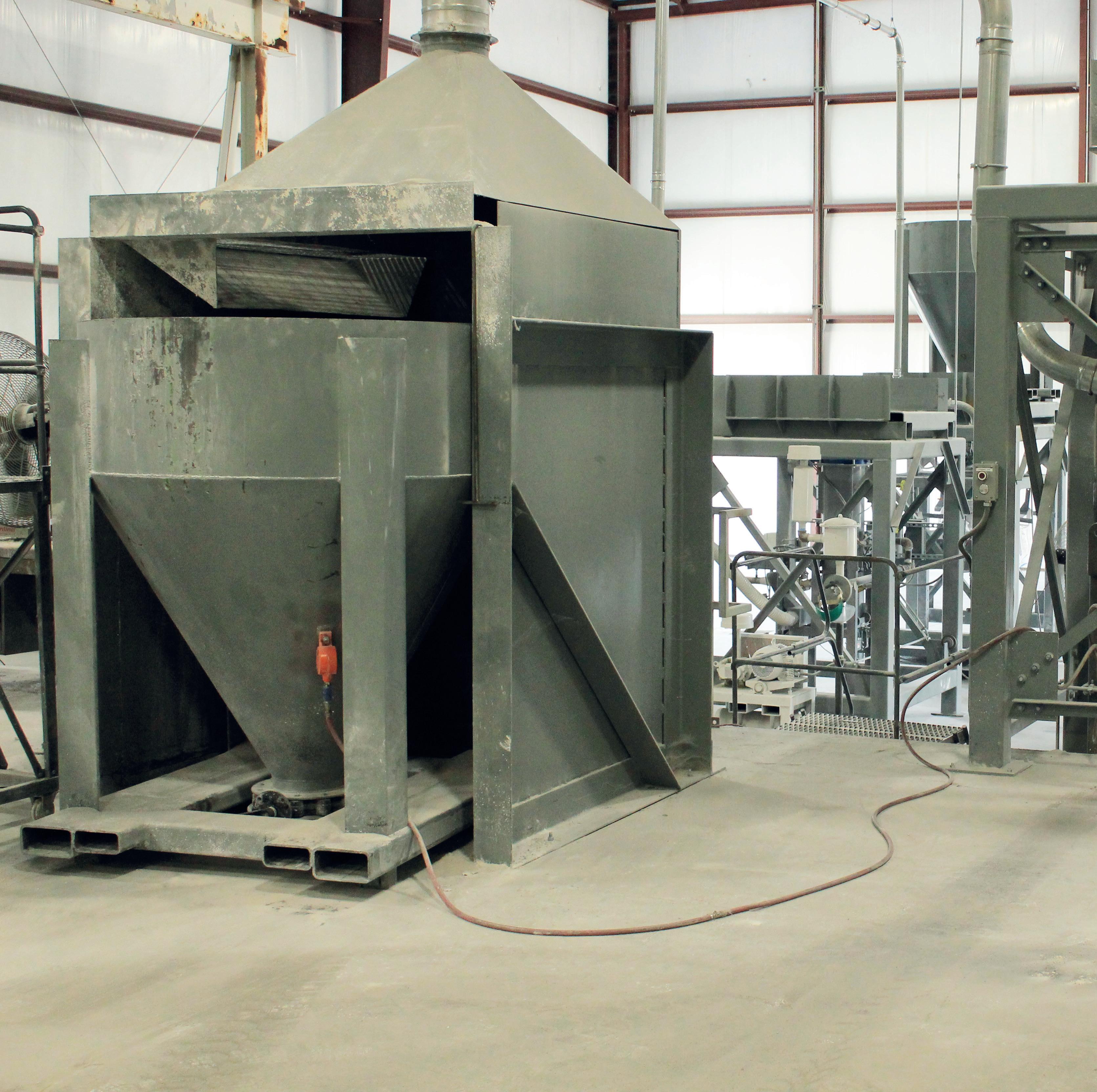
5 minute read
Company profi le: SSRC
US refractory specialist enters new era
In June 1987, Wally Evans stood in an empty horse stable near the heart of Alabama. A company was formed to help the global glass industry with a focus on value, speed, and purity.
As he stood in the stable, he could not imagine that his son, Luke Evans, would later redefine the company. The next chapter for Special Shapes Refractory Company (SSRC) was developed from customer drive solutions to improve their current and future capabilities.
