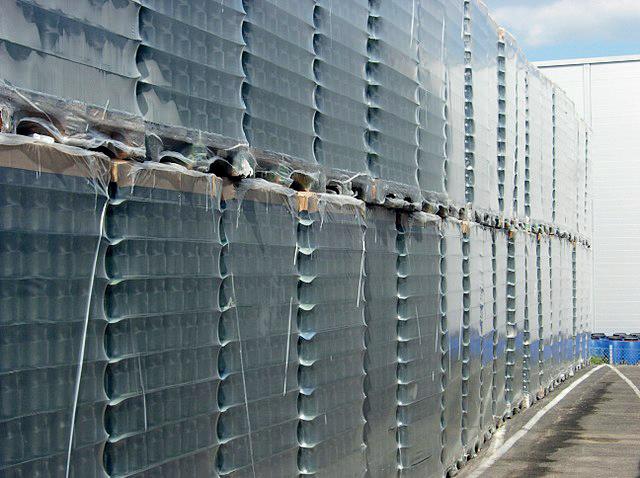
8 minute read
Glass packaging: Talos Recycling
Minimising plastic waste in the glass industry
Talos Recycling is helping to ensure container glass manufacturers achieve their sustainability goals throughout the entire supply chain, working alongside manufacturers such as Ardagh to recycle their used flexible plastic packaging back into a closed-loop manufacturing process. Jamie Gibson* reports.
Sustainability is a core value in the glass industry and glass itself is a perfect model for the circular economy, as it can constantly be recycled back into new glass packaging.
One of the challenges facing the industry is to ensure the whole supply chain is just as sustainable.
The benefits of using flexible plastic packaging within the glassmaking supply chain are well-established. Transporting glass containers (jars and bottles) from the manufacturer’s warehouse to the customers’ filling lines, and then on to the end consumer via retailers and the licensed trade, is a critical part of their journey.
The containers must be loaded securely onto pallets for safe and efficient transportation: flexible plastic packaging protects the glass containers, ensuring they arrive at their final destination in as perfect condition as they left the warehouse.
Depending on the content of the plastic packaging, once used, it can be recycled back into new plastic packaging.
By using a product that not only contains recycled material, but is, itself, 100% recyclable, a circular economy model can be achieved, eliminating waste and lowering carbon emissions: each tonne of plastic that is recycled back into the manufacturing process saves 1.5 tonnes of carbon1 .
� Glass bottles on pallets wrapped in flexible plastic packaging.
Marpak Extrusions is a UK-based manufacturer of flexible plastic packaging, supplying the major UK glass manufacturers. Recognising the need for glass manufacturers to be able to reduce plastic waste and use flexible plastic packaging with recycled content, Jamie Gibson and Matt White set up sister company Talos Recycling, which collects their customers’ plastic packaging waste and turns it into pellets.
These pellets are used to create new plastic packaging, with a minimum of 30% recycled content, using Talos Recycling’s mechanical recycler at its factory in Leeds, UK.
Continued>>
� The recycling process - used film being recycled back into pellets.
