

PWR EXCELLENCE
SAFETY, HEALTH, &ENVIRONMENT
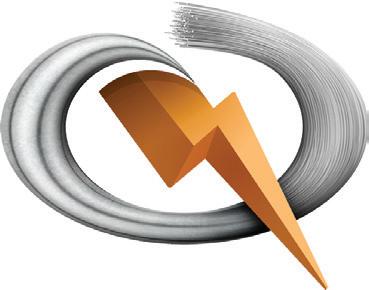

our PEOPLE are the HEART of everything we do. “ ”
Quanta
BECAUSE
PWR EXCELLENCE SAFETY, HEALTH, & ENVIRONMENT
Introduction
Message from Leadership
SH&E Philosophy
SH&E Overview
Six Strategic Imperatives
Eight PWR Excellence – SH&E Elements
• Leadership Commitment and Employee Engagement
• SH&E Strategy and Resources
• The Capacity Model
• Driver Safety Framework
• SH&E Systems
• SH&E Operations
• Professional Development and Training
• Continuous Improvement and Innovation
SH&E Journey to Excellence
SH&E Snapshot of Resources and Systems
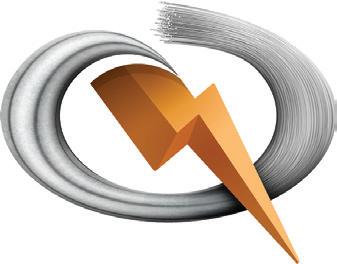
BECAUSE WE CARE
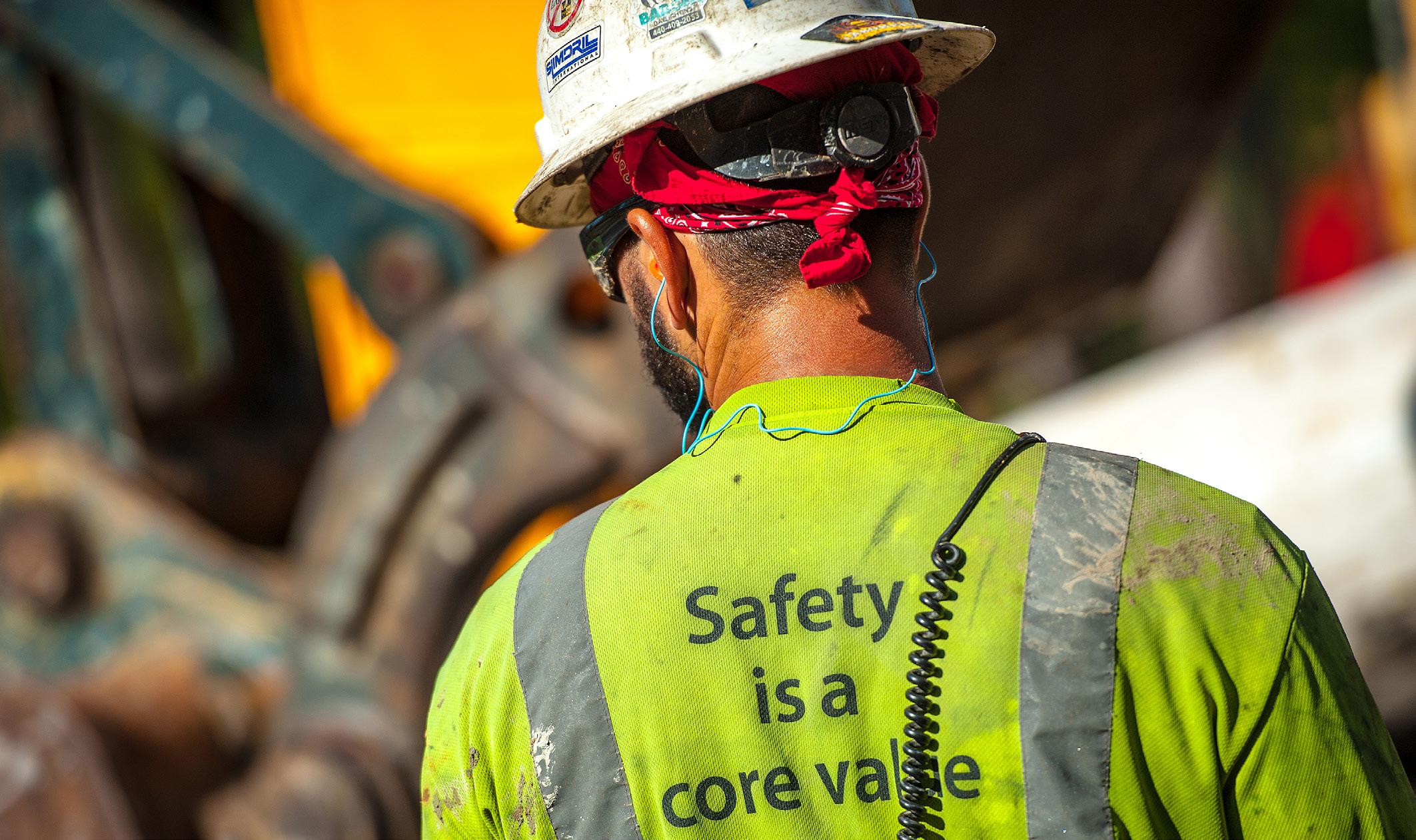
Just like lights are powered by electricity, Quanta Services is powered by thousands of heartbeats that span across our organization. We are the power of people.
Safety is not the first thing, but how we do everything. We are deeply committed to the health and safety of our employees, customers, contractors, and the communities we serve.
Our relentless pursuit of safety excellence drives a powerful culture where people are at the heart of all our actions. To demonstrate our commitment to our employees, this book exemplifies our framework to PWR Excellence in Safety, Health, & Environmental (SH&E).
Inside you’ll see what it takes to design, implement, evaluate, and enhance systems that deliver a culture of innovation and continuous improvement in all aspects of SH&E throughout Quanta.
Through our commitment to world-class SH&E, we aim to not only influence our company, but positively impact the industries we serve. This commitment underscores why we stand as true leaders in our field, shaping a future where safety is not just a practice but a way of life.