The legacy of what was built has stood the test of time while improving the nimbleness and rapid turnaround times are a cornerstone of SSRC.
Monolithic plant
SSRC has seen increased sales volumes for precast shapes and monolithic materials. It has increased capacity and expanded its plant operations.
The construction of the monolithic plant (above) was completed in 2021 along with the new laboratory. It decided to build its own monolithic plant as the company wanted to have vertical control of inputs into raw materials selection and cost.
It provide additional in-house quality control procedures and reduce the cost for additional testing, ultimately reduce cost for costumers. This also provides a reduced lead time for monolithic materials for its precast shapes.
Lastly, it provides a new segment for SSRC to establish partnerships, and create new monolithic
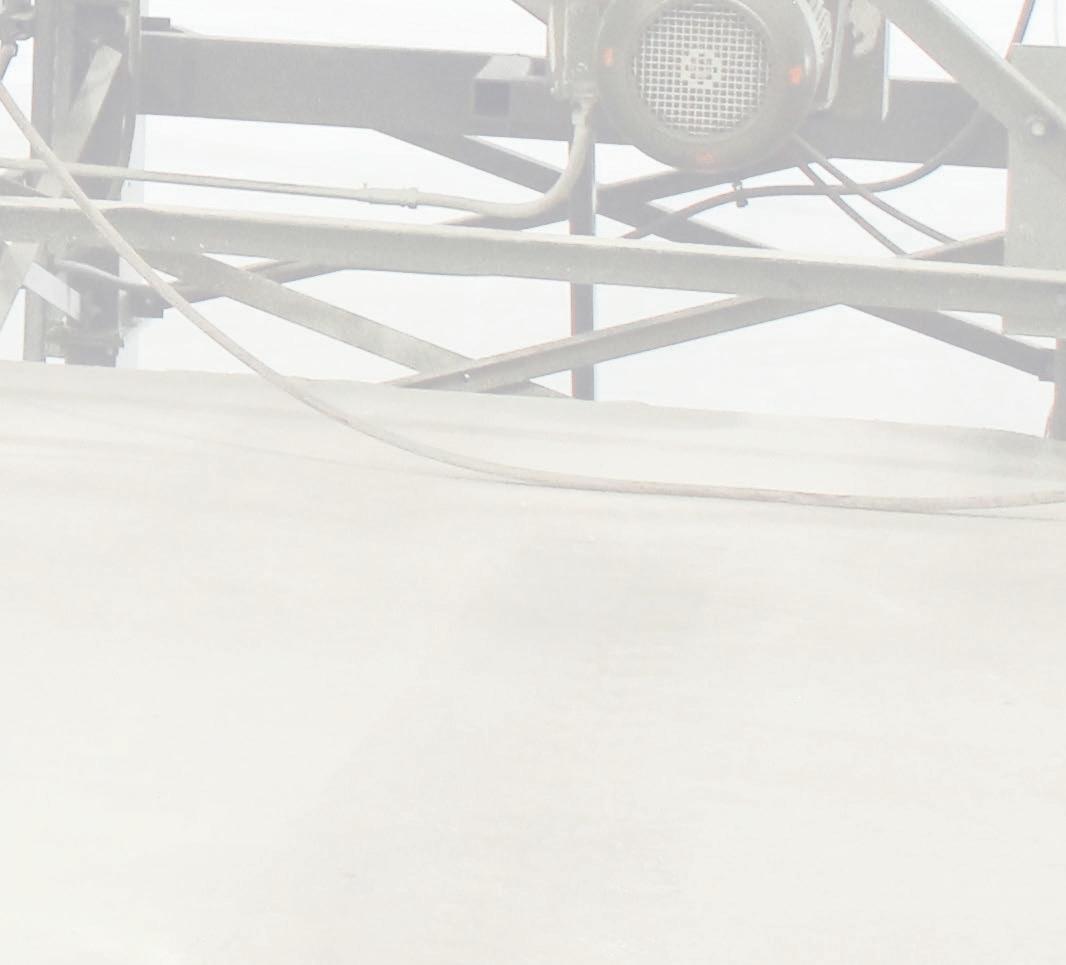
US refractory supplier Special Shapes Refractory Company (SSRC) has expanded its plant operations with a new monolithic plant and laboratory. Andrew Pea* discusses how the investments have improved reliability and helped meet increased demand for glassmaking equipment.
