
5 minute read
Forming technology: Siemens
Siemens servo drive improves indexing times
Siemens has produced a servo drive system that can increase the number of cycles per minute for machinery. Matthias Porzig1, Tobias Feige2 and Dominic Ackerschewski3 discuss how this shorter index time has influenced Ambeg’s output.
� Pic 1. Chuck lifting device: transfer station from the A part to the B part. The transfer must be fast to remain high quality.
At up to 60 cycles per minute, Ambeg Dr. J. Dichter is taking the output of its glass forming machines to a new level. A high level of automation, high-performance servo drives at cycle time-related (connection) points and the know-how of perfect interaction, has led to the shorter index time. Other benefits include a consistently high product quality and a reduced rejection rate.
As a manufacturer of machines for tubular glass packaging, Ambeg has constructed machines for products such as bottles, syringe barrels and cartridges. Rotary indexing machines produced by this family-owned company are still operating today according to a proven principle: a rotary conveyor feeds glass tubes to a central rotary indexing table, known as the ‘A’ part.
� Pic 2. Up to 60 cycles per minute: automated rotary indexing machines for pharmaceutical and cosmetic glass products from Ambeg are reliable and productive, thanks to consistent, end-to-end high-performance components from Siemens.
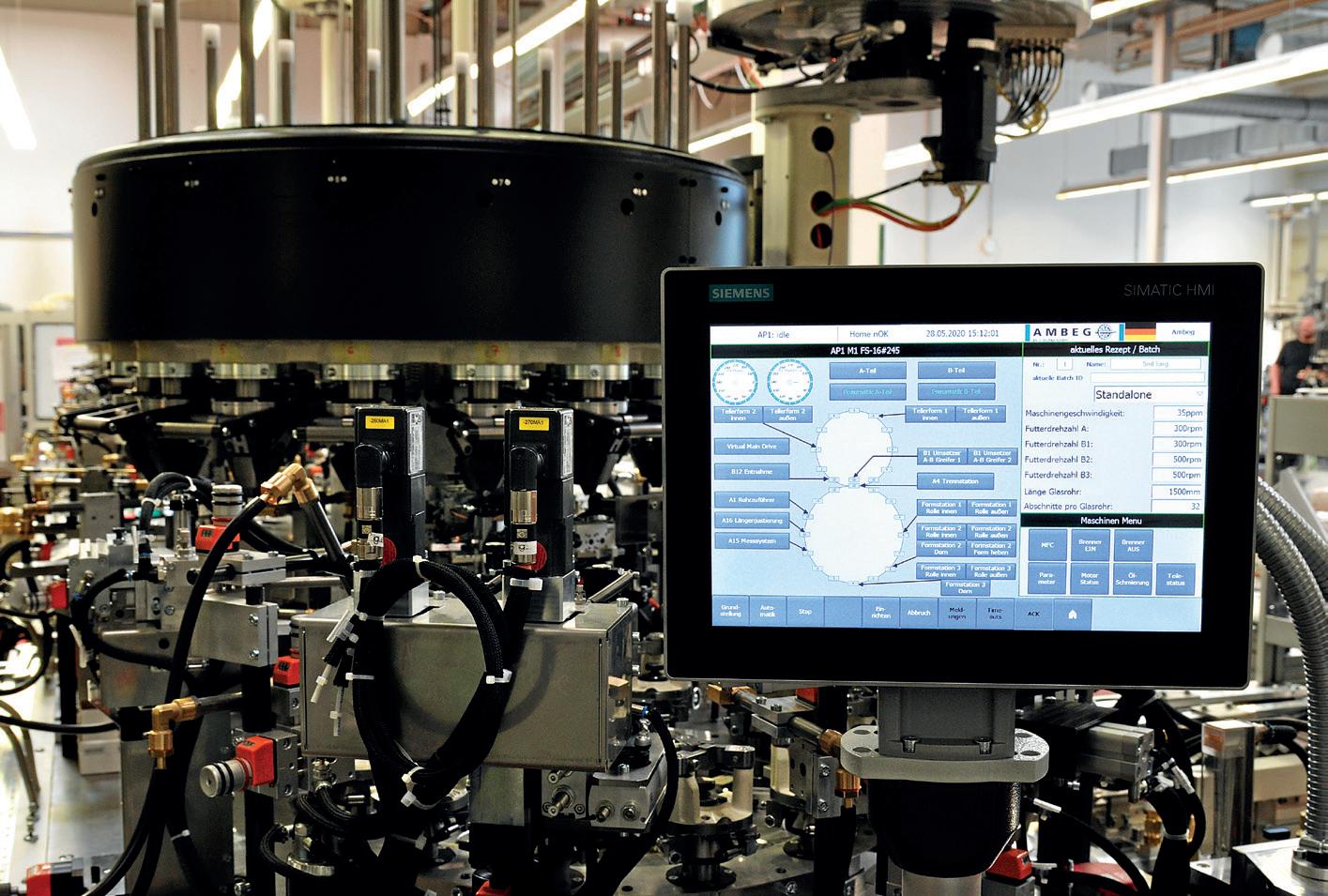

� Pic 3. Connected to a Simatic S7-1500TF via Profinet, new Sinamics S210 single-cable servo converters synchronise the traversing movement of the roll tongs precisely and highly dynamically. � Pic 4. Compact powerhouses: Simotics S-1FK2 servomotors provide three times the torque of the previous solution; with only one cable, they’re also easier to seal against oil.
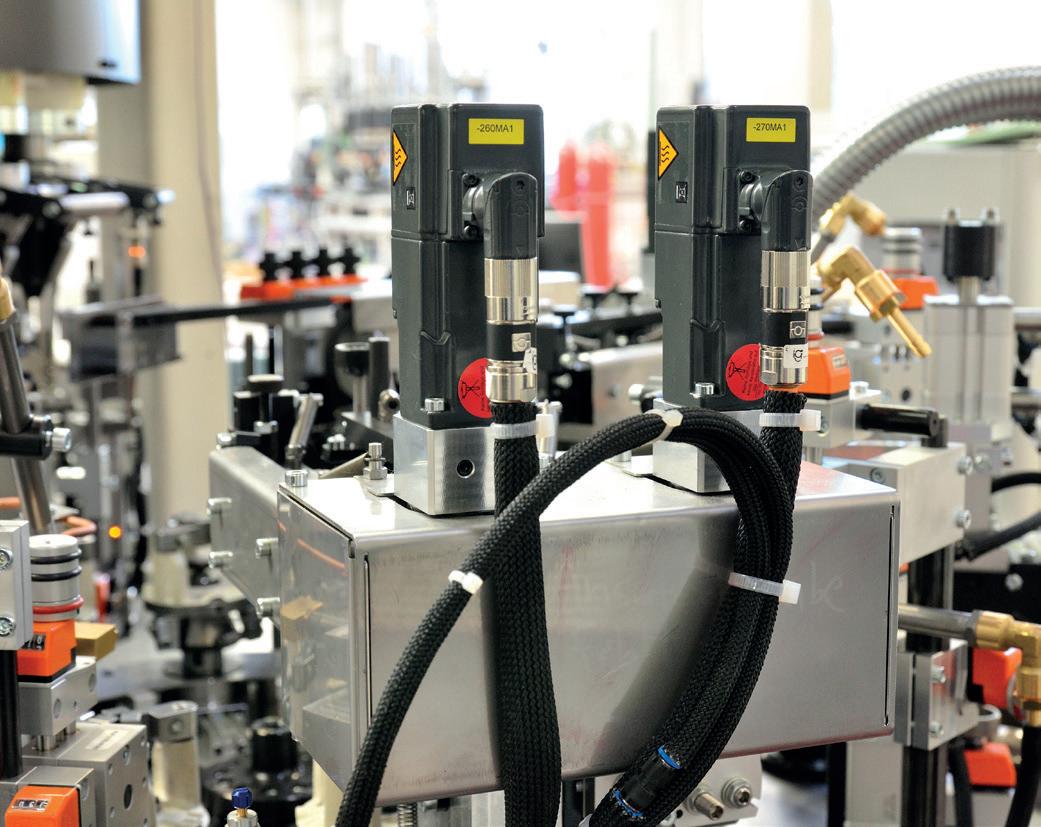
These tubes are partially heated several times over burners and gradually formed using roll tongs at multiple stations. After being transferred to a second rotary indexing table – the ‘B’ part – the base or (in the case of syringe barrels, for example) the open, opposite end of the glass container is formed (Pic 1). The speed of the A part determines output, which is why it is the focus of further development.