QUANTA LEADERSHIP
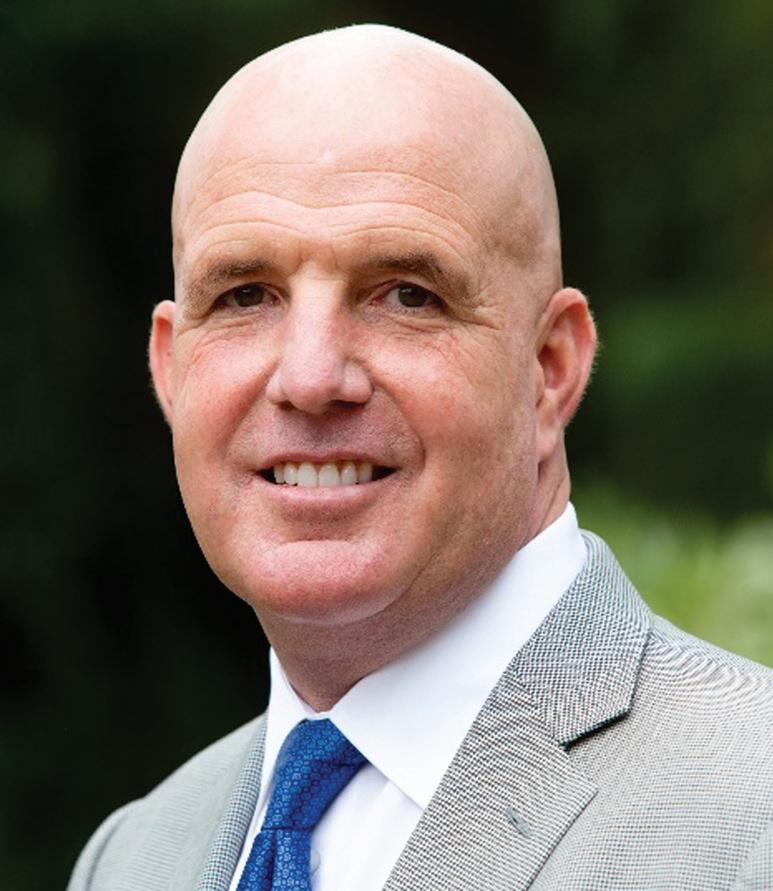
When it comes to safety at Quanta, we are world-class, and we do things right. Within this framework, we’ve given a platform for the continued growth of our safety culture. We believe we are industry changing and industry leading. We want our companies, customers, and competition to embrace it.
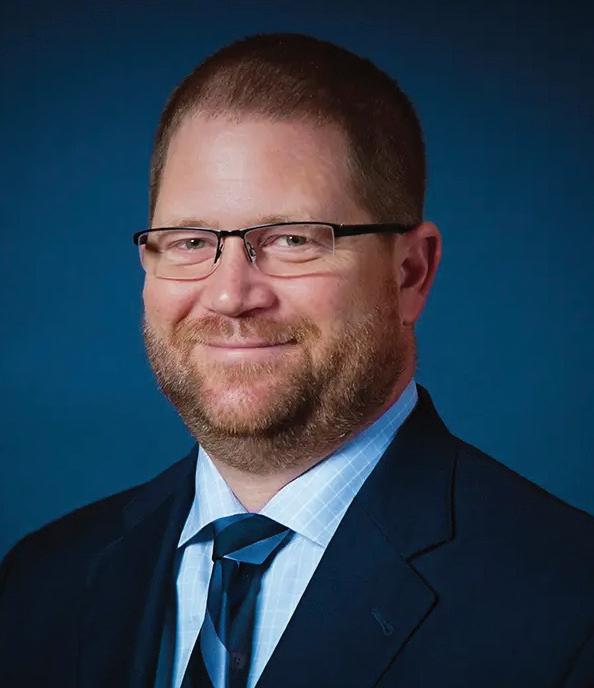
”MATT COMPHER
SVP - SAFETY, HEALTH, AND ENVIRONMENTAL
“Our employees are at the core of what we do. We will do everything we can to support them, protect them, and get everyone home to their families every night. To achieve this, we have to think about safety differently. By formalizing and maturing our SH&E programs, we will have sustainable success throughout our family of companies.
SH&E PHILOSOPHY
As Quanta’s operations expand and the markets we serve evolve, we will never lose sight of our mission to support OpCo excellence by providing professional and specialized services through collaboration.
Our approach to obtain repeatable, sustainable, and better SH&E performance is built on the principles of:
• Enabling operating companies to care for and support their employees by providing resources that assist in the journey to excellence
• Creating a culture where Quanta’s human performance principles found in The Capacity Model are foundational to the way we do business
• Understanding the perspective of our operating companies by forging relationships that earn trust and respect among our peers
PARADIGM SHIFT
• We are thinking about Safety differently.
• Quanta-Developed Human Performance – We understand that people are fallible.
• Prevention will always be a key element to our program.
• We will always plan and execute our work as if failure is going to happen today.
• We will build capacity into our work to absorb failure without causing harm.
• While focused on severity, we will not lose sight of frequency.
• Safety is the presence of capacity, not the absence of unwanted events.
• A learning-based approach allows us to continuously adapt, adjust, and improve.
• Enhancing competencies of hazard prevention, capacity for failure, and operational learning throughout the organization
• Fostering a collaborative environment where operating companies and individuals can learn from each other
• Striving for continued innovation and solution development that help operating companies reach their potential and build capacity in all aspects of their business
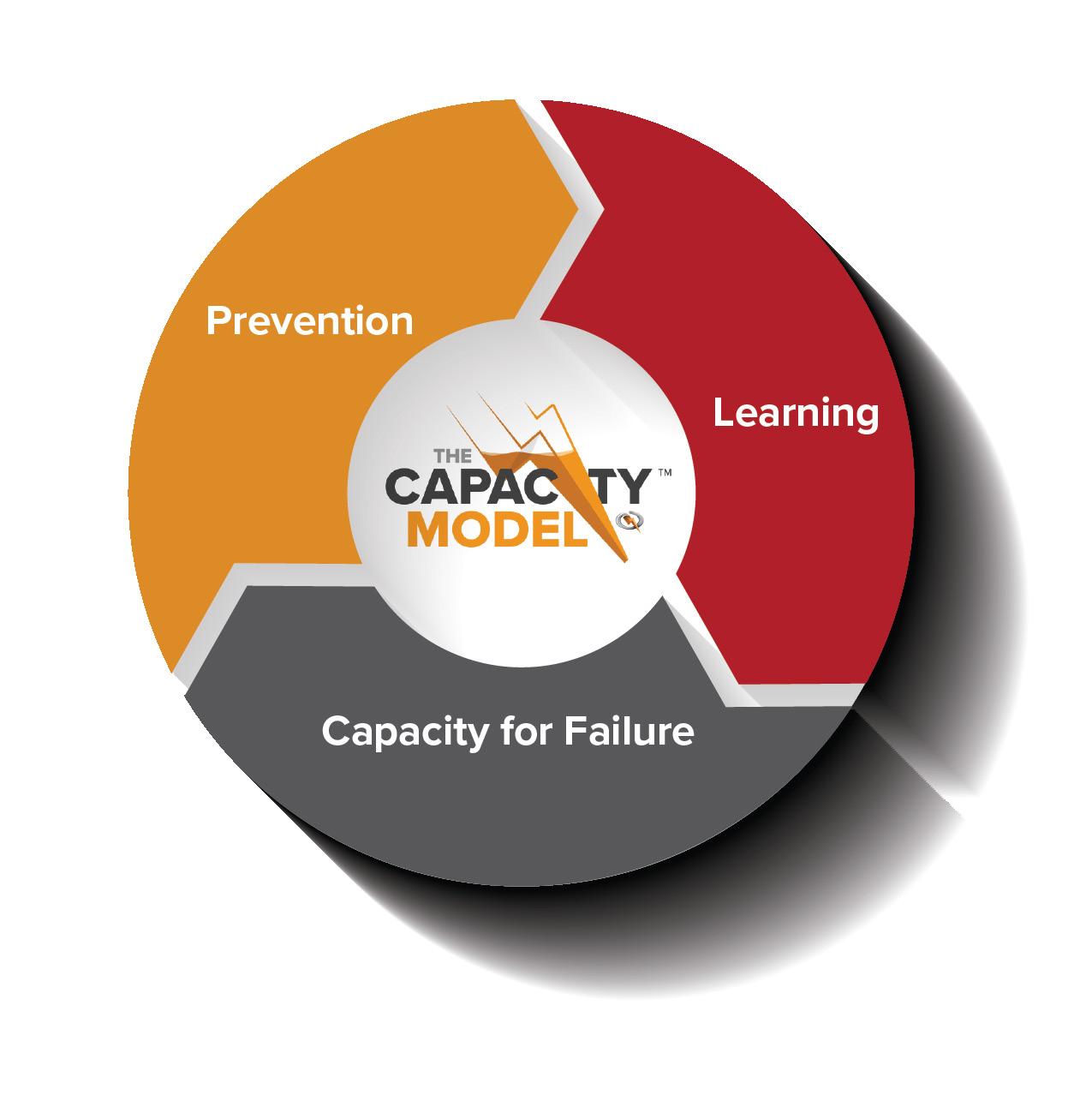
In order to achieve our vision of eliminating life-threatening, life-altering, and life-ending events, our Operating Companies will incorporate the concepts and practices of The Capacity Model into their operations with a focus on identifying what’s STKY on our jobsites, designing the capacity to fail safely into all Quanta systems and work practices, and assuring controls are in place, functioning, and effective.