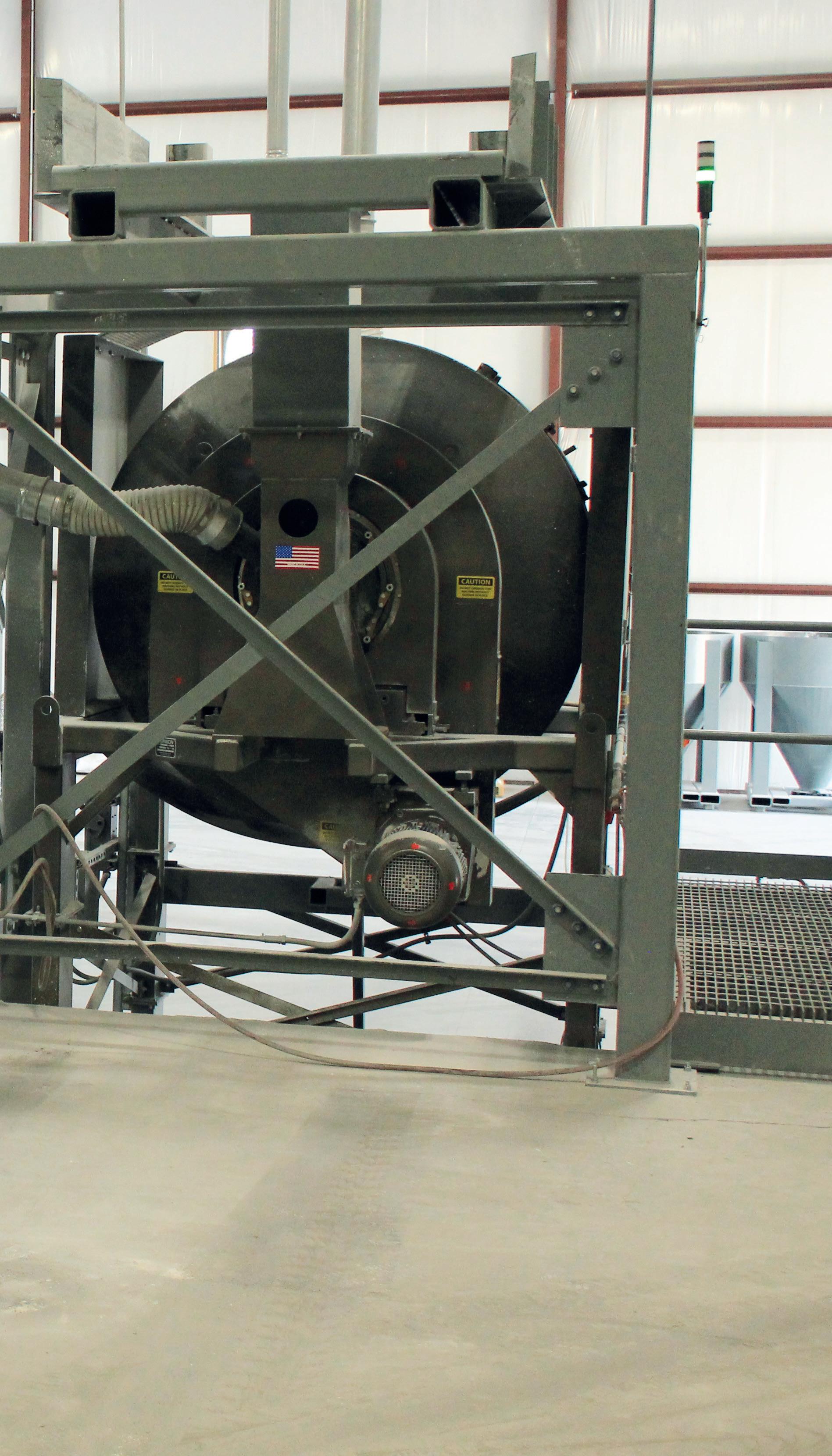
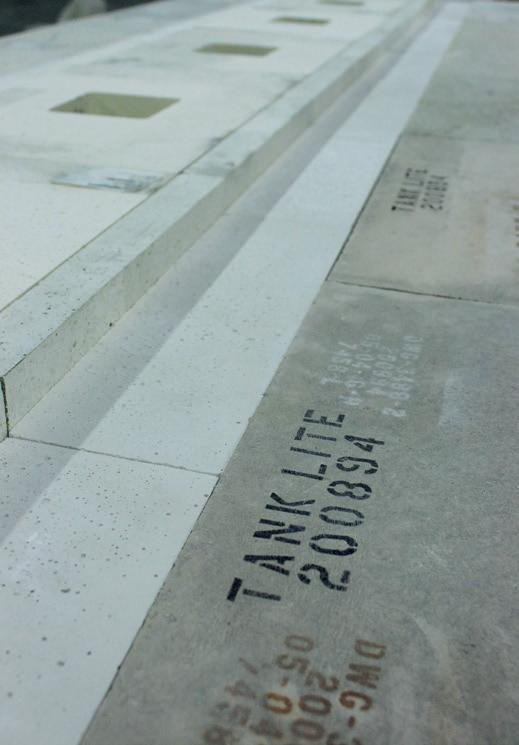

Monolithic Plant.�
� Additional QAQC Process Control. materials for hot repairs in glass.
