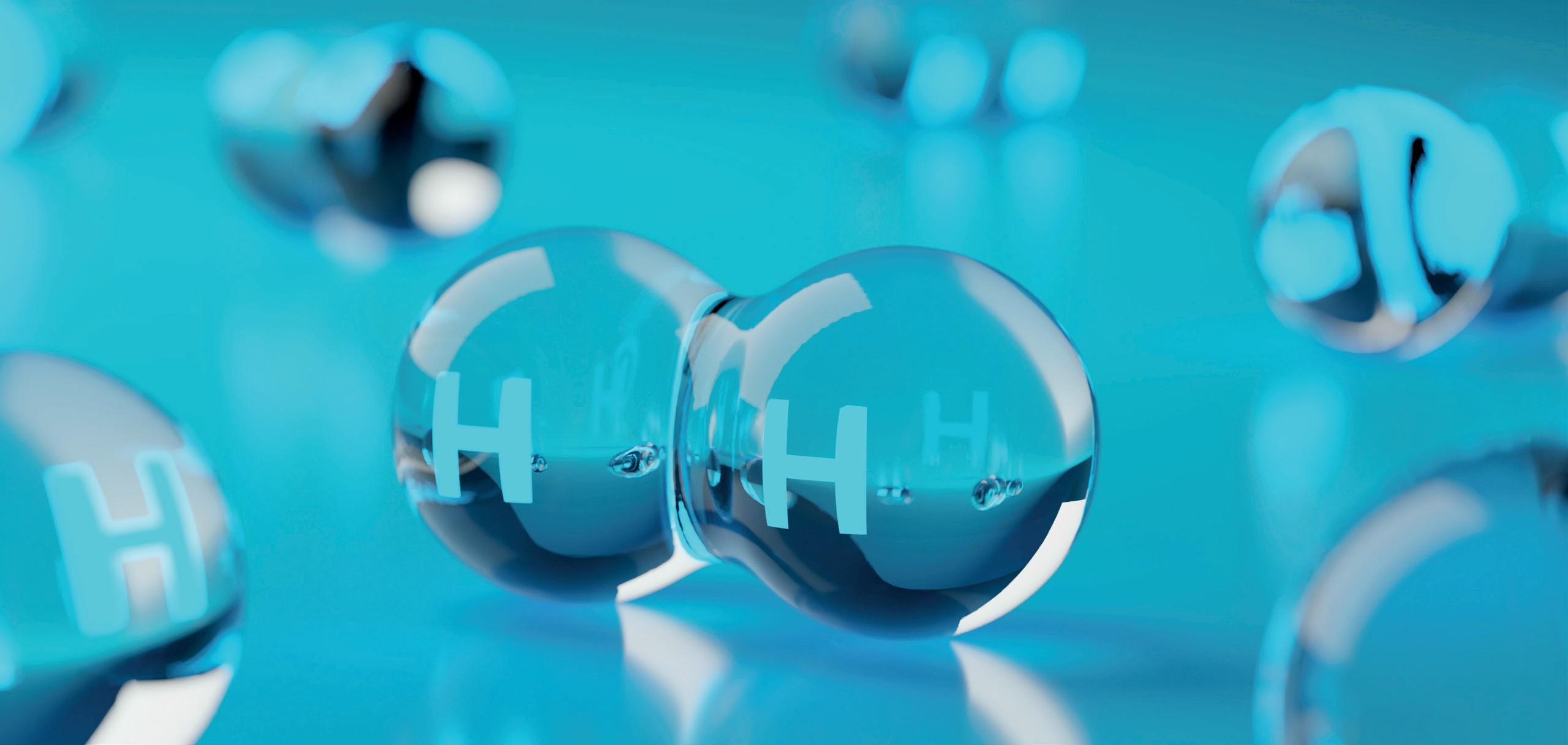
7 minute read
Hydrogen: Air Liquide
Preparing burners for the H2 transition in glass production
A. Bâ*, C. Guiberteau*, J. Caudal*, X. Paubel*, L. Jarry. * S. Gersen, B. Slim, R. Zeijlmaker** outline a programme for testing and adapting Air Liquide’s oxy-burners to the new H2 era.
Historically, the industry has favoured natural gas as an energy source because it is an established technology, with low price, ease of control and the fact that there is no special requirement for storage facilities. A first improvement of thermal efficiency and productivity was reached by the oxy-combustion in those sectors.
