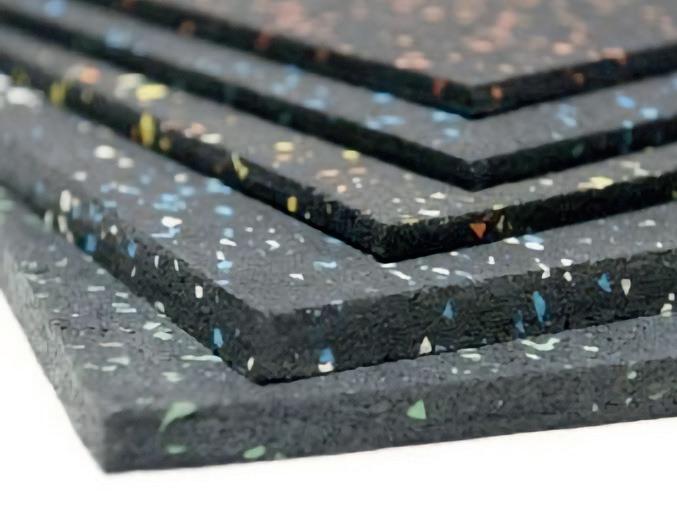
6 minute read
Mescole con gomma devulcanizzata
Approfondimento di carattere tecnico-scientifico Mescole con gomma devulcanizzata
Fig. 1 - Lastre con gomma riciclata
Fig. 2 - Schema sui vantaggi del riutilizzo della gomma Attualmente i manufatti in gomma che hanno terminato la loro vita e gli scarti di lavorazione dell’industria della gomma non sono più da considerarsi rifiuti da smaltire, ma possono essere concepiti come una materia prima da riutilizzare per dar vita a nuovi prodotti. Molte aziende hanno profuso un impegno unico su questa tematica, promuovendo un sempre maggiore impiego della gomma da recupero in tante applicazioni utili nella vita quotidiana (vedi figura 1), portando negli anni un beneficio concreto alla collettività e all’ambiente. L’obiettivo dell’industria italiana del settore è quello di produrre quantità sempre maggiori di mescole in gomma che, senza pregiudicare le caratteristiche prestazionali del prodotto finito, possano comprendere l’utilizzo di materiali rigenerati e/o devulcanizzati e/o di recupero. Tale nuovo indirizzo strategico coglie due interessanti obiettivi: da un lato il prodotto che si realizza acquisisce anche un miglior grado di sostenibilità grazie all’impiego di polverino di gomma proveniente da manufatti che hanno terminato il loro ciclo di vita, dall’altro si riducono i volumi di rifiuti prodotti dall’industria della gomma, con un indiscutibile vantaggio ambientale (figura 2). Il riutilizzo della gomma ha assunto un’importanza considerevole solo in tempi relativamente recenti, ma in realtà il processo è iniziato in tempi lontani (inizi del secolo scorso), quando tutta la produzione di articoli in gomma proveniva esclusivamente da lattice di gomma naturale. Dopo una sostanziale crescita iniziale dell’attività di riciclo, si è verificata una drastica riduzione provocata dal crescente utilizzo della gomma sintetica proveniente dalla lavorazione del petrolio (Anni Venti). Intorno agli Anni Quaranta e Cinquanta il prezzo delle gomme sintetiche, sempre più concorrenziali rispetto al lattice di gomma naturale, ha reso meno conveniente il processo di riutilizzo della gomma. Questo trend si è nuovamente invertito quando si sono cominciate a incontrare difficoltà nello smaltimento degli articoli in gomma a fine vita e si è compreso che occorreva operare nella direzione di un recupero dei materiali.
