
6 minute read
Hot End technology: Waltec
Waltec moves towards better ‘economics’ for press lines
Fig 1. The servo technology will allow � glassware factories to increase their sustainability and efficiency.
www.glass-international.com Herman Green* reports that Waltec’s next-generation ESERVO press technology and powered performance components are driving the sustainable optimisation of hot end processes.
Many in-market pressing machines and processes for tableware, cookware, glass bricks, insulators, washing-machine windows and other pressed products are still powered by obsolete technologies. Although most of the time these are still functional, they no longer comply with today’s economical and environmental requirements.
This has become a huge challenge for older glassware factories. Survival and profitability are connected to investments in smart and clean technology now more than ever. Shareholders, owners, banks and other investors are pushing this agenda more and more. Validating investments in new machines is no longer based solely on speed and output. It has become essential to reach compulsory targets related to resource efficiency, cost reduction, lowering environmental impact and boosting supply chain values. As such, new technology transitions are quickly transforming costs into revenue.
Investments in contemporary ESERVO technology can increase profits and upgrade existing press lines (or add new ones). Servo-driven key components reduce energy consumption whilst improving efficiencies and output - in other words ‘eco-nomics’ (Fig 1).
Waltec’s starting point is an average glassware factory specialised in the production of pressed items and running with 20 to 40-year-old presses. Some of these presses are still powered by obsolete, energy-intensive pneumatics whilst others are running on more recent proportional hydraulics - but are still outdated and very inefficient. Switching to servo-driven press technology will generate the following sustainable benefits and savings.
Servo powered pressing cylinder
The ESERVO pressing cylinder (Fig 2) generates a heavy-duty pressing force of up to 20 tons and saves up to 85% on energy costs compared to conventional hydraulics (Table 1).
Hydraulic oil changes are no longer required and, as such, reduce maintenance costs while contributing to a cleaner environment. Lower emissions (operator health) and less danger (oil fire) leads to better safety on the shop floor.
Servo powered main closer
Available for hinged/split mould items, such as beer mugs, only.
Conventional mould closing and locking is empowered by a pneumatic driven cylinder in which both movement and force are not controllable. High compressed air consumption, extensive wear and tear of mould-edges, oil vapour pollution and limited cycle speed are the limitations of this older technology.
The new generation of main closers improves both the closing process repeatability and accuracy (Fig 3). Using a strong and energy-efficient servo motor saves up to 80 m³/h of compressed air at a standardised 5 bar operating pressure (Table 2). High precision movement and soft-touch closing and locking extend the life cycle of the mould. High-speed mould locking up to 0.1 seconds saves valuable time when pressing.
Servo powered pusher for pushing article into the annealing lehr
Pneumatic cylinders drive conventional pushers with horizontal and vertical strokes, but this consumes a large amount
Savings compared to SINGLE GOB 6T
proportional hydraulic cylinder 118.000 kW/year
pneumatic cylinder (compressed air) 1.700.000 m³/year DOUBLE GOB 6T SINGLE GOB 16T
236.000 kW/year 294.000 kW/year
3.400.000 m³/year 2.900.000 m³/year
� Table 1. Savings of proportional hydraulic cylinder compared to pneumatic cylinder.
Savings compared to SINGLE GOB
pneumatic main closer (compressed air) 118.000 kW/year
� Table 2. Savings of a pneumatic main closer (for hinged/split mould items only).
DOUBLE GOB
236.000 kW/year
Savings compared to
pneumatic pusher (compressed air) ESERVO PUSHER
59.000 /year
� Table 3. Savings of a pneumatic pusher.
Savings shown in the tables are based on 24/7 operations, 350 days per year, on the basis of best practice management estimates requiring local on site validation and cross-checking with our technical service unit. Reference is an upgraded cookware/tableware press.
� Fig 2. The pressing cylinders could save factories up to 85% in energy costs. � Fig 3. The highly precise main closer will save valuable time when pressing.
