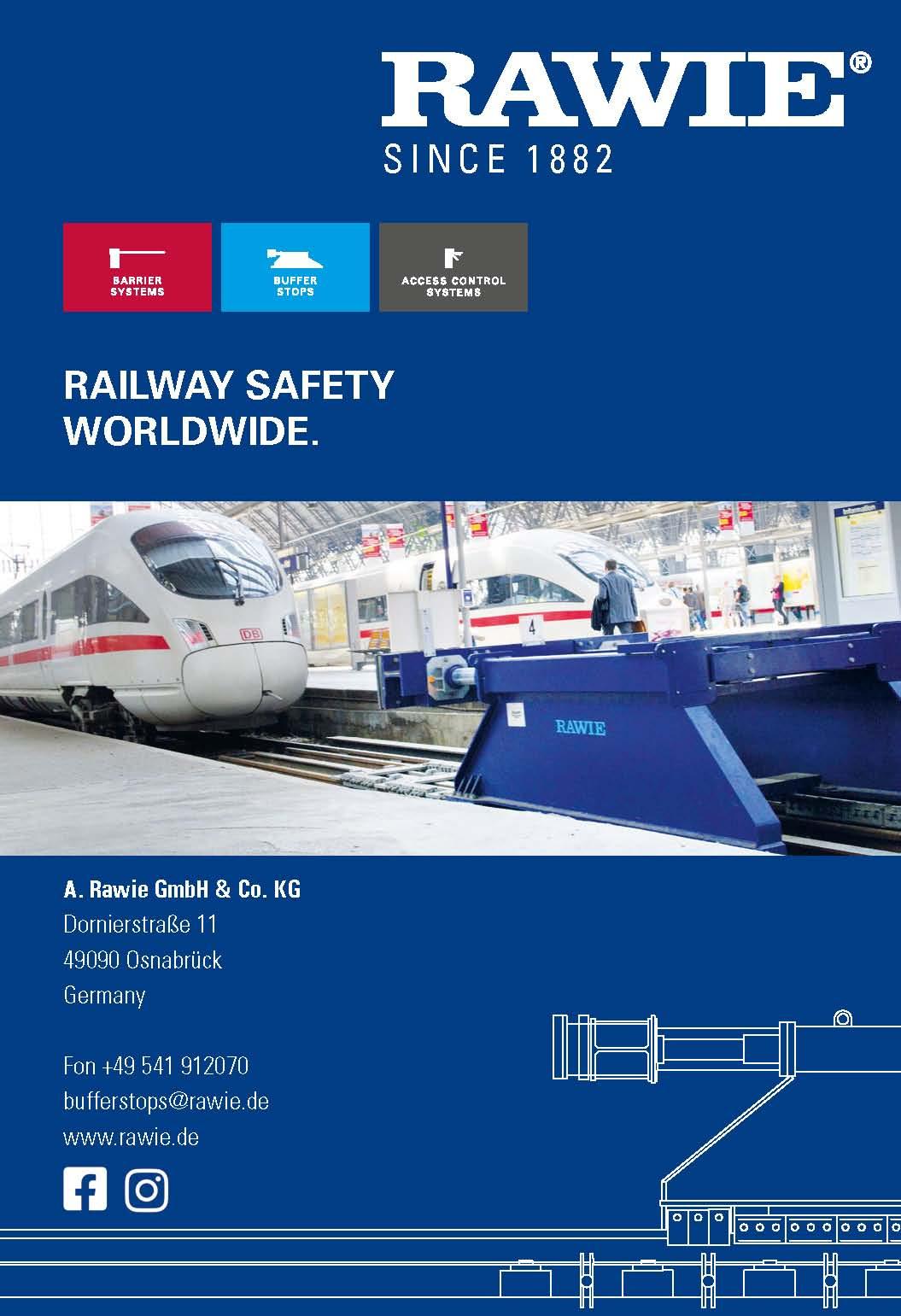

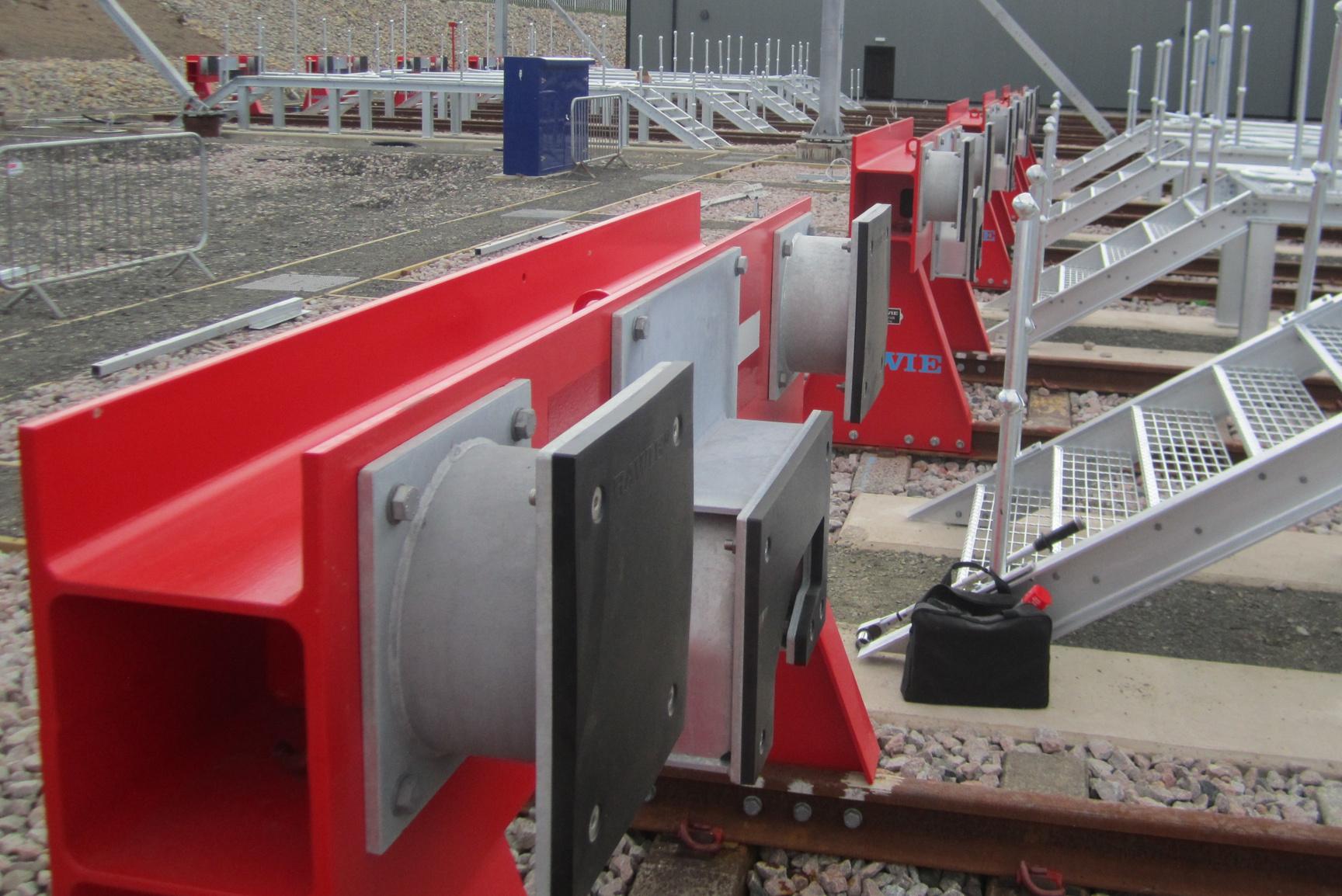

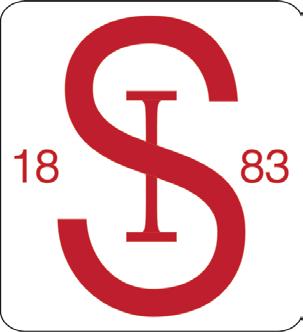
RAWIE Friction Buffer Stops provide track end protection worldwide
They can be designed to suit all types of rolling stock, accomodatiing varied train weights and speeds.
Supplied in the UK & Ireland by:
H.J. Skelton & Co. Ltd.
Tel: 01635 866877
E-Mail: sales@hjskelton.com
Web: www.hjskelton.co.uk
The tenth edition of the Rail Professional Supply Chain Directory is the most comprehensive to date. Each year this reference book has grown with the industry and expanded as the industry has expanded. As new bodies have formed and new concepts of what the railway should be have coalesced in the public’s mind, this Directory brings together all the major players and stakeholders across every layer of the industry.
Separated into seven sections, you will find within these pages a complete overview of the UK rail sector as it exists in 2024. Regulatory bodies, infrastructure companies, franchise holders and passenger and freight operating companies. We have also included articles on every relevant topic and listings of all organisations that are affiliated with the rail industry.
Organised into colour-coded sections, the first half features all the relevant bodies divided into the categories mentioned above. Each profile provides a short history of the organisation, its purpose and structure and any recent or future activities. There is also a list of each company’s key personnel and contact information.
The first section, Government and Regulatory, features profiles of all Government bodies with a responsibility for rail at both the national and sub-national level as well as other organisations that advise the Government on matters relating to rail safety and consumer protection.
The second, Infrastructure, looks at companies responsible for major projects, such as Network Rail and HS2.
The third and fourth sections look at companies that hold rail franchises, holding companies, and the passenger operating companies that operate trains on the routes.
The fifth section holds profiles on all the major freight operating companies in the United Kingdom.
The second half of the directory features editorials on a wide variety of topics including consulting, energy, geotechnical engineering, innovation, rolling stock, supply chain, safety, training and much more.
There are billions of pounds of contracts being awarded over this year and many of the companies that fulfilling those contracts are featured here.
Particular focus this year is given to the professional bodies and membershipbased associations that play a key role in communicating the importance of the railways to the public and acting as an intermediary between the industry and the wider supply chain. The newly formed Rail Partners, born out of the Rail Delivery Group, hosted a series of events throughout 2023 and look set to continue being a staple of the calendar for 2024. The importance of groups such as the Railway Industry Association, Chartered Institute of Railway Operators, Rail Partners, Rail Forum and others will only grow throughout 2024 as we await to see how the money that is being diverted from HS2 will be spent.
The government’s decisions on HS2 will deliver £36 billion of savings that will be reallocated to Network North, an ambitious pipeline of alternative transport projects which will drive growth and connectivity in the great towns and cities across the North.
The public perception of HS2 haunted that project for years and whatever we might think of the decision to curtail it that is now the direction the country is heading in. The frequent changes of plan and stop-start projects, especially in the Midlands and the North have made us all wary of getting overexcited but we need only look to the capital for an example of what great new transport infrastructure can look like.
The success of the Elizabeth Line will be as interesting to historians as it is to policymakers and hopefully both groups hold it up as an example of what the industry can achieve and the enthusiasm with which the public will embrace it.
Rail’s importance to this country goes back just shy of two centuries and this time
next year we will begin preparations to mark the bicentenary as 2025 looks set to play host to a year-long programme called Railway 200. 2024, however, will be marked by the commencement of Network Rail’s seventh Control Period. CP7 begins in April and will run until 31 March 2029. Network Rail has secured £27.5 billion of government funding for the period with £16.5 billion of its own income making up a total of £44 billion of investment funding for the five years of CP7.
So, what can we expect from this coming year? Previous years saw volatility in the industry due to multiple factors with investment, the lack of visibility and consistency in upcoming rail work, delayed decision-making on major projects like HS2 and Transpennine Route Upgrade, the Williams Rail Review, Brexit and then Covid all forcing the industry to throttle back any forward momentum and revise expectations.
The rapid growth experienced by the passenger railway throughout the noughties and the tens suffered a moratorium for the pandemic years but that has now effectively ended. Spring figures for 2023 showed demand came to within 89.7 per cent of pre-Covid levels, according to National Rail Trends statistics, published by the Office of Rail and Road (ORR).
The Government’s £44 billion commitment to CP7 is an important recognition of the economic and social value of rail and its role in supporting the country’s economy. The focus will be on meeting customer needs, achieving financial sustainability, operational efficiency and environmental sustainability.
All this serves the continuous goal of building the type of railway that we want to see in this country, one that can demonstrate its plans for climate change adaptation and build on the opportunities identified by the Plan for Rail.
The Secretary of State has asked the leadership of the Department for Transport (DfT), Great British Railways Transition Team (GBRTT) and Network Rail to work together to provide industry leadership until legislation is in place.
Great British Railways is the clear destination for the industry and by working together industry leaders can achieve the whole-railway thinking that will allow for the smoothest of transitions once the legislation needed to create GBR has passed through Parliament.
The Department for Transport provides strategic direction and funding to the railways in England and Wales and buys rail franchises and projects. Their work is directed and overseen by the Secretary of State for Transport and their team
The Department’s work is directed and overseen by the Secretary of State, Mark Harper MP, and his Ministerial team which is made up of four MPs and one Lords Minister. The Minister of State for Rail Huw Merriman MP is directly involved in rail. The DfT rail portfolio is organised into three separate groups:
• Rail Strategy and Services Group
• Rail Infrastructure Group
• High Speed Rail Group
The Rail Strategy and Services Group is led by Conrad Bailey, who oversees:
• Developing strategy and policy for the rail sector in the context of broader government policy
• Managing the department’s overall expenditure on rail services and infrastructure
• Ensuring delivery of major projects and programmes including the:
• £5.7 billion Intercity Express Programme
• £7 billion Thameslink programme
• £14.8 billion Crossrail programme (jointly with Transport for London)
• Delivering the ongoing programme of rail franchises
• Effective sponsorship of: British Transport Police, Network Rail, Office of Rail and Road, Rail Accidents Investigation Branch, Transport Focus
The Rail Infrastructure Group is led by David Hughes. This portfolio includes Northern Powerhouse Rail and the Integrated Rail Plan, the Transpennine Route Upgrade, Restoring Your Railway, other Network Rail enhancements, East West Rail and Crossrail.
The High Speed Rail Group is led by Alan Over and responsible for the High Speed 2 programme and is on the executive committee level for the department’s work on a number of other major rail projects. These projects include East West Rail, Northern Powerhouse Rail and Crossrail 2. He is a member of the department’s executive committee and board.
Network Rail is a central Government body which operates as a ‘not for dividend’ company regulated by the Office of Rail and Road. It owns, operates, maintains and develops Britain’s railway and is responsible for ensuring that the railway is safe and reliable. As NR’s sole Member, the Secretary of State for Transport is accountable to Parliament for the activities and performance of Network Rail. A framework agreement published in July 2019 stipulates that the Secretary of State has the power to appoint and dismiss the Chair of Network Rail and approve the board’s suggested candidate for Chief Executive. The Secretary of State also determines the Rail Investment Strategy and Statement of Funds Available which contain the Government’s plans for investment on the network.
The DfT oversees the British Transport Police Authority (BTPA) and Transport Focus. The Chair and Board members of the BTPA are appointed by the Secretary of State for Transport directly. Transport Focus has a board of non-executive members appointed by the Secretary of State for Transport (a Chair and five members). Transport Focus is the statutory independent consumer watchdog for Britain’s rail passengers. The TF Board has three other members (in addition to the five appointed by the SofS) who are appointed by Scottish Ministers, the National Assembly for Wales and the London Assembly. The British Transport Police Authority is the oversight body for the BTP, the specialist police force for the rail network across Great Britain.
The Office of Rail and Road is the independent safety and economic regulator for the railways. The Secretary of State appoints the Chair and other Board members. The Secretary of State issues the ORR with general guidance in respect of the exercise of its rail functions. The ORR is responsible for assessing whether the Secretary of State’s proposals are deliverable by Network Rail within the level of public funding available.
London and Continental Railways (LCR) is wholly owned by the Department
of Transport and High Speed Two (HS2) Limited is an executive non-departmental public body, sponsored by the Department for Transport.
The East West Railway Company (EWRC) is a non-departmental public arm’s length body set up by the Government to accelerate the East West Rail project – a new rail link between Cambridge and Oxford. EWRC works with the Department for Transport. The Rail Accident Investigation Branch (RAIB) works with the DfT but independently investigates accidents to improve railway safety and inform the industry and the public.
KEY PERSONNEL
Secretary of State for Transport: Mark Harper MP
Minister of State for Transport (Rail and HS2): Huw Merriman MP
Parliamentary Under Secretary of State: Baroness Vere of Norbiton
Director General, High Speed Rail Group: Alan Over
Director General, Rail Strategy and Services Group: Conrad Bailey
Director General, Rail Infrastructure Group: David Hughes
CONTACT INFORMATION
Address: Great Minster House
33 Horseferry Road
London SW1P 4DR
Tel: 0300 330 3000
Email: dft@dft.gov.uk
Visit: www.dft.gov.uk
PW150-PVC-6.38m
PW150-PVC-6.55m
PW150-VC-1.03m
A2AS_SO9132_5799A
A2AS_GU2000006761
A2AS_SO9132_6199A
CF225-PVC-13.42m
A2AS_GU2000006760
A2AS_GU2000006759
A2AS_GU2000006758
PW150-VC-1.04mPW150-VC-19.68m
-PP-13.11mCF
CF-PP-13.35m
CF225-PVC-12.88m
A2AS_SO9132_6495E
EC0-CO-505.83m
PW675-CO-89.23m
A2AS_GU2000006746
PW150-VC-1.65m PW600-CO-92.03m
A2AS_GU2000006750
PW150-VC-2.09m
A2AS_GU2000006747
CF225-12.99m
Transport Scotland is the national transport agency for Scotland, responsible for the ScotRail and Caledonian Sleeper franchises as well as planning and delivering rail policy, strategy and development in Scotland
The Transport Scotland Rail Directorate is responsible for planning and delivering rail policy, strategy and development. It carries out appraisals of capital projects, advises on rail investment decisions and provides the specification of railway outputs that the Scottish Government will wish to buy. The Rail directorate is also responsible for managing the ScotRail and Caledonian Sleeper franchise contracts, specifying and funding Network Rail’s high-level delivery responsibilities in Scotland, and liaising with the Office of Rail and Road in specifying and funding the outputs expected from Network Rail.
Transport Scotland has invested over £9 billion in the railway since 2007, which has resulted in:
• New fleets of modern electric trains.
• New and improved services through the ScotRail and Caledonian Sleeper franchises.
• 47 miles of new railway, including the Borders Railway.
• 252 miles of electrified lines.
• 16 new stations.
ScotRail services has moved into Scottish Government ownership as the ScotRail franchise has ended. The services will be provided within the public sector, by an arm’s length company owned and controlled by the Scottish Government. This is a result of the Scottish Government’s decision to run ScotRail services through what is known as the ‘Operator of Last Resort’. ScotRail staff will transfer to the new Scottish Government owned entity, with their terms and conditions protected. Transport Minister, Jenny Gilruth, has expressed an interest in working closely with wider partners including women’s organisations and British Transport Police to improve the public transport system, make it safer and build on the work already underway.
Transport Scotland’s vision, as set out in the National Transport Strategy (NTS2), is for Scotland to have a sustainable, inclusive, safe and accessible transport system which will help to deliver a healthier, fairer and more prosperous Scotland for communities, businesses and visitors. The second Delivery Plan for Scotland’s National Transport Strategy has been published, setting out the actions underway for 2022 to 2023. It recognises the key role that transport has in reducing inequalities, delivering inclusive economic growth, improving health and wellbeing, and tackling the climate emergency. At the heart of the Strategy is the recognition to deliver a step-change in behaviour and provide attractive, affordable, accessible and sustainable travel options.
Transport Scotland is an executive agency of the Scottish Government and is accountable to Parliament and the public through Scottish Ministers. Transport Scotland also provides input from a Scottish perspective on reserved rail issues such as: European directives, cross-border rail franchises, the Equality Act and safety and standards.
The rail freight sector is a vital part of Scotland’s economy. The Scottish Government’s vision is for a competitive, sustainable rail freight sector that plays a significant and increasingly important role in Scotland’s economic growth and provides a safer, greener and more efficient way of transporting goods and materials.
This vision is backed by a £25 million Scottish Strategic Rail Freight Fund for the period 2019 to 2024. The fund will support the development and delivery costs of proposals for minor-medium freight interventions aimed at improving the capacity and capability of the Scottish network for rail freight.
There are currently 360 railway stations in Scotland. Network Rail manages Glasgow Central and Edinburgh Waverley. The railway station at Prestwick Airport is owned and managed by the airport authority. The rest are leased to and operated by ScotRail. Scottish stations have improved significantly after considerable investment over the last few years. ScotRail has invested around £20 million in delivering front line improvements to passenger facilities at stations. The Scottish Government announced in 2019 a £25 million investment into rail freight over the next five years in a bid to strengthen the industry.
Transport Scotland aims to make travel as accessible and affordable as possible. To achieve this, we offer concessionary travel for young Scots, disabled travellers, over 60s and ferry passengers. They are committed to ensuring that their facilities are maintained and improved over the course of the current franchise, with further investments being made at stations to support smart ticketing and integrated travel.
Investment includes enhanced cycle facilities, upgraded ticket vending machines, multi-modal customer information screens and smart ticketing equipment.
KEY PERSONNEL
Interim Chief Executive:
Hugh Gillies
Director of Rail: Bill Reeve
Interim Director of Transport
Strategy and Analysis:
Fiona Brown
Director of Low Carbon
Economy: Stuart Greig
CONTACT INFORMATION
Address: Buchanan House, 58 Port Dundas Road
Glasgow G4 0HF
Tel: 0141 272 7100
Email: info@transport.gov.scot
Visit: www.transport.gov.scot
We’re with you every step of the way
RSSB works for the whole rail industry. But some organisations have more specific questions – which could be critical to the future of their business. So we make our experts available on a project basis, too.
As we’re responsible for the first-principles engineering that defines rail standards and best practice, you’ll get consultants working at the cutting edge of rail, whose whole-system expertise lets them identify the most effective solutions.
RSSB’s consultancy services are another way we’re supporting safer, smarter rail.
Find out how we can help you at: www.rssb.co.uk/expertsinrail
Transport for Wales (TfW) was set up by Welsh Government in 2016 to oversee public transport in Wales
Transport for Wales (TfW) is a not-for-profit organisation wholly owned by the Welsh Government which exists to drive forward the Welsh Government’s vision of a high quality, safe, integrated, affordable and accessible transport network that the people of Wales are proud of.
The Transport for Wales Board is made up of the Chair, Chief Executive, four independent non-executives and two executive members. Its role is to provide effective leadership for TfW, monitor performance and promote high standards of public finance, all whilst meeting the requirements of its remit as set by the Welsh Government.
From 2023, an £800 million investment will ensure that 95 per cent of journeys are on new trains. More than half the trains will be assembled in Wales. By December of that year, an extra 285 (29 per cent) more services will run every weekday, including improvements on the Ebbw Vale, Cambrian and Heart of Wales lines and the North Wales Metro (Wrexham Bidston). A new service will link Cardiff and Liverpool via Wrexham.
This will create more than six hundred new jobs, including two hundred new ontrain customer service staff, and add thirty apprenticeships per year. A £15 million fund will make stations more accessible. Accessibility issues are addressed by the TfW accessibility panel made up of members who are disabled and older people with a varying range of experience of rail travel. They meet monthly and as required throughout the year with the aim to consistently innovate accessibility policies and advise TfW how to support disabled, deaf and older customers in order for them to have a seamless travel experience. On top of that at least 1,500 new car parking spaces will be created and by 2023 the availability and quality of ticketing facilities will be transformed.
Transport for Wales focuses on planning, commissioning and managing efficient transport by creating transport networks fit for the future that will contribute to the long-term sustainability of Wales.
The intention is to create a rail service that benefits the whole of Wales, as well as
communities along the border in England and to this end Transport for Wales is:
• Working to bring the rail service into line with the regulations for persons of reduced mobility ensuring everyone can benefit from a better service.
• Committed to meeting the requirements of the Welsh Language Standards by providing better Welsh Language services.
• Improving integration with active travel routes making it easier for people to walk and cycle to and from stations.
• Working with bidders to ensure they invest in the skills of their staff and suppliers and that local people have opportunities for employment.
• Investing around three-quarters of a billion pounds to transform the valley lines to Treherbert, Aberdare, Merthyr Tydfil, Rhymney and Coryton, electrifying around 107 miles of track and upgrading infrastructure to enable improved journey times and more trains every hour.
During 2021/22 TfW worked on the development of a new marketing campaign ‘The Real Social Network’. It is Wales’ first multimodal public transport campaign and promotes walking, cycling, bus and rail use as a sustainable way to travel. This shift towards sustainable transport involves changing the way individuals travel, by improving their travelling experience, making sustainable transport more affordable, and improving integrated journey planning.
An extensive programme of testing and commissioning is being carried out on one of the two Stadler built trains, which made maiden voyages into Canton depot, Cardiff in late November 2021. There is a £800 million investment in new trains from manufacturer, Stadler in order to invite a new era of train travel for customers.
The South Wales Metro is an integrated public transport network for the Cardiff Capital Region which will involve electrifying around 170 kilometres of track, upgrading
stations and signalling and building at least five new stations. TfW has continued its work on the Metro Central Programme to establish an integrated transport hub, and provifr better connections whilst creating more sustainable travel choices.
The Swansea Bay Metro will transform public transport in the Swansea Bay area, TfW will be introducing new trains on services through the Swansea Bay area, increasing capacity on services to West Wales and between South West Wales and Manchester. From 2024, TfW will be introducing a first-class service between Swansea and Manchester on their new trains.
TfW are continuing to invest in the transformation of public transport in Wales with a focus on creating a joined-up network where integrated ticketing and reliable services make it the easiest option for people travelling across Wales.
KEY PERSONNEL
Chief Executive: James Price
Executive Director of Finance and Governance:
Heather Clash
Communications Director: Lewis Brencher
Transport Operations Director: Alexia Course
Rail Programme Director: Karl Gilmore
Safety and Sustainability Director: Leyton Powell
Director of Planning, Development and Advisory Services: Geoff Ogden
Commercial and Customer Experience Director: David O’Leary
Development Director Mid, North and Rural Wales: Lee Robinson
Director of People and Organisational Development: Lisa Yates
IT and Digital Services Director: Dave Williams
CONTACT INFORMATION
Address: Llys Cadwyn
Pontypridd CF37 4TH
Tel: 029 2167 3434
Email: contact@tfw.wales
Visit: www.tfw.wales
The BTP is split into three divisions covering London and the South East of England, The Pennines, Midlands, South West and Wales, and Scotland. Their mission is to protect and serve the railway environment and its community, keeping levels of disruption, crime and the fear of crime as low as possible.
BTP employs 3,123, police officers, 233 PCSOs (Police Community Support Officer), 306 special constabulary officers and 1,452 police staff. Due to Covid-19 related travel restrictions, the rail network experienced a significant reduction in passenger numbers. At the start of the third national lockdown in January 2021, Network Rail and Transport for London (TfL) managed stations saw just 15-20 per cent of normal passenger use. This reduction in passengers resulted in a change in demand on the Force in terms of crime. In the initial stages of the pandemic crime levels were extremely low (around 30 per cent of previous levels) but returned to near normal levels in late 2020 (around 80 per cent of previous recorded crime).
Targeted intelligence-led deployments and proactive policing operations under Operation Viking and Operation Engulf to deter, disrupt and detect violent crime, resulted in a 29 per cent reduction in these types of crimes. These operations, together
with other crime prevention tactics, such as the deployment of knife arches, contributed to an increase in the number of weapons seized by 13 per cent (752 during 2019/20 compared with 851 during 2020/21).
During 2020/21, BTP officers and PCSOs intervened in 25,997 cases involving vulnerable people. This included identifying and safeguarding children and young people, responding to people in mental health crisis and dealing with domestic abuse, stalking and harassment.
Every five years BTPA sets out medium and long-term objectives for the British Transport Police in a Strategic Plan. This is in addition to the athree-yearly policing plans, which cover objectives for the threeyear period from the date of the plan’s publication. In 2022, the BTP's 2022-27 Strategic Plan was published. You can read more about the strategic plans in the British Transport Police Authority section.
In 2020 BTP launched the Moving the Needle action plan, setting out its commitment to tackle racism and unconscious bias and make BTP a fairer more inclusive police force. Moving the Needle is an ambitious, wide-ranging plan which has been drawn up through
discussion with a cross section of the Force’s employees.
KEY PERSONNEL
Chief Constable: Lucy D’Orsi
Deputy Chief Constable: Alistair Sutherland
Assistant Chief Constable: Charlie Doyle
Assistant Chief Constable: Sean O’Callaghan
B Division – Chief Superintendent: Chris Casey
C Division – Chief Superintendent: Allan Gregory
D Division – Chief Superintendent: Gill Murray
Head of Corporate Communications:
Allison Potter Drake
CONTACT INFORMATION
Address: Force Headquarters, 25 Camden Road
London NW1 9LN
Tel: 0800 40 50 40
Email: first_contact@btp.pnn.police.uk
Visit: www.btp.police.uk
The British Transport Police Authority (BTPA) is responsible for ensuring an efficient and effective police force for the railways
With the passing of the Railways and Transport Safety Act 2003, the BTPA was established to oversee the British Transport Police (BTP), review its performance and allocate funding for its budget. It also deals with complaints, recruitment, and managing relationships with the rail industry.
The Authority is responsible for setting objectives for British Transport Police (BTP) before the beginning of each financial year. The BTPA announces these objectives, as well as its strategic direction and performance review of the Force by publishing its annual Policing Plan, Strategic Plan and its Annual Reports. The Policing Plan contains the Force’s priorities for the year and the financial resources expected to be available to deliver the plan. The Strategic Plan sets out the Authority’s medium and long-term strategies for policing the railways. At the end of each financial year, the Annual Reports cover the policing of the railways in that year. The BTPA is also responsible for recruitment of Chief Officers and BTP senior Directors.
2022/23 was the first year of our new strategy, which covers the period 2022-27. This Strategic Plan aims to deliver a secure place for passengers, a hostile place for those who would do harm and a safe place for vulnerable people encountered on the network. We will do this in partnership with the rail and underground industry, wider law enforcement, safeguarding agencies and passenger groups.
Our strategic objectives for 2022-27 are:
• Crime prevention and safeguarding to reduce the likelihood of people coming to harm on the railways.
• Target our efforts to ensure fewer victims of the most serious crime.
• Innovate and collaborate with our stakeholders to reduce disruption.
• Build the trust and confidence of passengers and rail staff to defeat criminality together.
• Generate value for money through the exploitation of technology, adapting to meet the future.
• Build a modern and inclusive Force where our people are well-equipped, well-trained, well-led, well-cared for and reflect the best of our communities.
BTP will work with industry, security and wellbeing agencies to ensure that everyone who works on or uses the railways to travel for leisure or work feels safe and is confident to do so.
As well as billing the rail industry for the costs of running the BTP, the BTPA determines the budget of the police force and oversees large financial projects. The Authority maintains the accounts of BTP and has them audited each financial year. For 2021/22 the BTPA set a core policing budget of £328.1 million for policing Great Britain’s railways. A total of £255.5 million has been allocated to overground rail services and £72.6 million for London Underground.
The BTPA enters into Police Service Agreements (PSAs) with TOCs and FOCs, PSAs require payment from the train companies to the BTPA in exchange for the policing of the railway and associated property.
When a new rail franchise is awarded by the Department for Transport, the winning company is usually required to enter into a new or existing PSA with the BTPA.
KEY PERSONNEL
Chairman: Ron Barclay-Smith
Deputy Chairman: Andy Cooper
Chief Executive and Accounting Officer: Hugh Ind
Chief Financial Officer, Deputy Chief Executive
and Treasurer: Sarah Church
Communications Manager: Katie Stanton
Member Engagement Manager: Raquel Cortes
CONTACT INFORMATION
Address: 25 Camden Road
London NW1 9LN
Camden Street, London NW1 0EG
Tel: 07900 394397
Tel – Media: 0300 123 9104
Email: btpa-enquiries@btp.police.uk
Visit: www.btpa.police.uk
Lifting and inspection equipment you can rely on for all maintenance of rail vehicles.
With 40 years’ experience on heavy duty lifting solutions, Totalkare combines world class products with industry leading support to facilitate effective maintenance and repair.
HEAVY DUTY
SYNCHRONISED
RELIABLE
6,000 - 14,000KG
COMPLIANT WITH DIFFERENT RAIL GUAGE SYSTEMS
HYDRAULIC LIFT PLATFORM
The Department for Infrastructure (DfI) was formed in May 2016 and operates under the direction and control of the Minister for Infrastructure
DfI is staffed by civil servants who are accountable to the Minister for Infrastructure.
The Minister is a member of the Northern Ireland Executive and accountable to the Northern Ireland Assembly. The Permanent Secretary, Julie Harrison, is the Accounting Officer for the Department and the Minister’s principal adviser. Julie Harrison chairs the Departmental Board, which directs the delivery of Corporate Governance within the Department.
Details of the arrangements which have been established to ensure proper and effective management of the Department’s affairs are set out in the Corporate Governance Framework. The Departmental Board comprises a further five executive members and two non-executive, independent members.
The Department provides capital and revenue grant funding to Translink for Northern Ireland Railways to operate rail services. The funding helps maintain and develop the rail infrastructure, allows rail services to operate safely and efficiently and helps make public transport an attractive alternative to private transport.
Public Transport Division carries out the governance function of Translink on behalf of DfI and monitors spend of the grant allocated to Translink against plans, ensuring that projects demonstrate value for taxpayers’ money and expenditure falls within budgetary limits.
The Infrastructure Investment Plan for Scotland 2021-2022 to 2025-2026 was published on 4 February 2021. It sets out a long-term vision of infrastructure in Scotland, which supports an inclusive, net zero carbon economy and includes details on over £26 billion of major projects and large programmes, some of which includes:
• Glasgow Subway Modernisation –includes a smartcard ticketing system linked to wider integrated ticketing; new
rolling stock and signalling; refurbished stations with improved accessibility including replacing escalators.
• Future Transport Fund – capital to support a range of low and zero carbon investment
• Rail Decarbonisation Action Plan- We will decarbonise Scotland's passenger rail services by 2035, ahead of the UK's target of 2040.
The Department has responsibility for the licensing, safety certification and safety authorisations of all mainline, light railways and heritage railways operating in Northern Ireland in exercise of the powers conferred on it under the Railway Safety Act (Northern Ireland) 2002. The Department regulates railway safety to ensure all Railway Undertakings, Infrastructure Managers and heritage rail operators comply with regulatory duties to provide a safe rail network. In addition, the Department is the Competent Authority for assessing compliance with technical standard on the rail network.
The Northern Ireland Transport Holding Company (NITHC) is a public corporation and its responsibilities include holding and managing property assets and the oversight, in terms of support, control and supervision, of its private limited subsidiary companies, the principal ones being Ulsterbus, Metro (previously Citybus) and Northern Ireland Railways, trading jointly as Translink. It is expected to operate commercially and has a duty to operate in line with Ministerial policy.
The chairman and other directors of the Holding Company shall be appointed from among persons who appear to the Minister to have had wide experience of, and to have shown capacity in, transport, industrial, commercial or financial matters or to have
other adequate or suitable experience, and the Minister in appointing them shall have regard to the desirability of including among them persons who are directors of, or concerned in the management of, the subsidiaries of the Holding Company.
The Travel Survey for Northern Ireland (TSNI) started in 1999 and is produced by the Analysis, Statistics and Research Branch (ASRB) of the Department for Infrastructure. It collects information on how and why people travel within Northern Ireland, and details information on journeys taken by mode of travel and purpose of journey. Covid-19 has had a knock-on effect on the usual publication timetable of the reports, therefore the 2020 report was published on 10 March 2022, and instead of the report covering its usual three year period, it only reports as a single year.
KEY PERSONNEL
Minister for Infrastructure: John O'Dowd
Permanent Secretary: Katrina Godfrey
Deputy Secretary – Resources, Governance and EU Group: Declan McGeown
Director of Safe and Sustainable Travel Division: Chris Hughes
Director of Finance: Susan Anderson
Director of Corporate Policy and Planning Division: Sian Kerr
Director of Transport Policy Division: Liz Loughran
Director of Gateways and EU Relations: Bernie Rooney
Director of Public Transport Division: Jackie Robinson
Head of Internal Audit: Tracey Woods
CONTACT INFORMATION
Address: Department for Infrastructure, Departmental Co-ordination Unit, Clarence Court 10-18 Adelaide Street, Belfast BT2 8GB
Tel: 028 9054 0540
Email: info@infrastructure-ni.gov.uk
Visit: www.infrastructure-ni.gov.uk
Formed on 1 April 2011, the Greater Manchester Combined Authority is run jointly by the leaders of the ten councils and the Mayor of Greater Manchester
ver the last decade several devolution agreements have been signed between Government and the GMCA.
These agreements brought new powers and responsibilities to the region, including transport. To deliver these devolution agreements, it was decided that Greater Manchester should have an elected Mayor to act as a directly elected point of accountability for the GMCA.
The GMCA is both a political entity and an organisation in its own right. The political part of GMCA provides direction, governance, and oversight of the work they do on behalf of the city region for our residents and businesses. GMCA as an organisation translates that political direction into action through teams of dedicated experts across a range of functions and services.
As a political entity, GMCA comprises the ten local authorities that make up the city region. The Authority is Chaired by the Mayor, Andy Burnham and is led by the Chief Executive, Eamonn Boylan. Functional executive bodies, such as Transport for Greater Manchester (TfGM), are responsible for the delivery of services with the Transport for Greater Manchester Committee (TfGMC) and its sub committees managing the TfGM and creating the transport policy on behalf of the GMCA, however some decisions still require approval by the GMCA. TfGM delivers the GMCA’s transport policies, by coordinating transport networks across the region, deciding where to invest transport funding, and owning and running the Metrolink tram service. TfGM is a key partner in Rail North and Transport for the North.
The GMCA gives local people more control over issues that affect their area.
It means the region speaks with one voice and can make a strong case for resources and investment. There corporate objectives include:
1. Deliver core and devolved services for the public.
2. Secure, and manage, funding and investment at Greater Manchester level for agreed activity.
3. Work with the ten local authorities in Greater Manchester to drive collective activity that puts Greater Manchester at the forefront of tackling social, economic, and environmental issues.
4. Ensure Greater Manchester is speaking with one voice – developing, leading and implementing our evidence-based strategies, building our networks and partnerships and influencing policy.
GMCA coordinates transport services through the public body Transport for Greater Manchester (TfGM).
Greater Manchester Transport Strategy 2040
Greater Manchester Transport Strategy 2040 sets out Greater Manchester’s longterm ambition for transport. The vision is for Greater Manchester to have ‘Worldclass connections that support long-term sustainable economic growth and access to opportunity for all’. It sets out a strong commitment to provide a transport system which: supports sustainable economic growth and the efficient and effective movement of people and goods; improves the quality of life for all by being integrated, affordable and reliable; protects the environment and supports our target to be net zero carbon by 2038 as well as improving air quality; and capitalises on new technology and innovation.
The Five-Year Transport Delivery Plan provides the detail of the schemes to be delivered to support progress towards the longer-term ambitions and targets. As additional funding is secured in the future, subsequent updates of the Delivery Plan will identify the schemes that provide the detail for the broad interventions identified in the 2040 Transport Strategy document.
Transport for Greater Manchester
Transport for Greater Manchester (TfGM) is the local government body responsible for delivering Greater Manchester’s transport strategy and commitments. TfGM implements the decisions made by GMCA and the Greater Manchester Transport Committee GMTC to improve transport services and facilities in Greater Manchester. TfGM owns Metrolink – the UK’s largest light rail network – and plan for its future, including the new Trafford Park line.
KEY PERSONNEL
Mayor: Andy Burnham
Chief Executive: Eamonn Boylan
Head of Communications: Sarah Keaveny
CONTACT INFORMATION
Address: Tootal Buildings
56 Oxford Street, Manchester M1 6EU
Tel: 0161 778 7000
Email: enquiries@greatermanchester-ca.gov.uk
Visit: www.greatermanchester-ca.gov.uk
Established in July 2000 and officially known as London Transport Users Committee, London TravelWatch is sponsored and funded by the London Assembly, which is part of the Greater London Authority, and is independent from the transport operators. The Assembly also appoints its board members, supported by staff who carry out the day-to-day work.
London TravelWatch is interested in the passenger experience of all the services operated and licensed by Transport for London.
The casework team, as well as dealing with appeals, also handle enquiries about Penalty Fare Notices and Penalty Charge Notices. However, the team is only able to ensure that the appeal process has been correctly followed and does not have the power to overturn a decision that has already been made.
As a statutory appeals/consumer body London TravelWatch is always keen to engage with members of the public and listen to their feedback about the transport issues they may face. To get involved, you can sign up to the digital community and receive regular news updates and helpful information on the latest things happening in transport across London.
London TravelWatch’s remit is set by Parliament and, as a result, there are some issues that it is unable to address.
London TravelWatch regularly publishes its research into matters of concern to London transport users. In 2023 it published Left behind Londoners – Digital Exclusion and Disadvantage in London transport which looked at Londoners who had been unable to travel due to a lack of access to a smartphone or digital device. The research involved conducting surveys of Londoners and conducting interviews with organisations that advocate for impacted groups.
Another report looked at Rail Reform and what Londoners chief concerns were –discovering that:
‘We are particularly interested in how individual stations will be staffed, how accessible they will be, options for buying tickets and whether passengers will be able to access facilities such as lifts, waiting rooms and toilets.’
Michael Roberts
Chief Executive of London TravelWatch
• Two thirds of Londoners told us they would be put off from using the railways if the frequency of their train was cut in future.
• Less than half of people were satisfied with current levels of crowding on trains, despite this having got much better in the last two years due to fewer people travelling.
• Only 39 per cent of people surveyed consider the railways to be good value for money.
• 38 per cent of people were dissatisfied with toilet facilities at stations, and many were also dissatisfied with the availability of bike and car parking.
• 17 per cent of disabled passengers were very dissatisfied with connections with other forms of transport and 18 per cent with step-free access in stations and boarding trains.
• 58 per cent of people said they got most of their information about changes to their train service at the station, higher than any other option – online, social media, apps or alerts.
In the summer 2023, in collaboration with Transport Focus, London TravelWatch facilitated a public consultation on proposed changes to ticket offices and received over 680,000 responses combined. In the consultation responses from the public and stakeholders, concerns were raised around accessibility, safety and security, issues with ticket machines and how stations will be staffed in future.
KEY PERSONNEL
Chair: Arthur Leathley
Deputy Chair: Alan Benson MBE
Chief Executive: Michael Roberts
Head of Communications: David Murdoch
Head of Casework: Susan James
Head of Campaigns and Advocacy: Alex Smith
CONTACT INFORMATION
Correspondence address: London TravelWatch
PO Box 5594 Southend on Sea SS1 9PZ
Tel: 020 3176 2999
Email: info@londontravelwatch.org.uk
Visit: www.londontravelwatch.org.uk
Twitter / X: twitter.com/LonTravelWatch
Digital community: mailchi.mp/londontravelwatch/ sign-up-for-updates
Kilborn Consulting Limited is an independent railway engineering consultancy and design business, with over 21 years of railway experience.
We specialise in the design of new and altered railway Signalling & Telecoms systems for the UK railway infrastructure.
Our areas of specialism are:
•Signalling and Telecoms Consultancy, including technical advice & support;
•Asset Condition Assessments, Correlation and Surveys;
•Signalling & Level Crossing Risk Assessments;
•Feasibility and Optioneering Studies;
•Concept and Outline Signalling Design;
• Telecoms Option Selection Reports (including AiP), Reference System Design and Detailed Design;
•Detailed Signalling Design;
•Competency Management & Assessments;
•Signal Sighting assessments, covering the full Signal Sighting Committee process with a competent Chair.
The new office which is located in the heart of Wellingborough can accommodate all staff and visitors alike and offer widespread views across Wellingborough and the surrounding green spaces
We would be delighted to welcome you to our office to discuss your requirements and how we can support you to achieve those.
Kilborn Consulting Limited 6th Floor, South Suite, 12 Sheep Street Wellingborough, Northamptonshire NN8 1BL
Email: pmcsharry@kilbornconsulting.co.uk
Phone: 01933 279909
www.kilbornconsulting.co.uk
The National Infrastructure Commission carries out in-depth studies into the UK’s major infrastructure needs and makes recommendations to the government
The National Infrastructure Commission (NIC) is an executive agency of the Treasury that provides impartial, expert advice and makes independent recommendations to the Government on economic infrastructure.
The Commission functions in an open and transparent manner, building consensus around its recommendations and engaging across parties and with the public, policymakers, infrastructure experts and relevant bodies.
Recommendations made by the NIC represent the views of the Commission and are not a statement of Government policy. However, the Government is required to respond formally to the Commission’s National Infrastructure Assessment and specific studies it undertakes.
The NIC engages closely with devolved administrations and bodies under their jurisdictions as appropriate, particularly on matters where the respective infrastructure policy responsibilities of the UK government and devolved administrations interact.
The Commission undertakes research into specific transport proposals when asked to do so by government, but also advises on broader questions of policy and approach to planning upgrades and new investment in road, rail, and other transport modes.
The National Infrastructure Commission is charged with preparing a National Infrastructure Assessment once every five years, looking at the long-term needs of the main sectors of the UK’s economic infrastructure, including energy, transport, digital communications, waste, water and floods risk management.
The first National Infrastructure Assessment was published in July 2018, and the second in October 2023. The second Assessment made a series of recommendations for meeting the UK’s infrastructure needs up to 2050.
Its core proposals include:
• Taking a clear decision that electrification
is the only viable option for decarbonising buildings at scale, getting the UK back on track to meet its climate targets and lowering energy bills by fully covering the costs of installing a heat pump for lower income households and offering £7,000 support to all others.
• Investing in public transport upgrades in England’s largest regional cities to unlock economic growth, improving underperforming parts of the national road network and developing a new comprehensive and long term rail plan which will bring productivity benefits to city regions across the North and the Midlands.
The Assessment recommendations represent a major long-term programme of investment in the UK’s infrastructure. This includes proposing substantial funding for major public transport schemes in a number of city regions, in addition to significant funding for rail schemes particularly serving the North and Midlands. To ensure the latter is spent effectively and in the wake of the decision to cancel the northern legs of High Speed 2, the Commission called for a comprehensive long term plan to address the capacity and connectivity challenges facing city regions in the North and Midlands.
The Assessment also proposes additional investment in the maintenance and renewal of existing transport infrastructure on both a national and local level, and planning for the effects of climate change.
The government has committed to respond to the second Assessment in 2024, alongside an updated National Infrastructure Strategy.
In March 2021 the government asked the NIC to report on how to maximise the benefits of infrastructure policy and investment specifically for suburban areas and towns. At the conclusion of the six month study, the Commission set out how transport and digital connectivity plays an important role in supporting the
economic development of towns, and is best achieved as part of a long term strategy that complements a wider place based plan for a town.
However, the report found that the present funding system for local transport hinders the development of effective strategies. It called for a simplification of the current system of multiple competitive funding pots, and recommended that county and unitary authorities should receive devolved five year infrastructure budgets to enable long term planning.
The government’s formal response, published in August 2022, acknowledged the importance of devolution and repeated commitments made to extend the number of areas with devolved powers, but indicated that five-year budgets will be a matter of negotiation in each devolution deal.
KEY PERSONNEL
Chief Executive: James Heath
Chair: Sir John Armitt CBE
Deputy Chair: Julia Prescot
Commissioner: Professor Sir Tim Besley CBE
Commissioner: Neale Coleman CBE
Commissioner: Dr Michele Dix CBE
Commissioner: Andy Green CBE
Commissioner: Professor Jim Hall
Commissioner: Professor Sadie Morgan OBE
Commissioner: Kate Willard OBE
Commissioner: Nick Winser CBE
CONTACT INFORMATION
Address: 7th Floor, Windsor House, Victoria Street London SW1H 0TL
Email: enquiries@nic.gov.uk
Visit: www.nic.org.uk
X: @NatInfraCom
reputation as one of the largest rolling stock recyclers in the UK, winning nationally released tenders from several of the main rail operating companies.
The head office is located in Rotherham, South Yorkshire at Clarence Metal Works with the company’s gantry cranes and three derrick cranes making the site quite distinctive.
established in 1920 by Clarence Frederick Booth and since that time has continued to be generations of the Booth family.
associated with the scrapping of diesel and electric locomotives since the 1960s and has an the largest rolling stock recyclers in the UK, winning nationally released tenders from operating companies.
CF Booth rolling stock division has achieved both ISO 9001 and 14001 standards and has invested heavily in developing the infrastructure to handle all kinds of rolling stock including more than 1,500 metres of rail sidings, which allows us to accommodate a substantial amount of rolling stock. Work continues at present with rail vehicles being brought in through a connection to Network Rail and the proximity of the railway sidings to roads give this side of the business a high profile with many wagons, carriages, underground and departmental stock being processed. In addition, our extremely competitive buying process and quick payment terms mean that for many companies wishing to dispose of their rolling stock, CF Booth Ltd is the first port of call. Besides processing rolling stock for their residual ferrous/non ferrous metals, we also salvage any or all components that may be required by railway preservationists.
Rotherham, South Yorkshire at Clarence Metal Works with the company’s gantry cranes making the site quite distinctive.
CF Booth Ltd is one of the leading metal recycling companies in the UK. Established in 1920 by Clarence Frederick Booth, the business has grown from a local metal trader into one of the largest independently run recycling companies in Europe and is nearing its 100th year anniversary. CF Booth has been associated with the scrapping of diesel and electric locomotives since the 1960’s and is now one of the largest rolling stock recyclers in the UK, working with several of the main rail operating companies.
The current Rolling Stock Manager, Christopher Davis, says: “We are proud to be playing a major role in supporting the UK national rail industry and extremely proud to provide a valuable service to railway enthusiasts and preservationists throughout the UK as they continue to restore rolling stock vehicles to their former glory for future generations to enjoy. We value the relationship we have built up with preservationists and enthusiasts over the years’’.
CF Booth rolling stock division has achieved both ISO 9001 and 14001 standards and has invested heavily in developing the infrastructure to handle all kinds of rolling stock including more than 1,500 metres of rail sidings, which allows us to accommodate a substantial amount of rolling stock. Work continues at present with rail vehicles being brought in through a connection to Network Rail and the proximity of the railway sidings to roads give this side of the business a high profile with many wagons, carriages, underground and departmental stock being processed.
We are more than just a metal recycler, our continued investment in infrastructure and quality personnel has put us at the forefront of the metal recycling industry. Working with global businesses and international brands has made us think differently and strive to continue our development.
In addition, our extremely competitive buying process and quick payment terms mean that for many companies wishing to dispose of their rolling stock, CF Booth Ltd is the first port of call. Besides processing rolling stock for their residual ferrous/non ferrous metals, we also salvage any or all components that may be required by railway preservationists.
Our rolling stock asbestos removal/disposal service is supported by Demex Ltd a part of the CF Booth Group. Their fully trained and accredited operatives use the very latest equipment and techniques to safely strip out and dispose of asbestos. Besides processing rolling stock for their residual ferrous/non-ferrous metals, we also salvage any or all components that may be required by Railway Companies and Railway Preservationists.
The current Rolling Stock Manager, Christopher Davis, says: “We are proud to be playing a major role in supporting the UK national rail industry and extremely proud to provide a valuable service to railway enthusiasts and preservationists throughout the UK as they continue to restore rolling stock vehicles to their former glory for future generations to enjoy. We value the relationship we have built up with preservationists and enthusiasts over the years’’.
9 View, analyse and report on your data with our comprehensive cloud platform
9 Get real-time alerts and take action before you receive a non-compliance
9 Monitor multiple locations simultaneously
has achieved both ISO 9001 and 14001 standards and has invested heavily in handle all kinds of rolling stock including more than 1,500 metres of rail sidings, accommodate a substantial amount of rolling stock. Work continues at present with rail vehicles connection to Network Rail and the proximity of the railway sidings to roads give this side with many wagons, carriages, underground and departmental stock being processed. competitive buying process and quick payment terms mean that for many companies rolling stock, CF Booth Ltd is the first port of call. Besides processing rolling stock for ferrous metals, we also salvage any or all components that may be required by railway
9 Add weather, gas, dust and vibration data through bolt-on modules
9 Flexible subscriptions that can be changed at any time
Manager, Christopher Davis, says: “We are proud to be playing a major role in supporting and extremely proud to provide a valuable service to railway enthusiasts and UK as they continue to restore rolling stock vehicles to their former glory for future the relationship we have built up with preservationists and enthusiasts over the years’’.
The NECA is the legal body that brings together the seven councils of County Durham, Gateshead, Newcastle, North Tyneside, Northumberland, South Tyneside and Sunderland
The North East Combined Authority’s ambition, as set out in its Transport Manifesto is to provide affordable, attractive, reliable, safe, healthy transport choices for businesses, residents and visitors while enhancing the environment.
Working with partners, the NECA provides leadership and a united voice on key strategic transport issues, links strategic transport planning with economic priorities, provides strong representation on transport issues of national significance including rail, air travel, strategic road network and ports as well as providing more effective coordination to enable improvement to the area’s public transport network.
Previously overseen by the Tyne and Wear Integrated Transport Authority (ITA), in 2014 the responsibilities and assets of the ITA were transferred to the NECA. From that date the Tyne and Wear Integrated Transport Area was dissolved. NEXUS manages the functions which it previously delivered within the Tyne and Wear area.
NEXUS is the trading name of the Tyne and Wear Passenger Transport Executive. NEXUS is an independent organisation. It was created in 1969 by the Tyneside Passenger Transport (Designation) Order 1961 in accordance with the Transport Act 1968 and is responsible for overseeing work and ensuring good governance. The vast majority of these responsibilities have been delegated to a committee of NECA – the Transport North East (Tyne and Wear) SubCommittee.
Some responsibilities, such as the setting of transport levies and the approval of the regional transport strategy are discharged by the Authority’s principal decision-making body – the NECA Leadership Board. The NECA has prepared and submitted a bid on behalf of the seven local authorities which aims to obtain in excess of £100 million in funding which will be invested in major improvements to sustainable transport in the area.
The aim of this bid is to help close the area’s productivity gap through better connectivity and more mobility, enabling growth, reducing congestion and improving air quality and public health at the same time.
The Tyne and Wear Metro serves Newcastle upon Tyne, Gateshead, South Tyneside, North Tyneside and Sunderland. When the Metro opened to the public in August 1980 it was Britain’s first light rapid transit system and was the first railway in the country to be truly wheelchair compatible.
region’s programme envisages a £467 million investment in public transport, sustainable transport and supporting capital investment.
The system was progressively opened in phases through to 1984 when the full 34 miles of the original network became operational with the opening of the line into South Shields. In its first year of full operation there were more than sixty million passenger journeys. The local rail network was privatised in 1996, however, Tyne and Wear PTE, Nexus as it is now called, kept responsibility for the operation of the Metro. The Metro wasextended to Sunderland in April 2002.
In March 2018 the Department for Transport (DFT) launched a Call for Proposals for city region authorities wishing to obtain capital funding from its Transforming Cities Fund (TCF). On 28 November 2019 the North East region submitted an ambitious and integrated programme of capital investments to the Department for Transport, seeking funding from the Transforming Cities Fund. The
KEY PERSONNEL
Head of Paid Service: Patrick Melia
Deputy Head of Paid Service: John Hewitt, Jonathan Tew
Chief Finance Officer: Paul Darby
Policy and Scrutiny Officer: Gavin Armstrong
CONTACT INFORMATION
c/o South Tyneside Council
Town Hall & Civic Offices
Westoe Road
South Shields NE33 2RL
Tel: 0191 643 5339
Email: enquiries@northeastca.gov.uk
Visit: www.northeastca.gov.uk
Our lifts and escalators are helping to improve access for all in infrastructure hubs right across the UK.
Birkenhead Park
Cardiff Station
Edinburgh Haymarket
Glasgow Queen Street
King’s Cross
Leeds Station
Luton Airport
Manchester Piccadilly
Nottingham Hub
Paddington Station
Waterloo Station
Watford Junction
Every product maintained locally via our UK network of lift engineers. Call us today on 01264 343692
We know we can help.
The Office of Rail and Road is a non-ministerial government department and is the independent economic and safety regulator for Britain’s railway
The Office of Rail and Road (ORR) is responsible for protecting the interests of rail users now and in the future. ORR does this by holding Network Rail (and in future Great British Railways) to account and keeping the railway safe by regulating the rail industry’s health and safety performance. It also holds HighSpeed1 Ltd (HS1) to account and makes sure that the rail industry is competitive and fair.
ORR holds National Highways to account for its performance and efficiency, and it has economic regulatory functions in relation to railways in Northern Ireland and the UK section of the Channel Tunnel.
Keeping Britain’s railway safe
Britain has one of the safest railways in Europe for passengers and workers. With more than 100 HM Railway Inspectors dedicated to keeping every railway safe – from the mainline network, London Underground to light rail, trams, and the heritage sector –ORR works with the rail industry to identify, assess, and manage safety issues.
Inspectors are out on the network every day ensuring all train and freight operating companies and Network Rail manage passenger and workforce health and safety risks appropriately. ORR also offers advice, guidance and conducts research to promote continuous improvement.
ORR’s inspectors carry out investigations into breaches of health and safety law on the railway and take both informal and formal enforcement action, and as a last resort, ORR can prosecute a company for health and safety failings when things go wrong.
The railway network needs to be run for the benefit of the whole country. ORR oversees Network Rail (and in the future Great British Railways), holding it to account for its performance and service – overseeing whether it is delivering value for money –for passengers, the freight industry, and taxpayers.
As part of this, ORR monitors Network Rail’s train punctuality performance and upkeep of rail assets. ORR is also responsible
for determining operator access when disputes arise between Network Rail and operators.
As outlined in the Williams-Shapps Plan for Rail, the role of Network Rail is changing through rail reform. ORR’s role will adapt to reflect these changes and ensure ORR remains a strong independent body overseeing Great British Railways. This is essential to maintaining accountability, transparency, and efficiency across the network.
ORR also holds HS1 to account for the performance of its railway for train services, upkeep of the network and that it meets its efficiency targets. ORR is working with the French rail regulator Autorité de Régulation des Activités Ferroviaires (ARAF) to promote competition, full transparency, and fair access to the Channel Tunnel.
ORR works to ensure that rail markets are competitive and fair – for passengers, freight customers, railway operators and taxpayers. ORR does this by integrating its economic, competition and consumer functions and powers.
For consumers, ORR plays a key role in improving the rail passenger experience for which it has regulatory responsibility, taking prompt and effective action to improve the service that passengers receive where it is required.
ORR also sets guidance on the standards train and station operators must meet on assisted travel. They do this through; ensuring train companies provide accurate and timely information, particularly during disruption, handling complaint procedures seamlessly, and monitoring how train and station operators handle these situations.
As the accredited primary provider of railway industry official statistics, ORR publishes a range of statistics, including railway performance, rail usage (both passenger and freight) and safety. This open data and information about the rail industry promotes transparency and a better understanding of Britain’s railway.
The trustworthiness, quality and value of ORR statistics are overseen by the UK Statistics Authority’s regulatory arm – the Office for Statistics Regulation.
ORR regulates Network Rail including setting the targets it must achieve and reporting regularly on its performance. ORR also regulates health and safety standards and compliance across the whole rail industry. It oversees competition and consumer rights issues – driving a better deal for rail passengers and taxpayers. ORR regulates the HighSpeed1 link to the Channel Tunnel. ORR also holds National Highways to account for its performance and efficiency against government set targets.
KEY PERSONNEL
Chair: Declan Collier
Chief Executive: John Larkinson
Director of Economics, Finance and Markets: Will Godfrey
Director, Corporate Operations: Vinita Hill
HM Chief Inspector of Railways and Director, Railway Safety: Ian Prosser CBE
Director of Railway Planning & Performance: Feras Alshaker
Director of Strategy, Policy and Reform:
Stephanie Tobyn
Director of Communications: Russell Grossman
CONTACT INFORMATION
Tel: 020 7282 2000
Visit: www.orr.gov.uk
Address: 25 Cabot Square
London E14 4QZ
RAIB became operational in October 2005 as the independent body which investigates accidents and incidents on mainline railways, metros, tramways and heritage railways throughout the UK
Lord Cullen’s inquiry report into the Ladbroke Grove rail accident in 1999 recommended the creation of an organisation to independently investigate railway accidents to improve safety.
RAIB employs specialist investigators, inspectors and principal inspectors. These staff typically have a railway, academic or investigative background and RAIB gives them additional extensive training in railway operations, railway engineering and accident investigation. RAIB also has a dedicated team who provide essential business support, giving it a total of 43 staff.
RAIB investigations are focused solely on improving safety. RAIB are not a prosecuting body and do not apportion blame or liability. Possible breaches of legislation are dealt with by other organisations, usually the police and safety authorities.
RAIB’s responsibilities are to:
• Investigate causes of railway accidents and incidents where it believes investigation will bring safety learning to the industry.
• Identify the factors that may lead to a similar accident or make the consequences worse.
• Highlight gaps in the railway industry’s safety defences that are revealed during investigations.
• Make recommendations to prevent the same thing happening again.
• Increase awareness of how railway accidents happen and cooperate with other investigation organisations nationally and internationally to share and encourage good practice.
• RAIB’s scope of activity includes the UK mainline networks (Network Rail and Northern Ireland Railways), the London Underground and other metro systems, tramways, heritage railways and the UK part of the Channel Tunnel.
Operators of these railways and tramways have a legal duty to notify RAIB of certain
types of accidents and incidents. RAIB also monitors operations on the major networks through various industry reporting systems and may also proactively follow up events featuring in such systems.
RAIB has a duty to investigate all serious railway accidents as defined by law.
These include derailments and collisions of rolling stock resulting in the death of a person, serious injuries to five or more people, or extensive damage to rolling stock, infrastructure or the environment. They will also investigate incidents and accidents which, under slightly different circumstances, could have led to a serious accident, and which have an obvious impact on railway safety regulation or the management of safety. RAIB may produce a safety digest as alternative to a full investigation, where the safety learning from an event has been identified by a previous investigation or relates to compliance with existing rules.
Whenever RAIB investigates, it publishes the results as an investigation report. These reports will almost always include recommendations to improve safety. The branch can direct recommendations towards any organisation or person that they think is best placed to implement the changes required. This includes railway and nonrailway, private and public sector bodies.
While directed at specific end implementers, recommendations are addressed to the relevant railway safety authority, or to other public bodies. This is because the law requires these authorities to ensure that RAIB’s recommendations are considered and, where appropriate, acted upon. The authorities are required to report back to RAIB details of any implementation measures, or the reasons why no action is being taken. Details of the status of recommendations are published on the RAIB website.
In addition to recommendations, RAIB may include learning points in its investigation reports and safety digests
where there is good practice that might be adopted by others, or where a reminder to the industry to reinforce compliance with existing procedures or standards might be appropriate.
Based in operational centres in Derby and Farnborough, RAIB is able to respond quickly to accidents in any part of the UK. RAIB’s current priorities are:
• Maintaining the production of highquality, timely investigations
• Keeping up with changes in technology and industry structure.
• Recruiting, developing and keeping the right expertise
• Continued positive engagement with the rail industry and other statutory bodies.
• Preserving and enhancing RAIB’s international contacts
• Resolving (with other AIBs and the Chief Coroner) issues around legal judgements that set out how coroners and the AIBs interact.
• Working with other railway accident investigators in the UK to share good practice and to help improve the quality of investigations.
KEY PERSONNEL
Chief Inspector of Rail Accidents: Andrew Hall
CONTACT INFORMATION
Tel: 01332 253300
Email: enquiries@raib.gov.uk
Visit: www.raib.gov.uk
Address: The Wharf, Stores Road
Derby DE21 4BA
We make the world of infrastructure a safer place. We keep your network moving.
KITE Projects are an expert in the design and supply of handrail and access systems, and complex engineering solutions for infrastructure projects. We inspire and are inspired by safe and sustainable engineering.
All KITE Systems ensure safe access goes beyond compliance, and our products are designed to exceed industry standards.
We recognise the power of connection – be that bringing communities together, or joining networks, KITE Systems enable this to happen.
Contact our team if you have a project that requires a permanent access solution.
Managing environmental factors have never been more in focus.
KITE Systems offer sustainable engineering solutions for challenging conditions.
kite-projects.co.uk / 01962 886290
sales@kite-projects.co.uk
The RSSB (Rail Safety and Standards Board) is an independent body, working with its 88 member companies to drive improvements in the British rail system
Drawing on experience and expertise from across the sector, it brings all aspects of light rail safety under one roof while providing a central resource where colleagues can access the latest guidance and standards documentation.
Its role is to help the rail industry continually improve its health and safety performance in order to reduce risk to rail employees, passengers and the public at large. RSSB does this through developing standards, providing analysis and insight to health and safety data, carrying out research, promoting sustainability principles, and facilitating the industry’s technology strategy.
• RSSB’s strategic priorities are:
• Supporting healthy and safe collaboration and informing industry decisions to reduce risk and harm.
• Supporting enhanced performance and efficiency updating standards, modernising systems, informing and enabling innovation.
• Supporting the application of sustainability principles
RSSB members include Network Rail and other infrastructure managers, all the train operating companies (TOCs), all the freight operating companies (FOCs), rolling stock leasing companies (ROSCOs), infrastructure contractors, and suppliers.
The SRE is a pan-industry group of rail industry leaders, committed to sustainability leadership who will be responsible for a new Sustainable Rail Strategy. The group will oversee and promote the development of an ambitious, affordable, and coherent sustainability programme to make rail the leading mode of sustainable transport.
SRE’s representatives are drawn from: Chiltern Railways by Arriva, Crossrail, Department for Transport, DB Cargo, Eversholt Rail, HS2, Network Rail, Office of Rail and Road, Rail Operations Group, Rail Delivery Group, Rail Freight Group, Railway
Industry Association, RSSB, Siemens, Transpennine Express.
On 4 April 2019, RSSB published its 20192024 Business Plan, outlining how it will work over the next five years to support a safer railway into Control Period 6 (CP6) and beyond. Setting out how RSSB will meet a range of industry priorities and challenges to put passengers first, the plan focuses on the crucial areas of safety, health and wellbeing, sustainability, efficiency, innovation and the future post-Brexit.
RISAS is the Railway Industry Supplier Approval Scheme. It ensures that suppliers of critical products have the appropriate systems, processes, competence, resources, facilities and procedures. Companies undergo a challenging assessment by a Railway Industry Supplier Approval Body (RISAB). The assessment involves on-site interviews and evaluations to get proof that the company can meet the standards expected.
A successful assessment leads to the award of a RISAS certificate. This is evidence that an independent, robust, rigorous and transparent assessment of the supplier has taken place, by experts.
These details are added to the RISAS website which holds a searchable database of companies who hold RISAS certificates and details the products and services they cover. RSSB manages the scheme on behalf of the rail industry providing its profile and governance. RSSB also accredits the RISABs.
RISQS is recognised and supported by the rail industry as the most effective means of deriving assurance and managing supply chain risk. It gives the industry’s 100-plus buyer members the assurance to do business with confidence with 4,000 supplier members. It’s an open, fair and transparent way for them to be formally recognised as capable providers of products and services to the GB rail market, on a smart, quick, easy web-based platform. Suppliers can be
audited once via RISQS for their capabilities avoiding the need for them to be subjected to multiple, duplicate auditing from different buyers.
CIRAS is an independent, not-for-profit confidential reporting service, funded by its members. Its ambition is to improve the health, safety and wellbeing of staff and passengers across the transport sector. Transport workers can get in touch and CIRAS listens to their concerns in complete confidence.
CIRAS raises the concern with the relevant company and sends the response back to the person who raised the concern so that they know what action has been taken. CIRAS members use the intelligence they receive from reports to reduce risk, improve safety and wellbeing, and foster a positive safety culture. CIRAS also works with its 2,000-strong member community to share learning and good practice.
Starting out as a charity working with one train operator over 20 years ago, today CIRAS members span construction, transport operators including bus, light rail, tram, urban metros and mainline rail, and the transport supply chain. CIRAS is part of the RSSB Group.
KEY PERSONNEL
Chair: Mike Brown
Chief Executive Officer: Mark Phillips
Chief Financial Officer: Hannah Kingsley
Chief Operating Officer: Johnny Schute
CONTACT INFORMATION
Address: The Helicon, 1 South Place
London EC2M 2RB
Tel: 020 3142 5300
Email: enquirydesk@rssb.co.uk
Visit: www.rssb.co.uk
The Greater Glasgow Passenger Transport Executive (GGPTE) was created in 1972 to oversee all suburban railways in the Glasgow area. In the 1980s it was replaced by Strathclyde Passenger Transport Executive (SPTE). In 1996, the Executive was reincorporated as a body consisting of councillors drawn from the twelve Council Areas which succeeded Strathclyde Region.
In 2006 Strathclyde Passenger Transport Executive (and Authority), along with the WESTRANS voluntary regional transport partnership, was replaced by Strathclyde Partnership for Transport (SPT). It is part of the transport framework created by the Scottish Government, which is made up of a national transport agency, Transport Scotland, and seven Regional Transport Partnerships. As part of this reorganisation SPT gained responsibility of the region’s transport planning; analysing all travel needs and developing the transport system for now and the future.
SPT is the largest of the seven regional transport partnerships. SPT’s role involves planning and delivering transport solutions for all modes of transport across the region, in conjunction with member councils and industry partners. It runs the Glasgow Subway, a host of specialist bus services and is responsible for delivering public transport.
The Partnership consists of 20 elected members representing the twelve constituent authorities in the west of Scotland and between seven and nine appointed members.
In March 2021 the Chair and Vice-Chairs of SPT presented a proposal to evolve SPT into ‘Transport for Strathclyde’, a more powerful authority in control of one network across the region. It called for a new parliamentary Bill to empower the body and a ‘public transport social contract’ with the public which guarantees access to work, health, education and recreation – ‘without breaking the bank or planet’.
Glasgow has the largest network of suburban railway lines in the UK outside of London. SPT is no longer involved in the everyday operation of the rail network. The rolling stock was operated on behalf of SPT by First ScotRail (also part of FirstGroup) until March 2015, since April that same year Abellio ScotRail has operated rail services under the ScotRail brand.
The Glasgow Subway is the only underground metro system in Scotland. Originally built for the Glasgow District Subway Company, the railway first opened in 1896. The Subway is generally recognised as the world’s third oldest underground railway, after London and Budapest. And the only one that has never been expanded from its original route.
The Subway forms a circle in the centrewest of Glasgow and carries 13 million passengers each year. The entire route is underground, contained in twin tunnels, 15 stations are distributed along the route length of over six miles. Eight of the stations are north of the River Clyde which dissects the circular route.
In 1977, Greater Glasgow Passenger Transport Executive closed it for major modernisation works. The railway in its present form reopened for operation on 16 April 1980. Now part of SPT, the railway is one of the few in the UK remaining in public ownership and is ‘vertically integrated’, which means SPT’s responsibility covers all aspects of operation and infrastructure.
In 2016, SPT took a significant step forward in improving its Subway and is currently undergoing its biggest modernisation programme in more than 30 years. A £288 million funding package for the work is being supported by the Scottish Government. As well as the new trains, the Subway’s signalling equipment, control systems and control centre will all be replaced, and the upgrade will include
new platform screen doors. Glasgow Subway modernisation continues at a rapid pace. Having now completed all 15 stations including two city centre flagship stations all with the intent to; improve accessibility, introduce more smart technology ticketing, and provide a fresher look to its stations, all while minimising disruption.
SPT is passionate about its commitment to reducing its carbon footprint through finding ways of adopting sustainable policies and practices where possible. Work is ongoing across SPT to identify measures to improve energy efficiency, reduce water consumption and minimise waste. SPT also have a JourneySharing community, helping commuters connect where they have similar journey details to save money, and reduce CO2 emissions.
Once the modernisation plan is complete, and it has been fully tested, the Subway will move from its current partially automatic trains to Unattended Train Operations (UTO). SPT administers a range of integrated travel tickets, such as ZoneCard, Roundabout and Daytripper giving discounted fares on buses, trains, ferries and the Subway.
KEY PERSONNEL
Chief Executive: Valerie Davidson
Director of Finance & Corporate Support: Lesley Aird
Director of Transport Operations: Richard Robinson
CONTACT INFORMATION
Address: 131 St Vincent Street
Glasgow G2 5JF
Tel: 0141 332 6811
Email: enquiry@spt.co.uk
Visit: www.spt.co.uk
We are experts in delivering network reliability for high speed railways through whole-life asset management. We own the total solution and its performance.
A reliable service makes travel more convenient, easier for passengers to plan journeys and gives them confidence they will arrive on time.
Transport for Greater Manchester (TfGM) is a not-for-profit local Government body responsible for delivering the transport strategy set by the Greater Manchester Combined Authority (GMCA)
More than 5.8 million journeys are made across Greater Manchester’s transport network each day (excluding walking and cycling). TfGM coordinates transport networks across the region, works with the GMCA and the ten local authorities on the development and delivery of new projects, and owns and runs the Metrolink tram service (the UK’s largest light rail network). It is developing the Bee Network – a high volume, low fare Londonstyle transport system integrating buses, trams, walking and cycling and – ultimately – local rail services.
TfGM builds and manages bus stations and transport interchanges, provides travel planning and timetable information to passengers, and promotes walking and cycling as safe and healthy choices.
TfGM assets include the Metrolink network, with 99 stops and 147 tram vehicles, 36 Park & Ride sites (including rail and guided busway), twelve Free Buses and 52 Yellow School Buses, the Cycle Hire scheme, more than a dozen transport interchanges, and many other properties.
The Greater Manchester rail network is now used by around forty million passengers a year. This is an increase of thirty per cent over the past decade and TfGM has an influential voice in developing the best possible rail services in Greater Manchester.
Following the Trailblazer Deeper Devolution Deal, which was agreed between Greater Manchester and the Government in March 2023, TfGM and the Great British Railways Transition Team are working to deliver a more locally accountable and integrated rail network in the city-region.
In 2021, TfGM marked ten years since its inception after a reform of local government in Greater Manchester granted the Greater Manchester Passenger Transport Executive (GMPTE) more powers and led to a rebranding.
Since the rebranding, TfGM has delivered many high profile and successful projects and schemes, including:
• The £1.5 billion ‘Phase Three’ Metrolink expansion between 2010 and 2015, which saw new lines through dozens of local communities, with extensions to Rochdale via Oldham, Ashton-under-Lyne, East Didsbury, Manchester Airport and a new line through Manchester city centre.
• The £350 million Trafford Park line in March 2020, adding a further 5.5 kilometres of track and six new stops to serve one of the region’s major employment, leisure and retail destinations.
• New transport interchanges in Rochdale, Ashton, Altrincham, Wythenshawe and Bolton, while Radcliffe and Wigan now enjoy new, state-of-the-art bus stations.
• The TravelSafe Partnership – a multiagency body led by TfGM and Greater Manchester Police, that takes an intelligence-led, problem-solving approach to tackling crime and ASB on public transport.
Since Government announced proposals for the City Region Sustainable Transport Settlement (CRSTS) in 2021, GM has embarked on the roll-out of a long-term infrastructure pipeline that will see delivery of the schemes set-out in GM’s Transport Strategy 2040. Whilst the infrastructure pipeline is funded primarily through the CRSTS, other funding streams including Active Travel Funding (ATF), Local Electric Vehicle Charging Infrastructure (LEVI) funding and Zero Emission Bus Regional Areas (ZEBRA) funding take the overall programme funding to c£1.5 billion over the period to March 2027. Coupled with Government’s recent announcements regarding CRSTS 2, GM has the basis of a c£4 billion infrastructure pipeline to March 2032.
The principles that underpin the pipeline are built upon Government’s and GM’s shared vision for driving growth and productivity through infrastructure investment; levelling-up services towards the standards of the best; and decarbonising transport, especially promoting modal shift from cars to public transport, walking and cycling.
The programmes that make up GM’s integrated and sustainable transport investment pipeline within the current CRSTS investment period to March 2027 include:
• Development of schemes to expand the Metrolink network, together with Tram Train and guided busway routes.
• Working alongside rail industry partners, to improve the reliability, capacity and customer experience of rail travel –including work to progress and deliver GM’s Access for All (AfA) programme and the first contactless pilot for touch-in/ touch-out pay-as-you-go rail services in Greater Manchester in 2025.
KEY PERSONNEL
Interim Chief Operating Officer: Alex Cropper
Managing Director and Finance and Corporate
Services Director: Steve Warrener
Head of Rail Programme: Simon Elliott
Communications Officer: David Stevenson
CONTACT INFORMATION
Address: 2 Piccadilly Place, Manchester M1 3BG
Tel: 01612 244 1000
Email: hello@beenetwork.com
Engineering a better future for our planet and its people
We’re committed to lead our clients, and partners across the infrastructure ecosystem, to engineer this better future for our planet and its people.
atkinsrealis.com
Transport for London (TfL) is the integrated transport authority responsible for delivering the Mayor of London’s strategy and commitments on transport
Every day around 30 million journeys are made across the network and TfL keeps the city moving, runs the day-to-day operation of the Capital’s public transport network and manages London’s main roads.
The services operated include London Underground, London Buses, Docklands Light Railway, London Overground, TfL Rail, London Trams, London River Services, London Dial-a-Ride, Victoria Coach Station, Santander Cycles and the Emirates Air Line. TfL provides modern ways to pay through Oyster and contactless payment cards and provides live travel information via the app TFL Go, which allows users to get live updates on their journey, and advises on the most accessible routes for those with reduced mobility.
The TfL programme of transport capital investment is one of the world’s largest. It is modernising Tube services and stations, transforming the road network and making it safer, especially for more vulnerable road users such as pedestrians and cyclists. It is also working hard to help customers with reduced mobility access stations, as one third of London underground stations are now step-free.
The Elizabeth line
The Elizabeth line was built by Crossrail Ltd, a company joint sponsored by TfL and the Department for Transport. Crossrail broke ground at Canary Wharf in May 2009, and began tunnelling in May 2012.
TfL Rail services started running between Liverpool Street and Shenfield in May 2015, and between Paddington and Heathrow (and later Reading) in 2018 – these would become the eastern and western branches of the Elizabeth line once opened, with ten new stations opening through central London on 24 May 2022.
TfL has overall responsibility for the train frequency specifications, standards for station facilities and overall performance as well as fares and revenue management. The Elizabeth line's full peak timetable commenced on 22 May 2023, with 24 trains per hour between Paddington and Whitechapel, as well as more services
between Liverpool Street National Rail station and Gidea Park, and an increase in peak services from Reading with reduced stops. It was also the first time that direct services ran from Shenfield to Heathrow Airport. At a total of more than 250 million journeys in 18 months, the Elizabeth line has already become one of the most used railways in the country as it continues to provide greater connectivity and faster journey times, and support new housing, jobs and economic growth.
The Docklands Light Railway (DLR) opened in 1987 and operates as an automated light metro system with performance and dependability among the best in the UK. The DLR network of 45 stations has multiple connections with the Tube, buses, National Rail, Overground, river and coach services. The DLR is currently the busiest light railway in the UK, with around 1.8 million journeys made on the network each week. The DLR is operated by KeolisAmey Docklands (KAD) under a franchisee contract awarded by TfL. It operates the trains and stations with TfL maintaining much of the network. A contract was awarded to Construcciones y Auxiliar de Ferrocarriles, S.A (CAF) in June 2019 to replace some of the oldest trains operating on the network.
The new fleet of walk-through trains are expected to start entering passenger service from 2024 providing a number of customer improvements, including the latest audio and visual real-time travel information, air conditioning and mobile device charging points.
TfL is responsible for London Overground –a group of orbital lines serving many areas of the Capital. Launched in 2007, around a third of all Londoners are within walking distance of a London Overground station. There are six London Overground routes that, together, form an outer London orbital network. This route travels through 23 London boroughs, as well as southern Hertfordshire and serves 113 stations. Upgrades to London Overground stations is ongoing, including a new entrance and stepfree access at Surrey Quays station.
In November 2016 Arriva began to manage the network’s stations and trains on a day-to-day basis. Network Rail manages and maintains most of the track and signals, as London Overground is part of the National Rail network.
TfL took over the running of London Trams in 2008 and completely refurbished
the Trams network which had been created eight years earlier. London Trams offer frequent services from Croydon to Wimbledon, Beckenham Junction, Elmers End and New Addington. TfL sets the specifications for tram frequency and overall performance, is responsible for fares and revenue, carries out maintenance, and plans and funds improvements and extensions to the network. The tram network has 17 miles of track, 34 trams in the fleet and 39 stops. It serves seven National Rail stations and more than fifty bus routes. Tram Operations (TOL), a subsidiary of First Group, operates trams day-to-day under a franchisee agreement with TfL. TOL’s contract will expire in 2030.
London Underground, better known as the Tube, opened in 1863, it is the world’s oldest underground railway network, and one of the largest. The Tube spans 272 stations and over eleven lines. TfL is responsible for all aspects of the Tube’s operations including running the trains, stations and control centres, making sure the Tube is safe and secure, and collecting and protecting fares revenue as well as the maintenance and renewal of most of the infrastructure used by the Tube, although some services run over track that is the responsibility of Network Rail.
As the city continued to recover from the pandemic, and despite hybrid working becoming more of a norm TfL figures show
that tube ridership increased by more than 25 per cent between the months January and February of 2022. With stations in the heart of London’s financial district, like Bank and Canary Wharf seeing ridership numbers back on track.
KEY PERSONNEL
Commissioner: Andy Lord
Director of Communications & Corporate Affairs:
Matt Brown
Interim General Counsel and Board Secretary:
Andrea Clarke
Chief Capital Officer: Stuart Harvey
Chief Finance Officer: Rachel McLean
Interim Chief Operating Officer: Glynn Barton
Chief Safety, Health and Environment Officer: Lilli Matson
Chief Customer & Strategy Officer: Gareth Powell
TFL’s Director of Customer Operations: Nick Dent
CONTACT INFORMATION
Address: Palestra, 197 Blackfriars Road
London SE1 8NJ
Tel: 0343 222 1234
Email: Contact via website
Visit: www.tfl.gov.uk
• Rumour has it that the Bakerloo line was created after a group of businessmen complained that they couldn't get to and from Lord's Cricket Ground quickly enough.
• Opened in 1863, The Metropolitan Railway between Paddington and Farringdon was the first, urban, underground railway in the world.
• One third of London Underground stations are now step-free.
• The average additional journey time required for step-free journeys has now been reduced to around 6.7 minutes, comparing to 9.5 minutes back in 2016.
• Her Majesty became the first reigning monarch to travel on the London Underground in 1969, when she opened the Victoria line.
• Although a number of Jubilee line stations are among the Underground's newest, the line also serves some stations that originally opened over one hundred years ago.
• No other city is as defined by its transport system as London.
Transport for the North is the country’s first Sub-national Transport Body, formed to transform the transport system across the North of England, providing the infrastructure needed to drive economic growth
Transport for the North became England’s first Sub-national Transport Body in April 2018, bringing together the North’s 20 Local Transport Authorities and eleven Local Enterprise Partnerships to enable the North to speak with one voice on the transport infrastructure investment needed to drive transformational growth and rebalance the UK economy.
The Strategic Rail programme is key to ensuring the synergies between the North’s classic rail network, the Northern Powerhouse Rail programme, Transpennine Route Upgrade (TRU), through the Integrated Rail Programme (IRP), are fully optimised.
In operational terms, the programme partners with the Department for Transport in overseeing and managing the region’s biggest rail operators – Northern Trains Limited and TransPennine Express. The Rail North Partnership, informed by the advice and guidance of the Rail North Committee and the Department for Transport, oversees and manages the performance and delivery targets of these operators and works to ensure they are both fit for purpose and future-proofed.
The Northern and TransPennine Express rail services run through 25 local authority areas, including the 20 authorities that sit on the Partnership Board of Transport for the North. They engage regularly with representatives from all 25 authorities through our Rail Officer Reference Group.
Northern Powerhouse Rail is a major strategic rail programme that will deliver radical improvements to train service frequencies and journey times, to better connect the key economic areas in the North of England. The programme will transform east-west rail travel across the region to enhance connectivity, capacity and reliability.
By linking the east and west of the North, as well as linking with HS2, Northern Powerhouse Rail will deliver vastly improved regional rail connections, providing modern,
high-speed, low-carbon services which will improve the passenger experience, and encourage a modal shift from cars to trains, contributing greatly to the decarbonisation agenda.
Northern Powerhouse Rail will also release capacity in the existing rail network, supporting improvements in the local and freight services on which much of the region depends, as well as improving connectivity to international gateways including Manchester Airport.
The programme will connect the major urban centres of the North, and under-served communities, to generate opportunity, attract investment, create jobs and move the North towards a more integrated economy that will ‘level-up’ the region and boost UK productivity
The North’s economy will flourish with proper investment. To maximise and expand upon this ambition, the North’s creaking rail infrastructure must be improved.
Ultimately, Northern Powerhouse Rail – delivered in full alongside the Transpennine Route Upgrade – will define the North’s economic prosperity for the rest of this century, boosting jobs and growth, while also playing a significant role in reducing carbon emissions in the region and delivering tangible transformational benefits to people and business.
Transport for the North (TfN) and Department for Transport (DfT), working with delivery partners Network Rail and HS2 Ltd, has carried out substantial work to develop options in each NPR corridor. New lines and significant improvements to existing lines would free up capacity and reduce disruption, enabling more services on local lines, increasing opportunities for both workers and consumers.
Transport for the North produces a regular podcast on all things transport and the Northern Powerhouse, covering topics such as devolution, levelling up, economic growth, productivity, investment and more. It is available via the TfN website and on Spotify and Soundcloud. The All Points North e-newsletter highlights the top stories each week – sign up via the TfN website.
‘TfN continues to use its evidencebased approach to make the case for strategic transport improvements across the whole of the North.Martin Tugwell, Chief Executive of Transport for the North
KEY PERSONNEL
Chair: Lord Patrick McLoughlin
Chief Executive: Martin Tugwell
Rail and Roads Director and Deputy Chief Executive: Darren Oldham
Finance Director: Paul Kelly
Strategy, Policy and Communications Director: Katie Day
CONTACT INFORMATION
Address: Level 6, Town Hall Extension, Lloyd Street
Manchester M2 5DB
Tel: 0161 244 0888
Email: info@transportforthenorth.com
Visit: www.transportforthenorth.com
Led by the Mayor of the West Midlands, the WMCA brings together 18 local councils and three Local Enterprise Partnerships to oversee the transfer of powers and funding from Whitehall to the West Midlands
The authority consists of 18 local authorities and four Local Enterprise Partnerships (LEPs) working together to move powers from Whitehall to the West Midlands and its locally elected politicians. It includes the seven metropolitan West Midlands councils (constituent authorities), ten non-constituent authorities/councils and one observer council, as well as the Mayor of the West Midlands.
The transport arm of the WMCA is Transport for West Midlands (TfWM) which coordinates investment to improve the region’s transport infrastructure and create a fully integrated, safe and secure network. It is also responsible for assessing and planning for the region’s future transport needs so the network can meet the demands of businesses and a growing population.
The expansion of the Midland Metro tram system is just one of the many projects that TfWM is delivering to help meet those future needs. Where they are adding:
• Up to 50 extra trams.
• New control, communications and passenger information systems.
• An upgraded depot, control room and maintenance.
The Midlands Rail Hub is a £2 billion package of improvements to transform east-west rail connections. The project was awarded £20 million in the March 2020 Budget to develop the scheme to outline business case. The plans outline a programme of new and upgraded infrastructure that will be implemented in phases between now and 2033. It will strengthen rail links between Leicester, Nottingham, Coventry, Derby, Hereford and Worcester, improve services to Wales and the South West and allow more people to access HS2.
The WMCA has been a strong advocate for the planned HS2 line and has put in place
a £4.4 billion HS2 Growth Strategy to make the most of HS2 arriving in the West Midlands. As part of this Growth Strategy there is a Local Connectivity Package of 20 transport schemes to effectively ‘plugin’ the two new HS2 stations to local transport network.
These schemes include the transformational East-West Metro with tram extensions to Dudley/ Brierley Hill and through East Birmingham to North Solihull and the HS2 Interchange station.
The region is looking to reverse some the Beeching cuts by reopening rail lines to passenger services for the first time in decades. These include the Camp Hill line serving suburbs in South Birmingham and the line between Walsall and Wolverhampton. University station in Edgbaston, is undergoing major redevelopment with new station buildings, bridges and platforms to accommodate the 3.5 million passenger journeys it sees every year. Doubling the capacity of what is already considered one of the busiest railway stations in the country will provide huge safety benefits, improve customer experience, and enable the station to meet future demand, whilst also contributing to tackling the climate emergency.
Local rail services are co-managed by the West Midlands Rail Executive (WMRE) – a partnership of 16 local transport authorities – and the Department for Transport under the West Midlands franchise. Services are run by West Midlands Trains (a joint venture between Abellio, East Japan Railway Company and Mitsui) but branded West Midlands Railway.
The blueprint setting out what is needed to level up the region was launched by the West Midlands Combined Authority in October 2022. The Levelling Up Growth Prospectus sets out how the West Midlands Combined Authority is working as a region to tackle
the various challenges they face, and how they aim to fire up the regional economy by driving forward a new, green industrial revolution while attracting major private sector investment.
The prospectus looks at ways to expand its existing levelling up programme with:
• More flexible funding to build affordable, zero carbon homes and unlock stalled investment through new Investment Zones.
• New ways to encourage people onto public transport through mobility credit schemes, new e-mobility powers, and a dynamic role in Great British Railways
• Powers to help key growth sectors for the region flourish and drive innovation in low carbon businesses such as electric car manufacturing; battery production; low carbon, modular homes; and utilities such as wind and solar power.
• Greater control and influence over investment into the region’s energy system so it is more resilient to price hike shocks and able to speed up the decarbonisation of infrastructure and industry.
The Levelling Up Growth Prospectus serves as long term vision for the West Midlands.
KEY PERSONNEL
Chief Executive Officer: Laura Shoaf
Director of Programme Development: Sandeep Shingadia
Director of Rail: Malcolm Holmes
Director of Policy, Strategy and Innovation: Mike Waters
Director of Communications: Siobhan Bassford
Director of Operations: Clare Boden-Hatton
CONTACT INFORMATION
Address: 16 Summer Lane, Birmingham
West Midlands B19 3SD
Tel: 0121 200 2787
Email: customer.services@tfwm.org.uk
Visit: www.wmca.org.uk
Transport Focus is the independent transport user watchdog. Its mission is to get the best deal for rail passengers
With a strong emphasis on evidence-based campaigning and research, Transport Focus ensures that it knows what is happening on the ground. It uses its knowledge to influence decisions on behalf of passengers to secure improvements and make a difference.
Transport Focus is the voice of transport users. It carries out research on transport user experiences and needs for the future. This includes the large scale National Rail Passenger Survey where over 50,000 rail passengers give their views on rail journeys twice a year.
Transport Focus is an executive nondepartmental public body, sponsored by the Department for Transport. It is run by a management team (see more below) and led by a Board of non-executive directors.
It has existed in one form or another since 1947. It was formed by the Transport Act as the Central Transport Consultative Committee (CTCC) plus a network of regional Transport Users’ Consultative Committees. Over the years it has changed its name as it took on responsibility for bus, coach and tram passengers, and then road users.
Transport Focus makes major decisions at Board meetings, held in public four times per year. Decisions are also made at monthly management team meetings.
Transport Focus can have up to 14 Board members. The Scottish Government, Welsh Government and the Greater London Authority each appoint a member to the Board. The remaining appointments are made by the Secretary of State for Transport. Recruitment to the Board is based on merit. Appointments are regulated by The Office of the Commissioner for Public Appointments.
KEY PERSONNEL
Chair: Nigel Stevens
Chief Executive: Alex Robertson
Director: Natasha Grice
Resources Director: Nigel Holden
CONTACT INFORMATION
Address: Albany House
86 Petty France, London SW1H 9EA
Tel: 0300 123 0860
Email: info@transportfocus.org.uk
Visit: www.transportfocus.org.uk
Established in 2018, the Light Rail Safety and Standards Board (Light Rail SSB) is committed to further improvements to what is already one of the safest forms of public transport
LRSSB is structured by the LRSSB Board which consists of the Chief Executive Officer (CEO), Non-executive Chair, 4 Bonexecutive Directors, the Managing Director of UKTram and an ORR Observer. At the end of 2023, LRSSB and ORR signed an MOU agreeing to work together more closely
Drawing on experience and expertise from across the sector, it brings all aspects of light rail safety under one roof while providing a central resource where colleagues can access the latest guidance and standards documentation.
After significant investment, the launch of the updated TAIR platform took place in March 2023. The introduction of this new platform, aligned with feedback from the sector, has delivered enhanced usability and dashboards. The new platform provides improved integration with existing databases, enhanced user interface and navigation, improved reporting output, integrated sector dashboards and enabled ready for future integration of regulatory reports – e.g., RIDDOR.
The launch event of the upgraded TAIR platform was attended by senior executives
from all UK light rail networks and owners, in addition to members of the ORR, and featured a keynote address by Deputy Chief Inspector of Railways Richard Hines. Extensive work has been undertaken to populate TAIR with multiple years of individual networks’ historical data, thus building a foundation for the networks to continue the work themselves. The work undertaken by LRSSB, in conjunction with individual operators, allows more accurate assessment of event frequency to determine levels of risk.
With strong support from across the wider light rail community, and funding from the Department of Transport, the LRSSB is also taking the lead on numerous research projects.
Initial successes have included the review and revision of a wide range of existing guidance documents, the roll-out of an acclaimed hazard perception training system and award-winning research into driver fatigue monitoring systems.
The work of the LRSSB team is also supported by two working groups for Heads of Safety and Duty Holders which bring together safety professionals and senior figures from across the sector.
The LRSSB is currently working in partnership with the RSSB, industry experts, academics, statutory organisations and Network Rail to research and develop the optimum wheel/rail profile for proposed routes that will see trams operate on mainline tracks.
At the same time, it is working with similar partners to draw up a comprehensive best practice guide that aims to reduce the costs of future projects and the time it takes to deliver them. This will enable rail services to be extended on-street through city centres to centrally located stops and offer higher frequency services, increasing personal mobility and improving access to key city centre activity sites.
This should pave the way for many future collaborations between LRSSB and RSSB as both organisations look to identify opportunities to improve both sectors.
Over the past year, the LRSSB has also worked with Network Rail and Transport for Wales on the development of a signalling system for the tram-train system under construction in Cardiff.
KEY PERSONNEL
Chief Executive: Carl Williams
Administration Manager: Erica Pearson
Safety Assurance: Mark Ashmore
Head of Engineering Safety & Innovation:
Craig O'Brien
Head of Commercial: Jamie Swift
Data Analyst: Mohamed Hefny
CONTACT INFORMATION
Address: LRSSB, 16 Summer Lane
Birmingham, B19 3SD
Email: info@lrssb.co.uk
East West Railway Company (EWR Co) was set up by the Secretary of State for Transport in 2018 to develop East West Rail, a railway with customers and communities at its core
The company’s role is to oversee the work already underway on East West Rail between Oxford, Bedford and Milton Keynes, to develop the case for the section between Bedford and Cambridge, and to integrate the two sections of the project to get the best results for all the communities between Oxford and Cambridge.
East West Railway company works with four key stakeholders: The Department for Transport, Network Rail, East West Rail Alliance, East West Rail Consortium. In January 2021, the Government announced £760 million to support the new East West Rail line.
The investment means further vital construction work can begin and represents an important milestone in the East West Rail project. The funding is for part of the line between Oxford and Bletchley/Milton Keynes and means this section of East West Rail is expected to be up and running by 2025. Delivery of this stage is expected to provide work for 1,500 people, injecting an estimated £1.1 billion pounds into the local economy.
The first section of railway on East West Rail Phase Two was successfully commissioned over the August Bank Holiday weekend in 2021.
In the Chancellor’s Autumn statement of 2022, the Government confirmed its commitment to EWR and the East West Railway Company is now in the process of finalising recommendations for consideration by Government in the early part of 2023.
East West Rail intends to create a new direct connection between Oxford and Cambridge. Serving communities across the area, it intends to bring faster journey times and lower transport costs as well as ease pressure on local roads.
East West Rail is planned to be delivered in three Connection Stages:
• Connection Stage One: Oxford to Bletchley and Milton Keynes
• Connection Stage Two: Oxford to Bedford
• Connection Stage Three: Oxford to Cambridge
Network Rail was responsible for developing the first part of the East West Rail, connecting Oxford with Bicester, and is a partner in a construction alliance to deliver Connection Stage 1 of the project, where East West Railway Company and Network Rail are acting as the Department for Transport’s joint sponsors.
East West Railway Company is now developing the route to enable services to run to Cambridge via Bedford and plans to seek statutory powers under the Planning Act 2008, following a period of extensive consultation.
KEY PERSONNEL
Chief Executive: Beth West
Chair: Neil Sachdev
Strategy Director: Will Gallagher
Programme Delivery Director: Ian Parker
Engineering Director: Simon Scott
CONTACT INFORMATION
Address: 1 Grafton Gate, Midsummer Blvd, Milton Keynes Mk9 1Fb
Tel: 0330 1340067
Email: contact@eastwestrail.co.uk
On 20 November 2017, Groupe Eurotunnel changed its name to Getlink, the group manages cross-Channel transport for passenger vehicles, trucks, Eurostar passengers and rail freight trains which travel through the Channel Tunnel
In 1802, French mining engineer
Albert Mathieu-Favier put forward the first ever design for a cross-Channel fixed link based on the principle of a bored two-level tunnel. Twohundred years later, Eurotunnel became the first private company to be granted a rail operator’s licence valid across Europe, following the liberalisation of rail freight.
25 per cent of the trade between the UK and the European union is carried through the tunnel, with 320 daily trains, more than half of which carry goods.
Each year, Eurotunnel safely transports more than 20 million passengers, 1.6 million trucks, 2.6 million cars, two billion tonnekilometres of freight and, eventually, one gigawatt of electricity.
Since 18 September 2021, a new crossChannel freight service has been open to all transporters, using an unaccompanied mode through the Channel Tunnel. The crossing is managed by Eurotunnel Le Shuttle Freight and operates 24 hours a day and six days per week. Departures are from the Group’s two terminals in Calais or Folkestone with a capacity of 8,300 trailers per year. The Eurotunnel Border Pass allows transporters to speed up the border crossing by digitising their administrative exchanges with the border authorities.
This new rail service, which emits 40 times less CO2 than ferries (compared to Calais-Sheerness route), enables customers to decarbonize their logistic chain by choosing rail. The modal shift also contributes to the French government’s objectives of doubling the share of rail in freight transport by 2030 and to UK government plans to decarbonise freight set out in the Green Industrial Revolution plan.
At the end of 2021, Eurotunnel and CargoBeamer signed a partnership for the launch of a new, 100 per cent unaccompanied rail freight transport service across the Short Straits, from Calais to Ashford. The extension of the rolling motorway from Perpignan to Ashford is a logical step in developing a future international intermodal network between
the Channel and the Mediterranean.
A second route from Domodossola, in the Alps region, to Calais was also extended to Ashford after its launch in early October 2021.
This action plan in line with the 2019-2025 Environment Plan, will enable the Group to reduce its carbon footprint by 30 per cent by 2025. Its deployment has already saved nearly 40 GWh per year on traction electricity.
The Energy Efficiency plan is built on concrete actions such as in-depth moderation of daily use by all employees and partners of the Group (reduction of heating instructions in buildings, eco-gestures oriented towards lighting or digital uses in particular), the continued development of eco-driving, and even accelerating bulb replacements with LEDs in the Concession. All these actions will generate up to nine per cent additional savings by 2024 on auxiliary consumption, i.e., up to 5 GWh.
At the start of 2022, Getlink and CAT Group launched a new cross-Channel rail freight service transporting Toyota vehicles, for a period of six years, between Toton (UK) and Kolin (CZ) via Onnaing (FR). This new traffic alone represents growth of +15 per cent in annual cross-Channel freight on a like-for-like basis, compared to 2021. It will significantly reduce CO2 emissions by promoting the modal shift of more than 8,500 trucks to rail per year, thus avoiding the emission of more than 8,000 tonnes of CO2
In 2022, Salesforce, the global leader in Customer Relationship Management (CRM) was selected to support Eurotunnel’s digital transformation journey and enhance engagement with customers by leveraging Salesforce Marketing Cloud. Eurotunnel will leverage the Salesforce platform to further improve the services it offers to
its customers and create the outstanding travel experiences at the core of its strategic ambition.
As an innovative player, Eurotunnel Le Shuttle will continue to improve passenger experience using digital solutions and best practice. Eurotunnel Le Shuttle was the first cross-channel operator to deploy a digital wallet to speed their customer’s journey through the Terminals.
The Salesforce Marketing Cloud solution will enable Eurotunnel to engage with customers across multiple channels in a more personalised manner and bring them great value at every point of their journey.
KEY PERSONNEL
Chief Executive Officer: Yann Leriche
Deputy CEO: François Gauthey
Chief Operating Officer – Corporate:
Michel Boudoussier
Chief Operating Officer – Safety and Ethics:
Philippe de Lagune
Chief Operating Officer – Europorte: Pascal Sainson
Safety, Sustainable Development and Business
Services Director: Patrick Etienne
Commercial Director – Concession: Jo Willacy
Chief Executive Officer – ElecLink: Steven Moore
CONTACT INFORMATION
Address: UK Terminal, Ashford Road
Folkestone, Kent CT18 8XX
Tel: 0844 335 3535
Email: communication.internet@getlinkgroup.com
Visit: www.getlinkgroup.com
High Speed 1 (HS1) is the UK’s first section of high-speed rail and operates along a 68-mile-long railway between St Pancras International in London and the Channel Tunnel
Operating as both a domestic and international service, the line carries passengers from St Pancras International in London to the Channel Tunnel and connects with the international high-speed routes between London and Paris, London and Brussels and London and Amsterdam. HS1 Ltd has the 30-year concession to own and operate HS1, as well as the stations along the route: St Pancras International, Stratford International, Ebbsfleet International and Ashford International. In July 2017 HS1 Ltd was acquired by a consortium comprising of funds advised and managed by InfraRed Capital Partners Limited and Equitix Investment Management Limited.The cost of construction was £6.2 billion.
HS1’s domestic service, Southeastern High Speed, was introduced in 2009 and transports passengers from St Pancras International to Kent. Journey times to Ebbsfleet International are only 17 minutes, with Ashford International just 37 minutes from St Pancras. In 2018, approximately 15.7 million journeys were made on Southeastern High Speed.
In 2017, HS1 Ltd published a report entitled ‘10 Businesses at 10 Years’. The report presents real life examples of how HS1 has helped ten of the most exciting businesses in Kent to grow and prosper.
An accompanying survey of leading Kent businesses showed that:
• 91 per cent of those asked said that their business has benefitted from HS1
• 89 per cent said that HS1 has made Kent a more attractive place to set up a business
• Over one third said that HS1 was a factor when choosing to set up their business in Kent
• Over 80 per cent said that HS1 had helped their business grow
• One hundred per cent said that HS1 will play an important role in the future growth of Kent.
Dyan Crowther, CEO of HS1 Limited, said:
‘As the nation’s first and only high-speed railway, HS1 has been a catalyst for growth,
generating economic, cultural and social value in the regions it serves and the UK more widely.’
Passengers using HS1 have doubled since launch, with services carrying over twenty million domestic and international passengers each year and with an unrivalled average delay per train of just eight seconds.
A report independently produced by Visit Kent and tourism economists Destination Research revealed that for every HS1 leisure journey made to Kent in 2016, £81 was added to Kent’s local economy.
Almost 6,000 tourism sector jobs in Kent have been created and supported by HS1 with the total economic contribution to Kent’s visitor economy, since domestic HS1 services began, estimated at over £311 million. The findings demonstrate further the remarkable growth of Kent’s visitor economy, the value of which has increased by £1 billion since 2003. Kent’s visitor economy is now worth in excess of £3.8 billion and it is expected that the line will provide at least £10 billion of further regenerative benefits over the next 50 years.
HS1 Ltd is in a state of readiness for freight operating companies to operate high-speed services on the network. Being a highspeed railway network, which provides high economic value to its customers, there are significant benefits to be seen by freight operating companies, in particular those who deliver time critical commodities to its customers. As such, the high-speed rail network provides a dynamic transport infrastructure which leads to substantial commercial benefits for organisations.
Approximately 50 million people visit St Pancras International every year, for both the station’s retail offering and its rail services to Europe and Kent. Passenger numbers on the high-speed line are set to rise to 127 per cent by 2044. The total number of trains on HS1 is at 73,402 (201819). This is mostly attributed to the increase in timetabled international services which are up 386 compared to 2017-18. In 2018, HS1 Ltd announced that it would be working closely with other infrastructure managers to help develop new routes, including a direct passenger service to Bordeaux.
KEY PERSONNEL
Chairman: Keith Ludeman
Chief Executive Officer: Dyan Crowther
Chief Financial Officer: Mark Farrer
General Counsel & Corporate Services Director: Lucy Clarke-Bodicoat
Commercial Director: Wendy Spinks
Engineering Director: Richard Thorp
CONTACT INFORMATION
Address: 5th Floor, Kings Place, 90 York Way
London N1 9AG
Tel: 020 7014 2700
Email: info@highspeed1.co.uk
Visit: www.highspeed1.co.uk
is Great Britain’s new high-speed railway. HS2 Ltd is the company responsible for developing and promoting HS2. It is an executive nondepartmental public body, sponsored by the Department for Transport
HS2 is Great Britain’s new highspeed, railway and is the first new intercity railway to be built north of London in over a century. HS2 is Britain’s biggest build, comprising 140-miles of track, four brand-new, state-of-the art stations, two depots, 32 miles of tunnel, and 130 bridges.
Running at speeds of up to 225 miles per hour, HS2’s British-built bullet trains will provide zero-carbon journeys between the UK’s two largest cities, Birmingham and London, reducing journey times by 40 per cent, to just 49 minutes.
Four new HS2 stations – London Euston, Old Oak Common in West London, Interchange in Solihull, West Midlands and Curzon St in Birmingham will serve the new high-speed line.
Services will continue to Manchester, the North West and Scotland using the conventional railway network, cutting journey times.
By better connecting Britain’s biggest economic centres and catalysing plans for inner-city regeneration, HS2 will generate opportunities for the creation of thousands of new jobs and homes as well as boosting economic growth.
Multi-billion pound regeneration plans are in place for the land surrounding HS2’s new stations. This is set to deliver thousands of new homes and jobs as well as new offices, public spaces and leisure facilities.
HS2’s construction is delivering significant economic benefits now, years before the first trains run.
Construction of the new, high-speed line is well underway, with work taking place across 350 active sites between the West Midlands and London. HS2 will build some of Britain’s longest viaducts, spanning valleys, lakes and rivers, specially designed to minimise noise and vibration. The 2.1-mile Colne Valley viaduct near West London will be the UK’s longest rail bridge. HS2 stations will be amongst the most environmentally
sustainable buildings in the world. In addition to the four new stations, HS2 will include the construction of two major depots, 32 miles of tunnel and nine miles of viaduct.
At the peak of construction, ten giant tunnel boring machines will bore and line the tunnels that the high-speed trains will pass through.
Businesses and employees in every region and nation of the UK are helping to build HS2. Since 2016, £11.5 billion worth of contracts has been awarded by HS2’s construction partners. 94 per cent of all contracts have been awarded to Britishbased businesses. 57 per cent of contracts have been awarded to SMEs – companies with 250 or fewer employees.
Journeys on HS2 will be zero carbon from day one of operations, with its fleet of trains running on electrified tracks, powered by sustainable energy. HS2 is creating a new ‘Green Corridor’ running alongside the railway. The Green Corridor programme is the single largest environmental project in the UK. It aims to create a network of bigger, better-connected, climate resilient habitats and new green spaces for people and wildlife to enjoy. Seven million new native trees and shrubs will be planted.
Over 30,000 people are currently working on the project and more than 3,200 Britishbased businesses are helping to build it.
HS2 will include the construction of four brand new stations. HS2’s stations will be amongst the most sustainable stations in the world. Interchange station, near Solihull in the West Midlands was the first railway station anywhere in the world to be awarded BREEAM ‘outstanding certification, closely followed by Old Oak Common station in West London.
A measure of sustainability for new and refurbished buildings, this award puts these two stations in the top one per cent of buildings in the UK.
HS2 is designed with ‘green tunnels’, cuttings and embankments to help blend the railway into the natural surroundings.
HS2 employs construction workers, specialist engineers, architects, designers and project managers drawn from across the UK and beyond. Over 30,000 jobs are currently supported by the HS2 programme. Over 1,380 apprentices have started work on HS2, and more than 3,800 people who were previously unemployed, have found work on the project.
HS2 will leave a legacy of environmentally responsible travel, economic regeneration and technological innovation for generations to come.
KEY PERSONNEL
Executive Chair: Sir John Thompson
Chief Railway Officer: Emma Head
Chief Financial Officer: Alan Foster
Civils Delivery Director: David Speight
Stations and Systems Delivery Director: Chris Rayner
CONTACT INFORMATION
Address: Two Snowhill, Snow Hill Queensway Birmingham B4 6GA
Tel: 0808 143 4434
Email: HS2enquiries@hs2.org.uk
Visit: www.hs2.org.uk
LCR is a skilled commercial developer and the UK Government’s regeneration and placemaking expert. It has a 25-year track record of creating exciting new destinations for people to live, work and experience
LCR uses its skills in land assembly, placemaking and development to unlock regeneration opportunities. Its unique position on the cusp of the public and private sectors allows it to transform the most complex sites, using an imaginative approach to problem solving to bring forward schemes that deliver homes and jobs, and create value from public sector real estate assets. The team’s considerable experience includes the delivery and sale of the High Speed 1 railway and the associated multibillion-pound, mixed-use developments at King’s Cross and Stratford City – two of London’s most successful regeneration stories.
LCR’s current projects include the £1.1 billion regeneration of the Mayfield site in Manchester. Working with U+I as its development partner, the project will deliver a mixed use community at a 24-acre site adjacent to Piccadilly station.
In Stratford, east London, LCR and Lend Lease are continuing to bring forward International Quarter London (IQL) – a £2.4 billion urban regeneration which will deliver four million sq.ft of Grade A office space, new homes and community facilities, within a 22-acre site. Nearly one million sq.ft of office space is already let or pre-let at IQL, to organisations including the FCA, Transport for London, Cancer Research UK and the British Council.
In central London, LCR is delivering a new retail, restaurant and leisure destination in the heart of the South Bank. Set to open in Spring 2021, it will feature 135,000 sq ft of local, independent and national retail and leisure operators. LCR has also transformed the nearby railway arches at Leake Street into a creative and leisure destination, populated by local independent businesses and startups.
Using expertise gained from delivering some of the UK’s most successful regeneration projects, LCR collaborates with local authorities, LEPs, government agencies and private developers to deliver
outstanding developments. It provides long-term support and forms joint venture partnerships to create the conditions to ensure every destination reaches its full potential, with a focus on driving public value through delivering meaningful outcomes, not short-term returns.
LCR was formed in 1994 to bid for the contract to build and operate the Channel Tunnel Rail Link (CTRL) and to own the UK arm of the Eurostar International train service. It won the bid in 1997 and spent the following ten years delivering on its promises for High Speed 1, until it sold a 30-year concession for the project for £2.1 billion to a consortium of Borealis and Ontario Teachers’ Pension Fund. LCR then moved from the private to public sector, becoming a limited company wholly owned by the Department for Transport.
KEY PERSONNEL
Chairman: Nick Markham
Interim Chief Executive: Peter Hawthorne
Development Director: Adrian Lee
Asset Management Director: Lucy Robinson
Managing Director for Strategic Partnerships:
Jamie Kerr
CONTACT INFORMATION
Address: 20 Cranbourn Street, London WC2H 7AA
Tel: 020 7391 4300
Email: info@lcrproperty.co.uk
Visit: www.lcrproperty.co.uk
The West Midlands Combined Authority, the design consortium of Egis, Tony Gee and Pell Frischmann, and contractor Colas Rail (supported by their suballiance partners Colas Limited, Barhale, Bouygues UK and Auctus Management Group) came together to form the Midland Metro Alliance in July 2016
Each of the partner companies brings a complementary area of expertise to the alliance. The real focus, however, is on leaving a legacy of skills and experience for the region, even after the extensions are complete and helping the West Midlands attract regeneration and investment.
The Midland Metro Alliance is working with Transport for West Midlands on a number of projects for the West Midlands Metro network, each in differing stages of development, design or delivery.
As part of the Wolverhampton Interchange, the West Midlands Metro extension will run from a junction with the existing West Midlands Metro system close to the current terminus at Wolverhampton St. George’s through to Wolverhampton Railway Station. West Midlands Metro will stop at the city’s Bus Station on Pipers Row, before continuing to Wolverhampton Railway Station, allowing easy interchange with other modes of transport.
in an area of the region where most journeys are completed by private vehicle.
The Secretary of State for Transport has announced that he has decided to make the Midland Metro (Birmingham City Eastside Extension) Order and relevant documents to this order can be found via the Statutory Information tab below.
The Birmingham Eastside Metro extension to Digbeth will serve the High Speed 2 (HS2) station at Curzon Street, separating from the existing West Midlands Metro line at Bull Street. The route is planned to consist of 1.7 kilometres of twin track running from Bull Street to a new terminus at High Street Deritend. The scheme includes four additional West Midlands Metro stops serving the east of Birmingham City Centre.
The extension will service the Eastside regeneration area offering connections with
New Street, Moor Street and Snow Hill Railway Stations, in addition to the new HS2 station. The scheme also includes a new bus interchange adjacent to Clayton Hotel Birmingham to provide an efficient bus, Sprint and coach interchange with HS2.
Each project has an overarching Project Sustainability Plan, detailing how the project is to contribute to the sustainability objectives and how the project will manage any environmental impacts.
All new projects are registered with CEEQUAL and will complete a CEEQUAL Assessment to assess the sustainability of the scheme against a benchmark of industry best practice. The CEEQUAL process is externally verified giving assurance of the quality of the awards.
All new construction works will also register with the National Considerate Constructors Scheme (CCS). The CCS is a voluntary code of practice that seeks to minimise any disturbance or negative impact (in terms of noise, dust and inconvenience)
sometimes caused by construction sites to the immediate neighbourhood; eradicate offensive behaviour and language from construction site; and recognise and reward the constructor’s commitment to raise standards of site management, safety and environmental awareness beyond statutory duties. As with CEEQUAL the code offers an external validation of the scheme performance against industry best practice.
CONTACT INFORMATION
Address: 4th Floor Alpha Tower, Suffolk St Queensway, Birmingham B1 1TT
Tel: 0121 643 8729
Email: communications@metroalliance.co.uk
Visit: www.metroalliance.co.uk
Network Rail is a public sector arm’s length body, giving it commercial and operational freedom. Its main customers are the TOCs and FOCs which provide services on Network Rail’s infrastructure.
Network Rail owns, operates and develops Britain’s 20,000 miles of railway track, 30,000 bridges, tunnels and viaducts and the thousands of signals, level crossings and 20 of the UK's largest stations.
In 2014, Network Rail began devolving day-today responsibility for railway businesses to eight strategic geographical areas. In late 2018, new Chief Executive Andrew Haines announced plans to deepen devolution, with 14 routes sitting under five new regions – Scotland’s Railway, Wales and Western, North West and Central, Southern and Eastern. These new regions became operational in June 2019.
On 1 April 2019, the rail industry introduced a new, more detailed and precise set of measures to better understand train performance. The additional ‘on time’ measures reflect that good performance needs to be delivered throughout the whole journey and that every minute matters for passengers.
The official measure of punctuality used up until then, known as public performance measure (PPM), considers trains to be punctual if they are five or ten minutes after schedule, for short and long-distance journeys respectively, at their destination, but the new measures report cancellations and the proportion of trains arriving to the minute at every station on the timetable.
Network Rail also measures its safety performance using a model produced by the Rail Safety and Standards Board (RSSB). It measures safety from the perspective of passengers at stations and all aspects of interaction between the general public and the railway.
Network Rail runs five-year long Control Periods which it uses to determine priorities for investment. Each Control Period begins on 1 April and ends on 31 March to coincide with the financial year. Control Period 7 begins in April 2024.
The Strategic Freight Network (SFN) aims to create a network of freight capable rail corridors across Britain by upgrading the existing network and building new infrastructure at key locations to allow more freight to travel on rail. Schemes currently underway include gauge clearance, train lengthening and capacity building.
With railway from the borders of Scotland to the nation’s capital, Eastern region is critical to the success of Britain. It is an incredibly busy region, operating some of the busiest and most congested rail lines in the country, transporting large numbers of commuters to and from busy cities including Newcastle, Leeds, Sheffield, Derby, Norwich, Cambridge and London. The region is also home to other major transport hubs including three
airports and 13 freight ports, connecting millions of people every day to city, town, coast and country, to friends and family, jobs and leisure, as well as goods to businesses here and abroad.
North West and Central
North West & Central (NW&C) is the ‘Backbone of Britain’ – the economic spine linking the United Kingdom’s main cities, connecting workers with jobs, people with loved ones and bringing goods to market.
The infrastructure runs from London Euston and Marylebone in the south through the Chiltern and West Midlands regions, the North West of England and Cumbria before joining with Scotland at Gretna. NW&C is home to the West Coast Mainline, the busiest mixed-use railway in Europe, serving London, Birmingham, Manchester, Liverpool, Edinburgh and Glasgow.
Southern
The new Southern region serves passengers and freight operators from Devon in the West to Kent in the East and links Wessex, Sussex and Kent as well as Network Rail High Speed.
Birmingham, Manchester and Liverpool, directly serving London Heathrow, Europe’s busiest international airport and providing connections to Cardiff, Bristol, Birmingham, Manchester, and London Gatwick airports. Wales and Western supports leisure and
Abellio is one of the UK’s largest transport groups, operating four rail franchises, as well as 740 buses on 52 London bus routes
Over 15,000 people are employed across its operating companies, which collectively serve over a million passengers in England and Scotland every day. A wholly owned subsidiary of Dutch rail operator Nederlandse Spoorwegen, Abellio was founded in 2002 to take advantage of the liberalisation of the European transport sector, and it now has operations in the UK and Germany.
Abellio first entered the UK transport market in 2003 and has since established itself as one of the UK’s foremost rail owning groups, accounting for nearly one in five of all UK rail customers – the largest it has been in its operating history.
Its UK rail franchises are Merseyrail (a 50:50 venture with Serco), Greater Anglia (a
60:40 venture with Mitsui), West Midlands Trains (a 70:15:15 venture with Mitsui and JR East) and East Midlands Railway.
After taking its first steps into the London bus market in 2009, the company now runs around eight per cent of all London bus services. Abellio wants to make it easier to travel, by providing comfortable, reliable journeys which are simple for people to plan, buy and use. To this end, the company is investing heavily across its UK rail franchises to transform its services, improve its customers’ experience and help to deliver a sustainable zero carbon future. Through its £3 billion investment in new trains for all its operating companies, Abellio is delivering more seats and services.
This investment and innovation reflect Abellio’s strong commitment to improving
its customers’ experience by delivering the more reliable, simple and sustainable transport services they rightly expect.
A new UK-run transport company is set to operate four of the country’s rail passenger services and over 50 London bus routes by the end of this year. A management buyout from the state-owned rail company, Nederlandse Spoorwegen will pave the way for a new UK-based company to take over all Abellio UK’s existing services, serving millions of rail and bus passengers in London, Liverpool, the Midlands and East Anglia. The new company will be called Transport UK Group Limited.
Led by Managing Director Dominic Booth, who has decades of experience running public transport services in the UK, this deal has been widely welcomed by industry partners and experts. Completion of the buyout deal is subject to formal approval from partners including the Department for Transport, Transport for London and Merseytravel as well as regulatory consent from the Office for Rail and Road.
KEY PERSONNEL
Managing Director Abellio UK: Dominic Booth
Chief Operating Officer Rail: Dave Kaye
Financial Director: Chris Harris
Managing Director Rail Retailing and Digital Business: Stewart Fox-Mills
UK New Trains Project & Fleet Director, and ScotRail COO: Alex White
Human Resources Director: Andrew Meadows
Director of Communication: Allan Watt
Managing Director, Abellio Group: Angelique Magielse
CONTACT INFORMATION
Address: 5th Floor, The Culzean Building
36 Renfield Street, Glasgow G2 1LU
Tel: 0141 320 0620
Email: communications@abellio.co.uk
Visit: www.abellio.com/uk
Arriva UK Trains operates multiple rail services through the open access model the concession model, or passenger service contract, two franchises and one concession
The CrossCountry network is the most extensive rail contract in the UK. Stretching from Aberdeen to Penzance, and from Stansted Airport to Cardiff, it calls at more than 120 stations. Based in Birmingham, CrossCountry connects seven of Britain’s ten largest cities, delivering services every weekday that equate to some forty million passenger journeys a year. CrossCountry has been awarded five stars under the EFQM ‘Recognise for Excellence’ accreditation and the coveted UK Excellence Award by the British Quality Foundation.
Chiltern Railways provide scheduled passenger services along the M40 corridor between London Marylebone and Birmingham Moor Street, to Aylesbury via Amersham. Following an investment of £250 million, Chiltern Railways run a service between Oxford and London Marylebone, on which route they enjoy a successful partnership with Bicester Village.
Chiltern remains one of Britain’s most popular and reliable train operating companies, regularly scoring in the top quartile of all operators for customer satisfaction and punctuality in national rail passenger surveys.
Grand Central is an established fully commercial train operating company connecting the North East of England and Yorkshire to London under an open access agreement. It has been providing high quality rail services since 2007 and delivers customer satisfaction that is regularly among the highest scoring of all operators. Grand Central has done this while growing passenger numbers and introducing real competition on the East Coast Main Line, exerting downwards pressure on ticket costs for passengers.
Arriva Rail London operates the London Overground network under contract to Transport for London (TfL). The seven and half year concession commenced in November 2016, with the network linking 23 of London’s 33 boroughs.
Working in partnership with TfL, Arriva Rail London has delivered improvements for customers through more frequent services, new trains, better facilities and improved interchanges, and has developed stations and lines to meet increasing passenger
demand. The partnership also supports new homes (such as new links to Barking Riverside), jobs around stations and the environment.
Arriva’s TrainCare business provides maintenance depots and servicing facilities for electric and diesel trains. In recent years, Arriva TrainCare has grown following substantial investment in developing heavy maintenance work.
Operating from five depots in strategic locations across the country, Arriva TrainCare currently provides overnight and heavy maintenance services to several train operating companies and ROSCOs, along with post production support for new train manufacturers.
Arriva Road Transport Services offer rail replacement, minibus and taxi provision, duplicate transport services and event transportation hire across the UK.
KEY PERSONNEL
Arriva CEO: Mike Cooper
Arriva Chief Financial Officer: Christian Goeseke
Managing Director UK Trains: David Brown
Arriva UK Trains Finance and Commercial Director:
Amanda Furlong
CONTACT INFORMATION
Address: Arriva plc, Admiral Way, Doxford
International Business Pk, Sunderland SR3 3XP
Tel: 0191 520 4000
Email: enquiries@arriva.co.uk
Visit: www.arriva.co.uk
First Rail is the UK’s largest rail operator, with many years of experience running all types of passenger rail operations across the country; comprising long-distance, commuter, regional and sleeper services
First Rail operates four Department for Transport contracted services
– Avanti West Coast, Great Western Railway, South Western Railway and TransPennine Express. Alongside this it also runs two open access operators – Hull Trains and Lumo. It also operates London Trams on behalf of Transport for London.
First have proposed and delivered over £650 million capital investment into the franchises since 2006. Since they began running rail operations, they have introduced more than 740 additional vehicles across various franchises, which has also led to the creation of new depot facilities and jobs.
The customer app for First operating companies has been downloaded more than one million times; First is working with councils to introduce smart ticketing and has led one of the largest roll outs of free Wi-Fi on the UK rail network.
Owner
First Group owns Great Western Railway (GWR) which operates the Great Western rail franchise area. This includes South Wales, the West Country, the Cotswolds, and large parts of Southern England. On 30 March 202 FirstGroup signed a Direct Award with the Department for Transport to continue operating GWR services until 31 March 2023, with a possible extension of up to one further year.
The South Western Rail franchise was awarded to FirstGroup and MTR in March 2017. They began operating the network on 20 August 2017 and will continue until at least August 2024. SWR operates almost 2,000 services per day across the network, providing commuter, inter-urban, regional and long distance services to passengers in south west London and southern counties of England.
First Group introduced refurbished trains to the Portsmouth-London line in late 2019, with new suburban rolling stock due in the next few months. Timetable changes in May and December 2019 added more than 350 new services per week.
First Group also owns TransPennine Express which provides vital connections
between key cities in the North of England and Scotland.
TransPennine Express operates intercity services on three main routes:
• North TransPennine
• South TransPennine
• North West and Scotland
Frist Group will operate the franchise until at least 2023, and during that time TPE is overseeing an investment which lead to an 80 per cent rise in capacity at the busiest times of the day and increase connections between the largest cities in the North and Scotland by 55 per cent by 2019.
TPE has now begun to introduce 220 new carriages, and new services, including Liverpool to Glasgow, and extending its East Coast route from Newcastle to Edinburgh.
First Group open access operation of Hull Trains began service in 2000, making 90 journeys a week between London, Hull and intermediate stations, and transporting more than a million people annually – an increase of more than ten times since inception. First Group have secured track access rights to operate the service until 2029.
First Group operates the London Trams network on behalf of Transport for London, which sees patronage of around 29 million passengers per year. Passenger numbers have increased by more than ten million since the start of operations.
KEY PERSONNEL
Non-Executive Chairman,
Chair of the Nomination Committee: David Martin
Chief Executive Officer: Matthew Gregory
Managing Director – First Rail: Steve Montgomery
Chief Financial Officer: Ryan Mangold
Group Employee Director: Ant Green
CONTACT INFORMATION
Address: 395 King Street, Aberdeen, Scotland
AB24 5RP
Tel: 01224 650100
Email: contactus.fec@firstgroup.com
Visit: www.firstgroupplc.com
Go-Ahead Group provides 20 per cent of all passenger journeys in the UK through its operating companies, Govia Thameslink Railway (GTR)
In October 2022 it became a private limited company, sold to a consortium comprising of the Australian bus operator Kinetic and the infrastructure specialists Globalvia. It employs 27,000 people in the UK and overseas, who work hard to deliver safe, reliable and value-for-money services for passengers.
Go-Ahead has a devolved approach to the management of its bus and train operating companies. They are run autonomously, are locally branded, and the management teams are empowered to respond directly to the
needs of the local communities they serve. Working in this way ensures Go-Ahead retains strong local expertise and can focus on the needs of customers and adapt quickly to changing conditions in local markets.
It is the largest operator of bus services in London, running around a quarter of London’s buses and outside of London, its regional bus services account for around eleven per cent of the UK market.
Go-Ahead also runs bus services in Singapore and Australia began running services in Ireland in 2018. The company has a rail contract in Norway.
Go-Ahead’s UK rail operation (Govia) is a joint venture between Go-Ahead (65 per cent) and Keolis (35 per cent). In the years since the privatisation of rail operations, Go-Ahead’s rail division has delivered profitability, strong cash flow and good returns on capital; and continues to do so.
Govia Thameslink Railway (GTR)
Govia Thameslink Railway (GTR) began operating in September 2014 with Great Northern and Thameslink routes. Southern and Gatwick Express routes were integrated in July 2015. It is the largest and busiest single rail franchise in the UK: in terms of passenger numbers (around 20 per cent of all train passenger journeys), trains, revenue and staff (6,500 people employed).
The franchise encompasses King’s Lynn in the north and Brighton in the south, serving London as well as several important regional centres including Cambridge, Luton, Peterborough, Portsmouth and Southampton. It also provides direct links to major airports (Gatwick and Luton) as well as St Pancras International.
GTR was awarded a National Rail Contract in March 2022 by the DfT which will run to at least April 2025 with the potential for a further extension.
KEY PERSONNEL
CEO of Go-Ahead: Miguel Ángel Parras
Chief Financial Officer: Ian Grose
Chief People Officer and Group Company Secretary: Carolyn Ferguson
CEO – Bus: Matt Carney
CEO – Rail: Patrick Verwer
Strategy and Transformation Director: Louis Rambaud
Customer and Commercial Director: Mark Anderson
CONTACT INFORMATION
Address: The Go-Ahead Group
4 Matthew Parker Street, Westminster London SW1H 9NP
Tel: 020 7799 8999
Email: communications@go-ahead.com
Visit: www.go-ahead.com
Keolis operates public transport networks on behalf of three hundred transport authorities around the world. It is now present in 16 countries across four continents
Established in the United Kingdom since 1996 and employing 9,500 people across its businesses, Keolis has become a reference public transport operator due to its operation of several emblematic train, tram and metro networks including:
• Govia, the joint venture created between Keolis UK (35 per cent) and its partner Go-Ahead (65 per cent), which operates Govia Thameslink Railway (GTR), the train network in the London area, since 2014.
• KeolisAmey, the joint venture created in 2014 by Keolis UK is a British company specialising in the operation and maintenance of transport networks Docklands Light Railway (DLR), the automatic metro network, since 2014 – Keolis (70 per cent) and Amey (30 per cent) and Greater Manchester's Metrolink, the UK's largest tram network, since 2017 – Keolis (60 per cent) and Amey (40 per cent).
• Tramlink Nottingham, the joint venture formed by Keolis UK (80 per cent) and Wellglade Limited (20 per cent) which has operated Nottingham's tram network since 2011.
KeolisAmey Metrolink, a joint venture
between Keolis and Amey, took over operations and maintenance of Manchester’s Metrolink for a period of up to 10 years from July 2017.
The KeolisAmey Metrolink tram system is the largest of its kind in the UK. It serves 99 stops across eight different lines along almost 103 kilometres of track, with a fleet of 120 modern trams catering for more than 34 million journeys a year.
KeolisAmey Docklands was awarded the franchise in July 2014 to operate and maintain the Docklands Light Railway in London until at least 2024.
Govia is a joint-venture between Keolis (35 per cent) and The Go-Ahead Group (65 per cent). As the country’s busiest rail operator, Govia is responsible for 5,500 services and more than one million passengers per day. It operates two major commuter rail franchises, Southeastern and GTR (Govia Thameslink Railway), serving over 500 stations.
GTR, which stands for Govia Thameslink Railway, is the largest train operating company in the UK and was created following the merger of Great Northern, Thameslink, Southern and Gatwick Express in July 2015.
Keolis is part of the Tramlink consortium responsible for the operation, maintenance and ongoing expansion of the Nottingham tram system. In December 2011, Tramlink entered into a PPP (Public-Private Partnership) agreement for 22 and a half years. Together Keolis, Trent Barton, Alstom and Vinci, are the industrial shareholders in the Tramlink Nottingham concession company.
KEY PERSONNEL
Chairman of Keolis UK: Sir Derek Jones
CEO: Alistair Gordon
Chief Financial Officer: Virginie Merle
Managing Director of KeolisAmey Docklands: Abdellah Chajai
CONTACT INFORMATION
Address: Evergreen House North, 160 Euston Road London NW1 2DX
Tel: 020 3691 1715
Email: comms@keolis.co.uk
Visit: www.keolis.co.uk
MTR Corporation was established in 1975 with a mission to construct and operate an urban metro system for Hong Kong
In June 2000, it was re-established as MTR Corporation Limited and was listed on the Stock Exchange of Hong Kong in October 2000. In December 2007, the operations of the government-owned rail operator, the Kowloon-Canton Railway Corporation, were merged into MTR. The merged rail network comprises nine commuter railway lines, a light rail network and an airport express link with an average weekday ridership of more than 5.6 million passengers in Hong Kong. MTR also operates high speed rail services, connecting Hong Kong to cities in mainland China.
Globally, MTR delivers services for over 13 million people each day, more than 4.7 billion journeys every year.
Acknowledged as one of the world’s leading operators of metro, commuter and airport rail systems, MTR also has a successful international consulting business and is a recognised world leader in Rail + Property development, managing shopping malls, retail units, apartments and other major buildings along some of its lines.
MTR offers worldwide railway consultancy and contracting services. Clients served include metro companies, government authorities and rail system suppliers in the Mainland of China, India, Australia, the Middle East and Southeast Asia.
In China, MTR operates the Beijing Metro Lines 4, 14,16 and 17 and the Daxing Line extension, Shenzhen Metro Longhua Line and the Hangzhou Metro Lines 1 and 5. Further projects and concessions in development include Shenzhen Metro Line 13, and property projects in Hangzhou and Tianjin.
In Australia, MTR operates and manages the Melbourne Metro and Sydney Metro Northwest Line which is a Public-Private Partnership (PPP) project.
MTR also operates and manages Stockholm Metro, the MTR Express intercity service between Stockholm and Gothenburg, the Stockholm Commuter Rail System and Mälartåg regional train service in Sweden.
In the UK, MTR’s portfolio brings together rail operations, infrastructure, and transport-focused property development. Connecting people and communities for over 15 years, MTR has an established track record of excellence. It operated the London Overground in partnership with Arriva for ten years, and currently operates the Elizabeth line on behalf of Transport for London, and South Western Railway in partnership with FirstGroup.
An award-winning operator, MTR is known for its innovation and transformative rail solutions.
The Elizabeth line is the most significant addition to London’s transport network in a generation, providing new journey options, cutting travel time, and supporting regeneration across the capital. As the line’s operator, MTR provides passengers with the best possible experience when travelling on this world-leading transport infrastructure, covering all aspects of train and passenger service operations including:
• The operation of 28 stations, serving 41 stations in total.
• Running more than 700 services a day, with over four million passenger journeys each week.
• Operating a fleet of 70 brand new highcapacity trains, 200-metre long, each featuring nine walk-through carriages.
MTR Elizabeth line was named Passenger Operator of the Year 2023 at the National Rail Awards and Rail Operator of the Year 2023 at the National Transport Awards.
KEY PERSONNEL
CEO UK: Steve Murphy
CONTACT INFORMATION
Address: MTR Corporation Limited
Third floor, 123 Pall Mall, London, SW1Y 5EA
Visit: www.mtreurope.com
Serco has global expertise in the design, setting up, operation, and maintenance of heavy rail, metro and light rail operations across the globe – from the turnkey operation of the Dubai Tram to redefining a luxury experience on the Scottish Caledonian Sleeper
Caledonian Sleeper
Serco began operating Caledonian Sleeper in April 2015 after it was selected by Transport Scotland to manage the new 15- year franchise back in May 2014. Total revenue to Serco over the franchise period is estimated at up to £800 million, of which approximately £180 million will be in the form of franchise payments.
In 2019, Caledonian Sleeper’s service was transformed when it debuted 75 new carriages across its Highlander and Lowlander routes – delivering on a commitment made when the contract was won. The fleet, built at a cost of £150 million, has been part funded by capital grants from Scottish Ministers and from the UK Government.
Dubai Metro
Serco first began operating and maintaining the initial ten stations on the Red Line from the official opening of the Dubai Metro in 2009. Expansion of the Metro has seen
the Red Line grow to 29 stations, while the Green Line, opened in 2011, added an additional 20 stations. The Red Line expansion for Expo 2020 adds 15 kilometres and connects seven stations. At that point, the Dubai Metro will have a total network length of 90 kilometres and over 120 trains running at peak times. Serco’s more than 2,000 employees on the Dubai Metro continue to deliver excellent operational performance and record numbers of passenger journeys.
Merseyrail is a 50/50 JV between Serco and Abellio. Serco have redesigned the model of delivering a city region wide rail transit system through a model of operational excellence by focussing on delivering high levels of predictability, reliability, punctuality, trust, safety and customer service. All of which has led to Merseyrail consistently being at or around the top of the league on customer satisfaction and operational performance.
SRTS is part of Serco’s Transport business, which operates various transport services around the world (primarily rail but also air, sea and road related). A specialist provider of Rolling Stock Testing & Commissioning (T&C) and technical assurance services, it is uniquely placed to provide a deep technical and practical insight into GB railway operations. Today it has over 50 years’ experience across a broad range of rolling stock and infrastructure technical services through the rolling stock development lifecycle. SRTS provides engineers at client depots and routes across the GB rail network. SRTS works closely with train manufacturers to successfully deliver extensive and complex rolling stock testing programmes at sites and other worldwide test tracks and depots.
KEY PERSONNEL
Chairman: John Rishton
Group Chief Executive Officer: Rupert Soames OBE
Chief Executive Officer, Serco UK and Europe:
Mark Irwin
Group Chief Financial Officer: Nigel Crossley
Managing Director, Transport for the UK & Europe:
John Whitehurst
Group Human Resources Director: Anthony Kirby
Group General Counsel and Company Secretary: David Eveleigh
Group Strategy and communications Director: Kate Steadman
CONTACT INFORMATION
Address: Serco House, 16 Bartley Wood Business Park Bartley Way, Hook Hampshire RG27 9XB
Tel: 01256 745900
Email: generalenquiries@serco.com
Visit: www.serco.com
Avanti West Coast operates the 400-mile long west coast route that serves cities including Birmingham, Manchester, Liverpool and London, as well as Scotland and North Wales
Under the West Coast Partnership, a joint venture between FirstGroup and Trenitalia which celebrated its first anniversary in December 2020, First Trenitalia is committed to delivering a range of passenger enhancements for InterCity West Coast services including new and upgraded trains, simplified fares, more destinations and improved onboard experience.
The programme will transform all 56 of Avanti West Coast’s Pendolinos which have served routes between London, Birmingham, Manchester, Liverpool, Glasgow, and Edinburgh for close to 20 years, clocking up more than 270 million miles – enough to go to the moon and back more than 500 times.
Rail manufacturer Alstom will oversee the refurbishment at their new depot in Widnes in the North West securing 100 skilled jobs. The first refurbished Pendolino was returned to service in April 2022, boasting as the UK’s biggest train upgrade with some of its new features including:
• 25,000 new, ergonomic Standard Class seats.
• Conversion of one First Class carriage on each of the 35 eleven-carriage Pendolinos to provide more than 2,000 extra Standard Class seats.
• The introduction of a new onboard shop.
• Improved lighting and new interior carpets.
• Greater use of technology with customerfriendly passenger information screens.
• Power points at every seat.
• New carpets throughout using sustainable British wool.
The upgrade programme will run until 2024 when the last of the 56 strong fleet is expected to leave Widnes. UK suppliers will benefit from 80 per cent of the £117 million investment, which is financed by Angel Trains, one of the UK’s leading train Asset Management companies.
West Coast Partnership will invest £1 million plus as part of the University of Leeds’s plans for The Institute for High Speed Rail and System Integration. The
research tie-in will help deliver a UK centre of excellence for rail engineering in the Leeds City Region and is intended to drive improved customer experience and operation of HS2.
When fully operational, the Institute will be capable of simulating the conditions found on busy rail networks, the findings of which will play a key part in the shaping of HS2 services.
Avanti West Coast has launched a new fund to encourage ideas to improve stations and local communities along its route. The Customer and Communities Investment Scheme (CCIS) encourages applications from projects that address regeneration challenges and tackle social needs across the regions served by Avanti West Coast. The money will be awarded to the successful bidders over a two-year period.
This investment by the inter-city operator is part of its focus to support projects across the routes and regions they serve and create a difference that benefits the community. There are three phases of the CCIS, which spans five years and is set to provide a total of £5.5 million in funding.
For more information on what kind of social, environmental, and economic development issues are eligible for the scheme, please visit: www.avantiwestcoast. co.uk/about-us/sustainability/ community-hub
KEY PERSONNEL
Interim Managing Director: Steve Montgomery
Exec Director, Finance: Craig Forster
Exec Director, Commercial: Sarah Copley
Operations Director: Nick Westcott
Exec Director, Customer Experience: Natasha Grice
Exec Director, Projects: Michael Weston
Exec Director, Technology: Rob Tyler
Marketing Director: Mike Greenup
CONTACT INFORMATION
Address: Victoria Square House
Victoria Square, Birmingham, B2 4DN
Customer Support Phone: 0345 528 0253
Email: customer.resolutions@avantiwestcoast.co.uk
Visit: www.avantiwestcoast.co.uk
Home to mainland Britain’s first electric tramway, the Blackpool Tramway is the last surviving first-generation tramway in the UK
The oldest part of the tramway, along Blackpool Promenade, was opened on 29 September 1885, originally using conduit collection. The electric supply was converted to overhead power four years later.
Over 130 years later and 2017 was a redletter year for the Tramway as September saw the eightieth anniversary of the Brush Car tram and in October a collection of illuminated heritage trams paraded along the promenade for the first time in the tramway’s history.
Over five million passengers rode the Tramway in 2016 and in 2012 it underwent renewal efforts which saw modern light rail trams operating along the eleven miles of coastline. The £100 million redevelopment was completed in April 2012 and involved the relaying of track and the building of a new depot.
Other upgrades included a brandnew fleet of Bombardier trams that have reduced journey times by up to 15 minutes. Bombardier’s trams have level boarding and step-free interiors as well as designated disabled/pushchair areas. The vehicles are 32 metres long, split into five sections and can accommodate up to 222 passengers.
Heritage Blackpool is unique to the UK as it has the freedom to operate unmodified vintage trams throughout the year under its heritage brand, Blackpool Heritage Tram Tours. The Heritage Tram Tours have gone from strength-to-strength since 2014 and is a fine example of modern day voluntary working, with up to ninety per cent of its workforce being volunteers.
There are twelve different types of car that have been used on the tramway over its 133-year lifespan, with some travelling around the world, like the iconic Boat car which was used in the USA during the 1970s.
The Blackpool Tramway won the award for the Most Improved System in 2020/21. Blackpool Trams saw a resurgence in customer numbers after the Blackpool
staycation boom brought about by travel restrictions in the wake of the Covid lockdown. Coupled with seamless ticketing and low fares, the Tramway extension is well on its way to completion as it opened for testing in June 2022 and is set to open in the Spring of 2023 to provide an integrated train, tram and bus network for Blackpool.
The improvements previously made to the tramway received such a positive response from the public that at the end of 2018 Blackpool Transport alongside Blackpool Council began further upgrades. The existing tramway service operates between Starr Gate and Fleetwood Ferry from approximately 05.30 until 23.30, with a peak service every ten minutes.
The tramway extension will leave the existing route at North Pier, via a two-way double track junction. The route will cross the Promenade highway and enter Talbot Square, which is being remodelled to provide segregation of trams and highway traffic. The existing pedestrian signals on the Promenade will be replaced by a signalled
intersection. A new eastbound tram stop is to be located in Talbot Square, to allow interchanges with the existing North Pier tram stops. Beyond Talbot Square, a double track alignment continues eastwards in the centre of the highway.
KEY PERSONNEL
Managing Director: Jane Cole
Director of Organisational Development: Karen Cooper
CONTACT INFORMATION
Address: C/O Blackpool Transport
Services Limited, Rigby Road
Blackpool FY1 5DD
Tel: 01253 473001
Email: enquiries@blackpooltransport.com
Visit: www.blackpooltransport.com
c2c operates services between Fenchurch Street and Shoeburyness, serving 26 stations in East London and South Essex
Built and operated by the London Tilbury & Southend Railway in the 1850s, the current c2c rail service has operated under a number of different names and ownership during its 160-year lifespan. The line was once known as the Seaside line until spending a few unfortunate years nicknamed the ‘Misery Line’ in the 1990s after privatisation, with fifty years of nationalisation in between. Trenitalia paid £72.6 million for c2c after being awarded a Pre-Qualification Questionnaire Passport enabling it to bid for franchises without needing to resubmit corporate data.
c2c currently serves 26 stations on the London, Tilbury and Southend Railway line from London Fenchurch Street to the northern Thames Gateway area of southern Essex including Grays, Leigh-on-Sea and Southend-on-Sea. The main route from Fenchurch Street to Shoeburyness is 63 kilometres with a fastest journey time of 58 minutes.
As c2c is mainly a London commuter railway and the typical journey is between 40 and 80 minutes, it does not offer First Class seating. Its Class 357s have standard high density ‘3 + 2’ seating to meet high demand at peak times, however 17 trains were converted into a metro style with ‘two and two’ seating and grab handles.
London Underground’s District line connects with c2c indirectly at Tower Hill (for Fenchurch Street) and directly at West Ham, Barking and Upminster. Tickets are fully interchangeable between the two operators. There are also interchanges at Limehouse and West Ham with Docklands Light Railway and at Barking and Upminster with London Overground.
The Transport Focus survey of October 2022, which interviewed rail passengers across the country, revealed that c2c tops the league with 96 per cent overall satisfaction rate among the passengers surveyed. c2c also comes in first place among train operators for punctuality/ reliability, with 96 per cent of passengers saying they were satisfied and 91 per cent
saying they were satisfied in terms of the level of crowding.
c2c has also led the rail industry in being the first company to introduce customer friendly new products such as Automatic Delay Repay for customers whose journeys are delayed, Flexi-Season tickets for parttime workers, and Personal Punctuality Reports which allow customers to track exactly how punctual the trains that they were on have been.
The c2c app called c2c Live provides a one-stop-shop for c2c passengers with everything from personalised journey information to buying tickets, and even paying for car parking.
Developed with IBM, this is the first app made by a UK rail company to include nationwide door-to-door public transport journey planning, enabling users to plan a route for any journey anywhere in the UK.
Other developments include the c2c Smart card which allows c2c season ticket holders to switch from paper tickets to an Oyster-style tap-and-go smartcard ticket they can use anywhere on the c2c route.
KEY PERSONNEL
Managing Director: Rob Mullen
Engineering Director: Jeff Baker
Delivery Director: Laura McEwen
Finance Director: Philip Leney
Commercial Director: Clare McCaffrey
HR Director: Donna Thorpe
CONTACT INFORMATION
Address: 2nd Floor, Cutlers Court
115 Houndsditch, London EC3A 7BR
Tel: 0345 744 4422
Email: contact@c2crail.co.uk
Visit: www.c2c-online.co.uk
From Sunday 25 June 2023 the Caledonian Sleeper services have been provided by the Scottish Government
The night of Friday 23 June saw the last Caledonian Sleeper services run under Serco’s management when the Caledonian Sleeper franchise expired almost eight years and three months since Serco’s inaugural service departed from Fort William on Tuesday 31 March 2015. It operates as a separate business from ScotRail, as part of Scottish Rail Holdings (SRH). Caledonian Sleeper runs on two routes – the Lowlander and the Highlander. The Lowlander route connects Scotland’s two biggest cities, Glasgow and Edinburgh, with the capital of the UK, stopping at Carlisle and then at Watford Junction before arriving at London Euston early in the morning.
The Highlander connects London with Aberdeen, Fort William and Inverness, leaving London Euston in the evening before splitting into three at Edinburgh Waverley in the early hours of the morning. The three sections arrive at Aberdeen, Inverness and Fort William.
The Caledonian Sleeper serves 48 stations overall – 43 in Scotland and five in England – and is a key part of Scotland’s transport offering that delivers unique journey and tourism opportunities. Services run in
both directions six nights a week, with the trains calling at dozens of other stations along the way.
In 2019, the service took a giant leap forward with the introduction of its new trains – 75 carriages debuting across the Lowland and Highland routes. The fleet, built at a cost of £150 million, has been part funded by capital grants from Scottish Ministers and from the UK government.
Designed to accommodate the modern-day traveller, the trains offer accommodation ranging from new comfort seats for the budget traveller to rooms with double beds and en-suites – for the first time in the history of Caledonian Sleeper. Other features are included on the new trains, such as a hotel-style key card entry system, charging panels and Wi-Fi throughout the train.
Since March 2022, Caledonian Sleeper has consistently increased forward sales. As a result, the service has achieved the highest ever forward bookings with every individual period seeing record sales. This has been in large part due to the innovation of allowing
guests to book up to twelve months in advance, a unique feature of the service that Serco introduced when it started managing the service. As part of this increase, there have been record sales through the dedicated website, Sleeper.scot, since January 2022. 2022 was the best year ever for the service as it recovered from Covid; the year saw the highest revenue since the start of the franchise with guest levels back to pre-covid.
Caledonian Sleeper has worked to ensure the best possible experience for guests with access needs. With a new range of accessible accommodation, the service is committed to ensuring accessible guests have the space they need to travel comfortably and safely between London and Scotland.
Since 2015 the Caledonian Sleeper has partnered with ARRAN Sense of Scotland to supply their guests with bath and shower gels, shampoo, conditioner, handwashes and body lotions. Since the start of October 2022 all of their fleet has been fitted with eco-friendly refillable dispensers to replace the single use plastics in the Caledonian Double and Club rooms, reducing virgin plastic use by 81 per cent and liquid waste by use to 75 per cent.
KEY PERSONNEL
Managing Director: Kathryn Darbandi
Commercial & Procurement Director: Graham Kelly
CONTACT INFORMATION
Address: 1-5 Union Street
Inverness IV1 1PP
Tel: 0330 060 0500
Email: enquiry@sleeper.scot
Visit: www.sleeper.scot
Running along the M40 corridor to destinations in Buckinghamshire, Oxfordshire and Warwickshire and longdistance services to the West Midlands along two routes. Services on the Chiltern Main Line run from London Marylebone to Birmingham Snow Hill, Stratford-upon-Avon and Oxford, with some peak-hour services to Kidderminster.
Chiltern Railways also runs trains on the London to Aylesbury Line to Aylesbury (with some trains terminating at Aylesbury Vale Parkway instead), on the Princes Risborough to Aylesbury and Oxford to Bicester branch lines.
Chiltern Railways is part of the Arriva group, one of the leading providers of passenger transport in Europe. In 2022, 18.5 million passenger journeys were carried on Chiltern’s services.
Chiltern intends to deliver easier, greener, and better rail services through investment in new trains over the next decade. The vision was developed following research that Chiltern commissioned to ask customers, stakeholders and colleagues what they wanted Chiltern to look like from their perspective by 2030.
The Office of Rail and Road’s latest statistics show that Chiltern has the third oldest trains by operator, with an average age of 28.9 years. While the operator’s fleet ages, the communities it serves continue to grow, highlighting the need for a strategic plan to deliver a modern, greener railway.
Chiltern Railways has been awarded a new contract which includes commitments to continue working towards decarbonising and modernising its fleet. Chiltern is working with Magtec on the Hybrid DMU project with Angel Trains, Britain’s leading train asset management company. The £4 million Class 165 Hybrid DMU project aims to reduce carbon and gaseous emissions, whilst addressing local air quality and noise pollution issues. The Hybrid DMU train’s electric drive offers improved acceleration compared to its diesel-only counterparts, potentially reducing journey times for
passengers. Its smart drive system is able to detect proximity to stations or depots, switching to battery power to cut emissions and noise in populated areas. Magtec’s new range-extender generators charge the traction battery and deliver power to the traction motor. They are smaller and more efficient than existing diesel engines and comply with the latest emissions standards. The battery is also recharged by the train’s regenerative braking system, increasing overall efficiency and further reducing emissions.
Chiltern Railways launched HybridFLEX, Britain’s first 100mph capable batterydiesel hybrid train into passenger service in February 2022. It is formed of a 20-yearold diesel train that has been fitted with a powerful battery allowing it to run solely on battery power when departing and arriving at stations. This train runs between Aylesbury and London and significantly cuts CO2 emissions, saves fuel and reduces noise and air pollution.
HybridFLEX is the product of a four-year partnership between Chiltern Railways, Porterbrook and Rolls-Royce.
KEY PERSONNEL
Managing Director: Richard Allan
Commercial & Customer Strategy Director: Andrew Camp
Engineering and Safety Director: Tim Sayer
Finance Director: Richard Johnson
CONTACT INFORMATION
Address: Banbury ICC, Merton Street
Banbury, Oxfordshire OX16 4RN
Tel: 0345 600 5165
Email: customer.service@chilternrailways.co.uk
Visit: www.chilternrailways.co.uk
Since 2007 CrossCountry has provided passenger services to more parts of Great Britain than any other train operator, including operating the country’s longest passenger service from Aberdeen
In October 2020 DfT entered into a unique Operating Cost Franchise Agreement with Arriva UK Trains Ltd to operate passenger rail services on Cross Country. The core term of this contract ended on 15 October 2023 with a National Rail Contract replacing it.
The National Rail Contract with Arriva UK Trains Ltd includes the addition of capacity to replace the remaining highspeed trains which are being retired, the refurbishment of both the existing Cross Country train fleets and the introduction from December 2024 of direct daily services between Cardiff and Yorkshire, the North East and Edinburgh.
In 2023 Alstom signed an eight-year extension to its Train Services Agreement (TSA) with CrossCountry in the UK. Under the agreement, Alstom will continue to maintain, overhaul, service and clean 252 vehicles of the CrossCountry fleet (34 Class 220 Voyagers and 24 Class 221 Super Voyagers) at their primary depot, Central Rivers. In addition, seven Voyagers will move to CrossCountry when they are released from service with Avanti West Coast to bolster the CrossCountry fleet and enable service uplifts.
The contract extension, valued at around £825 million, further secures this long-term partnership and is evidence of the trust placed by the customer.
The contract includes management of all planned (preventative) and unplanned (corrective) maintenance; all required overhaul activities; cleaning, and light maintenance services on the vehicles; vehicle servicing; service delivery support (including 24/7 telephone help line); vehicle cleaning (daily and periodic); depot management; shunting; obsolescence monitoring and management, and accident/ vandalism repair.
Within the agreement, the fleet will be installed with an Intelligent Engine Stop Start (IESS) system, which will drive a reduction in fuel usage, emissions, and operational costs. Additionally, the collaboration team will continue with other fuel savings measures to build on the weight reduction initiatives already undertaken, or
underway, which will substantially reduce the emissions produced from the fleet.
Owned by Beacon Rail, the Voyagers are running across the CrossCountry network, from Aberdeen, Scotland, to Penzance, England.
Alstom's Voyager and Super Voyager inter-city trains have already served passengers across England, Scotland and Wales for over two decades. Operating at speeds of up to 200 km/hour, they have clocked up over 414 million miles of service.
During the partnership over 34,000 Personal Safety Scouting badges were awarded and the scheme was recognised for its achievements in several awards by rail industry and external organisations, including the International CSR Excellence and Peer Awards, against strong competition from some of the largest UK and European brands and businesses.
CrossCountry continues its commitment to delivering actions that benefit the customers and communities that it serves. In 2020 it established a new regionalised management structure, with directors and teams responsible for making its products and services more relevant to customers and local stakeholders.
A partnership with the Newcastle College Rail Academy continues to support educating the students, by promoting the diverse and widespread careers across the rail sector. Through this partnership CrossCountry has donated over £50,000 worth of IT equipment as well as being a key contributor to events helping students to get a better overview of the industry.
CrossCountry also supports many Community Rail Partners along its network, working on a variety of activities to strengthen their work bridging the gaps between rail and the wider community. This has included supporting award-winning collaborative projects such as ‘Dwell Time’ focused on raising awareness of mental wellbeing, featuring art, poetry and writing along the Penistone Line as well as nationally and even internationally.
CrossCountry has helped fund transformative regeneration projects such as the ‘Whistlestop café’ in partnership with the Derwent Valley CRP, transforming old and unused heritage station buildings into enterprising and useful spaces, and other projects to establish tourist information hubs and support local community food banks.
KEY PERSONNEL
Managing Director: Tom Joyner
Service Delivery Director: Mark Goodall
Human Resources Director: Zoe Kennedy
Finance Director: Harj Singh
Customer Director: Colette Casey
Regional Director, North East & Scotland: Ben Simkin
Regional Director, West Midlands & North West: John Robson
Regional Director, East Midlands & East Anglia: Richard Morris
Regional Director, West & Wales: Sarah Gould
CONTACT INFORMATION
Address: 5th Floor, Cannon House
18 The Priory Queensway
Birmingham B4 6BS
Tel: 0344 736 9123
Email: info@crosscountrytrains.co.uk
Visit: www.crosscountrytrains.co.uk
Prior to the Covid-19 pandemic, Edinburgh Trams enjoyed yearon-year growth, with annual patronage levels peaking at around 7.5 million per year. In June 2023 Edinburgh Trams extended the line by three miles in a £200 million project. Trams will now run from Edinburgh Airport, Gyle Centre, Edinburgh Park and Murrayfield Stadium across the City centre to eight brand new stops conveniently located along Leith Walk, The Shore, directly outside the doors of Ocean Terminal and at Newhaven.
The extension has proved popular with the tram’s busiest month ever coming in August 2023, recording more than 1.2 million customer journeys. Trams operate every seven minutes from 6am to midnight, seven days a week.
Edinburgh Trams picked up two awards in 2023, winning Transport Operator of the Year at the Scottish Transport Awards and Project of the Year for the Trams to Newhaven extension project at the Global Light Rail Awards.
Regular users of trams and buses in the city can use the Ridacard, which gives the best value travel whenever it’s used. Fully contactless, one-week, four-week and annual tickets can be stored on the card, with the latter two offering savings on the weekly rate.
Passengers are also able to use their smartphones for travel by using Edinburgh Trams’ free app. It provides users with live information on the quickest way to reach their destination and enables m-tickets to be downloaded and activated as needed.
A new feature was added to the app in November 2015 that for the first time allowed users to ‘share’ tickets, so tickets can be sent through the smartphone’s native sharing technology such as Bluetooth, AirDrop, e-mail, social media or text. Edinburgh Trams, and its sister company Lothian Buses, also partnered with Google Maps from the beginning of 2016 to provide real-time travel information.
KEY PERSONNEL
Managing Director: Lea Harrison
Chief Executive – Transport for Edinburgh: George Lowder MBE
Head of Operations: Sarah Singh
Head of Safety and Projects: Colin Kerr
HR Manager: Sue Bucher
CONTACT INFORMATION
Address: 1 Myreton Drive
Edinburgh EH12 9GF
Tel: 0131 338 5780
Email: customer@edinburghtrams.com
Visit: www.edinburghtrams.com
Operated by MTR Elizabeth line (MTREL), a one hundred per cent subsidiary of MTR Corporation, the Elizabeth line is part of the TfL network and has interchanges with the London Underground, DLR, London Overground and National Rail
June 2023 marked one year of the Elizabeth line, with more than 150 million passenger journeys made in the first year alone it topped national tables for being the most ‘on time’ railway in the country.
The Elizabeth line is the most significant addition to London’s transport network in a generation, providing new journey options, cutting travel time and supporting regeneration across the capital. Customers can travel direct between Reading, Heathrow and Abbey Wood and between Shenfield and Heathrow via Paddington, taking advantage of record journey times with up to 24 trains per hour in each direction through central London with around 4.1 million journeys made each week. In 2023 it was crowned
The Elizabeth line is London’s first accessible railway. It is the result of the biggest infrastructure project in a generation and, as a concept, can trace its history back over a century. Lifts have been installed at every Elizabeth line station to ensure step free access from the street all the way to the platform. The enhancements to the older stations have included improving accessibility at the ticket office windows and wider entrances to ticket halls.
The railway connects the mainline stations at Paddington and Liverpool Street with Heathrow Airport and Reading in the west, and with Shenfield and Abbey Wood in the east. It increases central London’s rail
capacity by ten per cent, taking pressure off some of the Underground’s busiest interchanges.
Each of its fast air-conditioned walkthrough trains are nine carriages long, with space for up to 1,500 people.
Work on the line’s 42 kilometres of tunnels started in 2011, with eight huge Tunnel Boring Machines (TBMs) completing the task in four years. The main phase of station building and systems installation took place between 2016 and 2021, with each new station in turn handed over to Transport for London (TfL).
A new depot at Old Oak Common houses and maintain 42 of the Elizabeth line’s 70 new trains at a time.
The trains use up to 30 per cent less energy by tapping into the electricity produced whilst braking and then pumping that back into the power supply, just like a Formula One car. The trains have three double doors per side which open onto a clear area which allows for easier access to the metro-style and bay seating within. Other features include multiple wheelchair dedicated areas and mixed-use seating that can be flipped up to accommodate wheelchairs.
KEY PERSONNEL
Managing Director for MTR Elizabeth Line: Mike Bagshaw
Concession Director: Nick Arthurton
People & Culture Director: Claire Metcalfe
Finance and Business Systems Director: Ben Milway
Train Service Delivery Director: Nick Westcott
Customer Experience Director: Paul Parsons
CONTACT INFORMATION
Address: Palestra, 197 Blackfriars Road, London SE1 8NJ
Tel: 0343 222 0000
Email: Contact via website
Visit: www.mtrel.co.uk
Jointly operated by Iarnród Éireann (IE) and NI Railways (NIR) Enterprise operates on the Belfast to Dublin line. The Great Northern Railway (Ireland) (GNR(I)) introduced the service as the ‘Enterprise Express’ in August 1947 in an attempt to compete with air travel which was challenging the railways as Swissair and Pan Am both began using Shannon Airport as a stop-off on transatlantic flights in the Spring of that year.
The initial service ran between Belfast Great Victoria Street station and Dublin Amiens Street station, which was renamed Dublin Connolly in 1966. Customs checks were limited to the Belfast and Dublin terminals to reduce journey times by ensuring that journeys were non-stop.
In October 1950 the service was extended beyond Dublin to Cork. This proved unsuccessful and ceased in September 1953 when the governments of the Republic of Ireland and Northern Ireland nationalised the GNR as the Great Northern Railway Board (GNRB). In October 1958 the GNRB was dissolved and its assets and liabilities were split between Córas Iompair Éireann (CIÉ) and the Ulster Transport Authority (UTA) – the predecessors of Iarnród Éireann (IÉ) and Northern Ireland Railways (NIR) respectively.
Following the completion of the Belfast Central Line Project, the Belfast terminal moved to Belfast Central station in 1976. The service was upgraded in September 1997 with a new timetable and new coaching stock from French train makers De Dietrich Ferroviaire (now Alstom DDF). At this point the service, which had operated under either the IÉ or NIR brands, was branded separately as Enterprise.
The service has suffered disruption, particularly during the Troubles, when it was regularly halted by bomb threats. Since the Northern Ireland peace process, however, such disruption has diminished. Renewed investment in recent years has seen the line upgraded to continuously welded track capable of ninety mph running along the southern part of the route, as part of Iarnród Éireann’s rail network upgrades.
The Northern Ireland section of the line was also upgraded to run at speeds
along the Dublin-Belfast corridor and how both Northern Ireland and the Republic of Ireland plan to develop the railway.
The Enterprise Strategic Development Plan seeks approval to start procurement of new fleet and fund a detailed Technical & Feasibility study for journey time improvement options.
An hourly Belfast – Dublin service could be achieved within five years with a journey time of less than two hours.
Longer term, additional improvements could be achieved with investment in line electrification to achieve further frequency improvements and a journey time of potentially 90 mins or less.
The three initiatives laid out in the plan are:
• Introduction of an hourly service frequency between the two cities.
• Infrastructure enhancements to improve journey times and connections.
• Electrification through investment in infrastructure and rolling stock.
of ninety mph on many sections of the line. The Enterprise brand aims to be politically neutral, there are no Irish Rail or NI Railways logos inside or outside the train, only Enterprise specific branding, all announcements are made in English and not in Irish, and purchases are dual priced in Pounds Sterling as well as in Euros.
Operating eight services in each direction, Monday to Saturday and five journeys in each direction on Sundays, the journey takes just over two hours. If an Enterprise set is unavailable, either a NIR or an IÉ set can be used. Both NIR and IÉ have equipped a number of their DMUs to each other’s specifications so they may be used in the event of a breakdown.
Enterprise put out a document titled the ‘Strategic Development Plan’ in June 2018, detailing the projected population growth
• The long-term goal of electrification set out in the plan recommends replacing the existing rolling stock with electrically powered units by 2035. A new fleet of nine train sets would be required to permit an hourly service.
KEY PERSONNEL
CEO: Jim Mead
Director Infrastructure Manager: Don Cunningham
Chief Financial Officer: Aidan Cronin
Director Human Resources: Ciaran Masterson
Commercial Director: Gerry Culligan
CONTACT INFORMATION
Address: Enterprise c/o Iarnród Éireann
HQ, Connolly Station, Amien Street
Dublin 1, D01 V6V6 Eire
Tel: +353 1 836 6222
Email: info@irishrail.ie
Visit: www.irishrail.ie/enterprise
Since 1984, Gatwick Express has operated as the only non-stop train service between
Gatwick Express operates 160 services carrying around 13,000 travellers a day and covers around 1.6 million miles a year. Running between London Victoria station and Gatwick Airport, the airport train service departs every 15 minutes, enabling passengers to
reach the airport, which is located directly beneath the train’s south terminal, in around 30 minutes.
A new look Gatwick Airport station opened in November 2023. Eight new escalators and five new lifts provide a step change for
accessibility. Easier journeys between train and plane will benefit passengers across the wider network, helping keep trains running on time by removing the congestion on platforms that delay trains.
Passengers travelling on the Brighton Main Line are already seeing the benefits of the project thanks to track upgrades that have helped reduce journey times between Brighton and London to one hour on some services.
The existing station concourse is also bigger and better than ever before with new customer information systems, more ticket gates, a dedicated passenger assistance point enhancing the passenger experience and helping people move through the station more quickly.
The new concourse will now act as the new entrance for people accessing the airport terminal, while the existing concourse will be for people exiting. The existing station concourse, station footbridges and the South Terminal linkspan have been refurbished and reconfigured to provide a seamless oneway system to the airport from the train station.
KEY PERSONNEL
Chief Executive Officer: Patrick Verwer
Chief Operating Officer: Angie Doll
Engineering Director: Steve Lammin
Infrastructure Director: Keith Jipps
Head of Safety & Health: Emile MacDonald- Williams
Marketing and Communications Director: Myriam
Walburger
Head of Engineering and Asset Management:
Dave Hickson
Head of Network Operations: Mark Boon
CONTACT INFORMATION
Address: 1st Floor, Monument Place
24 Monument Street, London EC3R 8AJ
Tel: 0345 850 1530
Email: customerservices@gatwickexpress.com
Visit: www.gatwickexpress.com
The Glasgow Subway carries eight million passengers each year, and is currently undergoing its biggest modernisation programme in more than 30 years
The 15 stations of the Subway are distributed over a six mile circuit of the West End and City Centre of Glasgow, with eight stations to the North of the River Clyde and seven to the South. There are two lines: an outer circle running clockwise and an inner circle running anticlockwise.
Glasgow Subway saw its busiest period for some time with more than 470,000 journeys completed during the 2023 UCI Cycling World Championships. The first weekend of the event saw more than 132,000 journeys, the busiest weekend overall since 2018.
The Subway is open 06:30 to 23:40 Monday to Saturday and 10:00 to 18:12 on Sundays.
The full-scale upgrade will ensure that the highest quality of service is delivered to the 40,000 passengers who use the Subway every day. The Glasgow Subway is 120-years old and is the third oldest underground system in the world behind London and Budapest. A £288 million funding package for the work is being supported by the Scottish Government and rebuilding work is happening right across the network.
Key improvements to accessibility, safety and information provision are being introduced. With progress to date including; St Enoch Station with its two new glass canopies has undergone the most comprehensive transformation bringing new life to the historic St Enoch Square. As well as Buchanan Street Station which has also undergone modernisation complete with new travelators which acts as a very important link to Queen Street Station.
In 2011/12, Strathclyde Partnership for Transport (SPT) secured funding from the Scottish Government to fully upgrade and modernise the Subway. This included the refurbishment of all 15 stations, a strand of work which was completed in 2022.
In 2013, SPT also introduced a new Smartcard ticketing system as part of the modernisation programme which has
revolutionised ticketing options across all forms of transport in the region with train and bus operators all developing smart ticketing options. SPT are continuing to work with other travel operators to develop more integrated travel options for commuters. In the future the Subway Smartcard could be used seamlessly between different transport modes (such as bus, train and ferry) and even to buy other everyday items such as coffee on the way into work.
With more than 230,000 Subway Smartcards now in operation, SPT continues to work with transport operators and Transport Scotland to develop more integrated ticketing opportunities across the region.
In 2016, SPT announced a significant step forward in the modernisation programme with the award of contract for the new rolling stock, signalling and equipment to the Stadler Bussnang AG/ Ansaldo STS (now Hitachi) Consortium. The contract worth £200 million will include the 17 new Subway trains which are of the same length and size as existing rolling stock but made up of four-car sets as opposed to the current three-car sets. They also feature open gangways to maximise the space available. The first of the new trains was on show at InnoTrans 2018, the international Trade Fair for transport technology in Berlin, by leading manufacturer Stadler.
As well as the new trains, the Subway’s signalling equipment, control systems and control centre will all be replaced bringing improved availability and reliability to passengers. The system will include new platform screen doors, which will be ‘half height’ to preserve as much space and openness within the stations as possible while still maintaining passenger safety and security.
Once the new full system is in place – trains, signalling, operational control centre, platform screen doors – and has been fully tested, the Subway will move from its current partially automatic trains to Unattended Train Operations (UTO).
KEY PERSONNEL
Chief Executive Strathclyde Partnership for Transport: Valerie Davidson
CONTACT INFORMATION
Address: Broomloan Depot, Robert St Lanarkshire, Glasgow G51 3HB
Tel: 0141 332 6811
Email: enquiry@spt.co.uk
Visit: www.spt.co.uk
Govia Thameslink Railway (GTR) operates the Great Northern, Thameslink, Southern and Gatwick Express routes
GTR is the largest and busiest single rail franchise in the UK: in terms of passenger numbers (around 25 per cent of all UK rail journeys), trains, revenue and staff (7,574 people employed).
The franchise encompasses King’s Lynn in the north and Brighton in the south,
serving London as well as several important regional centres including Cambridge, Luton, Peterborough, Portsmouth and Southampton. It also provides direct links to major airports (Gatwick and Luton) as well as St Pancras International.
KEY PERSONNEL
Chief Executive Officer: Angie Doll
Chief Financial Officer: Ralph Pidsley
Chief Customer Officer: Mark Pavlides
Customer Services Director: Jenny Saunders
Safety, Health and Security Director: Samantha Facey
CONTACT INFORMATION
Address: 1st Floor, Monument Place
24 Monument Street, London EC3R 8AJ
Tel: 0345 026 4700
Email: communications@go-ahead.com
Visit: www.thameslinkrailway.com
Social: @TLRailUK
More and more passengers are not able to hear audio announcements on trains.
Televic GSP’s Speech-to-Text solution converts real-time audio announcements into text.
The transcription can be seamlessly integrated into other onboard systems for diverse applications. Enhance the experience for everyone on board!
Learn more at www.televic.com/televicgsp or contact us at televicgsp@televic.com
Grand Central’s first route was launched in December 2007 and linked London Kings Cross with York and the North East.
In May 2010, this was joined by the West Riding service, linking Doncaster, Bradford and West Yorkshire with London – most recently adding Low Moor in 2017. In August 2014, Grand Central was granted an extension of its operating rights until December 2026.
In early 2024 Grand Central trains will be able to stop at Peterborough after proposals were given the go-ahead by the Office of Rail and Road. Travellers will be able to reach more places in the north of England direct, including Bradford and Sunderland. Two services will leave London King's Cross in the morning on weekdays, heading to Bradford and Sunderland, and southbound trains will stop at Peterborough in the afternoon before heading to London.
Grand Central connects Yorkshire and the North East to London with two routes.
Five daily services on the North East to London route run between Sunderland and London King’s Cross calling at Hartlepool,
Eaglescliffe, Northallerton, Thirsk and York. This route is known as the North Eastern service.
Four daily services which run on the Yorkshire to London route operate between Bradford Interchange and London King’s Cross calling at Halifax, Brighouse, Mirfield, Wakefield Kirkgate and Doncaster. Some services also call at Pontefract Monkhill. This is known as the West Riding or West Yorkshire service.
In May 2018 Grand Central commenced operating services on the West Coast Main Line from London Euston to Blackpool after the Office of Rail and Road granted fellow Arriva subsidiary Alliance Rail Holdings access rights for ten years.
ORR figures showed from April 2022 to March 2023 Grand Central had the highest relative usage at 113 per cent, compared to the same period in 2019.
In the Summer of 2020, the Transport Focus National Rail Passenger Survey (NRPS) reported that Grand Central enjoyed an overall customer satisfaction score of 95 per cent, as well as topping the Value for Money table with a passenger rating of 74 per cent. Travellers also reported a 95 per cent satisfaction rate with Grand Central’s
punctuality, and strongly improved scores for onboard aspects of the journey following a £9 million refurbishment programme.
Grand Central Rail introduced e-ticketing towards the end of 2017, allowing customers to buy tickets online and display them on their mobile or tablet device. Instead of queuing at stations or waiting for tickets to be delivered, customers can now pay for their fare online. Available on desktop and mobile devices, tickets stay available until ten minutes before departure and after purchasing customers receive an email with a downloadable PDF that features a barcode scanned by crew and ticket gates.
Grand Central has a six-month reservation window which is continually updated on a rolling basis. Grand Central was able to make the upgrade after adopting the new Rail Availability & Reservation Service (RARS) system and working with its suppliers.
Grand Central operates an all-Adelante fleet, with its ten Class 180 trains receiving extensive refurbishment and updates to improve passenger comfort in 2018. Due to issues with the 180s in 2023, Grand Central has introduced one Voyager 221 units to the fleet to ensure it can fulfil its timetable. The two Voyager 221 units each consist of five carriages and 276 seats.