WE ARE CHANGING THE WAY WE DO SAFETY.
P W R EXCELLENCE – SH&E OVERVIEW
Achieving operational excellence demands a clear understanding of business goals, systems thinking, and a culture of caring above everything else. Below is our structured methodology for accomplishing our mission.
OUR WHY
STRATEGIC IMPERATIVES
CONTINUOUS IMPROVEMENT & INNOVATION
SHAREHOLDERVALUE
PROFESSIONAL DEVELOPMENT & TRAINING
SH&E ELEMENTS
SH&E OPERATIONS
PEOPLEEMPOWERING
LEADERSHIP COMMITMENT & EMPLOYEE ENGAGEMENT
ENTREPRENEURIAL CULTURE
BECAUSE WE CARE
OPERATIONAL EXCELLENCE
SH&E STRATEGY & RESOURCES
SAFETYWORLD-CLASS &TRAINING
DEFFERENTIATINGSOLUTIONS
THE CAPACITY MODEL
DRIVER SAFETY FRAMEWORK
SH&E SYSTEMS
At the core of who we are is a belief that we do what we do Because We Care. Our WHY inspires our team to do whatever it takes to protect our family of employees and ensure they go home every day to the ones they love. Quanta’s Strategic Imperatives guide SH&E to align our vision and actions to support the continued growth and success of the company. We collaborate with operating companies to advance their SH&E programs and processes by referencing the PWR Excellence –SH&E Elements. SH&E Management must be built into how we plan, execute, and learn from work.
SIX STRATEGIC IMPERATIVES
Our purpose within the Quanta Corporate SH&E team will be driven by the relentless pursuit of achieving Quanta’s six imperatives. Each Operating Company should set goals, define objectives, and set actionable plans that chart the course for driving long-term, sustainable value creation.
The image below outlines the comprehensive approach to targeting the most significant opportunities throughout the company. This strategy is a collaborative effort between Quanta, the Regions/Standalones, and Operating Company personnel.
1 2 3 4 5 6
WORLD-CLASS SAFETY AND TRAINING
• Strive to eliminate life-threatening, life-altering, and life-ending events (STKY Actuals)
• Prevent motor vehicle accidents to save lives and reduce injuries.
• Support the development and execution of a world-class training program
DIFFERENTIATING SOLUTIONS
• Innovative approach to safe execution of work
• Customers have an understanding and confidence in our approach to safety, health, and environment.
• Quanta is the preferred business partner to our customers
OPERATIONAL EXCELLENCE
• Operating Companies’ SH&E performance is repeatable, sustainable, and continuously improving
• Strategic acquisitions that expand operations and maintain safety standards
EMPOWERING PEOPLE
• Be the preferred workplace for SH&E professionals and craft skill labor
• Employ the top SH&E professionals in the industry
INCREASE SHAREHOLDER VALUE
• World-Class SH&E performance
• Industry leading ESG program
• High ROI for shareholders
ENTREPRENEURIAL CULTURE
• Consistent safety philosophies and principles throughout Regions/ Standalones
• Autonomous SH&E systems at Regions/ Standalones
By aligning our efforts to support the continued growth and success of the company, our actions will be direct and specific, ensuring we are efficiently striving towards the ongoing progress of safety, health and environmental performance and the elimination of life-threatening, life-altering, and life-ending events throughout all of Quanta.
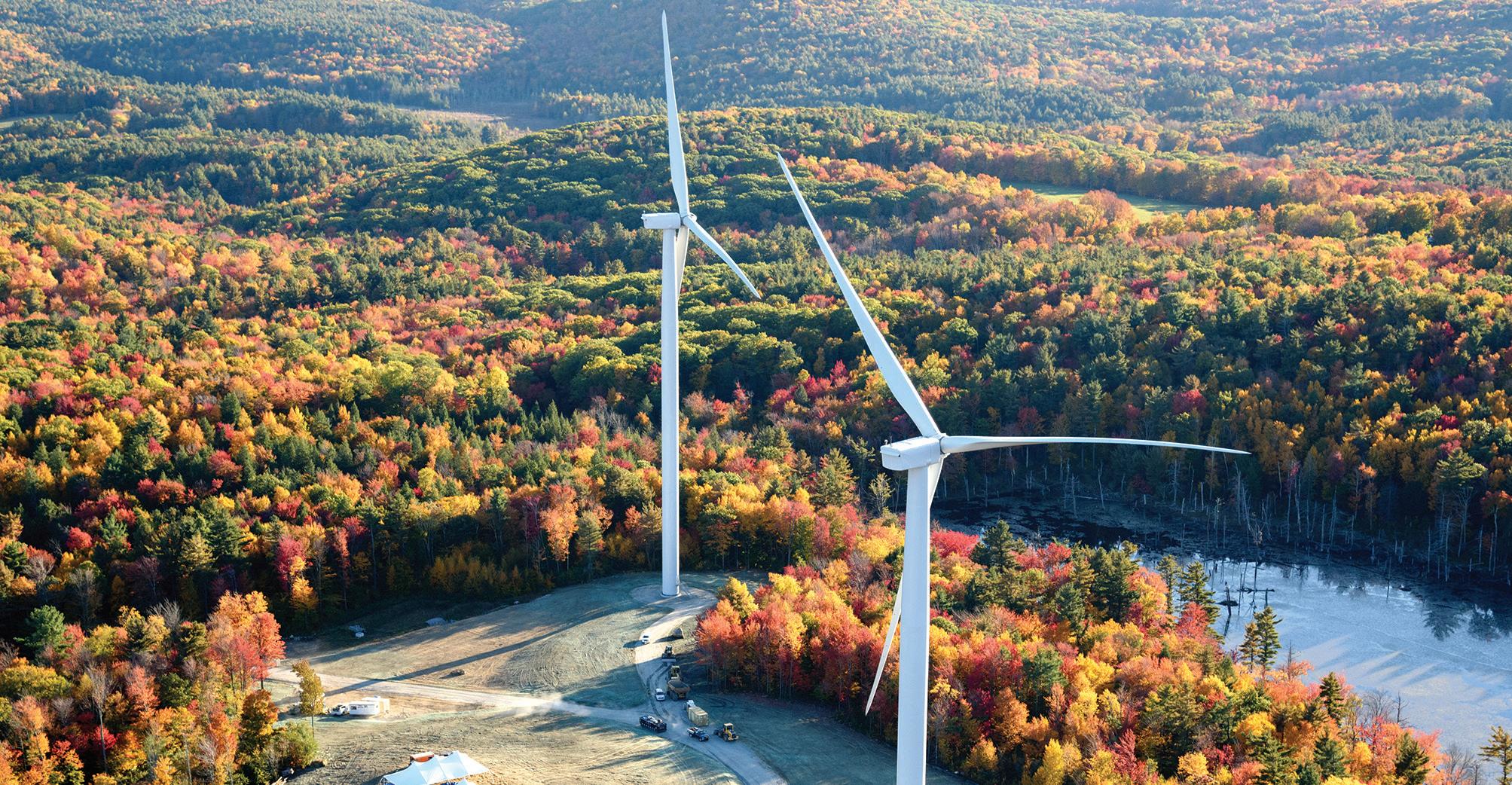
P W R EXCELLENCE – SH&E ELEMENTS
The PWR Excellence - SH&E Elements outlined in this section are strategically designed to support the journey of building mature systems and achieving a high level of SH&E performance that is repeatable, sustainable, and better at each OpCo. We view safety as a dynamic process to be managed, rather than an outcome to be achieved.
