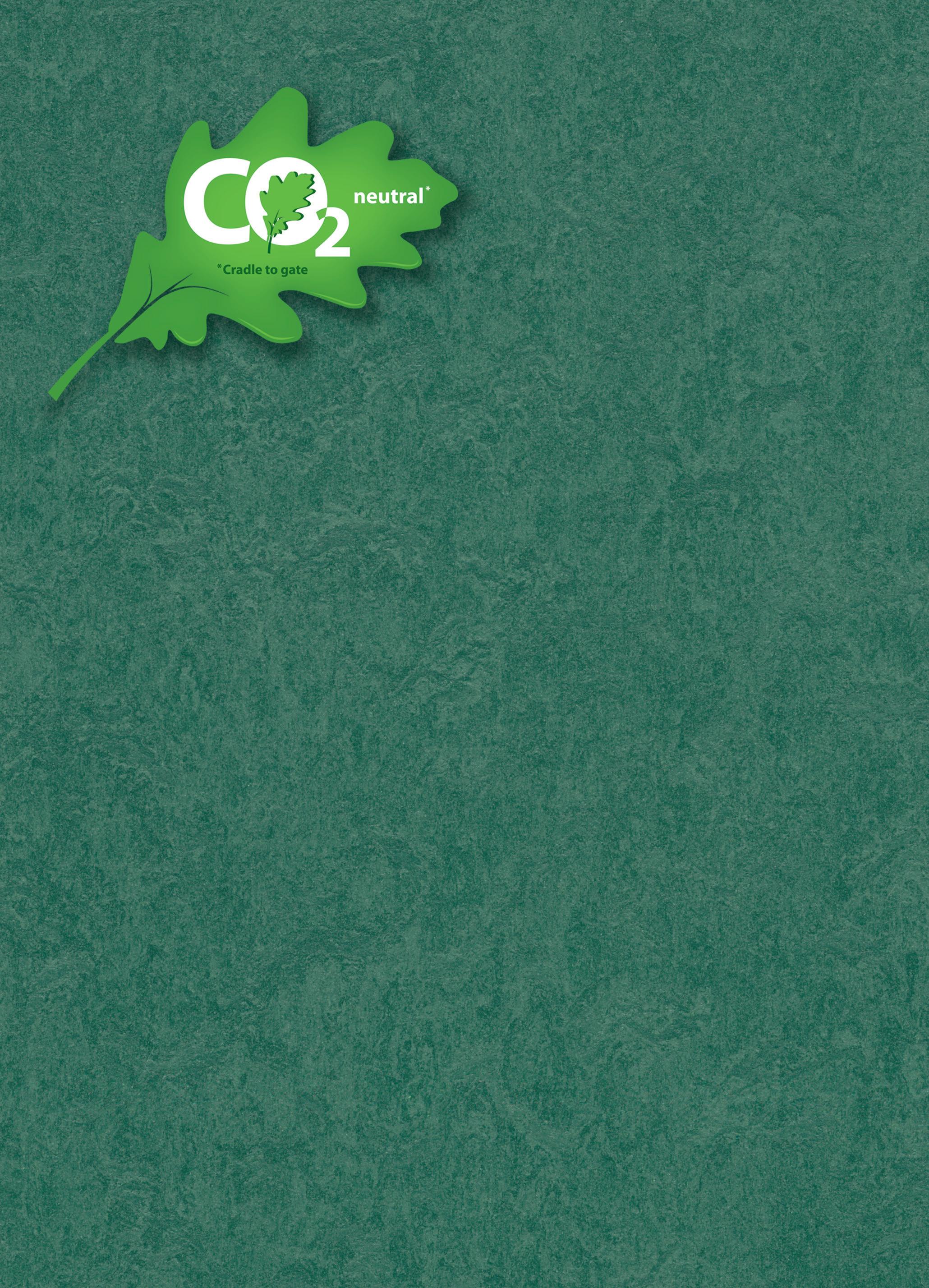
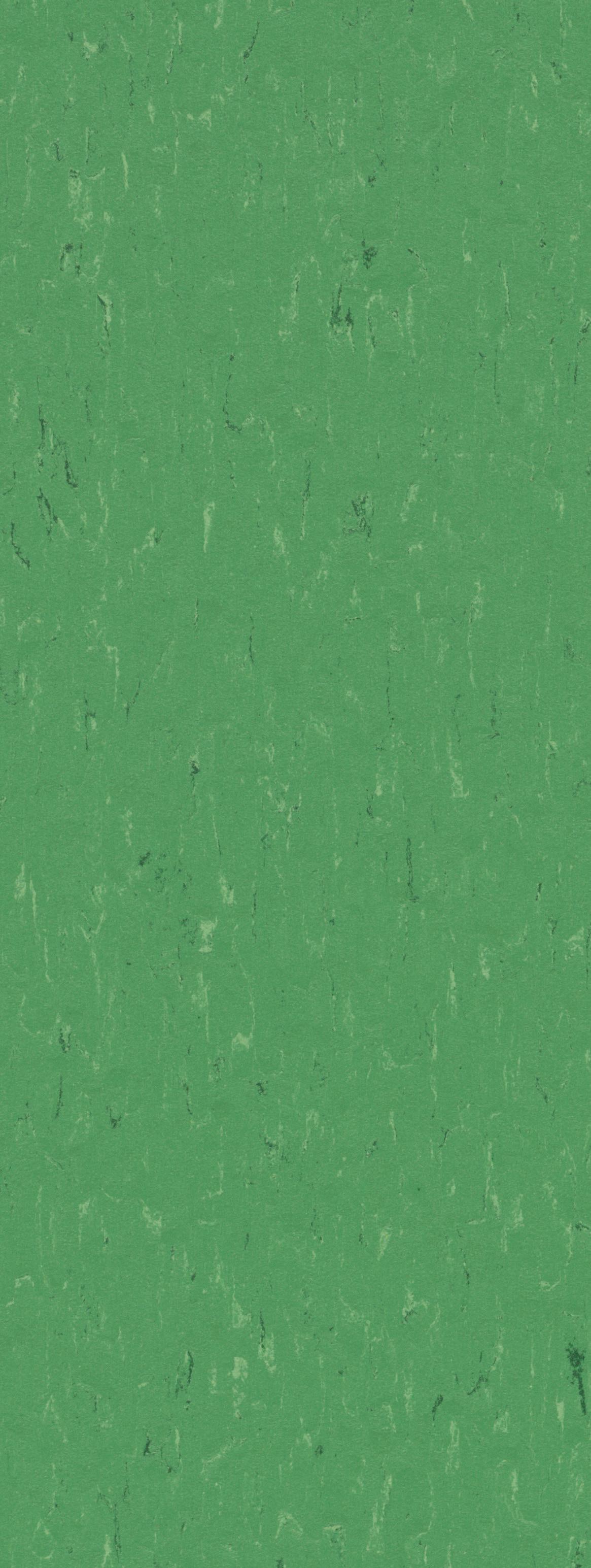


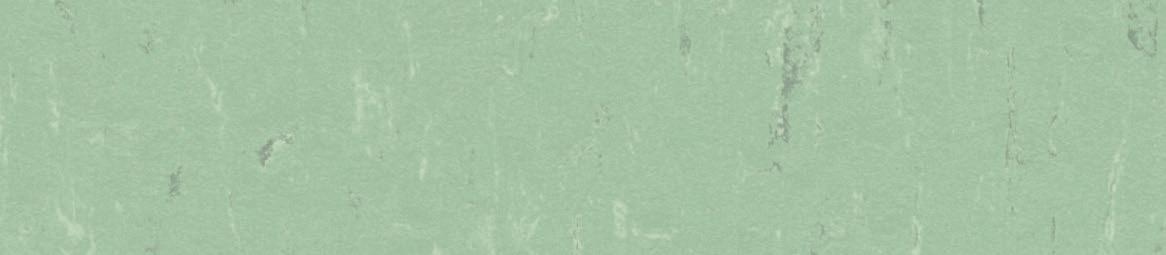
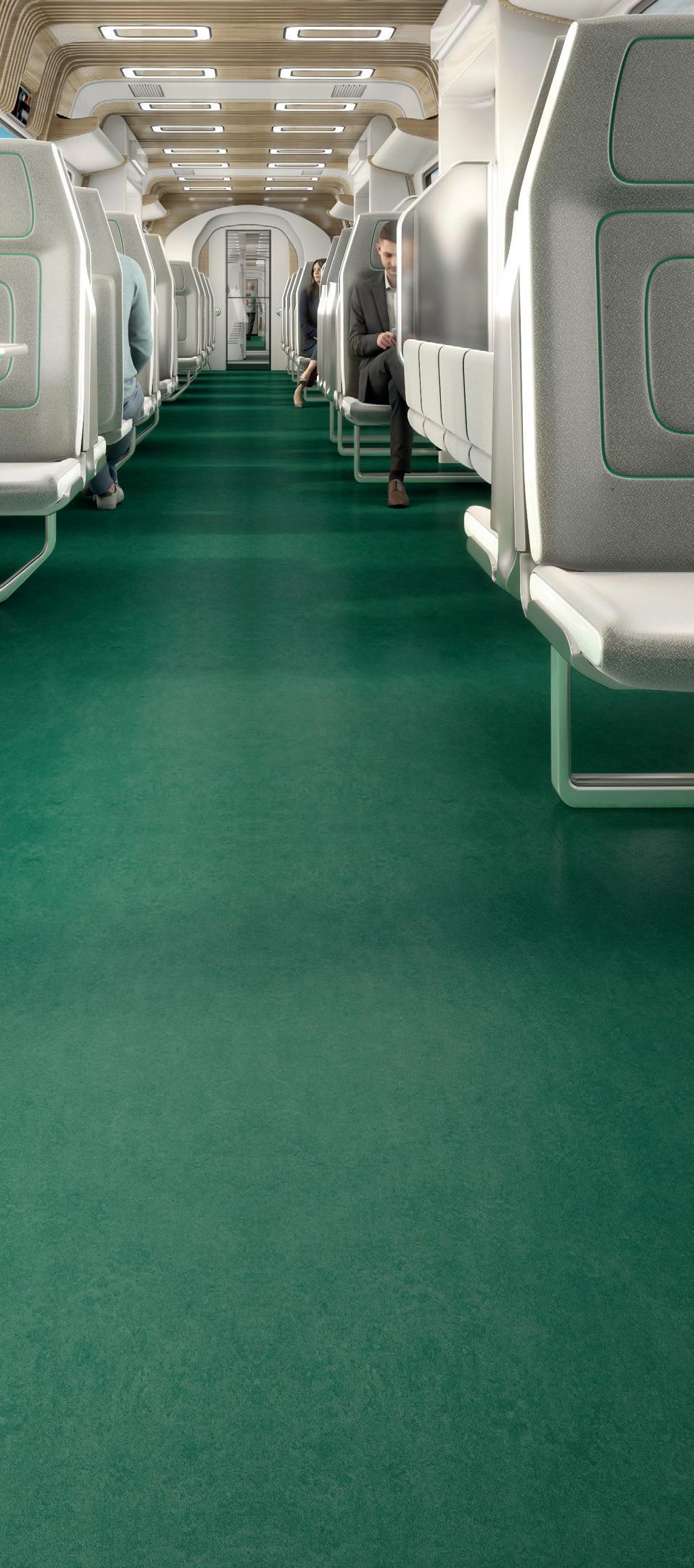
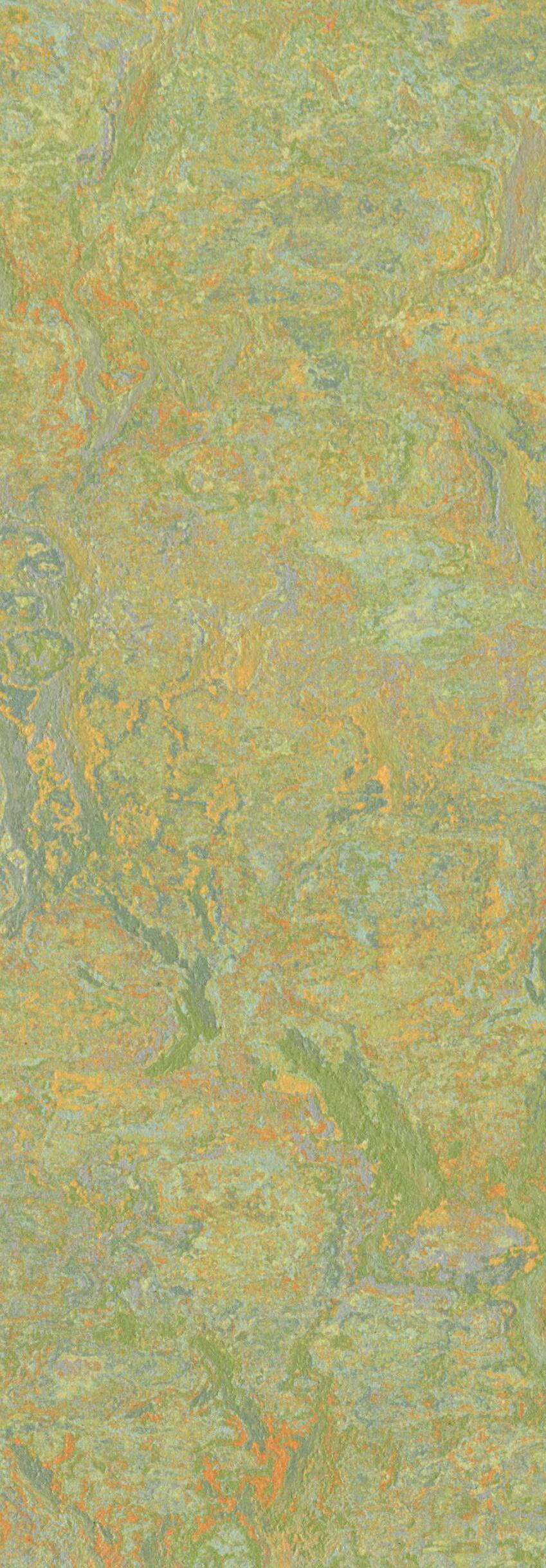

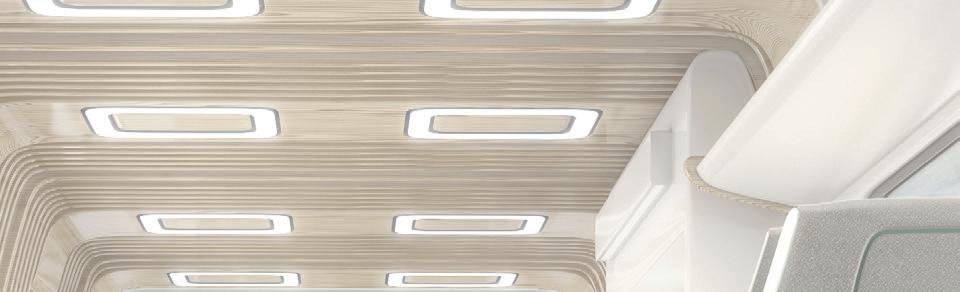

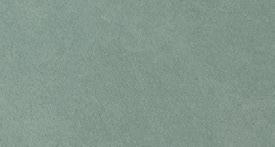

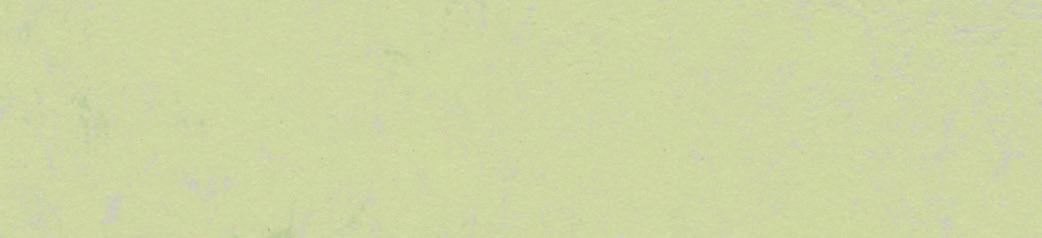
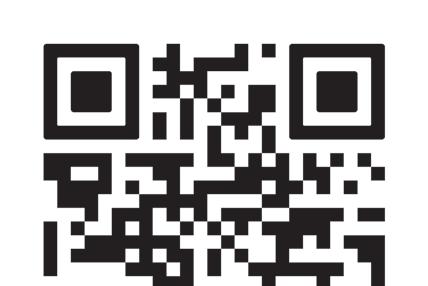
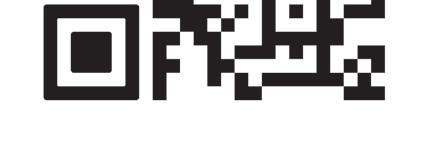
CLEM
Clem O'Rourke is the advanced modelling lead at Frazer-Nash consultancy and has been involved in the rail industry for over 5 years. Clem is currently Frazer-Nash's rail data science innovation lead and developed the concept which won the RIA innovation award in 2020.

innovation award winning delay predictions, to developing rail freight energy calculators to help understand the potential routes to net zero.
What is your role within Frazer-Nash Consultancy?
I hold two complementary roles with FNC, I am the advance modelling group leader and also the data science rail innovation lead. In these roles, I head a team of data scientists working across a wide range of industries, and also help shape and steer our data science focussed innovation proposals for the rail industry.
This role is very varied, with day-to-day activities varying from initial discussions with potential collaboration partners or customers, developing proposals against specific challenges to rolling up my sleeves and writing some code.
One of the strengths of FNC is our crossdomain experience; a large amount of our rail work comes from applying techniques and methods developed in other industries (often nuclear or defence) to help solve challenging railway issues. A key aspect of my role is to help provide the technical translation of concepts into rail market, helping to smooth their introduction and implementation.
What success have you experienced in the last twelve months and how do you measure success?
Success, to me, means effectively solving problems which matter. Global warming is a massive threat to our way of life, and delivery of a successful railway is key to reaching net zero. However, the railway needs to adapt to reach its full potential. As such any project which helps the railway reach its potential, matters.
Want to know more about Frazer-Nash Consultancy
Tel: 01925 40 40 00
Email: rail@fnc.co.uk
Visit: www.fnc.co.uk/rail
How did you get started in the industry?
I first became involved in the rail industry about five years ago, with my first projects focussing on how a predictive maintenance tool Frazer-Nash Consultancy initially developed for the Royal Navy might be applied to the rail industry. This project is a good example of the work we often deliver to the railway, taking and adapting learning we have gained from other domains, and applying it to deliver value, quickly.
Since then, my involvement has spread significantly, touching on a wide range of aspects of the industry – ranging from depot modelling, schedule eight risk modelling,
Finding problems that matter is only half the problem. To deliver success, you must also effectively solve that problem. Without an appropriate route to deployment and use, the best ideas and solutions are glorified shelfware. As such any successful project must have a clear vision and route to integration into the railway.
With that criteria in mind, there are two projects which spring to mind. Firstly, under a First of a Kind SBRI competition we have developed PosITrack in collaboration with Evifile. PosITrack uses AI to help support the optimisation of railway possessions. The delivery of possessions effectively is key to a successful railway, and PosITrack helps planners and Person In Charge of Possession (PICOPs) to optimise each railway possession ensuring effective delivery. PosITrack is integrated into Evifiles possession management platform, providing an easy and simple route to deployment.
Secondly, as part of the RSSB DECARB project, we have created a freight energy calculator, which gives detailed energy and emissions for user defined consists and routes. This tool allows different power setups to be compared and for infrastructure gaps to be thought of energy gaps rather
than distance. Through RSSB, we are using the tool to help produce insights into the network and future loco requirements.
Tell us about Frazer-Nash Consultancy. We are a systems engineering consultancy firm, with over 1,000 employees working across a wide range of domains including defence, nuclear, power and rail. With roots going back to Archie Nash engineering firm, the current form of FNC has grown significantly from a management buyout in early 1990s, roughly doubling every five to seven years. Everything we do is underpinned by our four key values:
• We care.
• We are trusted.
• We deliver success.
• We want to do things that matter.
These values guide everything we do, helping ensure our staff and clients feel valued and making the world a better place. In the rail market we are best known for our safety work but increasingly our innovation winning data science services are gaining traction.
When a client comes to you with a particular problem, what’s your process for coming up with a solution, and how closely do you work with clients throughout the projects?
As a company we like to work on the most challenging projects. This is where we feel we add the most value and our experience from other domains brings the most benefits. Whilst no one project is the same, our approach can be broken into a number of high-level steps.
The first step is always to ensure you understand what the client’s problem is, what constraints they have and to understand their thoughts around integration. Often is this is best done through a face-to-face discussion but depending on the client this can be constrained due to the rules of the framework.
Once we have a good understanding of the clients needs, the next step is to flesh out potential approaches and work out what partners we might need to develop and/or deliver the solution. I am a strong believer that collaboration delivers stronger and better solutions, so where we have partners with existing products or services which can complement our proposal, we look to form partnerships. Depending on the contracting mechanism, the outline approach is either turned into a formal proposal, or, if allowed, presented to the client for comments.
Once on contract and delivering, we look to engage with our clients frequently, getting their feedback and guidance on the project’s direction. The exact methods used vary significantly depending on the project and the client’s appetite, but as a rule of thumb for innovation projects we often look to form across industry steering groups which meet quarterly, for client specific projects, a more regular drumbeat is often used.
What are your plans going forward to ensure Frazer-Nash Consultancy services are still around for years to come?
Our services are constantly evolving in response to both market pull and technology evolution. Within data science, the rate of development is staggering, with seemingly more and more powerful tools available. The potential for these tools to provide benefits to the railway is obvious, but they need to be surrounded with the appropriate levels of assurance for they can be used.
Through our involvement in the defence sector, we work at the cutting edge of data science, testing and understanding the latest methods. I expect we will continue to cross pollinate the understanding and research we do in this area to the railway, coupling with our strong track record in assurance to deliver services and products which will make a big difference to the railway.
With the roll out of the Great British Railway, there is also a unique opportunity to develop more holistic approaches to maximise the potential of the railway. Our systems engineering heritage and approach are very well suited to this, and I expect that this will be an area of growth for ourselves.
What are your views on collaborative working?
Collaboration is often key to the delivery of a successful project. Without strong integration and deployment methods, good ideas and projects become shelfware, wasting money and effort. This is particularly true in the innovation space, where there are a number of established SMEs who offer high quality solutions which are well suited to be augmented through a targeted innovation development.
Furthermore, I am a strong believer in not repeating work unless crucial – it demotivates the staff working on the project and often delivers poor value to the client. By partnering with and augmenting existing solutions, the timescales to deployment are often shorter, and the barriers to exploitation are lower.
In the last year alone we have partnered with DRS, evifile, Systra and Lampada Solutions to deliver successful projects.
In terms of technology, how do you anticipate things might change in the next five to ten years?
As I mentioned above, the pace of development in data science is staggering. Machine Learning and Artificial Intelligence offer significant benefits across a wide arc of the rail sector. These tools give the potential
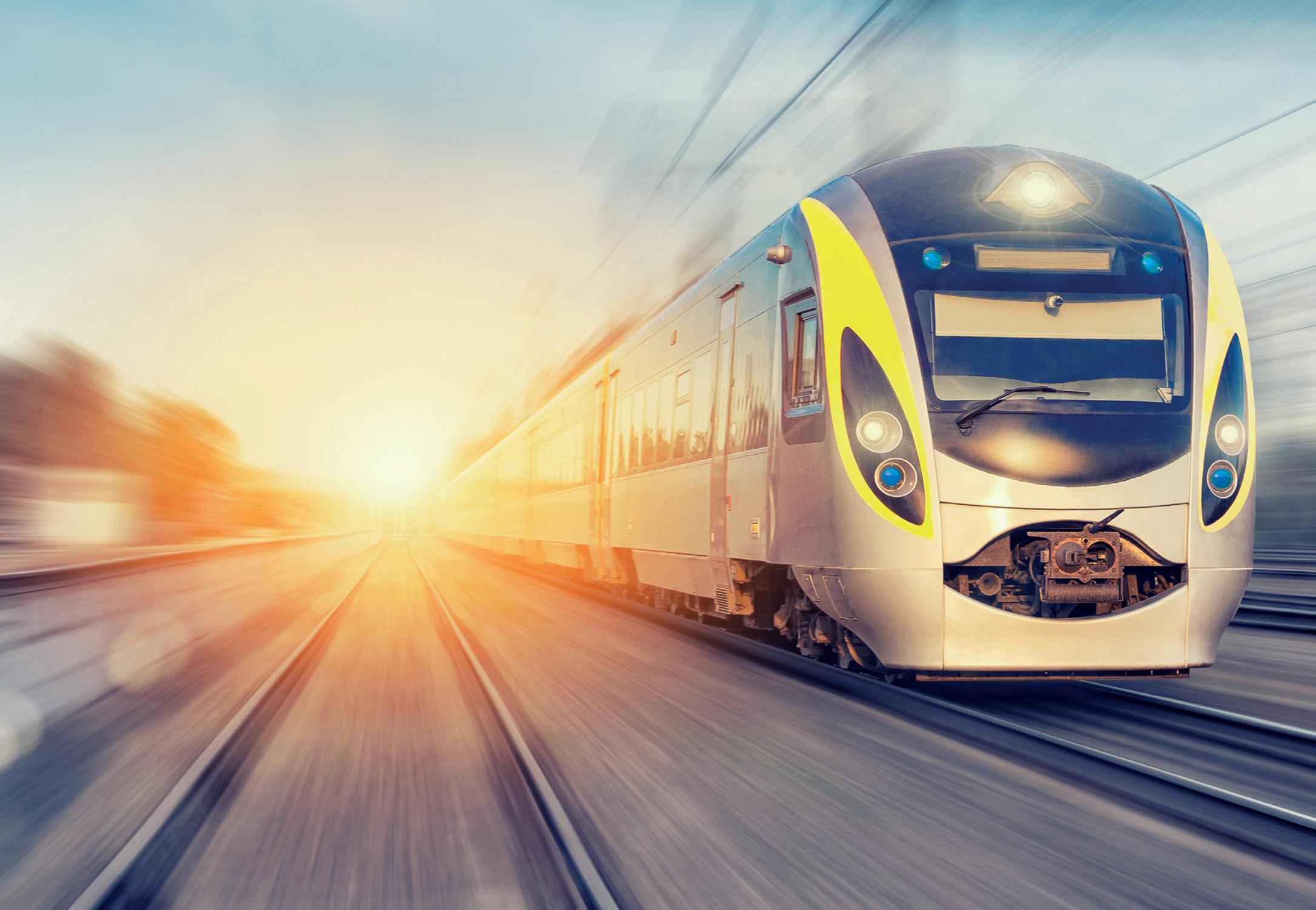
to revolutionise the data collection and analysis of the railway, offering methods to successfully move towards predictive maintenance for the majority of assets on the railway.
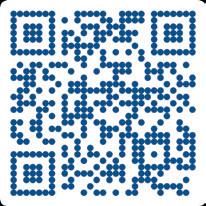
However caution will be needed to provide the appropriate level of assurance for these tools; concepts like Explainable AI are crucial for these tools to become fully embedded into decision making processes. Understanding the regulatory and safety considerations of concepts like human in the loop or human over the loop will be key to the total value these systems will unlock.
It is worth noting that ML and AI require significant amounts of high quality data to operate. The cost effective collection of this data will be key to enable their use and I am excited by concepts like kinetic energy recovery devices which can power sensors without significant rolling stock upgrades. If shown to be cost effective, these devices offer the potential to democratise data across ageing assets.
Finally, and away from data science, I expected the deployment and development of systems like ETCS and local regenerative braking and power for freight wagons will offer the ability for the railway more and more congested networks, creating capacity and lowering costs.
Taking the 3D Perspective
3D scanning and 3D printing can benefit the rail industry at all stages
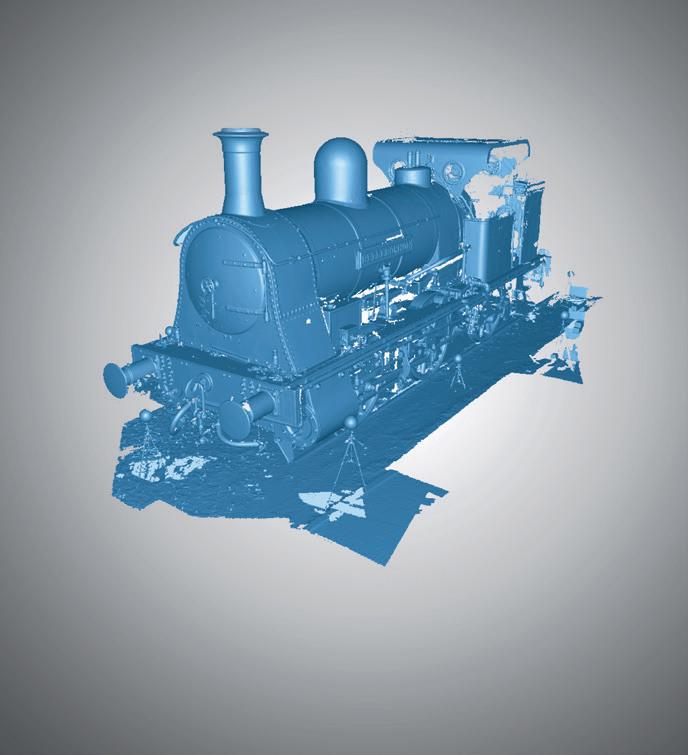
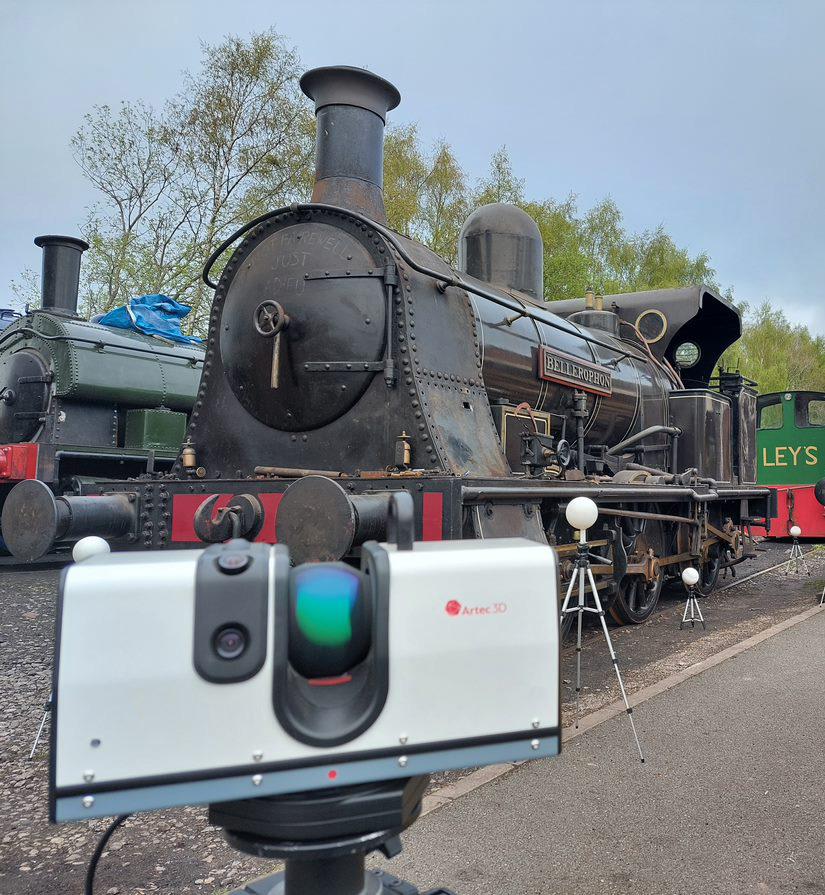
3D Scanning is a fast and efficient process used for analysing a realworld object or environment to collect data on its shape and possibly its appearance, like its colour.
The collected data can then be used to construct digital 3D models used for inspection, reverse engineering or 3D printing typically. Parts ranging from several millimetres in size to planes, trains and automobiles can be scanned with high accuracy and relative ease.
The use of 3D scanning is now being deployed in an ever-growing range of industry sectors – aerospace, medical, automotive, rail, R&D as well as tool making and product development. From engineering, to design, manufacturing, testing, development and quality assurance to name a few. There are many benefits to employing a handheld 3D scanner such as the Artec Leo or the Zeiss T-Scan Hawk 2, in all stages of the manufacturing process.
As industry leading 3D Printing, 3D Scanning, Reverse Engineering and Inspection specialists, Central Scanning Ltd is the only Artec 3D Ambassador & Gold Certified reseller in the UK. A leader in its field, providing 3D scanning equipment and related software. The company is also part of the #HandsOnMetrology network and can
provide pre-sales, installation, training and ongoing support.
In addition to its 3D scanning capabilities, the company offers a comprehensive 3D printing service utilising its in-house 3D printers from Stratasys, MarkForged, Ultimaker and Prusa. Central Scanning Ltd can print in a wide variety of materials and has the full colour multi-material Stratasys J750 printer.
The expertise of its engineers, combined with the 3D scanning and 3D printing equipment and related software they have, allows them to offer a comprehensive service to a wide range of clients and are used to working under NDA conditions. They work in their air-conditioned premises or can travel to most facilities to meet the project needs.
Central Scanning Ltd has released a brand-new #HandsOnMetrology handheld 3D Scanner. 31 January 2023 saw the global release of the Zeiss T-Scan Hawk 2, a lightweight 3D laser scanner designed and manufactured by Zeiss, who are renowned for high accuracy, and repeatable measuring equipment.
The new scanner, weighing less than one kilogramme is a highly portable 3D Scanner that is travel friendly and provides a user-friendly scanning experience working directly within the highly acclaimed Zeiss Quality Suite software. Scanning is
performed using remote workflow; there are four buttons on the scanner that allows the software to be navigated without using the laptop from up to ten metres away.
You can also ‘GO BIG’ with the new Satellite mode which enables the scanning of larger objects without the need of traditional photogrammetry. This has no compromise on accuracy and is easier using the positioning laser grid projected from the scanner onto the object being scanned.
There are different laser modes and a ‘deep pocket’ mode allowing you to scan deep into the features on parts and a highresolution mode called scan details, allowing
‘The Rail Industry is a very exciting sector for 3D scanning, reverse engineering, inspection and 3D printing. We work with vintage and modern rail companies throughout the industry and the addition of the Zeiss T-Scan Hawk 2 enhances the offering provided to the sector. Being hand-held with high accuracy, resolution and repeatability, the fit is perfect to cover many applications.’
Nick Godfrey Managing Director at Central Scanning Ltd.
targeted capture of highly detailed items such as text on castings or engravings on a coin for example.
As a business, Central Scanning is very excited by this new scanner as it provides metrology grade accuracy, combined with a large volume and un-paralleled portability.
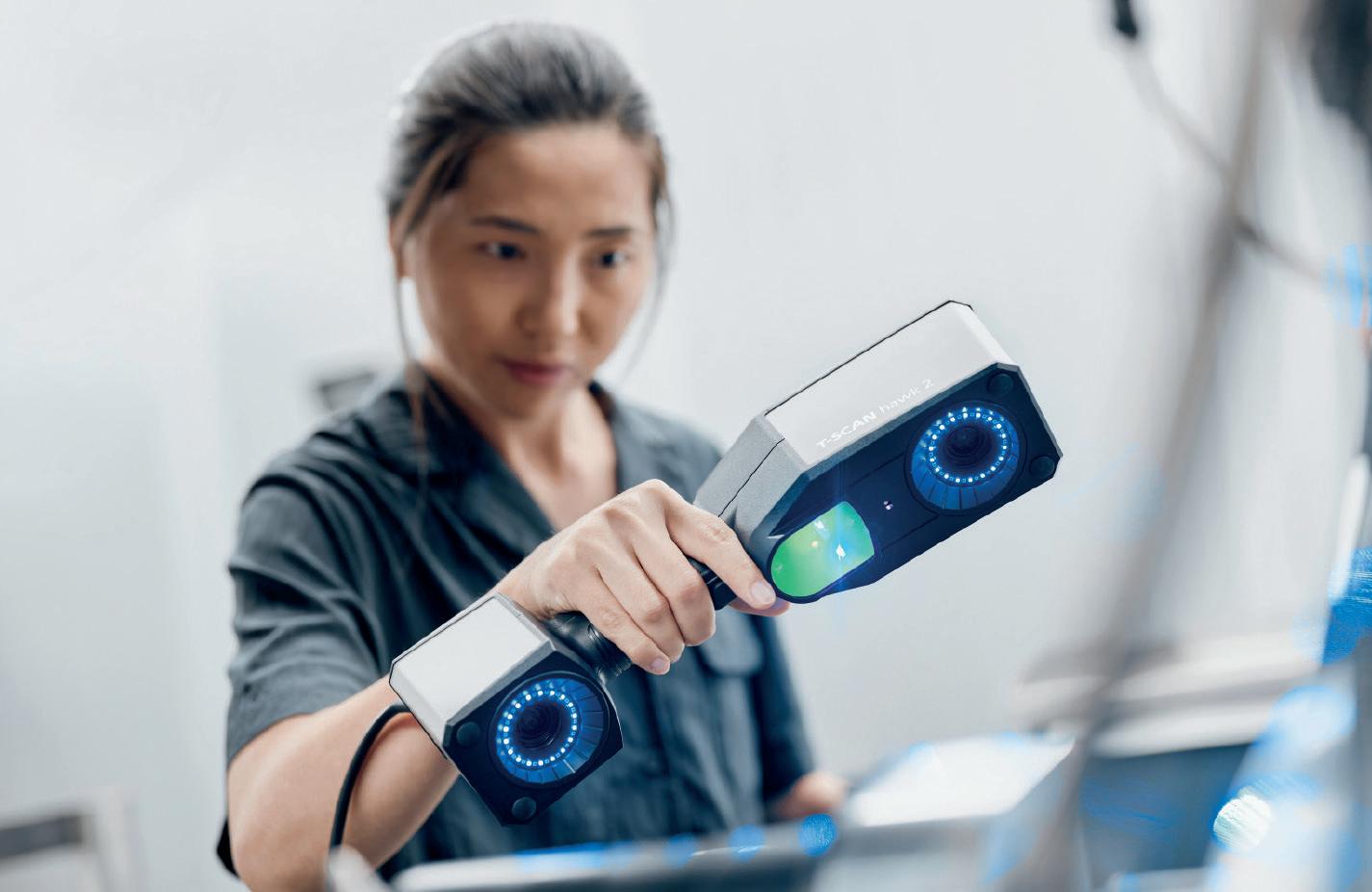
The Zeiss Quality Suite software not only allows for the collection of scan data but also the full measurement of the data compared to either a nominal 3D model or another approved sample part. For the more indepth analysis of the data, the ‘Pro’ version of the software provides the ability to write
inspection templates and report trends from the results.
Data collection, reverse engineering, inspection/validation of a wide range of objects are where these types of 3D Scanners are used and being highly portable, this increases the applications where this technology can be deployed. Gone are the days when the item has to be bought to the ‘measuring room’. The T-Scan Hawk 2, 3D Scanner can be easily taken to the item, making the process much easier, hence the slogan ‘Take it, Make it’ which is frequently seen alongside the T-Scan Hawk 2.
Central Scanning is not exhibiting at the Rail Live show this year. To find out more about how its products and services can help you, get in touch via the contact information below.
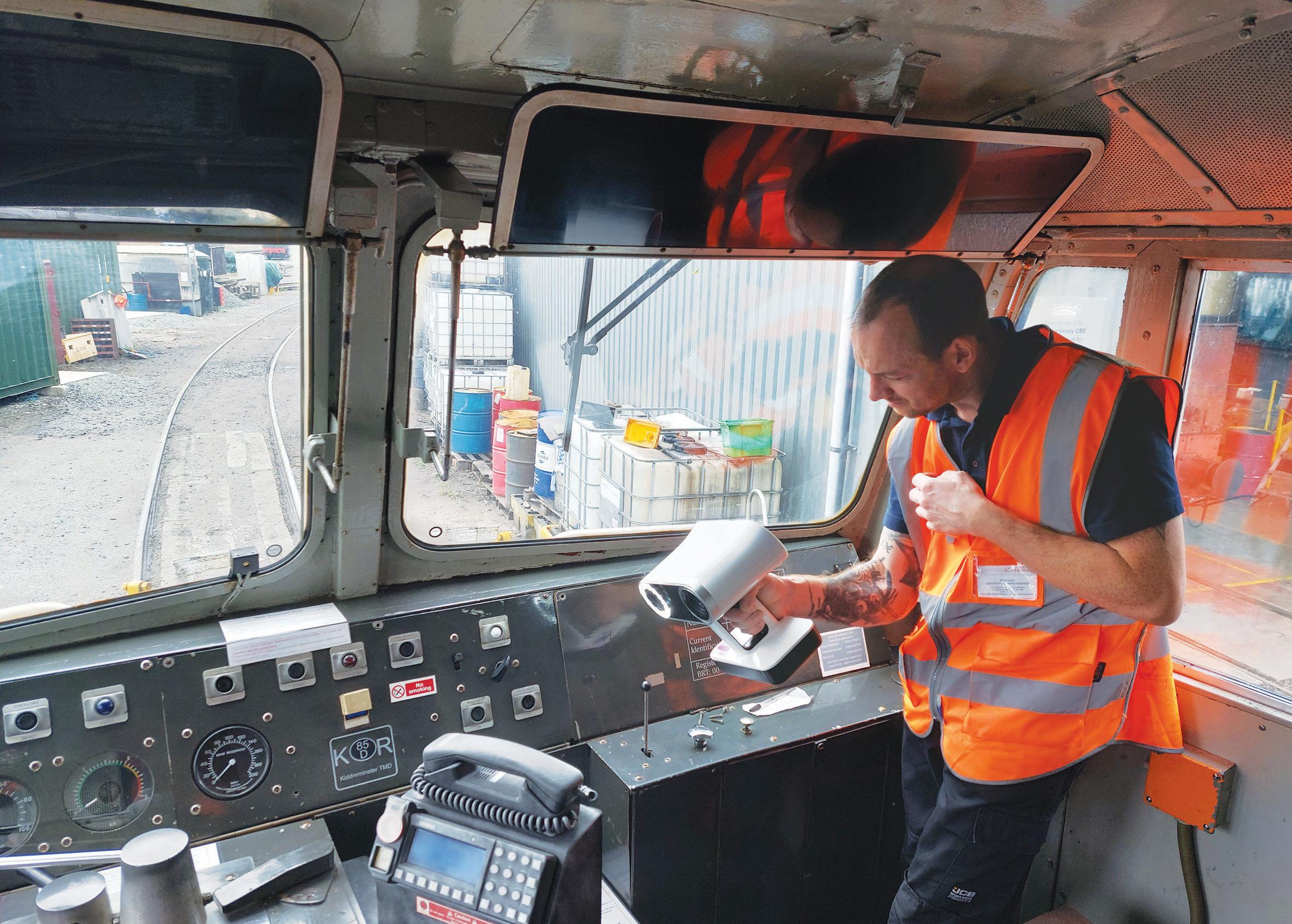
Tel: 01527 558282
Email: info@central-scanning.co.uk
Visit: www.central-scanning.co.uk
Address: Central Scanning Ltd
Unit 9, Wildmoor Mill, Mill Lane, Wildmoor, Bromsgrove, B61 0BX
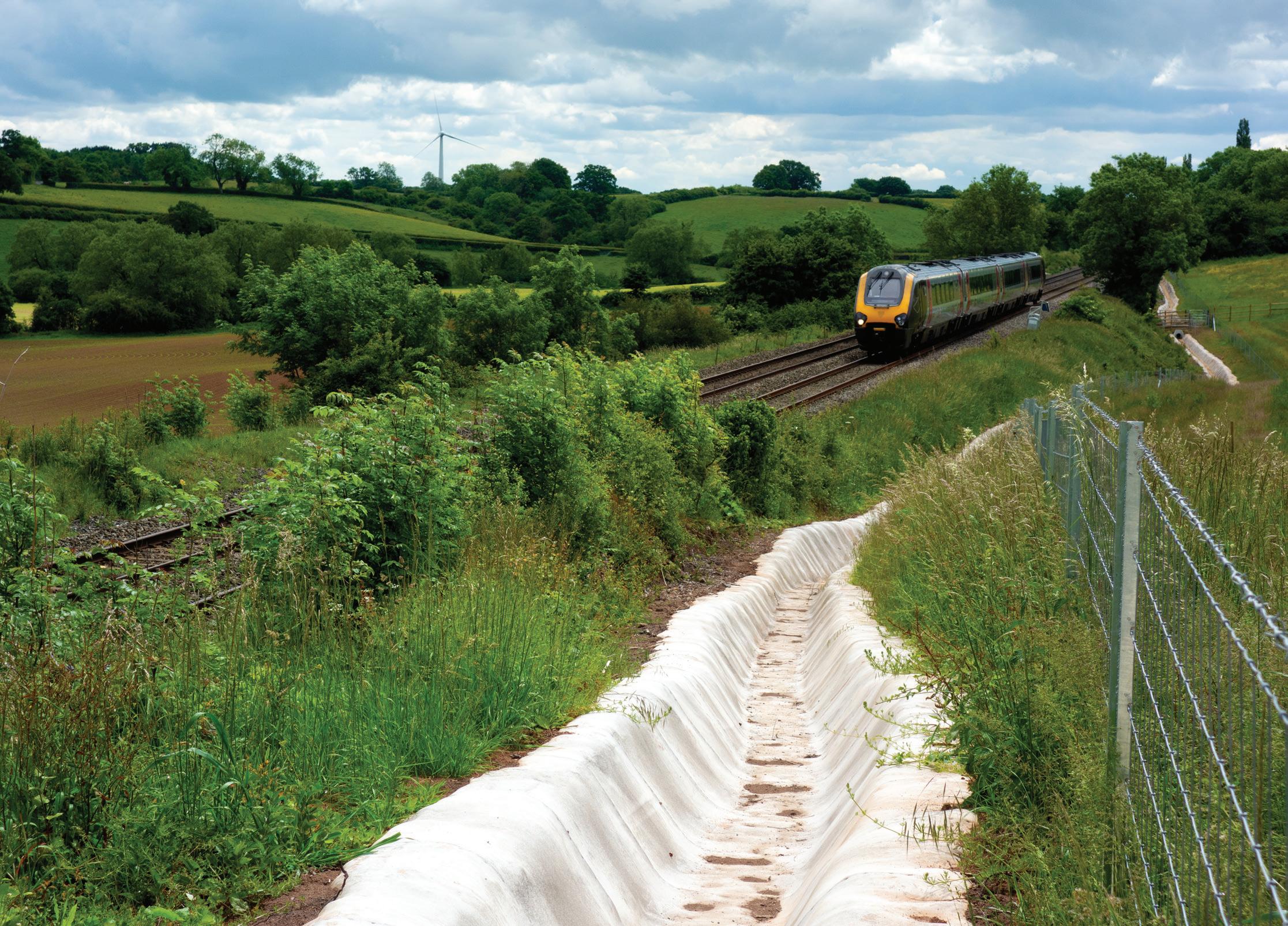
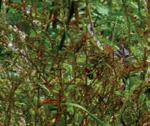

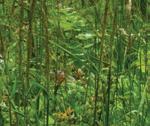
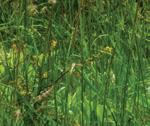
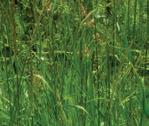
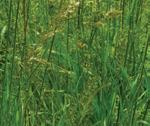
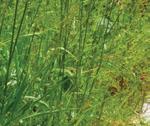
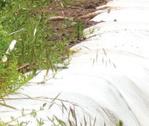
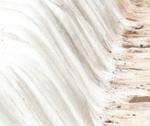
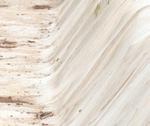


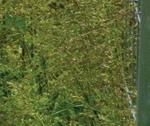
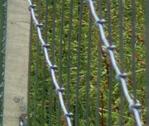

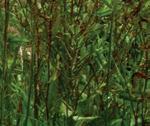
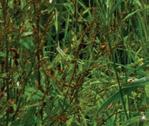
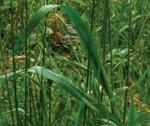
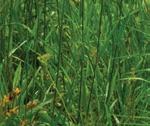
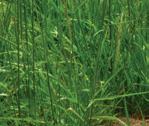
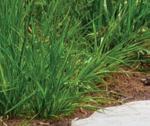
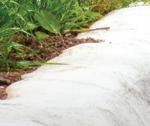
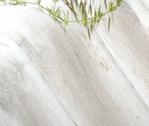

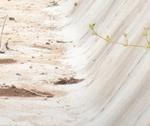
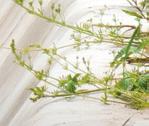
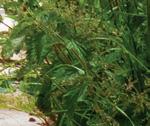
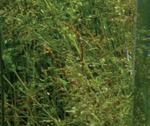
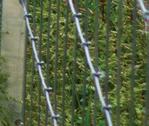
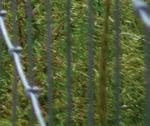
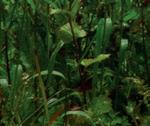

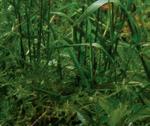
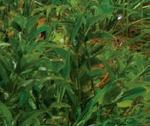
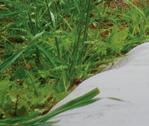
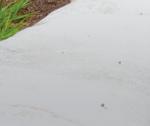
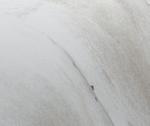

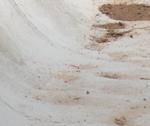
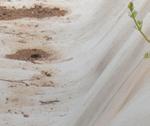
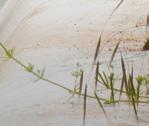

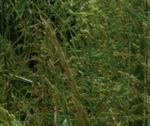
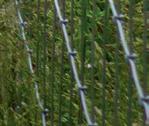
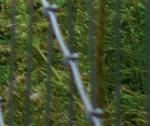
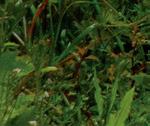
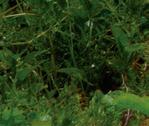
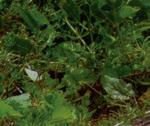
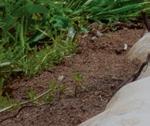
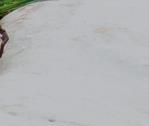
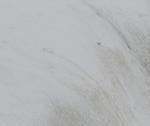
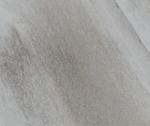
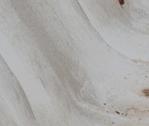
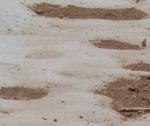
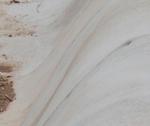
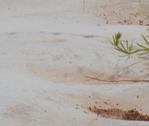
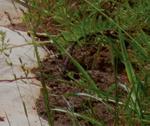
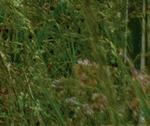
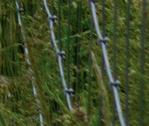
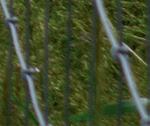
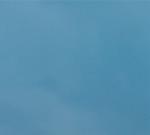

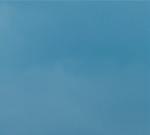
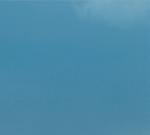
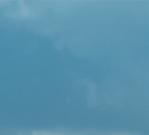
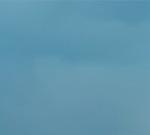
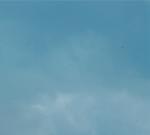
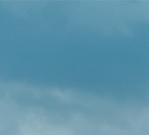
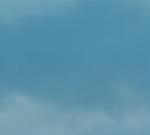
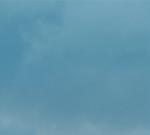
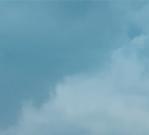
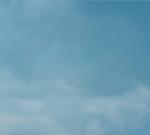
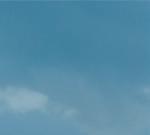
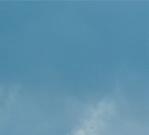
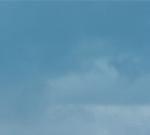
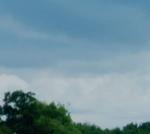
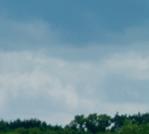
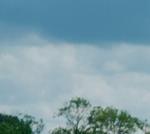
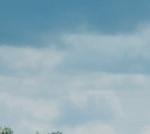
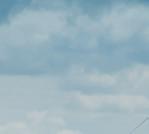

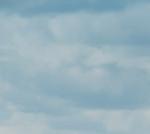
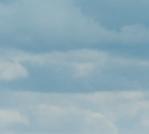
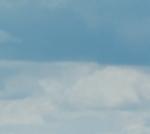
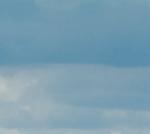
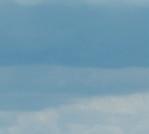
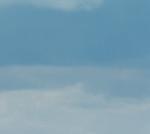

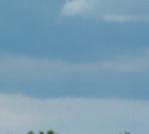
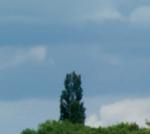
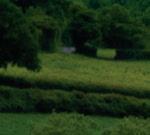
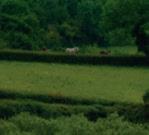

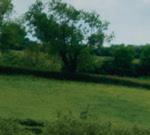
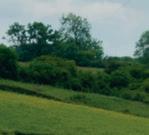
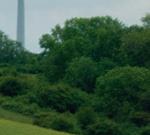
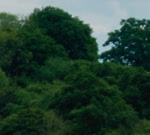
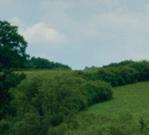
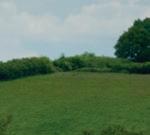
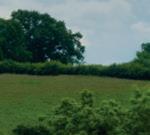
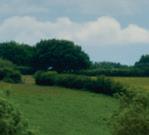
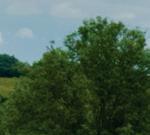
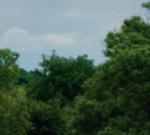
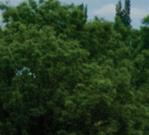
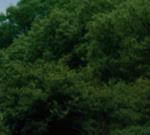
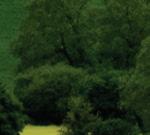
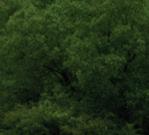

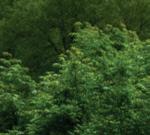
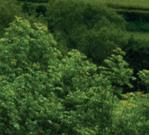
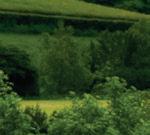
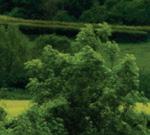

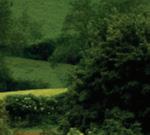
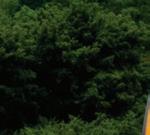
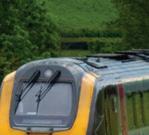
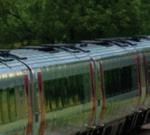
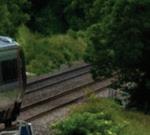
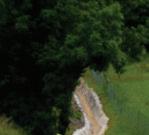
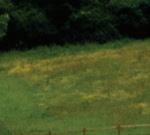
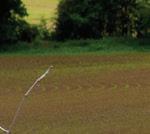
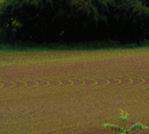

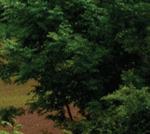
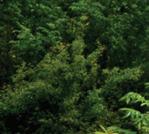
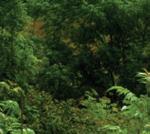
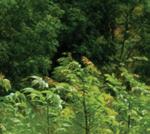
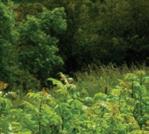
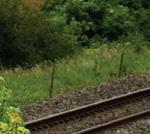
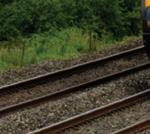
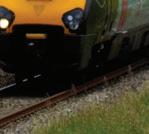
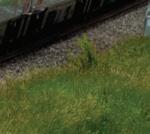
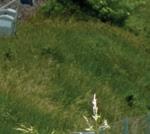


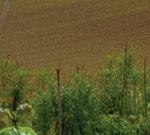


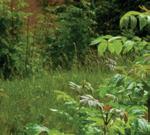
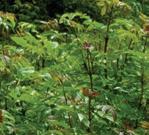
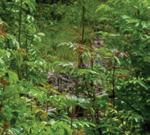
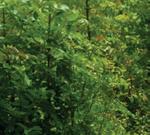
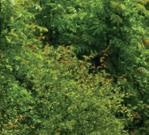
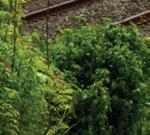

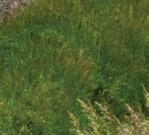
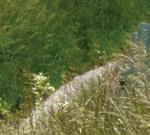
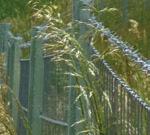

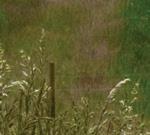
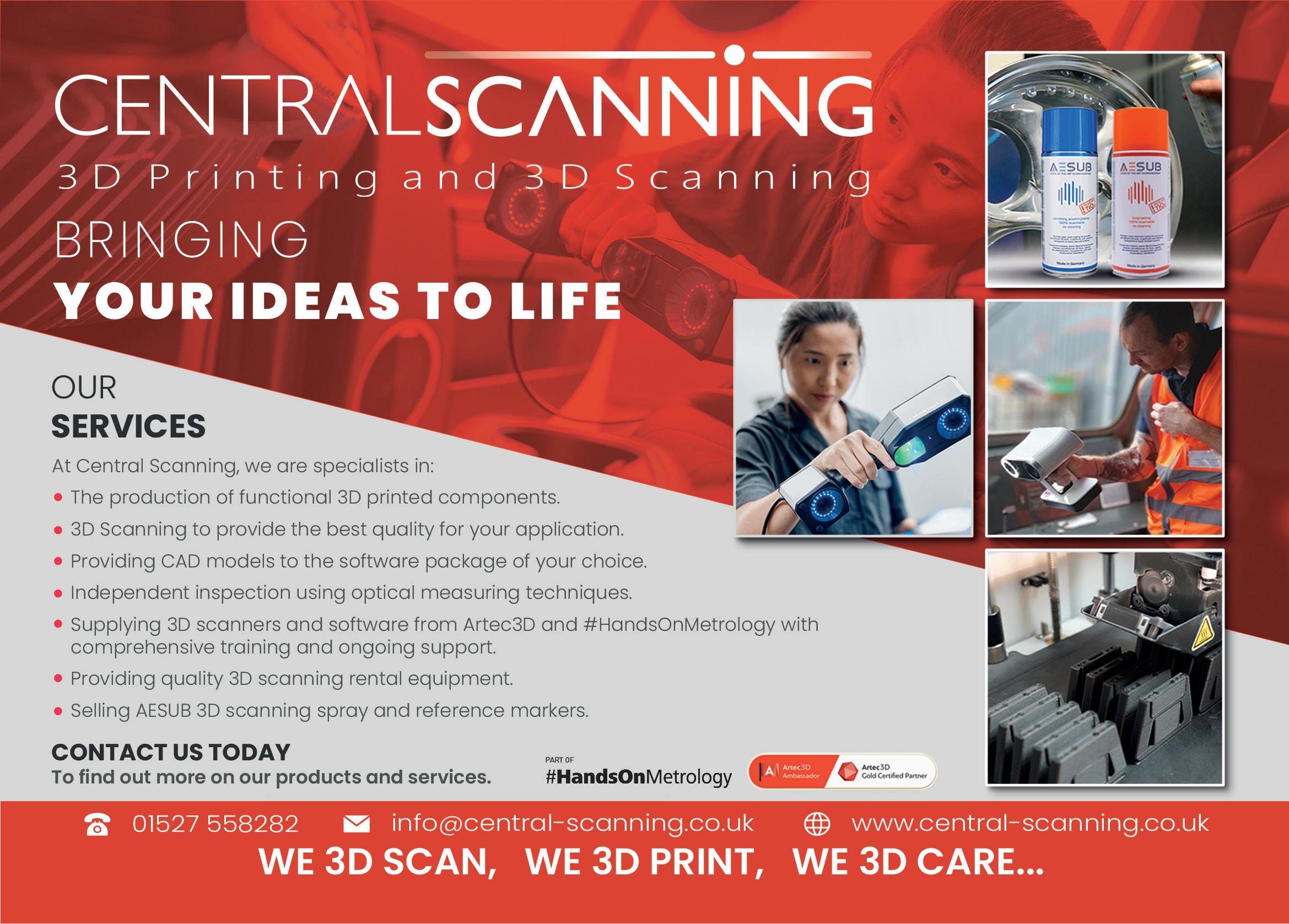
Passenger Information in All Seasons
Axiomtek’s EN 50155 18.5” Open Frame Railway Monitor for Passenger Information System – P718O
ADVANCED FEATURES OF P718O
• EN 50155 compliance.
• 18.5" Full HD TFT LCD.
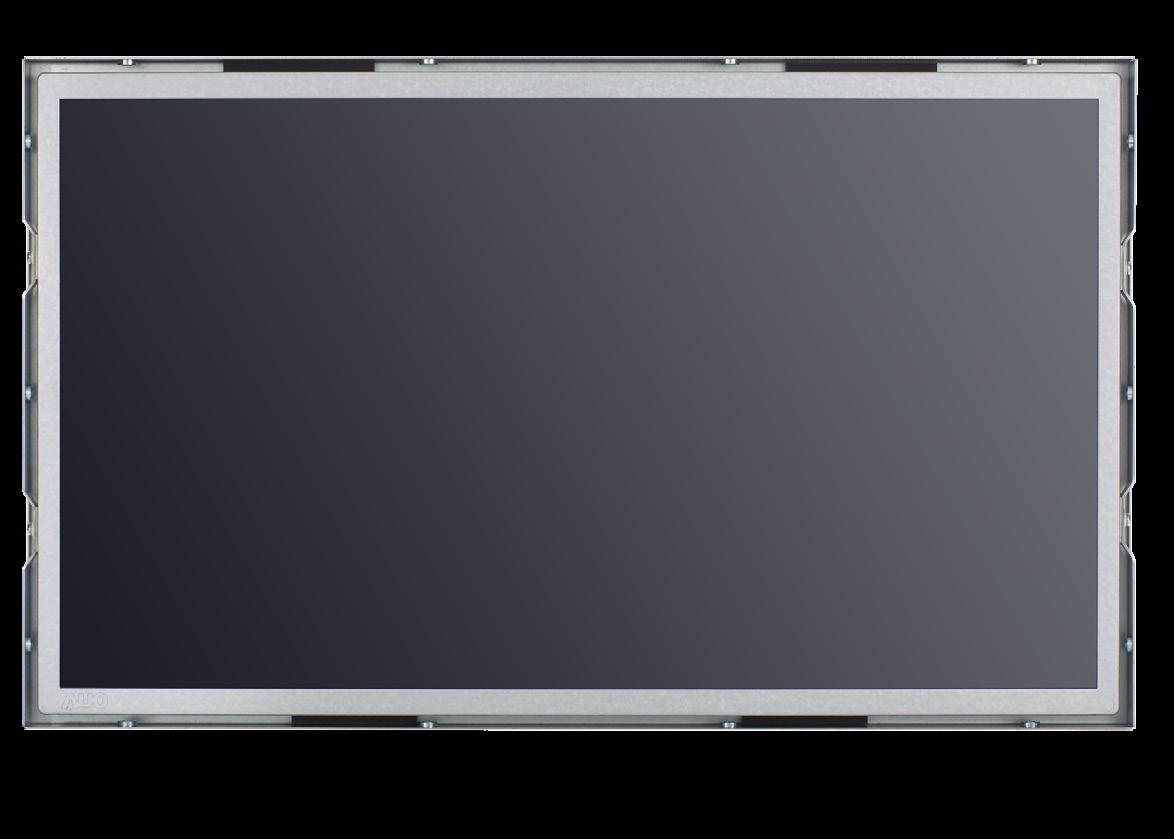
• Wide viewing angle and high brightness of 500 nits.
• HDMI, DVI-D, and VGA video inputs.
• 24 to 110 VDC power input.
• Supports VESA arm (100 x 100 mm).

