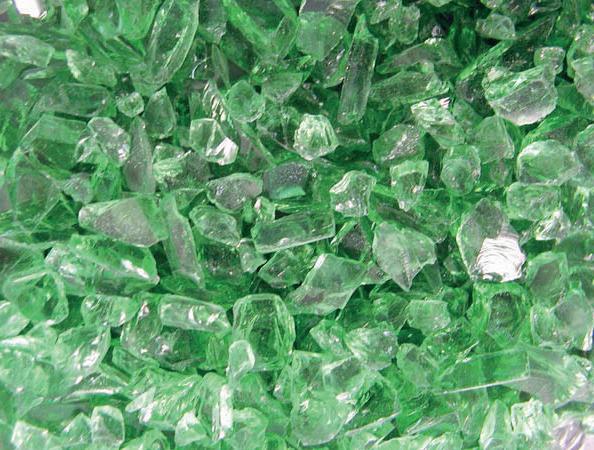
7 minute read
Recycling: Krysteline
Recycling: The process of economic recovery and use of ALL waste glass
Steve Whettingsteel* discusses some of the challenges in creating truly sustainable glass and outlines a series of refinement solutions.
Contrary to popular belief it is a technical impossibility for all used or recycled glass to be considered as furnace ready feedstock.
However unfortunately the public, industry and legislators have been misled to believe that ‘bottle to bottle’ is the only true form of glass recycling.
While this is the ideal in a utopian circular economy, in reality globally in excess of 50 million tonnes of glass is produced annually, with less than 40% being used for new glass production.
Therefore, not considering any other end markets for the processed waste glass results in a large percentage ending up in landfill as daily cover or used as a low value aggregate substitute
Where possible remelt cullet should always be the primary marketplace for recycled glass, however limitations of furnace capacity in many countries, low cost of imported glass, colour disparity, quality, contamination, location, and economics have proven over decades to be the principle challenge in creating sustainability.
The Myth of Bottle to Bottle
A further challenge is the long chain CO2 cost of delivering glass to a furnace, the claimed CO2 benefit of using cullet does not account for its recovery, recycling, transport, nor the disposal to landfill of the glass which is not suitable for remelt (pic 1).
Having a clear demonstrable CO2 value for cullet or other glass products along any part of its recovery, processing and re-use should be part of any responsible strategy, and to use the glass in a way where the true CO2 cost of each product or market determines its use.
Contrary to popular belief efficient and effective alternative markets for glass unsuitable for remelt can play a substantial in the overall reduction in CO2 of the glass recycling industry.
Many governments and authorities blindly sign up to the policy of ‘the only true glass recycling is the production of new glass’, not considering the total capacity of furnaces within an economic distance, or the matter of what coloured cullet requirements these furnaces have.
This often leads to a glass recycling programme to collapse or indicate disproportionally high cost, eventually having to concede landfill daily cover as material having been recovered and repurposed to meet recycling rates and targets.
It is often touted that optical sorters can recover cullet at 3mm, which of course they can, but how efficiently and at what cost per tonne?
There is a natural balance of economics in glass recycling which is lacking in clarity.
This lack of clarity is detrimental in creating long term stability of the whole glass recycling process.
Supporting the development of low CO2 sustainable alternative uses for the glass unsuitable or uneconomic for use as cullet should be championed, not derided.
Their use provides economic stability for the recycler, as well as improving overall cullet quality and availability.
� Pic 1. Green colour sorted remelt quality cullet.
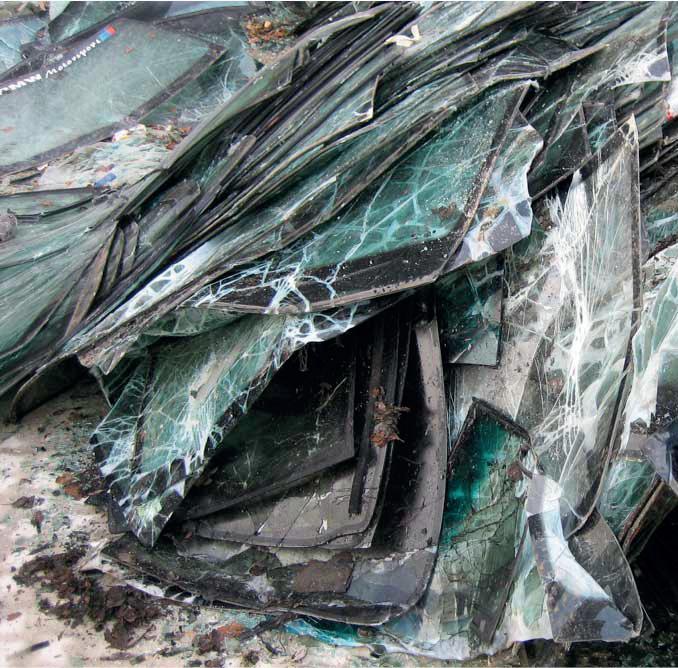
Keeping Waste Glass out of Landfill
Glass that cannot be used for remelt is often sized <10mm (1/2”) and contaminated with Ceramic, Stone and Porcelain (CSP) among other materials. This glass is certainly the most challenging aspect of glass recycling due to its high levels of multi product contaminates, putrescibles and organics, as well as being uneconomic for optically sorting (Pic 2).