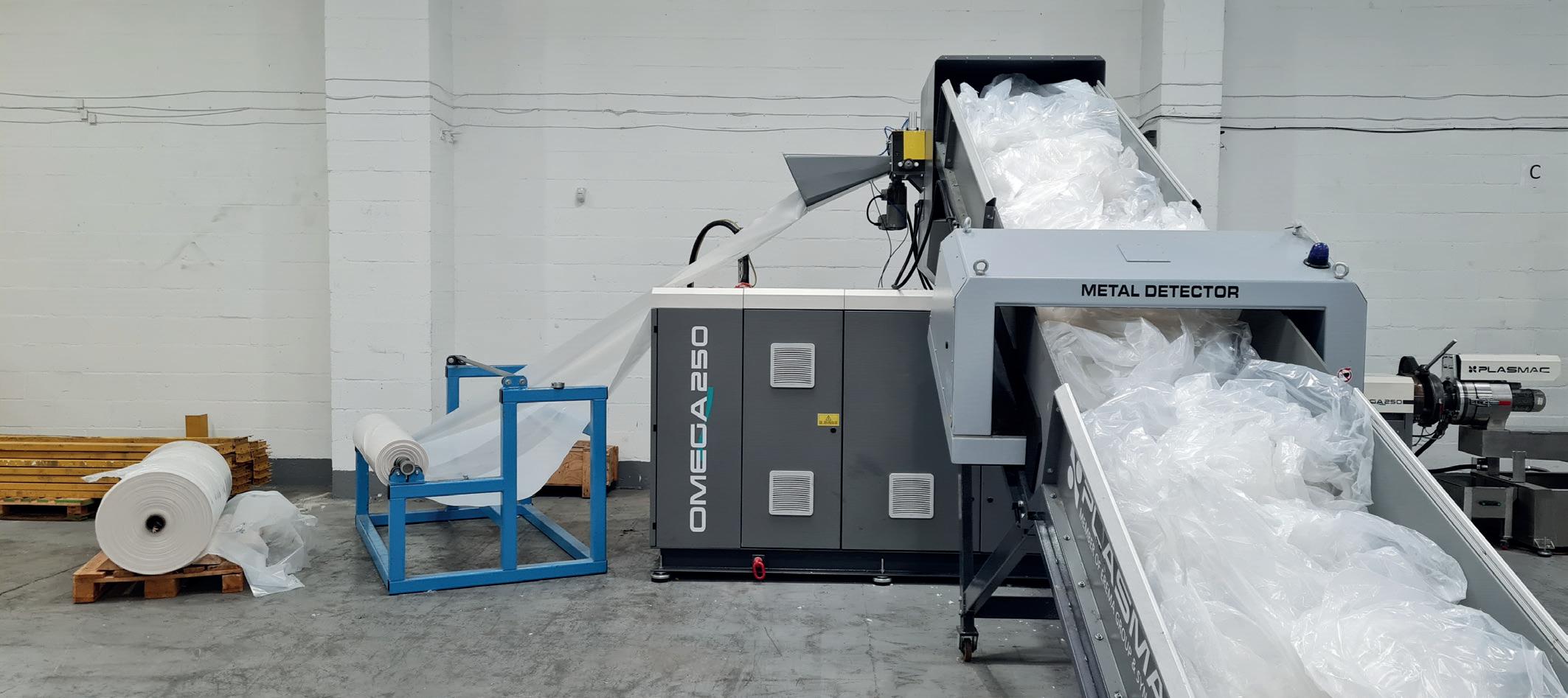
CASE STUDY: ARDAGH GLASS PACKAGING
Ardagh Glass Packaging-Europe (AGP-E) is now using a sustainable, recycled base foil product to give stability to its glass containers when in transit to customers, created using the waste plastic packaging material from its Doncaster manufacturing facility.
Developed with suppliers Marpak and Talos Recyling during an initiative to reduce waste, the flexible plastic packaging material, called Fuse Seal, outperforms the standard, non-recycled material in terms of strength and costeffectiveness. Made from 30% waste plastic shrink-wrap, it can be recycled multiple times.
All waste shrink-wrap at the Doncaster facility is now recycled in a closed loop system. AGP-E bales the used shrink wrap from the shop floor, which is then collected by Marpak and Talos Recyling. To avoid unnecessary transport, the suppliers collect the bales as a consolidated load when delivering shrink wrap packaging to AGP-E.
At Marpak and Talos Recycling, the material is graded and segregated for re-use. It is re-granulated into pellets and re-used to make up 30% of the new Fuse Seal product. The remaining 70% is new LDPE (Low Density Polyethylene), which is also recycled into other products. Fuse Seal’s 30% recycled content also means it will not be subject to the UK Government’s 2022 Plastic Packaging Tax.