The glass industry today is investigating different options to reach carbon neutrality by 2050.
As glass furnaces have long lifetimes, on average over 12 years and sometimes up to 20 years, their conversion with new cleaner melting technologies could start by 2030, in order that all plants would be

� Fig 1.Natural gas and oxygen flow distributions for the Air Liquide glass melting FC burner.
� Fig 2. Laminar flame speed, adiabatic flame temperature (A) and the strain rate with H2 concentration (α) in the fuel blend (B). ready by 2050.
Clean hydrogen is one possible option to replace fossil fuels (notably NG or fuel oils) as feedstock and hydrogen-based solutions will play a pivotal role in the energy decarbonisation.
Air Liquide has set up a programme for testing and adapting its oxy-burners to the new H2 era. In that frame, upgrading its burners portfolio, together with acquiring knowledge to allow having technically proven and efficient solutions for different applications are the top priority activities currently in progress.

Technical approach
In the frame of the H2 programme, Air Liquide’s existing burners are being tested and adapted to be used with hydrogen. In the first phase of this programme, the main criteria to evaluate the burner performance include the flame characteristics and stability aspects, NOx emissions and heat transfer.
The strategy for safe gas handling, and usage of typical instruments for measurements, as well as flame detection sensors, were also evaluated. Based on those criteria, several tests were carried out at different installations: � Tests at the combustion platform of Air Liquide’s R&D centre (Innovation Campus Paris) where installations such as combustion chambers, valve trains

� Fig 3. Pictures from the tests of Melting-FC burners carried out at Air Liquide’s R&D facilities.
to handle and control different types of gases and their blends, as well as advanced diagnostics tools to evaluate and measure burner performance and flame characteristics are available. � Other results were obtained through partnerships involving major industrial actors, such as in the project ‘Hydrogen as a fuel for heating processes’ led by DNV and CelSian [1] . � Evaluation and investigation at university laboratory scale in order to study fundamental details of flame structure, including thermodynamic calculations useful to understand the combustion mechanisms, and provide criteria to evaluate the results at industrial scale. Within this programme, tests at Rouen University (France, CORIA laboratory) are currently underway.
Air Liquide FC burners for glass manufacturing
Within the glass melting burner solutions from Air Liquide, Alglass FC is a patented technology where fuel and oxygen are introduced into the furnace through a configuration of separate injectors, producing a luminous flat and broad flame. This was the type of burner used for the experimental work presented in this paper.
In the glass melting FC burner, oxygen is injected at lower velocity from two injectors located at the top of the burner block. This directs the oxygen flow towards three natural gas (NG) jets of fuel located in the bottom of the block. Fuel and oxygen are mixed and burned outside the block into the furnace, creating a wide flame coverage over the glass melt.
The control of the flame shape and luminosity is obtained by adjusting the secondary oxygen flow rate (10% to 30% of the total oxygen), which is injected around each of the three natural gas injectors at the bottom of the block. Increasing this secondary oxygen flow
