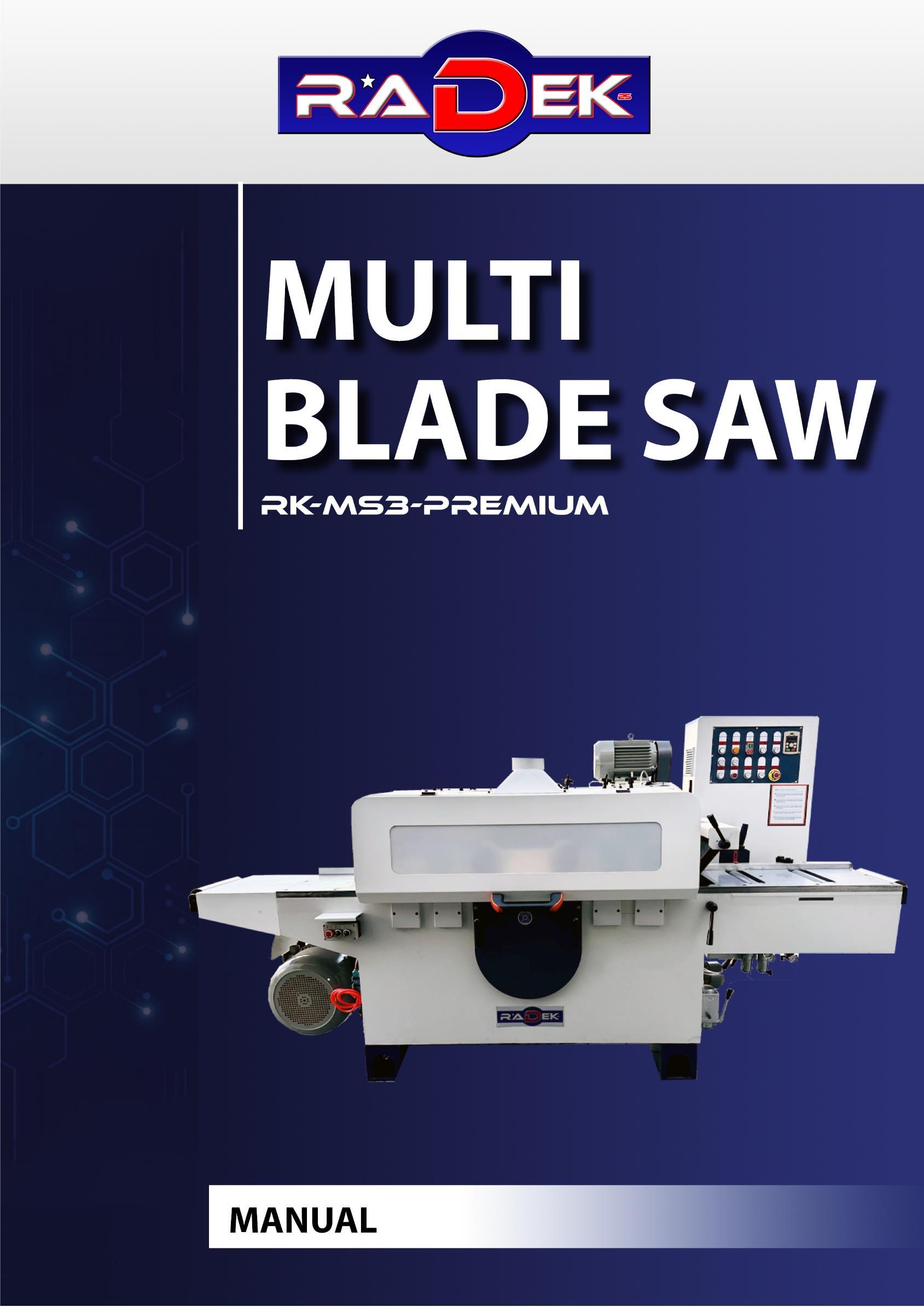
1.General safety rules
2.Overview of the machine tool
3.Main technical parameters
4.Handling and installation of machine tools
5.Operation of the machine tool
6.Installation and adjustment of saw blade
7.Lubrication and maintenance of machine tools
Eight. Bearing parts list
9.Detailed list of wearing parts
10.Common faults and troubleshooting methods
11.Random accessories
Dear Customer:
Welcome to use the woodworking machinery series products
The machine you purchased may differ from this manual in some details, but as long as you adjust the operation according to the provisions of this manual, it will not affect the safe operation of the machine.
This machine is carefully designed and manufactured by our company with excellent quality. Ensuring the safe operation of the machine and the personal safety of the operators is one of the important principles of our company. If operated correctly, it can fully guarantee safe production.
