CAPA Management Software |CAPA
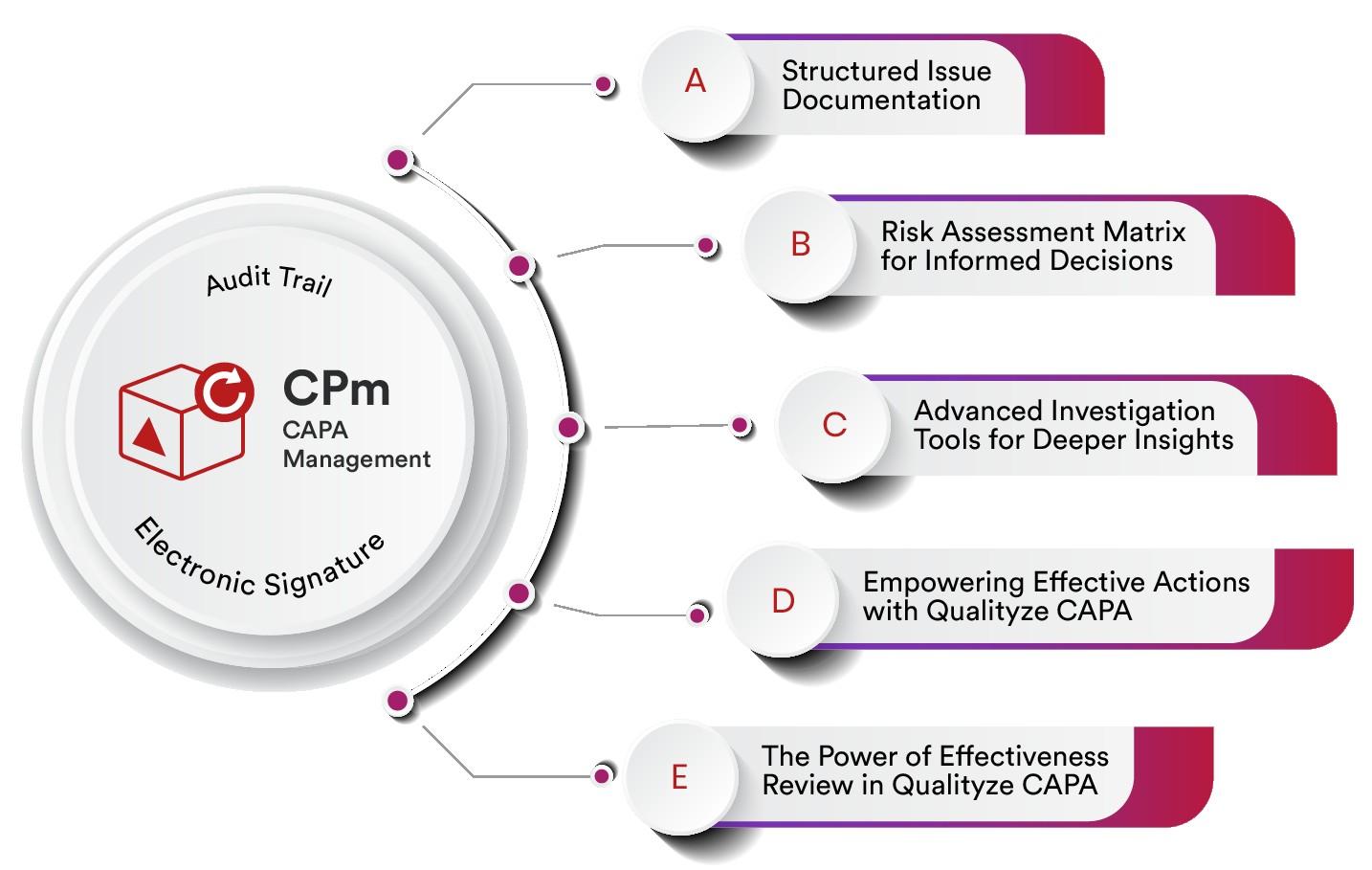
In today's competitive business landscape, organizations strive to deliver products and services that meet the highest quality standards. Achieving and maintaining quality excellence is a critical factor in gaining a competitive edge and building a strong reputation in the market. One of the key pillars of effective quality management is the implementation of a robust Corrective and Preventive Action (CAPA) system. In this article, we will explore the significance of CAPA in quality management and how it can help businesses achieve operational excellence.