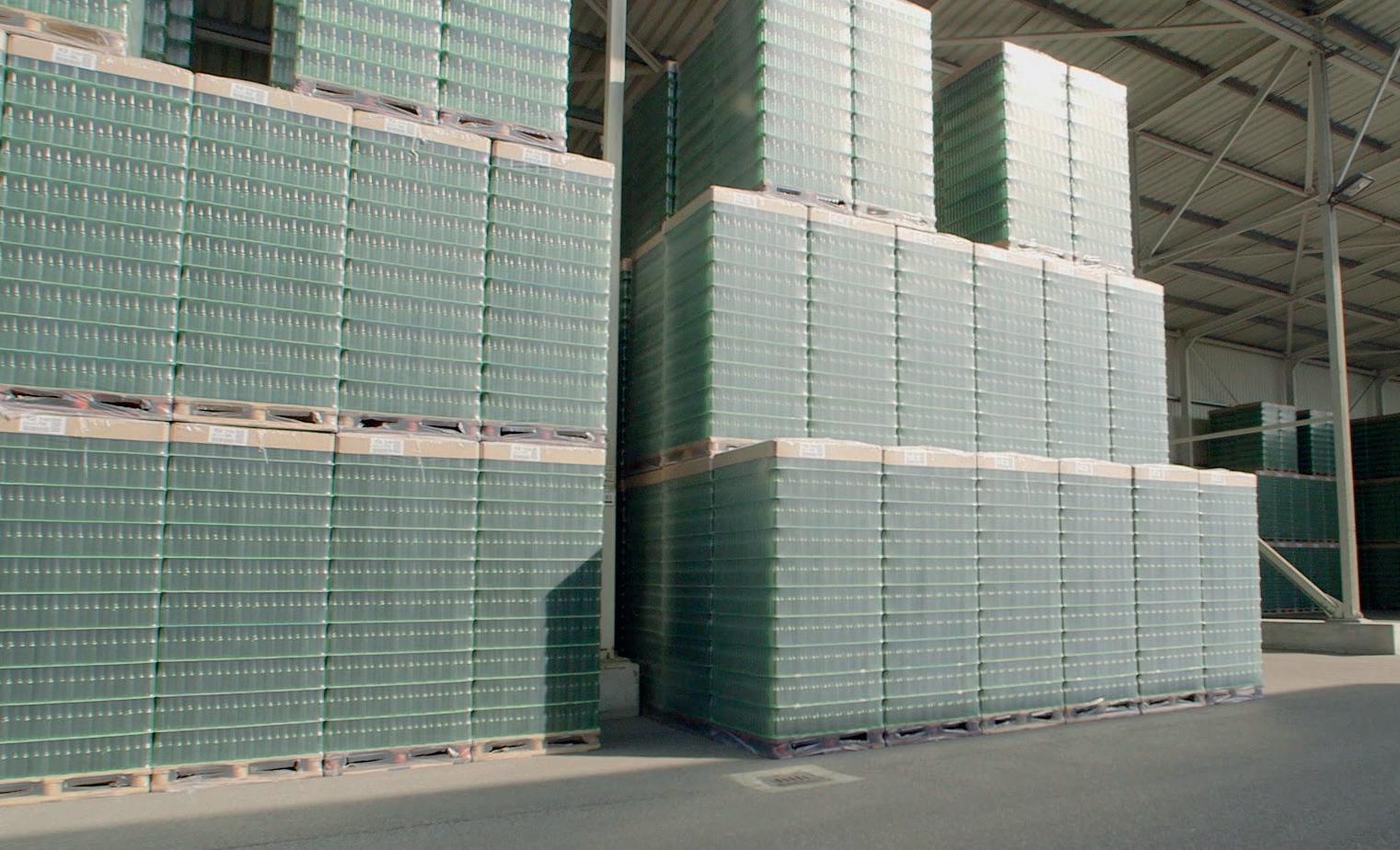
The process provides a way for glass manufacturers to ensure that the plastic packaging used to transport their glass containers, is created in a closedloop, circular economy model, as well as complying with the UK’s Plastic Packaging Tax requirements.