• -25°C to +55°C wide operating temperature range.
• Supports 5 OSD keys on the front bezel.
As leader relentlessly in research, development, and manufacturing of innovative and reliable industrial computer products of high efficiency –Axiomtek is pleased to introduce its P718O, an EN 50155 compliant 18.5-inch Full HD open frame monitor designed for Passenger Information System (PIS) for railway. Featuring a sunlight-readable 500-nit high brightness display and wide viewing angles, the P718O is viewable in high ambient light conditions. In addition, the durable monitor supports a wide operating temperature range of -25°C to +55°C and a wide range power input of 24V to 110V DC, making it suitable for various rail environments, such as trains, stations, tunnels, and platforms.
Violet Hsu, a product manager at Axiomtek: ‘Axiomtek’s P718O is designed for delivering multi-media information and entertaining content such as real-time route information, destination notifications, advertisements, captain announcements, etc. To serve the diverse needs of the rolling stock sector, this 18.5” railway passenger information system has an overall thickness of under 50 mm and comes with an open frame design, allowing customers to easily
apply customized appearance and integrate with existing infrastructure. Vibration resistance in accordance with EN 61373 Category 1, Class B and interference immunity in accordance with EN 50121-3-2 Table 1, the rugged P7180O works flawlessly on moving trains. In addition, the open frame display offers on-screen display (OSD) controls on the top side as well as I/O ports on the bottom side for easy maintenance and operation.’
The user-friendly P718O provides multiple video inputs including VGA, DVI-D, and HDMI. The 18.5-inch railway display has flexible mounting options including VESA arm (100 x 100 mm) and wall mount. In addition, one RS-232 is available for remote control. The P718O is now available for purchase.
Company profile
Axiomtek has experienced extraordinary growth in the past 30 years because of its people, its years of learning which resulted in tremendous industry experience, and a desire to deliver well-rounded, easy-tointegrate solutions to its customers. These factors have influenced the company to invest in a growing team of engineers
including software, hardware, firmware, and application engineers. For the next few decades, Axiomtek’s success will be determined by its ability to lead with unique technologies for AIoT and serve key markets with innovatively-designed solution packages of hardware and software – coupled with unmatched engineering and value-added services that will help lessen the challenges faced by its systems integrator, OEM and ODM customers and prospects alike. Axiomtek will continue to enlist more technology partners and increase collaborations with its growing ecosystem who are leaders in their fields. With such alliances, the company will create synergy and better deliver solutions, value, and the expertise its customers need.
Tel: +44-161-2093680
Email: info@axiomtek.co.uk
Visit: www.axiomtek.co.uk
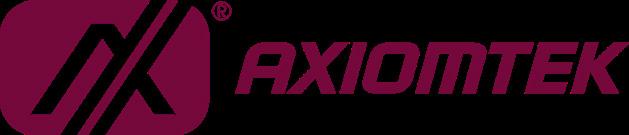
STEVE WHITMORE MANAGING DIRECTOR OF ENGAUGED
Steve is a Chartered Engineer with a detailed knowledge of railway infrastructure along with a good appreciation of railway rolling stock and operations. He has 39 years’ experience in a mix of railway contracting, design, consulting and client roles, being accountable for engineering design, project and business management. He has developed and led multi-discipline teams in partnering and collaborative environments.
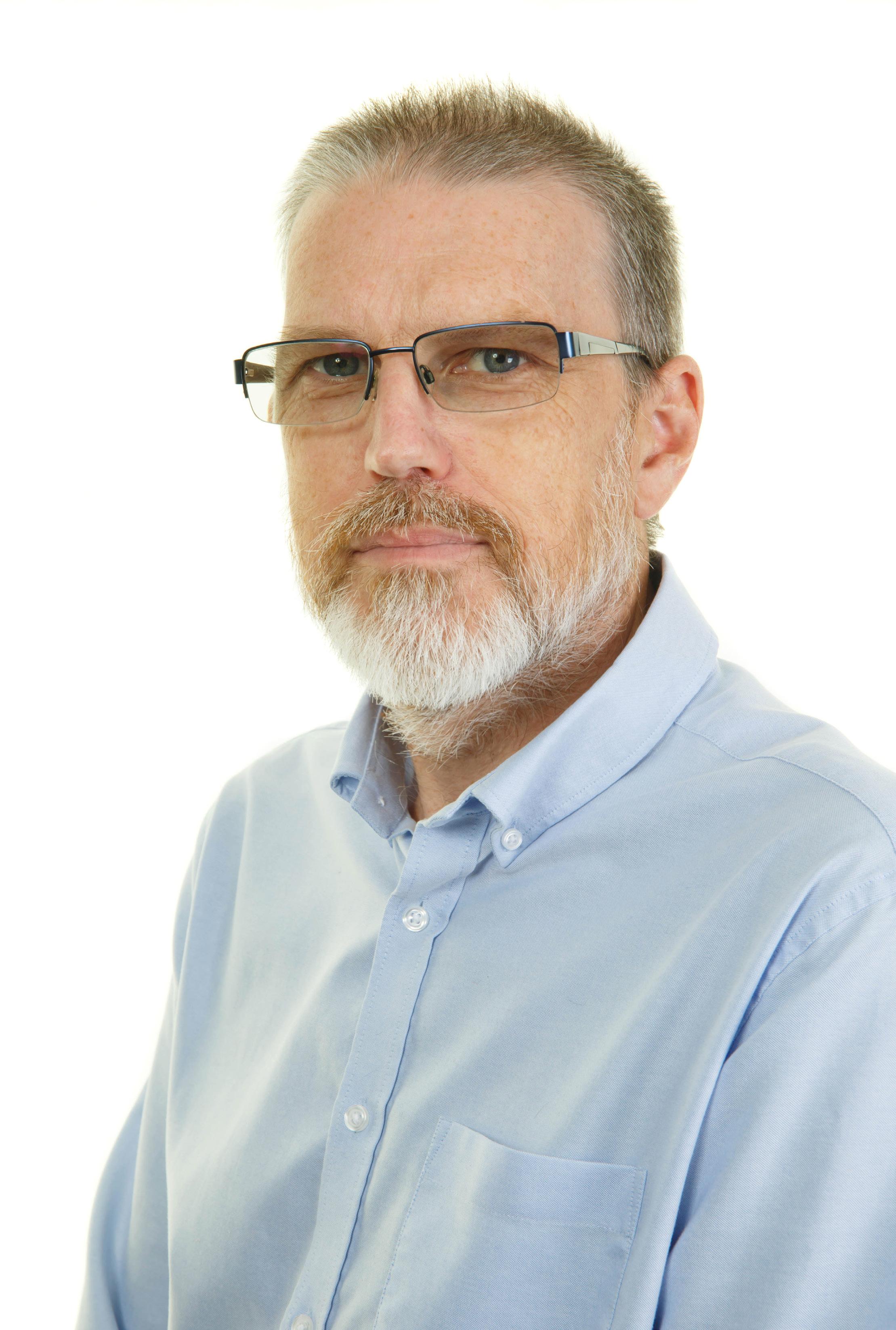
Tell us about enGauged
enGauged Ltd is a rail infrastructure design practice. We have a focus on building and civil engineering design with our in-house resources and can collaborate with our supply chain partners to provide a multidiscipline delivery if our clients require it. We are based in Crewe in the north west of England and we have members of the team in west London and Glasgow which enables us to deliver to all nations and regions of the rail network.
We are a small and growing team delivering design for stations, depots and lineside civils. We also support principal contractors during construction with the design of temporary works.
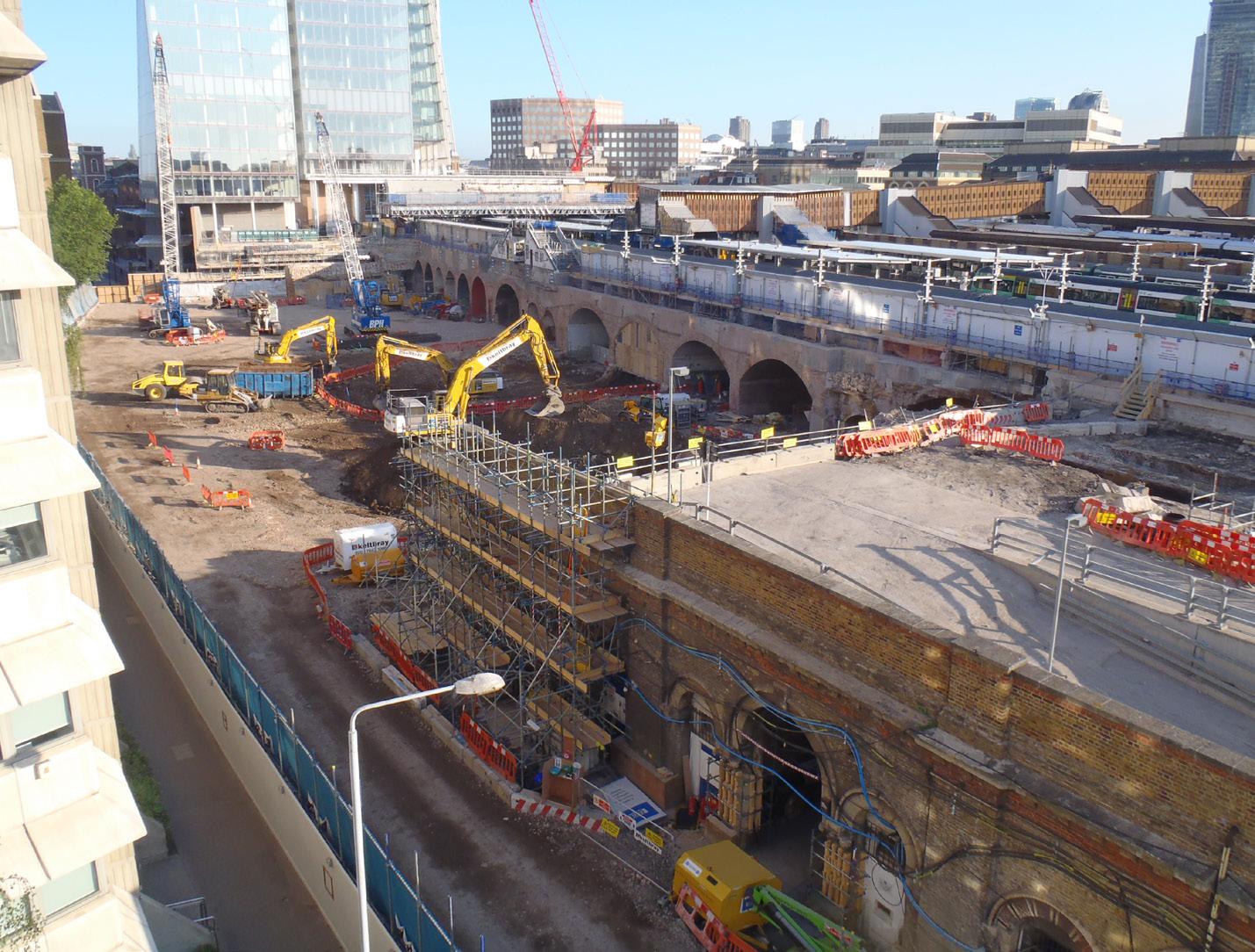
We have been building our accreditations over the past few years and are now proud to have an Integrated Management System (IMS) in place with certification to ISO 9001, ISO 14001 and ISO 45001. In addition to this we subscribe to the Rail Industry Suppliers Qualification Scheme (RISQS) and hold Audited status across the building, civil engineering and temporary works codes. We also manage our own trackside competencies through Sentinel.
Tell us about your career before enGauged?
I started my career in 1983 when I left school at the age of 15 and started working for British Rail (BR) as an apprentice electrician in the loco works in Crewe. I served a four-year technical apprenticeship and gained my HNC in Electrical Engineering. BR was a good organisation for staff development and I was fortunate to be able to move into civil engineering after my apprenticeship. I joined the Area Civil Engineers Office in Crewe in 1987 as a Technical Officer and progressed through the technical grades over the following years into management.
Alongside this I was undertaking a part-time degree in civil engineering. This I completed in 1994 and, as did many others, found myself navigating the new world of railway privatisation. I remained in contracting organisation GTRM, later Carillion, for two years and then joined Owen Williams Railways (now part of Amey). I spent a number of years as a Resident Engineer on bridge and structures work and an interesting assignment in the late 1990s supporting the Transport and Works Act submission for the West Coast Main Line upgrade works.
I joined First Engineering (now Babcock) in the year 2000 to help develop the consultancy office in Birmingham, progressing to Acting Regional Manager. In 2003 I joined Jacobs to become Regional Manager for the rail team in Midlands (Birmingham and Derby Offices). I was the Engineering Manager for the design work Jacobs delivered in relation to the Thameslink St Pancras Station box where
my responsibility was to co-ordinate the technical delivery of the design for overhead line, track alignment and track slab.
In 2005 I joined Network Rail. I initially led the engineering team for the delivery of stations, depots and buildings contracts across the north of England and Scotland.
I was appointed Programme Engineering Manager for the National Buildings portfolio in 2006 where I provided technical leadership, supported initiatives such as Safety by Design, Competence Management, and CDM. I also led the introduction of Structural Eurocodes into the NR business and presented a paper to the ICE conference on Structural Eurocodes.
In 2010 I was appointed as Engineering Manager for the London Bridge Station Redevelopment project as part of the Thameslink Programme. This was an excellent team to be part of and we have delivered a lasting legacy for the station and the surrounding area. My role was to lead the NR integrated engineering delivery team embedded with the delivery contractor and their supply chain. I was also the Building and Civils Lead Discipline Engineer for the Thameslink Programme providing technical leadership and assurance across all projects.
When did you first start the company?
I had opportunity to leave Network Rail and start trading through my own business in 2015. This was a daunting move to leave a full-time employee position at 17:00 on the Thursday evening before the Easter weekend, heading for the pub and my leaving drinks, with nothing lined up except a week away on holiday. An hour later and a couple of phone calls, my first contract landed working with Capita leading their design delivery on High
Speed 2. And no holiday as they wanted an immediate start! Fortunately, the work has kept coming and I’ve not looked back since.
What was the inspiration behind starting enGauged?
I saw a lot of design work over the years where solutions were not economic or well developed. Buildability was missed out of the loop and the designs often lacked practicality for site installation. I felt I could provide a better service and I’m still here 8 years on with repeat business from a small number of clients so I must be doing something right? Our company strap line is ‘Design with Build in Mind’ for that reason. As enGauged, we need to be adding value. In an industry which is publicly funded, we need to be making every penny count. Minimum Viable Product is the current industry focus and we need to make sure that we achieve requirements without over design.
What is your USP (Unique Selling Point)?
Our USP is that we are rail focussed. We operate primarily in the rail industry. This means we have day to day workload using standards and approval mechanisms that we operate with day in and day out. The team are familiar with the systems and processes our clients need in rail. It means that we can add value but smoothing the path to a compliant, accepted design. We understand the risks and opportunities that face our clients in rail. Being a small business also makes us agile and we can be responsive to changes in our client’s needs.
What are some standout projects you’ve been involved in over the years?
We have been fortunate to be invited to work on a number of interesting projects over the past eight years. Two or three stand out for me particularly at this moment. However, the development of the Overhead Line (OLE) pile cap, which is now in the UK Master Series design suite, is one which we can point to as adding significant value.
A fabricator approached us in 2016 and asked for some support with the NR deign approvals for a prototype pile cap for use on Great Western Electrification (GWEP). Once through the design and approvals, the use of the cap spread and interest arrived from the Midland Main Line Electrification project. We continued to develop the cap design to accommodate the project requirements and along with some other supporting design work, helped increase the use of 610 piles on the project and remove a good percentage of concrete foundations from the project. This saved the project a seven-figure sum in civils works. Work like this is why I set up enGauged.
The railway of tomorrow needs innovation and will face the challenge of doing things differently. We are still working with the team on Midland Main Line
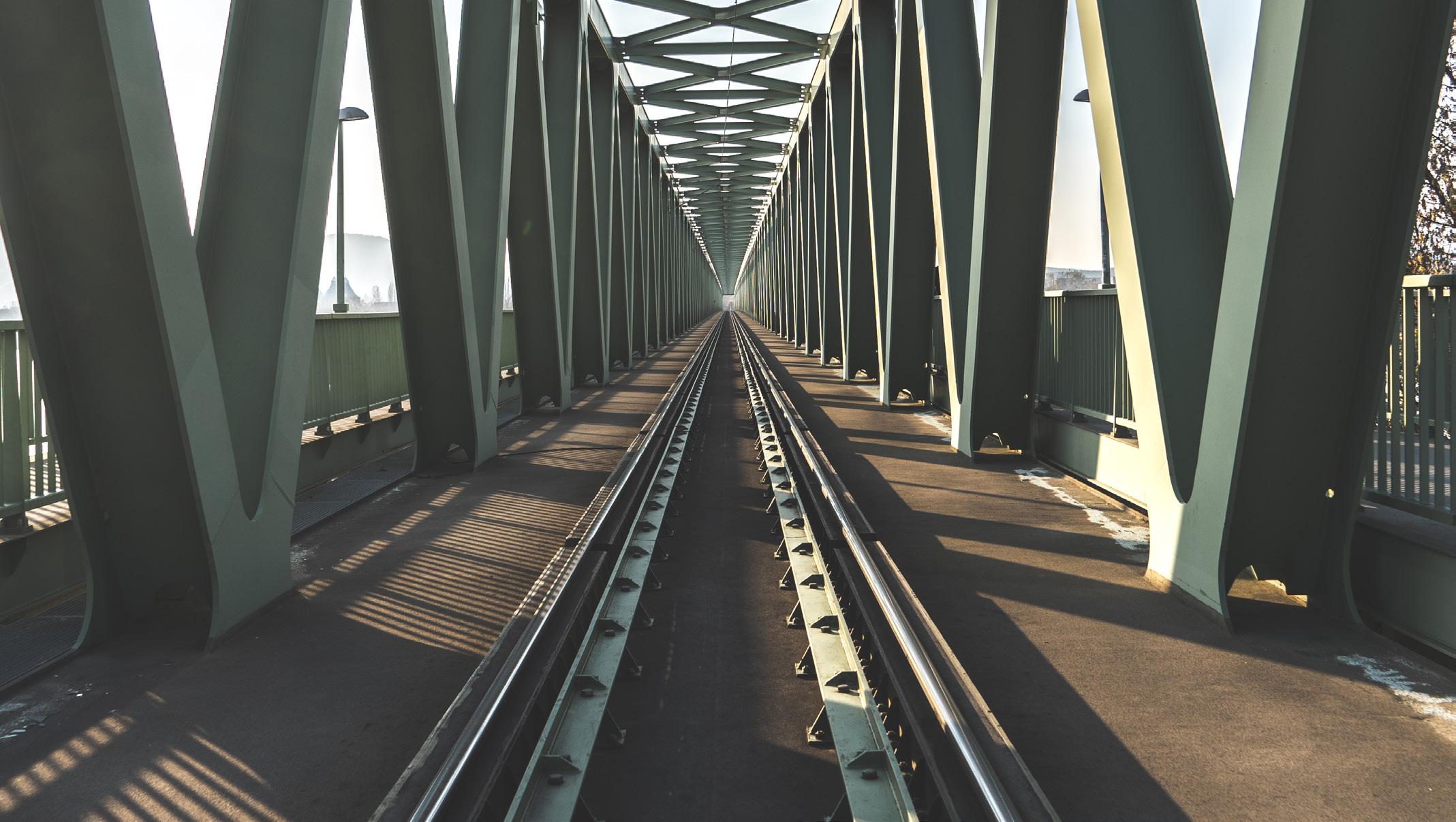
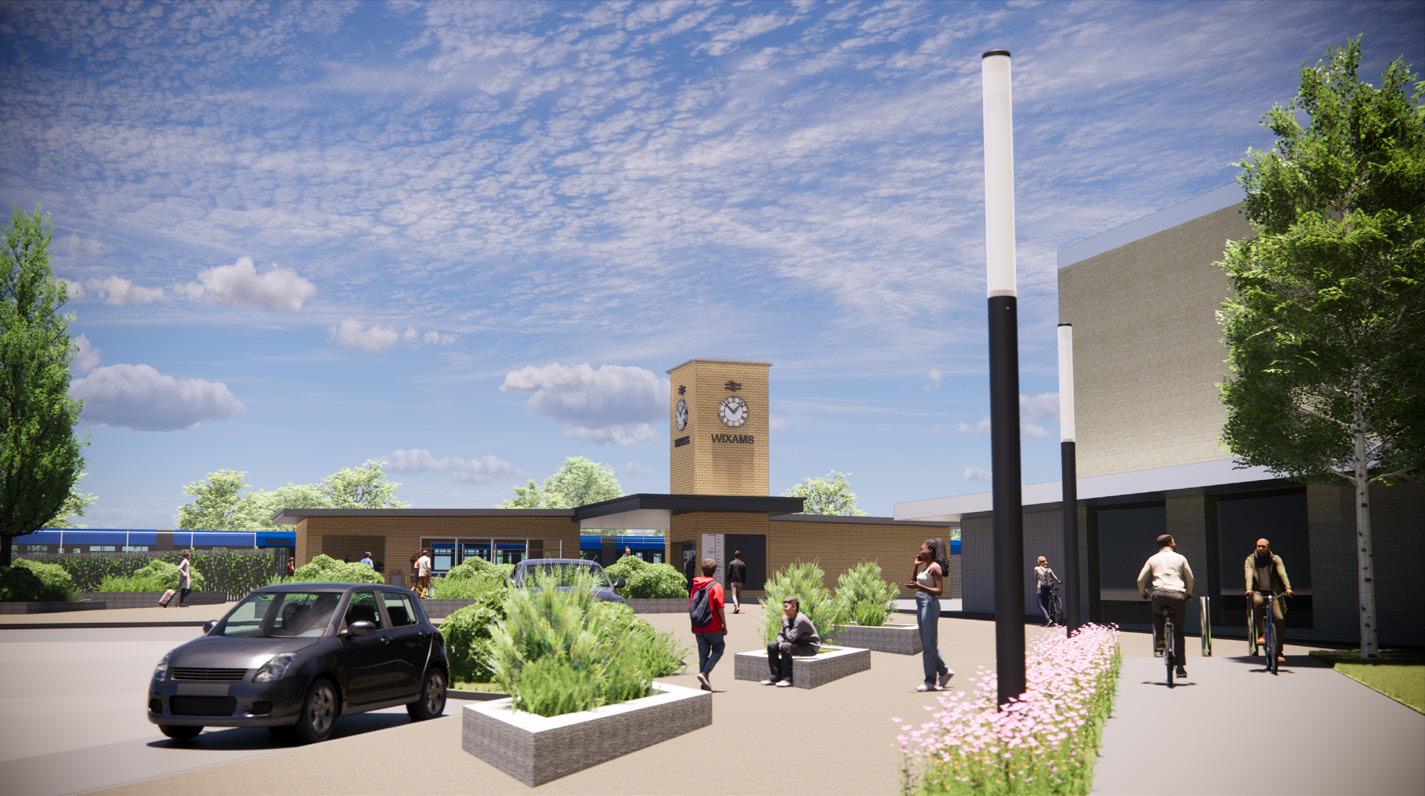
looking at alternative solutions to problems and seeking more efficient ways to deliver the minimum viable product.
What types of companies do you collaborate on projects with?
Our collaboration is mainly with other SMEs, often to deliver a multi-discipline
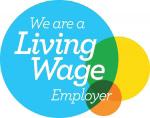
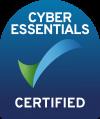
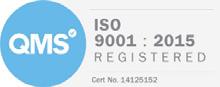
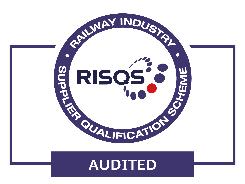
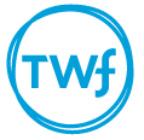
project. One particularly exciting project is the outline design of a new station on the Midland Main Line south of Beford, at Wixams. This work is being led by Kilborn Consulting who are the lead player on contract to Bedford Borough Council to deliver the outline design. Kilborn has drawn together a collaboration of SMEs to cover each railway discipline.
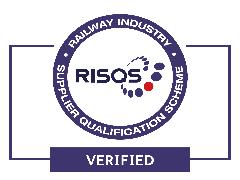
We are providing civils, earthworks, structures, highways and architecture design. The agility of the team of SMEs is key to being able to respond to client needs and support them through decision making. The benefit of SMEs comes through when you have director level people actively involved in the day-to-day design and helping push the decision making. I have to say that the SME community in the rail industry I come into contact with is very strong and very collaborative.
What kind of challenges do you face?
I have been very fortunate to have some good friends in the industry who have trusted me to deliver work for them and have helped us grow and develop. (They know who they are and I’m very grateful for the help). It is much tougher than I gave credit for as a new player to enter the marketplace. The rail industry has a heavy ask in terms of accreditation which drives a high overhead.
Cashflow is always in the forefront. Most clients are excellent at paying on time. As an SME this is critical, one missed invoice payment can swing the account from black to red very quickly. Procurement delays and projects slipping dates with work moving to the right on the programme creates challenges to understand resource levels. A month delay at the start of a job is a month of costs with no income. As an industry, we need to iron out the authority processes to make sure we have the right funding in place at the right time and that contracts can be then be placed on time, giving good visibility through the whole supply chain beneath the Tier 1s.
One frustration I do have is that whilst government and the industry in general support SMEs, it is quite often that I may find myself excluded from a tender opportunity because turnover doesn’t meet a level, or my financial status doesn’t signal the wealth equivalent to that of a small country. It needs to be realised that the most value can often be realised from micro enterprises, those with a turnover less than £2 million who often have a very experienced, but small team. Things are steadily improving on this front but I suspect it will take some time yet before all the corporate procurement processes in large client organisations find ways to benefit from micro enterprises.
My other plea at this point is for tender feedback. The need to receive feedback is key to any business learning and developing. I have a large number of projects currently in a tender status, some of them now months old, and no feedback on whether the job is won, lost, cancelled, delayed, or the reasons why. So please can any bid managers reading this give your supply chain some feedback.
How can the industry tackle its skills shortage and how do you recruit/retain/ train your staff?
The industry is suffering from a boom-andbust approach to taking on and training new people, in particular engineers. The years leading into and just after privatisation in the 1990s, there we very few organisations in the new commercial world that took on new entrants to the industry on formal training schemes. This, coupled with a national decline in engineering graduates, has presented a large gap in the skills market and the volume of principal engineers we now have in the industry is insufficient.
I have taken the approach to recruit for behaviour and train for skill. I have also struck up a relationship with the local college and have been supporting T-Level students with their industry placement. One such student is finishing his course this year and will transition to a full-time role with us.
How do you make your business a good place to work?
I have tried to keep a focus on the people I employ. If people are happy in the workplace, they will do a good job. It’s important to develop a culture where people feel valued. I have tried to bring new people into the industry and sponsor their development. Empowerment is also important. People need to feel that they can make decisions and that their opinion counts for something. We have regular team meetings and encourage everyone to contribute ideas to improve the system and processes we operate to.
I am also keen that the team develop themselves to their potential. I have supported people doing part-time education to enhance their skills and knowledge.
Last year we undertook Investors in People and after assessment, we have been awarded Silver. This was particularly pleasing and underlines the work to develop and invest in the team.
What’s your view on Professional Development?
I am very supportive of professional development. I am a chartered engineer and a member of four professional engineering institutions, ICE, IStructE, CIBSE and PWI. I receive value in different ways from all of them, but I am most active in the PWI, which I joined 33 years ago.
I became a member of the committee in what was then the North Wales Section in early 2000s and represented the section on Council of Management until the reorganisation in 2010. I have since had the privilege of being President (2012-2014) and have supported the PWI Board in a number of ways since then.
I am keen that my team are all pursuing continued professional development and engineering institutions provide a great source of learning in this area. I think it is important for individuals to have the recognition that comes from professional registration, whether that be at EngTech, I.Eng or C.Eng level. The routes to membership have adapted over recent years and there are now a number of pathways open for people to attain recognition. I would recommend looking at the PWI website for further information.
ENGAUGED LTD
enGauged Ltd is a privately owned small to medium enterprise (SME) design practice based in Crewe. It covers the whole of the UK with an increasing portfolio of projects with Tier-1 clients. The primary focus is the rail industry with its core discipline being civil and structural engineering and the capability to deliver multidiscipline projects through its supply chain partners.
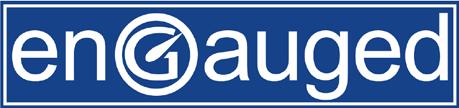
Want to know more about enGauged Ltd?
Tel: 01270 255 731
Email: enquiries@engauged.co.uk
Visit: www.engauged.co.uk
‘The railway of tomorrow needs innovation and will face the challenge of doing things differently. We are still working with the team on Midland Main Line looking at alternative solutions to problems and seeking more efficient ways to deliver the minimum viable product.’
RIC KIRMAN BUSINESS AREA MANAGER RAIL & MONITORING AT KOREC GROUP
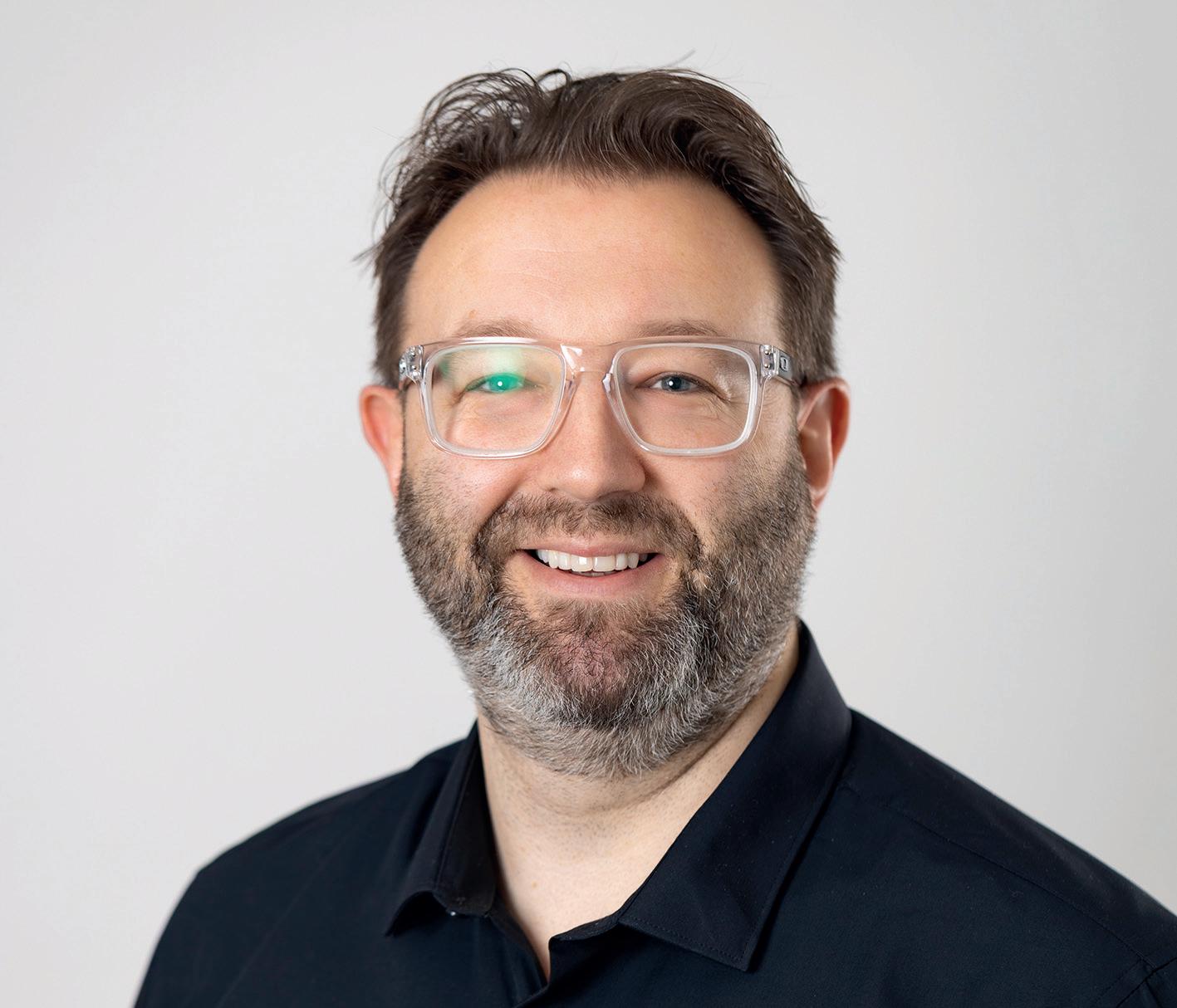
Ric Kirman is the Rail and Monitoring Manager at KOREC Group and the driving force behind this growing area of the business. With a background in business development, team leadership and customer engagement and with extensive experience within the rail industry, he is renowned for his motivational skills and excellent communication.
What is your role within KOREC Group?
I am the Business Area Manager for Rail and Monitoring. Rail and Monitoring is one of the specialist business areas within the KOREC Group; each area offers industry specific advice, support, training and consultancy ensuring we can deliver the very best service for our customers. KOREC Group offers an award-winning service in geospatial solutions to its varied customer base as well as a range of digital construction solutions.
We are one of Trimble’s largest distributors which enables us to bring world class solutions to our customers but always tailored to the demands of a UK market.
Key to the success of this team is our focus on using dedicated industry specialist sales consultants and industry certified Applications Engineers. Within my team alone we have over 50 years’ experience in the rail industry and over 70 years’ within the monitoring sector, this is what helps set us apart from our competition, we understand your challenges.
Tell us about KOREC Group
Our mission statement sums up KOREC Group perfectly: Our mission is to empower you to measure, map and manage the natural and built environment.
We’ve been established for over 50 years and our strength lies with the relationships we have with our customers and our partners. We have a strong company culture, (KOREC Group is an Investor in People and an Investor in Wellbeing). Our customers often share their appreciation of the KOREC team’s willingness to go ‘above and beyond’ to help support them in the more challenging situations.
How have the products and services you offer developed over the years?
KOREC
KOREC specialises in providing measurement solutions, surveying equipment and mapping systems for the geospatial, engineering and construction sectors in the UK. If you want to know more about KOREC, get in touch via the contact information below.
Want to know more about KOREC Group?
Tel: 07966251781
Email: ric.kirman@korecgroup.com
Visit: www.linkedin.com/showcase/korec-rail/
KOREC is the vital link between Trimble’s global leading solutions and the UK Rail Industry. We have a very strong relationship with Trimble Rail and that means that feedback from UK customers can directly influence developments from Trimble and consequently our customers see the results of this in later generations of hardware and software. A great example of is the Trimble IMU going from a wired system to wireless.
The GEDO Track Survey System’s been with us for a number of years and there have therefore been many iterations of this modular system that make it extremely versatile and at the same time, incredibly user friendly. Several GEDO developments we’ve seen were driven by UK customer feedback. We also have our own KOREC in-house software development company called K-Matic. This year K-Matic has developed field data capture and data sharing software specifically for Network Rail. This ability to offer full workflows and customised applications is a huge strength within our rail systems portfolio.
When a client comes to you with a particular problem, what’s your process for coming up with a solution, and how closely do you work with clients throughout the projects?
In almost every situation, there’s a 99 per cent chance we’ve come up against this problem before and can usually offer a solution straight away. Our team has over 50 years’ of experience between us and we can also draw upon Trimble’s global rail knowledge. However, our first priority is always to listen and to truly understand the challenge before we move on to advice, demonstrations, site trials where required, and of course a solution.
We work in partnership with our customers and regard our approach as a relationship, not a transaction. We offer our customers the highest level of consultation and comprehensive training and when they are out in the field we offer 24-hour support because they tell us that ‘the best ability is availability’. Going back to all of that experience we have, it means we understand the pressures of the rail industry and how important it is that our customers can deliver their projects safely, effectively and on budget.
What would you say is the most exciting technology in the industry?
For me, without a doubt, the ability to collect, use and share point cloud data captured by 3D Laser Scanners. 3D laser scans are so incredibly easy to undertake.
This is one of the reasons they’re so powerful and one of the reasons they’re being embraced by the rail industry to great effect. The use of point cloud data is not standardised yet, but I predict that within 5 years it will become the norm.
What’s particularly important with point cloud data is of course how you can turn it into usable data for informed decision making and that’s where the office software comes in. In KOREC’s case, this is Trimble’s GEDO Scan Office. Features within this software enable you to carry out so many tasks: platform gauging, clash detection, height and stagger surveys, asset data collection and much, much more. GEDO Scan Office is tailored to the rail industry and its predefined reports, tools and easy workflows make it incredibly useful in this time constricted industry to get the results you need quickly.
As well as using a 3D Laser Scanner mounted on the GEDO track measurement trolley, let’s not forget that they can also be used on a tripod to provide data for hard to access areas such as tunnels and bridges and for other applications such as asset management and station refurbs. In short, a point cloud captured once can be revisited for many different purposes. Think of the cost savings.

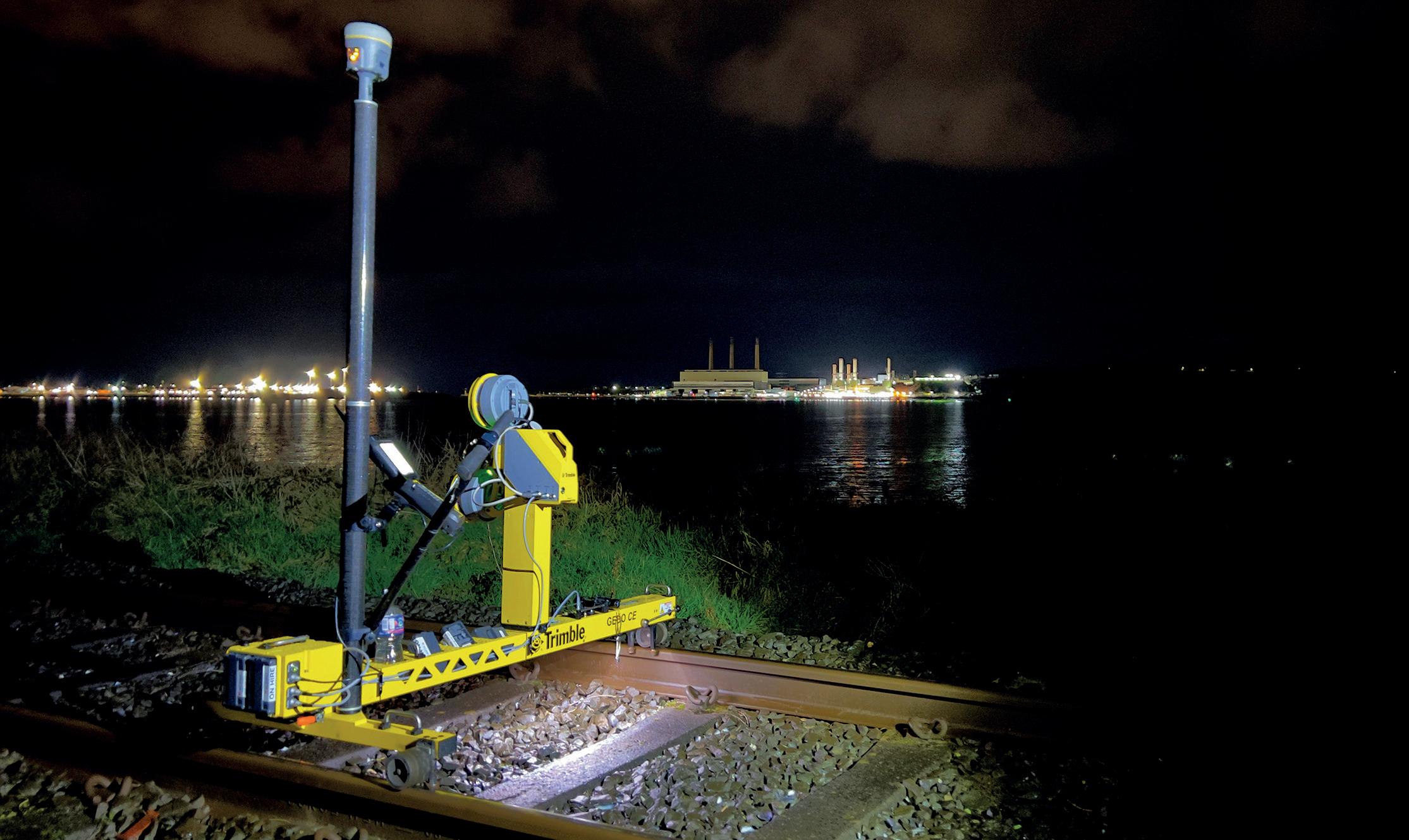
What are some of the biggest challenges this sector currently faces?
Looking ahead, it’s evident that the rail industry faces three particular challenges; a people and skills shortage, increased
pressure to deliver more work of higher accuracy despite a decrease in track access time and finally, the constant challenge of keeping our railways safe both for those who use them and those who work on them.
Our customers come to us with very specific needs that reflect the challenges they face, namely to get ‘boots off ballast’ which means achieving much more whilst you are actually on site. With the solutions we have, gathering data on site has never been so quick, easy or safe.
Whilst there is a wealth of knowledge within the industry, we are all growing older and that means we need to recruit young and talented people to retain this level of knowledge. This has always been a challenge, it’s not common to hear a child saying they want to be Track Maintenance Engineer when they grow up!
We also have the demands of Europe’s largest rail project, HS2, to contend with as the track installation phase draws closer. Whilst this is very exciting, it will draw professionals from other areas of the industry which could have a knock-on effect resulting in staff shortages elsewhere.
‘Our mission is to empower you to measure, map and manage the natural and built environment.’
What are some potential solutions?
Technology! Or more specifically, technology that can tackle safety, efficiency and accuracy. It has to be user friendly, fast, efficient and accurate. We’re not always dealing with surveyors in our industry but with rail professionals and technical staff, so from a manufacturer’s point of view, we must create systems that not only have a fast, easy learning curve and are therefore usable by anyone on track, but they must also deliver excellent survey results.
A great example of this is Trimble’s GEDO CE 2.0 IMS GX50 Scan Solution. Our customers are achieving results 50x faster than traditional methods for overhead line surveys. We’ve seen these results in practice on a trial in the Severn Tunnel. The GX50 completed the job on site within 8 hours compared to the same survey undertaken using traditional methods (height stagger gauge and laser measurement) which took 450 hours and five members of staff. The GEDO GX50 IMS Scan solution, required just one member of staff, (but we sent two) so we allowed three other engineers to focus on other important works. (https://bit. ly/40CAOlu).
This is a perfect example of achieving great results, far faster and with fewer people on track, plus we now have a digital twin of
the tunnel that can be used for many, many other applications and other departments.
Our industry uses some really cool hardware and software and can be at the forefront of global rail. We should embrace this and let it help us attract a tech savvy generation of new workers who have grown up with the smart phone.
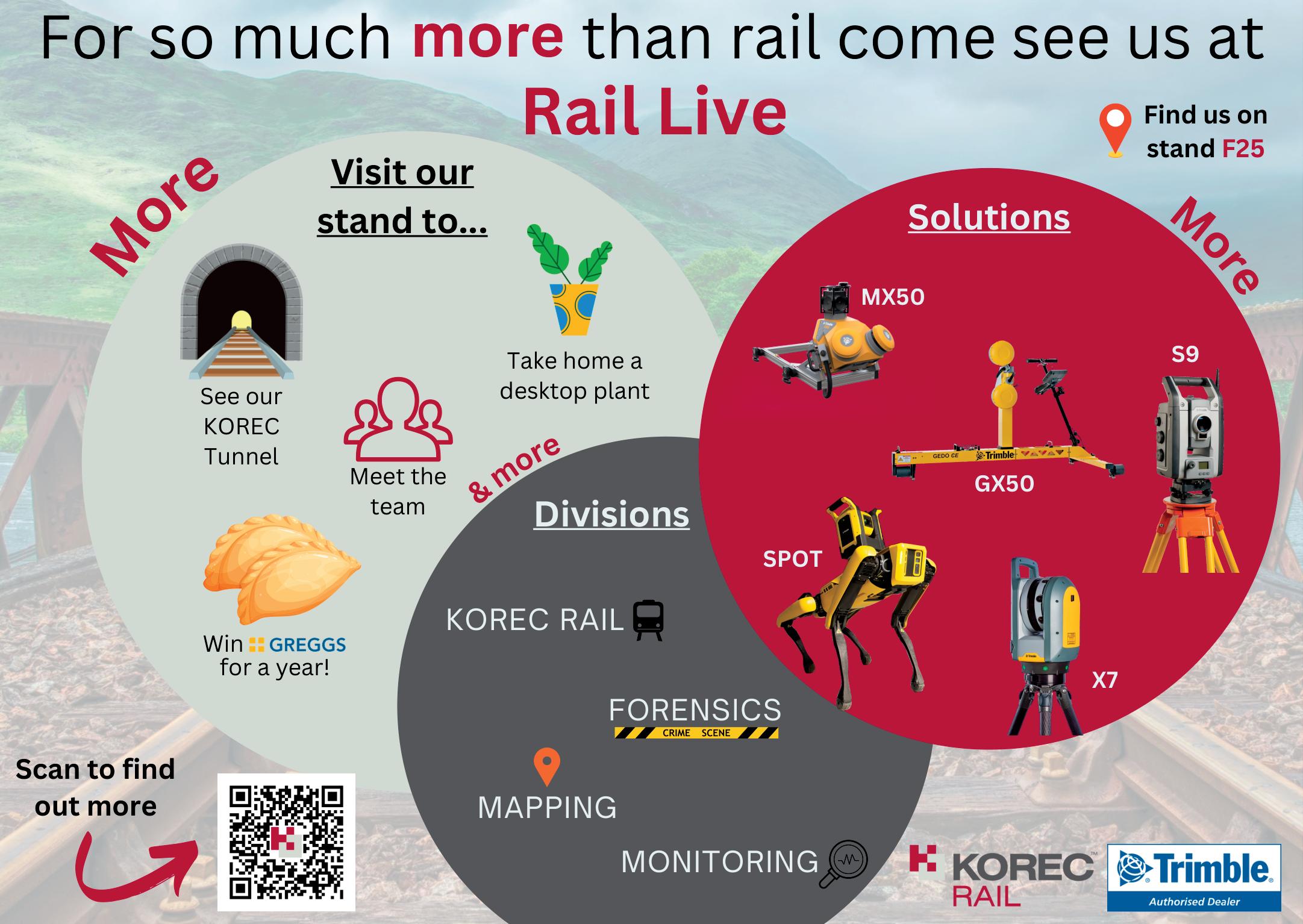
How do we attract them? Cool tech and professional education. Apprenticeships are a great place to start along with working with Network Rail and academia in general. We are constantly impressed by the level of apprentices that we work with in the private sector and now is the time to ensure that we are upskilling them sufficiently to take on the challenges of the rail industry over the next 10, 20 or 30 years.
What are your views on collaborative working?
As both technology and working methods evolve, it’s vital that the whole industry moves towards a more collaborative approach with a focus on reducing any duplicated effort. Our customers are aware that this is the way forward, we hear it from them every day.
What’s holding them back? The ability to share data that they have in a meaningful way to induce that more collaborative
approach. In particular, 3D Laser Scanning is a major driver towards collaborative working – why not share point cloud data for multiple uses? In this area, we’ve seen a great addition with Cintoo Cloud technology. Cintoo Cloud allows users to stream huge 3D data from any desktop or laptop via a web browser, and provides the tools and technology to compare scans to CAD models or scans to scans and enable large-scale collaboration and management of the reality data.
An added benefit of this collaboration is that if the engineer who gathered the data is on leave, that data is still available for everyone on the project via a securely hosted cloud server (ISO 27001 accredited). Whilst we are familiar with BIM models as a useful ‘single source of truth’, digital twins are still not commonly found within the rail industry despite their vast benefits. This would definitely be a fruitful step towards better collaboration.
We’re seeing evidence of this approach on flagship schemes. For example, we’ve been working with several of Network Rail’s key delivery partners who’ve embraced Trimble’s GEDO technology and KOREC solutions whilst working on key projects. They’ve seen tangible benefits of using the GEDO system and allowing collaboration by sharing data with other project partners.
RAIL LIVE 2023
On 21 and 22 June 2023 the UK’s largest rail exhibition returns to Long Marston Rail Innovation Centre in Warwickshire
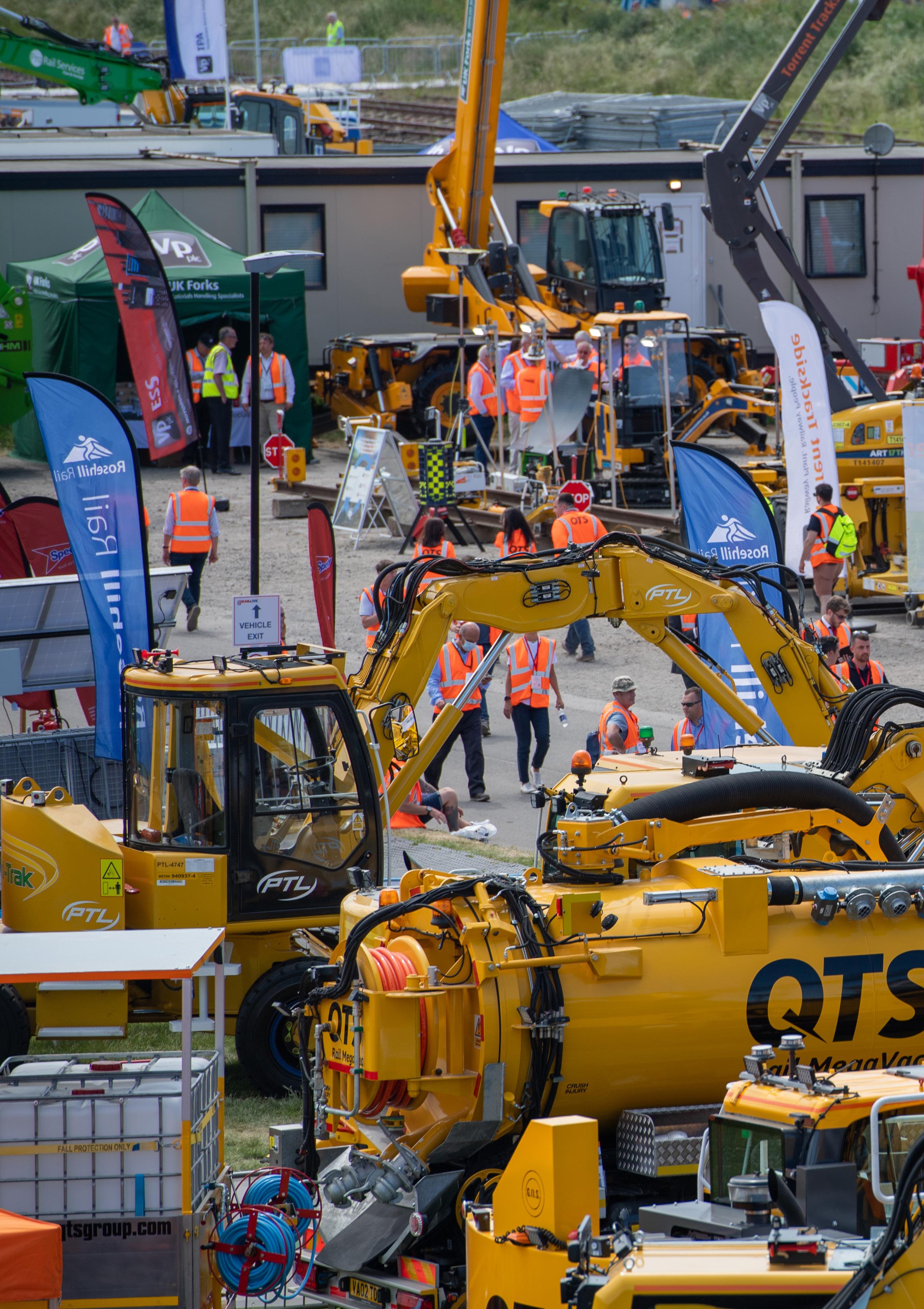
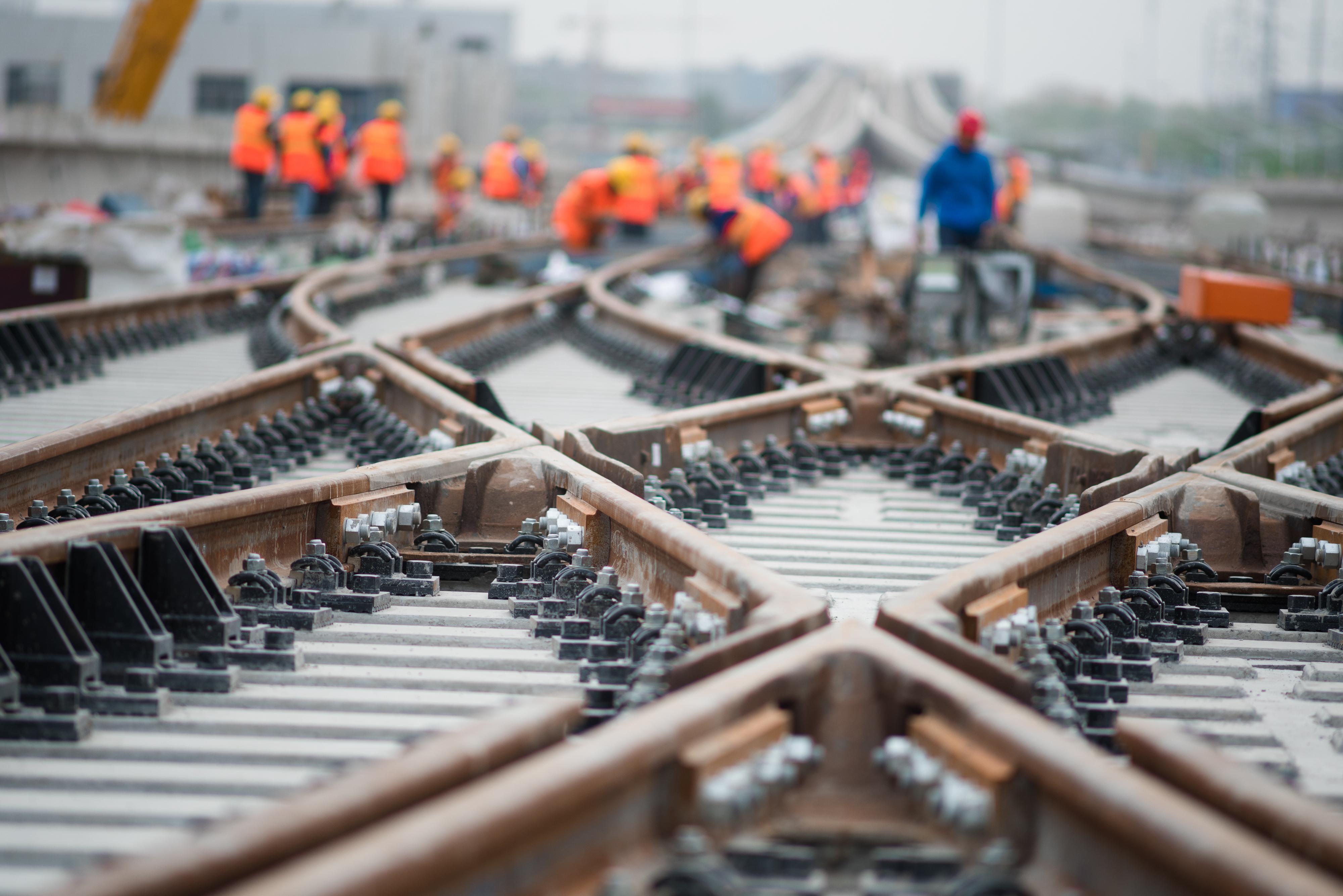
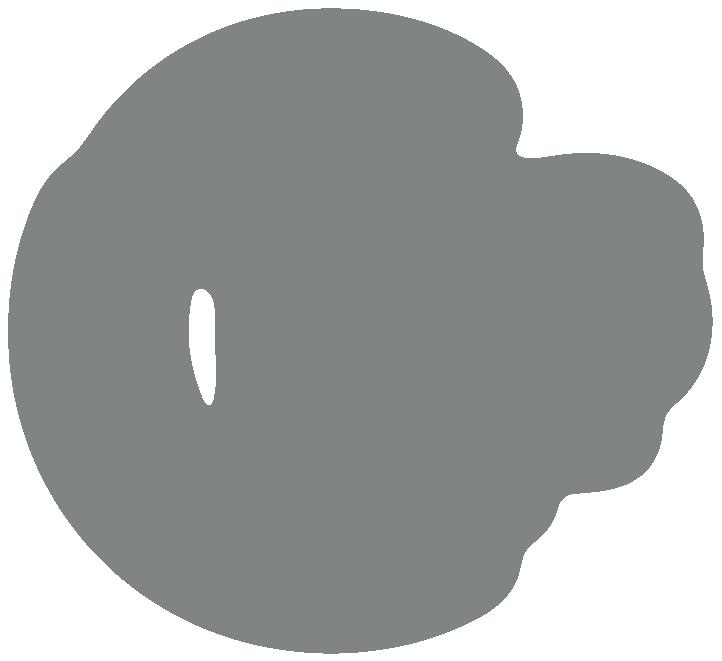
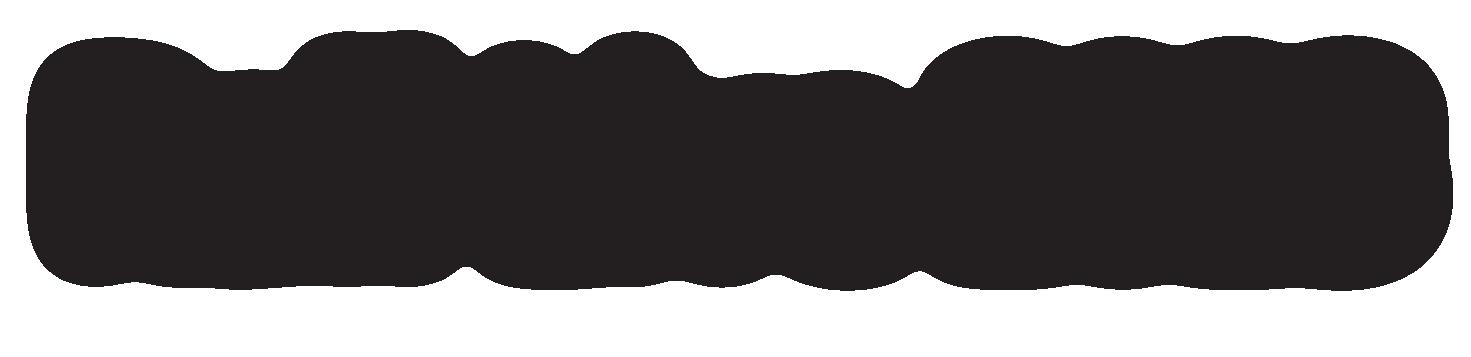
10:30 – 11:00
Next Steps in Rail Regulation: PR23 and beyond
John Larkinson – Chief Executive ORR (Office of Rail & Road) on ORR’s role in rail reform, PR23 draft determination, Train service performance and Safety over the last year.
RAIL LIVE 2023 SCHEDULE
WEDNESDAY 21 JUNE
11:15 – 11:45
Where next? The future of British Railways with Andrew Haines
Andrew Haines, Network Rail Chief Executive and Great British Railways Transition Team Lead, joins Nigel Harris to share his views on the coming months and years for Britain’s railways.
Including:
• How do we rebuild the railways from three years of uncertainty and disruption?
• The path to reform – creating Great British Railways.
• How can the railway better meet the needs of its customers?
12:00 – 12:30
Digital signalling: The next generation railway
Digital signalling is a centrepiece of a 21st century railway. It offers a safer, higher performing, more resilient, more efficient, better skilled, more productive, and greener railway that works better for passengers, users and taxpayers.
The East Coast Digital Programme has brought together Network Rail, operators, suppliers and Government in a pioneering industry and commercial partnership to deliver the introduction of digital signalling to the southern part of the East Coast Main Line.
A panel led by Ed Akers, Network Rail’s Principal Programme Sponsor, ECDP, will explore how the open boundary and user centric approach is generating innovation and building the capability and experience required for the first ever transition to digital signalling to an intercity main line in Britain.
THURSDAY 22 JUNE
13:15 – 13:45
Update on HS2: Overview and insights
A progress update on HS2, highlighting milestone achievements and gathering momentum ‘on the ground’ building HS2. Mark Thurston, Chief Executive Officer at HS2 will also reflect on some of the lessons learned so far from building Britain’s new high-speed railway.
14:00 – 14:30
Why diversity and inclusion matters. Understanding the barriers women face in your organisation.
With a strong reputation for delivery and getting the best from people, Emma Porter, Managing Director at Story Plant, providing specialist operated road rail vehicles to the UK’s railway industry. Emma shares insights into some of the issues that women may encounter in their career. She provides tips for dealing with these issues effectively and productively.
10:30 – 11:00
Innovations that deliver benefits today and tomorrow – the supply chain perspective
From digital to advanced materials, from new practices in design, planning and delivery to new approach to maintenance and renewals – the UK railway industry is innovating every day.
Milda Manomaityte, Innovation Director at the Railway Industry Association will share examples of cutting edge innovation from its members.
11:15 – 11:45
Rail Reform as a catalyst for the future with Peter, Lord Hendy of Richmond Hill
Peter, Lord Hendy of Richmond Hill, Chair of Network Rail, will deliver a speech about the challenges facing the railway, how plans for reform will boost innovation across the industry, and how Great British Railways will help to focus the industry on delivering what passengers need.
Lord Hendy will also discuss plans for the 200th anniversary of the railway in 2025..
12:00 – 12:30
H&S Challenges going forward and in
CP7
For 15 years, ORR has had a vision of zero industry caused fatalities and reducing risk, achieved by moving towards excellence in Health and Safety Management. This is not about gold plating but about doing the right thing and continuous improvement. To help the sector achieve this, ORR developed the Risk Management Maturity Model and worked with the sector to improve it.
Ian Prosser, Director of Railway Safety and HM Chief Inspector of Railways at ORR will focus on key areas the sector should focus on, the financial difficulties the industry faces and the significant organisational changes many parts of the sector are headed towards.
13:15 – 13:45
Network Rail Commercial Procurement
Network Rail Commercial Procurement team will be presenting a panel session at Rail Live.
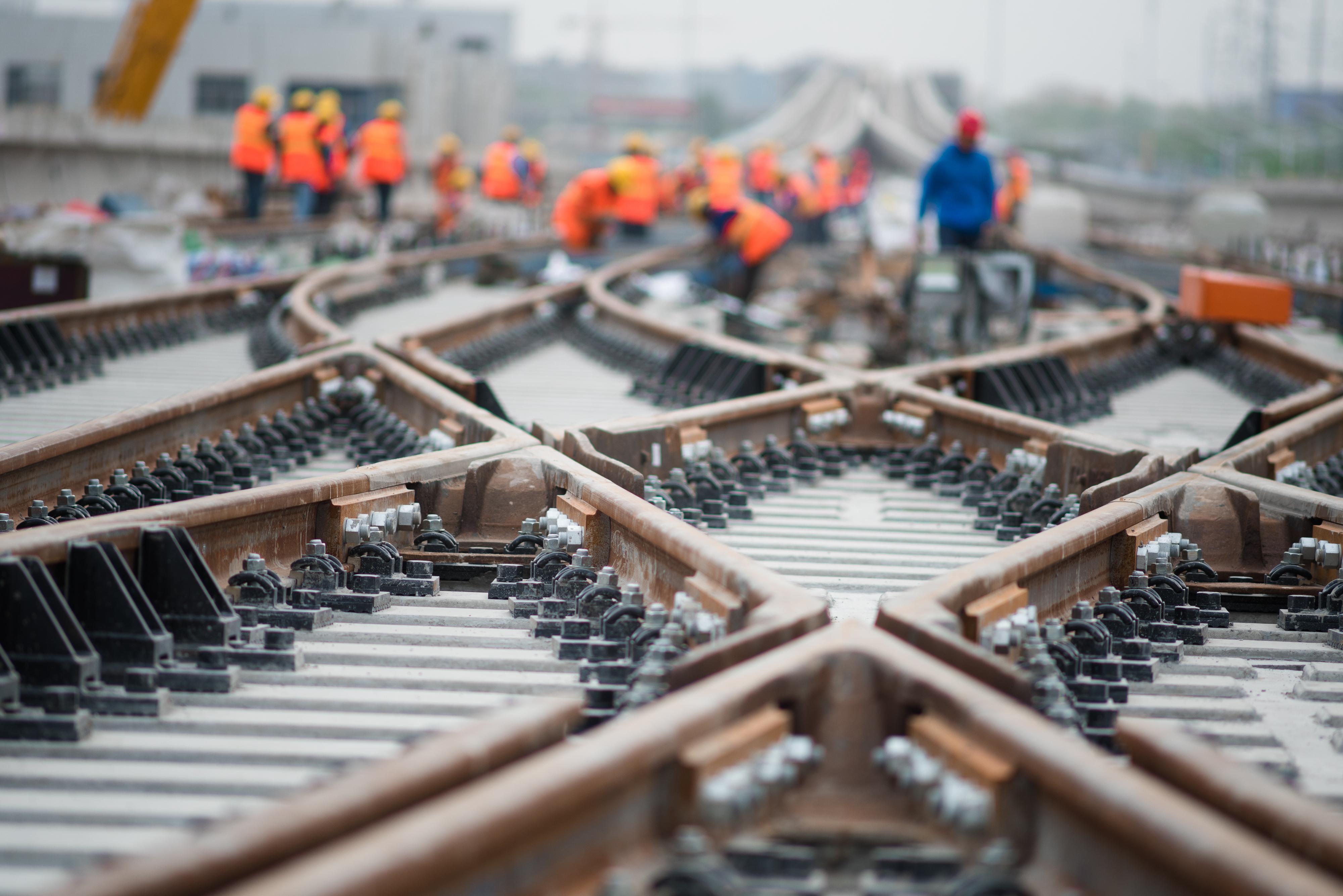
14:00 – 14:30
Aerial Derived Data – Reaching New Heights
A look at the many new use cases for drone use within the rail industry, the challenges and opportunities of the BVLOS journey as well as an overview of our new camera system (MACS) that will offer a superior level of details and with AI be able to produce an end product that will benefit a multitude of user groups.
Speakers:
• Rikke Carmichael, Head of Air Operations
• Bradley Sparkes, National Drone Manager
• Sean Leahy, National Aerial Survey Specialist
As the largest outdoor rail exhibition in the UK, Rail Live brings thousands of rail professionals together in a real railway environment to explore the latest innovations, make valuable connections, and help businesses to save time and money.
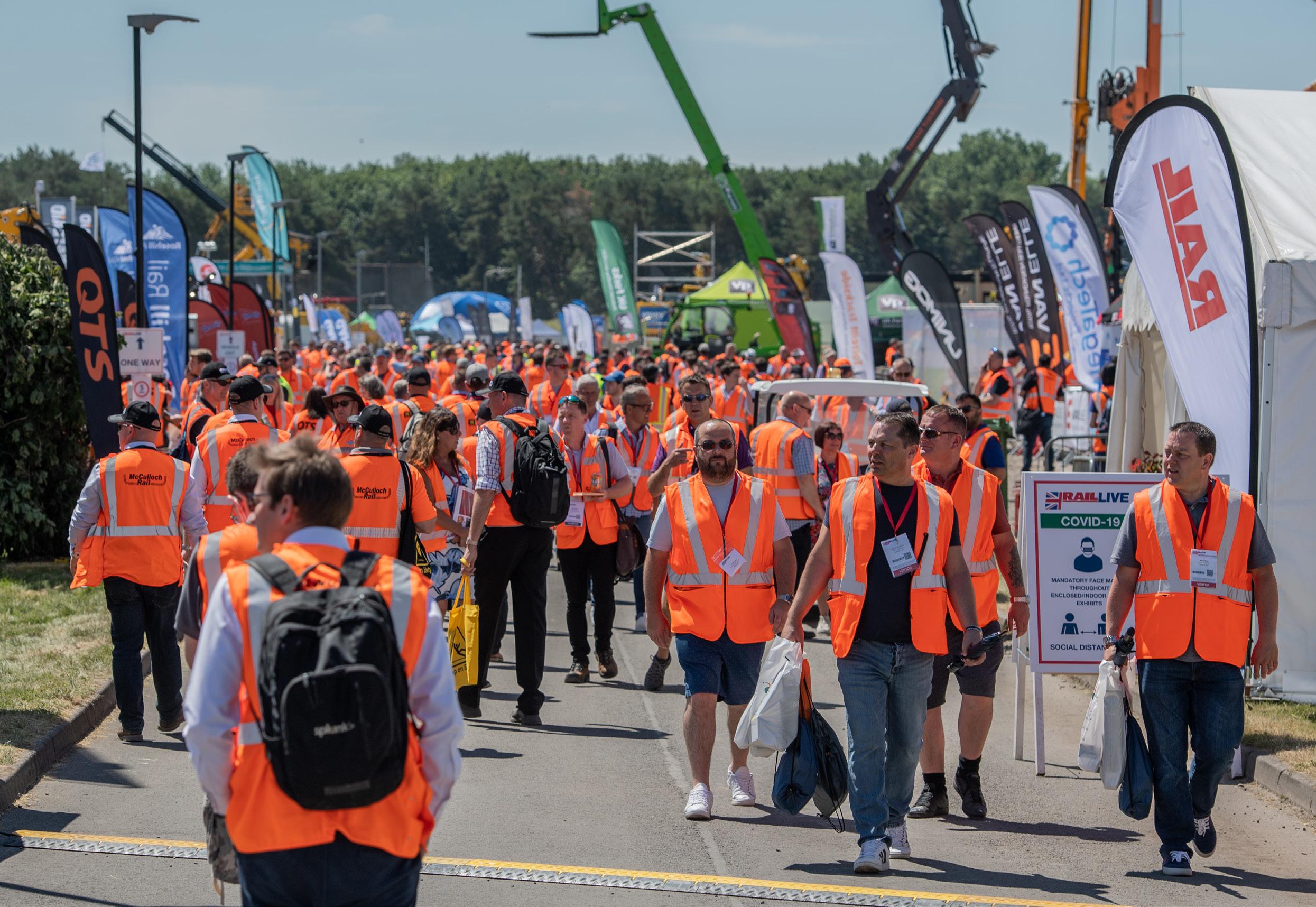
At Rail Live you’ll be able to:
• Evaluate products and services from leading suppliers in a real railway environment via live plant demonstrations and make faster, more informed decisions by comparing thousands of pieces of kit.
• Discover new, more efficient ways of working through the insights provided by industry experts including Mark Thurston (HS2), Peter Lord Hendy of Richmond Hill (Network Rail) and Milda Manomaityte (RIA).
• How the rail industry will move towards a more environmentally sustainable future and discover best practices.
With both Network Rail and HS2 attending Rail Live 2023, this is your best opportunity to connect with key decision makers within the rail industry and discuss the changing landscape so you can plan for the future.
Off track features
Stop by at the Network Rail Village to see the following:
• Sentinel – Sentinel is one of the rail industry's core safety systems, allowing users to check authority to work before
going trackside. Drop by and take a look at the new user interface and find out how you can request and download your own virtual Sentinel card.
• Research & Development Team – The team are a focal point for research, development and innovation. At Rail Live they will be exhibiting a variety of innovative items including: the Felix Laser Robot, a high performance switch system (HPSS) points operating equipment demonstrator and a variety of smaller displays encompassing their current projects.
• Intelligent Infrastructure – Intelligent Infrastructure is a digital transformation programme – helping Network Rail to improve asset management and to provide the basis for a ‘predict and prevent’ maintenance strategy – using apps and tools to take raw data and transform it into intelligence, to support effective decision making.
• Commercial & Procurement – The team from Commercial and Procurement will be on hand to meet and speak with current and potential suppliers.
• SPEED – Swift, Pragmatic and Efficient Enhancement Delivery. To help provide a better service for passengers and freight users.
• Track Demo Viewing Platform – The track work and equipment demonstration taking place on the tracks next to the Network Rail Village will include a viewing platform, providing a clear view of what’s taking place.
• Wales and Western Safety Campaign
Vehicle – The W&W Safety Campaign
Vehicle is a flexible communications vehicle which has can be used to act as a focal point for engaging people, one to one or in groups through use of its internal and external video screens, audio speakers or a human speaker. It has internal and external seating to enable a more comfortable engagement session.
‘I would encourage you to get around and talk to as many people as you can, because in my visit I genuinely have spoken to people I would never have seen before. That’s one of the joys of this dynamic, and it’s why I’m a real passionate supporter of Rail Live.’
Andrew Haines, Chief Executive of Network Rail
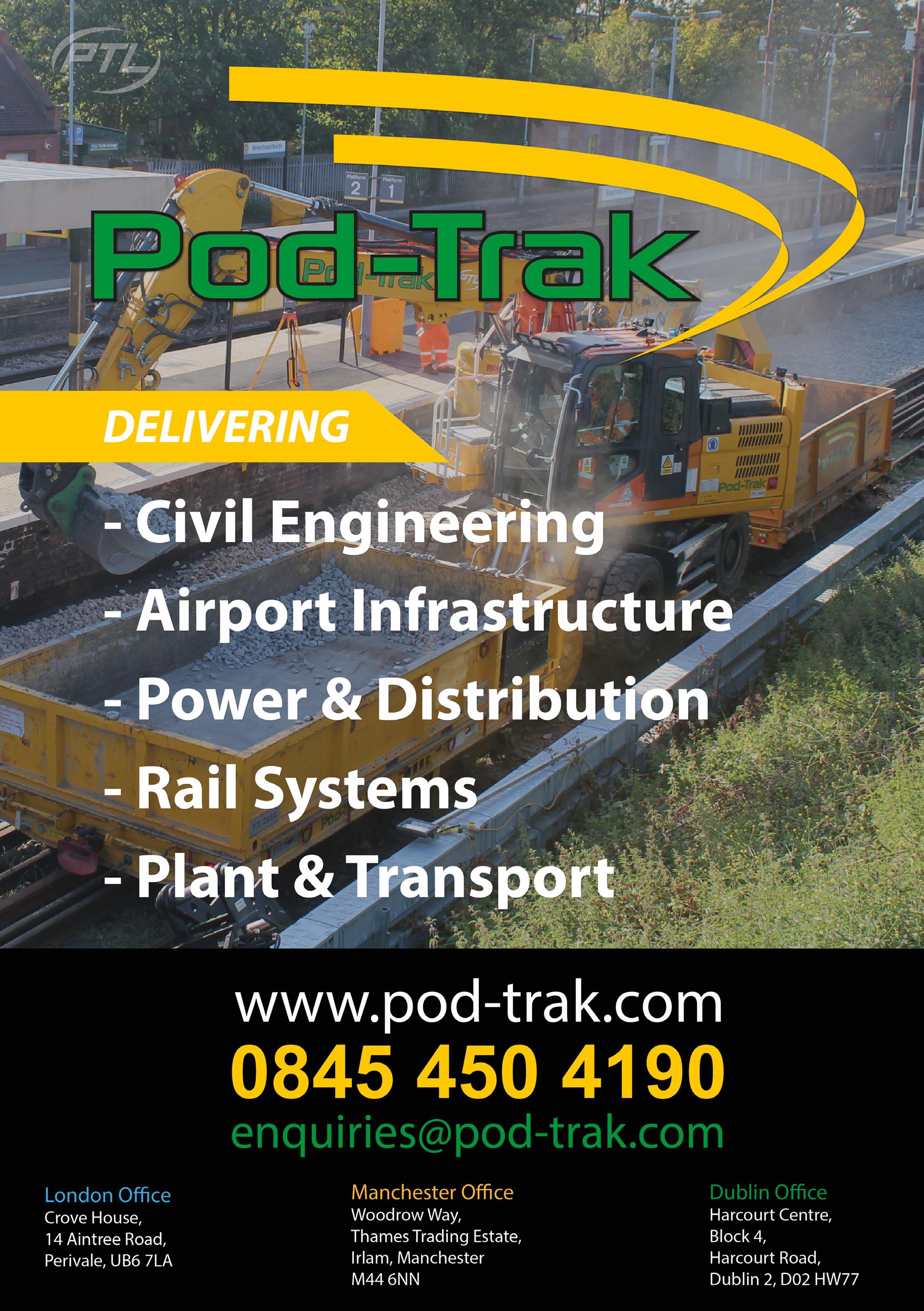
MARTIN OSMAN CONSULTANCY DIRECTOR AT CHEVRON GREEN SERVICES
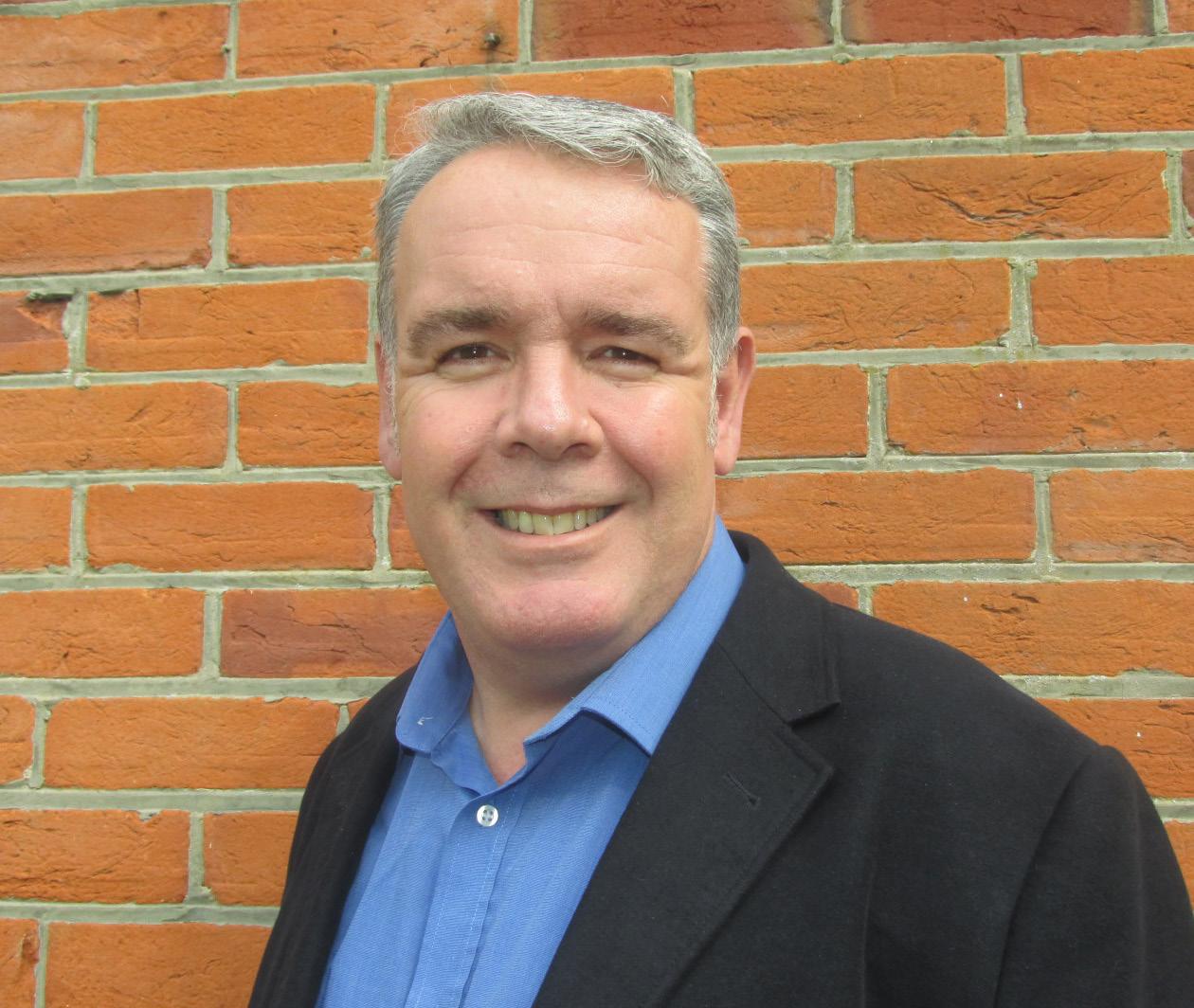
Martin is a Chartered Arboriculturist and joined Chevron Green Consultancy at inception as Director in 2021 having previously led an arboriculture and environmental consultancy business for seven years. Before that, Martin worked for Tier 1 contractors in strategic asset management, combining his technical experience with a strategic approach to his work.
CHEVRON GREEN SERVICES