KEY PERSONNEL
Chief Operating Officer: Sean English
Finance Director: Carol Bainbridge
Head of Commercial: Nick Clarke
Head of HR: Angela Newsome
CONTACT INFORMATION
Address: Grand Central Rail,
Northern House, 9 Rougier Street
York YO1 6HZ
Tel: 0345 603 4852
Email: customer.services@grandcentralrail.com
Visit: www.grandcentralrail.com
The Great Northern Franchise operates trains between London and the east of England, including Cambridge, Peterborough and King’s Lynn
Since 2016 Great Northern has invested in new trains and increased services. It has doubled overall capacity on the Cambridge to London route and installed new air-conditioned trains from Cambridge to King’s Lynn.
At the end of 2019, Great Northern completed a £240 million train fleet renewal and introduced 25 six-carriage Siemensbuilt Class 717 units on the route between London Moorgate and Stevenage, Hertford North and Welwyn Garden City. The new trains have capacity for 943 people, an eleven per cent increase on the old 313 trains they replaced. The new 717s also feature a ‘snow mode’, which changes the way the brakes work to improve reliability in snowy conditions.
In late November Great Northern commuters began travelling to the City of London in trains controlled by cutting-edge digital in-cab signalling (European Train Control System, or ETCS), giving them a more reliable, greener service.
This was a significant milestone for the £1.4 billion government-funded East Coast Digital Programme (ECDP), set to improve journeys along the East Coast Mainline, from London to north of Peterborough, providing the foundations for the expansion of digital signalling across the UK network.
Introducing digital signalling on this busy commuter line is an important first stage in the ECDP, which will see the first introduction of digital ETCS to an intercity mainline in Great Britain. Progressively, more trains will operate with digital signalling, as more Great Northern drivers are trained to use the technology. Traditional signals will be kept at the side of the track until everyone is trained and the old system can be switched off.
Drivers using digital ETCS aren’t told to stop and go by fixed signals at the side of the track. Instead, they drive according to a target speed set by the system in their cab that is kept continually updated about the location of other trains by a multitude of beacons positioned along the track. The system effectively allows drivers to ‘see’ much further ahead than line-of-sight signals would ever allow, meaning trains can run more efficiently.
The next phase of the ECDP will see digital signalling introduced between Welwyn Garden City and Hitchin, on the East Coast Mainline. The first digitally signalled trains are expected to operate on this section of the route by the end of 2025.
KEY PERSONNEL
Chief Executive Officer: Angie Doll
Engineering Director: Steve Lammin
Infrastructure Director: Keith Jipps
Head of Safety & Health: Emile MacDonald- Williams
Marketing and Communications Director: Myriam Walburger
Head of Engineering and Asset Management: Dave Hickson
CONTACT INFORMATION
Address: 1st Floor, Monument Place
24 Monument Street, London EC3R 8AJ
Tel: 0345 026 4700
Email: customerservices@greatnorthernrail.com
Visit: www.greatnorthernrail.com
Great Western Railway (GWR), operates trains across the Great Western franchise area, which includes South Wales, the West Country, the Cotswolds, across southern England and into London
GWR provides high speed, commuter, regional and branch line train services, and before the covid-19 pandemic helped over 100 million passengers reach their destinations every year. GWR has been awarded a National Rail Contract to continue operating the Great Western network, which shall run up to 21 June 2025, with the potential for a further three years at the Secretary of State’s discretion.
In late November 2023, the reopened Dartmoor Line marked 550,000 journeys made in the first two years of the previously mothballed rail line re-entering service. An impact evaluation of the Dartmoor Line is currently being conducted. This research aims to assess the extent to which the Line has delivered against the anticipated benefits for the local community since its re-opening. The evaluation will conclude next year with findings expected to be
published in Spring 2024. The Dartmoor Line’s success has seen the Government commit to provide £13.4 million from the Levelling Up Fund for an additional station, an Okehampton Parkway.
Okehampton Station was named as the Small Station of the Year at the National Rail Awards 2023.
Three new Great Western Railway stations opened in 2023, the first being Reading Green Park which sits on the Reading to Basingstoke line, with half-hourly services running north to Reading and south to Basingstoke through the day. The second was Marsh Barton in Exeter and the third was Portway Park & Ride in Bristol, which was the first new station in Bristol in almost a century. Regular services will run from the accessible, single-platform station seven days a week along the Severn Beach railway line, taking passengers into the city centre of Bristol in just 24 minutes.
KEY PERSONNEL
Managing Director: Mark Hopwood
Engineering Director: Simon Green
Customer Service and Transformation Director: Richard Rowland
Director, Compliance, Sustainability & Environment:
Joe Graham
Finance Director: Duncan Rimmer
Development Manager: Mike Preece
GWR Head of Strategic Service Development:
Matt Barnes
Business Assurance and Strategy Director:
Joe Graham
CONTACT INFORMATION
Address: Milford House, 1 Milford Street
Swindon SN1 1HL
Tel: 0345 700 0125
Email: visit website for all enquiries
Visit: www.gwr.com
Greater Anglia operates 1,300 train services per day across 133 stations. With the inception of the new franchise in October 2016, Abellio announced it would invest £1.4 billion in fleet replacement which resulted in 33,000 new train seats at morning and evening peak travel times. Greater Anglia is owned by Transport UK which also operates East Midlands Railway and West Midlands Trains, as well as the Merseyrail rail concession in a joint venture with Serco.
As part of a £1.4 billion investment in transforming train services in East Anglia. Greater Anglia is currently in the process of replacing all trains in its fleet with brand new ones, which are all longer, with more seats, USB and plug sockets, fast free Wi-Fi, air conditioning and improved accessibility features as well as dedicated cycle spaces.
Throughout 2021, Greater Anglia introduced new commuter trains to replace all the company’s old trains on Great Eastern Main Line routes between Liverpool Street and Southend Victoria, Braintree, Southminster, Stowmarket, Ipswich, Colchester, Clacton, Walton-on-the-Naze and Harwich. In March 2021, the first of 133 Aventra Class 720 trains being built by Alstom in Derby was introduced on the Clacton to London route. In September of the same year, the trains ran for the first time on the Harwich and Walton-on-theNaze branch lines.
The full introduction of new trains are now in service on every single route in the Greater Anglia network, with many routes operated exclusively by new trains.
Greater Anglia’s reported carbon emissions decreased by 17 per cent between April 2022 and March 2023 – that’s over 67,000 tonnes according to a report by independent environmental consultancy, WSP. This is the third year in a row that the train operator has reduced its carbon emissions.
Over the last few years, Greater Anglia has introduced new more energy-efficient trains, cut waste, increased recycling and
worked with partners and communities on projects to improve sustainability and biodiversity at stations.
They have also worked to install wireless energy management systems at rail stations to ensure heating and lighting are used efficiently and taken steps to reduce water consumption.
In a first for the rail industry, Greater Anglia has pioneered online virtual tours for its entire new train fleet to help people travel with confidence. The virtual train tours have been designed for all of Greater Anglia's new train types to support journey planning, give customers a clearer picture of what they can expect on board and reduce anxiety about travelling.
They are particularly aimed at helping disabled customers who are wanting to check how accessible their journey is.
Virtual tours are available for Greater Anglia’s entire fleet of new trains and also for 15 of the train operator’s stations and are available at https://www.greateranglia.
co.uk/travel-information/your-journey/virtualtours on any device.
The virtual tours help people to navigate their journey, find out where facilities are located and plan in advance. They can use the virtual tours to ‘walk through’ the train or station using the navigation tools.
KEY PERSONNEL
Managing Director: Jamie Burles
Engineering Director: Martin Beable
Commercial Director: Martin Moran
Asset Management Director: Simone Bailey
HR Director: Katy Bucknell
Finance Director: Michael Robertson
Client & Program Director: Andrew Goodrum
Train Service Delivery Director: Jay Thompson
CONTACT INFORMATION
Address: 18-20 St Andrew's Street
London, EC4A 3AG
Tel: 0345 600 7245
Email: contactcentre@greateranglia.co.uk
Visit: www.greateranglia.co.uk
Hull Trains is a non-franchised, open-access operator running up to 94 direct services a week from Hull and the East Yorkshire region direct to London King’s Cross
In 2023 Hull Trains increased its number of journeys by 31 per cent having delivered 358,000 journeys compared to 270,000 in the same quarter in 2022.
Rolling stock
Hull Trains’ high-tech bi-mode, electric and diesel, trains are one of the most modern and innovative trains on the UK rail network. The Hitachi inter-city fleet has consistently ranked inside the top 10 for reliability, often being three times more reliable than the industry average. The Paragon Fleet replaced the old Class 180 fleet following a £60 million investment in 2019. Each train in the fleet carries a name
Awards success
For the second consecutive year, Hull Trains was named ‘Best in Class’ The Golden Spanners which recognise the most reliable train fleets in the railway industry. Hull Trains was also recognised as ‘Best Place to Work’ at 2023’s Hull Live Business Awards alongside being awarded the top employer accolade at the Women in Rail Awards.
KEY PERSONNEL
Managing Director: Martijn Gilbert
Service Delivery Director: Louise Mendham
Head of HR: Deborah Birch
Head of Safety and Sustainability: Michael Powell
Head of Operational Safety: Mark Shepherd
Head of Commercial: Tom McFall
Head of Fleet: Richard Vernon
Head of Customer and Stakeholder Engagement:
Paul Jackson
CONTACT INFORMATION
Address: South Wing, Cherry Court
36 Ferensway, Hull HU2 8NH
Ferensway, Hull HU1 3UT
Tel: 0345 071 0222
Email: customerservices.hull@hulltrains.co.uk
The A1 Loo Hire Rail Division has been providing welfare facilities for the rail industry for over 10 years.
Accredited by RISQS and PTS safety trained we’re the perfect partner for rail construction work.
Bowsers for transporting fuel and water.
Powering both plant and personnel, T&M have a wide range of tankers to assist
Providing the vital supply link, our larger bowsers are the perfect option for transporting vast quantities to your location, while smaller bowsers offer a nimble alternative.
T&M work with your crew to help meet specific requirements, carrying out intelligent innovations and modifications that help form an integral part of any rail construction project.
Our bowsers help ensure a seamless process from start to finish
LNER runs from London Kings Cross to Leeds, York, Newcastle, Edinburgh Waverly, Glasgow, Aberdeen and Inverness. The company is owned by the Department for Transport (DfT). LNER took over the InterCity East Coast franchise in June 2018, after the previous privately owned operator Virgin Trains East Coast returned it to the Government following sustained financial difficulties.
In late November 2023 CAF was awarded the contract to supply a fleet of tri-mode intercity trains for LNER. Based on CAF's Civity platform, the ten state-of-the-art ten-car trains will enter passenger service on the LNER-operated East Coast Main Line (ECML). On electrified routes the trains will use pantographs to draw power from overhead lines and on sections of the route which are not electrified will use either a combination of battery and diesel power modes, or battery-only mode.
Environmental benefits will be realised during the arrival and departure from stations when in battery mode, eliminating emissions, including harmful NOx, and significantly reducing noise pollution.
The transition from electric to self-power mode and vice versa can be undertaken when the train is stationary or in motion.
The battery can recharge in both electric and diesel mode. The trains will be equipped with CAF Signalling proprietary European Rail Traffic Management System (ERTMS) digital signalling, helping reduce energy consumption and emissions by regulating speed, acceleration, and braking. ERTMS also enables reduced minimum distance and time between trains and ensures automatic activation of train safety functions if necessary.
The new tri-mode fleet will be assembled at CAF's Newport manufacturing facility in South Wales. The contract also includes an eight-year maintenance services agreement with an option to extend.
LNER is proposing to continue to move away from traditional retailing, further enriching the digital retailing experience. The plans would bring its people closer to customers, with more colleagues deployed across station concourses and platforms to assist customers wishing to purchase tickets or asking for help or information. Teams will have mobile devices enabling them to sell the vast majority of ticket types and will also be there to assist customers using ticket vending machines.
LNER’s plans include the retention of ticket offices at Edinburgh Waverley, Newcastle, York, Doncaster, Peterborough
and London King’s Cross, which will continue to offer the same range of products and opening times.
Under the proposals LNER plans to repurpose travel centres at Berwick-uponTweed, Darlington, Durham, Grantham, Newark Northgate, Retford, and Wakefield Westgate, with colleagues supporting customers on the stations and proposals to create a modern station retailing experience. LNER is responsible for ticket retailing and passenger assist at eleven stations, as well as Edinburgh Waverley and London King’s Cross, all of which will continue to be staffed by LNER colleagues from the first to the last train and passenger assist will remain.
LNER is continuing to invest in its stations as it welcomes record numbers of customers back to rail. In a UK first, a Family Lounge has been introduced at London King’s Cross station and waiting rooms have been refurbished across the route. Further investment is planned to make rail even more accessible, giving people greater confidence to travel by train. LNER has also committed to multi-million-pound investments at Darlington, Doncaster and Peterborough.
KEY PERSONNEL
Managing Director: David Horne
Commercial Director: David Flesher
Engineering Director: Dr Linda Wain
Customer Experience Director: Claire Ansley
Safety and Operations Director: Warrick Dent
Finance Director: James Downey
CONTACT INFORMATION
Tel: 0345 722 5333
Email: customers@lner.co.uk
Visit: www.lner.co.uk
Address: East Coast House 25 Skeldergate, York YO1 6DH
EC100-CO-47.55m
A2AS_SO9133_5502A
PW600-CO-91.63m
A2AS_GU2000006767
PW150-PVC-6.38m
A2AS_SO9133_5400B
A2AS_GU2000006764
A2AS_GU2000006765
PW150-VC-1.03m
A2AS_SO9132_5799A
A2AS_GU2000006761
PW600-CO-89.66m
A2AS_GU2000006766
PW225-PP-13.29m
A2AS_SO9133_6401B
CF-PP-12.84m
A2AS_GU2000006763
A2AS_SO9132_6199A
CF225-PVC-13.42m
FD0-GR-38.06m
A2AS_SO9133_6500D
A2AS_GU2000006762
A2AS_SO9132_6599A
A2AS_GU2000006759
A2AS_SO9132_5490B
A2AS_SO9132_5490A
A2AS_GU2000006760
A2AS_GU2000006758
PW600-CO-91.96m
A2AS_GU2000006749
EC0-CO-505.83m
PW150-VC-8.28m
A2AS_SO9132_5385A
PW675-CO-89.23m
A2AS_GU2000006745
A2AS_GU2000006746
PW150-VC-7.41m
A2AS_SO9132_5382A
FD0-GR-41.01m
-PP-13.11mCF
CF-PP-13.35m
A2AS_GU2000006755
A2AS_GU2000006757
A2AS_SO9132_6495E
A2AS_GU2000006753
A2AS_GU2000006750
PW150-VC-2.09m
PW600-CO-92.03m
A2AS_GU2000006748
CF225-12.99m
CF225-PVC-44.85m
A2AS_GU2000006747
CF225-PVC-27.92m
A2AS_GU2000006744
A2AS_GU2000006743
A2AS_SO9132_5482E
A2AS_GU2000006740
A2AS_SO9132_5581A
A2AS_SO9132_6084C
A2AS_SO9132_6184E
Cp-08 Cp-06
PW225-PVC-13.29m
PW150-VC-3.62m
PW0-PVC-20.21m
PW150-PP-8.15m
A2AS_GU2000006742
A2AS_SO9132_6183D
PW225-PP-16.49m
A2AS_SO9132_5382B
PW675-CO-20.19m
A2AS_GU2000006739
PW150-PVC-7.47m
A2AS_SO9132_5381A
A2AS_GU2000006737
A2AS_SO9132_5981B
A2AS_GU2000006738
CU4000-CO-68.53m
PW150-VC-2m
PW675-CO-8.61m
PW150-VC-0.84m
A2AS_SO9132_6079C
SC1
A2AS_GU2000006735
A2AS_GU2000006734
PW150-PVC-8.54m
A2AS_SO9132_6179A
A2AS_SO9132_6179B
Arriva Rail London took over the London Overground network in November 2016 and supports TfL in delivering further improvements for customers on the already hugely popular network. The vast majority of the London Overground network is operated on Network Rail tracks, which are also used by other rail operators, freight and maintenance services. 187 million journeys were made on the Overground in the year 2019/20, compared to just 33 million when it launched in 2007/8. One third of Londoners live within walking distance of a London Overground station and overall satisfaction scores were at 87 per cent on the Spring 2020 National Rail Passenger Survey.
A fleet of 106 trains operate on the network comprising 49 four-car and 57 fivecar electric trains. These trains make around 17,000 station stops each day. In 2020, Class 710 ‘Aventra’ trains began operating on the West Anglia routes, replacing the legacy fleet of Class 315s and 317s. The new Class 710 trains feature walk-through carriages, airconditioning, live network information and improved accessibility.
New London Overground trains run on all services to Liverpool Street from Chingford, Cheshunt and Enfield Town stations. Over half of London Overground stations have step-free access from street to platform. A further five stations are proposed to be made step-free by 2024 as part of the Department for Transport's Access for All scheme. Transport for London has built a four-kilometre extension (1.5 kilometres of new track) of the London Overground Gospel Oak to Barking route into the Barking Riverside development in the London Borough of Barking and Dagenham.
The extension provides an essential rail link to support the development of Barking Riverside, serving both new and existing residents. The opening of the new station in July 2022 completes the first extension of London Overground since 2015. Barking Riverside station is fully step-free, bringing the total of step-free stations across London Overground to more than 60.
KEY PERSONNEL
Managing Director: Steve Best
Head of Performance: Paul Western
CONTACT INFORMATION
Address: Palestra, 197 Blackfriars Road
London SE1 8NJ
Tel: 0343
1234
Email: overgroundinfo@tfl.gov.uk
Visit: www.tfl.gov.uk/overground
The London Overground, known to Londoners as the Orange Line, launched in 2007 and runs along a circular route around inner London, connecting 23 boroughs of the capital city and parts of southern Hertfordshire
Lumo trains run on the East Coast Main Line and call at Newcastle, Morpeth and Stevenage, helping to improve regional connectivity while offering alternatives to Newcastle and Luton airports
Lumo is an open-access operator, not subject to franchising and aims to create over 13 million additional passenger journeys in the next decade as well as reducing carbon emissions by encouraging travellers to use greener, electric travel. It will contribute as much as £250 million to the UK economy over ten years.
Owned by FirstGroup, Lumo has invested £15 million on digital and IT infrastructure and £100 million on the manufacture and maintenance of five brand new, state-of-theart Hitachi AT300 intercity electric trains.
Lumo has invested £2 million in a Training Academy to develop a freshthinking generation of rail colleagues, focused on passenger wellbeing and on-board customer service, harnessing new technology and caring for vulnerable passengers.
Since launching in October 2021 Lumo has run over 6,000 services, carrying over two million passengers. Lumo aims to contribute £250 million to the economy in the next ten years, create over one hundred new jobs and generate over one million extra seats on the network every year. It is an ‘open access’ train operating company, meaning it does not receive state funding, and has invested £100 million to manufacture and maintain five one hundred per cent electric trains, built by Hitachi.
Other services include LumoEats, an at seat catering offer which will allow customers to purchase on board from our catering trolley or pre-order food via the app from a range of high street brands, LumoLuggage – a bespoke courier service designed to sustainably transport oversized, heavy luggage, and LumoGo, an all-in-one
free Wi-Fi and entertainment centre that will allow customers to tweet, work, and play on the go.
KEY PERSONNEL
Managing Director: Martijn Gilbert
CONTACT INFORMATION
Address: 4th Floor, Central Square South
Orchard Street
Newcastle-upon-Tyne NE1 3PG
Tel: 03455280409
Email: lumopr@grayling.com.
Visit: www.lumo.co.uk
The network consists of 39 stops along 17 miles of track, on a mixture of street track shared with other traffic, dedicated track in public roads, and off-street track consisting of new rights-of-way, former railway lines, and one section of alignment (not track) shared with a third rail electrified Network Rail line.
The network has four lines that coincide in central Croydon, with eastbound termini at Beckenham Junction, Elmers End and New Addington, and a westbound terminus at Wimbledon, where there is an interchange for London Underground.
Tramlink is operated with 35 vehicles. The original fleet comprised 24 articulated low floor Flexity Swift CR4000 trams built by Bombardier Transportation. In 2006, the CR4000 fleet was refurbished, with the buslike destination blinds being replaced by an electronic dot system.
Stadler Rail has since supplied six Variobahn trams similar to those used by Bybanen in Bergen, Norway and the first entered service in 2012. In August 2013, TfL ordered additional Variotrams, for use on the Wimbledon to Croydon link.
Since 2000, the number of passengers on the network has increased from 14 million to around 30 million today, and this is expected to reach nearly 60 million by 2030. An upgrade to the trams network is acknowledged to be needed to accommodate this growth. Trams for Growth summarises TfL’s proposed 20-year plan to accommodate growing demand, improve reliability and support the regeneration of Croydon town centre and the wider south London.
Passenger numbers are expected to grow to nearly 60 million by 2030, Trams 2030 summarises TfL’s proposed plan to accommodate growing demand, improve reliability and support the regeneration of Croydon town centre. Trams 2030 sets out TfL’s ongoing works (including the Wimbledon line enhancement programme), the current proposals including major upgrades and expansions to the network, such as Dingwall Road Loop, and the longer term plan for trams in south London.
The original fleet comprised 24 articulated low floor Flexity Swift CR4000 trams built by Bombardier Transportation in Vienna numbered beginning at 2530, continuing from the highest-numbered tram 2529 on London’s former tram network, which closed in 1952. In 2006, the CR4000 fleet was refurbished, with the bus-like destination blinds being replaced by an electronic dot system. In 2009 the fleet was repainted into a new green livery. In January 2011, Tramtrack Croydon opened a tender for the supply of ten new or second hand trams from the end of summer 2011. The trams will be used between Therapia Lane and Elmers End. On 18th August 2011, TfL announced that Stadler Rail had won a £16 million contract to supply six Variobahn trams. They entered service in 2012. In August 2013, TfL ordered an additional four Variotrams for delivery in 2015, for use on the Wimbledon to Croydon link, an order which was later increased to six. This brought the total Variotram fleet up to ten in 2015 and twelve in 2016 when the final two trams were delivered. The tram supports
a set of up to seven cars, is available as a unidirection or a bi-directional vehicle. It has a lightweight construction and meets the crash standard conforming to EN 15227. The individual way in which TRAMLINK can be developed and built is demonstrated by the configuration options: track gauges of 900, 1,000 or 1,435mm, different lengths and widths, and even a version to run without overhead contact lines are all possible. The interior can be configured and equipped individually; the positioning of the doors can also be adapted to suit requirements.
KEY PERSONNEL
General Manager, London Trams: Mark Davis
Director of Rail and Sponsored Services at TfL: Jonathan Fox
CONTACT INFORMATION
Address: Palestra, 197 Blackfriars Road, London
SE1 8NJ
Tel: 0343 222 000
Email: Contact via website
Visit: www.tfl.gov.uk/modes/trams
Over 150 years ago the first trains ran on the first underground railway the world had ever seen, today the London Underground is the fourth largest underground network in the world
Each year the London Underground carries over one billion people across the nation’s capital, the same number as the United Kingdom’s National Rail network. The network is just under 250 miles in total length, with just over one station for every mile track there are eleven lines serviced by 270 stations. Opened in 1863, the first journey was on what is today the Circle, Hammersmith & City, and Metropolitan lines from Paddington (Bishop’s Road) to Farringdon Street.
For the first one hundred years the Underground, nicknamed the Tube, was funded by private companies, the current operator, London Underground, is a wholly owned subsidiary of Transport for London (TfL).
At the end of 2023 TfL the Tube reached four million journeys a day. Midweek ridership on the Tube is now regularly above 3.7 million journeys and up around 6.5 per cent compared to last year, with ridership on Monday and Friday now regularly above three million journeys a day. Weekend ridership also continues to grow, with several Tube stations around central London already close to or exceeding levels seen before the pandemic. Ridership on the Night Tube and Night Overground services shows that around 60,000 journeys take place on a Friday night between 0030 and 0430, and close to 70,000 journeys on a Saturday night between 0030 and 0430.
More than a third of the 272 London Underground stations are step-free with 24 new step-free access stations since 2016. TfL is working closely with Camden Council to develop plans to deliver accessibility upgrades at West Hampstead and Finchley Road Tube stations and with Brent Council for plans on Alperton station.
In 2022 TfL trialled a mini ramp at step-free stations on the Jubilee line. It was designed to provide additional support and reassurance for customers to cross a small gap between the platform and train.
Following a successful pilot with 63 per cent of respondents saying they would be more likely to travel with the mini ramp, TfL will be introducing it at all Tube stations that are fully step-free by spring 2024 and is looking to introduce it to other parts of the TfL network where possible in the future.
In order to keep up with the pace of growth London experienced at the turn of the new millennium, multiple changes were made to the Underground’s organisational structure and operating procedures. The first change came with the creation of TfL in the Summer of 2000.
For four years the Underground was reorganised into a public-private partnership (PPP) where private infrastructure companies carried out upgrades and maintenance work on the system. This arrangement was short lived however and in 2003 the London Underground became a subsidiary of TfL. Of the two private companies that had been working on the Underground as part of the PPP scheme, one went into administration in 2007 and TfL assumed control of the other in 2010.
Passenger fares account for 92 per cent of the current operational expenditure.
The Underground is a world-famous brand, with ridership records broken almost every day during the 2012 London Olympics. The Tube carried athletes and spectators across the city during the sporting event and one year later was ranked as the most improved brand according to London’s Buzz rankings. In May 2017 TfL struck its first global licensing deal, looking to capitalise off the iconic London Underground imagery with products like designer chairs using tube seat patterns and creating new designs using Harry Beck’s schematic underground network map. The classic aesthetic has been used unofficially for years, with various products like t-shirts adorned with the famous phrase ‘mid the gap’ embossed over the roundel sign and other fashion items incorporating the famous visuals.
KEY PERSONNEL
TfL Commissioner: Andy Lord
TfL Chief Finance Officer: Rachel McLean
TfL Director of Rail and Sponsored Services:
Tricia Ashton
TfL Director of Customer Operations – London
Underground: Nick Dent
CONTACT INFORMATION
Address: Palestra, 197 Blackfriars Road
London SE1 8NJ
Tel: 0343 222 1234
Email: Contact via website
Visit: www. tfl.gov.uk/modes/tube
The Merseyrail commuter network incorporates two lines, the Northern Line and the Wirral Line
The self-contained network operates over 600 regular services per day, every 15 minutes, to 68 stations throughout the Liverpool City Region, including four underground stations in the city centre that receive services every few minutes, with its Liverpool Central station being one of the busiest outside of London.
The City Line refers to local and regional stopping rail services out of the main line platforms of Liverpool Lime Street railway station. Many of the City Line routes are shared with inter-city express services and are operated by Northern Trains.
Merseyrail is a 50:50 joint venture between Serco and Abellio, run as a concession agreement with governing body Merseytravel. As part of the Liverpool City Region Combined Authority, Merseytravel delivers transport projects that support the economic growth of the region.
Serco and Abellio took over from Arriva Trains Merseyside in 2003, winning a 25year contract. The company operates a fleet of 59 trains and employs 1,200 people.
In February 2017, Merseytravel ordered 52 new EMUs from Stadler for a complete fleet renewal. The modern Stadler EMUs are future-proofed, having been prepared for the retrofit of ERTMS and dual voltage equipment, and thus comply with the Liverpool City Region Long Term Rail Strategy. On 26 August 2021, Stadler handed over the first of 53 trains to Liverpool City Region. In July of that year trials undertaken on new Stadler-built trains using battery technology were successfully completed, paving the way to the potential expansion of the Merseyrail network, with services reaching as far as Wrexham and Preston.
Merseyrail has partnered with local schools in the Liverpool City Region alongside the Rail Ombudsman to educate a new generation of rail users on safety when using the network. The Rail Ombudsman has launched the ‘Young Person’s Train Guide’ – a rail byelaw campaign aimed at young people empowering them to use trains confidently. The campaign seeks to target
and address this problem by supplying interactive exercise packs to schools and youth groups that can either be completed by young adults independently, or as part of the PSHE curriculum through teacherled worksheets, competitions and blog style content.
Merseyrail will be introducing this into the work it does with schools such as Maricourt High School in Maghull on travel confidence and rail safety – a positive addition to the work the rail operator already does with many schools across the Liverpool City Region.
KEY PERSONNEL
Managing Director: Andy Heath
Commercial Director: Suzanne Grant
Human Resources Director: Jane English
Safety and Engineering Director: Mike Roe
Operations Director: Zoe Hands
Finance and Transformation Director: Paul Bowen
CONTACT INFORMATION
Address: Merseyrail, 9th Floor Rail House
Lord Nelson Street, Liverpool L1 1JF
Tel: 0151 555 1111
Email: comment@merseyrail.org
Visit: www.merseyrail.org
Metrolink is the largest light rail network in the country, with more than 100 kilometres of track and 147 vehicles – which equates to just under half of the entire tram fleet in the UK
Built in three phases over three decades, the network serves Bury, Oldham and Rochdale in the north, Ashton-underLyne in the east, Eccles and MediaCityUK in the west, and Altrincham, Wythenshawe, Chorlton, Manchester Airport and East Didsbury in the south. Construction work on the transformational £165 million Second City Crossing (2CC) finished in late 2016 – the final phase of a £1.5 billion investment to expand the network.
In 2023 Transport for Greater Manchester (TfGM) appointed leading rolling stock engineering consultancy DB ESG to deliver its tram safety improvement programme. The Rail Accident Investigation Branch (RAIB) recommended that light rail networks deliver programmes to prevent the risk of serious accidents from tram overspeeding or driver inattention following the tragic event at Sandilands in Croydon where a tram overturned.
Metrolink trams are already fitted with a device that applies the emergency brake in the event of a driver becoming incapacitated and the signalling system has several built-in protections. DB ESG working in partnership with Sella Controls, will design, install, test and commission the Driver Vigilance Devices (DVD) and Tram Overspeed Protection Systems (TOPS) to the Metrolink fleet of trams.
To prevent over-speeding, Metrolink’s fleet of 147 trams will be equipped with the new systems that will use GPS and other information to determine the location and speed of the tram. The system utilises Sella Controls UK Rail approved Tracklink® III and EKE Electronics TRAINNET® technologies to provide the TOPS and DVD System. In the event of over-speeding, the driver will be alerted, and if there is no response the brakes will be applied automatically. The protection system will operate independently of other tram monitoring systems. To ensure drivers remain alert, an upgrade will be applied to the traction brake system and if no movement is detected input will be requested from the driver.
The tram network’s touch in/ touch out system allows customers to travel quickly, securely and flexibly across the network without the need to download an app or buy a paper ticket. Initially launched in July 2019, it was further enhanced following the roll-out of the Bee Flex Weekly in September 2021 and by 17 September more than five million contactless journeys.
The Bee Network is TfGM’s vision for an integrated transport system which will join together buses, trams, cycling and walking by 2024, with rail incorporated by 2030, to transform how people travel in Greater Manchester.
KEY PERSONNEL
Head of Metrolink: Danny Vaughan
Managing Director: Guillaume Chanussot
CONTACT INFORMATION
Address: Metrolink Trafford Depot
Warwick Road, Stretford, Manchester M16 0GZ
Tel: 0161 205 2000
Email: customerservices@metrolink.co.uk
Visit: www.metrolink.co.uk
Northern covers an area taking in Newcastle and Carlisle across to Liverpool and Manchester, then to Huddersfield and Nottingham
Northern is the second largest train operator in the UK, employing some 7,000 people and running regional and commuter services across the north of England. Northern provides more than 2,500 local and regional train services every day across the north of England, serving a population of nearly 15 million. There are more than one hundred million passenger journeys made on the network each year.
Northern Trains Limited is owned by DfT OLR Holdings Limited (DOHL), which took on the operation of Northern rail services on 1 March 2020.
In recent years, Northern has introduced 100 new trains as part of a £500 million investment in regional rail.
New line
A new Northumberland Line is set to open in 2024. The completed project will result in an upgrade of 18 miles of
track to provide local communities with enhanced connectivity between Newcastle to Ashington. Construction is already well underway at Ashington station and platform, which will be the northern-most point on the line and will whisk people to the centre of Newcastle in just over half an hour.
Neville Hill depot
Every day, a team of engineers and support staff at Neville Hill service 34 trains from nine different fleets and carry out more than 500 safety and service critical tasks. Their work supports 260 direct and 825 indirect passenger services a day. Since it become sole operator of the depot in 2021, Northern has completed a site-wide cleanup, integrated teams for more efficient working, improved security, refurbished facilities for staff and improved safety with the installation of illuminated walkways.
KEY PERSONNEL
Managing Director: Tricia Williams (From Spring 2024)
Safety and Environment Director: Mike Roe
Commercial Director: Mark Powles
Strategic Development Director: Rob Warnes
Programme Director: Emma Yates
Engineering Director: Jack Commandeur
Finance Director: Richard Hinds
Regional Directors: Craig Harrop, Kerry Peters
Strategic Development Director: Rob Warnes
People Director: Lisa Leighton
Head of Operational Standards: Mark Gardner
Head of Service Planning: Paul Headon
Head of Property: Jayne Breen
CONTACT INFORMATION
Address: Northern House, York YO1 6HZ
Tel: 0800 200 6060
Email: enquiries@northernrailway.co.uk
Visit: www.northernrailway.co.uk
Nottingham Express Transit (NET) offers a green, convenient and affordable way to travel through the City and the surrounding areas
MET was the first tramway in the country to be fully accessible, meeting the Disability Discrimination Act guidelines. Following the opening of two new extensions in 2015, Nottingham’s popular tram network now stretches 20 miles across the city and wider conurbation. From Hucknall and Phoenix Park to the north of Nottingham to Clifton in the south and Toton in the west, the network has a total of 51 stops including key locations such as Old Market Square in the heart of the city, Nottingham railway station, the Queens Medical Centre and the prestigious NG2 business park. The award-winning system first opened in 2004 and is now operated and maintained by Nottingham Trams Ltd (Keolis) on behalf of concessionaire Tramlink Nottingham.
In December 2011, the consortium was awarded a 23-year concession by Nottingham City Council to manage the delivery of the NET Phase Two expansion project and the ongoing operation of a network which has fast become a real success story.
Over the past few years, the operator has made a range of changes to its service including the implementation of Zero Tolerance fare evasion campaigns which have been running since the pandemic and have resulted in a 200 per cent increase in penalty fares issued each month. The company remains committed to reducing fare evasion and has been working with enforcement personnel to improve surveillance, safety and working practices.
The network operates a 37-strong mixed fleet of Bombardier Incentro AT6/5 and Alstom Citadis 302 trams, all maintained within its Wilkinson Street depot headquarters. NET took delivery of 22 Citadis models in preparation for the expansion of the network while the Incentro trams have been in operation since 2004 and recently underwent a major refurbishment programme.
In addition to adopting a fresh, new look they are also benefitting from a full mechanical overhaul, replacement floors and new interior fittings aimed at boosting reliability, comfort and accessibility.
All of Nottingham’s trams have been named in recognition of historic characters, well-known literary figures, scientists, community leaders, actors and sports stars related to the city.
KEY PERSONNEL
Director and General Manager: Chris Wright
Head of Operations: Trevor Stocker
HR Manager: Maria Dobney
Customer Service Manager: Constantina Samara
CONTACT INFORMATION
Address: NET Depot, Armstrong Way, Wilkinson Street Nottingham NG7 7NW
Tel: 0115 824 6060
Email: info@thetram.net
Visit: www.thetram.net
Pre Metro Operations runs the Stourbridge Shuttle and is dedicated to expanding its light rail services across the West Midlands
Pre Metro Operations (PMOL) was founded in 1999 as an independent train operation company with the aim to establish innovative and low-cost light rail transit services on branch lines across the UK.
The company first saw the potential to help connect the Stourbridge community with the rest of the Black Country using light rail technology on the Stourbridge Town to Stourbridge Junction branch line.
Using two newly constructed Class 139 LPG fuelled, flywheel hybrid railcars, PMOL ran light rail transit services on the branch line with high reliability and efficiency; providing Sunday service on the line for the first time since 1914.
The Stourbridge Shuttle currently operates seven days a week with basic tenminute frequency. The reliability of the service currently stands in the region of 99.8 per cent having operated 500,000 miles and completed over six million passenger journeys to date. The service has become ever popular within the local community. PMOL now runs the service on behalf of the West Midlands Railway franchise and is scheduled to do so until 2026.
In light of the Restoring Your Railway DfT initiative, promoted by the Government, the company is ready to work with scheme developers, transport franchises and investors looking to establish cost-effective and green solutions that will restore Britain’s railway connectivity using a highly effective business model, vast amounts of experience, and over two decades of expertise in the light rail industry.
Not being tied to any one vehicle manufacturer, the company is also working with leading UK light rail innovators to create a brighter, cleaner, and greener future for Britain’s railways.
Pre Metro is currently pursuing a second service between Stourbridge and Brierley Hill, titled the Stourbridge Dasher, that can provide a mixed-use case for the dual-track heavy rail freight line between Stourbridge Junction and Round Oak Steel works.
The company is currently working on a strategy document for transport professionals regarding transport integration within Stourbridge and Brierley Hill which can provide a template for light rail integration at sites across the country and reestablish the Stourbridge to Walsall transport corridor.
KEY PERSONNEL
Managing Director and CEO: Philip R Evans
Company Chairman: Geoff Lusher
Company Secretary: Steve Jasper
Director: Professor Alan Wenban-Smith
Director: Mathew Taylor
Head of Operations: Andrew S. Merrell
Press & Marketing Officer: Charlie Merrell
CONTACT INFORMATION
Address: 54-56 Hagley Rd, Stourbridge
DY8 1QD
Tel: 01384 441385
Email: info@premetro.org
Visit: www.premetro.co.uk
Over the last forty years ScotRail has introduced new stations, new trains, reopened disused railway lines and modernised rail services across Scotland
ScotRail is the national railway franchise of Scotland and since April 2022 has been operated by an arm’s length company owned and controlled by the Scottish Government called Scottish Rail Holdings (SRH).
ScotRail provides over 94 million passenger journeys each year, with over 2,300 intercity, regional and suburban rail services a day, more than 340 stations, and 1,016 trains serving Scotland’s railway.
Between 2014 and 2019 Scotland’s Railway electrified 325 kilometres of the country’s central railway network. This investment supported the introduction of a new £370 million fleet of 70 faster, greener, modern electric trains, the class 385 built by Hitachi, with 44 per cent more capacity for customers.
More than 76 per cent of passenger and 45 per cent of freight journeys are already electrified on Scotland’s Railway, and rail is already the most sustainable mode of public transport, contributing only one per cent of Scotland’s overall transport carbon emissions.
On 8 April the last of ScotRail’s upgraded Inter7City high speed trains has arrived in Scotland. The upgraded Inter7City high speed trains initially operated on the East Coast mainline between Aberdeen and Edinburgh, but now run on the following routes serving all seven Scottish cities. The refurbishment programme was carried out by Wabtec Doncaster (coaches) and Brush Traction Loughborough (power cars) from late 2017 through to 2021.
More than 7.7 million journeys were made with ScotRail during August 2023. The passenger journeys, made between 1 August and 31 August, reached 89 per cent of prepandemic levels and mark a year-on-year growth of 35 per cent.
Several high-profile events, including the renowned Edinburgh Festivals, the exhilarating UCI Cycling World Championships, and captivating international rugby at Scottish Gas Murrayfield Stadium, contributed to the
surge in numbers. Off-peak travel across the network surpassed pre-pandemic numbers and reached its highest level since 2015. Peak time and commuter travel also saw growth in August, with 3.1 million journeys made – a 31 per cent year-on-year rise.
In 2022 ScotRail and Hitachi Rail celebrated four years of Class 385 passenger service, which has delivered record reliability and shorter journey times for passengers on Scotland’s Central Belt. Upon its introduction, ScotRail’s Express train became Scotland’s fastest train and was the UK’s most reliable new fleet for twelve months. It has remained in the top three for UK train availability ever since. Over the past year, the fleet has an average of 52,212 MTIN (meaning Miles per Technical Incident), which is over three times higher than the industry average. In total, the British built train has carried approximately 34.3 million passengers to their destinations. The fleet of 70 trains has racked up 26,557,229 zero-emission miles, which is the equivalent of travelling from Earth to Venus.
Being 100 per cent electric, the Class 385 is already playing a major role in decarbonising Scotland’s railways by 2035. It has reduced CO2 emissions by 72 per cent, a carbon saving of 41,432 tonnes CO2e. This is equivalent of saving the CO2 emissions from over 14,600 return flights between London and Tokyo, or the construction of over 800 homes.
This milestone in passenger service is also a celebration of collaboration between ScotRail, Transport Scotland, Network Rail and Hitachi Rail – ‘Team Scotland’. The commuter fleet was built at Hitachi Rail’s UK factory in County Durham and was part of £1.3 billion investment in new trains and infrastructure funded by the Scottish Government and Network Rail.
Now entering the fifth phase of the redevelopment project, work is underway to expand the station concourse which will make way for an enhanced station forecourt
and building with glazed roof, creating a brighter, and more modern station.
North Lanarkshire Council are also carrying out work to overhaul the public realm outside the station building to create a new transport hub, with support from the Glasgow City Region City Deal.
This includes an expanded bus facility, new station access road, car drop-off area and blue-badge parking, as well as improved facilities for taxis and pedestrian and cycle access.
Once complete, it will improve links between bus and train services as well as reducing congestion in the town centre.
The £14.5 million project will deliver a host of further benefits for customers including improved ticket retailing facilities, an enhanced retail environment with food and drink offering, and refurbished waiting facilities.
KEY PERSONNEL
Scotland’s Railway Managing Director: Alex Hynes
Chief Operating Officer: Joanne Maguire
Customer Operations Director: Phil Campbell
Service Delivery Director: David Simpson
Head of Economic & Community Development: James Ledgerwood
CONTACT INFORMATION
Address: First floor, Atrium Court
50 Waterloo Street
Glasgow G2 6HQ
Tel: 0344 811 0141
Email: customer.relations@scotrail.co.uk
Visit: www.scotrail.co.uk
South Western Railway provides commuter inter-urban, regional and long distance services to passengers in South West London and southern counties of England and Island Line services on the Isle of Wight
South Western Railway (SWR) was awarded the South Western franchise in March 2017, and took over from South West Trains on 20 August 2017. SWR is owned 70/30 by FirstGroup and MTR. The company operates commuter services from London Waterloo to south west London and suburban and regional services in Surrey, Hampshire and Dorset, as well as regional services in Devon, Somerset, Berkshire and Wiltshire. It is one of the largest train operators in the country with stations across South West London, Surrey, Hampshire, Berkshire Dorset, Wilshire, Somerset, and Devon.
In Spring 2023, Just a few weeks short of its 85th birthday, Malden Manor station underwent a transformation to make it a much brighter and more welcoming place to travel from. As part of SWR’s ongoing station redecoration plan, Malden Manor was completely redecorated, both inside and out, including on its platforms, which have also been fitted with new benches. The booking hall had its information panels refreshed and over the Summer the station was fitted with a defibrillator as part of
SWR’s drive to install the life-saving devices at all of its staffed stations.
SWR intends to install publicly accessible automated external defibrillators at all 154 of the staffed stations on its network. The defibrillators will be placed in protective cabinets as close as possible to the front entrance of the stations, to be used day or night in the event of cardiac incidents at or near stations.
Network Rail and SWR worked with Richmond and Hillcroft Adult Community College (RHACC), London School of Mosaic, Surbiton Art Trail and Friends of Surbiton Station to install ten William Blake inspired detailed mosaics at Surbiton station. The Blake Mosaics, which form part of a set of 70 mosaics created by Southbank Mosaics to commemorate Blake’s time in Lambeth between 1790 and 1800, were originally installed in the underground tunnels, streets, and walkways of Lambeth around London Waterloo station.
SWR is investing £1 billion in a new fleet of 90 Arterio trains for its Reading, Windsor and South West London suburban routes.
SWR currently operates eight Class 158 Express Sprinters, 32 Class 159 Turbo
trains, 45 Class 444 Desiro trains, 127 Class 450 Desiro trains, 84 Class 455 trains, the Class 707 Desiro City train, the Class 458 Coradia Juniper train and five Class 484 trains on the Island Line.
KEY PERSONNEL
Managing Director: Claire Mann
Chief Operating Officer: Stuart Meek
Service Delivery Director: Lyndsey Robson-Malone
Customer and Commercial Director: Peter Williams
Planning and Performance Director: Steve Tyler
Head of Sustainability: Amy Dickinson
CONTACT INFORMATION
Address: Friars Bridge Court
41-45 Blackfriars Road
London SE1 8NZ
Tel: 0345 600 0650
Email: Contact via website
Visit: www.southwesternrailway.com
Southeastern has been running the train service between London and Kent and parts of East Sussex since 2006. One of the busiest networks in the country, it carries more than 400,000 people every day. It includes the UK’s first domestic high-speed service with Javelin trains. The operation of all Southeastern services transferred from London South Eastern Railway (LSER) to SE Trains Limited on 17 October 2021.
All 112 of Southeastern’s Class 375 ‘Electrostar’ train fleet are receiving atseat power sockets, including USB points, new LED lighting and energy metering, which means that the railway only pays for the power it uses, as part of a £10 million upgrade to Southeastern’s mainline train fleet.
In Autumn 2023, Southeastern teamed up with Siemens Mobility and Eversholt Rail to develop a fully automated vehicle inspection system. The new technology will be installed at the Ramsgate train maintenance facility, and it will use a series of high sensitivity cameras and optical laser sensors to collect and analyse data about the condition of the Mainline fleet. AVI will check each train’s brake pads, collector shoes, wheel profiles, as well as the wheel tread thickness. It will also run underframe inspections to ensure everything is in good working order.
The mass of data captured by AVI will allow Southeastern to run a more efficient on-demand maintenance programme by not carrying out work that isn’t needed. It means targeted maintenance rather than automatic changes after a set mileage.
It also helps to improve safety by running consistent measurement and component assessments that can send out immediate safety alerts, as well a 48-hour forecast of failures.
Three new separate, but linked, information systems developed by Southeastern with its partners have included a dynamic route map showing real-time status on every route and station (developed by FabDigital); an information management system which
allows much better identification of priority trains and travellers, especially during disruption, and an improved customer information system.
Other improvements include more informative announcements with a personal touch, prior notice about how busy a particular train is and advertising if passenger facilities (lifts or toilets for example) are out of action.
Southeastern’s Service Quality Regime monitors the service that it provides on board its trains and stations, through a mixture of mystery shopping and auditing. These measure key aspects of facilities and customer service. The operator’s weekly audits show that four in five passengers score the operator highly for its customer service.
KEY PERSONNEL
Managing Director: Steve White
Engineering Director: Mark Johnson
Head of Information Delivery: John Till
Technical Services Engineer: Nada Abouelhiga
Passenger Services Director: David Wornham
Commercial Director: Alicia Andrews
HR Director: Scott Maynard
Finance Director: Paul Barlow
CONTACT INFORMATION
Address: Friars Bridge Court, 41-45 Blackfriars
Road, South Bank, London SE1 8NZ
Tel: 0345 322 7021
Email: Contact via website
Visit: www.southeasternrailway.co.uk
Southern operates routes in south London, between central London and the south coast, through East and West Sussex, Surrey and parts of Kent and Hampshire
Southern manages 156 stations and operates around 300 new or refurbished trains. It is a subsidiary of Govia, a joint venture between transport groups Go-Ahead and Keolis, and has operated the South Central rail franchise since August 2001 and the Gatwick Express service since June 2008.
In July 2015, the franchisee was subsumed into GTR, but the Southern and Gatwick Express brand identities were retained alongside those of Thameslink and Great Northern.
GTR has introduced 12 Class 171 vehicles for Southern. Southern operates the majority of commuter services from its Central London terminals at London Bridge and London Victoria to South London and
Sussex, as well as regional services in parts of Hampshire, Kent and Surrey.
It also provides services between Milton Keynes and Croydon via the West London Line. It also operates services from Brighton to Southampton and South Croydon to Milton Keynes Central.
KEY PERSONNEL
Chief Executive Officer: Angie Doll
Chief Financial Officer: Ralph Pidsley
Chief Customer Officer: Mark Pavlides
Customer Services Director: Jenny Saunders
Safety, Health and Security Director: Samantha Facey
CONTACT INFORMATION
Address: 1st Floor, Monument Place
24 Monument Street, London EC3R 8AJ
Tel: 0345 127 2920
Email: comments@southernrailway.com
Visit: www.southernrailway.com
Stagecoach Supertram has been serving the city of Sheffield since 1994 with four tram lines calling at 50 stops
LeppingsLaneMIDDLEWOOD
HillsboroughParkHillsboroughBamforthStreetLangsett/PrimroseView InfirmaryRoadShalesmoorforKelhamIsland
NetherthorpeRoad
UniversityofSheffield forWestendHospitals
WestStreetCityHallCathedralCastleSquare
MALINBRIDGE
FitzalanSquare/PondsForge
HydePark
CricketInnRoadNunnerySquareWoodbournRoad
AttercliffeArena/OlympicLegacyPark ValleyCentertainmentCarbrookMeadowhallSouth/Tinsley
MEADOWHALLINTERCHANGE
WhiteLaneBirleyLaneBirleyMoorRoadHackenthorpe
DonetskWayMossWayforPeaksCollege
CrystalPeaksBeighton/DrakeHouseLane
WaterthorpeWestfield
HALFWAY
SheffieldStation/HallamUni
GranvilleRoad
TheSheffieldCollegeParkGrangeCroftParkGrange
ArbourthorneRoadSpringLaneManorTopHollinsendGleadlessTownend
Herdings/LeightonRoad
The tram is owned by the South Yorkshire Passenger Transport Executive, which built the network at a cost of around £240 million. It was opened in stages between 1994 and 1995 and was run by South Yorkshire Supertram (SYSL) until 1997, when Stagecoach bought the concession for £1.15 million that gives it control until 2024.
The tramway is served by eight park and ride sites enabling easy parking for car users wishing to complete their journey by tram. Four sites offer paid for parking and the other three sites have free designated parking.
Railway Overhead Line Equipment (OLE) distributes electricity to trains at 750 volts DC, which is considerably more than the power on most tram systems. Around 14.5 million passengers use the tram every year.
Tram Train innovation
Tram train vehicles that can operate on both mainline rail and tram tracks rolled out on 25 October 2018, making it possible to make a single journey between tram stops and conventional rail stations.
Three Tram Trains an hour travel on the Supertram network from Sheffield Cathedral to Meadowhall South, before proceeding over a new section of track linking the tram line to the rail track called the Tinsley Chord and on to the national rail network to Parkgate Retail Centre via Rotherham Central station.
The Government funded programme is a partnership between South Yorkshire Passenger Transport Executive (SYPTE), Network Rail, Stagecoach Supertram and
Northern Rail to pilot this pioneering technology. The seven Stadler built tram trains have been in public service since September 2017.
Staff
Around 330 employees maintain and operate the trams from the Nunnery depot.
KEY PERSONNEL
Managing Director: Tim Bilby
Corporate Communications Manager:
Sian Freestone-Walker
CONTACT INFORMATION
Address: Nunnery Depot, Woodbourn Road
Sheffield S9 3LS
Tel: 0114 272 8282
Email: supertram.enquiries@supertram.com
Visit: www.stagecoachbus.com/supertram
The Stansted Express ferries passengers from Stansted Airport to central London in just 47 minutes, connecting to the Central, Hammersmith and City, Metropolitan, Circle, Victoria and Jubilee Lines
Stansted Express trains leave from a station directly below Stansted Airport every 15 minutes, reaching the London Underground station of Tottenham Hale in 36 minutes and London Liverpool Street in 47 minutes.
The Stansted Express service is operated by Abellio Greater Anglia in a franchise that will last until 2025.
Unlike the Heathrow Express and the Gatwick Express, which require the purchase of premium tickets to use the services, normal rail tickets are valid on the Stansted Express.
Customers can purchase tickets six months in advance and are able to access their ticket within the Stansted Express app.
During the Summer months capacity on the service is expanded by 5,000 seats to accommodate increased holiday travel. This is made possible by increasing the number of carriages on the trains from eight carriages to twelve.
A First-Class ticket on Stansted Express gives passengers access to airport security FastTrack. The same ticket also allows for unlimited luggage.
KEY PERSONNEL
Managing Director: Jamie Burles
CONTACT INFORMATION
Address: 11th Floor, 1 Stratford Place
Montfitchet Road, London E20 1EJ
Tel: 0345 600 7245
Email: contactcentre@greateranglia.co.uk
Visit: www.stanstedexpress.com
Translink runs public transport services across Northern Ireland, with the operations of NI Railways, Ulsterbus, Metro and Glider managed under a single team. Translink carries 1.5 million passengers every week and operates over and maintain 300 miles of rail track.
Translink aims to operate a zero-emission fleet across the network by 2040, with 21 new Class 4000 CAF train carriages entering service on the NI Railways network at the end of 2021. In the coming years, Translink will introduce a fleet of new bi-mode trains for use on the NI Railways network, as well as working towards the electrification of the rail network by 2035. Translink is also participating, along with colleagues in Irish Rail and other key stakeholders, in an allIreland Strategic Rail Review, initiated by Government Ministers in Northern Ireland and the Republic of Ireland, to discuss potential expansion and greater connectivity across the island-wide railway network, as well as participating in the UK Government’s Union Connectivity Review.
KEY PERSONNEL
Group Chief Executive: Chris Conway
Deputy Group Chief Executive: Gordon Milligan
Chief Operating Officer: Phillip O’Neill
Chief Financial Officer: Patrick Anderson
Director of Engineering & Sponsorship: Clive Bradberry
Director of Infrastructure & Projects: John Glass
Director of Service Operations: Ian Campbell
Corporate Communications Manager: Lynda Shannon
CONTACT INFORMATION
Address: 22 Great Victoria Street
Belfast BT2 7LX
Tel: 028 9066 6630
Email: feedback@translink.co.uk
Visit: www.translink.co.uk
Ballycarry
Renowned as the global market leading depot protection system, the SMART DPPS™ delivers physical protection from vehicle movements to rail depot staff whilst providing visual and audible warnings.
• Protects staff and equipment
• Ensures safe and controlled movement of rail vehicles into and out of the depot
• Allows train maintenance operations to be conducted without endangering the safety of staff or damaging infrastructure
It is:
• Fully configurable, flexible and functional
• Proven in use and installed globally
• Capable of interfacing with third party equipment including signalling systems.
• Adaptable to the safe requirements of the depot
On 28 May 2023 TransPennine Express service will transfer to a new Government operator – DOHL. North TransPennine runs from Newcastle to Manchester Airport, Redcar/ Middlesbrough to Manchester Airport, Scarborough to Liverpool, Edinburgh to Liverpool and Hull to Manchester Piccadilly. South TransPennine runs from Cleethorpes via Doncaster and Sheffield to Manchester Airport and North West and Scotland runs from Liverpool and Manchester Airport to Preston, Oxenholme, Carlisle, Penrith, Edinburgh and Glasgow.
Making Journeys Better: A Prospectus gives clear detail of the issues TPE has faced during the past two years as well as outlining how TPE, under DOHL, will work to make things better, having completed an in-depth review of the business. Through the long-term plan TPE will also deliver a number of short-term initiatives designed to give a better and more reliable service to its customers. Those initiatives include a ticket sale to thank customers for sticking with TPE and to encourage others to travel by rail, an amended timetable and fleet to simplify operations and boost reliability, a programme of toilet improvements on trains, the recovering of all seats on trains, and a refresh of the older trains (Class 185s) to include the replacement of carpets and an interior deep clean.
The Carbon Literacy Trust has formally recognised TPE as Carbon Literate. The accreditation, awarded by the Carbon Literacy Trust, is internationally recognised and demonstrates recipients are prioritising action to tackle the climate crisis. TPE has cut its carbon emissions by 18 per cent since 2019 and its Nova train fleet, which includes bi-mode and electric trains, helps reduce customers’ CO2 contribution by 77 per cent compared to travelling by car.
In an important stride towards sustainability, TPE has also announced its near-term science-based targets have been validated by Science Based Target initiative (SBTi). TPE's scope one and two near-term targets align to the latest climate science from the IPCC.
Managing Director: Chris Jackson
Commercial Director: Darren Higgins
Head of Sustainability: Nicola Martin
Fleet Director: Paul Staples
Major Projects Director: Chris Nutton
Customer Service and Operations Director: Kathryn O’Brien
Service Planning Director: Ben Holmes
Strategy Director: Louise Ebbs
Finance Director: Carolann James
CONTACT INFORMATION
Address: 7th Floor, Bridgewater House
60Whitworth Street, Manchester M1 6LT
Tel: 0345 600 1671
Email: tpecustomer.relations@firstgroup.com
Visit: www.tpexpress.co.uk
The Tyne and Wear Metro was the first modern light rail system in the UK when it opened in 1980. It now has sixty stations on a 46-mile network that connects Newcastle Airport with South Hylton on the Green Line and St James with South Shields on the Yellow Line.
Stadler, the Swiss train manufacturer, are building a total of 46 new Metro trains on behalf of Nexus. The new fleet will enter service in phases over the next two years. Stadler has delivered three new trains to North East England so far, and more are set to arrive later this year. The Class 555 Stadler train is a unique design for Metro and in the months ahead will undergo rigorous testing to ensure that it interfaces correctly with signalling systems and other Metro infrastructure.
Metro drivers will also start a process of training at the controls of the new train. The new trains have been designed and shaped by customers, and in response to vast consultation will include modern features such as linear seating, charging points, air conditioning and will deliver a step-change in accessibility.
Among the new features will be an automatic sliding step at every door to enable seamless boarding, making travel easier for Metro’s 50,000 wheelchair passengers as well as people with children’s buggies, luggage or bicycles.
The final stabling areas for all 46 new Metro trains is in the final stages of completion with all tracks successfully installed as part of the £70 million rebuild of Gosforth Depot. The old Metro depot buildings were demolished over the summer to make way for the new sidings, which will provide the required space to stable the new Stalder trains when they are not being used for service. Nexus, the public body which owns and manages Metro, said the completion of this latest phase of the depot construction work was another important step towards the Gosforth Dept construction project being completed.
A total of 17 new sidings for train stabling have been created over the entire area of the Gosforth depot site – which has been home to the Tyne and Wear Metro for 43 years. The final eight new sidings, which are areas of newly installed track, located where the depot’s old maintenance sheds
once stood, were completed this week. The installation of new overhead lines, signalling equipment, walkways and lighting is in progress, in preparation for a line closure in January where the contact wire will be installed and energised so the sidings can be entered into service.
KEY PERSONNEL
Managing Director: Martin Kearney
Operations Director: Kevin Storey
Director of Finance and Resources: John Fenwick
Transport Strategy Director: Philip Meikle
Customer Service Director: Huw Lewis
CONTACT INFORMATION
Address: Nexus House, St James Boulevard
Newcastle upon Tyne NE1 4AX
Tel: 0191 203 3333
Email: contactmetro@nexus.org.uk
Visit: www.nexus.org.uk
The Venice-SimplonOrient Express operates a luxury service from London to Venice, taking in Paris and Verona on the way
Operated by luxury travel company Belmond, the Venice Simplon-Orient-Express (VSOE) epitomises the glamour and elegance of the Golden Age of travel. Taking luxury seekers from London to Venice and stopping off at other places across the European continent at cities like Paris, Berlin, Budapest, Istanbul, Prague, Vienna and Verona.
For the first time in its history, the Venice Simplon-Orient-Express will embark on a new journey connecting two iconic destinations: Paris and Portofino. Its first alpine journey headed to the French Alps on December 21, 2023, and it will be repeated in December 2024. Following the huge success of the introduction of Grand Suites and Suites onboard the train, eight new Suites will join the rake in 2024, bringing a total of 16 Suites and 6 Grand Suites to the Venice Simplon-Orient-Express.
VSOE runs services between March and November. The journey is not intended as a functional rail service taking passengers from A to B, but as a five-star experience in every sense of the word.
Belmond operates 47 luxury hotels, restaurants, tourist trains and river cruises in 24 countries and that standard comes across in the accommodation, dining and overall experience of the VSOE.
The VSOE continental leg contains 18 carriages – twelve sleeping cars, three dining cars, a bar car and two former sleepers, which provide accommodation for the staff and storage rooms for luggage and supplies.
By day the twin-cabin rooms look out on the European countryside flying by and by night the rooms are transformed into bedrooms.
The carriages were refurbished in 2017 to bring them up to date with modern standards of safety and comfort. In March 2018 the ‘Grand Suites’ were launched, each of these suites feature a private bathroom and living area fashioned after the 1920s ‘art deco’ style designed by Wimberly Interiors.
2021 brought new Grand Tour routes crisscrossing through Europe. Embark on a thrilling voyage connecting some of the continent's most vibrant cultural hubs. Explore the elaborate canals of Amsterdam – taking in the world-class museums by day
and sampling the Dutch cuisine by night –before boarding the train for your overnight adventure.
KEY PERSONNEL
Executive Vice President and Chief Financial
Officer: Martin O’Grady
Vice President, Legal: Abigail Hunt
Vice President, Trains & Cruises: Gary Franklin
Director of Sales, Trains & Cruises: Lucy Clark
CONTACT INFORMATION
Address: Shackleton House, 4 Battle Bridge Lane, London SE1 2HP
Tel: 0845 077 2222
Email: reservations.uk@belmond.com
Visit: www.belmond.com
Formerly known as Seco Rail, Colas Rail is a rail freight operator that is a subsidiary of French industrial group Bouygues
Colas Rail Limited is part of the Colas Rail Group, a Colas company – the organisation is split into four different sections – Rail Infrastructure, Rail Services, Urban Rail, High-Speed Rail.
Rail Infrastructure
Colas Rail is a leading provider of railway infrastructure services – providing design, engineering, project management, construction and maintenance solutions for the light rail, metro, mainline and highspeed markets.
Some of the schemes it delivers include:
• Track Installation, Renewal and Maintenance.
• Signalling.
• Electrification (Overhead Catenary Systems and 3rd Rail).
• High Voltage and Traction Power.
• Rolling Stock Refurbishment and Maintenance.
In 2019, Colas Rail UK won a ten-year contract for the South Rail Systems Alliance (SRSA) across three Network Rail regions in the South of the UK – Western & Wales, Southern and Anglia. The framework creates an alliance between Network Rail, Colas Rail Ltd, and AECOM providing an integrated delivery model for the development, design and construction of track renewals on plain line, switches and crossings.
Rail services
Services include the operation and maintenance of On Track Plant, which includes operating and maintaining the largest, most advanced fleet of On Track Plant in the UK, and Rail Freight, Rolling Stock Refurbishment and Maintenance, as well as Rail Grinding and Milling services.
The extended depot in Rugby accommodates On Track Plant and Locomotives up to 148-metre long and undertakes the servicing and repair of On Track Machines, On Track Plant and Locomotives.
Colas Rail currently operates an extensive fleet of railway assets: 130 locomotives, 500 wagons and two track-laying trains. As well as three ballast clearing machines, 32 ballast tampers, three stabilisers, 13 ballast
regulators, 55 road-rail vehicles, 15 loaders, and three concreting trains, across the 20 countries in which it operates.
Included in this collection are several ‘Specialist Wagons’ including eight ‘Slinger’ rail delivery and recovery gantry wagons, one high capacity 125T Kirow crane KRC 1200 UK, 16 PEM LEM switch handling units (PEMs/LEMs) and two Track Relaying Machines (TRM).
Colas Rail has over 25 years’ experience in designing and delivering Light Rail systems in more than 50 cities around the world. In the UK it delivers design, construction and maintenance for light/metro rail projects, the company works in partnership with its customers to identify optimal engineering and value-based solutions through Early Contractor Involvement.
Urban Rail transit offers low energy consumption and high efficiency travel, opening up under-populated areas and aiding regeneration. Increasingly becoming an integral part of urban planning, it provides one of the most convenient and safest modes of transportation within inner city areas – enhancing regional quality of life and having a positive impact on the local community, the environment and the economy.
The Midland Metro Alliance (MMA) was established in 2016 and consists of a consortium of partners including the West Midlands Combined Authority and Colas Rail Ltd. It was established to contribute to the social and economic regeneration of the West Midlands – with the aim of extending the tram network by a further 32 kilometres by 2026.
Construction started in June 2017 with the Birmingham Centenary Square Extension, completed in 2019. Further works include the tramway extensions to Wolverhampton City Centre and Edgbaston due to enter operation in 2021. Dependent on financing, the network will extend to the east of Birmingham, to link the future highspeed line, High Speed 2 (HS2) and towards the airport with the East BirminghamSolihull branch.
With over 35 years’ experience managing and delivering high-speed rail projects, the Colas Rail Group have delivered on a variety of projects harnessing a successful track record.
Colas Rail built 74 kilometres of new highspeed double track line from the Channel Tunnel to Fawkham Junction in north Kent, with a design speed of 300 kph, including the OCS and Mechanical and Electrical equipment and services.
KEY PERSONNEL
CEO: Jean- Pierre Bertrand
Deputy CEO: Stephens Haynes
Rail Freight Director: Simon Ball
CONTACT INFORMATION
Address: Dacre House, Dacre St Westminster, London SW1H0DJ
Tel: 020 7593 5348
Email: info@colasrail.co.uk
Visit: www.colasrail.co.uk
DB Cargo UK is the largest rail freight haulier in the UK. It operates freight and infrastructure services, as well as passenger charter trains throughout the UK
The company was born in 1996 when assets from the former British Rail freight business were used to form English Welsh and Scottish Railway (EWS). In 2007 Deutsche Bahn AG acquired all shares in the company and in 2016 renamed it DB Cargo UK.
Maritime Intermodal
In October 2021, DB Cargo UK announced plans to lease its Mossend EuroTerminal rail freight facility to Maritime Intermodal. The Lanarkshire depot provides intermodal freight transfer between rail and road and is well-placed at the centre of Scotland’s road network, next to the M8 motorway linking Glasgow and Edinburgh. The announcement came two years after Maritime Intermodal took over the lease of DB’s intermodal rail freight facilities in Wakefield, West Yorkshire and Trafford Park in Manchester. Under the terms of that agreement:
• DB Cargo UK was contracted to run Maritime Intermodal’s rail operations out of Felixstowe and Southampton.
• Maritime Intermodal took on responsibility for DB Cargo UK’s terminals in Trafford Park, Manchester and Wakefield in West Yorkshire, thus strengthening the road haulier’s national network of strategic hubs.
• Maritime Intermodal took responsibility for DB Cargo UK’s existing intermodal customers on its Felixstowe and Southampton services.
Contracts
DB Cargo UK signed a ten-year contract with Brett Aggregates in 2020. The contract will see DB Cargo UK transport millions of tonnes of sea-dredged products every year from Brett’s marine aggregates terminals in Ipswich, Cliffe and Newhaven.
DB Cargo UK was awarded a five-year haulage contract with Tarmac in 2020. This has welcomed a boost for the rail freight company which already runs a range of services for Tarmac to and from Mountsorrel Quarry in Leicestershire and its aggregates facility in Angerstein Wharf, Greenwich, London.
DB Cargo UK has been awarded a twoyear contract to transport china clay for Imerys. DB Cargo UK also signed a fiveyear ‘hook and haul’ contract to transport
supplies of sustainable biomass to Drax. Each train will carry around 1,650 tonnes of sustainable biomass to Drax Power Station, which provides flexible and reliable renewable power for millions of UK homes and businesses.
DB Cargo UK has also secured a new three year deal with fellow rail freight company GB Railfreight (GBRf) to undertake the maintenance of ten Class 60 locomotives for them as well as providing technical infield support.
In 2023 CWE Ltd, an independent supply, maintenance, and logistics partner to the rail industry, signed a twelve-month framework agreement with DB Cargo UK. The partnership will ensure that more parts and services are readily available, reducing downtime and assisting in the movement of the 36.7 million net tonnes of goods transported by DB Cargo UK annually.
In October 2018, UK manufacturing was given a major boost with the opening of DB Cargo UK’s new £6 million steel logistics centre in the West Midlands. Construction took more than twelve months and saw the German-owned freight operator more than double the size of its existing facility in Knowles Road, Wolverhampton, which receives imported steel from as far afield as Holland and Sweden.
The £6 million project was one of the largest investments in rail freight in the past five years and seen as a major vote of confidence in the UK’s continuing ability to trade and attract inward investment post-Brexit.
The state-of-the-art logistics centre is used by some of the world’s biggest steel companies including ArcelorMittal, Tata Steel and SSAB; providing a major boost to local businesses that use their products in their manufacturing processes.
KEY PERSONNEL
Chief Executive Officer: Andrea Rossi
Chief Financial Officer: Deb Hardy
Chief Transformation and Digitalisation Officer: Rohan Kapoor
Head of Sales: Roger Neary
CONTACT INFORMATION
Address: Lakeside Business Park
South Yorkshire DN4 5PN
Tel: 01302 575000
Email: uk.dbcargo@deutschebahn.com
Visit: www.uk.dbcargo.com
Operating
DRS has a uniquely flexible and efficient fleet of locomotives and rolling stock. Its fleet of Class 88, 68, 66, 57 and 37 locomotives allow it to deliver freight services across the network. The Class 88 is a state-of-theart bi-mode locomotive, the only dual powered locomotive in the UK. It can run on overhead electricity and offers industry leading CO2 savings, but also up to 500 miles on diesel power when no overhead lines are available.
Unique amongst UK rail freight businesses, DRS is not only fully accredited
to ISO 9001 quality management and ISO 14001 environmental standards, but has also achieved the occupational health and safety approval BS OHSAS 18001.
DRS’s UK-wide operations are delivered from a national network of fully equipped depots and facilities, supported by a 24/7 control centre. Supporting DRS’s core business of delivering safe, secure and reliable transport services for some of the most sensitive and demanding loads is an ever-expanding portfolio of key rail activities.
DRS operates a unique fleet of locomotives matched with a flexible
team of highly trained, fully experienced staff, providing a comprehensive range of infrastructure support services including:
• Autumn Rail Head Treatment Trains (RHTT).
• Winter snow clearance utilising DRS’ own MSP-fitted locomotives and Network Rail Independent Snow Ploughs and Beilhack Ploughs.
• Overhead line ‘ice breaking’ service.
• MPV weed-spraying operations.
• S&C Video MPV Operation.
• A variety of Test Trains, including Network Rail Saloon services.
In addition to these key services, DRS also supports Supply Chain Operations for Network Rail with the extensive resources required to facilitate its infrastructure renewal requirements, including the provision of Network Services, Bulk Ballast Services, Delivery Trains and Possession Services.
In April 2021, Nuclear Transport Solutions (NTS), a specialist nuclear transport organisation, was launched. NTS is part of the Nuclear Decommissioning Authority (NDA) group and specialises in the operational, commercial, engineering, legal, and regulatory expertise that underpin nuclear transport and logistics operations.
Operating from a network of more than thirty depots and sites, from Georgemas in the far north of Scotland to Devonport on the south coast, Nuclear Transport Solutions operate seven fully nuclear capable regional railheads that are positioned to support decommissioning and new build activities, and safe, high-security stabling facilities at strategic locations.
KEY PERSONNEL
Interim Rail Director: Julie Nerney
Senior Business Manager: Sabrina Brannan
Senior Operations Planning Manager: Sam Dixon
CONTACT INFORMATION
Address: Direct Rail Services
Regents Court, Baron Way, Carlisle
Cumbria CA6 4SJ
Tel: 01228 406600
Email: communications@drsl.co.uk
Visit: www.directrailservices.com
Freightliner is an intermodal and bulk haulage rail freight company operating in
Founded in 1965 in the UK, Freightliner has since expanded into Continental Europe.
After a few years operating only intermodal services from ports like Southampton and Tilbury to Birmingham, Manchester and others, Freightliner began operating infrastructure trains for Network Rail in 1999. In the first ten years after privatisation Freightliner trebled the number of services it ran. Freightliner and sister company Pentalver are owned by Genesee & Wyoming Inc. (G&W). G&W owns or leases 116 freight railroads worldwide organised in eight locally managed operating regions with 7,300 employees serving 3,000 customers.
Freightliner is the leading UK intermodal rail freight operator for the transportation of maritime containers with a comprehensive network offering the complete logistics package or trunk rail moves.
Operating around a hundred services daily, Freightliner moves over 770,000 maritime containers per year from the deepsea ports of Felixstowe, Southampton and London Gateway to all major conurbations in the UK, offering total coverage of the UK network. The combined Pentalver/ Freightliner road fleet consists of more than 350 modern tractor units and over 900 trailers to compliment the rail operations, providing a total logistics solution to their customer base.
Located in Doncaster Frenchgate Centre. The Operational Training Academy will prepare Freightliner’s freight train drivers for the introduction of in-cab digital signalling on the East Coast Main Line – South. The academy, funded by Network Rail as part of the East Coast Digital Programme (ECDP), marks another milestone for both Freightliner and ECDP as the second location dedicated to upskilling of drivers on European Rail Traffic Management System (ERTMS) operations. The site’s location further promotes Freightliner’s investment in its northern operations.
Beyond its role in training, Freightliner envisions these academies as spaces for fostering connectivity and collaboration among ECDP colleagues.
With 75 per cent of Freightliner’s direct carbon emissions coming from diesel traction, there has been a focus on seeking alternative fuels that can provide the same performance as diesel but with significant reductions in carbon emissions and air quality benefits.
In 2021 Freightliner carried out trials to verify alternatives fuels that could be used in unmodified locomotives without loss of power. From running a series of test trains, including the heaviest freight train on the network with no reduction in horsepower, confirmed air quality benefits and significant reductions in carbon emissions.
Freightliner now offers the use of alternative fuels such as Hydrotreated Vegetable Oil (HVO). Carbon emissions are roughly 90 per cent lower than diesel on average, with air quality benefits including a 14 per cent reduction in nitrogen oxides and 18 per cent lower ultra-fine particulates. HVO is a drop-in fuel that can be used without any alteration to a locomotive engine and supports as a transitional fuel on the path to a net zero economy.
Switching to electric traction boosts environmental benefits even further cutting carbon emissions up to 95 per cent compared with road haulage and reducing air pollution. Freightliner endorses the Department for Transport’s Decarbonisation Plan, which prioritises infill electrification of short stretches, sometimes only a few miles, to open whole routes to end-to-end electric traction.
With its fleet of 23 electric locomotives, Freightliner is the UK’s biggest provider of electric freight traction and with the lowercost gap-filling electrification projects, it would unlock substantial carbon savings and air quality benefits, taking the early steps towards full decarbonisation of the network and increasing the economic, social, and environmental benefits of UK rail freight.
KEY PERSONNEL
Chief Executive Officer: Tim Shoveller
Head of Sustainability: Chris Cleveland
Chief Financial Officer: Will Wright
Chief Commercial Officer: Andrew Daly
Safety & Sustainability Director: Louise Ward
CONTACT INFORMATION
Address: 6th Floor, The Lewis Building, 35 Bull Street Birmingham B4 6EQ
Tel: 03330 169545
Email: info@gwrr.co.uk
Visit: www.freightliner.co.uk
GB Railfreight (GBRf) is the third largest rail freight operator in the United Kingdom, transporting goods for a wide range of customers
GBRf’s £3 million building opened in August 2021, accommodates GBRf’s traincrew and office staff including its 24-hour control centre, training and operations departments, as well as the asset management team. The building plays host to three new purpose-built classrooms and state-of-the-art simulators which will be used to develop future generations of talent from the local area and beyond.
Upgrade to Eastleigh and Bescot LDCs for Network Rail
GBRf has completed two major upgrade projects funded by Network Rail worth over £1.5 million, aimed at improving vital Local Distribution Centres (LDCs) in Eastleigh and Bescot.
Both LDC’s act as a focal point for the shunting, marshalling and preparation of trains needed to support vital engineering works carried out by Network Rail.
The work on Eastleigh LDC, in Hampshire, has been two years in the making with GBRf replacing old cabins with updated facilities that provide full recreational capability, offices for management, a meeting room, as well as a vantage point that overlooks the yard. Alongside this, GBRf undertook a car park overhaul, maximising the potential parking for those operating onsite.
GB Railfreight (GBRf) renewed its contract with Tarmac for five years from January 2020 to 31 December 2025. GB Railfreight (GBRf) and Rail Stone Solutions (RSS) signed two contracts to support construction on the first phase of HS2.
The deals, with HS2 contractors EKFB (Eiffage, Kier, Ferrovial BAM Nuttall) and BBV (Balfour Beatty VINCI) will see GBRf join forces with RSS to deliver aggregates by rail to the high-speed rail project’s main construction compounds.
As part of the deal with EKFB, GBRf will support the training of new train drivers at their new state-of-the-art twin-simulators near Peterborough where the UK’s first and only full-cab freight European Rail Traffic Management System (ERTMS) simulator centre is located.
GBRf and Stadler have signed an agreement that will see Stadler Rail Services be responsible for all aspects of service and maintenance GBRf’s latest hybrid locomotives from 2025. Beacon Rail will own the new hybrid fleet, and GBRf will be the lessee. The UK government’s electrification rollout, when complete, will enable the Class 99s to run on electricity across all UK routes and reduce emissions by 585,000 tonnes of carbon per year. High quality and reliable servicing is critical to ensuring the fleet can deliver this impact.
GBRf has agreed with Stadler that they will maintain the 30 locomotives at a new depot in Leicester, where they will receive tailored maintenance solutions to ensure a high quality of service. Stadler will manage overhauls, spare parts, material supplies, vehicle repairs, mobile service support, data and maintenance software.
GBRf has a seven-year deal with Caledonian Sleeper Ltd to continue hauling the Caledonian Sleeper coaches with Class 92s and Class 73s to haul the service, with the length of the new agreement offering the potential opportunity to consider incorporating GBRf’s new bi-mode Class 99 locomotives in the future. Utilising the Class 99s would create a significant reduction in the volume of carbon created by the service.
Having provided services since 2015, this agreement remains in line with the original 15-year contract length – until 2030. At a time when the service is seeing the highest levels of demand, the continuity of GB Railfreight’s service will minimise disruption for guests during this transition period for the Caledonian Sleeper.
KEY PERSONNEL
Chief Executive Officer: John Smith
Commercial Director: Liam Day
Production Director: Ian Langton
Finance Director: Karl Goulding- Davis
Asset Director: David Golding
Business Development Director: Tim Hartley
General Infrastructure Manager: Alex Kirk
CONTACT INFORMATION
Address: LONDON HQ, 3rd Floor
55 Old Broad Street, London EC2M 1RX
Tel: 020 7904 3393
Email: info@gbrailfreight.com
Visit: www.gbrailfreight.com
0161 793 8127 (Manchester)
01670 590300 (Cramlington)
The MOSA division of Wilkinson Star Ltd is the sole importer and after sales service agent for the full range of Engine Driven Welder Generators, Generating Sets & Lighting Towers manufactured by MOSA Italy, a company founded in 1963.
MOSA Engine Driven Welder Generators, together with MOSA Generating Sets & Lighting Towers are supplied to a wide range of industry sectors in the UK including plant & tool hire, welding & engineering distributors, power generation specialists, Network Rail, Crossrail & London Underground contractors together with many overseas projects requiring the use of reliable equipment.
With the backing of Wilkinson Star and a commitment to customer service, product innovation, competitive pricing and stock availability, MOSA offers you – the customer, a quality product with first class support.
Apart from providing strategic direction to the group, Rail Operations (UK) incorporates a Project Management Office (PMO) to deliver support to major projects, both within the group itself and to external customers. Examples of this include:
• ERTMS support to Crossrail.
• Train planning support to Orion.
• Procurement of the UK’s first fleet of trimode class 93 locomotives.
Rail Operations (UK) specialises in train movements relating to rolling stock delivery, testing, maintenance, modification and refurbishment programmes. Train operations include new build deliveries, train testing, fault-free running and mileage accumulation of new rolling stock.
Current fleet support includes fleet maintenance, modification and refurbishment programmes, fleet cascade or transfer programmes, vehicle / fleet testing (e.g. ETCS fitment) and infrastructure-train interface testing.
Rail Operations (UK) also provides storage regimes to support new build, off lease and redundant rolling stock.
• Passenger (ECS), ad-hoc freight or engineering rolling stock movements.
• Traction and rolling stock movements for private owners / operators.
Rail Operations (UK) also has a fleet of dedicated locomotives which have been modified with electrical brake translation equipment and a range of coupler types to enable direct coupling to, and through automatic brake control of, most UK EMU types. This negates the need to use historic barrier and translator type vehicles.
Delivering innovation and diversification to the UK rail industry the Rail Operations group of companies provides a range of specialist services to the UK rail industry. These services are principally in support of the rolling stock leasing, manufacturing and engineering sectors and involve everything from project management through to the
delivery and testing of new train fleets. Rail Operations Group partnered with the Barrow Hill Roundhouse to provide a shuttle service to the 2021 Rail Ale Festival. On 4 August 2021 Rail Operations Group operated Retro Railtours’ first tour since 2019.
Traxion is a specialist rolling stock management company delivering services related to rolling stock storage and disposals. Today’s rolling stock storage programmes require suitable storage facilities, within which, a varying range of rolling stock servicing or maintenance regimes are provided. Traxion can tailor to include the following:
• Wheel Bearing Rotations.
• Weekly Inspections.
• Transit of the unit to and from an approved engineering provider for more in-depth inspection.
• Arrange with Rail Operations Group transit to and from originating depot to storage.
• Asset surveys and reports to clients at their request.
Orion started trading in 2020, delivering high speed logistics services across the UK using re-purposed passenger trains employing bi-mode traction systems. Orion has already ordered the first class 769 ‘Flex’ units which will be used to convey light goods and parcel type commodities. These trains can operate over all UK rail routes and will serve national and regional logistics hubs, terminal, principal and regional stations and deep sea and inland ports.
On 16 February 2021, Rail Operations (UK) completed a Sale and Purchase Agreement with Heathrow Airport Limited, the parent company of Heathrow Express, to acquire the fleet of five Class 360/2 multiple units, plus spare parts.
On 14 January 2021 Stadler and Rail Operations (UK) signed a framework agreement for the supply of thirty Class 93 tri-mode locomotives. The advanced locomotives will significantly reduce CO2
emissions for both rail freight as well as potential passenger transport services, underscoring Stadler’s green credentials and demonstrating its commitment to decarbonisation. Deliveries are expected to start in early 2023.
KEY PERSONNEL
Group President: Karl Watts
Chairman: Neil Bennett
Chief Operating Officer: David Burley
Production Director: Paul Orchard
CONTACT INFORMATION
Address: First Floor, Wyvern House, Railway Terrace, Derby DE1 2RU
Tel: 01332 343295
Email: info@railopsgroup.co.uk
Visit: www.railopsgroup.co.uk
Victa Railfreight is an UK owned business and whilst independent, it maintains a close relationship with all the major players in the rail freight sector
Victa Railfreight holds a UK wide Non-Passenger Train Operators Licence that has enables it to offer ‘last mile’ shunts, local tripping and rail freight feeder services and ‘short line’ capability to a wide customer base as well as ground staff provision for passenger and freight train operating companies. The company acts as principal operators at Dove Holes Quarry in the Peak District on behalf of Cemex UK and at Tilbury on behalf of Forth Ports, in both cases providing both expertise and shunting and train preparation services at these busy locations. In addition, it delivers a large number of safety related training courses to the freight community and also advises on a
wide range of safety, operations and logistics related subjects.
Victa Railfreight offers safety and sustainability evaluations to customers in the form of its Rail Freight Terminal Management packages which facilitate continuous improvement in the safety, operation and sustainability of rail freight facilities. Victa Railfreight has expertise in providing rail solutions for construction projects and is completing an eight-year involvement with the building of the Elizabeth Line under London. Prior to this it provided support to the construction of High Speed 1, Heathrow T5 and other similar projects.
Victa Railfreight is one of the longest standing members of the Railfreight Group
with Managing Director Neil Sime recently completing his two terms as Chair.
Victa currently employs around 70 staff and has a turnover of c£3.5 million. Its dedicated team have long established expertise in the rail industry and freight sector in particular. Victa Railfreight has a reputation for innovation and collaborative working that is driving the business forward and would be delighted to discuss our services with prospective clients.
KEY PERSONNEL
Managing Director: Neil Sime
Contract & Resources Manager: Debbie Simmons
Head of Operations & Safety: Paul Verghese
Third Party Services Manager: Colette Ranford
CONTACT INFORMATION
Address: Unit 1 The Viewpoint
Boxley Road, Boxley Road, Maidstone
Kent ME14 2DZ
Tel: 01622 690978
Email: enquiries@victa-railfreight.com
Visit: www.victa-railfreight.com
Manchester Metrology LTD are pioneers and innovators of metrology offering specialist contract measurement services using the latest metrology technologies and equipment. Offering support across the UK and worldwide. Our attention to detail and helpful attitude towards our customers are among the many positive attributes which distinguish the company as a benchmark metrology company.
Hiring, purchasing and training on all portable metrology equipment available
www.manchester-metrology.co.uk
Manchester MetrologyMetrology is an ever-expanding field, with progress being made all the time, from game changing technological advances to new software developments and updates
It can be challenging to keep up with technical progress and it pays to seek some expert advice before investing in new metrology solutions. A wellknown authority in the sector is the UK-headquartered Manchester Metrology. The business continually invests in the latest innovative hardware to ensure it can offer the customer the best that is on the market. Within the rail industry, the company supports projects from manufacturing to installation. Its equipment and engineers have supported manufactures to achieve design intent on products, which then reduces timescales for assembly.
The company conducts full 3D scans of working areas to give the customer the ability to obtain dimensions and to plan where they can add additional assemblies. Customers can add their designed product to the CAD model to ensure it will fit into already busy areas (a particular challenge at offshore sites).
Manchester Metrology provides on- and off-site inspection, scanning and measurement services, as well as in-depth training for software such as CAM2 & Polyworks. Its extensive stock also allows the firm to hire out metrology equipment such as portable coordinate measurement machines (CMMs), laser trackers, 3D scanners and laptops with metrology software installed and ready to go. This allows the company to answer any metrology need a customer may have.
CMMs offer the ultimate solution for components that require the highest accuracy. Manchester Metrology has a range of bridge CMMs (small, medium, and large), all of which can run both PC-DMIS and PolyWorks software. The flexibility of size and software allows the company to use each machine for its individual strengths. With a maximum part volume of 2.5 metres by two metres by one metre, it can accommodate a wide variety of parts. All machines can be programmed online or offline and can run one off or multi-
piece inspections. With the use of CAD models, complex geometries and shapes can be compared to their nominal position or surface. Once programmed, the CMM offers automated inspection with little input needed from the operator. Inspection programs can also be optimised to ensure the quickest and most efficient run times.
As well as stocking innovative technology and providing efficient service, the company is also an official reseller of the Peel 3 3D scanner. This is a professional-grade 3D scanner for an incredibly low price –making it a popular choice for engineering applications. Weighing less than 1kg, the Peel 3 is capable of scanning structures with incredible accuracy and displaying them on a computer using CAD.
Manchester Metrology recently acquired Apex Metrology. Apex Metrology boasts a global footprint in the industrial sector, offering a wealth of experience in CMM applications and efficient, comprehensive solutions. The company’s robust quality assurance credentials are underscored by its ISO9001 & ISO17025 certifications. From
its base at the Midlothian Metrology Centre, located near the esteemed Edinburgh Technopole Science Park, Apex has been at the forefront of innovative solutions, a testament to its commitment to quality and development.
The amalgamation of Manchester Metrology’s state-of-the-art technology and Apex’s wide-reaching industrial experience promises to deliver an unprecedented portfolio of metrology services. This merger is poised to not only enhance the service offerings for existing customers but also attract new clients seeking the reliability and expertise that the joint force now guarantees.
Tel: 0161 637 8744
Email: info@manchester-metrology.co.uk
Visit: www.manchester-metrology.co.uk
Indestructible Paint Ltd are a UK based Coatings manufacturer, with over 45 years’ experience supplying coatings to the Aerospace and Defence Industries worldwide.
This technology is now available for use within the rail sectors, offering corrosion, chemical and heat protection in aggressive operating conditions, extending the operating life for customer assets.
RWIP120 Coating Range for Underframe Equipment.
After 7 days air curing or force curing for 30 minutes at 125°C, the coating will pass
• CR/PE0102
• EN45545-2 R1 / R7 / R9 Fire Testing.
• Heat resistance: 48 hours at 204°C (400°F)
• Heat resistance: 100 hours at 180°C (356°F)
• Hot oil immersion: 8 hours in ASTM Fluid 101 (ASTM D 471) at 177°C (350°F) showing no peeling or softening
• Hot lube oil immersion: 100 hours at 150°C (302°F)
• Fuel resistance: immersion in ASTM ref fuel B for 4 hours at room temperature without peeling or softening
• Fuel resistance: room temperature immersion 100 hours
• Corrosion resistance: exposure to heat (48 hours at 400°F) cross scratched X withstands 350 hours salt spray ASTM B117
• Heat Salt Fog Resistant to 10 cycles: each cycle, 4 hours at 250°C (300°F) then 20 hours salt fog
• Resistant to temperatures down to -50°C
If you do have any enquiries regarding our range of Rail products, please contact our Sales Department
Tel: +44(0)121 702 2485
www.indestructible.co.uk 16-25 Pentos Drive, Birmingham, B11 3TA, United Kingdom
A highly versatile and robust epoxy coating system has now been introduced by specialist coatings manufacturer, Indestructible Paint Ltd
With key benefits for use within the rail industry.
The RWIP120 product has been developed from over four decades of experience in aerospace coating technology which has been used in the most challenging global environments.
Indestructible Paint’s RWIP120, which is fully compliant with CR/PE0102 Repainting of Rail Vehicles specification, and fully fire tested to EN45545 (R1, R7 and R9) offers a range of performance benefits and, significantly, is available as either a one or two coat system.
• Heat resistance: 48 hours at 204°C (400°F).
• Heat resistance: 100 hours at 180°C (356°F).
Underframe coating objectives can often be achieved by the use of the system as a single 120-micron primer/finish coating in a semi-gloss finish, or as a two-coat system with 60-micron primer and an additional 60-micron finish coat.
Indestructible Paint’s RWIP120 has been proven on a range of substrates, many of which are a common feature in the rail sector. These include steel, aluminium, galvanised and composite surfaces which all gain from the composition of the epoxy and its chemical bonding characteristics. The cured coating is a tough chemically resilient finish that has been tested against a variety of corporate and national standards.
The system is part of a family of coatings that have been developed at Indestructible Paint which are based on high grade, twopart epoxy coatings that have a long and successful track record in the Aerospace and Land Defence sectors.
The performance capability of the RWIP120 range covers a long list of challenges faced by rail operators. From impact, chip and scratch resistance to the ability to withstand high temperatures, high humidity environments, all are key benefits as are proven resistance to abrasion, salt spray and wash plant operations.
After seven days air curing or force curing for 30 minutes at 125°C, the RWIP120 coating will pass:
• Hot oil immersion: eight hours in ASTM Fluid 101 (ASTM D 471) at 177°C (350°F) showing no peeling or softening.
• Hot lube oil immersion: 100 hours at 150°C (302°F).
• Fuel resistance: immersion in ASTM ref fuel B for four hours at room temperature without peeling or softening.
• Fuel resistance: room temperature immersion one hundred hours.
• Corrosion resistance: after exposure to heat (48 hours at 400°F) cross scratched X withstands 350 hours salt spray ASTM B117.
• Heat Salt Fog Resistant to ten cycles: each cycle, 4 hours at 250°C (300°F) then 20 hours salt fog.
• Resistant to temperatures down to -50°C.
When required the RWIP120 can be overcoated with the RWIP48, an air drying two pack Low VOC Polyurethane finish coat, specially developed for use within the Rail and Associated Industries on rolling stock and is available as a Matt to Full Gloss finish in a range of BS and RAL Colours.
RWIP48000 is part of a family of coatings developed by Indestructible Paint Ltd and is manufactured from a high grade two-part Polyurethane system initially procured for use on aerospace applications. Indestructible subsequently take this resin binder system to manufacture a range of low VOC coatings
intended for Rail, Industrial, Transport and Architectural applications, ideally suited for use on vehicle bodyshells, interior and exterior components. The composition of the Polyurethane and its chemical bonding allow use on a range of substrates including ferrous and non-ferrous metallics and a wide range of composites. The cured coating is a tough chemically resilient finish that has been tested against a variety of corporate and national standards, and fire tested to EN45545 (R1 and R7).
Benefits include:
• Low VOC (less than 420gms/litre) high build finish.
• High Performance two pack finishes.
• Designed for spray application, or by brush / roller.
• Excellent hardness; chemical resistance and flexibility.
• Excellent gloss retention on exterior weathering.
• Suitable for use on items where cold or low temperature cure is a necessity and
high-performance finish is required.
• Superb obliteration.
• Suitable for use as a solid colour finish or as a base coat/clear system.
Other developments from Indestructible Paint Ltd are a range of thin film intumescent coating which, when intumesced, forms a barrier to protect the substrate from burning for a specific number of minutes dependant on thickness, and when used in conjunction with a heat absorbing primer they are suitable for application in hot areas typically found under a train, for example, around an exhaust area/motors.
The Intumescents perform on a range of substrates, including metals, timber and composites, suitable for both air- and forceddrying, the coatings maintain excellent adhesion – including, importantly for the rail sector, where high air movement is present.
The Intumescent Range:
• RWIP1000 – air drying single pack Water based Intumescent emulsion specially developed to provide enhanced fire resistance to timber, fibre boards and composite substrates. Specially developed for use within the rail industry on vehicle components and civil installations on various substrates. Available as a Matt, finish, in White and Grey. Applied as a single coat or two coat application, the product and can be overcoated with itself, combining excellent application characteristics with fast drying characteristics. The product is designed for internal situations, and is a genuine water-based intumescent, safe to store, handle and apply.
• RWIP2000 – two component water based acrylic intumescent coating for timber, aluminium and other combustible
Test Time
substrates that require protection from the effects of fire. Suitable for application by spray or brush and can be air dried or force cured. The coating is designed to be part of a composite system that will inhibit the surface spread of flame and provide an insulative barrier layer, preventing heat degradation of the underlying substrate.
• RWIP3000 – two component epoxy based air drying/force drying Intumescent coating specially developed to provide enhanced fire resistance to metallic, timber, and composite substrates. Specially developed for use within the Rail Industry on vehicle components and on civil installations, designed to be more resistant to high air movement and maintain excellent adhesion properties after the product has intumesced.
Available in a White Matt Finish. RWIP3000 is usually applied as a system of primer/sealer (substrate dependant) intumescent coat and can then be overcoated with a two component epoxy or Polyurethane topcoat if required.
As a clear demonstration of the performance capability of the RWIP3000 epoxy intumescent, Indestructible Paint points to a specific testing operation centred on exposure to an 1100°C flame, with the flame positioned 10cm from a 4mm anodised aluminium substrate, the panel condition remained satisfactory, with internal pressure maintained, after a five-minute exposure period, by comparison, over the same period a non-coated panel distorts and deteriorates before splitting, exploding and completely melting. Similarly, the Indestructible Paint coating has been shown to maintain heat resistance when exposed to 180°C heat source for more than one hundred hours.
Effect of 1100 degC. Burner
Uncoated Panel Panel coated with RWIP3000
One minute Panel distorted outwards Panel and coating intact
Two minutes Deterioration rapidly decreasing Intumescent barrier formed with adhesion to substrate
Two + minutes
Explosion. Panel splits, centre blows out Intumescent barrier formed with adhesion to substrate
Five minutes Panel completely melted. Condition satisfactory. Internal pressure maintained
INDESTRUCTIBLE PAINT LTD RAIL PRODUCT RANGE
• Epoxy Range – RWIP120 – Primer + Finish coat / Primer Finish coat (one coat system).
• Polyurethane – RWIP48 – Finish coat for exteriors/interiors, matt to full gloss.
• Intumescent Coating – RWIP1000 – 1K water based acrylic emulsion intumescent.
• RWIP2000 – 2K water based acrylic intumescent.
• RWIP3000 – 2K epoxy solvent based intumescent.
• Thermochromic Range – Reversible and Non Reversable systems.
• RWIP-INFRACOAT – Water Based 1K maintenance coating for infrastructure.
• RWIPTHIN/1 – General Purpose Degreaser / Cleaning Solvent.
• IPSTRIP500 – Environmentally friendly Paint Stripper.
• RUSTETA – Rust Conversion Coating.
RWIP3000 intumesced
Typical performance to exposure to 1100 degrees C flame showing product fully intumesced.
Two 0.6-meter panels of 4mm anodised aluminium. One coated with RWIP3000 @ 300 microns dft. and the other left uncoated. Both are pressurised to five psi. An SAE 15cm diameter propane burner (116350 BTU) is positioned 10cm from the centre of each panel.
Address: 19-25 Pentos Drive
Sparkhill, Birmingham B11 3TA
Tel: 0121 702 2485.
Email: sales@indestructible.co.uk
Visit: www.indestructible.co.uk
With
50 years experience under his belt, for seasoned rail operator Steve Derrick, working in the industry isn’t simply a job – it’s a way of life
Away of life which has seen him involved in everything from project engineering and contract management through to senior project/programme and general management roles. Now, that includes running his own consultancy. By way of background, Steve’s rail career began in 1974 as a Junior Technical Officer for British Rail in Croydon, before taking on a variety of positions over the following five decades, ranging from track/maintenance renewals and contract management through to lead project engineer and area general manager roles.
But when faced with retirement in 2014, Steve wasn’t ready to walk away, instead deciding to ‘rally the troops,’ collecting up former colleagues to create his own business – AARC Professional Services Limited, a specialist rail consultancy, run by railway people, for railway people. The company brings together like-minded rail professionals, with the common aim of delivering expert support and advisory services to the rail industry, built upon a shared motivation to provide clients with outstanding outcomes by:
• Helping clients achieve their goals.
• Through strategic and technical expert advice.
• Across a range of disciplines.
• From the frontline through to the boardroom.
AARCPS’s formation was also based on a desire to stem the ‘brain drain’ experienced by the industry in recent years. Steve explains: ‘When launching AARCPS, I was conscious of the significant changes affecting the rail industry, which I felt posed a real danger of the industry losing invaluable knowledge and experience when long standing professionals left. One of our initial aims was to help address this by redeploying some of those people and skills where they could make a positive and meaningful impact.’
Another key driver for Steve was a genuine belief in the need for a thriving and successful rail industry and a desire to give something back to a sector that has looked after him for so long – a mindset shared by all of AARCPS’s associates. It’s this extensive experience which sees Steve and co able to provide support across all levels of the industry, from frontline through to the boardroom. AARCPS also has a national reach, providing a fast, flexible and sustainable service throughout the UK, with clients in England, Scotland and Wales.
AARCPS specialises in the following areas:
• Rail Operations including network operations, maintenance operations and train operations. Its team of associates can provide support across all aspects of rail operations, covering both short-term tactical rail operational requirements, as well as more strategically focused rail operational issues.
• Projects & Engineering including bid management, change management, programme/project management and engineering management. AARCPS covers the complete project lifecycle, from prefeasibility and bid management through to implementation and project close-out.
• Safety & Assurance including risk management, safety management and assurance management. All of AARCPS’s associates have worked directly in a safety conscious environment and fully understand and appreciate the importance of a strong safety culture,
helping clients to meet their core safety requirements.
• Rail Training including training development and training delivery. Its associates are experienced in the design and delivery of skills/bespoke rail training, tailored to suit each client’s specific needs, and can also carry out assessments and assist in the verification process where required.
Steve continues: ‘Our main motivation is to help clients achieve their goals through the delivery of strategic and technical expertise, either working independently or as part of a team - all our associates are strong advocates of collaboration and the benefits it can bring. With a fast growing team, currently standing at 23, AARCPS also provides real strength in depth, with each of our associates bringing with them a particular set of skills, honed over a lifetime of service in the rail sector.
‘It’s also important to note that we’re a particularly close knit organisation, with almost everyone having worked together before in a previous capacity and all of us sharing the common goal of providing a professional, collaborative and friendly though determined approach to all that we do, bringing about outstanding results.’
Projects that Steve and team have supported include the following:
• Electrical Control Operator (ECO)
Training for Amey Infrastructure
Wales – AARCPS has been providing
operational training for AIW, which was appointed by Transport for Wales (TfW) as the managing agent for its extensive programme of electrification, signalling recontrol and upgrade, track doubling and station improvements. Following the successful provision of signaller training, AARCPS was also retained by AIW to conduct ECO training – directly linked to TfW’s upgrade of the Core Valley Lines’ upgrade, which includes provision of 25Kv OLE electrification and the siting of an electrical control room (ECR) at a new integrated control centre (ICC) at Taffs Well. This assignment has involved the recruitment, training and assessment of an ECO resource to manage electrical supply and emergency response for the newly installed OLE and associated infrastructure, with eight new AIW staff taking part in a bespoke training package.
• Updates to Health and Safety Management System for Network Rail – AARCPS was commissioned to help Network Rail remodel its overarching health and safety management system into an accessible tool for continuous improvement in risk management, which is integrated with its wider management systems and operating model and which recognises the need for devolved,
customer focused decision making. The remodeled system follows the RM3 Risk Management Maturity Model and has been informed by a gap analysis of current processes, identification of best practice and stakeholder engagement. It recognises Network Rail’s safety certification and authorisation commitments and other requirements of the Railways & Other Guided Transport Systems Regulations (ROGS) and Railways Interoperability Regulations, while covering all Network Rail’s business activities.
• Rail for London Infrastructure (RfLI) on the Elizabeth line – AARCPS was initially engaged by RfLI’s Head of Maintenance for the Elizabeth line (London’s East to West railway) to provide a report on each maintenance business areas’ readiness for taking over the railway at ROGS. The assignment was extended to support Crossrail’s hand-over of stations, portals and rail wide systems by assuring the necessary information and training was sufficient to enable the maintainer to mobilise. With AARCPS acting as sponsor's representative, the business benefits were achieved by delivering a fault reporting system link between operational control systems and
AARC
Maximo (the maintenance workbank system), which enabled operators to initiate a response team directly from the control system. Since entering revenue service, AARCPS has also been working with the heads of departments to improve the concept of the RTIM (Real Time Infrastructure Manager) working 24/7 on the control floor, as well as continuing to support the Elizabeth line’s Infrastructure Manager.
With regards to the future development of the business, AARCPS’s objective is to continue to evolve at a controlled pace, continuously building its pool of expertise, whilst simultaneously developing the business offer, though ‘never at the expense of the quality of service provided.’ To find out how AARCPS can help your organisation, please get in touch using the details below.
Tel: 07841 611657
Email address: info@aarcps.co.uk
Visit: www.aarcps.co.uk
Run by railway people, for railway people
Services Limited draws from over five decades of experience to provide expert support to the industry.
We are a railway consultancy bringing together likeminded rail professionals with a common aim to deliver outstanding outcomes by..
• Helping clients achieve their goals...
• Through strategic and technical expert advice...
• Across a range of disciplines...
• From the frontline through to the boardroom
Whether you’re looking for high level advice & guidance or direct project support, we’re here to help you deliver excellent outcomes.
WCL follows three core values – integrity, collaboration and simplicity – to reduce risk, streamline, and achieve success for rail projects worldwide
WCL is an agile and fastgrowing consultancy firm, developing and delivering major works for customers across the rail sector. Working with large corporates and SMEs, it brings together the best minds in planning, programming, engineering and management.
WCL specialises in integrated solutions for complex projects, complementing its customer’s existing team with hand-picked experts, offering tailored insights and support, and ensuring they get exceptional outcomes. WCL serves a growing range of clients across the globe, from Network Rail to Tier 1 suppliers, as well as operators at every level.
WCL has a record for success across some of the largest signalling schemes in recent UK history, including projects for Network Rail and TfW. It simplifies multi-faceted works, overcomes obstacles and reduces risk, with expert assurance and support every step of the way.
WCL provides best-in-class engineers and construction professionals, combined with a systems thinking approach, to deliver added value at every stage of your project lifecycle.
WCL cultivates integrity and success through unified handling of finances, operations and project development. It is supported by its wealth of in-house commercial experience, plus relationships with a number of key strategic partners. WCL will work to make sure you complete on budget, on schedule, and in alignment with stakeholder expectations – leading to fewer risks and more opportunities.
Large, complex or multi-discipline projects require smart working to avoid conflicting
interests, inefficiency and uncertainty. WCL creates real integration that not only works – it lasts. The company collaborates with clients to design purpose-built processes and improved controls, helping them better define, measure and achieve success at both project and programme levels.
WCL specialises in big projects and their unique challenges. With roles including lead strategic support for the £738 million multidisciplinary overhaul of rail infrastructure in South Wales, as well as lead consultancy services for Network Rail’s CP6 Wessex Works Delivery, the company has established itself as central to success in a number of the UK’s largest rail works programmes.
In complex, multi-stakeholder project and programme environments, persistent bottlenecks or blind spots can lead to major issues. WCL helps by offering a fresh, expert perspective as specialist change-makers. Through its work with Network Rail on
the CP6 Wessex Works, for example, its intervention – focused on stakeholder communication, culture, problem-solving and process efficiency – led to their portfolio of work doubling in year one and increasing by a further 50 percent in year two.
In addition to its involvement in major programmes of work across the UK, such as the Core Valley Lines in Wales and Transpennine Route Upgrades (TRU), WCL has extended its consultancy services to New Zealand and its national operator, KiwiRail.
Through its success in the original advisory and review role, providing constructability and staging arrangements, WCL was further engaged to deliver broader project management and engineering support for optioneering and tender workstreams.
WCL has since established an incountry presence and continue its rapid growth, now working on signalling design
“Thank you for all the invaluable help and support WCL has provided to the Wessex Works Delivery team over the past two years. The difference from what it was like before to what Works Delivery was like under your guidance has been huge…”
Senior Sponsor, Network Rail
“Thank you WCL Rail for your valued input to the BASRE and BEJR projects. All of these major projects present different challenges, however having your expertise and skills set seamlessly integrate into our one team approach is truly appreciated. This is what contributes to successful projects as we saw at the weekend with the on time hand back of the complex Stage F on Bristol East Junction blockade.”
Project Director, Alstom
“CVL is a hugely ambitious programme which will ultimately provide life changing benefits to our customers, the people and communities who live in South Wales and surrounding areas. WCL have played a lead role in delivering the signalling workbank to date with recent highlights including the complex TAM A commissioning earlier in 2023. WCL have seamlessly integrated and delivered within our one team approach and I wish to express my thanks to them for their ongoing contribution and continuous support to deliver."
Programme Manager, Core Valley Lines Transformation Programme
“With significant experience in big project delivery, WCL have been able to provide an honest and experienced insight into some of our biggest programme integration risk areas and proactively offer and manage solutions. I can only recommend them.”
Project Director, Amey Infrastructure Wales
and its effective integration into the wider Wellington Master Plan, as well as project management of major re-signalling upgrades in Wellington Station and the Wairapa lines.
From WCL's work across the UK and New Zealand, plus discussions with colleagues and partners elsewhere in the world, it’s clear that demand for talented and experienced consultants/resources is a global challenge. WCL has responded proactively by securing a sponsorship license with the UK government to employ and issue visas for overseas workers, allowing it to bring scarce and specialist resource into the country.
WCL continues to gather and act on important industry insights such as these through its expert advisory services and ongoing work on major rail infrastructure projects; as a result, WCL has established itself as a leading choice for networks, operators and suppliers around the world looking to secure the best consultancy support for success – both today, and tomorrow. Get in touch today for a free discussion about your project and to find out more about how WCL can help.
Tel: 01666 837708
Email: info@wclrail.co.uk
Visit: www.wclrail.co.uk
LinkedIn: wcl-rail-ltd
‘With significant experience in big project delivery, WCL have been able to provide an honest and experienced insight into some of our biggest programme integration risk areas and proactively offer and manage solutions. I can only recommend them.’
Project Director, Amey Infrastructure Wales
Radius Group specialises in providing expertise on projects that are logistically challenging, require performance in tight and enclosed spaces, involve large and or unusually shaped plant or equipment,
whilst always being extremely time sensitive. The group is widely regarded by its clients as their specialist problem solvers; helping to manage and mitigate specific project risks. Early engagement is key; the team is typically called upon early within projects
when other specialist contractors and suppliers are unable to provide a safe or technically acceptable solution.
For each specialist sector that it serves, Radius Group has also developed unique operational methods and manufactured
LARGE OBJECTS. SMALL SPACES. INNOVATIVE SOLUTIONS.
equipment of its own original design. To assist with projects within the rail sector for example, Radius Group owns and operates the only London Underground approved escalator sledge, capable of carrying up to 450kgs down escalators to specific project locations.
Industry leading project documentation ensures a quick and smooth process, giving you reassurance that the operation is in safe hands. Utilising cutting-edge software and planning tools, technology is always at the forefront.
Radius Group offers a full turnkey solution to include off-site warehousing, ontime delivery, off-load servicing and on-site lifting and plant movement to point of use of various types of mechanical equipment.
Radius Group has vast experience in the rail sector, having recently completed the installation of the ventilation, power, ticket machines, gates and comms-equipment on London Underground Northern Line Extension, working with clients to deliver a safe and successful installation.
Radius has also completed the mechanical installation of the water-cooled Platform Air Handling Units installed at Victoria, Piccadilly, Central and Bakerloo lines. These units were delivered using engineering trains and required a complex quad lift using four lifting beams clamped to the tunnel ring bolts.
The Radius Plant Installation Team were also heavily involved in the planning and execution of the following works on Crossrail, which were delivered on-time and in-budget:
• Non-Traction Power Installation to point of use.
• OHLE Switchboard Installation to point of use.
• StationUPS Installation to point of use.
• LV Switchgear at various Crossrail stations.
• Tunnel vent shaft fans and associated components installation.
When the delivery of new equipment for forty London Underground substation upgrades was required, in addition to 15 sub-station upgrades for Network Rail, Radius was the obvious choice to provide the end-to-end lifting solutions. Radius has an impressive success and safety record on projects involving lifting/handling and installing heavy plant within both surface and sub surface environments.
Radius Group recently completed the upgrade of ‘Connect’, London Underground’s radio, transmission, and operational CCTV communications technology system, used daily by the TfL staff. Radius supported Thales in its bid to win the scheme and once successful, works took place over a two-anda-half-year period, to complete the upgrade
of over 290 locations for the London based client. Radius Group was instructed to work on the system to plan, and implement the replacement all the dated communication cabinets, across 290 locations.
Radius has extensive knowledge of all aspects of the London Underground System, and the stringent procedures needed to work in the Underground environment. Their skilled team has a staggering combined one hundred years of knowledge and experience on the Underground system, and ensure all standards are met and passed on every site. Radius utilises a variety of methods including but not limited to Hydraulic Gantries, Hydraulic Skidding Systems, Versa Lift, Industrial & All Terrain Forklift, Stair Robots, A-Frames, Hoists, Engineering Trains and Cranes.
Coupled with the Plant Installation offering is the Radius Contract Lift Division, offering a vast range of contract lifting services from lorry loader through to telehandler, mobile, spider to crawler crane, and tower crane through to helicopter lifts.
The industry-leading contract lifting expertise is complimented by the Radius Tower Crane Division. Radius has access to the world’s largest crane bank through its partnership with NFT. Combining its own technical engineering knowledge, plus the manufacturers (Manitowoc Potain) global technical support makes Radius a world-leading provider in the Tower Crane business.
Tel: 01604 622865
Email: info@radiusgroup.co.uk
Visit: www.radiusgroup.co.uk
can be complex and require a comprehensive approach to solve.
For more information visit: www.infinitivegroup.co.uk
That’s why we offer a range of professional services across the entire project lifecycle, and develop cutting-edge products to support you from project conception through to operations and maintenance.
With our proven track record of success and commitment to delivering exceptional service, you can trust us to help you overcome any transportation challenge.
With renewed interest in continuous improvement programmes, how can data support a future-focused industry?
After a long-term focus on capital projects such as new rolling stock fleets, industry attention is shifting once again to continuous improvement programmes led and implemented at both a regional and local level.
However, any continuous improvement activity – often built around frameworks such as the Shewhart cycle or DMAIC (Define-Measure-Analyse-Improve-Control) methodology – relies strongly on the quality, consistency and timeliness of the data it’s based on.
The industry is now comfortable with monthly performance metrics such as mean distance before failure in benchmarking performance. This data-driven approach creates a shared technical and operational reality which can be used both to identify pain points and align stakeholders with an end goal: most vitally the end-users, who must be able to see that the project addresses pain points which align with their experience and envision how any potential solution can be integrated with their daily life. At this stage the end goal might be as broad as improvements in MDBF or as specific as reduction in door irregularities.
The additional challenge comes from using data to articulate root cause and develop effective solutions. Infinitive Group’s work in industry has identified that companies tend to be aware of both their problems and the potential of data as a tool for resolving them. Many are stuck in one of two positions; either their data doesn’t seem to have the necessary resolution to divine the issue, or the sheer volume of data makes identification of signal in the noise beyond their current capability.
Fortunately, there are more tools than ever for addressing both issues. Infinitive Group has helped clients adopt a variety of approaches to make sense of available data streams, including machine learning, data modelling and AI applications. Even where organisations believe they lack the data to reach a conclusion, examination of existing disparate data streams often identifies correlations and synergies which can be used to reach intelligent and actionable conclusions.
It doesn’t matter what the challenge is – once a solution has been identified the only way to confirm its effectiveness is by monitoring measures of the output, both at the project and the broader operational
level. Modern data tools are of great value here too, allowing automated processing and monitoring of data for a consistent and meaningful measure.
This is the stage where early engagement with end-users and data-driven buy in from stakeholders pays dividends; the project either finds that the problem is solved (and that users can have confidence in an appropriate and effective solution) or articulates a gap between expectation and reality which can be addressed as a team for additional project cycle.
The additional project cycles are where the data-driven approach really comes into its own, however. Whether it’s a Shewhart/Plan-Do-Check-Act cycle, cycle or a transition, or a transition to Lean methodology, for any continuous improvement effort the data is what demonstrates that the project is having the intended effect, identifies further opportunities for improvement, and underpins the business case. The cycle is self-reinforcing; establishing a route to change using consistent data and KPIs offers operational improvements, then savings and justification of costs, then revealing new ways of working and further potential for improvements as teams grow more experienced and capable.
Infinitive Group recently brought this approach to a metro system experiencing earthing failures with their PSD earthing arrangements. The failures were safetyaffecting and caused significant disruption to normal operations. The operator was fortunate enough to have a data-rich environment and suspected that it was possible to prevent this issue through identifying precursor incidents, but was struggling to identify the relevant signal in the copious quantities of data the modern network produced every day.
Most critically, there was an open question around the number of potential failure conditions present on the network.
This kind of critical failure is always accompanied by a sense of urgency, and this was no exception. Infinitive mobilised quickly to capture all the available data and let the operator focus on maintaining a safe and satisfactory service. Interrogation of the common factors to the failure were established to establish the parameters of the failure; robust and consistent data systems were used to interrogate the data and find patterns; critical precursor failures to the earthing issue were quickly identified and the scale of the issue quantified.
At every stage the approach to data supported the work; it gave internal and external stakeholders confidence both that the problem had been correctly identified and the pattern behind the precursors was genuine, and that the proposed response
was commensurate with the scale of the issue. Creation of a shared data-led conversation kept all parties informed and working in the same direction.
This approach holds true even where project requirements are abstract and data is sparse to non-existent. Infinitive were offered a challenge by an industry partner working with a client on a new infrastructure project. The client was hanging cables in a new tunnel system and sought efficiencies beyond their current manual approach. Critically the sag between cable stanchions achieved during fitment had significant implications for cable tension over the required service temperature range of 125°C, and was highly dependent on ambient temperature during fitment. The necessary data was gathered manually, translated into fitment parameters and then manually checked later on, resulting in rework of the hung cable.
Infinitive identified the potential for hardware capable of capturing the relevant data and automating the process, and after extensive requirements capture with the client began development of what would become the IRRIS system. Fitted to their partner’s automatic cable installation vehicle, Infinitive’s millimetre wave radar system captured stanchion position with a high degree of accuracy despite the challenges of the poorly lit and contamination-heavy work environment.
The integrated system was able to produce fitment parameters and cable adjustments in real time and inspected the fitted cable as it went. The client benefited from efficiencies in construction and also from a new stream of consistent automated data for assurance purposes.
Whatever the method used, improvement programmes rely on metrics to establish the current state, articulate problems and opportunities, and confirm the effectiveness of solutions. Modern data approaches offer an opportunity to do this and bring stakeholders along for the journey – if industry can grasp the opportunity.
Address: 7 Lakeview House
Bond Avenue, Bletchley
Milton Keynes MK1 1FB
Tel: 01908 018900
Email: info@infinitivegroup.co.uk
Visit: www.infinitivegroup.co.uk
EN 50155: Isolation and EMC immunity
EN 45545-2: Fire protection
EN 61373: Shock and vibration immunity
Input voltage range: 2:1/4:1/12:1
3-years warranty
For more information, datasheet and certifications please visite our website www.tracopower.com
In the modern railway sector, the drive towards heightened passenger satisfaction and operational efficiency is unyielding. A significant leap towards these goals is the integration of advanced Passenger Information Systems (PIS) and Driver Cab Applications. These systems provide real-time updates, travel information, and entertainment to passengers, while also furnishing critical operational data to train drivers.
Central to these systems are robust and reliable monitors and panel PCs capable of enduring the challenging railway environment. Relec Electronics, a notable supplier in the railway electronics domain, offers a comprehensive range of EN50155 compliant monitors and panel PCs, meticulously engineered to simplify system integration, and enhance both passenger and driver experiences.
The EN50155 standard is synonymous with quality and reliability in railway electronics, ensuring equipment resilience against severe temperature fluctuations, vibrations, and other harsh conditions inherent to railway applications. Relec's
EN50155 compliant monitors and panel PCs are crafted to meet these rigorous standards, making them an ideal choice for deployment in both Passenger Information Systems and Driver Cab Applications.
Relec’s panel PCs epitomise durability, reliability, and functional excellence crucial for modern railway operations. Here are the key features that underscore its suitability:
Relec’s offerings, bearing the EN 50155 certification, have passed all requisite safety tests for electronic equipment on railway vehicles. Their rugged design, characterized by an IP65/NEMA 4 rated aluminium front bezel, effectively shields against dust, liquid spillage, and contaminants, ensuring seamless operation in harsh railway conditions.
Engineered with a fanless cooling mechanism, promoting silent operation and reduced maintenance and most importantly increased reliability and lower down time.
15″ Railway Approved Panel PC Back
The importance of secure I/O connections and power input in a vibrating train environment is paramount. Relec’s products feature IP65-rated M12-type I/O connectors, designed to protect serial, USB, Gigabit LAN, and DC power input connections against severe shock and vibration.
The modules boast a 10.4-inch ultra-bright, sunlight-readable SVGA TFT LCD display with 1,000-nit brightness levels, ensuring optimal visibility even under direct sunlight, which is crucial for both passengers and drivers.
While touchscreen controls are standard, certain actions are more intuitively executed via physical buttons. Relec’s front bezels can be customized to integrate a UIC61201 standard keypad, offering hotkeys and shortcuts for swift access to frequently used functions, enhancing user experience across various locomotive types.
The heart of the Panel PCs is the Intel® Atom® processor E3845 running at 1.91GHz, engineered to handle multi-tasking applications, delivering consistently reliable performance for railway tasks. Units also come with a standard 4GB DDR3 memory onboard, with the capability to expand up to 8GB as needed. They also come with two PCI Express Mini Card slots, facilitating wireless network connections and storage expansion, enhancing its adaptability to various operational needs.
Monitors and Panel PCs operate efficiently within a broad temperature range of -25°C to +70°C, making it resilient in harsh environmental conditions and fully compliant with EN50155 class OT3.
Optional features include a 5-wire resistive touchscreen for intuitive interaction and quick response.
Through Power over Ethernet (PoE), panel PCs facilitate remote surveillance by connecting to onboard IP cameras, displaying live video feeds from inside and outside passenger cabins. Wireless connectivity to cellular networks enables real-time communication with monitoring centres, ensuring a seamless flow of information. I/O ports provides a wide array of I/O outlets including two isolated RS-232/422/485 serial ports, one isolated CAN bus, two isolated Gigabit LAN ports, two USB 2.0 ports, one isolated DIO (6-IN/2OUT), and an isolated DC power input for versatile connectivity.
In conclusion, the integration of EN50155 compliant monitors and panel PCs is a transformative stride for railway operators aiming to enhance both Passenger Information Systems and Driver Cab Applications. Relec Electronics is at the forefront of this transformation, offering a blend of cutting-edge technology and stringent industry standards, promising
a harmonious blend of reliability and innovation in delivering an enriched railway experience.
To find out more about the groundbreaking railway approved Panel PCs, visit the Relec Electronics website or contact our sales team at sales@relec.co.uk.
Established in 1978, Relec Electronics is a UK-based distributor specialising in power conversion and display technologies. With a strong emphasis on customer service and an unmatched product range, Relec Electronics works alongside top-tier manufacturers to provide industry-leading solutions that meet the most exacting standards.
Tel: 01929 555 800
Email: sales@relec.co.uk
Visit: www.relec.co.uk
Climate change is making track drainage a more critical issue than ever before. Lanes Group plc is using its national reach and impressive service portfolio to help customers respond to the challenge
The response to a call that Project Manager John Barkley took serves to illustrate the can-do mentality and capability in the rail division at Lanes Group plc. A tier one contractor had a remit to remove a 123-metre length of 496mm-diameter twin wall drainage pipe from the 6ft within Network Rail infrastructure.
Part of the scope was to redirect the 496mm drainage pipe to the down cess side to enable the client to install S&C. The works included deep excavation using temporary works.
A 224-metre length of 225mm-diameter plastic drainage pipe also had to be installed, with all work completed in the available possession.
It was the sort of project that, ordinarily, would be planned over several months. The start date for this scheme was just three weeks away.
Despite these pressures, the project at a new logistics park in Northamptonshire was completed in eleven shifts over two weeks in November 2023. Work had to be managed flexibly due to stops caused by the discovery of hidden assets. But it was completed on time.
The client was impressed. ‘At Lanes, we see one of our main tasks as taking away our clients’ pain’ said John Barkley, a 25year veteran of the rail industry, having previously worked for multiple tier one contractors. ‘We can solve the problems, so they don’t have to.’
It is an approach that is winning Lanes, supported by its rail specialist subsidiary, UKDN Waterflow (LG), which holds a principal contractor licence (PCL), increasing volume of rail work. The size and capabilities of Lanes, the UK’s largest independent drainage and utilities specialist, is also a factor.
The company has 20 commercial depots dotted all across England, Wales and
Scotland, from Aberdeen to Plymouth.
These are backed by 16 specialist utilities and service hubs. The services they deliver include pipe lining, digital network installation, industrial cleaning, wet/dry heavy vacuumation, tankering, professional services and, of course, rail maintenance.
It is the geographical spread of these resources and the high level of expertise and experience of the Lanes teams that rail contractors value.
The company has been active in the rail sector for more than 30 years. It is well known in the industry for its work for Transport for London (TfL) on the London Underground. Lanes is the main drainage maintenance contractor on the Tube. It also delivers a major FM contract for TfL covering buildings and structures
maintenance, plumbing, locks and gates, and vegetation control, among other tasks.
Its teams also deliver drainage services for London Overground and on large stretches of the Elizabeth Line. The challenges of delivering rail services in long tunnels, arguably, makes Lanes primary rail drainage experts.
The company is now implementing a strategy to leverage this know-how on behalf of other rail clients across the UK. This involves integrating its UKDN Waterflow (LG) teams within the Lanes Division. At the same time, more drainage engineers at depots across the UK are being put through PTS training.
This is turning what was once an ad hoc rail drainage services into a powerful and highly-capably national one, capable
of responding flexibly to any rail drainage project, anywhere in the country.
The skills and qualifications of UKDN Waterflow (LG) technical managers are key. John Barkley is a contractor’s responsible engineer (CRE). A colleague is a contractor’s engineering manager (CEM).
If necessary, the team can develop their own environmental plans and construction phase plans, as well as bespoke work package plans and task briefing sheets, and carrying out walk-outs for clients. They can also carry out full lifecycle project management, from intake and initiation to closure. If a client wants that ‘pain’ taken away.
These are capabilities that Bill Waring, Lanes Group Rail (LGR) Lead, is finding rail contractors are keen to know more about. ‘There is no other rail supplier that can deliver the drainage, and related underground services, in the way Lanes can on a national basis’ he said.
‘The offer is all but unique. At a time when rail contractors and Network Rail are looking to work collaboratively across multiple, complex projects, with stretching efficiency and sustainability objectives, I believe Lanes has a compelling proposition. We are also looking to work with delivery partners across all types of rail infrastructure. Lanes is already working extensively on HS2 in the Midlands.
‘We also deliver drainage services on tram networks, strategic rail freight interchanges, and rail maintenance depots, and we have the capacity to do much more.’
Lanes can flexibility deliver five key services – individually or as part of a coordinated work programme – for tier one contractors
anywhere in the UK. The first is the broad range of drainage services that can be delivered through LGR – including CCTV surveys, drain unblocking, track drainage and culvert cleaning, pipe and culvert lining, and track drainage renewal.
For example, Lanes is a national leader in ultraviolet cured in place pipe (CIPP) lining. In 2022, it installed the largest ever UV liner in a 1,800mm stormwater drain in Corby. Its teams have also installed numerous liners in rail culverts. This expertise is backed by the project management expertise of John Barkley and his colleagues at UKDN Waterflow (LG), and their civils know-how.
The third is the fibre-optic ducting installation expertise of Lanes subsidiary Lanes Infrastructure, which can support the digital networks needed by modern rail systems. LGR also has its own inhouse drain rail survey capability, with the Unmanned Aerial Vehicle (UAV) equipment, software and Network Rail flight approvals to carry out aerial surveys over tracks and other rail infrastructure.
Finally, Lanes Professional Services, which delivers site engineering surveys and investigations, plus ground and infrastructure design services, has a strong focus on the rail sector.
Bill Waring said: ‘Combining all these services allows Lanes to provide a highly agile turnkey drainage investigation, maintenance and improvement service for rail contractors. The efficiencies and sustainability advantages, combined with potential cost and time savings, are proving attractive to clients.’
An ongoing works programme to survey track drainage at 22 locations across the Western and Wales Region is a case in point.
LGR is carrying out the surveys for Colas as part of a CP7 plan to upgrade track drainage at flood hotspots.
Network Rail has announced it is doubling its investment in measures to tackle climate change, spending £1.6 billion over the next five years. A significant portion of that money will be spent on drainage upgrades.
The Colas survey work, project managed by John Barkley, can draw on drainage teams from Lanes depots across the south of England and Wales.
Data is being analysed at Lanes’ national CCTV survey processing centre in Manchester, ensuring reports are prepared to Colas’s precise requirements and provided in a timely way.
John Barkley said: ‘The programme is going extremely well. We have a good relationship with colleagues at Colas. As we have depots across the survey region, we are completing the work flexibly and sustainably, with the smallest possible carbon footprint.’
A commitment to sustainability is a strong element of LGR’s service offer. Lanes has the UK’s largest fleet of recycler jet vac tankers. These can filter and reuse their water, making best use of the resource, improving productivity by 62 per cent and reducing journeys during work shifts. Lighting towers used at night run on hybrid generators, reducing fuel consumption and carbon footprints by up to 94 per cent and minimising noise levels.
Similarly, onsite accommodation and welfare units are eco- and user-friendly with green functionality that greatly reduces CO2 emissions and running costs.
LGR Director Martin Balcombe said: ‘Strong collaborative relationships are at the heart of high performance rail programme work. We are always determined to foster such relationships. Lanes understands the goals of our rail clients and can deliver drainage and other work packages that act as a one-stop shop, leveraging high levels of value for both them and end-use customers alike.’
Address: Lanes Group
16 Lamson Road
Rainham RM13 9YY
Tel: 01708 528770
Email: railenquiries@lanesgroup.co.uk
Visit: www.lanesfordrains.co.uk
LinkedIn: www.linkedin.com/company/339851
Facebook: www.facebook.com/LanesGroupplc
Twitter: twitter.com/LanesForDrains
Coljoint have a vast knowledge and understanding of the railway industry methods of installations, we can complete full electrical installs, refurbishments, rewires or upgrades of the railway stations, station carparks, substations, TP huts, DNO cabinets, whether that sits within the depots, track or non-track side locations
Daniel Collins founded Coljoint in November 2013.
Coljoint electrical services is an electrical installation company based in the UK, covering Greater London and the Southeast. Coljoint specialises in the complete installation of electrical services for Domestic, Commercial, Industrial and Rail services including the installation of MV/LV distribution systems.
How long has Coljoint been in business?
I set up Coljoint in November 2013, so this year, we are in our tenth year. Happy anniversary Coljoint!
Where did the ‘name’ Coljoint come from?
I wanted a name that was short, personal, but not too personal that it couldn’t become a brand, the COL stands for Collins, and the JOINT stands for cable jointing. My wife and I came up with the name, we did some research on Google, and on companies’ house, and there were not any similar companies with our name, so we went with COLJOINT LIMITED.
What was the inspiration behind starting Coljoint?
While working for Balfour Beatty ‘Traction Power’ I felt like there was a market for a small electrical company, able to offer the specialist services that normally a bigger
company could only offer. It was never my intention to leave Balfour Beatty, but as time went on, my passion for wanting to try something on my own, came stronger, so I made the jump in 2014.
Tell us about your career before Coljoint?
I completed my electrical apprenticeship with Balfour Beatty, my first project at the age of 16 was the refurbishment of the Royal Opera House at covert gardens, but after two years I was transferred to their Rail division ‘Traction Power’ at Greenwich, it was a much smaller team than I was use too, but they were a unique team, specialising in the refurbishment and upgrades of LUL substations, when I joined they were upgrading the Northen line, we were contracted to replace the complete switchgear and the associated cabling within the substations. Our teams were small groups of four to five operatives, working days or nights to get the job done. It was here I really started to enjoy my time at
Want to know more about Coljoint?
Tel: 0333 210 0343
Email: info@coljoint.co.uk
Visit: www.coljoint.co.uk
work, we had a great team, many of which I am still very good friends with today.
At the age of 21, I had built up the knowledge and respect of my engineers to be trusted to run my own sites, this came with a company van, a mobile phone, and a company credit card, when I left Balfour Beatty in 2014, I had completed 18 years’ service, obtaining a JIB grade of an ‘technical supervisor’ running three to four sites with a squad size of around 15-20 men.
When did you become a cable jointer?
I was already experienced in many methods of containment installations but when joining the traction division, I learnt how to install HV & LV switch panels and the cabling connections between the two, within a short period, I became a cable jointer, joining cables ranging between 230v to 33KV, I can joint lead to XLPE, with either heat shrink, cold shrink or resin style joints.
How have you seen Coljoint grow over the ten years?
In the early days, I was rewiring houses and completing small remedial works for my local estate agent. I was able to earn a week’s money in just four days, so being self-employed seemed OK. We quickly grew to a team of four after only trading for two years, with three electricians on the tools and me jumping on and off the tools when not pricing new works, seem to work well, we were now able to start taking on larger projects. We now employ five office staff, two apprentices, five site leads/ supervisors and 22 electricians with a fleet of twelve vans.
What kind of challenges have you faced since having your own business within the electrical industry?
Balancing the workloads, it is always a challenge, we either seem to be too busy and wondering if we should turn work away or so quiet, we are having to let contractors go. Managing cash flow is another challenge, the key to any business growth is cash flow. We’ve been quite lucky securing projects
to date to allow us to jump from one client to another.
How do you make your business a good place to work?
I believe if you treat people how you want to be treated you will always create an environment where people want to work as they can trust you. I’d like to think that anyone that works for Coljoint feels like
they're in a position where they can contact me directly, any problems or issues which arise, we would work with them to find a solution.
Our office management is in constant communication with our site leads ensuring that the office mentality, of our forward thinking approach is pushed down the line to our site leads and electricians under them, this ensures that our teams feel like they are part of the company as opposed to the office just barking orders when required.
I regularly make site visits to see our teams, and praise them on the quality of the installs, the sites are always clean and tidy, it’s almost like they knew I was coming.
What kind of products and services does Coljoint offer?
We have a vast knowledge and understanding of the railway industry and the different methods of installations, we can complete full electrical installs, refurbishments, rewires or upgrades of the railway stations, station carparks, substations, TP huts, DNO cabinets, whether that sits within the depots, track, or non-track side locations.
We also have a commercial side to the business, which can offer the complete electrical design, installation, and commissioning package. Our works consist of electrical fit outs and refurbishments of offices, bars, and shops.
We have quite a passion for smart lighting systems, we have completed many, automotive homes installations, integrating smart lighting system, home cinema rooms, swimming pools, CCTV, which all integrates with their music and TV systems, it’s the opposite spectrum to rail but it has its own
challenges which we really enjoy and gives a lot of job satisfaction when completed well.
What projects you are currently working on?
For the past three years we have been assisting Bam Nuttall, on their CP6 works. We were contracted to complete the electrical installation for their, NSCD safer isolation packages, to date we have successfully completed 52 sites, and helped towards Bam Nuttall in achieving, a gold site award, twelve silver site awards and a load of bronze site awards, issued by Network Rail.
We were also awarded Trimley Station rewire, in Norwich by the KN Group (Circet). The works consisted of a new 100a DNO supply followed by a full rewire of the station platform, carpark, and the 100-yearold heritage foot bridge crossing the track.
We are completing a large show at Waterloo Station for a private client, we are transforming the old Waterloo Eurostar carpark into an Alice in wonderland walk through themed show. We have already completed a small restaurant/bar, located within the sidings, called the ‘Rosarium,’ this was phase one of three to get the public aware of the show, which is coming, now were doing the downstairs bar and the show area which is due to open June 2024.
We have covered a lot of the Workspace group projects, Workspace provides small offices for small companies, they tend to buy old, derelict warehouses and convert them into multi occupancy offices, to serve smaller businesses to date we have refurbished 22 Offices.
During 2021-22, we completed a large domestic project, it was a new build for a private client which consisted of 185
lighting circuits, fed from seven lighting control panels over three floors, our client wanted to build his dream home, incorporating all electrical services as a smart home automation system. Coljoint worked closely with him to ensure all aspects were able to be controlled by one device.
What other rail projects have you completed over the last five years?
Before starting works on CP6, we were picking up a lot of works from Kier on CP5, they were only small contracts, mainly completed during weekend shutdowns, but it gave us the opportunity to show people what Coljoint can offer:
• Power Supply Projects – Sim 119 signaling works - 70 x LOC’s.
• Laing O’Rourke – Bond Street Station –256 LVAC terminations.
• Kier – New FSP Works.
• Kier – HVMS Legacy works.
• Kier – NSCD Phase 1 works.
• Kier – Sim 119 signalling works 312 x LOCs.
• McNicholas – Sim 119 signalling works –70 x LOCs.
• IPS Power – Cable jointing Ashford shopping centre.
When a client comes to you with a particular problem, what is your process for coming up with a solution, and how closely do you work with clients throughout the projects?
All of our works to date on the rail have been fully design sites, if only it was as straight forward as that, most designs only show the final layout, which is fine for a new build, but nothing is new on the rail, so how
do we get from A to D when B & C are still in situ, with Coljoint’s years of experience on the railway our clients can rest assured that we can assist in finding a solution to overcome this, by working closely with
our clients we are normally able to pick up on any of these issues at the early site surveys, so by the time the install team gets to site the problem is already resolved and programmed in.
What new projects are you moving onto?
We have recently submitted a few new tenders, our works over the past five years has put us in a strong position moving into CP7, so we are looking forward to 2024 with some interesting things coming up!
What success have you gained over the years?
For me ‘success’ has come in two parts. Firstly, our clients. We still work with most of our original clients, they have stuck by us allowing us to grow under them, which now puts us in a position to take on their bigger projects, we have always been loyal and transparent with our costs and upheld our client’s end goal. Ensuring the projects are completed on time and within budget. Furthermore, our clients have been recommending us to their circle of friends, giving us continuation of works and even more growth. For every project we worked on, we would almost always gain a new client.
Second would be maintaining the quality of installs, from growing Coljoint from a one-man band to a larger team, ensuring we maintain the same quality of install, has always been my goal, the saying ‘you’re only as good as your last project’ is so true. We have achieved this but recruiting the right people, while assisting with completing in house training, and allowing our team to see a progression path within Coljoint, so by investing in operatives, we have maintained our quality of install and offering job security at the same time.
What is next for Coljoint?
I often get asked, what is my five-year plan. Well, I would like to continue with Coljoint’s steady growth as seen over the last five years, growing slowly has allow us to maintain our quality across our teams.
We have recently employed a Quality Compliance Manager to assist us in the office with completing our electrical designs as well as ensuring our site teams are installing to the current standards, we have introduced in house CPD training to bring our electricians up to date with the latest IEE electrical regulations to the 18th edition amendment 2.
With the new technology changing so quickly, we are seeing the wiring regulations being updated more regularly, as they are rapidly trying to keep up with the times.
I would like to think we are in the driving seat for being able to advise our clients, with the latest requirements to meet their electrical requirements on their projects. We have just redesigned our website to show case our recent works complete, hopefully to put us in a good position for CP7.
Bender is one of the world’s leading providers of solutions that make electrical infrastructures smart and safer.
An approved Network Rail supplier, Bender UK has worked in the industry for over two decades to ensure maximum availability, prevent downtime, maintain uptime, and ensure operational efficiency.
Bender continuous insulation monitoring and earth fault location solutions measure system status and pinpoint the location of failure and degradation, and issue warnings and alarms to improve rail safety and services for staff and passengers.
Bender’s rail capability includes monitoring signal power, points heating, rail crossings, underground networks and rolling stock, supported by predictive maintenance and software solutions.
www.bender-uk.com
Yannick Longbottom, Rittal’s Vertical Market Manager for Rail & Telecoms, describes the company’s best practice approach to safeguarding
Rittal offers infrastructure solutions for all aspects of railway technology, across the railway Telecoms and Signalling network at stations, trackside, and in tunnels, supplying Network Rail, ScotRail and Crossrail. Passenger numbers are rising on the UK’s railways, with industry predictions suggesting there could be an extra one billion rail journeys by the mid-2030s (Network Rail). This extra demand means that additional capacity is urgently required.
The challenges facing the network are around how to upgrade and modernise ageing infrastructure and legacy systems while avoiding the huge cost and disruption created by large capital construction projects, as well as managing more hightech equipment.
The aim is to expand the scope of the existing infrastructure to increase the
number of trains and connections, while also creating a more reliable service with minimum upheaval to passengers.
To deliver this, management has turned to targeted conventional interventions, along with digital technology deployed
across the network. This is now supporting the development of new signalling and telecoms technology, to optimise performance and reliability and keep passengers better informed about train running and delays.
All this has created an exponential growth in the amount and speed of data collection, gathering and processing to allow engineers to support operational delivery, and support better monitoring and maintenance of existing assets.
There is a concern, however, as to how all this new digital equipment can be adequately protected. Much of it has needed to be placed trackside and on station platforms. This means, of course, that it is vulnerable to acts of theft, vandalism, and extreme weather events, as well as the kind of shocks, vibration, temperature
fluctuations, moisture and/or dust ingress that are impossible to avoid near a busy railway line.
Aside from these environmental issues, there is also a need to create and maintain the inner working conditions that are required by the technology for optimum performance and longevity.
Technology of this sophistication and sensitivity requires a closely controlled operating space to work reliably, costeffectively, and to its full capacity, over its lifetime. Electrical components struggle under extremes of temperature – both hot and cold – and problems with external applications that have been heated by solar gain have been rising in recent years. The reason is largely because the UK has seen ten of its warmest-ever years since 2003, according to the Met Office records, and that’s a trend which is likely to continue.
Of course, the heat doesn’t just encroach from outside. The technology itself also generates considerable amounts of heat; and this only increases with more electronic and electrical power.
All these considerations mean that, as well as the type of technology that is employed, close attention has to be paid to the specification of the enclosures that house that technology.
Where legacy applications are still in use, these tend to be housed in enclosures that are based on outdated, legacy design principles. These older enclosures are not designed for housing the latest equipment, and any attempt to do so is likely to cause components to overheat, as well as allow excess ingress of contaminants, and create an increase in internal condensation.
Where this has happened, rail systems are routinely failing, railway lines are being closed, and the network has been beset with
communications issues. Maintenance on railways is expensive and never without risk – and this work is arguably avoidable.
So, how does the rail industry tackle these problems and increase its resilience in a cost-effective way; one that is futurefocused and based on ‘right first time’?
In answering this, we need to consider a modern enclosure’s design and build principles, including construction, design, materials, testing and IP ratings to understand how they can all affect an enclosure’s ability to keep the elements out, while maintaining optimal conditions for modern electrical and electronic components.
Enclosures can be constructed as single- or double-skinned units (i.e. two material layers separated by an air gap). New digital technology of this type typically needs to be housed in double-skinned enclosures for the following reasons:
• Temperature management.
• Lower condensation.
• Higher security.
Solar gain, where heat is absorbed directly from the sun’s rays, is significantly reduced with double-skinned enclosures because the air gap between the two skins creates a buffer between the inner compartment (containing the equipment) and the sun.
A single-skinned enclosure will essentially act as a radiator, absorbing and then dispersing heat. This process will only add to the heat already inside the enclosure, much of which is generated by the equipment itself.
As we’ve indicated, system components typically fail more frequently as
temperatures rise. In this case, the difference in the internal temperature between double- and single-skinned housing can be as much as 15oC.
These are entirely preventable failures, but ones that will require engineers to be deployed, along with the purchase and transport of replacement equipment, and of course the removal and waste of the broken equipment, all of which increases both op-ex and its carbon footprint.
If excess heat doesn’t cause outright equipment failure, it will almost certainly reduce its working life; some electrical components designed to last for ten years at 35oC temperatures, may only last for one year in 70oC.
Note: An outdoor enclosure should also have some form of climate management in place, whether that is passive, using louvres and filters, or active from fans creating a throughput of air to help remove the heat. Unfortunately, in high summer ambient temperatures, neither option may offer much in terms of heat transference. In these circumstances, cooling based on refrigeration is required. This will require a fully sealed enclosure; something that seems to be the direction of travel for many applications.
Condensation inside an enclosure can cause water droplets to form on the inside enclosure surface and pool on the floor. With single-skinned enclosures, these pools of water will collect around the electrical equipment, creating a very real risk of the equipment shorting out. In double-skinned enclosures, the condensation tends to collect between the inner and outer walls.
Some applications have tried applying insulation boards to the inside surfaces
of single-skinned enclosures to manage internal temperatures. But lining an enclosure in this way prevents it from being ventilated, and ventilation is always vital to prevent condensation forming.
Enclosures are large, conspicuous, and often sited in publicly accessible areas, making them a potential target for thieves. A welldesigned enclosure made of interlocking, carefully configured panels can provide greater security, making it much more difficult for would-be thieves to gain access to the technology, such as telecoms equipment and batteries.
Some enclosures are constructed as shells rather than panels, but this makes them a lot more difficult and expensive to repair. Any damage to one side will mean the whole enclosure will need to be removed from site, to be either fixed or replaced. Similar damage to an enclosure made of panels is considerably easier to repair; the damaged panel is simply removed and replaced. Not only is this far quicker, it lowers the cost of the repair, ensures the system is up and running again sooner, and again, it lowers the carbon footprint.
That’s not to say that single-skinned enclosures are never effective; for certain applications, they are fine e.g. where the equipment is mainly cabling.
Stainless steel or galvanised steel are popular material choices for enclosures, largely because they typically last a long time. However, aluminium is often a better and more cost-effective solution for rail applications outdoors. It is relatively cheap, and much lighter than steel, so heavy lifting gear isn’t necessarily required. It also has impact properties that are less prone to cracking compared with stainless steel and any exposure to water will create a layer of aluminium oxide that bonds to the surface and doesn’t flake (unlike the rust on a stainless steel enclosure). Powder-coating the aluminium will add an additional layer of protection and help extend the lifetime of the enclosure.
Smaller systems can be housed in GRP enclosures, ideally with Class 2 protection (i.e. insulated to 1,000 volts). GRP enclosures will need outdoor approval ratings because of their potential to fade/discolour and warp in the heat. Nevertheless, they’re a good option for small remote communications or telemetry devices, relays, and terminal boxes, as well as lighting systems.
As mentioned earlier, enclosures placed near railway lines must be able to withstand challenges like shock and pressure, and nowhere is this more obvious than within tunnels. Enclosures located in tunnels must be tested and certified to be capable of withstanding the pressure differentials created by fast-moving passing trains; these differentials are so powerful, they can easily remove an enclosure door. They must, of course, also be fire resistant.
IP ratings for outdoor enclosures are widely misunderstood. They are designed to be an indication of the protection offered by the enclosure against solid and water ingress. However, they are based on tests carried out under laboratory conditions, which don’t replicate conditions by a railway line.
An IP66 rating, for example, tests the enclosure door seal resilience under high water pressure. But this is not a good indication of its resilience in the face of wintery weather where rainwater which collects and can freeze against the door, causing it to expand with such force that it will split the seal. Plus, IP ratings will be broken anyway, every time an engineer opens the door.
Rather than IP66, rail engineers would almost always be better off choosing an IP55 rating, which is more than sufficient for UK outdoor conditions, coupled with an enclosure design that protects the seal; for example a physical barrier between the door seal and external environment. This can be achieved in a number of ways but a protruding roof canopy or rainwater strip to stop rainwater from being trapped between the door and the body wall is one of them.
These features will ensure that an outdoor enclosure will last longer, and they provide better protection for the equipment inside because the seals stay intact.
As we’ve outlined above, the current speed of innovation and development is so great, that planning ahead for further changes isn’t a luxury – it’s a necessity. Modular systems offer cost-effective housing for modern technology, thanks to their rapid scaling potential.
They provide a fast, effective option for expansion and for combining services such as signalling, communications and power, each separated by hard divides and with independent door controls for enhanced security.
Choosing the right enclosures for assets spread across a divested rail network is an area that should always be given close attention if the systems within them are to be adequately protected.
Temperature control and condensation can quickly knock-out electrical equipment, causing disruption and misery for passengers, as well as increased capex and a higher carbon footprint for the rail companies.
To ensure the product selected will provide a long-term cost-effective solution, it always makes sense to involve a company which has both the relevant expertise and the widest range available.
Tel: 01709 704000
Email: information@rittal.co.uk
Visit: www.rittal.co.uk
The next level of inter-car jumper solutions
■ Longer lifetime due to optimised design against water, dust and ice
■ Time savings during the whole installation process due to free access from all directions
■ Weight savings due to the replacement of distribution boxes and shorter cable runs
■ High flexibility due to full compatibility with the whole Han® HPR portfolio (retrofit)
HARTING has developed new solutions for rail vehicles which focus on the safety and durability of the entire infrastructure. These products are part of a complete system of cabling that extends from the vehicle roof to the underfloor distribution.
The Han® HPR (High Pressure Railway) VarioShell is a housing system which has been specially designed for jumper applications. Thanks to a circumferential internal seal and mounting frame, the two-piece housing/hood achieves an IP69K rating. As the cover is removable, the housing/hood can be installed from both inside and outside the rail vehicle. This also simplifies servicing and maintenance because the housing cover can be opened and faulty conductors or contacts replaced without disconnecting all the connections.
The contours of the VarioShell allow dirt deposits to slide off while channels guide water away from the housing screws so that rust does not form. Special curvatures on the upper side ensure that ice and snow slide off without exerting pressure on the wall and housing, increasing service life.
The VarioShell is an open system that also houses mounting frames, cable managers and shielding plates to route and hold cables with different diameters. It can be used as a surface or panel mounted housing and is a robust alternative to distribution boxes for installation on the roof, outer wall or bogie.
The Han® HPR HPTC (High Performance Transformer Connector) has been developed to meet all the requirements of the rail market. Hoods, housings and cable glands have been optimised for outdoor use, ensuring the connection between pantograph, transformer and train busbar remains stable over the long term. Existing contours on the transformer can be reused, meaning design changes are unnecessary.
This product has been specially designed for simple assembly, maximum safety and to minimise the number of components used. A crimped contact on the cable side is inserted into a three-part, touch-proof
insulating body and there is a cable gland that protects against dust and moisture whilst also forming part of the shielding, absorbing residual currents and transferring them to the housing.
The hoods and housings are metallically contacting on all sides, which means the cover and underside are connected across the entire contact surface. This is a new development, being the first transformer connector that is specially designed for shielded connections. Collecting and discharging residual currents is achieved with the Han® HPR HPTC P800 thanks to its two separate contact zones. It is directly connected to the flange housing by a surface on the underside and there is a thread on the upper side for a potential grounding, which dissipates the remaining residual currents.
Neither shrinking nor taping are required in the assembly process and the interfaces are quick to prepare; simply crimp the contacts, insert the insulating body with shield contact into the housing, close the cover, and the cable side is ready. Two coding elements in the panel mounted housing enable 16 different possible combinations and one connector is enough for the transformer connection, meaning there is no risk of confusion.
The Han® HPR TrainPowerLine (TPL) replaces existing solutions such as UIC, power or Y-distributors for train busbars. It is tailored to modern trains running in a network and offers weight advantages of up to ten kilogrammes per rail vehicle compared to previous standards. As a result, very little space is required to reliably supply all the electrical equipment and systems of the train.
Following requests from customers, the application was simplified considerably. A uniform solution replaces the many variants that were previously required for busbar construction and the number of parts used has been significantly reduced. At the same time, safety is top priority: male and female contacts are designed to be touch-proof and there are ground potentials on the top and bottom of the housing. The contours of the
TPL also effectively remove dirt and ice to the sides.
Previous interfaces for the underfloor were often hard-wired. The TPL is designed so that all connection points are now pluggable. The housings are equipped with Han® HC Modular high-current contacts that transmit power up to 800 A / 5100 V DC / 3000 V AC. The housing is based on the Han® HPR design and is made of corrosionresistant aluminium die castings. Therefore, the TPL is ideally suited for use in harsh environmental conditions and outdoor applications.
This interface is a uniform connector design for the entire underbody distribution system of a train. Its advantages include shorter installation times, more economical use of materials, weight reduction and standardised assembly processes.
HARTING is also constantly innovating products and solutions to drive advancements in transportation. Currently, there is an ongoing drive towards weight reduction within the rail vehicle construction sector as manufacturers strive to minimise energy consumption to improve efficiencies. One way of delivering savings is reducing the weight of components.
With the Han-Eco®, HARTING has developed new innovations for their industry standard Han connector series. The range contains a series of hoods and housings manufactured from high-performance, glass fibre-reinforced, polyamide plastic, which offer substantial weight savings compared to traditional metal connectors.
By switching from metal to Han-Eco®, you can achieve substantial weight savings of up to 50 per cent per connector. As well as being lightweight, Han-Eco® also supports modular inserts, meaning data, signal and power options can all be combined into one standard-sized industrial connector. Not only does this make them versatile, but it also further reduces the space requirement for connectors within the train. Han-Eco® complies with standards IEC 61948 and EN 45545-2 HL3 and is fire-resistant according to UL94 V0.
HARTING are also supporting retrofit solutions for the European Train Control System (ETCS) and have a wide range of railapproved products and solutions to support this challenge.
Interior fitting and retrofit work in trains is often awkward due to restricted space conditions, meaning easy installation is crucial. The M12 PushPull is the solution, offering handling, time saving and reliability benefits. M12 PushPull uses a tool-free connection, meaning the assembly density can be significantly increased, helping to save valuable space.
Used in combination, HARTING’s preLink® system and Ha-VIS EtherRail® cables allow you to build secure data networks in trains. EtherRail® cables are specially designed for railway requirements whilst the preLink® contact block allows you to pre-fabricate data cables outside the carriage before installing them, resulting in a reliable, simplified assembly.
As well as product systems, HARTING also offers customised solutions for rail vehicle technology. With specialisms including cable assemblies, box builds and inter-car jumpers for the rail market,
HARTING uses its experience to design and create custom solutions that meet your exact requirements. All customised products are built and tested at their fully IRIS-certified manufacturing facility in Northampton and are based on market-leading connectors from the extensive HARTING range, including M12 and Han-Modular®.
The company has recently retained their prestigious Silver Quality Performance Level award from the International Railway Industry Standard (IRIS). Silver Performance is currently the second highest performance level issued by IRIS and is a significant achievement for HARTING, making them one of only two UK companies to receive Silver status and putting them in the top five per cent globally of all IRIS certified companies.
Inter-car jumpers are designed to run connections between train carriages, including roof or underfloor systems, ensuring a reliable supply of data, signals and power along the train. The Han-Modular® series allows you to create a versatile solution by combining individual inserts for different transmission media into standard-sized industrial connector housings.
The series offers over a hundred different inserts, enabling a wide range of customisable combination options.
For example, as the demand for data communications in rail vehicles increases, powerful network and data interfaces are required to power information systems and fast, reliable internet access. The Han® Gigabit module enables Cat. 7A transmission in the inter-vehicle area and delivers higher frequency bandwidth for the flow of data. The interface is also shock and vibration resistant according to EN 61373 and shielded against electromagnetic interference (EMC).
No matter what the degree of complexity, HARTING have the capacity to produce bespoke, project-specific solutions to suit your needs, including installing components, efficiently routing cable harnesses and fabrication. To further assist you, their design team can create a 3D CAD visualisation of your build beforehand to ensure absolute accuracy before manufacturing begins.
To learn more about HARTING’s range of rail products and solutions, get in touch via the contact information below.
Email: salesUK@harting.com
Visit: www.harting.com/UK/en-gb/markets/ transportation
A professional and customer focused accredited laboratory with experience in diverse industrial sectors testing products for vibration, climatic, corrosive atmospheres, ingress protection and shock
Axis Test Laboratories is a provider of comprehensive environmental testing that enables designers and engineers to qualify and evaluate the behaviour and performance of their products whilst ensuring all legal requirements are satisfied. With experience in offshore, deep sea, rail, road and military product approvals, the procedures employed by Axis Test Laboratories can be applied to highlight where the exposure to environmental conditions can present a potential hazard or cause performance issues to equipment.
The company was established in 2010 to meet the testing requirements of the marine and subsea sectors, and has expanded so it now provides environmental testing to industries ranging from; rail, military, aerospace, industrial, as well as packaging and transportation testing.
The team are on hand to offer extensive advice, drawing from the experiences of an expert team of Engineers to guide customers through every step of the testing process.
This expertise allows Axis Test Laboratories to provide insight and potential solutions, to shorten development times and help reduce the costs by finalising an optimal design as quickly as possible.
Vibration testing involves the repeated oscillation about a central point at a specific level and frequency, meant to mimic the effects of ‘shaking’ experienced by products in everyday use. This shaking can be a result of nearby reciprocal machinery or the uneven road surface experienced during transportation from factory to customer. Imbalances in the construction can stress the materials and cause metal fatigue, which can result in cracks, fractures and breakages resulting in the product not being able to carry out its intended function and potentially resulting in injury. Vibration testing identifies weaknesses in the construction and can locate problems before they occur.
The assessment is not just limited to the physical observations. For many
products, full functionality is a requirement, particularly for safety critical equipment. As part of the vibration test schedule at Axis Test Laboratories, inputs and outputs of systems can be monitored to ensure no loss in signal or degradation of performance and that the equipment under test continues to function as normal both after and during any testing experience.
Axis Test Laboratories can offer tailored testing strategies to give a broad analysis of how a product is affected by exposure to corrosive atmospheres. Multiple exposure periods are offered, ranging from several days to multiple weeks depending on the specified requirements.
Corrosion testing involves creating a damp, warm, high concentration salt atmosphere in which a product can be observed to see how resistant the materials are to the corrosive effects of the chemicals which occur naturally in outside conditions.
The effects of a corrosive atmospheres can adversely affect the performance of
products, and can even render products useless. Corrosion testing, as performed at Axis Test Laboratories is an efficient way to ensure the effectiveness of protective coatings and to identify any areas that may cause issues over the lifetime of a product.
Climatic testing is useful in various industries to examine the effects that extremities of environmental conditions have on the functionality and reliability of products. Climate can affect the structural integrity of materials, can contribute to unexpected problems with electronics and interfere with safety critical sensors.
Performed to the highest of good engineering practices and by the methods outlined in BS EN 60068. Testing is carried out with accreditation from UKAS ensuring confidence in the robustness of the practices, precision of the equipment and accuracy of reporting.
The following conditions are trialled as part of the climatic testing at Axis Test Laboratories:
• Cold – simulates the effects of freezing conditions and general areas of low temperature such as what may be experienced in the Arctic and Siberia.
• Dry heat – ideal for simulation of hot, dry conditions such as engine rooms and deserts.
• Humidity – this test can detect problems caused by damp atmospheres. Changing humidity and temperature can cause condensation to form in areas of the product which may inhibit correct operation.
It is essential that rail equipment is proven to be safe and reliable, and is able to withstand any harsh environment. Axis Test Laboratories provides a range of suite testing to ensure that all equipment meets the rail industry requirements.
The types of testing done includes:
• Vibration.
• Shock and bump.
• Salt mist and corrosive atmospheres.
• Cold, Dry heat, Cyclic Humidity, High/ Low Temperature Storage.
• EMC, Stress and Voltage Testing.
The unique business model Axis Test Laboratories employs enables customers to send their equipment from anywhere in the world to their laboratory in Durham for environmental testing, and receive a full test report back within ten days or less of the completion of testing. For more information or to speak to the team, get in touch via the contact information below.
Tel: 0191 3784653
Email: info@axistestlaboratories.co.uk
Visit: www.axistestlaboratories.co.uk
Address: Axis Test Laboratories
Unit 11A, Oakway Court, Meadowfield Industrial Estate, Meadowfield, Durham DH7 8XD
Ever since Forbo Flooring Systems began making floor coverings, starting with linoleum more than one hundred years ago, the company has been committed to creating better environments in all the spaces in which people, work, live, travel, relax, learn and play
Today, with a vastly increased range of product choices, it remains every bit as passionate about sustainable floor coverings.
At the forefront of sustainable entrepreneurship for over three decades, Forbo was the first in using Environmental Product Declarations (EPD’s). This remains a transparent way to calculate the environmental impact of its raw materials and processes, as well as the products lifecycle.
When it comes to product design and production, Forbo follows the 4R principle of `Reduce, Reuse, Recycle and Renew` for all its collections. The design process is central to reducing raw material requirements, reusing factory waste, recycling old products and employing renewable raw material. Following green design principles means working with circular economy principles in mind as well. Furthermore, one hundred per cent of the electricity Forbo buys for all of its production sites, comes from renewable sources
Marmoleum FR² and Marmoleum Striato FR are linoleum floor coverings made from natural materials. Floor coverings associated with sustainability, durability, high quality and innovative design. Created using a high percentage of natural raw materials, with renewable and recycled content, offering a sustainable solution to rail interior design.
As part of the Marmoleum product range, Marmoleum FR2 and Striato FR products are climate positive (cradle to gate) without offsetting. In simple terms, they absorb more carbon dioxide (CO2) during the growth of their plant-based ingredients such as flax, jute and resin, than is released during the manufacturing and transportation processes.
The result is a net positive impact on reducing greenhouse gases in the atmosphere from cradle to gate.
Marmoleum FR² is also naturally bacteriostatic, meaning it actively prevents the growth of harmful bacteria. In fact, it has been independently proven to suppress the spread and growth of numerous infections, including MRSA, Norovirus and C Difficile. This protection is active from the point of installation and will not diminish in quality over time.
What’s more, it is a floor covering solution that is easy to clean and maintain as well as durable, safe and comfortable for both wheeled and foot traffic. Awarded the prestigious Allergy UK Seal of Approval as, with the correct cleaning and maintenance regime, it won't harbour dust mites, contributing to a better indoor environment for all.
All Marmoleum FR² floor coverings include Topshield pro, a double layer, UV cured finish that is scratch, and scuff resistant, easy to maintain and ensures long-lasting appearance retention. The Topshield pro finish features a two-layer system that can be repaired or refreshed in cases of damage or after many years of use. Because the floor lasts for so long and is so easy to clean, Marmoleum FR² has a low cost of ownership.
Thanks to its unique construction, Flotex FR is one of the world’s most hygienic textile floor coverings available on the market. A flocked floor covering that combines the cleaning properties and durability of a resilient with the comfort, slip resistance and acoustic properties usually associated with textiles. In addition, it is a textile floor covering that can be digitally printed, allowing for great design freedom.
Containing over 70 million upright fibres per square metre, Flotex FR is exceptional at capturing fine dust particles and allergens in the air, significantly improving the air quality within rail vehicles. Vacuuming Flotex FR removes twice as many allergens
than from conventional carpet due to its design allowing it to be cleaned down to the base of the pile. This is why Flotex is the only textile floor covering to receive the Allergy UK Seal of Approval.
Flotex FR floor coverings are waterproof and washable with many different cleaning products. Importantly, it is fast drying, maximising the efficiency of the cleaning process. When tested against six other carpet constructions, Flotex FR far outperformed its competition, having only 0.57 per cent moisture remaining two hours following cleaning.
Stopping up to 95 per cent of walked-in dirt and moisture, effective entrance floor coverings can prolong the life of your rail vehicle interior floor coverings and finishes, as well as greatly reducing cleaning costs and the risk of slipping. With almost 50 years of experience, Coral FR offers you the best entrance flooring solutions for your entrance areas on board rail vehicles.
As an alternative to fully adhering the floor covering to the subfloor, Coral FR can
also be supplied with alternative backing types for quicker and easier installation and replacement.
Coral Brush FR, Coral Duo FR and Coral Welcome FR entrance floors all use Econyl® yarn which is made from used and abandoned fishing nets. Using Econyl® is a way to reduce existing waste, avoid additional manufacturing-related pollution, and keep the consumption of natural resources and energy to a minimum.
All the waste yarn from the Coral FR production is re-used by the yarn supplier and virtually zero landfill is achieved by the manufacturing plant.
Tel: 01773 744121
Email: transport@forbo.com
Visit: www.forbo-flooring.com/rail
RSS Infrastructure (RSSI) has been at the forefront of safety innovations in the rail sector. Recognising the immense safety potential of geofencing, RSSI has been instrumental in championing its adoption
Geofencing is fast becoming the industry standard for bolstering track worker situational awareness and worksite visibility. Its applications aren't limited to the rail infrastructure; it can be used across worksites where workers might be exposed to hazards, such as moving vehicles or machinery.
Introduced as part of Network Rail's commitment to innovation, geofencing received product acceptance in September 2022. Its implementation is underway across various Network Rail routes, with several principal contractors already leveraging its benefits.
Jason Fidoe, TWS Technical Manager said: ‘RSS Infrastructure is a trusted partner in the innovative application of geofencing technology within the rail industry. Our mission is to elevate safety standards, boost operational efficiency, and deliver solid asset management and tracking solutions.
By collaborating with Tended, we combine their technical expertise and our proven track record in implementing successful track safety solutions to bring about a transformative change in the rail sector.’
Understanding geofencing
Geofencing is a geospatial technology that establishes a 'virtual' geographic boundary or zone. When these boundaries are crossed, real-time alerts are triggered. In the context of safety, geofencing can be a lifesaver. Companies can set out precise, safe working areas, and workers with wearable devices receive alerts if they venture out of these zones. This enhances situational awareness and ensures workers are clear about safe entry points and routes on a site. Additionally, geofencing can be employed to set up exclusion zones, especially in areas with operational machinery, ensuring that workers and machinery do not come into unintended contact.
While large enterprises might find investing in geofencing equipment and training feasible, smaller businesses find it more challenging to justify the investment. Recognising this gap, Jason saw an opportunity to collaborate with accredited geofencing technology providers, Tended. The solution? A managed service that makes geofencing technology accessible to a broader range of projects.
Launched in July 2023, this service adheres to the Trackworker Protection and Warning Systems Standard. RSSI even offers businesses the option to engage a geofencing-certified Controller of Site Safety (COSS) for project support through its managed service.
RSSI understood the importance of demonstrating the tangible benefits of geofencing to potential clients. Through live demonstrations, clients could witness the technology in action, appreciate its ease of use, and experience firsthand the alerts when moving out of safe zones. These initiatives showcased the lightweight nature of the devices and their seamless integration with workers' PPE and reassured workers of the added layer of safety it provides.
There are numerous brain functions that can lead to a loss of situational awareness, which in high risk environments, can be fatal. In the rail industry, minor mistakes can escalate into significant issues. Instead of demanding constant vigilance from individuals, which is unrealistic, Tended realised the focus should be on leveraging technology to enhance human abilities.
Geofencing technology stands out in this regard. It combines advanced GPS systems, like those in drones, with a planning system designed for the rail
sector. Its primary purpose is to establish virtual safety zones for track workers. With centimetre precision, wearable devices can determine a wearer's proximity to the zone boundary. If a worker strays outside the safe zone boundary, the device emits an alert, directing them back to safety. More than immediate risk prevention, this technology gradually influences behaviour, promoting safety-first habits.
Jules Reed, Head of Behavioural Science at Tended said: ‘Consistent feedback is essential for habit development. Geofencing wearables provide real-time feedback, acting as a continuous reinforcement tool. This constant reinforcement can make safety behaviours instinctive for workers, enhancing the overall safety culture.’
Situational awareness is more than just being alert. It involves understanding your environment, intertwined with cognitive functions and biases. Our brains, while designed for survival, sometimes conflict with the requirements of highrisk settings. Technology bridges this gap, not replacing human judgement but augmenting it. Effective situational awareness today combines human intuition with technological expertise, collaboratively reducing risks and promoting a sustained safety culture.
The benefits of geofencing technology are threefold: it enhances worker safety, boosts efficiency, and improves asset tracking on worksites.
• Protecting Workers on Track – geofencing technology is a game-changer for track worker safety. It provides an additional layer of protection, alerting teams if they leave their safe zones. This helps them regain situational awareness, driving safer behaviours and decisions on site.
• Improving Operational Efficiency –geofencing technology can streamline your operations. With rail-specific map overlays that include ELRs, miles and chains, you can easily and precisely place geofence zones, protection assets, and safe access points. This reduces setup time and enhances project efficiency.
• Asset Management and Tracking –geofencing technology is vital in asset management and tracking. It ensures that teams and assets are precisely where they need to be, confirms the removal of equipment from the line upon project completion, enhances accountability, and reduces the risk of loss or theft.
With extensive experience in Track Warning Systems and worksite management, RSSI has developed a comprehensive Geofencing service for the rail sector. This service includes three key offerings:
• Fully Managed Service – RSSI will handle everything from consultation and planning to supplying qualified staff
who distribute wearable devices, conduct safety briefings, manage the planning dashboard and worksite, and ensure safe working zones.
• Planning Service – for businesses that buy geofencing wearables but lack the time, resources, or expertise to set them up, RSSI's TWS planning department is ready to help with detailed planning services.
• Dry Hire Option – for businesses that own geofencing wearables and have fluctuating needs, RSSI offers a flexible dry hire service to accommodate varying requirements. These services are designed to provide additional safety and efficiency and are tailored to each business's needs.
These services, designed with precision and expertise, will improve safety and efficiency and are tailored to the unique needs of each business or worksite.
The potential of geofencing extends beyond the rail sector. RSSI's vision includes exploring its applications in other areas, such as light rail or construction projects, and other sectors, such as civils, highways
and utilities. Plans are also underway to utilise geofencing for creating exclusion zones around moving machinery, further enhancing safety across various operational scenarios.
In conclusion, geofencing is undeniably gaining ground across the rail sector, offering a blend of enhanced safety, operational efficiency, and ease of deployment. With pioneers like RSS Infrastructure leading the way, the future looks promising for this transformative technology.
For more insights into RSS Infrastructure's work with geofencing technology, contact Jason Fidoe, Technical Manager, at jason.fidoe@rssinfrastructure.com or on 07769 645202.
Tel: 0330 113 0004
Email: info@rssinfrastructure.com
Visit: rssinfrastructure.com
Concrete Canvas is a flexible, cement-filled fabric that hardens when hydrated. Its unique properties make it an ideal solution for a wide range of rail applications, including crest drainage, slope protection, weed suppression and erosion control.
Concrete Canvas® (CC) is a flexible, concrete-filled geosynthetic that hardens on hydration to form a thin, durable and waterproof concrete layer. CC combines the robustness of a precast or poured concrete solution with the ease of installation and reduced permeability of a geomembrane. CC allows concrete construction without the need for plant or mixing equipment, offering a rapid, lower-carbon, environmentally sensitive solution for erosion control and weed suppression applications. Essentially, it's Concrete on a Roll™.
CC is manufactured in South Wales and exported to over 100 countries worldwide from its purpose-built headquarters, incorporating state-of-the-art R&D laboratories and a demonstration park.
The speed and ease of installing CC mean it is well suited to time-critical track-side work, reducing line possession and improving safety. Eliminating issues associated with rebound from shotcrete and the large plant and equipment required for traditional concreting methods means rail works can continue without line closures. CC is certified with a durability of over 120 years when used in erosion control applications – HS2 requires a 120-year design life for products; this provides vital accreditation to the physical properties, design and installation guidance of CC, enabling designers to ensure they are specifying a quality material.
With tightening budgets and a greater focus on increasing the efficiencies of current assets rather than building new ones, CC offers a unique solution for the remediation of existing infrastructure. CC can improve the industry by utilising existing assets, reducing waste and contractor burden. One Bulk Roll of CC
equals two 6m³ ready mix trucks; therefore, one 40ft vehicle movement would cut down on 32 mixer trucks.
CC is an industry-accepted alternative to conventional concrete that has been widely used by Network Rail across the UK for over 14 years and is one of a few products included in the Network Rail Standardised Task Portal. Route Directors, Senior Asset Engineers (Drainage) and minor works teams across the five Network Rail regions and their 13 routes have specified the geosynthetic.
CC has been extensively used through CP4, CP5 and CP6. Most route network framework contractors have installed CC, including QTS, Balfour Beatty, BAM Nuttall, Costain, AmcoGiffen, Alun Griffiths and Story Contracting. CC has been specified on numerous projects for Network Rail, Transport for London, Translink NI Railways and others. Typical applications for Rail in the UK include channel lining, culvert repair and weed suppression.
During three control periods, the company has been fortunate to be involved in over 600 Network Rail schemes across the UK. Some recent standout projects include the installation of Concrete Canvas® for the rapid lining of crest drainage channels across several Network Rail routes, including work at Slochd, Charfield and Bath Road Cutting. It was specified over ST4 poured concrete to line crest perimeter drainage channels on different compounds at HS2; this application is typically required to prevent saturation of embankments and potential slip onto a track below as a result. For all projects, the ease and speed of installation allowed contractors to increase workers' health & safety by minimising the time on site, reducing line possession during the works and providing a lower carbon alternative to conventional concrete lining methods.
As a supply chain partner with Network Rail since 2009, CC has worked and collaborated with most Tier 1 and Tier 2 consultants and contractors in the rail sector
across the UK. As a manufacturer, CC can provide expert support at all project stages, from pre-design to completion, with regional technical sales support, specification and installation guidance.
Recently, a new product range has been developed to reduce further the environmental impact of the original Concrete Canvas® material whilst delivering even higher performance for the customer. The new T-series has 33 per cent less embodied carbon than standard CC, providing more than 63 per cent savings when used to replace conventional poured concrete for erosion control applications. The new material also has 25 per cent higher abrasion resistance providing longer-lasting protection.
The T-series was a vast project for Concrete Canvas, with thousands of hours in research by the R&D team with well over 150 documents carefully being checked,
updated and re-issued by the Marketing Department to launch successfully in June 2022.
CC Ltd is working hard to reduce the company's environmental footprint and is proud that by replacing conventional concrete solutions, CC products sold to date are estimated to have saved over 3000 tonnes of CO2 emissions globally. The T-series product line mentioned previously has 33 per cent less embodied carbon than the original CC and is building on this legacy as we advance.
The introduction of the T-series has already seen several of its key benefits utilised by clients in the Rail Sector and beyond to help them deliver their KPIs and objectives to reduce embodied carbon on projects.
One of the biggest challenges to the railway network in recent years has been extreme weather conditions. Long-term
trends show changing weather patterns with increasing average and maximum daily temperatures with drier summers, wetter winters, and severe storms. The increased risk of weather-related events such as floods and landslips causing delays, rising operating costs and increased safety risks along the network is a genuine issue.
There has been increased investment in CP6 and a focus on weather resilience, which has led to long-term asset resilience improvements, reducing the number of assets susceptible to adverse weather. Drainage management has also been enhanced, focussing on the importance of water management around rail infrastructure to prevent saturation of slopes and minimise the risk of landslips.
An example of use is a recent multiagency scheme, headed by the Environment Agency with National Highways and Network Rail collaboration to provide an erosion protection solution to a Network Rail embankment as part of an overall flood alleviation scheme in Birmingham. The use of Concrete Canvas showed the materials' innovative approach to solving issues the original poured concrete design presented to the contractor regarding the project's buildability.