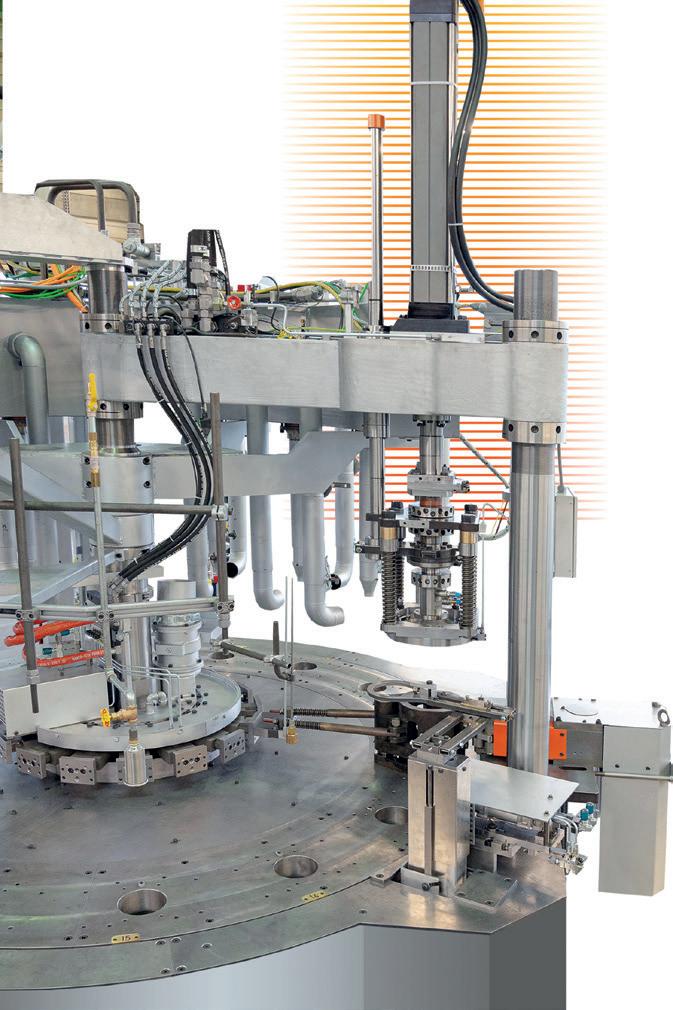
of compressed air and the movements are difficult to control. Installing a servo pusher (Fig 4) in this part of the process saves up to 10 m³/h of compressed air (Table 3).
The servo pusher operates by using two servomotors, each one being independently responsible for either horizontal or vertical movement. Speed and movement consequently becomes 100% precise, repeatable and controllable when pushing the product into the annealing lehr. Smooth and soft touch movement guarantees lower rejection levels for scratched and damaged glass. The absence of pneumatic valves also lowers maintenance costs.
By switching to ESERVO press technology, the ‘eco-nomics’ for this glass factory may total up to 130 m3/h compressed air saving, 80% less energy consumption and 20% higher output. Servo technology is also more precise and highly repeatable.
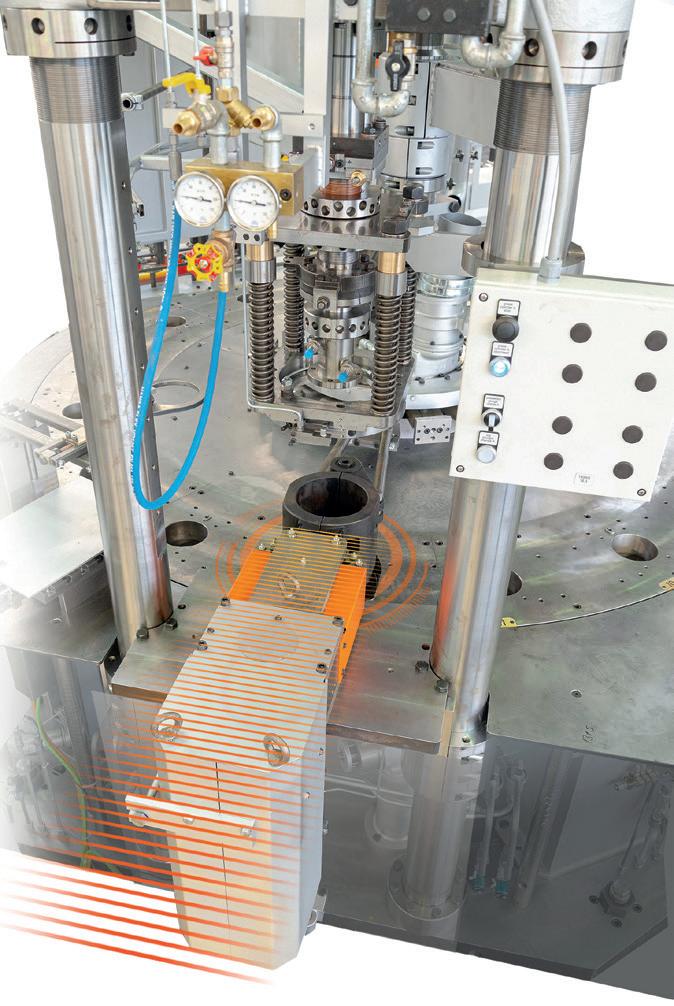
� Fig 4. By using two servomotors, the servo pusher becomes 100% precise.