Operating companies should reference these elements when building and maintaining their SH&E programs. They must think of their program as a true system where effective performance is based on the interaction and interdependencies of all system parts. It’s important to look beyond individual parts and instead focus on how those parts work together as a whole to achieve specific goals or outcomes.
By looking at their SH&E program with this perspective, it will help OpCos analyze and solve complex problems, improve efficiency, and drive long-term, resilient SH&E success.
The structure of the PWR Excellence elements was built upon several industry standards and system frameworks. These management system frameworks include:
• ISO 45001
• ANSI Z10
• API 1173
• OSHA VPP and Challenge Programs
• OSHA’s Recommended Practices for Safety and Health Programs
• NSC’s Nine Elements of a Successful Safety & Health System
Common elements between each of the referenced standards and frameworks have been identified, blended with Quanta’s SH&E focus areas, and put into categories within the framework that enable a unity between all core components. These identified elements are:
1. Leadership Commitment
2. SH&E Strategy and Resources
3. The Capacity Model
4. Driver Safety Framework
5. SH&E Systems
6. SH&E Operations
7. Professional Development
8. Continuous Improvement
and Employee Engagement and Training and Innovation
LEADERSHIP COMMITMENT & EMPLOYEE ENGAGEMENT SH&E STRATEGY & RESOURCES CONTINUOUS IMPROVEMENT & INNOVATION
PROFESSIONAL DEVELOPMENT & TRAINING
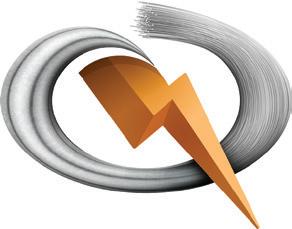
SH&E OPERATIONS THE CAPACITY MODEL
DRIVER SAFETY FRAMEWORK
SH&E SYSTEMS
Ensuring the presence, functionality, and seamless interaction of these elements is crucial for constructing high-performing SH&E systems.
LEADERSHIP COMMITMENT AND EMPLOYEE ENGAGEMENT
When senior managers consistently exhibit a sincere and unwavering commitment to Safety, Health, and Environment (SH&E), their dedication becomes a cornerstone value embraced by employees. In a robust Safety, Health, and Environmental program, managerial leadership plays a pivotal role in overall safety, with every individual contributing to shared safety responsibilities. Senior managers establish the strategic direction, managers craft effective practices and procedures, and employees carry out these practices while offering crucial feedback. Clarity in roles and responsibilities, coupled with accountability, forms the bedrock for effectively managing SH&E performance.
ESTABLISHED SAFETY CULTURE:
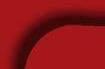
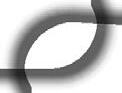
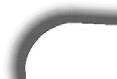


GUIDANCE

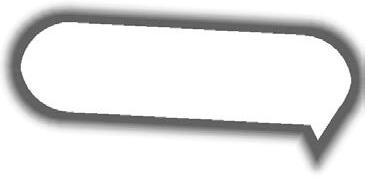
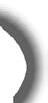




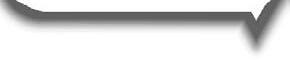
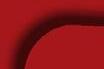
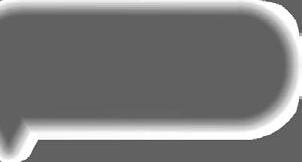
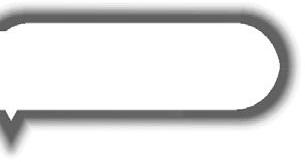
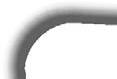



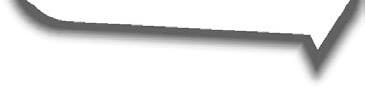
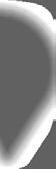


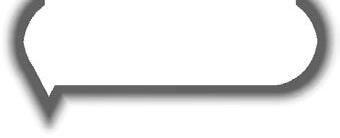

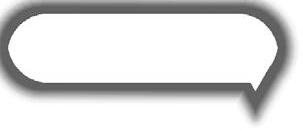
This list gives some examples of how your OpCo can demonstrate leadership commitment and encourage active employee participation:
• Clearly outline the roles and engagement of top management in the Safety, Health, and Environmental program.
• Define how leadership is involved in the day-to-day operation, evaluation, and communication of the SH&E program.
• Formulate a well-documented SH&E policy to serve as the cornerstone for the Safety Management System (SMS), ensuring widespread communication of this policy across the Operating Company.
• Align the OpCo’s business plan, performance review, incentive programs, and recognition systems with leading indicators, harmonizing them with the OpCo’s SH&E goals and objectives.
• Create clear and open communication channels for safety-related information.
• Establish a psychologically safe environment by fostering a culture that encourages employees to openly discuss safety concerns, ensuring they feel secure and valued in sharing their insights without fear of negative consequences.
• Regularly communicate SH&E program requirements, expectations, and updates throughout the company.
• Institute a process that promotes employee involvement and encourages active participation of the SH&E program.
• Conduct regular safety committee meetings involving representatives from all organizational levels to deliberately discuss safety issues, review incident trends, and make recommendations for improvements.
• Implement feedback mechanisms enabling employees to communicate SH&E questions, comments, suggestions, and concerns to supervisors and management effectively.
• Consistently assess and enhance safety procedures by understanding the “Blue Line”, incorporating employee feedback and adapting to evolving circumstances through regular reviews and updates.