Chevron Green Services is a leading provider of commercial vegetation management and aboriculture services across the UK. They also provide environmental consultancy services to help clients create sustainable environments by developing and improving maintenance and management schemes.
Want to know more about Chevron Green Services?
Tel: 0330 174 4386
Email: consultancy@ChevronGS.com
Visit: www.ChevronGS.com
What is your role within Chevron Green Services?
I am the Director and divisional lead of Chevron Green Consultancy which is a division of Chevron Green Services, providing professional advisory services to our clients. My role involves working with our exceptional arboricultural and environmental specialists to deliver the services required from our clients. I also work on developing our current services and providing new services where required. A big part of my role is to look at how we innovate and embrace new technology. As industry leaders we are constantly looking at how we can improve process and deliver efficiencies, whilst continuing to provide the high standard of work our clients expect.
Tell us about Chevron Green Services
Chevron Green Services provide environmental consultancy, arboriculture services and commercial vegetation management throughout the UK. We have been managing and maintaining our landscapes and natural environment for almost twenty years. In that time, we have built our reputation on knowledge, respect and appreciation for the green spaces that make up our beautiful land.
Our mission is to protect them while also ensuring that they are maintained in such a way that they do not endanger road users or the general public.
Chevron Green Consultancy is driven by the desire to work with clients to save them time, money and resources while at the same time, protecting the environment.
We started out primarily in the highways sector but we see an opportunity to bring our expertise to the rail sector, working with clients who need our operational experience in grass and hedge management, arboriculture and tree works, de-vegetation and landscaping services as well as clients who would benefit from our professional advice and consultancy services.
How have your products and services developed over the years?
The Consultancy team have been providing arboricultural surveys, landscape management, tree and vegetation services since 2014. Understanding the interactions of nature and that no one specimen lives in isolation, we grew to incorporate an ecological and environmental consultancy capacity into our portfolio, dovetailing them both into the blended services which we can offer today.
We embrace technology where possible within our sector and have certainly moved forward from paper based onsite data gathering. Now we're using digital, phone and tablet recording. We’re also looking at how we can use technology within our environmental and arboricultural roles to provide long term data gathering surveys
and remote sensing. Not only does this have an environmental benefit in reducing footfall on site, but it also provides us, and our clients with more accurate data. This is an emerging market, but the potential usefulness of the information harvested is extremely exciting and will have significant benefits in helping our clients deliver more sustainable services.
What types of companies do you collaborate on projects with?
As with technology and innovation, we embrace collaboration in all its guises, whether that is internally between the arboriculture and ecological parts of the business, the professional services and operational divisions or with contractors and subcontractors.
We have been involved in some key alliance collaborations, with multiple disciplines and multiple companies working together in regional areas and externally with individual contractors on singular and multi-disciplinary projects.
We also have several accreditations and allegiances with charity organisations including Grown in Britain and the Species Recovery Trust. Our work with these organisations ensures we’re lending our expertise to the companies that can help effect change beyond our industry. We are delighted to be able to support these charities in a practical way.
We recently started a project with Anglia Ruskin University and the Peoples Trust for Endangered Species to co-deliver a research project into the use of cameras for small mammal surveys. This knowledge exchange and innovative approach is fundamental to the perspective we take at Chevron Green Services. If successful, we’ll share our findings to help the industry as a whole develop mammal survey best practice in more sustainable and environmentally friendly ways.
What are some of the biggest challenges this sector currently faces?
There are several challenges within the environmental industry none of which are easy to resolve or are any less challenging than the next. I know from first-hand experience that one of our challenges has been the skills shortage currently enveloping the arboricultural, forestry
and environmental sectors, for both the operations and professional services divisions.
Currently everything and everyone requires as a quick fix without much thought placed on retaining mature habitats, ancient woodlands, mature and veteran trees, marshlands, heathlands, and mature grasslands, but instead would remove these natural assets and replace them with some new ones close by or by planting a few trees as mitigation.
Often the trees are planted in locations which are unsuitable, or the wrong species has been selected or the aftercare operations are not completed to a satisfactory standard, these factors all result in the planting schemes failing.
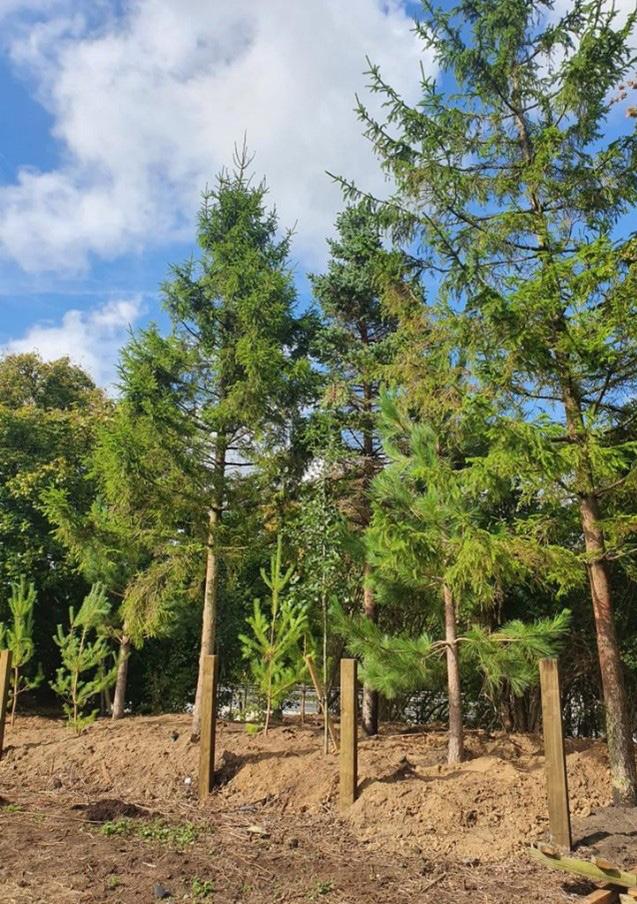

The real problem lies in the loss of relationships, habitats and loss of ecosystems that have been built by the living organisms in these mature habitats over several decades or even hundreds of years. These cannot be re-engineered by planting a few trees nearby.
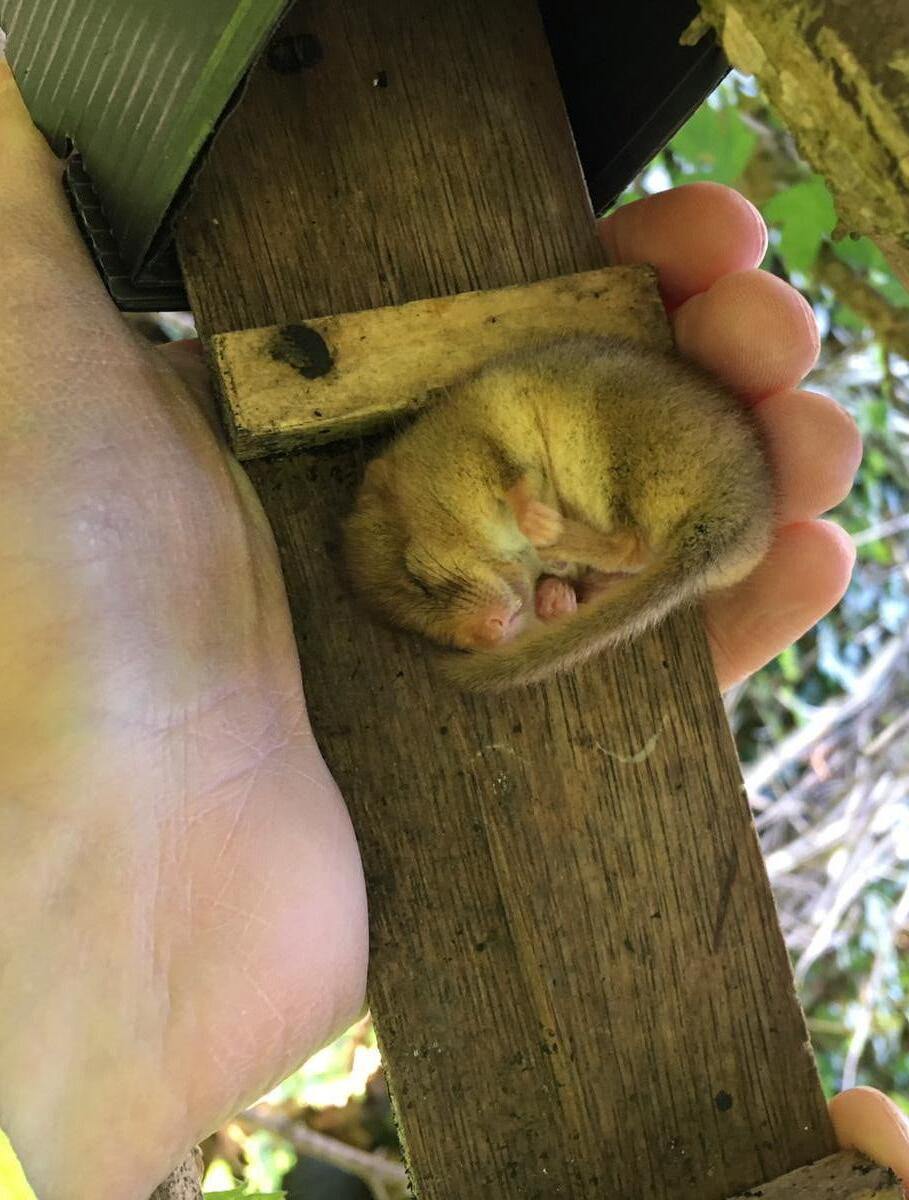
A mature oak tree can provide habitat for hundreds of species above ground with birds, caterpillars, spiders, moths, beetles, squirrels, bats, insects, mosses, liverworts and over 300 species of lichens. Whilst underground mycorrhizal fungi interactions provide a symbiotic relationship which is developed through years of cohabitation. These are the losses which are hurting the biodiversity in the UK, and these are the losses which will take decades to recover.
Do you think the rail industry could be greener and what is your organisation’s green strategy?
Absolutely. It is our responsibility as an industry to collectively work on ways to create a sustainable future. It requires a shift in mindset from everyone, not just in the approach to financing projects, but also in terms of truly embracing sustainable strategies and embracing the mature habitats within our landscape.
We can, as in other infrastructure industries, look at the mature habitats
‘A mature oak tree can provide habitat for hundreds of species above ground with birds, caterpillars, spiders, moths, beetles, squirrels, bats, insects, mosses, liverworts and over 300 species of lichens.’
‘The potential for the rail sector to make a real difference to the protection of our natural habitats and biodiversity is huge.’
and look to preserve, enhance them in line with best practices, whilst also looking outside of the rail estate boundaries to see where enhancement of the wider landscape and environment can be undertaken. The linear assets can be connected to provide linked ecosystems within the borders and then further linked to embrace the wider landscape and the natural assets located nearby.
Chevron Green Services’ mission is to help provide biodiverse habitats for generations to come, which encompasses the vision of habitats to have the allowance to grow into thriving mature eco communities.
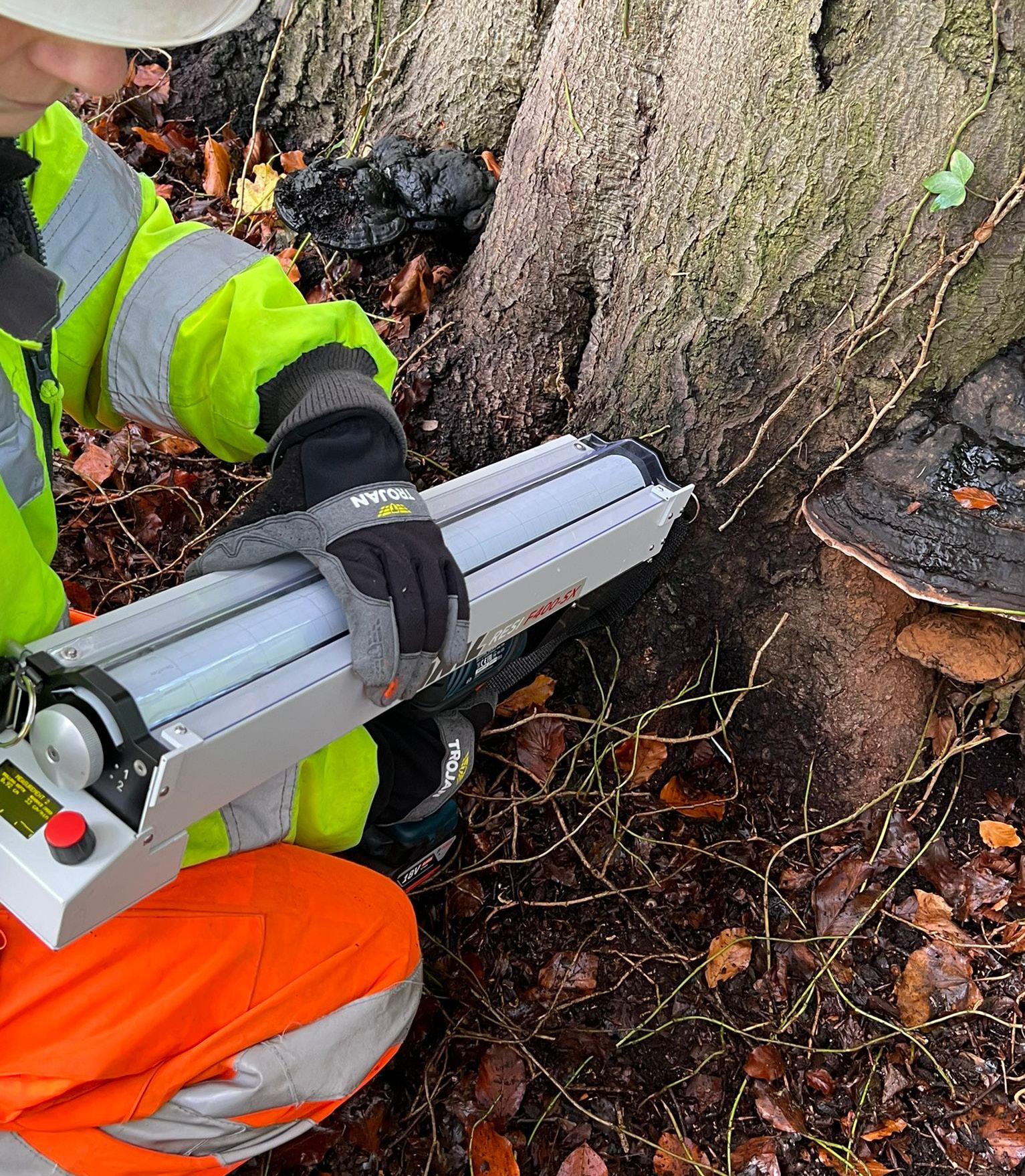
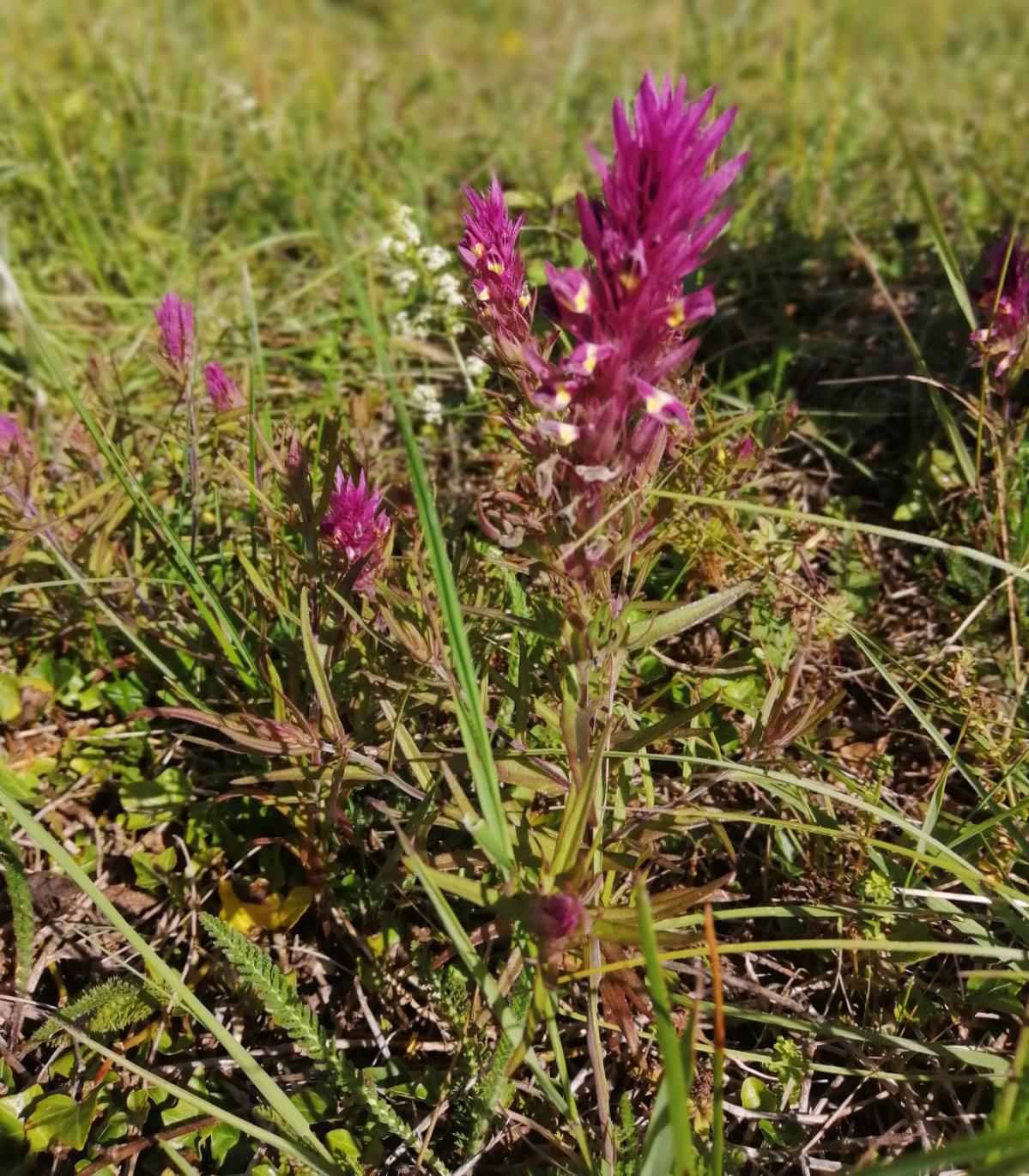
How can we make the rail industry a place people want to work in?
We need to demonstrate to the prospective worker, operative, designer, engineer that the rail industry is innovative, at the forefront of technology not just for the rail itself but also for all the other disciplines working daily within the confines of the rail estate boundary.
The rail industry needs to highlight its safety standards and innovations, the
environmental advances, the social value of the networks and working within the industry, well-being and health advances and benefits for works whilst showing that this is a growth industry not just for now but one that is forward thinking and will be a rewarding challenge for years to come.
What are your views on collaborative working?
We embrace collaboration at all levels, I would struggle to find any of our projects delivered over the past couple of years which has not had some degree of collaboration involved in the successful design, mobilisation, delivery, and conclusion of it.
Every step of the project process can and has been enhanced by discussing and implementing the view, experiences, knowledge, and competencies of others either within our organisation, our supply chain partners, our client base or even with our competitors. I do believe that collaboration widens the competency pool and if managed effectively and more importantly openly, it is an unbelievably valuable asset and key to operational success.
At some point, every company will face the question of how to continue maximising earnings from their current business practice whilst also investing enough in innovation so they can turn a profit in the future. How can a company achieve the necessary creativity to innovate without compromising their existing business?
Employees are the be all and end all of a company, especially in a consultancy where the service is the employees themselves. There are a couple of well-known and used phrases: ‘look after the employees and they will look after the clients’ and ‘train people well enough so they can leave, treat them well enough so they don't want to’ these work just the same for creativity, innovation, ideas, and investment into the company.
Many of my staff have been with me for a while now and I ensure they are looked after, respected, encouraged and empowered to speak up and informed of all things that are happening within the division through regular meetings, updates, and discussions.
Sometimes the best, most simple and effective ideas come from the newest member of the staff and therefore I would say the best way to succeed, is to listen to the ones that are helping you push forward.
‘We’ve started a project with Anglia Ruskin University and the Peoples Trust for Endangered Species to co-deliver a research project into the use of cameras for small mammal surveys.’
‘We work with the rail sector to see how they can deliver a more sustainable and environmentally friendly service.’
Providing environmental consultancy, arboriculture services and commercial vegetation management nationwide.
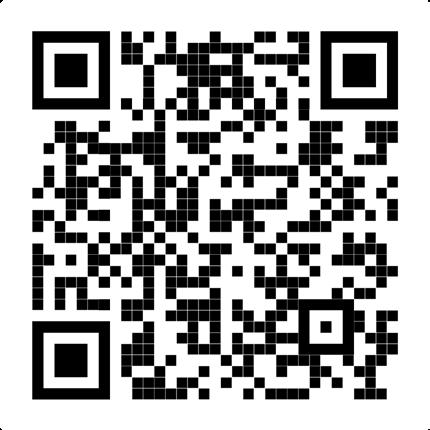
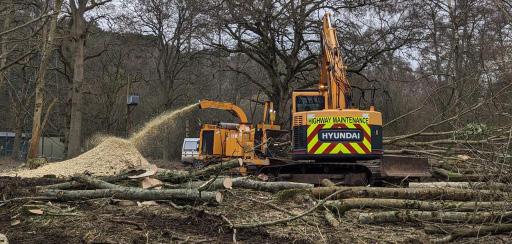
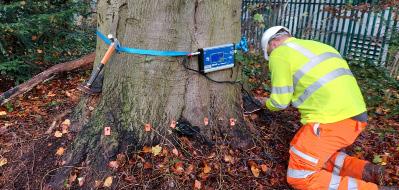
Chevron Green Services keeps the natural world and sustainability at the heart of everything we do. We’re here to help you plan for the long-term life cycle of your projects. Forefront of our approach is achieving inclusion and integration into the wider environment, providing biodiverse habitats for generations to come.
We work in collaboration with our advisory division, Chevron Green Consultancy to provide an end-to-end solution, including: consultancy and advisory services, project delivery and maintenance for all your landscape, environmental and arboriculture requirements.
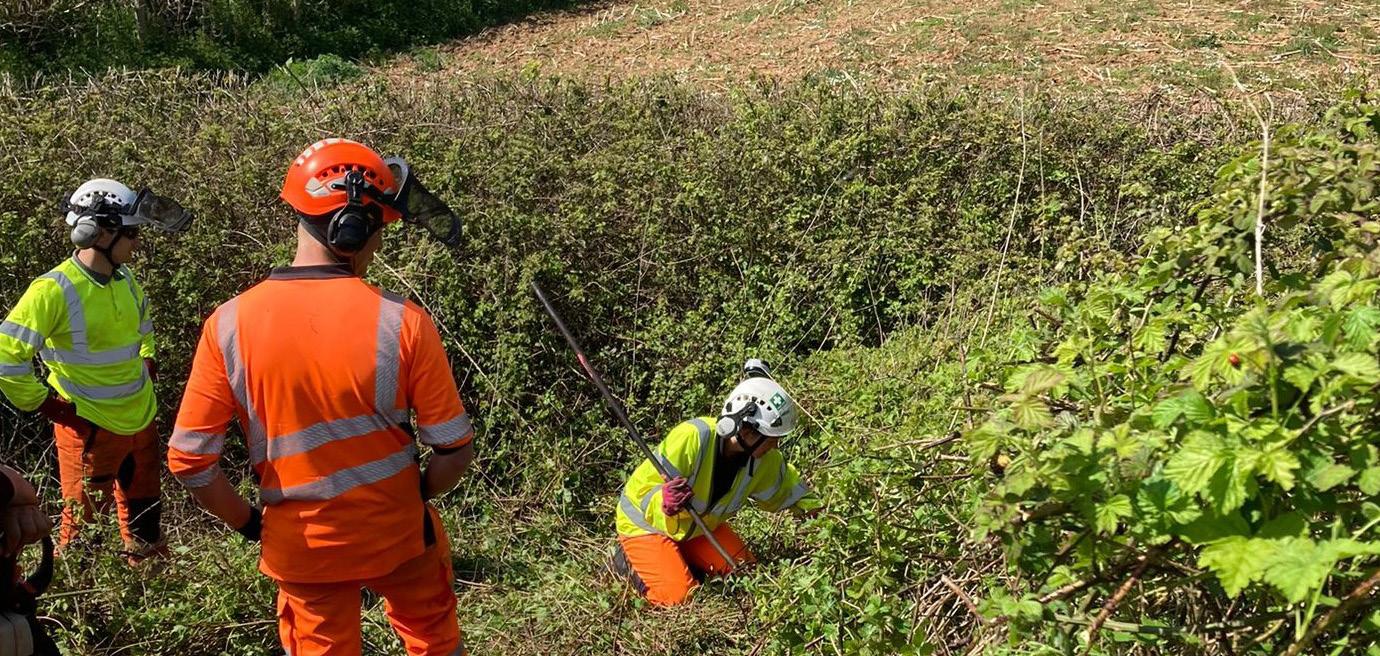
With over 20 years experience in vegetation management, we’re arboriculture experts, constantly innovating to ensure we are providing the safest and most efficient service available. We work with clients in the public and private sectors to maintain, manage, control, and enhance natural environments.
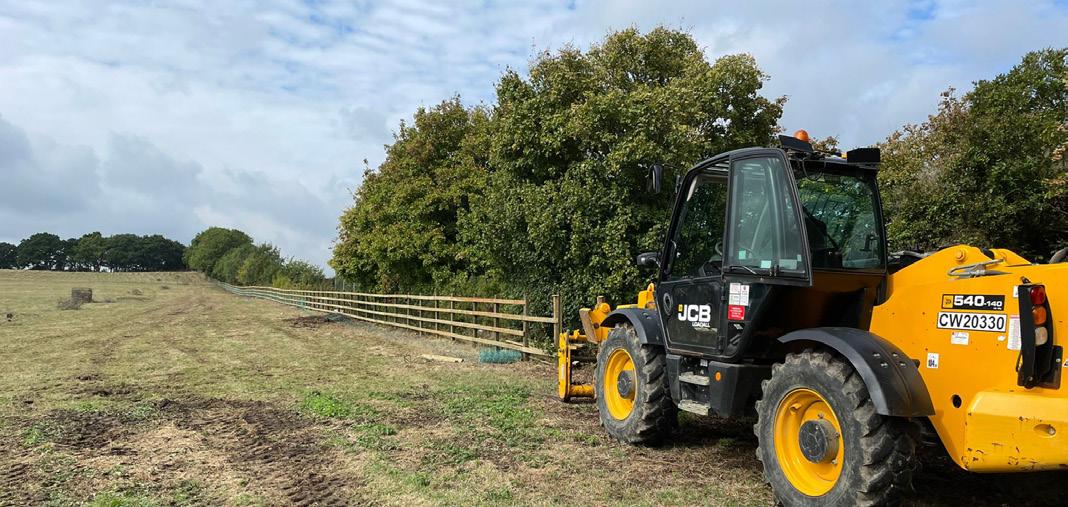
KEVIN BABSTOCK UK SALES AND CUSTOMER SERVICE MANAGER AT ADVANCED NEW TECHNOLOGY LTD. (ANT)
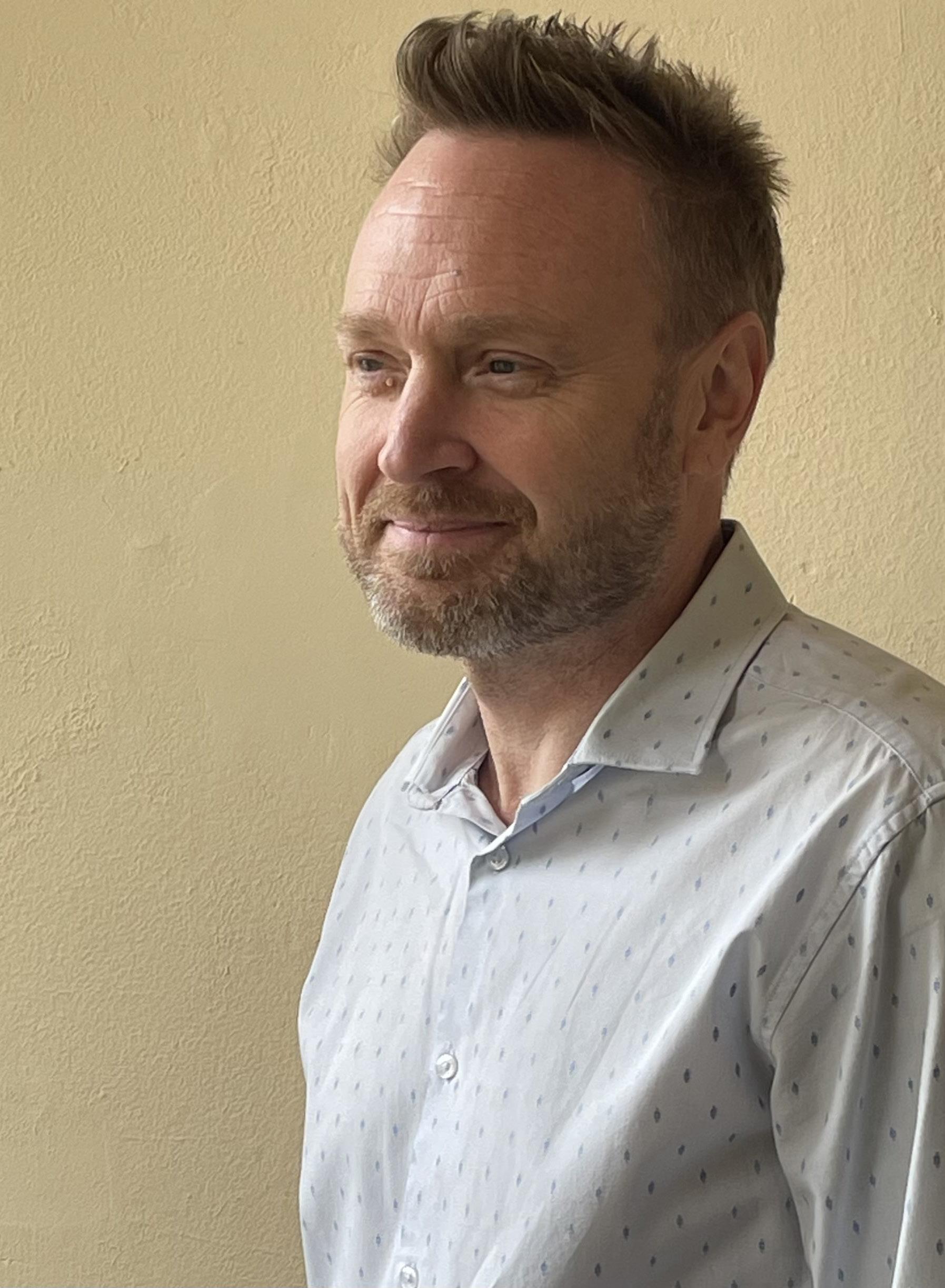
Kevin Babstock is a successful sales and customer service manager with an in-depth knowledge of sales processes. He specialises in understanding the key requirements and challenges presented by the software development sector and delivers solutions and account management skills in order to maximise client satisfaction.
ADVANCED NEW TECHNOLOGY LTD
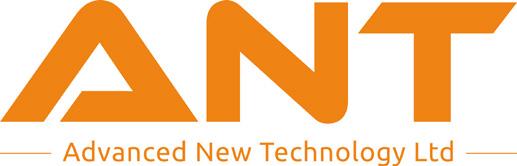
ANT was established in 1986 and since then has been providing customers with bespoke mobile apps and web applications for multi-national companies like MTR whilst also offering off the shelf customisable solutions. ANT are market leaders in the Apps and Web back end systems we supply, making ANT an exciting, innovative, dynamic company.
Want to know more about ANT?
Tel: 01825 713 058
Email: sales@a-n-t.com
Visit: www.a-n-t.com/
How long has Advanced New Technology Ltd. (ANT) been in business?
Based in Nutley East Sussex, Advanced New Technology Ltd (ANT) was established in 1986 programming Psion mobile handheld computers, for Health and Safety recording and quickly became a specialist in developing Safety Management and Risk Tracking Applications. Our experienced professional team have developed and implemented multiple purpose-built systems and applications for a range of clients across the UK who are leaders in their industries including regional airports, councils, facilities management companies and Train Operating Companies.
What is your role within Advanced New Technology Ltd. (ANT)?
I joined ANT as the Sales and Customer Service Manager at the start of the Covid restrictions in 2020. Within this role I oversee our sales process, which includes the initial consultation to understand how they would best benefit from our software solutions. For many of our customers this is an exciting part of getting to know our company and becoming familiar with what type of system we could offer. Knowing that we will support them at every opportunity makes it less daunting for some customers. There is always the element of the unknown in starting a new venture, with the majority of our clients being very happy with the ongoing service they receive.
Once there is some kind of agreement in place, I work supporting the system design process to ensure the development and launch will meet or exceed the customers’ requirements. When a system has been integrated, we like to visit regularly to support the customer and to understand how the system is working in situ. By supporting the customer in this way, it helps both parties to understand the challenges the client faces and how the systems we develop can be enhanced to benefit our customers further.
This has been an integral part of my role in understanding customer requirements and how we can deliver them effectively whilst continually surpassing their expectations. As a team effort, this involves working closely with the software developers as well as the Admin and Help Desk Teams.
Which sectors do you work in?
ANT works within all sectors and can help companies requiring comprehensive Safety Management and Risk Tracking software across many business models from small independent companies to large corporations. For the rail industry we have developed large and small scale specialised software for regional TOCS including MTR Elizabeth Line, SouthEastern, GTR, Greater Anglia, WM Railway, Northern Rail, East
Midlands Railway and Arriva Rail London.
All the companies that we work with require the ability to undertake audits and risk tracking measures to ensure compliance is met or preferably exceeded, based on industry specifications. Our systems typically cater for unlimited licenses to use our mobile app(s) to undertake audits conveniently on site, as well as undertaking directly on their customised web system, as frequently as required. Our auditor apps which include SQR and PGI allow for actions to be raised to the appropriate responsible person(s) with defined timescales for these actions to be closed.
Reporting and analysis is key, so our standard audits dashboards are included, and we can provide additional exports and reports that streamline the reporting process. We can also integrate into third party systems and allow API Access level for integrations into platforms such as PowerBI. Once a system is in place within a company it quickly becomes an indispensable tool for all levels within the business.
Sectors such as airports, councils, facilities management, or TOC may require Accident or Incident Reporting applications which can provide local managers a 72 Hour review of the reported incident as well as an investigation stage if required. We work to empower local managers to track accidents and incidents and to check that the correct health and safety measures are in place. These are just a handful of our applications which all sectors can benefit from.
How has the technology developed since you started in the industry?
Since Covid, businesses are looking for ways to become more streamlined and cost effective. Enhancements and affordability in software development and devices has helped businesses report quicker and more effectively if they invest in the right technology. Every year devices are becoming more powerful with more storage. Faster processing power accelerates the processing of large amounts of data from remote sites.
In addition, Wi-Fi/Data coverage is continually improving and as most people have a device, they are used to working with some form of technology, and it’s more readily available, which has helped remove barriers in introducing software solutions.
Over the last few years there has been a sharp increase in the use of Teams Meetings and remote working tools. On face value this has meant that people have needed to embrace technology and now have considerable experience and daily use of it in the working environment. It has also increased our accessibility for remote meetings with our customers, which in many instances has made supporting our customers easier and more efficient.
What types of products and services do you offer?
Over the years ANT have developed a range of purpose-built software solutions to increase safety management risk tracking.
For the rail industry, this includes auditing, such as Planned General Inspections or Service Quality Regime, and risk tracking such as suicide prevention and accidents, for instance. These all have assisted in TOCs becoming safer, cleaner, and improving customer satisfaction, whilst reducing costs.
PGI (Planned General Inspections) allows the audit to be completed in more than one visit. While there is a set question set, the auditor can customise the assets, for instance, they can add up to 17 platforms for a station during setup, and these can all be renamed, so that their location is instantly recognisable. This ensures that each asset is assessed and taken into consideration, rather than an auditor completing a standard audit template, which may not be relevant.
This aids reporting and provides a true reflection of the audited assets. It also makes a big difference when they have any outstanding actions to know exactly where these are within the station.
Our Foundit (lost property software) has helped hundreds of customers get repatriated with their lost items. TOCs have benefitted from a reduction in the lost property held on the network and the admin resources to look after it, as well as gaining transparency and increasing customer satisfaction in their services.
If customers have an idea or a requirement to fulfil a task, we can help turn this from an idea into a working software solution. We are always happy to talk through potential software solutions. As we have undertaken development for all types of requirements, we are most likely to already have something which has been developed which we can implement onto a system of your own.
What is your USP (Unique Selling Point)?
It’s hard to choose just one as ANT, Advanced New Technology Ltd, have so many positive things going for it.
As a software development company, we have designed systems for many businesses with each software package bespoke to the needs of the client. One of our USP’s is our specialist knowledge in being able to interpret the customers’ requirements to build a system that exceeds their expectations and requirements at a competitive price.
All our solutions are built and developed in-house using our own frameworks and libraries for various platforms, PC and Mobile. We are not developing plugins on top of existing CRM systems so we are not restricted by limitations of the base
software, we can literally develop anything the client requires of us. This has included various completely bespoke solutions provided to TOC’s. i.e. Roster Template Tools, Fleet Recovery Systems, Berth Monitoring Tools.
Throughout the process, from initial introductions to a product being imbedded within a company the system designers, admin and I are on hand to support, offer advice and answer any questions.
Offering ongoing support and advice throughout the lifetime of the product is a huge part of what we do, and clients are unlikely to find another competitively priced system parallel to what we can provide. Clients’ conscious about the money they spend on internal administration costs may benefit by using the types of services and solutions we offer.
How have the products and services you offer developed over the years?
Businesses would previously have to purchase purpose-built devices, now a mobile device (tablet/phone) can be used to undertake a multitude of different tasks. In short, the software solutions are now easier to use.
Continuing to build our systems with easier and more intuitive operating systems and user interfaces, means that accessibility and availability to each level of the business continues to be a key factor when designing software and how it will work within a business. Not only that, but the ease and speed at which it can be used, means a much bigger saving on administrative time and cost now, in comparison to when the system was first developed.
Our customers are becoming more integral to the software design process, providing feedback at each development stage, and using a beta version in situ prior to the final system being implemented, rather than just sold an ‘off the shelf’ system. This means that the specific customer’s system is tailored more to meet their needs and industry standards, which would not be possible from a one shoe fits all approach.
What are some major projects you’re currently working on?
A major project that is continually evolving is the Service Quality Regime (SQR) System. This was introduced by the Department for Transport at the beginning of 2021, and for the TOCs that are included was a massive undertaking. The SQR project meant that TOCs needed a software system that could record a complete asset register of all customer facing assets on its trains and within stations. Once this was completed, each TOC was required to undertake a defined amount of station and train audits each period, with any station failures then requiring a further audit to confirm if the failure had been fixed or resolved, again, within a defined timescale. Should it still be outstanding, a final audit could be undertaken where the asset is determined fixed or in breach.
The SQR system was built to support the TOCs management, the third party auditing company, as well as the departments responsible for resolving any failures raised. It is essential that the DfTs defined reporting requirements are met every period, so the system has many dashboards, exports, and reporting features to enable each teams’ users to report and analyse the extensive data which is collected. The level of records and data available within the system is more than any other system we have built and continues to grow.
We have numerous dashboards for the auditors and their management team specifically. One example is the revisits dashboard, so that auditors can effectively plan their workloads for revisits, and the third party auditing company can assign/ reassign auditors internally.
As this concept has now been tried and tested and has reached the end of its developmental phase, it would be an ideal time for any new TOC clients wanting to implement the enhanced SQR system.
What are some standout projects you’ve been involved in over the years?
ANT have been involved in many projects that have aided the rail industry, a significant project was the development of iSafety for MTR. iSafety includes seven recording applications: two Safety Tour applications, five station compliance audits, bespoke reporting and results linking directly into COMPASS, MTRs own inhouse system. This system took four years to develop, working collaboratively with different stakeholders within MTR and went on to win an award for Safety Initiative of the Year. ANTs Software is now integral within MTR and how it operates its safety and risk management, as it allows easy reporting and data analysis and with the COMPASS integration, it effectively allows for any issues and failures to be raised and resolved to the required standard effectively.
In terms of technology, how do you anticipate things might change in the next five to ten years?
We anticipate that more companies may ask for further integration with APIs as linking various systems data strengthens its reporting and analysis capabilities. We have found that there has been an increase in the use of the single sign-on or multi factor authentication to access client’s systems, which increases the systems data security and provides extra elements of reassurance.
An exciting new development on the market might be e-ink devices. Once they are more readily available, we may receive requests for our auditing software to be compatible with it, as some auditors may enjoy the experience of writing their answers instead of typing them. This may be preferable for some when they have a lot of information to collect. The e-ink devices may also help the task force to be more focused on their workload.
Another different development for the future may be in 3D mapping. We already have the technology to plot where an asset is against the station map during the setup of stations for our SQR, (Service Quality Regime System), they can also plot where an asset has been determined a failure. This assists the relevant teams in identifying the correct asset and rectifying the issue faster. 3D mapping may become more beneficial as a solution for asset registers or providing more detail on where a failure or noncompliance has occurred, with handheld devices becoming more powerful this may become a powerful solution for many industries.
While some people seem excited for Artificial Intelligence, we don’t imagine this would change much within the next five to ten years. But sometimes technology advances because of the interest from the end consumers or a ground-breaking idea becomes available.
What makes this such an exciting time for innovation in the rail sector?
Technology can move at a fast pace and can evolve from customers wanting the technology to assist in more ways. So innovative ideas from a new breed of personnel, other industries or from another country are crossing into the rail industry, which can only benefit the rail and software industry as developers face new and exciting challenges. despite the challenges of Covid, it has played a big part in how the rail networks work and what customers expect from them, this has made the TOCs review how they can be more effective. So, innovation for reducing costs, and improving customers’ expectations and supporting their employees to conduct their roles effectively has been necessary.
‘Offering ongoing support and advice throughout the lifetime of the product is a huge part of what we do, and clients are unlikely to find another competitively priced system parallel to what we can provide.’
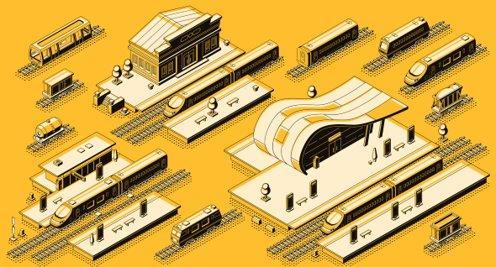