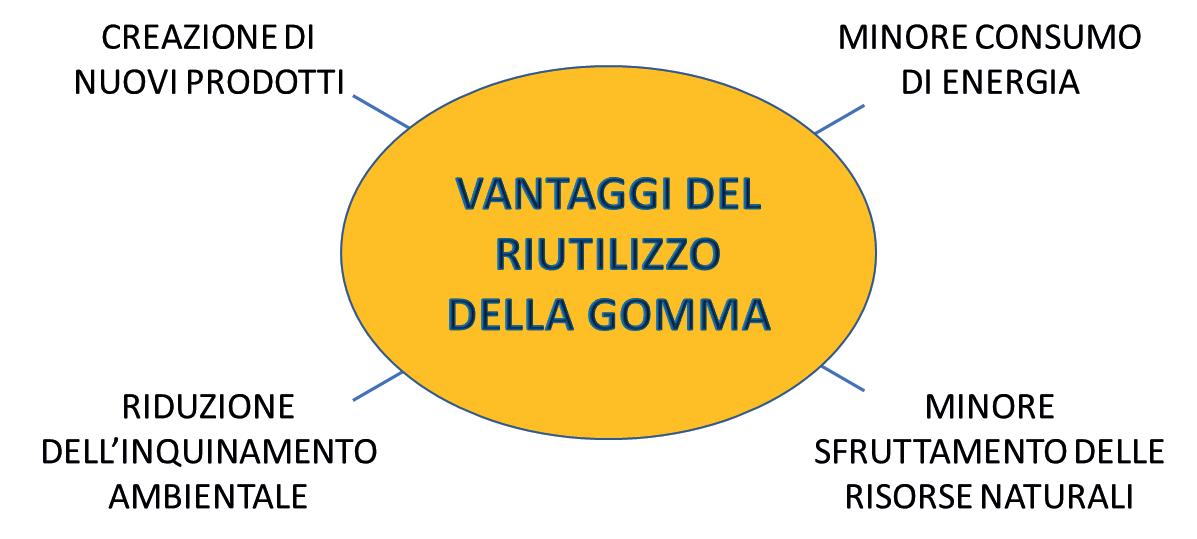
Riutilizzo degli pneumatici
Più della metà della produzione mondiale di manufatti in gomma è rappresentata dagli pneumatici. La gomma ottenuta dal riciclo dei PFU (Pneumatici Fuori Uso) è ormai un materiale ampiamente utilizzato in tutto il mondo, ad esempio per la realizzazione di superfici sportive, asfalti (figura 3), isolanti acustici, arredi urbani ecc. Se opportunamente trasformato in olio combustibile, il PFU può anche essere impiegato per il recupero energetico [1]. Inoltre, in Italia, è stato emanato uno specifico Decreto Ministeriale, n. 78 del 31 marzo 2020 “End of Waste PFU”, che stabilisce criteri specifici (con relativi riferimenti normativi UNI) rispetto ai quali la gomma derivante da PFU cessa di essere considerata rifiuto. Grazie all’attività di recupero e riciclo (figura 4) effettuata nell’ultimo decennio nel nostro Paese, è stato possibile evitare sia l’emissione di milioni di tonnellate di anidride carbonica sia una considerevole e inutile spesa per nuove materie prime, stimabile in diversi milioni di euro [2, 3]. Il processo di riciclo avviene normalmente attraverso i seguenti passi operativi: 1. Raccolta e stoccaggio dei prodotti in gomma che s’intende riciclare. 2. Frantumazione della gomma, generalmente, attraverso l’u-

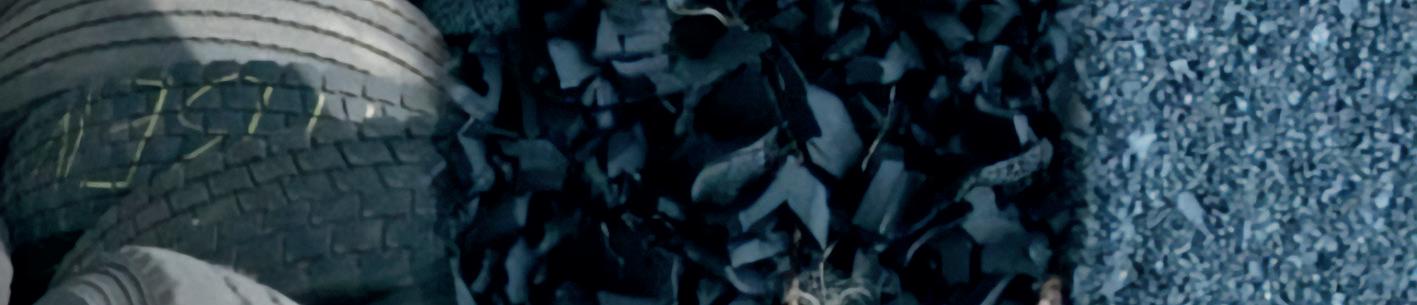
tilizzo di trituratori rotanti. Tale processo può essere ripetuto diverse volte, allo scopo di raggiungere la granulometria richiesta dalle successive lavorazioni del materiale. 3. Separazione della gomma da acciaio e fibre tessili eventualmente presenti. I procedimenti necessari per raggiungere il grado desiderato di pulizia e uniformità del materiale possono essere diversi e può accadere che si debbano ripetere uno o più di tali procedimenti per ottenere un prodotto che soddisfi gli standard richiesti. 4. Devulcanizzazione, ossia il processo mediante il quale si scindono i legami chimici tra elastomeri e zolfo, creati attraverso la vulcanizzazione e responsabili delle proprietà elastiche e di resistenza meccanica della gomma.