There are also a number of ‘harder to recycle’ glass products that while they cannot be recycled in a local MRF, can be recycled by dedicated glass processing plants. These include but are not limited to: heat treated glass (such as Pyrex or drinkware), laminated glass (such as window glass or car windshields), pharmaceutical glass, solar panels and CRT.
The challenge within the glass recycling industry is to create a sustainable low CO2 product from 100% of the glass entering the recycling facility.
The majority of recycling plants around the world are either mandated or prefer to target the recovery of remelt cullet as a known market and to dispose the <10mm glass to landfill or low value aggregates, losing any of its CO2 benefit. A practice that has gone unchanged for decades.
However, there is hope, industry and academia are cooperating around the world to create high value low CO2 products and marketplaces for this challenging material: 1. Cementitious materials, as supplements to Ordinary Portland Cement (OPC) � A green ultra-high-performance glass concrete (UHPGC) with a compressive strength (fc) of up to 220 MPa � UHPGC provides technological, economical, and environmental advantages compared to traditional ultrahigh-performance concrete (UHPC).
2. Silicon Fertilisers � Increased yield by up to 300% • Improved cell structural strength of the plant
3. Foam glass � This material is incredibly lightweight and can be used to build walls, regulate heat in refrigerating equipment, as an hydroponic substrate, or used as floating and filtering material. It is an advanced heat insulating material, easily cut and cemented. � Classification A1 when tested to BS EN 13501-1, contributing to the fire safety of a building.
4. Fibreglass and glass wool � Thermal Insulation, making it warmer in winter and cooler in summer. � Improves the acoustic insulation of walls, floors and roofs. � Classification A1 when tested to BS EN 13501-1, contributing to the fire safety of a building.
5. Water filtration � Using crushed glass as a water filtration medium for swimming pools, car washes and wastewater treatment plants has become more commonplace over the years. � Due to the characteristics of Imploded glass, the use as a filtration medium is well suited and has a higher filtration power compared to sand. It also lasts longer, in many cases glass has been known to remain effective up to 10 years, compared to two to three years with sand. Additionally, in many remote locations and Islands around the world no remelt industry exists and exporting specialist sands and powders is prohibitive. Specialised small-scale glass refinement plants are available at very economic rates; these being designed with adequate
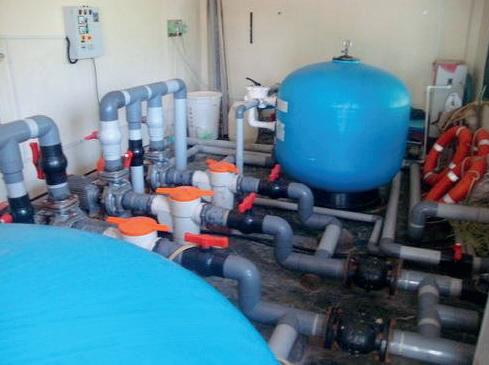
� Pic 3. An example of an alternative recycled glass marketplace - Water filtration
flexibility to create products to suit local demand. In some cases, the creation of aggregate substitute for French drains, trench fill and pre-cast concrete blocks; may be the only low CO2 possibility, so efficient low cost processing should be deployed.
The Benefits of Alternative Marketplaces
Not only do alternative end markets solve the problem of waste glass going into landfill: In some cases, it replaces the need for mining of virgin materials and prevents the shipping and haulage of sands and powders from many locations around the world (pic 3).
All markets must offer environmental and economic benefits, focusing on the needs of each individual client and establishing an inclusive strategy ensures the commercial viability of glass recycling no matter its location or traditional constraints.
Such solutions create sustainability and employment locally, open up new revenue streams and offer the recycler the opportunity to choose which marketplace it will produce for based on the costeffective conditions and requirements of the region, always working alongside remelt where possible, but always making use of 100% of all glass and avoiding landfill at all cost.
Companies and organisations are actively looking to reduce their carbon footprint and environmental impact by sourcing local suppliers, using recycled materials or saving energy for example.
All three of these examples could be met by a recycling facility that is open to supplying a number of end markets, including remelt, ensuring that 100% of glass which enters the gate has an end market and a sustainable value.
This would keep transportation costs down, creating use locally for a product that would otherwise go to landfill.
Increasing demand for recycled materials will only strengthen and stabilise the marketplace as well improving the economics of a MRF driving investment.
Innovation is required and a desire to understand and mandate greater diversity and sustainability for all glass.
In fact, research has shown many recycled glass products offer technical benefit over those being displaced, as well benefiting from the characteristics and properties of glass which underline its credentials through sustainability. This is only possible through well-designed cost-effective technology focused on enhancing quality and consistency.
Inclusive approach
Krysteline is well placed to provide sustainable glass recycling and refinement solutions across a spectrum of markets and locations, all considerate of their CO2 footprint.
Our strategic and inclusive approach offers solutions for the processing and recovery of 100% of all waste glass.
By considering the feedstock and delivering technology that provides clients with the means to produce high quality end products that service the demand of traditional marketplaces and also to assist in the development and growth of sustainable alternative marketplaces.
Specialising in processing and refinement of the glass generally perceived as being too poor or too difficult to process.
We have worked with most types of glass, from multi-layer bullet proof glass, through to car windshields, industrial flat glass, and the challenging MRF glass and 10mm fines. Our machinery is used globally to produce recycled glass products ranging from expendable abrasives and foam glass to water filtration and cement, and of course cullet for the production of containers. We aim to keep 100% of waste glass out of landfill! �
*CEO, Krysteline Technologies, Southampton, UK https://www.krysteline.com