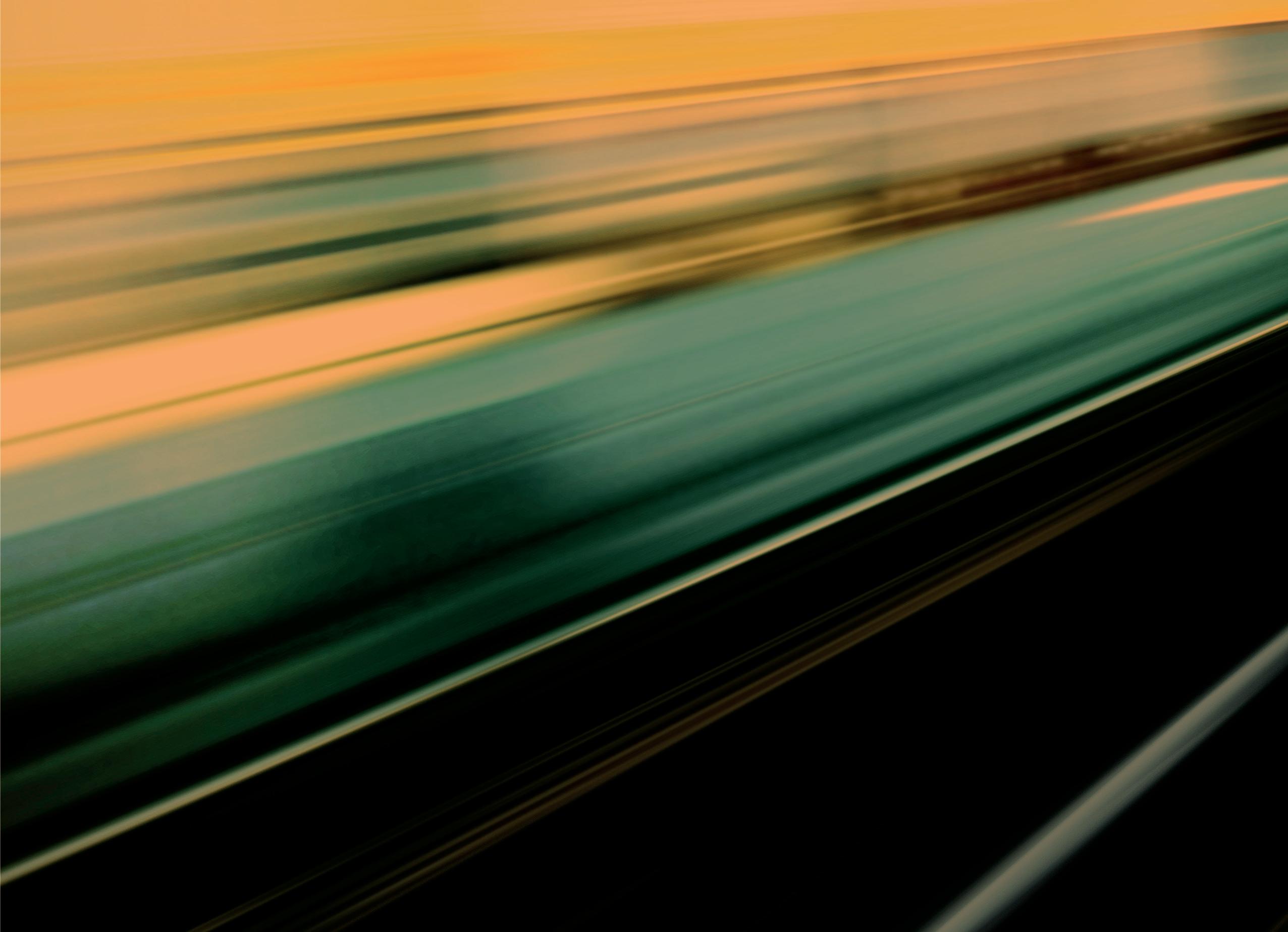
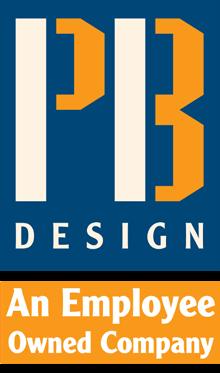
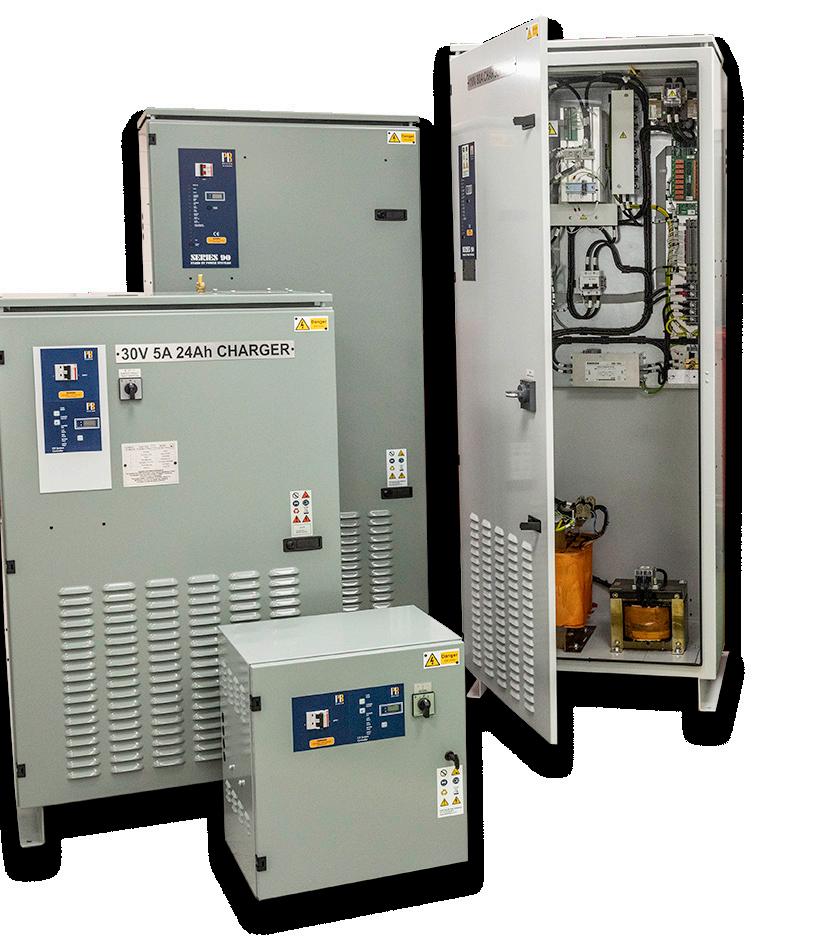
CHRIS RENSHAW BUSINESS OPERATIONS MANAGER AT A. BRATT & SON LTD (BRATTS LADDERS)
An avid golfer that is as competitive at work as he is on the course, Chris Renshaw is Business Operations Manager at Bratts Ladders after starting out as their delivery driver. He is a qualified Ladder instructor and a member of the Ladder Association Council.
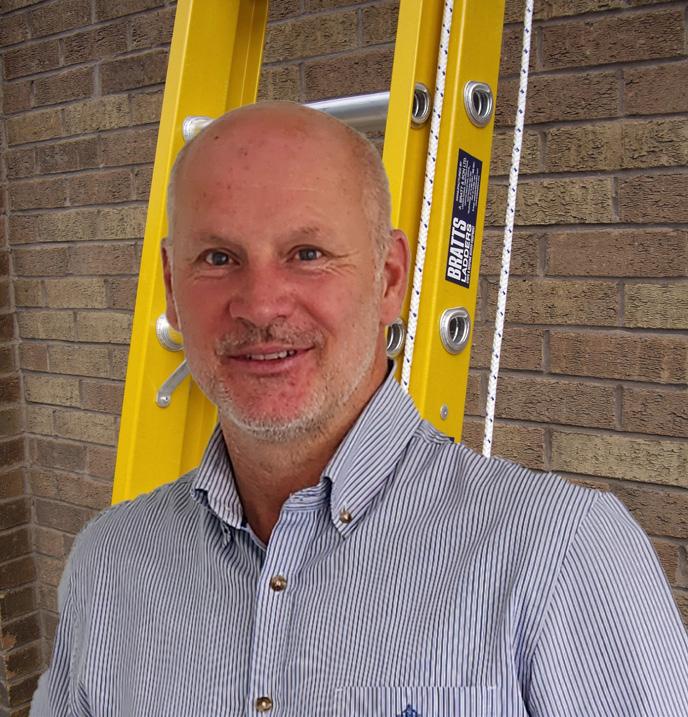
BRATTS LADDERS
Bratts has been making ladders since 1895, supplying the Railways since 1938 and the Electricity industry since 1953. They are a British Standards licenced UK manufacturer, producing non-conductive Timber and Glassfibre ladders, stepladders, platforms and specialist access equipment for industrial use. They supply every major UK electricity, rail, telecom, gas, chemical, oil, aviation and construction company and similar industries worldwide.
Want to know more about Bratts Ladders?
Tel: 0115 986 6851 or 07836 710824
Email: chris@brattsladders.com
Visit: www.brattsladders.com
What is your role within Bratts Ladders?
Over the time I have spent here, I have taken over a few roles. My main day to day is the dealing of any sales related queries. A lot of Bratts requests are of a combination of standard off the shelf access equipment and those of a more bespoke nature. This then requires site visits, discussing with the client the best way to tackle their access issues.
Bratts also offer Ladder Association credited ladders courses, to which I am our Lead Trainer.
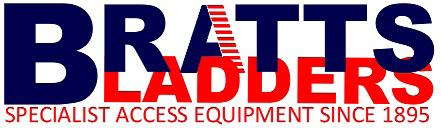
How did you start at Bratts Ladders and when did you join?
A long time ago, 2003 as a Delivery driver –and I’m still considered one of the newbies here. We are a small company and we had one 7.5 tonne lorry. A friend of a friend said they needed a driver, and so here I am.
How long has your company been in business?
Since 1895. Founded by Alfred John Bratt, the Great Grandfather of our current Managing Director, Stephen Bratt. A long running family business that we are so proud of, its written on our shirts.
Tell us about Bratts Ladders.
Bratts has had a long history in the manufacturing of Timber ladders. Utility companies, telecommunications and of course widely in the rail sector. Around the mid-1990s we then started to develop our Glass Fibre range. This allowed us to compete with other sector markets, but at the same time, offer a more diverse range for our long-standing existing customers.
What types of products and services do you offer?
We specialise in non-conductive access equipment, ranging from ladders, stepladders and other bespoke
requirements. Increasingly, customers are needing case specific access. A simple ladder or step just does not always work. We use our experience and knowledge to help overcome any such ‘obstacles’.
Training has seen a massive importance in day-to-day workings. Due to our long history, experience and knowledge gained, it puts us in an advantageous position to offer the training courses we do, a user course to give learners all the knowledge needed to use equipment properly and an inspectors course to qualify a learner to competently inspect the equipment, ensuring it is safe to use.
Some companies prefer to keep their access equipment inspections independent from themselves, we are only too happy to attend and carry out the inspections on their behalf.
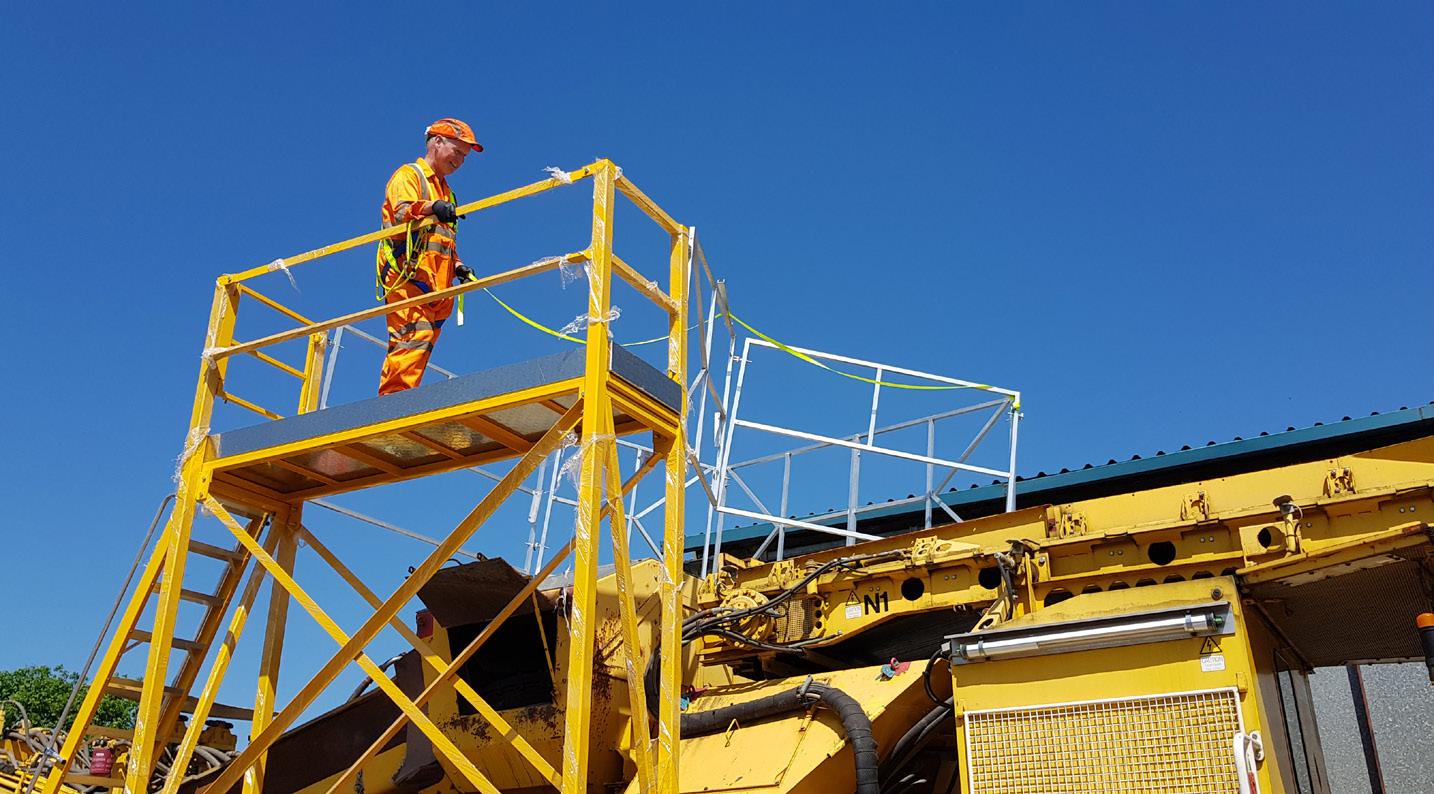
How have the products and services you offer developed over the years?
Our product still to this day is industry driven. We started with a pointer ladder for the window cleaner. Then local business’ wanted ladders and stepladders. Electricity companies recognised the need for non-conductive. The rail industry saw the same need. Coal boards understood that underground they needed spark free equipment. And then, Health and Safety.
What are some major projects you’re currently working on?
HS2 has contracted a company to construct the concrete sections of the tunnels. An issue that this company experienced is the transport of these components. They have devised an award nominated solution to this but required safe access to the machine. They invited us to help, if we could, and that is exactly what we did. An access ladder on a rail that allows them to achieve the perfect access point.
Network Rail required access to a satellite machine by its maintenance engineers. We have created a platform system for them
to have ease of ingress/egress, and to have sure, safe and secure standing areas while carrying out their tasks.
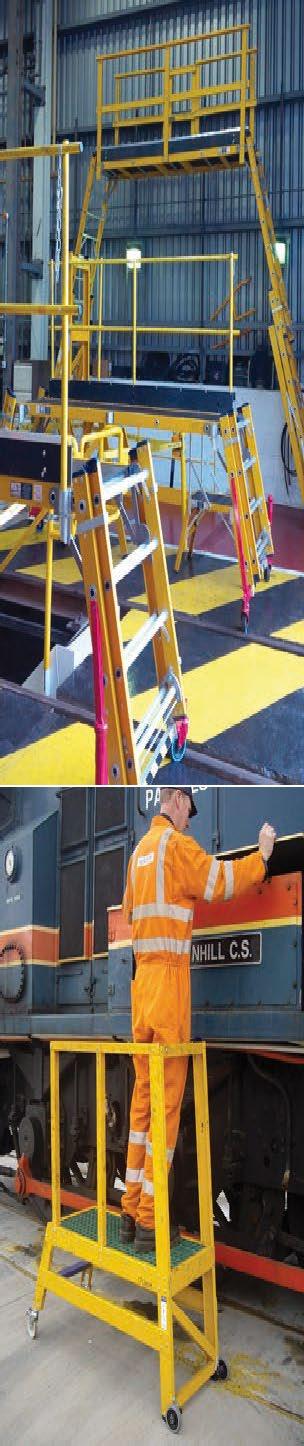
Alstom have asked us to work a prototype for them to allow many of their engineers to continue work on the construction of their projects, offering them a sturdy platform at a height of approximately 350mm with a handrail to increase their own personal stability.


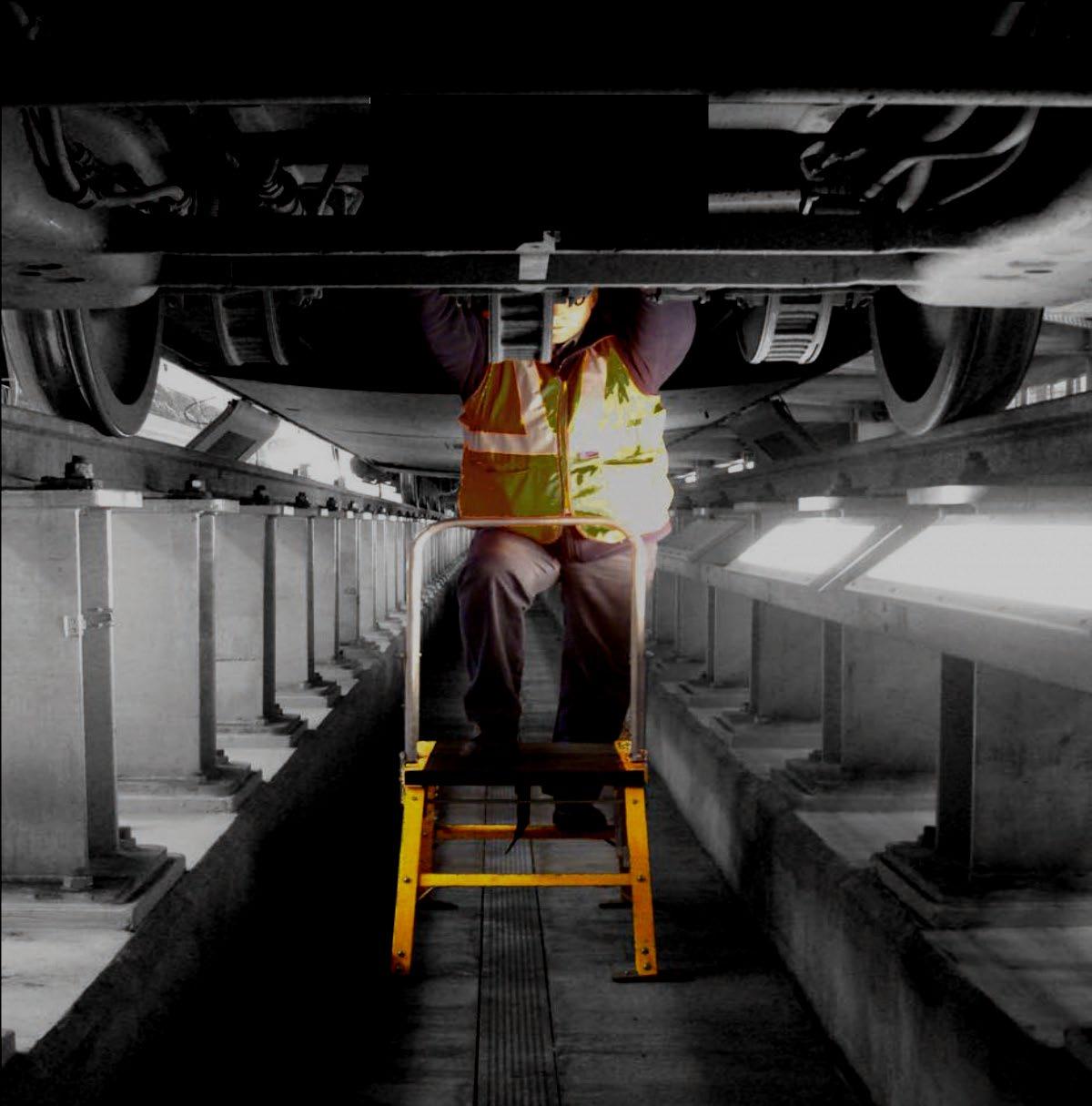
We are now receiving more requests to assist engineers to go down into an excavation. We are currently working on an Excavation ladder to do exactly that.
How do you work with the supply chain within this sector?
Bratts are foremost an approved verified supplier to many of the rail companies. That said, some companies use more facility companies like Cromwell Tools, Arco etc… We still work in partnership with them also.


With the coming launch of Great British Railways, how do you anticipate your place within the supply chain changing?
For us we feel it will not. We see our role continuing in the same manner.
How have you seen the industry change over the years?
Health and Safety. We have seen with the much-needed demand for a better, safer environment to work in, the greater push to have ‘the best piece of kit’ for the job. The most suitable, the most practicable and still, the most user friendly.
What are your views on collaborative working?
It is what we have always done. Our whole product is a partnership with someone. It’s not always good to have just one individual saying how things are to be done. Many ideas, many thoughts, much feedback allow us to hopefully get it right.
How do you make your business a good place to work?
Smile. At some stage we will all wind each other up. My mum always said to me: ‘If you don’t laugh, you’ll cry!’ I try to live by that every day. And tolerance. We all do things in a unique way. Understanding that and accepting that means we can all move in our own comfortable way, but still striving forward to the same goal.
At some point, every company will face the question of how to continue maximising earnings from their current business practice whilst also investing enough in innovation so they can turn a profit in the future. How can a company achieve the necessary creativity to innovate without compromising their existing business?
Our long-term business plan has been perfected for over a century. We understood early not to ‘reinvent the ladder’! Our commitment to ISO9001:2015 enables us to work and communicate closely with our customer base to innovate and drive new products.
Quality by Design
CHRIS MANNING HEAD OF RAIL AND INFRASTRUCTURE AT SUMO SERVICES LTD.
Chris has worked in the survey industry for 28 years, specializing for much of this time in the rail sector. He has worked with a range of key clients and projects, including TFL, Network Rail and HS2. Chris leads all rail activities for SUMO Services Ltd, throughout the UK.
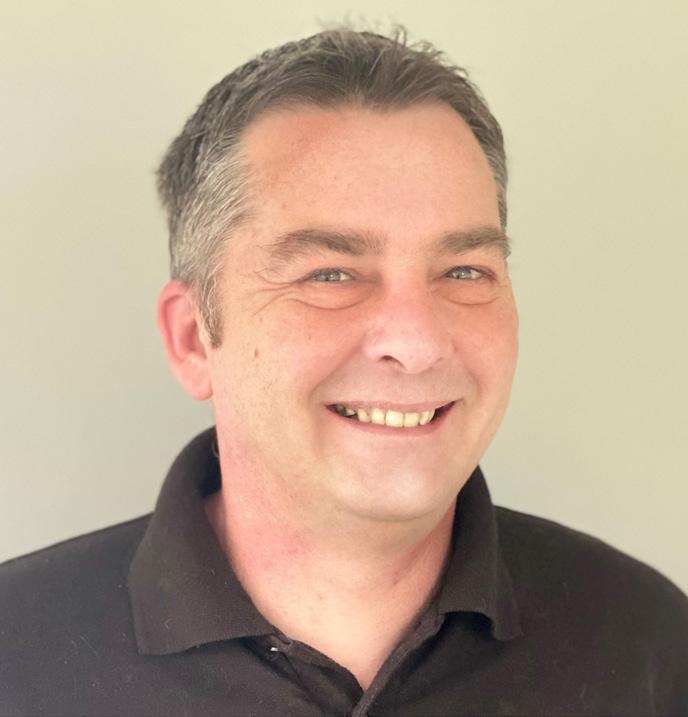
What is your role within SUMO Services Ltd.?
I am the Head of Rail and Infrastructure, leading a team of experienced surveyors. All of my surveyors hold the Personal Track Safety (PTS) certification. The team works across the UK using a diverse range of survey techniques tailored to each client’s needs.
I am responsible for ensuring SUMO meets and exceeds the service levels our clients expect. Also, that our high standards are kept to retain our Railway Industry Supplier Qualification Scheme (RISQS) accreditation, so that we can continue to sponsor our own staff and remain flexible to our client’s needs.
I also closely manage our rail client relationships, proactively engaging with them to both check the progress of projects and look for ways to improve our services. I represent SUMO at trade events and continually look for and evaluate new technologies to add to our portfolio of survey services.
What success have you experienced in the last twelve months and how do you measure success?
The imposed lockdowns throughout the Covid-19 pandemic forced us to radically rethink how operationally we could streamline, deliver and improve the services we provide. One of the positive outcomes of this, which we still employ, is the implementation of flexible working, in terms of job roles and responsibilities, skills, working hours and work-based locations. This unprecedented period meant we had to accelerate our programme to provide a much more flexible workforce at a lower cost. This has been achieved by delivering a training program that has increased the skills of each surveyor meaning we can employ a much more agile and flexible approach when scheduling clients’ projects.
SUMO GROUP
The SUMO Group is a multi-disciplinary survey business and is committed to maintaining the highest possible standards in all aspects of surveying.

Want to know more about SUMO Services?
Tel: 01726 816069
Email: chris.manning@ sumoservices.com
Visit: www.sumoservices.com
Another valuable measure is employee engagement, which has improved through regular company updates on the organization’s current situation, progress against KPI and future initiatives by our Group Managing Director. This ensures that all staff are aware of the positive progress we make against the challenges we face.
The above successes have meant that in the last twelve months sales income from Rail clients has risen by over ten per cent. This was achieved by implementing many more initiatives than listed here, and we have a dedicated workforce that is keen to continue delivering improvements to all areas of the business.
How has technology developed since you started in the industry?
28 years ago, surveys needed a minimum two-man team using traditional survey methods. As a result, site times were longer, and we were only picking up limited
information based on what the surveyors physically recorded and captured.
The introduction of LASER scanners in the early 2000s marked the start of a rapid evolution of survey techniques. It meant that data was rapidly captured, saving onsite time. Furthermore, the quality and quantity of the data recorded has improved dramatically, such that the entire site is now captured, removing the need for repeat visits to site if additional survey information is subsequently requested by the client.
Unmanned Aerial Vehicles (UAVs) have also made an appearance in the last few years and are revolutionising survey techniques. Because they can capture vast areas quickly and cost-effectively, they are becoming a real point of interest. SUMO is actively working to incorporate UAV technology across the entire range of services they offer, and I am liaising with our UAV team to maximise the potential this technology can offer the rail industry.
Finally, the rapid advancement in artificial intelligence is also going to change the way data is analysed, providing quicker and more cost-effective services, which will ultimately benefit our clients.
Which sectors do you work in?
SUMO works across a huge range of sectors with teams who specialise in Rail, Construction, Infrastructure, House Building, Heritage, Facilities Management, Energy and Renewables. In fact, any sector where surveys of land, buildings, services and structures are required.
What is your USP (Unique Selling Point)?
SUMO is unique because we can offer an integrated service across a range of specialisms according to each client’s specific needs. We provide a comprehensive service, which means our clients do not need to source a range of different suppliers. Our range of specialists, investment in technology and our flexibility saves our clients time and money, whilst providing a high-quality product.
What types of products and services do you offer?
Our survey services can be split into six areas:
• Rail – providing mainly 3D laser scanning of building and structures for the production of 3D models, 2D plans, sections and elevations of the railway, local ground models, and all associated signage, equipment and utilities that accompany the rail.
• Archaeology Geophysics – using geophysical surveys to investigate nearsurface objects and obstacles. They deliver archaeological prospection for the assessment of both green and brownfield sites, for example as part of the planning application process.
• Engineering Geophysics – again using geophysical techniques to investigate the types of materials and structures below the ground that could be relevant to engineering design and problem resolution, such as unknown voids, rebar, sewers or culverts.
• UAVs – using drones we can provide photogrammetry, thermal imaging and multispectral imaging. Applications include producing largearea topographical surveys, heat loss surveys, and inspection and monitoring of structures and buildings where the height or access precludes normal survey methods.
• Topographical – using the latest robotic total stations and GPS surveying units, quick and accurate 2D plans are generated illustrating all the details of the surveyed area.
• Utility Detection and Mapping – using detection technology including electromagnetics, signal-induced threading and ground penetrating radar to locate pipes, drainage systems, electricity cables, telecoms and fibre optics, we can identify where services are located, including where they enter your boundaries and buildings.
What are some standout projects you’ve been involved in over the years?
Our day-to-day projects cannot be construed as ‘stand-out,’ but do deliver essential information to clients, however a couple of projects come to mind that we have been engaged in. Firstly, we were part of the project team for the Birmingham New Street station redevelopment. The client needed a 3D model of the existing complex, partly because they wanted to incorporate as much of the existing unusual structure into the new development as possible. This was delivered and helped to isolate and eliminate any potential construction issues, before any physical work took place. Walk-through animations of the new development were also produced, giving the client the ability to virtually walk through and experience the design, while still in early concept.
Another interesting project we were involved in, was the reconstruction of Shakespeare’s original Globe Theatre. Because the building was built using traditional materials, and these move as the organic material matures and settles, this meant that over time, the building plans no longer accurately reflected the structure. This in turn made designing and building stage sets difficult, as there were no longer any accurate plans available. To resolve this problem, we surveyed the theatre and created an accurate 3D model of it, which means that the Shakespeare Globe Trust can now confidently design sets knowing they will fit the structure, saving time and money.
Using our 3D Laser Scanning technology, we have also created 3D models that enabled projection mapping for high profile
light shows, including events such as the Buckingham Palace Jubilee light show and the Washington Monument Apollo 50 anniversary.
When a client comes to you with a particular problem, what’s your process for coming up with a solution, and how closely do you work with clients throughout the projects?
A great example of this, was illustrated on a project that a major first tier contractor asked us to help with. They had a major project underway, which was to create an exciting arrival experience for a major city, costing many millions of pounds in improvement works. During construction, the client became concerned about the possible presence of hidden attenuation tanks in the construction area. There were no records to confirm their existence and digging trial holes could become costly, risky and very time-consuming.
They called SUMO in and after an initial reconnaissance of the site with the client to ascertain their concerns, we employed a multi-geophysical survey over the site of 1000sq metres. Using low-frequency ground penetrating radar (GPR) backed up with an electromagnetic ground conductivity survey, we revealed eight well-defined parallel anomalies crossing the site with responses similar to those expected from attenuation tanks. The GPR data, indicated that these were approximately 0.9 metres beneath ground level and also found unexpected areas of reinforced concrete, buried under asphalt.
This data was key to the client, and saved both time and money for the project, which continued to be delivered on time, due to our support.
How can the industry tackle its skills shortage and how do you recruit/retain/ train your staff?
Finding skilled surveyors that have a crosssection of the skills SUMO needs is very difficult. Colleges don’t offer specific training across the various survey options that we need our staff to be trained to be able to undertake. Therefore, we have deployed our own SUMO ‘apprenticeship scheme’ whereby we recruit college leavers, who have probably studied in the construction arena and put them through our own training program. This is a combination of technical classes and working alongside experienced surveyors, to gain valuable on-the-job experience. After a period of time, they are assessed, and if appropriate become independent multiskilled surveyors in their own right. This approach has been very successful and instrumental in delivering various department’s growth.
Retention of staff can be difficult, but as stated in a previous answer, getting all staff engaged and knowledgeable about the business’s current position and goals,
contributes to making them feel included. This is no easy feat with remote-based staff, but is an approach that is successful for us.
Having a progression/succession plan is also vital. By holding regular 1 to 1’s with our staff, we find out what their aspirations are, and in turn, they understand our vision for their long-term future.
Do you think the rail industry could be greener and what is your organisation’s green strategy?
Of course, all industries can become greener and the rail sector is very in tune with this message and delivering improvements as quickly as possible. SUMO doesn’t have the biggest carbon footprint, but we can’t be complacent. Being a service provider, one of our biggest contributors is running a fleet of vehicles for our surveyors. Therefore, we employ careful planning and scheduling of client projects with minimal travel as a point of focus.
We have surveyors based throughout the UK and as you can imagine, efficient scheduling is not always possible, as it is dependent on external issues, such as when customers have access to the survey site and our other project commitments, but having multi-skilled surveyors is key in allowing us maximum flexibility. Our fleet of vehicles also meets the current standards for the Ultra London Low Emission Zone (ULEZ) and we are currently looking at electric variants as alternatives. This is an ongoing process, and we continually are looking at other ways to reduce our carbon footprint further.
What are your views on collaborative working?
In the 28 years that I have been working in the industry, we have moved from a model where the client specifies their requirements and we deliver that without necessarily questioning it, to a collaborative, partnership approach, where we troubleshoot the problem, or desired client outcomes, and come up with a range of solutions, before agreeing on the final specification. We also work in a much more agile manner, adjusting and liaising with the client when a job is underway, to achieve the desired outcomes at high quality and in the most cost-effective way. Therefore, collaborative working is a necessity and not an option. SUMO offers solutions to client’s problems, but we could not do that without working with those clients and other stakeholders.
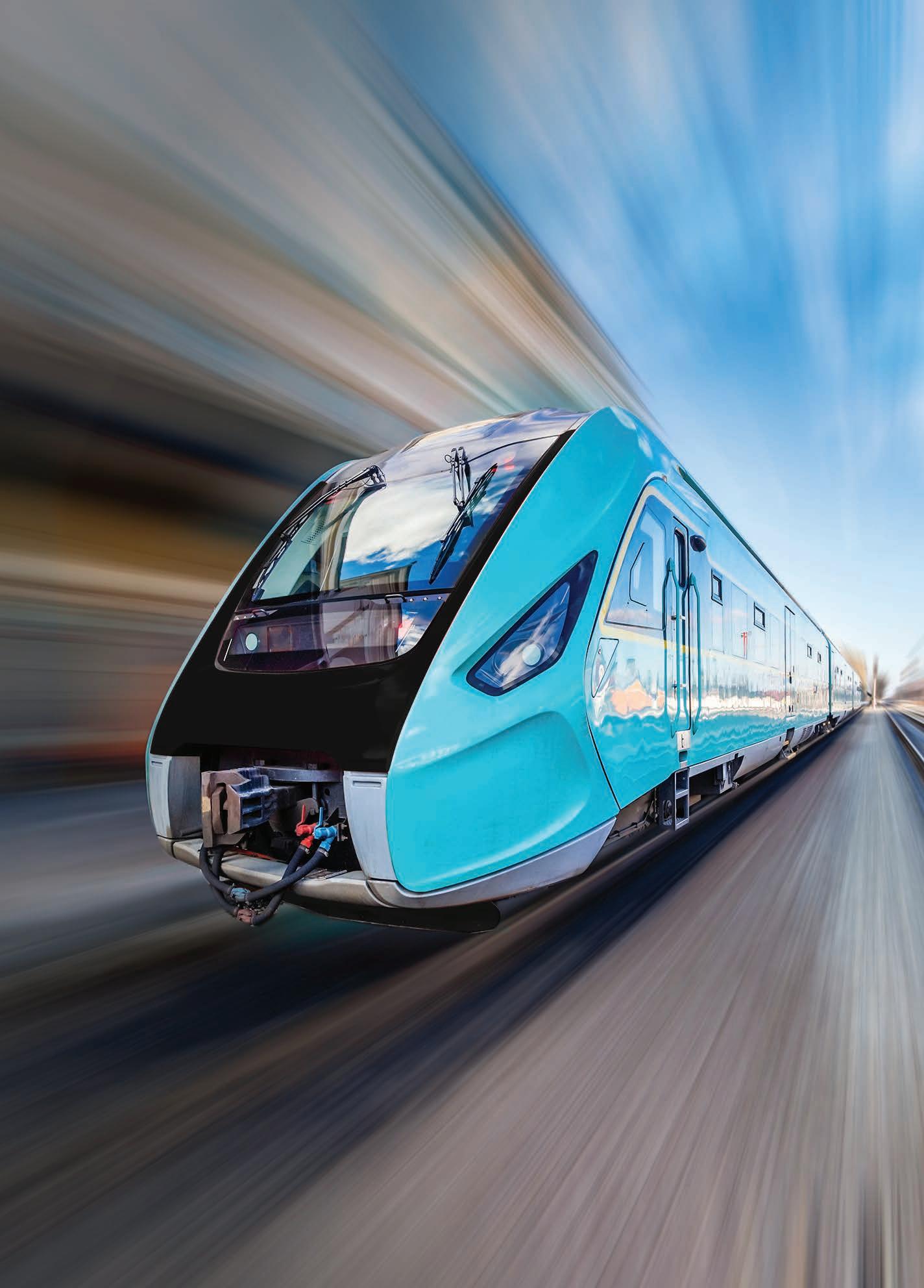
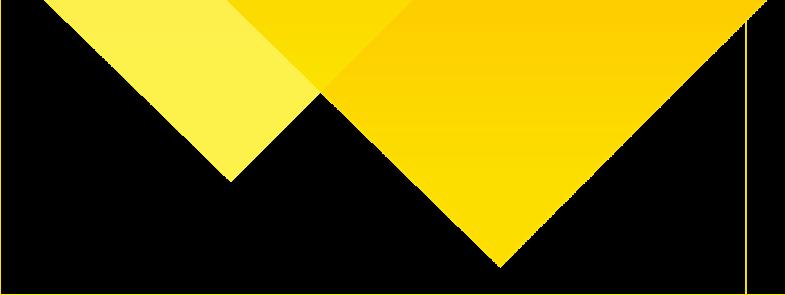
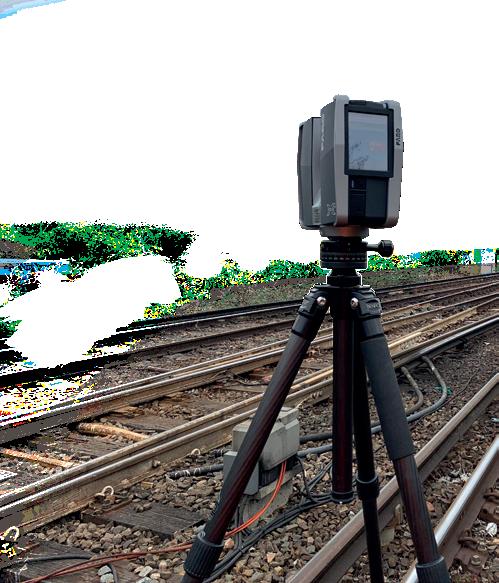

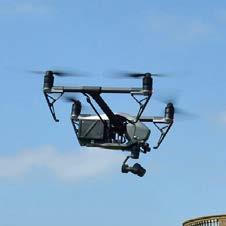
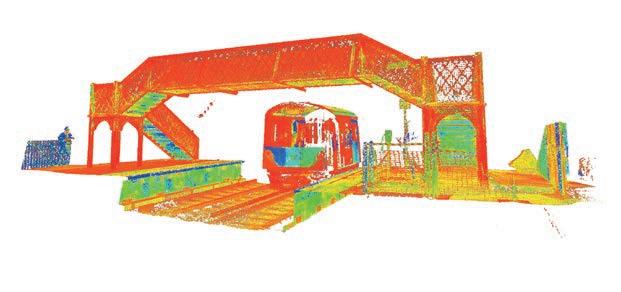
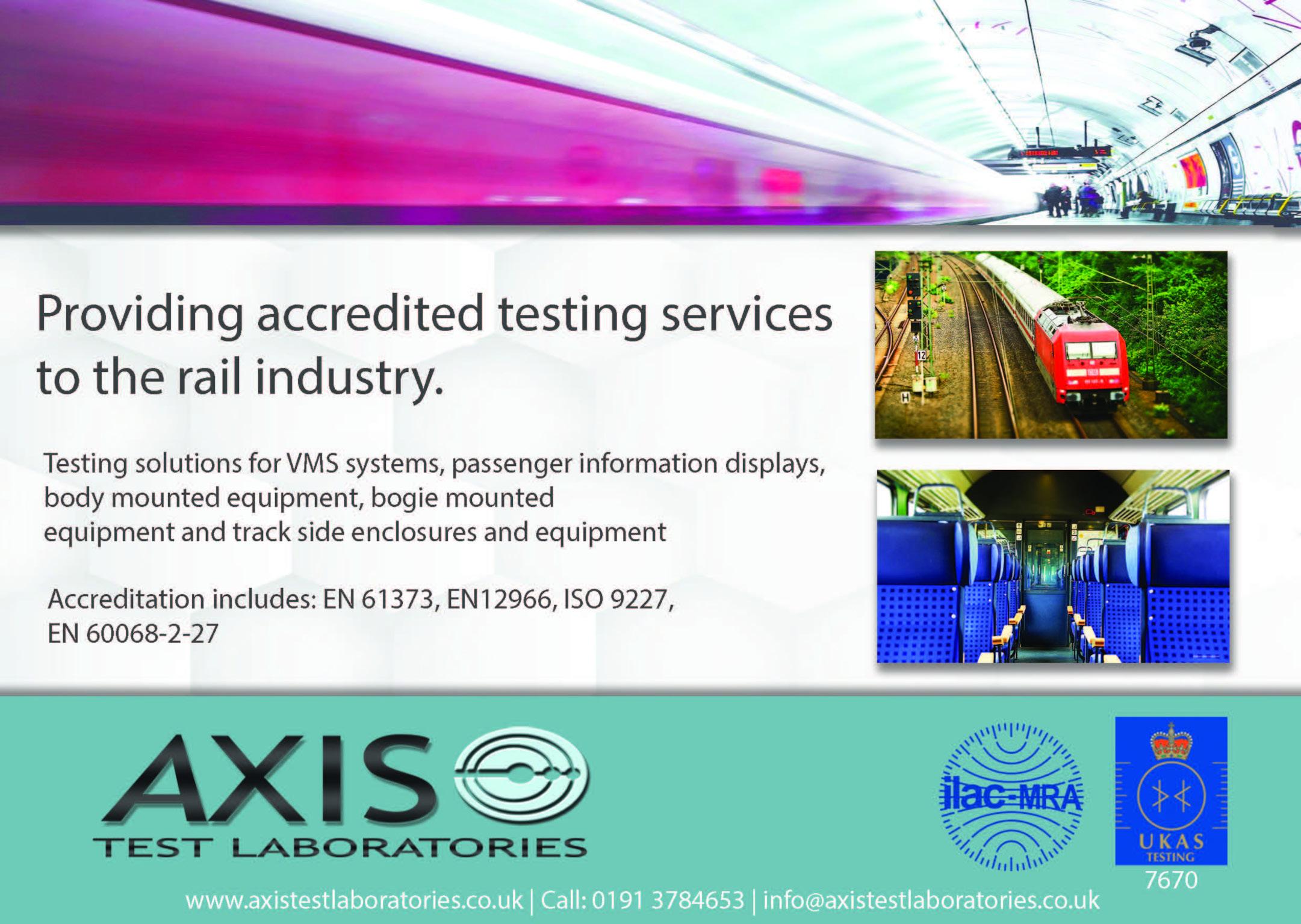
A Constantly Replenishing Supply Chain
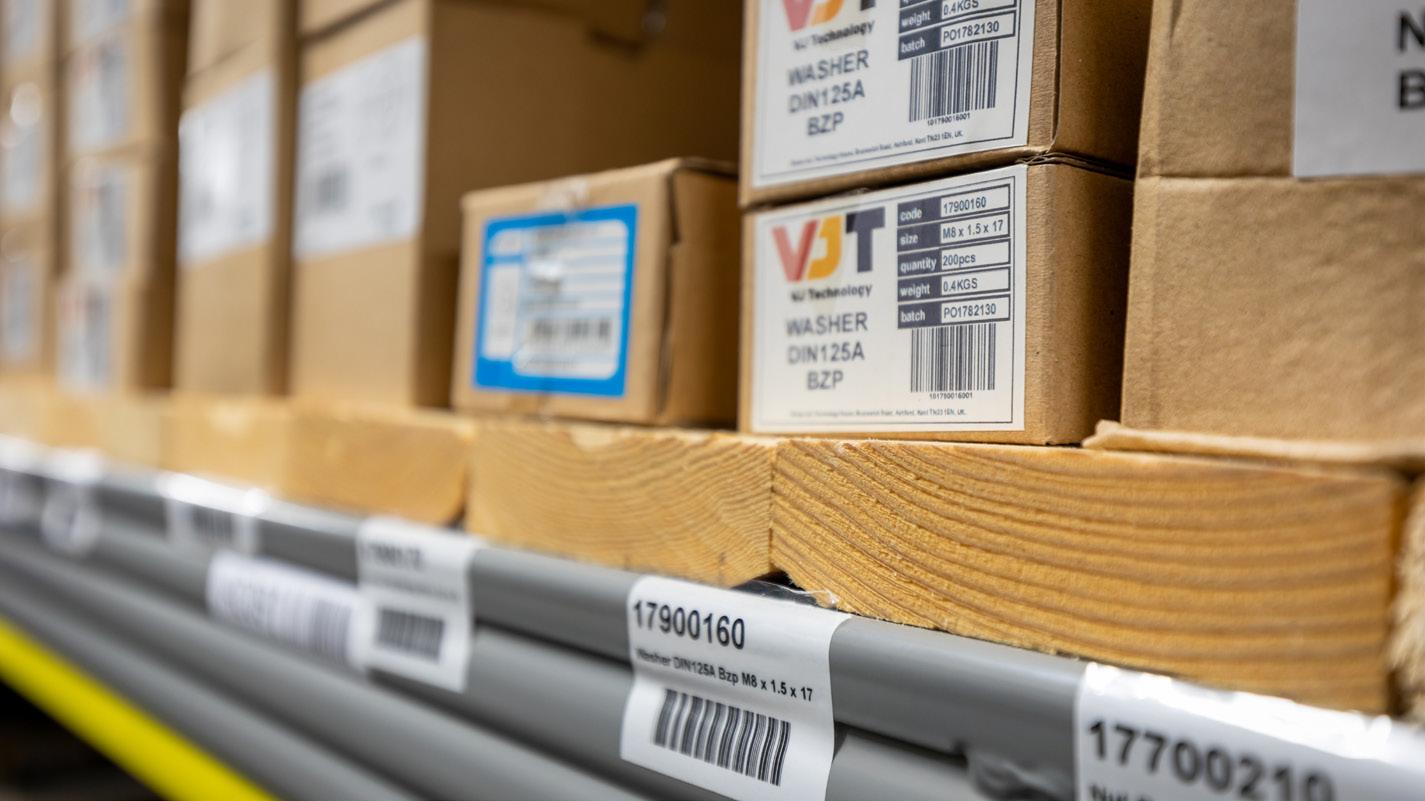
Align JV chooses unique onsite procurement solution to support HS2 construction
Align, the joint venture between Bouygues Travaux Publics, a subsidiary of Bouygues Construction, Sir Robert McAlpine, and VolkerFitzpatrick, a subsidiary of VolkerWessels that is delivering the Central 1 portion of HS2 Phase One, has chosen a next generation procurement delivery solution which can result in up to 70 per cent reduction in carbon emissions previously caused by daily deliveries to site, as part of its ongoing commitment to supporting sustainability and innovation in the sector.
Inspired by the Amazon Locker solution, the secure by design VJ iStore® (patent pending) is located at Align’s site in Rickmansworth and consists of a 40 ft high bespoke modular shipping container which acts as a vending machine. It will help ensure that Align’s supply chain contractors can be fed a constant supply of their most used products that can be clicked and collected in a matter of minutes directly on-site at the point of need.
Over 30 different Align contractors are authorised to procure and collect from the VJ iStore®, a unique solution from VJ Technology. There are almost 300 sperate items within the store ranging from bolts,
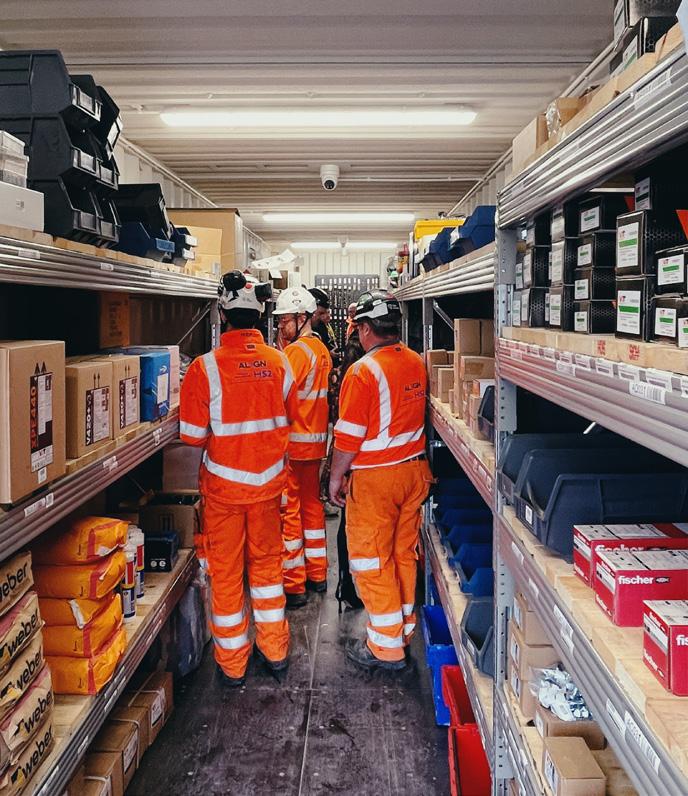
washers, nails, sealants, hand tools, paints, lubricants, mechanical anchors, locks, foams and brooms.
Products are available 24/7 which in turn increases productivity significantly and are only paid for once they have been collected, positively impacting cashflow. It is replenished once every 10 to 14 days as managed by the active stock control system resulting in an up to 70 per cent reduction in carbon emissions previously caused by daily deliveries to site.
Electra Thanopoulou, Buyer at Align, said: ‘As an early adopter of this solution we were able to work closely with VJ Technology to help them refine the offering, which we believe is an exciting development which helps address a number of challenges we face. Perhaps most importantly though the reduction in daily deliveries that reduce our impact on both the environment and the local communities we operate in.’
Peter Mckeown, Cross Passage Superintendent, Align said: ‘We use the VJ iStore® 24/7 and so far 25 per cent of our orders have been out of hours – before 8am or after 5pm – and 15 per cent have been on weekends. Previously this could have resulted in project delays and or rescheduling, but this solution enables us to continue.’
Andrew Mobbs, CEO at VJ Technology said: ‘These are challenging times for the sector and we are on a mission to de-risk the construction and infrastructure supply chain, playing our part to help projects finish on budget and on time. Everything we do revolves around how we can make things easier and better for the customer and The VJ iStore® is just another step in this journey and is absolutely a part of our longterm growth strategy.’
Andrew joined VJ Technology as the CFO in January 2020. After successfully guiding the business through that period he became CEO in July 2021. Andrew has created a highly customer focussed culture and an environment that enables everyone to innovate which has driven consistent profitable growth.
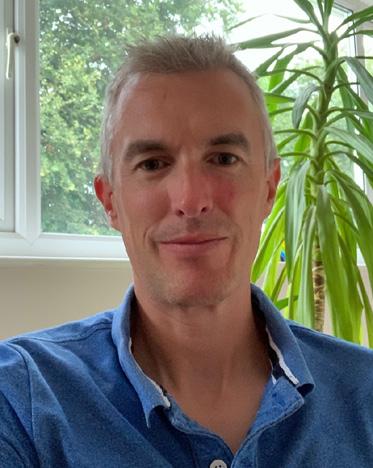
Premier global manufacturer of components and kits for railway applications

In addition to supplying individual components, the global companies of STAUFF and their authorised system partners use the STAUFF Line approach to support Original Equipment Manufacturers with the supply of custom-designed and ready-to-install fluid power lines from connection to connection and also provide supplemental services that create added value: · Components · Systems · Services · Contact
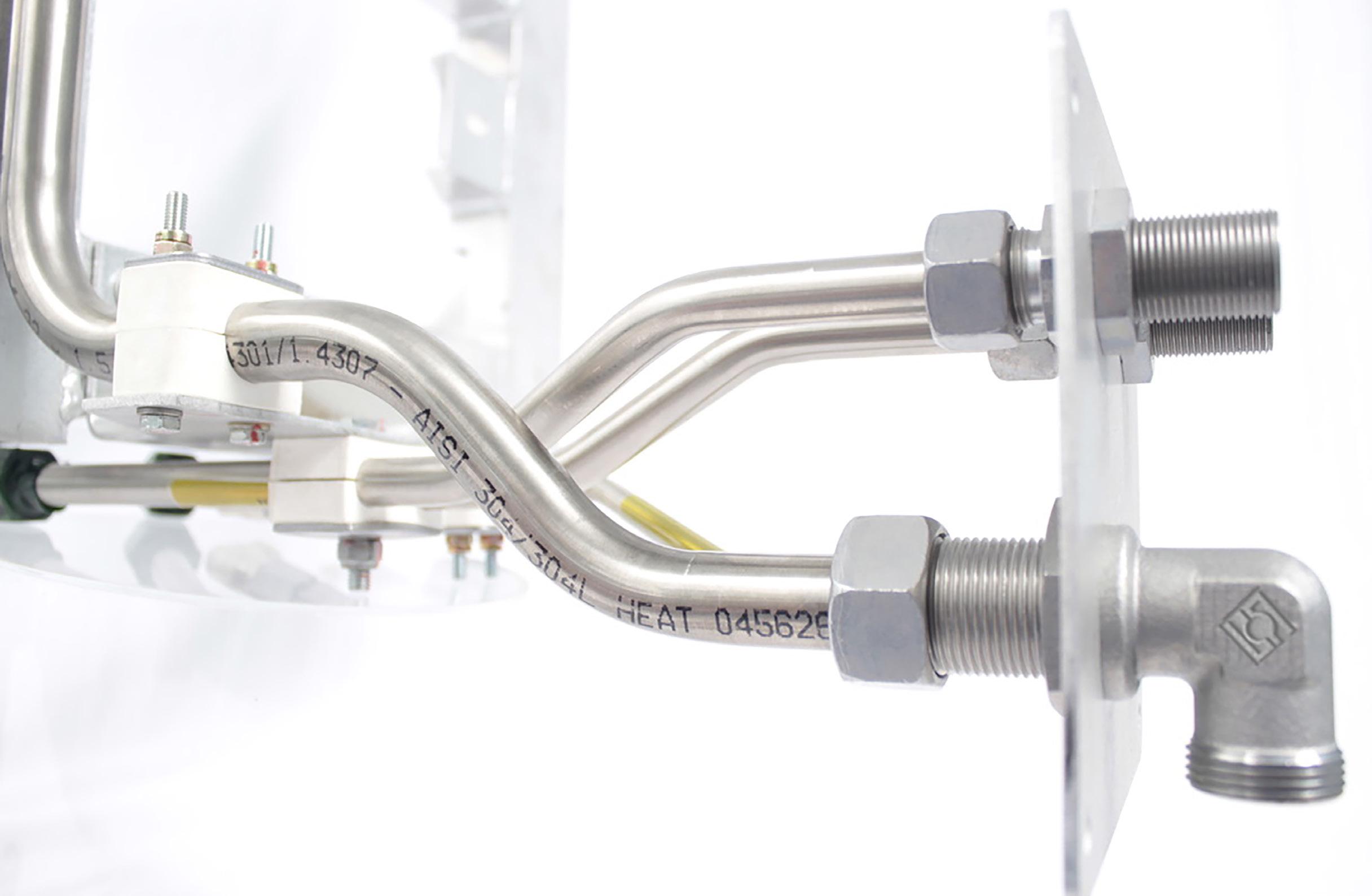
The STAUFF Line process is adopted by global OEMs to successfully achieve cost savings in rolling stock manufacture.
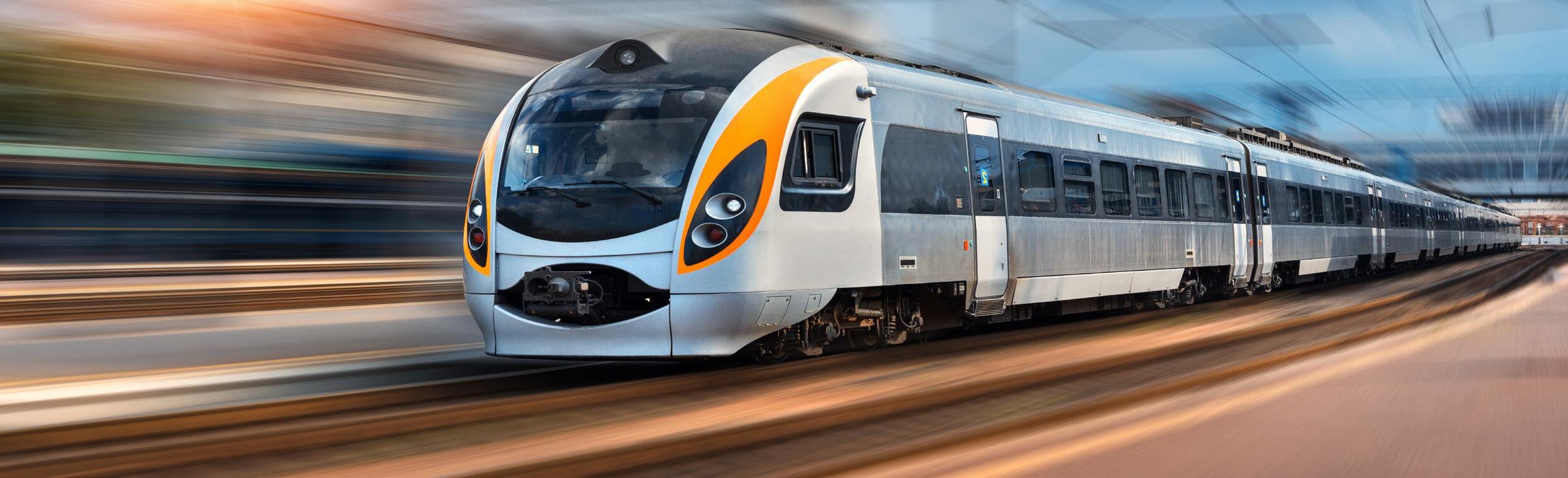
Sheffield Tel: 0114 251 8518
Email: sales@stauff.co.uk
Aberdeen Tel: 01224 786166
Email: sales@stauffscotland.co.uk
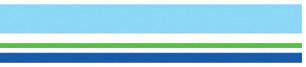
Ireland Tel: 02892 606900
Email: sales@stauffireland.com
Southampton Tel: 023 8069 8700
Email: sales@stauffsouthampton.co.uk
www.stauff.co.uk
Nuclear Success at the Northern Power Women Awards
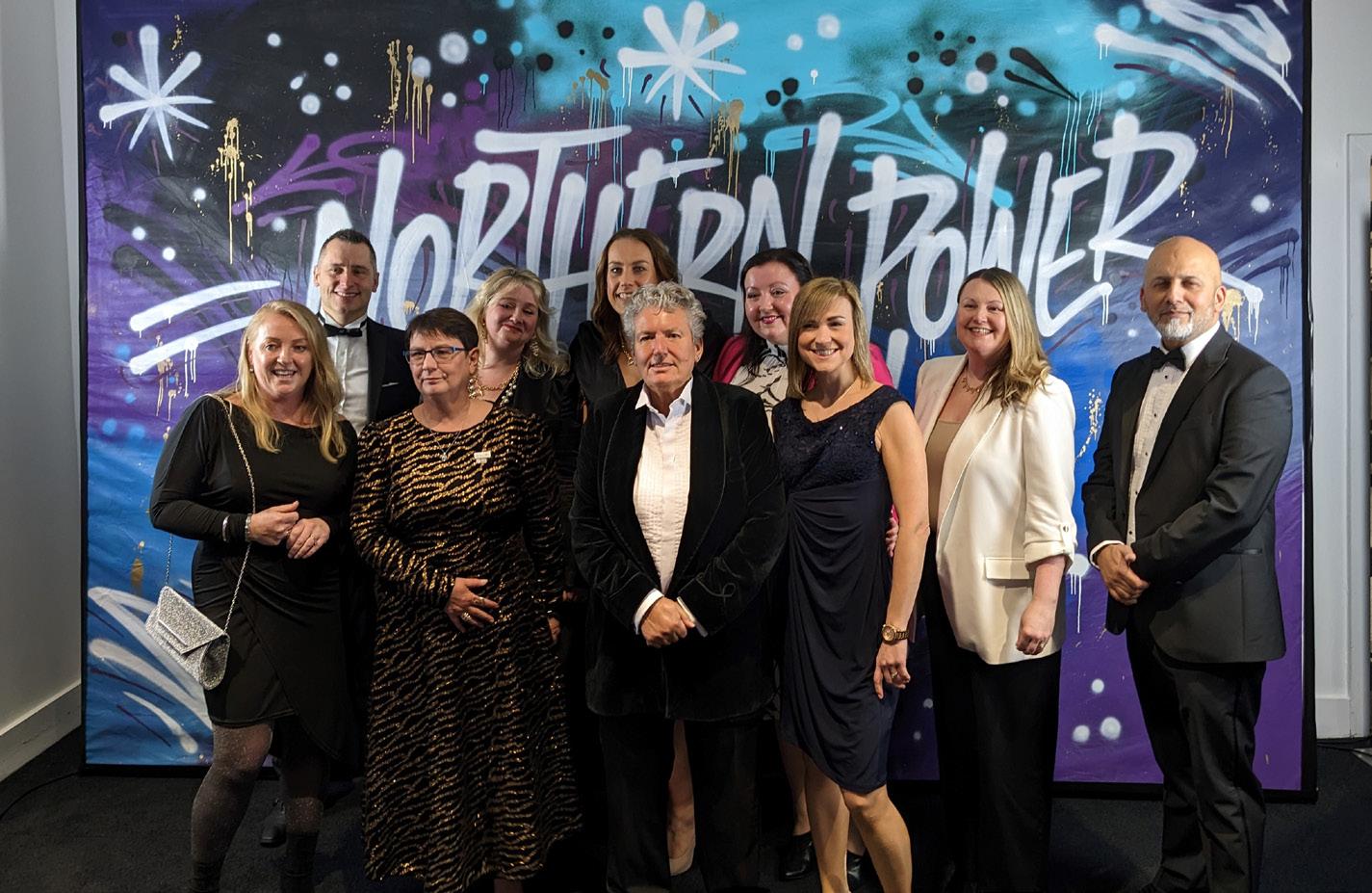
Organisational diversity has long been overlooked within businesses, with many not understanding the true impact of a diverse and healthy culture. But it’s something I’m passionate about and resolutely committed to achieving within NTS. So, when NTS won Northern Power Women’s esteemed award for medium organisation, I was extremely proud. I’ve been championing diversity and inclusion all my life and I wanted to ensure NTS was doing absolutely everything it could to attract and retain the most diverse
workforce - regardless of gender, sexuality, disability, or religious belief.
What makes an organisation great is its workforce and to be truly great, you need a diverse talent pool. If you look around the table and everyone is the same as you, chances are they will have the same ideas as you, which isn’t great for innovation or diversity of thought. In my experience the more challenging circumstances an organisation is in the greater need for diversity of thought.
People can sometimes mistakenly believe that if you’re championing one person you’re
somehow repressing another, but that’s not how diversity and inclusion works. We want to encourage everyone to feel welcome and included at NTS and we’ve made great strides in that over the last couple of years.
Our strategy included encouraging more women into the business. We operate in predominantly male-dominated industries – nuclear, shipping and rail – and we needed to improve on that to bring in those fresh, new ideas and ultimately help us move forward.
The Women Returns Programme was a great initiative to help attract female professionals, who’d had a career break for whatever reason, to return to the workplace. It encouraged those who’d spent time away from work to come back and that they’d be supported in doing so.
Many professionals might need to take time out for family or health reasons, and we wanted to ensure they’d not only be supported through the process but that this ‘time out’ experience might bring a new outlook on things, and that’s so valuable to us at NTS.
We got a number of fantastic individuals though this programme and they’ve all brought huge benefits to NTS and our culture.
We’ve also been working hard to get underrepresented groups to apply for roles within our business. We’ve had vacancies for train drivers, and before we launched female-centred recruitment campaigns, they made up only a small part of our workforce.
Since we’ve been actively targeting female drivers, we’ve increased the numbers employed by 16 per cent in our recent London-based recruitment drive, which is a fantastic achievement.
I want to make it clear, however, that there is no bias involved in the recruitment process, we want the best people for a role, so all names, gender and other identifiable information is removed in the recruitment process.
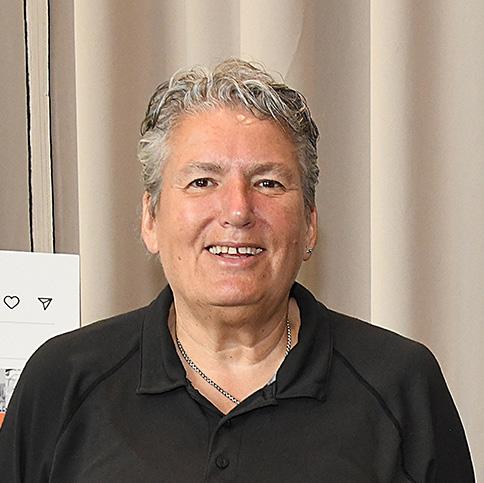
This was about attracting diverse individuals, bringing them to the table, and on an equal footing to everyone else who applied. That’s how you get the best, you increase your pool of applicants and only the outstanding candidates make it through the process.
The award we’ve received for this excellent work is a huge boost, it’s not about the kudos, but it shows that we’re a place where everyone can work and feel valued and we’re on the right track.
There’s still a way to go but the message I want to get across loud and clear is that NTS is a place to feel included, valued and appreciated, no matter who you are or where you’re from.
A diverse and inclusive culture is what we are striving for, recognising and adapting to each individual to ensure, even if you’ve never thought about nuclear, shipping or rail, that we’re the top of your list for employment and somewhere you will thrive.
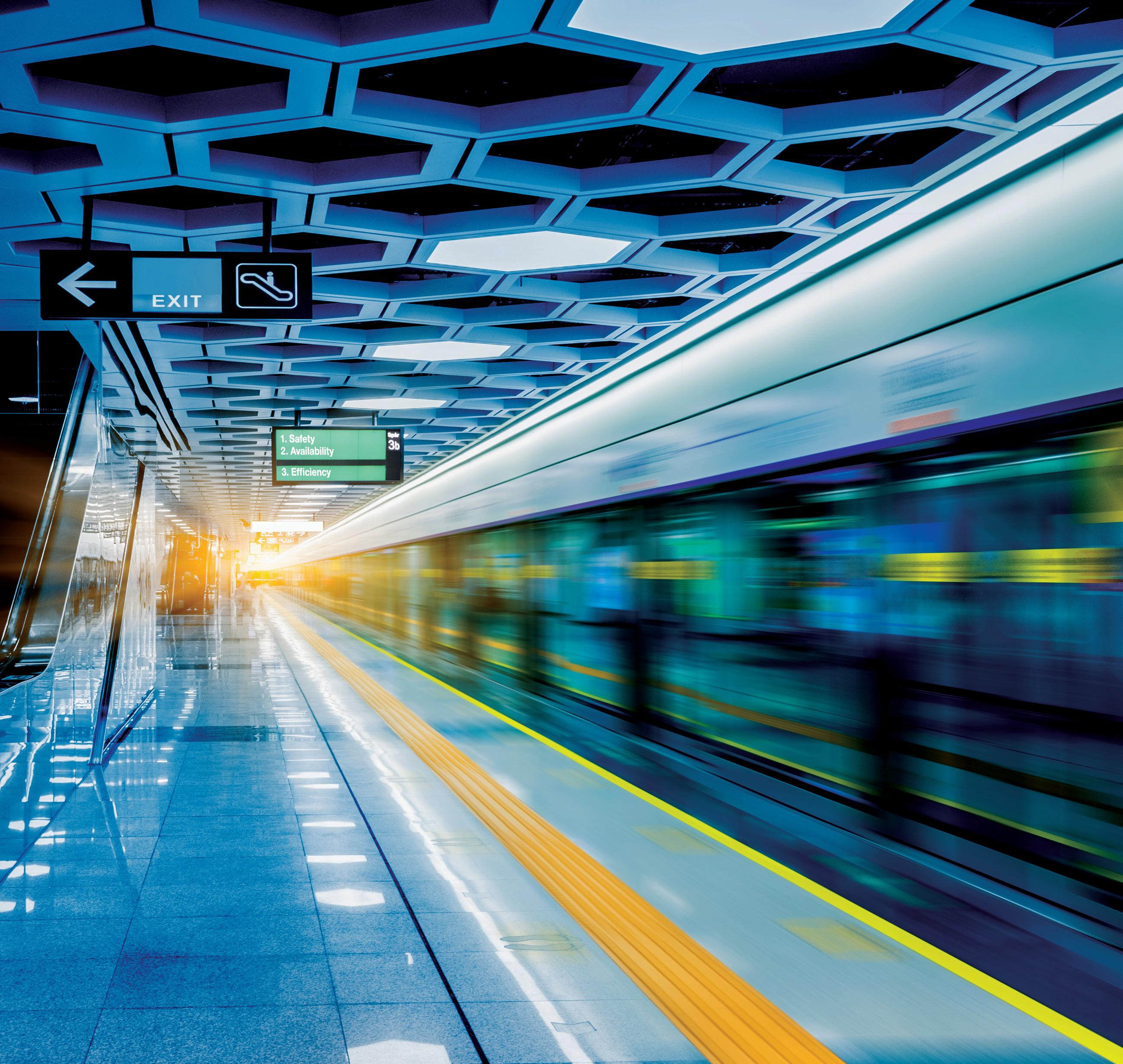
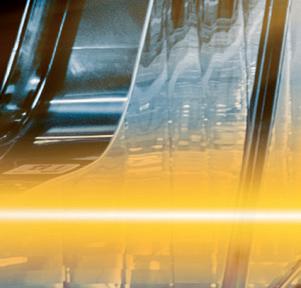
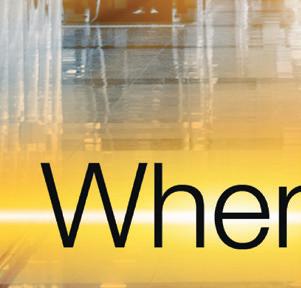
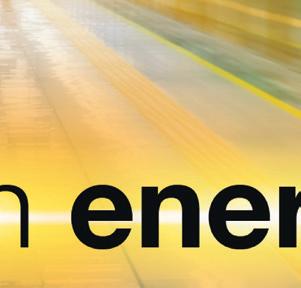
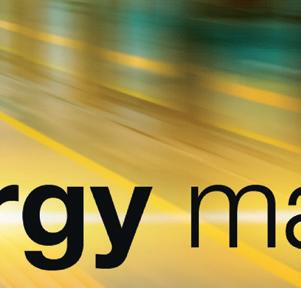
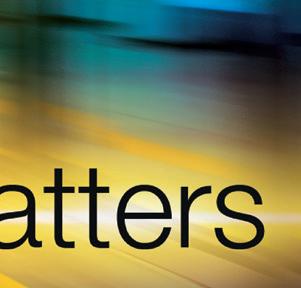
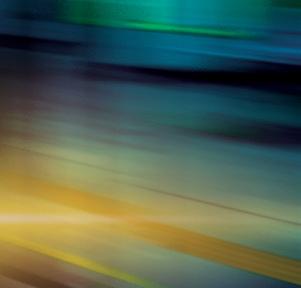
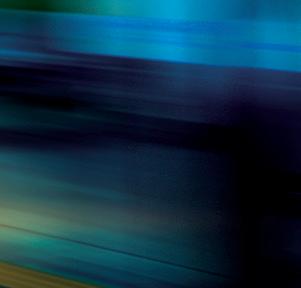
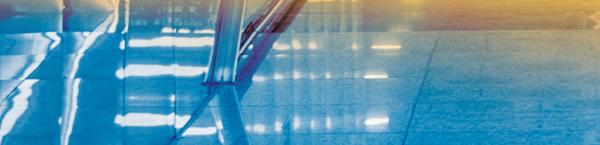