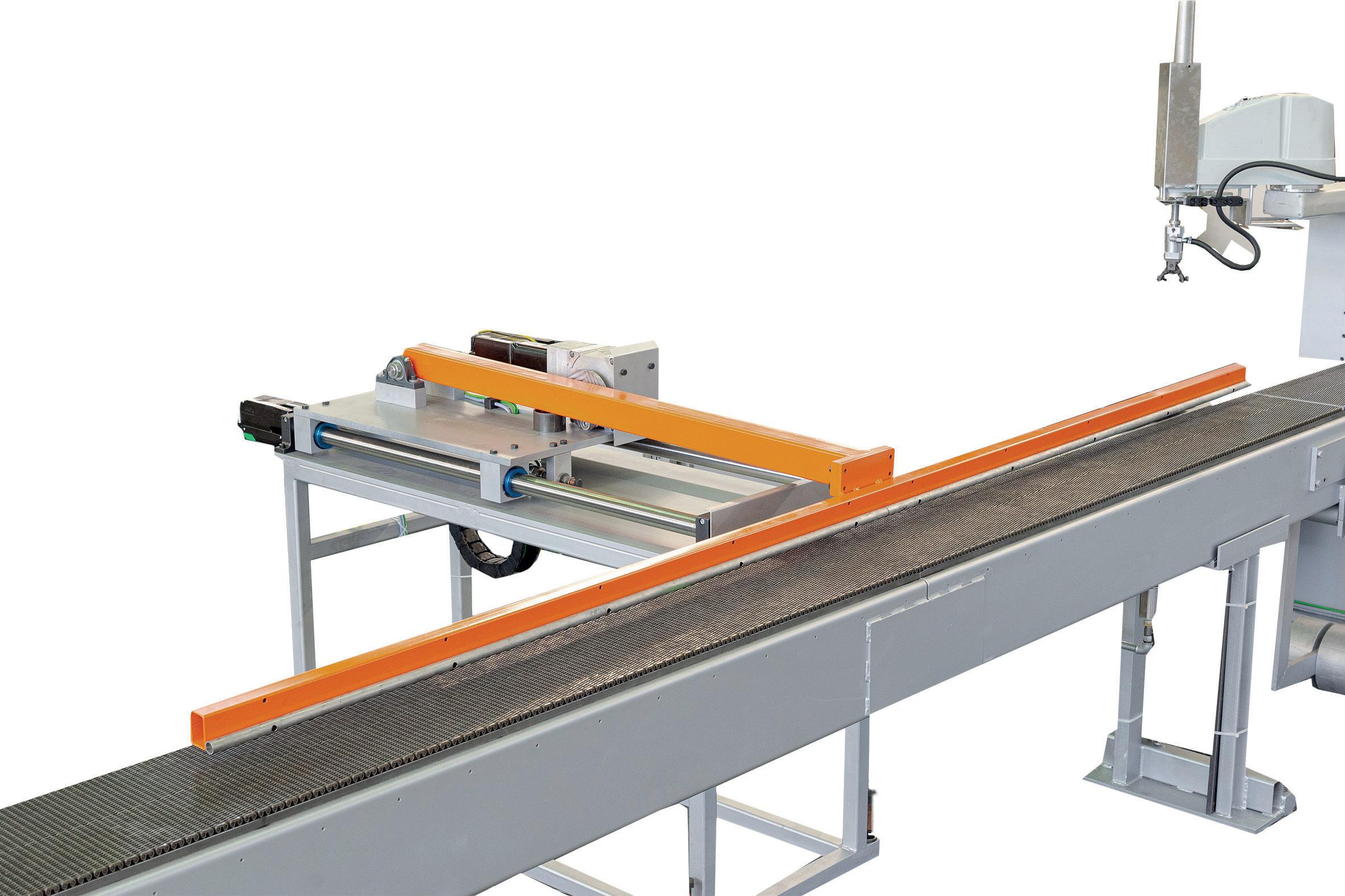
As a result, this factory has two options moving forward: upgrade its existing press lines or opt-in for new press lines. Based on the previous data, it can balance the available capex against the potential investments, benefits and savings more easily.