The GWP saving on this scheme alone, compared to ST4 poured concrete was a massive 66 per cent. All parties had approved and accepted the original material. Still, after the launch of the new T-series formulation, even better-embodied carbon savings than initially expected were achieved.
CCT-series is already reducing the amount of embodied carbon emitted by the rail sector. Since launch last year, Concrete Canvas has sold over 12600m² of material to the rail sector across the UK at just under £330,000. The switch to the T-series has saved 175 tonnes of CO2, equivalent to approximately 28.5 days of airline flight or over 8,000 trees absorbing CO2 in a year.
The new product ranges are a large step forward in evolution for the GCCM material class used in the rail sector, and the company is still innovating. Since day one, Concrete Canvas has strived to provide the best material possible for erosion protection with continuous innovation critical to the company's growth, evolving and moving towards a better, greener, and brighter future for the rail sector.
Tel: 0345 680 1908
Email: info@concretecanvas.com
Visit: www.concretecanvas.com
Social megatrends such as urbanisation, eco-efficiency, digitisation and automated driving are shaping new technologies. And it ’s not just the vehicle subsystems and products that are getting more intelligent − services are keeping pace: remote diagnostics, predictive maintenance and innovative connectivity solutions add genuine value for vehicle manufacturers, operators and passengers alike.
At Knorr-Bremse in the UK, we provide end-to-end digitisation and automation, boosting transportation capacity with automated processes and digital solutions, and improving efficiency and availability to make rail freight faster, more flexible, and more accessible to schedule.
| rail.knorr-bremse.com |
As part of Network Rail’s technical strategy, they are continuing to drive and promote research and development into new ideas and technologies to address challenges faced
WM Plant Hire is proud of its continued work with contractors across the UK, exploring the best application of long reach and Spider excavator machinery to achieve the most efficient delivery on both maintenance and emergency operations. Long reach and spider excavator specialists, WM Plant Hire, with a wide-ranging fleet from four to 115 tonnes continue to invest ensuring the team has the capability to tackle almost
every eventuality. Whilst the reach is always a major factor, access constraints usually dictate the size of the machine and so the company continues to extend its offering in this specialist market. Their fleet includes:
• Wide track, low ground pressure long reach machines.
• Ten to 16-metre zero-tail swing excavators – fully rotating within the width of the tracks.
• ‘Spider’ or ‘Walking’ excavators up to 16 tonnes.
By investing in some of the largest Spider machines in the UK, this enables its clients to work on steep slopes, in deep water and overcome obstacles such as fencing and safety barriers to achieve a rapid response. With powerful hydraulics up to one hundred per cent more than equivalent size tracked machines, these larger Spiders offer more versatility with the capacity to handle heavier attachments for more varied applications. In addition, by offering experienced and dedicated long reach
operators, the company believes they can give the customer the very best in safe and productive working.
WM Plant Hire has developed its expertise over 30 years working on numerous high-profile contracts including HS1, HS2, Evergreen, Crossrail, West Coast Mainline and Hope Valley Upgrades together with numerous emergency schemes – most recently Nuneham Viaduct. By prioritising client relationships, the company facilitates open communication necessary to ensure optimum plant selection by Network Rail contractors and efficiencies achieved thereby in operations. The crucial understanding developed between parties in turn helps promote the exploration of new ideas, pushing boundaries in delivery.
As a specialist plant hire business, the company is committed to safety, working with equipment manufacturers on machine specification to enhance safety features wherever possible to meet the stringent requirements of rail operations.
Most recently this has been evident in their Euromach Spider excavator specifically customised with a dedicated inbuilt winch, which can be anchored to plant at the top of an embankment as a secondary fail safe. This machine can travel where conventional
tracked machines cannot. This approach was adopted by BAM Nuttall at Sevenoaks on a regrading scheme where the machine was able to work safely on an embankment above a live railway line.
WM Plant Hire offers the full range of machine control systems (height, lift, slew, envelope control) as well as additional safety features including LED lighting, 360 degree all-vision cameras with boom and dipper cams to maximise safety. This includes the latest Network Rail approved X-watch full envelope control system to manage machine movement near to the rail line, used in some challenging locations at Hope Valley and on an embankment repair at Hook.
The addition of the Euromach Spider with the latest stage V engine also demonstrates the company’s continued commitment as part of the supply chain to help clients work toward net zero targets.
‘We continue to invest across our fleet in machines with better fuel consumption and environmental credentials, demonstrating cleaner and more efficient operations; ensuring our clients are able to use alternative greener fuels such as HVO; as well as exploring better ways to record our own carbon footprint’ said Director Damian McGettrick
As a Chartered Civil Engineer and past Chairman of the ICE West Midlands region,
his engineering knowledge has improved productivity through efficiency and sustainable engineering practices, which he is keen to help deliver for his clients.
Ensuring clients select the machinery to facilitate the most efficient operations is important to WM Plant Hire as evidenced in their collaboration at Hook with Universal Piling and VolkerFitzpatrick. A failure of an embankment resulted in the mainline from Southampton to London being reduced to one operational line. Following the emergency installation of piles to stabilise the bank, WM Plant Hire assisted with the install of 1,200 soil nails to depths of up to 25 metres. A range of long reach excavators were supplied to suit the varied locations and included the 24 tonne (16-metre reach), 40 tonne (18-metre reach) and 46 tonne (22-metre reach) long reach machines.
Mark McIntyre, Construction Manager at Universal Piling commented: ‘Using WM Plant Hire is time saving for us as Director Damian and his operational team understand and anticipate our attachment requirements and their machines are always ‘ready to go’ without us needing to carry out additional fabrication for our masts to work.’
The company’s specialist heavy lifting configuration offered on some of their
machines also provided the additional lifting capacity required to handle the larger drill masts for the soil nailing operations at Hook.
Rail schemes on embankment sites or around bridges often face real challenges with access constraints. Innovative approaches using machines within the WM fleet have improved efficiencies in overcoming some of these problems. Where tracked long reach options are just not an option the ‘Spider’ machine comes into its own.
At Sevenoaks this provided BAM Nuttall with the additional reach required on a slope length in excess of 40 metres. The Spider, capable of working on steep slopes around 40 degrees, worked in tandem with a 22-metre-long reach excavator and reprofiled the toe of the slope passing back material to the long reach for removal. Fitted with a tilt-rotate unit the Spider machine was able to regrade the slope to any angle required.
At Nuneham viaduct it was limitations of height and water that were factors overcome by the Spider. Working with Teignmouth Maritime Services it was able to overcome the challenges of low headroom by lowering
itself while working from a pontoon underneath the Viaduct. Its extendable boom allowed the specialist excavator to reach out and lift the temporary piles which had been cut off by their divers.
With emergency rail schemes rapid response can be of the essence. With the largest fleet of long reach in the UK including the longest reach at 32 metres, WM Plant Hire are well resourced to support emergency schemes. Following a landslip in Kent –efficient communication between their clients, hauliers, police, and Network Rail ensured that the 30-metre super long reach, mobilised in two loads due to its considerable size, reached its destination at Selling Tunnel within days.
Customer service and investing in the best equipment is particularly important to this family business. Looking to improve efficiency and widen the applications of their specialist equipment has led to discussions with the Story Contracting geotechnical team, who had recognised the impressive hydraulic and lifting capacity of the Spider machines.
WM Plant Hire has been working with Lee Healey, Head of Technical Services at Story Geotech and his team to trial the use of these specialist excavators for drilling applications using a large TEI mast attachment. Utilising machinery capable of traversing slopes could provide a unique opportunity to undertake Ground Investigations and in-situ testing, as well as installing monitoring systems and implementation of soil reinforcement/ regrade of earthworks.
WM Plant Hire is looking forward the future development of this ‘Spider’ methodology versus conventional bespoke temporary works platforms, as it could lead to greater efficiency, less disruption to the public and environment and greater utilisation of staff.
Tel: 01746 769555
Email: info@wmplanthire.com
Visit: www.wmplanthire.com
Established in 1999, Lankelma has grown
With nearly 20 years of experience working in the rail industry, Lankelma can perform fast and effective ground investigations in all areas of the trackway.
Boasting a team of qualified, highly experienced field operatives, and an extensive fleet of specialised CPT rigs, all of which can be mobilised anywhere in the UK at short notice. CPT is a technique for soil testing that is ideal for rail investigations due to it being a clean, quiet, and quick method coupled with the ability achieve deeper penetration (depending on the geology). Clearly work on the rail is a time sensitive endeavour, and this makes CPT ideal for on track investigations, providing a highly accurate and easily repeatable assessment of soil conditions. A CPT is performed by pushing an instrumented cone into the ground at a constant rate, with measurements recorded every 20mm.
CPT investigations characterise subsurface materials in situ, produce continuous profiles, and determine soil parameters including soil type, in situ stress conditions and shear strength for use in geotechnical design. High quality results are available in real-time which allows engineers to take decisions on site during the ground investigation. This is particularly useful when identifying the best locations for further investigation, especially as detection of potential problems is of paramount importance on the railway, and can expedite the program of works at all levels of the project.
As the use of CPT in railway investigations has grown, Lankelma has developed specialist rail CPT plant and equipment specifically designed for ground investigations in the four main rail environments: track bed, embankments, tunnels and stations. These rail CPT plant can be used with the full range of standard and specialist cones to fulfil a variety of testing requirements including soil analysis, magnetometer detection, and seismic wave testing. Provided there is sufficient reaction force and a power supply, CPTs can be carried out almost anywhere, and in almost any material.
One of the biggest innovations in rail CPT site investigation over the years, has been Lankelma’s one-of-a-kind road-rail CPT truck – the world’s first dedicated rail CPT truck. Arriving by road and accessing the track from level crossings or authorised road rail access points (RRAP) using the central turntable mechanism and rail wheels. This capability of the self-contained truck allows rapid deployment of operatives and equipment to numerous test locations, meaning multiple CPTs can be achieved in quick succession in the four-foot. The rail CPT truck has significantly improved productivity and efficiency in on-rail site investigation.
For ground investigations on other areas of the trackway, Lankelma’s rail excavatormounted CPT unit is the answer. The CPT unit attaches to the arm of an RRV
excavator; the excavator manoeuvres the self-contained unit to each test position. Testing can be carried out in the cess, sixfoot, ten-foot, up and down embankments and cuttings.
Site investigations in challenging environments like tunnels and stations are also possible. Lankelma has developed lightweight, hand-mobilised, CPT rams suitable for testing positions with access restrictions, including confined spaces and into vertical walls. These rams which are bolted into position to gain the necessary reaction force and can test in otherwise impossible to reach locations minimising enabling works and reducing cost and time loss. The same equipment, which is electrically powered, and therefore quiet, is suitable for testing within open stations, tunnels or on platforms.
Lankelma have been involved in rail investigations for electrification schemes, emergency slips/faults on track, track upgrades and embankment stability work.
The rail CPT truck helped gather high quality ground information for the reconstruction of a failed section of railway embankment at Wrecclesham, Surrey. Network Rail discovered that a 250-metre section of the embankment had failed, causing the track to settle. Emergency stabilisation works allowed safe reopening of the line and work began to find a permanent solution. Lankelma carried out ten CPTs over a single shift along the failed
section. Tests were carried out through one-metre thick ballast and into the sand and clay below, to a maximum depth of eleven metres. This information proved invaluable to project engineers needing to characterise the embankment material and the geology beneath.
Ground investigations to support Network Rail’s South Wales Re-Signalling project involved working over a series of seven-hour Saturday night shift possessions. Lankelma’s rail CPT truck was ideal, able to efficiently travel along the 35-track-mile length of the scheme and carry out multiple CPTs during the short possessions, covering new signals, location cases and Functional Supply Points.
The Edinburgh Glasgow Improvement Programme (EGIP), delivered by Network Rail, involved modernisation and upgrades of key junctions, plus electrification of the rail network. Lankelma, working for ABC Electrification (a joint venture of Alstom, Babcock and Costain), carried out more than 250 CPTs to depths of twelve-metre in sands and soft, sensitive clays on the railway over 90 nightshifts. Testing was carried out using Lankelma’s two rail units – rail CPT truck and excavator-mounted CPT unit. Geotechnical data was used directly in the design of the overhead line equipment
support structures and for station remodelling along the route.
Following the identification of embankment instability on several rail assets in Hampshire and Somerset, Lankelma responded to the needs of an urgent requirement for geotechnical definition by delivering preliminary soil stratification, pore pressure and geotechnical parameter derivations within one week of completion. The rail CPT truck and excavator-mounted CPT unit working in conjunction, carried out investigations at three sites over ten twelve-hour shifts.
As part of a scheme to improve London’s transport network, Lankelma were procured to carry out CPTs at Finsbury Park tube station. Using a lightweight mobile CPT unit anchored to the walls of the station’s stairwell, horizontal testing was performed. Four horizontal CPTs were pushed 14 metres into the wall to provide an assessment of the current structural arrangement.
In each case, Lankelma’s fast and effective methods, performed by skilled crew operating specially designed equipment, expedited the progress of works and provided invaluable information with minimum disruption unmatched by alternative methods.
A rail track facility at Lankelma’s head office facilitates development of its rail-specific CPT units and maintenance of equipment. In-house mechanics ensure all rail plant is compliant with standards so they can offer a first-class service to clients.
Lankelma continues to offer an expanding array of testing options with the ambition to fulfil any shift pattern required.
Lankelma is RISQ accredited, trading as a specialist ‘plant hire’ company under Network Rail’s Plant Operator Scheme (POS), and all on-track rail plant are VAB approved.
Lankelma also expanded its rail capabilities with a second track-mounted CPT unit. The latest addition is cutting edge technology and will assist to speed up rail investigations.
Tel: 01797 280 050
For over four decades, McGinley Support Services has distinguished itself as a leader in the UK's rail infrastructure sector
The company’s steadfast commitment to identifying, sourcing, and placing exceptional talent has made it a go-to resource for both employers and jobseekers in this critical industry. Renowned for its comprehensive staffing solutions, the company stands out not only for its commitment to quality but also for its embrace of diversity and inclusivity. These core principles were recently acknowledged, as McGinley Support Services was named one of the Top 100 Apprenticeship Employers in England.
The complex nature of rail infrastructure requires a staffing solution that exceeds mere role fulfilment. McGinley Support Services understands that its recruits must be adept in safety regulations, project management, and continual professional development. Specialising in Track Labour, Trades & Labour, Tunnelling Services, Project Works, Professional & Technical, S&T, E&P and Welding, Grinding & Burning Services, the company offers staffing solutions tailored to meet these high demands.
Inclusion is not a buzzword at McGinley Support Services; it is a core value. The achievement of a diverse workforce is central to the company’s mission as a provider of recruitment services. McGinley Support Services actively enhances its workforce by creating and offering opportunities for underrepresented groups – including women, individuals from BAME backgrounds, those with disabilities, or participants in various CSR programmes like Prison Leavers, Homeless to Work, the longterm unemployed, and Apprenticeships. This diverse workforce not only enriches the company culture but allows the company and the clients it works with to be reflective of the society we live in which brings a range
of experience and skills. McGinley Support Services’ business culture reflects that belief.
The company's dedication to nurturing talent and entry level careers has been recognised at a national level, with its inclusion in the list of Top 100 Apprenticeship Employers. This accolade reflects McGinley Support Services' long-standing efforts to develop new apprenticeships, promote diversity, and achieve apprenticeship goals. As an award-winning Flexi Job Apprentice Agency, McGinley Support Services can
design apprenticeship programmes which are designed to work in construction and infrastructure projects creating environments where the apprentice is at the centre of the programme. This has supercharged the effort to introduce new entrants into the infrastructure market.
In an industry where a skills gap looms large, McGinley Support Services goes beyond recruitment to include comprehensive training and development programmes. Every employee is not just qualified but is developed to excel in their roles, thereby setting new industry standards.
Compliance with legal requirements is just the starting point. McGinley Support Services’ commitment to ethics, safety, and professional conduct surpasses industry norms. This dedication to quality is reflected in its involvement in some of the UK’s largest infrastructure projects, including those in airports, energy, metro, ports, roads, telecoms, waste, and water sectors.
Understanding that no two projects are the same, McGinley Support Services offers customised staffing solutions. Whether the need is for a short-term workforce or a long-term team of specialists, the company possesses the resources and expertise to deliver without compromise.
McGinley Support Services not only addresses immediate staffing needs but also prepares for future industry challenges. A culture of continuous learning and advancement ensures that the workforce is ready for the ever-evolving landscape of rail infrastructure. With its unique blend of quality, diversity, and professionalism, McGinley Support Services is more than a staffing
agency; it is a partner in progress for the UK’s rail & civil engineering infrastructure. As the sector continues to grow and adapt, McGinley Support Services will evolve alongside it, offering robust, adaptable, and inclusive staffing solutions that set new industry benchmarks.
For more information, get in touch via the contact information below.
Tel: 0845 5435953
Email: info@mcginley.co.uk
Visit: www.mcginley.co.uk
Discover in-depth insights and strategies on rail infrastructure with whitepapers and reports. Scan the QR code to access these expert resources.
SATEBA UK (formerly Sateba Stanton Precast) has a rich history in working with clients to resolve project needs
From noise and vibration mitigation sleepers used on HS1 and the Elizabeth Line to levelling bolt holes in sleepers used on Midland Metro SATEBA UK supports the needs of the track environment and the people who install it.
SATEBA UK is one of 13 manufacturing sites across nine countries that form the SATEBA Group, a European leader in precast concrete solutions for sustainable Rail Infrastructure, developed in a safe and responsible way.
Key benefits of working with
SATEBA include:
• A range of innovative products proven in the UK and overseas.
• More than 35 years of High Speed Rail experience combined with a century of infrastructure expertise.
• Offsite manufacturing at a central UK location with well-connected distribution links.
• Collaboration with an expert team of rail engineers in anything precast, combining high performance with sustainability.
• Bespoke, adaptive, flexible design options, working to your project needs.
The company’s portfolio includes products for metro, tram, tube, suburban (light rail), high speed rail and mainline rail. These include noise and vibration attenuation sleepers, integrated sleepers, sleeper fittings, digital tracking technology, pole foundations, drainage channels, embankment access stairs, cable troughs and made to design, bespoke products.
SATEBA 312 technology is available in a variety of sleeper types: twinblock, monoblock or bearers, and can accommodate any type of fastening. They are suitable for high speed, mainline and urban lines.
When the Eurostar arrives in London, it does so with serenity. This is partly thanks to the SATEBA S312 twinblock booted slab track sleeper, designed to respond to the noise and vibration mitigation requirements
of London tunnels with various levels of performance (5db – 15db). This reinforced sleeper is approved by Network Rail with Certificate of Acceptance PA05/06822.
The M312 monoblock high attenuation booted sleeper, is the result of a joint development between SATEBA and Alstom. The sleeper mass combined with the resilient boot provides extremely high levels of acoustic performance (insertion gain is >20db) comparable to the performance of traditional floating slab track and can be installed up to 10 times faster!
M312 sleepers were used on the Elizabeth Line (Crossrail) project which benefited from safe, easy, rapid installation of up to 250 metres per day, using the same installation methodology as the twin block booted sleepers.
Another key advantage of the booted 312 systems is how easy they are to maintain or replace thanks to the rigid boot.
All of these benefits result in significant savings in cost, programme and maintenance over traditional floating slab track insitu installation. In certain circumstances it is estimated that the M312 track can be up to 30 per cent less costly to construct.
The SATEBA TW120 sleeper system is used for embedded rail slab track construction and can be used with all fastening systems. This solution allows for rapid installation and accurate alignment of the track by using levelling inserts precast into the sleeper blocks resulting in significant cost and time savings on both construction and programme. As a result the TW120 system only requires concreting up to the underside of the rail foot and can then be finished with a variety of materials e.g. grass, asphalt, and block paving.
Around 20,000 SATEBA TW120
Sleepers have been supplied to the Midland Metro line in the UK and are the common sleeper type for light rail construction throughout Europe.
Carbon Reduction and Sustainability
Decarbonization is a major focus of SATEBA’s environmental strategy. SATEBA’s specialist R&D team have developed pioneering sustainable sleepers using the latest technology, resulting in new profiles with less material, and the incorporation of fibres and materials with high performance properties. Other developments include products made using recycled steel and decarbonated cement known as
green cement with the lowest possible clinker content.
The company also buys raw materials as close as possible to production sites to limit transport related CO2 emissions.
Precast concrete is highly recyclable so often used in other products or backfill for highway projects.
Each sleeper has a validated carbon value (EPD), guaranteeing a reduced CO2 impact. This is only the beginning as SATEBA is committed to ever decreasing decarbonization to further contribute to preserving the environment. This includes SATEBA targets of ten per cent carbon reduction by 2026 and a 30 per cent carbon reduction by 2030.
Always at the forefront of innovation and deeply committed to reducing the carbon impact of infrastructure, SATEBA, together with VAPÉ RAIL, is part of an ambitious circular economy project known as ECOTRACK™ dedicated to the reuse of track products. Watch out for further company innovations and updates.
Precast Concrete Credentials
Accreditations include RISQS, ISO 9001, ISO 14001 and ISO 45001. Projects supplied include:
• Grand Paris Express (current supplier)
• Elizabeth Line (Crossrail)
• High Speed 1 (CTRL)
• TGV in France
• ICE in Germany
• Light Rail schemes including Nottingham (NET), Manchester and the Midland Metro.
For further information, get in touch via the contact information below.
Tel: 07534 131046
Email: daniel.cross@sateba.com
Visit: www.sateba.uk
Highly flexible, EN 45545-compliant insulation materials for railway vehicles; reliable thermal protection and condensation control on refrigerant pipework and air ducts
Improving space and energy efficiency is a key challenge for today’s railway industry. Armacell’s thermal and acoustic insulation products and sustainable foam cores optimise the weight-to-performance ratio. What’s more, they increase passenger safety and comfort. Our innovative solutions are used in rail vehicles all over the world, where they ensure safe and smooth operation.
When railway vehicles are designed and constructed, the safety of passengers and staff is of the highest priority. The level of safety has been increased successively over the past years and today all materials used must fulfil the highest fire protection requirements. The introduction of EN 45545-2 sees the legislation being further tightened and standardised throughout Europe.
Armaflex Rail thermal insulation, manufactured by flexible technical insulation market leader Armacell, is the first closed-cell insulation material to offer greater fire safety for railway passenger vehicles.
Armacell offers flexible, closed-cell insulation materials with integrated fire protection for railway vehicle construction: All Armaflex Rail products meet the high requirements of the new European fire protection standard EN 45545. They achieve hazard level HL2 or 3. According to EN 45545 Armaflex Rail SD-C and Armaflex Rail ZH-C can even be installed in trains operated on underground track sections or in tunnels. The innovative materials – including halogen-free and covered insulation materials – have very good fire properties and develop extremely little smoke.
Armaflex Rail products protect refrigerant pipework, air ducts and other components against energy losses and condensation. Because the elastomeric insulation materials are highly flexible, installation is unbeatably fast and easy.
The energy required for heating and air conditioning passenger rail vehicles can account for 30 to 40 percent of the total energy use. With Armacell’s thermal insulation, rail operators can reduce costs and meet the growing demand for increased energy efficiency and an enhanced weightto-performance ratio.
Armaflex Rail products at a glance Armacell provides innovative system solutions for insulating refrigeration and air-conditioning systems in vehicles ranging from trams to high-speed trains. The new technologies ensure more safety and comfort on the tracks.
• Armaflex Rail SD – elastomeric insulation material achieves HL2, R1 under EN 45545 and is also classified under the national fire protection standards NFPA 130 and DIN 5510-2. The Microban® technology for additional protection against bacteria and mould contributes to a healthy indoor climate.
• Armaflex Rail SD-C – the first closedcell insulation material for use in areas requiring the highest hazard level – HL3. The product is based on Armaflex Rail SD and is equipped with a shiny, silver covering. The attractive surface is UVresistant, protects the insulation material against mechanical impact and is very easy to clean.
• Armaflex Rail ZH – the first halogenfree, closed-cell insulation material to
achieve the classification HL2, R1 under EN 454545. The product not only has very good flame-retardant properties and low smoke density, it also minimizes the risk of secondary damage. Acidic fire gases cause damage to property leading to costs many times higher than those of the actual fire loss. In a fire, the halogenfree Armaflex Rail ZH does not release corrosive gases which, in combination with the fire-fighting water, could form aggressive acids.
• Armaflex Rail ZH-C – the first halogenfree, closed-cell insulation material for applications with the highest requirements regarding the materials used. Armaflex Rail ZH-C achieves hazard level HL3, R1 and can even be used in sleeping cars and couchettes which are rated operating class 4 and run on underground track sections or in tunnels. The shiny metallic, UV-resistant covering is easy to clean and so flexible that it regains its shape after mechanical impact such as knocks and blows.
In a fire, low smoke density can be of vital importance in order to allow passengers and staff to escape and be rescued quickly and safely. For this reason, the new European standard EN 45545-2 defines tighter requirements for the fire behaviour of materials and components. In accordance with their classification as R1 materials, technical insulation materials are tested under ISO 5658-2 (spread of flame), ISO 5660-1 (heat release, smoke development and mass loss rate) and EN ISO 5659-2 (optical smoke density and smoke gas toxicity).
Because they are closed-cell insulation materials with low thermal conductivity and high resistance to water vapour transmission, Armaflex Rail products provide installations with reliable, long-term protection against energy losses and condensation. As is the case with all Armaflex products the Armaflex Rail products have a ‘built-in’ vapour barrier. Unlike conventional insulation materials which have to be protected against moisture penetration with a separate vapour barrier, in Armaflex the resistance to water vapour transmission is built up throughout the entire insulation thickness. The Microban® technology provides additional protection against harmful microbes such as bacteria and mould.
Armaflex Rail products are supplied as tubes, sheets, selfadhesive sheets and tapes in the usual insulation thicknesses. A great advantage of the synthetic rubber, which becomes particularly apparent in the tight installation situations in rail vehicle construction, is the highly flexible nature of the material. The homogenous, three-dimensionally linked structure of the elastomeric insulation allows the sheets to be cut neatly without the release of dust or fibre particles which could pose a health threat if breathed in. The high flexibility of the material allows it to be fitted simply even on complex fittings and equipment. Application times can be further reduced by using self-adhesive sheets.
ArmaPET
Armacell also manufactures ArmaPET foam core insulation, made from fully recycled PET plastic bottles material.
ArmaPET Struct FR is a halogen-free product with very low smoke generation and reduced smoke toxicity that enhances rail passenger fire safety. Achieving EN 45545-2 compliance up to hazard level HL3. ArmaPET can be used for rail vehicle flooring, walls, ceilings, doors and body work as well as a lightweight core for tables.
ArmaPET Struct provides a durable final product with superior impact resistance to ensure long-term performance, fewer repairs and easy maintenance in use.
Armacell is a world leader in flexible insulation foams for the equipment insulation market and also a leading provider of engineered foams. In 2015, the company with currently approx. 2,900 employees and 24 production plants in 15 countries generated net sales of EUR 540.2 million.
In addition to ARMAFLEX, the world’s leading brand for flexible technical insulation, Armacell offers thermoplastic insulation materials, covering systems, fire protection and noise control solutions as well as special foams for a multitude of industrial applications. In recent years, Armacell has developed new insulation systems for the oil and gas market, core foams for composite materials, and low-smoke products that have set new standards in the industry. Armacell´s products make a significant contribution to global energy efficiency.
Address: Armacell
Robert-Bosch-Str. 10
48153 Münster, Germany
Tel: +49 251 7603-0
Fax: +49 251 7603-448
Email: info@armacell.com
Visit: www.armacell.eu
The primary business focus of TRB Lightweight Structures has traditionally been the rail sector, but the company has proven its versatility and adaptability by branching out into hybrid and electric vehicles, medical devices, and more
It is constantly developing lighter and more sustainable materials for use across various markets, and these new solutions are now being widely applied to rolling stock. TRB Lightweight Structures Ltd. (TRB), based in Huntingdon, Cambridgeshire, is a leading tier 1 manufacturing and engineering company, offering comprehensive conceptto-delivery and rolling stock refurbishment services using its in-house production, engineering and laboratory testing facilities. The company has been working with the rail industry for more than 40 years, designing and manufacturing a wide range of interior and exterior components for both new build
and refurbished rolling stock, including flooring, doors, partitions, galleys and storage units.
TRB is proud of its strong reputation as an International Railway Industry Standard (IRIS)-approved supplier of engineered parts and complete systems to leading train builders worldwide, including Hitachi, Alstom and CAF. The company is also DIN 6701 certified, and registered and approved by the Railway Industry Supplier Qualification Scheme (RISQS).
One of TRB’s core strengths is its capacity to develop, test and validate innovative lightweight metal and composite materials, which can be supplied to original equipment manufacturers (OEMs) as either individual components or fully assembled, ready-to-install units. In recent years, the company has continued to research and manufacture a range of lightweight structural components based on more environmentally friendly materials for use in different sectors.
The 2016 Paris Agreement to reduce CO2 emissions has resulted in numerous mergers, collaborations and major capital investments by the global transport
industry to develop hybrid and electric vehicles. Transport companies have therefore been placed under pressure to rapidly adapt their manufacturing processes in order to stay in line with ever-changing legislation, as well as the public’s demand for cleaner modes of transport. TRB believes that advanced composites are a crucial part of this move towards greener travel, as they make rolling stock lighter, faster, more energy efficient and cheaper to maintain. TRB’s ultimate strategic goal – which is central to its business ethos – is to help reduce overall transport emissions by offering OEMs lightweight alternatives based on sustainable materials.
TRB’s design and materials processing capabilities now include a broad selection of alternative lightweight composite materials for the rail sector – such as modified epoxy glass prepreg, fire retardant foam cores and select thermoplastic materials – that comply with the latest and most stringent fire, smoke and toxicity guidelines detailed in EN 45545. The company’s main production facility in Huntingdon is also DIN 6701 (Parts 1-4) A1 type certified
for the bonding of safety-critical rail vehicle parts. Switching to bonding where possible eliminates the need for many fixings – further reducing weight, while improving assembly productivity and reducing overall production costs – and this comprehensive certification allows the construction of bonded rail vehicle products under any of the four DIN 6701 A1-3 and Z type classifications. This includes safetycritical products requiring A1 approval for applications where part failure during use risks endangering passengers, and TRB currently manufactures and supplies emergency detrainment door systems, driver cab doors and passenger exit doors.
TRB works in close partnership with its rail customers to continually devise new designs that minimise weight, reduce maintenance, repair and overhaul (MRO) costs, and improve safety. This service covers a wide range of potential applications, with past
projects including the development of a new lightweight composite antenna cover for Hitachi and Alstom Transport, and the reverse engineering of a stiffer and lighter coupler hatch for the West Coast Pendolino.
TRB is also proud to have been working closely with Transport Design International (TDI) over the last few years to develop the composite bodyshell design of the Revolution VLR (Very Light Rail), which was launched in early 2022. The brief for this project was to create a lighter vehicle with reduced energy consumption, while still maintaining the same structural strength and adhering closely to both industry safety standards and governmental decarbonisation goals. To achieve these aims, TRB and TDI together developed modular wall panels composed of moulded carbon fibre laminates with a recycled foam core. The partnership also employed a unique polyfurfuryl alcohol (PFA) bioresin – a sustainable alternative to the commonly used phenolic resins. The Revolution VLR is 40 per cent lighter than the equivalent traditional heavy rail vehicles, with reduced energy consumption and CO2 emissions.
TRB has extensive experience in the refurbishment of rolling stock, providing high quality, lightweight solutions for
a number of common problems. This knowledge and expertise covers everything necessary for refurbishing doors, internal partitions, floors and roofs, including a detailed survey and quote, reverseengineering and finishing specific parts to meet customer needs. The company’s expertise covers everything from assessment and reverse engineering of components to improving maintenance efficiency, all while reducing the overall cost of components. TRB’s comprehensive service offering comprises all manner of processes to ensure that refurbished products stand up to the demanding rail environments. This includes stripping down panels, replacing worn materials – such as handles and rubber trims – fixing water ingress problems, filling dents repainting, and a host of additional services, all tailored to precisely meet each customer’s particular needs.
TRB has made major strategic investments to grow its capabilities, while also running continuous improvement programmes across the business to increase efficiency, reduce costs, and raise quality even higher. Looking forward, the TRB management team plans to make further strategic investments and establish additional partnerships with specialist technology providers that complement its capabilities. Richard Holland, Managing Director of TRB, explained: ‘We will continue to invest in product innovations and technologies to provide end-to-end manufacturing and refurbishment services across all transport sectors. We are dedicated to meeting the dynamic needs of this vital industry, and to supporting sustainability goals by further developing our repertoire of environmentally friendly materials.’
The clear aim is for TRB to continue to grow by focusing on providing its customers with complete solutions that meet their evolving needs, and by responding directly to the growing global socio-economic pressure for greener, more sustainable products.
Tel: 01480 588050
Email: sales@trbls.com
Visit: trbls.com/rail
In the realm of rail travel, the intrinsic value of light for our wellbeing and health is universally acknowledged
It orchestrates our sleep-wake cycles, invigorates our daily routines, and enhances our focus. The presence of abundant light not only fosters a sense of safety but also aids in spatial orientation. For a span of over three decades, Twinfix has been a stalwart in the provision of well-illuminated spaces. Throughout the United Kingdom, Twinfix has worked its magic, aiding the rail industry in the transformation of stations into secure and welcoming environments, alleviating the rigors of travel.
Twinfix, armed with its proficiency in polycarbonate and roof glazing, is committed to developing state-of-theart, safe, and high-quality solutions. This commitment finds particular significance within the rail network, where the preservation of historical buildings necessitates meticulous and considerate approaches to restoration and refurbishment.
Twinfix's range of roof glazing products seamlessly marries the aesthetic appeal of traditional glass with the advantages of contemporary material technology, ensuring that historic railway stations bask in the embrace of natural light once more. This impact transcends the realm of enhanced travel experiences, contributing to a reduction in reliance on electric lighting, ultimately resulting in lower carbon emissions and a more environmentally friendly planet.
As masters of polycarbonate, Twinfix has perfected the art of emulating the timeless allure of traditional glass through their array of polycarbonate products. Even intricate designs, such as the Georgian Wire, can be faithfully replicated. Polycarbonate, with its substantial weight savings compared to glass, allows support systems and roofs to maintain their authentic appearance while adhering to building regulations. Moreover, polycarbonate outlasts glass, resisting UV damage and exhibiting remarkable strength and durability.
Maintenance and cleaning become effortless, ensuring a persistent source of natural light. When it comes to ensuring the safety and durability of roofing systems, Twinfix has emerged as a trusted name in the industry. The Multi-Link-Panel Non-Fragile (NF) roofing system has been a catalyst in redefining perceptions of roof safety.
The Twinfix Multi-Link-Panel NF roofing system is endowed with a wealth of safety features that prioritise the protection and well-being of individuals. Constructed with high-quality polycarbonate material, known for its exceptional strength and durability, the system ensures that the roof can withstand diverse environmental conditions and potential impacts without the risk of shattering or fragmenting.
This innovative system incorporates a unique Multi-Link design that securely interlocks the panels, creating a stable and
robust roofing structure. This eliminates the risk of panel dislodgment or collapse, even under the duress of substantial stress or severe weather conditions. With these features in place, the Twinfix MultiLink-Panel NF roofing system stands as a dependable and secure solution for the safeguarding of individuals and properties beneath it, making it a preferred choice for railway stations across the UK.
A recent instance of the transformative power of Twinfix's solutions can be witnessed at Pembroke Dock Station. Steeped in history and character, this station opened its doors in 1863 and evolved in the early 1900s, including the addition of fully glazed canopies over the station entrance and platform following the Great Western Railway's takeover of Pembroke and Tenby.
Now a Grade II listed building nestled within a conservation area, Pembroke Dock station underwent a revival as part of the £24 million Wales Station Improvement Scheme. The project encompassed the restoration of the station canopies, designed to withstand the test of time. The principal contractor, AmcoGiffen, undertook the renewal of the station, while meticulously adhering to the specifications that preserved the historic design and character of the station.
AmcoGiffen enlisted the expertise of Twinfix, a family business with nearly three decades of experience in the polycarbonate
roof glazing market. With a team of specialists in polycarbonate and roof glazing, Twinfix is dedicated to developing the latest and most cost-effective roof glazing products.
In the process of revitalising Pembroke Dock station, Twinfix supplied its MultiLink-Panel non-fragile roofing system to replace the existing glazing, which had grown old, tired, and discoloured. Notably, the innovative Georgian wired MultiLink-Panel NF roof-glazing emerged as an ideal fit for the refurbishment project at Pembroke. While it was essential to preserve the station's character through a sympathetic restoration, it was equally crucial to transcend a like-for-like replacement. Traditional materials, despite their resemblance, often come with inherent disadvantages.
Georgian wired polycarbonate, a 6mm solid polycarbonate sheet with a dimpled surface that mirrors the Georgian wired glass it replaced, stands out for its longevity and low maintenance. Beyond aesthetics, the focus was also on enhancing roof safety. The Multi-Link-Panel system earned the classification of non-fragile in accordance with the ACR(M)001:2019 roofing test, a significant safety update in line with modern-day requirements.
Furthermore, the access hatches at Pembroke Dock were designed to facilitate entry from underneath, enhancing the safety of the roof. These access hatches seamlessly integrated with the glazing, meeting the heritage demands of this historic station.
The importance of off-site construction in the rail industry cannot be overstated. Panel manufacture and assembly within the Twinfix factory have streamlined installation, leading to swifter and more error-free outcomes. Any necessary corrections are executed before the panels reach the site. Vicky Evans, Managing Director at Twinfix, lauds the myriad advantages of the nonfragile Multi-Link-Panel, particularly its crucial safety feature. The Georgian wired polycarbonate glazing seamlessly aligns with the station's historical appearance while incorporating essential safety features.
Chris Howchin, Capital Delivery Programme Manager at Network Rail, lauds Twinfix's contribution, highlighting the brighter and better canopy at Pembroke, which harmoniously complements the station's character. The safety features, including resilient polycarbonate panels and sturdy fixing mechanisms, ensure that the canopy will remain in excellent condition for years to come.
Paul Childs, Company Secretary for the Railway Heritage Trust, emphasises the trust's support for Network Rail's choice to partner with Twinfix in the restoration of the canopies. The restoration was conducted with sympathy and consideration for the historic structure.
The installation at Pembroke Dock station serves as a splendid example of the Georgian wired Multi-Link-Panel system in action. Twinfix, AmcoGiffen, and Pembroke Dock station all have every reason to be proud of the refurbished premises.
So, the next time you find yourself at a well-illuminated and welcoming railway station, take a moment to appreciate the natural light filtering through the roof. You might just be witnessing a touch of the magic that Twinfix brings to rail travel, making your journey brighter and better.
Tel: 01925 811311
Email: enquiries@twinfix.co.uk
Visit: www.twinfix.co.uk
bespoke torque control solutions specially
From humble beginnings 80 years ago, in a small workshop, to the latest purpose-built factory, Norbar has pioneered many of today’s solutions for torque control
Incorporated in 1943, the ‘North Bar Tool Company’ became the first company in Britain to commercially manufacture torque wrenches. The initial demand was driven by the need for the gasket-less cylinder head of the Rolls Royce Merlin engine to be accurately tightened. Bill Brodey and his partner Ernest Thornitt obtained a licence from Britain's wartime Government to begin the manufacture of torque wrenches and Norbar was born.
Norbar specialises in the manufacture and worldwide distribution of torque tools for torque tightening, measurement and calibration, as they are engaged solely in the design, development and production or torque tightening and measuring equipment. Their main customers include manufacturers, and engineering services who operate within a wide range of industries including transportation and rail industry.
Norbar’s involvement in the transport industry begins with the manufacturers, and extends through the life of vehicles and rolling stock. It also plays a key role in the infrastructure element of transport, building and maintaining road and rail networks. The company provides the industry with ergonomic tools including; torque wrenches that are easy to read and adjust, power tools that emit low levels of noise and vibration, and torque measurement instruments.
Norbar has worked to manufacture a torque wrench that addresses the market needs, and is both fast and light to adjust with the clearest possible scale. Another version of the industrial wrench that has found great success in the rail track maintenance industry is the 1 11/16” bi-square wrench. It was produced at the request of the rail industry for torque tightening rail fishplate
bolts. It eliminates the possibility of sockets or square drives being left on the railway track by integrating the 1 11/16” socket permanently onto the end of the wrench.
EvoTorque® are electronic torque tools designed for applying torque to threaded fasteners. The unique ‘Intelligent Joint Sensing’ technology will accurately tighten to the correct torque without the risk of excess overshoot or undershoot that is common in other electric tools. EvoTorque® tools give continuous (non-impacting) rotation and are quiet in use. EvoTorque® tools utilise patented technology to give unprecedented joint control from hard through to soft joints. They are available in both mains-electric and battery-powered ranges. The battery tool version EvoTorque® Battery Tool (EBT) shown on the previous page is a transducer controlled battery powered torque tool that is designed for
accurately applying torque to threaded fasteners with data memory and data transfer capabilities.
Pneumatic torque tools are handheld, air driven, non-impacting torque delivery tools intended to tighten and loosen nuts, bolts and threaded fasteners. However they do come with various health and safety risks as they involve the operator being subjected to high levels of noise and vibration, but Norbar’s PneuTorque® is a rotating pneumatic torque wrench that features almost no vibration and low levels of noise. PneuTorques have been used on many transport infrastructure projects including bridge and tunnel construction.
The importance of keeping torque tools in peak calibration condition is well established. The main reasons that more companies do not perform calibration checks on their own wrenches are the cost of testers and fears over the complexity of the testing equipment. Norbar’s TruCheckTM torque wrench testers are cost effective being significantly cheaper than most similar products on the market and simpler to use. TruCheckTM was designed specifically with the needs of automotive and transport workshops in mind.
The importance of torque control
Torque is defined as any force or system of forces that tends to cause rotation about an axis. In order to control this many methods exist to join the two or more parts together, and typically the threaded fastener is what is used to streamline this process.
The threaded fastener clamps parts together with a tension that exceeds the external forces leading them to separate. It is vital that the initial tension is correct, as if its too low varying loads act on the bolt and it will quickly fail, and if initial tension is too high the tightening process may cause bolt failure. Finding the correct balance is done by specifying and controlling the tightening toque.
Whilst Norbar produces an extensive range of standard equipment, there are times when something outside the standard range is required, and Norbar’s engineer to order service can be beneficial.
As an ISO 9001 company, Norbar both designs and manufactures special equipment to meet customer specifications. These projects range from modified torque wrench end fittings to complete torque and angle control of multi-spindle nut runners.
Relevant European Safety Directives are applied where appropriate, giving further assurance that the engineer to order equipment is of the highest standard.
Case study: London Underground Norbar Torque Tools’ Specialist Engineering Department has developed a unique torque tool for London Underground. The new tool has been developed to solve a specific engineering challenge, namely the removal and refit of the inter-car coupler mounting bolts on the fleet of 47 Bombardier 09 Stock trains used on the Victoria Line in London and maintained at the Northumberland Park depot.
The inter-car coupler mounting bolts are accessed from the underside of the train, either from the pit road or with the train jacked up. The coupler mounting has four bolts with a significant boss in the middle that houses the Absolute Position Reader (APR). Of the four bolts, the upper two were particularly difficult to access due to them being deeper up into the train and surrounded by other hardware. The bolts are required to be tightened to a torque of 1,050 N·m.
London Underground’s tool supplier, Hayley Group, contacted Norbar with the remit of providing one tool to reach all of the bolts on the coupler.
The Norbar solution was to use a PneuTorque® PTS tool with a specially developed drive that is slim, long and offset from the PTS square drive, with a series of gears arranged in line and driving each
‘My colleagues and I were very impressed by your entire manufacturing operation, and it was evident from the tour the standards you achieve are impeccable. It's comforting to know we're in good hands, and we proudly promote the use of your equipment internally.’
Michael Millard National Repair Improvement Manager for The Automobile Association
other. This enables all of the bolts on the Bombardier 09 Stock trains to be reached during maintenance.
In addition, the gearbox of the tool is supplied with quick change reaction arms in order to reach all of the bolts and safely take torque reaction from the tool. The aluminium bodied gearbox can also be positioned on the bolt before the driving tool is coupled. This significantly reduces the total weight that has to be lifted and makes the location of the offset gearbox and its reaction plate much easier.
Norbar’s website features a toque tension calculator, to use the calculator visit: https:// www.norbar.com/Support/Calculators/TorqueTension-Calculator
For more information and to view an example list of projects previously delivered by Norbar visit: https://www.norbar.com/ Support/Services/Engineer-to-Order
Tel: 01295 270333
Email: enquiry@norbar.com
Visit: www.norbar.com
Address: NORBAR TORQUE TOOLS LTD.
Wildmere Road
Banbury, Oxfordshire OX16 3JU United Kingdom
Dyer & Butler, part of M Group Services’ Transport Division, delivers specialist engineering services to the UK’s rail and aviation sectors as well as providing expertise in adjacent markets.
Putting Health, Wellbeing & Safety of people first
Engaging and empowering everyone to deliver and grow
Our Vision
Helping deliver our clients business needs
Conducting ourselves respectfully, being open, accountable & honest in all of our operations
To be the leading provider of essential infrastructure to the transport sector in the UK.
McCulloch Group is a Scottish based company that provides the world’s railways with their innovative solutions to improve safety and efficiency on track
Now operating in the UK, Europe, North America and Australasia, McCulloch Group’s fleet of machines take on railway maintenance tasks that would otherwise be time consuming, costly, and sometimes dangerous, to carry out manually.
Founded 30 years ago, McCulloch Group was founded on a desire to do better. Solving problems is at the core of the business, as is innovation – and have been since the very first product, the TRT™, was invented by the McCulloch brothers in a yard, in a small Scottish village.
30 years, and many products later – the fleet of machinery was recently enhanced yet again, with the creation of McCulloch Group’s first all-electric piece of kit – the
TRTe. For decades, the challenge on the railways has always been safety. McCulloch Group was born of innovation; creating technical solutions that make on-track work safer for all. Whilst rail infrastructure projects still have their dangers, the new challenge is one that, if tackled properly, will save the planet.
With government targets encouraging more and more of the countries companies and infrastructure agencies to set their own ambitious sustainability goals, providers of infrastructure solutions – need to get greener. The TRTe™ is a step towards this, one which will make a sizeable contribution to the move towards zero emission working practices. Here’s a breakdown of the McCulloch fleet and the problems it’s solving across the world’s railways.
The invention that kick-started it all, was the Trac Rail Transposer (the TRT), a mobile, remote-controlled machine which lifts and moves sizeable lengths of rail and associated ironwork across project landscapes. In the last 15 years it’s operated in the UK with 99.7 per cent proven reliability and is now trusted by infrastructural organisations such as Network Rail, Paris Metro, London Underground and Kiwi Rail. It also has a variety of attachments which minimize the need to bring other equipment on to the track, including a rail saw, a plough, and a jib arm.
The Rail Saw attachment releases zero emissions and carries out the functions of a hydraulic long arm saw. With full use possible from a standing position, this attachment not only minimises additional machinery on site but also protects the workforce from fatigue and back injury due to its position.
Moving on to the Plough attachment, again this piece of supplementary kit clears the majority of ballast from the side of the track and from sleeper ends, without bringing a further machine on site. The TRT Plough eliminates manual handling and fatigue and can work on most track types. On one project, you can have multiple TRT and plough systems working in conjunction with each other.
The final attachment, the mounted Jib Arm, allows for the safe and easy lifting of track furniture. This attachment for the TRT operates off of the TRT’s own power supply, again minimising emissions that would be generated by hiring a separate piece of kit entirely. The Jib is capable of lifting various track furniture up to a maximum of 990kgs.
This patented system removes and replaces rail panels swiftly and safely. Another remotecontrolled piece of technology, the Panel Lifter creates an instant exclusion one which eliminates any handling issues and keeps on track teams safe while panels are removed and replaced. It works incredibly quickly,
meaning it’s a more efficient process – an incredibly important factor to consider on projects with limited possession timescales.
The MMPV is a self-mounting, self-propelled vehicle which, with a crane attachment, can also be self-loading. It can be adapted to a variety of tasks on the railways and is best put to use in environments where significant volumes of materials and track furniture need to be moved, where waste and equipment need to be removed from the infrastructure, and where track occupation times are limited due to scheduled train movements.
The McCulloch InfiniTy (previously known as the TCT) is a solution that lifts, transports, and dispenses cable from pre-wound cable reels. Again – it’s an entirely remote-controlled piece of kit and
so completed this task more safely and efficiently than traditional methods. The rubber tracked machine is easily moveable across the infrastructure and can lift and dispense reels of cable up to 1,600mm in diameter and two metric tons in weight.
To find out more about the McCulloch Group products, visit mccullochgroup. com or follow them on LinkedIn to see the machines hard at work on the world’s railways.
Whilst safety and efficiency will always be a top priority for those operating in rail, the last decade has also brought a new challenge – one which is going to require the transformation of how we work, to solve.
Net Zero targets are now firmly in place across governments and businesses across the UK, Europe, and wider globe. As we, as an industry, try to clean up our act in a significant enough way to actually achieve
the ambitious targets, as problem-solvers our next challenge is to create a Net Zero Solution.
In September 2022, the TRTe – the newest member of the McCulloch Group fleet, was launched. The TRTe offers all the same services as the TRT but with the added benefit of being entirely electric. It has been designed in response to the climate crisis and the need for rail organisations to meet ambitious Net Zero targets. Entirely battery powered, the TRTe also reduces noise pollution on track, an issue which is faced by many projects operating near residential areas.
By providing the industry with an effective, all-electric solution McCulloch Group plays its part in transforming the industry, acting as a catalyst for change.
Reasons to use McCulloch products
McCulloch Group’s motto is ‘we’re built for rail people, by rail people’ – meaning it understands the day-to-day challenges faced by companies and on-track teams alike. Here are just a few of the useful features you’ll find across the fleet:
• Many products are entirely remote controlled, meaning a safety exclusion zone is created when operating.
• Products can be operated during the day, or at night.
• Most of the fleet can operate in completely live environments.
• The kit is designed to move on rubber tracks, meaning it can easily move around uneven track landscapes and around track furniture.
• Much of McCulloch kit is incredibly agile, meaning it can easily move within difficult environments such as tunnels, bridges and other tight spaces.
• For large projects, some of the products can be used in conjunction with others to create a system. This means that even the largest quantities and volumes of track and line can be manoeuvred.
• McCulloch products are now trusted worldwide, with fleets in operation as far afield as Autralasia, North America, and Malaysia.
• McCulloch Group is a trusted partner to companies like Affective Rail, the Paris Metro, London Underground, Kiwi Rail, and Network Rail.
With 30 years of successful business now past – McCulloch Group is excited for all that the future holds, here with its domestic operations in the UK, and internationally as it takes on more work on the world’s railways.
Tel: +44 (0)330 0130 010
Email: sales@mccullochgroup.com
Visit: www.Mccullochgroup.com
Address: Riverside Works, New Mill Road, Kilmarnock, KA1 3JG UK
LinkedIn, Tik Tok, Facebook, Instagram and Youtube at McCulloch Group
Operated during the day or at night
Brush strip solutions from Kleeneze-KOTI are perfect for sealing doors, compartments and sensitive equipment against uncontrolled air infiltration, energy loss, rodents, dirt, noise and cold smoke without impairing moving parts.
Escalator SAFETYSTRIP™ helps prevent sidewall entrapment on escalators and walkways. Simple to install and maintain, SAFETYSTRIP complies fully with EN115 and A17 codes.
Trackside ducting and electrical enclosures are irresistible places for determined rodents to squeeze in and make a nest. Approved by Network Rail, RODENTBRUSH™ protects vital signal and electrical cables from gnawing rodents.
Whatever you need to seal or protect, get in touch and we’ll be happy to help
T +44 (0)117 958 2450
E sales@ksl.uk.com
www.kleenezeko�.co.uk
Founded back in 1923 and now part of the KOTI group of companies, Kleeneze-KOTI are the leading manufacturer of brush strip products in the UK
From humble beginnings selling household brushes door to door around Bristol, Kleeneze-KOTI now design and manufacture flexible brush strip seals and solutions for all aspects of the rail, automotive and aerospace sectors.
Brush strip is one of the most adaptable sealing products available and much like Bristol’s own industrial heritage and evolution, Kleeneze-KOTI are continually developing practical solutions to today’s problems.
Many of their dedicated team have over 30 years’ experience in providing bespoke solutions, and because they focus entirely on brush strip, Kleeneze-KOTI have built up an unrivalled knowledge and expertise that enables them to provide innovative solutions across all industries.
Minding the gap
Wherever there are sliding or pivoting parts, brush strips seals the gap perfectly. From cab control levers to signalling and points covers, brush strip seals prevent the intrusion of rodents, dirt and contaminants. Sliding platform screen doors fitted with fire retardant brush strip seals, suppress underground train noise, improve station climatic control and help keep platform environments cleaner. Gaps between sliding train carriage doors and internal panels are discretely sealed with custom formed brush strip, preventing accidental entrapment and foreign objects fouling the door operating system.
Passenger safety
Escalator Safetystrip is a durable brush deflector designed to provide a tactile reminder to passengers to keep away from the hazard zones between the moving step and the stationery sidewall and reduce the risk of an entrapment incident.
First installed on London Underground escalators in 1982, Escalator Safetystrip has been protecting passengers from sidewall entrapment for over 35 years. Successfully fitted to over 400 escalators across the
existing network, Escalator Safetystrip and platform screen door seals will also protect the expected 200 million passengers on the new Elizabeth Line due to open in 2022.
Electrical enclosures, junction boxes and trackside ducting are warm dry places, irresistible to rodents. There are many points of access through which a determined rodent can squeeze and make a nest and problems occur because rats love to chew. As they gnaw through the protective plastic casing they dangerously expose the vital electrical and data cable.
Specially designed RODENTBRUSH
is easy to use, and incredibly effective in deterring rodents. Unlike other forms of pest control, RODENTBRUSH can be easily removed for routine maintenance and then replaced for ongoing cable protection. Rodent brush can be exposed to all elements, allows air to circulate and water to drain away.
Always here to help
As a close knit and dedicated team, KleenezeKOTI are proud of the products and service they provide. They offer a complete design, advisory and manufacturing service, providing friendly assistance in all aspects of problem solving with brush strip technology. So whether you are a designer, specifier or end user, their brushes may provide the perfect solution. Simply contact their friendly customer service team or ask one of the technical team to visit via the contact information below.
Tel: 01179 582 450
Email: sales@ksl.uk.com
Visit: www.kleenezekoti.co.uk
An EAL Assured quality course, delivered over 5 days on site with you
A brand-new, regulated, course that provides your Team Leaders with all the Production management and control skills needed to run today’s modern railway depot effectively.
Using independent multi-disciplinary advice to set up and deliver major rail programmes with our proven full project life-cycle capability.
Let’s support you on your journey ahead, talk to an expert at www.gleeds.com
It seems several years since I was a team leader, but I can still remember my time in the role with fondness It was a great position being able to directly control and manage a fair portion of your daily activity. The close contact with your team offers rewards when you see improvements in productivity and performance, and just seeing people improve from your inputs and guidance is so rewarding. It can be a tough role too at times as you try to balance the demands of managing scheduled delivery with the needs and desires of your team. I don’t think I realised when I was a Team Leader, how important the role was.
But are we letting our Team Leaders down? And hurting business performance at the same time.
Team Leader is a tough role to balance; they are right in the mix of things, needing to be connected to their teams and yet also managing multiple activities in a complex technological environment, often with moving targets to achieve. It might be said, ‘a hard tight rope to walk and get right.’ Team leaders are pivotal in turning direction from the plan into action and
ultimate effective output. No train runs on your network without it being touched by production, overseen by a team leader. Without effective, well-skilled team leaders an organisation will always struggle to deliver to a plan. We often talk of Production teams being ‘the engine’ of a maintenance business; well, team leaders have control of the accelerator!
Yet do we set them up to succeed in this vital role? Many papers split the role into leadership (people) and management (things).
Leadership is best described as being about inspiring others to perform at their optimum ability, with management best described as being able to effectively use all the available systems, processes, and resources at your disposal to achieve the required results.
Additionally, the rail Team Leader has full technical authority for work on the trains in the depot, giving three key aspects to the team leader competency skills required:
• Leadership competence.
• Technical (on train) competence.
• Production Management competence.
Typically, organisations spend a reasonable amount of time training and developing people’s leadership competence, often termed soft skills. There are many providers of leadership training, ourselves included; and several good products such as Insights® and situational leadership® have emerged over many years undertaking such development. It is an area that in most businesses is covered reasonably well.
Technical (on train) capability, being regulated by ROGS in our safety critical world, is amply covered from a development perspective. It must be as it is part of the legal compliance around competence management. And often is the only part of the three legs of team leader’s competence that is assessed… discussion for another article I’m sensing!!
But we are not so great at teaching our junior leaders the skills and importance of production management. How to manage the depot or department effectively and efficiently. Typically, we leave that to learning through osmosis, which will always lead to degradation of business capability over time. Train drivers are taught to drive the train, then they have route training layered on top; airline pilots learn to fly, then have airline and other cockpit management training layered on top. This additional (role-specific) training provides the required competence for the person to deliver optimum results. And let us be honest, as travelling public we prefer our pilots being competent! Airline mechanics pass their basic licence and then have system and organisation training to give the full competence in role. So, why don’t we do this in rail – as part of formalised development?
Well interestingly, as an industry, we used to teach production management competence; in the good old British Rail (BR) days, in fact some people reading this article will recall the NEBSS courses that were run, a very well received course. The BR NEBSS course systematically took prospective Team Leaders through many aspects required, everything from H&S, to employment law, to depot safety, to quality procedures… production efficiency – basically, the full
range of skills and knowledge required to perform the job well. Observationally, we lost many good things when BR broke up, EngPro hope to replace a little bit of it with this brand new course.
Our CS08 course has taken that old BR course, updated and modernised it to fit with the modern depots, trains, and working styles. It leaves the soft skills training to one side as that is covered well by most organisations, and if it isn’t then we always have CS01.
An EAL approved professional level training course, that following successful exam and work-based assignment returns a recognised certificate for your team leaders; The Modern Production Supervisor (Rail Vehicle Maintenance). Giving them a sense of pride in the role by raising the professional bar of these key individuals, improving their depth of knowledge, and in turn incrementally improving the depot management and output performance.
Running for five days the Course covers:
• Brief introduction to rail history, and application today.
• Understand the typical TOC organisation and where the TL fits in.
• Discuss the future challenges rail maintenance will have to tackle in the PSC world.
• The ‘big three’ that control availability.
• Routine maintenance –production control.
• Defect management and improving MTTR.
• Maintenance programmes and optimisation.
• Planning and scheduling effectively.
• Use Method Study approach to streamline production tasks.
• Contract and contractor management.
• Developing the competence of their team.
• Assigning work well.
• Operational communications.
• Running the effective shift brief.
• The perils of the 02:30 email.
• Safety management and risk assessments.
• The critical 60 minute after an incident – gathering and protecting perishable evidence.
• Quality control and assurance and the TL role in delivering this.
• Managing practical drift.
• Reporting performance (of train).
• KPI and metrics and how to use more effectively.
• TRUST 701D and delay attribution.
• LOTO, tool control, and governance boards.
• Technical publications and their origin and upkeep.
• Introduction to RCM ? and the future of maintenance.
• Reporting and learning cultures.
• Human performance limitations –recognising when your team is limited.
• EAM and other modern systems.
Logistics: At the moment we are running this course onsite at (or near) your location, which works well for our larger clients. Releasing team leaders for the course will always be a challenge especially for smaller organisations. In 2024 we will be running some open access courses in London (and Manchester) to cater for individuals and smaller organisations. We are also happy to discuss forms of licencing the product to train internally – reducing your costs.
More details of the certification and the course can be found at: https://engpro.co.uk/ cs08-workshop
EngPro is a boutique consultancy and training organisation specialising in maintenance professionalism and efficiency improvements. We are in our eighth year of business during which time our highly experienced small team have trained over 1000 delegates. As well as this we also train incident/near miss Investigations to RSSB standard, maintenance efficiency programmes, and managing change in the maintenance world – a very dynamic course. All our training immerses the delegate in topic with several in-class exercises and selfreflection.
HOWARD LEACH
C.Eng
Maintenance management professional in rail and aviation with extensive experience in both fields. We focus on the people in the system.
Tel: 07841029276
Email: howard@engpro.co.uk
Visit: www.engpro.co.uk
The future of rail infrastructure & asset monitoring
Discover unparalleled insights with future-proof, self-learning technology. Our award-winning Trains with Brains® rail portfolio delivers one of the most comprehensive head-to-toe monitoring solutions available today. Proven in the field, operations and maintenance teams worldwide are experiencing enhanced e ciency, reduced costs, and prolonged asset lifespan with this ground-breaking technology. We are shaping a smarter, more e cient, and sustainable future for rail transportation, where innovation meets reliability. Scan
Damage to the overhead line and pantograph poses significant issues in the rail industry, costing the UK rail network alone over £100 million annually, and causing severe service disruption and reputational damage
Transmission Dynamics, a UKbased, multi-award winning, global innovator, and Industrial Internet of Things solutions provider, has been working with clients to identify and resolve these issues with its market-leading Pantograph Damage Assessment System (PANDAS) since 2008. Building on this success, the latest innovation, PANDAS-V®, incorporates a camera unit, providing critical footage of incidents detected. Deployed in various regions across the UK and multiple countries, PANDAS-V® is significantly reducing service disruption and saving costs globally.
Michael Dobbs, Principal Engineer for Network Rail Northwest and Central Region, emphasises the severity of dropper wire faults in particular, stating these incidents: ‘Are one of the main causes of overhead line related train delays and disruption.’
Statistics from the NW&C region ‘show 518 incidents over last five years, resulting in 51,307 minutes of train delays and estimated £5.7 million of associated cost.’
He added: ‘PANDAS-V is playing a critical role in identifying and immediately reporting all problematic locations.’
With twelve initial systems currently deployed across Class 390 trains in this region, PANDAS-V® has brought about transformative change. Ndaba Moyo, Senior Contact Systems Engineer, Network Rail (NW&C) stated: ‘Having installed our first PANDAS® system in August 2021 this technology now provides critical actionable intelligence, that has allowed us to focus less time on fault identification and more time on fault remediation. It has had a vast impact on our ability to inform and prioritise our operations and maintenance, leading to less delays resulting from overhead line incidents.’
Below are examples of some of the faults identified and reported by this powerful technology.
These issues regularly cause dewirements and cost the industry an estimated £1 million to £1.5 million each time.
PANDAS-V® provides invaluable intelligence regarding these infrastructure faults, immediately notifying rail stakeholders of issues identified which could lead to potential dewirements. These issues are efficiently found using GPS tracking and effectively reported with visual footage, allowing Network Rail engineers to plan remedial work before attending the location, within the same day if necessary.
Traditionally, preventing such faults requires regular manual inspections, with maintenance teams walking miles of ballast to assess the condition of the overhead line. However, these methods prove to be timeconsuming, costly, and often fail to identify emerging faults before they escalate. The longer a fault remains undetected and unresolved, the more catastrophic the resulting damage.
In fact, during one week in September 2023, two separate regions in the UK suffered dewirement incidents, as a result of issues that had been successfully identified and reported by PANDAS-V(R)®. These incidents have led to a significant cultural and operational shift within Network Rail, to ensure these critical alerts are prioritised, ensuring faults are resolved before further damage and disruption occurs.
The need for more efficient and reliable railway monitoring methods has become paramount for rail operators and infrastructure maintainers worldwide. Subsequently, the digitalisation of the railway through remote condition monitoring has become essential. In pursuit of innovation, Transmission Dynamics continues to lead the industry with the groundbreaking solution, PANDAS-V®.
PANDAS-V® combines advanced IIoT sensor technology and unique, innovative design to provide a comprehensive solution for the rail industry. A roof-mounted camera, synchronised with a pantographmounted wireless accelerometer, detects changes in overhead line conditions as the train travels. This synchronisation triggers video captures of potential issues based on impacts, generating invaluable ten-second clips, and pinpointing precise locations for immediate analysis through automatic and instantaneous reporting to relevant stakeholders. What sets PANDAS-V® apart is its real-time onboard processing using Machine Learning, saving critical time in fault identification, and allowing stakeholders to implement fault remediation works appropriately and before the issue causes further damage.
Traditionally, similar systems require one to two weeks of post-processing, a delay that PANDAS-V® eliminates entirely
by reporting such issues within one minute from detection with its train-borne instrumentation. Faults identified by PANDAS-V® today are typically serviced by Network Rail with immediate effect, on the same day and often within just one hour.
PANDAS-V® is engineered to operate in some of the most arduous outdoor environments, from heavy rain and high winds to extreme temperatures ranging from -40°C to +85°C and deliver reliable performance during both day and night. As such, it is now in successful operation across a wide spectrum of climates, ranging from scorching Indian summers to freezing Canadian winters. A key feature enhancing its robustness is the incorporation of a patented dual-arm wiper-scraper mechanism with automatic rain detection. This innovative design ensures consistent and reliable visibility, even in adverse weather conditions. Remarkably, this mechanism eliminates the need for frequent cleaning of the lens, a common issue caused by carbon deposits that can impair visual clarity after just a few days of operation.
The combination of this market-leading hardware, high-quality video footage, and onboard edge processing with selflearning image processing algorithms, propels PANDAS-V® to the forefront of rail infrastructure monitoring, making it not only advanced but also future-proof in its capabilities. As well as reporting impacts and identifying issues such as broken dropper wires, misaligned neutral sections, pantograph flip, arcing and bird strikes, PANDAS-V® offers a comprehensive range of additional critical measurements related to pantograph and overhead line performance.
Currently, these measurements encompass parameters such as pantograph height, wire stagger, and carriage sway.
Soon, the system will incorporate features like carbon wear monitoring and contact force measurement (uplift), enhancing its diagnostic capabilities even further.
By harnessing cutting-edge technology, PANDAS-V® provides real-time data and insights, enabling operators to make informed decisions promptly. This proactive approach not only minimises downtime but also significantly reduces the likelihood of costly repairs, resulting in substantial financial savings for operations, all while enhancing safety and extending the lifespan of railway infrastructure.
Key impact themes include:
• Maximised operational efficiencies through preventative rather than reactive maintenance, enabling operations and maintenance engineering teams to plan, mobilise and undertake maintenance when issues occur. Network Rail have already reduced some of their manual inspection intervals from every six weeks to every eleven weeks following the adoption of this technology.
• Increased safety by reducing boots on ballast. Having previously been physically walking and searching miles of rail network for new and known faults, PANDAS V® can provide visibility of the entire network during live passenger service. Using these insights to prevent incidents associated with pantograph and overhead line defects, which could cause catastrophic incidents such as dewirements, provides exponential increases in the safety of the network, its passengers, and its workers.
• Reduced delays caused by infrastructure faults and unplanned maintenance. Engineers are now made aware of issues
quickly and can plan a suitable time/place to undertake the resolutions required without disruption to services and keeping boots off ballast. With dropper wires alone causing more than 10,000 minutes of delays in one region of the UK network, PANDAS V® is having a vast impact on service reliability, reporting such events within one minute of occurrence.
• Reduced costs come from the above operational efficiencies, the resulting reduction in costly delays and remediation works, and the extension of asset life as a result of more proactive operations and maintenance works. Michael Dobbs, Principal Engineer at Network Rail stated: ‘The PANDAS® system could have prevented more than £5.9 million worth of costs over the last five years on the Class 350 trains alone.’
With this proven impact on reducing delays, improving maintenance practices, and enhancing rail service reliability, PANDAS-V® is poised to play a pivotal role in revolutionising the way rail infrastructure is monitored. Transmission Dynamics is committed to continuing its global rail sector collaborations in order to lead the future of rail infrastructure monitoring worldwide.
Tel: 01915 800 058
Email: support@jrdltd.co.uk
Visit: www.transmissiondynamics.com
Non-armored and armored Flame-retardant Wrapping Tube Cable using SpiderWeb Ribbon (FR-WTC-SWR) for rail, underground and metro applications.
Range of ultra-high fibre density cable designs including 288, 432 and 864 fibres both non-armored and armored variants specifically intended for OVERGROUND RAIL TUNNEL and UNDERGROUND network applications.
www.fujikura.co.uk
HD
• Illustration is 432 fibre over-ground double-jacket design
• Cable can be jointed in 4-5 hours compared to 20+ hours using traditional loose tube cables and conventional installation methods.
• Small and lightweight compared to traditional designs
• Fully dry (gel-free) construction
• 12 Fiber Spider Web Ribbon (SWR)
• CPR Class B2ca-s1a,d0,a1
Inner sheath (FRPE, Yellow)
Corrugated steel tape
12F Spider Web Ribbon in each bundled unit
Water blocking tape
Strength member (FRP)
Water blocking material
Ripcords
Outer sheath (FRPE, Black)
Diamond Hire and Sales have invested in innovative electric machinery which can make your site carbon neutral, free of HAV, and compliant with all aspects of manual handling with just one call
Our equipment is your gateway to a cleaner and safer working environment, carbon free, remote operation and minimal labour costs; the future looks safer with Diamond Hire and Sales.
The workplace environment is different today, there are many mandatory conditions that have to be attended to, that’s why innovation is so important as it helps us to meet those requirements without compromising the job in hand. We know the concrete is still very hard and heavy, that has not changed it’s just how we go about removing it! Traditional methods are not acceptable as they don’t meet legislation, so the future has to come from innovation as they combat the issues and provide the answer, ‘Safe working for all’ on time and within budget.
Part of a full range of models to suit your environment, the automated Minnich Rock Drill is ideal for rock drilling, vertical or horizontal dowel bars and anchor holes in concrete. The robotic electric Brokks is perfect for controlled demolition, whether breaking or crunching these machines demolish concrete like no other. For removing debris, look no further than the Hi-Tip electric Twinca barrow with 800kg load capacity, this one-man operation makes light work of shifting rubble. Last but not least is our very own Sindrilla, the first patented hands-free drilling solution for those everyday holes, you can drill all day long, free from drill rotation and HAV, the Sindrilla is compact, mobile and dustless.
This drill is essential for future railway projects, perfect for dowel bar drilling, induction line drilling, anchor hole drilling and hydraulic bursting prior to removing unwanted concrete. It mitigates HAV to the
operator due to its remote operation and keeps workers safe. The drill penetrations are fast, cost effective and reliable ensuring accurate placement of dowels and fixings after drilling.
Brokks
Our Brokks are the robots that you need. It enables your business to keep up with Health and Safety vibration legalisation along with commercial pressure. They are small in size meaning they can fit into tight spaces; however, they boast a hydraulic system that runs on a low flow/high pressure principle which gives them enormous strength. These Brokks do not emit any fumes and keeps
noise pollution at a minimum. Hiring or purchasing this excellent piece of Swedish engineering from us will guarantee safety and a faster, cleaner, and more accurate job. Perfect for those challenging railway projects where health and safety is paramount.
Twincas
This is your perfect machine for the clean-up process and is a necessity for those labour intensive clear up jobs. The Twinca HI-Tip Electric Dumpers are battery powered and omit no noise or fumes whilst in operation. Allowing operatives to use the machine inside or outside all day on a full charge. It can hold up to 800kg debris and with the
press of a button can dump its load into your skip. Operatives have no fatigue or manual handling concerns when operating the walk behind Twinca Hi-Tip Dumper.
Sindrilla
Our very own percussive mobile drill that will leave you with the perfect dustless hole that is clean and accurate ready for your chosen bar or anchor. It is rig mounted
and offers a perfect hands-free drilling solution for those everyday percussive holes. Omitting no vibration exposure to the operator, they are safe from HAV and can be used all day.
Our equipment which is available to hire is safe, robust, and very cost effective, it can be delivered to your project by contacting us directly. It provides solutions to those everyday site constraints that all
construction managers and workers face each and every day. This is the new method of working, a glimpse into the future and we are happy to share it with you.
Tel: 01252 524141
Email: info@diamondhiresales.co.uk
Visit: www.diamondhiresales.co.uk
PULS DIN-Rail power supplies are authorised by NRAP for use on railway infrastructure for which Network Rail is the manager under ROGS regulations
PULS Power the specialist manufacturer of high reliability DIN-Rail power supplies provides a range of reliable, efficient and robust DIN-Rail power supplies specifically for railway applications. Using technology based on designs already proven in tens of thousands of industrial applications worldwide PULS power supplies also feature DIN-Rail mounting to enable simple integration into cabinets and enclosures both on board rolling stock and trackside.
Performance requirements for electronic systems in railway applications are challenging on several fronts; failures cannot be tolerated, even under extreme mechanical stress over an extended temperature range. Further, the input voltages in railways differ from those experienced in industrial applications ruling out the use of standard commercial grade devices. PULS railway approved power supplies are ideally suited to the latest infrastructure projects such as HS2 and extensions to underground rail networks.
PULS railway specific power supplies may be used in a wide range of applications within the train and on the track including, central power, air conditioning, communication and infotainment systems, signaling technology and train protection systems. PULS products are deployed in major infrastructure investments such as the SBB (Swiss Federal Railways) where power supplies have been installed along the railway track in some 800 electrical cabinets all over Switzerland for the control of power lines for the trains. Critical to this contract was the ability of PULS to deliver and support the chosen product types for many years after design-in, while also delivering cost savings over the existing installation.
PULS continue to innovate and have recently introduced the new FIEPOS range of rugged IP67 rated power supplies which need no protective enclosure. These power supplies provide an intelligent distributed power solution and may be mounted in close proximity to, or actually on, the
load. This reduces installation costs and simplifies commissioning while introducing increased flexibility and the ability to easily reconfigure systems.
PULS railway range of power supplies provide one hundred per cent greater mains failure bridging time than required by the railway standard EN 50155 (S2), are weather resistant with all PCBs having conformal coating as standard and are completely convection cooled simplifying installation, further increasing reliability and minimising system noise.
Fully EN 50155 certified PULS DIN-Rail power supplies are classified according to T3, TX, C2 and S2 for use on rolling stock. They also meet EN 61373 for shock and vibration, EN 50121-3-2 for EMC requirements and EN 45545-2 for fire protection on a railway vehicle according to hazard level HL3.
Five models from the PULS QS Series have been awarded full acceptance certification by Network Rail for use with
signaling equipment in environments not exceeding 95 per cent relative humidity. The Network Rail product acceptance process is required for products intended for use on or about rail infrastructure and ensures they are safe, reliable, fit for purpose, compatible and do not export unacceptable risks to the infrastructure. Only accepted products, (except those allowed by NR/ L2/RSE/100/05) may be used on rail infrastructure.
Three of the Network Rail approved PULS DIN-Rail power supplies feature the advanced PULS ‘Hiccupplus’ overload protection mode. These employ technology innovations to overcome the problems associated with early hiccup protection circuits which were considered too sensitive when used in conjunction with motors or loads that are equipped with large input capacity, running power supplies in parallel or battery charging. Th ese are the QS40.241 with a DC output of 24V/40A, and the
QS20.481.C1 and QS20.241.C1 with outputs of 48V/10A and 24V/20A respectively and feature conformal coating.
The two other approved DIN-Rail power supplies are the QS10.481.C1 providing an
output of 48V/5A and the QS5.241.A1 rated at 24V/5A, which are also conformal coated.
PULS DIN-Rail power supplies offer system designers and installers’ uncomplicated assembly and permits flexible
positioning of the devices. Optional wall and side mounting brackets offer alternative mounting options. Spring-clamp terminals provide shock and vibration resistance, making installation intuitive and facilitates simple wiring without tools.
Key features of the PULS QS Series of DIN-Rail power supplies include a wide input range from 100 to 240Vac, and a very wide operating temperature from -40⁰C to +70⁰C (depending on model) without derating (+60⁰C to +70⁰C with derating), typical efficiency greater than 94 per cent and operation in environments with up to 95 per cent maximum relative humidity. All models have a nominal 110Vdc input with a wide voltage fluctuation tolerance of -30 to +40 per cent and are available with an output voltage range from 24 to 28VDC with power ratings of 100, 200 and 400W.
For more information on PULS DIN-Rail railway power supplies, get in touch with them via the contact information below.
Tel: 01525 841 001
Email: sales@puls.co.uk
Visit: www.pulspower.com
WAVE TECHNOLOGY
ADAPTABLE F I T
COLOR CODE
SIMPLIFIED SELECTION
COATING
ANTI - FOG & ANTI-SCRATCH
UNIVERSAL was engineered to combine strength, flexibility, and ergonomics in a light yet panoramic eyewear. Through these innovative goggles, bold adventurers can explore the furthest reaches of time and space. As they venture outward, they can have peace of mind that their eyes are protected with confidence in their enhanced vision.
IT’S TIME TO RISE TO THE CHALLENGE.
The beauty of the universe resides in the equilibrium found between the elements that compose it, each of them, having a clear purpose.
UNIVERSAL was engineered to combine strength, flexibility, and ergonomics in a light yet panoramic goggle, leading to a model adapted for both the wearer and the working environment. Indeed, UNIVERSAL concentrates all Bollé Safety’s latest lens and frame technologies in just over 100g.
OF RESEARCH AND DEVELOPMENT, BOLLÉ SAFETY UNVEILED THEIR LATEST SAFETY GOGGLE : UNIVERSAL. THIS ICONIC MODEL ENCOMPASSES ALL THE BRAND’S EXPERTISE AND REACHES NEW HEIGHTS IN TERMS OF ERGONOMICS, COMFORT AND STYLE. IT OFFERS OPTIMAL PROTECTION FOR EVERY USER IN ANY WORK ENVIRONMENT.
The purpose of PPE eyewear is first and foremost to protect the vision of the wearer from harmful elements, from shards to liquids or gas. UNIVERSAL has reached the highest level of protection under EN166 certification (B-rated). Available in several versions, each adapted to a specific work environment to offer more peace of mind & efficiency for the worker. For the most demanding jobs, a pivoting faceguard can be easily attached to UNIVERSAL’s main frame, so that every worker may be safe, regardless of the risk they face.
While many eyewear brands claim to protect the eye, Bollé Safety goes beyond with UNIVERSAL and offers enhanced effectiveness and efficiency.
When developing safety eyewear, one of the first challenges manufacturers are confronted with is the product’s fit. Indeed, while every user’s face shape is different, the protection of a goggle is as good as its fit. The solution found by Bollé Safety with their UNIVERSAL model resides in a simple yet effective feature: its Wave technology.
UNIVERSAL’s TPR soft frame was indeed equipped with the company’s latest innovation: a unique threefold bellows design that allows the model to morph and adapt perfectly to every user’s face structure. As a result, wearers benefit from a superior protection without any compromise on comfort, even in the long-term.
Through UNIVERSAL, Bollé Safety also introduces a new concept by employing a visible color code on their goggles’ straps and flexible frames. Its mission is to simplify the selection process for the wearer based on his/her work constraints, improve visibility, and allow site safety managers to ensure proper use of PPE, even from a distance.
Because the best safety goggle requires the best lens coating, UNIVERSAL is coated with Bollé Safety’s exclusive PLATINUM formula. This K & N certified lens technology offers a resistance to fogging that is 100 times more efficient than the required standard. The product also maintains its properties even after 100 cleanings, thanks to its dipping application process which enhance its robustness.
With an enhanced vision, users can be more aware of their environment, which leads to two positive effects for both the user and his/her company: Increased efficiency while reducing the risk of accidents in the workplace.
UNIVERSAL offers the promise of enhanced efficiency and peace of mind, essential for users to RISE TO THE CHALLENGE.
bolle-safety.com
Sealed Vented Welding Neoprenesuppliers to the
“We have the hose world in our hands”
In April 2018, AB Hoses was approached by RSSB and DB-ESG to develop a sander for the purposes of the DVRS pilot trial on the 323 fleet
AB Hoses was selected as preferred supplier in August 2018 due to its proven capability in variable rate sanding, as is seen with Class 220 and 221 Diesel Electric Multiple Units for Arriva Cross Country, and also its ability to develop bespoke sander equipment within a relatively short timeframe; 16 weeks from concept to installation for Arriva Cross Country.
Other sanding equipment competitors either stated that it would not be possible for them to develop variable rate sanding or quoted a minimum of one to two years for the development of a bespoke DVRS sander to RSSB, which would have resulted in the risk of the trial not going ahead at all or the funding being unavailable in later years. However, AB Hoses quoted 23 weeks for production of DVRS with twelve weeks for fitment as a commitment to supporting the development of data on DVRS and braking performance in the industry. The trial 323 units were completely installed with DVRS by April 2019.
In addition, AB Hoses also made the decision to undertake production of the sanding equipment as a non-profit project i.e. AB Hoses did not make any margin at all. This was decided due to the desire to be involved in a meaningful trial, having shared ownership of investment into the project with RSSB which makes for effective teamwork, whilst remaining the leaders in innovation of sanders in the industry as opposed to turning a profit. This commitment to RSSB saw AB Hoses invest into research and development, explore new technology ideas and test
emerging products available on the market, ultimately exploiting the existing AB Hoses products and using them as a platform to demonstrate capability.
Based on AB Hoses general and sander specific operational experience, it was recommended to undertake a series of comprehensive HAZID/HAZOP workshops, for full life cycle from design, validation and verification, installation, operation, maintenance, evaluation, removal etc be conducted involving competent operational staff from all parties. This process enabled all safety concerns to be identified and recorded, in particular where challenges and outcomes had potential to influence or change the design of the sanding equipment and its interactions with the train and Instrumentel’s monitoring equipment.
This documented process clearly defined the outputs required and took several iterations/workshops with all team members to agree the scope of work and to what extent I.e. the level of detail e.g. IP ratings of particular equipment, types of material to be used, performance level indicators etc. Ultimately with such safety critical equipment and the nature of the installation and operation, the entire project came under the scrutiny and approval of Ricardo Rail to the mandatory applicable standards i.e. Railway group standards, European Normalised standards, and Statutory law. However, as this process was undertaken in collaboration, the expectation for AB hoses to deliver sanding equipment to these requirements was communicated and set from the outset by means of a technical requirements document and also an applicable list of the relevant standards
to the application. This process assisted in ensuring good working relations between all team members as no lines were blurred as a result.
Like any team working on a project, success depends entirely on the contribution of every member. It was imperative that all team members had a sense of personal ownership within the project; for RSSB this was quantifying their research as leaders of the rail industry to achieve continuous improvement in health and safety performance of the railways, for WMT this trial could result in a route to the removal of the autumn timetable and provide longer term capacity gains and for AB Hoses and Instrumentel this was the incentive to develop the equipment at the forefront of technology and innovation that could achieve RSSB’s objective and maintain their own position of market leaders in their expertise. This shared vision enabled the team to work harder for the project as everyone had an invested interest in its success or failure.
Tel: 01246 208831
Email: sales@abhoses.com
Visit: www.abhoses.com
Address: AB Hoses & Fittings Limited
Units 5-7, Warwick Street Industrial Estate Chesterfield S40 2TT
Huck fasteners are used in many tough engineering applications, although their function is simple – to hold components together – there are a wide variety of designs and sizes available. These fasteners have been designed to cope with extreme stress and vibration, providing strength and facilitating lighter, stronger, more durable structures. Huck Fasteners are commonly used in railcars, railway tracks, rolling stock, aerospace, truck suspensions and chassis, bridge construction, heavy defense vehicles and mining/quarrying applications. In fact, anywhere that fastener failure is not an option.
Direct-tension HuckBolt’s and structural blind fasteners can often be a faster, more cost efficient, and safer alternative to traditional processes. Fasteners are an important engineering component; therefore, product reliability is key. Due to the complex working environment, traditional bolted joints often experience self-loosening (gradual loss of preload) over their working life, which can cause a decrease in the structures strength and loss of joint integrity.
The key difference between HuckBolt and conventional fastener installations is found in the structure of the threads of each of the fastening systems. Instead of the deep threads required to achieve a tolerance fit between conventional nuts and bolts, the HuckBolt pin requires only shallow locking grooves into which the collar is swaged. Th e shallow design of the locking grooves allows for a much larger pin root radius, which contributes significantly to the fatigue strength – up to five times that of a conventional nut and bolt.
For years, welding was seen as the only way to ensure the integrity of joints in demanding load-bearing or high-vibration structures. Today there are alternatives to
welding, the direct-tension, swaged Huck BobTail® Lockbolt is a uniquely engineered fastener. It is a two-part fastening system that consists of a pin and a collar. This enables the structure to be easily preassembled by hand allowing for additional alterations and checks. Th e fastener is then installed using a direct tension technique, in which the pin is pulled and the collar is simultaneously swaged into the locking grooves of the pin, deforming the collar into the grooves and swaging the material forward. Th is action develops the high clamp force.
The Huck BobTail has been designed to provide superior joining strength and offers fast, secure and simple installation. Even taking into consideration the need to drill holes, installing a Lockbolt is significantly faster than welding a joint and a quick visual inspection is all that is required to confirm the accuracy and quality of the installation.
HuckBolt’s can be effectively used with virtually any metal, and disparate metals with dissimilar coefficients of thermal expansion present no problems. Varying piece sizes in a joint are readily accommodated, and surface finishes are not harmed. Most importantly, HuckBolt’s are proven to hold up over years of service in demanding high-stress, high-vibration environments.
The Huck BobTail 12,14,16, 20mm and one-inch diameters, after lengthy and vigorous independent testing, has gained the prestigious Allgemeine bauaufsichtliche Zulassungen (German national technical approval) from the world renowned DIBt (Deutsches Institut für Bautechnik) for use in both static and dynamic applications in civil engineering. The approval concludes
that retorque/re-tension of an installed Huck BobTail LockBolt is not possible and also not necessary, and connections do not require maintenance regarding preload. Joints fastened together by BobTail large diameter LockBolts, within the range specified, are maintenance free.
Star Fasteners have been a Huck fastener distributor for over thirty years and are the UK’s largest stockists. Star Fasteners work closely with their customers to understand their applications and suggest new products that they may not have initially considered for a project. They can do this thanks to the knowledge and experience that they have within the market.
Tel: 0115 9324939
Email: sales@starfasteners.co.uk
Visit: www.starfasteners.co.uk
The experience of recent years has shown that relays have by no means lost their importance in the age of digitalisation. On the contrary, they are taking on ever more specialised functions
ComatReleco AG, incorporated in 1970, is a Swiss headquartered global supplier of high-quality relays and contactors of any kind. The core competencies are industrial relays, timing relays, monitoring relays and contactors. The electromechanical relay was invented in 1835 by Joseph Henry, who is mainly known as the inventor of the electromagnetic phenomenon of selfinduction and mutual induction. Henry was only really interested in the science of electricity, and the relay was a laboratory trick to entertain students.
Henry’s invention remained relatively unknown for several decades, but it became widespread in the 1860s with the development of the telegraph and telephone. In 1941, Konrad Zuse used electromechanical relays to build the world's first functioning computer Z3. Today, electromechanical relays have disappeared from computers.
Although fewer logic circuits are realised with the help of industrial relays nowadays, the relay is gaining in importance as an interface between logic and load due to the increasing use of process control systems and controllers. In their daily work,
designers are mainly guided by the specified values such as 10 A at 250 VAC or 10 A at 30 VDC with a width of 15.6 mm (interface relay) or 22.5 mm or 38 mm (industrial relay). It is quite often not considered that these specifications refer to the ohmic load.
Experience has shown that statements such as ‘we have always used the relay, but never had any problems before – why now?’ are first asked to the supplier. In most cases, however, it turns out that the type of signals to be switched has changed. This is because the levels of the signals to be switched are becoming smaller and smaller and the loads are becoming more and more inductive. Nevertheless, the proven relays with their standard contacts continue to be used.
It is not the stable current that stresses the contact, but the actual switching operation in connection with load size and load type. Therefore, the ratio of the switching current to the stable continuous current must be considered. In case of a resistive load, switching current and continuous current are approximately identical. With a lamp load, however, the
switching current can be up to twenty times the continuous current due to the cold resistance of the filament. Motors, valves and contactors, on the other hand, are inductive consumers that are characterised by an inrush current that can be five to ten times higher. The switching peaks of valves can also be up to twenty times the continuous current. These inductive loads also cause strong switch-off sparks. Capacitor loads and very long cables are a special case. Here, the switching currents can reach forty times the continuous current.
If the switching contacts are opened under high DC loads, an electric arc is formed that can lead to fast wear or even welding of the contacts. Thanks to the magnetic field of a blow magnet, the Lorentz force acts on the electric arc, which is ‘blown away’ or ‘pushed away’ and thus extended as a result.
Some manufacturers specify the utilization categories for switching elements according to IEC/EN 60947. However, usually only the utilization categories AC-1 and DC-1 are specified, whereby the utilization categories
AC-1 and DC-1 are described according to IEC/EN 60947-5-1 as resistive loads, precisely as ‘non-inductive or only slightly inductive loads (resistive loads)’. But in practice, the user hardly ever finds a resistive load. Here, the utilization categories for inductive loads are needed to find the right relay for the respective application.
For the utilization categories for DC voltage, the standard refers to the calculation of the load limit curve, here the time constant t = L/R is evaluated. Resistance heaters are resistive loads (t = 0.95) and are classified in class DC-1. DC-13 includes electromagnets with 6 x P (continuous load in W) and DC-14 are electromagnets with economy resistors (IE = 10 x IB; t = 15 ms).
Basically, the categories DC-1 and DC-13 are of interest for an industrial relay. The utilization category DC-13 describes the control of electromagnets, auxiliary current switches, contactors and solenoid valves where the inrush current is less than or equal to the rated current, but the cut-off voltage peak can reach fifteen times the rated voltage.
The influence of the inductances on the switching capacity of a contact can be illustrated by the typical relay power curve. A normal contact reaches its limits under inductive load even at low currents. With the knowledge of this problem, ComatReleco has created a complete product range for these applications. These special relays in the sizes of the standard industrial relays (38 and 22.5 mm) make it possible to switch even higher direct currents reliably due to their contact architecture.
The basic condition for a satisfactory relay service life is the correct selection of the relay type. If inductive loads have to be
switched, it is generally recommended to connect the load in order to eliminate the disturbance at the point of generation. For alternating current with an RC element or a VDR, for direct current with an RC element or a free-wheeling diode. This measure is rewarded by lower interference and a considerably longer contact life.
With capacitive loads, only a series resistor or a choke can help. If the designer does not have data of the connected devices, ComatReleco relays can be fitted directly with a protective circuit.
Relays have some very good properties that make them ideal components for coupling between systems. The galvanic separation between the coil and the contacts makes isolation between systems easy. The choice of coil voltages is wide and does not limit the voltage and current values of the contacts. It is relatively easy to select a relay to interface between a 24 V DC control circuit and a 230 V AC circuit. Relay coils are almost immune to overvoltage and EMC. There are also no software malfunctions. Due to the mechanical nature and simplicity of a relay, it has predictable behaviour in the event of a fault. However, there is no such thing as a one- fits-all relay. Knowing the application exactly is crucial for optimal dimensioning.
Usually, the actuation of the relay is manageable. It is more challenging when it comes to the load. It is not only important to know the voltage and current of the load, but also whether the load is resistive, inductive or capacitive. The switching interval, the switching frequency and special ambient conditions have an influence on the selection of the relay. The utilization categories according to IEC/EN 60947 help to characterise the application cases considering the operating conditions. Depending on the application and when
specified correctly, relays offer reliable solutions in railway applications in many cases and are therefore state-of- the-art even today. Relay -based designs are usually simpler than electronic controls with software and this also simplifies certification.
With one of the widest product portfolios of Relays and Contactors including customized solutions ComatReleco serves customer within the segments of industrial automation and building installation technology as well as transport and railway. Built with latest solid-state technologies, using the traditional electro-mechanical design or a combination of both. For more than 20 years, ComatReleco products have found their way into rail vehicles and their subcomponents such as toilet systems, HVAC, doors, etc.
Based on customer feedback, continuous improvements, and adaptations to comply with the standards, the product range has been continuously expanded over the past years.
ComatReleco’s CMS-10R IoT messaging system, often referred to as remote relay or SMS butler, secures contact with your assets.
One of the newer additions to the product range is the remote relay, the CMS-10R monitoring and control system. Despite the connected world, there are always situations where there is no internet access, the PLC control is unavailable, or monitoring is required outside the existing IT infrastructure. For these cases, ComatReleco has developed a remote relay with an integrated eSIM for 4G, 3G, 2G communication that works worldwide. The system includes an IoT cloud and an app for smart phones.
The world today is full of uncertainties. Nevertheless, we need to look forward and continue to grow our business as you and we did during the pandemic. A workplace where you can develop, share and evolve and the satisfaction of having done a good job will help us innovate and prepare for the future.
Tel: +41 31 838 55 77
Email: info@comatreleco.com
Visit: comatreleco.com
LinkedIn: ComatReleco AG
Address: ComatReleco AG
Bernstrasse 4 3076 Worb
Switzerland
With
J-Flex offers an extensive range of unique elastomer materials for Surface, Sub-Surface, Tunnel and Rolling Stock applications
J-Flex EPDM, Silicone and Neoprene and Vamac® materials are tested and approved to EN45545-2 and many other certifications, including LUL S1085 compliance and are designed specifically for low smoke low toxicity requirements, particularly with regards to enclosed space applications.
This makes them ideal for all safety critical applications in rail, mass transit, marine vessels, oil & gas, public transport and heavy goods vehicles. With resistance to corrosion, moisture, salt and light fuels, they offer outstanding flexibility, strength and durability. This includes environmental resistance – withstanding Ozone, U.V., rain and frost – meaning outdoor applications such as lighting systems and enclosures are kept water and dust tight.
Vamac® for example has excellent abrasion resistance, so is ideal where
wear is a concern – one notable use being protection of cables laying on ballast trackside. Gaskets and seals for enclosures such as lighting fixtures, battery boxes/ covers and the like will prevent the ingress of environmental factors.
Extruded seals are perfect for glazing partitions, door portals and floor covings. Anti-vibration gaskets and mouldings come into play for seating mounts and floor vibration dampening. As you can imagine, our various elastomers can perform many functional and critical roles within Surface, Sub-Surface, Tunnel and Rolling Stock applications. With various degrees of hardnesses being available, and gaskets, seals and mouldings being achievable in virtually any required dimensions, the possibilities are endless.
The following page should gives some food for thought but with so many
possibilities, maybe there’s something you have in mind that isn’t shown? Get in touch, we love a challenge and providing solutions!
Materials that can be supplied:
• EPDM
• Silicone
• Vamac®
• Silicone Sponge
• Neoprene Sponge
• Natural Rubber
Which can be supplied as:
• Calendered Sheet Rubber.
• Cut Gaskets; Joints and Strips.
• Precision Moulded Components.
• Extruded Profiles and Sections.
• Vulcanised Joined Profile Frames.
• Laminated Composites (rubber and sponge).
• Sponge/Foam Sheets or cut parts.
• Machined Plastics and sheets.
• Seals.
J-Flex’s extensive range of unique elastomer materials are tested and approved to EN45545-2 and many other certifications, including LUL S1085 compliance. J-Flex can also cross reference international standards, providing the best solutions – matching or alternative – that meet or exceed your specifications. The company’s extensive knowledge of the worldwide rubber market means it can usually source any specific material requirements you have.
Established in 1984, J-Flex is a privately owned company involved in the manufacturing & distribution of high
performance rubber products. Over this time they have gained an enviable reputation for high quality manufactured rubber components, elastomer sheetings and vacuum forming consumables, backed up with excellent customer service.
Trackside applications include:
• Cable Jacketing.
• Signal Cable Hose.
• Cable Ductings.
Material data sheets, test reports and samples are available upon request.
Datasheets and A Guide to Flame Retardant, Low Smoke, Low Toxic Rubber Materials can be downloaded at www.j-flex.com/productmarket/rail-and-mass-transit
Tel: 01777 712400
Email: sales@j-flex.com
Visit: www.j-flex.com
Address: J-Flex Rubber Products
Units 1 & 2 London Road Business Park
Retford, Nottinghamshire, DN22 6HG
LinkedIn: j-flex-rubber-products
Facebook: JFlexRubber
Twitter: JFlexRubber
for Transportation Gateway
Fanless Embedded System with Intel Atom® Processor E3940 for Vehicle PC
Key Features
CE and FCC certified and ISO 7637-2 compliant
Intel Atom® processor E3940
Supports 9 to 36 VDC and 12/24 VDC typical in-vehicle power input
Smart Ignition for power on/off schedule, vehicle battery protection, and different power modes
Axiomtek – a world-renowned leader relentlessly devoted to the research, development, and manufacturing of innovative and reliable industrial computer products of high efficiency – is proud to announce its tBOX110, a compact fanless transportation embedded system now EN 45545-2, EN 50155 certified. The tBOX110 is designed with low power consumption and heavy-duty construction that can withstand challenging day-to-day operational conditions. It accommodates varying voltage demands, effortlessly adapting to different environments.
The reliable transportation system supports 12/24 VDC typical automotive power input with smart ignition, or 24 to 110 VDC for railway use and a widerange 9 to 36V DC power input for general purposes. The tBOX110 is powered by the Intel Atom® x5-E3940 processor and has a wide operating temperature range of -40°C to +70°C and 3Grms vibration resistance. Its comprehensive verification and certification provide a more sustainable and safer solution for transportation applications.
The DIN-rail and wall-mountable tBOX110 measures only 164 x 128 x 44 mm and weighs 1.0 kg. The compact size ensures that it can fit in various space-constrained environments. The tBOX110 is equipped with one DDR3L-1866 SO-DIMM for up to 8GB of system memory. It also has one internal 2.5” SATA drive and one mSATA for extra storage needs. There are two full-size Rev.1.2 PCI Express Mini Card slots – one USB/PCIe with external SIM socket and one mSATA/USB/PCIe with external SIM socket – for high integration. Equipped with smart ignition power control, the tBOX110 enables to schedule power on/off events to protect the vehicle battery from unstable voltage and supports different power modes.
Axiomtek's tBOX110 offers comprehensive transportation gateway solutions, catering to a wide range of applications, from in-vehicle to railway. This transportation-grade embedded system not only meets ISO 7637-2 standards but also
has full certification to EN 45545-2 and EN 50155. By choosing the tBOX110, customers can benefit from significant cost savings and reduced waiting time, since they have no longer needed to bear verification fees or lengthy certification processes. This makes the tBOX110 a highly efficient and reliable choice for transportation-related projects. With the innovative and reliable safe shutdown feature, the tBOX110 safeguards critical components and data during power disruptions or emergencies.
Customers could also easily setup power on/off scheduling in the BIOS menu. It ensures the longevity and optimal functionality of the devices as well as making tBOX110 a responsible and environmentally conscious choice for energy saving solution.
The tBOX110 also offers rich I/O interfaces to ensure seamless connectivity and performance across transportation applications. For in-vehicle applications, the tBOX110 features two RS-232/422/485 with shield grounding, two isolated CANBus with SocketCAN, two RJ-45 10/100/1000 Mbps Ethernet ports (Intel® I210-IT), and one DB9 8-bit programmable DIO.
While for railway applications, it offers four isolated RS-232/422/485 with shield grounding, two M12 A-coded 10/100/1000 Mbps Ethernet ports (Intel® I210-IT), two M12 X-coded 10/100/1000/10000 Mbps
Ethernet ports (Intel® I210-IT), and one isolated 4-in/4-out DIO (terminal block). Two HDMI 1.4b with keylock, two USB 3.0, one reset button, one power button, one remote switch, and four antenna openings are available. Moreover, the tBOX110 is compatible with Windows® 10 64-bit and Ubuntu 20.04.
Advanced Features of tBOX110:
• EN 45545-2 and EN 50155 certified; ISO 7637-2 compliant.
• Intel Atom® x5-E3940 processor.
• Fanless and wide operating temperatures from -40°C to +70°C.
• Supports 9 to 36VDC and 12/24VDC typical in-vehicle power input.
• •Supports 24 to 110VDC for railway power input.
• Compact size with multiple COM, CANBus, and DIO for communication.
• Smart Ignition for power on/off schedule, vehicle battery protection, and different power modes.
Tel: +44-161-2093680
Email: info@axiomtek.co.uk
Visit: www.axiomtek.co.uk
Capitol Industrial Batteries - the perfect power solution.
Here at capitol industrial batteries, we have operated as an independant battery manufacturer assembly plant sales and service agent since 2004.
We have the ability to match customers’ requirements for wet lead acid, gel VRLA and lithium type batteries. whilst also offering bespoke manufacturing for client needs.
We pride ourselves on supporting the market through our stock holding facility as part of our business model which allows us quick delivery upon product orders. the following describes us we make supply maintain a full range of types with regards to our own direct replacement range of products ..... capitol are fully aware and committed to support the evolving market in terms of the electrification and decarbonisation agendus
RAILWAY
which are current thus future proofing the ability to supply any product type to support the long term running of alternative fuel powered trains.... ... since 2004 we have been acutely aware of the need of localised battery production within the uk ... which is why we continue with the final assembling of our batteries here in Cumbernauld and is something we pride ourselves on.
We have the backing of our major existing manufacturing partners for this. Aligned to our own business model in place to keep on establishing our company as a reliable and safe option for battery product and service.
MATERIALS HANDLING AVIATION GSE AUTOMOTIVE RENEWABLE ENERGY
By offering a bespoke customer driven level of service from manufacturing through to consultation and collaboration stages of discussion we can tailor individual battery types from our dedicated range of product specifically for use in Rail applications. Visit: www.capitolbatteries.com
Capitol Industrial Batteries - perfect power solution
Whether you require batteries repaired, overhauled or replaced, Capitol are trusted and relied upon by a wide range of UK rail industry companies, who have come to know that we deliver on our promises to provide exacting standards of product, service, ongoing technical support and commitment in all aspects of our business dealings.
Multi-million pound ongoing investment in plant and people is driving export success at William Cook Rail and keeping the British company at the forefront of the design, manufacture and overhaul of safety-critical components for the global rail industry
The company serves international rolling stock builders and operators including Alstom, Siemens and Transport for London from its world leading foundry, machining and workshop facilities in Leeds, West Yorkshire. Its products are on trains around the world, including the UK, France, Germany, Canada, India, Australia and the United States.
William Cook Rail has secured substantial new work this year, including a multimillion-pound contract with Transport for London to overhaul mechanical and electrical systems on Jubilee Line trains. The work will be completed on a tight turnaround time to keep the line running as usual.
William Cook Rail is the Original Equipment Manufacturer of the wedgelock
autocoupler, in service on all deep Tube lines, and has overhauled thousands of coupler systems and components for the capital’s transport service in the past.
The company also won new export orders with several European tram and train builders in 2023 to design and manufacture complex cast steel components used in the construction of bogie frames, beating fierce competition from elsewhere on the continent.
Across the Atlantic, William Cook Rail has continued its work with Alstom North America manufacturing precision components in a specialist grade of stainless steel for the Long Island Rail Road in New York – one of the busiest commuter lines in the world. The components will extend the life of the fleet and reduce the noise of the trains to improve comfort for passengers.
This export success comes as a result of sustained investment in plant and machinery at William Cook Rail, including a brand new full-service paint shop in 2023. The facility brings in-house the capability to coat everything from individual components to complete bogie frames, all to rail industry standards.
The company has also added millions of pounds worth of new CNC machining centres to its already extensive and modern machine shop, which includes a Correa FOX gantry milling machine, capable of accommodating complete bogie frames, and a top-of-the-range Correa Norma five-axis CNC machining centre.
These latest investments follow a multi-year programme of upgrades to the company’s steel foundry, fabrication, heat treatment, machining and metrology facilities and an expansion of its coupler and bogie overhaul workshops.
Mr William Cook – Group Commercial Director for the William Cook Group – said: ‘Our ambition is to be a ‘one-stop’ shop for design, manufacture and overhaul of safetycritical rolling stock subsystems. Doing everything in-house, under one roof, reduces our reliance on subcontractors and shortens turnaround times for our customers.’
Against a backdrop of soaring energy costs and the UK’s transition to net zero, William Cook Rail has successfully reduced its energy consumption by investing in highefficiency equipment and reorganising its manufacturing operations.
Its new high efficiency heat treatment furnaces help achieve the superior mechanical qualities required for the ultra high-strength but lightweight steel components demanded by the rail industry. Meanwhile new extraction units reduce the factory’s emissions and improve working conditions for employees.
Combined, these efforts have led to a 60 per cent reduction in gas consumption and a 15 per cent reduction in electricity
consumption over the last year, without any fall in production output.
Mr Cook said: ‘William Cook Rail is investing for the long term to develop our world-leading foundry, machining and workshop facilities and our workforce of highly skilled engineers, technicians and apprentices, helping to create a sustainable future for British manufacturing capabilities.
‘We are proud that the world’s major train builders come to William Cook Rail for safety-critical components that they can rely on. We’re also proud to manufacture and export from the North of England, despite the sad lack of a British rolling stock builder and decades of under-investment in the North’s rail infrastructure.’
William Cook Rail holds certification from the Railway Industry Supplier Approval Scheme (RISAS), which ensures key suppliers can become recognised as bestin-class at delivering the most challenging and high-risk products and services. It is also one of only 19 British manufacturers to meet the International Railway Industry Standard (IRIS), the leading quality benchmark for the global rail sector. This covers the company’s management systems for the manufacturing, machining, assembly and overhaul of safety critical components for rolling stock builders and operators across the world.
William Cook Rail is part of William Cook Holdings, a specialist manufacturing group serving the defence, rail and energy sectors. The Sheffield-headquartered group has over 500 employees and five factories across the north of England, with sales of over £70 million in 2023.
In addition to brand new state-of-the-art facilities, William Cook Rail has also continued its investment in the next generation of industry talent, taking on nine apprentices in 2023. The company has a strong track record in the development of engineering talent and has built close links with local education providers in a bid to encourage more ambitious and enthusiastic young engineers to pursue a career in the rail industry.
The apprentices – ranging in age from 16 to 19 years old – are working in a variety of roles including Mechatronics, Technical Support, CNC Machining, Metrology and Welding.
Barry Swift, Executive Director at William Cook Rail, said: ‘We are great believers in giving young people an opportunity to develop careers as engineers. To succeed in the global rail industry, you need to invest in the future and bring young people into an environment where they can learn new skills.
‘They find it very rewarding to be able to contribute to finished products that are running on railways throughout the world. Equally, our experienced engineers find it very exciting to be able to share their
knowledge with the new recruits. It gives everyone a spring in their step.’
William Cook Rail’s apprenticeship scheme is proving to be a successful route into the rail industry. In a workforce of 123 people, 20 are either in apprenticeships or fresh out of training. They are being guided by some of the most experienced engineers in the industry: the company has just handed out long service awards to four members of staff with a combined tenure of 137 years.
Tel: +44 (0)113 249 6363
Email: rail@cook-rail.co.uk
William Cook Rail
Cross Green
Leeds LS9 0DX
England
Aura Brand Solutions regularly works in close contact with the highest level of suppliers to bring its customers’ projects to life. Taking on contracts across all sectors but mainly specialising in large, complex branding projects where it can utilise the team’s rail expertise and project management skills. In the last year alone, Aura Brand Solutions had the opportunity to work on several high-profile projects that are now coming to fruition – with incredible results that showcase its close partnerships.
Some of Aura Brand Solutions’ most recent notable work includes:
• Heathrow Express – Full refurbishment, including supply and apply of exterior rail carriage branding, as well as labels and branding for interiors of 14 x 4 car sets.
• SouthWest Railway and Greater Anglia – Supply and application of branding to new build trains, through the C2C train operator.
• Irish Rail – Recently awarded a £1.2 million livery contract with Irish Rail, after an extensive tender process.
Aura Brand Solutions has also been hard at work providing refurbishment services to Transport for Wales Class 150 trains, supplying them with heat reflect window films, which are used to control the ambient temperature of their trains.
In the coming months, with energy bills due to rise, the specialised window films will help to reduce heat inside the train –leading to less costs for running interior air conditioning units. The films also work to retain heat in the winter months, which will help with spiralling heating costs.
Alongside this offering, Aura Brand Solutions’ has also been supplying window protection films to various rail operators to protect their rolling stock from graffiti and vandalism attempts.
Aura was also recently awarded the full supply and application for 68 sets of livery for Cairo Monorail, in partnership with Alstom.
Currently under construction in Cairo, Egypt, the Monorail will be the largest
driverless monorail system in the world. Alstom are leading the project in designing, constructing, operating and maintaining the two lines. One line will connect the New Administrative City with East of Nile covering 57 kilometres, and the second line will connect West of Nile with Giza covering 42 kilometres.
The new Monorail will provide improved mobility for the citizens of Cairo, able to transport 45,000 passengers per hour in each direction, along with reduced traffic congestion and environmental impact.
In an age where sustainability is at the forefront of business, it’s incredibly important to continue using cutting-edge products and solutions. Aura will always champion state-of-the-art solutions that transform the face of the rail industry.
In line with this, the Cairo Monorail will be produced from the highly versatile 3M Envision range film, further strengthening our sustainable ambitions.
The range includes the 3M Envision Print Wrap Film 480, which is a non-PVC, highquality film that has twelve years durability, and can amazingly be used for both external and internal application. It also has a sixyear warranty, a slower burn rate with less smoke giving 4.5x longer evacuation time
and is equipped to withstand the UV rays and high temperatures in Cairo.
Through its ongoing partnership with 3M, Aura has used the phenomenal 3M Envision Print Wrap Film 480 on other several projects and continue to gain great feedback from clients. Another sustainability initiative that Aura has regularly used on fleets, but recently adopted for rail livery, is the RE:CYCLE system. This solution gives decommissioned train wraps a new lease of life as a sustainable product, and drastically reduces carbon footprints.
As part of the GreenBrand portfolio, this system is zero waste to landfill or incineration and provides a complete lifecycle service through utilising existing materials. Once stripped down, PVC graphics are then compacted and turned into bales that are taken away to be further recycled into products, such as plastic furniture, traffic cones, and road barriers.
This recyclable film is responsibly manufactured in the UK and utilises existing materials, providing proven durability and performance. Alongside this, over the course of the past three months, Aura has successfully negotiated terms to become one of four companies globally to sign a five-year framework agreement with Alstom.
This agreement will see Aura become one of the main approved suppliers of Alstom globally, opening up the opportunity to take on extensive international rail projects of various offerings – including maintenance, design, and paint refurbishment.
Aura’s Director of Rail, Tim Locke, negotiated this joint commitment following several months of discussions with Alstom’s head office in Paris to allow Aura to bid for more work. This will include offering Aura’s comprehensive services, including our industry-leading online portal, digital printing processes, and customer services hub to a host of new customers.
If you’re looking for comprehensive, expert rail branding solutions, get in contact with Aura Brand Solutions via the contact information below.
Tel: 07774 473 707
Email: tlocke@aurabrands.com
Visit: aurabrands.com
LinkedIn: www.linkedin.com/company/860668
Address: Freemantle Road, NR33 0EA
Derbyshire Geotechnical Ltd is an established Rope Access Geotechnical installation service provider with a strong track record of Quality, Competitive Pricing and Safety
From its base in the Derbyshire Peak District, Derbyshire Geotechnical’s Ltd’s teams of Certified and experienced IRATA Operatives undertake a broad range of specialised Rope Access Geotechnical services installing stabilisation mechanisms (Rock Anchors, Soil Nails & Rockfall Mesh etc) in hard to reach/working at height situations.
Using fully qualified and time served experienced IRATA Qualified Rope Access Technicians work includes de-vegetation, large/difficult tree removal, the installation of rock anchors, soil nails, rockfall mesh, erosion matting and catch fences. Roof inspection and bolting in mines and tunnels.
Still considered a relatively young company, Derbyshire Geotechnical Ltd was established in 2017 and has in this short period of time built a good reputation as a safe, reliable Geotechnical Rope Access operator that delivers top quality installations at a very competitive price. This wealth of experience in the industry enables Derbyshire Geotechnical Ltd to design and build projects like the ones listed below.
De-vegetation involves the removal of weeds and dangerous or obstructive vegetation from either a structure, slopes or rock faces. This can be done to assist inspection, remove potential hazards or as preparation of a face or slope for further works. Then the cleared area may then be treated with an herbicide in order to restrict or reduce regrowth.
Rockfall containment
Rockfall containment normally involves the installation of a strong fence or barrier (An approved Debris or Catch Fence) that is placed on or bat the base of a slope or beneath a rockface to catch debris, and protect structures, plants and persons beneath. Derbyshire Geotechnical Ltd is frequently recommended by Catch Fence manufacturers (E.g Geobrugg) as an
installer. The company can also offer Catch Fence Inspection and maintenance services where these structures are already installed.
These are Geotechnical Installations, usually anchors and/or soil nails and rockfall mesh that provides long term stabilisation for over-steepened or unstable soil slopes. The strength of the soil/slope is increased by drilling, installing and grouting hollow bar anchors into the slope in a regular pattern. The anchors are installed in conjunction with a geotextile erosion matting or a combined rockfall mesh and geotextile layer which is secured to the slope by the anchors.
Rock Face Stabilisation involves the securing of unstable rock faces. This can be achieved in three ways:
• De-scaling – removing loose materials such as rock and overburden by hand, and for large blocks with airbags, to leave sound rock that requires little further intervention apart for regular inspection.
• Installation of Rock Anchors and Dowels – Anchor holes are drilled using either a hand operated pneumatic drill or more frequently a rock drill and drill mast mounted on a drilling frame or 360 excavator. Strong Steel Anchor Bars (Usually a Galvanised High Yield Steel Gewi Bar) is then inserted into the anchor holes and affixed into place with either a resin or cement grout, and these can hold both rock mesh and sections of rock face into place.
• Installation of Rockfall Mesh – Often used in addition to the installation of
Facing systems encourage vegetation growth and enhances the stability of the soil slope through soil retention. This is done through the use of a variety of anti-erosion and soil retention geo mats, but can alternatively be done with semi rigid geocell baskets or reno mattresses installed on steeper slopes or where high erosion rates can be anticipated. These facings may be tied back with soil nails or driven earth anchors.
Although not typically a core area of work for the company, Derbyshire Geotechnical Ltd is able to offer structural repair services such as re-pointing, brickwork and concrete repairs.
Over the years Derbyshire Geotechnical Ltd has developed business relationships with clients such as; AMCO Giffen, Aggregate Industries, Bam Nuttall, Breedon Aggregates, Hanson UK (Heidelburg Aggregates & Materials), Keller Geotechnique, National Trust, TARMAC, and numerous local authorities.
In addition to the company’s regular work Derbyshire Geotechnical Ltd also works for the film industry offering Rope Access Support for works including on site safety cover and the installation of items/ equipment on to set for filming. Such works has included providing support on the new Mission Impossible 7 filming and Emmerdale.
‘I wish to express our thanks for the work of your team and associates. The team were courteous and professional throughout. Communication was excellent and we were able to safely make our contribution by clearing the track of vegetation and liberated stone. The team could not have worked harder during the two days.’
Kevin Bunting (Assessor & Track Support – Steeple Grange Light Railway)
‘Thanks Simon. The team – as usual – were great to work with.’
Jenna Roberts (Quarry Manager –Tytherington Quarry)
‘Great job, great team, if you ever require a reference either written or verbal, I will be happy to oblige.’
Robert Wood (Property Owner, Huddersfield Area)
As the company grows it endeavours to stay true to its mission statement to provide a safe, reliable, professional, and excellent value for money service to all of its clients in the UK and beyond, whilst striving for continual improvement.
For more information about the services that can be provided by Derbyshire Geotechnical Ltd Rope Access Operators and specialists please contact the team via the contact information below.
KEY PERSONNEL
Managing Director: Simon Brooks
Operations Manager: Charlie Scouler
Office Manager: Nicola Lait
Accounts Manager: Zoe Green
CONTACT INFORMATION
Address: Derbyshire Geotechnical Ltd
C/O Torr Croft
Pittlemere Lane (Off A623)
Tideswell Moor, Nr Buxton
Derbyshire SK17 8JF
Tel: 01298 931030
Email: admin@d-geo.co.uk
Visit: www.d-geo.co.uk
Safety is of paramount importance to our railways; whether we are referring to ensuring safe journeys for the travelling public, or the guaranteed provision of a safe working environment for our lineside colleagues it is imperative that safety really does come first
The Office of Road and Rail Regulation (ORR) in June 2023’s periodic review (ORR PR23 Draft Determination executive summary) states that when holding Network Rail to account in the coming Control Period, CP7, it will focus on the following four objectives:
• Safety – the rail network must be maintained in a safe condition for all of
its users, workers and the public.
• Performance – the railway must be customer-focused, making effective use of its capacity to deliver passenger and freight services that are punctual and reliable.
• Asset sustainability – assets must be planned and managed to deliver their greatest value over the course of their operational lives.
• Efficiency – Network Rail must be subject to stretching but realistic efficiency targets.
With safety paramount, the introduction of the safe walking route instruction in 2005 specified the railway must have an authorised walkway alongside the track for the workforce and passengers, should they need to be evacuated from a train in an
emergency. In spite of this instruction, it is well documented by Network Rail that the largest proportion of mainline workforce specified injuries were due to slips, trips and falls, the majority of which were caused by obstructions on walkways or due to uneven surfaces (Health and Safety Executive).
Quite often the ‘safe walking route’ that runs along the cess is nothing more than a rough path constructed from aggregate, tarmac or timber, which all create significant safety, environmental, maintenance and repair issues as they suffer from the impact of the weather and environment. Critically, it is also commonplace for the railway to feature separate cable management solutions (CMS) that require considerable space in an already constrained and safety critical area. Cable management systems, also referred to as cable troughs, are traditionally manufactured from concrete, and are therefore difficult to modify and are prone to cracking and can therefore never be deemed to be safe walking routes, official or unofficial.
The railway relies on an inordinate amount of power and communications cables alongside the track to operate lineside equipment, collate and deliver data, and ultimately ensure the uninterrupted running of the network. The integrity and value of these assets is only as good as the protection offered by the lineside cable management systems, from wear and tear, extreme weather and theft and vandalism.
The latest Network Rail National Performance Affecting Cable Theft Impact Summary found there were 51 incidents of theft in 2021/2022, resulting in 3,071 train journeys affected and 32,250 delay minutes caused. During the first half of 2023 Network Rail estimated that the theft of metal, particularly cables, from the railway represented a cost to the taxpayer £1.1 million in Wales and Borders route alone. When interviewed in 2021, Network Rail’s Director of Incident Management and
Operational Security James Nattrass said cable theft caused circa 22,000 hours of passenger delays in the previous four years and resulted in costs of £61 million.
In response to these known industry challenges, Trough-Tec Systems (TTS) developed a pioneering, sustainable and easy-to-install anti-slip walkway system, which provides all the benefits of the standard Green Trough CMS range but is designed to be fully compliant with the railway’s safe walking route instructions. The TTS walkway system thus provides dual functionality and helps maximise the useable space within the cess. Green Trough boasts many features including:
• Manufactured from one hundred per cent recycled polymer.
• All cable trough sizes EPD certified.
• Anti-slip coated.
• The Bimagrip surface results in zero static which improves safety and avoids any shorting of lineside electrical equipment.
• Tolerant to thermal expansion.
• One tonne weight bearing, with a tentonne option – capable of withstanding human foot traffic and road-rail vehicle loads.
• Protects against theft and vandalism as standard.
• Removable and re-lockable lids, enabling easy maintenance and access to increase cable capacity at a later date.
• Up to 82 per cent lighter than traditional concrete equivalents: all individual units, base + lid are compliant with a singleperson lifting.
• Provides up to 70 per cent more internal capacity than concrete equivalents.
• Three times faster to install than other options.
• Requires less labour and no plant to install.
• Can be provided in modular
Substantially lighter than concrete alternatives, the Green Trough Walkway Systems mitigate the risk of musculoskeletal injury, including back, arm and wrist strains during installation or harm to limbs if accidently dropped when carrying the product.
The Walkway system's non-slip surface provides a much safer working environment for track walkouts and inspections.
The dual function Green Trough Walkway System creates easy and safe site access to maintain lineside equipment. With an expected lifespan of 50 years, the product requires minimal maintenance, enhancing workforce safety.
Lockable lids protect against vandalism and bases have a built-in security system to further protect against cable theft, helping to protect the operational railway and mitigate the need for the workforce to be on site to deal with such incidents.
Green Trough is an environmentally friendly alternative to traditional CMS as it is manufactured from one hundred per cent recycled polymer, more specifically post-consumer household waste. Boasting a 50-year design-life Green Trough is re-recyclable at end of life, and at the time of writing is believed to be the only fully PADs approved cable trough system that has received Environmental Product Declaration certification (EPD). Circa 7,000 tonnes of household waste was recycled in total in 2022 in relation to the manufacture of Green Trough.
Efficiency
Designed and manufactured to be lighter and easy to install, the Green Trough Walkway System is three times quicker to install, creating significant time and cost efficiencies. Delivered as ready to install kits, the risk for damage during transit and installation is minimal. This substantially reduces the potential for rework, which is usually estimated at a quality rejection rate of one in 20 metres for equivalent traditional alternative products.
‘As an industry….we will deliver £4 billion of efficiencies by pursuing better value and doing more for less by 2024.’
Network Rail
combinations with different components to enable a multitude of route configurations.
• Optional handrail option, that is selfsupporting so need no auguring or postfixing concrete.
Tailor made solutions as standard
In addition to the core product range, and in response to clients’ needs TTS has consistently designed and introduced innovative products including an elevated system for Green Trough, composite replacement lids for existing concrete troughs, and the anti-slip walkway system.
TTS is more than simply a product provider: the company actively seeks to work with its clients on a partnership basis across small to major projects to ensure that it provides a full-service proposition; in this way product innovations unlock process improvements. TTS is able to work with stakeholders to eliminate problems that arise when key components such as theirs are considered within the original design process, and not merely considered as an ancillary product.
By embedding itself within project design and delivery teams, TTS ensures that certain problems can be designed out, thus avoiding costly rectifications which would occur otherwise. Exemplar projects on which TTS has worked in this way include the Great Western Electrification project (GWEP), Northern Hub, Northwest Electrification projects and East West Rail.
The East West Rail project is a great example of early contractor involvement. By working in collaboration with the East West Rail Alliance (EWRA) TTS gained an in-depth understanding of the project requirements and was able to recommend alternative designs, product modifications
and installation solutions. As a result, TTS was able to incorporate site-specific configuration requirements into their offering and create an innovative ‘ready to assemble’ kit of parts, establishing a ‘construction to production’ approach to meet EWRA requirements.
A first for the UK rail industry and thought to be a first worldwide, there is no comparable combined cable management and safe walkway product delivered in an easy-to-install kit on the market on a likefor-like basis. The sustainable base product and innovative kit format have created significant benefits for EWRA including:
• Ability to order exact quantities –minimising waste and reducing delivery costs and associated carbon emissions.
• Creates time efficiencies – no time wasted by staff in storage compounds picking abstract parts from a huge inventory, eliminating the risk of mis picking.
• Guaranteeing the right components are delivered to exact locations and correct installations.
• Contributes to right first time installation.
• Minimises time and costs associated with snagging lists as mistakes are eliminated from a product and design perspective.
• Enhances workforce safety by reducing the volume of activity and time on site for installation.
• Minimising plant and equipment requirements.
Traditionally, ancillary civils products are not considered during the project design phase and are usually procured late in the process. Applying systems thinking to the product and elevating it from just a cable management and walkway system to an innovative off-site manufacture and
modular construction kits has transformed the way design, production and installation teams work together, which is pioneering for the industry.
This innovative approach is a practical example of ‘doing more for less’ by avoiding unnecessary costs to what could be a very mundane but potentially expensive, occupational and operational safety-critical problem. This is an ongoing industry challenge and commitment set by NR and GBR.
Further benefits of working in this way are multiple: this approach also ensures contingency supplies become unnecessary, and by working as TTS did across multiple project teams, lessons learned in real time, were reported and avoided instantaneously as well as informing the delivery of subsequent projects.
As the Department for Transport states: ‘Major projects are often asked to deliver against aggressive timescales set early in their lifecycle. They are expected to deliver to schedule and budget and to be right first time.’
By working in conjunction with much larger stakeholders, and much earlier on, TTS have proved that their early involvement as described above pays dividends for all, maximising the design and cost-efficiency of projects and possessions, and providing a cable management and walkway system that significantly improves a project’s costs, carbon footprint, health and safety considerations and overall lifecycle.
Email: ttsinfo@hird.group
Visit: www.hirdtts.com
RJW Engineering was set with the task of overhauling an old antiquated system that had danger written all over it
Why are we using metal road pins on a network driven by electricity? This was the question presented to NWR, and the answer was simply, we don’t know! Currently, metal road pins are either driven into the ground (cat scan required), driven into sand bags that lose the sand once pierced, wedged between bricks or logs or whatever can be found lying around. There is no set system, it’s whatever goes. The safety netting is often left loose, just falling over, therefore resulting in little to no protection.
Let’s address the main issue – metal road pins. This will seriously injure or kill someone if it strikes a cable, visit the website in the contact information section to watch the NWR safety video which explains all.
RJW Engineering decided immediately to move away from a conductive material, the metal road pins. If these were to be driven into the ground then they needed to be non-conductive. The trials soon showed the recyclable plastic road pin with its cross section design was very effective, RJW Engineering’s team then replaced the sharp point of the metal road pin with a much safer rounded bull nose.
The way the netting was hung over the hook was also questioned, this has now been replaced with a unique slotted end allowing the netting to be located within the road pin, this also added a big advantage when storing and transporting the pins, now taking up far less room and not becoming tangled with each other.
There is now a replacement for the metal road pin, but know it’s not always going to be driven into the ground. The sandbags currently used are a disposal commodity, and the use of bricks, logs or whatever can be found is totally unacceptable.
Staying with a recyclable plastic, RJW Engineering designed a tapered base so it can be turned to accommodate a flat or slopping surface. A central slot was added
to locate the road. Given the storage and transport has been improved for the road pin, the team then added a small locating boss and recess to the new non-conductive base enabling them to be stacked on top of each other and held in place, now giving compact easy storage alongside the nonconductive road pins.
This new patented system is now fully non-conductive, easier to store, transport and deploy. Each and every deployment is a uniform system across the board, and will meet health and safety standards.
An additional lighting system located in the slotted end of the road pin is also available. In conjunction with Birmingham university this system is now readily available creating a safe working environment for staff, workers and customers. For more information get in touch via the contact information below.
Tel: 01384 442852
Fax: 01384 442920
Mobile: 07860 588918
Email: rjweng@btinternet.com
Visit: rjwengneering.co
Address: 70 Walker Avenue, Stourbridge, West Midlands DY9 9EL
‘Currently, metal road pins are either driven into the ground … trials soon showed the recyclable plastic road pin with its cross section design was very effective … (the) team then replaced the sharp point of the metal road pin with a much safer rounded bull nose … this new patented system is now fully non-conductive, easier to store, transport and deploy.’
From new construction to refurbishment, the rail sector’s needs are as wide as the UK network is extensive
Safety is of paramount importance – the need to ensure safe and efficient use of all equipment and methods extends both to the workforce and rail-users alike. In these instances, proven scaffolding systems and experienced back-up are vital and integral to contractors’ successful project completion. A system capable of adaptation to a range of operational needs is a fundamental requirement.
Layher’s Allround equipment, featuring the widely used Bridging Truss, is a prime example. Developed to integrate fully with the Layher system and designed in response to the need for fast, controlled installation, bridging spans of up to 30 metres can be achieved – typically to provide temporary access between platforms, and for installation across active lines.
Supplemented by stair systems with DDR-compliant handrails and the versatile
Layher Protect panel design – used, for example, to create effective screens between bridging structures and the rail lines below – mean the majority of rail installations’ access needs can be met.
Possession time: an essential factor Sean Pike, Layher’s UK MD comments: ‘From our choice of scaffolding designs to purpose-developed equipment, we have always been fully aware of rail users’
needs and work closely with contractors and operating companies to deliver optimum results.
‘We are fully aware, that possession times are key during rail works and can often be linked to penalty clauses arising from project overruns.’
The installation speed and simplicity of Layher designs have been proven to make a major contribution in this regard, “particularly as many of our structures can be assembled trackside or even offsite for craning into position during closure periods,” Sean Pike concludes.
The light weight, ease of handling and minimum components of the Layher system, together with equipment storage and transportation efficiencies are key planning and operational considerations. The proven gains arising from the use of the Layher system throughout the rail sector have been recognised by contractors across the UK.
A 16-metre span was required to provide passenger access between platforms during repairs of an existing bridge. The system was installed between two Layher stair systems, each featuring non-slip GRP surfaces, temporary lighting and Layher’s Protect screening panels. The structure was installed at a greater height than normal to enable drivers to maintain clear sight of the signalling system, and the contractor was able to complete with just one overnight possession.
Two sections of Layher Allround Bridging spanning six and 14 metres respectively were to be supported by a central tower
to create a wide public walkway alongside service connections via two external cantilevered scaffolds. This build took place at ground level for the two spans to be craned into position overnight – minimising possession time – while the design also accommodated loading that allowed the central support to have been removed if required.
A team at another location carried out a full pre-build of a structure off-site to ensure track possession requirements were kept to a minimum. The bridge was craned into place during a single overnight possession. Two DDA-compliant Layher public access staircases were also fitted. By combining previous experience gained by using Layher equipment with the commitment of their specialist team, delivery was completed safely, on time and within budget.
A structure spanning some 30 metres across two train lines, and incorporating two bridges – one for construction use, the other to carry some of the location’s 60,000 commuting passengers daily – had highly complex design, health and safety and programming requirements. The Layher design was erected in a total of just four days but remained in position for some 18 months. The structure was an excellent example of the Layher bridging system’s versatility in accommodating stringent site conditions including the absence of access for crane usage and intermittent track closures resulting directly from such a busy train line.
A mobile temporary roof was required to follow refurbishment work as it progressed along a structure above a primary rail
hub. The contractor employed the Layher Allround system, including decking panels in order to provide protection below and as support for a rolling birdcage giving access to the roof. Movement of the entire roof structure was undertaken each time in an average of just 40 minutes, and by only four people.
For another contract, just two weekend periods were allocated for installation of a Layher bridge in contrast with the three weekends that would be needed with traditional material. In the event, only one weekend was required. Additionally, the two days anticipated for fitting ply-board screening along a 31-metre total span was completed in just 90 minutes by instead using Layher Protect panelling. Protect panels create an appearance that is markedly removed from that of a building site.
With storage and transportation benefits also to the fore, the gains arising from the use of Layher equipment throughout the rail sector are clear-cut and are well set to enable our work with contractors in the field to stay fully on track.
Tel: 01462 475 100
Email: info@layher.co.uk
Visit: www.layher.co.uk
Sean Ballard, Group Managing Director at
Security is becoming a more prominent consideration in the Rail Industry. As part of the UK’s critical infrastructure, all rail networks and hubs (stations and power) must be protected regardless of the volume or usage. When it comes to the rail network there is an inherent need for such security measures in the form of various products and services, which are key to the protection of assets and the users.
Our products are designed to blend in with the environment or build in which they are used, yet are manufactured to provide performance such as ventilation and cooling for instance with our Steel Louvre Systems and examples of use include transformer or power rooms, tunnel or shaft ventilation, and then other product examples include steel security and fire doors which restrict and control critical access areas and of course provide up to four hours fire resistance.
Newer to our range and particularly relevant to areas which have Trackside embankments or areas close to Electrified Rail or Cables are our GRP Walkways, Platforms and Access Stairs.
GRP is widely specified due to the nonconductivity of the product yet has the integral strength for weight loading.
These can be brightly coloured with integrated grip on the grid and define safe passageways or access for rail workforce staff as well as passengers in the event of emergencies.
As specialists in providing bespoke Security Solutions to the Rail Industry, Sunray have provided a number of products in applications where security for electrical switch gear, tailored pressure relief measures for escape routes, plant room ventilation, station security, fire compartmentation as well as specialist Blast and Fire protection consideration, all of which is uniquely designed for a specific project.
Due to the nature of Rail infrastructures, we often find ourselves working with complex design solutions where practicality
and design must harmonise, yet functionality and performance is critical. This can present challenges, however our ability to ‘tailor’ product ensures we blend seamlessly into any given structure.
We manufacture all products at our factories in Ashford, which ensures the control, quality, and timely delivery of product to meet customer expectation. We also regularly test on site in association with the BRE (British Research Establishment) especially for those projects requiring ‘one off’ type scenarios. This ensures our Rail
clients benefit from our proven history and track record of investing in design and innovation. As pioneers of the niche, when it comes to Security Doors and Systems, we will always strive to build the impossible yet blend with the environment. This makes us well placed for working with the Rail Sector so we can provide tailor made solutions to exceptional criteria’s and demands the industry often faces.
Sunray continues to invest heavily into R&D, keeping ahead the of the everchanging regulations.
Tomorrow’s products will require even more security and protection and given Sunray’s capabilities and experience we are well placed to assist this critical infrastructure and industry.
For more details, get in touch with our specialist team via the contact information below.
Sean Ballard is Group Managing Director at Sunray Engineering
Tel: 01233 639039
Email: sales@sunraydoors.co.uk
Visit: www.sunraydoors.co.uk
Foresight is not about predicting the future’ said the science fiction author and futurist Karl Schroeder, ‘it's about minimising surprise’. Given the unpredictable nature of today’s supply chains, ‘minimising surprise’ may seem like an unrealistic goal – but it needn’t be. Here Keith Kentish, regional vice president at TFC, an AFC Industries company, explains how a global sourcing partner can improve strategic decision-making in the UK’s rail industry –including in relation to change management.
Most industries, including rail, are understandably concerned about supply chains; including the future effects of current geopolitical situations on commodity prices and availability. The stakes are high – supply chain management and sourcing can have a significant impact on customer experience, service continuity, productivity and the ability for rail companies to achieve net zero carbon emissions targets.
Despite concerns and the negative headlines, good supply chain networks are more reliable. Demand for products across all commodities soared in the wake of the Covid-19 pandemic but, more recently, a global slowdown has meant there is more capacity.
Suppliers now have excess stock levels of several C-Class products – small industrial components like fasteners, tooling, consumables and personal protective equipment (PPE). C-Class products are typically considered nonstrategic, low in value but high in number, and administratively time-consuming for businesses.
To get a wider picture of the current status of supply chains, we can look at the stability and continuity of commodity prices. Naturally, rail professionals will worry when prices go up; for instance, it isn’t long ago that we saw significant increases in steel and stainless steel costs in the fastener market. However, commodity prices have now mostly plateaued, or at least the rate of increase has slowed significantly.
All of which brings us to global sourcing, the practice of sourcing from the global market for goods and services across geopolitical boundaries. When sourcing engineered components globally, rail professionals’ main focus should be predicting the next curveball – whether that happens to be changing commodity prices or shifting manufacturer-supplier dynamics. To minimise such surprises, resilience and reliance must be the mantras for today’s supply chain professionals.
Manufacturers are rightly focused on their main business priorities, which typically include optimising production efficiency, improving product quality and new product introduction (NPI) programs. These companies have little time or resources to dedicate to the headache that is sourcing and managing the continued availability of administratively heavy C-Class products.
Let’s say a company sources its C-Class products from 20 different suppliers. What does that mean for the business? The answer is 20 vendor relationships that must be managed, multiple orders to raise and hundreds of prices to negotiate among fluctuating market levels. If these companies do not have C-Class products of the right quality, quantity and price, at the right place and time, there can be dire consequences, especially for rail passengers.
So, what can rail companies do to overcome these obstacles? Well, imagine if, rather than dealing with multiple vendors, you could deal with just one reliable source? This is where a global sourcing partner can change the game.
Let’s talk through an example. One of the world’s largest manufacturers of laboratory products, has historically sourced and purchased its C-Class products from various different suppliers – but the company wished to save time and resources invested across the products it was buying. To achieve this, it approached TFC to become its global
sourcing and vendor managed inventory (VMI) partner.
For this prospective customer, TFC first compiled a list of all its present vendors and the C-Class items it was buying from each. This process identified that a number of C-Class electronic products could be purchased as comparative brand items elsewhere, for reduced costs, while maintaining, or in many instances, improving the product quality.
For processes like these, TFC audits suppliers around the globe and does so either face-to-face, using a third party or electronically. As part of the audit, the supplier must agree to TFC’s own policies –not only regarding quality and service, but also ethical behaviours such as sustainability or not using child labour. A global sourcing partner’s expertise is about being able to manage a global supply network based on trusted relationships with vendors.
But how does this partnership help rail companies ‘minimise surprise’? A good example is TFC’s proactive territory research, which means monitoring and benchmarking alternative territories for the supply of products. For instance, if the changing geopolitical situation means it is no longer time- or cost-effective to source parts from a certain country or region, TFC can quickly and efficiently re-align the supply source. At the moment, there is real potential in Slovakia, Slovenia, Poland, Turkey and India
– all countries that are coming to the fore in producing top quality C-Class components.
On the one hand, proactive territory research may identify an opportunity where the customer could buy better quality products that are manufactured abroad, rather than domestically. On the other, the research might support rail companies in quickly onshoring, or at least nearshoring, their manufacturing. In 2020, The Railway Industry Association (RIA) joined Reshoring UK, a collaboration of industrial engineering associations, to support RIA members that are looking to fill gaps in their supply chains by connecting manufacturers with trusted, accredited UK suppliers.
Lastly, a global sourcing partner can help its customers navigate the impacts of import levies. One example is the antidumping duty (ADD) applied to Chinese products imported into the European Union (EU). Or there are new regulations like the Carbon Border Adjustment Mechanism (CBAM) that will require importers of certain energy-intensive goods to pay a levy.
The overall picture
You may be thinking, how is a global sourcing partner able to manage so many vendors and transactions quickly and effectively? It can be managed by combining
the skills of an experienced and trained team with the right tools. TFC uses a custom enterprise resource planning (ERP) system coupled with the right business intelligence (BI) reporting software. This makes it possible to look at supplier and supply data across the TFC Group, and consider the overall picture with vendor relationship management achieved through a number of key performance indicators (KPIs) including service, quality, pricing and more.
TFC is also unique in that its procurement specialists are from engineering and manufacturing backgrounds. Not only do its specialists understand manufacturers’ C-Class product requirements from first-hand experience, they also benefit from continued training and personal development – with a goal that in time all of TFC’s central team will be qualified to Level 6 in the CIPS Professional Diploma in Procurement and Supply (MCIPS) to give customers the best strategic direction and advice – including in relation to change management.
Going forward, better change management will be crucial for international businesses. They cannot predict the future, but they can plan for all eventualities. With a global sourcing partner like TFC, it is certainly possible to minimise surprise.
TFC, an AFC Industries company, is one of the leading suppliers of engineering products in Europe, with an unrivalled reputation over 60 years for providing exceptional design development, the best components and bespoke production line inventory solutions, all from one organisation. Our customers experience exemplary customer service and added value technical solutions to help them achieve breakthroughs in product advancement, innovation and significantly raised standards of manufacturing efficiency.
To learn more about how TFC can support you as a global sourcing partner, visit its website or get in touch via the contact information below.
Tel: 01435 860349
Visit: https://www.tfc.eu.com/
Email: AScrafton@tfc.eu.com
Twitter: @TFCLtd
LinkedIn: https://www.linkedin.com/company/tfc-ltd/
It’s never been more difficult to manage supply chains. External pressures caused by inflation, Covid, Brexit and the war in Ukraine have complicated an already challenging situation and component shortages and delayed deliveries are causing huge upheaval in the industry
This state of disruption has become the new normal and emphasises the importance of proactive supply chain management and collaboration. The supply chain must react rapidly to volatility, uncertainty, complexity, and ambiguity. This means changing the emphasis from Just in Time to Just Right.
Part of the way that TVS SCS is helping the industry to get products at the right time is by launching the new online service www.tvsrailspares.com.
TVS Rail Spares was launched to introduce to the rail sector some of the features that, as individuals, we all expect from a modern purchasing process, like online order tracking, live web pricing and availability information and free delivery.
The future of rail procurement is online like it is in other industries. TVS Rail Spares offers a unique rail-specific online catalogue with more than 10,000 items available, and this is continuing to grow every day.
The TVS Rail Spares brand is based upon three key core values:
• Easy to use – online catalogue with total transparency and no hidden costs.
• Great service – including free next-day delivery on stocked items.
• Value for money – competitive pricing on a large range of material.
TVS stocks over 2,500 items at our warehouse in Chorley, Lancashire, across 37 different product categories, including Signalling, OLE, Telecoms, Consumables, Tools and Safety & PPE. Its service consolidates material from over 400 suppliers and makes it easy to get the key rail spares equipment that you need when you need it.
This key service helps ensure the right material is in the engineer's hands, ready
for installation at the right time. But it’s not all that TVS SCS offers, as it has sustainability and supply chain transformation at the heart of what it does.
Sustainability is a dominant theme in our daily lives. It is becoming increasingly important for businesses to play their part by developing their sustainability roadmaps and engaging their employees and customers as part of their journey. Coupled with today’s rising supply chain costs, it is clear that there are significant benefits for companies who seriously consider the value in refurbishing, re-using, and recycling their assets.
ensure that any repaired or refurbished equipment is ordered from stock and reused first before any new equipment needs to be re-ordered.
TVS Supply Chain Solutions understands the value of asset care management. Its reverse logistics and refurbishment solutions open up benefits to the rail sector which include improved efficiency, cost reductions, and high levels of sustainability – and support them on their journey to Net Zero. From its experience of parts supply and the associated inventory management, TVS SCS knows that there are huge opportunities within multiple equipment categories for us to apply our asset care management strategy. This means that, by repairing or refurbishing old and or worn equipment, it is possible to significantly reduce the amount of new replacement equipment that businesses need to purchase.
In addition to this, and to further support the ongoing use of refurbished equipment, our systems automatically
This is how we are supporting businesses to reduce their costs and overall inventory –and reduce their carbon footprint.
TVS SCS provides a complete end-to-end reverse logistics solution, with a sortation and triage service which includes:
• Receiving returned parts.
• Logging of serialised assets.
• Segregation and sortation into appropriate streams.
• Refurbishment.
• Returns to the asset owner or recycling as required.
With several years’ experience of sift and sort, TVS SCS can separate serviceable/nonserviceable assets and then repatriate them to the owner as per the specified customer process. This saves you time to focus on your operational requirements.
Items that can be refurbished rather than scrapped in this process provide cost savings on your bottom line. It also takes away the challenge of whether you should buy new, as well as supporting your green credentials and drive to achieving Net Zero status.
TVS SCS can carry out a variety of inspection and testing regimes in line with customers’ specific requirements. This provides peace of mind that product is compliant and eliminates risk of any health and safety issues. For utility customers, TVS SCS inspects electricity meters including power up and testing of the units, and, for gas meters, it carries out pressure and leakage testing.
TVS SCS recycle waste items from the sortation process in accordance with the relevant legislation, using a range of recycling management solutions to minimise and, where possible, eliminate waste to landfill.
As a final solution offering, TVS SCS provides storage and logistic services for those items that are serviceable. Using its warehouse management systems, it can identify those assets that have undergone refurbishment and ensure that these are always called off out of stock ahead of brand-new parts, always ensuring the most efficient inventory levels.
TVS SCS has invested heavily in technology, for optimum management of the asset care cycle. It uses artificial intelligence to support the process, generating efficiencies which are passed through the supply chain.
The conveyor production system, which enables the logging of serial numbers at speed, is automated using radio frequency scanners. This brings enhanced accuracy to our process and allows through-life asset tracking.
TVS SCS has developed technological innovations so we can use image data capture to enable fault identification. This provides high-resolution photographs that can be used to identify any damage or condition issues affecting the assets. This benefits customers, as TVS SCS can provide this information to further support their warranty claims and returns processing.
By using the expertise of TVS SCS to manage your assets, you will benefit from a robust supply chain network that effectively negates the chance of disruption. TVS SCSs supply chain is, by design, agile and innovative. It uses cutting-edge technology to streamline movement and processing. This means the team can adapt to the
demands of a quickly moving sector whilst simultaneously providing cost savings. Ultimately, TVS SCS creates a high level of operational efficiency which delivers maximised profitability potential and protects the environment.
TVS SCS’ industry expert, Steve Welch, has 20 years of experience working in the rail industry alongside projects, logistics and supply chain management expertise, allowing him to identify areas of opportunity and growth within your supply chain.
If you would like to start a conversation about how we can transform your supply chain, get in touch with Steve by the contact information below.
Tel: 07501 187758
Email: steve.welch@tvsscs.com
PBH have a long history in railway surveying and have always ensured that our teams have expertise in both innovative surveying techniques alongside track safety training.
This has enabled PBH to expand our survey team to include COSS, ES, SWL1, SWL2 and Protection Controllers, all supported by five experienced Safe Work Planners providing quality access planning. This experience enables us to internally plan, manage and safely deliver surveys to support tight programme constraints in all parts of the UK.
With extensive knowledge of track access planning requirements, our RISQS accredited planning team are fully trained and competent with the expertise needed to support delivery of all workstreams safely. The knowledge and experience of working nationally allows our team of professionally qualified staff to provide a full spectrum of planning support services. We can support the delivery of programmes of all sizes in all corners of the UK.
We have the capability to plan long and short-term track access using all resources available to keep your programme on track. PBH Planning also pride ourselves on the production of quality safety critical paperwork compliant with NR/L2/OHS 019 to ensure the safe delivery of all work on site.
The wealth of knowledge and experience within our team allows us to offer bespoke services enabling the planning and management of tailor-made programmes to suit your requirements and ensure a service of the highest standard. We can also look at alternative approaches to help deliver challenging programmes. PBH Planning has over 40 years combined experience working with Network Rail Maintenance, Track Renewals and many principal contractors and we have helped to deliver many programmes on behalf of all of our clients safely and on time.
PBH have surveyed plain-line sites across the UK supplying data to many of the principal contractors. Each PBH surveyor has extensive componentry knowledge which, coupled with modern surveying techniques, ensures a final deliverable that meets and often exceeds the current Network Rail standards.
Complex S&C surveys require the highest degree of knowledge and understanding of the permanent way infrastructure. The PBH team is highly skilled and trained in carrying out S&C surveys, with many years of experience of working closely with our in-house design teams to undertake these projects. Our survey teams work efficiently with single-operator robotic instrumentation and mass data capture systems to ensure that track access is utilised in the most efficient way possible.
PBH Surveys provide structure gauge clearance surveys in compliance with Network Rail Standard NR/L2/TRK/3203. To ensure the safe passage of trains, surveys are carried out as part of the
suite of gauging standards which manage risk relating to gauging compatibility, structural clearances, passing clearances and calculation of stepping clearances on the infrastructure.
All gauging surveys are carried out with the latest compliant equipment utilising track mounted Abtus Routescans, Balfour Beatty Lasersweep, Robel Platform Gages and track mounted laser scanners on Track Measuring devices (TMDs). Gauging surveys include rail geometry collected from both TMDs and conventional topographical methods.
The Permanent Way Design team within PBH Rail offers full clearance analysis through ClearRoute providing Network Rail National Gauging Database reports.
When surveying some of the largest and most complex structures on the network, PBH harness the benefits of laser scanning to ensure a more robust deliverable.
Some of the benefits of laser scanning include:
• Entire and accurate dimensions
• A repeatable 3D environment allowing for easy navigation
• Geo-referenced information which can be linked to design projects
• Provision of an accurate basis to build infrastructure models
• Safe non-contact data capture even in difficult or dangerous places to access
• A ‘Capture-All/Capture-Once’ methodology to reduce the need for site revisits
• An insurance policy against future scope creep – the data is there even if not required at the project outset
PBH Surveys offer PAS128 compliant Utilities Surveys to allow designers to know what is potentially beneath them when preparing and working on a site. This can help mitigate potential issues when
breaking ground or positioning large plant and machinery during construction works, which may cause damage to services passing through the site.
PBH use the latest detection techniques including Electromagnetic Detection, signal induced threading and Ground Penetrating Radar (GPR) to locate utilities.
At PBH, we provide a range of monitoring services which can be tailored to suit the requirements of our client. Utilising a range of techniques, we are currently involved in monitoring track, structures and embankments on the railway infrastructure throughout the UK. The techniques deployed on these projects range from traditional track monitoring using retro reflective targets and total stations, to automatic wireless mesh networks which can deliver movement information in real time via an online web portal.
Our tender stage consultation services aid our clients to consider monitoring provisions and solutions at the procurement and bid stages.
The PBH Monitoring team have close working relationships with several leading global suppliers of monitoring equipment to provide monitoring solutions through all stages of construction and maintenance.
UAV surveys collect data using small remotely piloted aircraft systems, otherwise known as unmanned aerial vehicles (UAVs). PBH UAV operational platforms can be legally flown in wind speeds up to 20mph, and at heights up to 400 feet.
UAVs will be operated within line of sight of the pilot, or within 500 metres, whichever is the lesser of the two. PBH Surveys operate UAVs under a Permission for Commercial Operation (PfCO) with the Civil Aviation Authority (CAA), with permission to operate multi-rotors (≤20kg).
The platforms currently utilised to carry out work are either:
A. A multi rotor UAV with a payload operating a 100mp camera, or B. A multi roto UAV with a 20mp camera/HD .mp4 video recorded
UAV Surveys are a fantastic way to record orthomosaics and detailed 3D models of areas where poor quality, outdated or limited data is available.
Depots, although part of the railway infrastructure often pose a different set of challenges. Some examples of this would be:
• Typically, depots are open when the railway network is closed
• Generally, tracks are in a poor condition as maintenance is reduced due to the low speeds permitted
• Often depots have a collection of varying materials and S&C ages which requires a wealth of experience when trying to identify
Some depots have stabled stock that cannot be moved - PBH are well versed in selecting appropriate survey techniques to minimise the problems this may cause for a complete survey deliverable.
Depots also require staff to communicate with depot managers to agree local safeworking arrangements on closed/open lines within the depot. This requires a clear understanding of depot layouts to work in close proximity to stabled trains and ensure minimal gaps are left in survey data.
PBH Surveys can deliver outputs directly tailored to client requirements:
• ‘Traditional’ Linework/linestyles 2D Drawings – dgn/.dwg
• ‘Traditional’ 3D Wireframe Drawings –.dgn/.dwg
• ‘Simple Hybrid’ 3D Wireframes/ Solid Models – combining traditional track surveys with 3D Solid models of complicated structures - dgn/. dwg/.rvt/.msh
• ‘Complex Hybrid’ 3D Wireframes/ Solid Models – Full solid models of all infrastructure supplemented with traditional topographic surveys - dgn/. dwg/.rvt/.msh
• Total 3D Solid Models – No traditional Linework. - dgn/.dwg/.rvt/.msh
• All deliverables can be tailored to suit time/cost budgets.
• Outline Detail – Building Shapes/ groundforms – representative components.
• Medium Detail – Building Shapes/ Features – basic componentry accurately depicted.
• High Detail – WYSIWYM “What You See Is What You Model” Accurate depictions of all features required in specification.
• Rendered High Detail – Photorealistic Models used for heritage grade/planning applications etc
Below are some examples of different projects that PBH Rail has worked on.
Network Rail realised that the Covid-19 pandemic would cause a reduced train service. As a result, a potential blockade could be secured on the West Coast Mainline covering Kilsby Tunnel to undertake the renewal of 800 yards of drainage and 870 yards of track. PBH got the call ten days before the blockade was due to start, requesting a full survey and design. PBH mobilised survey resources to complete the survey over one weekend night shift, processed the data and delivered to the design team within three days. The design team turned the design around within a week in time for the renewal to start.
PBH is delivering detailed S&C surveys for the CRSA Alliance across multiple
regions. PBH undertake all access planning, paperwork and Safety Critical Staff for the client to ensure efficient delivery of both surveys and client design. A large percentage of PBH’s staff have extensive experience in this type of work which is demonstrated by our capacity to supply the large amount of survey data that is required when renewing S&C. Our regional based survey teams and internal planning resource services allow any changes to the delivery programme to be actioned quickly and safely.
Through CP6, PBH Rail is delivering Plain Line surveys across LNE, LNW, Anglia and Scotland for CRSA and Network Rail Works Delivery. This results in an annual combined workbank of circa 300 sites, ranging from Plain Line, Gauge Clearance, Drainage and S&C. Our in-house Planning, Survey, Track Design and OLE Design allows one point of contact for the client which ensures the demanding delivery timescales are met.
PBH are regularly commissioned to undertake monitoring across a variety of projects. We are experienced in the use of remote web-based monitoring and conventional monitoring. Projects range from the monitoring of tracks, buildings, embankments and railway infrastructure such as tunnels, bridges and arches. PBH have developed bespoke monitoring solutions to meet the client’s needs.
Newton Heath was surveyed by PBH due to various concerns raised by the Depot Manager regarding the condition of the structure, therefore a survey was required to assess what repairs were needed to be undertaken. We installed and coordinated a new grid tied to Snake Grid TPEN11 utilising six-hour GNSS observations as per the Northern Programmes standard.
A mix of traditional topographical survey, UAV survey and terrestrial laser scanning was undertaken in order to deliver this project in the most efficient manner. The final deliverables were delivered to LOD300 standard along with our usual 3D dgn, registered point cloud and full NR3100 standard survey report. A flythrough of the site was created in order to assist the client with their design from the comfort of their own desk, minimising the need for further site walkouts.
Tel: 07487 717 900
Email: matt.chilton@pbhrail.com
Visit: www.pbhrail.com
Helping organisations become Verified Carbon Neutral in a measurable, meaningful and potentially self-funding way
Auditel is a team of carbon footprint consultants which helps organisations reduce their carbon emissions and costs at the same time. Its Net Zero carbon consultants and carbon footprint experts help its clients on their journey towards Net Zero by simplifying the process. Auditel begins with a couple of easy steps, which could lead you to be verified as Carbon Neutral within twelve months, to an internationally recognised standard. Using its procurement expertise, Auditel makes sure any action taken to improve your environmental credentials have a strong and potentially self-funding business case
because the company truly believes that being Carbon Neutral doesn’t need to cost the Earth.
With the UK Government’s commitment to a low carbon world and net zero targets by 2050, the drive to carbon neutrality and achieving net zero is dominating organisations’ future decision-making. However, many organisations believe the changes that they will have to make to achieve net zero carbon emissions will be time-consuming, costly and with all the conflicting information, a little daunting.
This is far from the truth, as there are many incentives to help businesses become greener and leaner without costing the earth.
Using Auditel’s simple four step process experienced carbon neutral consultants can help your organisation demystify and provide clarity to this complex subject of achieving net zero. Auditel’s carbon management consulting services deliver expert guidance and resources so you can achieve an NQA or BSI recognised specification for carbon neutrality (PAS 2060) as soon as possible, while you progress on the longer-term net zero journey.
Founded in 1994, Auditel was established to help organisations make effective and informed procurement decisions within a rapidly evolving energy market. Since then, the company has built a strong network of over one hundred procurement and carbon consultants and is now one of the leading Cost, Procurement and Carbon Solutions in the UK. Auditel’s Procurement and carbon footprint consultants work alongside your existing Finance, Operational and Procurement teams providing the external guidance your organisation requires.
Auditel helps its clients on their journey to Net Zero without the usual associated costs, for many it is self-funding and for some its actually profitable. The company delivers solutions that will enable your organisation to achieve independent accreditation of carbon neutrality. By combing the expertise of its Carbon Strategy Group with its experience in cost management, and partnering with the British Standards Institute, Auditel is assisting clients towards currently the only internationally recognised standard PAS2060.
In the current challenging economic climate, organisations are battling with the desire to drive growth and profitability, whilst investing in low carbon emitting technologies to reduce their carbon footprint and speed up their journey to achieving Net Zero. With the UK firmly embedded in the Fourth Industrial Revolution, in which disruptive technologies and trends are changing the way we live and work, the need for an organisation’s procurement function to embrace new ideas and technologies within their supply chain has never been greater.
It is not uncommon when we first engage with an organisation that they believe that their procurement is under control, and any improvements we could achieve would be insignificant and not worth pursuing. Many organisations believe that ‘as long as the spend is within budget and the supplier is delivering in accordance with the contract and service level agreement, then all is well.’
This is a natural response, and Auditel fully understands this initial reaction. However, without independent benchmarking and validation of pricing, service level arrangements and now the impact that supplier has on your Carbon Footprint, it’s impossible to know if you are receiving value for money or have the right supplier to help you achieve your carbon reduction plans.
From its 27 years of experience, working with thousands of clients, organisations are typically over-paying for goods and services by up to 50 per cent whilst missing out on innovation. If addressed, this can have a dramatic reduction on your Carbon Footprint and the profitability of your organisation.
Auditel believes that any claims made regarding GHG emissions (Carbon Footprint) needs to stand up to the closest scrutiny. With an increasing demand from consumers, investors, media, staff, and the public for accurate and meaningful measurement of an organisations carbon footprint, it has never been more important to ensure our clients can trust in our work.
All member firms of Auditel are required to have every Carbon Footprint Report they produce verified as an accurate and true reflections of the subjects’ emissions. This internal verification process will assess the inventory work and subsequent report content, based on either PAS2060:2014, PPN 06/21 or ISO 14064-1 requirements.
All internal verification will be carried out to ISO 14064-3 standards by a financially independent arm of the Auditel network. Which will be another member firm with no financial interest in the project being verified.
With every Auditel Carbon Inventory & Report having a separate Verifiers Statement following this stringent internal review process, you can trust in the work it produces and stand tall in a world increasingly plagued by false or misleading environmental claims.
Auditel believes that a small investment of time and money at the early stages of your carbon journey to ensure accurate reporting, will deliver long term benefit and reduced risk as the world’s media increasingly holds us all to account for our environmental claims.
Carbon reduction and cost reduction
Auditel’s carbon footprint consultants have been hand-picked to join Auditel due to their lifetime of experience gained during senior careers within their chosen area of expertise. Auditel understands its client’s business challenges, having worked in their sector implementing thousands of similar projects over the last 27 years.
Auditel’s consultants really know what ‘best value’ looks like and can uncover opportunities to decarbonise, reduce costs, improve supplier service and quality, and deliver innovation into your supply chain. Auditel’s knowledge and understanding of the supplier markets provide you with an enhanced negotiating position and by using its bespoke analytical tools and tendering processes, the company can deliver impressive results quickly, with limited disruption or input needed by you and your staff.
Negotiating from a position of knowledge, Auditel’s specialists will help you avoid any contractual pitfalls that would disadvantage your organisation. Having supply-side expertise on your team ensures that any contracts that are put in place between you and your suppliers will be reviewed in detail, to safeguard your organisation from unfair clauses and protect you from unjustified price rises. During
• Resource – dedicated resource that adds considerable weight to your current procurement and sustainability team.
• Knowledge – detailed procurement and decarbonisation knowledge of what best value looks like and how to achieve it.
• Expertise – hand-picked procurement specialists negotiating on your behalf, who have long careers working in over one hundred different expenditure areas.
• Tools – unique carbon foot printing and procurement analytical tools that make sense of complex dataallowing you to make informed decisions.
• Buying Power – access to serious buying power due to supplier relationships and unique pricing frameworks exclusive to Auditel.
the implementation process, Auditel’s specialists, who will be working alongside your employees, will ensure they are fully trained and supported in dealing with the supplier – eradicating maverick spend and holding suppliers to account, whilst adhering to the agreed prices and service levels.
Tel: 07904 378911
Email: barry.harwell@auditel.co.uk
Visit: auditel.co.uk/barryharwell
We are experienced at engineering fully welded single or multiple room railway equipment containers designed to accommodate LV and MV Switchgear, UPS and batteries.
• Custom-designed railway modules and acoustic containers
• Relocatable Equipment Buildings (REBs)
• Control instrument and switchgear modules
Decades of durability built into every module.
Moore Concrete have been supplying the Civil Infrastructure, Agricultural and Building markets across the UK & Ireland for 45 years. In recent years, the company has worked on multiple rail projects, including the 4.5-kilometre extension of the Gospel Oak to Barking London Overground line. This consisted of three areas; precast elements for the main station construction, parapet units along the elevated rail viaduct leading into the station, and bespoke retaining walls creating a ramp between the existing rail line and the viaduct.
The most unusual items manufactured were the ‘platform tables’, which support the main platform areas while providing access and protection to various service runs. Construction is currently ongoing at the new Belfast Transport Hub. The flagship infrastructure project is being built with the aim of strengthening essential transport services and improving connections throughout the city and surrounding areas. Moore Concrete supplied bespoke platform units and retaining walls for the new hub.
The completed hub will make Belfast more accessible for everyone, enabling those travelling to the city, for either work or leisure, to do so via a clean mode of transport. This will also help reduce individual car usage and contribute to decarbonisation.
Moore Concrete is working hard to develop environmentally friendly, sustainable products for its customers. Working with Queens University Belfast, the company is leading the way in this sector.
As a company, Moore Concrete has a world-class vision. In line with this, its goal is to be an industry leader in environmentally friendly precast concrete manufacture through the development of the Net Zero Pathway which has two streams: ‘Challenging Ourselves and Challenging Our Customers’.
In Challenging Ourselves, Moore Concrete target its own carbon footprint and energy expenditure. The Challenging Our
Customers stream researches and offers the viable environmentally friendly alternatives to carbon-hungry concrete for customers. This means not only producing precast concrete in an environmentally friendly way, but also producing products that enable customers and projects to meet and exceed environmental targets.
ISO 14001 is used as the basis for managing its environmental obligations and achieving internal environmental objectives and targets. These objectives are communicated throughout the company to increase environmental awareness.
Moore Concrete strives to be at the forefront of not only green manufacturing, but greener products, enabling its customers to achieve their environmental goals. The three-year Knowledge Transfer Partnership with Queens University Belfast is underway in order to further research and implement other low carbon options in precast.
Currently, Moore Concrete has several processes in place to reduce the impact its manufacturing has on the environment:
• Recycling of materials – all scrap steel and timber used at Moore Concrete is recycled.
• 100 per cent renewable energy – Moore Concrete’s factory is 100 per cent powered by onshore wind energy.
• Science based targets – Moore Concrete is one of only two UK based precast concrete manufacturers with an approved Science Based Target. Science-based targets provide companies with a clearly defined path to reduce emissions in line with the Paris Agreement goals. The company has committed to reduce greenhouse gas emissions by over 42 per cent by 2030, while this will have a major impact on carbon emissions it will also driver the company’s innovation
towards more sustainable manufacturing processes.
• Recycling water supply – the team at Moore Concrete go to great lengths to ensure it recycles as much water as possible during the manufacturing
process, where all excess water from manufacturing and washouts is cleaned and recycled. Water used in manufacturing is sourced from a borehole by pumping water directly from the borehole to the production teams, where
this minimises the use of a mains water supply. This results in the amount of energy required to supply the factory with water being greatly reduced.
• Localised supply chain – 80 per cent of Moore Concrete suppliers are based locally, this not only reduces transport emissions but supports the local economy.
• Determined pursuit of low carbon concrete – reducing the amount of cement in concrete mixes has been an ongoing process for over 20 years now at Moore Concrete, due to evolving technology it can currently produce precast concrete products with a mix including up to 66 per cent GGBS (ground granulated blast slag). This lowers the CO2 content of the concrete by over 50 per cent.
Durable Low Carbon Marine Concrete
Moore Concrete has recently completed a research project to develop highly durable, corrosion resistant concrete mix designs for use in marine infrastructure. The new optimised mix design displays improvement over the current 40 per cent GGBS mix and the use of this in future projects should see Moore Concrete perform better in production and use.
Data:
Concrete mix: 80% GGBS
Cube Strength: 60MPa
Cement Type: IIIB
SCM GGBS
Cement Content: 450kg/m3
w/c ratio 0.4
SCM content 80%
Aggregate size: 20mm
Admixtures: Superplasticiser
Slump class: SF2
STRENGTH: C50/60
Moore Concrete has published EPDs for a range of its products. EPDs are used to quantify environmental information on the lifecycle of a product. The recently published EPDs are just the beginning, Moore Concrete is working towards producing these for the wide range of products across the business. Having EPDs available enables the company to be transparent with its customers about the environmental performance of the products as well as
allowing it as a company to easily identify areas where positive changes can be made moving forward.
Cement free concrete
Cement free concrete, with the strength and integrity of current concrete mixes, is the goal. Moore Concrete is able to produce some of the products completely cement free already and is continuously testing new mixes on this front to extend the use of nonferrous reinforcement materials.
GGBS (Ground Granulated Blast Slag) is a cementitious material which can be used to replace Portland Cement. The source of GGBS has a carbon footprint of 32kg CO2 eq/t, compared to Portland Cement at 884kg CO2 eq/t. This mix has been rated A++ using the recommendations published in the Low Carbon Concrete Routemap.
Moore Concrete is continuing to develop the mix design of its 80 per cent GGBS mix to improve workability and finish. 80 per cent GGBS mixes have a long curing period before formwork can be stripped, this needs to be accommodated within the works programme.
Basalt rebar
Basalt rebar is used as an environmentally friendly alternative to steel. Basalt is naturally resistant to attacks from alkali, water or chemical – making it perfect for use in the marine environment, where corrosion is continuous concern. Basalt reinforced structures may be designed to the code ACI 440 which allows for greater design crack widths, as the durability risk to the unit is reduced.
Using non-ferrous reinforcement in coastal locations, allows the cover to reinforcement to be reduced hence reducing the overall section size. The unit design with basalt fibre rods, in place of steel reinforcement, reduces the unit volume by 25 per cent. Basalt rebar is also significantly lighter than steel rebar, while retaining greater strength properties.
By using basalt rebar, as opposed to steel, Moore Concrete are able to design smaller, lighter units which allow for a significant carbon reduction in both production and transport – without compromising structural integrity.
Moore Concrete recently attended the Flood & Coast exhibition in Telford where it had an example of low carbon concrete on show. What you see here is an L-Wall produced with an 80 per cent GGBS mix and basalt rebar. By substituting cement and steel for more environmentally friendly material, the carbon footprint of this particular product is reduced significantly. The GGBS has a carbon footprint of 32kg CO2 eq/t compared to Portland Cement at 884kg CO2 eq/t. These are just some of the initiatives underway at Moore Concrete to help contribute to a more sustainable future for the UK construction industry.
Tel: +4428 2565 2566
Email: sales@moore-concrete.com
Visit: www.moore-concrete.com
Orbital Fasteners is a leading distributor of fixings, fasteners, tools and power tools in the UK with over 40 years of experience in product, application know-how and customer service
The Orbital Fasteners product range continues to expand and its reliable next day delivery service is second to none. The 50,000 sq. ft Watford warehouses has in excess of six million of stock and is backed up by a further £10 million of stock that is delivered regularly at 8am from Orbital Fasteners primary supply partners.
With over 40 years of experience in product, application know-how and customer service. The product range continues to expand so you can now choose from over 300 manufacturers and 27,000 products.
Orbital Fasteners is proud to stock an extensive range of fasteners, fixings, professional tools, tool consumables and power tool accessories which range from the likes of Bosch cordless drills to diamond blades and cores, screwdriver bits and other site essential products.
Orbital Fasteners fully understands the importance of having the right fasteners and tools for the job and that having the reassurance that you’re purchasing products from a reputable and established manufacture is of uttermost priority.
With this in mind, Orbital Fasteners is proud to offer professional power tools from manufacturers including Bosch, Rotabroach and Hole Maker Technology as well as consumables and accessories which includes the likes of dormer drill bits, saw blades, holesaws and arbors, to outline just a few. If you’re looking for the highest quality products at the best possible online prices, you’re in capable hands and the experienced team are always on hand to assist if you have any queries or questions.
In addition to an extensive range of power tools, hand tools and consumables, Orbital Fasteners is proud to offer free next day delivery over £25 on all orders which fall into the delivery area. There will always be times when you need replacement tools and consumables quickly and the service is intended to fully cater for those needs.
Solar panels have been installed on the roof of the 14,500 sq. ft main warehouse which now generates more electricity than the warehouse consumes and returns the excess back to the national grid. Installing these solar panels has reduced Orbital Fasteners’ energy bills and carbon footprint.
Bolts and bolting products
Whether you’re looking to purchase hexagon head high tensile set screws, hexagon head tensile bolts, HSFG, holding down bolts or a whole host of other types of fasteners and fixings, you’ll find it in stock. The most commonly stocked surface
finish in use is Cr3 bright zinc plated. Hot dipped galvanised finishes are becoming ever more popular, particularly in the rail industry sector. Typical applications for this very widely used product include steel fabricators, machine builders, automotive applications and the construction industry.
Customer service
Orbital Fasteners employs more than 90 people, the sales office and trade counter opens at 7.00am Monday to Friday. Each day they process more than 1,200 orders and offer nationwide delivery via its fleet of 16 vans and hundreds more by parcel carrier. Many of these orders are placed through the
Orbital Fasteners website which shows stock holding and prices 24/7.
Deliveries to central London construction sites is their speciality and Orbital also offer an ‘Early Bird’ or same day delivery solution if required.
Orbital Fasteners was awarded the BS5750 Pt 2 (stockist) in July 1992 and then qualified to BS EN ISO9002:1994. The company’s continuing compliance to BS EN ISO9001:2015 demonstrates the commitment Orbital Fasteners has in both quality products and first-class customer service. This standard is recognised internationally as the benchmark for quality assurance systems and is held by companies who wish to conform to customer needs relating to quality and service.
Limited companies and sole traders with a minimum of three years trading may apply for a business credit account.
All applications received will be assessed using our credit reference system by EXPERIAN. A business account will allow your company 30 days credit, simplifies tracking your previous purchase history and can be linked to the website.
Whatever your needs in terms of fasteners, tools and consumables, Orbital Fasteners welcomes you to browse the
wide range available on its website and if you require something specific but cannot find it on the site, the experienced and knowledgeable team are able to advise on availability or suitable alternatives so get in touch via the contact information below.
Tel: 01923 777 777
Email: sales@orbitalfasteners.co.uk
Visit: www.orbitalfasteners.co.uk
PlasmaTrack technology ends ‘Leaves on the Line’ delays to autumnal timetables and increases the UK network capacity delivering ‘Summer braking conditions all year round’
Autumnal delays on the rail network have been estimated to the cost the UK £350 million every year. PlasmaTrack is a railway technology business which is focused on unlocking predictable and optimized braking for the UK rail network. It will achieve this using its patented high energy plasma system, to remove & retard the formation of low friction contamination on the railhead (‘Leaves on the Line’) and thereby returning the rail head to summer braking conditions.
The vision for the business is to deliver a multi-product portfolio around predictable and optimised braking solutions for the Rail Industry. Leading a revolution in rail network operation through closer running of railway vehicles and a safe increase in network capacity.
Over the next three to five years the sales of PlasmaTrack Cleaning and Track Monitoring systems will gain traction with UK and global network operators as the only full turnkey solution to enable closer running of rail vehicles.
The technology was born out of an Innovate UK SBRI (Small Business Research Initiative) feasibility study launched by the Railway Safety and Standards Board (RSSB) for predictable and optimised braking. The end goal of this industry calling is to increase the UK rail network capacity through closer running of rail vehicles.
Plasma is well established in other industries for cleaning, sterilization, and surface deposition.
Plasma Track has developed Intellectual Property for a plasma cleaning system suitable for the railways. It eradicates track contamination through thermal ablation, such as leaf layer, and turns the track from ‘Autumnal’ to ‘Summer Braking’ conditions.
PlasmaTrack has two main track cleaning products:
1. Low speed PlasmaTrack system –Delivering track cleaning within a possession up to 7.5kph. This system uses energy sources suitable for mounting on a Road-Rail Trailer pulled by road-rail service vehicle or a dedicated Road-Rail Vehicle.
2. High speed PlasmaTrack system – This system will deliver a solution for faster running and more efficient rail head track treatment (RHTT) trains, up to 95 kph. This modular system can be placed onto multi-purpose vehicles (MPVs) or wagons and outperforms water jetting by 50 per cent on speed and 40 per cent on cleaning efficiency.
PlasmaTrack cleaning systems enable summer braking conditions all year round and will lead to the end of Autumnal timetabling. Rapid deployment off rail to target hotspots removes scheduling challenges. Faster treatment without consumable materials eases maintenance scheduling. The cleaning systems are nontoxic, with zero water table impact and lower fuel consumption per treatment kilometre.
In addition to track cleaning systems
PlasmaTrack has also developed a system for sensing and evaluating the track condition. This was developed with support from the National Physical Laboratory (NPL) utilizing a novel application of RAMAN spectroscopy. This is the first technology which has analysed the railhead contaminant on live
track in the UK and can be used to predict changes in the track conditions, indicate which cleaning regime should occur and confirm a successful intervention has occurred returning the track to suitable braking conditions.
This is embodied in three different products:
1. Handheld for use by on Track Engineers.
2. Trackside data logging module.
3. On vehicle dynamic monitoring system.
PlasmaTrack sensing systems will give Improved service delivery through prediction of conditions and proactive intervention. Less disruptions to service by removing unscheduled maintenance. Addressing serious issues of stress and defensive driving. Giving confidence to engine drivers to operate based on real-time conditions.
PlasmaTrack’s ultimate goal is to enable the development of a miniaturised passenger and freight train-borne system. This would replace current onboard sanding cleaning systems with a PlasmaTrack adhesion guaranteeing product. Active
during braking and initial traction acceleration, the PlasmaTrack solution replaces on train grit applicators (also known as sanders). It will also have a cumulative effect for the entire network, cleaning the track for following trains.