In order to help you use this machine safely and correctly, in order to give full play to the performance of this machine tool, please read this manual in detail before installing this machine, and be fully familiar with it.
In case of any problem that cannot be solved with the help of the manual, please contact our technical service department, they will be happy to give you any assistance you need.
1. General safety rules:
1.The operation, maintenance and maintenance of this machine must be carried out by fully trained and qualified personnel who must be familiar with the features, functions and safety rules of this
machine.
2.Every approved operator or maintenance and maintenance personnel must study this manual carefully and understand it thoroughly before operating this machine.
3.This machine is a special equipment designed for the processing of wood strips, louvers, high-precision small-sized wood, etc., and is not allowed to be used for other purposes. Consideration should be given to preventing misuse.
4.Safety contents include: safety guidelines, safety rules, accident prevention and safety signs and reliable and correct operation of machine tools.
5.In addition to the safety rules in this manual, the general occupational safety rules and local safety regulations and regulations must also be observed.
6.Prevent the designed safety device and safety production instructions from being damaged.
7.The obvious safety signs on the machine tool should be prevented from being damaged.
8.If the safety signs and safety devices cannot meet the safety requirements, they should be repaired or eliminated immediately.
9. The machine tool workplace should be kept clean and tidy. Do not store anything that affects safe operation on the machine or within the safe area.
10. The installation or maintenance of electrical equipment must be carried out by qualified personnel. The machine tool must be grounded reliably to avoid the danger of electric leakage. After any electrical installation or repair, tests should be carried out for electrical safety features.
11. The operator should not wear loose clothes; the cuffs should be fastened; those with long hair should wear a work cap; and gloves should not be worn. It is best not to wear jewelry and other accessories while working. When necessary, wear safety protection such as eyes, ears, masks, etc.
12. The machine and the slip point must be slipped before starting the machine. And check that all safety devices are reliable.
13. Before the following situations, the power switch of the machine tool should be in the off position: (when checking, measuring; when doing maintenance, maintenance, and setting work; when removing the protective cover; when opening the door or cover to observe the internal conditions; when leaving the machine tool .)
14. Do not remove any safety cover or cover at will during the operation, and it is strictly forbidden to start the machine with incomplete safety protection device.
15. It is strictly forbidden to touch the parts of the machine that are running or not completely stopped, and it is strictly forbidden to disassemble any parts of the machine when the machine is running
or not completely stopped.
16. The operator is not allowed to leave when the machine tool is running or not completely stopped.
17. For mechanical or electrical maintenance, the power supply must be cut off.
18. Before replacing or installing the saw blade/blade, you must carefully check whether the saw blade/blade is defective, and the power must be cut off before installation. Pay attention to the balance state of the tool shaft, and it is strictly forbidden to install an unbalanced tool.
19. The chip hood should be connected to a vacuuming device (the power of removing raw material is not less than 4 KW).
20. The processed wood shall not have hard objects such as iron nails, sand and gravel.
21. Before starting the machine tool, you must first check whether the saw blade/blade is installed tightly, whether the spindle is locked, and whether the spindle can rotate freely.
22. Do not change the speed when the machine tool is stopped to prevent damage to the continuously variable transmission; after starting each shift, please idling the handle of the continuously variable transmission mechanism at high and low gears several times to prevent rusting.
23. According to the hardness and thickness of the processed wood,
reasonably select the feed speed and the number of saw blades to avoid overloading.
24. Cleaning and maintenance should be done after the work is completed. When cleaning, it is recommended not to blow with compressed air, but to clean with a brush.
25. The calculation method of the number of data sheets allowed to be installed:
N=P/0.75B
N The number of saw blades allowed to be installed (integer);
P Motor power (KW)
B height of sawing wood (CM);
Note: Taking pine wood as an example, N slightly increases or decreases with the hardness of the wood. Please note that the working current of the motor should not exceed the rated current value.