Plastic Packaging Tax
In Europe, a tax on all non-recycled plastic packaging waste came into force on January 1, 2021 designed to encourage the use of recycled, rather than new plastic. Where plastic packaging has less than 30% recycled content, the EU charges €800 per tonne of plastic to member states, rather than businesses, but the expectation is that member states will introduce their own plastic taxes to fund their liability to the EU.
The UK’s Plastic Packaging Tax will come into force from April 2022. A charge of £200 per tonne will be applied to manufacturers using plastic packaging that contains less than 30% recycled content and will apply to plastic packaging produced in, or imported into, the UK. This provides a clear economic incentive for businesses to use more recycled material in their plastic packaging, which will also help to achieve their sustainability goals.
Plastic packaging can be even more sustainable
As well as being created from recycled plastic waste, plastic packaging can be made more sustainable by using biobased ingredients in the production of the plastic itself.
Plastic is made from polymers; Marpak uses chemical industry giant Braskem’s sugarcane-derived bio-based polymers in their blend, to create more environmentally-friendly plastic packaging. Braskem’s green polyethylene is produced from sugarcane from 100% renewable sources, which helps to reduce greenhouse gases in the atmosphere and is entirely recyclable.
Marpak also offers a down-gauged, lighter-weight, flexible packaging material, which reduces costs, the tonnage of plastic produced, and the CO2 emitted.
If a glass manufacturer opts to reduce the thickness of its plastic packing from 80 microns to 70 microns, for example, based
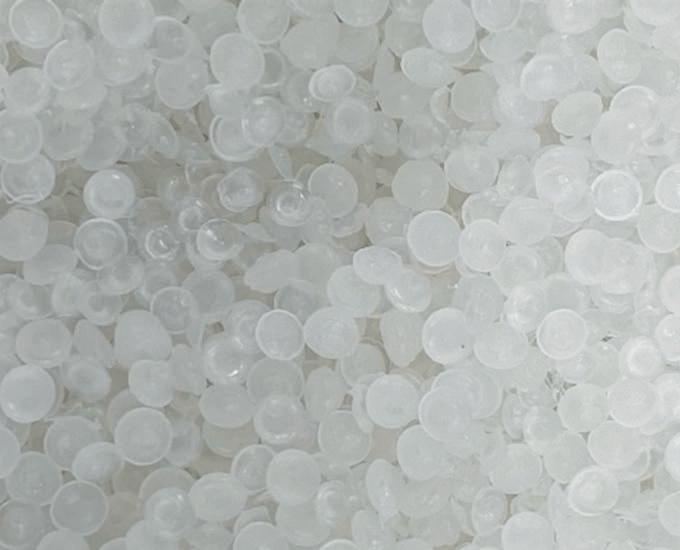
� Pellets - used plastic packaging can be recycled back into pellets to be reused in the manufacturing process. on an annual usage of 2000 tonnes, the weight saving equates to the equivalent of c.200 tonnes per year and approximately a 12.5% CO2 reduction. This is achieved without any loss in strength or quality of the material: a win-win for both the glass manufacturer and the environment.
Closing the loop
Plastic packaging used during transit in the container glass industry can meet manufacturers’ sustainability goals if manufacturers opt to downgauge the weight of their product, use bio-polymers in the blend, and recycle used material back into the production process.
The issue of tackling plastic packaging waste in the glass industry starts with collaboration between the glass manufacturer and their plastic packaging supplier and ends with both sides achieving their sustainability goals. �
1 Source: http://www.wrap.org.uk/content/fast-factsplastics
*Director, Talos Recycling, Leeds , UK Email: jamie.gibson@talosrecycling.co.uk Website: www.talosrecycling.com
� Shrink-wrapped bottles on pallets
Constraint Programming in glass production scheduling
Sylvain Leroy* and Tanguy Lapegue** outline how constraint programming (CP) technology could save glass manufacturers hours of planning time. This would provide more opportunities to test what-if scenarios and complete tasks of higher-added value, ultimately leading to global performance optimisation.
Most glassmakers face similar issues when it comes to production planning, because a complex set of interlocutors and IT systems are usually requested. To plan effectively, managers must orchestrate data from sales, stocks and production, as well as juggling with varied and disparate data types (e.g. Excel sheets, ERP information, written reports, etc.).