This is the on train 21st century solution to track adhesion. The solution gives independence of environmental conditions, leading to predictable and optimized braking enabling closer running of vehicles to ERTMS & ETCS. Ultimately, it increases passenger capacity on the same infrastructure, addressing the problem of the doubling of passenger journeys over the last 20 years.
The team completed the technological development through three phases of grant funding managed by the RSSB. Phase 1 Feasibility, Phase 2 Demonstrator. Phase 3 Prototype. During this time, it has published and had granted several patents with respect to plasma track cleaning and track sensing, as well as many scientific papers around low adhesion intervention.
Subsequently it has completed a successful on network trial with Network Rail Wales in Autumn 2020.
It has also demonstrated the High-Speed product on a full-scale rolling track and bogie with Knorr-Bremse in Germany on its ATLAS test rig in 2022. This showed efficacy at 95 kph completely removing leaf layer from the track and returning the braking conditions to maximum levels.
Network Rail launched a PIN (Periodic Indicative Notice 02/06/2020) for new track cleaning innovations. PlasmaTrack is the only UK based innovation, selected by Network Rail, for live line testing ahead of three other potentials.
Autumn testing on East Lancashire heritage lines with Network Rail Future Technology Trial in 2022, showed efficacy for cleaning the track at over 95kph, with its High Speed product.
The team has grown from a bias in engineering design & science to include commercial experience from the Railway industry. The board includes Julian Swan CEO and Alastair Burton CFO. Its advisory board includes Abi Broadley (Rail Consultant, ex Managing Director of Aquarius Rail), Neil Welch (Director WRAIL Consultancy Limited; ex Business Manager of Seasonal Delivery Network Rail), Nick
Coutts (Advisor to Co-founders), Pete Wild (Commercial Advisor).
With this team, PlasmaTrack’s initial market will be track cleaning in the UK through Network Rail. Further markets include European, North American, and far Eastern rail markets.
OEM train manufacturers & Train Operating Companies (TOC) are the key target for the onboard Passenger / Freight train mounted system. PlasmaTrack systems will bring the dawn of closer running rail vehicles on every network through predictable and optimised braking.
Tel: 07748767688
Email: julian@plasmatrack.co.uk
Visit: plasmatrack.co.uk
RHTT - MPV plasma cleaning 95kph
Road to rail plasma cleaning 7.5kpg
Mobile track condition monitor
Live network track condition data logging
Driver feed-back track condition sensing
Passenger & freight vehicle plasma adhesion system
‘Competency’, but they are not the same thing
Everyone in the rail industry understands the importance of training to impart skills and knowledge to staff. This is particularly important for engineers who are working on the infrastructure. We need to make sure that they have had suitable training for the work that they are undertaking. However, training shouldn’t be the end of the process, it is just the beginning.
Training for Signal Engineers is our speciality, and it is important the engineers start with an understanding of how electricity works and how this relates to signalling equipment such as signals, points and warning systems. They can then build up their specific skills. Within Signal Engineering this is usually a pathway such as Installation, Testing or Maintenance. There are several courses that they can complete, but these should relate to the work that
they are undertaking so that they can move onto the next stage. This is because training only imparts skills and knowledge at the time of the course. More time is needed before this becomes ingrained and moves from the short-term memory to the longterm memory. Here at PMTandA we provide training for Signal Engineers across a range of skills. We can bring our mobile classrooms to local depots so that the engineers don’t have to travel for training.
Mentoring is important so that when engineers return to the workplace after training, they have someone who can make sure that they can implement what they have learnt in the live working environment. The mentor is also there to help answer questions and guide the engineer in the correct way of completing their work. When we all learn a new skill, we always need someone to run things past just to make sure that we are doing things correctly. Mentors therefore play a vital role in the learning process. As the engineer becomes more confident and proficient the mentor can then take a step back and just oversee what the engineer is doing.
Competence is the culmination of training and experience. It demonstrates that the engineer has the knowledge and skill in a particular area. The amount of training and experience (often under the watchful eye of a mentor) can vary depending on the complexity of the skill, and the amount of experience the engineer is able to gain. In Signal Engineering the primary way of demonstrating competence is with the IRSE (Institution of Railway Signal Engineers) Licencing scheme.
This scheme was created by British Rail and London Underground after the Clapham Rail crash in the 1980s. It allows engineers to demonstrate their level of competence in a particular type of engineering. For example a Testing Engineer may start their career with a Test Assistant licence, but over the years with training and mentoring they can work their way up to a Principles Tester and Tester in Charge IRSE Licence. The applicant must provide evidence of training and work experience as well as giving detailed examples of work they have undertaken, along with supporting evidence. This is a bit like doing an NVQ and is a way of proving competence and knowledge in a particular skill, which is a step up from just being trained. PMTandA provide IRSE assessments across the UK and abroad.
Authority to Work provides the detail to the competence qualification. For example, an engineer may be deemed competent as a
Points Fitter, but it doesn’t say what types of points they are competent to install. This is where the ATW comes into play, as this provides the details of what equipment on each railway system the individual can work on. This considers the training and competence of the engineer, alongside their experience.
Skills Fade happens when we don’t use our skills and knowledge regularly. Because we work in a safety critical industry, we must make sure that our competence is regularly tested to make sure that we haven’t forgotten anything. That is why many of the rail competencies are tested regularly. For example, for the IRSE scheme the licence holder must demonstrate their competence every five years.
Assessors, Trainers and Mentors are key to this process of training and assessment. Therefore, we need to make sure that we have trained and qualified people undertaking these roles. The learners can only gain skills if they have knowledgeable and qualified people imparting these skills and knowledge. As well as being skilled in the technical skill they are imparting, they also need to be competent as Trainers, Assessor and Mentors. Here at PMTandA we provide training and assessment for these qualifications, which are not specific to any particular sector.
Quality Assurance is key in making this all work. If we don’t have a system that checks that the training and assessment has been carried out to the correct level, then everything will fall like a deck of cards. Each organisation needs to ensure that it has quality systems in place for their organisation to make sure their trainers and assessors are working at the correct level. If they are doing a formal qualification, then they are usually required to have the Internal Quality Assurer (IQA) qualification. A good example of this would be the IRSE Licencing scheme. We can provide these qualifications for your organisation.
Continuous Professional Development (CPD) Is the culmination of all this and more. It is about each individual keeping
themselves up to date. Part of this is what we have described above, but it can also include informal learning opportunities such as webinars, reading books and magazines, shadowing experienced engineers etc.
What is the future of training and assessment?
This is an interesting question. We can all agree that signalling training and assessment needs to continue into the future. However, technology has moved on at such a pace so that we now have more options than ever to be creative in the way that we train and assess learners. Some of the ways in which we currently use technology to our advantage at PMTandA is online electronic portfolios, online learning, video calls for assessment, recording of observations and questioning, online tests that mark themselves and Virtual Reality. All of these are just tools that we use and don’t replace the role of the trainer and assessor. For example, even though we may use an online test, if a learner gets a question wrong they still need time with the assessor to go through why they got it wrong and make sure they understand what was the correct answer and why.
Going forward we can look towards how we can make our training and assessment better with the use of tools such as Augmented Reality and Artificial Intelligence. These should be used to enhance the training and assessment process so that the engineer can learn in a way that is as close to the live railway as possible.
Tel: 01874 620 704
Email: enquiries@pmtanda.co.uk
Visit: www.pmtanda.co.uk
LinkedIn: PMTandA
provide companies with the skills, knowledge and certifi to ensure that works on the railway are carried out efficiently and safely as well as in full compliance with Network Rail Standards.
Seaton Rail are one of the leading railway training and assessment providers Our courses are delivered by professional, full-time trainers who know how to get their message across. We can also tailor course content and format to meet your specific requirements. Our courses are delivered at our modern training centres in Bridlington, and Glasgow where we have excellent facilities, lunch is provided, unlimited free hot and cold drinks and free wi-fi. We also arrange training to meet the requirements of our Clients shift patterns including early, late and night turns of duty. Training is also available at the weekends, or at a premises of your choice.
Seaton Rail’s Railway and Track Safety Training Courses provide companies with the skills, knowledge and certification to ensure that works on the railway are carried out efficiently and safely as well as in full compliance with Network Rail Standards.
Courses we deliver (both initial and recertification):
•Personal Track Safety
•Working Near or Adjacent to the DC Conductor Rail (DCCR)
•Lookout
•Individual Working Alone
Seaton Rail are one of the leading railway training and assessment providers, recently graded GOLD (outstanding) by NSAR. Our courses are delivered by professional, full-time trainers who know how to get their message across. We can also tailor course content and format to meet your specific requirements. Our courses are delivered at our modern training centres in Bridlington, Goole, York, Rotherham, Warrington and Glasgow where we have excellent facilities, lunch is provided, unlimited free hot and cold drinks and free wi-fi. We also arrange training to meet the requirements of our Clients shift patterns including early, late and night turns of duty. Training is also available at the weekends, or at a premises of your choice.
Courses we deliver (both initial and recertification):
•Personal Track Safety
Seaton Rail’s Railway and Track Safety Training Courses provide companies with the skills, knowledge and certification to ensure that works on the railway are carried out efficiently and safely as well as in full compliance with Network Rail Standards.
•Working Near or Adjacent to the DC Conductor Rail (DCCR)
•Lookout
•Individual Working Alone
•Controller of Site Safety (OLP and CRP LLT)
•Protection Controller
•Level Crossing Attendant
•Points Operator
•Engineering Supervisor
•Safe Work Leader 1 and 2 Conversion
Seaton Rail are one of the leading railway training and assessment providers, recently graded GOLD (outstanding) by NSAR. Our courses are delivered by professional, full-time trainers who know how to get their message across. We can also tailor course content and format to meet your specific requirements. Our courses are delivered at our modern training centres in Bridlington, Goole, York, Rotherham, Warrington and Glasgow where we have excellent facilities, lunch is provided, unlimited free hot and cold drinks and free wi-fi. We also arrange training to meet the requirements of our Clients shift patterns including early, late and night turns of duty. Training is also available at the weekends, or at a premises of your choice.
•Safe System of Work Planner
•Possession support
•OLEC 1
•Industry Common Induction
• Person in Charge of Possession
Telephone: 01262 608 313
Workplace assessments
•Individual Working Alone
Seaton Rail’s Railway and Track Safety Training Courses provide companies with the skills, knowledge and certification to ensure that works on the railway are carried out efficiently and safely as well as in full compliance with Network Rail Standards. Seaton Rail are one of the leading railway training and assessment providers, recently graded GOLD (outstanding) by NSAR. Our courses are delivered by professional, full-time trainers who know how to get their message across. We can also tailor course content and format to meet your specific requirements. Our courses are delivered at our modern training centres in Bridlington, Goole, York, Rotherham, Warrington and Glasgow where we have excellent facilities, lunch is provided, unlimited free hot and cold drinks and free wi-fi. We also arrange training to meet the requirements of our Clients shift patterns including early, late and night turns of duty. Training is also available at the weekends, or at a premises of your choice.
•Controller of Site Safety (OLP and CRP LLT)
•Protection Controller
•Level Crossing Attendant
•Points Operator
•Engineering Supervisor
•Safe Work Leader 1 and 2 Conversion
•Safe System of Work Planner
•Possession support
•OLEC 1
•Industry Common Induction
• Person in Charge of Possession
Workplace assessments we deliver:
•Controller of Site Safety (Including OLP, CRP LLT and PC)
•Engineering Supervisor
•Safe System of Work Planner
•Possession Support
• Person in Charge of
•Individual Working Alone •Controller of Site Safety (Including
Telephone: 01262 608 313
•Individual Working Alone
•Controller of Site Safety (Including OLP, CRP LLT and PC)
Web: www.seaton-rail.com
•Engineering Supervisor
Email: training@seaton-rail.com
•Safe System of Work Planner
•Possession Support Person in Charge of Possession
Althon Headwalls are a cost-effective alternative to in-situ concrete structures for connecting pipework discharging into open watercourses
Althon Limited manufactures and distributes specialist water management products to the construction industry. They design and manufacture precast concrete headwalls to meet Sewers for Adoption and Severn Trent Guidelines. Their product range includes flap valves, penstocks and stop logs. Additionally, trash screens, outfall safety grilles, penstock chambers and a large range of commercial and industrial application drainage channels.
Althon Limited is part of the MAG Group of Companies. MAG Group Limited is a privately owned UK based business operating since 1982. MAG Group has six subsidiary companies concentrating on the manufacture and supply of specialist products for the construction industry and retail markets.
The MAG Group employs around 70 people and has a customer base throughout the UK and worldwide having traded in over 50 countries to date. MAG Group Limited anticipates significant growth in 2023 with Group turnover set to exceed £25 million.
Precast headwalls are an important part of most SUDS drainage schemes, preventing erosion at the point of discharge into watercourses such as attenuation ponds, detention basins, rivers, ditches and swales.
• Althon Headwall Drainage Standards & Guidelines.
• Designed to BS EN 1992-1-1 (EC2) standards.
• Manufactured to BS EN 15258 & BS EN 13369 standards.
• Severn Trent Water specifications for rectangular precast outfalls.
• Headwalls to Anglian Water's S104 adoptable standards.
• Angled ranges that meet the Environment Agency’s ‘Standard rules SR2015 No 27’.
• Selected ranges meet the Sewers for Adoption 7th Edition guidelines to be adopted by local Water Authorities and comply with the Water Industry Regulations 2011.
Althon’s headwalls can be factory fitted with accessories such as outfall safety grilles, Kee Klamp® handrails, flap valves and penstocks. Althon is also able to provide additional precast elements, such as diffuser blocks, stepped baffle blocks, extended spillways with cascade panels and in some instances precast steps. The company is happy to help design a precast concrete outfall and spillway to site-specific requirements.
Althon is the UK’s leading manufacturer and supplier of precast headwalls with associated accessories available in the UK. If you cannot find the product you are looking for, get in touch and their sales team will be happy to assist. Althon is constantly uploading new ranges and new drawings to their website and is confident they will be able to meet your spillway and outfall requirements.
Althon has supplied HS2 as well as several other rail projects with precast concrete headwalls complete with kee klamp handrail and flow control devices. Ordered through the contractor they can deliver anywhere in the country with its own transport. Factory fitting accessories means the concrete does not have to be drilled on site. This saves time on the installation and has great health and safety benefits. Wherever possible, Althon will deliver their headwalls with factory fitted accessories still attached for faster offload and installation.
Althon offers a range of specialist water management and flood prevention products such as HDPE flap valves, ductile iron flap valves, penstocks, Wastop inline nonreturn valves, stop logs, Tideflex duckbill
and Checkmate valves. It offers flanged, wall mounted and tidal flap valves and can offer wall mounted and inline penstocks. As standard the HDPE flap valves and penstocks have a 50-year design life.
Althon manufactures and distributes flap valves in HDPE, cast iron and stainless steel. Flap valves and flap gates are a type of nonreturn valve (NRV) used to prevent flooding and to stop water back-flowing up pipework connecting into ponds, ditches, swales, rivers and marine or tidal environments.
Their range of flap valves includes wall mounted flap valves, tidal flap valves, flange mounted flap valves as well as push fit and pipe mounted flap valves. Althon can manufacture valves to suit site specific installation requirements and operating water pressures. They're able to design and manufacture bespoke flap valves for square,
rectangular or elliptical openings or provide additionally reinforced ballast flap valves for when the valve is subject to wave action.
Althon flap valves can be factory fitted to precast concrete headwalls and chambers. For installation on site, Althon supplies their flap valves with an EPDM seal, stainless steel fixings and chemical anchors.
Althon penstock valves are for the control and isolation of water. Penstock sluice gates can be mounted directly to an existing flat surface, or factory fitted to a precast headwall or concrete penstock chamber or fixed in-line with an existing pipe run negating the requirement for a manhole.
Althon has a range of penstock sluice valves designed for manhole chambers and for use alongside Flow Controls. Outside of the standard range of penstock valves, as detailed below, Althon can assist with
• Manufactured in controlled factory conditions and can be made to accommodate multiple pipe openings.
• Pipe invert level and opening can be specified to site specific requirements.
• Fast, easy and safe to install and do not require any on-site formwork or shuttering.
• We supply flap valves, penstocks and other flow control devices factory fitted.
• Headwalls supplied with Kee Klamp® handrails and fixing points cast in at the factory.
• A range of outfall safety grilles and trash screens factory fitted.
• A headwall range that complies with Sewers for Scotland, Sewers for Adoption Guidelines and Severn Trent specification.
• Angled ranges that meets the Environment Agency’s ‘Standard rules SR2015 No 27’
the design and supply of penstocks to suit square openings, non-standard size pipe openings and can supply penstocks to suit operating pressures dictated by site requirements.
Althon penstocks are typically manufactured in HDPE and stainless-steel grade 316L. Althon keeps large stocks of the most common sizes but will be pleased to assist with any bespoke fabrication requirements you may have.
A penstock is essentially a gate valve to control or isolate the flow of water. Penstocks are also used to control water levels to ponds, reservoirs and wetland areas.
Address: MAG Group Building
Vulcan Road South, Norwich, Norfolk NR6 6AF
Tel: 01603 488700
Email: sales@althon.co.uk
Visit: www.althon.co.uk
LinkedIn: Althon Limited
The Railway Industry Association (RIA) is the national, award-winning trade association for UK-based suppliers to the railway industry, with activity in all Nations & Regions of the UK
Established almost 150 years ago, RIA has 350+ member companies from across the supply chain. As the voice of the UK rail supply community, RIA supports the delivery of a bigger and better rail industry, representing the sector as an essential generator of economic growth, jobs and investment, supporting a low carbon form of mass transit for communities across the UK. RIA regularly engages with Ministers and their Shadows and civil servants in the UK and devolved governments. It works closely with all the major rail clients across the country, and collaborates with a range of industry partners to help drive positive change in the sector, on areas such as:
• Smooth, visible and certain pipelines of rail work.
• Major rail projects and significant enhancements.
• Rolling stock manufacturing and refurbishing.
• Decarbonising the railway, including electrification, hydrogen and battery traction, and embodied infrastructure carbon.
• Gaining benefits from retail solutions and data advances, to improve customer experience and railway performance.
• Developing world-class innovation in all rail disciplines.
• Skills, including equality, diversity and inclusion.
• Supporting SMEs.
RIA offers its members a whole host of benefits, helping them to navigate and succeed in the rail industry. These benefits include:
• Representing members’ interests to Government and other political decisionmakers an influencers, major clients, regulators, and other bodies.
• Offering a forum for dialogue between members.
• Keeping members up to date with industry news and information.
• Providing a platform for members to showcase their positive news stories or developments.
• Promote exports of members’ products and services.
RIA holds regular events with politicians of all parties for members to join, feed into consultations, and run a range of campaigns on major issues for the industry. RIA hosts client workshops and meetings for members to engage directly with and feed back to clients including Network Rail, HS2, Transport for London (TfL) and East West Rail (EWR).
RIA also hosts visits at member sites with politicians as part of its Rail Fellowship Programme.
RIA runs a substantial events programme, holding over one hundred events every year. Many of these are Member Interest Groups, which cover a wide range of technical and policy-based subjects and in which RIA hears from senior industry figures on industry initiatives/major developments. Members can participate in rail industry committees or groups (eg. the SME Group or Public Affairs & Communications Network) to network with industry colleagues.
RIA holds two flagship conferences each year: the RIA Annual Conference in November and the RIA Innovation Conference in March. And in June it holds the Annual Dinner & RISE (Railway Industry Supplier Excellence) Awards.
RIA assists with the development of technical strategies, standards development, promoting innovation and sustainability,
and helping RIA members with product acceptance and staying up to date with the latest research and legislation. RIA does this at both UK and international levels, particularly promoting the interests of the UK railway supply industry in the European arena. It sends out five weekly mailings, as well as a range of other communications which you can tailor to suit your interests.
RIA’s Members’ News section of the website hosts press releases sent by members, which are then shared on its social media channels.
RIA hosts trade missions and events and has a close relationship with the Department for Business and Trade (DBT), who it often partners with. RIA regularly attends overseas trade shows and hosts pavilions in countries including India and Australia and offers members the opportunity to get involved.
If you are interested in joining RIA, please get in touch via the contact information below.
Tel: 020 7201 0777.
Email: membership@riagb.org.uk
Visit: RIAGB.org.uk
LinkedIn: Railway Industry Association
Twitter: @railindustry
Inspired by Innova�on
26-27 March, ICC Wales
2-day conference with a networking dinner
Inspiring keynotes, panel discussions, TechTalks, student challenges and Future Focus Zone
Large interac�ve exhibi�on with innova�on spotlight sessions presen�ng innova�ve services, products and solu�ons
Scan the QR code to register today or visit
www.riagb.org.uk/RIC2024
Strategic Partners
Pla�num Sponsors
Asbestos Removal Contractors Association (ARCA)
The Association is dedicated to promoting safety and professionalism throughout the licensed asbestos removal industry. As the UK’s leading association representing the interests of asbestos removal contractors and associated businesses ARCA provides guidance, asbestos training and support on all legislative requirements for members and their clients.
www.arca.org.uk
Associated Society of Locomotive Engineers and Firemen (ASLEF)
ASLEF is Britain’s trade union for train drivers. Its 23,500 members are employed in the train operating companies, the freight companies, London Underground and some Light Rapid Transport. The first recorded meeting was held on 7 February 1880.
www.aslef.org.uk
Association for Consultancy & Engineering (ACE)
The Association for Consultancy and Engineering (ACE) is the association for the UK’s professional consultancies and engineering companies operating in the social and economic infrastructure sectors. ACE champions infrastructure to government and other stakeholders, representing the views of around 450 members.
www.acenet.co.uk
Association for European Transport (AET)
The Association for European Transport is a European organisation for transport professionals. It provides networking opportunities to enable the exchange of ideas, information and opportunities among its 300 corporate and individual members, who are based in more than 35 countries.
www.aetransport.org/en-gb
Association for Project Management (APM)
The Association for Project Management (APM) is a professional membership organisation that sets the standards for the project profession and raises its profile. APM is the only chartered organisation representing the project profession in the world. As a registered charity, APM delivers best practice guidance for the project community, helping the profession deliver better.
APM currently has over 40,000 members and more than 400 corporate partners based in over 128 countries across the world.
www.apm.org.uk
Association of Fencing Industries (AFI)
AFI exists to promote safety, quality and professionalism throughout the UK, working to make the fencing industry stronger. We support our members with expert advice, exclusive benefits and encourage inter-member trading and collaboration. The AFI continually works to raise the profile and image of the UK fencing industry.
www.afiorg.uk
Association of Geotechnical and Geoenvironmental Specialists (AGS)
The Association of Geotechnical and Geoenvironmental Specialists (AGS) is a not-for-profit trade association established to improve the profile and quality of geotechnical and geoenvironmental engineering. The membership comprises UK organisations and individuals having a common interest in the business of site investigation, geotechnics, geoenvironmental engineering, engineering geology, geochemistry, hydrogeology, and other related disciplines.
www.ags.org.uk
Association of Railway Training Providers (ARTP)
The ARTP is the trade association for suppliers of training, assessment and development services to the rail
industry and has more than 50-member organisations.
www.artp.co.uk
Association of Technical Lightning & Access Specialists (ATLAS)
ATLAS has been representing the leading players in the lightning protection and specialist access sector since 1946. At the forefront of all industry developments, ATLAS is committed to improving working practices, technical excellence and the skills of the workforce to provide the highest quality service to the industry’s clients.
www.atlas.org.uk
The Association of Transport Coordinating Officers was formed in 1974, joining together senior public transport officers of local government across the UK. ATCO’s members include staff directly concerned with strategic policy development and implementation for securing passenger transport services for a wide range of public authorities.
www.atco.org.uk
The Automatic Door Suppliers Association (ADSA) formed in 1985 to ensure that its member companies offer superior levels of safety for pedestrian automatic doors. The members can advise on every aspect of automatic doors, from the initial selection and specification,through to installation. www.adsa.org.uk
British Drilling Association (BDA)
‘The British Drilling Association (BDA) is a trade association, formed in 1976, to look after the needs of the land drilling and geotechnical sector in its many formats. BDA members come together to raise standards; improve health & safety;
train and educate and promote industry skills, to all those involved in drilling and geotechnics. BDA members are expected to uphold the highest standards and we recommend that anybody that is procuring services or suppliers in this sector, do so from a BDA Member.
www.britishdrillingassociation.co.uk
British Fluid Power Association (BFPA)
Representing and supporting businesses in the hydraulic, pneumatic and motion control industries in the UK. The only voice for the industry in the UK, the BFPA aims to raise standards, share best practice, provide industry insights and promote fluid power as a vital technology in the engineering sector.
www.bfpa.co.uk
British Geophysical Association (BGA)
The British Geophysical Association is a Joint Association of the Geological Society of London and the Royal Astronomical Society. Its aims are to promote the subject of geophysics, and to strengthen the relationship between geophysics and the other natural sciences in the UK. Membership of the BGA is open to Fellows of either of the Parent Societies.
www.geophysics.org.uk
British Geotechnical Association (BGA)
We are the principal association for geotechnical engineers in the United Kingdom. We also perform the role of the Ground Board for the Institution of Civil Engineers, as well as being the UK member of the International Society for Soil Mechanics & Geotechnical Engineering (ISSMGE) and the International Society for Rock Mechanics and Rock Engineering (ISRM).
www.britishgeotech.org
British International Freight Association (BIFA)
The British International Freight Association is the trade association for UK-registered companies engaged in international movement of freight by rail, air, road and sea. It has around 1,500 corporate members who offer a wide range of services within these various modes of transport.
www.bifa.org/home
British Parking Association (BPA)
We are a not-for-profit organisation representing the UK parking and traffic management profession. We work with our 750 plus corporate members and stakeholders to support their communities, improve compliance by those managing and using parking facilities, and encourage fairness to achieve our vision of excellence in parking for all.
www.britishparking.co.uk
British Pest Control Association
BCPA is the leading UK trade association, representing organisations with a professional interest in the eradication and management of public health pests. We’re a not-for-profit organisation acting in the interests of our members and on behalf of the pest management industry in the UK.
www.bpca.org.uk
British Precast
Tracing its roots back to 1918, British Precast is the trade association of precast concrete manufacturers. The main aims of the federation are to promote precast concrete in the construction market and to disseminate information, through a range of industry representation and by shared knowledge, to add value to its member companies.
www.britishprecast.org
British Safety Industry Federation (BSIF)
The trade association for the Personal Protective Equipment (PPE) Regulation and has Primary Authority status with Trading Standards. The BSIF has active links with many government departments and over 130 representative Trade Bodies.The Federation has some 350 members, ranging from manufacturers and distributors of safety products through to test houses, certification bodies and specialist safety service providers.
www.bsif.co.uk
British Security Industry Association (BSIA)
The BSIA is the trade association representing the UK’s private security industry. Its members provide more than 70 per cent of the UK’s security products and services (by turnover) including electronic solutions such as access control and CCTV, as well as security guarding and consultancy services.
www.bsia.co.uk
British Standards Institution (BSI)
BSI is the business standards company that helps organizations all over the world make excellence a habit. For more than a century we have been challenging mediocrity and complacency to help embed excellence into the way people and products work. That means showing businesses how to improve performance, reduce risk and achieve sustainable growth. As a global leader in helping organizations improve, our clients range from high profile brands to small, local companies in 182 countries worldwide.
www.bsigroup.com
British Transport Police (BTP)
British Transport Police is responsible for policing the UK rail network nationally, protecting passengers, rail operators and their staff across the country. It also covers the London Underground, DLR, Midland Metro tram system, Croydon Tramlink, Sunderland Metro, Glasgow Subway and Emirates Airline. www.btp.police.uk
British Transport Police Authority (BTPA)
BTPA is the independent body responsible for ensuring an efficient and effective police force for rail operators, their staff and passengers. Its duties and functions are like those of the Scottish Police Authority or a police and crime commissioner in England and Wales, but it oversees a force that is responsible for policing a much wider area – the railways of Great Britain. www.btpa.police.uk
British Tunnelling Society (BTS)
The BTS is an Associated Society of the Institution of Civil Engineers (ICE). With a current membership of 788 individual members and 90 corporate members, it is one of the most vibrant gatherings of professional tunnellers in the world. www.britishtunnelling.com
Campaign for Better Transport Campaign for Better Transport is a national charity which works to make sustainable transport available to all and encourage its use. Campaign for Better Transport’s vision is for all communities to have access to high quality, sustainable transport that meets their needs, improves quality of life and protects the environment. www.bettertransport.org.uk
Chartered Association of Building Engineers (CABE)
The Chartered Association of Building Engineers (CABE) is a professional body and unifying voice within the construction sector. Bringing together members, who work across the life cycle of the built environment, specialising in a wide range of disciplines, CABE shares knowledge, raises standards and develops professional building engineers. www.cbuilde.com
Chartered Institute of Arbitrators (CIArb)
The Chartered Institute of Arbitrators (CIArb) is an international centre of excellence for the practice and profession of alternative dispute resolution (ADR). CIArb is passionate about promoting a harmonious society and helping people and organisations avoid, manage and resolve conflict through our global network of more than 21,500 members, students included. www.ciarb.org
Chartered Institute of Architectural Technologists (CIAT)
The Chartered Institute of Architectural Technologists is the lead qualifying body for Architectural Technology, representing those working and studying within the discipline. CIAT qualifies Chartered Architectural Technologists, MCIAT.
wwww.architecturaltechnology.com
Chartered Institute of Ecology and Environmental Management (CIEEM)
We are the leading professional membership body representing ecologists and environmental managers in the UK and Ireland. We are passionate about nature and pragmatic about the need to manage it in ways that add value to society. Our Registered Practices deliver the best outcomes for biodiversity, whilst supporting successful development.
www.cieem.net
Chartered Institute of Logistics and Transport (CILT)
The Chartered body for professionals involved in the movement of goods, people and their associated supply chains. Delivering career development, relevant information, essential networking and professional recognition. Promoting pride in your profession.
Delivering your development. Driving professional recognition. Providing essential news, guidance, and information.
Keeping you moving.
www.ciltuk.org.uk
Chartered Institute of Personnel and Development (CIPD)
The CIPD has been championing better work and working lives for over 100 years. It helps organisations thrive by focusing on their people, supporting our economies and societies. It’s the professional body for HR, L&D, OD and all people professionals – experts in people, work and change. With almost 160,000 members globally – and a growing community using its research, insights and learning – it gives trusted advice and offers independent thought leadership. It’s a leading voice in the call for good work that creates value for everyone.
www.cipd.co.uk
Chartered Institute of Procurement & Supply (CIPS)
CIPS is the largest organisation in the world dedicated to the procurement and supply profession and acts as the profession’s voice, supporting individuals and organisations to achieve excellence and providing the Global Standard in Procurement and Supply. It is the awarding body regulated by OFQUAL in England for procurement and supply management qualifications.
www.cips.org
Chartered Institution of Building Services Engineers (CIBSE)
CIBSE is the standard setter and authority on building services engineering. It publishes Guidance and Codes which are internationally recognised as authoritative and sets the criteria for best practice in the profession. The Institution speaks for the profession and so is consulted by government on matters relating to construction, engineering and sustainability. It is represented on major bodies and organisations which govern construction and engineering occupations in the UK, Europe and worldwide.
www.cibse.org
Chartered Institution of Civil Engineering Surveyors (CICES)
The Chartered Institution of Civil Engineering Surveyors (CICES) is an international qualifying body dedicated to the regulation, education and training of surveyors working within civil engineering. It has relevant competencies for geospatial engineers and commercial managers, leading to grades of membership and professional registration as chartered or incorporated engineer.
www.cices.org
Chartered Institution of Railway Operators
Chartered Institution of Railway Operators (CIRO)
CIRO exists for its members and the rail industry, promoting best practice and representing the interests of railway operators at all levels. It delivers membership services, learning opportunities and courses that are tailored specifically to the needs of the industry, many of which lead to internationally recognised qualifications www.ciro.org
Chartered Quality Institute (CQI) The Chartered Quality Institute (CQI) is the professional body for experts in quality management. We support individuals and organisations to improve the performance of their
business through quality management. With 19,000 members located in 130 countries, the CQI is uniquely placed to lead the global quality profession. We encompass the whole quality community, including quality management professionals (CQI members) and management systems auditors, through our International Register of Certificated Auditors (IRCA) members.
www.quality.org
City & Guilds
Since 1878 we have worked with people, organisations, and economies to help them identify and develop the skills they need to thrive. Everything we do is focused on developing and delivering high-quality training, qualifications, assessments, and credentials that lead to jobs and meet the changing needs of industry.
cityandguilds.com/about-us
Civil Engineering Contractors Association (CECA)
Representing civil engineering contractors, CECA builds and maintains the UK’s critical infrastructure networks in transport, energy, water, waste and communications. It has more than 300 members who are estimated to carry out around 70 per cent of all civil engineering activity in the UK. www.ceca.co.uk
Community Rail Network
Community Rail Network is the umbrella body for over 75 community rail partnerships across the UK, as well as more than 1,200 station adoption groups. It supports its members to be effective in benefiting their communities and railways, socially, environmentally and economically.
www.communityrail.org.uk
Community Transport Association (CTA)
The Community Transport Association (CTA) is a national charity that represents and supports providers of community
transport: thousands of local charities and community groups across the UK that all provide transport services that fulfil a social purpose and community benefit.
www.ctauk.org
CPT helps a dynamic bus and coach industry to provide better journeys for all, creating greener communities and delivering economic growth. They do this by representing around 900 members from across the industry be they large or small, bus or coach, operator or supplier.
www.cpt-uk.org
CIRAS is a confidential incident reporting and analysis service that delivers assurance for member organisations across the UK. It is a totally independent service governed by the ‘CIRAS Committee’, comprising representatives from the UK rail industry, TfL, UK Light Rail, Trams and other UK transport modes.
www.ciras.org.uk
CIRIA is a neutral, independent, notfor-profit body that links organisations with common interests and facilitates a range of collaborative activities that help improve the industry.
www.ciria.org
The Construction Industry Training Board (CITB) supports the skills needs of British construction – in England, Scotland and Wales. It attracts talent to the construction sector, so employers have an adequate recruitment pool, and encourages employers of all sizes to access the skills training necessary to grow their businesses.
www.citb.co.uk
Construction Plant-hire Association (CPA)
The Construction Plant-hire Association (CPA) is the leading trade association for the plant hire industry in the UK and CPA Members supply 85% of hired plant to the construction industry. Established for 75 years, the CPA has over 1,600 members, with premises in the City of London, and a permanent staff of experienced employees. The Association is governed by a Council of Members, who represent of plant-hire companies of all types and sizes throughout the country.
www.cpa.uk.net
Construction Products Association (CPA)
The Construction Products Association represents the UK’s manufacturers and distributors of construction products and materials. The sector directly provides jobs for 373,000 people across 23,884 companies and has an annual turnover of £61.2 billion.The Construction Products Association is the leading voice to promote and campaign for this vital UK industry.
www.constructionproducts.org.uk
Contract Flooring Association (CFA)
Members of the Association include Flooring Contractors, Manufacturers, Distributors and Consultants – large and small, operating from locations throughout the UK. Members work across a wide range of flooring finishes including carpets, underlays, vinyl, rubber, timber, adhesives and flooring accessories.
www.cfa.org.uk
Cycling UK
Since 1878 Cycling UK has worked for safer streets, opened up new traffic-free routes and inspired more people with the confidence to get on their bikes. We promote all forms of cycling to inspire people of all ages, backgrounds and abilities to ride. We support our members
and defend UK cyclists’ rights for safer roads, better infrastructure and legal protection.
www.cyclinguk.org
The Delay Attribution Board is an industry body established under the Network Code to ‘Lead, Monitor and Advise’ the Rail Industry on the attribution of train delays. The Board comprises representatives from Network Rail and Train Operators, with an independent Chair, providing knowledge and experience from across the industry.
www.networkrail.co.uk/dab
The government department, which is run by the Secretary of State for Transport, is responsible for the English transport network and a limited number of matters in Scotland, Wales and Northern Ireland. Among the DfT’s aims are to sustain economic growth, improve productivity through reliable and efficient transport networks and to enhance access for all to jobs, services, and social networks.
www.dft.gov.uk
The DSA’s mission is to promote the work of professional drilling and sawing contractors by highlighting the main advantages of cutting concrete with diamond tools, which include precision cutting within the shortest time scale, reduced noise, dust and debris and maintenance of structural integrity.
www.drillandsaw.org.uk
The regulatory body for the UK engineering profession, it holds the national Register of 230,000 Engineering Technicians (EngTech), Incorporated Engineers (IEng), Chartered Engineers (CEng) and Information and Communications Technology Technicians (ICTTech). The Council also sets and maintains the internationally recognised standards of professional competence
and ethics that govern the award and retention of these titles.
www.engc.org.uk
The EIA has more than 70 years’ experience in promoting trade and representing the interests and aspirations of the UK engineering manufacturing sector, particularly SME’s. It’s an accredited trade organisation for Department of International Trade, assisting UK SME’s in their participation at overseas engineering trade shows.
www.eia.co.uk
EPTO is the trade association of the European Passenger Transport Operators, whose members are the six largest private public transport companies in Eu rope. Established in 2006, EPTO promotes the development of a competitive market structure for the supply of public transport services. EPTO has worked closely with the European Commission in the development of transport policy particularly in the field of opening of the passenger transport market and competition law and membership is available to qualifying operators.
www.epto.net
Excellence Achievement Learning (EAL)
EAL is the specialist skills partner, awarding organisation, and EPAO for industry. We develop rail qualifications and deliver EPA informed by expertise and experience. Our rail portfolio spans all engineering disciplines; from track, traction and rolling stock, to signalling, telecoms, electrification, and overhead line. Contact us for a responsive skills solution service.
www.eal.org.uk
The Federation of Master Builders is the largest trade association in the UK construction industry, representing thousands of firms in England, Scotland, Wales and Northern Ireland. Established in 1941 to protect the interests of small and medium-sized (SME) construction firms, the FMB is independent and nonprofit making, lobbying for members’ interests at both the national and local level.
www.fmb.org.uk
The FPS is the industry body for foundation contractors. Members undertake piling and geotechnical works on construction projects. All FPS members are independently and regularly audited to ensure they represent the best quality in the industry. The standards expected are rigorous and encompass technical ability, quality management, sustainability, safety and training.
www.fps.org.uk
FTMRC are the largest Federation for traditional metal roof detailing and installation, demanding higher craft skills and knowledge. As well as the heritage sector, there is increasing demand for the knowledge and skills of FTMRC members, with modern architectural design fashion attracted by the wide variety of colours and finishes available, especially in the zinc product range.
www.ftmrc.co.uk
Fire Industry Association (FIA)
The FIA is the largest fire protection trade association in the UK with 1000 members. We are a not-for-profit organisation and a major provider of fire safety training. Our objective is to promote, improve and perfect fire protection methods, devices, services and apparatus. We achieve this through the representation of our members, providing technical support, guidance and opportunities for professional advancement through education and appropriate regulation.
www.fia.uk.com
Galvanizers Association (GA)
Galvanizers Association is the representational body for the hot dip galvanizing industry in the UK and the Republic of Ireland. Galvanizers Association (GA) has provided authoritative information and advice on hot dip galvanizing to users and potential users since it was first established in 1949.
www.galvanizing.org.uk
Greengauge 21
Greengauge 21 aims to promote a network approach to Britain‘s railways, through extending the reach of highspeed services (to Scotland, North Wales and across England) and showing how the existing network can best be freed up to improve local and regional services. It also carries out research to support the case for investment in rail in rural areas and improving freight and logistics services and links to ports and airports.
www.greengauge21.net
Ground Source Heat Pump Association (GSHPA)
The Ground Source Heat Pump Association (GSHPA) was formed in June 2006 to serve as the focal point for organisations with business interests in Ground Source Energy. The GSHPA encourages the growth and development of the ground source heat pump industry. www.gshp.org.uk
Guild of Master Craftsmen (GMC)
The Guild of Master Craftsmen is the UK’s most established membership association, representing trade and craftspeople recognised for their skill, integrity and expertise. See how we can support you at www.guildmc.com or to find a craftsperson in your area go to: www.findacraftsman.com
Health and Safety Executive (HSE)
We’re Britain‘s national regulator for workplace health and safety, preventing work-related death, injury and ill health. Our activities are supported by globally recognised scientific expertise. HSE does not endorse commercial products or companies including the Rail Professional reference book or other products or companies within this publication.
www.hse.gov.uk
Hire Association Europe (HAE)
SafeHire is a Private Standard developed by Hire Association Europe and Event Hire Association (HAE EHA) with the assistance of the Health & Safety Executive (HSE) and the Prefabricated Access Supplie rs’ and Manufacturers’ Association (PASMA). All HAE EHA members have to be SafeHire Certified to demonstrate competence and compliance in all the key areas of business activity, particularly H&S legislation.
www.hae.org.uk
INCOSE UK Ltd
Help to Grow:
Management Programme
Join 30,000+ senior leaders of small and medium sized business to boost business performance resilience and long-term growth. This 12-week 90% government funded programme has been designed to be completed alongside fulltime work. Learn through online and face-to-face sessions, alongside peer support and mentoring. Find out more about our programme here:
www.derby.ac.uk/HTG
Heritage Railway Association
The HRA is the UK’s trade association for heritage and minor railways, heritage tramways, cliff railways, and related museums and organisations. We represent our 300 members to national and regional government; provide business support, guidance and technical advice; and we help promote heritage rail which attracts 13million visitors each year.
www.heritagerailways.com
INCOSE UK is a Professional Engineering Institution licensed by the Engineering Council. INCOSE UK acts as the UK Chapter of the International Council on Systems Engineering (INCOSE), a not-forprofit membership organisation founded to develop and disseminate the interdisciplinary principles and practices that enable the realisation of successful systems.
INCOSE UK Offers members: professional development pathways, contact with local, working and interest groups, INCOSE UK Publications and networking events such as the Annual Systems Engineering Conference.
www.incoseonline.org
Industrial Rope Access Trade Association (IRATA)
The rope access technique developed by IRATA is used in a wide range of repair, maintenance, inspection and access work. Rope access methodology boasts an unrivalled safety record, short set-up and dismantling time, positive environmental benefits and removes the need for invasive access equipment or disruption to a worksite.
www.irata.org
Institute of Acoustics (IOA)
The Institute of Acoustics is the UK’s professional body for those working in
acoustics, noise and vibration. It was formed in 1974 from the amalgamation of the Acoustics Group of the Institute of Physics and the British Acoustical Society (a daughter society of the Institution of Mechanical Engineers). The Institute of Acoustics is a nominated body of the Engineering Council, offering registration at Chartered and Incorporated Engineer levels.
www.ioa.org.uk
The Institute of Asset Management (the IAM) is the international professional body for people and organisations involved in the acquisition, operation and care of physical assets. The IAM is dedicated to furthering knowledge and understanding of asset management.
www.theIAM.org
Institute of Cast Metals Engineers (ICME)
Our members include foundry workers, design engineers, metallurgists, moulders, patternmakers, CAD technicians, methods engineers, researchers, students and suppliers to the industry. The aim of the institute is to bring together people from all sectors and levels, to offer help and advice, technical support and professional development opportunities, helping our members make the most of their careers in the castings industry.
www.icme.org.uk
Open Door to all construction sectors, learn more about the Institute of Construction Management, your invite –contact the membership department for an ICM Information Pack. We will provide you with information about an Institute that cares about you, your profession, your employer and your customers in competent safety! National CDM Competence Registry™® launched 2018 –CDM4BIM Gateway™ launched 2019.
www.the-icm.co.uk
Institute of Corporate Responsibility and Sustainability (ICRS)
The UK’s professional body for corporate responsibility and sustainability. We help Individual members develop their careers by setting professional standards, qualifying their experience, recognising their achievements and supporting them through CPD. We help Organisational members by enabling them to demonstrate their organisation’s commitment to responsible and sustainable business, share best practice and build their CR and sustainability capacity through dedicated member events.
www.icrs.info
Institute of Corrosion (Icorr)
The institute is a learned body, offering training and certification in various corrosion mitigation disciplines. In addition to regional branches, it has two technical divisions: Corrosion Science and Corrosion Engineering, which provide an informal forum for the exchange of ideas and information relating to corrosion engineering issues.
www.icorr.org
Institute of Customer Service
The Institute of Customer Service is the professional body for customer service delivering tangible benefit to organisations and individuals so that our customers can improve their customers’ experience and their own business performance. The Institute is a membership body with a community of over 400 organisational members – from the private, public and third sectors –and many individual memberships.
www.instituteofcustomerservice.com
Institute of Directors (IoD)
The IoD represents, supports, and develops directors. With branches across the UK, membership provides access to information and professional advice, networking, and flexible working spaces, alongside influence on issues from tax to infrastructure. The Institute, a Royal Charter body since 1906, offers in-company training and professional
development for individual directors, with the Chartered Director programme at its pinnacle.
www.iod.com
Institute of Environmental Management and Assessment (IEMA)
IEMA is the professional body for everyone working in environment and sustainability. We provide resources, tools and knowledge sharing along with high-quality formal training to meet the needs of our members. We believe that together we’re positively changing attitudes to sustainability as a progressive force for good. Together we’re transforming the world to sustainability.
www.iema.net
Institute of Materials Finishing (IMF)
To provide a focus for Surface Engineering and Finishing activities worldwide through the fulfilment of the technical, educational and professional needs at all levels for both the individuals and companies involved in the coatings industry.
www.materialsfinishing.org
Institute of Materials, Minerals and Mining (IOM3)
IOM3 is a major UK engineering institution whose activities encompasses the whole materials cycle, from exploration and extraction, through characterisation, processing, forming, finishing and application, to product recycling and land reuse. It exists to promote and develop all aspects of materials science and engineering, geology, mining and associated technologies, mineral and petroleum engineering and extraction metallurgy, as a leading authority in the worldwide materials and mining community.
www.iom3.org
Institute of Rail Welding (IoRW)
Set up in 2002 by TWI (The Welding Institute) and Network Rail in the aftermath of the Hatfield disaster.
The IoRW is a focal point for good rail welding practice, development and competence and aims to raise awareness of rail welding throughout the industry.
www.iorw.org
Institute of Risk Management (IRM)
IRM is the leading professional body for risk management. We are an independent, not-for-profit organisation that champions excellence in managing risk to improve organisational performance. We do this by providing internationally recognised qualifications and training, publishing research and guidance and raising professional standards across the world. Our members work in all industries, in all risk disciplines and across the public, private and not-for-profit sectors. We’ve recently launched our new Certificate in Supply Chain Risk Management.
www.theirm.org
Institute of Spring Technology (IST)
IST are at the forefront of the spring making industry developing Spring Calculator Professional (SCP) the leading, go-to, spring validation software. Used to design, test and adapt springs under real world constraint s. We also provide ISO 17025 accredited testing, technical training, failure analyses and consultancy; giving impartial and informative advice to the world‘s spring making industry.
www.ist.org.uk
Institute of Transport Administration (IoTA)
The IoTA is a membership organisation dedicated to promoting professionalism in transport. Founded in 1944, it creates up-to-date training and best practice schemes to facilitate the educational needs of transport manager and/or operators.
www.iota.org.uk
The Institute of Workplace and Facilities Management (IWFM)
The Institute of Workplace and Facilities Management (IWFM) is the body for workplace and facilities professionals. We exist to promote excellence among a worldwide membership community of around 14,000 and to demonstrate the value and contribution of workplace and facilities management more widely. www.iwfm.org.uk/
Institution of Civil Engineers (ICE)
A global professional engineering institution that promotes and advances civil engineering. Established in 1818, ICE has more than 90,000 members, around a third of whom are based overseas. ICE qualifies civil engineering professionals, helps them exchange knowledge and best practice, and promotes their important contribution to society. www.ice.org.uk
Institution of Engineering and Technology (IET)
The Institution of Engineering and Technology (IET) is one of the world’s largest engineering institutions with over 168,000 members in 150 countries. It is also the most interdisciplinary – to reflect the increasingly diverse nature of engineering in the 21st century.
www.theiet.org
Institution of Engineering Designers (IED)
Founded in 1945, Chartered in 2012, the IED is the premier membership body representing engineering and product designers. We aim to support and inspire our members to achieve their career goals and professional aspirations. www.ied.org.uk
Institution of Environmental Sciences (IES)
The IES represents professionals from fields as diverse as air quality, land contamination and education – wherever you find environmental work underpinned by science. We utilise our network of professionals, educational institutions, researchers, and policymakers to stand up for science, scientists and for the natural world.
www.the-ies.org
Institution of Fire Engineers (IFE)
The IFE is a global professional membership body for those in the fire sector that seek to increase their knowledge, professional recognition and understanding of fire through a global discourse. With over 100 years of history, the IFE is instrumental in shaping a future world that is safer from fire. The IFE offers internationally recognised membership grades and fire-related qualifications and delivers more than 6,000 exams annually.
www.ife.org.uk
Institution of Mechanical Engineers (IMechE)
Established in 1847, the Institution has some of the world‘s greatest engineers in its history books. It is one of the fastest growing professional engineering institutions with operations around the world and more than 120,000 members working at the heart of the most dynamic industries.
www.imeche.org
Institution of Occupational Safety and Health (IOSH)
The Institution of Occupational Safety and Health is the Chartered body for health and safety professionals. With more than 50,000 members in over 130 countries, it’s the world‘s biggest professional health and safety organisation. IOSH sets standards, and supports, develops and connects its members with resources, guidance,
events and training. It’s the voice of the profession, campaigning on issues that affect millions of working people.
www.iosh.com
Institution of Railway Signal Engineers (IRSE)
Protecting the safety of all those who travel and work on railway systems worldwide. The IRSE is the professional institution for all those engaged in or associated with railway signalling and telecommunications, train control, traffic management and allied professions.
www.irse.org
Institution of Structural Engineers (IStructE)
IStructE is the world‘s largest membership organisation dedicated to structural engineering. The Institution leads and supports the development of structural engineering worldwide, in order to secure a safe and resilient built environment for all.
www.istructe.org
Intelligent Transport Systems UK (ITS UK)
ITS UK is the voice of the transport technology industry, with 150+ members from the public and private sector. It provides a national platform to support the roll out of technology for a cleaner, safer and more effective transport network, both at home and abroad.
www.its-uk.org.
International Air Rail Organisation (IARO)
The IARO is a worldwide organisation dedicated to spreading best practice and workable ideas for rail links to airports. The organisation enables the exchange of experience, ideas and information through access to its databases, workshops, seminars and via fellow members.
www.iaro.com
International Geosynthetic Society (IGS UK)
The aims of the IGS UK chapter are to collect and distribute knowledge about geosynthetics & their applications by facilitating conferences, symposiums, evening presentations & research in order to promote the advancement of the state of the art of geosynthetics & to improve the communication and understanding of geosynthetic products between designers, manufacturers and users of the products.
www.igs-uk.org
International Glassfibre Reinforced Concrete Association (GRCA)
GRC is a material that has been widely used within the railway industry, ranging from permanent formwork for bridges through to decorative cladding on stations and buildings. Many GRCA members have knowledge and experience of working within the rail sector and we would recommend contacting them using our members contact information which is available via our website.
www.grca.online
International Institute of Obsolescence Management (IIOM)
IIOM is the world’s largest not-forprofit professional body specialising in obsolescence management with chapters in five countries. Members include system and equipment manufacturers, asset owners and obsolescence solution providers. Individual members can attain internationally recognised professional development qualifications. With regular in-person meetings and webinars, members can share best practice and keep up to date with relevant legislation.
www.iiom.global
International Institute of Risk and Safety Management (IIRSM)
IIRSM is the professional home for everyone involved in managing risk. Our members work across all sectors of industry, worldwide and they lead the
way in managing risks to benefit people, society, government and business. We welcome individual and corporate members from all sectors of industry, including :construction; oil and gas; engineering; public sector; facilities; hospitality and healthcare, and more.
www.iirsm.org
International Transport Workers’ Federation (ITF)
The International Transport Workers’ Federation (ITF) is a democratic global union federation of nearly 700 transport workers trade unions representing around 20 million workers in 150 countries. The ITF works to improve the lives of transport workers globally, encouraging and organising international solidarity among its network of affiliates. The ITF represents the interests of transport workers’ unions in bodies that take decisions affecting jobs, employment conditions and safety in the transport industry.
www.itfglobal.org
Landscape Institute (LI)
The Landscape Institute (LI) is the chartered body for the landscape profession. It is an educational charity that promotes the art and science of landscape practice. The Li’s aim, through the work of its members is to protect, conserve and enhance the natural and built environment for the public benefit. The LI provides a professional home for all landscape practitioners including landscape scientists, landscape planners, landscape architects, landscape managers and urban designers.
www.landscapeinstitute.org
Lead Contractors Association (LCA)
The Lead Contractors Association was formed in 1984 to promote and protect quality standards in working with lead sheet. The LCA consists of specialist installer members and Industry associate members. All members are vetted, and their work graded on a regular basis. Only LCA members can provide a 25year guarantee of their work.
www.leadcontractors.co.uk
Lead Sheet Training Academy (LSTA)
The Lead Sheet Training Academy is at the forefront of training for those using lead or hard metals in the construction industry. LSTA operates from a modern purpose built training facility in Kent that includes full scale training rigs and a wellequipped environment in which to learn, re-creating real-life situations.
www.leadsheet.co.uk
Lifting Equipment Engineers Association (LEEA)
With origins dating back to 1943, the LEEA represents all those involved in the lifting industry worldwide. Some of the key areas that it operates in include training services, industry representation, technical support, health and safety and marketing.
www.leeaint.com
Light Rail Transit Association (LRTA)
Free of any trade or political affiliation, the UK-based not for profit is among the world’s leading organisations concerned with bringing better public transport –through light rail, tramway – to towns and cities worldwide.
www.lrta.org
Locomotive & Carriage Institution (L&CI)
The Institution was founded in 1911 and was then known as the Institution of Locomotive Inspectors and Foreman. Our present title was adopted in 1931. Since then we have continued to provide a knowledge of and interest in all aspects of the railway industry. Whilst based in Britain, we also have members in Czech Republic, Austria, Germany and Switzerland.
www.lococarriage.org.uk
Logistics UK
Logistics UK (formerly FTA) is the voice of the UK logistics industry, representing
the transport interests of companies that move goods by road, rail, sea and air. The Organisation delivers safe, sustainable and efficient logistics, raises awareness of the industry, informs its members about the latest compliance requirements and provides training schemes to improve the skills and knowledge of drivers and industry managers.
www.logistics.org.uk
The Mineral Products Association (MPA) is the trade association for the aggregates, asphalt, cement, concrete, dimension stone, lime, mortar and silica sand industries. It has a growing membership of 530 companies and is the sectoral voice for mineral products. MPA membership is made up of most independent SME quarrying companies throughout the UK, as well as the 9 major international and global companies.
www.mineralproducts.org
National Access & Scaffolding Confederation (NASC)
Founded in 1945 the NASC membership now accounts for a significant share of the UK’s total industry workload and is increasingly making its mark in Europe. Our members operate from locations throughout the UK.
www.nasc.org.uk
National Federation of Builders (NFB)
The National Federation of Builders (NFB) represents sole traders to large, billion pound construction companies and house builders across England and Wales, with turnover ranging from below £500,000 to £1.1 billion. As one of the UK’s longest standing trade bodies, it was created to represent the building profession and to promote conditions its members need to thrive and contribute to the economic success of the UK. www.builders.org.uk
National Federation of Demolition Contractors (NFDC)
NFDC is the longest-established trade body representing the UK demolition industry, having championed industry standards and promoted the value of using accredited demolition contractors for over 80 years. We are proud that many local authorities and developers choose NFDC members to conduct demolition works nationwide. A full list of audited and accredited demolition contractors can be found via a searchable database on our website. www.demolition-nfdc.com
National Federation of Roofing Contractors (NFRC)
The National Federation of Roofing Contractors Limited (NFRC) is the UK’s largest roofing trade association. With a history spanning 130 years, NFRC has established itself as the voice of the roofing industry, constantly adapting to change and innovation to ensure its members are at the fore front. www.nfrc.co.uk
National Railway Museum
Home to iconic locomotives and an unrivalled collection of engineering brilliance, we celebrate the past, present and future of innovation on the railways. Dedicated to igniting our visitors’ curiosity about the people, places and engineering marvels behind the railways, we put our passion for amazing stories into everything we do. www.railwaymuseum.org.uk
National Skills Academy for Rail (NSAR)
The National Skills Academy for Rail is an organisation established to enable the sector to deliver a modern and efficient, world class railway through the development of a highly skilled and productive workforce. www.nsar.co.uk
National Transport Trust
The Trust is the only British charity established to promote and encourage the preservation and restoration of the UK’s transport heritage, including rail, road and air. Founded in 1965, it provides advice and assistance, organises public events and works to secure suitable accommodation and maintenance facilities for historic items.
www.transporttrust.com
National Union of Rail, Maritime and Transport Workers (RMT)
Formed after a merger of the National Union of Railwaymen and the National Union of Seamen, The RMT is a British trade union for workers from almost every sector of the transport industry. Protecting its members’ pay and conditions, it currently represents more than 80,000 people. www.rmt.org.uk
Near Surface Geophysics Group (NSGG)
NSGG aims to advance, encourage and support the study and practice of near-surface geophysics, predominantly restricted to depths of investigation down to 500m. Areas of application include hydrogeology, engineering, archaeology, forensic science, environmental investigations and monitoring, mineral exploration, hazard assessment and geological mapping. www.nsgg.org.uk
Network Certification Body (NCB)
Network Certification Body (NCB) provides a system-wide approach to railway assurance and certification on infrastructure, vehicle and freight projects, both UK and worldwide. Our knowledge of the processes and our connections throughout the railway industry give us the unparalleled ability to provide solutions that work for you. www.net-cert.co.uk
Office of Rail and Road (ORR)
The Office of Rail and Road (ORR) is responsible for protecting the interests of rail and road users. ORR’s railway health, safety, economic and road functions overall are driven by UK legislation. ORR is accountable to Parliament and the public to protect the people who use, interact or work on the railway; ensure fair access to a rail network; ensure National Highways delivers its major programme of investment and other performance commitments; and protect the interests of future users by working with the industry and funders as they develop the network of tomorrow.
www.orr.gov.uk
Painting and Decorating Association (PDA)
The UK’s largest trade and employers’ Association for painters and decorators in the industry. The Painting & Decorating Association has members across the length and breadth of the country and has been committed to encouraging best practice since1894.
www.paintingdecoratingassociation.
co.uk
Perimeter Security Suppliers Association (PSSA)
The Perimeter Security Suppliers Association (PSSA) is the trade association for companies manufacturing, installing or supplying independently tested and rated high security perimeter protection products. PSSA members undergo strict vetting and criteria checks ensuring that accepted industry requirements are met to give end users confidence in the product received. www.pssasecurity.org
Permanent Way Institution (PWI)
The Permanent Way Institution is a modern professional technical engineering institution for rail engineers. Its main objectives are to collect and share technical knowledge and best practice from and within the rail industry; contribute to the raising of standards
through professional registration and increase the competency of rail engineers at all levels through its services. Individual & corporate membership available.
www.thepwi.org
Pipe Jacking Association (PJA)
Dedicated to best practice for the cost effective and environmentally sensitive installation of utility services underground. The PJA provides: Detailed design advisory publications based on industry best practice. Case studies covering a range of applications and typical carbon savings. CPD lectures for clients and design teams. Presentations and animations to explain the technology. Research at leading universities and student teaching resources. Carbon calculator demonstrating carbon savings of nondisruptive methods.
www.pipejacking.org
Rail Delivery Group (RDG)
The Rail Delivery Group brings together Britain’s rail companies to deliver a better railway. All passenger and freight rail companies are members of the RDG, as well as Network Rail and HS2. RDG provides services and support to our members enabling them to transform and deliver a successful railway, benefiting customers, taxpayers and the economy.
www.raildeliverygroup.com
Rail Forum
The Rail Forum is a national industry body with 380+ members. The Rail Forum actively supports the national rail agenda and strategy, encouraging collaboration, promoting members’ capabilities, leading a number of skills initiatives and supporting innovation, safety and export priorities. The Rail Forum is owned and governed by its members with a Board drawn from member companies.
www.railforum.uk
Rail Freight Group (RFG)
The leading representative body for rail freight in the UK, RFG’s members include ports, terminal operators, equipment suppliers and support services. It campaigns to ensure politicians and key decision makers are well informed, enabling them to make the right decisions for rail freight and UK logistics. www.rfg.org.uk
Rail Industry Contractors Association (RICA)
RICA was established in 1999 to represent the interests of small and medium enterprises in the rail industry. Its focus is on helping member companies grow through active engagement with major customers as well as influencing the direction of the industry on safety and commercial matters.
www.rica.uk.com
Rail Safety and Standards Board (RSSB)
RSSB provides research, analysis, and insight to help the industry work together to deliver a better, safer railway. As a membership based rail industry body, RSSB includes train and freight operating companies, infrastructure managers, contractors, rolling stock leasing companies and suppliers, and our work involves partnerships with academia and other railways across the world .
www.rssb.co.uk
Rail Supply Group (RSG)
The Rail Supply Group (RSG) is the leadership body for the rail supply sector, working in partnership with Rail Delivery Group to set the direction for the industry. We bring Government and the private sector together to champion the rail supply chain, focusing on four areas of work: driving growth; accelerating innovation; doubling exports and improving skills.
www.railsupplygroup.org
Rail Wagon Association Limited (RWA)
A rail industry trade body whose members have a commercial interest in the safe and efficient operation of railway wagons in the UK. It engages with developments and initiatives by participation in industry committees and liaising with government, standard setters, Network Rail and regulatory bodies. RWA is a member of UIP, the European grouping of wagon trade bodies.
www.railwagon.org
Railfuture
Railfuture is the UK’s leading independent organisation campaigning for better rail services for passengers and freight. The voluntary group represents rail users and has around 20,000 affiliated and individual members. Over the past 50 years it has played a major part in getting more than 370 new and reopened stations and more than 500 miles of route to join the network.
www.railfuture.org.uk
Railway Benefit Fund (RBF)
The Railway Benefit Fund is a charity that provides support to current, former and retired railway staff and their dependents across the UK. We’ve been here for railway people since 1858 and today, thanks to the generosity of our supporters, we’re able to offer help to those who need us. From financial grants and confidential advice, to online tools and a legal helpline, we provide a range of services designed to support through life’s unexpected events.
www.railwaybenefitfund.org.uk
Railway Children
Every day vulnerable children and young people end up at UK railway stations with no one else to turn to. We’ve teamed up with the British Transport Police (BTP) to create a safety net – and a safety network – for those children who need our help the most. And we’re here to help them for as long as it takes.
www.railwaychildren.org.uk
Railway Civil Engineers’ Association (RCEA)
The RCEA exists to foster professional development and exchange knowledge and experience between railway engineers. The Association’s main areas of expertise include main line, London Underground and light rail. It works with other engineering disciplines through the Railway Engineering Forum and Young Railway Professionals to develop strategies for the UK network.
www.rcea.org.uk
The Railway Enginemen’s Assurance Society was established in 1865 and its ethos is the same today as it was then: to provide financial security through Savings Plans and to support its members and their families affected by death or injury that permanently prevents them from carrying out their duties.
www.enginemens.co.uk
Railway Heritage Trust
The Trust gives grants towards the restoration and regeneration of historic (listed) buildings and structures on the national network and is often consulted on applications for listed building consent and planning. Since it was founded in 1985, the RHT has awarded more than 1,900 grants worth in excess of £62 million.
www.railwayheritagetrust.co.uk
Railway Housing Association (RHA)
Railway Housing Association owns over 1,500 rented homes in 24 local authority areas in addition, we also manage 73 leasehold properties for older people. We are proud of our heritage and retain our charitable values whilst being committed to the future provision of accessible homes and services to meet housing need.
www.railwayha.co.uk
Railway Industry Association (RIA)
The Railway Industry Association (RIA) is the voice of the UK rail supply community. RIA has 350+ member companies in a sector that contributes £43 billion of economic benefits and employs 710,000 people. RIA members cover products and services and include both multi-national companies and SMEs (60% by number).
www.riagb.org.uk
Railway Industry Supplier Approval Scheme (RISAS)
Railway Industry Supplier Qualification Scheme (RISQS)
The official rail industry scheme for supplier assurance. Buyers of products and services throughout Great Britain’s rail industry including Network Rail, TfL, train and freight operating companies and rolling stock organisations – use RISQS as its supplier qualification service. The scheme helps suppliers sell into the industry by providing an open, fair and transparent way for them to be formally recognised as capable providers of products and services.
www.risqs.org
Railway Mission
Railway Mission provides independent, impartial, confidential short-term pastoral support to all railway staff and members of the public affected by railway operations. Our work complements the welfare services provided by rail employers. Our chaplains also act as chaplains to British Transport Police and support suicide prevention and mental health. Registered charity in England and Wales (1128024) and in Scotland (SC045897). A company limited by guarantee registered in England and Wales (06519565)
www.railwaymission.org
Railway Tie Association (RTA)
Consisting of retired senior managers from the wider rail industry, the society has more than 700 members with meetings on a monthly basis. There are regular talks and discussion on current topics, and updates on news of colleagues, pensions and travel facilities.
www.rros.org.uk
The Royal Academy of Engineering is harnessing the power of engineering to build a sustainable society and an inclusive economy that works for everyone.
www.raeng.org.uk
The Royal Incorporation of Architects in Scotland (RIAS) was founded in 1916 as the professional body for all chartered architects in Scotland and is the foremost architectural institute in the country dealing with architecture and the built environment. The RIAS offer a wide range of services and products for architects, students of architecture, construction industry professionals and all those with an interest in the built environment and the design process.
www.rias.org.uk
Railway Heritage Designation Advisory Board
The Railway Heritage Designation Advisory Board has 12 members, consisting of individuals in the rail industry, archives and records offices, museum world, and heritage railway. It meets three times a year to recommend artefacts and records for designation by the Board of Trustees of the Science Museum.
www.sciencemuseumgroup.org.uk/ about-us/railway-heritage-designationadvisory-board/
RISAS ensures key suppliers can become recognised as best-in-class at delivering the most challenging and high-risk products and services for the GB mainline railway. The scheme currently covers suppliers of critical products and services for the overhaul of rolling stock assets and components in the rail vehicle after-market sector. Work is now underway to transform RISAS including an expanded scope.
www.risas-online.org
The Railway Tie Association is the forum for the interests and needs of all groups that depend on the wood crosstie for their business success. Our mission since 1919: To ensure that the engineered wood crosstie system continues to evolve and improve in order to remain cost-effective and meet the everchanging requirements of track systems around the world.
www.rta.org
The RIBA is a global professional membership body driving excellence in architecture. We serve our members and society in order to deliver better buildings and places, stronger communities and a sustainable environment. Being inclusive, ethical, environmentally aware and collaborative underpins all that we do.
www.architecture.com
We are RICS. Everything we do is designed to effect positive change in the built and natural environments. Through our respected global standards, leading professional progression and our trusted data and insight, we promote and enforce the highest professional standards in the development and management of land, real estate, construction and infrastructure.
www.rics.org
The association campaigns for an efficient, world-class transport system for Scotland; sustainable public transport for rural and urban communities; city streets free from road traffic pollution and congestion; coordinated train, bus and ferry services; and high-speed rail for Scottish Intercity and Anglo-Scottish routes.
www.sapt.org.uk
The Scottish Building Federation was established in 1985 working with its members to bring together ideals, collective needs and collaborative business practices. SBF continues to represent the interests and aspirations of its members throughout Scotland. The membership is made up of hundreds of different types of companies including large, medium-sized and small businesses working within construction and general contracting.
www.scottish-building.co.uk
The SPOA is the only trade association representing all business involved across the Scottish Plant Industry. Founded in 1950, we have, and will always act and advocate for our members in the various challenges the industry faces. We are proud to now have record membership of over 350 member organisations.
www.spoa.org.uk
SOE works to advance Operations Engineering for the benefit of everyone through education, training, study and research. SOE also establishes and maintains standards of competence and conduct for those engaged in Operations Engineering professionally, with an emphasis on enhancing public safety. Through its Professional Sectors of IRTE, IPlantE, Operations, BES and Environmental, SOE directly influences the road transport, plant and engineer surveying sectors, developing best practice and improving compliance across the board.
www.soe.org.uk
Structural Timber Association (STA)
As the UK’s leading organisation representing the structural timber sector and associated supply chain companies, the STA has an objective to drive quality and product innovation through expert technical guidance and research –underpinned by education, training and event programmes.
www.structuraltimber.co.uk
The Survey Association (TSA)
The role of TSA is to promote best practice amongst its members, provide a forum for members for discussion, debate and continuing professional development and, to the wider audience such as engineers and architects, provide guidance on new methods and techniques and a list of suitably qualified and experienced companies.
www.tsa-uk.org.uk
Trades Union Congress (TUC)
The TUC is the voice of Britain at work. We exist to improve working life and promote equality for everyone. The TUC brings together more than 5.5 million working people who belong to our 48-member unions. We support trade unions to grow and thrive, and we stand up for everyone who works for a living. Every day, we campaign for more and better jobs, and a more equal, more prosperous country.
www.tuc.org.uk
Transport Focus
We are the independent transport user watchdog. Our mission is to get the best deal for passengers and road users. With a strong emphasis on evidencebased campaigning and research, we ensure that we know what is happening on the ground. We use our knowledge to influence decisions on behalf of passengers and road users to secure improvements and make a difference.
www.transportfocus.org.uk
Transport for London (TfL)
Transport for London (TfL) is the integrated transport authority responsible for delivering Mayor of London Sadiq Khan’s strategy and commitments on transport. It runs the day-to-day operation of the capital’s public transport network, including London Underground, London Overground, Docklands Light Railway, London Trams, London Buses and the Elizabeth line – London’s newest railway. It also manages London’s main roads and the Santander Cycles bicycle hire scheme.
www.tfl.gov.uk
Transport Benevolent Fund CIO
1923 to 2023: TBF has supported public transport workers during times of need for more than one hundred years. This not-for-profit membership charity offers a wide range of financial, health and welfare benefits should need, hardship, or distress arise. Membership costs just £1.25 a week, covering the member, their live-in partner and dependent children – that’s less than 20p a day! Registered charity in England and Wales no. 1160901, in Scotland SC047016. www.tbf.org.uk
Transport Salaried Staffs’ Association (TSSA)
Founded in 1897, the union for transport and travel employees represents around 30,000 administrative, managerial, professional and technical workers, ranging from engineers and senior managers to booking office staff and call centre workers.
www.tssa.org.uk
UK Rail Research and Innovation Network (UKRRIN)
The UK Rail Research and Innovation Network (UKRRIN) is a powerful collaboration between academia and industry, providing a step change in innovation in the sector and accelerating new technologies and products from research into market applications globally.
www.ukrrin.org.uk
The UKSTT (United Kingdom Society for Trenchless Technology) is a registered charity involved in the development and promotion of Trenchless techniques, sometimes termed No-Dig techniques. We should be of interest to all people involved in the installation of new and renewal or replacement of, pipes, sewers or cables. It should also be of special interest to government bodies, environmentalists, or anyone with concern over street works or traffic congestion.
www.ukstt.org.uk
UK Tram was established to enable key stakeholders in the UK tramway industry to present a single voice in dealing with government and statutory bodies to enable it to develop a coordinated and structured approach to regulation, procurement and standardisation within the industry.
www.uktram.co.uk
UNIFE – the European Rail Supply Industry Association, directly represents European companies responsible for the design, manufacture, maintenance and refurbishment of rail transport systems, subsystems and related equipment. UNIFE’s mission is to foster an environment where its members can provide railway systems to cater for the growing demands of rail transport.
Twitter: @UNIFE
www.unife.org
Unite, the country’s largest union, represents 12,000 members working in the rail industry, mainly in engineering and maintenance roles. The union engages with Network Rail and the railway employers to advance the pay and employment conditions of its members.
www.unitetheunion.org
The United Kingdom Accreditation Service (UKAS) is the sole National Accreditation Body for the UK. Its role is to check that organisations providing conformity assessment services (certification, testing, inspection and calibration) are meeting a required standard of performance. UKAS accreditation demonstrates an organisation’s competence, impartiality and performance capability against internationally recognised standards. For further information please visit www.ukas.com
In order to secure the future of rail, YRP promotes the rail industry as a great place to work, inspires the next generation of railway talent and develops the future leaders of the industry.
www.youngrailpro.com
The Urban Transport Group brings together and promotes the interests of Britain’s largest urban areas on transport. Our full members are Transport for West Midlands, Merseytravel (Liverpool City Region), Nexus (Tyne and Wear), South Yorkshire Mayoral Combined Authority, Transport for Greater Manchester, Transport for London, West Yorkshire Combined Authority. We also have associate members between them our members serve over 24 million people. www.urbantransportgroup.org
Women in Rail is a charity comprising men and women from the UK rail sector, working alongside undertakings and stakeholders in the industry to support the development, promotion and attraction of women in the railway and, more broadly, improve gender balance, equality, diversity and inclusion in the UK rail sector.
www.womeninrail.org
Academic & Research Institutions
Institute of Railway Research
Institute of Railway Research – University of Huddersfield
National College for High Speed Rail
TECHNO CTA Limited
University of Birmingham
Central / Local Government
Department for Infrastructure (Belfast)
Department for Transport (DfT)
Greater Manchester Combined Authority (GMCA)
London TravelWatch
National Infrastructure Commission (NIC)
North East Combined Authority (NECA)
Office of Rail and Road (ORR)
r2p UK Systems Ltd
SOCOTEC UK Ltd
South Yorkshire Passenger Transport
Executive
Transport Focus Transport for Greater Manchester Transport for London (TfL)
Transport for the North Transport for Wales
Transport Scotland
West Midlands Combined Authority
Franchise Owners
Arriva UK
FirstGroup PLC
Go-Ahead Group Plc Keolis (UK) Ltd
MTR Corporation Limited
Serco Group Plc
Stourbridge Shuttle – Pre Metro Operations Ltd
Strathclyde Partnership for Transport (SPT)
Infrastructure Owners Crossrail Ltd
East West Rail
Getlink (formerly Eurotunnel)
High Speed 1 (HS1 Ltd)
High Speed Two (HS2) Ltd
London Continental Railways (LCR)
Midland Metro Alliance
Network Rail
Sensonic
Cable Management / Cable Troughing
Sensonic TTS (Trough-Tec Systems)
Professional Organisation
Asbestos Removal Contractors Association (ARCA)
Associated Society of Locomotive Engineers & Firemen (ASLEF)
Associated Train Crew Union (ATCU)
Association for Consultancy & Engineering (ACE)
Association for Project Management (APM)
Association of Fencing Industries (AFI)
Association of Geotechnical and Geoenvironmental Specialists (AGS)
Association of Railway Training
Providers (ARTP)
Association of Technical Lightning & Access Specialists (ATLAS)
Association of Transport Coordinating Officers (ATCO)
Automatic Door Suppliers Association (ADSA)
British Drilling Association (BDA)
British Fluid Power Association (BFPA)
British Geomembrane Association (BGA)
British Geophysical Association (BGA)
British Geotechnical Association (BGA)
British International Freight Association (BIFA)
British Parking Association (BPA)
British Pest Control Association (BPCA)
British Precast
British Safety Industry Federation (BSIF)
British Security Industry Association (BSIA)
British Standards Institution (BSI)
British Transport Police (BTP)
British Transport Police Authority (BTPA)
British Tunnelling Society (BTS)
Campaign for Better Transport Capel (CS) Ltd
Chartered Association of Building Engineers (CABE)
Chartered Institute of Arbitrators (CIArb)
Chartered Institute of Architectural Technologists (CIAT)
Chartered Institute of Ecology and Environmental Management (CIEEM)
Chartered Institute of Logistics and Transport (CILT)
Chartered Institute of Personnel and Development (CIPD)
Chartered Institute of Procurement & Supply (CIPS)
Chartered Institution of Building Services Engineers (CIBSE)
Chartered Institution of Civil Engineering Surveyors (CICES)
Chartered Institution of Railway Operators (CIRO)
Chartered Quality Institute (CQI)
City & Guilds of London Institute (C&G)
Civil Engineering Contractors Association (CECA)
Community Rail Network Community Transport Association (CTA)
Confederation of Passenger Transport UK (CPT)
Confidential Incident Reporting & Analysis Service (CIRAS)
Construction Industry Research and Information Association (CIRIA)
Construction Industry Training Board (CITB)
Construction Plant-Hire Association (CPA)
Construction Products Association (CPA)
Contract Flooring Association (CFA)
Cycling UK
Delay Attribution Board (DAB)
Department for Transport (DfT)
Drilling and Sawing Association (DSA)
Engineering Council Engineering Group – The
Geological Society Engineering Industries Association (EIA)
European Passenger Transport Operators (EPTO)
European Transport Conference – Training for Transportation Professionals
Excellence Achievement Learning (EAL)
Federation of Master Builders (FMB)
Federation of Piling Specialists (FPS)
Fire Industry Association (FIA)
Freight on Rail
Galvanizers Association (GA)
Greengauge 21
Ground Source Heat Pump Association (GSHPA)
Guild of Master Craftsmen (GMC)
Health and Safety Executive (HSE)
Heritage Railway Association
High Speed Rail Industry Leaders (HSRIL)
Hire Association Europe (HAE)
HKA
Incose UK Ltd
Industrial Rope Access Trade Association (IRATA)
Institute of Acoustics (IOA)
Institute of Asset Management (IAM)
Institute of Cast Metals Engineers (ICME)
Institute of Construction Management (ICM)
Institute of Corporate Responsibility and Sustainability (ICRS)
Institute of Corrosion (ICorr)
Institute of Customer Service
Institute of Directors (IoD)
Institute of Environmental Management and Assessment (IEMA)
Institute of Materials Finishing (IMF)
Institute of Materials, Minerals and Mining (IOM3)
Institute of Rail Welding (IoRW)
Institute of Risk Management (IRM)
Institute of Spring Technology (IST)
Institution of Civil Engineers (ICE)
Institution of Engineering and Technology (IET)
Institution of Engineering Designers (IED)
Institution of Environmental Sciences (IES)
Institution of Fire Engineers (IFE)
Institution of Mechanical Engineers (IMechE)
Institution of Occupational Safety and Health (IOSH)
Institution of Railway Signal Engineers (IRSE)
Institution of Structural Engineers (IStructE)
Intelligent Transport Systems UK (ITS UK)
International Air Rail Organisation (IARO)
International Geosynthetic Society (IGS UK)
International Glassfibre Reinforced Concrete Association (GRCA)
International Institute of Obsolescence (IIOM)
International Institute of Risk and Safety Management (IIRSM)
International Liaison Group of Government Railway Inspectorates (ILGGRI)
International Transport Workers’
Federation (ITF)
Landscape Institute (LI)
Lead Contractors Association (LCA)
Lead Sheet Training Academy (LSTA)
Lifting Equipment Engineers
Association (LEEA)
Light Rail Transit Association (LRTA)
Locomotive & Carriage Institution (L&CI)
Logistics UK
Mineral Products Association (MPA)
National Access & Scaffolding
Confederation (NASC)
National Federation of Builders (NFB)
National Federation of Demolition
Contractors (NFDC)
National Federation of Roofing Contractors (NFRC)
National Railway Museum
National Skills Academy for Rail (NSAR)
National Union of Rail, Maritime and Transport Workers (RMT)
Near Surface Geophysics Group (NSGG)
Network Certification Body (NCB)
Office of Rail and Road (ORR)
Painting and Decorating Association (PDA)
Perimeter Security Suppliers Association (PSSA)
Permanent Way Institution (PWI)
Pipe Jacking Association (PJA)
Rail Alliance
Rail Delivery Group (RDG)
Rail Forum (RF)
Rail Freight Group (RFG)
Rail Industry Contractors Association (RICA)
Rail Plant Association (RPA)
Rail Safety and Standards Board (RSSB)
Rail Supply Group (RSG)
Railfuture
Railway Benefit Fund (RBF)
Railway Children
Railway Civil Engineers Association (RCEA)
Railway Employees & Public Transport Association (REPTA)
Railway Enginemen’s Assurance Society
Railway Heritage Designation
Advisory Board
Railway Heritage Trust
Railway Housing Association (RHA)
Railway Industry Association (RIA)
Railway Industry Supplier Approval Scheme (RISAS)
Railway Industry Supplier Qualification Scheme (RISQS)
Railway Mission
Railway Study Forum (RSF)
Retired Railway Officers’ Society (RROS)
Royal Academy of Engineering (RAEng)
Royal Incorporation of Architects in Scotland (RIAS)
Royal Institute of British Architects (RIBA)
Royal Institution of Chartered
Surveyors (RICS)
Science, Engineering and Manufacturing
Technologies Alliance (SEMTA)
Scottish Association for Public
Transport (SAPT)
Society of Operations Engineers (SOE)
SOCOTEC UK Ltd
Stone Federation
Structural Timber Association (STA)
Survey Association (TSA)
TECHNO CTA Limited
Trades Union Congress (TUC)
Transport Benevolent Fund CIO
Transport Focus
Transport for London (TfL)
Transport Salaried Staffs’
Association (TSSA)
Transport Trust
UK Rail Research and Innovation Network (UKRRIN)
UK Society for Trenchless Technology (UKSTT)
UK Tram
UNIFE
Unite the Union
United Kingdom Accreditation
Service (UKAS)
Urban Transport Group
VVB Group
Women in Rail
Young Rail Professionals (YRP)
Regulatory
British Transport Police (BTP)
British Transport Police Authority (BTPA)
Confidential Incident Reporting & Analysis Service (CIRAS)
JVR Consultancy Ltd
Rail Accident Investigation Branch (RAIB)
Rail Delivery Group (RDG)
Rail Safety and Standards Board (RSSB)
Railway Industry
Scheme (RISAS)
Railway Industry Supplier Qualification
Scheme (RISQS)
SOCOTEC UK Ltd
TECHNO CTA Limited
Leasing / Hire Locomotives
Browns Fasteners Ltd
Direct Rail Services Ltd
Eversholt Rail Limited
Porterbrook Leasing Company Limited
r2p UK Systems Ltd
Leasing / Hire Rolling Stock
Browns Fasteners Ltd
Direct Rail Services Ltd
Eversholt Rail Limited
Porterbrook Leasing Company Limited
r2p UK Systems Ltd
Light Rail, Tram & Metro
Browns Fasteners Ltd
Camel Precast
Cleshar Contract Services Ltd
E-Tech Components UK Ltd
Elite Ground Support Services
GHD
Greenwood Engineering
Infrastructure Training Services Ltd
Leewood Projects Ltd
Parry People Movers Ltd
r2p UK Systems Ltd
Xrail Group
Train Operator (Freight)
Browns Fasteners Ltd
Camel Precast Colas Rail Ltd
DB Cargo (UK) Limited
Direct Rail Services Ltd
Forwardis UK Ltd
Freightliner Group Limited
GB Railfreight
r2p UK Systems Ltd
Rail Operations Group Ltd
Riviera Trains Ltd
SLC Operations
Victa Railfreight Ltd
Train Operator (Passenger)
Alliance Rail Holdings
Blackpool Tramway
Browns Fasteners Ltd
c2c Rail Ltd
Caledonian Sleeper
Camel Precast
Chiltern Railways
CrossCountry
East Midlands Trains
Edinburgh Trams
Elizabeth line
Enterprise
Eurostar International Ltd
Gatwick Express
Glasgow Subway (SPT)
Govia Thameslink Railway (London)
Grand Central Rail
Great Northern Rail
Greater Anglia
Heathrow Express
Hull Trains
KeolisAmey Docklands Ltd
London North Eastern Railway (LNER)
London Overground
London Tramlink
London Underground Ltd (TfL)
Merseyrail
Metrolink
Northern Ireland Railways
Northern Trains Ltd
Nottingham Express Transit
r2p UK Systems Ltd
Scotrail
South Western Railway
Southeastern
Southern
Stagecoach Supertram
Stansted Express
Stourbridge Shuttle – Pre Metro
Operations Ltd
TransPennine Express
Tyne & Wear Metro
Venice Simplon-Orient-Express
Wales and Borders
West Midlands Metro
West Midlands Trains
OPERATION & MANAGEMENT
Accreditation / Compliance / Assessment
Acutest (Head Office)
Adfil
AEGIS
Andrew Reid
Applied Industrial Systems (AIS)
ARC Academy UK Ltd
Arco Professional Safety Services Ltd
Arup (Head Office)
AssessTech
Auditel (U.K.) Limited
Aura Brand Solutions
Book my Course Training Courses
Bridgeway Consulting Limited
C2E Consulting
Capel (CS) Ltd
Darcy Spillcare Manufacture Ltd
Data Acquisition & Testing Services Ltd
DB ESG DGauge Ltd
Ebeni Limited
Electromagnetic Testing Services Ltd
Era Technology
Eurofins
SGS
SMARTbrief – Part of Junction 9 Network Ltd
SOCOTEC UK Limited
T&RS Engineering Ltd
The
Unipart
Warringtonfire
Watson
Acoustic
KP
McNealy
Strategic
ABB
Consult
Tyrolit Ltd
UK Power Networks Services
UKDN Waterflow Ltd
UKRL – UK Rail Leasing Ltd
Unipart Rail
Upshot UK Ltd
VGC Rail Projects
Warringtonfire
XEIAD
Xrail Group
Clearance Services
Grange Archive Services
MAL Explosive Ordnance Disposal Ltd
Orbis Protect
Collaborative Working
AARC Professional Services Limited
ABB Electrification Products
Adfil Aecom
Agility3 Modelling and Simulation
Amey TPT
Andrew Reid
Arup (Head Office)
Aura Brand Solutions
Babcock International
Buckingham Group Contracting Ltd
C2E Consulting
Cadenza Transport Consulting Ltd
Capel (CS) Ltd
Cygnet Projects Ltd
DM Development Coaching Ltd
Elite Ground Support Services
Encompass Engineering
Ensafe Consultants
Everlast Group Ltd
EviFile Limited
Excell Rail Ltd
Fourway Communication Ltd
G-volution Ltd
GES Consulting Ltd
GHD
GIRO
Gleeds
Ground Transportation Systems, Thales UK
Harmonic Limited
Imtech/Dynniq
Institute of Railway Research
J. Murphy & Sons Ltd
Jacobs UK Ltd
JFC Civils UK
Journeycall – Part of the ESP Group
Kiepe Electric UK Ltd
LogiKal Projects
Loram UK Ltd
Lundy Projects
Morson Human Resources Ltd t/a
Morson Talent National Composites Centre
Novus Rail Ltd
Oakes Power Services Ltd
Pipex Ltd
PlasmaTrack Ltd
Project Control Tools
Purcell
Royal Haskoning DHV
Schoenemann Design
Serco Rail Technical Services
Severn Partnership
Siemens
Signature Rail Limited
Skanska Construction UK Ltd
SLC Rail
Stannah Lift Services – Major Projects
Steconfer
Steelway Fensecure Ltd
Strategic Rail Consultants Ltd
TBAT Innovation Limited
TenBroeke Company Limited
The Consultancy Company
TRL
TSP Projects
TVS Supply Chain Solutions Ltd
TXM Consult
Tyrolit Ltd
UK Power Networks Services
Unipart Rail University of Birmingham
Van Elle Rail
VGC Labour Solutions
VGC Personnel
VGC Rail Projects
VisiLean
Warringtonfire
Welding Alloys Group
Xrail Group
Commercial
Schoenemann Design
TBAT
TXM
Ensafe
Real-Time
Technology Services Ltd
TenBroeke Company Limited
The Consultancy Company
The Ecology Consultancy
The OPC
The Rail Estate Consultancy Ltd
The Railway Consultancy Ltd
Thomson Ecology Ltd
Trackmaps
Transport Investigations Ltd
Trelleborg Antivibration Solutions
Trimble UK
TRL
TSP Projects
TVS Supply Chain Solutions Ltd
TXM Consult
Tyrolit Ltd
UK Power Networks Services
UKRL – UK Rail Leasing Ltd
Unipart Rail
Vettica BV
VGC Personnel
Vigier Rail AG
WAGO Limited
Walker Training & Consultancy Ltd
Warringtonfire
Waterman Group
Watson & Watson Health and Safety
Consultants Limited
WCL Rail
Sirenum
SNC-Lavalin (formerly known as Interfleet)
Sqills
Sunbelt Rentals Limited
Triscan Systems Ltd
Trueform
TSG Fleet TVS Supply Chain Solutions Ltd
Tyrolit Ltd
Tyrone Fabrication
UKRL – UK Rail Leasing Ltd
Unipart Rail
Unistrut University of Birmingham
Vettica BV
VisiLean Weston Analytics
WEYTEC
Xanta Limited
Xrail Group
19 Inch Racks, Enclosures & Cabinets
ABB Electrification Products
ABI Electronics Ltd
Andrew Reid
Axiomtek UK Ltd
Bernstein Ltd
Cannon Technologies Group Limited
Captec
Data Acquisition & Testing Services Ltd
FREQUENTIS UK Limited
Fujikura Europe Ltd
Harland Simon Power Solutions
HARTING Ltd
HUBER+SUHNER (UK) Ltd
ICEE Managed Services Ltd
Industrial Communication Products Ltd
Jaltek Systems
Mayteck Ltd
Orbital Fasteners
TVS Supply Chain Solutions Ltd
Tyrone Fabrication
Unipart Rail
DATA Systems / Management
3SL
ABB Electrification Products
Adaptive Modules Ltd
Amaro Group Andrew Reid
Arup (Head Office)
AssessTech
BELDEN
Brand-Rex Ltd
Captec Common Time Ltd
Data Acquisition & Testing Services Ltd
Data Techniques
Dorma Kaba Ltd
Electroustic Ltd
Emico Limited
Esoterix
Eurotech
EviFile Limited
Firstco
FREQUENTIS UK Limited
Fujikura Europe Ltd
Galldris Services Ltd
GHD
GIRO
Ground Transportation Systems, Thales UK
HaRMUK Ltd
Ideagen Ltd
Imtech/Dynniq Jacobs UK Ltd
Jaltek Systems
Journeycall – Part of the ESP Group
JVR Consultancy Ltd
Kadfire
Kiepe Electric UK Ltd
MacRail Systems Ltd
Met Office
Mitsubishi Electric Europe BV
Nexus Alpha Low Power Systems Ltd
Oltec Group
Omnicom Balfour Beatty
Pandrol PD Devices Ltd
Penton UK Ltd
Perpetuum Ltd
Postfield Systems Ltd
PULS UK Ltd
Railweight
Scisys UK Ltd
Sensonic
Serco Rail Technical Services
Smartwater Technology Ltd
Telent Technology Services Ltd
Tracsis PLC
Trimble Rail Solutions
Trolex Ltd
TSG Fleet
TVS Supply Chain Solutions Ltd
UK Power Networks Services
Unipart Rail
Unistrut
University of Birmingham
Zircon Software Ltd
Fare Collection
Axiomtek UK Ltd
Common Time Ltd
GHD
Parkeon Ltd
Scheidt & Bachmann UK Ltd
Transport Investigations Ltd
Vettica BV
Intelligent Transport Systems
Adaptive Modules Ltd
Andrew Reid
Axiomtek UK Ltd
Coeval (Ltd)
Data Acquisition & Testing Services Ltd
Diamond Point International
Encompass Engineering
FREQUENTIS UK Limited
Galldris Services Ltd
GIRO
HARTING Ltd
HORIBA MIRA Ltd
Jaltek Systems
JR Dynamics Ltd
r2p UK Systems Ltd
RUGGED MOBILE Systems Ltd
Sensonic
Signature Rail Limited
University of Birmingham
Vettica BV
IT Hardware / Software / Consultancy
3SL
ABB Electrification Products
Adaptive Modules Ltd
AEGIS
Agility3 Modelling and Simulation
Andrew Reid
Applied Industrial Systems (AIS)
Arup (Head Office)
AssessTech
Azteq Solutions Ltd
BELDEN
CADFEM UK CAE Ltd
Captec
Common Time Ltd
Data Acquisition & Testing Services Ltd
Diamond Point International
Electroustic Ltd
Encompass Engineering
Esoterix
Eurotech
EviFile Limited
Forgetrack Ltd
FREQUENTIS UK Limited
Freshwater
Fujikura Europe Ltd
Galldris Services Ltd
GIRO
HaCon (UK)
Hawkgrove Limited
HUB Auto ID Ltd
Human Reliability
Industrial Communication Products Ltd
Jabero Consulting
Journeycall – Part of the ESP Group
Kadfire
Legion Limited
LogiKal Projects
MacRail Systems Ltd
Met Office
Nexus Alpha Low Power Systems Ltd
Omnicom Balfour Beatty Penton UK Ltd
Primary
Ltd
Ground Transportation Systems, Thales UK
HaCon (UK)
HARTING Ltd
Imtech/Dynniq
Industrial Communication Products Ltd
Infotec Ltd
Jaltek Systems
Kadfire
Kiepe Electric UK Ltd
LPA Connection Systems
LPA Group Plc
Mitsubishi Electric Europe BV Nexus Alpha Low Power Systems Ltd
Nomad Digital (Head Office)
Parkeon Ltd
Penton UK Ltd
Petards
r2p UK Systems Ltd
RUGGED MOBILE Systems Ltd
Schaltbau Transportation UK Ltd
Siemens
Signature Rail Limited
Stadler Rail Management AG
Strategic Rail Consultants Ltd
Telegartner UK Ltd
Telent Technology Services Ltd
Teleque Ltd
Televic GSP
Tracsis PLC Trainfx Ltd
Trolex Ltd
Unipart Rail
Vettica BV
Wabtec Rail Limited
Xrail Group
Radio Communications & Equipment
ABI Electronics Ltd
Alan Dick Communications Ltd
Andrew Reid
Babcock International
BELDEN
Chatterbox Limited
Co-Channel Electronics Ltd
Common Time Ltd
DAC Limited
Data Acquisition & Testing Services Ltd
Data Techniques
DB ESG
dBD Communications
DNH WW Ltd
Electroustic Ltd
Emico Limited
Eyedot (Europe) Ltd – Electronic Repair and Maintenance
Firstco
Fourway Communication Ltd
FREQUENTIS UK Limited
Galldris Services Ltd
Ground Transportation Systems, Thales UK
HUBER+SUHNER (UK) Ltd
Imtech/Dynniq
Industrial Communication Products Ltd
J. Murphy & Sons Ltd
Jaltek Systems
Kiepe Electric UK Ltd
LPA Connection Systems
LPA Group Plc
Marlec Engineering Co Ltd
Ogier Electronics Limited
Orbital Fasteners
OSL Rail Limited
Siemens
Spotcom Ltd
Stadium IGT
Sunbelt Rentals Limited
Swann Group Ltd
Telegartner UK Ltd
Telent Technology Services Ltd
Teleque Ltd
Televic GSP
Trainfx Ltd
TVS Supply Chain Solutions Ltd
Unipart Rail
Upshot UK Ltd
– Electronic Repair and Maintenance
VR Experiences / Training Software
Agility3 Modelling and Simulation
Wireless Data Communications
Eyedot (Europe) Ltd – Electronic Repair and Maintenance
Softil Ltd
Spotcom Ltd
Design Services
ABB Electrification Products
Actavo Building Solutions
Adaptive Modules Ltd
Adfil
Aecom
AJC Trailers Ltd
Amida Ltd
Andrew Reid
Arktis Endurance Textiles Ltd
Arup (Head Office)
Astley Signs
Aura Brand Solutions
Axiomtek UK Ltd
Babcock International
Baqus Group Plc
Belvoir Rail Ltd
Bender UK Ltd
Bespoke by Evans
BPR Architects Ltd
CADFEM UK CAE Ltd
CECL – Global
Craig & Derricott Ltd
Creactive Design
Crouch Waterfall
Cundall Lift & Escalator Consultants
Data Acquisition & Testing Services Ltd
DB ESG
DCA Design International
Design and Analysis Ltd
DGauge Ltd
Dura Composites Ltd
Duvine Limited
enGauged Limited
Ensafe Consultants
Everlast Group Ltd
Firstco
FJD Consulting and Design
Fourway Communication Ltd
Freshwater
Furrer + Frey GB Ltd
GALL ZEIDLER Consultants
Galldris Services Ltd
Gatecare Ltd Solar Powered Gate Systems
GES Consulting Ltd
GHD
Giffen Group Ltd
Global Rail Construction Ltd
GT Engineering (Markyate) Ltd
Human Reliability
iLECSYS Rail Ltd
ISC Best Practice Consultancy
ISVR Consulting – University of
Southampton
J. Murphy & Sons Ltd
Jacobs UK Ltd
Jafco Tools Ltd
Jaltek Systems
James Fisher Testing Services
JFC Civils UK
Kadfire
Kiepe Electric UK Ltd
Legion Limited
Lundy Projects
Magrenko Ltd
Marchantcain Group
Millcroft Group
MLM Consulting Engineers Ltd
Morrison Utility Services Limited
Murphy Geospatial
National Composites Centre
Newgate (Newark) Ltd
Nicoll Russell Studios
Nortek Global HVAC UK Ltd
Novus Rail Ltd
Oakes Power Services Ltd
Oltec Group
OSL Rail Limited
Parry People Movers Ltd
PBH Rail
Pipex Ltd
PlasmaTrack Ltd
Power Jacks
Priestman Goode
Purcell
Relinea – GRP Systems Ltd
Remedy Geotechnics Ltd
Ricardo Rail
Royal Haskoning DHV
RSS Infrastructure Ltd
Sadler Brown Architecture
Schoenemann Design
SLC Rail
Softech Global Ltd
Specialised Tools and Equipment Ltd
Standish Engineering Co Ltd
Stewart Signs Rail
Strategic Rail Consultants Ltd
SubVision Surveys Ltd
Telent Technology Services Ltd
Trelleborg Antivibration Solutions
TSP Projects
TTS (Trough-Tec Systems)
TXM Consult
Tyrone Fabrication
UK Power Networks Services
Unipart Rail
Van Elle Rail
VGC Rail Projects
Waterman Group
Wentworth House Rail Systems Limited
XEIAD
Xrail Group
Design Consultancy
Analysis by Firth
BPR Architects Ltd
Capel (CS) Ltd
Eyedot (Europe) Ltd – Electronic Repair and Maintenance
GES Consulting Ltd
Rapid Ramp
Tangerine
Driver Only Operations
GES Consulting Ltd HARTING Ltd
Loram UK Ltd
r2p UK Systems Ltd
Engineering Consultancy
ABB Electrification Products
ABI Electronics Ltd
ABM Manufacturing
Adfil
Alan Dick Communications Ltd
Allan Webb Ltd
Andrew Reid
Bender UK Ltd
Bridgeway Consulting
ISVR
RSS Infrastructure Ltd RUAS
SAP Ecology and Environmental Ltd
SEP Rail Services
Smart Rail Services Limited
Steconfer
Structural Soils Ltd (Castleford Office)
TCS Geotechnics
TVS Supply Chain Solutions Ltd Tyrolit Ltd
Vigier Rail AG
Anti-icer
Arrow Solutions
Camel Precast
Asbestos Services
ABP Associates Limited
B&B Industrial Dismantling Limited
CF Booth Limited
Ensafe Consultants
Everlast Group Ltd
Galldris Services Ltd
Geo-Environmental Services Ltd
NATAS ASBESTOS Ltd
OTM Learning Rhodar Limited
RSS Infrastructure Ltd
Bird Control
Reactive Group Services
Bulk Sample Analysis
Ensafe Consultants
Galldris Services Ltd
Geo-Environmental Services Ltd
NATAS ASBESTOS Ltd
SEP Rail Services
Carbon Assessment
FJD Consulting and Design
Cost & Carbon reduction
G-volution Ltd
Welfare Hire Nationwide Ltd
Ecological Services
4 Acre Ecology
Coeval (Ltd)
Elite Ground Support Services
GS Ecology
Environment Protection
3M
ACCON UK Limited
Aecom
APPS UK Ltd
Arup (Head Office)
Avondale Environmental Services Ltd
Baker Consultants Ltd
Bridgeway Consulting Limited
Cleshar Contract Services Ltd
Coeval (Ltd)
Darcy Spillcare Manufacture Ltd
Elite Ground Support Services
Ensafe Consultants
RS
RUAS
SAP
SOUNDEX
The
Three Shires
TSP Projects
Vigier
Flood Risk Assessment
Capel (CS)
Geotechnical
Aarsleff
ABG Geosynthetics
ACS Testing
Amida Ltd
Arup (Head Office)
Babcock International
BAM Ritchies CAN
CC Ground Investigations Ltd
Coffey Geotechnics Ltd
Concept Engineering Consultants Ltd
Cygnet Projects Ltd Derbyshire Geotechnical Ltd Dr. Sauer & Partners Elite Ground Support Services
Galldris Services Ltd GenAir UK Ltd
Geo-Environmental Services Ltd
GeoAccess
Geotechnical Engineering Ltd
Henderson Thomas Associates Limited
Ischebeck Titan Ltd
J. Murphy & Sons Ltd
Jacobs UK Ltd
James Fisher Testing Services Keller Ltd
Korec Group
Live Trakway | Barriers | Bridges | Lights
MLM Consulting Engineers Ltd
Neary Rail and Construction
NTS Premier Services
OSL Rail Limited
Plowman Craven Ltd
Prolec Ltd
Quantum Geotechnical Limited
RSK
RUAS
Sensonic
SEP Rail Services
Severn Partnership
SOCOTEC Monitoring UK Ltd
SOCOTEC UK Limited
Soil Engineering Geoservices Limited
Sonic Drilling Ltd
Spectrum Contracting Services Limited
Steconfer
Structural Soils Ltd (Castleford Office)
TCS Geotechnics
Tencate Geosynthetics
Terram & Tubex
The Bionic Eye
Topdrill Ltd
TSP Projects
Upshot UK Ltd
Uretek UK
Van Elle Rail
Verdant Solutions Ltd
ZF UK Laser Limited
Geotechnical Rope Access
Derbyshire Geotechnical Ltd
Noise & Vibration Control 3M
A-Plant Rail
ACCON UK Limited
Arco Professional Safety Services Ltd
Arup (Head Office) British Steel
Cirrus Research
Data Acquisition & Testing Services Ltd
Galldris Services Ltd
GHD
GMT Rubber-Metal-Technic Ltd
Gramm Barrier Systems Ltd
Henderson Thomas Associates Limited
Ischebeck Titan Ltd
ISVR Consulting – University of Southampton
J. Murphy & Sons Ltd
Kleeneze – Koti Ltd
Nord-Lock Group
NRL
UK Ltd
The Consultancy Company
TRL
TVS Supply Chain Solutions Ltd
Tyrolit Ltd
VGC Rail Projects
Vigier Rail AG
White Lion Engineering Ltd
Underwater Inspections / Services
Bridgeway Consulting Limited
Cygnet Projects Ltd
Galldris Services Ltd
GeoAccess
GPS Marine Contractors Ltd
Jacobs UK Ltd
James Fisher Testing Services
Jotun Paints (Europe) Ltd
Jumo Instrument Co Ltd
MLM Consulting Engineers Ltd
Northern Divers
OSL Rail Limited
Upshot UK Ltd
Vivax – Metrotech Ltd
XEIAD
Vegetation Control
AGS One (Anti Graffiti Systems)
Arco Professional Safety Services Ltd
Avondale Environmental Services Ltd
Babcock International
Bodacc Ltd
Bridgeway Consulting Limited
Buck & Hickman
CAN CCS Jeweltone Ltd
Civil Rail Solutions Ltd
Cleshar Contract Services Ltd
Colt Construction Limited
Cygnet Projects Ltd
Elcot Environmental
Encompass Environmental Ltd
Enduramaxx Limited
Epicuro Protective Materials Ltd
Galldris Services Ltd
GeoAccess Ground Control Limited
Infrastructure Training Services Ltd
J. Murphy & Sons Ltd
Jafco Tools Ltd
Keystone Environmental Ltd
Korec Group
Lineside Structure Maintenance Ltd
Liniar Ltd
Martin Castle Ltd
Mitie Pest Control Ltd
MLM Consulting Engineers Ltd
Neary Rail and Construction
NTS Premier Services
OSL Rail Limited
Polypipe Civils & Green Urbanisation
Red Viking Rail Ltd
RSS Infrastructure Ltd
RTG Rail Services Limited
Running Rail Ltd
SEP Rail Services
Spectrum Contracting Services Limited
Steconfer STEGO (UK) Ltd
Stobart Rail
TCS Geotechnics The Bionic Eye
Three Shires Ltd
Trackmaps
Verdant Solutions Ltd
Vital – Head Office
Walker Construction (UK) Ltd
Wrekin Products Ltd
XEIAD
Winterisation
Arrow Solutions
Camel Precast
Elite Ground Support Services
Facility Management
Acutest (Head Office)
Alchemy Metals Ltd
Andrew Reid
Armorgard Security Products
Baldwin Boxall Communications Ltd
CCS Jeweltone Ltd
Cygnet Projects Ltd
Dexeco Ltd (subsidary of Dextra Group plc)
Durham Lifting
Eldapoint Ltd
Ensafe Consultants
Everlast Group Ltd
HBI Haerter AG
Leadec Lista UK Ltd
MENNEKES
Premier Pits
Pulsar Instruments Plc
Recycling Management
Rexel
Snap-on Industrial
Steconfer
TBA Protective Technologies Ltd
The SES Group
Tyrolit Ltd
WEYTEC
Facility Management Equipment
A-Plant Rail
Acutest
SLC Rail
Steconfer
Newgate (Newark) Ltd
NSS Group – Nationwide Specialist Services
Recruitment & Training
AARC Professional Services Limited Adfil AEGIS
Arco Professional Safety Services Ltd
Atom Training Centre
Blueprint Recruitment Ltd
Bridgeway Consulting Limited
C2E Consulting CCL Rail Training Civil Rail Solutions Ltd
Cygnet Projects Ltd
Daniel Owen Ltd
Equipe Group
Excell Rail Ltd
Harvey Thomas
ICEE Managed Services Ltd
INFRA Skills Ltd Intertrain UK Ltd
Intuitive Interm & Executive Search Ltd
Lineside Structure Maintenance Ltd
Maxim Recruitment
MSA Safety – Latchways PLC
National College for Advanced Transport & Infrastructure (NCATI)
OPC Assessment Pendersons Ltd
PM Training and Assessing Ltd
Pulsar Instruments Plc
Relinea – GRP Systems Ltd
RSS Infrastructure Ltd
Samuel Knight International – Rail
Recruitment
Steconfer
Tec Training (GB) Ltd
The SES Group
Trackmaps
TVS Supply Chain Solutions Ltd
TXM Recruit
Tyrolit Ltd
Walker Training & Consultancy Ltd
Assessment
AARC Professional Services Limited
Capel (CS) Ltd
SMARTbrief – Part of Junction 9
Network Ltd
Southside Rail Training Ltd
Education Training
ARC Academy UK Ltd
Atom Training Centre
Babcock International
C2E Consulting
Cleshar Contract Services Ltd
DM Development Coaching Ltd
Equipe Group
Era Technology
Essempy
Freshwater
HPC Asset Services & Hygiene Pro
Clean Ltd
HSS Hire PLC
Infrastructure Training Services Ltd
Multimodal
NATAS ASBESTOS Ltd
NewRail
NTS Premier Services
Pendersons Ltd
Pennant PLC
People 1st
PM
Rail
Seaton
Smartwater
Southside
Tec
Trackmaps
Infrastructure Training Services Ltd Intertrain UK Ltd
J. Murphy & Sons Ltd
Kopta Training
Korec Group
McGinley Support Services (Infrastructure) Ltd
Morson Human Resources Ltd t/a
Morson Talent
MSA Safety – Latchways PLC
Multimodal NATAS ASBESTOS Ltd
National College for Advanced Transport & Infrastructure (NCATI)
Neway Training Solutions Limited
NewRail North Yorkshire Moors Railway
NRL NTS Premier Services
Oltec Group
OPC Assessment
Pendersons Ltd
Pennant PLC
People 1st
PM Training and Assessing Ltd
PPS Rail
Pristine Condition Ltd
ProActive Recruitment Services
PTRC Education and Research Services Ltd.
Pulsar Instruments Plc
Qualitrain
Rail Operations Group Ltd
Real Skills Training Limited
RSK
RSS Infrastructure Ltd
RT Training Solutions Ltd
Schaeffler (UK) Ltd
Seaton Rail Limited
Siemens
Signet Solutions
SKF (UK) Limited
SMARTbrief – Part of Junction 9
Network Ltd
Smartwater Technology Ltd
Southside Rail Training Ltd
Spitfire Steconfer
Tec Training (GB) Ltd
TECHNO CTA Limited
The Consultancy Company
The QSS Group Limited
The SES Group
Trackmaps
Trackwork Ltd
Transport Investigations Ltd
TVS Supply Chain Solutions Ltd
Tyrolit Ltd
Van Elle Rail
Victa Railfreight Ltd
Vivax – Metrotech Ltd
Waterfront Conference Company
Watson & Watson Health and Safety
Consultants Limited
Wilde Analysis Ltd
XEIAD
Inspection Services
ABB Electrification Products
AEGIS
Aura Brand Solutions
Bridgeway Consulting Limited
Clow Group Ltd
Data Acquisition & Testing Services Ltd
Durham Lifting
Ensafe Consultants
Era Technology
EviFile Limited
Fuel Storage Systems Ltd
Fugro
Geismar UK Ltd
GeoAccess
Giffen Group Ltd
HaRMUK Ltd
Inspectahire Instrument Co. Ltd
Intertek NDT & Materials Testing
James Fisher Testing Services
Kiepe Electric UK Ltd
Kilborn Consulting Limited
Manchester Metrology Ltd
Martin Castle Ltd
Millcroft Group
MLM Consulting Engineers Ltd
Murphy Geospatial
NATAS ASBESTOS Ltd
Northern Divers
Novus Rail Ltd
NSS Group – Nationwide Specialist Services
Omnicom Balfour Beatty
Perpetuum Ltd
SGS Correl Rail Limited
SOCOTEC UK Limited
Standish Engineering Co Ltd
Steconfer
Sulzer Electro Mechanical Services UK
T&RS Engineering Ltd
Trackwork Ltd
Trimble Rail Solutions
TXM Consult
Upshot UK Ltd
VGC Rail Projects
Warringtonfire Waterman Group
XEIAD
Xrail Group
Zetica Rail
Training, Leasing & Onsite
Inspection Services
Durham Lifting
Inspectahire Instrument Co. Ltd
Intertek NDT & Materials Testing
Manchester Metrology Ltd
Insurance
JOBSON JAMES RAIL – INSURANCE
SJL Insurance Services
Square Mile Broking Ltd
Insurance & Risk Management
HaRMUK Ltd
JOBSON JAMES RAIL – INSURANCE
Square Mile Broking Ltd
Legal Services
Clifford Chance LLP
Dentons
DWF LLP
Ensafe Consultants
Freeths LLP
HaRMUK Ltd
Kennedys Law LLP
Mariel Irvine Solicitors
Norton Rose Fulbright
Simmons & Simmons
SLC Rail
Southside Rail Training Ltd
Transport Investigations Ltd
Lone Worker Protection
Orbis
Novus Rail Ltd
Orbis Protect
Pandrol
Senceive Limited
Sensonic
Serco Rail Technical Services
Topdrill Ltd
Trimble Rail Solutions
Non Destructive Testing
ACS Testing Ltd
Houghton International Inspectahire Instrument Co. Ltd
Out Of Hours Response Centre
Orbis Protect
Procurement Services
Alan Dick Communications Ltd
Allan Webb Ltd APPS UK Ltd
Auditel (U.K.) Limited
C2E Consulting
Capel (CS) Ltd
Excell Rail Ltd
Eyedot (Europe) Ltd – Electronic Repair
and Maintenance
GALL ZEIDLER Consultants Gardiner & Theobald LLP
GHD HKA
RPS
Engineering Ltd
Wilde Analysis Ltd
Research Testing
AMG Superalloys Ltd
Axis Test Laboratories Ltd
Data Acquisition & Testing Services Ltd
EMC Hire Ltd
Eurofins York
Firstco
G-volution Ltd
Great Central Railway Plc
Henderson Thomas Associates Limited
Institute of Railway Research – University of Huddersfield
JR Dynamics Ltd
Kiepe Electric UK Ltd
National Composites Centre
NewRail
Pipex Ltd
RSK
SLC Rail
Standish Engineering Co Ltd
Telent Technology Services Ltd
TRL
Unipart Rail University of Birmingham
Van Elle Rail
Wilde Analysis Ltd
XEIAD
Safety & Security
AARC Professional Services Limited
AbsTracked Solutions Ltd
ACCON UK Limited
Adfil
Advanced New Technology
AEGIS
Alchemy Metals Ltd
Andrew Reid
Applied Industrial Systems (AIS)
APPS UK Ltd
Arco Professional Safety Services Ltd
Arctic Air Solutions Ltd
Arktis Endurance Textiles Ltd
Armorgard Security Products
Atex Global Ltd
Axiomtek UK Ltd
Baldwin Boxall Communications Ltd
Barkers Fencing
Bernstein Ltd
Bolle Safety
Bradgate Containers
C.Scope International Ltd
Cable Services Group
CAP Productions Limited
Cirrus Research
Complete Cyber
Coretech Solutions Ltd
Creative Composites Ltd
Cygnet Projects Ltd
Delmatic
Duvine Limited
E2S Warning Signals
Elite Precast Concrete Ltd
Encompass Engineering
Encompass Environmental Ltd
Engineered Composites Ltd
ESR Technology
Everlast Group Ltd
EviFile Limited
Express Medicals Ltd
FREQUENTIS UK Limited
Galldris Services Ltd
GES Consulting Ltd
Gramm Barrier Systems Ltd
GRID Innovations
HARTING Ltd
Haywood & Jackson Fabrications Ltd
HBI Haerter AG
Hydram Engineering Limited
ICEE Managed Services Ltd
Indestructible Paint Limited
ISVR Consulting – University of Southampton
JR Dynamics Ltd
JSP Limited
Kee Systems
Key Fasteners
KITE Projects
Kleeneze – Koti Ltd
Leadec Lineside Structure Maintenance Ltd
LKQ Coatings
Martin Castle Ltd
MCL Rail
Medigold Health
MENNEKES
MSA Safety – Latchways PLC
Newgate (Newark) Ltd
Noble MED Solutions Ltd
Oasys Ltd
OPC Assessment
Orbis Protect
Orbital Fasteners
PBWel
Pramac-Generac UK
PRBX (Powerbox) UK
Protec Direct
ProtectHear
PULSAR®
Railway Safety Solutions Ltd
Raptor Supplies Ltd
Relinea – GRP Systems Ltd
Rexel
Rhodar Limited
Safeaid Limited
Sensonic
Serco Rail Technical Services
Sicuro UK – Monitored Security Solutions
Sirenum
Smyth Composites Limited
Star Fasteners (UK) Ltd (Huck Fastener
Distributor)
STAUFF UK Ltd
Steconfer
Teleque Ltd
The SES Group
Torrent Trackside Transport Benevolent Fund CIO
Trelleborg Antivibration Solutions
Trimble
Triptex Limited
TVS Supply Chain Solutions Ltd
Tyrolit Ltd
Warringtonfire
WEYTEC
Accident Investigator / Investigations
Aecom
Dellner Ltd
Galldris Services Ltd
GES Consulting Ltd
HaRMUK Ltd
Human Reliability
JVR Consultancy Ltd
Kilborn Consulting Limited
MLM Consulting
Ltd
Schaltbau Transportation UK Ltd
STAUFF UK Ltd
TVS Supply Chain Solutions Ltd
WEYTEC
Control Panels
ABB Electrification Products
AMELEC Instruments
Andrew Reid
Applied Industrial Systems (AIS)
Austin-Lenika Project Services Ltd
Axair Fans UK Limited
Axiomtek UK Ltd
Baldwin Boxall Communications Ltd
Bernstein Ltd
FREQUENTIS UK Limited
Galldris Services Ltd
GES Consulting Ltd
Harland Simon Power Solutions
HARTING Ltd
Human Reliability
ICEE Managed Services Ltd
IXYS UK Westcode Ltd
LC Switchgear Limited
MENNEKES
Moorecorp Ltd
R Baker (Electrical) Ltd
STAUFF UK Ltd
Sulzer Electro Mechanical Services UK
TVS Supply Chain Solutions Ltd
WEYTEC
Control Room Equipment
WEYTEC
Control Room Solutions
WEYTEC
Cybersecurity
Complete Cyber
Derailment Investigation & Re-Railing of
Derailed Vehicles
Alma Rail Limited
Galldris Services Ltd
JR Dynamics Ltd
Railway Support Services
Disabled Refuge Systems
Baldwin Boxall Communications Ltd
Disabled Toilet Alarms
Baldwin Boxall Communications Ltd
Drug / Alcohol Testing
Amtrain (Midlands) Ltd
ARC Academy UK Ltd
Atom Training Centre
Ayrshire Medical Services Ltd
Express Medicals Ltd
Galldris Services Ltd
JVR Consultancy Ltd
Med-Fitplus Ltd
Medigold Health
Noble MED Solutions Ltd
Railmed
VGC
Axiomtek
Cable
Dorma
Ayrshire
Derma
Everlast
Galldris
Healthcare
Amtrain
Derma
Med-Fitplus Ltd
Medigold Health
NTS Premier Services
Rail Operations Group Ltd
Railmed Ltd
SC Johnson Professional
The QSS Group Limited
LPCB Security Rated Housings &
Firstco Galldris Services Ltd
GES Consulting Ltd
Gleeds
GRID Innovations
HaRMUK Ltd
HBI Haerter AG
Ideagen Ltd
Imtech/Dynniq Infrastructure Training Services Ltd
Intertek – Production and Integrity Assurance
J. Murphy & Sons Ltd
Jacobs UK Ltd
JVR
Bolle Safety
Elite Ground Support Services
Galldris Services Ltd
JVR Consultancy Ltd
Lindström Group LKQ Coatings
MC Electronics Ltd
MSA Safety – Latchways PLC
Optical Coating Technologies
PBWel
Pronto Direct
Protec Direct
ProtectHear
PULSAR®
Rapid Fire Supplies
Rexel
Safeaid Limited
SC Johnson Professional
Spartan Safety Ltd
Techpol Ltd
Tower Supplies
TVS Supply Chain Solutions Ltd
Public Address Systems
Baldwin Boxall Communications Ltd
Rescue Services
Arco Professional Safety Services Ltd
Crittall Windows Limited
Cygnet Projects Ltd
Galldris Services Ltd
Martin Castle Ltd
MSA Safety – Latchways PLC
Syndicate Alpha Ltd
Trackmaps XEIAD
Risk / Safety Assessment
1st Line Defence Ltd
AARC Professional Services Limited
Abbott Risk Consulting Ltd
Advanced New Technology
AEGIS
Alan Dick Communications Ltd
Applied Industrial Systems (AIS)
Arco Professional Safety Services Ltd
Atex Global Ltd
Auctus Management Group
Barkers Fencing
C.Scope International Ltd
Cirrus Research
Cleshar Contract Services Ltd
DB ESG
DGauge Ltd
Ebeni Limited
Encompass Engineering
Era Technology
AJC Trailers Ltd
Alan Dick Communications Ltd
Alchemy Metals Ltd
Andrew Reid
Arktis Endurance Textiles Ltd
Armorgard Security Products
ATEC Fire & Security
Atex Global Ltd
Blok ‘N’ Mesh
Bosch Security Systems UK Brammer
Buck & Hickman
Dorma Kaba Ltd
Emico Limited
ExMesh Security Products
Fone-Alarm Installations Ltd
Galldris Services Ltd
ICEE Managed Services Ltd
J. Murphy & Sons Ltd
Leadec
Legion Limited
Lingwood Security Management Limited
NATAS ASBESTOS Ltd
Newgate (Newark) Ltd
NTS Premier Services
Oltec Group
Onis Consulting Limited
Orbis Protect
Pragmasis Limited
ProActive Recruitment Services
Quartix Ltd
r2p UK Systems Ltd
Red Viking Rail Ltd
Redscan Cyber Security Ltd
Sensonic
Smartwater Technology Ltd
SMP Electronics / Samalite Products
Steelway Fensecure Ltd
Syndicate Alpha Ltd
The SES Group
Trackmaps
Transport Investigations Ltd
Trelleborg Antivibration Solutions
TVS Supply Chain Solutions Ltd
Tyrolit Ltd
Unilite Limited
Vital – Head Office
WEYTEC
Security Fasteners
Barkers Fencing
CAP Productions Limited
Galldris Services Ltd
JR Dynamics Ltd
Key Fasteners
MSA Safety – Latchways PLC
MSA
Skelair
Snap-on Industrial
South Survey Ltd
Limited
Sovereign Hydroseal LP
Stannah Lift Services – Major Projects
Star Fasteners (UK) Ltd (Huck Fastener
Distributor)
Structural Soils Ltd (Castleford Office)
Sunbelt Rentals Limited
TBA Protective Technologies Ltd
TCS Geotechnics
TenBroeke Company Limited
Torrent Trackside
Total Steelwork & Fabrication Ltd
TVS Supply Chain Solutions Ltd
Twinfix Limited
Tyrolit Ltd
Tyrone Fabrication
UK Power Networks Services
Vigier Rail AG
VolkerFitzpatrick
VolkerRail
Warringtonfire
Westcotec Limited
BIM (Building Information Modelling)
ABA Surveying Ltd
ABB Electrification Products
ACO Technologies Plc
Agility3 Modelling and Simulation
Amberg Engineering AG
Anderton Concrete, part of Ibstock
Andrew Reid
Arco Professional Safety Services Ltd
Aworth Survey Consultants
BPR Architects Ltd
Bridgeway Consulting Limited
Buckingham Group Contracting Ltd
BWB Consulting
CCTV Drainage Surveys – Midland Survey
Crouch Waterfall
D2 Rail & Civils Ltd
EOS Geomatics
Everlast Group Ltd
EviFile Limited
FJD Consulting and Design
Galldris Services Ltd
Geo-Environmental Services Ltd
GHD
Leadec
Maccaferri Ltd
MSA Safety – Latchways PLC
NATAS ASBESTOS Ltd
Nicoll Russell Studios
Nortek Global HVAC UK Ltd
Novus Rail Ltd
Polypipe Civils & Green Urbanisation
RUAS
Sadler Brown Architecture
SEP Rail Services
UK Power Networks Services
VolkerFitzpatrick
Bridge Building / Maintenance
Aarsleff Ground Engineering
ABG Geosynthetics
Actavo Building Solutions
Adomast Manufacturing Limited
Aecom
Alltask
Amida Ltd
Andrews Fasteners Limited
APB Construction (UK) Limited
Applied Industrial Systems (AIS)
Arbil Rail
Arco Professional Safety Services Ltd
BAM Ritchies Bodacc Ltd
Bradleys Metal Finishers
Bridgeway Consulting Limited
Britannia Construction Ltd
Browns Fasteners Ltd
Buckingham Group Contracting Ltd
Cairn Cross Civil Engineering Limited
CAN Cintec International Ltd
Cleshar Contract Services Ltd
Colt Construction Limited
Concrete Repairs Limited
Crouch Waterfall
Cygnet Projects Ltd
DGauge Ltd
DWG Infraco Ltd
Elite Ground Support Services
Ensafe Consultants
Epicuro Protective Materials Ltd
FA Clover & Son Ltd
Flexcrete Technology Ltd
FP McCann Ltd
Freyssinet Furse Galldris Services Ltd
Gradus Ltd
Graham Construction
Grenrose Scaffolding Ltd
Ground Control Limited
Gunform International Ltd
Gurit (UK) Ltd
Haywood & Jackson Fabrications Ltd
Henry Williams Ltd
Hilti (Gt. Britain) Ltd
Holemasters
Indestructible Paint Limited
Infrastructure Training Services Ltd
Klingspor Abrasives Limited
Lanes for Drains
Leadec
Links Signs Ltd
Mabey Hire Limited
Maker Coating Systems Ltd
MAL Explosive Ordnance Disposal Ltd
Marchantcain Group
McLaughlin & Harvey Ltd
McNealy Brown Ltd
Millcroft
Civil
Latchways PLC
Murphy Geospatial
Neary Rail and Construction
Newgate (Newark) Ltd
Nord-Lock Group
Nortek Global HVAC UK Ltd
NTS Premier Services
OSL Rail Limited
Padley & Venables
Pod-Trak
POS Services
Poundfield Precast
Premier Pits
PRV Engineering Ltd
Red Viking Rail Ltd
Relinea – GRP Systems Ltd
RSS Infrastructure Ltd
RTG Rail Services Limited
Running Rail Ltd
Severn Partnership
Shire Structures Ltd
Skanska Construction UK Ltd
SLC Rail
Smyth Composites Limited
Sonic Drilling Ltd
Sovereign Hydroseal LP
Steelway Fensecure Ltd
Taziker Industrial Limited
TCS Geotechnics
TECHNO CTA Limited
The Bionic Eye
Torrent Trackside
Total Steelwork & Fabrication Ltd
Trackwork Ltd
Trendrail Ltd – Specialists in Engineering
TSP Projects
Tufnol Composites Ltd
Twinfix Limited
Tyrolit Ltd
Tyrone Fabrication
Van Elle Rail
Vigier Rail AG
Vivax – Metrotech Ltd
Viztek Ltd
VolkerFitzpatrick Walker Construction (UK) Ltd
Welfare Hire Nationwide Ltd
West Maintenance Services
Wood Group Industrial Services Ltd
XEIAD
Consulting Civil & Structural Engineers
ABG Geosynthetics
Adfil
Adomast Manufacturing Limited
Amberg Engineering AG
APPS UK Ltd
Bridgeway Consulting Limited
BWB Consulting
Capel (CS) Ltd
CECL – Global
Concrete Repairs Limited
Crouch Waterfall
Cygnet Projects Ltd
DWG Resins
Ensafe Consultants
Everlast Group Ltd
FJD Consulting and Design
GALL ZEIDLER Consultants
Galldris Services Ltd
GeoAccess
Gurit (UK) Ltd
HBI Haerter AG
Henderson Thomas Associates Limited
HKA
JNP Group
KP Acoustics
Leadec
Links Signs Ltd
Maker Coating Systems Ltd
Morgan Sindall Construction & Infrastructure Ltd
Newgate (Newark) Ltd
PBH Rail
Relinea – GRP Systems Ltd
RSS Infrastructure Ltd
Shire Structures Ltd
StressMap
TenBroeke Company Limited
Tyrolit Ltd
Vigier Rail AG
Welfare Hire Nationwide Ltd
Contractors Principle
ABB Electrification Products
Actavo Building Solutions
Adfil
Adomast Manufacturing Limited
AM1 Projects Ltd
Amida Ltd
APB Construction (UK) Limited
APPS UK Ltd
Arup (Head Office)
Avondale Environmental Services Ltd
Babcock International
BAM Ritchies
Bridgeway Consulting Limited
Britannia Construction Ltd
Buckingham Group Contracting Ltd
Capel (CS) Ltd
Cleshar
Leadec
PBWel
Rexel
Zeta
Polycarbonate
Leadec
Precast
Sandel
TBA
Server
ABB
Capel (CS)
Captec
Galldris
Hydram
Kingsley Plastics Limited
Kleeneze – Koti Ltd
Leadec
Mayteck Ltd
Signage ABB Electrification Products
Adaptive Modules Ltd
Apcoa Parking (UK) Ltd
Arco Professional Safety Services Ltd
Astley Signs
Aura Brand Solutions
Ballast Tools UK Ltd
BCM GRC Ltd
Brammer Buck & Hickman
Capel (CS) Ltd
Coeval (Ltd)
Everlast Group Ltd
Ferrograph Limited
FLI Structures
Galldris Services Ltd
Giffen Group Ltd
GT Engineering (Markyate) Ltd
Horizon Group
J. Murphy & Sons Ltd
Jafco Tools Ltd
Kadfire Kroy Europe Ltd
Leadec
Lexicraft Ltd
Links Signs Ltd
LPA Channel Electric
Maker Coating Systems Ltd
Merson Group
Millcroft Group
MLM Consulting Engineers Ltd
Neary Rail and Construction
Nord-Lock Group
Novus Rail Ltd
Ogier Electronics Limited
Optical Coating Technologies
Powdertech (Corby) Ltd
PULS UK Ltd
Pulsar Instruments Plc
RSS Infrastructure Ltd
Running Rail Ltd
Rydon Signs Ltd
Selectequip Ltd
Shire Structures Ltd
Smartwater Technology Ltd
Specialised Tools and Equipment Ltd
Stewart Signs Rail
Stocksigns Ltd
Torrent Trackside
Total Steelwork & Fabrication Ltd
TVS Supply Chain Solutions Ltd
USC Hydraulics
Viztek Ltd
Walker Construction (UK) Ltd
West Maintenance Services
Westcotec Limited
Zeta Specialist Lighting
Specialist Bridge Installer
Osprey Shipping Limited
Sprayed Concrete Specialist
Capel (CS) Ltd
Gunform International Ltd
Leadec
Structural Engineering Design
Adfil
Adomast Manufacturing Limited
Amberg Engineering AG
Arrk Europe Ltd
Asset International Structures
Bridgeway Consulting Limited
Browns Fasteners Ltd
BWB Consulting
Capel (CS) Ltd
CECL – Global
Crouch Waterfall
Cygnet Projects Ltd
EOS Geomatics
Everlast Group Ltd
FJD Consulting and Design
GALL ZEIDLER Consultants
Galldris Services Ltd
Gurit (UK)
Had-Fab
Leadec
Martin
Morgan
PBH
RUAS
Shire
StressMap
Services Ltd GenAir UK Ltd
Holemasters Indestructible Paint Limited
JR Dynamics Ltd JSP Limited Leadec
Lineside Structure Maintenance Ltd
Links Signs Ltd
Martin Castle Ltd
MENNEKES
Pramac-Generac UK
Recycling Management
Rhodar Limited
RUAS
Site Contract Personnel (SCP)
Smyth Composites Limited Star Fasteners (UK) Ltd (Huck Fastener Distributor)
TBA Protective Technologies Ltd
TVS Supply Chain Solutions Ltd
Tyrolit Ltd
Urban Hygiene Ltd
Warringtonfire
Wilcomatic Limited
Blast Cleaning Equipment & Consumables
APPS UK Ltd
CryoGen
Cygnet Projects Ltd
Enduramaxx Limited
Galldris Services Ltd
GenAir UK Ltd
Leadec
Links Signs Ltd
Rapid Fire Supplies
Rhodar Limited
TVS Supply Chain Solutions Ltd
USC Hydraulics
Blast Work PPE
CryoGen
Derma Shield Skincare
Galldris Services Ltd
GenAir UK Ltd
JSP Limited
Leadec
TBA Protective Technologies Ltd
TVS Supply Chain Solutions Ltd
USC Hydraulics
Building & Structures Maintenance
3M
Aarsleff Ground Engineering
Adomast Manufacturing Limited
Aecom
AGS One (Anti Graffiti Systems)
Alan Dick Communications Ltd
Alltask Amberg Engineering AG
Amida Ltd
Ampteam
Arco
Auctus
Bradleys
Ltd
APPS UK Ltd
Excell Rail Ltd
Galldris Services Ltd
GeoAccess
Leadec
Polypipe Civils & Green Urbanisation
Sateba UK (formerly Sateba
Stanton Precast)
SBC Rail Specialist Engineering Services Ltd
Steconfer
Torrent Trackside
TVS Supply Chain Solutions Ltd
Electrical
Actemium UK
Acutest (Head Office)
AM1 Projects Ltd
Andrew Reid
Arthur Flury (UK) Ltd
ATAM (UK) Ltd
BAND-IT Company Ltd
Barnbrook Systems Ltd
Bender UK Ltd
Bernstein Ltd
British Cables Company
C.Scope International Ltd
Cable Services Group
CEF
CHH Conex Ltd
Data Acquisition & Testing Services Ltd
Duvine Limited
EasyStart Batteries
Gordon Services UK Ltd
HARTING Ltd
HGI Generators International
HUBER+SUHNER (UK) Ltd
Hydrostatic Extrusions Limited
HYTORC
ICEE Managed Services Ltd
iLECSYS Rail Ltd
Jaltek Systems
LC Switchgear Limited
Leadec
Marshall-Tufflex Ltd
MENNEKES
Mosdorfer Rail Ltd
MTM Power Messtechnik
Mellenbach GmbH
Oakes Power Services Ltd
Overhead Line Engineering Limited
PBH Rail
PBWel
Pod-Trak
Polypipe Civils & Green Urbanisation
PRBX (Powerbox) UK
Provertha Connectors, Cables & Solutions GMBH
Prysmian UK
PSG Ltd
PULS UK Ltd
Rexel
Roxtec Ltd
RS Electrical (RSE) Ltd
Samuel Taylor Ltd
Sateba UK (formerly Sateba
Stanton Precast)
Shenton Group
Slingco Limited
SPL Powerlines UK
Stäubli Electrical Connectors
Steconfer
Sulzer Electro Mechanical Services UK
Sunbelt Rentals Limited
T-UK Tecnologic UK
Time 24
Torrent Trackside
Traco Electronic AG
Traction Rail Electrical Ltd
TVS Supply Chain Solutions Ltd
Tyrone Fabrication
UK Power Networks Services
Unipart Rail
VolkerRail
Batteries
Alan Dick Communications Ltd
DMS technologies
Duvine Limited
EasyStart Batteries
Harland Simon Power Solutions
HARTING Ltd
Hoppecke Industrial Batteries Limited
Marlec Engineering Co Ltd
Moorecorp Ltd
Oakes Power Services Ltd
PB Design & Developments Ltd
PULS UK Ltd
Rexel
Rotronics Battery Management Solutions
TVS Supply Chain Solutions Ltd
Tyrone Fabrication
USC Hydraulics
Battery Chargers
Actemium UK
DMS technologies
Duvine Limited
EasyStart Batteries
Eyedot (Europe) Ltd – Electronic Repair and Maintenance
Harland Simon Power Solutions
Arlington Fleet Group Cabel UK
Capel (CS) Ltd
CPC Battery Services Ltd
EasyStart Batteries
Enersys Limited
Gaia Converter
Houghton International
Hydrostatic Extrusions Limited
iLECSYS Rail Ltd
IXYS UK Westcode Ltd
Jumo Instrument Co Ltd
Mallatite Rail
Mecc Alte UK
MTM Power Messtechnik
Mellenbach GmbH
Oakes Power Services Ltd
PRBX (Powerbox) UK
PULS UK Ltd
R Baker (Electrical) Ltd
REO (UK) Ltd
Rexel
Rotec Hydraulics
Shenton Group
Siemens
Steconfer
Sulzer Electro Mechanical Services UK
Torrent Trackside
Traco Electronic AG
TVS Supply Chain Solutions Ltd
UK Power Networks Services
Unipart Rail
Wabtec Rail Limited
Semiconductors
Capel (CS) Ltd
GD Rectifiers USC Hydraulics
Shore Supply Systems
ABB Electrification Products Bender UK Ltd
Duvine Limited
Gaia Converter
LC Switchgear Limited
PULS UK Ltd
Rexel
Unipart Rail
Switchgear
ABB Electrification Products
Actemium UK
ADE Power
AM1 Projects Ltd
AMELEC Instruments
Cable Services Group
Duvine Limited
Gaia Converter Harland Simon Power Solutions
Hydrostatic Extrusions Limited
iLECSYS Rail Ltd
JCK Ltd
LC Switchgear Limited
MTM Power Messtechnik
Mellenbach GmbH
Oakes Power Services Ltd
PBWel
PSG Ltd
Rexel
Samuel Taylor Ltd
Steconfer
Time 24
TVS Supply Chain Solutions Ltd
Tyrone Fabrication
UK Power Networks Services
VolkerRail
Transducers & Signal Conditioning
Equipment
AMELEC Instruments
Barnbrook Systems Ltd
Bender UK Ltd
Duvine Limited
Jaltek Systems
MPEC Technology Ltd
PSG Ltd
Rexel
Steconfer
TVS Supply Chain Solutions Ltd
USC Hydraulics
Electrification Equipment / Services 3M
A-Plant Rail
Aecom
Amida Ltd
Arthur Flury (UK) Ltd
Arup (Head Office)
ATL Transformers Ltd
Babcock International
Bradgate Containers
Brecknell Willis
Cable Services Group
Cairn Cross Civil Engineering Limited
Cintec International Ltd
Cleshar Contract Services Ltd
Data Acquisition & Testing Services Ltd
DGauge Ltd
Dorma Kaba Ltd
Duvine Limited
EasyStart Batteries
Emico Limited
EviFile Limited
FLI
Furrer
g2 Energy Ltd
Giffen Group Ltd
Had-Fab Limited
Henry Williams Ltd
iLECSYS
Norbar Torque Tools Ltd
Nord-Lock Group Nortek Global HVAC UK Ltd
Onis Consulting Limited
Padley & Venables
PBWel
Platipus Anchors Ltd Power Jacks
Predator Trailers Ltd
Probst Handling Equipment
Quality Precision Engineering Ltd
R Baker (Electrical) Ltd
Raptor Supplies Ltd
Rexel
RSS Infrastructure Ltd Schaeffler (UK) Ltd Sefac UK Ltd
Selectequip Ltd
Serco Rail Technical Services
Skanska Construction UK Ltd
Slingco Limited
SMP Electronics / Samalite Products
Snap-on Industrial Sonatest Ltd
Specialised Tools and Equipment Ltd
SPL Powerlines UK
Stahlwille Tools Limited
Star Fasteners (UK) Ltd (Huck Fastener Distributor)
Staytite Ltd
Steconfer
Steelway Fensecure Ltd
TFC Ltd – Head Office
Thermit Welding (GB) Ltd
Thomson Engineering Design Ltd
Torrent Trackside
Tufnol Composites Ltd
TVS Supply Chain Solutions Ltd
Tyrolit Ltd
Unilite Limited
USC Hydraulics
Vivax – Metrotech Ltd
Fasteners
BAND-IT Company Ltd Browns Fasteners Ltd
Raptor Supplies Ltd
Star Fasteners (UK) Ltd (Huck Fastener Distributor)
TFC Ltd – Head Office
Trojan Special Fasteners Ltd
USC Hydraulics
Multidisciplinary Engineering
Cadenza Transport Consulting Ltd
Capel (CS) Ltd
FJD Consulting and Design
Route Feasibility Studies
Cadenza Transport Consulting Ltd
The Railway Consultancy Ltd
Station Feasibility Studies
Cadenza Transport Consulting Ltd
The Railway Consultancy Ltd
Painting & Coating 3M
Adomast Manufacturing Limited
AGS One (Anti Graffiti Systems)
Anochrome Technologies
APPS UK Ltd
Aura Brand Solutions
Barkers Fencing
Concrete Repairs Limited
CryoGen
Cygnet Projects Ltd
Everlast Group Ltd
Galldris Services Ltd
GenAir UK Ltd
Highland Galvanizers
Hydram Engineering Limited
Indestructible Paint Limited
Joseph Ash Galvanizing
Links Signs Ltd
LKQ Coatings
Optus Anti-skid surfacing systems
PSG Ltd
Sherwin-Williams Protective & Marine Coatings
Silenzio Panels Ltd
Standish Engineering Co Ltd
Sulzer Electro Mechanical Services UK
Total Steelwork & Fabrication Ltd
TrAchem Ltd
TVS Supply Chain Solutions Ltd
USC Hydraulics
West Maintenance Services
Corrosion Protection 3M
AGS One (Anti Graffiti Systems)
Anochrome Technologies
APB Construction (UK) Limited
APPS UK Ltd
Arrow Solutions
Aura Brand Solutions
Bradleys Metal Finishers
British Steel
Colt Construction
PB
Profin
Silenzio
Galldris
LKQ Coatings Maker Coating Systems Ltd
Mallatite Rail
Profin Protective Finishing Ltd
Sulzer Electro Mechanical Services UK
TVS Supply Chain Solutions Ltd
West Maintenance Services
Wet Paint Spray Finishing
ABM Manufacturing
Anochrome Technologies
APPS UK Ltd
Aura Brand Solutions
Bradleys Metal Finishers
CryoGen
Cygnet Projects Ltd
Dyer Engineering Ltd
Galldris Services Ltd
Hydram Engineering Limited
Indestructible Paint Limited
LKQ Coatings Maker Coating Systems Ltd
Mallatite Rail
Paintmaster Trade Paints Manufacturer
Profin Protective Finishing Ltd
PSG Ltd
Sulzer Electro Mechanical Services UK
Techpol Ltd
TVS Supply Chain Solutions Ltd
Zinc Metal Spraying
Anochrome Technologies
APPS UK Ltd
Bradleys Metal Finishers
CryoGen
Galldris Services Ltd
Impreglon UK
Paintmaster Trade Paints Manufacturer
Profin Protective Finishing Ltd
Sulzer Electro Mechanical Services UK
Total Steelwork & Fabrication Ltd
TVS Supply Chain Solutions Ltd
Plant Hire
A-Plant Rail
AB Hoses & Fittings Ltd
Advante – Oasis® Welfare
Aquarius Railroad Technologies Ltd
Arbil Rail
ATI Tank Hire Limited
Avondale Environmental Services Ltd
Babcock International
Brian Doogue Haulage Ltd
CCF Plant Hire Ltd – t/as Access Plant
Durham Lifting
Eldapoint Ltd
Facelift
Freyssinet
Geismar UK Ltd
Hilti (Gt. Britain) Ltd
HSS Hire PLC
J. Murphy & Sons Ltd
Lankelma Ltd
Live Trakway | Barriers | Bridges | Lights
Lundy Projects
Metcalfe Plant Hire Limited
MGF Ltd
Millcroft Group
Morgan Sindall Construction & Infrastructure Ltd
Pennys Group Ltd
Pontoon Works Ltd
Pramac-Generac UK
Probst Handling Equipment
Rail Freight Services
Rail Vac
Readypower Rail Services Group Ltd
Skelair International Ltd
Specialist Engineering Services Ltd
SRS Rail System International Ltd
Stobart Rail
Torrent Trackside
TPA Rapid Rail Access
TXM Plant Ltd
Tyrolit Ltd
Van Elle Rail
Vivax – Metrotech Ltd
VolkerRail
Rubber
Nufox
Rubber Products
USC Hydraulics
Scaffolding Labour & Access
Anderton Concrete, part of Ibstock
Arco Professional Safety Services Ltd
Bridgeway Consulting Limited
Capel (CS) Ltd
Crouch Waterfall
CryoGen
Cygnet Projects Ltd
Dura Composites Ltd
Everlast Group Ltd
Excell Rail Ltd
Henderson Thomas Associates
Bradgate
EviFile Limited
Frauscher Sensortechnik
ABI Electronics Ltd
Aecom
AEG Power Solutions Ltd
AEI Cables
Alan Dick Communications Ltd
Amaro Group
AMELEC Instruments
Amida Ltd
Anderton Concrete, part of Ibstock
Arup (Head Office)
ATL Transformers Ltd
Babcock International
Bender UK Ltd
Bernstein Ltd
Bradgate Containers
Bridgeway Consulting Limited
Captec
Collis Engineering Ltd
Craig & Derricott Ltd
Data Techniques
DB ESG
DMS technologies
Duvine Limited
Electroustic Ltd
Eyedot (Europe) Ltd – Electronic Repair and Maintenance
FLI Structures
Furse
Gatecare Ltd Solar Powered Gate Systems
GHD
Giffen Group Ltd
Global Rail Construction Ltd
Ground Transportation Systems, Thales UK
GT Engineering (Markyate) Ltd
HARTING Ltd
Henry Williams Ltd
Hill and Smith Ltd t/a Variable
Message Signs
Hitachi Information Control Systems
Hitachi Rail Europe
HJ Skelton and Co. Ltd
HUBER+SUHNER (UK) Ltd
iLECSYS Rail Ltd
IXYS UK Westcode Ltd
Jacobs UK Ltd
Jumo Instrument Co Ltd
KEC Limited
Keltbray Group
Kilborn Consulting Limited
LEM Regional Office UK
LPA Channel Electric
Mallatite Rail
Mors Smitt (A Wabtec Company) NRL
Optical Coating Technologies
OSL
Schaltbau Transportation UK Ltd
Schneider Electric Ltd
Schweizer Electronic Ltd
Sheerspeed Shelters Ltd
Siemens
Signal House Group – Collis Engineering
Signet Solutions
SigTech Rail Stadler Rail Management AG
Steconfer
Strategic Rail Consultants Ltd
Swann Group Ltd
Time 24
Trackmaps
Trans-Tronic Ltd
TSP Projects
TVS Supply Chain Solutions Ltd
Unipart Dorman
Unipart Rail University of Birmingham VolkerRail
WEYTEC
Wrekin Circuits Ltd
Xrail Group
Zircon Software Ltd
Signalling Surge Protection
ABB Electrification Products
AMELEC Instruments
Bender UK Ltd
Bridgeway Consulting Limited
Eyedot (Europe) Ltd – Electronic Repair and Maintenance iLECSYS Rail Ltd
IXYS UK Westcode Ltd
Keltbray Group PBWel
PD Devices Ltd PSG Ltd
PULS UK Ltd
Roxtec Ltd
SigTech Rail
Steconfer
TVS Supply Chain Solutions Ltd
Stations
Anderton Concrete, part of Ibstock
Andrew Reid
APPS UK Ltd
Astley Signs
Baldwin Boxall Communications Ltd
Bridgeway Consulting Limited
Cable Services Group
Crouch Waterfall
Dura Composites Ltd
Duvine Limited
Galldris Services Ltd
Haywood & Jackson Fabrications Ltd
Henderson Thomas Associates Limited
Kleeneze – Koti Ltd
Lineside Structure Maintenance Ltd
Memolub Lubrication Systems
Pod-Trak
Rexel
RUAS
Sateba UK (formerly Sateba Stanton Precast)
Silenzio Panels Ltd
Smyth Composites Limited
Steconfer
Sunbelt Rentals Limited
TenBroeke Company Limited
Torrent Trackside
Total Steelwork & Fabrication Ltd
Twinfix Limited
Tyrolit Ltd
VolkerFitzpatrick
Station Equipment / Services
ABB Electrification Products
Aecom
Amey TPT
Anderton Concrete, part of Ibstock
Andrew Reid
APPS UK Ltd
Arup (Head Office)
Baldwin Boxall Communications Ltd
Bradleys Metal Finishers
Bridgeway Consulting Limited
Cable Services Group
Camel Precast
Capel (CS) Ltd
Captec
Craig & Derricott Ltd
Cycle-Works Cyclepods Ltd
Duvine Limited
Emico Limited
Eurotech
Eyedot (Europe) Ltd – Electronic Repair and Maintenance
FDB Electrical Ltd
FJD Consulting and Design
Power
Bradgate Containers
Dyer Engineering Ltd
Had-Fab Limited
Kingsley Plastics Limited
TVS Supply Chain Solutions Ltd
Tyrolit Ltd
Structural Fasteners & Tools
BAND-IT Company Ltd
Raptor Supplies Ltd
Star Fasteners (UK) Ltd (Huck Fastener Distributor)
Sub-Contract Laser Cutting
ABM Manufacturing
CAP Productions Limited
Dyer Engineering Ltd
Hydram Engineering Limited
Laser Process Ltd
Surface Preparation Equipment
Bridgeway Consulting Limited
CryoGen
Links Signs Ltd
StressMap
Tyrolit Ltd
Surveying & Inspection
ABA Surveying Ltd
Amberg Engineering AG
Arco Professional Safety Services Ltd
Bridgeway Consulting Limited
BWB Consulting
C.Scope International Ltd
Capel (CS) Ltd
CCS Jeweltone Ltd
Concrete Repairs Limited
Crouch Waterfall
Cygnet Projects Ltd
Data Acquisition & Testing Services Ltd
Ensafe Consultants
Everlast Group Ltd
Galldris Services Ltd
GeoAccess
Geoterra
Henderson Thomas Associates Limited
ISVR Consulting – University of Southampton
JNP Group
JR Dynamics Ltd
JWG Survey & Engineering Ltd
KP Acoustics
Lankelma Ltd
Level X NDT
Malcolm Hughes
Martin Castle Ltd
Northern Divers
Novus Rail Ltd
PBH Rail
RUAS
Senceive Limited
SEP Rail Services
Specialist Engineering Services Ltd
Steconfer
Structural Soils Ltd (Castleford Office)
Sulzer Electro Mechanical Services UK
Trimble Rail Solutions
UK Power Networks Services
Warringtonfire
3D Laser Scanning
ABA Surveying Ltd
Agility3 Modelling and Simulation
Amberg Engineering AG
Bridgeway Consulting Limited
BWB Consulting
Central Alliance Ltd
Data Acquisition & Testing Services Ltd
Drone Tech Aerospace Ltd
EOS Geomatics
Galldris Services Ltd
GeoAccess
Henderson Thomas Associates Limited
JWG Survey & Engineering Ltd
MAL Explosive Ordnance Disposal Ltd
NATAS ASBESTOS Ltd
PBH Rail
Plowman Craven Ltd
SEP Rail Services
StressMap
Sulzer
3D
ABA
Agility3 Modelling and Simulation
Amberg Engineering AG
Bridgeway Consulting Limited
BWB Consulting
CCTV
Data
Drone
SEP
Aerial Photography ABA
Concrete Repairs Limited
Galldris Services Ltd
GeoAccess
MAL
PBH
Ordnance Disposal Ltd
Structural Soils Ltd (Castleford Office)
SubVision Surveys Ltd
Measurement Surveys
ABA Surveying Ltd
Agility3 Modelling and Simulation
Amberg Engineering AG
Aworth Survey Consultants
Bridgeway Consulting Limited
Capel (CS) Ltd
CCTV Drainage Surveys – Midland Survey
Central Alliance Ltd
Cygnet Projects Ltd
Data Acquisition & Testing Services Ltd
Drone Tech Aerospace Ltd
EOS Geomatics
Everlast Group Ltd
Galldris Services Ltd
GeoAccess
Henderson Thomas Associates Limited
ISVR Consulting – University of Southampton
JR Dynamics Ltd
JWG Survey & Engineering Ltd
KJ Hall Surveyors Ltd
MAL Explosive Ordnance Disposal Ltd
NATAS ASBESTOS Ltd Novus Rail Ltd PBH
RUAS Schenck Process Ltd
SEP Rail Services
South Survey Ltd
Specialist Engineering Services Ltd
Xrail Group
Non Destructive Testing
Capel (CS) Ltd GeoAccess
Level X NDT
SEP Rail Services
Obstacle Detection
ABA Surveying Ltd
Bridgeway Consulting Limited
Data Acquisition & Testing Services Ltd
Galldris Services Ltd
GeoAccess
Groeneveld Lubrication Solutions
Henderson Thomas Associates Limited
MAL Explosive Ordnance Disposal Ltd
PBH Rail
SEP Rail Services
PAS:128 Surveys
ABA Surveying Ltd
Bridgeway Consulting Limited
CCTV Drainage Surveys – Midland Survey
Galldris Services Ltd
GeoAccess
MAL Explosive Ordnance Disposal Ltd
SEP Rail Services
Structural Soils Ltd (Castleford Office)
SubVision Surveys Ltd
Rope Access
Arco Professional Safety Services Ltd
BAM Ritchies
Bodacc Ltd
Brammer
Bridgeway Consulting Limited
Buck & Hickman
CAN
CCS Jeweltone Ltd
MAL
Mitie
Overhaul Services
ABB Electrification Products
Alan Dick Communications Ltd
Capitol Industrial Batteries Systems Limited
Data Acquisition & Testing Services Ltd
Durham Lifting
Eyedot (Europe) Ltd – Electronic Repair and Maintenance
Semcon Product Information UK Ltd
Serco Rail Technical Services
Standish Engineering Co Ltd
Unipart Rail
USC Hydraulics
Track Adfil
AEGIS
Anderton Concrete, part of Ibstock
APPS UK Ltd
Armorgard Security Products
B H Railway Infrastructure Consultants Ltd
BarChip EMEA Ltd
Bernstein Ltd
Bradgate Containers
Bridgeway Consulting Limited
Buckingham Group Contracting Ltd
C.Scope International Ltd
Cable Services Group
Coveya Ltd
Creative Composites Ltd
Data Acquisition & Testing Services Ltd
DLR Elastomer Engineering
Duvine Limited
E2S Warning Signals
Eland Cables Ltd
Elwood International Ltd
Engineered Composites Ltd
Excell Rail Ltd
GAI – Tronics (A division of
Hubbell Limited)
Galldris Services Ltd
HJ Skelton and Co. Ltd
Holemasters
Hydram Engineering Limited
HYTORC
JR Dynamics Ltd
Kluber Lubrication
LC Switchgear Limited
Marshall-Tufflex Ltd
MATISA (U.K) Ltd
McCulloch Rail
MH Southern & Company Ltd (Timber)
Newgate (Newark) Ltd
Orbital Fasteners
Pandrol
PBH Rail
PBWel
PcP Gratings Ltd
Pendersons Ltd
PlasmaTrack Ltd
Prysmian UK
PSG Ltd
PULS UK Ltd
Railcare Sweden Ltd
RSS Infrastructure Ltd
RWB Group
Safeaid Limited
Schweizer Electronic Ltd
Senceive Limited
Sensonic
SigTech Rail
Skelair International Ltd
Snap-on Industrial
Specialist Engineering Services Ltd
Star Fasteners (UK) Ltd (Huck Fastener
Distributor)
Steconfer
Strail (UK) Ltd
Sunbelt Rentals Limited
TCS Geotechnics
Torrent Trackside
Trackmaps
Triptex Limited
TTS (Trough-Tec Systems)
TVS Supply Chain Solutions Ltd
Tyrolit Ltd
Unipart Rail
Vigier Rail AG
VolkerFitzpatrick VolkerRail
Welfare Vans 4 Less
CESS
Elwood International Ltd
Conductor Rail Heating
AM1 Projects Ltd
Bridgeway Consulting Limited
Cable Services Group
Galldris Services Ltd
LC Switchgear Limited
Steconfer
TVS Supply Chain Solutions Ltd
Elevated Cable Trough System
PcP Gratings Ltd
Flood Response
RWB Group
Level Crossings Aecom
AEGIS
Alma Rail Limited
AM1 Projects Ltd
Anderton Concrete, part of Ibstock
Arup
Padley
Pandrol
PBH
Freight Services
Railweight RS Clare & Co Limited
RSS Infrastructure Ltd
Safeaid Limited
Sateba UK (formerly Sateba
Stanton Precast)
SBC Rail
Selectequip Ltd
Serco Rail Technical Services
Sheerspeed Shelters Ltd
Sicut Enterprises Ltd
Skelair International Ltd
SMP Electronics / Samalite Products
Smyth Composites Limited
Snap-on Industrial
Sonatest Ltd
Specialised Tools and Equipment Ltd
Specialist Engineering Services Ltd
Spectrum Contracting Services Limited
SRS Rail System International Ltd
Star Fasteners (UK) Ltd (Huck Fastener Distributor)
Steconfer
Steelway Fensecure Ltd
Sunbelt Rentals Limited
SVR Plastics
TCS Geotechnics
Terram & Tubex
Thermit Welding (GB) Ltd
Tiflex Ltd – Trackelast Specialist Rail
Solutions
Track Maintenance Equipment Limited
Trackmaps
Trackwork Ltd
Trendrail Ltd – Specialists in Engineering
Triptex Limited
TTS (Trough-Tec Systems)
TVS Supply Chain Solutions Ltd
Ltd
ME
Newgate (Newark) Ltd
Schaltbau
Steconfer TVS
Unipart
Kaymac Marine & Civil Engineering Ltd
Kite Group Ltd
Lindapter International LKQ Coatings
Lockinex (UK) Limited
McGinley Support Services (Infrastructure) Ltd
Midland Alloy Ltd
NRL
Pandrol
Pod-Trak
PRV Engineering Ltd
Raptor Supplies Ltd
Riverview Welding Services
RSS Infrastructure Ltd
Sheerspeed Shelters Ltd
Specialised Tools and Equipment Ltd
Steconfer
Steelway Fensecure Ltd
Sulzer Electro Mechanical Services UK
Thermit Welding (GB) Ltd
Trendrail Ltd – Specialists in Engineering
TVS Supply Chain Solutions Ltd
Tyrolit Ltd
Vital – Head Office
VolkerRail
ROLLING STOCK & TRACTION
Air Horns & Valves ISVR Consulting – University of Southampton
Marsh Bellofram Europe Ltd
STAUFF UK Ltd
TVS Supply Chain Solutions Ltd
UKRL – UK Rail Leasing Ltd
Zollner UK Ltd
CET Systems
Bingham Rail (DS) Ltd Design and Analysis Ltd
GBR-Rail Ltd
Schaltbau Transportation UK Ltd
Vogelsang
Wilcomatic Limited
Depots APPS UK Ltd
Armorgard Security Products
Aura Brand Solutions
Buckingham Group Contracting Ltd
Dura Composites Ltd
Duvine Limited
EngPro Solutions
Galldris Services Ltd
GBR-Rail Ltd
Gramm Barrier Systems Ltd
Haywood & Jackson Fabrications Ltd
Houghton International
Incap Electronics UK Ltd
KITE Projects
LC Switchgear Limited
Lista UK Ltd
LKQ Coatings
Majorlift Hydraulic Equipment Limited
MENNEKES
MSA Safety – Latchways PLC
Newgate (Newark) Ltd
Noble MED Solutions Ltd
PBWel
Permalok Fastening Systems Ltd
Pramac-Generac UK
Premier Pits
Rexel
Specialist Engineering Services Ltd
Standish Engineering Co Ltd
Steconfer
TenBroeke Company Limited
Time 24
Total Steelwork & Fabrication Ltd
Totalkare TrAchem Ltd
TVS Supply Chain Solutions Ltd
TXM Consult
Unipart Rail
VolkerFitzpatrick
VolkerRail
Wickens Engineering Ltd
Wilkinson Star Ltd
Cleshar
Haywood
HGI Generators International Hilti (Gt. Britain) Ltd
ICEE Managed Services Ltd
iLECSYS Rail Ltd
Infrastructure Training Services Ltd
J. Murphy & Sons Ltd
Jotun Paints (Europe) Ltd
Depot Workshop Equipment
ABB Electrification Products
Airguard Filters Ltd
APPS UK Ltd
Arbil Rail
Arlington Fleet Group
Armorgard Security Products
Brammer
Buck & Hickman
Craig & Derricott Ltd
Duvine Limited
FDB Electrical Ltd
Galldris Services Ltd
GT Engineering (Markyate) Ltd
Harmill Systems Limited
IFC Inflow
Jigsaw M2M Limited
Klingspor Abrasives Limited LKQ Coatings
Lucy Zodion Ltd
MENNEKES
Newgate (Newark) Ltd
Permalok Fastening Systems Ltd
Pramac-Generac UK
Premier Pits
Rapid Fire Supplies
Rexel
Sefac UK Ltd
Semmco Ltd
Star Fasteners (UK) Ltd (Huck Fastener Distributor)
Totalkare TrAchem Ltd
TSG Fleet Tufnol Composites Ltd
TVS
DB ESG
Dellner Ltd
Diamond Rail Services
Duvine Limited
Dyer Engineering Ltd
EngPro Solutions
Eyedot (Europe) Ltd – Electronic Repair and Maintenance
Freightliner Group Limited
Galldris Services Ltd
GDM Heat Transfer Ltd
GT Engineering (Markyate) Ltd
Houghton International
Houghton International
IFC Inflow
IGW International n.v
Incap Electronics UK Ltd
IXYS UK Westcode Ltd
James Troop & Co Ltd
Jigsaw M2M Limited
Johnson Security
Lista UK Ltd
LKQ Coatings
LPA Group Plc
LUR Ltd
M Barnwell Services Ltd
Nord-Lock Group
OLD Engineering Co Ltd
PBWel
Permalok Fastening Systems Ltd
Perpetuum Ltd
Premier Pits
Rowe Hankins Ltd
Rubirail
Sabre Rail Services Ltd
Schaltbau Transportation UK Ltd
Sefac UK Ltd
Semcon Product Information UK Ltd
SKF (UK) Limited
Specialist Engineering Services Ltd
Standish Engineering Co Ltd
Star Fasteners (UK) Ltd (Huck Fastener
Distributor)
Tecforce Ltd
Thermacom Ltd
Time 24
Total Steelwork & Fabrication Ltd
Totalkare
TrAchem Ltd
Tufnol Composites Ltd
TXM Consult
UKRL – UK Rail Leasing Ltd
Unipart Rail
VolkerFitzpatrick Wabtec Rail Limited
Welding Alloys Group
William Cook Rail Ltd
ZF Services UK Ltd
Zonegreen
Specialist Depot Equipment
Maintenance
APPS UK Ltd
Bingham Rail (DS) Ltd
Duvine Limited
Galldris Services Ltd
GBR-Rail Ltd
Incap Electronics UK Ltd
LC Switchgear Limited
Leadec
LKQ Coatings
PBWel
Premier Pits
Specialist Engineering Services Ltd
Star Fasteners (UK) Ltd (Huck Fastener
Distributor)
Steconfer
Totalkare
VolkerFitzpatrick
Storage Systems & Handling
Wickens Engineering Ltd
Washing Systems – Vehicles
AB Hoses
Aqua-Solv
Browns Fasteners Ltd
Derma Shield Skincare
USC Hydraulics
Lubrication Systems
Bijur Delimon International
Galldris Services Ltd
Jigsaw M2M Limited
Kluber Lubrication
ME Railway Research Group, University of Sheffield
Memolub Lubrication Systems
RS Clare & Co Limited
TrAchem Ltd
Triscan Systems Ltd
TVS Supply Chain Solutions Ltd
UKRL – UK Rail Leasing Ltd
USC Hydraulics Wilcomatic Limited
Hydraulic Equipment
CAP Productions Limited
Fairway Hydraulics Limited
Galldris Services Ltd
HTL Group Ltd
HYTORC
Micro-Mesh Filtration Star Fasteners (UK) Ltd (Huck Fastener Distributor)
STAUFF UK Ltd
Tidyco Ltd
Torishima Service Solutions Europe Limited
– Fluid Power Division
Totalkare
USC Hydraulics
On-Board Services
AEGIS
Axiomtek UK Ltd
Duvine Limited
Encompass Engineering
GAI – Tronics (A division of
Hubbell Limited)
GD Rectifiers
HARTING Ltd
HaslerRail AG
HaslerRail Secheron UK
HUBER+SUHNER (UK) Ltd
Industrial Communication Products Ltd
MTM Power Messtechnik
Mellenbach GmbH
Nomad Digital (Head Office)
PRBX (Powerbox) UK
Rolls-Royce Solutions UK Ltd
RUGGED MOBILE Systems Ltd
Catering / On-Train Services
DB ESG
Office Depot r2p UK Systems Ltd
On-Board Entertainment
AEGIS
Arlington Fleet Group
Axiomtek UK Ltd
Belvoir Rail Ltd
DAC Limited
Electroustic Ltd
Eyedot (Europe) Ltd – Electronic Repair and Maintenance
HARTING Ltd
Icomera
Industrial Communication Products Ltd
Nomad Digital (Head Office) r2p UK Systems Ltd
Schaltbau Transportation UK Ltd
Televic GSP
Trainfx Ltd
Wabtec Rail Limited
On-Board Power Supply Equipment
ABB Electrification Products
Armacell UK
Duvine Limited
GD Rectifiers
IXYS UK Westcode Ltd
James Troop & Co Ltd
Moorecorp Ltd
MTM Power Messtechnik
Mellenbach GmbH
Powertherm Contracting Services
PRBX (Powerbox) UK
PULS UK Ltd
r2p UK Systems Ltd
Relec Electronics Ltd
Rolls-Royce Solutions UK Ltd
WISKA UK
On-Board Train Comms
Axiomtek UK Ltd
Eyedot (Europe) Ltd – Electronic Repair and Maintenance
GAI – Tronics (A division of
Hubbell Limited)
HARTING Ltd
HaslerRail AG
HaslerRail Secheron UK
Industrial Communication Products Ltd
Nomad Digital (Head Office)
PULS UK Ltd
r2p UK Systems Ltd
RUGGED MOBILE Systems Ltd
Softil Ltd
Passenger WiFi
Axiomtek UK Ltd
HARTING Ltd
HUBER+SUHNER (UK) Ltd
Industrial Communication Products Ltd
Nomad Digital (Head Office) PULS UK Ltd
r2p UK Systems Ltd
On-Track Plant
King Vehicle Engineering Ltd
Pramac-Generac UK Railcare Sweden Ltd
Specialist Engineering Services Ltd
Spectrum Contracting Services Limited
Star Fasteners (UK) Ltd (Huck Fastener Distributor)
STAUFF UK Ltd
Pennys Group Ltd
Petards Premier Pits
Prysmian UK Record Electrical Associates Ltd
Rolls-Royce Solutions UK Ltd
Roxtec Ltd
Samuel Taylor Ltd
Schweizer Electronic Ltd
Semcon Product Information UK Ltd
Serco Rail Technical Services
Slingco Limited
Stadler Rail Management AG
Standish Engineering Co Ltd
Star Fasteners (UK) Ltd (Huck Fastener
Distributor)
Sulzer Electro Mechanical Services UK
Time 24
TRB Lightweight Structures Ltd
Trelleborg Antivibration Solutions
Tribo “LLC Bilotserkivskiy Zavod Tribo Ltd’’
Trimble Rail Solutions
TVS Supply Chain Solutions Ltd
Tyrolit Ltd
UKRL – UK Rail Leasing Ltd
Unipart Rail
Voith Turbo Limited
Axles / Wheelsets / Suspension AEGIS
AJT Engineering Ltd
AME-3D
Arlington Fleet Group BG Steels Ltd
Browns Fasteners Ltd
DB ESG
Ferrabyrne Limited
Freightliner Group Limited GMT Rubber-Metal-Technic Ltd
IGW International n.v
Indestructible Paint Limited
ISVR Consulting – University of Southampton
Jumo Instrument Co Ltd
LUR Ltd
M Barnwell Services Ltd
ME Railway Research Group, University of Sheffield
Mini Gears Group
Nord-Lock Group
OLD Engineering Co Ltd Perpetuum Ltd
Premier Pits
Sabre Rail Services Ltd
Serco Rail Technical Services
SKF (UK) Limited
Stadler Rail Management AG
Standish Engineering Co Ltd
STAUFF UK Ltd
Sulzer Electro Mechanical Services UK
Tecforce Ltd
Trelleborg Antivibration Solutions
TVS Supply Chain Solutions Ltd
UKRL – UK Rail Leasing Ltd
Unipart Rail
Voith Turbo Limited
Wabtec Rail Limited
White Lion Engineering Ltd
William Cook Rail Ltd
ZF Services UK Ltd
Bogie Jumpers
HUBER+SUHNER (UK) Ltd
Bogies Running Gear AEGIS
AJT Engineering Ltd
Arlington Fleet Group
BG Steels Ltd
Brodie Engineering Limited
Browns Fasteners Ltd
David Brown Gear Systems Limited
DB Cargo (UK) Limited
GMT Rubber-Metal-Technic Ltd
Gurit (UK) Ltd
IGW International n.v
Indestructible Paint Limited
Jumo Instrument Co Ltd
KEC Limited
LUR Ltd
M Barnwell Services Ltd
ME Railway Research Group, University
of Sheffield
Mini Gears Group
Nord-Lock Group
OLD Engineering Co Ltd
Perpetuum Ltd
Powertherm Contracting Services
Serco Rail Technical Services
SKF (UK) Limited
Stadler Rail Management AG
Standish Engineering Co Ltd
STAUFF UK Ltd
Trelleborg
Inter-Vehicle
Passenger
DGauge
Group Limited
Houghton International
IFC Inflow
Indestructible Paint Limited
James Troop & Co Ltd
Jumo Instrument Co Ltd
Powertherm Contracting Services
Rolls-Royce Solutions UK Ltd
Rubirail
Trelleborg Antivibration Solutions
UKRL
Unipart Rail
Voith Turbo Limited
Wabtec Rail Limited
Rolling Stock Components
AB Hoses & Fittings Ltd
ABB Electrification Products
ABM Manufacturing AEGIS
Aerco Ltd
Airguard Filters Ltd
AJT Engineering Ltd
AME-3D
AP Diesels Ltd
Arlington Fleet Group
Arrk Europe Ltd
Axair Fans UK Limited
Beakbane Ltd
Belvoir Rail Ltd Bender UK Ltd
BG Steels Ltd
Brecknell Willis
Browns Fasteners Ltd
BTRoS Interiors and Cabling Division
CAP Productions Limited
Capital Seating
CF Booth Limited
Charcroft Electronics
Craig & Derricott Ltd
Dartford Composites Ltd
Datum Composites
David Brown Gear Systems Limited
Dellner Ltd Design and Analysis Ltd
Dorma Kaba Ltd
Dyer Engineering Ltd
EBC Brakes
Ferrabyrne Limited
Flexicon Ltd
GD Rectifiers
GDM Heat Transfer Ltd
GMT Rubber-Metal-Technic Ltd
Grayson Thermal Systems
Greenwood Engineering
GT Engineering (Markyate) Ltd
Gurit (UK) Ltd
HaslerRail AG
HaslerRail Secheron UK
Hayley Rail
Houghton International
Hydram Engineering Limited
HydraPower Dynamics Ltd
I M Kelly R&A Ltd
IFC Inflow
IGW International n.v
Indestructible Paint Limited
IXYS UK Westcode Ltd
J-Flex Rubber Products
JR Dynamics Ltd
Jumo Instrument Co Ltd
KEC Limited
Kingston Engineering Co (Hull) Ltd
Kleeneze – Koti Ltd
Kluber Lubrication
LEM Regional Office UK
LPA Channel Electric
LUR Ltd
M Barnwell Services Ltd
Marsh Bellofram Europe Ltd
Maycast – Nokes Precision Engineering
Mettex Electric Co Ltd
Micro-Mesh Filtration
Midland Alloy Ltd
Mini Gears Group
MTM Power Messtechnik
Mellenbach GmbH
Nord-Lock Group
Nufox Rubber Ltd
Oleo International
Omnicom Balfour Beatty
Parker Hannifin
PD Devices Ltd
Pro-Style Ltd
Prysmian UK
PSV Wipers Ltd
Record Electrical Associates Ltd
Rowe Hankins Ltd
Roxtec Ltd
Sabre Rail Services Ltd
Samuel Taylor Ltd
Schaeffler (UK) Ltd
Schaltbau Transportation UK Ltd
Schaltbau-ME
Serco Rail Technical Services
Shield Batteries Ltd
SKF (UK) Limited
Stadler Rail Management AG
Standish Engineering Co Ltd
Star Fasteners (UK) Ltd (Huck Fastener
Distributor)
STAUFF UK Ltd
Sulzer Electro Mechanical Services UK
Tecforce Ltd
Televic GSP
Tiflex Ltd – Trackelast Specialist Rail
Solutions
Time 24
TRB Lightweight Structures Ltd
Trelleborg Antivibration Solutions
Tribo “LLC Bilotserkivskiy Zavod Tribo Ltd’’
Trolex Ltd
TVS Supply Chain Solutions Ltd
UKRL – UK Rail Leasing Ltd
Unipart
Rolling
LUR
Maycast
Precision Engineering
McGeoch Technology Ltd
Mettex Electric Co Ltd
Midland Alloy Ltd
Novograf
Parker Hannifin
Permalok Fastening Systems Ltd
PSI Technologies Ltd
Samuel Taylor Ltd
Serco Rail Technical Services
Slingco Limited
Stadler Rail Management AG
Standish Engineering Co Ltd
Star Fasteners (UK) Ltd (Huck Fastener Distributor)
Sulzer Electro Mechanical Services UK
Tecforce Ltd
Techpol Ltd
Televic GSP
Time 24
TRB Lightweight Structures Ltd
Trelleborg Antivibration Solutions
Tribo “LLC Bilotserkivskiy Zavod Tribo Ltd’’ Trolex Ltd
Tufnol Composites Ltd
TXM Consult UKRL – UK Rail Leasing Ltd
Unipart Rail
Voith Turbo Limited
Wabtec Rail Limited
William Cook Rail Ltd
Seating
Capital Seating Star Fasteners (UK) Ltd (Huck Fastener Distributor)
Special Lightweight Insulating Materials
Cecence Ltd
Structural Fasteners & Lockbolts
AME-3D
Orbital Fasteners Star Fasteners (UK) Ltd (Huck Fastener Distributor)
Train Heating & Airconditioning
Belvoir Rail Ltd
Browns Fasteners Ltd
Coulstock & Place Engineering Ltd
Grayson Thermal Systems
Gurit (UK) Ltd
Nortek Global HVAC UK Ltd
Star Fasteners (UK) Ltd (Huck Fastener
Distributor)
STAUFF UK Ltd
Sulzer Electro Mechanical Services UK
Train to Ground Communication
HUBER+SUHNER (UK) Ltd
Waste Removal
APPS UK Ltd
Browns Fasteners Ltd
CF Booth Limited
Pennys Group Ltd
REACT Specialist Cleaning Ltd
Rhodar Limited
STAUFF UK Ltd
Rolling Stock Disposal /
Scrap Netal Dealers
CF Booth Limited
Seating
Capital Seating
Speed / Pressure Indicators & Gauges
Acutest (Head Office)
Data Acquisition &
1st Line Defence Ltd
Unit 3 Maple Park, Essex Road Hoddesdon EN11 0EX
T: 01992 446974
E: info@1stlinedefence.co.uk
W: www.1stlinedefence.co.uk
1stinRail
1d North Crescent, Cody Road London E16 4TE
T: 020 7474 1459
E: info@1stinrail.co.uk
W: www.1stinrail.co.uk
21st Century Technology
12 Charter Point Way, Ashby-De-La-Zouch Leicestershire LE65 1NF
T: 0844 871 7990
E: info@21stplc.com
W: www.21stplc.com
360 Vision Technology Ltd
7 Seymour Court, Manor Park Runcorn Cheshire WA7 1SY
T: 0870 903 3601
E: info@360visiontechnology.com
W: www.360visiontechnology.com
3Di International Limited 1 Ham Business Centre, 53 Brighton Road Shoreham-by-Sea West Sussex BN43 6RE
T: 01273 464883
E: 3di@dial.pipex.com
W: www.3di-international.com
3M Bracknell 3M Centre, Cain Road Bracknell Berkshire RG12 8HT
T: 0870 608 0050
E: bondingsolutions.uk@3mukcit.freshdesk.com
W: www.3m.co.uk
3SL Suite 2, 22a Duke Street
Barrow-in-Furness Cumbria LA14 1HH
T: 01229 838867
E: salesdetails@threesl.com
W: www.threesl.com
3Squared Ltd
Fountain Precinct, Balm Green Sheffield S1 2JA
T: 0333 121 3333
E: hello@3squared.com
W: www.3squared.com
3Ways Railway & Construction Services Ltd
Unit 8 & 9, Thurrock Commercial Park Purfleet Ind. Park South Ockenden RM15 4XA
T: 01708 680160
E: info@3waysrcs.co.uk
W: www.3waysrcs.co.uk
4 Acre Ecology is an ecological consultancy offering expert advice and services, based on sound, scientific data. We provide services including species (bat, Badger, GCN, reptile, Dormouse) and habitat surveys, mitigation design, site management plans, protected species licencing, planning advice and Ecological Clerk of Works.