Introduction to CAPA
Corrective Action and Preventive Action is a systematic approach to identifying, investigating, and addressing the root causes of quality issues within an organization. It involves a set of defined steps that help in understanding the problem, implementing corrective actions, and preventing similar issues from recurring in the future. CAPA software focuses on continuous improvement and is an integral part of quality management systems such as ISO 9001.
The Role of Corrective Action and Preventive Action in Quality Improvement
Corrective Action and Preventive Action plays a pivotal role in driving quality improvement initiatives within an organization. By addressing the root causes of quality issues, CAPA helps in preventing their recurrence and reducing the overall
number of non-conformities. This, in turn, leads to enhanced customer satisfaction and increased trust in the brand.
Steps in the CAPA Process
The Corrective Action and Preventive Action process typically involves the following steps:
Problem Identification
The first step in the Corrective Action and Preventive Action process is to identify the problem or non-conformity. This could be done through various means such as customer complaints, internal audits, or monitoring quality metrics. The key is to capture the problem accurately and document it for further analysis.
Root Cause Analysis
Once the problem is identified, the next step is to conduct a thorough root cause analysis. This involves investigating the underlying factors that contributed to the issue. Techniques such as the 5 Whys, fishbone diagrams, and Pareto analysis are commonly used to identify the root causes effectively.
Corrective Actions
Based on the findings of the root cause analysis, appropriate corrective actions are developed and implemented. These actions aim to eliminate the root causes and address the problem at its source. It is essential to define clear objectives, assign responsibilities, and establish a timeline for implementing the corrective actions.
Preventive Actions
In addition to addressing the immediate problem, Corrective Action and Preventive Action also focuses on preventing its recurrence. Preventive actions are proactive measures taken to avoid similar issues in the future. This may include process improvements, employee training, updated documentation, or enhanced quality control measures.
Effectiveness Checks
Once corrective and preventive actions are implemented, it is crucial to evaluate their effectiveness. This involves monitoring the process or system to ensure that the desired improvements have been achieved and that the problem does not recur. If necessary, further adjustments or additional actions may be required to achieve the desired outcome.
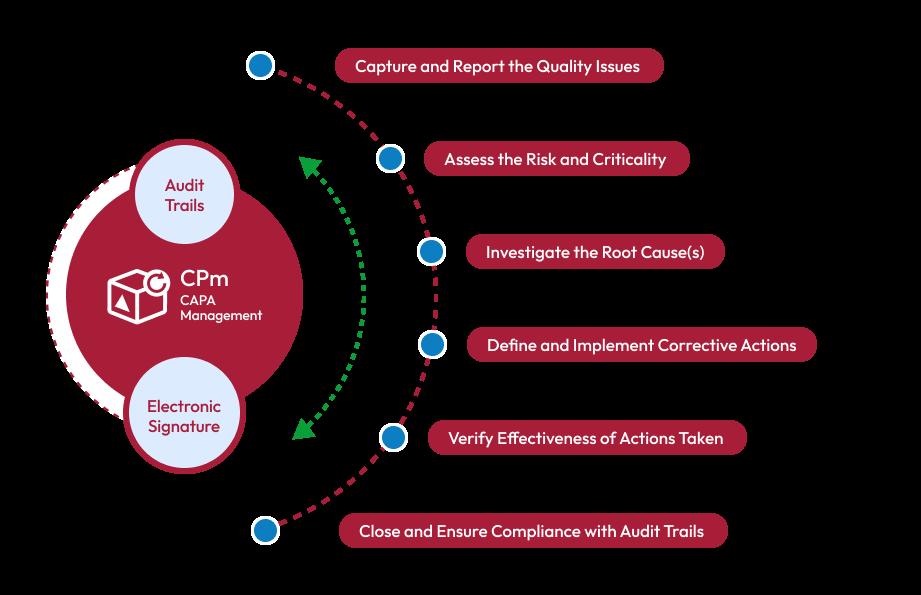