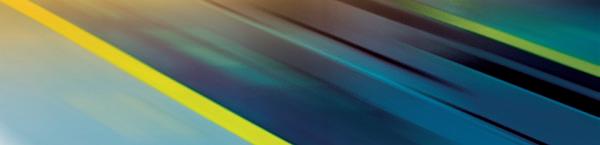
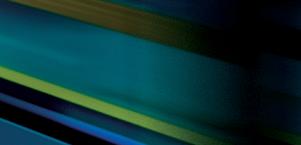
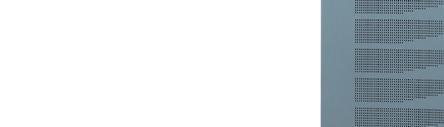
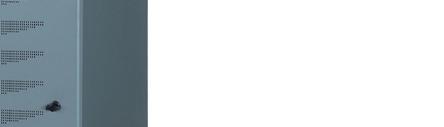
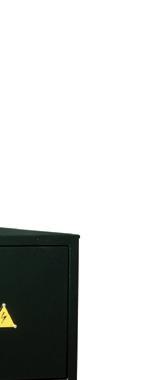
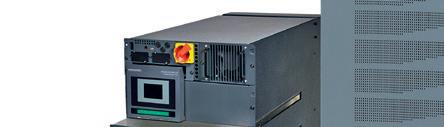
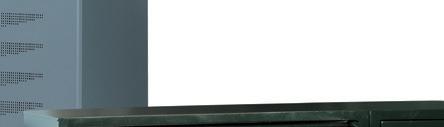
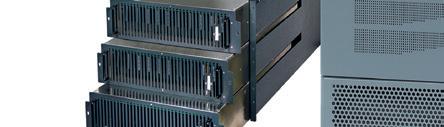
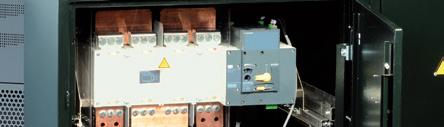
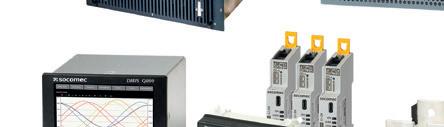
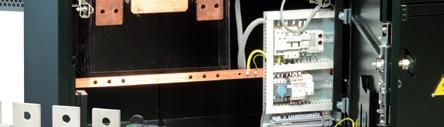
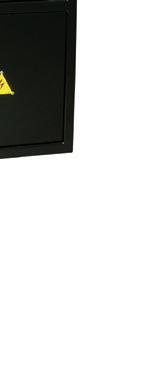
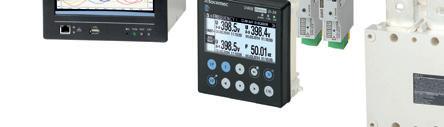
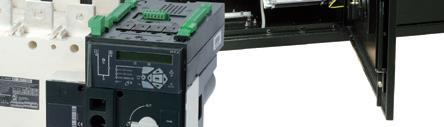
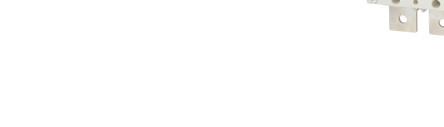
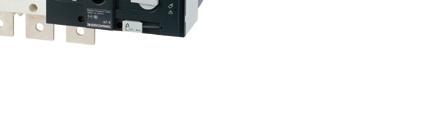
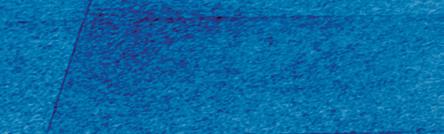
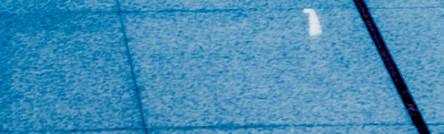
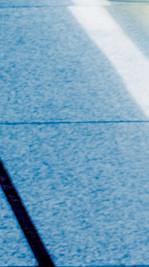
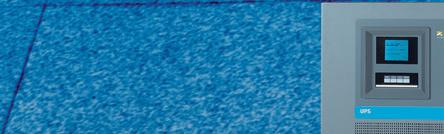
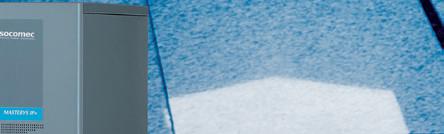
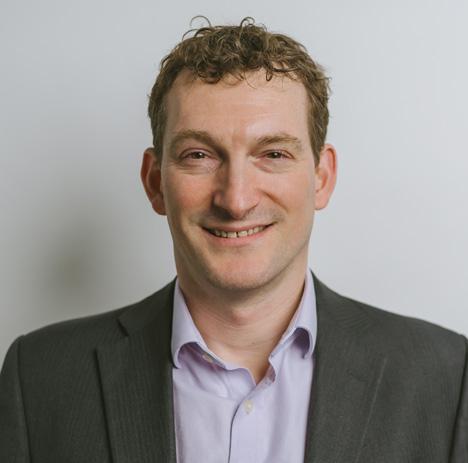
Two Years on from the Plan for Rail – Time is Running out to Deliver it
Andy Bagnall, Chief Executive of Rail Partners takes stock of the plan to revolutionise the country’s railways
Saturday 20 May marked two years since the government’s Plan for Rail was published, setting out a blueprint for transforming the way the railway is run in the interests of passengers. There was also speculation the Plan was about to be shelved. But rail is at a critical juncture and we must move quickly or risk missing the opportunity for successful reform.
It is no secret the railway is on life support and we have to correctly diagnose the problem before we can provide the right course of treatment – and there are many factors as to why we have arrived at this destination.
Even before the pandemic, the blurring of lines between respective roles and responsibilities of the Department for Transport, Network Rail as the public sector infrastructure manager, both private and public sector train operators and, more recently, the Great British Railways Transition Team, has left the railway with too many cooks preventing effective service delivery.
When Covid-19 hit, it not only disrupted travel patterns and commuter behaviour, but wreaked havoc with the railway’s finances on an unprecedented scale, compounded by the wider economic turbulence of inflation and slow growth.
Throw in the long drawn-out rail dispute currently undermining reliability across the network. Rail operators want to offer their people pay increases and job security but any deal must be affordable through reforms
to boost productivity, especially at a time when the government is taking all cost and revenue risk in the railway and setting all fares, meaning the taxpayer will fund any cost increases.
Two weeks ago we saw the operator Transpennine Express taken into public hands. The operator recognised it had not delivered the level of service customers had a right to expect but it took the entire blame for the complex cocktail of underlying causes driving the railway’s current challenges.
The Plan for Rail is the only blueprint available for rapidly delivering a better railway quickly. The alternative is sleepwalking into a spiral of decline with all the negative economic and environmental consequences that would entail.
The government needs to legislate to create Great British Railways – the public sector ‘guiding mind’ for the railways –aligning track and train in the customer’s interests. Legislation would provide a clear signal of intent from the government and re-establish defined relationships between government, the infrastructure manager and operators who directly provide the service to people using trains. It would also give certainty to freight operators who need a stable environment to attract goods from our congested roads.
As it stands, passenger operators are stuck on ‘National Rail Contracts’, which pay a flat fee to run specified services and do not give operators the commercial flexibilities to attract customers. These contracts were a necessary response to the pandemic but
are insufficient to drive recovery. Rapid introduction of contractual flexibility is essential and this can be done with or without legislation.
In the longer term, evolving the contractual model to create a variety of ‘Passenger Service Contracts’, reflecting the different requirements of the railway in different areas, is the key to harnessing operators to build a thriving network that can offer passengers a good service and value for money.
Fixing the railway is a collaborative effort. A reformed public-private partnership harnessing the expertise of the private sector under a new public body will drive growth and restore a railway that is fit for purpose for the passenger.
The time has come to implement the Plan for Rail and it cannot wait any longer.
RESPONDING TO LNER'S ANNOUNCEMENT THAT ITS TRIAL OF SINGLE LEG TICKET PRICING WILL BE EXPANDED TO COVER ITS ENTIRE NETWORK
“It is great news for customers that LNER’s trial of single leg pricing is expanding as the industry has been calling for this important step in simplifying fares for many years. We’d like to see people travelling across the whole network benefit from fares and ticketing reform, so want other operators to be rapidly afforded similar opportunities to trial this type of change.”
RESPONDING TO TRANSPORT SECRETARY MARK HARPER'S ANNOUNCEMENT THAT TRANSPENNINE EXPRESS’ CONTRACT WILL NOT BE RENEWED
“The decision not to extend TPE’s contract is very disappointing. Passengers need reliable services, but the operator’s issues were complex and largely beyond their control, especially in the context of industrial relations. It is essential that the Secretary of State delivers on his promise to return this contract to the private sector, which needs to be done at pace to secure the benefits that competitive tendering and private sector innovation deliver for customers and taxpayers.”
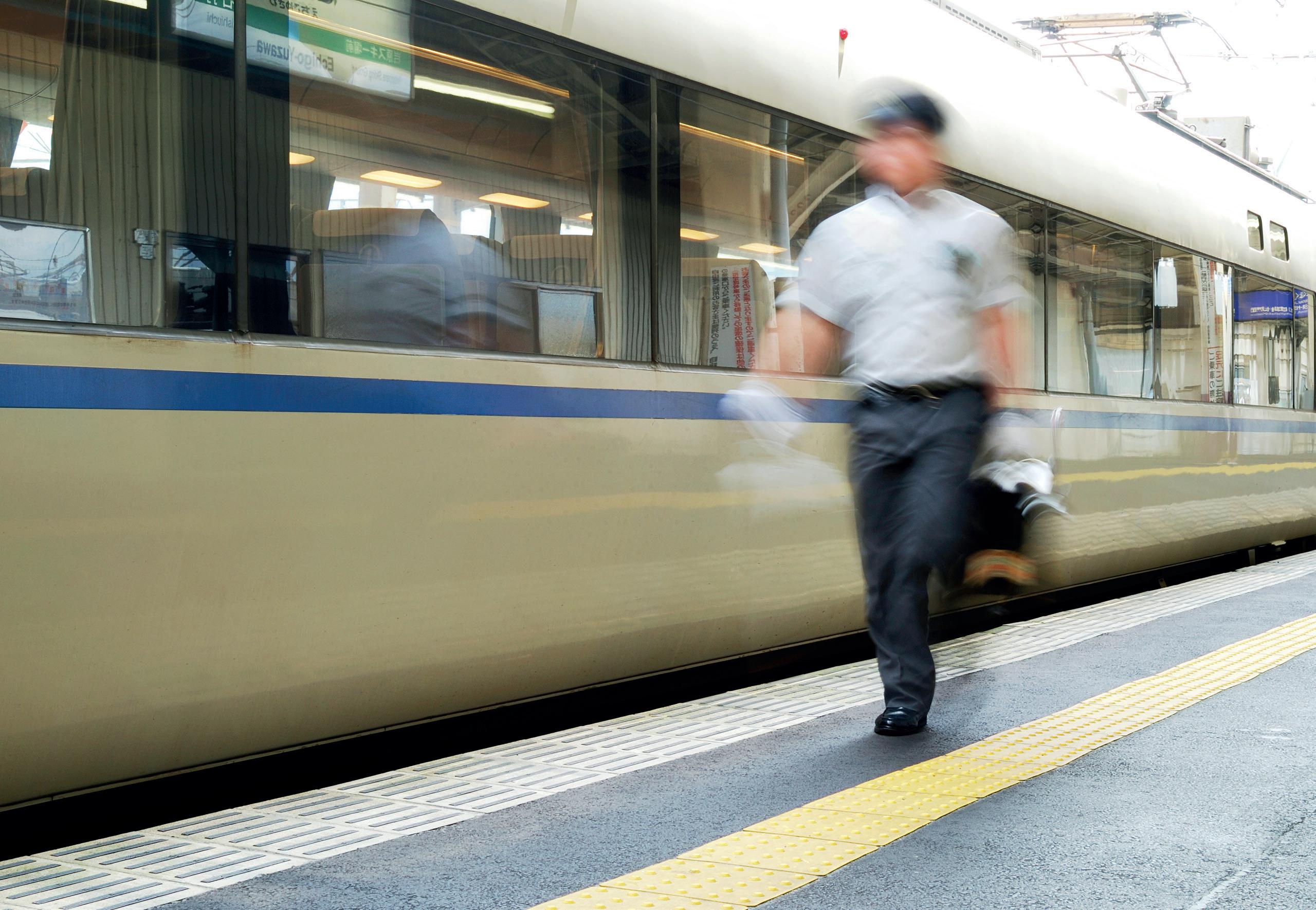
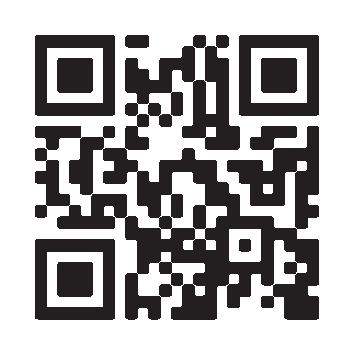
Fit more Square Vehicles through Round Tunnels
Using gauge clearance assessments to understand the available space on the railway, D/Gauge have successfully supported the industry for the last 15 years
Working on various projects such as new train designs and introductions, vehicle cascades, vehicle modifications and infrastructure and electrification projects – D/Gauge’s software is now also a trusted tool for many of the industry's engineers. The railway system represents a complex physical ecosystem that intertwines various components to enable the seamless movement of trains and passengers. Over the years, as upgrades and modernisation have taken place, the demands placed on the available railway space have significantly increased. This surge in demand necessitates careful consideration of gauge clearance, which is crucial to ensure that all physical aspects of the railway can coexist harmoniously.
What is Gauge Clearance?
Gauge clearance in the railway refers to the amount of space (or clearance) provided between the vehicles and the surrounding structures or assets along the tracks. It ensures that there is sufficient space for trains to pass through safely without any obstructions or clashes.
The primary purpose of gauge clearance is to maintain a safe distance between the trains and various elements near the tracks, such as platforms, bridges, tunnels, signals, overhead lines, and adjacent tracks. It is essential to ensure the safety and smooth operation of the railway system.
Gauge clearance is determined by the specific railway standards and regulations of each country or region. These standards specify the minimum distance required between the train and the nearby structures to prevent any potential interference or accidents. The clearance is typically measured spatially to accommodate the various dimensions of trains, including width, height, and any lateral movement they may have while passing through curves.
Overall, gauge clearance plays a critical role in maintaining the safe and efficient operation of trains within the railway network by providing the necessary space and clearance for their movement while ensuring the integrity of the surrounding infrastructure.
How can gauge clearance be used across the rail sector?
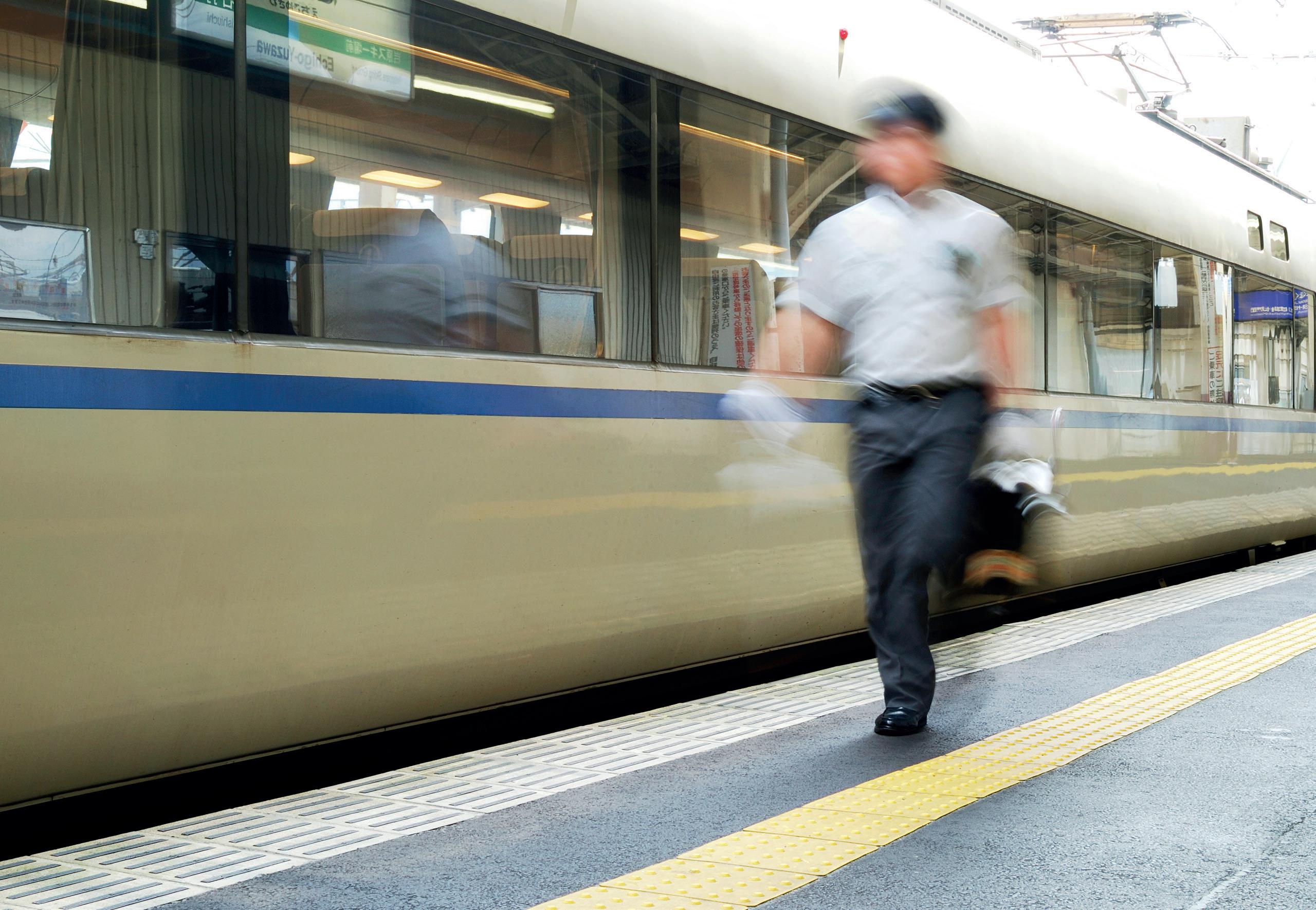
D/Gauge can offer clearance assessments for the rolling stock, infrastructure, and electrification markets. Whether looking at it from a vehicle or an infrastructure perspective, there is space to be found around the entire network. Typical gauging is conservative and works for most scenarios, though the commissioning of detailed gauge clearance assessments can be the deciding factor for many projects.
Infrastructure
Using gauging, asset owners and contractors can understand the impact of proposed
works, the extent of modifications required to improve clearance, and the potential costs. There are essential questions for Project Managers, Infrastructure Managers and Design Consultancies to ask, for example:
• Identification – Am I looking to identify structures which have tight clearances?
• Investigation – Do I need to analyse what is causing tight clearances, or causing clearances to change?
• Redesign – Should I need to consider clearance when redesigning track or structures?
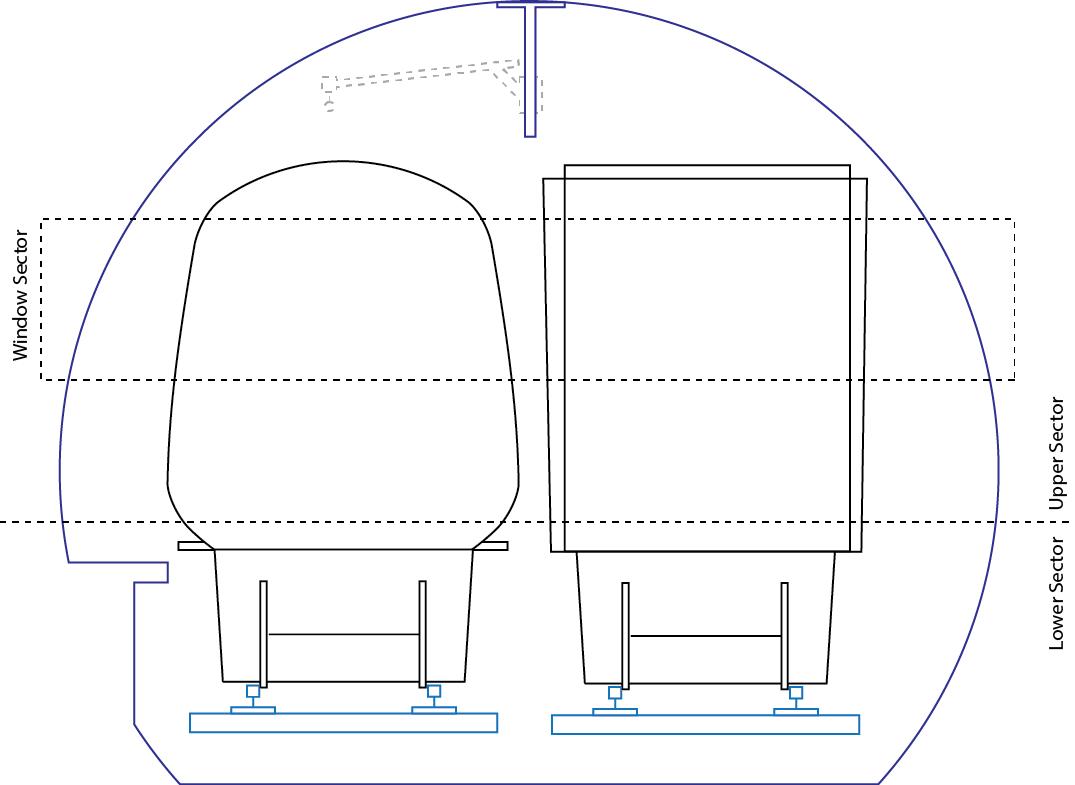
• Routing – Do we need to assess temporary vehicle movements, or out-ofgauge traffic?
Rolling Stock
D/Gauge support the Rolling Stock community with clearance studies during new train procurement, train introductions and retrospective modifications. When considering freight traffic DGauge are able to assess clearances of out-of-gauge loads.
There are some key questions that vehicle manufacturers, Rolling Stock Owners and Train Operating Companies can consider. These include:
• Procurement – Am I currently procuring new train fleets?
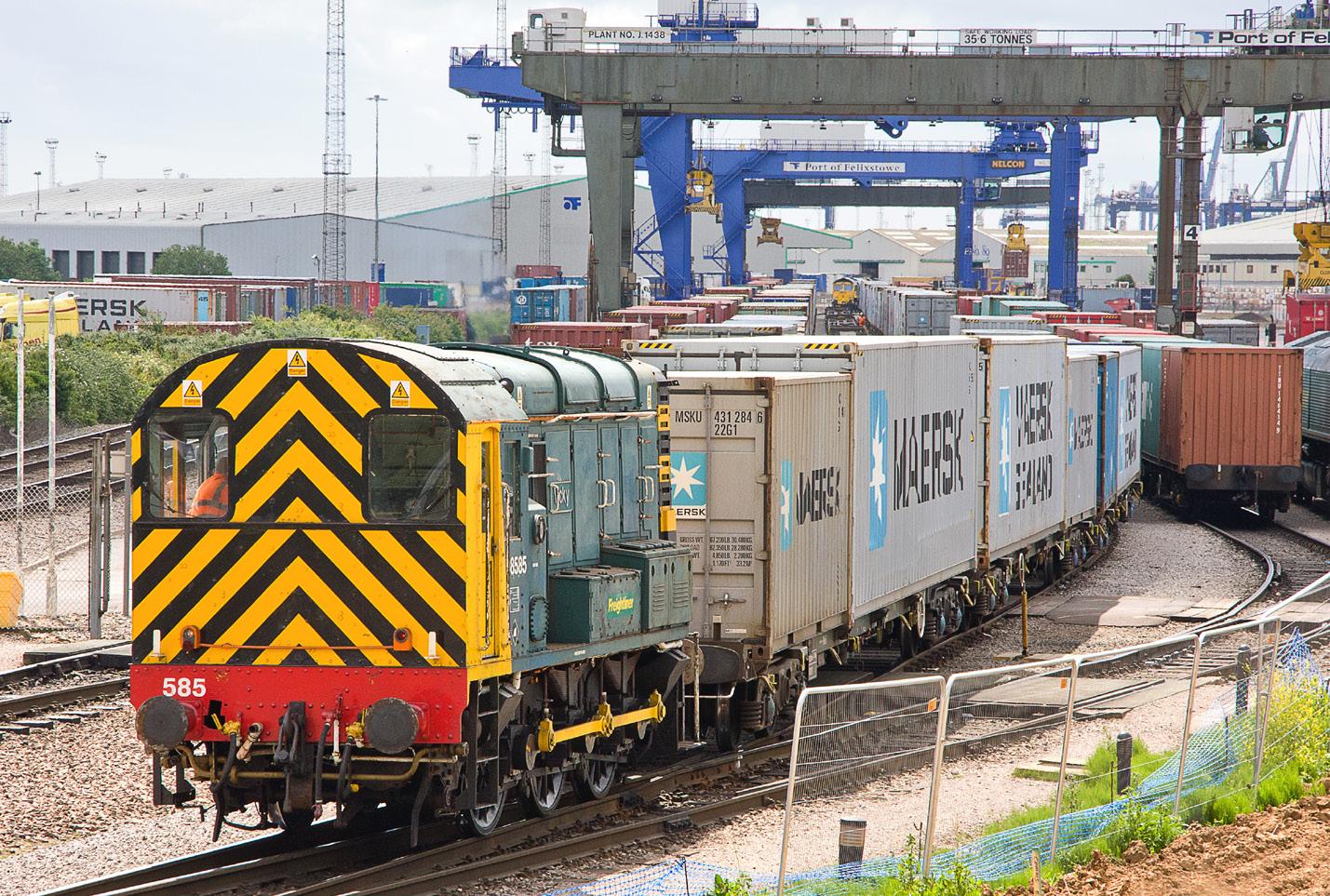
• Introduction – Will we be introducing a new train fleet, and need the assurance that it will fit?
• Modification – Are we planning modifications to existing fleets that could change the vehicle shape and mass?
• Freight – Do I want to run a freight load that does not conform to the route freight gauge?
Electrification
The electrification community can utilise clearance studies to investigate electrification feasibility, design, monitoring and dewirement assessments. As the UK looks to extradite its electrification schemes, D/Gauge has been able to apply
its innovative methods and technologies to help an electrified network become the reality.
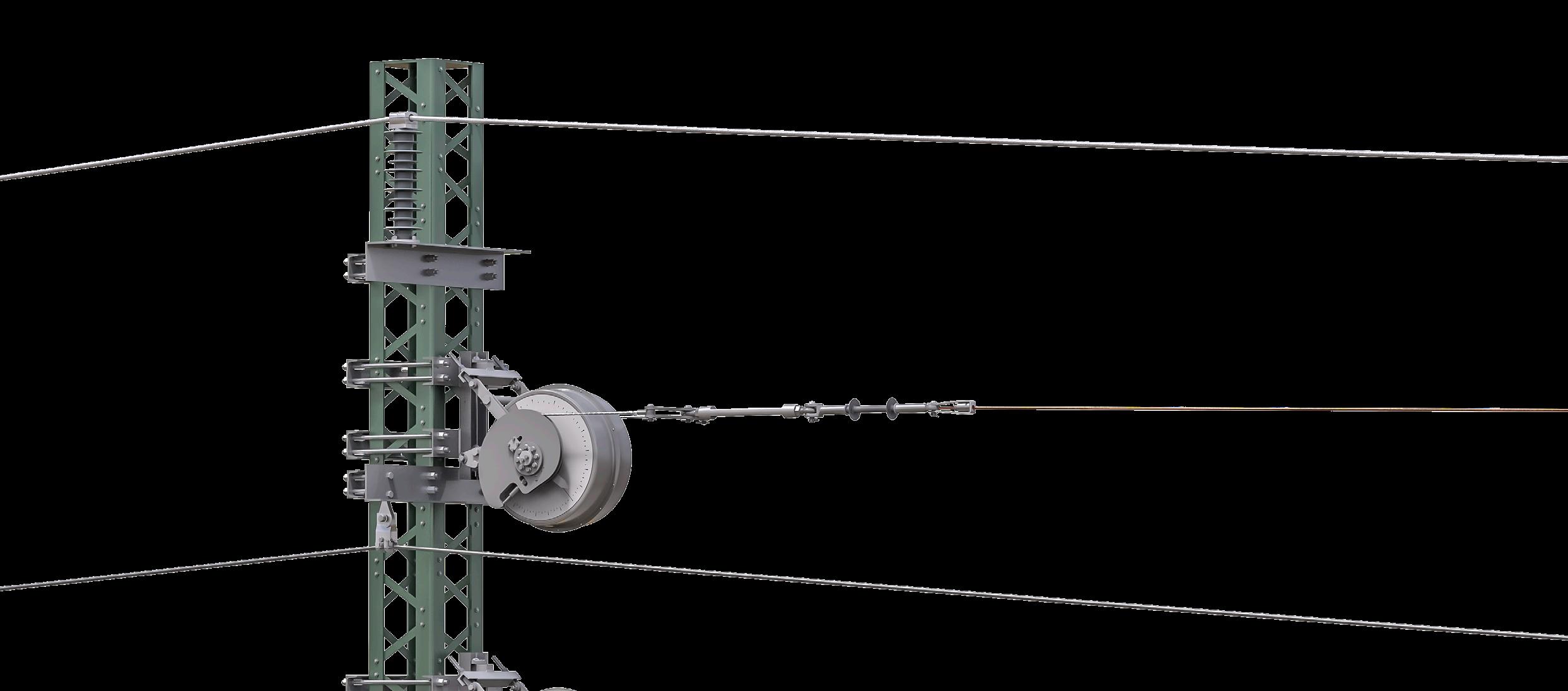
For OLE Installers, Electrification Projects and Alliances, or design consultancies, clearance should be considered by asking:
• Feasibility – Am I looking to retrofit overhead electrification into existing infrastructure?

• Design – Do I have to design for structures with tight or unacceptable electrical clearances?
• Monitoring – How do I monitor my overhead network for de-wirement risks and minimum electrical clearances?
Onto the next chapter
D/Gauge has been leading the way in gauging techniques and technology for the past 15 years, consistently pushing the boundaries and developing innovative methodologies. The commitment to research and development remains unwavering,

and heavy investment has been made in advancing gauging capabilities. Excitingly, D/Gauge has recently unveiled new methodologies specifically tailored for light rail environments and anticipates releasing these to software users later this year.
Collaboration has been integral to this success story, as D/Gauge has forged strong partnerships with various stakeholders and suppliers across the rail sector. Moving forward, there is an eagerness to build upon these collaborations, leveraging the collective expertise of industry players. One noteworthy partnership is with Cordel, a renowned specialist in infrastructure data capture, processing and management.
Together, D/Gauge and Cordel offer a comprehensive gauging and clearance management service, capitalising on combined strengths to deliver a seamless solution. A prime example of the benefits of a collaborative approach is with an ongoing project with Amtrak in the USA, where they are spearheading a complete modernisation of their clearance calculation and assessment processes. The focus is particularly on accommodating out-of-gauge, or ‘high and wide,’ freight traffic. D/Gauge hopes to extend its support to other international networks, contributing expertise and solutions in a similar manner.
In line with a commitment to sustainability, D/Gauge is actively involved in supporting decarbonisation efforts, specifically in the field of electrification. With the need to incorporate additional infrastructure in limited spaces for full electrification in the UK, the engineers have successfully challenged conservative gauging practices.
By introducing Probabilistic Gauging during the feasibility and design stages, the need for extensive physical interventions has been minimised, resulting in substantial cost savings amounting to millions of pounds.
In recent times, skills have taken clearance beyond national borders, with projects spanning Europe, North America, and Australia. As D/Gauge continues to explore international opportunities, it is eager to share the unique expertise and knowledge developed in the UK's gauging domain with the rest of the world, fostering innovation and progress in the global rail industry.
Tel: 01332 972360
Email:colin.johnson@dgauge.co.uk, stephen.pole@dgauge.co.uk
Visit: www.dgauge.co.uk
Address: 11 Brunel Parkway, Pride Park, Derby, DE24 8HR
Social: www.linkedin.com/company/dgauge
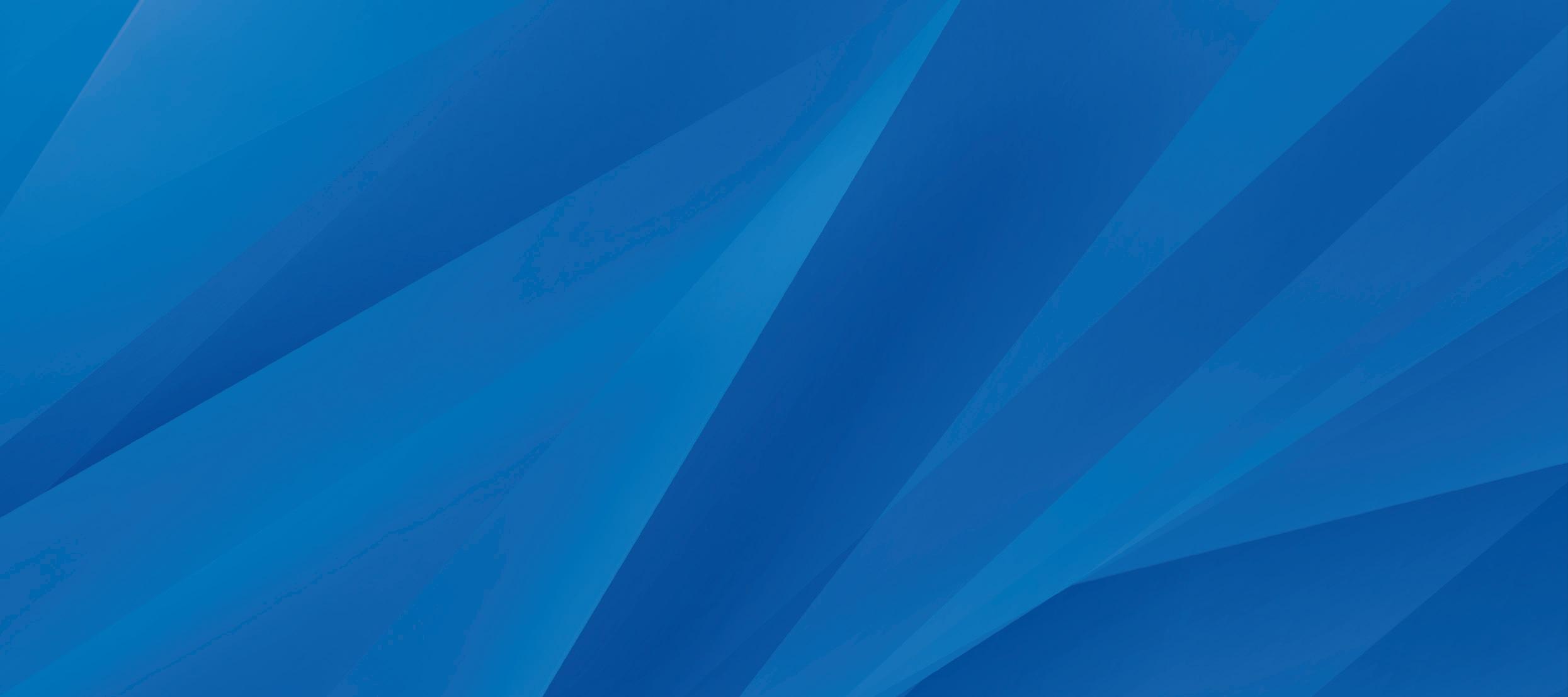
TENSOREX C+: Spring Automatic Tensoning Device
RAILWAY INFRASTRUCTURE SOLUTIONS
FOR TODAY´S AND FUTURE CHALLENGES
Our Expertise for Railway and Tramway:
- Railway Catenary Systems
- Tensioning
- Insulation technology
- Power supply
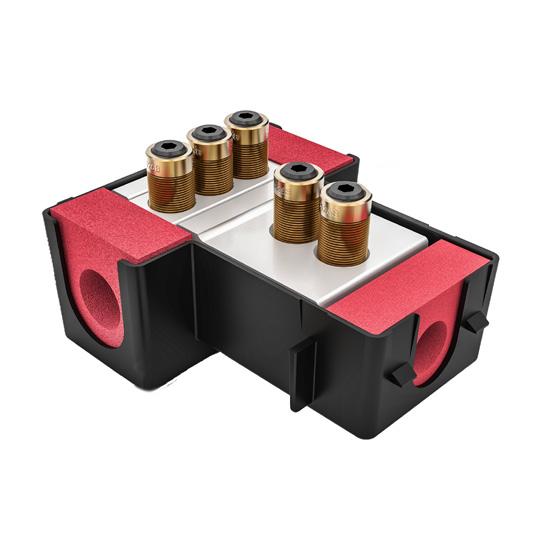
- Safety equipment
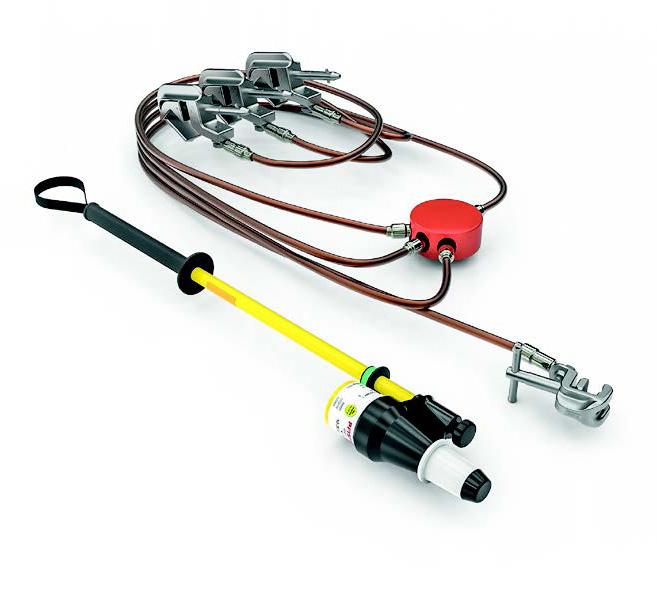
Insulators
Safety Equipment
Bonding Connectors
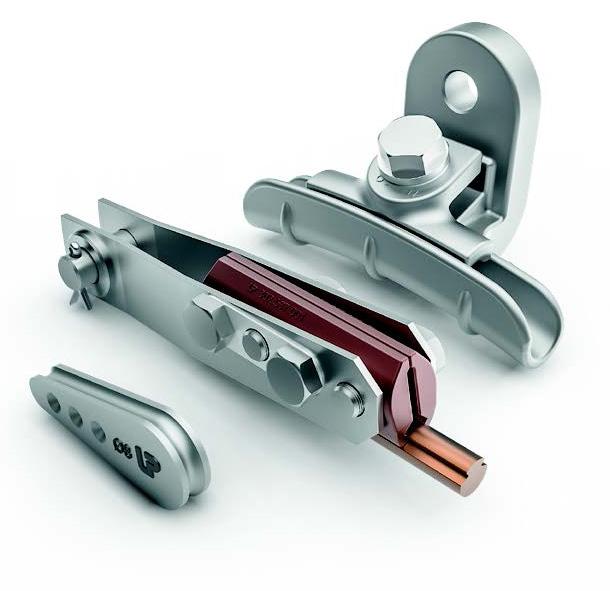
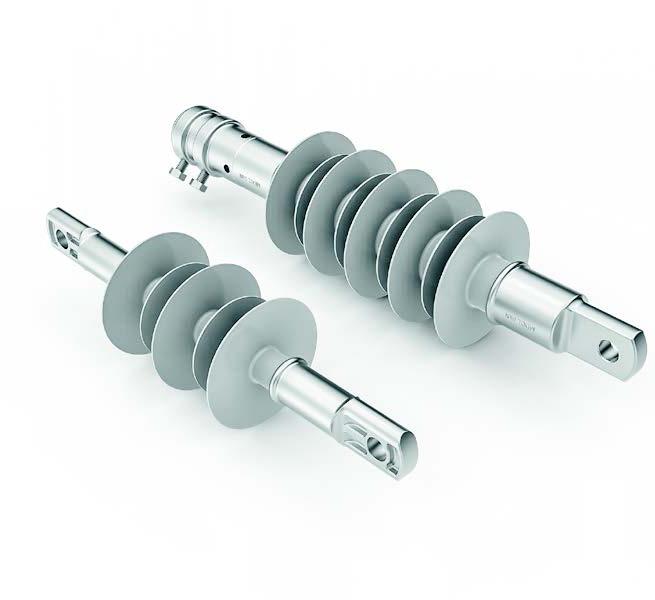
Catenary Clamps

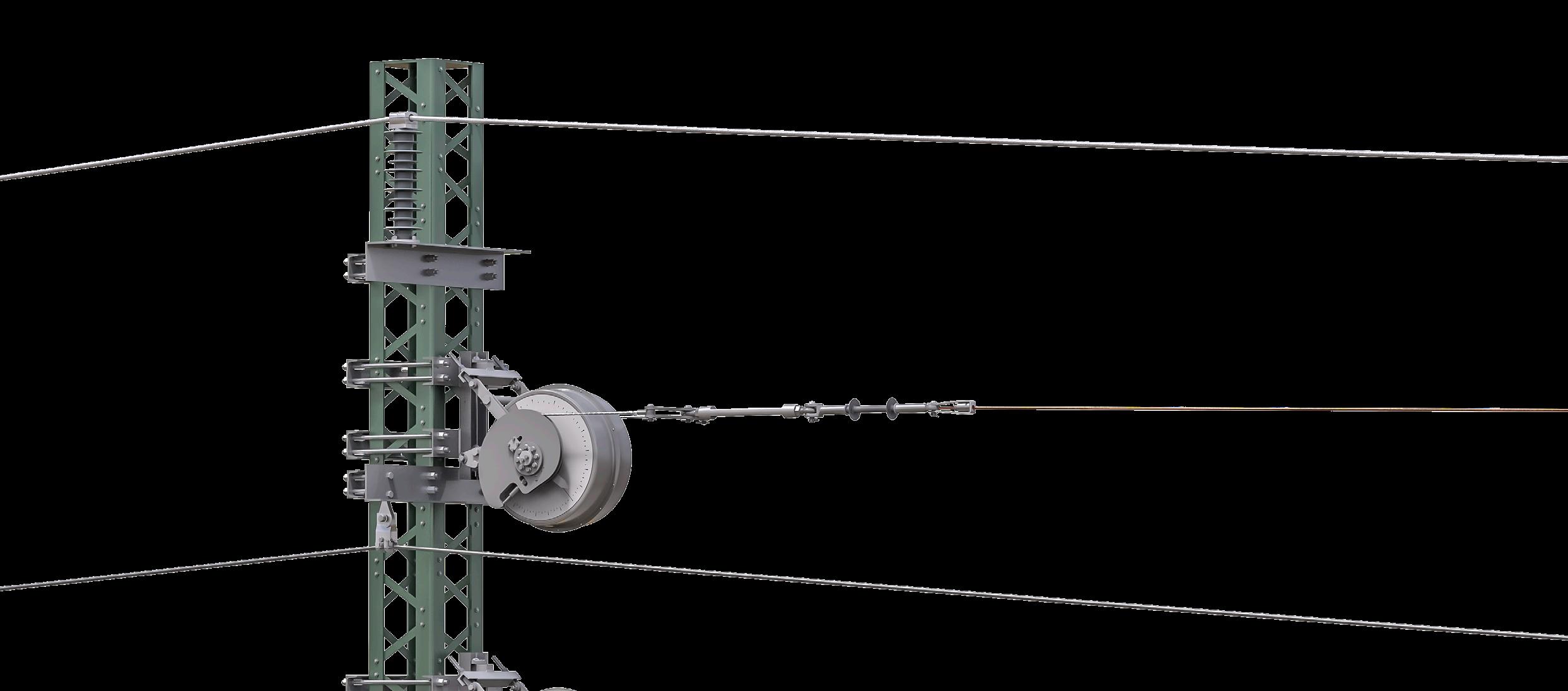
Mosdorfer Rail Ltd. 2 – 4 Orgreave Place, Orgreave Sheffield S13 9LU, South Yorkshire, UK Phone: +44 114 3878370
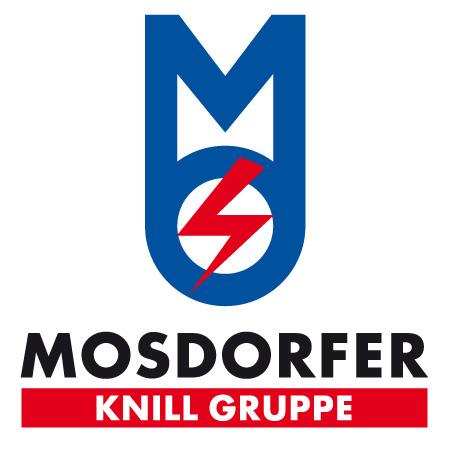
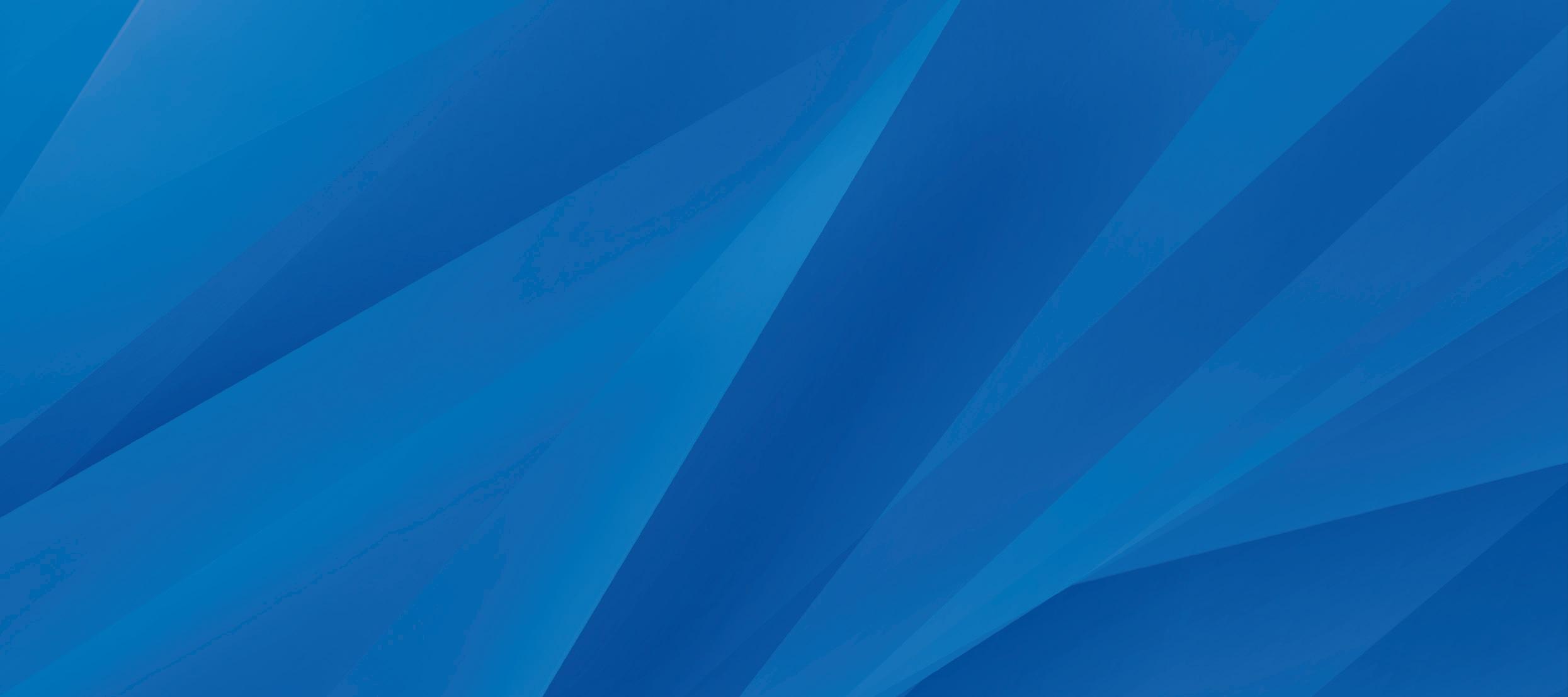
E-Mail: OrdersRailUK@mosdorfer.com
Droppers
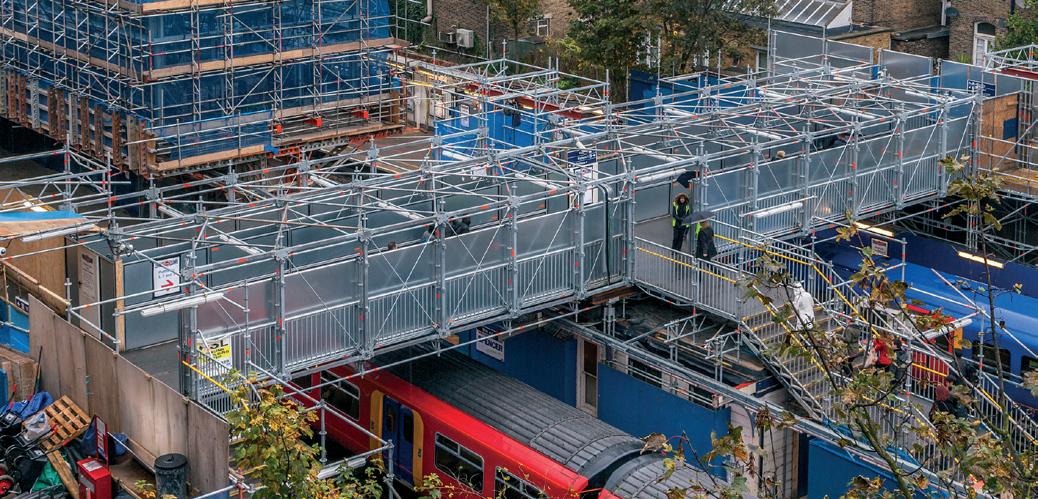

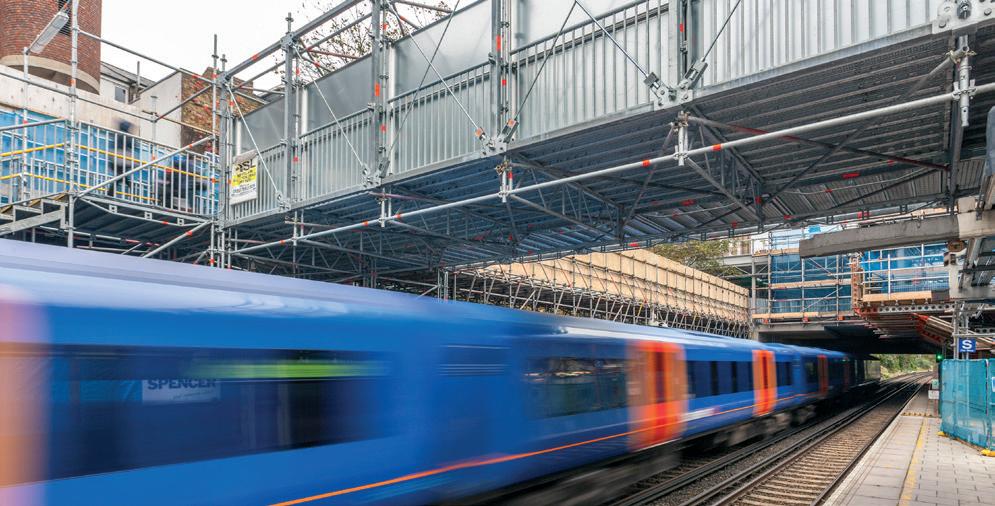
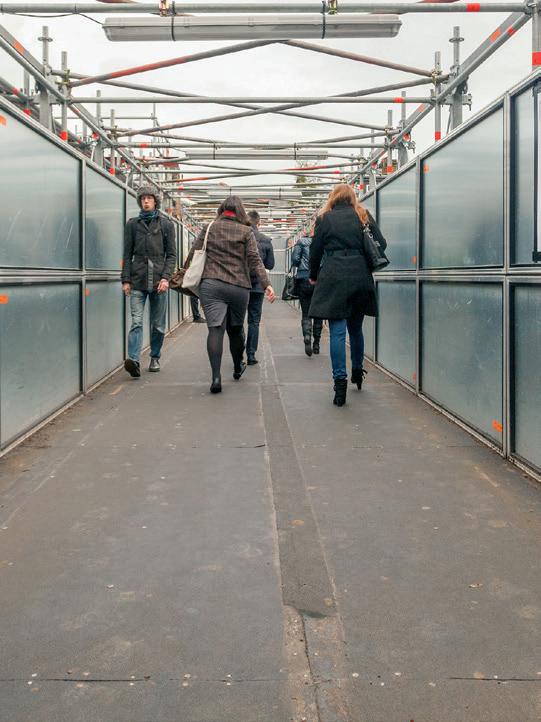

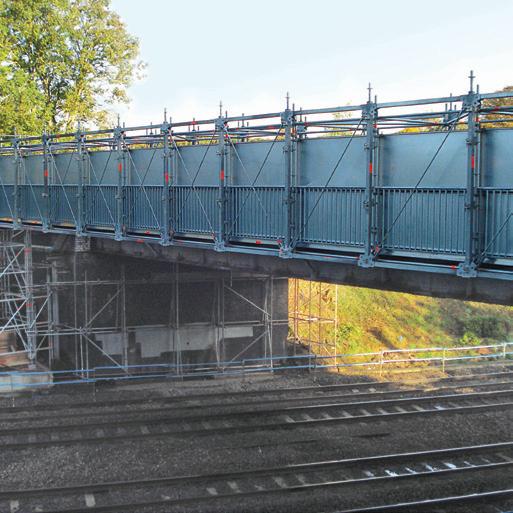
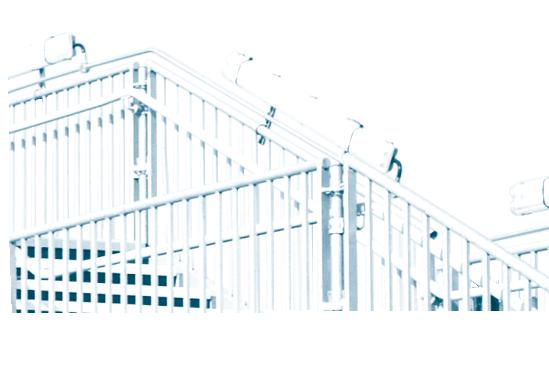


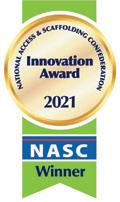
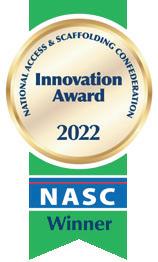


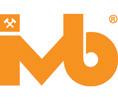




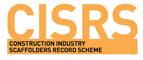

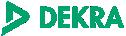
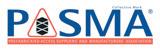

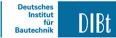



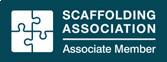

Safety Challenges on the UK’s Rail Network
Due to the high-risk nature of trackside environments, ensuring worker safety continues to be an industry priority, says Leo
Scott SmithRail, Tended created its high-precision geofencing wearable, which, in September 2022, received official product acceptance from Network Rail for use on UK railway infrastructure.
Tended’s geofencing solutiontransforming safety in rail
Geofences are virtual geographic boundaries, defined by digital coordinates. They can be created in any shape or location and there is no limit to how big a geofence can be, making them an incredibly flexible and useful tool for creating zones on a worksite.
As rail plays an important role in achieving net zero carbon emissions in the UK, focus on maintenance and upgrades are essential to ensure minimal disruption and a positive customer experience. It was recently announced in the statements of funds available (SoFas) that Network Rail will be provided with £49 billion to spend over CP7; much of which will be put toward renewal programmes that require people to work trackside. The people who carry out these essential works do so in hazardous environments where open lines and exposure to high-voltage electricity have the potential to cause severe injury or death.
A leading cause of many trackside incidents is due to diminishing worker situational awareness, which can contribute to avoidable accidents and near misses with trains. Typical safety protocols managed through paper-based diagrams, written documentation and physical barriers are
all subject to high costs as well as human error. Miscommunication, distraction, complacency and fatigue are just a few human factors that can lead to a loss of situational awareness, which, in high-risk environments, can be fatal.
To address these safety challenges and loss of situational awareness, Tended worked alongside Network Rail to develop an innovative solution to transform trackside safety. Having already had success developing safety wearables for safetycritical environments, Tended created a wearable solution to function as a sixth sense or 'tap on the shoulder' to alert a worker in real-time if they leave a position of safety. Alerting workers as soon as they enter hazardous areas or approach an open line augments their situational awareness, helping to stop preventable near misses and accidents.
Over three years and with rigorous R&D and live environment trials with Network
Tended uses geofencing technology to enable planners to define critical details on site before work starts. Using an online Planning Dashboard, planners can map out safe working zones with associated safe access points and plot the location of safety equipment. This means that in addition to defining safe zones, the technology can also be used to modernise site operations and allow planners to define the location of critical assets such as marker boards and possession limit boards, as well as easily pinpoint safe access points for workers. This will help to prevent unsafe events that arise from miscommunication or misinterpreted instructions, such as track workers accessing a worksite from the wrong location or before a line has been blocked.
The Planning Dashboard is accompanied by a small wearable device. Worn by workers, this device pinpoints their nearexact proximity to the planned geofence boundaries. If they cross a boundary, the Wearable alerts them in real-time through a combination of audio, visual and haptic alerts, providing an exigent warning that they should move back to safety and helping them regain situational awareness.
Using this technology in high-risk and safety-critical environments, such as on the railway, means that a high level of precision is essential. Tended’s system achieves an incredible accuracy of around 14 mm by using an existing network of beacons. Using this well-established network allows Tended to achieve highly accurate positioning
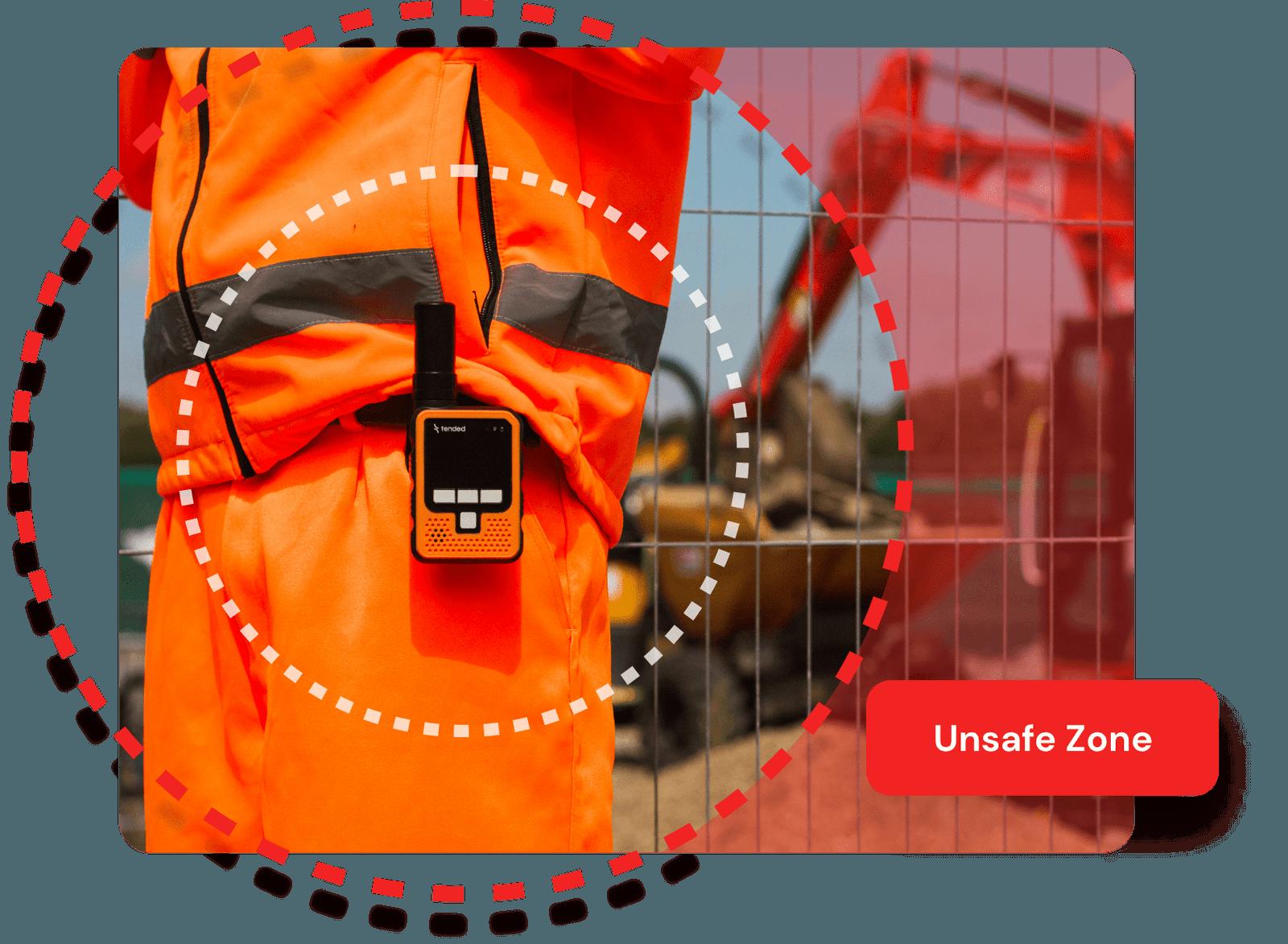
without the need for onsite infrastructure or set-up. Not only does it provide fail-safe coverage for remote and rural areas, but it also enables users to get going with the technology right away. On average, it takes less than ten minutes (including planning) to get the technology deployed onsite, saving valuable project time and costs by getting teams set up and onsite as quickly as possible.
Wearables and Psychology to instil sustainable behavioural change
The benefits of Tended’s Wearables to improve track worker safety is heavily underpinned by behavioural science. In the short term, the benefit of using the technology is that it provides a timely ‘tap on the shoulder’ to track workers to increase their situational awareness and provides a proactive solution to preventable accidents, helping them stay away from hazards and ultimately, saving lives.
Over time, this tap on the shoulder automatically prompts a behavioural change by increasing hazard perception. These adjustments to behaviour are normalised over time, and habitual use of the device nudges wearers into higher levels of situational awareness. These long-term behavioural changes mean that overall, workers will practise safer behaviours, not only contributing to their workplace welfare but also helping organisations to create safer, more efficient worksites for everyone.
Tended has a dedicated in-house behavioural science team who have contributed significantly toward the development of the technology since its inception to instil long-term behavioural change. The team also supports customers from onboarding, implementation and deployment to ensure successful workforce participation and engagement with the solution.