Last but not least, servo technology facilitates the Industry 4.0 Compliance. Digitalisation and collection of process data, in combination with operational analytics, can be used to stay ahead of the competition.
ESERVO technology, combined with

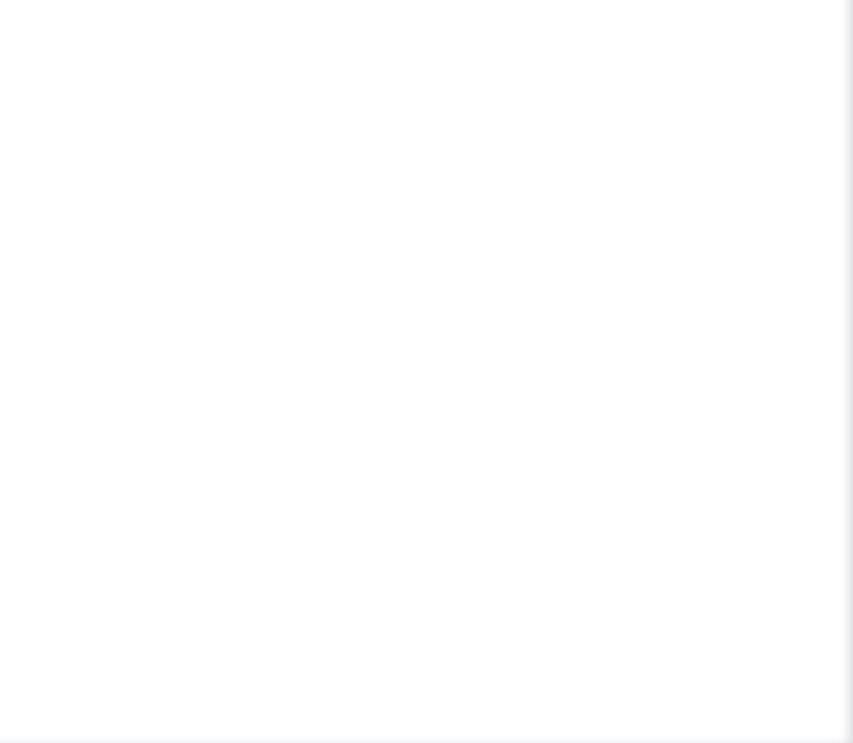
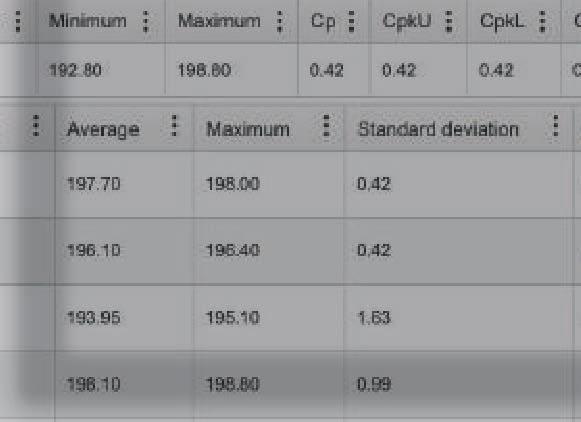
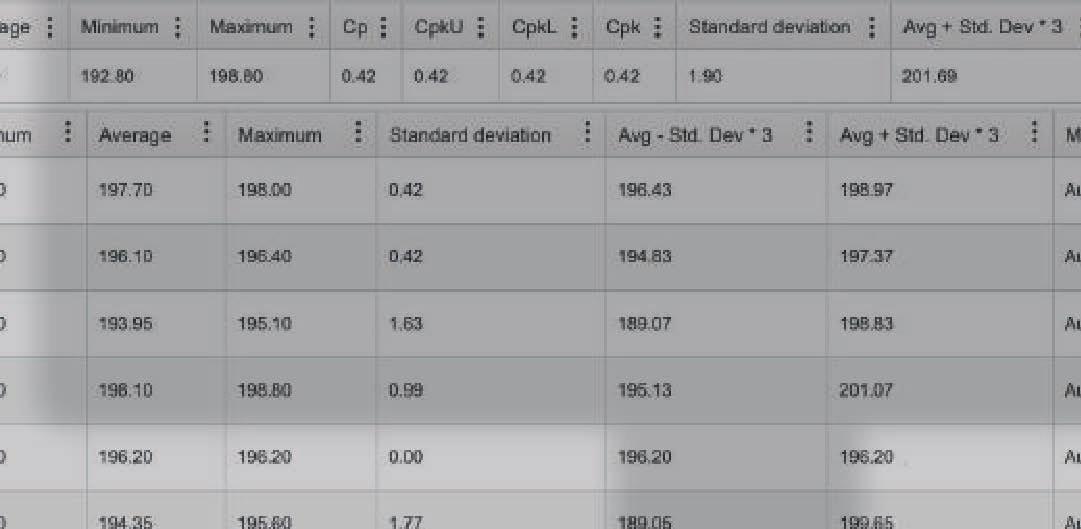
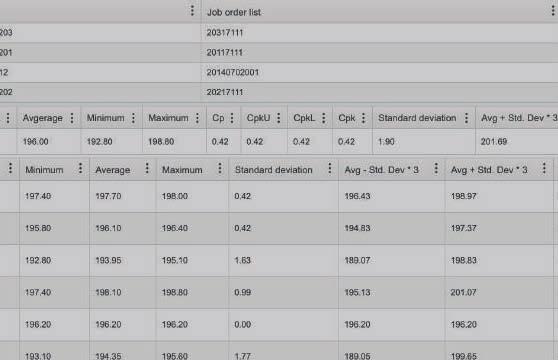
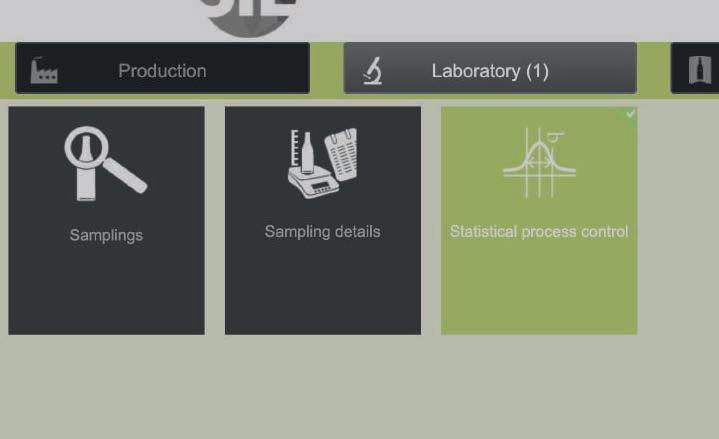