Machine tool overview
1.Appearance of the machine tool (see Figure 1)
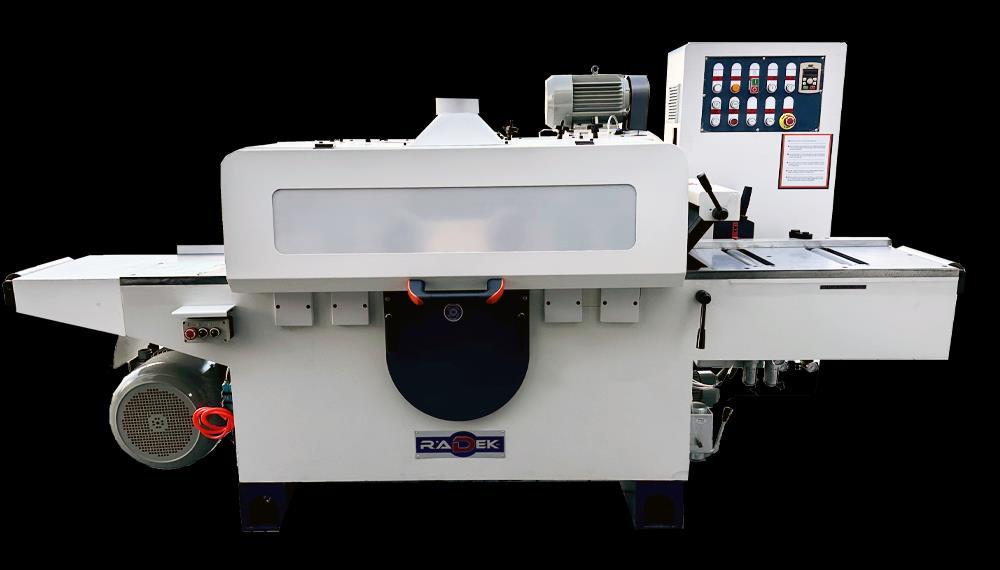
2.The use and characteristics of the machine tool:
This machine uses multiple saw blades to longitudinally cut the wood or plank into specific wood chips or strips. The whole process is automatically fed, and the sawing and cutting of the wood or plank is completed at one time. The production efficiency is very high. It is an ideal equipment for producing wooden strips. This product uses the power supply: three-phase alternating current, frequency 50Hz, voltage 380V.
3.Main technical parameters:
4.Handling and installation of machine tools.
1.This machine is a small device, suitable for transportation by forklift or crane. Please keep the balance of the machine when handling, and be careful during handling to avoid collision or tilt of the machine.
2.The machine must be placed on solid concrete, and the thickness of the concrete should not be less than 100mm.
3.Place a spirit level on the machine table, and use the inclined iron to adjust the level of the machine tool within 0.1/1 000.
4.Connect the power supply of the machine tool according to the electrical schematic diagram of the machine tool, and jog the saw shaft motor to see if the rotation direction is correct. If the steering phase On the contrary, please exchange the contact positions of any two wires in the power supply.
5.the operation of the machine tool (refer to Figure 1)
1.Axial movement adjustment mechanism of saw shaft (see Figure 2)
Loosen the two clamping bolts on the spindle seat at the rear of the machine tool, and turn the adjusting screw with a wrench to move the spindle and the spindle sleeve forward or backward along the inner hole of the spindle seat. After the spindle position is adjusted, Rotate the clamping bolt to prevent axial play.
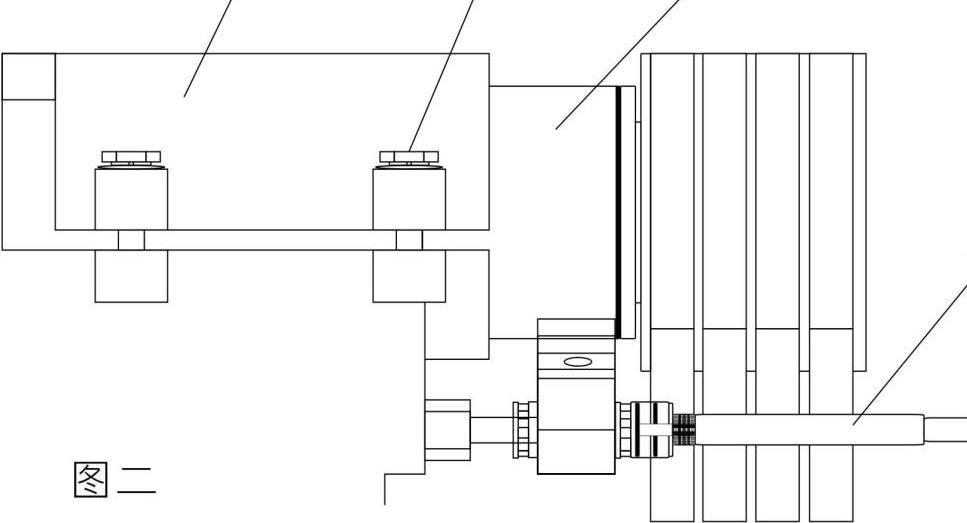
2.Feeding part:
After the feeding motor is variable speed, it is decelerated by the worm and worm gear, and the power is transmitted to the feeding wheel by the universal shaft. The pressure of the feeding wheel on the wood during the feeding process is realized by adjusting the pressure reducing valve on the pneumatic triplet to change the air supply pressure. The air supply pressure shall generally not be less than 0.4MPa. When the working resistance is large, the air
supply pressure can be appropriately increased according to the actual size.