With worker privacy a key consideration among organisations, it must be noted that the technology hasn’t been developed to monitor, track or record a user’s location
at any point. The real-time whereabouts of a device is only used to alert the wearer when they are no longer safe, protecting the privacy of workers and helping to encourage engagement with the technology. Once works have been completed, analytics and data trends provide safety leaders with insights about the overall safety of their worksites to support its continued, proactive and long-term improvements.
An innovative solution for the rail industry
On 3 September 2022, Network Rail issued their latest safety standard (NR/ L2/OHS/501 Module W4) which is a module that, for the first time, specifies the requirements for the use of geofencing on the railway. This new standard marks the start of a transformative era for track workers using wearable technology to keep them safe. By incorporating this technology into their Safe Systems of Work, organisations can better protect their workers and more effectively comply with safety standards. In doing so, we can pioneer the future of safety technology on the railway and lead the way for safer UK rail infrastructure for all.
Following product acceptance from Network Rail, as well as the release of their new geofencing standard, Tended’s technology is now being rolled-out to Network Rail routes and principal contractors.
The system is being applied on worksites for the likes of AmcoGiffen, Network Rail Wales and Borders, Network Rail North and East and most recently, Siemens.
Tended is working with these clients to integrate geofencing into their existing systems and processes to help improve the safety of its workers and strengthen site efficiency.
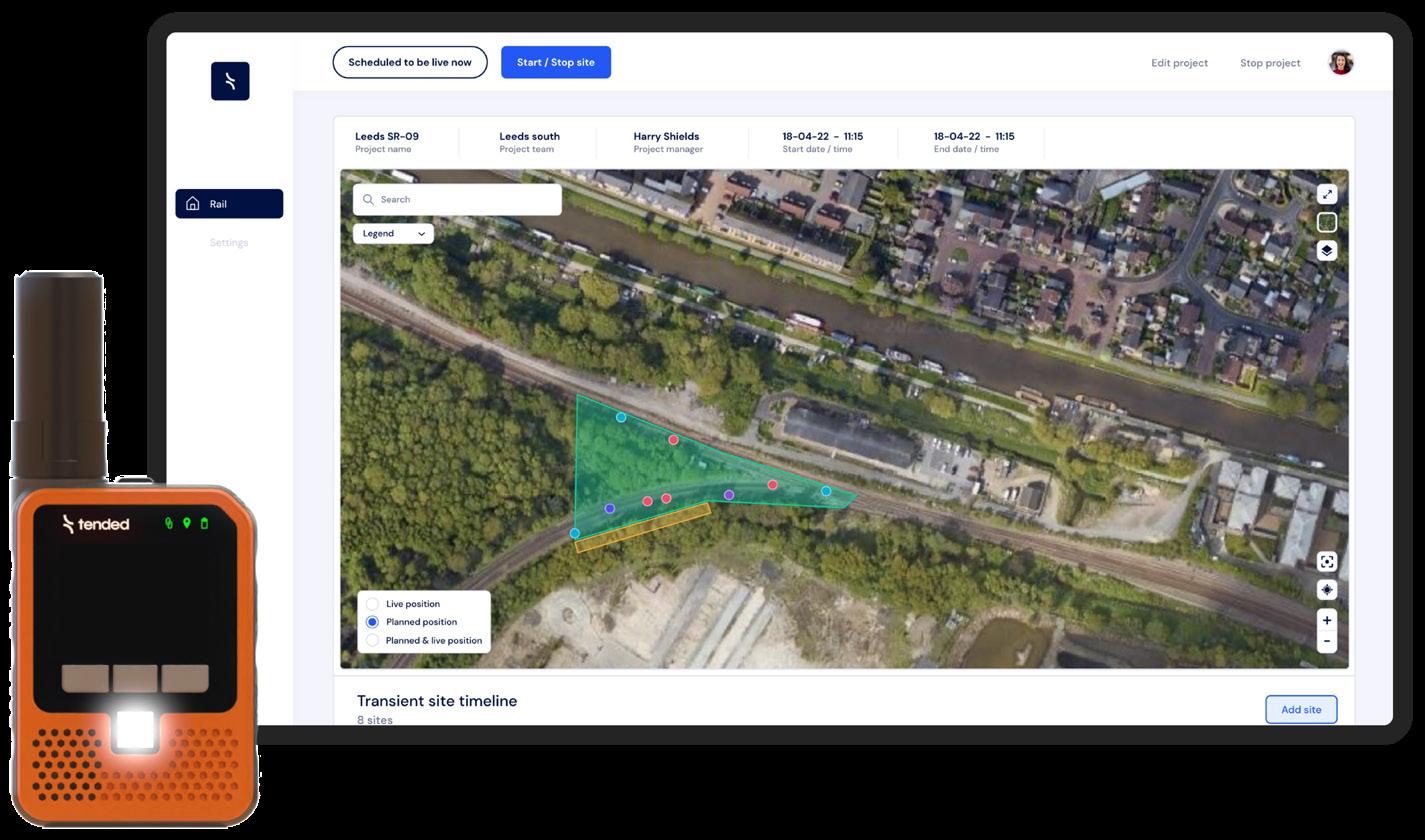
The system is currently being implemented by Siemens across locations around Northumberland in the Eastern region and around Welwyn on the East Coast Mainline. The technology is
being used to create safe zones for their trackside teams when conducting adjacent open line working or working within possessions. The Wearable’s alerts will then keep workers within these safe working zones and stop them from coming into the path of oncoming trains or close to electrical hazards.
Principal contractors Story Contracting and Morgan Sindall are also about to begin using Tended’s technology with their trackside workforce, with Morgan Sindall further applying it to the positioning of critical protection equipment. Tended’s system will be used for geotagging to help ensure the safe and correct placement of marker boards and other assets to monitor the movement of on-track plant and machines in real time.
The future of safety on the rail
While the rail industry has undergone a radical transformation in recent years, earning it a reputation as one of the safest and most reliable rail networks in the world, safety innovation to protect its trackside workers has been more modest. Each fatal incident is shocking and deeply distressing.
Tended has been instrumental in bringing geofencing to the forefront of the railway industry, helping to revolutionise track worker safety and onsite operations. By bringing this innovation and firstof-its-kind technology into the safetycritical railway industry, Tended is helping organisations transform the welfare of their trackside teams.
Earlier this year, Tended’s geofencing solution won the Safety and Security Excellence category at the Rail Business Awards, cited for its life-saving abilities. The solution also won the Engineering and Safety category at the 2022 Railway Innovation Awards, winning against tough competition from the likes of Network Rail and Thales.
Leo Scott Smith is the CEO and founder of award-winning safety technology startup Tended. He has been the driving force behind Tended’s transformative solutions for safety-critical industries, including the company’s advanced geofencing solution. Developed alongside Network Rail, this solution can help prevent accidents and near misses in the industry by helping workers regain situational awareness when they leave safe working limits. In 2021, Leo was named one of Forbes 30 Under 30. He was also named Midlands Startup Entrepreneur of the Year at the 2019 Great British Entrepreneur Awards.
Kilborn Consulting Limited is an independent railway engineering consultancy and design business, with over 21 years of railway experience.
We specialise in the design of new and altered railway Signalling & Telecoms systems for the UK railway infrastructure.
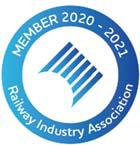
Our areas of specialism are:
•Signalling and Telecoms Consultancy, including technical advice & support;
•Asset Condition Assessments, Correlation and Surveys;
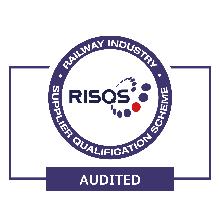
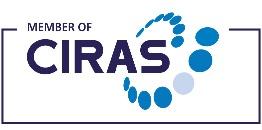
•Signalling & Level Crossing Risk Assessments;
•Feasibility and Optioneering Studies;
•Concept and Outline Signalling Design;
• Telecoms Option Selection Reports (including AiP), Reference System Design and Detailed Design;
•Detailed Signalling Design;
•Competency Management & Assessments;
•Signal Sighting assessments, covering the full Signal Sighting Committee process with a competent Chair.
The new office which is located in the heart of Wellingborough can accommodate all staff and visitors alike and offer widespread views across Wellingborough and the surrounding green spaces
We would be delighted to welcome you to our office to discuss your requirements and how we can support you to achieve those.
Kilborn Consulting Limited 6th Floor, South Suite, 12 Sheep Street Wellingborough, Northamptonshire NN8 1BL
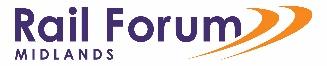
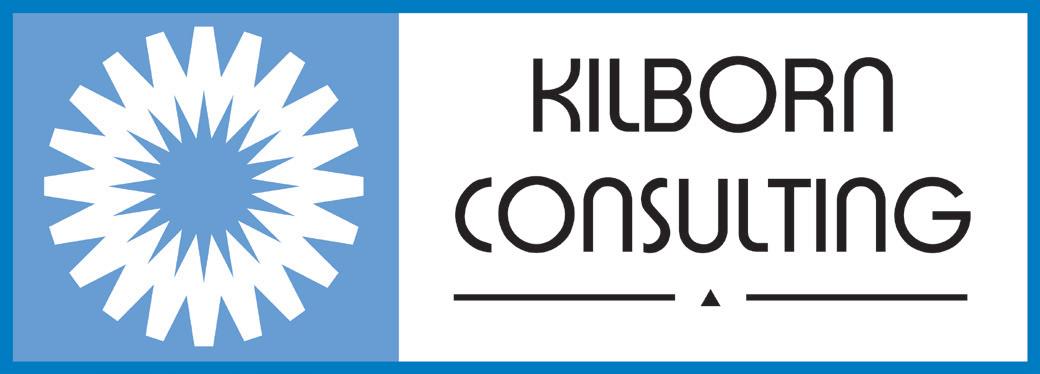
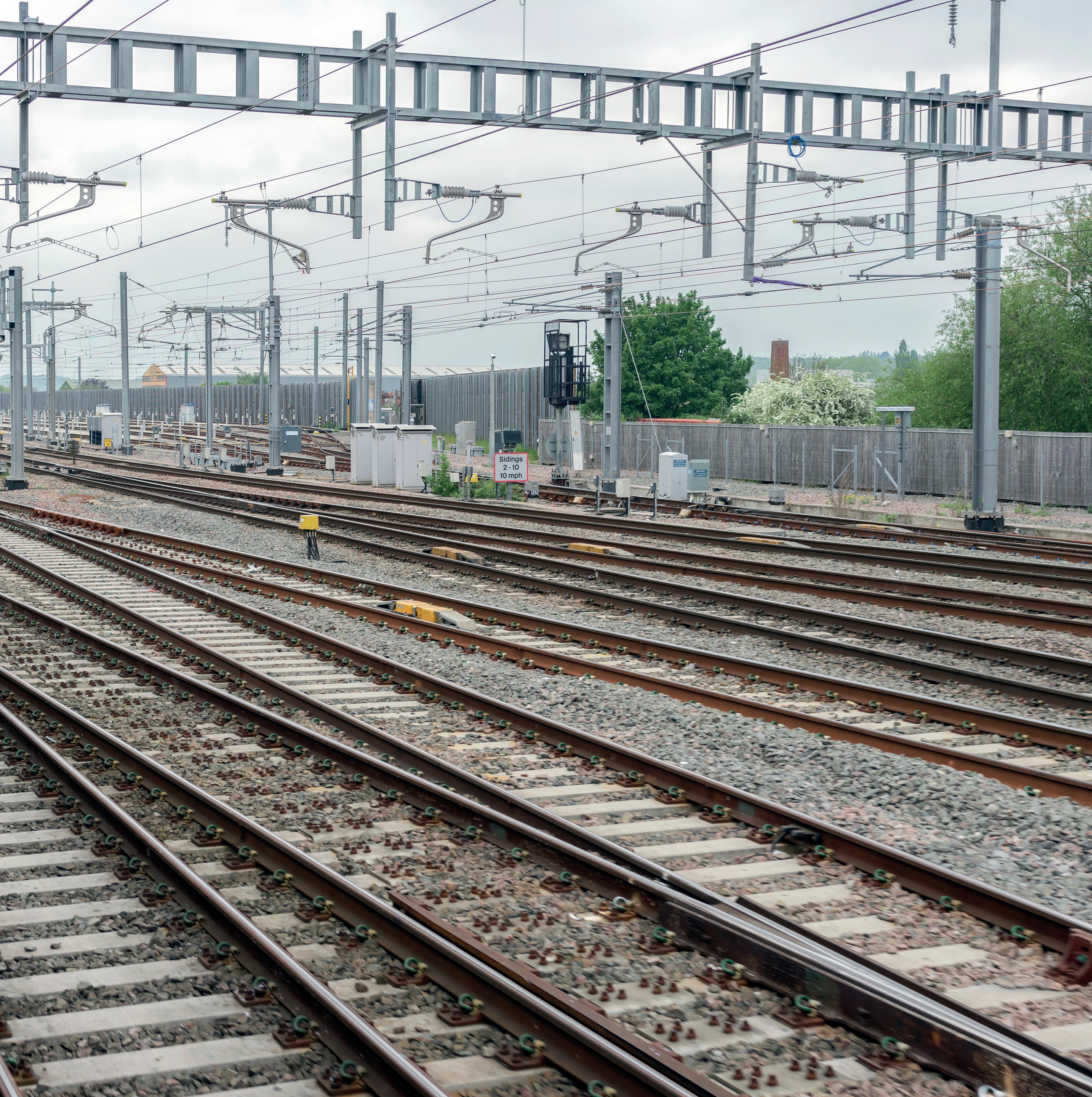
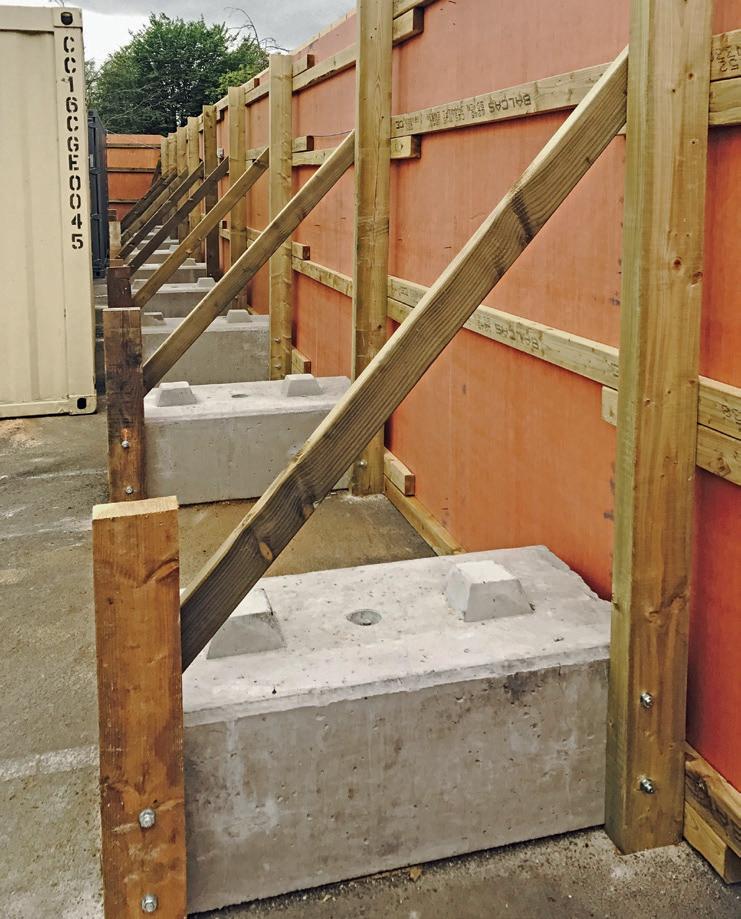
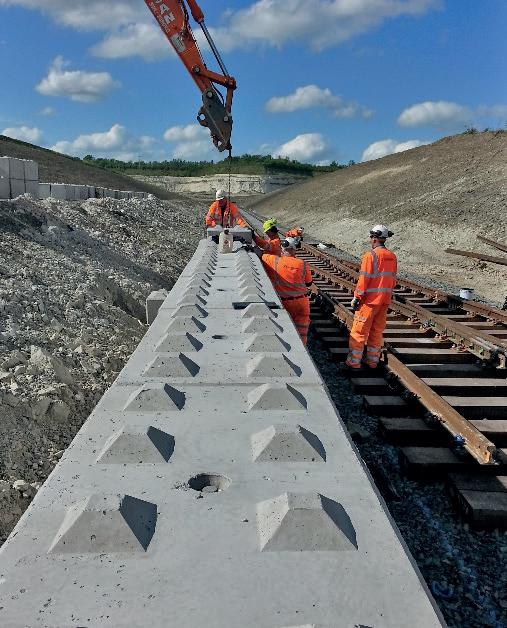
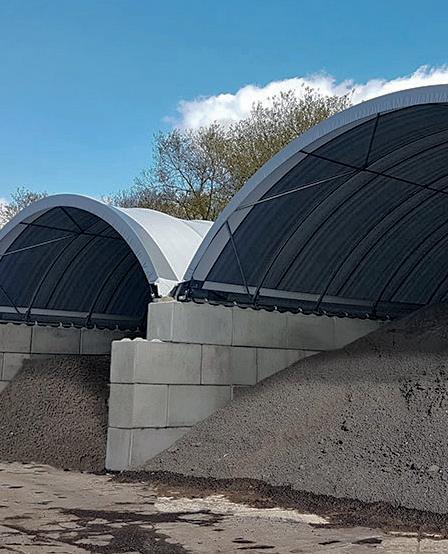
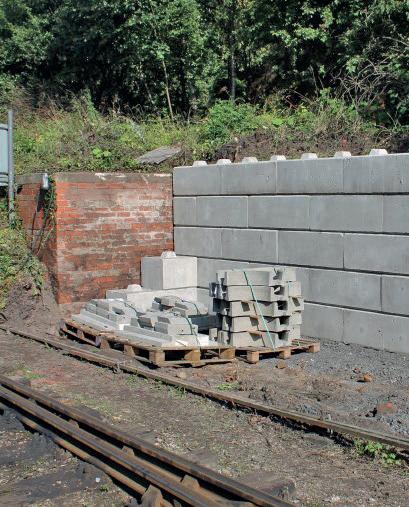
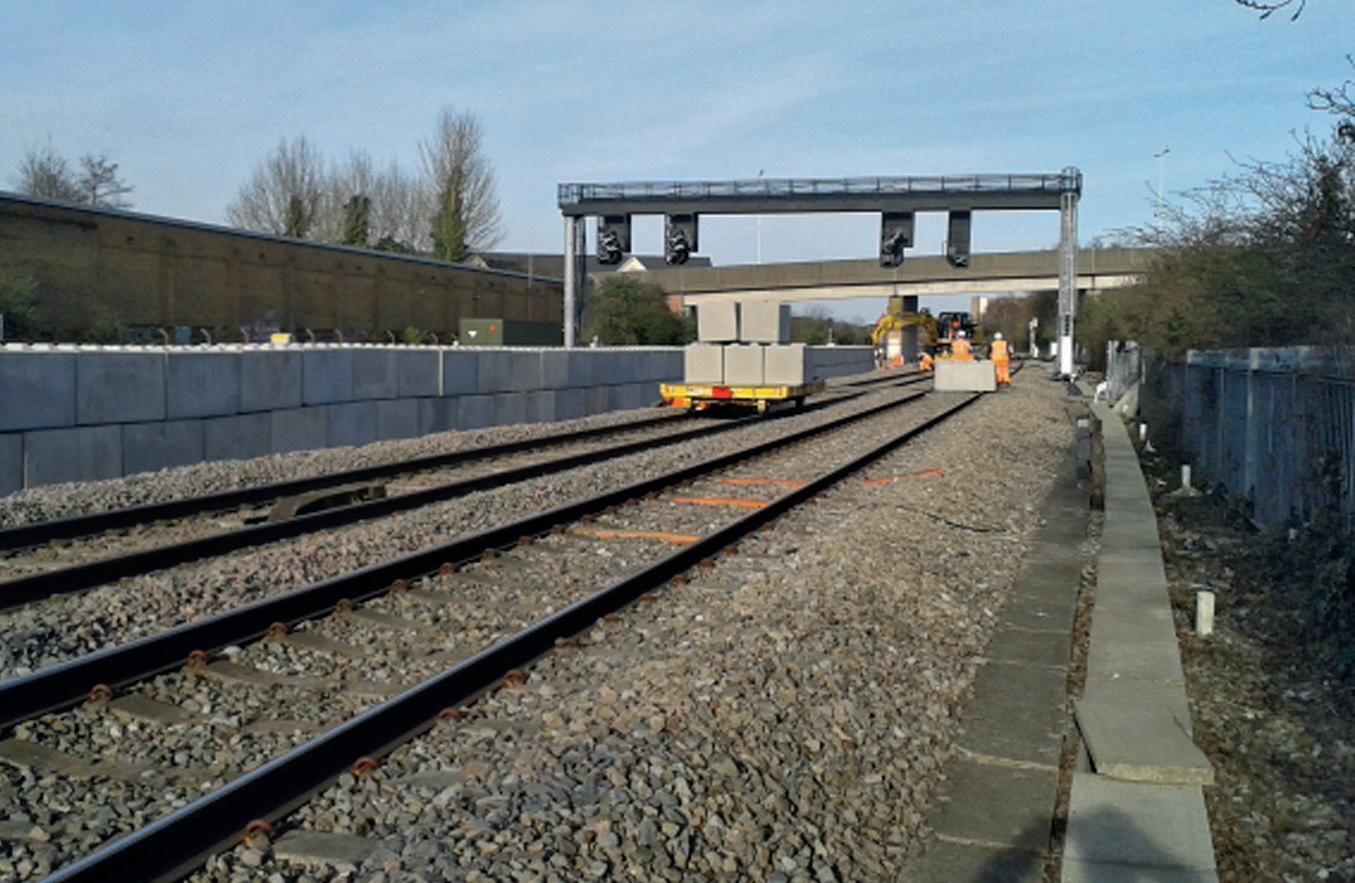
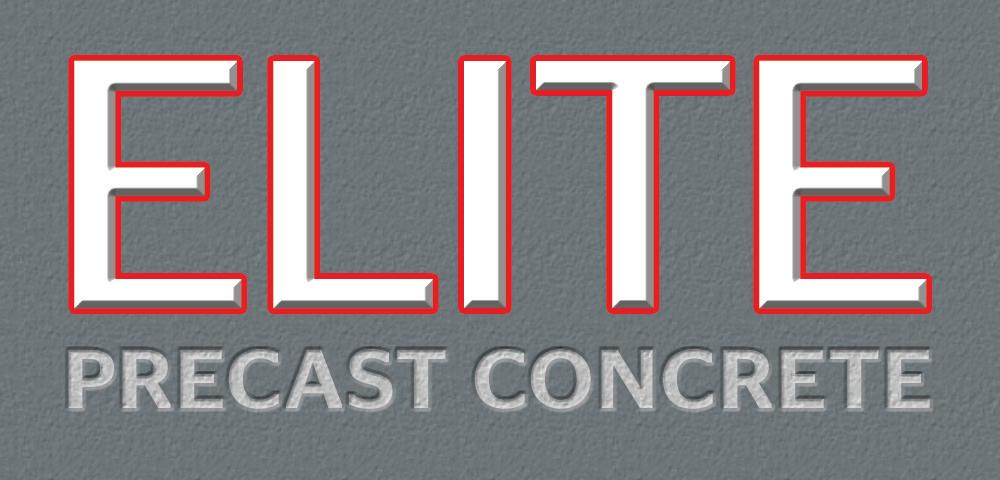
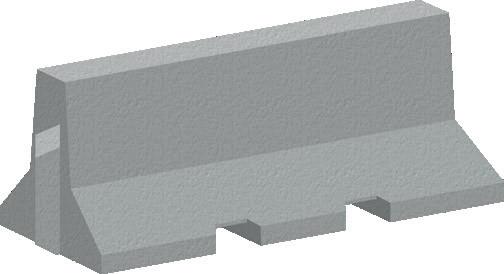
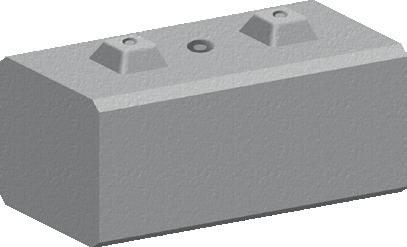

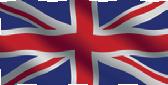
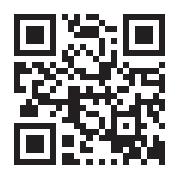
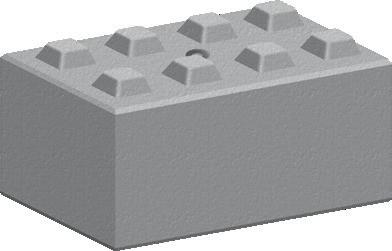
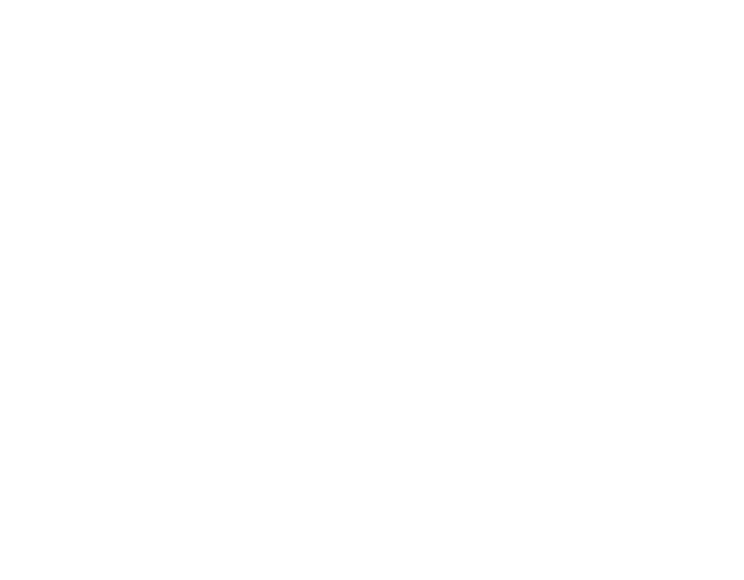
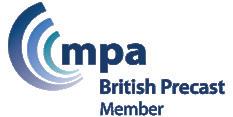
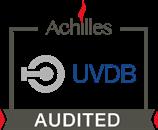
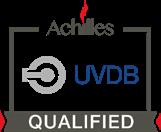
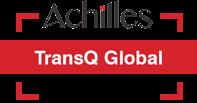
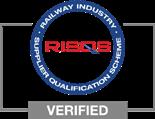

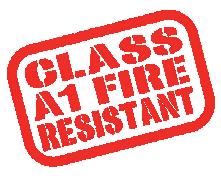
The Challenge of Rail Electrification
Asa Whitfield, Fellow of the Institution of Civil Engineers and rail electrification expert on what the UK is doing in this area and why, and whether goals will actually be reached
Like almost every other country, the UK signed up to the 2016 Paris Agreement on climate change and greenhouse gas emissions, and then followed this up with national targets. The goal for 2050 is net zero, which means almost no emissions, plus offsetting of any remaining residual ones.
According to the UN, transport accounts for a quarter of all emissions globally, so these goals won’t be reached without big changes in how we move ourselves and our goods around. In 2021, the government published its plan for decarbonising transport. This made significant pledges for road and rail. Other forms of transport, such as air, saw fewer specific or binding commitments, unfortunately.
What did government promise for rail?
Ambitiously, Decarbonising Transport promised to simply end the use of dieselpowered trains by 2040. The scale of the challenge involved here shouldn’t be underestimated; by the end of 2022, just 38 per cent of the rail system had been electrified. Further change is envisaged after 2040, with detail to come on how government will ensure a goal of running a wholly net-zero rail network by 2050.
There’s more than one reason to electrify the rail network. Electric trains have about half the carbon footprint of diesel-powered ones, but this is by no means the whole
of the picture. As the same source shows, even diesel trains are really pretty low in emissions compared to non-rail options. Road electric vehicles vary, but going by diesel train is probably better for the planet. For this reason, rail is only responsible for 1% of transport emissions.
So why the focus on electrifying rail? Partly, the obvious; if challenging overall targets are to be met, each bit of the economy must do its part. The other reason, though, is that net zero may be hard to achieve, even with all cars fully electric, unless more people are encouraged away from road and aviation. And if government is going to do that, naturally it makes sense to make the alternative less polluting and quicker, with journey times reduced using faster accelerating electric trains.
The plan is mostly line electrification, but don’t forget BEMUs
The pledge to phase out diesel trains by 2040 doesn’t constitute a promise to electrify the entire network by that date. It’s pretty clear this won’t happen. Rail electrification is expensive. It also results in a system that is sufficiently cheaper to run that it pays for itself, but government must spread that cost, so not every branch line will be electrified by 2040.
For some while afterwards, local journeys will often involve some option that isn’t diesel and isn’t an electrified line. That might
include a hybrid (diesel-electric as currently in place on the Greater West in places) or trains with hydrogen fuel cells, but price will have to fall quite a bit to seriously challenge the battery option, Battery Electric Multiple Units (BEMUs).
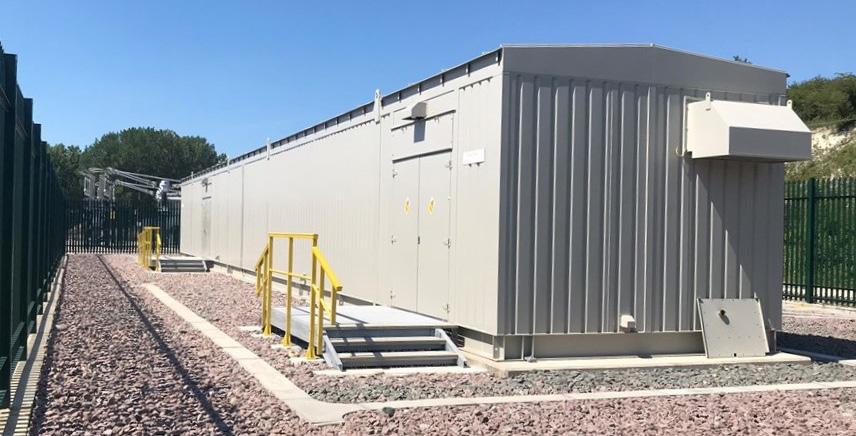
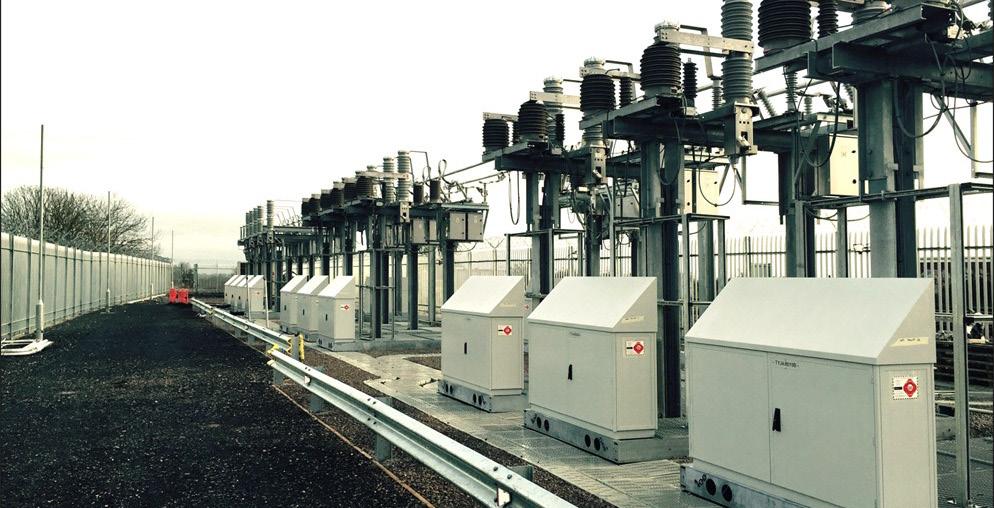
Rail electrification isn’t going smoothly
As mentioned, 38 per cent of our rail network is electrified, 38.1 per cent to be specific, up from 37.9 per cent one year before. It is apparent that there have been significant delays. The consensus explanation is that funding jumps wildly from year to year. These lurches cause missed targets, because erratic funding doesn’t support enough of a base of people with the relevant skillset:
‘Between 2009 and 2014, £200 million was invested in electrification. The plan for the following five years was for electrification schemes totalling £4 billion. This was an extraordinarily inefficient way to deliver electrification and contrasts with the steady rolling programme in European countries…with mistakes made owing to skills shortages’ says the Institution of Mechanical Engineers website.
Specialists are needed in this area
The company I founded, WCS, is one of the few that has had a consistent presence even in the lean years. Today there are over 40 of us, and a wide variety of projects, but initially there was 1, with most of
the work being civil engineering support for those bringing power to rail. As we discussed recently on our company blog, we’ve chosen deliberately to maintain that original focus as a significant strand, even as we diversified, ultimately folding it into a wider corporate strategy, SustainableFuture, that centres on building in-house expertise in areas that are expected to grow due to sustainability awareness.
Case studies
Because of this history and focus, we have built up considerable experience in rail electrification, including projects that have involved complex civil engineering challenges. Here are a few of the projects that exemplify this:
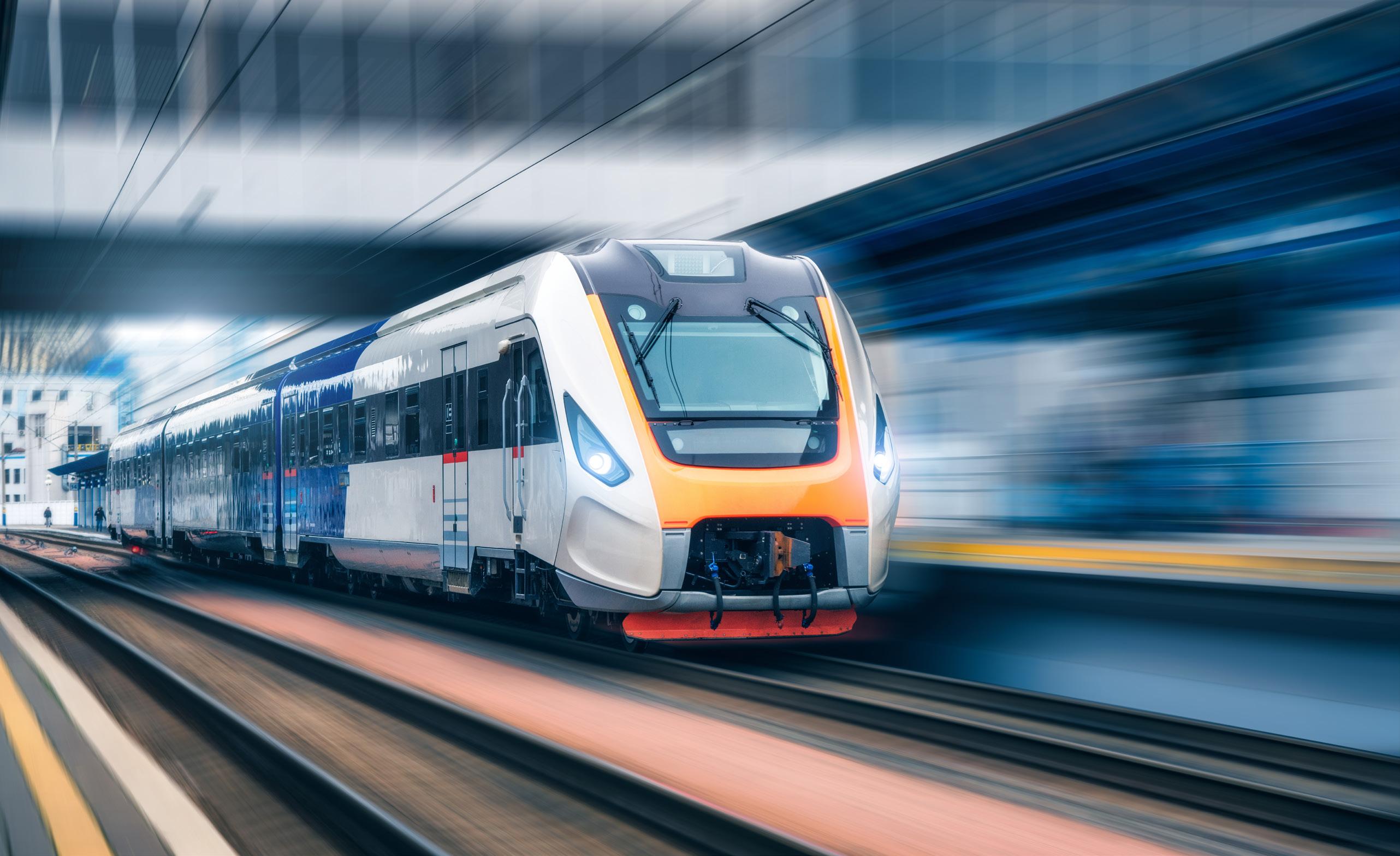
• Great Western Electrification Programme – Working with client UK Power Networks Services, we provided the civil design work on the biggest UK electrification project of the last decade, the Great Western Main Line Upgrade. WCS oversaw survey, design and checking of over 30 substation sites and associated HV feeder routes between Reading and Cardiff.
• Midland Mainline Upgrade – For the Midland Mainline Upgrade, WCS provided SPL Powerlines and Network Rail with survey and civil engineering design services for GRIP stages 4 and 5 on two packages of work (so far), including for new substation compounds, road-rail access points and pedestrian access points. WCS has also been able to provide electrical design through our supply chain relationships.
• Intercity Express Programme Doncaster Depot Power (IEPDDP) – For Hitachi Energy, we provided work to support a power upgrade to a major maintenance

depot, Doncaster Carr, as well as the East Coast Main Line. This was part of the Intercity Express Programme. Scope included civils design of two compounds to house a static frequency converter as well as a 33kV substation and 25kV feeder station. We also designed approximately 3.5km of cable feeder route to overhead line equipment connection points, crossing the East Coast Main Line using Under Track and Over Track Crossings, including converting an existing driver’s footbridge into an HV cable way.
• Northern Trains Battery Electric Multiple Units – We have also been supporting client UK Power Networks Services on an ongoing project to support the operation of Battery Electric Multiple Units by Northern Trains. WCS has been advising on a GRIP 3 option selection, risk and constraint analysis, plus outline design of substations and cable routes.
• London Underground: Piccadilly Line upgrade – Our work with familiar partner UK Power Networks Services includes projects for London Underground too. Substantial enhancements to Manor House and Cobourg Street substations were required to support a major upgrade to the Piccadilly Line. New cable routes were also needed, and Nick Lowe, Associate Director at WCS, was named as Lead Civil Engineer for the overall project.
Final Points
The government’s plans on net zero more widely, and rail electrification specifically, are cogent and imperative. We must all hope they are able to coordinate with train operating companies (TOCs) and others involved, and oversee delivery of the promised change by 2040.
More joined up thought on other modes of transport would do no harm. In the UK, most long-distance journeys are cheaper by air than rail, forcing passengers to choose between sustainable and affordable means of transport. Across the channel, governments are willing to absorb more of the cost of electrification, helping to avoid this and to encourage a switch to more sustainable travel options; some are taking even stronger action, with France recently banning short haul domestic flights. Still, progress is being made, and with thought and goodwill, we should all hopefully reach the terminus on our journey to net zero.
To learn more about WCS, please visit our contact page. To say hello in person, please stop in at stand M16 during Rail Live, where we look forward to continuing this discussion with contacts old and new, and catching up with partners and clients.
Asa Whitfield is the Managing Director of Whitfield Consulting Services (WCS).
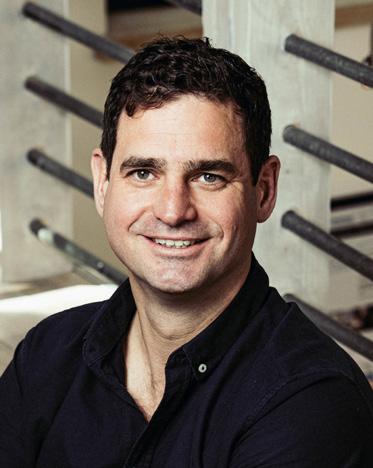
Founded in 2007, WCS is a growing and dynamic civil engineering design company serving multiple
Tier 1 contractors across the infrastructure sector. They have extensive experience working in the rail sector, encompassing civils and structures as well as electrification work. WCS also operates in the Power and Energy sector, delivering projects that support the UK’s NetZero agenda.
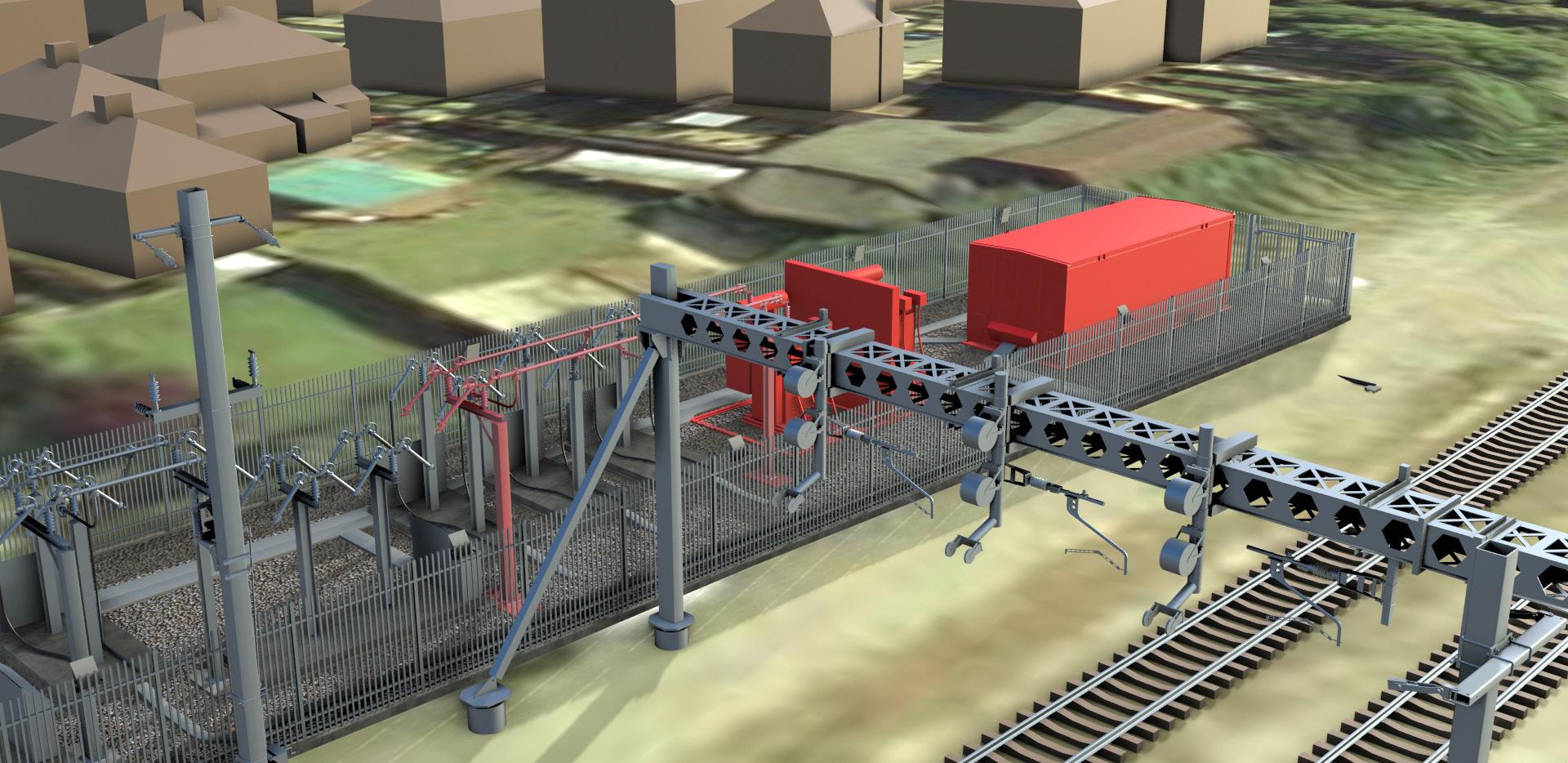

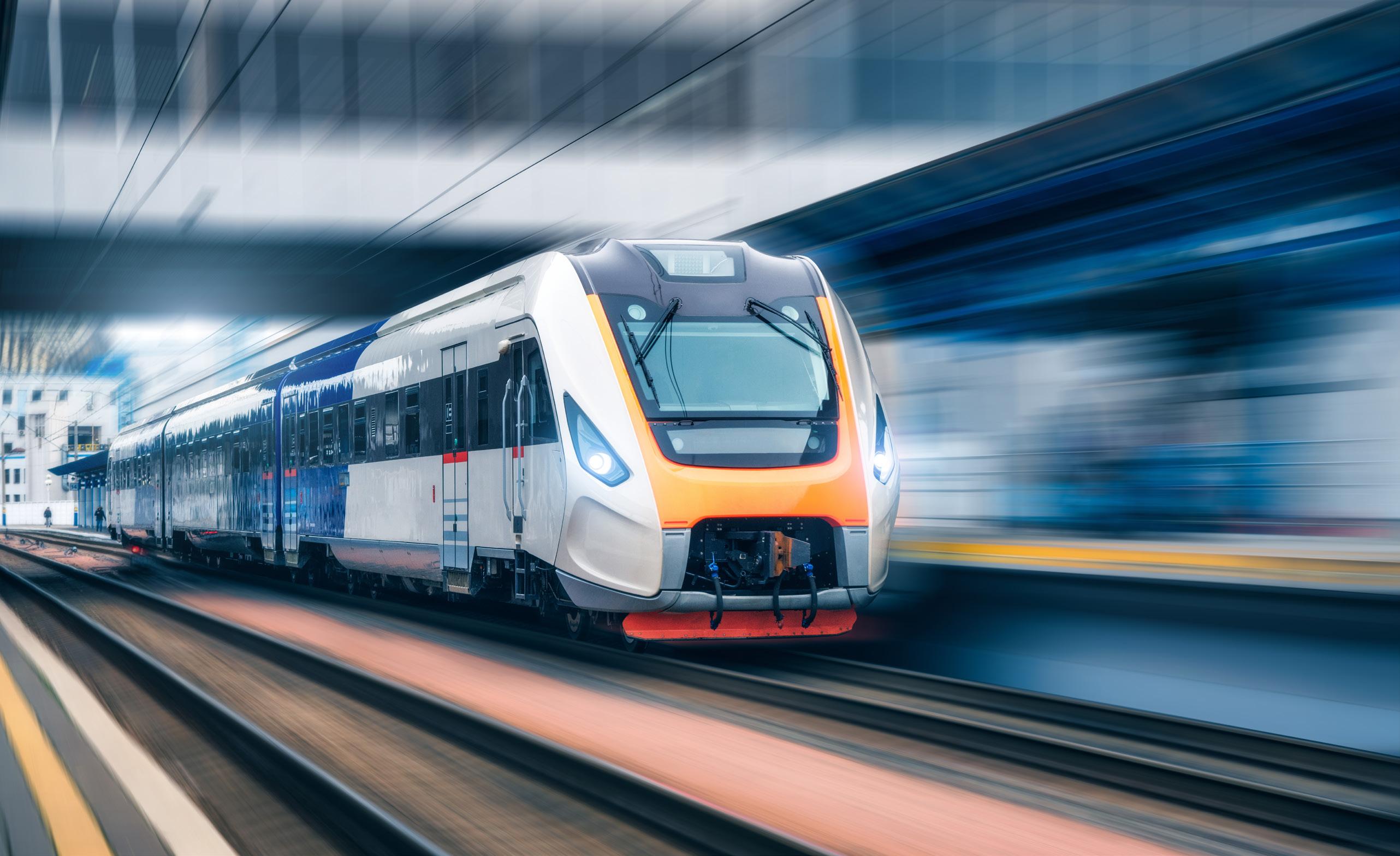
Dovetailed NTS Help Colleagues Stay Safe
Laura Hedley, Senior Occupational Psychologist at the OPC shares reflections on the inter-dependent safety-critical relationship between Controllers of Site Safety (COSS) and Signallers and how key Non-Technical Skills (NTS) closely fit together to keep track teams safe
1. Valuing and prioritising safety can be demonstrated by a COSS ensuring they prioritise their own and their teams’ safety vs. rushing to complete a job, so trains can resume or moving onto another job for cost-saving efficiencies. In the critical COSS/Signaller working relationship, this may mean that a Signaller would display the same NTS by not exerting pressure to complete a job ahead of schedule. If a job is taking longer than expected, the Signaller and COSS would work jointly to re-assess a plan. There’s a clear recognition by both parties that rushing is more likely to lead to errors, and jeopardise safety.
There are many relationships that are inter-dependent in the rail industry, where working together means a safer and more effective network, or a better customer experience. Yet, nowhere is this more important, safety-critical and as lifesaving as the relationship between a Controller of Site Safety (COSS) and a Signaller.
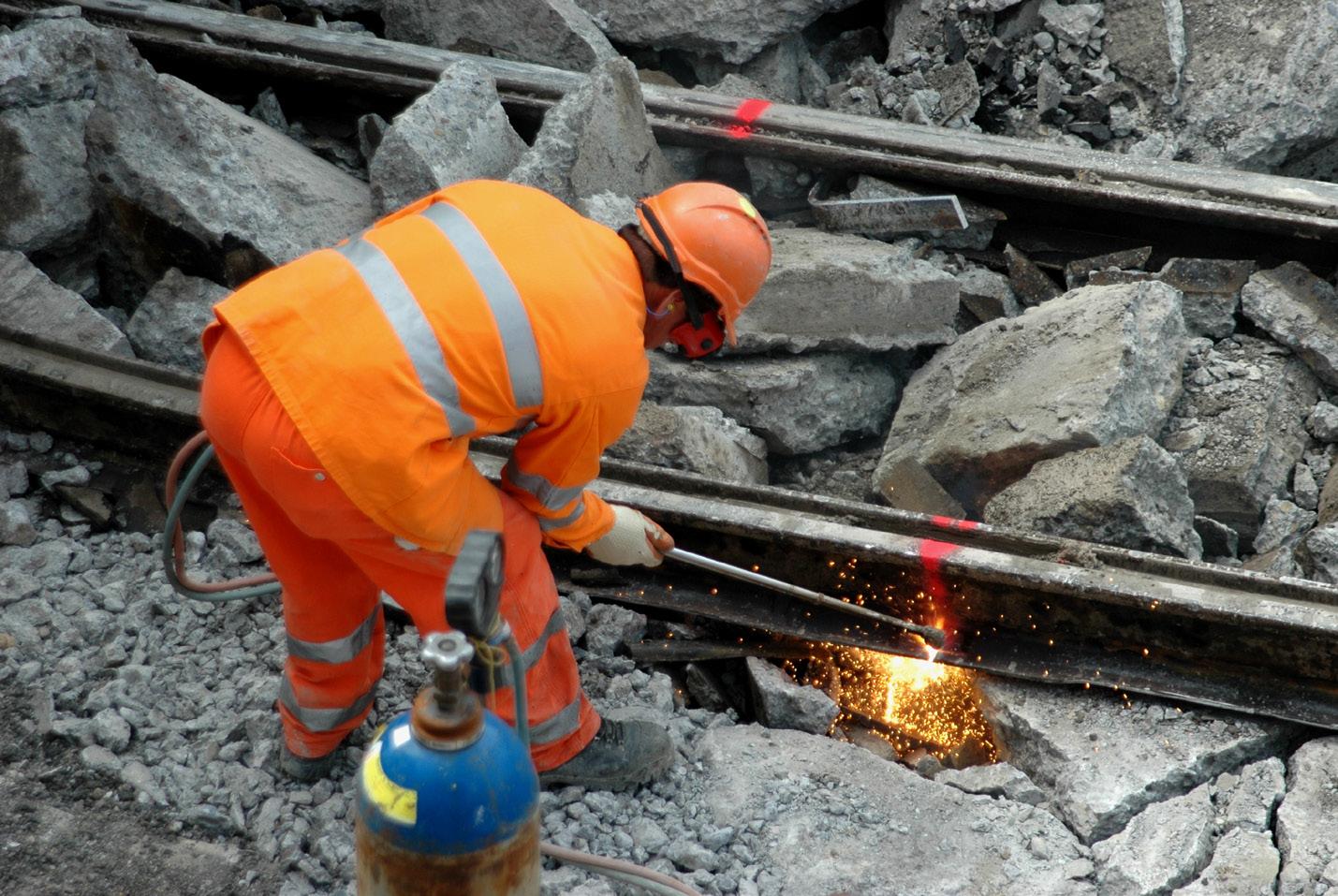
A COSS’s safety-critical role may be very varied on a daily basis – from patrolling a line section, repairing faulty points, to installing a major structure. It has significant and far-reaching accountabilities. As the person responsible for all site safety, if negligent, they risk prosecution should someone be harmed or killed. Having this weight of responsibility requires stringent training, relevant industry experience, a period of mentoring and certification to each specific level. Once qualified, they
undergo regular competency assessments and reviews to continue in the role.
Signallers are also a key safety-critical role with significant training requirements before commencing in post or progressing to a more senior grade. Alongside train movements, other key safety responsibilities are looking after train crew colleagues, and also a COSS and their team – Caring for their colleagues, ensuring their safety at all times.
So, what might some of the key NonTechnical Skills (NTS) be for these roles?
Safety, first and foremost
As both a COSS and Signaller are safetycritical roles, their first and foremost priority is safety over all other concerns. The safety of trains, train crews, rail passengers, and the track teams come first. There are three key NTS that all dovetail together to ensure effective and safe behaviours:
2. Maintaining safety vigilance. Both roles are very dynamic. A Signaller needs to stay focussed, alert and concentrate on changing information for their line section all the time. A COSS needs to remain vigilant to identify hazards and risks for the team. Both roles work on shift patterns, so being aware of the impact of fatigue or task repetition on their safety vigilance is key to maintaining safety.
3. Risk anticipation, time focus and risk management. A COSS with a strong NTS of risk anticipation will be proactively ‘scanning’ for risks – in themselves, their team, the job, and their environment. Proactive risk management starts well before the work in their planning and preparation of a job. During the course of a job, a safe and effective COSS is able to think through changing situations, anticipating consequences and proactively taking action to remove or reduce risks.
An Infrastructure Operations manager (IOM) said: ‘Some of the best COSS’s on my team look ahead of time, proactively thinking up front. They may tweak plans as they go along to keep everyone safe.’
Effective, accurate and proactive planning is a key NTS
A skilled and high performing COSS will plan all aspects of the job proactively, to a meticulous standard – seeing this as entirely their own responsibility. Their planning will be very systematic, collating information from all relevant sources, checking for accuracy and reviewing all the details. They won’t leave planning to the last minute, be haphazard in it, or leave plans incomplete. Once on location, from a position of safety, they may do a last site-check comparison to make sure nothing has changed.
Because they ‘own’ the plan they will have a sound understanding of it, enabling them to communicate it and complete the team safety briefing assertively, with confidence. Being sure of the plan allows them to encourage others to work to it too; recognise any non-compliance and call a halt to work if it’s not progressing safely – as per the plan! They won’t be afraid to re-work a plan even if this causes a delay or takes additional or personal time. Meticulous planning is paramount and it’s a foundational aspect
of their character and safety-critical performance as a COSS.
An IOM commented: ‘An outstanding COSS will have a really strong NTS of assertiveness. They’re willing to speak up, confidently challenging something when it’s unsafe – They’re not afraid to ‘stand down’ their crew and call a complete stop. Even if the request is from someone more senior than themselves.’
Sound planning from a COSS helps a Signaller keep them safe
When interacting with the Signaller, the COSS’s coherent and effective planning will be very apparent. They’ll be able to communicate their requirements clearly, with succinct knowledge of the blockage location and points positions. They’ll also
have a realistic understanding of the time required to complete the job. This will make it easier for a Signaller to complete all the necessary approval paperwork to put the line blockage in place, and give them clarity for onward communication to Train Drivers or the next shift’s signal person.
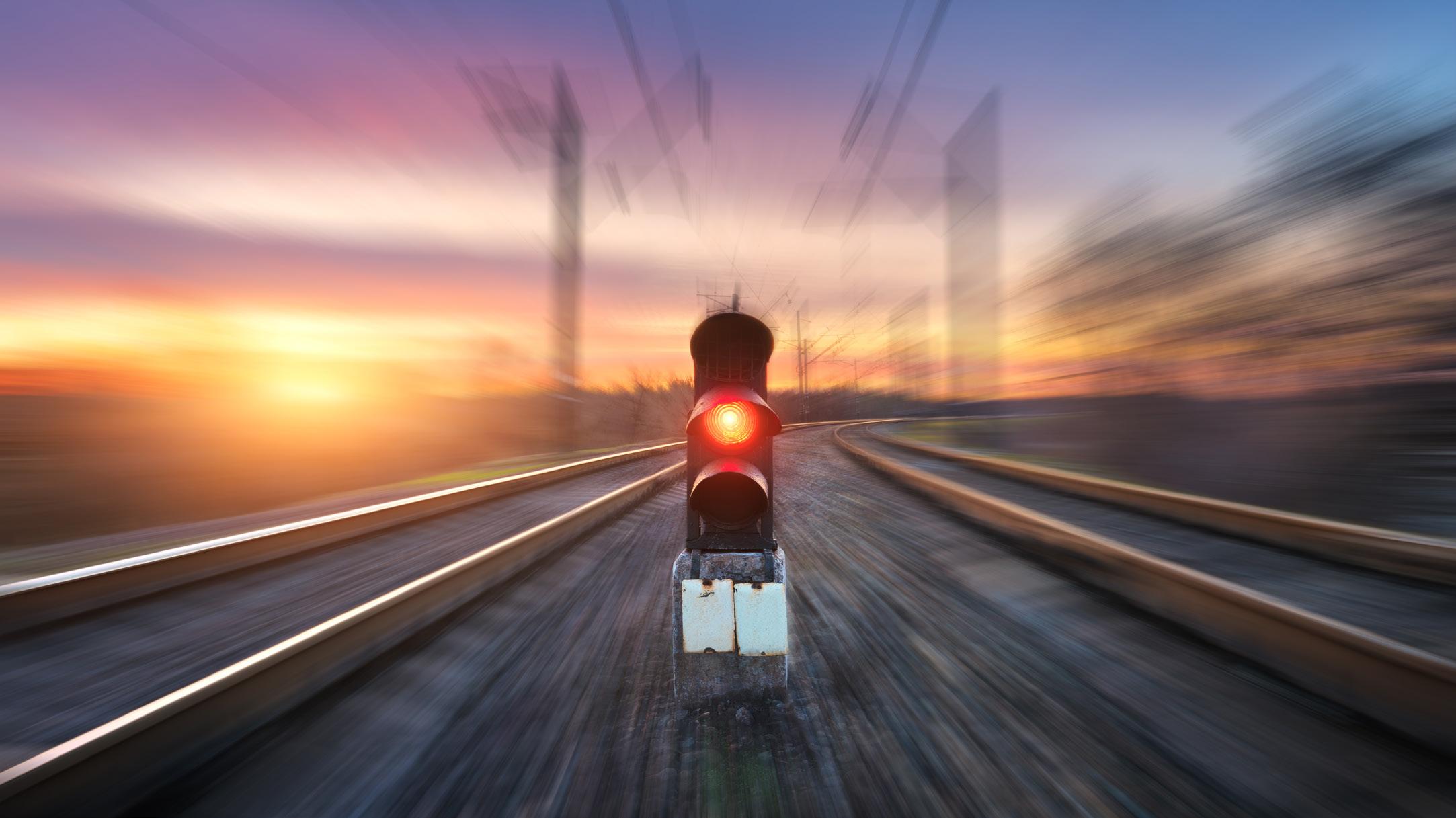
A Signaller’s NTS of effective decision making
As planning is a key NTS for a COSS, the dovetail fit is a Signaller’s NTS of effective decision-making. Their section of track and all the associated train or line activities on it are their full responsibility.
Effective and timely decisions are not made jumping to conclusions or by making assumptions. A systematic, analytical and calm step-by step approach is more likely
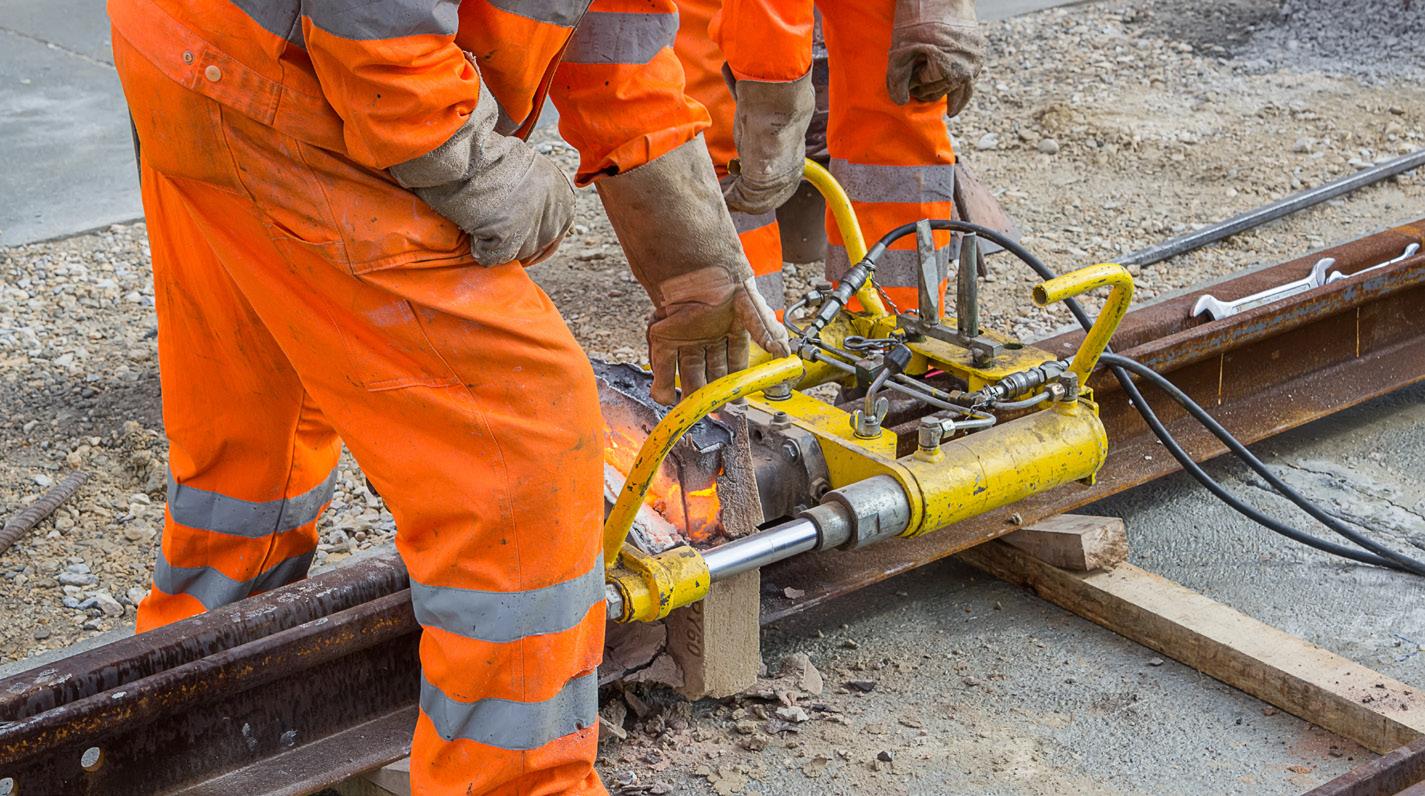
‘Some of the best COSS’s on my team look ahead of time, proactively thinking up front. They may tweak plans as they go along to keep everyone safe.’
to yield a safer solution. A good Signaller will listen and receive all the relevant information; assess it for gaps and collect any further missing facts. It’s protocol to repeat information they’ve received for checking purposes. Once they’re satisfied they have all the correct information they can implement a line blockage with confidence and authority.
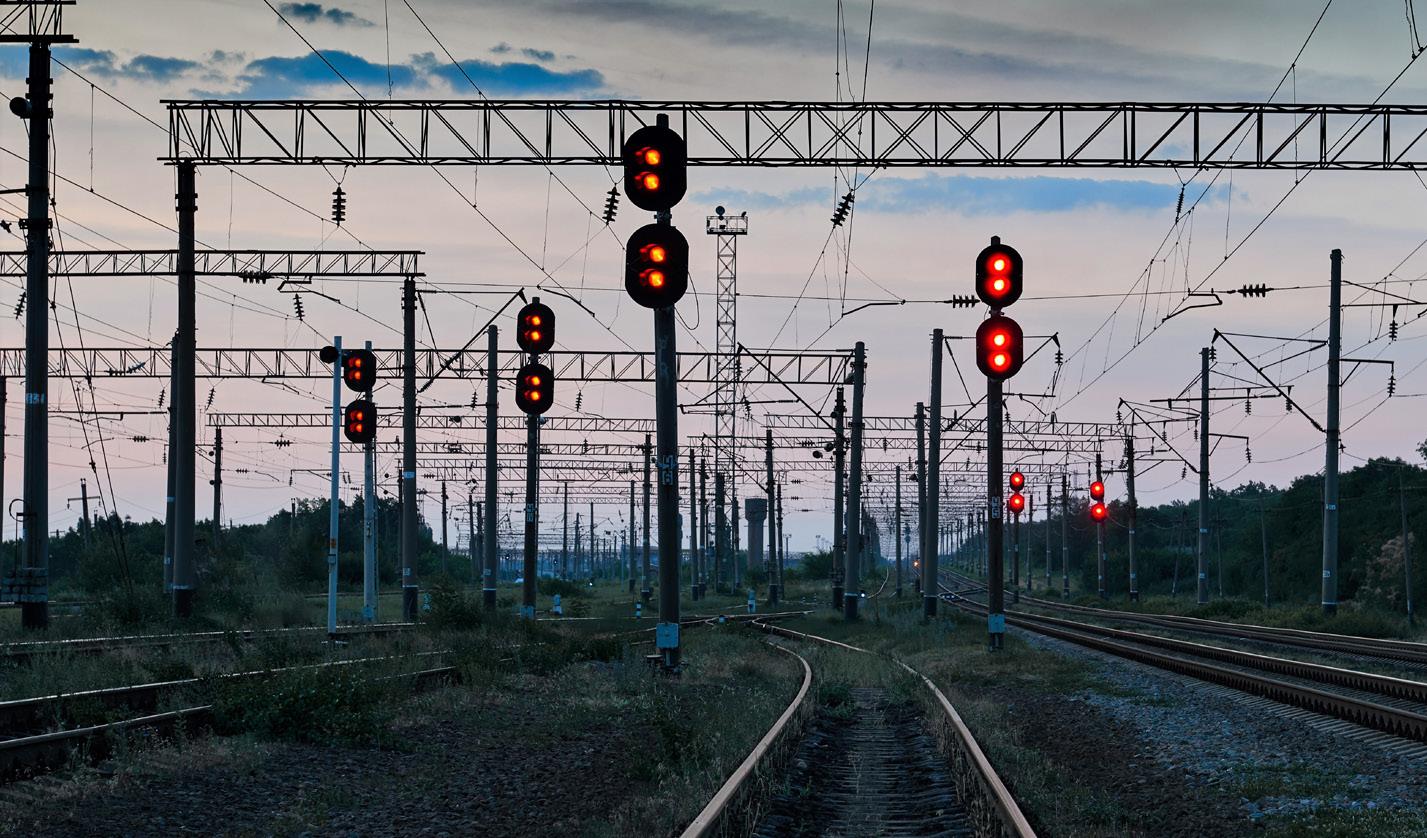
The NTS of conscientious checking
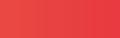
Thorough planning and conscientious checks fit together hand-in-hand. An experienced and effective COSS will conscientiously check everything – especially their teams’ certification, competence and fitness to work. Alongside personnel checks they’ll review work detail, location, access points, equipment or PPE requirements –systematically and thoroughly. They’ll undertakes checks, personally, more than once, giving a final sign-off before leaving for the job. They will not leave this responsibility to another team member or succumb to rushing checks – even if this means a delayed start to the job. Conscientious checking helps save lives.
An IOM said: ‘Some of the best COSS’s I’ve worked with will take ownership for any errors. First, they’ll use it for personal learning and development. Then they’ll also share their mistake with younger, less experienced engineers, and be a real advocate for that particular NTS. Helping them to use it to stay safe.’
NTS of effective communication
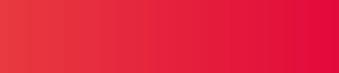
Effective communication is crucial to both a COSS and a signalling role. All communication, written or verbal, whether with a group or with an individual needs to be clear, concise, and following a logical order. Regardless of accent, it’s important that individuals receiving information can follow everything without any ambiguity. Coherent communication by a COSS during a safety briefing, to their team, is essential. An experienced and competent COSS will deliver a safety briefing with confidence,
sticking to protocols. They’ll actively engage with the team, checking that everyone has heard and understood everything. Clear and concise communication between a COSS and a Signaller is crucial for the safety of all concerned. It’s key that processes are followed meticulously when agreeing a line blockage, location and duration. There is no room for misunderstanding through over-familiarity or slang-terms. An exemplary Signaller will stick to communication process steps, regardless of how familiar they may be with the COSS or the work required.
So, what NTS initiatives might help improve track workers’ safety?
The OPC have psychologists who are safetycritical, Human Factors (HF) specialists, who’ve been implementing NTS and Human Factors work with UK and international rail clients for over 25 years. They can help identify what NTS are required in any safety critical role and support in their use during a recruitment process. They run successful NTS training that helps to upskill frontline staff and managers on what NTS are all about and how to use them to develop and enhance safety performance. Following a safety incident, the OPC also support with Post-Incident Assessments (PIA) that can identify the HF root causes of the incident.
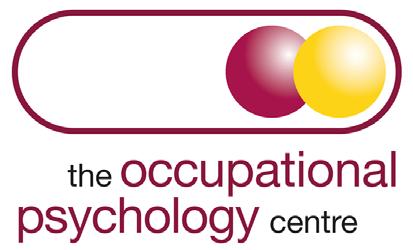
The OPC regularly undertakes PIA with a wide range of operatives to help rail managers uncover the underlying NTS or HF causes of an incident. These PIA are often accompanied by development plans or training initiatives that might assist the employees’ NTS development after an incident.
Many within the industry can recall instances where safety critical personnel may not have applied NTS. This may have led to work being carried out on open lines or in unsafe conditions. In some cases, this may have arisen from one or more NTS shortfall. Perhaps mis-communication on points locations, careless checking, insufficient up-front planning time or poor
detail. Other occasions may have been down to over-familiarity between individuals leading to inadequate checking processes or a reticence to assert themselves when challenged. Any of these NTS shortfalls can easily lead to a track team working on an open line to traffic with the potential for serious injury or fatalities.
An IOM commented: ‘When it goes wrong, and there’s an incident, an NTS gap can sometimes be evident. Root causes of an incident are much less likely to be attributed to what a personnel member has learnt or their technical competence. It’s much more likely to be about their behaviour – what they’ve done or not done.’
Using effective recruitment tools that help assess for key NTS
OPC Assessment has a wide range of assessment tools that can help identify the key NTS when recruiting for many safety-critical roles such as Signallers and COSS. Some of these include: The Risk and Time Focus Questionnaire (RTQ) that helps profile a candidate’s behaviours and attitudes towards risk anticipation, risk management and time focus. The RSJT (Railway situational Judgement Test) is specifically designwed to assess a candidates’ safety judgements, checking and conscientiousness abilities for a safety critical role. Additionally, the Safe Personality Questionnaire (SAFEPQ) assesses for four personality factors; Cautiousness, Conscientiousness, Resilience and Rules Focus that are linked to safe behaviours in the rail industry. Some of these tools have been statistically linked with training and job performance in rail employees. So, there’s evidence to show that these tests do work. They can help to identify safety-critical employees who are more likely to perform better in training and be safer on the job. They can also be used for development purposes with existing employees too.
I can sum up by saying it is good to recognise that we all have a part to play in keeping each other safe. Working together, matching and complimenting each other’s skills to get the job done, keep the network running and deliver customer service –whilst improving safety standards. Seeing the application of NTS in other safety-critical roles, alongside Train Drivers is a really positive step and another milestone in the industry-wide implementation of them.
Smart integrated solutions that and costs. minimise energy maintenance
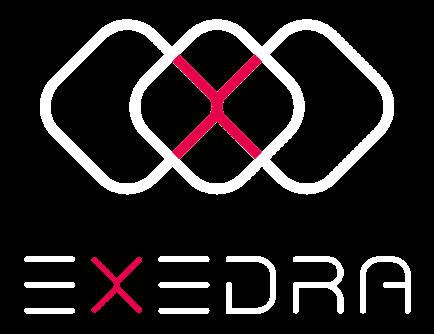