P W R EXCELLENCE ELEMENT 2:
SH&E STRATEGY AND RESOURCES
Developing a strategic approach is paramount for seamlessly integrating Safety, Health, and Environment into your company’s overarching business plan. Key considerations in theplanning process can include: identifying actions necessary to establish a safe work environment, designating responsible parties, determining required resources, and establishing timelines. The strategic plan, documented for achieving SH&E targets, should align seamlessly with the Operating Company’s overall business objectives. It should become an inherent and routine aspect of operations, subject to ongoing tracking, monitoring, and assessment. Goals may vary, ranging from broad organizational objectives to more focused targets within specific departments, activities, or processes.
E M
Measurable goals can be tracked, allowing you to see your progress. They also tell you when a goal is complete.
GUIDANCE
Are you able to take action to achieve the goal? Actionable goals ensure the steps to get there are within your control.
Be realistic and avoid overwhelming and unnecessary stress and frustration by making the goal realistic.
A date helps us stay focused and motivated, inspiring us and providing something to work toward.
This list offers examples to guide your Operating Company in formulating a strategic approach for Safety, Health, and Environment:
• Define SH&E goals and objectives that are transparent, achievable, quantifiable, and directly aligned with the company’s mission.
• Implement a process to periodically review and communicate new annual SH&E goals and objectives, ensuring alignment with evolving organizational needs.
• Consult with field level workers to ensure their concerns and needs are incorporated into the development of the SH&E strategy.
• Determine how the OpCo will measure and monitor progress toward SH&E goals and objectives, fostering accountability and continuous improvement.
• Provide adequate resources for the establishment, integration, monitoring, and continuous improvement of all SH&E activities.
• Assign dedicated personnel to implement and achieve the defined SH&E objectives, ensuring a focused and effective approach.
• Develop a comprehensive communication plan to share the SH&E goals and objectives throughout the organization, providing updates regularly based on indicators and milestones.
• Articulate and approve SH&E objectives ahead of the budget cycle, ensuring that necessary resources are identified and appropriate funding is allocated to support safety initiatives effectively.
P W R EXCELLENCE ELEMENT 3: THE CAPACITY MODEL
To foster a safer work environment and mitigate the risk of injuries, illnesses, and environmental impacts, it is essential to understand and plan for the potential hazards inherent in your work. The primary objective is to systematically assess and manage these hazards, ensuring that employees can carry out their tasks safely and efficiently.
Aligned with contemporary safety management concepts, The Capacity Model (TCM) adopts a proactive approach to eliminate life-threatening, life-altering, and life-ending events. TCM places a strong emphasis on understanding human performance principles and integrating the capacity to fail safely into our work processes. Operating Companies are tasked with the responsibility of developing and implementing a robust process for seamlessly integrating The Capacity Model into how they plan, execute, and learn from work.
GUIDANCE
This list outlines key practices for your Operating Company to proactively anticipate, recognize, evaluate, and control hazards, incorporating The Capacity Model (TCM) into daily operations:
• Evaluate potential Safety, Health, and Environmental risks and hazards across all work processes through robust risk assessments.
• Engage top management in Leadership Playbook sessions to craft a strategic integration plan for The Capacity Model.
• Utilize the TCM Maturity survey to gauge your OpCo’s integration progress, identifying areas of strength and opportunities for improvement.
• Implement tools like Job Safety/Hazard Analysis (JHA), Job Safety Analysis (JSA), or Field Level Hazard Assessments (FLHA) to evaluate and control hazards at the field level.
• Enhance hazard recognition by incorporating the Energy Wheel into all job planning and hazard evaluation processes.
• Develop a systematic approach to eliminate or control the risks associated with various hazards, including STKY (Stuff That Kills You).
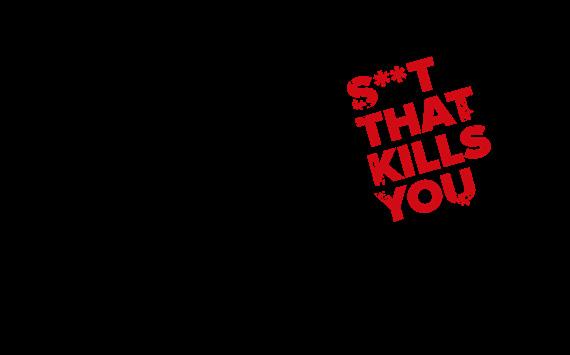
• Facilitate STKY Controls Framework sessions with the goal of developing STKY Controls for all identified critical tasks.

• Engage in on-site STKY discussions with field crews to evaluate hazards, assess control implementation, and identify additional measures as needed.
• Establish a process for verifying and monitoring the effectiveness of controls implemented in the field.
• Actively support a culture of operational learning and continuous improvement, fostering an environment where lessons learned contribute to ongoing safety enhancements.
• Seamlessly integrate TCM philosophy and principles into the OpCo’s training curriculum to enhance workforce proficiency.
P W R EXCELLENCE ELEMENT 4: DRIVER SAFETY FRAMEWORK
Safety, Health, and Environmental excellence must include safe fleet operations. Quanta and its operating companies are unwavering in their commitment to establishing a comprehensive fleet safety program. The primary objective is to proactively prevent motor vehicle accidents, preserve lives, and minimize injuries. To realize this commitment, each Operating Company is tasked with the responsibility of developing and implementing a robust process for the safe management and operation of motor vehicles.
GUIDANCE
This list gives some examples of how your OpCo should develop and integrate a driver safety framework:
• Implement procedures that address the initial evaluation and ongoing monitoring of driver eligibility.
• Maintain an inspection and maintenance program for both Commercial Motor Vehicles (CMV’s) and Non-Commercial Motor Vehicles (Non-CMV’s).
• Implement clear and comprehensive operational driving polices, including but not limited to:
• General Vehicle Use Requirements
• Seat Belts
• Pre and Post Trip Inspections
• Spotters
• Parking procedures and 360° Walk-Around
• Cargo Securement
• Hazardous Materials
• Personal and After-Hours Use of Company Vehicles
• Personal Vehicle Use for Company Business
DRIVER SAFETY FRAMEWORK
• Establish a driver safety training program that addresses requirements for new drivers (e.g., orientation), continuing education, and instances where remedial education is required.
• Develop procedures that address the reporting and documentation requirements for all motor vehicle incidents.
• Maintain comprehensive driver qualification/personnel files for each driver in accordance with local, state, and federal guidelines. Additionally, keep vehicle inspection and maintenance files, along with an accident register.
• Comply with any additional guidance provided within Quanta’s overarching Driver Safety Framework, ensuring alignment with company-wide safety standards and best practices.
• Capture and analyze data pertaining to driver behavior, leveraging this information to actively monitor and promote positive behavioral changes.

P W R EXCELLENCE ELEMENT 5: SH&E SYSTEMS
A comprehensive Safety, Health, and Environmental program within a company often relies on a variety of documents, technology systems, and information to efficiently oversee and enhance workplace safety. Maintaining accurate records is essential, enabling management to document safety policies and procedures while providing reliable data for analysis, informed decision-making, continuous improvement measurement, and reporting trends. Additionally, staying current with relevant regulations and standards is crucial to ensure compliance with federal, state, and local regulations.
GUIDANCE
This list offers insights on how your Operating Company can establish and maintain effective systems and internal processes for managing SH&E:
• Develop internal SH&E programs, policies, and procedures that align with all international, federal, state, local, and client safety, health, and environmental requirements.