60 cycles per minute
Whereas the limit of ‘traditional’ servo machines is approx. 40 cycles per minute, the latest developments by Ambeg are already reaching 60 cycles - the output of one product per second (Pic 2).
“The indexing time from station to station is also critical for quality,” says Matthias Langer, Head of Engineering at Ambeg, “because the faster the indexing, the more time that remains for forming and the more gently and precisely the glass can be formed. We literally fight for every millisecond.”
Manufacturers of high-end products, such as syringe barrels for the pharmaceutical industry, whose subsequent processes are highly automated, have to deliver glass that is absolutely precise and of a consistently high quality.
� Pic 5. Simotics S-1 FK7 servomotors also synchronise interaction between the material feeder and rotary indexing table in the A part.
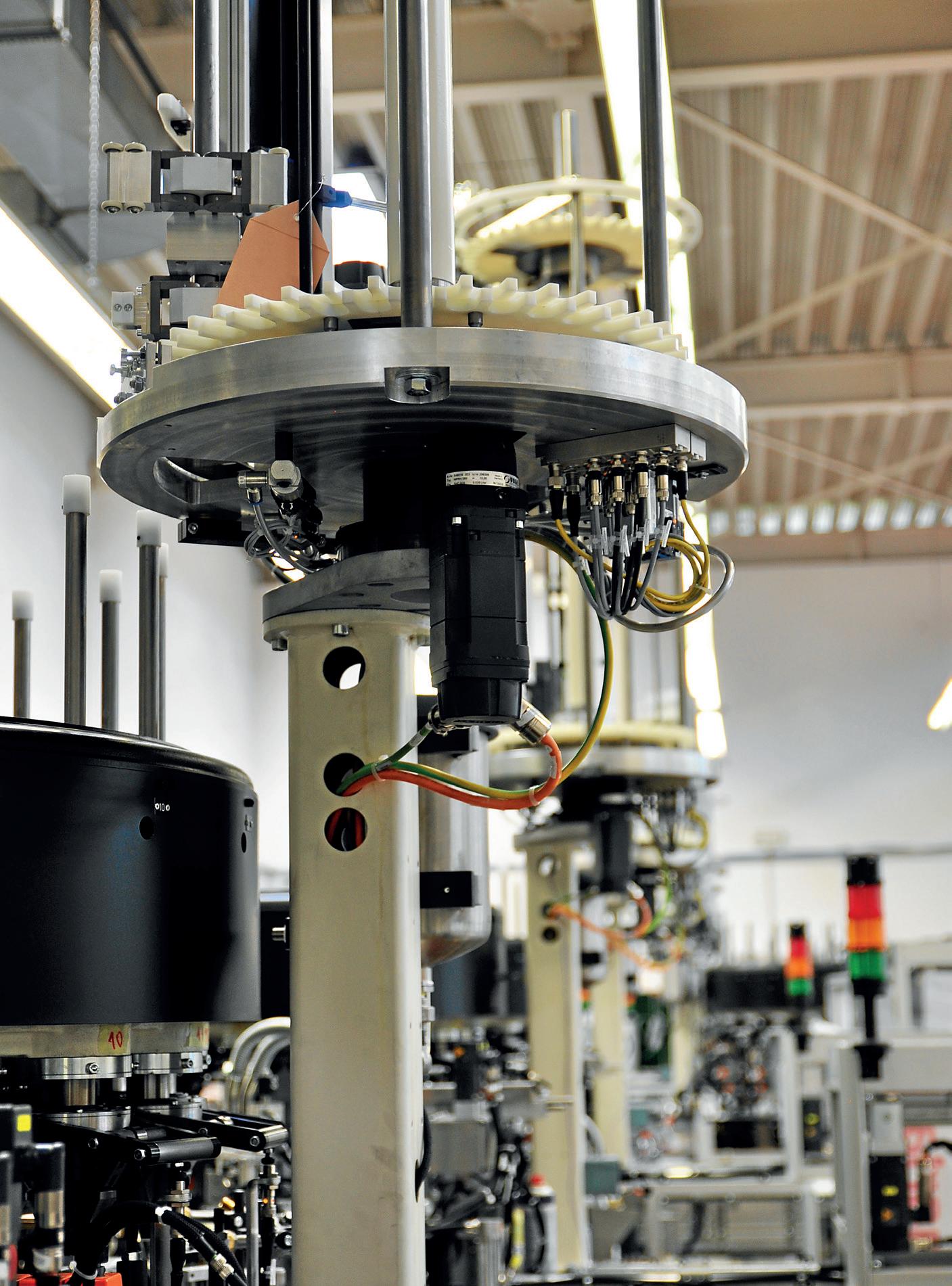
End-to-end automation
Servo drives have long been the norm for the rotary indexing machines at the glass tube feeder, the two rotary indexing tables, the forming tongs and other auxiliary equipment. The demand for a much higher performance has resulted in a new, comprehensive automation and drive concept, as well as in Ambeg’s choice of Siemens for its drives. Consequently, in addition to controllers and HMI devices from the Simatic product range, the company has since been using Sinamics converters and Simotics S servomotors provided by the automation specialists.
“We want to automate as consistently as possible,” is our motto. For this reason, the machine builder ultimately converted the drive system for the forming tongs to a latest-generation Siemens solution: a Sinamics S210 single-cable servo system (Pic 3) and matching Simotics S-1FK2 servomotors (Pic 4).
This has yielded a number of benefits. Due to the holistic automation concept in the TIA environment, diagnostics are already a standard functionality and require no additional configuration.
Converters from the modular Sinamics S120 series and Simotics S servomotors were already being deployed wherever higher performance was required. Like the new Sinamics S210, they also communicate with the Simatic PLC via Profinet IRT and, when necessary, via the fail-safe Profisafe protocol.
Controllers for every task
The functionality required of a machine or line determines the performance of the controller selected. The Simatic S71500 portfolio supports finely scalable solutions – from standard CPUs in various performance classes and fail-safe F CPUs for safety-related tasks to technology CPUs for more sophisticated motion control functions.
The latter are the first choice when cam and positioning functions are required. The highly dynamic, synchronous processes of the glass tube feeder and rotary table in the A part or the coordinated lifting and in-feed motion at the shaping tongs are notable examples (Pic 5). As a result, Ambeg is able to implement highly dynamic and precisely reproducible motional sequences that combine high quality with maximum productivity.
High-end application processes
The Berlin-based company wasn’t a leading innovator, nor was it constantly on the lookout for new technologies that would introduce further improvements. What pushed Ambeg’s proven technology to its limits was the demand, on the part of prominent pharmaceutical customers, for 60 cycles per minute.