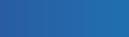
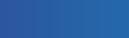
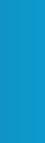


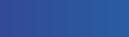



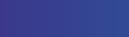
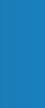



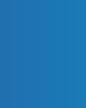

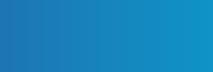

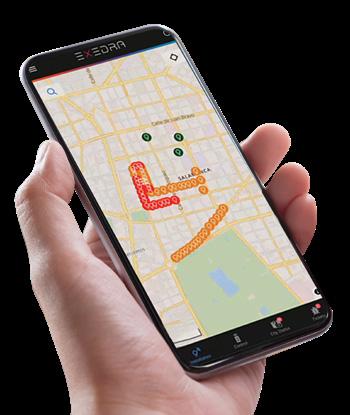




- Whilst prioritising safety and comfort. Talk




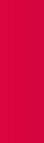
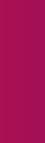





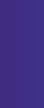

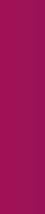





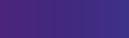


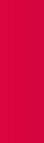
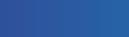
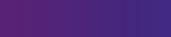
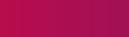


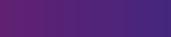

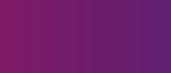
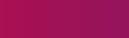
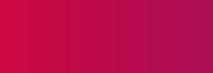
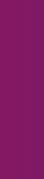
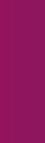


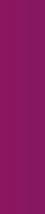
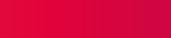

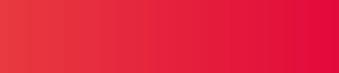

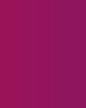


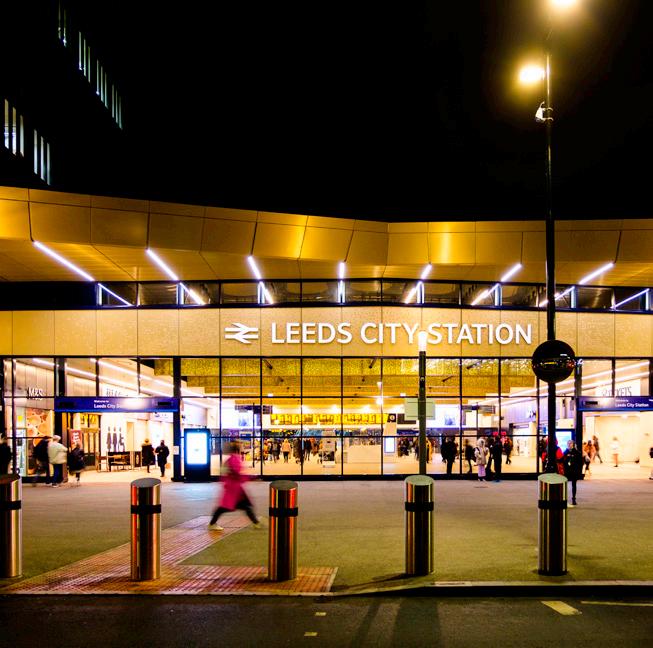

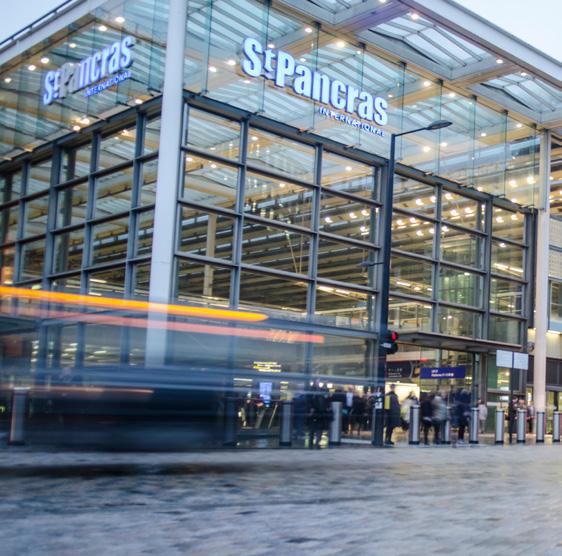
A Geogrid for Demanding Geotechnical Conditions
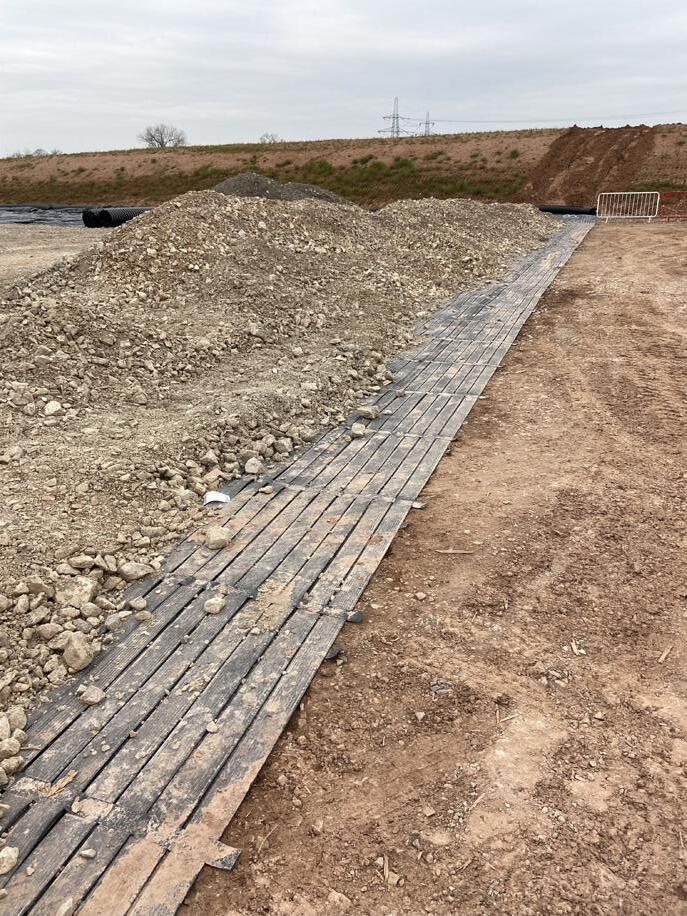
Whenever construction is carried out upon soft or unstable ground, there is the possibility of settlement: this can include geological effects caused by subsidence, sink holes as well as man-made effects, such as mining voids
On the other hand, when overburden on native ground is largely increased, such as with the construction of new embankments, there is the issue of differential settlement or collapse.
Differential settlement can be controlled by the construction of a basal platform to spread the loading upon the ground. In extreme circumstances, this platform can also be supported upon piles, for example within embankments supporting critical road or rail infrastructure. The performance of this platform can be enhanced by using high strength geosynthetic geogrids, which absorb, spread, span or dissipate the vertical loads downwards into the ground or piles. This can often lead to an increase in the pile spacing and therefore offer a significant cost saving through the reduction in number of piles within the basal platform.
Maccaferri Paralink® is a unique high
performance geogrid for use in demanding geotechnical applications where high loads, seismic events or aggressive ground conditions are encountered. Developed in the 1970s, it is the oldest and most proven geogrid of its kind available on the market. Paralink® has been used extensively across the world to span soft ground, piled foundations and voids.
With a BBA certified design life of 120 years, Paralink® offers the most beneficial partial safety factors (including creep, installation damage and chemical resistance), which on average allows 70 per cent of the ultimate tensile strength to be used as the long term design strength value at 120 years.
Paralink® has recently been supplied to the HS2 project for use as part of a basal platform over piles supporting construction of a new embankment on the outskirts of Birmingham. Grades of varying strengths
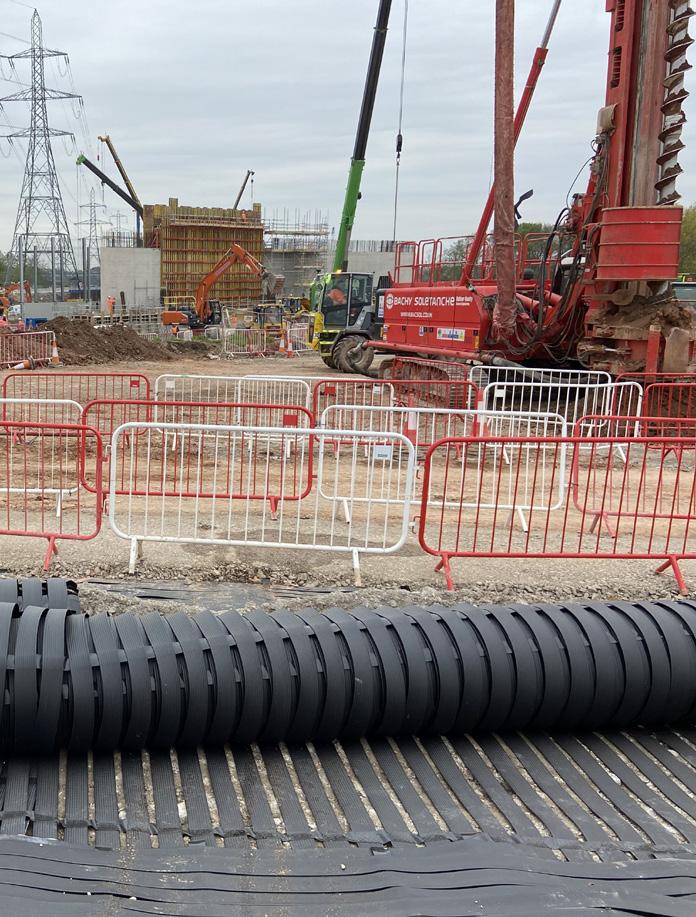
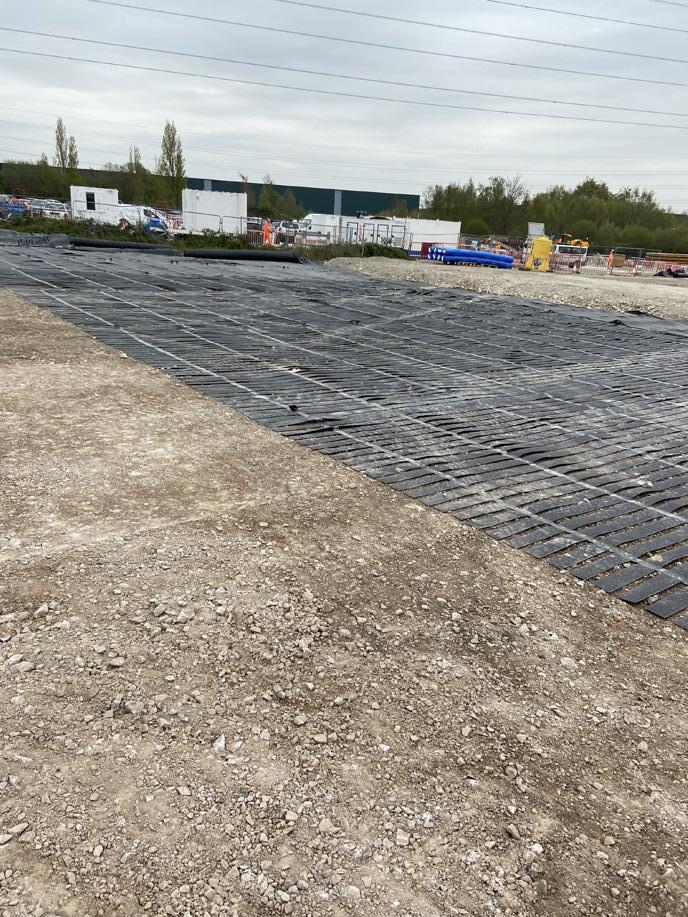
950kN/m to 1,600kN/m were selected to cope with the high loads imparted by the embankment fill and trafficking loads.
Paralink® has also been used on HS2 within a reinforced soil retaining embankment designed to support a temporary track realignment at a location in West London. Paralink® 1200kN/m strength geogrid was selected by the designers to accommodate the high loading conditions on the embankment resulting from the location of large gantry cranes next to the diverted rail track.
Tel: 01865 770 555
Email: Info.uk@maccaferri.com
Visit: www.maccaferri.com/uk/
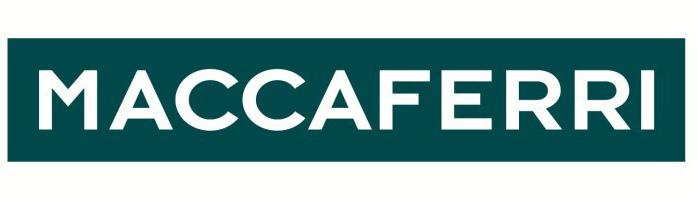


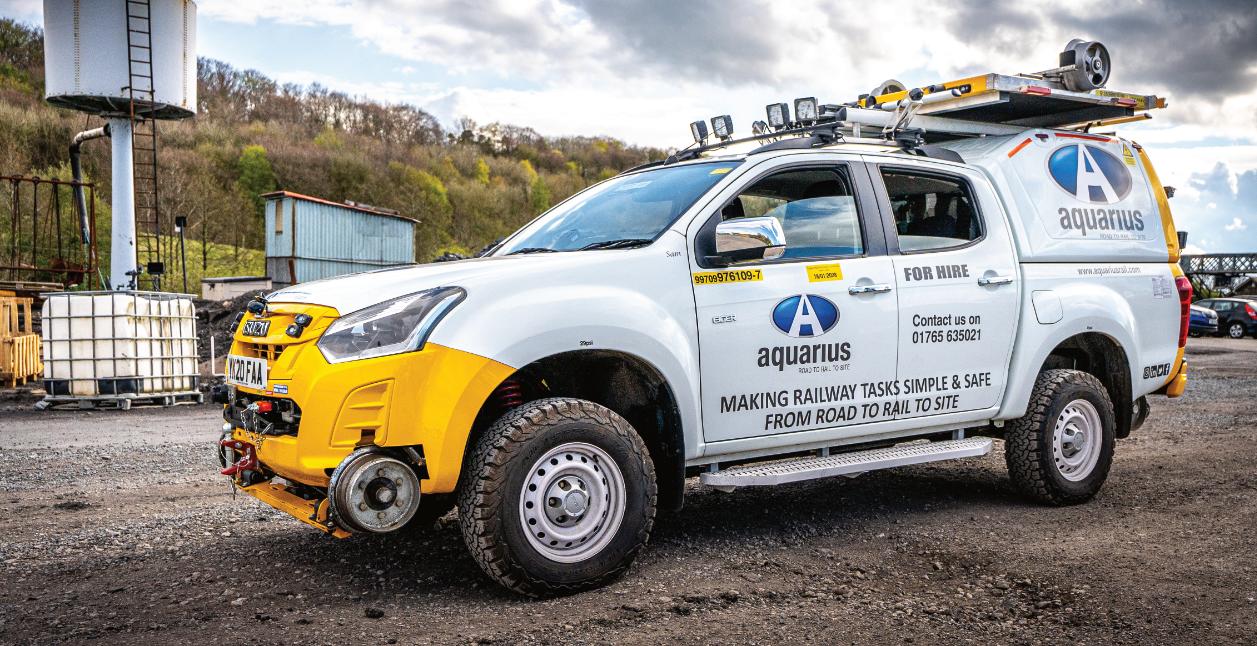
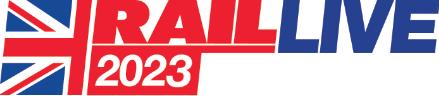
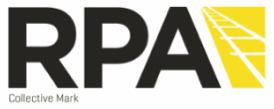

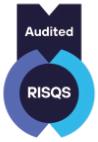
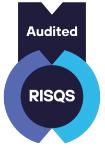
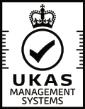

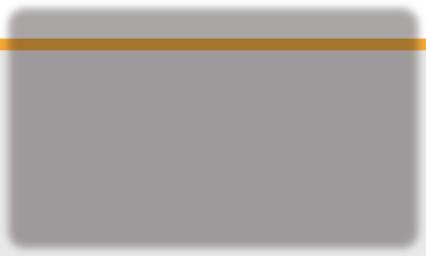
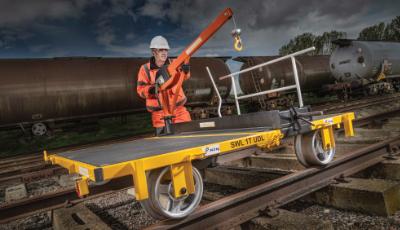
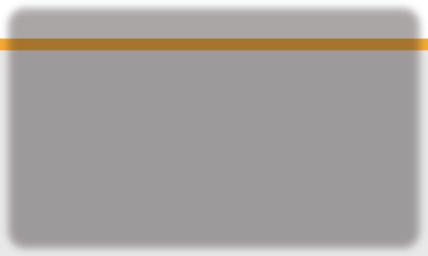
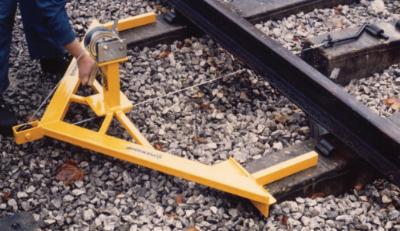
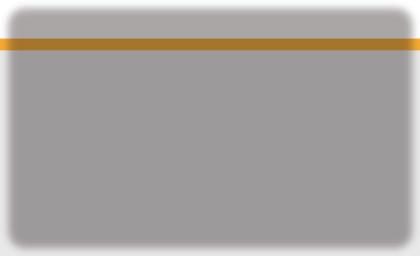

Smart Integrated Lighting Solutions
Rising fuel prices, the growing problem of road congestion and the need to move towards sustainability make rail more than ever the most appropriate means of transport. There has never been a better time to reduce costs and build confidence in outdoor areas
For over 115 years, Schréder, an independent, family-owned company, has dedicated itself to exploring everything there is about the potential of light, constantly pushing the boundaries of technological innovations. Expertise, passion, innovation, and sustainability drive 2,600+ employees to use the power of light for the safety and well-being of all, from
public spaces to higher-risk environments, such as railway stations, commuter routes and carparks, where the consequences of a dark or dimly lit area can lead to injuries.
In May 2022, Woolwich railway station was opened for the first time to the public as part of the Elizabeth Line, after Crossrail announced the handover of ownership to TFL (Transport for London). Operating up to twelve trains per hour travelling
to Canary Wharf and Central London, this ‘new’ station was built by Balfour Beatty Kilpatrick and designed by Weston Williamson, Mott MacDonald, and Arup Group (engineering).
Crossrail describes the station as a ‘portal connecting the elements of the surrounding heritage listed buildings and the large retail units, to enhance the experience both in and out of the station.’ Additionally, their
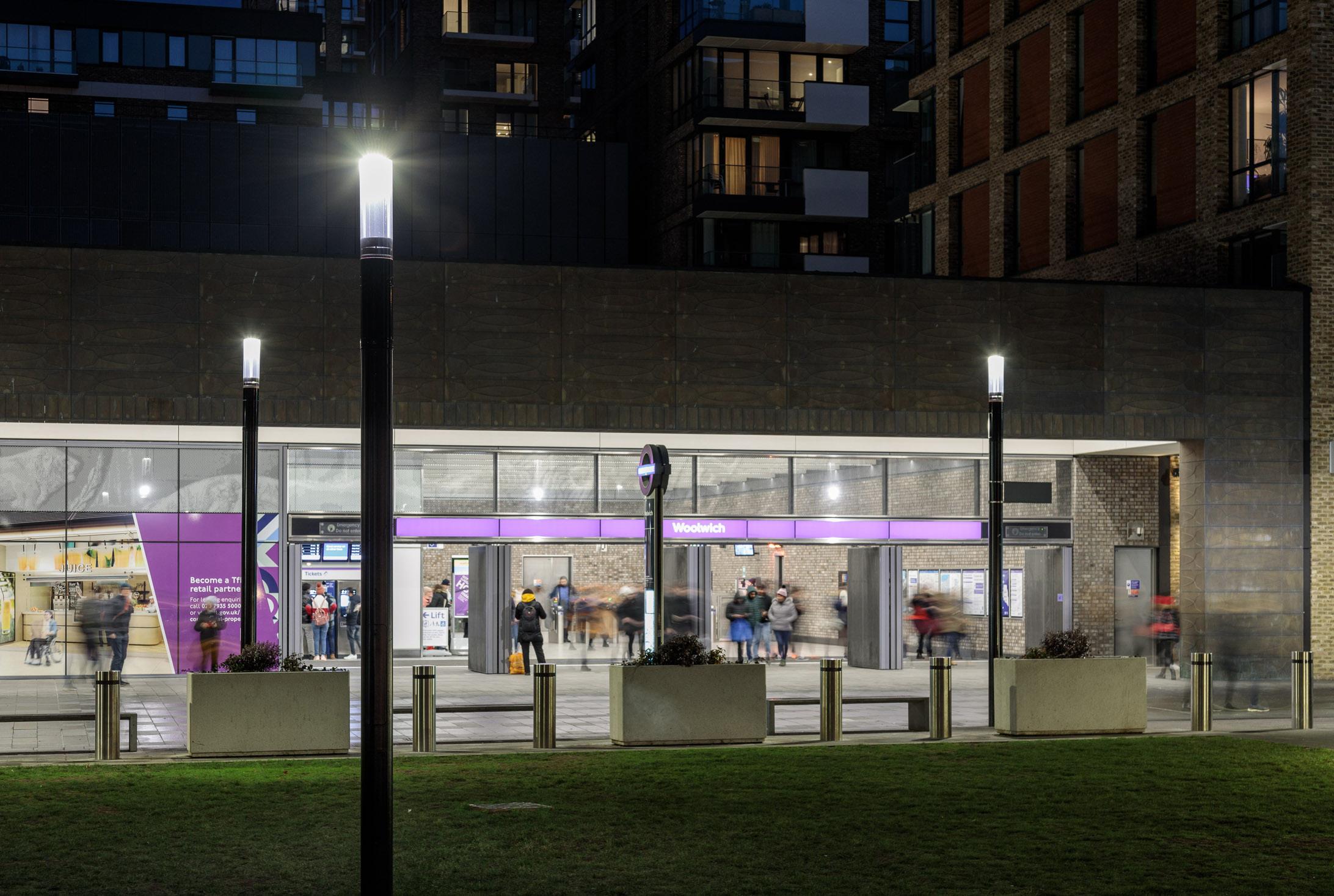
unique urban realm design not only improves the experience for visitors inside, but also connects the station to the wider town centre.
Amongst the complimentary and architecturally thoughtout designs surrounding the station, you can also find multiple 5.2-metre Schréder black polyester SHUFFLE units, at the forefront of the station, directing and helping people travel with ease. 360° and 180 ° camera modules were added to the multifunctional Schréder SHUFFLE columns creating a safe, pleasant place, informing and entertaining people, whilst the relighting of the approach roads – Station way, with SENSO lanterns and Woolwich New Road with AXIA GEN 2 blends into the area elegantly, guiding people safely from main street to station.
The comfortable ambient lighting creates attractive environments, while state-of-theart surveillance cameras, with digital zoom or fully motorised control, keeps an eye on people and their valuables such as bicycles, deterring the unwary and providing a sense of security.
Schréder takes the smart LED

With energy prices relentlessly rising, there has never been a better time for local authorities to reduce overhead costs, prioritise safety and build confidence in outdoor areas. Money is often wasted on poorly designed systems which don’t benefit the comfort of the commuters/ travellers or your finances, and what people don’t know is that installing the optimal lighting solution for each area of the station also offers significant financial savings too.
Schréder’s EXEDRA, is a remote-control system which allows you to monitor, meter and manage in a lighting network. It is a complete solution based on open standards and protocols. Schréder’s EXEDRA offers a unique combination of state-of-the-art technology and an easy-to-use web interface to control each luminaire, at all times, through a secure internet connection. With bi-directional communication, the operating status, energy consumption and possible failures can be monitored. As a result, this improves efficiency: accurate real-time data and energy savings of up to 85 per cent.
Whether it is the station forefront, carparks, platforms, footbridges, tunnels, junctions, or maintenance pits, Schréder’s dedicated systems offer solutions to suit YOUR space. Schréder’s expertise enables any environment to be transformed into a safe, sustainable, and cost-effective place
where the commuters can travel with ease and no worries. Schréder’s lighting systems also require less maintenance than traditional discharge lamps, which means another reduction in costs.
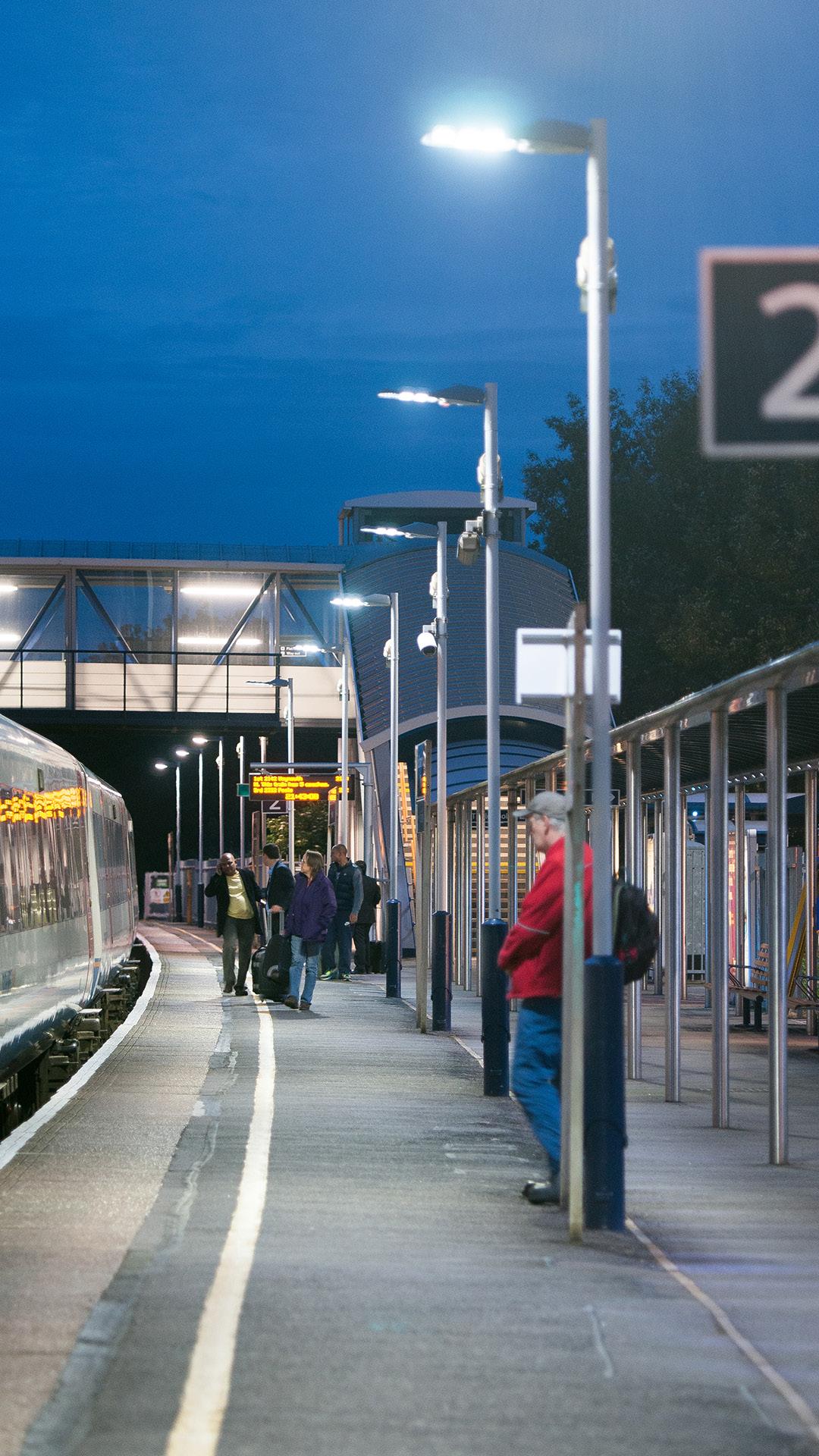
However, connecting your luminaires is not just about adding in a control system to the products you are having installed, it’s much more than that. It is about control of the area you are lighting, it’s about the space the lights are in and the people who are using that space, it’s about delivering solutions beyond lighting for electric mobility, security, information, and entertainment. Is the light right for type of areas? Are you lighting an area to reduce the crime rate? What type of lighting will attract people to use that space? And do you need to dim the light during certain hours of the night but have the control to be able to make them bright again should there be an emergency? Are you wanting to look for energy efficient lighting, a more sustainable solution that reduces your costs?
So, by taking all of this into consideration, the place, the space, the people, the light, the control, let’s get connected!
Why Urbis Schréder?
High quality, yet energyefficient and low-maintenance lighting provides a strategic asset for the development of a sustainable and beneficial railway infrastructure. Urbis Schréder’s wide range of lighting solutions for the rail industry, combined with the company’s expertise and outstanding heritage in delivering breakthrough projects, creates the best possible experience for passengers and staff in the station environment.
Critical to delivering a safe and pleasant passenger experience inside and in the vicinity of a station is appropriate lighting solutions. New technology also offers the rail industry the ability to improve station lighting and significantly reduce cost. By combining traditional street lighting, LED handrails, continuous tiled lighting, and ground level inclination lighting; it is possible to create a bright and effective environment. The improved visibility reduces the risk of crime in a station environment and increases passenger confidence.
Schréder’s solutions are not just limited to rail, but also extend to interior and exterior lighting such as workspace, roads, architectural buildings, urban deco, sports, cities/communities etc. As the company has done so for many years, it provides beneficial LED alternatives to luminaires with fluorescent lamps and can offer a uniform and comfortable lighting suited to any area of choice, whether that’s interior or exterior, helping enhance spaces and create places, people love to live, learn, travel, and play in.
To find out how Schréder can support your vision for connected, safe and sustainable places get in touch via the contact information below.
Tel: 01256 354446
Email: sales@urbis-schreder.com
Visit: www.schreder.com
LinkedIn: Urbis Schréder
Address: Urbis Schréder
Sapphire House Lime Tree Way, Basingstoke RG24 8GG
Custom Flooring for your Rail Interior
Forbo Flooring’s wide portfolio of rail floor and wall covering collections are designed in-house and made a working reality with modern printing and manufacturing techniques
The results combine inspiring designs with the required performance – no matter what combination of floor and wall coverings are selected. Forbo’s portfolio has been designed, so that the entrance systems, carpets, textile floor coverings and resilient floorcoverings are available in contrasting and complementary colourways.

Forbo’s experienced designers can help at any stage in the design process, depending on what involvement you require. If you are
looking for ideas, re-coloration of existing designs in its current collections or help with the development of a totally custom design that will work perfectly with your rail interior design scheme, then Forbo can guide you through the whole process.
Forbo also offers a cut to shape and size service, whether it is a complete rail floorcovering carriage layout or the addition of logos and signage, the possibilities are endless. From an initial concept, detailed drawing, or computer file, the design team will prepare a flooring design that is
transferred electronically to the cutting machines. These computer-controlled machines represent state-of-the-art cutting technology and produce precision cut items, accurate to a fraction of a millimetre.
Coral FR: textile clean-off entrance systems
If you are looking to make a statement with your entrance flooring, and don’t see exactly what you are looking for in the Coral FR standard collections (Coral Classic FR, Coral Brush FR, Coral Duo FR, Coral Welcome FR), then custom colourways are always an option. Forbo can match to physical samples, NCS, RAL or Pantone colours. Inset logos can also be designed and incorporated into Coral FR entrance flooring.
Marmoleum FR² / Striato FR: linoleum floor coverings
With over 140 references across a variety of marbled, patterned, and solid design effects, Forbo aims to offer real design freedom and options for the vast majority of rail interior design concepts. However, whenever a customised flooring solution is required, it is important to note that re-coloration is offered across all of the Marmoleum FR2 and Striato FR collections. So, you can achieve any of the designs in your own chosen colourway.
Flotex FR: textile, flocked floor coverings
This unique high-density textile substrate allows for customisation using rotary or digital printing technologies.
Flotex Colour FR is a rotary printed collection of four semi plain designs each with a full colour palette. Flotex Vision FR is a collection of over 500+ high definition digitally printed references ranging from abstracts with an intricate colour spectrum to realistic images of natural materials. There is the also the option for recoloration of any of the existing designs from these two collections.
Alternatively, you can choose to create your own Flotex FR masterpiece using Forbo’s bespoke design service alongside its high-definition print technology. The high-definition print technology allows for larger scale pattern repeats and vivid lifelike colours providing ultimate design flexibility.
Coral Move Vision FR: broadloom carpets
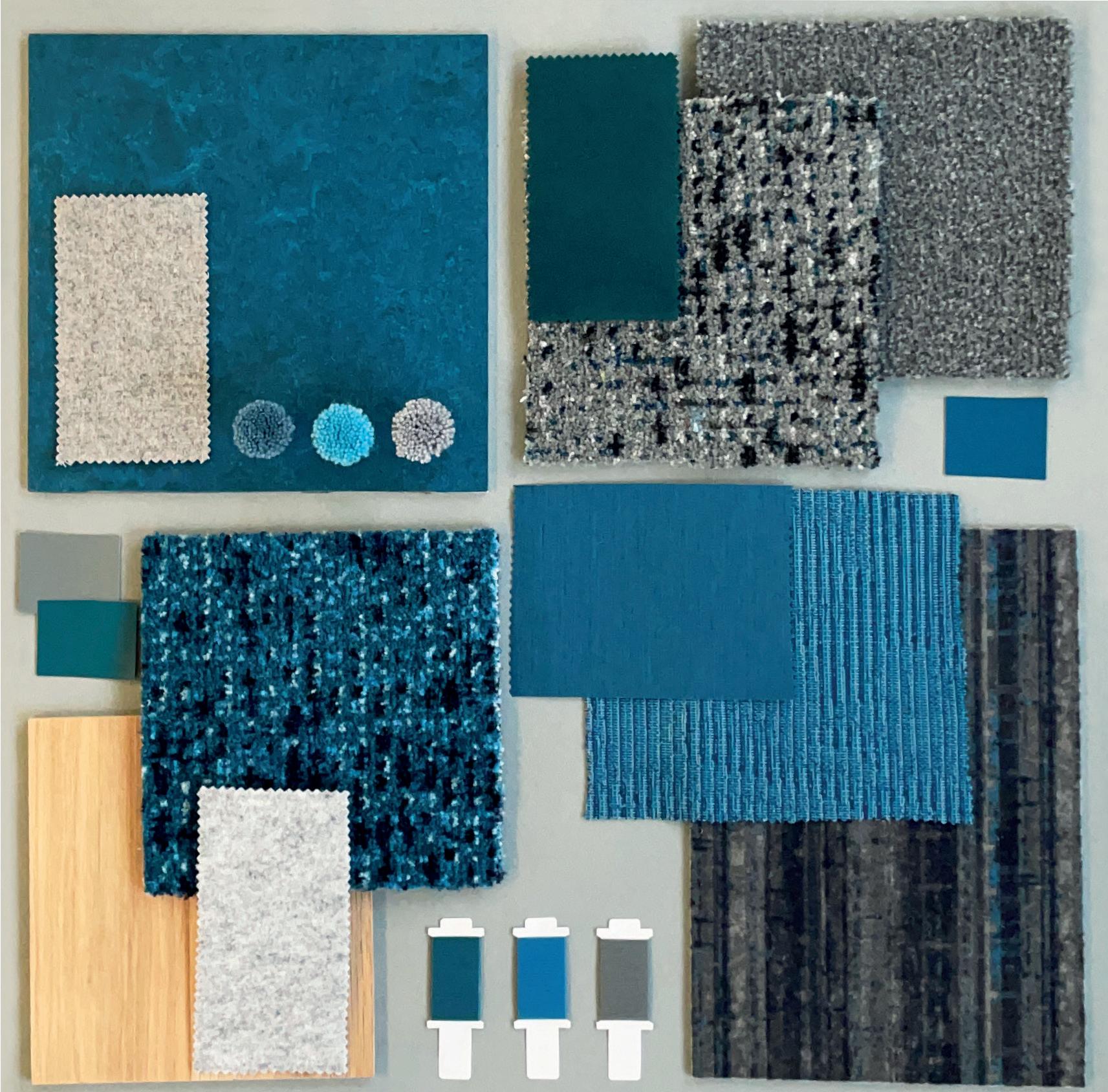
Depending on the desired aesthetic, the Forbo design team will advise whether a tufted (Coral Move FR) or a digitally printed (Coral Move Vision FR) solution will give you the best result for your rail project. The dedicated design team will work with you to match carpet design and colour requirements on an individual project by project basis.
Coral Move FR is manufactured to a bespoke tufted design specification, giving design flexibility. Different tufting design styles can give very different overall aesthetics. There is a wide selection of yarn colourways, and special colours can be matched to NCS, RAL, Pantone references as required.
Coral Move Vision FR uses a digital printing process, allowing for far greater customisation possibilities in terms of both design and colour. The digital printing process makes non-linear type designs possible, is perfect for complicated designs or when there are a variety of colourways within a design.
Fleet FR: textile wall and ceiling coverings
Fleet FR is offered in four standard colourways, however custom colourways can also be supplied upon request, to match any NCS, RAL or Pantone colour, enabling specific colours to complement any interior design scheme.
Tel: 01773 744121
Email: transport@forbo.com
Visit: www.forbo-flooring.com/rail
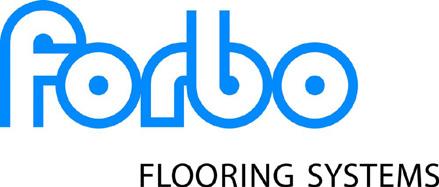
Feeling is Believing –Build, Test, Refine
CAD renderings and VR or AR environments can certainly help to gather feedback from users to inform the design process. However, even at their best, these technologies can lack the level of fidelity that hands on experience can provide to build confidence among stakeholders.
Efficient translation of ideas into suitably representative physical assemblies that can be tested and evaluated is one of the key challenges to reducing development lead times.
DCA is always looking for new ways to speed up the process of turning 3D CAD data into physical rigs, models and prototypes. Many of the products the company designs are small enough to be held in one hand, and rigs and prototypes for these can be rapidly prototyped using a range of in-house 3D printers and 5-axis CNC machinery centres. Transportation mock-ups are however, generally far larger and scale is often a problem for these machines.
The recent introduction of large scale CNC machining at DCA gives it the ability to profile much larger parts far more quickly than previous manual methods allowed, working directly from the design team’s 3D CAD data.
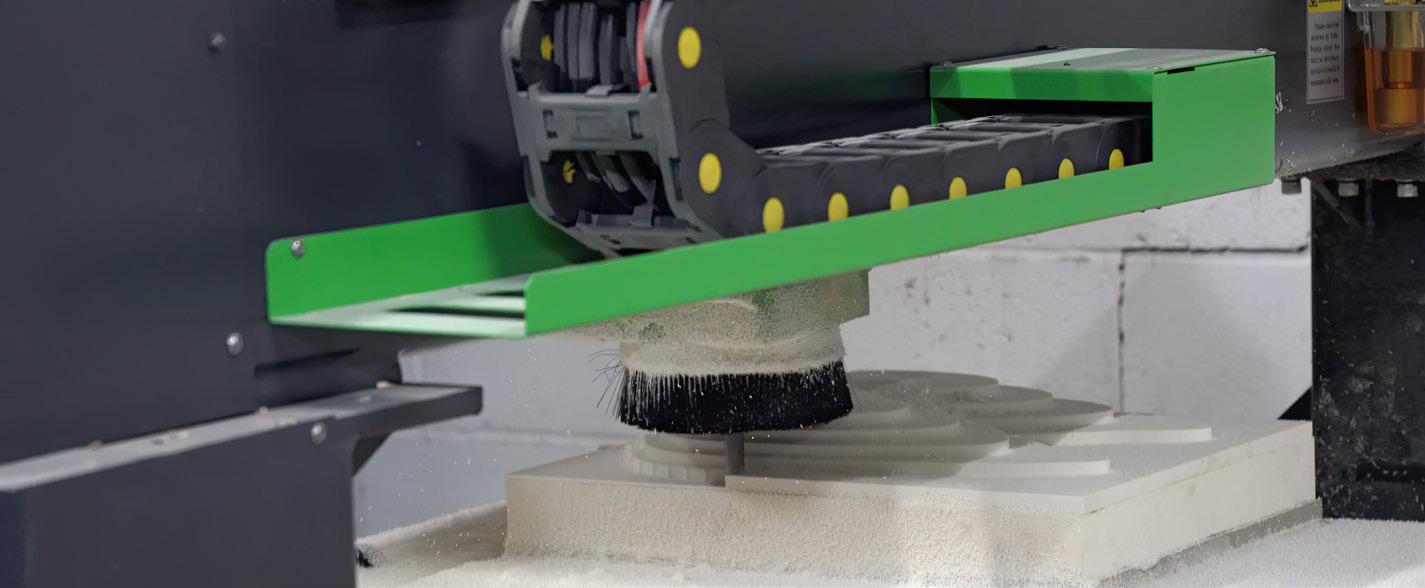
The resulting large profiled sections are then assembled and finished by an experienced team of model makers and technicians to create full size rigs and mock-ups in the workshops. Using Human Factors (HF) expertise to review these with a suitable cross section of users and stakeholders provides the feedback necessary to establish how well the criteria for, say, comfort or anthropometric compliance can be achieved.
The process that DCA now offers links 3D CAD generated design data to an initial desk based HF review, followed up quickly with physical testing. For a large proportion of any new vehicle proposition, using dimensional checks of CAD data against
established anthropometric data for the target operating region enables DCA to analyse and determine whether a design can meet the requirements of all the relevant regulations, the contractual demands and best practice expectations, including those for customers with disabilities and special needs. However, there will always be some issues that cannot be resolved by such a desk based assessment and need to be tested practically using physical rigs or mock-ups.
A good example of this is the forthcoming introduction of Rail Industry Guidance GMGN2696. This addresses the need to assess passenger seat comfort. A key part of the process is to establish just how well a seat
design meets the objectives that determine comfort. The criteria are laid out by a series of tables with scores that are obtained by measurement, in the first instance from 3D CAD data. The next and vital part of the process is to run physical tests on the seat.
As part of DCA’s response to this new Guidance, it has created its own seat comfort test rig, complete with a set of buttock profiles to simulate passenger loading on the seat. In combination with pressure pad instrumentation, this test rig has allowed it to test and assess the potential comfort of proposed seat geometries and cushion profiles and materials before committing to pre-production solutions and user trials.
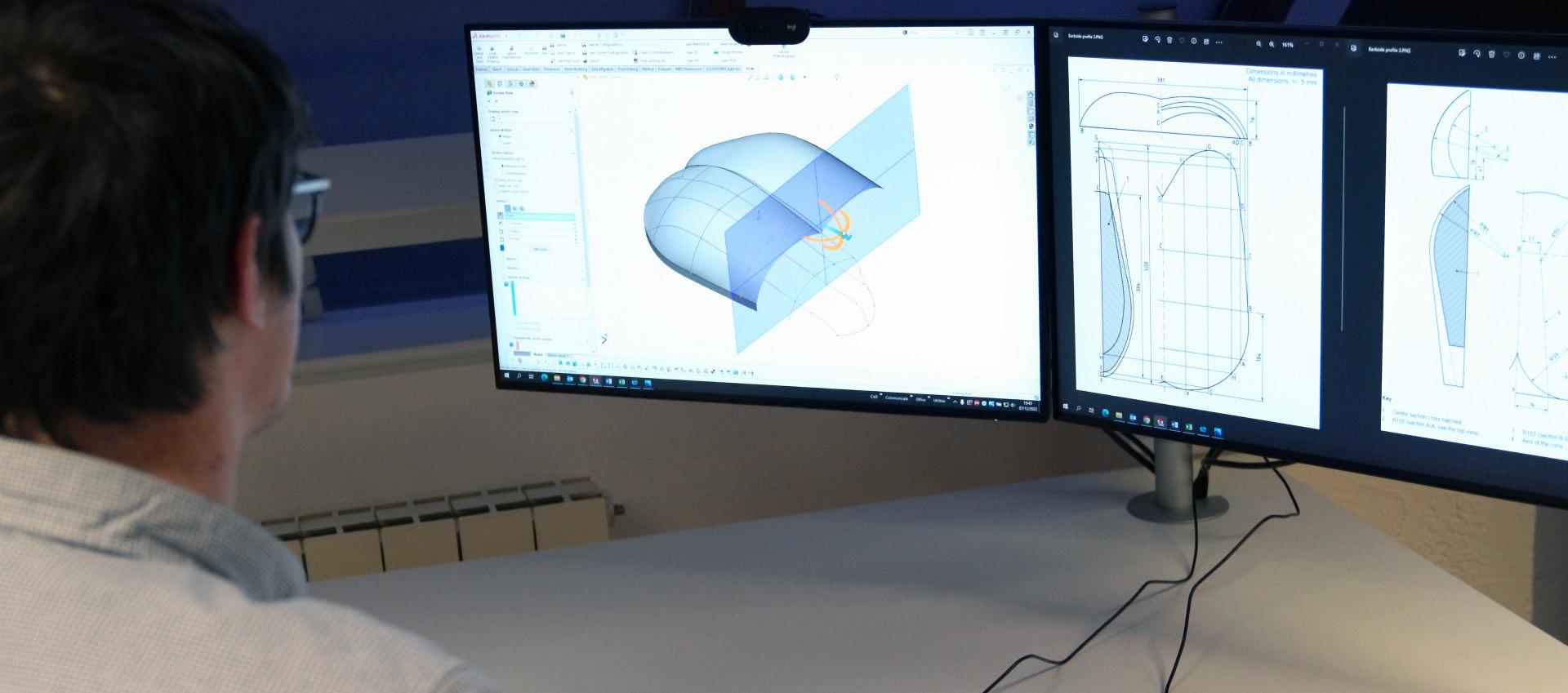
When it comes to assessing the design of products that we are expected to interact with, to sit on, climb on, grip, push or pull, there is no substitute for physically interacting with them
DCA provides several quick and practical solutions that enable it to test its larger scale product design propositions. The first option combines a simple functional rig produced quickly using its 3D CNC router in structural foam or unfinished wood/ MDF with a Virtual Reality (VR) model overlay. The use of real time rendering and a VR headset enables true user interactions to take place, say a task analysis or a sequence of control events, with the action taking place in the virtual world while the mock-up provides just the physical touch points.
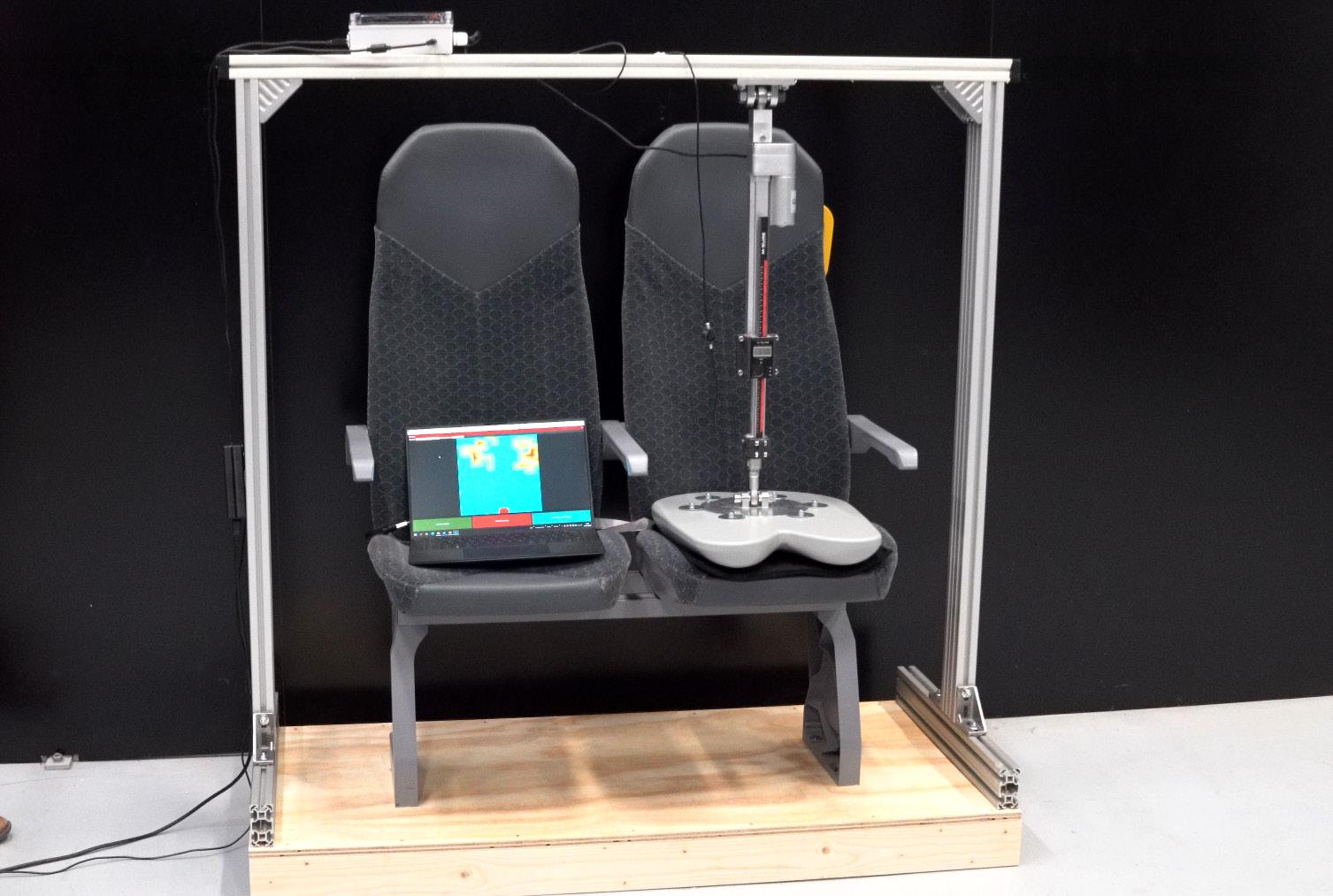
The second option uses a rapid build process to construct representative visual prototypes. For most of us, being able to see and touch a physical model provides the most tangible feedback. Being able to look round a model that represents the actual design vision allows a personal engagement to take place. In the context of a train driver’s cab or a car interior, which deals with a complex 3D environment, it is hard to convey the design experience through visuals or VR alone. Vitally for mass transit solutions such physical mock-ups allow simultaneous interactions with multiple users drawn from a representative range of customer groups. Such interactions can incorporate boarding and disembarkation trials, including under emergency conditions.
The aim with this process is to establish quick results and confidence in the designs. By keeping all the activities during this rapid build, interactive review process in–house and using its own skilled team of designers, ergonomists, engineers, model makers and technicians, DCA controls the process and can gain valuable insights early on. This enables changes or improvements to be made and assessed while a design idea is still in its infancy before critical financial decisions have to made. This in turn, encourages more design options to be assessed, including some that might be considered too high risk without such physical assessment procedures. The time saved and flexibility to change or adapt, leading to better design outcomes, makes the investment in this interactive design and development process well worth making.
EN 45545 Approved Cable Glands and Entries...
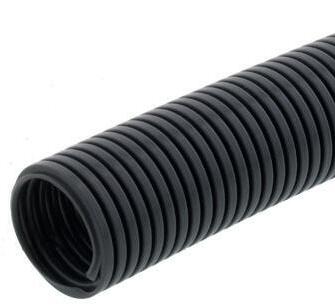
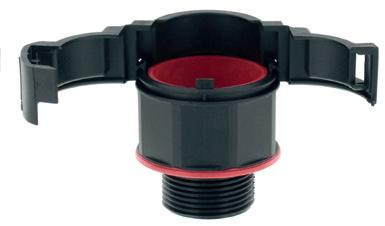
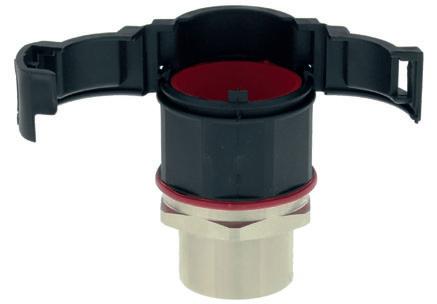
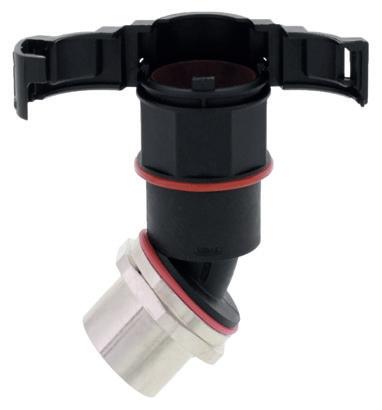
Tel: 01926499461
Email: transport@dca-design.com
Visit: www.dca-design.com

For over 100 years WISKA have been at the forefront of cable management design and innvoation. This level of expertise has resulted in the development of our lastest range of products, introducing The Railway Series by WISKA.