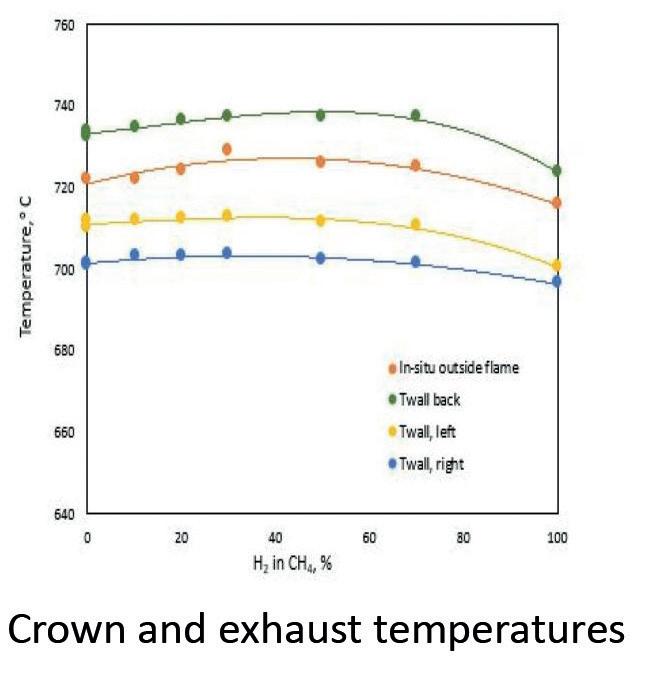
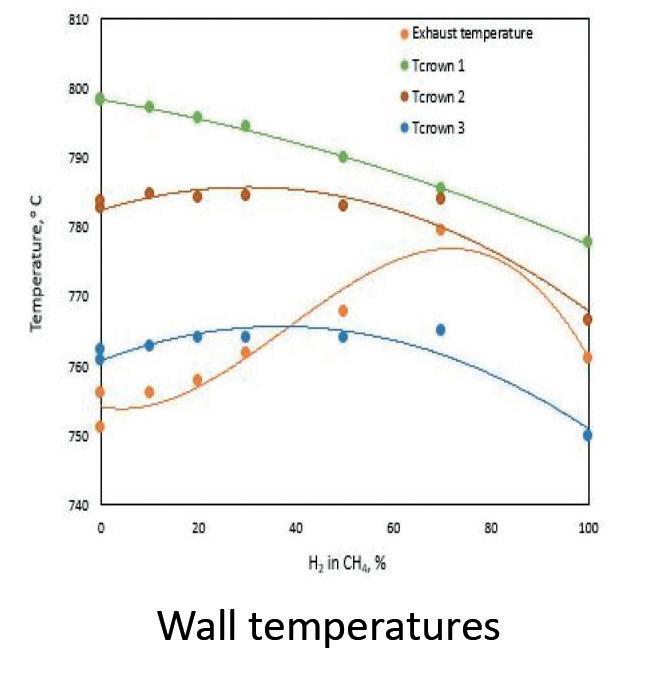
� Fig 4. Temperatures in the furnace crown and walls.
results in faster mixing between natural gas and oxygen and thereby produces a shorter flame. Lower secondary oxygen flow delays the oxygen and gas mixing producing a longer flame. In both situations, the flame peak temperature is reduced because the primary oxygen jets separated from fuel jets are diluted with the furnace gases before they intersect each other.
Results
Numerical calculations
A first insight into H2 flames specific properties can be obtained through standard laminar flames calculations. In air combustion, the adiabatic flame temperature of hydrogen flames is higher than that of methane flames. Whereas with pure oxygen, the difference between hydrogen and methane flames temperature is not significant. The laminar flame speed also shows a high increase with H2 content in the fuel, having a remarkable impact particularly in the oxy combustion case. The tendency to flame extinction given by the calculated strain rate is also highly dependent on the H2 concentration in the fuel blend and, it shows in air and oxygen cases, that flames with higher H2 concentration are more stable. Particularly, in the case of pure oxygen, the flame exhibits a higher resistance to extinction compare to air, providing in this way better flame stability and flexibility in the operation. In general, these properties provide insight into the burner design in order to control velocities, flame structure and stability, as well as the potential NOx formation due to higher temperatures.
In the frame of the project lead by DNV and CelSian, the Air Liquide standard version of Melting-FC Burner was operated with various H2/CH4 blends, going from 100% CH4 to 100% H2 without changing any burner design parameters and keeping constant the thermal input. Similarly, during all the tests performed in parallel on Air Liquide facilities it was observed that oxy-fuel combustion allowed the use of the standard oxyburners designed for NG, for the whole range of H2 enrichment, from 0% vol to 100% H2
[2] .
Digital and IR cameras were used to visualise the flame structure. In general,
only small changes could be observed in the flame shape with the H2 flame compared with NG flames. The visual flame length was similar in both cases.
In all the tested configurations carried out at the different facilities, a stable combustion was observed without any overheating at the burner exit, over the whole range of H2 concentration tested.
NOx emissions
All the tests that were carried out so far with oxy-fuel combustion showed the NOx emissions resulting from the Air Liquide Melting-FC Burner during operation at different H2 concentrations in the fuel. The results obtained by DNV clearly state that a reduction in NOx emissions of 21% could be achieved when switching to full H2 operation.
Heat transfer
Replacing part of the NG with H2 can also have some consequences on the heat transfer. Temperature measurements carried out during the tests at DNV, using fixed thermocouples installed in the crown and furnace’s walls, showed a slight reduction in temperature with H2 concentration in the fuel blend, see Fig 4. This is in agreement with the higher heat absorbed in the cooling floors at the same conditions showed in Fig 5. Switching to H2 improves the heat transfer to this zone of the furnace, adding the strong contribution of the convection heat transfer due to the velocity changes upon hydrogen concentration.