Production scheduling is, therefore, one of the daily headaches of glassmakers. One question many operations personnel ask themselves every day is ‘how can I effectively and efficiently schedule my production batches’? While on one hand, the goal is to not use excessive resources to carry out the schedule, on the other, the goal is to optimise performance and ensure on-time delivery to customers.
Hence the interest for a solution that adapts to the unique environment of each company and integrates a powerful calculation ‘engine’ to ensure optimum scheduling for maximum production yield.
The key challenge for management is to allocate the company’s human resources to tasks with high added value to remain competitive.
The integration of the latest generation tools will support ‘empowered human’ approaches and generate a positive and modern impression among employees.
Headquartered in France, Cosling is a company that provides software solutions for planning and scheduling problems, making better use of key resources. The company was founded in 2014 by two PhD scientists, whose expertise included process optimisation, mathematical modelling and constraint programming.
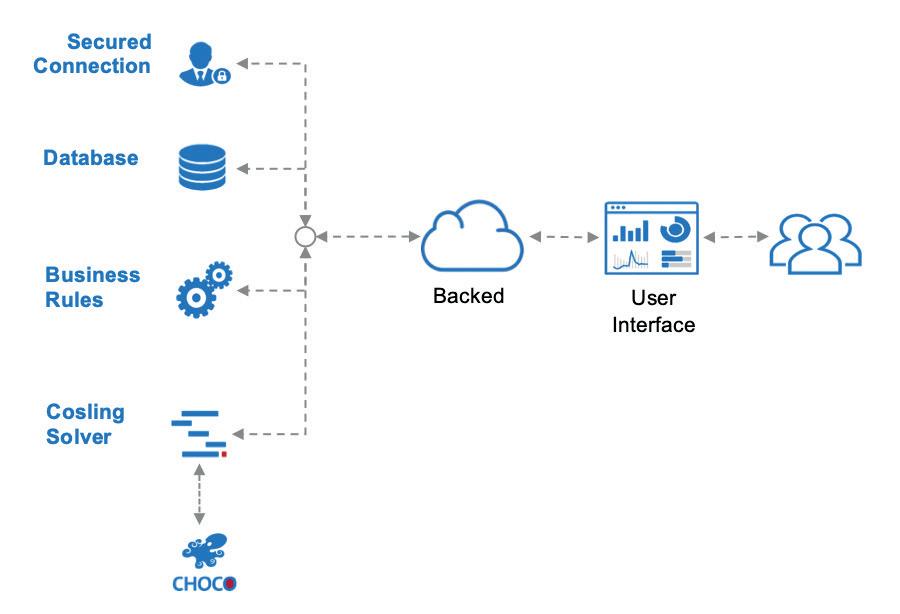
� Fig 1. Software architecture of Cosling Scheduler.
Cosling CEO Jean-Guillaume Fages has been awarded twice for his thesis on artificial intelligence and constraint programming1 .
Constraint programming
CP is a programming paradigm that belongs to the wide field of artificial intelligence (AI). It is a declarative language that enables modelling optimisation problems through variables, domains and constraints. Variables represent choices to make, such as the employee to be assigned to a task.
Each variable is associated to a domain that defines its alternative values, such as qualified workers for a given task. Variables are linked by constraints, which state logical properties that must be respected to get a feasible solution, such as making sure no employee is working on two tasks simultaneously.
Once a decision problem has been modelled within CP, it can be given to a CP Solver, i.e. a programming library whose purpose is to find a feasible solution to a given model. Several CP Solvers could be used, each one with its own interface, language, strength and weakness.
The well-known Choco Solver is one of the best CP Solvers that enables a very good trade-off between performance and ability to be finely tuned; the Institut Mines Telecom (IMT) Atlantique in France developed the solver.
Based on this technology, Cosling has developed a scheduler, with interactive graphical user interfaces, data management and advanced algorithms (Fig. 1). Such a solution has already proven