4 Acre Ecology
The Little House, Lower Crescent Minster Lovell Witney OX29 0SD
T: 01993 864958
E: info@4acreecology.co.uk
W: www.4acreecology.co.uk
4 Rail Services Ltd
Unit 11, Iron Bridge Close Great Central Way London NW10 0UF T: 020 8955 1700
E: enquiries@4-rail.com
W: www.4-rail.com
40Seven Limited
Cross Green Ind. Estate, Cross Green Way Leeds LS9 0SE
T: 0113 201 9700
E: info@40seven.com
W: www.40seven.com
42 Technology Ltd
5-6 Meadow Lane, St Ives Cambridgeshire PE27 4LG
T: 01480 302700
E: answers@42technology.com
W: www.42technology.com
80:20 Communications
Hadleigh House, 232 High Street
Guildford Surrey GU1 3JF
T: 01483 447380
E: hello@8020comms.com
W: www.8020comms.com
8Point8 Support Limited
Units 10-12, Yorkshire Way, West Moor Park
Armthorpe Doncaster DN3 3FE
T: 01302 965050
E: info@8point8support.com
W: www.8point8support.com
A Hingley & Son (Timber) Ltd
Nether Lane, Hazlewood Belpher Derbyshire DE56 4AP
T: 01773 550055
E: sales@hingleytimber.co.uk
W: www.hingleytimber.co.uk
A-Plant Rail
102 Dalton Avenue, Birchwood Park Warrington Cheshire WA3 6YE
T: 0845 602 1304
E: rail@aplant.com
W: www.aplant.com
A&E Systems Europe
3 Charles Wood Road, Dereham Norfolk NR19 1SX
T: 01362 694915
E: uk@ae-sys.com
W: www.ae-sys.com
A&M EDM Limited
Unit 25, Mornington Road Smethwick West Midlands B66 2JE
T: 0121 558 8352
E: info@amedm.co.uk
W: www.amedm.co.uk
A&M Electrical Services Ltd
Unit 9, 194 Commerce Park
Stephenson Road Washington NE37 3HR
T: 0191 419 1519
E: info@amelectricals.com
W: www.am-electricals.com
A1 Group Silver Birches, Highland Avenue Wokingham Berkshire RG41 4SP
T: 0118 989 4652
E: info@a1groupcomp.co.uk
W: www.a1groupcomp.co.uk
AA Security Ltd
57 Green Lane, Ilford Essex IG1 1XG
T: 020 8514 0861
E: info@aasecurity.co.uk
W: www.aasecurity.co.uk
Aalco Metals Ltd Parkway House, Unit 6 Parkway Ind. Estate Pacific Avenue Wednesbury WS10 7WP
T: 01932 576820
E: info@aalco.co.uk
W: www.aalco.co.uk
AARC Professional Services Limited is a railway consultancy drawing on five decades of experience to provide expert support to the industry. We comprise likeminded professionals who deliver outstanding outcomes by:
• Helping clients achieve their goals…
• Through strategic/technical expert advice… Across a range of disciplines…
• From frontline through to boardroom
AARC Professional Services Limited
1 Lant Close, Kings Bromley Staffordshire DE13 7JW
T: 07841 611657
E: info@aarcps.co.uk
W: www.aarcps.co.uk
Aaron Rail Ltd
Bramhall Moor Tech Park, Pepper Road
Hazel Grove Stockport SK7 5BW
T: 0161 302 3670
E: enquiries@aaronrail.co.uk
W: www.aaronrail.co.uk
Aarsleff Ground Engineering
Hawton Lane, Balderton
Newark Nottinghamshire NG24 3BU
T: 01636 611140
E: info@aarsleff.co.uk
W: www.aarsleff.co.uk
Aati Rail Limited
11 Swinborne Drive, Springwood Ind. Estate Braintree Essex CM7 2YP
T: 01376 346278
E: info@aati.co.uk
W: www.aati.co.uk
AB Connectors Ltd / TT Electronics
Mountain Ash, Abercynon Rhondda Cynon Taff Wales CF45 4SF
T: 01443 740331
E: sales@ttabconnectors.com
W: www.ttabconnectors.com
The UK’s leading hose suppliers to the rail industry. We are a dynamic and engaged, delivery focused, supplier of products and services in the rail industry. We have been in business for over 20 years, building an enviable reputation for successfully doing things that others say can’t be done. “We have the hose world in our hands“.
AB Hoses & Fittings Ltd
Units 5-7, Warwick Street Industrial Estate Chesterfield S40 2TT
T: 01246 208831
E: sales@abhoses.com
W: www.abhoses.com
AB Precision (Poole) Limited
1 Fleets Lane, Poole Dorset BH15 3BZ
T: 01202 665000
E: enquires@abprecision.co.uk
W: www.abprecision.co.uk
AB Turnkey Solutions Ltd
Unit 2-3, The Enigma Centre, Bilton Road Bletchley Milton Keynes MK1 1HW
T: 01908 644748
E: sales@abturnkey.co.uk
W: www.abturnkey.co.uk
AB2000 Ltd
95 Westburn Drive, Cambuslang Glasgow Scotland G72 7NA
T: 0141 646 1212
E: enquiries@ab2000.co.uk
W: www.ab2000.co.uk
ABA Surveying Ltd
The Lansbury Estate, Lower Guildford Road Woking Surrey GU21 2EP
T: 01483 797111
E: info@abasurveying.co.uk
W: www.abasurveying.co.uk
Abacus Lighting Ltd
Oddicroft Lane, Sutton-in-Ashfield Nottinghamshire NG17 5FT
T: 01623 511111
E: sales@abacuslighting.com
W: www.abacuslighting.com
ABB Electrification Products
Tower Court, Foleshill Enterprise Park Courtaulds Way Coventry CV6 5NX
T: 024 7636 8500
E: info@abb.co.uk
W: www.abb.com
Abbey Pynford Foundation Systems Ltd 2-6 Bilton Way, Luton Bedfordshire LU1 1UU
T: 01442 212112
E: Info@abbeypynford.co.uk
W: www.abbeypynford.co.uk
Abbi Access Services Ltd
Clwyd Close, Hawarden Ind. Estate Manor Lane Hawarden CH5 3PZ
T: 01244 629919
E: admin@abbiaccess.com
W: www.abbiaccess.com
ARC provides independent professional consultancy and assessment services to rail operators, suppliers, regulators and Government bodies in the UK and Australia. We support our clients in the approvals process through effective and efficient management of safety risks and the achievement of a safer railway.
Abbott Risk Consulting Ltd
11 Albyn Place, Edinburgh EH2 4NG
T: 0131 220 0164
E: rail@consultarc.com
W: www.consultarc.com
Abel Systems Ltd Station Road, Tupton Chesterfield Derbeyshire S42 6DA
T: 01246 851175
E: sales@abelsystems.co.uk
W: www.abelsystems.co.uk
Abellio UK HQ 5th Floor, The Culzean Building 36 Renfield Street Glasgow G2 1LU
T: 0141 320 0620
E: customer.care@abellio.co.uk
W: www.abellio.com
Aberdeen & Grampian Chamber of Commerce
The Hub, Exploration Dr, Aberdeen Energy Park Bridge of Don Aberdeen AB23 8GX
T: 01224 343900
E: info@agcc.co.uk
W: www.agcc.co.uk
ABG Construction & Mineral Tools Ltd
Charterhouse Road
Coventry CV1 2BJ
T: 024 7635 6344
E: info@abgtools.com
W: www.abgtools.com
ABG Geosynthetics
E7 Meltham Mills Road, Meltham Holmfirth HD9 4BS
T: 01484 852096
E: enquiries@abgltd.com
W: www.abg-geosynthetics.com
ABI Electronics Ltd
Dodworth Business Park, Barnsley South Yorkshire S75 3SP
T: 01226 207420
E: sales@abielectronics.co.uk
W: www.abielectronics.co.uk
Able Piling
U2 Sharlands Rd Ind Est, Sharlands Road
Newgate Lane Fareham Hampshire PO14 1RD
T: 01489 797600
E: sales@frankifoundations.co.uk
W: www.frankifoundations.co.uk
Abloy UK
Portobello Works, School Street
Willenhall West Midlands W13 3PW
T: 01902 364500
E: info@abloy.co.uk
W: www.abloy.co.uk
ABM has 3 interlinked buildings in North Coventry with 160,000 ft2 of Manufacturing Capacity in Stainless Steel and Aluminum. Our Press Shop, 3D 5 axis Lasers , Roll Mills, Brake Press’s, Painting Facility, Fabrication and Assembly Cells provide Exterior and Interior parts for our Rail, Construction and Automotive Customers. ISO 9001 & IATF 16949 approved.
ABM Manufacturing
56 Bayton Road, Bayton Ind. Estate Exhall Coventry CV7 9EL
T: 02476 100 567
E: sales@abm-manufacturing.com
W: abm-manufacturing.com
ABM Precast Solutions Ltd
Ollerton Road, Tuxford Newark Nottinghamshire NG22 0PQ
T: 01777 872233
E: precast@abmeurope.com
W: www.abmprecast.co.uk
Abnormal Load Services – ALS
Building 3, Eltherington Bus Pk 1305 Hedon Road Hull, East Yorks HU9 5QD
T: 01482 796214
E: info@als-europe.com
W: www.abnormal-loads.com
ABP Associates Limited
8 Chancerygate Bus Ctr, Manor House Avenue Millbrook Southampton SO15 0AE
T: 02380 528571
E: marvin.sexton@abp.uk.com
W: www.abp.uk.com
Abracs Ltd
Abracs House, George Cayley Drive Clifton Moor York YO30 4XE
T: 01904 789997
E: abracs@abracs.com
W: www.abracs.com
ABS Consulting Ltd
EQE House, The Beacons, Warrington Road Birchwood Cheshire WA3 6WJ
T: 01925 287300
E: enquiriesuk@abs-group.com
W: www.abs-group.com
ABS Consulting Ltd (London Office)
ABS House, 1 Frying Pan Alley London E1 7HR
T: 020 7377 4422
E: info@abs-group.com
W: www.abs-group.com
Absoft Ltd
Davidson House, Aberdeen Innovation Pk Balgownie Road Aberdeen AB22 8GT
T: 01224 707088
E: info@absoft.co.uk
W: www.absoft.co.uk
AbsTracked Solutions is a highly respected safety, assurance and competence management consultancy, specialising in the railway and airport sectors. Our core workstreams include regulatory submissions, change management, project safety assurance and accident investigation. For information on these services or for a demonstration of our tablet-based electronic competence management application, please visit ‘Contact Us’ at www.AbsTracked.co.uk.
AbsTracked Solutions Ltd
AbsTracked House, 120 Birches Lane South Wingfield Derbyshire DE55 7LZ
T: 07872 609 619
E: enquiries@abstracked.co.uk
W: www.abstracked.co.uk
Abtus Limited
Falconer Road, Haverhill Suffolk CB9 7XU
T: 01440 702938
E: sales@abtus.com
W: www.abtus.com
ACAL BFI UK Ltd
3 The Business Centre, Molly Millars Lane Wokingham RG41 2EY
T: 0118 978 8878
E: sales-uk@acalbfi.co.uk
W: www.acalbfi.co.uk
Acanthus Architects LW
Voysey House, Barley Mow Passage London W4 4PN
T: 020 8994 2288
E: design@acanthuslw.com
W: www.acanthuslw.com
Accelerator Solutions Ltd
Elizabeth House, 6th Floor
39 York Road London SE1 7NQ
T: 0845 260 6886
E: info@acceleratorsolutions.com
W: www.acceleratorsolutions.com
Accenture
9-10 St Andrew Square
Edinburgh EH2 2AF
T: 0131 718 3501
E: info@accenture.com
W: www.accenture.com
Access Design & Engineering Marsh Road, Middlesbrough Cleveland TS1 5JS
T: 01952 588788
E: sales@access-design.co.uk
W: www.access-design.co.uk
Access Disputes Committee
1 Eversholt Street, Floor 8 London NW1 2DN
T: 020 7554 0601
E: sec.adc@btconnect.com
W: www.accessdisputesrail.org
Access IS
18 Suttons Bus Park, Reading Berkshire RG6 1AZ
T: 0118 966 3333
E: sales@access-is.com
W: www.access-is.com
ACCON UK are specialists in noise and vibration for railway projects. As one of the leading expert consultancies in railway noise, vibration, and ground-borne noise, with over 30 years’ experience in rail projects, we are able to provide specialist consultancy services covering planning, construction, operation and investigation of noise issues.
ACCON UK Limited
Unit B Fronds Park, Frouds Lane
Aldermaston Reading RG7 4LH
T: 0118 971 0000
E: enquiry@accon-uk.com
W: www.accon-uk.com
Accord Marketing Ltd
Endeavour House, 189 Shaftesbury Avenue
Covent Garden London WC2H 8JR
T: 020 7395 9655
E: enquiries@accordmarketing.com
W: www.accordmarketing.com
Accurate Section Benders
Dawley Brook Road, Kingswinford West Midlands DY6 7AU
T: 01384 402402
E: sales@accuratesectionbenders.co.uk
W: www.accuratesectionbenders.co.uk
Aces Compressors
Unit 4 Tower Estate, Warpsgrove Lane
Chalgrove Oxfordshire OX44 7XZ
T: 01865 891522
E: info@acescomp.co.uk
W: www.acescomp.co.uk
Acheson + Glover
4 Marlin Office Village, 1250 Chester Road
Castle Vale Birmingham B35 7AZ
T: 0121 747 0202
E: specifications@ag.uk.com
W: www.ag.uk.com
Achilles Information Ltd
30 Western Avenue, Milton Park
Abingdon Oxfordshire OX14 4SH
T: 01235 861118
E: enquiries@achilles.com
W: www.achilles.com
ACM Composite Bearings Ltd
Derwent Way, Wath West Ind Estate Rotherham South Yorkshire S63 6EX
T: 01709 874951
E: sales@acmbearings.co.uk
W: www.acmbearings.co.uk
ACO Technologies Plc
ACO Business Park, Hitchin Road
Shefford Bedfordshire SG17 5TE
T: 01462 816666
E: technologies@aco.co.uk
W: www.aco.co.uk
Acorel
Unit 23, Braintree Ent Centre
46 Springwood Dr Braintree CM7 2YN
T: 01376 324825
E: info@acorel.com
W: www.acorel.com
Acorn Group – Head Office Somerton House, Hazell Drive Newport NP10 8FY
T: 01633 660000
E: branch@acornpeople.com
W: www.acornpeople.com
Acorn Industries Ltd
Unit A Denby Way, Hellaby Ind Estate Rotherham South Yorkshire S66 8HR
T: 0800 876 6441
E: info@acorn-ind.co.uk
W: www.acorn-ind.co.uk
Acousteel
Naylor Court, Patterson Road Blaydon-on-Tyne Tyne & Wear NE21 5SD
T: 0191 499 0244
E: sales@nislimited.com
W: www.acousteel.com
Acoustic Sensing Technology UK Ltd
22nd Floor City Tower, Piccadilly Plaza Manchester M1 4BT
T: 0161 413 9615
E: office@acousticsensing.co.uk
W: www.acousticsensing.co.uk
Acrastyle Limited
North Lonsdale Road, Ulverston Cumbria LA12 9DP
T: 01229 583232
E: enquiries@acrastyle.co.uk
W: www.acrastyle.co.uk
ACS Testing Ltd
Unit 14, Blackhill Road West Poole Dorset BH16 6LE
T: 01202 622858
E: testing@acstesting.co.uk
W: www.acsgroupofcompanies.co.uk
Actaccom Ltd (Actiform Group)
Queens Buildings, Lowlands Road Mirfield West Yorkshire WF14 8LX
T: 01924 498557
E: sales@actiformgroup.co.uk
W: www.actiformgroup.co.uk
Actavo Building Solutions
Unit 1 First Floor, Calder Close Calder Park Wakefield WF4 3BA
T: 0330 102 5544
E: building.uk@actavo.com
W: www.actavo.com
Actemium UK
Unit 3, Elmdon Trading Estate
Bickenhill Lane Marston Green B37 7HE
T: 02392 269960
E: automation.sales@actemium.co.uk
W: www.actemium.co.uk
Acumen Design Associates Ltd
Holborn Hall, 193-197 High Holborn London WC1V 7BD
T: 020 3026 4560
E: info@acumen-da.com
W: www.acumen-da.com
Test equipment specialists with over 32 years’ experience.
Equipment Supply: Great stock availability, expert support, technical on-site demonstrations (with further training available) Hire: Fully calibrated stock and technical support.
Calibration/Repair (UKAS/Traceable): Four service centres for UK-wide coverage.
• 65,000 calibrations/yr
• 450 calibration days at customer premises/yr
• 11,000 component-level repairs/yr
• Certificate management software
Corporate website: www.acutest.net/
Test Instrument Supply website: www.acutestdirect.co.uk/
Acutest (Head Office)
Century Road, High Carr Business Park
Newcastle-under-Lyme Staffordshire ST5 7UG T: 01782 563030
E: sales@acutest-ukti.co.uk
W: www.acutest.net
Acutest (Northern Office)
Unit 4, Evans Bus Centre, Durham Way South Newton Aycliffe Bus Park County Durham DL5 6ZF
T: 01782 563030
E: sales@acutest-ukti.co.uk
W: www.acutest.net
Acutest (Scotland Office)
Unit 2 Jubilee Court, Montrose Avenue Hillington Park Glasgow G52 4LB
T: 01782 563030
E: sales@acutest-ukti.co.uk
W: www.acutest.net
Acutest (Western Office)
Acutest 61 Macrae Road, Eden Office Park Ham Green Bristol BS20 0DD
T: 01782 563030
E: sales@acutest-ukti.co.uk
W: www.acutest.net
Adam Smith Conferences
14 Gray’s Inn Road
London WC1X 8HN
T: 020 8004 5707
E: info@adamsmithconferences.com
W: www.adamsmithconferences.com
Adamson Associates 6th floor, 1 Canada Sq, Canary Wharf
London E14 5AB
T: 020 7418 2068
E: info-uk@adamson-associates.com
W: www.adamson-associates.com
Adaptive Modules Ltd
Lorna House, 103 Lorna Road
Hove East Sussex BN3 3EL
T: 01273 830929
E: sales@adaptivemodules.com
W: www.adaptivemodules.com
Adare SEC
Byron House, Willow Drive
Nottingham NG15 0DP
T: 01623 727500
E: enquiries@adaresec.com
W: www.adaresec.com
ADAS (Cambridge) Battle Gate Road, Boxworth Cambridge CB23 4NN
T: 01954 268200
E: enquiries@adas.co.uk
W: www.adas.uk
ADAS Uk Ltd (Head Office)
Spring Lodge, 172 Chester Road
Helsby WA6 0AR
T: 01928 726006
E: enquiries@adas.co.uk
W: www.adas.co.uk
Addagrip Terraco Ltd
Addagrip House, Bell Lane Ind Estate
Uckfield East Sussex TN22 1QL
T: 01825 761333
E: sales@addagrip.co.uk
W: www.addagrip.co.uk
Addleshaw Goddard LLP
Milton Gate, 60 Chiswell Street London EC1Y 4AG
T: 020 7305 5692
E: info@addleshawgoddard.com
W: www.addleshawgoddard.com
ADE Power
Hellaby Industrial Est, Hellaby Lane Rotherham S66 8HN
T: 01977 657982
E: enquiries@adeltd.co.uk
W: www.adeltd.co.uk
Adecco Group UK & Ireland
Millennium Bridge House, 2 Lambeth Hill London EC4V 4BG
T: 020 7403 0978
E: headoffice@adeccogroup.com
W: www.adecco.co.uk
Adeo Construction Consultants
Oakhurst Business Park, Wilberforce Way Southwater West Sussex RH13 9RT
T: 01403 821770
E: enquiries@adeo.uk.com
W: www.adeo.uk.com
Adey Steel
Falcon Industrial Park, Meadow Lane Loughborough LE11 1HL
T: 01509 556677
E: mail@adeysteel.co.uk
W: www.adeysteelgroup.co.uk
Adfield Group
The Granary, Beckbury Shifnal Shropshire TF11 9DG
T: 01952 752500
E: hello@adfield.co.uk
W: www.adfield.co.uk
Adfil
Devonshire House, 60 Goswell Road Barbican London EC1M 7AD
T: 01482 863777
E: info@adfil.co.uk
W: www.adfil.com
Adomast manufacture a comprehensive range of high performance and specialist construction chemicals for civil engineering and railway applications. Included are a diverse and high quality range of cementitious and epoxy and polyester resin based protective/ repair compounds. We also offer bespoke manufacturing where products can be specifically designed for exacting applications.
Adomast Manufacturing Limited
Units 1 & 2, Barkston Road
Carlton Ind Estate Barnsley S71 3HU
T: 01226 707863
E: enquiries@adomast.co.uk
W: www.adomast.co.uk
ADP Group Ltd
Firing Close Farm, Wickwar
Wotton Under Edge Gloucestershire GL12 8PE
T: 01454 227115
E: info@adpgroupltd.com
W: www.adpgroupltd.com
ADS Group Limited (Farnborough)
Show Centre, ETPS Road, Farnborough Aerodrome Hampshire GU14 6FD
T: 020 7091 4500
E: enquiries@adsgroup.org.uk
W: www.adsgroup.org.uk
ADS Group Limited (Head Office)
Salamanca Square, 9 Albert Embankment London SE1 7SP
T: 020 7091 4500
E: enquiries@adsgroup.org.uk
W: www.adsgroup.org.uk
ADT Fire & Security
Security House, The Summit Hanworth Road Sunbury on Thames TW16 5DB
T: 01932 743229
E: sales@adt.co.uk
W: www.tycoint.com
Advance Electronics Ltd
Advance Park, Wrexham Wales LL14 3YR
T: 01978 821000
E: sales@aelgroup.co.uk
W: www.aelgroup.co.uk
Advance Training & Recruitment
Stamford House, 91 Woodbridge Road Guildford Surrey GU1 4QD
T: 01483 361061
E: info@advance-trs.com
W: www.advance-trs.com
Advanced Building Composites (ABC) Ltd Civils House, Cemetery Road
Telford Shropshire TF4 2BS
T: 01952 504288
E: sales@abc-uk.com W: www.abc-uk.com
Advanced Chemical Etching Ltd (ACE)
31-34 Hortonwood 33, Telford Shropshire TF1 7EX
T: 01952 416666
E: info@ace-uk.net W: www.ace-uk.net
Advanced Engineering Techniques Ltd (AET UK)
9-15 Holbrook Avenue, Holbrook Ind Estate
Halfway Sheffield S20 3FF
T: 0114 247 5725
E: sales@aetuk.com W: www.aetuk.com
Advanced Handling Ltd
Newcombe Way, Orton Southgate Peterborough PE2 6SE
T: 01778 345365
E: sales@advancedhandling.co.uk
W: www.advancedhandling.co.uk
Advanced New Technology
Pippingford Park Manor, Nutley Uckfield TN22 3HW
T: 01825 713058
E: info@a-n-t.com W: www.a-n-t.com
Advanced Resource Managers (ARM)
Langstone Tech Park, Langstone Road Havant Hampshire PO9 1SA
T: 023 9222 8228
E: hello@arm.co.uk W: www.arm.co.uk
Advanced Selection Ltd
30 Bell Street, Romsey Hamsphire SO51 8GW
T: 023 8074 4455
E: office@advancedselect.co.uk
W: www.advancedselect.co.uk
Advantage Resourcing (London & City)
No 1 Poultry
London EC2R 8EJ
T: 020 7390 7000
E: infoaruk@advantageresourcing.com
W: www.advantageresourcing.co.uk
Advantage xPO
No 1 Poultry
London EC2R 8EJ
T: 020 7390 7000
E: info@advantagexpo.com
W: www.advantagexpo.com
Advante – Oasis® Welfare
10/11 Argent Court, Sylvan Way Basildon Essex SS15 6TH
T: 01268 280500
E: sales@advante.co.uk
W: www.advante.co.uk
Advantech Unit 3 Gunnery Terrace, Duke of Wellington Ave
Royal Arsenal Woolwich London SE18 6SW
T: 020 8836 9732
E: embedded@advantech.eu
W: www.advantech.eu
AE Engineering Ltd Unit 3, Maritime Street Fleetwood Lancashire FY7 7PB
T: 0800 987 5434
E: info@ae-engineering.co.uk
W: www.ae-engineering.co.uk
AE Harris & Co (Birmingham) Ltd
109-138 Northwood St
Birmingham B3 1SZ
T: 0121 200 3700
E: sales@aeharris.co.uk
W: www.aeharris.co.uk
AE Oscroft & Sons Limited
Washford Ind Estate, Heming Road
Redditch Worcestershire B98 0EA
T: 01527 502203
E: info@aeoscroft.co.uk
W: www.aeoscroft.co.uk
AE Yates Ltd
Cranfield Road, Lostock Ind Estate Lostock Bolton BL6 4SB
T: 01204 696175
E: civils@aeyates.co.uk
W: www.aeyates.co.uk
Aecom
Tricentre 3, Newbridge Square Swindon SN1 1BY
T: 01793 508500
E: enquiries@aecom.com
W: www.aecom.com
Aedas Group Ltd
Ivory House, St Katharine Docks London E1W 1AT
T: 020 3764 5450
E: London@aedas.com
W: www.aedas.com
AEG Power Solutions Ltd
Electric Avenue, Enfield Middlesex EN3 7XU
T: 01992 719200
E: sales@aegps.com
W: www.aegps.com
AEGIS has been operating in the UK for 25 years. Through our Engineering and Independent Certification businesses we offer engineering expertise, innovative solutions and a full suite of Certification Services to the international rail industry, including Passenger Rolling Stock, Freight, On Track Plant & Machines, Signalling, Telecoms, Civil Infrastructure and Electrification.
AEGIS
29 Brunel Parkway, Pride Park Derby DE24 8HR
T: 01332 384302
E: sales@aegisengineering.co.uk
W: www.aegisengineering.co.uk
AEI Cables Durham Road, Birtley
Chester-le-Street County Durham DH3 2TD
T: 0191 410 3111
E: sales@aeicables.co.uk
W: www.aeicables.co.uk
Aerco Ltd
17 Lawson Hunt Ind Park, Broadbridge Heath Horsham West Sussex RH12 3JR
T: 01403 260206
E: sales@aerco.co.uk
W: www.aerco.co.uk
Aerolux Ltd
91 Chorley Road, Blackpool Lancashire FY3 7XQ
T: 01253 396670
E: sales@aerolux.co.uk
W: www.aerolux.co.uk
Aeropair are a 25 year old, Worldwide, Aircraft and Railway Carriage Interior Production and Repair company with vast experience on all Composite, Plastic and metallic machined and formed parts to include seating with a range of over 5000 parts, with JV’s In Asia and India for the supply of Multiple Fabric solutions. Bespoke VVIP & VIP Interiors also supported.
Aeropair Ltd
5 Neil Street, Meadowside Street
Renfrew Scotland PA4 8TA
T: 0141 886 7005
E: enquiries@aeropair.co.uk
W: www.aeropair.co.uk
AF Switchgear Ltd
Nunn Brook Road, Sutton-In-Ashfield Nottinghamshire NG17 2HU
T: 01623 555600
E: sales@afswitchgear.co.uk
W: www.afswitchgear.co.uk
Afford Rent A Car Royal Oak Garage, City Road Fenton Stoke-on-Trent ST4 2PX
T: 01782 848627
E: info@affordrentacar.co.uk
W: www.affordrentacar.co.uk
AGD Equipment Ltd
Avonbrook House, 198 Masons Road Stratford Ent Park Stratford CV37 9LQ
T: 01789 292227
E: info@agd-equipment.co.uk
W: www.agd-equipment.co.uk
AGD Systems Ltd
White Lion House, Gloucester Road Cheltenham GL51 0TF
T: 01452 854212
E: sales@agd-systems.com
W: www.agd-systems.com
Agency Brazil
54 Marshall Street, Soho London W1D 7AZ
T: 020 7785 7383
E: london@agencybrazil.com
W: www.agencybrazil.com
Aggregate Industries UK Ltd (Leicestershire)
Bardon Hill, Coalville
Leicestershire LE67 1TL
T: 01530 510066
E: aggregates@aggregate.com
W: www.aggregate.com
Aggregate Industries UK Ltd (Scotland)
Duntilland Quay, Salsburgh
Shotts North Lanarkshire ML7 4NZ
T: 01698 870811
E: aggregates@aggregate.com
W: www.aggregate.com
Aggregate Industries UK Ltd (Somerset)
Edwin Sims House, Vallis Road
Frome Somerset BA11 3EG
T: 01373 456789
E: aggregates@aggregate.com
W: www.aggregate.com
Aggreko UK Ltd Kimpton Ind Estate, 14 Sandiford Road
Sutton SM3 9RD
T: 0345 824 7365
E: hire@aggreko.co.uk
W: www.aggreko.co.uk
AGH Engineering Ltd Mill House, North Street York North Yorkshire YO1 6JQ
T: 01904 545040
E: info@aghengineering.co.uk
W: www.aghengineering.co.uk
Agility3 Modelling and Simulation
Unit 7 Titmore Court, Titmore Green Hitchin Hertfordshire SG4 7JT
T: 01438 488066
E: info@agility3.co.uk
W: www.agility3.co.uk
AGS One (Anti Graffiti Systems)
Unit D, Prospect House, Hyde Business Park Brighton BN2 4JE
T: 01273 690059
E: info@agsone.co.uk
W: www.agsone.co.uk
AHL Resourcing Solutions Ltd
Unit B3, Hillborough Bus Park
Sweechbridge Road Herne Bay Kent CT6 6TE
T: 01227 362415
E: info@ahlsolutions.co.uk
W: www.ahlsolutions.co.uk
AHR Group Limited
5-8 Harwick Street London EC1R 4RG
T: 020 7837 9789
E: london@ahr.co.uk
W: www.ahr.co.uk
AIA Worldwide Ltd
200 Aldersgate Street London EC1A 4HD
T: 020 7993 1300
E: contactus@aia.co.uk
W: www.aia.co.uk
Ainscough Crane Hire Limited Bradley Hall, Bradley Lane Standish Lancashire WN6 0XQ
T: 0800 272 637
E: info@ainscough.co.uk
W: www.ainscough.co.uk
Air Products PLC Hersham Place, 41-61 Molesey Road Hersham Walton On Thames KT12 4RZ
T: 0800 389 0202
E: apukinfo@airproducts.com
W: www.airproduct.co.uk
Air Rail News Ltd
Link House, 140 Tolworth Broadway Surbiton KT6 7HT
T: 020 8339 6124
E: info@globalairrail.com
W: www.globalairrail.com
Air Sea Scotland Ltd Eagle House, 159 Wright Street
Renfrew Renfrewshire PA4 8AN
T: 0141 887 8877
E: admin@airseascotland.co.uk
W: www.airseascotland.co.uk
Airguard Filters Ltd Unit 16, Watery Lane Ind Estate Willenhall West Midlands WV13 3SU
T: 0333 323 2684
E: sales@airguardfilters.co.uk
W: www.airguardfilters.co.uk
Airport Operators Assocation
3 Birdcage Walk, London SW1H 9JJ
T: 020 7799 3171
E: info@aoa.org.uk
W: www.aoa.org.uk
Airquick Ltd
Brunel Business Park, Jessop Close Newark Nottinghamshire NG24 2AE
T: 01636 640480
E: sales@airquick.co.uk
W: www.airquick.co.uk
Airtec International Ltd
40 Couper Street, Glasgow Scotland G4 0DL T: 0141 552 5591
E: enquiries@airtecinternational.co.uk
W: www.airtecinternational.com
AJ Paveley & Co
416 Golden Hillock Road, Birmingham West Midlands B112QH
T: 0121 772 1739
E: sales@ajpaveley.com
W: www.ajpaveley.com
AJ Wells Architectural Enamel Bishop’s Way, Newport Isle of Wight PO30 5WS
T: 01983 537766
E: enamel@ajwells.co.uk
W: www.ajwells.com
AJC Retail Solutions Ltd
1 Bilton Way, Luton Bedfordshire LU1 1UU
T: 01582 727760
E: info@ajcretailsolutions.co.uk
W: www.ajcretailsolutions.co.uk
AJC Trailers Ltd
Unit 10, Cosgrove Way
Luton Bedfordshire LU1 1XL
T: 01582 486663
E: info@ajc-trailers.co.uk
W: www.easycabin.co.uk
AJT Engineering Ltd
Craigshaw Crescent, West Tullos
Aberdeen AB12 3TB
T: 01224 871791
E: info@ajt-engineering.co.uk
W: www.ajt-engineering.co.uk
Aker Solutions
Building 6, Chiswick Park
566 High Road London W4 5YS
T: 020 8987 2000
E: info@akersolutions.com
W: www.akersolutions.com
AKKA Aeroconseil UK
4 Brabazon Office Park, Gold Course Lane Filton Bristol BS34 7PZ
T: 0117 974 9820
E: aeroconseil-uk@aeroconseil.com
W: www.akka-technologies.com
Al-Vac UK Limited
Beecroft Nursery, Queen Anne Drive
Wimborne Dorset BH21 3BA
T: 01202 668001
E: mike@al-vac.co.uk
W: www.al-vac.co.uk
Alan Dick Communications Ltd
Unit 11 Billet Lane, Normanby Ent Park
Scunthorpe North Lincolnshire DN15 9YH
T: 01724 292200
E: info@alandickcomms.com
W: www.alandickcomms.com
Alcad
1st Floor Unit 5, Astra Centre
Edingburgh Way Harlow CM20 2BN
T: 01279 772555
E: alcad@alcad.com
W: www.alcad.com
The Alchemy Metals Group is an independent company trading scrap metal and waste across the UK. We work in partnership with business from a wide range of industries helping them manage their scrap metal and waste, maximise their financial returns and address key issues such as sustainability and environmental impact.
Alchemy Metals Ltd
Cavendish Point, Cavendish Road Stevenage SG1 2EU
T: 01438 745307
E: enquiries@alchemymetals.co.uk
W: www.alchemymetals.com
ALControl Oil & Fuel Labratories Ltd (Conwy) Unit 6, Conwy, Morfa Enterprise Park
Parc Caer Seion Conwy Gwynedd LL32 8FA
T: 01492 574750
E: oilinfo@alcontrol.com
W: www.alcontrol.com
ALE Heavylift – Head Office
2 Parker Court, Staffordshire Tech Park Stafford ST18 0WP
T: 01889 272500
E: info@ale-heavylift.co.uk
W: www.ale-heavylift.com
ALE UK Ltd
G/F Lunar House, Mercury Business Park Wycombe Lane Buckinghamshire HP10 0HH
T: 01628 810777
E: info.uki@al-enterprise.com
W: www.al-enterprise.com
Alere Healthcare Connections Ltd
U8 Prospect Bus Park, Langston Road
Loughton Essex IG10 3TR
T: 0845 677 3002
E: sales@alerehealthcareconnections.com
W: www.alerehealthcareconnections.com
Alere Toxicology PLC (Formerly Concateno UK)
21 Blacklands Way, Abingdon Business Park Abingdon OX14 1DY
T: 01235 861483
E: toxeu.enquiries@alere.com
W: www.aleretoxicology.com
Alexandra
West Park House, Thornbury Bristol BS35 2NT
T: 0333 600 1111
E: customercare@alexandra.co.uk
W: www.alexandra.co.uk
Alfred Bagnall & Sons (North)
6 Manor Lane, Shipley West Yorkshire BD18 3RD
T: 01274 714800
E: info@bagnalls.co.uk
W: www.bagnalls.co.uk
All Clothing & Protection Ltd
U6-7 Manor Park Ind Est, Station Road South Southampton Hampshire SO40 9HP
T: 023 8042 8003
E: sales@allclothing.co.uk
W: www.allclothing.co.uk
Allan J Hargreaves Plant Engineers Ltd Longmeadow Lane, Red Marsh Ind Estate Thornton Cleveleys FY5 4JT
T: 01253 859677
E: enquiries@ajhplant.com
W: www.ajhplant.com
Allan Webb Ltd
Red Lodge, Bonds Mill Stonehouse GL10 3RF
T: 01453 824581
E: sales@allanwebb.co.uk
W: www.allanwebb.co.uk
Allelys Heavy Haulage Ltd
Benavon, The Slough Studley Warwickshire B80 7EN
T: 01527 852408
E: heavyhaulage@allelys.co.uk
W: www.allelys.co.uk
ALLEN & YORK Ltd
Farrs House, Cowgrove Wimborne Dorset BH21 4EL
T: 01202 888986
E: info@allen-york.com
W: www.allen-york.com
Allen Watson Ltd
Rowhook Manor Estate, Rowhook Horsham RH12 3PS
T: 01403 790772
E: sales@allenwatson.com
W: www.allenwatson.com
Allerton Steel
Thurston Road, Northallerton North Yorkshire DL6 2NA
T: 01609 774471
E: contactus@allertonsteel.co.uk
W: www.allertonsteel.co.uk
Alliance Inspection Ltd
Unit 9, Old Marsh Farm Barns
Old Marsh Farm Rd Sealand Chester CH5 2LY
T: 01244 952531
E: enquiries@allianceinspection.co.uk
W: www.allianceinspection.co.uk
Alliance Rail Holdings
Northern House, Rougier Street York YO1 6HZ
T: 01904 628904
E: info@alliancerail.co.uk
W: www.alliancerail.co.uk
Allied Insulators Ltd
Unit 5, Scotia Road Bus Park
Fitzgerald Way Tunstall Staffs ST6 4HN
T: 0845 481 0208
E: enquiries@alliedinsulators.com
W: www.alliedinsulators.com
Allies & Morrison
85 Southwark Street London SE1 0HX
T: 020 7921 0100
E: newprojects@alliesandmorrison.com
W: www.alliesandmorrison.com
Allison Enterprises Ltd
East Fordell, Glenfarg
Perth Scotland PH22 9QQ
T: 01577 830003
E: info@allisonenterprises.co.uk
W: www.allisonenterprises.co.uk
Allport Cargo Services Ltd
Allport House, 1 Cowley Business Park
Cowley Uxbridge UB8 2AD
T: 01895 206000
E: info@uk.allportcargoservices.com
W: www.allportcargoservices.com
Allsee Technologies Ltd
Unit 5 Woodgate BP, Kettles Wood Drive Birmingham B32 3DB
T: 0121 421 4458
E: info@allsee-tech.com
W: www.allsee-tech.com
Alltask
Alltask House, Commissioners Road Medway City Estate Strood ME2 4EJ
T: 01634 298000
E: enquiries@alltask.co.uk
W: www.alltask.co.uk
Alltype Fencing Specialists Ltd
Ye Wentes Wayes, High Road Langdon Hills Essex SS16 6HY
T: 01268 545192
E: sales@alltypefencing.com
W: www.alltypefencing.com
Ally Structures Unit 5a, Aviation Park, Flint Road Saltney Ferry Chester CH4 0GZ
T: 01244 531889
E: sales@allystructures.co.uk
W: www.allystructures.co.uk
Alma Rail Limited 176 Chesterfield Road, North Wingfield Chesterfield Derbyshire S42 5LA
T: 01246 852621
E: info@almarail.co.uk
W: www.almarail.co.uk
Alpeco Ltd
66-69 Rabans Close, Aylesbury Buckinghamshire HP19 8RS
T: 01296 619510
E: sales@alpeco.co.uk
W: www.alpecoltd.com
Alpha Adhesives & Sealants Ltd
Llewellyn Close, Sandy Lane Ind Estate Stourport Worcestershire DY13 9RH
T: 01299 828626
E: sales@alpha-adhesives.co.uk
W: www.alpha-adhesives.co.uk
Alpha Electronics Ltd (Southern) U6-7 Spectrum Bus Park, Bircholt Road Maidstone Kent ME15 9YP
T: 01622 690187
E: sales@alpha-electronics.com
W: www.alpha-electronics.com
Alpha Sheetmetal Ltd Unit 7, Naylor Road Sweetbriar Ind Est Norwich NR3 2BZ
T: 01603 486108
E: sales@alphasheetmetal.com
W: www.alphasheetmetal.com
Alpha Technologies Europe Ltd
Twyford House, Thorley Bishop’s Stortford Hertfordshire CM22 7PA
T: 01279 501110
E: customerservice-EMEA@alphatechnologies.com
W: www.alphatechnologies.com
Alphatek Hyperperformance Coatings Ltd
A5 Cuba Ind Estate, Bolton Road North Ramsbottom BL0 0NE
T: 01706 821021
E: postbox@alphatek.co.uk
W: www.alphatek.co.uk
Alsim System Building Limited Stockholm Road, Hull East Yorkshire HU7 0XW
T: 01482 372525
E: enquiry@alsim.co.uk
W: www.alsim.co.uk
Alstom Transport UK Ltd
Inspira House, Martinfield
Welwyn Garden City AL7 1GW
T: 01707 383700
E: sales@transport.alstom.com
W: www.alstom.com
Alstom UK
The Place, 175 High Holborn London WC1V 7AA
T: 020 7438 9230
E: AES-UK@alstom.com
W: www.alstom.com
Alter Lanscapes Ltd
Weels Farm, Lochwinnoch Renfrewshire Scotland PA12 4LD
T: 01505 842201
E: enquiries@alterfencing.com
W: www.alterlandscapes.co.uk
Althon are the UK’s leading designer, manufacturer and distributor of Precast Concrete Headwalls with the largest range in the UK. These can be specified with factory fitted accessories including penstocks, flap valves, handrails & trash screens. Althon’s website has a Headwall Specifier Tool, making it easy to identify the most appropriate models & accessories.
Althon Limited MAG Group Building, Vulcan Road South Norwich Norfolk NR6 6AF
T: 01603 488700
E: sales@althon.co.uk
W: www.althon.co.uk
Altran UK Shackleton House, 4 Battle Bridge Lane London SE1 2HP
T: 020 3117 0700
E: reception@altran.com
W: www.altran.co.uk
Altro Works Road, Letchworth Hertfordshire SG6 1NW
T: 01462 489516
E: enquiries@altro.com
W: www.altro.com
Alucast Limited Western Way, Wednesbury West Midlands WS10 7BW
T: 0121 556 6111
E: sales@alucast.co.uk
W: www.alucast.co.uk
Alumasc Water Management Solutions Station Road, Burton Latimer Kettering Northamptonshire NN15 5JP
T: 01536 383810
E: info@alumascwms.co.uk
W: www.alumascwms.co.uk
Aluminium Lighting Company Ltd
Croeserv Ind Estate, Eastern Avenue Cymmer Port Talbot SA13 3PB
T: 01639 852502
E: sales@alulight.co.uk
W: www.aluminium-lighting.com
Aluminium Special Projects Ltd (ASP Group) Unit 39 Second Avenue, The Pensnett Estate Kingswinford West Midlands DY6 7UW
T: 01384 291900
E: help@aspgroup.co.uk
W: www.aspgroup.co.uk
Alun Griffiths Ltd
Waterways House, Merthyr Road Llanfoist Abergavenny NP7 9PE
T: 01873 857211
E: enquiries@alungriffiths.co.uk
W: www.alungriffiths.co.uk
AM Sensors Ltd Chedzoy Lane, Chedzoy Bridgewater Somerset TA7 8QS
T: 01278 448374
E: info@amsensors.com
W: www.amsensors.com
AM1 Projects Ltd 111 Hopewell Drive, Chatham Kent ME5 7NP
T: 01634 400033
E: info@am1projects.co.uk
W: www.am1projects.co.uk
Amantys Power Electronics Ltd
Compass House, Vision Park
Histon Cambridge CB24 9AD
T: 01223 652530
E: info@amantys.co.uk
W: www.amantys.co.uk
Amaro Group
Unit J2, Knights Park Ind Estate
Knights Road Strood Rochester ME2 2LS
T: 0845 207 1190
E: equiries@amarogoup.co.uk
W: www.amarogroup.co.uk
Amazon Medical Limited
Carrington Bus Park, Carrington Manchester M31 4XL
T: 0161 776 4336
E: sales@amazonmedical.co.uk
W: www.amazonmedical.co.uk
Amberg Engineering AG
Trockenloostrasse 21, 8105 Regensdorf-Watt
Switzerland
T: +41 44 870 91 11
E: information@amberg.ch
W: ambergengineering.com
Amberol Ltd
The Plantation, King Street
Alfreton Derbyshire DE55 7TT
T: 01773 830930
E: sales@amberol.co.uk
W: www.amberol.co.uk
AmcoGiffen
Whaley Road, Barugh Barnsley S75 1HT
T: 01226 243413
E: info@amcogiffen.co.uk
W: www.amcogiffen.co.uk
AME-3D
Momentum House, Church Lane Dinnington Sheffield S25 2RG
T: 01909 550 999
E: info@ame-3d.co.uk
W: www.ame-3d.co.uk
45 Years Quality Manufacturing and Supply of Signal Conditioning, Process Monitoring and Control Instrumentation for the process industry sectors. Seismic qualified Non-Smart, Non-uProcessor based, Type A instruments for SIL 1, SIL 2, SIL 3 rated Safety System Loop applications, as well as Network Rail Approved Non-intrusive AC/DC Current Transducers.
AMELEC Instruments
5 Cochran Close, Crownhill Milton Keynes Buckinghamshire MK8 0AJ
T: 01908 567003
E: sales@amelec-uk.com
W: www.amelec-uk.com
Ametek Airscrew
111 Windmill Road, Sunbury-on-Thames Middlesex TW16 7EF
T: 01932 765822
E: mail.airscrew@ametek.co.uk
W: www.ametekaerospaceanddefense.com
Amethyst Surveys Ltd Unit 2 Davy Court, Central Park Rugby Warwickshire CV23 0UZ
T: 01788 566740
E: enquiries@amethystsurveys.com
W: www.amethystsurveys.com
Amey Rail 10 Furnival Street, London EC4A 1AB
T: 0800 521660
E: customercontact@amey.co.uk
W: www.amey.co.uk
Amey TPT 3rd Floor, 10 Furnival Street London EC4A 1AB
T: 020 7921 2930
E: enquiriesTPT@amey.co.uk
W: www.tpt.amey.co.uk
AMG Superalloys Ltd
Fullerton Road, Rotherham South Yorkshire S60 1DL
T: 01709 828500
E: info@amg-s.com
W: www.amg-s.com
Amida Ltd
1st Floor, Victoria House
1 Leonard Circus London EC2A 4DQ
T: 020 7033 3100
E: london@amida-recruit.com
W: www.amida-recruit.com
AMOT
Western Way, Bury St Edmunds Suffolk IP33 3SZ
T: 01284 762222
E: info@amot.com
W: www.amot.com
Ampetronic Ltd
Unit 2 Trentside, Business Village Farndon Road Newark NG24 4XB
T: 01636 610062
E: support@ampetronic.co
W: www.ampetronic.co
Amphenol Ltd
Thanet Way, Whitstable Kent CT5 3JF
T: 01227 773200
E: info@amphenol.co.uk
W: www.amphenol.co.uk
Amplicon
Centenary Ind Estate, Hollingdean Road
Brighton BN2 4AW
T: 01273 570220
E: sales@amplicon.com
W: www.amplicon.com
Ampteam Ltd
5/6 Charlotte Street
Dudley West Midlands DY1 1TD
T: 01384 252777
E: unifold@ampsteam.co.uk
W: www.ampteam.co.uk
AMS Acoustics Ltd
104 Fox Lane
London N13 4AX
T: 020 8886 4060
E: info@amsacoustics.com
W: www.amsacoustics.co.uk
AMS No-Dig Ltd
Brigg Road, Scunthorpe DN16 1AP
T: 01724 294294
E: enquiries@amsnodig.com
W: www.amsnodig.com
AMT Coffee Ltd
1 Knightsbridge Green
London SW1X 7NE
T: 020 3772 4000
E: feedback@amtcoffee.co.uk
W: www.amtcoffee.co.uk
AMT Sybex Ltd
The Spirella Building, Bridge Road Letchworth Hertfordshire SG6 4ET
T: 01462 476400
E: info@amt-sybex.com
W: www.amt-sybex.com
Amtrain (Midlands) Ltd
A38 Southbound, Rykneld Street Fradley Staffordshire WS13 8RD
T: 01283 792633
E: info@amtrain.co.uk
W: www.amtrain.co.uk
AN Wallis & Co Ltd Greasley Street, Bulwell Nottingham NG6 8NG
T: 0115 927 1721
E: info@an-wallis.com
W: www.an-wallis.com
AN4 Group Ltd
8 The Windmills, St Marys Close Alton Hampshire GU34 1EF
T: 01420 544440
E: sales@an4group.com
W: www.an4group.com
Analysis by Firth Suite 101A Standish Cen, Cross Street Standish wigan WN6 0HQ
T: 01257 427667
E: info@abyf.co.uk
W: www.abyf.co.uk
Analysys Mason Limited
Bush House, North West Wing Aldwych London WC2B 4PJ
T: 020 7395 9000
E: enquiries@analysysmason.com
W: www.analysysmason.com
Anchor Systems (International) Ltd
Units 44-46, Rowfant Business Centre
Wallage Lane Rowfant W Sussex RH10 4NQ
T: 01342 719362
E: info@anchorsystems.co.uk
W: www.anchorsystems.co.uk
Anderselite Ltd (Head Office)
115 Southwark Street, London SE1 0JF
T: 020 7743 7500
E: contactus@anderselite.com
W: www.anderselite.com
Anderselite Ltd (Salford Office)
Adamson House, 2 Centenary Way Salford Manchester M50 1RD
T: 0161 832 7577
E: contactus@anderselite.com
W: www.anderselite.com
Anderson Acoustics Unit 9, Baden Place Crosby Row London SE1 1YW
T: 020 3176 7909
E: hello@andersonacoustics.co.uk
W: www.andersonacoustics.co.uk
Ibstock is a leading UK manufacturer of precast concrete products for the rail sector, drawing on decades of experience to become the industry’s most trusted supplier. We are the leading supplier of UK manufactured Signal Bases, Platform Solutions, Cable Protection and Cable Theft Deterrents to the rail industry, with an extensive product line-up which deliver lower embodied carbon product options.
Anderton Concrete, part of Ibstock
Units 1&2, Cosgrove Business Park, Soot Hill, Anderton Cheshire Northwich CW9 6AA
T: 0333 234 3434
E: anderton.rail@ibstock.co.uk
W: www.ibstock.co.uk
Andover Trailers Limited 75 Columbus Way, Walworth Ind Estate Andover Hampshire SP10 5NP
T: 01264 358944
E: sales@andovertrailers.co.uk
W: www.andovertrailers.co.uk
Andreas STIHL Ltd STIHL House, Stanhope Road Camberley Surrey GU15 3YT
T: 01276 20202
E: enquiries@stihl.co.uk
W: www.stihl.co.uk
Andrew Reid 240 Blackfriars Road, London SE1 8NW
T: 020 7332 0500
E: general@andrewreid.co.uk
W: www.andrewreid.co.uk
Andrews Fasteners Limited Unit 8, Latchmore Park Latchmore Road Leeds LS12 6DN
T: 0113 246 9992
E: sales@andrewsfasteners.co.uk
W: www.andrewsfasteners.uk
Andrews Signs & Engravers Ltd
Units 5 & 6, Rawcliffe Ind Estate Manor Lane York YO30 5XY
T: 01904 400800
E: sales@andrewssigns.co.uk
W: www.andrewssigns.co.uk
Andy Foan Ltd
15 Bloomsbury Drive, Nuthall Nottingham NG16 1RJ
T: 07584 191412
E: SandC@andyfoan.co.uk
W: www.andyfoan.co.uk
Angel Trains Limited
123 Victoria Street London SW1E 6DE
T: 020 7592 0500
E: communications@angeltrains.co.uk
W: www.angeltrains.co.uk
Anglia Land Surveys Ltd
Bowthorpe Hall Road, Bowthorpe Hall Norwich NR5 9AA
T: 01603 749600
E: mail@als-surveys.com
W: www.als-surveys.com
Anglia Metal Ltd
Good Hope Close, Normanton Ind Estate Normanton West Yorkshire WS6 1TR
T: 01924 223744
E: sales@angliametal.com
W: www.anglianmetal.com
Anglian NDT Limited
27 Haverscroft Ind Est, New Road
Attleborough Norfolk NR17 1YE
T: 01953 457070
E: info@angliandt.com
W: www.anglianndt.com
Animal Systems Ltd
4 St Mary’s Courtyard, East Farm, Codford Warminster Wiltshire BA12 0PG
T: 01985 800300
E: admin@animalsystems.co.uk
W: www.animalsystems.co.uk
Anixter (UK) Ltd
Unit A, The Beacons, Warrington Road Risley Warrington WA3 6GB
T: 01925 848039
E: railsales@anixter.com
W: www.anixter.com
Anochrome Technologies Anochrome Group, Wood lane
Fordhouses Wolverhamton WV10 8HN
T: 01902 397 333
E: enquiries@anochrome-group.co.uk
W: www.anochrome.com
Another Level Car Parks Ltd
Tweedale Way, Oldham OL9 7LD
T: 0845 345 3835
E: info@anotherlevelcarparks.co.uk
W: www.anotherlevelcarparks.co.uk
Ansaldo STS UK Ltd
Hudson House, Platform 1 Victoria Station London SW1V 1JT
T: 020 3574 4980
E: info@ansaldo-sts.com
W: www.ansaldo-sts.com
ANT Telecommunications Limited Unit 5, The Courtyard, Meadowbank Furlong Road Bourne End, Bucks SL8 5AU
T: 01494 833100
E: info@anttelecom.co.uk
W: www.anttelecom.co.uk
Antagrade Electrical Limited
6 Verity Court, Middlewich Cheshire CW10 0GW
T: 01606 833299
E: enquiries@antagrade.co.uk
W: www.antagrade.co.uk
Antal International Network 64 Baker Street, Marylebone London W1U 7GB
T: 020 7467 2520
E: info@antal.com
W: www.antal.com
Anthony Brookes Surveys Ltd
Unit 2, Thornbury Office Park Midland Way Thornbury BS35 2BS
T: 01454 419133
E: absurveys@aol.com
W: www.anthonybrookes.com
ANV Measurement System
Beaufort Court, 17 Roebuck Way Milton Keynes MK5 8HL
T: 01908 642846
E: info@noise-and-vibration.co.uk
W: www.noise-and-vibration.co.uk
Aon Ltd
The Aon Centre, The Leadenhall Building 122 Leadenhall St London EC3V 4AN
T: 020 7623 5500
E: enquiries@aon.com
W: www.aon.com
AP Diesels Ltd are a leading common rail diesel injector and pump remanufacture specialist, providing all makes including Cummins, MTU, Caterpillar, injectors. We are the only company in Europe with a successful remanufacturing program for Cummins QSK, HPI, ISL, ISX and XPI, also MTU L’Orange series 2000/4000, CAT C7/C9, 3408/3412.
AP Diesels Ltd
25a Victoria Street, Englefield Green Egham Surrey TW20 0QY
T: 01784 437228
E: office@apdiesels.com
W: www.apdiesels.com
AP Webb Plant Hire Ltd
Common Road, Stafford Staffordshire ST16 3DQ
T: 01785 241335
E: info@apwebbplanthire.co.uk
W: www.apwebbplanthire.co.uk
APA Design Ltd
Suite 4.1, Litchurch Plaza Litchurch Lane Derby DE24 8AA
T: 01332 299022
E: infoderby@apadesign.co.uk
W: www.apadesign.co.uk
APB Construction (UK) Limited Grange Business Centre, River Works Grange Lane Sheffield S5 ODP
T: 01709 541000
E: info@apbcon.co.uk
W: www.aeyates.co.uk
Apcoa Parking (UK) Ltd
Wellington House, 4-10 Cowley Road
Uxbridge Middlesex UB8 2XW
T: 01895 272500
E: uk.sales@apcoa.com
W: www.apcoa.com
APD Communications Ltd
Newlands Centre, Inglemire Lane Hull HU6 7TQ
T: 01482 808300
E: info@apdcomms.com
W: www.apdcomms.com
Aperio Systems Limited
Level 17, Dashwood House
69 Old Broad St London EC2M 1QS
T: 020 7256 4090
E: info@aperioltd.com
W: www.aperioltd.com
Apex Cables Limited
Saint Johns Road, Meadowfield Ind Estate Durham DH7 8RJ
T: 0191 378 7900
E: info@apexcables.co.uk
W: www.apexcables.co.uk
Apex Engineering Ltd
Unit B5 Southgate, Commerce Park
Frome Somerset BA11 2RY
T: 01373 469977
E: office@apexengineering.co.uk
W: www.apexengineering.co.uk
Apex Engineering Services Ltd
F7 Waterfront Studios, 1 Dock Road
London E16 1AH
T: 020 7018 1635
E: enquiry@apex.uk.net
W: www.apex.uk.net
Apex Engineering Solutions
9 York Place Leeds LS1 2DS
T: 0113 245 3309
E: leeds@apexes.co.uk
W: www.apexes.co.uk
Apex Rail GmbH
Winkelriedstrasse 56, Lucerne Switzerland 6003
T: 00 41 41 220 2451
E: info@apex-rail.com
W: www.apex-rail.com
API Capacitors
Leyden Works, Station Road
Great Yarmouth Norfolk NR31 0HB
T: 01493 652752
E: info@api-capacitors.com
W: www.api-capacitors.com
Apollo Chemicals Ltd
Sandy Way, Amington Ind Estate Tamworth Staffordshire B77 4DS
T: 01827 54281
E: enquiries@apollo.co.uk
W: www.apollo.co.uk
Application Solutions (Safety and Security) Ltd
Unit 17, Cliffe Ind Estate
Lewes East Sussex BN8 6JL
T: 01273 405411
E: sales@asl-control.co.uk
W: www.asl-control.co.uk
Applied Card Technologies Ltd Langley Gate, Kington Langley Chippenham Wiltshire SN15 5SE
T: 01249 751200
E: info@weareact.com
W: www.weareact.com
Applied Industrial Systems (AIS)
IH 1.16 Q West, 1110 Great West Road Brentford Middlesex TW8 0GP
T: 020 8747 2130
E: info@applied.co.uk
W: www.applied.co.uk
Applied Inspection Ltd
Mosley Street, Burton-on-Trent Staffordshire DE14 1DW
T: 01283 515163
E: burtoninfo@appliedinspection.co.uk
W: www.appliedinspection.co.uk
Approved Hydraulics Ltd
Unit 1 Avery Trad Est, Kenwood Road North Redditch Stockport SK5 6PH
T: 0161 480 0869
E: sales@approvedhydraulics.co.uk
W: www.approvedhydraulics.co.uk
Approved Inspector Services Limited
14 Berkeley Street London W1J 8DX
T: 020 7491 1914
E: info@approvedinspector.co.uk
W: www.approvedinspector.co.uk
APPS UK Ltd
Paisley Works, 14 Windover Road
Huntingdon Cambridgeshire PE29 7EB
T: 01480 458888
E: sales@appsuk.com
W: www.apps-group.com
APR Services
Block B, 1st Floor, Queens Road
Barnet Hertfordshire EN5 4DL
T: 020 8449 9143
E: mail@aprservices.net
W: www.aprservices.net
APT Controls Group
Unit 1, Maxted Corner
Maxted Road Hemel Hempstead HP2 7RA
T: 020 8421 2411
E: webenquiries@aptcontrols.co.uk
W: www.aptcontrols.co.uk
APT Skidata Ltd
Unit 1, Maxted Corner
Maxted Road Hemel Hempstead HP2 7RA
T: 020 8421 2411
E: enquiries@aptskidata.co.uk
W: www.aptcontrols.co.uk
Aqua Fabrications Ltd
Belmont House, Garnett Place
Skelmersdale Lancashire WN8 9UB
T: 01695 51933
E: sales@aquafab.co.uk
W: www.aquafab.co.uk
Aqua-Solv Solutions Ltd
5 Malt Kiln Road, Plumley Knutsford Cheshire WA16 OTS
T: 01565 740600
E: info@aquasolvsolutions.com
W: www.aquasolvsolutions.com
Aquarius Railroad Technologies Ltd Old Sleningford Farm, North Stainley
Ripon North Yorkshire HG4 3JB
T: 01765 635021
E: enquiries@aquariusrail.com
W: www.aquariusrail.com
AquaSpira Limited
Profile Park, Junction Street
Nelson BB9 8AH
T: 01282 608510
E: info@aquaspira.com
W: www.aquaspira.com
Aquobex Limited
Building 69, Building Research Estab
Bucknalls Lane Garston Watford WD25 9XX
T: 01923 518582
E: sales@aquobex.com
W: www.aquobex.com
Arbil Rail
Providence Street, Lye Stowbridge West Midlands DY9 8HS
T: 0845 600 4332
E: rail@arbil.co.uk
W: www.arbil.co.uk
ARBOR Technology UK Ltd Unit 32, Walker Avenue
Wolverton Mill Milton Keynes MK12 5TW
T: 01908 310100
E: sales@arbor-uk.com
W: www.arbor-uk.com
Arburies Ltd
Waterside House, Station Road
Irthlingborough NN9 5QF
T: 0845 463 5180
E: enquiries@arburies.co.uk
W: www.arburies.co.uk
Arbus Ltd
Ellis Square, Selsey
Chichester West Sussex PO20 0AY
T: 01243 606219
E: info@arbus.co.uk
W: www.arbus.co.uk
ARC Academy UK Ltd
17-18 Centre Court, Treforest Ind Estate
Pontypridd South Wales CF37 5YR
T: 01443 842856
E: info@arcacademyuk.com
W: www.arcacademyuk.com
Arcadis
Arcadis House, 34 York Way
London N1 9AB
T: 020 7812 2000
E: UKenquiries@arcadis.com
W: www.arcadis.com
Archbold Logistics Ltd
Birch Industrial Estate, Whittle Lane
Heywood Lancashire OL10 2SX
T: 01706 627201
E: enquiries@archbold.co.uk
W: www.archbold.co.uk
Archerdale Ltd
Hirstwood Works, Hirstwood Road
Shipley West Yorkshire BD18 4BU
T: 01274 595783
E: sales@archerdale.com
W: www.archerdale.com
ArchOver Ltd 5th Floor, 40 Gracechurch Street
London EC3V 0BT
T: 020 3021 8100
E: info@archover.com
W: www.archover.com
Arco Limited PO Box 21, 1 Blackfriargate
Hull HU1 1BH
T: 0330 390 2050
E: customer.service@support.arco.co.uk
W: www.arco.co.uk
Arco Professional Safety Services Ltd
Unit 5, 6, 7, Raleigh Hall Ind Estate
Swynnerton Road Eccleshall ST21 6JL
T: 0330 390 0822
E: info@arcoservices.co.uk
W: www.arcoservices.co.uk
Arconic Fastening Systems Ltd
Unit C, Stafford Park 7
Telford Shropshire TF3 3BQ
T: 01952 290011
E: info@afsglobal.net
W: www.afsglobal.net
Arctic Air Filtration Overpressure Systems
Unit 2 Mill Works, Gregorys Mill Street Worcester WR3 8BA
T: 01905 616664
E: julian@arcticaircon.co.uk
W: www.arcticaircon.co.uk
Arctic Air Solutions Ltd
Unit 2, Mill Works Worcester WR3 8BA
T: 01905 616664
E: info@arcticairsolutions.co.uk
W: www.arcticairsolutions.co.uk
Ardent Management Ltd
Print Rooms, 164-180 Union Street London SE1 0LH
T: 020 3693 2500
E: info@ardent-management.com
W: www.ardent-management.com
Ardmore Construction Limited
6 Wharf Studios, 28 Wharf Road London N1 7GR
T: 020 8344 0300
E: info@ardmoregroup.co.uk
W: www.ardmoregroup.co.uk
Ark Signalling Consultancy Ltd
Lower Granary, Cornwells Farm Marden Kent TN12 9NS
T: 01622 902880
E: enquiries@arksignalling.co.uk
W: www.arksignalling.co.uk
Arktis Endurance Textiles Ltd
Unit 3 Peek House, Pinhoe Trading Estate Exeter EX4 8JN
T: 01392 201614
E: info@arktis.co.uk
W: www.arktisltd.co.uk
Arlington Fleet Group Railworks Gate 2, Campbell Road Eastleigh Hampshire SO50 5AD
T: 023 8069 6789
E: info@arlington-fleet.co.uk
W: www.arlington-fleet.com
ARM Engineering
Langstone Tech Park, Langstone Road Havant Hampshire PO9 1SA
T: 023 9222 8228
E: hello@arm.co.uk
W: www.arm.co.uk
Armacell develops innovative and safe thermal, acoustic and mechanical solutions that create sustainable value for its customers. ArmaFlex Rail is the world’s first closed-cell insulation to meet EN 45545-2 fire protection requirements, and is ideal for the protection of refrigerant pipework and air ducts on railway vehicles.
Armacell UK
Mars Street, Oldham Lancashire OL9 6LY
T: 0161 287 7100
E: info.uk@armacell.com
W: www.armacell.co.uk
Armcon Limited
Armcon Business Park, London Road South Poynton Cheshire SK12 1LQ
T: 01625 856680
E: sales@armcon.com
W: www.armcon.com
Armitage Communications
Mill House, Wandle Road London Croydon CR0 4SD
T: 020 8667 9660
E: info@armitage-comms.co.uk
W: www.armitage-comms.co.uk
Armorduct systems Ltd
Building 9, The Pensnett Estate
Kingswinford West Midlands DY6 7TG
T: 01384 233445
E: sales@armorductsystems.co.uk
W: www.armorductsystems.co.uk
Armorgard Security Products
Unit 14-16 Standard Way, Fareham Indsutrial Park
Fareham Hampshire PO16 8XB
T: 023 9238 0280
E: sales@armorgard.co.uk
W: www.armorgard.co.uk
Arnold Laver & Co Ltd
Bramall Lane, Sheffield South Yorkshire S2 4RJ
T: 0114 223 0300
E: marketing@laver.co.uk
W: www.laver.co.uk
ARR Craib Transport Ltd
Howe Moss Drive, Kirk Hill Ind Estate
Dyce Aberdeen AB21 0GL
T: 01224 771122
E: info@arr-craib.co.uk
W: www.arr-craib.co.uk
Arriva Rail London
Overground House, 125 Finchley Road Swiss Cottage London NW3 6HY
T: 020 3031 9200
E: communications@arrivarl.co.uk
W: www.arrivaraillondon.co.uk
Arriva Traincare
2 Cranham Court, Arden Square
Crewe Cheshire CW1 6HA
T: 01270 508000
E: info@arrivatc.com
W: www.arrivatc.com
Arriva UK
Admiral Way, Doxford Int Bus Park
Sunderland SR3 3XP
T: 0191 520 4000
E: enquiries@arriva.co.uk
W: www.arriva.co.uk
Arrk Europe Ltd
Nuneaton Tech Centre, Caldwell Road Nuneaton Warwickshire CV11 4NG
T: 024 7658 0700
E: ntc@arrkeurope.com
W: www.arrkeurope.com
Arrow County Supplies (Head Office)
Arrow House, Longden Road Shrewsbury SY3 9AE
T: 01743 283600
E: response@arrowcounty.com
W: www.arrowcounty.com
Arrow Solutions
Rawdon Road, Moria Swadlincote Derbyshire DE12 6DA
T: 01283 221044
E: sales@arrowchem.com
W: www.arrowchem.com
Artcom Tradebridge Ltd
Unit 2a, Strathallan Airfield
Auchterarder Perthshire PH3 1LA
T: 01764 663000
E: info@artcom-tradebridge.com
W: www.artcom-tradebridge.com
Artel Rubber Co Ltd
Unit F, Springfield Bus Park
Alcester Warwickshire B49 6PU
T: 01789 774099
E: sales@artelrubber.co.uk
W: www.artelrubber.com
Artelia Group
High Holborn House, 52-54 High Holborn London WC1V 6RL
T: 020 7269 0450
E: enquiries@uk.arteliagroup.com
W: www.uk.arteliagroup.com
Artemis Intelligent Power Ltd
Unit 3, Edgefield Ind Estate
Loanhead Midlothian EH20 9TB
T: 0131 440 6269
E: enquiries@artemisip.com
W: www.artemisip.com
Arthur D Little Ltd
Merlin Place, Milton Road Cambridge CB4 0DP
T: 01223 427100
E: enquiries.uk@adlittle.com
W: www.adlittle.co.uk
Arthur Flury manufactures reliable, precisionmade OLE components which have contributed for many years to the safety and efficiency of the UK rail network. Our Milton Keynes office provides local support and liaises with our Swiss factory to ensure that we consistently meet our UK customers’ expectations.
Arthur Flury (UK) Ltd
Unit 218, Milton Keynes Bus Ctr Foxhunter Drive Milton Keynes MK14 6GD T: 01908 686766
E: info@aflury.co.uk
W: www.aflury.co.uk
Arthur J Gallagher Limited
The Walbrook Building, 25 Walbrook London EC4N 8AW
T: 020 7204 6000
E: ukenquiries@ajg.com
W: www.ajginternational.com
Arup (Head Office)
8-13 Fitzroy Street London W1T 4BQ
T: 0121 213 3000
E: rail@arup.com
W: www.arup.com
ARUP (Manchester Office)
6th floor, 3 Piccadilly Place
Manchester M1 3BN T: 0161 228 2331
E: manchester@arup.com
W: www.arup.com
ARUP (Newcastle Office)
Central Square, Forth Street
Newcastle upon Tyne NE1 3PL
T: 0191 261 6080
E: newcastle@arup.com
W: www.arup.com
AS Peck Engineering 116 Whitby Road, Ruislip Middlesex HA4 9DR
T: 01895 621398
E: info@aspeckeng.co.uk
W: www.aspeckeng.co.uk
Asbestos Removal Contractors Association (ARCA)
Unit 1, Stretton Bus Park 2 Brunel Drive Stretton DE13 0BY
T: 01283 566467
E: info@arca.org.uk
W: www.arca.org.uk
Ascertus Limited
Office 305, 1 Northumberland Avenue
Trafalgar Square London WC2N 5BW
T: 020 3126 4960
E: contactus@ascertus.com
W: www.ascertus.com
ASCO Joucomatic Ltd
Pit Hey Place, West Pimbo Skelmersdale Lancashire WN8 9PG
T: 01695 713600
E: enquiries.asco.uk@emerson.com
W: www.asco.com
Ascom (UK) Ltd
Wall Island, Birmingham Road Lichfield WS14 0QP
T: 0121 353 6151
E: sales@ascom.co.uk
W: www.ascom.com
ASD Lighting PLC Mangham Road, Bardot Hall Ind Estate Rotherham S61 4RJ
T: 01709 374898
E: info@asdlighting.com
W: www.asdlighting.com
ASD Ltd. T/A Kloeckner Metals UK
Valley Farm Road, Stourton Leeds West Yorkshire LS10 1SD
T: 0113 254 0711
E: enquiries@kloeckner.com
W: www.kloecknermetalsuk.com
ASD Ltd. T/A Kloeckner Metals UK Daventry Alvis Way, Royal Oak Ind Estate
Daventry Northamptonshire NN11 8QQ
T: 01327 876021
E: daventry@kloeckner.com
W: www.kloecknermetalsuk.com
Ashurst Broadwalk House, 5 Appold Street London EC2A 2HA
T: 020 7638 1111
E: enquiries@ashurst.com
W: www.ashurst.com
ASI Solutions Limited
Office 610, Milton Keynes Bus Ctr
Linford Wood Milton Keynes MK14 6GD
T: 01908 246000
E: enquiry@asisolutions.co.uk
W: www.asisolutions.co.uk
Aspin Consulting Ltd (Midlands) Nunn Brook Road, Huthwaite Nottinghamshire NG17 2HU
T: 01623 446100
E: info@aspingroup.com
W: www.aspingroup.com
Aspire Consultants – Keltbray Unit 12 Weston Road, Crewe Hall Ent Park Crewe CW1 6UA
T: 01270 254176
E: info@aspirerail.co.uk
W: www.keltbray.com
Assembly Solutions Limited
Nile Street, Bolton Lancashire BL3 6BW
T: 01204 521999
E: sales@assembly-solutions.com
W: www.assembly-solutions.com
Assertis
2-6 Boundary Row London SE1 8HP
T: 020 3207 9663
E: info@assertis.co.uk
W: www.assertis.co.uk
AssessTech are the UK’s leading provider of electronic competence management software and training consultancy, all focused on delivering a safer railway for the UK. They work with 85% of the UK’s rail network providing services to customers such as Great Western Railway, Northern, Southeastern, Greater Anglia, Heathrow Rail and Eurostar.
AssessTech
41 Church Road, Guildford
Surrey GU1 4NQ
T: 01483 338646
E: info@assesstech.com
W: www.assesstech.com
Asset ID Limited
70a High Street, Shepperton Middlesex TW17 9AU
T: 01932 269900
E: sales@assetid.co.uk
W: www.assetid.co.uk
Asset International Structures
Suite 5 Brecon House, William Brown Close
Llantarnam Cwmbran NP44 3AB
T: 01633 499830
E: info@assetint.co.uk
W: www.assetint.co.uk
Asset Management Consulting Limited
221 St John Street, Clerkenwell
London EC1V 4LY
T: 020 7688 2828
E: enquiries@amcl.com
W: www.amcl.com
Asset-Pro Ltd
Concorde House, 24 Cecil Pashley Way Shoreham Airport West Sussex BN43 5FF
T: 0845 121 0101
E: enquiries@asset-pro.com
W: www.asset-pro.com
Associated British Ports (Ayr)
Port Office, North Harbour Street
Ayr Ayrshire KA8 8AH
T: 01292 281687
E: ayr@abports.co.uk
W: www.abports.co.uk
Associated British Ports (Garston)
Port Office, Garston Liverpool Merseyside L19 2JW
T: 0151 427 5971
E: garston@abports.co.uk
W: www.abports.co.uk
Associated British Ports (Swansea & Port Talbot) Harbour Office, Lockhead King’s Dock Swansea West Glamorgan SA1 1QR
T: 0870 609 6699
E: swansea@abports.co.uk
W: www.abports.co.uk
Associated British Ports – Head Office 2nd Floor, 25 Bedford Street London WC2E 9ES
T: 020 7430 1177
E: pr@abports.co.uk
W: www.abports.co.uk
Associated Rewinds Ireland Limited Whitestown Road, Tallaght Business Park Dublin D24 EV62
T: 00 35 314520033
E: contact@associatedrewinds.com
W: www.associatedrewinds.com
ASLEF is Britain’s trade union for train drivers. Its 23,500 members are employed in the train operating companies, the freight companies, London Underground and some Light Rapid Transport. The first recorded meeting was held on 7 February 1880.
Associated Society of Locomotive Engineers & Firemen (ASLEF)
77 St John Street, Clerkenwell London EC1M 4NN
T: 020 7324 2400
E: info@aslef.org.uk
W: www.aslef.org.uk
Associated Society of Locomotive Engineers & Firemen (ASLEF)
77 St John Street, Clerkenwell London EC1M 4NN
T: 020 7324 2400
E: info@aslef.org.uk
W: www.aslef.org.uk
Associated Train Crew Union (ATCU) PO Box 763, Cudworth Barnsley S72 8YD
T: 01226 716417
E: headoffice@atcu.org.uk
W: www.atcu.org.uk
Associated Utility Supplies Ltd Riverside House, Colliers Way Clayton West Huddersfield HD8 9TR
T: 01484 860575
E: sales@aus.co.uk
W: www.aus.co.uk
Association for Consultancy & Engineering (ACE) Alliance House, 12 Caxton Street London SW1H 0QL
T: 020 7222 6557
E: consult@acenet.co.uk
W: www.acenet.co.uk
Association for European Transport (AET) Forester House, Doctors Lane Henley-in-Arden B95 5AW
T: 01564 793552
E: info@aetransport.org
W: www.aetransport.org
Association for Project Management (APM)
Ibis House, Regent Park Summerleys Road Princes Risborough HP27 9LE
T: 0845 458 1944
E: info@apm.org.uk
W: www.apm.org.uk
Association of Fencing Industries (AFI) 19 Omega, Thurston Road
Northallerton DL6 2NJ
T: 020 8253 4516
E: info@afiorg.uk
W: www.afiorg.uk
Association of Geotechnical and Geoenvironmental Specialists (AGS)
Forum Court Office 205, Devonshire Hse Bus Ctr
29-31 Elmfield Rd Bromley BR1 1LT
T: 020 8658 8212
E: ags@ags.org.uk
W: www.ags.org.uk
Association of Railway Training Providers (ARTP)
Kelvin House, RTC Business Park London Road Derby DE24 8UP
T: 01332 360033
E: info@artp.co.uk
W: www.artp.co.uk
Association of Technical Lightning & Access Specialists (ATLAS)
6-8 Bonhill Street London EC2A 4BX
T: 0844 249 0026
E: info@atlas.org.uk
W: www.atlas.org.uk
Association of Transport Coordinating Officers (ATCO)
Hermes House, St John’s Road
Tunbridge Wells Kent TN4 9UT
T: 07757 944689
E: ellie.thornley@atco.org.uk
W: www.atco.org.uk
Assystem UK Ltd
Club Street, Bamber Bridge
Preston PR5 6FN
T: 01772 645000
E: communication@assystem.com
W: www.assystem.co.uk
AST Language Services Ltd Unit 8, Ayr Street
Nottingham NG7 4FX
T: 0115 970 5633
E: enquiries@astls.co.uk
W: www.astlanguage.com
Ast Rail (Ast Signs Ltd)
The Box, Eden Bus Park, Penrith Cumbria CA11 9FB
T: 01768 892292
E: info@astsigns.com
W: www.astsigns.co.uk
Astley Signs
Redforrest House, Queens Court North Earlsway Team Valley NE11 0BP
T: 03332 300 440
E: enquiries@astley-uk.com
W: www.astley-uk.com
Aston University
Aston Triangle
Birmingham B4 7ET
T: 0121 204 3000
E: thehub@aston.ac.uk
W: www.aston.ac.uk
Astute Global / Astute Electronics Ltd
Astute House, Rutherford Close
Stevenage Hertfordshire SG1 2EF
T: 01438 909909
E: sales@astute.global
W: www.astute.global
AT Kearney Limited
Adelphi, 1-11 John Adam Street
London WC2N 6HT
T: 020 7468 8000
E: reception.london@atkearney.com
W: www.atkearney.com
ATA Recruitment Ltd
Derby Conference Centre, London Road
Derby DE24 8UX
T: 0808 164 2000
E: info@ata-recruitment.co.uk
W: www.ata-recruitment.co.uk
ATAM (UK) Ltd
The Fluid Power Centre, Watling Street
Nuneaton Warwickshire CV11 6BQ
T: 02476 326060
E: sales@atam.uk.com
W: www.atam.uk.com
ATB Special Products
Unit 11, Waterfall Lane
Cradley Heath West Midlands B64 6PU
T: 0121 698 3100
E: spsales@atb-sp.com
W: www.atb-motors.com
ATEC Fire & Security
1 Element Court, Hilton Cross Bus Park Featherstone Wolverhampton WV10 7FE
T: 0330 058 0050
E: info@atec-security.co.uk
W: www.atec-security.co.uk
Atex Global Ltd
12 Radway Road, Southampton Hampshire SO15 7PW
T: 0800 756 5305
E: sales@atexglobal.com
W: www.atexglobal.com
ATG Access Ltd
CoBaCo House, North Florida Road
Haydock Ind Estate Merseyside WA11 9TP
T: 0845 675 7574
E: enquiries@atgaccess.com
W: www.atgaccess.com
ATI Tank Hire Limited
Yarmouth Business Park, Thamesfield Way
Great Yarmouth Norfolk NR31 0DN
T: 01493 441747
E: info@atitanks.co.uk
W: www.atitankhire.co.uk
Created by the integration of long-standing organisations dating back to 1911, AtkinsRéalis is a world-leading professional services and project management company dedicated to engineering a better future for our planet and its people. We create sustainable solutions that connect people, data and technology to transform the world’s infrastructure and energy systems. We deploy global capabilities locally to our clients and deliver unique end-to-end services across the whole project lifecycle.
AtkinsRéalis
Nova North, 11 Bressenden Place London SW1E 5BY
T: 020 7121 2000
E: info@atkinsrealis.com
W: www.atkinsrealis.com
ATL Transformers Ltd
Hanson Close, Manson Street Middleton Manchester M24 2HD
T: 0161 653 0902
E: sales@atltransformers.co.uk
W: www.atltransformers.co.uk
Atlantic Design
Branch Hill Mews, Branch Hill London NW3 7LT
T: 020 7435 1777
E: enq@atlanticdesign.uk.com
W: www.atlanticdesign.uk.com
Atlantic Geomatics (UK) Ltd
Enterprise House, Gillan Way Penrith Cumbria CA11 9BP
T: 01768 483310
E: enquiries@atlanticgeomatics.co.uk
W: www.atlanticgeomatics.co.uk
Atlas Copco Compressors Ltd
Swallowdale Lane, Hemel Hempstead Hertfordshire HP2 7HA
T: 0845 601 0001
E: uk.enquiries@uk.atlascopco.com
W: www.atlascopco.com
Atmos Recruitment Ltd
Timberlake Barn, Stock Lane
Congresbury North Somerset BS49 5JL
T: 01934 835779
E: getintouch@atmosrecruitment.com
W: www.atmosrecruitment.com
Atom Services 408 Trocoll House, Wakering Road Barking Essex IG11 8PD
T: 020 8591 5140
E: info@atom-services.co.uk
W: www.atom-services.co.uk
Atom Training Centre 4th Floor, The Clockhouse
East Street Barking IG11 8EQ
T: 020 8591 5140
E: admin@atomtraining.co.uk
W: www.atomtraining.co.uk
ATOS
Second Floor, MidCity Place
71 High Holborn London WC1V 6EA
T: 0800 783 3040
E: ukwebenquiries@atos.net
W: www.atos.net
Attobus Ltd
Unit D2, Watlington Ind Estate Cuxham Road Watlington OX49 5LU
T: 01628 537300
E: sales@attobus.com
W: www.attobus.com
Auctus Management Group The Atlas Building, 16 Portland Street Aston Birmingham B6 5RX
T: 0121 366 8800
E: info@auctusmg.co.uk
W: www.auctusmg.co.uk
Auditel is a leading Cost, Procurement & Carbon Solutions Company. We help organisations reduce carbon emissions whilst also reducing costs. Carbon (GHG) projects are carried out by BSi Associate Consultants to internationally recognised PAS 2060 and PAS 2080, specifications which when verified can substantiate your carbon neutrality, and reduction claims.
Auditel (U.K.) Limited
1 Andromeda House, Calleva Park Aldermaston RG7 8AP
T: 07904 378911
E: barry.harwell@auditel.co.uk
W: www.auditel.co.uk/barryharwell
Augean Plc
4 Rudgate Court, Walton Wetherby North Yorkshire LS23 7BF
T: 01937 844980
E: aec-sales@augeanplc.com
W: www.augeanplc.com
Aura Brand Solutions are one of Europe’s leading branding experts – supplying full rail refurbishments, project management, and rolling stock rebranding. Over the years we’ve packaged this with complementary services, such as in-house design, marketing and social media, and site audits, to deliver a full suite of flexible project solutions.
Aura Brand Solutions
Freemantle Road, Lowestoft Suffolk NR33 0EA
T: 0845 052 5241
E: info@aurabrands.com
W: www.aurabrands.com
Aurora Lifts Ltd (Head Office) West Yoke, Michaels Lane, Ash Sevenoaks Kent TN15 7EP
T: 01474 879858
E: info@aurora-lifts.co.uk
W: www.aurora-lifts.co.uk
Austin Reynolds Ltd
Augustine House, Gogmore Lane Chertsey Surrey KT16 9AP
T: 01932 568888
E: sales@austinreynolds.co.uk
W: www.austinreynolds.com
Austin-Lenika Project Services Ltd
Unit 5c Hillthorpe Farm, Knoll Lane Preston Lancashire PR4 4TB
T: 01772 619573
E: sales@austin-lenika.co.uk
W: www.austin-lenika.co.uk
Autins Group PLC
Central Point One, Central Park Drive
Rugby Warwickshire CV23 0WE
T: 01788 578300
E: sales@autins.co.uk
W: www.autins.co.uk
Autoclenz Limited Stanhope Road, Swadlincote Derbyshire DE11 9BE
T: 01283 550033
E: sales@autoclenz.co.uk
W: www.autoclenz.co.uk
Autodrain Rotherwell Haigh, Leeds West Yorkshire LS26 0SB
T: 0113 205 9332
E: info@autodrain.net
W: www.autodrain.net
Autoglass
1 Priory Business Park, Cardington Bedford Bedfordshire MK44 3US
T: 01234 273636
E: customer.services@autoglass.co.uk
W: www.autoglass.nett
Automatic Door Suppliers Association (ADSA)
13 Tamworth Ent Centre, Philip Dix House Corporation Street Tamworth B79 7DN
T: 01827 216136
E: info@adsa.org.uk
W: www.adsa.org.uk
Automotive Trim Developments (ATD)
Priory Mill, Charter Avenue Coventry West Midlands CV4 8AF
T: 024 7669 5150
E: info@autotrimdev.com
W: www.autotrimdev.com
AV Birch Limited Aldenham Business Park, Muckley Cross Bridgnorth WV16 4RR
T: 01767 14418
E: enq@avaccess.co.uk
W: www.avaccess.co.uk
AV Coatings
13 Tamworth Ent Centre, Philip Dix House Corporation Street Tamworth SA18 1PE
T: 01269 825507
E: info@avcoatings.co.uk
W: www.avcoatings.co.uk
AV Dawson Ltd
Parc Howard Ind Estate, Cwmgors Ammanford Carmarthenshire TS2 1UT
T: 01642 219271
E: enquiries@av-dawson.com
W: www.av-dawson.com
Avalon Abseiling Ltd Avalon House, 45 Tallon Road Hutton Brentwood Essex CM13 1TG
T: 01277 500100
E: enquiries@avalonpro.co.uk
W: www.avalonpro.co.uk
Avanti West Coast North Wing Offices, Euston Station London NW1 2HS
T: 07500 122941
E: richard.stanton@avantiwestcoast.co.uk
W: www.avantiwestcoast.co.uk
AVL Reach Ltd International House, 124 Cromwell Road London SW7 4ET
T: 020 7559 1302
E: info@avlreach.co.uk
W: www.avlreach.co.uk
Avondale Environmental Services Ltd Fort Horsted, Primrose Close Chatham Kent ME4 6HZ
T: 01634 823200
E: info@avondaleuk.com
W: www.avondaleuk.com
Avonwood Developments Ltd
Knoll Technology Centre, Stapehill Road
Hampreston BH21 7ND
T: 01202 868000
E: sales@avonwood.co.uk
W: www.avonwood.co.uk
AW Marketing (AWARE) Ltd
16 Craigweil Close, Stanmore Middlesex HA7 4TR T: 020 8954 9121
E: training_services@marketing-intelligence.co.uk
W: www.aw-marketing.co.uk
Aworth Survey Consultants
Norfolk House, Norfolk Way
Uckfield East Sussex TN22 1EP
T: 01825 768319
E: als@aworth.co.uk
W: www.aworth.co.uk
AWS Electronics Group
Croft Road, Newcastle-UnderLyme ST5 0TW
T: 01782 735200
E: sales@awselectronicsgroup.com
W: www.awselectronicsgroup.com
Axa Reim UK
155 Bishopsgate, Broadgate London EC2A 3XJ
T: 020 7003 2874
E: webmaster-com@axa-im.com
W: www.axa-im.com
Axair Fans UK Limited
Centre 500, Lowfield Drive
Wolstanton Staffordshire ST5 0UU
T: 01782 349430
E: sales@axair-fans.co.uk
W: www.axair-fans.co.uk
Axiom Rail
Doncaster Works, Hexthorpe Road
Doncaster South Yorkshire DN1 1SL
T: 01302 340700
E: sales@axiomrail.com
W: www.wabtec.com
With over 30 years of design and ISO certified manufacturing behind us, we have the comprehensive capabilities to efficiently help you bring your innovative products to market. We can take your project from inception to delivery and help you make your industry expertise and capabilities. You can trust your innovation to our technology and expertise.
Axiomtek UK Ltd
Peter House, Oxford Street
Greater Manchester M1 5AN
T: 01612 093680
E: info@axiomtek.co.uk
W: www.axiomtek.co.uk
Axis Cleaning and Support Services Ltd
London Head Office, 361-373 City Road
London EC1V 1LR
T: 020 7520 2100
E: site-enquiries@axis-css.co.uk
W: www.axis-css.co.uk
Axis Communications (UK) Ltd
1 Capability Green, Luton
Bedfordshire LU1 3LU
T: 01582 283760
E: info@axis.com
W: www.axis.com
Axis Group Integrated Services
London Head Office, 361-373 City Road
London EC1V 1LR
T: 020 7520 2100
E: site-enquiries@axis-security.co.uk
W: www.axis-groupservices.co.uk
Axis Recruitment UK Ltd
Unit 9, High Point Bus Village
Henwood Kent CT9 4JS
T: 01233 632294
E: info@axisjobs.com
W: www.axisjobs.com
A professional and customer focused accredited laboratory with experience in diverse industrial sectors testing products for vibration, climatic, corrosive atmospheres, ingress protection and shock. Axis provides comprehensive testing schedules tailored to individual customer requirements, utilising flexible scheduling to ensure rapid turnaround and short lead times.
Axis Test Laboratories Ltd
Unit 11A, Oakway Court
Durham DH7 8XD
T: 0191 378 4653
E: info@axistestlaboratories.co.uk
W: www.axistestlaboratories.co.uk
Axminster Carpets Limited
Woodmead Road, Axminster
Devon EX13 5PQ
T: 01297 630650
E: sales@axminster-carpets.co.uk
W: www.axminster-carpets.co.uk
Ayrshire Medical Services Ltd
4 Wellington Square, Ayr South Aryshire KA7 1EN
T: 01292 262770
E: info@ayrshiremedical.co.uk
W: www.ayrshiremedical.co.uk
Ayrshire Metals Limited
Royal Oak Way, Daventry
Northamptonshire NN11 8NR
T: 01327 300990
E: sales@ayrshire.co.uk
W: www.ayrshire.co.uk
AZPML
55 Curtain Road
London EC2A 3PT
T: 020 7033 6480
E: lon@azpml.com
W: www.azpml.com
Aztec Chemicals
Gateway, Crewe Cheshire CW1 6YY
T: 01270 655500
E: info@aztecchemicals.com
W: www.aztecchemicals.com
Azteq Solutions Ltd
Azteq House, Maxted Corner
Eaton Road Hemel Hempstead HP2 7RA
T: 01442 244444
E: info@azteq.com
W: www.azteq.com
B&B established 1984 has remained a family orientated company, providing a personal service delivered to high standards. Audited members of the NFDC, RISQS & holders of a full 3 year HSE Asbestos licence- Offering Demolition, Dismantling, Asbestos removal and surveying services to Local Authorities, Rail, Infrastructure, Health Authorities, Highways etc.
B&B Industrial Dismantling Limited
4 Queen Street, Worksop Nottinghamshire S80 2AN
T: 01909 477799
E: mail@dismantling.org.uk
W: www.dismantling.org.uk
B&M McHugh Ltd
429a Footscray Road, New Eltham
London SE9 3UL
T: 020 8859 7706
E: msg@mchughltd.co.uk
W: www.mchughltd.co.uk
B&S Group
Sovereign Way, Chester West Employment Park Chester CH1 4QJ
T: 01244 390215
E: info@bsgroupltd.com
W: www.bsgroupltd.com
Babcock International
33 Wiemore Street London W1U 1QX
T: 020 7355 5300
E: info@babcock.co.uk
W: www.babcockinternational.com
Bachy Soletanche (Southern Office) Foundation Court, Riverside Way
Watchmoor Park Camberley Surrey GU15 3RG
T: 01276 674940
E: enquiries@bacsol.co.uk
W: www.bacsol.co.uk
Badenoch & Clark
20 Blythswood Square
Glasgow G2 4BG
T: 0141 220 6460
E: info@badenochandclark.com
W: www.badenochandclark.com
Badgemaster Ltd
Hazelford Way Ind Est, Newstead
Nottingham NG15 0DQ
T: 01623 723112
E: customerservices@badgemaster.co.uk
W: www.badgemaster.co.uk
BAE Systems Plc Warwick House, PO Box 87
Surrey GU14 6YU
T: 01252 373232
E: baesystemsinfo@baesystems.com
W: www.baesystems.com
Baker Bellfield Ltd Display House, Hortonwood 7 Telford Shropshire TF1 7GP
T: 01952 677411
E: info@bakerbelfield.co.uk
W: www.bakerbelfield.co.uk
Baker Consultants Ltd
West Platform, Cromford Station Cromford Bridge Matlock DE4 5JJ
T: 01629 593958
E: info@bakerconsultants.co.uk
W: www.bakerconsultants.co.uk
Baker Rose Consulting LLP
53 Davies Street, Mayfair London W1J 5DU
T: 020 7788 4784
E: mailbox@bakerrose.com
W: www.bakerrose.com
Bakerail Services Ltd
4 Green Lane, Hail Weston St Neots Cambridgeshire PE19 5JZ
T: 01480 471349
E: info@bakerailservices.co.uk
W: www.bakerailservices.co.uk
BakerHicks
1 Warwick Tech Park, Gallows Hill Warwickshire CV34 6YL
T: 01926 567800
E: contact@bakerhicks.com
W: www.bakerhicks.com
Balcony Business Services Limited Clouds House, George Road Yorkley Gloucestershire GL15 4TL
T: 0845 456 8956
E: enquiries@balconybs.co.uk
W: www.balconybs.co.uk
Baldwin & Francis Ltd
President Park, President Way Sheffield S4 7UR
T: 0114 286 6000
E: enquiries@baldwinandfrancis.com
W: www.baldwinandfrancis.com
Baldwin Boxall Communications Ltd
Wealden Ind Estate, Farningham Road
Crowborough East Sussex TN6 2JR
T: 01892 664422
E: mail@baldwinboxall.co.uk
W: www.baldwinboxall.co.uk
Baldwins Crane Hire Ltd PO Box 2656, Station Road
Langley Middlesex SL2 4ZM
T: 01753 583872
E: info@baldwinscranehire.com
W: www.baldwinscranehire.com
Balfour Beatty Ground Engineering
Pavillion C2, Ashwood Park
Ashwood Way Basingstoke RG23 8BG
T: 01256 400400
E: enquiries-basingstoke@bbge.com
W: www.balfourbeatty.com
Balfour Beatty Rail
5 Churchill Place, Canary Wharf London E14 5HU
T: 020 7216 6800
E: info@balfourbeatty.com
W: www.balfourbeatty.com
Ballast Tools UK Ltd
7 Pure Offices, Kembrey Park Swindon Wiltshire SN2 8BW
T: 01793 697800
E: sales@btukltd.com
W: www.btukltd.com
Balls2 Marketing Ltd
The Old Chapel, 1c Welbeck Grove Allestree Derby DE22 2LS
T: 01332 559406
E: support@balls2marketing.co.uk
W: www.balls2marketing.com
Ballyclare Limited
102 The Oaks Business Park, Crewe Road Wythenshawe M23 9HZ
T: 0844 493 2808
E: info@ballyclarelimited.com
W: ballyclarelimited.com
Ballycommon Services
77a Boston Manor Road, Brentford Middlesex TW8 9JQ
T: 020 8568 7706
E: mail@ballycommon.co.uk
W: www.ballycommon.co.uk
Balvac Ltd
Unit 6 Puma Court, Kings Business Park Kings Drive Prescot L34 1PJ
T: 01928 719875
E: enquiries.balvac@balvac.co.uk
W: www.balvac.co.uk
Bam Construct UK Ltd
Breakspear Park, Breakspear Way
Hemel Hempstead Hertfordshire HP2 4UL
T: 01442 238300
E: enquiries@bam.co.uk
W: www.bam.co.uk
BAM Nuttall Ltd
St James House, Knoll Road Camberley Surrey GU15 3XW
T: 01276 63484
E: headoffice@bamnuttal.co.uk
W: www.bamnuttall.co.uk
BAM Ritchies Glasgow Road, Kilsyth Glasgow Scotland G65 9BL
T: 01236 467000
E: ritchies@bamritchies.co.uk
W: www.bamritchies.co.uk
Banagher Precast Concrete Mundford Road, Weeting Brandon Norfolk IP27 0PL
T: 0161 3000513
E: info@bancrete.com
W: www.banagherprecast.com
BAND-IT Company Ltd
Speedwell Ind Est, Staveley Chesterfield UK S43 3PF
T: 01246 479479
E: sfranklin@idexcorp.com
W: www.band-it-idex.com
Banlaw Systems (Europe) Ltd 1 Rosdendale Way, Blantyre Glasgow G72 ONJ
T: 01698 824431
E: info@banlawsystems.com
W: www.banlawsystems.com
Bapp Industrial Supplies Ltd (Head Office) Claycliffe Road, Barugh Barnsley South Yorkshire S75 1LR
T: 01226 388444
E: sales@bappbarnsley.co.uk
W: www.bapp.co.uk
Baqus Group Plc
2-3 North Mews London WC1N 2JP
T: 01202 204888
E: enquiries@baqus.co.uk
W: www.baqus.co.uk
BarChip EMEA Ltd Business Campus, 3013 Lake Drive Citywest Dublin 24 D24
T: 00 353 1 4693197
E: dcrehan@barchip.com
W: www.barchip.com
Barcodes for Business Ltd – Head Office
Unit 5, Deans Close
Steventon Oxfordshire OX13 6SZ
T: 01494 810101
E: enquiries@barcodesforbusiness.co.uk
W: www.barcodesforbusiness.co.uk
Barhale Limited
Barhale House, Bescot Crescent
Walsall WS1 4NN
T: 01922 707700
E: communications@barhale.co.uk
W: www.barhale.co.uk
Barkers Fencing Duke Street, Fenton Stoke on Trent Staffordshire ST4 3NS
T: 01782 319264
E: sales@barkersfencing.com
W: www.barkersfencing.com
Barkley Plastics Ltd 120 Highgate Street
Birmingham B12 0XR
T: 0121 440 1303
E: info@barkley.co.uk
W: www.barkley.co.uk
Barnbrook Systems Ltd
25 Fareham Park Road, Fareham
Hampshire PO15 6LD
T: 01329 847722
E: sales@barnbrook.co.uk
W: www.barnbrook.uk
Barnshaws Section Benders Ltd
Barnshaws Group, Tipton Road
Tivdale Oldbury West Midlands B69 3HY
T: 0121 557 8261
E: sections@barnshaws.com
W: www.barnshaws.com
Barnsley MBC
Wellington House, Wellington Street
Barnsley South Yorkshire S70 1WA
T: 01226 773555
E: communications@barnsley.gov.uk
W: www.barnsley.gov.uk
Basemap Ltd
Surrey Tech Centre, 40 Occam Road
Guildford Surrey GU2 7YG
T: 01483 688470
E: sales@basemap.co.uk
W: www.basemap.co.uk
BASF Plc
PO Box 4, Earl Road
Cheadle Hulme Cheshire SK8 6QG
T: 0161 485 6222
E: info@basf.com
W: www.basf.com
BATT Cables PLC
The Belfry, Fraser Road Erith Kent DA8 1QH
T: 01322 441166
E: battindustrial.sales@batt.co.uk
W: www.batt.co.uk
Battery Service Hub Ltd
Pegasus House, Riverside End Market Harborough Leicestershire LE16 7PU
T: 01858 433008
E: info@batteryservicehub.com
W: www.batteryservicehub.com
BAUER Technologies Ltd
Millers Three, Southmill Road
Bishops Stortford Hertfordshire CM23 3DH
T: 01279 653108
E: info@bauertech.co.uk
W: www.bauertech.co.uk
Bayham Ltd
Rutherford Road, Daneshill West Ind Est
Basingstoke RG24 8PG
T: 01256 464911
E: sales@tankgauges.co.uk
W: www.tankgauges.co.uk
BCM Construction Ltd
Devonshire House, 164 Westminster
Bridge Rd Waterloo London SE1 7RW
T: 020 7551 0998
E: info@bcmconstruction.co.uk
W: www.bcmconstruction.co.uk
BCM GRC Ltd
Unit 22, Civic Industrial Estate
Whitchurch Shropshire SY13 1TT
T: 01948 665321
E: info@bcmgrc.com
W: www.bcmgrc.com
Beacon Rail Leasing Ltd
4th Floor, 4 Matthew Parker St London SW1H 9NP
T: 020 3983 0898
E: rail@beaconrail.com
W: www.beaconrail.com
Beakbane Ltd
Stourport Road, Kidderminster Worcestershire DY11 7QT
T: 01562 820561
E: info@beakbane.co.uk
W: www.beakbane.co.uk
Bearward Engineering Ltd
Main Road, Far Cotton
Northampton Northamptonshire NN4 8HJ
T: 01604 762851
E: sales@bearward.com
W: www.bearward.com
Beaver 84 Ltd
Trinity Street, Off Tat Bank Road
Oldbury Birmingham B69 4LA
T: 0121 543 2950
E: sales@beaver84.co.uk
W: www.beaver84.co.uk
Bechtel Ltd
Park Royal, 2 Lakeside Drive
London NW10 7FQ
T: 020 8846 5111
W: www.bechtel.com
Bechtel Ltd (London Office)
11 Pilgrim Street London EC4V 6RN
T: 020 7651 7777
W: www.bechtel.com
Beck & Pollitzer Ltd
Burnham Road, Dartford Kent DA1 5BD
T: 01322 223494
E: dartford@beck-pollitzer.com
W: www.beck-pollitzer.com
Bedestone Ltd
Boulton House, 41 Ickneild Street
Hockley Birmingham B18 5AY
T: 0121 554 3283
E: info@bedestone.co.uk
W: www.bedestone.co.uk
Beeby Anderson Recruitment (B-A-R)
Wenlock Studios, 50-52 Wharf Road London N1 7EU
T: 020 3176 2666
E: contact@b-a-r.com
W: www.b-a-r.com
Beeswift Limited
West Wing, Delta House, Delta Point Greets Green Road West Bromwich B70 9PL
T: 0121 524 2323
E: sales@beeswift.com
W: www.beeswift.co.uk
BELDEN
Belden Inc., Edisonstraat 9
5928 PG Venlo The Netherlands
T: 00 31 773 878 555
E: emea.cic@belden.com
W: www.belden.com/rail
BELDEN
Manchester Intl Off Ctr, Suite 13
Styal Road Manchester M22 5WB
T: 0161 498 3749
E: manchester.salesinfo@belden.com
W: www.beldensolutions.com
Bell Plastics Lts t/a Safetytread
450 Blandford Road, Poole
Dorset BH16 5BN
T: 01202 625596
E: safetytread@bellplastics.co.uk
W: www.safety-tread.co.uk
Bellman Media Limited
More House Farm, Haywards Heath West Sussex RH17 7RE
T: 01444 471884
E: enquiries@bellman.co.uk
W: www.bellman.co.uk
Bellsure Supplies Ltd
Vision House, Bedford Road Petersfield Hampshire GU32 3QB
T: 01730 719292
E: info@bellsure.co.uk
W: www.bellsure.co.uk
Bellvedi
Berkhamsted House, 121 High Street Berkhamsted Hertfordshire HP4 2DJ
T: 020 3289 4894
E: info@bellvedi.com
W: www.bellvedi.com
Belvoir Rail Ltd Unit 13, Manvers Business Park High Hazels Road Cotgrave Notts NG12 3GZ
T: 0115 989 2760
E: enquiries@belvoir-rail.com
W: www.belvoir-rail.com
Belzona Polymerics Ltd Claro Road, Harrogate North Yorkshire HG1 4DS
T: 01423 567641
E: belzona@belzona.co.uk
W: www.belzona.co.uk
BEMA Rail Training
Metasi House, Unit 1 523 West Street Crewe CW1 3PA
T: 01270 501821
E: enquires@bemarailtraining.co.uk
W: www.bemarailtraining.co.uk
Benchmark Training Ltd
Warvey’s Place, Farncombe Estate Broadway Worcestershire WR12 7LJ
T: 01386 854387
E: info@benchmarktraining.com
W: www.benchmarktraining.com
Bender is a global pioneer of electrical safety technology. Bender rail technology is approved and proven in use on Network Rail infrastructure throughout the UK. Solutions include NR/L2/SIGELP/27725 compliant insulation monitoring and earth fault location systems, enabling the identification of developing faults and improving operational efficiency of rail networks.
Bender UK Ltd
The Old Tannery, Low Mill Business Park Ulverston Cumbria LA12 9EE
T: 01229 480123
E: industrialsales@bender-uk.com
W: www.bender-uk.com
Bentley Systems (UK) Ltd 20 Gracechurch Street, 9th Floor London EC3V 0BG
T: 020 7861 0900
E: info@bentley.com
W: www.bentley.com
Beresfords Flooring Ltd
New House Farm, Belper Road Bradley Ashbourne DE6 1LP
T: 01335 345111
E: info@bfl.uk.com
W: www.beresfordsflooring.co.uk
BERNSTEIN are a specialist manufacturer of Safety switches, Sensors & Enclosures (Fire Protection (EN45545-2)). Utilising UK based comprehensive value-added services to deliver world-class “one stop” solution services on a world-wide platform. BERNSTEIN continues to partner all leading rail companies, being a Safety Critically Approved Supplier to Siemens, Bombardier and London Crossrail project.
Bernstein Ltd
Unit 1 Tintagel Way, Westgate Aldridge West Midlands WS9 8ER
T: 01922 744999
E: sales@bernstein-ltd.co.uk
W: www.bernstein-ltd.co.uk
Berry Piling London Limited
Berry Piling Group, Axiom House 41 Balcombe Road Horley Surrey RH6 7HF
T: 01293 772422
E: sales@berrypilinggroup.co.uk
W: www.berrypilinggroup.co.uk
Berry Systems
Springvale Business, & Industrial Park Bilston Wolverhampton WV14 0QL
T: 01902 491100
E: sales@berrysystems.co.uk
W: www.berrysystems.co.uk
Berrymans Lace Mawer LLP (BLM)
King’s House, 42 King Street West Manchester M3 2NU
T: 0161 236 2002
E: info@blmlaw.com
W: www.blmlaw.com
Bersche-Rolt Ltd Stream House, Herons Ghyll Uckfield East Sussex TN22 4BY
T: 01825 713000
E: mail@bersche-rolt.co.uk
W: www.bersche-rolt.co.uk
Bespoke by Evans Bespoke Showroom, Parkway Denton Manchester M34 3SG
T: 0161 320 2121
E: design@evans-textiles.com
W: www.bespokebyevans.com
Bespoke Composite Panels
5 Stukeley Bus Centre, Blackstone Road Huntingdon Cambridgeshire PE29 6EF
T: 01480 435302
E: sales@bespokecompositepanels.com
W: www.bespokecompositepanels.com
Best Impressions
15 Starfield Road London W12 9SN
T: 020 8740 6443
E: talk2us@best-impressions.co.uk
W: www.best-impressions.co.uk
Betafence Limited PO Box 119, Shepcote Lane Sheffield S9 1TY T: 0114 256 7800
E: sales.sheffield@betafence.com
W: www.betafence.co.uk
Bethell Construction Limited
Dane House, Europa Park
Stoneclough Road Kearsley M26 1GE
T: 01204 439100
E: solutions@bethell.co.uk
W: www.bethell.co.uk
Beveridge Associates Partnership Limited
Regency House, Station Road
Harold Wood Essex RM3 0BS
T: 01708 336969
E: info@Beveridge-Associates.co.uk
W: www.beveridge-associates.co.uk
Beyond Interactive Communications Ltd
Ribble Saw Mill, Paley Road
Preston PR1 8LT
T: 0844 335 0390
E: info@beyondinteractive.co.uk
W: www.beyondinteractive.co.uk
BG Steels Ltd
Little Edge House, Eyam Hope Valley Derbyshire S32 5RE
T: 07831 759594
E: bj.hague@bgsteels.co.uk
W: www.bgsteels.co.uk
BGB Engineering Ltd
357 Dysart Road, Grantham Lincolnshire NG31 7NB
T: 01476 576280
E: sales@bgbinnovation.com
W: www.bgbinnovation.com
BHA
BHA Cromwell House, PO Box 302 Carshalton SM5 9AU
T: 0843 523 1024
E: contact@bhacromwell.co.uk
W: www.bhacromwell.co.uk
bhi Ltd
22 Woolven Close, Burgess Hill West Sussex RH15 9RR
T: 01444 870333
E: info@bhi-ltd.com
W: www.bhi-ltd.com
BHSF Occupational Health Ltd
G/F Suite Lyndon House, 62 Hagley Road Birmingham B16 8PE
T: 01527 577242
E: admin@bhsfoh.co.uk
W: www.bhsfoh.co.uk
Bibby Distribution 105 Duke Street, Liverpool Merseyside L1 5JQ
T: 0151 708 8000
E: info@bibbydist.co.uk
W: www.bibbydist.co.uk
Bidvest Noonan (UK) Limited
15 St Botolph Street, Aldgate London EC3A 7BB
T: 0203 319 1750
E: info@bidvestnoonan.com
W: www.bidvestnoonan.co.uk
Bijur Delimon International Ramsden Court, Ramsden Road Rotherwas Ind Est Hereford HR2 6LR
T: 01432 365000
E: info@bijurdelimon.co.uk
W: www.bijurdelimon.com
Bikeaway Strode Road, Newnham Industrial Estate Plympton Plymouth PL7 4AY
T: 01752 202116
E: sales@bikeaway.com
W: www.bikeaway.com
Binder Fastener Systems UK Limited
Unit 16a, John Bradshaw Court
Alexandria Way Congleton Cheshire CW12 1LB
T: 01260 272744
E: sales@binderuk.com
W: www.binderuk.com
Bingham Rail (DS) Ltd
Barrow Road, Wincobank Sheffield S9 1JZ
T: 0114 243 8441
E: info@binghamrail.com
W: www.binghamrail.co.uk
Bircham Dyson Bell LLP 50 Broadway, London SW1H 0BL
T: 020 7227 7000
E: enquiries@bdb-law.co.uk
W: www.bdb-law.co.uk
Bird & Bird LLP
12 New Fetter Lane London EC4A 1JP
T: 020 7415 6000
E: info@twobirds.com
W: www.twobirds.com
Bird Free Ltd
3 Tyndale House, Tyndale Lane London N1 2UL
T: 020 7359 9988
E: ian.smith@bird-free.com
W: www.bird-free.com
Birmingham Prototypes Limited
Unit 7, Madley Road Ind Estate
North Moons Moat Redditch B98 9NB
T: 01527 68071
E: info@birminghamprototypes.co.uk
W: www.birminghamprototypes.co.uk
Birmingham Specialities Ltd Lincoln Works, Moor Lane Witton Birmingham B6 7HE
T: 0121 356 5026
E: sales@bhamspec.co.uk
W: www.bhamspec.co.uk
Birtley Group
Mary Avenue, Birtley County Durham DH3 1JF
T: 0191 410 6631
E: info@birtleygroup.co.uk
W: www.birtleygroup.co.uk
Bisham Consulting
Cedar House, Glade Road Marlow Buckinghamshire SL7 1DQ
T: 01628 487000
E: contact@bishamconsulting.com
W: www.bishamconsulting.com
Bitmen Products
Tex Engineering Limited, Unit 35 Claydon Bus Pk
Gipping Road Ipswich Suffolk IP6 0NL
T: 01257 264403
E: info@tex-engineering.co.uk
W: www.tex-engineering.co.uk
Bitrez Limited
Bradley Hall Ind Estate, Bradley Lane Standish Wigan WN6 0XQ
T: 01257 425512
E: enquiries@bitrez.co.uk
W: www.bitrez.com
BJD Group
2 The Mill Rectory Farm, Farndon Road
Market Harborough Leicestershire LE16 9TU
T: 01858 455098
E: mailbox@bjdgroup.com
W: www.bjdgroup.co.uk
Black Diamond Security
Vision House, Durham Lane West Moor Park Doncaster DN3 3FE
T: 0800 804 8112
E: info@blackdiamondsecurity.co.uk
W: www.blackdiamondsecurity.co.uk
Blackbox Co UK Ltd
3 The Courtyard Bracknell RG12 2XB
T: 01344 513333
E: info@blackbox-co.com
W: www.blackbox-co.com
Blackbridge Communications Limited
Zetland House, 5-25 Scrutton Street London EC2A 4HJ
T: 020 7729 8969
E: hello@blackbridge.co.uk
W: www.blackbridge.co.uk
Blackpool Tramway (Blackpool Transport, Services Limited) Rigby Road Blackpool FY1 5DD
T: 01253 473001
E: enquiries@blackpooltransport.com
W: www.blackpooltransport.com
Blagg & Johnson Ltd
Newark Business Park, Brunel Drive Newark Nottighamshire NG24 2EG
T: 01636 703137
E: sales@blaggs.co.uk
W: www.blaggs.co.uk
Blake Morgan LLP
New Kings Court, Tollgate Chandlers Ford Eastleigh Hants SO53 3LG
T: 023 8090 8090
E: info@blakemorgan.co.uk
W: www.blakemorgan.co.uk
Our business is to improve the working environment in railway depots and to safeguard the workforce. For over 45 years, we have been designing, manufacturing, and installing local exhaust ventilation systems removing the diesel engine exhaust fumes at source. Many well-known railway companies rely on our experience and expertise.
Blaschke Umwelttechnik GmbH
Industriestrasse 13, 86405 Meitingen Germany
T: 00 49 8271 8169-0
E: info@hblaschke.de
W: www.hblaschke.de
Blocksil Ltd
Cathedral House, 5 Beacon Street Lichfield WS13 7AA
T: 01543 887840
E: info@blocksil.co.uk
W: www.blocksil.co.uk
Blok ‘N’ Mesh Unit 1, Hammond Rd Liverpool L33 7UL T: 0870 950 57 88
E: webteam@bloknmesh.com
W: www.bloknmesh.com
Bloomberg LLP 3 Queen Victoria Street London EC4N 4TQ
T: 020 7330 7500
E: inquiry1@bloomberg.net
W: www.bloomberg.com
Bloxwich Transport & Container Products Ltd
10 Cedars Bus Centre, Avon Road Cannock Staffordshire WS11 1QJ
T: 01543 435160
E: sales@bloxwichgroup.com
W: www.bloxwichgroup.com
Blue Chip Technology Chowley Oak, Chowley Oak Lane
Tattenhall Chester CH3 9EX
T: 01829 772000
E: sales@bluechiptechnology.com
W: www.bluechiptechnology.com
Blueprint Recruitment Ltd
6/7 Pentland House, Glenrothes Fife Scotland KY6 2A
T: 0159 263 1644
E: info@blueprint-recruitment.co.uk
W: www.blueprint-recruitment.co.uk
Blueprint Recruitment Solutions
Fartec, Carnac Court, Cams Hall Estate Fareham Hampshire PO16 8JY
T: 023 9260 3030
E: info@blueprintrecruit.com
W: www.blueprintrecruit.com
Bluesky PR Centurion House, 136-142 London Road St Albans Hertfordshire AL1 1PQ
T: 01582 790700
E: hello@bluesky-pr.com
W: www.bluesky-pr.net
BMAC Ltd
U13-14 Shepley Ind Est, South Shepley Road Audenshaw Manchester M34 5DW
T: 0161 337 3070
E: enquiries@bmac.ltd.uk
W: www.bmac.ltd.uk
BME Nitech Ltd
Unit 2a Nevis Bus Park, Blagownie Road Bridge of Don Aberdeen AB22 8NT
T: 01224 825320
E: sales@bmenitech.co.uk
W: www.bmenitech.co.uk
BMT Asset Performance Ltd
1st Floor, Berkeley Hse, The Square Lower Bristol Road Bath BA2 3BH
T: 01225 473727
E: info@bmtapl.com
W: www.bmtapl.com
BMT Group
Goodrich House, 1 Waldegrave Road
Teddington Middlesex TW11 8LZ
T: 020 8949 5544
E: enquiries@bmtmail.com
W: www.bmt.org
BNP Paribas Real Estate Portwall Place, Portwall Lane Bristol BS1 6NA
T: 0117 984 8400
E: realestate.press@bnpparibas.com
W: www.realestate.bnpparibas.co.uk
BOC Ltd
The Priestly Centre, 10 Priestley Road Guildford Surrey M28 2UT
T: 0808 278 4993
E: custserv@boc.com
W: www.boconline.co.uk
Bodacc Ltd
Unit 7, Griffin Entreprise Park
Penrhyndeudraeth Gwynedd LL48 6LE
T: 01766 238020
E: admin@bodaccltd.co.uk
W: www.bodaccltd.co.uk
Boddingtons Electrical Prospect House, Queenborough Lane
Gt Notley Braintree CM77 7AG
T: 01376 567490
E: info@boddingtons-electrical.com
W: www.boddingtons-electrical.com
Bodycote PLC Macclesfield Head Office Springwood Court, Springwood Close Macclesfield Cheshire SK10 2XF
T: 01625 505300
E: customer.response@bodycote.com
W: www.bodycote.com
Bodyguard Workwear Ltd
Adams Street
Birmingham B7 4LS
T: 0121 359 8880
E: info@bodyguardworkwear.co.uk
W: www.bodyguardworkwear.co.uk
Bollé Safety, the safety eyewear specialist. With a wide range of comfortable and protective safety and prescription eyewear, Bollé Safety has the right equipment for your unique needs. Led by innovation for over 130 years, we develop all our products and services to go beyond our users’ expectations.
Bolle Safety
C83 Barwell Bus Park, Leatherhead Road Chessington Surrey KT9 2NY
T: 020 8391 4700
E: sales@bolle-safety.co.uk
W: www.bolle-safety.com
BOMAG (Great Britain) Ltd
Sheldon Way, Larkfield Aylesford ME20 6SE
T: 01622 716611
E: gb@bomag.com
W: www.bomag.com
Bond Demolition Ltd
Unit 3B Ocean Park, Pant Glas Ind. Estate Caerphilly CF83 8DR
T: 02920 888 788
E: info@bonddemolition.co.uk
W: www.bonddemolition.co.uk
Bond Insurance Service Ltd
Salisbury House, 81 High Street
Potters Bar Hertfordshire EN6 5AS
T: 01707 291200
E: enquiries@bond-insurance.co.uk
W: www.bond-insurance.co.uk
Bonomi UK Ltd
The Fluid Power Center, Watling Street Nuneaton Warwickshire CV11 6BQ
T: 024 7635 4535
E: sales@bonomi.co.uk
W: www.bonomi.co.uk
Bonsers (Nottingham) Limited
No2 The Tractor Barn, Hall Farm Yard
Kirklington Newark NG22 8NN
T: 01636 815986
E: contact@bonsersrestoration.co.uk
W: www.bonsersrestoration.co.uk
Book my Course Training Courses
Book My Course Ltd, Diamond Way
Nene Park Irthlingborough NN9 5QF
T: 01933 233884
E: enquiries@bookmycourse.co.uk
W: www.bookmycourse.co.uk
Booth Industries International Ltd
PO Box 50, Nelson Street
Bolton Lancashire BL3 2AP
T: 01204 366333
E: enquiries@booth-industries.co.uk
W: www.booth-industries.co.uk
Booth-Muirie Ltd
South Caldeen Road, Coatbridge
Scotland ML5 4EG
T: 01236 345500
E: enquiries@boothmuirie.co.uk
W: www.boothmuirie.co.uk
Bosch Rexroth Limited
15 Cromwell Road, St. Neots
Cambridgeshire PE19 2ES
T: 01480 223200
E: info@boschrexroth.co.uk
W: www.boschrexroth.co.uk
Bosch Security & Saftety Systems
Broadwater Park, North Orbital Road
Denham UB9 5HJ
T: 0330 123 9979
E: service-enquiries@uk.bosch.com
W: www.boschsecurity.com
Bosch Security Systems UK
PO Box 750, Uxbridge
Middlesex UB9 5ZJ
T: 01895 878088
E: security.systems@uk.bosch.com
W: www.uk.boschsecurity.com
Bott Ltd
Bude-Stratton Bus Park, Bude
Cornwall EX23 8LY
T: 01288 357788
E: info@bottltd.co.uk
W: www.bottltd.co.uk
Bourton Group LLP
5 Cottesbrooke Park, Heartlands
Daventry Northamptonshire NN11 8YL
T: 01926 633333
E: info@bourton.co.uk
W: www.bourton.co.uk
Bowden Bros Ltd
Brickworks House, Spook Hill North Holmwood Surrey RH5 4HR
T: 01306 743355
E: sales@bowden-bros.com
W: www.bowden-bros.com
Bowmonk Ltd
Diamond Road, Norwich Norfolk NR6 6AW
T: 01603 485153
E: info@bowmonk.com
W: www.bowmonk.com
BPH Rail and Civil Engineering Ltd
Unit 8 Little Hyde Hall, Hatfield Heath Road
Sawbridgeworth Hertfordshire CM21 9HX
T: 01279 724913
E: enquiries@bphrail.co.uk
W: www.bphrail.co.uk
BPR Architects Ltd
The Boathouse, Embankment Putney London SW15 1LB
T: 020 8785 9983
E: info@bprarchitects.com
W: www.bprarchitects.com
Bradgate Containers design and manufacture a wide range of specialist equipment including containers and modules used in the rail sector for applications from traction electrification through to signalling supplies PSP’s and SSP’s. From fully welded to bonded panel, mild steel to stainless steel, at Bradgate we have the solution to fit the customer needs.
Bradgate Containers
Leicester Road, Shepshed Leicestershire LE12 9EG
T: 01509 508678
E: sales@bradgate.co.uk
W: www.bradgate.co.uk
Bradley Manufacturing
Junction 21 Bus Park, Gorse Street
Chadderton Oldham OL9 9QH
T: 01706 621421
E: web@bradleymanufacturing.com
W: www.bradleymanufacturing.co.uk
Bradleys Metal Finishers
49 Knightsdale Road, Ipswich Suffolk IP1 4JJ
T: 01473 461400
E: sales@bradleys-uk.com
W: www.bradleysmetalfinishers.com
Brady UK
Wildmere Ind Estate, Banbury Oxon OX16 3JU
T: 01295 228288
E: csuk@bradycorp.com
W: www.brad.co.uk
Brammer
Headway Road
Wolverhampton WV10 6PZ
T: 01902 395000
E: marketing.uk@brammer.biz
W: www.brammer.co.uk
Brand-Rex Ltd
West Bridgewater Street, Leigh Lancashire WN7 4HB
T: 01942 265500
E: sales@brand-rex.com
W: www.brand-rex.com
Brand8 PR
Round Foundry, Media Centre
Foundry Street Leeds LS11 5QP
T: 0113 394 4580
E: info@brand8pr.com
W: www.brand8pr.com
Brandauer
235 Bridge Street West, Birmingham West Midlands B19 2YU
T: 0121 359 2822
E: sales@brandauer.co.uk
W: www.brandauer.co.uk
Brandformula Ltd
Fourth Floor, 5 London Wall Buildings
Finsbury Circus London EC2M 5NS
T: 020 7265 7880
E: info@brandformula.co.uk
W: www.brandformula.co.uk
Brands2Life
2 Floor, Blue Fin Building
110 Southwark St London SE1 0SU
T: 020 7592 1200
E: info@brands2life.com
W: www.brands2life.com
Brass Agency (Head Office)
Moorfield House, Alma Road Leeds LS6 2AH
T: 0113 230 4000
E: hello@brassagency.com
W: www.brassagency.com
Bratts Ladders
Abbeyfield Road, Lenton Ind Estate
Nottingham NG7 2SZ
T: 0115 986 6851
E: sales@brattsladders.com
W: www.brattsladders.com
Braybrook Ltd
3c Sopwith Crescent, Hurricane Way
Wickford Essex SS11 8YU
T: 01268 763399
E: admin@braybrookltd.co.uk
W: www.braybrookltd.co.uk
Brazen (UK) PR & Content Marketing
Brazen House, 27 Great Ancoats Street
Manchester M4 5AJ
T: 0161 923 4994
E: info@wearebrazenpr.com
W: www.brazenpr.com
BRE Watford Bucknalls Lane Watford WD25 9XX
T: 0333 321 8811
E: enquiries@bregroup.com
W: www.bregroup.com
Breckenridge
Old Bond Store, Back of the Walls Southampton Hampshire SO14 3HA
T: 023 8043 3348
E: hello@breckenridge.agency
W: www.breckenridge.agency
Brecknell Willis PO Box 10, Chard Somerset TA20 2DE
T: 01460 260700
E: brecknellwillis@wabtec.com
W: www.brecknellwillis.com
Bremskerl (UK) Ltd 4b Ashmead Ind Estate, Ashmead Road Keynsham Bristol BS31 1TU
T: 0117 946 1600
E: online@bremskerl.com
W: www.bremskerl.de
Brett Aggregates Ltd
Brett House, Bysing Wood Road
Faversham Kent ME13 7UD
T: 01795 594000
E: aggssalesenquiries@brett.co.uk
W: www.brett.co.uk
Brett Aggregates Ltd Waldringfield Road, Brightwel Ipswich Suffolk IP2 8LY
T: 01473 811900
E: saleseastern@brett.co.uk
W: www.brett.co.uk
Brett Martin Ltd
24 Roughfort Road, Newtownabbey Co Antrim BT36 4RB
T: 028 9084 9999
E: mail@brettmartin.com
W: www.brettmartin.com
Brevia Consulting (Brevia Ltd) 5 Salamanca Place, Lambeth London SE1 7HP
T: 020 7091 1650
E: contact@brevia.co.uk
W: www.brevia.co.uk
Brian Cole Associates Ltd Orient House, Church Way Wellingborough Northamptonshire NN8 4HJ
T: 01933 440024
E: enquiry@bcal.co.uk
W: www.bcal.co.uk
Bridges Communications Limited York House, 5a Holly Hill Lane Sarisbury Green Southampton SO31 7AB
T: 01489 559976
E: team@bridgescommunications.co.uk
W: www.bridgescommunications.co.uk
Bridgeway Consulting Limited Bridgeway House, Riverside Way Nottingham NG2 1DP
T: 0115 9191111
E: enquiries@bridgeway-consulting.co.uk
W: www.bridgeway-consulting.co.uk
Briggs Equipment UK Ltd Orbital 7, Orbital Way Cannock Staffordshire WS11 8XW
T: 0330 123 9814
E: info@briggsequipment.co.uk
W: www.briggsequipment.co.uk
BriggsAmasco
Amasco House, 101 Powke Lane
Cradley Heath B64 5PX
T: 0121 502 9600
E: enquiries@birggsamasco.co.uk
W: www.briggsamasco.co.uk
Brintons Carpets Limited Stourport Road, Kidderminster Worcestershire DY11 7PZ
T: 01562 820000
E: contact@brintons.co.uk
W: www.brintons.co.uk
Britannia Construction Ltd
Britannia House, Staverton Tech Park Cheltenham Gloucestershire GL51 6TQ
T: 01452 859880
E: info@britanniaconstruction.co.uk
W: www.britanniaconstruction.co.uk
British Approvals Service For Cables (BASEC)
Presley House, Presley Way
Crownhill Milton Keynes MK8 0ES
T: 01908 267300
E: mail@basec.org.uk
W: www.basec.org.uk
British Cables Company provides the infrastructure cabling required for highly advanced, safety-critical rail systems to operate. Our products have gained Network Rail product approval for the full range of LSZH NR/PS/TEL/00015 (Trackside Comms), NR/L2/ SIG/30060 (Axle Counter) and BR1932 (SSI Datalink) variants.
British Cables Company
Delaunays Road, Blackley Manchester M9 8FP
T: 0161 741 2345
E: info@britishcables.com
W: www.britishcablescompany.com
British Chamber of Commerce
65 Petty France, Westminster London SW1H 9EU
T: 020 7654 5800
E: info@britishchambers.org.uk
W: www.britishchambers.org.uk
British Drilling Association (BDA)
Alphab House, Alfred Street Pinxton Nottinghamshire NG16 6NQ
T: 01773 778751
E: office@britishdrillingassociation.co.uk
W: www.britishdrillingassociation.co.uk
British Fluid Power Association (BFPA) Cheriton House, Cromwell Park Chipping Norton Oxon OX7 5SR
T: 01608 647900
E: enquiries@bfpa.co.uk
W: www.bfpa.co.uk
British Geological Survey Kingsley Dunham Centre, Keyworth Nottingham NG12 5GG
T: 0115 936 3100
E: enquiries@bgs.ac.uk
W: www.bgs.ac.uk
British Geomembrane Association (BGA)
8 Darwin House, Corby Gate Business Park Corby Northants NN17 5JG
E: office@britishgeomembraneassociation.co.uk
W: www.britishgeomembraneassociation.co.uk
British Geophysical Association (BGA)
c/o The RAS, Burlington House Piccadilly London W1J 0BQ
T: 020 7734 4582
E: secretary@geophysics.org.uk
W: www.britgeophysics.org
British Geotechnical Association (BGA)
1 Great George Street London SW1P 3AA
T: 020 7665 2007
E: bga@britishgeotech.org.uk
W: www.britishgeotech.org
British Gypsum Ltd
Gotham Road, East Leake
Loughborough Leicestershire LE12 6HX
T: 0115 945 1000
E: bgtechnical.enquiries@bpb.com
W: www.biritsh-gypsum.co.uk
British International Freight Association (BIFA) Redfern House, Browells Lane
Feltham Middlesex TW13 7EP
T: 020 8844 2266
E: bifa@bifa.org
W: www.bifa.org
British Mica Co Ltd
123 Barkers Lane, Bedford Bedfordshire MK41 9RR
T: 01234 327977
E: info@britishmica.co.uk
W: www.britishmica.co.uk
British Parking Association (BPA)
Chelsea House, 8-14 The Broadway
Haywards Heath West Sussex RH16 3AH
T: 01444 447300
E: info@britishparking.co.uk
W: www.britishparking.co.uk
British Pest Control Association (BPCA)
4a Mallard Way, Pride Park Derby DE24 8GX
T: 01332 294288
E: enquiry@bpca.org.uk
W: www.bpca.org.uk
British Precast
The Old Rectory, Main Street Glenfield Leicestershire LE3 8DG
T: 0116 232 5170
E: info@britishprecast.org
W: www.britishprecast.org
British Retail Consortium
2 London Bridge London SE1 9RA
T: 020 7854 8900
E: info@brc.org.uk
W: www.brc.org.uk
British Safety Council
70 Chancellor’s Road, Hammersmith London W6 9RS
T: 020 3510 8355
E: customer.service@britsafe.org
W: www.britsafe.org
British Safety Industry Federation (BSIF)
Bsif House, 3 Austens Mews
Hemel Hempstead Hertfordshire HP1 3AF
T: 01442 248744
E: enquiries@bsif.co.uk
W: www.bsif.co.uk
British Security Industry Association (BSIA)
Anbrian House, First Floor 1 The Tything Worcester WR1 1HD
T: 01905 342020
E: info@bsia.co.uk
W: www.bsia.co.uk
British Standards Institution (BSI) 389 Chiswick High Road, Chiswick London W4 4AL
T: 0345 080 9001
E: cservices@bsigroup.com
W: www.bsigroup.com
British Steel PO BOX 1, Brigg Road
Scunthorpe DN16 1BP
T: 01724 404040
E: rail@britishsteel.co.uk
W: www.britishsteel.co.uk
British Transport Police (BTP)
BTP Headquarters, 25 Camden Road London NW1 9LN
T: 0800 40 50 40
E: first_contact@btp.pnn.police.uk
W: www.btp.police.uk
British Transport Police Authority (BTPA)
The Forum, 5th Floor North 74-80 Camden St London NW1 0EG
T: 020 7383 0259
E: general.enquiries@btpa.police.uk
W: www.btpa.police.uk
British Tunnelling Society (BTS)
1 Great George Street London SW1P 3AA
T: 020 7665 2238
E: bts@ice.org.uk
W: www.britishtunnelling.com
Briton Fabricators Ltd
Watnall Road, Hucknall Nottingham NG15 6EP
T: 0115 963 2901
E: sales@britonsltd.co.uk
W: www.britonsltd.co.uk
Broadway Malyan (Weybridge Office)
3 Weybridge Bus Park, Addlestone Road
Weybridge Surrey KT15 2BW
T: 01932 845599
E: wey@BroadwayMalyan.com
W: www.broadwaymalyan.com
Brockhouse Forgings Ltd
Howard Street, West Bromwich West Midlands B70 0SN
T: 0121 556 1241
E: info@brockhouse.co.uk
W: www.brockhouse.co.uk
Brodie Engineering Limited
Bonnyton Rail Depot, Munro Place
Kilmarnock Ayrshire KA1 2NP
T: 01563 546280
E: mail@brodie-engineering.co.uk
W: www.brodie-engineering.co.uk
Brodies LLP
15 Atholl Crescent, Edinburgh Scotland EH3 8HA
T: 0131 228 3777
E: mailbox@brodies.com
W: www.brodies.com
Brogan Group UK Ltd
4 Falcon Gate, Falcon Way
Shire Park Welwyn Garden City AL7 1TW
T: 0333 358 0007
E: enquiries@brogangroup.com
W: www.brogangroup.com
Brokk UK Ltd
Unit 2a, Moss End Bus Village
Crooklands Milnthorpe LA7 7NU
T: 01539 566055
E: info@brokk.com
W: www.brokk.com
Brookvex IMS
Sandham House, Boundary Business Court
92-94 Church Road Mitcham Surrey CR4 3TD
T: 020 8687 5560
E: info@brookvexims.com
W: www.brookvexims.com
Browns Fasteners Ltd
PO Box 13, Deanfield Mills
Asquith Avenue Morley, Leeds LS27 9RE
T: 0113 252 2185
E: sales@brownsfasteners.co.uk
W: www.brownsfasteners.co.uk
Browse Bion
Unit 19/20, Lakeside Park
Medway City Estate Rochester Kent ME2 4LT
T: 01634 710063
E: sales@browsebion.com
W: www.browsebion.com
Brunel University
Kingston Lane, Uxbridge
Middlesex UB8 3PH
T: 01895 274000
E: ukeu-admissions@brunel.ac.uk
W: www.brunel.ac.uk
Bruton Knowles
Greybrook House, 28 Brook Street London W1K 5DH
T: 0845 200 6489
E: marketing@brutonknowles.co.uk
W: www.brutonknowles.co.uk
Bryan & Armstrong Ltd 22 Wenlock Road, Hoxton London EC1V 4PY
T: 020 7129 7075
E: enquiry@bryan-armstrong.com
W: www.bryan-armstrong.com
Bryan Cave Leighton Paisner LLP
Adelaide House, London Bridge London EC4R 9HA
T: 020 3400 1000
E: info@bclplaw.ccom
W: www.blplaw.com
Bryen & Langeley Ltd
6 Lagoon Road, Orpington
Kent BR5 3QX
T: 020 8850 7775
E: info@bryen-langley.com
W: www.bryen-langley.com
Bryn Thomas Cranes Ltd 421 Chester Road, Flint
Wales CH6 5SE
T: 01352 733984
E: sales@brynthomascranes.com
W: www.brynthomascranes.com
BSP Consulting (Nottingham Office) Head Office, 12 Oxford Street Nottingham NG1 5BG
T: 0115 840 2227
E: rail@bsp-consulting.co.uk
W: www.bsp-consulting.co.uk
BSP International Foundations Ltd
Claydon Business Park, Gipping Road
Great Blakenham Ipswich Suffolk IP6 0NL
T: 01473 830431
E: sales@bspif.co.uk
W: www.bsp-if.com
BSRIA Ltd
Old Bracknell Lane, West Bracknell Berkshire RG12 7AH
T: 01344 465600
E: bsria@bsria.co.uk
W: www.bsria.co.uk
BSV Recruitment Ltd
Lynton House, Station Approach Woking Surrey GU22 7PY
T: 01483 768600
E: info@bsvrecruitment.co.uk
W: www.bsvrecruitment.co.uk
BTROS electronics Unit 4b, Castlewood Bus Park Farmwell Lane Sutton-in-Ashfield NG17 1JF
T: 01773 814640
E: esales@btros.co.uk
W: www.btros-electronics.com
BTRoS Interiors and Cabling Division Litchurch Lane Works Derby DE24 8AD
T: 01332 257500
E: bdm@btros.co.uk
W: www.btros.co.uk
Buck & Hickman
National Distb Centre, Headway Road Wolverhampton WV10 6PZ
T: 01902 395000
E: enquiries@buckandhickman.com
W: www.buckandhickman.com
Buckingham Group Contracting Ltd Silverstone Road, Stowe Buckinghamshire MK18 5LJ
T: 01280 823355
E: bd@buckinghamgroup.co.uk
W: www.buckinghamgroup.co.uk
Buildbase Gemini One, 5520, Oxford Business Park Cowley Oxford OX4 2LL
T: 01865 871700
E: oxford@buildbase.co.uk
W: www.buildbase.co.uk
Building Design Partnership (BDP)
16 Brewhouse Yard, Clerkenwell London EC1V 4LJ
T: 020 7812 8000
E: london@bdp.com
W: www.bdp.com
Bulk Freight (Midlands) Ltd
Trent Lane, Castle Donington
Derby Derbyshire DE74 2NP
T: 01322 853358
E: sales@bulkfreight.co.uk
W: www.bulkfreight.co.uk
Bulkhaul Ltd
Brignell Road, Riverside Park Ind Est Middlesbrough Cleveland TS2 1PS
T: 01642 230423
E: info@bulkhaul.co.uk
W: www.bulkhaul.co.uk
Bunkabin
Tweedale Way Oldham OL9 7LD
T: 0345 456 7899
E: hires@bunkabin.co.uk
W: www.bunkabin.co.uk
Bunzl Greenham
Bunzl UK Limited, Greenham House 671 London Road Middlesex TW7 4EX
T: 0845 300 6672
E: sales@greenham.com
W: www.greenham.com
Bupa – Health Care Service Delivery
Battle Bridge House, 300 Grays Inn Road London WC1X 8DU
T: 020 7656 3710
E: BattleBridgeHouse@bupa.com
W: www.bupa.co.uk
Burges Salmon
One Glass Wharf Bristol BS2 0ZX
T: 0117 939 2000
E: marketing@burges-salmon.com
W: www.burges-salmon.com
Burrell & Mistry Ltd
7a Lambs Conduit Psge, Holborn London WC1R 4RG
T: 020 7092 3090
E: post@burrellmistry.com
W: www.burrellmistry.com
Burrows Electrical Limited Ansona Works, Steamer Terrace Chelmsford Essex CM1 1QP
T: 01245 267428
E: enquiries@burrowselectrical.com
W: www.burrowselectrical.com
Burtonwood Generator & Switchgear Services Ltd
Unit 2, Saint Michael’s Road
St Helens Merseyside WA9 4WZ
T: 01744 814444
E: info@burtonwoodgroup.com
W: www.burtonwoodgroup.com
Business Dispatch Ltd
Unit 3&4, Kingspark Bus Centre
152-178 Kingston New Malden Surrey KT3 3ST
T: 020 8605 1771
E: info@businessdispatch.co.uk
W: www.businessdispatch.co.uk
Butler & Young (BYL) Ltd
Unit 10, Airport House Purley Way Croydon CR0 0XZ
T: 020 8253 4900
E: enquiries@byl.co.uk
W: www.butlerandyoung.co.uk
BWB Consulting 5th Floor, Waterfront House Station Street Nottingham NG2 3DQ
T: 0115 924 1100
E: nottingham@bwbconsulting.com
W: www.bwbconsulting.com
BWCS Limited 6 Worcester Road, Ledbury Herefordshire HR8 1BN
T: 01531 634326
E: info@bwcs.com
W: www.bwcs.com
ByteSnap Design
2 Devon Way, Longbridge Tech Park Birmingham B31 2TS
T: 0121 222 5433
E: info@bytesnap.co.uk
W: www.bytesnap.co.uk
Bywater Training Ltd
Couchmore House, Littleworth Road Esher Surrey KT90 9TN
T: 0333 123 9001
E: contact@bywater.co.uk
W: www.bywater.co.uk
C.Scope International Ltd Kingsnorth Tech Park, Wotton Road Ashford Kent TN23 6LN
T: 01233 629181
E: info@cscope.co.uk
W: www.cscopelocators.com
C&S Equipment Ltd
15 Wingbury Courtyard, Leighton Road
Wingrave Buckinghamshire HP22 4LW
T: 01296 688500
E: sales@CandSequipment.co.uk
W: www.candsequipment.co.uk
c2c Rail Ltd
2nd Floor, Cutlers Court
115 Houndsditch London EC3A 7BR
T: 0345 744 4422
E: contact@c2crail.co.uk
W: www.c2c-online.co.uk
C2E Consulting
1-2 Broadgate Circle London EC2M 2QS
T: 07939 919141
E: enquiries@c2econsulting.co.uk
W: www.c2econsulting.co.uk
C3S Projects Ltd
Riverside House, Elland Bridge
Elland Halifax HX5 0SQ
T: 01422 313800
E: info@c3s.com
W: www.c3s.com
Cabel UK
8 Pillings Road, Oakham Rutland LE15 6QF
T: 01572 755168
E: info@cabeluk.com
W: www.cabeluk.com
Cabfind
Twelve Quays House, Egerton Wharf
Birkenhead Wirral CH41 1LD
T: 0843 658 1122
E: enquiries@cabfind.com
W: www.cabfind.com
Cable Detection Ltd
Unit 1 Blythe Park, Cresswell
Stoke-on-Trent ST11 9RD
T: 01782 384630
E: sales@cabledetection.co.uk
W: www.cabledetection.co.uk
Cable Dynamics Ltd
Unit 15, Binghams Pk Bus Centre
Potten End Hill Hemel Hempstead HP1 3BN
T: 01442 234808
E: enquiries@cabledynamics.co.uk
W: www.cabledynamcs.co.uk
Cable Jointing Services Ltd
North Farm House, Warden Law
Houghton le Spring Tyne & Wear DH5 8LX
T: 0191 512 6040
E: info@cablejointingservices.com
W: www.cablejointingservices.com
The Cable Services Group was founded in 1971 and is the UK’s leading Specialist Electrical Distributor. We stock and supply both cable and cable accessories to the domestic and international markets, and can provide full technical back up to our customers on all the products supplied.
Cable Services Group
Bridge House, Bridge Road Wrexham Ind Est Wrexham LL13 9PS
T: 01978 340450
E: rail@cableservices.co.uk
W: www.cableservices.co.uk
Cable Telecommunications Training Services Ltd
Jubilee Place, Lindum Business Park Station Road North Hykeham LN6 3QX
T: 01522 880900
E: info@cable-training.co.uk
W: www.cable-training.co.uk
Cablecraft (a part of Shoal Group Ltd)
Cablecraft House, Circle Business Centre
Blackburn Road Houghton Regis LU5 5DD
T: 01582 606033
E: sales@cablecraft.co.uk
W: www.cablecraft.co.uk
CACI Ltd
Kensington Village, Avonmore Road
London W14 8TS
T: 020 7602 6000
E: compliance@caci.co.uk
W: www.caci.co.uk
Cadenza Transport Consulting Ltd
8-10 South Street, Epsom Surrey KT18 7PF
T: 07786 430420
E: info@cadenza.co.uk
W: www.cadenza.co.uk
CADFEM UK CAE Ltd
Airport House, Purley Way
Croydon Surrey CR0 0XZ
T: 020 8256 0630
E: info@cadfemuk.com
W: www.cadfemukandireland.com
Cairn Cross Civil Engineering Limited
1 Cadman Court, Morley Leeds LS27 0RX
T: 0113 284 2415
E: info@cairncross.uk.com
W: www.cairncross.uk.com
Calco Services Ltd
5th Floor, Melrose House
42 Dingwall Road Croydon CR0 2NE
T: 020 8655 1600
E: careers@calco.co.uk
W: www.calco.co.uk
Calders & Grandidge
194 London Road, Wyberton Boston PE21 7HJ
T: 01205 358866
E: enquiries@caldersandgrandidge.com
W: www.caldersandgrandidge.com
Caledonian Sleeper
1 Union Street, Inverness Scotland IV1 1PP
T: 0330 060 0500
E: enquiry@sleeper.scot
W: www.sleeper.scot
Calibration, Maintenance & Repair (CMR) Ltd
Units 3-7, Home Farm Ind Park
Norwich Road Marsham Norfolk NR10 5PQ
T: 01603 279557
E: support@cmrcalibrate.co.uk
W: www.cmrcalibrate.co.uk
Calibre Search Ltd
7 Brewery Place, Brewery Wharf Leeds West Yorkshire LS10 1NE
T: 0113 234 6047
E: info@calibresearch.co.uk
W: www.calibresearch.co.uk
CallConfidential
The Town House, Market Street
Halisham East Sussex BN27 2AE
T: 01323 818030
E: info@callconfidential.com
W: www.callconfidential.com
Calverley Control Installations Ltd
Blacup House, Royds Close Leeds West Yorkshire LS12 6LL
T: 0113 279 6611
E: info@calverleycontrols.co.uk
W: www.calverleycontrols.co.uk
Camargue
7 Bayley Street London WC1B 3HB
T: 020 7636 7366
W: www.camargue.uk
Cambrian Transport Limited Green Farm, Country House Bristol Road Falfield Glos GL12 8DL
T: 01454 260319
E: enquiries@cambriantransport.com
W: www.cambriantransport.com
Camel Precast
Hoyle Mill Road, Kinsley
Pontefract West Yorkshire WF9 5JB
T: 01652 641 204
E: info@camelprecast.co.uk
W: www.camelprecast.co.uk
Camfaud Concrete Pumps Ltd
High Road, Thornwood Common Epping Essex CM16 6LU
T: 01992 560898
E: sales@camfaud.co.uk
W: www.camfaud.co.uk
Camira Fabrics Ltd
The Watermill, Wheatley Park Mirfield West Yorkshire WF14 8HE
T: 03330 324 568
E: transportfabrics@camirafabrics.com
W: www.camirafabrics.com
Camlin Rail (Headquarters)
31 Ferguson Drive, Knockmore Hill Ind Park Lisburn Lisburn BT28 2EX
T: 028 9262 6989
E: mail@camlingroup.com
W: www.camlingroup.com
Camlok Lifting Clamps Knutsford Way, Sealand Ind Estate Chester CH1 4NZ
T: 01244 375375
E: sales.uk@cmco.eu W: www.cmworks.com
Camozzi Automation Ltd
The Fluid Power Centre, Watling Street Nuneaton Warwickshire CV11 6BQ
T: 024 7637 4114
E: askus@camozzi.co.uk
W: www.camozzi.co.uk
Campaign for Better Transport Canopi, 7-14 Great Dover Street London SE1 4YR
T: 0300 303 3824
E: info@bettertransport.org.uk
W: www.bettertransport.org.uk
CAN Smeckley Wood Close, Chesterfield Trd Estate Chesterfield Derbyshire S41 9PZ
T: 01246 261111
E: info@can.ltd.uk
W: www.can.ltd.uk
Cannon Technologies Group Limited Stem Lane, Queensway
New Milton Hampshire BH25 5NU
T: 01425 632600
E: sales@cannontech.co.uk
W: www.cannontech.co.uk
CAP Productions Limited The Crescent, Hockley Birmingham B18 5NL
T: 0121 554 9811
E: sales@capproductions.co.uk
W: www.capprodcutions.co.uk
Capel (CS) Ltd 638 Cranbrook Road, Ilford Essex IG6 1HJ
T: 0208 518 5354
E: info@capelcsltd.com
W: www.capelcsltd.com
Capgemini UK 1 Forge End, Woking Surrey GU21 6BD
T: 01483 764764
E: centralmarketing.uk@capgemini.com
W: www.capgemini.com
Capita Property and Infrastructure Ltd 65 Gresham Street London EC2V 7NQ
T: 020 7709 4500
W: www.capitaproperty.co.uk
Capita Property Ltd (East Grinstead)
Capita Symonds House, Wood Street East Grinstead West Sussex RH19 1UU
T: 01342 327161
E: media@capita.co.uk
W: www.capitaproperty.co.uk
Capital Aluminium Extrusions Limited Cleator Moor Trd Estate, Cleator Moor Cumbria CA25 5QB
T: 01946 811771
E: enquiries@capalex.co.uk
W: www.capalex.co.uk
Capital Seating are UK distributors for Grammer Rail – manufacturer of highquality seating systems for both driver and passengers. Grammer set standards in comfort, ergonomics, design, modularity, safety and economic efficiency, whilst ensuring ongoing research to provide a steady flow of innovation. Capital offer a full refurbishment and parts service on all types of seating.
Capital Seating
Unit 1 Forward Park, Sheene Road
Gorse Hill Ind Estate Leicester LE4 1BF
T: 0116 216 9910
E: grammer@capitalseating.co.uk
W: www.grammer.co.uk
Capitol Group
Capitol House, 232 Tolworth Rise Tolworth Surrey KT5 9ND
T: 020 8330 7716
E: headoffice@thecapitolgroup.co.uk
W: www.thecapitolgroup.co.uk
Capitol Industrial Batteries is an independent manufacturer and supplier of all types of industrial, stationary, and transportation Batteries. As a recognised leader in service provision, Capitol Industrial Batteries works closely with its valued customers to develop, manufacture and deliver both traditional and alternative types of batteries for a wide range of equipment and applications.
Capitol Industrial Batteries Systems Limited
22 Napier Court, Wardpark North
Cumbernauld Glasgow G68 0LG
T: 01236 731982
E: info@capitolbatteries.com
W: www.capitolbatteries.com
Cappagh Construction
Cappagh House, 8 Waterside Way London SW17 0AB
T: 020 8947 4000
E: office@cappagh.co.uk
W: www.cappagh.co.uk
Capstone Recruitment
First Floor, Northumberland House Great Portland St London W1W 6QP
T: 020 3757 5000
E: london@capstone-recruitment.com
W: www.capstone-recruitment.com
Captec
7 Whittle Avenue, Segensworth Fareham PO15 5SH
T: 01489 866066
E: sales@uk.captec-group.com
W: www.captec-group.com
Capula Ltd
Orion House, Stone Business Park Staffordshire ST15 0LT
T: 01785 827000
E: contactus@capula.co.uk
W: www.capula.co.uk
Carlisle Warehousing Ltd
The Old Court House, Weobley Hereford HR4 8SG
T: 01544 318788
E: hfp@wwlgroup.co.uk
W: www.wwlgroup.co.uk
Carlton Die Castings Ltd 88 Greenhill Road, Paisley Scotland PA3 1RD
T: 0141 887 8355
E: sales@carltondie.com
W: www.carltondie.com
Carlton Technologies Ltd
Unit 4, Church View Bus Park
Coney Green Road Chesterfield S45 9HA
T: 01246 861330
E: sales@carltontech.co.uk
W: www.carltontech.co.uk
Carmet Tug Riverbank Road, Bromborough Wirral CH62 3JQ
T: 0151 327 8018
E: tugs@carmet.co.uk
W: www.carmettugs.co.uk
Carmichael UK
Head Office, 34 Upper High Street
Thame Oxon OX9 2DN
T: 01844 212058
E: info@carmichaeluk.com
W: www.carmichaeluk.com
Carnon Contracting
Wheal Jane, Earth Science Park
Baldhu Truro Cornwall TR3 6EE
T: 01872 560200
E: contracts@carnon-contracting.co.uk
W: www.carnon-contracting.co.uk
Carrington West is an award-winning recruitment agency, with a dedicated rail team since 2017. Providing skilled staff in a range of roles including rail design & consultancy, project delivery and blue collar. We work on contingent, preferred supplier or sole supplier agreements and are ISO 9001:2015, ISO 14001:2015, ISO27001:2013 accredited and RISQS and Achilles registered.
Carrington West 1000 Lakeside North Harbour, Western Road
Cosham Portsmouth P06 3EN
T: 023 9387 6000
E: info@carringtonwest.com
W: www.carringtonwest.com
Carter Jonas
One Chapel Place
London W1G 0BG
T: 020 3131 6264
E: info@carterjonas.co.uk
W: www.carterjonas.co.uk
Carters Flooring (Transport) Ltd
Unit 1 The Fulcrum, Low’s Lane
Stanton-by-Dale Derbyshire DE7 4QU
T: 0115 932 1691
E: info@carters-flooring.co.uk
W: www.carters-flooring.co.uk
Cartoozo
Keystone, Innovation Centre Croxton Road Thetford IP24 1JD
T: 020 7060 6772
E: sales@cartoozo.com
W: www.cartoozo.com
Cartyne Transport Co Ltd
440 Petershill Road, Springburn Glasgow Lanarkshire G21 4AA
T: 0141 557 1199
E: info@carntyne-transport.co.uk
W: www.carntyne-transport.co.uk
Carver Engineering Services Ltd
11 Brunel Close, Brunel Ind Estate Blyth Road Doncaster DN11 8QA
T: 01302 751900
E: info@carverengineering.com
W: www.carverengineering.com
Carwood Motor Units Ltd Herald Way, Binley
Coventry CV3 2RQ
T: 024 7644 9533
E: sales@carwood.co.uk
W: www.carwood.co.uk
Case CE UK Ltd
1st Floor, Barclay Court 2
Heavens Walk Doncaster DN4 5HZ
T: 0844 273 4339
E: eucaseceukroi@cnh.com
W: www.casece.com
Cass Hayward LLP York House, Welsh Street Chepstow Monmouthshire NP16 5UW
T: 01291 626994
E: office@casshayward.com
W: www.casshayward.com
Cast UK Ltd – Manchester Office
7 Jordan Street, Castlefield
Manchester M15 4PY
T: 0161 825 0825
E: hello@castuk.com
W: www.castuk.com
Cats Solutions (Cats Group)
Two Caen View, Rushy Platt
Swindon SN5 8WQ
T: 01793 432913
E: sales@cats-solutions.co.uk
W: www.cats-solutions.co.uk
Caval Limited
York House, 31 York Place
Leeds West Yorkshire LS1 2ED
T: 0113 203 1244
E: enquiries@planetcaval.com
W: www.planetcaval.com
Cavendish Media Ltd
Tower Bridge Bus Centre, 46-48 East Smithfield London E1W 1AW
T: 020 7265 1054
E: info@cavendishmedia.com
W: www.cavendishmedia.com
CB Frost & Co Ltd Green Street, Digbeth Birmingham B12 0NE
T: 0121 773 8494
E: info@cbfrost-rubber.com
W: www.cbfrost-rubber.com
CB Richard Ellis St Martin’s Court, 10 Paternoster Row London EC4M 7HP
T: 020 7182 2000
E: corpcomm@cbre.com
W: www.cbre.com
CBI (Confederation of British Industry)
CBI Head Office, Cannon Place
78 Cannon Street London EC4N 6HN
T: 020 7379 7400
E: enquiries@cbi.org.uk
W: www.cbi.org.uk
CC Ground Investigations Ltd Unit A2, Innsworth Technology Pk Innsworth Lane Gloucester GL3 1DL
T: 01452 739165
E: info@ccground.co.uk
W: www.ccground.co.uk
CCD Design & Ergonomics Ltd
Second Home, Spitalfields
68-80 Hanbury St London E1 5JL
T: 020 7593 2900
E: hello@designbyccd.com
W: www.designbyccd.com
CCF Plant Hire Ltd – t/as Access Plant
9 Orient Ind Park, Simonds Road
Leyton London E10 7DE
T: 020 8518 7400
E: hire@accessplant.co.uk
W: www.accessplant.co.uk
CCL Rail Training Room 104a, Rail House, Gresty Road
Crewe Cheshire CW2 6EA
T: 01270 897647
E: info@ccltraining.com
W: www.ccltraining.com
CCS Electronics
4 Aragon Court, Manor Park Cheshire WA7 1SP
T: 01928 579797
E: sales@ccselec.com
W: www.ccselec.com
CCS Jeweltone Ltd Bath Place Wharf, Downs Road Maldon Essex CM9 5HG
T: 01621 841 222
E: sales@jeweltonesolutions.uk
W: www.ccsjeweltone.com
CCS/Complete Composite Systems 503 Broadway, Letchworth Hertfordshire SG6 3PT
T: 01462 659876
E: info@completecomposite.co.uk
W: www.completecomposites.co.uk
CCTV Drainage Surveys – Midland Survey
Cromwell House, Westfield Road Southam Warwickshire CV47 0JH
T: 01926 810811
E: admin@midlandsurvey.co.uk
W: www.midlandsurvey.co.uk
CD Fencing & Construction Services Ltd
Cocklebury Road, Chippenham Wiltshire SN15 3QE
T: 01249 460187
E: info@cdfencing.co.uk
W: www.cdfencing.co.uk
CDH Recruitment Ltd
2 Cambridge Gardens, Hastings East Sussex TN34 1EH
T: 0845 126 2299
E: info@cdhrecruitment.co.uk
W: www.cdhrecruitment.co.uk
CDM-UK
The Sawmill, Sunnyside Road Quarter Scotland ML3 7XH
T: 01698 422551
E: info@cdm-uk.com
W: www.cdm-uk.com
CE Turner (Engineers) Ltd
Hudson Road, Saxby Road Ind Estate
Melton Mowbray Leicestershire LE13 1BS
T: 01664 564643
E: enquire@ceturner.co.uk
W: www.ceturner.co.uk
Cecence Ltd
Unit 6 Bunas Bus Park, Hollom Down Road Lopcomber Corner Hampshire SP5 1BP
T: 01264 781115
E: info@cecence.com W: www.cecence.com
CECL – Global
The Priory, Priory Road Wolston CV8 3FX
T: 07803 468 429
E: mail@cecl.global
W: www.cecl.global
Ceenorm UK Ltd
Unit 2 Highbridge Court, Stafford Park 1
Telford Shropshire TF3 3BD
T: 01952 212700
E: sales@ceenorm.co.uk
W: www.ceenorm.co.uk
CEEQUAL Ltd
Scheme Management Team, Bucknalls Lane
Watford WD25 9XX
T: 0333 014 7880
E: enquiries@ceequal.com
W: www.ceequal.com
CEF
Tom Mackie House, Station Road
Kenilworth Warwickshire CV8 1JJ
T: 01926 350018
E: naps@cef.co.uk
W: www.cef.co.uk
Celtic Recycling Limited
29-31 Clearwater Road, Queensway Meadows
Newport Gwent NP19 4ST
T: 01633 274700
E: info@celtic-recycling.co.uk
W: www.celtic-recycling.co.uk
Celtic Energy Ltd
9 Beddau Way, Castlegate Bus Park
Caerphilly CF83 2AX
T: 029 2076 0990
E: info@coal.com
W: www.coal.com
Cembre Ltd
Dunton Park, Kingsbury Road
Curdworth Sutton Coldfield B76 9EB
T: 01675 470440
E: sales@cembre.co.uk
W: www.cembre.co.uk
Censol Ltd
Forbes Close, Long Eaton Nottingham NG10 1PR
T: 0115 972 7070
E: info@censol.co.uk
W: www.censol.co.uk
Central Alliance
Alliance House, South Park Way
41 Business Park Wakefield WF2 0XJ
T: 01924 229889
E: info@central-alliance.co.uk
W: www.central-alliance.co.uk
Central Alliance Ltd
Alliance House, South Park Way
41 Business Park Wakefield WF2 0XJ
T: 01924 229889
E: info@central-alliance.co.uk
W: www.central-alliance.co.uk
Central Piling
Rawden Enterprise Park, Sixth Avenue
Halstead Essex CO9 2FL
T: 01787 474000
E: info@centralpiling.com
W: www.centralpiling.com
Centre for Policy Studies
57 Tutton Street, Westminster London SW1P 3QL
T: 020 7222 4488
E: mail@cps.org.uk
W: www.cps.org.uk
Centre for Regional Economic & Social Research Sheffield Hallam, City Campus Howard Street Sheffield S1 1WB
T: 0114 225 3073
E: cresr@shu.ac.uk
W: www.shu.ac.uk
Centregreat Rail Ltd Ynys Bridge, Heol yr Ynys Tongwynlais Cardiff CF15 7NT
T: 029 2081 5661
E: office@centregreat.net
W: www.centregreatrail.co.uk
Centrus Advisors
10 Queen Street Place London EC4R 1BE
T: 020 3846 5670
E: london@centrusadvisors.com
W: www.centrusadvisors.com
Centurion Safety Products Ltd
Howlett Way, Thetford Norfolk IP24 1HZ
T: 01842 754266
E: sales@centurionsafety.co.uk
W: www.centurionsafety.co.uk
Century PR
100 Pall Mall, St James London SW1Y 5HP
T: 020 7664 8790
E: info@centurypr.co.uk
W: www.centurypr.co.uk
Cerdic Foundries Ltd
Beeching Close, Chard Somerset TA20 1BB
T: 01460 64301
E: sales@cerdicfoundries.co.uk
W: www.cerdicfoundries.co.uk
Cermag Ltd
92/94 Holywell Road, Sheffield South Yorkshire S4 8AS
T: 0114 244 6136
E: sales@cermag.co.uk
W: www.cermag.co.uk
Established in 1920 CF Booth Ltd has an excellent reputation as one of the largest rolling stock recyclers in the UK, winning nationally released tenders from several of the main rail operating companies. CF Booth rolling stock division hold both ISO 9001 and 14001 standards and RISQS certified.
CF Booth Limited
Clarence Metal Works, Armer Street Rotherham Yorkshire S60 1AF
T: 01709 559198
E: chrisdavis@cfbooth.com
W: www.cfbooth.com
CGMS Ltd
Baston House, 140 London Wall
London EC2Y 5DN
T: 020 7583 6767
E: london@cgms.co.uk
W: www.cgms.co.uk
CH2M
2nd Floor, Quarnmill House
Stores Road Derby DE21 4XF
T: 01332 222621
E: hr@ch2m.com
W: www.ch2m.com
Chainings Ltd
Units 1 & 2, Harrow Park
Harrow Road Hereford HR4 0EN
T: 01432 356318
E: info@chainings.com
W: www.chainings.com
Chamber of Shipping
30 Park Street
London SE1 9EQ
T: 020 7417 2800
E: query@ukchamberofshipping.com
W: www.britishshipping.org
Chambre de Commerce Francaise de GB
Lincoln House, 4th Floor
300 High Holborn London WC1V 7JH
T: 020 7092 6600
E: mail@ccfgb.co.uk
W: www.ccfgb.co.uk
Change Recruitment Group
Clarendon House, 116 George Street
Edinburgh EH2 4LH
T: 0131 225 7744
E: mail@changerecruitmentgroup.com
W: www.changerecruitmentgroup.com
Chaos Design Ltd
32 High Street, Guildford
Surrey GU1 3EL
T: 020 3053 9140
E: info@chaosdesign.com
W: www.chaosdesign.com
Charcon Construction Solutions
Rowan House, Sheldon Business Park
Chippenham Wiltshire SN14 0SQ
T: 01249 463244
E: sales@charconcs.com
W: www.charconcs.com
Charcroft Electronics
Dol-y-Coed, Llanwrtyd Wells
Powys Wales LD5 4TH
T: 01591 610408
E: sales@charcroft.com
W: www.charcroft.com
Charles Endirect Ltd
Wessex Way, Wincanton Business Park
Wincanton Somerset BA9 9RR
T: 01963 828400
E: info@charlesendirect.com
W: www.charlesendirect.com
Charles Francis Cooper Ltd
3/F, 5 Temple Square, Temple Street Liverpool Merseyside L2 5RH
T: 0845 003 9545
E: info@charlesfranciscooper.co.uk
W: www.charlesfranciscooper.co.uk
Charles Ransford & Son Ltd
Station Street, Bishops Castle Shropshire SY9 5AQ
T: 01588 638331
E: info@ransfords.co.uk
W: www.ransfords.co.uk
Charter Security Ltd Suite 6, Ensign House
Admiral Way London E14 9XQ
T: 020 7515 0771
E: info@charter-security.co.uk
W: www.charter-security.co.uk
Chartered Association of Building Engineers (CABE)
Lutyens House, Billing Brook Road Weston Favell Northampton NN3 8NW
T: 01604 404121
E: info@cbuilde.com
W: www.cbuilde.com
Chartered Institute of Arbitrators (CIArb)
12 Bloomsbury Square London WC1A 2LP
T: 020 7421 7444
E: marketing@ciarb.org
W: www.ciarb.org
Chartered Institute of Architectural Technologists (CIAT)
397 City Road London EC1V 1NH
T: 020 7278 2206
E: info@ciat.org.uk
W: www.ciat.org.uk
Chartered Institute of Ecology and Environmental Management (CIEEM)
43 Southgate Street, Winchester Hampshire SO23 9EH
T: 01962 868626
E: enquiries@cieem.net
W: www.cieem.net
Chartered Institute of Highways & Transportation 119 Britannia Walk London N1 7JE
T: 020 7336 1555
E: info@ciht.org.uk
W: www.ciht.org.uk
Chartered Institute of Logistics and Transport (CILT) Earlstrees Court, Earlstrees Road Corby Northamptonshire NN17 4AX
T: 01536 740100
E: enquiry@ciltuk.org.uk
W: www.ciltuk.org.uk
Chartered Institute of Personnel and Development (CIPD)
151 The Broadway, Wimbledon London SW19 1JQ
T: 020 8612 6200
E: cipd@cipd.co.uk
W: www.cipd.co.uk
Chartered Institute of Procurement & Supply (CIPS) Easton House, Church Street Stamford PE9 3NZ
T: 01780 756777
E: info@cips.org
W: www.cips.org
Chartered Institution of Building Services Engineers (CIBSE)
222 Balham High Road London SW12 9BS
T: 020 8675 5211
E: membership@cibse.org
W: www.cibse.org
Chartered Institution of Civil Engineering Surveyors (CICES)
Dominion House, Sibson Road Sale Cheshire M33 7PP
T: 0161 972 3100
E: membership@cices.org
W: www.cices.org
Chartered Institution of Railway Operators (CIRO)
Beacon Bldg 2nd Floor, Stafford Ent. Pk West Weston Rd Stafford ST18 0BF
T: 0333 344 0523
E: info@railwayoperators.co.uk
W: www.ciro.org
Chartered Quality Institute (CQI) 2nd Floor, 10 Furnival Street London EC4A 1AB
T: 020 7245 6722
E: marketing@quality.org
W: www.quality.org
Chatterbox Limited 1 Guards Avenue, Caterham Surrey CR3 5XL
T: 01883 334792
E: support@chatterboxradio.com
W: www.chatterboxradio.com
Chela Ltd
68 Bilton Way, Brimsdown Enfield Middlesex EN3 6EJ
T: 020 8805 2150
E: sales@chela.co.uk
W: www.chela.co.uk
Chemical Industries Association
King’s Buildings, Smith Square London SW1P 3JJ
T: 020 7834 3399
E: enquiries@cia.org.uk
W: www.cia.org.uk
Cheshire Mouldings Unit 4, Abbotsfield Road
Sutton St Helens WA9 4HU
T: 0800 085 3475
E: enquiries@cheshiremouldings.co.uk
W: www.cheshiremouldings.co.uk
Chester Hydraulics PO Box 740, Unit 21 Calder Vale Rd Wakefield WF1 9RD
T: 01924 371161
E: information@grouprhodes.co.uk
W: www.grouprhodes.co.uk
Chesterfelt Ltd
Foxwood Way, Sheepsbridge
Chesterfield Derbyshire S41 9RA
T: 01246 268000
E: general@chesterfelt.co.uk
W: www.chesterfelt.co.uk
CHH Conex Ltd
4 Holford Way, Holford Ind Estate
Witton Birmingham B6 7AX
T: 0121 344 4229
E: enquiry@chhconex.com
W: www.chhconex.com
Chicago Glass Uk Ltd
Kingston House, Waterside Court Neptune Close Rochester Kent ME2 4NZ
T: 01634 735616
E: info@scratchremovers.co.uk
W: www.scratchremovers.co.uk
Chicago Pneumatic Zodiac Unit 4, Boundary Way
Hemel Hempstead Hertfordshire HP2 7SJ
T: 01442 838999
E: cp.marketing@cp.com
W: www.cp.co.uk
Chieftain Trailers 207 Coalisland Road, Dungannon Co Tyrone Northern Ireland BT71 4DP
T: 028 8774 7531
E: sales@chieftaintrailers.com
W: www.chieftaintrailers.com
Chiltern Railways Banbury ICC, Merton Street Banbury Oxfordshire OX16 4RN
T: 0345 600 5165
E: customer.service@chilternrailways.co.uk
W: www.chilternrailways.co.uk
Chiltern Railways (Marylebone)
Marylebone Railway, Personnel Department
Great Centrl House Melcombe Place NW1 6JJ
T: 020 7922 9520
E: recruitment@chilternrailways.co.uk
W: www.chilternrailways.co.uk
Chris Reeves Communications 20 Stanton Close, Epsom Surrey KT19 9NP
T: 020 8391 2741
E: info@chrisreevescommunications.co.uk
W: www.chrisreevescommunications.co.uk
Chris Wheeler Construction Ltd
Church Farm, Burbable Marlborough Wiltshire SN8 3AT
T: 01672 810315
E: cw.cw@btinternet.com
W: www.chriswheelerconstruction.co.uk
Chrysalis Rail Ltd Electra House, Electra Way Crewe Cheshire CW1 6GL
T: 01270 534683
E: info@chrysalisrail.com
W: www.chrysalisrail.com
Churchill Trading Services Ltd Unit 1, 40 Coldharbour Lane Harpenden Hertfordshire AL5 4UN
T: 01582 760055
E: helppoint@churchillservices.com
W: www.churchillservices.com
Cintec International Ltd have served the rail network for over 20 years in the stabilisation, repair and strengthening of its structures and high performance fixings for ancillary equipment. With a life expectancy of 120 years the Cintec system is the permanent structural solution in a large variety of substrates.
Cintec International Ltd
11 Gold Tops, Newport South Wales NP20 4PH
T: 01633 246614
E: solutions@cintec.com
W: www.cintec.com
Cirrus Research is dedicated to preventing hearing loss and environmental noise pollution. We help the rail industry keep workers safe and residents happy with easy-to-use equipment that provides accurate and reliable data. Manufactured with longevity in mind and backed by a 15-year warranty, Cirrus Research is the go-to partner for noise measurement solutions in the rail industry.