6. Installation and adjustment of saw blade (see Figure 1)
1.Select the appropriate saw pad according to the specifications of the required saw material, install the saw blade and saw pad on the spindle, use a special wrench to lock the nut and close the saw shaft cover.
2.Start the main motor, loosen the saw shaft locking handle, and then start the spindle lift motor, so that the saw blade cuts the wooden panel on the workbench. Raise the blade to the desired height. Then tighten the saw shaft handle.
3.When the actual distance between the saw blade and the front backing plate does not meet the requirements, you can pull the front backing plate adjustment handle to adjust the backing plate position or adjust the axial position of the spindle to control the distance between the data sheet and the backing plate.
7. Lubrication and maintenance of machine tools.
Lubrication Cycle Schedule
No. Machine parts
Number of recommended hole slip types Cycle
No. Machine parts
Number of recommended hole slip types Cycle No. Machine parts
Number of recommended hole slip types Cycle No. Machine parts
Number of recommended hole slip types Cycle
No. Machine parts
Number of recommended hole slip types Cycle
1 Saw shaft seat dovetail 1 Oil N46 Before adjustment
2 universal joints 10 calcium base grease ZG-3 one shift
3 Air source triplet l Oil N46
Check every day to ensure that there is no shortage of oil
adjustment
adjustment
3 Air source triplet l Oil
N46 Check every day to ensure that there is no shortage of oil 3 Air source triplet l Oil N46 Check every dayto ensure that there is no shortage of oil 3 Air source triplet l Oil
4 Column bearing seat 2 Machine pumping N46 Before adjusting the machine 4 Column bearing seat 2 Machine pumping N46 Before adjusting the machine
5 Screw and nut 4 Oil N46 once per shift
Feeding
Column bearing seat 2 Machine pumping N46 Before adjusting the machine
N46 Check every day to ensure that there is no shortage of oil
3 Air source triplet l Oil N46
Check every day to ensure that there is no shortage of oil
Column bearing seat 2 Machine pumping N46 Before adjusting the machine 4 Column bearing seat 2
5 Screw and nut 4 Oil N46 once per shift 5 Screw and nut 4 Oil N46 once per shift 5 Screw and nut 4 Oil N46 once per shift
Machine pumping N46 Before adjusting the machine
5 Screw and nut 4 Oil N46 once per
Feeding worm gear box 2
gear oil N460 once a year 7 Lifting worm gear box 3 Industrial gear oil N460 Once a year
8 Fuel pump 1 Oil N46 Check every day for no shortage of oil
Check every day for no shortage of oil 8 Fuel pump 1 Oil N46 Check every day for no shortage of oil
Fuel pump 1 Oil N46
Fuel pump 1 Oil N46 Check every day for no shortage of oil 8 Fuel pump 1 Oil N46 Check every day for no shortage of oil
Troubleshooting method
Troubleshooting method
1. Check the circuit and motor 1. Check the circuit and motor
No feeding or poor feeding 2. Check whether the pulley of the speed change mechanism is correct
No feeding or poor feeding 2. Check whether the pulley of the speed change mechanism is correct
3. Checkwhether thetransmissionsleeveis displaced and the flat key is falling off
4. Check whether the universal joint is bent or broken
5. Check whether the feed roller pressure and pressing depth are correct
6. Check whether the cutting amount is too large
3. Check whether the transmission sleeve is displaced and the flat key is falling off
4. Check whether the universal joint is bent or broken
5. Check whether the feed roller pressure and pressing depth are correct
6. Check whether the cutting amount is too large
The bed cover cannot be lifted 1. Check whether the lifting limit switch is turned on and whether the motor is out of phase
2. Check whether the drive shaft sleeve is displaced and the flat key is falling off
3. Check whether the lifting nut is worn
Loud noise 1. Check whether the bearing is damaged
2. Check that the saw blade is installed correctly
The motor cannot start 1. Overload, eliminate the cause of overload
2. Motor phase loss or under pressure start, check fuses and wiring
3. If the relay is faulty, check the working condition of the relay
The bed cover cannot be lifted 1. Check whether the lifting limit switch is turned on and whether the motor is out of phase
2. Check whether the drive shaft sleeve is displaced and the flat key is falling off
3. Check whether the lifting nut is worn
Loud noise 1. Check whether the bearing is damaged
2. Check that the saw blade is installed correctly
The motor cannot start 1. Overload, eliminate the cause of overload
2. Motor phase loss or under pressure start, check fuses and wiring
3. If the relay is faulty, check the working condition of the relay
1. One product instruction manual
2. One product certificate
3. One copy of packing list illustrate:
1.If the machine tool is inconsistent with the manual due to design improvement and other reasons, the machine tool ordered by the user shall prevail;
2.If you do not understand or are unclear, please ask our company. Our company is not responsible for any loss caused by blind work.