It’s also what inspired the design engineers to operate the rotary indexing table in the A part using an extremely rigid and precise direct drive from Siemens. Thanks to the Sinamics S120’s optimised control, machine vibrations can be reduced to a minimum despite an extremely high dynamic, which in turn protects the mechanical construction. This enables stable and low-maintenance high-end applications operating at 60 cycles per minute. �
1. Head of Technical Consulting and Promotion Drive Technology
2. Project Specialist Motion Control and Drive Technology in Technical Sales Support
3. Sales Manager for Digital Industries Siemens Digital Industries, Nuremberg, Germany
https://new.siemens.com/global/en/markets/glass-industry.html
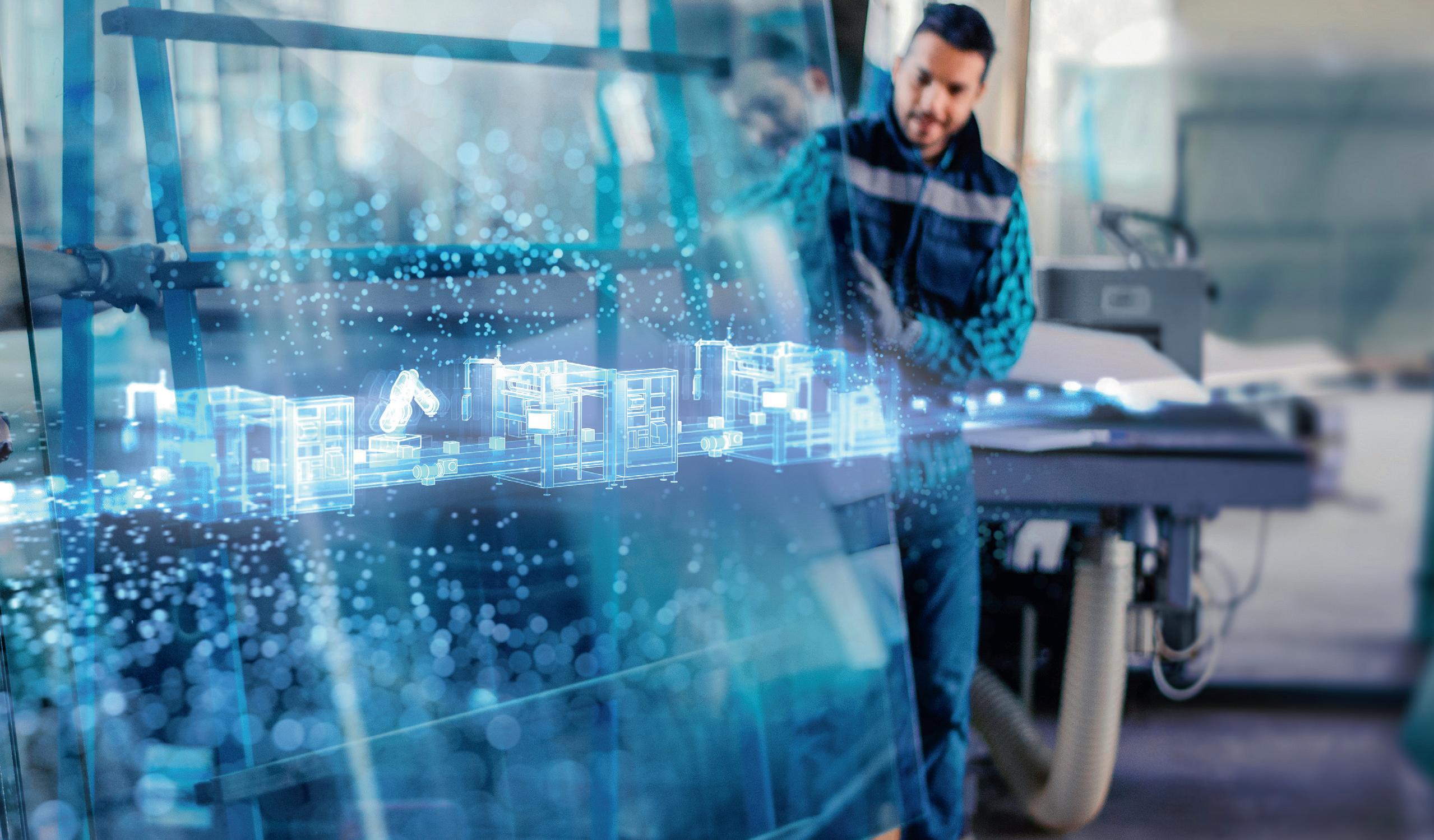