Cirrus Research
Acoustic House, Bridlington Road Hunmanby North Yorkshire YO14 0PH
T: 01723 891 655
E: sales@cirrusresearch.com
W: www.cirrusresearch.co.uk
CIS Services Ltd
Matrix House, Brook Road Rayleigh Essex SS6 7XL
T: 01268 773331
E: info@cisservices.co.uk
W: www.cisservices.co.uk
Cisco Systems Ltd
10 New Square Park, Bedfont Lakes Feltham TW14 8HA
T: 020 8824 1000
E: asksg@cisco.com
W: www.cisco.com
Citigate Dewe Rogerson
3 London Wall Buildings, London Wall London EC2M 5SY
T: 020 7638 9571
E: info@citigatedewerogerson.com
W: www.citigatedr.co.uk
City & Guilds of London Institute (C&G)
1 Giltspur Street, London EC1A 9DD
T: 020 7294 2468
E: general.enquiries@cityandguildsgroup.com
W: www.cityandguilds.com/about-us
Cityscape Recruitment Ltd
1st Floor Regency House, 43 High Street
Rickmansworth Hertfordshire WD3 1ET
T: 01923 750095
E: info@cityscapeltd.com
W: www.cityscapeltd.com
Civil Engineering Contractors Association (CECA) 1 Birdcage Walk, Westminster London SW1H 9JJ
T: 020 7340 0450
E: enquiries@ceca.co.uk
W: www.ceca.co.uk
Civil Rail Solutions Ltd 7 Henwood, Ashford Kent TN24 8DH
T: 01233 625464
E: ashford@crs-rail.co.uk
W: www.civilrailsolutions.co.uk
CJ Associates
26 Upper Brook Street London W1K 7QE
T: 020 7529 4900
E: info@cjassociates.co.uk
W: www.cjassociates.co.uk
Clancy Consulting Ltd 7th Fl, Northum House, 303-306 High Holborn London WC1V 7JZ
T: 020 3077 0970
E: enquiries@clancy.co.uk
W: www.clancy.co.uk
Clancy Consulting Ltd
Dunham Court, 2 Dunham Road
Altrincham Cheshire WA14 4NX
T: 0161 613 6000
E: enquiries@clancy.co.uk
W: www.clancy.co.uk
Clarendon Executive
12b Clarendon Road, Clarendon Dock Belfast Northern Ireland BT1 3BG
T: 028 9072 5750
E: enquiries@clarendonexecutive.com
W: www.clarendonexecutive.com
Clarity Visual Management
Melton House, Jackson Way
Melton East Yorkshire HU14 3HJ
T: 0845 838 0624
E: info@clarityvm.com
W: www.clarityvm.com
Clark-Drain Ltd Station Road, Yaxley
Peterborough PE7 3EQ
T: 01733 765317
E: sales@clark-drain.com
W: www.clark-drain.com
Clarke Demolition Company Ltd Sinks Pit, Main Road, Kesgrave Ipswich Suffolk IP5 2PE
T: 01473 736791
E: enquiries@clarkedemco.com
W: www.clarkedemco.com
Clayton Equipment Ltd Second Avenue, Centrum 100 Bus Park
Burton Upon Trent Staffordshire DE14 2WF
T: 01283 524470
E: contact@claytonequipment.co.uk
W: www.claytonequipment.co.uk
CLD Fencing Systems Unit 11, Springvale Bus Centre Millbuck Way Sandbach Cheshire CW11 3HY
T: 01270 764751
E: info@cld-fencing.com
W: www.cld-fencing.com
Clearview Intelligence Ltd
A4, Telford Road, Bicester Oxon OX26 4LD
T: 01869 362800
E: info@clearview-intelligence.com
W: www.clearview-intelligence.com
Clemtech
7 Falcon Court, Parklands Business Park Forest Road Denmead Hampshire PO7 6BZ
T: 023 9224 2690
E: enquiries@clemtech.co.uk
W: www.clemtech.co.uk
Cleshar Contract Services Ltd
Heather Park House, North Circular Road Stonebridge London NW19 7NN
T: 020 8733 8888
E: info@cleshar.co.uk
W: www.cleshar.co.uk
Cleveland Cable Co Ltd
Riverside Park Road, Middlesbrough Cleveland TS2 1QW
T: 01642 241133
E: sales@clevelandcable.com
W: www.clevelandcable.conm
Cleveland Steel and Tubes Ltd
Dalton Idustrial Estate, Thirsk North Yorkshire YO7 3JN
T: 01845 577789
E: sales@cleveland-steel.com
W: www.cleveland-steel.com
Clifford Chance LLP
10 Upper Bank Street, Canary Wharf London E14 5JJ
T: 020 7006 1000
E: info@cliffordchance.com
W: www.cliffordchance.com
Cloburn Quarry Company Ltd
Lanark, South Lanark Scotland ML11 8JR
T: 01555 663444
E: sales@cloburn.co.uk
W: www.cloburn.co.uk
Clow Group Ltd
185 Broad Street, Glasgow Scotland G40 2QR
T: 0141 554 6272
E: enquiries@clowgroup.co.uk
W: www.clowgroup.co.uk
Clyde & Co
St Botolph Building, 138 Houndsditich London EC3A 7AR
T: 020 7876 5000
E: info@clydeco.com
W: www.clydeco.com
Clyde Fasteners Ltd
5 Hawbank Road, College Milton East Kilbride G74 5ET
T: 01355 225451
E: info@clydefasteners.com
W: www.clydefasteners.com
CMA CGM (UK) Shipping Ltd
12 Princes Parade, Princes Dock Liverpool L3 1BG
T: 0151 227 1771
E: lpl.genmbox@cma-cgm.com
W: www.cma-cgm.com
CML Innovative Technologies Ltd
69-70 Eastern Way, Bury St Edmonds Suffolk IP32 7AB
T: 01284 714700
E: uksales@cml-it.com
W: www.cml-it.com
CMS Cameron McKenna Nabarro Olswang LLP
Cannon Place, 78 Cannon Street London EC4N 6AF
T: 020 7367 3000
E: communications@cms-cmno.com
W: www.cms.law
CMS Cepcor Precision Services Ltd
1 Vulcan Way, Hermitage Ind Estate
Coalville Leicestershire LE67 3AP
T: 01530 817000
E: sales@cmscepcor.com
W: www.cmscepcor.com
CMS Vibration Solutions Ltd
Unit 2, Lyncastle Road Warrington WA4 4SN
T: 023 8062 5568
E: info@cms-av.com
W: www.cms-av.com
Co-Channel Electronics Ltd
Victoria Road, Avonmouth Bristol BS11 9DB
T: 0117 982 0578
E: sales@co-channel.co.uk
W: www.co-channel.co.uk
Coast Communications and Marketing Ltd
Unit 5, Briston Orchard
St Mellion Cornwall PL12 6RQ
T: 01579 352600
E: info@coastmarcoms.co.uk
W: www.coastmarcoms.co.uk
Cobalt Telephone Technologies Ltd Intec 2, Wade Road
Basingstoke Hampshire RG24 8NE
T: 01256 869600
E: info@ctt.co.uk
W: www.ctt.co.uk
Coburg Banks Ltd
15 Wrens Court, Lower Queen Street Sutton Coldfield B72 1RT
T: 0121 362 2300
E: hello@coburgbanks.co.uk
W: www.coburgbanks.co.uk
Codra Software Limited
Regus House, Chester Business Park Heronsway Chester CH4 9QR
T: 01244 893221
E: sales-panorama@codra.fr
W: www.uk.codra.net
Coeval (Ltd)
Cumbernauld Bus Centre, 2nd Floor, Lennox House
Lennox Road Cumbernauld G67 1LL
T: 0141 255 0840
E: info@coeval.uk.com
W: www.coeval.uk.com
Coffey Geotechnics Ltd
Atlantic House, Atlas Business Park
Manchester M22 5PR
T: 0161 499 6800
E: contactus@coffey.com
W: www.coffey.com
COFRA Ltd
Orltons Barn, Orltons Lane
Rusper North Horsham RH12 4RN
T: 01293 871637
E: office@cofra.co.uk
W: www.cofra.co.uk
Cogitamus
11 Woodfield Road
Peterborough PE3 6HD
T: 01733 767244
E: info@cogitamus.co.uk
W: www.cogitamus.co.uk
Cogitare Ltd
South Bank Technopark, 90 London Road London SE1 6LN
T: 020 7717 1689
E: info@cogitare.biz
W: www.cogitare.biz
Cognisco Ltd Trent House, University Way Cranfield Bedford MK43 0AN
T: 01234 757520
E: information@cognisco.com
W: www.cognisco.com
Colas Rail Ltd
Dacre House, Floor 3 19 Dacre Street London SW1H 0DJ
T: 020 7593 5353
E: enquiries@colas.co.uk
W: www.colasrail.co.uk
Colchester Fuel Injection Ltd Haven Road, Colchester
Essex CO2 8HT
T: 01206 862049
E: enquiries@colfuel.co.uk
W: www.colfuel.co.uk
Coleman Construction And Utilities Ltd
Unit 1, Brook Way Business Park
Ivyhouse Lane Hastings TN35 4NN
T: 01424 714885
E: admin@coleman.eu.com
W: www.coleman.eu.com
Coljoint specialise in the complete installation of electrical services for Commercial, Industrial and Rail, including the installation of MV/LV distribution cabling systems. We collaborate with our clients to complete contracts of all sizes. We are NICEIC registered, based in the UK, covering Greater London and the Southeast.
Coljoint Limited
Unit 11, Kencot Close, Kencot Way
Erith Kent DA18 4AB
T: 0333 210 0343
E: info@coljoint.co.uk
W: www.coljoint.co.uk
Collaborative Project Management Services (CPMS)
64 Clifton Street, London EC2A 4HB
T: 0330 058 0653
E: info@cpmsrail.co.uk
W: www.cpmsrail.co.uk
Collett & Sons Ltd
Victoria Terminal, Albert Road
Halifax HX2 0DF
T: 08456 255 233
E: info@collett.co.uk
W: www.collett.co.uk
Collingwood Executive Recruitment
4 Portal Business Park, Eaton Lane Tarporley Cheshire CW6 9DL
T: 01829 732374
E: enquiries@collingwoodsearch.co.uk
W: www.collingwoodsearch.co.uk
Collins Bartholomew Ltd
Westerhill Road, Bishopbriggs Glasgow G64 2QT
T: 0141 772 3200
E: ask@collinsbartholomew.com
W: www.collinsbartholomew.com
Collis Engineering Ltd
Salcombe Road, Meadow Lane Ind Estate Alfreton Derbyshire DE55 7RG
T: 01773 833255
E: sales@collis.co.uk
W: www.collis.co.uk
Colman Rail Services
8 Fort House Bus Centre, Primrose Close Chatham Kent ME4 6HZ
T: 01634 888620
E: office@colmanrail.co.uk
W: www.colmanrail.com
Colour-Rail
558 Birmingham Road, Bromsgrove Worcestershire B61 0HT
T: 0121 453 6518
E: colourrail@aol.com
W: www.colourrail.com
Colt Construction Limited
Freightliner Road, Hull Yorkshire HU3 4UL
T: 01482 755755
E: info@colt-construction.co.uk
W: www.colt-construction.co.uk
Coltraco Ultrasonics
46 Mount Street, Mayfair London W1K 2SA
T: 020 7629 8475
E: info@coltraco.co.uk
W: www.coltraco.com
Coltraco Ultrasonics
Unit 1, Chewton Fields
Ston Easton Radstock BA3 4BX
T: 01761 241601
E: info@coltraco.com
W: www.coltraco.com
ComatReleco AG, incorporated in 1970, is a Swiss headquartered global supplier of high-quality relays and contactors. With its product portfolio including customised solutions, ComatReleco serves customers within the segments of industrial, automation and building installation technology as well as railway and transport (compliant with EN50155 and EN45545).
ComatReleco AG
Bernstrasse 4, CH-3076 Worb Switzerland
T: 00 41 31 838 55 77
E: info@comatreleco.com
W: www.comatreleco.com
CoMech Metrology Ltd
Derwent House, RTC Business Park London Road Derby DE24 8UP
T: 01332 867700
E: sales@comech.co.uk
W: www.comech.co.uk
Commend UK
Unit 20, M11 Busn Link, Parsonage Lane Stansted Essex CM24 8GF
T: 01279 872020
E: sales@commend.co.uk
W: www.commend.co.uk
Commercial Consultants (UK) Ltd
Commercial House, Great Northern Court Great Northern Rd Derby DE1 1LR
T: 01332 868291
E: submitcv@commercialconsultants.co.uk
W: www.commercialconsultants.co.uk
Commerz Bank AG
30 Gresham Street London EC2V 7PG
T: 020 7623 8000
E: ir@commerzbank.com
W: www.commerzbank.com
Commhoist Logistics Ltd
Pocket Nook Lane, Lowton Warrington WA3 1AB
T: 01942 269335
E: enquiries@commhoist.co.uk
W: www.commhoist.co.uk
Common Time Ltd
15 St Christophers Way, Pride Park Derby DE24 8JY
T: 0845 009 0028
E: info@commontime.com
W: www.commontime.com
Comms Design is a high-tech design and manufacturing organisation specialising in Digital In Cab Signalling and communication equipment for the rail industry. Our solutions cover embedded and application software development, fast-turnaround electronic hardware design, state-of-the-art radio coverage planning & simulation and the delivery of volume manufacture and supply.
Comms Design Limited
40 Freeman’s Way, Harrogate North Yorkshire HG3 1DH
T: 01423 895071
E: sales@commsdesign.net
W: www.commsdesign.net
Community Rail Network
The Old Water Tower Huddersfield HD1 1JF
T: 01484 548926
E: office@acorp.uk.com
W: www.communityrail.org.uk
Community Transport Association (CTA)
12 Hilton Street, Manchester M1 1JF
T: 0161 351 1475
E: info@ctauk.org
W: www.ctauk.org
ComNet Europe Ltd
8 Turnberry Park Road, Gildersome Morley Leeds LS27 7LE
T: 0113 307 6400
E: info-europe@comnet.net
W: www.comnet.net
Complete Cyber offers comprehensive Railway Cybersecurity services, including security risk assessments (NIS-D/NIS-D2, TS50701, IEC 62443), penetration testing, vulnerability assessments, security monitoring, and tailored cybersecurity training. Safeguarding critical railway assets, our experts enable proactive protection against evolving cyber threats.
Complete Cyber
Princess Risborough, Buckinghamshire HP27 9FA
T: 03301 331 959
E: contactus@completecyber.co.uk
W: www.completecyber.co.uk
Complete Drain Clearance
49 Weeping Cross
Stafford ST17 0AQ
T: 01785 665909
E: info@completedrainclearance.co.uk
W: www.completedrainclearance.co.uk
Complete Training Solutions Ltd
Unit 12 Glacier Bldgs, Harrington Road Brunswick Bus Park Liverpool L3 4BH
T: 0151 708 9785
E: info@completetrainingsolutions.co.uk
W: www.completetrainingsolutions.co.uk
Comtest Wireless International Ltd (UK Office) Badgemore House, Gravel Hill Henley-on-Thames Oxfordshire RG9 4NR
T: 01491 579512
E: contact@comtestwireless.eu
W: www.comtestwireless.eu
Concept Engineering Consultants Ltd
Unit 8, Warple Mews
Warple Way London W3 0RF
T: 020 8811 2880
E: si@conceptconsultants.co.uk
W: www.conceptconsultants.co.uk
Concerto
Somerset House, Strand London WC2R 1LA
T: 020 7404 4303
E: info@concerto.uk.com
W: www.concerto.uk.com
Created specifically for erosion control, containment and shelter applications, Concrete Canvas® (CC) products are part of a revolutionary class of new, innovative materials called Geosynthetic Cementitious Composite Mats (GCCMs). CC is a flexible, concrete filled geosynthetic which provides a thin and durable concrete layer when hydrated. Typically, 10-times faster to install than conventional concrete solutions; essentially, it’s Concrete on a Roll™.
Concrete Canvas Ltd Cowbridge Road, Talbot Green Pontyclun CF72 8HL
T: 0345 680 1908
E: info@concretecanvas.com
W: www.concretecanvas.com
Concrete Canvas Ltd Cowbridge Road, Talbot Green Pontyclun CF72 8HL
T: 0345 680 1908
E: info@concretecanvas.com
W: www.concretecanvas.com
Concrete Repairs Limited
Cathite House, 23a Willow Lane Mitcham Surrey CR4 4TU
T: 020 8288 4848
E: contact@crl.eu.com
W: www.crl.eu.com
Confederation of Passenger Transport UK (CPT) 22 Greencoat Place
London SW1P 1PR
T: 020 7240 3131
E: admin@cpt-uk.org
W: www.cpt-uk.org
Confidential Incident Reporting & Analysis Service (CIRAS)
The Helicon, One South Place London EC2M 2RB
T: 020 3142 5369
E: enquiries@ciras.org.uk
W: www.ciras.org.uk
Connect Communications
Millbank Tower, Millbank London SW1P 4QP
T: 020 7592 9592
E: info@connectpa.co.uk
W: www.connectpa.co.uk
I started in the 2 Way Radio industry to provide business communications where the ability to communicate instantly and to a number of people at once is important and sometimes vital. Connect supply, hire and install 2 Way Radio, Push To Talk, Body Worn Cameras and a Patrol System using Near Field Communications. As well as the rail industry we supply Recycling companies, Security and Facilities and others.
Connect Mobile Radio Watling Court, Orbital Plaza Cannock WS11 0EL
T: 02476 011750
E: sales@connectmobileradio.co.uk W: www.connectmobileradio.co.uk
Consarc Consulting Architects Limited
1 Canal Side Studios, 8-14 St Pancras Way London NW1 0QG
T: 020 7387 5060
E: mail@consarc.co.uk
W: www.consarc.co.uk
Consortia Integrated Services Appletree House, 4 Mapledale Road
Liverpool L18 5JE
T: 0151 294 3114
E: info@consortiais.com
W: www.consortiais.com
Constellation Lighting Ltd
Unit 1, Holbrook Rise, Holbrook Ind Estate Halfway Sheffield S20 3FG
T: 0114 247 9900
E: sales@constellationlighting.com
W: www.constellationlighting.com
Construction Composites Limited
Unit 35, Church Road Bus Centre
Sittingbourne Kent ME10 3RS
T: 01795 435535
E: info@constructioncomposites.com
W: www.constructioncomposites.com
Construction Industry Research and Information Association (CIRIA)
Griffin Court, 15 Long Lane London EC1A 9PN
T: 020 7549 3300
E: enquiries@ciria.org
W: www.ciria.org
Construction Industry Training Board (CITB) Bircham Newton, Kings Lynn Norfolk PE31 6RH
T: 0344 994 4400
E: welcome@citb.co.uk
W: www.citb.co.uk
Construction Marine Limited (CML)
The Coach House, Mansion Gate Drive Chapel Allerton Leeds LS7 4SY
T: 0113 262 4444
E: info@cml.uk.co
W: www.cml.uk.com
Construction Monitoring Control Systems Ltd Building 3, Room 14, Building Research
Establishment Watford WD25 9XX
T: 01923 682300
E: david@cmcsltd.co.uk
W: www.cmcsltd.co.uk
Construction Plant-Hire Association (CPA) 27-28 Newbury Street, Barbican London EC1A 7HU
T: 020 7796 3366
E: enquiries@cpa.uk.net
W: www.cpa.uk.net
Construction Products Association (CPA)
The Building Centre, 26 Store Street London WC1E 7BT
T: 020 7323 3770
E: enquiries@constructionproducts.org.uk
W: www.constructionproducts.org.uk
ConsultCarr Limited – Rail Sector Consultant
T: 07849 896270
E: richard@consultcarr.com
W: www.consultcarr.com
Containerlift Services Ltd PO Box 582, Great Dunmow Essex CM6 3QX
T: 0800 174 546
E: enquiries@containerlift.co.uk
W: www.containerlift.co.uk
Contract Flooring Association (CFA) Unit 23, Eldon Business Park Chilwell Nottingham NG9 6DZ
T: 0115 941 1126
E: info@cfa.org.uk
W: www.cfa.org.uk
Contract Sign Systems Ltd
Jon Davey Drive, Treleigh Ind Estate Redruth Cornwall TR16 4AX
T: 01209 313449
E: sales@contractsigns.co.uk
W: www.contractsigns.co.uk
Control Risks Group Ltd
Cotton Centre, Cotton Lane London SE1 2QG
T: 020 7970 2100
E: enquiries@controlrisks.com
W: www.controlrisks.com
Convention of Scottish Local Authorities (COSLA)
Verity House, 19 Haymarket Yard
Edinburgh Midlothian EH12 5BH
T: 0131 474 9200
E: info@cosla.gov.uk
W: www.cosla.gov.uk
Convert Ltd
Units K1 & K2, Gaywood Farm
Hole Lane Edenbridge Kent TN8 6SL
T: 01732 868131
E: info@convertltd.co.uk
W: www.convertltd.co.uk
Coombes Limited Unit 6, New Building
Winchester Road Petersfield GU32 3PB
T: 01730 231761
E: enquiries@coombesuk.com
W: www.coombesuk.com
Cooneen Group
23 Cooneen Road, Fivemiletown County Tyrone Northern Ireland BT75 0NE
T: 028 8952 1401
E: info@cooneen.com
W: www.cooneengroup.com
Cooper and Turner Ltd Templeborough Works, Sheffield Road Sheffield S9 1RS
T: 0114 256 0057
E: sales@cooperandturner.co.uk
W: www.cooperandturner.co.uk
Cooper Specialised Handling Ltd
Holly Farm Bus Park, Honiley Kenilworth Warwickshire CV8 1NP
T: 01926 658900
E: info@cooperhandling.com
W: www.cooperhandling.com
Corbett Keeling Limited
8 Angel Court, London EC2R 7HP
T: 020 7626 6266
E: info@corbettkeeling.com
W: www.corbettkeeling.com
Cordek Ltd
Spring Copse Bus Park, Slinfold
West Sussex RH13 0SZ
T: 01403 799600
E: info@cordek.com
W: www.cordek.com
Core Systems Software
Fusion Hive, North Shore Road
Stockton-on-Tees TS18N 2NB
T: 07946 170291
E: enquiries@coresystems-software.co.uk
W: www.coresystems-software.co.uk
Corehard Ltd
Viewpoint, Babbage Road
Stevenage Hertfordshire SG1 2EQ
T: 01438 225102
E: info@corehard.com
W: www.corehard.com
Coretech Solutions Ltd Unit 1 Moons Park, North Moons Moat Redditch B98 9PA
T: 01564 829722
E: getintouch@coretechsol.com
W: www.coretechsol.com
Corethree Ltd Suite 14, Building 3, Hatter Lane Croxley Green Bus Park Watford WD14 8YG
T: 0845 557 0475
E: info@corethree.net
W: www.corethree.net
Corex Honeycomb
5 Stukeley Bus Centre, Blackstone Road
Huntingdon Cambridgeshire PE29 6EF
T: 01480 435302
E: sales@corex-honeycomb.com
W: www.corex-honeycomb.com
Coriel Ltd
Uni of Nottingham, Geospatial Building Triumph Road Nottingham NG7 2TU
T: 0115 748 4486
E: info@coriel.co.uk
W: www.coriel.co.uk
Cory Brothers Shipping Agency Ltd
Haven Exchange, Felixstowe Suffolk IP11 2QX
T: 01394 674822
E: agency@corybrothers.com
W: www.corybrothers.com
Cory Riverside Energy
2 Coldbath Square, Clerkenwell
London EC1R 5HL
T: 020 7417 5200
E: info@coryenergy.com
W: www.coreyenegy.com
Costain Ltd
Costain House, Vanwall Business Park Maidenhead Berkshire SL6 4UB
T: 01628 842444
E: info@costain.com W: www.costain.com
Coulstock and Place provide a comprehensive service including motor repairs and air-conditioning fan motor overhauls, as well as new motor supply. We are also able to remanufacture air-conditioning compressors for the rail network and offer a complete range of cable management products and bespoke services.
Coulstock & Place Engineering Ltd
Units 1-7, Bankwood Lane Ind Est Rossington Doncaster DN11 0PS
T: 01302 865400
E: info@coulstockandplace.co.uk
W: www.coulstockandplace.co.uk
Covanburn Contracts Ltd
Unit 1, Colvilles Place, Kelvin Ind Estate
East Kilbride Glasgow G75 0PZ
T: 01355 208895
E: enquiries@covanburncontracts.co.uk
W: www.covanburn.co.uk
Coventry University Priory Street, Coventry CV1 5FB
T: 024 7765 7688
E: ukadmissions@coventry.ac.uk
W: www.conventry.ac.uk
Coverdale Specialist Contracting
Unit 3H, Nevendon Industrial Est Basildon Essex SS13 1DA
T: 01268 727555
E: sales@coverdalegroup.co.uk
W: www.coverdaleresinflooring.co.uk
Coveya Ltd
Coveya Ltd, Unit 1, St Ivel Way
Warmley Bristol BS30 8TY
T: 0800 915 9195
E: sales@coveya.co.uk
W: www.coveya.co.uk
Cowan Consultancy Limited
3 Turnberry House, 4400 Parkway Whiteley Hampshire PO15 7FJ
T: 01489 577488
E: consultants@cowanconsult.co.uk
W: www.cowanconsult.co.uk
Cowans Sheldon PO Box 9, Saltmeadows Road
Gateshead NE8 1SW
T: 0191 477 2271
E: info@cowanssheldon.co.uk
W: www.clarkechapman.co.uk
COWI UK Limited
Eastfield, Church Street
Uttoxeter Staffordshire ST14 5HU
T: 01889 563680
E: info_uk@cowi.com
W: www.cowi.com
Cox Wokingham Plastics Limited
Fishponds Road, Wokingham Berkshire RG41 2QH
T: 0118 977 4861
E: sales@cwpl.net
W: www.cwpl.net
Coyle have been providing recruitment services and solutions to the Rail industry since 1996. We are trusted partners to many rail contractors in the UK and developed industry leading rostering and fatigue management systems to safely and efficiently source, plan and deliver large numbers in multiple locations throughout the UK.
Coyle Personnel Limited
Hygiea, First Floor 66-68 College Road Harrow Middlesex HA1 1BE
T: 020 8861 3000
E: info@coyles.co.uk
W: www.coyles.co.uk
CP Plus Ltd
10 Flask Walk London NW3 1HE
T: 020 7431 4001
E: info@cp-plus.co.uk
W: www.cp-plus.co.uk
CP Power & Automation Ltd
3 Fairfield Court, Seven Stars Ind Estate Coventry West Midlands CV3 4LJ
T: 024 7621 4799
E: mail@cppowerautomation.com
W: www.cppowerautomation.com
CPC Battery Services Ltd 214 Red Lion Road, Surbiton Surrey KT6 7RA
T: 020 8397 1813
E: sales@cpcbatteries.co.uk
W: www.cpcbatteries.co.uk
CPC Project Services LLP
Quality House, 5-9 Quality Court
Chancery Lane London WC2A 1HP
T: 020 7539 4750
E: info@cpcprojectservices.com
W: www.cpcprojectservices.com
CPI Ltd (Crane Payment Innovations)
Coin House, New Coin Street Royton Oldham OL2 6JZ
T: 0161 678 0111
E: sales@cranepi.com
W: www.cranepi.com
CPRE Campaign to Protect Rural England
5-11 Lavington Street London SE1 0NZ
T: 020 7981 2800
E: info@cpre.org.uk
W: www.cpre.org.uk
CR Reynolds Group
Redcliff Court, Redcliff Road Hessle HU13 0EY
T: 01482 637373
E: info@crreynolds.co.uk
W: www.crreynolds.co.uk
Craig & Derricott Ltd Hall Lane, Walsall Wood Walsall West Midlands WS9 9DP
T: 01543 375541
E: sales@craigandderricott.com
W: www.craigandderricott.com
Cranage EMC Testing Limited
Tern Valley Bus Park, Wallace Way Market Drayton Shropshire TF9 3AG
T: 01630 658568
E: info@cranage.co.uk
W: www.cranage.co.uk
Crayside Consulting Limited
Thorne House, Queen Mary Avenue Basingstoke RG21 5PL T: 01256 329550
E: enquiries@craysideconsulting.co.uk
W: www.craysideconsulting.co.uk
CRC Industries Ltd
Ambersil House Wylds Rd, Castlefield Ind Estate Bridgewater Somerset TA6 4DD
T: 01278 727200
E: info.uk@crcind.com
W: www.crcindustries.com
CRC Industries UK Ltd
5 Aldermanbury Square London TA6 4DD
T: 01942 713667
E: sales@actioncan.com
W: www.crcindustries.com
Creactive Design
Unit 2, Trojan Business Centre
Tachbrook Pk Drive Warwick CV34 6RS
T: 01926 499124
E: info@creactive-design.co.uk
W: www.creactive-transport.co.uk
Creative Composites Ltd
1 Ferguson Road, Lisburn County Antrim Northern Ireland BT28 2FW
T: 028 9267 3312
E: enquiries@creativecomposites.co.uk
W: www.creativecomposites.co.uk
Creative Concern
Fifth Floor, Fourways House 57 Hutton Street Manchester M1 2EJ
T: 0161 236 0600
E: info@creativeconcern.com
W: www.creativeconcern.com
Creative Rail Dining PO Box 10375, Little Waltham Chelmsford Essex CM1 9JW
T: 01245 364051
E: enquiries@crdltd.co.uk
W: www.crdltd.co.uk
Creed Communications Limited 3 Tabley Court, Victoria Street Altrincham WA14 1EZ
T: 0161 359 5999
E: hello@creedcomms.co.uk
W: www.creedcomms.co.uk
Crestwood Environmental
1 & 2 Nightingale Place, Pendeford Business Park Wolverhampton WV9 5HF
T: 01902 229563
E: info@crestwoodenvironmental.co.uk
W: www.crestwoodenvironmental.co.uk
Crittall Windows Limited Francis House, Freebournes Road Witham Essex CM8 3UN
T: 01376 530800
E: info@crittall-windows.co.uk
W: www.crittall-windows.co.uk
CrossCountry 5th Floor, Cannon House, 18 The Priory Queensway Birmingham B4 6BS
T: 0344 736 9123
E: info@crosscountrytrains.co.uk
W: www.crosscountrytrains.co.uk
Crossrail Ltd
25 Canada Square, Canary Wharf London E14 5LQ
T: 020 3229 9100
E: helpdesk@crossrail.co.uk
W: www.crossrail.co.uk
As an established firm of Civil, Structural and Geotechnical Consulting Engineers Crouch Waterfall has extensive experience in the core areas of Bridges, Rail Infrastructure, Buildings, Temporary Works and Geotechnical Services. Formed in 1981, we have enjoyed steady growth with works carried out throughout the UK from three regional offices.
Crouch Waterfall
15 Apex Court, Woodlands Bradley Stoke Bristol BS32 4JT
T: 01454 270707
E: bristol@crouchwaterfall.co.uk
W: www.crouchwaterfall.co.uk
Crowd Dynamics 21 Station Road West, Oxted Surrey RH8 9EE
T: 01883 718690
E: enquiries@crowddynamics.com
W: www.crowddynamics.com
Crowle Wharf Engineers Ltd (CWE)
Wharf Road, Ealand
Scunthorpe North Lincolnshire DN17 4JW
T: 01724 710455
E: mark.lifsey@cwelimited.com
W: www.cwelimited.com
Crown International
Old Mill Road, Portishead Bristol BS20 7BX
T: 01275 818008
E: info@crown-international.co.uk
W: www.crown-international.co.uk
Croylek Ltd (Head Offices)
23 Ullswater Crescent, Coulsdon Surrey CR5 2UY
T: 020 8668 1481
E: sales@croylek.co.uk
W: www.croylek.com
CryoGen
Office 45-47, Chichester ENT Centre Terminus Road Chichester PO19 8FY
T: 01903 731 717
E: info@cryo-gen.co.uk
W: www.cryo-gen.co.uk
CSD Sealing Systems Baker Road, Nelson Park Ind Est Cramlington Northumberland NE23 1WQ
T: 01670 739970
E: enquiries@csdsealingsystems.co.uk
W: www.csdsealingsystems.co.uk
CSI Ltd – Computer Systems Intergration Garden Suites 1-4, Coleshill Manor South Drive Coleshill B46 1DL
T: 0800 108 8301
E: info@csiltd.co.uk
W: www.csiltd.co.uk
CSS Recruitment – Head Office
CSS House, 10-12 Manor Street Braintree Essex CM7 3HP
T: 01376 330700
E: reception@csspeople.co.uk
W: www.csspeople.co.uk
CTL Manufacturing Waterside House, Brunel Way Stonehouse Gloucestershire GL10 3SW
T: 01453 794100
E: ctl_sales@alpha3manufacturing.com
W: www.ctlmanufacturing.com
CTS Rail Services Ltd
The Railway Station, Green Road Newmarket CB8 9WT
T: 01638 669123
E: sales@ctsrailservices.co.uk
W: www.ctsrailservices.co.uk
CU Phosco Lighting Ltd Charles House, Great Amwell Ware Hertfordshire SG12 9TA
T: 01920 860600
E: enquiries@cuphosco.co.uk
W: www.cuphosco.co.uk
Cube Precision Engineering Ltd
Cakemore Road, Rowley Regis West Midlands B65 0QW
T: 0121 559 3096
E: sales@cubeprecision.com
W: www.cubeprecision.com
Cubic Transportation Systems – Europe Office
AFC House, Honeycrock Lane Redhill Surrey RH1 5LA
T: 01737 782200
E: info-eu@cubic.com
W: www.cubic.com
Cubis Systems
4 Silverwood Ind Estate, Lurgan Co Armagh BT66 6LN
T: 028 3831 3100
E: info@cubis-systems.com
W: www.cubis-systems.com
Cucumber Public Relations Ltd
61 High Street, Albrighton Wolverhampton WV7 3JG
T: 07812 600271
E: russ@cucumberpr.co.uk
W: www.cucumberpr.co.uk
Cundall Lift & Escalator Consultants
Fourways House, 57 Hilton Street
Manchester M1 2EJ
T: 0161 244 5660
E: manchester@cundall.com
W: www.cundall.com
Curotec
Unit 3, Tealgate, Charnham Park
Hungerford Berkshire RG17 0YT
T: 01488 662790
E: sales@curotec.eu
W: www.curotec.eu
Currall Lewis & Martin (Construction) Limited
Century House, 47 Century Road
Oldbury West Midlands B69 4AW
T: 0121 552 9292
E: enquiries@clmconstruction.com
W: www.clmconstruction.com
Currie & Brown Holdings Limited
12 Dumaresq Street, St Helier Jersey JE2 3RL
T: 020 7920 9220
E: enquiries@curriebrown.com
W: www.curriebrown.com
Cushman & Wakefield
125 Old Broad Street
London EC2N 3BQ
T: 020 3296 3000
E: procurement.emea@cushwake.com
W: www.cushmandwakefield.com
Customer Consulting Ltd
2 Queens Parade, Bath BA1 2NJ
T: 01225 827930
E: info@customerconsulting.com
W: www.customerconsulting.com
Cycle-Works
Unit 24, 8-9 Rodney Road
Southsea Portsmouth PO4 8DF
T: 023 9281 5555
E: info@cycle-works.com
W: www.cycle-works.com
Cyclepods Ltd
2 Betsoms Barn, Pilgrims Way Westerham Kent TN16 2DS
T: 0845 094 0490
E: info@cyclepods.co.uk
W: www.cyclepods.co.uk
Cycling UK
Parklands, Railton Road Guildford Surrey GU2 9JX
T: 01483 238301
E: cycling@cyclinguk.org
W: www.cyclinguk.org
Cygnet Projects Ltd
Unit 3, Wharf Road Ind Estate
Ealand North Lincolnshire DN17 4JW
T: 01724 622003
E: info@cygnet-projects.co.uk
W: www.cygnet-projects.co.uk
Cyril Orchard Group
Orchard House, 2 Bouverie Road West Folkestone Kent CT20 2RX
T: 01303 851000
E: folkestone@cyrilorchard.co.uk
W: www.cyrilorchard.co.uk
D Morgan Plc
New Hey, Chester Road
Great Sutton Ellesmere Port CH66 2LS
T: 0151 339 8113
E: contact@dmorgan.co.uk
W: www.dmorgan.co.uk
D-Grease UK Ltd
Shawfield Road, Carlton Ind Estate
Carlton Barnsley S71 3HW
T: 01226 777527
E: enquiries@d-grease.co.uk
W: www.d-grease.co.uk
D&D Rail Ltd
Time House, Time Square
Basildon Essex SS14 1DJ
T: 01268 520000
E: info@ddrail.com
W: www.ddrail.com
D2 Rail & Civils Ltd
1 Ridgefield, 16-18 King Street
Manchester M2 6AG
T: 0161 258 7534
E: info@d2rail.co.uk
W: www.d2rail.co.uk
DAC Limited
Union Mill, Watt Street
Sabden Lancashire BB7 9ED
T: 01282 447000
E: sales@daclimited.co.uk
W: www.daclimited.co.uk
Dacrylate Paints Ltd
Lindley’s Lane, Kirby-in-Ashfield Nottinghamshire NG17 8AL
T: 01623 753845
E: enquiries@dacrylate.co.uk
W: www.dacrylate.co.uk
DAF Trucks Ltd
Haddenham Business Park, Pegasus Way Haddenham HP17 8LJ
T: 01844 261111
E: reception@daftrucks.com
W: www.daf.co.uk
Daktronics UK Ltd
F16 Kestrel Court, Waterwells Drive
Quedgeley Gloucester GL2 2AT
T: 01454 413606
E: uksales@daktronics.co.uk
W: www.daktronics.com
Dale Power Solutions Ltd
Salter Road, Eastfield Ind Estate
Scarborough North Yorkshire YO11 3DU
T: 0330 999 3000
E: info@dalepowersolutions.com
W: www.dalepowersolutions.co.uk
Dalroad
Dalroad, Enterprise Way
Luton Bedfordshire LU3 4BU
T: 01582 505252
E: sales@dalroad.com
W: www.dalroad.com
Daniel Owen Ltd
Hadwyn House, Field Road Reading RG1 6AP
T: 0345 810 1020
E: info@danielowen.co.uk
W: www.danielowen.co.uk
Daniel Owen Ltd – Head Office
Hadwyn House, Field Road Reading RG1 6AP
T: 0118 952 1000
E: reading.office@danielowen.co.uk
W: www.danielowen.co.uk
Danny Sullivan & Sons
22 Barretts Green Road, Park Royal London NW10 7AE
T: 020 8961 1900
E: enquiries@dannysullivan.co.uk
W: www.dannysullivan.co.uk
Darcy Spillcare Manufacture Ltd
UB7 Chaucer Business Pk, Watery Lane
Kemsing Sevenoaks TW15 6QY
T: 01732 762338
E: web@darcy.co.uk
W: www.darcy.co.uk
Dartford Composites Ltd
Jubilee Works, Ness Road Erith Kent DA8 2LD
T: 01322 350097
E: sales@dartfordcomposites.co.uk
W: www.dartfordcomposites.co.uk
Data & Process Advantage Limited
Advantage House, Stowe Court Stowe Street Lichfield WS13 6AQ
T: 01543 401144
E: enquiries@dpadvantage.co.uk
W: www.dpadvantage.co.uk
DATS provide rail vehicle, infrastructure and component testing to EN, GMRT & UIC standards. Worldwide measurement, instrumentation, strain gauging and consultancy services. Component vibration and durability lab testing; sales, service, calibration and hire of dataloggers, instrumentation and sensors; commissioning services, operations, 125mph test locomotives & rolling hire are all available.
Data Acquisition & Testing Services Ltd
U4 Gainsborough Close, Gainsborough Bus Park Long Eaton Nottingham NG10 1PX
T: 01332 875450
E: enquiries@datsltd.com
W: www.datsltd.com
Data Techniques Unit 4, Gateway Business Centre Tom Cribb Road London SE28 0EZ
T: 020 8319 5640
E: sales@datatechniques.co.uk
W: www.datatechniques.co.uk
Datasys Limited 15 Queen Street, Wednesbury West Midlands WS10 7PT
T: 0121 270 4948
E: info@datasys.org.uk
W: www.datasys.org.uk
Datatrack | Part of The Triscan Group 4 Petre Court, Clayton Business Park Clayton-le-Moors Accrington BB5 5HY
T: 0845 350 300
E: info@datatrack.co.uk
W: www.thetriscangroup.com
Datum Composites
22 Longbridge Lane, Ascot Business Park Ascot Drive Derby DE24 8UJ
T: 01332 751503
E: composites@datum-patterns.co.uk
W: www.datum-patterns.co.uk
David Brown Gear Systems Limited Park Works, Lockwood Huddersfield Yorkshire HD4 5DD
T: 01484 465500
E: uk@davidbrown.com
W: www.davidbrown.com
David Simmonds Consultancy Ltd
Suite 4, Bishop Bateman Court
5-7 New Park St Cambridge CB5 8AT
T: 01223 316098
E: admin@davidsimmonds.com
W: www.davidsimmonds.com
Davies Turner & Co Ltd
Clipper Boulevard West, Edison’s Park Crossways
Dartford DA2 6QJ
T: 01322 277558
E: dartfordsales@daviesturner.co.uk
W: www.daviesturner.com
Davies Turner & Co Ltd (Manchester) Unit 8, World Freight Centre Europa Gate Manchester M17 1DY
T: 0161 873 4400
E: manchestersales@daviesturner.co.uk
W: www.daviesturner.com
Day Group Ltd
Transport Avenue, Great West Road
Brentford Middlesex TW8 9HF
T: 020 8380 9600
E: email@daygroup.co.uk
W: www.daygroup.co.uk
DB Cargo (UK) Limited
Lakeside Business Park, Carolina Way
Doncaster DN4 5PN
T: 01302 575000
E: uk.dbcargo@deutschebahn.com
W: www.uk.dbcargo.com/rail-uk-en
DB ESG
Derwent House, RTC Business Park London Road Derby DE24 8UP
T: 01332 483800
E: enquiries@dbesg.com
W: www.deutschebahn.com/dbesg
dBD Communications
2 Nobel Square, Burnt Mills Ind Estate Basildon Essex SS13 1LS
T: 01268 724538
E: sales@dbdcommunications.co.uk
W: www.dbdcommunications.co.uk
DBK Technitherm Ltd
Unit 11, Llantrisant Bus Park
Llanterisant Wales CF72 8LF
T: 01443 237927
E: info-uk@dbk-group.com
W: www.dbk-group.com
DC Advisory
5 King William Street London EC4N 7DA
T: 020 7856 0999
E: uk.enquiries@dcadvisory.com
W: www.uk.dcadvisory.com
DCA Design International
19 Church Street Warwick CV34 4AB
T: 01926 499461
E: info@dca-design.com
W: www.dca-design.com
Deepdale Engineering Co. Ltd Pedmore Road, Dudley West Midlands DY2 0RD
T: 01384 480022
E: sales@deepdale-eng.co.uk
W: www.deepdale-eng.co.uk
DEG Signal Ltd
Aspect House, Crusader Park Warminster Wiltshire BA12 8BT
T: 01985 212020
E: info@degsignal.co.uk
W: www.degsignal.co.uk
Dehn (UK) Ltd
Unit N8b, Meltham Mills Ind Est Meltham West Yorkshire HD9 4DS
T: 01484 859111
E: info@dehn.co.uk
W: www.dehn.co.uk
Deimos Space UK Ltd Building R103, Fermi Avenue Harwell Oxford OX11 0QR
T: 01235 567231
E: contact@deimos-space.com
W: www.deimos-space.co.uk
Delamode Plc
700 Avenue West, Skyline 120 Great Notley Braintree CM77 7AA
T: 01376 333000
E: info@delamode-group.com
W: www.delamode-group.com
Delatim Limited
Unit 33 IO Centre, Armstrong Road London SE18 6RS
T: 020 8853 9580
E: info@delatim.co.uk
W: www.delatim.co.uk
Delay Attribution Board (DAB) Floor 1, Mimet House 5a Praed Street London W2 1NJ
T: 07825 766727
E: DABOffice@networkrail.co.uk
W: www.delayattributionboard.co.uk
Dellner Ltd
Hearthcote Road, Swadlincote Derbyshire DE11 9DX
T: 01283 221122
E: info@dellner.com
W: www.dellner.com
Delmatic
The Powerhouse, Power Road Chiswick W4 5PY
T: 020 3184 2000
E: delmatic@delmatic.com
W: www.delmatic.com
Deloitte 2 New Street Square London EC4A 3BZ
T: 020 7936 3000
E: deloitteprecurement@deloitte.co.uk
W: www2.deloitte.com
Deltron Enclosures (Dem Manufacturing)
Deltron Emcon House, Hargreaves Way
Sawcliffe Ind Park Scunthorpe DN15 8RF
T: 01724 273206
E: sales@dem-uk.com
W: www.dem-uk.com
Demob Job Ltd
South Shields Bus Works, Henry Robson Way Station Road South Shields NE33 1RF
T: 0191 427 4655
E: enquiry@demobjob.co.uk
W: www.demobjob.co.uk
Dentons
One Fleet Place London EC4M 7WS
T: 020 7320 4001
E: info@dentons.com
W: www.dentons.com
Department for Business, Energy & Industrial Strategy
1 Victoria Street, London SW1H 0ET
T: 020 7215 5000
E: enquiries@beis.gov.uk
W: www.bis.gov.uk
Department for Infrastructure (Belfast) Co-ordination Unit, Clarence Court
10 Adelaide Street Belfast BT2 8GB
T: 028 9054 0540
E: dcu@infrastructure-ni.gov.uk
W: www.infrastructure-ni.gov.uk
Department For International Trade (London HQ) King Charles Street, Whitehall London SW1A 2AH
T: 020 7215 5000
E: enquiries@trade.gov.uk
W: www.gov.uk
Department for Transport (DfT)
Great Minster House, 33 Horseferry Road London SW1P 4DR
T: 0300 330 3000
E: dft@dft.gov.uk
W: www.dft.gov.uk
DePe Gear Company
Unit 1, Grove Road Ind Estate Fenton Stoke-on-Trent ST4 4LG
T: 01782 594114
E: sales@depe.co.uk
W: www.depe.co.uk
Deploy UK (Ltd)
Burdett House, 15-16 Buckingham Street London WC2N 6DU
T: 020 7434 0300
E: enquiries@deployuk.com
W: www.deployuk.com
Depot Rail Ltd
Unit 5, 6 Sanders Road
Gainsborough DN21 1RZ
T: 01427 392 000
E: admin@drail.co.uk
W: www.depotrail.co.uk
Derby Engineering Unit Ltd
Unit 22, Riverside Park, East Service Road
Raynesway Derby DE21 7RW
T: 01332 660364
E: sales@derbyengineeringunit.co.uk
W: www.derbyengineeringunit.co.uk
Derbyshire Geotechnical Ltd is one of the UK’s most experienced and dedicated Rope Access Operators. We offer a broad range of services, including de vegetation, large/difficult tree removal, rock anchoring, soil nailing, slope stabilization/installation of rockfall mesh/ erosion matting, inspection/repair of previously installed rockfall protection, supporting and enabling geotechnical/ecological surveys and inspection.
Derbyshire Geotechnical Ltd
C/O Torr Farm, Pittlemere Lane
Tideswell Moor Derbyshire SK17 8JF
T: 01298 931030
E: admin@d-geo.co.uk
W: www.d-geo.co.uk
Derma Shield Skincare
Unit 307, Springvale Ind Est
Cwmbran NP44 5BR
T: 01633 877569
E: info@dermashield.co.uk
W: www.dermashield.co.uk
Design & Projects Int Ltd
2 Manor Farm, Flexford Road
North Baddesley Hampshire SO52 9DF
T: 023 8027 7910
E: info@railwaymaintenance.com
W: www.railwaymaintenance.com
Design and Analysis Ltd
Unit 1, Lake View Drive
Sherwood Park Nottingham NG15 0HT
T: 0115 888 2666
E: info@designanalysis.co.uk
W: www.design-and-analysis.co.uk
Design Flooring Ltd
Unit 8, Montpelier Central Station Road Bristol BS6 5EE
T: 0117 942 6189
E: info@designflooringltd.co.uk
W: www.designflooringltd.co.uk
Design MAD Ltd
1st Floor Front, 42 Borough High Street
London SE1 1XW
T: 020 7403 4429
E: studio@designmad.london
W: www.designmad.london
Designplan Lighting
16 Kimpton Park Way
Sutton SM3 9QS
T: 020 8254 2023
E: sales@designplan.co.uk
W: www.designplan.co.uk
Destec Engineering Ltd
Five Mile Lane, Washingborough Lincoln LN4 1AF
T: 01522 791721
E: sales@destec.co.uk
W: www.destec.co.uk
Develop Training Limited
Derby Training Centre, Ascot Drive Derby DE24 8GW
T: 01332 253500
E: enquiries@developtraining.co.uk
W: www.developtraining.co.uk
Develop Training Limited – Swindon (South)
Swindon Training Centre, Frankland Road Blagrove Swindon Wiltshire SN5 8YF
T: 01793 507690
E: enquiries@developtraining.co.uk
W: www.developtraining.co.uk
Dewhurst Plc
Unit 9 Hampton Bus Park, Hampton Road West Feltham Middlesex TW13 6BD
T: 020 8744 8200
E: info@dewhurst.co.uk
W: www.dewhurst.co.uk
From platforms and station buildings to train care depots and car parks, Dexeco have lighting solutions to cover all areas across the railway estate. Dexeco have also provided bespoke solutions to heritage stations, maintenance pits, gantries and sidings using a combination of retro-fit gear trays and specially designed products.
Dexeco Ltd (subsidary of Dextra Group plc)
Brickfields Business Park, Gillingham Dorset SP8 4PX
T: 01747 858100
E: enquiries@dextragroup.co.uk
W: www.dextragroup.co.uk
DFDS Logistics
Nordic House, Western Access Road
Immingham Dock North East Lincs DN40 2LZ
T: 01469 575231
E: sales.uk@dfds.com
W: www.dfdslogistics.com
DGauge Ltd
11 Brunel Parkway, Pride Park Derby DE24 8HR
T: 01332 972360
E: info@dgauge.co.uk
W: www.dgauge.co.uk
DGSOL Creative Ltd
51 Solway Street West, Liverpool L8 0TY
T: 0775 991 8069
E: inquiry@dgsol.co.uk
W: www.dgsol.co.uk
DHL Freight
Beveridge Lane, Bardon Ind Estate
Coalville Leicestershire LE67 1UA
T: 0844 248 0844
E: freightservices@dhl.com
W: www.logistics.dhl
Offering a UK nationwide service in order to provide a comprehensive hire and sales package to the construction industry.
Specialising in both conventional and innovative eco equipment we hire and sale high-quality professional equipment to aid concrete cutting and controlled removal of concrete in order for our clients to complete their jobs independently, safely and on time.
Diamond Hire & Sales LLP
Elles House, 4B Invincible Road
Farnborough Hampshire GU14 7QU
T: 01252 524141
E: info@diamondhiresales.co.uk
W: www.diamondhiresales.co.uk
Diamond Point International Suite 13, Ashford House, Beauford Court, Sir Thomas Longley Rd Rochester Kent ME2 4FA
T: 01634 300900
E: sales@dpie.com
W: www.dpie.com
Diamond Rail Services Unit 3, Butterthwaite Lane
Ecclesfield Sheffield S35 9WA
T: 0114 257 0909
E: info@diamondrail.co.uk
W: www.diamondrail.co.uk
Diem Ltd
Merseyside Office, 11 Jubilee Road Formby Merseyside L37 2HN
T: 01704 870461
E: davidinman@diemltd.co.uk
W: www.diemltd.co.uk
Dieselec Thistle Generators Cadder House, 160 Clober Road Milngavie Glasgow G62 7LW
T: 0141 956 7764
E: sales@dtgen.co.uk
W: www.dieselecthistle.co.uk
Digital Barriers Services Ltd Belle House, Platform 1 Victoria Station London SW1V 1JT
T: 020 3553 5888
E: sales@digitalbarriers.com
W: www.digitalbarriers.com
Dilax Systems UK Ltd
Dalton House, 60 Windsor Avenue London SW19 2RR
T: 01908 607340
E: info@dilax.com
W: www.dilax.com
Direct Corporate Clothing Plc
Direct 2 Ind Park, Roway Lane Oldbury West Midlands B69 3ES
T: 0121 543 1333
E: info@directcorporate.co.uk
W: www.directcorporate.co.uk
Direct Insurance Corporate Risks
Cumberland House, 129 High Street Billericay Essex CM12 9AH
T: 01277 844360
E: info@direct-ins.co.uk
W: www.dicr.co.uk
Direct Link North 56 Beverely Gardens, Wembley Middlesex HA9 9QZ
T: 020 8908 0638
E: info@directlinknorth.com
W: www.directlinknorth.com
Direct Rail Services Ltd
Regents Court, Baron Way
Carlisle Cumbria CA6 4SJ
T: 01228 406600
E: enquiries@drsl.co.uk
W: www.directrailservices.com
Direct Track Solutions Limited
Unit 1c Midland Place, Midland Way Barlborough Chesterfield S43 4FR
T: 01246 810198
E: info@directtracksolutions.co.uk
W: www.directtracksolutions.co.uk
Distinction Training 1/F Oxford House, Sixth Avenue Doncaster South Yorkshire DN9 3GG
T: 01302 623362
E: distinctiontrain@aol.com
W: www.distinctiontrain.com
DJ Civil Engineering Ltd
4 Moorhey Street, Oldham Greater Manchester OL4 1JD
T: 01467 671892
E: info@djcivil.co.uk
W: www.djcivil.co.uk
Since 1895 DLR (Dexine) has been combining extensive knowledge of rubber materials, their properties, and processing techniques to develop bespoke mouldings, sheeting, and fabrications for the rail industry. The products DLR currently manufacture range from rail pads, AV mounts, gangway diaphragms and many other products, contact DLR to discuss your requirements.
DLR Elastomer Engineering
Unit 1A & B Leyland Business Park, Centurion Way Farington Leyland PR25 3GR
T: 01772 450930
E: sales@elastomer.co.uk
W: www.elastomer.co.uk
DM Development Coaching Ltd
The Mansion House, Calderstones Park Liverpool LI8 3JB
T: 0151 724 4439
E: info@dmdevelopmentcoaching.com
W: www.dmdevelopmentcoaching.com
DMA Europa Ltd
Europa Bldg, Arthur Dr, Hoo Farm Ind Estate Kidderminster Worcestershire DY11 7RA
T: 01562 751436
E: infoallenquiries@DMAEuropa.com
W: www.dmaeuropagroup.com
DMC Contracts Ltd
Unit 17-18, The Capstan Centre Thurrock Park Way Tilbury Essex RM18 7HH
T: 01375 845070
E: office@dmccontracts.co.uk
W: www.dmccontracts.co.uk
DMS technologies is well-known among Rail Engineers for Signalling Batteries & Chargers. We can also build battery packs using battery chemistries such as lead acid, NiMH & Lithium Ion. Through our sister company, Duvine, we provide power supplies for a wide range of applications including Axle Counters, Telecoms and Cathodic Protection.
DMS technologies
Belbins Business Park, Cupernham Lane Romsey Hampshire SO51 7JF
T: 01794 525400
E: sales@dmstech.co.uk
W: www.dmstech.co.uk
DNH WW Ltd 31 Clarke Road, Mount Farm Bletchley Milton Keynes MK1 1LG
T: 01908 275000
E: dnh@dnh.co.uk
W: www.dnh.co.uk
Dods Parliamentary Communications
11th Floor, The Shard, 32 London Bridge Street
London SE1 9SG
T: 020 7593 5500
E: customer.service@dodsgroup.com
W: www.dodsgroup.com
Dold Industries Ltd
11 Hamberts Road, Blackall Ind Estate
S Woodham Ferrers Chelmsford Essex CM3 5UW
T: 01245 324432
E: admin@dold.co.uk
W: www.dold.co.uk
Don and Low Ltd
Newfordpark House, Glamis Road
Forfar Angus DD8 1FR
T: 01307 452200
E: enquiries@donlow.co.uk
W: www.donlow.co.uk
Donald Insall Associates Ltd
12 Devonshire Street London W1G 7AB
T: 020 7245 9888
E: consultancy@insall-architects.co.uk
W: www.donaldinsallarchitects.co.uk
Donfabs & Consillia Ltd
The Old Iron Warehouse, The Wharf
Shardlow Derby DE72 2GH
T: 01332 799705
E: enquiries@consillia.com
W: www.donfabsandconsillia.com
Donseed UK Ltd
Lombard House, 145 Great Charles St
Queensway Birmingham B3 3LP
T: 020 7240 3007
E: info@donseed.com
W: www.donseed.com
Doran Consulting
Norwood House, 96 Great Victoria St Belfast BT2 7BE
T: 028 9033 3443
E: info@doran.co.uk
W: www.doran.co.uk
Dorma Kaba Ltd
Lower Moor Way
Tiverton Devon EX16 6SS
T: 0870 000 5625
E: info.uk@dormakaba.com
W: www.dormakaba.com
Dorset Woolliscroft
Falcon Road, Sowton Ind Estate Exeter Devon EX2 7LB
T: 01392 473037
E: info@dorsetwolliscroft.com
W: www.dorsetwoolliscroft.com
Dow AgroSciences Ltd
Capital Park, Fulbourn
Cambridge Cambridgeshire CB21 5XE
T: 01462 457272
E: DowAgroSciencesUK@dow.com
W: www.uk.dowagro.com
Downpatrick & County Down Railway Market Street, Downpatrick County Down Northern Ireland BT30 6LZ
T: 028 4461 5779
E: info@downrail.co.uk
W: www.downrail.co.uk
DP World London Gateway No 1 London Gateway, Stanford Le Hope Essex SS17 9DY
T: 01375 648300
E: enquiries@londongateway.com
W: www.londongateway.com
DPSS Cabling Services Ltd Unit 16, Chiltern Bus Village
Arundel Rd Uxbridge UB2 2SN
T: 01895 251010
E: info@dpsscabling.co.uk
W: www.dpsscabling.co.uk
Dr. Sauer & Partners 11 Langley Avenue, Surbiton Surrey KT6 6QH
T: 020 8339 7090
E: london@dr-sauer.com
W: www.dr-sauer.com
Dragados SA
Regin House, 1-58 Queen Street London EC4N 1SW
T: 020 7651 0900
E: info@dragados.com
W: www.dragados.com
Drainline Southern Ltd
Station House South, Mercer Road Horsham West Sussex RH12 3SR
T: 01273 269557
E: info@drainlinesouthern.co.uk
W: www.drainlinesouthern.co.uk
Draka
Chickenhall Lane, Eastleigh Hampshire SO50 6YU
T: 023 8029 5016
E: cableuk@draka.com
W: www.drakauk.com
Drallim Industries Limited
Druy Lane, Ponswood Ind Estate
St Leonards on Sea East Sussex TN38 9BA
T: 01424 205140
E: sales@drallim.com
W: www.drallim.com
DRB Power Transmission Ltd
First Avenue, Deeside Industrial Park
Deeside Flintshire CH5 2QR
T: 01244 280280
E: sales@drbgroup.co.uk
W: www.drbgroup.co.uk
Drilling and Sawing Association (DSA)
Unit 3, Brand Street
Nottingham NG2 3GW
T: 0844 879 3452
E: dsa@drillandsaw.org.uk
W: www.drillandsaw.org.uk
Drive Lines Technologies Ltd
45 Murdock Road, Bedford Bedfordshire MK41 7PQ
T: 01234 360689
E: enquiries@drivelines.co.uk
W: www.drivelines.co.uk
Drone Tech Aerospace Ltd
2 Alexandra Gate, Ffordd Pengam
Cardiff CF24 2SA
T: 07947 212 195
E: info@DroneTechAerospace.co.uk
W: www.DroneTechAerospace.co.uk
DS + A Ltd
Unity Chambers, 34 High East Street
Dorchester DT1 1HA
T: 01305 310500
E: enquiries@dsa.uk.com
W: www.dsa.uk.com
DSM Demolition Ltd
Arden House, Arden Road
Heartlands Birmingham B8 1DE
T: 0121 322 2225
E: info@dsmgroup.info
W: www.dsmdemolitiongroup.co.uk
DSV Road Ltd
Scandinavia House, Parkeston Harwich Essex CO12 4QG
T: 0844 880 0844
E: info@uk.dsv.com
W: www.uk.dsv.com
Dual Inventive Ltd
Drake House, Decoy Bank North
Doncaster South Yorkshire DN4 5JR
T: 01724 608020
E: info@dualinventive.com
W: www.dualinventive.com
dubSEO
Suite 16, West Africa House London W5 3QP
T: 020 8259 2120
E: hello@dubseo.co.uk
W: www.dubseo.co.uk
Dunbar and Boardman
2nd Floor, BTHA House
142-146 Long Lane London SE1 4BS
T: 020 7739 5093
E: dunbarboardman@tuv-sud.co.uk
W: www.tuv-sud.co.uk
Dunlop Adhesives
Longton Road, Trentham
Stoke-on-Trent ST4 8JB
T: 01782 591100
E: info@building-adhesives.com
W: www.dunloptrade.com
DuPont (UK) Ltd
4th Floor, Kings Court
London Road Stevenage Herts SG1 2NG
T: 01438 734000
W: www.dupont.co.uk
Dura Composites Ltd
Dura House, Telford Road
Clacton on Sea Essex CO15 4LP
T: 01255 440291
E: info@duracomposites.com
W: www.duracomposites.com
Durham Lifting
Britannia Testhouse, Romaldkirk Road
Middlesbrough Teesside TS2 1HB
T: 01642 240672
E: info@durhamlifting.co.uk
W: www.durhamlifting.co.uk
Dürr Technik UK Ltd
Unit 13 The Ind Quarter, Bath Business Park
Foxcote Avenue Peasedown St John BA2 8SF
T: 01761 422944
E: office@durrtechnik.co.uk
W: www.durr-technik.co.uk
Duvine Limited Unit A8, Sturmer End Industrial Estate Sturmer Road, Haverhill Suffolk CB9 7UU
T: 01440 706777
E: sales@duvine.co.uk
W: www.duvine.co.uk
DVR Ltd
Unit 1, Bentalls Business Park Pips Hill Basildon Essex SS14 3BN
T: 01268 530032
E: sales@dvr-ltd.co.uk
W: www.dvr-ltd.co.uk
DW Windsor Lighting Pindar Road, Hoddesdon Hertfordshire EN11 0DX
T: 01992 474600
E: info@dwwindsor.com
W: www.dwwindsor.com
DWF LLP
Dalmore House, 110 Queen Street Glasgow G21 3HD
T: 0141 228 8000
E: enquiries@dwf.law
W: www.dwf.co.uk
DWG Infraco Ltd No.2 The Lodge, Burrough Court
Melton Mowbray Leicestershire LE14 2QS
T: 01664 650666
E: info@dwguk.com
W: www.dwguk.com
DWG Resins
2 Burrough Court, Burrough-on-the-Hill
Melton Mowbray Leicestershire LE14 2QS
T: 0800 133 7517
E: info@dwgresins.co.uk
W: www.dwgresins.co.uk
DWS Advertising Ltd
51 Caroline Street, Limehouse London E1 0JG
T: 020 7780 9580
E: dws@dwsadvertising.co.uk
W: www.dwsadvertising.co.uk
Dyer & Butler’s rail capabilities cover a wide range of specialist engineering works and projects, including: civil works, track, power, electrification and station builds/upgrades across all rail routes in the UK.
With a Principal Contractor Licence, we predominately employ direct staff and labour to self-deliver the majority of our work.
Dyer & Butler
Mead House, Station Road, Nursling Southampton Hampshire SO16 0AH
T: 023 8074 2222
E: enquiries@dyerandbutler.co.uk
W: www.dyerandbutler.co.uk
Dyer Engineering Ltd
Solutions House, Morrision Road Ind Est
Annfield Plain County Durham DH9 7RU
T: 01207 288986
E: enquiries@dyer.co.uk
W: www.dyer.co.uk
Dynamic Track Solutions Limited
7 Haven House, Albemarle Street
Harwich Essex CO12 3HL
T: 01206 890380
E: manpower@dynamictracksolutions.com
W: www.dynamictracksolutions.com
DYWIDAG Ltd
Datum House, The Pavilions
Bridge Hall Lane Bury BL9 7NX
T: 0161 797 5511
E: info@dywidag-systems.com
W: www.dywidag.com
E-Leather Group – Global Headquarters Kingsbridge Centre, Sturrock Way Peterborough PE3 8TZ
T: 01733 843939
E: info@eleathergroup.com
W: www.eleathergroup.com
E-T-A Circuit Breakers Telford Close, Aylesbury Buckinghamshire HP19 8DG
T: 01296 420336
E: info@e-t-a.co.uk
W: www.e-t-a.co.uk
E-Tech Components UK Ltd
Unit 14 Park Court, Sherdley Business Park Maple View Skelmersdale WN8 9TG
T: 01744 762929
E: sales@e-tech-components.co.uk
W: www.etechcomponents.co.uk
E2S Warning Signals
Impress House, Mansell Road London W3 7QH
T: 020 8743 8880
E: sales@e2s.com
W: www.e2s.com
EA Technology Ltd Capenhurst Tech Park, Capenhurst Chester CH1 6ES
T: 0151 339 4181
E: sales@eatechnology.com
W: www.eatechnology.com
EAO Ltd Highland House, Albert Drive Burgess Hill West Sussex RH15 9TN
T: 01444 236000
E: sales.euk@eao.com
W: www.eao.com
EAS – East Anglian Sealing
Unit 3-8 Goldingham Hall, Bulmer Sudbury Suffolk CO10 7ER
T: 01787 880433
E: sales@easeals.co.uk
W: www.easeals.co.uk
East Midlands Trains Prospect House, No 1 Prospect Place Millennium Way Pride Park Derby DE24 8HG
T: 01332 867000
E: getintouch@eastmidlandstrains.co.uk
W: www.eastmidlandstrains.co.uk
East West Rail
Great Minster House, 33 Horseferry Road London SW1P 4DR
T: 0300 330 3000
E: info@eastwestrail.org.uk
W: www.eastwestrail.org.uk
East Yorshire Hydraulics Ltd
Harpings Road, National Avenue
Kingston-upon-Hull East Yorks HU5 4JF
T: 01482 440222
E: esales@eyh.co.uk
W: www.eyh.co.uk
Haze Batteries are one of the world leaders in UPS, Standby, Cyclic and Telecom battery power. Haze Batteries have been installed for many years on UK and Irish railways as well as across the world. Easystart Ltd (Haze’s UK and Ireland Distributor) hold large stocks in UK and have a full customer service and technical support to match
EasyStart Batteries
Unit 9, St Marks Road
Corby Northamptonshire NN18 8AN
T: 01536 203030
E: sales@easystartbatteries.co.uk
W: www.easystartbatteries.co.uk
EBC Brakes
Upton Valley Way East, Pineham Northampton NN4 9EF
T: 01604 583344
E: rail@ebcbrakesuk.com
W: www.ebcbrakesrail.com
Ebeni Limited
Hartham Park, Corsham Wiltshire SN13 0RP
T: 01249 700505
E: info@ebeni.com
W: www.ebeni.com
Eccles (UK Foundries FE) Ltd Portland Street, Walsall West Midlands WS2 8AA
T: 01922 613222
E: enquiries@ecccles-uk.co.uk
W: www.ecccles-uk.co.uk
Ecology By Design
Hampden House, Monument Park
Chalgrove Oxfordshire OX44 7RW
T: 01865 893346
E: hello@ecologybydesign.co.uk
W: www.ecologybydesign.co.uk
Econocom
Eton House, 18-24 Paradise Road
Richmond upon Thames TW9 1SE
T: 020 8940 2199
E: info.gb@econocom.com
W: www.econocom.co.uk
Ecus Ltd
Brook Holt, 3 Blackburn Road Sheffield S61 2DW
T: 0114 266 9292
E: contactus@ecusltd.co.uk
W: www.ecusltd.co.uk
Edesix Ltd
16 Firth Street, Edinburgh Scotland EH1 3LH
T: 0131 510 0232
E: sales@edesix.com
W: www.edesix.com
Edge Hill University St Helens Road, Ormskirk
Lancashire L39 4QP
T: 01695 575171
E: admissions@edgehill.ac.uk
W: www.edgehill.ac.uk
Edge Selection Ltd
Park House, Church Place Swindon Wiltshire SN1 5ED
T: 01793 698081
E: info@edgeselection.com
W: www.edgeselection.com
Edinburgh Trams
1 Myreton Drive
Edinburgh EH12 9GF
T: 0131 338 5780
E: customer@edinburghtrams.com
W: www.edinburghtrams.com
EFD Corporate
41 Caxton Court, Garamonde Drive Wymbush Milton Keynes MK8 8DD
T: 01908 560669
E: enquiries@efd-corporate.com
W: www.efd-corporate.com
Efficio Limited
33 Regent Street London SW1Y 4NE
T: 020 7550 5677
E: info@efficioconsulting.com
W: www.efficioconsulting.com
Eglin Concourse International Globe Works, Victoria Road
Sowerby Bridge West Yorkshire HX6 3AE
T: 01422 317601
E: eglin@racefurniture.com
W: www.eglinconcourse.com
EH Hassell & Sons Ltd
Newstead Ind Trd Estate Stoke-on-Trent ST4 8HX
T: 01782 644299
E: info@hassells.com
W: www.hassells.com
EHS Holdings Ltd t/as EHS Roofing 627 Kingsbury Road, Erdington Birmingham B24 9PP
T: 0845 634 3131
E: info@ehsroofing.net
W: www.ehsroofing.co.uk
EJOT UK Ltd
Hurricane Close, Sherburn Ent Park Sherburn-in-Elmet Leeds LS25 6PB
T: 01977 687040
E: rail@ejot.co.uk
W: www.ejot.co.uk
Eland Cables is a global supplier of rail & metro cable and accessories. Our comprehensive portfolio covers OHL, trackside power, signalling, telecoms and station cables including Network Rail PADS cables. Quality and compliance assured with our IECEE CBTL and ISO/IEC17025 accredited lab testing. Extensive stockholding, expert technical and industry support and leading logistics provided.
Eland Cables Ltd
10 Jamestown Road, London NW1 7HW
T: 020 7241 8759
E: rail@elandcables.com W: www.elandcables.com
Elastacloud Limited
34b York Way, Kings Cross London N1 9AB
T: 020 7859 4852
E: london@elastacloud.com
W: www.elastacloud.com
Elcot Environmental
Kingsdown Lane, Blunsdon Swindon Wiltshire SN25 5DL
T: 01793 700100
E: enquiries@elcotenviro.com
W: www.elcotenviro.com
Eldapoint Ltd
Charley Wood Road, Knowsley Ind Estate Knowsley Merseyside L33 7SG
T: 0151 548 9838
E: sales.manufacturing@eldapoint.co.uk
W: www.eldapoint.co.uk
Eldin Rail Limited
19 Sunnyside Road, Paisley Scotland PA2 6JN
T: 0141 577 8786
E: enquiries@eldin.co.uk
W: www.eldin.co.uk
Elecosoft UK Ltd
Parkway House, Pegasus Way
Haddenham Buckinghamshire HP17 8LJ
T: 01844 261700
E: info@elecosoft.com
W: www.elecosoft.com
Electren UK Ltd
2nd Floor, Regina House, 1-5 Queen Street London EC4N 1SW
T: 020 3651 3856
E: electrenuk@electren.co.uk
W: www.electren.co.uk
Electrification Solutions Ltd
6/F Trafford House, Chester Road
Manchester M32 0RS
T: 0161 509 7910
E: info@electrificationsolutions.co.uk
W: www.electrificationsolutions.co.uk
Electro-Motive Diesel Limited
Unit 25, Enterprise Bus Park
Carcroft Doncaster DN6 8DD
T: 01782 562900
E: emdlenquiries@progressrail.com
W: www.progressrail.com
Electromagnetic Testing Services Ltd
Pratts Fields, Lubberhedges Lane Stebbing Essex CM6 3BT
T: 01371 856061
E: info@etsemc.co.uk
W: www.etsemc.co.uk
Electrosteel Castings (UK) Ltd
Ambrose House, Broombank Road Trad Est Chesterfield Derbyshire S41 9QJ
T: 01246 264222
E: sales@electrosteel.co.uk
W: www.electrosteel.co.uk
Electroustic Ltd
32-36 Orchard House, Lodge Farm Business Ctr
Castlethorpe Milton Keynes MK19 7ES
T: 01908 307200
E: sales@electroustic.co.uk
W: www.electroustic.co.uk
Electus Recruitment Solutions Ltd Richmond House, Richmond Hill Bournemouth BH2 6EZ
T: 01202 296566
E: info@electusrecruitment.co.uk
W: www.electusrecruitment.co.uk
Elite Ground Support Services
1 Steel Close, Little End Road
Eaton Socon Cambs PE19 8TT
T: 0800 622 6838
E: sales@elite-gss.com
W: www.elite-gss.com
Elite KL Ltd
Elite House, 19a Sandy Way
Amington Ind Est Tamworth B77 4DT
T: 01827 300100
E: info@elitekl.co.uk
W: www.elitekl.co.uk
Elite Precast Concrete specialise in supplying the rail industry with a large variety of products for both temporary and permanent works, including Interlocking concrete blocks for retaining walls, refuges.
Elite are also the UK’s leading manufacturer of Kentledge blocks providing no dig solutions for hoarding and site security fencing.
The range includes concrete barriers for traffic management, vehicle containment barriers and hostile vehicle mitigation.
Elite Precast Concrete Ltd
Halesfield 9, Telford
Shropshire TF7 4QW
T: 01952 588885
E: sales@eliteprecast.co.uk
W: www.eliteprecast.co.uk
Elizabeth line Palestra, 197 Blackfriars Road
London SE1 8NJ
T: 0343 222 1234
W: www.tfl.gov.uk
Ellis is an expert in the design and manufacture of cable cleats and cable hangers, with decades of experience in the industry. In-house engineering capabilities allow for constant innovation and the creation of bespoke solutions for individual project specifications. Our strong network of worldwide distributors helps to deliver technical expertise to secure international rail projects.
Ellis Patents Ltd
High Street, Rillington
Malton North Yorkshire YO17 8LA
T: 01944 758395
E: sales@ellispatents.co.uk
W: www.ellispatents.co.uk
Elmatic Wentloog Road, Rumney Cardiff CF3 1XH
T: 029 2077 8727
E: sales@elematic.co.uk
W: www.elematic.co.uk
Eltek Power (UK) Ltd Cleveland Road, Hemel Hempstead Hertfordshire HP2 7EY
T: 01442 219355
E: info@eltek.com
W: www.eltek.com
Eltherm UK Ltd
Unit 7, Kingfisher Court Hambridge Road Newbury RG14 5SJ
T: 01635 255280
E: uk@eltherm.com
W: www.eltherm.com
Elwood International Ltd
Elwood House, Cross Road Albrighton Wolverhampton WV7 3RA
T: 01902 820345
E: info@elwoodinternational.com
W: www.elwoodinternational.com
EMC Hire is the UK’s largest rental company of EMC and RF test equipment. Whether required for limited funding, performing own testing, covering calibration periods or equipment breakdowns. In partnership with WEMEC ltd, EMC Hire offers an EMC turnkey solution through providing a central-hub for all EMCrelated needs, including consultancy.
EMC Hire Ltd
Unit 1, Ivel Road
Shefford Bedfordshire SG17 5JU
T: 01462 817111
E: info@emchire.co.uk
W: www.emchire.co.uk
Emeg Electrical Ltd
Unit 3, Dunston Place, Dunston Road Whittington Moor Chesterfield S41 8NL
T: 01246 268678
E: enq@emeg.co.uk
W: www.emeg.co.uk
Emerson Crane Hire Ltd
Emerson House, Freshwater Road Dagenham RM8 1RX
T: 020 8548 3900
E: info@emersoncranes.co.uk
W: www.emersoncranes.co.uk
Emico Limited
39 Mark Road, Hemel Hempstead Hertfordshire HP2 7DN
T: 01442 213111
E: contact@emico.co.uk
W: www.emico.co.uk
Eminox Limited
Miller Road, Corringham Road Ind Est Gainsborough Lincolnshire DN21 1QB
T: 01427 810088
E: enquiries@eminox.com
W: www.eminox.com
EMKA
Patricia House, Bodmin Road
Coventry CV2 5DG
T: 024 7661 6505
E: enquries@emka.co.uk
W: www.emka.com
EML Wildfire
The Albany Boathouse, Lower Ham Road
Kingston upon Thames Surrey KT2 5BB
T: 020 8408 8000
E: enquiries@wildfirepr.com
W: www.wildfirepr.com
Empark UK Ltd
Suite 4b, Stansted Courtyard
Parsonage Road Takeley CM22 6PU
T: 01279 879395
E: info@empark.co.uk
W: www.empark.co.uk
Emtelle UK Ltd
Haughhead, Hawick Scotland TD9 8LF
T: 01450 364000
E: info@emtelle.com
W: www.emtelle.com
Enable ID
10-12 The Courtyard, Timothy’s Bridge Road Stratford CV37 9NP
T: 020 8102 9541
E: hello@enableid.com
W: www.enableid.com
Encompass Engineering
T: 01332 323060
E: enquiries@encompass-engineering.com
W: www.encompass-engineering.com
Encompass Environmental provides comprehensive vegetation control services to the Rail Industry. Services include complete Weed Control, Vegetation and Tree Management to TOC Maintenance depots, Stations, Station car parks, FOC yards and major Port railheads.
Other services include Pest Control, Security Fencing and the eradication of Japanese Knotweed.
Encompass Environmental Ltd
Cushion Farm Barn, Laxfield Road Stradbroke Suffolk IP21 5JT
T: 01379 384200
E: enquiries@encompassenvironmental.co.uk
W: www.encompassenvironmental.co.uk
EnCon Construction Ltd
10 Deryn Court, Wharfedale Road
Pentwyn Cardiff CF23 7HB
T: 029 2073 5111
E: enquiries@encon.uk.com
W: www.encon.uk.com
Encore Personnel Services Ltd
Encore House, 32 Millstone Lane
Leicester LE1 5JN
T: 0116 262 0651
E: leicesterengineering@encorepersonnel.co.uk
W: www.encorepersonnel.co.uk
Enduramaxx Limited
Outgang Road, The Fen Baston Peterborough PE6 9PT
T: 01778 562810
E: enquiries@enduramaxx.co.uk
W: www.enduraspray.co.uk
Energi Recruitment Services Ltd
Cody Technology Park, Ively Road
Farnborough Hampshire GU14 0LX
T: 01252 413080
E: hello.eu@energi.uk.com
W: www.energi.uk.com
Enerpac
5 Coopies Field, Morpeth
Northumberland NE61 6JT
T: 01670 501650
E: sales-uk@enerpac.com
W: www.enerpac.com
Enersys Limited
Oak Court, Clifton Business Park
Wynne Avenue Manchester M27 8FF
T: 0161 794 4611
E: enersys.rail@uk.enersys.com
W: www.enersys.com
We are a privately owned small to medium enterprise (SME) design practice based in Crewe. We cover the whole of the UK with an increasing portfolio of projects with Tier-1 clients. Our primary focus is the rail industry with our core discipline being civil and structural engineering and the capability to deliver multi-discipline projects through our supply chain partners.
enGauged Limited
11 Macon Court, Herald Drive Crewe Cheshire CW1 6EA
T: 01270 255731
E: enquiries@engauged.co.uk
W: www.engauged.co.uk
We are one of the UK’s leading independent supplier of GRP Pultruded Profiles, Handrails, Fencing & Grating. One-hour turnaround on quotations, next day delivery and a free cutting service.
Product Areas:
GRP Pultruded Profiles
GRP Handrail
GRP Rods & Tubes
GRP Fencing
GRP Grating
GRP Anti Slip Products
GRP Interlocking Flooring
GRP Rebar
Engineered Composites Ltd
Unit B4, Borders 2 Industrial Pk River Lane Saltney Chester CH4 8RJ
T: 01244 676 000
E: info@engineered-composites.co.uk
W: www.engineered-composites.co.uk
Engineering Council
5th Floor, Woolgate Exchange 25 Basinghall St London EC2V 5HA
T: 020 3206 0500
E: info@engc.org.uk
W: www.engc.org.uk
Engineering Group – The Geological Society Burlington House, Piccadilly London W1J 0BG
T: 020 7434 9944
E: membership@geolsoc.org.uk
W: www.geolsoc.org.uk
Engineering Industries Association (EIA) 62 Bayswater Road London W2 3PS
T: 020 7298 6455
E: head.office@eia.co.uk
W: www.eia.co.uk
Experienced experts in maintenance planning and plan-led transformations. Delivering quality maintenance is one of the most significant ways of improving service performance of your fleet. First rate planning will deliver both quality and business efficiency improvements. EngPro improve your planning capability. Rail, Aviation, Bus and Automotive.
EngPro Solutions
1 Sherrard Way, Mytchett Camberley Surrey GU16 6AU
T: 07841 029276
E: contact@engpro.co.uk
W: www.engpro.co.uk
Enjoy Recruitment Group
c/o Crossley & Co, Royal Mews Cheltenham GL50 3PQ
T: 01242 252337
E: hello@enjoyrecruitmentgroup.co.uk
W: www.enjoyrecruitmentgroup.co.uk
Enotrac (UK) Ltd
Chancery House, St Nicholas Way
Sutton Surrey SM1 1JB
T: 020 8770 3501
E: info@enotrac.com
W: www.enotrac.com
EnPro Group Ltd
The Chubb Buildings, Fryer Street Wolverhampton WV1 1HT
T: 01902 925 307
E: enquiries@enprogroup.co.uk
W: www.enprogroup.co.uk
Ensafe Consultants
The Forge, Blisworth Hill Farm
Stoke Road Northampton NN7 3DB
T: 01604 878190
E: info@ensafe.co.uk
W: www.ensafe.co.uk
Ensto UK
Unit 6, Zeus House
16-30 Provost St London N1 7NG
T: 020 3750 0154
E: salesuk@ensto.com
W: www.ensto.com
Entech Technical Solutions Ltd
Unit 1 Grovelands, Business Centre
Hemel Hempstead HP2 7TE
T: 01442 898900
E: info@entechts.co.uk
W: www.entechts.com
Enterprise c/o Iarnrod Eireann, Connolly Station Amien Street Dublin D01 V6V6
T: 00 353 1 836 6222
E: info@irishrail.ie
W: www.irishrail.ie
Entire Engineering Ltd
Great Fenton Bus Park, Grove Road
Fenton Stoke-on-Trent ST4 4LZ
T: 01782 744444
E: sales@entire-group.co.uk
W: www.entire-engineerin.co.uk
Entrance Matting Systems Ltd
Freiston Ent Park, Priory Road Boston Lincolnshire PE22 0JZ
T: 01205 761757
E: info@entrance-matting.com
W: www.entrance-matting.com
EnviroWrap Solutions Limited
PO Box 11, Ashford Road
Tenterden Kent TN30 6AQ
T: 01233 860080
E: enquiries@envirowrap.eu
W: www.envirowrap.info
EOS Geomatics 29 Liddell Gardens, Kensal Rise
NW10 3QA
T: 07477 510958
E: info@eosgeomatics.co.uk
W: www.eosgeomatics.co.uk
EPC-UK Head Office Venture Crescent, Nix’s Hill Ind Estate Alfreton Derbyshire DE55 7RA
T: 01773 832253
E: info@epc-groupe.co.uk
W: www.epc-groupe.co.uk
Epicuro Protective Materials Ltd 54 Oxford Road, Denham UB9 4DN
T: 020 7125 0071
E: info@epicuro.co.uk
W: www.epicuro.co.uk
EPS UK Ltd Units N & O, Freeth Street Colwick Nottingham NG2 3GT
T: 0115 896 0486
E: sales@eps-uk.co.uk
W: www.eps-uk.co.uk
Epsilon Design Engineers Limited
1 Cadman Court, Morley Leeds LS27 0RX
T: 0113 284 2415
E: info@epsilondesign.uk.com
W: www.epsilondesign.uk.com
Equib Ltd
Suite 5, Grindleton Bus Centre
The Spinney Clitheroe Lancs BB7 4DH
T: 01200 449709
E: enquiries@equib.co.uk
W: www.equib.co.uk
Equipe Group
The Paddocks, Home Farm Offices
The Upton Estate Banbury OX15 6HU
T: 01295 670990
E: info@equipegroup.com
W: www.equipegroup.com
Era Technology Cleeve Road, Leatherhead Surrey KT22 7SA
T: 01372 367434
E: info@era.co.uk
W: www.era.co.uk
Eric Wright Civil Engineering
Sceptre House, Sceptre Way Bamber Bridge Preston PR5 6AW
T: 01772 698822
E: civils@ericwright.co.uk
W: www.ericwright.co.uk
Erith Holdings Ltd
Erith House, Queen Street Erith Kent DA8 1RP
T: 0370 950 8800
E: bd@erith.com
W: www.erith.com
ERM Ltd
2nd Floor, Exchequer Court
33 St Mary Axe London EC3 8AA
T: 020 3206 5200
E: ermuklondon.reception@erm.com
W: www.erm.com
Ernst & Young LLP
1 More London Place London SE1 2AF
T: 020 7951 2000
E: info@ey.com
W: www.ey.com
ESAB (UK) Ltd
Warlies Park House, House Shoe Hill Upshire Essex EN9 3SL
T: 01992 768515
E: info@esab.co.uk
W: www.esab.co.uk
ESB Environmental Ltd
16 Culimore Road, West Wittering West Sussex PO20 8HB
T: 01243 672455
E: sales@esb-environmental.co.uk
W: www.esb-environmental.co.uk
Esoterix
Esoterix Systems, Future Space
UWE North Gate Bristol BS34 8RB
T: 0117 4285755
E: info@esoterix.co.uk
W: www.esoterix.co.uk
ESP Group Hudson House, 8 Albany Street Edinburgh EH1 3QB
T: 0131 473 1594
E: espgroup@the-espgroup.com
W: www.the-espgroup.com
ESR Technology
202 Cavendish Place, Birchwood Park Warrington Cheshire WA3 6WU
T: 01925 843400
E: info@esrtechnology.com
W: www.esrtechnology.com
ESS Safeforce Essential House, Vaux Road Finedon Rd Ind Est Wellingborough NN8 4TG
T: 01933 443442
E: ess-safeforce@vpplc.com
W: www.ess-safeforce.com
Esseco UK
Calder Vale Road, Wakefield West Yorkshire WF1 5PH
T: 01924 234968
E: info@essecouk.com
W: www.essecouk.com
Essempy
1 Phoebe Lane, Church End Wavendon Milton Keynes MK17 8LR
T: 01908 582491
E: norman.price@essempy.co.uk
W: www.essempy.co.uk
ETA Enclosures (UK) Ltd
Unit 2 Ignite, Magan Way
Rotherham South Yorkshire S60 1FD
T: 01709 386630
E: info@eta-enclosures.co.uk
W: www.eta.it
ETS Cable Components Unit 4-6, Red Lion Road
Tolworth Surrey KT6 7QD
T: 01889 580282
E: sales@etscablecomponents.com
W: www.etscablecomponents.com
Eurofins York Unit 1 Arabesque House, Monks Cross Drive Huntington York YO32 9GW
T: 0330 430 3456
E: enquiryyork@eurofins.com
W: www.eurofins.co.uk/york
Eurolog Ltd
Orlando House, 3 High Street
Teddington Middlesex TW11 8NP
T: 020 8977 4407
E: info@eurolog.co.uk
W: www.eurolog.co.uk
European Passenger Transport Operators (EPTO)
Rue Saints Marie 6, 1080 Brussels
Belgium
E: info@epto.net
W: www.epto.net
European Rail Timetable
28 Monson Way, Oundle
Northamptonshire PE8 4QG
T: 01832 270198
E: editorial@europeanrailtimetable.eu
W: www.europeanrailtimetable.eu
Eurostar International Ltd Times House, Bravingtons Walk
Regent Quarter London N1 9AW
T: 0343 218 6186
E: traveller.care@eurostar.com
W: www.eurostar.com
Eurotech
2 Clifton Court
Cambridge CB1 7BN
T: 01223 411200
E: sales.uk@eurotech.com
W: www.eurotech.com
Evergrip Limited
Flaxley Road, Selby North Yorkshire YO8 4BG
T: 01757 212744
E: info@evergrip.com
W: www.evergrip.com
Everlast Rail have a wealth of experience both in new build and refurbishment sectors. We maintain our status as a market leading specialist in the building envelope. Offer a one stop approach to refurbishment and new build projects. Provide a highly experienced team of professionals with a proven track record.
Everlast Group Ltd
The School House, Parkfield Terrace
Pudsey Leeds LS28 6BS
T: 0113 255 2739
E: info@everlastgroup.co.uk
W: www.everlastgroup.co.uk
Eversholt Rail Limited
Ground Floor, WeWork 1 Waterhouse Square
138-142 Holborn London EC1N 2ST
T: 020 7380 5040
E: enquiries@eversholtrail.co.uk
W: www.eversholtrail.co.uk
EviFile Limited
The West Wing, Bowcliffe Hall Leeds LS23 6LP
T: 0113 859 1669
E: info@evifile.com
W: www.evifile.com
Evolution Cooling
Unit 10 Ash Court, Crystal Drive
Sandwell Business Park Smethwick B66 1QG
T: 0121 820 8946
E: info@evolution-cooling.com
W: www.evolution-cooling.com
Evolvi Rail Systems
2nd Floor, Reading Bridge House
George Street Reading RG1 8LS
T: 01732 598510
E: info@evolvi.co.uk
W: www.evolvi.co.uk
EWI Recruitment
222 Bishopsgate, The City London EC2M 4QD
T: 020 7877 8350
E: hello@ewirecruitment.com
W: www.ewirecruitment.com
Excalibur Screwbolts Ltd
Gate 3 Newhall Nursery, Lower Road Hockley Essex SS5 5JU
T: 01702 206962
E: info@excaliburscrewbolts.com
W: www.excaliburscrewbolts.com
Excell Rail Ltd
Rear of unit 5, Severn Road Pontypridd CF37 5SP
T: 01443 404201
E: requests@excellrail.co.uk
W: www.excellrail.co.uk
Excellence Achievement Learning (EAL)
Unit 2, The Orient Centre
Greycaine Road Watford Herts WD24 7GP
T: 01923 652400
E: customercare@eal.org.uk
W: www.eal.org.uk
Excess Baggage Company
Unit 2, Provident Ind Estate
Pump Lane Hayes UB3 3NE
T: 020 8897 5320
E: administration@excess-baggage.com
W: www.excess-baggage.com
Executive Careers Ltd
77a Victoria Road, Farnborough Hampshire GU14 7PL
T: 01252 377177
E: info@executive-careers.com
W: www.executive-careers.co.uk
Executive Compass®
Studio 5, The Kiln, Hoults Yard Walker Road Newcastle NE6 2HL
T: 0191 338 6975
E: info@executivecompass.co.uk
W: www.executivecompass.co.uk
ExMesh Security Products
PO Box 14, Longhill Ind Estate Hartlepool TS25 1PR
T: 01429 867388
E: fencing@exmesh.co.uk
W: www.exmeshsecurity.co.uk
Exol Lubricants Ltd
All Saints Road, Wednesbury West Midlands WS10 9TS
T: 0121 568 6800
E: sales@exol-lubricants.com
W: www.exol-lubricants.com
Expedient Recruitment Consultancy
Sovereign House, 12-14 Warwick Street Coventry CV5 6ET
T: 024 7671 4422
E: info@expedientrecruitment.co.uk
W: www.expedientrecruitment.co.uk
Experis UK (Manpower Group)
6 New Bridge Street London EC4V 6AB
T: 020 3122 0200
E: info@experis.co.uk
W: www.experis.co.uk
Express Catering
1 Meadow Close, Ilfracombe North Devon EX34 8JA
T: 0800 612 4172
E: info@expresscatering.biz
W: www.mobilecatering.biz
Express Medicals Ltd
8 City Business Centre, Lower Road London SE16 2XB
T: 020 7500 6900
E: workhealth@expressmedicals.co.uk
W: www.expressmedicals.co.uk
Extek Ltd PO Box 9460
Nottingham NG8 9FQ
T: 0115 849 6965
E: sales@extek.info
W: www.extek.info
Eyedot (Europe) Ltd – Electronic Repair and Maintenance
5 Devizes Trade Centre, Hopton Industrial Estate Devizes SN10 2EH
T: 01380 728 118
E: clive.huntley@eyedot.co.uk
W: www.eyedot.co.uk
F3G 34 St James Street London SW1A 1HD
T: 020 7766 8500
E: info@f3g.uk
W: www.f3g.uk
FA Clover & Son Ltd
14 Bardolph Road, Richmond Surrey TW9 2LH
T: 020 8948 6321
E: contracts@cloverpainting.com
W: www.cloverpainting.com
Fabric Architecture Ltd Red Stables, Yokehouse Lane Painswick Gloucester GL6 7QS
T: 01452 612800
E: info@fabarc.co.uk
W: www.fabricarchitecture.co.uk
Fabrikat (Nottingham) Ltd Hamilton Road, Sutton-in-Ashfield Nottinghamshire NG17 5LN
T: 01623 442200
E: sales@fabrikat.co.uk
W: www.fabrikat.co.uk
Facelift
Westside, London Road Hickstead West Sussex RH17 5LZ
T: 0844 225 4360
E: sales@facelift.co.uk
W: www.facelift.co.uk
Factair Limited
49 Boss Hall Road, Ipswich Suffolk IP1 5BN
T: 01473 746400
E: enquiries@factair.co.uk
W: www.factair.co.uk
Fairway Hydraulics Limited Unit 96a, Blackpole Trade Estate Worcester WR3 8TJ
T: 01905 457519
E: enquiries@fairwayhydraulics.com
W: www.fairwayhydraulics.com
Faithful & Gould Euston Tower, 286 Euston Road London NW1 3AT
T: 020 7121 2121
E: info@fgould.com
W: www.fgould.com
Faiveley Vapor Ricon Europe Ltd Meadow Lane, Loughborough Leicestershire LE11 1HS
T: 01509 635920
E: sales@vaporricon.co.uk
W: www.vaporricon.co.uk
Falco UK Ltd Unit 8 Leebrook Way, Leebrook Staffordshire ST13 7AP
T: 01538 380080
E: sales@falco.co.uk
W: www.falco.co.uk
Fantastic Media Ltd Hawthorne House, Dark Lane Birstall Leeds WF17 9LW
T: 0345 017 6090
E: info@fantasticmedia.co.uk
W: www.fantasticmedia.co.uk
Fast Track Management Services Ltd Unit 4 Century Court, Tolpits Lane Watford Hertfordshire WD18 9RS
T: 0845 165 6363
E: enquiries@ftrack.co.uk
W: www.ftrack.co.uk
Fawkes & Reece Ltd
68 Cornhill London EC3V 3QX
T: 020 7288 0166
E: recruitment@frlondon.co.uk
W: www.fawkesandreece.co.uk
FDB Electrical Ltd
Unit 20, Worton Hall Ind Estate
Worton Road Isleworth TW7 6ER
T: 020 8568 4621
E: rcdsales@fdb.uk.com
W: www.fdb.uk.com
Federation of Master Builders (FMB)
David Croft House, 25 Ely Place
London EC1N 6TD
T: 0330 333 7777
E: reception@fmb.org.uk
W: www.fmb.org.uk
Federation of Piling Specialists (FPS)
Forum Court, Office 205
29-31 Elmfield Rd Bromley Kent BR1 1LT
T: 020 8663 0947
E: fps@fps.org.uk
W: www.fps.org.uk
FEIN Industrial Power Tools UK Ltd
4 Badby Park, Hartlands Business Park
Daventry Northamptonshire NN1 8YT
T: 01327 308730
E: info@fein-uk.co.uk
W: www.fein.de
Fencing and Lighting Contractors Ltd
Unit 2, Sidney Robinson Bus Pk
Ascot Drive Derby DE24 8GW
T: 01773 531383
E: info@fencingandlighting.co.uk
W: www.fencingandlighting.co.uk
Feonic Technology Ltd
3e Newlands Science Pk, Inglemire Lane
Hull HU6 7TQ
T: 01482 806688
E: info@feonic.com
W: www.feonic.com
Fereday Pollard
30 Kings Bench Street
London SE1 0QX
T: 020 7253 0303
E: info@feredaypollard.com
W: www.fereday-pollard.co.uk
Ferrabyrne Limited
Fort Road, Littlehampton West Sussex BN17 7QU
T: 01903 721317
E: sales@ferrabyrne.co.uk
W: www.ferrabyrne.co.uk
Ferranti Technologies Ltd
Cairo House, Greenacres Road Waterhead Oldham OL4 3JA
T: 0161 624 0281
E: sales@ferranti-technologies.co.uk
W: www.ferranti-technologies.co.uk
Ferrograph Limited 1 New York Way, New York Ind Park Newcastle NE27 0QF
T: 0191 280 8800
E: info@ferrograph.com
W: www.ferrograph.com
FGD Ltd
Smestow Bridge, Bridgnorth Road
Wombourne Staffordshire WV5 8AY
T: 01902 893226
E: info@fgdltd.co.uk
W: www.fgdltd.co.uk
Fibox Ltd
Suite 25, Durham Tees Bus Centre
Orde Wingate Way Stockton-on-Tees TS19 0GD
T: 01642 604400
E: salesuk@fibox.com
W: www.fibox.co.uk
Fibrelite Composites Ltd Snaygill Ind Estate, Keighley Road Skipton North Yorkshire BD23 2QR
T: 01756 799773
E: enquiries@fibrelite.com
W: www.fibrelite.com
Ficode Technologies
Regus Business Centre, Fort Dunlop Fort Parkway Birmingham B24 9FD
T: 020 3695 0893
E: info@ficode.com
W: www.ficode.co.uk
Finance Birmingham – National Rail Supply
Growth Fund
Baskerville House, Centenary Square Birmingham B1 2ND
T: 0121 233 4903
E: enquiry@financebirmingham.com
W: www.financebirmingham.com
Finchpalm Ltd
42-44 Claredon Road
Watford WD17 1JJ
T: 01923 312337
E: info@finchpalm.co.uk
W: www.finchpalm.co.uk
Findlay Irvine Limited
Bog Road, Penicuik
Midlothian Scotland EH26 9BU
T: 01968 671200
E: sales@findlayirvine.com
W: www.findlayirvine.com
Finlay Group
Lakeside House, Ladford Covert Ind Park
Seighford Stafford ST18 9QL
T: 01785 282323
E: enquiries@finlay-group.co.uk
W: www.finlaygroup.com
Fintec Recruit
83 Princes Street
Edinburgh EH2 2ER
T: 0131 564 0755
E: info@fintecrecruit.co.uk
W: www.fintecrecruit.co.uk
Fircroft
Lingley House, 120 Birchwood Point
Birchwood Way Warrington WA3 7QH
T: 01925 281555
E: warrington@fircroft.com
W: www.fircroft.com
Fire Fogging Systems Ltd
149a Glasgow Road, Wishaw
Lanarkshire Scotland ML2 7QJ
T: 01698 386444
E: info@firefighting.co.uk
W: www.firefighting.co.uk
Fire Industry Association (FIA)
Tudor House, Kingsway Business Park
Oldfield Road Hampton TW12 2HD
T: 020 3166 5002
E: info@fia.uk.com
W: www.fia.uk.com
Fireclad Ltd
5th Floor, 120 Old Broad Street
London EC2N 1AR
T: 020 7628 6500
E: admin@fireclad.com
W: www.fireclad.com
Firecrest Services Ltd
Stables 4, Howbery Park
Wallingford Oxon OX10 8BA
T: 01491 832810
E: sales@firecrestservices.co.uk
W: www.firecrestservices.co.uk
Firetrace Ltd
Unit 22, Knightsdale Road
Ipswich IP1 4JJ
T: 01473 744090
E: info@firetrace.co.uk
W: www.firetrace.co.uk
First Class Partnerships Limited
46 New Broad Street
London EC2M 1JH
T: 020 3651 5745
E: info@fcpworld.net
W: www.fcpworld.net
First Components Limited
Wallows Ind Estate, Wallows Road
Brierley Hill West Midlands DY5 1QA
T: 01384 262068
E: info@firstcomponents.co.uk
W: www.firstcomponents.co.uk
Firstco
8 Celbridge Mews
London W2 6EU
T: 020 7034 0833
E: info@firstco.uk.com
W: www.firstco.uk.com
FirstGroup PLC
395 King Street, Aberdeen Scotland AB24 5RP
T: 01224 650100
E: contactus.fec@firstgroup.com
W: www.firstgroup.com
FirstGroup PLC – Resourcing Office Minton Place, Station Road
Swindon SN1 1DA
T: 01793 425656
E: careers@firstgroup.com
W: www.firstgroupcareers.com
Fischer Connectors UK
The Briars, 11 Waterberry Drive Waterlooville Hampshire PO7 7YH
T: 023 9245 9600
E: sales@fisherconnectors.co.uk
W: www.fisherconnectors.com
Fishbone Solutions
7 Pride Point Drive, Pride Park Derby DE24 8BX
T: 01332 899190
E: go-fish@fishbonesolutions.co.uk
W: www.fishbonesolutions.co.uk
Fission Recruitment Services
Unit 13 Venture Point, Stanney Mill Road
Ellesmere Port Chester CH2 4NE
T: 0151 356 5610
E: enquiries@fission.co.uk
W: www.fissionrecruitment.com
Fitzgerald Plant Services Ltd
Avondale Ind Estate, Avondale Way Cwmbran NP44 1TS
T: 01633 860693
E: info@fitzgeraldplant.co.uk
W: www.fitzgeraldplant.co.uk
FJD Consulting and Design
87 Caroline Street, Jewellery Quarter
Birmingham West Midlands B3 1UP
T: 0121 233 4786
E: simon.moon@fjdconsulting.co.uk
W: www.fjdconsulting.co.uk
Flagship Consulting Limited
Coppergate House, 16 Brune Street London E1 7NJ
T: 020 7680 7104
E: info@flagshipconsulting.co.uk
W: www.flagshipconsulting.co.uk
Flexcrete Technology Ltd
Tomlinson Road, Leyland Lancashire PR25 2DY
T: 0845 260 7005
E: web@flexcrete.com
W: www.flexcrete.com
Flexelec UK Ltd
Kings Park Ind Estate, Primrose Hill Kings Langley WD4 8ST
T: 01923 274477
E: sales@omerin.co.uk
W: www.flexelec.com
Flexicon Ltd
Roman Way, Coleshill Birmingham B46 1HG
T: 01675 466900
E: flexiconsales@atkore.com
W: www.atkore.com/flexicon
FLI Structures
Francis & Lewis Int Ltd, Waterwells Drive
Waterwells Bus Pk Quedgley Glos GL2 2AA
T: 01452 722200
E: sales@fli.co.uk
W: www.fli.co.uk
Flotec Industrial Limited
Unit 8 Pavilion Way, Loughborough Leicestershire LE11 5GW
T: 01509 230100
E: sales@floteconline.com
W: www.floteconline.com
Flowcrete UK Ltd
The Flooring Tech Ctr, Booth Lane Sandbach Cheshire CW11 3QF
T: 01270 753000
E: ukweb@flowcrete.com
W: www.flowcrete.com
FlowStone Industrial Flooring Ltd
The Shippon, Faenol Farm Ruthin Clywd LL15 2SP
T: 0800 009 6910
E: info@flowstonefloors.com
W: www.ukindustrialflooring.co.uk
Fluke UK Ltd
52 Hurricane Way, Norwich Norfolk NR6 6JB
T: 020 7942 0708
E: cs.uk@fluke.com
W: www.fluke.com
Focus 2000 Infrared Limited
3 Bridge Barns, Long Sutton Langport Somerset TA10 9PZ
T: 01458 241723
E: sales@focus2k.co.uk
W: www.focus2k.co.uk
Focus Resourcing Ltd
5 Richfield Place, 12 Richfield Avenue Reading Berkshire RG1 8EQ
T: 0118 956 7064
E: recruitment@focusresourcing.co.uk
W: www.focusresourcing.co.uk
Focus Security & Surveillance Ltd
Unit 1, The Hermitage Bus Park
Birchmoor Tamworth Staffs B78 1HS
T: 01827 898000
E: enq@focussecurity.co.uk
W: www.focussecurity.co.uk
Fone-Alarm Installations Ltd
59 Albert Road North, Reigate Surrey RH2 9EL
T: 01737 223673
E: enquiries@fonealarm.co.uk
W: www.fonealarm.co.uk
Presenting a truly comprehensive and compliant floor and wall covering product for rail vehicles, combining durability, excellent fire resistant properties and great aesthetics. Within the portfolio are textile entrance systems, linoleum, flocked flooring, carpets and textile wall coverings. Offering the widest range of products and within each product category, an array of design, colourway choices as well as bespoke options.
Forbo Flooring Systems UK Limited
High Holborn Road, Ripley Derbyshire DE5 3NT
T: 01773 744121
E: transport@forbo.com
W: www.forbo-flooring.com/rail
Force One Ltd
24 Long Hill Road, March Cambridgeshire PE15 0BL
T: 01354 655441
E: enquiries@forceoneltd.co.uk
W: www.forceoneltd.co.uk
Ford and Stanley Ltd
44 Royal Scot Road, Pride Park Derby DE24 8AJ
T: 01332 344443
E: rail@fordandstanley.com
W: www.fordandstanley.com
Forest of Dean Stone Firms Ltd
Bixslade, Stone Works Parkend Gloucestershire GL15 4JS
T: 01594 562304
E: info@fodstone.co.uk
W: www.fodstone.co.uk
Forever Group
204 Sutton Park Road, Kidderminster Worcestershire United Kingdom DY11 6LE
T: 0333 358 3808
E: sales@forever-group.co.uk
W: www.forever-group.co.uk
Forge Europa Ltd
The Old Railway, Princes Street
Ulverston LA12 7NQ
T: 01229 580000
E: infor@forge.co.uk
W: www.forge.co.uk
Forgetrack Ltd
Thistle House, 32a St Andrew Street
Hertford Hertfordshire SG14 1JA
T: 01992 500900
E: sales@forgetrack.co.uk
W: www.forgetrack.co.uk
Forkers Ltd
Golds Green House, Shaw Street
West Bromwich West Midlands B70 0TX
T: 0121 505 1010
E: admin@forkers.com
W: www.forkers.com
Fortel Services Ltd
The Forge, Old Perry Street Northfleet Kent DA11 8BT
T: 01902 603409
E: enquiries@fortel.co.uk
W: www.fortel.co.uk
Forwardis UK Ltd
Unit 17, 83 Crampton Street London SE17 3BQ
T: 020 7939 1900
E: sales@forwardis.co.uk
W: www.forwardis.com
Fosroc Ltd
Drayton Manor Bus Park, Coleshill Road Tamworth Staffordshire B78 3XN
T: 01827 262222
E: enquiryuk@fosroc.com
W: www.fosroc.com
Four Counties Training Ltd
49-51 Uxbridge Road London W5 5SA
T: 020 8840 5132
E: enquiries@fct.org.uk
W: www.fct.uk.com
Four Tees Engineers Ltd
1 Dewar Close, Segensworth West Fareham Hampshire PO15 5UB
T: 01489 885899
E: info@fourtees.co.uk
W: www.fourtees.co.uk
Fourway Communication Ltd
Unit A, Argyle Gate, Argyle Way
Stevenage Herts SG1 2AD
T: 01992 629182
E: enquiries@fourway.co.uk
W: www.fourway.co.uk
Foxwell Brown Ltd 20-22 Wenlock Road London N1 7GU
T: 020 7993 8479
E: inquiries@foxwellbrown.com
W: www.foxwellbrown.com
FP McCann Ltd Wisbech Road, Littleport Ely Cambridgeshire CB6 1RA
T: 01353 861416
E: sales@fpmccann.co.uk
W: www.fpmccann.co.uk
FPA Consulting Ltd
1 St Andrews House, Vernon Gate Derby DE1 1UJ
T: 01332 604321
E: enquiries@fpaconsulting.co.uk
W: www.fpaconsulting.co.uk
Francis Brown Ltd Hill Street East, Stockton on Tees Cleveland TS18 2HL
T: 01642 806000
E: sales@francisbrown.co.uk
W: www.francisbrown.co.uk
Francis Kirk & Son Ltd
Denton Hall Farm Road, Denton Manchester M34 2QN
T: 0161 336 2631
E: sales@franciskirk.com
W: www.franciskirk.com
Francis W Birkett & Sons Ltd St Peg Lane, Cleckheaton West Yorkshire BD19 3SL
T: 01274 873366
E: info@fwbirkett.com
W: www.westleygroup.co.uk
Frank Hand (Galvanizers) Ltd
Private Road 7, Colwick Ind Estate Nottingham East Midlands NG4 2AD
T: 0115 987 0508
E: enquiries@frankhand.co.uk
W: www.frankhand.co.uk
Frauscher Sensortechnik
Gewerbestraße 1, 4774 St. Marienkirchen
Austria T: 00 43 7711 29200
E: office@frauscher.com
W: www.frauscher.com
Freeths LLP
Cumberland Court, 80 Mount Street Nottingham NG1 6HH
T: 0115 936 9369
E: postmaster@freeths.co.uk
W: www.freeths.co.uk
Freight Arranger West View, Brownshill Stroud Gloucestershire GL6 8AQ
T: 01453 367150
E: enquiries@freightarranger.co.uk
W: www.freightarranger.co.uk
Freight on Rail 70 Cowcross Street London EC1M 6EJ
T: 07593 976548
E: philippa.edmunds@bettertransport.org.uk
W: www.freightonrail.org.uk
With businesses in the UK and Continental Europe, Freightliner is a leading provider of intermodal and bulk freight haulage. Operating services across the entire UK rail network, Freightliner transports maritime containers from all the main UK deep-sea ports as well as from a network of 12 owned and third party inland terminals.
Freightliner Group Limited 6th Floor, The Lewis Building 35 Bull Street Birmingham B4 6EQ
T: 03330 168556
E: info@gwrr.co.uk
W: www.freightliner.co.uk
FREQUENTIS UK Limited
Regal House, 70 London Road Twickenham TW1 3QS
T: 0203 005 0182
E: marketing@frequentis.com
W: www.frequentis.com
Freshfields Bruckhaus Deringer LLP
65 Fleet Street London EC4Y 1HT
T: 020 7936 4000
E: enquiries@freshfields.com
W: www.freshfields.com
Freshwater Boundary House, 91 Charterhouse Street London EC1M 6HR
T: 020 7067 1595
E: hello@freshwater-uk.com
W: www.freshwater-uk.com
Freyssinet Innovation House, Euston Way
Telford Shropshire TF3 4LT
T: 01952 201901
E: info@freyssinet.co.uk
W: www.freyssinet.co.uk
Fronius UK Ltd
Maidstone Road, Kingston Milton Keynes MK10 0BD
T: 01908 512300
E: info-uk@fronius.com
W: www.fronius.co.uk
Frontier Economics
71 High Holborn London WC1V 6DA
T: 020 7031 7000
E: information@frontier-economics.com
W: www.frontier-economics.com
FT Transformers Ltd
Unit 7 Cyclo Works, Lifford Lane Kings Norton Birmingham B30 3DY
T: 0121 451 3204
E: sales@ft-transformers.co.uk
W: www.ft-transformers.co.uk
FTI Group Ltd
Willmotts Business Park, Waterlip Shepton Mallet Somerset BA4 4RN
T: 01749 881920
E: support@fti-group.co.uk
W: www.fti-group.co.uk
Fuel Storage Systems Ltd
Unit 8 Silverwood Court, Fairfield Park Manvers, Rotherham South Yorkshire S63 5DB
T: 01226 753160
E: info@fuelstoragesystems.com
W: www.fuelstoragesystems.com
Fuelcare Ltd
Mercury House, Shrewsbury Bus Park Shrewsbury Shropshire SY2 6LG
T: 01743 360784
E: sales@fuelcare.com
W: www.fuelcare.com
Fugro
Fugro House, Hithercroft Road Wallingford OX10 9RB
T: 01491 820700
E: info@fugro.com
W: www.fugro.com
Fujikura is one of the world’s leading manufacturers of fibre optic cables and equipment for installation, measurement and testing.
The Fujikura name has become synonymous with fibre optic cable and fusion splicers and the company is a leading supplier to telecommunication companies around the globe.
Fujikura Europe Ltd
C51 Barwell Business Pk, Leatherhead Road Chessington Surrey KT9 2NY
T: 020 8240 2000
E: sales@fujikura.co.uk
W: www.fujikura.co.uk
Fujitsu 22 Baker Street London W1U 3BW
T: 01235 797711
E: askfujitsu@uk.fujitsu.com
W: www.fujitsu.com
Fullmen Limited
Fullmen Industrial Park, Kings Road Canvey Island SS8 0SF
T: 01268 683530
E: sales@fullmen.com
W: www.fullmen.com
Halo Plus2™ signal lamps Network Rail Approval (Certificate PA/05/965).
The signal lamps incorporate ultra-bright LED’s in various colours including BS1376 Class B and other configurations. The Halo Plus2 ™ has a 3-Position rocker switch for halogen spot or signal operation. Switching between colours is by top-mounted, colour coded push buttons.
Furneaux Riddall & Co Ltd
Alchorne Place, Portsmouth Hamsphire PO3 5PA
T: 023 9266 8621
E: info@furneauxriddal.com
W: www.furneauxriddall.com
Furnitubes International Ltd
3/F Meridian House, Royal Hill Greenwich London SE10 8RD
T: 020 8378 3200
E: sales@furnitubes.com
W: www.furnitubes.com
Furrer + Frey GB Ltd
Winchester House, 1st Floor
19 Bedford Row London WC1R 4EB
T: 020 3740 5455
E: gb@furrerrey.ch
W: www.furrerfrey.ch
Furse
Wilford Road
Nottingham NG2 1EB
T: 0115 964 3700
E: enquiry@furse.com
W: www.furse.com
Fusion People 3700 Parkway, Solent Business Park Whiteley Fareham Hampshire PO15 7FJ
T: 01489 865200
E: enquiries@fusionpeople.com
W: www.fusionpeople.com
Future Industrial Services Limited
Colt Business Park, Witty Street Hull East Yorkshire HU3 4TT
T: 01482 214244
E: enquiriesyorkshire@futureindustrial.com
W: www.futureindustrial.com
Future Talent Recruitment Ltd
32 Enterkin Street, Shettleston Glasgow Scotland G32 7BA
T: 0141 573 6650
E: info@futuretalentrecruitment.co.uk
W: www.futuretalentrecruitment.co.uk
Futurelink Group Kings House, Home Park Estate Kings Langley Hertfordshire WD4 8LZ
T: 01923 277900
E: sales@futurelinkgroup.co.uk
W: www.futurelinkgroup.co.uk
FW Cables Ltd
Unit 2, Boultbee Business Units
Nechells Place Birmingham B7 5AR
T: 0121 685 3000
E: sales@fwcables.co.uk
W: www.fwcables.co.uk
G-Tech Copers Limited Freightliner Road, Hull East Yorkshire HU3 4UR
T: 01482 755855
E: info@g-techlimited.co.uk
W: www.g-techlimited.co.uk
G-volution Ltd
Trym Lodge, 1 Henbury Road Westbury on Trym Bristol BS9 3HQ
T: 0117 9596470
E: simon.pickess@g-volution.com
W: www.g-volution.com
G&M Power Plant Ltd 31 Anson Road, Martlesham Heath Suffolk IP5 3RG
T: 01473 662777
E: sales-pt@gmpp.co.uk
W: www.gmpp.co.uk
G&M Tex Ltd
Unit 69, Claydon Business Park Great Blakenham Ipswich IP6 0NL
T: 01473 662777
E: sales@gmtex.co.uk
W: www.gmtex.co.uk
g2 Energy Ltd
Olney Office Park, 1 Osier Way
Olney Buckinghamshire MK46 5FP
T: 01234 482482
E: enquiries@g2energy.co.uk
W: www.g2energy.co.uk
G4S PLC
Southside, 105 Victoria Street London SW1E 6QT
T: 020 8770 7000
E: enquiries@uk.g4s.com
W: www.g4s.com
GABE
12 Church Street, Omagh Co Tyrone BT78 1DG
T: 028 8224 0391
E: info@gabrielhughes.com
W: www.gabrielhughes.com
Gable (UK) Ltd
17-19 Station Road, Hayling Island
Hampshire PO11 0EA
T: 023 9246 6416
E: gable@gable.co.uk
W: www.gabel.co.uk
GAC Rail Ltd
New Works, Burnley Road
Halifax West Yorkshire HX6 2TF
T: 01422 836091
E: sales@gacrail.co.uk
W: www.gacrail.co.uk
GAI – Tronics (A division of Hubbell Limited)
Brunel Drive, Stretton Park
Burton Upon Trent Staffordshire DE13 0BZ
T: 01283 500500
E: sales@gai-tronics.co.uk
W: www.gai-tronics.com
Gaia Converter
18 Rue Caroline Aigle, BP 26 33186
LE HAILLAN CEDEX FRANCE 33816
T: 07983 633202
E: salesUK@gaia-converter.com
W: www.gaia-converter.com
GALL ZEIDLER Consultants
102-104 Park Lane, Croydon Surrey CR0 1JB
T: 0208 686 6887
E: office-uk@gzconsultants.com
W: www.gzconsultants.com
Gallagher Security (Europe) Ltd
Unit 5, Eastboro Fields
Hemdale Bus Park Nuneaton CV11 6GL
T: 024 7664 1234
E: sales.eu@security.gallagher.com
W: www.gallagher.com
Having established ourselves as one of the UK’s leading Rail and Civil Engineering solution providers, our rail division is committed to providing cost-effective solutions, operational excellence and delivery of a superior product to our client’s satisfaction. Our integrated selfdelivery model ensures collaboration, increased productivity, and innovation throughout the delivery of our projects.
Galldris Services Ltd
Galldris House, Pavilion Business Centre
Kinetic Crescent Enfield EN3 7FJ
T: 01992 763000
E: info@galldris.co.uk
W: www.galldris.co.uk
GallifordTry Rail
Pontefract Road, Normanton Wakefield West Yorkshire WF6 1RN
T: 01924 245650
E: info@gallifordtry.co.uk
W: www.gallifordtry.co.uk
Galvanizers Association (GA)
Wren’s Court, 56 Victoria Road
Sutton Coldfield B72 1SY
T: 0121 355 8838
E: ga@hdg.org.uk
W: www.galvanizing.org.uk
Gamatronic Colmworth Business Park, Eaton Socon Cambridgeshire PE19 8YT
T: 01480 479889
E: SalesUK.Gama@solaredge.com
W: www.gamatronic.co.uk
Ganymede
London Road
Derby DE24 8UX
T: 0333 011 2048
E: info@ganymedesolutions.co.uk
W: www.ganymedesolutions.co.uk
Gard Chemicals Ltd
Chapel Lane, Heckmondwike West Yorkshire WF16 9JP
T: 01924 403550
E: sales@gardchemicals.com
W: www.gardchemicals.com
Gardiner & Theobald LLP
10 South Crescent London WC1E 7BD
T: 020 7209 3000
E: london@gardiner.com
W: www.gardiner.com
Garic Ltd
Kingfisher Park, Aviation Road
Bury Lancashire BL9 8GD
T: 0844 417 9780
E: info@garic.co.uk
W: www.garic.co.uk
Gatecare Ltd Solar Powered Gate Systems
Unit N Tyson Courtyard, Weldon South Ind Estate
Corby Northamptonshire NN18 8AZ
T: 01536 266211
E: sales@gatecare.co.uk
W: www.gatecare.co.uk
Gateway Automation Ltd
Unit 8 Wainer Close, Lincoln East Midlands LN6 3RY
T: 01522 682255
E: info@gatewayautomation.co.uk
W: www.gatewayautomation.co.uk
Gatwick Express 1st Floor, Monument Place
24 Monument Street London EC3R 8AJ
T: 0345 850 1530
E: customerservices@gatwickexpress.com
W: www.gatwickexpress.com
Gauge Communication Suite S1, Unit 1, Verulam Ind Estate
224 London Road St Albans Herts AL1 1JB
T: 01721 853952
E: info@gauge-communication.com
W: www.gauge-communication.com
GB Inspection Systems Ltd
22a Cobbett Road, Burntwood Business Park
Burntwood Cannock Staffordshire WS7 3GL
T: 0121 351 5025
E: enquiries@gbinspection.com
W: www.gbinspection.com
GB Railfreight 3rd Floor, 55 Old Broad Street London EC2M 1RX
T: 020 7983 5124
E: info@gbrailfreight.com
W: www.gbrailfreight.com
GBR-Rail Ltd
Dartmouth House, Bawtry Road
Wickersley Rotherham S66 2BL
T: 0800 949 9575
E: sales@gbr-rail.com
W: www.gbr-rail.com
GD Rectifiers
Bentley House, 2 William Way Burgess Hill West Sussex RH15 9AG
T: 020 7983 5134
E: enquiries@gdrectifiers.co.uk
W: www.gdrectifiers.co.uk
GDM Coolers Manufacturing Ltd
Boston Ind Estate, Power Station Road
Rugeley Staffordshire WS15 2HS
T: 01889 574880
E: sales@gdmcoolers.co.uk
W: www.gdmcoolers.co.uk
GDM Heat Transfer Ltd
Boston Ind Estate, Power Station Road
Rugeley Staffordshire WS15 2HS
T: 01889 574880
E: sales@gdmcoolers.co.uk
W: www.gdmcoolers.com
GEC Anderson Limited
Oakengrove, Shire Lane
Hastoe Tring HP23 6LY
T: 01442 826999
E: info@gecanderson.co.uk
W: www.gecanderson.co.uk
GEDORE
Marton Street
Skipton BD23 1TF
T: 01756 706700
E: sales@gedoreuk.com
W: www.gedoreuk.com
GEE Communications
Unit 8a Charnwood Park, Clos Marion Cardiff CF10 4LJ
T: 0845 070 1204
E: enquiries@geecommunications.co.uk
W: www.geecommunications.co.uk
Gee Construction Co Limited
11 Argent Court, Sylvan Way Basildon Essex SS15 6TH
T: 01268 541654
E: marketing@geeconstruction.co.uk
W: www.geeconstruction.co.uk
Geismar UK Ltd
Salthouse Road, Brackmills Ind Estate Northampton NN4 7EX
T: 01604 769191
E: sales-uk@geismar.com
W: www.geismar.com
GEM Cable Solutions Ltd
Unit C, 165 Saint Albans Road Sandridge St Albans AL4 9NP
T: 01727 845750
E: sales@gemcable.co.uk
W: www.gemcable.co.uk
Gemma Lighting
Unit 3 Marshlands Spur, Farlington Portsmouth Hampshire PO6 1RX
T: 0800 999 5201
E: info@gemmalighting.com
W: www.gemmalighting.com
GenAir UK Ltd
Unit 28 & 29, Prothero Works
Bilport Lane Wednesbury WS10 0NT
T: 0844 775 0890
E: sales@genair.co.uk
W: www.genair.co.uk
Generator Power Limited
Foxbridge Way, Normanton Ind Estate Wakefield West Yorkshire WF6 1TW
T: 01924 220055
E: info@generator-power.co.uk
W: www.genetrator-power.co.uk
Gensler
Moretown
London E1W 1YW
T: 020 7073 9600
E: info@gensler.com
W: www.gensler.com
Genwork Ltd
Bromley Street, Lye Stourbridge West Midlands DY9 8HU
T: 01384 636588
E: sales@genworkltd.co.uk
W: www.genworkltd.co.uk
Geo-Environmental Services Ltd
Unit 7, Danworth Farm
Cuckfield Road Hurstpierpoint BN6 9GL
T: 01273 832972
E: mail@gesl.net
W: www.gesl.net
Geo-Rope Ltd
West Quarry, Ballachulish
Scotland PH49 4JP
T: 01855 811224
E: info@geo-rope.com
W: www.geo-rope.com
GeoAccess is an Asset Management business. Established to address the need for inspections on difficult access sites in the rail sector, we utilise our highly experienced Geotechnical and Structural Engineers coupled with UAVs, ROVs, Rope Access and Confined Space Techniques. By using tried and tested methods as well as implementing highly innovative cutting-edge techniques, we deliver efficient cost effective solutions.
GeoAccess
The Old Dairy, Pessall Lane Edingale B79 9JL
T: 0333 772 2315
E: info@geoaccess.co.uk
W: www.geoaccess.co.uk
Geobear
24 Eversholt Street London NW1 1AD
T: 0800 084 3503
E: info@geobear.co.uk
W: www.geobear.co.uk
GeoDesign Barriers Ltd
1 Chapel Street, Warwick West Midlands CV34 4HL
T: 01926 405590
E: contact@geodesignbarriers.com
W: www.geodesignbarriers.com
Geofabrics Ltd
Skelton Grange Road, Stourton
Leeds LS10 1RZ
T: 0113 202 5678
E: info@geofabrics.com
W: www.geofabrics.com
Georg UK Ltd
Unit 7-8, Dunstall Hill Estate
Gorsebrook Road Wolverhampton WV6 0PJ
T: 01902 715110
E: enquiries@georguk.com
W: www.georg-uk.co.uk
Geosynthetics Ltd
Fleming Road, Harrowbrook Ind Estate Hinckley Leicestershire LE10 3DU
T: 01455 617139
E: sales@geosyn.co.uk
W: www.geosyn.co.uk
Geotech Soil Stabilisation Ltd Suite 1b Market House, 19/21 Market Place Wokingham Surrey RG40 1AP
T: 0118 979 6897
E: info@geobind.com
W: www.geobind.com
Geotechnical Engineering Ltd
Centurion House, Olympus Park Quedgeley Gloucestershire GL2 4NF
T: 01452 527743
E: geotech@geoeng.co.uk
W: www.geoeng.co.uk
Geotechnical Observations Ltd
Peter Vaughn Building, 9 Avro Way, Brooklands Weybridge Surrey KT13 0YF
T: 01932 352040
E: info@geo-observations.com
W: www.geo-observations.com
Geotechnics Ltd
The Goetechnical Centre, 203 Torrington Avenue Tile Hill Coventry CV4 9UT
T: 024 7669 4664
E: mail@geotechnics.co.uk
W: www.geotechnics.co.uk
Geoterra
Winnington Hall, Winnington Lane Northwich Cheshire CW8 4DU
T: 01606 75755
E: info@geoterra.co.uk
W: www.geoterra.co.uk
GES Consulting Ltd
61 Islington Street, Ponsonby Auckland New Zealand 1011
T: 00 64 021 968 131
E: gillian@gesconsulting.co.nz
W: www.gesconsulting.co.nz
Getlink (formerly Eurotunnel) Channel Tunnel Group, UK Terminal Ashford Road Folkestone Kent CT18 8XX
T: 0844 335 3535
E: communication.internet@getlinkgroup.com
W: www.getlinkgroup.com
GEW 2 Ltd
Mansfield I-Centre, Hamilton Way Masfield Nottinghamshire NG18 5BR
T: 0345 508 2057
E: commercialteam@gew2ltd.co.uk
W: www.gew2.co.uk
GGR Group
Presentation House, Broadgate Broadway Bus Park Oldham OL9 0JA
T: 0161 683 2580
E: info@ggrgroup.co.uk
W: www.ggrgroup.co.uk
GHD 10 Fetter Lane London EC4A 1BR
T: 020 3077 7900
E: londonmail@ghd.com
W: www.ghd.com
GI Hopley Ltd
The Sidings Ind Estate, Cammock Lane Settle North Yorkshire BD24 9RP
T: 01729 823618
E: info@gihopleyltd.co.uk
W: www.gihopleyltd.co.uk
Gidov Oil & Logistics
1 New Line, Wrotham Kent TN15 7DA
T: 07729 229830
E: sales@addinol.co.uk
W: www.gidovlogistics.co.uk
Giffen Group Ltd
Unit T, Lyon Way St Albans Hertfordshire AL4 0LQ
T: 01727 869126
E: info@giffengroup.co.uk
W: www.giffengroup.co.uk
Giken Europe B.V.
15 Manchester Mews London W1U 2DX
T: 0845 260 8001
E: info@giken.co.uk
W: www.giken.co.uk
Gilgen Door Systems UK Ltd Crow House, Crow Arch Lane Ringwood Hampshire BH24 1PD
T: 0870 000 2424
E: info@gilgendoorsystems.co.uk
W: www.gilgendoorsystems.com
Gillespies
1 St John’s Square London EC1M 4DH
T: 020 7253 2929
E: admin.london@gillespies.co.uk
W: www.gillespies.co.uk
Gillieron Scott Acoustic Design 130 Brixton Hill London SW2 1RS
T: 020 8671 2223
E: ashley@gsacoustics.org
W: www.gsacoustics.org
Gilpin Demolition & Environmental
The Horsefields, Clay Pits Way
Newton Abbot Devon TQ12 3GP
T: 01626 249696
E: info@gilpindemolition.com
W: www.gilpindemolition.com
Gioconda Ltd
Unit 10 Woodfalls, Gravelly Walls Laddingford Kent ME18 6DA
T: 01622 872512
E: mail@gioconda.co.uk
W: www.gioconda.co.uk
GIRO
75 rue de Port-Royal E, Suite 500 Montréal, QC Canada H3L 3T1
T: 011 514 383 0404
E: info@giro.ca
W: www.giro.ca/en-ca
GKD Technologies 17 Cobham Road, Ferndown Wimborne Dorset BH21 7PE
T: 01202 971971
E: service@gkdtec.com
W: www.gkdtec.com
Glasdon UK Ltd
Preston New Road, Blackpool Lancashire FY4 4UL
T: 01253 600400
E: sales@glasdon-uk.co.uk
W: www.glasdon.com
Glasgow Subway (SPT)
Broomloan Depot, Robert Street
Glasgow G51 3HB
T: 0141 332 6811
E: enquiry@spt.co.uk
W: www.spt.co.uk
Gleeds provide independent, and multidisciplinary, consultancy services on some of the UK’s biggest rail projects. Working for clients including Network Rail, HS2, Crossrail, the DfT, ORR, Transport Executives and rolling stock providers. We take pride in our ability to deliver exemplar consultancy services through award winning infrastructure and construction advice.
Gleeds
95 New Cavendish Street London W1W 6XF
T: 0207 631 7000
E: london@gleeds.co.uk
W: www.gleeds.com
Glenair UK Ltd
40 Lower Oakham Way, Mansfield Nottinghamshire NG18 5BY
T: 01623 638100
E: sales@glenair.co.uk
W: www.glenair.com
Glendale Managed Services
The Coach House, Duxbury Hall Road Chorley Lancashire PR7 4AT
T: 01257 460461
E: info@glendale-services.co.uk
W: www.glandale-services.co.uk
For over 40 years GDS has delivered class leading displays and turn-key solutions, from innovative design and development, through manufacture, test and installation, commissioning and after-sales service. Our displays are designed to operate reliably and safely in all environmental conditions, be easily serviceable and offer long life.
Global Display Solutions Ltd
Unit 6 Cobham Centre, Westmead Ind Estate
Westlea Swindon SN5 7UJ
T: 01793 498027
E: uk@gds.com
W: uk.gds.com
Global Rail Construction Ltd
Unit 20, The IO Centre, Hatfield Business Park Hatfield Hertfordshire AL10 9EW
T: 0870 990 4407
E: enquiries@grcl.co.uk
W: www.grcl.co.uk
Global Transport Forum Ltd
3rd Floor, Petersham House
57a Hatton Garden London EC1N 8JD
T: 020 7045 0900
E: marketing@globaltransportforum.com
W: www.globaltransportforum.com
GlobalData
John Carpenter House, 7 Carmelite Street London EC4Y 0BS
T: 020 7936 6400
E: info@globaldata.com
W: www.globaldata.com
Glow New Media Ltd
501 Cotton Exchange, Bixteth Street Liverpool L3 9LQ
T: 0151 707 9770
E: info@glow-internet.com
W: www.glow-internet.com
GLS Coatings Ltd Unit 1-2 Broncoed Ct, Broncoed Business Park Mold Flitshire CH7 1HP
T: 01352 753494
E: info@glsgroupuk.com
W: www.glscoatings.co.uk
GLW Engineering & Construction Ltd
Three Acres, Railway Junction South Creek Road March Cambs PE15 8SD
T: 01945 464637
E: info@glwengineering.co.uk
W: www.glwengineering.co.uk
GME Springs Unit C, GME Industrial Estate Coventry CV6 5NN T: 024 7666 4911
E: info@gmesprings.co.uk
W: www.gmesprings.co.uk
GMT Rubber-Metal-Technic Ltd
The Sidings, 7 Station Road
Guisley Leeds LS20 8BX
T: 01943 870670
E: sales@gmtrubber.com
W: www.gmtrubber.com
Go-Ahead Group Plc
4 Matthew Parker Street, Westminster London SW1H 9NP
T: 020 7799 8999
E: Enquiries@go-ahead.com
W: www.go-ahead.com
GOBOTiX Ltd
140b Longden Coleham Shrewsbury SY3 7DN
T: 01743 387030
E: sales@gobotix.co.uk
W: www.gobotix.co.uk
GoCustom Clothing
Units 12b+c Orleton, Road Ludlow Business Park Ludlow SY8 1XF
T: 0330 223 3321
E: sales@kingflw.com
W: www.gocustomclothing.com
Gold Group Ltd
5th Floor, East Grinstead House Wood Street West Sussex RH19 1UZ
T: 01342 330500
E: info@goldgroup.co.uk
W: www.goldgroup.co.uk
Golder Associates (UK) Ltd
20 Eastbourne Terrace
London W2 6LG
T: 020 7423 0940
E: info@golder.com
W: www.golder.com
Goldschmidt Holding GmbH
Hugo-Licht-Str. 3, Leipzig
Germany 04105
T: 00 49 341 355918-0
E: info@goldschmidt.com
W: www.goldschmidt.com
Goldsmiths University of London
New Cross London SE14 6NW
T: 020 7919 7171
E: course-info@gold.ac.uk
W: www.gold.ac.uk
GoMedia Services Ltd
Evergreen House North, Grafton Place London NW1 2DX
T: 020 3691 1870
E: enquiries@gomedia.io
W: www.gomedia.io
Goodflex Rubber Company Ltd
Unit 4 Weston Ind Est, Honeybourne North Evesham Worcestershire WR11 7QB
T: 01386 841480
E: info@goodflexrubber.com
W: www.goodflexrubber.com
Goodlight
Unit 7, J4 Camberley, 15 Doman Road
Camberley Surrey GU15 3LB
T: 01276 691230
E: sales@goodlight.co.uk
W: www.goodlight.co.uk
Established in 1993, Gordon Services UK is an Electro-Mechanical engineering company providing a fast, comprehensive and cost effective service for the railway industry. Now a leading force in the overhauling of components & products from all types of rolling stock throughout the UK including a full state of the art Powder Coating Facility with a large 6m Oven.
Gordon Services UK Ltd
Unit 8 Dawes Farm, Ivy Barn Lane
Ingatestone Essex CM4 0PX
T: 01277 352895
E: mark.hardy@gsl-uk.co.uk
W: www.gordonservicesukltd.co.uk
GOS Tool & Engineering Services Ltd
Heritage Court Road, Gilchrist Thomas Estate
Blaenavon Gwent NP4 9RL
T: 01495 790230
E: enquiries@gosengineering.co.uk
W: www.gosengineering.co.uk
Govia Thameslink Railway (London)
1st Floor, Monument Place
24 Monument Street London EC3R 8AJ
T: 0345 026 4700
E: customerservices@thameslinkrailway.com
W: www.thameslinkrailway.com
GPL Civil Engineering Ltd
GPL Group, PO Box 516
Salford M5 0BJ
T: 0161 745 7888
E: enquiries@gplgroup.co.uk
W: www.gplgroup.co.uk
GPS Marine Contractors Ltd
GPS Marine House, Upnor Road, Lower Upnor Rochester Kent ME2 4UY
T: 01634 892010
E: enquiries@gpsmarine.co.uk
W: www.gpsmarine.co.uk
Graco BVBA
Slakweidestraat 31, B-3630 Maasmechelen
Belgium 3630
T: 0032 8977 0700
E: info@graco.com
W: www.graco.com
Gradus Ltd
Chapel Mill, Park Green
Macclesfield Cheshire SK11 7LZ
T: 01625 428922
E: imail@gradus.com
W: www.gradus.com
Grafters Recruitment Consultants Ltd
7a Bolton Road, Eastbourne East Sussex BN21 3JU
T: 01323 737010
E: info@graftersrecruitment.com
W: www.graftersrecruitment.com
GRAHAM
1 Seaward Place, Centurion Business Park Glasgow G41 1HH
T: 0141 418 5550
E: info@graham.co.uk
W: www.graham.co.uk
Graham Construction
5 Ballygowan Road, Hillsborough Co Down Northern Ireland BT26 6XH
T: 028 9268 9500
E: info@graham.co.uk
W: www.graham.co.uk
Gramm Barrier Systems Ltd
18 Clinton Place, Seaford East Sussex BN25 1NP
T: 01323 872243
E: info@grammbarriers.com
W: www.grammbarriers.com
Grand Central Rail
Grand Central Rail, Northern House
9 Rougier Street York YO1 6HZ
T: 0345 603 4852
E: customer.services@grandcentralrail.com
W: www.grandcentralrail.com
Grange Archive Services
Unit 2A, 185 Tame Road, Witton
Birmingham West Midlands B6 7DA
T: 0121 769 0832
E: enquiries@grangearchive.co.uk
W: www.grangearchive.co.uk
Granger Reis Limited
Vertigo, Cheese Lane
Bristol BS2 0JJ
T: 0844 800 0799
E: info@grangereis.com
W: www.grangerreis.com
Grantham Coates Surveys Limited
2 Arden Court, Arden Road
Alcester Warwickshire B49 6HN
T: 01789 764420
E: info@gcsurveys.co.uk
W: www.gcsurveys.co.uk
Grants Of Shoreditch Ltd
Grant House, Prospect Way Brentwood Essex CM13 1XD
T: 01277 236190
E: office@grantsint.com
W: www.grantsint.com
Gravity London 69 Wilson Street London EC2A 2BB
T: 020 7330 8810
E: info@gravitylondon.com
W: www.gravitylondon.com
GrayBar Ltd
10 Fleming Close, Park Farm Ind Estate
Wellingborough Northamptonshire NN8 6UF
T: 01933 676700
E: sales@graybar.co.uk
W: www.graybar.co.uk
GRAYLING (Birmingham Office)
The Assay Office, Newhall St Birmingham B3 1BF
T: 0121 265 2760
E: info@grayling.com
W: www.grayling.com
Grayson Thermal Systems
Wharfdale House, 257 Wharfdale Road Tyseley Birmingham B11 2DP
T: 0121 700 5600
E: info@graysonts.com
W: www.graysonts.com
Great Central Railway Plc
Great Central Station, Great Central Road Loughborough LE11 1RW
T: 01509 632323
E: sales@gcrailway.co.uk
W: www.gcrailway.co.uk
Great Northern Rail
1st Floor, Monument Place
24 Monument Street London EC3R 8AJ
T: 0345 026 4700
E: customerservices@greatnorthernrail.com
W: www.greatnorthernrail.com
Greater Anglia 11th Floor, One Stratford Place Montfitchet Road London E20 1EJ
T: 020 3356 2650
E: contactcentre@greateranglia.co.uk
W: www.greateranglia.co.uk
Greater Manchester Combined Authority (GMCA) Churchgate House, 56 Oxford Street Manchester M1 6EU
T: 0161 778 7000
E: enquiries@greatermanchester-ca.gov.uk
W: www.greatermanchester-ca.gov.uk
Greengauge 21
28 Lower Teddington Rd, Kingston-upon-Thames Surrey KT1 4HJ
T: 07785 242506
E: co-ordinator@greengauge21.net
W: www.greengauge21.net
Greenvale Capital LLP 3rd Floor, 1 Vere Street London W1G 0DG
T: 020 3230 3707
E: info@greenvalecapital.com
W: www.greenvalecapital.com
Greenwood Consultants Limited Synergy House, Beauclare Close Leatherhead Surrey KT22 8UB
T: 01372 277943
E: info@greenwoodconsultants.com
W: www.greenwoodconsultants.com
Greenwood Engineering
H.J. Holstvej 3-5 C, 2605 Brøndby
Denmark
T: 00 45 3636 0200
E: greenwood@greenwood.dk
W: www.greenwood.dk
Grenrose Scaffolding Ltd
Grenrose House, Compton Road
Stevenage Hertfordshire SG1 2EE
T: 01438 813948
E: office@grenrose.co.uk
W: www.grenroe.co.uk
GRID Innovations
1 Gibfield, Enterprise Centre
Atherton Greater Manchester M46 0SU
T: 0800 2335988
E: info@grid-i.co.uk
W: www.fatiguemanager.com
Grimshaw Architects
57 Clerkenwell Road
London EC1M 5NG
T: 020 7291 4141
E: info@grimshaw.global
W: www.grimshaw.global
GripDeck UK
Unit 1 Chancers Farm, Fossett Lane Colchester Essex CO6 3NY
T: 01206 242494
E: mail@gripdeck.co.uk
W: www.gripdeck.co.uk
Groeneveld Lubrication Solutions
Gelders Hall Road, Shepshed
Loughborough LE12 9NH
T: 01509 600033
E: info@groeneveld-group.com
W: www.groeneveld-lubrication-solutions.com
Ground Control Limited
1st Fl Kingfisher House, Radford Way
Billericay Essex CM12 0EQ
T: 0800 334 5606
E: info@ground-control.co.uk
W: www.ground-control.co.uk
Ground Developments Ltd
Burnhouse Ind Estate, Whitburn Scotland EH47 0LQ
T: 01506 884405
E: info@grounddevelopments.co.uk
W: www.grounddevelopments.co.uk
Ground Source Heat Pump Association (GSHPA)
39 Dryburgh Road London SW15 1BN
T: 0330 223 4302
E: info@gshp.org.uk
W: www.gshp.org.uk
Ground Transportation Systems, Thales UK Quadrant House, 4 Thomas More Square
Thomas More Street London E1W 1YW
T: 020 3300 6000
E: transportationcommunication@ ukthalesgroup.com
W: www.thalesgroup.com
Groundforce (VP PLC)
Central House, Beckwith Knowle
Otley Rd Harrogate North Yorkshire HG3 1UD
T: 0800 169 5269
E: info@groundforce.co.uk
W: www.groundforce.uk.com
Groundwise Searches Ltd is a leading provider of PAS128 level D – Utility Mapping Desk Top Searches. Covering the UK and Ireland, we source the most up to date and detailed utility asset location data, offering clients an efficient and comprehensive dial before you dig service.
Groundwise Searches Ltd
Suite 6, Princess Caroline House
1 High Street Southend-on-Sea SS1 1JE
T: 01702 615566
E: mail@groundwise.com
W: www.groundwise.com
GroupCytek Ltd
Unit 3 The Bus Centre, Woodford Park Ind Est
Barlow Drive Winsford CW7 2GN
T: 01606 226000
E: projects@groupcytek.com
W: www.groupcytek.com
GRP Grating Systems
1st Floor The Villa, Astley Hall Drive
Astley Manchester M29 7TX
T: 01942 878062
E: info@grpgratingsystems.co.uk
W: www.grpgratingsystems.co.uk
GRS Roadstone (GRS Group)
10 Goldsmith Way, Eliot Business Park Nuneaton CV10 7RJ
T: 024 7658 0800
E: info@grsbagging.co.uk
W: www.grsroadstone.co.uk
GS Ecology
Suite 9, Beacontree Court
Beacontree Plaza Reading RG2 0BS
T: 0118 975 9387
E: info@gsecology.co.uk
W: www.gsecology.co.uk
GT Engineering (Markyate) Ltd
Unit 5 Caxton Park, Caxton Road Bedford Bedfordshire MK41 0TY
T: 01234 905555
E: info@gtengineering.co.uk
W: www.gtengineering.co.uk
Guidance Automation Ltd
Unit 2, Meridian South Meridian Bus Park Leicester LE19 1WY
T: 0116 243 6250
E: info@guidanceautomation.com
W: www.guidanceautomation.com
Guild of Master Craftsmen (GMC)
166 High Street, Lewes East Sussex BN7 1XU
T: 01273 478449
E: theguild@thegmcgroup.com
W: www.guildmc.com
Gunform international ltd have carried out numerous contracts nationwide within the rail network. Works including tunnel strengthening and repairs, bridge and station concrete repairs, slope and ground stabilisation works. Utilising Gunite and SHOTCRETE, PRESSURE POINTING AND GROUTING. Gunform have RISQS certification and all operatives have pts training.
Gunform International Ltd
33 Carsthorne Road, Carr Lane Ind Estate Hoylake Cheshire CH47 4FB
T: 0151 632 6333
E: info@gunform.com
W: www.gunform.com
Gunnebo UK Ltd
Fairfax House, Pendeford Business Park Wobaston Road Wolverhampton WV9 5HA
T: 0370 600 6665
E: service.uk@gunnebo.com
W: www.gunnebo.co.uk
Gurit (UK) Ltd
St Cross Business Park, Newport Isle of Wight PO30 5WU
T: 01938 828000
E: contact@gurit.com
W: www.gurit.com/rail
H Goodwin (Castings) Ltd
155 Stafford Street, Walsall
West Midlands WS2 8EY
T: 01922 633511
E: enquiries@hgoodwin.com
W: www.hgoodwin.com
H&M Security Services
476-478 Lakshall Road
London E4 9HH
T: 020 8523 2227
E: info@hmsecurityservices.co.uk
W: www.hmsecurityservices.co.uk
H&S Decorating Specialists Ltd
1 Wellesley Avenue, Richings Park
Iver Buckinghamshire SL0 9AU
T: 01753 654123
E: info@hsgroup.co.uk
W: www.hsgroup.co.uk
HA Marks Ltd
1 Beadman Street, West Norwood
London SE27 0DN
T: 020 8659 6918
E: info@hamarks.com
W: www.hamarks.co.uk
Hack Partners
WeWork Old Street, 41 Corsham Street
London N1 6DR
T: 07724 811099
E: hello@hackpartners.com
W: www.hackpartners.com
HaCon (UK) Exchange House, 494 Midsummer Boulevard Milton Keynes Buckinghamshire MK9 2UB
T: 0845 835 8688
E: info@hacon.de W: www.hacon.de
Had-Fab Limited
MacMerry Ind Estate, Tranent East Lothian EH33 1RD
T: 01875 611711
E: sales@hadfabltd.co.uk
W: www.hadfab.co.uk
Hafren Security Fasteners Unit 23, Mochdre Ind Estate Newtown Powys SY16 4LE
T: 01686 621300
E: sales@hafrenfasteners.com
W: www.hafrenfasteners.com
Haigh Rail Ltd Unit 2, Crompton Business Park
Crompton Road Doncaster DN2 4PW
T: 01302 342188
E: info@haighrail.com
W: www.haighrail.com
Haki Limited
Magnus, Tame Valley Ind Estate
Tamworth Staffordshire B77 5BY
T: 01827 282525
E: info@haki.co.uk
W: www.haki.com
Haldo Developments Ltd
Western Way West, Bury St Edmunds Suffolk IP33 3SP
T: 01284 754043
E: info@haldo.com
W: www.haldo.com
Halfen Ltd
A1/A2 Portland Close, Houghton Regis Dunstable Bedfordshire LU5 5AW
T: 01582 470300
E: info@halfen.co.uk
W: www.halfen.co.uk
Halifax Rack and Screw Cutting Co Limited
Coronation Works, Armytage Road
Brighouse West Yorkshire HD6 1QA
T: 01484 714 667
E: halifaxrackandscrew@gmail.com
W: www.halifaxrs.com
Hall Bros (Groundwork) Limited
Garrolds Farm, Benfleet Essex SS7 3DZ
T: 01702 523807
E: enquiries@brothers-hall.co.uk
W: www.brothers-hall.co.uk
Hammond ECS Ltd
Canal Road, Cwnbach Aberdare CF44 0AG
T: 01685 884813
E: enquiries@hammond-ecs.com
W: www.hammond-ecs.co.uk
Hampton Knight Ltd
Vantage House, Sandy Hill Bus Park
Tamworth Staffordshire B77 4DU
T: 01827 65999
E: enquiries@hamptonknight.co.uk
W: www.hamptonknight.co.uk
Hankinson Painting Contractors
Cotton Place, 2 Ivy Street
Wirral CH41 5EF
T: 0333 996 6223
E: info@hankinson.co.uk
W: www.hankinson.co.uk
Hanson Cement
Ketton Works, Ketton Rutland PE9 3SX
T: 0330 123 4525
E: sales@hanson.com
W: www.hanson.co.uk
Hanson Springs Ltd
Hanson Place, Gorrells Way
Rochdale Lancashire OL11 2PX
T: 01706 510600
E: railsprings@hanson-springs.co.uk
W: www.hanson-springs.co.uk
Hardstaff Barriers Hillside, Gotham Road
Kingston On Soar Nottingham NG11 0DF
T: 0115 983 2304
E: enquiries@hardstaffbarriers.com
W: www.hardstaffbarriers.com
Harland Simon Power Solutions
Bond Avenue, Bletchley
Milton Keynes Buckinghamshire MK1 1TJ
T: 01908 565656
E: sales@hsups.co.uk
W: www.harlandsimonups.com
Harmill Systems Limited
Unit P, Cherrycourt Way
Leighton Buzzard Bedfordshire LU7 4UH
T: 01525 851133
E: support@harmill.co.uk
W: www.harmill.co.uk
Harmonic Limited
The Hatchery, Eaglewood Park llminster Somerset TA19 9DQ
T: 01460 256500
E: enquiries@harmonicltd.co.uk
W: www.harmonic.co.uk
HaRMUK Ltd
3 Westfield House, Millfield Lane York YO26 6GA
T: 01904 220297
E: info@harmuk.com
W: www.harmuk.com
Harp Visual Communications Limited
Unit C4, Segensworth Bus Centre
Segensworth Road Fareham Hampshire PO15 5RQ
T: 01329 844005
E: sales@harpvisual.co.uk
W: www.harpvisual.com
Harrington Generators International
Ravenstor Road, Wirksworth Matlock Derby DE4 4FY
T: 01629 824284
E: info@hgigenerators.com
W: www.hgigenerators.com
Harrisons Engineering Lancashire Ltd
Judge Walmesley Mill, Longworth Road Billington Clitheroe BB7 9TP
T: 01254 823993
E: info@harrisonsengineering.co.uk
W: www.harrisons-engineering.co.uk
Harsco Rail Ltd
Unit 1, Chewton Street Eastwood Nottingham NG16 3HB
T: 01773 539480
E: uksales@harsco.com
W: www.harscorail.com
Hartecast Ltd
City View House, Union Street Manchester M12 4JD
T: 0161 820 6906
E: info@hartecast.co.uk
W: www.hartecast.co.uk
The HARTING Technology Group, specialists in connectivity solutions for Power, Signals and Data, have used their extensive knowledge of the rail sector to offer customised assemblies such as Inter Car Jumpers for Power and Data, in-car networking and enclosure assemblies from their purpose built UK facility in Northampton.
HARTING Ltd
51 Caswell Road, Brackmills Ind Estate Northampton NN4 7PW
T: 01604 827500
E: salesuk@harting.com
W: www.harting.com
Harvard Technology Ltd
Tyler Close, Normanton Wakefield West Yorkshire WF6 1RL
T: 0113 383 1000
E: info@harvardtechnology.com
W: www.havardtechnology.com
Harvey Thomas
86-90 Paul Street London EC2A 4NE
T: 0203 995 2007
E: harveythomasmarketing@gmail.com
W: www.harvey-thomas.com
Haskoll
39 Harrington Gardens London SW7 4JU
T: 020 7835 1188
E: info@haskoll.co.uk
W: www.haskoll.co.uk
HaslerRail AG
Freiburgstrasse 251, 3018 Bern
Switzerland
T: 00 41 31 990 71 11
E: info@haslerrail.com
W: www.haslerrail.com
HaslerRail Secheron UK
Un A2 Brookside Bus Pk, Greengate Middleton Manchester M24 1GS
T: 0161 655 6614
E: info@haslerrail.com
W: www.haslerrail.com
Havas People
The HKX Building, 3 Pancras Square London N1C 4AG
T: 020 7022 4000
E: info@havasmg.com
W: www.havaspeople.com
Hawker Siddeley Switchgear Ltd
Unit 3, Blackwood Business Park
Newport Road Blackwood NP12 2XH
T: 01495 223001
E: sales@hss-ltd.com
W: www.hss-ltd.com
Hawkgrove Limited
Rural Entreprise Centre, The Showground
Shepton Mallet Somerset BA4 6QN
T: 01373 710777
E: info@hawkgrove.co.uk
W: www.hawkgrove.co.uk
Hawkins/Brown 159 St John Street London EC1V 4QJ
T: 020 7336 8030
E: mail@hawkinsbrown.com
W: www.hawkinsbrown.com
Hawsons
Pegasus House, 463a Glossop Road
Sheffield S10 2QD
T: 0114 266 7141
E: email@hawsons.co.uk
W: www.hawsons.co.uk
Hayley Rail
Shelah Road, Halesowen
West Midlands B63 3XL
T: 0121 585 5841
E: rail@hayley-group.co.uk
W: www.hayley-group.co.uk
Hays – Head Office
250 Euston Road London NW1 2AF
T: 020 7383 2266
E: customerservice@hays.com
W: www.hays.co.uk
Haywood & Jackson Fabrications Ltd
Denton Drive, Northwich
Cheshire CW9 7LU
T: 01606 47777
E: info@haywoodandjackson.co.uk
W: www.haywoodandjackson.co.uk
HBC-radiomatic (UK) Ltd
Building 5, Bay 1, First Avenue, Pensnett Trading Estate
Kingswinford West Midlands DY6 7TW
T: 0121 503 6930
E: sales@hbc-radiomatic.co.uk
W: www.hbc-radiomatic.co.uk
HBI Haerter Consulting Engineers focus on the design and planning of ventilation, aerodynamics, environmental control, mechanical equipment, and safety of rail tunnels and underground systems. HBI offers the entire range of services – from first feasibility studies, measurements, detail studies, project execution up to refurbishment and optimisation during operation.
HBI Haerter AG
Bahnhaldenstrasse 7, 8052 Zürich Switzerland
T: 00 41 44 289 39 00
E: info.be@hbi.ch
W: www.hbi.eu
HBPW LLP
43 Bridgegate, Retford Nottinghamshire DN22 7UX T: 01777 869896
E: mail@hbpwconsulting.co.uk
W: www.hbpw.co.uk
HD Sharman Ltd
High Peak Works, Chapel-en-le-Frith
High Peak Derbyshire SK23 0HW
T: 01298 428122
E: info@hdsharman.co.uk
W: www.hdsharman.co.uk
Health and Safety Executive (HSE)
Redgrave Court, Merton Road
Bootle Merseyside L20 7HS
T: 0300 003 1747
W: www.hse.gov.uk
Health and Safety Laboratory
Harpur Hill, Buxton Derbyshire SK17 9JN
T: 020 3028 2000
E: hslinfo@hsl.gsi.gov.uk
W: www.hsl.gov.uk
Heat Exchange Group
Unit 3 Greens Industrial Park, Calder Vale Road, Wakefield WF1 5PH T: 0300 124 0495
E: sales@heatexchangegroup.co.uk
W: heatexchangegroup.co.uk
Heathrow Express
The Compass Centre, Nelson Road
Heathrow Airport Hounslow TW6 2GW
T: 0345 600 1515
E: sales@heathrowexpress.com
W: www.heathrowexpress.com
Heavenly Group Ltd
15 Little Green, Richmond
Surrey TW9 1QH
T: 020 7554 3355
E: london@weareheavenly.com
W: www.heavenly.co.uk
Heinrich Georg (UK) Limited
Units 7-8, Dunstall Hill Estate
Gorsebrook Road Wolverhampton WV6 0PJ
T: 01902 715110
E: enquiries@georguk.com
W: www.georguk.com
Helifix (Sustainable Structural Solutions)
The Mille, 1000 Great West Road
Brentford London TW9 9DW
T: 020 8735 5200
E: sales@helifix.co.uk
W: www.helifix.co.uk
HellermannTyton Ltd
Sharston Green Bus Park, 1 Robeson Way
Wythenshawe Manchester M22 4TY
T: 0161 945 4181
E: sales@hellermanntyton.co.uk
W: www.hellermanntyton.co.uk
Help Point Ltd
Unit 19 Lakeside Park, Medway City Estate Rochester Kent ME2 4LT
T: 01634 723174
E: sales@helppoint.co.uk
W: www.helppoint.co.uk
HemingwayDesign
15 Wembley Park Drive, Wembley Middlesex HA9 8HD
T: 020 8903 1074
E: info@hemingwaydesign.co.uk
W: www.hemingwaydesign.co.uk
Henderson Thomas Associates Limited Unit 6, Little Mundells
Welwyn Garden City Hertfordshire AL7 1EW
T: 01707 327 785
E: testing@hendersonthomas.co.uk
W: www.hendersonthomas.co.uk
Henley Business Group 1st Floor, 47 Bury New Road Prestwich Manchester M25 9JY
T: 0800 012 1416
E: info@henleybusiness.com
W: www.henleybusiness.com
Henry Williams Ltd
Dodsworth Street, Darlington County Durham DL1 2NY
T: 01325 462722
E: sales@hwilliams.co.uk
W: www.hwilliams.co.uk
Hepworth Group – B Hepworth and Co Ltd
2-4 Merse Road, North Moons Moat Redditch Worcestershire B98 9HL
T: 01527 61243
E: rail.web@b-hepworth.com
W: www.hepworthrail.co.uk
Heritage Railway Association
c/o The Railway Station, Havenstreet Ryde Isle of Wight PO33 4DS
T: 0800 756 5111
E: contact@hra.uk.com
W: www.heritagerailways.com
Hertford Controls Ltd
14 Ermine Point, Gentlemens Field Westmill Road Ware Herts SG12 0EF
T: 01920 467578
E: info@hertfordcontrols.co.uk
W: www.hertfordcontrols.co.uk
Heskins Ltd
Churchill Rd Ind Estate, Brinscall Lancashire PR6 8RQ
T: 01254 832266
E: mail@heskins.com
W: www.heskins.com
Hevertech
Unit 2, Treefield Ind Estate Gildersome Leeds LS27 7JU
T: 0113 238 3355
E: enquiries@hevertech.co.uk
W: www.hevertech.co.uk
HGI Generators International Ravenster Road, Wirksworth Derbyshire DE4 4FY
T: 01629 824284
E: sales@hgigenerators.com
W: www.hgigenerators.com
High Speed 1 (HS1 Ltd) 5th Floor, Kings Place
90 York Way London N1 9AG
T: 020 7014 2700
E: info@highspeed1.co.uk
W: www.highspeed1.co.uk
High Speed Rail Industry Leaders (HSRIL)
T: 07984 647367
E: hsril@wearefield.co.uk
W: www.rail-leaders.com
High Speed Two (HS2) Ltd
Two Snowhill, Snow Hill Queensway Birmingham B4 6GA
T: 0808 143 4434
E: HS2enquiries@hs2.org.uk
W: www.hs2.org.uk
High Value Manufacturing Catapult Regus Building, Blythe Valley Bus Park
Shirley Solihull B90 8AD
T: 01564 711540
E: info@hvm.catapult.org.uk
W: www.hvm.catapult.org.uk
Highland Galvanizers
Pinefield Parade
Elgin IV30 6FG
T: 01343 548855
E: highlandgalvonizersuk@gmail.com
W: www.higalv.co.uk
Hill & Smith Holdings Plc
Westhaven House, Arleston Way
Shirley West Midlands B90 4LH
T: 0121 704 7430
E: enquiries@hsholdings.co.uk
W: www.hsholdings.co.uk
Hill and Smith Ltd t/a Variable Message Signs
Unit 1, Monkton Bus Park North
Mill Lane Hebburn Tyne & Wear NE31 2JZ
T: 0191 423 7070
E: sales@vmstech.co.uk
W: www.vmstech.co.uk
Hill Dickinson Legal Services
The Broadgate Tower, 20 Primrose Street London EC2A 2EW
T: 020 7283 9033
W: www.hilldickinson.com
Hillmoore Fire Protection Ltd
Unit 10 Clipper Park, Thurrock Park Way
Tilbury Essex RM18 7HG
T: 01628 890122
E: info@hillmoorefire.co.uk
W: www.hillmoorefire.co.uk
Hilti has been supplying the rail industry for a number of years & a number of our products are Network Rail &/or LUL approved. Traditionally we have supplied tools & fastening solutions, that have been well received within the industry offering both productivity gains and H. & S. benefits.
Hilti (Gt. Britain) Ltd
No.1 Circle Square, 3 Symphony Park Manchester M1 7FS
T: 0800 886 100
E: gbsales@hilti.com
W: www.hilti.com
Hingley Transport Limited
4 Talbots Lane, Brierley Hill West Midlands DY5 2YX
T: 01384 262221
E: enquiries@hingleytransport.co.uk
W: www.hingley-transportltd.co.uk
Hird Rail Development
Clifford House, Lady Bank Drive Lakeside Doncaster DN4 5NF
T: 01302 952040
E: info@hirdrail.com
W: www.hirdrail.com
Hire Association Europe (HAE) 2450 Regents Court, The Crescent
Solihull B37 7YE
T: 0121 380 4600
E: membership@hae.org.uk
W: www.hae.org.uk
Hire Station Fields Farm Road, Long Eaton Nottingham NG10 3FZ
T: 0370 990 0999
E: hirestation@vpplc.com
W: www.hirestation.co.uk
Hitachi Information Control Systems
Solstice House, Middleton Drive Bradford on Avon Wiltshire BA15 1GB
T: 01225 860140
E: info@hitachi-infocon.com
W: www.hitachi-infocon.com
Hitachi Rail Europe
7th Floor, 40 Holborn Viaduct
London EC1N 2PB
T: 020 7970 2700
E: rail.enquiries@hitachirail-eu.com
W: www.hitachirail-eu.com
Hitachi Rail Global
1 New Ludgate, 60 Ludgate Hill London EC4M 7AW
T: 020 3904 4000
E: rail.enquiries@hitachirail-eu.com
W: www.hitachirail-eu.com
HJ Skelton and Co Ltd are the appointed sales agents for Rawie in the UK and Eire. Rawie manufacture a wide range of railway buffer stops and wheel stops. Rawie hold product approval for many users throughout the world.
HJ Skelton and Co. Ltd
9 The Broadway, Thatcham
Berkshire RG19 3JA
T: 01635 866877
E: info@hjskelton.com
W: www.hjskelton.co.uk
HKA
3200 Daresbury Park, Daresbury
Warrington Cheshire WA4 4BU
T: 01928 756 500
E: helenwalker@hka.com
W: www.hka.com
HMG Paints Ltd
Riverside Works, Collyhurst Road
Manchester M40 7RU
T: 0161 205 7631
E: sales@hmgpaint.com
W: www.hmgpaint.com
Hobby Homes 5 St Andrews Way
London E3 3PA
T: 020 7537 6500
E: sales@hobbyhomes.com
W: www.hobbyhomes.com
Hodge Clemco Ltd
36 Orgreave Drive, Handsworth
Sheffield S13 9NR
T: 0114 254 8811
E: sales@hodgeclemco.co.uk
W: www.hodgeclemco.co.uk
Hogia Transport Systems Ltd St James House, 13 Kensington Square
London W8 5HD
T: 020 7795 8156
E: sales@hogia.com
W: www.hogia.com
HOK International
Qube, 90 Whitfield Street
London W1T 4EZ
T: 020 7636 2006
E: london@hok.com
W: www.hok.com
Holden Aluminium Technologies Ltd
Unit 5, Station Road
Bromyard Herefordshire HR7 4QT
T: 01885 482222
E: info@holdenaluminium.com
W: www.holdenaluminium.com
Holdtrade (UK) Ltd
No 1 The Rubicon, 51 Norman Road
Greenwich London SE10 9QB
T: 020 8293 5999
E: holdtrade@holdtrade.co.uk
W: www.holdtrade.co.uk
Holemasters
Suite 14, Blackpool Tech Mgmt Ctr
Faraday Way Blackpool FY2 0JW
T: 01253 892890
E: enquiries@holemasters.co.uk
W: www.holemasters.co.uk
Hollingworth Bissell
Albert Buildings, 49 Queen Victoria St
London EC4N 4SA
T: 020 7653 1994
E: information@hblaw.co.uk
W: www.hblaw.co.uk
Hollywell Building Services Ltd
New Barnes Mill, Cottonmill Lane
St Albans Hertfordshire AL1 2HA
T: 01727 810555
E: helpdesk@hollywell.co.uk
W: www.hollywell.co.uk
Holmatro UK
Unit 6 Easter Park, Lenton Lane Nottingham NG7 2PX
T: 0115 973 8590
E: ukrescue@holmatro.com
W: www.holmatro.com
Holophane Europe Ltd
Bond Avenue, Bletchley
Milton Keynes Buckinghamshire MK1 1JG
T: 01908 649292
E: info@holophane.co.uk
W: www.holophane.co.uk
Homegrown Timber (Rail) Ltd
Courtlands, Antlands Lane
Shipley Bridge Surrey RH6 9TE
T: 01293 821321
E: rail@homegrowntimber.com
W: www.homegrowntimber.com
Honeywell Safety & Productivity Solutions
Honeywell House, Skimped Hill Lane
Bracknell Berkshire RG12 1EB
T: 01344 656000
W: www.honeywellaidc.com
Hoppecke Industrial Batteries Limited
Unit 2 Lowfield Drive, Centre 500
Wolstanton Newcastle ST5 0UU
T: 01782 667305
E: rail@hoppecke.co.uk
W: www.hoppecke.co.uk
HORIBA MIRA Ltd
Watling Street, Nuneaton Warwickshire CV10 0TU
T: 024 7635 5000
E: rail@horiba-mira.com
W: www.horiba-mira.com
Horizon Group
Unit 15b, Britannia Road
Milnsbridge Huddersfield HD3 4QF
T: 01484 460909
E: sales@thehorizon-group.co.uk
W: www.thehorizon-group.co.uk
Horton Automatics Ltd
Horton Wood 31, Telford Shropshire TF1 7YZ
T: 01952 670169
E: sales@horton-automatics.ltd.uk
W: www.horton-automatics.ltd.uk
Hosiden Besson Ltd
12 St Josephs Close, St Josephs Trading Est Hove East Sussex BN3 7EZ
T: 01273 860000
E: info@hbl.co.uk
W: www.hbl.co.uk
Hottinger Bruel & Kjaer UK Ltd Jarman Way, Royston Hertfordshire SG8 5BQ
T: 01223 389800
E: info@hbkworld.com
W: www.hbkworld.com
Houghton International
Beacon Road, Trafford Park Manchester M17 IAF
T: 0161 874 5000
E: info@houghtonintl.com
W: www.houghtonintl.com
Houghton International
Houghton International, Ronnie Mitten Works
Shields Road NE6 2YL
T: 0191 234 3000
E: info@houghton-international.com
W: www.houghton-international.com
Howe Green Ltd
Marsh Lane, Ware Hertfordshire SG12 9QQ
T: 01920 463230
E: info@howegreen.co.uk
W: www.howegreen.co.uk
Howells Railway Products Ltd
Longley Lane, Sharston Ind Estate
Wythenshawe Manchester M22 4SS
T: 0161 945 5567
E: info@howells-railway.co.uk
W: www.howells-railway.co.uk
HPC Asset Services & Hygiene Pro Clean Ltd
2 Grange Court, Harnett Drive
Milton Keynes MK12 5NE
T: 0800 024 8090
E: info@hpc-assetservices.com
W: www.hygieneproclean.com
HR Kilns Ltd & HR Fibreglass Unit 5 & 7, Gorsey Place
Gillibrands Skelmersdale WN8 9UP
T: 01695 557711
E: sales@hrkilns.com
W: www.hrfibreglass.co.uk
HRS Services Ltd
The Maltings, 81 Burton Road Sheffield South Yorkshire S3 8BZ
T: 0800 030 4391
E: info@hrsservices.co.uk
W: www.hrsservices.co.uk
HS Carlsteel Engineering Ltd Suite B, Hailey Road Ind Estate
Erith Kent DA18 4AU
T: 020 8312 1879
E: admin@hscarlsteel.co.uk
W: www.hrcarsteel.co.uk
HS Jackson and Son (Fencing) Ltd Stowting Common, Ashford Kent TN25 6BN
T: 0800 408 4739
E: security@jacksons-fencing.co.uk
W: www.jacksons-security.co.uk
HSQE Ltd
22 Brownsea Drive, Wickford Essex SS12 9LB
T: 0333 733 1111
E: info@hsqe.co.uk
W: www.hsqe.co.uk
HSS Hire PLC
25 Willow Lane, Mitcham Surrey CR4 4TS
T: 020 8936 7307
E: hire@hss.com
W: www.hss.com
HSS Training
76 Talbolt Road, Old Trafford Manchester M16 0PQ
T: 0845 314 2283
E: training@hss.com
W: www.hsstraining.com
HTA Group Ltd
Units 7040-7060, Middlemarch Bus Park
Siskin Parkway Coventry CV3 4PE
T: 024 7651 6100
E: sales@htagroup.co.uk
W: www.htagroup.co.uk
HTL Group Ltd 45 Colbourne Avenue, Nelson Park Ind Estate
Cramlington Northumberland NE23 1WD
T: 01670 700000
E: info@htlgroup.com
W: www.hiretorque.co.uk
Huawei Technologies (UK) Ltd
300 South Oak Way, Green Park Reading Berkshire RG2 6UF
T: 0118 920 8000
E: transportation@huawei.com
W: e.huawei.com
HUB Auto ID Ltd
Unit D, Bartonfields Centre
Barton Blount Church Broughton DE65 5AP
T: 01509 357080
E: info@hub-autoid.co.uk
W: www.hub-autoid.co.uk
HUBER+SUHNER (UK) Ltd
Telford Road
Bicester Oxfordshire OX26 4LA
T: 01869 364100
E: railway-marketing@hubersuhner.com
W: www.hubersuhner.com/en
We are committed to replace conventional construction methods with providing ingenious and sustainable solutions applying state of the art and highly effective technical textiles. With top-class engineering solutions and more than 150 years of expertise in manufacturing, coating and tailoring of technical textiles.
Huesker Ltd
1 Quay Business Ctr, Harvard Court Calver Road Warrington WA2 8LT
T: 01925 629393
E: info@huesker.co.uk
W: www.huesker.co.uk
Hull Trains
South Wing, Cherry Court
36 Ferensway Hull HU2 8NH
T: 0345 071 0222
E: customerservices.hull@hulltrains.co.uk
W: www.hulltrains.co.uk
Human Reliability
1 School House, Higher Lane Dalton Wigan Lancashire WN8 7RP
T: 01257 463121
E: info@humanreliability.com
W: www.humanreliability.com
Hurley Palmer Flatt Ltd
NWS House, 1e High Street Purley Surrey CR8 2AS
T: 020 8763 5900
E: info@hurleypalmerflatt.com
W: www.hurleypalmerflatt.com
HUSQVARNA CONSTRUCTION, is a leading producer within the light construction equipment business. The range includes machines and services for concrete sawing & drilling, concrete surfaces & floors, and remote demolition, as well as diamond tools for the construction industry.
Husqvarna Construction
Unit 4 Glenmore Centre, Waterwells Business Pk
Quedgeley Gloucester GL2 2AP
T: 0344 844 4569
E: husqvarna.construction@husqvarna.co.uk
W: www.husqvarnacp.co.uk
Hutchinson Engineering Ltd
Everite Road, Widnes Cheshire WA8 8PT
T: 0151 422 9990
E: info@hutchinsonengineering.co.uk
W: www.hutchinsonengineering.co.uk
HV Wooding Range Road Ind Estate, Range Road Hythe Kent CT21 6HG
T: 01303 264471
E: sales@hvwooding.co.uk
W: www.hvwooding.co.uk
HW Martin (Fencing Contractors) Ltd
Fordbridge Lane, Blackwell Alfreton Derbyshire DE55 5JY
T: 01773 860600
E: recycling@hwmartin.com
W: www.hwmartin.com
Hydram Sheet Metalwork supplies metal products, components and precision sheet metal fabrications to market leading companies in industries such as rail, bus, lighting, furniture, earth-moving machinery and white goods. Hydram’s success is founded on customer satisfaction, aiming to achieve maximum productivity & quality by working closely with customers to establish long term partnerships.
Hydram Engineering Limited
Avenue One, Chilton Ind Estate Chilton County Durham DL17 0SG
T: 01388 720222
E: enquiries@hydram.co.uk
W: www.hydram.co.uk
HydraPower Dynamics Ltd
Saint Marks Street, Birmingham West Midlands B1 2UN
T: 0121 456 5656
E: salesoffice@hdl.uk.net
W: www.hydrapower-dynamics.com
Hydraulic & Offshore Supplies Ltd
Offshore House, Southwick Ind Estate
Sunderland SR5 3TX
T: 0191 549 7335
E: hos@hos.co.uk
W: www.hos.co.uk
Hydraulic Pumps UK Ltd
Summit 2, Mangham Road, Barbot Hill Ind Estate Rotherham S61 4RJ
T: 01709 360370
E: sales@hydraulicpumps.co.uk
W: www.hydraulicpumps.co.uk
A Scottish based company for over 50 years producing conductors for many uses including switchgear, aerospace, railway traction equipment and transformers.
Cuponal™ is a Co-extruded copper clad aluminium (CCA) which is produced as busbars, rods and wire for high and low-voltage electrical distribution.