Your SPC under supervision

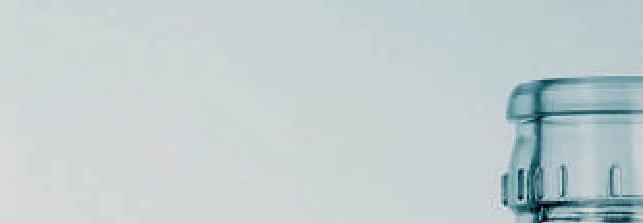
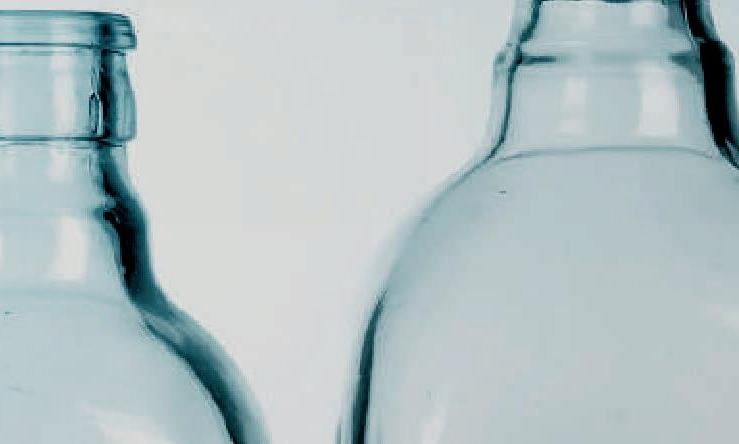
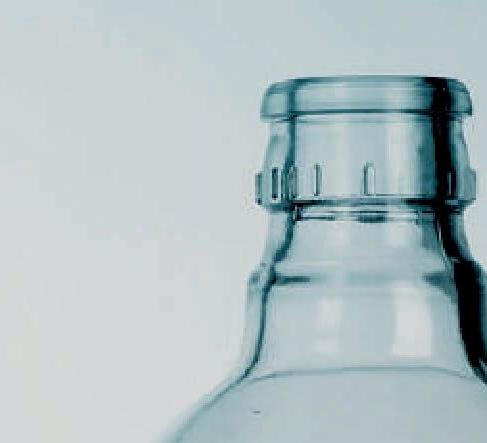
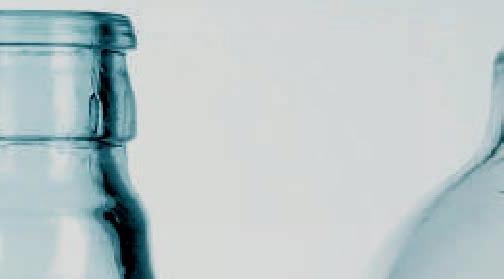
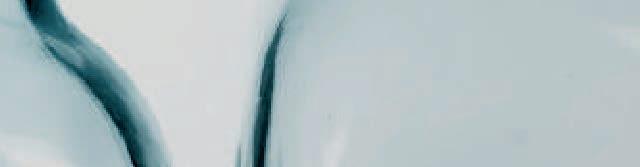
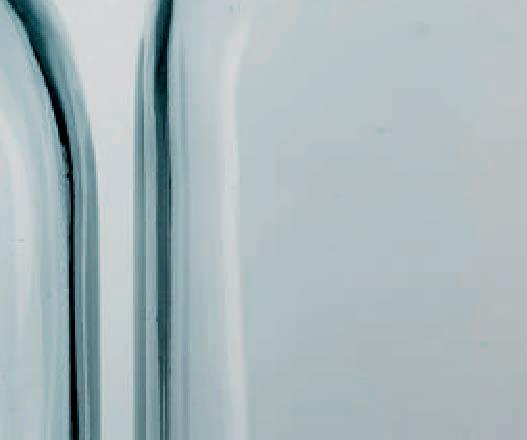
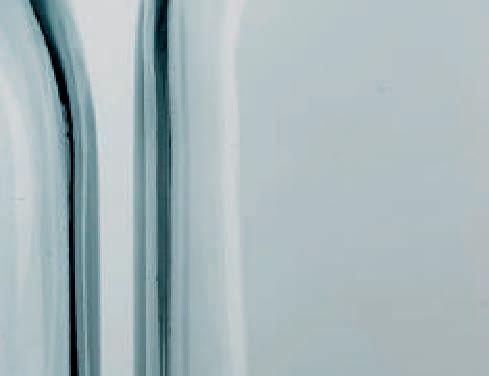
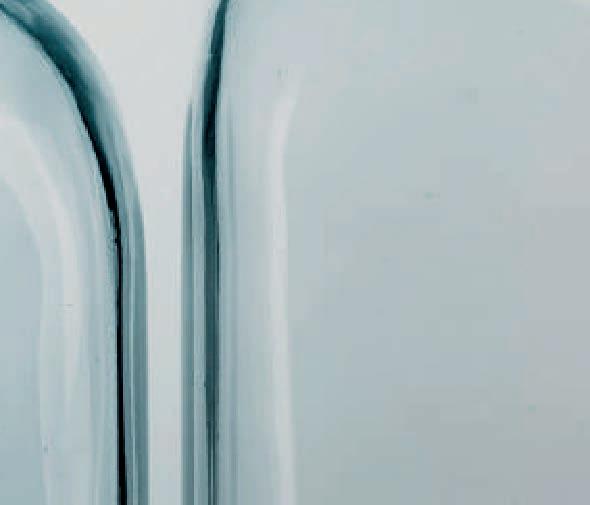
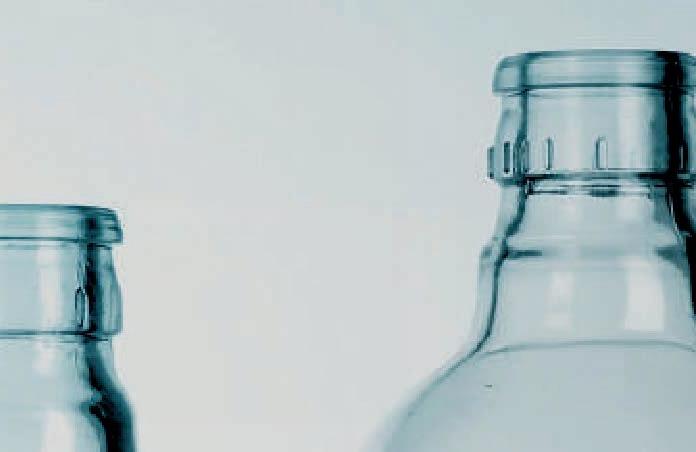
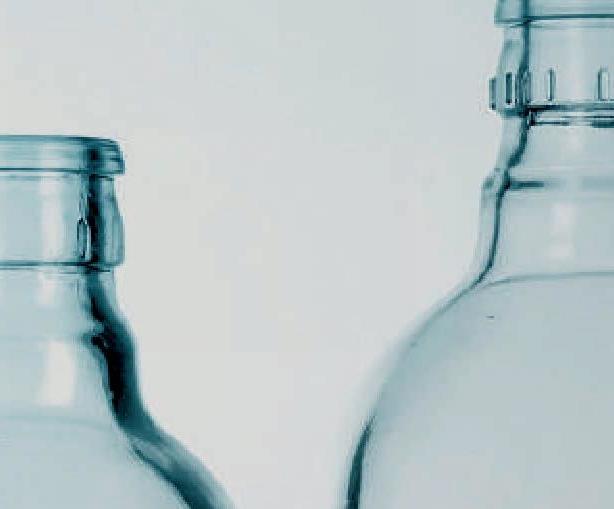
Waltec’s WTRACK productivity software, can improve data-driven processes and take Waltec’s ‘eco-nomics’ to the next level.
A Waltec customer, who recently upgraded its existing press configuration with ESERVO press cylinders as well as other components, had this to say about its experience: “We must admit, that up to today, we are by far exceeding our targets related to cost and energy savings, speed and efficiency.
“Commissioning this new technology with Waltec’s team went very fast, was hassle-free and reliable.
“Our ramp-up times have improved and our forming process became more safe and sustainable.
“Consequently, the team is running a more stable and predictable process simultaneously collecting data for further process improvements”. �
*Global Sales Director, Waltec Maschinen, Wilhelmsthal, (Steinberg), Germany https://www.waltec.de/
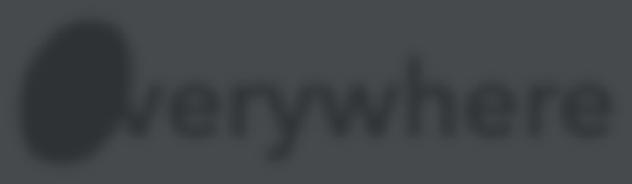