• Utilize various software and program solutions to assist in the management and organization of data, including incident and claim management and training record retention.
• Establish processes for the inspection, maintenance, and tracking of equipment and tools to ensure their reliability and safety.
• Implement a robust Document Management System (DMS) that allows for centralized storage, version control, and access control of documents.
• Ensure that documented information is available for all relevant workers at all levels and functions, as well as any relevant external interested parties. (e.g., training records, OSHA logs, JHAs, jobsite safety observations, etc.)
• Define clear document lifecycle stages, including creation, review, approval, publication, and archival. Implement workflows to automate these processes.
• Use standardized document templates to ensure consistency in formatting and content, making it easier to update information uniformly.
• Develop formal change control procedures to manage updates and revisions to critical documents, ensuring that changes are tracked, reviewed, and approved.
• Establish balanced metrics and monitoring systems to assess the performance of the OpCo’s safety and health management efforts, providing valuable insights for continuous improvement.
P W R EXCELLENCE ELEMENT 6: SH&E OPERATIONS
Effective day-to-day management of a safety program and its field execution demands a proactive approach, elevating safety to an integral aspect of a company’s operations. Regulatory compliance forms the foundational bedrock upon which any Safety, Health, and Environmental program is constructed. As the program matures, it becomes imperative to evolve towards more progressive safety management techniques and procedures, ensuring the sustainability and repeatability of SH&E operations. By cultivating a robust safety culture, embracing innovative safe work methods, and consistently reviewing and enhancing safety practices, Operating Companies can establish and sustain a safe working environment for their employees.
GUIDANCE
This list gives some examples of how your OpCo should effectively manage a safety program’s day-to-day operations:
• Document departmental and individual Safety, Health, and Environmental roles, responsibilities, and authorities.
• Meet or exceed the expectations outlined within Quanta’s Regional Safety and Training Standards.
• Meet or exceed the expectations outlined within Quanta’s Environmental Handbook.
• Adhere to regulatory requirements while also integrating advanced processes in key focus areas that will elevate the standard of safety.
• Identify and implement industry best practices to continually enhance SH&E performance.
• Actively monitor and address regulation changes and emerging compliance issues related to SH&E.
• Manage SH&E coordination with subcontractors’ activities, implementing a subcontractor vetting and management process.
• Create, implement, and maintain a process(es) needed to prepare for and respond to potential emergency situations.
• Strengthen the job planning process by utilizing effective tools and resources, such as Grounding Plans, Wire Stringing Plans, etc.
• Conduct regular jobsite safety audits and inspections to assess compliance with safety policies and procedures, identifying areas of improvement and ensuring adherence to safety policies and procedures.
• Encourage employees to report safety incidents and near-misses, including STKY-p and STKY-success. Analyze incident data to identify trends, root causes, and opportunities for prevention.
P W R EXCELLENCE ELEMENT 7:
PROFESSIONAL DEVELOPMENT AND TRAINING
Organizations attaining Safety, Health, and Environmental excellence demonstrate their commitment through the implementation of effective training and professional development processes. Such organizations meticulously plan and execute SH&E training, ensuring a systematic and well-defined approach. This encompasses vital components like needs assessments, curriculum design, and the development of a competency evaluation strategy that is consistently applied. At Quanta, our focus goes beyond constructing projects; we are dedicated to the development and growth of our people.
GUIDANCE
This list gives some examples of how your OpCo should build your workforce to become leaders of their craft and true safety champions:
• Conduct a thorough training needs assessment to determine the specific SH&E training curricula tailored to job roles, tasks, and industry regulations (e.g. training matrix).
• Set clear, measurable, and observable learning objectives that articulate the desired knowledge, skills, or behaviors participants should acquire.
• Customize training content and materials to address hazards and safety concerns specific to the company’s operations.
• Incorporate regulatory requirements into training programs and competency evaluations.
• Involve employees in the development and feedback processes to enhance the relevance and engagement of training programs.
• Ensure that instructors are qualified, experienced, and possess a comprehensive knowledge in the subject matter.
• Provide ongoing opportunities for instructors to stay current with updated regulations and safety best practices.