Hydrostatic Extrusions Limited
Arran Road, North Muirton
Perth Scotland PH1 3DX
T: 01738 494500
E: sales.hydrostatic@bruker.com
W: www.bruker.com
HYTORC
Unit 25 Moorland Way, Nelson Park Ind Estate Cramlington NE23 1WE
T: 01670 363800
E: info@hytorc.co.uk
W: www.hytorc.co.uk
I C Consultants Ltd
58 Prince’s Gate, Exhibition Road London SW7 2QA
T: 020 7594 6565
E: consultant-support@imperial.ac.uk
W: www.imperial-consultants.co.uk
I M Kelly R&A Ltd
The Moorings Bus Park, Channel Way Exhall Coventry CV6 6RH
T: 024 7664 4026
E: email@imkellyrail.co.uk
W: www.imkra.co.uk
iBlocks Ltd
189 Bermondsey Street London SE1 3UW
T: 020 7234 9060
E: info@iblocks.co.uk
W: www.iblocks.co.uk
ICB Group
Virginia House, 35-51 Station Road
Egham Surrey TW20 9LB
T: 01784 608100
E: reception@icbgroupuk.com
W: www.icbgroupuk.com
ICEE manufactures high-quality, bespoke equipment enclosures, offering a complete, lifecycle service including design, fabrication, fit-out, installation, maintenance, refurbishment and related support. We typically partner with infrastructure operators and principal contractors requiring our specialist resources. A major strength is standards compliance including ISO, RISQS and other key safety and quality certifications.
ICEE Managed Services Ltd
20 Arnside Road, Waterlooville Hampshire PO7 7UP
T: 02392 230 604
E: info@icee.co.uk
W: www.icee.co.uk
ICL Solutions Ltd
10 Rochester Court, Anthony’s Way Rochester Kent ME2 4NW
T: 01634 717784
E: info@iclsolutions.co.uk
W: www.iclsolutions.co.uk
Icomera
Victory House, Quayside
Chatham Kent ME4 4QU
T: 0870 446 0461
E: sales@icomera.com
W: www.icomera.com
Icon Polymer Group Ltd
Thrumpton Lane, Retford Nottinghamshire DN22 6HH
T: 01777 714300
E: info@iconaerotech.com
W: www.iconaerotech.com
ICTS (UK) Limited
South Block, Entrance D, Tavistock House
Tavistock Square London WC1H 9LG
T: 020 7874 7576
E: info@icts.co.uk
W: www.icts.co.uk
ID Computing Ltd
Marble Hall, 80 Nightingale Road
Derby DE24 8BF
T: 01332 742654
E: enquiries@idcomputing.co.uk
W: www.idcomputing.co.uk
Ideagen Ltd
Ergo House, Mere Way
Ruddington Nottinghamshire NG11 6JS
T: 01629 699100
E: sales@ideagen.com
W: www.ideagen.com
Ideas Limited
Sanderum House, Oakley Road
Chinnor Oxfordshire OX39 4TW
T: 01844 355474
E: info@ideas.ltd.uk
W: www.ideas.ltd.uk
Idom Merebrook Limited
Cromford Mills, Mill Lane
Matlock Derbyshire DE4 3RQ
T: 01773 829988
E: info.derbyshire@idom.com
W: www.merebrook.co.uk
IFC Inflow
3 Ryder Way, Basildon Essex SS13 1QH
T: 01268 596900
E: sales@ifcinflow.com
W: www.ifcinflow.com
IFPL
Elm Lane, Calbourne Newport Isle Of Wight PO30 4JY
T: 01983 555900
E: enquiries@ifpl.com
W: www.ifpl.com
IFS Laboratories Ltd
Textile Innovation, House 1 Lyons Road
Trafford Park Manchester M17 1RN
T: 0161 505 0650
E: info@ifs-labs.com
W: www.ifs-labs.com
Igus UK
Caswell Road, Brackmills Northampton NN4 7PW
T: 01604 677240
E: sales@igus.co.uk
W: www.igus.co.uk
IGW International n.v
Kampveldstraat 51, Oostkamp Belgium B-8020
T: 0032 5082 6907
E: info@igwpower.com
W: www.igwpower.com
iLECSYS Rail Ltd
1 Kites Park, Summerleys Road
Princes Risborough Buckinghamshire HP27 9PX
T: 01442 828387
E: enquiry@ilecsys.co.uk
W: www.ilecsysgroup.co.uk
Impact Executives Ltd
Heron Tower, 110 Bishopsgate London EC2N 4AY
T: 020 7314 2011
E: info@impactexecutives.com
W: www.impactexecutives.com
Impact Security and Medical Training Ltd Unit 15 Peartree Bus, Centre Peartree Road Colchester Essex CO3 0JN
T: 01206 562366
E: info@impact-security.com
W: www.impact-security.com
Imperial College London Room 761, South Kensington Campus Imperial College London SW7 2AZ
T: 020 7594 7091
E: me.admissions@imperial.ac.uk
W: www.imperial.ac.uk
Impreglon UK
Kingsbury Link, Trinity Road Piccadilly Tamworth B78 2EX
T: 01827 871400
E: info@impreglon.co.uk
W: www.impreglon.co.uk
Imtech/Dynniq Hazelwood House, Lime Tree Way Basingstoke Hampshire RG24 8WS
T: 01256 891800
E: sales@dynniq.co.uk
W: www.dynniq.co.uk
In2Global Ltd
104 Dunstable Road, Studham Dunstable Bedfordshire LU6 2QL
T: 01582 873447
E: info@in2global.com
W: www.in2global.com
Incap Electronics UK Ltd
Croft Road, Newcastle-under-Lyme Staffordshire ST5 0TW
T: 01782 753200
E: salesuk@incapcorp.com
W: www.incapcorp.com
Incorporatewear
Edison Road, Hams Hall, National Dist Park Coleshill B46 1DA
T: 01675 432200
E: enquiries@icwuk.com
W: www.incorporatewear.co.uk
Incose UK Ltd
The Dyers Building, 21 Silver Street
Ilminster Somerset TA19 0DH
T: 01460 298217
E: enquiries@incoseuk.org
W: www.incoseuk.org
Incremental Solutions
York Science Park, Innovation Centre
Innovation Way York YO10 5DG
T: 01904 435100
E: contact@incrementalsolutions.co.uk
W: www.incrementalsolutions.co.uk
Independent Glass Co Ltd
540-550 Lawmoor Street, Dixon Blazes Ind Estate Glasgow G5 0UA
T: 0141 429 8700
E: toughened@independent.glass.co.uk
W: www.independentglass.co.uk
Indestructible Paint Ltd – a UK based Coatings manufacturer, with over 45 years’ experience supplying coatings to the Aerospace and Defence Industries worldwide. This technology is now available for use within the rail sectors, offering corrosion, chemical and heat protection in aggressive operating conditions, extending the operating life for customer assets.
Indestructible Paint Limited 19-25 Pentos Drive, Sparkhill Birmingham B11 3TA
T: 0121 702 2485
E: sales@indestructible.co.uk
W: www.indestructible.co.uk
INDO Lighting Ltd
Units 18-19, Chancerygate Bus Centre Manor House Avenue Southampton SO15 0AE
T: 020 3051 1687
E: info@indolighting.com
W: www.indolighting.com
Industrial and Financial Systems, IFS UK Ltd
Artisan, Hillbottom Road High Wycombe HP12 4HJ
T: 01494 428900
E: info.uk@ifsworld.com
W: www.ifsworld.com
Known by our brand name INDUSTRIALCOMMS
we are a dedicated Business to Business (B2B) supplier serving the needs of the UK Rail Infrastructure and Rollingstock sectors. Our product offering spans from Trackside WAN/LAN solutions to 4G/LTE/GSM-R transmission systems to OnBoard Train Wi-Fi and communication solutions.
Industrial Communication Products Ltd
The Angel Business Centre, 1 Luton Road Toddington Bedfordshire LU5 6DE
T: 020 3086 9569
E: sales@industrialcomms.com
W: www.industrialcomms.com
Industrial Door Services Ltd
Adelaide Street, Crindau Park Newport NP20 5NF
T: 01633 853335
E: enquiries@indoorserv.co.uk
W: www.indoorserv.co.uk
Industrial Rope Access Trade Association (IRATA) 3 Eurogate Bus Park, Trinity Road Ashford TN24 8X
T: 01233 754600
E: info@irata.org
W: www.irata.org
Industrial Workwear Ltd
Unit 16, Consett Business Centre Consett County Durham DH8 6BP
T: 0808 178 1938
E: sales@industrialworkwear.com
W: www.industrialworkwear.com
Industrilas GB
Unit 3, Cedar Court, Halesfield 17 Telford Shropshire TF7 4PF
T: 01952 850 416
E: sales.gb@industrilas.com
W: www.industrilas.com
Infinitive Group is a specialist consultancy and engineering technology business that sit at the intersection of operational know-how and information technology. Working with customers to extract, transform and visualise information using Machine Learning and Analytics combined with our expertise to deliver business outcomes that generate revenue, optimise cost and mitigate risk.
Infinitive Group Ltd
7 Lakeview House, Bond Avenue Bletchley Milton Keynes MK1 1FB
T: 01908 018900
E: info@infinitivegroup.co.uk
W: www.infinitivegroup.co.uk
Infor Global Solutions
Infor House, 1 Lakeside Road
Farnborough GU14 6XP
T: 01252 556000
E: ukmarketing@infor.com
W: www.infor.co.uk
Infotec Ltd
The Maltings, Tamworth Road
Ashby De La Zouch Leicesterhire LE65 2PS
T: 01530 560600
E: sales@infotec.co.uk
W: www.infotec.co.uk
Infrasafe UK Limited
Railsafe House, Whiteley Road
Blaydon Tyne & Wear NE21 5NJ
T: 0191 499 0024
E: enquiries@infrasafe.co.uk
W: www.infrasafe.co.uk
Infrastructure Training Services Ltd
Heather Park House, North Circular Road
Stonebridge London NW19 7NN
T: 020 8733 8888
E: info@cleshar.co.uk
W: www.cleshar.co.uk
Infrata
3rd Floor, 5 Chancery Lane
London WC2A 1LG
T: 020 7406 7464
E: info@infrata.com
W: www.infrata.com
Ingersoll Engineers
1 Northumberland Avenue, Trafalgar Square London WC2N 5BW
T: 020 7872 5666
E: info@ingersollengineersuk.com
W: www.ingersollengineersuk.com
Initiate Consulting Ltd
40 Great Portland St, London
W1W 7LZ
T: 020 7357 9600
E: info@initiate.uk.com
W: www.initiate.uk.com
Inline Track Welding Ltd
Ashmill Business Park, Ashford Road Lenham Maidstone ME17 2GQ
T: 01622 854730
E: info@inlinetrack.co.uk
W: www.inlinetrackwelding.co.uk
Innova Care Concepts
Unit 700, Street 5, Thorp Arch Estate
Wetherby West Yorkshire LS23 7FZ
T: 0345 034 1450
E: enquiries@innova.uk.com
W: www.innovacareconcepts.com
Innuscience
44 Burners Lane, Kiln Farm
Milton Keynes MK11 3HD
T: 020 3239 8317
E: uk@innuscience.com
W: www.innuscience.com
Inside Out Group (Europe) Ltd
190 North Gate, Basford Nottingham NG7 7FT
T: 0115 979 1719
E: info@insideoutgroup.co.uk
W: www.insideoutgroup.co.uk
Insight Security (UK Head Office)
Units 1 & 2, Cliffe Ind Estate
South Street Lewes East Sussex BN8 6JL
T: 01273 475500
E: info@insight-security.com
W: www.insight-security.com
Inspectahire Instrument Co. Ltd
Inspectahire, Badentoy Road
Bandentoy Ind Est Portlethen AB12 4YA
T: 01224 789692
E: enquiries@inspectahire.com
W: www.inspectahire.com
Installation Technology
Unit 13, Headley Park Area 10
Headley Road East Woodley Reading RG5 4SW
T: 0118 969 9777
E: info@installationtechnology.com
W: www.installationtechnology.com
Institute for Collaborative Working (ICW)
Suite 2, 21 Bloomsbury Square
Bloomsbury London WC1A 2NS
T: 020 3051 1077
E: enquiries@icw.uk.com
W: www.instituteforcollaborativeworking.com
Institute of Acoustics (IOA) Silbury Court, 406 Silbury Boulevard Milton Keynes MK9 2AF
T: 0300 999 9675
E: ioa@ioa.org.uk
W: www.ioa.org.uk
Institute of Asset Management (IAM) St Brandons House, 29 Great George Street Avon Bristol BS1 5QT
T: 0845 456 0565
E: office@theiam.org
W: www.theiam.org
Institute of Cast Metals Engineers (ICME)
National Foundry Centre, Tipton Road
Tipton West Midlands DY4 7UW
T: 0121 752 1810
E: info@icme.org.uk
W: www.icme.org.uk
Institute of Construction Management (ICM) 24 Landport Terrace, Portsmouth Hampshire PO1 2RG
T: 07958 959133
E: info@the-icm.co.uk
W: www.the-icm.co.uk
Institute of Corporate Responsibility and Sustainability (ICRS) 21 Holborn Viaduct London EC1A 2DY
E: info@icrs.info
W: www.icrs.info
Institute of Corrosion (ICorr)
5 St. Peters Gardens, Marefair Northampton NN1 1SX
T: 01604 438222
E: admin@icorr.org
W: www.icorr.org
Institute of Customer Service Bridge House, 4 Borough High Street London SE1 9QQ
T: 020 7260 2620
E: info@instituteofcustomerservice.com
W: www.instituteofcustomerservice.com
Institute of Directors (IoD)
116 Pall Mall London SW1Y 5ED
T: 020 7766 8888
E: membership@iod.com
W: www.iod.com
Institute of Environmental Management and Assessment (IEMA)
Saracen House, Crusader Road City Office Park Lincoln LN6 7AS
T: 01522 540069
E: info@iema.net
W: www.iema.net
Institute of Materials Finishing (IMF) Exeter House, 48 Holloway Head Birmingham B1 1NQ
T: 078 763 47787
E: info@materialsfinishing.org
W: www.materialsfinishing.org
Institute of Materials, Minerals and Mining (IOM3)
297 Euston Road London NW1 3AD
T: 020 7451 7300
E: membership@iom3.org
W: www.iom3.org
Institute of Rail Welding (IoRW)
Granta Park, Great Abington Cambridge CB21 6AL
T: 01223 899567
E: iorw@twi.co.uk
W: www.iorw.org
Institute of Railway Research
Queensgate Huddersfield HD1 3DH
T: 01484 473572
E: irr.info@hud.ac.uk
W: research.hud.ac.uk/institutes-centres/irr/
Institute of Railway Research – University of Huddersfield Queensgate, Huddersfield HD1 3DH
T: 07849 896270
E: r.carr@hud.ac.uk
W: research.hud.ac.uk/institutes-centres/irr/
Institute of Risk Management (IRM) 2nd Floor, Sackville House London EC3M 6BN
T: 020 7709 9808
E: enquiries@theirm.org
W: www.theirm.org
Institute of Spring Technology (IST) Henry Street Sheffield S3 7EQ
T: 0114 276 0771
E: ist@ist.org.uk
W: www.ist.org.uk
Institution of Civil Engineers (ICE) One Great George Street, Westminster London SW1P 3AA
T: 020 7665 2012
E: membership@ice.org.uk
W: www.ice.org.uk
Institution of Engineering and Technology (IET) Futures Place, Kingsway Stevenage Hertfordshire SG1 2AY
T: 01438 313311
E: postmaster@theiet.org
W: www.theiet.org
Institution of Engineering Designers (IED) Courtleigh, Wiltshire BA13 3TA T: 01373 822801
E: ied@ied.org.uk
W: www.ied.org.uk
Institution of Environmental Sciences (IES) First Floor, 6-8 Great Eastern St London EC2A 3NT
T: 020 3862 7484
E: info@the-ies.org
W: www.the-ies.org
Institution of Fire Engineers (IFE) 64-66 Cygnet Court, Timothy’s Bridge Road Stratford CV37 9NW
T: 01789 261463
E: info@ife.org.uk
W: www.ife.org.uk
Institution of Mechanical Engineers (IMechE) 1 Birdcage Walk, London SW1H 9JJ
T: 020 7222 7899
E: enquiries@imeche.org
W: www.imeche.org
Institution of Occupational Safety and Health (IOSH)
The Grange, Highfield Drive Wigston Leicester LE18 1NN
T: 0116 257 3100
E: reception@iosh.com
W: www.iosh.com
Institution of Railway Signal Engineers (IRSE) 4th Floor, 1 Birdcage Walk Westminster London SW1H 9JJ
T: 020 7808 1180
E: hq@irse.org
W: www.irse.org
Institution of Structural Engineers (IStructE) International HQ, 47-58 Bastwick Street London EC1V 3PS
T: 020 7235 4535
E: pr@istructe.org
W: www.istructe.org
Instrumentel’s condition-based monitoring rail products are being increasingly adopted by rail operators and maintainers to deliver efficiency and maintenance savings. From train door diagnostics to energy meters and HVAC system monitors, Instrumentel products provide rapidly retrofittable, cost effective solutions for improved asset monitoring in the rail industry.
Instrumentel Ltd
Unit 6, Landmark Court
Leeds LS11 8JT
T: 0113 831 4725
E: enquiries@instrumentel.com
W: www.instrumentel.com
Insync Corporate Healthcare Ltd
Excalibur Drive, Thornhill
Cardiff CF14 9BB
T: 029 2076 1550
E: enquiries@insynchealth.co.uk
W: www.insynchealth.com
Intec (UK) Ltd
Brunel House, 9 Penrod Way
Heysham Lancashire LA3 2UZ
T: 01524 865555
E: intec@velosi-intec.com
W: www.velosi-intec.com
Integrated Utility Services Ltd
Unit 8, Brindley Way
41 Ind Estate Wakefield WF2 0XQ
T: 0800 073 7373
E: enquiries@ius.co.uk
W: www.ius.co.uk
Integrated Water Services Ltd Green Lane Walsall WS2 7PD
T: 0345 600 6028
E: contact@integrated-water.co.uk
W: www.integrated-water.co.uk
Intelligent Data Collection Ltd
Unit 2 Cordwalls House, Cordwalls Street Maidenhead Berkshire SL6 9SL
T: 0845 003 8747
E: info@intelligent-data-collection.com
W: www.intelligentdatacollection.com
Intelligent Locking Systems Bordesley Hall, Alvechurch Birmingham B48 7QA
T: 01527 68885
E: info@ilslocks.co.uk
W: www.ilslocks.co.uk
Intelligent Transport Systems UK (ITS UK) Suite 107, Tower Bridge Bus. Ctr
46-48 East Smithfield St E1W 1AW
T: 020 7709 3003
E: contact@its-uk.org
W: www.its-uk.org.
Interclamp – Handrail Systems
Meyrick Owen Way, The Dockyard Pembroke Dock Pembrokeshire SA72 6WS
T: 01646 683584
E: info@interclamp.com
W: www.interclamp.com
Interflon UK Ltd Crofton House, Crofton Road Stockton on Tees Cleveland TS18 2QZ
T: 01642 615002
E: sales@interflon.co.uk
W: www.interflon.com
Intermodality Ltd
Owlsbrook House, New Pond Lane Heathfield East Sussex TN21 0NA
T: 0845 130 4388
E: info@intermodality.com
W: www.intermodality.com
International Air Rail Organisation (IARO)
Suite 3, Charter House
26 Claremont Road Surbiton KT6 4QZ
T: 020 8390 0000
E: patrick.hicks@iaro.com
W: www.iaro.com
International Geosynthetic Society (IGS UK)
Sir Henry Doulton House, Forge Lane
Etruria Stoke on Trent ST1 5BD
T: 01782 276700
E: committee@igs-uk.org
W: www.igs-uk.org
International Glassfibre Reinforced Concrete Association (GRCA) PO Box 1454
Northampton NN2 1DZ
T: 0330 111 4722
E: info@grca.online W: www.grca.online
International Institute of Obsolescence (IIOM)
Unit 3 Curo Park, Frogmore St Albans Hertfordshire AL2 2DD
T: 01727 876029
E: admin@theiiom.org
W: www.theiiom.org
International Institute of Risk and Safety Management (IIRSM)
77 Fulham Palace Road
London W6 8JA
T: 020 8741 9100
E: info@iirsm.org W: www.iirsm.org
International Liaison Group of Government Railway Inspectorates (ILGGRI) 25 Cabot Square
London E14 4QZ
T: 020 7282 2000
E: ilggri@orr.gsi.gov.uk W: www.ilggri.org
International Transport Workers’ Federation (ITF)
49-60 Borough Road London SE1 1DR
T: 020 7403 2733
E: mail@itf.org.uk
W: www.itfglobal.org
Intersect Recruitment
Business Design Centre, 52 Upper Street
London N1 0QH
T: 020 7812 0632
E: info@intersectglobal.co.uk
W: www.intersectglobal.co.uk
Interserve Plc
Interserve House, Ruscombe Park Twyford Berkshire RG10 9JU
T: 0118 932 0123
E: info@interserve.com
W: www.interserve.com
Intertek – Production and Integrity Assurance
Unit 12-15, Longwood Road
Manchester M17 1P2
T: 0161 875 7600
E: production.assurance@intertek.com
W: www.intertek.com
Intertek NDT & Materials Testing
10a Victory Park, Victory Road
Derby DE24 8ZF
T: 01332 275700
E: ndt@intertek.com
W: www.intertek.com
Intertrain UK Ltd
Balby Court, Balby Carr Bank
Carr Hill Doncaster DN4 8DE
T: 01302 815530
E: sales@intertrain.biz
W: www.railway-training-courses.com
Intoware Limited
Ingenuity Centre, Jubilee Campus Nottingham NG7 2TU
T: 01159 778 969
E: hello@intoware.com
W: www.inotware.com
Intuitive Interm & Executive Search Ltd
T: 07801 995094
E: say-hello@intuitiverecruitment.com
W: www.intuitiverecruitment.com
Invertec Interiors Ltd
Unit 1-6 Trimdon Court, Trimdon Grange Ind Est
Trimdon Grange County Durham TS29 6PE
T: 01429 882210
E: info@invertec.co.uk
W: www.invertec.co.uk
Invictus Resource Ltd
Radway Green Bus Centre, Building 01
Office 45-47 Crewe CW2 5PR
T: 01270 875393
E: info@invictusresource.co.uk
W: www.invictusresource.co.uk
IOM Consulting Ltd
Research Avenue North, Riccarton Edinburgh Midlothian EH14 4AP
T: 0131 449 8000
E: info@iom-world.org
W: www.iom-world.org
IPEX Consulting Limited
Liberty House, 222 Regent Street
London W1B 5TR
T: 020 3642 5893
E: info@ipexconsulting.com
W: www.ipexconsulting.com
Iprosurv Technology Centre
South Yorkshire S60 5WG
T: 0114 4055 007
E: info@iprosurv.com
W: www.iprosurv.com
IPS Communication Ltd
53 Ullswater Crescent, Coulsdon Surrey CR5 2HR
T: 020 8655 6060
E: sales@ips-ltd.co.uk
W: www.ips-ltd.co.uk
IQM Software
U/2 Hove Tech Centre, St Joseph’s Close
Hove East Sussex BN3 7ES
T: 01293 226136
E: support@iqmsoftware.co.uk
W: www.iqmsoftware.co.ik
IQPC Ltd 129 Wilton Road
London SW1V 1JZ
T: 020 7368 9300
E: enquire@iqpc.co.uk
W: www.iqpc.co.uk
IRITS Events Ltd
Kemp House, 152 City Road
London EC1V 2NX
T: 020 7112 5357
E: hello@irits.org
W: www.irits.org
Ironside Farrar
111 McDonald Road
Edinburgh EH7 4NW
T: 0131 550 6500
E: mail@ironsidefarrar.com
W: www.ironsidefarrar.com
Ironsides Lubricants
Shield Street, Stockport Cheshire SK3 0DS
T: 0161 477 5858
E: enquiries@ironsidelubricants.co.uk
W: www.ironsideslubricants.co.uk
IRS Surfacing Technologies Ltd
Unit 8, Abbey Lane Ind Estate
Burscough Lancashire L40 7SR
T: 01704 89633
E: info@irsltd.co.uk
W: www.irsltd.co.uk
Irvine-Whitlock
Brickstone House, Priory Business Park Bedford Mk44 3JW
T: 01234 832300
E: enquiries@irvine-whitlock.co.uk
W: www.irvine-whitlock.co.uk
IS Consultancy Ltd
Skinner House, 35-40 Bell Street
Reigate Surrey RH2 7BA
T: 01737 228990
E: isc@isconsult.net
W: www.isconsult.net
IS-Rayfast
2 Lydiard Fields, Swindon Wiltshire SN5 8UB
T: 01793 616700
E: uksales@is-rayfast.com
W: www.is-rayfast.com
ISC Best Practice Consultancy
Market Hall Offices, Market Street Okehampton Devon EX20 1HN
T: 01837 54555
E: isc@ischq.com
W: www.isc-bestpracticeconsultancy.co.uk
Ischebeck Titan Ltd
John Dean House, Wellington Road Burton Upon Trent DE14 2TG
T: 01283 515677
E: sales@ischebeck-titan.co.uk
W: www.ischebeck-titan.co.uk
ISS Labour Ltd
Unit 12, The Albion, Brunel Avenue Salford Manchester M5 4BE
T: 0161 743 4480
E: info@isslabour.co.uk
W: www.isslabour.co.uk
IST Power Products Ltd
64-66 Percy Road, Leicester LE2 8FN
T: 0116 283 3321
E: sales@istpower.com
W: www.istpower.com
ISVR Consulting – University of Southampton University Road, Southampton SO17 1BJ
T: 023 8059 2162
E: rail@isvr.co.uk
W: www.isvr.co.uk
ITAL Group Limited
Unit 2/3 Ridgeway, Office Park Bedford Road Peterfield GU23 3QF
T: 0330 022 5022
E: sales@ital-uk.com
W: www.ital-uk.com
ITE Group plc
The Studios, 2 Kingdom Street London W2 6JG
T: 020 3545 9400
E: enquiry@ite-exhibitions.com
W: www.ite-exhibitions.com
ITSO Ltd
Aurora House, Deltic Avenue Rooksley Milton Keynes MK13 8LW
T: 01908 255455
E: info@itso.org.uk
W: www.itso.org.uk
IXC UK Ltd
Innov Birmingham Campus, Faraday Wharf Holt Street Birmingham B7 4BB
T: 0121 250 5717
E: connect@ixc-uk.com
W: www.ixc-uk.com
IXYS UK Westcode Ltd
Langley Park Way, Langley Park Chippenham Wiltshire SN15 1GE
T: 01249 455500
E: sales@ixysuk.com
W: www.ixysuk.com
J Lewis (Auto Electrical) Ltd
21 Impresa Park, Pindar Road Hoddesdon Hertfordshire EN11 0DL
T: 01992 469781
E: info@jlae.co.uk
W: www.jlae.co.uk
J Morgan Consulting Ltd
6 Linnet Drive, Stowmarket Suffolk IP14 5UB
T: 07941 160470
E: jem@jmclimited.com
W: www.jmclimited.com
Since 1984, we have supplied into a wide range of markets, including Rail & Mass Transit, where we provide a wide range of unique elastomer materials & components for both rolling stock and trackside applications, tested and approved to EN45545-2 plus many other certifications. Visit our website or contact us.
J-Flex Rubber Products
Units 1 & 2, London Rd Bus. Park Retford Nottinghamshire DN22 6HG
T: 01777 712400
E: sales@j-flex.co.uk
W: www.j-flex.com
J. Murphy & Sons Ltd
Hiview House, Highgate Road London NW5 1TN
T: 020 7267 4366
E: mail@murphygroup.co.uk
W: www.murphygroup.com
Jabero Consulting
22 Church Road, Tunbridge Wells TN1 1JP
T: 01892 535730
E: info@jaberoconsulting.com
W: www.jaberoconsulting.com
Jacobs UK Ltd 1180 Eskdale Road, Winnersh Berkshire RG41 5TU
T: 0118 946 7000
E: info@jacobs.com
W: www.jacobs.com
Jafco Tools Ltd
Access House, Great Western Street Wednesbury West Midlands WS10 7LE
T: 0121 556 7700
E: sales@jafcotools.com
W: www.jafcotools.com
Jaltek is a leading AS9100 and ISO 13485 accredited UK electronics design and manufacturing company providing solutions for a range of multinational and start-up companies working in a wide variety of industries. Our services include conceptual design, PCBA layout, fast turnaround NPI, manufacture and test and final product assembly, offering a single service or complete solution.
Jaltek Systems Unit 13 Dencora Way, Sundon Park Luton Bedfordshire LU3 3HP
T: 01582 578170
E: info@jaltek.com
W: www.jaltek.com
James Fisher Testing Services Unit 10, City Business Park Easton Road Bristol BS5 0SP
T: 01761 414939
E: enquiries@jftesting-services.com
W: www.jftesting-services.com
James Troop & Co Ltd
4 Davy Road, Astmoor Ind Estate Runcorn Cheshire WA7 1PZ
T: 01928 566170
E: sales@jamestroop.co.uk
W: www.jamestroop.co.uk
James Walker Devol
U2 Faulds Park Ind Est, Faulds Park Road Gourock Scotland PA19 1FB
T: 01475 657360
E: customerservice.devol@jameswalker.biz
W: www.devol.com
Janson Bridging (UK) Ltd
Unit 1, The Ridgeway Bus Park Bedford MK44 3DE
T: 01767 641469
E: info@jansonbridging.co.uk
W: www.jansonbridging.co.uk
Japanese Knotweed Group Ltd
Rose Cottage, Birchwood Lane Caterham CR3 5QD
T: 01883 336602
E: simon@japaneseknotweedgroup.co.uk
W: www.japaneseknotweedgroup.co.uk
JB Corrie & Co Ltd Frenchmans Road, Petersfield Hampshire GU32 3AP
T: 01730 237100
E: sales@jbcorie.co.uk
W: www.jbcorie.co.uk
JCK Ltd Pippin Grove, 628 London Road Colnbrook SL3 8QH
T: 0207 100 3783
E: info@jckltd.com
W: www.jckltd.com
JD Neuhaus Ltd
Unit 9 & 10, Kirkton Avenue
Pitmedden Road Dyce Aberdeen AB21 OBF
T: 01224 722751
E: info@jdneuhaus.co.uk
W: www.jdngroup.com
JDA Software (Berkshire Office)
3 The Arena, Downshire Way
Bracknell Berkshire RG12 1PU
T: 01344 354500
E: info@jda.com
W: www.jda.com
Jeep Rail Ltd
Room 211, Digital Media Centre
County Way Barnsley S70 2JW
T: 01226 720720
E: enquiries@jeeprail.com
W: www.jeeprail.com
Jenkins & Potter
1st Floor, 67-74 Saffron Hill
London EC1N 8QX
T: 020 7242 8711
E: london@jenkinspotter.co.uk
W: www.jenkinspotter.co.uk
Jermyn Street Design
34 Galena Road, Hammersmith London W6 0LT
T: 020 8563 5000
E: sales@jsd.co.uk
W: www.jsd.co.uk
Jestico + Whiles Sutton Yard, 65 Goswell Road London EC1V 7EN
T: 020 7380 0382
E: info@jesticowhiles.com
W: www.jesticowhiles.com
Jewers Doors Limited
1 Juno Place, Stratton Business Park
Biggleswade Bedfordshire SG18 8XP
T: 01767 317090
E: postroom@jewersdoors.co.uk
W: www.jewersdoors.co.uk
JFC Civils UK
Hardwick Road, Astmoor Ind Estate Runcorn Cheshire WA7 1PH
T: 01928 583391
E: sales@jfccivils.com
W: www.jfccivils.com
JFM Associates
The Old Fire Station, Alexander Road Birmingham B27 6ER
T: 0121 706 9485
E: recruit@jfmassociates.co.uk
W: www.jfmassociates.co.uk
Jigsaw M2M Limited
Clayton Green Bus Pk, Library Road
Clayton-le-Woods Chorley PR6 7EN
T: 01942 616 278
E: info@jigsawfuel.com
W: www.jigsawfuel.com
JMC Recruitment Solutions Ltd
First Floor, Unit 1, Exeter Int Office Park
Exeter Devon EX5 2HL
T: 01392 268310
E: info@jmc-groupltd.co.uk
W: www.jmc-groupltd.co.uk
JMD Developments (UK) Ltd
Audby Grange, Audby Lane Wetherby LS22 7FD
T: 01937 587777
E: enquiries@jmddevelopments.co.uk
W: www.jmddevelopments.co.uk
JMD Railtech Limited (UK Office)
JMDR Rail Tech Centre, Kettlestring Lane
Clifton Moor York YO30 4XF
T: 01904 477661
E: mail@jmdrailtech.com
W: www.jmdr.com
JNP Group
Woodvale House, Woodvale Road
Brighouse West Yorkshire HD6 4AB
T: 01484 400691
E: brighouse@jnpgroup.co.uk
W: www.jnpgroup.co.uk
We insure the Railway Supply Chain. We are RISQS accredited and the market leader by a huge margin with over 650 railway clients. We are the rail experts on hand to support with insurance solutions, free railway contractual liability advice and commercial support through our rail events.
Call Keven Parker Head of Rail on 07816 283 949.
JOBSON JAMES RAIL – INSURANCE
30 St Paul Square
Birmingham B3 1QZ
T: 07816 283949
E: info@jjrail.co.uk
W: www.jjrail.co.uk
John Anthony Signs Ltd
Claydons Lane, Rayleigh Essex SS6 7UU
T: 01268 777333
E: contact@johnanthonysigns.com
W: www.johnanthonysigns.com
John Bell Pipeline Co Ltd Units 3-4 Camiestone Rd, Thainstone Ind Estate Inverurie Aberdeenshire AB51 5GT
T: 01224 714514
E: sales@jbpipeline.co.uk
W: www.jbpipeline.co.uk
John G Russell (Transport) Ltd Deanside Road, Hillington Glasgow G52 4XB
T: 0141 810 8200
E: sales@johngrussell.co.uk
W: www.johngrussell.co.uk
John Laing Group PLC 1 Kingsway, London WC2B 6AN
T: 020 7901 3200
E: enquiries@laing.com
W: www.laing.com
John McAslan & Partners
7-9 William Road London NW1 3ER
T: 020 7313 6000
E: mailbox@mcaslan.co.uk
W: www.mcaslan.co.uk
Johnson Security
Orchard Ind Estate, Toddington Gloucestershire GL54 4EB
T: 01242 621362
E: sales@johnson-security.co.uk
W: www.johnson-security.co.uk
Johnson Surfacing Limited
Sebastian House, 204 Ashgate Road Chesterfield Derbyshire S40 4AL
T: 01246 231871
E: sales@johnsonsurfacing.co.uk
W: www.johnsonsurfacing.co.uk
Jointing Technologies
Bellsize Close, Norton Canes Staffordshire WS11 9TQ
T: 01543 450555
E: enquiries@jointingtech.co.uk
W: www.jointingtech.co.uk
Jonathan Lee Recruitment
The Maltings, Mount Road Stourbridge West Midlands DY8 1HZ
T: 01384 397555
E: consult@jonlee.co.uk
W: www.jonlee.co.uk
Jonathan Roberts Consulting (JRC) Bridge House, Wanstrow Somerset BA4 4TE
T: 07545 641204
E: jr@jrc.org.uk
W: www.jrc.org.uk
Joseph Ash Galvanizing: your next stop for metal finishing services.
With eight strategically located plants and a large transport fleet, we offer technical expertise, premium quality, and a first-class service when galvanizing, shot blasting and powder coating steel for the UK’s railways. From station canopies to platforms, and lighting columns to bridges, we’re experts in treating all types of railway steel fabrications.
Joseph Ash Galvanizing
The Alcora Building 2, Mucklow Hill Halesowen West Midlands B62 8DG
T: 0121 504 2573
E: sales@josephash.co.uk
W: www.josephash.co.uk
Jotun Paints (Europe) Ltd Stather Road, Flixborough Scunthorpe North Lincolnshire DN15 8RR
T: 01724 400000
E: enquiries@jotun.co.uk
W: www.jotun.co.uk
Journeycall – Part of the ESP Group
3 James Chalmers Road, Arbroath Enterprise Pk Kirkton Ind Estate Arbroath DD11 3QR
T: 01241 730300
E: businessdev@journeycall.com
W: www.the-espgroup.com
JPCS Limited Rejuvo House, The Sidings Hampton Heath Malpas Cheshire SY14 8LU
T: 01948 820696
E: info@jpcs.co.uk
W: www.jpcs.co.uk
We provide services ranging from simple coaching and mentorship to complete business transformation. Covering strategy development, new product and service development, market analysis and intelligence, pipeline creation and company profile development. We will work with you to develop business and will unpick any issue preventing you from succeeding.
JPL Diversified Ltd
3 Heritage Mews, Elsecar Barnsley South Yorkshire S744 8EJ
T: 07935 788604
E: john@jpldiversified.co.uk
W: www.jpldiversified.co.uk
Transmission Dynamics is a multi award winning, global Internet of Things solutions provider offering remote condition monitoring solutions to global asset owners and operators. Their Rail sector portfolio offers market leading solutions via their ‘trains with brains’ portfolio, which delivers increased reliability and safety while decreasing delays and associated costs.
JR Dynamics Ltd 1 Innovation Way, Northumberland Business Park Cramlington NE23 7FP
T: 0191 580 0058
E: wsupport@jrdltd.co.uk
W: www.jrdltd.com
JRE Precision Engineering Ltd 18 Bakewell Road, Loughborough Leicestershire LE11 5QY
T: 01509 610580
E: info@jreuk.com
W: www.jreuk.com
JSD Research & Development
14-15 Globe Park, Mossbridge Road Rochdale OL16 5EB
T: 01706 646959
E: info@jsdrail.com
W: www.jsdrail.com
JSM Group Ltd
Sterling House, Mutton Lane Potters Bar Hertfordshire EN6 3AR
T: 0800 035 0708
E: enquiries@jsmgroup.com
W: www.jsmgroup.com
JSP Limited Worsham Mill, Minster Lovell Oxford OX29 0TA
T: 01993 826050
E: uksales@jsp.co.uk
W: www.jspsafety.com
Judge 3D
Oakpark Business Park, Alington Road Little Barford St Neots PE19 6WA
T: 01480 211080
E: info@judge3d.com
W: www.judge3d.com
Jumo Instrument Co Ltd
Jumo House, Temple Bank Riverway Harlow Essex CM20 2DY
T: 01279 635533
E: info.uk@jumo.net
W: www.jumo.co.uk
Jumpstart 6 Atholl Crescent, Edinburgh Scotland EH3 8HA
T: 0333 305 9184
E: helpinghand@jumpstartuk.co.uk
W: www.jumpstartuk.co.uk
Jungle Green MRC Ltd
79 Coldharbour Road, Westbury Park Bristol BS6 7LU
T: 0117 914 4921
W: www.junglegreenmrc.co.uk
JVR Consultancy Ltd
635 Bath Road, Slough Berkshire SL1 6AE
T: 01628 56 52 56
E: info@jvrconsultancy.com
W: www.jvrconsultancy.com
JWG Survey & Engineering Ltd
46 Hamilton Square, Birkenhead CH41 5AR
T: 0151 342 1671
E: admin@jwg.org.uk
W: www.jwg.org.uk
K&M McLoughlin Decorating Ltd 2nd Floor, 94 Silver Street Enfield EN1 3TW
T: 020 8370 7910
E: info@kmdecorating.co.uk
W: www.kmdecorating.co.uk
Kadfire
Unit 1, Little Forge Road, Park Farm North
Redditch Worcestershire B98 7SF
T: 01527 595880
E: production@kadfire.com
W: www.kadfire.com
KAEFER Ltd
Riverside House, Rolling Mill Road
Viking Ind Est Jarrow NE32 3DP
T: 01623 781200
E: infouk@kaefercd.com
W: www.kaeferltd.co.uk
Kaler Engineering Ltd
Kaler House, George Summers Close Rochester Kent ME2 4NS
T: 01634 723565
E: enquiry@kaler-group.co.uk
W: www.kaler-group.co.uk
Kaymac Marine & Civil Engineering Ltd
Osprey Business Park, Byng Street Landore Swansea SA1 2NR
T: 01792 301818
E: enquiries@kaymacltd.co.uk
W: www.kaymacmarine.co.uk
KBH On-Train Media Limited
Union House, 182-194 Union Street London SE1 0LH
T: 020 7207 5333
E: sales@kbhontrainmedia.co.uk
W: www.kbhontrainmedia.co.uk
KEC Limited
Orpheus House, Calleva Park Aldermaston Berkshire RG7 8TA
T: 0118 981 1571
E: sales@kec.co.uk
W: www.kec.co.uk
Kee Safety
Cradley Business Park, Overend Road Cradley Heath West Midlands B64 7DW
T: 01384 632188
E: sales@keesafety.com
W: www.keesafety.co.uk
Kee Systems supplies and installs handrails, guardrails, access platforms and walkways constructed from Kee Klamp@ and Kee Access@ fittings. We have provided safety solutions for the industry on many projects including DDA compliant handrails within stations, safety barriers for working at height on viaducts and bridges and trackside safety fences.
Kee Systems
Thornsett Works, Thornsett Road Wandsworth London SW18 4EW
T: 020 8874 6566
E: sales@keesystems.com
W: www.keesystems.com
Keller Ltd
Oxford Road, Ryton on Dunsmore
Coventry CV8 3EG
T: 024 7651 1266
E: foundations@keller.com
W: www.keller.co.uk
Kelly Rail
Kelly House, Fourth Way Wembley Middlesex HA9 0LH
T: 020 8424 0909
E: info@kelly.co.uk
W: www.kelly.co.uk
Kelly Services UK Ltd
3rd Floor, 100 Cannon Street
London EC4N 6EU
T: 020 3040 1900
E: londoncity@kellyservices.co.uk
W: www.kellyservices.co.uk
Keltbray Group St Andrew’s House, Portsmouth Road
Esher Surrey KT10 9TA
T: 020 7643 1000
E: info@keltbray.com
W: www.keltbray.com
Kemada Limited Protec House, Cropton Road Ilkeston Derbyshire DE7 4BG
T: 01332 325050
E: sales@kemada.co.uk
W: www.kemada.co.uk
Kemp Recruitment Ltd
Third Floor, Pine Court, Gervis Road Bournemouth Dorset BH1 3DH
T: 0330 440 2323
E: info@kemprecruitment.com
W: www.kemprecruitment.com
Kennedy Pearce Consulting Ltd 1st Floor, 50 St Mary Axe
London EC3A 8FR
T: 020 3846 0750
E: london@kennedypearce.com
W: www.kennedypearce.com
Kennedys Law LLP 25 Fenchurch Avenue
London EC3M 5AD
T: 020 7667 9667
E: enquiries@kennedyslaw.com
W: www.kennedyslaw.com
Kent & East Sussex Railway – Heritage Railway
Tenterden Town Station, Station Road
Tenterden Kent TN30 6HE
T: 01580 765155
E: enquiries@kesr.org.uk
W: www.kesr.org.uk
Kent Modular Electronics Ltd (KME)
621 Maidstone Road, Rochester
Kent ME1 3QJ
T: 01634 830123
E: sales@kme.co.uk
W: www.kme.co.uk
Kent PHK Ltd
Kent House, Lower Oakham Way
Mansfield Nottinghamshire NG18 5BY
T: 01623 421202
E: enquiries@kentphk.co.uk
W: www.kentgroup.com
Keolis (UK) Ltd
Evergreen House North, 160 Euston Road London NW1 2DX
T: 020 3691 1715
E: comms@keolis.co.uk
W: www.keolis.com
KeolisAmey Docklands Ltd
Castor Lane, Poplar London E14 0BL
T: 020 7363 9500
E: reception@keolisameydlr.co.uk
W: www.keolisameydocklands.info
Kernow Model Rail Centre (KMRC)
98a Trelowarren Street, Camborne Cornwall TR14 8AN
T: 01209 714099
E: sales@kernowmodelrailcentre.com
W: www.kernowmodelrailcentre.com
KeTech Systems Ltd
Glaisdale Drive East, Bilborough Nottingham NG8 4GU
T: 0330 057 8450
E: info@ketech.com
W: www.ketech.com
Key Fasteners
Unit A3 Lakeside Park, Neptune Close Rochester Kent ME2 4LT
T: 01732 820101
E: enquiries@keyfasteners.co.uk
W: www.keyfasteners.co.uk
Keyline Builders Merchants Ltd
Unit S3, 8 Strathkelvin Place Kirkintiloch Glasgow G66 1XT
T: 0141 777 8979
E: rail@keyline.co.uk
W: www.keyline.co.uk
Keyline Rail
Keyline National, Rail Office Grove Road Northfleet Kent DA11 9AX
T: 0344 892 2677
E: rail@keyline.co.uk
W: www.keyline.co.uk
Keystone Environmental Ltd
The Old Barn, Park Farm Buildings Tetbury Gloucestershire GL8 8TT
T: 01666 503687
E: info@keyenv.co.uk
W: www.keyenv.co.uk
Keystone Training Ltd
Front Suite, 1st Floor, Charles House
149 Gt Charles St Birmingham B3 3HT
T: 07939 997954
E: esther.patrick@keystonetrainingltd.co.uk
W: www.keystonetrainingltd.co.uk
For over 25 years, Keytracker has dedicated their time and expertise to crafting tailored solutions for many businesses including those within the railway operations. The innovation of their mechanical systems, key control software, electronic cabinets, and intelligent lockers, has allowed railway organisations to manage and monitor the usage of their keys and assets while also enforcing accountability among their staff members.
Keytracker – Head Office & Factory
Station Road, Rowley Regis
West Midlands B65 0JY
T: 0121 559 9000
E: sales@keytracker.com
W: www.keytracker.com
KGJ Price Rail Contractors Ltd
Pant Glas Ind Estate, Bedwas
Caerphilly Wales CF83 8DR
T: 029 2088 9220
E: enquiries@kgjprice.co.uk
W: www.kgjprice.co.uk
KH Engineering Services Ltd
4 Crayside, Five Arches Bus Park
Maidstone Road Sidcup Kent DA14 5AG
T: 020 8309 3100
E: enquiries@khengineeringservices.co.uk
W: www.khengineeringservices.co.uk
Kiepe Electric UK Ltd
2 Priestley Wharf, Holt Street
Aston Birmingham B7 4BN
T: 0121 359 7777
E: enquiries@kiepe-electric.co.uk
W: www.kiepe-electric.co.uk
Kilborn Consulting Limited is an independent railway engineering consultancy and design business, specialising in the design of new and altered signalling and telecoms systems for UK and Ireland railway infrastructure. Our core services cover technical advice and consultancy, and concept, outline and detailed design for main line and private railways.
Kilborn Consulting Limited
6th Floor, South Street, 12 Sheep Street
Wellingborough Northamptonshire NN8 1BL
T: 01933 279909
E: mail@kilbornconsulting.co.uk
W: www.kilbornconsulting.co.uk
Kilfrost is a supplier to the rail networks all over The UK and Europe. Our Kilfrost Rail, TDIce and TDIce Plus are used to di-ice and prevent icing on Rails, Rolling Stock, Third Rail and Pantograph lines. Our products are also used to clear Ballast piles.
Kilfrost Ltd
Albion Works, Haltwhistle
Northumberland NE49 0HJ
T: 01434 320332
E: info@kilfrost.com
W: www.kilfrost.com
Kilnbridge Construction Services Ltd
McDermott House, Cody Rosd Business Park South Crescent London E16 4TL
T: 020 7511 1888
E: office@kilnbridge.com
W: www.kilnbridge.com
King Rail
Riverside, Market Harborough
Leicestershire LE16 7PX
T: 01858 467361
E: info@king.uk.com
W: www.king.uk.com
King Vehicle Engineering Ltd
Riverside, Market Harborough
Leicestershire LE16 7PX
T: 01858 467361
E: info@kingtrailers.co.uk
W: www.king.uk.com
King’s College London Strand London WC2R 2LS
T: 020 7836 5454
E: ucas.enquiries@kcl.ac.uk
W: www.kcl.ac.uk
For over 35 years’ Kingfisher have a been creating quality lighting solutions. Utilising the latest technologies including GRP and reflector-based systems, we manufacture high performance, low glare and sustainable exterior solutions that stand the test of time. Explore our dedicated Rail range, with a variety of specially developed luminaires and accessories to perfectly enhance any project.
Kingfisher Lighting
Ratcher Way, Forest Town Mansfield Nottinghamshire NG19 0FS
T: 01623 415900
E: sales@kingfisherlighting.com
W: www.kingfisherlighting.com
Kingfisher Productions PO Box 110, Cullompton
EX15 9AZ
T: 0333 121 0707
E: sales@railwayvideo.com
W: www.railwayvideo.com
Kingsley Plastics Limited
The Airfield, Winkleigh Devon EX19 8DW
T: 01837 83154
E: sales@kingsleyplastics.co.uk
W: www.kingsleyplastics.co.uk
With origins dating back to 1919 Kingston Engineering are one of the UK’s leading specialist manufacturers and producers of bespoke Power Screws.
We offer a variety of specialised engineering services based on using materials and specifications to suit customer’s exact needs along with accreditation to ISO9001-2015.
Kingston Engineering Co (Hull) Ltd
Pennington Street, Hull East Yorkshire HU8 7LD
T: 01482 325676
E: sales@kingston-engineering.co.uk
W: www.kingston-engineering.co.uk
Kitchen Civils Ltd
Unit 2-4 Jet Park, Newport East Yorkshire HU15 2PR
T: 01430 410044
E: info@kitchencivils.co.uk
W: www.kitchencivils.co.uk
Kite Group Ltd
19 Bankhead Drive, Edinburgh EH11 4DW
T: 0131 333 4413
E: isla.mcgill@kirtegroupltd.com
W: www.kitegroupltd.com
We make the world of infrastructure a safer place. We keep your network moving. KITE Projects are an expert in the design and supply of handrail and access systems, and complex engineering solutions for infrastructure projects. We inspire and are inspired by safe and sustainable engineering.
KITE Projects
Littleton Lane, Nr Sparsholt
Winchester Hampshire SO21 2LS
T: 01962 886290
E: sales@kite-projects.co.uk
W: www.kite-projects.co.uk
KJ Bownes & Sons
2 Bungalow, Wallingwells Worksop Nottinghamshire S81 8DA
T: 01909 731647
E: info@kjbownes.com
W: www.kjbownes.co.uk
KJ Hall Surveyors Ltd
22 Bower Hinton, Martock
Somerset TA12 6JY
T: 01935 823423
E: admin@kjhsurvey.co.uk
W: www.kjhsurvey.co.uk
Kleeneze-Koti is the UK’s leading brush strip manufacture, providing sealing, cleaning, safety and rodent control solutions across the rail industry. Whether you need standard Superseal or Rodentbrush for next day delivery, or a custom made solution, our friendly and efficient customer service team will be happy to help.
Kleeneze – Koti Ltd
Ansteys Road, Hanham Bristol BS15 3SS
T: 0117 958 2450
E: sales@ksl.uk.com
W: www.kleenezekoti.co.uk
Klingspor Abrasives Limited
Dukeries Bus Centre, 31-33 Retford Road Worksop Nottinghamshire S80 2PU
T: 01909 712310
E: sales@klingspor.co.uk
W: www.klingspor.co.uk
Kluber Lubrication
Unit 10 Longbow Close, Bradley Huddersfield West Yorkshire HD2 1GQ
T: 01422 205115
E: sales@uk.klueber.com
W: www.klueber.com
KMC International
308 London Road, Hazel Grove Cheshire SK7 4RF
T: 0161 818 2448
E: info@kmcinternational.com
W: www.kmcinternational.com
KN Group (UK)
221 Dover Road, Slough Berkshire SL1 4RF
T: 020 3668 9600
E: info@knns.ie
W: www.kngroup.com
Knorr-Bremse Platform Screen Doors Westinghouse Way, Hampton Park East Melksham Wiltshire SN12 6TL
T: 01225 898765
E: neil.ponsillo@knorr-bremse.com
W: www.rail.knorr-bremse.com
Knorr-Bremse Rail Systems UK Ltd is a member of the global Knorr-Bremse Group, a world leader in braking and sub-systems for rail vehicles.
We supply the entire portfolio of Knorr-Bremse cross-connected rail systems technology including braking, HVAC, power supply, sanding, and integrated digital control and monitoring technology to rail vehicle builders, maintainers and operators in the UK & Ireland.
Knorr-Bremse Rail Systems (UK) Ltd
Westinghouse Way, Hampton Park East Melksham Wiltshire SN12 6TL
T: 01225 898700
E: info@knorr-bremse.com
W: www.rail.knorr-bremse.com
Knowledge Transfer Network
Suite 218, Business Design Centre
52 Upper Street London N1 0QH
T: 0333 340 3250
E: enquiries@ktn-uk.org
W: www.ktn-uk.co.uk
Komplete Group
Suite 2 Floor 3, Cardinal Square
10 Nottingham Road Derby DE1 3QT
T: 01332 349255
E: enquiries@komplete-group.com
W: www.komplete-group.com
Kopta Training
18 Lavant Street
Petersfield Hampshire GU32 3EW
T: 01703 711202
E: info@kopta.co.uk
W: www.kopta.co.uk
Korec Group
34-44 Mersey View, Blundellsands House
Brighton le Sands Liverpool L22 6QB
T: 0151 931 6701
E: info@korecgroup.com
W: www.korecgroup.com
KP Acoustics 1 Galena Road
London W6 0LT
T: 020 8222 8778
E: info@kpacoustics.com
W: www.kpacoustics.com
KPMG Boxwood Limited
10th Floor, 15 Canada Square
London E14 5GL
T: 020 7694 1700
E: info@kpmgboxwood.co.uk
W: www.kpmgboxwood.co.uk
KPMG Legal & Financial Services
15 Canada Square, Canary Wharf
London E14 5GL
T: 020 7311 1000
W: www.kpmg.co.uk
Kranlyft UK Ltd
Unit 1 IO Centre, Cabot Park
Avonmouth Bristol BS11 0QL
T: 0117 982 6661
E: info@kranlyft.co.uk
W: www.kranlyft.co.uk
Kroy Europe Ltd
Unit 2, 14 Commercial Road
Reading Berkshire RG2 0QJ
T: 0118 986 5200
E: info@kroyeurope.com
W: www.kroyeurope.com
Kusch+Co Ltd
48-50 St John Street
London EC1M 4DG
T: 020 7336 7561
E: info-uk@kusch.com
W: www.kusch.com
Kwik-Klik Hoardings Ltd
10-14 Ward Street, Bradford West Yorkshire BD7 3PR
T: 01274 525660
E: info@kwik-klik.co.uk
W: www.kwik-klik.co.uk
KWT Global 60 Charlotte Street
London W1T 2NU
T: 020 7632 7687
E: info@kwtglobal.com
W: www.kwtglobal.com
L&W Contractors
L&W House, Stane Street
Billinghurst West Sussex RH14 9AE
T: 01403 784286
E: enquiries@lwcontractors.co.uk
W: www.lwcontractors.co.uk
LAE Welfare Vehicle Solutions
Unit 1 Garnett Place, Skelmersdale
WN8 9UB
T: 0169 555 6865
E: info@lae-ltd.com
W: www.laevehiclerental.co.uk
Laing O’Rouke Infrastructure – Head Office
Bridge Place 1 & 2, Anchor Boulevard Crossways Dartford Kent DA2 6SN
T: 01322 296200
E: info@laingorourke.com
W: www.laingorourke.com
Lamplas Ltd
Castleside Ind Estate, Consett Co Durham DH8 8JA
T: 01207 502474
E: sales@lamplas.co.uk
W: www.lamplas.co.uk
Lancaster University
Bailrigg, Lancaster LA1 4YW
T: 01524 65201
E: ugadmissions@lancaster.ac.uk
W: www.lancaster.ac.uk
Land & Water Services Ltd
Weston Yard, Albury
Guildford Surrey GU5 9AF
T: 0844 225 1958
E: enquiries@land-water.co.uk
W: www.land-water.co.uk
Landscape Institute (LI) 107 Grays Inn Road, London WC1X 8TZ
T: 0330 808 2230
E: contact@landscapeinstitute.org
W: www.landscapeinstitute.org
Lanes for Drains 300 Lansdowne Road, Monton Eccles Manchester M30 9PJ
T: 0800 526 488
E: sales@lanesgroup.co.uk
W: www.lanesfordrains.co.uk
Lanes Group Rail has been supporting the UK’s rail networks since 1992. Its services include CCTV, drone and ground surveys, drainage cleaning and installation, and chamber and pipe rehabilitation. Lanes delivers what its client partners need, where and when they need it, with highly motivated, agile, expert teams.
Lanes Group Rail
16 Lamson Road Rainham RM13 9YY
T: 01708 528770
E: railenquiries@lanesgroup.co.uk
W: www.lanesfordrains.co.uk
Lanes Rail (Part of Lanes Group)
17 Parkside Lane, Parkside Ind Estate Leeds LS11 5TD
T: 0113 385 8400
E: marketingdepartment@lanesgroup.co.uk
W: www.lanesgroup.com
Langley Holdings PLC Enterprise Way, Retford Nottinghamshire DN22 7HH
T: 01777 700039
E: info@langleyholdings.com
W: www.langleyholdings.com
LanGuard Ltd
Packs Hill Farm, Station Road
Lutterworth Leicestershire LE17 6JN
T: 01858 880898
E: info@languard.co.uk
W: www.languard.co.uk
Lankelma are first-class providers of cone penetration testing (CPT) and specialist ground investigations in the rail environment. We have over 10 years of experience working in the rail industry using our bespoke rail units and working nationwide to offer high-quality ground investigations in all areas of the trackway.
Lankelma Ltd
Coldharbour Barn, Coldharbour Lane Iden East Sussex TN17 7UT
T: 01797 280050
E: info@lankelma.co.uk
W: www.lankelma.com
Lansons
24a St John Street
London EC1M 4AY
T: 020 7490 8828
E: consultancy@lansons.com
W: www.lansons.com
Largam Limited
Unit 9, Oak Ind Park, Great Dunmow Essex CM6 1XN
T: 01371 876121
E: plant@largam.co.uk
W: www.largam.co.uk
LARS Communications Ltd
Keer Bridge Depot, Scotland Road
Carnforth Lancashire LA5 9RQ
T: 01524 727910
E: info@lars.co.uk
W: www.lars.co.uk
Laser Process Ltd
Keys Park, Cannock Staffordshire WS12 2GE
T: 01543 495000
E: sales@laserprocess.co.uk
W: www.laserprocess.co.uk
Lavender International
Unit 7, Sheffield Road Penistone Station Sheffield S36 6HP
T: 01226 765769
E: enquiries@lavender-ndt.com
W: www.lavender-ndt.com
Proven in a long list of rail industry applications, Layher’s scaffolding, access and protection systems provide safe, versatile solutions. Modular design optimises each installation while tailored product systems, such as temporary footbridge options and public access stairs complete with DDA handrail, deliver clear advantages for the workforce and public alike.
Layher Ltd Works Road, Letchworth Hertfordshire SG6 1WL
T: 01462 475100
E: info@layher.co.uk
W: www.layher.co.uk
LB Foster Rail Technologies (UK) Ltd Stamford Street, Sheffield S9 2TX
T: 0114 256 2225
E: sales@lbfoster.co.uk
W: www.lbfoster.eu
LC Switchgear Limited
Unit 16, St Josephs Bus Park
St Josephs Close Hove East Sussex BN3 7ES
T: 01273 770540
E: sales@lcswitchgear.com
W: www.lcswitchgear.com
LCM Environmental
The Oil Depot, Wyre Street Padiham Lancashire BB12 8DF
T: 0808 164 4570
E: hello@lcmenvironmental.co.uk
W: www.lcmenvironmental.co.uk
Lead Contractors Association (LCA)
Centurion House, 36 London Road East Grinstead West Sussex RH19 1AB
T: 01342 317888
E: info@leadcontractors.co.uk
W: www.leadcontractors.co.uk
Lead Sheet Training Academy (LSTA)
Unit 10 Archers Park, Branbridges Road
East Peckham Tonbridge Kent TN12 5HP
T: 01622 872432
E: info@leadsheet.co.uk
W: www.leadsheet.co.uk
Leadec Leadec House, 2 Academy Drive Warwick CV34 6QZ
T: 01926 623550
E: info-uk@leadec-services.com
W: www.leadec-services.com
Leadership Champions (UK) Limited
Westlands, Long Buckby Road
Daventry NN11 2LT
T: 01327 705910
E: info@leadership-champions.com
W: www.leadership-champions.com
Leca UK
Regus House, Herons Way Chester Bus Park Chester CH4 9QR
T: 0844 335 1770
E: enquiries@leca.co.uk
W: www.leca.co.uk
Lee Warren Fabrication & Design Ltd
Unit 6-9, Silverdale Road Ind Est
Hayes Middlesex UB3 3BL
T: 020 8813 7474
E: info@leewarren.co.uk
W: www.leewarren.co.uk
Leemark Spinnings
186 Drews Lane, Ward End Birmingham West Midlands B8 2SL
T: 0121 773 5444
E: enquiries@leemarkspinnings.co.uk
W: www.leemarkspinnings.co.uk
Leewood Projects Ltd
38 Deacon Road, Kingston upon Thames Surrey KT2 6LU
T: 020 8541 0715
E: info@leewoodprojects.co.uk
W: www.leewoodprojects.co.uk
Legion Limited
Hamilton House, Mabledon Place
Bloomsbury London WC1H 9BB
T: 020 7793 0200
E: info@legion.com
W: www.legion.com
Legrand Electric Limited
Great King Street North Birmingham B19 2LF
T: 0370 608 9000
E: legrand.sales@legrand.co.uk
W: www.legrand.co.uk
Leica Geosystems Ltd
Hexagon House, Michigan Drive
Tongwell Milton Keynes MK15 8HT
T: 01908 513400
E: uk.sales@leica-geosystems.com
W: www.leica-geosystems.com
Leighfisher Ltd
New City Court, 20 St Thomas Street
London SE1 9RS
T: 020 7939 6100
E: leighfisheradmin@leighfisher.com
W: www.leighfisher.com
LEK Consulting
40 Grosvenor Place London SW1X 7JL
T: 020 7389 7200
E: info@lek.com
W: www.lek.com
LEM Regional Office UK
West Lancs Inv Centre, Whitemoss Business Park
Skelmersdale Lancashire WN8 9TG
T: 01942 388440
E: luk@lem.com
W: www.lem.com
Leoni Tailor-Made Cables UK Ltd
Units 12-14, Boythorpe Bus Units
Dockwalk Chesterfield S40 2QR
T: 01246 558618
E: machinery-sensors@leoni.com
W: www.leoni.co.uk
Lesmac (Fasteners) Ltd
73 Dykehead St, Queenslie Ind Estate
Queenslie Glasgow G33 4AQ
T: 0141 774 0004
E: sales@lesmac.co.uk
W: www.lesmac.co.uk
Level Crossing Installations Ltd
Canterbury Bus Centre, 18 Ashchurch Road
Tewkesbury Gloucestershire GL20 8BT
T: 01684 278022
E: enquiries@levelcrossinginstallations.co.uk
W: www.levelcrossinginstallations.co.uk
Level X NDT
11 Salisbury Grove, Giffard Park
Milton Keynes MK14 5QA
T: 0844 5855 638
E: consult@levelxndt.com
W: www.levelxndt.com
Lexicraft Ltd
2 Bromborough Pool, Business Park
Price’s Way Bromborough Wirral CH62 4LP
T: 0151 647 9281
E: sales@lexicraft.co.uk
W: www.lexicraft.co.uk
Ley Hill Solutions Limited
Beech House, 9 Cheyne Walk
Chesham Buckinghamshire HP5 1AY
T: 01494 772327
E: info@leyhill.com
W: www.leyhill.com
Leyland Auto Ltd
Unit 220 Cocker Road, Walton Summit Ind Est
Preston Lancashire PR5 8BP
T: 01772 695000
E: sales@leylandauto.com
W: www.leylandauto.com
Lifting Equipment Engineers Association (LEEA)
3 Ramsay Court, Kingfisher Way
Hinchingbrooke Cambridgeshire PE29 6FY
T: 01480 432801
E: mail@leea.co.uk
W: www.leeaint.com
Light Rail Transit Association (LRTA)
c/o 8 Berwick Place, Welwyn Garden City Hertfordshire AL7 4TU
T: 0117 951 7785
E: office@lrta.org
W: www.lrta.org
LightGreen Power Ltd
Suite 1, Bishop Bateman Court
Thompson’s Lane Cambridge CB5 8AQ
T: 01223 852497
E: sales@lightgreenpower.co.uk
W: www.lightgreenpower.co.uk
Lighthouse (UK) Ltd
Unit 23, Charnwood Business Park North Road Loughborough LE11 1LE
T: 01509 264500
E: sales@lighthouse.uk.com
W: www.lighthouse.uk.com
LimitState Ltd
The Innovation Centre, 217 Portobello
Sheffield S1 4DP
T: 0114 224 2240
E: info@limitstate.com
W: www.limitstate.com
Linbrooke Services Ltd
Unit 3/4, Sheffield Business Park
Churchill Way Chapeltown S35 2PY
T: 0844 800 0983
E: communications@linbrooke.co.uk
W: www.linbrooke.co.uk
Lindapter International
Lindsay House, Brackenbeck Road Bradford West Yorkshire BD7 2NF
T: 01274 521444
E: enquiries@lindapter.com
W: www.lindapter.com
Lindhurst Engineering Ltd
Midland Road, Off Station Road
Sutton-in-Ashfield Nottinghamshire NG17 5GS
T: 01623 557420
E: sales@lindhurst.co.uk
W: www.lindhurstengineering.co.uk
Lindström Group
6 Caxton Park, Caxton Road Bedford MK41 0TY
T: 01234 343555
E: sales.uk@lindstromgroup.com
W: www.lindstromgroup.com
Linear Guidance Illumination Limited
Scientific House, Turnpike Ind Estate Newbury Berkshire RG14 2LR
T: 01249 819638
E: info@lineargi.com
W: www.lineargi.com
Linear Recruitment
18 Paradise Square
Sheffield S1 2DE
T: 0114 263 4888
E: rail@linearrecruitment.co.uk
W: www.linearrecruitment.co.uk
Lineside Structure Maintenance Ltd Works Depot, Lilac Grove Beeston Nottingham NG9 1PF
T: 0115 922 5218
E: info@lineside.co.uk
W: www.lineside.co.uk
Lineworx Ltd
Basepoint Centre, Cressex Business Park
High Wycombe Buckinghamshire RH12 1TL
T: 0333 900 0939
E: info@lineworx.co.uk
W: www.lineworx.co.uk
Lingwood Security Management Limited 6 Penrod Way, Heysham
Lancashire LA3 2UZ
T: 01524 852275
E: sales@lingwoodsecurity.com
W: www.lingwoodsecurity.co.uk
Liniar Ltd
Flamstead House, Denby Hall Bus Park Denby Derbyshire DE5 8JX
T: 01332 883900
E: sales@liniar.co.uk
W: www.liniar.co.uk
Liniar Retaining Systems
Flamstead House, Denby Hall Business Park Derbyshire DE5 8JX
T: 01332 883900
E: info@liniar.co.uk
W: www.liniar.co.uk
Linklite Systems Ltd
29 Waterloo Road, Wolverhampton WV1 4DJ
T: 0345 862 0236
E: sales@linklite.co.uk
W: www.linklite.co.uk
Links Signs Ltd Drury Lane, St Leonards East Sussex TN38 9BA
T: 01424 424423
E: info@linkssigns.co.uk
W: www.linkssigns.co.uk
Linsinger: Linsinger Maschinenbau is a renowned company specializing in the design and manufacturing of state-of-the-art rail milling machines. With decades of experience, Linsinger provides innovative solutions for the efficient maintenance and modernization of rail infrastructures worldwide. Their advanced technologies and commitment to the highest quality standards make Linsinger a leading partner in the railway industry.
Linsinger Maschinenbau Gesellschaft m.b.H
Dr. Linsinger Strasse 23-24, A-4662 Steyrermuhl
Austria
T: 0043 7613/8840
E: office@linsinger.com
W: www.linsinger.com
Lionweld Kennedy Flooring Limited Marsh Road, Middlesbrough TS1 5JS
T: 01642 245151
E: sales@lk-uk.com
W: www.lk-uk.com
LISTA is the recognized market leader in Europe in respect to workspace and storage equipment. We have set the standard for quality and durability. The selection of cabinets, workstations and shelving systems can be combined to make your workspace work. Our products currently used by over 100,000 satisfied customers.
Lista UK Ltd
14 Warren Yard, Warren Farm Wolverton Mill Milton Keynes MK12 5NW
T: 01908 222333
E: info.uk@lista.com
W: www.lista.co.uk
Listers Geotechnical Consultants Limited
Slapton Hill Barn, Blakesley Road
Slapton Northamptonshire NN12 8QD
T: 01327 860060
E: info@listersgeotechnics.co.uk
W: www.listersgeotechnics.co.uk
Littlewood Fencing Ltd
North Trade Road, Battle
East Sussex TN33 9LJ
T: 01424 775333
E: info@littlewoodfencing.co.uk
W: www.littlewoodfencing.co.uk
Live Trakway | Barriers | Bridges | Lights Bramley Vale, Chesterfield Derbyshire S44 SGA
T: 0870 076 7676
E: enquiries@liontrackhire.com
W: www.livetrakway.com
LKQ Coatings
Newberry House, Michigan Drive Tongwell Milton Keynes MK15 8HQ
T: 01908 517777
E: enquiries@lkqcoatings.com
W: www.lkqcoatings.com
LML Products Ltd Unit L1, Redman Road Calne Wiltshire SN11 9PR
T: 01249 810000
E: sales@lmlproducts.co.uk
W: www.lmlproducts.co.uk
Lockinex (UK) Limited
Lockinex Works, Hammonds Drive Eastbourne East Sussex BN23 6PW
T: 01323 737626
E: sales@lockinex.com
W: www.lockinex-store.com
Locktec Ltd
Units 7-11, Midlothian Innov Centre
Pentlandfield Roslin EH25 9RE
T: 0131 445 7788
E: sales@locktec.co.uk
W: www.locktec.co.uk
Loco Diesel Suppliers
123oil, 1 Beecholme Court
143 Lichfield Road B74 2RY
T: 0845 257 1377
E: sales@123oil.co.uk
W: www.123oil.co.uk
Locomotive & Carriage Institution (L&CI)
35 Fairacres, Ruislip Middlesex HA4 8AN
E: membership.sec@lococarriage.org.uk
W: www.lococarriage.org.uk
Logic Engagements Ltd
45-47 High Street, Cobham Surrey KT11 3DP
T: 01932 869869
E: info@logicrec.co.uk
W: www.lovelogic.co.uk
LogiKal Projects
Level 3, 27-29 Cursitor Street London EC4A 1LT
T: 020 7404 4826
E: info@logikalprojects.com
W: www.logikalprojects.com
Logistics UK
Hermes House, St John’s Road Tunbridge Wells Kent TN4 9UZ
T: 03717 11 22 22
E: enquiry@logistics.org.uk
W: www.logistics.org.uk
London Bridge Associates Ltd
Cranhurst Lodge, 37-39 Surbiton Hill Rd Surbiton KT6 4TS
T: 020 8399 8614
E: welcome@lba.london
W: www.lba.london
London Business Conferences Group (LBCG)
2nd Floor, 64 Great Eastern Street London EC2A 3QR
T: 0845 867 8109
E: info@lbcg.com
W: www.lbcg.com
London Communications Agency
8th Floor, Berkshire House
High Holborn London WC1V 7AA
T: 020 7612 8480
E: lca@londoncommunications.co.uk
W: www.londoncommunications.co.uk
London Continental Railways (LCR)
20 Cranbourn Street, London WC2H 7AA
T: 020 7391 4300
E: info@lcrproperty.co.uk
W: www.lcrproperty.co.uk
London North Eastern Railway (LNER)
East Coast House, 25 Skeldergate
York North Yorkshire Y01 6DH
T: 0345 722 5333
E: customers@lner.co.uk
W: www.lner.co.uk
London NorthWestern Railway
134 Edmund Street
Birmingham B3 2ES
T: 0333 311 0006
E: Contact.LNR@wmtrains.co.uk
W: www.londonnorthwesternrailway.co.uk
London Overground
Palestra, 197 Blackfriars Road
London SE1 8NJ
T: 0343 222 1234
E: overgroundinfo@tfl.gov.uk
W: www.tfl.gov.uk
London Tramlink
Palestra, 197 Blackfriars Road
London SE1 8NJ
T: 0343 222 1234
W: www.tfl.gov.uk
London TravelWatch
Europoint, 5-11 Lavington Street
London SE1 0NZ
T: 020 3176 2999
E: info@londontravelwatch.org.uk
W: www.londontravelwatch.org.uk
London Underground Ltd (TfL)
Palestra, 197 Blackfriars Road
London SE1 8NJ
T: 0343 222 1234
W: www.tfl.gov.uk
Loram UK Ltd
Loram House, 7 Mallard Way
Pride Park Derby DE24 8GX
T: 01332 293035
E: enquiries@loram.co.uk
W: www.loram.co.uk
Loughborough University
Epinal Way, Loughborough
Leicestershire LE11 3TU
T: 01509 222222
E: enquiries@lboro.ac.uk
W: www.lboro.ac.uk
Lowery Ltd
Ashley Place, Hanworth Lane
Chertsey Surrey KT169JX
T: 01932 564248
E: info@lowery.co.uk
W: www.lowery.co.uk
LPA Channel Electric
Bath Road, Thatcham
Berkshire RG18 3ST
T: 01635 864866
E: enquiries@lpa-channel.com
W: www.lpa-group.com
LPA Connection Systems
Light & Power House, Shire Hill
Saffron Walden Essex CB11 3AQ
T: 01799 512800
E: sales@lpa-connect.com
W: www.lpa-group.com
LPA Group Plc
Shire Hill, Saffron Walden Essex CB11 3AQ
T: 01799 512800
E: enquiries@lpa-group.com
W: www.lpa-group.com
LPA Lighting System
Ripley Drive, Normanton Wakefield West Yorkshire WF6 1QT
T: 01924 224100
E: enquiries@lpa-light.com
W: www.lpa-group.com
LPA Transport Plus Light & Power House, Shire Hill Saffron walden Essex CB11 3AQ
T: 01799 512800
E: enquiries@lpa-connect.com
W: www.lpa-group.com
Lucy Zodion Ltd
Station Road, Sowerby Bridge
West Yorkshire HX6 3AF
T: 01422 317337
E: sales@lucyzodion.com
W: www.lucyzodion.com
Lundy Projects
3rd Floor Regent House, Heaton Lane
Stockport SK4 1BS
T: 0161 476 2996
E: mail@lundy-projects.co.uk
W: www.lundy-projects.co.uk
LUR Ltd
Wheel Forge Way, Trafford Park Manchester M17 1EH
T: 0161 886 0300
E: contactus@lur.co.uk
W: www.lur.co.uk
Lutze Limited
Unit 3 Sandy Hill Park, Sandy Way Amington Tamworth B77 4DV
T: 01827 313330
E: sales.gb@lutze.co.uk
W: www.lutze.com
Lyndon Scaffolding
Valepits Road, Garretts Green Birmingham B33 0TD
T: 0121 789 7979
E: enquiries@lyndonscaffolding.co.uk
W: www.lyndonscaffolding.co.uk
M Barnwell Services Ltd
Reginald Road, Smethwick West Midlands B67 5AS
T: 0121 429 8011
E: sales@barnwell.co.uk
W: www.barnwell.co.uk
M Buttkereit Ltd
Unit 2, Britannia Road Ind Est Sale Cheshire M33 2AA
T: 0161 969 5418
E: sales@buttkereit.co.uk
W: www.buttkereit.co.uk
M Seals UK Ltd
Quartz Close, Enderby Leicester LE19 4SG
T: 0116 275 4720
E: sales@m-seals.co.uk
W: www.m-seals.co.uk
M&I Materials
Hibernia Way, Trafford Park Manchester M32 0ZD
T: 0161 864 5449
E: mi@mimaterials.com
W: www.mimaterials.com
Mabanaft Ltd
Floor 5, Portland House Cardinal Place London SW1E 5RS
T: 020 7802 3300
E: info@mabanaft.co.uk
W: www.mabalive.co.uk
Leading temporary works specialist with a national engineering team and the UK’s widest range of temporary works equipment. At the forefront of our industry for 60 years, building a reputation for engineering and service excellence. Expertise includes groundworks, propping, jacking, formwork and falsework systems, temporary access solutions, temporary bridges, and structural and environmental monitoring.
Mabey Hire Limited
Scout Hill, Ravensthorpe Dewsbury WF13 3EJ
T: 0845 741 3040
E: info@mabeyhire.co.uk
W: www.mabeyhire.co.uk
For over 140 years Maccaferri have been at the forefront of the civil engineering industry. Maccaferri design, manufacture and install innovative, long-lasting and environmentally friendly solutions across the UK and Ireland. Maccaferri have a global presence and the HQ is based in Italy. Maccaferri are always engineering a better solution.
Maccaferri Ltd
9 Blenheim Office Park, Fenlock Road Long Hanborough Oxfordshire OX29 8LN
T: 01865 770555
E: info@maccaferri.com
W: www.maccaferri.com/uk
Macdonald & Company (Recruitment)
2 Harewood Place, Hanover Square London W1S 1BX
T: 020 7629 7220
E: connect.uk@macdonaldandcompany.com W: www.macdonaldandcompany.com
Macemain + Amstad Ltd Boyle Road, Willowbrook Ind Estate Corby Northamptonshire NN17 5XU
T: 01536 401331
E: sales@macemainamstad.com
W: www.macemainamstad.com
MacRail Systems Ltd Units 1 & 2, Morston Court
Aiscombe Way Weston Super Mare BS22 8NG
T: 01934 319810
E: info@macrail.co.uk
W: www.macrail.co.uk
Macrete Ireland limited
50 Creagh Road, Toomebridge Co Antrim BT41 3SE
T: 028 7965 0471
E: info@macrete.com
W: www.macrete.com
MacRoberts LLP
Capella, 60 York Street
Glasgow G2 8JX
T: 0141 303 1100
E: maildesk@macroberts.com
W: www.macroberts.com
Maddox Consultancy Limited Oakdene, Rectory Road
Little Burstead Billericay CM12 9TR
T: 020 7588 8800
E: info@maddoxconsultancy.co.uk
W: www.maddoxconsultancy.co.uk
Magdalene
Magdelene House, Compass Point Bus Park St Ives PE27 5JL
T: 01480 357777
E: enquiries@magdalene.co.uk
W: www.magdalene.co.uk
Magrenko Ltd Brookfield Drive, Cannock Staffordshire WS11 0JR
T: 01543 572016
E: sales@magrenko.com
W: www.magrenko.com
Majenta PLM Ltd
5 Medway Court, University Way Cranfield Tech Pk Cranfield MK43 0FQ
T: 01234 757695
E: sales@majentaplm.com
W: www.majentaplm.com
An independent manufacturer of the best quality, specialist, lifting equipment for automotive, aerospace, rail and other applications. We seek to take the load and risk out of moving heavy assemblies so that our customers can work safely and efficiently. Our range is engineered to keep on performing, ensuring that operational downtime is minimised.
Majorlift Hydraulic Equipment Limited
Arnolds Field Estate, Wickwar Glos GL12 8JD
T: 01454 299299
E: sales@majorlift.com
W: www.majorlift.com
Maker Coating Systems Ltd
Unit 5, Oak Bus Units, Thorverton Road Matford Bus Park Exeter EX2 8FS
T: 01392 822600
E: sales@makercoating.com
W: www.makercoating.com
MAL Explosive Ordnance Disposal Ltd
MAL EOD Ltd, Bulloch House
10 Romford Place Liverpool L3 9DG
T: 0151 528 2204
E: enquiries@mal-eod.com
W: www.mal-eod.com
Malcolm Hughes
65 Cross Street, Sale Manchester M33 7HF
T: 0800 833 312
E: surveythis@mhls.co.uk
W: www.malcolmhughes.co.uk
Malcolm Rail
Railport Approach, DIRFT South Crick Northamptonshire NN6 7JZ
T: 01788 822122
E: contact@whm.co.uk
W: www.malcolmgroup.co.uk
Mallatite
Hardwick View Road, Holmewood Chesterfield Derbyshire S42 5SA
T: 01246 593280
E: groupsales@mallatite.co.uk
W: www.mallatite.co.uk
Mallatite Rail
Unit B Baltic Park, Saltmeadows Road Gatesehead Tyne and Wear NE8 3DA
T: 0191 933 1740
E: railsales@mallatite.co.uk
W: www.mallatite.co.uk
Maltaward
Unit 7 Wellingham Way, Holmbush Potteries Faygate Horsham West Sussex RH12 4SE
T: 0800 043 2742
E: admin@maltaward.co.uk
W: www.maltaward.co.uk
Mammoet UK Ltd (Head Office)
Beatrix House, Tyne View Terrace Wallsend Tyne & Wear NE28 6SG
T: 0191 263 9222
E: sales.uk@mammoet.com
W: www.mammoet.com
Manchester Metrology LTD are pioneers and innovators of metrology offering specialist contract measurement services using the latest metrology technology and equipment. Offering support across the UK and worldwide our helpful attitude towards our customers are among the many positive attributes which distinguish the company as a benchmark metrology company.
Manchester Metrology Ltd
Unit 3, The Wellington Centre
Whitelands Road Ashton-Under-Lyne OL6 6UY
T: 0161 637 8744
E: info@manchester-metrology.co.uk
W: www.manchester-metrology.co.uk
Manchester Metropolitan University
All Saints Building, Manchester M15 6BH
T: 0161 247 2000
E: enquiries@mmu.ac.uk
W: www2.mmu.ac.uk
Mansell Recruitment Group
Mansell House, Priestly Way
Crawley West Sussex RH10 9RU
T: 01293 404050
E: recruitment@mansell.co.uk
W: www.mansell.co.uk
Marchantcain Group
1 Banner Park, Wickmans Drive
Coventry CV4 9XA
T: 02476 100 321
E: business@marchantcain.com
W: www.marchantcain.com
Mardix Rail Castle Mills, Aynam Road Kendal Cumbria LA9 7DE
T: 01539 720161
E: sales@mardix.com
W: www.mardix.com
Mariel Irvine Solicitors
1 Luke Street, London EC2A 4PX
T: 020 7608 2275
E: irvine@marielirvine.com
W: www.marielirvine.com
Maritime Transport UK
Maritime House, Clickett Hill Road
Felixstowe Ipswich 1P11 4AX
T: 01394 617300
E: enquiries@maritimetransport.com
W: www.maritimetransport.com
Market Research Society
The Old Trading House, 15 North Burgh Street London EC1V OJR
T: 020 7490 4911
E: info@mrs.org.uk
W: www.mrs.org.uk
Marks Barfield Architects 50 Bromells Road London SW4 0BG
T: 020 7501 0180
E: info@marksbarfield.com
W: www.marksbarfield.com
Marl International Ltd
Marl Business Park, Ulverston Cumbria LA12 9BN
T: 01229 582430
E: enquiries@marl.co.uk
W: www.leds.co.uk
When you need power at off grid sites for professional equipment, our specialist team of experienced engineers will find a renewable energy solution to suit. We are Marlec, the UK’s longest standing renewables company of 40 years, manufacturer of micro wind turbines and designer of wind & solar power systems.
Marlec Engineering Co Ltd
Rutland House, Trevithick Road
Corby Northants NN17 5XY
T: 01536 201588
E: sales@marlec.co.uk
W: www.marlec.co.uk
Marsh Bellofram Europe Ltd
Unit 9, Castle Park
Queens Drive Nottingham NG2 1AH
T: 0115 993 3300
E: sales@marshbellofram.co.uk
W: www.marshbellofram.co.uk
Marsh Ltd (Risk Consulting)
1 Tower Place West London EC3R 5BU
T: 020 7357 1000
E: info@marsh.com
W: www.marsh.com
Marshall-Tufflex Ltd
55-65 Castleham Road, St Leonards on Sea TN38 9NU
T: 01424 856600
E: sales@marshall-tufflex.com
W: www.marshall-tufflex.com
Marshalls CPM
Marshalls CPM, Mells Road
Mells Somerset BA11 3PD
T: 0117 981 4500
E: salesemail@marshalls.co.uk
W: www.cpm-group.com
Martin Castle Ltd
MCL Unit T4, Leyton Ind Village
Argall Avenue London E10 7QP
T: 020 8558 5688
E: info@martincastleltd.com
W: www.martincastleltd.com
Marton Geotechnical Services Ltd
Rougham Ind Estate, Rougham
Bury St Edmunds Suffolk IP30 9ND
T: 01359 271167
E: info@mgs.co.uk
W: www.mgs.co.uk
Masabi Ltd – Head Office
Unit 1, 37 Bevenden Street London N1 6BH
T: 020 7089 8860
E: enquiries@masabi.com
W: www.masabi.com
MATISA (U.K) Ltd Dawes Lane
Scunthorpe DN15 6UW
T: 01724 786160
E: matisa@matisa.co.uk
W: www.matisa.ch
Matrax Ltd
Kestrel Court, Harbour Road
Portishead Bristol BS20 7AN
T: 01275 390600
E: contact@matrax.co.uk
W: www.matrax.co.uk
Matrix Booking 18 Soho Square
London W1D 3QL
T: 0203 951 8291
E: info@matrixbooking.com
W: www.matrixbooking.com
Matt Black Systems
Unit D, Broom Road Bus Park Broom Road Poole BH12 4PA
T: 01202 731731
E: mail@mattblacksystems.com
W: www.mattblacksystems.com
Matterson Cranes
45 Regent Street, Rochdale Lancashire OL12 0HQ
T: 01706 649321
E: matterson@pctgroup.co.uk
W: www.mattersoncranes.co.uk
Mattinson Partnership
Unit 109, The Print Room
164-180 Union St London SE1 0LH
T: 020 7960 2555
E: gmk@mattinsonpartnership.com
W: www.mattinsonpartnership.com
Max Fordham & Partners
42-43 Gloucester Cres London NW1 7PE
T: 020 7267 5161
E: post@maxfordham.com
W: www.maxfordham.com
Maxim Power Tools
40 Couper Street, Glasgow Scotland G4 0DL
T: 0141 552 5591
E: enquiries@maximpower.co.uk
W: www.maximpower.co.uk
Maxim Recruitment
87b Queens Road, Clarendon Park Leicester LE2 1TT
T: 0800 689 4841
E: uk@maximrecruitment.com
W: www.maximrecruitment.com
Mayarail Ltd Canberra House, 10 First Avenue Finningley Doncaster DN9 3GA
T: 0330 016 9779
E: Compliance@mayarail.co.uk
W: www.mayarail.co.uk
Maycast – Nokes Precision Engineering Factory Lane West, Halstead Essex CO9 1EX
T: 01787 477021
E: enquiries@maycast.co.uk
W: www.maycast.co.uk
Mayflower Engineering Ltd Coleridge Road, Sheffield South Yorkshire S9 5DA
T: 0114 244 1353
E: info@mayflower-engineering.co.uk
W: www.mayflower-engineering.co.uk
Maylarch Environmental Ltd
Oakwood, Oakfield Ind Estate Eynsham Oxfordshire OX29 4TH
T: 01865 883 829
E: Enquiries@maylarch.co.uk
W: www.maylarch.co.uk
Maynes Coaches
Cluny Garage, March Road Ind Estate Buckie Scotland AB56 4BU
T: 01542 831219
E: info@maynes.co.uk
W: www.maynes.co.uk
Mayteck Ltd
Unit 8, The Old Print Works Fishponds Road Wokingham RG41 2QX
T: 0800 048 5207
E: sales@mayteck.co.uk
W: www.mayteck.co.uk
MC Electronics Ltd
61 Grimsdyke Road, Hatch End Pinner Middlesex HA5 4PP
T: 020 8428 2027
E: info@mcelectronics.co.uk
W: www.mcelectronics.co.uk
McAuley Engineering
21 Ballymena Road, Ballymoney County Antrim Northern Ireland BT53 7ET
T: 028 2766 6646
E: sales@mcauleyengineering.co.uk
W: www.mcauleyengineering.co.uk
McCulloch Group design and create bespoke and patented machines which eliminate manual handling and improve the accuracy and productivity of installations across railway infrastructure projects. Using McCulloch technology, worldwide rail track maintenance and construction projects are completed in less time with reduced operational costs. The core principle of the business is innovation.
McCulloch Rail
Riverside Works, New Mill Road
Kilmarnock Ayrshire KA1 3JG
T: 0330 0130 010
E: marketing@mccullochgroup.com
W: www.mccullochgroup.com
McGeoch Technology Ltd
86 Lower Tower Street
Birmingham B19 3PA
T: 0121 687 5850
E: sales@mcgeoch.co.uk
W: www.mcgeoch.co.uk
McGinley Support Services (Infrastructure) is a specialist provider of contingent labour and recruitment, focused on Rail & Civil Engineering. Supporting clients, main contractors and their supply chain, we recruit and manage PTS, Safety Critical & Civils labour safely, on a 24/7 basis. Contact us for all your labour requirements.
McGinley Support Services (Infrastructure) Ltd
Ground Floor, Hyde, 38 Clarendon Road Watford WD17 1JW
T: 0845 543 5953
E: info@mcginley.co.uk
W: www.mcginley.co.uk
MCL (Martin Childs Ltd)
1 Green Way, Swaffham Norfolk PE37 7FD
T: 01760 722275
E: enquiries@martinchilds.com
W: www.martinchilds.com
MCL Group Industries Ltd
New Street, Biddulph Moor
Stoke on Trent Staffordshire ST8 7NL
T: 01782 375450
E: sales@mcl-grp.co.uk
W: www.themclgroup.co.uk
Dedicated to providing the highest quality rail storage, training and fleet servicing solutions across the UK.
Services also include materials handling, shunter hire, groundstaff hire, road-rail facilities, rollingstock refurbishment, servicing facilities including CET and fuelling.
MCL Rail
9 Park Square East, Vicarage Chambers
Leeds LS1 2LH
T: 0203 280 6390
E: enquiries@mclrail.co.uk
W: www.mclgroup.uk
McLaughlin & Harvey Ltd
15 Trench Road, Mallusk
Newtonabbey Belfast BT36 4TY
T: 028 9034 2777
E: mclh@mclh.co.uk
W: www.mclh.co.uk
McNealy Brown Ltd
Units 14-17, Craft Marsh Trading Est Gas Road Sittingbourne ME10 2QB
T: 01795 470592
E: info@mcnealybrown.co.uk
W: www.mcnealybrown.co.uk
MDG Rail
Yew Tree House, Broad Lane
Wolverhampton WV11 2RG
T: 0121 296 2051
E: info@mdgrail.com
W: www.mdgrail.com
MDS Transmodal Ltd
5-6 Hunters Walk, Canal Street
Chester CH1 4EB
T: 01244 348301
E: web.enquiries@mdst.co.uk
W: www.mdst.co.uk
ME Railway Research Group, University of Sheffield Dept Mechanical Eng, Mappin Street Sheffield S1 3JD
T: 0114 222 7760
E: D.I.Fletcher@Sheffield.ac.uk
W: www.merail.co.uk
Mecc Alte UK
6 Lands End Way, Oakham Rutland LE15 6RF
T: 01572 771160
E: info@meccalte.co.uk
W: www.meccalte.com
Lifting and handling specialist, Mechan supplies a wide range of equipment for rail depots, including its flagship lifting jacks, bogie drops and traversers.
The firm is part of the CIM Group, one of the industry’s most ambitious full-service suppliers and also offers unrivalled technical support, encompassing design, maintenance and refurbishment.
Mechan Limited
Building 5, Davy Industrial Park
Prince of Wales Rd Sheffield S9 4EX
T: 0114 257 0563
E: info@mechan.co.uk
W: www.mechan.co.uk
Med-Fitplus Ltd
45 Circus Road, St. John’s Wood London NW8 9JH
T: 0203 869 0026
E: info@med-fitplus.co.uk
W: www.med-fitplus.co.uk
Medicals Direct Group Limited
Buckingham House East, The Broadway Stanmore HA7 4EB
T: 0845 108 0446
E: info@wearemdg.com
W: www.wearemdg.com
Medigold Health
Medigold House, 1 Queensbridge Northampton NN4 7BF
T: 0845 127 8888
E: enquiries@medigold-health.com
W: www.medigold-health.com
Memolub Lubrication Systems
Unit 5, The Green Ind Est Clun Shropshire SY78LG
T: 01584 874220
E: lube@s2lube.com
W: www.lubricationuk.com
We are the ideal partner as we advise you on site and recommend the most suitable plugs and sockets for you. We have developed numerous individual solutions in the past to meet different requirements. The very close cooperation and coordination with our customers is always the central aspect of each technological development.
MENNEKES
Unit4, Crayfields Industrial Park, Main Road, St Paul’s Cray Orpington Kent BR5 3HP
T: 01689 833 522
E: sales@mennekes.co.uk
W: www.mennekes.co.uk
Merseyrail
9th Floor Rail House, Lord Nelson Street
Liverpool L1 1JF
T: 0151 555 1111
E: comment@merseyrail.org
W: www.merseyrail.org
Merson Group
2 Young Place, Glasgow
Scotland G75 0TD
T: 01355 243 021
E: enquiries@mersongroup.com
W: www.mersongroup.com
Met Office
Fitzroy Road, Exeter
Devon EX1 3PB
T: 01392 885680
E: enquiries@metoffice.gov.uk
W: www.metoffice.gov.uk
Metcalfe Plant Hire Limited
Gilwilly Road, Gilwilly Ind Estate
Penrith Cumbria CA11 9BL
T: 01768 868686
E: enquiries@metcalfe-plant-hire.co.uk
W: www.metcalfe-plant-hire.co.uk
Metis Conferences Ltd
27 Gloucester Street, WC1N 3AX
T: 07426 377301
E: victorkinlock@metisrail.com
W: www.metisconferences.com
Metrel UK Ltd
U/16 1st Qtr Bus Park, Blenheim Road Epsom Surrey KT19 9QN
T: 01924 245000
E: sales@metrel.co.uk
W: www.metrel.co.uk
Metrolink
Trafford Depot, Warewick Road South
Stretford Manchester M16 0GZ
T: 0161 205 2000
E: customerservices@metrolink.co.uk
W: www.metrolink.co.uk
Mettex Electric Co Ltd
Thorpe Way, Banbury Oxfordshire OX16 4SP
T: 01295 250826
E: sales@mettex.com
W: www.mettex.com
MGA Group (Marten Gibbon Associates Ltd)
10 Maltings Place, 169 Tower Bridge Road London SE1 3JB
T: 020 7186 5101
E: contact@mga-ideas.com
W: www.mga-ideas.com
MGF Ltd
Grant House, Lockett Road Wigan WN4 8DE
T: 01942 402700
E: enquiries@mgf.ltd.uk
W: www.mgf.ltd.uk
MGS Demco (Coventry Office)
Hayford Close, Aldermans Green Ind Est Aldermans Green Coventry CV2 2QB
T: 024 7660 2323
E: info@mgs.co.uk
W: www.mgs.co.uk
M H Southern are Timber Importers & Sawmillers based in the North East. We specialise in supplying the Rail Industry with a range of Large Sectional Timbers including Douglas Fir, Ekki, Opepe and German Whitewood. Also, our range of Fencing and general Carcassing Timbers together with our Milling & Treatment facilities enable us to offer a wide range of products and UK wide delivery.
MH Southern & Company Ltd (Timber)
Green Lane Sawmills, Felling
Gateshead NE10 0JS
T: 0191 489 8231
E: sales@mhsouthern.co.uk
W: www.mhsouthern.co.uk
Mick George Ltd
6 Lancaster Way, Ermine Business Park
Huntingdon PE29 6XU
T: 0800 587 3329
E: sales@mickgeorge.co.uk
W: www.mickgeorge.co.uk
Micro-Mesh Filtration
Innovation House, Dabell Avenue
Blenheim Ind Est Nottingham NG6 8WA
T: 0115 975 2929
E: enquiries@micro-mesh.co.uk
W: www.micro-mesh.co.uk
Middlemarch Environmental Ltd
Triumph House, Birmingham Road Coventry CV5 9AZ
T: 01676 525880
E: admin@middlemarch-environmental.com
W: www.middlemarch-enviromental.com
Midland Alloy Ltd
Unit 1, Stafford Park 17
Telford Shropshire TF3 3DG
T: 01952 290961
E: sales@midlandalloy.com
W: www.midlandalloy.com
Midland Metro Alliance 4th Floor Alpha Tower, Suffolk St Queensway Birmingham B1 1TT
T: 0121 643 8729
W: www.metroalliance.co.uk
A well respected Achilles audited professional firm of Chartered Land and Engineering Surveyors with over 30 years’ experience committed to utilising state of the art surveying and imaging technology in order to provide a wide range of deliverables to the Rail Industry.
Mike Worby Survey Consultancy Ltd
37 Ramblers Way, Welwyn Garden City Hertfordshire AL7 2JU
T: 01707 333677
E: survey@mw-sc.co.uk
W: www.mw-sc.co.uk
Mikerry Rail Ltd
Unit 1, Pontsarn Road
Merthyr Tydfil CF48 2TN
T: 01685 377011
E: admin@mikerryrail.co.uk
W: www.mikerryrail.co.uk
Milestone Project Management Solutions
Great West House, Great West Road Brentford London TW8 9DF
T: 020 8326 5760
E: info@milestoneuk.com
W: www.milestoneuk.com
Millcroft Group Salutation House, 1 Salutation Road Greenwich London SE10 0AT
T: 020 8305 1988
E: sales@millcroft.co.uk
W: www.millcroft.co.uk
Mills Ltd
13 Fairway Drive, Fairway Ind Estate Greenford Middlesex UB6 8PW
T: 020 8833 2626
E: sales@millsltd.com
W: www.millsltd.com
Mineral Products Association (MPA) Gillingham House, 38-44 Gillingham Street London SW1V 1HU
T: 020 7963 8000
E: info@mineralproducts.org
W: www.mineralproducts.org
Mini Gears Group
Top Gear House, Bletchley Road
Heaton Mersey I.E. Stockport SK4 3ED
T: 0161 432 0222
E: enquiries@minigears.co.uk
W: www.minigears.co.uk
Mitie Pest Control Ltd
Unit 1 Athelney Way, Cheltenham Gloucester GL52 6RT
T: 0345 017 1069
E: mpc.sales@mitie.com
W: www.mitie.com
Mitsubishi Electric Europe BV
Travellers Lane, Hatfield Hertfordshire AL10 8XB
T: 01707 288180
E: automation@meuk.mee.com
W: gb3a.mitsubishielectric.com
MJ Quinn Intergrated Services (Head Office) Finwell House, 26 Finsbury Square London EC2A 1DS
T: 020 7993 0731
E: enquiry@mjquinn.co.uk
W: www.mjquinn.co.uk
MJ Rees & Company Ltd
A1 Vantage Office Park, Old Gloucester Road Hambrook Bristol BS16 1GW
T: 01454 252930
E: survey@mjrees.co.uk
W: www.mjrees.co.uk
MK Surveys
1 Potters Lane, Kiln Farm Milton Keynes MK11 3HE
T: 01908 565561
E: mail@mksurveys.co.uk
W: www.mksurveys.co.uk
MK Test Systems ATE House, Westpark 26 Wellington Somerset TA21 9AD
T: 01823 428702
E: sales@mktest.com
W: www.mktest.com
MLM Consulting Engineers Ltd North Kiln, Felaw Maltings 46 Felaw Street Ipswich Suffolk IP2 8PN
T: 01473 231100
E: contact@mlmgroup.com
W: www.mlmgroup.com
MMRA Ltd
10 Fleet Place, 4th Floor London EC4M 7RB
T: 020 7651 0590
E: info@mmra-cert.com
W: www.mmra-cert.com
MobiHub Crown House, 183 High Street Bottisham Cambridge CB25 9BB
T: 01223 813151
E: info@mobihub.com
W: www.mobihub.com
Mobil Baustoffe GmbH Trimburgstr. 2, 81249 München
Germany
T: 00 49 8989 5457 40
E: office@mobil-baustoffe.com
W: www.mobil-baustoffe.com
Modern Eon | Lighting Services in UK Lighting House, Church Road London SE19 2ET
T: 020 8650 9690
E: info@moderneon.co.uk
W: www.moderneon-light.com
Mole Solutions Ltd Church Farm House, Grafton Road Geddington NN14 1AJ
T: 01480 413141
E: info@molesolutions.co.uk
W: www.molesolutions.co.uk
Momentum Services Ltd (Euro Star)
Times House, Bravingtons Walk Regent Quarter London N1 9AW
T: 020 7843 5619
E: info@momentumltd.eu
W: www.momentumservicesltd.com
Mono Design Ltd
16 Scarsdale Avenue, Littleover
Derby DE23 6ER
T: 01332 361616
E: info@monodesign.co.uk
W: www.monodesign.co.uk
Moore Concrete have been involved in numerous civil engineering projects, working in conjunction with key contractors to manufacture bespoke precast concrete units. This experience has led to Moore Concrete building a high level of expertise, in manufacturing units for coastal, road, rail, construction and architectural schemes.
Moore Concrete Products Ltd
Caherty House, 41 Woodside Road, Ballymena
Co. Antrim Northern Ireland BT42 4QH
T: 028 2565 2566
E: info@moore-concrete.com
W: www.moore-concrete.com
Moorecorp Ltd
9 Millfield Close, Flitwick Bedford MK45 1LB
T: 01525 717075
E: sales@moore-ltd.com
W: www.moorecorp.co.uk
Morgan Advanced Materials PLC
473 Foleshill Road, Coventry West Midlands CV6 5AQ
T: 024 7670 2802
E: info@morganplc.com
W: www.morganadvancedmaterials.com
Morgan Hunt Limited (London Office)
9th Floor, 125 London Road
London EC2Y 5AS
T: 020 7419 8900
E: info@morganhunt.com
W: www.morganhunt.com
Morgan Marine, part of Morgan GRP established 1965, leads the field in the design manufacture and installation of both GRP and Steel equipment housings, as well as the largest portfolio of LPCB security rated products available in the UK these are certified to LPCB up to level SR 4 D10. These include doors, window bar-sets, ventilation louvres, cages and access covers.
Morgan Marine Ltd Llandybie, Ammanford
Carmarthenshire Wales SA18 3GY
T: 01269 850437
E: sales@morgan-marine.com
W: www.morgan-marine.com
Morgan Sindall Construction & Infrastructure Ltd Corporation Street, Rugby Warwickshire CV21 2DW
T: 01788 534500
E: info.infrastructure@morgansindall.com
W: www.construction.morgansindall.com
Morgan Sindall Group Kent House, 14-17 Market Place London W1W 8AJ
T: 020 7307 9200
E: enquiries@morgansindall.co.uk
W: www.morgansindall.com
Morganite Electrical Carbon Ltd Upper Forest Way, Morriston Swansea SA6 8PP
T: 01792 763000
E: meclsales@morganplc.com
W: www.morgancarbon.com
Morris Site Machinery Station Road, Four Ashes Wolverhampton WV10 7DB
T: 01902 790824
E: info@morrismachinery.co.uk
W: www.morrismachinery.co.uk
Morrison Utility Services Limited
Abel Smith House, Gunnels Wood Road Stevenage Hertfordshire SG1 2ST
T: 01438 743744
E: communications@mgroupservices.com
W: www.morrisonus.com
Mors Smitt (A Wabtec Company)
Graycar Business Park, Burton Upon Trent Staffordshire DE13 8EN
T: 01283 722650
E: msu_sales@wabtec.com
W: www.mors-smitt.com
Morson Human Resources Ltd t/a Morson Talent Adamson House, 2 Centenary Way Salford Manchester M50 1RD
T: 0161 707 1516
E: enquiries@morson.com
W: www.morson.com
Mosdorfer Rail offer innovative product solutions for High-Speed, Commuter and Light Rail OCS systems. Our in-house technology is developed for the production of safe and reliable materials and products. Mosdorfer offer connectors and systems for the electrification of railway lines:
• Tensorex® C+ Tensioning Device Droppers
• Catenary Fittings
• Insulators Tools
• Safety Equipment
Mosdorfer Rail Ltd
2-4 Orgreave Place, Orgreave Sheffield S13 9LU
T: 0114 478 8500
E: ordersrailuk@mosdorfer.com
W: www.knillgruppe.com
Motorail UK Limited
QRTC, Station Road Long Marston Stratford-on-Avon CV37 8PL
T: 01789 721995
E: info@motorail.co.uk
W: www.motorail.co.uk
Movement Strategies
31-35 Kirby Street, Farringdon London EC1N 8TE T: 020 3540 8520
E: info@movementstrategies.com
W: www.movementstrategies.com
Moxa UK
Sanderrum Centre, 30a Upper High Street
Thame OX9 3EX
T: 01844 355601
E: uk@moxa.com
W: www.moxa.com
MPEC Technology Ltd
6 Pinnacle Way, Pride Park Derby DE24 8ZS T: 01332 363 979
E: enquiries@tracsis.com
W: www.mpec.co.uk
MPH Construction Ltd
Bromfield House, Bromfield Ind Estate Queens Lane Flintshire CH7 1XB
T: 01352 755151
E: info@mphconstruction.co.uk
W: www.mphconstruction.co.uk
MR Site Services Ltd
Unit 6, Worcester Trading Est Worcester WR3 8HR
T: 01905 755055
E: welding@mrsiteservices.co.uk
W: www.mrsiteservices.co.uk
MRI Software
9 King Street, London EC2V 8EA
T: 020 3861 7100
E: emeasales@mrisoftware.com
W: www.mrisoftware.com
MRL Eye Limited
Alfred House, Ropewalk Knottingley West Yorkshire WF11 9AL
T: 01977 622000
E: info@mrl-limited.co.uk
W: www.mrl-limited.co.uk
MSA Safety – Latchways PLC
Hopton Park, Devizes Wiltshire SN10 2JP
T: 0800 066 2222
E: info.gb@msasafety.com
W: www.msasafety.com
MTAG Composites Ltd are a leading manufacturer of many different types of composite mouldings, using a variety of resin systems and reinforcements to suit the needs of their customers’ requirements. All of which conform to the most stringent British and European standards. MTAG also offer a complete on-site painting and assembly service, which allows them to deliver parts ready for installation.
MTag Composites Ltd
Coldham Road, Coningsby Lincolnshire LN4 4SE
T: 01526 343790
E: enquiries@mtagcomposites.com
W: www.mtagcomposites.com
MTM Power Messtechnik Mellenbach GmbH
Zirkel 3, 98744 Schwarzatal Germany
T: 0049 367 05 / 6 880
E: info@mtm-power.com
W: www.mtm-power.com
MTR Corporation Limited Samuel House, 6 St Alban’s Street London SW1Y 4SQ
T: 020 7766 3500
E: mtr@mhpc.com
W: www.mtreurope.com
MTR Elizabeth Line
63 St Mary Avenue London EC3A 8NH
T: 020 7444 0213
E: communications@mtrcrossrail.co.uk
W: www.mtrcrossrail.co.uk
Muirhead – Scottish Leather Group Operations Baltic Works, Kilbarchan Road Bridge of Weir Scotland PA11 3RH
T: 01505 691730
E: marketing@muirhead.co.uk
W: www.muirhead.co.uk
Multimodal
69 Fulham High Street London SW6 3JW
T: 020 7384 7700
E: info@clarionevents.com
W: www.multimodal.org.uk
Murphy Geospatial
39-41 North Road London N7 9DP
T: 020 3598 3775
E: info@murphygs.com
W: www.murphygs.com
My Visual Management
The Willows Studio, Pakenham Bury St Edmunds Suffolk IP312JT
T: 01359 305010
E: info@myvisualmanagement.co.uk
W: www.myvisualmanagement.co.uk
MYM Recruitment
80-82 Rainey Street, Magherafelt Northern Ireland BT45 5AJ
T: 028 7939 7108
E: team@mymrecruitment.com
W: www.mymrecruitment.com
NAL Limited Weir Lane Worcester WR2 4AY
T: 01905 427100
E: sales@nal.ltd.uk
W: www.nal.ltd.uk
NATAS ASBESTOS Ltd
Earles Court, Forshaw Heath Lane Solihull B94 5LT
T: 0870 751 1880
E: info@natas.co.uk
W: www.natas.co.uk
National Access & Scaffolding Confederation (NASC)
4th Floor, 12 Bridewell Place London EC4V 6AP
T: 020 7822 7400
E: enquiries@nasc.org.uk
W: www.nasc.org.uk
National College for Advanced Transport & Infrastructure (NCATI)
2 Lister St, Birmingham B7 4AG
T: 0330 120 0375
E: enquiries@ncati.ac.uk
W: www.ncati.ac.uk
National College for High Speed Rail
2 Lister Street Birmingham B7 4AG
T: 0330 120 0375
E: enquiries@nchsr.ac.uk
W: www.nchsr.ac.uk
National Composites Centre Bristol & Bath, Science Park Emersons Green Bristol BS16 7FS
T: 0117 370 7600
E: info@nccuk.com
W: www.nccuk.com
National Federation of Builders (NFB) Spectrum House, Suite AF29 Gatwick RH6 0LG
T: 0345 057 8160
E: info@builders.org.uk
W: www.builders.org.uk
National Federation of Demolition Contractors (NFDC)
Resurgam House, Paradise Hemel Hempstead Hertfordshire HP2 4TF
T: 01442 217144
E: info@demolition-nfdc.com
W: www.demolition-nfdc.com
National Federation of Roofing Contractors (NFRC) 31 Worship Street London EC2A 2DY
T: 020 7638 7663
E: helpdesk@nfrc.co.uk
W: www.nfrc.co.uk
National Infrastructure Commission (NIC)
Finlaison House, 15-17 Furnival Street London EC4A 1AB
T: 020 7270 4624
E: enquiries@nic.gov.uk
W: www.nic.org.uk
National Railway Museum Leeman Road, York North Yorkshire YO26 4XJ
T: 0333 016 1010
E: nrm@nrm.org.uk
W: www.nrm.org.uk
National Skills Academy for Rail (NSAR) 11 Carteret Street London SW1H 9DJ
T: 020 3021 0575
E: enquiries@nsar.co.uk
W: www.nsar.co.uk
National Union of Rail, Maritime and Transport Workers (RMT) Unity House, 39 Chalton Street London NW1 1JD
T: 020 7387 4771
E: info@rmt.org.uk
W: www.rmt.org.uk
Nationwide Data Collection Ltd Haseley Office, Centre Firs Lane Haseley Warwick CV35 7LS
T: 01926 485504
E: enquiries@nationwidedatacollection.co.uk
W: www.nationwidedatacollection.co.uk
Natural Cement Distribution Ltd 10-11 Fountain Parade, Mapplewell Barnsley South Yorkshire S75 6FW
T: 01226 381133
E: enquiries@naturalcement.co.uk
W: www.naturalcement.co.uk
Navigant Consulting 5th Floor, Woolgate Exchange 25 Basinghall St London EC2V 5HA
T: 020 7469 1111
E: contactus@navigant.com
W: www.navigant.com
Naylor Drainage Ltd
Clough Green, Cawthorne
Barnsley South Yorkshire S75 4AD
T: 01226 790591
E: drainage@naylor.co.uk
W: www.naylor.co.uk
NBC Environment Limited
The Mews, Snetterton Park
Snetterton Norfolk NR16 2JU
T: 0333 567 2020
E: enquiries@nbcenvironment.co.uk
W: www.nbcenvironment.co.uk
NCC Group
XYZ Building, 2 Hardman Boulevard
Spinningfields Manchester M3 3AQ
T: 0161 209 5200
E: response@nccgroup.trust
W: www.nccgroup.trust
NDE Clarke Pitchline Ltd
NDE Buildings, Aldbourne Road
Coventry CV1 4EQ
T: 02476 222272
E: sales@ndepower.com
W: www.ndepower.com
Near Surface Geophysics Group (NSGG)
The Geological Society, Burlington House
Piccadilly London W1J 0BG
T: 020 7434 9944
E: info@nsgg.org.uk
W: www.nsgg.org.uk
Neary Rail and Construction
9 Coal Pit Lane, Atherton
Manchester M46 ORY
T: 0845 217 7150
E: info@neary.co.uk
W: www.neary.co.uk
NÉOS Superform Limited
Cosgrove Close, Worcester WR3 8UA
T: 01905 874300
E: info@neosintl.com
W: www.neosintl.com
Network Certification Body (NCB)
Groung Floor Caldecotte, The Quadrant
Eldergate Milton Keynes MK9 1EN
T: 01908 784002
E: ncbenquiries@networkrail.co.uk
W: www.net-cert.co.uk
Network Rail
1 Eversholt Street London NW1 2DN
T: 020 7557 8000
W: www.networkrail.co.uk
Network Rail (Manchester)
Square One, 4 Travis Street
Manchester M1 2NY
T: 0161 880 3936
W: www.networkrail.co.uk
Networkers International plc
1450 Parkway, Solent Business Park Whiteley Hampshire PO15 7AF
T: 01489 882500
E: info@networkerstechnology.com
W: www.networkerstechnology.com
New Holland Construction
Cranes Farm Road, Basildon
Essex SS14 3AD
T: 01268 533000
E: customerservice.na@newholland.com
W: www.newholland.com
Neway Training Solutions Limited
Kelvin House, RTC Business Park
London Road Derby DE24 8UP
T: 01332 360033
E: enquiries@neway-training.com
W: www.neway-training.com
Newcastle College Rail Academy
Williams Street, Felling Gateshead Tyne & Wear NE10 0JP
T: 0191 200 4486
E: rail@ncl-coll.ac.uk
W: www.newcastlecollege.co.uk
Newcastle University
Newcastle Upon Tyne
Tyne & Wear NE1 7RU
T: 0191 208 6000
E: pg-info@ncl.ac.uk
W: www.ncl.ac.uk
We are the UK’s leading supplier of robust and reliable automatic and manual barriers, gates and height restrictors. Whether you’re looking for a simple barrier or large commercial gate we provide quality bespoke British made vehicle access solutions, from design concept, to manufacturing, installation and after-service.
Newgate (Newark) Ltd
Brunel Drive, Newark Nottinghamshire NG24 2DE
T: 01636 700172
E: sales@newgate.uk.com
W: www.newgate.uk.com
NewRail
Newcastle University, Stephenson Building Kensington Terrace Newcastle NE1 7RU
T: 0191 208 5821
E: newrail@newcastle.ac.uk
W: www.ncl.ac.uk
Newsom Consulting Ltd
Evergreen House, North Grafton Place London NW1 2DX
T: 020 3026 3870
E: enquiries@newsomconsulting.co.uk
W: www.newsomconsulting.co.uk
Nexus Alpha Low Power Systems Ltd
London House, 7 Prescott Place
Clapham London SW4 6BS
T: 020 7622 6816
E: info@nexusalpha.com
W: www.nexusalpha.com
Nexus Recruitment Solutions
139 High Street, Portishead Bristol BS20 6PY
T: 0845 025 111
E: nexus@nexus-resources.co.uk
W: www.nexus-resources.co.uk
NG Bailey (Bailey Rail)
3rd Floor, The Angel Building
407 St John Street London EC1V 4AB
T: 020 7843 0200
E: generalenquiries@ngbailey.co.uk
W: www.ngbailey.com
Nicoll Russell Studios
111 King Street, Broughty Ferry Dundee DD5 1EL
T: 01382 778966
E: design@nrsarchitects.com
W: www.nrsarchitects.com
NightSearcher Limited
Unit 4 Applied House, Fitzherbert Spur Farlington Portsmouth PO61TT
T: 023 9238 9774
E: sales@nightsearcher.co.uk
W: www.nightsearcher.co.uk
NMB Minebea UK Ltd
Doddington Road Lincoln LN6 3RA
T: 01522 500933
E: enquiries.lincoln@nmb-minebea.com
W: www.nmb-minebea.com
Nmcn
The County Estate, Huthwaite
Sutton-in-Ashfield Nottinghamshire NG17 2HW
T: 01623 515008
E: pr@nmcn.com
W: www.northmid.co.uk
Nobel Fire Systems
7 Quest Park, Moss Hall Road Bury Lancashire BL9 7JZ
T: 01706 625777
E: info@nobel-fire-systems.com
W: www.nobel-fire-systems.com
Noble MED Solutions Ltd
2nd Floor, 12 Town Quay Wharf
Unit 12 Abbey Road Barking IG11 7BZ
T: 0737 720 6539
E: info@noblemedsolutions.com
W: www.noblemedsolutions.com
Nokia 740 Waterside Drive, Aztec West Bristol BS32 4UF
T: 01454 467000
E: info@nokia.com
W: www.nokia.com
Nomad Digital (Head Office)
5th Floor, One Trinity
Broad Chare Newcastle NE1 2HF
T: 020 7096 6966
E: experts@nomad-digital.com
W: www.nomad-digital.com
Norbar, the world’s foremost specialist in torque control, has a longstanding association with the rail industry. Our involvement starts with the manufacturers and extends through the life of the rolling stock, the networks and infrastructure. We offer pneumatic, electronic and manual torque multipliers, industrial torque wrenches, calibration and special products services.
Norbar Torque Tools Ltd
Wildmere Road, Banbury Oxfordshire OX16 3JU
T: 01295 753600
E: sales@norbar.com
W: www.norbar.com
Nord-Lock Group Kingsgate House, Newbury Road Andover Hampshire SP10 4DU
T: 01264 355557
E: enquiries@nord-lock.com
W: www.nord-lock.com
Norelem Ltd Innovation Centre, Longbridge Birmingham B31 2TS
T: 0121 222 5322
E: info@norelem.co.uk
W: www.norelem.co.uk
Nortek Global HVAC UK Ltd
Fens Pool Avenue, Brierley Hill West Midlands DY5 1QA
T: 01384 489 700
E: reznorsales@nortek.com
W: www.reznor.eu
North East Combined Authority (NECA)
Quadrant Colt Bus Park, The Silverlink North North Tyneside NE27 0BY
E: enquiries@northeastca.org.uk
W: www.northeastca.gov.uk
North Highland Consulting 120 Holborn London EC1N 2TD
T: 020 7812 6460
E: info@northhighland.com
W: www.northhighland.com
North Yorkshire Moors Railway 12 Park Street, Pickering North Yorkshire YO18 7AJ
T: 01751 473799
E: admin@nymr.co.uk
W: www.nymr.co.uk
Northern Divers specialise in underwater and surface civil engineering providing teams of divers and trained water personnel to carryout works above and below water. Bridge inspections and repairs, scour protection, river reinstatements, inland waterway repairs, maintenance, salvage, structural inspections and repairs, hydrographical and topographical surveys, prioritising customer satisfaction and cost-effectiveness.
Northern Divers Oslo Road, Sutton Fields Ind Est Hull HU7 0YN
T: 01482 227276
E: contact@northerndivers.co.uk
W: www.northerndivers.co.uk
Northern Ireland Railways
22 Great Victoria St, Belfast
Northern Ireland BT2 7LX
T: 028 9066 6630
E: feedback@translink.co.uk
W: www.translink.co.uk
Northern Precision Ltd
Unit 3, Durham Lane, Armthorpe
Doncaster South Yorkshire DN3 3FE
T: 01302 836010
E: sales@npfasteners.com
W: www.npfasteners.com
Northern Trains Ltd
Northern House, York North Yorkshire YO1 6HZ
T: 0800 200 6060
E: enquiries@northernrailway.co.uk
W: www.northernrailway.co.uk
Norton & Associates Ltd
32a High Street, Pinner Middlesex HA5 5PW
T: 020 8869 9237
E: mail@norton-associates.co.uk
W: www.nortonandassociates.co.uk
Norton Rose Fulbright
3 More, London Riverside London SE1 2AQ
T: 020 7283 6000
E: marketing@nortonrosefulbright.com
W: www.nortonrosefulbright.com
Nottingham Express Transit NET Depot, Armstrong Way Wilkinson Street Nottingham NG7 7NW
T: 0115 942 7777
E: info@thetram.net
W: www.thetram.net
Novah Ltd
Unit 12, Jenson Court
Astmoor Ind Estate Runcorn WA7 1SQ
T: 01928 242918
E: sales@novah.co.uk
W: www.novah.co.uk
Novograf
10 Langlands Place, East Kilbride Glasgow G75 0YF
T: 01355 900100
E: hello@novograf.co.uk
W: www.novograf.co.uk
Novus Rail Ltd Solaris Centre, New South Prom Blackpool FY4 1RW
T: 01253 478027
E: admin@novus-rail.com
W: www.novus-rail.com
NQA Certification Ltd Warwick House, Houghton Hall Park Dunstable Bedfordshire LU5 5ZX
T: 0800 052 2424
E: info@nqa.com
W: www.nqa.com
NRL Building 5, Glasshouse Bus. Park Wigan Lancashire WN3 6GL
T: 01324 625231
E: enquiries@nrl.co.uk
W: www.nrlrail.co.uk
NRL 2 Norman Court, Albion Road Barnsley South Yorks S71 3TE
T: 01942 614650
E: enquiries@nrl.co.uk
W: www.nrlrail.co.uk
NSI Group Ltd
Whitacre Rd Ind Estate, Nuneaton Warwickshire CV11 6BY
T: 024 7637 5656
E: sales@nsigroup.co.uk
W: www.nsigroup.co.uk
NSS Group – Nationwide Specialist Services 239 Ashley Road, Hale Altrincham Grt Manchester WA15 9NE
T: 0161 223 8100
E: salessupport@nssgroup.com
W: www.nssgroup.com
NTS Premier Services
UK House, 315 Collier Row Lane Romford Essex RM5 3ND
T: 01708 733200
E: info@ntsps.co.uk
W: www.ntsps.com
Nu Star Material Handling Ltd
Lakeside, Ednaston Bus Centre
Ednaston Derby DE6 3AE
T: 0115 880 0070
E: enquiries@nu-starmhl.com
W: www.nu-starmhl.com
Nufox reputation within the Rail Industry, comes from providing solutions from concept to finished production.
Our engineers and technical experts have knowledge in all aspects of the industry, this is the foundation of our manufacturing capability and includes all areas from material, to rubber extrusion and above all quality.
Our products include door seals, glazing strips, gaskets and bespoke fabrications.
Nufox Rubber Ltd Unit 1 Bentley Avenue, Middleton Manchester M24 2GP
T: 0161 655 8800
E: sales@nufox.com
W: www.nufox.com
Oakes Power Services Ltd Suite 2010, 6-8 Revenge Road
Lordswood Chatham Kent ME5 8UD
T: 01634 940796
E: info@ops-ltd.co.uk
W: www.oakespowerservices.co.uk
Oakland Group LLP
1 Aire Street, Leeds West Yorkshire LS1 4PR
T: 0113 234 1944
E: hello@theoaklandgroup.co.uk
W: www.theoaklandgroup.co.uk
Oasys Ltd
Central Square, Forth Street
Newcastle NE1 3PL
T: 0191 238 7559
E: oasys@arup.com
W: www.oasys-software.com
Oasys Ltd
8 Fitzroy Street, London W1T 4BJ
T: 0207 755 4515
E: oasys@arup.com
W: www.oasys-software.com
Octane Holding Group Ltd
Peace Street, Bradford BD4 8UF
T: 0113 201 2460
E: info@octane.uk.com
W: www.octane.uk.com
Office Depot
501 Beaumont, Leys Lane
Leicester LE4 2BN
T: 0116 232 3425
E: ukcustomerservice@officedepot.com
W: www.online.officedepot.co.uk
Office of Rail and Road (ORR)
25 Cabot Square London E14 4QZ
T: 020 7282 2000
E: contact.cct@orr.gov.uk
W: www.orr.gov.uk
Office Twelve
2 Exploration Drive, Pioneer Park Leicester LE4 5JD
T: 0344 801 2012
E: hello@officetwelve.com
W: www.officetwelve.com
Ogier Electronics Limited U13 Sandridge Park, Porters Wood St Albans Hertfordshire AL3 6PH
T: 01727 853521
E: enquiries@ogierelectronics.com
W: www.ogierelectronics.com
Ogle Models & Prototypes Ltd
Birds Hill, Letchworth Hertfordshire SG6 1JA
T: 01462 682661
E: info@oglemodels.com
W: www.oglemodels.com
OLD Engineering Co Ltd
Plot 1, Sketchley Lane Ind Est Burbage Leicestershire LE10 3EN
T: 01455 612521
E: sales@oldengineering.co.uk
W: www.oldengineering.co.uk
Oldham Engineering Ltd
Castle Iron Works, Overens Street Oldham Lancashire OL4 1LA
T: 0161 627 5822
E: sales@oldham-eng.com
W: www.oldham-eng.com
Oleo International Grovelands, Longford Road Exhall Coventry CV7 9NE
T: 024 7664 5555
E: sales@oleo.co.uk
W: www.oleo.co.uk
Olleco
Northampton Road, Blisworth Northampton NN7 3DR
T: 01604 857030
E: enquiries@olleco.co.uk
W: www.olleco.co.uk
Oltec Group
Oltec House, 18 Beecham Court Smithy Brooke Road Wigan WN3 6PR
T: 01942 829101
E: info@oltecgroup.com
W: www.oltecgroup.com
OLTIS Group a.s. Dr. Milady, Horákové 1200/27a 779 00
T: 00 420 588 208 555
E: oltis@oltis.cz
W: www.oltis.cz
Omnicom Balfour Beatty
Eboracum House, Clifton Park Avenue York YO30 5PB
T: 01904 778100
E: info@omnicomengineering.co.uk
W: https://omnicombalfourbeatty.com
One Way Resourcing Limited
U6-7 Cross House Centre, Cross House Road Southampton Hampshire SO14 5GZ
T: 023 8098 1600
E: info@oneway.co.uk
W: www.oneway.co.uk
Onis Consulting Limited
8 Bradley Drive, Grantham Lincolnshire NG31 7WW
T: 07930 115709
E: robin@onis-consulting.co.uk
W: www.onis-consulting.co.uk
OnTrac Ltd
Baltimore House, Baltic Business Quarter Gateshead Tyne & Wear NE8 3DF
T: 0191 477 4951
E: enquiries@on-trac.co.uk
W: www.on-trac.co.uk
We’re a leading provider of psychometric tests and exercises in the transport sector. Our tools are designed to identify capabilities in current employees and potential in job applicants. For businesses without in-house expertise, we also provide trained assessors and a Bureau Service to manage assessment testing for any sized recruitment process.
OPC Assessment
One Wellstones, Watford Hertfordshire WD17 2AE
T: 01923 234646
E: admin@theopc.co.uk
W: www.theopc.co.uk/assessment
Open Technology Ltd
1 Woodlands Court, Albert Drive Burgess Hill West Sussex RH15 9TN
T: 01444 230660
E: info@opentechnologyuk.com
W: www.opentechnologyuk.com
Opentree Ltd
Cabinet House, Ellerbeck Court Stokesley Bus Park Stokesley TS9 5PT
T: 01642 714471
E: info@opentree.co.uk
W: www.opentree.co.uk
Optasense Ltd
Cody Technology Park, Ively Road
Farnborough Hampshire GU14 0LX
T: 01252 392000
E: contact@optasense.com
W: www.optasense.com
Optical Coating Technologies Unit 8, Lagrange Lichfield Road Tamworth B79 7XD
T: 01827 63489
E: info@optical-coatings.com
W: www.optical-coatings.com
Optosafe Ltd
15 Spiersbridge Way, Spiersbridge Bus Park Thornliebank Glasgow G46 8NG
T: 0141 428 3482
E: cctv@optosafe.co.uk
W: www.optosafe.co.uk
Optus Anti-skid surfacing systems
22 Tarran Way North, Moreton Wirral Merseyside CH46 4UA
T: 0151 604 0001
E: info@optus.co.uk
W: www.optus.co.uk
Orano Projects Limited Suite 7 Hitching Court, Abingdon Business Park Abingdon Oxfordshire OX14 1RA
T: 01235 555755
E: abingdon@oranoprojects.uk
W: www.oranoprojects.uk
Orapi Applied Ltd Spring Road, Smethwick West Midlands B66 1PT
T: 0121 525 4000
E: info@orapiapplied.com
W: www.orapiapplied.com
Orbis Protect Beaufort House, Cricket Field Road Uxbridge UB8 1QG
T: 08000 830 850
E: rail@orbisprotect.com
W: www.orbisprotect.com
Orbital Fasteners is a leading online & telesales distributor of fixings, fasteners, tools & power tools specialising in next day delivery to construction sites and factories in and around London via our own van fleet and nationally via carrier.
Orbital Fasteners Olds Approach, Tolpits Lane Watford Herts WD18 9XT
T: 01923 777777
E: sales@orbitalfasteners.co.uk
W: www.orbitalfasteners.co.uk
Osborne Rail
Fonteyn House, 47-49 London Road Reigate Surrey RH2 9PY
T: 0800 025 8008
E: enquiries@osborne.co.uk
W: www.osborne.co.uk
OSL Global
The Railway Exchange, Weston Road Crewe Cheshire CW1 6AA
T: 0845 271 9171
E: enquiries@oslglobal.com
W: www.oslglobal.com
OSL Rail Limited
The Railway Exchange, Weston Road Crewe Cheshire CW1 6AA
T: 0845 271 9171
E: enquiries@o-s-l.uk.com
W: www.oslglobal.com
Osprey Shipping Limited
9 Portis Fields, Bristol Road Portishead BS20 6PN
T: 01275 460608
E: hello@osprey.group
W: www.osprey.group
OTM Learning
630 High Road, Woodford Green IG8 0PS
T: 020 3093 1828
E: social@otmlearning.com
W: www.otmlearning.com
Overhead Line Engineering Limited
4b Mallard Way, Pride Park Derby DE24 8GX
T: 01332 342122
E: contact@ole-limited.co.uk
W: www.ole-limited.co.uk
Overseas Trade Shows Agency (OTSA)
Montgomery Exhibitions, 9 Manchester Square London W1U 3PL
T: 020 7886 3000
E: otsa@otsa.net
W: www.otsa.net
Oxford Plastic Systems Ltd
Enstone Business Park, Enstone Chipping Norton Oxfordshire OX7 4NP
T: 01608 678888
E: sales@oxfordplastics.com
W: www.oxfordplastics.com
P Ducker Systems Ltd
Olympus House, Stephenson’s Way Wyvern Bus Park Derby DE21 6LY
T: 01332 280195
E: info@pdslimited.co.uk
W: www.pdslimited.co.uk
PA Consulting Group
10 Bressenden Place London SW1E 5DN
T: 020 7333 5865
E: info@paconsulting.com
W: www.paconsulting.com
PACE Networks
4 The Hayloft, Far Peak Northleach GL54 3AP
T: 01285 323525
E: info@pace-networks.co.uk
W: www.pace-networks.co.uk
Padley & Venables – Quality Tools, Made in Britain, Proven Worldwide.
Demolition Tools, Contractors’ Tools, Rock Drilling Tools.
P&V have been manufacturing quality tools in the UK for over 100 years – using up to date manufacturing methods and production processes to ensure the best possible product where it matters most.
Padley & Venables
Callywhite Lane, Dronfield Sheffield S18 2XT
T: 01246 299100
E: sales@padley-venables.com
W: www.padley-venables.com
Pageantry Electronic Systems Ltd
Argent Court, Hook Rise South Surbiton KT6 7NL
T: 020 8391 8360
E: sales@pageantry.co.uk
W: www.pageantry.co.uk
Paint Inspection Ltd (Head Office)
61 High Street, Fareham Hampshire PO16 7BG
T: 0845 463 8680
E: admin@paint-inspection.co.uk
W: www.paint-inspection.co.uk
Painting and Decorating Association (PDA)
32 Coton Road, Nuneaton Warwickshire CV11 5TW
T: 024 7635 3776
E: info@paintingdecoratingassociation.co.uk
W: www.paintingdecoratingassociation.co.uk
Paintmaster Trade Paints Manufacturer
Unit 12-17, Bingswood Ind Estate Whaley Bridge Derbyshire SK23 7LY
T: 01663 733633
E: orders@paintmaster.co.uk
W: www.paintmaster.co.uk
Palmers Scaffolding UK Ltd
331 Charles Street, Glasgow Scotland G21 2QA
T: 0141 553 4040
E: info@palmersgroup.co.uk
W: www.palmersgroup.co.uk
Pandrol defines the industry standard across rail fastening systems and aluminothermic welding. Our products and services extend to designing, developing and manufacturing equipment to make constructing and maintaining railways more efficient. Our smart control systems increase productivity, monitor track conditions and improve the overall track life cycle.
Pandrol Gateford Road, Worksop Nottinghamshire S81 7AX
T: 01909 476101
E: info@pandrol.com
W: www.pandrol.com
Panduit (Europe) Ltd
West World, Westgate London W5 1UD
T: 020 8601 7200
E: emea-customerservices@panduit.com
W: www.panduit.com
Paperless Construction
3 Westfield House, Millfield Lane
Nether Poppleton York YO26 6GA
T: 01904 373081
E: info@paperlessconstruction.co.uk
W: www.paperlessconstruction.co.uk
Paragon ID
Stockholm Road, Sutton Fields Hull HU7 0XY
T: 01482 826343
E: info@bemrosebooth.com
W: www.bemrosebooth.com
Specialists in innovative design and product development to enhance service life of train control systems and equipment, using cost effective digital solutions to deliver problem solving solutions to heavy and light rail networks.
Park Signalling Limited
Holdsworth Mill, Houldsworth Street
Reddish Stockport SK5 6DA
T: 0161 219 0161
E: sales@park-signalling.co.uk
W: www.park-signalling.co.uk
Parkeon Ltd
10 Willis Way, Poole Dorset BH15 3SS
T: 01202 339339
E: sales_uk@parkeon.com
W: www.parkeon.co.uk
Parker Hannifin
Tachbrook Park Drive, Tachbrook Park
Warwick CV34 6TU
T: 01926 317878
E: parker.uk@parker.com
W: www.parker.com
Parry People Movers Ltd
Parry House, Overend Road
Cradley Heath West Midlands B64 7RD
T: 01384 569553
E: info@parrypeoplemovers.com
W: www.parrypeoplemovers.com
Partex Marking Systems (UK) Ltd
Units 61-64 Station Rd, Coleshill
Birmingham B46 1JT
T: 01675 463670
E: sales@partex.co.uk
W: www.partex.co.uk
Partline Limited
Dockfield Road, Shipley West Yorkshire BD17 7AZ
T: 01274 531531
E: sales@partline.co.uk
W: www.partline.co.uk
Pascall+Watson
The Warehouses, 10 Black Friars Lane London EC4V 6ER
T: 020 3837 2500
E: info@pascalls.co.uk
W: www.pascalls.co.uk
Passcomm Limited
24 Tatton Court, Kingsland Grange Warrington Cheshire WA1 4RR
T: 01925 821333
E: sales@passcomm.co.uk
W: www.passcomm.co.uk
Passenger Transport Networks
49 Stonegate, York Yorkshire YO1 8AW
T: 01904 611187
E: info@passengertransportnetworks.co.uk
W: www.passengertransportnetworks.co.uk
Pathfinder Tours
Stag House, Gydynap Lane
Inchbrook Woodchester Glos GL5 5EZ
T: 01453 835414
E: office@pathfindertours.co.uk
W: www.pathfindertours.co.uk
Pauley Interactive (Head Office)
Bletchley Leys Farm, Whaddon Road
Milton Keynes MK17 0EG
T: 020 3432 8680
E: info@pauley.co.uk
W: www.pauley.co.uk
PAYE Stonework and Restoration Ltd
Stationmasters House, Mottingham Station Approach London SE9 4EL
T: 020 8857 9111
E: ask@paye.net
W: www.paye.net
Payzone UK Limited
Andmore House, Unit 4 Triangle Court Cheshire Bus Park Northwich CW9 7YL
T: 01606 566600
E: info@payzone.co.uk
W: www.payzone.co.uk
PBH rail are a well-established survey and design company delivering Track/OLE survey and design nationally, delivering small scale single discipline design to large scale multidisciplinary services. We have a team of 70 experienced staff and work with our partners in Signalling, Civils and E&P providing a one-stop shop for clients.
PBH Rail
The Old Coach House, 4a Custance Walk York North Yorkshire YO23 1BX
T: 01904 655666
E: enquiries@pbhrail.com
W: www.pbhrail.com
PBWel
Unit 1, Leafield Way, Corsham Corsham Wiltshire SN13 9SW
T: 01225 811449
E: sales@pbwel.com
W: www.pbwel.com
PCE Instruments UK Ltd Unit 11, Southpoint Bus Park Ensign Way Southampton SO31 4RF
T: 023 8098 7030
E: info@industrial-needs.com
W: www.pce-instruments.com
PCL Industrial Cleaning & Coating Ltd PO BOX 455, St Helens WA10 9GA
T: 0161 672 7432
E: info@pclicc.co.uk
W: www.pclicc.co.uk
PcP Gratings Ltd Enterprise Drive, Four Ashes Wolverhampton WV10 7DF
T: 01902 791792
E: sales@pcpgratings.co.uk
W: www.pcpgratings.co.uk
PD Devices Ltd
Old station Yard, South Brent Devon TQ10 9AL
T: 01364 649248
E: info@pddevices.co.uk
W: www.pddevices.co.uk
PE Systems Ltd Unit 2, Hindley Green Bus Park
Leigh Road Wigan WN2 4TN
T: 01942 260330
E: sales@pe-systems.co.uk
W: www.pe-systems.co.uk
PEL Services Ltd Unit 1-2, Belvue Business Centre Northolt Middlesex UB5 5QQ
T: 0333 123 2100
E: info@pel.co.uk
An Employee Owned Company
PB Design & Developments Limited is a proud manufacturer/partner of PADS approved chargers for our Rail, Metro & Underground customers. In addition, our battery chargers, UPS, batteries and system services are trusted in all types of AC and DC standby power applications. Customer service and satisfaction, plain and simple.
PB Design & Developments Ltd
Hithergreen Ind Estate, Clevedon North Somerset BS21 6XT
T: 01275 874411
E: sales@pbdesign.co.uk
W: www.pbdesign.co.uk
PB Metal Finishing Systems Ltd
Unit 11, Eclipse Trading Estate
Sedgley Road Tipton DY4 8DQ
T: 0121 522 3513
E: info@pbmetalfinishingsystems.com
W: www.pbmetalfinishingsystems.com
W: www.@pel.co.uk
Peli Products (UK) Ltd
Peli House, Peakdale Road Brookfield Glossop SK13 6LQ
T: 01457 869999
E: sales@peliproducts.co.uk
W: www.peliproducts.co.uk
Pendersons Ltd
Pendersons House, Pleasant Street Stoke-on-Trent ST6 3DL
T: 01782 832090
E: info@pendersons.com
W: www.pendersons.com
Penna Plc (London Central Office)
Millennium Bridge House, 2 Lambeth Hill London EC4V 4BG
T: 020 3849 2777
E: info@penna.com
W: www.penna.com
Pennant PLC Parkway House, Palatine Road
Northenden Manchester M22 4DB
T: 0161 947 6940
E: rail@pennantplc.co.uk
W: www.pennantplc.co.uk
Penningtons Manches (Solicitors)
125 Wood Street, London EC2V 7AW
T: 020 7457 3000
E: info@penningtons.co.uk
W: www.penningtons.co.uk
Pennys Group Ltd
Green Street, Ston Easton Somerset BA3 4BY
T: 01761 241387
E: info@pennysgroup.co.uk
W: www.pennysgroup.co.uk
Penso Woodhams Road, Coventry Warwickshire CV3 4FX
T: 024 7621 7760
E: info@penso.uk.com
W: www.penso.co.uk
Penspen Ltd
Darpen House, 3 Water Lane Richmond Surrey TW9 1TJ
T: 020 8334 2700
E: info@penspen.com
W: www.penspen.com
Penton UK Ltd
Unit 2, Teville Industrials
Dominion Way Worthing BN14 8NW
T: 01903 215315
E: sales@pentonuk.co.uk
W: www.pentonuk.co.uk
People 1st Hospitality House, 11-59 High Road East Finchley London N2 8AB
T: 020 3074 1222
E: info@people1st.co.uk
W: www.people1st.co.uk
Percipere
Suite 424, The Atrium 1 Harefield Road Uxbridge UB8 1EX
T: 07860 806104
E: percipereuk@gmail.com
W: www.percipere.co
Perimeter Security Suppliers Association (PSSA)
Unit 19, Omega Business Village
Thurston Road Northallerton DL6 2NJ
T: 020 8253 4509
E: admin@pssasecurity.org
W: www.pssasecurity.org
Permali
Permali Gloucester Ltd, Bristol Road Gloucester Gloucestershire GL1 5TT
T: 01452 528282
E: marketing@permali.co.uk
W: www.permali.co.uk
Permalok has been supplying Huck© fasteners and tooling to the rail market for over 25 years. We are able to supply from stock Huck© lockbolts and blind fasteners for use in both Permanent Way and rolling stock. We also stock Huck© tooling and offer a tooling repair/ hire service.
Permalok Fastening Systems Ltd
Unit 1a, Plumtree Ind Estate Harworth Doncaster DN11 8EW
T: 01302 711308
E: info@permalokfastening.co.uk
W: www.permalokfastening.co.uk
Permanent Way Institution (PWI)
5 Mount Crescent, Warley Brentwood CM14 5DB
T: 01277 230031
E: secretary@pwi.org
W: www.thepwi.org
Permaquip Ltd
Old Sleningford Farm, North Stainley Ripon North Yorkshire HG4 3JB
T: 01623 513349
E: sales@permaquip.co.uk
W: www.permaquip.co.uk
Perpetuum Ltd
Unit 7 The Quadrangle, Abbey Park Ind Estate Romsey SO51 9DL
T: 023 8076 5888
E: info@perpetuum.co.uk
W: www.perpetuum.com
Petards
390 Princesway, Team Valley
Gateshead Tyne & Wear NE11 0TU
T: 0191 440 1104
E: rail@petards.com
W: www.petards.com
Peter Alvey – Freelance Photographer
Alvey & Towers, 8 Nether Street
Harby Leicestershire LE14 4BW
T: 01949 861894
E: office@alveyandtowers.com
W: www.peteralvey.com
Petrotechnics Ltd
Pavilion 3, Craigshaw Business Park
Craigshaw Road Aberdeen AB12 3QH
T: 01224 337200
E: info@petrotechnics.com
W: www.petrotechnics.com
PFB Recruitment Ltd
13 Cromwell Road, Eynesbury St Neots Cambridge PE19 2HP
T: 01480 702005
E: paul@pfbrecruitment.com
W: www.pfbrecruitment.com
Phixos Limited
Teme House, Whittington Road
Whittington Worcester WR5 2RY
T: 01905 368580
E: contact@phixos.co.uk
W: www.phixos.co.uk
Phoenix Contact Ltd
Halesfield 13, Telford
Shropshire TF7 4PG
T: 0845 881 2222
E: info@phoenixcontact.co.uk
W: www.phoenixcontact.co.uk
Picturascope Ltd
Suite 5.2a, 140 Tabernacle Street
Shoreditch London EC2A 4SD
T: 020 7099 8635
E: info@picturascope.com
W: www.picturascope.com
Pilz Automation Technology
Pilz House, 3 Little Colliers Field
Corby Northamptonshire NN18 8TJ
T: 01536 460766
E: sales@pilz.co.uk
W: www.pilz.co.uk
Pinnacle PSG
1st Floor, 6 St Andrews Street
Holborn London EC4A 3AE
T: 020 7017 2000
E: enquiries@pinnaclegroup.co.uk
W: www.pinnaclepsg.co.uk
Pipe Jacking Association (PJA)
6 Burroughs Bank, Lightmoor Telford TF4 3QS
T: 0345 0705201
E: graeme.monteith@pipejacking.org
W: www.pipejacking.org
Pipex Ltd
Devon Ent Facility, 1 Belliver Way
Roborough Devon PL6 7BP
T: 01752 581200
E: fgssales@nov.com W: www.pipexpx.com
Pirtek (UK) Ltd
199 The Vale, Acton London W3 7QE
T: 020 8749 8444
E: info@pirtek.co.uk W: www.pirtek.co.uk
Pivovar Ltd Station Yard, York Road
Elvington North Yorkshire YO41 4EL
T: 01904 607197
E: sales@pivovar.co.uk
W: www.pivovarorders.co.uk
Plascoat Systems Ltd
Farnham Trading Estate, Farnham Surrey GU9 9NY
T: 01252 738220
E: sales@plascoat.com
W: www.plascoat.com
Using green energy to clear the residue on tracks, PlasmaTrack will restore the track to a dry, clean and uncontaminated state. Our Plasma technology, enables trains to run as if it were summer all year round, leading to increased capacity and closer running trains.
PlasmaTrack Ltd
Unit 149, The Light Box, 111 Power Road
Chiswick London W4 5PY
T: 07748 767688
E: julian@plasmatrack.co.uk
W: www.plasmatrack.co.uk
Plasser & Theurer
Plasser UK Ltd, Manor Road
West Ealing London W13 0PP
T: 020 8998 4781
E: info@plasser.co.uk
W: www.plasser.co.uk
Plastech Limited
Park Industrial Estate, Liverpool Road
Wigan WN4 OYU
T: 01942 717110
E: info@plastechtitan.co.uk
W: www.plastechtitan.co.uk
Plastic Coatings Limited
Ham Lane, Kingswinford West Midlands DY6 7JY
T: 0800 008 6903
E: enquiries@plastic-coatings.com
W: www.plasticcoatings.co.uk
Platinum Resources
1 Fore Street, London London EC2Y 9DT
T: 020 7242 9944
E: info@platinumresources.co.uk
W: www.platinumresources.co.uk
Platipus Anchors Ltd
Kingsfield Bus Centre, Philanthropic Road Redhill Surrey RH1 4DP
T: 01737 762300
E: info@platipus-anchors.com
W: www.platipus-anchors.com
Plowman Craven Ltd
2 Lea Business Park, Harpenden Hertfordshire AL5 5EQ
T: 01582 765566
E: webenquiry@plowmancraven.co.uk
W: www.plowmancraven.co.uk
Creating a skilled workforce is our aim. We provide training and assessment for companies looking to develop their staff. Our areas of expertise are: Trainer, Assessor and IQA national qualifications
• IRSE Licencing
Signalling Training & Assessment
• Level 2, 3 and 4 Apprenticeships incorporating traditional railway courses.
PM Training and Assessing Ltd
The Courtyard Granary, Standard Street Crickhowell Powys NP8 1BP
T: 01874 620 704
E: enquiries@pmtanda.co.uk
W: www.pmtanda.co.uk
PMC Foundations and Underpinning Ltd
10a Ellery Street, Peckham London SE15 3RL
T: 020 7639 7642
E: info@pmcfoundations.co.uk
W: www.basementunderpinning.co.uk
PMC Marketing
Pantiles Chambers, 85 High Street
Tunbridge Wells TN1 1XP
T: 01892 506992
E: info@pmcmarketing.co.uk
W: www.pmcmarketing.co.uk
Pneumatrol Limited
West End Business Park, Blackburn Road
Oswaldtwistle Accrington BB5 4WZ
T: 01254 872277
E: sales@pneumatrol.com
W: www.pneumatrol.com
Pochins Ltd
Brooks Lane, Middlewich Cheshire CW10 0JQ
T: 01606 833333
E: info@pochins.com
W: www.pochins.com
Pod-Trak offers bespoke engineering solutions to clients across the UK and Ireland who seek an innovative approach to the construction and maintenance of transport infrastructure in the Railway, Airport and Civil Engineering sectors. Our specialist Divisions cover Railway Electrification, Civil Engineering, Permanent Way, Communications and Airports & Stations.
Pod-Trak
Crove House, 14 Aintree Road
Perivale London UB6 7LA
T: 020 8998 0010
E: enquiries@pod-trak.com
W: www.pod-trak.com
Poise Group Ltd
Fleet House, 8-12 New Bridge Street London EC4V 6AL
T: 020 3086 9400
E: info@poisegroup.uk
W: www.poisegroup.uk
Polgain Cams, Camshafts & Precision Engineering
1 Crown Score, Off Whapload Road Lowestoft NR32 1JH
T: 01502 532880
E: info@polgain.co.uk
W: www.polgain.co.uk
Polypipe Civils & Green Urbanisation
Charnwood Business Park, North Road
Loughborough LE11 1LE
T: 01509 615100
E: civilsenquiries@polypipe.com
W: www.polypipe.com
Polysafe Level Crossings Systems Ltd 25 King Street Ind Est, Langtoft
Peterborough PE6 9NF
T: 01778 560555
E: polysafeoffice@polysafe.co.uk
W: www.polysafe.co.uk
Pontoon Provider Haycocks Lane, West Mersea CO5 8SS
T: 01206 382317
E: Ben@pontoonprovider.co.uk
Pontoon Works Ltd
The Old Glove Factory, Bristol Road
Sherborne Dorset DT9 4HP
T: 01935 814950
E: office@pontoonworks.co.uk
W: www.pontoonworks.co.uk
Portaramp UK Limited Units 3 & 4, Dolphin Business Park
Shadwell Thetford Norfolk IP24 2RY
T: 01953 681799
E: sales@portaramp.co.uk
W: www.portaramp.co.uk
Portastor Ltd
New Lane, Huntington York YO32 9PR
T: 0845 601 1276
E: action@portastor.com
W: www.portastor.com
Porterbrook Leasing Company Limited
Ivatt House, 7 The Point
Pinnacle Way Derby DE24 8ZS
T: 01332 285050
E: enquiries@porterbrook.co.uk
W: www.porterbrook.co.uk
POS Services
Cunningham House, 19-21 Westfield Lane Harrow Middlesex HA3 9ED
T: 020 8931 8757
E: info@posservicesuk.com
W: www.posservicesuk.com
Positive
Willoughby House, 439 Richmond Road Richmond TW1 2AG
T: 020 8744 4350
E: enquiries@positive.co.uk
W: www.positive.co.uk
Postfield Systems Ltd
53 Ullswater Crescent, Couldson Surrey CR5 2HR
T: 020 8655 6080
E: accounts@postfield.co.uk
W: www.postfieldsystems.wixsite.com
Poundfield Precast
The Grove, Creeting St Peter Ipswich Suffolk IP6 8QG
T: 01449 723150
E: enquiries@poundfield.com
W: www.poundfield.com
Powdertech (Corby) Ltd
Cockerell Road, Phoenix Park
Corby Northamptonshire NN17 5DU
T: 01536 400890
E: pcl@powdertech.co.uk
W: www.powdertechcorby.co.uk
Powelectrics
12 Ninian Park, Tamworth Staffordshire B77 5ES
T: 01827 310666
E: sales@powelectrics.co.uk
W: www.powelectrics.co.uk
Powell Dobson Architects Ltd
Suite 1F Building One, Eastern Business Park Old St Mellons Cardiff CF3 5EA
T: 0333 320 1001
E: cardiff@powelldobson.com
W: www.powelldobson.com
Power Continuity Ltd
Kemp House, 152 – 160 City Road London EC1V 2NX
T: 08450 558455
E: powercontinuity8@gmail.com
W: www.powercontinuity.co.uk
Power Jacks
Kingshill Commercial Pk, Prospect Road
Westhill Aberdeenshire AB32 6FP
T: 01358 285100
E: sales@powerjacks.com
W: www.powerjacks.com
Power System Services Ltd
Carrwood Road, Sheepbridge Chesterfield S41 9QB
T: 01246 268800
E: info@powersystemservices.co.uk
W: www.powersystemservices.co.uk
Power Systems International Ltd
Carina House East, Sunrise Parkway Linford Wood Milton Keynes MK14 6LS
T: 01494 871544
E: info@powersystemsinternational.com
W: www.powersystemsinternational.com
Power Testing Limited 33 Hanbury Road, Widford Ind Estate Chelmsford Essex CM1 3AE
T: 01245 266800
E: info@powertesting.co.uk
W: www.powertesting.co.uk
Powernetics International Ltd
Power House, Jason Works Clarence Street Loughborough LE11 1DX
T: 01509 214153
E: sales@powernetics.co.uk
W: www.powernetics.co.uk
Powertherm Contracting Services
Powerherm Ltd, Francis House Orgreave Drive Sheffield S13 9NR
T: 0114 288 9119
E: info@powertherm.co.uk
W: www.powertherm.co.uk
Pozzoni (Altrincham office) Woodville House, 2 Woodville Road Altrincham WA14 2FH
T: 0161 928 7848
E: architects@pozzoni.co.uk
W: www.pozzoni.co.uk
PP Group of Companies Ltd
Profiles Point, Drury Lane
Oldham Greater Manchester OL9 7PH
T: 0161 938 8080
E: sales@ppgroupltd.co.uk
W: www.ppgroupltd.co.uk
PPS Rail
Unit 22 Rufford Court, Hardwick Grange Warrington Cheshire WA1 4RF
T: 01925 813897
E: enquiries@pps-rail.co.uk
W: www.ppsrail.co.uk
Pragmasis Limited
78 Castlehall, Tamworth Felspar Road Tamworth B77 4DP
T: 01827 286267
E: info@pragmasis.com
W: www.securityforbikes.com
Pramac-Generac UK
Pramac House, Tunstall Arrow South Stoke on Trent ST6 5GF
T: 01270 445777
E: uk@pramac.com
W: www.towerlight.com
PRB Consulting The Town House, Market Street
Hailsham East Sussex BN27 2AE
T: 01323 887186
E: info@prb-consulting.co.uk
W: www.prb-consulting.co.uk
PRBX (Powerbox) UK
Suite 57-58 Lynx House, Basepoint Bus Centre Caxton Close Andover SP10 3FG
T: 01264 326457
E: info.uk@prbx.com
W: www.prbx.com
PreCast Advanced Track Ltd
Meadow Cottage, Hatton Farm Hatton Warwick CV35 7EY
T: 01926 484080
E: info@precastadvancedtrack.com
W: www.precastadvancedtrack.com
Predator Trailers Ltd
53 Dungorman Road, Dungannon Co Tyrone Northern Ireland BT71 6SD
T: 028 3754 8889
E: info@predator100.com
W: www.predator100.com
Premier Calibrations Ltd
219 Bentley Road, Doncaster South Yorkshire DN5 9TB
T: 01302 787333
E: premcal@premier-calibration.co.uk
W: www.premier-calibration.co.uk
Premier Pits
Town Drove, Quadring Spalding Lincolnshire PE11 4QP
T: 01775 821222
E: info@premierpits.com
W: www.premierpits.com/railpits
Premier Rail are specialists in installing, upgrading and maintaining of all types of level crossings and road rail access points across the UK. As approved installers of Rosehill Rail, Strail and Polysafe, Premier Rail offer the complete turnkey solution in the installation, removal and upgrading of level crossings and RRAPs.
Premier Rail Services
Plumtree Industrial Est, Plumtree Road Bircotes Doncaster DN11 8EW
T: 01302 738020
E: info@premier-rail.co.uk
W: www.premier-rail.co.uk
Priestman Goode
150 Gt Portland Street
London W1W 6QD
T: 020 7580 3444
E: studio@priestmangoode.com
W: www.priestmangoode.com
Primary Image Ltd
Business Hub, 10 Elmer Approach
Southend-on-Sea Essex SS1 1LW
T: 01702 680690
E: hello@primaryimage.com
W: www.primaryimage.uk
Primat Recruitment
Falcon Court, Preston Farm Bus Park
Stockton on Tees TS18 3TU
T: 01642 130300
E: primatrecruitment@worleyparsons.com
W: www.primatrecruitment.com
Prime Rail Solutions Ltd
Dartford Road, March
Cambridgeshire PE15 8AE
T: 01733 462420
E: info@primerailsolutions.com
W: www.primerailsolutions.com
Pristine Condition Ltd
Unit 1, Centenary Business Park
Station Road Oxfordshire RG9 1DS
T: 01491 414464
E: info@pristinecondition.com
W: www.pristinecondition.com
Pro-Link Europe Limited
Irene House, Five Arches Bus Park
Maidstone Road Sidcup Kent DA14 5AE
T: 020 8309 2700
E: enquire@prolink-europe.com
W: www.prolink-europe.com
Pro-Style Ltd
Unit 7b Crondal Road, Bayton Road Ind Estate Coventry CV7 9EP
T: 024 7636 7441
E: info@pro-style.co.uk
W: www.pro-style.co.uk
Pro-Tek Engineering
Unit 1, Waterloo Industrial Pk
Waterloo Road Bidford on Avon B50 4JH
T: 01789 490490
E: enquiries@protekeng.co.uk
W: www.protek-eng.co.uk
ProActive Recruitment Services
78 York Street, Marylebone London W1H 1DP
T: 020 7993 6049
E: enquiries@proactiverail.co.uk
W: www.proactiverail.co.uk
Probst Handling Equipment
Unit 2 Fletcher House, Stafford Park 17 Telford TF3 3DG
T: 01952 292733
E: sales@probst-handling.co.uk
W: www.probst-handling.co.uk
Professional Lifting Services Limited
Unit 7, Parkview Works
870 Penistone Road Sheffield S6 2DL
T: 0114 285 5488
E: mail@plsltd.co.uk
W: www.plsltd.co.uk
Profin Protective Finishing Ltd
Unit 33, Crossgate Road
Park Farm Ind Est Redditch B98 7SN
T: 01527 524126
E: sales@profingroup.co.uk
W: www.profingroup.co.uk
Progress Rail Services UK Ltd
Headrig Road, South Queensferry
West Lothian Scotland EH30 9SH
T: 0131 319 3700
E: prsuk.sales@progressrail.com
W: www.progressrail.com
Project 7 Consultancy UK Ltd
Westpoint House, 5 Redwood Place
Peel Park East Kilbride G74 5PB
T: 0844 568 6840
E: enquiries@project7consultancy.com
W: www.project7consultancy.com
Project Control Tools offer simple software solutions for Rail and Construction. Our benefits reach all areas of the business by reducing project spend and increasing efficiencies through the capture and automation of Site Information.
We enable a seamless transition in Digital Transformation, providing efficient and costeffective solutions for your business.
Project Control Tools
Office 16, East Durham Bus Ctr
Station Town Wingate Durham TS28 5HD
T: 0191 731 9933
E: fin.gregory@projectcontroltools.co.uk
W: www.projectcontroltools.co.uk
Project EU Ltd
Strathallan House, Midland Road
Hemel Hempstead Hertfordshire HP1 4LS
T: 0845 680 0193
E: intouch@project.eu.com
W: www.project.eu.com
Project Leaders Ltd
137b Minnis Road, Birchington Kent CT7 9NS
T: 01843 847848
E: info@projectleaders.co.uk
W: www.projectleaders.co.uk
Prolec Ltd 25 Benson Road, Nuffield Ind Estate
Poole Dorset BH17 0GB
T: 01202 681190
E: info@prolec.co.uk
W: www.prolec.co.uk
Pronto Direct Unit 8 Hornsby Square Basildon Essex SS15 6SD
T: 01268 414418
E: support@prontodirect.co.uk
W: www.prontodirect.co.uk
Propeller Studios First Floor, Alexander House Bus Ctr
40a Wilbury Way Hitchin SG4 0AP
T: 01462 440077
E: info@propeller-studios.co.uk
W: www.propeller-studios.co.uk
Protec Direct Unit 1 Britannia Park, Trident Drive Wednesbury WS10 7XB
T: 0870 333 3081
E: sales@protecdirect.co.uk
W: www.protecdirect.co.uk
Protec Fire Detection Plc Protec House, Churchill Way Nelson Lancashire BB9 6RT
T: 01282 717171
E: sales@protec.co.uk
W: www.protec.co.uk
ProtectHear 18 Eve Street, Louth Lincolnshire LN11 0JJ
T: 01507 604322
E: enquiries@protecthear.co.uk
W: www.protecthear.co.uk
Proteq Northern Ltd 96 High Street, Epworth Doncaster DN9 1JS
T: 01427 872572
E: info@proteq.co.uk
W: www.proteq.co.uk
Provertha Connectors, Cables & Solutions GMBH Westring 9, Pforzheim Germany 75180
T: 07824 444612
E: chris.osborn@provertha.com
W: www.provertha.com
PRV Engineering Ltd
Pegasus House, Polo Grounds New Inn
Pontypool Gwent NP4 0TW
T: 01495 769697
E: enquiries@prv-engineering.co.uk
W: www.prv-engineering.co.uk
Prysmian UK
Chickenhall Lane, Eastleigh Hampshire SO50 6YU
T: 023 8029 5555
E: cables.marketing.uk@prysmiangroup.com
W: uk.prysmiangroup.com
PSD Group
21 Perrymount Road, Haywards Heath West Sussex RH16 3TP
T: 01293 802039
E: haywardsheath@psdgroup.com
W: www.psdgroup.com
PSG Ltd
2 Bordon Trading Estate, Old Station Way Bordon Hampshire GU35 9HH
T: 01428 651246
E: info@paintservices.com
W: www.paintservices.com
PSI Technologies Ltd Technology House, Stratfield Park Elettra Avenue Waterlooville PO7 7XN
T: 02392 233611
E: sales@psitech.co.uk
W: www.psitech.co.uk
PSR Solutions
8th Floor, 140 Aldersgate Street London EC1A 4HY
T: 020 3800 0050
E: info@psrsolutions.co.uk
W: www.psrsolutions.co.uk
PSS Folgate Road, North Walsham Norfolk NR28 0AJ
T: 01692 406017
E: sales@pss.co.uk
W: www.pss.co.uk
PSV Glass Hillbottom Road, High Wycombe Buckinghamshire HP12 4HJ
T: 01494 533131
E: railsales@psvglass.co.uk
W: www.psvglass.com
PSV Wipers Ltd
18 Kempton Road, Keytec 7 Business Park Pershore Worcestershire WR10 2TA
T: 01905 350500
E: sales@psvwipers.com
W: www.psvwipers.com
PTP Associates Limited
The Lodge, 21 Harcourt Road Dorney Reach Berkshire SL6 0DT
T: 01628 776059
E: info@ptpassociates.co.uk
W: www.ptpassociates.co.uk
PTRC Education and Research Services Ltd.
22 Greencoat Place London SW1P 1PR
T: 020 7348 1970
E: info@ptrc-training.co.uk
W: www.ptrc-training.co.uk
Pullman Instruments (UK) Ltd
Chatsworth House, Chatsworth Terrace Harrogate North Yorkshire HG1 5HT
T: 01423 720360
E: sales@pullman.co.uk
W: www.pullman.co.uk
PULS is focused entirely on development and production of DIN-rail power supplies. We concentrate our engineering knowledge, resources and energy on one goal: To be the best in this technology.
Our range consists of: Single-Phase Power Supplies, Three-Phase Power Supplies, DC/ DC Converters, Buffer Units, DC-UPS Battery Modules and Redundancy Modules.
PULS UK Ltd
Cranfield Innov Cntr, University Way Cranfield MK43 0BT
T: 01525 841001
E: sales@puls.co.uk
W: www.pulspower.com/uk/home
Pulsar Instruments Plc
Evron Centre, John Street Filey YO14 9DW
T: 01723 339 715
E: sales@pulsarinstruments.com
W: www.pulsarinstruments.com
PULSAR®
Eagle Road, Redditch
Worcestershire B98 9HF
T: 01527 962012
E: sales@pulsaruk.com
W: www.pulsaruk.com
Purcell
15 Bermondsey Square, Tower Bridge Road London SE1 3UN
T: 020 7397 7171
E: info@purcelluk.com
W: www.purcelluk.com
PWC Strategy& (UK) Ltd
7 More London Riverside London SE1 2RT
T: 020 7583 5000
E: london.information@strategyand.pwc.com
W: www.strategyand.pwc.com
PWS Technical Services Ltd
The Media Centre, 7 Northumberland Street
Huddersfield West Yorkshire HD1 1RL
T: 01484 508380
E: info@pwstechnicalservices.co.uk
W: www.pwstechnicalservices.co.uk
QA Weld Tech Ltd
2a Bowes Road, Riverside Park Ind Est Middlesbrough TS2 1LU
T: 01642 222831
E: enquiries@qaweldtech.com
W: www.qaweldtech.co.uk
QCS (Lanark) Ltd
97 St Leonard Street, Lanark Scotland ML11 7BJ
T: 01555 660467
E: enquiries@qcscleaning.co.uk
W: www.qcscleaning.co.uk
QED Scaffolding Ltd
Lock Street, St Helens Merseyside WA9 1HS
T: 01744 751117
E: enquiries@qedscaffoding.com
W: www.qedscaffolding.com
Qinesis
Walton Business Centre, Walton Upon Trent Derbyshire DE12 8ND
T: 0845 873 9274
E: growth@qinesis.com
W: www.qinesis.com
QinetiQ
Cody Technology Park, Building A7 Ively Road
Farnborough Hampshire GU14 0LX
T: 01252 392000
E: railservices@QinetiQ.com
W: www.QinetiQ.com
QTS Group
Rench Farm, Drumclog Strathaven South Lanarkshire ML10 6QJ
T: 01357 440222
E: info@qtsgroup.com
W: www.qtsgroup.com
Qualitrain
26 Royal Scot Road, Pride Park
Derbyshire DE24 8AJ
T: 01332 345205
E: info@qualitrain.co.uk
W: www.qualitrain.co.uk
Quality Precision Engineering Ltd
1 Coldhams Road
Cambridge CB1 3EW
T: 01223 215333
E: qpe-ltd@hotmail.co.uk
W: www.qpe-ltd.co.uk
Quantum Geotechnical Limited
Ty Berwig, Bynea
Llanelli Camarthanshire SA14 9ST
T: 01554 744880
E: enquiries@quantum-geotech.co.uk
W: www.quantum-geotech.co.uk
Quantum Mouldings Ltd
Whitehouse Road, Kidderminster
Worcestershire DY10 1HT
T: 01562 747975
E: sales@quantummouldings.co.uk
W: www.quantummouldings.co.uk
Quantum Seating Ltd
Priory Mill, Charter Avenue
Coventry CV4 8AF
T: 024 7669 5150
E: info@quantumseating.com
W: www.quantumseating.com
Quartix Ltd
Chapel Offices, Park Street Newtown Wales SY16 1EE
T: 0870 013 6663
E: enquiries@quaratix.net
W: www.quartix.net
Queen Mary & Westfield College
Mile End Road London E1 4NS
T: 020 7882 5555
E: admissions@qmul.ac.uk
W: www.qmul.ac.uk
Quest Global
G/F Derwent House, RTC Business Park London Road Derby DE24 8UP
T: 01934 421500
E: info@quest-global.com
W: www.quest-global.com
Quickmap Limited
PO Box 12
London SE5 9PN
T: 020 7813 3397
E: info@quickmap.com
W: www.quickmap.com
Quiligotti Terrazzo Tiles UK Rake Lake, Clifton Juction Manchester M27 8LP
T: 0161 727 9798
E: sales@quiligotti.co.uk
W: www.quiligotti.co.uk
Quinshield Ltd
Capel Hendre Ind Estate, Capel Hendre Ammanford Carmarthenshire SA18 3SJ
T: 01269 832220
E: sales@quinshield.com
W: www.quinshield.com
R Baker (Electrical) Ltd
Evans Road, Speke Liverpool L24 9PB
T: 0151 486 6760
E: mail@rbaker.co.uk
W: www.rbaker.co.uk
R Bance & Co Ltd
Cockcrow Hill House, St Mary’s Road Surbiton Surrey KT6 5HE
T: 020 8398 7141
E: enquiries@bance.com
W: www.bance.com
R.M.Smith Fencing Ltd Duck Island Lane Ringwood Hampshire BH24 3AA
T: 01425 476 617
E: smithfencinguk@gmail.com
W: www.smith-fencing.co.uk
R&B Switchgear Services Ltd
Switchgear House, The Courtyard Green Lane Heywood Manchester OL10 2EX
T: 01706 369933
E: info@rbswitch.co.uk
W: www.rbswitchgeargroup.com
r2p UK Systems Ltd
Unit 1, Charlwood Court, County Oak Way Crawley West Sussex RH11 7XA
T: 01293 887308
E: uk@r2p.com
W: www.r2p.com
Racon Management Services Limited 5th Floor, 38 Waterloo Street Glasgow G2 7DA
T: 0141 248 3038
E: Info@racon-ms.com
W: www.racon-ms.com
Our experienced project teams & installation crews provide a fully managed logistics service to clients within the London underground infrastructure. Specialising in deliveries to platform level using the only LU approved escalator sledge with a SWL of 450 Kgs. Also providing logistics solutions for power & ventilation within the LU infrastructure and can also supply all your contract lift needs.
Radius Group Mainland House, Gladstone Close Northampton NN5 7AY
T: 01604 622865
E: info@radiusgroup.co.uk
W: www.radiusgroup.co.uk
Rail Accident Investigation Branch (RAIB) The Wharf, Stores Road Derby DE21 4BA
T: 01332 253300
E: enquiries@raib.gov.uk
W: www.gov.uk
Rail Alliance Quinton Rail Tech Ctr, The Junction,Station Rd Long Marston Stratford-on-Avon CV37 8PL T: 01789 720026
E: info@railalliance.co.uk
W: www.railalliance.co.uk
Rail Delivery Group (RDG) 2nd Floor, 200 Aldersgate Street London EC1A 4HD
T: 020 7841 8000
E: info@raildeliverygroup.com
W: www.raildeliverygroup.com
Rail Forum (RF)
Chief Executive Officer, Lonsdale House Quaker Way Derby DE1 3HD
T: 01332 593550
E: info@railforum.uk
W: www.railforum.uk
Rail Freight Group (RFG)
7 Bury Place London WC1A 2LA
T: 020 3116 0007
E: contact@rfg.org.uk
W: www.rfg.org.uk
Rail Freight Services 1st Fl Mill House, Station Approach Harlow Essex CM20 2EL
T: 01279 630890
E: enquiries@railfreightservices.co.uk
W: www.railfreightservices.co.uk
Rail Images
5 Sandhurst Crescent, Leigh-on-Sea Essex SS9 4AL T: 01702 525059
E: info@railimages.co.uk
W: www.railimages.co.uk
Rail Industry Contractors Association (RICA) c/o Hill House Cottage, Misbrooks Green Road Beare Green Dorking RH5 4QQ
T: 07557 404727
E: enquiries@rica.uk.com
W: www.rica.uk.com
Rail Manche Finance Times House, Bravingtons Walk Regent Quarter London N1 9AW
T: 020 7042 9961
E: dh@rmf.co.uk
W: www.rmf.co.uk
Rail Operations Group Ltd 6 Snow Hill London EC1A 2AY
T: 020 7002 7710
E: info@railopsgroup.co.uk
W: www.railopsgroup.co.uk
Rail Order Ltd
11 Billet Lane, Normanby Ent Park Scunthorpe North Lincolnshire DN15 9YH
T: 01724 292860
E: sales@rail-order.co.uk
W: www.rail-order.co.uk
Rail People Solutions Ltd
1 The Old Flour Mills, Mill Road
Buckden Cambridgeshire PE19 5WX
T: 07825 050554
E: glenis.reagon@rpsltd.uk
W: www.railpeoplesolutions.uk
Rail Personnel
Level 13, 141 Thomson Road
Wanchai Hong Kong
T: 00 852 2753 5636
E: info@railpersonnel.com
W: www.railpersonnel.com
Rail Plant Association (RPA)
27/28 Newbury Street, Barbican London EC1A 7HU
T: 020 7796 3366
E: rpa@cpa.uk.net
W: www.cpa.uk.net
RSSB is a membership-based rail industry body which includes train and freight operating companies, infrastructure managers, contractors, rolling stock leasing companies and suppliers. Our work involves partnerships with academia and other railways across the world.