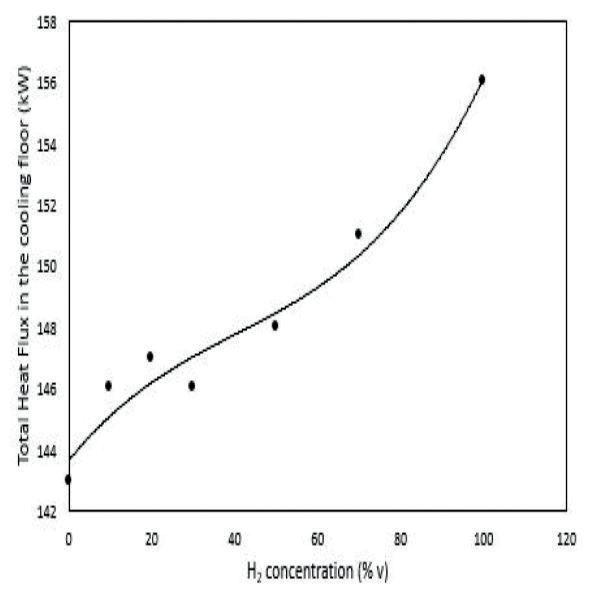
� Fig 5. Heat transfer to the cooling floors with H2 concentration in the fuel blend.
Conclusion
In general, after a complete analysis of different test campaigns, it is possible to conclude that all results are encouraging. Positive impacts have been identified so far regarding materials, flame stability and combustion efficiency, as well as NOx emissions. We observed a good performance of the Air Liquide Glass Melting FC oxy-fuel burner technology, ensuring flame stability and reliability over the whole range of H2 enrichment in the NG/CH4, from 0% to 100%.
These results confirm this burner as a cost-effective solution for the transition from natural gas to full H2, having in mind its performance and also the utilisation of existing installations and equipment for gas handling and safety purposes. �
References
1. https://www.dnv.com/article/ hydrogen-as-a-fuel-for-hightemperature-heating-processes-219385 2. Caudal, J.; Paubel, X.; Jarry, L.; Del Corso, F. Hydrogen as a source of combustion energy for glass melting. Glass International, February 2021
*Air Liquide **DNV Campus Groningen

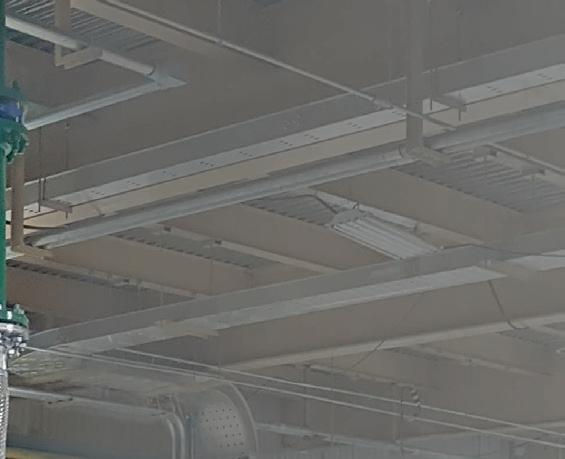
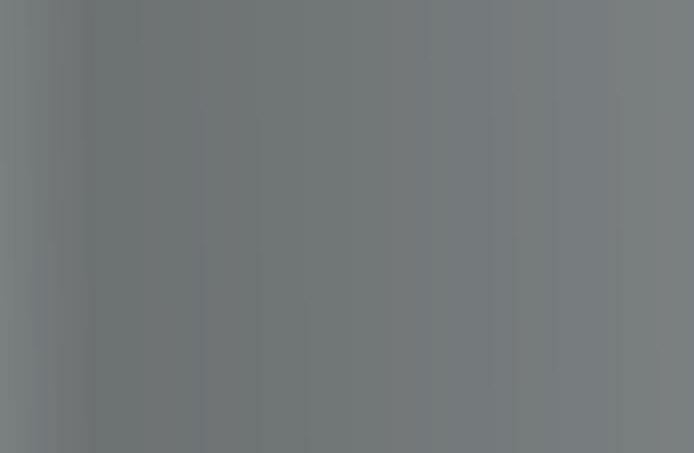