It is now in complete control from a Quality Control standpoint of everything: from incoming raw materials to fi nished monolithic products and completed precision, precast shapes.
In 2019, the company broke ground on the multi-million dollar monolithic plant, capable of manufacturing 13,000 metric tons per year.
Four new direct jobs were created in the monolithic plant, while indirectly, three additional jobs within SSRC organisation were created. The advantages for its customers include a reduced cost of SSRC’s products, a reduction in the lead times for monolithic materials as well as precast shapes, and an increase in product quality.
Its in-house laboratory is a newly-built dedicated room for the team to work in.
It contains a rapid fi re furnace for quality control on incoming raw materials as well as a particle size analyser. It has also installed a cold crusher, weight controls and other manual gauges.
Team
Operations Director Greg Clark and his team are tasked with preventing manufacturing imperfections as well as the quality assurance team confi rming the purity of the materials. Overall, reliability of the materials has improved since the induction of the new plant and procedures.
For SSRC to continue to bring solutions to the market, a new team was created. Ralph Blythe has been assigned with the task of bringing new monolithic materials to market. Ed Reeves and Somnath Mandal, both ceramic engineers, are focused on the glass industry and are collaborating for the next generation of refractory materials.
One of the next developments from SSRC will provide customers with more energy effi cient refractory materials. By decreasing the thermal conductivity, the furnace will be able to consume less energy thus bringing a more sustainable material to the end user.
Continued>>

Sustainability is a key theme within SSRC and it has worked on its existing materials that would have similar performance but with less thermal conductivity.
The reduction in thermal conductivity would ultimately mean that the customer can install a more energy efficient insulation package, reduce installation time (while using less refractory), and decrease the cost of their furnace (removing more expensive insulating materials). Its ceramic engineers are working on providing quantitative data that would provide information on what that reduced thermal conductivity would look like. The second phase the group is working on is providing modelling data to provide a visual representation of the efficiency. A final test phase would be to install the materials in a furnace and provide data in a working environment.
As of late 2020, Bob Hunter is the new Director of Sales and Marketing tasked with building new monolithic business while maintaining the legacy glass industry.
Andrew Pea and Joe Fretz are continuing to build the container, fiber, float and other glass segments while Wes Broussard is entrusted with providing the solutions for monolithic customers. SSRC has seen revenue growth domestically but has also seen a rapid expansion internationally from agile and prompt delivery. Its international expansion has occurred in two segments: pre-cast shapes for the glass industry and monolithic materials.
For pre-cast shapes it has built an international network in Europe, Asia, South America and Mexico. This has come with adding agents in South America and Europe as well as by providing more of its pre-cast shapes to those locations.
It has seen increased demand for its monolithic materials in South America, alongside more enquiries from European customers.
It states that the driving factor in its international growth is the increased demand for bonded products for hot repairs, its competitive pricing for cold repairs, increased energy efficiency compared to competitors, and the high quality materials customers expect in their furnaces.
� Cold crusher and particle sizer.
Identity
The next generation of SSRC has been ushered in by the rebranding of the company in 2021. A new emphasis on marketing literature showcases the path forward while recreating the company’s website provides a more user-friendly structure.
While modernising the identity, the voice of SSRC will continue to provide experience and knowledge to global organizations. SSRC has so far joined ACERS, Glass Futures, Glass Packaging Institute, Glass Art Society and Louisiana Chemical Industry Alliance already in 2022.
SSRC will continue to improve refractory and monolithic materials for the glass industry for decades to come.