• Regularly assess and update professional development programs to ensure that it remains relevant and effective in preventing accidents and promoting a safe working environment.
• Allocate ample resources, both in terms of time and budget, to ensure the development and delivery of impactful safety training.
• Establish a comprehensive career progression plan specifically tailored for safety professionals. This plan should be designed to systematically cultivate the knowledge, skills, and behaviors needed for them to evolve into more adept and seasoned leaders in the field of safety.
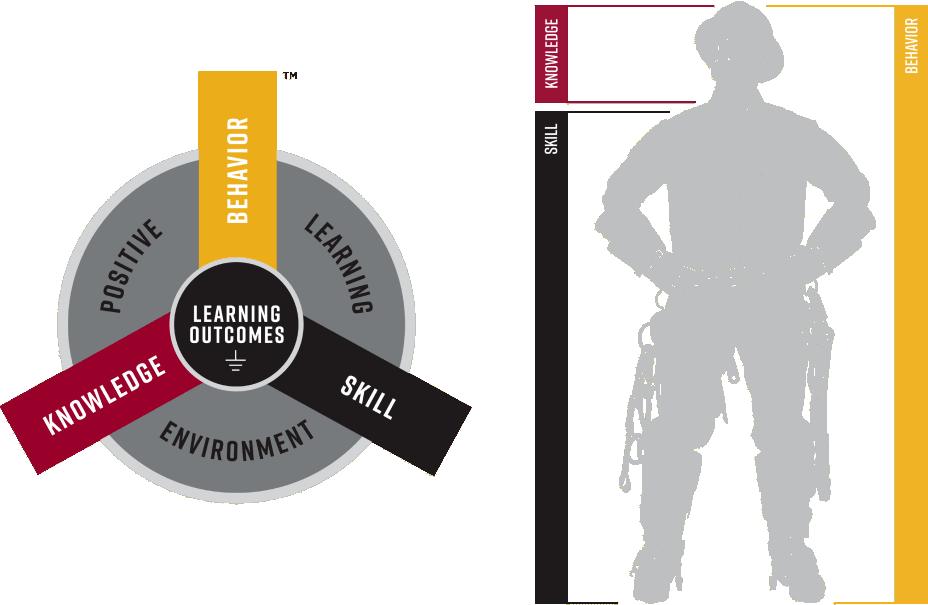
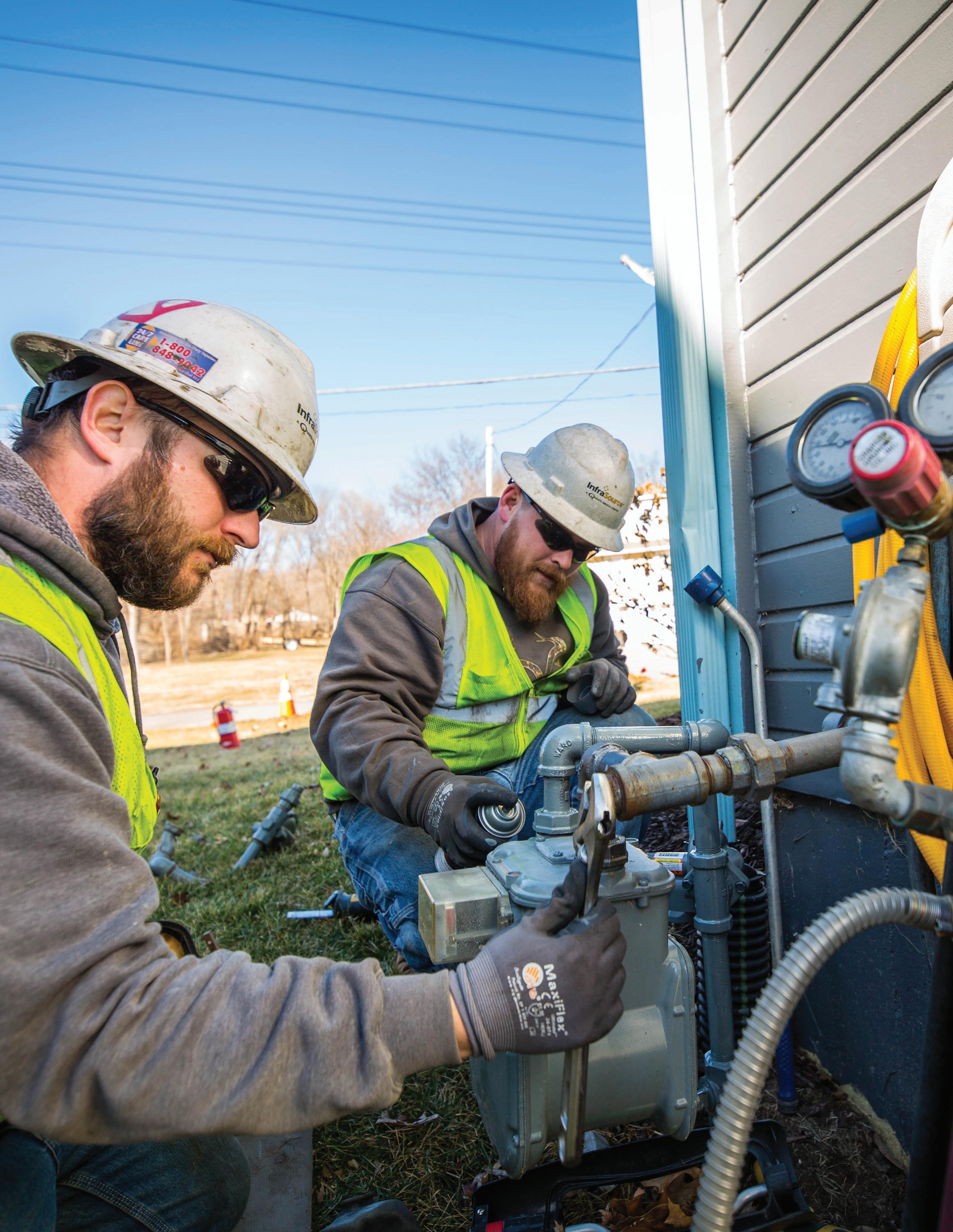
P W R EXCELLENCE ELEMENT 8:
CONTINUOUS IMPROVEMENT AND INNOVATION
Continual improvement and innovation are vital to ensuring the adaptability of your Safety, Health, and Environmental management system in a dynamic work environment. The ongoing pursuit of enhanced SH&E performance in your organization involves always looking to identify new work methods and implement improved safety controls, empowering workers with the tools essential for the safe and effective execution of their tasks.
True improvement goes beyond retrospective analysis and lessons learned from the past. It requires a proactive stance, actively considering emerging risks and deliberately searching for opportunities to enhance safety through system and technological innovations. This forward-thinking approach ensures that your SH&E program not only evolves but remains ahead of potential challenges in the ever-changing landscape of the work environment.
GUIDANCE
This list outlines strategic and operational choices for your Operating Company to foster continuous refinement of SH&E programs and processes:
• Regularly analyze safety data, including incident reports, near-miss reports, and safety performance metrics. Identify trends and patterns, focusing improvement efforts on areas with high potential for STKY events.
• Utilize various approaches to operational learning (e.g.; Learning Teams, Blue Line Understandings, Jobsite discussion, Post-event learning, etc.), enhancing the breadth and depth of learning experiences.
• Conduct thorough investigations when incidents occur, delving into the underlying causes rather than merely addressing the symptoms.
• Encourage employees at all levels to actively participate in safety initiatives, as they often provide valuable feedback on potential hazards and improvement opportunities.
• Foster a positive safety culture where employees are empowered to speak up about safety concerns and suggest system improvements, without fear of reprisal.
• Periodically review and update safety policies, procedures, and emergency response plans to align with changing circumstances, technologies, and regulations.
• Ensure that senior management is actively involved in and committed to the continuous improvement of safety. Their support is essential to driving change throughout the organization.
• Embrace innovation in safety, constantly exploring and implementing new solutions to provide employees with tools and strategies that enhance the safety of their work environment.
SH&E JOURNEY TO EXCELLENCE
OPTIMIZING
INITIATING
• Safety is not a core value, and incidents are often reacted to after they occur.
• Minimal safety policies and procedures are in place.
• A lack of safety culture and employee involvement in safety initiatives.
PROGRESSING
• Compliance with safety regulations and standards becomes a focus.
• Basic safety policies and procedures are established and enforced.
• Safety initiatives are primarily driven by external regulations.
• Safety processes and practices are integrated into daily operations.
• Employees are involved in identifying and mitigating hazards.
• A growing safety culture emphasizes prevention and proactive measures.
LEADING
• A strong safety culture is established, with safety as a core value.
• Safety performance metrics and goals are set and regularly achieved.
• Continuous improvement and innovation in safety processes are common.
TRANSFORMING
• Safety is ingrained in the company’s DNA, with a holistic approach to safety.
• A culture of safety leadership exists at all levels of the organization.
• Best practices in safety management are continually pursued and refined.
• Safety is a competitive advantage and a source of pride for the organization.
It’s understood that every OpCo will be in different stages of their management system’s maturity level, with some further along the journey than others. The image above represents a progression through various stages, with each stage representing a higher level of safety performance and culture.
The goal for any organization is to advance its safety maturity over time, continually improving safety practices, culture, and performance to create a safer and healthier work environment for employees. This SH&E Journey to Excellence provides a framework for self-assessment and goal-setting in this regard.
Quanta’s SH&E Team is there to support the continued growth of each OpCo’s SH&E program. With subject matter experts in a variety of fields, each OpCo has a plethora of resources to utilize.