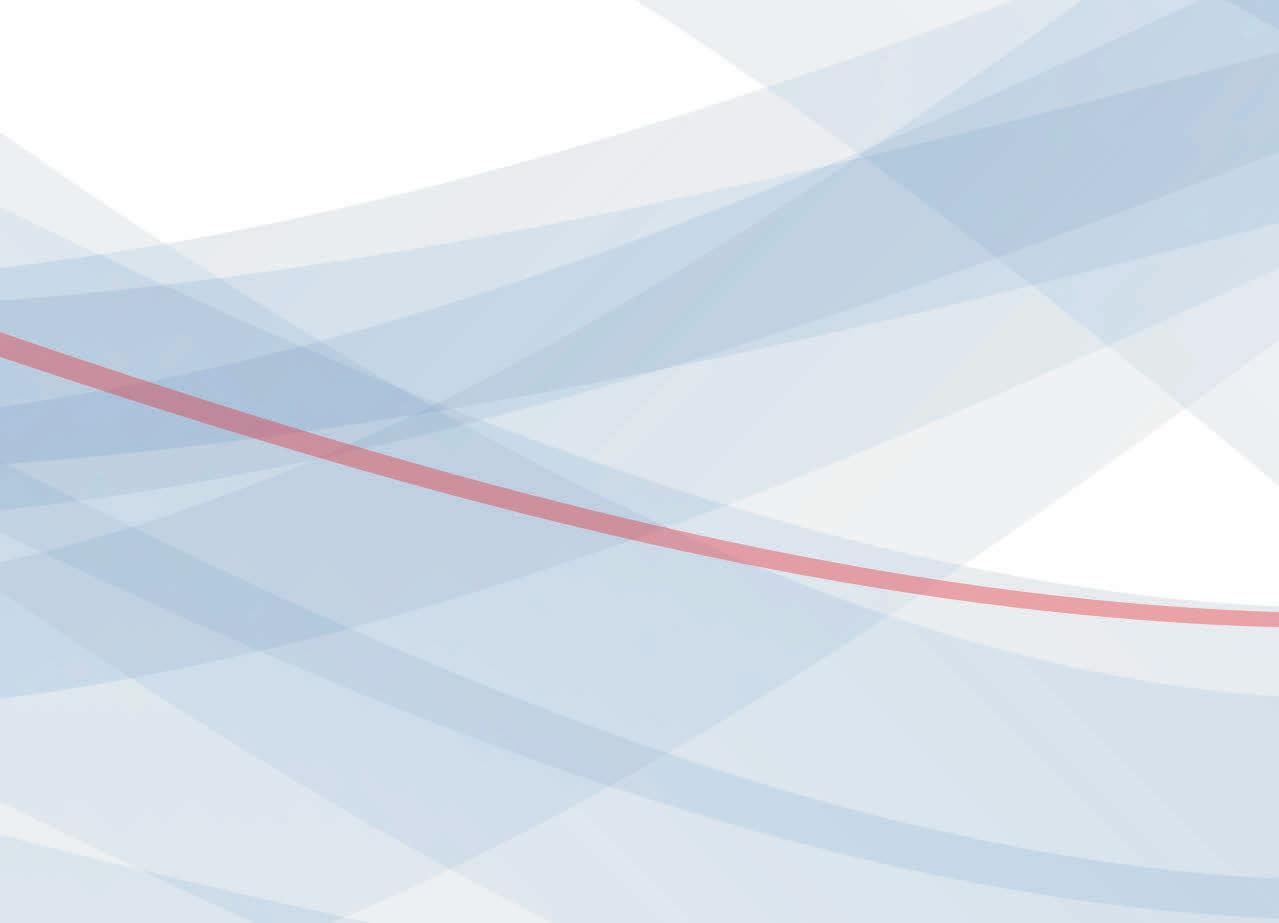
The Railway Series is a comprehensive range of industry-specific cable glands and conduit solutions in accordance with EN 45545.
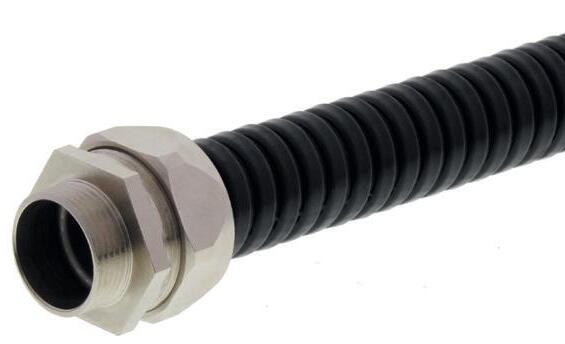
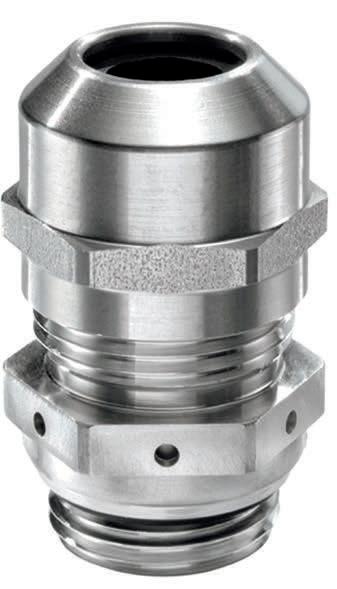
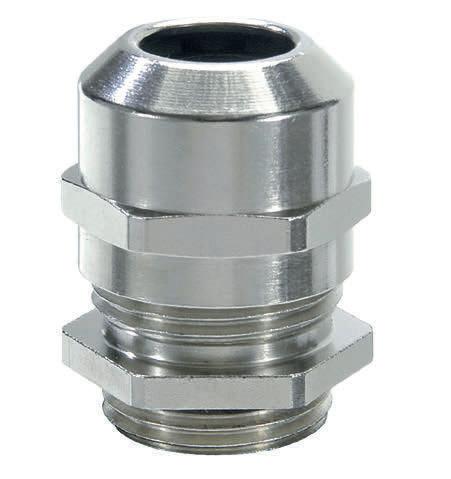

Need an expert? Speak to us today.
01208 816062 / 01208 816708 / www.wiska.co.uk / info@wiska.co.uk
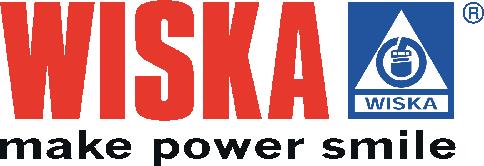
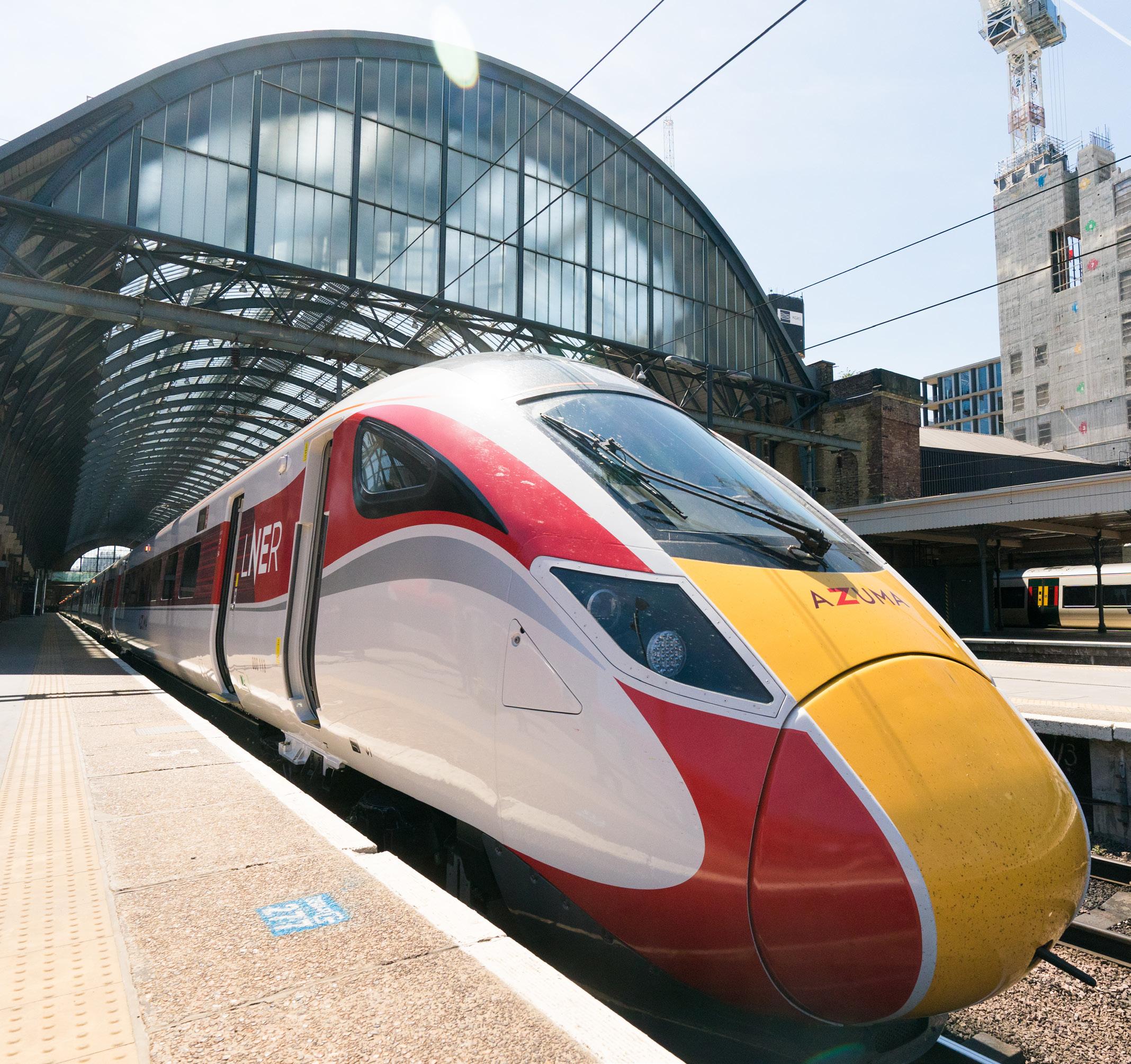
Going from Strength to Strength
Fast becoming recognised and specified as a key supplier to the Rail Industry, Step on Safety is currently enjoying huge growth in demand for their anti-slip GRP access solutions
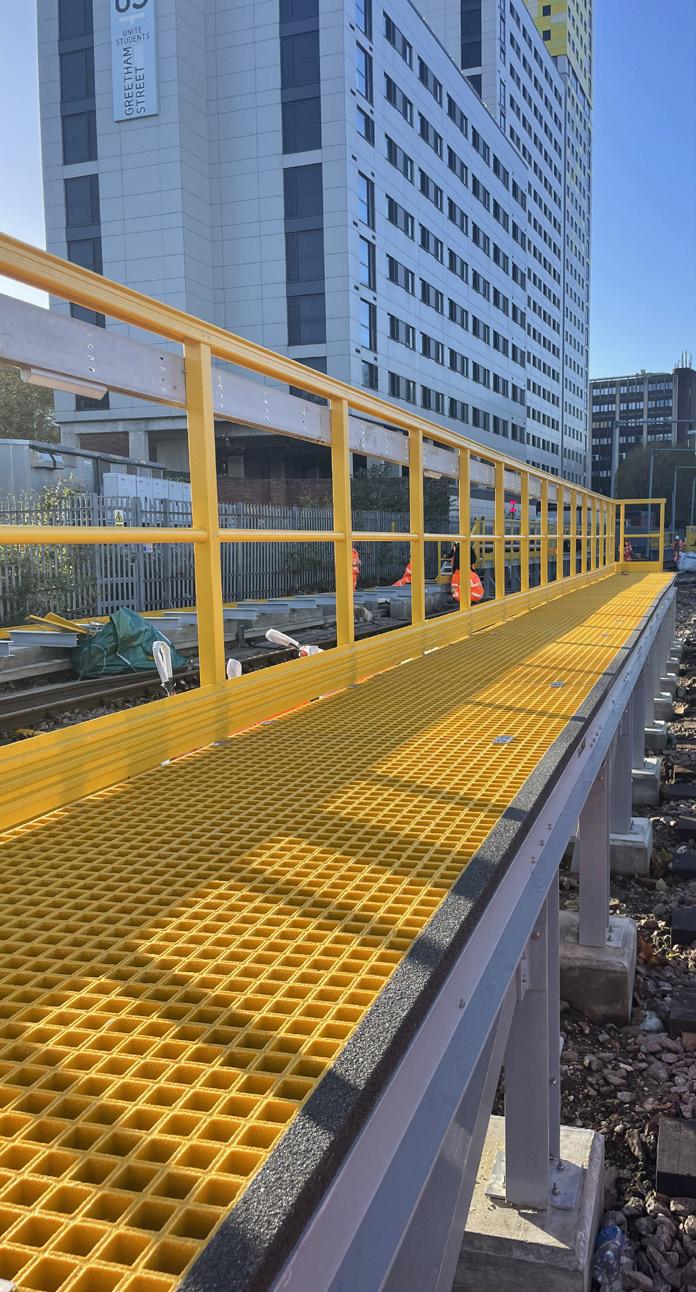
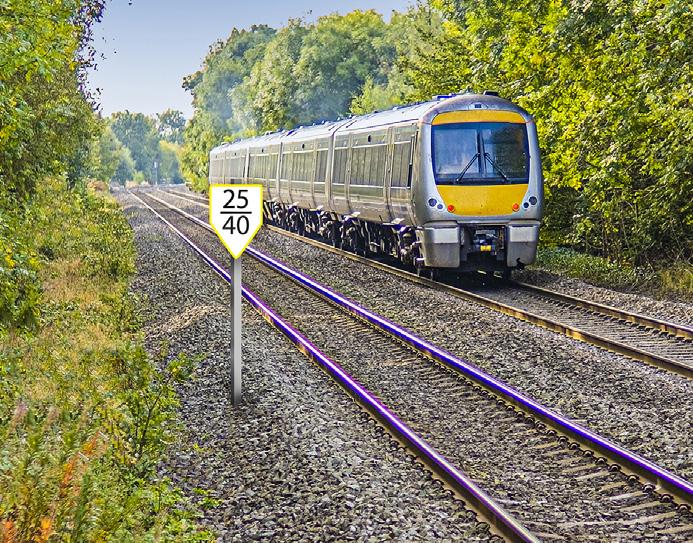
In the first part of 2023 they’ve supplied embankment staircases for 25 locations in Scotland – with more in the pipeline – and have begun production of 26 staircases bound for Wales. In the Southern regions, 40 Driver’s Access Platforms (DAPs) ranging from ten metres to 55 metres long can be seen across depots in Wimbledon, Guildford and Portsmouth. Made using GRP profiles, QuartzGrip® Open Mesh Grating and SafeRail™ Handrail, the platforms provide a hi-vis, anti-slip landing point for drivers and maintenance crews to access trains safely.
The staircases and platforms are all built at the SoS Suffolk headquarters before being shipped out in modules for installation. A second workshop is being built to allow them to increase the number of fabricator teams to meet the current demand and to provide the space that these huge projects demand.
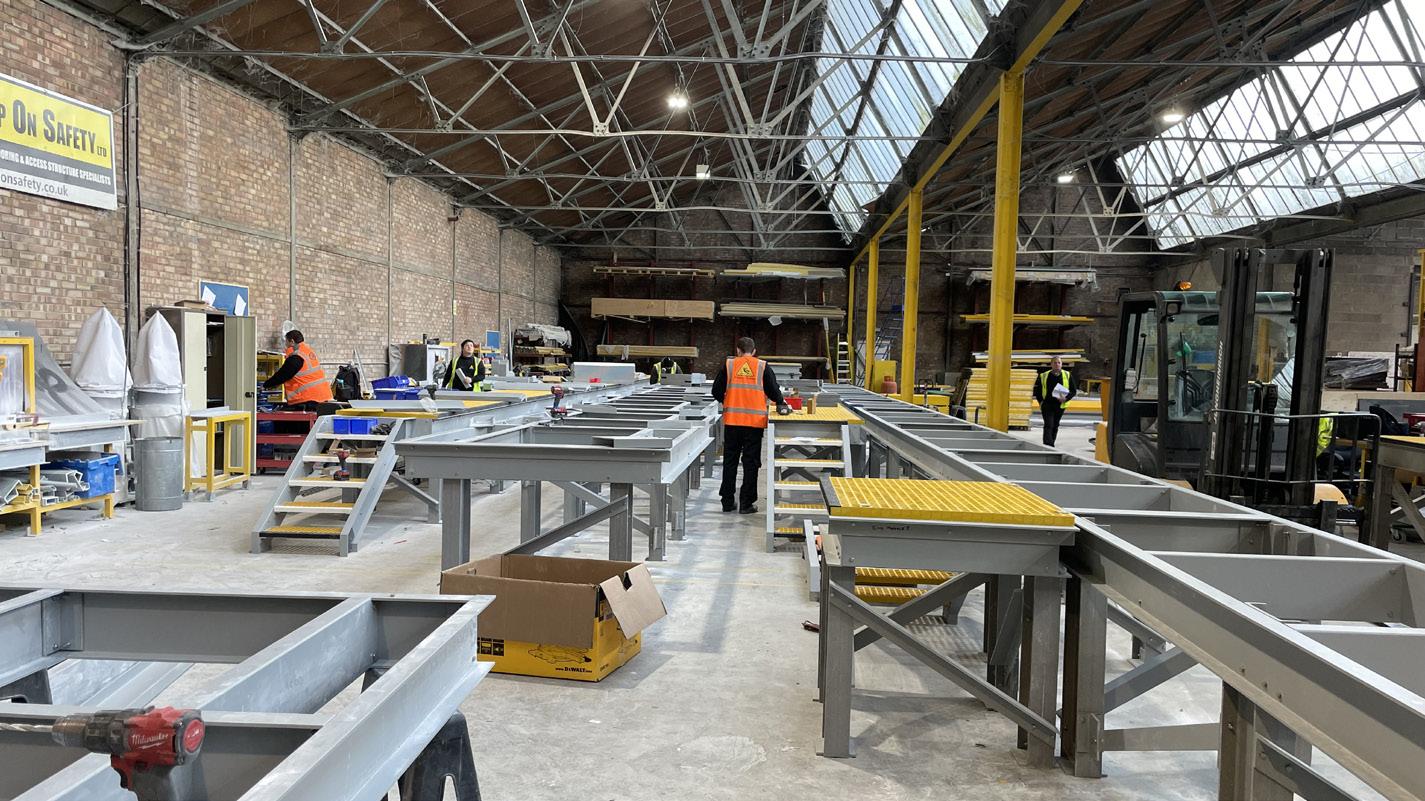
Introducing LitePost™
Developed with the engineers at FJD Consulting Ltd, LitePost™ is a combined post and foundation system made entirely
from GRP and designed to stay safely in place without the need for concrete anchors. Simply dig a hole, position the post and backfill. The design allows the soil or ballast to hold the post securely in position, preventing it from twisting or leaning. When the equipment is no longer needed, it can be dug out and reused. And, because it’s made from Glass Reinforced Plastic, it’s lightweight, it won’t rust and has zero scrap value.
LitePost™ will be available in a number of configurations to suit low-level and high-level signage, SPTs, small electrical equipment housings and signals/indicators. The cost savings in installation time and materials they’ll offer are huge. It’s being officially launched at Rail Live 2023 and you’ll be able to see on the Step on Safety Stand and on the Network Rail one. If you want to know more before then, get in touch with the Step on Safety Rail Team.
Tel: 01206 396 446
Email: sales@steponsafety.co.uk
Visit: www.steponsafety.co.uk
On Track for a Greener Future
Torrent Trackside is a business built for rail
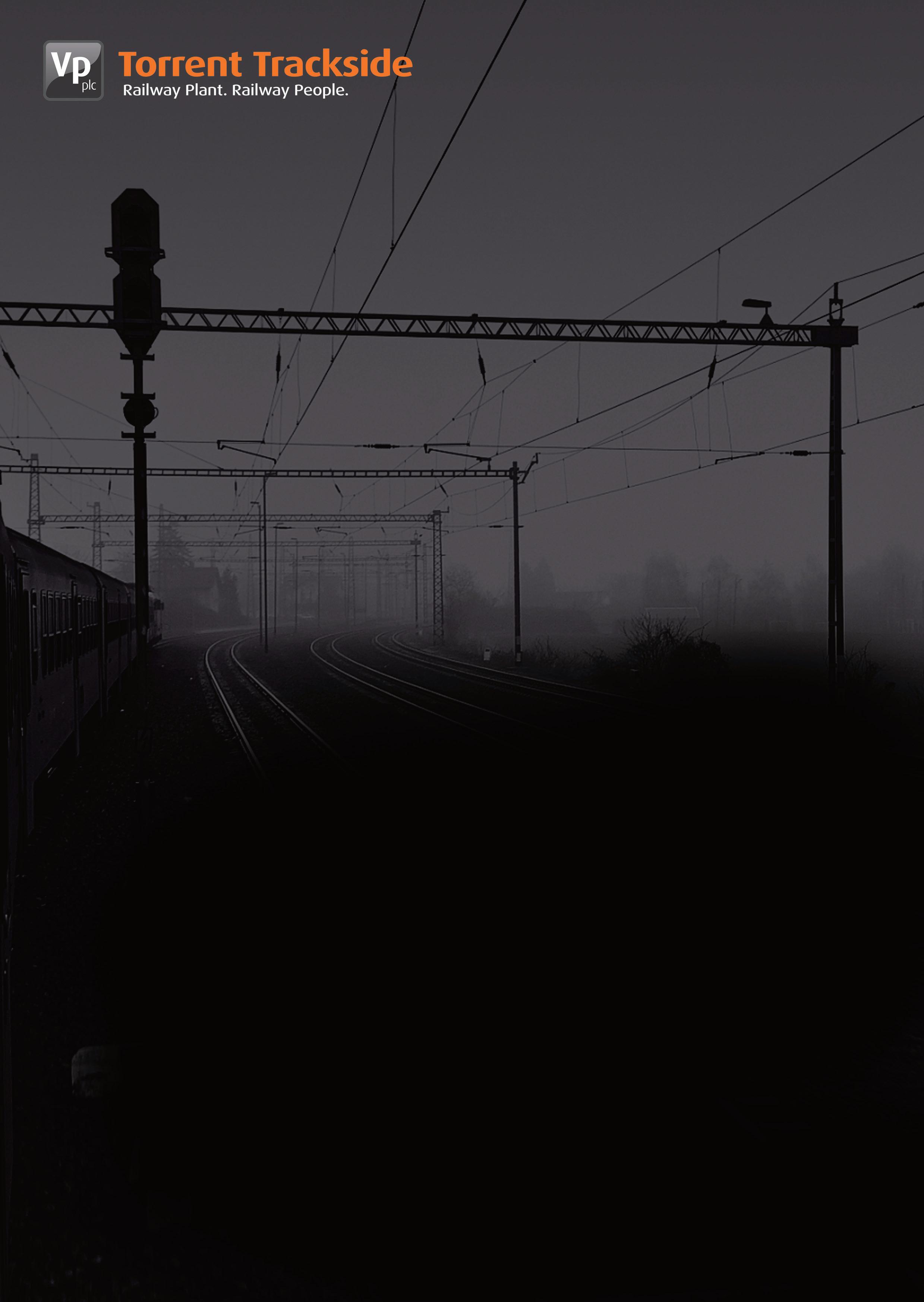
We are committed to investing in the latest battery powered tools, lighting and equipment which provide outstanding levels of power and efficiency The advantages of battery power include:
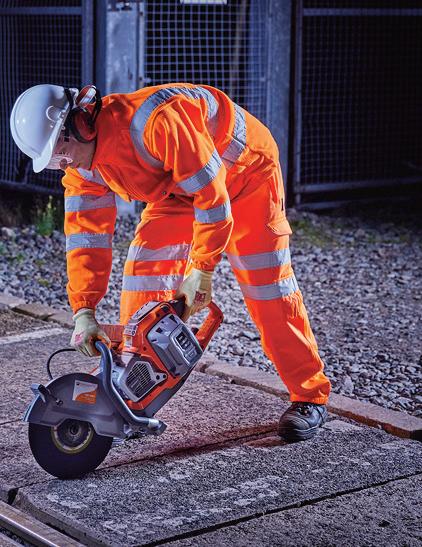
l Zero emissions - better for the environment and safer for the operator
l Instant power at the flick of a switch - no tugging on pull cords
l Significant reduction in HAVs - up to 80% for some tools
l Battery tools are smaller, lighter and easier to transport
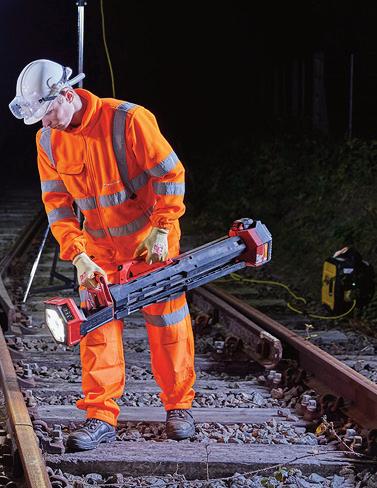
l Noise Reduction - ideal for built up residential areas and night time working
Download our brochure
As part of our commitment to a greener future Torrent Trackside will no longer be printing brochures To view or download our new brochure scan this QR code or visit the brochures section on our website: www.torrenttrackside.co.uk/brochures/
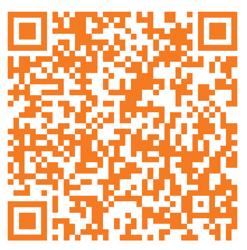
Torrent Trackside will be exhibiting at this year’s Rail Live Come and see all our new battery and solar products at the Vp Village, Stand G7, main concourse

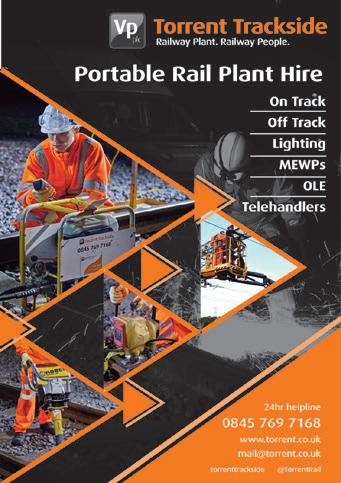
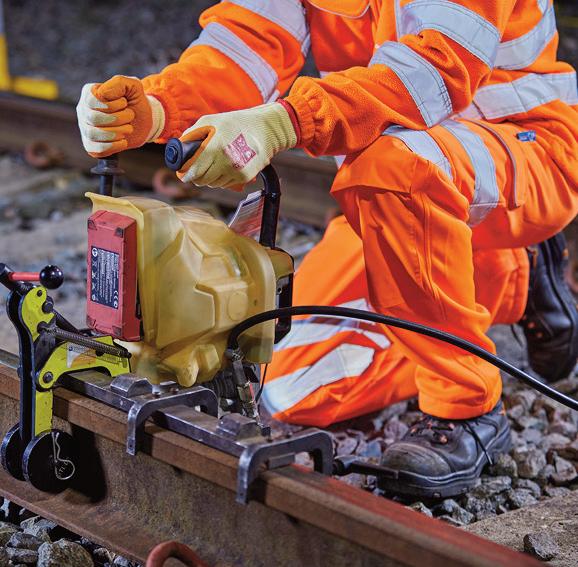
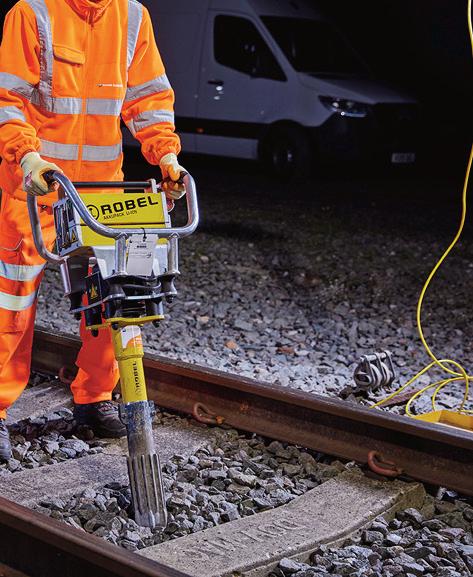

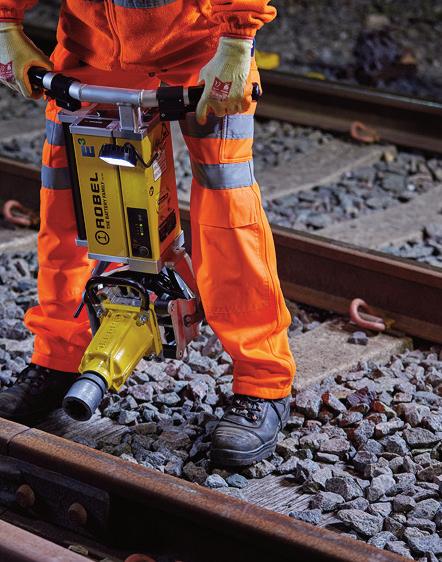
l Battery and solar lighting is powerful, lightweight and silent r 24hr helpline 0845 769 7168
www.torrent .co.uk mail@torrent .co.uk


@TorrentRail

Reduce your Maintenance Unit Costs (MUC)
The Permaquip MUC Revolution shows you the way. Permaquip’s team of industry experts is dedicated to helping you find simple and safe solutions that work for unique challenges. With this cutting-edge technology and unparalleled industry knowledge, the team is confident that they can help you reduce your MUC and optimise your budget.
The approach is simple – send in your challenges and the company will show you a Permaquip solution that works for you. The answer may be one of the existing products, or the team will work with you to develop a new innovation that's tailored to your unique requirements.
To talk to Permaquip about your challenges, meet the Permaquip team on Stand F11 at Rail Live on 21 and 22 June 2023.
Permaquip and Aquarius Rail are poised to continue their growth, providing unparalleled rail products to customers here
in the UK and around the world. Permaquip recently announced the appointment of Richard Cradock as Product and Service Development Manager. Richard brings over 30 years of rail experience, having worked globally for companies such as British Rail and Geismar.
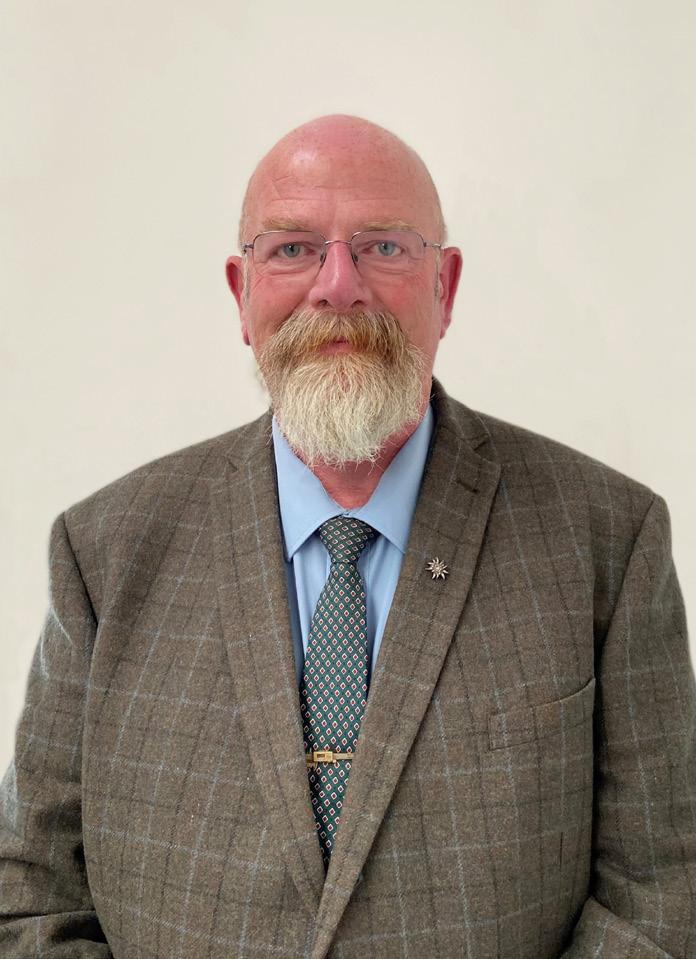
‘We are thrilled to welcome Richard to our team’ said Scott Harrison, Chief Operating Officer at Permaquip. ‘His extensive rail experience and knowledge of the industry will be a tremendous asset to our company as we continue to provide the best rail plant systems to our customers, both nationally and internationally.’
Coupled with the experience of the existing team, Richard's appointment reaffirms Permaquip's commitment to delivering solutions to the most critical issues our customers face in track renewal and maintenance.
For more information, visit: www.permaquip.co.uk
Bollé Safety Presents Universal Goggle
To protect the eyes of industry professionals and ensure their optimal safety, Bollé Safety is launching Universal Goggle, the premium iconic model of its new range of goggles. The goggle is designed with an accordion-style bellows system that allows the goggle to conform to the user's face and evenly distributes the goggle’s pressure across the face. This ensures an optimised fit for each morphology and individual. The bi-material frame is made with TPR1 for greater flexibility and comfort, and PC2 for better impact resistance and optical clarity. The product is compatible with prescription glasses as slots on the goggle allow most prescription glasses to fit perfectly under the goggle without creating any pressure points.
Finally, the Universal Goggle can be easily dismantled allowing materials (TRP, PC and Nylon) to be recycled separately and packaged in a high-density polyethylene bag that is 100 per cent recycled and recyclable. This model is also compatible with a face shield that aims to protect the lower part of the face. This face shield clips easily and intuitively onto the Universal Goggle.
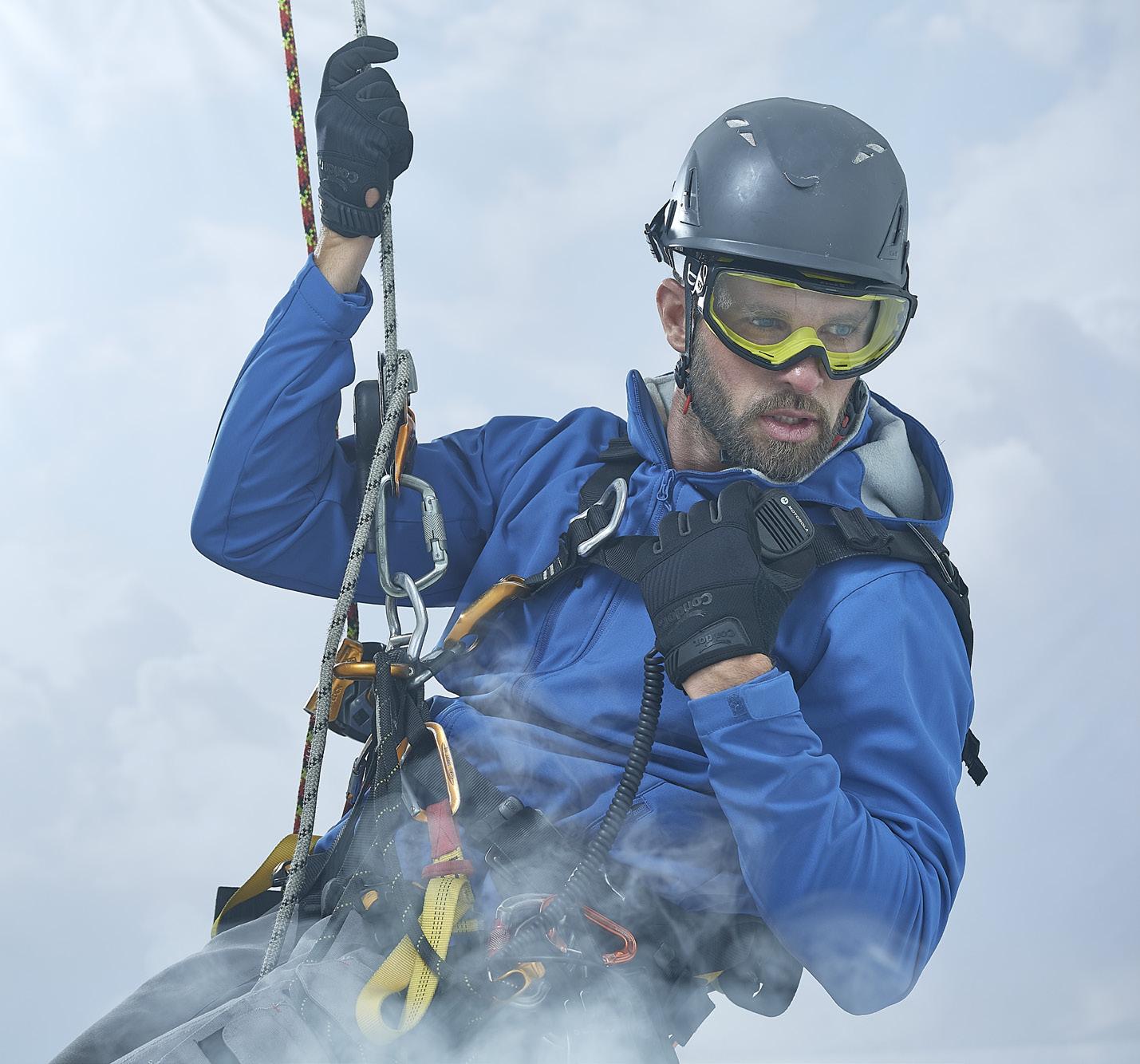
SYSTRA bolsters UK-IRL business with two strategic appointments
Llewelyn Morgan joins SYSTRA as Head of Innovation and Dr Peter Weldon joins as Director of Net Zero Transport.
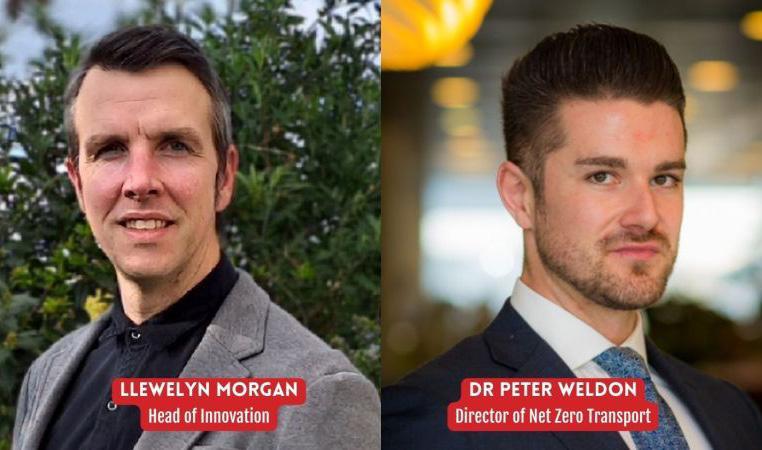
The Tyne and Wear Metro has appointed a new Operations Director. Kevin Storey has taken over the responsibility for overseeing the day to day running of services on the network following a successful recruitment process.
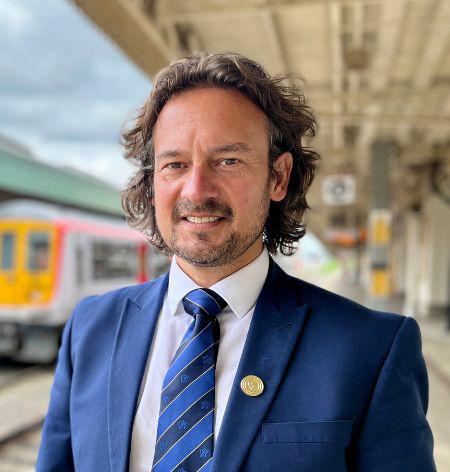
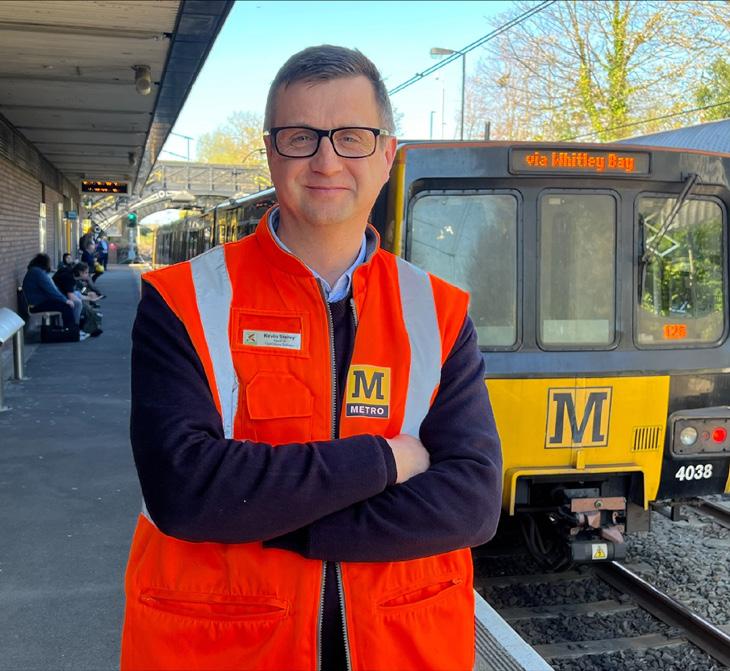
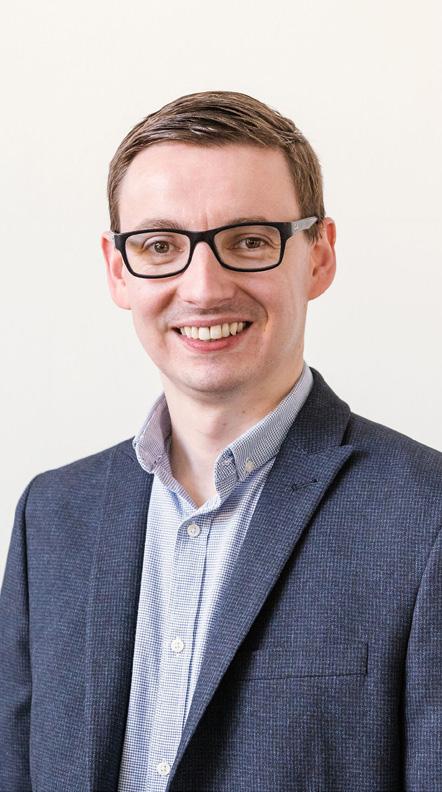
Jacobs directors appointed to RIA Board and elected Chair of RIA Consultants Group
Jacobs Transportation Growth Director
Europe John Downer has been appointed to the Board of the Railway Industry Association (RIA). Jacobs Director of Market Solutions Europe Jessica Ellery was also recently elected Chair of the Railway Industry Association Consultants Group, representing the rail consultancy and design community.
Outgoing Chair hands over to Lancashire County Council’s Rail Development Manager
Chair of the Clitheroe Line and East Lancashire Community Rail Partnership, Melanie Taylor is handing over the chair of the CRP to Mike Cliffe, Lancashire County Council’s Rail Development Manager. Melanie Taylor will continue as a director of Community Rail Lancashire and will remain extensively involved in rail in the county in her new role as Group Leader for Public Transport at Blackpool Council.
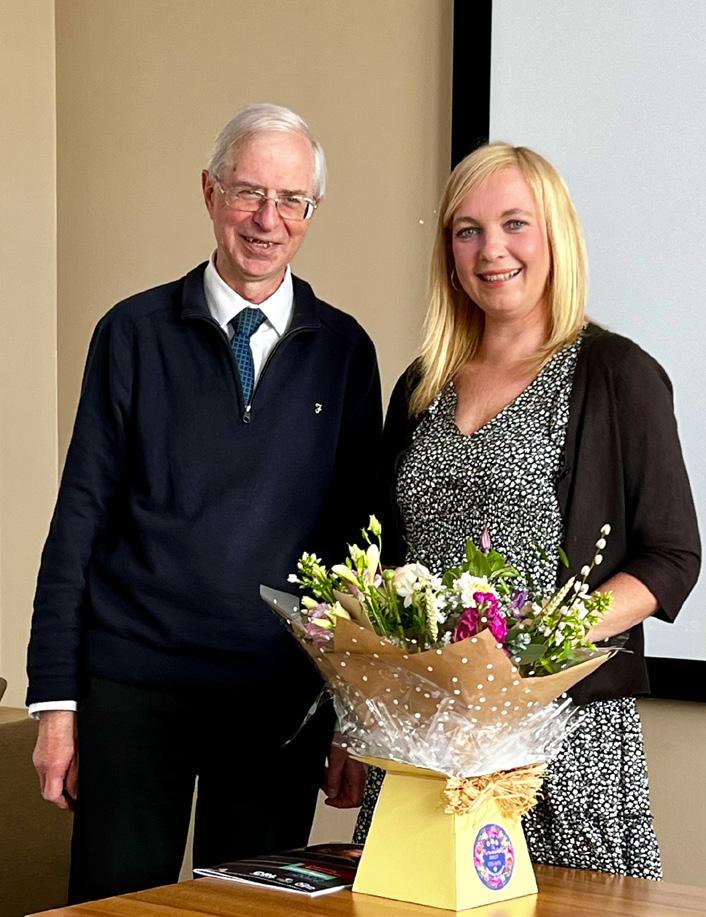
Network Rail has appointed three new directors in the Wales & Western region Nick Millington MBE moves into the permanent role of route director on the Wales and Borders route. Marcus Jones has been appointed as the new route director for the Western route, alongside Sophie Bancroft who takes on the role of operations director, also for the Western route.
Skanska UK appoints President and CEO
Previously a member of Skanska UK’s Executive Management Team, Katy Dowding took up her new role as President and CEO on Tuesday 2 May.
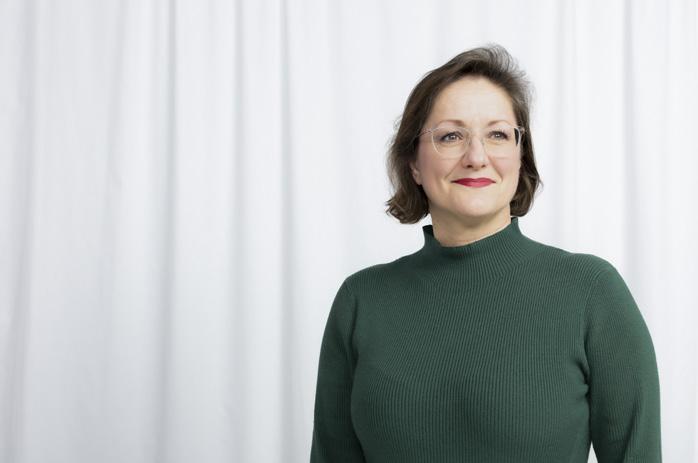
Pandrol promotes senior leader to head up commercial and sales John Dowie has been appointed Chief Commercial & Sales Officer of Pandrol in a move that sees him promoted following him joining the company in 2022.
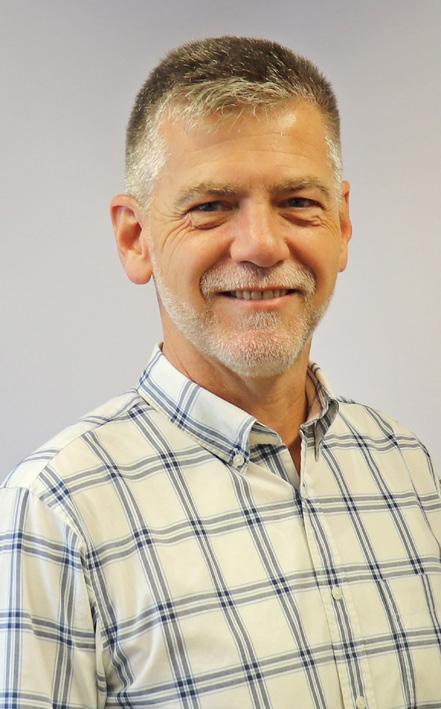
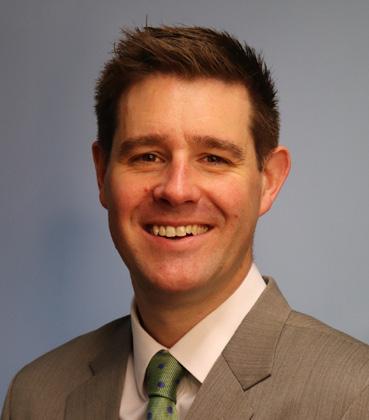
Arriva Rail London welcomes new Head of Performance Delivery
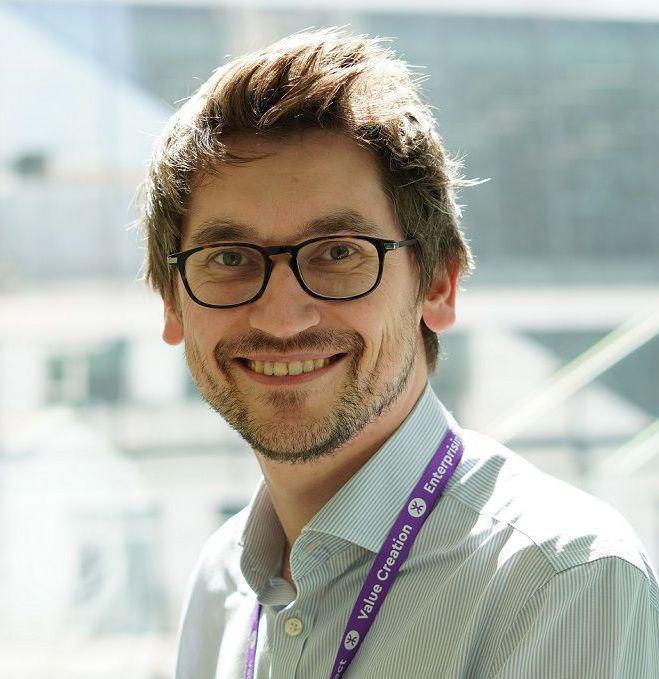
Arriva Rail London has appointed Jon Bradley as Head of Performance Delivery, a newly created role in the Operations team.
HS1 Ltd appoints first Strategy & Regulation Director
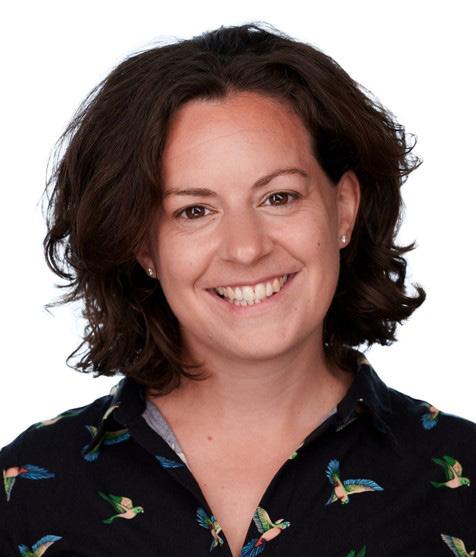

HS1 Ltd – the owner and operator of High Speed 1, the UK’s first section of highspeed rail – has announced the appointment of Mattias Bjornfors as its first-ever Strategy & Regulation Director as the company looks to bolster its regulatory affairs expertise at a crucial time in the rail sector.
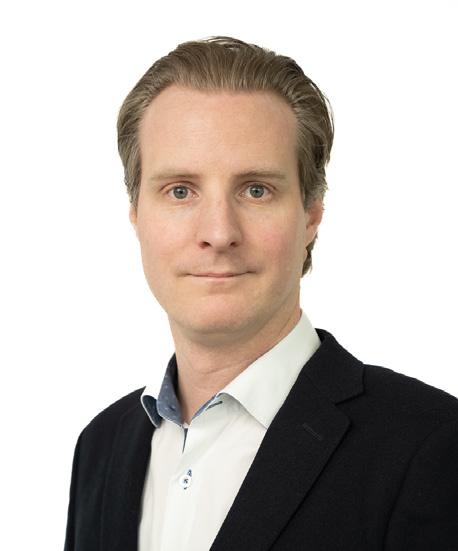
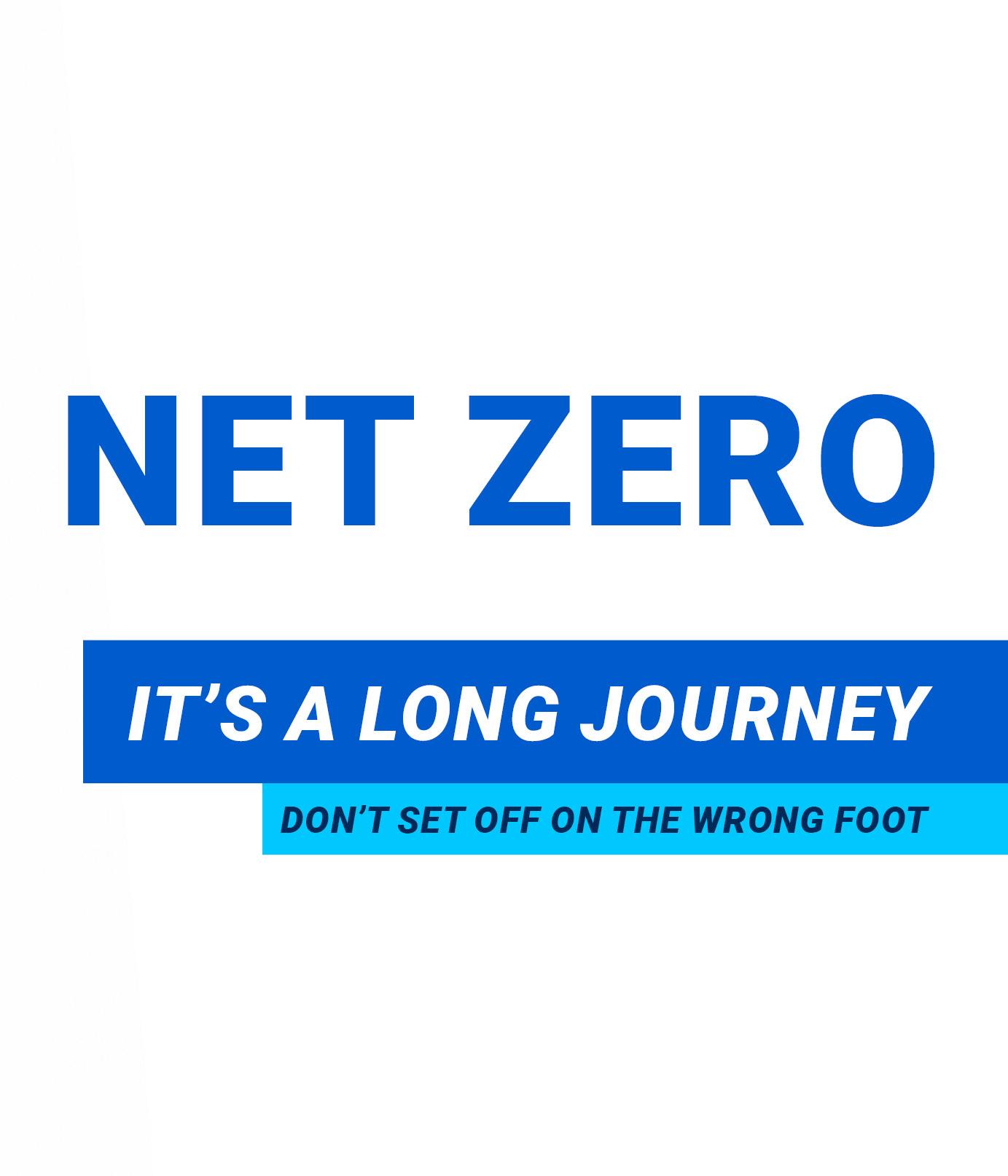
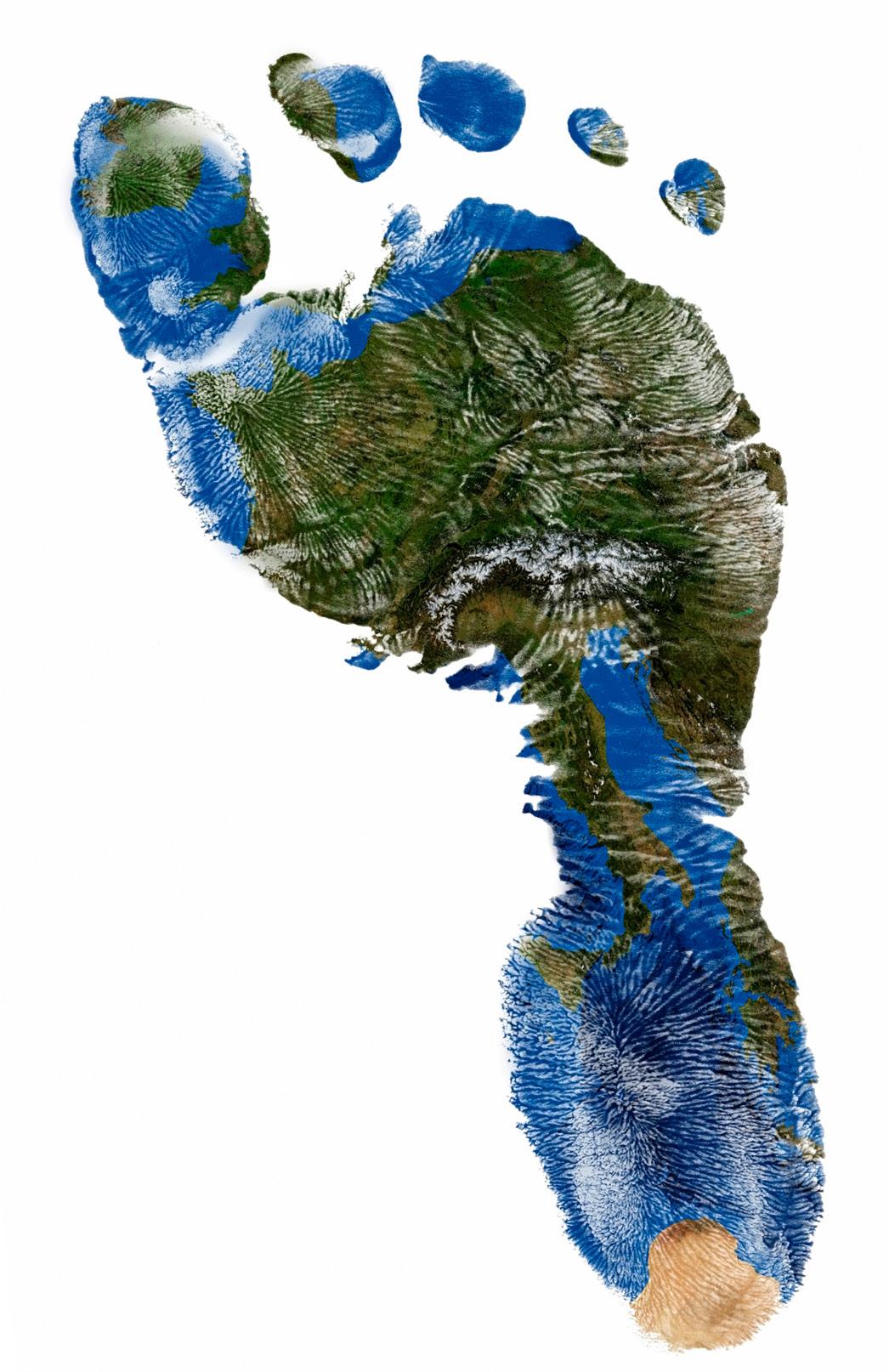
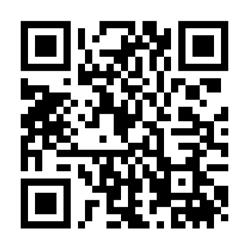
Delivering assured solutions for the UK rail industry

The UK rail industry needs to adapt their existing energy infrastructures to keep up with evolving customer demand.
We take the time to understand individual rail energy requirements which allows us to develop technologically advanced solutions tailored to our clients needs to increase productivity and decarbonise infrastructure.
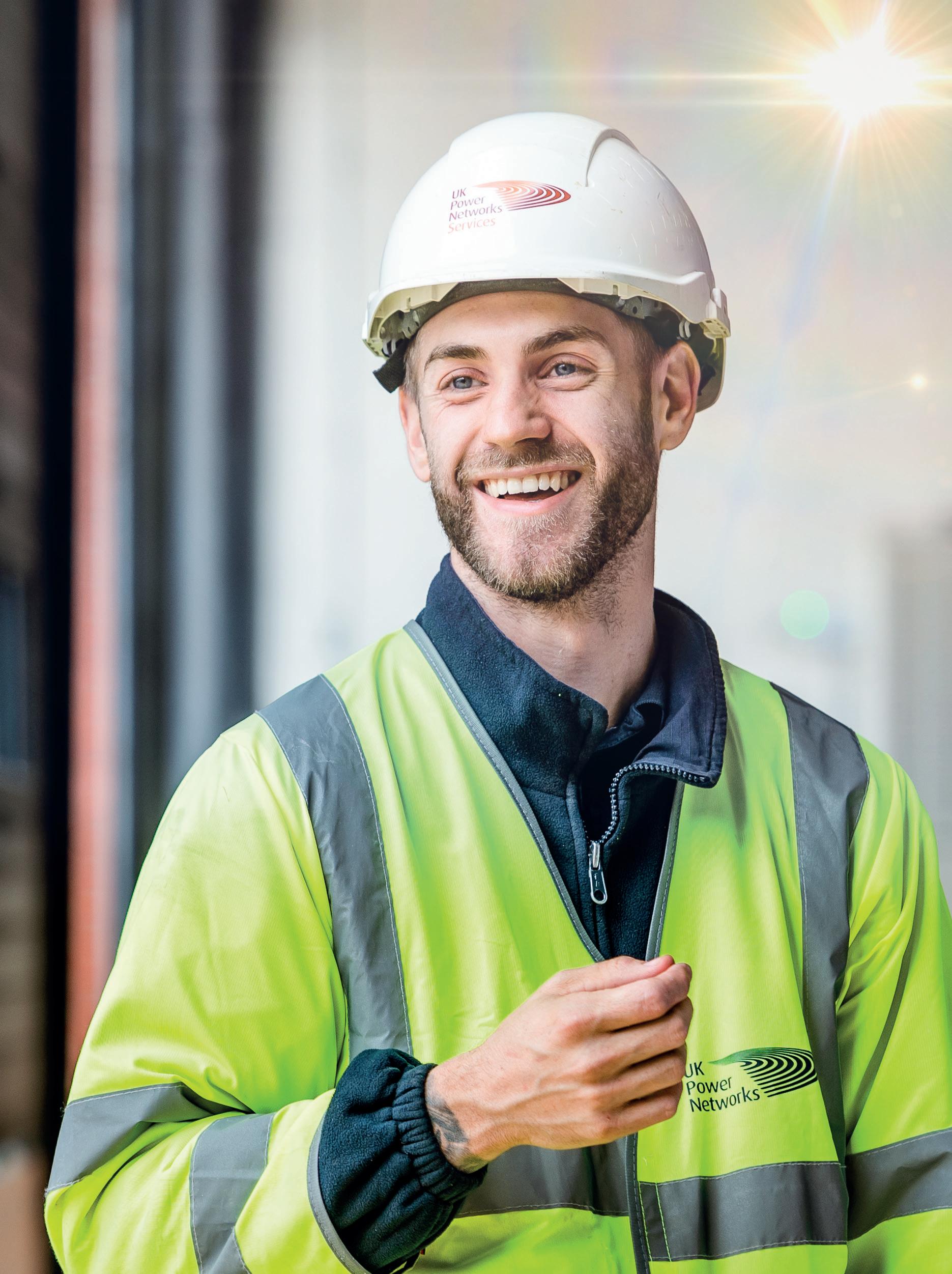