Bringing the experience of the research and development team as well as the knowledge of the sales team show exhibits the core values of the company. At the same time, the new monolithic plant ensures the highest quality materials are provided.
With most refractory manufactures’ lead times have continued to increase, SSRC can still provide some of the quickest manufacturing lead times. The next era of the company has been created to provide ‘better solutions, faster.’ �
� Monolithic plant and materials. SSRC, Bessemer, USA www.ssrco.com
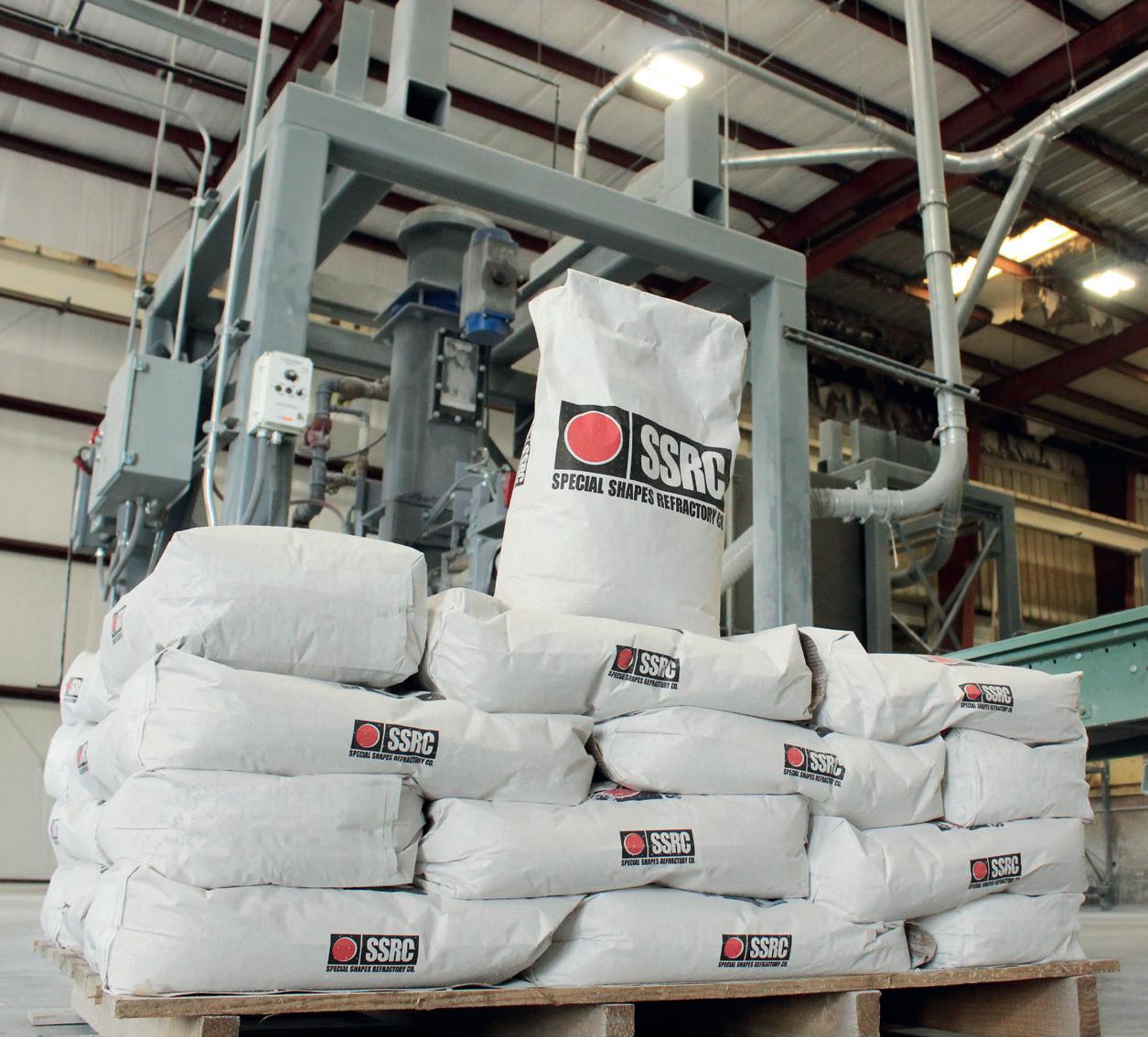