Rail Safety and Standards Board (RSSB)
The Helicon, One South Place London EC2M 2RB
T: 020 3142 5300
E: enquirydesk@rssb.co.uk
W: www.rssb.co.uk
Rail Spares Limited
Unit 1 Bonnyton Ind Est, Munro Place Kilmarnock Ayrshire KA1 2NP
T: 01563 535463
E: sales@railspares.com
W: www.railspares.com
Rail Supply Group (RSG)
c/o 22 Headfort Place London SW1X 7RY
T: 07801 301259
E: rsgenquiries@raildeliverygroup.com
W: www.railsupplygroup.org
Rail Technology Ltd
4 Noon Croft, Alrewas
Burton On Trent DE13 7EA
T: 01283 790012
E: info@railtechnologyltd.com
W: www.railtechnologyltd.com
Rail Training International Ltd
North Suite, Parsonage Offices Church Lane Canterbury Kent CT4 7AD
T: 01227 769096
E: rtiuk@rti.co.uk
W: www.rti.co.uk
Rail Vac
4 Sarum Place
Hemel Hempstead HP2 6DP
T: 01442 244970
E: info@railvac.com
W: www.railvac.com
Rail Vision Europe Ltd
2 Cygnus Court, Beverley Road
Castle Donington Leicestershire DE74 2SA
T: 01509 672211
E: enquiries@rail-vision.com
W: www.rail-vision.co.uk
Rail Waiting Structures
Dyffryn Business Park, Llantwit Major Road
Llandow Vale of Glamorgan OF71 7PY
T: 01446 795444
E: sales@shelters.co.uk
W: www.shelters.co.uk
Railcare Sweden Ltd
Unit 1 Derwent Park, 214-216 London Road
Derby DE1 2SX
T: 01332 647388
E: info@railcare.co.uk
W: www.railcare.co.uk
Railfuture
14 Ghent Field Circle, Thurston Suffolk IP31 3UP
E: info@railfuture.org.uk
W: www.railfuture.org.uk
Railmed Ltd
Office A&B Lawrence Hse, The Street
Hatfield Peverel Essex CM3 2DN
T: 01245 382473
E: info@railmed.co.uk
W: www.railmed.co.uk
Railnews Ltd (Industry Publication)
95 Wellingborough Road, Finedon
Wellingborough NN9 5LG
T: 01438 281200
E: contact@railnews.co.uk
W: www.railnews.co.uk
RailPoint
Unit 1, Little Forge Road, Park Farm North
Redditch B98 7SF
T: 01527 595880
E: hello@railpoint.co.uk
W: www.RailPoint.co.uk
RailTech Solutions Ltd
Holbeck Rail Depot, Bridge Road
Holbeck Leeds LS11 9UG
T: 0118 903 6045
E: team-rts@rts-solutions.net
W: www.rts-solutions.net
RAILTEX 2022 – Mack Brooks Exhibitions Ltd
Mack Brooks Exhibitions, Romeland House
Romeland Hill St Albans AL3 4ET
T: 01727 814400
E: railtex@mackbrooks.co.uk
W: www.railtex.co.uk
Railway Benefit Fund (RBF) 1st Floor, Millennium House
40 Nantwich Road Crewe CW2 6AD
T: 0345 241 2885
E: info@railwaybenefitfund.org.uk
W: www.railwaybenefitfund.org.uk
Railway Brake Services Ltd
Unit 2 Sidings Ind Est, Wetmore Road
Burton On Trent DE14 1SB
T: 01283 440102
E: support@railwaybrakeservices.co.uk
W: www.railwaybrakeservices.co.uk
Railway Children
1 The Commons, Sandbach Cheshire CW11 1EG
T: 01270 757596
E: hello@railwaychildren.org.uk
W: www.railwaychildren.org.uk
Railway Civil Engineers Association (RCEA)
1 Great George Street, Westminster London SW1P 3AA
T: 020 7665 2238
E: rcea@ice.org.uk
W: www.rcea.org.uk
Railway Convalescent Centre
Bridge House, 2 Church Street Dawlish Devon EX7 9AU
T: 01626 863303
E: bookings@rch.org.uk
W: www.rch.org.uk
Railway Electrical Services Ltd St Bartholomews Church, Hallams Fields Road Ilkeston DE7 4AZ
T: 0115 944 4608
E: info@rail-elec.co.uk
W: www.railwayelectricalservices.co.uk
Railway Employees & Public Transport Association (REPTA)
4 Brackmills Close, Forest Town Mansfield NG19 0PB
T: 01623 646789
E: candarolle@btinternet.com
W: www.repta.co.uk
Railway Engineering Associates Ltd
125 Boden Street Glasgow G40 3PX
T: 0141 556 0415
E: postmaster@rea.uk.com
W: www.rea.uk.com
Railway Enginemen’s Assurance Society
727 Washwood, Heath Road
Birmingham B8 2LE
T: 0800 328 9140
E: info@enginemens.co.uk
W: www.enginemens.co.uk
Railway Forgings & Castings Ltd
Unit 51, Woodcock Ind Estate
Warminster Wiltshire BA12 9DX
T: 01985 846000
E: sales@railwayforgingsandcastingsltd.co.uk
W: www.railwayforgingsandcastingsltd.co.uk
Railway Heritage Designation Advisory Board Science Museum, Exhibition Road London SW7 2DD
T: 01904 686242
E: smgrailheritage@sciencemuseum.ac.uk
W: www.sciencemuseum.org.uk
Railway Heritage Trust
1 Eversholt Street London NW1 2DN
T: 020 7904 7354
E: rht@railwayheritagetrust.co.uk
W: www.railwayheritagetrust.co.uk
Railway Housing Association (RHA)
Bank Top House, Garbutt Square Neasham Road Darlington DL1 4DR
T: 0800 028 7428
E: info@railwayha.co.uk
W: www.railwayha.co.uk
RIA is the voice of the UK rail supply community, with over 300 companies in membership. We help to grow a sustainable, high-performing, railway supply industry, and to export UK rail expertise and products. We promote and represent our members’ interests to policy makers, clients and other stakeholders in the UK and overseas.
Railway Industry Association (RIA)
Kings Buildings, 16 Smith Square
London SW1P 3HQ
T: 020 7201 0777
E: ria@riagb.org.uk
W: www.riagb.org.uk
Railway Industry Supplier Approval Scheme (RISAS)
The Helicon, 1 South Place
London EC2M 2RB
T: 020 3142 5376
E: risas.admin@rssb.co.uk
W: www.risas.co.uk
Railway Industry Supplier Qualification Scheme (RISQS)
The Helicon, 1 South Place London EC2M 2RB
T: 020 3142 5300
E: admin@risqs.org
W: www.risqs.org
Railway Mission
Rugby Railway Station, Station Approach Rubgy Warwickshire CV21 3LA
T: 0203 887 7000
E: office@railwaymission.org
W: www.railwaymission.org
Railway Moulds & Systems Ltd PO Box 5317, Hove
East Sussex BN52 9TP
T: 01435 813946
E: sales@r-m-s-ltd.com
W: www.railwaymoulds.com
Railway Safety Solutions Ltd 5 Ellingham Road, Shepherds Bush London W12 9PR
T: 020 7459 4825
E: enquiry@railwaysafetysolutions.com
W: www.railwaysafetysolutions.com
Railway Study Forum (RSF)
Earlstrees Court, Earlstrees Road
Corby Northamptonshire NN17 4AX
T: 01536 740100
E: membership@ciltuk.org.uk
W: www.ciltuk.org.uk
Railway Support Services provide a fully nationwide breakdown and recovery service for all train operating companies and depots. The very nature of derailments requires a 24/7 service which we provide on a call-out basis. Wheelskating of defective vehicles is also undertaken at short notice as is Class 08 locomotive hire and maintenance.
Railway Support Services
Unit 15, Rye Farm, Dunton Lane
Wishaw Sutton Coldfield B76 9QA
T: 0870 803 4651
E: info@railwaysupportservices.co.uk
W: www.railwaysupportservices.co.uk
Railway Systems Consultants Ltd
Church View, Knockhundred Row
Midhurst West Sussex GU29 9DQ
T: 01730 813280
E: rsc@rscuk.com
W: www.rscuk.com
Railway Wheelset & Brake Ltd
1/F G2, 12 Leeds Road Sheffield S9 3TY
T: 0114 303 0705
E: sales@railwaywheelset.co.uk
W: www.railwaywheelset.co.uk
Railweight Foundry Lane, Smethwick West Midlands B66 2LP
T: 0845 246 6714
E: sales@railweight.co.uk
W: www.averyweigh-tronix.com
Rainford Solutions Ltd
Rainford House, Mill Lane, Rainford St Helens Merseyside WA11 8LS
T: 01744 889886
E: sales@rainfordsolutions.com
W: www.rainfordsolutions.com
Ram Services Limited
Holyoake House, 240-244 Lowerhouse Lane Burnley Lancashire BB12 6NG
T: 01282 452211
E: sales@ramservices.co.uk
W: www.ramservices.co.uk
Ramboll UK Ltd
Carlton House, Ringwood Road Southampton SO40 7HT
T: 023 8081 7500
E: southampton@ramboll.co.uk
W: uk.ramboll.com
Ramtech Electronics Ltd
Ramtech House, Castlebridge Office Vlg Castle Marina Road Nottingham NG7 1TN
T: 0115 957 8282
E: info@ramtech.co.uk
W: www.ramtech.co.uk
Rapid Fire Supplies 2430/2440 The Quadrant, Aztec West Almondsbury Bristol BS32 4AQ
T: 03330 150 330
E: cs@rapidfiresupplies.co.uk
W: www.rapidfiresupplies.co.uk
Rapid Ramp (wheelchair ramp manufacturer, supplier and installer)
10 Menzies Road, St Leonards on Sea TN38 9BB
T: 01424 714646
E: sales@rapidramp.co.uk
W: www.rapidramp.co.uk/public-buildings
Raptor Supplies Ltd 6 Hessel Road, London W13 9ES
T: 020 3287 5224
E: sales@raptorsupplies.co.uk
W: www.raptorsupplies.co.uk
Rawlplug Ltd
Skibo Drive, Thornliebank Ind Estate Glasgow G46 8JR
T: 0141 638 7961
E: rawlinfo@rawlplug.co.uk
W: www.rawlplug.co.uk
RE Systems
Systems House, Deepdale Business Park
Bakewell Derby DE45 1GT
T: 01629 813961
E: enquiries@re-systems.co.uk
W: www.re-systems.co.uk
Providing field operations teams a world-class field management solution that enables them to grow rapidly – save time, increase productivity, and ensure compliance. Tirelessly committed to listening to client needs, and putting it into practice, the system has since grown exponentially.
Re-Flow
The Mount, 72 Paris Street Exeter EX1 2JY
T: 01392 574001
W: www.re-flow.co.uk
Reach Engineering & Diving Services Ltd Cottage Leap, Rubgy Warwickshire CV21 3XP
T: 01788 570077
E: reds@red-services.co.uk
W: www.red-services.co.uk
REACT Specialist Cleaning Ltd
115 Hearthcote Road, Swadlincote Burton-on-Trent Derbyshire DE11 9DU
T: 01283 550503
E: react@reactsc.co.uk
W: www.reactsc.co.uk
Reactec Ltd
Vantage Point, 3 Cutlins Road Edinburgh EH11 4DF
T: 0131 221 0920
E: info@reactec.com
W: www.reactec.com
Reactive Group Services Broadley Grove Halifax HX2 0RN
T: 01925 393707
E: info@reactivegroupservices.com
W: www.pigeon-control.co.uk
Readypower Rail Services Group Ltd
620 Wharfedale Road, Winnersh Reading Berkshire RG41 5TP
T: 0118 977 4901
E: info@readypower.co.uk
W: www.readypower.co.uk
Real Skills Training Limited
Real House, 215 Crosby Road South Liverpool L21 4LT
T: 0151 257 6969
E: info@real-skills.co.uk
W: www.real-skills.co.uk
Real-Time Consultants Ltd 25 Trenchard Street Bristol BS1 5AN
T: 0117 917 1500
E: contact@rtc.co.uk
W: www.rtc.co.uk
REC Ltd
Osprey House, Pacific Quay
Broadway Manchester M50 2UE
T: 0845 676 9303
E: info@recltd.co.uk
W: www.recltd.co.uk
Record Electrical Associates Ltd
Longford Trading Estate, Thomas Street
Stretford Manchester M32 0JT
T: 0161 864 3583
E: info@reauk.com
W: www.reauk.com
Recycling Management
Trevor Street Ind Est, Trevor St Nechells Birmingham B7 5RG
T: 0121 328 5000
E: info@recman.com
W: www.recyclingmanagement.com
Red Viking Rail Ltd
1 Cavendish Court, South Parade
Doncaster South Yorkshire DN1 2DJ
T: 01302 260380
E: enquiries@redvikingrail.co.uk
W: www.redvikinggroup.co.uk
RedRay Limited
Lantern House, 39-41 High Street
Potters Bar Hertfordshire EN6 5AJ
T: 01707 662997
E: enquiries@redray.co.uk
W: www.redray.co.uk
Redscan Cyber Security Ltd
The Shard, 32 London Bridge Street London SE1 9SG
T: 0800 107 6098
E: info@redscan.com
W: www.redscan.com
Regeneris Consulting Ltd
Faulkner House, Faulkner Street
Manchester M1 4DY
T: 0161 234 9910
E: manchester@regeneris.co.uk
W: www.regeneris.co.uk
Regenesis Cambridge House, Henry Street Bath BA1 1BT
T: 01225 618161
E: europe@regenesis.com
W: www.regenesis.com
Reinforced Earth Company Limited
Innovation House, Euston Way
Telford TF3 4LT
T: 01952 204357
E: info@reinforcedearth.co.uk
W: www.reinforcedearth.co.uk
Relec Electronics are your go-to for reliable power and display solutions in the railway sector. We’re all about keeping your projects powered and visible, no matter the demand. From sturdy power supplies to clear, userfriendly screens, we’ve got the tech to enhance your railway systems. Explore our range today!
Relec Electronics Ltd
Animal House, Justin Business Park Sandford Lane Wareham, Dorset BH20 4DY
T: 01929 555700
E: sales@relec.co.uk
W: www.relec.co.uk
Reliable Contractors
301 Northdown Road, Margate
Kent CT9 3PA
T: 020 3887 7801
E: info@reliablecontractors.co.uk
W: www.reliablecontractors.co.uk
Relinea – GRP Systems Ltd
14 Crosshill Road, Crumlin Co Antrim BT29 4BQ
T: 028 9447 0010
E: info@relinea.com
W: www.relinea.com
Reme Industrial Flooring Ltd
Manor Farm, 73 The Green
Rawcliffe East Yorkshire DN14 8QF
T: 01405 839529
E: info@remeflooring.co.uk
W: www.remeflooring.co.uk
Remedy Geotechnics Ltd
ICON Centre, Daventry Northants NN11 0QB
T: 01327 304826
E: admin@remedygeotechnics.com
W: www.remedygeotechnics.com
Remlive Ltd PO Box 189, Bingley West Yorkshire BD16 3UY
T: 01274 562135
E: enquiries@remlive.com
W: www.remlive.co.uk
Rendel Ltd
200 Great Dover Street London SE1 1SA
T: 020 7654 0500
E: london@rendel-ltd.com
W: www.rendel-ltd.com
REO (UK) Ltd
Unit 2-4 Callow Hill Rd, Craven Arms Bus Park
Craven Arms Shropshire SY7 8NT
T: 01588 673411
E: main@reo.co.uk
W: www.reo.co.uk
Repair Protection & Maintenance Limited
Roall Lane, Kellington North Yorkshire DN14 0NY
T: 01977 663111
E: info@rpmltd.co.uk
W: www.rpmltd.co.uk
Resonate Group Ltd
Hudson House, 2 Hudson Way
Pride Park Derby DE24 8HS
T: 01332 221000
E: enquiries@resonate.tech
W: www.resonate.tech
Resource Rail Ltd
Building C-E Goldwell Court, Goldwell Lane Ashford Kent TN25 7DX
T: 01233 610628
E: info@resourcerail.co.uk
W: www.resourcerail.co.uk
Resourcing Solutions Limited
Thames Valley HQ, Ruscombe Business Park Ruscombe Reading RG10 9JW
T: 0118 932 0100
E: marketing@resourcing-solutions.com
W: www.resourcing-solutions.com
Retired Railway Officers’ Society (RROS)
26 Chester Way London SE11 4UR
T: 020 7582 2395
E: malins.rw4@btopenworld.com
W: www.rros.org.uk
Revitaglaze Ltd
Unit 2 Swanwick, Business Park Bridge Road Southampton SO31 7GB
T: 020 3384 0220
E: enquiries@revitaglaze.com
W: www.revitaglaze.com
Rex Advertising Limited
The Observatory, 40 Clerkenwell Close London EC1R 0AW
T: 020 7336 4585
E: info@rexadvertising.co.uk
W: www.rexadvertising.co.uk
With extensive expertise in supporting the rail sector a robust supply chain, and added value solutions, we keep your operation running efficiently, cost-effectively and compliant, especially where access to PADS approved products are required. We offer lighting and switchgear design, energy surveys, Solar & EV solutions, intelligent stock management systems, asset repair management and other bespoke services via our specialist teams.
Rexel
FM National Contact Centre, 1120 Europa Boulevard
Gemini Business Park Warrington WA5 7UW
T: 0333 400 7917
E: customer.connect@rexel.co.uk
W: www.rexel.co.uk
RGB Network Recruitment Solutions
14-15 Lower, Grosvenor Place
London SW1W 0EX
T: 020 7932 2800
E: info@rgb.co.uk
W: www.rgb.co.uk
RHL Recruitment Holdings Ltd
The Cedars, Church Road
Ashford TN23 1RQ
T: 01233 658000
E: recruitment@rhl.co.uk
W: www.rhl.co.uk
Rhodar Limited
Astra Park, Parkside Lane
Leeds West Yorkshire LS11 5SZ
T: 0800 834 669
E: info@rhodar.co.uk
W: www.rhodar.co.uk
Rhomberg Sersa (UK) Ltd
Unit 2 Sarah Court, Yorkshire Way
Doncaster DN3 3FD
T: 0300 303 0230
E: info.uk@rhomberg-sersa.com
W: www.rhomberg-sersa.com
RIB Software (UK) Ltd
3rd Floor Abbey House, 74-76 St John Street London EC1M 4DZ
T: 020 8629 7088
E: info@rib-software.co.uk
W: www.rib-software.co.uk
Ricardo Energy & Environment
1 Frederick Sanger Road, Surrey Research Park Guildford GU2 7YD
T: 01483 544944
E: enquiry-ee@ricardo.com
W: www.ee.ricardo.com
Ricardo Rail 30 Eastbourne Terrace London W2 6LA
T: 01235 753683
E: railUK@ricardo.com
W: rail.ricardo.com
Ricardo UK Ltd Shoreham Tech Centre, Old Shoreham Road
Shoreham-by-Sea West Sussex BN43 5FG
T: 01273 455611
E: info@ricardo.com
W: www.ricardo.com
Richmond Electronic Services Ltd
42 Hurricane Way, Norwich Norfolk NR6 6JB
T: 01603 416304
E: admin@richmondelectronic.co.uk
W: www.richmondrepair.co.uk
Richmond Interior Supplies Ltd Units 2-4, Chichester Business Ctr Chichester Street Rochdale Lancs OL16 2AU
T: 01706 525623
E: info@richmonds-ltd.co.uk
W: www.richmonds-ltd.co.uk
Rider Hunt Leeds
Quarry Dene Lodge, Westwood Lane Leeds LS16 8HH
T: 0113 294 7291
E: leeds@rhms.uk.com
W: www.riderhunt.co.uk
Rider Industrial Services
Windfall House, Strawgate Lane Stapleton Darlington DL2 2QW
T: 01325 351570
E: info@riderindustrial.co.uk
W: www.riderindustrial.co.uk
Riegens UK Ltd 230 Avenue West, Skyline 120 Braintree Essex CM77 7AA
T: 01376 333400
E: riegens-lighting@riegens-lighting.com
W: www.riegens.co.uk
Riggots & Co Ltd
U/X Lodge Lane Ind Est, Tuxford Newark Nottinghamshire NG22 0NL
T: 01777 872525
E: webenquiries@riggott.co.uk
W: www.riggott.co.uk
Rimex Metals UK Ltd
Aden Road, Enfield Middlesex EN3 7SU
T: 020 8804 0633
E: sales@rimexmetals.com
W: www.rimexmetals.com
RINA Cleeve Road, Leatherhead Surrey KT22 7SA
T: 01372 367350
E: info@rina.org
W: www.rina.org
RIS Consultants (NW) Ltd
Unit 1, The Workshops, Marcus Street Birkenhead Wirral CH41 1EU
T: 0800 978 8659
E: info@risgroup.co.uk
W: www.risgroup.co.uk
Ritherdon & Company Ltd
Lorne Street, Darwen Lancashire BB3 1QW
T: 0800 138 7410
E: info@ritherdon.co.uk
W: www.ritherdon.co.uk
Enclosure systems which satisfy the highest demands for trackside and signalling are one of Rittal’s hallmarks. High performance IT racks, power-distribution components, perfectly tuned climate control units and robust outdoor solutions round off the unique all-embracing enclosure range from a global player in the business of innovation.
Rittal Limited
Braithwell Way, Hellaby Ind Estate Rotherham South Yorkshire S66 8QY
T: 01709 704000
E: information@rittal.co.uk
W: www.rittal.co.uk
Riverview Welding Services
Unit 7, Quell Farm Ind Estate Greatham Lane Pulborough RH20 2ES
T: 01798 875676
E: sales@riverviewwelding.co.uk
W: riverviewwelding.com
Rivet Holdings Limited
Unit 3, Keys Business Village
Keys Park Road Hednesford WS12 2HA
T: 0121 766 5445
E: sales@rivetwise.co.uk
W: www.rivetwise.co.uk
Riviera Trains Ltd 116 Ladbroke Grove London W10 5NE
T: 020 7727 4036
E: enquiries@riviera-trains.co.uk
W: www.riviera-trains.co.uk
RJC Lowloaders Ltd
Units 1-2 Federal Est, Newton Road Higham Ferrers Northamptonshire NN10 8HW
T: 01933 419350
E: info@rjclowloaders.co.uk
W: www.rjclowloaders.co.uk
Established 1989, we specialise in prototype manufacturing, 1 off to small batch runs. Working in metals, plastics, associated materials. RJW turn concept into reality. Inventing ideas, taking them to market and have achieved a place in the Guinness book of records for the largest copper pipe fitting in the world.
RJW Engineering Ltd
70 Walker Avenue, Stourbridge West Midlands DY9 9EL DY9 9EL
T: 01384 442852
E: rjweng@btinternet.com
W: www.rjwengineering.co
RLE International
1 Endeavour Drive, Feastival Bus Park Basildon Essex SS14 3WF
T: 01268 247900
E: info@rle.co.uk
W: www.rle.international
RMD Kwikform Foundation House, Brickyard Road Aldridge Walsall WS9 8BW
T: 01922 743743
E: info@rmdkwikform.com
W: www.rmdkwikform.com
RMF Construction Services Ltd
Unit 2 Oughton Road, Highgate Birmingham B12 0DF
T: 0121 440 7970
E: info@rmfconstruction.co.uk
W: www.rmfconstruction.co.uk
RMI Engineering Ltd
Woodlands Farm, Tye Lane
Bramford Suffolk IP8 4LA
T: 01473 657511
E: info@railmarine.co.uk
W: www.railmarine.co.uk
RMS Rail Projects Ltd
2 White House Close, New Road
Laxey Isle Of Man IM4 7BA
T: 01388 526203
E: documentcontroller@britamrail.com
W: www.rmslocotec.com
Robens Centre For Occupational Health & Safety
1 Huxley Road, The Surrey Research Pk
Guildford GU2 7RE
T: 01483 686690
E: info@rcohs.com
W: www.rcohs.com
Robert Lewis Signs Limited
Hill Farm, Sealwood Lane
Linton Derbyshire DE12 6PA
T: 01283 760765
E: robert@robertlewissigns.co.uk
W: www.robertlewissigns.co.uk
Robert West Consulting Country House, St Mary’s Street
Worcester WR1 1HB
T: 01905 28288
E: worcester@robertwest.co.uk
W: www.robertwest.co.uk
Robin Mackenzie Partnership (RMP)
Unit 1 7Hills Bus Park, Bankhead Crossway
South Edinburgh EH11 4EP
T: 0345 062 0000
E: rmp@napier.ac.com
W: www.rmp.biz
Robinson Mesh Products Limited
Unit 4 Enterprise Park, Newton Heath
Manchester M40 3AL
T: 0161 681 6810
E: sales@robinsonmeshproducts.co.uk
W: www.robinsonmeshproducts.co.uk
Robinsons Tree Service Ltd
Beech Farm, Coopers Green Lane St Albans Hertfordshire AL4 9HW
T: 01727 848111
E: robinsonstreeservice@ robinsonstreeservice.org.uk
W: www.robinsonstreeservice.co.uk
ROC Recruitment
37 Duke Streeet London W1U 1LN
T: 020 7318 1400
E: reception@roc.co.uk
W: www.roc.co.uk
Rochling Engineering Plastics (UK) Ltd
Waterwells Bus Park, Waterwells Drive
Gloucester GL2 2AA
T: 01452 727900
E: sales@roechling-plastics.co.uk
W: www.roechling.com
Rock Fall UK
Major House, Unit 1/3, Wimsey Way
Alfreton Derbyshire DE55 4LS
T: 01773 608616
E: sales@rockfall.com
W: www.rockfall.com
Rock Rail Holdings Ltd
Capital Tower, 91 Waterloo Road
London SE1 8RT
T: 020 3170 0870
E: info@rockinfrastructure.com
W: www.rockinfrastructure.com
Rockwool Ltd
Pencoed, Bridgend
Wales CF35 6NY
T: 01656 862621
E: customersupportcentre@rockwool.co.uk
W: www.rockwool.co.uk
Rocol Rocol House, Wakefield Road
Swillington Leeds LS26 8BS
T: 0113 232 2700
E: customer.services@rocol.com
W: www.rocol.com
Rodgers Leask Limited
St James House, St Mary’s Wharf
Mansfield Road Derby DE1 3TQ
T: 01332 285000
E: rllderby@rodgersleask.co.uk
W: www.rodgersleask.com
Roger Bullivant Limited
RB Walton Park, Hearthcote Road Swadlincote Derbyshire DE11 9DU
T: 01332 977300
E: info@roger-bullivant.co.uk
W: www.roger-bullivant.co.uk
MTU is the core brand of Rolls Royce Power Systems providing High Speed Diesel Engines to Mainline Locomotives, Shunters, Railcars and Infrastructure Vehicles. MTU have served the Rail market for over 90 years and today offer full propulsion system solutions including recently launched Hybrid Powerpacks for Railcars.
Rolls-Royce Solutions UK Ltd
Unit 29, The Birches Industrial Estate
East Grinstead West Sussex RH19 1XZ
T: 01342 335450
E: uk.sales@mtu-online.com
W: www.mtu-solutions.com
Romag
Leadgate Ind Estate, Consett
County Durham DH8 7RS
T: 01207 500000
E: sales@romag.co.uk
W: www.romag.co.uk
Romax Technology
Nottingham University, Innovation Park Triumph Road Nottingham NG7 2TU
T: 0115 951 8800
E: sales@romaxtech.com
W: www.romaxtech.com
Romsey Reclamation Ltd
Oak Tree Farm, Dunbridge Lane Awbridge Romsey SO51 0GQ
T: 01794 342252
E: info@romseyreclamation.com
W: www.romseyreclamation.com
Ron Hull Demolition Limited
Mangham Road, Parkgate Rotherham South Yorkshire S62 6EF
T: 01709 524115
E: info@ronhull.co.uk
W: www.ronhulldemolition.co.uk
Ronacrete Ltd
Ronac House, Flex Meadow Harlow Essex CM19 5TD
T: 01279 638700
E: sales@ronacrete.co.uk
W: www.ronacrete.co.uk
Roofcare London
6 Claremont Road
Surbiton KT6 4QU
T: 020 8485 9639
E: roofcarelondon@gmail.com
W: www.roofcarelondon.co.uk
Rose Plant Hire (Whittlesey) Ltd
Padholme Road East, Peterborough Cambridgeshire PE1 5XL
T: 01733 557575
E: info@roseplanthire.co.uk
W: www.roseplanthire.co.uk
Rosehill Rail
Spring Bank Mills, Watson Mill Lane
Sowerby Bridge West Yorkshire HX6 3BW
T: 01422 839610
E: info@rosehillrail.com
W: www.rosehillrail.com
Rösler UK Limited
1 Unity Grove, Knowsley Bus Park
Prescot Merseyside L34 9GT
T: 0151 482 0444
E: rosler-uk@rosler.com
W: www.rosler.com
RotaBolt Ltd
Peartree Business Park, Peartree Lane
Dudley DY2 0UW
T: 01384 214442
E: sales@rotabolt.co.uk
W: www.rotabolt.co.uk
Rotabroach Ltd
Burgess Road Sheffield S9 2YL
T: 0114 221 2510
E: info@rotabroach.co.uk
W: www.rotabroach.co.uk
Rotec Hydraulics
Unit 1 Venture Way, Priorswood Estate
Taunton Somerset TA2 8DE
T: 01823 348900
E: sales@rotec.net
W: www.rotec.net
Rothwell Electrical Services Limited
Unit 3, Yorvale Bus Pk, Hazel Court James Street York YO10 3DR
T: 01904 413172
E: enquiries@rothwellelect.co.uk
W: www.rothwellelect.co.uk
Rotork PLC
Brassmill Lane Bath BA1 3JQ
T: 01225 733200
E: rotorkuk.sales@rotork.com
W: www.rotork.com
Rotrex Winches
Wimsey Way, Alfreton Trading Estate
Alfreton DE55 1AR
T: 01773 603997
E: sales@rotrexwinches.co.uk
W: www.rotrexwinches.co.uk
Rotronics Battery Management Solutions Queen Street, Darlaston West Midlands WS10 8JF
T: 0121 526 8185
E: info@rotronicsbms.com
W: www.rotronicsbms.com
Routescene Mapix Technologies Ltd, 54 Timber Bush Edinburgh EH6 6QH
T: 0844 409 9530
E: sales@routescene.com
W: www.routescene.com
Rowe Hankins Ltd. Power House, Mason Street Bury Lancashire BL9 0RH
T: 0161 765 3000
E: sales@rowehankins.com
W: www.rowehankins.com
Roxburgh EMC (DEM Manufacturing)
Deltron Emcon House, Hargreaves Way Sawcliffe Ind Park Scunthorpe DN15 8RF
T: 01724 273200
E: sales@dem-uk.com
W: www.dem-uk.com
Roxtec cable, pipe and conduit seals have been tested and approved by London Underground and Network Rail. Our solutions protect rail assets and rolling stock against fire, smoke, water damage, rodents, gas, vibration, humidity, dust and electromagnetic interference. The certified seals can be used in many applications including traction power, signalling and rail control, communications, tunnels and bridges, railway stations and rail yards.
Roxtec Ltd
1st Floor, Power House Mason Street Bury BL9 0RH
T: 0161 761 5280
E: info@uk.roxtec.com
W: www.roxtec.com
Royal Academy of Engineering (RAEng)
Prince Philip House, 3 Carlton House Terr London SW1Y 5DG
T: 020 7766 0600
E: webmaster@raeng.org.uk
W: www.raeng.org.uk
Royal Haskoning DHV
Rightwell House, Bretton Peterborough PE13 8DW
T: 01733 334455
E: info@uk.rhdhv.com
W: www.royalhaskoningdhv.co.uk
Royal Incorporation of Architects in Scotland (RIAS) 15 Rutland Square
Edinburgh EH1 2BE
T: 0131 229 7545
E: info@rias.org.uk
W: www.rias.org.uk
Royal Institute of British Architects (RIBA)
66 Portland Place London W1B 1AD
T: 020 7580 5533
E: info@riba.org
W: www.architecture.com
Royal Institution of Chartered Surveyors (RICS) Parliament Square, 12 Great George Street London SW1P 3AD
T: 024 7686 8555
E: contactrics@rics.org
W: www.rics.org
RPC Contracts Ltd Quarryfields, Ruthin Denbighshire LL15 2UG
T: 01824 709102
E: contracts@rpcltd.co.uk
W: www.rpcltd.co.uk
RPS – Railway Project Services
2 Brook Park, Gaddesby Lane
Rearsby Leicestershire LE7 4ZB
T: 01664 494098
E: contact@rps-team.co.uk
W: railwayprojectservices.co.uk
RPS Group Plc
20 Western Avenue, Milton Park
Abingdon Oxfordshire OX14 4SH
T: 01235 438000
E: rpsmp@rpsgroup.com
W: www.rpsgroup.com
RS Clare & Co Limited
8-14 Stanhope Street Liverpool L8 5RQ
T: 0151 709 2902
E: info@rsclare.co.uk
W: www.rsclare.com
RS Electrical (RSE) Ltd Brookside Ind Estate, Station Street Longport Stoke-on-Trent ST6 4ND
T: 01782 575316
E: rseltd@btconnect.com
W: www.rselectric.co.uk
RSK Spring Lodge, 172 Chester Road
Helsby Cheshire WA6 0AR
T: 01928 726006
E: communications@rsk.co.uk
W: www.rsk.co.uk
RSS Infrastructure has created a range of integrated infrastructure solutions, including Construction & Civils, Magnetic Track Safety, Overhead Line Electrification, Possession Planning, Safety-Critical Resource, Signalling, Track Warning Services, Vegetation Management and Welding Services. We are the UK’s sole provider of Track Warning Systems.
RSS Infrastructure Ltd Tech Block, Gee Business Centre Holborn Hill Aston West Midlands B7 5JR
T: 0330 113 0004
E: info@rssinfrastructure.com
W: www.rssinfrastructure.com
RT Infrastructure Solutions
91 Dales Road, Ipswich Suffolk IP1 4JR
T: 01473 242330
E: resource.admin@rt-is.co.uk
W: www.rt-is.co.uk
RT Training Solutions Ltd
91 Dales Road, Ipswich Suffolk IP1 4JR
T: 01473 242344
E: info@rttsolutions.co.uk
W: www.rttsolutions.co.uk
RTG Rail Services Limited Unit 10, Ilford Trading Estate
Paycocke Road Basildon Essex SS14 3DR
T: 0330 119 4450
E: info@rtgrail.co.uk
W: www.rtgrail.co.uk
RUAS
2 Imperial Courtyard, Imperial Park Newport NP10 8UL
T: 01633 835123
E: contact@ruas.co.uk
W: www.ruas.co.uk
Rubirail Victoria Buildings, 27 Victoria Road Draycott Derbyshire DE72 3PS
T: 01332 872483
E: info@rubirail.co.uk
W: www.rubirail.co.uk
RUGGED MOBILE Systems Ltd
The Carriage House, Brynkinalt Bus. Ctr Chirk Wrexham LL14 5NS
T: 01691 900222
E: sales@rm-systems.co.uk
W: www.ruggedmobilesystems.co.uk
Rullion Engineering
Aldermary House, 10-15 Queen Street London EC4N 1TX
T: 020 3251 1250
E: london.engineering@rullion.co.uk
W: www.rullion.co.uk
Running Rail Ltd
The Whitehall Centre, Whitehall Road Medway City Estate Rochester Kent ME2 4DZ
T: 01634 739010
E: info@runningrail.com
W: www.runningrail.com
Rust-Oleum UK Ltd PO Box 261, Chester-Le-Street County Durham DH3 9EH
T: 024 7671 7329
E: info@rust-oleum.eu
W: www.rust-oleum.eu
RWB Group
Kinetic Business Centre, Theobald Street Elstree WD6 4PJ
T: 0800 488 0658
E: operations@rwbgroup.co.uk
W: www.rwbgroup.co.uk
Rydon Signs Ltd
Unit 3 Peek House, Pinhoe Trading Estate Venny Bridge Exeter EX4 8JN
T: 01392 466653
E: sales@rydonsigns.com
W: www.rydonsigns.com
S&T Cover Limited
Railway Goods Yard, Dutton Lane Eastleigh Hampshire SO50 6AA
T: 023 8098 9545
E: enquiries@s-tcover.co.uk
W: www.s-tcover.co.uk
Sabre Rail Services Ltd
Grindon Way, Heighinton Lane Bus Pk
Newton Aycliffe County Durham DL5 6SH
T: 01325 300505
E: sales@sabrerail.com
W: www.sabrerail.com
SACO AEI Polymers UK Ltd. Sandwich Ind Estate, Sandwich Kent CT13 9LY
T: 01304 616171
E: uksales@sacoaei.com
W: www.sacoaei.co.uk
Sadler Brown Architecture
11-12 Riverside Studios, Amethyst Road
Newcastle NE4 7YL
T: 0191 265 7080
E: info@sadlerbrown.co.uk
W: www.sadlerbrown.co.uk
Safeaid Limited 16 Arnside Road, Waterlooville Hampshire PO7 7UP
T: 023 9225 4442
E: sales@safeaid.co.uk
W: www.safeaid.co.uk
SafetyKleen
Profile West, 950 Great West Road Brentford Middlesex TW8 9ES
T: 020 3814 8700
E: skuk@safetykleen.eu
W: www.safetykleen.eu
Salesforce
EMEA Limited, Village 9, Floor 26 Salesforce Tower 110 Bishopsgate London EC2N 4AY
T: 0800 092 1223
E: info@salesforce.com
W: www.salesforce.com
Samuel James Engineering is one of the UK’s leading suppliers of LV switchgear and control gear systems for the Rail Industry. We design, manufacture and commission LV (low voltage) Switchgear and Control Panels, Panel Boards, Automatic Changeover Panels, PSPs, FSPs, DNOs, Shore Supplies and UPS Panels.
Samuel James Engineering
Beresford Avenue, Coventry CV6 5LZ
T: 02476 835 000
E: sales@samuel-james.co.uk
W: www.samuel-james.co.uk
Samuel Knight’s rail consultants specialise in recruiting Project Leadership, Project and Site Management, Commercial, Planning, H&S, Design, IOT, Blue Collar and Safety Critical Staff. We operate across Civil Engineering, Construction, Electrification, Signalling, Rolling Stock and Digital Rail in the UK and overseas.
Samuel Knight International – Rail Recruitment
Pure Offices, Harbour Road Portishead Bristol BS20 7AN
T: 01275 404777
E: rail@samuel-knight.com
W: www.samuel-knight.com
Samuel Taylor Ltd is a UK manufacturing company supplying formed metal components to a global customer base.
Founded in 1899, it has a long history in the UK Rail industry, supplying electrical contacts both as components and sub-assemblies to customer specifications. Typical products are for use in electromechanical switches.
Samuel Taylor Ltd
Arthur Street Canal, Lakeside Redditch B98 8JY
T: 01527 504910
E: info@samueltaylor.co.uk
W: www.samueltaylor.co.uk
Sangwin Group of Companies
Dansom Lane South, Hull East Yorkshire HU8 7LN
T: 01482 329921
E: sales@sangwin.co.uk
W: www.sangwin.co.uk
SAP (UK) Ltd Clockhouse Place, Bedfont Road
Feltham Middlesex TW14 8HD
T: 0870 608 4000
E: info@sap.com W: www.sap.com
SAP Ecology and Environmental Ltd
2 Dunloe Terrace, Eaglesfield Dumfries & Galloway DG113PD
T: 01461 500754
E: enquiries@sapecology.co.uk
W: www.sapecology.co.uk
Sarens
Booth House, Riverside Park Road Middlesborough TS2 1UT
T: 01642 621621
E: info@sarens.com W: uk.sarens.com
Sateba UK are experts in vibration mitigation, ballasted and slab track sleepers and bearers, with over 35 years’ experience supplying to light rail and high speed lines. Including HS1, Elizabeth Line, Midland Metro. Our team of experts work collaboratively with clients to adapt designs to challenging project needs.
Sateba UK (formerly Sateba Stanton Precast) Littlewell Lane, Stanton-By-Dale Ilkeston Derbyshire DE7 4QW
E: salesuk@sateba.com
W: www.sateba.uk
Savigny Oddie Ltd
Wallows Ind Estate, Wallows Road Brierley Hill West Midlands DY5 1QA
T: 01384 481598
E: info@savigny-oddie.com
W: www.savigny-oddie.co.uk
SBC Rail
Littlewell Lane, Stanton by Dale Ilkeston Derbyshire DE7 4QW
T: 0115 944 1448
E: info@stanton-bonna.co.uk
W: www.stanton-bonna.co.uk
SBL-Rail
14 Woodland Crescent, Prestwich Manchester M25 9WQ
T: 07813 930687
E: info@sbl-rail.co.uk
W: www.sbl-rail.co.uk
SC Johnson Professional Denby Hall Way, Denby DE5 8JZ
T: 01773 855100
E: talktous@scj.com
W: www.scjp.com/en-gb
Schaeffler (UK) Ltd
Unit 308, Fort Dunlop Fort Parkway Birmingham B24 9FD
T: 0121 313 5830
E: info.uk@schaeffler.com
W: www.schaeffler.co.uk
Schaltbau Transportation UK Ltd
Unit 2, Patriot Drive Rooksley Milton Keynes MK13 8PU
T: 01908 224140
E: sales@schaltbau-transportation-uk.com
W: www.schaltbau.com
Schaltbau-ME
Springvale Ind Estate, Woodside Way Cwmbran Wales NP44 5BR
T: 01633 877555
E: sales@schaltbau-ME.com
W: www.schaltbau-ME.com
Scheidt & Bachmann UK Ltd
U7 Silverglade Bus Park, Leatherhead Road Chessington Surrey KT9 2QL
T: 01372 230400
E: info@scheidt-bachmann.co.uk
W: www.scheidt-bachmann.co.uk
350
Schenck Process Ltd
Unit 3 Alpha Court, Capitol Park
Thorne Doncaster DN8 5TZ
T: 01302 321313
E: enquiries@schenckprocess.co.uk
W: www.schenckprocess.com
Schneider Electric Ltd
2nd Floor, 80 Victoria Street London SW1E 5JL
T: 0870 608 8608
E: sales@schneider-electric.co.uk
W: www.schneider-electric.co.uk
Schoenemann Design
Friar Gate Studios, Ford Street
Derby DE1 1EE
T: 01332 258345
E: andrew@schoenemanndesign.co.uk
W: www.schoenemanndesign.co.uk
School of Engineering
University of Edinburgh, Sanderson Building
The King’s Bldngs Edinburgh EH9 3FB
T: 0131 650 6554
E: infopoint@ed.ac.uk
W: www.eng.ed.ac.uk
Schroff UK Limited
Grovelands Bus Centre, Boundary Way
Hemel Hempstead Hertfordshire HP2 7TE
T: 01442 240471
E: sales.uk@pentair.com
W: www.pentairprotect.com
Science, Engineering and Manufacturing Technologies Alliance (SEMTA)
Head Office, Unit 2, The Orient Centre
Greycaine Road Watford Herts WD24 7GP
T: 0845 643 9001
E: customerservices@semta.org.uk
W: www.semta.org.uk
Scisys UK Ltd
Methuen Park, Chippenham Wiltshire SN14 0GB
T: 01249 466466
E: info@scisys.co.uk
W: www.scisys.co.uk
Scotrail Atrium Court, 50 Waterloo Street Glasgow Scotland G2 6HQ
T: 0141 335 5050
E: customer.relations@scotrail.co.uk
W: www.scotrail.co.uk
Scott Bader Co Ltd Woolaston, Wellingborough Northamptonshire NN29 7RL
T: 01933 663100
E: enquiries@scottbader.com
W: www.scottbader.com
Scott Brownrigg Limited
77 Endell Street London WC2H 9DZ
T: 020 7240 7766
E: enquiries@scottbrownrigg.com
W: www.scottbrownrigg.com
Scott Cables Ltd
Unit 7 Merlin Park, Airport Service Road Portsmouth Hampshire PO3 5FU
T: 023 9265 2552
E: sales@scottcables.com
W: www.scottcables.com
Scott Hughes Design Ltd
The Flint Glass Works, 64 Jersey Street Manchester M4 6JW
T: 0161 605 0831
E: mail@scotthughesdesign.co.uk
W: www.scotthughesdesign.co.uk
Scott Parnell, a leading Civils Merchant in the UK has a dedicated Rail Team. Our Rail specialists are committed to providing the very best service. Alongside our standard merchant range, Scott Parnell specialise in introducing the UK Rail Sector to innovative products to offer efficiencies through cost and installation.
Scott Parnell Rail Unit 18, Asheton Farm Bus Centre Stapleford Abbotts Essex RM4 1JU
T: 020 8805 5797
E: rail@scottparnell.com
W: www.scottparnellrail.com
Scottish Association for Public Transport (SAPT)
11 Queens Crescent, Glasgow Scotland G4 9BL
T: 07760 381729
E: sapt@btinternet.com
W: www.sapt.org.uk
Scottish Woodlands Ltd – Head Office Research Park, Riccarton
Edinburgh EH14 4AP
T: 0131 451 5154
E: enquiries@scottishwoodlands.co.uk
W: www.scottishwoodlands.co.uk
SCP Colwyn Chambers, 19 York Street
Manchester M2 3BA
T: 0161 832 4400
E: info@scptransport.co.uk
W: www.scptransport.co.uk
SCQ Ltd
8 Kimpton Link, 40 Kimpton Road Sutton Surrey SM3 9QP
T: 020 8644 4416
E: info@ashleygroup.co.uk
W: www.ashleygroup.co.uk
Screwfast Foundations Ltd
1st Floor, 4 Sandridge Park Porters Wood Hertfordshire AL3 6PH
T: 01727 735550
E: info@screwfast.com
W: www.screwfast.com
Sea Training International
Sguboriau, Y Felinheli
Wales LL56 4QP
T: 01248 673200
E: training@seatraining.co.uk
W: www.seatraining.co.uk
Search Consultancy Limited
198 West George Street
Glasgow G2 2NR
T: 0141 272 7777
E: glasgow@search.co.uk
W: www.search.co.uk
Seaton Rail is a leading supplier to Network Rail, Principal Contractors and leading industry specialist contractors for the provision of Possession, Isolation & Railway Safe System of Work Planning, Training and Workplace Assessment, Drugs & Alcohol Screenings, Medical Screenings, Labour Supply and On Track Protection and Warning services.
Seaton Rail Limited
Unit B Enterprise Way, Bessingby Ind Estate
Bridlington East Yorkshire YO16 4SF
T: 01262 608313
E: info@seaton-rail.com
W: www.seaton-rail.com
Secured By Design
1st Floor, 10 Victoria Street
London SW1H 0NN
T: 020 3862 3999
E: enquiries@police-cpi.co.uk
W: www.securedbydesign.com
Seetru Limited
Albion Dockside Works
Bristol BS1 6UT
T: 0117 630 6100
E: enquiries@seetru.com
W: www.seetru.com
Sefac UK Ltd
Oldberrow Manor, Ullenhall Warwickshire B95 5PF
T: 0121 582 0367
E: sales@sefac-lift.co.uk
W: www.sefac-lift.co.uk
Select Plant Hire
Bridge Place, Anchor Boulevard Dartford Kent DA2 6SN
T: 01322 732732
E: infouk@selectplanthire.com
W: www.selectplanthire.com
Selectaglaze Ltd
Alban Park, Hatfield Road St Albans Hertfordshire AL4 OJJ
T: 01727 837271
E: enquiries@selectaglaze.co.uk
W: www.selectaglaze.co.uk
Selectequip Ltd
Unit 7, Britannia Way Lichfield Staffordshire WS14 9UY
T: 01543 416641
E: sales@selectequip.co.uk
W: www.selectequip.co.uk
Selective Recruitment Solutions Ltd
13 Vineyard Chambers, Abingdon Oxford OX14 3PX
T: 01235 462900
E: info@selective-group.com
W: www.selective-group.com
Sella Controls Ltd
Carrington Field Street, Stockport Cheshire SK1 3JN
T: 0161 429 4500
E: reception@sellacontrols.com
W: www.sellacontrols.com
Semcon Product Information UK Ltd Semcon House, Edgehill Drive Warwick CV34 6NH
T: 01926 642935
E: sales@semcon.com
W: www.semcon.com
Semmco Ltd
9 Kestrel Way, Goldsworth Park Ind Est Woking Surrey GU21 3BA
T: 01483 757200
E: sales@semmco.com
W: www.semmco.com
The world’s most reliable, robust, long lasting and cost effective wireless asset condition monitoring system, explicitly designed for Rail/ Civil infrastructure. Senceive’s FlatMesh platform/products solve challenging structural/ geotechnical monitoring problems by using unique technology which combines: low power, ultra-long life, low energy intelligent computing; high precision, high stability and high resolution sensors.
Senceive Limited
Davy Avenue, Knowlhill Milton Keynes MK5 8PB
T: 0800 033 7731
E: info@senceive.com
W: www.senceive.com
Sentinel Lightening Protection & Earthing Ltd
Unit 6a Suite 2, East Bridgford Bus Park
Kneeton Road East Bridgford NG13 8PJ
T: 0115 961 0520
E: enquiries@sentinellp.com
W: www.sentinel-lightning.co.uk
SEP Rail Services
1 Exchange Square, Middlesborough
TS1 1DE
T: 01904 403 322
E: info@seprail.co.uk
W: www.seprail.co.uk
Sepura PLC
9000 Cambridge Research, Park Beach Drive
Waterbeach Cambridge CB25 9TL
T: 01223 876000
E: customer.support@sepura.com
W: www.sepura.com
Sercal Ltd
Unit 1 Littleton Bus Pk, Littleton Drive
Huntington Cannock WS12 4TR
T: 01543 570074
E: enquiries@sercal.co.uk
W: www.sercal.co.uk
Serco Group Plc 16 Bartley Wood, Business Park Bartley Way Hook Hampshire RG27 9XB
T: 01256 745900
E: generalenquiries@serco.com
W: www.serco.com
Serco Rail Technical Services
Derwent House, RTC Business Park London Road Derby DE24 8UP
T: 0330 109 8852
E: enquiries.srts@serco.com
W: www.serco.com/srts
Serfis Construction and Engineering Ltd
9a Church Street, Kidderminster Worcestershire DY10 2AD
T: 01562 822082
E: info@serfis.co.uk
W: www.serfis.co.uk
Serpro Ltd
Units 1008-1009, Hart St Comm Cntr Hart Street Maidstone ME16 8RF
T: 01622 236303
E: accounts@serpro.co.uk
W: www.serpro.co.uk
Servepro Plc Ltd Network Rail Depot, The Old Carriage Works Holgate Park Drive York YO24 4EH
T: 01904 654158
E: info@serveproplc.com
W: www.servproplc.com
SeSys Ltd
1 Rotherbrook Court, Bedford Road Petersfield Hampshire GU32 3QR
T: 01730 230530
E: info@sesys.com
W: www.sesys.com
Setec Ltd
11 Mallard Way, Derby Derbyshire DE24 8GX
T: 01249 704394
E: info@setecltd.co.uk
W: www.setecltd.co.uk
Severfield UK Ltd
Severs House, Dalton Airfield Ind Est Thirsk North Yorkshire YO7 3JN
T: 01845 577896
E: sales@severfield.com
W: www.severfield.com
Severn Partnership Lambda House, Hadley Park East Telford Shropshire TF1 6QJ
T: 01952 676775
E: info@severnpartnership.com
W: www.severnpartnership.com
Seymour Harris Limited 58 Oxford Street, Digbeth Birmingham B5 5NR
T: 0121 600 7420
E: info@seymourharris.com
W: www.seymourharris.com
Seymourpowell The Factory, 265 Merton Road
London SW18 5JS
T: 020 7381 6433
E: reception@seymourpowell.com
W: www.seymourpowell.com
SGS Correl Rail Limited
Gee House, Holborn Hill Birmingham B7 5PA
T: 0121 326 9900
E: gb.rail@sgs.com
W: www.sgs.com
SGS Engineering (UK) Ltd
1 West Side Park, Belmore Way Raynesway Derby DE21 7AZ
T: 01332 576850
E: sales@sgs-engineering.com
W: www.sgs-engineering.com
SH Lighting Ltd
Salcombe Road, Meadow Lane Ind Estate
Alfreton Derbyshire DE55 7RG
T: 01773 522390
E: sales@shlighting.co.uk
W: www.shlighting.co.uk
Shannon Survey Ltd (C.G Surveying Ltd)
Gerrards House, Theobald Street
Borehamwood Hertfordshire WD6 4RT
T: 020 8953 1333
E: sales@shannonsurvey.co.uk
W: www.shannonsurvey.co.uk
Sheerspeed Shelters Ltd
Unit 3, Diamond House, Reme Drive
Heathpark Ind Est Honiton Devon EX14 1SE
T: 01404 46006
E: sales@sheerspeed.com
W: www.sheerspeed.com
Sheffield Hallum University City Campus, Howard Street Sheffield S1 1WB
T: 0114 225 5555
E: enquiries@shu.ac.uk
W: www.shu.ac.uk
Shelley Signs Ltd
54 Cartmel Drive, Harlescott Shrewsbury Shropshire SY1 3TB
T: 01743 460996
E: sales@shelleysigns.co.uk
W: www.shelleysigns.co.uk
Shenton Group
Shenton House, Walworth Road
Walworth Bus Park Andover SP10 5LH
T: 0344 888 4445
E: sales@shentongroup.co.uk
W: www.shentongroup.co.uk
Shepherd PR Limited 24a Market Place, Ashbourne Derbyshire DE6 1ES
T: 01335 368020
E: info@shepherd-pr.com
W: www.shepherd-pr.co.uk
Sherborne Sensors
1 Ringway Centre, Edison Road Basingstoke RG21 6YH
T: 01256 630300
E: sales@sherbornesensors.com
W: www.sherbornesensors.com
Sherwin-Williams Protective & Marine Coatings Tower Works, Kestor Street Bolton Lancashire BL2 2AL
T: 01204 521771
E: sales.uk@sherwin.com
W: www.sherwin-williams.com
Shield Batteries Ltd 277 Stansted Road, Bishops Stortford Hertfordshire CM23 2BT
T: 01279 652067
E: info@shieldbatteries.co.uk
W: www.shieldbatteries.co.uk
Shield Security Services (Yorkshire) Ltd
7 Earls Court, Priory Park East Kingston Upon Hull East Yorkshire HU4 7DY
T: 01482 300833
E: sales@shield-security.co.uk
W: www.shield-security.co.uk
Shire Structures Ltd
The Chapel, Barnsley Hall Road
Bromsgrove Worcestershire B61 0SZ
T: 01527 579933
E: engineers@shire-uk.com
W: www.shire-uk.com
Shrink Polymer Systems (UK)
Unit E3, Crown Way, Crown Park Ind Estate Rushden Nothants NN10 6FD
T: 01933 356758
E: info@shrinkpolymersystems.co.uk
W: www.shrinkpolymersystems.co.uk
Sibcas Ltd
Easton Road, Bathgate West Lothian EH48 2SF
T: 01506 633122
E: enquiries@sibcas.co.uk
W: www.sibcas.co.uk
Sicuro UK – Monitored Security Solutions
23 Saffron Court Laindon Essex SS15 6SS
T: 0800 9991 888
E: info@sicuro.co.uk
W: www.sicuro.co.uk
Sicut Enterprises Ltd
152 City Road London EC1V 2DN
T: 020 8123 6685
E: info@sicut.co.uk
W: www.sicut.co.uk
Siemens 7th Floor, Euston House, 24 Eversholt Street London NW1 1AD
T: 020 7874 6772
E: info.mobility.gb@siemens.com
W: www.siemens.co.uk
Siemens Mobility
Ashby Park, Ashby de la Zouch
Leicestershire LE65 1JD
T: 01530 258000
E: uk.mobility@siemens.com
W: www.siemens.co.uk
SIG PLC
Signet House, 17 Europa View Sheffield Bus Park Sheffield S9 1XH
T: 0114 285 6300
E: info@sigplc.com
W: www.siggroup.com
SIGMAT Limited
Birkbecks, Water Street
Skipton North Yorkshire BD23 1PB
T: 01756 701522
E: info@sigmat.co.uk
W: www.sigmat.co.uk
Signal House Group – Collis Engineering
Salcombe Road, Meadow Lane Ind. Estate
Alfreton Derbyshire DE55 7RG
T: 01773 833255
E: sales@signalhouse.co.uk
W: www.collis.co.uk
Signalling Engineering
The Mount,, Barrow Hill Sellinge
Ashford Kent TN25 6JQ
T: 01303 764344
E: admin@sigtechrail.co.uk
W: www.sigtechrail.co.uk
Signature Aromas Ltd
Signature House, 65-67 Gospel End Street
Sedgley West Midlands DY3 3LR
T: 01902 678822
E: enquiries@signaturearomas.co.uk
W: www.signaturearomas.co.uk
Signature Rail Limited
6 St Mary’s Court, Blossom Street
York YO24 1AH
T: 01904 639091
E: info@signaturerail.com
W: www.signaturerail.com
Signet Solutions
Kelvin House, RTC Business Park
London Road Derby DE24 8UP
T: 01332 343585
E: enquiries@signet-solutions.com
W: www.signet-solutions.com
SignPost Solutions
Unit 5 Clarendon Drive, The Parkway
Tipton West Midlands DY4 0QA
T: 0121 506 4771
E: sales@signfix.co.uk
W: www.signfix.co.uk
SigTech Rail
Dane Rise, Dog Kennel Lane
Lyminge Kent CT18 8ER
T: 01303 764344
E: office@sigtechrail.co.uk
W: www.sigtechrail.co.uk
Sika Ltd
Watchmead Ind Estate
Welwyn Garden City AL7 1BQ
T: 01707 394444
E: sales@uk.sika.com
W: www.gbr.sika.com
Silentblock UK Ltd
Wellington Road, Burton upon Trent
Staffordshire DE14 2AP
T: 01283 741741
E: info@silentbloc.co.uk
W: www.silentbloc.co.uk
Silenzio Panels Ltd
73 Swaisland Drive, Crayford
Kent DA1 4HY
T: 01322 557520
E: sales@silenzio.co.uk
W: www.silenzio.co.uk
Silicone Engineering Limited
Blackwater Road, Greenbank Business Park
Blackburn Lancashire BB1 3HJ
T: 0845 674 4747
E: enquiries@silicone.co.uk
W: www.silicone.co.uk
Sill Lighting (UK) Ltd
4 Goodson Mews, Wellington Street
Thame Oxon OX9 3BX
T: 01844 260006
E: sales@sill-uk.com
W: www.sill-uk.com
Silver Fox Limited
2 Swallowfields, Swallowcourt
Welwyn Garden City Hertfordshire AL7 1GY
T: 01707 373727
E: sales@silverfox.co.uk
W: www.silverfox.co.uk
SilverRail Technologies
The Heal’s Building, 22 Torrington Place London WC1E 7HJ
T: 0845 834 1069
E: info@silverrailtech.com
W: www.silverrailtech.com
Simmons & Simmons
City Point, One Ropemaker Street
London EC2Y 9SS
T: 020 7628 2020
E: enquiries@simmons-simmons.com
W: www.simmons-simmons.com
Sirenum
1st Floor Winston House, 349 Regents Park Road
London N3 1DH
T: 020 3137 2842
E: rail@sirenum.com
W: www.sirenum.com
Site Contract Personnel (SCP)
Hollinwood Business Ctr, Albert Street Failsworth Oldham OL8 3QL
T: 0333 999 7995
E: elliot@sitecontractpersonnel.co.uk
W: www.sitecontractpersonnel.co.uk
Site Vision Surveys Ltd
19 Warwick Street, Rugby Warwickshire CV21 3DH
T: 01788 575036
E: enquiries@svsltd.net
W: www.svsltd.net
SJL Insurance Services Suite C, The Kays Building
23 The Tything Worcester WR1 1HD
T: 01905 27775
E: info@sjl-insurance.com
W: www.sjl-insurance.com
Skanska Construction UK Ltd
Maple Cross House, Denham Way
Maple Cross Rickmansworth WD3 9SW
T: 01923 423100
E: enquiries@skanska.co.uk
W: www.skanska.co.uk
Skelair International Ltd
Units 1 & 2a, Holmes Chapel Bus Park
Manor Lane Holmes Chapel CW4 8AB
T: 01477 539100
E: enquiries@skelair.com
W: www.skelair.com
SKF (UK) Limited
Sundon Park Road, Luton Bedfordshire LU3 3BL
T: 01582 490049
E: marketing.uk@skf.com
W: www.skf.co.uk
Skill Scaffolding Ltd
Skill House, Andes Road Nursling Southampton SO16 0YZ
T: 023 8077 7750
E: enquiries@skillscaffolding.co.uk
W: www.skillscaffolding.co.uk
SLC Investments
111 Edmund Street, Birmingham England B3 2HJ
T: 0121 285 2622
E: Enquiries@slcinvestments.co.uk
W: https://slcrail.com
SLC Operations SLC Operations, 35 Station Road Kings Norton Birmingham B38 8SN
T: 0121 227 5756
E: enquiries@slcoperations.com
W: www.slcoperations.com
SLC Property
4 Brindleyplace, Birmingham B1 2LG T: 0121 285 2622
E: enquiries@slcproperty.co.uk
W: www.slcproperty.co.uk
SLC Rail
4 Brindleyplace, Birmingham B1 2LG
T: 0121 285 2622
E: enquiries@slcrail.com
W: www.slcrail.com
Slender Winter Partnership Limited The Old School, London Road Westerham Kent TN16 1DN
T: 01959 564777
E: swp@swpltd.co.uk
W: www.swpltd.co.uk
Slingco Limited Station Road, Facit Whitworth Lancashire OL12 8LJ
T: 01706 855558
E: sales@slingco.com
W: www.slingco.com
Smart Component Technologies Ltd Cooper Buildings, Arundel Street Sheffield S1 2NS
T: 0114 360 0009
E: info@smartcomptech.com
W: www.smartcomptech.com
Smart Moves Recruitment Ltd
1st floor Silbury Court, 362 Silbury Boulevard Milton Keynes MK9 2AF
T: 01908 308788
E: info@smartmovesrecruitment.co.uk
W: www.smartmovesrecruitment.co.uk
Smart Rail Services Limited
12 Beech Grove, Weaverham Northwich Cheshire CW8 3JA
T: 07540 887458
E: enquiries@smartrailservices.com
W: www.smartrailservices.com
SMARTbrief – Part of Junction 9 Network Ltd St Johns Innovation Ctr Cowley Road Cambridge, CB4 0WS
T: 07971 498113
E: jhall@j9imaging.co.uk
W: www.smart-brief-app.co.uk
Smartwater Technology Ltd
27 Queen Anne’s Gate London SW1H 9BU
T: 0800 521 669
E: enquiries@smartwater.com
W: www.smartwater.com
SMC Pneumatics UK Ltd
Vincent Avenue, Crownhill
Milton Keynes Buckinghamshire MK8 0AN
T: 01908 563888
E: sales@smcpneumatics.co.uk
W: www.smcpneumatics.co.uk
Smith Brothers & Webb / Britannia
Washing Systems
Britannia House, Arden Forest Ind Estate Alcester Warwickshire B49 6EX
T: 01789 400096
E: sales@sbw-wash.com
W: www.sbw-wash.com
Smith Cooper Limited
St Helen’s House, King Street Cathedral Quarter Derby DE1 3EE
T: 01332 332021
E: derby@smithcooper.co.uk
W: www.smithcooper.co.uk
Smiths Rail (Smiths Metal)
Stratton Business Park, London Road Biggleswade SG18 8LB
T: 01767 604704
E: info@smithmetal.com
W: www.smithmetal.com
SmoothtraxGroup
4 Oaklands Road, Petersfield GU32 2EZ
T: 07941 458180
E: contact@smoothtraxgroup.co.uk
W: www.smoothtraxgroup.co.uk
SMP Electronics / Samalite Products
Unit 6 Border Farm, Station Road Chobham Woking GU24 8AS
T: 01276 855166
E: sales@smpelectronics.com
W: www.samalite.com
Specialists in bespoke GRP Dagger Boards, Lightweight GRP Coping, GRP Glazing (Georgian wired), Ballast Boards and well as anti-slip stair treads and flooring. Excellent customer service; all products made (to various thicknesses, size and colour – with or without fire ratings) in our factory in Carnoustie, Scotland.
Smyth Composites Limited
Unit 10, Panmure Ind Estate Carnoustie Angus DD7 7NP
T: 01241 855799
E: admin@scomp.co.uk
W: www.scomp.co.uk
SNA Europe Ltd (Bahco Tools)
Moorhead Way, Bramley Rotherham Yorkshire S66 1YY
T: 01709 731731
E: info.uk@snaeurope.com
W: www.bahco.com
Snap-on Industrial
38a Telford Way, Kettering Northamptonshire NN16 8UN
T: 01536 413904
E: rail@snapon.com
W: www.snapon.com
SNC-Lavalin (formerly known as Interfleet)
SNC-Lavalin House, Pride Parkway Pride Park Derby DE24 8HX
T: 01332 223000
E: groupcommunications@snclavalin.com
W: www.snclavalin.com
Society of Operations Engineers (SOE)
22 Greencoat Place London SW1P 1PR
T: 020 7630 1111
E: webmaster@soe.org.uk
W: www.soe.org.uk
Socomec U.K. Limited
Units 7-9, Lakeside Business Park Broadway Lane Cirencester GL7 5XL
T: 01285 863300
E: info.uk@socomec.com
W: www.socomec.co.uk
SOCOTEC Monitoring UK Ltd
34 Bell Lane, Uckfield East Sussex TN22 1QL
T: 01825 701801
E: monitoring@socotec.com
W: www.socotec.co.uk/monitoring
SOCOTEC UK Limited
SOCOTEC House, Bretby Business Park Ashby Road Burton Upon Trent DE15 0YZ
T: 01283 554400
E: salesuk@socotec.com
W: www.socotec.co.uk
SOCOTEC UK Ltd
Bretby Business Park, Ashby Road
Bretby Burton upon Trent DE15 0YZ
T: 07449 910401
E: vivin.vijay@socotecuk.com
W: www.socotec.co.uk
Softech Global Ltd
Softech House, London Road
Albourne West Sussex BN6 9BN
T: 01273 833844
E: info@softechglobal.com
W: www.softechglobal.com
Softil Ltd
24 Raoul Wallenberg St, Building D
Tel-Aviv Israel 6971924
T: 00 972 3750 9610
E: amir.angel@softil.com
W: www.softil.com
Sohal Shopfronts & Shutter Ltd
71 Elmstead Rd, Seven Kings
Ilford East London IG3 8AY
T: 07469 171423
E: sohalshutters@gmail.com
W: www.sohalshopfronts.com
Soil Engineering Geoservices Limited
Parkside Lane, Dewsbury Road
Leeds LS11 5SX
T: 0113 271 1111
E: enquiries@soil-engineering.co.uk
W: www.soil-engineering.co.uk
SolarFire Systems
Ledgers Farm, Forest Green Road
Fifield Berkshire SL6 2NR
T: 01628 902107
E: sales@solarfiresystems.com
W: www.solarfiresystems.com
Solaris Technologies Ltd
Manchester Bus Park, 3000 Aviator Way
Manchester M22 5TG
T: 0161 266 1860
E: info@solaristechnologies.co.uk
W: www.solaristechnologies.co.uk
Solid Applications Ltd
Old Market Place, Market Street
Oldbury B69 4DH
T: 0121 544 1400
E: info@solidapps.co.uk
W: www.solidapps.co.uk
Solution Rail Ltd
26 The Ridgeway, Watford Hertfordshire WD17 4TN
T: 020 3589 6715
E: enquiries@solutionrail.co.uk
W: www.solutionrail.co.uk
Sonatest Ltd
Dickens Road, Old Wolverton Milton Keynes Buckinghamshire MK12 5QQ
T: 01908 316345
E: sales@sonatest.com
W: www.sonatest.com
Sonic Drilling Ltd
Thornhills Farm, Love Lane Betchton Cheshire CW11 2TT
T: 01477 500177
E: info@sonic-drill.co.uk
W: www.sonic-drill.co.uk
Soprema UK
Soprema House, Freebournes Road
Witham Essex CM8 3UN
T: 0330 058 0668
E: info@soprema.co.uk
W: www.soprema.co.uk
Sortimo International Ltd
11-17 Ravenhurst Court, Birchwood Warrington Cheshire WA3 6PN
T: 01925 831636
E: info@sortimo.co.uk
W: www.sortimo.co.uk
SOUNDEX Temporary Noise Control
Raven Group, The Old Dairy
Southfield Avenue Northampton NN4 8AQ
T: 0800 814 4422
E: enquiries@soundexsolutions.com
W: www.soundexsolutions.com
We are UK suppliers for RS targets, which have been used extensively in connection with railway works for a number of years. The monitoring targets allow for measurements to be taken accurately and safely and can be used for remote monitoring of bridges, tracks, railways and surrounding structures preventing closedown.
South Survey Ltd
21 Deanfield Court, Clitheroe Lancashire BB7 1QS
T: 01200 429870
E: sales@southsurvey.co.uk
W: www.surveyorsequipment.co.uk
South Western Railway
Friars Bridge Court, 41-45 Blackfriars Road
South Bank London SE1 8NZ
T: 0345 600 0650
E: customerrelations@swrailway.com
W: www.southwesternrailway.com
South Yorkshire Passenger Transport Executive
11 Broad Street West Sheffield S1 2BQ
T: 0114 276 7575
E: communications@sypte.co.uk
W: www.sypte.co.uk
Southampton Solent University East Park Terrace
Southampton SO14 0YN
T: 023 8201 3000
E: ask@solent.ac.uk
W: www.solent.ac.uk
Southdowns Environmental Consultants Ltd
16 Station Street, Lewes East Sussex BN7 2DB
T: 01273 488186
E: enquiries@southdowns.eu.com
W: www.southdowns.eu.com
Southeastern Second Floor, 4 More London Riverside London SE1 2AU
T: 0345 322 7021
W: www.southeasternrailway.co.uk
Southern
1st Floor, Monument Place 24 Monument Street London EC3R 8AJ
T: 0345 127 2920
E: comments@southernrailway.com
W: www.southernrailway.com
Southern Ecological Solutions
Sudbury Stables, Sudbury Road
Downham Essex CM11 1LB
T: 01268 711021
E: officeadmin@ses-eco.co.uk
W: www.ses-eco.co.uk
Southside Rail Training Ltd
The Loft, Lees Road, Brabourne Lees Ashford Kent TN25 6QE
T: 07719 304668
E: info@southsiderailtraining.com
W: www.southsiderailtraining.com
Sovereign Hydroseal LP
32-02 Vernon Blvd, PO Box 6466 Astoria, NY 11106
T: 00 1 646 649 5878
E: info@sovereignhydroseal.com
W: www.sovereignhydroseal.com
SpaceandPeople are commercialisation space specialists who market, sell and administer exhibition and promotion space in high footfall venues including train stations. We work with brands, businesses, promoters and agencies seeking space for retail, promotions and brand experience, to increase passenger engagement, generate an additional income stream for venues and ensure placements adhere to compliance requirements.
SpaceandPeople
3rd Floor, Delta House 50, West Nile Street
Glasgow G1 2NP
T: 033 33 401 500
E: marketing@spaceandpeople.co.uk
W: www.spaceandpeople.co.uk
SpanSet UK Ltd
Telford Way, Middlewich
Chesire CW10 OHX
T: 01606 737494
E: customerservices@spanset.co.uk
W: www.spanset.co.uk
Spartan Safety Ltd
3 Waltham Park Way, Billet Road
Walthamstow London E17 5DU
T: 020 8527 5888
E: info@spartansafety.co.uk
W: www.spartansafety.co.uk
SPCM Ltd 2nd Floor, Afon Building Worthing Road Horsham RH12 1TL
T: 0333 900 0939
E: office@spcm.co.uk
W: www.spcm.co.uk
Specialised Tools and Equipment Ltd Unit 15 Riverside Court, Don Road Sheffield South Yorkshire S9 2TJ
T: 0114 383 0110
E: sales@specialisedtools.co.uk
W: www.specialisedtools.co.uk
Specialist Compliant Coatings Ltd
26 Heathfield, Stacey Bushes
Milton Keynes MK12 6HR
T: 01908 320546
E: info@sccgb.co.uk
W: www.sccgb.co.uk
A leading service provider to the Rail Industry with over 20 years rail engineering experience across the UK. Delivering safe and reliable railway infrastructure solutions for our partners on many diverse and challenging projects.
Supplier of safety critical labour, rail plant, POS, minor civil works and leaky feeder communication systems.
Specialist Engineering Services Ltd SES House, Unit 3 Balby Court Balby Carr Bank Doncaster DN4 8DE
T: 01302 756800
E: info@ses-esg.com
W: www.ses-esg.com
Specialist Plant Associates Ltd Airfield Road, Hinwick Wellingborough Northamptonshire NN29 7JQ
T: 01234 781882
E: info@specialistplant.co.uk
W: www.specialistplant.co.uk
Spectrum Contracting Services Limited 107 Bridge Street, Swinton Manchester M27 4DN
T: 0161 711 0399
E: rail@spectrum-group.uk.com
W: www.spectrum-group.uk.com
Spectrum Freight Ltd PO Box 105, Chesterfield Derbyshire S41 9XY
T: 01246 456677
E: sales@spectrumfreight.co.uk
W: www.spectrumfreight.co.uk
Spectrum Technologies Ltd
Western Avenue, Bridgend
Mid Glamorgan CF31 3RT
T: 01656 655437
E: sales@spectrumtech.com
W: www.spectrumtech.com
Spence Ltd
Macmillan House, Paddington Station
London W2 1FT
T: 020 7387 1268
E: info@spenceltd.co.uk
W: www.spenceltd.co.uk
Spencer Group Mill Lane, Barrow upon Humber North Lincolnshire DN19 7BD
T: 01469 532266
E: think@thespencergroup.co.uk
W: www.thespencergroup.co.uk
Spencer Rail (Head Office)
One Humber Quays, Wellington Street West Hull Yorkshire HU1 2BN
T: 01482 766340
E: think@thespencergroup.co.uk
W: www.thespencergroup.co.uk
Spitfire
Kirkhill House, Broom Road East Glasgow G77 5LL
T: 0141 639 6880
E: info@spitfireconsultancy.com
W: www.spitfireconsultancy.com
Spitfire Tours PO Box 824, Taunton TA1 9ET
T: 0870 879 3675
E: info@spitfirerailtours.co.uk
W: www.spitfirerailtours.co.uk
SPL Powerlines UK
Unit 4, Potteric Carr Ind Est
Potteric Carr Road Doncaster S Yorks DN4 5NP
T: 01302 344377
E: office.uk@powerlines-group.com
W: www.powerlines-group.com
Spotcom Ltd
74 Bridge Street, Titchfield Fareham Hants PO14 3QL
T: 07787 522704
E: Andrew@Spotcomltd.co.uk
W: www.SpotcomLtd.co.uk
SPX Flow Rail Systems
Unit 7, Thames Gateway Park Choats Road Dagenham RM9 6RH
T: 020 8526 7100
E: sales@spxflow.com
W: www.spxflow.com
SQES Ltd
24 Highfield View, Barlby Selby YO8 5HB
T: 07968 825774
E: suzanne@sqes.co.uk
W: www.sqes.co.uk
Sqills Palatijn 3, 7521 PN, Enschede
The Netherlands
T: 00 31 0 88 774 557 0
E: info@sqills.com
W: www.sqills.com
Square Mile Broking Ltd
Lloyd’s, Gallery 4 12 Leadenhall St London EC3V 1LP
T: 020 3725 5706
E: rail@squaremilebroking.com
W: www.squaremilebroking.com
SRL Technical Services Limited Holbrook House, Little Waldingfield Sudbury Suffolk CO10 0TF
T: 01787 247595
E: srlweb@srltsl.com
W: www.srltsl.com
SRPS Railtours
82 Busby Road, Carmunnock Glasgow G76 9BJ
T: 0131 202 1033
E: railtours@srps.org.uk
W: www.srps.org.uk
SRS with a history of over 30 years and is a leading supplier of Road Rail plant. The range of equipment comprises of access platforms, cranes, bridge inspection, drum carriers for both OLE and ground cables. Each vehicle is supplied with a highly trained operator, in addition SRS can supply OLEC linesmen.
SRS Rail System International Ltd
3 Riverside Way, Gateway Business Park Bolsover Derbyshire S44 6GA
T: 01246 241312
E: info@srsrailuk.co.uk
W: www.srsrailuk.co.uk
Stadium IGT
Woodside Road Ind Est, Woodside Road Eastleigh Hampshire SO50 4ET
T: 023 8061 0818
E: sales@stadium-igt.com
W: www.stadium-igt.com
StadiumTM
Unit 5, Coventry West Midlands CV2 5DB
T: 024 7518 9999
E: info@stadiumtm.co.uk
W: www.stadiumtm.co.uk
Stannah is an independent British lift company that was founded in 1867. Its maintenance and repair division holds Network Rail maintenance contracts for hundreds of lift products across the network. Its major projects team supplies new lifts and escalators as well as modernisation works across the UK rail network, as well as other infrastructure projects.
Stannah Lift Services – Major Projects
Watt Close, East Portway Bus. Pk Andover Hampshire SP10 3SD
T: 01264 343777
E: contact@stannah.co.uk
W: www.stannahlifts.co.uk
Stansted Express
11th Floor, 1 Stratford Place Montfitchet Road London E20 1EJ
T: 0345 600 7245
E: contactcentre@greateranglia.co.uk
W: www.stanstedexpress.com
Stanway Consulting Ltd
Aztec West, 2440/2430 The Quadrant Almondsbury Bristol BS32 4AQ
T: 01454 878991
E: info@stanwayconsulting.co.uk
W: www.stanwayconsulting.co.uk
Stadler provides high-speed trains, intercity trains, regional and commuter heavy rail trains, underground trains, tram-trains and trams, as well as service and signalling. With a keen focus on the environment, its products feature state-of-the-art technology, offering maximum comfort for passengers. They are safe, reliable, innovative, comfortable and built to last.
Stadler Rail Management AG
Stadler Rail AG, Ernst-Stadler-Strasse 1 9565 Bussnang Switzerland
T: 00 41 71 626 21 20
E: stadler.rail@stadlerrail.com
W: www.stadlerrail.com
Staff Absence Solutions Limited
The Old Courthouse, Chapel Street Dunkinfield Cheshire SK16 4DT
T: 0161 478 4560
E: info@staffabsencesolutions.com
W: www.staffabsencesolutions.com
Stagecoach Supertram
Nunnery Depot, Woodbourn Road Sheffield S9 3LS
T: 0114 272 8282
E: supertram.enquiries@supertram.com
W: www.stagecoachbus.com
Stahlwille Tools Limited
Unit 2 D, Albany Park Ind Estate Camberley Surrey GU16 7PL
T: 01276 24080
E: sales@stahlwille.co.uk
W: www.stahlwille.co.uk
Standish Engineering Co Ltd
Mayflower Works, Bradley Lane
Standish Lancashire WN6 0XF
T: 01257 422838
E: info@cnc-machining.co.uk
W: www.standishengineering.co.uk
Star Fasteners; a global Huck® fastener distributor.
Stock includes an extensive range specifically for the rail industry, track and permanent way engineers including Lockbolts, the new BobTail® & associated tooling.
If structural strength, resistance to vibration & loosening are a requirement – choose Huck fasteners.
Many years of application experience ensures unrivalled technical support.
Star Fasteners (UK) Ltd (Huck Fastener Distributor)
Unit 1, 44 Brookhill Road Pinxton Nottinghamshire NG16 6RY
T: 0115 932 4939
E: sales@starfasteners.co.uk
W: www.starfasteners.co.uk
Stäubli Electrical Connectors
Stäubli House, Presley Way Crownhill Milton Keynes MK8 0ES
T: 01908 265544
E: ec.uk@staubli.com
W: www.staubli.com/electrical
STAUFF UK Ltd
500 Carlisle St East, Off Downgate Drive Sheffield S4 8BS
T: 0114 251 8547
E: sales@stauff.co.uk
W: www.stauff.co.uk
Staytite Ltd are a major supplier and stockist of Railway Fasteners used on S&C and P/Way applications. This includes Hardlock Nuts, approved for use on Fishplates and a growing list of S&C applications. In addition, we can supply the full range of fasteners and other components through VMI systems –www.hard-lock.co.uk.
Staytite Ltd
Staytite House, Coronation Road
High Wycombe Buckinghamshire HP12 3RP
T: 01494 462322
E: info@staytite.com
W: www.staytite.com
Steconfer
Estrada Nacional 3, Km 46,5, 2000-531
Póvoa de Santarém Portugal
T: 00 351 912 952 136
E: comercial@steconfer.com
W: www.steconfer.com
Steel Line Ltd
Unit 27b Orgreave Drive, Sheffield
South Yorkshire S13 9NR
T: 0114 288 0622
E: enquiries@steelline.co.uk
W: www.steelline.co.uk
Steel Protection Consultancy Ltd
PO Box 6386, Leighton Buzzard Bedfordshire LU7 6BX
T: 01525 852500
E: info@steel-protection.co.uk
W: www.steel-protection.co.uk
Steelway Fensecure Ltd
Queensgate Works, Bilston Road Wolverhampton WV2 2NJ
T: 01902 451733
E: marketing@steelway.co.uk
W: www.steelway.co.uk
Steer Davies Gleave
28-32 Upper Ground London SE1 9PD
T: 020 7910 5000
E: ukinfo@steergroup.com
W: www.steerdaviesgleave.com
STEGO (UK) Ltd Unit 12, 1st Quarter Business Pk Epsom Surrey KT19 9QN
T: 01372 747250
E: info@stego.co.uk
W: www.stego.co.uk
Step on Safety Ltd supplies bespoke GRP platform, trackside and depot access solutions to the rail industry; Embankment Staircases, Drivers’ Access Platforms, Maintenance Platforms, End of Platform Steps, Catchpit & Trench Covers and more.
Step on Safety
Factory Lane, Brantham Suffolk CO11 1NH
T: 01206 396446
E: sales@steponsafety.co.uk
W: www.steponsafety.co.uk
Stephen Craven Building Design Ltd Town Hall, Market Place Settle North Yorkshire BD24 9EJ
T: 01729 824754
E: stephen.craven@tiscali.co.uk
W: www.stephencraven.org
Stephen George and Partners LLP 85 Tottenham Court Road London W1T 4TQ
T: 020 3755 5178
E: enquiries@stephengeorge.co.uk
W: www.stephengeorge.co.uk
Stewart Hindmarsh Advertising Ltd Cedars Lodge, The Cedars Ashbrooke Sunderland SR2 7TW
T: 0191 564 0300
E: everything@sh-advertising.co.uk
W: www.sh-advertising.co.uk
Stewart Signs Rail Trafalgar Close, Chandlers Ford Ind Est Eastleigh Hampshire SO53 4BW
T: 023 8025 4781
E: sales@stewartsigns.co.uk
W: www.stewartsigns.co.uk
Stirling Maynard Stirling House, Rightwell Bretton Peterborough PE3 8DJ
T: 01733 262319
E: enquiries@stirlingmaynard.com
W: www.stirlingmaynard.com
STM Security Group (UK) Ltd
Solar House, 1-9 Romford Road
Stratford London E15 4LJ
T: 020 3597 4264
E: businessenquiries@stmgroupltd.com
W: www.stmgroupltd.com
Stobart Rail Aviation Way, Lake District Airport Carlisle CA6 4BY
T: 01228 882300
E: info@stobartrail.com
W: www.stobartrail.com
Stocksigns Ltd
43 Ormside Way, Redhill Surrey RH1 2LG
T: 01737 774072
E: info@stocksigns.co.uk
W: www.stocksigns.co.uk
Stockton Engineering Management Ltd
Minster House, 272-274 Vauxhall Bridge Victoria London SW1V 1BB
T: 020 7931 9898
E: info@stocktonlondon.com
W: www.stocktonlondon.com
Stone Federation Channel Business Centre, Ingles Manor Castle Hill Avenue Folkestone Kent CT20 2RD
T: 01303 856123
E: enquiries@stonefed.org.uk
W: www.stonefed.org.uk
Stonewest has been delivering its own brand of excellence for many decades. Whether it be in the area of principal contracting, building refurbishment, restoration, conservation or new build masonry, our award winning company can offer each and every Client the assurance of unrivalled knowledge in traditional and modern building methods.
Stonewest Ltd
4 Millbank, Westminster London SW1P 3JA
T: 020 8684 6646
E: info@stonewest.co.uk
W: www.stonewest.co.uk
A Step Change in Railway Economy and Efficiency.
The company, an ORR licenced TOC, specialises in providing effective and efficient passenger services utilising lightweight railway technology on non-electrified railways. This approach enables conventional railway services on branch lines, tramways or lightly used railways to be provided at a fraction of current railway operating costs and with increased reliability.
Stourbridge Shuttle –
Pre Metro Operations Ltd
54-56 Hagley Road, Stourbridge West Midlands DY8 1QD
T: 01384 441325
E: premetro@aol.com
W: www.premetro.co.uk
STRAIL (UK) Limited supplies products made from 95% recycled vulcanised rubber, using resilience to protect track geometry and reduce transmission of noise and vibration to the environment. STRAIL is a long-established UK supplier for level crossing systems, with a range that include heavy duty and sleeper spacing independent systems.
Strail (UK) Ltd
Room 2, 1st Floor, 3 Tannery House
Tannery Lane Woking GU23 7EF
T: 01483 222090
E: info@strail.com
W: www.strail.com
Strand7 UK Ltd
The Stables, Church Street
St Neots Cambridgeshire PE19 2BU
T: 01480 211011
E: info@strand7.co.uk
W: www.strand7.co.uk
Stratec Ltd
Stratec Ltd, Ellon AB41 9RG
T: 07468 711621
E: giles.clarke@stratec-geo.com
W: www.stratec-geo.com
Strategic Rail Consultants Ltd
Fourth Floor, Suite 6 12 Pepper Street London E14 9RP
T: 020 7537 2444
E: enquiries@strategicrail.co.uk
W: www.strategicrail.co.uk
Strathclyde Partnership for Transport (SPT)
131 St Vincent Street
Glasgow G2 5JF
T: 0141 332 6811
E: enquiry@spt.co.uk
W: www.spt.co.uk
Street Crane Company Limited
Chapel-en-le-Frith, High Peak
Derbyshire SK23 0PH
T: 01298 808853
E: website@streetcrane.co.uk
W: www.streetcrane.co.uk
StressMap
Venables Building, The Open University Walton Hall Milton Keynes MK7 6AA
T: 01908 653452
E: contact@stressmap.co.uk
W: www.stressmap.co.uk
Structural Adhesives Limited
The Adhesive Buildings, Units 12-13a
Marlow Rd Ind Est Leicester LE3 2BQ
T: 0116 289 4655
E: enquiries@structuraladhesives.co.uk
W: www.structuraladhesives.co.uk
Structural Fabrications Limited
2 Castings Road, Sir Francis Ley Ind Pk South Derby DE23 8YL
T: 01332 747400
E: sales@structural-fabrications.co.uk
W: www.structuralfabrications.co.uk
Structural Repairs
46 The Arches, Windsor Berkshire SL4 1QZ
T: 0300 030 1822
E: hello@structuralrepairs.com
W: www.structuralrepairs.com
Structural Soils Ltd (Bristol Office)
The Old School, Stillhouse Lane
Bedminster Bristol BS3 4EB
T: 0117 947 1000
E: ask@soils.co.uk
W: www.soils.co.uk
Structural Soils, an RSK company, provides an award-winning full Ground Investigation and Testing Service to the rail sector using dedicated staff and equipment for this unique working environment. Highly experienced in the rail sector, we can offer innovative solutions to meet your requirements on projects of all scales.
Structural Soils Ltd (Castleford Office) The Potteries, Pottery Street Castleford West Yorkshire WF10 1NJ
T: 01977 552255
E: ask@soils.co.uk
W: www.soils.co.uk
Structural Soils Ltd (Glasgow Office) 65 Sussex Street, Glasgow Scotland G41 1DX
T: 01414 180 471
E: ask@soils.co.uk
W: www.soils.co.uk
Structural Soils Ltd (Hemel Office)
18 Frogmore Road, Hemel Hempstead Hertfordshire G41 1DX
T: 01442 416 660
E: ask@soils.co.uk
W: www.soils.co.uk
Structural Soils Ltd (Tonbridge Office)
Anerley Court, Half Moon Lane
Hildenborough Tonbridge TN11 9HU
T: 01732 833 111
E: ask@soils.co.uk
W: www.soils.co.uk
Structural Soils Ltd (Wigan)
Unit 1 Forton Road, Wheatlea Industrial Estate
Wigan Lancashire WN3 6YD
T: 01942 825052
E: ask@soils.co.uk
W: www.soils.co.uk
Structural Systems (UK) Ltd
12 Collett Way, Southall Middlesex UB2 4SE
T: 020 8843 6500
E: enquiries@structural-systems.co.uk
W: www.structuralsystemsuk.com
Structural Timber Association (STA)
The e-Centre, Cooperage Way Bus Vlg
Alloa Scotland FK10 3LY
T: 01259 272140
E: office@structuraltimber.co.uk
W: www.structuraltimber.co.uk
Studio Egret West Limited
3 Brewhouse Yard London EC1V 4JQ
T: 020 7549 1730
E: hello@egretwest.com
W: www.egretwest.com
Subscan UDS Ltd
Subscan House, 126 Whitehall Road Leeds LS12 1AE
T: 0344 499 5220
E: info@subscan.com
W: www.subscan.com
SubVision Surveys Ltd
Mapline House, 14 Bull Lane Rayleigh Essex SS6 8JD
T: 0845 567 5677
E: info@subvisionsurveys.co.uk
W: www.subvisionsurveys.co.uk
Sulzer Electro Mechanical Services UK 193 Camp Hill
Birmingham B12 0JJ
T: 0121 766 6161
E: service.birmingham@sulzer.com
W: www.sulzer.com
Sunbelt Rentals Limited
102 Dalton Ave, Risley
Warrington WA3 6YE
T: 0808 196 8639
E: NROC@sunbeltrentals.co.uk
W: www.sunbeltrentals.co.uk
Sunray Engineering are leading designers, manufacturers and installers of steel doorsets and louvre products. Our comprehensive portfolio provides bespoke solutions for a variety of project applications through innovative design, technical expertise and dependable quality and service. All our high quality steel door products are designed and manufactured in the UK.
Sunray Engineering Ltd
6 Kingsnorth Ind Est, Wotton Road Ashford TN23 6LL
T: 01233 639 039
E: sales@sunraydoors.co.uk
W: www.sunraydoors.co.uk
Super Rod S-O-T Ltd
Furlong Lane, Burslem Stoke on Trent ST6 3LE
T: 01782 832444
E: info@superrod.co.uk
W: www.superrod.co.uk
Superfine Manufacturing Limited Orchardbank Ind Estate, Forfar Angus Scotland DD8 1TD
T: 01307 463538
E: sales@superfine.co.uk
W: www.superfine.co.uk
Surbon Consulting 3a Minton Place, Victoria Road Bicester Oxfordshire OX26 6QB
T: 07799 626196
E: info@surbonconsulting.com
W: www.surbonconsulting.com
Surface Finishing Equipment Group Unit 10 Armstrong Road, Armstrong Ind Estate Washington NE37 1PR
T: 0191 415 3030
E: marketing@sfeg.co.uk
W: www.sfeg.co.uk
Survey Association (TSA)
Northgate Bus Centre, 38 Northgate Newark-on-Trent Nottinghamshire NG24 1EZ
T: 01636 642840
E: office@tsa-uk.org.uk
W: www.tsa-uk.org.uk
Sussex Blast Cleaning Ltd Unit 35, Station Road Ind Estate
Hailsham East Sussex BN27 2ER
T: 01323 849229
E: info@sussexblastcleaning.co.uk
W: www.sussexblastcleaning.co.uk
SVR Plastics Units 5/6, Greenhey Place
East Gillibrands Skelmersdale WN8 9SA
T: 01695 50717
E: enquiries@svrplastics.co.uk
W: www.svrplastics.co.uk
SW Global Resourcing Ltd (Scotland) 270 Petershill Road, Springburn Glasgow Scotland G21 4AY
T: 0141 557 6133
E: Admin@sw-gr.com
W: www.sw-gr.com
Swann Group Ltd Kent House, 60 Priory Street Tonbridge Kent TN9 2AH
T: 01732 770813
E: sales@swanngroupltd.com
W: www.swanngroupltd.com
Swansea University
Singleton Park, Swansea Wales SA2 8PP
T: 01792 205678
E: study@swansea.ac.uk
W: www.swansea.ac.uk
Sweco UK
Grove House, Mansion Gate Drive
Leeds LS7 4DN
T: 0113 262 0000
E: info@sweco.co.uk
W: www.sweco.co.uk
Sweetnam & Bradley Ltd
Industrial Estate, Gloucester Road
Malmesbury Wiltshire SN16 0DY
T: 01666 823491
E: enquiries@sweetnam-bradley.com
W: www.sweetnam-bradley.com
Founded in 1936 by Hellmuth Swietelsky, the company is now one of Austria’s biggest specialist construction companies with an annual turnover close to € 3 billion. Our Bahnbau division owns and operates one of the largest on track machine fleets in Europe and its U.K. based business and has the most modern fleet of on track machines in the country.
Swietelsky Construction Company Limited
1st Floor Suite 1, Sycamore House 290 Bath Street Glasgow G2 4JR
T: 0141 212 5630
E: office@swietelsky.at
W: www.swietelsky.com
Swift Industrial Supplies Suite 1, Venture Park
Selborne Road Alton Hampshire GU34 3HL
T: 01420 592540
E: info@swift360.co.uk
W: www.swift360.co.uk
Sydac Limited
The Derwent Bus Centre, Clarke Street
Derby DE1 2BU
T: 01332 299600
E: sales@sydac.co.uk
W: www.sydac.com
Syndicate Alpha Ltd 210 Church Road London E10 7JQ
T: 0203 642 9510
E: info@syndicatealpha.co.uk
W: www.syndicatealpha.co.uk
Synectics
3-4 Broadfield Close, Sheffield South Yorkshire S8 0XN
T: 0114 255 2509
E: sales@synecticsglobal.com
W: www.synecticsglobal.com
Synoptix Limited
10 Brabazon Office Park, Golf Course Lane Filton Bristol BS34 7PZ
T: 0117 943 0707
E: info@synoptix.co.uk
W: www.synoptix.co.uk
Syntax Consultancy
Derwent Business Centre, Clarke Street Derby DE1 2BU
T: 01332 293605
E: hello@syntaxconsultancy.com
W: www.syntaxconsultancy.com
System Electrical Ltd
Unit 23 Mold Bus Park, Mold Flintshire CH7 1XP
T: 01352 750010
E: info@system-electical.com
W: www.system-electrical.com
System 7 is a leading provider of cutting-edge railway maintenance solutions. Specializing in the design and development of state-of-the-art equipment, System 7 delivers innovative tools for the efficient inspection, maintenance, and modernization of rail networks globally. With a focus on advanced technology and unwavering commitment to quality, System 7 is a trusted partner in advancing railway infrastructure.
System7 Rail Holding GMBH
Gewerbegebiet Süd 11, 4664 Laakirchen Austria
T: +43 7613 44700
E: office@s7-rail.com
W: www.s7-rail.com
Systra UK Ltd
5th Floor, Lancaster House 67 Newhall Street Birmingham B3 1NQ
T: 0121 393 4841
E: info_uk@systra.com
W: www.systra.co.uk
T Sumner Smith Ltd
Unit A, Clayton Green Bus Park Library Road Chorley PR6 7EN
T: 0333 311 4400
E: info@tssinfrastructure.com
W: www.tssinfrastructure.com
T-UK Tecnologic UK
Unit 1, Farnborough Bus Centre Eelmoor Road Farnborough, Hants GU14 7XA
T: 01252 377 600
E: sales@tecnologicuk.co.uk
W: www.t-uk.co.uk
Moving Rail Projects Forward Together
Powering both plant and personnel, T&M have a wide range of bowsers to assist. Providing the vital supply link for crew, our larger bowser models are the perfect option for transporting vast quantities of fuel and water to your location, whilst smaller bowsers offer a nimble alternative for moving around the site.
T&M Bowser Solutions
T&M House, Star Road Ind Est
Partridge Green West Sussex RH13 8RA
T: 01293 774 500
E: info@tmplant.co.uk
W: bowser-hire.com
T&R Test Equipment Ltd
15-16, Woodbridge Meadows Guildford GU1 1BJ
T: 01483 207428
E: sales@trtest.com
W: www.trtest.com
T&RS Engineering Ltd
Unit 8 Buccaneer Drive, Fountain Court Hayfield Lane Doncaster DN9 3QP
T: 01302 315011
E: mail@trsengineering.co.uk
W: www.trsengineering.co.uk
Tamura Europe Ltd
Clark Avenue, Porte Marsh Ind Estate Calne Wiltshire SN11 9BS
T: 01380 731700
E: business@tamura-europe.co.uk
W: www.tamura-europe.co.uk
Tanfield Engineering Systems Ltd
Tanfield Lea Ind Est N, Stanley Co Durham DH9 9NX
T: 01207 521111
E: info@tanfieldengineeringsystems.com
W: www.tanfieldengineeringsystems.com
Tangerine
Unit 9 Blue Lion Place, 237 Long lane London SE1 4PU
T: 020 7357 0966
E: mail@tangerine.net
W: www.tangerine.net
Tarmac
Portland House, Bickenhill Lane
Solihull Birmingham B37 7BQ
T: 0121 737 5375
E: pr@tarmac.com
W: www.tarmac.com
TATA Consultancy Services
33 Grosvenor Place London SW1X 7HY
T: 020 7245 1800
E: contact.us@tcs.com
W: www.tcs.com
Taylor Technology Solutions Limited
Richmond Court, 128 Maidstone Road
Sidcup Kent DA14 5HS
T: 020 8320 9944
E: sales@taylortechnologysystems.com
W: www.taylortechnologysystems.com
Taziker Industrial Limited
Unit 6 Lodge Bank, Crown Lane Horwich Lancashire BL6 5HY
T: 01204 468080
E: sales@ti.uk.com
W: www.ti.uk.com
TB Davies (Cardiff) Ltd Lewis Road
Cardiff CF24 5EB
T: 029 2132 0000
E: info@tbdavies.co.uk
W: www.tbdavies.co.uk
TBA Protective Technologies Ltd are specialist UK manufacturers of the highest performance technical textiles for use in critical fire, thermal and protective applications. Greatly experienced in the provision of fire and slashresistant materials used within rail passenger seating, working with seat manufacturers to meet relevant European and International test standards.
TBA Protective Technologies Ltd
Transpennine Trade Est, Gorrells Way
Rochdale Lancashire OL11 2PX
T: 01706 647422
E: info@tba-pt.com
W: www.tba-pt.com
TBAT Innovation Limited
Unit 3, Bradley Court, Trent Lane
Castle Donington Derbyshire DE74 2UT
T: 01332 819740
E: info@tbat.co.uk
W: www.tbat.co.uk
TCS Geotechnics
Units 2 & 5, Tetbury Close
Martland Park Wigan WN5 0LA
T: 01942 218597
E: sales@tcs-geotechnics.co.uk
W: www.tcs-geotechnics.co.uk
Tec Training (GB) Ltd
1 Dock Road, London E16 1AH
T: 020 7476 1111
E: info@tectraining.co.uk
W: www.tectraining.co.uk
Tecalemit
Eagle Road, Langage Business Park Plymouth Devon PL7 5JY T: 01752 219111
E: sales@tecalemit.co.uk
W: www.tecalemit.co.uk
Tecforce Ltd
Litchurch Lane, Derby Derbyshire DE24 8AA
T: 01332 268000
E: sales@tecforce.co.uk
W: www.tecforce.co.uk
Technical Programme Delivery Ltd
Systems House, 10 Heathfield Close Binfield Heath Henley On Thames RG9 4DS
T: 01932 228710
E: dir@tpd.uk.com
W: www.tpd.uk.com
TECHNO CTA Limited
7 Pier Parade, London E16 2LJ
T: 0207 055 0877
E: info@technocta.co.uk
W: www.technocta.co.uk
Technocover Ltd (Incorporating Technorail)
Henfaes Lane, Welshpool Powys Wales SYL1 7BE
T: 01938 555511
E: sales@technocover.co.uk
W: www.technocover.co.uk
Technology Resourcing Ltd
Technology Centre, Surrey Research Park Occam Road Guildford GU2 7YG
T: 01483 302211
E: recruit@tech-res.co.uk
W: www.tech-res.co.uk
Techpol Ltd
Unit 4 Rushy Platt, Wootton Bassett Road Swindon Wiltshire SN5 8WQ
T: 01793 871550
E: enquiries@techpolltd.com
W: www.techpolltd.com
Tecocraft LTD
311 Green Lane, Ilford
Essex IG3 9TL
T: 07833 027277
E: info@tecocraft.com
W: www.tecocraft.co.uk
Teepee Electrical
Teepee House Unit 6, Leamore Lane Bloxwich, Walsall West Midlands WS2 7DG
T: 01922 408 571
E: sales@teepee-electrical.co.uk
W: www.teepeeelectrical.co.uk
TEK Seating Ltd
14 Decimus Park, Kingstanding Way
Tunbridge Wells Kent TN2 3PG
T: 01892 515028
E: sales@tekseating.co.uk
W: www.tekseating.co.uk
Telegartner UK Ltd Unit 1, A1(M) Business Centre
157 Dixons Hill Rd Hertfordshire AL9 7JE
T: 01707 636600
E: info@telegaertner.co.uk
W: www.telegaertner.co.uk
Telent is a leading technology company in the design, build, support and management of the UK’s critical digital infrastructure, utilising decades of experience in mission critical communications and technology. Our expertise, partnerships and committed teams make Telent the partner of choice for organisations at the forefront of the digital revolution.
Telent Technology Services Ltd
Point 3, Haywood Road
Warwick CV34 5AH
T: 01926 693000
E: talktotelent@telent.com
W: www.telent.com
The Teleque Wireless radio platform announcer is a cost-effective and visible upgrade to existing PA systems. It significantly enhances station operations, increasing the mobility and safety of its platform staff. The Teleque T101 conforms to the National Rail product specification for wireless connectivity (NR/L2/ TEL/30147) and is fully PADS approved.
Teleque Ltd
71-75 Shelton Street
London WC2H 9JQ
T: 01243 278785
E: info@teleque.co.uk
W: www.teleque.co.uk
Televic Rail designs, produces and maintains communication and control systems for the rail market. For more than 30 years Televic Rail has been a leading trusted partner for railway operators and train builders all over the world and has equipped more than 60.000 vehicles with on-board solutions.
Televic GSP
Televic Rail HQ, Leo Bekaertlaan 1 8870 Izegem Belgium
T: 0032 5130 3045
E: televicgsp@televic.com
W: www.televic.com/en/televicgsp
Temple Group Ltd
The Woolyard, 52 Bermondsey Street London SE1 3UD
T: 020 7394 3700
E: enquiries@templegroup.co.uk
W: www.templegroup.co.uk
TenBroekeCo is a firm of multi-disciplinary independent expert advisers on infrastructure, with specialist knowledge in railways, depots and stations. We have taken leading roles in many high-profile UK projects including Canary Wharf Crossrail Station, Jubilee Line, Thameslink, Old Oak Common, Ramsgate and internationally in Turkey, Iraq, India and Bangladesh.
TenBroeke Company Limited
39 North View Crescent, Epsom Downs Epsom Surrey KT18 5UW
T: 01737 211300
E: paul.tweedale@tenbroekeco.com
W: www.tenbroekeco.com
TenCate Advanced Composites UK Amber Drive, Langley Mill Nottingham NG16 4BE
T: 01773 530899
E: tcacsales@tencate.com
W: www.tencatecomposites.com
Tencate Geosynthetics PO Box 773, Telford Shropshire TF7 9FE
T: 01952 588066
E: service.uk@tencategeo.com
W: www.tencategeo.eu
Teneo Blue Rubicon 5th Floor, 6 More London Place London SE1 2DA
T: 020 7260 2700
E: info@teneo.com
W: www.teneo.com
Tenmat Ltd (Railko Ltd)
Ashburton Road West, Trafford Park Manchester M70 1RU
T: 0161 872 2181
E: webenquiry@tenmat.com
W: www.tenmat.com
Tensar International Ltd Cunningham Court, Shadsworth Bus Park Blackburn BB1 2QX
T: 01254 262431
E: info@tensar-international.com
W: www.tensar.co.uk
Terra Solutions Limited
3 Carnbane Bus Park, Shepherds Way Newry Co. Down BT35 6QH
T: 028 3026 9848
E: info@terrasolutions.co.uk
W: www.terrasolutions.co.uk
Terram & Tubex
Blackwater Trading Est, The Causeway Maldon Essex CM9 4GG
T: 01621 874200
E: info@terram.com
W: www.terram.com
TES 2000 Ltd Heath Business Park, Grange Way Colchester Essex CO2 8GU
T: 01206 799111
E: info@tes2000.co.uk
W: www.tes2000.co.uk
Testo Ltd
Newman Lane, Alton Hampshire GU34 2QJ
T: 01420 544433
E: info@testo.co.uk
W: www.testo.com
TFC, an AFC Industries company, is a full-service industrial distributor offering Vendor Managed Inventory services, vending, kitting, and other supply chain solutions to manufacturers, utilities, distributors, and users of C-Class components.
TFC is the sole UK supplier of Smalley Springs, Retaining Rings and ARaymond Quick Connectors with unsurpassed quality and expert, collaborative engineering team.
TFC Ltd – Head Office
Hale House, Ghyll Industrial Estate Heathfield East Sussex TN21 8AW
T: 01435 866011
E: Enquiries@tfc.eu.com
W: www.tfc.eu.com
The Bionic Eye Unit 7, Brook Business Centre Cowley Mill Road Uxbridge UB8 2FX
T: 01753 653456
E: info@thebioniceye.co.uk
W: www.thebioniceye.co.uk
The Consultancy Company
9 Fenlock Court, Blenheim Office Park Long Hanborough Oxford OX29 8LN
T: 01993 883421
E: info@the-consultancy.co.uk
W: www.the-consultancy.co.uk
The Cylinder Service Centre Ltd
Sedling Road, Washington Tyne & Wear NE38 9BZ
T: 0191 416 6288
E: sales@cylinder.co.uk
W: www.cylinder.co.uk
The Deritend Group Ltd
Cyprus Street, Wolverhampton West Midlands WV2 4PA
T: 01902 426354
E: wolverhampton@deritend.co.uk
W: www.deritend.co.uk
The Ecology Consultancy
Tempus Wharf, 33a Bermondsey Wall London SE16 4TQ
T: 020 7378 1914
E: marketing@ecologyconsultancy.co.uk
W: www.ecologyconsultancy.co.uk
The Greenbank Group UK
Hartshorne Road, Woodville Derbyshire DE11 7GT
T: 0845 0707 097
E: info@greenbankgroup.com
W: www.greenbankgroup.com
The Imagination Factory Ltd
Power Road Studios, 114 Power Road Chiswick London W4 5PY
T: 07748 767688
E: julian@imaginationfactory.co.uk
W: www.imaginationfactory.co.uk
The Input Group
Input House, 103 Ashbourne Road
Derby DE22 3FW
T: 01332 348830
E: office@inputgroup.co.uk
W: www.inputgroup.co.uk
The National Engineering & Construction Recruitment Exhibition
Floor 2, 2-4 St Georges Road
Wimbledon SW19 4DP
T: 020 8394 5200
E: ner@vmgl.com
W: www.engineerjobs.co.uk
With over 30 years of rail industry experience, we provide specialised psychological and HR solutions for gaps in (safety) performance, talent acquisition, and support for employee development. Our particular interest is in human factors and safety-critical role performance, as well as why people make mistakes and have safety incidents.
The OPC
One Wellstones, Watford Hertfordshire WD17 2AE
T: 01923 234646
E: admin@theopc.co.uk
W: www.theopc.co.uk
The Pied Piper Pest Control Company Ltd
301 Hall Lane, 301 Hall Lane
E4 8NU
T: 0800 9993999
E: thepiedpiperpestcontrol@gmail.com
W: www.thepiedpiper.co.uk
The QSS Group Limited
2 St George’s House, Vernon Gate Derby DE1 1UQ
T: 01332 221400
E: enquiries@theqss.co.uk
W: www.theqssgroup.co.uk
The Rail Estate Consultancy Ltd
12 Bridge Wharf, 156 Caledonian Road London N1 9UU
T: 020 7837 1114
E: mail@railestate.co.uk
W: www.railestate.co.uk
The Railway Consultancy Ltd
1st floor South Tower, Crystal Palace Station London SE19 2AZ
T: 020-8676-0395
E: info@railwayconsultancy.com
W: www.railwayconsultancy.com
The SES Group
The Barrows, Roydon Road Harlow CM19 5DY
T: 020 3858 0528
E: enquiries@thesesgroup.co.uk
W: www.thesesgroup.co.uk
The SFS Manufacturing Group Ltd
Unit 3, Finway
Luton Bedfordshire LU1 1TR
T: 01582 509250
E: sales@sfsgrp.com
W: www.sfsgrp.com
The Spencer Group
One Humber Quays, Wellington Street West Hull HU1 2BN
T: 0113 815 0015
E: think@thespencergroup.co.uk
W: www.spencerrail.co.uk
The Tankbusters & Tankbusters Commercial Ltd
Langworth Junction Mansfield
T: 01623 741351
E: info@tankbusters.co.uk
W: www.tankbusters.co.uk
The Think Tank
40 Clifton Street London EC2A 4DX
T: 020 7831 2225
E: info@thinktank.org.uk
W: www.thinktank.org.uk
The Trainline PO Box 23972, Edinburgh EH3 5DA
T: 0333 202 2222
E: customer.relations@thetrainline.com
W: www.thetrainline.com
The Write Angle
20 Eaton Avenue, Buckshaw VIllage Chorley Lancashire PR7 7NA
T: 01772 450990
E: hello@thewriteangle.co.uk
W: www.thewriteangle.co.uk
Thermacom Ltd
Kelvin House, Preston Road Reading Berkshire RG2 0BE
T: 0118 918 1400
E: sales@thermagroup.com
W: www.thermagroup.com
Thermit Welding (GB) Ltd
87 Ferry Lane, Rainham
Essex RM13 9YH
T: 01708 522626
E: info@thermitwelding.co.uk
W: www.thermit-welding.co.uk
Thomas Radford
1 Broad Gate, The Headrow Leeds LS1 8EQ
T: 0113 834 5546
E: info@thomasradford.co.uk
W: www.thomasradford.co.uk
Thomson Ecology Ltd
Compass House, Surrey Research Park Guildford Surrey GU2 7AG
T: 01483 466000
E: enquiries@thomsonecology.com
W: www.thomsonecology.com
Thomson Engineering Design Ltd
Units 2a and 3 Crab Tree Road, Forest Vale
Industrial Estate
Cinderford GL14 2YQ
T: 01594 826611
E: sales@thomsondesignuk.com
W: www.thomsonrail.com
Thornton & Lowe 40 Higher Bridge Street Bolton BL1 2HA
T: 01204 238046
E: hello@thorntonandlowe.com
W: www.thorntonandlowe.com
Three Shires Ltd
Piper Hole Farm, Eastwell Road Scalford Leicestershire LE14 4SS
T: 01664 444604
E: enquiries@threeshires.com
W: www.threeshires.com
TICS (Global) Ltd
PO BOX 139 Sandall Lane, Kirk Sandall Ind Estate Doncaster DN3 1WZ
T: 01302 888631
E: info@tics-ltd.co.uk
W: www.tics-ltd.co.uk
TIDE Services trading as Geodesys Osprey House, 1 Percy Road
Huntingdon Cambridgeshire PE29 6SZ
T: 0800 085 8050
E: customer.services@geodesys.com
W: www.geodesys.com
Tidyco Ltd
Nottingham Road Derby DE21 6BW
T: 01332 851300
E: sales@tidyco.co.uk
W: www.tidyco.co.uk
Specialised in the manufacture of resilient track support materials, designed to reduce ground borne vibration.
Rail products include Sleeper/baseplate pads. Under Sleeper Pads, S&C pads, strip pads. Under ballast mats, stray current protection mats, structural protection mats. Fire retardant rail pads, Floating Slab Track (FST) bearings, crane rail strip pads.
Tiflex Ltd – Trackelast Specialist Rail Solutions Tiflex House, Liskeard Cornwall PL14 4NB
T: 01579 320808
E: sales@tiflex.co.uk
W: www.trackelast.com
Timbermat Ltd
Battersea Road, Heaton Mersey Ind Est Stockport Cheshire SK4 3EA
T: 0161 442 3157
E: info@timbermat.co.uk
W: www.timbermat.co.uk
Time 24 are one of Europe’s largest Rail Contract Manufacturers for the supply of Electromechanical Assemblies and Wiring Harnesses. Fully ISO22163(IRIS) approved and with facilities in both the UK and the low cost Czech Republic, Time 24 have a world class customer base for both Rolling Stock and Infrastructure Applications. Time 24 assemblies are now on over 30,000 UK Rail Carriages.
Time 24
19 Victoria Gardens, Burgess Hill West Sussex RH15 9NB
T: 01444 257655
E: info@time24.co.uk
W: www.time24.com
Timeplan Solutions Ltd
12 The Pines, Broad Street Guildford Surrey GU3 3BH
T: 01483 452283
E: info@timeplansolutions.com
W: www.timeplansolutions.com
Tony Meadows Associates Ltd
3 Fitzroy Mews, Fitzrovia London W1T 6DF
T: 020 7388 0004
E: tma@tma.uk.com
W: www.tma.uk.com
Topdrill Ltd
7 Deeping Gate, Stonebridge
Milton Keynes Buckinghamshire MK13 0DE
T: 01908 321925
E: info@topdrill.co.uk
W: www.topdrill.co.uk
Torishima Service Solutions Europe Limited – Fluid
Power Division
Unit 5, Berrington Road, Sydenham Ind. Estate
Royal Leamington Spa Warwickshire CV31 1NB
T: 01926 420847
E: salestfp@torishima.co.uk
W: www.torishimaservice.co.uk/fluid-power
Torrent Trackside
1st Floor, Ventura House
Ventura Park Road Tamworth Staffs B78 3HL
T: 0845 769 7168
E: mail@torrent.co.uk
W: www.torrent.co.uk
Total Connections 2009 Ltd
Unit 2, Clark Avenue
Calne Wilts SN11 9BS
T: 01249 812 707
E: sales@tc2009.co.uk
W: www.tc2009.co.uk
Total Rail Solutions (TRS)
Crossways, Stephenson Road
Houndmills Basingstoke RG21 6XR
T: 01962 711642
E: info@totalrailsolutions.co.uk
W: www.totalrailsolutions.co.uk
Total Steelwork & Fabrication Ltd
Warrington Central, Trading Estate
Bewsey Road Warrington WA2 7LP
T: 01925 234320
E: info@totalsteelfabs.com
W: www.totalsteelfabs.com
Total Training Company (UK) Ltd
365-369 Olton Boulevard, East Olton Solihull West Midlands B27 7DP
T: 0121 706 0851
E: info@total-training.uk.com
W: www.total-training.uk.com
Totalkare’s railway lifting jacks are perfect for depots and workshops. Available in lifting capacities from 5,500kg to 50,000kg per jack, they are heavy duty and reliable.
The jacks can be used in configurations of 4 to 128 columns, with computerised control units providing easy synchronicity, enabling the lifting of a single carriage or series of rail cars.
Totalkare Block G1, Dandy Bank Road
Pensnett Trad Est Kingswinford DY6 7TD
T: 0121 585 2724
E: sales@totalkare.co.uk
W: www.totalkare.co.uk
Tower Supplies
3 Yarrow Road, Tower Park Poole Dorset BH12 4TS
T: 01202 718000
E: sales@towersupplies.com
W: www.towersupplies.com
Townscape Products Fulwood Road South, Sutton-in-Ashfield
Nottinghamshire NG17 2JZ
T: 01623 513355
E: sales@townscape-products.co.uk
W: www.townscapeproducts.co.uk
TP Matrix Ltd
Prince Of Wales Bus Pk, Vulcan Street
Oldham Greater Manchester OL1 4ER
T: 0161 626 4067
E: enquiries@tpmatrix.co.uk
W: www.tpmatrixrail.co.uk
TPA Rapid Rail Access
Claylands Avenue, Worksop Nottinghamshire S81 7DJ
T: 0870 240 2381
E: info@vp-tpa.com
W: www.vp-tpa.com
We bring a wealth of specialist rail industry experience, sector knowledge, strategic and commercial planning expertise and a track record of delivering projects to the highest standard, with our partners. Installing, testing and managing major work projects, from complex large renewal works, to multi-faceted dynamic systems test sessions.
TPS Limited (Track Protection & Signalling)
Warlies Park House, 11 Old School Block Horseshoe Hill Upshire EN9 3SL
T: 01992 245560
E: info@uk-tps.com
W: www.uk-tps.com
Trace Heating Projects Ltd
Green End House, 33d Greens End Road
Meltham Holmfirth West Yorkshire HD9 5NW
T: 01484 859700
E: sales@traceheatingprojects.co.uk
W: www.traceheatingprojects.co.uk
TrAchem Ltd
Unit 2 Holmeroyd Bus Pk, Holmeroyd Road Carcroft Doncaster DN6 7EG
T: 01302 723111
E: info@trachem.co.uk
W: www.oil-store.co.uk
Track Maintenance Equipment Limited 2 Station Road Ind Est, Liphook Hampshire GU30 7DR
T: 01428 724701
E: sales@tmeltd.co.uk
W: www.tmeltd.co.uk
Tracklink is a leading UK supplier of railway equipment, tools and technology. We are also the market leader in calibration services for railway specific instruments and non-railroad specific equipment such as insulation testers and digital thermometers.
Tracklink is committed to providing the best possible standard of service to all its clients.
Tracklink UK Ltd
Unit 5, Miltons Yard Petworth Road Witley, Surrey GU8 5LH
T: 01428 685902
E: enquiries@tklink.co.uk
W: www.tklink.co.uk
Trackmaps PO Box 5259, Beckington
Frome BA11 9DD
T: 0845 300 1370
E: sales@trackmaps.co.uk
W: www.trackmaps.co.uk
Trackway Solutions Limited
Unit 727a, Street 2
Thorp Arch Estate Wetherby LS23 7FX
T: 0845 241 8555
E: info@trackwaysolutions.co.uk
W: www.trackwaysolutions.co.uk
Trackwork Ltd
PO Box 139 Sandall Lane, Kirk Sandall Ind Estate Doncaster DN3 1WZ
T: 01302 888666
E: info@trackwork.co.uk
W: www.trackwork.co.uk
TRACO POWER has been the leading manufacturer of DC/DC converters and AC/DC switching power supplies for industrial or railway applications.
TRACO POWER offer a wide selection of DC/DC converters that meet the stringent requirements for mobile and stationary railway applications in accordance to EN50155 standard: Increased EMC immunity against surge, burst, radiated and conducted disturbance
Traco Electronic AG
Sihlbruggstrasse 111, 6340 Baar
Switzerland T: 00 41 43 311 45 11
E: info@tracopower.com
W: www.tracopower.com
Tracsis PLC
Nexus, Discovery Way Leeds LS2 3AA
T: 0845 125 9162
E: info@tracsis.com
W: www.tracsis.com
Tracsis Transport Consultancy
33 Brunel Parkway, Pride Park Derby DE24 8HR
E: consultancy@tracsis.com
W: www.tracsis.com
Traction Rail Electrical are a family-owned specialist railway electrification contractor, for all third-rail distribution enhancement and upgrade schemes. With a wealth of ETE experience within the internal management team, we have the capabilities for all DC cabling design and installation, negative bonding and CRE design / construction support.
Traction Rail Electrical Ltd
Unit D4, Lomer Farm
Wrotham Road Meopham DA13 0AN
T: 0203 146 1157
E: thecompany@tractionrail.com
W: www.tractionrail.com
Trades Union Congress (TUC)
Congress House, Great Russell Street London WC1B 3LS
T: 020 7636 4030
E: info@tuc.org.uk
W: www.tuc.org.uk
Trainfx Ltd
4 Newmarket Court, Newmarket Drive Derby DE24 8NW
T: 01332 366175
E: enquiries@trainfx.com
W: www.trainfx.com
Trans Data Management Ltd
12 Raleigh Court, Priestley Way Crawley RH10 9PD
T: 01293 516691
E: info@trans-data.com
W: www.trans-data.com
Trans-Tronic Ltd
Whitting Valley Road, Old Whittington Chesterfield S41 9EY
T: 01246 264260
E: sales@trans-tronic.co.uk
W: www.trans-tronic.co.uk
Transit Cable Products
2 Jane’s Court, Cambridge Cambridgeshire CB1 3JJ
T: 01223 655664
E: info@transitcableproducts.co.uk
W: www.transitcableproducts.co.uk
TransPennine Express
7th Floor, Bridgewater House
60 Whitworth St Manchester M1 6LT
T: 0345 600 1671
E: tpecustomer.relations@firstgroup.com
W: www.tpexpress.co.uk
Simply known as TBF, this not-for-profit membership charity has been providing help and support to its members in the public transport industry for more than 100 years. It offers its members a wide range of financial, health and welfare benefits should need, hardship and distress arise. Membership costs £1.25 a week, covering the member, their livein partner, and dependent children.
Transport Benevolent Fund CIO
Suite 2.7 The Loom, 14 Gowers Walk London E1 8PY
T: 0300 333 2000
E: help@tbf.org.uk
W: www.tbf.org.uk
Transport Focus
Albany House, 86 Petty France London SW1H 9EA
T: 0300 123 0860
E: info@transportfocus.org.uk
W: www.transportfocus.org.uk
Transport for Greater Manchester
2 Piccadilly Place, Manchester M1 3BG
T: 0161 244 1000
E: customer.relations@tfgm.com
W: www.tfgm.com
Transport for London (TfL)
Ashfield House, 7 Beaumont Avenue
West Kensington London W14 9UY
T: 0843 557 3455
W: www.tfl.gov.uk
Transport for London (TfL)
4th Floor, 14 Pier Walk
London SE10 0ES
T: 0343 222 1234
W: www.tfl.gov.uk
Transport for London (TfL)
5th Floor Central, Templar House
81-87 High Holborn London WC1V 6NU
T: 020 7038 4503
W: www.tfl.gov.uk
Transport for London (TfL)
Palestra, 197 Blackfriars Road London SE1 8NJ
T: 0343 222 0000
W: www.tfl.gov.uk
Transport for the North 2nd Floor, 4 Piccadilly Place
Manchester M1 3BN
T: 0161 244 0888
E: info@transportforthenorth.com
W: www.transportforthenorth.com
Transport for Wales
South Gate House, Wood Street Cardiff CF10 1EW
T: 029 2167 3434
E: contact@transportfor.wales
W: www.tfw.gov.wales
Transport Investigations Ltd
Unit 65 The Oaks, Manston Business Park
Ramsgate Kent CT12 5FD
T: 01843 593595
E: info@transportinvestigations.co.uk
W: www.transportinvestigations.co.uk
Transport Salaried Staffs’ Association (TSSA)
2nd Floor Walkden House, 17 Devonshire Square London EC2M 4SQ
T: 020 7387 2101
E: enquiries@tssa.org.uk
W: www.tssa.org.uk
Transport Scotland
Buchanan House, 58 Port Dundass Road
Glasgow G4 0HF
T: 0141 272 7100
E: info@transport.gov.scot
W: www.transport.gov.scot
Transport Trust
First Floor, 26 Station Approach
Hinchley Wood Esher Surrey KT10 0SR
T: 020 7928 6464
E: info@transporttrust.com
W: www.transporttrust.com
Tratos Ltd 10 Eagle Court, Britton Street
Farringdon London EC1M 5QD
T: 0845 413 9990
E: uk@tratos.eu W: www.tratos.eu
Travel Compensation Services Ltd
Unit 55, 2 Cromar Way
Chelmsford Essex CM1 2QE
T: 020 3794 4346
E: info@travelcompensationservices.com
W: www.travelcompensationservices.com
IRIS approved, TRB Lightweight Structures is a Tier 1 supplier to the UK and European train builders, providing high-quality, lightweight solutions – including doors, partitions and detrainment systems.
TRB also offers a comprehensive rolling stock refurbishment service that includes surveying, reverse engineering, stripping and rebuilding and paint or vinyl wrap finishing.
TRB Lightweight Structures Ltd 12 Clifton Road, Huntingdon Cambridgeshire PE29 7EN
T: 01480 447400
E: info@trbls.com W: www.trbls.com
Helping you remove unwanted vibration and noise. Trelleborg Antivibration Solutions make improvements people can feel physically. With quality, testing and compliance built in, our customers can have the confidence they’re dealing with a true partner that understands their challenges and joins them on the frontline of innovation.
Trelleborg Antivibration Solutions
1 Hoods Close
Leicester LE4 2BN
T: 0116 267 0300
E: antivibration@trelleborg.com
W: www.trelleborg.com
Tremco Illbruck Limited
Coupland Road, Hindley Green Wigan WN2 4HT
T: 01942 251400
E: uk.info@tremco-illbruck.com
W: www.tremco-illbruck.com
Trendrail Ltd – Specialists in Engineering Unit 4, Wilcock Road, Old Boston Trade Estate Haydock WA11 9SR
T: 01942 721432
E: info@trendrail.com
W: www.trendrail.com
Trent Instruments Ltd
Units 8 & 9, Genesis Business Park
Midland Way Nottingham NG7 3EF
T: 0115 978 5333
E: sales@trentinstruments.co.uk
W: www.trentinstruments.co.uk
Trenton Fire Ltd
Murdock House, 30 Murdock Road
Bicester OX26 4PP
T: 01869 366545
E: enquiries@trentonfire.co.uk
W: www.trentonfire.co.uk
Trevally Engineering Ltd
4 The Avenue, Hale Cheshire WA15 0LX
T: 0161 657 3783
E: andrew.knowles@trevallyengineering.com
W: www.trevallyengineering.com
TRI Control Systems
Colham Green House, Colham Green Road
Uxbridge Middlesex UB8 3QQ
T: 01895 257500
E: enquiries@tricontrols.com
W: www.tricontrols.com
Tribo “LLC Bilotserkivskiy Zavod Tribo Ltd’’ 95 Levanevskogo street, Bila Tserkva 09108 Kiev Region Ukraine
T: 00 38 050 488 5609
E: office@tribo.com.ua
W: www.tribo.ua
Trimble Rail Solutions
Fenward House, Arkle Road Sandyford Dublin
T: 00 353 1 539 8700
E: rail@trimble.com
W: www.rail.trimble.com
Trimble Tekla UK Trimble House, Gelderd Road Morley Leeds LS27 7JP
T: 0113 887 9790
E: tekla.sales.uk@trimble.com
W: www.tekla.com
Trimble UK Hillside House, Parkway North 1500 Stoke Gifford Bristol BS34 8YU
T: 0117 203 3500
E: info@atriumsoft.com
W: www.trimble.com
Triptex Limited Suite 301, 51 Pinfold Street Birmingham B2 4AY
T: 0121 371 0800
E: info@triptex.co.uk
W: www.triptex.co.uk
Triscan Systems Ltd 4 Petre Court, Clayton Business Park
Clayton-le-Moors Accrington Lancs BB5 5HY
T: 01254 350302
E: info@triscansystems.com
W: www.triscansystems.com
Tritech Group Bridge Road North, Wrexham Ind Estate Wrexham North Wales LL13 9PS
T: 01978 661111
E: sales@tritechgroup.co.uk
W: www.tritechgroup.co.uk
TRL
Crowthorne House, Nine Mile Ride Wokingham Berkshire RE40 BGA
T: 01344 773131
E: enquiries@trl.co.uk
W: www.trl.co.uk
Trojan Special Fasteners Ltd 18 Fortnum Close, Kitts Green Birmingham B33 0LG
T: 0121 789 8586
E: trojan.fasteners@gmail.com
W: www.trojansf.co.uk
Trolex Ltd
Newby Road, Hazel Grove Stockport Cheshire SK7 5DY
T: 0161 483 1435
E: sales@trolex.com
W: www.trolex.com
TRS Staffing Solutions 8th Floor, York House
Kingsway London WC2B 6UJ
T: 020 7419 5800
E: info-uk@trsstaffing.com
W: www.trsstaffing.com
Trueform Unit 12, Pasadena Trading Estate Pasadena Close Hayes Middlesex UB3 3NQ
T: 020 8561 4959
E: sales@trueform.co.uk
W: www.trueform.co.uk
TSG Fleet, supply and install products and services to the commercial fleet industry. UK wide 24/7 maintenance and installation services for fuel dispensers, fuel management systems, wireless and analogue tank gauges, above and below ground fuel, diesel and water holding tanks. TSG also carry out site audits, including DSEAR assessments.
TSG Fleet
Platts Common Ind Est, Hoyland Barnsley South Yorkshire S74 9SE
T: 0333 015 3001
E: enquiries.uk@tsg-solutions.com
W: www.tsg-solutions.com
TSP Projects
Meridian House, The Crescent York YO24 1AW
T: 01904 454600
E: tsp.communications@tspprojects.co.uk
W: www.tspprojects.com
TTG Technology (Europe) Ltd
1st Floor, 6 Munro Road, Springkerse Ind Estate Stirling FK7 7UU
T: 01786 448535
E: enquiries@ttgeurope.com
W: www.ttgtransportationtechnology.com
TTPP Construction Consultants
1/F Crowne House, 56-58 Southwark Street London SE1 1UN
T: 020 7940 6500
E: enquiries@ttpp.coo.uk
W: www.ttpp.co.uk
TTS supplies Green Trough cable management systems (CMS), combined anti-slip walkway/ CMS and a range of accessories for rail, utilities, and power generation industries, offering elevated options where space is restricted. Manufactured from 100% recycled household waste, Green Trough is halogen free, UV-resistant, boasts a 50-year design-life and incorporates anti-theft features as standard. EPD Certified.
TTS (Trough-Tec Systems)
Clifford House, Lady Bank Drive Lakeside Doncaster DN4 5NF
T: 01302 343633
E: ttsinfo@hird.group
W: www.ttsrail.co.uk
Tufnol Composites Ltd
Wellhead Lane, Perry Barr Birmingham B42 2TN
T: 0121 356 9351
E: info@tufnol.co.uk
W: www.tufnol.com
Tunnelling Accessories Ltd
Sidney Little Road, Churchfields Ind Estate St Leonards-on-Sea East Sussex TN38 9PU
T: 01424 854112
E: info@tunnellingaccessories.co.uk
W: www.tunnellingaccessories.co.uk
Turbex Limited
Unit 1 Riverwey Ind Pk, Newman Lane Alton Hampshire GU34 2QL
T: 01420 544909
E: sales@turbex.co.uk
W: www.turbex.co.uk
Turbo Power Systems Ltd
1 Queens Park, Queensway North Gateshead Tyne & Wear NE11 0NX
T: 0191 482 9200
E: info@turbopowersystems.com
W: www.turbopowersystems.com
Turkington Holdings Limited James Park, Mahon Road
Portadown Co. Armagh BT62 3EH
T: 028 3833 2807
E: info@turkington-holdings.com
W: www.turkington-construction.com
Turner & Townsend Group
One New Change London EC4M 9AF
T: 020 7544 4000
E: lon@turntown.co.uk
W: www.turnerandtownsend.com
TVS Supply Chain Solutions provide companies in the rail sector with a wide range of procurement strategies, coupled with innovative supply chain and logistics solutions. Our unique services and solutions provide our clients with cost savings and efficiencies and allows them to concentrate on their core business activities.
TVS Supply Chain Solutions Ltd Logistics House, Buckshaw Avenue
Chorley Lancashire PR6 7AJ
T: 01257 265 531
E: rail@tvsscs.com
W: www.tvsscs.com
TWI Certification
Granta Park, Great Abington Cambridge CB21 6AL
T: 01223 899000
E: twicertification@twi.co.uk
W: www.twicertification.com
The chosen product for rail and depot rooflights is the Multi-Link-Panel NF (Non Fragile). The Multi-Link-Panel is an innovative polycarbonate glazing product that, due to its fix and link method of installation, is incredibly quick to fit, making it an excellent choice for installation where possession times are an issue.
Twinfix Limited
201 Cavendish Place, Birchwood Park Birchwood Warrington WA3 6WU
T: 01925 811311
E: enquiries@twinfix.co.uk
W: www.twinfix.co.uk
TXM Consult
Quarnmill House, Stores Road Derby DE24 4XF
T: 07741 664 290
E: info@txmconsult.com
W: www.txmconsult.com
TXM Plant Ltd
23 Linford Forum, Rockingham Drive Linford Forum Milton Keynes MK14 6LY
T: 01908 443000
E: sales@txmplant.co.uk
W: www.txmplant.co.uk
TXM Projects Unit 21, Monkspath Business Park Solihull B90 4NZ
T: 0121 516 3739
E: info@txmprojects.co.uk
W: www.txmprojects.co.uk
TXM Recruit is a specialist Engineering and Technical recruitment agency, providing temporary, contract and permanent workforce solutions via PSL, MSP and RPO engagement models. Formed by engineers, TXM Recruit remains in the ownership of people who have an extensive history of working within the engineering and recruitment industry.
TXM Recruit
2 Grange Court, Harnett Drive
Wolverton Mill Milton Keynes MK12 5NE
T: 07824 817056
E: info@txmrecruit.co.uk
W: www.txmrecruit.co.uk
Tyne & Wear Metro
Nexus House, St James Boulevard
Newcastle upon Tyne NE1 4AX
T: 0191 203 3333
E: contactmetro@nexus.org.uk
W: www.nexus.org.uk
Tyrolit Ltd
Eldon Close, Crick Northampton NN6 7UD
T: 01788 823738
E: gborder@tyrolit.com
W: www.tyrolit.co.uk
In 30+ years, Tyrone Fabrication has grown to be a market-leading supplier of intelligent enclosures solutions.
We produce advanced steel equipment enclosures, location cases and REB’s for the transportation, communications and power supply industries and global organisations count on our turn-key products to keep data secure/services operational.
Our bespoke systems will be YOUR ultimate solution.
Tyrone Fabrication
87 Goland Road, Ballygawley Co. Tyrone, Northern Ireland BT70 2LA
T: +44 (0) 28 8556 7200
E: info@tyrone.co.uk
W: www.tyrone.co.uk
U+I Group PLC
7a Howick Place
London SW1P 1DZ
T: 020 7828 4777
E: hello@uandiplc.com
W: www.developmentsecurities.com
UK Composite Decking
Redhill House, Hope Street Chester CH4 8BU
T: 01244 689 317
E: admin@ukcompositedecking.co.uk
W: www.ukcompositedecking.co.uk
UK Power Networks Services provides energy infrastructure solutions to global energy challenges, delivering resilience, cost efficiency and sustainability. They deliver in highly complex and challenging environments, including working on Europe’s busiest runways, trackside on the UK’s fastest mainline railway and at nuclear sites, ports and military facilities.
UK Power Networks Services
Newington House, 237 Southwark Bridge Road London SE1 6NP
T: 0207 397 7845 / 07938 740407
E: enquiries@ukpowernetworks.co.uk
W: www.ukpowernetworksservices.co.uk
UK Rail Ltd
Unit 4, Hollies Business Park
Hollies Park Road Cannock WS11 1DB
T: 01543 575704
E: info@ukrail-ltd.com
W: www.ukrail-ltd.com
UKRL is your comprehensive railway services and engineering partner providing rail vehicle and component overhaul, maintenance & repair, including UK-wide mobile support. We provide passenger train servicing, cleaning and refueling using our 150,000-litre capacity refueling point and modern train-care facility including CET. Able to service 4 vehicles simultaneously.
UKRL
Leicester TMD
Beale Street Leicester LE2 0AA
UK Rail Ltd (Birmingham)
8th Floor, 1 Victoria Square Birmingham B1 1BD
T: 01543 575704
E: info@ukrail-ltd.com
W: www.ukrail-ltd.com
UK Rail Research and Innovation Network (UKRRIN)
c/o RSSB, The Helicon 1 South Place London EC2M 2RB
T: 020 3142 5300
E: ukrrin@rssb.co.uk
W: www.ukrrin.org.uk
UK Railtours PO Box 350, Welwyn Hertfordshire AL6 0WG
T: 01438 715050
E: info@ukrailtours.com
W: www.ukrailtours.com
UK Society for Trenchless Technology (UKSTT) Camden House, Warwick Road
Kenilworth Warwickshire CV8 1TH
T: 01926 513773
E: admin@ukstt.org.uk
W: www.ukstt.org.uk
UK Tram
Centro House, 16 Summer Lane Birmingham B19 3SD
T: 0121 214 7104
E: info@uktram.co.uk
W: www.uktram.co.uk
UKDN Waterflow Ltd
Block A The Courtyard, Langley Business Park Waterside Drive Slough SL3 6EZ
T: 0333 344 9099
E: bids@ukdnwaterflow.co.uk
W: www.ukdnwaterflow.co.uk
UKIDesk
Office One, 1 Coldbath Square Farringdon London EC1R 5HL
T: 0203 372 4303
E: info@ukidesk.co.uk
W: www.ukidesk.co.uk
UKRL – UK Rail Leasing Ltd
Leicester TMD, Beal Street Leicester LE2 0AA
T: 0116 262 2783
E: info@ukrl.co.uk
W: www.ukrl.co.uk
Ultra Electronics Ltd PMES Towers Business Park, Wheelhouse Road Rugeley Staffordshire WS15 1UZ
T: 01889 503300
E: enquiries@ultra-pmes.com
W: www.ultra-pmes.com
UNIFE Avenue Louise 221, B-1050
Brussels Belgium
T: 0032 2626 1260
E: general@unife.org
W: www.unife.org
Unilite Limited Winyates Way, Moons Moat Ind Estate Redditch Worcestershire B98 9FG
T: 01527 584344
E: sales@unilite.co.uk
W: www.unilite.co.uk
Our LED signalling solutions have been enhanced with the addition of the Lightweight Signalling Solutions, Assisted Lift Trunnion options and Wayside Signal Ranges – designed collaboratively to meet the changing needs of signalling within the Rail industry.
Unipart Dorman
Wennington Road, Southport Merseyside PR9 7TN
T: 01704 518000
E: dorman.enquiries@unipartdorman.co.uk
W: www.unipartdorman.co.uk
Unipart Rail are experts in delivering performance improvements for their customers through new Technology and Supply Chain solutions for the Rail Industry. As preferred supply partner for many rail customers and a critical part of their supply chain, the service provided enables them to deliver for their customers and improve the performance of the railway.
Unipart Rail
Jupiter Building, First Point Balby Carr Bank Doncaster DN4 5JQ
T: 01302 731400
E: enquiries@unipartrail.com
W: www.unipartrail.com
Unistrut
Delta Point, Greets Green Road West Bromwich B70 9PL
T: 0121 580 6300
E: enquiries@unistrut.com
W: www.unistrut.co.uk
Unite the Union
Unite House, 128 Theobald’s Road Holborn London WC1X 8TN
T: 020 7611 2500
E: executive.council@unitetheunion.org
W: www.unitetheunion.org
United Kingdom Accreditation Service (UKAS) 2 Pine Trees, Chertsey Lane
Staines TW18 3HR
T: 01784 429000
E: info@ukas.com
W: www.ukas.com
United Springs Ltd Mandale Park, Norman Road Rochdale Lancashire OL11 4HP
T: 01706 644551
E: united-springs.uk.info@sogefigroup.com
W: www.united-springs.com
UniTrunk – Harlow
Unit G Flex Meadow, Merring Way
The Pinnicles Harlow CM19 5SR
T: 01279 444481
E: harlow@unitrunk.co.uk
W: www.unitrunk.co.uk
UNITRUNK Ltd
Blaris Ind Estate, Altona Road
Lisburn County Antrim BT7 5QB
T: 01279 444481
E: lisburn@unitrunk.co.uk
W: www.unitrunk.co.uk
Univar Specialty Consumables
USC House, Vanguard Tame Park
Wilnecote Tamworth Staffs B77 5DY
T: 01827 255216
E: univarsc@univar.com
W: www.univarsc.com
University of Birmingham
Edgbaston Campus, Edgbaston Birmingham B15 2TT
T: 0121 414 2626
E: railway@contacts.bham.ac.uk
W: www.birmingham.ac.uk/railway
University of Central Lancashire
Preston Lancashire PR1 2HE
T: 01772 201201
E: cenquiries@uclan.ac.uk
W: www.uclan.ac.uk
University of East Anglia
Norwich Research Park, Norwich Norfolk NR4 7TJ
T: 01603 456161
E: communications@uea.ac.uk
W: www.uea.ac.uk
University of Hertfordshire
Hatfield
Hertfordshire AL10 9AB
T: 01707 284800
E: ask@herts.ac.uk
W: www.herts.ac.uk
University of Hull
Hull
East Yorkshire HU6 7RX
T: 01482 346311
E: admissions@hull.ac.uk
W: www.hull.ac.uk
University of Liverpool Foundation Building, Brownlow Hill Liverpool L69 7ZX
T: 0151 794 2000
E: irro@liv.ac.uk
W: www.liv.ac.uk
University of Manchester Oxford Road
Manchester M13 9PL
T: 0161 306 9200
E: enquiries@manchester.ac.uk
W: www.manchester.ac.uk
University of Salford
The Crescent, Salford M5 4WT
T: 0161 295 5000
E: enquiries@salford.ac.uk
W: www.salford.ac.uk
University of Southampton
Highfield
Southampton SO17 1BJ
T: 023 8059 8454
E: enquiries@rruk.soton.ac.uk
W: www.southampton.ac.uk
University of Strathclyde
16 Richmond Street, Glasgow Scotland G1 1XQ
T: 0141 552 4400
E: admissions-engineering@strath.ac.uk
W: www.strath.ac.uk
University of the West of England (UWE Bristol) Frenchay Campus, Coldharbour Lane Bristol BS16 1QY
T: 0117 965 6261
E: infopoint@uwe.ac.uk
W: www.uwe.ac.uk
University of Warwick Engineering
School of Engineering, University of Warwick Coventry CV4 7AL
T: 024 7652 2046
E: eng-pgadmissions@warwick.ac.uk
W: www.warwick.ac.uk/tunnelling
University of York Heslington York YO10 5DD
T: 01904 320000
E: ug-admissions@york.ac.uk
W: www.york.ac.uk
Unwin Safety Systems
Unwin House, The Horsehoe Coat Road Martock Somerset TA12 6EY
T: 01935 827740
E: sales@unwin-safety.co.uk
W: www.unwin-safety.com
Upshot UK Ltd
260 Bentley Way, Ampress Park Lymington Hampshire SO41 8JW
T: 01590 670845
E: info@upshot-uk.com
W: www.upshot-uk.com
Urban Hygiene Ltd
Unit 9, Sky Business Park
Robin Hood Airport Doncaster DN9 3GN
T: 01302 623193
E: enquiries@urbanhygiene.com
W: www.urbanhygiene.com
Urban Security Guards
Unit 32, DRCA Business Centre
33 Charlotte Despard Ave, SW115JE
T: 020 3617 8314
E: contactus@urbansecurityguards.co.uk
W: www.urbansecurityguards.co.uk
Urban Transport Group
Wellington House, 40-50 Wellington Street
Leeds LS1 2DE
T: 0113 251 7204
E: info@urbantransportgroup.org
W: www.urbantransportgroup.org
With over 100+ years of experience and refinement of our approach to lighting, Urbis Schréder’s unparalleled experience in lighting city centres, roads, bridges, tunnels, buildings, and workspaces enables us to develop solutions for tomorrow’s needs, connecting global expertise with a local perspective to build legacies for future generations.
Urbis Schréder Ltd
Sapphire House, Lime Tree Way
Hampshire Int Bus Park Basingstoke, Hampshire RG24 8GG
T: 01256 354446
E: sales@urbis-schreder.com
W: www.uk.schreder.com/en
Uretek UK
Colin Saunders Inv Ctr, Newburn Road
Banbury Oxford OX16 9PA
T: 0800 084 3503
E: info@geobear.com
W: www.geobear.co.uk
Uroven Ltd
45 Station Road
Henley on Thames Oxfordshire RG9 1AT
T: 01494 845444
W: www.uroven.co.uk
USC Hydraulics
Hozier Street
Carluke Lanarkshire ML8 5DW
T: 01555 772474
E: sales@uscltd.co.uk
W: www.uschydraulics.com
Utility Equipment Limited 28 Longwood Road, Trafford Park Manchester M17 1PZ
T: 0161 850 0456
E: enquiries@utility-equipment.com
W: www.utility-equipment.com
Vac UK Ltd
Woodstock Business Park, Meek St Oldham Greater Manchester 0L2 6HL
T: 0800 047 3296
E: info@vacukltd.co.uk
W: www.vacukltd.co.uk
VAE UK Ltd
Sir Harry Lauder Road, Portobella
Edinburgh EH15 2QA
T: 0131 322 7210
E: info@voestalpine.com
W: www.voestalpine.com
Valmont Stainton Ltd
Unit 5 Dukesway, Teesside Ind Estate
Thornaby Stockton-on-Tees TS17 9LT
T: 01642 766242
E: stainton@valmont.com
W: www.valmont-stainton.com
Van Elle Rail
Kirkby Lane, Pinxton
Nottinghamshire NG16 6JA
T: 01773 580580
E: info@vanellerail.com
W: www.vanellerail.com
Vaughan Plant Haulage Ltd
Unit1, Frogs Ditch Farm
Shepston Lane Hayes UB3 1RN
T: 020 8991 6886
E: info@vaughanplanthaulage.com
W: www.vaughanplanthaulage.com
Vector Foiltec Ltd
Archway House, 1-3 Worship Street
Shoreditch London EC2A 2AB
T: 020 8821 2900
E: GB@vector-foiltec.com
W: www.vector-foiltec.com
Venesta Limited
1st Floor, Units 19-22, St George’s Square
Gravesend Kent DA11 0TA
T: 01474 353333
E: marketing@venesta.co.uk
W: www.venesta.co.uk
Venice Simplon-Orient-Express Shackleton House, 4 Battle Bridge Lane London SE1 2HP
T: 0845 077 2222
E: reservations.uk@belmond.com
W: www.belmond.com
Veolia 8th Floor, 210 Pentonville Road London N1 9JY
T: 020 7812 5000
E: info@veolia.co.uk
W: www.veolia.co.uk
Verdant Solutions Ltd High Street, Hartfield East Sussex TN7 4AE
T: 01892 770470
E: office@verdantsolutions.ltd.uk
W: www.verdantsolutions.ltd.uk
Vertemax Limited
Spinney House, Wilcox Close Aylesham Kent CT3 3EP
T: 01227 711072
E: info@vertemax.com
W: www.vertemax.com
Vertical Access Ltd
Tame Bank, Unit E211, Warmco Industrial Park Mossley OL5 9AY
T: 01457 838722
E: info@verticalaccess.co.uk
W: www.verticalaccess.co.uk
Vertiv
TOR, St Cloud Way Maidenhead SL6 8BN
T: 023 8061 0311
E: contact@vertivco.com
W: www.vertivco.com
Vettica BV Galerij 33, 1411 LH Naarden
The Netherlands
T: +31 651899435
E: info@vettica.com
W: www.vettica.com
VGC Labour Solutions Cardinal House, Bury Street Ruislip HA4 7GD
T: 0845 620 1201
E: recruitment@vgcgroup.co.uk
W: www.vgcgroup.co.uk
VGC Personnel Cardinal House, Bury Street Ruislip HA4 7GD
T: 0845 620 1201
E: vgcpersonnel@vgcgroup.co.uk
W: www.vgcgroup.co.uk
VGC Rail Projects Cardinal House, Bury Street Ruislip HA4 7GD T: 0845 620 1201
E: enq@vgcgroup.co.uk
W: www.vgcgroup.co.uk
Viaduct Ltd 2, The Court, Bohortha
Portscatho Truro Cornwall TR2 5EY T: 01872 581978
E: info@viaduct.uk.com
W: www.viaduct.uk.com
Victa Railfreight Ltd
Unit 1, Viewpoint, Boxley Road
Penenden Heath Maidstone Kent ME14 2DZ
T: 01622 690978
E: enquiries@victa-railfreight.com
W: www.victa-railfreight.com
Vidiwave Ltd
Unit 5, Beaufont Court, Roebuck Way Knowlhill Milton Keynes MK5 8HL
T: 01908 690090
E: info@vidiwave.co.uk
W: www.vidiwave.com
Viewtec Signs Ltd
Unit 9 Rani Drive, Basford Nottingham NG5 1RF
T: 0115 942 1511
E: sales@viewtecsigns.co.uk
W: www.viewtecsigns.co.uk
Vigier Rail AG
Industriezone 2, CH-3225
Müntschemier
T: 00 41 32 312 98 50
E: info@vigier-rail.ch
W: www.vigier-rail.ch
VINCI Construction Grands Projets Great West House GW1, Great West Road Brentford Middlesex TW8 9DF
T: 02085 871 882
E: info@vinci-construction.co.uk
W: www.vinci-construction-projets.com/en/
VIP-Polymers Ltd
15 Windover Road, Huntingdon Cambridgeshire PE29 7EB
T: 01480 411333
E: sales@vip-polymers.com
W: www.vip-polymers.com
VisiLean
2 Lakeside Drive, Park Royal London NW10 7SQ
T: 07949 007437
E: info@visilean.com
W: www.visilean.com/
Visual Security Services UK Ltd
U/30 Coppice Trd Estate, Walter Nash Road West Kidderminster DY11 7QY
T: 01562 747241
E: enquiries@visualsecurityltd.co.uk
W: www.visualsecurityltd.co.uk
Vital – Head Office
The Mill, South Hall Street Ordhall Lane Salford M5 4TP
T: 0161 836 7000
E: info@vital.uk.com
W: www.vital.uk.com
Vitec Webber Lenihan Ltd
7 Village Way, Greenmeadow Springs Bus Park Cardiff CF15 7NE
T: 029 2062 0232
E: info@vitecconsult.com
W: www.vitecwebberlenihan.com
Vivax – Metrotech Ltd
Unit 1 B/C, The Polden Business Ctr Bristol Road Bridgewater TA6 4AW
T: 01793 822679
E: salesuk@vxmt.com
W: www.vivax-metrotech.com
Viztek Ltd
15E Southwick Ind Es, Riverside Road Sunderland Tyne & Wear SR5 3JG
T: 0191 516 6606
E: info@viztekltd.co.uk
W: www.viztekltd.co.uk
Vizwear Ltd
Enfield Ind Estate, Enfield Street Wigan WN5 8DB
T: 01942 219709
E: info@vizwear.com
W: www.vizwear.com
Vogelsang is a leading supplier of fixed and mobile sanitary and wastewater disposal units to the rail industry. From fixed CET pumping units – non-spill, non-freeze – to mobile pumping units, which can safely be used on passenger platforms. Units also have the capacity to refresh the clean water supply.
Vogelsang
Gateway, Crewe Gates Ind Est.
Crewe CW1 6YY
T: 01270 216 600
E: sales.uk@vogelsang.info
W: www.vogelsang.info
Voith Turbo Limited
Unit 49, Metropolitan Park Bristol Road Greenford UB6 8UP
T: 020 8436 1070
E: turbo.uk@voith.com
W: www.uk.voithturbo.com
VolkerFitzpatrick
Hertford Road, Hoddeson
Hertfordshire EN11 9BX
T: 01992 305000
E: enquiries@volkerfitzpatrick.co.uk
W: www.volkerfitzpatrick.co.uk
VolkerRail
Eagre House, J3 Business Park
Carr Hill Balby Doncaster DN4 8DE
T: 01302 79 11 00
E: info@volkerrail.co.uk
W: www.volkerrail.co.uk
Von Roll UK
42 Wharfedale Road, Bradford West Yorkshire BD4 6SG
T: 01274 687777
E: cs.europe.uk@vonroll.com
W: www.vonroll.com
Vortex Exhaust Technology Ltd
53 Tower Road, Globe Industrial Estate Grays Essex RM17 6ST
T: 01375 372037
E: enq@vortexexhausttechnology.com
W: www.vortexexhaust.com
Vossloh Cogifer UK Limited
80A Scotter Road, Scunthorpe North Lincolnshire DN15 8EF
T: 01724 862131
E: contact-uk@vossloh-cogifer.com
W: www.vossloh.com
VP PLC
Central House, Beckwith Knowle
Otley Road Harrogate HG3 1UD
T: 01423 533400
E: enquiries@vpplc.com
W: www.vpplc.com
VTG Rail UK Ltd
Two Parklands, Parklands Business Park
Birmingham West Midlands B32 9PZ
T: 0121 421 9180
E: salesuk@vtg.com
W: www.vtg.com
Vulcanite UK
PO Box 456, Newcastle Upon Tyne Tyne & Wear NE3 9DR
T: 0191 490 6203
E: sales-uk@vulcanite.com
W: www.vulcanite.com
Vulcascot Cable Protectors Ltd
Unit 12, Norman-D-Gate, Bedford Road
Northampton NN1 5NT
T: 0800 035 2842
E: sales@vulcascot.co.uk
W: www.vulcascot.co.uk
VVB Group 3rd Floor, 25 Watling Street London EC4M 9BR
T: 01268 711845
E: info@vvb-eng.com
W: www.vvb-eng.com
Wabtec Rail Limited
PO Box 400, Doncaster House
Hexthorpe Road Doncaster DN1 1SL
T: 01302 340700
E: wabtecrail@wabtec.com
W: www.wabtecrail.co.uk
Wacker Neuson Ltd (Head Office)
WN Place, Beacon Way Stafford ST18 0DG
T: 01785 785700
E: uk.orders@wackerneuson.com
W: www.wackerneuson.co.uk
Wade Spring Ltd
Highfield Street, Long Eaton Nottingham NG10 4GY
T: 0115 946 3000
E: info@wade-spring.co.uk
W: www.wade-spring.co.uk
WAGO Limited
Triton Parak, Swift Valley Ind Estate
Rugby Warwickshire CV21 1SG
T: 01788 568008
E: ukmarketing@wago.com
W: www.wago.com
Wales and Borders
Evergreen House North, 160 Euston Road
London NW1 2DX
T: 020 3691 1715
E: comms@keolis.co.uk
W: www.keolisamey.cymru
Walker Construction (UK) Ltd
Park Farm Road, Folkestone Kent CT19 5DY
T: 01303 851111
E: admin@walker-construction.co.uk
W: www.walker-construction.co.uk
Walker Training & Consultancy Ltd
The Office Suite, The Transport Depot Mercer Road Warnham, W.Sussex RH12 3RL
T: 01403 250089
E: info@walkertraining-consultancy.co.uk
W: www.walkertrainingconsultancy.co.uk
Wall to Wall Communications Ltd
Unilink House, 21 Lewis Road Sutton Surrey SM1 4BR
T: 020 8770 1007
E: info@walltowallcomms.co.uk
W: www.walltowallcomms.co.uk
Ward Recycling Donald Ward Ltd, Moira Road Woodville Derbyshire DE11 8DG
T: 0345 337 0000
E: enquries@ward.com
W: www.ward.com
Warringtonfire
Holmesfield Road, Warrington Cheshire WA1 2DS
T: 01925 655116
E: info.warrington@warringtonfire.com
W: www.warringtonfire.com
Washington Metal Works
Bath Road, Felling Gateshead Tyne & Wear NE10 0LH
T: 0191 469 4466
E: contact@wmwgroup.co.uk
W: www.washington-metalworks.co.uk
Washtec UK Ltd
Unit 14a Oak Ind Park, Great Dunmow Essex CM9 1XN
T: 01371 878800
E: sales@washtec-uk.com
W: www.washtec-uk.com
Waterfront Conference Company
Fleet House, 8-12 New Bridge Street London EC4V 6AL
T: 020 7067 1597
E: conference@thewaterfront.co.uk
W: www.waterfrontconferencecompany.com
Waterman is a leading global infrastructure and environmental consultancy providing sustainable multidisciplinary rail engineering solutions to private and public sector rail clients. We have extensive experience in all aspects of railway infrastructure, including station and depot design, maintaining and upgrading structures, heavy and light rail schemes and underground networks.
Waterman Group
Pickfords Wharf, Clink Street London SE1 9DG
T: 020 7928 7888
E: mail@watermangroup.com
W: www.watermangroup.com
Wath Group
Unit 1 Bedford Park, Barnsley Road
Wath Upon Dearne Rotherham S63 6DQ
T: 01709 867900
E: info@wath.co.uk
W: www.wathgroup.com
Watson & Watson Health and Safety Consultants Limited
F1, Wheatley House, 3 Diamond Avenue
Kirkby In Ashfield Nottinghamshire NG17 7GP
T: 01623 753654
E: watsonsafety@gmail.com
W: www.watsonandwatsonsafety.co.uk
Wavesight Limited
13 Dencora Way, Luton Bedfordshire LU3 3HP
T: 01582 578160
E: sales@wavesight.com
W: www.wavesight.com
A forward-thinking project consultancy company delivering tomorrow’s railway.
Based on a wealth of experience delivering major complex infrastructure projects, WCL offer consultancy services for Project & Programme Management, Engineering & Design, Construction, Commercial and Integration & Controls, with Integrity, Collaboration and Simplicity at the heart of everything we do.
WCL Rail
20 Newtown, Hullavington Wiltshire SN14 6EP
T: 01666 837708
E: info@wclrail.co.uk
W: wclrail.co.uk
WDS Components Limited
Grangefield Ind Estate, Richardshaw Road Pudsey Leeds LS28 6LE
T: 0113 290 9852
E: sales@wdscomponents.com
W: www.wdscomponents.com
Webro (Long Easton) Limited
Vision House, Meadow Brooks Bus Park Long Eaton Nottinghamshire NG10 2GD
T: 0115 972 4483
E: info@webro.com
W: www.webro.com
Wedge Group Galvanizing Ltd
Stafford Street, Willenhall West Midlands WV13 1RZ
T: 01902 601944
E: sales@wedge-galv.co.uk
W: www.wedge-galv.co.uk
Weighwell Engineering Ltd
Weighwell House, Woolley Colliery Road Darton Barnsley S75 5JA
T: 0114 269 9955
E: sales@weighwell.com
W: www.weighwell.com
Welding Alloys Group
The Way, Fowlmere
North Royston Hertfordshire SG8 7QS
T: 01763 207500
E: info@welding-alloys.com
W: www.welding-alloys.com
Welfare Hire Nationwide Ltd
Unit F, Rosie Road
Trident Park Normanton WF6 1ZB
T: 0845 600 6670
E: info@welfarehire.com
W: www.kellinggroup.com/welfare-hire
Welfare Vans 4 Less Royal Oak Garage, City Road
Stoke on Trent ST4 2PX
T: 01782 848627
E: info@affordrentacar.co.uk
W: www.welfarevans4less.co.uk
Wenlock Spring Water Ltd
Wolverton, Church Stretton
Shropshire SY6 6RR
T: 01694 781277
E: enquiries@wenlockspring.co.uk
W: www.wenlockspring.co.uk
Wentworth House Rail Systems Limited
Preston Brook Office, U2 Wellfield Bus Park
Preston Brook Runcorn WA7 3FR
T: 01270 448405
E: enquiries@railelectrification.com
W: www.railelectrification.com
West London Security Ltd
22-36 Paxton Place, West Norwood London SE27 9SS
T: 020 8676 4300
E: info@wls.ltd
W: www.westlondonsecurity.com
West Maintenance Services
27 Riverside,, Sir Longley Road
Medway City Estate Rochester, Kent ME2 4DP
T: 07831 173464
E: westservices@me.com
West Midlands Combined Authority 16 Summer Lane, Birmingham West Midlands B19 3SD
T: 0121 200 2787
E: customer.services@tfwm.org.uk
W: www.westmidlandscombinedauthority.org.uk
West Midlands Metro 16 Summer Lane Birmingham B19 3SD
T: 0345 835 8181
E: customerservices@westmidlandsmetro.com
W: www.westmidlandsmetro.com
West Midlands Railway 134 Edmund Street, Birmingham B3 2ES
T: 0333 311 0039
E: contact.wmr@wmtrains.co.uk
W: www.westmidlandsrailway.co.uk
West Midlands Trains 134 Edmond Street
Birmingham B3 2ES
T: 0333 311 0039
E: questions@wmtrains.co.uk
W: www.wmtrains.co.uk
West Yorkshire Combined Authority (Metro) Wellington House, 40-50 Wellington Street Leeds LS1 2DE
T: 0113 251 7272
E: enquiries@westyorks-ca.gov.uk
W: www.westyorks-ca.gov.uk
Westcotec Limited
34 Bertie Ward Way, Rash’s Green Ind Est Dereham Norfolk NR19 1TE
T: 01362 853124
E: sales@westcotec.co.uk
W: www.westcotec.co.uk
Westermo Data Communications Ltd
Talisman Bus Centre, Duncan Road Park Gate Southampton SO31 7GA T: 01489 580585
E: sales@westermo.co.uk
W: www.westermo.co.uk
Westgate Communications
58 Cobden Road, Sevenoaks Kent TN13 3UB
T: 01732 779087
E: info@westgatecomms.com
W: www.westgatecomms.com
Westley Engineering Ltd
120 Pritchett Street, Aston Birmingham B6 4EH
T: 0121 333 1952
E: info@westleyengineering.co.uk
W: www.westleyengineering.co.uk
Westlin Group
Building 388/8, Liberator House
Prestwick KA9 2PT
T: 01292 678444
E: enquiries@westlingroup.com
W: www.westlingroup.com
Weston Analytics
Munnelly House, 84-88 Pinner Road
Harrow HA1 4LP
T: 0203 854 1876
E: sales@westonanalytics.com
W: www.westonanalytics.com
Weston Partnership
Sparrow Hall, Brighton Road
Lower Beeding West Sussex RH13 6TL
T: 01403 891514
E: info@westonpartnership.co.uk
W: www.westonpartnership.co.uk
Westshield Ltd
Ashcroft House, Bredbury Park Way
Chadderton Stockport SK6 2SN
T: 0161 682 6222
E: info@westshield.co.uk
W: www.westshield.co.uk
Wetton Cleaning Services Ltd
Estate House, 2 Pembroke Road
Sevenoaks Kent TN13 1XR
T: 0845 433 4101
E: sales@wettons.co.uk
W: www.wettons.co.uk
WEYTEC
City Reach, 7th Floor, Suite 3,
5 Greenwich View Place London E14 9NN
T: 002 7536 1940
E: info.uk@weytec.com
W: www.weytec.com
Wharton Electronics Limited
Unit 15, Thame Park Bus Centre
Wenman Road Thame OX9 3XA
T: 01844 260567
E: sales@wharton.uk
W: www.wharton.co.uk
Wheelsets UK Ltd
Canklow Meadows Ind Est, West Bawtry Road Rotherham South Yorkshire S60 2XL
T: 01302 322266
E: martin@wheelsets.co.uk
W: www.wheelsets.co.uk
Wheelsure Holdings PLC (Tracksure Ltd)
8 Woburn Street, Ampthill Bedfordshire MK45 2HP
T: 01525 840557
E: info@wsgroupglobal.com
W: www.wsgroupglobal.com
Whitcher Wildlife Ltd
Cliff Edge, Cliff Road
Darfield Barnsley S73 9HR
T: 01226 753271
E: info@whitcher-wildlife.co.uk
W: www.witcher-wildlife.co.uk
White Cross Rubber Products
White Cross, White Cross Street Lancaster LA1 4XS
T: 01524 585200
E: info@wcrp.co.uk
W: www.wcrp.uk.com
White Knight Specialist Portable Lighting Alchorne Place
Portsmouth PO3 5PA
T: 023 9266 8624
E: info@whiteknight.uk.com
W: www.whiteknight.uk.com
White Lion Engineering Ltd 49 Church Street, Melbourne Derbyshire DE738EJ
T: 07768 192369
E: brown.cc@btinternet.com
Whitmore Europe Ltd
Unit 9, Foster Avenue, Woodside Park Ind Est Dunstable Bedfordshire LU5 5TA
T: 01707 379870
E: info-uk@whitmores.com
W: www.whitmores.com
Whoosh Media
Suite 38-41, The Hop Exchange 24 Southwark St London SE1 1TY
T: 020 7403 6763
E: info@whooshmedia.co.uk
W: www.whooshmedia.co.uk
For over 40 years, Wickens design, manufacture and install heavy duty storage systems to a wide customer base. Our range includes cantilever racking, structural pallet racking, coil racking, rack clad buildings, safety barriers and a variety of other bespoke storage systems. Wickens has ISO 9001:2015, CE marking and RISQS accreditation.
Wickens Engineering Ltd
1 Shire Business Park, Wainwright Road Worcester WR4 9FA
T: 01905 456780
E: sales@wickens.co.uk
W: www.wickens.co.uk
Wifi Spark
5 Cranmere Court, Lustleigh Close Matford Bus Park Exeter EX2 8PW
T: 0344 848 9555
E: info@wifispark.com
W: www.wifispark.com
Wilcomatic Limited
Unit 5 Commerce Park, 19 Commerce Way
Croydon Surrey CR0 4YL
T: 020 8649 5768
E: sales@wilcomatic.co.uk
W: www.wilcomatic.co.uk/rail-wash-systems
Wilde Analysis Ltd
Whitworth House, 28 Charles Street
Stockport SK1 3JR
T: 0161 474 6886
E: info@wildeanalysis.co.uk
W: www.wildeanalysis.co.uk
Wilkinson Star is one of the UK’s leading importers and distributors of welding and industrial equipment.
We offer a comprehensive range of JASIC welding equipment, MOSA welder generators, generators and lighting towers, FIAC air compressors, F-Tech fume extraction equipment and sanitising systems.
Wilkinson Star Ltd
Shield Drive, Wardley Ind Estate
Worsley Manchester M28 2WD
T: 0161 793 8127
E: wilkinsonstar.sales@wilkinsonstar.com
W: www.wilkinsonstar247.com
WilkinsonEyre
33 Bowling Green Lane, Clerkenwell London EC1R OBJ
T: 020 7608 7900
E: info@wilkinsoneyre.com
W: www.wilkinsoneyre.com
William Cook Rail works with train builders and operators to design, manufacture and overhaul safety-critical components and systems for the global rail industry.
William Cook Rail is part of the William Cook group, a £60 million specialist engineer in the defence, rail and industrial sectors.
William Cook Rail Ltd Cross Green, Leeds LS9 0DX
T: 0113 249 6363
E: rail@cook-rail.co.uk
W: www.william-cook.co.uk
William Hackett Lifting Products Ltd Oak Drive, Lionheart Enterprise Pk Alnwick Northumberland NE66 2EU
T: 01665 604200
E: info@williamhackett.co.uk
W: www.williamhackett.co.uk
Wind River UK Ltd
47 Pure Offices, Kembrey Park
Swindon Wiltshire SN2 8BW
T: 01793 230474
E: customer_advocate@windriver.com
W: www.windriver.com
Wireless CCTV Ltd
Charles Babbage House, Kings Way Business Park Rochdale Greater Manchester OL16 4NW
T: 01706 631166
E: sales@wcctv.com
W: www.wcctv.co.uk
WISKA UK
Unit 7, Hurling Way, St Columb Major Bus Pk
St Columb Major Cornwall TR9 6SX
T: 01208 816062
E: info@wiska.co.uk
W: www.wiska.co.uk
WiTest Equipment Ltd
15-16 Woodbridge Mdws, Guildford Surrey GU3 3JS
T: 01483 207428
E: sales@trtest.com
W: www.trtest.com
WJ Project Services Limited
11 Bell Lane, Monks Kirby
Rugby Warwickshire CV23 0QY
T: 07957 641976
E: info@wjpservices.com
W: www.wjpservices.com
UK’s long reach excavator specialists, with machines ranging in size from 4-110 tonnes and ability to reach 30 metres. 25 years in the rail sector has developed expertise and allowed us to enhance our offering helping clients overcome challenges faced with machines ideal for working on steep slopes, tight constraints, or soft ground (‘Spider,’ zero tail-swing, LGP).
WM Plant Hire
Manor Farm Lane, Bridgnorth Shropshire WV16 5HG
T: 01746 769 555
E: info@wmplanthire.com
W: www.wmplanthire.com
Women in Rail
London Fruit & Wool EXC, 1 Duval Square London E1 6PW
T: 020 8432 4320
E: wr@womeninrail.org
W: www.womeninrail.org
Wonderland Agency Thames Works Studios, Church Street Chiswick London W4 2PD
T: 020 3056 6848
E: info@wonderland-agency.com
W: www.wonderland-agency.com
Wood Group Industrial Services Ltd Kirkstone House, St Omers Road Gateshead Tyne & Wear NE11 9EZ
T: 0191 493 2600
E: wgis.comms@woodgroup.com
W: www.woodgroup-isl.com
Woodward Diesel Systems Lancaster Centre, Meteor Business Park Cheltenham Rd East Gloucester GL2 9QL
T: 01452 859940
E: corpinfo@woodward.com
W: www.woodward.com
Woodway Engineering Ltd Lower Road, Barnacle Coventry CV7 9LD
T: 024 7684 1750
E: sales@woodwayengineering.com
W: www.woodwayengineering.co.uk
Working At Height Ltd Amberley Court, Old Elstead Road Milford Surrey GU8 5EB
T: 01483 415410
E: info@workingatheightltd.com
W: www.workingatheightltd.com
Worldline 1 Trinity Court, Broadlands Wolverhampton WV10 6UH
T: 0121 717 4100
E: infowl@worldline.com
W: www.worldline.com
Wrekin Circuits Ltd 29/30 Hortonwood 33, Telford Shropshire TF1 7EX
T: 01952 670011
E: sales@wrekin-circuits.co.uk
W: www.wrekin-circuits.co.uk
Wrekin Products Ltd
Europa Way, Britannia Enterprise Pk Lichfield Staffordshire WS14 9TZ
T: 01543 440440
E: sales@wrekinproducts.com
W: www.wrekinproducts.com
Wring Group Ltd
Vale Lane, Bedminster Bristol BS3 5RU
T: 0117 923 1320
E: info@wringgroup.co.uk
W: www.wringgroup.co.uk
WSP Group – Basingstoke
Mountbatten House, Basing View Basingstoke Hampshire RG21 4HJ
T: 01256 318800
E: info@wspgroup.com
W: www.wspgroup.com
WSP Parsons Brinckerhoff
The Lansdowne Building, 2 Lansdowne Road Croydon Surrey CR9 2ER
T: 020 8667 2002
E: contactus@wspgroup.com
W: www.wspgroup.com
WT Fabrications (NE) Ltd
Boathouse Lane Stockton-on-Tees TS18 3AW
T: 01642 619191
E: enquiries@wtfabrications.com
W: www.wtfabrications.com
Xanta Limited
130 Fleet Street London EC4A 2BH
T: 020 7583 4500
E: enquiries@xantarail.com
W: www.xantarail.com
XEIAD
Clarendon Court, Manners Avenue
Ilkeston Derby DE7 8EF
T: 0115 931 9000
E: 42@xeiad.com
W: www.xeiad.com
Xrail Group Boardman House, 64 Broadway
Stratford London E15 1NT
T: 0345 060 0700
E: enquiries@xrailgroup.com
W: www.xrailgroup.com
Yaplex Ltd
Derby Road Bus Park, Derby Road
Clay Cross Chesterfield S45 9AG
T: 01246 860114
E: sales@yaplex.co.uk
W: www.yaplex.co.uk
Yardene Engineering 2000 Ltd
Daux Road, Billingshurst West Sussex RH14 9SJ
T: 01403 783558
E: sales@yardene.co.uk
W: www.yardene.co.uk
Yeltech Ltd
300 Cathedral Hill, Guildford Surrey GU2 7YB
T: 0845 052 3860
E: info@yeltech.com
W: www.yeltech.com
Young Rail Professionals (YRP)
Derby Carriage, & Wagon Works
Litchurch Lane Derby DE24 8AD
E: info@youngrailpro.com
W: www.youngrailpro.com
Youngman® Group Limited
The Causeway, Maldon Essex CM9 4LJ
T: 01621 745900
E: uk.customercare@wernerco.com
W: www.youngmanaccess.com
YY Security Installations Ltd
Unit 2 & 3, Hillstone Court
Empson Street Bow E3 3LT
T: 01895 271400
E: projects@yysecurity.com
W: www.yysecurity.co.uk
Z-Tech Control Systems Ltd
Unit 4 Meridian, Buckingway Bus Park
Anderson Road Cambridge CB24 4AE
T: 01223 653500
E: admin@z-tech.co.uk
W: www.z-tech.co.uk
Zarges (UK) Ltd
8 Holden Avenue, Saxon Park Ind Estate
Bletchley Milton Keynes MK1 1QU
T: 01908 641118
E: sales@zarges.co.uk
W: www.zarges.com
Zaun Limited
Steel Drive, Wolverhampton West Midlands WV10 9ED
T: 01902 796699
E: info@zaun.co.uk
W: www.zaun.co.uk
ZEP UK Limited
PO Box 12, Tanhouse Lane Widnes Cheshire WA8 0RD
T: 0151 422 1000
E: info@zep.co.uk
W: www.zep.co.uk
Zeta Specialist Lighting
Telford Road, Bicester Oxfordshire OX25 4LB
T: 01869 322500
E: info@thezetagroup.com
W: www.zetaled.co.uk
Zetica Rail
Zetica House, Southfield Road
Eynsham Oxfordshire OX29 4JB
T: 01993 886682
E: rail@zetica.com
W: www.zetica.com
ZF Services UK Ltd Abbeyfield Road
Lenton Nottingham NG7 2SX
T: 0333 240 1123
E: info.zf-services-uk@zf.com
W: www.zf.com
ZF UK Laser Limited
Unit 9 Avocado Court, Commerce Way Trafford Park Manchester M17 1HW
T: 0161 871 7050
E: info@zf-uk.com
W: www.zf-uk.com
Zigma Ground Solutions
Unit 11 M11 Bus Link, Parsonage Lane
Stansted Essex CM24 8TY
T: 01279 647021
E: sales@tufftrak-safety.com
W: www.zigmagroundsolutions.com
Zircon Software Ltd
Bellefield House, Hilperton Road
Trowbridge Wiltshire BA14 7FP
T: 01225 764444
E: info@zirconsoftware.co.uk
W: www.zirconsoftware.co.uk
Zollner UK Ltd
Clayton Business Centre, Midland Road Leeds LS10 2RJ
T: 0113 270 3008
E: office@zollner-uk.co.uk
W: www.zoellner.de
Zonegreen specialise in modern rail depot protection systems and are regarded as the world market leaders with the SMART Depot Personnel Protection Systems (DPPSTM). The system, installed throughout the UK and across the world, allows the safe and efficient control of train movements within depots, protecting both staff and infrastructure.
Zonegreen
Sir John Brown Building, Davy Industrial Park Prince of Wales Rd Sheffield S9 4EX
T: 0114 230 0822
E: info@zonegreen.co.uk
W: www.zonegreen.co.uk
Zuken
1500 Aztec West, Almondsbury Bristol BS32 4RF
T: 01454 207800
E: sales-uk@zuken.com
W: www.zuken.com
Workforce
Rockfall
Hoarding