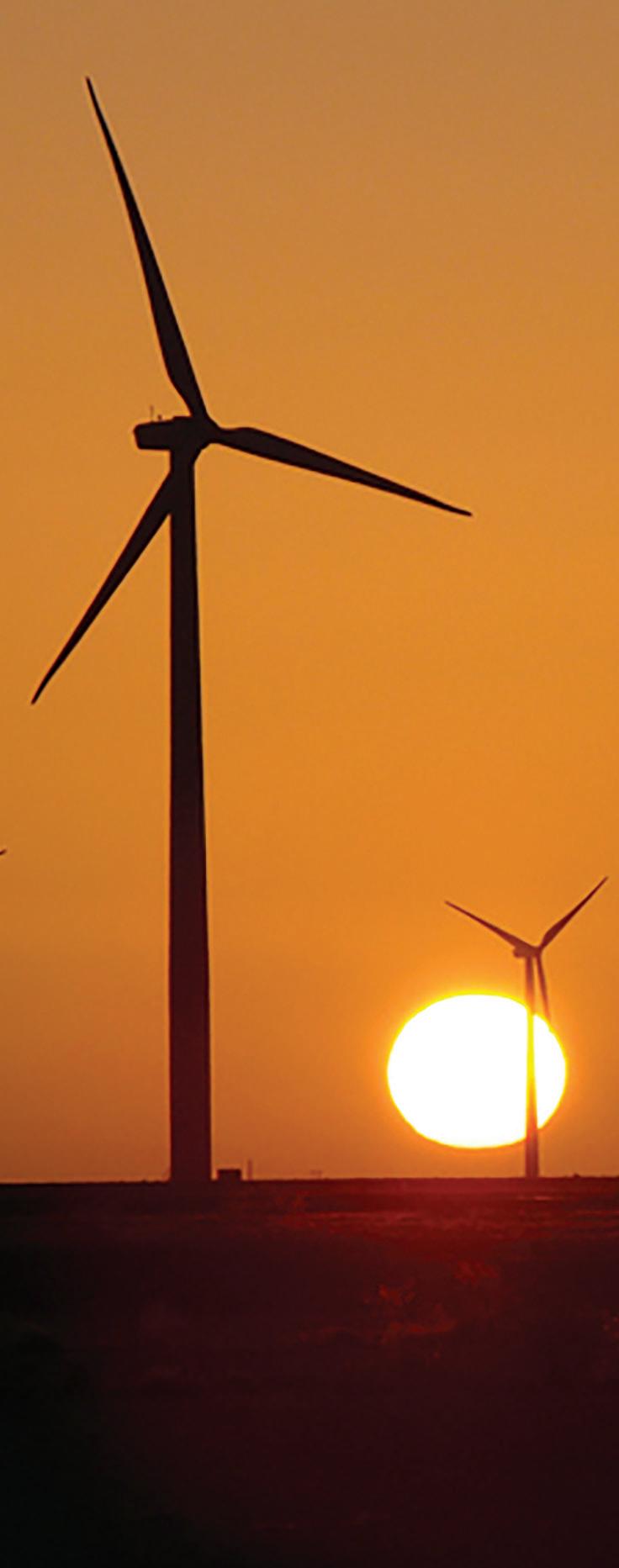
SH&E RESOURCES AND SYSTEMS (APPENDIX)

Library of Policies (Regulatory Support)
Environmental Handbook (Environmental Support)
Regional Safety and Training Standards
Safety Emphasis Program
PWR UP Safety Professional Development Program
QCentral / SharePoint
Storm Support
M&A Due Diligence and Integration
Avetta (Sub-Contractor Management Support)
Sologic (Incident Investigation Support)
The Capacity Model Resource Center
SH&E Snapshot Brochure

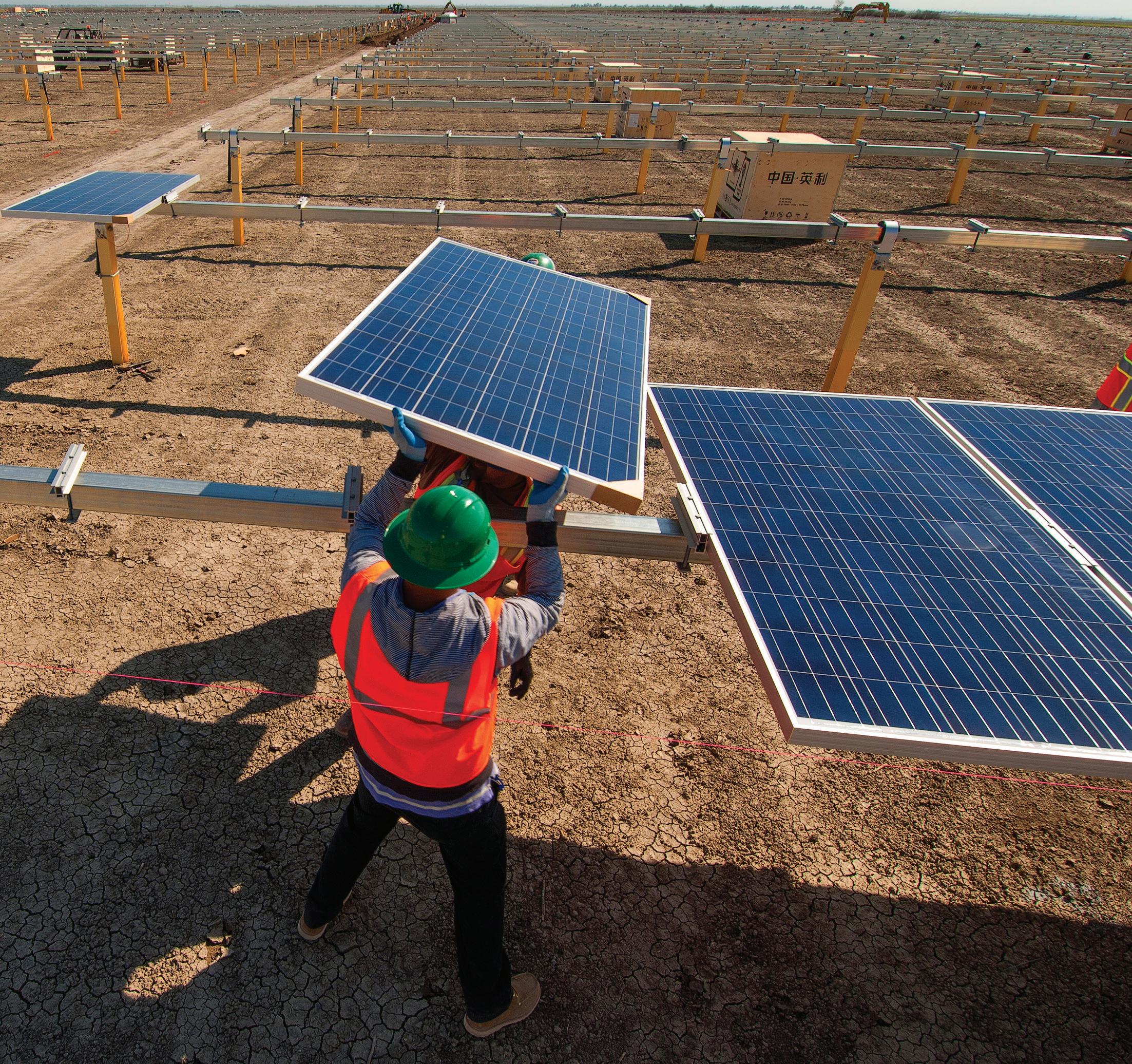
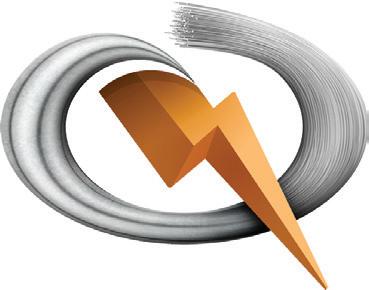
Quanta Services. All Rights Reserved.