Quest’ultima fase del processo è la più critica, poiché la vulcanizzazione non è, in linea di principio, un processo reversibile e una devulcanizzazione completa dovrebbe corrispondere alla scissione selettiva del reticolo, senza la rottura delle catene principali dei polimeri. Tuttavia, è molto difficile rompere selettivamente i legami zolfo-zolfo (S-S) e/o i legami carbonio-zolfo (C-S) senza intaccare la catena principale del polimero, cioè senza rompere i legami carbonio-carbonio semplici (C-C) e doppi (C=C). In genere, i campioni trattati con tale processo subiscono rigenerazione, cioè una combinazione di devulcanizzazione (scissione legami S-S) e degradazione (scissione legami C-C e/o C=C), risultando miscele di gomma devulcanizzata e di gomma degradata, di caratteristiche fisico-meccaniche inferiori [4]. Il processo di devulcanizzazione può essere realizzato mediante differenti modalità: a. chimiche: al polverino di gomma vengono aggiunte determinate quantità di reagenti chimici, applicando successivamente alte temperature e pressioni elevate; b. conultrasuoni: la devulcanizzazione avviene mediante l’attività sinergica dell’energia ultrasonica, del calore, della pressione e dell’azione meccanica alla quale il materiale viene sottoposto; c. con microonde: applicabile solamente a materiali che presentino caratteristiche di polarità adatte; d. biologiche: basate sull’utilizzo di specifici microrganismi in grado di attaccare i legami dello zolfo.
L’effetto della devulcanizzazione e quello della degradazione polimerica (breakdown) sono già stati affrontati proprio da Cerisie sulla rivista MacPlas 378 (agosto/settembre 2020), dove è stato mostrato che per stabilire entrambi i suddetti contributi è necessario effettuare misure sperimentali e un calcolo teorico (Horikx) [4].
Attività svolte dal Cerisie
Da sempre al servizio delle aziende che svolgono l’attività di devulcanizzazione della gomma, il laboratorio Cerisie si occupa dello studio e della preparazione di mescole che includono nella loro formulazione anche gomma devulcanizzata o polverino. Nello specifico, il processo di consulenza inizia sempre con un audit con il cliente, il quale è responsabile del processo di devulcanizzazione, al fine di registrare tutte le informazioni/osservazioni sulla composizione e sulla caratterizzazione del materiale originario. Il materiale devulcanizzato è sottoposto alla determinazione del grado percentuale di devulcanizzazione. Quest’analisi si basa sull’assorbimento del solvente (swelling) da parte del materiale. La gomma sottoposta al processo di devulcanizzazione assorbe una quantità maggiore di solvente rispetto al materiale vergine, aumentando tanto più il suo volume, quanto maggiore è stata la devulcanizzazione avvenuta al suo interno. Possiamo idealizzare questo effetto immaginandolo come l’allargamento di una maglia della rete che si produce eliminando un nodo (crosslink), creando così spazio per ospitare un numero maggiore di molecole di solvente. La determinazione del grado percentuale di devulcanizzazione è un’analisi regolamentata dalla norma ASTM D6814, che indica l’esatto procedimento da seguire. Le misure di swelling sono già state descritte, sempre da Cerisie, nel numero di dicembre 2019/gennaio 2020 (MacPlas 374). Presso il laboratorio Cerisie si procede con la preparazione di un congruo numero di mescole al Banbury, sostituendo percentuali differenti dei componenti maggioritari (polimeri e carica) con il materiale devulcanizzato, per stabilire la variazione delle caratteristiche fisico-meccaniche delle mescole contenenti diverse percentuali di materiale devulcanizzato rispetto alle caratteristiche della mescola realizzata esclusivamente con materie prime vergini. Se necessario è possibile aggiungere alle mescole una miscela di vulcanizzanti ottimizzati per questo scopo, composti da ossido di zinco (ZnO), zolfo e acceleranti. Infine, le mescole così ottenute sono sottoposte a caratterizzazione fisico-meccanica, sia sul crudo che sul vulcanizzato: in tabella 1 sono elencate alcune delle prove principali effettuate su tali mescole.
Fig. 4 - Dagli pneumatici al polverino
[1] https://www.ecotyre.it [2] https://www.ecopneus.it/ [3] Chapter 7 of Tire Waste and Recycling [4] Experimental Validation of the Horikx Theory to Be Used in the Rubber Devulcanization Analysis - Saïd Seghar, Lucia Asaro, Nourredine Aït Hocine
TAB. 1 - PRINCIPALI PROVE EFFETTUATE SULLE MESCOLE CRUDE E SU QUELLE VULCANIZZATE Prove sulle mescole crude Prove sulle mescole vulcanizzate Viscosità Mooney Densità
Vulcanografo con rotore (ODR)
Durezza Vulcanografo senza rotore (MDR) Trazione (carico e allungamento) Compression Set Resistenza all’abrasione